{"pages":{"page":[{"#text":"TRADE SHOW PREVIEW 36 PETplanet insider Vol. 11 No. 11/10 www.petpla.net Schaefer Förderanlagen- und Maschinenbau GmbH Palletising, sorting and pallet inspection systems Palletising system specialist Schaefer says that the highlight of its display will be its MultiROB HighS palletising machine, which has a low level infeed and a divided loading plate in the palletising head. With capacity in excess of 500 layers/hr, claimed layer forming time is less than 7s. Capable of palletising up to 62,000 1.5l PET bottles/hr, non-returnable packs and single bottles can be mixed and arranged in one machine. PatternBuilder features an upgraded configuration table and RoboTurn pack turner. It is designed to keep movement and travelling distance to the minimum, has a small footprint and low power consumption. Schaefer’s QualiPal II pallet inspection system is intended to ensure safe transport and stacking in high rack warehouses. CompactStack is an automatic destacker for nested pallet stacks. www.schaeferpal.de Plast Engineering Knauff Complete PET line in a container Plast Engineering Knauff will be showcasing its Compact A 4C fully automatic stretch blow mould bottling, filling and labelling plants. The unusual feature of these plants is that they are designed to be installed in standard 12m (40ft) transport container units. The Compact A 4C manufactures up to 2,800 PET 500 to 1,500ml bottles/hr from preforms. The PET bottles are automatically disinfected by UV radiation and transferred directly to the filling station, which fills them with UV disinfected drinking water. They are then closed with UV radiated caps, labelled, and covered with tamper-evident sleeves. Ready-for-sale bottles are discharged through a window in the container wall. The production units require an 80kW power connection and a source of drinking water; an EC connection for electrical power and two-inch pipe coupling for water are built into the outside of the container. On request, the system can be supplied complete with a diesel generator and water purification system. www.plastics-equipments.de www.pet-equipments.de Hall 5 | Booth 423 Hall 7 | Booth 206 Kaeser Kompressoren Energy-saving boosters and compressed air systems Hall 4 | Booth 423 Kaeser Kompressoren will be presenting its latest range of products and developments, including its new dry-running rotary screw compressors. The highlight of the stand will be its ‘Airbox Center’, which it describes as a compact compressor system offering high-quality, all-in-one compressed air generation, treatment and storage. Visitors to the stand will also be able to see the company’s latest range of rotary blowers, which are designed for efficient air delivery; and systems for effective heat recovery. Energy-saving boosters for PET bottle production will be on display, as well as complete compressed air systems. www.kaeser.com Invista Barrier resins Invista will display its portfolio of barrier PET packaging resins. The company’s barrier portfolio includes PolyShield resin, a monolayer PET barrier resin that meets the shelf life and barrier requirements of oxygensensitive food and beverages, including beer. Also on display wlll be OxyClear barrier resin, a crystal clear oxygen ingress barrier tailored for oxygen-sensitive food and beverages, such as juice, wine and sauces. Hall 4 | Booth 143","@ID":38} "MARKET SURVEY 26 MARKETsurvey11/10 Company name Sidel Group Postal address Telephone number Web site address Contact name Function Direct telephone number Fax E-Mail Via La Spezia 241 43100 Parma, Iitaly +39 0521 9991 http://www.sidel.com Mr. Stefano Baini Filling Product Manager +39 0521 / 999249 +39 0521 / 999299 stefano.baini@sidel.com 1. Machine designation / model number Eurotronica FM-S Eurotronica FM-C Eurotronica FM-LT Selecta C Eurostar MS 2. Number of filling heads (range: from/to) 32-144 48-192 48-192 36-50 24-50 3. Filling speed/output - based on 1 litre PET bottles a. Still water (1 litre bph) 16,000 -80,000 6,000-16,000 b. Carbonated drinks with 8 g CO² (1 litre bph) 13,000 -68,000 9,000-15,000 4,000-13,000 c. Milk (1 litre bph) d. Fresh fruit juice (1 litre bph) Beer:12,000-50,000 4. Filling process Pressureless (still drinks) Yes Yes Yes Yes Pressure filling (carbonated drinks) Yes Yes Yes Yes Hot filling Yes Yes Cold aseptic filling Juices with high pulp content 5. Type of filling valve and metering system Volumetric with flowmeters Volumetric with flow meters -long tube Mechanical isobarometric, volumetric Company name Fogg Filler KHS GmbH Serac Postal address Telephone number Web site address Contact name Function Direct telephone number Fax E-Mail 3455 John F Donnelly Dr. Holland MI 49424, USA +1 616-786-3644 www.foggfiller.com Susan Lamar Sales/Marketing +1 616-738-0261 +1 616-786-0350 slamar@foggfiller.com Juchostrasse 20 44143 Dortmund, Germany +49 231 569-0 www.khs.com Heinz Hillmann Produktmanager +49 671 852 2714 heinz.hillmann@khs.com 12 Route de Mamers, F- 72400 La-Ferté-Bernard +33 2 40 60 28 28 www.serac-group.com Fabienne Cheriaux Marketing +33 2 43 60 29 55 facheriaux@serac.fr 1. Machine designation / model number Similar models in different sizes, F4, F4.1, F6.2, F8 and F9 DRV, computer controlled volumetric filling machine, for carbonated softdrink NV, computer conntrolled volumetric filling machine, for still water and juice (cold and hot) SESL & SAS4 2. Number of filling heads (range: from/to) 12-90 48 - 180 36 - 144 8 - 90 3. Filling speed/output - based on 1 litre PET bottles a. Still water (1 litre bph) 1,800-36,000 up to 72,000 up to 68,000 48,000 b. Carbonated drinks with 8 g CO² (1 litre bph) No filling of carbonated products up to 55,000 Ø c. Milk (1 litre bph) 1,800-36,000 48,000 d. Fresh fruit juice (1 litre bph) 1,800-36,000 up to 55,000 up to 44,000 48,000 4. Filling process Pressureless (still drinks) Fogg gravity fills hot and cold ESL products Yes Yes Gravimetric filling tank Pressure filling (carbonated drinks) Yes No Ø Hot filling Yes Yes Gravimetric filling tank Cold aseptic filling No No Gravimetric filling tank Juices with high pulp content No up to 10% Gravimetric filling tank 5. Type of filling valve and metering system Mechanical/gravity valve Valve with swirl modul for foam free filling, volumetric system with MID Non contact, free flow filling valve with MID, ( magnetic inductive flowmeter ) Magnetic Valves and net weigh","@ID":28} "REGIONAL MARKET REPORTS 16 PETplanet insider Vol. 11 No. 11/10 www.petpla.net from 22 springs. This value model has become the best selling volume brand in France. In 2008 Pierre Castel sold shares to co-founder Papillaud. Alma, with a sales turn-over of €900 million, was too large for Papillaud alone to buy. Therefore a financial deal was arranged for Papillaud to become the majority share holder with 51%, while the remaining 49% was taken by a JapaneseAmerican partnership called Otsuka Beverages Co. Previously, Roxane had already worked together with Otsuka to create the Crystal Geyser in the United States. The situation today is that the Alma Group (Roxane) holds the number one market position bottling and marketing mineral water in France, from a dedicated range of mineral water springs, with brand names such as St. Yorre, Vichy Celestins, Thonon, Pierval, Chateldon, Courmayeur and Cristaline, Verniere, Rozana. The Alma Group (Roxane) has 34 production sites, 68 production lines, 3,000 employees, and fills 4 billion bottles (in 2008). For Otsuka Pharmaceutical Europe, with a 49% share in Alma, the acquisition was a milestone, since it provided a platform for further expansion into Europe in addition to having a strong foothold in the European mineral water business. A visit of the Roxane plant in Ferriere de Brochard For Roxane it all started in Ferriere de Brochard: the mineral springs, the first filling, the expanding factory. Today there are tower blocks in the once idyllic valley - for PET and for sweeteners. Products such as Cola (own Roxane brand), fruit drinks, carbonated water and tea are all filled here. At La Ferriere de Brochard, there are a total of 4 lines, blowing, filling, capping, labelling and packing. Sidel, Serac and Krones have supplied the core of machines. Preforms are produced in-house, at a central point, on 3 Husky systems (72 cavities, 300t capacity). The man Papillaud The entire concept and strategy of Alma-Roxane became clear to us after a few, inevitably provocative, verbal exchanges: The concept and strategy of the company with all subsidiaries for water and CSD bottling is Pierre Papillaud and vice versa - Pierre Papillaud the man, character and personality is Alma-Roxane. He drives the company. He makes the decisions. He works from morning to night “with small breaks”, he explains. He orders the equipment. He can set the machines for optimised production. He is in charge of his advertising and his public image. He is on top – seemingly facing and challenging everybody in his way or in the way of PET and his business. He likes his good people. For those people he is the father, he takes care of them. “You don’t exist, just the company exists. The company that makes you,” he says. Despite the fact that the man with the wide suspenders, sitting behind the desk, initially did not want to tell us anything – ““I have no secrets. I have nothing to tell and I Daily industry news and opinion FoodBev.com Images: screen© Irochka,bottle© FilipeVarela, tomato©Mailthepic,carton©Photoeuphoria,cheese© EdytaPawlowska,glass ©KonstantinTavrov, orange© LesCunliffe,bean©Monika3stepsahead,biscuit© Picsfive, strawberry©BraendanYong |Dreamstime.com Making a splash online now FoodBevcom A world of food and drink","@ID":18} "REGIONAL MARKET REPORTS 14 PETplanet insider Vol. 11 No. 11/10 www.petpla.net March 29, 2010 Danone Research Danone Research – Packaging, a key in-house expertise for Danone Frédéric Jouin, Global Packaging Platform Director, Danone Reserach We met: Frederic Jouin, Global Packaging Platform Director, who is in charge of the entire R&D Packaging of the Danone Waters and Dairy Divisions. He came to Danone in 1997 after leaving Yves St. Laurent, where he developed packaging for perfumes. After 9 years in different positions in R&D Packaging for Danone Dairy Products, he moved to Product Development for Danone Dairy and was promoted in his today’s office in October 2009. ‘Bringing health through food to as many people as possible’, Danone R&D is committed to Danone’s mission “Irrespective of age and irrespective of where in the world one lives, health is always intimately related to diet. Danone was born from that conviction now inscribed at the heart of its mission: ‘Bringing health through food to as many people as possible’. This ambition is largely based on the commitment and skills of the R&D teams. These skills are grouped in Danone Research, a worldwide organization present in some fifteen countries, employing about 1200 personnel, and maintaining a network of almost 200 scientific cooperations worldwide. The dialogue between Danone researchers and outside research teams, such as those of the universities and specialised private and public research organisations, generates and enables the sharing of knowledge, advancing and comparing working hypotheses. The complementarity gives rise to high-level scientific cooperation on the company’s strategic axis. Science is fundamental to the products created by Danone R&D. Science is placed in the service of consumers in order to build and maintain their health capital throughout their lives while offering accessibility to the greatest number and maintaining the pleasure of good food.The fields of expertise cover domains as varied as nutrition, human physiology, immunology, food engineering, microbiology, molecular biology, biochemistry, food safety, product development, sensory evaluation. Packaging is also an in-house expertise aiming at delivering the best pack in every hand, according to the Danone’s mission. The packaging experts of Danone Research are working on three principal axes ensuring the safety and innocuousness of the packaging with respect to the product contained, reducing the environmental impact of packaging, with the aim of decreasing our carbon footprint by 30% by 2012, stimulating innovation projects in order to identify new packaging solutions compatible with the sensory properties of the product, health benefits and consumer expectations. The R&D Global Packaging Platform lead by Frédéric Jouin is made in two parts The part of it working for Danone Dairy is based in this R&D center. The part dedicated to Danone Waters is located in Evian in order to be close to a factory with key competencies on materials/polymers and technologies of ISBM & caps workshops including equipments for bottles and caps production and testing plus a training center. The team, in connection to the local R&D Pack teams located in the countries is in charge of the qualification of new materials, of the design of any new bottle or cap design and makes recommendations about supplier’s equipment, packaging formats – all under the banner: “Best pack in every hand.” The task of WW R&D Pack team is indeed enormous and ambitious, as Danone produces in 58 plants world wide with 80 filling lines, most of them integrated with blowing. The current sitation of machines used within the Danone Waters Factories around the world is spread as followed Husky & Netstal for injection moulding Sidel, Sipa and Krones for blowing and filling Sacmi and Krones for labelling. 250,000t of PET resin are converted globally each year, of which 100,000t of PET resin are converted in France (25,000t are from post-consumer, recycled material). Packaging strategy This worldwide R&D Pack organization is focussing on 3 main tasks: Ensure safety and quality of the products to all consumers. Reduce significantly the carbon foot print of the Danone products: Bring packaging innovations on the market visible for consumers. Frédéric Jouin, emphasising the priorities of research in general: “Quantity is an issue, quality is a must.”","@ID":16} "MARKET SURVEY 27 Gero Von Stackelberg Product Manager Sensitive Products +49 172 7114982 Gero.Stackelberg@sidel.com Guillaume Rolland Product Manager - Aseptic Filling +39 521 999 141 +39 521 959 009 Guillaume.Rolland@sidel.com Hotfill Ultra Clean for carbonated beverages Cold Chain Aseptic Eurostar HS Europa WM Veloce \"mech\" Veloce FM Combi Predis FMc Combi Predis FMm Sensofill FMa / Combi Predis Fma 48-180 32-120 40- 90 40-108 70 -130 24 -72 32-120 16,000-72,000 15,000-62,000 8,000-45,000 11,000-58,000 18,000-36,000 8,000- 40,000 10,000-60,000 Beer: 10,000-54,000 10,000-48,000 10,000-48,000 8,000-40,000 10,000-60,000 Yes Yes 4°C Yes 18°C up to 94°C up to 94°C Yes Yes Yes, up to 10x10x10mm No Yes Yes Mechanical gravity level Contact filling with mechanical filling valve with level control Contact less filling with inductive flowmeter Contact filling with inductive flowmeter Contact less filling with inductive flowmeter Magnetic filling valve with Flowmetering control Sacmi Filling S.p.A. Krones AG Via E. Ferrari, 1 43058 Ramoscello di Sorbolo (PR) - Italy +39 0521 695411 www.sacmifilling.it Matteo Quaini Sales General Manager +39 0521 695411 +39 0521 695400 info@sacmifilling.it Böhmerwaldstr.5 93073 Neutraubling, Germany +49 9401 / 70-0 www.krones.com Georg Setz Product Manager Filling Technology +49 9401 / 70-4346 +49 9401 / 70-3056 georg.setz@krones.com Vega Alfa Volo-Mas Solo-Mas Modulfill 32-192 32-168 32-192 16-168 16 -216 10,000-72,000 10,000 - 72,000 10,000 - 72,000 10,000 - 72,000 up to 72,000 10,000-60,000 10,000 - 60.000 up to 65,000 7,000 - 40,000 7,000 - 40,000 up to 60,000 10,000-60,000 10,000 - 60,000 10,000 - 60-000 10,000 - 60,000 up to 60,000 Yes yes yes yes Volumetric filling system, net weight filling system, heigh filling system Contactless filling system Yes no yes no Volumetric filling system, net weight filling system, heigh filling system Short tube or long tube filling systems, contactless filling system Yes yes yes yes Volumetric filling system, net weight filling system, heigh filling system Short tube or long tube filling systems, contactless filling system No no no no PETAsept L, PETAsept D Short tube or long tube filling systems, contactless filling systems / volumetric or net weight filling systems Yes yes yes yes Heigh filling system, Pre dosing system Contactless filling systems / volumetric or net weight filling systems, long tube filling system, full bore filling / contactless / for pulp, fibers or fruit pieces Mechanical or electropneumatic / vent tube Mechanical / vent tube electronic volumetric / flowmeter electronic volumetric / flowmeter Volumetric filling system, net weight filling system Magnetic flow meter","@ID":29} "BOTTLES 43 PETbottles PETplanet insider Vol. 11 No. 11/10 www.petpla.net Double body for Pom Under its brand name of “Pom”, the Dutch company Pom Wonderful B.V., Amsterdam is marketing the fruit drink made from 100% juice which is bottled in the USA. Depending on the flavour, which may be pomegranate / blueberry or pomegranate/cherries , the printed bottles feature printed screw caps in different colours with a tear-off tamper-proof guarantee. www.pomwonderful.eu SEALING COMPOUNDS FOR CROWN CORKS AND CLOSURES Granulen®PVC free– non PVC liner for pry–off crown corks Granulen®OS– sealing compound capable of trapping oxygen extending flavour stability and shelf life for beer Granulit® S CR–PVC dry blend for pry–off crown corks Granulit®S CR/TO– PVC dry blend for twist corks Granulen® ROPP– non PVC liner for aluminium closures Granulon®– liners for plastic closures, application by out–shell moulding or in–shell moulding technology Plastisols– for crown corks and aluminium closures Address: D PLAST a.s. Luzkovice 206 CZ-763 11 Zlin Czech Republic e-mail: info@dplast.cz fax: +420 577 610 170 tel: +420 577 610 111 Fun without calories Under the brand name of “Fun One“, the Danish company Kavli is marketing 0.5l soft drinks concentrate with no added sugar for mixing in a very wide range of flavours in easy to handle, clear PET bottles. According to the manufacturer, 5l of drink can be made out of the concentrate, 100ml of which delivers only 1kcal. A wraparound body label printed with the necessary information and a screw cap with a tamper-evident seal that can be torn off completes the packaging for this beverage. www.fun.dk Slim bottle for syrup Eckes-Granini Austria is offering 0.7l of fruit syrup in a very wide range of flavours in a tall, slim PET bottle. The bottle features a body label and a screw snap closure with a dispenser section and integral embossed brand name. A laminate die-cut lid that needs to be pulled off prior to use seals the bottle and keeps it safe during transport and storage. www.yo-fruchtsirup.at Yellow PET for kids The German company sonicdrink Marketing GmbH of Mainz is selling 0.5 litre packs of various fruit juices in eye-catching yellow PET bottles. The wraparound labels are printed with SpongeBob images from licensor Viacom International. A screw-on cap, injection-moulded in two colours, which can be operated using one hand only and with a tear-off tamper-proof guarantee complements the appearance of the packaging. www.sonic-drink.de China soya in PET The Danish company O. Kavli AS based in Hvidovre is offering 300 ml real Chinese soy sauce in a round, special shape PET bottle. The clear bottle features a label printed with information and a red, screw-on hinged cap. In the PET bottle the soy sauce has a shelf life unopened of approximately 1 year. www.kavli.dk","@ID":45} "PETcontents 11/10 4 PETplanet insider Vol. 11 No. 11/10 www.petpla.net INSIDE TRACK 3 Editorial 4 Contents 6 News 42 Products 44 Bottles 44 Patents BUYER’S GUIDE 45 Get listed! TRADESHOW PREVIEWS 32 drink technology India, Mumbai, November 18 - 20, 2010 34 Brau Beviale, Nuremberg, Germany, November 10 -12, 2010 REGIONAL MARKET REPORT 10 France - Part 3 MATERIAL / RECYCLING 22 Cost efficiency in PET resin production PREFORM PRODUCTION 24 A rapid guide to perfect preforms - Part 16 MARKET SURVEY 22 Suppliers of filling equipment BOTTLING /FILLING 30 ‘Green Plan’ for eco-friendly water bottling Page 30 Page 22 Page 38 Page 40","@ID":6} "TRADE SHOW PREVIEW 39 PETplanet insider Vol. 11 No. 10/10 www.petpla.net Strong fresh air for PET-bottle industry Gainnew heights in savings and energy-efficiency with the new oil-free ZD compressor Time to gain new heights. The highly energy efficient ZD compressor, with superior screw and booster technology, offers Class Zeroquality air and is extremely silent with no vibrations. Theair-cooledZD provides you anexceptional reliability, no water consumption, while driving down investment and installation cost. It all adds up to sustainable productivity for today’s challenging low carbon economy. This new ZD is The answer for all your high pressure 40 bar applications. For more information, visit www.atlascopco.com/petcompressors Rudolf Wild GmbH & Co KG Natural sweeteners and flavours Wild will be exhibiting the latest results of its ongoing drive to develop natural alternatives for flavourings and sweeteners. The latest of these is Stevia, which is derived from tropical plants common to the Americas. With extracts possessing up to 300 times the sweetness of sugar, Stevia fits into the demand for low-carbohydrate, low-sugar sweetening ingredients. Wild says that its products open up new opportunities for breweries, mineral water companies and soft drinks manufacturers. Beer-based drinks sweetened with Stevia join a range including near-water, tea and nectar drinks. Wild will be showing ideas for beer-mix products and for alcohol-free malt-based drinks, as well as products with fruit pulp, tea drinks and alcohol-free ciders. www.wild.de Hall 1 | Booth 119 Nate Filling machines and flow meters Czech company Nate (nápojová technika a.s.), which is based in Chotěboř, will have on its stand a working example of its PETblok 40/4/8 filling machine in ultra-clean execution mode. The machine will subsequently be installed at the Clean Water Company, which produces mineral water in Novosibirsk, southern Siberia. Nate also makes a range of flow meters for mineral water, soft drinks, CSD and beer applications, for pressurised filling PET bottles between 0.2 and 3l, with output capacity from 2,000 to 30,000bph. the company says that, among other features, changes in fill volumes can be accommodated without adjusting the valve. The filling process is controlled from the filling machine’s control system and its electro-pneumatic control enables adaptation to different types of drinks and gas concentration. The company’s volumetric fillers with flow meters are suitable for CSD, dairy-based, higher viscosity and other non-carbonated beverages. www.nate.cz Hall 5 | Booth 431-433","@ID":41} "REGIONAL MARKET REPORTS 17 PETplanet insider Vol. 11 No. 11/10 www.petpla.net will not tell you anyway.”- he told us a lot about himself, his aims and ambitions. Two major topics have priority on his agenda. In these topics he is both aggressor and defender, provoking and under pressure. The aware public is his arena for the conflict. No. 1 topic – tap water versus bottled water A campaign was launched by Syndicat des Eaux D’Ilede-France (Sedif), the public water utility that serves four million inhabitants in the region surrounding Paris. Sedif was spreading its message through posters that displayed bottles resembling known brands (Papillaud’s Cristaline for instance) and labelled “Eau du Robinet” or tap water. The posters carried provocative texts like “You’re free to pay 100 times more” or “Ideal for those living on the fifth floor without a lift” and “What could be more environmental than no packaging at all?” Being the bottler of France’s most popular mineral water Papillaud hit back with a campaign similar provocative - implying that the capital’s tap water is undrinkable and polluted. In the name of his “eau minérale” Cristaline he covered Paris with posters showing an open lavatory with a red cross and a tagline: “I do not drink water that I use.” No 2 topic – France 5 versus Syndicat des Eaux de Sources The television network France 5 on 14th of March reported about plastics in general and categorically stated that “it is difficult to recycle plastics”. The Syndicat des Eaux de Sources (Sedif) disproved this officially. Papillaud with less diplomacy insisted, when we met him: “PET is not plastic. Because PET can be recycled to 100%.” It may be difficult to argue that collecting and recycling plastics is an easy job. And PET surely is plastics. But the issue indiscriminately carried into the TV public is a sensitive issue – in view of the 3.5 billion litres of water consumed in France and 7.2 billion litres bottled in France, as well as putting the jobs of 2,500 to 3,000 French people at risk as well as in view of the many recycling projects that exist to the use of recycled material in new bottles by beverage companies. Papillaud himself has started reprocessing PET – fully committed, yet apparently without much pleasure. The flakes, which he at present produces, are – so far – subsequently extruded and granulated at added cost. But whatever this entrepreneur started he has eventually carried through to success against all odds. This will surely and in future include making food grade PET resin for new bottles to be filled.","@ID":19} "BOTTLING / FILLING 31 PETplanet insider Vol. 11 No. 11/10 www.petpla.net Georg Menshen GmbH & Co. KG Industriestraße 26 | 57413 Finnentrop Fon +49 2721 518113 | Fax +49 2721 518115 contact@menshen.com | www.menshen.com • no measuring out of dosage volume necessary • user-friendly one-hand-use • no over dosing • environmental-friendly and efficient one2dose®, the innovative dosing system. A measured dosing system with a flip top cap. Enabling easy, exact and clean dosing with only one hand! Intelligent packaging, easy dosing. final product of this process is a Canada and USA-approved food-grade pellet. This turnkey line was supplied by Starlinger, of Austria, which was chosen because of its convincing performance during the SSP process and overall low energy consumption in converting clean r-PET flakes into pellets. These pellets are then used to produce the preforms. Lighter bottle design made of rPET resin Ice River Springs is currently in the process of lightweighting its existing 500ml water preforms from 9.94g to 8.67g; the intention is to have everything completed by spring of 2011. The challenge with lightweighting is that the processing window on the blow moulding machines becomes very narrow. However, the company has been able to make this work. The current closure is the Corvaglia design (see also PETplanet 7+8/2010) and weighs 0.97g. Ice River Spring’s goal is to have a cap and bottle under 10g combined weight. These 100% rPET bottles will have small labels made of recycled paper and cases will be produced without cardboard to further minimize packaging. www.iceriversprings.com RPET plant at Ice River Spings The Starlinger SSP line is located in one of Ice River Springs bottling plants","@ID":33} "NEWS 7 PETplanet insider Vol. 11 No. 11/10 www.petpla.net Unisensor nominated for technology and innovation award Professor Dr. Gunther Krieg, Dipl.- lng. (FH) Dirk Fey and Dipl.-lng. (FH) Jürgen Bohleber have been nominated for the “Deutscher Zukunftspreis 2010“for the Powersort 200 high-speed laser spectroscopy-based plastics sorting system. The award is for outstanding technical, engineering or scientific innovations already on the market. The Federal President of Germany will present the award at a televised gala event in Berlin on December 1, 2010. Powersort 200 uses highspeed laser spectroscopy to identify contaminants in recycled plastic that are missed by conventional methods. The Powersort system identifies the ‘good material’ in a plastic flake or pellet flow based on its specific opto-electronic spectrum, separating it from various contaminants in a single process step. The detection system excites plastic particles with laser light and analyses the light spectrum that the individual parts then emit. Powersort 200 separates material that differs from the reference spectrum of the ‘good material’. It can evaluate up to a million spectra per second and can detect even tiniest particles with accuracy. Unisensor’s product portfolio includes internationally patented systems for the recycling, beverage, gas, and printing industries and for energy technology. Further information on the award: www.deutscher-zu-kunftspreis.de www.unisensor.de New management appointments at Sacmi Ermes Belicchi has been appointed general manager of Sacmi Labelling. He joined the company in 2005 and was in charge of its production planning and EDP systems from 2007 until taking up his new post. John Bruno Pasqua, an Australian of Italian origin, has been appointed commercial manager of Sacmi Verona. He has extensive experience of the labelling business and joins Sacmi from Sidel, where he had responsibility for commercial operations in the Americas, and for R&D and marketing. www.sacmi.com","@ID":9} "TRADE SHOW PREVIEW 38 PETplanet insider Vol. 11 No. 11/10 www.petpla.net Resilux NV New developments in barrier technology Dutch company Resilux has some new products in its barrier technology, which it will be demonstrating and explaining at Brau Beviale. The company’s in-house team has developed a range of barrier preforms and bottles in multilayer and monolayer formats. They include ResiOx 3-6-9 barriers against O2 ingress, suitable for juices, wines and sauces; ResiC barriers against CO2 loss for CSD products; ResiBlock 0-2-4 light barrier for dairy; resiMid and ResiMax barriers agasnt CO2 loss and O2 ingress, designed for beer packaging. www.resilux.com Hall 5 | Booth 323 Bericap Lightweight closures and necks also save CO2 The Bericap stand will illustrate the variety of caps the company produces, its drive to reduce weight and consequent CO2 savings. It offers five different generic closure designs for PCO 1881, including the DoubleSeal SuperShorty Eco (DS SuS eco), which weighs only 2,1g, which is suitable for carbonated beverages with up to 8g CO2 /l. Bericap offers a still version (DS SuS Still), which includes an antisabotage feature and can be applied with same chucks as DS SuS eco. The company has also developed numerous custom designed closures for PCO 1881. The company’s Hexalite range is designed for PET 29/25 and PET 26/22 standards for still beverage bottles. North America will soon see the current 43mm hotfill neck finishes superseded by 38mm; visitors to the stand will be able to discuss its solutions, as well as one-piece closure technology and two- and three-piece sports caps. Bericap says that, by the end of Q1/2011 it will have converted more than 50% of its beverage closure capacity to lightweighted closures. It estimates that the resin savings will contribute to reducing CO2 emissions by 60,000t/a. www.bericap.com Hall 4 | Booth 515","@ID":40} "TRADE SHOW PREVIEW 40 PETplanet insider Vol. 11 No. 11/10 www.petpla.net GEA Procomac New aseptic filler for low/medium speed lines GEA Procomac’s new Modulbloc aseptic filling machine is designed for low to medium speed aseptic lines. The company says that it is a compact machine, featuring ancillaries units and cap sterilisation on the same frame. It includes strong chemical action for cap and bottle treatment. Visitors to the stand will be able to discuss the company’s EcoSpin, the latest generation of its high-speed wet PAA-based aseptic filling bloc. GEA Procomac says that it features shorter rinsing time and reduced footprint. Also on show will be its Fillstar CX and FX volumetric electronic fillers with magnetic flow meters. Fillstar CX is designed for still and carbonated products with and without pulps and fibres, and Fillstar FX series for still products. Sterilbeam is a new energy-based cap steriliser, which uses electron emitters. GEA Procomac staff will be on hand to discuss the company’s research and development of electron beam technology as an alternative medium for decontamination. www.procomac.it Hall 7 | Booth 602 Sipa PET bottles for hotfill applications Sipa will not have working machinery on its stand but the area will not be empty. The company will be showing the latest examples of its drive to reduce bottle weight, cut energy consumption, save space, reduce machine maintenance needs (and downtime) and minimise waste. Its slogan for the show is ‘Less and More’; the ‘More’ side is represented by higher outputs, improved efficiency, faster cycles, quicker changeovers, wider process windows and greater flexibility. The stand will demonstrate industrial applications of several hot-fill bottles which do not have vacuum absorption panels. Immediately prior to capping, after filling at 85-87 deg Centigrade, a dose of liquid nitrogen is added at 1.5 bar. As the beverage cools and contract, internal pressure remains at 0.2-0.3 bar, to ensure rigid packaging and to aid labelling. The system is also claimed to save costs in labelling. www.sipa.it Hall 7 | Booth 335 Injectoplast Multi-functional system closures Ijectoplast (Kunststoffverarbeitungsges.m.b.H)in Waidhofen at the Thaya, Lower Austria will present its range of beverage closures, as well as the competence as a development partner for new closure systems. This position corresponding to the market position has thus been adapted to the company’s brand identity. From “IP Injectoplast” to “Injectoplast - Effective Closure Systems”. With this new positioning, the company is presented to the public for the first time at the Brau Beviale 2010. A steadily increasing share of the company’s capacity is invested in the new development of closures. A concrete example is reflected in screw caps, with foil seals of containers, which can be simultaneously removed in the opening operation. Another example is the closure system with integrated additive container, which was developed in cooperation with the mould manufacturing company KTW. When opened, the contained additive (liquid or powder) is released and dosed to the underlying liquid. As a result, color effects or chemical reactions can be initiated. Hall 4 | Booth 500 Gernep GmbH Labelling is all wrapped up! Gernep, an established manufacturer of labelling machines located in Southern Germany, will once again be presenting the most up-to-date technologies in the shape of a wide range of different labelling systems at. For the wraparound labelling of PET bottles or other container formats using hot melt adhesive there is a choice of two different types of machines. The first, for processing pre-cut paper or plastic labels from the label magazine, is represented by the Rollina Series machines, whilst the second is the innovative Rollfed for labelling with off-theroll foil labels. GERNEP has developed its Labetta-SK Series as a self-adhesive labelling system. Innovative and exclusive design labels are, according to the manufacturer, just as feasible as the processing of no-label-look or water-resistant plastic labels. Not only re-tooling times but also the time taken for cleaning and maintenance work are considerably shorter than, for example, using the wet adhesive systems. Gernep’s approach to wet adhesive labelling as a system is illustrated by its Labetta series. The combination of wet and self-adhesive labelling offers special flexibility in terms of user potential. In order to accommodate the full range of requirements of the processing industry, Gernep has developed its Labetta Duo Series. The Labetta Duo type labelling machines as well as the Labetta type can be fitted by way of option with a mechanical or photo-electric container alignment facility. At the customer’s request the machines can also be fitted with a seal (self-adhesive) as well as wet adhesive labelling in the shape of an L or a U. www.gernep.de Hall 7 | Booth 222","@ID":42} "REGIONAL MARKET REPORTS 11 PETplanet insider Vol. 11 No. 11/10 www.petpla.net We met: Sophie Dournier-Delamare (Evian Public Relations Department at Evian-Les-Bains on Lake Geneva) Evian waters, which are collected in an agricultural (60%) and wetland (10%) area of 35 km2 and at an altitude of 850m, then travel through layers of sedimentation to an altitude of 400m and Evian Les-Bains on Lake Geneva. The journey through the rock takes 20 years, during which period it experiences filtration and enrichment with minerals - the origin of Evian as pure and healthy mineral water. To ensure sustainability (as well as to safeguard water quality and the environment) the waters pumped are limited to what the catchment area can provide. In recent years the Evian volumes have declined due to the economic crisis and the government’s campaign in favour of tap water. One could almost see the economic situation as a blessing in disguise for the water reserves. Sophie Dournier-Delamare (Evian Public Relations Department at Evian Les-Bains on Lake Geneva) and her assistants receive and host 20,000 visitors annually. The plant tours definitely add flavour to an already existing good image of Evian waters. Highly motivated ladies convey the Evian philosophy, the Evian commitment and mission, to the public in an almost missionary approach. PETplanet had the privilege of a VIP tour with the very knowledgeable Sophie Dournier, whose academic background is packaging engineering. She is head of the PR team, loves her job, loves Evian, and is responsible for what we know about Evian. And as we tour, talk and listen, we inevitably touch on the emotional basis of this multibillion litre and multimillion Euro business of Evian. It is this blend of intellectual conviction and emotional involvement which motivates people and makes them work best. But there is business too. Evian’s business was water, is water and will always be high-end high quality water - pure water with mineral ingredients for health. People want water. They also need 1.5l per day, we learned. So business should almost be guaranteed. But today business for the water producers is not secure since the government started to promote tap water. Thus Evian reacted and started campaigning - far beyond the basic aim of securing business alone. The people of Evian call it the “great plan”, i.e. the commitment to sustainability, which is a commitment in the political, environmental, social and economical arena. As the waters from the Evian springs are the same at all times and should be so, the action plan has to do very much with packaging and thereafter with logistics. 95% of Evian waters are filled in PET bottles. PET, in the official eye of the French government, seems to be regarded as an environmental burden (see also report about our Alma Roxane visit). Evian reacted gently with their action plan on four major fronts: Protection of the catchment area with sensitive inclusion of the people living there. Packaging, with analysis of the status quo, a reduc- tion of use of PET material (light weighting), water and","@ID":13} "REGIONAL MARKET REPORTS 20 PETplanet insider Vol. 11 No. 11/10 www.petpla.net March 30, 2010 Valorplast in Paris Valorplast - “The need might exceed the amount collected.” Géraud Delorme – Directeur Général of Valorplast We met: Géraud Delorme – Directeur Général. Recycling is the hottest topic for PET markets in France: Our discussions with Geraud Delorme at Valorplast are already reflected in great detail in “The PET Story” in first edition of “Focus on France”. Therefore we attend to the critical topics only and in brief: The conflict: Recycling of post-consumer PET bottles replaces virgin PET resin and saves resources. If bottle-to-bottle recycling is managed professionally its use of PET for bottling helps secure the environment. Such is the position of the industry. “What could be more environmental than no packaging at all?” This is the position of the government organisation Syndicat des Eaux D’Ile-de-France (Sedif), hoping that its campaign will further the acceptance of tap water. Both Eco Emballage and Valorplast play an important role in easing the conflict and pacifying the conflicting parties. Granulate versus flakes Numerous steps are involved in the process from postconsumer bottles to food-approved granulate or flakes. Experts argue whether the recycled material should be in the form of granulate or flakes. Apparently the dirt of the incoming material (used bottles) are cause of the problem: Granulate, no doubt, are cleaned during the process of extrusion (Reference: Erema at APPE in Beaune) and is less sensitive for reprocessing. Clean(er) post-consumer bottles are needed to be fed into a flake production system. Cleaning afterwards, for instance by Gneuss filtration, in the preform system when injection moulding, is still considered critical. (Reference: Krones at Norpa Plast in Lille, owned by Alma Roxane). Blending virgin with recycled PET Industries have given themselves ambitious targets. It is common practice already to blend 25% recycled material when making new bottles. Danone targets 75% and Alma, in the forefront of the controversy with the “Syndicat”, targets even 100%. The highest targets set by the industries seem unrealistic or at least problematic. The volumes necessary can almost certainly not come from used bottles. Already today the requirements exceed supply. Apart from the 24.5%, which returns to the beverage industry, recycled PET is successfully used by other industries such as for fibre (52%) for sheeting (20%) strapping and others. If beverage receives more volume, fibre, sheeting, strapping and others will receive less. Visions Eco Emballage will have to collect more. Their focus will be on big towns, on high-rise apartment blocks. Valorplast will step up accordingly, is used as an educational tool as well. The waste prevention policy by municipalities seems to be counter-productive in this respect, since PET and recycled PET are valuable resources for industry providing work and employment. Géraud Delorme, Directeur Général of Valorplast, therefore warns: “There is a strong commitment from fillers and sheet makers to re-use PET. Big demand exists. The need might exceed the amount collected.” Géraud Delorme knows PET conversion and PET recycling from experience when he was Managing Director from 1996 to 2004 with what was then Amcor PET France, before becoming Director of Valorplast. His experience makes him the right man to bring the conflicting parties (syndicat and industry) to the table for the benefit of all. Reg i ona l mar ke t repor t France part 4 - Issue 12/2010 APPE Beaune, APPE Bierne, Retal","@ID":22} "imprint EDITORIAL PUBLISHER Alexander Büchler, Managing Director HEAD OFFICE heidelberg business media GmbH Landhausstr. 4 69115 Heidelberg, Germany phone: +49(0)6221-65108-0 fax: +49(0)6221-65108-28 info@hbmedia.net EDITORIAL Doris Fischer fischer@hbmedia.net Michael Maruschke Ruari McCallion Tony O´Neill Ilona Trotter Wolfgang von Schroeter Anthony Withers MEDIA CONSULTANTS Ute Andrä andrae@hbmedia.net Miriam Kiesler kiesler@hbmedia.net phone: +49(0)6221-65108-0 fax: +49(0)6221-65108-28 France, Italy, Spain, UK Elisabeth Maria Köpke phone: +49(0)6201-878925 fax: +49(0)6201-878926 koepke@hbmedia.net LAYOUT AND PREPRESS Exprim Kommunikationsdesign Matthias Gaumann | www.exprim.de READER SERVICES Kay Krüger reader@hbmedia.net PRINT WDW Druck GmbH Gustav-Throm-Straße 1 69181 Leimen-St.Ilgen Germany WWW www.petpla.net | india.petpla.net PETplanet insider ISSN 1438-9459 is published 10 times a year. This publication is sent to qualified subscribers (1-year subscription 149 EUR, 2-year subscription 289 EUR, Young professionals’ subscription 99 EUR. Magazines will be dispatched to you by airmail). Not to be reproduced in any form without permission from the publisher. Note: The fact that product names may not be identified as trade marks is not an indication that such names are not registered trademarks. 3 PETplanet insider Vol. 11 No. 11/10 www.petpla.net EDITORIAL dear readers, EDITORIAL This edition of PETplanet Insider 11/10 contains part 3 of our regional market report on France with reports on Evian and Danone, the Alma Group-Roxane, SBECM and Valorplast. The final Part 4 of “Focus on France” will follow – with reports on APPE in Beaune and Bierne and on Retal. We are gratified to have received so many positive comments from the market about our publications so far and thus feel that we should express our gratitude to those, who have made such reporting possible. At the risk of repeating ourselves, we have to say once again that indepth and comprehensive regional PET market reporting is possible only with the help and support of those industries actively working in these markets. In most cases the highest level of support comes from companies, mostly makers of machines and systems, who are successfully involved and eagerly engaged in their markets, and who, as a spin-off from the investigations carried out by PETplanet Insider, can see an opportunity to communicate with their customers. Referring to “Focus on France” readers should know: We owe our thanks to Eddy Fery from Husky and Bertrand Guillet from Sidel for their readiness to open discussions, as well as for organising tours and most of our visits. With them we took an insight look into PET France and visited prominent converters and fillers. (See our visit reports in PETplanet 10/10, to be continued in issues 11/10, and 12/10) Alain Viron from Netstal joined us at our meeting with PDG. The efforts of Martina Bottarel from Sipa were appreciated - shining an Italian light on this complex French PET market - , despite the fact that Schweppes-Orangina, Sipa’s important customer did not open the gates for PETplanet. The role of Krones in the PET markets of France may (we admit) be understated. We saw impressive Krones equipment in operation at CocaCola in Bierne and heard the controversial comments of Pierre Papillaud of Alma Roxane about the Krones recycling plant, but we failed to listen to the o-tone (o for original) from the local Krones people in Paris. Amongst others one more gentleman should be mentioned here: Geraud Delorme, Director General of Valorplast. Thanks are due to him for explaining concepts and systems of recycling PET in France. We understood through him that the re-processing and re-use of PET bottles is crucial for the future of the entire PET industry especially in this country. We are certain that only by these joint efforts and friendly co-operation could we write our stories and do justice to the French PET market and its participants. Yours, Wolfgang von Schroeter","@ID":5} "BOTTLING / FILLING 30 PETplanet insider Vol. 11 No. 11/10 www.petpla.net Bottle production from 100% recycled material ‘Green Plan’ for eco-friendly water bottling leadership Ice River Springs of Ontario, Canada, is in the final stages of installing their own PET recycling plant, which will produce its own 100% recycled PET for water bottles. The aim is to reduce its carbon footprint by closing the loop for plastics and re-processing post consumer PET that is currently either shipped overseas or applied in North America for single-use products. Shortage of rPET in the market In 2008, Ice River Springs launched its ‘Green Plan’: which incorporates a number of initiatives intended to make the company the most environmental friendly water bottler in the world. The strategy focuses on efficiency, renewable energy (primarily geothermal and solar) and packaging reduction. At the same time, the company also began to experiment with recycled resins. It purchased recycled resins from PET recycling specialist Phoenix Technologies and found that it was possible to make a 100% recycled PET bottle, but only if the resin was in pellet form. Flakes from rPET could not be processed with the demanded level of reliability – for example, it was unable to maintain constant pressure during preform production. In 2009, the company began selling water in bottles that contained rPET (either 100% or 50%) to some of their major Canadian customers. However, they quickly realized that there was a general shortage of available rPET in the market. Many Ontario recyclers are used to selling their baled PET bottles to Asia. The only way Ice River Springs could convert all of its products over to rPET plastic was if it could supply the material to itself; the company therefore decided to go for its own in-house PET recycling system. If successful, Ontario recyclers would no longer need to sell baled PET bottles to Asia, further reducing transportation emissions. Furthermore, purchases of PET baled plastic on this scale in Ontario would provide a stable demand for baled post consumer plastic, stabilising prices and making recycling centres more economically feasible. The equipment: washing line and pelletizing/SSP line The company proceeded to install two production lines. The first was the washing line, which was installed in a new facility located about 25km from the main factory. The facility is located on the existing trucking route for Ice River trucks in order to backhaul the baled material and minimize freight cost and emissions. It is designed to purchase PET bottles in baled form from recycling centres & bottle depots, sort them for colour, type of plastic and metal/paper content, wash them, grind them into flakes and then sort the flakes for colour and type of plastic. The final product is clean PET flake material. The equipment for the washing line was supplied by several different vendors, including Italy’s Amu and Ariostea; Titech of Norway; Sortex, from the UK; and others. The second line is the pelletising & SSP (Solid State Polycondensation) line, which is located in one of Ice River Springs’ existing bottling plants. It is designed to take clean PET flake material from the washing line, melt it down, send it through a melt filter and then pelletize it. The pellets are then sent into an SSP unit that removes contaminants. The","@ID":32} "Vol.6 PETplanet print PREFORM PRODUCTION 24 PETplanet insider Vol. 11 No. 11/10 www.petpla.net The Rapid Guide to Perfect Preforms by Rick Unterlander and Ottmar Brandau Troubleshooting guides have suffered in the past from being locked away in offices and not being available to the people that actually need them. Considering the high cost of machine and tools high scrap rates can be a costly proposition eating away at already tight margins. PETplanet’s “Rapid Guide to Perfect Preforms” takes a different approach. Bound in laminated paper that is easy to clean off, the small format of the book of 108mm by 151mm (4.25” by 6”) allows easy storage in back pockets or tool boxes. It has been written for the people on the floor of injection moulding companies to support their daily work in making the best preforms possible. The product of two industry experts, Rick Unterlander and Ottmar Brandau, it gives concrete advice on 35 of the most common problems in preform manufacture, most illustrated by pictures. From high AA levels to wavy bodies processors can find help when they need it. Read chapter 16 of the story... PETplanet print vol.6 The Rapid Guide to Perfect Preforms machine no./name 16. IV Loss Symptom: The resin IV (Intrinsic Viscosity) has been reduced by more than 0.04dl/g between resin and preform. This cannot be seen in the preforms, rather it needs to be tested in a laboratory with an IV tester or melt viscometer. Cause: The melt has been hydrolytically or severely thermally degraded during processing. Solutions: 1. Check dryer for alarms and correct as necessary. A high dewpoint (above –40ºC (–40ºF)) may cause extrusion problems and must be rectified. The resin must be dried below 50ppm of water to minimize IV loss during melting. 2. Check for adequate resin drying time in hopper (should be around 4h at 175ºC (347ºF) and up to 6h at 160ºC (320ºF)). 3. Check all temperature readings and correct if necessary. PET resin should be melted at about 280ºC (536ºF) +/- 10ºC (18ºF). Excessive temperatures may degrade the melt. 4. Check all %-controlled temperature settings and minimize if possible. %-controllers provide no temperature feedback and require fine tuning. 5. Check that all thermocouples are properly inserted and contacting the bottom of the wells. 6. Check extruder back pressure and minimize if possible. Back pressure should be sufficient to provide good melt mixing, but not too much to cause excess shear. Typical range is 15 – 20bar (200 – 300psi). 7. Check screw rpm and minimize if possible. Screw speed should be reduced as much as possible to minimize shear heating, yet still recover within the cycle time of the machine. The stopped time at the end of recovery should be about 2sec to offset any fluctuations during screw recovery. 8. Check to ensure incoming resin IV was within specification (resin supplier). 9. Check hardware for worn, damaged or failed components, specifically the resin handling and storage area for excess moisture (silos), dryer hopper (especially the cone), resin in-feed line, and machine and mould heaters.","@ID":26} "PREFORM PRODUCTION 29 PETplanet insider Vol. 11 No. 11/10 www.petpla.net Y O U R PA R T N E R F O R B L O W M O U L D S . Benef i t of 30 Years of Exper ience in Blow Mould Manufactur ing! Sidel • SIG • Krones • SIPA • MAG • ADS • Kosme • Nissei a. o. Röders GmbH / Scheibenstr. 6 / 29614 Soltau / Germany / www.roeders.de Telephone +49 5191-603-53 / Fax +49 5191-603-36 / E-Mail mold@roeders.de For our subsidiaries in China, USA and Latin America please check our website. PET STRETCH BLOW MOULDS VISIT US Hall 5 Booth 419 Nov. 10 - 12, 2010 Table of Contents i. ................. About the Authors ii. ..........................Introduction Chapter 1.. ......................AA Level High 2.. ................ Accordion Preform 3.. ...............Air hooks / Streaks 4.. ....................... Black Specks 5.. .............................. Bubbles 6.. ..........................Burn Marks 7.. .....Colour Streaking / Peeling 8.. ..........................Crystallinity 9.. ........................ Drool Marks 10.. .................................. Flash 11.. ................. Gate Depressions 12.. ....................... Gate Peeling 13.. ......... Gate Voids / Pin Holes 14.. ................. Internal Gate Sink 15.. ........................Internal Sinks 16.. ................................ IV Loss 17.. ....................Long Gate Nub 18.. .......................Milky Preform 19.. .................... Moisture Marks 20.. ....... Neck Finish out of Round 21.. ............... Parting Line Crease 22.. ........ Parting Line Deformation 23.. ................. Preform Yellowing 24.. .......................... Short Shots 25.. .................................. Sinks 26.. ................................. Splay 27.. ................... Stretched Necks 28.. ............................. Stringing 29.. .................Surface Blemishes 30.. ................. Thread Flow Lines 31.. TSS (Top Sealing Surface) Sink 32.. ...............................Unmelts 33.. ........ Wall Thickness Variation 34.. .........................Wavy Body 35.. ..........................Weld Lines prices in EUR + VAT. 1- 3 exemplar each 129,- € 4 - 10 exemplar each 99,- € 10 exemplar each 69,- € fax: +49 (0) 6221-65108-28 info@hbmedia.net www.petpla.net Order your copy now! Spiral Binding Laminated Cover Sheet Tape and eyelet for easy hanging","@ID":31} "TRADE SHOW PREVIEW 34 PETplanet insider Vol. 11 No. 11/10 www.petpla.net Brau Beviale 2010 in Nuremberg, Germany will host 1,400 exhibitors. At this year’s important exhibition for the beverage industry some 34,000 visitors from November 10–12, 2010 are expected at the fairground in Nuremberg. At hall 7A at Brau Beviale the Exhibitors Forum and the two theme pavilions are located. The “Energy & Water” theme pavilion, which is organized together with the Competence Pool Weihenstephan of Munich Technical University, focuses on renewable energy, rational energy conversion, cogeneration units, contracting, disinfection, and recovery, analysis and treatment of water. The “Future Beverage Industry 20XX” theme pavilion ventures a look into the future of the beverage industry. The beverage industry faces great challenges: How can costs be cut? What technologies help to increase production? How can quality management be improved? Wirtschaftsvereinigung Alkoholfreie Getränke (wafg), the German employers association of non-alcoholic beverage manufacturers, offers a workshop for its members and exhibition visitors. The exchange of opinions on “Beverage packages – Challenges for beverage producers” starts at 2 p.m. on Thursday afternoon (11.11.) in the Neu-Delhi room of CCN Ost. The PETnology Europe Conference in Tokio hall of CCN Ost will take place on Monday and Tuesday before the exhibition starts (8./9.11.). The exhibition centre will be open from 9 a.m. to 6 p.m. In this tradeshow preview we bring you a short preview of the exhibitors of particular interest to Pet bottle fillers. KHS Combined operator-machine interface KHS Gmbh will be showing its newly-developed HMI (human-machine interface) machine operator system, which the company developed in collaboration with Fraunhofer IAO Institute. The graphic design of the interface is the work of Projekttriangle Design Studio. KHS says that the new HMI is that it brings together a number of machine operator interfaces to form a uniform system. Both individual machines and entire production lines can be controlled and monitored on a single interface. The company says this is a first. The user interface is claimed to offer greater ease-of-use, with recognisable and easilymemorable icons and clear, interactive handling instructions. The HMI system has been conferred a ‘red dot’ quality award by Design Zentrum Nordrhein-Westfalen. www.khs.com Hall 5 | Booth 127 Aptar Food + Beverage Caps and closures solutions Aptar Food + Beverage is part of the Aptargroup family of companies, along with Aptar Beauty + Home and Aptar Pharma. It designs, develops and manufactures dispensing systems for leading food and beverage manufacturers. Aptar will be exhibiting a range of dispensing solutions and will be talking to visitors about its global distribution and support network, as well as discussing tailor-made and specialized solutions for the beverage market. www.aptar.com Hall 4 | Booth 336","@ID":36} "TRADE SHOW PREVIEW 37 PETplanet insider Vol. 11 No. 10/10 www.petpla.net Dr Thiedig + Co KG Oxygen measuring equipment Berlin-based company Dr. Thiedig+Co KG will present Digox 6.1, the latest example of its oxygen analyzing equipment for beverages. It is available in either stationary or portable forms. TPO – total packaging oxygen – measurement can be integrated into the machine as an option. The company says that the machine offers clear and intuitive control systems, which are optimised for daily operational procedures. Results of total oxygen calculations in bottles and cans is available after only 10min. Up to 500 data sets can be saved internally, prior to direct loading onto a PC for documentation and evaluation. The Digox 6.1 is used for measuring oxygen in laboratories and in-line, for example at the storage tank, after filtration, at the filler and for material deliveries. The machine features direct measurement of oxygen by means of the membrane-less Thiedig sensor and built-in, automatic Thiedig Active Calibration. The measuring electrode is in direct contact with the measuring medium and can respond to changes in the oxygen concentration in less than 10s. www.thiedig.com Hall 4 | Booth 322","@ID":39} "MATERIAL / RECYCLING 22 PETplanet insider Vol. 11 No. 11/10 www.petpla.net Melt-To-Resin (MTR) technology - Elimination of the solid-state post-condensation (SSP) process Cost-efficiency in PET resin production (USA) in September 2009, with the second line coming on-line in June 2010. MTR technology eliminates the need for solid-stating: High-molecular PET material with almost the required intrinsic viscosity is obtained directly during melt polycondensation by means of a special high-viscosity finishing reactor - the so-called Discage MV Reactor. The chief advantage of the MTR technology is that the cost-intensive SSP stage is no longer required. Major savings relate to a reduction in electrical and heating energy due to the following: there is no heating of the PET precur- sor chips as solid-stating is eliminated the nitrogen circuit with its booster blowers and nitrogen purification unit is also eliminated for the same reason the 2-reactor melt-phase process replaces multi-stage reactor cascades the so-called Espree reactor does not require agitators process steam is used to generate a vacuum by means of steam jets. It is said that this proprietary technology from Uhde Inventa-Fischer improves the energy efficiency of PET production by about 40% compared to the conventional route with an SSP stage. In addition, preform manufacturers and bottle producers appreciate the high quality of MTR resin, and many well-known brand owners have approved MTR resin for their bottle production. Recent experience also indicates that converters may benefit from the fact that less energy is required for melting MTR resin due to its significantly lower degree of crystallinity compared to SSP material. Flake-To-Resin (FTR) technology - Uniform virgin-like bottle resin from recycled PET flakes Flake-To-Resin (FTR) technology is Uhde Inventa-Fischer’s proprietary recycling technology for food-grade PET packaging. FTR has been cleared by the US Food and Drug Administration (FDA) for food contact applicaPET production plant using MTR technology PET is produced by polymerising the feedstocks purified terephthalic acid (PTA), isophthalic acid (PIA) and ethylene glycol (EG) using a melt polycondensation process. Conventional routes have commonly required a subsequent solid-state post-condensation (SSP) step to further increase the molecular weight of the polymer. During this so-called solid-stating, PET precursor chips are typically subjected to a temperature above 210°C, and a counterflow of purified nitrogen is used to avoid polymer degradation. However, the SSP stage is energyconsuming and as it is an extra step, it also has the disadvantage of requiring additional plant equipment and operating personnel. MTR - technology In 2007 Uhde Inventa-Fischer’s MTR technology was introduced to the PET industry. Three world-scale MTR plants with a total production capacity of more than 800,000t/a have already come on-stream. The world’s biggest MTR plant was commissioned for Indorama in Alabama Energy costs have become a crucial cost factor for producers of PET. Annual energy costs can amount to up to 8 million euros for an output of 200,000t/a and in general, energy prices are expected to increase even further. Low energy consumption during the production of PET bottle resins therefore creates a competitive advantage for PET producers. New technologies from Uhde Inventa-Fischer, such as the Melt-To-Resin (MTR) technology and the Flake-To-Resin (FTR) technology, help PET producers to improve energy efficiency.","@ID":24} "REGIONAL MARKET REPORTS 10 PETplanet insider Vol. 11 No. 11/10 www.petpla.net Part 3 France by Wolfgang von Schroeter The tour through through France went into second week, when visiting the big fillers Evain/Danone and Alma-Roxane. From SBECM we learned that PET converters need to adjust to smaller markets in France. With Valorplast the very vital and sensitive topic of recycling PET in France received attention once more high lighting the political and technical conflicts as well as the need of exceeding amounts of used bottles to be collected. March 25, 2010 Evian (Danone) in Amphion-Les-Bains at Evian Evian (Danone) “We chose PET for environmental reasons.” Sophie Dournier-Delamare, Evian Public Relations Department Regional market reports France Part 3","@ID":12} "BOTTLE MAKING 33 PETplanet insider Vol. 11 No. 11/10 www.petpla.net Time Company Speaker Topic November 18th 2010 10:00 am - 11:00 am Block 1 - Beverage packaging in PET Part 1 10:00 am - 10:30 am M&G Finanziaria S.r.l. Ms Cécile Bourland Poliprotect, technical innovation in PET 10:30 am - 11:00 am Piovan S.p.A. Mr Giorgio Santella Energy efficient solutions for PET preform production 11:00 am - 12:00 am Block 2 - Beverage packaging in PET Part 2 11:00 am - 11:30 am Netstal-Maschinen AG Mr Stefan Bock Performance of PET preform production system 11:30 am - 12:00 am Sidel Group Mr Torsten Kaiser Packaging of sensitive beverages in PET 12:00 am - 01:00 pm Block 3 - Beverage packaging in PET Part 3 12:00 am - 12:30 am GEA Process Engineering India Mr Valerio Cazzato Filling aseptic 12:30 am - 01:00 pm Atlas Copco (India) Ltd. Mr Aneek Roy Energy efficient ways of using compressed air in bottling 01:00 pm - 02:00 pm Break 02:00 pm - 03:00 pm Block 4 - Caps and closures for beverages 02:00 pm - 02:30 pm Sacmi Mr Rajesh Sharma Closures - New developments 02:30 pm - 03:00 pm Company to be confirmed Speaker to be confirmed Topic to be confirmed 03:00 pm - 04:00 pm Block 5 - Water treatment 03:00 pm - 03:30 pm EUWA H.H. Eumann GmbH Mr Michael Eumann Best available technology in brewery water treatment 03:30 pm - 04:00 pm Norit N.V. Mr Oliver Meckler Norit AirLift MBR – Wastewater reuse in breweries 04:00 pm - 05:00 pm Block 6 - Technology in dairy packaging and processing 04:00 pm - 04:30 pm Colormatrix Europe Ltd. Mr Luc Vervynck Technology in dairy packaging processing 04:30 pm - 05:00 pm Siemens AG Mr Pratish Sheth Integrated solutions for maximum efficiency November 19th 2010 10:00 am - 11:00 am Block 7 - Hotfill technology 10:00 am - 10:30 am KHS GmbH Mr Frank Haesendonckx Cost optimization in PET hotfilling by challenging technology 10:30 am - 11:00 am Krones AG Mr Hans Hiendl Hot processing and filling: Soft drinks and fruit juices with/without fruit pieces and slurry 11:00 am - 12:00 am Block 8 - Brewing and beverage technology Part 1 11:00 am - 11:30 am Vin Service Dispensing Group Mr Riccardo Guadalupi News and advantages using draught beverage technology 11:30 am - 12:00 am Denwel EU s.r.o. Mr Marc Bolliger Efficient water deaeration and precise high gravity blending 12:00 am - 01:00 pm Block 9 - Brewing and beverage technology Part 2 12:00 am - 12:30 am Norit N.V. Mr N. Ashok Babu Norit's clean & sustainable brewing and beverage technology 12:30 am - 01:00 pm Danfoss Industries Pvt. Ltd. Mr John Unbehaun VLT Conveyor solutions - OneGearDrive and FC/D 302 Inverters for the beverage industry 01:00 pm - 02:00 pm Break 02:00 pm - 03:00 pm Block 10 - Brewing and beverage technology Part 3 02:00 pm - 02:30 pm Ziemann India Pvt. Ltd. Mr Arun Kumar Engineering and design of turn-key breweries 02:30 pm - 03:00 pm Institute Of Brewing And Distilling Mr Simon Jackson Why technical education and qualification are integral to production excellence 03:00 pm - 04:00 pm Block 11 - Beverage packaging in cartons, cans and glass Part 1 (Duesseldorf Fairs) 03:00 pm - 03:30 pm Sacmi Mr Satish Kanaginhal Complete solution for PET bottling line 03:30 pm - 04:00 pm Company to be confirmed Speaker to be confirmed Topic to be confirmed 04:00 pm - 05:00 pm Block 12 - Beverage packaging in cartons, cans and glass Part 2 (Duesseldorf Fairs) 04:00 pm - 04:30 pm Company to be confirmed Speaker to be confirmed Topic to be confirmed 04:30 pm - 05:00 pm Company to be confirmed Speaker to be confirmed Topic to be confirmed Data are subject to change. Final version expected for 08.11.2010 Exhibitor forum","@ID":35} "PETpatents www.verpackungspatente.de 44 PETplanet insider Vol. 11 No. 11/10 www.petpla.net Tool for bottle manufacture International Patent No. WO 2010 / 058098 A2 Applicant: Sidel Participations, Octeville sur Mer (FR) Date of Application: 17.11.2009 The patent describes the structure and the function of a tool for manufacturing a plastic bottle with a specially moulded floor area. Folding bottle International Patent No. WO 2009 / 027224 A2 Applicant: Nestlé Waters Management & Technology, Issy-les-moulineaux (FR) Date of Application: 12.8.2008 Plastic bottle with reversible compression facility through integrated fold lines to save space in transport, storage and return operations. Once on site, the bottle can subsequently be easily restored to its original shape. The application has been filed internationally. Reinforcing ribs International Patent No. WO 2010 / 053251 A1 Applicant: CJ Cheildjedang Corp., Seoul (KR) Date of Application: 24.8.2009 Oval plastic container with resealing cap. The container, which is of “lightweight / thinwalled” construction is fitted with specially mounted reinforcing ribs to provide optimum protection for the product during transport and storage. Drinks container International Patent No. WO 2010 / 054734 A2 Applicant: Schäfer Werke GmbH, Neunkirchen (D) Date of Application: 20.10.2009 Simple construction, easy to operate container made from PET with a compressed gas cartridge (also made from PET) for storing and discharging liquids. Preform with pourer International Patent No. WO 2010 / 054059 A1 Applicant: Procter & Gamble Comp., Cincinnati (US) Date of Application: 5.11.2009 Concept and process for manufacturing a preform with an integrated pourer has been registered internationally. Based on this preform, even bottles of different shapes can be manufactured / blow moulded. Beverage pouring spout European patent granted No. EP 1966059 B1 Applicant: Bapco Closures Research Ltd., Woking (GB) Date of application: 19.12.2006 A reduced weight, resealable hinged closure designed to be screwed onto a bottle is described in this application. The tamper evident closure is designed for use as a one-handed sports cap.","@ID":46} "MATERIAL / RECYCLING 23 PETplanet insider Vol. 11 No. 11/10 www.petpla.net tions. The technology can be integrated into production plants which use the above-mentioned MTR technology. The FTR technology consists of two steps: Firstly, impurities are eliminated and then the PET bottle resin is reformed. In the first step, post-consumer PET flakes are melted and ethylene glycol is added to the melt to partially depolymerize the PET molecules. The long PET molecular chain is broken into smaller sections, which reduces the viscosity of the polymer melt. Then a fine filtration of the low-viscosity melt removes impurities. In the second step, the partially depolymerized PET is blended with virgin prepolymer during the polymerization process and the low-molecular-weight material is polymerized to PET bottle polymer. The process leads to a virgin-like bottle resin which is ready for use in preform production and does not need blending at the preform production site. The blend uniformity of the resin is even reported to be superior to mixes of recycled and virgin pellets. As the post-consumer bottle flakes used in the FTR® process can replace up to 50% of PET production feedstocks, the resulting feedstock cost savings can be added to the profit usually made with a conventionally designed PET plant. www.uhde-inventa-fischer.com Enjoy completeness Sacmi Imola S.C. Via Selice Prov.le, 17/a 40026 Imola (BO) Italy Tel. +39 0542 607111 - Fax +39 0542 642354 E-mail: sacmi@sacmi.it www.sacmi.com Sacmi offers turnkey solutions for the beverage and packaging industry: complete bottling lines for product preparation, container manufacture, filling and closing, labelling and final packaging operations. The extensive experience acquired since the company was established in 1919, in addition to its reputation for supplying advanced technology, financial solidity and a network of 70 companies throughout the world, enables Sacmi to meet all your requirements wherever you are. Melt-To-Resin (MTR) process Flake-To-Resin (FTR) process","@ID":25} "BOTTLE MAKING 32 PETplanet insider Vol. 11 No. 11/10 www.petpla.net dti India Around 90 exhibitors from twelve countries are presenting their products and services on a total of 1,300 m² of exhibition space – drink technology India (dti), which is taking place in Mumbai at ‘Bombay Exhibition Centre’ from November 18 to 20, 2010 The companies represented at dti are displaying the complete range of beverage and liquid food technology. There is a special focus on the requirements of the Asian, and especially the Indian, market, with trade visitors from India and the adjacent regions being specifically targeted. The organiser of dti is MMI India, a subsidiary of Messe München International (MMI). “In this region there is a huge demand for the latest technology for producing, filling and packaging beverages and liquid food. Our aim is to bring this demand and the technological solutions of the Western industrial countries in particular together in the place where that demand is,” explains Petra Westphal of MMI, who is responsible for drinktec, the world’s leading trade fair for beverage and liquid food technology held in Munich, and also for dti. And many well-known drinktec exhibitors will also be present at dti. Exhibitor forum Information on current products and innovations is available to trade visitors both at the exhibitors’ stands and in the Exhibitor Forum, where representatives of the exhibiting companies present their products and solutions. The lectures are divided into blocks of topics and you can view the topics and speakers in the table on the next page. In parallel with dti, one of the world’s leading research institutes in the brewing industry, the Versuchs- und Lehranstalt für Brauerei (VLB), based in Berlin, is holding a three-day seminar aimed at technical managers from breweries and beverage producers. Joint trading platform with International PackTech India After two events held in 2007 and 2008, both planned as conventions with an accompanying exhibition, dti is taking place as a trade fair in Mumbai for the first time. The progression from convention to trade fair has also necessitated a change of venue, and dti is moving from its previous location of the Grand Hyatt Hotel lobby to the Bombay Exhibition Centre. International PackTech India (www.packtech-india.com), organised by Messe Düsseldorf and its subsidiary Messe Düsseldorf India, is taking place at the same time and at the same location as dti. Trade visitors will greatly benefit from this merger, because the two fairs will form a large joint trading platform for customers from both the packaging and the beverage and liquid food industries. www.drinktechnology-india.com On 18 November drink technology India will take place in the Bombay Exhibition Centre for the first time A. Ziemann Gmbh | Abc Compressors - Arizaga Bastarrica Y Cia, S.A. | Ace Technologies | Advance Info Media & Events | Advanced Enzyme Technologies Ltd. | Ambicon Brewpub Pvt Ltd | Amd Industries Ltd | Anton Paar India Pvt. Ltd. | Atlas Copco Compressor Sales | Barry Wehmiller International Resources Pvt Ltd | Brauwelt International (Fachverlag Hans Carl) | Buhler (India) Pvt. Ltd. | Centec Rrr Systems And Sensors Private Limited | Cipriani Harrison Valves Pvt. Ltd. | Closure Systems International (I) PrivatE Limited | Colormatrix | Danfoss Industries Pvt. Ltd. | Dase-Sing Packaging Technology Co., Ltd. | Della Toffola Spa. | Digmesa Ag | Doemens Academy Gmbh | Dsm Food Specialities | Dw Plastics N.V. | Ecokrin Hygiene Pvt Ltd | Euwa Water Treatment Plants | Food, Marketing And Technology | Food And Processing World | Gardner Denver Ltd | Gea Process Engineering (India) Pvt. Ltd. | Globalmalt Gmbh & Co. Kg | Gruppo Mossi & Ghisolfi - M&G Finanziara S.R.L. | Guangzhou Vanta Packing Machinery Co. Ltd | Haendler & Natermann Gmbh | Holland Colours | Hypro Engineers | The Institute Of Brewing & Distilling | Jiaxing Haoneng Packing Co., Ltd. | Khs Gmbh | Khs Machinery Pvt. Ltd. | Kieselmann Gmbh | Kosme Srl Unipersonale | Kraussmaffei Technologies Gmbh | Krones Ag | Lambrechts N.V. | Lehui Industry | Magplastasia Pvt Ltd | Manifattura Tubi Gomma S.P.A. | Manjushree Technopack Limited | Mht Mold & Hotrunner Technology | Mold-Masters Technologies (P) Limited | Moretto S.P.A. | Netstal-Maschinen Ag | Nexgen Drying SystemS Pvt. Ltd. | Norit India Pvt Limited | Nsf International | Parle Agro Pvt. Ltd. | Petplanet Insider, Heidelberg Business Gmbh | Piovan India | Polyone Polymers India Pvt. Ltd. | Praj Industries Ltd. | Processed Food Industry | Radical Waters | Reliance Industries Ltd. | Repi S.P.A. | Sacmi | Saffron Media Pvt. Ltd. (Food And Beverage News) | Sap Media Worldwide Limited | Schulz, Kaspar | Sidel India Pvt.Ltd. | Siemens | Spiritz | Srithai Superware Public Company Limited | Tech-Long Packaging Machinery Ltd. | Technopet Industries | Times Infomedia | Trade4india.Com | Tradeindia.Com | Vacuum Barrier Systems Sprl | Vibrofloors World Group | Vin Service Dispensing Group | Vlb Berlin | Weyermann® Specialty Malts | Wittemann India | Yudo Hot Runner India Pvt. Ltd. | Ziemann India Pvt. Ltd. | Ziemann Ludwigsburg Gmbh | Exhibitors November 18 - 20, 2010","@ID":34} "25 PET bottle-to-bottle recycling plants Caps and closures Conveyers for preforms and empty bottles Preforms Preform moulds and SBM moulds Two-stage SBM machinery Preform and single stage machinery Resins and additives Filling equipment Compressors Suppliers of filling equipment for beverages in PET Our detailed survey, in a special edition of PETplanet devoted to the Brau – Beviale trade fair, includes some of the best known suppliers of filling equipment for PET bottles. Most of the manufacturers are based in Italy (GEA Procomac, Sacmi, Sidel and Sipa, closely followed by Germany (Krones and KHS) and one company from USA, Fogg Fillers. The requirements for the equipment are high: amongst them, reducing operating costs, saving space, increasing plant efficiencies, and implementing the latest technologies to take into account the most stringent hygiene and health and safety regulations. The aim is to achieve needs-based solutions for various drinks and package sizes. For this reason the range of machinery offered by individual companies is correspondingly large. It goes without saying that every company offers various special features with their systems: unfortunately, for reasons of space, we are unable to provide full descriptions. Full details of the various machines and optional equipment can be obtained from the relevant company. Whilst the publishers have made every effort to ensure that the information is up to date, no claims are made regarding completeness or accuracy. 11/10 MARKETsurvey Company name Sipa GEA Procomac SpA Postal address Telephone number Web site address Contact name Function Direct telephone number Fax E-Mail via Caduti del Lavoro n. 3 31029 Vittorio Veneto (TV) Italy 0039 0438 911511 www.sipa.it Matteo Tagliaferri Marketing and Communication +39 0438 912273 +39 0521 548111 matteo.tagliaferri@zoppas.com Via Fedolfi, 29 43038 Sala Baganza (Parma) - Italy +39 0521 839411 www.procomac.it Flavio Slavadori Sales Director +39 0521 839490 +39 0521 833879 flavio.salvadori@geagroup.com 1. Machine designation / model number Isofill P Isotronic Stillfill S Stillfill R\\HR Unitronic 2. Number of filling heads (range: from/to) 20-160 40-160 20-130 20-130 20-130 24 -168 3. Filling speed/output - based on 1 litre PET bottles a. Still water (1 litre bph) 60,000 63,000 63,000 No 63,000 12,000 - 60,000 b. Carbonated drinks with 8 g CO² (1 litre bph) 51,000 (CMW) 60,000 (CMW) No No NO 8,000 - 48,000 c. Milk (1 litre bph) No No No No 45,000 (Fresh Milk) 6,000 - 48,000 d. Fresh fruit juice (1 litre bph) 45,000 (Clear) 50,000 (Clear) 63,000 (Clear) 48.000 45,000 (Clear) 6,000 - 60,000 4. Filling process Pressureless (still drinks) Yes Yes Yes Yes Yes Yes Pressure filling (carbonated drinks) Yes Yes Yes Hot filling Yes Yes Cold aseptic filling Yes Juices with high pulp content Yes Yes 5. Type of filling valve and metering system Isobaric mechanical level filling valve Isobaric volumetric filling valve Mechanical gravity filling valve Mechanical gravity filling, valve with recirculation Gravity volumetric filling valve Mechanical, electronic with flow measuring","@ID":27} "TRADE SHOW PREVIEW 35 PETplanet insider Vol. 11 No. 10/10 www.petpla.net This amazes even the professionals: oval shapes can also be blow-moulded. Using ProShape – the latest module for the kronesContiform. www.krones.com Brau Beviale 2010 Nürnberg 10 – 12 November Hall 7A, Stand 206 Kiefer Werkzeugbau GmbH Full design, process development and mould-manufacturing Kiefer will be showcasing ist full range of services at Brau Beviale. Over the past 20 years the company has expanded to become a toolmaking specialist, focused on plastic processing. An independent toolmaker, Kiefer produces round running stretch blow machines that are used on equipment from companies such as Krones, Sidel, KHS/SIG and Sipa; and linear stretch blow machines deployed on equipment from Sipa, Kosme, ADS and Tetra Pak. Kiefer says that it provides complete design, process development and mould-manufacturing is in close collaboration with customers. It is currently focused heavily on design for weight reduction in PET bottles. www.kiefer-mold.de Hall 5 | Booth 407 Sidel Developments in labelling, pasteurisation and energy reduction Sidel Group says that it has doubled investment in R&D since 2007. It will be showing some results of that expenditure at Brau Beviale 2010, under the themes of sustainability, saving and flexibility. The company’s stand will feature Sidel’s recent developments in labelling solutions for self-adhesive, cold glue, sleeve and roll-fed applications. The goals with its latest offers in these areas are to improve flexibility, raise productivity and enhance quality. The stand will feature a new pasteurisation solution that the company claims delivers savings in both water and energy usage. Visitors to the Sidel stand will also be able to discuss the company’s ECO Services offer, which is aimed at optimising existing machines’ productivity while reducing energy use. www.sidel.com Hall 5 | Booth 121","@ID":37} "zoom zoom fax: +49-6221-65108-28 info@hbmedia.net www.petpla.net ANA LY S I S OF A L L E S S ENT I A L P E T BOT T L E COMPONENT S WOR L DWI D E PETpla.net Zoom sheds light on the mysteries surrounding the manufacturing processes of leading PET bottle manufacturers and provides a comprehensive analysis of the PET bottles of this world. Get the results online. Professional. Precise. Up-to-date. Global. Join the inner circle and become a real insider! a Why not give it a try, and download some sample data? Go to zoom.petpla.net ! It’s sure to impress! PETpla.net Zoom Analysis of all essential PET bottle components worldwide Photo: ©suzannmeer - Fotolia.com","@ID":30} "REGIONAL MARKET REPORTS 12 PETplanet insider Vol. 11 No. 11/10 www.petpla.net Product and production 1,100 people in total. 950 employees in the factory operating three shifts. Site of 52 hectares of which 91,000 m2 is covered by buildings PET resin converted: about 100,000t/a 75% virgin and 25% recycled PET granulate are currently being used. 50/50 being targeted in two further steps. Recycled material is obtained from France Plastiques Recyclage, in which Danone has a stake, in order to secure constant quality and continuous quantity. Preforms are made 100% in-house on 11 Husky systems with cavities of 32 (one unit), 48 (6 units) and 96 (4 units). A total of 14 filling lines 12 lines for blowing/filling PET bottles with all downstream equipment and representing 94% of the filled volume 1 line for filling glass bottles with downstream equipment and representing 5% of the filled volume 1 line for filling sprays and representing 1% of the filled volume. Blowers All blowers are from Sidel. Of the 12 PET lines 3 are Combibloc blowing/filling systems from Sidel. 2 of the Combiblocs are running in parallel with same downstream equipment. Average capacity per PET line is 36,000bph. Large AGVs (Automated Guided Vehicles) move pallets between lines and to and from the storage area. Evian, with 11km of railway track on its land, is committed to ship 70% of production by rail, in line with the Evian “Eco system”. By rail the waters travel to several distribution centres for domestic sale and also for export. Bottle formats: 0.33l, 0.5l, 0,75l, 1l, 1.5l and 2l. Production figures: 100t of PET converted per day (maximum) 20,000 preforms per hour per moulding machine (maxi- mum) 4.5 million preforms produced per day (maximum) 24,000bph per machine (average) for bottles weighing between 11g and 40g. 6 million bottles filled each day (maximum) 1.45 billion bottles filled in 2009 1.3 billion litres filled in 2009 energy savings, rail transport; what is called an Eco package. Recycling, actively pursued in general, targeting 50% and eventually 100% of recycled material to be used for new bottles (bottle-to-bottle); waste management. Carbon footprint (CO 2 ) reduction to near zero in the production of Evian; compensation measures for remaining CO 2 (e.g. re-plantating of mangroves in Senegal); carbon neutral by 2011. The above “great plan” is beneficial to the productivity of Evian’s plant. It is also intended to improve the acceptability of the company and the product by the public. The Evian statement about PET is very much in contrast to the governmental approach: “We at Evian chose PET because of our environmental commitment. It is the safe material to protect the purity and quality of our waters.” History The first water was found and bottled in 1789. The waters in the following years were used as part of a cure for sick patients. Behind Danone stand two extraordinary personalities: Daniel Carasso, who sold the first yoghurt under the Danone brand in 1919. In 1966 Danone produced 580 million servings of yoghurt per year. Antoine Riboud, who in 1966 was Chairman and Chief Executive of the newly created BSN, the second largest manufacturer of glass of France, before divestment. In the 1970s BSN took up a position in the food industry by acquisition and mergers. Both were bold, visionary entrepreneurs who met in 1972 and decided to unite their businesses, making Danone a global brand. A new plant for Evian waters was built in Amphion-lesBains, 7 km from Evian-les-Bains. Bottling was done in glass and clay jars. PET arrived at Evian in 1981 and was mainly used for exports to the US market in 1 litre formats. In the mid 1990s there was a changeover from PVC to PET. The BSN Group changed its name to Danone to reflect the international nature of the business. The Group today: €14.982 billion sales in 2009. Danone proudly claim: World number 1 in fresh dairy products. World number 2 in bottled waters World number 2 in baby nutrition European number 1 in medical nutrition SAEME (Societé Anonyme des Eaux Minérales d’ Evian) is part of the Bottled Waters Division of the Danone Group in France, with net sales in 2007 of € 1.9billion in total and 2,600 employees in France - sources production from several springs located in France. The leading brand in volume terms is Evian with its very famous name in bottled water. There are also Volvic, Badoit, Salvetat.","@ID":14} "REGIONAL MARKET REPORTS 19 PETplanet insider Vol. 11 No. 11/10 www.petpla.net For further information, visit www.khs.com/service KEEPING YOUR LINE RUNNING IS WHAT WE STAND FOR. Long lasting, safe, and efficient: Original spare parts from KHS. Come and visit us at the Brau Beviale Hall 5 Booth 127 Formats: Smallest size: 15 grams for 0.33l bottles Greatest size: 91 grams for 5.0l bottles Preforms and caps for the well-known commodities - CSD, water, juice. Plans exist for packaging milk and wine. Barrier moulding is also under consideration, especially for wine. French customers include the Nestlé Group (Perrier, Vittel). Exports to the UK, Germany, Spain and the Caribean. 40 employees of which 15 are in the PET production area, and 12 for caps and closures. Equipment 8 Husky preform systems, 300t clamping force, 48//60/72 cavities. Production is fully-automated. Pallets for 300kg bins moving in and out of production room, to and from outside storage on automated conveyors. Production facilities are temperature and humidity controlled. Incoming air is filtered. All aimed at ensuring a top quality product. 14 Netstal and Ferromatik injection moulding machines for caps and closures each with 48/72 cavities. Jean-Luc Didouan comments, “No independent converter needs more than 72 cavities in a machine.” Company future In the 27 years of preform manufacturing, the company has grown continuously with the market, until 5 years ago, when the market started to decline. In France, with the water and CSD producers moulding 70% and more of their own requirements the available markets for converters is getting even smaller. Jean-Luc Didouan: “The biggest markets are decreasing. We are not inactive and are looking for alternatives. Lightweighting and the use of recycled material are no miracle solutions for a small company like ours. Part of the decline we can and must compensate by in-house measures such as increased productivity but we also have to look for other applications. As a private company we are flexible, can adjust and must adjust.”","@ID":21} "PETproducts 42 PETplanet insider Vol. 11 No. 11/10 www.petpla.net Energy-saving cap feeder Sidel has launched a new range of cap feeders, named Aidlin Eco, which it says are designed to consume as little as one-tenth the electricity used by traditional models. The new feeder does not use air for any functions, including cap propulsion and off-spec products. However, the company claims that Aidlin Eco is capable of producing flat caps at a rate exceeding 120,000/h – more than five times the speed of its predecessor, the Aidlin Premier. The well-established cap orientation principle is maintained. Caps are carried from a large storage hopper towards an adjustable speed bump by cleats, linked together by an articulated chain. The speed bump inclines the cleats and gravity makes poorly oriented caps fall out. The chain has a lateral curvature; after the speed bump, the caps enter a corridor that guides them to a wheel for sorting and elevation. Any units that are poorly oriented or missing tamper-proof rings are automatically ejected via a magnetic finger system. On-spec caps are continuously conveyed by the wheel, which is equipped with a brushless motor, and then elevated in a vertical column to the required height and direction in order to feed the capper. The new range’s electricity consumption, including the off-spec cap ejection system, has been cut by 90%, compared to standard compressed-air cap feeders, and by 50%, compared to the ventilated-air cap feeder. The installed power is 0.7 kW. www.sidel.com W. Amsler Equipment’s ‘one-stop shop’ for liquid filling machinery W. Amsler Equipment Inc., the Canadian manufacturer of all-electric, reheat stretch-blow moulding machines and related equipment, has expanded its custom line of filling equipment with the announcement of a single-source service for turnkey filling operations. The company’s solutions are targeted for tight manufacturing footprints, expansion of existing filling lines, and turnkey operations. Amsler produces equipment for a broad range of liquid filling applications including beverage, edible oil, household cleaners, and pharmaceuticals. Its rotary monoblock filling lines are made of stainless steel and all rinsing, filling, and capping operations are enclosed. The unit can be built with Hepa filtration and serve as its own clean room. Filling lines can be set up independently or inline with an Amsler linear or rotary blow moulder. Other equipment available includes, bottle unscramblers, labellers, shrink bundlers, stretch wrappers, date code printers, palletisers, and other downstream packaging solutions. www.amslerequipment.net Quadrel’s track-and-trace barcode labeller American company Quadrel Labeling Systems has launched an integrated trackand-trace system that prints a serialized EPC code on each bottle, while labels are printed with another EPC barcode. The codes are captured and automatically uploaded into a Video Jet (ePedigree) database for full tracking of each unit. The Versaline system features Allen Bradley controls, Emerson servo motors, Cognex vision and Videojet printing, and ePedigree technologies. Quadrel says that it can be used for front/back, wraparound and custom applications. o. www.quadrel.com Moretto S.p.A. Via dell’Artigianato 3 - 35010 Massanzago (PD) ITALY Tel. +39 049 93 96 711 - Fax +39 049 93 96 710 www.moretto.com The most ambitious project in the history of the dehumidification. Drying Revolution designed by Moretto Hall 5 - Stand 5B58","@ID":44} "REGIONAL MARKET REPORTS 15 PETplanet insider Vol. 11 No. 11/10 www.petpla.net March 18, 2010 Alma Group – Roxane in La Ferriere de Brochard Alma Roxane – Pierre Papillaud - the man, character and personality is Alma-Roxane. We met: Pierre Papillaud, Chairman According to the French beverage data and statistics, Alma Group is a leading company in terms of soft beverage volume produced in France. Cristaline from Alma Roxane is in the lead in terms of brands in France. The company has the biggest share (more than 20% in 2008) in French markets of bottled water. Pierre Papillaud is chairman of the Alma Group and part owner. Some will call him an unpredictable personality of the French beverage market; others consider him the charismatic builder of a beverage empire in France in competition with the global giants such as Danone and Nestlé. Company history in brief At the beginning of the 1990s consolidation and its regulatory consequences in the French bottled beverage market was still essentially dominated by single source mineral water produced by the three owners of what were then the best known national brands – Nestlé, Danone and Neptune. The owners of Neptune soon realised, however, that if they wished to compete nationally with the other two, a new approach was required and so the multi-source spring water concept of Cristaline was born. In 1992 the Cristaline brand was created by Neptune, which spread country-wide in numerous regions of France. Neptune, located in the South of France and owned by Pierre Castel, and Roxanne located in the North owned by Pierre Papillaud, eventually formed the Alma Group as a joint venture sourcing water Cristaline - a multi-source spring water concept","@ID":17} "REGIONAL MARKET REPORTS 18 PETplanet insider Vol. 11 No. 11/10 www.petpla.net March 29, 2010. SBECM in Paris (Société des Bouchages, Emballages et Conditionnements Modernes) SBECM - “Markets for converters are getting smaller… we must adjust.” Jean-Luc Didouan, President of SBECM We met: Jean-Luc Didouan, President of SBECM in Paris. The head office is located in Paris, although production of preforms and caps is located in Lavardac in the Southwest of France. The Paris office is not only for convenience, but is the commercial office for sales and company administrative functions, and for easy contact with customers. History The business was started by the parents of Jean-Luc Didouan in 1961. Initially caps and closures made from aluminium and steel were manufactured but rapidly plastic manufacturing became the core business. At the same time, the Perrier Group, looking for a safe, secure and reliable supplier, took a participation in SBECM, but left the management with the founders. In 1983 SBECM entered the PET market and was the second company in France purchasing Husky preform systems. Jean-Luc Didouan took over in 1994 as president and has been running the business since that time. Product and production 70% of turnover is preform business, 30% caps and clo- sures and other minor products About 10,000t of PET are converted per annum but so far very little recycled material is used. About 600 million preforms were injection moulded in 2009 (available capacity near 1 billion).","@ID":20} "PETnews 6 PETplanet insider Vol. 11 No. 11/10 www.petpla.net Mold-Masters acquires Abba Systems, announces MasterPET brand Hot runner solutions supplier Mold-Masters has completed the purchase of Abba Systems of Brantford, Ontario. Abba Systems and Mold-Masters have been working together in a marketing alliance to build PET preform moulds since 2009. Bruce Catoen, Vice President of Business and Product Development, said that Abba’s expertise in preform stack manufacturing complements Mold-Masters’ core strengths. The acquisition comes after the companies had been working together for a period of nine months. The Abba Systems PET business is changing its name, from iPET to MasterPET (MPET). Abba Systems was founded in 1993 and is a global supplier of precision machined solutions. It employs 78 people and is located in Brantford, Ontario. www.moldmasters.com Sidel opens SA subsidiary October 12 saw Sidel South Africa host its inaugural customer conference in Johannesburg, which focused on ‘Sustainability in Packaging’. The company established its South African subsidiary in June 2010. Based in Johannesburg, it provides sales and support to customers in South Africa itself, Namibia, Botswana, Zimbabwe, Zambia, Malawi, Tanzania, Mozambique, Lesotho and Swaziland. Sidel has an existing installed base of more than 400 machines in Southern Africa. The region is viewed as a growing market in all types of beverage business. According to Euromonitor, 3.5 billion litres of beer and 4 billion litres of CSD were consumed in South Africa in 2009. Forecasts for 2010 to 2014 are also positive. “We plan to bring additional resources onboard soon in order to offer more service capabilities and competences,” said Mart Tijsmann, Sidel President and CEO. “We are confident that economic growth in the future will continue to drive beverage consumption in Southern Africa.” www.sidel.com Changes in Husky’s Americas sales organisation Husky Injection Molding Systems has announced that Mike Urquhart, Vice-President, Latin America Sales since 2007, is to assume leadership responsibility for Husky’s customer relationships throughout the Americas. The appointment comes after the announcement by Carmen Lowe, VicePresident North American Sales, of his intention to retire. Mr Lowe joined Husky in 1987; Mr Urquhart has been with the company since 1980. www.husky.ca Arabian filling company chooses Corvaglia cap solution The Masafi company, of Dubai, United Arab Emirates, is an established supplier in the Gulf region of natural mineral water, fresh and natural fruit juices and other products. It has been using its own-manufactured standard closures for cold-fill products and imported two-piece caps for hot-fill from Australia. After the conclusion of a successful trial period, Masafi is now using one-piece hot-fill caps it produces itself on a 16-cavity tool supplied by Corvaglia, of Eschlikon, Switzerland. Corvaglia has been selling the one-piece concept to companies in several Latin American companies. After the market launch of the cap by an international beverage filler in Mexico, Corvaglia presented the one-piece hot-fill cap to Masafi. Initial trials used 38mm caps; following minor modifications to the filling equipment, the concept was accepted and Masafi has now become the first beverage filler in the Middle East to produce its own hot-fill caps, using a 16-cavity tool supplied by Corvaglia. The one-piece caps are claimed to offer a number of economic and environmental advantages. They are made from one type of material – HDPE – and processed in a single injection moulded step. Corvaglia says that fillers can cut costs by more than 30%, compared to conventional multi-piece hot-fill caps, from savings in machinery, materials and processing. A critical point is the transition period from overpressure, which is cause by hot filling and occurs immediately after filling, and the vacuum that occurs after the bottle is cooled down. It is also vital that the cap is leakproof at the second stage, in order to avoid ingress of cooling water. Corvaglia claims to achieve secure seals by design and product geometry. The twostart 38mm closure, when screwed down, provides sufficient tension for a perfectly tight seal, which is maintained by deformation of the cap during cooling. Corvaglia reports that other beverage fillers in the Middle East have also declared an interest in its hot-fill cap system. www.corvaglia.ch Supply agreement for Husky and Toyo Machinery and Metal Co. Husky Injection Molding Systems has formed a strategic supply agreement with Toyo Machinery and Metal Co., Ltd. Toyo will provide components and assemblies to be integrated into the new H-PET AE and H-MED AE systems that Husky launched at the K 2010 Show in Dusseldorf. Husky says that the new systems will complement its Hylectric platform-based product line and will offer quality and performance but in a smaller size. All functions within the workcell will be managed by the company’s PC-based Polaris Control system. www.husky.ca","@ID":8} "NEWS 8 PETplanet insider Vol. 11 No. 11/10 www.petpla.net Continued growth in plastic closures market report Market research organisation Ceresana’s recently-published plastic caps and closures report forecasts continued growth in the market and increase in sales revenue, to more than €2 bn a year by 2017. More than 200 bn plastic closures were sold throughout Europe in the past year, 60 bn more than at the start of the decade. Growth is expected to average 2.3% a year, with consequent increase in revenues. Downward pressure on prices of commodified products is expected to be offset by the continuing trend towards greater complexity. “More functionality, better technical characteristics, and convenience are in demand, in addition to weight reduction, energy saving during production, and recycling,” said Oliver Kutsch, owner of Ceresana. Manufacturers, of both caps and closures and production machinery, are expected to profit primarily from an increased use of plastic packaging for foods and drinks, where PP and PE are increasing market share. Significant growth is forecast for beer, yoghurt, milk products, and sports drinks segments. Production and consumption of plastic caps and closures is growing most strongly in Russia, Poland, and Turkey, where manufacturers are currently investing in mass production of standardised products, such as screw-caps for PET bottles. Producers in Western Europe are focussing on complex closures systems, such as those with built-in seals and dosing devices for medications. The 1100-page study analyses production, consumption, imports, exports, and revenue in the plastic closure market in 31 European countries and presents information on the most important varieties of closure types: advantages, application possibilities, legal situations, disposal, and recycling. It also includes a producer directory with profiles of 379 closure manufacturers. www.ceresana.com/en/market-studies/industry/plastic-caps Uhde Inventa-Fischer to build new MTR plant for Octal Octal Petrochemicals, headquartered in the Sultanate of Oman, recently signed a contract with Uhde InventaFischer (Uhde) of Berlin, Germany, to build a 550,000 tpy plant for the production of PET resin. The contract for delivery of two lines unique to Octal will use Uhde’s proprietary MTR Melt-to-Resin technology. The plant will be built at Octal’s existing PET complex in Salalah, Oman, and will make the company the world’s largest single-site packaging-grade PET manufacturer. Its existing plant also uses MTR technology to produce APET sheet and bottlegrade chips. Uhde will provide technology, expertise, engineering, process equipment such as Espree and Discage reactors, auxiliary and utilities processes, site supervision and commissioning support for the PET polycondensation plant. Uhde says that its MTR technology offers advantages in quality, investment costs, raw material usage and utilities consumption, resulting in a significantly lower carbon footprint of the production, compared to other technologies. In just a year since it ramped up production at the world’s first integrated PET resin and PET sheet plant, Octal has established itself as a leader and one of the most energy efficient PET manufacturers in the world. www.uhde-inventa-fischer.com www.octal.com 175 years of Starlinger This year marks the 175th anniversary of flexible woven plastic packaging and PET recycling technology specialist Starlinger & Co GesmbH. Starting life as a small mechanic’s workshop in 1835 under the name of Franz Laubek, the company has evolved from a specialist in stationary steam engines and drive elements to a leading supplier to the textile industry. From the 1920s to the 1940s, it became known as supplier of winders and auxiliary equipment, such as lace and trimming machines, to the Austrian textile industry. The acquisition of Starliger by Erna and Franz Xaver Starlinger-Huemer, in 1959, can be regarded as the foundation for today’s company. It began exporting with the introduction of circular looms for weaving fabric from plastic tapes and broke into the PET market in 2005, with the introduction of PET reprocessing lines. With offices in the USA, India, Russia, China and Brazil, the company is a globally-recognised supplier of flexible woven plastic packaging and a leader in PET recycling and refining. It has grown from within and by acquisition and now employs more than 920 people across the world. Despite the economic downturn, the company expects to achieve its highest turnover ever during 2010. Its notable anniversary year has seen a series of significant upgrades and new product launches, which were on display at the K Show in Dusseldorf, October 27 - November 3, 2010. www.starlinger.com 2011 Packaging Conference, Las Vegas The 2011 Packaging Conference, organised by Plastic Technologies, Inc. (PTI) and SBA-CCI, Inc., will be held February 7-9, 2011 in Las Vegas at the ARIA Resort at CityCenter. Aimed at businesses in the supply chain, exhibitors and delegates are expected to range from retailers and brand owners to resin suppliers, technology providers, equipment manufacturers, and converters. It is also expected to include presentations on sustainability, market analysis, merger predictions, plastic resin supply/ demand and emerging technologies/ applications. Among the keynote speakers will be Dr. Anne Roulin, Nestlé’s global head of packaging and design, who will be giving a presentation on Opportunities and Challenges in Food and Beverage Packaging. The session will include a discussion on emerging technologies and legislative trends projected to shape the face of packaging. Registration is $1,995; an early registration discount of $200 is available to those registering prior to January 14. Fees include two nights accommodation at the ARIA Resort at CityCenter, conference sessions and proceedings, breaks, lunch and a Monday evening reception and networking opportunity. www.thepackagingconference.com www.sba-cci.com www.plastictechnologies.com","@ID":10}]}}
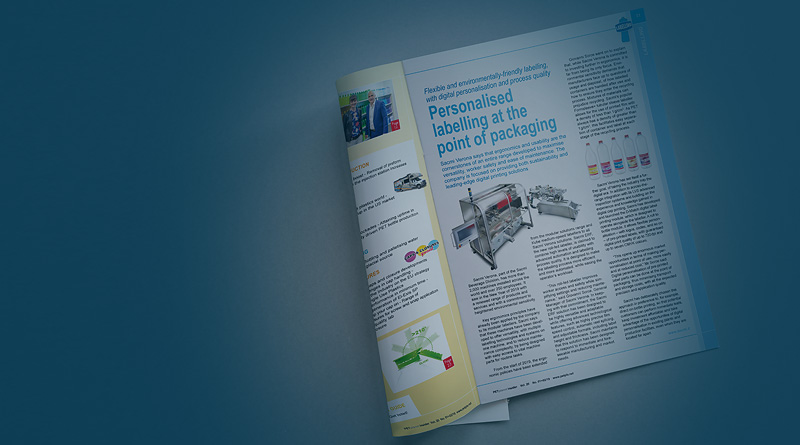