{"pages":{"page":[{"@ID":4, "The all-new PET-LINE comes with a variety of advantages to maximize output and minimize costs: • Maximum compatibility with legacy molds and PMC • Shortest cycle times for increased output • Lowest level of energy consumption to minimize the ecological footprint • Improved 100 % rPET processing to enable the circular economy • New control unit including Smart Operation to ensure easy, fast and safe start-up and production • Now available with 3000 and 4000 kN clamping force More details on www.netstal.com FLIPPING THE WORLD OF PET UPSIDE DOWN AND EVEN SIDEWAYS THE ALLNEW PETLINE WITH SIDE ENTRY."},{"@ID":29, "EDITOUR PETplanet Insider Vol. 23 No. 10/22 www.petpla.net 27 69% bottle-to-bottle recycling The Swiss Association PRS (PET Recycling Switzerland) was established in 1990 and offers industryrelated solutions on a voluntary basis. While beverage producers and importers pay a charge for each bottle, the bottle itself is deposit-free. Consumers return their bottles to a collection point which is separate from other household waste. Thus, of the 42,880 t of bottles that are in circulation, 45,893 t are put back into the cycle annually, i.e. more tonnes than from officially sold PET bottles. This is the equivalent of a collection rate of 107%. 33,414 t of rPET are produced for bottle-to-bottle recycling once all foreign matter and non-recyclable PET residues have been removed. In Switzerland, coloured PET bottles are also being reprocessed, generating 16,190 t of white rPET, 7,578 t of blue, 7,577 t of green, 1,722 t of brown and 348 t coloured rPET. This means that 69% of new material can be saved in Switzerland (source of all figures: PRS / 2021). www.resilux.com www.polyrecycling.ch K 2022 Düsseldorf, 19-26 October Hall 09/Stand 9C29 F.l.t.r.: Roland Rinderer COO, Manuel Peter CTO and Daniel Sommer CSO"},{"@ID":70, "TRADE SHOW PREVIEW PETplanet Insider Vol. 23 No. 10/22 www.petpla.net 53 material which can be processed as a recycled material on an industrial scale to create food packaging. This innovation sees partner companies pave the way for removing the need to downcycle packaging products other than bottles, and opens up an opportunity for recycling or even upcycling. This would substantially extend the range of uses for PET and rPET. In addition to the bottle-to-bottle cycle, this also means that the establishment of bottle-to-cup or even a cup-to-bottle recycling is conceivable. Injecting at 1,400mm per second The modified rPET being processed at the show comes from drinks bottles recycled in the plants of packaging and recycling specialists Alpla Group, who are headquartered in Hard, Austria. Other partner companies involved in the show exhibit are Brink (Harskamp, Netherlands) for the mould and IML automation and IPB Printing (Reusel, Netherlands) for the labels. An Engel e-speed 280/50 injection moulding machine is the heart of the production cell. Engel specifically developed this hybrid machine with its electrical clamping unit and hydraulic injection unit for the high performance requirements of thin-wall injection moulding. The new high-performance injection unit achieves injection speeds up 1,400mm per second at a maximum injection pressure of up to 2,600 bar when processing small shot weights with an extreme wall-thickness to flow path ratio. To process rPET, Engel combines the new injection unit with a plasticising unit from in-house development and production specifically designed for processing recycled material. During plasticising and injection, the viscosity of the PET is configured for thin-wall injection moulding. The new Engel e-speed supports the processing of arbitrary recycled materials up to 100% rPET. Taking different label trends into account Engel is presenting a mould at the K’ show which can process different labels at the same time. This sees the partners respond to the globally different trends in in-mould labelling which are in line with the EPBP and/ or Recyclass recommendations in the EU, and with the specifications from the Association of Plastic Recyclers (APR) for the USA. The dyes used on in-mould labels for the American market and its requirements can be washed off as the intent is to recycle the labels and the application for this market. A different technology is used in Europe: an in-mould label which floats off in the recycling process making it easy to separate the dyes and the label from the PET. www.engelglobal.com www.alpla.com Containers are being produced directly from rPET in thin-wall injection moulding at the K’ show 2022. ES PROCESS on energy consumption, PET RECYCLING PLANT Compact process, modular design equipment space. CONTACT US TO LEARN MORE ! WWW.BO-RE-TECH.COM | +86-573-85120186 | SALES@BO-RE-TECH.COM"},{"@ID":64, "PETplanet Insider Vol. 23 No. 10/22 www.petpla.net 62 PETbottles Beverage + Liquid Food Functional water by Hohes C The best prerequisite for getting noticed in a new market segment is a well-known brand name. Hohes C - in 1958 the producer of the first ready-to-drink orange juice, bottled in a brown bottle - has now launched three functional waters. The three variants, Immune, Energy and Antiox Water taste like lime-ginger, orange-passion fruit and cassis-mint, come without added sugar or sweeteners and contain only 3kcal/100ml. Each variant contains specific vitamin supplements. Each 750ml is filled in a climate-neutral bottle made of 100% rPET, decorated with a sleeve label with colour gradient and large brand lettering, and closed with a silver-coloured screw cap with first-removal safety device. www.hohesc.de"},{"@ID":32, "EDITOUR PETplanet Insider Vol. 23 No. 10/22 www.petpla.net 30 Business is booming for waste sorting systems Recycling in Spain by Kay Barton Around 160km to the northeast of Barcelona is the small Catalonian town of Roses. Here in 2004, Norwegian recycling equipment provider Tomra installed a local branch when it took over the former local distributor. This was in response to a recycling situation that was changing for the better. With the Packaging Waste Law enacted in 1998 that stipulated new EPR requirements for manufacturers, and with the foundation of the EPRO (extended producer responsibility organisation) Ecoembes, a non-profit environmental organisation, the topic of recycling and responsibility for it was now brought into more general focus. European funding for the construction of collection and sorting facilities in Spain and Portugal did the rest and helped bring about success. Since the start, almost 800 sorting systems have already been sold in Spain and Portugal, the company has a local market share of around 60% and 30 employees now work at the Spanish site. Judit Jansana, Commercial Director and Head of Tomra Sorting Spain, discusses the current recycling situation in the country and the role her company plays. Interview with Tomra Sorting S.L. 3 August 2022 We met: Mrs Judit Jansana, Managing Director Judit Jansana has been with Tomra for almost 15 years. From 2007, she was Head of Technical Office for seven years, before finally becoming Managing Director in the autumn of 2014. “Commodas, the company that Tomra bought in 2004, then owned a unique x-ray technology that could identify and separate Zorba waste, i.e. mixed metal waste with a significant proportion of aluminium,” she explains to us. “This helped us into new business opportunities in the field of metal sorting. After the creation of our office here in Roses, we were also able to turn our attentions to the South American market, thanks to the common language and the cultural similarities. Naturally, the waste import ban in China and changes to the Basel Convention also had a positive effect on our activities,” says Mrs Jansana. “Because of the new waste law in Spain, which was passed in April of this year and that stipulates a landfill Visit us at K 2022 Hall 11, stand I37 19-26 October, Dusseldorf, Germany Tomra’s Managing Director Judit Jansana at her desk"},{"@ID":72, "OUTER PLANET 70 PETplanet Insider Vol. 23 No. 10/22 www.petpla.net OUTER PLANET Making nanodiamonds out of PET What goes on inside planets like Neptune and Uranus? To find out, an international team headed by the Helmholtz-Zentrum Dresden-Rossendorf (HZDR), the University of Rostock and France’s École Polytechnique conducted an experiment: They fired laser flashes at a thin PET film and investigated what happened. One result was that the researchers were able to confirm their earlier thesis that it really does rain diamonds inside the ice giants at the periphery of our solar system. And another was that this method could establish a new way of producing nanodiamonds. The group has presented its findings in the journal Science Advances. The conditions in the interior of icy giant planets like Neptune and Uranus are extreme: temperatures reach several thousand degrees celsius, and the pressure is millions of times greater than in the earth’s atmosphere. Nonetheless, states like this can be simulated briefly in the lab: powerful laser flashes hit a film-like material sample, heat it up to 6,000 °C for the blink of an eye and generate a shock wave that compresses the material for a few nanoseconds to a million times the atmospheric pressure. “Up to now, we used hydrocarbon films for these kinds of experiment,” explains Dominik Kraus, physicist at HZDR and professor at the University of Rostock. “And we discovered that this extreme pressure produced tiny diamonds, known as nanodiamonds.” Using these films, however, it was only partially possible to simulate the interior of planets – because ice giants not only contain carbon and hydrogen but also vast amounts of oxygen. When searching for suitable film material, the group hit on an a substance well-known to readers of this publication: PET. “PET has a good balance between carbon, hydrogen and oxygen to simulate the activity in ice planets,” Kraus explains. The team conducted its experiments at SLAC National Accelerator Laboratory in California, the location of the Linac Coherent Light Source, a powerful, accelerator-based X-ray laser. They used it to analyse what happens when intensive laser flashes hit a PET film, employing two measurement methods at the same time: X-ray diffraction to determine whether nanodiamonds were produced and so-called smallangle scattering to see how quickly and how large the diamonds grew. A big helper: oxygen “The effect of the oxygen was to accelerate the splitting of the carbon and hydrogen and thus encourage the formation of nanodiamonds,” says Dominik Kraus, reporting on the results. “It meant the carbon atoms could combine more easily and form diamonds.” This further supports the assumption that it literally rains diamonds inside the ice giants. The findings are probably not just relevant to Uranus and Neptune but to innumerable other planets in our galaxy as well. While such ice giants used to be thought of as rarities, it now seems clear that they are probably the most common form of planet outside the solar system. The team also encountered hints of another kind: In combination with the diamonds, water should be produced – but in an unusual variant. “So-called superionic water may have formed,” Kraus opines. “The oxygen atoms form a crystal lattice in which the hydrogen nuclei move around freely.” Because the nuclei are electrically charged, superionic water can conduct electric current and thus help to create the ice giants’ magnetic field. In their experiments, however, the research group was not yet able to unequivocally prove the existence of superionic water in the mixture with diamonds. This is planned to happen in close collaboration with the University of Rostock at the European XFEL in Hamburg, the world’s most powerful X-ray laser. In addition to this rather fundamental knowledge, the new experiment also opens up perspectives for a technical application: the tailored production of nanometer-sized diamonds, which are already included in abrasives and polishing agents. In the future, they are supposed to be used as highly-sensitive quantum sensors, medical contrast agents and efficient reaction accelerators, for splitting CO2 for example. “So far, diamonds of this kind have mainly been produced by detonating explosives,” Kraus explains. The scientists’ vision: A high-performance laser fires ten flashes per second at a PET film which is illuminated by the beam at intervals of a tenth of a second. The nanodiamonds thus created shoot out of the film and land in a collecting tank filled with water. There they are decelerated and can then be filtered and harvested. The essential advantage of this method in contrast to production by explosives is that “the nanodiamonds could be custom cut with regard to size or even doping with other atoms,” Dominik Kraus emphasises. www.hzdr.de In the experiment, a thin sheet of simple PET plastic was shot at with a laser. The strong laser flashes that hit the foil-like material sample briefly heated it up to 6,000 °C and thus generated a shock wave that compressed the matter to millions of times the atmospheric pressure for a few nanoseconds. The scientists were able to determine that so-called nanodiamonds formed under the pressure. (Photo: Blaurock / HZDR)"},{"@ID":3, "EDITOUR PETplanet Insider Vol. 23 No. 10/22 www.petpla.net 28 Sorting waste streams A vital element in plastic recycling is the homogenous sorting of different plastics. Sorting by colour is also important, especially in PET bottle recycling, where Sesotec has made a name for itself. The company is now also tackling the PET tray sector. PETplanet spoke to Michael Perl, Group Director Sales Division Sorting Recycling. Sesotec GmbH / June 17, 2022 We met: Michael Perl, Group Director Sales Division Sorting Recycling Brigitte Rothkopf, Director Corporate Communication The better the sorting, the better the subsequently produced rPET. This truism is growing in significance with the increasing streams of rPET. Sesotec uses infrared to sort for example PVC, PLA and multi-material bottles (also with sleeves) and trays from the PET bottle streams, with systems achieving a purity of 99.8 to 99.9%. After the article sorting the bottles are shredded, washed, dried and sorted by airstream before the flakes are cleaned again by means of a flake sorter which are also manufactured by Sesotec. These systems identify foreign material and sort pieces by colour. Sesotec itself builds the systems with a high vertical range of manufacturing; the associated electronics are also developed in house. According to information from Michael Perl, Group Director Sales Division Sorting Recycling, the high vertical range of manufacturing ensures the flexibility and quality of the systems as well as of the assembly. For him, trends in sorting include larger throughput quantities, a reduced loss of accept material and improved sorting performances including sorting algorithms based on AI to handle also higher contaminated plastic fractions. Including glass cullet sorters, systems for mixed plastics, metal and electronic scrap, a total of around 2,200 Schönberg systems are running worldwide in recycling applications. The Sesotec systems are designed for the needs of the individual sorting application – so there are individual sorting systems for plastic bottles and trays, for film, for flakes and regrind, for glass cullets as well as for metal and electronic scrap. Tour Sponsors: Bottles on the pilot plant system PET bottles collected by customers and delivered to the pilot plant to adapt the sorting system perfectly to the bottle streams The same also applies to flakes sent by customers. Michael Perl"},{"@ID":67, "PETnews 6 NEWS PETplanet Insider Vol. 23 No. 10/22 www.petpla.net Driving global harmonisation for recyclability RecyClass and the US based Association of Plastics Recyclers, the international association representing the plastics recycling industry, reinforce their collaboration to drive worldwide harmonisation of plastic packaging recyclability. The basis of this collaboration is a shared vision of science-based design for recycling guidelines and protocols for recyclability assessments. This partnership is indispensable to drive unified, fact-based approach to recyclability and to bring clarity for the whole value chain, specifically brand owners and retailers who operate in multinational markets. “RecyClass mission, beyond supporting the industry in redesigning plastic packaging and boosting recycled material in new products, is to harmonise the approach toward recyclability assessment”, said Fabrizio di Gregorio, Technical Director at Plastics Recyclers Europe. “Given the similarities when it comes to the products placed on the markets globally, such harmonisation can help make the packaging production systems more efficient and at the same time accelerate significantly the transition toward circularity”, he added. This collaboration includes establishing a common workplan to align and review the existing documents with an objective to identify potential gaps, consolidate existing methodologies and map additional testing methods. The first deliverables, focused on aligning the guidelines and protocols for flexible plastics, are expected at the beginning of 2023. “The purpose of design guides is to ensure packages can be processed through the recycling infrastructure with the highest yield and best quality impact. Since the European and North American recycling infrastructures operate on many of the same principles, it is possible to harmonise much of the guidance. I’m excited that RecyClass and APR are making efforts to communicate and coordinate. These efforts benefit the entire packaging industry and circular economy,” said Curt Cozart, Chief Operating Officer at APR. The two organisations endorsed a common definition of recyclability back in 2018 which stipulates that to be considered recyclable, a product must be able to be collected and sorted in sufficient quantities. It must be as well compatible with existing industrial recycling processes or be available in sufficient quantities to justify the development of new recycling processes to become a raw material for new products. This partnership is an important effort to harmonise the standards available on the market. RecyClass, together with APR, is prone to collaborate with other organisations willing to make plastic products compatible with recycling and deliver on the EU targets of making all plastic packaging recyclable by 2030. www.recyclass.eu www.plasticsrecyling.org Plant for chemically recycled PET Köksan PET Packaging Industry Co. introduces its new chemically recycled PET production with its patented (pending) process technology with a total capacity of 300 tons per day. According to the company the plant is designed to produce 100% rPET resin which will be ready to use for both bottle grade and textile applications. Köksan uses two CP lines with 600 tons line capacity each per day for PET resin production and is now adding a third line made by Polytex with a unique energy saving production process, according to the management. The high IV rPET CP 300 tons/day project CP for various packaging and textile grade applications has been officially launched on August 29, 2022. Chemical recycling through the glycolysis process is turning PET into bis-hydroxyethyl terephthalate (BHET) monomers which are already being used in CP lines up to 50%. The plant will be fully up and running for operation by the end of 2023. www.koksan.com Help us shape the circular economy! Technically-minded and keen to protect the climate? Relish a challenge and want to help find the right people to do something about the plastic waste on our planet? Then Krones Recycling Solutions is the right place for you! For more than 20 years, we have been developing innovative technologies to keep valuable packaging materials within a closed loop – and to take our vision of a sustainable industry from Flensburg out into the wider world. There is more to do than ever, which is why we are now looking for committed individuals to join our team – for example in the following areas: Mechanical/electrical design and automation Process engineering Product management Erection and commissioning at customers' premises worldwide Employee management Maybe you share our vision of a waste-free world, but don't see your abilities reflected fully in any of these job areas? Then why not send us an unsolicited application? Because job titles are not what matters to us. What is important is who you are and what you can do. Any questions? Please contact Astrid Schwartz (astrid.schwartz@krones.com) for more information. We look forward to receiving your application (including all relevant documents). These can be uploaded in just a few clicks on our careers portal at www.krones.com."},{"@ID":69, "TRADE SHOW PREVIEW PETplanet Insider Vol. 23 No. 10/22 www.petpla.net 55 TRADE SHOW PREVIEW 55 accumulating in recesses of the neck area of the preform mould. Both serve to extend maintenance intervals and enhance the ability of an injection system to process high levels of rPET is enhanced. Digital innovation A zone on digitalisation will feature the latest solutions in the technical services package, called the Echo System. This makes it possible to have full control of system performance, increasing efficiency and optimising costs. It allows users to access information on any of the company’s machines anywhere in the world, at any time. Sustainability Capabilities at the service of downstream partners to reduce consumption of materials, energy, water, and compressed air will also be highlighted, as well as the proficiency to create containers that use the highest possible levels of not only rPET but also alternative resins. It is of importance to the company that the materials are not only recyclable in theory, but also in practice. Sipa is also shining the light on AWArPET, the new brand to communicate the company’s approach in the design and production of primary and secondary packaging according to environmental affairs. The company’s product design experts are involved in the development of thousands of new packaging designs every year, and in all of these, they are guided by the three Rs – Reduce, Reuse, Recycle. www.sipa.it Thanks to the Echo System, operators have control of system performance, efficiency and costs. BOTTLE TO BOTTLE RECOVERY MOISTURE CONTENT CONTROL PROCESS CONSISTENCY EXTREME BLENDING FLEXIBILITY MAKING THE DIFFERENCE ON PET. Hall 11 Stand H56 Stand H66 moretto.com follow us"},{"@ID":28, "EDITOUR PETplanet Insider Vol. 23 No. 10/22 www.petpla.net 26 A closed loop of 69% rPET in Switzerland The Swiss Association PRS (PET Recycling Switzerland) has managed to achieve a PET bottle-to-bottle recycling rate of 69%. PETplanet visited a Resilux plant in Switzerland which converts bottles into rPET on three machines and sometimes injection-moulds and stretch-blows them into rPET preforms and bottles. Poly Recycling is a subsidiary of Resilux Switzerland that converts collected bottles into rPET on three machines. There are two Erema and one Starlinger processing machines in the plant which have a total capacity of 90 tonnes per day. The bottles are routinely sorted, washed and crushed prior to them being processed. The main difference compared to other markets is that in Switzerland bottles are pre-sorted by colour which means that Poly Recycling receives bales that are rich in colour. As PRS and its members in the drinks industry both want to produce coloured rPET bottles, the rPET plant makes blue, green and brown rPET as well as the white rPET variety. There are still bottles that have PVC labels. Here, Poly Recycling is trying to remove the films by means of wind separation. However, a minimal acceptable residue remains in the flakes. In the neighbouring Resilux plant, rPET preforms are made from rPET with 25% to 100% rPET content, depending on the wish of the customer, says Daniel Sommer, Sales Director at DACH. Here, the ‘3 Ps’ have been written on the flag to express that PET packaging is not waste, but a valuable raw material. These stand for “Inspired by People”, “Safe for the Planet” and “Protecting your Product” and express the idea of a sustainable future in the company’s philosophy. Multinational brands in particular ask for 100% rPET preforms which Resilux’s Chief Operating Officer Roland Rinderer believes is crucial from a technological perspective. Given that high recycling quotas in Switzerland have been in place for a long time and with PET having been reprocessed several times, such a high rPET content can create a yellow or grey haze. In his opinion, this could be prevented by always incorporating about onethird new material into each preform which would in principle result in a recycling rate of 69%. The PET itself is not affected by repeated reprocessing. “Our preform department uses Netstal machines and Otto Hofstetter moulds. The preforms are examined on a conveyor belt before they fall into boxes. Preforms are checked with an IMD Vista Pecu Lux system. “The IMD Vista Peco Lux is a robust and straightforward system that has served us well and within which all our preform machines are integrated”, says Rinderer. Just as PET bottles are recycled, the boxes are also reused either as pallet or cardboard ones. Bottles that arrive at Resilux’s Poly Recycling plant are pre-sorted in four colours: white, blue, green and brown. Tour Sponsors:"},{"@ID":20, "MATERIALS / RECYCLING PETplanet Insider Vol. 23 No. 10/22 www.petpla.net 18 Masterbatch for hot fi ll packaging No compromise on processability A lot of food and beverage products require a long shelf life, so they require filling at high temperatures to remove harmful bacteria or microorganisms which might damage or interact with the product. Normally the hot filling temperatures range from 80 °C up to 90 °C, depending on the specific product. A special masterbatch has been developed to increase the crystallinity of PET without compromising its processability resulting in a considerable increase in thermal and oxygen barrier properties. Hot fill for PET bottles presents many challenges, starting from the thermal resistance of the material itself, to the resistance to implosion to avoid deformation and to the oxygen barrier properties to ensure a longer shelf life. The current hot fill technology available on the market use hot moulds at 140-160 °C. It is feasible with special blow moulding machines that have a specific blowing system capable of blowing through perforated stretching rods and systems of special valves that allow the recirculation of air to lower the temperature of the containers below 100 °C, with an increase in the cycle time. “This technology can be very effective but often it is not easy to have a high enough output of bottles, let’s say in excess of 5 million, to justify the investment in a dedicated special ISBM or SBM machine,” explains Giovanni Sonzogni, CEO and Innovation Director of GS4Plastic. “In addition, it is often necessary to use special hot fill PET grades with a high Tg, in order to guarantee a high thermal resistance, and this further increases the cost of the final packaging,” he concluded. The Italian start-up GS4Plastic SB detected the need for a process that allows the production of a hot fill packaging with a high thermal MATERIALS resistance and a good barrier property against O2 that can be obtained simply, cheaply and with low cycle times. GS4Plastic patented a special masterbatch called FastPET, that is claimed to increase the crystallinity of PET without compromising its processability; this results in an increase in thermal and oxygen barrier properties. It is possible to use FastPET for the production of hot fill bottles in single stage stretch blow moulding (ISBM) without the need to use special hot mould technologies. FastPET is added to PET or rPET in the feeding of the extruder together with other additives, such as pigments or others, says GS4Plastic. The recommended dosing percentage is lower than 1% in weight. Thus the bottles made with this special masterbatch are 100% recyclable in the existing PET supply chain. With FastPET it is possible to make a monolayer container resist up to 88 °C, thus making it suitable for the hot fill process without either the use of special PET or expensive technologies, says the company. Increased shelf life by up to 12 months With the additive, it is possible to increase the barrier properties, and consequently the shelf life of the products by up to 12 months, states GS4Plastic. The increase must be evaluated based on the type of product and on the design of the preform/ bottle. ISBM tests with 3 or 4 stations, have been carried out, and in addition to confirming the increase in properties, a surprisingly significant reduction in the cycle time has been found. As an example, the start-up tested an 18 g bottle produced on a 4 station machine with a mould cooled to 13 °C with a cycle time of 17.5 s. It was found that with the masterbatch it was possible to achieve a cycle time of 15.5 s. The only disadvantage is the loss of transparency of the bottle. The masterbatch acts on the crystallinity of PET, and a slight loss of optical properties is therefore to be expected. The patented masterbatch called FastPET is claimed to increase the crystallinity of PET without compromising its processability."},{"@ID":44, "42 TRADE SHOW PREVIEW PETplanet Insider Vol. 23 No. 10/22 www.petpla.net High-performance machines for cosmetics, pharma & packaging PackSys Global will present 6 machines which have been manufactured in Switzerland, the FlexSeamer, FlexMaster, Box Butler, Prestige 45, TEM Plus and the CapLab. CapLab is an in-line, automatic integrated unit for testing the functionality of a closure’s tamper evident (TE) band. In optional combination with a vision inspection system which can select closures by cavity number, CapLab takes samples from the slitting / folding machine outfeed and measures inline the pull-off strength of the closure’s TE band. The unit can be connected in-line to a system producing closures with moulded TE bands rather than slit TE bands. Further, the company will present the Swiss Altitude series of tubes made in some of the differently sustainable ways their machines can produce them. The tubes present some of the most iconic Swiss mountains. And finally, partners like Huhtamaki or Buy Food with Plastic will be present at the Packsys booth for a few days. www.packsysglobal.com VACUNITE® definiert den Maßstab für Leistungsfähigkeit im Bottle-to-Bottle Recycling neu: Höchste Dekontamina- tionseffizienz für kompromisslose Lebensmitteltauglichkeit, rPET-Granulate mit besten Farbwerten, Top IV-Stabilität, Kompaktheit der Anlage sowie ein geringer Energieverbrauch über den gesamten Prozess sorgen für überzeugende Sicherheit, Produktivität und Qualität. Vereint Vakuum- & Stickstoff-Technologie erema-group.com K22 MAIN BOOTH: Hall 9 / Booth C09 OUTDOOR AREA: FG-CE03 Packsys Global Hall 3 Booth D90 Smart new hot runner systems, controllers and auxiliary injection units Mold Master will be showcasing new hot runner systems, controllers, and auxiliary injection units. These solutions includes comprehensive bio-resin/PCR processing solutions (including co-injection) for producing high-quality parts related to sustainable applications, a PET-Series 2-stage PET preform hot runner system and the Axiom TG single stage bottle hot runner system. In addition, customers can view recent innovations, exclusive to Mold Masters, such as Symfill technology, TC-connect technology and a manifold plastic leakage detection. The company will also be showcasing their latest control products that incorporate enhanced integration options, modernised functionality, and smart capabilities. www.moldmasters.com Mold-Master Hall 1 Booth C05 Saving resources Every Eisbär dryer can handle throughputs between 250 and 5,000kg/h. To be more attractive in regards of saving resources, the company creates material drying system without the need of any cool water supply. To keep wear parts as well as filters sustainable, Eisbär made them reusable by being cleanable. Since Covid outbreak in March 2020, there was a big movement toward the willingness of customers to remote installations. Remote installations are a good possibility to save money, resources, and the environment for all parties. Eisbär is keeping the focus on easy handling, low energy consumption and a few moving wear parts. www.eisbaer.at Eisbär Hall 10 Booth G32"},{"@ID":47, "MARKET SURVEY 37 PETplanet Insider Vol. 23 No. 10/22 www.petpla.net Sacmi Imola S.C. Krones AG Newamstar Packaging Machinery Co., Ltd. Via Selice Prov.le 17/A Imola (BO) Italy +39 0542 607111 www.sacmi.com Mr Stefano Severi Sales Area Manager +39 0542 607553 stefano.severi@sacmi.it Böhmerwaldstr. 5 93073 Neutraubling, Germany +49 9401 70 0 www.krones.com East Xinjing Road, Zhangjiagang Economic & Technological Development Zone, Jiangsu 215618, P.R. China +86 512 5869 1111 www.newamstar.com Marketing Manager +86 512 5699 3303 market@newamstar.com No Yes Yes No Yes Yes No Yes Yes Yes Yes and high frequency Yes No Equipped with recovery system Yes Yes Yes Yes Yes Yes Yes Yes Yes Yes Yes Yes Yes Yes Yes Camera with special peripheral lens to control 360° of the sidewall, real 3D technology for 360° precise inspection Yes Yes Yes, +/- 1° Yes Yes Yes, +/- 1mm Yes Yes Yes, both inkjet or laser printed, through proprietary AI algorithms Yes Yes Camera 360° with real 3D technology Yes Yes No Yes Yes Up to 150mm 50-105mm Up to 50-250mm Up to 340mm 60-340mm & closure diameter 27-46mm Up to 100-470mm Single or multi push devices Yes, without air consumption Up to 72,000bph Up to 84,000bph 1,000-72,000bph Panorama supervisor Yes KHS GmbH Newamstar Packaging Machinery Co., Ltd. Juchostraße 20 44143 Dortmund, Germany +49 231 569-0 www.khs.com Mr Manfred Härtel Product Manager Filling +49 231 569-0 manfred.haertel@khs.com East Xinjing Road, Zhangjiagang Economic & Technological Development Zone, Jiangsu 215618, P.R. China +86 512 5869 1111 www.newamstar.com +86 512 5699 3303 market@newamstar.com Innofi ll PET DRV Innofi ll PET NV XGF 48/216 32/144 20-120 0.1/3.0 0.1/3.0 0.25-15 Up to 82,000 Up to 82,000 1,200-81,000 Up to 82,000 Up to 82,000 Up to 48,000 Up to 72,000 Up to 36,000 Up to 50,000 Up to 36,000 Up to 60,000 Up to 60,000 Up to 36,000 Yes Yes Yes Yes No Yes Yes Yes Yes No No Yes No Yes Yes Volumetric fi lling system; pneumatic cylinder; MID (inductive fl ow meter); Mass-fl ow (Coriolis) Volumetric fi lling system; pneumatic cylinder; MID (inductive fl owmeter); Mass-fl ow (Coriolis) Water valve, hot fi lling valve, isobaric valve, electronic valve; fl owmeter fi lling, weight liquid level inspection CSDwarm-fi lling up to 24°C; simple fi lling valve; compact unit; slow & fast-fi lling; gentle fi lling with low foaming; no beverage loss during production; PTFE-sealing technology prevents aroma transfer Contact-free fi lling Intelligent Factory Management Platform"},{"@ID":68, "TRADE SHOW PREVIEW PETplanet Insider Vol. 23 No. 10/22 www.petpla.net 48 viscosity or variable input viscosities. In combination with Gneuss’ rotary filtration technology, a high melt purity is guaranteed. Quality assurance can be provided with an online viscometer VIS for measuring melt viscosity. As demand for PET bottle flakes outpaces supply and processors are looking for alternative feedstock (e.g. to fulfil recycled content mandates) the MRSjump offers a solution for PET thermoform, film or fibre recycling, while the newly developed MRS cutter compactor makes it possible to use low bulk density materials. In parallel, with company headquarters only about 200 km from the show, a complete PET sheet extrusion line with an Omnimax recycling machine - consisting of an MRSjump 70, Gneuss’ deep vacuum system and a fully-automatic filtration system RSFgenius 75 - and a sheet downstream with a 500mm wide extrusion will be running in Gneuss’ technical centre open to visitors. Omniboost recycling machine including polyreactor jump Additionally, an Omniboost recycling machine with a polyreactor jump will be operating in the company’s technical centre for an online demonstration. The jump can lift the IV value of a PET melt up to 0.95dl/g. In the jump the polymer passes over several slow turning elements which create a polymer film, the surface of which is constantly renewed. The reactor vessel is kept under vacuum, through which volatile substances are reliably removed. By regulating the residence time in the reactor, the vacuum, the fill level and the speed of rotation of the agitating devices, the polycondensation reaction can be altered to achieve the required product properties. The jump is a robust and reliable liquid state polycondensation system (LSP) and a compact, quick and efficient alternative to conventional solid-state systems (SSP). It enables direct reintroduction of the polymer into the production process without the need to remelt the PET. www.gneuss.com Omniboost recycling machine with Jump polyreactor, MRS extrusion system, rotary filtration systems and 3C rotary feeder (QKDQFHG FDYLWDWLRQ 6XSHULRU WRRO VWHHO %DODQFHG +5 V\\VWHP 0ROG# '3: 2QH 6WRS 6ROXWLRQ )RU 6LQJOH 6WDJH ,6%0 0ROGV 0ROGV 6XSSOLHG *OREDOO\\ ^ŝŶŐůĞ ^ƚĂŐĞ DŽůĚƐ ZZZ DFPHGULQNWHF FRP VDOHV#DFPHGULQNWHF FRP 3K &5($7,1* 02/'6 :,7+ $ ',))(5(1&( \"DNF %SJOLUFD 4PMVUJPOT --1 9LVLW XV +DOO %RRWK F 'ÙVVHOGRUI *HUPDQ\\ 2FW p 02/'6 )25 $6% 0% 0 '3+ '3: $2., 6,3$ HWF "},{"@ID":9, "7 NEWS PETplanet Insider Vol. 23 No. 10/22 www.petpla.net product development caps & closures design high cavitation moulds multi-component moulds closure production systems after sales service competent – professional – inspiring +43 5572 7272-0 | sales@z-moulds.com | www.z-moulds.com Visit us @K-SHOW Düsseldorf, Oct. 19-26th Hall 10 Booth G32 z Alpla and PTT Global Chemical open Thailand’s largest plastics recycling plant Following 18 months of construction and installation, the Alpla Group and PTT Global Chemical are opening a stateof-the-art Envicco recycling plant in Thailand. With an annual production capacity of 30,000 t of recycled PET and 15,000 t of recycled HDPE, it is one of the largest recycling plants for these plastics in Asia. With this plant, the two companies will strengthen the region’s circular economy and supply the growing markets with high-quality recycled material. Located in an economic zone on the coast of the southeastern province of Rayong, the plant is equipped with the latest recycling technology and production lines to manufacture high-quality plastic recyclates with approval from the USFDA. The opening on September 13 was attended by, among others, Alpla Chairman Günther Lehner, Kongkrapan Intarajang (CEO and President, GC), Dietmar Marin (Alpla Managing Director Recycling) and Bernd Wachter (Alpla Corporate Director Circular Economy & Recycling Asia). “Demand for recycled, sustainable packaging materials is rising sharply in Southeast Asia, and high-quality plastics have a key role to play here. With this new plant, we are now applying our many years of expertise in the treatment and processing of packaging made from post-consumer recycled resins in Thailand,” explains Bernd Wachter. Alpla will supply its production facilities in Asia with recycled material and is also fostering the circular economy at the local level. With the plant, majority shareholder GC supports sustainable development in the region, moving it towards resource-conserving business and lifestyles. “Today, GC is proud to reveal that Envicco is ready for commercial operation. Used plastics within the Kingdom of Thailand will make up 100% of the raw materials processed by Envicco ’s cutting-edge production technologies to transform used plastics into valuable products,” says Kongkrapan Intarajang. “The Envicco production plant is part of our long-term circular economy strategy to fully realise GC’s value chain. It also has the added benefit of creating jobs within the community while simultaneously aligning with the Thai government’s BioCircular-Green Economy Model.” The Envicco team will comprise approximately 180 employees at the start of production. Future plans: Bottle-to-bottle recycling The 30,000m2 plant is on a plot of land measuring a good 90,000 m2 at the Map Ta Phut Industrial Estate. There is, therefore, also space for future capacity expansions. “We have long-term plans to promote the bottle-to-bottle cycle not only here in Thailand, but across Asia and other regions around the world. Carbon emissions and waste can be reduced through optimised resource consumption,” emphasises Dietmar Marin. www.alpla.com www.pttgcgroup.com F.l.t.r.: Bernd Wachter (Alpla Corporate Director Circular Economy & Recycling Asia), Dietmar Marin (Alpla Managing Director Recycling), Günther Lehner (Alpla Chairman), Kongkrapan Intarajang (CEO and President, GC), Georg Weingartner (Austrian Commercial Counsellor in Bangkok) and Korn-eak Thamrongwang (Alpla Large Scale Project Manager Asia) at the opening of the Envicco plant."},{"@ID":38, "MARKET SURVEY 36 PETplanet Insider Vol. 23 No. 10/22 www.petpla.net Filling inspection systems Company name KHS GmbH Pressco Technology Inc Heuft Systemtechnik GmbH Postal address Telephone number Web site address Contact name Function Direct telephone number E-Mail Juchostraße 20 44143 Dortmund, Germany +49 231 569-0 www.khs.com Mr Helmut Schmitt Project & Production Manageement Inspection Technology +49 231 569 10124 helmut.schmitt@khs.com 29200 Aurora Road, Cleveland, OH USA +1 440 498 2600 www.pressco.com Mr Tom Murphy VP, Sales & Customer Service +1 440 498 2600 sales@pressco.com Am Wind 1, 56659 Burgbrohl, Germany +49 2636 56 0 www.heuft.com Mr Sjoerd van Laar Product Manager +49 2636 2431 Sjoerd.Van.Laar@heuft.com Fill level control Infrared No Yes X-ray Yes Yes Yes Gamma Yes No, too unsafe Camera Yes, high frequency controll Yes, high frequency Yes Contamination control Foreign Substance Inspection (sniffi ng) for empty refPET bottles No Yes Closure inspection Yes Presents of cap Yes Yes Yes Crooked cap Yes Yes Yes Lifted cap Yes Yes Yes Wrong cap Yes Yes Yes Tamper evident band control Yes Yes Yes Camera: 360° / sensor Yes, both Yes Yes Label inspection Torn label Yes Yes Vertical / horizontal misalignment Yes Yes Yes Best-before date control Code presence inspection No Yes Camera: 360° / sensor Camera and sensor Yes Yes Pressure leak detector Squeezer No Yes Applicable bottle type Diameter 40-110mm Up to 150mm in standard up to 200 mm Height 150-360mm Up to 400mm in standard up to 400 mm Rejecting bottle Into bin and onto collecting table Push reject and diverter reject options available Yes Inspection speed PET: up to 86,000 bph Over 3,000ppm 72.000 cph with 360° inspection included. Otherwise up to 144.000 cph Monitoring Filler-/sealer management Filler valve, capper head correlation Yes Filling Equipment Company name Krones AG Fogg Filler SMI S.p.A. Postal address Telephone number Web site address Contact name Function Direct telephone number E-Mail Böhmerwaldstr. 5 93073 Neutraubling, Germany +49 9401 70 0 www.krones.com Mr Philipp Schön Product Manager Filling Division +49 9401 4567 philipp.schoen@krones.com 3455 John F Donnelly Dr Holland, MI 49424, USA +1 616 786 3644 www.foggfi ller.com Mr Karl Walby Sales Manager +1 616 786 3644 karl.walby@promachbuilt.com Via Carlo Ceresa, 10 24015 San Giovanni Bianco, Italy +39 0345 40111 www.smigroup.it Mr Pietro Volpi Marketing Dept. Manager +39 0345 40316 pietro.volpi@smigroup.net 1. Machine designation / model number Modulfi ll F2 - F12 (2' fi lling bowl to 12' fi lling bowl) Blowing, fi ller and capping machine in Ecobloc confi guration; rinser, fi ller and capper machine in Monobloc confi guration 2. Number of fi lling heads (range: from/to) 16-216 6-120 9-126 3. Min to max bottle contents (in liters) 0.1-5 0.05-5 0.25-10 4. Filling speed: output (bph) (min to max): 20bpm - 1,200bpm Eco: 1,000-36,800 Mono: 1,000-55,000 specifi y: 1l bottle / still water (bph) Up to 72,000 38-746 Eco: 36,800 Mono: 44,000 1l bottle / CSD (bph) Up to 65,000 No carbonated beverages Up to 24,000 1l bottle / Milk (bph) Up to 60,000 38-786 Up to 33,500 1l bottle / Juice (bph) Up to 60,000 38-786 Up to 34,400 5. Filling process Pressureless (still drinks) Yes Yes - gravity fi ll Yes Pressure fi lling (carbonated drinks) Yes No Yes Hot fi lling Yes Yes - gravity fi ll Eco: no Mono: yes Cold aseptic fi lling Yes Yes - cold fi ll - esl and near aseptic No Juices with high pulp content Yes Yes - gravity fi ll with special agitation system No 6. Type of fi lling valve and metering system Volumetric fi lling system: inductive and mass-fl owmeter, net weight fi lling system with weighing cell and height fi lling systemwith electronic fi ll height measuring Gravity fi lling valves Electronic volumetric fi lling valves Flowmeters (metering system) 7. Special features (short description/keywords) Monotec (starwheel columns with servo drives), cap disinfection (UV light / PAA / H2O2, optional), clean room cover, foam cleaning system, nitrogen injection system, automatic CIP-cups, capcade, Bloc solutions Hot fi ll, cold fi ll, ESL fi ll, spirits fi ll; all pourable liquids that are noncarbonated Compact modular frame, with a wide choice of customisation options; operating and maintenance costs dramatically cut; easy and quick format changeover, with no need to replace mechanical components"},{"@ID":65, "PATENTS PETpatents www.verpackungspatente.de PETplanet Insider Vol. 23 No. 10/22 www.petpla.net 63 A sturdy plastic bottle base International Patent No. WO 2021 / 261290 A1 Applicant: Suntory Holdings Ltd., Osaka (JP) Application date: 11.6.2021 This specially designed base area ensures bottle stability while using as little material as possible. The shape and contours of the reinforcing grooves stand out in the illustration. Shape of the base area International Patent No. WO 2021 / 261292 A1 Applicant: Suntory Holdings Ltd., Osaka (JP) Application date: 11.6.2021 This specially designed base area ensures bottle stability while using as little material as possible. The shape and contours of the reinforcing grooves stand out in the illustration. A variable base International Patent No. WO 2021 / 261578 A1 Applicant: Yoshino Kogyosho Co. Ltd., Tokyo (JP) Application date: 25.6.2021 The design aims to compensate for changes in pressure inside the bottle with a specially formed base area that does not alter the bottle’s outer shape. An asymmetrical bottle International Patent No. WO 2021 / 249798 A1 Applicant: Sidel Participations, Octeville-sur-Mer (FR) Application date: 31.5.2021 An asymmetrically designed PET bottle in the area between the bottle shoulder and its base, in this case, five-sided which prevents the container from twisting, A lightweight bottle International Patent No. WO 2021 / 247728 A1 Applicant: Niagara Bottling LLC., Diamond Bar, (US) Application date: 2.6.2021 Shaping and design of a preform so that the thread – and thus the weight of the associated cap – are optimised. An opaque preform International Patent No. WO 2021 / 260463 A1 Applicant: Colormatrix Holdings Inc., Wilmington (US) Application date: 1.6.2021 The application describes a preform that consists of a special material that provides protection from the light thus avoiding problems such as material distribution at fixed points."},{"@ID":41, "39 TRADE SHOW PREVIEW PETplanet Insider Vol. 23 No. 10/22 www.petpla.net Circular Economy Forum at K 2022 This year will once again see a Circular Economy Forum held at K in Düsseldorf, The Trade Fair for Plastics & Rubber, from 19 to 26 October 2022. On the outdoor premises between Halls 10 and 16, the VDMA (German Engineering Federation) as organiser and 13 of its member companies will demonstrate the importance of technology in the implementation of the circular economy in the plastics industry. With machines running visitors can see how plastic waste is converted into high-quality regranulates or how recyclates are processed into attractive, highly functional and recyclable products by means of various processing methods. The Circular Economy Forum picks up on all three guiding topics of K 2022 – Circular Economy, Climate Protection, Digitalisation. Because high tech is also required to optimise manufacturing processes and make them ever more efficient – as another measure besides the recycling of plastic products to save CO2. Both approaches are not conceivable without digitalisation. It is, for instance, the enabler for digital product passports and globally applicable traceability standards. The linking of all components in the production line is considered the prerequisite for optimising processes. On the topic of data exchange between machines the VDMA has initiated a showcase that makes the live data of integrated machines visible on the basis of OPC UA, at the VDMA Dome and also retrievable by smartphone. The VDMA Dome at the centre of the Forum will serve as an information point and meeting place. But it will also provide an overview of important technology-relevant process steps in the plastic circular economy. By means of “The Machine” installation nearly 40 companies with over 50 submissions will present their technology highlights for the Circular Economy. Technologies range from sorting, shredding, washing and regranulating, or material handling to the most important converting processes not forgetting downstream process steps. In this second part of our preliminary report, you can find out what K has to offer especially in the field of PET! www.k-online.de TRADE SHOWpreview Focus on recyclate processing, circular economy and digitalisation The Institute for Plastics Processing in Industry and Craft at RWTH Aachen University (IKV) will show three processes in operation. The focus of the presentation will be on the topics of recyclate processing, circular economy and digitalisation. IKV will be presenting a batch variation tolerant process control for recyclate processing in injection moulding, an example from the portfolio for material characterisation of the Centre for Analysis and Testing of Plastics (KAP) and an additive manufacturing technology for the production of large-volume components with load-case tailored layers. Also at the IKV booth, the deep-tech start-up company IonKraft, which has its roots at IKV, will present its prototype machine for coating large-volume blow mouldings for the first time to the public. www.ikv-aachen.de IKV Hall 14 Booth C16 BEYOND THE HORIZON PROCESS SOLUTIONS FOR POLYMER RECYCLING AND SOLID STATE POLYMER UPGRADING Polymetrix, a Sanlian Buhler Company, provides process technology including EPCM services for the polymer recycling and manufacturing industry. Leading supplier of rPET systems and integrated rPET plants for single line capacities up to 70’000 tons per year. www.polymetrix.com www.slhpcn.com"},{"@ID":5, "imprint EDITORIAL PUBLISHER Alexander Büchler, Managing Director HEAD OFFICE heidelberg business media GmbH Hubweg 15 74939 Zuzenhausen, Germany phone: +49 6221-65108-0 fax: +49 6221-65108-28 info@petpla.net EDITORIAL Kay Barton Heike Fischer Gabriele Kosmehl Michael Maruschke Ruari McCallion Anthony Withers WikiPETia. info petplanet@petpla.net MEDIA CONSULTANTS Martina Hirschmann hirschmann@petpla.net Johann Lange-Brock lange-brock@petpla.net phone: +49 6221-65108-0 fax: +49 6221-65108-28 LAYOUT AND PREPRESS EXPRIM Werbeagentur | exprim.de Matthias Gaumann READER SERVICES reader@petpla.net PRINT Chroma Druck Eine Unternehmung der Limberg-Druck GmbH Danziger Platz 6 67059 Ludwigshafen, Germany WWW www.hbmedia.net | www.petpla.net PETplanet Insider ISSN 1438-9459 is published 10 times a year. This publication is sent to qualified subscribers (1-year subscription 149 EUR, 2-year subscription 289 EUR, Young professionals’ subscription 99 EUR. Magazines will be dispatched to you by airmail). Not to be reproduced in any form without permission from the publisher. Note: The fact that product names may not be identified as trademarks is not an indication that such names are not registered trademarks. 3 PETplanet Insider Vol. 23 No. 10/22 www.petpla.net Copyright of front cover by: Messe Düsseldorf/ctillmann Dear readers, Drinktec 2022 has closed its doors, the first international fair for our sector after the disruption of the pandemic. From a personal perspective, I was extremely pleased; we met all PETlers again, and it was good to shake hands again and to look into each other’s eyes. Martin Hammerschmid, CEO Gernep, had repeatedly questioned the costs of trade fairs in previous years. At this year’s Drinktec he told me that he would never want to question the trade fair again, so great is the need for suppliers and processors to meet and interact in person in an intense way. Perhaps Petra Westphal summed up the importance of Drinktec best: “The future of the industry is being shaped here.” However, she also self-critically mentioned the rollercoaster ride in the preparations for this year’s event. There were significantly fewer exhibitors (2022: 1,002 instead of 2017: 1,749) and significantly fewer visitors (50,000 instead of 76,000). But the proportion of overseas visitors did increase slightly (2022: 70% instead of 2017: 67%), demonstrating the international importance of the event. We can only agree with the view of Volker Kronseder, Krones. This is how he summed up the fair: “When you walk through the halls ... you finally see people from different nations communicating with each other face to face again”. Personally, I am pleased that Drinktec and with it our PETpoint are back and I look forward to the next meeting in Munich in 2025. Yours, Alexander Büchler"},{"@ID":33, "EDITOUR PETplanet Insider Vol. 23 No. 10/22 www.petpla.net 31 tax, a ban on single-use plastics and an EPR system for textiles, we are currently working mostly on projects relating to textile recycling, but also on the recovery of PET flakes because of the high demand for the separation of rPET and bottle cap flakes. We assume that, because of EU legislation, the trend towards a circular economy and increasing trademark holder engagement with sustainability issues, our recycling activities will increase in the coming years.” Even if precise figures regarding overall growth and specifically the growth of PET sorting are not currently given, we’re told that with Tomra’s technologies Autosort Flake and Innosort, PET flake sorting will demonstrate continual growth. Autosort is the bestseller here, while X-Tract takes this lead in metal cleaning. Incidentally, the new generation of X-Tract with enhanced functionality had just been unveiled. “Basically, what we’re seeing,” says Mrs Jansana, “is a clear need in the industry for high-quality recycling end products, larger and more precisely working systems with high material throughput, and overall more lines per facility. The larger PET providers are expanding and upgrading their systems for higher capacities and are relying more heavily on process automation, the same with PET flake sorting.” There are also trends towards the recovery and processing of PET trays, coloured PET and above all, the PET waste generated inhouse in the manufacturing process. The issue of tethered caps will also create a need for in-house sorting facilities, as significantly more bottles will now be returned with caps. Mrs Jansana explained that in the worst days of the pandemic, Tomra’s activities were maintained in accordance with the situation, and sales and service were carried on in person and also online, which worked well. She summarises the future of the Spanish branch as follows: “We are planning to bring new products and applications onto the market and to further develop existing products. There is a particular focus on plastics and materials like metals, paper, textiles and wood. Furthermore, we are also continuing to work on digital solutions, such as our cloud-based data platform Tomra Insight, to optimise sorting processes.” www.tomra.com Tour Sponsors: Close-up of Tomra’s Autosort Flake"},{"@ID":6, "PETcontents 4 PETplanet Insider Vol. 23 No. 10/22 www.petpla.net 10/2022 Page 54 TOP TALK 12 Sidel’s food, home and personal care initiative - Interview with Sidel’s new Global Vice President, Mr Pascal Lefèvre MATERIALS / RECYCLING 15 New PET hydrolase - Enzyme discovered in human saliva microbes could be used to decompose PET-based plastics 16 Improved characteristics - Clay-based additive triples gas barrier properties and boosts strength & UV resistance 18 No compromise on processability - Masterbatch for hot fill packaging EDITOUR 20 Product quality, shelf life and food safety for PET - Additive and colour masterbatches from Switzerland 22 Innovating for sustainability 26 A closed loop of 69% rPET in Switzerland 28 Sorting waste streams 30 Recycling in Spain - Business is booming in waste sorting systems 32 Always the right atmosphere 33 Virtually maintenance-free injection moulds MARKET SURVEY 35 Suppliers of filling equipment & inspection systems TRADE SHOW PREVIEW 39 K’ show 2022, preview part 2 47 Degassing and decontamination technologies 50 Digitalisation and process control, the wider concept of sustainability 52 Processing rPET in thin wall injection moulding 54 High productivity, low consumption & sustainability 56 Wide range of vision inspection systems 58 PET Technologies to debut at K’ show 59 Four moulding technologies - Focusing on packaging sustainability & efficiency BUYER’S GUIDE 64 Get listed! INSIDE TRACK 3 Editorial 4 Contents 6 News 60 PET bottles for home & personal care 62 PET bottles for beverage + liquid food 63 Patents 70 Outer Planet Page 26 MATERIALS Page 22"},{"@ID":13, "EDITOUR PETplanet Insider Vol. 23 No. 10/22 www.petpla.net 23 in the Ashfield district of Nottinghamshire. We met at the Kirkby in Ashfield facility; the third factory is around three kilometres away, in Sutton in Ashfield. The Sutton site has been the centre of PET production but all plastics bottle, carton and closure manufacture is in the process of being centralised in Kirkby. Total company revenues now are in the region of £50 million a year (€60 million). On the plastics side of the business, Robinson’s supplies customers in chemical, domestic cleaning, personal care, food – predominantly foodservice, as opposed to retail but, during the tour of the plant, we saw some packaging for Tesco’s, a very well-known UK high street retailer. Its customer roll also includes Unilever, Procter & Gamble, Reckitt Benckiser and SC Johnson. “We make bottles for Radox shower and bath gels, bleach bottles, squeezy bottles for sauces, rigid jars and pots for chilled soups. Wherever you shop, you will potentially be buying products sold in Robinson packaging,” Helene explains. PET, PP and HDPE Around 70% of its UK plastic production is for food and beverage but that market represents less than half of the Poland factories’ output, which is oriented to homecare and personal care. The Denmark plant is primarily focused on home care; its food and drink activity is mainly supplying larger-capacity containers for foodservice and catering. Currently, its plastics packaging output is approximately 35% each in PET and PP, and 30% in HDPE. “I think there is a market shift towards PET, because it’s the easiest to drive recycled content,” Dr Roberts said. However, demand for rPET is outstripping supply, at the moment, and the UK is a long way from selfsufficiency. Indorama Ventures finally closed its recycling plant in County Durham, in the North-East of England, in 2017; the largest recycling plant in the country is now Monoworld Recycling, located at Rushden, Northamptonshire, at the southern end of the East Midlands. Robinson does what it can within those operational challenges. Improving recyclability “We stopped using carbon black because of the impact on recyclability and now use alternative additives. We are also moving away from polystyrene – we only had a small amount but our production now is essentially PT, PP and HDPE,” Dr Roberts said. “There’s no reason why any of these materials cannot be recycled. My drive is to get to DNC boosters Turnkey all-in-one system • Compact powerhouse with a footprint of only 2.35 m² ,QLWLDO SUHVVXUH XS WR EDU ² ÀQDO SUHVVXUH XS WR EDU • Plug and play: ready for immediate operation 3UHPLXP HˣFLHQF\\ ,( PRWRU GHOLYHUV LPSUHVVLYH SHUIRUPDQFH DQG HQHUJ\\ VDYLQJV • Sigma Control 2 controller: RSWLPXP HˣFLHQF\\ DQG QHWZRUN FDSDELOLW\\ ,QGXVWULH www.kaeser.com 19. – 26. October 2022 Fair Düsseldorf Hall 11 | Stand H 65 A tray of robot-packed 1 l bath/shower bottles with 50% rPET content"},{"@ID":62, "PETplanet Insider Vol. 23 No. 10/22 www.petpla.net 60 PETbottles Home + Personal Care Micellar Water with vitamin C Beiersdorf is adding a var iant wi th vi tamin C to its steadily growing micellar water segment. Micelles are designed to help gently and softly cleanse the skin. The 400 ml vegan water is f i l led in a bott le made of 95% recycled material with coloured accents. The back label is coloured orange on the inside, and together with the transparent front label and the two-tone hinged lid closure, it makes for an attractive package design. www.nivea.de Cleaner in signal colour S h i p - S h a p e i s a cleaner specially designed for the quick and easy cleaning of all surfaces in hairdressing salons and especially for removing hairspray residues from mirrors and chairs. The cleaner, which is manufactured in the USA and comes in a signal colour, is filled into a handy bottle with a 250ml capacity and a lockable pump sprayer. Brushes and combs can also be thoroughly cleaned by soaking them in ShipShape. www.king-research.de Conical bottle for shampoo The “Bioderma” brand, which belongs to Naos Deutschland GmbH, sells 400ml of a gentle, skin-caring and soothing shampoo in an eye-catching, high-quality bottle. The slightly conical, green coloured bottle is directly printed and closed with a matching coloured, one-handed hinged lid closure with a dosage opening. www.bioderma.de"},{"@ID":45, "43 TRADE SHOW PREVIEW PETplanet Insider Vol. 23 No. 10/22 www.petpla.net The fine art of PET bottle-to-bottle recycling Star l inger recycl ing technology will showcase the RecoStar PET art, the company’s latest plant model in the field of PET recycling. In addition to Starlinger’s established technology solutions such as good decontamination performance for food contact applications and rPET pellet quality, the new plant is characterised by low energy consumption and considerably simplified maintenance processes. For 35 years now, Starlinger recycling technology has been involved in processing plastic waste so that it can be used as an alternative resource to virgin materials. Starlinger recycling plants are used the world over to recycle used plastics from a wide variety of sectors, thus counteracting the problem of waste and scarcity of resources. Ideally, closed packaging cycles are created – as is the case with PET beverage bottles. “What happens in the PET bottle-tobottle recycling process to turn a used mineral water bottle back into a new mineral water bottle can be called high art,” says Paul Niedl, Commercial Director at Starlinger recycling technology. “It is a composition, a synthesis of experience combined with the latest scientific knowledge and high technological standards. Our new RecoStar PET art embodies 20 years of experience in the field of PET food contact recycling. In addition, technical improvements have been made to make the plant easier to maintain and even more energy-efficient – in times like these, this is an important issue, especially in Europe. But we don’t want to give too much away in advance – at K 2022 and our Dynamic Days in Schwerin, interested parties can learn about the RecoStar PET art and all its technological innovations in great detail.” The pre-drying unit and the extruder of the new RecoStar PET art will be on display at the Starlinger recycling technology stand in Hall 9, and the SSP reactor at the Starlinger stand in Hall 16. The company will also be showcasing machine solutions from the fields of polyester fibre/ filament recycling and recycling of postconsumer polyolefins, including odour reduction technology. Starlinger Dynamic Days in Schwerin – spotlight on PET & post-consumer plastics recycling On 26 and 27 October 2022 Starlinger recycling technology will also be holding its “Dynamic Days” in-house exhibition at its Schwerin site in Germany, where the new RecoStar PET art and a RecoStar dynamic recycling plant will be in operation. Interested customers will have the option of travelling from Düsseldorf to Schwerin via Rostock and back again on their chosen day by means of a charter flight and bus transfers. www.starlinger.com Starlinger Hall 16 Booth B47"},{"@ID":71, "MARKET SURVEY 35 PETplanet Insider Vol. 23 No. 10/22 www.petpla.net 10/2022 MARKETsurvey Supplier of filling equipment and filling inspection systems It’s time to present some state-of-the-art filling equipment and filling inspection systems in our annual market survey. Please have a look at the up to date technical details provided by: Sacmi Imola S.C., SMI S.p.A., Sipa S.p.A, Pressco Technology Inc., KHS GmbH, Newamstar Packaging Machinery Co., Ltd., Heuft Systemtechnik GmbH, Krones and Fogg Filler. Although the publisher has made every eff ort to make sure that the information in this survey is up to date, no claims are made regarding accuracy and completeness. Filling Equipment Company name Sipa Postal address Telephone number Web site address Contact name Function Direct telephone number E-Mail Via Caduti del Lavoro n. 3 31029 Vittorio Veneto (TV), Italy +39 0438 911 511 www.sipasolutions.com Mr Matteo Tagliaferri Marketing and Communication +39 0438 911 511 matteo.tagliaferri@zoppas.com 1. Machine designation / model number Isofi ll P Stillfi ll Evo Flextronic C Flextronic SE/S Isotronic Flextronic W Bigfi ll 2. Number of fi lling heads (range: from/to) 20-140 20-140 30-180 20-180 20-100 20-96 12-36 3. Min to max bottle contents (in liters) 0.125-3 0.125-3 0.125-3 0.125-3 0.125-3 0.125-3 3-20 4. Filling speed: output (bph) (min to max): specifi y: 1l bottle / still water (bph) 60,000 62,000 60,000 62,000 (S: 63,000) 50,000 36,000 18,000 (5 l ) 1l bottle / CSD (bph) 51,000 (CMW) 55,000 (CMW) 50,000 1l bottle / milk (bph) 62,000 50,000 36,000 1l bottle / juice (bph) 53,000 62,000 5. Filling process Pressureless (still drinks) Yes Yes Yes Yes Yes Yes Yes Pressure fi lling (carbonated drinks) Yes Yes Yes Hot fi lling Yes Yes Yes (S: no) Cold aseptic fi lling Yes Juices with high pulp content Yes Yes (S: no) 6. Type of fi lling valve and metering system Isobaric mechanical level fi lling Mechanical gravity fi lling Isobaric volumetric fi lling valve Gravity volumetric fi lling valve Isobaric mechanical level fi lling valve Electronic weight fi ller Gravity volumetric fi lling valve 7. Special features (short description/keywords) AISI 316L SS valve, product defl ection without defl ector on the fi lling tube, quick changeover for different neck diameters, automatic dummy bottle insertion, mobile vent tube, centralised remote fi ll level adjustment AISI 316L SS valve, product defl ection without defl ector on the fi lling tube, quick changeover for different neck diameters, seperated bottle air return, hot fi ll kit for product recirculation, constant and controlled recirculation rate in bottle, centralised remote fi ll level adjustment no bottle no fi ll system AISI 316L SS valve, product defl ection without defl ector on the fi lling tube, quick changeover for different neck diameters, automatic dummy bottle insertion, magnetic fl ow meter product control, fi lling speed control, XFill confi guration without tank on board, dry pressurisation separated bottle air return AISI 316L SS valve, no contact between valve and bottle neck, quick changeover for different neck diameters, ultra clean version available, magnetic fl ow meter product control, fi lling speed control, automatic dummy bottle insertion, XFill confi guration without tank on board AISI 316L SS valve, electro-pneumatic level fi ller for glass, PET and RefPET bottles, quick changeover for different neck diameters, automatic dummy bottle insertion, mobile vent tube, centralised remote fi ll level adjustment AISI 316L SS valve, no contact between valve and bottle neck, quick changeover for different neck diameters, load cell integrated in the bottle neck support, 3 positions membrane valve fi lling speed control, automatic dummy bottle insertion AISI 316L SS valve, no contact between the valve and the bottle neck, quick changeover for different neck diameters, ultra clean version available, 3 positions membrane valve fi lling speed control, automatic dummy bottle insertion, high fl ow performance Resins & additives Preform machinery Preform production & inspection systems Preform & SBM mould manufacturer SBM 2-stage Compressors Caps & closures & inspection systems Filling equipment & inspection systems Recycling machinery Palletising & shrink film machinery"},{"@ID":23, "EDITOUR PETplanet Insider Vol. 23 No. 10/22 www.petpla.net 21 the company, the whole idea is seen as feasible for both transparent and opaque containers that have good recycling properties as is the case with PET. Being PET the only polymer able to offer tray to tray or bottle to bottle food grade use of mechanically recycled rPET, this project showcase the company’s understanding of market needs, and its translation into functional additives that replace non circular polymers. Markets, customers and sustainability “Today’s markets, whether in India, Brazil, North America or Europe, are largely regulated through legislation and no longer necessarily by the customer”, said Mr Egger. “Legislators play a crucial role in shaping the circular economy and in increasing the market’s involvement in innovative products. The issue for us is more about the dynamics. We are looking to strengthen our efforts to encourage the uptake of monomaterial PET packaging along with our innovascan GPS NPSF , 4IPX EFUBJMT 888 */53\"7*4 $0. 8PSMEXJEF 4FSWJDF 7*4*0/ */41&$5*0/ 4:45&.4 GPS QMBTUJD QBDLBHJOH 7JTJU VT )BMM \" #PUUMFT $POUBJOFST tions, as well as greater use of rPET and making it easier for customers to make the switch to these products”. In addition to its focus on products that contribute to circularity in recycling, Sukano is also committed to sustainable manufacturing and practices, including technical upgrades to its machinery worldwide. As a result, extruders at all facilities are subject to constant technical improvements, with the proof of concepts process completed in advance of customer testing which is a benefit when it comes to speeding-up project launches and ensuring consistency of performance. The Swiss plant has also just been expanded with the introduction of a new extrusion line and material silos. As part of the company’s sustainability strategy and in addition to continuous expansion of its automation practices, 2,000 solar panels were recently mounted on the factory roof to reduce emissions and generate their own sustainable energy supply with a total output of 725,000 kW/h. www.sukano.com"},{"@ID":60, "TRADE SHOW PREVIEW PETplanet Insider Vol. 23 No. 10/22 www.petpla.net 58 PET Technologies to debut at K show PET Technologies’ stand at K2022 – its first ever – will present its solutions for improved energy consumption and other savings and feature its range of stretch blow moulding machines (SBM) that can handle sizes from 100ml up to 40 l containers, including five US gallon jugs and 30 l beer kegs. PET Technologies prides itself on its willingness and ability to meet customers’ special needs and adapt its machines accordingly. It will demonstrate technologies that can produce a mirror-like smooth finish, as well as manufacturing equipment equipped with four and five-axis machining centres, with spindle processing speeds up to 42,000 rpm. The company says that it can produce linear and rotary blow-moulds for all European brands of SBM machines. PET Technologies Hall 14 Booth A72 Faster and cooler than ever optiSTACK saves your time and money! German Technology Special designs that will be seen on the stand include a transparent Boston round water bottle with a black cap and minimalist label, branded as Yulong water, from China. The lower part is finished with sharp edges, to give the impression that the bottle is emerging from dense ice. The bottle was designed and developed in accordance with the PET stretch blow moulding process, the capabilities of the customer’s SBM machine and the restrictions of the existing filling line and market trends. PET Technologies says that its machines offer customers low energy consumption within compact general dimensions; flexibility of bottle shapes and formats; easy access to internal components for simpler maintenance; and a wide network of service centres. www.pet-eu.com"},{"@ID":42, "40 TRADE SHOW PREVIEW PETplanet Insider Vol. 23 No. 10/22 www.petpla.net rPET100 Designed for recycling. Made from recycling. • Heat resistant • Fully recyclable • Thermoformable like PET BENEFITS HOT CUPS · DAIRY PRODUCTS · INSTANT SOUPS · TO-GO MEALS · COFFEE LIDS foodgrade without compromise Closure portfolio & injection mould technology Alongside the latest closure solutions, Corvaglia will unveil the “adaptive flex-band” injection mould technology. This technology is claimed to combine different – and in some cases conflicting – requirements of beverage bottlers and consumers. Above all, the technology is intended to offer advantages for tethered caps: the key objective for beverage bottlers is finding closure solutions that can be easily applied to the bottles on an industrial scale. This makes it easy to ensure high productivity and reduce scrap at the same time. For this purpose, a flexible tamper-evident band has become established for conventional closures. Consumers, in turn, prefer a convenient opening and closing experience. Consumer tests have revealed that this requires locking it in the open position with a large opening angle. The locking mechanism requires hinges, which are produced in the injection moulding process using slides in the injection moulds in Corvaglia’s solution. Slides can be used to design a wide range of different hinges. Combining both requirements in a single closure solution is difficult to implement from a technological point of view. Thanks to the new injection mould technology, however, Corvaglia considers itself now in a position to combine these two demands. The company’s sales representatives from all regions of the world will be on hand at the fair to explain the technology in detail. www.corvaglia.ch Combination of both advantages of the adaptive flex-band concept. On the left the flex-band, on the right the hinges with large opening angle. Corvaglia Hall 12 Booth B36-02"},{"@ID":17, "MATERIALS / RECYCLING PETplanet Insider Vol. 23 No. 10/22 www.petpla.net 15 Enzyme discovered in human saliva microbes could be used to decompose PET-based plastics New PET hydrolase Researchers in Thailand have discovered that an enzyme found in human saliva has the capacity to decompose certain forms of PET. Chayasith Uttamapinant, from the Vidyasirimedhi Institute of Science and Technology (Vistec) in Rayong, Thailand, and Worawan Bhanthumnavin, from Chulalongkorn University, Bangkok, Thailand, and their teams and colleagues, investigated whether humans, who consume vast amounts of food and beverages that have been packaged in PET, may have evolved the ability to digest microplastics. Landfill sites and harbours have already been found to be promising sites for finding bacteria that have adapted to consume or make use of plastics. The candidate bacteria have evolved enzymes, known as PET hydrolases, which can break PET down into smaller molecules. The teams did not discover any PET-digesting ability in the human gut but they did find a new hydrolase, which they named MG8, while searching a public metagenome database that contains samples from seawater and human saliva. The teams were able to attribute the likely source of the enzyme to gram-negative bacteria that may reside in human saliva. These bacteria are similar to strains found near the “Pacific trash vortex”, which have also evolved to produce PET hydrolases. Their paper, published in the journal Angewandte Chemie, reports that this newly discovered hydrolase performs better than many other known bacterial PET hydrolases. It can be produced using biotechnological methods and could be put to use in plastic recycling or for functionalising plastics. In their quest for enough material to perform their experiments, the teams modified a bacterium that can be cultured in laboratories to produce the enzyme. They easily recovered an active form of the MG8 enzyme from a denatured form, which can be isolated in large amounts. This discovery indicates a high level of potential for scaling up in the future. The team discovered that MG8 can not only decompose PET with ease but, with a small modification, it can also bind to it, highly effectively. They achieved this by modifying the protein sequence, replacing one of the naturally occurring amino acids (serine) at the active site with an unnatural amino acid: DAP (diaminopimelic acid). DAP is a characteristic of cell walls of some bacteria; it is often found in the peptide linkages of NAM-NAG (amino sugars present in the peptidoglycan layer of bacteria) chains that make up the cell wall of gram-negative bacteria. The modified enzyme was found to immediately adhere to PET powder. The report paper suggests that, in this form, it could be used as a vehicle for functionalising PET surfaces, increasing its versatility in medical devices and enhancing the versatility of rPET. While it looks promising, MG8 is still at an early stage of development. Consumer-grade PET plastics with high crystallinity cannot be decomposed by it yet, for example. Further research will be necessary to reach the stage where a whole plastic water bottle can be dissolved in a simple solution containing the enzyme. Dr Chayasith Uttamapinant is a lecturer in the School of Biomolecular Science & Engineering, Vidyasirimedhi Institute of Science and Technology (VISTEC), Rayong, Thailand. The Uttamapinant group develops chemical biology technologies to study proteoforms and local translation, bioremediation tools, and open-source molecular diagnostic platforms. Dr Worawan Bhanthumnavin is an Associate Professor at the Chemistry Department of Chulalongkorn University, Bangkok, Thailand. Her lab has broad interests in synthetic methodological development for bioactive compounds, fluorescent probes and sensors, as well as biological applications of these synthetic molecules. The research paper was published in Angewandte Chemie. The full article can be found at: Discovery and Genetic Code Expansion of a Polyethylene Terephthalate (PET) Hydrolase from the Human Saliva Metagenome for the Degradation and Bio-Functionalization of PET. https://onlinelibrary.wiley.com Some additional information was found and included in this article by Ruari McCallion, PETplanet Insider Editor-at-large. The hydrolase can be produced using biotechnological methods and could be put to use in plastic recycling or for functionalising plastics (source: Wiley-VCH, ‘Angewandte Chemie’). MATERIALS"},{"@ID":51, "8 NEWS PETplanet Insider Vol. 23 No. 10/22 www.petpla.net Adler Industrial Solutions acquires R&D / Leverage Adler Indust r ial Solut ions, Inc. announced it has acquired R&D/Leverage, Co. This transaction marks the third acquisition by Adler in the past year and gives the company expanded scale, a broader capability set, and European manufacturing facilities that serve a global customer base. Headquartered in Lee’s Summit, Missouri, R&D is a leading manufacturer and supplier of mould types for the food and beverage, personal care, and healthcare markets. Founded in 1975 by Ivan and Ardith Drienik, the company was a pioneer in developing complex tooling solutions for the injection moulding and blow moulding industries. Today, R&D has over 250 employees split between its 180,000-square-foot and 60,000-square-foot manufacturing facilities in Lee’s Summit, Missouri, and Nottinghamshire, England, respectively. “The acquisition of R&D is a milestone addition for Adler. The capabilities and skillsets of the R&D team are second to none and will only further raise the core competencies of the Adler group,” said Philipp Gruner, CEO of Adler. “Adding adjacent markets such as blow moulds, injection stretch blow moulds, preform moulds and higher complexity injection system moulds to our capabilities allows Adler to offer more services to our existing and future customers while expanding our geographic reach within the United States and internationally.” As a part of Adler, R&D / Leverage will benefit from additional resources and investment. Ardith Drienik said the acquisition is the ideal pathway forward for the company that she and her husband, Ivan, founded and dedicated their lives to building. “When I met the Adler founders, I knew I had found the right buyer. I wanted someone that shared my husband’s love of manufacturing and engineering, and someone who appreciates the value and contributions of the employees. I feel Ivan would agree with this decision that the Adler team’s track record, energy, and vision will make them the ideal stewards of this amazing company,” said Mrs. Drienik. www.adlertooling.com www.rdleverage.com Kilian Braunsdorf becomes CEO of Paccor Kilian Braunsdorf has been appointed Chief Executive Officer (CEO) of Paccor, a global player in the plastic packaging industry. He succeeds Andreas Schuette, who steps down from his role with the completion of the acquisition of Paccor by the Faerch Group (as of September 1, 2022). Under the new ownership, Paccor intends to accelerate the transition towards circular packaging and provide its customers with new and innovative packaging solutions. Kilian Braunsdorf (47) joined the company in July 2020 as a Member of the Executive Board and has since served as Chief Financial Officer (CFO). Prior to joining Paccor, he held global leadership positions in the packaging industry. He started his career in Auditing and Management Consulting and holds a degree in Industrial Engineering. Kilian Braunsdorf succeeds Andreas Schuette, who served as CEO of Paccor since March 2019. Being part of the Faerch Group is stated to bring numerous benefits to Paccor and its customers. The joint geographical footprint of more than 30 production sites with around 6,000 employees across Europe, the US and Asia brings the company closer to its customers. “Paccor will continue to operate as a separate company and provide its customers with the products and services they know and expect from Paccor,” Lars Gade Hansen, CEO of the Faerch Group, said. “A comprehensive investment programme for supporting material conversion into circular solutions, expanding the operational platform and in R&D will be quickly brought into play,” he concluded. The Paccor UK business is not part of the acquisition and was hived off prior to the transaction. www.paccor.com RadiciGroup: acquisition of Ester Industries Ltd. completed RadiciGroup High Performance Polymers acquired the Engineering Plastics business of the Indian company Ester Industries Ltd. Last May, RadiciGroup announced this action aimed at strengthening its internationalisation strategy, with an investment of around 35 million euros: the transaction allows RadiciGroup - in India since 2006 - to further reinforce its local presence through the acquisition of one of the main and historic players on the Indian market. For RadiciGroup this is a significant industrial investment in which Ester Industries Ltd is selling its newly-built production plant in the city of Halol (Gujarat), West of India: compound lines, R&D laboratories, customers/suppliers contracts as well as its leading brand Estoplast which includes different types of compounds used primarily in the electrical/electronic and telecommunications markets. Ester Industries Ltd - one of the leading Indian producers of polyester films, engineering plastics and special polymers - has seen in RadiciGroup the ideal partner to follow up on its consolidated experience in the engineering polymers business, in order to focus on the packaging film sector, a business the Indian firm intends to continue and strengthen. The new production site, under construction, will become operational at the beginning of 2023, following the various transfers of tangible and intangible assets. As a result of the acquisition, the Group aims to achieve total annual sales in the Indian market of more than EUR 50 million. www.radicigroup.com"},{"@ID":61, "TRADE SHOW PREVIEW PETplanet Insider Vol. 23 No. 10/22 www.petpla.net 59 Focusing on packaging sustainability & effi ciency Four moulding technologies Three of the four Nissei ASB machines being demonstrated will be making their global debuts at the K’ show 2022. The first global debut is the PF36/9-12000, a 1.5-step injection stretch blow moulding machine producing a 12 l bag-in-box super light-weight container for water server. The second debut is the ASB-12M-2INJ: A 1-step double layer injection stretch blow moulding machine producing a 300ml airless pump bottle with PET outer & PP inner layer. And finally the third debut is a PM-100/111N. A vertical clamp compact preform injection moulding machine producing 13.5 g preforms at a speed of 14,700 pph. Nissei ASB Hall 14 Booth B38 Nissei ASB will also demonstrate live moulding of a returnable & refillable PET bottle on an HSB-4N machine using its well-established double blow heat-set process via its HSB series reheat stretch blow moulding machines. A 1 l sparkling water bottle with 1.5 gas vol., designed compatible with popular German industry standard for sparkling water, with a weight of 53 g serves as sample. With an rPET content of 30% the reuse cycles are more than up to 25 times. The double blow heat-set process that is the main feature of the HSB series machines, generates high crystallinity (density) of the material together with less stress in the moulded bottle which combine to provide improved thermal stability and greater resistance to environmental stress cracking, ensuring high reusability rates even at much lighter weight than current industry standards. In a typical production scenario, a single HSB-4N machine will produce up to 20 million returnable & refillable PET bottles per year, and with each having a lifetime of more than 25 cycles, represents the equivalent of 500 million single use bottles, says Nissei ASB. At end of life, refillable PET bottles can be bottle-to-bottle recycled or converted into rPET for other new products, typically reducing their carbon footprint by an additional 25%. ASB is no stranger to the returnable & refillable PET bottle industry; the company developed and launched the first returnable & refillable PET bottles for juices and soft drinks in the German market during the country’s first “green wave” way back in 1989. With the resurgence in interest and public demand for refillable packaging, not only in Germany but also globally, ASB is well placed to take advantage by utilising its broad packaging expertise as well as its capable moulding equipment. 12l bag-in-box for water server The bag-in-box water delivery service is already an established market in Japan where Nissei ASB has been a key player, providing moulding solutions for the popular sized 12 l and 9 l light-weight PET water containers. This packaging concept provides a wide range of benefits at the point of delivery, for consumer safety, and contributes to sustainability by reduction of resin consumption. Airless pump double layer container ASB’s patented double layer moulding process enables containers to be moulded with an inner and outer layer in the body and/or neck section in a variety of thicknesses, configurations, moulding order, or resins as required to provide additional flexibility and value to the moulded product. The ASB-12M-2INJ is based on the ASB-12M model, re-engineered with twin injection units and a six-station rotary table that comprise two separate injection and cooling stations. Preform moulding machine The K’ show 2022 marks the global debut of ASB’s new PM-100, compact injection machine, developed for preform manufacture where small to medium scale production of high quality preforms is required. In keeping with ASB’s design philosophy, the PM-100 utilises vertical clamping with mould indexing being conducted by a rotary table traversing through injection, cooling and eject stations with operations being carried out simultaneously in each station. A complete set of lip cavities is mounted at each station so that moulded preforms remain held by the neck until final ejection from the machine. The machines will be displayed at the show with a full line of matched moulding ancillary equipment that the company is able to supply, such as preform unscrambler, chillers, compressors, mould temperature controllers, etc. ASB’s booth will also be exhibiting a range of developments and packaging technologies including Zero Cooling, heat resistant PET containers, bag-in-box, canted/tilted neck bottles, HDPE bottles by ISBM, thick wall / base cosmetic bottles, etc. www.nisseiasb.co.jp"},{"@ID":43, "41 TRADE SHOW PREVIEW PETplanet Insider Vol. 23 No. 10/22 www.petpla.net The future of dry ice cleaning in the plastics industry Cleaning tools, moulds and surfaces is one of the most quality- and cost-critical manufacturing steps in the plastics industry. To help make this process more efficient, Cold Jet provides several effective dry ice solutions. They are claimed to enable soft, non-abrasive cleaning of delicate contours and fine cavities of injection moulds. Commonly used for environmentally-friendly cleaning blasting is dry ice in the form of blocks, discs, nuggets and pellets. Depending on the cleaning application, a choice can be made between a 3mm dry ice pellet blasting system or Cold Jet scraping technology, which uses any form of dry ice. Typically used in the plastics industry, the compact, electric, single-hose, low-pressure blasting systems with patented micro-particle scraping technology are used for dry ice blocks. In addition, at K show, Cold Jet will present its latest novelty, the i³ MicroClean2 and the PCS60 with patented particle control technology. Manufacturer Cold Jet also offers systems that combine dry ice pellet production and dry ice blasting in one system (Combi system) and is capable of integrating with a robot. In addition to its dry ice-based cleaning systems, Cold Jet is a supplier of high quality dry ice production equipment to both industrial gas and end users around the world, producing the highest quality dry ice available. www.coldjet.com Sustainable packaging with the KMD 78.2 Speed Kiefel’s packaging specialists will be demonstrating a Speedformer KMD 78.2 speed producing a tray made from an rPET film with a thickness of 0.35mm - light, stable and sustainable. The steel rule machine is just as at home in large volume production as it is with smaller quantities. The interaction of servo motor drives, an optimised symmetrical toggle lever system and particularly robust cast steel tables offer high efficiency along the entire service life. With the Kiss-Cut system the machine guarantees maximum uptime and precision with its high punching quality and reliability, says Brückner. The separately driven plug assist provides material savings, high levels of process control and product quality. During machine development, the focus was on energy efficiency, for example of the heating elements or the drives, which all have an energy recovery system. The new KMD generation saves material. The film feed table with rollers prevents scratches and particle contamination. It enables reliable and safe film transport. The forming area of the machines uses the entire width of the film. The servo motor-driven components, the forming air speed and the cutting force are responsible for speed and accuracy. Ergonomic tool changing systems make tool changes quick and easy. Operation of the machines can be grasped quickly - thanks to the machine visualisation, the human-machine interface (HMI). The production process is clearly visualised on a dashboard on a screen attached to the machine. Machine operators can thus monitor the machine status and forming process at a glance. Settings, adjustments and test runs are carried out intuitively via the HMI. Supported by clear diagrams and animations as well as step-by-step instructions, machine training time and adjustment processes are reduced to a minimum. www.kiefel.com Cold Jet Hall 11 Booth G12 Kiefel Hall 3 Booth E90 The KMD 78.2 steel rule machine will be demonstrated live at the K trade fair."},{"@ID":7, "TRADE SHOW PREVIEW PETplanet Insider Vol. 23 No. 10/22 www.petpla.net 51 The rPET approach: extended range and products The recyclable material par excellence, PET has been the focus of the industry’s development efforts for years. Such developments concern both the technology - presses capable of processing higher percentages of recycled resins - and research into new materials and applications. For several years now, all standard Sacmi IPS models have been able to process up to 100% rPET and up to 50% PET in recycled flake form. The in-press hopper to be presented by Sacmi at the K’ show allows for further acceleration on this front by increasing the flake share to 70-75%. The single hopper optimises the flakegranule mix without the complexities that stem from having to manage two distinct processing hoppers. This proposal offers process simplification, which Sacmi combines with intense Research & Development into the use of PET instead of other resins (for example, to replace the traditional polystyrene used in the dairy sector). Thanks to its skilled Rigid Packaging Laboratory team and their understanding of materials and processes, Sacmi will also preview some of its latest producible items - such as new yogurt cartons made of transparent PET - that are driving sustainability by opening up new opportunities from both a product and market perspective. CCM technology The ability to design new products - such as PET dairy cartons - stems directly from the specific characteristics of the compression process, such as the lower material extrusion temperature, the absence of both, the gate and the hot runners in the mould. This results in a greater freedom to manage recycled and/or high-viscosity materials and the ability to manufacture light, high-quality, high-performance products. In the context of key development trends in the PET sector, the K fair offers the opportunity to showcase the latest generation of controls on CCM cap presses, such as the CMFlow extruder which reduces total electricity consumption on the press by up to 9%. With a 35mm screw connected directly to the motor, and a footprint as small as 1 meter, CMFlow can process up to 200 kg/h of resin - the same as a conventional 75mm extruder. In-the-field tests have demonstrated up to 50% fewer black spots: all other factors remaining equal. In addition to the new extruder, Sacmi customers can count on nextgen CCMs able to mount the new Smart Pack, a digital package that incorporates on-board sensors and controls. These boost plant availability, extend the lifespan of its components and simplify the workers’ tasks by reducing process errors, says Sacmi. The vision system Classy AI Applying Artificial Intelligence to vision systems can result in cuttingedge product checks, which can potentially be extended to achieve improved, proactive process management. Integrated on the PVS156 preform vision system displayed at the fair, Classy AI is a new tool that lets manufacturers perform immediate classification of defect types via a user-friendly dashboard. It covers everything from the most common defects to those that would be extremely difficult to spot without the expert eye of a highly trained technician. The result of Sacmi’s R&D on the software and relative control algorithms, Classy AI lets users examine categories of defects: in practice, the operator has a dashboard illustrating the detectable defect types. These are grouped into ‘families’ (accidental, technological, decoration-OCR, measurements, specific), providing a clear overview of the area of the object affected by a problem and compiling quality statistics. If an issue arises, a specific icon comes on, indicating the exact defect type and the affected area. Moreover, the operator is provided with statistics and info on trends. AI helps to treat the defect not as a ‘mathematical’ association between an acquired image and certain parameters but identifies exactly what the defect is in terms of the main defect families and sub-families, arriving at further levels of specificity that register the product type, the size and the technological process in use. Proposed as an integral part of the PVS 156 preform control system, it is set to be integrated on all Sacmi CVS vision systems as part of a new approach that puts the human factor back at the center of the operator-machine-software ecosystem. www.sacmi.com +44 78175 32087 +34 676 986 962 sales@petmachinery.com petmachinery.com Looking to sell your used PET machinery? We can help you. We offer a free valuation service, 50 years of industry experience, and a global network that guarantees you the best market value. Contact us today to find out more. THE INDUSTRY EXPERTS"},{"@ID":40, "EDITOUR PETplanet Insider Vol. 23 No. 10/22 www.petpla.net 32 Always the right atmosphere Strong growth in the PET recycling sector has led to a substantial increase in turnover for the supplier Eisbär in Götzis, Austria. The PET sector has doubled in 2.5 years. PETplanet spoke to CEO Martin Spiegel about particular developments in the rPET sector. Eisbär is a traditional manufacturer of dryers and dehumidifiers for the PET sector. What was once always part of the machines has now been developed by Eisbär as a plug and dry application. “The user only wants two buttons on the machine, i.e. an “on” and an “off”, says Spiegel. The compact module consists of a dryer for PET granulate and flakes, a drying hopper and conveyor for low material flows. As well as simplicity of operation, Spiegel is increasingly focusing on the issue of low-impact drying, particularly in the rPET area. High temperatures can cause the material to degrade, resulting in a yellow or grey haze. Eisbär offers a twostep solution in which the material is initially dried at low temperatures Tour Sponsors: so far have the capacity of 12,000 l, with the biggest dryer operating at 6,000 kg/h. www.eisbaer.at Mr Martin Spiegel, CEO at Eisbär A ‘plug and dry’ dryer Advanced rPET plant and only later heated to the required 170 °C to 180 °C. As well as preventing the appearance of the yellow or grey haze, the process is also more energy-efficient than a one-step system. In the meantime, Eisbär is responsible for overall planning at the plant, particularly for more complex challenges. Drying and recrystallisation are taken into account. Depending on material flow, benzenes caused by PVC residues can also be removed. By switching from open to closed recirculation systems, energy consumption can be significantly reduced. As a result, 100,000m3/h of air are circulated per hour. Finally, energy efficiency is now an important element within the total cost of ownership. The largest crystallisers built The right tools and expertise to help with your rPET goals! Agr is uniquely positioned to support your venture into rPET bottle manufacturing with a powerful combination of Process Control tools, Process Consultants, and decades of industry experience. AGRINTL.COM • +1.724.482.2163"},{"@ID":1, "EDITOUR PETplanet Insider Vol. 23 No. 10/22 www.petpla.net 22 Innovating for sustainability by Ruari McCallion Robinson PLC has a long history of innovation. In recent years it has gone from a privately-owned to stock exchange listed company, recruited a new CEO, has expanded its operations and locations and is investing in equipment and systems. Dr Helene Roberts, CEO, explained the strategy, tactics and market demands that are driving them. Interview with Robinson PLC June 29, 2022 We met: Dr Helene Roberts, CEO Mrs Alexandra Greenwood, Group Marketing Assistant Robinson PLC started as a familyowned business in Chesterfield, Derbyshire, in 1839 – nearly 200 years ago. John Robinson was a chemist who had a pharmacy business, selling medicines. He founded the company that still bears his name because he wanted to sell pills and medicines in convenient packages, rather than loose, which was the practice at the time. “I have seen the original box that John Robinson made. It’s a really beautiful little box; it was actually made to hold pills for a gentleman’s dog – a veterinary remedy for the dog’s ‘constitution’; stomach problems,” said Dr Helene Roberts, CEO of Robinson plc. “It was, literally, the very first pillbox. John and subsequent generations were very innovative; either coming up with ideas themselves or adapting good ideas they saw elsewhere.” Helene reeled off a list of innovations that Robinson’s invented, including the world’s first crepe bandage, supplied at the behest of Florence Nightingale for wounded soldiers in the Crimean War and the world’s first disposable nappies – CosiFit, introduced years before Pampers and others appeared on the scene. Its first high-profile foray into plastic packaging was in the 1950s: a hard plastic bowed disc for the top of a Smarties tube – a very popular sweet then and now. Robinson was already making the spiral form tube so it was logical to take the next step. Geographical and product expansion But that was then and this is now. Robinson divested from healthcare products even before it went from a privately-owned firm to becoming listed on London’s Alternative Investment Market, 15 years ago. It still makes packages from board but its growth – and its future – is dominated by plastics. Dr Roberts was recruited to the company at the end of 2019; just in time for the Covid pandemic and economic disruption. “Obviously, the timing wasn’t ideal!” Dr Roberts said, with a rueful smile. “We are an expanding company and we just started the process of acquisition of a business in Denmark when the pandemic struck and travel stopped.” The acquisition, of Schela Plast, completed in February 2021. The factory is located in Billund, Jutland, which is also the home of Lego. It has a payroll of around 45 people and comprehensive production capability from cap to bottle. “We have a number of customers, including Unilever, located in Germany and elsewhere in Northern Europe and we are committed to offer them effective support wherever they are,” she explained. “Closures can travel quite long distances but bottles tend to be more local; it makes sense to transport fresh air only so far.” Increasing recycling in Denmark Schela Plast is the third Robinson’s factory in Europe, following the establishment of another two in Poland. The Denmark operation was established in 1971, offers extrusion blow moulded (EBM) packaging and produced more than 50 million items during 2021, its golden anniversary year. Robinson Schela Plast has formed an alliance with three other companies, Nopa Nordic A/S, Aage Vestergaard Larsen A/S and Dansk Affald A/S, to meet Nopa Nordic’s demand for packaging made from locally-sourced recycled materials. That need dovetailed very well with Robinson’s declared priority of increasing recycled content in its own products and making the company a circular, sustainable manufacturer. That objective was one of the reasons Dr Roberts was recruited; she had been driving the sustainability agenda since working on the development of the first responsible packaging plan at British retailer Marks & Spencer, in 2004. UK plants: consolidation In the UK, the company currently has three factories: one in Chesterfield, near to its original site, and two Tour Sponsors: Robinson’s Stanton Hill site (picture by Signs Express) Dr Helene Roberts, CEO of Robinson PLC"},{"@ID":66, "PETplanet Insider Vol. 23 No. 10/22 www.petpla.net 61 BOTTLES Slim bottle for shampoo L’Oreal has a shampoo on offer under the brand “Mythic Oil”, which is supposed to provide the hair with special care and moisture thanks to the long-known properties of the substances myrrh extract and argan oil. 250ml are filled in a specially shaped and coloured bottle. When the bottle is moved, the oily viscosity of the contents becomes visible. An adhesive strip and matching printed labels give the bottle an exotic look. A hinged lid with a dosing opening that can be opened with one hand completes the product packaging. www.lorealprofessionnel.de Stylish bottle for hair tonic Reuzel, a supplier of products for hair, beard and skin care, focuses on stylish looks for its packaging, sometimes with a vintage effect. One example is the bottle for a hair tonic for styling hair. The transparent, waisted bottle with embossing on the side is filled with 500ml of the coloured tonic up to under the cap, which contributes to a special look. The label with an old barber’s chair as logo underlines the vintage look. The product is dispensed via a pressed-in dosing insert in the neck of the bottle, which is closed with a screw cap. www.reuzel.com propakwa propakwa Give your business a boost and discover innovation in packaging, plastics, food processing, labelling and print in West Africa at the region s largest B2B trade event. Taking place at the Landmark Centre in Lagos, Nigeria, Propak will set the stage for reconnecting the West African manufacturing community. www.propakwestafrica2022.com/register2022 propakwa www.propakwestafrica.com The Largest Packaging, Plastics, Food Processing, Labelling and Print Exhibition inWest Africa 30+ COUNTRIES VISITORS 5,000+ SPONSORED BY BRANDS 200+ REGISTER FREE TODAY Thomas Salussolia +44 (0) 207 886 3028 Thomas.salussolia@montgomerygroup.com CONTACT US TODAY"},{"@ID":16, "TOP TALK PETplanet Insider Vol. 23 No. 10/22 www.petpla.net 14 PETplanet: Are customers interested more in complete lines or is it in specific machinery and equipment to be added to existing equipment? Pascal Lefèvre: In the food segment, in the edible oil business or sauce & dressing, our expertise mainly relies on delivering complete lines. In the HPC segments, most enquiries are for stand-alone equipment. PETplanet: What role does the sale of downstream equipment play in your planning? Pascal Lefèvre: End-of-Line equipment is key. It is the ‘backbone’ of our FHPC activity, with a growing need to bring agile and low energy consumption solutions. At Sidel we always plan for customer solutions that cover the complete production line process, right up to packaging and palletising products ready to be transported to supermarkets and wholesalers. By choosing Sidel, the customer has a one-stop shop for all their packaging needs, including downstream equipment such as packing, palletising and intralogistics systems. PETplanet: How has your business been affected by the global demand for rPET in containers? What changes in your equipment designs have been adopted as result? Pascal Lefèvre: Several aspects of recent legislation are driving beverage industry trends and there’s an increasing focus on sustainability. The European Single Use Plastics Directive (SUP), for example, impacts the circular economy of PET, defining the collection targets for PET beverage bottles to be at 77% in 2025 and 90% in 2029. It also requires increasing the share of rPET in beverage bottles, up to 25% by 2025 and 30% by 2030. We are witnessing the impact of the consumer’s lifestyle on the industry. On-the-go consumption and healthy living trends are continuously increasing and they are forcing the beverage industry to downsize bottle formats in some beverage categories, like carbonated soft drinks (CSD) and aseptic. On the food, home and personal care side, we face a growing demand to use rPET and our expertise in this field supports our customers in reaching their own sustainability targets. PETplanet: What is the market demand in terms of PET packaging for FHPC from your point of view and do you expect any changes, such as sustainability ambitions driven by brand owners? Pascal Lefèvre: The FHPC markets have different challenges. They are large but also very fragmented and growing constantly. The rapidly increasing importance of e-commerce reduces the accuracy of sales forecasts and puts pressure on margins and consequently has a strong impact on manufacturing. Consumers demand personalised products in terms of health and convenience at affordable prices. All this, together with sustainability and digitalisation requires new thinking at every level. Furthermore, bottle weight reduction is a strong demand, in order to reduce the amount of plastic tonnage consumed while maintaining the required mechanical constraints of the container. PETplanet: Which differences in packaging and demands can you observe when you compare this segment with the beverage segment? Pascal Lefèvre: In the FHPC markets, production lines are smaller than in beverages but much more agile and flexible. With the SKU proliferation generated by e-commerce, our customers need to change formats very often, and they need to do so quickly and efficiently. We also see a change in the case counts; customers are going to both lower and higher case counts, in order to cater for the needs of increased personalisation. PETplanet: What challenges, changes, and opportunities for Sidel have resulted from the Covid-19 situation? Pascal Lefèvre: Covid-19 has led to shortages in components, notably semi-conductors, and that has had an impact on the global packaging industry, impacting lead times and forcing costs up. As mentioned earlier, e-commerce has grown rapidly during the pandemic and this has led to less certainty in sales forecasts for manufacturing. However, we are experiencing strong demand for our products and services and are working to refresh and renew our face-to-face contact with customers. The pandemic and its causes have raised consumer concerns about food safety. To address these, we believe that food and beverage manufacturers are likely to pay more attention to food safety and traceability in every step of production. That can be reached by upgrading their existing solutions or by investing in equipment that is in compliance with regional, global and European food safety standards. PETplanet: Are there any defined investments/purchases that will align with the target for trebling FHPC by 2030? Pascal Lefèvre: Internal capabilities will be a core investment for Sidel and will include the utilisation of a comprehensive range of blowers and end-of-line solutions, including packers and palletisers, for any type of primary and secondary packaging. Sidel also offers complete or partial integrated lines in categories like edible oil, sauces & dressing, coffee and more. Nevertheless, we do not exclude the possibility of working on partnerships or acquisitions in order to cover the food, home and personal care markets we have selected. www.sidel.com"},{"@ID":15, "TOP TALK PETplanet Insider Vol. 23 No. 10/22 www.petpla.net 13 TOP TALK 13 focus needs to be placed on delivering sustainable and environmentally conscious products and packaging that will meet or exceed the standards of those currently available. PETplanet: How many employees work at Sidel overall? Pascal Lefèvre: 5,119 employees. (Source: Tetra Laval Annual Report 2021/2022) PETplanet: What is your current turnover overall? Pascal Lefèvre: 1.4 billion euros in net sales. (Source: Tetra Laval Annual Report 2021/2022) PETplanet: How many Sidel machines are roughly in use globally for this segment? Pascal Lefèvre: Around 15,000 machines have been sold globally to the FHPC segment. PETplanet: How has the company grown over the last years? Pascal Lefèvre: Growth has been consistent across recent years. Obviously, the pandemic was a shock to everyone but the ways in which we’ve developed, especially in CSD and aseptic markets, is a testament to the hard work of everyone at Sidel. PETplanet: Which markets are of specific interest for you at the moment and why? Pascal Lefèvre: We are committed to the FHPC segment’s transition to sustainable packaging solutions in response to growing consumer demand, ensuring that manufacturers can play their part in the journey to net-zero. The FHPC market is a vast and interesting one and I think longterm solutions are a priority in it. The markets related to hair care, liquid hand soap and home care are of specific interest to us, due to our expertise in designing and blowing bottles on our preferential heating blow moulding machines. The food market is also of great interest as this is where our packing and palletising solutions can handle most customer requests. (MKMXEP VEXMSREP TVSƤXEFPI ;LEX IPWI# SACMI.COM 300 4VIJSVQ MRWTIGXMSR ERH TVSGIWW IRLERGIQIRX MRGPYHIH DIGITAL (MKMXEP TVSGIWW GSRXVSP VIEGLIW TVIZMSYWP] YRXLMROEFPI PIZIPW STIRMRK YT XLI MRHYWXV] XS -S8 WGIREVMSW RATIONAL 7%'1- 4VIJSVQ :MWMSR 7]WXIQ MRGPYHIH JSV EHZERGIH GSQTVILIRWMZI TVSGIWW GSRXVSP PROFITABLE '330 TSWX GSSPMRK MRWMHI GSSPMRK W]WXIQ\r WLSVXIRW G]GPI XMQIW ERH PIEHW XS QSVI TVSƤXEFPI TVSHYGXMSR momic"},{"@ID":36, "44 TRADE SHOW PREVIEW PETplanet Insider Vol. 23 No. 10/22 www.petpla.net 40mm ultra-compact mould pitch PETform has developed a new PET hot runner system allowing for an ultra-compact vertical mould pitch of 40mm. On the cold half, the company has developed a robust mould stack design for 28 and 30mm necks where the mould pitch can be set at 45mm x 100mm. For neck diameters of 25 mm or less, it is possible to reduce the mould pitch down to 40mm x 95mm. With the lower pitch come a number of benefits: it allows for higher cavitation and higher production rates while energy consumption in the hot runner is reduced, as surface for heat loss per cavity is reduced. This also reduces the load on the chiller for cooling the backing plates. Also reduced is material degradation in the hot runner with shorter flow path (lower shearing and residence time) as the per cavity stress on the clamping unit and the energy consumed for opening and closing the mould. The lower pitch also increases overall clamping surface to absorb clamping force, thus increasing mould life. As of the present, the highest cavitation generally being run on these 300 t machines is predominantly 48 drops and in a few cases 72 drops. PETform says that with the technology, convertors can increase their production rates to up to two times, shot size and plasticising capability permitting. www.petform.co PETform Hall 1 Booth E23 Moretto Hall 11 Booth H56/H66 PETform CEO Shurid Mody next to the 96-cavity mould wi th a pi tch of 45 mm x 100 mm for the Husky GL/ LX/XL 300 machine Global approach, Italian roots Technology, sustainability and connectivity will characterise the new Moretto products that will be exposed at the K fair as the new dosing and feeding solutions for micro moulding and small productions available also for use in the clean room. Thanks to their compactness they can be installed stand alone or on the IMM. Among the solutions dedicated to recycling, Moretto will present the new granulators of the GMK series which ensure uniform and constant granulation minimising the dust formation. The small size structure allows it to be placed next to the processing machine, thus optimising production spaces. The implementation of more compact solutions then allows production to be increased by reducing energy consumption and noise pollution. Among the novelties the volumetric doser DVM8 which ensures the maximum perfection of microdosing. Connectivity that optimises processes Modern production plants are intelligent, flexible and data-driven. The amount of data generated that must be correctly processed to support decisions and make processes even more efficient is enormous. Having the right equipment for data management becomes essential. Mowis is the software platform developed by Moretto to supervise and manage the entire production process. A modular and self-configurable tool, usable on-site or remotely, which through the OPC UA protocol creates total connectivity among machines, processes, departments and plants and makes the management of complex systems easy. Moretto operates in a complicated business, both for the high level of innovation that characterises the sector and for the well-known critical issues related to the massive use of plastic products. In spite of this the company has been able to identify a winning strategy developing solutions with a high technological content that contribute to the progress and optimisation of processes in a sustainable way and respecting the environment. www.moretto.com"},{"@ID":21, "MATERIALS / RECYCLING 19 PETplanet Insider Vol. 23 Clearly it is possible to colour the bottle, thus masking the effect of the masterbatch. (Fig. 2) The additive is potentially a suitable and efficient alternative solution to the heat set technology, for food and aerosol application. In addition, FastPET could be used for the production of refillable and returnable PET bottles, because they can be washed safely in any dishwasher. To conclude, the main advantages given by the additive according to GS4Plastic are: Suitable for usage with 100% rPET Increase in the oxygen barrier properties, so to achieve a shelf life of up to 12 months Increase the thermal properties of PET up to 88 °C (dishwasher safe) Reduced investments in machinery and mould for hot fill Reduction of cycle time Food grade approved. www.gs4plastic.com Fig 2 The masterbatch acts on the crystallinity of PET, and a slight loss of optical properties is therefore to be expected. It is possible to colour the bottle, thus masking the effect of the masterbatch."},{"@ID":35, "EDITOUR PETplanet Insider Vol. 23 No. 10/22 www.petpla.net 33 Virtually maintenance-free injection moulds z-moulds is known for its excellent product design, long shelf life, low maintenance and flexible use of cavity inserts. PETplanet wanted to know more about the technology and visited Michael Fink, Vice President, Sales and Marketing, at z-moulds at the Dornbirn site in Austria. Tour Sponsors: Many years ago, z-moulds decided on an unusual approach. Each individual cavity with an ejector and cooling element for a moulded cap has its own four slides. This removes the standard slides, the cavities cannot jam even if the plates are not completely aligned with one another which can easily happen if, for example, the cooling system fails. The result is a service life of over 10 years with many millions of cycles without the mould having to be refurbished. Putting it simply, you can compare it to a three- or four-legged chair. The former always stays stable and does not wobble. The z-moulds system is like this in that the mould itself is not damaged even if the plate stucks for any reason when the mould is closed. On the other hand, with a four-legged chair, the floor must always be level and all the legs the same length, meaning that if I put a beer mat under one leg, the chair does not wobble. Similarly, with a standard mould, the slides must always work perfectly with the plates precisely aligned with one another, otherwise the mould will be damaged. Beer mats are not appreciated in the cap mould. The patented system is called z-slides, with a more recent development being the z-slides extended. These extended slides can mould undercuts in the caps up to the total shell height. Thus, the straps on the tethered cap can be moulded such that they almost reach the top of the cap. One example of this is the UCL Tethered Peacock Design Cap. UCL Tethered Peacock Design The normal z-slides and the extended ones fit into the same mould. So with a new cap design, it is no longer necessary to change the mould, only the cavity insert. As it is self-centring, the user can do this on site directly on the machine. The standard 70mm pitch is suitable for nearly all applications. Beside the 70mm pitch there is also a standard for bigger caps with 85mm and 105mm pitch. The Austrians are now working on a smaller pitch given the current trend towards using smaller cap diameters. In the factory itself, there are fully automated processing machines that produce cavities with their format parts which are assembled into moulds at the end of the process. Mould-validating machines from almost all injection-moulding machine manufacturers can be found at the far end of the production area. However, the customer can always bring in their own equipment to try out if they wish so. www.z-moulds.com Mr Michael Fink, Vice President, Sales and Marketing, at z-moulds Ltd. The z-slides cavity stack. You can clearly see the compact design, four slides form the outer contour. The ejector and cooling element are integrated within the cavity."},{"@ID":52, "TRADE SHOW PREVIEW PETplanet Insider Vol. 23 No. 10/22 www.petpla.net 50 Digitalisation and process control, the wider concept of sustainability The Sacmi range has been developed to transform sustainability into opportunity and make it a source of competitive advantage, as the latest generation of machines and control systems on show shall demonstrate. Behind these solutions lies the use of new eco-sustainable materials and an approach to quality control that makes extensive use of AI. This means simplifing workers’ tasks, making line management more proactive and optimising man-machine resources, says Sacmi. Sacmi Hall 13 Booth A63 New IPS 300: state-of-the-art performance IPS 300 is the latest Sacmi preform press. It completes a range that has been on the market for 10 years, providing solutions that offer best performance, low consumption, fast set-ups and quick changeovers. Like the IPS 400, the new IPS 300 features high compatibility with various mould types, including those produced by third parties. Workers’ tasks are streamlined at every stage - from start-up to size changeovers and control of auxiliary units. From a product perspective, the IPS 300 is designed to work with 24-cavity moulds for 48mm necks and up to 96 cavities for 30mm necks. Further opportunities include a 128-cavity configuration for 26/22mm necks, taking advantage of the Nano Pitch patented solution from MHT, the main partner of Sacmi concerning mould supplying. A unique solution within today’s range of available technologies, says Sacmi. The new IPS 300 press has a lock-to-lock time of 2 seconds and fast cycle times, characteristics that stem from the patented Cool+ after-cooler (inside cooling system) which improves thermal efficiency and boosts productivity. In terms of versatility, the IPS 300 has a wide range of plasticising units (from 625 to 1,220 kg/h) and various kits designed to streamline system use and enhance finished product quality. At 0.2 kWh/kg, the IPS 300 has a low energy consumption. This is achieved via a combination of kinetic energy recovery system (KERS) and adaptive self-tuning. The IPS 300 can incorporate the PVS 156, a preform vision system designed and manufactured by Sacmi, with the aim to meaningfully contribute to the IPS process, without affecting the press footprint. PVS156 performs a accurate and precise inspection of the preform, providing detailed statistic and reports, also based on cavity number; each preform is weighted and its temperature is detetected in different positions. A 96-cavity mould is typically inspected in less than 5 minutes, corresponding to about 1,200 preforms per hour, says Sacmi. The company considers these numbers to be very interesting on an absolute level and even more significant when compared to the accuracy and repetitiveness of the inspection that a trained operator can perform in the same amount of time."},{"@ID":19, "EDITOUR PETplanet Insider Vol. 23 No. 10/22 www.petpla.net 29 The most recent development is the increasing market demand for identification systems for PET trays. These systems must have appropriate sensors to distinguish between the monolayers of multilayer trays. Like with PET bottles, only monolayers can actually be brought back into the recycling system as approved material. And this brings us back to Perl’s wishes for the sector. For him it’s important that packaging design is recycling design. Only monolayer materials can be prepared for true recycling. Additives like optical brighteners and oxygen blockers make a true recycling more difficult too. Also collection rates must be increased. These days, it is in too many cases still not economical to extract recyclable plastics from the general waste streams. Political frameworks must provide accompanying support for recycling to take place within the country and also ensure that the material remains within the country. And plastic recycling must not be restricted to PET; PP/PE, PS and other plastic types can also be prepared. www.sesotec.com PETplanet at Sesotec’s premises in Schönberg, Germany Sorting systems with chute are suitable for removing contaminants or impurities from material that has already been shredded. INNOVATIVE TECHNOLOGIES THAT PUT RECYCLED CO2 INTO WORK FOR A CLEANER, HEALTHIER PLANET. VISIT COLD JET HALL 11, BOOTH 11G12 Discover the possibilities of dry ice cleaning in a live demo at our booth. Learn more at coldjet.com i n f o . e u @ c o l d j e t . c o m + 3 2 ( 0 ) 1 3 5 3 9 5 4 7 C o l d J e t B V , Z o n e 1 R e s e a r c h p a r k 3 3 0 , 1 7 3 1 Z e l l i k , B e l g i u m WATER FREE WASTE FREE CHEMICAL FREE REDUCE EMISSIONS RECYCLED PRODUCT"},{"@ID":58, "TRADE SHOW PREVIEW PETplanet Insider Vol. 23 No. 10/22 www.petpla.net 56 Wide range of vision inspection systems Intravis GmbH will present a wide range of inspection solutions from its product portfolio at this year’s K’ trade show, both at its booth and at several partner booths. Intravis Hall 11 Booth A56 sive statistics correlating the average application angle with the capper’s tool. This allows malfunctions of a tool to be detected at short notice. In addition, the CapWatcher FC inspects the bottle for damage, presence and correct positioning of the closure, and records the fill level of the bottle. New washdown design for high splash protection The CapWatcher FC is completely designed in the new washdown design. Dr Gerd Fuhrmann: “The washdown design is intended for Intravis systems that are located exclusively in the wet area of the filling lines behind the filler. Thanks to the specific design, the inspection unit and the associated control cabinet are splashproof all around and meet the hygiene requirements of the fillers.” The design simplifies cleaning of the system as the exterior is designed to drain off any water. In addition, the interior of the CapWatcher FC is easily accessible. Besides the CapWatcher FC, the label inspection system LabelWatcher is now available in the washdown design. Janina Orlowski, Product Manager at Intravis: “With the washdown design on the LabelWatcher, we are once again significantly expanding its application possibilities. Each component is individually enclosed and thus optimally protected during ongoing operation and cleaning.” The LabelWatcher is already established on the market and is used for the comprehensive decoration inspection of bottles, jars, cans and containers. CapWatcher Q-Line: new separation methodology for tethered caps Additionally, Intravis will present its new and further developments of the CapWatcher Q-Line which is tailored to the challenges of tethered cap inspection. Intravis will show an exhibit of this inspection system for caps at the booth 15/D22 of Sumitomo (SHI) Demag. What is new is the way the closures are separated during the inspection. Whereas the system previously used a star wheel to separate the caps from above, a positive, lateral star wheel separation is now selected. Gerd Fuhrmann: “The external shape and stability of tethered caps pose a challenge for separation, especially as the caps are becoming thinner and thinner. With our new form-fit, lateral star wheel separation, our systems ensure perfect separation and positioning of the caps even at the highest speeds. In the process, the closures are handled gently and carefully.” Due to a software logic that has been optimised for the non-rotationally symmetrical outer appearance of the caps, the tethered caps no longer have to be aligned. This further simplifies the separation process. IntraVisualizer: new version as cloud-based solution The CapWatcher Q-Line exhibited is equipped with the latest version of the IntraVisualizer. The software solution already serves many companies as a trend detection and analysis tool for optimising production processes. In doing so, the software accesses the multitude of product-related quality data from all Intravis inspection systems in a production plant, analyses them in detail, and uses them to determine trends and important information for the quality, manufacturing, and management teams. A new feature is that the IntraVisualizer is now offered as a cloud-based solution. Markus Juppe, CMO at Intravis says, “The benefits of a cloud-based solution are many for our customers. For example, they do not have to The applications range from the new CapWatcher FC and different variants of the IMLWatcher to the CapWatcher Q-Line, which is optimised for the inspection of tethered caps and will be presented with the latest version of the IntraVisualizer analysis software. Dr Gerd Fuhrmann, CEO of Intravis GmbH, is already looking forward to the trade show: “We will undoubtedly generate a lot of attention with our exhibits and new developments.” CapWatcher FC At the Intravis booth visitors will receive extensive information on the latest system in the product portfolio, the CapWatcher FC. With it, Intravis introduces for the first time a new inspection technology that uses index markings to inspect the application angle. With the help of five side cameras, the system detects whether the closure is screwed on in the target position or whether it has been screwed on too far or not far enough. The vision inspection system is guided by markings on the closure and neck support ring that are barely perceptible to the end user. If these markings are within a tolerated range of each other, the system assumes that the closure has been completely and correctly fitted and releases the bottle for packaging. The production line operator also receives comprehen-"},{"@ID":74, "EDITOUR PETplanet Insider Vol. 23 No. 10/22 www.petpla.net 24 the point where we are predominantly using recycled materials. The immediate goal is to reach the 30% level, which is where the Plastics Tax comes in, but I would like to go beyond that and really drive it. We can do it with the right models.” Dr Roberts’ background and experience is very much about sustainability, in its broader sense: environmental responsibility and commercial success. “It’s truly about ESG – environmental, social and corporate governance,” she said. It’s the social side of sustainability as well as the environmental impacts we have. It’s about the purpose of the business and about driving the best benefit for our people, for all our stakeholders: shareholders, employees, customers and the final consumers.” Robinson’s Sustainability Pledge became active in March 2021. The most visible manifestation is a change in signage, to a sage green colour – restrained, rather than ‘in your face’ – and the ubiquity of its Five Pillars, graphically represented in the illustration below. It includes staff well-being as well as environmental commitments to Zero Waste to landfill by 2021; achieve Sustainable Buildings by 2025; and to be Net Carbon Positive by 2030. It is currently ahead of its targets. Commercial competitiveness Businesses still have to be competitive. Customers may say nice things about sustainability and environmental responsibility but they are still going to want competitively-priced supplies. “If you look at carbon, it’s about energy and energy is based on money – so the lower the carbon, the more cost-effective it can be,” Dr Roberts continued. “What it does change is your investment plan and how you view those investments. If we are buying a new machine, I’m not going to choose one that’s environmentally unsound or perform worse than one of our current machines. It has to be better, to be lower carbon, to be more efficient and cheaper to run, using less energy and fewer people. It needs to drive efficiency within the business.” The environmental dovetails neatly with the commercial. “In terms of materials, it is our customers who ultimately make the choice; it’s their specification. We will strive towards using as much recycled content as possible. Security of supply is, of course, essential for all our products,” she explained. “It is very much about having the right relationships with your suppliers.” Security of supply is very much a concern, after the pandemic and the Russia-Ukraine war. British plastics manufacturers did not have to shut down during Covid-19 because of fall in demand – if anything, demand from medical suppliers ramped up and more than replaced downturns elsewhere; but the British Plastics Society reckoned that more than half of businesses in the converting sector had to shut down lines because they could not get raw materials. It illustrates that Robinson’s contention that environmental and commercial sustainability are inextricably interlinked. Management systems and maintain the legacy of innovation Robinson’s is also in the process of replacing its management IT system. While the existing technology works fine as it is, the new one will have extended capabilities in quality control, planning and forecasting. We concluded our visit with a tour of the factory floor at Kirkby in Ashfield, which is currently devoted to PP and HDPE containers but space is being made for the PET lines that are coming over from the Sutton site. Production is a mixture of automated and manual, for agility and responsiveness. Robinson’s has a history of innovation. We asked how that is being manifested now. “We work with Unilever, P&G and other companies, all of whom have sophisticated brand managers and undertake a huge amount of consumer research on what they want and so, realistically, I’m not going to be able to add any value on design,” Dr Roberts said. “Where we add value is by searching to find out how to make the product more efficiently, make it lighter, make it faster, how to reduce the environmental impact and to increase the use of raw materials without compromising quality.” www.robinsonpackaging.com An operator packs PET bottles."},{"@ID":11, "MATERIALS / RECYCLING PETplanet Insider Vol. 23 No. 10/22 www.petpla.net 16 Clay-based additive triples gas barrier properties and boosts strength & UV resistance Improved characteristics US-based startup Berkm reports encouraging test results with no impact on recyclability or transparency and seeks additional funding for scale-up. Berkm Inc, which is based in the Boston, Massachusetts, area of the USA, is an advanced materials startup company that is working on commercialising a new type of clay-based additive for the PET plastic industry. It has secured exclusive licensing for technology developed from 25 years of research at Professor Tsung Yen Tsai’s laboratory at Chung Yuan Christian University, Taiwan. Berkm says that the additive offers a number of potential advantages for PET packaging manufacturers, especially in the food and beverage sectors. It is claimed to enable the practical and commercial production of small (100-200ml) CSD bottles, while reducing the amount of plastic per PET container, leading to savings in raw materials costs. The company further maintains that costs can also be saved in pretreatment for hot-fill applications; reduction or elimination of UV blockers; and that the qualities of recycled PET can also be improved. The particular characteristics of PET that have been shown to be improved during testing are: strength (increased by 66%); distortion caused by heat (37%); gas barrier properties (increased by a factor of 29); and UV resistance (up by a factor of 52). These improvements are claimed to be achieved while maintaining current levels of transparency. The latest round of testing, undertaken by third-party agencies, demonstrated that CSD bottles made with Berkm’s clay-based additive showed a tripling of gas barrier properties, compared with conventional PET, at a loading of 0.3%. Barrier properties can be further increased without compromising transparency, up to 1.2% loading. Berkm claims, in addition, that the improved characteristics are achieved not only without harming recyclability but can actually help bottle-to-bottle recycling when added during in-situ PET polymerisation. It can also be added during mechanical recycling and still improve gas barrier performance and strength, by 37% and 25%, respectively. Industrial scale-up trials were completed in May 2022. The platform technology can be applied to improve the CO2 barrier and O2 barrier properties and does not need different chemistries for different gases. Clay particles in the additive create a tortuous path for gas to travel. In December 2021, Berkm filed a new patent that extended its technology to polyethylene (PE) and polypropylene (PP). Several paid pilot projects are currently being undertaken with a range of brand owners and packaging companies. Berkm is now engaged in fundraising to expand production capacity and engage partners for scale-up. www.berkm.co PET bottles (hazy ones) made via conventional clay technologies and bottles made via Berkm’s technology (transparent one on the right). TEM image of clay layers in PET polymer matrix. The image shows a high degree of exfoliation of clay layers. Clear PET bottles made via Berkm’s clay technology MATERIALS"},{"@ID":22, "EDITOUR PETplanet Insider Vol. 23 No. 10/22 www.petpla.net 20 Additive and colour masterbatches from Switzerland Product quality, shelf life and food safety for PET by Kay Barton When it comes to the use of masterbatches and additives in the production of PET containers, all roads eventually lead to the family-run company Sukano AG. The global specialist with its main office in Schindellegi, around 30 minutes south of Zurich, has been manufacturing these products for use in a range of sectors and applications since the business was first established at the end of the 1980s. In terms of revenue, about two-thirds of the products end up in the packaging sector and approximately 80% in food applications. The company has a global presence employing 200 staff and claims not to have lost any of its trailblazing spirit. CEO Norman Egger took the time to speak to PETplanet about demand for packaging solutions, including recycling and sustainability. Interview with Sukano AG 9 August 2022 We met: Mr Norman Egger, CEO Local to global Founded in 1988, Sukano specialises in slip and anti-block additive masterbatches for PET film applications which are still among today’s bestsellers. “Sustainable business models and innovative products while at the same time working closely with our customers have always been our focus”, said Mr Egger, CEO since 2017, as we began our interview. A local business later became a global one with the addition of two company sites established over the years in order to be as close as possible to the customer. The Malaysian facility focuses on clients in the Asia-Pacific region, with the US plant in South Carolina concentrating on American markets. Mr Egger explains the strategy. “With our set-up on three continents, we can offer a flexible service on a regional level. For example, we can develop products in one place and manufacture them anywhere.” Product portfolio and latest developments As well as an extensive and standard portfolio ranging from colours to special additives, the manufacturer also offers customised projects and product developments to meet customers specific requirements or to address market trends for PET bottles and trays as well as other end applications in market segments such as durable goods, building and construction or healthcare applications. “Recycling and circularity are particularly important for us,” said Mr Egger. “All our PET masterbatches are designed to be recycled while some may also be reused. Our products allow the use of both recycled material and increased recyclate in processing and subsequent end use. We also support our customers in moving from complex packaging designs to monomaterial packaging”. “Applications where our additive and colour masterbatches are found include dairy, water, and carbonated soft drinks PET bottles be that transparent or opaque containers. We offer a complete rPET portfolio. From colours, which are designed for detectability, light barriers to protect the content, or additives to improve and recover the mechanical properties of the polymer. Our chain extender additive enables the use of a variable quality range of rPET and allows higher rPET content in the final part.” Just to name a few functionalities the company offers, as well processing aids, light protection additives, impact modifiers or combi masterbatches. The “CPET light” project launched last year with the company Illig showed where the food packaging sector is heading. Specially developed additives produced by Sukano, together with temperature control and a modified mould for material processing prepared by Illig, have enabled thermo-formed containers for use in microwaves and for hot filling that are heat-resistant up to 100 °C to be successfully produced. Traditional market materials such as polypropylene or other materials could face competition in this area and, according to Tour Sponsors: Sukano’s CEO Norman Egger"},{"@ID":12, "10 NEWS PETplanet Insider Vol. 23 No. 10/22 www.petpla.net Koch Technology Solutions and Ioniqa Technologies partner to scale up recycling technology Koch Technology Solutions (KTS), a Koch Engineered Solutions company, and Ioniqa Technologies B.V. (Ioniqa) announced a partnership to scale up and commercialise Ioniqa’s PET recycle technology in the plastics industry. As part of this collaboration, KTS has committed to invest up to €30M in Ioniqa. Ioniqa has developed a process that utilises low-grade post-consumer PET to produce a feedstock that displaces virgin raw materials used in the production of polyester products. Ioniqa has successfully demonstrated this technology in The Netherlands’ 10KTA production facility. KTS and Ioniqa’s partnership will work to address the growing demand for recycled content in the 30 million metric tonnes per annum PET market. Ioniqa’s technology offers a solution to PET waste that is currently non-recyclable, turning the waste into materials suitable for high quality food grade applications such as beverage bottles. KTS and Ioniqa consider the technology as a disruptor in the PET industry providing a sustainable economic recycle proposition to conventional manufacturing routes. The partnership will drive a circular process that addresses environmental impacts of the current PET industry. Tonnis Hooghoudt, CEO and Founder of Ioniqa said “After the scaling of our technology to a 10KTA depolymerisation plant in The Netherlands, this KTS partnership is a major stepping stone for Ioniqa in commercialising its technology on a global level. Our expertise in breaking down plastic waste into virgin-like monomers matches seamlessly with KTS’ track record in designing and licensing PET production processes worldwide.”. www.ioniqa.com www.kochtechsolutions.com Acquisition of Herbold Meckesheim completed The acquisition of the engineering company Herbold Meckesheim, has formally been completed. Herbold Meckesheim will be integrated with Coperion’s recycling product lines into its new recycling business unit that plans to offer complete solutions for plastics recycling processing. Coperion intends to combine its strengths as an international industrial and technological leader with Herbold Meckesheim, a specialist in mechanical recycling of plastics and plastic waste, and to form a united business approach together. Herbold Meckesheim will continue to operate at its existing location and retain its name. Both companies will combine their capabilities in the field of recycling and integrate to build modular systems and plant solutions that cover a broad sector of the circular economy, as well as large sections of the globe with their combined sales and service network. The recycling business unit plans to offer complete solutions leveraging both Coperion and Herbold Meckesheim’s complementary technologies. From mechanical processing — shredding, washing, separating, drying, and agglomerating of plastics — to bulk material handling, feeding and extrusion, as well as compounding and pelletising, this business unit encompasses the complete process chain. With their combined global service network that supports installations and start-ups, competent and rapid service is also available on site, states the company. Additionally, state-of-the-art test centres for product development as well as customer trials are available to customers. Before interested parties make significant investments, they can undertake in-depth testing of every process step in the test labs. The recycling business unit plans to offer complete plants and systems for recycling PET, polyolefins, film, or rigid plastic. From mechanical processing to solvent-based and chemical recycling to complete solutions for highly automated to modular recycling lines. Engineering and service during the equipment’s entire operating life is also available. www.coperion.com www.herbold.com Werner Herbold, CEO, Herbold Meckesheim GmbH (left) and Markus Parzer, President, Polymer Division, Coperion (photo: Coperion GmbH, Stuttgart)"},{"@ID":73, "Sponsors to date The worldwide round trip with EDITOURS Back to Europe The second part of PETplanet’s bipartite Drinktec Editour is right ahead! After the successful first part “From Down Under to Japan” in 2020, our second stage of the project takes us back to the flourishing European hub where we will be exploring the latest technologies, news, innovations and developments that move our PET industry. It is time for a new start, for renewal and for developing new ways of thinking. During and especially after the pandemic, it will be vital to make every effort to get the global economy back on track in the medium term. Sustainability will be the key. Once again, PETplanet will be at the forefront. It will again be a partner in Drinktec, the world’s leading beverage trade fair, which is to be held in Munich from 12-16 September 2022. After the success of our previous Drinktec Road Shows, in 2017 in South East Asia and 2020 in Australasia, we will be back on the road in Europe for a whole year. Starting in Autumn 2021 with our Editourmobil, we will be ready for a new get-together with the industry. We will be revealing the results of our meetings and discussions at Drinktec with the leading thinkers in PET processing, packaging and recycling. Apart from new technologies we will be also taking stock of how things stand. We will be asking how global thinking might change as a result of Covid-19. How will bilateral business relationships cope with the aftermath of the pandemic? What opportunities will there be for the drinks industry and its suppliers? Our planning, in terms of precise timeframes and details of the countries to be visited will be flexible, in order to take account of the rapidly changing pandemic situation. However, this much we can confidently say: in these challenging times we, as the voice of the PET industry, will be at the very heart of the roadshow as usual and are already looking forward to welcoming you back on board the Editourmobil! Share this exciting experience with us! Interested in being interviewed? barton@petpla.net Let Your Inspiration Flow. 7KH (XURSHDQ 5RDG 6KRZ PART2 Empowered by drinktec Interested in becoming a Sponsor? sales@petpla.net Autumn 2021 - 2022"},{"@ID":59, "TRADE SHOW PREVIEW PETplanet Insider Vol. 23 No. 10/22 www.petpla.net 57 maintain their own IT infrastructure to use the IntraVisualizer and therefore do not have to maintain it. We take care of updates automatically - and without affecting the users. Furthermore, our customers are now completely flexible: they can connect as many systems as they like and no longer come up against capacity limits.” The cloud solution also enables all information to be displayed on mobile devices. IMLWatcher: experience different inspection options The IMLWatcher is a system for quality inspection of products with inmould labels that is well established in the market. Intravis will be represented with it at a total of three partner booths. At the booth of Enelkon Automation (12/ A43) Intravis will show an IMLWatcher, which is integrated into a robot handling system of Enelkon. Ten cameras carry out a 360° inspection of the labels per shot, as well as an inner inspection and an inspection for short shots on four round cups each. The IMLWatcher at the Wittmann Battenfeld booth (15/C06) is integrated into a robot handling system - namely the IML handling system from Beck Automation. Its ten cameras inspect drinking cups from four cavities. In addition to 360° inspection of the labels and inspections of the interior and for short shots, this IMLWatcher also offers special software functions. These include a long-term image memory, extended cavity statistics, a prewarning stage when a tolerance range is foreseeably exceeded, and extensive user administration. The IMLWatcher presented at Sumitomo (SHI) Demag (15/D22) together with Campetella Robotic Center S.r.l. follows a different concept. In this case, the ten cameras are installed on a conveyor belt and inspect the labels of the eight different cavities 360° for quality. In addition, the system performs a quality control of the bottom label and reads both a data matrix code and a barcode. New preform development at Nissei ASB Open House Event As part of the K show, Intravis will also participate in live system demonstrations at Nissei ASB Machine’s Dusseldorf facility and, together with Delta Engineering, present a new development for preform inspection. The DCI 500, an inspection system offered by Delta Engineering, incorporates various inspection stations from Intravis’ PreWatcher Offline. The system performs mouth inspection, preform body and thread inspection for contamination, and colour inspection using a spectrometer. All three partners are happy to accept registrations for the demonstrations that will take place daily at the Nissei ASB machine plant during the trade show. Intravis machinery can be find at the following boothes: Intravis: 11/A56 Sumitomo (SHI) Demag: 15/D22 Enelkon: 12/A43 Wittmann Battenfeld: 15/C06 www.intravis.com Starlinger"},{"@ID":54, "TRADE SHOW PREVIEW PETplanet Insider Vol. 23 No. 10/22 www.petpla.net 52 Processing rPET in thin wall injection moulding In cooperation with partners Alpla Group, Brink and IPB Printing, Engel is promising to present a quantum leap for the packaging industry. For the first time, thin-walled containers made of PET can be produced in a single injection moulding process step. Austrian injection moulding machine manufacturer Engel is processing recycled material (rPET) at its stand. An Engel e-speed injection moulding machine with a newly-developed and powerful injection unit is being used to do this. Engel Hall 15 Booth C58 Featuring a wall thickness of 0.32mm, the transparent, round 125ml containers are representative of a whole genus of packaging, especially in the food industry. Thanks to integrated in-mould labelling (IML), the containers are ready-for-filling as soon as they leave the production cell. The special feature in this application is the material. The thin-walled containers are produced directly from rPET in a single step. Up to now it has only been possible to process PET in thick-walled parts such as bottle preforms in injection moulding. The final packaging format was created in a second step of the process – by blow moulding for example. Bottle-to-cup and cup-to-bottle as the target Under the European Plastics Pact, the intent is for all plastic packaging to contain 30% recycled material and to be 100% recycling capable by 2025. The typical materials for packing foods in thin-thin-walled containers are polyolefins or polystyrene. However, experts estimate that it will be impossible to achieve the stated objectives with these materials. And the recycling flows lack the approval of the European food authority, EFSA. Recycled PET offers a solution for avoiding penalties and special taxes here. Although the price for PET is high right now, this makes the material a cost- effective alternative. Efsa has approved numerous recycling processes for PET, ensuring that the material is available in Europe. PET offers the benefit of a close recycling loop already being in place. To date, PET is the only packaging Thanks to the new high-performance injection unit, thin-walled containers made of PET and rPET can be produced on the Engel e-speed injection moulding machine."},{"@ID":14, "TOP TALK PETplanet Insider Vol. 23 No. 10/22 www.petpla.net 12 Interview with Sidel’s new Global Vice President, Mr Pascal Lefèvre Sidel’s food, home and personal care initiative In April 2022 Sidel announced the appointment of Pascal Lefèvre as the new Global Vice President. He will develop and drive Sidel’s food, home and personal care (FHPC) strategy, meeting the unique needs of FHPC markets and delivering flexible, eco-friendly, tailor-made solutions that will address the new and complex retailing and distribution challenges facing customers. PETplanet: Could you please give us some information on your personal background, experience and activities in the plastics and/or packaging industry prior to Sidel? Pascal Lefèvre: I graduated with a Master’s from ISG Paris Business school and subsequently held a number of management positions with B2B businesses in the packaging equipment industry, specifically in blow moulding, labelling and injection equipment. I joined Sidel in 2020 as Vice President Europe & Central Asia for the FHPC market and was then appointed Global Vice President of food, home and personal care. PETplanet: Which key projects did you successfully manage in the past (probably in a similar sector)? Pascal Lefèvre: When the iconic Italian brewery Birra Peroni, part of Asahi Group Holdings Ltd, decided to upgrade its glass bottling operations as a result of a growing domestic market and trends towards premium beer in the UK and the US, its new line featured Sidel’s latest innovation: the Evofill glass filler, with its cuttingedge technology and hygienic, nobase design. PETplanet: What are your main targets and challenges as Sidel’s new VP for food, home and personal care? Pascal Lefèvre: FHPC markets are large and fragmented but are steadily growing, despite the current shortage crisis. Sidel can provide innovative solutions that offer the flexibility, operability and product care demanded by these fast-moving and rapidly evolving market segments, while drawing on existing capability and expertise. We are looking to triple this key part of our business by 2030. PETplanet: What is the main strategic approach to fulfil this target of tripling the FHPC business segment by 2030 and how will it be achieved? Pascal Lefèvre: By establishing this new initiative, we can work flexibly and be much more agile. We are developing a new portfolio of machines and solutions that addresses the needs of the FHPC sectors. It is not only the high-speed machines but also our customers require mid-capacity equipment that reduces resource consumption and is flexible in any way. PETplanet: How important is the topic of sustainability in the FHPC sector for you personally and what needs to be done here globally from your very own point of view? Pascal Lefèvre: Sustainability is crucial in the FHPC sectors. We see that our customers require mid-capacity equipment that reduces resource consumption and is flexible. One product worth mentioning is Cermex Evopack, a secondary packaging unit. It reduces product repacking by managing those activities directly at the production line, thus cutting waste and energy consumption. Globally, more Sidel’s Global Vice President Pascal Lefèfvre Sidel is developing a new portfolio of machines and solutions that addresses the needs of the FHPC sectors. by Kay Barton"},{"@ID":48, "46 TRADE SHOW PREVIEW PETplanet Insider Vol. 23 No. 10/22 www.petpla.net EISBÄR TROCKENTECHNIK GMBH / Wuhrmühle 22 / A–6840 Götzis / T +43 5523 55558-0 / F –50 / cool@eisbaer.at / www.eisbaer.at RECYCLING Conveying Drying Crystallizing Mixing&Dosing Decontamination Testing MEET US AT THE K SHOW! HALL 10, BOOTH G32 Odour minimisation in granulates and regrinds Kreyenborg has developed sustained, high-level expertise in plastics recycling, with solutions for decontamination of PCRPET, crystallisation, drying, and heating of bulk materials, using infrared technology. Further development of this technology has brought to the fore its newest member among its products, the IR-Fresh - a modular system for the safe and efficient reduction of unpleasant odours in plastics. In the first process step, an infrared module installed above the material bed heats the material quickly and directly to the optimum temperature level for the plastic in question. In this process, the continuous rotation of the drum ensures a homogeneous mass flow with a defined dwell time (applying the first-in/first-out principle). By means of the rotating and mixing elements integrated in the spirals, the material is continuously mixed in the drum with constant surface exchange. Combined with controlled heating, this ensures considerable odour elimination, even within a short residence time. In the second process step, the remaining odourous substances in the regrind or granules are removed by a thermal-physical cleaning process in the IR-Fresh Conditioner. This IR-Fresh Conditioner - an insulated hopper - keeps the material to be decontaminated within a temperature range that’s ideal for the decontamination process by means of a hot purge-gas. Good results for deodorisation and decontamination can be achieved through the interaction of the main process parameters of airflow, temperature, and residence time. Through its modular design, the IRFresh process can be used continuously in two stages both for regrind - before the extrusion process - and for granules - after the extrusion process. Likewise, it is also possible to integrate the IR-Fresh Conditioner as a sole process step in the process chain, or to operate it as a standalone solution continuously, as well as discontinuously. The system presented is also suitable as a retrofit solution for integration in existing plants. In cooperation with the customer, Kreyenborg will develop a solution - also in conjunction with pilot plant trials - that is optimally tailored to the customer’s individual processing needs. www.kreyenborg.com Kreyenborg Hall 9 Booth A27"},{"@ID":49, "TRADE SHOW PREVIEW PETplanet Insider Vol. 23 No. 10/22 www.petpla.net 47 Degassing and decontamination technologies Gneuss presents their new series of Omni recycling machines: the MRS extrusion technology has proven itself as an alternative for the reprocessing of contaminated materials like polyester, polystyrene, polypropylene or polyethylenes. Gneuss Hall 9 Booth A22 In combination with the Gneuss rotary filtration systems and optimised vacuum technology, customisable recycling lines tailor-made for a specific material can be engineered. Several Letters of Non-Objection (LNOs) from the FDA, EFSA conformity and local approvals in Latin America confirm the decontamination efficiency of the technology. Samples of PP tubs for food applications made with 30% post-consumer PP and PS sheet made from 30% post-consumer PS, processed on the Omni recycling machines with MRS extruders and RSFgenius filtration systems, will be on display. Omni recycling machine for post-consumer fibre or thermoform reclaim The company will be showing its new machinery for recycling needs with a complete Omni recycling machine featuring a new 3C rotary feeder, an MRSjump 70 extruder, a fully automatic melt filtration system RSFgenius 90 and an online viscometer VIS, for the processing of 200 kg/h (450 lbs/h) of undried and uncrystallised polyester (PET) thermoform reclaim. 3C rotary feeder The newly developed 3C rotary feeder makes it possible to use low bulk density materials without any external processing steps. A conveyor belt feeds shredded reclaim material into the hopper, where a fast-rotating disc with knives cuts, compacts and pre-conditions the material. The knives add energy into the material and start the heating and degassing process before the material is automatically fed into the MRSjump extruder. MRSjump The MRS extruder is based on conventional single screw technology but is equipped with a multiple screw section for devolatilisation. It enables efficient and gentle decontamination of PET, whilst achieving the requirements for direct food contact standards. The MRS extruder permits the processing of rPET directly into high quality end products such as packaging sheet, strapping tape or filaments without pre-drying by using a simple and rugged vacuum system. This is achieved by means of its unique and patented processing section. The multi rotation section is a drum containing multiple satellite single screws, driven by a ring gear and pinion transmission. The satellite screws rotate in the opposite direction to the main screw. This disproportionately increases the surface exchange of the polymer melt. A large opening for venting, exposing the full length of the satellite screws, is completely under vacuum. This provides good and unrestricted access to the polymer melt, the surface of which is constantly replaced at a high rate by the action of the satellite screws in the multiple screw section. The surface area and the surface area exchange rate, available for devolatilisation, are greater than in other extrusion systems, says Gneuss. As the thermal and mechanical stress on the polymer melt is minimised, PET processed on the MRS extruder has good optical and mechanical properties. The new MRSjump has a longer, modified version of the Multi Rotation Section, which is claimed to ensure both a longer residence time of the material and more surface area exchange under vacuum. The longer multi rotation section, coupled with a powerful vacuum system operating at 1mbar, can be used to boost the viscosity of rPET and to hold it at a stable level in spite of variations in the input material. There is thus no need for any liquid phase (LSP) or solid-state polymerisation (SSP). With the stabilisation and/or increase of the intrinsic viscosity in the extrusion process, the MRSjump is claimed to be well suited to recycling e.g. PET film waste or fibre reclaim – applications for which direct recycling with one single extrusion step was previously impossible due to low intrinsic Gneuss Omnimax recycling machine with MRSjump extrusion system, rotary filtration system and 3C rotary feeder"},{"@ID":56, "TRADE SHOW PREVIEW PETplanet Insider Vol. 23 No. 10/22 www.petpla.net 54 Visitors to the Sipa stand can take part in a “full immersion” experience of what is possible in PET, rPET and new resins, through use of live production demonstrations and live links to remote operations. They are intended to give a deep insight into the company’s capabilities in providing customised solutions with the flexibility to adapt to fast-changing markets, across diverse technologies. Sustainability and digitalisation will be among key focus points. Single-stage ISBM technology Running all through the show will be a single-stage ISBM (injection stretch-blow moulding) system which Sipa will be using to demonstrate how flexible the technology can be in production of a wide variety of highquality containers – in this case, cosmetic bottles. The ability to respond to fast-changing customer and market requirements is more important than ever today, especially with the current substantial shortfall in availability of glass bottles. Based on the above, quick changeover is one of the key elements for a successfull growth and ESC SP is equipped with a state-of -the art feature for quick, easy and safe tooling change. The fact that the company has an extensive in-house mould design and production is an additional advantage for the customer. Injection mould making Sipa will also demonstrate its ability to develop and produce highperformance, high-cavitation preform injection moulds. On display will be one of the highest worldwide cavitation moulds. It has been optimised to enable the highest preform production rate, especially when it runs on the XForm high-performance injection moulding system, says the company. Also important for the future will be Sipa’s capacity to respond to customer calls for design modifications driven by changes in legislative requirement for bottle caps, which are likely to affect bottle neck designs. Sipa’s preform moulds incorporating a system for keeping injection moulds ultraclean, even when processing post-consumer recycled PET, will also be demonstrated. Videos will introduce Xactive-Cleaning for hot halves and Xvacuum-Cleaning for cold halves. These are systems that have been developed to avoid the accumulation of dust generated above all during processing of rPET. Xvacuum-Cleaning takes care of residues Sipa Hall 13 Booth B11 High productivity, low consumption & sustainability Sipa will be showing its wide expertise in PET container design and production technologies at the K show, focused on sustainable solutions based on reduced consumption of utilities and virgin fossil-based materials, and increased use of rPET and alternative resins. 180-cavity preform injection mould A selection of rPET bottle shapes developed by Sipa"}]}}
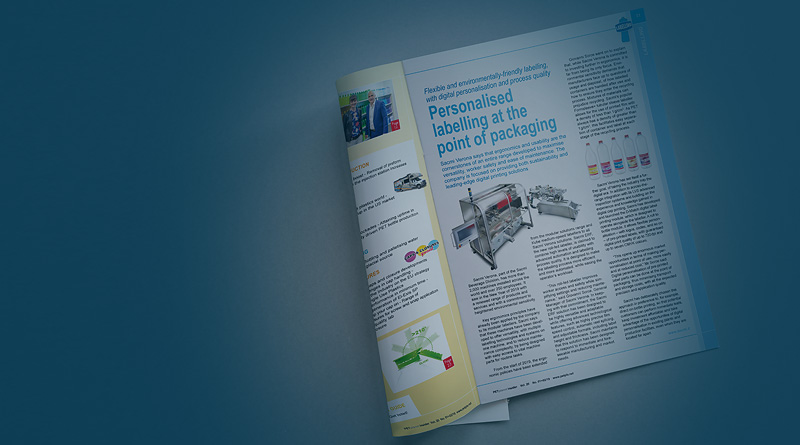