The CircuTray-UP project – PET tray packaging recycling
Although PET packaging is produced in large quantities and is one of the most common types of modified atmosphere packaging, it is rarely if ever recycled. Despite the established state of the art in sorting non-bottled PET packaging, the most common processing route for such packaging ends in incineration. The CircuTray-UP project, which is funded by the German Federal Ministry of Education and Research (BMBF) as part of the Plastics Recycling Technologies (KuRT) initiative, aims to close the loop for PET trays by establishing a value chain from innovative recycling strategies to the production of rPET-based tray packaging.
The field of packaging structures encompasses a wide range of plastics, with PET being one of the most commonly used plastics for flexible food packaging after polyolefins such as PE. PET tray packaging with a production volume of 1,070 kt/a including PET film in the EU27+3 in 2022 [PET Market in Europe. State of Play. Production, collection & recycling data 2022], is used both for simple items such as fruit and vegetables and for more challenging items such as meat and cheese, which require modified atmosphere packaging. While only single-layer structures are required for low-value items, high-value items in modified atmosphere packaging usually require a multi-layer structure containing PE, EVOH, PA and adhesives. Such a conglomerate of plastics poses a problem for conventional mechanical recycling, as different processing conditions are required and the polymers do not dissolve into each other. While multi-layer structures are an obvious problem for mechanical recycling, single-layer PET is a problem in itself. The mechanical and thermal properties of PET used for trays, such as different melt viscosities, melting temperatures and intrinsic viscosities, differ significantly from bottle PET, resulting in limited compatibility with the well-established bottle PET recycling.
In Germany, PET-based plastics are collected by the Dual Systems Germany (DSD) and sorted accordingly into waste fractions of non-food PET bottles and trays with different compositions and a majority tray fraction containing both single and multi-layer structures. While the mixed PET fractions are partially recycled and mainly used in low-value applications, the majority tray fraction often ends up in plants for energy recovery.
Pressure from legislator
According to the latest revision of the European Plastic Packaging Waste Regulation (PPWR), touch-sensitive packaging with PET as the main polymer, including food contact packaging, must contain at least 30 per cent recycled material by weight in 2030 and at least 50 per cent by weight in 2040. In addition, at least 70% of the packaging must be recyclable. None of the proposed minimum values can currently be achieved on an industrial scale. As the PPWR is on its way into legislation, a solution to this waste problem must be found soon, otherwise this type of packaging will have to be replaced by more recyclable packaging.
Several market players have already partially addressed the problem, but not sufficiently solved it. Some have tried to take the delamination route (Repetco Spain, Linpac Packaging Ltd), others have addressed the issue of adhesives (BASF), while others have chosen the mechanical recycling route for monolayer structures only (Klöckner Pentaplast). In 2022, the recycling capacity for PET trays was 57 kt/a, with the Netherlands, Spain and France contributing the most. [PET market in Europe. State of Play. Data on production, collection and recycling 2022]
Advancing the recyclability one step at a time
The CircuTray-UP project, which is funded by the German Federal Ministry of Education and Research (BMBF) as part of the Plastics Recycling Technology Initiative (KuRT), addresses the entire value chain by looking at sorting, waste processing, advanced recycling processes, film processing and packaging production in order to close the loop for PET trays. The strategic partners of the project committee, led by the Fraunhofer Institute for Process Engineering and Packaging IVV in Freising, are ZWS Recycling GmbH, Unisensor Sensorsysteme GmbH, Lömi GmbH, Reifenhäuser GmbH & Co. KG, Silverplastics GmbH and Öko-Institut e.V.
With the technologies available, a recycling cycle from waste to food packaging is to be established. The aim is to provide tray packaging produced from recycled single and multi-layer PET trays as early as 2026, which will replace today’s PET trays when they are ready for the market (Fig. 1).
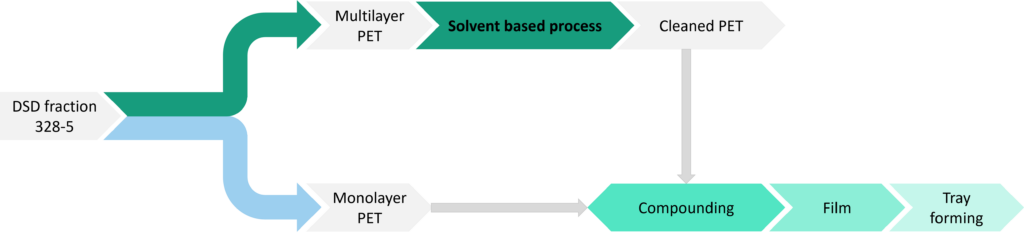
Municipal plastic waste is sorted using near-infrared sensors in the recycling centres. This results in waste fractions 328-1 to 328-5, which are heavily enriched with PET, the latter consisting mainly of PET trays. This waste is usually cut into flakes and washed for further processing. This task is tackled by ZWS Recycling. Due to the higher stiffness and brittleness of PET trays compared to PET from bottles, a large amount of fines accumulate during washing, which are often of limited use for further processing. A reduction in fines is to be achieved by developing suitable washing technologies with a design optimised to minimise material breakage.
With Unisensor’s flake-based sorting technology, the flakes are sorted into a high-purity single-layer PET fraction and a multi-layer PET fraction, both of which are ready for further processing by mechanical and solvent-based recycling.
The Fraunhofer IVV’s solvent-based recycling aims to selectively remove the non-PET components from the multi-layer flakes to produce pure PET flakes. Previous projects have already demonstrated the applicability of such a process for mixed plastics. In an earlier project, PET flakes were obtained that are suitable for the production of films. With this film, it was also possible to produce three-dimensional trays using a thermoforming process (Fig. 2, heading picture).
This solvent-based recycling process, which is currently being carried out on a small technical scale, is to be scaled up to the size of a pilot plant in order to gain deeper insights for further scaling up to an industrial scale.
At the same time, packaging orientated to the “Design for Recycling” guidelines is being developed that can contain a recycled content that exceeds the prescribed minimum. Such a design requires functional barrier technologies to ensure that there is no contact between the product and the rPET, as required by European legislation and necessary for modified atmosphere packaging. Suitable functional barrier technologies that prevent the migration of substances from rPET into the product during the typical storage period have already been identified and investigated prior to this project. Of the functional barrier technologies investigated, coextruded virgin PET film, PET lacquer, laminated virgin PET film and SiOx coating, both laminated virgin PET film and SiOx coating offer similar performance, although only laminated PET film can be thermoformed after application. Usually PE and EVOH are used for such barriers, but to make this packaging mechanically recyclable, a laminated PET film is chosen as the functional barrier.
After washing and processing, processed and purified mono- and multilayer waste PET fractions are to be turned back into a film consisting of a sandwich structure with at least one laminated PET virgin material layer for food contact. Once Reifenhäuser has obtained the films, silverplastics will thermoform them into new trays, which can be tested on existing packaging lines. In order to prove suitability for food contact, the recyclate is analysed for non-intentionally added substances (NIAS) and the barrier is tested using a migration test in order to collect data for modelling potential storage durations.
In order to demonstrate the ecological viability of the recycling chain, the processing chain is analysed and evaluated by the Öko-Institut using a life cycle assessment, whereby the recycling scheme competes with incineration with energy recovery and the production of new, modern virgin PET trays. A use case with a recyclate content of 66 per cent by weight and at least one additional life cycle is assumed. In addition, the production of the developed packaging is evaluated from an economic point of view.
As the status of recycling technologies for PET trays poses a significant problem for the entire value chain involved with PET trays, cooperation is welcome. Quarterly meetings are planned for all those involved in the PET tray value chain.