Improving compressed air efficiency in PET applications
The Water Compressor is a step forward in compressed air systems, according to Augwind, its developer. With a successful R&D project demonstrating its effectiveness, it is now seeking partners to help demonstrate and develop to the next stage.
Augwind’s Water Compressor system takes a different approach to compressed air from conventional solutions. It is an evolution of Augwind’s AirBattery, an energy storage technology developed by Dr Or Yogev around 15 years ago, while he was in California. The ‘Golden State’ had a wide range of energy resources, including oil and, more recently, wind and solar power. Dr Yogev was working at the time with a solar power company and he recognised the need for some kind of storage system to manage renewables, to harvest wind energy when wind was blowing but demand was low – such as at night – and, similarly, to release energy back into the grid during periods of higher demand. The conventional thought had been to create big batteries that harness the energy in the form of compressed air; Dr Yogev took a step to the side and thought of something different.

“His original idea was to place an underground tank beneath each wind tower. Excess energy generated by the turbine would compress air within the tank and the network of wind turbine-fed tanks would become a distributed energy storage asset,” said Ido Ben-Yehuda, Head of Marketing with Augwind. “The solution has evolved, dramatically, since then.”
Augwind, headquartered in Yakum, Israel, was established in 2012, to develop and exploit Dr Yogev’s idea and to realise the AirBattery energy storage system – a novel combination of pumped-hydro and compressed air energy storage. After accomplishing the development of its proprietary underground tanks, that are used for the compression and expansion process of the AirBattery, Augwind realised that this element has already commercial value for industrial compressed air applications – buffering between compressed air generation and consumption, optimising the energy bill and productivity of large compressed air systems. This underground tank was commercialised under the name AirSmart. Today, over 70 AirSmart installations are operating on daily basis at some of the largest industries in Israel and recently in Italy. AirSmart clients include companies operating on the mineral mining and processing industries, food and beverage, plastics, cement, steel and more. Among Augwind’s customers are companies such as Unilever, Iscar (an IMC Group company) and Tempo, the Israeli producer of Heineken and PepsiCo.
Raising the game with underground storage
AirSmart is essentially a compressed air buffer system. Instead of supplying directly, the air is accumulated in underground tanks located between the compressor room and the machinery. This allows supply to be optimised. That idea of buffer storage is not new, of itself, but the installation, charging technology and management all are. Compressed air buffering systems traditionally take up a lot of space; what Augwind achieved was the development of technologies that enable the large CE-certified tanks to be installed underground – under car parks, logistics or other areas, which means that valuable working spaces can be kept in productive activity, while enabling huge, compressed air reservoirs. The system offers energy cost savings of more than 20% of compressor’s electricity consumption, according to Ido and Augwind.
To realise the AirBattery system, one of the challenges that had to be overcome was keeping the air cool that was undergoing compression. Augwind has achieved it by using water as both the compressing agent and as a cooling medium – and the location of the tanks underground also helps to maintain a constant temperature.

Water for compression
Compressors in traditional air system use an electric motor to rotate metal pistons that pump to compress air, these motors are replaced by hydraulic water pumps. The ‘liquid piston’-water is pumped into a chamber and compresses the air in it over 20% more efficiently than conventional compression. This is due to the inherently higher efficiency of water pumps, and the near-isothermal process that results in negligible energy losses, according to Dr Yogev.
A demonstration system, built in 2023 at Augwind’s R&D site in the Arava area in Israel, is made up of three pumps, two compression chambers that serve as the liquid-piston, and another chamber as a reservoir of compressed air, typically held at 7 bar, although 42 bar is theoretically possible by adding two pumps in series. When pressure falls, the upstream elements are called upon to replenish the reservoir. This happens automatically and pressure is maintained at a constant level, enabling fluctuating demand to be met without inefficient surges and shutdowns. Compression happens slowly, so the air does not heat up as much as in conventional systems; heating air is a waste of energy. Traditional compressors address this issue by cooling the air between compression stages. The slow liquid piston process provides ongoing heat exchange between the compressed air, the water, and the ground the tanks are buried in; the air is kept at a near-constant temperature, so energy consumption remains low throughout the process.
The concept has been successfully validated, and the company is looking at prospect sectors, including glass blowing and mainly PET bottle production.
Applications to PET
“This is the core principle. After more than seven years of learning experience with AirSmart, and after accomplishing the compression process at our R&D site, we understood that our liquid piston mechanism has a unique value proposition for industrial compressed air applications,” said Ido. “Our technology offers a number of energy consumption and operating cost advantages to PET bottle converters and filling operations. However, it is a larger scale system and it is not a cheap option for SME businesses.”
“At the moment, we are competing with 25 to 42 bar oil-free compressors – of which 70% of applications are PET blowing,” he continued. “Our focus now is on PET applications between 2,000 m3/h and 10,000 m3/h. Based on the performance at our R&D site, a Hydro Air system running at 4,000 m3/h at 32 barg [33 bar absolute assuming atmospheric pressure of one bar] average consumption would be 526 kW.”
Augwind reckons that full ROI (return on investment) of the capital expenditure would be achieved within four years, based on electricity at € 0.10 per kWh and € 0.20 per cubic metre of water, through energy savings alone.
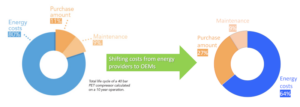
Switching cost from Opex to Capex
Augwind’s Water Compressor is claimed to be at least 20% better than the current best in class in terms of energy consumption, and that is before considering the elimination of need for cooling water. As the compressing medium is water, there are potential advantages in regulatory decarbonisation schemes, as well as lower operations and management costs; the entire system is claimed to be more efficient than conventional technology because correct pressure is always maintained and is constantly available. There are no losses from continual shutdowns, stops, idling and restarts.
“These are the main advantages of our liquid-piston Water Compressor: lower electricity bills; no oil in the system; and no need for running cooling water,” said Ido. “We bring great ROI for any market that strives for carbon reduction and increased energy efficiency by accumulating long term energy savings. We are now seeking and looking forward to recruiting partners for demonstrator units and to work with us in developing the technology further.”