PEF, polyester material of the future
by Michael Thielen, Publisher of Renewable Carbon Plastics Magazine
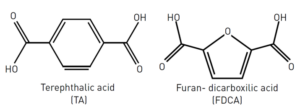
There is no doubt that plastics based on fossil raw materials are problematic in terms of climate change and limited resources. In many cases, plastics made from renewable raw materials already represent an interesting alternative. A comparatively new biobased plastic is polyethylene furanoate (PEF). Chemically, the aromatic polyester material is similar to the well-known commodity plastic PET, which is made from monoethylene glycol (MEG) and terephthalic acid.
While biobased MEG is already being used in some cases for PET, the production of terephthalic acid from renewable raw materials has not yet been sufficiently developed. With the biobased furandicarboxylic acid (FDCA), PEF can therefore be a 100% biobased alternative for PET. Compared to PET, PEF is also characterised by improved properties, such as higher structural strength, better thermal properties and strongly improved barrier behaviour.
PEF can be used for a variety of commercial applications, including bottles, films, food packaging, textiles, carpets, electronics applications and in the automotive sector.Another advantage of PEF is that it can be processed on the same equipment that is used for PET, other polyesters and often even other plastics. In many cases, only changes to the process parameters are required, as is usually the case when switching between different materials.
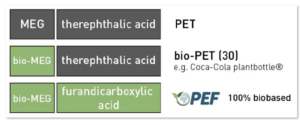
(Source: Renewable Carbon Plastics)
Properties
PEF is comparable to PET in many respects: It is a transparent and relatively rigid polymer. However, there are some notable differences between PEF and PET. PEF has a glass transition temperature of 86 °C, which is ~10 °C higher than PET.
In the packaging industry, the remarkable barrier properties of PEF represent a significant improvement over PET. PEF has a ten times higher oxygen- and a 15 times higher CO2 barrier and two and a half times as high a water vapour barrier as PET. In addition, the strength and modulus of PEF are significantly higher than those of PET. For brand owners and packaging developers, the improved properties of PEF offer a range of innovation opportunities such as extending shelf life, further reducing bottle weight, smaller packaging for carbonated drinks and replacing glass with PEF for oxygen-sensitive products.
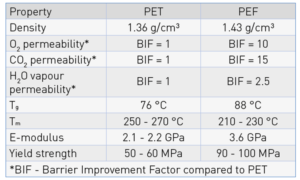
Due to its similarity to PET, PEF can be recycled using the same processing steps as the many known PET recycling processes. It has also been shown that PEF has a limited impact on the rPET stream, which have led to (interim) endorsements of PET/PEF multilayer bottles to enter the PET bottle recycling stream in Europe (EPBP limited to a market penetration of 5%) and US (APR).
PEF World Congress
Due to the properties of PEF and its production from 100% renewable raw materials, a whole range of companies around the world are already developing FDCA and PEF production. The Dutch company Avantium (Amsterdam) is opening its flagship plant for the production of FDCA in Delfzijl, The Netherlands, in October. Reason enough for the trade journal Renewable Carbon Plastics (formerly bioplastics Magazine) to organise the first PEF World Congress together with the Horizon 2020 project PEFerence. The 2-day hybrid conference (on-site and online) will take place on October 30 and 31 in Düsseldorf, Germany.