US market key focus for growth
AF Compressors: celebrating three decades in the United States
It was not long after the emergence of PET in the beverage industry in the late 1970s and early 1980s that Atelier François (AF Compressors) noticed an increase in demand for oil-free air compressors, driven by the US market. After selling several machines to a US-based global producer and supplier of PET plastic containers and preforms for the food and beverage industry, the decision was made to establish a presence in the US. AF USA Inc., based in Atlanta, GA, was founded in 1995, and by the end of the 1990s, was already contributing no less than 25% of the company’s sales in US dollars.
“The US market remains at the forefront of focus for our global organisation. Many key customers globally are based in the United States, which has a direct impact on our relationships abroad,” states Gareth Smith, Area Sales Manager of AF USA. As the US demand for PET plastic continues to grow, AF Compressors has positioned itself as a key player in providing energy-efficient solutions to meet these needs. The company, which has dedicated 99% of its business focus to the PET industry over the last 40 years, boasts a global market share of 60-65% with its oil-free piston compressors Their efficient designs are widely used across the US.
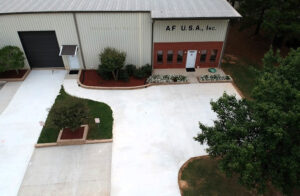
Today, AF USA has a team of 22 employees providing comprehensive support to clients across the US, Canada, and the Caribbean. This includes everything from new compressor installations to preventive maintenance and troubleshooting. The team’s deep engineering expertise, cultivated over decades, helps clients optimise their operations, expand facilities, and replace equipment from other suppliers.
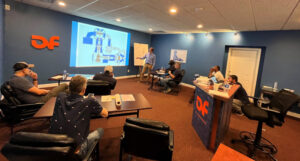
In Carrollton, Georgia, the company also has a 5,750-square-foot warehouse that stores over $1m worth of spare parts, ensuring that AF USA can meet the needs of its growing customer base. The AF Training Academy, located at the US headquarters, is offering extensive training programs for both AF technicians and clients. Courses cover everything from compressor operation and maintenance to safety and troubleshooting, helping customers maximise the efficiency and lifespan of their equipment.
Smith continued, “We are consolidating our leading position on an actual 100% AF service presence, while developing new technologies and accompanying our customers through their challenges in terms of global sustainability. Our compressor systems are engineered and mechanically designed for ‘energy sobriety’ and this is a key fact to positively respond to the climate challenges in the USA and the Americas as well as anywhere else in the world.” Thus, the company is responding to customer requests that differ little in the USA from those of customers in other parts of the world:
“Energy savings / TCO, flexibility, after-sales service & support, ease of maintenance and training of onsite personnel are all areas of focus brought consistently to our attention.“
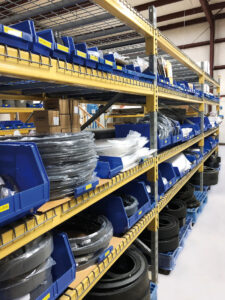
But there are also a few special characteristics of the US market: AF is beginning to see a push from the end-user to bring full PET production lines in-house to reduce the costs of transporting empty containers, and other associated outsourced costs. A direct consequence of this change of approach is that the end-user is playing a more direct role in supplier selection, including direct procurement of PET compressors and overall maintenance /
management of the equipment. Smith went on, “This has created a challenge for us as it is even more important for us to educate these customers on proper installation, operation, and ongoing maintenance in order for the user to achieve optimal efficiency and long-term sustainability of our equipment.”
Focus on energy efficiency, sustainability & costs
AF Compressors also places a strong emphasis on incorporating customer feedback into the design and functionality of its compressors, with a focus on energy savings and cost reduction. The company developed the adjustable Air Flow System (AFS), which allows for 0-50-100% load regulation, enabling customers to achieve immediate power savings and long-term efficiency gains. The system can be retrofitted to existing compressors, requires zero maintenance, and extends the lifespan of equipment by maintaining stable operating temperatures.
In partnership with Schneider Electric, the Smart Inverter Starter (SIS) has been created, which is claimed to be a cost-effective alternative to full-size variable speed drives (VSDs). This solution provides energy-saving benefits during compressor startup without requiring special motors or cabling and can be retrofitted on existing units, according to AF.
The company’s patented All-In-One (AIO) system combines high and low-pressure air supply in a single compressor, reducing both investment and service costs. AF offers a Multi-Compressor Management System that optimises energy use across multiple compressors by balancing load distribution and extending service intervals.
Additionally, AF’s Heat Recovery System captures up to 80% of the heat generated during compression, allowing customers to reuse the energy for other processes, further enhancing efficiency and sustainability.
Smith comments, “All of these systems have been developed based on customer demand and on what we have learned from the challenges our customers face.”
Increasing local presence
Looking ahead, AF USA is committed to expanding its market share while maintaining a strong focus on customer service. “We know that the best service makes the best presales and is the right way to increase our presence over time.” So the company is building on their local presence to improve responsiveness rather than relying on third party agents.
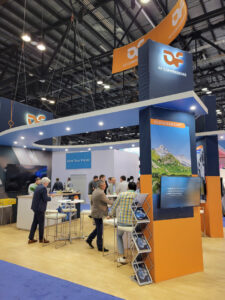
This also included AF USA’s participation in NPE in May. Located in the bustling Bottle Zone, AF Compressors was strategically positioned alongside its OEM blow moulding partners. “The Bottle Zone was the perfect location for us,” Smith noted. “Being positioned next to major OEMs, allowed us to showcase our products to a wide audience. Our neighbour had multiple SBM machines producing non-stop all week with high and low-pressure air supplied by our 40 bar, 1,000 cfm compressor.”
One of AF’s major highlights at the event was powering several production lines in real-time. Their 40 bar compressor supplied high and low-pressure air to multiple OEM blow moulding machines, creating a live demonstration of how their compressors drive the high-efficiency production of PET bottles. Gareth Smith ended on a positive note: “Seeing visitors engage with the equipment and witness entire production lines, from compressed air to resin melted down into preforms, to newly blown bottles, and knowing that we are such an important part of our partners’ exhibition is exciting and humbling at the same time,” Smith concludes.