Closures from the Saudi province of Qassim
Potential for the Gulf region and beyond for bottled water
The foundation stone for the water bottle cap manufacturer Cap House Plastic Factory was laid in 2012 in the small town of Ar Rass in Qassim, just under 100 kilometres southwest of the Saudi Arabian provincial capital of Buraida. The idea was developed by General Manager Yousef Alassaf after realising the constantly increasing demand for safe, packaged drinking water in the country and not least because there was still a lack of suppliers in precisely this segment in the country. Today, the company produces with its Plasticap brand not only for Saudi Arabia, but also for many neighbouring countries and GCC states and is also interested in the potential in African countries. In conversation with the passionate entrepreneur, we learnt how passion and vision go hand in hand.
Meeting with Cap House Plastic Factory
We met: Mr Yousef Alassaf, General Manager
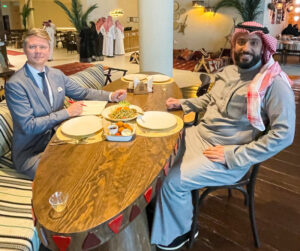
It all began in 1977 with a family-owned baking factory. “My father,” explained 37-year-old Yousef Alassaf, “wanted to produce his baked goods on a larger scale and bought fully automated equipment from Japan. This was before I was born, but by the age of 16 I was helping out in the factory for my pocket money. It was my first contact with a real production environment and I learnt to appreciate the benefits of higher output. Later, during my studies in Alabama, I visited the Thyssen Krupp steel plant in Calvert. At that time, I was totally impressed by the high turnover of the company with just 16 employees, and I realised once again that I felt at home in the field of highly automated production.”
When the idea of his own factory in the beverage packaging sector came up, Mr Alassaf was initially interested in preform production. His close contact with Eng. Abdullah Obeikan, CEO of the Obeikan Investment Group, a group that is primarily active in the fields of digitalisation and education, but also in packaging, ultimately advised him that a cap business would make even more sense, as there were no companies specialising in this field at the time.
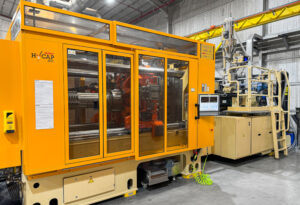
Cap House, which is ISO 22000:2018, ISO 9001:2015 and HACCP:2003 certified by TÜV Austria, now produces 2.9 billion 29/25, 1.22g closures a year under the “Plasticap” brand, so far exclusively for bottlers of still water. “When production started back then, we used injection moulding machines from Taiwanese manufacturer Jon Wai, each with 220t and 24 cavities for 30/25 caps. After a few years, however, it became clear that we needed to increase capacity and quality. This is where Husky and Corvaglia came into play.”
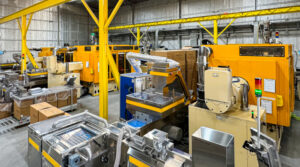
The setup now includes three Husky HyCap 4.0 systems with Corvaglia moulds, of which the first machine with 300t force and 72 cavities was delivered in 2018 and went into operation in April 2018. This was followed in 2020 by a second HyCap 4.0, 400t with 96 cavity mould and in 2023 a third HyCap 4.0, 400t also with a 96-cavity mould. All injection moulding machines are equipped with IMD Vista closure inspection systems. Sabic supplies the raw material for the caps, together with masterbatches from Avient, which are now supplied to around 20 regular customers, including Azbah, Berain, Najran, Rest Water, View and many more. In addition to GCC countries, more and more countries in Africa are also attracting business interest. 47 employees work at Cap House.
“We are also planning to expand into other segments in the future, such as CSD, juices, milk or possibly non-food,” says Mr Alassaf. According to its own estimates, Cap House is probably in fourth or fifth place in terms of market share among the five major converters Oasis, Gulf Packaging, Alsad and Takween.