Once local, now global: PET production in Oman
Two years ago, Alpek Polyester acquired OCTAL, the largest PET resin and PET sheet manufacturer in the GCC, thus marking its expansion into global markets beyond the Americas and Europe. We visited the plant in Salalah and discussed bottle grade PET resin, sheet production, chemical recycling, and the Gulf market in general.
The Alpek Polyester Middle East (APME) plant is a state-of-the-art modern manufacturing facility for production of bottle grade PET resin and sheets, with a combined capacity of close to 1 million t/a. With Uhde Inventa-Fischer’s MTR technology, a differentiated, sustainable, and efficient PET resin production process, they eliminate a crucial step in conventional manufacturing, resulting in 63% less electricity consumption compared to traditional technologies, leading to a shorter cycle time for customers.
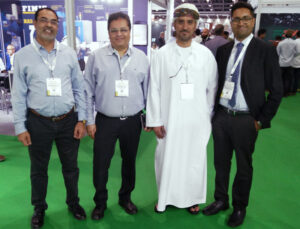
The facility benefits from its strategic location, which is close to the Port of Salalah, a major hub for connecting raw materials from Asia, that allows rapid delivery of finished goods, resin and sheets, to global markets. The site can store more than 3,000 TEUs (Twenty-foot Equivalent Units) within its peri-meters and includes container cleaning facilities.
According to the company, the market in the GCC is dominated by the water segment which contributes to around 70% of bottle grade PET resin. APME’s WG02 grade is the most popular to service this segment and is regularly supplied to major regional and international brands. Furthermore, the use of MTR technology for PET production ensures a very low acetaldehyde content in its products, which is particularly important for water producers as it achieves the best product characteristics.
APME’s strengths include just-in-time (JIT) delivery in trucks by road to regional markets like the UAE, KSA, Kuwait, Qatar, Yemen, and Jordan. Their strategic location adjacent to Salalah port enables them to ship product to over 75 countries around the world from US East Coast to Japan main ports, with short transit times.
The market in Oman and that of the neighbouring Gulf states is, according to the company, a stable market with the prospects of solid growth.
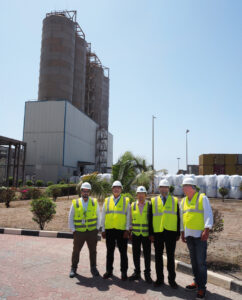
“Offering unique products to our customers is key to our success, especially in today’s competitive market where cost optimisation is crucial. We are a preferred supplier instead of just a one-off vendor in the highly volatile commodity market.” stated Senior Sales Director – PET Resin, Prashant Boloor and he also emphasised the popularity of fast reheat grades owing to increasing energy cost globally and growing awareness among brands on reducing CO2 generation targets.
As a leader in sustainability and promoting a circular economy, APME is already contributing by offering its Single Pellet Technology (SPT) which is chemically recycled PET with up to 25% recycled content to their customers in the region. Many brands have shown interest in the product due to its excellent quality and how it supports their commitment towards sustainability.
Ajith Ravindranath, Sales Manager, comments: “Our aim is to ensure best quality product available to our customers, at an affordable price and on time to serve the beverage industry, FMCG and many other markets.”
As an innovative market player, Alpek Polyester presented closures made of PET in NPE 24. As long as it remains transparent, it can be reprocessed with the bottle in both chemical recycling and mechanical recycling which ensures recycling at its best to avoid complications in the initial separation process.
With increased focus on sustainability, the plant is heavily invested in recycling capabilities including production of resin & sheets with rPET content using the chemical recycling process.
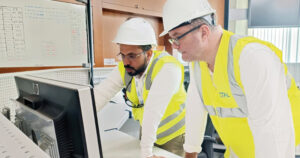
Used PET bottles in the form of high-quality flakes are sourced to be made into bottle-grade again. Andrea Frigerio, Site Quality & Continuous Improvement Manager, stated: “We make sure that the quality of the flakes is as consistent as possible. Everything goes into the reactor described below, where unwanted substances like other polymers (PP/HDPE) are removed. Another positive aspect of chemical recycling is that the material is only heated once in the reactor. As a result, it is not prone to grey or yellow haze. APME’s PET resin and single pellet technology meets FDA & EFSA standards.”
The melt-to-resin (MTR)
The melt-to-resin (MTR) process is a fully integrated one-step process that provides bottle-grade IV PET melt directly from the discage reactor (finisher). PET is produced from the raw materials purified terephthalic acid (PTA), isophthalic acid (PIA) and ethylene glycol (EG) using a melt polymerisation process. Conventional processes have in common that they require a second, subsequent solid condensation step (SSP) to further increase the molecular weight of the polymer. Alpek Polyester uses the MTR process, in which the IV increase takes place before the granulate is produced. This makes the material more uniform; thicker or thinner granules or dust have the same material properties. As the granulate is not subsequently heated again in the SSP, the acetaldehyde content is significantly lower, which is a decisive advantage for water bottle grades. In addition, the MTR process has a clear advantage in producing bottle-grade PET in terms of overall costs, energy consumption, plant flexibility, fixed costs, raw material utilisation and maintenance costs.
Alpek Polyester, a leading global producer of PTA and PET, closed the acquisition of OCTAL Holding for US$620m on June 1, 2022, as the agreement signed was subject to regulatory approvals. OCTAL, a major producer of PET film and bottle grade PET resin with a capacity of over 1 million t/a, operates plants in Oman, Saudi Arabia, and the USA. The acquisition expands Alpek Polyester’s portfolio to include the direct-to-sheet PET film segment (DPET). Alpek has an installed capacity of 5.8 million t/a and operates 32 plants in Mexico, the USA, the UK, Brazil, Argentina, Canada, Oman and Saudi Arabia.