PEF: A bio-based alternative to PET with lower environmental impact
At the PEF World Congress in Düsseldorf this October, Dr Ángel Puente, Senior Expert at the nova-Institut GmbH, presented on the topic “PEF – A circular bio-based plastic with improved properties and environmental performance.” As part of the EU-funded PEFerence project, Dr Puente is evaluating the environmental impact of polyethylene furanoate (PEF). PETplanet caught up with him to discuss how PEF compares to PET and examine its potential advantages.
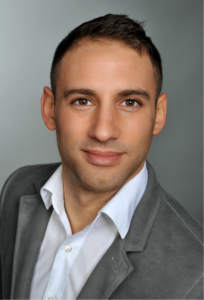
PETplanet: At the nova-Institute you are part of the EU-funded PEFerence project. Could you briefly describe the project’s goals and your specific role within it?
Dr Puente: The PEFerence project aims to establish a sustainable value chain for producing polyethene furanoate (PEF), a 100% bio-based and fully recyclable plastic developed by Avantium (NL). PEF offers a renewable carbon-based alternative to fossil-based plastics like PET in applications such as bottles, films and fibres. My role in the project is to assess the environmental advantages of PEF using the established ISO LCA methodology.
PETplanet: You have assessed various products made from PEF, such as monolayer bottles and PET/PEF multilayer bottles. Are bottle applications the primary focus for PEF?
Dr Puente: PEF is indeed an excellent material for bottle applications. Its superior barrier properties — especially against oxygen and carbon dioxide — make it an ideal choice for monolayer and multilayer bottles, ensuring extended shelf life for beverages and reducing food waste. Additionally, its fully bio-based and recyclable nature aligns perfectly with the growing demand for sustainable packaging solutions. However, bottles are just one of the many applications where PEF can excel. Thanks to its remarkable mechanical strength and thermal stability, PEF can also replace traditional materials like ABS in certain application and is well-suited for films used in flexible packaging, which can replace conventional plastics in snack wrappers, pouches, and more. In textiles, PEF fibres can offer a bio-based alternative to polyester, catering to industries aiming to reduce their dependence on fossil-based materials.
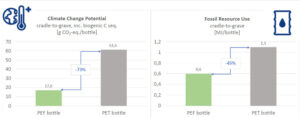
PETplanet: How do the barrier properties of PEF compare to PET, and what other characteristics make it particularly suitable for bottle applications?
Dr Puente: One of the standout features of PEF is its exceptional barrier performance. PEF offers up to 10 times better oxygen barrier and approximately 16-20 times better carbon dioxide barrier compared to PET. These properties significantly extend the shelf life of beverages, making it an ideal material for packaging sensitive products like carbonated drinks, juices, and even beer. This advantage also helps reduce food and beverage waste, aligning with global sustainability goals. Another advantage is that PEF can be processed in existing PET processing lines, therefore no additional investment is needed.
PETplanet: When you compared the environmental impact of PEF to PET, what did the profiles reveal? What environmental impacts were most relevant, and how did they differ?
Dr Puente: As an example, in monolayer bottles application, the LCA showed that the use of PEF would result in significant reductions (up to -73%) in greenhouse gas emissions (GHG) over the bottles’ life cycle compare to those of PET (Fig. 1). PEF bottles would also contribute to remarkably less finite resource consumption of fossil fuels (-45%), largely due to the use of 100% renewable feedstocks and the good barrier and mechanical properties of PEF enabling light-weighting designs. These results are remarkable, since these impact potentials are two of the most relevant environmental impact categories in the current political agenda driving the transition from fossil to renewable feedstocks.
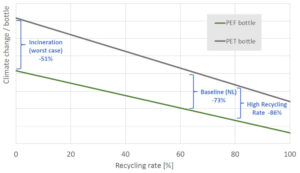
PETplanet: In comparing end-of-life scenarios like incineration and recycling with respect to climate impact, you project that PEF bottles could reach a similar recycling rate as PET bottles, which could offer up to an 86% advantage for PEF (Fig. 2). Given that PEF currently lacks established recycling streams, how would a comparison look between a recycled PET bottle and an incinerated PEF bottle?
Dr Puente: PEF has proven fit-for-purpose with existing sorting and recycling facilities and can be recycled mechanically in a similar way using the same equipment used to recycle PET. The European PET Bottle Platform (EPBP) has provisionally approved the recyclability of PEF in the European recycling market for bottles, although in the future a separate recycling stream would have to be set up for final recycling. In this respect, PEF can easily be distinguished from PET and other plastics using near-infrared technology. This will allow PEF to be sorted from any PCR or deposit system waste streams once the market has grown sufficiently to enable an individual PEF material recycling stream. Our study showed that a rPET bottle would need to contain approximately 85% recycled content to match the carbon footprint of a virgin PEF bottle.
PETplanet: By 2030, PET bottles in Europe must have an average of 30% recycled content. How does the carbon footprint of a PET bottle with this 30% recycled content compare to a vPEF bottle?
Dr Puente: Based on our assessments, a virgin PEF bottle would still have a 48% lower carbon footprint than a PET bottle with 30% recycled content. As PEF enters the market and recycling streams for PEF are further developed, its carbon footprint could decrease even further, reinforcing its role as a 100% bio-based and recyclable packaging solution.
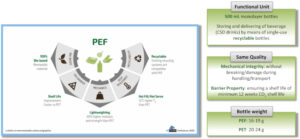
PETplanet: The production of PEF requires intermediates such as fructose and other plant-based feedstock. In 2022, EU demand for bottle-grade PET was 3.4 million tonnes. If this demand were fully met with plant-based PEF, what would that mean in terms of agricultural land requirements?
Dr Puente: To make the change to a fully sustainable future we need to switch to sustainable carbon sources. With recycling alone, we will not be able to meet the full demand. Therefore, next to recycling we need to switch to plant-based materials. Materials that have a good fit with the feedstock (efficient conversion) and a performance that can, at least, compete with the current incumbent. PEF is a material that fulfils these criteria.
The feedstocks required for PEF production is sourced from sustainably grown, high-efficient crops. In any case, the focus should not be solely on land use but on integrating any bio-based material production into landscapes in a way that balances environmental, social, and economic priorities. Today, plant-based plastics only make up a miniscule land use. Ultimately, there is a need to shift away from fossil feedstocks to achieve climate change mitigation and bio-based materials are part of the solution. With thoughtful planning, policy support, and technological advancements, bio-based feedstocks and materials can contribute to a more sustainable future without compromising food security or ecosystems.
PETplanet: How significant do you see the role of government policy in supporting the adoption of PEF?
Dr Puente: Government policy plays a crucial role in supporting the adoption of PEF by setting clear regulations and incentives that promote sustainability. Policies that encourage the use of bio-based and recyclable materials such as regulations on eco-design and product standards, extended producer responsibility (EPR) schemes, and stricter recycling and renewable carbon content targets for materials can accelerate PEF’s market penetration.
PETplanet: Thank you very much!
PEFerence receives funding from the Bio-based Industries Joint Undertaking (JU) under the European Union’s Horizon 2020 research and innovation programme. The JU receives support from the European Union’s Horizon 2020 research and innovation programme and the Bio-based Industries Consortium.