Half the space is needed…
The CapWatcher Compact by Intravis
The new CapWatcher Compact from Intravis combines a sorting, feeding and inspection unit for the quality control of plastic closures in a single, compact solution. Based on many talks with customers, the system addresses one of the largest problems in modern production facilities – the availability of space! The CapWatcher Compact saves up to 50% of the floor space compared to conventional solutions and simultaneously maintains Intravis’ renowned commitment to quality.
Photo top: An insight into the CapWatcher Compact
Efficiency and precision in a limited space
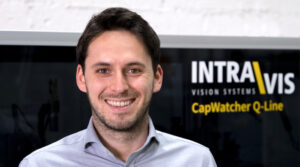
Manufacturers of plastic packaging are increasingly faced with the challenge of fitting more and more production capacity into limited space. This is where the CapWatcher Compact comes into play: It combines three previously separate elements of the plastic closure production line – sorting, feeding and inspection – in one compact housing, without compromising on functionality or inspection quality. “With the CapWatcher Compact, we have created a solution that takes our customers’ production realities into account. We offer a reliable 100% inspection with minimal space requirements,” explains Marius Pötting, Product Manager Caps & Closures at Intravis.
Development in dialogue with the customer
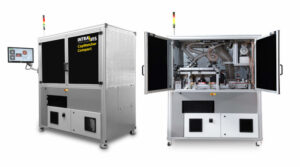
The impetus for the development of the CapWatcher Compact came from customer requests over the last year. “During the last year, some of our customers came to us and said, that in the future it will be harder for them to use our solutions, since the space in their production lines will be more and more limited. They were very sorry for that since they appreciated our sophisticated systems”, explains Marius Pötting. Intravis realised that there is a requirement to enable the proven inspection performance in a significantly smaller space. Within six months, Intravis created an initial prototype. However, it quickly became clear that simply reducing the footprint of the inspection system would not provide the necessary space savings. Only by combining several downstream elements, the necessary reduction in space requirements would be achieved. So, in a second project phase, the Aachen-based company also developed and implemented an integrated sorting and feeding technology and finally brought the system to market maturity. “Of course, it helped that we have been developing and building feeding solutions for plastic closures ourselves for many years in addition to vision inspection systems,” says Marius Pötting. As a result, the system now has a footprint of just 2.4 m² and therefore offers nearly the same inspection performance in half the space of a conventional setup.
Technical features of the CapWatcher Compact
The CapWatcher Compact offers numerous technical functions for inline plastic closure inspection:
- Integrated hopper and conveyor technology: The integrated hopper offers a capacity of up to 140 l. The feeder uses the familiar waterfall principle to efficiently transport closures into the inspection section.
- Comprehensive quality assurance: In addition to the standard modules for inner and outer closure inspection, unique and market-proven modules for micro hole inspection and cavity number reading are implemented. The top wall inspection (e.g. for inspecting prints for contamination etc.) is also available as an option.
- High speed: With an inspection performance of up to 40 closures per second, the system meets high-speed requirements.
- Second ejector: Despite the limited space, a second ejector is integrated, which can be used for sorting out quality shots or blacklisting, for example.
- Wide product range: The CapWatcher Compact is designed for the inspection of common CSD closures as well as tethered caps.
- Product-specific settings: The electrically adjustable jet height is saved for each product, and it automatically adjusts when changing products.
- Fault and jam detection: The system automatically recognises (by implemented sensors), when faulty moulded closures become jammed, and localises the position precisely. This ensures uninterrupted and fluent production.
- Ease of maintenance: Despite the compact construction, the design allows easy access to all components thanks to doors on all sides.
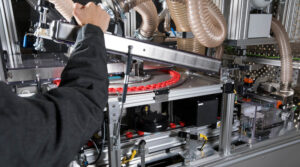
To complete the downstream equipment, customers only need a cooling conveyor and a packaging unit in addition to the CapWatcher Compact. However, Intravis can also supply these elements as a turnkey supplier.
Solution for modern production requirements
With its compact design, the CapWatcher Compact addresses one of the most urgent problems in the industry: Limited space in production halls. Particularly in Europe, attempts are being made to produce more and more in the same or smaller space. With the integration of sorting, feeding and inspection in one unit, Intravis now offers a space-saving and efficient solution. “The CapWatcher Compact shows how important it is to adapt flexibly to the needs of customers. It is yet another example of how we at Intravis see ourselves as a partner to our customers. We are always ready to take on new challenges. With the CapWatcher Compact, we are proud that we have created again great value for our customers as well as our industry in general,” summarises Marius Pötting.