Tethered caps assembly
Highspeed system – all processes integrated
Contexo has developed a patented all-in-one system designed to enhance the speed and efficiency of tethered cap assembly. By integrating the cutting process, the system aims to improve production reliability while also offering greater flexibility for implementing new closure designs.
For over 30 years, Contexo has been designing systems for complex closures and complete systems manufactured in plastic. This was the basis for the next step: the new, patented concept of the all-in-one system for single- and multi-part tethered caps. A machine platform was developed and designed that integrates all necessary processes in one system: from assembly to folding and roll slitting of the TE band to closing and packaging. The advantages of the concept are a small footprint, reduced costs and less energy consumption, says Contexo.
Capacity growth
The system is based on continuous-motion rotary presses to guarantee maximum output rates. This kind of speed is reached using a central tower that assembles the part, while feeder satellites guide them at a precisely controlled rate; a system that places minimal stress on the part. The integrated slitting unit eliminates the need to invest in expensive and high-maintenance injection moulds, says Contexo. Filigree in-mould operations are replaced by simple, safe processes, as material no longer has to be pressed through narrow channels. The integrated folding and roll cutting of the TE strip is claimed to be more stable in the production process: the TE bridges are not stressed or damaged during handling, the downstream process and assembly. At the same time, high speed and repeatability are guaranteed in the production process in order to reduce costs and increase safety.
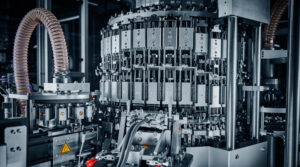
Inspection before and after assembly
Contexo employs a quality control method where each component is inspected prior to assembly, and the finished closure is inspected afterward. To ensure efficiency, the inspection systems are integrated inline with the assembly machine and operate in synchronisation with it. The camera stations used inspect the typical elements inside and outside the closure. This results in technically flawless products which are then sent for further processing. The machine is claimed to be user-friendly with 360° accessibility, changeable slitting unit and low maintenance thanks to mechanical components.
Product design
Whereas previously there were restrictions in terms of shape and appearance, eye-catching designs are now possible with the Contexo system. The vulnerability of the TE bridges is eliminated, and the rotating mould axis makes unusual shapes possible. Closures without TE bridges are feasible. Contexo states that their systems offer a space-saving and effective alternative for manufacturing closures. Their machines can produce cost effectively because the company works with standardised machine concepts and a full, in-house technology spectrum.
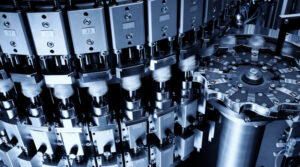
Sports Cap: Contexo´s highspeed machines show that the combination of continuous motion and inline quality control can set a new standard for high output rates and high-quality parts. Every six-hundredth of a second, a new beverage closure is assembled, folded, inspected three times, and packed. The continuous-motion rotary system enables high-performance production, achieving speeds of 920 closures per minute or approximately 1.3 million closures per day.