“We do not feel that the market is any quieter”
Interview with Michael Fink, CEO of Z-Moulds
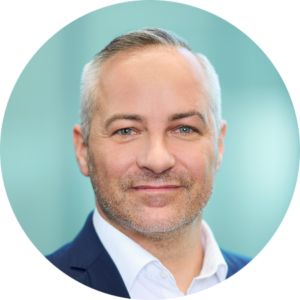
PETplanet: Dear Mr Fink, z-werkzeugbau became the Z-Group. May I ask you to recapitulate the milestones and how theses enabled Z-Moulds to achieve its leading position in the market?
Mr Fink: z-werkzeugbau had three different business units in different market segments 2023: Z-Moulds, in the caps & closure market for high-performance injection moulding systems, Z-Microsystems in the medical sector, specialised in microfluidic products for lab-on-a-chip applications and Z-Prototyping as a specialist in additive manufacturing. In order to offer these three areas their full development potential, these three business units were spun off into their own independent companies. What remained was the Z-Group, as a service provider and parent company. This way the newly established z-moulds GmbH has now independency in orienting and growing in the packaging market.
PETplanet: In recent years, for example, the new EU directives on tethered caps have boosted development in the caps mould sector. Since then, the market has become somewhat quieter. Where do you see future development opportunities in cap mould production?
Mr Fink: Actually, we do not feel that the market is any quieter. On the one hand, there are still a lot of developments in improving the current tethered solutions and on the other hand, the new requirements came across with new standards for bottle finishes, which will now be adapted in other continents outside of Europe as well. Therefore, there is still lots of movement in the caps & closure market globally.
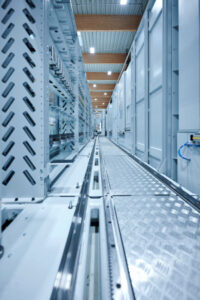
PETplanet: The topic of sustainability plays a major role in the EU directives, as well as in a future-orientated company. What are the three most important components for sustainable business at Z-Moulds?
Mr Fink: When it comes to environmental sustainability, our company can certainly be seen as one of the pioneers or early implementers. When we built our new building in 2016, we paid attention to sustainable raw materials and integration into the beautiful natural landscape of Austria from the very beginning. Our ultra-modern automated manufacturing centres fit seamlessly into a pleasant wooden facade. The electricity comes from a photovoltaic system on the roof above. Also simple things like cleverly organised waste management to reduce and recycle is key. We think each simple and small act of reducing carbon footprint counts.
PETplanet: This year will once again be a particularly eventful one for the beverage industry – the Drinktec and K trade fairs are of course the big highlights in autumn. But spring will also kick off with Chinaplas for the Chinese market, for example. Where will our readers and friends of PETplanet find Z-Moulds and can you already tell us whether you have any special news in store?
Mr Fink: Our exhibition year in 2025 will start with the Plastimagen in Mexico, followed by the Plastico Brasil in São Paulo and Chinaplas in Shenzhen. Then we will participate at two well-known industry conferences, the AMI Plastic Closure Innovations and the PETnology. The Autumn, as mentioned, will end the year with Drinktec, K-Show and also the Gulfood in Dubai. – And yes, of course, we will always be able to display new developments and innovations.
PETplanet: Thank you very much for the interview and we are delighted to present the latest innovations from Z-Moulds now:
The new 26/22 mm GME 30.40 with tethered function
Lightweight: Weighing only 1.7 g, the 26/22 mm closure is claimed to be the lightest closure in its category on the market. Despite its lightweight design, it offers robustness and can be stored effortlessly in large containers such as octabins. This combination of low weight and high durability makes it a goodsolution for a wide range of applications, says Z-Moulds.
Technical design: The sophisticated technical design of the closure ensures it is claimed to outperform comparable substitute products. With a larger opening angle than competitors – particularly compared to products from Z-Moulds – it enhances user-friendliness. Customers benefit from easier handling, providing a real advantage, especially for high-consumption products.
Manufacturing technology: The closure is made from high-quality HDPE and is designed for production with moulds ranging from single-cavity up to 128-cavities. It boasts a short cycle time of around 3 s. This efficiency enables high production capacity while maintaining consistent quality.
Sustainability and cost efficiency: The 26/22 mm GME 30.40 is sustainable thanks to the patented z-slides technology; the tamper-evident (TE) band is directly moulded, eliminating the need for subsequent folding and cutting processes. This results in material savings and less production costs. This development underscores Z-Moulds’ commitment to resource-efficient manufacturing while providing a competitive advantage.
Compatibility and adaptability: The closure can be easily integrated into existing filling systems. Without requiring changes to machines or processes, it can be immediately used on lines already designed for GME 30.40 closures. This saves time and costs during conversion and ensures smooth implementation.
High standards: The closure’s performance has been specifically tailored to meet the stringent requirements of renowned companies like Coca-Cola and Pepsi. With a carbonation level of up to 4.5 CO2 vol%, the closure demonstrates its versatility and reliability in demanding applications.
“The 26/22 mm GME 30.40 with tethered function combines lightweight design, technical sophistication, sustainability, and compatibility in an unparalleled manner. This closure makes one thing clear: innovation means not only improving existing standards but redefining them,” stated Mr Fink.