New directions for an established stationery manufacturer
Plastic packaging for personal care and cosmetics
Success stories can sometimes be unplanned or triggered by an external impulse. This is what happened to Prima Pens & Packaging, which was previously just called Prima Pens and was a well-known brand for all kinds of writing utensils. You may have guessed: it didn’t stay that way, on the contrary. A good 20 years ago, the company with its production site east of Cairo began to develop a new business area, which centred on packaging for non-food items. And all because a well-known household goods manufacturer had the idea that the company, with its expertise in plastics processing for pens, could also be a good partner in the field of plastic packaging. They were right.
Interview with Prima Pens & Packaging // September 9, 2024
We met: Mr Tarek Zayed, General Manager
A good 60 kilometres north-east of Cairo city lies the town of Badr, in whose industrial zone we had arranged to meet GM Tarek Zayed, more precisely in the Prima Pens & Packaging factory. The company, which started out in 1993 as a stationery factory and manufacturer of school supplies under the name ‘Yosran Company’, is firmly in family hands. Tarek Zayed, who studied history and then took several courses in business administration, has been part of the management team since 2013, following in his father’s footsteps. Around four years ago, the company changed its name to Prima Pens and the addition of ‘Packaging’ also followed in order to raise awareness of this area of the company, which is often still unknown to many brand connoisseurs. “We started our business with school supplies such as pens,” recalled Mr Zayed, with whom we were sitting in the meeting room. The Prima brand is still a leading manufacturer in this area today.
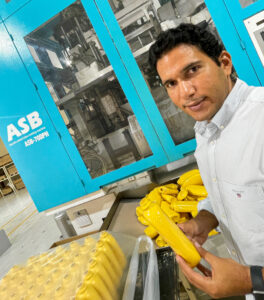
“In 2003, my father received a surprising enquiry from Henkel, who asked him if he could blow mould PE and PP bottles for them and if he would be prepared to invest in the appropriate equipment. Of course, we had experience in injection moulding due to our plastic processing for pens, but the topic was new to us. In the end, we agreed, purchased a Taiwanese Parker EBM machine and got started in 2004. Over the course of the next ten years, the business with the household portfolio ran parallel to the stationery business. However, there was no reason for us to expand further, as the stationery business was booming. But then L’Oréal came knocking on our door.” The cosmetics giant, which had recently opened a plant in Egypt, was looking for a partner to manufacture a special fliptop cap, but was apparently not very impressed with the technical setup and applications when it visited the plant, and so the topic was initially taken off the table again. At the time, Prima Pens & Packaging had around 50 injection moulding machines for stationery products. “At the end of 2014, however, L’Oréal contacted us again about the feasibility of producing two different bottles for filling a hair care product and hair dye in plastic bottles and we agreed,” explained Mr Zayed. Production continued to pick up, and in 2015, bottles were added for Reckitt Benckiser. L’Oréal also needed more bottles as well as caps.
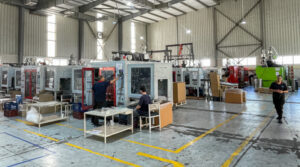
In 2017, the converter started producing PE shampoo bottles for L’Oréal’s Elvive brand on a 4-cavity machine. “After a year and a half, they asked us for a chat. They wanted to convert all of their shampoo bottles to PET packaging and orientated themselves on their European production facilities, where they produced their PET bottles using two-stage technology, which doesn’t make sense for the Egyptian market due to the much lower demand for huge quantities. We advised a one-step process, but this was not an option and unfortunately the deal didn’t go through,” said Mr Zayed. Instead, the cosmetics manufacturer commissioned a different converter, where the business relationship would continue to this day. Finally, in 2022, Mr Zayed’s father wanted to enter this sector due to the noticeable increase in demand for PET in the market. “He told me that we absolutely had to get involved, otherwise we would be excluding potentially important customers, so we bought a PET single-stage machine, an Aoki AL-500LL 50S.” When L’Oréal approached again, this time for 200 ml and 600 ml PET bottle formats for their Ultra Doux haircare brand, and agreed to single-stage production, the company invested in a Nissei ASB-70DPH with R&D Leverage mould, which has now been operating at the plant since May 2023, producing various bottle formats for L’Oréal, including rPET processing, still a fairly new topic in the country. Five different recyclate variants are sourced from the recycler Bariq, two from Far Eastern producers. A second ASB-70DHP has been ordered and is on its way, as the first one is currently working to capacity, we were told.
Looking at the figures, Mr Zayed said: “PET packaging currently accounts for about 20% of the total of about 9 million bottles a year and apart from a small portion on the Aoki, we produce everything on our ASB machine. Overall, we have a turnover of more than US$5 million for the packaging sector in general and this part is growing by around 20% a year.” L’Oréal is the largest customer with 20% of the total turnover and the converter is the main supplier for closures with around 5 million units.