The bigger the better – and lighter
Cypet Technologies claims big savings for extra large containers
Cypet Technologies, which is located near Nicosia, Cyprus, has made a speciality of designing and manufacturing large capacity PET containers. Later in 2025 it will be launching a 1,000 l container in partnership with a company in South Asia, and a similar sized Intermediate Bulk Container (IBC). We spoke to Michalis Sideris, the company’s Business and Technical Development Director.
Photo top: F.l.t.r.: Michalis Sideris, Head of Business and Technical Development, and Constantinos Sideris, Director & General Manager at Cypet Technologies
Cypet Technologies was established in 2013 by Michalis Sideris’ father, Constantinos Sideris, who had a chemical engineering background and many years’ experience in the plastics industry; he had been running a trading company in Cyprus. It now employs 25 people at its Nicosia HQ and an additional 15 people at its facility in India. Innovative design was a strength from the start.
As a start-up, the company was not in a position to take on the established and global businesses, whose scale of operations meant that it was impossible to compete in the mainstream market on price or, realistically, on technology. But Mr Sideris Senior had a clear vision of where he wanted the business to be: in larger-sized containers. He was also in possession of a patented process to make such containers through single-stage injection stretch blow-moulding, which – he maintained – would save operators time, material and energy. As these are the three factors that are most likely to push up costs, the Sideris family and Cypet Technologies believed they were on to a winner – and so it has proved. Cypet has established itself in its niche with a combination of innovation and demonstrable cost saving technologies.
Simpler, cheaper – and larger
“Our machinery uses a single clamping unit to open and close the injection mould and to blow them but it was the layout of the two moulds inside the machine that was a novel innovation,” Michalis said. “When we developed that first machine, we thought that the main benefit would be a simpler and cheaper machine. We subsequently found that our machine was capable of making much larger containers than were available at the time. Back then, the maximum container size that could be blown was 30 l, which is a popular beer keg size. The Cypet machines were capable of going up to 120 l blow-moulded containers, which was demonstrated via a live production demo at the 2019 K’ Show.”
This capability took Cypet well into areas that were traditionally dominated by HDPE, although its mission was, initially, to drive the market to PET containers as a more environmentally friendly alternative to traditional materials.
Sustainability
“PET is the most sustainable plastic packaging available. It is recyclable indefinitely and another way of making it sustainable is to produce your plastic packaging using the lowest amount of energy possible. These two factors were the main motivation for establishing Cypet,” Michalis explained.
Cypet also saw that the ISBM market was ripe for disruption, with two Japanese companies dominating the market. As a start-up, it took some time to convince potential customers that its innovations were going to deliver their promises but it has now, while remaining a niche player, established itself as a serious contender, with customers in 20 countries on all five continents. And it was customers themselves who identified the potential for the Cypet technology.
“By the time we reached machine number three, we were already blow-moulding 50 l beer kegs for a specific application in Australia. It was the market that guided us into looking at larger containers,” he explained.
Innovation and invention lead to big savings
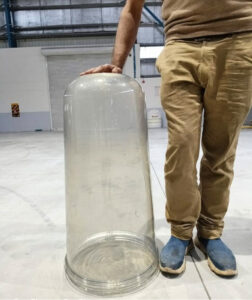
Cypet has built its reputation with features including handles moulded into the container, not added after, and designs that use less material and need less energy to produce than conventional HDPE or other materials. Anyone can make larger containers with thicker walls but that means more material and more energy expended on heating the material, as well as blowing and manipulating it.
When PET is stretched, it becomes much stronger than stretched HDPE, which means that manufacturers can obtain the same strength and capacities with rather less material. Michalis gave as an example a 5 l jerrycan. The lightest HDPE 5 l can requires 140 g of material. A PET container (handle included) can be made with just 100 g: 35% saving on material and with consequent energy costs.
Savings extend right the way up the range. The largest container the company makes now is 120 l. It explored 220 l drums but saw that the market for them was shrinking; they were being replaced with IBCs, the familiar cuboid containers that are packaged within a wire cage.
The bigger the better – and lighter
“We undertook a lot of calculations and simulations and we found that, in theory, it would be possible to design a bigger version of our machine that could blow mould containers as large as 1,000 l,” Michalis explained. “We were able to demonstrate in theory that an IBC made of PET could be much lighter and use much less material. It could reduce the cost of production by so much that it would remove the need to return an IBC bottle, wash it out and redeploy it. You could just send the package back, remove the used, dirty bottle and put a brand new, clean one, inside and ship it out to the market again.” The discarded IBC would be recycled.
The immediate project is for a 1,000 l container for water, for India, which will offer an economic and sustainable alternative to traditional packaging. Cypet plans to launch a demonstrator of the water tank by the end of April and the IBC project is expected to be ready by Summer 2025.
Material, energy and labour savings
“We estimate that our technology will achieve around 40% material savings on both water tanks and IBCs, compared to the HDPE versions. This means that material per IBC will come down from 12 to 15 kg in HDPE to less than 10 kg in PET. A saving of 5-6 kg for each water tank or IBC is absolutely huge in raw material costs, alone.”
The energy and cycle time savings offered by ISBM compared to rotary moulding are similarly impressive. Rotary moulding cycle time is up to five times longer than ISBM and energy costs are between 30- and 80% higher, depending on the product being moulded, as rotary moulds must be heated and kept hot for a long time and then allowed to cool down. Labour costs are also higher because of the extended opening and closing process. The advantages are clear but going from 120 l bottles to 1,000 l containers was still a big step up.
From virtual world to real time solutions
“We had to engineer everything from first principles. We used all the tools that we had available, from design to simulations, including structural injection moulding and blow moulding, and we strove to do the best possible job in the simulation world first,” Michalis explained. “To make sure we could achieve what we had done in the simulation, we added a lot of extra provisions on our machines and our models to be able to ensure even better control of the process, above what the simulations showed that was needed, so that we could be as foolproof as possible and maximise the chances of success.”
The new, extra-large range of containers required a significant investment, which has been achieved with the involvement of a strategic partner in India. The next step will be to introduce the bulk water containers and IBCs commercially and to convince users across the world – for this is a global market – that the promised savings can indeed be achieved. The figures should speak for themselves.
Cypet is not only focusing on the big picture, if 1,000 l containers can be called that. Later in 2025 it will be launching its Pro Series, which will take the productivity of ISBM machines to a new level in the 20 ml to 50 l space. 2025 looks like an exciting year for Cypet, all round.