The first rPET bottle from Qatar: Visit to Polytech
Polytech is a classic converter for water preforms and caps. 50% of production goes to the sister company Rayyan Water. This makes Polytech half an in-house producer. We spoke to Plant Manager Nallasivam Singaraj.
Interview with Polytech Plastic Industries // September 19, 2024
We met: Nallasivam Singaraj, Plant Manager
Photo top: Polytech has two lorries to serve the nearby customers. Mr Nallasivam Singaraj, Alexander Büchler and Vivek Chaturvedi, Quality Manager at Polytech (from left to right) took a look at one of them from the inside.
The company began life in 2017 with the factory equipped with a Husky HyPET 400 t system with 96-cavity moulds and a Husky HyCAP225 complete system with Husky 48-cavity closure mould and downstream IMD inspection equipment. In the wake of the embargo imposed by other Gulf states, Polytech doubled its capacity in 2019 by adding a further Husky HyPET system and a Husky HyCAP system. Capacities now stand at 1 million preforms and 1.4 million caps. Polytech also blows 5-gallon PC water containers. The standard sizes for water are 200 ml, 330 ml, 500 ml and 1.5 l. The caps for the bottles fit on 29/25 or 30/25 necks.
Nallasivam Singaraj is and always has been a technician through and through. When he started at Polytech in Doha in 2017, he was also assigned to the sales division. As a technician, this was a new experience. But he clearly liked it, otherwise he would no longer be running Sales today. He looks after around 10 to 11 customers. Many of them are located within a radius of 5 km. However, the company also exports to Kuwait, the UAE and India. Half of its production goes to the water bottler Rayyan. Like Polytech, Rayyan belongs to Al Rabban Holding in Qatar. The second major customer is Coca-Cola. He makes no secret of the fact that he worked for Coca-Cola for many years. Singaraj is therefore familiar with the internal processes there and can provide his customers with a comprehensive range of preforms and caps for water bottles.
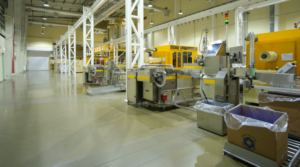
Singaraj enters into 3-month contracts with many customers. Therefore, he can take possible fluctuations in material prices into account. However, there are also always short-term contracts. With water preforms in particular, he must ensure that the acetaldehyde (AA) content does not exceed the required value. He usually uses scavengers for short-term contracts. For long-term contracts where the purchase quantities are agreed well in advance, he produces the preforms in advance and stores them for four weeks. So the AA limit also fits. To ensure that fluctuations in temperature and humidity do not affect the preforms over the four weeks, not only the production area but also the warehouses are air-conditioned. In general, the factory makes an exceptionally well-kept impression. Every last corner is clean and tidy, all the boxes are neatly positioned on the pallets and the reusable mesh boxes for preform transport look as good as new. The production area is cleaner than many a kitchen. The factory’s Coca-Cola past is clear to see.
And who would have thought it? Here we found the first 100% rPET water bottle on our round trip! To mark the 2022 FIFA World Cup, Rayyan launched a light blue 500 ml bottle (13.5 g) with a 30/25 neck finish. It is still available for certain target groups, but generally consumers prefer material made from virgin material.