Manufacturing blow moulds for PET bottles
Four steps, one supplier: design, manufacturing, sampling & testing
For half a century, Röders GmbH is manufacturing PET blow moulds, delivering high-precision solutions. With its experience the company offers solutions for a wide range of blow moulds, applications and designs. The moulds are produced for all 2-stage PET bottles for various industries all over the world.
As the industry continues to evolve, packaging manufacturers face increasing demands for lightweight, sustainable, and cost-effective solutions. Röders has continuously adapted to these challenges, ensuring that their moulds meet market expectations, and exceed them with their innovations and in-house developments. The company develops customised mould solutions, optimising bottle performance and production efficiency.
A seamless process
Efficiency is critical in today’s fast-paced beverage industry. That’s why Röders offers a complete solution from design, manufacturing, sampling, and testing. This integrated approach is claimed to ensure short reaction and lead times and to eliminate compatibility concerns. Röders’ moulds are engineered for rotary or linear stretch blow moulding machines, eg. from KHS, Krones, Sidel, or Sipa and others.
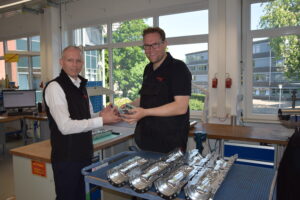
In its ISO 9001-certified bottle testing laboratory, Röders analyses every bottle to meet the high industry standards. Equipped with state-of-the-art machinery, Röders offers a comprehensive range of tests, including: top load resistance, drop impact, carbonation retention, thermal stability, wall thickness and section weight distribution. Röders has been certified by PepsiCo for many years and more recently also authorised by Coca-Cola. If needed, customised tests are carried out to meet individual requirements.
Speed and flexibility
In the competitive PET packaging industry, time-to-market is everything. Thanks to Röders’ modern production and in-house high-speed machining technology, moulds can be delivered in short time. According to Röders, the mould change systems combined with specialised coatings for durability, provide added value by reducing downtime and extending mould lifespan.
Röders actively supports its customers with on-site process optimisation and machine conversions for a smooth transition to new bottle designs. Whether working with standard PET or rPET, Röders helps to fine-tune blowing parameters for weight reduction (lightweighting to cut material costs), energy efficiency with low-pressure blowing, or stretch ratios for improved material distribution. This work supports customers achieving their sustainability goals and helps brands to reduce their carbon footprint.
Advanced blow moulding technology
Röders has a long history of pioneering developments in PET stretch blow moulding. Together with Corpoplast, Röders introduced this technology for beverage packaging in 1975, moving from PVC to PET long before it became the industry standard. Since then, they have worked closely with market leaders developing advanced mould solutions that have shaped the industry. Today, Röders produces over 6,000 moulds annually in Soltau, Germany. Their ability to adapt quickly to market changes, combined with customer-driven R&D, contributes to their strong position in PET blow mould technology.
Röders at SaudiFood Manufacturing, drinktec & Gulfood Manufacturing
As Röders celebrates 50 years of innovation, the company remains committed to driving progress in PET packaging. To showcase their latest developments, Röders will be exhibiting at SaudiFood Manufacturing in Riyadh, Gulfood Manufacturing in Dubai and drinktec in Munich.