Why speed alone isn’t enough
Smart prototyping: De-risking bottle design with data-driven insights
In the world of fast-moving consumer goods (FMCG), brands and converters operate under immense pressure to launch new packaging quickly. Rapid prototyping has become an industry norm, yet simply producing a bottle faster is no longer enough. Advances in virtual simulation, 3D-printed moulds, and lab-scale testing are reshaping how bottle designs are refined and optimised, ensuring better performance and reducing risks before mass production begins.
BMT’s method of a data-driven approach to bottle development combines virtual simulation, 3D printed moulds, and lab-scale stretch blow moulding. Their methodology – measure, digitise, execute – focuses on gathering insights rather than relying solely on iterative testing. By capturing critical information about material behaviour, blowing dynamics, and final bottle performance, the design process can be refined, reducing lead times and mitigating risks associated with production.
Engineering confidence before production begins
At the core of this approach is BMT’s proprietary SBM simulation, which uses advanced material models to virtually assess the preform to bottle design before any physical prototype is made. This allows engineers to predict bottle formation, identify areas for optimisation, and verify performance virtually – long before production tooling is considered. By making smarter decisions at this stage, costly modifications down the line can be avoided.
Advanced testing capabilities
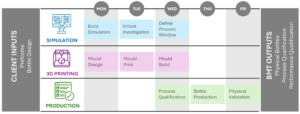
Using Blowscan, BMT’s lab-scale SBM machine, small batches of bottles are produced under controlled conditions. Integrated with Thermoscan technology, the full temperature profile of the preform is captured. Simultaneously, pressure data and material distribution are tracked in real time, providing a detailed picture of exactly how the bottle is formed. This level of analysis provides engineers with precise information to optimise preform geometry, material selection, and processing parameters for efficient scale-up.
3D-printed mould tools
Traditionally, creating prototype bottles required expensive metal mould tools and access to an industrial SBM machine, adding time and cost to the development process. By 3D printing the mould tool, BMT reduces the time from concept to prototype from weeks to days. The tooling is designed to work seamlessly with Blowscan, so engineers can test and iterate designs rapidly, all while generating performance data that informs final production decisions.
Performance validation
To assess the viability of 3D printed mould technology, BMT conducted a comparative study, forming two sets of bottles using the same blowing recipe – one from a 3D printed mould, the other from a traditional metal tool. The results confirmed equivalency across all critical parameters. Geometrically, both bottles had identical maximum diameters and lengths, indicating no difference in shrinkage post-demoulding. Top-load performance for the printed-mould bottle was just 2.3% lower, well within acceptable limits. Mechanical testing of sidewall samples showed axial and hoop modulus differences of only 7% and 1% respectively. Wall thickness difference between the two was minimal – just 2.5% on average. These findings suggest that BMT’s 3D printed mould technology can reliably produce bottles that mirror production-grade quality. More importantly, when combined with Blowscan and simulation tools, this allows customers to move from concept to confident validation in a matter of days – not weeks – without compromising on performance.
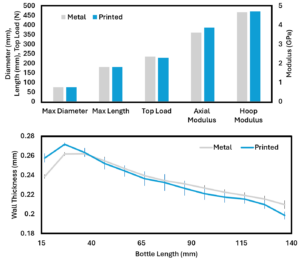
Packaging smarter, not just faster
Originally, BMT offered prototyping services using machined metal moulds, providing high-fidelity results at the cost of time. While this met the needs of traditional development timelines, it became clear that today’s FMCG market demands something more agile. The introduction of 3D printed tooling, in-house SBM simulation, and advanced lab-scale blowing technology has transformed the offering. It’s no longer just about prototyping; it’s about delivering actionable insight, fast. This approach aims to provide manufacturers with confidence in their preform and bottle design and process before committing to full-scale production. Whether working with internal designs or those provided by the client, the BMT process is designed to optimise every stage of development – from virtual validation to physical formation, from prototype to production. By integrating virtual validation with physical testing, companies can streamline development, reduce costs, minimise material waste, and accelerate innovation.