StackTeck: Overmoulding Cube applications
StackTeck Systems Ltd. announces a successful introduction of technology for overmoulding PET preforms with multiple layers. The first overmoulding system has been designed to achieve a light barrier for light sensitive applications. The system incorporates two preform moulds used in concert with a Niigon rotary cube injection moulding machine, using its horizontal rotating table and dual injection units. The rotary cube rotates 180 degrees during every cycle, bringing the first shot parts to a second cavity for overmoulding the second shot.
“We are very pleased with the new system, which provides competitive cycle times while dramatically reducing the overall part weight and light blocking additives of a monolayer bottle by means of a multi-shot process. This results in a dramatic reduction in part cost, while delivering improved light barrier properties. We chose to work with StackTeck and Niigon, as innovative suppliers who bring state-of-the-art capabilities to high volume moulding systems,” said Russell Gray, COO of Ngoc Nghia Industry.
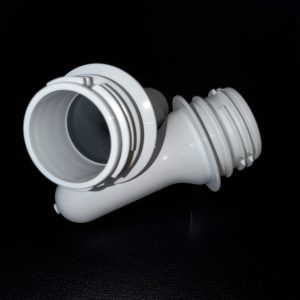
“The StackTeck mould includes an advanced Yudo hot runner, which helps improve our part quality with superior hot runner balance. At the same time, the hot runner pressure drop is much lower than conventional hot runners, which enables the moulding of the thin layers needed for this multi-layer part design.” Mr Gray continued, “It’s an exciting technology to work with, we’ve expanded our testing to include parts with pearlescent colours in the inner layer and clear PET in the outer layer; the final parts have a glossy, “candy-apple” look that gives great shelf appeal and significant savings over a monolayer bottle with 100% blended pearlescent colours. We see opportunities for cosmetics and personal care packaging beyond the original focus on beverage packaging.”
Rick Unterlander, General Manager of PET at StackTeck, explains the set up: “This technology is distinct from traditional co-injection, because an inner layer is initially moulded on one side of the cube, then rotated 180 degrees where the outer layer is over-moulded. Both moulding stages operate as conventional injection moulding processes, which is simpler to set up, maintain, and run continuously in comparison to a more complex co-injection system. It’s comprised of two standard moulds, with stacks designed to accurately and repeatably produce the individual layers of the preform.”
Overmoulding with rPET possible
Instead of the light barrier approach, this technology can be used with significant rPET content in the overmoulded shot. For some applications, up to 75% of the total part weight can be moulded with rPET on the outside surface, which is much higher than some competing preform moulding processes.
- Cost reduction through isolation of non-virgin materials from product contents (regrind/flake); use of lower cost materials; reduced additive/colourant content.
- Increased use of recycled material/rPET which addresses environmental concerns and/or government regulations.
- The development of new approaches to applications requiring light barrier/shielding such as dairy.
- New product differentiation.