“Our activities are circular and local”
Recycling plastic packaging
Our last visit in Spain is already close to the French border. In the north-east, 20 km from the Atlantic coast, a good acquaintance, Mikel Urain, an expert in the PET industry, welcomes us to his company EkoRec. We are curious about his new company and torture the Editourmobile the last kilometres through the Spanish heat.
Mikel Urain has been in the PET industry for about 15 years. At ABC Compressors as Global Sales & Technical Service Director CCO, then as General Manager at BeandBe Beverages. Now he welcomes us in the mid of pressed and tied PET bales. In his office he tells us about his company EkoRec.
“Ekorec Group was created in 2012 as a key player on Spanish circular economy. Part of our industrial equipment and background comes from the extinguished textile activity that was performed in our facilities. Ekorec industrial know-how on recycling and PET transformation was powered in 2021 through the merge operation with its mother company Bascotecnia (EPC Engineering Group created in 1976). The resulting industrial group is a unique example of integrated circular economy adding recycling activities with PET transformation and engineering consultancy. Three factories are located on 75,000 m2 of industrial space and house four business units. Not to forget the company’s own combined heat and power plant;” Mikel explained.
EkoRec integrates in the same industrial area PET recycling plant and rPET sheet, reducing CO2 footprint of the whole process. “Our activities are circular and local. Taking care and controlling the whole flow from each individual bottle recycling act to the processed rPET sheets and flakes that will close the loop and become again a sustainable packaging solution,” Mikel mentioned. He continues, “Our facilities and production machinery allow us to be flexible with our customers and offer highest food grade products under BRC certification. We recycle post consumer and post industrial bottles, preforms and PET sheet into new raw materials for bottle-to-bottle granule production and rPET sheet. Our sheet production business unit manufactures 100% rPET sheet, multilayer and medium – high barrier sheets.
We manage full logistics to final destinations, with regular deliveries to main industrial areas in Spain and Europe.”EkoRec works in high demanding sectors such as food & beverage, automotive and pharma-medical industry. “Therefore, quality is a strong value that rules all we do. 100% of our rPET flakes and any raw material used for our plastic processing goes through our quality department and laboratory. Our general processes and procedures are certified under ISO9001 and our products do have BRC Packaging Materials certification.”
In the PET recycling area, we see a state-of-the-art sorting and recycling equipment from STF Germany with sorting technology of Sesotec. “We have a warehousing capacity for bales and flakes of about 3,000 t and a production capacity of 15,000 t a year. Our own quality flakes are called Eko PET. We also process random samples and laboratory analyses for control before delivery, as well as specific checks for raw density, colours, adhesive residues, foreign plastics, impurities, grain size distribution and residual moisture.”
Mikel told us that the Packaging Division has been providing sustainable solutions for the food, pharmaceutical and industrial sectors since 1996. “We work closely with the fruit and vegetable sector on the Mediterranean coast, the Atlantic fishing industry, the Spanish jam and meat industry, the bakery industry through out Europe and a wide range of pharmaceutical and industrial applications. To produce packaging material for these industries EkoRec use Bandera and Reifenhauser machinery. The multilayer sheet lines produce 2,000 kg/h with up to five layers. A third PET sheet line is planned for 2024,” he summarised. There are two more business units under the roof of EkoRec, the Engineering Projects & Power Generation. The engineering projects focuss on realising plastic circular economy, water treatment e.g. urban water treatment plants or any project that has to do with general waste recycling. The group has its own office and staff for African EPC operations in Angola.
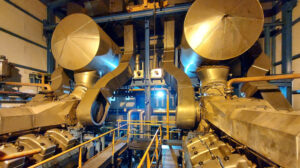
In the power generation area, Mikel leads us into a somewhat deserted-looking part of the factory premises. “True to our environmental responsibility, our combined heat and power plant covers all the electricity and heat needs of our production facilities. In this way, we avoid supply from less environmentally friendly sources and feed our excess electricity into the general grid.
The cogeneration plant consists of a cycle combined by two Rolls Royce natural gas engines, developing a power of 5,100 KWe plus a 269 kWe condensation Dresser Rand steam turbine. The thermal utilisation of the cogeneration plant is used for the production of: factory steam used in the production of polyester fibre, PET film, PET recycling and operates as district heating for neighboring industries; the hot water for the absorption refrigeration group and the steam for use in the condensing steam turbine.”
Impressed by this holistic view of the circular economy, we have to say goodbye to Mikel, to whom we must decline an invitation for lunch with a guilty conscience, as our schedule is pressing. We thank him for his willingness to provide information and his hospitality and wish him every success with EkoRec!