128 beverage caps every 1.9 seconds
Netstal, W223
Netstal’s Cap-Line system solution offers performance and efficiency on a small footprint
At the NPE, Netstal, together with their system partners and customer Alltrista, will be presenting a powerful production system for lightweight beverage closures. The 26 mm water closures are produced in a mould with 128 cavities. The system runs with a cycle time of 1.9 seconds.
With the Cap-Line, Netstal now offers injection moulding machines specifically pre-configured for closure applications. The exhibition machine is based on the high-performance Elios platform and is pre-configured with various equipment features for the efficient production of beverage closures. The Cap-Line 4500’s all-electric clamping unit with a dry cycle time of 1.4 seconds enables fast cycle times of less than 2 seconds. Thanks to the optimised barrier screw, a smaller injection unit is used. The new design ensures a higher plasticising performance and a better degree of homogenisation. Further options are available for individual optimisations, such as the four-key Smart Operation control panel or the adaptive system pressure reduction for additional energy savings.
High productivity, low floor space requirement
The complete system running on the Netstal booth with a 128-cavity mould from Z-Moulds and Intravis peripherals is identical to production systems used by the US contract manufacturer Alltrista. 26 mm tamper-evident caps for still water are produced. Thanks to a new design, Z-Moulds was able to make the mould as small and light as a 96-cavity mould. This results in decisive advantages for closure manufacturers. Compared to previous 128-cavity moulds, the Z-Moulds mould fits into a machine with a smaller column distance. Due to the compact design, less mass has to be moved, which has a positive effect on the cycle time: “Running a mould with 128 cavities at a cycle time of less than 2 seconds is a world first,” says Netstal’s Head of Business Unit Caps and Closures, Horst Kogler. “Alltrista is the first in the world to produce with 128 cavities and a cycle time of 1.9 seconds. They produce more than 3.1 billion closures on two lines. More output per square metre of production area is currently not possible,” he added.
The complete production system requires only around 50 m2 floor space.
In addition, there are further cost savings and a smaller environmental footprint thanks to the low power consumption of the more efficient and smaller machine. With 128 cavities, Netstal says, the line consumes around 12% less electricity than competitor machines operating with only 96 cavities. Furthermore, Alltrista was able to make the closures themselves more sustainable by reducing the weight of the closures by roughly 25% compared to previous industry benchmark, without compromising performance. Over the 3.1 billion closures per year that this program produces annually, the total amount of resin being removed from the product exceeds 930,000 kg/a.
Downstream with in-line quality laboratory
Downstream, the finished caps pass through the equipment of system partner Intravis until they are filled into octabins. The central element is the Cap Watcher Q-Line, which enables a comprehensive 360° full inspection of the closures. With an accuracy in the hundredths of a millimetre range, the system checks up to 80 closures per second for more than 40 quality criteria. The cavity-related inspection is carried out with up to nine high-resolution cameras. Sophisticated tests, such as the patented temperature measurement and the non-contact micro-hole inspection, have been implemented for quality assurance of closure production.
Alltrista – contract manufacturer from South Carolina
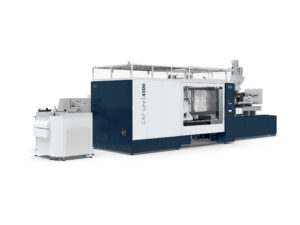
At Alltrista, two identical system solutions for cap production are currently in operation. Alltrista Plastics LLC specialises in high-volume precision manufacturing. From rigid packaging and custom moulded solutions to assembly, filling, and kitting, Alltrista supports customers in the medical, healthcare and consumer goods industries with a wide range of products and services.
Alltrista attaches great importance to continuously improving its own sustainability. The company was audited by Ecovadis in 2023 and received the silver medal for its sustainability performance to date. Alltrista ranked in the 88th percentile of all EcoVadis rated companies, and top 7% among its peers.
Alltrista will be present at the Nets-tal booth during the NPE with its own staff to provide information from the customer’s perspective. For detailed information on all the company’s services, Netstal also recommend a visit to stand S22065 in the South Hall, where Alltrista will be showcasing their full offering of products and services in contract manufacturing and injection moulding.