{"pages":{"page":[{"@ID":40 "COMPRESSORS PETplanet Insider Vol. 25 No. 09/24 www.petpla.net 38 Adekom introduces KSP series high-pressure compressor for bottle blowing Oil-free high-pressure compressor series launched Adekom, a well-known Asian compressor manufacturer, has unveiled the KSP series screw+piston tandem high pressure compressor. This system features a skid-mounted combination of a first-stage oil-free screw compressor and a second-stage oil-free piston booster, designed to provide stable and energy-efficient performance. The KSP series delivers 5.0 - 30.5m³/min of oil-free air at 40 bar pressure, meeting ISO8573-1 Class 0 air quality standards, and operates continuously on a 24/7 basis, says Adekom. One of the key advancements in the KSP series is its completely oil-free operation. The system incorporates a water-injected screw as the first stage, which serves multiple functions, including lubrication, cooling, sealing, and noise reduction, all while delivering high-quality oil-free air. The company says that no special treatment for the discharge water is required to meet environmental protection requirements. The food-grade stainless steel construction of the screw air-end casing, star wheel bracket, and entire pipeline ensures that the system remains oil-free. The KSP series boasts enhanced reliability due to its use of corrosion-resistant food-grade stainless steel components. The lubrication water absorbs compression heat, allowing the compressor to run at lower temperatures. This temperature control is claimed to extend the machine’s operational life and to improve overall reliability. Energy efficiency is another focal point of the new system. Equipped with a permanent magnet frequency inverter drive, the KSP series offers a wide range of regulation and minimises energy consumption. Additionally, maintenance has been streamlined, with fewer consumables, lower costs, and an automatic waterchanging device that allows water replacement without stopping the unit. The system is remote control-ready, featuring advanced PLC technology that ensures full digital control and automation. Cloud-based monitoring and predictive maintenance capabilities further enhance operational efficiency. With two decades of experience in the food and beverage industry, Adekom claims to design every compressor from the ground up to meet the high standards of quality and performance for the PET industry. www.adekom.com.hk COMPRESSORS"},{"@ID":58 "BOTTLE MAKING 23 PETplanet Insider Vol. 25 No. 09/24 www.petpla.net CHANGE YOUR PERSPECTIVE CUSTOMIZED COMPLETE LINES PREFORMS AND CONTAINERS PRODUCTION SYSTEMS SINCRO BLOC SOLUTIONS FILLING & SECONDARY PACKAGING SOLUTIONS TOOLING SOLUTIONS vbr-voѲࢼomvĸ1ol \" bv |_; omѲ vrrѲb;u om |_; l-uh;| -1ࢼm] -v - om;ňv|or v_orĶ 1-r-0Ѳ; o= o@;ubm] you a full range of vhbѲѲv vr;1bC1 |o |_; ;mࢼu; ruo1;vv ث =uol |_; 7;vb]m -m7 ruo71ࢼom o= ru;=oulvĶ loѲ7v -m7 1om|-bm;uvĶ r |o |_; u;-Ѳb-ࢼom o= 1olrѲ;|; Ѳbm;vĸ ); -u; -Ѳvo ;|u;l;Ѳ Y;b0Ѳ; bm ruob7bm] mbt; -m7 _b]_Ѳ 1v|olb;7 voѲࢼomv =ou |_; lov| 7b;uv; l-m=-1|ubm] u;tbu;l;m|vĸ $_; b7;-Ѳ r-u|m;u |o _-um;vv ou bl-]bm-ࢼom -m7 0ubm] ou ruof;1|v =uol r;ѲѲ;| |o r-ѲѲ;|ĸ PACKAGING DESIGN AND ENGINEERING"},{"@ID":19 "MOULD MAKING PETplanet Insider Vol. 25 No. 09/24 www.petpla.net 17 Arnaud: All our spare parts are meticulously manufactured at our facility in Saint-Remi, QC, Canada, ensuring exceptional quality and consistency. We back every part with a standard one-year warranty, and for components such as oven chains and cams, we offer extended warranties due to their enhanced durability. Our team is actively focused on developing new products designed to significantly reduce operating costs, creating excitement among our clients. With our comprehensive range of alternative parts for the bottling industry and our agile approach to evolving needs, we evaluate patents strategically and innovatively to continually offer cutting-edge solutions. PETplanet: For which spare parts do you receive the most enquiries? What are your delivery times? Arnaud: Our valves and guides are unmatched in the market, delivering exceptional operating cost savings, particularly in energy efficiency, that set them apart from any other products available. We sell thousands of these units annually and ensure they are always in stock, ready to ship within a week. Additionally, we keep a selection of the most sought-after cams on hand, available for delivery within 2-3 weeks. Our moulds shells and oven chains are also standout products at UM, consistently meeting the high demands of our clients. Moreover, a crucial aspect of our business is providing personalised components such as spindle tips, grippers, and entry/ exit wheels, which are vital for the operation of blow moulding machines. We frequently receive requests for these customised parts and are fully equipped to manage and fulfill such projects with precision. PETplanet: You offer specialised spare parts & individual solutions. Format conversions are also possible with your parts. It is noticeable that you are particularly well positioned in the filling sector, (e.g. at Krones). Are you planning to expand your machine portfolio in the future? Arnaud: Looking ahead, our vision is to become the go-to partner for all our clients’ needs across the entire bottling industry production line. We are continually expanding our product catalogue to align with this vision, ensuring we offer comprehenProtecting Product Integrity With Torus gauges, you can rest assured all of your inspection requirements are covered. Would you like to know more? Email us for more information. [email protected] Wall thickness Thread, body & thickness Burst pressure Top load, weight & volume Internal diameter Total Quality Laboratory Measuring your plastic containers quickly, accurately and reliably sive solutions that cover every aspect of our clients’ operations. Stay tuned, additional service lines key to our clients will be announced in the near future. PETplanet: Your business is facing a lot of competition. How do you feel about the global market situation? Where do you see future markets for yourself? Arnaud: We remain committed to what we do best: being responsive to our clients and delivering solutions and services that offer exceptional value. Our focus on innovation drives us to continually expand our offerings, enhance our production capabilities, and invest in technology to adopt new business practices. We are confident in our abilities but recognise the challenges ahead. Adapting to the rapidly evolving environment - both within our company and in the broader market - is crucial. Technological advancements, particularly in user experience, will be key to our future success. Our primary markets include the US, Canada, and Mexico, where we continue to strengthen our presence. In Europe, we are growing, though market dynamics vary due to different client types. We are also seizing significant opportunities in the Middle East and Africa, where we see substantial demand and rapid growth, and we are pursuing these markets with strategic intent. PETplanet: Thank you very much for sharing your insides and knowledge with us! Arnaud: It is our pleasure. Thank you for your time and interview! www.um-inc.com"},{"@ID":38 "COMPRESSORS PETplanet Insider Vol. 25 No. 09/24 www.petpla.net 36 Controller improves effi ciency & reliability of high-pressure reciprocating compressors Increased monitoring capabilities Ingersoll Rand has introduced the ESP-7800 series high pressure reciprocating controller, designed to improve the efficiency and reliability of high-pressure reciprocating compressors. The controller is suitable for both new installations and retrofitting existing systems, providing enhanced monitoring and operational capabilities. The ESP-7800 controller includes advanced monitoring tools that track over 14 critical data points, providing real-time diagnostics. This feature is claimed to allow users to identify potential issues early, reducing downtime and improving operational awareness. In addition, the system’s 3-step load control, managed by a programmable logic controller (PLC), intelligently adjusts compressor output to match demand. It allows for up to 50% flow reduction, ensuring that the compressor matches demand without shutting off. This helps optimise energy consumption and may lead to significant cost savings. The controller is housed in a durable NEMA 4 enclosure and features a user-friendly colour touchscreen display. This interface allows operators to easily adjust settings and monitor key performance parameters. The ESP-7800 is compatible with both fixed and variable speed motors. It integrates seamlessly with Ingersoll Rand’s WH- and VH-Series compressors and offers Internet of Things (IoT) capabilities for remote monitoring. It can also connect with third-party platforms, enabling predictive maintenance and analytics. Customer success story An early adopter of the ESP-7800 has reported significant operational improvements: “The panel detected high temperature alarms that led us to discover a plugged aftercooler and oil cooler. This early warning helped us avoid serious damage. Additionally, the ability to adjust setpoints, like oil temperature, allowed us to optimise performance without exceeding spec limits.” www.irco.com product development caps & closures design high cavitation moulds multi-component moulds closure production systems after sales service +43 5572 7272-0 | [email protected] | www.z-moulds.com z NEXT SHOWS FAKUMA Friedrichshafen, Oct. 15-19th GULFOOD Manufacturing Dubai, Nov. 5-7th INSPIRING PARTNER COMPRESSORS"},{"@ID":50 "BOTTLE MAKING 22 PETplanet Insider Vol. 25 No. 09/24 www.petpla.net Flexibility and fast changeovers “This is across all sizes. That flexibility is very important to us and it’s not something you always get in the medium to low production end of the market. We run in weights from 17 g to 35 g, and around 23.5 g for the halflitre and 20 oz bottles. We have found changeovers to be very impressive. Within 21 minutes I can go from running one bottle to another,” John said. With Flexblow technology, not only regular bottles but also 1-gallon containers with a wider neck can be produced. Saving costs and increased sustainability “We’ve significantly optimised our logistics process, reducing the number of trucks required for packaging transportation from 60 to just eight. This efficiency not only slashes costs but also minimises CO2 emissions, reinforcing our commitment to sustainability,” John said. “We were finding leaks in boughtin bottles, sometimes running through entire consignments. We would get credit from our suppliers but we were losing an awful lot of product and it impacted our reputation. We have eliminated that completely, as well as unformed bottles and cloudiness,” he said. The complete solution Total packaging cost audit and business case: Flexblow made a free total packaging source analysis and a business case in which it was shown how much English Mountain will save with self manufacturing. Turn-key equipment solution: Flexblow provided a comprehensive turn-key solution by delivering a blower, bottle accumulation system, and all necessary peripheral equipment. This complete package was designed to seamlessly integrate into existing production line, ensuring efficient and reliable operation from start to finish. Preform sourcing platform: Flexblow recommended preforms most suitable for English Mountain Spring products. 10-point project implementation and aftersales: Flexblow ensured the successful completion of the project and continued to support English Mountain Spring Water, ensuring their satisfaction with the product and service after the initial sale. Relationship: Flexblow continues to provide periodic consulting services to assist with packaging solutions. Custom shape value: English Mountain Spring Water Company stands out with its unique custom bottle designs, leveraging this distinctiveness to differentiate their brand in a competitive market. www.fl exblow.com “We’re saving around 60% over what we were paying for bottles alone, plus freight charges. We’ve eliminated management costs of returning faulty product. We’re saving on credit notes we had to give our customers, as well, and on warehousing.” www.englishmountainh2o.com Achieve your sustainability goals and produce your best product Agr’s Process Pilot system provides personalized process control response to each unique bottle GHVLJQ EORZPROGHU ȴQJHUSULQW Ȃ VDIHO\\ DQG TXLFNO\\ 1R ELJ GDWD MXVW UHOLDEOH GDWD ZZZ DJULQWO FRP Process Pilot+®"},{"@ID":30 "MARKET SURVEY 28 PETplanet Insider Vol. 25 No. 09/24 www.petpla.net 09/2024 MARKETsurvey Compressors Compressors – not often in the spotlight perhaps, yet a vitally important component of PET production, and with significant potential of energy saving. Our annual market survey takes a closer look at these unsung heroes of the PET industry, featuring compressor manufacturers and their product range: AF Compressors, Siad Macchine Impianti, ABC Compressors, Kaeser Kompressoren, Atlas Copco Airpower, Adekom Asia Pacific Limited and Dalgakiran Compressed Air Technologies. Although the publishers have made every eff ort to ensure that the information in this survey are up to date, no claims are made regarding completeness or accuracy. Resins & additives Cap producers, systems & inspection systems Preform machinery Preform production & inspection systems Preform, cap & SBM mould manufacturer SBM 2-stage Compressors Filling equipment & inspection systems Palletising & shrink film machinery Recycling machinery Company name AF Compressors, Ateliers François S.A. Siad Macchine Impianti ABC Compressors Kaeser Postal address Telephone number Web site address Contact name Function Direct telephone number E-Mail Ateliers François, Rue Côte d'Or 274, Liège 4000, Belgium +32 4 229 70 10 www.afcompressors.com Mr Pascal Heyden Marketing Manager + 352 26 95 66 28 [email protected] Via Canovine, 2/4 24126 Bergamo, Italy +39 035 327611 www.siadmi.com Mr Giovanni Brignoli Compr. Div. Food & Beverage Product Leader +39 035 327609 [email protected] Azitaingo Industrialdea, 6, 20600 Eibar, Gipuzkoa, Spain +34 943 820 400 www.abc-compressors.com Mr Gonzalo Gabarain Global Sales & Marketing Director +34 647 413 760 [email protected] Carl-Kaeser-Str. 26, 96450 Coburg, Germany +49 9561 640-0 www.kaeser.com Mr Henry Beyer Product Manager +49 9561 640-5017 [email protected] 1. Machine designation / model number CE & L (high pressure) OPC (low pressure) BS Line Vito Next Horizon Synchro | Horizon Synchro LP | X-PET Sigma PETAir 2. Number of models in range 30 (high pressure), 22 (low pressure) 19 32 30+ models 25 3. Output in m³/hour 150 - 3,300 m³/h (high pressure); 432 - 3,480 m³/h (low pressure) 1,000 - 6,000 100 - 6,000 200 - 6,600 336 - 2,772 4. Compressor type High pressure blowing air (up to 40 bar) Oil-free reciprocating piston compressor \"all-in-one\" skid Low pressure air 7-10 bar, possibilities from 3 to 15 bar (2 stages) Low pressure screw Low pressure oil-free piston compressor Screw type High pressure blowing air (up to 40 bar) 20-40 bar, possibilities down to 15 bar (3 stages) High pressure piston (booster) Piston High pressure oil-free piston compressor (atmospheric up to 40 bar) Piston type Integrated system All in one system, high & low pressure simultaneously Atmospheric compressor including VSD with largest regulation range from 18% to 100% of the capacity 5. Lubricated or oil-free Oil-free 100% oil-free compressor class 0 Low pressure compressor Oil-free 6-15 bar Oil-free 100% oil-free compressor class 0 Lubricated Booster compressor Oil-free 0-40 bar Oil-free Not needed, it's atmospheric HP compressor Lubricated Integrated system Yes Yes Atmospheric 100% oil-free compressor class 0 6. Machine layout L shape V V and H (horizontal) Horizontal opposed cylinders, forces balanced and virtually no vibrations V (2 cylinder), W (3 cylinder) 7. Number of compressor stages 3 stages, 3 cylinders for HP, 2 stages, 2 cylinders for LP 2 screw + 2 booster = 4 total 3 2 for LP and 3-4 for HP 1+1 8. Are special foundations required ? No No No No, virtually no vibrations No 9. Cooling system Evaporative or radiator system Water Water Water cooled (closed cooling tower or aerocooler) Air (water option) 10. Belt or direct drive V-belt transmission Belt drive Direct drive Low pressure compressor V-belt transmission Direct drive Direct drive Direct Booster compressor 0-40 bar, V-belt transmission Belt drive Not needed, atmoshperic HP direct drive Belt Integrated system Direct drive"},{"@ID":48 "EVENT REVIEW PETplanet Insider Vol. 25 No. 09/24 www.petpla.net 46 Compact preform system for long and heavy preforms (HOD) by Alexander Büchler At its in-house exhibition, Otto Systems presented its newly developed injection moulding system designed for producing 5 to 20 l Home and Office Delivery (HOD) preforms. The Swiss company, with its strategic focus on special applications outside the mass market showcased a 160 t system that allows for the efficient production of large-volume preforms, which traditionally would require a larger system to achieve a comparable output. The Swiss achieve the compact design thanks to an outward-bending toggle mechanism, intelligently arranged cooling stations on the post-mould cooling unit and an in-house developed injection unit. The external, electrically driven toggle levers, developed in collaboration with partner BMB, enable a significant stroke of nearly 1m, while maintaining a compact structure. On the 160 t system presented, eight preforms for one-way PET water containers weighing 330g and measuring 304mm in length have been produced per cycle. With a cycle time of 36 seconds, the system achieves an output of 800 preforms per hour. The two-row compact mould design helps reduce width, making the system smaller and more cost-effective without compromising on cooling-efficiency. The limitation, given by the mould, to two cooling stations can be enhanced to four postcooling stations through the chosen layout of the take-out plate. Thanks to the duplication of the EOAT to 2+2 cooling stations high cooling efficiency is ensured. The proprietary injection unit balances plasticising and injection performance, incorporating Otto Systems’ innovative Time Safe Unit (TSU). This TSU manages the extended holding pressure required for large and thickwalled preforms, allowing the screw to perform large dosing strokes at moderate rotational speeds with an ideal residence time. This combination results in optimal homogeneous plastification, ensuring superior process conditions. In addition to the 160 t machine shown, Otto Systems is expanding the HOD-Series with a larger 240 t system designed to produce preforms up to 400mm in length and shot weights of up to 10kg. This model will also be capable of producing preforms for MW 5-gallon containers weighing 680700g, demonstrating Otto Systems commitment to innovation and market adaptability. The extended clamping unit ensures flexibility and efficiency, even for the most demanding applications such as beer keg preforms. The compact, high-performance HOD-Series is engineered for specialised applications, with a strong focus on energy efficiency and cost-effectiveness. Reflecting Otto Systems’ strategic focus on special applications outside the mass market, the 160 t and 240 t systems demonstrate Otto Systems leadership in the production of large, heavy preforms for various sectors, while ensuring maximum productivity in minimal space. www.otto-systems.com The 160 t HOD-Series as shown during the Otto Systems open house Mould and cooling station Outward-bending toggle mechanism Otto Systems’ new Techcenter in Uznach, Switzerland"},{"@ID":13 "EDITOUR PETplanet Insider Vol. 25 No. 09/24 www.petpla.net 11 Mr Najmuddin, who has a master in Business Administration and is a Science Graduate, has been with the company since its inception in 1993. He has two daughters and a son, all of whom are currently in North America. “I’m probably the oldest employee here,” he said with a laugh at the small meeting table in his office. “My boss, Mr Ali Hashim, calls me the co-founder of the company because I’ve been here so long.” In fact, he is also something like the visionary backbone of the company. “When I started here, I quickly realised that PET had huge potential, but that it also needed some official qualifications if the company was to be recognised by the market leaders in the beverage industry. Just think of the high requirements of bottlers like Pepsi, for example. I then helped to drive the process of these qualifications forward and we sat down with PepsiCo and Coca-Cola to clarify what the quality requirements would be for a collaboration.” The fact that feelers had already been put out in the direction of packaging for the pharmaceutical industry as a further parallel project benefited the requirements of the multinational drinks manufacturers, as the necessary high requirements could already be more than met here. Mr Najmuddin explained: “We already had a lot of experience in injection moulding and were able to secure our first deals with pharmaceutical manufacturers for the sophisticated closures that we produced. By the start of 1995, we were already fully qualified and approved which enabled us to start producing preforms on commercial basis for Pepsi, Coca-Cola and Nestlé. On the pharmaceutical side, the company supplied bottles and closures to the Saudi Pharmaceutical Industries & Medical Appliances Corporation (Spimaco) first, and then went on to supply several other pharma companies in the region. Today, around 80% of the preforms and closures go into water applications, the rest into CSD, milk and juice. Working round the clock in day and night shifts, around 7 billion preforms and an equal number of closures are produced annually in Jeddah, and around 2 billion at the plant in Riyadh. 60% of the CSD closures are currently two-piece, but there is a shift towards more one-piece closures. For water, preforms can be produced for 200ml, 250ml, 330ml (most represented), 500ml, 600ml, 650ml and 1.5 l, for CSD for 250ml, 400ml, 500ml, 1 l and 2.25 l. 25% of the products are exported mainly in the Middle East and North Africa region. Keeping in view the circular economy, 3P is well equipped with the facilities to produce 100% rPET preforms or preforms blended with the vPET as per customer demand. Among the various support services, 3P group established an in-house inherent tooling workshop with CNC machines where prototype moulds and machine parts can be fabricated. The films division, which belongs to 3P, is mainly active in wrap-around label production for the local as well as international brand beverages, but also produces shrink film for multipacks, plastic bags including printing and the Sufra rolls, a type of disposable tablecloth. The company mainly sources its raw materials from Sabic. In fact 3P claims to be one of the largest customers of Sabic worldwide. The turnover for the entire Group in 2022 totalled USD 533.3 million, of which around 20% was attributable to the 3P flexible division which employs about 250 people. 3P setup: Jeddah plant 3 x Husky HyPET 500HPP5e 14x Husky HyPET 400/HPP4 8 x Husky G-lines still active 5 x Husky HyCAP 4 400 6 x Husky Hylectric 400 4 x Sacmi CCM 64 1 x Sacmi CCM 24 2 x Sacmi 32 inactive/for sale 3 x Blow moulding EBM 4 x ASB 70 DPH ISBM 1 x Aisa for collapsible tubes Riyadh plant 5 × Husky HyPET 500 HPP5e 3 × Husky HyCAP 4 www.3p-gulf.com Husky HyCAP closure moulding systems in action Just produced: Mohammed Najmuddin with a water preform F.r.t.l.: Mohammed Najmuddin, Kay Barton and Ahmed Salhi in front of a Husky HyPET HPP5e system"},{"@ID":29 "BOTTLING / FILLING PETplanet Insider Vol. 25 No. 09/24 www.petpla.net 27 Coca-Cola Bottlers Nepal’s journey with Sipa-supplied complete fi lling line Boosting efficiency and sustainability In the vibrant heart of Kathmandu, Bottlers Nepal Limited has been a key player in the country’s beverage industry for over four decades. The bottler has been dedicated to manufacturing, packaging and distributing a diverse array of soft drinks and packaged drinking water under renowned brand names such as Coca-Cola, Sprite, Fanta, Coke Zero, and Kinley. The company has recently upgraded its production capabilities by installing a new filling line supplied by Sipa. The move is part of the company’s effort to increase efficiency and minimise environmental impact. Located in the bustling Balaju industrial district, Bottlers Nepal’s facility boasts packaging lines for both returnable glass and PET bottles, equipped to meet the dynamic demands of the market and ensure consumers can enjoy their favourite beverages. At the core of Bottlers Nepal’s success is a team comprising over 600 employees, supported by an extensive value chain and distribution network. In a move to enhance its production capabilities and minimise environmental impact, Bottlers Nepal recently invested in a state-of-the-art filling line supplied by Sipa. This transformative technology is claimed to represent a significant milestone for both Bottlers Nepal and the beverage industry in Nepal. Mr Ike Yu Hang, Supply Chain Director at Bottlers Nepal Limited shared, “At Coca-Cola Beverages Nepal, we always strive to keep ourselves updated with relevant trends and operations. The new line investment allows us to align with our long-term strategy and sustain our position as the undisputed leader in the beverages market in Nepal. The plant we have in Balaju was first established in 1979 and we are proud of its consistent performance over more than four decades, refreshing the nation with Coca-Cola beverages along with the investments to maintain and upgrade our lines.” The filling line’s advanced automation allows for the handling of various bottle sizes and formats, ensuring flexibility in production and meeting diverse consumer preferences. Moreover, it is designed with energy-efficient components and design features to contribute to the company’s sustainability initiatives and to minimise resource consumption and waste generation. Equipment deployed at Bottlers Nepal’s facility includes a Sincro Bloc that combines an Xtra 8 rotary stretchblow moulding unit with a Flextronic C 54-9 volumetric filler, a Massblend 27 blending and carbonation unit, a Rollmatic 15 T labeller, a Genius PTF palletiser, and an SPF/E stretch wrapper for the pallets. These systems are instrumental in maintaining efficiency, reliability, and quality throughout the production process, says Sipa. Through initiatives focused on water conservation, energy efficiency, and waste reduction, Bottlers Nepal strives to minimise its environmental footprint while maximising positive social impact. The upgrade comes as part of broader efforts to remain competitive in Nepal’s beverage industry while also addressing environmental challenges. www.sipasolutions.com Saurav Thapa (right) from Bottlers Nepal and Kasi Viswanath (2nd f.r.) of Sipa, along with their colleagues, stand proudly before the Sipa production line. Sipa line in production of Fanta bottles"},{"@ID":5 "imprint EDITORIAL PUBLISHER Alexander Büchler, Managing Director HEAD OFFICE heidelberg business media GmbH Hubweg 15 74939 Zuzenhausen, Germany phone: +49 6221-65108-0 [email protected] EDITORIAL Kay Barton Heike Fischer Gabriele Kosmehl Michael Maruschke Ruari McCallion Anthony Withers Editorial & WikiPETia. info [email protected] MEDIA CONSULTANTS Martina Hirschmann [email protected] Johann Lange-Brock [email protected] phone: +49 6221-65108-0 LAYOUT AND PREPRESS EXPRIM Werbeagentur Matthias Gaumann www.exprim.de READER SERVICES [email protected] PRINT Chroma Druck Eine Unternehmung der Limberg-Druck GmbH Danziger Platz 6 67059 Ludwigshafen, Germany WWW www.hbmedia.net | www.petpla.net PETplanet Insider ISSN 1438-9459 is published 10 times a year. This publication is sent to qualified subscribers (1-year subscription 149 EUR, 2-year subscription 289 EUR, Young professionals’ subscription 99 EUR. Magazines will be dispatched to you by airmail). Not to be reproduced in any form without permission from the publisher. Note: The fact that product names may not be identified as trademarks is not an indication that such names are not registered trademarks. 3 PETplanet Insider Vol. 25 No. 09/24 www.petpla.net I started my tour through Oman, Qatar and Kuwait at the PRS Middle East & Africa 2024 in Dubai. A recycling fair in a region without recycling. It was small, but the 125 exhibitors made a pleasant show of it. For visitors from outside the Gulf States – especially those from Africa – there were many rPET suppliers and plant manufacturers from India, China and other countries represented. However, the search for regional recycling companies was fruitless. The issue of rPET is non-existent in countries that have crude oil reserves and can obtain virgin PET cheaply. At best, in-house recycling makes sense, at least for the production of plastic sheets. I spoke to recycling system providers at the PRS about why this is the case. Christoph Wöss, Business Development Manager of the Erema Group for the Bottle Application division: “We have two recycling plants at two locations in the region, each with a capacity of 1,600 kg/h, to directly recycle offcuts from sheet production. In Saudi Arabia, we also operate a preform production facility at Bariq. But in the Emirates or Oman? No, not a single bottle-to-bottle (b-to-b) system. People are not used to collecting rubbish; it all ends up in landfill. In the future, the idea of sustainability will also reach here, but I can’t tell you when that will be.” Christian Lechner, Regional Sales Manager at Starlinger: “There is no bottle-to-bottle recycling here. Virgin PET is so cheap and no consumer wants a slightly grey bottle. As there is a lack of b-to-b recycling, bottlers can also easily produce opaque bottles for energy drinks or fruit juices that are no longer suitable for b-to-b recycling due to their colour. By contrast, some manufacturers make sure that the bottles of exported drinks do not disrupt the recycling stream. It remains to be seen when the pressure for sustainability will be felt in these parts.” Peter Hartel, Head of Sales CN/MEA, Krones Recycling GmbH: “We have invested a lot of manpower in Krones Recycling GmbH in Flensburg and Neutraubling, which has been independent since July. We believe that PET recycling is a very important building block for the acceptance of the PET bottle. Only in this region has the topic not yet arrived, possibly blocked by the large local virgin PET manufacturers. One cracker after another is put into operation here.” Yours, Alexander Büchler Dear readers,"},{"@ID":45 "43 EVENT PREVIEW PETplanet Insider Vol. 25 No. 09/24 www.petpla.net Finke Hall A4 - Booth 4208 Colour meets sustainability Karl Finke GmbH & Co. KG, a leading producer of highquality masterbatches and colour solutions, is focusing on sustainability, especially in products with high recycled content and support for design-for-recycling. The company’s latest developments aim to help plastics processors achieve sustainability goals while maintaining vibrant colours. Finke’s proprietary process allows its Fibaplast masterbatches to be used in polyolefins with a high proportion of recycled material. By encasing recycled cores in a thin layer of virgin material, the full colour spectrum is maintained. The Fibafekt range enables interference colours on dark substrates. The company’s Fibasol liquid colourants are suitable for colouring plastics with high recyclate content. They are claimed to provide independence from carrier materials, high efficiency, and are compatible with most thermoplastics, including those with significant recycled content. New products from the Fibaplast masterbatch series for laser marking, the Fibatec uncoloured additive batch series with special functions and the Fibaplast NIR detectable black masterbatches help to meet design-for-recycling requirements for plastic packaging. An expansion of the range for laser markings enables dark markings within transparent plastics such as PET, PC or PMMA and coloured laser markings in many colours and shades on black, carbon black-coloured plastics. Fibatec is a new uncoloured additive batch series with special functions based on various carrier polymers. The Fibatec UVA additive batches is claimed to provide plastic products with UV protection. This enables the production of colourless bottles for the food and cosmetics sectors. The additive batches are free of benzotriazoles, PAAs and PAHs and contain neither CMR substances nor SVHCs and comply with the regulations for food contact plastics in the EU, the USA and China. They are approved for packaging and registered according to REACH and in the corresponding chemical inventories in the USA and China. The Fibatec UVA additive batches are available on the basis of bottlegrade PET or rPET, among others. Finke also has developed a Fibaplast NIR detectable black masterbatche to improve the sortability of packaging waste using NIR systems. The formulation contains no carbon black pigments so that even black plastics are easily detected during sorting in NIR systems. www.fi nke-colors.eu BOTTLE TO BOTTLE RECOVERY MOISTURE CONTENT CONTROL PROCESS CONSISTENCY EXTREME BLENDING FLEXIBILITY moretto.com follow us MAKING THE DIFFERENCE ON PET. Hall B3 Stand 3208"},{"@ID":49 "PATENTS PETpatents www.verpackungspatente.de PETplanet Insider Vol. 25 No. 09/24 www.petpla.net 47 Container with grooves Internal. Patent No. WO 2024 / 015278 A1 Applicant: Krones Inc., Franklin (US) Application date: 10.7.2023 The application describes several variants of circumferential grooves and base mouldings on how a weightreduced container or bottle can still be sufficiently stable. Coupling drinking bottle Internal. Patent No. WO 2024 / 015448 A1 Applicant: Hattab Global Corp., Arlington (US) Application date: 12.7.2023 A plastic bottle has a special outer shape that allows several bottles to be coupled together to save space. Packaging material can also be saved when combining a unit. Reusable bottle Internal. Patent No. WO 2024 / 009183 A2 Applicant: S.I.P.A.,. Vittorio Veneto (IT) Application date: 29.6.2023 The application is for a reusable PET bottle that can withstand a large number of washing cycles with a specific cleaning agent. Stackable container Disclosure no. DE 102022118053 A1 Applicant: B. Braun Avitum AG, Melsungen (DE) Application date: 19.7.2022 Stackable container for medical/pharmaceutical preparations made of a thermoplastic material. Neck for container spout Utility model DE 202023105564 U1 Applicant: Betapack S.A.U., Irun Gipuzkoa (ES) Application date: 25.9.2023 A neck with a thread is attached to the spout of a thin-walled container to stabilise the container and to attach a lid. Improved container Internal. Patent No. WO 2024 / 023167 A1 Applicant: Alpla Werke Alwin Lehner GmbH & Co KG, Hard (AT) Application date: 26.7.2023 Extrusion-blown container with a screw thread. The interaction with the screw-on lid ensures the necessary stability and tightness."},{"@ID":8 "PETnews 6 NEWS PETplanet Insider Vol. 25 No. 09/24 www.petpla.net Indorama Ventures, Dhunseri and Varun beverages joint venture plans multiple recycling facilities in India Indorama Ventures Public Company Limited, through its direct subsidiary – IVL Dhunseri Petrochem Industries Limited – and Dhunseri Ventures Limited have formed a joint venture with Varun Beverages Limited, PepsiCo’s second-largest bottling company globally outside the US, to establ ish several greenfield state-of-the-art PET recycling facilities in India. The joint venture has already begun the construction of two PET recycling facilities, planned for completion within 2025, with potential for more. One facility is in Kathua within the Jammu Division of the Indian Union territory of Jammu and Kashmir, situated in Northern India, while the other is in Khurdha within the State of Odisha, located in Eastern India. The aim is to reach 100 kt/a capacity of recycled PET across all the facilities when combined. This initiative aligns with the escalating demand for rPET content in India, driven by both regulatory mandates and a collective effort towards a circular economy for PET. The surge in demand reflects a significant shift, with projected volumes increasing from approximately 400 kt in 2025-2026 to over 1 million tons by 2031. Mandates such as the Indian government’s compulsory requirement of 30% recycled plastic content in plastic packaging by 2025-2026, escalating to 60% by 2028-2029, underscores the urgency and importance of this transformation. Moreover, this move aims to effectively cater to the needs of India’s beverage brand owners, many of whom have established ambitious sustainability goals in line with regulatory directions. The amalgamation of the three industry leaders is claimed to bode well for bolstering the region’s recycling infrastructure. As regulatory frameworks increasingly advocate for heightened usage of recycled content, the joint venture is positioned to play a pivotal role in meeting these evolving requirements. Indorama Ventures is the world’s largest producer of rPET resins widely used in food and beverage packaging. Since 2011, the company has operated PET recycling facilities, gradually expanding its global footprint. www.indoramaventures.com Husky Technologies announces leadership transition: Bradley Selleck appointed CEO, John Galt to become Chairman Hu s k y Te c h n o l o g i e s announced that Chief Operating Officer Bradley Selleck will assume the role of CEO, effective October 1st. The current CEO, John Galt, will transition to the role of Chairman. This leadership change is part of a long-term succession plan designed to maintain stability and position the company for continued growth. Husky, a portfolio company of Platinum Equity, is a global provider of innovative solutions and services primarily for the beverage, consumer goods and medical device markets. “John has been preparing the company for this for several years and I commend him and the team for taking such a thoughtful and deliberate approach,” said Louis Samson, Co-President of Platinum Equity. “Brad is a uniquely talented executive and key architect of the company’s current operating model. He has made a material and multi-faceted contribution to Husky since joining approximately three years ago and has proven beyond any doubt that he’s up to the task and ready to take the reins.” Galt has been with Husky since 1985 and served as CEO since 2005. During his tenure, he played a central role in the company’s transformation into a global leader in industrial technology. In recent years, Galt has worked closely with Selleck and the management team to strengthen the company’s market strategy, with an increased focus on sustainability and essential markets. Selleck joined Husky in 2022, bringing more than 25 years of experience in operations and supply chain management. As CEO, he plans to continue advancing the company’s strategic priorities, including sustainable practices and innovation. Galt will continue to play an active role in the company as Chairman, with a focus on sustainability advocacy and supporting the leadership team in areas such as customer and investor relations. www.husky.co Yash Lohia, representative of IVL Dhunseri, and Executive President Petchem Special Projects, and Chairman of the ESG Council of Indorama Ventures"},{"@ID":22 "BOTTLE MAKING 20 PETplanet Insider Vol. 25 No. 09/24 www.petpla.net English Mountain Spring Water Company boosted packaging quality with the installation of a blowing line from Flexblow Tennessee two-step by Ruari McCallion Ruari McCallion, PETplanet Insider’s Editor-at-Large, spoke to English Mountain Spring Water’s founder and CEO, John Burleson, about building a brand from a small base and the big step up in quality and consistency and the reduction in costs achieved with the installation of a PET bottle blowing line from Lithuanian company Flexblow. English Mountain Spring Water Company faced a range of challenges with its bottles, which it was buying in from external suppliers. Quality issues and lack of consistency were leading to losses of product, refunds to disappointed customers and a cost base that was inhibiting profitability and growth. At the time, the decision to bring bottle blowing in-house seemed a difficult one to make but it turned out very well. The line it bought from Lithuanian company Flexblow has pretty much eliminated quality problems and thus improved relations with customers, as well as helping to cut costs and make budgeting more manageable. The story hinges on persistence by Flexblow and a willingness to listen on the part of John Burleson, CEO of English Mountain Spring Water, who smiled as he recalls how the relationship developed. “I first met Flexblow at the NPE plastics show in Orlando, Florida, in 2018. Mr Martynas, the Service Manager, had been emailing me but I’d said that I wasn’t ready for a blow moulder at that time. Well, he took it upon himself to drive all the way from Orlando, overnight and all day, and he arrived late in the afternoon, as I was getting ready to go home,” he said. He reckoned that he couldn’t turn Martynas away as he’d driven so far and listened to what he had to say. Although John Burleson wasn’t ready to invest in a blow moulding line at that time, they agreed to keep in touch, which Flexblow did, diligently but not intrusively. Meeting customer needs “In 2022, we started getting serious. Gintautas [Gin] Maksvytis, the General Manager of Flexblow, came over from Lithuania with about four staff. They toured our facility and he said he really wanted us to have a Flexblow machine. After their visit, we conducted a follow-up to gather feedback. A packaging manufacturer in Georgia assured us that Flexblow produces robust and reliable systems. I still wasn’t sure but they put together a very attractive package and, in 2022, we finalised everything,” John continued. What English Mountain Spring Water got was a Flexblow Auto Quality, a pharmaceutical grade stretch blow moulding unit that had been shown at Pack Expo 2022 . Preferential heating catered for the company’s specific bottle shapes. Installation and final commissioning in August 2023 was the latest milestone on a journey that had started in 1992, when John became interested in bottled water as a business. His original intention was to be solely a contract supplier but prospective customers themselves wanted suppliers to have a brand and market presence themselves. By 1997, he had acquired a 5,000 sq ft (465m2) facility and was soon producing with two second-hand bottling lines. A five-gallon (US) line filled 100 bph; the second line filled one gallon HDPE plastic bottles. A PET line was added in May 1998. Building a reputation “We started selling to small, Momand-Pop operations, convenience stores owned by private individuals, rather than corporates, and the like – unconventional outlets, you might think,” John said. “One of our products was distilled water, displayed in glass door coolers that we provided and installed.” A virtually non-existent marketing budget meant that English Mountain had to build its reputation by hard work and word of mouth. Fortunately, Tennessee is the kind of area where local roots and neighbourly service count for a lot. “We were growing and the home delivery side was doing very well. Customer service was what we based our business around,” he said. “Our big break came in 1999 when we won a water tasting competition in Berkeley Springs, West Virginia. It was an international competition; we competed against every Nestlé brand, Boss was there, brands from all over – some from Sweden and Belgium The Flexblow Auto Quality line was installed in August 2023"},{"@ID":33 "MATERIALS / RECYCLING PETplanet Insider Vol. 25 No. 09/24 www.petpla.net 15 MATERIALS / RECYCLING 15 ing bottle weight, smaller packaging for carbonated drinks and replacing glass with PEF for oxygen-sensitive products. Due to its similarity to PET, PEF can be recycled using the same processing steps as the many known PET recycling processes. It has also been shown that PEF has a limited impact on the rPET stream, which have led to (interim) endorsements of PET/PEF multilayer bottles to enter the PET bottle recycling stream in Europe (EPBP limited to a market penetration of 5%) and US (APR). PEF World Congress Due to the properties of PEF and its production from 100% renewable raw materials, a whole range of companies around the world are already developing FDCA and PEF production. The Dutch company Avantium (Amsterdam) is opening its flagship plant for the production of FDCA in Delfzijl, The Netherlands, in October. Reason enough for the trade journal Renewable Carbon Plastics (formerly bioplastics Magazine) to organise the first PEF World Congress together with the Horizon 2020 project PEFerence. The 2-day hybrid conference (on-site and online) will take place on October 30 and 31 in Düsseldorf, Germany. www.pef-world-congress.com Property PET PEF Density 1.36 g/cm³ 1.43 g/cm³ O2 permeability* BIF = 1 BIF = 10 CO2 permeability* BIF = 1 BIF = 15 H2O vapour permeability* BIF = 1 BIF = 2.5 Tg 76 °C 88 °C Tm 250 - 270 °C 210 - 230 °C E-modulus 2.1 - 2.2 GPa 3.6 GPa Yield strength 50 - 60 MPa 90 - 100 MPa *BIF - Barrier Improvement Factor compared to PET Table 1: Intrinsic properties of amorphous PET and PEF Digital manufacturing line for plastic caps SACMI.COM Continuous compression molding solution: digital, smart, cost-effective. Conceived, designed and produced by SACMI. DIGITAL & PROFITABLE Line ready for advanced Smart Pack and Smart Care services to provide more effective synergy with HERE M.E.S. features. SMART & RELIABLE Reliable controls and immediate overview of the process via AI-based inspection systems integrated into all the processes. COMPACT &IWX MR GPEWW WTIGMƤG IRIVK] GSRWYQTXMSR CCM maximizes output rates per bay and is the most sustainable solution. momic"},{"@ID":12 "EDITOUR PETplanet Insider Vol. 25 No. 09/24 www.petpla.net 10 Packaging solutions from a single source “We want to become a key supplier for the beverage industry” Jeddah-based company and greenfield project 3P Gulf Packaging Systems, founded in 1992, is a market leader in plastic packaging and products in Saudi Arabia and the region, serving the beverage and food, pharmaceutical, personal care and home care sectors. Its most important products include preforms, closures, tubes, disposable plastic products, plastic tableware, films and labels. Meeting with 3P Gulf Packaging System Co. February 21, 2024 We met: Mr Mohammed Najmuddin, VP Operations Mr Ali Hashim, VC & CEO Mrs Randa Hashim, Business Development Manager Mr Vipin Vellipoyil, Tooling Workshop Manager Mr Ahmed Salehi, PET Production Manager In the PET segment alone, the conversion volume in Jeddah for PET reaches 7,000 t per month. In comparison: the company started with 70 t when it was founded. A total of nine plants belong to the 3P Group in Jeddah involved in producing products in rigid and flexible packaging. Another plant in Riyadh became operational in 2023 processing around 3,000 t of PET per month in the preforms and closures segment. In addition to the MENA region, the customer base extends to over 40 countries, which is due in particular to the production of shrink and stretch film. In an interview with VP Operations, Mr Mohammed Najmuddin, VC & CEO Mr Ali Hashim and Business Development Manager Mrs Randa Hashim, we gained a comprehensive insight into the market giant’s business. With his business idea in 1960, Mr Hashim Sr, the father of today’s CEO Mr Ali Hashim, wanted to support and serve pilgrims on their journey to Makkah in the south-western Saudi region of Hejaz. He began producing footwear for them and making jerry cans for carrying the holy water from the Zamzam well. Three years later, he started the first commercial factory in Jeddah for everyday household items under the name Arabian Gulf Manufacturers (AGM). The bestknown brand that emerged from this, “Gulfmaid”, contributed significantly to the company’s success story over many years and Mr Hashim increasingly recognised the potential of plastics processing. 1992 marked the start of the Gulf Packaging System Company (GPS) that was later brought under the umbrella of Prime Plastic Products more popularly known as “3P”, which still adorns the company logo today. The current CEO, Mr Ali Hashim already knew the markets and suppliers well from previous experience and so the idea was to be able to offer a complete solution from a single source in the field of packaging, mainly for bottles and closures, primary and secondary packaging - including printing and everything that goes with it. In the 1990s, the immense construction boom in many Gulf states ensured plenty of external investment, which favoured further growth and expansion of 3P. For example, the company’s subsidiary Gulf Manufacturers was established in Egypt to produce plastic pipes. F.l.t.r.: Mohammed Najmuddin, Ali Hashim, Randa Hashim and Kay Barton Talking to Mohammed Najmuddin in his office Sacmi machinery for closures EDITOUR"},{"@ID":11 "9 NEWS PETplanet Insider Vol. 25 No. 09/24 www.petpla.net Taste trends at CBB 2024 raw materials, agents and additive area 2024 China Brew China Beverage (CBB) will be held at the Shanghai New International Expo Center from October 28 to 31. A leading event for the Asian wine, beverage, liquid dairy products, liquid condiments, and edible oil industries, CBB is part of the Drinktec global network. It covers key aspects of the industry, from raw materials and auxiliary materials to processing technology and equipment, packaging technology and equipment, general equipment and parts, packaging containers and materials, and modern warehousing and logistics. It also highlights cutting-edge themes such as intelligent manufacturing, Industry 4.0, innovative packaging, food safety and health, energy efficiency management, and green and sustainable development. With rising living standards and growing health consciousness, the beverage and dairy industries are innovating to offer flavours that are both healthy and trendy. CBB 2024’s dedicated area for raw materials, agents, and additives will highlight key trends. Personalisation and trendiness: New flavours in beer, beverages, and dairy products - such as new hops and fruitinfused drinks - will inspire personalised, fashionable tastes. Natural and healthy: The focus will be on natural, healthpromoting ingredients, showcasing growth potential in craft beers, functional drinks, and plant-based beverages. A tasting journey on the tip of the tongue: Raw materials, agents and additive areas at CBB 2024 are intended to offer an interactive experience, allowing attendees to explore the diverse styles of raw materials, auxiliary materials, and additives. Visitors can sample diverse hops and explore healthy beverages, offering a hands-on experience of flavour trends. This area will serve as the starting point for a high-tech journey through the entire beverage and liquid food industry chain, including wine, beverages, dairy products, condiments, and edible oils. www.chinabrew-beverage.com"},{"@ID":36 "COMPRESSORS PETplanet Insider Vol. 25 No. 09/24 www.petpla.net 34 AF Compressors: celebrating three decades in the United States US market key focus for growth by Gabriele Kosmehl It was not long after the emergence of PET in the beverage industry in the late 1970s and early 1980s that Atelier François (AF Compressors) noticed an increase in demand for oil-free air compressors, driven by the US market. After selling several machines to a US-based global producer and supplier of PET plastic containers and preforms for the food and beverage industry, the decision was made to establish a presence in the US. AF USA Inc., based in Atlanta, GA, was founded in 1995, and by the end of the 1990s, was already contributing no less than 25% of the company’s sales in US dollars. “The US market remains at the forefront of focus for our global organisation. Many key customers globally are based in the United States, which has a direct impact on our relationships abroad,” states Gareth Smith, Area Sales Manager of AF USA. As the US demand for PET plastic continues to grow, AF Compressors has positioned itself as a key player in providing energy-efficient solutions to meet these needs. The company, which has dedicated 99% of its business focus to the PET industry over the last 40 years, boasts a global market share of 60-65% with its oil-free piston compressors Their efficient designs are widely used across the US. Today, AF USA has a team of 22 employees providing comprehensive support to clients across the US, Canada, and the Caribbean. This includes everything from new compressor installations to preventive maintenance and troubleshooting. The team’s deep engineering expertise, cultivated over decades, helps clients optimise their operations, expand facilities, and replace equipment from other suppliers. In Carrollton, Georgia, the company also has a 5,750-square-foot warehouse that stores over $1m worth of spare parts, ensuring that AF USA can meet the needs of its growing customer base. The AF Training Academy, located at the US headquarters, is offering extensive training programs for both AF technicians and clients. Courses cover everything from compressor operation and maintenance to safety and troubleshooting, helping customers maximise the efficiency and lifespan of their equipment. Smith continued, “We are consolidating our leading position on an actual 100% AF service presence, while developing new technologies and accompanying our customers through their challenges in terms of global sustainability. Our compressor systems are engineered and mechanically designed for ‘energy sobriety’ and this is a key fact to positively respond to the climate challenges in the USA and the Americas as well as anywhere else in the world.” Thus, the company is responding to customer requests that differ little in the USA from those of customers in other parts of the world: “Energy savings / TCO, flexibility, after-sales service & support, ease of maintenance and training of onsite personnel are all areas of focus brought consistently to our attention.“ But there are also a few special characteristics of the US market: AF is beginning to see a push from the end-user to bring full PET production lines in-house to reduce the costs of transporting empty containers, and other associated outsourced costs. A direct consequence of this change of approach is that the end-user is playing a more direct role in supplier selection, including direct procurement of PET compressors and overall maintenance / management of the equipment. Smith went on, “This has created a challenge for us as it is even more important for us to educate these customers on proper installation, operation, and ongoing maintenance in order for the user to achieve optimal efficiency and longterm sustainability of our equipment.” Focus on energy efficiency, sustainability & costs AF Compressors also places a strong emphasis on incorporating customer feedback into the design COMPRESSORS The AF USA Inc. premises in Atlanta, GA The AF Training Academy is offering extensive training programs for both AF technicians and clients."},{"@ID":32 "COMPRESSORS PETplanet Insider Vol. 25 No. 09/24 www.petpla.net 30 Improving compressed air efficiency in PET applications by Ruari McCallion The Water Compressor is a step forward in compressed air systems, according to Augwind, its developer. With a successful R&D project demonstrating its effectiveness, it is now seeking partners to help demonstrate and develop to the next stage. “His original idea was to place an underground tank beneath each wind tower. Excess energy generated by the turbine would compress air within the tank and the network of wind turbine-fed tanks would become a distributed energy storage asset,” said Ido Ben-Yehuda, Head of Marketing with Augwind. “The solution has evolved, dramatically, since then.” Augwind, headquartered in Yakum, Israel, was established in 2012, to develop and exploit Dr Yogev’s idea and to realise the AirBattery energy storage system - a novel combination of pumped-hydro and compressed air energy storage. After accomplishing the development of its proprietary underground tanks, that are used for the compression and expansion process of the AirBattery, Augwind realised that this element has already commercial value for industrial compressed air applications - buffering between compressed air generation and consumption, optimising the energy bill and productivity of large compressed air systems. This underground tank was commercialised under the name AirSmart. Today, over 70 AirSmart installations are operating on daily basis at some of the largest industries in Israel and recently in Italy. AirSmart clients include companies operating on the mineral mining and processing industries, food and beverage, plastics, cement, steel and more. Among Augwind’s customers are companies such as Unilever, Iscar (an IMC Group company) and Tempo, the Israeli producer of Heineken and PepsiCo. Raising the game with underground storage AirSmart is essentially a compressed air buffer system. Instead of supplying directly, the air is accumulated in underground tanks located between the compressor room and the machinery. This allows supply to be optimised. That idea of buffer storage is not new, of itself, but the installation, charging technology and management all are. Compressed air buffering systems traditionally take up a lot of space; what Augwind achieved was the development of technologies that enable the large CE-certified tanks to be installed underground – under car parks, logistics or other areas, which means that valuable working spaces can be kept in productive activity, while enabling huge, compressed air reservoirs. The system offers energy cost savings of more than 20% of compressor’s electricity consumption, according to Ido and Augwind. To realise the AirBattery system, one of the challenges that had to be overcome was keeping the air cool that was undergoing compression. Augwind has achieved it by using water as both the compressing agent and as a cooling medium – and the location of the tanks underground also helps to maintain a constant temperature. Setup example of a compressor, production machinery and an underground AirSmart buffer chamber COMPRESSORS Augwind’s Water Compressor system takes a different approach to compressed air from conventional solutions. It is an evolution of Augwind’s AirBattery, an energy storage technology developed by Dr Or Yogev around 15 years ago, while he was in California. The ‘Golden State’ had a wide range of energy resources, including oil and, more recently, wind and solar power. Dr Yogev was working at the time with a solar power company and he recognised the need for some kind of storage system to manage renewables, to harvest wind energy when wind was blowing but demand was low – such as at night – and, similarly, to release energy back into the grid during periods of higher demand. The conventional thought had been to create big batteries that harness the energy in the form of compressed air; Dr Yogev took a step to the side and thought of something different."},{"@ID":37 "COMPRESSORS PETplanet Insider Vol. 25 No. 09/24 www.petpla.net 35 and functionality of its compressors, with a focus on energy savings and cost reduction. The company developed the adjustable Air Flow System (AFS), which allows for 0-50-100% load regulation, enabling customers to achieve immediate power savings and long-term efficiency gains. The system can be retrofitted to existing compressors, requires zero maintenance, and extends the lifespan of equipment by maintaining stable operating temperatures. In partnership with Schneider Electric, the Smart Inverter Starter (SIS) has been created, which is claimed to be a cost-effective alternative to full-size variable speed drives (VSDs). This solution provides energy-saving benefits during compressor startup without requiring special motors or cabling and can be retrofitted on existing units, according to AF. The company’s patented All-InOne (AIO) system combines high and low-pressure air supply in a single compressor, reducing both investment and service costs. AF offers a MultiCompressor Management System that optimises energy use across multiple compressors by balancing load distribution and extending service intervals. Additionally, AF’s Heat Recovery System captures up to 80% of the heat generated during compression, allowing customers to reuse the energy for other processes, further enhancing efficiency and sustainability. Smith comments, “All of these systems have been developed based on customer demand and on what we have learned from the challenges our customers face.” Increasing local presence Looking ahead, AF USA is committed to expanding its market share while maintaining a strong focus on customer service. “We know that the best service makes the best presales and is the right way to increase our presence over time.” So the company is building on their local presence to improve responsiveness rather than relying on third party agents. This also included AF USA’s participation in NPE in May. Located in the bustling Bottle Zone, AF Compressors was strategically positioned alongside its OEM blow moulding partners. “The Bottle Zone was the perfect location for us,” Smith noted. “Being positioned next to major OEMs, allowed us to showcase our products to a wide audience. Our neighbour had multiple SBM machines producing non-stop all week with high and low-pressure air supplied by our 40 bar, 1,000 cfm compressor.” One of AF’s major highlights at the event was powering several production lines in real-time. Their 40 bar compressor supplied high and lowpressure air to multiple OEM blow moulding machines, creating a live demonstration of how their compressors drive the high-efficiency production of PET bottles. Gareth Smith ended on a positive note: “Seeing visitors engage with the equipment and witness entire production lines, from compressed air to resin melted down into preforms, to newly blown bottles, and knowing that we are such an important part of our partners’ exhibition is exciting and humbling at the same time,” Smith concludes. www.afcompressors.com The company’s 5,750 square-foot warehouse stores over $1+ million worth in spare parts. AF’s booth at this year’s NPE"},{"@ID":21 "PREFORM PRODUCTION PETplanet Insider Vol. 25 No. 09/24 www.petpla.net 19 identical temperature distribution along the length for a specific preform type, despite a significant 18% reduction in water flow rate. This reduction cut costs associated with the pump and also contributed to a decrease in overall energy consumption. This significant reduction in water usage, together with Sacmi’s water treatment and recycling initiatives, energy efficient machines, clean energy utilisation and emissions reduction demonstrates their commitment to sustainable success. BMT says that Thermoscan, as part of a sustainable manufacturing strategy, offers an array of advantages for the packaging industry, including brand owners, converters and preform manufacturers. It serves as a tool for quality control, ensuring consistent high-quality production and mitigating process drift caused by oven degradation and environmental factors. It quantifies and addresses variations between sites and machines. When discrepancies arise between batches during production, Thermoscan compares their absorption behaviour. It also generates a representative temperature profile usable in simulations for efficient virtual analysis, ultimately saving time, resources, and money. BMT’s Thermoscan to measure the preform temperature profile after injection moulding led to an 18% reduction in water flow rate while maintaining the production of high-quality preforms for stretch blow moulding. www.bmt-ni.com The Thermoscan measures and analyses preform temperature profiles to enhance resource efficiency, reduce operational costs, and minimise environmental impact."},{"@ID":46 "44 EVENT PREVIEW PETplanet Insider Vol. 25 No. 09/24 www.petpla.net CONTEXO GMBH Tel. +49 (0) 7181 / 606-100 [email protected] www.contexo-automation.de HIGHSPEED ASSEMBLY MACHINES CARTON CLOSURES POUCHES, CANS AND MORE PET CLOSURES + TETHERED CAPS Meet us at Fakuma! Hall A5 – Booth 5215 Coperion & Herbold Meckesheim, Hall A6 – Booth 6312 High-efficiency technologies for processing and recycling plastics Coperion and Herbold Meckesheim will demonstrate their expertise in producing entire systems using virtual animation: Both a complete compounding plant as well as an entire system for recycling plastic will be available to view. The processes involved can be experienced digitally with the aid of simulations, and visitors will be able to peer into individual key components and their functions. Rotors fromHerbold Meckesheim granulators will be on display in various sizes for many applications. Efficient plants for recycling a variety of plastics Along with individual components, Coperion and Herbold Meckesheim deliver entire systems for plastics recycling. From mechanical processing – shredding, washing, separating, drying and agglomerating of plastics – to bulk material handling as well as feeding and extrusion all the way to compounding and pelletising, such plants cover the entire plastics reclamation process chain. Currently, Coperion and HerboldMeckesheim are producing an entire bottle-to-bottle recycling system for Indian preform and plastic packaging manufacturer Magpet Polymer Pvt Ltd. This plant handles every process step from mechanical processing of used PET bottles to discharging highquality PET granulate, using a ZSK twin screw extruder with fully attuned peripherals to meet every need. Magpet awarded the contract for this PET recycling plant to Coperion and Herbold Meckesheim as they have coordinated their technologies and are committed to produce efficient plastic recycling solutions that consistently and reliably deliver high PET recyclate quality. Recycling test centre In its fully equipped test centres, Coperion and Herbold Meckesheim offer customers the ability to test a variety of plastic recycling processes and technologies under actual production conditions even before investing. At Herbold Meckesheim, within its 800m2 facility in Meckesheim, Germany, there is a complete washing line for cold and hot washing as well as every size reduction solution from shredders and granulators to pulverisers or plastic compactors for densification. In 2023, Coperion launched the operation of the Recycling Innovation Center in Weingarten, Germany, with stateof-the-art, individually configurable recycling plants where recyclate can be conveyed, fed, extruded, compounded, pelletised and deodorised. Both test centres complement each other perfectly to simulate and test the recycling of plastics. Smart solutions for classic compounding tasks Along with recycling, at this year’s Fakuma, Coperion will present versatile and efficient uses of its ZSK and STS twin screw extruders as well as its feeding and conveying technologies for classic compounding tasks. At the beginning of this year, Coperion introduced a re-worked version of the ZSK 18 Megalab laboratory extruder. With its optimised design, it now offers more flexibility and safety in handling, says the company. Using the newly developed patent-pending feeding platform, up to four feeders can be placed over the extruder’s intake barrel with great variability, allowing ingredients to be added flexibly into the compounding process. Likewise, Coperion’s ProRate Plus feeder line features new developments. With the ProRate Plus-MT twin screw extruder and the new ProFlow bulk solid activator, an efficient feeding solution for powder additives is now available. www.coperion.com www.herbold.com"},{"@ID":43 "41 EVENT PREVIEW PETplanet Insider Vol. 25 No. 09/24 www.petpla.net Erema, Hall A6 - Booth 6314 Versatile recycling technologies to meet increasing expectations Over the past 25 years, the Vacurema series of machines has become established for the production of food-safe rPET. Erema technologies for the recycling of PO materials have also already been approved by anAmerican food safety authority: the combination of the Intarema TVEplus with the ReFresher module allows recycled PO pellets from defined input streams to be reused in food packaging in proportions of up to 100%. By decontaminating the plastic and removing unwanted odours effectively, the technology opens up further high-quality applications for recycled pellets made using collected post-consumer material. These can be used in the automotive, home and design products, and for sensitive personal care products, for example. In the EU, the permit for foodsafe recycled pellets is based on a “novel technology” (Regulation 2022/1616). Erema supports recycling companies in generating data and evidence for the EFSA assessment process. Higher recycling capacities require larger volumes and more versatile processes As the demand for recyclates increases, so does the need to expand capacities by using larger machines. For recycling PET materials, Erema supplies large-scale systems with throughputs of up to 6t/h. The company has also built machines for recycling polyolefins with a throughput of over 4t/h. In addition to throughput, material-specific processes are decisive for increasing recycling capacities. Erema’s range of products also includes solutions for compounding, such as the Corema series, which combines an Erema extruder with twin screw technology. PCU TwinScrew technology, which features a direct combination of the patented PreConditioning Unit (PCU) and a twin screw extruder, is also ready to take on challenging homogenisation processes. These machines, as well as the new DuaFil Compact and various filter solutions, are available for trials at the Erema customer centre and in the R&D lab. Digital assistance systems also make a major contribution to efficiency in plastics recycling. BluPort is Erema’s online customer platform that is viewed as cutting edge in the recycling industry. BluPort contains apps for quality control and machine maintenance. The PredictOn app, for example, collects real-time data and enables predictions to be made about upcoming maintenance work, which increases machine uptime and productivity. The Spare Parts Online App makes it much easier to order spare parts. www.erema-group.com With Netstal’s leading preform injection molding technology. Our PET-Line impresses with broadest compatibility, maximum throughput, exceptional ĆďĆēĈĚ ĆħĄĊĆďĄĚ ĐđĕĊĎĂč đēĐĄĆĔĔĊďĈ Đć ē÷ìû Ăďą other challenging recyclates, and with its intuitive Axos control unit. Wemaximize your đēĐąĖĄĕĊĐď ĆħĄĊĆďĄĚ Preforms Fakuma I B3-3119"},{"@ID":27 "BOTTLING / FILLING PETplanet Insider Vol. 25 No. 09/24 www.petpla.net 25 BOTTLING / FILLING 25 Sterile water was produced by non-heat sterilisation using medium-pressure UV lamps and sterilisation filters. These were mixed in the aseptic blender and filled aseptically by filler. More than 10,000 media-filled bottles were incubated per test. After one week of incubation at 30°C, all bottles were visually inspected to ensure there were no spoilt bottles. This media fill test was carried out three times, and afterwards, all tests confirmed zero spoilage. These test results confirmed the confidence in Green Aseptic and allowed production to start, as planned, on April 1, 2024. Creating future standards The history of aseptic packaging began in the 1960s. The technology fills heat-sterilised products into sterilised packs in an aseptic environment. Products that cannot be heat sterilised are filtered and sterilised using a 0.2μm sterilisation filter. However, 0.2μm sterilisation filters have been reported to allow ultra-small and filterable bacteria to pass through. DNP tested the UV resistance of these bacteria and found UV irradiation conditions that kill UV-resistant filterable bacteria at 12Log or more. By combining medium-pressure UV lamps with 0.1μm sterilisation filters, DNP successfully produced sterile water with the same level of sterility as conventional heat sterilisation without heating. This patented technology has enabled significant decarbonisation and energy savings in liquid processing equipment for low and high-acid beverages. DNP is committed to using its long-established aseptic technology to solve today’s societal challenges and contribute to the realisation of a sustainable society. www.dnp.co.jp/eng/group/aseptic-systems MP-UV lamps and sterilisation filters Aseptic filler ? SEE HOW MUCH YOU CAN SAVE HALL B3, STAND 3108 70% LESS ENERGY MAINTENANCE COSTS 90% LESS 70% REDUCTION IN CO2e 50% MORE PRODUCTIVITY The savings will vary based on your circumstances and should be reviewed with our sales team. [email protected] www.maguire.com Discover your potential savings. With just a few clicks, you’ll gain valuable insight into how ULTRA will positively impact your bottom line. 1. Go to ultra.maguire.com 2. Input your data. 3. Receive your customized PDF report of potential savings via email."},{"@ID":10 "8 NEWS PETplanet Insider Vol. 25 No. 09/24 www.petpla.net Chile inaugurates first plant to produce beverage bottles from recycled plastic Chile has launched its first plant dedicated to producing beverage bottles from recycled plastic. The facility, named Re-Ciclar, is a joint venture between Coca-Cola Andina and Coca-Cola Embonor, representing a US $35 million investment. The plant aims to recycle over 350 million bottles annually and integrate food-grade recycled material into Coca-Cola’s packaging in Chile. Re-Ciclar is noted for its use of sustainable technologies and is expected to generate 25,000 indirect jobs nationwide. It is combining state-of-the-art equipment imported from Italy, Japan, and Austria. The plant is part of a broader initiative to increase the recycled content in Coca-Cola bottles, starting with 15% rPET by 2025, with plans to reach 100% in the future. Re-Ciclar has a collaborative and inclusive model through strategic alliances with all members of the recycling chain, including grassroots recyclers, small, medium, and large managers, local governments, and territorial organisations, among others. In 2024, it expects to collect around 10,000 t of PET alongside its partners, including the National Association of Recyclers of Chile, Latitud R, La Ciudad Posible, and the collective action of citizens. www.embonor.cl Corvaglia Group strengthens expertise in the Board of Directors At an extraordinary general meeting of Corvaglia Group in mid-August 2024, Marc Aeschlimann was elected to the Board of Directors. To strengthen the division operations, the sole Shareholder, Romeo Corvaglia sought to expand the Board of Directors, leading to the selection of Mr Marc Aeschlimann. The Board of Directors now consists of Romeo Corvaglia (Chairman), Karel Strub (Vice Chairman) and Marc Aeschlimann (Member). Marc Aeschlimann is CEO of the Schaffner Group. Schaffner (now part of TE Connectivity) is a global leader in electromagnetic solutions that ensure the reliable operation of electronic systems. Previously, Marc Aeschlimann was CEO of companies such as the R&S Group, Pfiffner Messwandler AG and held various leadership positions within the Franke Group. Marc Aeschlimann originally studied electrical engineering at ETH Zurich and graduated with a Master of Science. He then completed an MBA at the USC Marshall School of Business. www.corvaglia.com Factory Acceptance Test of first commercial-scale PET cap manufacturing system completed Origin Materials, a technology company focused on sustainable materials, announced the successful completion of the Factory Acceptance Test for its Origin CapFormer System, which is claimed to be the first commercial-scale system for manufacturing PET caps and closures. The system uses thermoforming, slit-and-fold technology and proprietary design elements to enable the production of PET caps at a large scale. The test demonstrated over 98% manufacturing efficiency, validating the system’s performance specifications. Origin’s Co-CEO and Co-Founder, John Bissell, noted that the system addresses long-standing industry demand for PET caps, offering a commercially viable solut ion for PET-based packaging. The CapFormer System is designed to enhance recycling efforts by enabling 100% PET container-to-container recycling for the first time. The system is poised to produce PET caps for a variety of industries, including beverages, food packaging, and medical products. Origin’s PCO 1881-compatible caps, made from either virgin or recycled PET, will be available in Q4 2024, with PCO 1881-compatible tethered caps and other cap types to follow. www.originmaterials.com"},{"@ID":51 "45 EVENT PREVIEW PETplanet Insider Vol. 25 No. 09/24 www.petpla.net Netstal Hall B3 – Booth 3119 Medical technology application Netstal will demonstrate the production of 10 ml syringe barrels with Luer-Lock adapters using its all-electric Elion MED injection moulding machine with a 1,750kN clamping force. The process uses a precision eight cavity mould from Fostag and COC material from Topas, with a cycle time of approximately 20s. Integrated systems from Mouldflo, Motan Colortronic, and HB-Therm are claimed to ensure precise thermal control, material preparation, and temperature regulation. Automation is managed by SKA, featuring high-speed part removal, thermal imaging, and process data tracking, all linked to a unique identifier via QR code. The Elion MED machine operates with advanced control technology, including Axos9 and Responsive Filling Control (RFC), to ensure exact shot weight within validated tolerances. Additionally, cooling processes are monitored using Mouldflo’s thermal control system to maintain strict component quality. The SKA handling system removes the finished syringes and places them on a conveyor belt. The system communicates with the machine via Euromap 77 interface, providing real-time process data for consistent medical-grade production quality. www.netstal.com Cold Jet, Hall B3 – Booth 3110 New performance standards in dry ice blasting technology Cold Jet, well known for dry ice technology, will be presenting its new Aero 2 Ultra Series. This new product line has been designed to support the plastics industry in mastering the challenges of increasing efficiency. The Aero 2 Ultra machines are characterised by moisture-resistant mechanics and an advanced ultra-cold performing motor. The all-metal gearboxes improve durability, reliability and efficiency. The machine stability has also been upgraded with completely new proprietary control firmware and motor drivers, said Cold Jet. The Aero2 Ultra Series was developed to meet diverse needs: a plastics processor can clean many types of surfaces with one machine, such as the surface of injection moulds, deburring as well as injection screws. Cold Jet’s environmentally friendly dry ice is also used in the industry for deburring and de-flashing plastic parts. Duroplast parts (sometimes also thermoplastic parts) and the part geometries are not always suitable for tumbling. Cold Jet’s solutions for this are often fully automated. In a live demo, Cold Jet will show deeper insights into the processes. www.coldjet.com"},{"@ID":53 "BOTTLE MAKING 21 PETplanet Insider Vol. 25 No. 09/24 www.petpla.net from Bosnia Herzegovina. We were featured on TV and major news outlets and we found that distributors whose doors we had been knocking on for years were now calling us and wanting to do business.” For the next three years, English Mountain Spring Water grew at about 300% annually. That rate of growth is extremely hard to maintain and even to cope with but hard work and growing production lines enabled the company to capitalise and stabilise. It continued entering and gaining outstanding results at competitions across the world, including in Paris, France, where it won Bronze Medal three times in a row. There seems to be something special about its water, that it can compete with high-profile French brands in their own country. Natural goodness “Our source is a natural spring. We sit on about 145 acres (around 60 hectares) of land which is covered in virgin timber. The mountain is mostly limestone but there’s no hard water. It’s naturally alkaline – it comes out at about 7.8 pH – and there’s no industry close to us,” John continued. “The spring has what I would deem a perfect mineral blend. The key to water is having no taste; you don’t want it to leave an aftertaste, you want it to refresh you. Our slogan is ‘engineered by nature, bottled with perfection’; we say God made it, we just clean it up and put it in a bottle!” At many competitions, English Mountain was the only entrant that was packaging in PET and HDPE, rather than glass. Its early adoption of plastic packaging made it something of a pioneer. “A five-gallon (US) bottle made of glass is pretty heavy. It weighs in at around 80 pounds (36 kg) and it’s potentially dangerous. I met someone at a show who had a scar on his neck from a bottle that separated while he was carrying it. We decided early that we were not going to use glass, if it could be avoided.” Setting trends English Mountain’s five gallon bottles were made of PC (polycarbonate) and they deliberately went with clear plastic, rather than the fashionable cobalt tint, because they didn’t want customers to think they were hiding anything. PET was selected for smaller, eight-ounce (250ml equivalent) bottles, for presentation and flavour; John found that there was always a residual plasticky taste in foil-topped HDPE packages. Whether PCB or PET, the packages are lighter to transport than glass and there was hope that they would be recycled. “I looked at buying bottling lines at the time but the cost was just prohibitive,” he explained. “I went round a number of factories that bottled for Pepsi-Cola, for example, and I was advised that I needed an annual output of around 10 million units to make it worthwhile. That has always been my benchmark.” Stepping up a gear By 2017, English Mountain had reached 10 million/year and it was time to look seriously at blowing their own bottles. But John didn’t build up his company by rushing headlong into things and this was no exception. “There were some smaller units coming in from China but I was in contact with people who used them and had some bad experiences. As time went on, the equipment started to work better for small bottles and prices began to come down. That potential investment began to make more sense.” Apart from the economics of buying in, English Mountain was finding that quality and consistency of bought-in supplies was, increasingly, leaving something to be desired. There were too many failures and loss of product. It was getting expensive and was beginning to have a reputational impact. Flexblow came onto the scene at just the right time. “When their team came to see us, Gin was particularly impressed with how we manage our facility and he made clear that he wanted to make English Mountain Spring Water a showpiece. They listened to what we wanted, brought us a newly-designed moulder with preferential heating for a specific shape of bottle that I requested, and adapted their machine to suit. I decided that I could not pass up the opportunity and that’s when we pulled the trigger,” said John. The Flexblow Auto Quality line was installed in August 2023. It consists of a linear blow moulder, infeed system, compressor, chiller and fully automatic bulk packaging system. As its name suggests, it has fully automatic operational package: the operators simply input bottle parameters and the machine calibrates automatically. The machine also features integrated automatic quality assurance systems that eliminate any defective bottles, ensuring that only quality products proceed down the line. It is currently running in four-cavity format, producing 6,200 20-ounce (one Imperial pint or 568ml) containers per hour. It can also produce 12 fl oz/340ml packages at 6,000 to 6,200 bph. “Altogether we have six model sets: 12 fl oz, 20 fl oz, a couple of versions of 500ml and a 1 l. We have just ordered four more mould sets and we are bringing in tall and slender bullet bottles,” he said. “Our family of packages goes up to 1.5 l, all with 28mm neck finishes. But, with this machine, we can also run 38mm neck finish, which we can use with a one-gallon PET mould that we propose to roll out in the Fall of this year.” English Mountain Spring Water ran about 2.5 million bottles through the Flexblow machine from August to the end of 2023 and it is on track for five million before the end of July 2024."},{"@ID":52 "40 EVENT PREVIEW PETplanet Insider Vol. 25 No. 09/24 www.petpla.net organized by co-organized by 30. + 31. October 2024 Düsseldorf, Germany Maritim Airport Hotel ONLINE, Live-Stream World Congress Platinum Sponsor KOREA PACKAGING ASSOCIATION INC. Media Partner Premium Media Partner Supporter Diamond Sponsor www.pef-world-congress.com JOINING PLASTICS FÜGEN VON KUNSTSTOFFEN REGISTER NOW Sumitomo (SHI) Demag, Hall B1- Booth 1105 Eight IntElect machines at Fakuma Sumitomo (SHI) Demag exhibits will focus on demonstrating the tools and solutions that will conserve resources and increase performance in an economical, space and timesaving way. Featuring eight smaller-footprint IntElect machines, four on the main booth (B1-1105), and four more supporting partner showcases, demonstrating the switch to all-electric injection moulding to reduce environmental impact. Having developed an IntElect for every market segment, including automotive, electronics, packaging, medical and consumer, the company will present how they are now assisting processors to save even more energy. Energy efficient packaging machines Processing packaging materials in the most efficient way directly addresses one of the major operating expenses for mass-packaging moulders – energy consumption. Business Development Director Packaging, Arnaud Nomblot and his team will demonstrate advantages of switching to all-electric. Citing examples of up to 70% reduction in energy costs, this year’s packaging exhibit features an IntElect 2 S 220/660-1400, efficiently manufacturing four decorated food containers in PP, with an integrated IML side entry robot. The exhibit features a four-cavity mould tool from Société Nouvelle Caulonque. Feeding labels with precision into the packaging machine is an automated IML system supplied by Pagès Group, with iPB Printing B.V. supplying the high-quality labels and Total Energies providing the material. Providing greater processing transparency to help run machines at their most efficient, Sumitomo (SHI) Demag will unveil its advances in myAssist and how further optimisations offer processors even deeper data insights. These newest upgrades, summarised by the company as the ultimate ‘digital process companion’, present easy to read dashboards, consumption data and KPIs, all defined by the end user. The ability to connect and oversee digital data across multiple machines in a single production facility is also available. www.sumitomo-shi-demag.eu"},{"@ID":57 "The worldwide round trip with PET world in the Middle East In a spectacular project taking us well into 2024, we will be travelling in a wide variety of ways to various countries and regions of the Middle East with different mobile editors. There we will interview machine manufacturers, the supply industry, bottle and beverage producers, as well as PET recyclers and everyone involved in the process chain. What market-specific trends are there now or will arise in the future? What developments and technologies are in vogue on the consumer and plant construction site in some of the hottest regions of the world? What special requirements are there? What role do topics such as food safety, shelf life and sustainability play in PET packaging and how are companies preparing themselves for the coming years? This, and much more we will be discussing face-to-face with all the key players and then our results will be presented to you in a series of must-read reports in PETplanet Insider. Please join on this enchanting voyage to the world of PET in the Middle East. We look forward to welcoming you on board! Our previous Road Shows at a glance 2010-2011-2012-2013-2014-2015- 2016-2017-2018-2019-2020-2022 Interested in being visited? [email protected] Autumn 2023 - 2024 6 countries numerous interviews with PET companies Sponsors to date Editour The Middle East Roadshow"},{"@ID":6 "PETcontents 4 PETplanet Insider Vol. 25 No. 09/24 www.petpla.net 09/2024 EDITOUR 10 “We want to become a key supplier for the beverage industry” - Packaging solutions from a single source MATERIALS / RECYCLING 12 From bottles to preforms to rPET - Spanish processor relies on recycling equipment from Germany 14 PEF, polyester material of the future - First PEF World Congress in Düsseldorf, Germany MOULD MAKING 16 The importance of high-quality spare parts PREFORM PRODUCTION 18 18% reduction in water flow rate - Thermoscan technology enables Sacmi to achieve water savings in injection moulding BOTTLE MAKING 20 Tennessee two-step - English Mountain Spring Water Company boosted packaging quality with the installation of a blowing line from Flexblow BOTTLING / FILLING 24 Aseptic filling system with non-heated water sterilisation 26 Hattrick in Colombia - South American beverage multi Postobón installs three KHS lines 27 Boosting efficiency and sustainability - Coca-Cola Bottlers Nepal’s journey with Sipa-supplied complete filling line MARKET SURVEY 28 Suppliers of compressors COMPRESSORS 30 Improving compressed air efficiency in PET applications 34 US market key focus for growth - AF Compressors: celebrating three decades in the United States 36 Increased monitoring capabilities - Controller improves efficiency & reliability of high-pressure reciprocating compressors 38 Oil-free high-pressure compressor series launched - Adekom introduces KSP series high-pressure compressor for bottle blowing EVENT PREVIEW 39 Fakuma 2024 preview EVENT REVIEW 46 Compact preform system for long and heavy preforms (HOD) OUTER PLANET 54 Biodegradable polymers in various environments BUYER’S GUIDE 48 Get listed! INSIDE TRACK 3 Editorial 4 Contents 6 News 47 Patents COMPRESSORS Page 10 Page 16 Page 39 EDITOUR"},{"@ID":28 "BOTTLING / FILLING PETplanet Insider Vol. 25 No. 09/24 www.petpla.net 26 South American beverage multi Postobón installs three KHS lines Hattrick in Colombia With over 50 million inhabitants, Colombia is the second-largest state in South America after Brazil and one of the most substantial growth markets on the continent. Colombia’s best-selling beverage producer is Postobón, a big player that exports its products to 27 different countries worldwide. In the InnoPET BloFill, KHS combines stretch blow moulding technology with energy-efficient, flexible filling machinery. (Photos: Juan Cristobal Cobo) Its vast and highly diverse portfolio includes water and soft drinks as well as primarily juice, teas, energy drinks, beer and coffee. In its role as contract filler, the company bottles Pepsi, Gatorade, Mountain Dew and Seven Up, plus Lipton Tea and Heineken beers. Of its 71 facilities, 20 are production sites that accommodate more than 100 filling lines, 20 of which are used for PET bottles. The company’s two largest complexes are located in the capital Bogotá, a metropolis of ten million, and in Malambo, a suburb of Barranquilla in the north of the country, where a greenfield project designed to house a total of eleven lines was begun in 2018. Three block systems Whereas in the past Postobón’s long-term relations with KHS focused on the supply of stretch blow moulders, in 2018, the Colombian bottler opted for its first block system. The first procured line includes an InnoPET TriBlock for water in plastic containers that comprises a stretch blow moulder, labeller and filler. At a maximum capacity of 54,000 bph, the line is technically convincing with consistent neck handling from the preform to the bottled product. With the KHS’ Bottles & Shapes program, a 600ml bottle was specifically developed for this application that saves 10 g of material and weigh. One particularly remarkable attribute in the dry section of the line is the multifuel burner on the Innopack Kisters SP that enables the shrink tunnel to be flexibly heated by either natural or propane gas. In Postobón, the installation and the work performed by the team on site the company ordered two more block systems within the space of 18 months. The second KHS line went into operation in Bogotá in 2021. This is also a turnkey filling line where a BloFill duo block for the hotfilling (HotFill+) of juice, tea and energy drinks with optional nitrogen dosing forms the heart of the line. Finally, the third KHS line was installed at the aforementioned site in 2023 – with a TriBlock for carbonated beverages such as Pepsi Cola. “We value KHS as one of the world’s most renowned manufacturers of plant engineering,” says César Bohórquez, who as national project manager for Postobón coordinates the implementation of all strategic growth projects. “We’re impressed by their pioneering technological standards for high-speed lines. We count on KHS with respect to the growth of our business as one of our key technology partners. They develop extensive and efficient systems for our processes that perfectly meet Postobón’s growth requirements.” The most recent project to come out of the two companies’ technological partnership is a new KHS InnoPET Blomax V stretch blow moulder. Integrated into an existing PET line by Postobón’s own converter Iberplast at the Caloto bottling plant, with its 20 cavities it can produce up to 45,000 bph in sizes ranging from 500ml to 1 l. On the line, the containers are filled with beverages such as juice, tea and energy drinks at temperatures of up to 85 °C. Sustainable and climate-friendly It was important to the Colombians that the beverage containers use as little plastic as possible, besides quality and efficiency, sustainability and protection of the climate are further major issues the bottler invests considerable sums of money in. In 2021, approximately US$ 30 million were spent on various social and environmental programs. Postobón’s biggest water brand Aqua Cristal is filled into bottles made entirely of rPET that themselves are fully recyclable. All told, the legal requirements for the avoidance of waste are more than met: for instance, the Colombians are proud of the fact that 72% of the packaging materials circulated by the company are recovered and reused. This figure even runs to 95% for glass bottles. Any reduction in the amount of material used for the company’s PET bottles must not be allowed to have a detrimental impact on their stability, however. On the small-format bottles for juice and tea, whose weight has been cut from 22 to 20 g, this is mainly prevented by nitrogen being injected into the head space, thus increasing the interior pressure in the container until it’s first opened. The six feet on the bottle base provide added rigidity and sturdiness. www.khs.com www.postobon.com Postobón’s wide range of products not only includes juice, soda pop and energy drinks but also other carbonated soft drinks, water, beer, tea and coffee."},{"@ID":7 "MATERIALS / RECYCLING PETplanet Insider Vol. 25 No. 09/24 www.petpla.net 13 Crystal Thumb Up Our extended SportCaps range Biarritz NEW In sport, you never settle for less. That’s why we strive for the perfect closures, also when it comes to sustainability. Many closures, such as Biarritz and Monet, are made from a single material, making them easy to recycle. In addition, our sport closures are easy to handle, have integrated tamper evidence solutions and are suitable for cold, dry, or wet aseptic filling. So take the leap – and opt for more sustainability. NEW Monet Visit us at BrauBeviale Hall 4, Booth 219 Contact us and arrange your line trials now! www.bericap.com New mono-material caps for optimized recyclability Going the extra mile for you"},{"@ID":9 "7 NEWS PETplanet Insider Vol. 25 No. 09/24 Z-Moulds Pty. Ltd. appoints David Chalmers as Vice President of new Sydney branch Z-Moulds has announced the expansion of its operations with the establishment of a new sales and service branch in Sydney, Australia. The new branch, Z-Moulds Pty. Ltd., became officially operational in September, marking a key step in the company’s growth. The expansion is aimed at enhancing service and product availability to customers across the region. David Chalmers’ experience in the closure and packaging industry spans over 30 years. His journey with Z-Moulds began in 2011, during his tenure at Coca-Cola Europacific Partners (formerly CocaCola Amatil), where he played a pivotal role in the company’s decision to self-manufacture both closures and preforms. Before joining CCEP, Chalmers had already built a strong foundation in the industry, having served as a Senior Technical Specialist at the Asahi Group for five years and as a Commercial Service Manager at the Pact Group for over a decade. During his t ime at CCEP, Chalmers col laborated wi th Z-Moulds on the Sylon closure project, an initiative that achieved recognition within the Coca-Cola system for its innovations in closure design, weight reduction, and cycle time efficiency. Under his leadership at CCEP, the company installed 11 Z-Moulds systems across Australia and Indonesia. The appointment of Chalmers is seen as a strategic move to strengthen Z-Moulds’ presence in Australia and further i ts commi tment to providing advanced solutions in the closure and packaging sector. www.z-moulds.com CREATING FUTURE STANDARDS Japan’s leading Aseptic PET Filling System Provider. Our website Our solution high quality reliable technology safe & secure"},{"@ID":20 "PREFORM PRODUCTION PETplanet Insider Vol. 25 No. 09/24 www.petpla.net 18 Thermoscan technology enables Sacmi to achieve water savings in injection moulding 18% reduction in water flow rate Blow moulding machinery manufacturer Sacmi has significantly reduced water consumption in PET bottle production by integrating BMT’s Thermoscan technology to optimise their injection moulding cooling processes. The Thermoscan, a patented precision offline instrument developed by Blow Moulding Technologies (BMT), measures and analyses preform temperature profiles to enhance resource efficiency, reduce operational costs, and minimise environmental impact. The temperature of the preform after injection moulding plays a crucial role in both its quality and energy consumption. Optimising cooling during injection moulding offers a range of benefits, including enhanced resource efficiency, faster cycle times and reduction in energy usage, which consequently reduce operational costs per part. Scrap rates are decreased and there are savings in raw materials, too, further reducing environmental impact. BMT, based in Belfast, Northern Ireland, are pioneers of stretch blow moulding (SBM) technology for sustainable packaging solutions. It believes that data driven measurement is essential for improvement and optimisation. Sacmi identified BMT’s Thermoscan as a suitable stand-alone solution to accurately measure and digitise their cooling process. Thermoscan is a patented precision offline instrument that simultaneously measures the internal and external temperature profiles of preforms extracted from the production line and uses proprietary software to analyse and evaluate through-thickness temperature distribution. It quantifies the influence of key machine parameters on the preform temperature profile and displays their direct impact on the integrated screen. Instant feedback provides operators with the means to systematically explore various process combinations and optimise production lines. “Using Thermoscan, we can get the right data to make critical decisions,” said Francesco Macchia, PET Injection Moulding Specialist, Sacmi. In a recent case study, Sacmi methodically adjusted flow rate to optimise their injection moulding cooling process, with the intention of reducing operational costs. It first configured their machines to a preset process that produced high-quality preforms, then used Thermoscan to measure temperature distribution and establish a reference profile. Sacmi then systematically reduced water flow rate, measuring the preform temperature profile with each change, while maintaining constant cycle times and heating conditions. Thermoscan provided quantitative comparison against the target profile, enabling data-driven decisions and eliminating subjectivity from the process. The graph shown in Figure 1, generated by Thermoscan, displays preform temperature profiles of the initial (reference) and final (optimised) processes. It demonstrates nearly Figure 1: Thermoscan temperature profiles with varying flow rate"},{"@ID":44 "42 EVENT PREVIEW PETplanet Insider Vol. 25 No. 09/24 www.petpla.net Motan, Hall B1 - Booth 1111 Advanced dosing and mixing solutions Motan, known for materials management, presents new additions to its portfolio of reliable and precise gain-in-weight dosing and mixing units, particularly for the medical and pharmaceutical sectors. Additionally, the Motan Group will highlight its Swift brand, known for combining high quality with exceptional price-performance ratios. Flexible and reliable dosing, FDA-compliant The Gravicolor 310 and 610 Gravimetric dosing and mixing units feature Motan’s cone dosing system, allowing precise mixing of up to eight materials with recipe accuracy. Their modular design ensures optimal performance, flexibility, and reliability in injection moulding, blow moulding, and especially extrusion applications. For the medical and pharmaceutical industries, the company introduces the Gravicolor 110 med. This FDA-compliant unit, designed for injection moulding, blow moulding, and extrusion, utilises vertical slide technology for precise mixing of up to four materials, ensuring maximum recipe accuracy. All Gravicolor units are equipped with the enhanced Intelliblend analysis function, which records and documents recipes, materials, and operating environments. This selfoptimising system ensures users achieve the best possible working point continuously. Swift brand The Motan Group’s Swift brand will showcase several products claimed to emphasise simplicity and efficiency: sDry 250 dry air generator: It offers energy efficient drying with good dewpoints and advanced features as standard. sCompact dry air dryer: Available in various sizes, for single or twin processing machine applications. The flexible dryer with integrated conveying and the option of controlling a dosing & mixing unit via its full colour touch display. sConvey Hos material loaders: Cost-effective and efficient conveying process automation. sColor V additive dosing & mixing unit: Ideal for masterbatch and regrind dosing applications, offering quick delivery and cost-effective performance. www.motan-group.com Engel Halle A5 - Booth 5203 Solutions with a focus on customer benefit At the heart of Engel’s presentation are high-precision injection moulding machines designed for modern production environments, with enhanced material and energy efficiency. The fully electric e-mac 500 injection moulding machine, with a clamping force of 5,000 kN, is claimed to combine high performance with energy efficiency and a compact design. Its clamping drive and iQ motion control digital assistance system reduce energy consumption by up to 30% compared to hybrid or hydraulic machines, according to Engel. The e-mac 500 is versatile, with optional expansion packages, making it suitable for energy-intensive processes. At the trade show, it will be producing 4 l containers with in-mould labelling. Tie-bar-less technology Engel has optimised its e-victory 100 for high-precision liquid silicone rubber (LSR) applications. With a 256 cavity mould, it is claimed to achieve a cycle time of 12 s and to ensure consistently high part quality. Thanks to Engel’s tiebar-less technology, the entire platen surface is utilised, thus optimising clamping force. Plug-and-play solutions for the European market Engel is introducing the new generation of t-win machines from its Wintec brand, featuring over 20 new options. These include iQ clamp control for optimising clamping force, reducing waste, energy use, and tool wear, and iQ hold control, which automatically adjusts holding pressure to speed up volume production. Many more options will be available by the end of 2024. Additionally, Engel will showcase the victory 160, producing fittings at the show, as well as digital assistance systems that optimise the production process from design to volume production and service. In the “Automation Expert Corner,” Engel will present solutions with viper linear robots, easix articulated robots, and conveyor systems, all seamlessly integrated into Engel’s control systems for process optimisation. www.engelglobal.com"},{"@ID":41 "39 EVENT PREVIEW PETplanet Insider Vol. 25 No. 09/24 www.petpla.net TRADE SHOWpreview Fakuma 2024, the 29th edition of the international trade fair for plastics processing, is set to take place from October 15 to 19 in Friedrichshafen, Germany. The event will feature a variety of highlights, including the second edition of the “Round Table at Fakuma” discussion on digitalisation, a dedicated start-up area, an exhibitor forum with expert presentations, and the unveiling of the “cradle to cradle” design concept at the opening press conference. Organisers anticipate a strong international presence, with 12 halls and two foyers fully utilised for the event. The ‘Round Table at Fakuma’ will take place on Tuesday, 15 October 2024 at 4pm. Under the heading ‘Digitalisation – Top or Flop?’, a select group of experts will discuss which digital tools can really help the plastics industry meet the challenges ahead. The five panellists, Prof Dr Michael Braungart, founder and scientific director of Braungart EPEA, Philipp Lehner, CEO of the Alpla Group, Guido Frohnhaus, Managing Director for Technology at Arburg, Prof Dr-Ing Hans-Josef Endres from the Institute of Plastics and Circular Economy at Leibniz University Hanover and Prof Dr-Ing Thomas Seul from the Schmalkalden University of Applied Sciences will assess the state of digitalisation in the industry. The panel will examine the extent to which digitalisation offers solutions in the areas of sustainability and the shortage of skilled workers. The Fakuma roundtable will be moderated by Dipl-Ing Markus Lüling, editor-in-chief of K-Profi. All interested parties are invited to attend the discussion; participation is free of charge. www.fakuma-messe.de ASIA 13–14 November 2024 Marina Bay Sands, Singapore 2024 will see the launch of the Plastics Recycling Show Asia. PRS Asia will be held in Singapore in November 2024. Register for FREE entry at: www.prseventasia.com Organised by Supported by In association with MIDDLE EAST & AFRICA 10-12 September 2024 Dubai 1-2 April 2025 RAI, Amsterdam Held in"},{"@ID":31 "MARKET SURVEY 29 PETplanet Insider Vol. 25 No. 09/24 www.petpla.net Company name Atlas Copco Adekom (Asia Pacific) Limited Dalgakıran Compressed Air Technologies Postal address Telephone number Web site address Contact name Function Direct telephone number E-Mail Boomsesteenweg 957, 2610 Wilrijk, Belgium www.atlascopco.com Mr Kris Vermeulen Global Product Manager PET +32 3 870 2111 [email protected] Suite 2311, 23/F., BEATower Millennium City 5, 418 Kwun Tong Rd, Kwun Tong, Kowloon, Hong Kong +852 2177 0757 www.adekom.com.hk Mr Raymond Chan Director + 852 977 80 500 [email protected] Eyup Sultan Mah. Muminler Cad. No:70 Sancaktepe / Istanbul, Turkey +90 216 311 71 81 www.dalgakiran.com Mr Alp Halil Yörük Strategic Marketing Director +90 216 311 71 81 [email protected] 1. Machine designation / model number ZP, ZP VSD ZD FF, ZD VSD FF ZD Xtend ZD Flex KSP-20/40PM Rotary screw, reciprocating and turbo compressors 2. Number of models in range 3 18 56 2,500 11 standard models 25 3. Output in m³/hour 170 - 835 902 - 4,195 500 - 7,500 400 - 10,000 from 360Nm3/h to 1,800Nm3/h 0.16 - 20,000 4. Compressor type 55 - 132 820 - 4,100 90 - 900 / 85 - 315 55 - 2,500 / 55 - 315 Skid mounted screw+piston booster tandem design Low pressure air Separate unit needed, full range available Separate unit needed, full range available Included; fi xed 10bar Included; to choose 6-10bar Yes, available as option, up to 15bar Tidy, D Series High pressure blowing air (up to 40 bar) 3-stage piston 2-stage screw + adsorption dryer + 2-stage piston 2-stage screw + adsorption dryer + 2-stage piston 2-stage screw or 3-stage turbo + adsorption dryer + 1- or 2-stage piston Yes, standard design in 30bar/40bar Pet Master, turbo compressors Integrated system Fixed speed & VSD range Fixed speed & VSD range Fixed speed & VSD range Fixed speed & VSD range Matching skid mounted HP air dryer + HP inline fi lters available DPR-D 5. Lubricated or oil-free Oil-free Oil-free, Class0 Oil-free, Class0 Oil free, Class0 Version A: 100% class 0 oil-free design; Version B: class 1 with oil content in discharge air 0.01ppm Low pressure compressor Piston 2-stage screw + adsorption dryer 2-stage screw + adsorption dryer 2 stage screw or 3 stage turbo + adsorption dryer In one skid Scroll Booster compressor Piston 2-stage piston 2-stage piston 1- or 2-stage piston In one skid Booster series Integrated system Air cooled Adiabatic water cooling available Adiabatic water cooling available Adiabatic water cooling available Available as option Eagle 6. Machine layout Balance opposite piston Oil-free screw balance opposite piston Oil-free screw balance opposite piston Oil-free screw or Centrifugal Balance opposite piston See below 7. Number of compressor stages 3 4 4 3 or 4 or 5 1st stage screw airend: single stage or 2-stage for energy saving; 2nd stage reciprocating booster pump head: two stage Single and double 8. Are special foundations required ? Industrial fl oor, no need for thick concrete or anchoring Industrial fl oor, no need for thick concrete or anchoring Industrial fl oor, no need for thick concrete or anchoring Industrial fl oor, no need for thick concrete or anchoring No 9. Cooling system Not needed (integrated) Seperate water system: Dry fan, adiabatic or evaportive type Seperate water system: Dry fan, adiabatic or evaportive type Seperate water system: Dry fan, adiabatic or evaportive type Air-cooled / water-cooled models available No 10. Belt or direct drive Low pressure compressor Belt Gearbox Gearbox Gearbox, direct drive Direct drive Tidy, Inversys Plus Booster compressor Belt Belt Belt Belt Direct drive Pet Plus, Inversys DPR, Impetus Integrated system Yes, refrigerant dryer Yes, energy-free adsorption dryer Yes, energy-free adsorption dryer Yes, energy-free adsorption dryer DVK-D, Inversys Plus"},{"@ID":3 "No.9 2024 www.petpla.net D 51178; ISSN: 1438-9452 30 . 09 . 24 M A G A Z I N E F O R B O T T L E R S A N D B O T T L E - M A K E R S I N T H E A M E R I C A S , A S I A , E U R O P E A N D A L L A R O U N D T H E P L A N E T PETplanet is read in 159 countries MARKETsurvey Suppliers of compressors Page 28 COMPRESSORS EDITOUR Page 39 Page 30 Page 10"},{"@ID":34 "COMPRESSORS PETplanet Insider Vol. 25 No. 09/24 www.petpla.net 32 up as much as in conventional systems; heating air is a waste of energy. Traditional compressors address this issue by cooling the air between compression stages. The slow liquid piston process provides ongoing heat exchange between the compressed air, the water, and the ground the tanks are buried in; the air is kept at a near-constant temperature, so energy consumption remains low throughout the process. The concept has been successfully validated, and the company is looking at prospect sectors, including glass blowing and mainly PET bottle production. Water for compression Compressors in traditional air system use an electric motor to rotate metal pistons that pump to compress air, these motors are replaced by hydraulic water pumps. The ‘liquid piston’-water is pumped into a chamber and compresses the air in it over 20% more efficiently than conventional compression. This is due to the inherently higher efficiency of water pumps, and the near-isothermal process that results in negligible energy losses, according to Dr Yogev. A demonstration system, built in 2023 at Augwind’s R&D site in the Arava area in Israel, is made up of three pumps, two compression chambers that serve as the liquid-piston, and another chamber as a reservoir of compressed air, typically held at 7bar, although 42bar is theoretically possible by adding two pumps in series. When pressure falls, the upstream elements are called upon to replenish the reservoir. This happens automatically and pressure is maintained at a constant level, enabling fluctuating demand to be met without inefficient surges and shutdowns. Compression happens slowly, so the air does not heat Water Compressor setup COMPRESSORS Water Compressor demo site"},{"@ID":35 "COMPRESSORS PETplanet Insider Vol. 25 No. 09/24 www.petpla.net 33 Applications to PET “This is the core principle. After more than seven years of learning experience with AirSmart, and after accomplishing the compression process at our R&D site, we understood that our liquid piston mechanism has a unique value proposition for industrial compressed air applications,” said Ido. “Our technology offers a number of energy consumption and operating cost advantages to PET bottle converters and filling operations. However, it is a larger scale system and it is not a cheap option for SME businesses.” “At the moment, we are competing with 25 to 42 bar oil-free compressors – of which 70% of applications are PET blowing,” he continued. “Our focus now is on PET applications between 2,000m3/h and 10,000m3/h. Based on the performance at our R&D site, a HydroAir system running at 4,000m3/h at 32 barg [33 bar absolute assuming atmospheric pressure of one bar] average consumption would be 526kW.” Augwind reckons that full ROI (return on investment) of the capital expenditure would be achieved within four years, based on electricity at €0.10 per kWh and €0.20 per cubic metre of water, through energy savings alone. Switching cost from Opex to Capex Augwind’s Water Compressor is claimed to be at least 20% better than the current best in class in terms of energy consumption, and that is before considering the elimination of need for cooling water. As the compressing medium is water, there are potential advantages in regulatory decarbonisation schemes, as well as lower operations and management costs; the entire system is claimed to be more efficient than conventional technology because correct pressure is always maintained and is constantly available. There are no losses from continual shutdowns, stops, idling and restarts. “These are the main advantages of our liquid-piston Water Compressor: lower electricity bills; no oil in the system; and no need for running cooling water,” said Ido. “We bring great ROI for any market that strives for carbon reduction and increased energy efficiency by accumulating long term energy savings. We are now seeking and looking forward to recruiting partners for demonstrator units and to work with us in developing the technology further.” www.aug-wind.com Cost structure (sources: Augwind)"},{"@ID":14 "MATERIALS / RECYCLING PETplanet Insider Vol. 25 No. 09/24 www.petpla.net 12 Spanish processor relies on recycling equipment from Germany From bottles to preforms to rPET The company Nosoplas, which was founded in 1996 in Bergondo, Galicia, Spain, by our interview partner Jose Carlos Piñeles, initially specialised in PET bottle blowing on the Iberian Peninsula before producing its own preforms some years later and increasingly focusing on rPET processing and production from 2012. Recycling systems from the German manufacturer Britas are used for this – the company recently added a fully automatic Britas band melt filter to the line. With an expected recycling throughput of around 43,000 t of post-consumer PET bottles this year, Nosoplas is contributing to the current massive demand for food-grade recyclate. Britas ABMF-1050-PET-C “Our original business was blow moulding PET bottles for CocaCola bottlers in Spain and Portugal,” explained General Manager Jose Carlos Piñeles in our interview. The company founder has been working in the packaging industry since 1986 and knows it like the back of his hand. “We later moved into injection moulding and started producing our own preforms in 1999, before turning our attention to sustainable packaging and rPET in 2012.” And the demand for high-quality recycled PET in Spain and Portugal proves the company right. “We definitely wanted to be one step ahead of the competition in this important area. Meanwhile, in addition to this factory in Bergondo, we have also been operating another one in the centre of the country in the city of Tarancon, Cuenca, since 2020 for logistical reasons.” The company currently sells around 42,000 t/a of rPET pellets. The corresponding post-consumer PET bottles are sourced exclusively from the EU. “Like everywhere else, we are confronted with a natural variability in the quality of the collected raw material. This is currently the major challenge for all recyclate producers who want to produce high-quality material that can ultimately be used in food contact,” explained Mr Piñeles. Legally prescribed minimum quantities of recyclate in packaging would then drive demand even higher. “We produce rPET with different viscosities, depending on customer requirements. The most common range is from 0.76 to 0.84, with 0.80 being in high demand for bottle-to-bottle.” In the process, the flakes are inspected using an inspection system before they are fed into a wet cutting system and finally a Solid State reactor via a drying, extrusion and filter melting process using Britas equipment. The ABMF-1050-PET-C band melt filter was recently added to the line and ensures that the process is characterised by a particularly high degree of filtration and that very little waste is produced during the process, which, according to the company, leads to the lowest costs for consumables. In addition to the beverage industry, which accounts for over 90% of Nosoplas’ output and whose main customers are Coca-Cola European Pacific Partners (CCEPP) bottlers, the recyclate produced is also used in the textile and detergent sectors. Nosoplas uses around half of the company space at both sites, around 1,000m2 each, for rPET production and employs a total of 110 people. And the company is growing rapidly: we were told that turnover had doubled since the Tarancon plant opened, reaching US$ 130 million in 2023. Competitors in the market include Novapet, Plastipak, Alpla and Retal. “What sets us apart is our comprehensive customer service, flexibility and adaptability to customer requirements,” concluded Mr Piñeles. Nosoplas is currently planning further investments and expansion in the areas of sustainability and energy reduction. www.linkedin.com/company/nosoplas-sl by Kay Barton"},{"@ID":39 ""},{"@ID":54 "BOTTLING / FILLING PETplanet Insider Vol. 25 No. 09/24 www.petpla.net 24 Aseptic filling system with non-heated water sterilisation Water is the main ingredient in soft drinks. To achieve decarbonisation in soft drink production process, Dai Nippon Printing Co., Ltd. (DNP) has developed a new generation of Green Aseptic, a processing system for non-heat sterilisation of water. DNP’s PET bottle aseptic filling solution for low-acid beverages using non-heat sterilisation was installed at a major beverage producers’ factory in Shizuoka Prefecture, Japan, with production starting in April 2024. Due to increased demand the new factory was built in March 2024 to produce soft drinks and provide warehousing facilities. With the DNP system, the product concentrate is heat sterilised in a small UHT steriliser and diluted with non-heat sterilised, but sterile water. After being mixed in an aseptic blender, the product is filled with an aseptic filler. Compared to the conventional method of sterilising product liquids using UHT sterilisers alone, this new aseptic processing achieves approximately 80% decarbonisation and energy savings, said DNP. This new sustainable system is called Green Aseptic. Green Aseptic Mount Fuji’s underground water is naturally filtered over a long period of time. The company uses this water as a raw material to produce clear, fullflavoured tea and mineral water. To make the tea, carefully selected tea leaves from Japan are steeped in hot water within an extractor to maximise the flavour and richness of the tea leaves. They are then sterilised in a small UHT steriliser and sent to an aseptic tank. High-temperature, shorttime sterilisation in the UHT steriliser preserves the original flavour and colour of the teas. Water is pumped up from approximately 180m below ground and, after removing foreign matter, is sterilised using powerful UV lamps and sterilisation filters. DNP focused on Atlantium’s HOD system, which uses mediumpressure UV lamps that have proven their worth as disinfection devices for raw water in beverage production. After repeated sterilisation tests in the laboratory, the lamps were modified to specifications for use in aseptic zones. The sterilisation filters are automatically subjected to ‘integrity testing’ where the pore sizes of the filters are checked before and after production to ensure that sterility is not compromised, while maintaining the precise aseptic conditions. To further extend the life of the 0.1μm sterilisation filters, DNP’s F0 solution has been installed, performing SIP on these filters, minimising the effects of thermal damage to the filters. By combining these particular Atlantium medium-pressure UV lamps and customised 0.1μm sterilisation filters, DNP produce sterile water for low-acid beverages in large quantities without heating. UHT-sterilised tea extract and virtually carbon-free sterile water are aseptically mixed at a high dilution factor. Then 500ml PET bottles are aseptically filled at 36,000bph. All conventional heat-sterilised sterile water used for rinsing bottles, closures and chambers in the aseptic filling machine has been replaced by non-heated, sterile water. Aseptic verification Aseptic verification was carried out to determine whether the Green Aseptic system was as sterile as a conventional UHT steriliser. This verification was conducted on site by Aseptic Systems Co., Ltd. (APS), DNP’s aseptic technology department. The method was to first heat sterilise a highly concentrated pH7 media broth in the small UHT steriliser."},{"@ID":16 "MATERIALS / RECYCLING PETplanet Insider Vol. 25 No. 09/24 www.petpla.net 14 First PEF World Congress in Düsseldorf, Germany PEF, polyester material of the future by Michael Thielen, Publisher of Renewable Carbon Plastics Magazine There is no doubt that plastics based on fossil raw materials are problematic in terms of climate change and limited resources. In many cases, plastics made from renewable raw materials already represent an interesting alternative. A comparatively new biobased plastic is polyethylene furanoate (PEF). Chemically, the aromatic polyester material is similar to the well-known commodity plastic PET, which is made from monoethylene glycol (MEG) and terephthalic acid. HO Terephthalic acid (TA) OH O O Furan- dicarboxilic acid (FDCA) HO OH O O O Figure 1: Building blocks of PET (terephthalic acid) and PEF (furandicarboxylic acid) (Source: Renewable Carbon Plastics) While biobased MEG is already being used in some cases for PET, the production of terephthalic acid from renewable raw materials has not yet been sufficiently developed. With the biobased furandicarboxylic acid (FDCA), PEF can therefore be a 100% biobased alternative for PET. Compared to PET, PEF is also characterised by improved properties, such as higher structural strength, better thermal properties and strongly improved barrier behaviour. PEF can be used for a variety of commercial applications, including bottles, films, food packaging, textiles, carpets, electronics applications and in the automotive sector. Another advantage of PEF is that it can be processed on the same equipment that is used for PET, other polyesters and often even other plastics. In many cases, only changes to the process parameters are required, as is usually the case when switching between different materials. Properties PEF is comparable to PET in many respects: It is a transparent and relatively rigid polymer. However, there are some notable differences between PEF and PET. PEF has a glass transition temperature of 86 °C, which is ~10 °C higher than PET. In the packaging industry, the remarkable barrier properties of PEF represent a significant improvement over PET. PEF has a ten times higher oxygen- and a 15 times higher CO2 barrier and two and a half times as high a water vapour barrier as PET. In addition, the strength and modulus of PEF are significantly higher than those of PET. For brand owners and packaging developers, the improved properties of PEF offer a range of innovation opportunities such as extending shelf life, further reducPET bio-PET (30) e.g. Coca-Cola plantbottle® 100% biobased MEG therephthalic acid therephthalic acid bio-MEG furandicarboxylic acid bio-MEG Figure 2: PEF can be a 100% biobased alternative for PET (Source: Renewable Carbon Plastics) Higher Tg (by about 10°C) Lower Tm (by about 30- 40 °C) Improved barrier to CO2, O2 and water vapor. Better metal adhesion 16—20x better CO2 barrier Light weighting potential (60% higher modulus &strength) Bio-based with PET-like mechanical properties 10x better O2 barrier PEF can be processed in existing PET lines PEF is complementary to PET PEF for flexible packaging PEF for CSD PEF resin General PEF for rigid packaging PEF for fibres & textiles PEF for oxygen sensitive drinks Figure 3: PEF application examples (Picture: Avantium)"},{"@ID":56 "OUTER PLANET 54 PETplanet Insider Vol. 25 No. 09/24 www.petpla.net OUTER PLANET Biodegradable polymers in various environments The world’s leading poster on biodegradability has been updated by the Nova team of experts: current standards and certifications as well as the latest scientific findings. The biodegradation of a material is a process that depends on the complex biological conditions at each site. In addition, only a handful of polymers have the inherent ability to biodegrade in different environments. Therefore, specific standards and certificates have been developed in recent years to provide a framework for declaring whether or not a product can biodegrade in an environment. Scientific verification and certification of the communication of environmental claims is becoming increasingly important under the Green Claims Directive. Biodegradability is one environmental claim that will need to be verified by third party certification. In order to improve the understanding of biodegradation and biodegradability and their certification, a group of experts came together a few years ago to develop a poster showing which polymers biodegrade in which environments according to established standards and certification schemes. This group includes experts from the Nova Institute (Germany) together with a number of leading experts from Normec OWS (Belgium), Hydra Marine Science (Italy/ Germany), IKT Stuttgart (Germany), Wageningen University & Research (The Netherlands) and in cooperation with Din Certo (Germany) and TÜV Austria (Austria/Belgium). The expert group met again this year to discuss the latest scientific evidence in the field of biodegradable polymers in order to make meaningful changes to the poster. The generic classification on the poster is only supported by tests performed in the context of certification. Therefore, the expert group decided to include the biodegradability of polycaprolactone (PCL) in additional environments: soil, freshwater, marine and anaerobic conditions. In addition, a new certification for marine biodegradability has been published by Din Certo in 2023, based on ISO 22403, the standard that provides requirements for marine biodegradability, and is now mentioned on the poster. A new poster design and a more precise definition of biodegradation and biodegradability complete the update for this year. www.nova-institute.eu"},{"@ID":55 "MOULD MAKING PETplanet Insider Vol. 25 No. 09/24 www.petpla.net 16 The importance of high-quality spare parts by Heike Fischer A machine should run, run, run and run... To keep it that way, the wearing parts of the machines must be replaced regularly. The Canadian company UM Inc. is a well-known manufacturer of alternative spare parts for blow moulding, filling, sealing and labelling machines for PET as well as for form-fill-seal machines, serving over 500 clients in more than 40 countries. PETplanet spoke to Arnaud Vital, President & CEO of the company, to learn more about the company’s portfolio, the market situation and high demanding spare parts. PETplanet: Dear Arnaud, may I kindly ask you to introduce your company in a few words? Arnaud: UM Inc., a premier Canadian enterprise, excels in manufacturing and supplying top-tier industrial components for the bottling industry. Our specialisation in blow moulding is complemented by our expertise in providing high-quality parts for filling, sealing, and labelling machines. Founded in 1976 as a local machine shop handling bespoke orders, UM Inc. embarked on a transformative journey in the 1990s with our strategic entry into the PET market. This pivotal move catalysed a period of strong growth, leading us to expand into a state-ofthe-art facility in Saint-Remi, QC. Three years ago, I had the privilege of acquiring UM Inc., and alongside our exceptional team, we have driven remarkable progress. This year alone, we are on a trend of a two-fold growth on our sales! We now proudly serve over 500 clients across more than 40 countries, and our global footprint continues to expand. PETplanet: Machine manufacturers provide their customers with maintenance and warranty services for machine parts. When do customers usually turn to you? Arnaud: At UM, our goal is to support our clients at every stage of the production process, enabling them to save valuable resources without compromising on quality or lead time. We aspire to be more than just a supplier; we aim to be a trusted partner, ready to assist with production issues and swiftly get machines back up and running. Our agility and proactive approach reflect our respect for time and our commitment to finding solutions. We have carefully built the UM brand around three core principles: quality, price, and lead time, all while maintaining a partnership-oriented approach. Each year, we invest significantly in expanding our product offerings to meet our clients’ evolving needs. By strategically enhancing functionality and strength, we ensure that our solutions continue to drive success for our clients. Our engineers are dedicated to making the right choices to support and improve their operations. We believe that by consistently doing what’s best for our clients, success naturally follows. PETplanet: You have published an impressive list of partners and customers from the blow moulding and filling industry on your homepage. This speaks for the high quality of your spare parts and comprehensive service. What costs do your customers save if they order spare parts from you instead of from the manufacturer of the original machine? Arnaud: Over the years, we have built robust client partnerships through a strategic and focused approach that remains at the heart of our operations. Our ability to deliver cost savings is a significant competitive advantage, with savings typically around double the industry average, all while maintaining uncompromised quality and competitive lead times. We pride ourselves on being leaders in providing alternative spare parts, but our process is meticulously strategic. We carefully select parts that offer the most potential for improvement, ensuring we deliver enhanced value to our clients. For instance, our moulds shell line is a standout success, where we consistently surpass expectations in quality, pricing, and lead times. PETplanet: Where do you produce your spare parts? Do you offer guarantees on your spare parts and have you patented them?"},{"@ID":2 "No.9 2024 www.petpla.net D 51178; ISSN: 1438-9452 30 . 09 . 24 M A G A Z I N E F O R B O T T L E R S A N D B O T T L E - M A K E R S I N T H E A M E R I C A S , A S I A , E U R O P E A N D A L L A R O U N D T H E P L A N E T PETplanet is read in 159 countries MARKETsurvey Suppliers of compressors Page 28 COMPRESSORS EDITOUR Page 39 Page 30 Page 10"},{"@ID":4
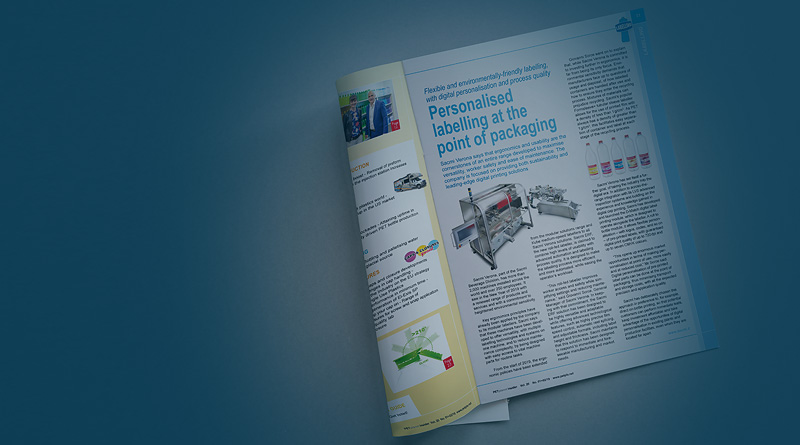