{"pages":{"page":[{"#text":"Vol.6 PETplanet print PREFORM PRODUCTION 24 PETplanet insider Vol. 11 No. 05/10 www.petpla.net The Rapid Guide to Perfect Preforms by Rick Unterlander and Ottmar Brandau Troubleshooting guides have suffered in the past from being locked away in offices and not being available to the people that actually need them. Considering the high cost of machine and tools, high scrap rates can be a costly proposition eating away at already tight margins. PETplanet’s “Rapid Guide to Perfect Preforms” takes a different approach. Bound in laminated paper that is easy to wipe clean, the small format of the book of 108mm by 151mm (4.25” by 6”) allows easy storage in back pockets or tool boxes. It has been written for the people on the floor of injection moulding companies to support their daily work in making the best preforms possible. The product of two industry experts, Rick Unterlander and Ottmar Brandau, it gives concrete advice on 35 of the most common problems in preform manufacture, most illustrated by pictures. From high AA levels to wavy bodies processors can find help when they need it. PETplanet print vol.6 The Rapid Guide to Perfect Preforms machine no./name Continued on page 29 MHT MOLD & HOTRUNNER TECHNOLOGY Dr. Ruben-Rausing-Str. 7 | D-65239 Hochheim/Ma Tel. +49(0) 6146-906-0 | www.mht-ag.de Lightweight threads are literally on everyone’s lips. After all, the smallest PET saving per preform soon amounts to hundreds of thousands of Euros for major bottlers each year. Looking to convert your mold to a new thread and need an experienced partner? MHT Mold & Hotrunner Technology offers all lightweight solutions on the market, including: • PCO1881 (17 mm / 3.8 g) • 28-21 ComPetCap® (21 mm / 3.9 g) • 29/25 (12.6 mm / 2.4 g) Lightweight Engineering made in Germany MHT: Your specialist for lightweight solutions!","@ID":26} "CCL Label Auto-Sleeve® producer a complete range of stretch sleeves suitable for all common PET container regardless of shape. The natural elasticity of Triple S® material feels like a second skin regardless of whether the bottle is full or empty and the tight fit even helps down-weighted bottles to keep their shape. Stretch Sleeves - The recycling friendly Decoration CCL Label Auto-Sleeve® can offer solutions to the evergrowing need of the PET Bottle Market to address increasingly important environmental concerns as its stretch sleeves require no glue or heat for application simply because the material’s natural elasticity ensures a snug fit to the container while allowing easy, contamination free separation for recycling purposes . Already used in major filling operations in the UK, Europe and even further afield, CCL Label can offer 3 types of Stretch Sleeves: Triple S® (Super Stretch Sleeves) compete very favourably against shrink sleeves from the environmental and cost point of view. The high elasticity of the Triple S® film, coupled with recently developed stretchable inks allow them to apply sleeves to bottles with curved label panels. Modified Stretchprovides a glue and heat free solution for containers requiring label application to slightly contoured areas thereby providing a more environmentally-friendly decoration than a comparable Roll-on-Shrink-on label. Standard Stretchis ideal for all sizes of traditional straight wall PET and HDPE containers and provides a superior alternative to Wraparound OPP labels in that there is no glue required and the sleeve clings well to the container after purchase regardless of how full or empty it may be. With in-house extrusion of proprietary film blends designed for your application, CTP 12 colour CCL Label Auto-Sleeve® When the environmental footprints of both Triple S® and other labelling types (Shrink, OPP wraparound and RoSo) are compared, Triple S® comes out on top by a clear margin. The combination of lower material requirements, no solvents for sealing and no need for shrink tunnels, means that the advantages of Triple S® are not only environmental but economical in that the on-bottle cost is some 30% less than shrink on a like for like basis. Types of Sleeve Triple S® Super Stretch Sleeves save up to 40% of material CCL Industries Inc. a world leader in the development of labelling solutions and specialty packaging for consumer products and healthcare industries signed a licensing agreement with Krones AG to develop and market Triple S® stretch sleeve applicator systems for common global customers in the soft drinks market. Under the terms of the transaction Krones will have the right to market next generation applicator machine systems for Triple S® sleeves under patents owned by CCLfor a one time fee. CCL Label will continue to supply Tripe S® sleeves to customers adopting the technology. Guenther Birkner, Group Vice President of CCL Label’s Food and Beverage business commented: \"Krones is recognized as the premier supplier of labelling equipment to the beverage industry globally. This license will allow us to accelerate the deployment of our technology much faster than with our own resources and leaves CCL to focus on its core business of label supply.\" Krones acquires rights to Triple S® labelling technology Flexo Plate making, a dedicated Graphics Department and over 25 years’ worldwide activity, CCL Label Auto-Sleeve has both the experience and the technology to respond promptly and efficiently to your Marketing needs whether they be for a simple design change, a major rebranding or a promotion requiring unique alpha-numerical codes inside each sleeve. CCL Label Auto-Sleeve® is situated in Volkermarkt, Austria www.ccl-label.com/voelkermarkt/","@ID":37} "BOTTLING / FILLING 41 PETplanet insider Vol. 11 No. 05/10 www.petpla.net Operational details The wide range of products means that the filling line at Gerolstein often has to be switched from one product to another. With the Solarjet HD only a few manual adjustments are needed - the machine operator simply calls up the product code on the control box and all of the required laser settings are automatically installed for operation. For every laser application the right focus is important, i.e. aiming the laser correctly onto the product surface. To make this easy for the operators at Gerolsteiner the Bluhm engineers have installed a special laser stand on the production line, which thanks to the small size of the laser marking head was no problem. Using a fine screw adjuster the laser beam can be exactly and correctly positioned in the x and y axes, ensuring that the required sharp focus is quickly achieved. On another line at Gerolsteiner Brunnen the marking is carried out not on the bottle conveyor line but before labelling, directly onto the PE film label roll. This has the advantage that any changes in the bottle eter do not affect the coding. In order to set the various positions for correct laser coding of the label a laser stand is used with push-button setting of the correct height by an electric motor. Wrap around labels for multi-packs To make handling of the Gerolsteiner PET bottles more convenient for the consumer the company has developed a new type of retail pack - a so-called “bottle clip” for six Gerolsteiner bottles. For maximum stability there is a wraparound sleeve on the lower part of the six-pack. The newly developed retail pack of course also needs an EAN 13 bar code. This code is applied by way of a label on the side and on the end face of the pack using a special six-pack printer-dispenser from Bluhm. For this job a LegiAir series printer/labeller with a Zebra Pax printing module is used. Of course each different product requires its own EAN 13 barcode label. Here again, to simplify the work of the operator all of the product parameters are stored in an industrial PC integrated into the Legi-Air printer. Access to the control software is via a simple touchscreen interface where the operator simply calls up the required product code. All of the appropriate EAN settings are then automatically uploaded. Up to 50 barcode labels per minute are applied to the sides of the six-pack, with no direct contact, using the socalled “tamp-blow” process. On the production line the six-packs are then rotated in order for a second barcode label to be applied on the end face. This means that at the supermarket checkout the price can be scanned without having to manhandle a large six-pack * Bluhm Systems is part of the international BluhmWeber group www.bluhmsysteme.com The required product code can easily be called up on the touch screen of the integrated PC. Label with EAN 13 barcode. The laser beam thermally alters the outer surface of the product.","@ID":43} "NEWS 7 PETplanet insider Vol. 11 No. 05/10 www.petpla.net : #326-1, Taejeon-dong, Gwangju-si, Gyeonggi-do, 464-805, R. O. Korea. Tel: +82 31 763 5621 Fax: +82 31 763 5623 E-mail: [email protected] URL: www.pnstech.co.kr Rotary type whole surface inspection system for preforms Model: PS-21GP De¿ciency caused during preform production is prevented through the full scan by rotating the preform in the rotary type. Automatic Illumination Control system by computer program and semi-permanent illumination. High credibility is recognized for the self diagnostic feature in the system which prevents trouble state. Shutting down the machine is possible to prevent failure in inspection. Available for gate cutter unit inside the machine as an option with no further space required. Using ultra high density semi-permanent blade enable to remove completely. Using Mirror Tracking Inspection System enables to inspect side-wall perfectly without any missing zone or dead zone. Option: Gate Cutter Rotary type whole surface inspection system for PET Bottle Model: PS-21RP High technology inspection equipment with High Resolution Camera installed that detects unknown substances over 0.5mm at 99.5%. Height adjustment is possible for bottle sizes from 0.35L to 2.0L which shows higher compatibility compared to other competitors. The self diagnostic feature installed in the system immediately alerts problems, preventing failure of inspection. Synchronized monitoring images, de¿ciencies, and production screen enables. The operator to control quality and alerts the de¿ciencies and production progress. Semi-permanent simple structure of the parts and spare parts. Mechanical structure system to operate easily. Using Mirror Tracking Inspection System enables to inspect sidewall perfectly without any missing zone or dead zone. Vacuum hold by Pusher Head Discharge Rotation Down Up Infeed Neck ¿nish(Sealing Surface) Lateral Neck Outwall Sidewall Lateral Neck Inner wall Sidewall Bottom Preform & Bottle Machine Vision Inspection System Cut / Ovality Bottom / Neck Innerwall CCD Camera LED","@ID":9} "PETproducts 42 PETplanet insider Vol. 11 No. 05/10 www.petpla.net Recycling line recoSTAR PET iV+ Ongoing PET recycling innovation, quality and state-of-the-art technology, a full range of consulting services – brought to you by Starlinger. Visit us at: K 2010, Duesseldorf, Germany Oct. 27 – Nov. 3, Hall 9, Booth D 21 www.starlinger.com Automatic handle insertion Siapi has developed an automatic system for inserting handles on two-stage linear blowers: This patented system makes it possible to configure the blow-molding system with the insertion of the handle directly in the mould. This system is designed for 5 gallon PET containers and for the Wide Mouth container range. The HandleMatic System will soon be used with 4 cavity blow-moulding machines for containers up to a 3 liter capacity. SIAPI has recently delivered 3 machines with this technology to the American market for 5 US gal. containers for a customer implementing an important project to change from polycarbonate to PET. www.siapi.it High-speed single-piece cap production Italian company Sacmi Imola SC debuted its new CCM48S compression press at Chinaplas 2010 in Shanghai. The machine has been designed and developed for the production of singlepiece caps for mineral water, hot filling and CAF (cold aseptic filling) bottles. Built by the Closures & Containers Division, the CCM48S on display featured a mould for the production of S30-14type single-piece HDPE (high density polyethylene) caps with a diameter of 30 mm, weighing just 1.9 grams. The machine was demonstrated alongside Sacmi CCM (continuous compression moulding) units. The Automation & Inspection Systems division presented several quality control solutions including the Surveyor 900, a laboratory X-ray inspection machine that allows nondestructive non-intrusive analysis. www.sacmi.com Preform moulding and closure manufacturing systems At Chinaplas 2010, Husky Injection Molding Systems was showcasing the range of tooling, systems and services it offers across a wide variety of beverage applications, including water, carbonated soft drinks, beer, wine and tea. Husky had two systems in operation at the show. A 96-cavity HyPETT 400 preform moulding system with High Performance Package (HPP) will run a 13.3 gram EcoBaseT preform at a cycle time of 7.0s. The 72-cavity HyCAP 300 system is capable of producing PCO 1881 CSD closures weighing 2.3 grams at 3.5s cycles. Also on show was the company’s PET mould refurbishment services, which are intended to maintain preform quality for customers through regular mould maintenance and refurbishment. The company has had a mould manufacturing presence in the Far East since 1971. Its Shanghai Technical Centre opened in 2004 and has been expanded several times since then. www.husky.ca","@ID":44} "CAPPING / CLOSURES 36 PETplanet insider Vol. 11 No. 05/10 www.petpla.net You will feel better having made the right decision. Reduce your energy consumption. Gesellschaft Wärme Kältetechnik mbH Friedrich-Ebert-Str. 306 · D-58566 Kierspe Tel. +49 2359 665-0 · www.gwk.com Mould inserts Temperature control technology Water treatment Cooling technology Temperature controllers Chillers Energy saving cooling systems advantages of such packages include the fact that such PET bottles are heavy and use a high amount of resin. They are, as a result, costly and not in line with requirements for a good carbon footprint. Two-piece closures need relatively high application torques and consequently present a high opening torque, with the seal breaking after a few degree of rotation. Furthermore, costs for two-piece closures are relatively high due to their two-component construction: HDPE or PP shell and thermoplastic elastomer liner. New trend for one-piece hot fill closure The disadvantages of two-piece hot fill closures made it apparent that a new trend for one-piece hot fill closures was necessary. To support its customers in their cost reduction efforts Bericap built a special closure for hot fill processes on the base of its DoubleSeal closure system. It was created in 2002 and the first market introduction was in China in 2003. The DoubleSeal one-piece closure system for hot fill application was made available in three sizes: 28, 38, and now also for 33mm versions. The double-sealing feature, with an inner boreseal and outer seal, secures strong sealing performances during the hot fill treatment, transport and storing, and under extreme temperatures or environmental conditions. The new design of hot fill closure needed to withstand a very challenging hot fill process. After the capping of the hot filled product, the inversion step is used to pasteurise the bottle headspace. A temperature of 80°C up to 92°C, depending on the product, lasting for about 30 seconds will meet bottle and closure. An optional (but widely used in Asia) hot shower – usually of chlorinated water at 65°C plus – will follow for another 10 minutes. The intensive heat treatment leads, first, to inflation of the bottle and also affects the neck, which leads to slight ovalisation. Cooling at around 40°C results in bottle contraction. DoubleSeal one-piece closures demonstrated reliable performance and achieved tight and secure seal of the package. The slit tamper-evident band provides safety and integrity of the package for consumers. A further advantage for the consumers is the convenient opening torque needed to open the bottle. Bericap’s introduction of the 38mm one-piece hot fill closure in the Chinese market led to the securing of several new contracts, establishing the trend for a the package and application type. Products packed were mainly juices and energy drinks. Since the 2003 introduction in China, other contracts followed in Italy, Germany and Kazakhstan. To date, Bericap has produced more than 1.2 billion 38mm one-piece hot fill closures.The 28mm DoubleSeal hot-fill closure was also launched to the market in China, again in 2003 and for filling fruit juices, jointly with a multinational client. The same closure has also penetrated the market in India and Russia, where it is used by several of Bericap’s SK 38/16 S DS HF Hot-fill product capped with SK 38/16 S DS HF","@ID":38} "MATERIAL / RECYCLING 20 PETplanet insider Vol. 11 No. 05/10 www.petpla.net Influx of PET imports into the EU – changes ahead? The market for PET has undergone some pronounced changes in recent years. Temporary closures or total shutdown of production plants in Europe, along with the commissioning of new production capacity in the Middle East, are significant factors that have brought about some fundamental changes to the global volume of foreign trade in PET. Another key factor is the levying of anti-dumping duties on PET from countries outside Europe exporting to the EU. This can have a decisive effect on the flow of PET, as numerous examples can testify. PETPlanet Pulse, PETplanet’s monthly price index, has collected information on PET imports into the EU to illustrate these changes. We are talking about goods with the Harmonized System Code 39076020*. Market experts have helped us check and edit the figures to ensure their validity. of 2009 saw the Artenius PET plant in Wilton/UK (now part of the South Korean KP Chemical company) at a standstill, although production is expected to resume in the second 2009: EU imports of PET top 872 kmt The most significant influx of PET imports with a viscosity number of at least 78 ml/g was recorded by the 27 EU States (EU27**) in 2009 with a total of 872 kmt (2008: 580 kmt; 2007: 494 kmt) (see Fig.1). The marked increase in imports in 2009 by comparison to previous years may be explained primarily by the shutdown of various European production facilities. In March 2009 the Invista Resins & Fibres plant in Offenbach/Germany closed; this plant had a capacity of 210, 000t/a. No bottlenecks were reported, indeed the closure led to the remaining European PET productions experiencing increased demand. However in March 2009, the Artenius PTA production plant in the UK, with an annual capacity of 500 000 tonnes a year, had also suffered an unexpected collapse which forced Artenius to declare force majeure for PTA. All Western European PET producers were affected by the shortage of the input material PTA – and, this in the peak season. The end of the first half Fig. 1: PET imports into the EU from 2003 to 2009 PET imports into the EU","@ID":22} "REGIONAL MARKET REPORTS 11 PETplanet insider Vol. 11 No. 05/10 www.petpla.net Flour and water Bakhresa Meeting in the headquarters and from here guided by Mr. Said Salim Bakhresa (seen on the right) through his extensive operation. Flour and water were the basis of Mr. Said Salim Awadh Bakhresa’s success story. And although they are so different - one is dry and powdery, the other is wet and runny - when put together they react in a superb way. Bread is made! And if we consider that flour in sacks, water in PET, and bread, all have to be transported, we have almost completely described Mr. Bakhresa’s empire. 30 years ago he started up a small business from nothing, but soon came the first flour mill. Later he established his own transport company, a sack factory and of course a large commercial bakery. A little outside the mainstream came ice cream and juice factories. Using the same logic that he applied when developing his other businesses, he turned, in 2001, to the business of “packaged water”. The water was initially packaged in 200ml pouches, but the government did not like it, and soon stepped in. The empty pouches were blowing about all over the place and disfiguring the landscape, so they were banned. But Mr. Bakhresa had taken a liking to the water business and in 2006 he installed his first bottle filling line, from Ave, with an output of 10,000 PET bottles per hour (350ml). This line is now fully occupied and so he is installing a second line with an output of 12,000bph, also 350ml. The bottle blower is from Chumpower, the filler is Kosme and the labeller is from Sacmi. The site of the plant is the oldest in the group and a flour mill, a bakery and the 350ml water filling operation are all on the same site. However, there is no room for expansion, and a new site was sought in the local area, where, in 2006, the biggest corn mill in the country was built. It was installed by Bühler with the best technology available. A third of all PET bottles collected in Tanzania arrive at the new Sorema/Erema Bottle-to-Bottle recycling plant (from left to right: Dinesh Cranonkar, Mechanical Engineer, Alexander Büchler, PETplanet, Vinod M. Shetye Process Engineer, and Shadab Alam Electronic Engineer At that time there was also space on the site to meet the rapidly growing demand for water in PET. Filling lines for 0.5, 1.0, 1.5, 3.0 and 6.0l were brought together in the new location. The blowers were supplied by Chumpower. The blown bottles are conveyed to a buffer silo from where they go to the filling lines - mainly Italian manufacture, e.g. Ave. It soon became clear that Mr. Bakhresa could save money by moulding his own preforms and so now there are 6 Nissei ASB preform systems to cover in-house requirements. The preforms for 0.35l weigh 12g, for 0.5l they weigh 15 and 16g, and for 1l 23 to 26g. All of the bottles are fitted with the same still water cap, which weighs 1.8g. Also new is the Netstal 2000 preform system (with Mr. Arumugam and Alexander Büchler)","@ID":13} "BOTTLING / FILLING 40 PETplanet insider Vol. 11 No. 05/10 www.petpla.net Lasers to help quench consumers’ thirst At Gerolsteiner Brunnen, Germany, a new filling line running at 28,000 bph uses a Bluhm Systems* Solarjet Heavy Duty (HD) 30 watt laser to ensure that every single one of their bottles of mineral water is marked with the correct expiry date and product traceability data. ing cable can be up to 15 metres long. Noteworthy features include a special lens technology that allows marking with a 30 watt laser where normally a much more powerful class of laser would be needed. The Solarjet HD is water-cooled and so is suitable for the highest levels of performance. It has IP65 protection and so is proof against external factors such as water and dust. This means that the robust equipment is suitable for use in the beverage industry as well as applications such as found in the cosmetics and pharmaceutical sectors, or anywhere where a great deal of water and/or steam is used for cleaning down the production environment. Technical performance When coding products using a laser the surface of the product is thermally altered; a small fraction of the outer surface is burned away. Hence the required heat energy has to work on the product for a specified amount of time. The shorter the time available for this burning process to be carried out the higher the laser output must be. If the product surface is highly reflective, as for instance PET film, then the combination of time and power has to be precisely adjusted. To simplify the work of the laser Gerolsteiner Brunnen have arranged for a coating of particularly black ink on the area of the PE label to be marked. This allows for faster coding and produces a result with greater contrast. Cost and efficviency factors Thanks to its extremely compact construction the Solarjet Laser can be conveniently installed in any production environment. The laser tube has an expected lifetime of 30,000 operating hours, and this refers only to the time during which the laser beam is active. The device needs no consumables or servicing other than electricity and an occasional wipe with a duster, which helps reduce running costs. This could be an important factor for lines running 24/7. “A large percentage of our output is exported around the world. Last year alone we exported 265 hectolitres. Every country has its own specific requirements regarding product marking and so we need a system with maximum flexibility, that codes products very quickly and is easy to operate,” explains Roland Schlösser, coordinator of technical planning at the mineral water plant in Gerolstein. “To make traceability of our products easier and more precise we wanted to mark the bottles not only with the expiry date but also with details of the batch number and the machine used to fill them, plus the exact date and time”. 30 Watts have got what it takes With this requirement in mind Gerolsteiner Brunnen, a leader in the bottled mineral water sector, approached Bluhm Systems. Bluhm, a manufacturer of various marking and coding systems, located at Unkel am Rhein in Germany, recommended the Solarjet laser. The device consists of a compact laser unit and a separate, very small control unit. The connectUp to 50 barcode labels per minute are applied to the side of the six-pack with no physical contact. The coding can be clearly read on the black background.","@ID":42} "NEWS 8 PETplanet insider Vol. 11 No. 05/10 www.petpla.net P E T C O R E C O L U M N Biodegradation – what’s in a word? Biodegradation as a word is very confusing to non experts. The dictionary defines it as the process of being broken down by bacteria. Members of the public will tell you that plastics don’t biodegrade and they will tell you plastics stay in the environment for years, as though this were a bad thing. It is acknowledged that plastics need to be fit for purpose and have a required service lifetime. In the view of many however, if plastics biodegrade, break down or “disappear” they would be more environmentally friendly materials. Do they expect them to degrade as soon as they hit the ground? What is the full environmental cost of “true” biodegradable plastics? These are the plastics that are based on food crops such as corn. In this process industrialists extract the organic carbon from plants grown using modern agricultural techniques. It is this long and convoluted process that many claim to be environmentally friendly. The biopolymer industry uses phenomenal amounts of energy. The energy drain starts with the manufacture of tractors, seed drills, fertilizer spreaders, harvesting and drying equipment. It uses energy from fossil fuels and electricity. In addition, the water footprint for crops is high. There are many factors to be considered when calculating the total environmental cost of supplying this “renewable resource”. Is renewable the right description for this type of product? Surely this is a once-through system? Crops are grown as a feedstock, harvested as a chemical resource, put through an industrial process and at the end of their life are degraded to greenhouse gas (carbon dioxide) and water. There is no re-use, no second life for these products, certainly no recovery of the energy used to make them. Who amongst us feels this type of process is the way forward? Can we afford to waste this or, for that matter, any other resource? The term renewable resource should be replaced by the term repeatable resource as crops can be re-sown. Perhaps an even more confusing use of the word biodegradation is the peculiar case of forced biological action. Here specific chemicals (additives) are mixed with conventional polymers in such a way that microbes can break down the additive in the plastic, weakening the polymer matrix and resulting in very, very fine but pure polymer particles. This is another waste of materials. Whilst we need technological understanding and technical expertise, all conventional polymers can be recycled over and over again – they are a truly renewable resource. However, the use of “eco friendly”, biodegradable additives produces many non eco friendly problems. It takes a truly renewable resource, a conventional polymer, and renders it completely non-renewable by breaking it down into a form that cannot be recovered, even using the very high level of development skills demonstrated by the plastics recycling industry. Biodegradable additives in plastics packaging, especially PET, have been recognised as a major concern for the recycle industry. Claims from manufacturers that their additives have no effect on PET recycling are not backed by publication of any scientific evidence that this is so. In particular there has been no approach to the EPBP (the European PET Bottle Platform) or APR (Association of Postconsumer Plastics Recycling) so that these types of additives can be fully evaluated and approved by those with an interest in the recycling of PET. Indeed, APR has published its serious concern about this type of technology and the impact of such additives on the recycling process. As well as other outlets, RPET can be used for all virgin PET applications including many that stress durability and physical performance. Buyers of RPET want not only the sustainability features of recycled material, but assurance of performance. Degradable additives that weaken products or shorten the useful life of PET will have a negative impact on postconsumer PET recycling. As we have reported before, in 2008 46% of all PET containers were collected for recycle in Europe, a great track record we feel sure will continue. This sustainability must not be sacrificed on the altar of biodegradation. www.petcore.org Extension of FDA approval for recycled PET The US Food and Drug Administration (FDA) has approved the use of food and ready-prepared meal packaging and containers made of up to 100% recycled PET (rPET) produced on Vacurema recycling equipment, even if temperatures rise above 120°C (250°F) during the heating process. The approval applies to both microwave and conventional oven cooking. Vacurema PET recycling equipment is made by Erema Engineering Recycling Maschinen und Anlagen Ges.m.b.H (Erema). The systems are already approved under FDA categories ‘C’ to ‘H’; they are now approved under FDA category ‘J’. All of the approvals apply to existing rPET pellets produced by Vacurema recycling machines as well as new equipment. The company specialises in the development, manufacturing and worldwide distribution of plastic recycling systems and technologies for the plastics processing industry. It has sales and servicing companies in the USA, China and Japan, as well as 50 local representatives in countries across the world. www.erema.at Indian plastic packaging business expands Parle Agro, the Indian food and beverages enterprise, is aiming to increase its preform production capacity by 21% in financial year 2010/11. This is in addition to the increase of 17% already achieved in 2009/10. Parle Agro recently installed a KM 96 cavity machine and a Husky HyPET 72 cavity machine at its Silvassa plant, in the Indian Union Territory of Dadra and Nagar Haveli. The company has commissioned its second preform manufacturing plant in Orissa and plans to set up its third plant in South India by early 2011. The company says that it plans to increase its presence in the oil, confectionery and pharmaceutical segments and to seek new customers in the liquor sector, which is seeing a shift from glass to PET bottles. The company’s PET division supplies preforms to customers in the bottled water, readyto-drink beverages, carbonated drinks, edible oil, confectionery and pharmaceutical segments. Its product range in terms of neck type are 30/25mm (water application); PCO neck (carbonated & juice application) and short neck (water). Parle Agro sells brands such as Frooti and Appy Classic in the Indian market but 60% of its PET perform production is supplied to external customers in India, SE Asia and Africa. www.parleagro.com","@ID":10} "MARKET SURVEY 27 Intergulf Ltd - Empol Retal Iberia S.L.U Khalid Seaport, P.O.Box 6131, Sharjah, . UAE +97165029284 www.empol.com Murali Krishna / Vinod Kanchan Business Development Manager +97165029244 / +97165029246 +97165285720 [email protected] Ctra.Comarcal C-35, 17451 Sant Feliu de Buixalleu - Girona (Spain) 00 34 972 865730 Pere Plademunt Mateu General Manager 00 34 972 865730 00 34 972 865731 [email protected] No ( Only monolayer barrier preforms) No No No No No CO2 & O2 barrier, UV absorber, Fast Heat Set Resin & Hot Fill Resin etc., Colourants (Colormatrix) , kimired, samplas 1. Preforms with 30/25 high neck finish for Mineral Water/2. Preforms with 28mm PCO/ BPF neck finish for CSD/ 3. Preforms with 38mm 3 start neck finish / Dairy products. / 4. Preforms with 29/21 and 36/29 snap on neck finish for edible oil applications./ 5.Preforms with 38 mm 2 start for Hot Fill applications. / 6. PETGard (CO2 &O2 ) speciality barrier preforms for up to 500 ml single serve CSD and for oxygen sensitive products. 40g PCO 1810; 43 g PCO 1810 45 g PCO 1810; 38,70g PCO 1881 43,70g PCO 1881; 41,86g PCO 1881 25g PCO 1810; 26g BPF 1810 51g PCO 1810; 47g PCO 1810 49,5g PCO 1810; 39g PCO 1810 41g PCO 1810; 45g PCO 1810 42g BPF; 40g BPF; 44g BPF 46g BPF; 48g BPF ; 51,5g BPF 22g OIL 29/21; 24g OIL 29/21 27g OIL 29/21; 86g 48/40 91g 48/40; 23g obrist; 30 g 30/25 31g 30/25; 39g 30/25; 36g 30/25 38g 30/25; 13,5g 30/25; 12,5g 30/25 27g 30/25; 18g 30/25 S G T Gastro PET d.o.o. Constar International Manjushree Technopack Limited 3,rue de l'île Macé 44 412 Reze, France +33 (0)2 40 05 09 37 www.sgt-pet.com Mrs Le Claire Sales administration +33 (0)2 40 05 02 88 +33 (0)2 51 70 01 55 [email protected] Kotna ulica 5, 3000 Celje Slovenia +386 3 425 80 30 www.gastropet.si Primož Agrež General Manager +386 3 425 80 30 +386 3 425 80 31 [email protected] 1 Crown Way Philadelphia, PA USA 215.552.3735 www.constar.net Pattie Chiaffa Sales 215.552.3735 215.552.3707 [email protected] #60 E, Manjushree Technopack Limited, Bommasandra Industrial Area, Bangalore - 560099 India +91-080-43436200 www.manjushreeindia.com Ankit Kedia Associate Director +91-080-43436254 +91-080-27832245 [email protected] No No Yes No No No Yes No No PLA preforms PP No All colours UV Blocker AA reducer Colours as per the specifications of the customer UV blockers, AA blockers UVI, CO2 , O2 UV Additive and Oxygen Scavenger O2 scavenger, CO2 scavenger, Reheat Additive, White colour for UHT milk, gliding agent, Still Water, Mineral Water, Carbonated soft drink, Oil & vinegar, Household producst, Cleaning products, Juice & milk, Wine CO2 & O2 barriers, any barrier material according to customer needs available. Monolayer preforms PCO 28mm 1810 (33,3g - 48g), PCO 28mm 810- light (18,5g - 24,5g), Bericap 38mm 3 start (16g - 41,5g), PCO hybrid, PLA preforms Colourants, Water, CSD, Food, Beer, Liquor, Hotfill, Household Goods, Personal Care, 2oz to 3L 28mm PCO (1810 Neck) with 15, 17,25,25.5, 27, 39, 48g; 28 mm PCO (1881 Short Neck) with 23.7, 25.7, 37.7g; 28mm PCO (Thick Neck) with 27 and 47g; 28mm Alaska (26.7mm Three with 15.6, 22 and 35.6g30/25mm (Three Start) with 22g","@ID":29} "MATERIAL / RECYCLING 19 PETplanet insider Vol. 11 No. 05/10 www.petpla.net Two new LCA studies indicate PET’s environmental advantage over glass or aluminium The Life Cycle Assessment 2010, carried out by the Ifeu Institute for Energy and Environmental Research Heidelberg GmbH (Ifeu), found that PET bottles have shown an improved ecological performance in all areas of the value chain. In 2009, disposable PET bottles’ share of the mineral waters market reached 68.1% and is tending to increase. Disposable PET bottles for mineral waters and refreshment drinks are being collected through a deposit system, are recycled through a closed material loop and eventually provide a high quality raw material for recycling. The Life Cycle Assessment found that, today, 81.3% of the researched market of mineral waters and refreshment drinks show an ecological equivalence with benchmark multiuse glass bottles. Dr. Jürgen Bruder, general director of the German Association for Plastics Packaging and Films - IK Industrievereinigung Kunststoffverpackungen e.V, said at a press event in April 2010 that the Ifeu report reflected the continuing ecological development of PET disposable drinks packaging that was identified by the GDB life cycle assessment in 2008. The survey used the same methods and effect categories and priorities in previous lifecycle assessments, in order to ensure accurate comparison. Technological advances in the entire process chain (PET manufacturing, PET bottle fabrication, filling, distribution and recycling) were taken into account. The categories examined were PET disposable drinks packaging and other marketrelevant drinks packagings such as returnable PET and glass for storage/repeat use (0,7l) and instant use (0.7l) for noncarbonated and carbonated mineral waters and refreshment drinks. The report shows improvements for the 1.5l non-returnable PET bottle in almost all categories. Under the headings of climate change, fossil resource consumption, summer smog, acidification, terrestrial pollution, and human toxicity/respirable dust, improvements between 30-55% were recorded, compared with the last life cycle assessment by the Association of German Wells (Genossenschaft Deutscher Brunnen e.G (GDB)) in 2008. Contributory factors included bottle weight reduction (-14%); increased recycling (25-35% recycled PET); decrease in distribution distances (-38%); and reduced energy and process water consumption (-30% and -36%) in contributing to equality to returnable glass in the reusable 0.7l reference point. PET returnable bottles reached a higher total score than any of the packaging systems examined. Helmuth von Grolman, managing director of Deutsches Dialog Institut, observed that the packaging directive and mandatory deposit measures have contributed strongly to the closing of the lifecycle loop in the case of single use PET bottles, and consequent saving of resources. The current return rate of 1.5l single use PET bottles has been reported as now reaching 98.5%. EREMA Engineering Recycling Maschinen und Anlagen Ges.m.b.H. Freindorf · Unterfeldstr. 3 · P.O.B. 38 · A-4052 Ansfelden/Linz · Austria Phone +43/732/3190-0 · Fax +43/732/3190-23 · [email protected] We know how. www.erema.at VACUREMA Prime Up to 10% IV increase without energy intensive classic SSP process FDA approved, ILSI-conform Very low total energy consumption from 0,25Kw/kg pellet only More than 100 plants delivered worldwide YOUR MOST ECONOMIC WAY TO HIGH QUALITY BTB REGRANULATE PET BOTTLE RECYCLING BY VACUREMA","@ID":21} "MATERIAL / RECYCLING 23 PETplanet insider Vol. 11 No. 05/10 www.petpla.net Y O U R PA R T N E R F O R B L O W M O U L D S . Benef i t of 30 Years of Exper ience in Blow Mould Manufactur ing! Sidel • SIG • Krones • SIPA • MAG • ADS • Kosme • Nissei a. o. Röders GmbH / Scheibenstr. 6 / 29614 Soltau / Germany / www.roeders.de Telephone +49 5191-603-53 / Fax +49 5191-603-36 / E-Mail [email protected] For our subsidiaries in China, USA and Latin America please check our website. PET STRETCH BLOW MOULDS 2002 – 2003 when Australia exported 17 / 19 kmt PET to the EU. Two points should be made on the issue of dumping/anti-dumping: we need to differentiate between dumping and items sold at a lower price as a result of higher productivity or lower costs. The key factor which defines dumping is NOT the ratio of the export price and the ruling market price in the country to where the PET is imported. The definition of dumping is if the export price is much lower than the price that would be achieved in the originating country. For this reason it may happen that it is not the entire complement of the goods (goods with a certain customs tariff number) from a country that has the anti-dumping duty levied on it, but only the goods from one or more manufacturers who sell their goods at dumping prices in the EU. At the beginning of May the Federal Ministry of Commerce, Family and Young People in Vienna/ Austria issued a statement via its publicly accessible home page that temporary anti-dumping duties are to be charged on PET with the Harmonized System Code 39076020 originating from Pakistan, Iran and the UAE as of June 3, 2010 at the latest. Responding to a request for information from PETPlanet Pulse, it was confirmed that these temporary anti-dumping duties will in any event apply for a period of six months; during this time a study will be undertaken into whether final anti-dumping duties of five years’ duration are to be introduced on goods from the countries specified. *As regards PET featuring the Harmonized System Code 39076020 we are dealing here with PET in its primary form with a viscosity number of 78 ml/g or more (the PET type which is predominantly used for the manufacture of preforms and beverage bottles). **Where the article mentions the EU, this refers to the 27 countries that have belonged to the EU since 2007. Where annual figures prior to 2007 are given in the graphics or in the article, the flow of goods referred to here relates to the countries that belong to the EU today. These are AT, BE, BG, CY, CZ, DE, DK, EE, ES, FI, FR, GB, GR, HU, IE, IT, LT, LU, LV, MT, NL, PL, PT, RO, SE, SI, SK. ***The source of the figures forming the basis of the article and the graphics is Eurostat. pulse The monthly PET price index! Subscribers to PETplanet Insider receive - in addition to the magazine - a monthly PET price newsletter: the PETplanet pulse. With informed comment and prices for both virgin PET and recycled material, PETplanet pulse is essential reading for the PET industry. For further details, please contact: [email protected]","@ID":25} "BOTTLING / FILLING 33 PETplanet insider Vol. 11 No. 05/10 www.petpla.net For further information, visit www.khs.com/service. KEEPING YOUR LINE RUNNING IS WHAT WE STAND FOR. Long lasting, safe, and efficient: Original spare parts from KHS. milliseconds. No water is required and machine validation is easier, as it can be carried out without any biological indicator tests. Only doses delivered to caps need to be measured. Sterilbeam can treat multiple cap formats, sizes and geometry on the same line. It reaches up to 5 Log Reduction and is claimed to reduce operational costs by 1/3. It is an FDA approvable process. Vaporized hydrogen peroxide bottle sterilisation GEA Procomac’s HPstar is a VHP (vaporized hydrogen peroxide) aseptic sterilisation system that has been developed as an alternative to PAA for dedicated applications. The HPstar machine consists of three carousels (bottle heater, VHP steriliser and air rinser). After preheating with high-temperature sterile air, bottles are transferred to the VHP steriliser and sprayed with H 2 O 2 gas vapour, which is injected into bottles at 60°C and over 3,000ppm concentration. H 2 O 2 is continuously delivered using a centralised manifold. An air rinsing carousel performs rinses bottles before they enter the filling machine, to eliminate any residuals. The HPSTAR carousels are placed within a new mini isolator, which uses less space and is easier to control because mechanical parts inside it are reduced to a minimum: there are no valves on the vaporiser and air rinsing carousels. Fifth generation aseptic filler GEA Procomac’s 5th generation of wet PAA-based aseptic filling bloc, Ecospin, offers consumption and investment cost optimisation through considerable reductions in rinsing time and footprint. www.procomac.it","@ID":35} "25 Suppliers of Preforms This year our market overview lists more than 18 manufacturers of preforms from 11 countries. Strongly represented are India and France, closely followed by Saudi Arabia and Germany. (Once again, there is no sign of Artenius, although the reason probably has something to do with the re-structuring activities of LA Seda which are still in full swing. Other major players are also conspicuous by their absence*). On the technology side, our survey reflects the trend indicating that the PCO 1881 is becoming increasingly established on the market. In 2009 there were 6 companies offering preforms in alternative materials (PLA/ PP) in their range or could deliver them on request, whilst in 2010 8 firms purport to fall into this category. Deriving any sort of trend from these figures would be presumptuous; what seems to have happened is that, during this year, companies have come on-stream who were not in evidence last year and who are now making their presence felt in this sector (e.g. SBECM and Constar.) As always, the range of products is broad and we hope that our survey will pinpoint the local bottle blowers as well as the appropriate products and suppliers. Here we should not forget to mention that many of the global suppliers have local branches: it is impossible to list them all here but their details can of course be found on the relevant company websites. Although the publishers have made every effort to ensure that the information in this survey is up to date no claims are made regarding completeness or accuracy 05/10 MARKETsurvey PET bottle-to-bottle recycling plants Caps and closures Conveyers for preforms and empty bottles Preforms Preform moulds and SBM moulds 2-stage SBM machinery Preform and single stage machinery Resins and additives Filling equipment Compressors Company name M/s. AMD Industries Ltd. Gulf Packaging System Co S.B.E.C.M. Parle Agro Pvt. Ltd. Savola Plastics Division Postal address Telephone number Web site address Contact name Function Telephone Fax E-mail 18, Pusa Road, Ist Floor, Karol Bagh, New Delhi -110 005 India +91 9811118736 www.amdindustries.com Mr. Adit Gupta Director -Business Development +91 9811118736 +91 11 28753591 [email protected] P.O. Box 20266, Jeddah 21455 Saudi Arabia +96626360099 www.gulf-pack.com Bader Abdullah Sales Manager +966548813009 +9666082716 [email protected] Rue de la plaine 47230 Lavardac, France +33 (0)5 53 97 41 00 www.sbecm.com Jean-Luc Didouan General Manager +33 (0)5 53 97 41 00 +33 (0)5 53 65 85 97 [email protected] Western Express Highway, Sahar - Chakala Road, Parsiwada, Andheri (E), Mumbai 400099, India +9122 - 6734 8000 www.parleagro.com Asha 9122 - 67348296 +9122 - 66935050 [email protected] Saudi Business Center, 6th Floor, Madina Road, P.O Box 34495, Jeddah 21468, Saudi Arabia +966 2 657 3333 http://www.savolaplastics.com Azhar Kangi President +966 2 2687780 +966 2 652 6680 [email protected] Multilayer preforms (yes/no) No No No No In process PEN preforms (yes/no) No No Yes No Yes Preforms in alternative materials (PP/PLA) NA No Possible No List of additives available NA Nylon for Barrier / AA Seavenger / colour AA scavengers, blockers, Colouring agents, O2 absorbers We add only master batch for making colored preforms All barrier additives for UV, Oxygen & Carbon dioxide. Preform range Preforms for CSD , MW , Oil, Juice Caps for CSD, juice, water bottles Laminate tube for tooth paste Bottles , Jars for food Neck finish : 30/25 High and Low, PCO 28 (1818,1881), BPF, 48/41. Study for special neck finish possible. Preform weight : from 15 to 91g Preforms in various weight categories – basic product range in terms of neck type: 30/25 mm ( water application ) ; PCO neck ( carbonated and juice application ) & short neck ( water application ) 28mm PCO / BPF Neck - various sizes 3025 Neck - various sizes 37mm 2 start Neck - various sizes (In process) 38mm 3 start Neck - various sizes 45 Neck - various sizes 29/21 Oil Neck - various sizes","@ID":27} "REGIONAL MARKET REPORTS 12 PETplanet insider Vol. 11 No. 05/10 www.petpla.net the high season the preform systems run around the clock and in winter 66 percent of the time. All of the preforms are for Bakhresa’s own use. Lawrence Silverious (on the left), Controller of the Bakhresa Group, holds all the reins With such a high consumption of bottles it is also logical to think about caps. After initial trials with injection moulding machines the company invested a few years ago in a Sacmi compression moulding machine with 24 cavities. The first Sacmi line, a CCM 24, was installed in 2007. The second line, again with 24 cavities, has just been installed. The cap they produce is for all bottles up to 1.5l. The output is high - 36,000 caps/minute at a 2.4s cycle time. Both CCM lines are producing a 30x25 light-band “hook” closure of about 1.8g, developed by Sacmi, which guarantees excellent sealing performance. Recently Bakhresa has started to print the logo directly on the top of the closure (on both lines) and high quality is guaranteed by the fact that compression technology allows the production of caps without the “gate scar” typical of injection moulded parts. It is easy to see the huge demand for PET that the group has - and Mr. Bakhresa would not be Mr. Bakhresa if he did not have his finger on the pulse of the whole operation. At the last “K” exhibition in Düsseldorf three years ago Mr. Bakhresa visited the Erema stand to learn more about PET recycling. Erema recommended that he use the Vacurema line. The discussions were positive and the next day Mr. Bakhresa signed an order for the Vacurema Advanced. The model he ordered, the 1310T, has a PET recycling capacity of about 500kg/h. It was also recommended that he invest in a Sorema plant to wash and shred post-consumer bottles, producing clean flakes ready for the Vacurema. The Sorema equipment was also ordered there and then at the “K” exhibition. So it was that at the end of last year, the first bottleto-bottle recycling plant in East Africa was set up. Here again the company chose state-of-the-art technology and now have a plant producing 10 tonnes of FDA approved granulate per day from post-consumer bottles and in-house scrap. This is not enough to meet the company’s in-house demand of up to 40 tonnes per day but enough to reduce their materials costs. In Tanzania there has long been a system to collect PET bottles, which were shipped to China. Now Mr Bakhresa buys about 30% of them. Despite the huge distances in Tanzania and the at times very variable road conditions, Bakhresa has managed to make the water brand available everywhere in the country. The price for the consumer is affordable at 1.40 US dollars for 12 x 0.5l bottles. At this level Bakhresa believes that he has about a 50 % share of the still water market. Vinod M. Shetye and Dinesh Cranonkar show the products at the recycling plant. In the foreground the light blue washed and sorted flakes from post-consumer bottles and behind is the PET granulate, also tinted light blue. It is hardly surprising that this new plant was soon bursting at the seams and so one year ago more land was reserved in the town for preform production. Since demand had grown even further the old Nisseis were no longer sufficient and investment was made in new technologies. The main requirement was that they wanted to move into higher output machines. The company had had good experience with Engel and their the cap moulding machines, so the first new preform system was an Engel machine. Since Engel subsequently pulled out of the preform business Bakhresa, had to turn, only a few months later, to another supplier for their continued expansion programme. The choice fell on the PET-Line 2000 kN system from the Swiss company Netstal. The system includes a 48-cavity tool from MHT and fits nicely into the production area. It is also noted for its high level of after sales service. Only a few months after its installation it became clear that the next preform machine would be another Netstal. This is now ordered and is on the way. What is not certain is whether, with the rapid expansion in the preform workshop, the Nissei ASBs will actually be moved there. If this happened the workshop would already be full. In total Bakhresa now has capacity for 2.3 million preforms per day - without the new Netstal system which is on the way! In","@ID":14} "REGIONAL MARKET REPORTS 13 PETplanet insider Vol. 11 No. 05/10 www.petpla.net “Powered by nature” New Acetaldehyde Scavenger Liquid colours and additives for PET www.repi.it Preserves the natural taste of water Can reduce AA in PET preforms, by more than 75% No plate-out and sublimation Meets EU and FDA food contact regulations Suited for bottle-to-bottle recycling Can be blended with REPI liquid colours Available in liquid and masterbatch versions SenzAATM is a trademark of INVISTA Sitting right in the heart of the tourist area of Northern Tanzania, close to the Serengeti National Park and against a backdrop of the 5895 metre high Mount Kilimanjaro, is the town of Moshi. On the edge of town is the spring from which the “Kilimanjaro” premium mineral water is drawn and filled by Bonite Bottlers, with no further treatment. Driving across the factory premises is like visiting a small town. Well-manicured parkland is interspersed with homely-looking buildings. If it were not for the busy lorry and forklift traffic it would be a nice place for a short vacation. “Yes! There used to be even more garden area but it had to give way and allow us to expand,” were the words of Zoeb Hassuji, MD of Bonite Bottlers, when he welcomed us to the site. “We set great store by an environmentallyfriendly approach to our business. The gardens are just a part of it”. The company has also cut down on energy and water consumption. With refillable bottles, for instance, the water usage has been cut from 7l to 3.3l, per litre of product filled. The in-house biological water purification plant with a capacity of 1,000 m³/day cleans up the waste water and feeds it into the fish ponds or to the sprinkler system in the gardens. Outside of the factory the owner, Reginald Mengi, has established a reforestation programme for Kilimanjaro. In 14 years 39 million new trees have been planted. In this way the company also supports the local population with social and humanitarian programmes. Bonite Bottlers","@ID":15} "REGIONAL MARKET REPORTS 16 PETplanet insider Vol. 11 No. 05/10 www.petpla.net NBL fills 9 different Coca-Cola products in 3 different sizes of PET bottle. And that was our second surprise - Coca-Cola in 0.5l bottles! While the rest of the Coca-Cola world is discussing whether that type of small container (known in the industry as a “can killer”) could possibly meet the minimum shelf life requirements, Fernandes has launched the 0.5l PET bottle with just 6 weeks shelf life - and he is very pleased with it. The monolayer PET package comes in at a solid 28.7g with a properly stretched side wall providing an acceptable level of barrier for such a size container – quality control and consistent processes being the basis. “The PET part of our business is making giant strides and our 0.5l size has been accepted with open arms by the consumers. The 0.5l PET bottle costs significantly more than refillable glass in production so that out in the market, instead of charging 28 Kenyan Shillings (about 45 US cents) for glass, we are charging 40 Shillings. Despite the higher price, consumers like the single trip PET with a recloseable cap for when they are on the move. It was not easy to find room in the packed schedule of Sergio Fernandes, Country Supply Chain Manager, for a brief discussion. However, we did finally manage it - although even during the photo session he received a few telephone calls. Kenya is a dream market for Coca-Cola: Pepsi doesn’t fill here, and apart from a few imported bottles has no significance in the market. Also, there are only a few local CSD bottlers. Coca-Cola has a firm grip on 50% of the Coca-Cola filling in Kenya, with the rest being shared by six small bottlers. So why take this difficult step? “We want to grow locally. We launch new flavours, as for example we did last year with Schweppes Novida, a fruity, malt-based non-alcoholic drink, or this week with Fanta Pineapple, but this doesn’t give us the growth stimulus that we are looking for. The glass bottle may be cheaper but is not suitable for people on the move, and we face a lot of competition here from juices and water - all in PET. So what was the obvious answer? Coke in PET bottles for people on the move. After our success, Coca-Cola Sabco in Uganda and Mozambique will follow suit and offer Coke in PET over there this year. A major challenge was of course the 6-week shelflife for the 500ml pack, whilst larger pack sizes are not so critical and have a much longer shelf-life. A key factor is the internal company organisation. Only small batches are produced, which are carefully released from stock on a “first in, first out” basis. This means that the bottle will be in the hands of the consumer within a few days, if not hours. For Caroline Cherono Keror, Production Unit Leader, small batches mean running a different product on each shift, and here she has high praise for the new PET line from Krones, which can actually handle this high degree of flexibility. A product changeover, with the same bottle size, takes about one hour. As everywhere within Coca-Cola every product has its own bottle shape so that the one-hour changeover time is mainly spent changing over the moulds in the stretch blow moulder. After a few shifts, when all of the products with the same fill volume have been run down the line there is a volume changeover. Here, in addition to changing the blow-mould, there are format changes to be made down the whole line. In total Caroline’s team needs 2 hours for this. To avoid having to change over the capping section for water bottles as well it was decided to leave still water also with a PCO 28 neck. Caroline Cherono Keror, Production Unit Leader, explained the plant layout and operation to us in great detail The fact that the whole line has been problem-free since the beginning is, according to production manager Mwenda Ruona Kageenu, thanks to the fact that 10 of their employees spent up to a month at Krones in Germany for intensive training. “Although all of my employees have had years of experience on the glass lines it was important for us that we had total mastery of the PET line right from the beginning,” was his comment on the subject of training overseas. The line has been designed as a fully automatic line for up to 22,000bph, starting with the preform unloader and going right through to the palletiser, which automatically stacks the 6-pack, 12-pack or 24-pack trays in units suitable for handling by fork-lift. In the warehouse full pallets are stacked three high. The preform manufacturer, Safepak, also from Nairobi, supplies monolayer preforms for water (15g/300ml, 18g/500ml, 28g/1l and 35g/1.5l). The range for CSD filling covers 28gr/500ml, 32gr/1l and 52g/2l. Between the unloader and palletiser sits a Contiform S12 blocked with a 60 head volumetric filler. After the 4,000 bottle buffer there is a Contiroll labeller which handles 18 different labels, one for each product filled. A particular challenge for Krones was presented by the narrow passageways in the production hall. In addition to limited floor space and a large number of support columns in the hall, they also had to cope with a number of integrated offices to half the height of the building. Some of the offices just had to go, but the preform conveyor from the unloader to the blow-moulder is still somewhat longer than it would otherwise be, the cooling system sits right next to the blow-moulder, the dry end has a few more curves than normal but nevertheless the palletiser is right there where the glass filling line also ends - ideal for the warehousing logistics.","@ID":18} "CAPPING / CLOSURES 34 PETplanet insider Vol. 11 No. 05/10 www.petpla.net Some like it hot PET bottles for hot-fill applications were first introduced in North America in the 1990s and have been widely adopted across the world since then. The majority of closures have been two-piece but they have several disadvantages, including weight and complex process requirements. Developments in one-piece closures have enabled them to become more and more widely adopted as solutions for hotfill products. The market for hot fill products Hot fill applications have been around for decades in, for example, the fruit juice bottling business. All juices, nectars and juice drinks filled in glass bottles in the past have been bottled under hot fill conditions in order to decontaminate the packaging material (the inside of the bottle and the closure) with the hot beverage itself (between 85 and 92°C in general). They also help to achieve a long shelf life, ranging from several months up to one year, depending on the type of juice, the temperature of the liquid and its time in contact at hot temperature during filling. The PET bottles introduced for the first hot fill applications had some specific designs in common. The body, which had to be temperature-stable, includes absorption panels to control deformations caused by variations of temperature and vacuum created during cooling. The neck needed to have a relatively thick wall, even crystallized initially, in order to withstand the distortion during the hot fill process and to provide heat stability. In the beginning, closures were (and still are, in many instances) twopiece, built with an elastomeric liner applied inside the closure shell. It provides a secure seal once screwed on the bottle neck with a high torque. DisDoubleSeal 28 HF Chart 2: North America: development of hotfilled juices, energy drinks, etc. (Source: Bericap) Chart 1: Europe: development of aseptically filled juices, energy drinks, etc. (Source: Bericap) Bericap’s one-piece closure for hotfill - in Asia since 2003 Global development of filling processes replacing glass bottles with alternative packaging systems differed in regions across the world. In Europe, the glass bottle was replaced mainly by PET aseptic systems, which still dominate today (see chart 1). Hot fill applications in North America moved into PET bottles in the 1990s and the trend continues, unbroken, up to the present day (see chart 2). Asia began hot fill applications with glass and moved to PET bottles around the year 2000. It is now, following a health trend, turning to aseptic applications, which promise better product quality because of shorter-period heating, thus minimising distortion of vitamins in the filled product.","@ID":36} "NEWS 9 PETplanet insider Vol. 11 No. 05/10 www.petpla.net New ‘Aptar Group’ branding for Emsar, Seaquist, Indigo by Valois, and Pfeiffer Airlessystems, Emsar, Indigo by Valois, Pfeiffer, Seaquist Closures, Seaquist Perfect Dispensing and Valois are to be rebranded by their longstanding parent company as Aptar Group. The business recently announced that it would, in 2010, undertake a strategic realignment of its business lines in order to focus on three market segments: Aptar Beauty + Home, Aptar Food + Beverage and Aptar Pharma. Aptar Food + Beverage will be fully operational by early 2011. Production and sales will be organised on a regional basis, with the backing of global development teams. It will, in addition, further focus on innovation in dispensing systems, the company says. www.aptar.com Renaming of Amcor business Michigan-based Amcor PET Packaging has been renamed Amcor Rigid Plastics, as a result of the reorganisation of seven business units following the US$1.9 billion acquisition of parts of Alcan Packaging by Amcor Ltd. Amcor Rigid Plastics consists of Amcor PET Packaging; Bericap North America, a plastic closures joint venture between Amcor and the Bericap Group; and the plastics container unit of Alcan’s global pharmaceutical business. Bill Long, who had been president of Amcor PET Packaging, will head up the new business. The company said that the acquisition of Alcan’s pharmaceutical rigid container business will complement Amcor’s current plastics packaging business, which produces PET packaging for the beverage, food, and non-food industries. Alcan’s rigid container pharmaceutical business produces containers made of PP, PE, and PET for over-the-counter drugs, vitamins, and other pharmaceutical needs. www.amcor.com Low-output rebranding reflects acquisition In early 2009, Krones AG increased its shareholding in Kosme SRL, of Roverbella, Italy, to 100 per cent and extended its market reach into low-output beverage and filling technology. Kosme is comprised of two business units: Kosme GmbH in Austria and Kosme s.r.l. in Italy. Since spring 2010, the new subsidiaries have been using the Krones logo but with a difference: the Kosme corporate colour of orange has been retained. The company says that this is intended to denote the overall group affiliation while ensuring that Kosme equipment remains easily identifiable. Kosme Italy focuses primarily on labelling, filling, packaging and conveyor technologies, with output ranges up to approximately 18,000 containers an hour. Kosme Austria is responsible for developing and manufacturing stretch blow-moulding technology. Kosme will work with Krones AG in research and development, so that it can incorporate empirical feedback from Krones technology in its own products. Its customers can also use Krones’ worldwide LifeCycle Service. www.krones.com","@ID":11} "BOTTLE MAKING 31 PETplanet insider Vol. 11 No. 05/10 www.petpla.net Generously configured curve radii counteract possible jamming on the bends and thus contribute to avoiding bottle jams and backing up. The segments which are manufactured from stainless steel (AISI304, ST1.4301) are laid out to suit the individual bottling line and overall operational requirements of the customer. They are delivered and set up and commissioned using expertise sub-contracted from the individual air segments maker. The company also plans and supplies transport conveyors for filled, capped and labelled bottles as well as for packaged products, right up to the palletiser and end of the line equipment. In such cases the controls of all conveyors from empty bottle air conveyors to the filled bottle and endof-line finished package conveyors are integrated into one central control cabinet. In addition the company can offer: defining the targeted total scope plant design – philosophy of the line – autocad supported calculations of speed and accumu- lation detailed technical planning – auto- cad supported project management for complete lines supervision of installation and com- mission until runoff and efficiency testing. The company endeavours to take all aspects of the bottling line into account. www.glocon.de DEUTSCHE EDELSTAHLWERKE, Obere Kaiserstr., D-57078 Siegen / Auestr. 4, D-58452 Witten Who knocks PET bottles into shape? CorroPlast® – the ultimate steel for all-stainless mould sets. Air conveyor Netstal PETline 48 preform system SBM system Corpoplast Blomax 6","@ID":33} "REGIONAL MARKET REPORTS 10 PETplanet insider Vol. 11 No. 05/10 www.petpla.net Tanzania & Kenya Circumnavigating Kilimanjaro by Alexander Büchler On the borders of Tanzania and Kenya Kilimanjaro towers to a height of around 6000 metres. For our East Africa Special we circumnavigated it, starting in the south-east of Tanzania at Dar- Es- Salaam. Despite its not being the capital, the government has its seat in this coastal location. It was from here that the local fire water, Bakhresa, set out to conquer the country. In addition to bottles and caps, the company also produces its preforms itself. We also took the opportunity to have a look at the company’s roots in flour production. On we went northwards, right to the foot of Kilimanjaro itself. This is where the headquarters of Bonite, the Coca Cola bottler for the region, are located. Bonite has a kind of symbiotic relationship with the mighty mountain. Bonite is involved in a number of environmental and social undertakings geared to the mountain. Nevertheless, the company also reaps huge benefits from Kilimanjaro. The high numbers of tourists streaming into the region ensure a good level of sales. Heading north we came to Nairobi in Kenya. Here we also met with the local Coca Cola bottler, a company belonging to the Sabco Group. In the case of both CC bottlers we found up to the minute machine technology coupled with good local distribution facilities. Whereas Bonite tends to rely on recyclable glass for operations in the small volumes sector, in Nairobi they have broken through into the PET era, even for smaller volumes. Macroeconomic Data Tanzania Area ................................................... 945,087 km2 Population............................................ 41,048,532 GNP/Head of population ......................... 415 US$ All figures 2006/07 Kenya Area .................................................... 580367 km2 Population............................................ 39,002,772 GNP/Head of population ......................... 845 US$ All figures 2006/07 © Henry Schmitt - Fotolia.com Regional market reports Tanzania / Kenya","@ID":12} "CAPPING / CLOSURES 39 PETplanet insider Vol. 11 No. 05/10 www.petpla.net functional requirements as well-established standard caps. The benefits of “X-Light” are obvious: these caps are 40% lighter, which translates into considerable material savings – and cycle times are cut by 25%,” Rainer Klass points out. The 96-cavity mould tool cycles at 3s for the 1g cap. The caps, which were optimised in shape and weight, are not only superior in terms of production, material and costefficiency, but also facilitate handling at the filling line. Schöttli is convinced that the new “X-Light” screw caps will become established in the market: they save costs and the mould concept ensures safe, reliable, flexible and cost-efficient production. International customers are expected to welcome the new product, which offers cost-efficiency in combination with convenience, easeof-use and a “green” image. International expansion Schöttli is expanding its international market presence by means of strategic acquisitions. The first of these happened in China, where the Swiss company took over s-mouldtech (Suzhou) in October 2008. At the Chinese facility a qualified team of 40 employees manufactures injection moulds for the production of caps and closures. In future Schöttli’s parent company, Mould Technologies Holding, will intensify its activities in the US market. “We want to be with our customers and move into their markets with them. This includes providing localised services,” points out coowner and CEO Martin Schöttli. www.schoettli.com The 96 cavity mould tool cycles at 3s for the 1g cap International Trade Fair No. 1 for Plastics and Rubber Worldwide k-online.de in the world for you! The most important trade fair “It’s K time” means that about 3,000 exhibitors from over 50 countries present the latest products and concepts – from standard to high-tech solutions. With its first-class range of exhibits, both in terms of quantity and quality, K is the most important business and contact platform for the industry worldwide. In 19 halls, everyone is represented, from the market leaders to the niche market suppliers who decide the future of the industry. Be there when the world-class suppliers of plastics and rubber meet in Düsseldorf! Messe Düsseldorf GmbH Postfach 1010 06 40001 Düsseldorf Germany Tel. +49(0)211/45 60-01 Fax +49(0)211/45 60-6 68 www.messe-duesseldorf.de New +++ The K Innovation Compass +++ from mid-September +++ at www.k-online.de/2550","@ID":41} "MATERIAL / RECYCLING 22 PETplanet insider Vol. 11 No. 05/10 www.petpla.net 800,000t/a during this year. The EU is a key target market for Oman (significant EU foreign trade partners are listed in Fig.3). Italy: biggest PET market, biggest PET importer According to a leading market expert, the total requirement for PET (with a viscosity number of 78 ml/g) was 2. 927 million tonnes in the 27 states of the EU and Switzerland in 2009. Italy alone accounted for 292 kmt of PET. According to market experts, and based on information from a variety of sources, more than 50% of Italy’s PET requirements came from outside the EU. Italy’s import quota according to various data amounts to between 55 to just under 70 per cent. Figures for other EU countries vary: in 2009, Spain imported 77 kmt, the UK 48 kmt and France 42 kmt from non-EU countries. Germany, which is one of the five EU countries with the highest requirement for PET, imported a mere 23 kmt from non-European states in 2009. Anti-dumping duties drastically reduce imports Alongside the plant closures in Europe, anti-dumping duties, levied by the EU Commission under certain conditions, affect the import of PET into the EU. Taking China and Australia as examples (see Fig. 4): in August 2004 an anti-dumping duty amounting to 184 Euro per tonne was levied on PET (bearing the Harmonized System Code 39076020) from both countries and this remained valid for five years in each case. In 2003 138 kmt PET were still being imported from China into what are now the 27 EU member states. Because of the imposition of an anti-dumping duty in 2004, imports totalled only 51kmt. After that, imports first soared to 104 kmt, before continuously falling back, until, in 2009, only 9 kmt PET from China was still getting into the EU. Another example is Australia. In 2009 the EU levied a €128 per tonne duty on exports from this country and the EU imported only 1.2kmt PET, of which 0.2kmt was sold to Ireland and 1 kmt to Italy. This compares with Fig. 4: Effects of anti-dumping duties on Imports from China into the EU (All figures: Source: Eurostat) anti-dumping duty","@ID":24} "MATERIAL / RECYCLING 18 PETplanet insider Vol. 11 No. 05/10 www.petpla.net LCA: the advantages of PET A newly released life-cycle inventory of single-serving soda containers concludes that PET plastic bottles offer a better environmental footprint than aluminium cans or glass bottles. For further information please contact: [email protected] www.gabriel-chemie.com Innovation Don’t compromise on quality. PremiumMasterbatches for Superb Products. $ (( /0 * Kielce May 25–28, 2010 2%/%0 1/ 0 , ( /0,+( The complete lifecycle study was conducted by Franklin Associates* for the PET Resin Association (PETRA)**. It compared total energy, solid waste and greenhouse gas emissions per 100,000 ounces of soft drinks packaged in typical 20-oz PET bottles, 8-oz glass bottles, or 12-oz aluminium cans. The PET bottles showed appreciably lower numbers across the board. Greenhouse gas emissions for the PET bottles registered 59% less than aluminium and 77% less than glass. Franklin calculated the greenhouse gas emissions for the PET bottles at 1,125lbs (approximately 510kg) of CO2 equivalents, compared to 2,766lbs (c. 1,258kg) for aluminium and 4,949 lbs (c. 2,250kg) for glass. Total energy use for the PET bottles amounted to 11 million BTU per 100,000 oz of soft drink, compared to 16 million BTU for aluminium and 26.6 million BTU for glass. Solid wastes amounted to 302lbs (137 kg) for PET bottles, 767lbs (348kg) for aluminium, and 4,457lbs (2,025kg) for glass. Solid waste volume was 0.67yd² (0.6m²) for PET, 0.95yd²(0.855m²) for aluminium, 2.14yd² (1.9m²) for glass. “Since 2005, PET containers have been the subject of several independent lifecycle analyses and PET has consistently shown itself to be a sound environmental choice whether compared to glass, metal or other plastics,” said PETRA Executive Director Ralph Vasami. After PETRA received the preliminary LCI report on the soft drink containers, it asked Franklin to recalculate its findings on the basis of 10,000 equally sized 12-oz. containers. The PET bottles still showed advantages over aluminium and glass in terms of lower greenhouse gas emissions and solid wastes, while total energy use was deemed comparable for all three materials. The lifecycle inventory for both analyses covered extraction of raw materials through container fabrication as well as post-consumer disposal and recycling. The post-consumer disposal and recycling calculations included transport to a landfill or incinerator, equipment operations at a landfill and energy recovered by an incinerator, but excluded incinerator and landfill emissions. Postfabrication transport to the filling site, filling, distribution, storage, retail use and consumer use were excluded. www.petresin.org/news.asp *Franklin Associates, Ltd., founded in 1974, provides consulting services in lifecycle assessment and solid waste management to clients in the public and private sectors. www.fal.com **PETRA (the PET Resin Association) is the industry association for North America’s producers of PET. www.petresin.org Please note: all metric conversions are approximate values. Conversion rates lbs/kg: 1:2.2; cubic yards/cubic metres: 1:0.9.","@ID":20} "BOTTLES 43 PETplanet insider Vol. 11 No. 05/10 www.petpla.net PETbottles Personal Care International PackTech India 2010 www.packtech-india.com 18–20 November 2010 Bombay Exhibition Centre Mumbai/India 6th International Exhibition and Conference for the Packaging- and Processing Industry Messe Düsseldorf GmbH P.O. Box 101006 40001 Düsseldorf Germany Phone +49/211/4560-7739/-7741 Fax +49/211/4560-7740 [email protected] [email protected] www.messe-duesseldorf.de Supported by Sponsors and Conference Organisers www.drinktechnology-india.com International trade fair for beverage and liquid food technology 18–20 November 2010 Bombay Exhibiton Centre, Mumbai/India www.drinktechnology-india.com Powered by Partner: Supported by: Contact: Messe München International India Pvt. Ltd. • 23, Deccan Court, S.V. Road, Bandra (West), Mumbai – 400 050, India • Phone (+91 22) 26 45-21 01/02/03 • [email protected] Eco-refill in PET Henkel in Boulogne-Billancourt, France, are selling the 3-litre refill pack of X-Tra liquid detergent in a tall, rectangular PET bottle. Using the refill pack, that carries front and rear labels, the handy 1 litre standard retail pack can be filled as required. The company promotes the pack as being very ecologically friendly and making significant savings in packaging material. Skin-friendly washing up liquid Specially developed for allergy sufferers with sensitive skin, the 500 ml pack of “dalli med” washing up liquid from DalliWerke of Stollberg in Germany is sold in a white, slightly waisted, PET bottle with an integrated grip feature. The front and back labels, designed to match the shape of the bottle, and the blue, screw-on push-pull closure, which simplifies one-handed operation, makes a nicely presented pack. Gentle shampoo The “Iroise“ brand shampoo sold by the French cosmetics manufacturer Scanark of Ivry-Sur-Seine is an extra gentle shampoo in an interestingly designed 250 ml PET bottle. On the front is a colourfully printed “no-label look” label, and the rear label is printed on the inner surface with a floral motif. At the point of sale this produces surprising 3D effects, depending on the angle of the light. The co-injected two colour hinged cap with a detent hold in the open position, is the perfect complement to this modern cosmetics pack. Hand wash in PET Biocos, the French cosmetics manufacturer from Sarcelles, is selling “Hyacos” hand wash and hand care lotions in crystal clear PET bottles of various sizes. These cleansing products are designed for use without the need for flowing water and dry on their own within 30 seconds. Suitably-designed “no-label look” labels and modern hinged closures strongly support the cosmeceutical character of the products and nicely finish off their look at the point of sale.","@ID":45} "MATERIAL / RECYCLING 21 PETplanet insider Vol. 11 No. 05/10 www.petpla.net quarter of 2010. The company’s plant in Spain also stopped production. This was compounded by the shutdown of the Invista Plant, resulting in a reduction of 300, 000t of the three plants in the second half of 2009. Together, these three plants had an annual capacity of 600, 000t/a. The French company Tergal also closed its Gauchy PET production plant in the autumn of 2009. Given these shutdowns, it is no surprise that imports rose significantly (see Fig. 2) South Korea – a dominant force It will come as no surprise that South Korea has been one of the top exporters to the EU for a number of years. In 2002 South Korea was already supplying 122 kmt of PET to the EU**; in subsequent years quantities fluctuated between 121 kmt and 177 KMT; in 2009 the EU states imported a total of 256 kmt PET from South Korea alone. The United Arab Emirates (UAE) have developed into the second largest supplier, with EU imports accounting for 199 kmt of the total 872 kmt produced by the UAE. Oman is also making an impact on the EU statistics, currently producing 300,000t (January 2009 figures, of which 53 kmt went to the EU), and this is expected to increase to a capacity of Fig. 2: PET imports into the EU in 2009 Fig. 3: PET imports into the EU from 2007 to 2009 - biggest suppliers","@ID":23} "REGIONAL MARKET REPORTS 14 PETplanet insider Vol. 11 No. 05/10 www.petpla.net Bonite Bottlers Ltd is the Coca-Cola licensee in Northern Tanzania. F.l.t.r.: Zoeb T. Hassuji, Managing Director, Christopher Loiruk, General Sales Manager, Alexander Büchler, and Peter Mayagils, Quality Manager The extent to which the company has integrated nature, the environment, and above all Kilimanjaro, into its philosophy can be seen most clearly in the business-like and down-to-earth office of Christopher Loiruk. There is a window that covers the full width of the room giving an uninterrupted view of Kilimanjaro, and, by lowering one’s eyes a little from the mountain itself, the bustling activity on the Bonite site can be seen. Filling under licence from Coca-Cola is the mainstay of the operation. Because of the size of Tanzania, Coca-Cola has appointed four regional licensees, with Bonite being responsible for the northern area. Filling is mainly done in refillable glass at up to 30,000 bph. Only the 1.5 litre bottle is made from PET and weighs in at 48 grams. It carries a PCO 28 cap. The new blocked blowing/filling line from Krones is already in operation. The valves are designed to handle still water and also CSDs. From left, Christopher Loiruk, Alexander Büchler and Peter Mayagils The labeller is located at the dry end Because Coca-Cola is the main business, all of the filling lines must meet Coca-Cola standards. “That may demand a higher level of investment but we can be sure that our quality is of a high standard,” explained Peter Mayagils. The latest example of the drive to quality is the very recently installed Krones line for filling water and CSDs. The Contiform S 12 stretch blow moulder feeds bottles directly to the rinser, which is mechanically blocked with the Contiform and the 70-head volumetric filler. The labeller, also from Krones, is located at the end of the dry area. The whole line has a capacity of 20,000 bph. This new line complements another Krones line, used to fill water, which itself is only 5 years old and is composed of separate machines. This “old” line was brought in to replace the original PVC line. The new glass filling line is also from Krones. “We did buy a filling line from another supplier about 10 years ago. It included an integrated Krones packer and we were so pleased with the service from Krones when compared with the service we got for the rest of the line that we ordered our next lines from Neutraubling,” said Christopher Loiruk. “Full steam ahead” for preform production. Christopher Loiruk and Peter Mayagils at the material dryer for the Husky Hypet 120 With the two Krones PET lines the company still has only 32,000 bph capacity, but today that is still more than the volume of water filled. “Up to now we have limited ourselves to selling our premium water only in the area covered by our Coca-Cola licence. Now we distribute the water across the whole country. Our first successes, for example, were in Dar Es Salaam. We are gradually work-","@ID":16} "PETnews 6 PETplanet insider Vol. 11 No. 05/10 www.petpla.net Graham Packaging announces agreement to purchase China Roots Packaging Graham Packaging Company Inc. (NYSE:GRM), which is based in York, Pennsylvania, has announced that its subsidiary, Graham Packaging Company, L.P., expects to acquire China Roots Packaging PTE Ltd., a plastic container manufacturing company located in Guangzhou, China. Its customers include several global consumer product marketers. The company has signed a Share Purchase Agreement to acquire 100% of the shares of Roots Investment Holding Private Limited, which will be the sole equity holder of China Roots, from Malaysian company PCCS Group Berhad. This will be Graham Packaging’s first operation in China. The transaction is expected to complete during the second quarter of 2010. Graham Packaging designs, manufactures and sells customised blow moulded plastic containers for the branded food and beverage, household, personal care/speciality and automotive lubricants product categories. It produces more than 20 billion container units a year at 80 plants in North America, Europe and South America. www.grahampackaging.com Engel management changes Hans Wobbe (57) is to leave the management of Engel Holding on July 31, 2010 for personal reasons. Mr Wobbe held responsibility for technology and production; his duties will now be assumed by Peter Neumann, CEO. The owning family and the management expressed regret at Mr Wobbe’s decision and their thanks to him for his work. www.engelglobal.com Invista Europe Polymer & Resins business reorganisation and management changes Invista Polymer & Resins’ primary European production facility, in Gersthofen, Germany, produces a wide-variety of DMT- and PTA-based polyesters for technical, textile, film and packaging applications. Invista is now offering an R&D service, based at Gersthofen, to the market. The company says that its continuous pilot-scale polyester polycondensation line at the R&D centre has the flexibility to produce customised polyesters via DMT or PTA. The line allows scaling-up of supply from small trial quantities to various bulk market quantities from one source, depending on customer needs. The key focus areas for the business remain the provision of high-value packaging resins, like PolyShield resin, specialty polymers and DMT sales, as well as a portfolio renewal of technically-challenging polymers. At the end of 2009 Ottmar Schmidt was appointed to the role of general manager of the European Invista Polymer & Resins business. He has over 20 years of industry experience including more than 15 years in the DMT and polyester businesses. www.INVISTA.com Organisational restructuring at La Seda Spanish company La Seda de Barcelona, S.A. has announced that the company is to be restructured into two distinct operational units: packaging and recycled PET. Mr. Martin Hargreaves, who will be responsible for site performance, operations and commercial functions, will lead the packaging division. The recycled PET division will be headed by Mr. José Antonio Alarcón, who will be responsible for PET production sites and the recycled PET sites in Balaguer and Italy. Mr. Abelardo López has been appointed as the new corporate and financial manager of the Group. As well as the financial area, he will be responsible for organisation, systems, and human resources and legal departments. www.laseda.es Krones reports loss for 2009; returns to profit in Q1 2010 Krones AG, the beverage filling and packaging company, reported a loss in the 2009 business year of €34.5 million but achieved increased sales and a return to profit in the first quarter of 2010, with earnings before tax (EBT) of €13.2 million (€9.1 million after tax). The executive and supervisory boards will propose to the AGM that no dividend is paid in respect of the 2009 trading year. Krones reported that demand in the packaging machinery market fell in 2009 by more than 25% worldwide and affected all geographic areas except China. Order bookings in 2009 were down by 17.6% from 2008, to €1,916.0 million; consolidated sales fell 21.7%. The executive board had, at the end of 2008, launched its ‘Conversions’ programme in order to adjust the company to the realities and effects of falling markets. The company increased its free cash flow during 2009 by around five per cent, to €82.5 million. As at December 31 2009, the Group had no debts with banks and held net liquidity of more than €135 million. Sales of €533.5 million in Q1 2010 were up 10.6% on the previous year’s. Bookings during 2009 rose in each quarter and accelerated during the first three months of 2010, during which time it received orders totalling €550.4 million – a rise of 32.8% over Q1 2009. Orders at the end of March totalled €905.3 million. Bookings during Q1 2010 were particularly good from Asia, China, Africa and the Middle and Near East. Demand remained weak in the USA, Eastern Europe and Russia but Central and Western Europe showed indications of gradual recovery. The executive board anticipates growth in sales of five to 15% in 2010 and expects a further uptrend in 2011, assuming no significant change in the situational framework. www.krones.com","@ID":8} "MARKET SURVEY 26 MARKETsurvey 05/10 Company name PET-Verpackungen GmbH Deutschland Westbridge PET Containers PDG Plastiques Resilux NV Postal address Telephone number Web site address Contact name Function Telephone Fax E-mail Gewerbegebiet 4, 98701 Großbreitenbach Germany +49 3 67 81 / 4 80 - 4 57 www.pet-verpackungen.de Hubert Rebhan Projects & Sales +49 3 67 81 / 4 80 - 4 53 +49 3 67 81 / 4 80 - 4 52 [email protected] 3838E - 80 Ave SE Calgary, AB T2C 2J7 403-248-1513 www.westbridge.ca Sharon Pokolm Sales Manager 403-207-7720 403-248-1199 [email protected] ZI secteur 2, 45330 Malesherbes, France 33 2 38 34 61 95 www.pdg-plastiques.com Francois Desfretier General Manager 33 2 38 34 61 95 33 2 38 34 63 82 [email protected] Damstraat 4 9230 Wetteren, Belgium +32 (9) 365 74 74 www.resilux.com Philippe Blonda Director of Marketing and Sales +32 (9) 365 74 76 +32 (9) 365 74 75 [email protected] Multilayer preforms (yes/no) yes No Yes Yes PEN preforms (yes/no) upon request No Yes Yes Preforms in alternative materials (PP/PLA) upon request Yes Yes Yes List of additives available colours, oxygen scavengers, UV-blockers, slip-agents, AA-scavengers, brighteners, PA-based barriers UV, Oxygen Scavenger, PCR, Bio additive light barrier Prelactia - Oxygen barrier - colored preforms, Recycled PET (RPET) UV-blockers, colours, multiple barrier additives Preform range standard preforms with 28mm PCO finish from 14.5g (e.g. for 0.25l bottles) to 54g (e.g. for 2.0l bottles) including, preforms with 28mm PCO finish and octagonal neckring. Preforms with PCO1881 short neckand other customized neck finishes. 38mm 2-Start and 3-Start Bericap preforms for wide mouth applications; 92g preforms with Bericap 48-41 finish for large containers. Preforms are also available as multilayer with tailor-made barrier properties Finish Category 28mm 410 28mm 410 28mm 415 28mm 400 28mm 100 33mm 400 33mm 400 CRC 29mm Rical 32mm Rical 28mm Kerr 33mm Kerr 3mm Stelvin 38mm Portola 38mm Alcoa 28mm PCO Gram weight 20.5; 23.5 36.5; 42.5; 48.5 36,5; 42.5; 48.5 36.5; 42.5; 47.5 34.5; 40.5; 47.5 30.5; 36.5; 54 56 36.5; 41.5 48.5 39.5; 45.5; 86 83.5; 90 71 59.5; 75.5; 83.5 87.5 19.6; 25; 35; 42; 47; 55; 76 29/25 short : 8 - 11,7 - 23,5 - 28g 30/25 high: 17,5-25-26-28-31-33-36-39g 30/25 low: 17,5-25-26-28-31-33-36-39g 38mm 3 start: 26 - 44 - 50gr 38mm 3 start: 28g Prelactia 100% light barrier for UHT milk long shelf-life 48/41: 55 - 62g 27/32: 6,5gr dairy and smoothies 25/20: 6,5 - 8g dairy Ø28 BPF: 42 - 44 - 48 - 60g 29/23: 24 - 33 chemical BVS 30H60: 50g Wine (high oxygen barrier) ultra-lightweighting 2,4g preform Overmoulding technology for 2 layers preforms Standard monolayer preforms: Weights: 9g-124g Neck finishes: PCO 1810, PCO 1881, PCO 8- sided, BPF, 38mm 3 & 2 thread, Detergent, Oil, Crown Cork, Ketchup, 29-25 short, 30/25 low, 30/25 high, 48-40 Bericap, Wine Barrier preforms (Monolayer & Multilayer)/ ResiOx 3-6-9 protects products against oxygen ingress/ ResiC for carbonated products/ • Resimid & Resimax protects beer • Resiblock 0-2-4 for milk and other products that are light sensitive Hot fill - For Filling at 85°C ; Refill Company name Pearl Drinks Limited Alpla Werke, Alwin Lehner GmbH & Co KG PETform (Thailabd) Limited Postal address Telephone number Web site address Contact name Function Telephone Fax E-mail 702,Anasal Bhawan, 16,K.G.MARG New Dehli-110001, India 011-46470200,41520227,41520442 jaipuria.co.in Vijay Walia Sales and Marketing 011-41520442,46470227, 9811020870 011-23327747 [email protected] Mockenstrasse 34, A-6971 Hard, Austria + 43 / 5574 / 602 - 0 www.alpla.com Hermann Riedlsperger Head of Sales, PET Business + 43 / 5574 / 602 - 513 [email protected] 75/102 Ocean Tower 2, 37th Floor, Soi Sukhumvit 19 (Wattana), Asoke Road, Kwang Klongtoey Nua, Khet Wattana, Bangkok 10110, Thailand (66 2) 6616661 www.indorama.net Pramod Dubey VP- Marketing 66 81 9371978 (66 2) 6616664-5 [email protected] Multilayer preforms (yes/no) No yes No PEN preforms (yes/no) No no No Preforms in alternative materials (PP/PLA) No yes No List of additives available Green colour, Emerlad Green, Turquoise Green all standards in the market None Preform range 28mm neck, 20.9g csd clear, 25.5g CSD clear and emerald green, 27.7g CSD clear, 52g CSD clear & green, 28mm diameter three start alaska neck, 22g clear, 30mm diameter three start alaska neck, 21.5g clear, 25.5g clear Preforms for beverage, food, cosmetic and household industry. Preforms with standard and customised necks. Preforms with barrier properties in mono and multilayer technology. More than 25 preform production plants in Europe. Specialized in In-House operations at customer's plant. 17.02g 30/25 mm, 25.50g PCO 28mm, 27.71g PCO 28mm, 40.02g PCO 28mm, 43.02g PCO 28mm, 45.50g PCO 28mm, 52.10g PCO 28mm","@ID":28} "BOTTLE MAKING 30 PETplanet insider Vol. 11 No. 05/10 www.petpla.net Used but not spent Systems supplier offers complete range of PET machinery, plant layout support and services. Older machines (“used but not spent“) represent an investment choice worthy of consideration - and not only in times of tight financial circumstances. Such value analysis usually pays off and applies equally to equipment for the production of preforms and bottles made from PET, PEN or PLA. Since 1994 Glocon Technical Supplies & Trading GmbH of Schwerin in Northern Germany has offered such equipment as well as systems/process related support services including support for process relevant auxiliary equipment such as resin dryers, dehumidifiers, chillers, compressors and tooling. Following inspection Glocon buys pre-used equipment and transfers it to its plant, sets it up for production, repairs and overhauls it there after another thorough audit. Before shipping it to a buyer it is testrun – usually assisted by the buyer’s technical staff. In 2004 the company moved into its own factory premises in Schwerin with 3000 m2 under roof, renovated and partitioned it into a workshop, separate blow and injection moulding equipment installation and test run areas, spare parts, a walled-in high rack spare parts storage section, support equipment room for the 40-bar blow air compressor and the PET-bottle regrinding mill and the office area. The two assembly halls are equipped with overhead crane runways. The technical assistance encompasses advice on bottle design (inclusive of lightweighting efforts) as well as on preform compatibility and pertinent lab testing. Glocon counsels on machine and auxiliary equipment sizing and layout, installation and startup services, line relocation, overhaul, upgrading and retrofitting with the objective of extending and/ or enhancing the useful life of existing PET-process and support equipment. In order to also serve the downstream side of the process more fully Glocon have reinforced their technical team and now provide layout engineering services as well as supplying conveyor systems for blown bottles - either air conveyors for cylindrical bottles or vacuum conveyors for special custom containers. They have supplied and commissioned such bottle transfer conveyors for CSDs (PCO1810-28mm) as well as for 38 mm iced tea applications. The equipment offers the following features: automatic adjustment for bottles with 28 mm and 38 mm neck finishes by electronically remote-controllable pneumatic cylinders symmetrical guide rail adjustment (both guide rails) asymmetrical guide rail adjustment (single guide rail) straight-line channel layouts, differ- ing customised layouts, customised curves and ups and downs climbing and descending channel layouts automatic shunting systems from 1 to 2 channels or 1 to 3 channels, as well as 2 to 2 and 3 to 3 channels Other details that make a difference are support ring guides with gentle handling plastic strips (project and client dependent with clips as wear parts) or, if staff is at a premium and maintenance must be minimised, metal guides (cold hardened stainless steel) with minimised coefficient of friction. Along the length of the air channels inspection hatches are arranged at regular distances in a clearly laid out manner. The driving air stream passes through individually selected filtering stages and applies pressure and air volumes to suit individual transport and hygiene requirements. Careful manufacture of the air channel segments, often using precision manual skills, ensures precision assembly of the conveyor and so minimises bottle jams that may otherwise occur on the line during production. Filled bottle conveyor Transporting system","@ID":32} "CAPPING / CLOSURES 38 PETplanet insider Vol. 11 No. 05/10 www.petpla.net “One Stop”strategy a success for Swiss mould maker Swiss injection mould maker Schöttli AG specialises in the production of highperformance moulds with a high number of cavities, combining high output and short cycle times, as well as the company’s end-to-end Cax concept and the pooling of all core competences under one roof. Tried and tested modular concept Widespread globalization and the corresponding pressure to reduce costs create an ongoing demand for injection moulds with an ever higher number of cavities. This is the core competence of Schöttli AG, be it single face or stack moulds. Schöttli’s modular concept for tool design has proven very successful. Optimised over many years, this concept applies to the construction and production of all of the company’s injection moulds, even those designed for complex closures. The modular concept is said to offer several advantages: The clamp system with its uniform opening geometry allows maximum freedom of product design. Cavities in close proximity to each other allow a compact mould design and the selection of the smallest possible injection moulding machine for production. Optimum temperature control and the deployment of innovative material and coating combinations promote very short cycle times. Components are optimised for mould and production so as to ensure easy exchangeability of functional elements and low maintenance. In addition the cavities are easily accessible, which facilitates the correction of errors without the need for removing the mould from the machine. “X-Light” economises on material and costs Increasingly strict environmental directives in industrialised nations have had a significant impact on the closures industry. The positive effect is that the environmentally friendly use of material resources also reduces production costs. “The idea of using less material to protect the environment is motivating”, says Rainer Klass, Product Manager of Schöttli’s packaging department. Developed by the company as a result of customer and market analyses, the new “X-Light” screw cap proves that saving material does not necessarily compromise product functionality. “Two years ago standard screw caps had an average weight of about 1.6g. The “X-Light”, which is produced in our 96-cavity mould presented at the NPE in 2009, meets the same The 1g “X-Light” is a development of Schöttli AG","@ID":40} "PETbottles 44 PETplanet insider Vol. 11 No. 05/10 www.petpla.net Lightweight 38mm closures for new dairy product Bericap’s redesign of its SK 38/16 LC 2-piece closure claims to save of around 15% of resin compared to its predecessor. The closure has a slit interbead band with vent slot design and is suitable for high-speed aseptic line handling. The new SK 38/16 LC 2-piece closure has been selected for a new dairy product from Coca-Cola China, which has been launched in three different flavours: pineapple, peach and mango. First bottles of the new dairy drink have been available in the markets since September 2009. The company says that its light-weighted SK38/16 closure will help its customers in their efforts to reduce packaging costs and to reduce consumption of non-renewable raw materials. www.bericap.com PET bottle for imported French vodka line. Spirits and liqueur importer White Rock Distilleries, of Maine, USA, has introduced a 375ml bottle from Amcor PET Packaging, which reflects the characteristic look of the company’s 1.75L Pinnacle Vodka brand PET container. White Rock converted its 1.75L bottle from glass to PET in 2006, which enabled it to cut material and production costs up to 50%, while preserving its brand image. The 44.5g custom bottle has a glass-like appearance and a metal ROPP closure for high topload strength. Bottle with additive Cedevita, a beverage producer from Zagreb in Croatia, is selling “Cedevita Go” (a vitamin drink with nine different vitamins) in a PET bottle with a special cap. While the cap is being unscrewed a small chamber in the cap is opened and an orange-coloured powder is released into the clear contents of the bottle, and shaken. The shaking dissolves the powder and the freshly mixed vitamin drink is ready for consumption. An appetising and informative shrink sleeve label completes this convenient 355 ml pack. New upside-down bottle from Knorr Unilever Germany of Hamburg are packaging their 500 ml “Tomato Joe” brand ketchup in an inverted PET bottle. The bottle is tamperproofed by way of an aluminium foil over the neck. The hinged lid is screwed on over the foil seal. When the lid is opened the sauce can be dispensed though a star-shaped orifice in the cap. Suitably shaped front and rear labels carry the commercial data and information on the product. Mousse in a PET bottle “bebe – young care“ is a brand owned by the cosmetics manufacturer Johnson + Johnson of Düsseldorf and includes a150 ml non-soap cleansing mousse in a clear PET bottle. A snap-fit foamer pump on the bottle is protected at the POS by a clear cover. When looking at the product through the “no-label” look front label it appears pink in colour thanks to the coloured label on the back of the bottle.","@ID":46} "BOTTLING / FILLING 32 PETplanet insider Vol. 11 No. 05/10 www.petpla.net Sterilization and aseptic filling systems GEA Procomac has recently introduced a range of sterilisation and aseptic filling systems, including a cap steriliser that uses electron beams, vaporized hydrogen peroxide bottle sterilisation, and the fifth generation of its wet PAAbased aseptic filling bloc. Electron beam cap sterilisation GEA Procomac’s ‘Sterilbeam’ cap steriliser is integrated with the company’s cold aseptic filling technology. Fed by a cap sorter, it is mounted on the top platform of a filling machine and it is the first machine in the beverage industry to employ electron beam cap sterilisation. Simple electron emitters, similar to common cathode-ray tubes, are used to produce electrons and convey them into beams. These are directed to cap surfaces and kill any possible microorganisms present by breaking and forming new chemical bonds in their molecules. The caps roll on guided rails and are sterilised by the e-beam as they pass in front of the emitter windows. The e-beam emitters are completely isolated from the external environment and shielded with lead. The company says that the advantages include a simpler process, as only voltage, current and time are monitored and there is no chemicals consumption, except for a small amount of hydrogen peroxide needed for environmental sterilisation. Energy is available on site allowing a shorter transmission chain; there are no residuals of sterilisation on the final product; and treatment time is in terms of GEA Procomac’s Sterilbeam cap sterilizer uses electron beams","@ID":34} "REGIONAL MARKET REPORTS 15 PETplanet insider Vol. 11 No. 05/10 www.petpla.net ControLine Motan control technology www.motan-colortronic.com Overall network controls to optimise your materials logistics in plastics processing –– Your partner for materials handling – worldwide –– A clear overview! Europe North: motan-colortronic gmbh Tel.: +49 6175 792 167 Europe South: motan-colortronic ag Tel.: +41 62 889 29 29 ing to establish a national market share in double figures,” Zoeb T. Hassuji explained to us. As part of this project the bottle was redesigned. Whilst previously it was a normallooking bottle with ribs, the shoulder of the new bottle is proudly emblazoned with a relief image of Mount Kilimanjaro. There is a narrower, grip area that also carries the wraparound label. The lower part of the bottle is decorated with tilted crowns. The PCO 28 cap has been retained and so switching the line over to the 1.5l Coca-Cola bottle is not a problem. Thanks to the superb mineral water that is filled direct from the spring with no form of treatment, the company has succeeded in positioning “Kilimanjaro Water” as a premium product. The 0.5 litre bottle is sold in retail stores at about 0.30 US Dollars. In addition 1.0 litre and 1.5 litre bottles are available. For the future the company also plans to develop and market other products. These include, for example, flavoured water or carbonated water. It was their high quality requirements that prompted Bonite to install a preform production line. First came a 24-cavity Husky HyPET 120 with moulds for 18g/0.5l, 23g/1l and 36g/1.5l preforms. To be able to increase their capacity Bonite have now also ordered another HyPET, this time a HyPET 225 with 48 cavities for the production of 0.5l preforms. “The preforms being sold in the region didn’t come up to our requirements and imports from the Gulf States, because of local taxes here, were too expensive,” said Christopher Loiruk, explaining the company’s decision. The “glass killer” Nairobi Bottlers Limited Coca-Cola Sabco Sergio Fernandes, Country Supply Chain Manager Mwenda Ruona Kageenu, Production Manager Caroline Cherono Keror, Production Unit Leader Solomon Lutta, Trade Marketing Manager When we visit emerging markets or developing countries we are fairly well used to seeing edible oil and water as the dominant products packaged in PET, and for CSDs to be mainly packaged in refillable glass. We were therefore rather surprised when we accepted the invitation of Sergio Fernandes, Country Supply Chain Manager of Nairobi Bottlers Limited, Coca-Cola Sabco, to see their production facility. Alongside 6 bottling lines for refillable glass was a brand new PET line for CSDs and water. In 2009 it filled almost 500 million bottles.","@ID":17} "PREFORM PRODUCTION 29 PETplanet insider Vol. 11 No. 05/10 www.petpla.net Symptom: The outer surface of the preform gate / dome area has indentations, usually formed in a circular pattern around the nub. The depression can be smooth or wrinkled in appearance. Cause: The gate area is deformed during the initial mould opening sequence (core side separating from cavity side) due to the preform not releasing freely from the cavity. Solutions: 1. Check water cooling temperature. This should be 7 – 10ºC (45 - 50ºF) for optimum cooling. 2. Check water cooling flow to mould. This should be at the mould manufacturers rating (for a given preform size and cavitation). 3. Check that the cooling time is sufficient for the preform being moulded. This typically ranges from about 1 to 3sec depending upon the preform wall thickness. Add time if necessary to increase shrinkage for better release. 4. Check that the hold (packing) time is not excessive for the preform being moulded. Reduce as necessary to minimise swelling. 5. Check that the hold (packing) pressure is not too high to cause excessive swelling, especially in the last zone. Reduce as necessary. 6. Check that transition position is set to about 13% of shotsize + cushion. Lower values may result in overfilling. 7. Check all temperature readings and correct if necessary. PET resin should be melted at about 280ºC (536ºF) +/- 10ºC (18ºF). 8. Check that all thermocouples are properly inserted and contacting the bottom of the wells. 9. Check that the decompression (pullback) time and position is not too little. This should be set high enough to ensure the melt pressure is being released, yet as low as possible to minimise the risk of drawing in air. Typical settings for valve gated moulds are: Time = 0 – 1sec; Distance = 0 – 10mm. Non-valve gated moulds may require higher values to minimise gate stringing. 10. Check the valve gate open delay timer and increase as necessary to release preform pressure. Typical settings are 0 – 0.3sec. This adjustment must work together with decompression (pullback) time. 11. Check hardware for worn, damaged or failed components, specifically the mould gate inserts, valve stems, and clogged core / cavity cooling channels. 11. GateDepressions PETplanet print Vol. 6: The Rapid Guide to Perfect Preforms by Rick Unterlander and Ottmar Brandau fax: +49 (0) 6221-65108-28 [email protected] www.petpla.net Order your copy now! Table of Contents i....................About the Authors ii............................Introduction chapter 1......................... AA Level High 2....................Accordion Preform 3.................. Air hooks / Streaks 4...........................Black Specks 5..................................Bubbles 6............................. Burn Marks 7........ Colour Streaking / Peeling 8.............................Crystallinity 9............................Drool Marks 10..................................... Flash 11.....................Gate Depressions 12...........................Gate Peeling 13.............Gate Voids / Pin Holes 14.................... Internal Gate Sink 15...........................Internal Sinks 16................................... IV Loss prices in EUR + VAT. 1- 3 exemplar each 129,- € 4 - 10 exemplar each 99,- € 10 exemplar each 69,- € 17....................... Long Gate Nub 18.......................... Milky Preform 19........................Moisture Marks 20...........Neck Finish out of Round 21.................. Parting Line Crease 22............ Parting Line Deformation 23.....................Preform Yellowing 24............................. Short Shots 25..................................... Sinks 26.....................................Splay 27...................... Stretched Necks 28................................ Stringing 29.................... Surface Blemishes 30.................... Thread Flow Lines 31....TSS (Top Sealing Surface) Sink 32..................................Unmelts 33............Wall Thickness Variation 34............................ Wavy Body 35............................. Weld Lines","@ID":31} "CAPPING / CLOSURES 37 PETplanet insider Vol. 11 No. 05/10 www.petpla.net No one knows your plant better than you yourself. That’s why we customise our lines to suit your visions – never the other way round. Just tell us your destination: we’ll find the route, supply the equipment, and stay with you until you arrive where you want to go. There’s only one thing you’ll never get from us: limitations. Because you are the sole arbiter of what’s possible. www.krones.com You want it? We build it! The machines of the ErgoBloc L have been awarded the enviro seal, by virtue of their minimised media consumption. the company’s multinational customers. After seven years in production, the company has gathered expertise from more than one billion commercial one-piece 28mm hot fill closures. Significant potential for onepiece hot fill closures The juices and sports drinks market in North America is so far a relatively virgin market for one-piece hot fill closures and remains probably the biggest market still using two-piece closures today. This means there are, potentially, huge savings available for the beverage filling industry if it converts to lighter packaging materials. From the closure manufacturer’s perspective, the goal is to develop a system that simultaneously resists hot fill conditions and also allows the use of lightweight neck finishes, with reduced neck wall thickness and consequent cost savings and carbon footprint improvement. Bericap is now offering a new hot-fill initiative to the market: neck wall thicknesses as low as 2mm (0.08”) together with a newly-modified onepiece 38mm closures – as a first step. Initial results have established that even thinner neck walls, together with a DoubleSeal one-piece closure show no leakages during the hot fill process - the packages remain absolutely tight. The DoubleSeal system maintains and supports the neck wall between the inner boreseal of the closure and its outer seal. Neck distortion is limited during the hot fill process, leading to proper tightness of the closure and thus securing the integrity of the beverage in its package. This initial success encourages minimising neck wall thickness further. Final weight savings for the 38mm neck alone of approximately 2.5g are projected. A similar development can be predicted for the 28mm DoubleSeal one-piece closure: the future neck finish for a hot fill bottle will be most probably the same as used for carbonated soft drinks (CSD) products today. When conversion from PCO 1810 hot fill neck to PCO 1881 standard finish becomes possible, a total weight saving for closure and neck of approximately 33% seems feasible. These savings are based on the 28mm DoubleSeal one-piece closure - a two-piece closure could not achieve it. www.bericap.com Lipton Ice tea capped with a DoubleSeal 28 HF","@ID":39} "imprint EDITORIAL PUBLISHER Alexander Büchler, Managing Director HEAD OFFICE heidelberg business media GmbH Landhausstr. 4 69115 Heidelberg, Germany phone: +49(0)6221-65108-0 fax: +49(0)6221-65108-28 [email protected] EDITORIAL Doris Fischer [email protected] Ruari McCallion Tony O´Neill Ilona Trotter Wolfgang von Schroeter Anthony Withers MEDIA CONSULTANTS Ute Andrä [email protected] Miriam Kiesler [email protected] phone: +49(0)6221-65108-0 fax: +49(0)6221-65108-28 France, Italy, Spain, UK Elisabeth Maria Köpke phone: +49(0)6201-878925 fax: +49(0)6201-878926 [email protected] READER SERVICES Kay Krüger [email protected] LAYOUT AND PREPRESS EXPRIM Kommunikationsdesign www.exprim.de PRINT WDW Druck GmbH Gustav-Throm-Straße 1 69181 Leimen-St.Ilgen Germany WWW www.petpla.net | www.pet-point.net PETplanet insider ISSN 1438-9459 is published 10 times a year. This publication is sent to qualified subscribers (1-year subscription 149 EUR, 2-year subscription 289 EUR, Young professionals’ subscription 99 EUR. Magazines will be dispatched to you by airmail). Not to be reproduced in any form without permission from the publisher. Note: The fact that product names may not be identified as trade marks is not an indication that such names are not registered trademarks. 3 PETplanet insider Vol. 11 No. 05/10 www.petpla.net EDITORIAL dear readers, The same thing done by two different people is not necessarily the same thing. How can it be that Krones, at its Annual Press Conference, designated 2009 as having been one of its most difficult years whilst Husky, Netstal and Hofstetter are talking about one of their best years in the PET business? As far as the preform system manufacturers are concerned, possible savings in materials here as a result of the new base geometry and the new cap have seen a return on investment within two years, in some cases within just one year. This meant that it was easy, even in times of crisis, to scrape the last few cents together and to invest in new systems. The consistent increase in the price of PET (which, according to our research for the PETplanet Pulse price index, is already back up to the level of June 2008) has, in particular, had the effect of spurring this process. Unfortunately the stretch blow moulding and bottling plant manufacturers have not been able to profit from this trend towards more lightweight PET bottles. Their installations last for ever and, if anything, a new cap can also be produced on the old plant using a couple of mouldings. Return on investment on bottling plants is difficult to estimate. In this respect the Krones situation is typical of manufacturers of complete systems. Quite simply, you need the plant before you can do any bottling. It’s only when we compare the old plant with the new investment that we arrive at an ROI. And that is quite often outside the 10-year margin. So the fact that Krones Financial Director Hans-Jürgen Thaus does not envisage a return to the boom levels of 2008 until 2013 / 2014 is not to be wondered at. As long as the complete systems manufacturers do not succeed with their new plants in saving you, as bottlers, 0.4 Eurocents per bottle, we are looking at achieving ROI over 2 years (assuming a plant investment of 1.2 million Euros at 25,000 bph 6000 hours per year). It will take them at least two years to even get on to the final straight that the preformers have been targeting for years. In addition to cost reduction measures and the modular principle, Krones and the other complete system manufacturers should not lose sight of this goal, otherwise it could well be doubtful whether the high level last seen in 2008 can in fact be achieved again in 2014. Yours A. Büchler","@ID":5} "PETcontents 05/10 4 PETplanet insider Vol. 11 No. 05/10 www.petpla.net BUYER’S GUIDE 44 Get listed! BOTTLE MAKING 30 Used but not spent BOTTLING / FILLING 28 Sterilasiatiion and aseptic filling systems CAPPING / CLOSURES 34 One-piece closure for hotfill 38 “One-Stop” strategy a success for Swiss mould maker REGIONAL MARKET REPORT 10 Tanzania - Kenya MATERIAL / RECYCLING 18 LCA - The advantages of PET 20 Influx of PET imports into the EU - changes ahead? PREFORM PRODUCTION 24 The Rapid Guide to Perfect Preforms - Part 11 MARKET SURVEY 21 Suppliers of preforms INSIDE TRACK 3 Editorial 4 Contents 6 News 42 Products 43 Bottles - Personal Care 44 Bottles - Food and Beverages 51 Patents Page 10 Page 38 Page 40","@ID":6}]}}
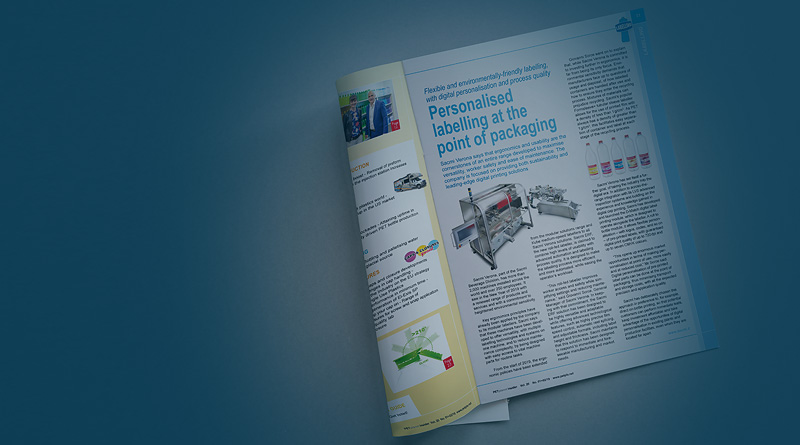