"MARKET SURVEY 43 Shinkong Synthetic Fibers Corp. Invista Resins & Fibers GmbH DAK Americas LLC Pearl Engineering Polymer Ltd 8fl, 123, Nanking East Road, Section 2, Taipei, Taiwan, R.O.C. +886 2 2507 1251 www.shinkong.com.tw Mr. Andy Chen Deputy Manager +886 2 2506 5137 +886 2 2506 8047 [email protected] Philipp-Reis-Str. 2 65795 Hattersheim am Main/ Germany +1 704 586 7331 www.Polymers.INVISTA.com Mr. Torsten Schmidt Business Director PET Packaging Resins + 49 69 305 85583 + 49 69 305 49147 [email protected] 5925 Carnegie Blvd. Suite 500 Charlotte, NC 28209, USA +877-432-2766 or +704-940-7500 www.dakamericas.com George Rollend Senior Technical Manager +603-672-6403 +866-833-5069 [email protected] Flat No. 3, Whitefield, Ashok Nagar, Pune - 411007, India +91 20 65000318 www.pearlPET.com S.T. Kulkarni SR. Executive Director +91 20 65000318 +91 2117 235248 [email protected] Shinpet PolyClear PET, PolyShield® resin, OxyClear® resin Laser+ PET Resin PeplPET 0.76- 0.92 0.50-1.40 0.76- 0.92 0.74 to 1.05 0.73-0.86 0.45-1.40 5015W/5015X PolyClear Refresh PET 1101 Laser+ Pepl B105C, B107C 5015/5015W PolyClear Splash PET 3301 Laser+W Pepl B103C PolyShiedResin 2300 in combiantion with nylon-MXD6 OxyClearBarrier Resin 3500 Pepl B105C 5015W PolyClear PET T94N (Europe) & T94 Customized grades PolyClear Crystal PET 3302 Pepl SealPET 01, 03, 05 (high Co-polymer) 5511H PolyClear Preserve PET 2201 Laser+HS Pepl HR PET (for 84oC filling temperature) None 5016/5016W/5016X PolyClear Refresh PET 1101 Laser+W, Laser+, Laser+ HS PolyClear EBM PET 5505 for Extrusion Blow Molding Laser+ EBM, Laser+C Pepl PET OxyClear Barrier Resin (Oxygen Barrier), PolyShied®Resin 2300 in combiantion with nylon-MXD6 (Oxygen barrier and passive barrier) 5038 PolyShied Resin 2400 in combiantion with nylon-MXD6 ( passive barrier) PolyClear Conserve PET 1101 D Pepl EPET-02 , EPET-03 range, Pepl MoldPET (To replace thermoformed containors of PP / PET / PS etc., Pepl CPET-01, Pepl CPET 02, Pepl FRPET-01, Pepl FRMPET-01, Pepl B101H, Pepl B103H, Pepl B105H, Pepl B109JS ColorMatrix Valspar Holland Colours European Division Clariant Masterbatches Italy BASF Color Solutions Germany GmbH Unity Grove, Knowsley Business Park Knowsley, Merseyside, L34 9GT UK +44 151 632 8800 www.colormatrix.com Claudia Finamore Marketing Manager - Europe, Middle East & Africa +44 151 632 8800 +44 151 548 3800 [email protected] 2001 Tracy Street Pittsburgh, PA 15233 / USA +1-800-333-1144 www.valsparpackaging.com Lynn Spataro Market Manager +1-412-734-8544 +1-412-766-8953 [email protected] P.O. Box 720; 7300 AS Apeldoorn/ The netherlands +31/55/3680700 www.hollandcolours.com Flórián Balogh European Sales Manager Packaging +36/30/2397710 +31/55/3662981 [email protected] Via Lainate 26 Pogliano Milanese, IT -20010 www.clariant.com Marco Sinigaglia Head of Technical Assistance +39 02 9918 7614 +39 02 9918 7551 [email protected] Clevischer Ring 180 51063 Cologne (Germany) 0049 221 96498-0 www.basf.com/masterbatch Alice Scheuer Manager Customer Service 0049 221 96498-539 0049 221 96498-510 [email protected] ColorMatrix Advanced Liquid Colorant Systems Yes Yes Yes Yes Yes Yes Yes Yes Ultimate UV390 UV protection and Lactra - UV and visitble light protection for dairy/white container applications Yes Yes Yes Yes Yes Yes Yes Yes No Triple A - AA reducer Yes No Amosorb and Amosorb SolO2 valor Activ and valor ActivBloc for monolayer and multilayer containers Yes No Yes No Eze slip agents (liquid), reheat agent with improved resin recyclability properties (liquid), reheat agent for press addition (liquid), PET resin toners (liquid or powder) valor ActivBloc and valor Bloc for carbon dioxide barrier Yes Yes Yes Yes Yes","@ID":45} "BOTTLES 75 PETplanet insider Vol. 11 No. 10/10 www.petpla.net Booth16A21 Visit us at: K2010 Hall 2 Booth C09 2 to 96 Cavity Molds Single Stage Molds Complete Stacks Hot Runners Spare Parts Refurbishment Conversions Engineering Service Kisan Precision Co., Ltd. 33-4, Wonmi-Dong Wonmi-Gu, Bucheon City, Kyunggi-Do Korea Tel: +82-32-663-6377 Fax: +82-32-663-6379 WWW.KSMOLD.COM Shower cocktail Limited product editions with a seasonal flavour such as, for example, “Summer Cocktail“ are being offered by the drugstore chain Müller in Ulm, germany as part of its range of shower gels in 300 ml PET bottles under the ”Aveo“ brandname. The transparent bottles are filled with coloured product and sealed with a colour-matched, snap-on cap. The front and rear labels which are made from paper and adapted to suit the shape of the packaging ensure sophisticated presentation. www.mueller.de Fruity body spray Under the brand-name of “Fruttini“, the cosmetics manufacturer Mann & Schröder of Siegelsbach, Germany, is selling PET pump spray bottles for body spray in different sizes and variants (e.g. Ginger Passionfruit or Milky Orange). The handy, round PET bottles (containing 200 and 125 ml) are coloured and the pump sprayers - complete with additional safety snap-on lids - are colour-matched. Depending on the particular variant, they are decorated with paper self-adhesive labels or with non-label-look stickers. www.fruttini.de www.mann-schroeder.de For hygiene on the move The cosmetics manufacturer Mann & Schröder from Siegelsbach, Germany, owners of the brandname “Dulgon“ and, under its “Cadeavera“ brandname, the drugstore german chain Müller of Ulm are offering small 50ml PET-bottles with disinfecting hand gel for customers on the move. The small, transparent PET bottles with their practical screw/ snap-on closures will fit into anyone’s trouser pocket and can be very useful in a multitude of situations. Small, informative front and rear labels made from paper or plastic foil add a final marketing touch to the bottles. www.mueller.de www.mann-schroeder.de Müller puts its money on PET The German drugstore chain Müller, based in Ulm, is offering 250ml Wellness Bodylotion in a range of fragrances in a round PET bottle with a manuallyoperated dispensing pump. The bottles feature coloured non-labellook stickers on both sides and the screw-on pumps are colourmatched to suit the respective fragrances. www.mueller.de","@ID":77} "LABELLING 58 PETplanet insider Vol. 11 No. 10/10 www.petpla.net Sleeve and roll in one Sidel’s new Rollsleeve system offers material savings, attractive packaging and cost savings. According to the AWA Labeling and Product Decoration Markets Global Review 2010, the market for heat shrink labels is growing fast – it increased by 4.4% in 2009, a much higher rate than other types of labels. The trend is particularly strong in rapidly industrializing countries (South America, China and India). The reasons for the success of high-shrinkage full-body sleeve labels include enhanced potential for communication and information, because of their greater space, compared to traditional labels. As the film is heat-shrunk, it adapts to any surface and is not restricted by the container’s shape; furthermore, full-body sleeves help to strengthen the surface of thinner bottles, which offers increased potential for lightweighting containers. Full-body labels can also function as a light barrier and even as a seal, when it is used to cover the container cap – which, again, offers savings in materials and processing. No traces of glue are left on the bottle, making recycling easier. Sidel presented a newly developed labelling systems at the Sidel plant in Mantova, where they explained the four specific advantages of the new Rollsleeve: savings in costs, flexibility, quality and sustainability to the trade press. ess uses an MDO film (Machine Direction Orientation): this means that the film is stretched in the same direction as the machine. The converting phase thus has two fewer manufacturing steps: sleeve forming and welding are not needed. The company claims that this system achieves label material savings of up to 30%, compared to traditional TDO (Transverse Direction Orientation). Sidel Group estimates that, with a throughput of 200 million bottles per year, savings on the costs of label material alone can lead to ROI within 18 months. Rollsleeve can apply labels that are 50% thinner (down to 18 microns) than traditional sleevers, which usually require minimum thickness of 50 microns. As the label is tubed and wrapped around the bottle as it moves within the machine, the film is not stressed. Flexibility Rollsleeve can be simply changed from sleeving to hot glue roll-fed applications, in around ten minutes more than a normal format changeover. With a routine action started from the operator panel, it becomes a roll-fed machine using the same labelling unit. Rollsleeve can also be equipped with a module for partial body sleeve labels. It can label various kinds of packaging, including PET, in any shape and format. Sidel has successfully tested all the principal materials available on the market, i.e.: PET, recycled PET, PVC, PE, PP, OPS and PLA with thicknesses ranging from 18μm to heat-isolated 150 μm and up to 60% shrinkable. Quality Sidel’s ‘heat & cool’ sealing system is designed to deliver outstanding label finish. The sealing area can be positioned exactly to the edge of the label, so the final overlap has no visual or tactile flaws after shrinkage. The quality of labelling is maintained even at high speeds (up to 54,000bph) and does not depend on the height of the container. The tube label is not lowered from above, unlike traditional technology. Sustainability By effectively having two machines in one, Rollsleeve is claimed to offer Cost savings ‘Tubing’ takes place within the Rollsleve machine, rather than being sourced externally. Sidel is one of very few manufacturers in the world to offer this. The Rollsleeve tube creation proc-","@ID":60} "TRADE SHOW PREVIEW 66 PETplanet insider Vol. 11 No. 10/10 www.petpla.net Moretto S.p.A. Via dell’Artigianato 3 - 35010 Massanzago (PD) ITALY Tel. +39 049 93 96 711 - Fax +39 049 93 96 710 www.moretto.com X MAX, a technological challenge. Flowmatik, a continuous success. OTX, an ingenious intuition. The most ambitious project in the history of the dehumidification. Drying Revolution K 2010 Düsseldorf Hall 11 Stand 11H57 designed by Moretto Energy-saving injection blow moulding machines Jomar Corporation will exhibit two new injection blow moulding (IBM series) machines: the Model 85S Hybrid and the Model 20. The new 85S Hybrid features an electric screw drive rather than a hydraulic drive unit. Incorporated with Jomar’s accumulator system, this is claimed to enable operation with a 30hp motor, down from 75hp. Energy consumption is reduced by 36% compared with the standard Jomar machine with vertical plastifier and by 50% compared with a reciprocating screw machine. It will demonstrate a ten cavity, 4oz round bottle made from clarified PP, at approximately 3,600bph. Jomar is a global manufacturer of injection blow moulding machinery for pharmaceutical, health care, personal care, beauty, food, beverage and household products markets. www.jomarcorp.com Productivity, energy efficiency and flexibility from China Chum Power Machinery Corporation was the first company in Taiwan to build two stage PET stretch blow moulding machines and is certified to ISO-9001 and CE. It exports bottling machinery and complete turnkey projects to 70 countries. Chum Power’s stand will feature the latest generation of its Phoenix series, which is now fully-electric in operation. It will also show its large volume and jar series, which is designed for containers with volumes up to 12l and necks up to 200mm. The company’s L-Series machines feature servo motors and continuous heating for consistency, improved productivity and lower energy consumption. The company’s equipment can produce bottles from 20cc to 20 ; necks from 14 to 200mm and production levels up to 19,400bph. It serves water, CSD, wine, personal health care, homecare and hot fill markets. www.chumpower.com Jomar Corporation Hall 14 Booth A32 Chum Power Hall 14 Booth B34 From tools to integrated systems KTW (Kunststofftechnik Waidhofen a.d. Thaya GmbH) will be represented on the Wittmann-Battenfeld and Sumitomo-Demag stands at K 2010, in addition to its own. KTW will present an alternative mould cooling system, developed in collaboration with Ritemp Technologies. The system transfers heat from mould cavities to ‘water pockets’, which are designed into the contour of the cavities. Water within the cavities evaporates when heated, circulates to a cooled heat exchanger and is then condensed and returned. The Wittmann Battenfeld stand will feature simultaneous production and assembly of a two-part, multi-functional closure for cooking oil bottles within an injection mould. A 72-cavity high-performance mould for a PET bottle light closure will be demonstrated on the Sumitomo-Demag stand. www.ktw-group.com KTW Hall 1 Booth A10","@ID":68} "TRADE SHOW PREVIEW 61 PETplanet insider Vol. 11 No. 10/10 www.petpla.net This amazes even the professionals: oval shapes can also be blow-moulded. Using ProShape – the latest module for the kronesContiform. www.krones.com K 2010, Düsseldorf 27 Oct. – 3 Nov. Hall 13, Stand A73 Improving appearance and environmental performance Chroma’s new range of frosted PET colour concentrate additives has been designed to achieve the look of glass in PET containers. The company says processors will save up to 90% by eliminating the need for spray-painting. The new masterbatch can be formulated for acrylic, PC and PET and Chroma says that it works well in blow moulding, reheat blow moulding and sheet extrusion, allowing for frosted thermoformed containers. The company’s biodegradable additives for thermoplastic polyolefin resins are FDA and RoHS compliant. They lower the molecular weight of polymer compounds to allow quicker oxidative bonding and uses sunlight, heat and oxygen to initiate the oxidative degradation of high molecular weight polymer chains into low molecular weight compounds. www.chromacolors.com Chroma Corporation Hall 7.1 Booth C30 Extrusion and recycling The Extrusion Division (foils & sheets) of Italian company Amut SpA will exhibit a horizontal calender developed for extruded PET foil, featuring 700mm diameter main rolls and 450mm diameter inlet roll. Driven by individual brushless motors, with electronic adjustment of rolls gap, this calender is specified for foil production up to 1500kg/hr. It is equipped with central roll automatic cleaning. The Recycling Division will exhibit one of its automatic washers as well as other machines and key technology in PET bottle washing and recycling. The AX-Washer 15005000 model on display can treat 4.5t/h of material. Flakes can be re-used for bottle-to-bottle processes. Amut SpA Hall 16 Booth D43","@ID":63} "Vol.6 PETplanet print PREFORM PRODUCTION 40 PETplanet insider Vol. 11 No. 10/10 www.petpla.net The Rapid Guide to Perfect Preforms by Rick Unterlander and Ottmar Brandau Troubleshooting guides have suffered in the past from being locked away in offices and not being available to the people that actually need them. Considering the high cost of machine and tools high scrap rates can be a costly proposition eating away at already tight margins. PETplanet’s “Rapid Guide to Perfect Preforms” takes a different approach. Bound in laminated paper that is easy to clean off, the small format of the book of 108mm by 151mm (4.25” by 6”) allows easy storage in back pockets or tool boxes. It has been written for the people on the floor of injection moulding companies to support their daily work in making the best preforms possible. The product of two industry experts, Rick Unterlander and Ottmar Brandau, it gives concrete advice on 35 of the most common problems in preform manufacture, most illustrated by pictures. From high AA levels to wavy bodies processors can find help when they need it. PETplanet print vol.6 The Rapid Guide to Perfect Preforms machine no./name Continued on page 45 A: ","@ID":42} "MATERIAL / RECYCLING 30 PETplanet insider Vol. 11 No. 10/10 www.petpla.net PET bottleson the floor The PET enviroTuf carpet solution from Futuris Automotive Interiors provides an alternative to traditional automotive nylon carpet, while delivering both environmental and cost benefits. Recycled post-consumer PET bottles are used to produce the carpet yarn, which is tufted to produce carpet material that meets the demanding standards for automotive use. The company has received three awards at the global and prestigious Automotive News Pace Awards. Nylon vs PET – current situation PET tufted carpeting has, for many years, been considered an alternative to nylon for automotive carpets. However, despite advantages such as improved stain resistance and the possibility of using recycled soda and water bottles as feedstock, PET was not affordable because it meant using higher, more expensive carpet pile weights to meet automotive requirements for wear and resiliency. The industry generally considered this an intrinsic limitation of PET fibre, as attractive as using recycled water and soda bottles would be. Beside nylon, there are also tufted PP and Needle Punch PET as low cost options available as carpet materials. The process makes the difference Traditional tufting operations utilise steam boxes that reach temperatures of approximately 100°C (212 F) for around 10 -20s. Although this heating process is sufficient to texturise typical nylon & polypropylene yarn, it is not sufficient to ‘bulk’ tufted PET carpet fibres. Extensive experimentation determined that a temperature range of 115-137°C (240 – 280 F) for 20 – 40s is required to bulk the full range of PET yarn construction. With its PET carpet technology, Futuris Automotive is able to meet automotive carpet specifications regarding wear resistance and resilience at the same carpet face weight as nylon, by developing innovative fibre, tufting, and carpet construction technologies. Face fibres utilised in the carpets can be made from postconsumer recycled material (validated with 20-80% recycled content). Lower costs – and 100% recyclable As a result, Futuris is able to offer PET carpet at lower cost than nylon but with better appearance and","@ID":32} "REGIONAL MARKET REPORTS 26 PETplanet insider Vol. 11 No. 10/10 www.petpla.net Light industrial equipment such as conveyors is manufactured in Strasbourg, France Montreal, Canada Santiago, Chile Oporto, Portugal Manila, Philippines Moulds are also produced in Le Havre, France Atlanta, USA Guadalajara, Mexico Shanghai, China Sao Paolo, Brazil End of line equipment produced in Sao Paolo, Brazil and blowers for the Indian market in Pune, India Sidel is a world wide supplier in solutions for packaging of liquid foods. Le Havre, the site that we visited, is not only the site for assembly of the SBO (Sidel’s PET blowing range) and moulds. Le Havre is also the home of the service activities which created the reputation of Sidel as a solution provider with activities such as: Packaging development and design from preform to bottle, Feasibility and testing on permanently installed lines, Product manufacturing and supply of moulds, Assembly of PET blowers on the shop floor, Product care and adaptation to existing plant, Packaging and processing, i.e. innovative R&D for future equipment, Quality control And, since January 2009, MPPI. Product Development z-slidesTM Closure Mould Technology The patented closure mould technology breaks the sound barriers of conventional cycle times and puts - as a modular system - new scales in ease of maintenance and operation of moulds. High Cavity Moulds for the Packaging Industry For single- or multi-component parts Mould Technology Test Centre Production Support z-moulds a brand of z-werkzeugbau-gmbh Competent – professional – inspiring Hoechster Strasse 8 · 6850 Dornbirn, Austria · T +43 5572 7272-720 · www.z-moulds.com K-Show Meet us at hall 10 booth H46 MPPI MPPI is a fairly new division at Sidel helping the customer to make a perfect marriage between the package and the drink. Presumably based of the available knowledge from Tetra Laval, the new division enters into serious research of the beverage end product. The various impacts of the PET package on such an end product are established. Micro-organisms, light, oxygen or temperature can easily alter or even contaminate the highly sensitive beverage. Packages under changing environmental conditions are kept under scrutiny in the course of the investigations in order to be able to define a precise life expectancy. Sidel has integrated all of these aspects into a comprehensive and unique service. Whether taken together or à la carte, these services provide an industrial packaging solution that is optimised and adapted to the drink’s individual characteristics and to each of the principal considerations: marketing, shelf life and storage or distribution conditions. At the end of the day the beverage producer receives a scientifically proven proposal regarding his optimum PET package design - from graphic design to compatibility of the product. Marketing aspects are taken into consideration, including the visual impression. Even taste and smell are reflected in the proposed package design. History of Sidel Founded in the early 1960s, when a company called Lesieur produced edible oil and developed extrusion blow moulding machinery for its own purposes, i.e. to bottle edible oil, but also still water and wine (Mid 1970s PET was pushed into Europe by Coke and Pepsi.)","@ID":28} "TRADE SHOW PREVIEW 64 PETplanet insider Vol. 11 No. 10/10 www.petpla.net You will feel better having made the right decision. Reduce your energy consumption. Gesellschaft Wärme Kältetechnik mbH Friedrich-Ebert-Str. 306 · D-58566 Kierspe Tel. +49 2359 665-0 · www.gwk.com Mould inserts Temperature control technology Water treatment Cooling technology Temperature controllers Chillers Energy saving cooling systems 27Oct.-3Nov.2010 Hall 10 Stand J 39 Handle handling Siapi will be showing a new development in its HandleMatic system, which is used for inserting handles into the mould during the blowing phase. It is now enabled to apply the handle to the body or the neck of the bottle immediately after blowing. Over the past months, Siapi has supplied the HandleMatic 360° system to customers in N America, N Africa, N Europe and Russia. Uses include insertion of PET handles during the blowing phase in EA2S blow-moulding machines producing refillable 5gal, 680g water containers; insertion of HDPE handles after blowing in EA7 and EA4 machines producing oil bottles in formats up to 2l; insertion of HDPE handles on the bottle neck after blowing for the EA2S blow-moulding machine producing 20l bottles for the chemical sector; development of an ergonomic container handle for the EA2 and EA2M blow-moulding machines for the production of water and oil bottles up to 5l. www.siapi.it Siapi Hall 14 Booth C17 PET preform production IT system In addition to its next-generation range of equipment, previewed in the last edition of PETplanet Insider, Piovan will be showing its latest software. Part of its standard Win Factory supervision software, WinPET has been developed specifically for the PET preform production process. It runs in a Windows environment with a client/server architecture and connections to equipment through RS485 serial lines or Ethernet. WinPET is based on a platform that offers the option of displaying all the line’s equipment on a single page. It can also show work areas on different pages when dealing with complex systems. The main page can be structured to customer’s production process specifications. Other pages give a detailed list of the operating parameters for individual pieces of equipment, along with the operating data for the process as a whole. Data are stored continuously in a central database. WinPET will be shown in both demo version and live connection to a working system. www.piovan.com Piovan Hall 9 Booth C59","@ID":66} "TRADE SHOW PREVIEW 67 PETplanet insider Vol. 11 No. 10/10 www.petpla.net Strong fresh air for PET-bottle industry Glide intoa new eraof air-cooled, oil-free, and cost-efficient high pressure Time to gain new heights. The highly energy efficient ZD compressor, with superior screw and booster technology, offers Class Zeroquality air and is extremely silent with no vibrations. Theair-cooledZD provides you anexceptional reliability, no water consumption, while driving down investment and installation cost. It all adds up to sustainable productivity for today’s challenging low carbon economy. This new ZD is The answer for all your high pressure 40 bar applications. For more information, visit www.atlascopco.com/petcompressors Energy efficient medium-capacity stretch blow moulder Urola S.C., part of Spain’s Mondragon Corporation, will be exhibiting its new Urbi-6 stretch blow moulding machine. With six cavities and a capacity in excess of 9,000bph, it is targeted at the medium-sized production segment. The company says that this new machine has been designed to be the most compact in its class. It is claimed to offer better accessibility and improved energy efficiency, from a new air recovery system, named Earu. Also on the stand will be an M12 rotary machine with 12 cavities, capable of producing multilayer bottles up to 1.5l, for packaging milk, juices, sauces and other hot-fill products. The single head is claimed to offer uniformity in weight and technical characteristics, which offers lightweighting opportunities; low power consumption; and flexibility in output size. www.urola.com Urola Hall 14 Booth B14 Recycling screen changer The latest generation of screen changers from Maag are claimed to meet all requirements of direct recycling processes, including fabrication of food-wrap films from PET bottle flakes in a single process step. Maag’s new CSC/BF-PE range features fully automated screen cleaning, adjustable to any kind of process. Material needed for backflushing is collected in a permanently flushed accumulating space, which the company says helps to avoid variations in pressure and volume. It further asserts that the flow channel geometry is entirely free from any dead spots. The recycling screen changers are based on a doublepiston design, which operates without any additional seals. CSC / BF-PE screen changers will be available in a range of sizes and can be incorporated into existing extrusion lines. Maag Pump Systems AG Hall 9 Booth 5","@ID":69} "PREFORM PRODUCTION 45 PETplanet insider Vol. 11 No. 10/10 www.petpla.net 15. Internal Sinks Table of Contents i................................................... About the Authors ii........................................................... Introduction Chapter 1........................................................ AA Level High 2................................................... Accordion Preform 3..................................................Air hooks / Streaks 4.......................................................... Black Specks 5................................................................. Bubbles 6............................................................ Burn Marks 7........................................Colour Streaking / Peeling 8............................................................ Crystallinity 9........................................................... Drool Marks 10.....................................................................Flash 11....................................................Gate Depressions 12.......................................................... Gate Peeling 13............................................ Gate Voids / Pin Holes 14....................................................Internal Gate Sink 15.......................................................... Internal Sinks 16...................................................................IV Loss 17...................................................... Long Gate Nub 18......................................................... Milky Preform 19.......................................................Moisture Marks 20.......................................... Neck Finish out of Round 21..................................................Parting Line Crease 22........................................... Parting Line Deformation Symptom: Small round dimples that occur on the interior of the preform. Cause: Internal shrinkage has occurred after the external surface has solidified. Occurs while the preform is contained within the mould, typically due to better cavity side cooling vs. core side cooling. Solutions: 1. Check water cooling temperature. This should be 7 – 10ºC (45 – 50ºF) for optimum cooling. 2. Check water cooling flow to mould, especially the core side. This should be at the mould manufacturers rating (for a given preform size and cavitation). 3. Check that the valve stems are opening properly. A partially open valve stem may restrict melt flow. 4. Check to ensure that the valve gate compressed air pressure is sufficient to open the valve stems properly. Typical pressures are in the range of 8 – 10bar (120 – 145psi). 5. Check that the cooling time isn’t excessive for the preform being moulded. This typically ranges from about 1 to 3sec depending upon the preform wall thickness. Reduce time 23....................................................Preform Yellowing 24.............................................................Short Shots 25.....................................................................Sinks 26....................................................................Splay 27......................................................Stretched Necks 28................................................................Stringing 29....................................................Surface Blemishes 30....................................................Thread Flow Lines 31................................... TSS (Top Sealing Surface) Sink 32................................................................. Unmelts 33........................................... Wall Thickness Variation 34............................................................Wavy Body 35.............................................................Weld Lines fax: +49 (0) 6221-65108-28 [email protected] www.petpla.net Order your copy now! prices in EUR + VAT. 1- 3 exemplar each 129,- € 4 - 10 exemplar each 99,- € 10 exemplar each 69,- € if necessary to minimize the risk of non-uniform shrinkage while contained in the mould. 6. Check to ensure hold (packing) pressure isn’t too low, especially near the beginning of hold time. Adjust higher if necessary to fully fill out the preform. 7. Check that the hold (packing) time isn’t too little for the preform being moulded. Increase as necessary to optimize part weight. 8. Check all temperature readings and adjust as necessary. PET resin should be melted at about 280ºC (536ºF) +/- 10ºC (18ºF). 9. Check that the decompression (pullback) time and position is not excessive. This should be set as low as possible to minimize the risk of melt backflow into the nozzle tips, yet enough to eliminate drooling into the cavity from excess melt pressure. Typical settings for valve gated moulds are: Time = 0 – 1sec; Distance = 0 – 10mm. Non-valve gated moulds may require higher values to minimize gate stringing. 10. Ensure the mould neck insert and lock ring vents are clean. This will minimize melt flow resistance due to gas entrapment. 11. Check to ensure that no moisture exists on the moulding surfaces, either from water leaks or condensation. This may obstruct normal melt flow and cause filling problems. The environmental dewpoint should be below the chilled water temperature to eliminate the risk of condensation. 12. Check hardware for worn, damaged or failed components, specifically the core cooling tubes, valve stems, valve stem seals, and clogged core cooling channels.","@ID":47} "PRODUCTS 71 PETplanet insider Vol. 11 No. 10/10 www.petpla.net K2010 Hall 1 Stand E16 Testing for recyclates PTI (Plastic Technologies Inc) has announced that it is now offering recycling stream impact testing services for PET containers, including resins, additives, adhesives, labels, etc. The company says that this service is designed to help ensure quality in supplies. It is particularly intended to address concerns about new materials, including resins, additives and multilayer structures, entering the market and to assess their potential for causing problems of yellowness and haze in recycled PET. PTI is one of only two U.S. companies approved by the Association of Postconsumer Plastic Recyclers (APR) to provide testing services in conjunction with the organisation’s critical guidance documents. Companies can choose to engage in a preliminary ‘quick test’, which typically takes one to two weeks and can yield valuable information on the yellowing and hazing tendencies of new materials. Critical guidance testing typically requires a month, with end use application studies adding another month. Adhesive roll-fed labelling for high-performance bottling lines PE Labellers will be demonstrating its new ‘Adhesieeve’ roll-fed labelling technology at the Emballage exhibition in Paris, November 22-25. While it is a roll-fed machine, the company says that its design makes its operation as simple as adhesive but without the cleaning and environmental issues. It eliminates hot-melt and so makes labels totally recyclable, as well as removing any need for solvent cleaning. The company further claims that the new machine’s new cutting devices do not require any servicing or adjustment for various film thicknesses or temperature changes. The absence of blades means there is no need for sharpening. www.pelabellers.it www.plastictechnologies.com","@ID":73} "BOTTLE MAKING 50 PETplanet insider Vol. 11 No. 10/10 www.petpla.net A deep grip New generation of container handleware Called Deep Grip packaging, the technology enables significant grip depth (more than 25mm or 1inch on either side), with an extremely thin (less than 0.3mm or .01inch) grip “web” thickness. (The grip web is where the hole would be in traditional handled bottles.) The end result is a grip deep enough for the average hand to completely close around without fingers touching the container wall. The comfort and handling ability is similar to that experienced with a traditional handle. Additionally, container size capability is extremely broad - up to 6l or 1.5-gallons, and beyond. Maximum bottle diameter is 220mm or 8.6inches. The development is one of the first commercially-viable handle processes that harnesses the advantages of ISBM. Extrusion blow moulding is the process traditionally used to produce most handled bottles. ISBM enables lightweighting, higher output per cavity, mechanical benefits (top/ side load, drop and creep resistance) and smaller equipment footprint. The lightweighting (20-25%) is possible because, in addition to functionality, the grip geometry also provides structural benefits which enable a reduction in bottle gram weight. Bottles using the Deep Grip technology are made in a two-step process on Sidel equipment. The first step is conventional stretch blow moulding, followed by a proprietary secondary operation within the same machine which forms the handle. Because both the container and the handle are made from the same material, this eliminates downstream recycling issues and contributes to lightweighting objectives. Moreover ISBM allows the bottle to be blown and conveyed inline to the filling operation. This eliminates the additional step of manufacturing bottles in a different location (either within the same facility or remotely) and then transporting them to the production line. The objective was to create commercially-viable technology that is capable of producing up to 1,200bph/ cavity. Further, the process needed to be applicable to a broad range of ISBM bottle polymers including PET, HDPE, BOPP, PLA and others. A variety of grip diameters and profiles are also possible. Target markets include detergents, household cleaners, non-carbonated beverages (juices, ready-to-drink teas, water, etc.), milk, edible oil, motor oil, baby bottles and other segments which are currently marketed in containers with handles. The technology is also suitable for dry products and wide-mouth applications. Deep Grip technology is also suited for commercialization where high clarity is desired. For example, with larger PET containers with deeper grips, now commercially viable via ISBM, the capability opens the door to a variety of conversions. www.pti-europe.com www.sidel.com PTI-Europe, Yverdon-les-Bains, Switzerland, in partnership with Sidel, Le Havre, France, is globally marketing a process which uses injection stretch blow moulding (ISBM) to create a new type of container handle. The technology was developed jointly with Procter & Gamble. (PTI-Europe is a subsidiary of Plastic Technologies, Inc. Holland, OH.) Could new stretch blowmoulded bottle process threaten extrusion blowmolding of handleware? A new type of container handle with significant grip depth was developed by PTI-Europe, Sidel and Procter and Gamble.","@ID":52} "TRADE SHOW PREVIEW 62 PETplanet insider Vol. 11 No. 10/10 www.petpla.net Thin-walled preform claims shorter cycle-time and energy saving Swiss company Hofstetter will be showing its latest development in the field of thin-wall. It will be demonstrating a PET mould with 60 cavities at the K fair, which features an updated design that is claimed to offer improved energy efficiency and cost-effectiveness. Operated on a 200t moulding machine platform, this new generation of Hofstetter’s moulds is also delivered with OHXtreme coating. The company has been applying this coating for eight years and says that it delivers increased wear resistance in assembly group components. The original base preform was a 12.5g - 0.5l Bague 30/25. By analysing and redesigning every detail of it, the developers in Uznach, Switzerland have managed to achieve a weight reduction in the region of 1.65g. The main factors contributing to this cut in weight are a special, Hofstetter-designed neck; the ‘Cappello’ contour at the base and a market-leading level of preform wall thickness. In achieving these advances, Hofstetter says that it has drawn on its 40 years’ experience in the production of moulds for thin-walled packaging articles. The company also mentions that all the redesigned, weight-reducing components are already present in moulds now running at various customer operations. Hofstetter presents its redesigned mould as a step forward in the ongoing drive for shorter cycle times, while helping to reduce the associated high wear of mould parts. The new product is also claimed to reduce energy use and resources consumption in PET bottle production. As well as its new mould and preform design, Hofstetter will also be showing a new cube mould for the production of tubes with integrated moulded lid and in-mould-labelling. This system has been developed in cooperation with Engel and Beck. www.hofstetter.ch Hofstetter AG Hall 1 Booth A40 Starlinger & Co GmbH Hall 9 Booth D21 Recycling technology Starlinger Recycling Technology will be exhibiting three recycling lines and new developments in its recoStar line, which is designed for recycling of PE, PP, PA, PS, PET and other plastics. A recoSTAR universal 65 VAC with an output of up to 200kg/h will be in operation twice a day, processing PP sack fabric. This machine’s heavy-duty single-shaft cutter, arranged parallel to the extruder, enables it to process films and materials such as tapes, fibres and start-up lumps. A new feeder system means that ground material and granulate can both be processed, without an additional dosing unit. The recoStar basic 85 with an output of 450kg/h will be demonstrated on stand B47 in hall 16. It can be used for all polyolefins, technical plastics and foamed materials. It is equipped with an agglomerator for predrying and compacting. Starlinger says that its recoStarPET iV technology yields recycled PET with the same properties as virgin material and decontamination values which allow direct food contact. The company’s SSP (solid state polycondensation) reactor series now includes a 15,000l model and a flake-only solution. Other models include the recoStar direct recycler, which processes pre-ground and dry materials, and the recoStar compact, which is suitable for recycling polyolefin films either off-line or in-line. www.recycling.starlinger.com Efficient and economic recycling Austrian specialist company Erema will use the K Show to premier its new TVEplus recycling system. New developments include enhancement of degassing and homogenisation performance, as well as downstream components said to improve maintenance and cleaning. The stand will feature tailor-made systems for bottle-to-bottle-PET recycling systems and inline technologies for the direct production of materials from PET bottle flake. Erema says that its TVEplus technology facilitates the processing of even extremely difficult waste materials in a single pass. Vacurema technology enables processing of rPET that is suitable for food contact. Its recycling systems all feature the ecoSAVE technology introduced in 2010, claimed to reduce energy consumption by a further 10%. Erema subsidiary 3S, of Roitham, Austria, will be presenting a new system for measuring wear on extruder cylinders. Erema Hall 9 Booth C05","@ID":64} "NEWS 10 PETplanet insider Vol. 11 No. 10/10 www.petpla.net European PET bottle collection increases by more than 8% Latest trends in PET recycling show mixed growth Petcore (PET containers recycling Europe) announced today that European post-sorting PET collection reached 1.4 million tonnes in 2009, an increase of more than 8% on 2008. The overall collection rate in 2009 rose by nearly 2.5%, from 46% to 48.4%, of all PET bottles on the market. The 2009 share of fibres as an end use for recycled PET flake decreased from 45% to 40%, while the tonnage remained almost the same. The PET sheet market tonnage resumed its growth pattern, increasing from 22% to 27%. Blowmoulding continued to grow, with more than 22% going to this outlet in 2009. The strapping market was the hardest hit by the economic recession but still consumed 7%. It was estimated that there is a total mechanical reclamation capacity in the European region of 1.6m tonnes, which provides the impetus for the industry to increase the current collection rate beyond 50%. Exports to the Far East fell slightly, to 16% of collected PET; 67,000t of baled PET bottles were imported from outside the area. Of the collected bales that are reprocessed in Europe, 75% is usable PET. The remainder consists of caps, labels, residues, contamination such as foreign materials and other polymers. The continuing programme of bottle weight reduction means that caps and labels form a greater proportion by weight of the collected PET package. Petcore pronounced itself generally satisfied with the increased collection rates, as recycled PET is an increasingly sought-after feedstock in the PET value chain. Sustainable uses are being developed to utilise the growing supply of recycled PET, including new applications, into other bottles, fibre, sheet or strapping tape. Energy savings are the same, regardless of ultimate application. The EU has a target of 22.5% overall for plastics recovery. The rate for PET alone is higher in 23 countries that required by the current packaging waste legislation for all plastics. Petcore’s PET Profile publication has been updated to include reflect the 2009 collection figures. www.petcore.org PET engineering and development training in Brazil Plastic Technologies, Inc. (PTI), a global leader in PET design, development and engineering services, is bringing its technical expertise to the rapidly-growing Brazilian marketplace. It has signed an agreement with Centro de Tecnologia de Embalagem (Cetea) packaging technology research institution in the state of São Paulo. The organization is part of Ital, the Food Technology Institute of São Paulo. To help address the needs of its expanding marketplace, CETEA is organizing a technical, public PET seminar in Brazil, to be held on August 24-25 at Ital’s headquarters in Campinas, SP. PTI will be providing attending packaging and plastics companies with in-depth instruction on a wide range of PET topics including: basic polymer and PET chemistry; injection and blow moulding, package development, barriers, recycling and food grade rPET resins, quality assurance and testing. With the Brazilian marketplace positioned for rapid growth, brand owners and suppliers are looking for technical assistance to improve manufacturing expertise and quickly ramp up production. The educational seminar is designed to help companies achieve those objectives. Cetea was established in 1982 as a non-profit food packaging research centre. The resources generated from its products and services are directly allocated to ongoing improvement of its researchers, employees, facilities and equipment. It is a member of the International Association of Packaging Research Institutions – Iapri. www.cetea.ital.sp.gov.br Information on the PET seminar: http://www.cetea.ital.org.br/cetea/eventos/pti2010_apresentacao.htm www.plastictechnologies.com Short-neck closure introduced to North America Swiss company Corvaglia has launched its 26mm BTL (‘break-then-leak) short-neck closure in the important markets of the USA and Canada. Designed for still water, the company says that the cap itself is significantly lighter than its predecessor – 1g, compared with 1.65g – and enables a lighter bottle neck finish, reduced from 3.15 to 1.75g. With an annual volume of over 1 billion bottles and closures, Corvaglia claims that this this lightweighting development results in savings of over 2,000t of plastic material and a reduction in energy consumption of approximately 50%, while maintaining performance. Corvaglia’s CSN 26mm BTL was first launched by Ice River Springs Water Co. Inc. in Canada. US production followed in early 2009. Silver Springs Bottled Water Company of Florida has now used it, also. Both bottling companies were interested in packaging cost reductions, as well as the potential for energy saving at all stages of the production process. www.corvaglia.ch Bioplastics Award 2010 - call for entries Trade publications bioplastics Magazine and European Plastics News are to jointly judge and present the 2010 Bioplastics Award. The award will recognise innovation, success and achievement by manufacturers, processors and users of bioplastic materials. There will not be any separate categories; all nominations will be considered. Nominations are currently open for the award. In order to be eligible, the suggested company, product, or service must have been developed or on the market in 2009 or 2010. Companies can nominate their own product, service or development. Entries are encouraged from across the global bioplastics community; however, the winning company must send a representative to Düsseldorf, Germany on December 1/2, 2010; the winner will be announced during the 5th European Bioplastics Conference. www.bioplasticsmagazine.de/award.","@ID":12} "74 PETplanet insider Vol. 11 No. 10/10 www.petpla.net PETbottles Personal Care 1&5 New bottle for Sun Unilever France has re-styled its 500ml PET bottle for its “Sun“ brand Clear Sparkle Rinse Aid. The blue coloured bottle is slimmer. The front and rear labels are adapted to the shape and feature quality printing. The 2-section screw closure with integral dispensing section rounds off the packaging. To dispense, simply unscrew the top screw cap. Readily audible clicking signals indicate the relevant status - open or closed. www.sun-services.com or www.unilever.com Total concentrate in PET Swiss retailer Migros, based in Zurich, is selling its innovative, ecological liquid detergent “Total concentré“ in a 1.155l PET bottle. According to the manufacturer, with this detergent up to 70% cash and energy savings can be achieved by comparison to traditional detergents. Even at a washing temperature of 20°C the consumer can be sure of high washing performance. The triangular PET bottle is designed for ease of handling and the aluminium-coloured screw cap can also be used as a dispensing cup. To complement the modern liquid packaging, there is a shrink sleeve label precision-adapted to the out-of-round shape of the packaging. www.migros.ch Leather care in PET Under the brandname “Kleen-up“, the French company Tetrosyl of Wambrechies is selling 500ml creme for caring for the leather internal trim of motor vehicles in a PET bottle with an unusual shape. Front and rear labels reflecting the shape of the packaging as well as a golden screw cap round off the presentation of this high quality packaging. www.tetrosyl-france.com PET for Natura Verde 750ml light green fabric softener concentrate brand-name “Natura Verde“ is being sold by the consumer goods group Colgate Palmolive in France in a transparent PET bottle with a green dispensing screw cap. 20 years ago this combination – a sensitive ecological product in a plastic bottle – would have been unthinkable. An all-enveloping foil label and a green “nouveau“ sticker complete the PET packaging. www.naturaverdehome.com","@ID":76} "PETnews 8 PETplanet insider Vol. 11 No. 10/10 www.petpla.net MHT MOLD & HOTRUNNER TECHNOLOGY Dr. Ruben-Rausing-Str. 7 | D-65239 Hochheim/Mai Tel. +49(0) 6146-906-0 | www.mht-ag.de Lightweight threads are literally on everyone’s lips. After all, the smallest PET saving per preform soon amounts to hundreds of thousands of Euros for major bottlers each year. Looking to convert your mold to a new thread and need an experienced partner? MHT Mold & Hotrunner Technology offers all lightweight solutions on the market, including: • PCO1881 (17 mm / 3.8 g) • 28-21 ComPetCap® (21 mm / 3.9 g) • 29/25 (12.6 mm / 2.4 g) Lightweight Engineering made in Germany MHT: Your specialist for lightweight solutions! Chinaplas 2011 returns to Guangzhou, PR China, 17-20 May 2011. Chinaplas, billed as Asia’s leading plastics and rubber trade fair, will be taking place at the continent’s largest exhibition centre – the China Import & Export Fair Pazhou Complex - from May 17 to 10, 2011. Chinaplas was first held in 1983 and is again exclusively sponsored by Europe’s Association for Plastics and Rubber Machinery Manufacturers (EuroMAP) in China. It is the only event approved by the Global Association of the Exhibition Industry (UFI) for the plastics and rubber industries in China. China’s demand for plastics machinery is growing at an average annual rate of 6%. Total output of China’s plastic products in 2009 exceeded 44 million t, with a total output value of RMB 1 trillion ($147bn; €114bn). The total output value of China’s rubber product industry also topped RMB 430 billion ($63 billion). The Chinese government’s RMB 4 trillion ($580bn) stimulus package launched last year is expected to lead to a continued rise in domestic demand, with rapid increases in plastics and rubber application in household electrical appliances, automobiles and infrastructure facilities. Plastic product output in China is expected to maintain growth in 2011. Guangzhou is the capital city of the Guangdong Province, home of the Pearl River Delta light industrial region. Organisers Adsale Exhibition Services Ltd maintain that Chinaplas is an ideal platform for both Asian and European industry players to showcase their machinery and raw materials. The last Chinaplas was 30% overbooked, so 17 exhibition halls are planned to be reserved in Zones A and B of the China Import & Export Fair Pazhou Complex, a total of 150,000m. It is expected to have more than 2,200 exhibitors from 35 countries/regions, together with pavilions from Austria, Canada, France, Germany, Italy, Japan, UK, USA, PR China and Taiwan. Exhibitor and visitor registrations are now open and can be found at the official website: www.ChinaplasOnline.com PET+Drink Tech Asia 2010 With active participation and strong support from PET, Drinks, Liquid Food and packaging industry players, the fourth international PET + Drink Tech Asia 2010 exhibition, was held at Chennai Trade Centre, Chennai, Tamilnadu, India, from August 27 to 29, 2010.The show attracted participation from more than 40 exhibitors and over 5,000 visitors from across the world. Visitors were able to see displays across the whole spectrum of PET and beverage activities, including injection moulding and stretch blow moulding machines; bottle filling; capping and labelling equipment; closure systems; masterbatch; colourings and additives; fruit processing technologies and more besides. Exhibitors responded positively, reporting a significant amount of business generated during the show. Orders were placed for ancillary, auxiliary, raw material and finished goods handling equipment. Organisers Kesari Media and Events Pvt. Ltd confirmed that the fifth PET + Drink Tech Asia 2011 exhibition and seminar will take place at Milan Mela Showground and Exhibition Centre in Kolkata, India, from August 27 to 29, 2011. F.l.t.r.:Miriam Kiesler for PETplanet with Gaurav Bhardwaj, Executive Director, S.K. Bhardwaj, Chief Coordinator and S.P.Gautam, Business Development Manager.","@ID":10} "REGIONAL MARKET REPORTS 17 PETplanet insider Vol. 11 No. 10/10 www.petpla.net lenge for SGT. to be reduced by half - a challenge for SGT of course, but also for the machine/system supplier. Today in the Nantes and Alger factories there are 30 Husky systems with 48, 56 and 72 cavities. Both of plants transform 80,000t PET resin and manufacture over 2.5 Billion preforms per annum. Pellets of post consumer recycled material are blended with virgin at varying percentages up to 25%. (For 5 years, the Alger plant is manufacturing 600 million caps per year in 30/25 and PCO.) Local organisation SGT employs 70 people in Nantes, of which 45 work on the shop floor to operate and service the Husky injection moulding systems. Outstanding features of the SGT plant in Nantes are the AGVs (fully Automated Guided Vehicles), which calmly manoeuvre empty boxes and full boxes of preforms to and from the injection moulding systems and to an automated station supplying the empties and receiving the full boxes. No operator is involved under normal circumstances. The software takes care of the traffic flow (one-way traffic in a circle in the central manufacturing area), priorities and parking. “Internal transportation is not effected by labour problems such as absenteeism” we were told jokingly. “But it took an extensive introduction period with plenty of trials and training of staff. The investment has paid off in a short amortisation period.” Shop floor activities include a high degree of planning of manufacturing schedules in depth and detail. Monitoring systems allow tight control and spontaneous analysis, and swift reaction to abnormalities, thus ensuring high productivity (as stated: 96%).The factory was, at the time of our visit, working at “89% capacity”. SGT today is producing 120 to 130 preform designs ","@ID":19} "NEWS 9 PETplanet insider Vol. 11 No. 10/10 www.petpla.net Growing their own PET bottles Coca-Cola Co has launched a new bottle that is designed to be more recyclable than conventional PET packaging. The company’s ‘PlantBottle’ contains up to 30% plant content, in the form of monoethylene glycol (MEG) derived from sugar cane and molasses. Coca-Cola says that light weighting of PET bottles, of itself, is insufficient to address concerns over the environmental sustainability of branded packaging. Bottles have to have a certain minimum weight in order to maintain their shape; the PlantBottle concept is intended to address entire lifecycle issues, especially end-of-life recycling. It has been deliberately designed to be 100% recyclable, rather than biodegradable. The company is researching ways to use plant waste in PET production, which could lead to bottles made entirely of such material. Coke considered several options, including polylactic acid (PLA), before opting for plant-based MEG. While it feels that PLA is suitable for some packaging solutions, it decided that it was not appropriate for its purposes. The renewable PET used in the PlantBottle is sourced from an Asian supplier. PlantBottle debuted in late 2009 and is currently available on the West Coast of the USA and in Denmark, where it is used for Dasani-brand water. It was also featured at the Vancouver Winter Olympics. www.thecoca-colacompany.com IBWA recycling initiative in USA The International Bottled Water Association (IBWA) Board of Directors has endorsed a framework for a Material Recovery Program that it hopes will serve as the blueprint for local communities to increase community-based recycling in the USA. The organisation says that the initiative will “…assist in the development of new, comprehensive solutions to help manage solid waste in communities in the United States by having all consumer product companies work together with state and local governments to improve recycling and waste collection efforts,” according to Joseph K. Doss, IBWA President and CEO. The IBWA framework supports state-authorized public or private corporations that establish specific recycling goals in each community that are intended to increase recycling access and rates. It also supports schemes that generate revenues for grants from company producer fees as well as local and state government contributions; and that fund local government recycling infrastructure improvements and consumer education programs. It envisages such schemes dissolving when local recycling goals have been met. IBWA has said that it believes that increasing the recycling rates for all consumer products and packaging should be a top priority for all companies whose product or packaging is ultimately discarded. Its stated position is that locally run recycling programs are the most effective method of diverting solid waste from landfills and increasing recycling of consumer products and packaging. Founded in 1958, IBWA’s membership includes U.S. and international bottlers, distributors and suppliers. www.bottledwater.org","@ID":11} "PREFORM PRODUCTION 39 PETplanet insider Vol. 11 No. 10/10 www.petpla.net iFlow hot runner technology The proprietary design of the iFlow hot runner manifold has less pressure drop, fills more uniformly, runs lower AA levels and generates less preferential shear stress than conventional gun drilled manifolds. The valve gate and piston area has been purpose engineered for moulding PET, so it generates less PET dust, reduces crystallinity in the gate and makes inpress service easy. iFlow technology not only serves the needs of preform users but also those in a myriad of other plastic injection business categories. The specific hot runner technology for the iPET moulds has been proven in the plastics industry on thousands of applications for over 20 years. However, until 2008, this technology was not used in the PET moulding environment but the value for the customerer has been proven in PET systems at major preform converters in North America and Europe, as Mold-Masters claims. Issued by Bruce Catoen / Vice President, Business & Product Development, Mold-Masters Limited and Oliver Lindenberg / Business Manager Europe, Mold-Masters EMEA www.ipetsystems.com iPET cores iFlow manifold (open position) Request your badge at www.emballageweb.com - Code : XPETPLAN More information? Tel. : +33 (0) 1 76 77 12 80 – stephanie.dryander @comexposium.com International Packaging Exhibition 22/25 NOV. 2010 PARIS NORD VILLEPINTE FRANCE 100% INNOVATIVE & 100% SUSTAINABLE! When innovation makes the packagingof food-anddrink products smarter, more functional, more reliable and more attractive, and… designed with sustainable development in mind. Come and identify the most dynamic providers and the most relevant concepts for your market. Express your distinctive identity! EMBALLAGE 2010 offers you the breadth of a generalist trade show, combined with the depth of a multi-specialist exhibition, through new designs and spaces, specialised areas, conferences and original events.","@ID":41} "imprint EDITORIAL PUBLISHER Alexander Büchler, Managing Director HEAD OFFICE heidelberg business media GmbH Landhausstr. 4 69115 Heidelberg, Germany phone: +49(0)6221-65108-0 fax: +49(0)6221-65108-28 [email protected] EDITORIAL Doris Fischer [email protected] Michael Maruschke Ruari McCallion Tony O´Neill Ilona Trotter Wolfgang von Schroeter Anthony Withers MEDIA CONSULTANTS Ute Andrä [email protected] Miriam Kiesler [email protected] phone: +49(0)6221-65108-0 fax: +49(0)6221-65108-28 France, Italy, Spain, UK Elisabeth Maria Köpke phone: +49(0)6201-878925 fax: +49(0)6201-878926 [email protected] LAYOUT AND PREPRESS Exprim Kommunikationsdesign Matthias Gaumann | www.exprim.de READER SERVICES Kay Krüger [email protected] PRINT WDW Druck GmbH Gustav-Throm-Straße 1 69181 Leimen-St.Ilgen Germany WWW www.petpla.net | india.petpla.net PETplanet insider ISSN 1438-9459 is published 10 times a year. This publication is sent to qualified subscribers (1-year subscription 149 EUR, 2-year subscription 289 EUR, Young professionals’ subscription 99 EUR. Magazines will be dispatched to you by airmail). Not to be reproduced in any form without permission from the publisher. Note: The fact that product names may not be identified as trade marks is not an indication that such names are not registered trademarks. 3 PETplanet insider Vol. 11 No. 10/10 www.petpla.net EDITORIAL dear readers, EDITORIAL PET spearheading the flow of visitors Once again we are in exhibition season, this time the K Fair in Düsseldorf. Whilst the show dazzles with its 3,100 exhibitors from the field of engineering materials and finished products, you might want to investigate one or the other corner of the area covering almost 0.2 km² devoted to PET and closures. So if your shoe leather can stand the pace you can catch up with us on PET-related issues. You can read our report on page 60. A striking feature of the exhibition is that many exhibitors are using the plastic industry as a flagship for their other products. It is absolutely clear to all plastics users that the demands placed by PET on machinery and equipment are of the highest possible order. Machines have to work in every corner of the world, regardless of whether it’s 5,000 meters up in the Himalayas or in scorching 50°C heat in the Gulf States or in the high humidity of the sub-tropics. In developing countries there may be power failures to cope with but the plant still needs to be up and running again as soon as the power is restored. This applies to manufacturers of stretch blow-moulding machines, injection moulding machines and peripheral equipment. Machinery has to operate 24/7, producing high single shot weights super-fast, at the same time they need to feature extremely high plate rigidity so as to ensure that the large number of cavities is neatly filled. Mould cooling is an extremely comprehensive operation and the material supply chain also has to provide the hygroscopic PET dry and in sufficient quantities. To cap it all, there is fierce price competition for the finished preform, making sure that it also undergoes regular optimization and not overlooking the need for constant investment in tools and moulds. No other plastics application is so exacting, and sometimes contradictory, in the demands it makes on the plant at this extremely high level of output. No wonder that PET will be seen as THE jewel in the crown on K Fair stands. Enjoy strolling round the K Fair Yours, Alexander Büchler","@ID":5} "PREFORM PRODUCTION 36 PETplanet insider Vol. 11 No. 10/10 www.petpla.net An alternative preform production philosophy In 2009 Mold-Masters and Abba formed iPET and developed the iPET system first launched in 2009 (see Petplanet 10/2009, page 21) This system has taken the approach that a “better” mould is not necessarily a larger mould with more cavitation, more water and more resulting complexity. The people behind iPET consider a mould as better if it reduces the lifecycle cost of moulding. So the strategy of iPET is to offer a technology for preform manufacturing that aims to reduce infrastructure costs, energy consumption and cycle times while improving preform quality in the critical areas of AA levels, witness lines and ovality. In this article iPET explain their different approach. High cavitation and its drawbacks While there are certain countries and regions where it makes sense to employ high cavity moulds in order to achieve the highest possible output, there are also many places where lower output and higher flexibility is required. Historically, equipment suppliers to the PET industry have mainly focused on system output to reduce costs. Most of the efforts in improving preform moulding economics were focused on increased output per capital via post mould cooling and larger cavitation moulds. However, there are practical limits as to how many cavities can be put in a press and how many stages of post mould cooling can be added. And with the ever increasing price of energy today it is important that a moulder considers the energy and infrastructure costs of moulding preforms in balance with output per capital. Energy costs are now the second most costly element of preform conversion. Undeniable is the fact that if a 192 or 216 cavity mould has a quality issue, then the cost of lost production quickly mounts. In addition part weights have decreased significantly. Getting 144 Get more using less Mold-Masters/iPET Hall 1 Booth A39","@ID":38} "TRADE SHOW PREVIEW 69 PETplanet insider Vol. 11 No. 10/10 www.petpla.net Clarified PP bottle Chinese company Wei Li will exhibit an automatic two-stage reheat stretch blow moulding machine for the production of clarified PP bottles in a single or multi-cavity. It will demonstrate production of an improved clarified PP sport bottle, blown from a preform in one cavity using its MP02 semi-automatic reheat stretch blow moulding machine. Productivity is claimed to be 300-400 units/hr; two, four and six-cavity versions are also available. Advantages claimed for the two-stage reheat process over single-stage ISBM, include higher bottle strength and flexibility in design and applications, in PET and PP bottles up to 5l. The company also says that the the machine is easy to operate and to change over. Wei Li has 15 years’ experience in the development of PET/PP reheat stretch blow moulding technology and offers a range of standard and specialist machine for PET, PP, PC, etc. www.weiliplastics.com Wei Li Plastics Machinery Ltd Hall 13 Booth B82 Recycling line recoSTAR PET iV+ Ongoing PET recycling innovation, quality and state-of-the-art technology, a full range of consulting services – brought to you by Starlinger. Visit us at: K 2010, Duesseldorf, Germany Oct. 27 – Nov. 3, Hall 9, Booth D 21 www.starlinger.com","@ID":71} "CAPPING / CLOSURES 56 PETplanet insider Vol. 11 No. 10/10 www.petpla.net High-speed caps Sumitomo (SHI) Demag Plastics Machinery Gmbh will be launching a new generation of its El-Exis series at K 2010. The SP series will be represented by an El-Exis SP 300 model, which produces screw caps using a 72-fold mould made by KTW. The cap is a ‘shortneck’ model, designed for bottles containing still water for a discount grocery store. The caps are injection moulded from HDPE, are 26.7mm diameter and weigh 1.6g. they are produced in a cycle time of just a few seconds. After ejection, the caps pass a cooling line and are routed to a hopper system, which feeds into a 100% quality control. The parts are closely inspected for geometry and colour in an IMD Vista optical inspection system, before being stored in a filling machine. The production cell to be exhibited at K 2010 – which will be a complete production unit – has an output capacity of 100,000caps/h. The El-Exis series of machines is already well-established in the packaging industry. Sumitomo says that the new SP series incorporates the results of detailed analysis of the requirements of the packaging market, which are implemented in a number of improved components within the machine. Improved efficiency The SP series will be available with clamping forces ranging from 150 to 750t. Sumitomo says that the reliability of the machine’s existing hybrid drive, which has been enhanced for high dynamics and precision, makes it particularly suitable for high-speed applications. The efficiency and precision of the ejector have also been improved, with the intention of meeting its market’s specific requirements. The company claims that the enhancements and developments make the SP series ready to meet future needs, as well. Technological improvements have also been made on the injection side, with the intention of achieving highly dynamic injection and reproducibility. The dosing unit’s direct drive is frequency-controlled, low maintenance and claimed to be very efficient. The modifications mean that it is possible to achieve higher plasticising outputs, which help to shorten cycle times and raise productivity. The new features are supported by the NC 5 control system, fitted as standard, which offers ease of operation through a touch screen and key panel. Clamping and injection unit sequences are freely programmable. A special input function allows the user to adjust the dynamics of the machine to specific applications by means of a slide control, which also helps to save on cycle time in critical areas. Sumitomo (SHI) Demag says that the new features in the El-Exis SP series will deliver fast, economic, energy efficient and reliable production for high-speed injection moulding applications. www. sumitomo-shi-demag.eu Sumitomo Hall 15 Booth D22","@ID":58} "41 PET bottle-to-bottle recycling plants Caps and closures Conveyers for preforms and empty bottles Preforms Preform moulds and SBM moulds Two-stage SBM machinery Preform and single stage machinery Resins and additives Filling equipment Compressors Suppliers of resins, colours and functional additives for PET bottle production What could be more appropriate than to publish the market survey on resins and additives in the K Fair issue? Once again this year a large number of participants are featured, even though some of the big players like La Seda and Equipolymers in the resin sector are conspicuous by their absence. Anyone who hasn’t been included is cordially invited to contact the editors direct to make sure that they are not left out next year. It was a particular pleasure to see Pearl and Shinkong there this time. See for yourself how the companies, along with their respective product portfolios, are faring in a market characterised by turbulence as far as prices are concerned. When it comes to suppliers, although we may have fewer entries this year (and bearing in mind the just how many suppliers out there, the number we do have is certainly not exhaustive) more and more new suppliers are finding their way to us. One example this year is Chroma. The additives available include barrier improvement additives for sensitive beverages, UV blockers, brighteners and many other performance enhancers. Whilst the publishers have made every effort to ensure that the information is up to date, no claims are made regarding completeness or accuracy. 10/10 MARKETsurvey Resins Company name M&G Polimeri Italia SpA Postal address Telephone number Web site address Contact name Function Direct telephone number Fax E-Mail Via Morolense Km 1 - 03010 Patrica (Frosinone) - Italy +39/0775/84221 www.gruppomg.com Marilena Grecchi Area Sales Export and Marketing intelligence support +39/02/82273242 +39/02/82273314 [email protected] RESINS 1. Brand name of the resins Cleartuf 2. IV range a. of Homo-Polymers b. of Co-Polymers 0.76 ÷ 0.95 3. Speciality resins CSD Cleartuf ultra Water Cleartuf p76 / cleartuf p82 Beer Poliprotect Wine / liquors Poliprotect Personal care /pharmaceuticals Cleartuf p82 Slow crystallisation Cleartuf aquad 82 Hotfill Cleartuf p85 hf Pre-coloured Fast reheat Cleartuf ultra Other 4. Increased barrier properties Yes, with our poliprotect resins, launched in 2009: • Poliprotect apb with strong active and passive barrier incorporated (recommended for highly sensitive beverages, such as beer), • Poliprotect jb with active barrier incorporated (recommended for juices, dairy products, food), • Poliprotect pb with passive barrier incorporated (recommended for carbonated beverages). Poliprotect is made with m&g's proprietary bicopet technology, which allows producing a resin which includes all necessary barrier components in each single chip, making it easy and economical to use by converters as standard resin. Poliprotect's scavenger provides more than 18 months O2 shelf life. Its exclusive nylon, x17, developed in collaboration with BASF company grants perfect transparency to containers produced with poliprotect resins.Poliprotect contacts: cécile bourland ([email protected]) and raffaella serra (raffaella. [email protected]) 5. PEN mixes available No 6. Recycled blends available Yes 7. Special comments","@ID":43} "PETproducts 70 PETplanet insider Vol. 11 No. 10/10 www.petpla.net connecting comPETence® www.petnology.com Plastics · Engineering · Technology PETnology Europe 2010 XIII. Strategy and Technology Conference for the PET Packaging Industry November 8-9, 2010, Nuremberg prior to Brau Beviale Conference Organiser PETnology/tecPET GmbH P.O. Box 120 429 D-93026 Regensburg, Germany Phone: +49 941 870 23 74 Fax: +49 941 870 23 73 [email protected] Media Partners: Supporting Organisations: TM Zero-calorie natural sweetener Wild (Rudolf Wild GmbH & Co. KG) is now offering the food and beverage Sunwin stevia, which it describes as ‘top-quality natural stevia sweeteners’. Wild Flavors, Inc, holds significant investments in manufacturer Sunwin International, which allows the company to monitor the entire production process for quality. Stevia is a natural, zero-calorie sweetener. The European Food Safety Authority (EFSA) issued a statement in April 2010, which said that stevia sweeteners with a steviol glycoside content of at least 95% were deemed to be safe for use in foods. Final confirmation of EU approval is anticipated. Wild Flavors’ stake in Sunwin International means that it has a secure supply of stevia and that it can offer manufacturers ‘turnkey’ solutions for the development of stevia-sweetened foods and beverages. www.wild.de Wild is offering the food and beverage industry Sunwin stevia, a zero-calorie natural sweetener with excellent taste. Single-minute mould Changeover In response to pressures for ever-faster production, Sidel has announced the launch of a new, quick-format changeover system. Sidel claims that its patented ‘Bottle Switch’ system achieves mould changeovers of less than a minute. The system incorporates a semi-automatic solution that places the blowing station to be changed directly in front of the operator. The mould support units are automatically unlocked and the operator then changes the moulds. Removal and installation of the mould support units can be achieved tool-free. Sidel claims that the new system offers greater ease-of-use; improved ergonomics; better safety; less labour and 50% reduction in machine downtime. A full-format changeover on an SBO 20 Universal2 can be cut to 18min ‘bottle to bottle’, with a single operator undertaking the work, compared with 33min for two operators previously. Full format changeover consists of replacing the stretching thrust units, body, shells and mould base. Sidel says that the new system is available in Options & Upgrades for the most recent generations of its SBO Universal blow moulders and will be available by end 2010 for all SBO Series2 and Combi machines. www.sidel.com","@ID":72} "REGIONAL MARKET REPORTS 20 PETplanet insider Vol. 11 No. 10/10 www.petpla.net Bottles to be filled are of HDPE or PET – with the PET portion growing. For complete and integrated blowing/filling and all downstream equipment Serac has worked closely with Sipa in the past, and is open for further cooperation in future. Two separately business units to be viewed separately: FDB – Food, Dairy, Beverages 60% especially aseptic and hygienic filling of dairy and fruit juices beverages, sauces... and APS – Advanced Packaging Solutions 40% espe- cially filling of non-food, beauty and health. 40% of Serac’s business is in PET filling. 200 Serac machines for edible oil filled in PET containers are operating in markets. 77 aseptic lines in total and 31 aseptic lines in production filling dairy and other beverages in PET containers. The range of aseptic fillers offers capacities up to 45,000bph – the majority being in the range of 6,000 to 15,000bhp. References include big names such as Coca-Cola, Eckes Granini, Danone, Nestlé, Orangina Schweppes, etc… Organisation The group employs 400 people of which 250 are in France. Turnover (2009) – 80 million Euros. Major subsidiaries in USA, Malaysia and Brazil, which are doing well thanks to the boom of emerging countries. The business there compensates for the decline in Europe. The factory in France carries out assembly only. All components are outsourced. Test runs are carried out only in case of need and space available. 10 units can be assembled at the same time We saw 6 units in assembly on our visit. The total amounts to 40 to 45 units per annum. Strategies The marketing department claimed “performance and service” as milestones to the future. But surely, we suspected, a privately owned company with the products and size of Serac must also have, apart from the common marketing vocabulary, some essential high-tech differentiation against their competition to ensure survival. Serac apparently has such differentiation according to the explanations of Mr. Xavier Gourlaouen, namely: ”Serac has a philosophy which is both simple and efficient: Control the filling technology from A to Z.” 1. Weight filling This includes manufacture of its own electronic components (such as electronic filling cards) and development of its own filling algorithms. Thank to this approach, Serac propose optimised equipment sizing with a reduced number of nozzles. 2. Multiflow nozzle: Such nozzles allow almost perfect measurement simply by selecting a product on screen and offering three innovations: The automatic calculation of the optimum dosage for various liquids, conceived by an algorithm to achieve the ideal dosing cycle for a given product. Multiflow: the “intelligent” filling nozzle monitored by an electronic board which defines the optimum dose cycle. K 2010 STAND 10H46","@ID":22} "TRADE SHOW PREVIEW 68 PETplanet insider Vol. 11 No. 10/10 www.petpla.net Components for bulk material handling Kreyenborg Plant & Technology GmbH & Co. KG (KPT) specialises in development and manufacturing of infrared drums and components for bulk material handling, including silos, mixers and extruder feeding systems. The company recently delivered a continuous infrared drum for PET bottle flakes drying, with a maximum output of 3,500kg/h. Its stand will feature its latest product, a discontinuously working infra-red drum. The company says that this batch drum achieves quick material treatment through infra-red radiation, with high efficiency and low energy consumption, and is particularly suited for producers of masterbatches and special products. www.kreyenborg.de Kreyenborg Technology Hall 9 Booth A44 New solutions for demanding pelletising applications Automatik Plastics Machinery’s stand is to be organised around five ‘theme parks’, featuring tailor-made solutions for challenging applications in pelletising. This is the first major public appearance by Automatik following its merger with Maag Pump Systems AG. The integrated Combi-Crystal-PET (CC-PET) system combines pelletising, drying and direct crystallisation. Also on show will be its nextgeneration Sphero 70, which is designed for the production of spherical pellets from both new and recycled materials. It features streamlined process water flow and a new cutting chamber lock, which can be flipped open with one hand. The Centro 150 centrifugal dryer enables more exact dosing and homogeneous distribution in polymer melts. It is designed to provide quick access for cleaning and maintenance, low energy consumption, and easily replaceable parts. www.automatikgroup.com Automatik Plastics Machinery GmbH Hall 9 Booth A04 Fully electric blow moulding Meccanoplastica srl, of Florence, Italy, will be presenting its new range of fully-electric injection and extrusion blow moulding machines. Its new HL350/D blow moulding machine (400mm carriage translation, 60kN clamping force, max volume of 3l), a double workstation machine, incorporates a hydro-electric clamping system. Mould opening/closing movements, mould holder carriage translation, upward/downward movement of the blowing nozzles and parison thickness regulator are all regulated by a brushless type motor. The company is also introducing the new version of its Jet55/L injection blow moulding machine, which is equipped to make small 30 ml cosmetics containers in PET. The machine on display will have eight cavities producing 30ml PET packages. Meccanoplastca’s electric injection blow moulding machines are targeted mainly towards the medical-pharmaceutical and cosmetics industries. www.meccanoplastica.com Meccanoplastica Hall 14 Booth B18 Highly Profitable, High Margin Specialty Grade PET Bottle Grade Resin and PET Fiber and Textile Lines IMMEDIATELY AVAILABLE TO START MANUFACTURING (5) Solid State Polymerization (SSP) Plants (2) 300 Ton/Day SSP Lines (1) 300 Ton/Day SSP Plant Comprised Of (2) 150 Ton/Day Lines(SSP1/SSP2) (2) 15,000 Ton/Year SSP Lines (SSP1/SSP2) (7) Specialty Staple Fiber Continuous Polymerization Lines (2) 9,984 Lbs/Hr Polyester Fiber Spinning Lines (H6/H7) Fll Design (1) 9,200 Lbs/Hr Polyester Fiber Spinning Line(H5) Fll Design (1) 8,707 Lbs/Hr Polyester Fiber Spinning Line(H1) Fll Design (1) 8,500 Lbs/Hr Polyester Fiber Spinning Line(H4) Fll Design (1) 8,006 Lbs/Hr Polyester Fiber Spinning Line(H2) Fll Design (1) 7,800 Lbs/Hr Polyester Fiber Spinning Line(H3) Fll Design Contact IPP For A Complete Equipment List For Each Line (9) Resin Continuous Polymerization Lines (1) 41,887 Lbs/Hr Polymer (Resin) Line (1) 31,000 Lbs/Hr Polymer (Resin) Line(H12) Zimmer Design (1) 24,000 Lbs/Hr Polymer (Resin) Line(H11) Werner & Pfleiderer Design (2) 14,000 Lbs/Hr Polymer (Resin) Lines (H9/H10) Hitachi Design (1) 13,668 Lbs/Hr Polymer (Resin) Line (1) 9,300 Lbs/Hr Polymer (Resin) Line(H8) Fll Design (2) 35,000 Ton/Year Continuous Polymerization Lines (CP2/CP3) Specialty Grade Polyester Fiber, Specialty Textile And Specialty PET Contact IPP For A Complete Equipment List For Each Line (17) Spinning Lines (4) 4,990 Lbs/Hr Polyester Fiber Spinning Lines (H6/H7) Outflow Quench (2) 4,600 Lbs/Hr Polyester Fiber Spinning Lines (H5) Outflow Quench (2) 4,353 Lbs/Hr Polyester Fiber Spinning Lines (H1) Outflow Quench (2) 4,250 Lbs/Hr Polyester Fiber Spinning Lines (H4) Outflow Quench (2) 4,003 Lbs/Hr Polyester Fiber Spinning Lines (H2) Outflow Quench (2) 3,900 Lbs/Hr Polyester Fiber Spinning Lines (H3) Outflow Quench (3) 50 Metric Ton/Day 16-Position Spinning Machines Karl Fisher/EMS Design (19) Stretch Draw Lines (Good For Specialty Applications) (12) 5,727 Lbs/Hr Denier Drawing Frames (J6 - J9/J11 - J18) Fll Design (6) 4,581 Lbs/Hr Denier Drawing Frames (J1 - J5/J10) Fll Design (1) 100 Metric Ton/Day 2-Stage Draw Line (Stretch Line) Including Spares Contact IPP For A Complete Equipment List For Each Line (6) Filament Spinning Lines (2) 4,400 Ton/Year 48-Position Filament Spinning Lines Barmag Design (2) 1,500 Ton/Year 20-Position Filament Spinning Lines Barmag Design (2) 1,500 Ton/Year 10-Position Filament Spinning Lines Barmag Design Office +1 609 586 8004 Mobile +1 609 838 5925 Fax +1 609 586 5725 [email protected] Ron Gale President Contact IPP with any of your plant or equipment needs or if you know of plants that are for sale or shut down. Office +1 609 586 8004 Mobile +1 609 516 9107 Fax +1 609 910 4435 [email protected] Michael Joachim Director, Plants Dept. Office +1 609 586 8004 Mobile +1 609 510 2616 Fax +1 609 910 4435 [email protected] Sanjeev Rege VP, Global Plant Sales (2) 150 Ton/Day SSP Lines What PET Plant Or Process Do You Need? Contact IPP Today! +1-609-586-8004 www.ippe.com Over (775) Pieces Of DMT & PET Equipment Contact IPP For A Complete List And About The Specialty Systems For PET Available (171) Aluminum Storage Bins 22,210 to 187 cu. ft. (12) Hot Oil Boilers, including 50 MM BTU and (4) 35 MM BTU (5) Steam Boilers 150,000 to 87,400 Lbs/Hr (2) Pusher Centrifuges 39” (1 M) Siebtechnik Konturbex (7) Chillers 2,300 Ton to 1,500 Ton (13) Columns, including Koch Water Stripper Column and Complete Package Water Scrubbing VOC Elimination System (8) Centrifugal Compressors Centac and Demag (3) Reciprocating Compressors 1,135 M³/Hr @ 17.5 Bar Linde (17) Chip Dryers 6,500 Kg/Hr Gala (16) Conveyor Dryers 10’6” wide x 80’ Proctor Schwartz (24) Filter Presses, including (10) 54 Sq. Ft. (5 M²) Seitz Orion (3) Inert Gas Generating Systems 38,000 SCFH Complete Systems (21) Granulators & Pelletizers (13) Automatik and (8) Reiter (3) Incinerators (2) Waste Water and (1) Residue (13) Screens/Separators 1 M² SS Engelsmann Vibrating (312) SS Tanks 460,381 to 100 Gallon (18) Tow Cutters 366 Meter/Minute Lummus Mark V","@ID":70} "REGIONAL MARKET REPORTS 15 PETplanet insider Vol. 11 No. 10/10 www.petpla.net in Luxembourg we met: Eddy Fery, Business Manager PET Europe Eddy Fery, being in charge of Husky`s PET activities in France, described his and the company’s attitude: “We are leading in the market. But nevertheless we never lose focus on supporting all of our PET customers in France, regardless of size of operation,” says Fery. Husky has the largest customer base of injection moulding systems in France, checking with customers at regular intervals, making sure that the customer is satisfied and happy with the equipment and support they are receiving. All of the Luxembourg facilities are at the disposal of the French market, with mould and hot runner production and refurbishing, with project engineering, application know-how, installation, systems integration, spare parts delivery, customer training and service teams. All PET moulds and hot runners for France are designed and manufactured out of the Luxembourg facility. Husky injection moulding machines are coming from Canada or China. Eddy Fery comments: “The industry in France has yet to experience the economic upswing, no new large volume beverage products and no new commodities (yet) in sight. Husky’s present focus is on reducing customers’ operational costs. Most systems require a number of different moulds for multiple bottle formats. Light weighting creates added business for our customers. This appears to be on-going and typical for other developed markets too. The 1.5l bottle weight has been reduced by more than 40%. Initiatives continue.” Product and population More than 130 Husky injection moulding systems are operating in the market and need to be taken care of. Market share in France is 92%. With minor exceptions (PDG, Schweppes) all PET conversion from resin into preforms using 2-stage technology is carried out on Huskys. About 50% of the systems are with converters and 50% with fillers. These days the annual requirement in France is as low as 2 to 4 systems. Inside France the business is, according to Husky, driven by requirements for better productivity, light weighting and reduction of energy consumption. But as sales of new systems have slowed down, moulds and hot runners, light weighting conversions and a trend to multiple bottle designs, have created new and sustainable business. Local organisation Customers in France have access to service technicians, service coordinators, hot runner technicians and PET processing specialists.The French organisation comprises 5 service technicians, 1 service coordinator, 1 hot runner technician and 1 PET process specialist. Eddy Fery- age 44 – leads the team, and is Mr. Husky in France, 21 years with Husky in various sales and engineering functions: Area Sales Manager, Turnkey Manager, PET Key Account Manager (in this function he already worked closely with Nestlé, Danone and Roxane) then General Manager Services and Sales Africa, and Business","@ID":17} "MATERIAL / RECYCLING 31 PETplanet insider Vol. 11 No. 10/10 www.petpla.net Tufted PET Automotive Carpet recognised as ‘Game-Changing’ innovation Futuris Automotive Interiors is an Australian automotive components manufacturer for seat systems, interior trims and modular assemblies. The company employs approximately 1,200 people and generates revenue of about A$450 million. feel. PET carpet has excellent stain resistance qualities, which avoid the necessity of adding stain resistance chemicals into the fibre such as is found in nylon. Furthermore, unlike current nylon carpets, the PET carpet with an all-polyester carpet construction is 100% recyclable. Futuris’ PET floor carpet uses approximately 125 PET water bottles per vehicle as recycled content: up to 100 bottles for main floor carpet plus another 20-25 bottles for floor mats = 125 water bottles per vehicle. The first tufted PET carpet applications were in aftermarket floor mats, while the first fully carpeted car floors began in 2009, with the Pontiac G8 from GM Holden (Australia) and the upcoming Hyundai Santa Fe and Sonata models. www.futurisautomotive.com EREMA Engineering Recycling Maschinen und Anlagen Ges.m.b.H. Unterfeldstraße 3 . A-4052 Ansfelden . Austria . [email protected] We know how. PET Extrusion System VACUREMA® Prime to produce BTB pellets that are EFSA, FDA and brand owner approved www.erema.at CIC compact inline crystallisation system • lower AA (1 ppm possible) • higher crystallinity • less equipment Batch process guarantees defined decontamination time for each PET flake Continuous software control for • food contact, IV and other parameters Efficient decontamination and IV increase . low energy consumption, 0.30 to 0.33 kWh/kg Output capacity from 500 to 2,600 kg/h Hall 9 - Stand C05 27. Oct. - 3. Nov. 2010 WELCOME","@ID":33} "REGIONAL MARKET REPORTS 29 PETplanet insider Vol. 11 No. 10/10 www.petpla.net Vision Bertrand Guillet: One of the top concerns of Sidel is to provide sustainable solutions for the beverage inustry. “We want to be an innovative, responsible, reliable partner providing sustainable solutions for the beverage industry.” There is that word again! One of the top concerns for the beverage industries, and all those connected in France, is sustainability. “We feel we have an obligation towards the environment. Sidel products aim at lowering consumption of resin (lightweighting), also of electric power and water. In addition we support ECO Emballage in the promotion of collecting and re-using recycled material with the objective of saving resources, helping the image of PET and also safeguarding our own interests and business”, said Bertrand Guillet. Reg i ona l mar ke t repor t France part 3 - Issue 11/2010 SBECM, Evian/Danone, Valorplast, Alma Group -Roxane France part 4 - Issue 12/2010 APPE Beaune, APPE Bierne, Retal","@ID":31} "REGIONAL MARKET REPORTS 28 PETplanet insider Vol. 11 No. 10/10 www.petpla.net 1980: Sidel goes with PET. The first SBO was sold to an English customer in the United Kingdom for carbonated beverage. 1984: the first SBO high speed PET machine sold in the United States. Sidel’s American saga starts here. 1986: Sidel, with 120 SBOs in 80 countries, goes global.. Solutions for hot-fill and pasteurisable bottles were invented. The fastest SBO 40 (26,000 bph) crossed the Atlantic for delivery to SouthEastern Containers in 1989. Several innovative steps driven by Sidel: automation by computer management and control, first jars in PET, preferential heating, quick change, double-cavity for small capacity containers. At the same time (1995) the SBO 48/38 blows 50,000 small bottles for Pepsi in USA (24 moulds, 48 blow mould cavities and 38 oven modules resulting in 14 bottles/second). 1997: A new concept combining blow-moulding and filling. A technology without conveyors, compact, clean and economical. This is start of the Combi range. 1999: Actis, the internal plasma coating technology for carbonated, oxygen-sensitive drinks bottled in PET. 2005: A new generation of blow moulders with the SBO Universal range. 2006: Release of the high-speed range. SBO 34 runs at a speed of 61,200bph. 2007: Predis for preform sterilisation. An innovative dry decontamination system for preforms, using hydrogen peroxide (H 2 O 2 ) for the packaging of sensitive products. 2009: Sidel sells the 5,000th machine and promises:“ The adventure continues”. In 2001 PETplanet Top Talk spoke to Francis Olivier, the president of Sidel at that time, who said: “Innovation is perhaps my added value to the company.” He was CEO from 1972. He led the company until 2001, through the dark years of changing ownership into a phase of innovative design and development. “Every year I say to myself and my people: you have to have new ideas”, he is quoted in the interview. “Even knowledge and experience should not work against innovation. And as my first believe is innovation, I will quit in time.” Which he did at the age of 60 in 2001, when Tetra Laval was bidding for Sidel and Sidel went through a period of 2 years of standstill and stagnation awaiting European approval of the take-over. In 2003 the European Commission allowed the acquisition to go through. Euphoria returned to Le Havre under the leadership and with the capital of Tetra Laval. In 2005 Simonazzi, the prominent Italian maker of filling machines was acquired, making Sidel one of the three major global blowing/filling line suppliers. Simonazzi was able to add considerable experience and references of filling machines for beer to the enlarged Sidel group. In 2009 – with markets in depression – Sidel suffered losses, as did all the big players. There is a moderately optimistic outlook at Sidel for 2010. Recovery of the markets is essential for all, but especially for those whose first priority is customer service, because all those activities which are designed to ease life for the customer must be paid for by the supply of machinery. “There are good indicators that we are on track in 2010, despite the present downturn in economy and business”, we were told. That situation affects all of us, but some more and some less, including market leading Sidel. Product and production The Sidel group, with all of its own and/or acquired locations world wide, designs, manufactures, assembles, supplies and sells complete packaging lines for liquid food in three main categories: glass bottles, plastic and cans. In Le Havre the manufacturing focus is on the traditional business of stretch blow moulds and SBO blowers, with options such as Actis coating and Predis dry decontamination for Combi equipment. Sidel’s customer base in France is between 100 and 120 companies with about 400 systems installed, making Sidel the market leader. IMD Ltd. Switzerland / www.imdvista.ch Swiss Made … more than a VISION SYSTEM _Complete System Solution _INOX Line (all in stainless steel) _Vision System with COLOR cameras _Self-learn functions _Inline for 100% inspection _Easy & fast product change _Very compact Closure Testing Preform Testing","@ID":30} "REGIONAL MARKET REPORTS 18 PETplanet insider Vol. 11 No. 10/10 www.petpla.net Strategies The strategy of SGT is quite clear: The focus of SGT has been, and will be on multiple products, i.e. on any size of volumes with lots of shapes and designs. According to Frederic Mignot: “There are no small or important customers, we are able to match everyone’s characteristics. However we stand truly by our traditional and existing customers in the market. They enjoy priority. We will not sacrifice 30 years of work, just to become the supplier of a few large and important principals”. SGT customers are located all over France and 35% of French production is exported to foreign fillers. Presently, SGT offers a complete range of performs for several fields of activity : Neck ring 30/25 high and low neck (13g to 55g) Neck ring 29/25 (9g to 37g) – lighter preforms Neck ring PCO 1810 (16g to 54g) Neck ring PCO 1881 (18g to 24g) – lighter preforms Neck ring BPF (20g to 54g) Neck ring 38 (14g to 48g) Neck ring 48/40 (85g to 95g) Neck ring 21/29 (22g to 28g) Neck ring 28/410 (19g to 40g) Neck ring BVS 30 H (40g to 54g) For particular applications, SGT uses some additives or blends, to give the preforms UV barrier, oxygen, CO 2 characteristics. The plant is suitably equipped to use recycled material at any possible and approved rates. Asked about the future, his expectations and about SGT in 5 years time, Frédéric Mignot replied: “We go for continued diversification of products for a demanding clientele cost reduction by optimising and increasing our produc- tivity. one environmental policy through a widespread use of recycled materials, and one (already important) commitment to reduce the weight of packaging. Machine suppliers need to understand the nature of our business and the business of our customers. For SGT a reduction in cycle time is welcome, but of relatively little significance. What we primarily require for our business is systems - reliable and easy to operate (including mould changes), of high quality and adapted to our specific manufacturing enviroment.” During the interview, with SGT, Husky and PETplanet at the table, inevitably we were convinced that the cooperation between converter SGT and machine maker Husky has already produced satisfactory results - and not in 5 years time but already today. March 18, 2010 Serac in La Ferté Bernard ”Serac has a philosophy which is both simple and efficient: Control the filling technology from A to Z.” F.l.t.r.: Xavier Gourlaouen, General Manager FDB, Fabienne Chériaux and Aymeric Vague, both Marketing Managers, Serac One needs to be determined and very insistent to visit Serac. Because finding Serac in Pays de Loire, near Le Mans, is a challenge even with Tom Tom satellite navigation - no signposting! But we managed, and it was worth our while to see this manufacturer of filling and capping machines, who specialises in aseptic and hygienic lines. There we met: Fabienne Chériaux and Aymeric Vague, both of whom are marketing managers, recently employed as this mid-size company apparently saw the need not only to excel in technology, but also to promote their excellence in the market. Then we also sawXavier Gourlaouen, the General Manager of the Food Dairy and Beverages (FDB) Division, one of the company’s technical experts who left no questions unanswered and toured with us through the factory of FDB. Company history in the region Serac started as a one-man/one-family company 40 years ago, owned by the Graffin family. Today the management owns 15%, and financial investors another 15%, leaving the Graffin family with the majority in balance. Product and population The product line consists of machines for filling, dosing and capping. In-house technology and expertise are focussed on very sensitive products such as UHT and Extended Shelf Life milks, functional drinks and sensitive products such as refrigerated dairy beverages, fruits juices with pulp and added vitamins... and challenging products regarding foaming sensivity, shelf life, oxygen, sterility etc.","@ID":20} "REGIONAL MARKET REPORTS 21 PETplanet insider Vol. 11 No. 10/10 www.petpla.net Filling nozzle adjusted automatically and actuated by an electromagnet that provides a throttling effect to optimise each filling cycle according to the product’s characteristics The neck transfer technology (patented): The loadcell, a crucial part of the process intelligence in the filler supports directly the bottle by the neck. The Serac solution – according to Serac’s experts - looks trivial at first sight but is a small revolution for the customer. Format change-over is reduced and cleanliness significantly improved. Xavier Gourlaouen, who satisfied our curiosity, joined the engineering department of the company in 1997. He became project manager for aseptic projects supplied to Japan. He moved to design in 2004 and moved again to Chicago in 2005, returning in 2009 to be General Manager in charge of the FDB business unit. His curriculum vitae – from the basis of engineering to the top of the managerial tree - made him an experienced and valuable resource for Serac. Surely mid-size companies are dependent on people like him. March 23, 2010 Netstal Machinery AG Alain Viron, Sales and Applications Manager PET Systems for France and the Iberian Peninsular Alain Viron, Sales and Applications Manager, PET Systems, enjoys a unique and solitary status within the Netstal organisation. He reports directly to the PET Project Department of Netstal in Switzerland. He is responsible for Netstal’s PET sales and applications in France and on the Iberian peninsular. And in case of need – with his in-depth knowledge of machines and long-term experience in applications – he is a troubleshooter for the company globally. In France Netstal is behind Husky in numbers of PET systems operating in the market. Alain Viron commented: “When the PET boom started at end of the 1980s Netstal was weak and struggling for survival. (Then the company was bought by KraussMaffei, became member of the Mannesmann group and experienced a remarkable come-back). By that time the French market had already made a decision and one that we are still facing today.” Enjoy completeness Sacmi Imola S.C. Via Selice Prov.le, 17/a 40026 Imola (BO) Italy Tel. +39 0542 607111 - Fax +39 0542 642354 E-mail: [email protected] www.sacmi.com Sacmi offers turnkey solutions for the beverage and packaging industry: complete bottling lines for product preparation, container manufacture, filling and closing, labelling and final packaging operations. The extensive experience acquired since the company was established in 1919, in addition to its reputation for supplying advanced technology, financial solidity and a network of 70 companies throughout the world, enables Sacmi to meet all your requirements wherever you are.","@ID":23} "REGIONAL MARKET REPORTS 24 PETplanet insider Vol. 11 No. 10/10 www.petpla.net France do not only compete, but also cooperate with each other - when it makes sense technically, financially and for the customer’s interest. Latest developments at PDG have been on: Ultra-light preforms (2.4g, 6,0g,8.0g), short 29/25 neck, light barrier and recycled PET An outstanding PET application at PDG is “Prelactia”, which is an innovative technology for over moulding of preforms to produce bottles with an effective light barrier.. For this application Netstal developed in cooperation with PDG a 24 cavity preform production system for milk bottles. PETplanet has reported on Prelactia in PETplanet Insider issue No 5, 2008. Prelactia preforms for milk bottles Due to the material properties PDG claim the following advantages for “Prelactia”: Pure white bottles … 100% light barrier. The two layers mean that the use of additives can be reduced to 50% and even more compared with monolayer solutions. Weight reduction up to 30% (monolayer needs an ade- quate bottle wall thickness for light barrier). Novapet Dairy 2C (additives used in the polymerization process) Cooperation and development with additives suppliers for the use of different kinds of resin everywhere in the world: ColorMatrix (liquid) light and oxygen barrier (same oxygen barrier performance as a 6 layer HDPE bottle) Holland Colours - master batch supplier. 10% faster cycle time thanks to sequential injection compared with the monolayer solution. Despite all advantages the question referring to recyclables must still be addressed. Valorplast as well as APPE in Beaune had reservations, since the white post-consumer milk bottles could - so far - not be used for bottle-to-bottle applications due to the white and black colouring. The 5-year perspective Asked about PDG in 5 years time we received a cautious answer. Francois Desfretier: “We consider ourselves to be one of the most ambitious and demanding players in the market. Strong in terms of innovation rather than in overall size. Fair economic size is important, because economy supports people. A stable team to stand together, a stable, democratic, multifunctional unit with a strong feeling of unity.” With those ethics PDG are well prepared to support their customers. March 24, 2010 Sidel in Le Havre Sidel – changing from a French to a multinational company. Bertrand Guillet, Communication Group Vice President, Sidel Sidel was there at the beginning and since that time has always had a major influence on the direction taken by PET. We met : Bertrand Guillet – Communication Group Vice President. In Le Havre they call it “the campus” – a green and grassy area over rolling hills on the outskirts of the town. In amongst the idyllic scenery the architects have erected structures of steel and glass, which house Sidel’s design and development, sales and customer services, laboratories, administration and finance departments. Moulds are manufactured and blowers assembled. The campus concept dates back to the end of the 1990s and was constructed at that time. It was inaugurated in 1998 and today still looks futuristic. And although now more than 10 years old it symbolises the changes at Sidel. The emphasis is not only on functional machine manufacturing but is also on professional service, on consultation of - and advice to - the PET markets. An atmosphere of environmental well-being, which is created by the campus, is a welcome by-product, but is also considered as a precondition for top performance and achievement. With Bertrand Guillet we toured the campus, spoke with the divisional managers in person and in conference calls, so creating and confirming the overall impression of this globally active company.","@ID":26} "TRADE SHOW PREVIEW 65 PETplanet insider Vol. 11 No. 10/10 www.petpla.net Dosers, mixers and conveyors for plastic granulates Koch-Technik’s stand will feature many of its machines for mixing, dosing, conveying and drying plastic materials in operation. A new addition to the range, the Exako gravimetric direct dosing device for use on injection moulding machines, will make its international debut. It is claimed to offer highest standards of accuracy in dosing very small quantities and is designed to be easily integrated into Koch modular systems. Its Comko compressed air dryer has been designed for operation in immediate contact with the processing machine and is particularly suitable for drying small quantities of hygroscopic materials. The Eko series dryers are designed to deliver energy savings up to 20%, depending on material, with potential for more. Also on display will be dryers from the company’s KKT series; KEM direct dyeing machines; Graviko series dosers; and a number of new developments and upgrades. www.koch-technik.com Koch-Technik Hall 10 Booth A21 All-electric preform IJ system Husky will be launching its new H-PET AE preform injection moulding system at the K Show. The ‘AE” designation stands for ‘all electric’. The system is designed to complement Husky’s existing Hylectric-based product line, which includes the company’s HyPET, HyCap and HyPac systems. H-PET AE is smaller than the existing product lines and is intended to address the needs of consumers in emerging markets and low-volume or custom producers in the developed world. The H-PET AE, which is managed by the company’s PC-based Polaris Control system, will be demonstrated on Husky’s stand at the show. www.husky.ca Husky Hall 13 Booth A59","@ID":67} "PREFORM PRODUCTION 46 PETplanet insider Vol. 11 No. 10/10 www.petpla.net Volcanic Act Moretto Hall 11 Booth H57 Italian company Moretto has deployed a volcanic mineral and modular design concepts to help achieve high standards of efficiency, flexibility and effectiveness in its new range of Flowmax PET drying systems. The process of achieving good quality processes in drying plastic granulate materials involves the management and control of ten factors that influence the process. These are: type of material; granule size; bulk and density; dew point; resistance time; specific airflow; initial and final air moisture content; and viscosity. A further influence is how low the dewpoint is, which is the temperature at which moisture condenses on relatively cool surfaces. The lower the dew point, the more the air is able to absorb and remove moisture. The treatment of highly hygroscopic polymers, which tend to absorb moisture from the air, requires constant performance; automatically variable airflow; and high performance with a constant dewpoint at -65°C. Zeolites reduce energy consumption Italian ancillary equipment manufacturer Moretto SpA has introduced a new drying system for plastics, particularly PET, that uses zeolite minerals. Zeolites are of volcanic origin, formed where volcanic rocks and ash layers react with alkaline groundwater. They are aluminosilicate members of the family of microporous solids known as ‘molecular sieves’, a term that refers to a particular property of these materials, which is the ability to selectively sort molecules based primarily on a size exclusion process. Moretto says that the use of zeolites in its new Flowmax drying system The dewpoint of the material has major influence on the process of achieving good quality in the drying process","@ID":48} "MATERIAL / RECYCLING 33 PETplanet insider Vol. 11 No. 10/10 www.petpla.net impacts on MachinePoint’s business. Projects with African companies, especially in the north and west, are longer-term and require 24 months, on average, to be closed successfully. However, the regular flow of important enquiries means that Africa is in the top three markets for its PET machinery activities. MachinePoint is investing a lot in India, where it has a local sales office. Demand for good technology at competitive prices is strong in both India and Pakistan. South-east Asia is also an active market, which the company serves in collaboration with local organisations. The CIS area (Russia and neighbouring republics) declined from very busy prior to 2008 to low levels during the recession period. Rodriguez said that there are indications of recovery appearing now and a return to full activity is expected by mid-2011. The company also has a strong presence in Poland, eastern Europe’s largest market. Top brands sell best MachinePoint has a strategy of working only with top brands in each of its market sectors. The reason for this is that such equipment retains the residual value necessary to make them interesting for the used market. Furthermore, commercial operations on a global scale require a logistical infrastructure, which means that only equipment and brands with appropriate levels of infrastructure will be cost-effective for the used machinery business. In the PET beverage packaging market, MachinePoint trades preform, caps and closure systems; blow-moulding machines; filling lines for water, CSD and non-carbonated drinks; and carton packaging lines for juices and dairy products. The company says that Husky is the preferred brand for used injection moulding machinery. Its particular attributes are: leading position in the original equipment market; good shelf life; high residual value; and very strong after-sales service worldwide, which makes the required levels of maintenance practical. Most of the Husky equipment sold by MachinePoint is audited In the PET beverage packaging sector, MachinePoint trades preform machinery as well as caps and closure systems, blowing machinery and filling lines.","@ID":35} "PREFORM PRODUCTION 48 PETplanet insider Vol. 11 No. 10/10 www.petpla.net enables lower consumption of energy in the drying process, compared to conventional dryers. The system combines zeolites in its range of X Max dryers with its Flowmatik control system. Modular design gives flexibility and reduced energy consumption Moretto says that its X Max dryers are designed to offer constant performance levels, within a modular concept. X Max is a multi-tower system, which allows one or more dryers to be taken offline for servicing and maintenance, while the others continue in operation. By rotating servicing between the modules the system operates constantly at capacities up to 5,000kg/h, through a combination of between three and ten dryer units, connected to up to 32 hoppers. Air is automatically regulated according to need. Airflow to the units can be reduced in parallel, or one unit can be switched off while airflow is modulated between 50 and 100% among the units that continue to operate. This means it is not only possible to maintain production during essential maintenance, but also to flex capacity according to demand – which leads to lower overall energy consumption. A further benefit claimed by Moretto is better control of both thermal stress of the material being dried and reduction in variation of viscosity. The modular design of Flowmax means that the system achieves a constant average value, with a dew point of about -65°C. The Flowmatik control system calculates the airflow needed for each hopper. The central control unit collects the data on dryer need and manages airflow as required. Units that are not needed for production are put on standby. Different set-ups for different needs Moretto says that the Flowmax system can be installed with different configurations, according to need. Combinations of Flomatik Uni, Twin and Multi units with the X Max dryers come together to make up the required process. Flowmax Uni is made up of a battery of X Max units with a single hopper and is used for dehumidification of large quantities of plastics, up to 12,000kg/h. Flowmax Multi configuration is, as is name suggests, designed for the treatment of a number of materials in an efficient and functional manner. The Flowmax PET configuration is a complete, centralised system designed for process constancy, simple management and significantly reduced treatment costs. Where space is at a premium, Moretto says that it can develop PET systems with a dryer installed on board each single hopper. The control system uses a coloured touchscreen panel with ‘intuitive’ user interface, which requires input of only two parameters: the type of material and the throughput. The system then activates automatically and provides exactly the right quantity of process air. Higher capacity, recovered energy Conventional systems currently on the market have maximum capacities of around 4,000m³/h and generate throughout of up to 1,300kg/h, which corresponds to a 144-cavity machine – which means that, in effect, a single drying system will be dedicated to a single machine. Moretto says that Flowmax can process up to 8,000kg/h of PET, with a modular generator of 20,000m³/h. The company claims that a large, modular system has advantages over individual systems, including fewer working components and reduced risk of failure. Flowmax has been designed to make the most of its energy, by recovering and reusing every Watt. The major attraction of this, Moretto says, is that energy costs are reduced to the extent that ROI on each machine is achieved in two years; furthermore, as energy typically represents 90% of total costs over ten-year lifetimes, total savings have been calculated as equal to a new injection moulding machine. The company has simulated these savings on a battery of five 72-cavity machines with output of 3,600kg/h, in tests equating to European conditions: ambient temperature 20°C and relative moisture at 80%. Production is based on six hours of treatment at 180°C with specific airflow of 2.5 m³/h on 8,500h of production per year. www.moretto.com","@ID":50} "NEWS 12 PETplanet insider Vol. 11 No. 10/10 www.petpla.net Barrier resin obtains egulatory clearance for USA and Europe Invista, part of Kansas, USA-based Koch Industries, Inc, has obtained regulatory clearance for its OxyClear barrier resin for food and beverage packaging under the Federal Food, Drug, and Cosmetic Act and the European Union Packaging Directive for certain food types and processing conditions. Containers made with the newly-authorised barrier resin are completely clear but provide full shelf-life protection for oxygen-sensitive foods and beverages, such as fortified water, juice, wine, beer and dairy, as well as ketchup, sauces and other condiments. Invista says that both colourless and tinted containers made from OxyClear barrier resin are as clear as containers made from standard PET. The product is a two-component barrier system in which up to 3% of OxyClear resin, an oxidisable co-polyester, is added at the injection machine to PolyShield resin, the established barrier resin used in beer packaging. The oxygen barrier is activated when OxyClear resin additive is added to the injection machine. The additive is a high capacity, polyester-based oxygen absorber. It contains no nylon or nitrogen and Invista says that it exhibits significantly reduced yellowing during the recycling process, compared to other commercial oxygen scavengers. The company is in the process of reviewing recognition guidelines from the Association of Postconsumer Plastic Recyclers (APR) and/or the European Plastic Bottle Platform (EPBP). www.invista.com Drink Technology India 2010 – seeds in fertile soil The Bombay Exhibition Centre will be simultaneously hosting drink technology India 2010 (dti) and International PackTech India, the International Exhibition and Conference for the Packaging and Processing Industry, from 18-20 November 18-20 this year. dti, India’s International Trade Fair for Beverage and Liquid Food Technology, attracts manufacturers of beverages of all kinds and producers of liquid food from across India and neighbouring regions. The 2010 edition is, for the first time, organised as a joint event with International PackTech India, with a shared exhibitor forum. The organiser of dti is Messe München GmbH; International PackTech India is the responsibility of Messe Düsseldorf GmbH. The joint event provides a single large trading platform for customers from the packaging industry and from the beverage and liquid-food industry. India’s economy is one of the fastest-growing in the world. Some sectors of the beverage are predicted to see double-digit growth in coming years. Over the last five years, India’s imports of food processing and packaging machinery increased by 200% (2008: US$200 million). CSD has attracted foreign direct investments amounting to around $1049 million. The bottled water market has been estimated at $570 million (2008), with annual growth of 14.5%. Beer sales amounted to 1074 million litres in 2008. www.drinktechnology-india.com www.vdma.org www.messe-munchen.de New Sales Manager at MHT Volker Jährling has been appointed to succeed Rolf Steinmetz as manager of worldwide sales for MHT Mold / Hotrunner Technology AG in Hochheim/Main, Germany. Mr Jährling is a qualified engineer, specialising in plastics technology and has been involved the service and distribution of plastics processing machinery and fittings for over 30 years. He has been involved with support for customers in the packaging industry and was responsible for joint projects with MHT. www.mht-ag.de New Managing Director/Partner at CCT GmbH CCT GmbH has announced that 45-yr-old Rolf Steinmetz been appointed Managing Director/Partner, with effect from September 1, 2010. He now heads the Niedernhausen/ Hessen , germany,company together with the long-term Managing Director/ Partner, Dipl. Ing. Alexander Schmitz. The core competency of CCT GmbH is the development of closure technologies such as ComPETCap, MC29-01, 1881 and various patents as well as the projecting of turnkey projects for the beverages industry. www.cct-gmbh.com Plasma technology in plastics processing German research teams from RWTH Aachen University, Ruhr University, Bochum (RUB), and the University of Paderborn are collaborating in the examination of fundamental issues regarding the development of plasma-assisted processes for the deposition of functional layers. The German Research Foundation (DFG) has been sponsoring the trans-regional collaborative research centre (SFB/TRR 87) for plasma technology since July 1, 2010. A total of nine research institutes are participating in this joint project, officially titled ‘Pulsed high-power plasmas for the synthesis of nano-structured functional layers’. The SFB, initially financed for four years, is divided into three research areas: coating systems on metal substrates for tribological applications (project area A); new functional coatings to improve the barrier performance of plastic substrates (project area B). Project C will undertake support studies on elementary principles of plasma processes (project area C). The Institute of Plastics Processing (IKV) at RWTH Aachen University will perform research in two subprojects of project area B: the large-scale deposition of strain-tolerant barrier coatings on PET films and, based on the example of PP, the influence of material properties – e.g. orientations and internal stresses – on the plasma process. They will study the influence and the potential of high-performance plasmas, starting with the atom in the gaseous phase to the performance characteristics of new, theoretically conceived material systems. www.ikv-aachen.de","@ID":14} "PETbottles 72 PETplanet insider Vol. 11 No. 10/10 www.petpla.net SPHERO® underwater pelletizers Beautiful things are formed underwater. Your single source for comprehensive pelletizing solutions. Expert pre-sales advice and post-sales service included. www.automatikgroup.com Special highlight at K 2010: SPHERO – the new generation! Hall 9, Stand A04 PET angled for aroma The French aroma manufacturer Vahiné of Avignon (Mc Cormic France) is selling 200ml liquid aromas such as vanilla or orange blossom in a coloured, angular PET bottle. This has a snap-on re-closable lid with a dispensing lip and tear-off tamper-evident security strip. An attractive front label provides support for product and brand whilst informative rear labels supply the necessary product and retailing information. www.vahine.fr The taste of Shakeria “Shakeria“ is the name given by the Swiss retailer Migros to its new, foaming coffee drink, available in a number of different flavours. The shake packaging consists of a round, bulbous 250ml PET bottle with a screw cap. The bottle sports a pre-perforated shrink sleeve label by way of decoration which also extends to incorporate the cap. Before it can be opened the top section of the label has to be removed, in so doing disclosing a drinking straw stored located ready for use in an outer groove of the bottle. The straw is made up of two parts and is extendable. On insertion via the latch on the screw cap a small sealing membrane is penetrated. www.migros.ch Black for intrigue “Chino“ is what the Italian beverages manufacturer San Pellegrino of Milan calls its caffeine-free scene drink with the bitter taste of the Chinotto Orange. The drink is bottled into a black, bulbous PET bottle. The intriguing factor as far as the consumer is concerned is the dark colour of the beverage (reminiscent of Cola) and its unexpectedly bitter taste. The PET bottle is also decorated with a black shrink sleeve label and a printed, black screw cap with tear-off tamper-evident security strip. www.fuoindalcaro.org","@ID":74} "BOTTLING / FILLING 54 PETplanet insider Vol. 11 No. 10/10 www.petpla.net 200ml bottles can be capped with a normal closure or with sportscaps. Antartic has noted the rising sales of 330ml PET packages and intends to include that size in its private-label filling range when volumes are right in its customers’ own-brands, according to Manuel Machado. “The aseptic line will also enable us to try out new products, such as smoothies in 0.15l bottles, for example,” he said. Antartic now handles ten different PET containers, ranging from 200ml to 2l. While non-Intermarché contract bottling currently represents only 5% of the facility’s output, third-party orders on the aseptic lines account for 10%. The company’s original aseptic line handles 15 different products, running the same one for three to twelve hours and with formats changed about three times a week. Aseptic line 2 runs 20 different products, from two to eight hours continuously. “We’re trying to run this line for a whole week with just one or two bottle sizes,” Machado said. “Weekly format change-over times for the two aseptic lines account for approximately 25%, including disinfection, sterilisation and product and format change-over routines. That’s a good figure, even comparable to the times we’re getting for the non-aseptic soft-drinks lines - but we’re trying to improve on this by means of SMED (single-minute exchange of die) steps.” Legacy and modernity combined Antartic opted for an air conveyor on its new line, rather than a blowmoulder/filler monobloc, as it is the same system it has on Line 1. The company is comfortable with the buffering provided by the air conveyor; it believes it makes the line more flexible. The two lines run four to six days a week in three shifts, each with two operators and one technician. As well as the new line itself, Krones also supplied an AquaAsept sterile-water treatment unit and a VarioDos hygiene centre. Antartic is able to recycle peracetic acid from the bottle sterilisation process and to re-use it for cleaning the bottle exteriors, which reduces total chemical consumption. Fewer parts, faster handling On Line 1, Antartic can assemble two-, three-, four- and six-bottle shrinkpacks, for promotional purposes, or use a Robogrip, plus appropriate gripper tools, to load the containers on sales pallets without prior shrink-wrapping. Loading on Line 2 is restricted to full pallets; it is handled by robots from the Modulpal family. In the new Line 2, Antartic uses two Variopac Pro units; its Variopac Pro FS produces four- or six-packs, which a Variopac Pro TFS assembles into 24-bottle trays as needed. The new Variopac Pro has turned out to be an important component for the company. Its original model had more handling parts, which slowed down changeovers. The new unit enables everything to go faster. In addition to its Contiroll wraparound labeller, Antartic also integrated an inline Sleevematic in the second line for bottle sleeving, with a downstream Shrinkmat. Sleeving is used for 1l, premium squash (cordial) containers. The sleeves have lifelike pictures of strawberries, bananas, lychees, apricots in lifelike pictures printed on them. “Compared to the first aseptic line, the new PET-Asept line has shorter changeover times and peracetic-acid treatment is more reliable, Machado said. The company is also focusing on operator and maintenance staff training, which it has recognised as an important element in continued performance. “We will intensify operator training on a continuous basis. Our goal is efficiency.” In the new Line 2, Antartic uses two Variopac Pro machines. “We opted once again for an air conveyor, and not a blow-moulder/filler monobloc, simply because that’s the same system we have in Line 1”, says Machado. Antartic is the only producer of juices, syrups and soft drinks in the Intermarché Group.","@ID":56} "TRADE SHOW PREVIEW 60 PETplanet insider Vol. 11 No. 10/10 www.petpla.net K-Show 2010 ‘A foretaste of PET’ At K 2010 in Düsseldorf, Germany, from October 27 to November 3, some 3,100 exhibitors will once again be presenting their latest developments for all sectors of the industry. Companies from 57 countries have already registered to attend. The total leased exhibition space comes to 164,100m², about 60% of this being occupied by companies based outside Germany. The number of German exhibitors registered currently totals 1,058. Italy is traditionally the most strongly represented nation among the non-German exhibitors, and more than 400 Italian companies alone have booked a net space of 27,400 m² to showcase their products. Also strongly represented among the European countries are Austria, Switzerland, France and the Netherlands. 113 companies from the USA will be taking part - an increase in relation to K 2007. Furthermore, the contingents from China, India and Turkey have grown appreciably. Taiwan is as strongly represented as in 2007. Appearing for the first time are exhibitors from Armenia, Chile, Indonesia, Pakistan and Vietnam. In our latest issue we published many previews from suppliers to the PET bottle industry who will be exhibiting at the K show. This tradeshow preview gives you another foretaste of the show. Croda Polymer Additives Hall 7 Booth B13 ‘Greener and smarter’ additives Croda Polymer Additives, exhibiting under the campaign theme of ‘Better Brands’, has taken double its normal stand space at the K Show and will be presenting the latest developments in its range of plastics additives. These are designed to help eliminate the need for outer packaging and to reduce slip, block, static and to provide UV protection. Croda Coatings & Polymers will be coexhibiting, promoting its range of natural ingredients for engineering plastics. On the stand will be examples of Atmer 7510 concentrated slip agent; Solasorb UV absorbers; and Incroslip G slip and anti-block agents. The Atmer range also includes anti-static and anti-fog agents. www.croda.com Improved appearance and performance of liquid colours and additives Producers of PET bottles and preforms will find at the Repi S.p.A. stand its full portfolio of colours, additives and colour barriers for packaging and other applications. The Repi Remap additives range includes products that are designed to aid optimisation of processing parameters and to control manufacturing costs; and items intended to improve final product performance and enhance packaging quality. Remap colour barriers are designed to protect packaging content from UV, visible light, and from oxidation. Repi is headquartered in Northern Italy and has a distribution network covering Europe, North America and Russia, as well as a global commercial network. The company is ISO 9001:2008 certified. www.repi.it Repi SpA Hall 6 Booth B27","@ID":62} "PETcontents 10/10 6 PETplanet insider Vol. 11 No. 10/10 www.petpla.net INSIDE TRACK 3 Editorial 4 Contents 8 News 70 Products 72 Bottles 74 Bottles Personal Care 76 Patents BUYER’S GUIDE 77 Get listed! BOTTLE MAKING 50 A deep grip BOTTLING /FILLING 52 Aseptics for private label juices CAPPING / CLOSURES 56 High-speed caps LABELLING 58 Sleeve and roll in one REGIONAL MARKET REPORT 14 France Part 2 MATERIAL / RECYCLING 14 PET bottles on the floor 32 An international market place for used PET machinery PREFORM PRODUCTION 36 Get more using less 40 A rapid guide tp perfect preforms part 15 46 Volcanic act MARKET SURVEY 41 Suppliers of resins and additves for PET bottle production Page 50 Page 36 Page 58","@ID":8} "REGIONAL MARKET REPORTS 22 PETplanet insider Vol. 11 No. 10/10 www.petpla.net P.D.G. Plastiques S.A.S. in Malesherbes is Netstal’s biggest PET customer – with 9 PET systems, Hofstetter hot runners and Hofstetter moulds (as well as one ageing injection moulding machine for caps, soon to be replaced). Alain Viron recommended PDG for PETplanet in order to see the Netstal over-moulding process at work, i.e. one dark PET layer over-moulded with one white PET layer for bottling milk. As a matter of interest it should be mentioned that Netstal’s total number of machines installed in France is, to date, 1,450, mainly in heavy moulding, packaging and thin wall applications. This business is directed by the Netstal subsidiary in Paris with some 25 people for sales and service. March 23, 2010 P.D.G. Plastiques in Malesherbes PDG – specialising in specials Francois Defretier, PDG, left, and Alain Viron at the PDG plant Francois Desfretier is second generation owning and directing, running and living this mid-sized preform and bottle making company PDG, set in the idyllic rural landscape of Malesherbes, south of Paris. PDG is an independent family-owned company. With 43 workers on the shop floor and only 6 multifunctional people in sales, engineering, administrative and managerial functions PDG enjoys the leanest organisational structure we have seen in the PET business so far. Francois Desfretier – mechanical engineer – is, he tells us, fascinated by the business: “We concentrate on our essentials such as – selecting limited market segments and excelling in niches foreseeing trends, being right in decisions and sticking to them no experiments, no technology adventures, no financial adventures total commitment of management and team to the com- pany and to their customers. There is a live connection between the managerial culture and growing value of the company for all concerned (externally and internally) i.e. customers, employees, and even the PET market as such, since innovation belongs to everybody and the supplier of machine tools, such as Netstal’s PET systems, is a part of the scenario. Francois Desfretier says, “The conductor needs an orchestra. Managers need players. Innovation is not driven by unilateral decisions and managerial edicts, but by motivated staff in a democratic system. The human factor is all important.” Desfretier sees his own prime role in customer contact and developing the company’s technological direction. He is PDG’s public face, and as in many well-organised private businesses the finances are controlled by his wife. History of company PDG Plastiques was created in 1948 in Paris (plastic packaging by injection). 1962: PDG received Packaging Oscar for the plastic crates. Moved to Malesherbes. 1981: Jacques Desfretier bought the company. Development of base cup for CSD PET bottles. 1990: Start of PET preform activity in new modern plant. 2000: Start of PET bottles activity. 2006: 2 Packaging “Oscars de l’Emballage” for PET preforms (2.4g Nestlé Dairy product). 2008: Packaging “Oscar de l’Emballage” for Prelactia preforms (UHT milk bottle). Products and production The plant in Malesherbes covers 6,000m2 production area and 2 x 2,500 m2 storage. Preforms: 585 million PET preforms representing 75% of turnover 9 Netstal PET Systems + Hofstetter 48 cavity moulds (8 cavity mould for small runs) Bottles: PET bottles: 56 million units representing 25% of turnover 8 blowing machines, 2 and 4 cavities (7 Sidel and 1 ADS) 4 single-stage injection blowing machines (ASB Nissei) Markets PDG produce standard preforms in the larger volumes and “specialises in specials” in comparatively small to medium volumes for commodities such as water, dairy and UHT milk, and fruit juices, wine. Water business with Intermarché, St.Amand, Wattwiller, Ogeu. Dairy business with LSDH, Novandie, Nestlé. Juice business with Andros, LSDH. Specific preforms with special neck, weight or dimen- sions. Also special bottles between 5ml and 10l. For PDG’s blowing activity preforms are bought from other converters, including from APPE (barrier preforms), also from Resilux and SGT. Apparently PET converters in","@ID":24} "BOTTLES 73 PETplanet insider Vol. 11 No. 10/10 www.petpla.net Livio is back The German manufacturer of fine foods, Homann of Dissen, is promoting various Livio brand products with the slogan “Livio is back!” These include a 220ml pack of salad cream in a PET container. The inverted bottle is in the typical Livio shape and has a suitably styled snap-shut cap with a dispensing nozzle. The cap is screwed onto the container and has to be unscrewed by the consumer to remove the tamper-evident aluminium seal over the neck of the bottle. Front and rear paper labels carry the requisite product and commercial data. www.homann.de k-online.de in the world for you! The most important trade fair “It’s K time” means that about 3,000 exhibitors from over 50 countries present the latest products and concepts – from standard to high-tech solutions. With its first-class range of exhibits, both in terms of quantity and quality, K is the most important business and contact platform for the industry worldwide. In 19 halls, everyone is represented, from the market leaders to the niche market suppliers who decide the future of the industry. Be there when the world-class suppliers of plastics and rubber meet in Düsseldorf! Buy your ticket now +++ at an attractive price +++ in the Online Ticket Shop +++ at www.k-online.de/2130 International Trade Fair No. 1 for Plastics and Rubber Worldwide Quality and clarity Under the “Filippo Berio“ brandname the Italian company Salov, based in Massarosa is offering a litre of olive oil in a perfectly designed PET bottle. The square bottle, with its metallic gold-coloured label, settles well into the “front-facing“ position on the shelf and two lateral recessed grips ensure that the contents can be safely poured out and dispensed. A printed, gold-coloured screw cap complete with integrated tear-off, tamper-evident security strip provides the finishing touch to this premium quality packaging. www.filippoberio.com www.salov.com Bio lemonade in PET The French retail chain Cora is selling a 1l pack of organic lemonade, including lemon and cane sugar, in a slim, easy-grip, crystal-clear PET bottle. The bottle carries a wraparound label and a green screw cap with tear-off tamper evidence. About 20 years ago all of this would have still been technically and politically difficult, but would have been a disaster for PET’s competitors. www.cora.fr","@ID":75} "REGIONAL MARKET REPORTS 16 PETplanet insider Vol. 11 No. 10/10 www.petpla.net We met: Frédéric Mignot, President Directeur Général The PET converters SGT enjoyed substantial regular volume growth from 1997 to 2006. Ever since then no further growth is to be registered according to Frederic Mignot. But their output has been at or close to capacity. Profits have been stable thanks to higher productivity. How did SGT manage to maintain its profits, in times of market decline (when everybody else in the market is suffering and complaining) we asked ourselves during the visit? Company history in the region The family company wasfounded in the 1950s, making soap. Frederic Mignot is the third generation managing the company. In the process of diversification in 1981 the company launched a new activity in producing PVC material for water bottles. PVC (the material itself) suffered from extensive environmental pressure and the company became involved in PET in 1997. In 1997 SGT installed the first three Husky systems with 48 cavities and PET preform production was commenced with an immediate result and with a constant and double-figure growth, until sales of bottled water declined as a consequence of governmental action to improve tap water. But SGT can see the requirement for bottled water returning as the big supermarkets are presently commercialising their own brands. The losses in famous, large volume brands are thus likely to be compensated. Product and population SGT today is producing preforms internationally of 120 to 130 different designs for water, CSD, edible oil, vinegar, detergents, wine, beer, dairy products… Production is on 50 moulds with numerous conversion kits. The frequent mould changes, estimated at 1,000 per annum with 2 to 5 hours lost each time, represent a chalManger PET Europe. Today he is PET Regional Manager France and Iberia. He can see reasons to be optimistic about Husky’s future in France: “We have a win-win situation, for our customers and for us. Light weighting cuts costs for our customers, light weighting grows our mould business. Regardless of the economy, we are continuing to offer creative solutions to help our customers reduce costs.” France is a vast country. Injection moulders are evenly spread over the entire country. In the extreme West on the Atlantic coast we visited Societé Générale des Techniques (SGT). March 17, 2010 Societé Générale des Techniques (SGT) in Nantes “Focus of SGT has been and will always be on multiple products with a large range of preforms i.e. on smaller volumes with lots of shapes and designs, in order to offer a global solution to the customer demand.” Frédéric Mignot, Président Directeur Général, SGT, left, with Eddy Fery, Husky","@ID":18} "MAGAZ I NE FOR BOT T L E R S AND BOT T L E - MAK E R S IN THE AMERICAS, ASIA, EUROPE AND ALL AROUND THE PLANET india.petpla.net MAGAZINE FOR BOTTLERS AND BOTTLE-MAKERS IN THE AMERICAS, ASIA, EUROPE AND ALL AROUND THE PLANET INDIA SPECIAL SPECIAL ISSUE 2010 www.petpla.net D51178; ISSN:1438-9452 No. 06/10 21.06.10 PETplanet is read in 137 countries MAGAZINE FOR BOTTLERS AND BOTTLE-MAKERS IN THE AMERICAS, ASIA, EUROPE AND ALL AROUND THE PLANET Manufacturers of mould tools for PET bottle production MARKETsurvey Page 17 Regional market reports Vietnam Part 1 Page 10 www.petpla.net D 51178; ISSN:1438-9452 No. 07+08 2010 26.07.10 PETplanet is read in 137 countries MAGAZINE FOR BOTTLERS AND BOTTLE-MAKERS IN THE AMERICAS, ASIA, EUROPE AND ALL AROUND THE PLANET Manufacturers of stretch blow moulding machines MARKETsurvey Page 21 Regional market reports Vietnam Part 2 Page 10 n www.petpla.net D 51178; ISSN: 1438-9452 No. 09/10 01.09.10 PETplanet is read in 138 countries MAGAZINE FOR BOTTLERS AND BOTTLE-MAKERS IN THE AMERICAS, ASIA, EUROPE AND ALL AROUND THE PLANET Page 21 MARKETsurvey Suppliers of preform machinery and suppliers of single stage machinery Regional market reports France Part 1 Page 10 Visit us at Hall EN Booth 03A www.petpla.net fax: +49-6221-65108-28 | [email protected] | www.petpla.net name company function street city / zip code country phone fax email credit card number expiry date name on card date, signature Order / Registration form Become a subscriber! PETplanet subscriptions 1-year PETpla.net package 1) 3) 10 Issues € 149 1-year Young Professionals´ PETpla.net package 1) 2) 3) € 99 2-year extended PETpla.net package 1) 3) + free gift: a useful water dispenser for PETbottles € 289 All prices are in EUR + VAT. Magazines will be sent to you by airmail. Shipping is included. 1) Orders for subscriptions are made for the required term. The order is deemed to be tacitly extended for one year for 149 Euros, if not cancelled in writing three months prior to the due date. 2) Available to young employees (aged 35 and below) on presentation of copy ID card or similar proof of identity. 3) includes subscription (print and online) includes exclusive access to our online archive includes monthly PETplanet Pulse, the PET price index newsletter","@ID":46} "LABELLING 59 PETplanet insider Vol. 11 No. 10/10 www.petpla.net significant potential in terms of simplifying layout, reduced footprint and overall optimisation of production. As the very thin labels are sealed without glue or solvents, they also have environmental advantages. New SL 90 modular labeller - a high technology solution Sidel’s new SL 90 rotary modular labeller is equipped with modules for applying pressure-sensitive self-adhesive labels or cold-glue labels on various kinds of packaging. It says that maintenance levels are lower because its design has eliminated mechanical gears and transmissions. There is a growing market demand for single labellers capable of various applications, even combining them to label the same container – such as beer bottles, which have paper neck and self-adhesive body labels. The SL 90, which will soon also be available with other modules including a roll-fed module, has been developed by Sidel with the flexibility to label all kinds of packaging, both round and irregularly shaped, with fast changeover times and freedom in layout design. At the SL 90’s core is a carousel and transfer system (starwheels and screw feed) which have no gears and no contact. Its linear motor drive technology and direct motor drives require almost no maintenance and normal drivegear wear is eliminated. These features also aid machine access and cleaning. The Sidel pneumatically-assisted guards can open independently. The SL 90’s hygienic design makes it particularly suitable for labelling sensitive products, such as beer. The SL 90 is capable of both high-speed and very highspeed production; it can label up to 60,000 bph with both selfadhesive and cold-glue labels. Application of the label to the container can be adjusted electronically, while a vision system with several cameras orientates bottles, ensuring correct positioning. Its direct motor drives minimise energy consumption and the ergonomic design and easy access reduce cleaning and maintenance times. Special tilting and fixed feet and a support plate for the tilting labelling units, which move independently, allow the module structure to adjust easily to the slope of the floor. The self-adhesive labelling station allows handling of very light self-adhesive labels. Two labelling units can be fitted on the same module, which eliminates machine downtime when the reel runs out. Changeover uses a simple clip-in/ out shaft system. Air tensioning of the film reduces mechanical stress on the labels and thus reduces the risk of damage or breaking. The cold glue labelling station also has an ergonomic design and compact footprint, features simple format changeover and low maintenance, and its stainless steel structure is finished with anticorrosion treatment. www.sidel.com","@ID":61} "PREFORM PRODUCTION 38 PETplanet insider Vol. 11 No. 10/10 www.petpla.net good parts consistently in a mould is not as easy as it was several years ago. Lighter weights have allowed for faster cycles, but this has also increased the difficulty of moulding a quality part. Quality factors such as ovality, witness lines and gate quality are now more important than ever. The iPET approach: less means more Over the years, the engineering design of preform moulding efficiency has not changed significantly. The same philosophy of more water, more cavitation and more energy, all to make more parts per hour, dominated design criteria. The iPET technology, which was introduced by the company Mold-Masters in 2009, takes another approach. iPET has focused its attention on engineering a mould that combines stack and hot runner design in order to obtain cycle and process advantages during preform production. Or in the company’s own words: less means more. iCool technology: the “conformal cooling” The patented technology called iCool, allows iPET moulds to cool more evenly and more efficiently. The use of “conformal cooling” technology allows preform moulds to run significantly faster in existing injection moulding machines while improving the look of splitlines and ovality. According to the company, moulds with iCool technology require less than half the coolant flow compared to typical preform moulds and do not require mould cooling down to 7ºC. Conformal cooling provides much more uniform stack cooling and reduces the formation of cold and hot spots typically seen in areas of the preform mould that are difficult to cool using convention drilled lines. In addition turbulent flow can be engineered into the inserts at much lower flow rates than generally is seen in these types of moulds. iCool cooling concept vs. conventional concept Melt channel comparison","@ID":40} "MARKET SURVEY 42 Resins Company name ExpoPET Ltd. Indorama Ventures Ltd NovaPET, S.A. Postal address Telephone number Web site address Contact name Function Direct telephone number Fax E-Mail 2nd Floor Cardiff House Tilling Road London NW2 1L J United Kingdom +44 7825 447 506 www.expoPET.co.uk Samreen Hussain Business Manager +44 208 253 7044 +44 207 183 5276 [email protected] 75/102 Ocean Tower 2, 37th Floor Soi Sukhumvit 19 (Wattana) Bangkok 10110, Thailand +662 661 6661 www.indoramaventures.com W.G. Hoenderdaal Technical Services Manager +316 51809942 [email protected] Pº Independencia 21, 3º. 50001 Zaragoza (Spain) +34 976 216129 www.novaPET.es Mr. Miguel Angel Arto Business Development Director +34 976 216129 +34 901 021138 [email protected] Resins Europe USA Asia 1. Brand name of the resins Expo RamaPET Performance PET RamaPET NovaPET 2. IV range a. of Homo-Polymers 0,62 to 0,96 b. of Co-Polymers 0.75 - 0.87 dl/g 0.70 - 0.84 0.76 - 0.84 0,63; 0.76 - 0.95 0,72 to 0,82 3. Speciality resins CSD Expo A8, Expo A8+ R1, R1L, ES11, CB11E, Vorcalor 9921W NovaPET Lbs Soft, NovaPET Cr Water Expo A7, Expo A8 N1, N2, 9921W, 18696 ES11 R1, S1 NovaPET Mw Soft, Cr, Glasstar and X_treme Beer N1, 9921W, AQ01 N1, N2, N3 NovaPET Glasstar Wine / liquors N1, 9921W, 1708 R1, N1 NovaPET Glasstar Personal care /pharmaceuticals N1, 9921W, 1708 N1 NovaPET Glasstar Slow crystallisation 9921P 1708 N1 NovaPET Glasstar and NovaPET X_treme Hotfill R1 No Pre-coloured 1708 H1 NovaPET Dairy Fast reheat Expo A8FR R1, R1L, ES11, CB11E, Vorcalor 9921W NovaPET Lbs Soft Other ES11 R1; S2, S3, S4 NovaPET Dairy (Long Life Dairy Products) 4. Increased barrier properties Yes (UV for ultraviolet protection) Yes (Gases and light radiation) 5. PEN mixes available No No 6. Recycled blends available On request In preforms 7. Special comments RamaPET Easyflow, low IV (0.70) for thin walled applications, preforms and other injection moulded articles. Milk: UHT, ESL, milk shakes and yogurths. Additives MARKETsurvey 10/10 Company name Chroma Corporation Gabriel-Chemie Ges.m.b.H. Repi S.p.A. PolyOne Corporation Postal address Telephone number Web site address Contact name Function Direct telephone number Fax E-Mail 3900 W. Dayton Street McHenry, IL 60050, USA +815-385-8100 www.ChromaColors.com Stuart D. Swain Director of Sales and Marketing +815-759-2110 +815-385-1518 [email protected] Industriestr. 1 A-2352 Gumpoldskirchen +43 (0)2252 63630-0 www.gabriel-chemie.com Ing. Andreas Hinterberger Unit Manager Food Brand Packaging +43 (0)2252 63630-0 +43 (0)2252 62725-0 [email protected] Via B. Franklin 2 21050 Lonate Ceppino (VA) - Italy +39 0331 819511 www.repi.it Maurizio Amicabile Market Development Manager - Packaging [email protected] 6 Giällewee, 9749 Fischbach, Luxembourg 32 (0) 83 660 211 www.polyone.com Mr. Denis Keller Market Manager 32 (0) 83 660 360 [email protected] Additives and Colours for PET FDA sanctioned frosted color concentrates Liquid colours Yes Yes Microgranule colours Yes Yes Masterbatch colours Yes Yes Yes Yes UV protection additive (solid) Yes Yes Yes UV protection additive (liquid) Yes Yes AA reduction (solid) Yes Yes No AA reduction (liquid) Yes No Oxygen scavenger (solid) Yes No No Oxygen scavenger (liquid) No No Other PET additives in liquid or solid form Yes Yes Anti-yellow (liquid), process aid (liquid), IV enhancer (solid), blowing additive (liquid), optical brightener (liquid). In addition to liquid colours and additives, Repi supply Remap barrier colours for protection of the packaging content . Optical brighteners, slip agents","@ID":44} "MATERIAL / RECYCLING 34 PETplanet insider Vol. 11 No. 10/10 www.petpla.net by Husky itself, which helps with buyer confidence and sense of security. MachinePoint is also able to offer financing through its Finance division, which operates as a separate company dedicated to providing solutions for industrial equipment purchase. Second only to Husky in used injection moulding machinery is the PET-Line production system from Netstal. The leading brands (by demand) in used blow- and stretch blow-moulding equipment are Sidel, Krones, Sipa, Side, Nissei and Aoki – with local variations. IBM Nissei machines are popular in India; local technical services and OEM presence are significant factors influencing demand for used machinery in local markets. Key points The key to make it smoothly for buyers and sellers of used machinery, is to count with the right assessment during the whole process. MachinePoint team does consultive selling, where customers are experts on every technical, legal and logistic issue along the whole process. MachinePoint says that prospective purchasers need to bear certain important points in mind when buying used PET machinery. First, they need to ensure they have access to qualified engineering and maintenance providers in their region. The equipment has to be complemented by an assured supply of reliable and costefficient ancillary products. It is vital to have all the manuals and instructions. Dismantling, loading and packaging the machine should be personally supervised, in order to make certain that the equipment is not damaged during the process. The company is prepared to look after logistics tasks, such as arranging the right transport, insurances, legal issues, exportimport docs, etc. Sellers, too, have to be aware of the issues involved. The process can be complex and time-consuming; operators themselves are unlikely to have the experience and expertise in-house, which is where a company like MachinePoint can be invaluable, in providing access to an international network of lawyers, technicians, machine manufacturers, forwarders, riggers, brokers, dealers, agents and auctioneers. It bases its reputation on selecting the best machinery and providing the best available engineering and logistics service to its customers. It can deal with collection, legal agreements, dismantling, packaging, loading, transportation, customs formalities, commissioning or repairing the machinery. International scope MachinePoint Group is an internationally-operating organisation that is dedicated to providing what it calls ‘smart equipment solutions’ to selected niche markets. MachinePoint Used Machinery, as its name indicates, is the division dedicated to the trading of used machinery. It has a team over 40 people and a wellestablished international presence, which enables it to make international trading of used machinery easier and more secure for both buyers and sellers. It has sold machines in 85 different countries around the world, has experience and expertise in valuating used equipment and can be found in most of the major European markets. It has representation in Germany, Italy, Poland and Russia, as well as its European and world HQ in Spain, and maintains offices in North Africa, India and Turkey. It has strategic partnerships in Latin America, with OEMs worldwide and relationships with local sellers in various markets. The company has plans to further expand its global presence. The requirements for sellers vary, depending on their circumstances. For some, time is key in order to liberate space in their factories for new equipment. For others, price is the highest priority – which has led MachinePoint to turn down some equipment, as overpriced. New machinery has seen price decreases over the last few years and this affects used machinery prices, too. Some manufacturers would rather invest their time in getting maximum profitability in the sale of their used equipment. Rodriguez says that selling used equipment is time consuming and involves risks and there is an opportunity cost in committing resources to used machinery selling and not to core business. International transactions are complex, as are payment methods, as well. Dealing with certain countries’ letter of credit and local specifications can become complex and he recommends careful thought before committing to undertake such disposals without professional help. The group has also MachinePoint Finance, the division dedicated to provide financial solutions to the equipment industry and MachinePoint Food Technologies, a division that does turn key projects and process for the beverages, dairy and agro-food industry. www.machinepoint.com Most of the used Husky equipment sold by MachinePoint is audited by Husky itself","@ID":36} "MATERIAL / RECYCLING 32 PETplanet insider Vol. 11 No. 10/10 www.petpla.net An international market place for used PET machinery Demand for used PET equipment keeps rising Sales figures on the used PET machinery sector have been consistently growing over the last few years; more so than in other sectors, such as glass or cans packaging. Demand nearly doubled in 2009 compared to the previous year and has shown continued growth in 2010, according to specialist company MachinePoint Consultants SL. Founded in 1999 and based in Valladolid, Spain, it is a significant trader of used plastic and beverage machinery in the world. Demand has been particularly strong during the two years of recession. Cesar Rodriguez, founder & managing partner, says that the growth in sales means that the PET machinery niche segment has continued to invest in capital equipment, which frees up previouslyowned machines for processors who are working within tight budgets but still need good quality equipment. The key drivers contributing to the growth of the used-equipment sector include innovations and new technologies, coupled with high output sold plastics and beverage used machines are sourced in Europe. Concerning the PET machinery market, 50% come from Europe, the other 50% come from outside.The PET segment is more global, with only around half of equipment sourced from Europe while only 20% are sold in the EU. Whatever the market, the company says that distance seems to be of little concern when customers are searching for good quality used PET equipment. MachinePoint expects the market balance to keep shifting. The growth in emerging regions such as Latin America, west and southern Africa, the Middle East, India and south-east Asia leads to a fallback in Europe’s position. Latin America is particularly strong; companies appear to have already completely recovered from the recession and they are fully focusing on their future expansion plans. The African market has challenges with telecommunications, which machines and lower power consumption. Combining these criteria with new ancillary technologies and complementary services and products raise cost-effectiveness and attractions in the market. As a result, MachinePoint expects a pattern of stable growth in the demand for used PET equipment in upcoming years, in parallel with growth in demand for new machinery, especially in Latin America and Asia. The market is likely to see further internationalisation. Europe: largest market but international growth is strong MachinePoint sells 60% of used plastics equipment; 85% of all their According to MachinePoint, Valladolid, Spain, sales figures of used PET machinery have been constantly growing.","@ID":34} "80 PETplanet insider Vol. 11 No. 10/10 www.petpla.net Buyer’sguide Entries from 5,70 Euro/mm, Call +49-6221-65108-0 TOOLING PREFORM SYSTEMS BV Moulds & Robotics PET-related Services & Technologies C. Houtmanstraat 42 Emmen, The Netherlands Tel +31 (0) 591 679768 Fax +31 (0) 591 630616 [email protected] · www.tps.nl www.wtbvc.com Blow Molds for All Technologies, All Machine Types, All Sizes. Highest Quality, Fastest Delivery, Lowest Cost. Canada - 905-574-0010 [email protected] Poland - 48-81-820-5730 [email protected] UK - 44-1623-658-416 [email protected] China - 86-137-646-05384 [email protected] Argentina - 54-11-4753-1111 [email protected] 3.1 Preform moulds www.wtbvc.com Preform Moulds, Components, Refurbishments and Conversions. Highest Quality, Fastest Delivery, Lowest Cost. United States - 937-898-8460 [email protected] Poland - 48-17-860-1020 [email protected] UK - 44-1623-658-416 [email protected] Argentina - 54-11-4753-1111 [email protected] Tel. +39 041 57 99 111 [email protected] www.piovan.com 2.5.3 Dryers 200 West Kensinger Drive Cranberry Township, PA 16066, USA Tel.: +1-724-584-5500 [email protected] www.conairgroup.com 3.0 SUPPLIERS FOR STRETCH BLOW MOULDS AND PREFORM MOULDS Molds, Change Parts, SBM and Injection Molding Machinery for the PET/Bioplastics Industries 284 Pinebush Road Cambridge Ontario Canada N1T 1Z6 Tel: 001-519-624-9720 Fax: 001-519-624-9721 [email protected] www.hallink.com Production of blow moulds and PET mould parts tel.: +359 32 606 821 fax: +359 32 606 888 [email protected] www.itd.bg KHS Corpoplast KHS Corpoplast GmbH & Co. KG Meiendorfer Str. 203 22145 Hamburg Deutschland T +49 40 67907-0 F +49 40 67907-100 E-Mail: [email protected] www.khscorpoplast.com Specialist for PET Preform Injection Mold, Injection Stretch Blow Mold & PET Blow Mold www.moltechkorea.com Tel : + 82-11-224-1571 / + 82-32-684-0153 Fax: + 82-32-684-0139 [email protected] for North American market [email protected] for International market www.petkamold.com [email protected] www.pmci-solutions.com R&D -Integrated Solutions In Plastics Leverage - Integrated Industrial Design Hamilton Road Sutton-in-Ashfield Nottinghamshire, NG17 5LD England Tel: +44 1623 556287 Fax: +44 1623 552240 www.rdleverage.com 1009 SE Browning Avenue Lee’s Summit, Missouri MO. 64081, USA Tel: +1 816 525 0353 Fax: +1 816 524 5068 www.rdleverage.com PREFORM MOULDS / STRETCH BLOW MOULDS Tel: 0039 071 7500214 Fax: 0039 071 7501958 [email protected] · www.simexitaly.it PET Preform and Blow Molds for Different Application Guang Dong Xing Lian Precise Machinery Co., Ltd. Baoshi Rd, Xiabei, Pingzhou, Nanhai, Foshan, Guangdong, China Tel: (86-757) 8677 7168 Fax:(86-757) 8623 3168 E-mail: [email protected] Website: www.gdxl.com Otto Hofstetter AG Zürcherstrasse 73 8730 Uznach, Switzerland Tel. +41 55 285 22 11 Fax +41 55 285 22 44 [email protected] www.otto-hofstetter.com 50 Galaxy Blvd. #13 Toronto, Ontario M9W 4Y5, CANADA P- (+1) 416 213 9400 F- (+1) 416 213 9379 [email protected] www.rnaprecision.com 3.2 Stretch blow moulds Awanti Polymoulds Pvt. Ltd. 25/5A/1/2, Nanded, Sinhagad Rd., Pune - 411 041, INDIA Telefax: - 91 20 24392805 [email protected] www.awantipolymoulds.com PET engineering, bottle design, Prototyping, industrial blow mould and services - Rue du buisson Moreau 16100 Cognac FRANCE Tel : 0033 (0)5 45 36 63 50 www.sa-comep.fr [email protected]","@ID":82} "BOTTLING / FILLING 53 PETplanet insider Vol. 11 No. 10/10 www.petpla.net centres by a fleet of 15,000 trucks. The production operation is made up of 13 lines, including four for filling beverage cartons, one glass line for juices, a five-gallon PET water line, a five-litre PET water line, two lines for filling syrup in glass and metal bottles, one PET line each for soft drinks and water, plus two aseptic lines from Krones. Total production in 2010 is expected to reach around 100 million beverage cartons, 200 million PET containers and 20 million glass and metal bottles. Need for increased capacity Antartic’s first Krones PET-Asept line is rated at 12,000 2l PET bph, or 35 million fills a year, and is used for bottling ice tea and fruit-juice beverages. Juice filling was not the initial intention but the introduction of onelitre juice bottles was well received by consumers and, by 2006, the aseptically-bottled range included 4 million of these packages. Demand continued to rise, both within the Intermarché brands and more widely. As one very few aseptic PET bottling lines in France at that time, Antartic was able to contract-bottle third-party dealer’s juice brands as well. By 2008 the existing line had reached its capacity limits, so the company decided to commission a second aseptic line as soon as possible. Increased capacity, greater flexibility In order to make room for the new line (and to reflect changing market preferences) Antartic closed down an existing glass line, which was right next to the first aseptic line. The second line is specified for nearly double the first’s output - 60 million bpa, compared with 35 million, and provides Antartic with an option for distributing container sizes between the two. Perhaps paradoxically, the ‘small’ line fills the large containers (1.5l and 2.0l), and the ‘large’ line handles the smaller 200ml and 1l formats. The smaller, single-serve units had previously been packaged in glass; they, in particular, are seeing significant growth, thanks to migration of consumer behaviour patterns. The For the new line, Krones also supplied the AquaAsept sterile-water treatment unit and the VarioDos hygiene centre.","@ID":55} "REGIONAL MARKET REPORTS 25 PETplanet insider Vol. 11 No. 10/10 www.petpla.net The futuristic Sidel “campus” in Le Havre Bertrand Guillet has been with Sidel since 1992, responsible for internal and external communications. He put Sidels’ approach quite simply: “We have changed from being a machine maker to a solution provider for our customers – whether it is in blowing, which is our traditional business, or in any other discipline from resin to recycling.” “This industry has been evolving from PET pioneering via more sophistication, and finally to being able to offer complete integrated line solutions. Sidel has been part of this development and has played a driving role. It has been a top-speed ride - no time for breaks. And I do not believe that we have reached the end of the story. This PET material will still present us with, and will surprise us with, some new developments. Sidel has changed over the years from a French to a multi-national company; from blow moulding to complete solutions; from a machine maker to a solution provider.” Organisational structure today Sidel’s Swedish parent company, Tetra Laval, with its Swedish-American CEO and head office in Switzerland (with around € 11 billion of sales and 20,000 employees), is 100% owner of the three business units: De Laval, Tetra Pak and Sidel (the latter with about € 1 billion in sales and 5,000 employees). The global set-up is as follows: Packaging and filling equipment is manufactured in Le Havre, France Parma, Italy Mantova, Italy Beijing, China The plant in Malaysia was closed in 2009 and operations shifted to China.","@ID":27} "BOTTLING / FILLING 52 PETplanet insider Vol. 11 No. 10/10 www.petpla.net Aseptics for private label juices The trend towards aseptic processes, rather than hot-fill of juices filled into PET containers has led French company Antartic SAS to install a second aseptic PET line, for the production of private label juices for the Intermarché supermarket chain. Antartic commissioned its first PET-Asept line from Krones in 2005; the new line utilises the same technology but is one size larger. *Based on an article by Matthias Kreutz, Krones AG, Neutraubling Germany France’s Intermarché retailing chain is organised as a cooperative. Its business is made up of independent retailers, who operate under a shared family brand so as to benefit from synergies in purchasing and marketing. There are approximately 1,800 autonomous Intermarché markets in France; 200 in Portugal; 150 in Poland; and others in Belgium, Bosnia and Romania. Turnover in 2009 totalled €34 billion, with total market share having increased from 12.1 to 12.5% over the previous year. Growth came mainly from the food segment. Increased sales came from greater unit throughput, not just increased prices. In common with other retailers, Intermarché strengthened its range of inexpensive products by upgrading its own, private label brands. “Our target is to upsize the proportion of dealer’s brands in our sales mix from its current 38% to 40%,” said Antartic Director Manuel Machado’s firm conviction. This is in response to rising consumer demand for low-price, value products, which are increasingly served by private label offers. As Intermarché’s distinctive characteristic is its traditionally very high proportion of dealer’s brands, manufactured in-house, it could be expected to profit from this trend. Its own 60 facilities, which employ a total of 9,000 people, produce goods worth about €2.9 billion. More than 90% of these are foods and beverages. It operates its own fishing fleet, processes meat, makes milk and cooking oil and a range of beverages. In the liquid-food segment alone, its facilities include an edible-oil producer, a dairy, two wine bottlers, two bottlers for carbonated mineral and spring waters, plus five bottlers for still waters. Water, juices, syrup and soft drinks One of Intermarché’s water bottlers is Antartic, which is located in the village of St. Martin D’Abbat. 20km east of Orléans, and two hours south of Paris by road. With a payroll of 235, Antartic is the only producer of juices, syrups and soft drinks in the Intermarché Group, accounting for 330 million fills a year. Its products are carried to the group’s logistic Antartic Director Manuel Machado: “Our goal is efficiency.”","@ID":54} "PETpatents www.verpackungspatente.de 76 PETplanet insider Vol. 11 No. 10/10 www.petpla.net Engagement groove Disclosure No. DE 102007033621 A1 Applicant: Krones AG, Neutraubling (D) Date of Application: 17.7.2007 A preform for manufacturing a PET container is fitted with a peripheral groove that enables easier handling of the container, rendering superfluous the “collar“ that has hitherto been used to locate the bottle during manufacture, transport etc. and/or makes it possible to save material at this point and thus reduce the manufacturing costs. Improved riser pipe International Patent No. WO 2010 / 034983 A1 Applicant: Pritchard Ip Ltd., Puckeridge (GB) Date of Application: 22.9.2009 Riser pipe for a container having a device for discharging the content of the container. It is manufactured from a material that conveys (preferably) liquid product from outside the small pipe into the inside. This means enhanced removal of residue and it is no longer necessary to hold ”in the correct position” for spraying. Lighter bottle International Patent No. WO 2010 / 045325 A1 Applicant: The Coca-Cola Comp., Atlanta (US) Date of application: 14.10.2009 The weight of a plastic bottle has been reduced increasingly over a number of years in the interests of saving costs / resources. The international application describes the possibilities for savings in materials in the neck / orifice of a bottle without ignoring the requirements in terms of stability. Twist-proof security device International Patent No. WO 2010 / 046567 A1 Applicant: Bericap, Longvic (FR) Date of application: 22.10.2009 The closure mounted on a container opening is fitted with a tamper-evident band and a twist-proof security device which reliably removes the tamperevident band in response to even a slight twisting action. Double-wall container European Patent No. EP 2172400 A1 Applicant: Yoshino Kogyosho Co. Ltd., Tokyo (JP) Date of Application: 19.6.2008 The process for manufacturing a doublewall container complete with discharge device is described. The walls do not have to be connected with one another over their entire surface. Bottle base European Grant of Patent No. EP 1827989 B1 Applicant: Acqua Minerale San Benedetto S.p.A., Scorze (IT) Date of Application: 21.12.2005 The grant of European patent describes the base of a plastic bottle for holding a carbonated liquid. The base is designed so as to ensure stability when upright and/or to minimise the risk of tipping over.","@ID":78} "REGIONAL MARKET REPORTS 14 PETplanet insider Vol. 11 No. 10/10 www.petpla.net Part 2 France by Wolfgang von Schroeter For our “Focus on France” the facts, information and impressions published here were collected during meetings and outside the meetings, in talks on tour through the factories, during lunch and dinner as well as while travelling. The regional market report on France in fact started in Luxembourg, on the border of France, from where Husky conducts sales and service for all European countries, which includes the French PET market, (also for the Middle East, Africa and India,) March 16, 2010 Husky Injection Molding Systems SA in Luxembourg “Light weighting cuts costs for our customers, light weighting grows our mould business.” Eddy Fery, Business Manager PET Europe, Husky Regional market reports France Part 2","@ID":16}]}}
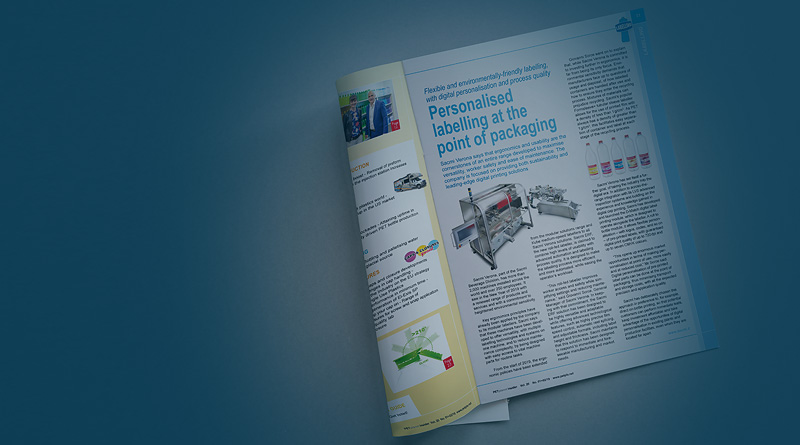