"PRODUCTS PETproducts 27 PETplanet insider Vol. 12 No. 01+02/11 www.petpla.net FoodBevcom A world of food and drink www.beverageawards.com functionaldrinks The only global awards scheme dedicated to the global functional drinks industry 6 categories – 24 awards Awards will be presented at the InnoBev Global Beverages Summit in Washington, DC, US March 2011 ENTER NOW Preform cooling system W. Amsler Equipment Inc. of Richmond Hill, Ont, the Canadian manufacturer of all-electric, reheat stretch-blow moulding machines, has announced a preform cooling system that uses increased airflow in the oven to reduce preform surface temperature. This results in minimal temperature differential throughout the preform, which induces less stress and creates faster moulding cycles, while reducing the chances of burning. The system uses infrared short-wave emitters but replaces the standard reflectors with a plenum. The airflow through the plenum slots cools each preform directly and more precisely. Instead of compressed air, Amsler uses its standard integrated filtered air supply at no additional cost in power consumption. Westbridge Inc., a Calgary, Alberta-based blow moulder of PET containers for CSD, water, and alcoholic beverages, has achieved a 13.3% improvement in productivity for its thickwalled (0.210-in) 1.75l PET alcoholic beverage bottles with a new preform cooling system on their Amsler two-cavity reheat stretch-blow machine. Amsler offers the preform cooling system as a retrofit on its full range of machines; Westbridge’s conversion kit was installed in less than four hours. www.amslerequipment.net Oxo-biodegradable cap for 5gal water bottles Norland International Inc. has introduced the industry’s first oxo-biodegradable cap for 5-gallon water bottles. The 55-mm LDPE caps, sold under the Earth Cap trade name, contain a proprietary additive, blended into the LDPE by a special mixing and drying system. It accelerates the degradation process, achieving total degradation in five to ten years, depending on environmental conditions. The additive does not affect either clarity or tensile strength. The injection-moulded cap has a biodegradable nonadhesive tamper-evident label and 2-mm foam seal, which makes the entire structure totally biodegradable. The caps have a two-year shelf life, are claimed to offer the same performance as current versions, and are FDA compliant. Once exposed to UV light, heat and moisture, the caps become brittle and break down into small pieces. When the molecular weight is sufficiently reduced, the broken down matter becomes a food source for bacteria or microbial activity. Caps containing the additive will degrade in landfills, ditches, rivers, and other water sources. They are fully recyclable and compatible with municipal collection and recycling systems. There is no contamination with the plastics recycling stream and industrial composting facilities are not required. Norland manufactures the caps at virtually the same cost as standard caps. They are commercially available in standard colours in the US and Far East/Pacific. www.norlandintl.com","@ID":29} "PET TOP TALK 11 PETplanet insider Vol. 12 No. 01+02/11 www.petpla.net John Galt of Husky: “Ownership, leadership and strategy are completely aligned on where we are taking the business.” We are here at K 2010 in Düsseldorf in the Husky booth, talking to John Galt, President and CEO of Husky Injection Molding Systems. Prior to becoming Robert Schad’s successor in 2005, John Galt was Vice President of Operations and COO. Prior to that he was Vice President Engineering in the Canadian based company. He gained a wealth of experience and business knowledge which would enable him to eventually lead Husky into a new epoch, from a predominantly family-owned and family-dominated company to the company owned by private equity finance, from PET pioneering to a profitable enterprise. art in preform and closure manufacturing solutions are still relatively immature, relative to what they could be. Therefore the prime duty for us is to continue to improve through technology, manufacturing efficiencies – to find a better way even in a saturated market. PETplanet: How far are environmentalists responsible for this market saturation? Is recycling the answer to protect the PET business against political interference? John Galt: PET packaging is the most environmentally friendly option - if you look at the product created, used and reused. We – the industry - ignored the opportunity to recycle material for a long time. Now the perception of PET packaging as an environmentally friendly product needs to be addressed. PETplanet: Given the linkage between the environment and the PET business, pressure is mounting on companies, especially in the highly significant bottled mineral water category. Public water companies are constantly improving tap water. John Galt: There’s a place for tap water. If you have access to clean quality drinking water, at the end of the day the consumer will make the decision. For us it’s about providing a packaging solution that meets the PETplanet: Dynamics have returned to the plastics markets, as seen here live at the show in Düsseldorf. John Galt: I don’t think the markets ever went away – not for food and beverage packaging . PETplanet: European injection moulding machine makers have suffered a 50% drop in order intake in 2009. We need to ask the question, how can industries survive and what are the recipes for survival, in view of these dramatic falls in sales and revenue. John Galt: We don’t have all the answers to that very big question. But to us, it’s fairly simple. Try to have the best products possible, continue to invest in R&D for leading technology, keep investing in customer service, develop a globally competitive cost structure so that regardless of swings in the economic cycles, regardless of where your competition will come from in the future, that you’re prepared. I don’t think that in principle that set of priorities has changed. PETplanet: France, for instance, is a saturated market. Growth is no longer the driver there. How does a company handle a saturated market, when growth is no longer the driving force? How does one operate in a saturated market? John Galt: There was a plaque on the wall in Robert’s office with a quote – my favourite quote from Thomas Edison that said “there’s always a better way - find it”. The state of the","@ID":13} "PETcontents 01+02/11 4 PETplanet insider Vol. 12 No. 01+02/11 www.petpla.net INSIDE TRACK 3 Editorial 4 Contents 6 News 27 Products BUYER’S GUIDE 29 Get listed! MARKET SURVEY 17 Suppliers of PET recycling plants for bottle-to-bottle recycling PREFORM PRODUCTION 22 New player in the preform tooling firmament TRADESHOW REVIEW 24 Brau - Beviale Nuremberg, November 2010 REGIONAL MARKET REPORT 8 France Part 5 PET TOP TALK 11 John Galt, CEO Husky Injection Molding Systems, Canada Page 11 Page 22 Page 24 SPECIAL: HEALTH AND BEAUTY CARE PACKAGING 16 Partnership for Progress 21 From HDPE to PET / One2dose / Joy creates a pleasant smiling effect 28 Partnership for Progress HEALTH&BEAUTY CARE PACKAGING","@ID":6} "PET TOP TALK 13 PETplanet insider Vol. 12 No. 01+02/11 www.petpla.net Revolution in PET-extrusion! Conical co-rotating MAS-extruder | perfect solution for A-PET, G-PET, PET Co-polymer … | prime pellet / melt quality (IV, b*, AA- content) | very low energy consumption | direct extrusion into sheet | stable melt pressure build up | small foot print paired with robust design | sizes available from 200 kg/h up to 1500 kg/h | suitable for food application M-A-S Maschinen- und Anlagenbau Schulz Gmbh A-4055 Pucking, Hobelweg 1 T: +43 7229 78 999, F: +43 7229 78 999 10 [email protected] www.mas-austria.com an approximate period of 5 years. Must we - customers and markets - be prepared for another change in the near future or mid term? What comes next? John Galt: Ownership changes, whether they are in the public or in the private market, are inevitable for any company. What’s also inevitable is that a private investor, at some point in time, will enter and at some time will exit. Those transitions to me should be anticipated by any company under such an ownership structure. Whether in the form of an IPO or in form of a sale to another private financial investor or potentially even a strategic company, I think that depends on the market. It also depends on the alignment and passion of management to support that direction. PETplanet: Next issue: Some years ago your then President explained to us Husky’s drive for diversification. PET systems of course were high on the agenda, and then machines for packaging. The next stage: Large machines for automotive and small machines for general purposes. It was a large portfolio of products. The essential objective was to become cost-effective through diversification. The pendulum has now swung back from diversification to segmentation and specialisation. Could you explain the reason for the strategy change? John Galt: We’re focussing on primary markets – which at this time are the food and beverage packaging industry as well as selected other niches such as for other packaging and medical where we think we can exploit the power of the system. Our thoughts were simple. If we were going to do something very well, we needed to focus. We focus now on markets that were large enough, we focus on markets that have a certain set of requirements, we focus on markets that we believed would be growing, we focus on markets that we believed would going to be global. We are channelling all of our energy into these businesses to achieve a leadership position. Where the company goes after that, is subject of future talks. PETplanet: Husky’s main focus used to be on high-tech, high performance, high quality. However, here in Düsseldorf on the Husky booth you are exhibiting a machine of lower output. This is sensational news at K 2010. Firstly Husky goes Toyo and secondly, fully electric! Two models have been unveiled: the H-PET low volume primarily for emerging markets, and the H-MED for clean room medical applications. Both systems are based on a Toyo design. Two questions spring to mind: What is the thinking behind the cooperation with Toyo? And why, after so many years refusing to go down this route, is Husky going electric? John Galt: What Robert said - which still holds true today -is that electric drive solutions have their place. The relationship between the performance, the cost and the reliability makes it the ideal choice for certain types of applications. Which the H-PET AE will do. What’s changed is the development in smaller drives. The speed of those drives, the reliability of the power and motion systems has reached the point where they represent a very attractive alternative - for the smaller sizes, where the demand on systems is reasonable. PETplanet: But Husky has a HyPET 90 tonner and you also have a HyPET 120 tonner to cope with a smaller number of cavitations? Is the new electric machine in competition to these? John Galt: Both lines will be offered. The customer will ultimately choose. It really depends on the applications. For short production runs, where you have longer cycles, more product change-over or less cavitation density the H-PET AE is likely to be a better solution. Where you are running a more traditional Husky application with ultra-high though-put of resin and","@ID":15} "PET TOP TALK 12 PETplanet insider Vol. 12 No. 01+02/11 www.petpla.net needs; where a packaged beverage is appropriate. I am not pessimistic looking at the future potential of bottled water. PETplanet: Any particular Husky input on the issue of recycling? John Galt: We address the controversial issue with a variety of different technologies, one example being our HyPET Recycled Flake system, to reliably provide food grade packaging out of non-food grade feed stock, i.e. unclean, but washed flakes. We use the filtration at the output of a twin screw extruder and before the shot pot to achieve a continuous rather than a discontinuous flow of material through the filters. PETplanet: In PET conversion the big innovative developments seem to us things of the past. No further increase of cavitations, no spectacular shortening of cycle time can be expected. Today’s innovations are marginal – mainly to adjust existing technology and improve productivity. John Galt: It depends how we define innovation and also what you call spectacular. I think one can expect the advancement of technology within the context of PET to take two directions. Both directions are innovative. First we look at what it should take to convert a PET pallet into a preform and ultimately into a bottle – from a theoretical viewpoint, excluding the particular machine execution. We hold this up as being our ideal, the goal we ought to have. And then we map out the existing production processes - in great detail from the context of resin, from energy, from cycle and from other sources of waste. And we investigate whether there is a gap between the current execution and that idea. The gap in our mind is waste - which will ultimately result in an evolution of the current platform combined with a revolution to eliminate some of the major barriers to waste. It will take a couple of years from now, but we will work on the elimination of waste. PETplanet: And the second innovative direction? John Galt: We simply look at the production of a PET preform. We are focused on lowering the cost of production and improving the quality and improving the flexibility for customers and design. Energy in the conversion process - electrical versus hydraulic - is only one very small percentage of the energy that should concern engineering and physics. A large amount of energy is lost in the entire process from preform production to the capped filled and labelled bottle stem to heat, to noise, to other things – and should be saved. The way the PET preform in a plant is conveyed from the preform machine up to the point where it’s ultimately blown and filled and capped and labelled. That entire process is today relatively immature compared to what it could be. So, that’s what I mean by barriers to be eliminated. PETplanet: If you claim line responsibility, does it mean that the owner of the blowing and filling line will also take over the injection moulding in-line? John Galt: Existing markets for converters will remain. Other markets – mainly brand owners - will develop, with an opportunity to integrate a significant proportion of the value chain, including injection moulding. I think the two markets can properly coexist. PETplanet: In 2001, we did an interview with Robert Schad, the founder of Husky and President at that time. Now since 2005, you, John Galt, are in charge of Husky. Big question: What has changed in the last five years? If I run through a list of the various topics, could you add your comments? Galt:Absolutely. PETplanet: Question 1: Ownership changed in 2007. Onex, a private equity financial investor, took 98 % of shares and took charge of the direction of the company. Any comment? John Galt: Onex didn’t take charge of the direction of the company at all. What was important to us in management, what was important to Robert at the time of the transition is that there are three fundamentals. Ownership, leadership and strategy are completely aligned on where we were taking the business. This we have achieved. PETplanet: Any particular advantage to being owned by a financial investor? John Galt: I don’t really see it very differently. When we were a public company, Robert still maintained a majority ownership position and therefore it helped to influence the direction. Under Onex, we’re a private company, there’s some cost savings due to not having to report publicly. we handle The management of the business the same as always. PETplanet: Almost all operative Husky management remained in office? John Galt: Yes. PETplanet: After the acquisition, no casualties, no losses? John Galt: Not those that I didn’t initiate. There’ve been changes, but the changes were all my decisions and those of my team, not anybody else’s and they’ve all been aimed at building a better group of people, a better team. PETplanet: The acquisition took place in 2007. Under normal circumstances financial investors buy and get out, sell to other investors within John Galt (centre), President and CEO Husky Injection Molding System, is top-talking with Wolfgang von Schroeter (right) and Alexander Büchler (left)","@ID":14} "TRADE SHOW PREVIEW 26 PETplanet insider Vol. 12 No. 01+02/11 www.petpla.net Blow-moulder/filler monobloc for lower output production Krones has launched a blow-moulder/filler monobloc, under the Kosme brand, aimed at lower-output or mid-tier producers. Synchroblock is designed for production runs of up to 8,000 containers/h. It combines Kosme’s stretch blowmoulding and filling technologies and operates without air conveyors. Simplified machine access allows moulds to be changed quickly and easily. The unit is designed to reduce operating costs, energy consumption and water use, and its cleaner layout is intended to facilitate faster changeover times and lower maintenance costs. An air recycling system is an option. The rotary blow-moulding machine demonstrated at Brau Beviale was rated at 2,000 containers/hr/cavity and able to produce containers ranging from 0.1 to 3.0l. Containers are passed via a transfer table, with transfer starwheels and base cooling by cold water spray, to the isobaric filler, which uses pneumatically controlled Krones VKP filling valves. The closer is incorporated with the filler, saving space. Several closers can be integrated in parallel. Synchroblock can be used for soft drinks, still water and beer. Krones also unveiled its new range of EvoGuard valves, which have been designed to be suitable for all commonly-used connection variants in the food and beverage industries. The valves incorporate standardised parts for double-seal, axial and radial seals. www.krones.com Stretch sleeves offer new options The Brau provided CCL with the opportunity to present its Triple S technology. The technology is a traditional stretch sleeve with a difference. According to CCL, the range of containers which can be labelled using stretch sleeves has opened up. Instead of being limited to containers with parallel or slightly curved label panels, CCL Label’s Super Stretch Sleeve (or Triple S) will allow customers to apply sleeves to bottles which could previously only be labelled with shrink sleeves. Features The high elasticity of the Triple S film, coupled with stretchable inks applied on a 10-colour press means that Triple S applications would typically use some 39% less material than a comparable shrink sleeve. Additional cost savings also on the application as there is no shrink tunnel neede compared to shrink techHigh speed lines sorted with precision The BBull Technology group of companies with offices in Königsbach-Stein, Germany, was presenting its ”Centro Snake“ transfer system. It was actually developed for fast-running canning lines but is also capable of processing any other type of container. Because of its unusual transfer technology featuring fingers which do not extend as we have been used to seeing them in the past but instead retract, each of the receptacles/containers can be tracked in exact synchronisation with the belt speed. This means that even “difficult“ containers, for instance, unstable or empty PET bottles, can be transferred with precision and without falling over. “Centro Snake“ is also suited to sample transfers (samplings). With this it is possible for entire samples series or even specifically targeted individual bottles to be extracted. Something else that is very interesting is a new application using “Stratec Image 4000“. In addition to the checks on level, labelling quality (positioning, askew, correct label), seal quality (fitting, height, broken links, colour and logo) or the text of the label (date of bottling, MFD, lot/ batch number) that we are used to seeing with BBull, this is special in that it makes it possible to check the quality of the plastic snap-rings. What used to be a reliable possibility only with a very high level of expenditure can now be achieved by “Stratec Image 4000“ using simple means. ”Stratec Compact Vision“ has been developed for small and medium-sized businesses. www.bbull.de nologies. Natural elasticity is all that is required to hold the sleeve in place. When the environmental footprints of both Triple S and other labelling types (Shrink, OPP wraparound and RoSo) are compared, Triple S comes out on top by a clear margin. Triple S license By acquiring a license for CCL´s patented label application process, Krones has obtained development and global marketing rights for TripleS. Canada-based CCL and Krones market the TripleS technology together, mainly to the beverage and dairy industries. The company maintains that TripleS sleeves are particularly well suited to individually designed and strikingly shaped containers. It is also confident companies that have committed to eco-awareness will be keen to examine the technology. This is because of the implications in terms of material usage and the recyclability of the container dress. www.ccllabel.com/voelkermarkt","@ID":28} "REGIONAL MARKET REPORTS 8 PETplanet insider Vol. 12 No. 01+02/11 www.petpla.net France The last but not least part of our Regional market report on France is dedicated to the interviews with Valérie Mure, General Manager Retal France, and Dominique Paul Vallée, Bericap France. Retal in St. Alban “The strategy is one of differentiation.” Valérie Mure, General Manager Retal France We met: Valérie Mure, General Manager Retal France For almost 10 years Retal, with its origins in Russia and the Ukraine (Uniplast), has been building its presence all over Europe, with PET resin production in Lithuania (Neo PET), and with preform plants in Bulgaria, Spain and France. Retal France is located in the centre of France, in St. Alban in the Rhône-Alpes – also conveniently located for the famous French waters such as Volvic, Evian and Badoit, as well as the neighbouring waters with the name of the town - Eaux Minérales St. Alban. Eddy Ferry from Husky, who accompanied us to St. Alban, and we were warmly welcomed by Valerie Mure, the General Manager. She is in charge of the French operation of Retal. She was born in St. Alban and grew up in St. Alban. Her father is the mayor of St. Alban since 20 years. She said, “Life is simple and straightforward here in St. Alban. We are very much attached to the history of the town, to its development. This is why I am here, why I joined the adventurous activity at Retal in 2003, as financial manager. I was appointed managing director myself last year, when Philip Blonda left.” Her background is financial. Her focus is financial. “Knowing your figures, you understand the company. You see everything. You can judge the actions and performance of each department and each individual.” And then she adds, charmingly, “But I don’t need to exert close control. I see us as a team. We are successful as only a team can be. We are good in quality, fast in reaction, good in service and close to our clients in terms of communication”. by Wolfgang von Schroeter (report Retal) and Alexander Büchler (report Bericap) Regional market reports France Part 5","@ID":10} "PREFORM PRODUCTION 22 PETplanet insider Vol. 12 No. 01+02/11 www.petpla.net New player in the preform tooling firmament There is not a machine manufacturer on the planet that has not made some attempt to erode Husky’s position as a market leader on the preform scene, but so far not one company has succeeded. In the medium and high performance range there has been no getting past this Canadian company. Only Netstal, Krauss-Maffei, Sipa and Sumitomo have managed to make any noteworthy inroads at all in this performance range. It is only in the preform tooling sector that one or two suppliers have managed to establish themselves. And this is precisely where a counter-reaction is now becoming discernible. As far as hot runner business is concerned, Husky and Mold-Masters have always been rivals, now Mold-Masters have put a complete preform system for 2011 on show at the K Fair to compete in the preform tooling sector as well. We spoke with Bruce Catoen, VP Product and Business Development for Mold-Masters. PETplanet: Bruce, at the most recent fairs you have expanded your preform program step by step, first of all at the NPE 2009 by presenting a hot side for preform tools, then, in September 2009, it was your collaboration with Abba and with that the idea of supplying complete tools. Now, at the K Fair, it’s the acquisition of Abba and the introduction of an all electric work cell and a quick change tooling system. results that are clearly better. And hopefully, in the long term, they will come to regard us as turnkey manufacturers of tools as well. Naturally, we are also looking forward to supplying complete tools. PETplanet: Why should your hot sides be better than those of your competitors? Bruce Catoen: All our competitors drill holes in steel. This means that no curves are possible. In this conventional approach various holes need to be drilled from different sides and plugged to prevent leakage. Depending on the system, this can result in dead spots in which material may accumulate and the sharp bends result in additional shear and stress on the moulding material. The results are increased injection pressure, uneven viscosity of the material and with this increased AA content and degradation. With our patented iFlow manifold design we can mill any geometry – including drawn-out curves – on two steel plates. We then fuse them together like 2 halves of a sandwich using a proprietary technique. This means that we are able to guarantee the same length of flow path and shear history for each mould cavity without any sharp corners or edges. The machine is able to fill the mould faster with significantly less injection pressure. The parts are filled more evenly resulting in a more even weight distribution and shrinkage. PETplanet: And you have acquired the iCool stack technology from Abba? Bruce Catoen: The iCool technology was developed as a joint effort between ABBA and Mold-Masters. The fundamental designs are based on a series of patents from Jobst Gellert, the founder of Mold-Masters. Using conformal cooling technology and proprietary manufacturing techniques we have been able to ensure more efficient routing of the cooling channels close to a mould cavity. Bruce Catoen, VP Product and Business Develoment, Mold-Masters Bruce Catoen: Yes, we thought originally that we could enable toolmakers to compete with Husky by supplying a leading edge hot runner solution using iFlow manifold technology. However, there were very few tool-makers interested in competing with Husky in this market. So we changed our approach and became preform toolmakers ourselves. Using our patented conformal cooling technologies, called iCool, we developed a complete mould solution for preform moulding. Then in September 2010 we purchased our stack supplier, Abba Systems, so that the customer can look forward to getting a 100% MoldMasters tool under the brand name MPET. PETplanet: How do you plan to bring your system closer to your customers? Bruce Catoen: In stages. We know that there are a very large number of tools out there in the marketplace. Here, for example, we are offering to replace the hot side only, so the customers will be able to see that, with the same machine and the same preform, we are achieving","@ID":24} "REGIONAL MARKET REPORTS 10 PETplanet insider Vol. 12 No. 01+02/11 www.petpla.net beverages, here the savings amount to 2g per bottle! Or our DoubleSeal 33mm cap which can replace the traditional 38mm cap: here we have cut each bottle down by 2.6g of PP and PET. We have also recorded a comparable achievement in the case of edible oil where we have been able to save up to 2.6g with the new 26/21 neck standard replacing the traditional 29/21 neck finish. Overall we have been able to reduce the CO 2 emissions by 15% within the last 3 years through such light weighting of 20% of our closures produced in France. PETplanet: France is the development centre for water caps and sports drinks caps, especially sports caps. Mr Vallée: As already discussed previously, France is a very dynamic country where caps are concerned, with very demanding customers in mineral and spring waters, national and international. Danone and Nestlé Waters also have their international R&D centres for water in France. These are some of the reasons why we have opted to develop caps for waters, and especially sports caps, here in France, with developments that are generally tested in France, then spread across the Bericap organization of 21 sites in 19 countries. PETplanet: Can you give us an idea of how the system works? You get an order from your affiliated companies to develop a particular type of cap? Or do you approach your colleagues with your new ideas? Mr Vallée: Our development activities start with the assessment of the closures needed by our sales people in close contact with the market, generally by our Market Coordinators based in Europe, but who are in daily contact with sales people from all our global affiliates. When the development project is approved, the closure involved is then developed in one of our four R&D centres, for example at Bericap France. The closure is fine tuned on a pilot line in France. The initial production run is generally begun in France before being moved to the Bericap factory that is in better situation - economically, technically or logistically - to supply the customers involved to their complete satisfaction. PETplanet: Many thanks for talking to us. ple, is where our new lightweight HexaLite 29/25 comes in, together with its light weight hinged sports cap Thumb’up 29/25. In third place are the JETs - Juice, Energy drinks. Tea and sports drinks – with screw and sports caps. PETplanet: To what extent does your home market of France differ from other markets? Mr Vallée: Here in France we have a large number of highly diverse neck finishes - the 28 series; 29/25; 30/25; 34/35, the 38 series as well as the 48 series, the upshot of which is that we produce the individual caps in relatively smaller quantities than in countries where 28 mm dominates the market. Whereas in Germany you may find 3 or 4 lines running adjacent to one another and producing the same cap, here in France the same caps are seldom run simultaneously on 2 or more lines. Naturally, this presents us with a logistical challenge. In addition there is the fact that, in France, the closures are embossed rather than printed to reduced hazards related to solvent migration and the closure design changes relatively quickly. PETplanet: So does this mean that you write off the moulds considerably faster than is the case in Germany? Mr Vallée: Of course, it requires more frequent investments in new moulds, increases our depreciations and makes the individual cap more expensive as it would be if the caps were all of same diameters, with same design for ten or twenty years; but if the market wants it, we can produce it. PETplanet: So, on average, what is the service life of a mould? Mr Vallée: Difficult to give an overall figure. We have moulds that run for 5 years and even more than 10 years without any modifications except regular maintenance and refurbishment; on the other hand, on some customised closures like sports caps or dispensing closures, we may have moulds that would not last more than the duration of a 3-years contract because of improvements required by the customers at the end of the contract. In this case we expect that the mould price is depreciated during the duration of the contract. PETplanet: When you talk about ’improvements’ what you really mean is savings in materials? Mr Vallée: Not just savings in materials. It can also include functionalities for better comfort and safety to final consumers. Although there is no getting away from the fact that this is definitely an area we focus on, where Bericap has taken a lot of light weighting initiatives. If you have a look at the environmental performance evaluation for a cap made on an industrial site like the Longvic factory of Bericap, you will find that in France 80% of the CO 2 generated is attributable to the material and very little to energy as it comes mainly from nuclear power stations. And this is the same for the production of bottles. This means that the most efficient way to reduce the carbon footprint of packaged beverages is to work on the geometry of the bottle necks and of the caps. Light weighted neck and cap geometries are a MUST today. Have a look at our development work from the PCO 28 to the DoubleSeal SuperShorty 28mm for carbonated drinks and you will notice we can save between 2 and 3g in material in relation to the closure and the neck of the bottle. Or our HexaLite for flat Bericap France: Bericap France is the second largest company of the Bericap Group, N°1 in France for plastic closures for the food and beverages sector. It employs 300 production staff at two factories. Vittel is a purely production location; Longvic, near Dijon, the second plant, relocated in 2007 on a brand new world class manufacturing site is also the head office of Bericap in France and home to the R&D department. It features a total of 130 injection moulding machines from 70 to 350t which are used to produce 10 billion cap components for a total of 7 billion caps each year. In conjunction with this the company processes 20,000t of material. The R&D Centre concentrates on caps for mineral waters, juices, sports drinks and syrups.","@ID":12} "PET TOP TALK 15 PETplanet insider Vol. 12 No. 01+02/11 www.petpla.net has an exceptional foundation but if Husky wasn’t around as an independent brand a hundred years from now, I would be disappointed. PETplanet: Bob Schad told us in his interview, that “leadership is the most important thing in business. But in the end, the team you assemble makes the difference”. Is this statement of your predecessor applicable to John Galt? John Galt: I was smart enough to realize earlier that surrounding yourself with people smarter than you is a very good thing to do. I spend truly 50% of my time on the team today, on valuating positions, leadership talent, development programmes, that’s the number 1 priority in our business. We know that we have to have the right people doing the right job. PETplanet: The organisation and structure of today’s company are more democratic, and adopt a more modern, human approach than used to be the case in the pioneering years. Right or wrong for Husky in 2010? John Galt: The direction of the company is ultimately my responsibility. But I think “democratic” is an interesting term. It would be foolish not to listen to somebody who has more knowledge about certain subjects. When we can’t reach consensus, I make the final decision. PETplanet: Is growth the key element in Husky’s future planning? Or is it profits? Or is it profits through growth? John Galt: Anybody who ignores the fact that a business must be profitable to continue to attract the support of an investor and be able to have their confidence to make the kind of longterm investments that are necessary is fooling himself. Every business has to have a reasonable level of profitability. It is absolutely necessary to have investor confidence. But on the other hand, if one focuses solely on profits, one might forego some of those future investments. It is a balance to be reached on growth, we want to grow, we want to grow consistently, we want to grow through serving our customers and we want to retain a level of profitability through that growth that allows us to continue to have investor confidence. PETplanet: Thank you very much.","@ID":17} "MARKET SURVEY 18 MARKETsurvey 01+02/11 Company name Erema Engineering Recycling Maschinen und Anlagen GmbH Sorema division of Previero N.srl Starlinger & Co. Ges.m.b.H. Postal address Telephone number Web site address Contact name Function Direct telephone number Fax E-Mail Unterfeldstr. 3 4052 Ansfelden, Austria +43 732 3190-0 www.erema.at Christoph Wöss +43 732 3190-352 +43 732 3190-23 [email protected] Via Per Cavolto 17 22040 Anzano del Parco, Italy +39 03163491250 www.sorema.it Dario Previero Sales Manager +39 031 63491250 +39 031 63491217 [email protected] Sonnenuhrgasse 4 1060 Wien +43 1 59955-0 recycling.starlinger.com Elfriede Hell, MBA General Manager Division Starlinger Rcycling Technology +43 1 599 55 241 +43 1 599 55 180 [email protected] Bottle to granulate Input variable: collected pressed bottles, various colours engineering of washing lines and / or turnkey projects with technologies available in the market Output: Granulate with approval Capacity[t/a] Floor space [m²] Which approvals Fresh water consumption per tonne output [m³/t] Consumption kWh per tonne output [kWh/t] Flakes to granulate Vacurema - 3 models: basic, advanced, prime Input variable: Flakes, coloured proportion max 5%, not much chlorine Basic flakes specifications: Higher contamination can influence pellet quality but are basically possible to process, after discussion and agreed by Erema. Moisture max. [%] 0,7; moisture variation [%/hr] +/- 0,1; bulk density [kg/m³] 300 – 500; bulk density variation [kg/m³/hr] +/- 50; Material Temp [°C] 15 – 50; material temp. variation [°C/hr] +/- 5; polymer density (amorphous) [kg/m³] 1350 appr.; PET type homopolymer DSC melting point [°C] 252 – 255; DSC onset for melting point [°C] 215; co-polymers + substitution elements ike IPA, DEG or CHDM have to be identified and their impact on processing has to be evaluated.; PVC max. [ppm] 10; glue max [ppm] 20; aluminium max [ppm] 25; HDPE, PP ...max [ppm] 25; foreign polymer particles total [ppm] 80; coloured PET flakes max [ppm] 50; PET dust max [%] 1 Output: Granulate with Approval FDA, EFSA (pending), ANVISA, ilsi, BGBI, and also from brand owners Capacity[t/a] up to 20,000 1,500t/a - 27,000t/a (6 sizes) Floor space [m²] depending on through-put and technology : 8 - 200 130m² - 540m² Which approvals FDA [cat. A-H&J]; efsa (pending); some brand owners (conf.); some national approvals (Austria, CH, Zona Mercursur, etc.) USA / FDA (cold-fill / hot-fill), Austria, Germany, via customer: France / AFSSA, Finland, Australia, Bolivia; follows EFSA requirements; brand owners Fresh water consumption per tonne output [m³/t] Depending on application and technology type but we have a closed loop system. approx. 0.15 Consumption kWh per tonne output [kWh/t] between 250 - 350 approx. 410 (depending on design) Bottles to flakes Input variable: collected pressed bottles, various colours same as flakes to granulate engineering of washing lines and / or turnkey projects with technologies available in the market Output: Flakes with/without approval FDA, efsa (pending) Capacity[t/a] up to 15,000 5,000-45,000 3,700 - 16,000 Floor space [m²] between 20-40 800 - 5,000m² approx. 150 Which approvals FDA, efsa (pending) not applicable FDA (cold-fill, hot-fill), follows EFSA requirements Fresh water consumption per tonne output [m³/t] Closed loop system 1 - 3 Consumption kWh/t output [kWh/t] 100 0.22 - 0.27 120 - 250 Miscellaneous Company also offers systems for Bottle-to-film yes: Vacurema inline sheet yes Bottle-to-fibre yes: Vacurema inline fibre yes Bottle-to-strapping yes: Vacurema inline strapping yes","@ID":20} "TRADE SHOW PREVIEW 24 PETplanet insider Vol. 12 No. 01+02/11 www.petpla.net Preforms and new bottle designs to the fore The PET-Verpackungen Germany presentation consisted of both standard preforms with 28mm PCO 1810 neck finish and a range of new solutions in weight-reduced neck areas. On show too were a variety of new preforms PCO 1881 standard, as well as 38mm 2- and 3-start neck finishes. The company also offers multilayer preforms with tailormade barrier solutions, designed for sensitive-fill goods. They are also producing PET bottles with capacities ranging from 20ml to 5l on five single-stage and two two-stage installations. Possible applications range from water, CSD and spirits as well as applications in relation to the cosmetics and detergents sector right through to foodstuff applications. One new in-house development was a wide mouth jar for powdered milk/coffee creamer. In the health and beauty care packaging sector PET Verpackungen has come up with a bottle family for hand sanitizers. A further new development that the people at PET Verpackungen have developed on their own initiative is a small 0.2l champagne ‘piccolo’ bottle. www.pet-verpackungen.de Identifying foreign matter Heuft has put forward a form of technology specially designed for inspecting filled stock. The Examiner XO is devoted to identifying foreign matter on the base of the bottle. Particles of metal, stones and many other high-density foreign bodies on the base of a bottle can be detected by the tried and tested impulse-commutated X-ray technology that characterises the Heuft Examiner XO. Foreign matter of this nature can reportedly be reliably traced even in supposed “blind“ areas such as glass and PET bottles filled with beer, mineral water, apple juice and other transparent liquids. The system can achieve an output of up to 72,000bph. Together with the standard visual side wall inspection, the Heuft Examiner XO is able to scan the full volume of the container in the course of foreign substance identification. In addition to this, Heuft has unveiled a system for sorting empty bottles. The Heuft SX is intended to prevent extraneous empties from adversely affecting the degree of efficiency of a filling line. The bottle sorting system is able to recognise up to 500 different types of container and can distinguish between a very wide diversity of bottle shapes, colours and materials. The system can also detect closures, integrating structures as well as ceramic labels and any broken bottles. Any empty bottles that are of a different type, are still sealed or are faulty will be re-routed by the Heuft SX before they have a chance to adversely affect the efficiency of the line. Automatic teach-in of up to 500 different types is possible and reproducible at the push of a button. The objective is to make it possible to change types quickly and ensure corresponding savings in time. www.heuft.com Beverage experts in Nuremberg The invitation extended to beverage specialists by Brau Beviale 2010 to visit Nuremberg, Germany, from November 10 -12, 2010 was the signal for the European beverage industry to turn out in force: 1,348 exhibitors and 32,617 technical and commercial management experts poured into the Nuremberg Exhibition Centre. The next Brau Beviale is scheduled to place in the Nuremberg Exhibition Centre from November 9-11, 2011 – with an important new feature: The PETpoint, the PET segment at drinktec, will also feature at Brau Beviale in Nuremberg, starting in 2011. The background to the collaboration exercise is the exceptionally fast innovation cycle in this segment. The organization of the pavilion rests in the hands of the drinktec team in Munich (see also page 3). The PETpoint 2011 will be marketed as part of visitor promotion for Brau Beviale. This time we have also managed to track down one or two innovations in the PET added value chain within the beverages sector.","@ID":26} "BOTTLE MAKING 21 PETplanet insider Vol. 12 No. 01+02/11 www.petpla.net From HDPE to PET Conversion projects, special containers and large sizes for detergent and healthcare markets from Siapi ‘one2dose’ for liquids, powders or granules Joy creates a pleasant smiling effect Aptar Beauty + Home is part of the Aptargroup family of companies, along with Aptar Food + Beverage and Aptar Pharma. The company creates innovative dispensing systems for businesses marketing fragrances, cosmetics, personal care and household products. The “Small Joy” Snap Top, available both with and without Aptar’s SimpliSqueeze technology, is part of their product range for the personal care market. The snap-on closure complete with a contoured finger recess not only creates aesthetic appeal, but also facilitates opening and closing for the consumer whilst remaining secure during transit. Sized for 125 - 250ml packages, the closure can also be inverted thanks to its flat lid and stable footprint. Aptar’s active hinge also ensures that the consumer can open the closure and dispense the product with just one hand. Due to the trend towards large volume packages, especially in the personal care and hair care markets, Aptar is planning to launch “Large Joy” Snap Top at the beginning of 2011. www.aptar.com The technology used by Siapi in its chosen fields of PET container stretch-blow machines and specialist niche markets, is applicable not only in food and beverage, but also in new sectors. The company’s R&D department has been working with customers and applying its flexible blower technology in developing several new applications for the detergent and healthcare sectors. Among the new products are three and fivelitre containers for windscreen washer liquid for Chemica Gmbh, one of its German customers. This project involved conversion from HDPE to PET, with the aim of providing a solution that maintained the functionality provided by the previous solution while fully exploiting the advantages offered by PET, such as a lighter container with high mechanical resistance. In the healthcare sector, Siapi technology was chosen by Larioplast for a specially-shaped container for Pasta del Capitano brand mouthwash. The two companies collaborated in developing a bottle blown from transparent preforms and involving very unusual stretch ratios. The ability to guarantee reliability and flexibility played a fundamental role in the choice of blower technology. www.siapi.it German company Menshen’s new ‘one2dose’ system is intended to provide highly accurate dosing of liquid, powder and granules in washing, dishwashing and detergents. It is designed with modern concentrates in mind and is claimed to virtually eliminate inaccurate measures, whether over or under-dosing. It is designed to be easy to use, with the simple move of upending the container for accurate measures to be dispensed. When the bottle is turned upside-down the defined quantity flows into a chamber. A partition wall and specially placed openings allow dispensing and dosing with a single 180° rotation. Menshen says that one2dose also adds visual enhancement to packaging at POS and on the shelf. www.menshen.com www.info-pg.com HEALTH&BEAUTY CARE PACKAGING A","@ID":23} "PETbottles 28 PETplanet insider Vol. 12 No. 01+02/11 www.petpla.net Personal Care Strong commitment to HBC Alpla of Hard, Austria, specialist on design and manufacture of PET bottles, is strong in the health and beauty care packaging sector. The bottles below are all manufacturd by Alpla and can be found in the drugstore shelves in of differnt countries. Transparent and easy to handle Global giant Colgate is retailing its branded liquid floor cleaner ”Ajax“ Europe-wide in a new design PET bottle. The crystal clear bottle has a striking handle featuring clearly visible grooves. The front and rear labels are adapted to suit the flat packaging and the cleaning product – with spring flowers fragrance – is light green in colour. The coloured screw cap which matches the packaging acts as a dispensing cap for the pack which is available in a 1l or 1.25l version. Crowned with style Stylish forms of packaging are becoming increasingly fashionable. The Unilever Group has carried out some adaptations to its PET bottles for fabric conditioner throughout Europe to take account of this trend. The changes implemented have been on the 750,1,000, 1,250, 1,500 and 2,000ml bottles. A specially moulded dispensing screw cap – a type of crown – puts the finishing touches to this modern approach to packaging. The bottles are manufactured in Spain and England. Nipped-in waist for recessed grip Within the framework of its worldwide interests, Procter & Gamble has made some improvements to its PET bottles for liquid detergent marketed under the name of ”Ariel“. The bottles now incorporate a nipped-in ‘waist’ which gives two recess grips, one to either side, a feature which makes dispensing significantly easier without adversely affecting the front design. The bottles, available in sizes 500, 1000, 1500 and 2000ml, have a 2-part dispenser cap closure which allows excess product to flow back into the bottle. The bottles are manufactured in Italy. www.alpla.at Heart-shaped Jars PET-Power has launched a series of heart-shaped PET jars in three sizes: 220ml, 420ml and a 1000ml. All three models have a 63 RTS neck finish. They can be used for cosmetics, including bath salts and hair care products, and for foods, such as sweets and spices. The jar is available with matching caps and also in different colours. The heart shape lends itself to several decorations, like labelling or sleeving. PET-Power says that the jars are ideal for special occasions like Valentine’s day, Christmas and Mothers’ Day. Free samples can be requested through the website. www.petpower.nl Bottles for Lifestyle Handwashes M&H Plastics, CRC Innovations and Chadwicks Sleeves have worked together to create a luxurious collection of hand washes especially designed to compliment home décor. Casa Dolce Casa (‘home sweet home’) has been created by a team of interior designers in four distinctive bottle styles, ranging from Crystal, a sleek grey/black/silver combination ideal for a contemporary minimalist city living, to Damask, a lush floral design in rich cream and dark pinks. CRC Innovations selected the 500ml Flat Base Boston Round PET bottle from M&H’s standard range, with a colourcoordinated metallised pump to add a touch of elegance and luxury. Chadwicks Sleeves produces the colourful stylish shrink sleeve packaging. M&H’s in-house decoration facilities include silkscreen printing, tampo pad printing, hot foil blocking, and labelling. www.mhplasics.com HEALTH&BEAUTY CARE PACKAGING AUU","@ID":30} "17 Bottle-to-bottle recycling plants Conveyors for preforms and empty bottles Caps and closures Preforms Perform moulds and SBM moulds Preform and single stage machinery 2-stage SBM machinery Compressors Filling equipment Resins and additives Suppliers of bottle-to-bottle recycling plants This is the second of our market surveys focusing on PET bottle to bottle recycling plants. It is of course difficult to make effective comparisons between the various technologies but at the end of the day the crucial factor is what goes in at the front and what comes out at the back. For this reason, we have limited ourselves to looking at a few relevant parameters. In order to make the comparisons between the systems fairer, we have opted for materials that are freely traded as the input variable. For bottles this is almost a worst case scenario – unsorted bottles in all colours, and pressed into bales, whereas with the flakes the quality is slightly higher, with only a few contaminants. Another important question is whether the recycled content has FDA approval. It is noticeable that not all suppliers give this information, even though it is a key point for decision-makers to opt for a particular system. But, as ever, we have given the contact details of the companies involved and they will be delighted to answer any questions you may have about system parameters. Whilst the publishers have made every effort to ensure that the information is up to date, no claims are made regarding completeness or accuracy. 01+02/11 MARKETsurvey","@ID":19} "PREFORM PRODUCTION 23 PETplanet insider Vol. 12 No. 01+02/11 www.petpla.net This saves 50% of cooling fluid and reduces cycle times by 5 to 15%. The technology has been tried and tested in production moulds for more than 18 months now. PETplanet: Here at the K Fair you are presenting a rapid tool change system for high-flexibility production under the name of Rapide. Bruce Catoen: Yes, we found many customers who are looking for a flexible system which would allow the moulding surface inserts to be changed from one design to another in 30min or less. Through some creative tool design from our product development team we were able to come up with a system which could change these parts in 15min without the need for a crane. PETplanet: And the secret? Bruce Catoen: We leave the entire mould in the machine and change only the stacks or mould inserts (arranged in racks of four) by hand. The sets of 3 inserts are mounted to holding blocks which reduce the number of bolts to be fastened to a minimum. The “modules” of 4 inserts are held to a weight that can be handled easily by hand. The robot on the unload side is not a linear robot – it’s an articulated robot. The operator pivots the robot to the side which enables him to get at the mould from both sides at the same time. Under normal operational circumstances the preforms for the cooling station are unloaded by the robot. PETplanet: This is the first time we have seen an articulated robot used to handle preforms. Does this not extend the unloading and hence the cycle time unnecessarily? Bruce Catoen: We are around 0.5 to 1sec second slower than a linear robot but with this system we also have our iCool and iFlow technology. This enables us to catch up. The most important thing however is the time saved during conversion. Normally you need 4h for a conversion but we take only 15min. You can work it out for yourself how many 5/10ths of a second go to make up this amount. PETplanet: The system runs on an all-electric machine from RP Injection from Italy. Will it also run on other machines? Bruce Catoen: All MPET moulds will run on any machine that is suitable for PET processing. We were very pleased to have RP Injection supply, for the K show, their standard allelectric machine with a screw and barrel specifically engineered for PET. The machine ran flawlessly at the show and it proved that a modified allelectric machine can work well for moulding preforms. PETplanet: So you don’t offer a complete system? Bruce Catoen: At present we are working with machine manufacturers with whom we can join forces for the supply of complete turnkey systems, not only our new Rapide but, our standard MPET moulds as well. We are looking at 2011 for the first system. PETplanet: Many thanks, Bruce. At K’ 2010, Mold-Masters was presenting a complete preform system called M-PET The system ran on an all-electric machine from RP Injection, Italy","@ID":25} "MARKET SURVEY 19 Zhejaing Boretech Co., Ltd. Amut S.p.A. Krones AG PTI Recycling Systems LLC Herbold Meckesheim GmbH 19K-1,07 Province Road, Pinghu Economic Development Zone, Pinghu City, Zhejiang, China +86-573-85120186 www.bo-re-tech.com Mr. Jimmy Chen Manager of Import & Export Dept. +86-573-85120186 +86-573-85113959 [email protected] Via Cameri 16 - 28100 Novara Italy +39 0321 6641 www.amut.it P. Milani President +39 0321 474200 [email protected] Böhmerwaldstraße 5 93073 Neutraubling, Germany +49 9401 70-0 www.krones.com Peter Hartel Sales Dept. PET-Recycling + 49 9401 70-5448 + 49 9401 70-91-5448 [email protected] 1440 Timberwolf Drive, Holland, Ohio, USA www.ptirecyclingsystems.com Stephen Hawksworth Director +1 419 867 5400 [email protected] Industriestr. 33, Germany-74909 Meckesheim +49 6226 932 0 www.herbold.com Mr. Siegfried Engel Vice President Sales +49 6226 932 0 +49 6226 932 495 [email protected] yes high quality flakes - ready to be SPP pellettized yes (Agglomerate) from 500kg/h to 4,000kg/h net clean product = from 3,600t/a to 29,000t/a 7,000 t/a to 14,000 t/a up to 36,000 t/a 2,500-4,500m² 800 - 2,000 m² approx 1,000m² FDA - LNO, EFSA 1m³/t, to be partially re-used into the process 1.0m³/t - 2.5m³/t approx 0.5 - 1m³/t according to plant size, 180-250kwh/t approx., depending on rated output of the plant and energy consumption for SSP System approx 545kWh/t high quality flakes - ready to be SPP pellettized yes from 500 kg/h to 4000 kg/h net clean product = from 3,600t/a to 29.000t/a 7,000 t/a to 14,000 t/a 10kt/a, 20kt/a modular systems that can be sized 1,000-2,000m² 800 - 2,000m² 260m² approx 64m² FDA - LNO, EFSA USFDA, Health Canada, EFSA up to 13,000 t/a (1 unit) 1m³/t, to be partially re-used into the process 1,0 m³/t - 2,5 m³/t 0.016m³/t 100kWh/t 548kwh/t approx 125 kWh/t high quality flakes - ready to be SPP pellettized 20,000t from 500kg/h to 4,000kg/h net clean product = from 3,600t/a to 29,000t/a 3,400t to 17,000t 1,800 2,500-4,500m² 600 - 1,200m² no FDA - LNO 6,000t/a - 30,000t/a 2 1m³/t, to be partially re-used into the process 1,0m³/t - 2,5m³/t 1,000m² - 3,000m² 110 according to plant size, 180-250 kwh/t approx., depending on rated output of the plant approx. 450 kwh/t yesfrom 5,000 to 20,000t/a capacity yes - size reduction and size reduction components. yes, bottle-to-packaging - PET bottles washing plants, turnkey systems, single components","@ID":21} "PET TOP TALK 14 PETplanet insider Vol. 12 No. 01+02/11 www.petpla.net ultra-high output of production, HyPET is still the best solution. PETplanet: So European customers would not be first in the queue for an H-PET? John Galt: We see H-PETs in mature markets; we see them also in developing economies that haven’t reached the scale or the infrastructure yet to support the higher volume system. PETplanet: Japanese machine builders used to be competitors to the Europeans – including Husky. Today they are significant partners with European companies. KraussMaffei are cooperating with Toshiba, and they also take the electrical drives from them. Demag Ergotech was bought by Sumitomo and imposes Japanese design on European machines. Even Engel enjoy a partnership with Mitsubishi. Now – we have heard - the Husky components on the H-PET are designed by Toyo and manufactured by Toyo and to cap it all, the entire system comes from China, assembled at your Shanghai factory. Being a bit provocative: Isn’t there a risk that Husky products may lose their distinct identity? John Galt: I need to correct you. The entire product isn’t coming from China. Not that we wouldn’t choose a component from China if we felt that the Chinese supplier had the best component in the world. That system has been engineered by Husky. When you look at the machine out there, you need to appreciate just what we have done! We have reengineered it, we’ve put the Polaris Control on it, we’ve put in the H-PET all of Husky’s PET knowledge in terms of preform manufacturing, injection performance, the interface between the robot and the mould, all of that has been designed and developed by Husky. I think there is a difference between re-branding and actually developing. Those systems – H-PET AE as seen at K - will continue to be controlled by the development resources at Husky. PETplanet: That answers our question but to change the subject slightly: what is Husky’s current thinking on global manufacturing. John Galt: Our injection moulding machines are assembled in Canada and China. Hot runners are manufactured in Singapore, Shenzhen, Shanghai serving the Asia-Pacific region. We have Luxemburg, we have small-scale manufacturing in Sao Paolo and we have Milton, Vermont. Hot runners are locally produced for the local markets – with exactly the same engineering, exactly the same quality standards. In 2011 we will begin manufacturing in Chennai, India. We build hot runners close to and in interaction with our customers. We require interaction with the customer to offer a good service. It is also impractical to ship a hot runner half way around the world. PETplanet: Husky injection moulding machines are assembled in Canada and in China. Globally sourced components, identical machines, same quality standards, same features. The only difference being where they are assembled. How about a global price for the global machine? John Galt: Assembly cost – which is low in China - is a relatively small factor in building a machine. On the other hand: Supply of machines out of Bolton to China for example involves tremendous costs in logistics. Ultimately, what we try to do is to not disadvantage our customers in any part of the world. We have a one-world pricing structure. So the answer to your question is one world, one product and a harmonized price. PETplanet: In this PETplanet series we are talking to leading personalities in the PET sector to discover what makes them tick, and how they have achieved success. John Galt, can you tell us a little bit about yourself, your background, technical, financial, managerial background? John Galt: I’m a mechanical engineer by education. My first job with Husky was in the print room. I worked as a mould designer, then worked in the service division for a year and a half in Luxemburg, went back, was involved in injection machine engineering, ran the machine business. PETplanet: Every door was open to you at Husky....? John Galt: I have had wonderful opportunities. I was a young man who found a perfect fit in Husky. I was fortunate enough to get to know Robert Schad early and I was inspired by what the company was doing. Its values are the same as my own. I think the two have merged into one. It’s an opportunity to test yourself. I think every engineer in the world, whether you’re making injection moulding machines, dish washers or anything else, would love to be given a chance to build the best product in the world. That’s what you live for. That’s what I’ve found here. PETplanet: So the leading person at Husky is an engineer as Bob Schad was? John Galt: Absolutely. PETplanet: Could you explain your personal contribution? What is your priority in the Husky business? John Galt: I want to be part of building a great company. I think Husky John Galt: “The direction of the company is ultimately my responsibility:”","@ID":16} "REGIONAL MARKET REPORTS 9 PETplanet insider Vol. 12 No. 01+02/11 www.petpla.net Despite an intimate knowledge of the monthly figures her contribution to the company indeed does not seem to be tight control, but rather giving direction and formulating the strategy of Retal France. And the strategy is: “Differentiation. We are different in comparison to the large preform producers. Our prime focus is on multi-layer. Our markets are growing, especially for juices and vegetable drinks. We are working at full capacity. In fact our capacity is overbooked. We are able to be selective. We can afford to turn down unreasonable orders.” It is a clear, well-defined strategy with a future orientation. History There are good reasons why Retal France is today located in St. Alban, and in particular next to the producer and bottler of Eaux Minérales St. Alban. The founder of the company, the Belgian Gust Gysen, placed the first blowing machine, and later an injection moulding machine, in-house at Eaux Minérales St. Alban in the 1996s. With addition of new injection equipment, he decided in 20012002 to build his own factory, also in St Alban. In 2003 multi-layer was started, when the first Husky/ Kortec system was purchased and put into operation. In 2007, the company was sold to the Russian-Ukrainian Retal, which at that time was expanding into the European Union. In same year Philip Blonda was installed as managing director. In 2008 Philip Blonda left and Valerie Mure took the managing director’s chair. Product and Production In 2009 Preform production in total 380 million preforms Multi-layer preforms 230 million preforms Mono-layer preforms 150 million performs In 2010, with added capacity: Preform production in total 500 million preforms Multi-layer preforms 320 million preforms Mono-layer preforms 180 million preforms As Retal’s market is rapidly growing, one more co-injection system is in the budget for next year Resin used: 15,000t of virgin PET annually. Supplied mainly by NeoPET (from the Retal group), and also by NovaPET (Spain). Retal sales: 80% into France, 6% to Germany, minor percentages to Spain, Turkey, and others. Customers for mono-layer preforms include Coca-Cola and Danone. Customers for multi-layer include Badoit (red) and Perrier, Joker. Annual sales € 23 million of which 90% is in preforms, 10% in caps. Preforms are the core business. The closure business was acquired with the company. Employment: 35 people of which 28 are in production. Equipment For closures: 4 Husky machines (24 to 48 cavities) Capacity in 2009: 450,000,000 caps/a Sales in 2009: 350,000,000 caps/a For preforms: 4 Husky/Kortec systems (48 to 72 cavities) 1 Husky system (96 cavities) Capacities see above. Valerie Mure considered the years between 2003 and 2008 to have been difficult years in the business, since the machines and the factory were leased. Ever since then the situation has eased and, with the pay-back and amortisation almost complete, Retal France strives to have a bright future. Bericap in Dijon “Our biggest market is that for carbonated beverages with 28mm neck finish” Dominique-Paul Vallée, CEO and Managing Director Bericap France We met: Dominique-Paul Vallée, CEO and Managing Director Bericap France Overall, there would appear to have been only a limited increase in the quantity of packaged beverages in France over the past few years. As a result, the bottlers are consistently being forced to promote their own brand at the Point of Sale by constantly introducing new products. In the final analysis this also affects manufacturers of sealing caps who need to supply what is, for the French market, an unusually high number of different neck finishes and different closure styles. We visited Bericap in France and spoke with Mr. Dominique-Paul Vallée, CEO and Managing Director PETplanet: Mr Vallée, around 3/4 of your turnover here in France is accounted for by caps for the beverages industry. What are the key sectors? Mr Vallée: Our biggest market is that of carbonated beverages (waters and soft drinks) with 28mm neck finish, with almost half of this segment converted now to the lightweight DoubleSeal SuperShorty PCO 1881. The next most important sector is the water sector; this, for exam-","@ID":11} "BOTTLE MAKING 16 PETplanet insider Vol. 12 No. 01+02/11 www.petpla.net Partnership for progress PET applications in the health and beauty care (HBC) business are growing and PETplanet is following these developments closely. Sidel, which is well-known for its expertise in the beverage market, also has customers in HBC, including Colgate. Sidel recently worked with Colgate on a benchmarking exercise that applied experience and methodology gained in the beverage industry to PET applications in HBC. An open partnership Colgate’s global operations include a wide-variety of Sidel equipment. After undertaking an initial survey, data and results were analysed and existing benchmarks established. The two companies held a wide-ranging meeting to review business opportunities and needs as well as basic issues that needed to change. Colgate wanted the ability to reach into the organisation, to provide feedback and drive change, with the ultimate goal of creating a strategic partnership and establishing open communication between the two enterprises. Colgate repeated the benchmark survey exercise twice, with results on each occasion showing improvement. The two companies continue to meet twice-yearly, to discuss issues of mutual benefit. Colgate provides feedback that helps Sidel improve its processes, and Sidel provides expert advice and innovations that benefit Colgate’s practices. Sidel also takes part in important internal Colgate processes and committees, in order to provide its industry expertise to this important commercial partner. During 2010, Colgate ordered seven Sidel blowmoulders worldwide, in order to increase its global production capacity. More than 50% of Colgate’s product portfolio in its Homecare Division, which is focused on the HBC market, is currently bottled in PET. Sidel’s relationship with the company began in the late 1980s with bottling processes but has now expanded, into supply of bottling equipment, packaging consulting and preventative services. “By using the beverage industry as a benchmark, Sidel has been able to provide their expertise from working within that industry,” said Elizabeth Mellone, Director of Home Care Global Design and Packaging. “We then see what we can apply successfully to the home care industry.” Sidel and Colgate operate together to turn the bottle concept into a final product that works technically and aesthetically. “Sidel has been able to bring a more holistic supply chain view to the services provided.” More than 50 % of Colgates’s product protfolio in its Homecare Division... ... is currently bottled in PET. HEALTH&BEAUTY CARE PACKAGING","@ID":18} "PETnews 6 PETplanet insider Vol. 12 No. 01+02/11 www.petpla.net Forum PET Europe to promote development of PET bottles Representatives of the pan-European PET bottle industry and its supply chain met in Paris on 23rd November to constitute Forum PET Europe, whose main goals are to create an environment to encourage innovation in PET bottles, to promote high quality recycling and to minimise risk to the reputation of PET. Founding members are the PET associations of France (Elipso) and Germany (Forum PET in der IK Industrievereinigung Kunststoffverpackungen e. V.), and Logoplaste S.A., from Portugal. It intends to act as a platform for the discussion of market and regulatory issues in the EU and to communicate with relevant stakeholders. The first President of Forum PET Europe is Jean-Marc Rostagno, Director Northern Europe of Artenius PET Packaging. Marcel de Botton, Chairman of Logoplaste S.A., Portugal, was elected vice-president. The Council includes Françoise Gerardi, General Manager of Elipso, France; and Dr. Jürgen Bruder, Director General of IK Industrievereinigung Kunststoffverpackungen e.V., Germany. www.forum-pet.de New CEO and board appointments at KHS Shareholders and the supervisory board of KHS GmbH Dortmund have made three appointments to the company’s executive management board. Prof. Dr.-Ing. Matthias Niemeyer becomes CEO of KHS GmbH on April 1, 2011. Prof. Niemeyer has been a member of the KHS Executive Management Board since September 14, 2009 and has been previously responsible for the Technology division. He will continue with responsibility for the Technology division. Current CEO Roland Flach will retire on March 31, 2011. Anke Fischer, current head of central controlling of Salzgitter AG, has been appointed chief financial officer and a member of the executive management board, effective February 1, 2011. She replaces Burkhard Becker, who will leave the board on January 31, 2011 and become chief financial officer of Salzgitter AG, effective February 1, 2011. Marc Hartmann, currently chief representative of KHS GmbH, has been appointed as a member of the executive management board, effective April 1, 2011. He will be responsible for project management and process and quality management. Other members of the board are Mr. Georg Michels (sales) and Prof. E.h. Dr.-Ing. Johann Grabenweger (production). www.khs.com Erratum In the market overview of issue 11/10 on suppliers of filling equipment, we incorrectly printed only part of the Sacmi machinery range. We apologise for this inadvertent error. Details of the full range of Sacmi equipment can now be found on the internet in the corrected version of the magazine. More xxhibitors and services at 25th Chinaplas, May 2011 The 25th edition of Chinaplas, the International Exhibition on Plastics and Rubber Industries, will be held at China Import and Export Fair Pazhou Complex, Guangzhou, PR China, from May 17 to 20, 2011. The confirmation of the India Pavilion brings the total of country and regional pavilions at the event to 11. Chinaplas will now be arranged under 12 themed zones, with the addition of the Rubber Machinery & Equipment; Industrial Services; and Bio-Plastics and Degradable Plastics zones. Over 20 enterprises have already reserved space in the Rubber Machinery & Equipment zone, in Hall 3.1. ChinaplasOnline.com, the official website, has been revamped and improved, with a search engine function that allows keyword searches in the website content and exhibitor’s data. The ‘Download Centre’ holds showrelated information, such as the visitor brochure, eNewsletter, etc. available for visitors to download. Japanese, Korean, Spanish, Italian, Russian and Arabic versions are now available. Latest show updates, transport and hotel information, and seminar details are available through Wap Chinaplas www.chinaplasonline.com/CPS11/Mobile New PET silo park for Indorama Polymers Rotterdam Indorama Polymers Rotterdam, a wholly-owned subsidiary of Thailand-based Indorama Ventures PCL, has commissioned a new silo park for storage of PET at its Rotterdam (NL) site. The park will enable the company to ship more PET resin directly from the factory to customers without intermediate and external storage. The 24 new silos provide additional storage capacity of 10,000t, in which Indorama keeps four different PET grades at all times. The company said that the new facility will enhance its flexibility in production and supply, reduce handling and, consequently, diminish the risk of contamination and the generation of dust or fines. The need for transport will also be reduced. The first direct shipments from the new facility started in November 2010. Indorama Polymers Rotterdam has a PTA capacity of 350,000t and 200,000t of PET. The company will further expand its PET capacity in Rotterdam by another 190,000t in 2012. www.indorama.com","@ID":8} "imprint EDITORIAL PUBLISHER Alexander Büchler, Managing Director HEAD OFFICE heidelberg business media GmbH Landhausstr. 4 69115 Heidelberg, Germany phone: +49(0)6221-65108-0 fax: +49(0)6221-65108-28 [email protected] EDITORIAL Doris Fischer [email protected] Michael Maruschke Ruari McCallion Tony O´Neill Ilona Trotter Wolfgang von Schroeter Anthony Withers MEDIA CONSULTANTS Ute Andrä [email protected] Miriam Kiesler [email protected] phone: +49(0)6221-65108-0 fax: +49(0)6221-65108-28 France, Italy, Spain, UK Elisabeth Maria Köpke phone: +49(0)6201-878925 fax: +49(0)6201-878926 [email protected] LAYOUT AND PREPRESS Exprim Kommunikationsdesign Matthias Gaumann | www.exprim.de READER SERVICES Kay Krüger [email protected] PRINT WDW Druck GmbH Gustav-Throm-Straße 1 69181 Leimen-St.Ilgen Germany WWW www.petpla.net | india.petpla.net PETplanet insider ISSN 1438-9459 is published 10 times a year. This publication is sent to qualified subscribers (1-year subscription 149 EUR, 2-year subscription 289 EUR, Young professionals’ subscription 99 EUR. Magazines will be dispatched to you by airmail). Not to be reproduced in any form without permission from the publisher. Note: The fact that product names may not be identified as trade marks is not an indication that such names are not registered trademarks. 3 PETplanet insider Vol. 12 No. 01+02/11 www.petpla.net After a break of over ten years PETpoint is once again back in Nuremberg at the Brau Beviale. Its precursor started life in 2000 as the “tenderest of shoots” in Hall 8 in the shape of a joint stand covering 450m². and shared with 18 other firms in Nuremberg. Even at this initial event the full spectrum of the PET industry was represented, from the materials side and extending to machinery and culminating in the converter. Two years later and we find PETpoint taking place as an independent event in Essen in close proximity, both temporally and spatially, to Interpack and side by side with Metpack, a canning industry exhibition, taking place simultaneously in the adjacent halls. Three years on and 2005 marks PETpoint’s debut in Munich under the drinktec umbrella. This time PETpoint occupied the whole of Hall A6. Four years further down the line and both exhibitors and visitors were forced to mark time pending the next PETpoint in 2009, this waiting period was only interrupted by the overseas events in Mumbai in 2007 and 2008. PETpoint migrated from the edge of Hall 6 into Hall B3 in the central area of drinktec. Many exhibitors were unhappy with the constantly increasing intervals between PETpoints (from 2 to 3 and now 4 years). Finally, their voices are being heard. Now PETpoint will be taking place every four years to coincide with drinktec in Munich and annually in Nuremberg to cover the years in between. Dr. Reinhard Pfeiffer Director of Messe München GmbH, sums the situation up as follows: “The PET industry is well known for its spirit of innovation and its fast pace. The existing 4-year cycle meant that drinktec was unable to do full justice to the requirements of the PET sector. Collaboration between Messe München and NürnbergMesse means that the PET industry will in the future be able to demonstrate its powers of innovation each year under the joint banner of PETpoint“. As founders and strategic partner of PETpoint we look forward to a reunion at the birthplace of PETpoint. Yours, Alexander Büchler EDITORIAL dear readers, EDITORIAL","@ID":5} "NEWS 7 PETplanet insider Vol. 12 No. 01+02/11 www.petpla.net Sidel ECO audit aims to cut energy consumption Sidel’s new ECO Audit joins ECO Booster and ECO EIT in its range of ECO services. ECO Audit is aimed at reducing energy consumption and production costs. Sidel conducted an ECO Audit for South African brewing company, SABMiller, in March 2010, with the intention of determining the environmental performance of its bottling line. The client company’s objective was to establish a reference point, in terms of method and results, in order to help in its drive to reduce energy, water consumption and CO 2 emissions by 25% per hectolitre (26 US gallons/21 Imperial) of beer produced. Sidel’s ECO Audit enabled the company to quantify the exact needs for each bottling step and to compare them with new technological standards. The audit also showed SABMiller how improved bottling efficiency can lead to a significant drop in water consumption, by more than 2m²/hr. Sidel’s ECO Audit is a snapshot of a complete line’s situation in full production. Its two major objectives are, first, to evaluate any gaps in production performance and energy consumption between the real operation of the line and its original specifications; and, second, to establish a reference point and identify levers for an improvement plan aimed at generating energy savings or improving performance quickly. The audit is also used to quantify subjective data on the line’s performance, with the intention of planning and implementing agreed targets. The process further helps to assess a line’s potential to achieve ‘world class’ production levels in the medium to longer term. It includes analysis of all consumptions on the line, such as power, air, steam, water and CO 2 , as well as line efficiency, machine reliability, changeovers, cleaning operations, shutdowns and other equipment performance indicators. Sidel engineers collect data on-site for a week, and the analysis and report is sent to the customer within three weeks after data collection is completed. The three principal focus areas are: excessive consumption by machines; consumption levels that vary with line productivity; and non-productive consumption, such as during changeovers and cleaning. www.sidel.com In Association with International PET Resales Ltd On the Instructions of the Official Liquidator Mr Neil Hughes, Hughes Blake SHANNON MINERALS LIMITED (In Liquidation)- Located: Limerick, Ireland PET BOTTLING PLANT • Sidel SBO 6 blow moulder • Cortellazi & Sachi fillers • Oxe & Sachi labellers • Sacmi Kristall mixer carbonator • SMI & SGB shrink wrappers • Berchi palletising plant • Atlas CopcoZD oil free compressor • Laboratory & other equipment TENDER CLOSING By 12 Noon GMT, Friday 4 March 2011 Viewing: Wednesday 2 &Thursday 3 March 2011, 10.00 – 16.00 & Morning of Sale, 9.00 – 12 Noon McKay, 4 Blackbourne Square, RathfarnhamGate, D.14, Ireland t. 003531 490 3130 f. 003531 490 3512 e. [email protected] View Photos & Download Full Catalogue From Our Website www.mckay.ie TENDER SALE La Seda de Barcelona sells PET production plant to Cepsa Química, S.A. The Seda Group has continued its process of divestment of nonstrategic assets with an agreement to sell its PET production plant located in San Roque, Cadiz, to Cepsa Química, S.A. Completion is expected within a few weeks, subject to agreement with employee organisations and regulatory authorities. The acquisition of Artenius San Roque will extend Cepsa Química’s presence in the polyester value chain. The San Roque plant has a production capacity of 175,000t/y, and is expected to be operational in early 2011. www.laseda.es AWS opens giant plastic sorting facility A little over 14 months after the original plant was devastated by a fire that destroyed its entire sorting and storage area, AWS Eco Plastics has unveiled its new plastic bottle sorting facility in Hemsworth, Lincolnshire, England. The official opening was carried out by Defra (Department of the Environment, Food and Rural Affairs) Director of Waste and Resources, Neil Thornton. The new factory is capable of processing more than 100,000t of waste plastic or 2,000,000,000 bottles per year and is the largest and most sophisticated in Europe. Valued at over £17 million, the facility features state-of-the-art equipment developed by leading manufacturers Stadler, Titech and Herbold, and is capable of processing a diverse range of plastic feedstocks. Seventeen Titech Autosort systems are incorporated into the new Hemswell facility and a further three systems were used as part of the interim solution prior to resumption of full production. The plant has a flexible output of 11 different streams of plastic and is virtually zero-waste. A key market for the new facility is the creation of food-grade PET, demand for which has risen strongly in the UK. Independent research has shown that products made with recycled plastic from the AWS Eco Plastic site are 68% less carbon-intensive than packaging made with virgin materials. The company plans to increase processing capacity at the site to 140,000t by mid 2011, just less than half the total of plastic bottles expected to be recycled in the UK during the year. AWS Eco Plastics is Europe’s largest recycler of mixed plastic bottles. www.awsecoplastics.com www.titech.com","@ID":9}
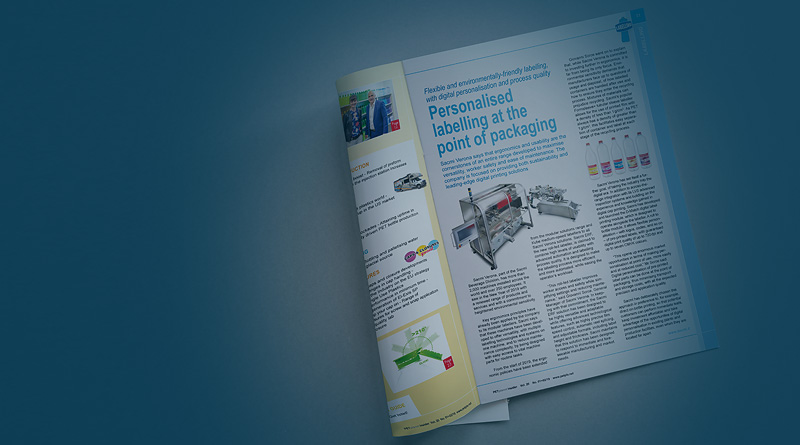