"BOTTLING / FILLING 30 PETplanet insider Vol. 12 No. 05/11 www.petpla.net A visit at PJSC „Erlan“ Biola Always at the top In our last issue we reported on the preform and caps manufacturer Retal Dnipro, Ukraine, and mentioned their cooperation with the bottler Biola at the same location. In part 2 of the Ukraine Story we take the opportunity of paying a visit to the highly innovative PJSC “Erlan” Biola. It was one of the first in Europe to bottle cold aseptic beverages in PET on a grand scale and they continue to be in the vanguard of technology. Now, following the introduction of lightweight bottle caps, the company has emerged as one of the first to manufacture lightweight shrink films. As a major national supplier of juices and CSD drinks in the Ukraine, PJSC “Erlan” Biola set its sights at an early stage on the aseptic bottling of fruit juices. On our last visit in 2005 there were already two aseptic lines of KHS in-situ, which together produced up to 48,000bph. Since then, a third high performance system – likewise from KHS – has been added. Since 2009, the plant has featured up to 44,000 bottling operations per hour. The bottling operation is fed by a Corpoplast Blomax 24. This plant is equipped with typical aseptic features such as ionised air for cleaning the preform and sterile air for blow moulding. Between stretch The bottling systems once more running at full capacity. This shows the aseptic plant with 0.5l bottling operations.","@ID":32} "BOTTLES 39 PETplanet insider Vol. 12 No. 05/11 www.petpla.net “Perfect skin starts at 20” Under the brand name “Aok“ and using the slogan “Perfect Skin starts at 20“, the German company Henkel of Düsseldorf is marketing a pore refining facial toner with peach extract in a natural design PET bottle. The clear product in just the right bottle, a non-label-look label to the front and the white inside section of the rear label ensure a simple, natural impression at the PoS. A screw-on pump dispenser makes an enormous difference when it comes to extracting the product. www.aok-kosmetik.de PET goes to war with blackheads Focussing particularly on the adolescent market, the corporate global concern Johnson & Johnson is marketing 200ml facial toner to combat blackheads in a PET bottle of attractive design throughout Europe. The transparent bottle, non-label-look labels to the front and rear and the bluish colour of the product invest the packaging with a discrete appearance at the PoS. The screwon, hinged lid in pink provides the perfect finishing touch to the whole ensemble. www.bebe.de Vitality with olive oil 500ml conditioning shampoo with olive oil is being marketed by the company Dr. Theiss Naturwaren Hamburg under the brand name ”medipharma cosmetics“ in a round, transparent PET bottle. Combining it with the clear bottle shows the greenish olive oil shampoo to particular advantage and gives a very natural impression. An all-round paper label with all the important product and trading information as well as a silvercoloured snap dispensing cap put the finishing touches to the packaging. www.medipharma.de White PET for kids The French trading group Cora from Marne-le-Vallee is marketing 250ml extra mild / care lotion for babies in a white PET bottle. The front and rear labels are designed appropriately to give the necessary product and trade information. A snap-on, 2-colour hinged lid that is easy to operate using only one hand ensures ease of dispensing. www.cora.fr","@ID":41} "BOTTLING / FILLING 32 PETplanet insider Vol. 12 No. 05/11 www.petpla.net Pepsi and KHS develop new process for hot filling of thin-walled PET bottles for Lipton tea It’s tea time! The Russian market for beverages, especially non-alcoholic drinks, is expanding rapidly. Pepsi Corporation took the decision to launch a brand of preservative-free Lipton Tea in order to capitalize on the opportunity. The company considered to possibilities for packaging without preservatives: aseptic cold filling and hot filling. The major perceived disadvantage of aseptic filling was the high capital investment and operating costs; hot-fill, by contrast, would cost about the same as a classic soft-drink filling line. However, there would be some additional costs involved in a traditional hot-fill line, for energy consumption and because of the need for heavier PET bottles, which would require vacuum compensation panels. Rajendra Gursahaney, Senior Director of Engineering, Pepsi Beverages Company, decided that the correct route would be to opt for hot-fill but to work to eliminate the disadvantages. The decision was crucial; if the project failed, the fast launch of preservativefree tea into the Russian market and a considerable sum of invested capital would both be at risk. Pepsi worked with KHS to develop a novel process that would deliver the objectives of timely launch, effective use of capital and acceptable operating costs. HotFill+ is the first hot filling process for bottling still, non-alcoholic beverages in thin-walled PET without the need for vacuum compensation panels. Mr Gursahaney: “The energy problem was solved pretty quickly. Together with KHS we developed an energy recovery process that recovered the heat from the warm water generated from the bottle cooler, to heat the incoming beverage.” In order to reduce the weight of the PET bottles, the companies develdid not work. Pepsi also took on significant risk in pursuing the project. Mr Gursahaney: “On the one hand, we had to invest in a blow moulder which, if it came to the worst, we couldn’t have used in the classic hot filling process. On the other, if the experiment failed, the production of Lipton Tea without preservatives would be delayed by six months. According to various studies, this would have meant that Pepsi would have lost a large share of the Russian market for tea.” A team of six people was established, who carried out the testing phase in the KHS Corpoplast laboratory. Mr Gursahaney: “The team was made up of specialists from KHS Corpoplast, from the KHS Filling Technology Department, and from the company responsible for nitrogen dosing. Lipton’s Technical Manager was also on site to assess the newly developed PET bottles from a technical and marketing point of view. In addition to this permanent team many employees from the companies involved in Hot filling without preservatives: Lipton Tea in PET bottles oped a means of putting nitrogen in the head space of hot-filled PET bottles, in order to compensate for any bottle shrinkage after filling. This eliminated the need for vacuum compensation panels. The idea came from an encounter with a company at Packexpo Beverage Exhibition in Chicago, which worked with nitrogen dosing. Mr Gursahaney: “I asked them if it could be possible to add nitrogen to a PET bottle that contains a hot beverage, in such a way that the nitrogen doesn’t penetrate the beverage but remains solely in the head space of the bottle. The answer was that they couldn’t give me any information as yet but would be willing to research the issue together with Pepsi. That was the first step towards HotFill+.” The research project additionally required a filling technology specialist and a specialist in PET bottle manufacture. The PET bottle manufacturer chosen was SIG Corpoplast, now KHS Corpoplast, with KHS as the partner for filling technology. Crucially, the two companies were prepared to share the risk of the project and to bear the investment cost if the idea","@ID":34} "PETpatents www.verpackungspatente.de 40 PETplanet insider Vol. 12 No. 05/11 www.petpla.net Reinforced bottle feet International Patent No. WO 2011 / 007734 A1 Applicant: Dai Nippon Printing Co. Ltd., Tokio (JP) Application Date: 9.7.2010 The individual “feet“ of a plastic bottle are provided with grooves so as to increase the stability of the feet and at the same time resistance to deformation / damage. Container label International Patent No. WO 2010 / 063919 A1 Applicant: Eos, Dizy (FR) Date of Application: 24.11.2009 An international patent application has been filed in respect of a label which is easy to make and to attach. This label is optimised for haptic characteristics including adhesion and display characteristics such as 3D brand logos and colouring. Bottle handling International Patent No. WO 2010 / 080731 A1 Applicant: Graham Packaging Comp., York (US) Date of Application: 4.1.2010 Specified in this patent is a bottle / bottle characteristics which simplify the packaging, despatch and movement of hot fill/ plastic bottles “formed under vacuum”. For this special “unalterable” contact points are established between the bottles. Sleeved preform US - Patent Nr. US 2008 / 0241447 A1 Applicant: Colgate Palmolive Comp., New York (US) Application Date : 4.4.2008 The preform for creating a container is encased in a type of sleeve aimed at the production of a special optical effect (colour gradient) during manufacture of the final container. The product can then undergo further pigmenting in order to enhance this effect. Compensating area for hot filling International Patent No. WO 2011 / 011183 A1 Applicant: Graham Packaging Comp., York (US) Application Date: 2.7.2010 In order to be able to compensate for the changes in volume that occur during hot filling and subsequent cooling without any “unattractive“ deformation, flexible deformation surfaces are integrated. In this application the surfaces are so designed as to ensure that any possible percentage change in volume has been amended. PET containers as preserving cans International Patent No. WO 2011 / 011182 A1 Applicant: Graham Packaging Comp., York (US) Application Date: 2.7.2010 PET container designed as an alternative to the traditional preserving can made from sheet metal. It also meets the requirements in terms of hot bottling, heating, pasteurisation and options for closure in relation to this type of packaging.","@ID":42} "BOTTLING / FILLING 28 PETplanet insider Vol. 12 No. 05/11 www.petpla.net Planning new factories for optimised production Expansion or greenfield? by Alexander Sixt, Divisional Manager Factory Planning, Krones AG, Neutraubling It is not unusual for Krones’ factory planning team to learn that it has just 18 months to get a customer’s new factory up, running and producing in market volumes. The request triggers a structured response, which takes all the client’s requirements and circumstances into account. Companies’ current situations vary. A beverage firm may be tied to a particular location and considering options for expansion. Another may be seeking to reduce headcount and to invest in automation. Yet another may be planning geographical expansion. Whatever the situation, it is the starting point from which the concept phase (pre-feasibility) is developed, leading to the initial proposal. The procedural framework for a complete new factory project begins with the clear definition of the goals. Detailed data has to be acquired and analysed, including product range, types of beverage, raw materials (including delivery, storage periods and quantities), the range of bottles handled and the closure and label variants. Pack sizes and pallet data complete the list. These particulars will be supplemented by individual, country-specific production variables, such as personnel expenses or energy costs. Precise definitions of these basic data, plus (where necessary) the decision-making process on the client’s side, are supported and assisted by Krones’ factory planning team. Expand on-site or greenfield location? The concept phase will usually have identified whether the project will be expansion at the existing location or construction of a new plant on a greenfield site – many beverage companies prefer the greenfield option. For practical reasons, the most sensible course is to commission a single vendor for the whole job; in a brewery, the brewhouse is closely connected to the building shell, so a coordinated approach with minimised interfaces makes sense. Krones has in-house capabilities for all the different technologies involved. Optimisation measures can achieve enhanced performance even when a new production site is not an option; new logistical solutions contribute towards increased efficiency in the production process within the existing space. When structural alterations during ongoing operation are involved, the factory planning team coordinates the necessary work in order to minimise disruption. In both greenfield and brownfield concepts, the function of all production sequences is the paramount consideration in the planning process. The essential aim is to provide optimised interfaces between production, filling, packaging and logistical operations. Besides the flow of goods, energy and media supply has to be designed to state-of-the-art standards for all production zones. Recovery systems or recirculation concepts for compressed air, hot water or steam are designed with optimised piping configurations, in order to achieve efficiency gains. TCO: the decision-clinching criterion The concept phase, which will last eight to twelve weeks, produces a choice of proposals for the planned product portfolio. The most important question in selecting from different options is the total cost of ownership (TCO). Using exemplification parameters, Krones can compare possible alternatives and identify priorities. Calculating the TCO may reveal that higher initial capital investment costs will enable the new facilities to pay for themselves quite quickly. For example, could the production operation The procedural framework for a complete new factory project begins with the clear definition of the goals.","@ID":30} "PET TOP TALK 12 PETplanet insider Vol. 12 No. 05/11 www.petpla.net PETplanet: What would you like to do if you were not managing a company? Otto Hofstetter: I like travelling. Getting to know people and new cultures. I find this just as exciting as technologies. Adopting the attitude of a blinkered specialist just makes you blind. The world is full of beautiful and interesting things. PETplanet: You are attracted by India, it’s at the top of your list of private projects. India’s ancient culture and the mentality of her people - what is it that a Swiss businessman finds so fascinating about India? Does India also provide you with a stimulus for the way you manage your business in Switzerland? Otto Hofstetter: Our first encounter with India was a shock both for my wife and for me. We thought we were well prepared but you have to go there and see it for yourself. Look, then go back and take another look; immerse yourself in it. As Europeans we either succumb to the foreignness of it all or we don’t go there again. Things are similar at a corporate level: watch, be patient, keep watching patiently and in the end you will find that things are moving forward slowly but surely. Business in India is a difficult matter. Our western mentality does not sit easily with the Indian mentality – we know that. We have to learn to live with the Indian mentality. PETplanet: Despite this – or perhaps even because of this – you have committed yourself doing business in India? Otto Hofstetter: We have made this commitment because we can see that our Indian friends are forging ahead and that they are very interested in steering a joint course with us. There is a belief in authority, which is not the style which we ourselves cultivate. However, there is a sizeable popular commitment, sometimes greater than that shown by people here in Switzerland. On product and production PETplanet: Everyone in the PET market is familiar with Otto Hofstetter products. Can you give us a resumé? Otto Hofstetter: In the PET sector we build moulds ranging from 2 cavities to 144 cavities. In addition, we have a design for a 192-cavity mould that we can build to order. In Europe we sell around 60% of the moulds we manufacture. Most of our moulds – from 48 to 128 cavities – are capable of running on a 350t injection moulding machine. We have developed this platform together with Netstal. The mould with 128 cavities on a 350 t machine represents an advantage over our competitors and is unparalleled. PETplanet: Is that one of the unique selling points that you cite? Stefan Zatti: “Maximum cavitation at minimum clamp force“: this is right at the top of the specification for our development staff. PETplanet: Ever since clocks were invented, Switzerland has been renowned for precision, quality and reliability. Does this sum up your philosophy in relation to your products? Otto Hofstetter: Mould precision plus reliability in terms of production and delivery schedules – these we rate pretty highly. In addition, we expect our moulds to make an impression due to their lengthy service life. PETplanet: Mr. Hofstetter, in your plant we see evidence of a spectacular development. Would you like to say a few words on the investments that you have made in the factory lately? Otto Hofstetter: Mr. Zatti and I have come up through production and manufacturing is our first love. We see the potential and the possibilities of better, more cost-effective production using new operating resources to respond to the challenges of the market place, which includes in particular the implementation of short delivery times. Lack of ability to deliver at short notice means that we lose orders. Often, it is not simply a matter of price but more of “are you able to deliver or not? ” This is what prompts us to reinvest 90% of our earned profit in production resources. We think this is the right way forward. PETplanet: What is noticeable is a harmonised flow of materials, then the automation in relation to the machine tools, plus the additional production area which means that everything is under one roof. Otto Hofstetter: Yes, that’s correct. We used to have various locations that we found it difficult to keep tabs on with our small management crew. We have merged these locations and optimised the work functions. Luckily we still had a land bank and were able to build. PETplanet: That’s an advantage and a disadvantage at the same time. You now have no space left for further expansion. Otto Hofstetter: You’re right there. But what it also means is that we shall be compelled to build a new plant at a different location or cooperate with a partner company or buy a similarly inclined business with matching aspirations – whatever is presumed to be the best option at the time. Otto Hofstetter: “The most important factor in achieving sustainable success is our production equipment, something which is constantly in need of replacement.”","@ID":14} "BOTTLE MAKING 21 PETplanet insider Vol. 12 No. 05/11 www.petpla.net 50 and 400mm. The material can be machined in DEW’s processing plants if required and can also, for example, be provided with cooling boreholes. “We provide customers with the entire process chain – starting with melting, then hot forming and heat treatment up to processing and storage service“, said Rolf Krusenbaum, head of sales plastic mould steel. The last few years has seen production Eisbär Material Drying PRODUCER MODEL LOW ENERGY CONSUMPTION LOW ENERGY CONSUMPTION LOWEST ENERGY CONSUMPTION ON THE MARKET RATING AAA Energy A Eisbär B C D E F G All the others A WWW.EISBAER.AT WUHRMÜHLE 22 / A-6840 GÖTZIS T +43 5523 55558-0 / [email protected] Michael Bauer, Director of the technical customer support, examines a plastic mould made of Corroplast FM. Large dimensions are forged on the forging press. in the PET bottle industry reach peak values in Europe and America. In Turkey, Asia – particularly China – and India, a marked increase can still be expected. DEW is intending to provide customers in all markets, including the growing economies in Turkey, China and the rest of Asia, with ’just-in-time’ service from its network of warehouses serving those countries. www.dew-stahl.com","@ID":23} "PETbottles 38 PETplanet insider Vol. 12 No. 05/11 www.petpla.net Personal Care Attractive PET box Henkel France is marketing 640 g (20 metered doses at 32g each) Gelpads in water-soluble PVA film for washing dark clothing at low temperatures and housed in an attractive PET box. Round labels front and rear convey the necessary consumer information and a single-section, snap-on hinged lid with integrated, detachable tamper-proof seal make this striking box a real eye-catcher on the shelves. www.mir-et-moi.com Henkel takes the vegetable option For their dishwashing liquid marketed under the “Terra“ brand name Henkel, Düsseldorf has opted overwhelmingly for product raw materials on a vegetable base. Attention is drawn to the transition – the shift away from petroleum-based raw materials – by means of an eye-catching allusion on the front label. The green bottle with the white screw cap and the tastefully printed paper labels adapted to the form of the packaging are factors that additionally foster the image of green sustainability. www.terra-henkel.de Environmentally-friendly parket cleaner Messrs. method products Inc., a company based in Sallaumines, are marketing their environmentally-friendly parquet cleaner in 739ml PET bottles of highly original shape. The bottle features peripheral beading – similar to a dinghy – so that there is never any problem holding the bottle and applying the cleaner using the screw-on, special design push-pull spray valve. Informative self adhesive labels are located in the central recessed section of this innovative bottle. www.methodhome.com The new aqua sensation The Hamburg cosmetics manufacturer Beiersdorf is marketing an invigorating wash gel – Aqua Sensation – in a 200ml PET bottle under the brand name ”Nivea Visage“. The round, non-slip, clear bottle is decorated with two non-labellook labels that ensure transparency. A 2-section hinge cap adapted to the shape enables straightforward, single-handed application and small white balls integrated in the product also mean enhanced product awareness at the PoS. www.nivea.com","@ID":40} "NEWS 9 PETplanet insider Vol. 12 No. 05/11 Think about it. Is your hot runner supplier just a supplier, or your partner? moldmasters.com/thinkaboutit [email protected] Mold-Mastersand theMold-Masters logoare trademarksofMold-Masters (2007)Limited. ©2011Mold-Masters (2007)Limited.All rights reserved. Large or small, complicated or simple, Mold-Masters has the depth, breadth and innovative problem solving to bring all your designs to production. As the world’s leading hot runner manufacturer with the most responsive customer service in the industry today, Mold-Masters offers a level of harmony you know you can trust. APPE gains Pan European BRC certification APPE (Artenius PET Packaging Europe) is the first major PET producer to gain the BRC/IOP Global Standard for Packaging and Packaging Materials across all of its European plants. The BRC (British Retail Consortium) Global Standards are a global product safety and quality certification programme used by 14,000 certificated suppliers in over 100 countries. The BRC/IOP Packaging and Packaging Materials Standard forms part of a suite of four technical standards, including food safety. Consumer Products and Storage and Distribution standards enable certification of the entire supply chain. BRC Global Standards are used by leading global retailers in supply chain management and for legal compliance. Certification verifies technical and functional performance and aids manufacturers’ fulfilment of legal obligations. All APPE’s plants in the UK, France, Spain, Belgium, Germany and Turkey were independently audited and current systems and practices, from factory hygiene to quality and the technical aspects of packaging, were assessed against the requirements of the Standard. www.packaging-int.com R&D/Leverage increases manufacturing and support capacity Four consecutive years of double-digit growth has led R&D/Leverage – UK to expand its manufacturing capacity by 40% percent in 2010. Recent new business wins in the UK and continental Europe have prompted the company to install another injection stretch blow moulding machine to its Product Solutions Laboratory (PSL), to further increase capacity. The PSL is a building-within-a-building that offers customers training modules and the capability to provide first-to-market samples. The company says that it can now qualify almost any product, including extreme shapes and extreme specifications, in-house. Earlier in 2011, the company added two new sales account managers to handle customers throughout northern and central Europe. Successful collaboration for R&D/Leverage – UK and Argo S.A. R&D/Leverage and Argo S.A. have successfully completed initial assignments for customers in three market sectors: personal care, health care and crop protection products. Argo S.A. is a single-source plastic packaging solutions provider serving customers in more than 30 countries throughout southern and eastern Europe, the Middle East and Africa. Based in Greece, it operates production facilities in its home country, Romania and Egypt. Its services include extrusion (and co-extrusion) blow moulding, injection blow moulding, injection stretch blow moulding, printing/labelling and assembly. www.rdleverage.com www.argo-sa.gr","@ID":11} "NEWS 8 PETplanet insider Vol. 12 No. 05/11 www.petpla.net A new complete closure system supplier with global footprint Husky Injection Molding Systems has announced the intention to acquire the Austrian KTW Group (see PETplanet issue 3, page 7). On the occasion of the inauguration of the new KTW development centre in Waidhofen / Thaya, Austria, Husky and KTW announced their strategy at a press conference. Formal completion of this transaction is expected in May 2011. KTW will play its role in the corporation as a leading manufacturer of injection moulds for plastic container closures. Their facilities include a development centre, a total of three mould manufacturing sites in Austria, Germany and the Czech Republic, with a total of 370 engineers and technicians. KTW thus complements the Husky programme, which includes injection moulding machines, PET preform tools of their own development and manufacture, as well as a complete range of hot runner technology. The KTW-mould technology covers the entire spectrum, from standard closures for beverage bottles to specific closures for “Personal Care” –to packaging, from detergent to grocery closures. Founded in 1979, KTW has developed under the leadership of the owner families Völker and Ziegler into a manufacturer of injection moulds for plastic closures of all kinds. Beginning with the Austrian parent plant in 1992, the families founded a branch in Chemnitz in the former East Germany and in 1999 in South Bohemia - Jindrichuv Hradec. The company’s specialisation remained focused on closure technology. The KTW Group employs 370 toolmakers and technicians. All three plants have similar facilities based on the same technology and performance standards. Husky and KTW have been working together on projects for more than 14 years - particularly closely in the Asian market for standard closure systems but in recent years increasingly on projects for non-standard fasteners. The Husky strategy aims, along with KTW, to offer complete closure systems. KTW will be the worldwide competence centre for closures within Husky - with the associated expansion of capacity meeting new demands. The strategy will focus on the following areas: For PET bottle production standard closures, the objective is centred upon providing complete solutions (machine, mould, and accessories) from a single source. Such facilities are operated as modules by the beverage industry. In the area of “non standard” closures – such as the typical “flip-top cap”, global proactive customers engage their suppliers to provide stronger accompanying support. This requires the expansion of the service centres, sales offices and also production sites in the growth markets of Asia, Latin America, and in North America. The trend towards the optimally adapted injection moulding system requires the ever closer integration of the individual – up to now independent - components in the injection moulding process and therefore a closing of ranks of the development departments of the component manufacturers. Optimisation of investment reflects the trend towards ever shorter project lead times. This requires new and optimised processes, especially in the global interaction with customers. The name and logo of KTW will continue to exist as a trade name. The development of integrated closure production systems will be intensified. In addition to focusing on the systems business, the business branch “single mould” remains unchanged in the programme. Existing customer relationships will continue to be served. www.husky.ca www.ktw-group.com Agr International expands process improvement services Agr International’s Process Improvement Consulting Service includes a team of professional consultants who work directly with process engineers and plant floor personnel to solve problems such as managing challenging lightweight applications and quality issues. Services include process control design; manufacturing process control; experimental design; statistical learning; and the recently-added material testing. The acquisition of West Analytical Laboratories by Agr International has enabled further expansion of the offerings available through the Consulting Service. The company now offers contaminant identification; non-volatile residue content and identification; qualitative identification of polymer and surfactants; glue content of PET, solvent extraction and quantification; ash content; plastic additive profiling; and lube analysis. Tests are performed at Agr’s ISO17025-accredited analytical testing laboratory, in Maumee, Ohio, USA. www.agrintl.com Krones returns to growth in 2010 Krones AG, the beverage filling and packaging technology company, has reported a return to profitability and growth in its financial and sales results for 2010. Consolidated sales were €2,173.3 million in 2010, a rise over the preceding year’s figure of €1,864.9 million (16.5%). Sales outside Europe showed the strongest growth, driven by rising demand in China, the rest of Asia and in South America. Almost 66% of the company’s 2010 sales were outside Europe. Booked orders at the end of 2010 were €908.7 million (2009: €888.5 million). Earnings before taxes improved to a total of €70.8 million, following a loss of €39.2 million in the preceding year. After-tax earnings were €50.9 million (2009: minus €34.5 million) and earnings per share were €1.68 euros (preceding year: minus €1.13). As at December 31, 2010, the group had no bank debt and possessed net liquidity of around €147 million, excluding the buyback of approximately 1.4 million of its own shares in 2009. At the end of 2010, the value of these shares was €66 million. The equity ratio was 40.2 % on the balance sheet reporting date. The Executive and Supervisory Boards of Krones AG will propose a dividend of €0.40 per share the 2010 business year to the AGM on June 15,2011; no dividend was paid in respect of 2009. The company has reported order bookings of €628.6 million in the first quarter, up 14.2% on the previous year on a like-for-like basis. Sales were also higher, by 13.7%, at €606.7 million. Earnings before taxes in the first three months of 2011 are higher as well. While noting that today’s markets are characterised by volatility, trend reversal and uncertainty, the company has confidently predicted growth of seven to ten per cent in 2011 and expects profit margins to return to a sustainable level of 7% in all segments. www.krones.com","@ID":10} "PETcontents 05/11 4 PETplanet insider Vol. 12 No. 05/11 www.petpla.net INSIDE TRACK 3 Editorial 4 Contents 6 News 34 Products 36 Bottles 38 Personal care BUYER’S GUIDE 41 Get listed! MARKET SURVEY 23 Suppliers of preforms BOTTLING / FILLING 28 Expansion or greenfield? Planning new factories for optimised production 30 Always at the top A visit at PJSC „Erlan“ Biola 32 It’s tea time Pepsi and KHS develop new process for hot filling of thin-walled PET bottles for Lipton Tea PET TOP TALK 10 “We are looking at making an acquisiton” Otto Hofstetter, Otto Hofstetter AG, Uznach, Switzerland PREFORM PRODUCTION 18 Neck finish out of round Troubleshooting - A hands on guide, part 20 Page 30 BOTTLE MAKING 20 The rule of hard blocks New metal alloy for PET mould manufacturing MATERIAL / RECYCLING 27 A better blend Insulation for higher productivity Page 10 Page 18 Page 20","@ID":6} "BOTTLING / FILLING 31 PETplanet insider Vol. 12 No. 05/11 www.petpla.net The new plant for manufacturing the shrink wrapping films reaches right up to the ceiling. blow moulding and the bottling block there is a 3.5min buffer stretch for the empty bottles. After that comes the wet sterilisation of the bottles. “We find that we are more flexible with wet sterilisation than with dry sterilisation. Once that’s done, we can fill the bottles with any of the products” says Felix Nosov. A total of 600 million b/a are processed through the cold aseptic facility at the plant. Water / CSD Parallel to this has been the development of the water/CDS area. A second plant near Kiev has now been added. There has also been a Blomax 24 there since 2009 although for CSD rather than for aseptic bottling operations. A total of 900 million bottling operations are carried out in this area alone. The bottle sizes vary from 0.5l to 2l. In May of last year ”Biola” converted all CSD products in one fell swoop to lightweight bottles with PCO 1881. “It took a lot of preparation but a gradual conversion operation was not an option as far as we were concerned“ said Felix. With their early breakthrough into PET aseptic technology in the newly developing Ukrainian cardboard packaging market, Biola have moved forward at a spanking pace: with the lightweight CSD PET bottles they are currently putting pressure on their customers. Nor can the Big Colas of this world rest easy. How much longer can they run with the lumbering PCO 28 in the Ukraine? Biola wouldn’t be Biola if it didn’t have one or two other surprises. In addition to a highly efficient storage facility for finished products, a textbook mixture / syrup area, a discharge station for paste-like base materials such as tomato puree, mango, banana etc. the plant has for some time now featured a film blowThe stretch blow moulding line is located at the dry end of the bottling plant, surrounded by haulage tracks and conveyor belts. Felix Nosov shows Alexander Büchler the new aseptic bottling line. Uniplast caps are not simply delivered to Biola, here we see a team from Husky and Corvaglia at Biola reviewing the cap fitting operation. ing line from Reifenhäuser. The precision shrink wrapping films made from multiple layer HDPE foils for repackaging are now being produced by Biola. In a joint development project with Reifenhäuser, “Biola “has been able, using innovative raw materials such as LLD-PE and metallocenes, to reduce the foil thickness from its former level of around 70μ to 50μ depending on the size/weight of the packaging. In addition to precision shrink wrapping films, the system is also capable of manufacturing laminated foils of similar thickness for laminating a range of substrates, in particular BoPET. By means of direct recirculation the system is able to recycle production waste itself. The installed annual capacity of the plant is approx. 3,000t and it is one of the first 3-shift plants for precision shrink wrapping films in the Ukraine. www.biola.ua","@ID":33} "BOTTLES 37 PETplanet insider Vol. 12 No. 05/11 www.petpla.net DRYING HAS NEVER BEEN THIS EFFICIENT: ETA plus® LUXOR - now available with ETAplus® ETAplus® considerably reduces energy consumption and protects materials. When it comes to drying, saving energy is a key concern. We have developed a system that combines airflow regulation with a temperature adjustment feature – that can be disabled if required –and efficient waste heat recovery. The result? A drying system that cuts energy consumption by up to 64%: ETAplus® . motan-colortronic gmbh [email protected] www.motan-colortronic.com Sports drink in PET The French sports equipment retailer Decathlon of Villeneuve d’Ascq is selling a 0.5l beverage under the brand name of ”aptonia“ which is specially aimed at sportsmen and women. The product, which is available in a range of flavours, is bottled in a handy, independently moulded PET bottle with an allround plastic label. The bottle is opened and re-sealed using a colour-matched, 2-section beverage cap which features a separate ring pull to ensure resistance to tampering, not only in the threaded area but also on the re-sealable hinged lid. www.aptonia.com Water from South Africa 500ml of spring water from the South African city on the Cape is being marketed by the European importer Drink and More of Hamburg under the brand name of ”Karoo“ in a PET bottle festooned with a number of injected motifs. The bottle sports a relatively smallformat belly label which gives all the essential product and trading information. The colour-matched plastic screw cap is fitted with a tear-off tamper proof guarantee and has “Pure Africa“ printed on it. www.drinks-and-more.com www.karoo.co.za High-quality design 280ml salad dressings in a range of flavours such as, for example, yoghourt or vinaigrette, are being marketed by Metro Cash & Carry under their own brand name of ”Finest Food“ using high-quality design PET packaging. The packaging, which is tailored to resemble a bottle, features a black shrink sleeve label of high quality. There is a large black, screw-on hinged lid adapted to the diameter, permitting precise, neat application and ensuring satisfactory re-closure. In order to avoid leaks, the packaging is sealed prior to opening by means of a composite-layer plate that needs to be removed. www.metro24.de","@ID":39} "BOTTLING / FILLING 29 PETplanet insider Vol. 12 No. 05/11 www.petpla.net be optimised with three filling lines instead of two? This would require less downtime from fewer changeovers, which will help to achieve higher output. Up to 850 project-specific parameters can be included in a separately ordered TCO computation. Once the client has decided to go ahead with the project, detailed engineering work and detailed planning of all sections of the job will take four to six months. The factory planning team has two variants available for the construction work. The beverage company can, of course, commission a local building firm to construct the shells. Krones will integrate and coordinate the interfaces to the technical equipment involved and ensure that all the requirements for high-performance kit are incorporated in the actual building. Alternatively, Krones, acting as the general contractor could commission and control a building subcontractor. The company works with global firms of consulting construction engineers, with branch offices worldwide. This means that specialists for all parts of the job are involved; they know the national framework conditions, laws, standards and any idiosyncrasies of the site in question, and are used to coordinated working on large-scale projects in an international context. These partners are usually bound by a FIDIC (International Federation of Consulting Engineers) based contract, which lays down binding project conditions for all parties. FIDIC offers a sample contract text as an internationally-recognised set of rules that serves as a basis for every international construction project. The factory planning team at Krones uses these standards for its major projects. Extensive advance auditing of all partners is done to ensure a high level of certainty for compliance with relevant quality requirements and deadlines. All vendors and subcontractors are audited by a benchmarking process, in order that effective procedures can be incorporated into project implementation. This approach assures a high level of transparency for the process of creating a new factory. The importance of local knowledge Local conditions continue to be a major focus in the planning phase and actual construction work. For a turnkey project in Vietnam, for instance, approximately 2,200 piles were driven 40m into swampy soil. In other projects, interfacing of PET and other packaging production facilities have been integrated into the project framework. In the construction phase, the team at Krones takes full responsibility for on-schedule completion of work. Project management includes interface management between the client’s project teams and Krones’ engineering people, coordination of the various parts of the job, site management and liaison with local vendors. It is vital to work hand in hand with the client’s specialists, since it is they who are most thoroughly familiar with the details of daily operation, which form the basis for their optimisation concepts. However, since a project cannot be allowed to tie up the entire knowledge capacity of a beverage plant, Krones looks after all the details – leaving the client free to focus on its core business. Different countries and different products Krones’ factory planning team offers concepts for food production or dairy plants, as well as soft drinks and beer. Its structured approach means that individual stages of the planning process can be ordered separately. The company’s factory planning team has planned and completed about 30 projects in countries as varied as Angola, Vietnam, New Zealand, India, Iran, the USA and Mexico, at plants with outputs of between two and four million hl/a. www.krones.com In both greenfield and brownfield concepts, the function of all production sequences... ...is the paramount consideration in the planning process.","@ID":31} "BOTTLING / FILLING 33 PETplanet insider Vol. 12 No. 03/11 www.petpla.net the experiment also came into the lab from time to time to see how we were progressing.” He also visited Hamburg several times during testing. Mr Gursahaney: “We tested various PET bottles with differing distributions of material to see how they behaved during hot filling, during the ensuing dose with a precisely stipulated amount of nitrogen, and during capping. Testing extended to the establishment of a manual filling line. We first filled each PET bottle with hot water. On the next station on the line an exact amount of nitrogen was added to each PET bottle. It was then capped and cooled with ice-cold water. After cooling each and every PET bottle was scrutinized down to the last detail.” Several thousand bottles went through the test phase. “Initially, KHS Corpoplast produced individual batches of 400 to 500 PET bottles. After testing one batch, we could assess where the weak points were in that PET bottle design. A new batch of PET bottles was then manufactured, tested, and again refined.” The test phase lasted for half a year, altogether, by which time the companies had developed a PET bottle that was found to be suitable for defined nitrogen dose after hot filling. The testing process then moved on to series production-level assessment and analysis, for which KHS rented a filling line in Germany. The HotFill+ process was tested with the latest design and, after filling 5,000 PET bottles, it was discovered that only about half met the requirements – the other half was either too unstable or too heavily inflated. Mr Gursahaney: “However, I reached the conclusion that the process itself worked. All we now had to do was to ensure that we duplicated the performance that had produced the perfectly filled PET bottles. Specifically, this meant that all three companies had to aim for a repeated accuracy of their process of almost 100%. I asked my partners if they thought this was possible. If, at this point, they had not agreed, the project would have been terminated. All three partners gave me a clear ‘yes’. This commitment led Pepsi to invest in its first KHS line in Yekaterinburg, which operates on HotFill+ technology. But the challenges were not yet over. Mr Gursahaney: “When we first started operating the filling line, we had a loss of over ten per cent. After further optimization, four weeks later we had a rejection rate of less than 0.1% – which we still have now and which is the norm for our type of industry. We are very satisfied with this. Pepsi reduced the weight of a 1.5l bottle from 63 to 48g, which saves approximately $2.5 million dollars a year in PET material costs, for just one filling line. “We now have three HotFill+ lines up and running at our plants in Yekaterinburg and Moscow. We now make an annual saving of 7.5 million dollars. Pepsi reports that, over the two years since the HotFill+ lines have been running, it has had no quality issues or complaints from either retailers or customers with PET bottles filled using the technology. HotFill+ was developed exclusively for Pepsi but the company has declined to patent it just for itself and has made it available for all interested organizations. www.khs.com Rajendra Gursahaney, Senior Director of Engineering, Pepsi Beverages Company MHT MOLD & HOTRUNNER TECHNOLOGY Dr. Ruben-Rausing-Str. 7 | D-65239 Hochheim/Main Tel. +49(0) 6146-906-0 | www.mht-ag.de Lightweight threads are on everyone’s lips. After all, the smallest PET saving per preform soon amounts to hundreds of thousands of Euros for major bottlers each year. Looking to convert your mold to a new thread and need an experienced partner? MHT Mold & Hotrunner Technology offers all lightweight solutions on the market, including: • PCO1881 (17 mm / 3.8 g) • MHT21LIGHT (21 mm / 3.9 g) • 29/25 (12.6 mm / 2.4 g) Engineering made in Germany MHT: Your specialist for lightweight solutions!","@ID":35} "PET TOP TALK 17 PETplanet insider Vol. 12 No. 05/11 www.petpla.net 17 are after, i.e. more output from the plants. In Western Europe the challenge lies in rapid tool change capability: Using smaller installations in the best possible way, changing tools faster, changing cavities fast. PETplanet: What the beverages industry is calling for is ”extended shelf life“. Which solution does Hofstetter favour? Stefan Zatti: We have found enquiries have fallen significantly. Even scavengers are being used less and less because the material costs too much. PETplanet: Every boom comes to an end. Is growth a condition for stable existence? Otto Hofstetter: If we want to keep our market position as No. 2 in the present environment we need to grow. In our principal market of Western Europe, to which we supply between 60 and 70% of our tools, we are in good shape. Approximately every 2-3 years a new generation of preforms comes along. PETplanet: And what if you don’t grow? Otto Hofstetter: The corporate structure and the flexibility of our operation enable us to cope with setbacks relatively easily. In 2002 and 2003 we suffered a 30% slump in market and sales. We reacted fast, cut working hours and sent people home. And managed to keep out of the red. Crises don’t upset us. As a family firm we may be dependent on profit as well but we have a long time horizon. PETplanet: To take a look at the classic ‘five year period’, are you thinking of making any acquisitions? Otto Hofstetter: We would like to make an acquisition, perhaps purchase a machine manufacturer. However, we have a high quality standard. We are looking for a partner who is just as good and sophisticated as we are – maybe even better. There is actually only one left .... But also amongst the Swiss mouldmakers, a meaningful supplementation and pooling of resources would be a possibility. We have no difficulty in imagining ourselves cooperating with a cap manufacturer in the PET sector at some point in the future.","@ID":19} "imprint EDITORIAL PUBLISHER Alexander Büchler, Managing Director HEAD OFFICE heidelberg business media GmbH Landhausstr. 4 69115 Heidelberg, Germany phone: +49(0)6221-65108-0 fax: +49(0)6221-65108-28 [email protected] EDITORIAL Doris Fischer [email protected] Michael Maruschke Ruari McCallion Ilona Trotter Wolfgang von Schroeter Anthony Withers MEDIA CONSULTANTS Ute Andrä [email protected] Martina Hischmann [email protected] Ursula Wachter [email protected] phone: +49(0)6221-65108-0 fax: +49(0)6221-65108-28 France, Italy, Spain, UK Elisabeth Maria Köpke phone: +49(0)6201-878925 fax: +49(0)6201-878926 [email protected] LAYOUT AND PREPRESS Exprim Kommunikationsdesign Matthias Gaumann | www.exprim.de READER SERVICES Kay Krüger [email protected] PRINT Chroma Druck & Verlag GmbH Werkstraße 25 67354 Römerberg Germany WWW www.petpla.net | india.petpla.net PETplanet insider ISSN 1438-9459 is published 10 times a year. This publication is sent to qualified subscribers (1-year subscription 149 EUR, 2-year subscription 289 EUR, Young professionals’ subscription 99 EUR. Magazines will be dispatched to you by airmail). Not to be reproduced in any form without permission from the publisher. Note: The fact that product names may not be identified as trade marks is not an indication that such names are not registered trademarks. 3 PETplanet insider Vol. 12 No. 05/11 www.petpla.net For a number of years now PET bottles have been acquiring an ever-increasing share of the market. What exactly is the reason for their obvious success? The consumer of course is the ultimate judge of cans, bottles, beverage cartons and PET bottles at the point of sale, but consistent improvements in technology developed by machinery and toolmakers are making the PET bottle better and lighter. These superficial arguments represent just one side of the coin. On the other side are the people in the background who promote the PET bottle with lots of good ideas plus a dash of boldness and persistence. We have met people like this all over the world. I would, however, like to take this opportunity of singling out two friends who, together, have succeeded in PET-ising an entire country. Yuriy Khmara and Felix Nosov have known each other since they were at school and have been jointly responsible for the introduction of the PET bottle in the Ukraine. Yuriy concentrates on preform production where he makes every individual gram count (see PETplanet issue 4/11); as for Felix, he focuses on the bottling side of the operation (see page 30). The photograph shows the two engaged in amicable, in-depth technical discussions on world matters and, of course, PET. Despite their friendship, we understand from sources close to both of them that Felix is one of Yuriy’s most demanding customers. This no doubt has something to do with the successful approach adopted by the pair in consistently presenting each other with new challenges and thus promoting the world of PET. Let’s wish them both many more years of friendship in the future! Yours Alexander Büchler EDITORIAL dear readers, EDITORIAL","@ID":5} "PET TOP TALK 11 PETplanet insider Vol. 12 No. 05/11 www.petpla.net Otto Hofstetter: I joined the firm in 1985. Back then, I was head of production. I am an engineer through and through. I have worked on the machines, and have expert knowledge of the majority of our machine tools. I won my spurs in production and subsequently managed it on an accountable basis for 10 years. I was lucky enough to have a father who had confidence in me and made funds available for investment. We invested significantly over those years – in production and factory equipment – confident that there was a future for sophisticated production in Switzerland and trusting in the quality and reliability of our Swiss workforce. The most important factor in achieving sustainable success is our production equipment, something which is constantly in need of replacement. PETplanet: Where do you feel that your corporate duties and responsibilities lie today? Otto Hofstetter: Naturally I see it as my duty to safeguard employment in the long term. This is what our employees appreciate and it is the reason why they give their unstinting commitment to the company. We have very few changes at the corporate level. We have a good mix of long-serving and recent recruits in our workforce. Back in 1958 my father embarked on the training of apprentices, and they continue to come through the ranks, thus benefiting both the staff themselves and the company. PETplanet: What has motivated you – as a person? Otto Hofstetter: On the one hand I get a kick out of technology and on the other I enjoy leading, endeavouring to motivate my staff, and to encourage them to act independently and on their own initiative. I am not like my father, who went for - what you might call - a very paternal style of management. I seek out people who are prepared to set out on a course with me and to move forward independently. I give them plenty of freedom. If they don’t make use of this freedom, they are unlikely to be comfortable here. PETplanet: And where would you say your added value for the company lies? Otto Hofstetter: The family structure represents added value. We are flexible in terms of thinking and fast-acting when we need to be. If we resolve to invest and the market suddenly changes in the course of the purchase, then we call a stop to the project and make an alternative decision. This is the advantage that a family business has over a big concern. We have short decision paths. We are able to act fast as need arises. PETplanet: As far as your own individual personality is concerned, duty and freedom of the private individual have entered a symbiotic relationship? Otto Hofstetter: Precisely. PETplanet: The plant is working at full capacity. This presumably means you have a full orderbook ? Otto Hofstetter: Indeed, we have. PETplanet: To what do you attribute the current boom? Otto Hofstetter: We have adopted a strategy of continuous improvement as far as tools are concerned and have responded to the challenging nature of today’s market, i.e. we have adapted the moulds to meet our customers’ expectations – as regards cycle time, service life and reliability – this is something on which we have been working consistently. PETplanet: But the market trends must have been helpful. Otto Hofstetter: It goes without saying that the trends exhibited in the markets are helpful. In particular in the Far East where the market is growing. And in Europe, where we as mouldmakers are benefiting from the materials savings potential of the PET bottle. There have been innovations in the threads sector. Many of our customers are having their moulds converted. Otto Hofstetter as a person PETplanet: The company Otto Hofstetter was established in 1955 and ever since that time it has been in the ownership of the Hofstetter family. You took over management of the company from your father in 1997, the second generation of the family to take the helm. Otto Hofstetter (left) is top-talking with Wolfgang von Schroeter (right)","@ID":13} "MATERIAL / RECYCLING 27 PETplanet insider Vol. 12 No. 05/11 www.petpla.net Insulation for higher productivity A better blend Conair’s insulated high-heat blenders help virgin/regrind PET producers achieve more accurate mixing, cut waste, reduce shutdowns and save energy. Increasing volumes of post-industrial and post-consumer recycled PET are being incorporated into products such as disposable food containers and polyester strapping for packaging and material handling. Conair, a global supplier of auxiliary equipment for plastics processors, says that its new, fully-insulated TrueBlend gravimetric blender can help manufacturers of products with high levels of recycled material to achieve significant energy savings and improve productivity. Conair’s high-heat Trueblend blender enables recycled and virgin materials to be kept separate until just before feeding into an extruder or moulding machine. This means that, for example, contamination in recycled PET need not shut down the entire production line. If contamination is discovered in the TrueBlend process, only the regrind stream needs to be cleaned up and production can continue using 100% virgin resin. Blended virgin pellets and regrind fluff, which have significantly different bulk densities and flow characteristics, reach the machine feed throat more quickly and have less opportunity to re-separate during conveying. The desiccant drying’s heat input is retained during blending, meaning less additional energy is needed for final processing. Conair’s insulated blenders have up to 2273kg/h capacity. The standard unit includes two material hoppers for virgin and regrind; systems with three, four or more hoppers are also available. Material hoppers are eatinsulated and have a 60° cone angle to encourage mass flow of material. Smooth interior walls ensure that all material spends the same amount of time in the hopper and prevents heat loss and moisture regain. All components have been specified to withstand temperatures up to 191°C and higher and electronic components are temperature-isolated. The conventional surge bin is replaced by another insulated drying hopper. All piping is insulated and all areas of the blender are blanketed with dry air to prevent moisture regain. The new blender models have a fully enclosed weighing and mixing section and the controlled environment makes the blenders accurate to within ±0.5% of setpoint on material weights. The standard microprocessor control adjusts after every dispense cycle, compensating automatically on the next batch for normal variations in dispensing, resin bulk density and particle geometry. After virgin and regrind are dispensed and weighed they are dumped into a multi-batch mixing chamber. Individual batches are mixed for a set time, averaging out any batch-to-batch differences. The control system has a full-colour 5.7in/140mm LCD touch-screen user interface. All setpoints are displayed simultaneously and after blend percentages have been entered, the blender automatically weighs the ingredients in the proper sequence and maintains. Up to 50 recipes can be entered and stored in the control for instant recall. Options include an integrated blender/loader control feature. www.conair.com Conair’s high-speed Trueblend gravimetric blender or recycled and virgin materials","@ID":29} "PET TOP TALK 16 PETplanet insider Vol. 12 No. 05/11 www.petpla.net Otto Hofstetter AG Otto Hofstetter AG – established in 1955 – is still in private ownership today. Otto Hofstetter Jr. is the second generation to head the company which today employs 185 staff, of whom 23 are apprentices. Production in Uznach/Switzerland covers an area of 11,000m². The company has an international outlook and exports almost 100% of its products. Sales trend 53 million CHF in 200 48 million CHF in 2009 59 million CHF in 2010 (highest ever turnover achieved) Hofstetter PET milestones: 1977 Production of the first 16cav. mould for PET preforms 1987 Development of 2-component technology 1998 Launch of 96-cavity moulds 2002 Presentation of 64/72 cavity moulds to fit into a 350t machine 2003 Launch of 144-cavity moulds to fit into a 600t machine 2005 New 96-cavity moulds with 38mm neck diameter based on a 350t machine (world’s first) 2007 128-cavity moulds based on a 350t machine (world’s first). 2009 60-cavity moulds based on a 200t machine (world’s first). 2010 Presentation of a thin wall preform produced with a 60-cavity mould during the K’2010. www.otto-hofstetter.com/pet In plastics production even the smallest metal fragments can have far-reaching consequences. Total machinery protection guarantees high productivity and optimizes machine utilisation. Foreign body detection and separation for production and recycling S+S offers comprehensive separation and sorting solutions for the entire PET product life cycle: for the protection of injection moulding machinery for preforms and closures as well as for separation or material sorting – from systems for whole bottle sorting to highly sensitive PET particle separation. All about PET S+S Separation and Sorting Technology GmbH Metal Detectors Metal Separators Magnetic Separators Sorting Systems www.sesotec.com/pet The existing 350t injection moulding machine is fitted with a relatively large mould for increased output and at the same time at lower costs. Since this mould was introduced we have succeeded in winning over many customers to this concept. A further example that we exhibited at K in Düsseldorf is thin wall preforms, which enable us to keep below the current ultra-sonic wall of 2mm wall thickness. Our long-term know-how gleaned from the thin wall packaging sector and stretching back over many years is helpful. Stability in the Hofstetter mould is a prerequisite for the high pressure levels which are in turn a precondition for even thinner walled preforms. On the challenges PETplanet: Developments in the PET business are currently moving solely in the direction of greater numbers of cavities and lightweighting. What technical requirements are there in addition? Stefan Zatti: In China, markets are where enormous growth is coming from. There it’s quantity they","@ID":18} "NEWS 7 PETplanet insider Vol. 12 No. 05/11 Performance Filling & Capping Labelling Blowing PET Engineering improves efficiency and profitability 2010 Engineering, design and consultancy company PET Engineering finished 2010 with record figures in terms of efficiency and profitability, following the implementation of its policy focus on costs, a series of investments and various strategic decisions. Costs and expenses were reduced by more than 12% compared to Year 2009, following a change in the structure and classification of costs and expenses. An internal reorganisation, reduction of waste and an improvement in teamwork have emphasised maintenance, improvement in product quality standards, services, and internal operations. EBITDA were more than 26%, 5% points higher than the previous record levels of 2008. Thanks to these record results, PET Engineering has decided to invest in vanguard instruments for its R&D area and to improve the architecture structure of the technological centre. The company’s continuing expansion policy has led to the opening of a new Commercial Agency Department in Barcelona, Spain, which is intended to provide better service to the Iberian and South American markets. www.petengineering.com APPE increases production of recycled PET APPE, a division of LSB and formerly known as Artenius PET Packaging Europe, has invested an additional €10 million at its dedicated PET recycling plant in Beaune, France. The investment will enable the company to increase the plant’s annual production by 40%, from 25,000 to 35,000t. The additional 10,000t output capacity has been achieved by the installation of (currently) the largest single washing line in Europe. An additional extruder, bringing the total at the plant to four, takes the washed flakes, ensures they are free from organic impurities and turns them into recycled pellets. The higher output is produced from over 46,000t of post-consumer PET, equivalent to removing around 1.5 billion PET bottles from the waste stream. APPE’s products made from recycled PET include SuperCycle food grade and Nu-Cycle non-food grade resins. SuperCycle is produced via a solid state polymerisation (SSP) process, which converts a PET bottle into food-grade material equivalent to virgin resin. 28,000t of the output at Beaune is SuperCycle material. The plant collects post-consumer PET from across Europe; 65% originates from France, 15% from Belgium, 10% from Germany and 7% from Italy. www.appepackaging.com","@ID":9} "BOTTLE MAKING 20 PETplanet insider Vol. 12 No. 05/11 www.petpla.net New metal alloy intended for more efficient PET bottle production The rule of hard blocks Deutsche Edelstahlwerke GmbH recently launched Corroplast FM, a new alloy intended as a primary material for preform moulds.It is intended to meet the industry’s need for greater efficiency, including improved machinability and metal hardness, without loss of corrosion resistance. Deutsche Edelstahlwerke GmbH (DEW) supplies the PET bottle industry with primary material for injection moulds for production of preform bottle blanks. Demand for bottles continues to increase. In 2009, a year of little economic growth, approximately 480,000t of PET were processed in Germany alone, mainly for use in the packaging industry and including PET bottles. Business pressures, including the need to improve competitive performance in international markets, mean that plastic manufacturers need to produce more and more bottles in less and less time – but without any loss of quality. Efficiency is the decisive factor. This also applies to the primary mould material made of specialty steel. In response to these demands, DEW has launched ‘Corroplast FM’. It presented this new material as its solution for increased requirements in process cost optimisation at Euromold in Frankfurt. “The trend for a few years now has been towards increasingly processed corrosion-resistant moulds, mould frames and superstructures,” said Michael Bauer, head of technical customer support for tool steel at DEW. “The PET bottle industry is a clear example. For reasons of efficiency, cavities for up to 192 preforms are now used in one single injection mould.” Increased numbers of cavities leads to increased machining complexity. DEW claims that Corroplast FM demonstrates significantly increased machinability, compared with other proven plastic mould steels, without reduction of corrosion resistance, and a good balance of those two features and metal hardness. Analysis and structure Development of the new material has taken more than two years. “In order to achieve the desired properties, we had to determine the optimum ratio of the alloy components – chromium, nickel, manganese and sulphur,” said Jens-Sebastian Klung, member of the department for development / material and process simulation. A particular challenge was homogenisation of the structure and the correct proportion of sulphur. In the right quantity, sulphur has a positive effect on the machining properties of specialty steel but it also decreases performance characteristics, especially in transverse direction, if the quantity is too high. Melting and subsequent secondary metallurgic treatment were adjusted in order to reduce this negative effect. The possible formation of embrittling delta ferrite was minimised through thermodynamic calculations, which further improves homogeneity of the structure and its resulting properties. The homogenous structure ensures not only that Corroplast FM remains corrosion-resistant – even in an environment marked by heat, condensation and coolant – but also provides stability for filigree components and limited cavity spacing. As well as PET bottle producers, the material is also claimed to offer advantages to the automotive industry (for the production of plastic and rubber parts); cosmetic and food industry packaging manufacturers; or any operation that needs complex, corrosion-resistant and easy-to-machine base and build up plates, mould frames or plastic moulds. Full service from scrap metal to preforms Following the successful completion of a series of experiments and tests, customers can now purchase Corroplast FM plastic mould steel as rolled or forged plate with a width of 1,000mm and a thickness between With the new material the processing/ production costs of the PET industry can be optimized. In the electric arc furnace selected scrap and certain alloying elements are melted.","@ID":22} "PREFORM PRODUCTION 19 PETplanet insider Vol. 12 No. 05/11 19 Table of Contents i............................................. About the Authors ii..................................................... Introduction chapter 1...................................................AA Level High 2............................................. Accordion Preform 3............................................Air hooks / Streaks 4.................................................... Black Specks 5........................................................... Bubbles 6...................................................... Burn Marks 7..................................Colour Streaking / Peeling 8...................................................... Crystallinity 9..................................................... Drool Marks 10...............................................................Flash 11.............................................. Gate Depressions 12.................................................... Gate Peeling 13...................................... Gate Voids / Pin Holes 14..............................................Internal Gate Sink 15.................................................... Internal Sinks 16.............................................................IV Loss 17.................................................Long Gate Nub 18................................................... Milky Preform 19................................................. Moisture Marks 20.................................... Neck Finish out of Round 21............................................Parting Line Crease 22..................................... Parting Line Deformation 23.............................................. Preform Yellowing 24.......................................................Short Shots 25...............................................................Sinks 26.............................................................. Splay 27................................................Stretched Necks 28..........................................................Stringing 29..............................................Surface Blemishes 30..............................................Thread Flow Lines 31............................. TSS (Top Sealing Surface) Sink 32........................................................... Unmelts 33..................................... Wall Thickness Variation 34......................................................Wavy Body 35.......................................................Weld Lines 8. Ensure the mould neck insert and lock ring vents are clean. This will minimize melt flow resistance due to gas entrapment. 9. Ensure the mould / robot alignment is accurate. 10. Ensure preform handling is not congested at the deposit locations and collection bins. 11. Reduce the robot ejection force to soften the contact of the neck finish with the conveyor. 12. Check to ensure that no moisture exists on the moulding surfaces, either from water leaks or condensation. This may obstruct normal melt flow and cause filling problems. The environmental dewpoint should be below the chilled water temperature to eliminate the risk of condensation. 13. Check hardware for worn, damaged or failed components, specifically the core cooling tubes, and clogged neck insert and core cooling channels. IN EVERY BOTTLE THERE IS ALL OUR KNOW HOW. RESEARCH & DEVELOPMENT A constant projection towards the future oriented to search not only for new materials but also new PET technologies of transformation and innovative materials. CONSULTANCY A concrete answer to all your questions. We put at your disposal all our know-how for every single requirement. PROTOTYPATION Prototypes of containers and innovative preforms in record times: you will be able to touch with your hands the bottles within a short time after approval of the design. DESIGN Creativity in search of elegance and refinement. Innovative designs, ergonomic structures, eye-catching and functional containers. We give a true shape to your product!","@ID":21} "MARKET SURVEY 25 Kimex, SA de CV Savola Plastics Division Constar, Inc Petform Thailand Ltd. Pearl Drinks Limited Km 26.5 Autopista México -Querétaro, Tlalnepantla 54020, Edo. De México, 52-55-53669030 Dr. Jorge Larrañaga Director -Business Development 52-55-53669059 52-55-53669031 [email protected] Saudi Business Center, Madina Road, 6th Floor, PO Box 34495, Jeddah 21468, Saudi Arabia +966 2 268 7782 www.savolaplastics.com Muthappan Annamalai General Manager - Business Devlopment +966 2 268 7785 [email protected] One Crown Way Philadelphia, PA, USA 215.552-3735 www.constar.net Dawn Little Sales +1 215 602 2670 +1 215 552 3707 [email protected] 75/101-102 Ocean Tower II 37 th Floor, Soi Sukhmvit 19 (Wathna), Asoke Road, Kloengtoey Nuer, Wathna, Bangkok 10110. Thailand. +66-26616661 www.indoramaventures.com Mr Pramod N Dubey, Head Marketing +66819371978 +66-26616664 [email protected] 802-Ansal Bhawan, 16,K.G.Marg, New Delhi-110001, India 011-41520442;46470200;46470227 www.jaipuria.co.in Vijay Walia Sales and Marketing +91 11-41520442,46470227 +91 11-23327747 [email protected] No No Yes No No No No No No Yes No RPET No No Colourants, UV blocker Barrier addtives for CO2, oxygen scavengers, UV blockers Oxygen scavengers, coulorants, UV protection, process aids No, as per requirements No 13 - 62g, PCO 1810, Corvaglia: 13g, 21g, 31g, 35g, 40g, 50g, 58g, Alaska Novembal 13g, Alaska 26.7g; 1844 14g, 21g, 27g, 31g, most preforms for CSD and still water Water 3025 and 28mm PCO; CSD 28mm PCO 1810 & 1881 2-piece; dairy & juices 38mm 3-start; hot fill 38mm 2-start thick neck sizes; edible oil 2921, 3629, 4236 neck sizes; cosmetics 17.02g 30/25 mm for water bottle; 25.50g PCO 28mm, 1810; 27.71g PCO 28mm, 1810; 40.02g PCO 28mm, 1810; 43.02g PCO 28mm, 1810; 45.60g PCO 28mm, 1810; 52.10g PCO 28mm, 1810; 24.20g PCO 28mm, 1881; 38.80 g PCO 28mm, 1881; 44.20g PCO 28mm, 1881; 50.8 g PCO 28mm, 1881; 50.8g PCO 28mm, 1881 22g 3-start Alaska 28mm; 21.5g 3-start Alaska 30mm; 25.5g 3-start Alaska 30mm; 20.9g PCO 28 mm CSD; 25.5g PCO 28mm CSD; 27.7g PCO 28mm CSD; 52 gPCO 28 mm CSD Novapet, S.A. APPE Société Générale des Téchniques Westbridge PET Containers Resilux NV Pº Independencia 21, 3º, 50001 Zaragoza, Spain +34976216129 www.novapet.es Mr. Miguel Angel Arto Business Development Director +34976216129 +34901021138 [email protected] Ellice Way, Wrexham Technology Park, Wrexham, Ll13 7YL, UK +44 1978 317 350 www.appepackaging.com Kinza Sutton Marketing Manager +44 1978 317 378 +44 1978 317 384 [email protected] 3 Rue De L'ile Mace 44412 Reze Cedex, France (33) 2 40 05 09 37 www.sgt-pet.com Frédéric Mignot +33 6 88 08 62 40 [email protected] 3838E - 80 Avenue SE, Calgary, Alberta, T2C 2J7, Canada 403-248-1513 www.westbridge.ca Sharon Pokolm Sales Manager 403-207-7720 403-248-1199 [email protected] Damstraat 4, 9230 Wetteren, Belgium +32 (9) 365 74 74 www.resilux.com Philippe Blonda Director of Marketing and Sales +32 9 365 74 76 +32 9 365 74 75 [email protected] No Yes No No Yes No Yes No No Yes No Yes No Yes - rPET Yes No Colourants, UV blocker, O2 and CO2 barrier, moisture O2 and CO2 scavenger, Anti UV, AA blocker, … Bio- degradable; UV blocker; Oxygen scavengers UV-blocker, colourants, multiple barrier additives Ø W 30/25 from 12,5g to 35g. Ø W 29/25 from 10,5g to 32g. Ø W 48/40 Bericap. From 77g to 82g. Ø PCO 1810. from 18,5g to 54g.; Ø PCO 1881. different weights. Peforms available clear / different colours Preforms for beverage, alcohol, food, dairy, personal care & home care applications, preform and container design, light-weighting, high performing multi-layer and mono-layer barriers, hot-fill, standard and non-standard preform sizes and weights, various necks and finishes, wide-mouth. 30/25 BH ET BB 13 - 50g; 29/25 8.9 - 36g; PCO 1810 16g à 52g; PCO 1881 21g; BPF 20.5 - 52g; COL38 14 - 72g; 48/40 85 -95 g; 21/29 22 - 25g; 28/410 19,5 - 40g; BVS30H 40 - 54g 24mm 410 - 20, 23; 28mm 400, 410, 415 - 36, 42, 47; 33mm 400 - 30, 36, 54; 33mm 400 CRC - 56; 29mm Rical - 36, 41; 32mm Rical - 48, 60; 28mm Kerr - 39, 45, 86; 33mm Kerr - 83, 90 97 (long Kerr); 38 mmPortola SCIII - 59, 75, 83; 30mm Stelvin - 65, 71; 38mmAlcoa - 87; 28mm PCO 1880 - 19, 24, 34, 42, 47, 55, 76; 28mm PCO 1881 - 19, 24, 34, 47 Standard monolayer preforms: Barrier preforms (Monolayer & Multilayer):• ResiOx 3-6-9 • ResiC • Resimid & Resimax • Resiblock 0-2-4; Hot fill; For Filling at 85°C; Refill","@ID":27} "Vol.6 PETplanet print PREFORM PRODUCTION 18 PETplanet insider Vol. 12 No. 05/11 www.petpla.net Neck Finish out of Round Part 20 of the “Rapid Guide to Perfect Preforms” * *by Rick Unterlander and Ottmar Brandau Troubleshooting guides have suffered in the past from being locked away in offices and not being available to the people that actually need them. Considering the high cost of machine and tools high scrap rates can be a costly proposition eating away at already tight margins. PETplanet’s “Rapid Guide to Perfect Preforms” takes a different approach. Bound in laminated paper that is easy to clean off, the small format of the book of 108mm by 151mm (4.25” by 6”) allows easy storage in back pockets or tool boxes. It has been written for the people on the floor of injection moulding companies to support their daily work in making the best preforms possible. The product of two industry experts, Rick Unterlander and Ottmar Brandau, it gives concrete advice on 35 of the most common problems in preform manufacture, most illustrated by pictures. From high AA levels to wavy bodies processors can find help when they need it. Read chapter 20 of the guide. fax: +49 (0) 6221-65108-28 [email protected] www.petpla.net Order your copy now! PETplanet print vol.6 The Rapid Guide to Perfect Preforms machine no./name Symptom: The range in neck finish ID as measured around its internal circumference is above 0.25mm (0.010”). Cause: Poor formation or external deformation of the neck finish. Solutions: 1. Check water cooling temperature. This should be 7 – 10ºC (45 – 50ºF) for optimum cooling. 2. Check water cooling flow to mould, especially the neck inserts and cores. This should be at the mould manufacturers rating (for a given preform size and cavitation). 3. Check to ensure hold (packing) pressure isn’t too low, especially near the beginning of hold time. Adjust higher if necessary to fully fill out the preform. 4. Check that the hold (packing) time isn’t too little for the preform being moulded. Increase as necessary to optimize part weight. 5. Check that the cooling time is sufficient for the preform being moulded. This typically ranges from about 1 to 3sec depending upon the preform wall thickness. Add time if necessary to improve solidification. 6. Maximize the cooling time of the robot. This should not be increased beyond the cycle time of the machine. 7. Check all temperature readings and adjust as necessary. PET resin should be melted at about 280ºC (536ºF) +/- 10ºC (18ºF).","@ID":20} "23 Bottle-to-bottle recycling plants Conveyors for preforms and empty bottles Caps and closures Preforms Perform moulds and SBM moulds Preform and single stage machinery 2-stage SBM machinery Compressors Filling equipment Resins and additives Suppliers of performs With 23 suppliers from 17 countries, we have in this issue compiled the most comprehensive market survey including both the number of preform suppliers and the various countries in which they are located. Meanwhile, different neck finishes have now established themselves in the marketplace, and seem to co-exist happily with each other. The product ranges of the suppliers are self-explanatory. We must again point out that, of course, many suppliers also have local branches, which we are unable to list in their entirety. Details of the relevant contact people are given below. Although the publishers have made every effort to ensure that the information in this survey is up to date, no claims are made regarding completeness or accuracy 05/11 MARKETsurvey Company name PDG Plastiques Retal represented by JSC Retal Europe PET-Verpackungen GmbH Deutschland Postal address Telephone number Web site address Contact name Function Direct telephone number Fax E-mail ZI secteur 2, 45330 Malesherbes, France 33 2 38 34 61 95 www.pdg-plastiques.com Francois Desfretier General Manager +33 2 38 34 61 95 [email protected] Konstitucijos av. 7, LT-09308 Vilnius, Lithuania +37052858400 www.retaleurope.lt Vidunas Stukonis Sales Director of Retal EU Group +37052858517 +37052858411 [email protected] Gewerbegebiet 4, 98701 Großbreitenbach +49 3 67 81 / 4 80 - 4 57 www.pet-verpackungen.de Hubert Rebhan Projects & Sales +49 3 67 81 / 4 80 - 4 53 +49 3 67 81 / 4 80 - 4 52 [email protected] Multilayer preforms (Yes/No) Yes Yes Yes PEN prefoms (Yes/No) Yes No upon request Preforms in alternative materials (PP/PLA) Yes No upon request List of additives available Light barrier Prelactia - Oxygen barrier colourants RPET Colourants, AA reducer Amosorb, Nylon, UV blocker Colourants, oxygen scavengers, UV-blockers slip-agents, AA-scavengers, brighteners, PA-based barriers Preform range 29/25 shorty : 8 - 11,7 - 22- 23 - 23,5 - 28g; 30/25 high: 17,5-25-26-28-31-33-36-39g; 30/25 low: 17,5-25-26-28-31-33-36-39g; 38mm 3 start: 26 - 33,5 - 44 - 50g; 38mm 3 start: 28gr Prelactia 100% light barrier for UHT milk long shelf-life; 48/41: 55 - 62g; 27/32: 6,5g dairy and smoothies; 25/20: 6,5 - 8g dairy; Ø28 BPF: 42 - 44 - 48 - 60gr; 29/23: 24 - 33g chemical; BVS 30H60: 50g Wine (high oxygen barrier); ultra-lightweighting 2,4g preform; Overmoulding-technology for 2 layers preforms PCO 1810 (15,8g,16,8g,18,5g,20g,20,5g,24g,25g,26,5g,28g,29g,30g, 31g,32g,33g,34g,35g,36g; PCO 1881 (20,7g,22,5g,22,7g,25g,26g,28g,29,5g,31,2g,38,7g,40,1g,4 0,2g,43,7g,46,7g,50,4g); PCO hybrid (23g,34,5g,35,5g,35,7g,37g,38g,39g,40g,41,5g); PCO Corvaglia (16,2g,22,9g,30g,32g,34g); BPF (18g,18,5g,20g,24g,26g,27,5g,32g,34g,36g,38g,39g,40g,41g,, 41.5g,,42g,47g,51,5g); 38 mm 2start (17,5g,18,5g,20g,28,5g,32g); 38 mm 3start (19,5g,21,5g,24,5g,27,5g,28g,35g,36g,39g); 48/41 low (77g,79g,80g,85g,86g,91g,145g); WM (30g,36g); Multilayer PCO 1810 (24g,26,5g,28g,35g,37g); Oil 29/21 (18g,21g,22g,24g,27g); Alaska Novembal 267 (12g,16,5g,20,7g,22,6g,30g,32g,34g); Obrist (21g,23g); 30/25 (12,5g,13,5g,14g,15,7g,18g,27g,30g,31g,32g, 34g,34,3g,36g,38g,39g); 29/25 (10g,12,5g,25,5g,29,5g) Complete range of standard preforms with 28mm PCO finish from 14.5 g (e.g. for 0.25l bottles) up to 54g (e.g. for 2.0l bottles); includingpreforms with 28mm PCO finish octagonal neckring(e.g. for German Petcycle customers); PCO1881 short neck; other customized neck finishes also available; 38mm 2-Start and 3-Start Bericap for wide mouth applications; 92g preforms with Bericap 48-41 finish for large containers. Majority of preforms available as multilayer with tailor-made barrier properties","@ID":25} "PETnews 6 PETplanet insider Vol. 12 No. 05/11 www.petpla.net Change of ownership for Husky Berkshire Partners LLC, the Boston based private equity firm, and Omers Private Equity Inc., the private equity arm of the Omers Worldwide group of companies, have announced that they have signed a definitive agreement to jointly acquire Husky International Ltd. and its subsidiaries from Onex Corporation and its affiliated funds. John Galt will continue as Husky’s President and CEO. Berkshire Partners LLC and Omers Private Equity Inc. expect to complete the transaction by the end of the third quarter of 2011. The management team of Husky is expected to be a significant investor in the business through continued equity ownership. Berkshire Partners is a private equity firm based in Boston, Mass, USA. It has aggregate capital of $6.5 billion. Omers Private Equity, headquartered in Toronto, Canada, has over $5.5 billion of investments under management and manages the private equity activities of Omers, one of Canada’s largest pension funds with over $53 billion in net assets. Financing will be provided by certain affiliates of Goldman, Sachs & Co., including its principal mezzanine fund; Morgan Stanley Senior Funding; RBC Capital Markets; and TD Securities Inc. TD Securities acted as financial advisor, and Weil, Gotshal & Manges LLP and McCarthy Tétrault LLP acted as legal counsel for the buyers. www.husky.ca www.berkshirepartners.com www.omerspe.com Uhde to build production plant in Turkey Uhde Inventa-Fischer has announced that it has been awarded a contract to build a PET production plant in Gaziantep, Turkey, for preform producer Koksan PET Packaging Industry Co. The plant will use Uhde Inventa-Fischer’s proprietary MTR technology to produce 216,000t/a of resin in various grades. The new plant will be built next to Koksan’s existing PET preform and bottling facilities in Gaziantep. Uhde Inventa-Fischer will provide basic and detail engineering, supply of all major plant equipment, supervision of construction and commissioning activities, as well as training of operating personnel. The MTR process is based on Uhde Inventa-Fischer’s Two-Reactor technology, which uses the patented Espree and Discage reactors to obtain required high-melt viscosities. A further investment for a second, identical, line is anticipated in the near future. www.uhde-inventa-fischer.com Thousands attend Sino-Pack / China Drinktec 2011 The 18th China International Exhibition on Packaging Machinery & Materials (Sino-Pack 2011) and The 15th China International Exhibition on Brewery, Beverage and Liquid Packaging (China Drinktec 2011) attracted 21,760 trade visitors from 80 countries. The event, which ran from March 9-11 2011 at the China Import & Export Fair Pazhou Complex (Area A), Guangzhou, PR China, is one of the leading packaging and beverage technology exhibitions in China. The organisers reported that the attendance was better than expected, with a higher number of trade and professional visitors than at the show’s previous edition. Visitors representing the food, beverage and household chemical industries came from China itself, elsewhere in Asia, Europe, the Middle East and the Americas, as well as delegations from Russia, India, Vietnam and other countries. A total of 390 exhibitors from more than 14 countries and regions had stands, including Bosch, KHS, KraussMaffei and Colormatrix from Europe, and Hongya, Mawell and Hong Bang from China. Chinese companies were particularly well represented, with strong delegations and visitor presence from the Pear River Delta industrial area. Trade associations from Korea, the UK, USA, Chinese Taipei and the People’s Republic of China (PRC) hosted their own pavilions. Around 20 symposiums were held during the exhibition, covering topics including Food Safety and the Development of Green Food Industry; Product Safety and the Development of Health Beverages; Low-Carbon Brewing Technology; Quality Control in the Pharmaceutical Industry; Product Development and Application of New Materials in Health Products; and Equipment Maintenance and Quality Control. The Premium Packaging Showcase attracted participation from 100 high-end packaging products enterprises from China, as well as leading designers who tpresented heir concepts on green packaging. Various ‘Business Matching’ activities brought buyers and exhibitors together and the organisers reported that over $20 million of business deals were discussed during the show. The exhibition was organised by Adsale Exhibition Services Ltd and the China Foreign Trade Centre (Group), supported by Guangdong Packaging Technology Association, Guangdong Provincial Pharmaceutical Management Board, Guangdong Brewing Information Technology Service Centre, ShenZhen Food Industry Association and Hong Kong Packaging Institute. The next Sino-Pack /China Drinktec 2012 will be held from March 7-9, 2012 at China Import & Export Fair Pazhou Complex (Area A), Guangzhou, PR China. www.ChinaSinoPack.com www.ChinaDrinktec.com","@ID":8} "MARKET SURVEY 24 MARKETsurvey05/11 Company name S.B.E.C.M. Alpla-Werke Alwin Lehner GmbH & Co. KG LuxPET SA (Plastipak) Parle Agro Pvt. Ltd. M/s. AMD Industries Ltd. Postal address Telephone number Web site address Contact name Function Direct telephone number Fax E-mail Rue de la plaine, 47230 Lavardac, France +33 (0)5 53 97 41 00 www.sbecm.com Jean-Luc Didouan General Manager +33 (0)5 53 97 41 00 +33 (0)5 53 65 85 97 [email protected] Mockenstrasse 34, 6971 Hard, Austria +43 5574 6020 www.alpla.com Hermann Riedlsperger Head of Sales - PET +43 5574 602 515 [email protected] Zone d’Activités Economiques, Rue Héierchen n° 4, 4940 Bascharage, Luxembourg +352 35 87 19 1 www.luxpet.com / www.plastipak.com Peter Van Ettro Sales Manager +352 35 87 19 248 +352 35 87 19 208 [email protected] Western Express Highway, Parsiwada, Andheri (E), Mumbai 400 099, Maharashtra, India + 91 22 6734 8000 www.parleagro.com Jitendra Kulkarni Sr. Manager - Technical +91 22 67348241; +91 22 67348237 +91 22 66935050 [email protected] 18, Pusa Road, 1st Floor, Karol Bagh, New Delhi - 110 005 +91 9811118736 www.amdindustries.com M/s. AMD Industries Ltd. Director -Business Development +91 11 46830202 +91 11 28753591 [email protected] Multilayer preforms (yes/no) No Yes No No No PEN prefoms (yes/no) Yes No No No No Preforms in alternative materials (PP/PLA) Possible Yes Yes No List of additives available AA scavengers, Blockers, Colouring agents, O2 absorbers, R-PET, etc.. all customary additives; AA blocker UV blocker O2 /CO2 scavengers O2 scavenger Preform range Neck finish : 30/25 High and Low, 29/25, PCO 28 (1818, 1881), BPF, 48/41. Study for special neck finish possible. Preform weight : from 15 to 91g Softdrinks: various neck versions from 0.25l to 2.5l Water: various neck versions from 0.25l to 5l; Edible oil: from 0.5l to 10l; Milk: various neck versions (2-start; 3-start); Home + personal care, lubricants: various neck versions PCO; ROPP; 3-Start; short neck; CTC; jar 22gm, 23gm with 30mm neck size; 25gm, 27gm, 28gm, 42gm, 44gm, 48 gm, 54gm with 28mm neck size ; 30 gm (Hot Fill) with 28mm neck size Company name Retal Iberia S.L.U Terrachim 97 AD Manjushree Technopack Limited Gulf Packaging System co Gastro PET d.o.o. Postal address Telephone number Web site address Contact name Function Direct telephone number Fax E-mail Ctra.Comarcal C-35, Km 66,147 , Nº147 , 2ºsector Parcela 5,17451 Sant Feliu De Buixalleu - Girona (Spain) 00 34 972 865730 Pere Plademunt Mateu General Manager +34 972 865730 +34 972 865731 [email protected] 6 Kupenite str., Sofia 1618, Bulgaria +359 2 955 63 22 www.terrachim.com Michail Kostov General Maneger +359 2 955 63 22 +359 2 955 63 25 [email protected] 60E, Bommasandra Indl. Area, Hosur Road, Bangalore 560099. India +91-80-4343 6200 www.manjushreeindia.com Ajay Nayak Chief Manager - Export Sales +91-80-4343 6293 +91-80-2783 2245 [email protected] Post box 20266, Jeddah 21455, K.S.A. 0096626360099 www.gulf-pack.com Mr. Badr Abdullah Sales Manager +96626360099 ext 107 +96626352111 [email protected] Kotna ulica 5, 3000 Celje, Slovenia +386 3 425 80 32 www.gastropet.si 3ULPRå General Manager +386 3 425 80 32 +386 3 425 80 31 [email protected] Multilayer preforms (yes/no) No No no No No PEN prefoms (yes/no) No No no No No Preforms in alternative materials (PP/PLA) No No Hot Fill resin, R-pet with 10% and 25% recyclate, M&G Poliprotect barrier resin PET PLA List of additives available Colourants, Kimired, Samplas Amosorb UV Blockers, Oxygen Scavenger - Amosorb, High IV range available (0.86 & 0.88) Low MOQ for special additive based preforms Colourants; AA blockers, UV blockers,Amosorb Preform range 40 gr PCO 1810, 43 gr PCO 1810, 45 gr PCO 1810, 38,70gr PCO 1881, 43,70gr PCO 1881, 25gr PCO 1810, 26gr BPF 1810, 51gr PCO 1810, 47gr PCO 1810, 49,5gr PCO 1810, 39gr PCO 1810, 41gr PCO 1810, 45gr PCO 1810, 42gr BPF, 40gr BPF, 44gr BPF, 46gr BPF, 48gr BPF , 51,5gr BPF, 22gr OIL 29/21, 24gr OIL 29/21, 27gr OIL 29/21, 27gr 30/25, 25,5gr 29/25, 29,5gr 29/25, 79gr 48/40, 86gr 48/40, 91gr 48/40, 23gr obrist, 30 gr 30/25, 31gr 30/25, 39gr 30/25, 36gr 30/25, 38gr 30/25, 13,5gr 30/25, 12,5gr 30/25, 27gr 30/25, 18gr 30/25, 14,5gr 30/25, 12,5gr 29/25, 10gr 29/25, 11,5gr 30/25 PCO: 10g; 19g;22g, 26g, 31g, 36g, 39g, 40g, 43g, 46g, 49g, 52g; 30/25: 14.5g, 16.5g, 28g, 30g, 32g; 29/21: 22g, 25.6g; 38mm: 21g, 28g, 38g, 48g,57g; 48mm: 57.5g, 80g, 86g, 115g, 123g, 130g; crown cork: 27,4 g 28MM PCO 1810; 14.6g 15g 17g 25g 25.5g, 27g, 39g 48g; 28MM PCO 1881 (New Short Neck); 23.7g 25.7g 37.7g 46.7g; 28mm PCO Thick Neck (For Hot fill up to 85º C ); 18.5g 27g 47g; 30 / 25 mm 3 Start; 22g; 28 mmAlaska 3 Start; 15.6g 22g 35.6g Mineral Water Application: 122 g upto 34 g - 30/25 HNF; 12.2 , 13g, 13.5g, 14g, 16g, 17g, 18g, 18.5g; 20g, 21.5g, 28g, 31.5g, 34g; 18 g 28 mm PCO upto 55g,18g, 19g, 21.5g, 22.6g, 24.4 g, 27g, 39g, 53.3g, 55g; 80.5g , 83g Nylon (in combination with Polyshield); preforms for water, CSD, juices, dairy products, beer, wine, detergents, cosmetical industry etc.) with required materials and additives. Extended experience with barrier technologies and additives. Range of preforms: PCO 28mm 1810 light: 18.5 - 24.5g PCO 28mm 1810: 33.3g - 48g Bericap 38mm: 16g - 41.5g PLApreform production. Complete support with PLAprojects.","@ID":26} "PETproducts 34 PETplanet insider Vol. 12 No. 05/11 www.petpla.net Idea-to-mould collaboration R&D/Leverage and Dr Pepper Snapple Group (DNS) have launched the first product of their ‘idea-to-mould’ collaboration: a new design for the 20-oz ‘Legacy’ bottle. The project began with consumer research and resulted in a package designed for efficient manufacture that enhanced both visual and tactile design elements and is intended to contribute to effective brand building. The new bottle will be used for DPS brands including 7Up, Sunkist soda, Canada Dry, Sun Drop, Squirt and other soft drinks in the company’s portfolio. DPS said that the package had to look good on the shelf, run efficiently in all its manufacturing locations and work in vending machines, as well as having aesthetic appeal to consumers. The entire process, including consumer work, was conducted in an accelerated 28-week ‘idea to mould’ process that included comprehensive qualitative and quantitative consumer validation. Specific ‘tactile tactics’ research tools were developed in order to identify consumer likes and dislikes. The tactile element was regarded as equally important as shape, graphics, label size and placement. www.rdleverage.com 1881 ‘light’ sport closure In response to the drive for sustainability in the beverage industry, dispensing systems manufacturer Aptar Food + Beverage, part of the Aptargroup, has announced the release of its light sport closure. The new product uses less plastic but without any reduction in performance. The lower profile of the 1881 light Original weighs 25% less than the 28mm PCO/BPF version, and is also claimed to enable weight savings on the preform. Aptar says that its new closure maintains the performance and aesthetics of its existing ‘Original Sports Closure’ system, including pressure containment up to 3bar; high flow rate; an active hinge; high transparency and a two-colour option for shelf appeal. The closure is available with a standard seven-millimetre opening or with a SimpliSqueeze silicone beverage valve, which is compatible with the PET recycling process. www.aptar.com Monobloc multi-dress labeller The offer held out by Krones AG is that its DecoBloc labelling system will make it possible to create a monobloc configuration synchronising a modularised labeller with a Sleevematic carousel, a Shrinkmat tunnel and a Linadry unit for predrying containers. The company says that the DecoBloc monobloc will run all labelling processes in common use, including cold-glue, pressure-sensitive, hotmelt or shrink and stretch sleeves. The machine’s docking stations have motorised height adjustment, which means that labelling stations can be prepared for product changeover at the touch of a button, regardless of the floor level involved. Different machine sizes offer outputs of up to 72,000 containers/h, with servomotors providing accurate dress positioning. There is also an option for camera-based alignment of the containers with embossed markings or special contours, with the intention of ensuring optimal positioning of labels or sleeves. www.krones.com ‘Next-generation’ hysteresis capping head After offering its BVK capping head for more than seven years, Bericap has announced the launch of its next-generation hysteresis capping head, designated BNX. The new machine provides application torque at an even narrower range than its predecessor, and independent of the head speed. The BNX is shorter, which makes it compatible with all major capper configurations currently on the market. The BNX capper is liquid tight, in order to prevent lubricant leakage, and application torque can be adjusted by hand, without special tooling. www.bericap.com","@ID":36} "PETbottles 36 PETplanet insider Vol. 12 No. 05/11 www.petpla.net Organic fertiliser Carrefour of France are selling1.2kg / 1 litre liquid fertiliser packs for flowering plants – brand name “Eco-Planet“ – in an opaque PET bottle with a large, informative, self-adhesive belly label. In the interests of better positioning on the shelf, the base and cap areas of the bottle are designed in a square format. The green screw cap is easy to grip and is secured by means of a tear-off tamper-proof strip. www.carrefour.com Clear classic lines The German cult brand “afri cola“ – currently owned by Mineralbrunnen Überkingen-Teinach AG – has been also available for some time now in 1l PET bottles. The typical palm – associated with the brand image – is still recognisable, if only dimly, but the dark product can be identified immediately through the transparent bottle. A paper label on the belly of the bottle is colour coded to distinguish between the different variations and provides trading information. A screw cap with pull-off tamperproof guarantee ring takes care of the necessary product security. www.afri.de Smooth-as-silk juice “Smooth-as-Silk Juice“ is the term used by the fruit juice producer Rapp´s Kelterei of Karben, Germany, to describe their orange juice in its 1l PET bottle. The bottle, which is also used for other juices, features an area in the centre which provides a handy grip point as well as an area for affixing a label plus a decorative base area in the form of raised injected patterns reflecting the nature of the product. The top section is designed as a kind of “dome“ and incorporates a colour-matched plastic screw cap with tear-off tamper-evident seal. www.rapps.de","@ID":38} "PET TOP TALK 15 PETplanet insider Vol. 12 15 PETplanet: You could work with a multitude of machinery manufacturers but have actually preferred to work with just one. Stefan Zatti: Our independence is from a certain point of view a problem. This is the reason why we are endeavouring to achieve a closer link with the machine builders. We are keen to penetrate new markets. We have ideas and are innovative. We are flexible when it comes to making decisions on prices – more flexible than many large companies. For future growth we need access to our own injection moulding machine. Husky started by building moulds and then machines and became a world market leader with this strategy. We reckon that this is something that Husky has done rather well. PETplanet: To keep to the point: marketing via references, i.e. by word of mouth, is the best bet for Swiss manufacturers. It’s a relaxed and moderate approach to policy which also helps save on costs. Would you say that this is a successful statement of your sales policy? Stefan Zatti: Of course, the company had been inward-looking for a long time- in the same way as many other Swiss companies. Top products – or so we thought – don’t need to go looking for customers, they sell themselves. This is an attitude that no longer has any place in our business. Our ambition is to demonstrate technological leadership to the world at large – by approaching customers ourselves on a regular basis, by adopting and implementing our customers’ ideas, which we receive in direct discussions. This service represents optimum marketing – or so we think. DEUTSCHE EDELSTAHLWERKE, Obere Kaiserstr., D-57078 Siegen / Auestr. 4, D-58452 Witten Who knocks PET bottles into shape? CorroPlast® – the ultimate steel for all-stainless mould sets. On innovation PETplanet: Turning now to complex high-tech applications that you regard as occupying a prime position in your development – can you elaborate on these? Otto Hofstetter: Reducing the pitch in the mould was a predominating theme. The moulds have become smaller and more compact. Market demand is for ever lighter as well as smaller preforms. In addition: we coat the tools and thus reduce the tearing forces. What we are also doing is giving the customer moulds featuring fewer maintenance intervals. PETplanet: Some examples? Otto Hofstetter: One example is the 128-cavity mould, a milestone in our development. The multi-cavity mould in this size is available on an existing Netstal machine platform.","@ID":17} "PET TOP TALK 10 PETplanet insider Vol. 12 No. 05/11 www.petpla.net Otto Hofstetter: “We are looking at making an acquisition“ In Uznach in Switzerland the economic boom is in full swing – and has been since last year – with every prospect of this continuing in 2011. It is in Uznach that Otto Hofstetter AG manufactures injection moulding tools, including the hot runners for high quality plastic packaging. Application areas include PET preforms (approx. 75% of total turnover) as well as thin wall packaging, cartridges and products for the agricultural sector. We travelled to Uznach, Switzerland for a PET Top Talk with Otto Hofstetter. One major factor which has contributed to the solid progress of the mould business is PET bottles for the beverages industry. This is a result firstly of the trend towards lightweight, materials-saving bottles and secondly of the increasing tendency of frequently switching to new bottle formats. Otto Hofstetter is participating in both trends. The numerous orders are doubtless the result of the current economic boom as far as moulds are concerned, but are also an indicator of the long-term, on-going work in the PET market carried out by Otto Hofstetter as a company. PETplanet Insider is continuing its series of Top Talks with Otto Hofstetter, focusing both on the company’s current success and on their long PET history. Otto Hofstetter goes back a long way, to the beginnings of PET and its introduction into the beverages market. We will also be taking the opportunity of speaking with the person who personifies Otto Hofstetter AG, namely, Otto Hofstetter himself, whose background and experience typifies a small- to medium-sized company. His story is both exemplary and interesting. This is what we were expecting when we travelled to Uznach on March 28, 2011 to interview Otto Hofstetter. And because, at Hofstetter, they attach great importance to teamwork, Stefan Zatti, Divisional Manager PET and Member of the Board, also took part in the discussions. PETTopTalk","@ID":12} "PET TOP TALK 14 PETplanet insider Vol. 12 No. 05/11 www.petpla.net 14 PETplanet: Does your planning allow for international production locations? Otto Hofstetter: Here in Uznach we are fortunate in having good resources in terms of personnel, highly trained skilled staff that we would not find abroad. It is also difficult to find people who are happy to take their expertise to India or China and to transfer the know-how. It is only once the staff problem has been resolved that we will look at taking our production abroad. PETplanet: Is Uznach in Switzerland the right location for deliveries to global markets? Otto Hofstetter: It goes without saying that Switzerland is the right location for manufacturing precision and quality. In sales we work alongside machine manufacturers and make use of their international organisational facilities. As far as service is concerned, we will probably be setting up further international strategic stations within the short term, because proximity to the client is an important factor – as it is, for example, in India. Currently our service and trouble-shooting engineers travel from Switzerland to our customers throughout the world. As things are today, a central service facility operating out of Switzerland is not a problem. PETplanet: Hofstetter, alongside Netstal, is perceived in the market place as a reputable company that tends to be respectable, solid and conservative rather than technically revolutionary, ingenious or innovative. Right or wrong? Otto Hofstetter: Yes and no. I think that, as the unit Netstal-Hofstetter we are conservative and reliable. As regards innovation, we are the driver of innovation in this partnership. In the last few years we have carried out further development work on the product; we have put forward proposals as regards cooling technology, including cycle times. We have ideas for robots. Our plan is to take our partners with us – for our mutual success. On market, marketing and strategy PETplanet: You once said with some regret: “We mould-makers are sandwiched between machine maker and converter, between the technical performance presented by the injection moulding machine and the customer requirement for a perfect process and a high quality end product”. It looks as though you fall between two stools. Otto Hofstetter: That used to be the case but things have changed. Today’s customers are more strongly focused on the mould-makers than they have been for years. What they have discovered is that the mould lies at the heart of the production line for PET preforms. This makes us as mould-makers very happy. PETplanet: You are cultivating contacts with the converters. What sort of volume of sales transactions do you achieve by way of direct contacts and how many with the machine manufacturers? Otto Hofstetter: We achieve approx. one third with the machine manufacturers and two thirds direct. Otto Hofstetter: “Mould precision plus reliability in terms of production and delivery schedules – these we rate pretty highly.”","@ID":16}
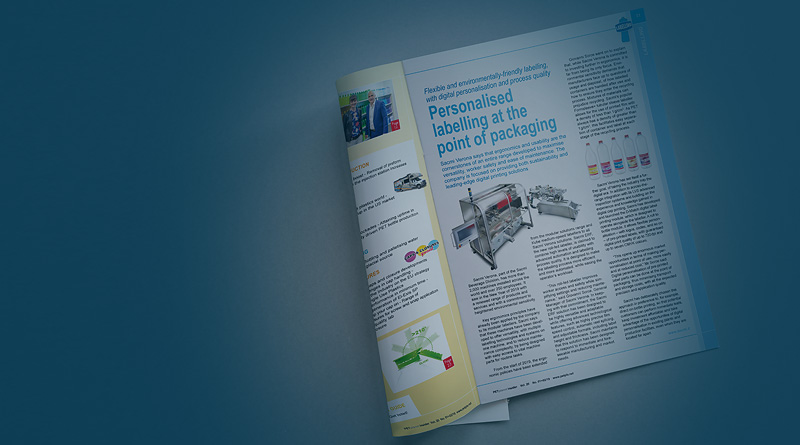