{"pages":{"page":[{"#text":"PRODUCTS 33 PETplanet insider Vol. 12 No. 07+08/11 www.petpla.net PETproducts Volumetric filling valves Sipa has developed a new series of volumetric filling valves: Isotronic SC for carbonated products and Unitronic SC for still products. These valves are designed to replace versions already present in the range. The aim was to achieve higher quality and levels of efficiency, while maintaining the key features of the previous generation. Both valves can modulate the filling speed to better suit the characteristics of the individual liquid product, avoiding turbulence, foaming and absorption of air into the product. The valves are characterised by high dosing precision, thanks to the use of magnetic flow meters. The valves can be equipped with additional elements allowing hot fill applications with re-circulation or with Ultra Clean. Special features allow the treatment of different bottle and neck sizes with reduced change-over times. All valves are made in stainless steel 316L and are solid and compact. There is a clear separation between the pneumatic parts and the parts in contact with the filling product, in order to avoid any problem with contamination. Each product/bottle size can be selected directly from the operator touch screen control panel. Electronic and pneumatic components are located in a box directly over the filling valve. The box is air-conditioned by a “vortex” system. Isotronic SC, the isobaric volumetric and electronic filling valve version, is suitable for filling liquids with or without gas into PET bottles. It is particularly suitable for filling liquids characterized by good conductivity, such as soft drinks, water and clear fruit juices. The bottles are held by the neck ring, no height adjustment of the machine is required and bottle sealing is guaranteed by a short stroke bottle lifter. Unitronic SC is the gravitational volumetric and electronic filling valve version, suitable for filling non carbonated conductive products like still water, juice, tea, energy drinks and milk in PET bottles. There is no contact between the valve and the bottle. Thanks to this feature, this version in particularly suitable for ultra clean solutions. Valves are very simple, product chambers do not come into contact with a single pneumatic part. The sealing is guaranteed by a pneumatic rise of the bottle lifter. www.sipa.com Integrated solution for dairy products and liquid food Italian company SMI, which has over 4,000 end-ofline packaging solutions and rotary stretch-blowmoulders for PET/PP containers installed worldwide, has launched a new, integrated solution branded as the EcoBloc Plus series. The machines feature integrated stretch-blowing, filling/capping and labelling of PET containers ranging from 200ml to 3l. the EcoBloc series, which does not have an integrated labeller, can handle containers with up to 10l capacity. EcoBloc and EcoBloc Plus systems are both suitable for bottling lines of milk, edible oil, still and carbonated drinks. They have been designed to be compact and feature technologies for synchronisation between the dry environment of the stretch-blowing module and the wet environment of the filling/capping module. The direct connection between the machine modules by means of transfer wheels reduces the number of machines installed and eliminates the need for a rinser, for accumulation conveyors and for conveyors between the blower, the filler/capper and the labeller. EcoBloc Plus systems are equipped with air recovery, which is claimed to provide up to 40% saving on air consumption. The area beneath the bottles is completely clear, which eases operator access for maintenance and cleaning operations. Electronic filling on EcoBloc Plus prevents any contact between the bottle and the filling valve, thus reducing moving mechanical parts. SMI says that the machines offer low cost of ownership and production capacities of up to 30,000bph. www.smigroup.it Bericap completes its range of one-piece closures for hotfill Bericap has been offering one-piece closures for hotfill applications since it launched its 38mm and 28mm closures on the Chinese market in 2003. These closures are now also in use in India, Russia, Central Asia and the Middle East. The company recently announced that Egyptian company Juhanya is now using Bericap closures for its hot-filled products, including Tingo juices. The company has now extended its hotfill closure offer with the launch of a 33mm closure, which features reduced wall thickness. Bericap is seeking to introduce thinner walls to 28mm and 38mm closures, also. Future hotflll applications with 28mm closures will, in future, use the same closures as CSD. All Bericap closures for hotfill are equipped with the company’s DoubleSeal system. www.bericap.com","@ID":35} "BOTTLE MAKING 16 PETplanet insider Vol. 12 No. 07+08/11 www.petpla.net Sokpol invests in growth with Sidel’s Predis FMa line A ‘sensitive’ affair Aseptic bottling technology is quickly becoming established in Poland, from where Sokpol supplies fruit juices to Eastern Europe, Portugal, France, Italy, and the US. It also has plants in Germany, the main consumer of fruit juices in Europe, and in Scandinavia. Prior to 2009, the company filled only cartons, glass bottles and jars. It has now been delivered its second Combi Predis line from Sidel. Sokpol’s plant in Myszków, near Katowice in Southern Poland, is located in a refurbished old factory. It was opened in 1992 by company president Roman Sobczyk and his wife, vice president Silvia Sobczyk. Over the past 19 years it has grown from a single TetraPak line to become one of the most innovative co-packers in Poland. The area’s well-developed road infrastructure enables it to supply its large supermarket group customers in its European markets. Sokpol has grown quickly since it decided to move into the 0.5l, 1.5l and 1.75l formats. It decided to buy its first Combi Predis FMa in 2008, which enabled Sokpol to aseptically blow, fill and cap its fruit juices in PET bottles in the same machine. However, the owners had no in-depth knowledge of PET or advanced sterilisation technologies. Its capabilities and capacities were not only limited technologically. Support and training boost performance “The company very much needed the full service support of an industrial partner who could help it realise its ambitions to become an innovative, growing company, able to meet modern market demands and changing consumer attitudes,” said Mr. Sobczyk. It turned to Sidel for expertise in co-ordination and support and implemented a training programme, which ran for seven months. It quickly noticed that its performance on new PET bottling lines improved. It saw a decrease in annual PET consumption, resulting in savings in raw material costs, as well as being more environmentally-friendly. Low operational costs, solid distribution networks and the emergence of new FMCG companies have made the consumer packaged goods industry extremely competitive and Mr. Sobczyk made the company’s objectives clear when he stated that Sokpol intended to consolidate its competitive position and create a strong brand. Its strategy is based on providing clients with high quality, good prices, and excellent service and support. Achieving its ambition of becoming a recognised player in the fruit juices, nectars, and soft drinks business is a challenge in itself, given the expectations of the domestic market and the requirements of the European Union. Progress is usually progressive but Sokpol took a significant step forward with the installation of the Combi Predis FMa system in 2009. In November 2010, the company decided to purchase a complete second, identical aseptic line, and to double its bottling capacity. In order to meet EU regulations and requirements, Sokpol has implemented Hazard Analysis Critical Control Point (HACCP), a method that aligns well with the guidelines supplied with Combi Predis FMa. The new line was delivered in April 2011. Sokpol, Poland, is a supplier of fruit juices for the markets of Eastern Europe, Portugal, France, Italy and has plants in Germany and Scandinavia sensitive BEVERAGES","@ID":18} "PETcontents 07+08/11 4 PETplanet insider Vol. 12 No. 07+08/11 www.petpla.net INSIDE TRACK 3 Editorial 4 Contents 6 News 33 Products 36 Bottles 38 Personal care 40 Patents MATERIAL / RECYCLING 12 High sun protection factor Developing a new sensitive product packaging solution: A case study BOTTLE MAKING 16 A ‘sensitive’ affair Sokpol invests in growth with Sidel’s Predis FMa line 18 Barriers without frontiers New coating technologies for beverage packages 21 Bottle developments for sensitive beverages Suppliers offer new PET bottle solutions BOTTLING /FILLING 30 Compact and dry PET Asept D Compact - the aseptic solution from Krones for the low output range 32 The next generation KHS launches dual-concept aseptic fillers PREFORM PRODUCTION 14 Parting line deformation A rapid guide to perfect preforms - part 22 MARKET SURVEY 23 Suppliers of single stage machinery BOTTLE MAKING 27 Single stage converters Single stage feature part 2 - A visit at PET Power, the Netherlands TRADESHOW REVIEW 35 Chinaplas, 2011 Page 12 Page 14 Page 27 BUYER’S GUIDE 41 Get listed! sensitive BEVERAGES","@ID":6} "PETpatents www.verpackungspatente.de 40 PETplanet insider Vol. 12 No. 07+08/11 www.petpla.net Plastic bottle European Grant of Patent No. EP 2049405 B1 Applicant: Sidel Participations, Octeville-sur-mer (FR) Application Date: 13.7.2007 A European patent has been granted for this process for manufacturing a plastic bottle with this particular shape base. Spray optimisation International Patent No. WO 2010 / 131066 A2 Applicant: Stormes Cuuvene Ltd., St. Peter Port (GB) Application Date: 15.5.2009 A pump sprayer is fitted with at least two riser tubes which guarantee product delivery regardless of position and permit optimum removal of residual quantities when the container is emptying. Depending on the requirement the “correct“ tube will be enabled. Pouch bottle European Grant of Patent No. EP 2050677 B1 Applicant: Krones AG, Neutraubling (D) Application Date: 1.10.2008 The European Grant of Patent describes a bottle preferably featuring a wall thickness of less than 0.05mm and having a specific volume relative to the grip area. The procedure used for its manufacture is also illustrated. Tamper-evident closure Disclosure No. DE 102009019362 A1 Applicant: Krones AG, Neutraubling (D) Application Date: 29.4.2009 In the interests of making the tamper-evident closure on a bottle cap even better and/or more readily identifiable a proposal has been put forward to fit a seal between the cap and the bottle which will be destroyed on opening the cap. Bottle for hot filling International Patent No. WO 2010 / 129402 A1 Applicant: Ball Corp., Broomfield (US) Application Date: 30.4.2010 Thin-walled PET bottle for hot fill applications. The shape of the bottle prevents any “oval” deformation of the container during cooling. Moulded bottle International Patent No. WO 2010 / 126829 A1 Applicant: Johnson & Johnson Consumer Comp. Inc. Skillman (US) Application Date: 26.4.2010 So as to suggest a usage to the consumer or to remind him of something, this plastic bottle is fitted with a neck similar to a “baby bracelet“, including the associated haptics.","@ID":42} "BOTTLING / FILLING 31 PETplanet insider Vol. 12 No. 07+08/11 www.petpla.net Thanks to the dry sterilisation process, no water is consumed during production for bottle and closure decontamination, nor during sterilisation of the product path and the filler’s cleanroom. The isolator, hygienically designed in conformity with EHEDG/3A, is first cleaned with caustic, then dried, and finally flooded with H 2 O 2 gas and decontaminated. Simultaneously, the product paths are cleaned with caustic and then sterilised in place (SIP) Minimal product losses Container sterilisation has been designed as a continuous process, so no switching valves are needed. This reduces the number of components and simplifies process monitoring. The filler’s aseptic filling principle provides for the product to come from above out of a rotating central tank with a static inlet, an axial face seal shuts off the gas phase, and the product does not pass through a manifold, all of which combines to minimise product losses. The filling valves are steamable, so no sterile water is required; the media used for CIP cleaning are returned via the isolator. At the closer, many critical components like the lifting cam and the reduction and stabilise the containers. The filling system permits the bottling of products containing chunks measuring up to 3 x 3 x 3mm (optionally up to 5 x 5 x 5ml). Product change-overs without intermediate flushing In order to avoid breaks in filling, the company has developed the following procedure: a product changeover can thus take place without any intermediate flushing. For this purpose, filling is continued until the tank runs empty, with a residual quantity remaining in the filling valve, which is topped up with the new product, whereupon the mixing phase is filled and rejected. This requires about two filler rotations, given a filler with a pitch circle diameter of 1,080mm and a pitch of 103mm, corresponding to 66 bottles. The new product can then be filled, without the isolator being affected by product residues. The elimination of intermediate disinfection ensures optimum availability. This enables long production cycles to be achieved of up to 48h with low-acid products and up to 72h with high-acid products. Availability is also boosted by shortened CIP/SIP times, with less than 3h from the last bottle to the first bottle. servodrives have been located outside the cleanroom. For closure sterilisation with H 2 O 2 , a static chute without any moving parts is used as a steriliser. This makes closure sterilisation affordable, simple and reliable, and avoids malfunctions on the closure path. The platform with stairs accommodates the valve rack, the central ventilation technology and the H 2 O 2 -sterilisable Hepa filters. Care has also been taken to ensure good access here to the treatment units. For the ventilation technology, an air route with monitored guidance was set up with supply air from the central zone, featuring inflow from above and extraction from below. A first reference system for the new PET-Asept D Compact was delivered to a German bottler early in 2011. Format [ml] Residues 0.5 ppm Residues 1 ppm 330 12,000 bph 12,500 bph 500 12,000 bph 13,000 bph 1,000 10,000 bph 12,000 bph 1,500 8,000 bph 9,000 bph 2,000 6,000 bph 6,750 bph PET-Asept D Compact – Maximum outputs for a pitch of 103mm when bottling still products www.krones.com The PET-Asept D Compact’s output range extends from 6,000 to 12,000bph: it can be installed as stand-alone machine or also as a monobloc with a stretch blow-moulder. sensitive BEVERAGES","@ID":33} "BOTTLE MAKING 17 PETplanet insider Vol. 12 No. 07+08/11 www.petpla.net Increased capacity and wider range “Our current capacity was and still is not enough,” Mr. Sobczyk said. “If we want to implement all of our projects and produce more effectively without, for example, having to change formats often, we needed a second line.” Both Combi Predis FMa complete lines will be able to fill more than 25,000bph (over 150 million/a) in 0.3l and 0.5l formats. Because of its greater filler capacity and cap change flexibility, Sokpol is aiming to run their new line with overall efficiency of over 90%. That is an ambitious goal but the company believes it is realistic. The Sidel aseptic filler has been found to permit continuous runs of 120h in high acid production, without intermediate sanitation. Cleaning and sterilisation can be completed in three hours, ‘bottle to bottle’. Sokpol’s new Combi Predis FMa will extend its bottling range and will produce 300ml, 500ml, 1.5l and 2l sizes, as well as a variety of capping formats such as sport caps for isotonic drinks for the ‘on-the-go’ market. From the environmental perspective, the Combi Predis FMa replaces bottle rinsing by peracetic acid (PAA) with dry decontamination of preforms using hydrogen peroxide vapor (H 2 O 2 ). The system reduces the number of machines and the overall footprint and delivers high decontamination performance without Predis and Combi Predis Sidel started with the dry preform decontamination by H 2 O 2 spray in 1998, with the Combi Disis. Originally the system was developed for liquid food products sold in the cold chain specifically for flavoured milk. A few years later, the system was introduced for UHT chocolate milk sold at ambient distribution. In 2006, the first Combi Predis with dry preform decontamination by H 2 O2vapor for ESL dairy products sold in the cold chain, with drinking yogurt as the first product in use, was launched. In 2008, Combi Predis was also sold for high acid, carbonated juices without preservatives at ambient temperature. Finally, the year 2009 marked the first Combi Predis for aseptic low acid products sold at ambient temperature, especially for UHT milk. The Combi Predis FMa replaces bottle rinsing by peracetic acid (PAA) with dry decontamination of preforms using hydrogen peroxide vapor (H 2 O 2) . The system reduces the number of machines and the overall footprint. It guarantees high decontamination performance without water consumption and uses only tiny amounts of chemicals. Sidel sold its 50th Combi Predis to Sokpol, Poland. water consumption, using only small amounts of chemicals. The time taken to heat preforms and the temperature level achieved during preform heating in the oven are sufficient to activate the small quantity of H 2 O 2 cold condensate and ensure even distribution on preform walls. This ensures a 100% bottle decontamination rate for a totally secure bottle production process. In combination with UV-C decontamination devices, air used for bottle blow-moulding and the air within the Combi keeps the bottles sterile until the filling and capping steps. The preform infeed uses ionization for dust removal, blow-moulding air is filtered to the 0.01 micron level and by-the-neck transfer of bottles under a controlled atmosphere all maintain The Sidel Combi Preis FMa line was delivered to Sokpol in April 2011 sterility. The continuous by-the-neck transfers and absence of any thermal stress on empty bottles have led to company to conclude that the Combi solution offers notable bottle lightweighting potential and greater bottle shape design freedom. Sokpol is converting technology to commercial advantage and using it to optimise the entire downstream packing process. By the end of 2011, it will have 19 different lines, including cartons, glass bottles, jars, aseptic and classic PET. The aseptic line takes up less space than other standard line configurations and the company has just finished construction of a 10,000m² storage depot, ready for its increased output. www.sidel.com sensitive BEVERAGES","@ID":19} "MATERIAL / RECYCLING 12 PETplanet insider Vol. 12 No. 07+08/11 www.petpla.net Developing a new sensitive product packaging solution: A case study High sun protection factor Protecting sensitive beverages while maintaining cost-effective production processes can present challenges in manufacture. UV light can cause reactions in UV-sensitive food and beverages that can result in changes in taste, odour and texture. The colour of juices can be affected, for example, as can the vitamin content. Colormatrix worked with a leading international brand owner to improve UV protection in a PET container. The company required a new container that could protect up to 390nm for highly sensitive products, as well as continue to protect less sensitive products. The key objectives were: Packaging weight reduction - Reduce the packaging weight by 10% without compromising its mechanical properties Better protection - The lightweight container had to protect the most sensitive products against UV light up to 390nm and below 10% transmission Reducing additive cost - Phase out old UV technology and replace with new more flexible, cost-effective and sustainable solution Increase recycle content- Increase the recycle content to 25% without compromising visual or mechanical performance. Challenges With light-sensitive products, improvements in one area can lead to problems in another. Lightweighting packaging, for example, makes it increasingly difficult to protect UV sensitive products, as the reduction in packaging weight typically reduces the wall thickness of the container. As a result, the use level of a UV blocker has to be increased to compensate for the reduced protection provided by the packaging wall. Increasing the use level of the UV blocker, however, not only increases cost, but can also lead to visual impact and contamination issues. Aesthetic quality can also be adversely affected by using higher levels of recyclate. Today’s packaging, ideally, has to accommodate a wide range of products with different UV sensitivities. As such, a more flexible and powerful single UV additive solution is required that does not impact the day-to-day manufacturing process. Addressing the issues In the original container, ColorMatrix’s UV blocker was dosed at 0.25%, providing UV protection up to 380nm using a 26g (500ml) container. The weight of the new container was reduced to 23.5g and accordingly, the wall thickness was reduced from average 0.40mm to 0.35mm. The manufacturer wanted to create a new container that not only needed to maintain the initial protection for low sensitive products, but also had to protect up to 390nm for highly sensitive content. sensitive BEVERAGES","@ID":14} "PETnews 6 PETplanet insider Vol. 12 No. 07+08/11 www.petpla.net Oystar and Sacmi to cooperate The Oystar Group, manufacturer of packaging machines, has concluded a cooperation agreement with the Italian Sacmi Group. The two companies aim to develop new market opportunities through integrated packaging solutions. The primary focus will be on the beverage industry. Above all, this cooperation will involve three core divisions. Thus plans are to combine Oystar Hamba Flexline filling machines with Sacmi blow moulding machines and in particular with the CBF machine (Compression-Blow Forming Technology). In the future, downstream solutions from Sacmi, such as those for labeling, palletizing or other end-of-line processes, are to be offered in combination with Oystar filling and packaging lines. And, finally, the two mechanical engineering companies also want to exploit synergies when it comes to the development of new and innovative solutions while profiting from their mutual know-how. “The portfolios of our two companies complement each other outstandingly,” underlined Sacmi CEO Pietro Cassani. “We will remain independent, but through this cooperation we will create genuine added value for our customers.” www.sacmi.com www.oystar-group.com PTI establishes new, independent closure testing lab Plastic Technologies, Inc. (PTI), Hollands, Ohio, USA, has established a new closure testing lab. “Closure manufacturers have traditionally offered testing support for their products, but up until now there really hasn’t been an independent closure evaluation and analysis lab. PTI’s new capability complements its previously-established bottle testing service. This means that brand owners wanting to test the performance of the entire package now have a one-stop place to go,” explains PTI’s Greg Fisher, Ph.D, who is responsible for overseeing the lab. Closure testing capabilities will include: application, top load vent, removal torque, opening performance, secure seal, carbonation retention, impact, barrier, scavengers, lubricants and others. The lab will also include a single-head capper to test reliable and reproducible capping, as well as a vision system to measure critical dimensions and facilitate tooling evaluations. Accurate analysis also is critical to ensure that packaging materials and structures haven’t been over engineered, thereby negatively affecting cost and source reduction initiatives. The total package approach also helps reduce the number of samples required to execute the tests and eliminates the need for correlated bottle data from one lab with closure information from another. PTI’s closure lab can analyze both plastic and metal closures for a broad variety of packaging applications. These include beverage, food, personal care, household chemicals and others. Fisher, the lab’s director, offers a significant amount of closure expertise, having previously worked for a leading closure manufacturer for almost a decade. www.plastictechnologies.com Krones re-structures its Supervisory and Executive Boards At the AGM in Neutraubling on June 15, 2011, the agenda for the shareholders of Krones AG included a vote on a revamped Supervisory Board. The following members of the Supervisory Board were re-appointed: Chairman Ernst Baumann (62), a former director of BMW AG, Norman Kronseder (48), farmer and forester, Dr. Jochen Klein (67), Managing Director of I-Invest GmbH, and Count Philipp von und zu Lerchenfeld (59), a member of the Bavarian State Parliament. The former President of Regensburg University, Prof. Dr. Erich Kohnhäuser (66), will be stepping down from the body upon conclusion of the AGM. Petra Schadeberg-Herrmann, (44) managing partner of Krombacher Finance GmbH, was newly elected to the Krones’ Supervisory Board. In the constitutive meeting following the AGM, the Supervisory Board of Krones AG decided upon the changes to the company’s Executive Board. After 15 years on the Krones AG’s Executive Board, the Deputy Executive Board Chairman, Hans-Jürgen Thaus (62), will be stepping down from it, with effect from 31 December 2011, having reached the contractually agreed age limit of 62. His successor as Financial Director is Christoph Klenk (47). An engineering graduate, Christoph Klenk has since 2003 been a member of Krones AG’s Executive Board, where he was responsible for Research and Development and Divisions. The successor to Christoph Klenk is the former Head of Research and Development, Thomas Ricker (43). A mechanical engineering graduate, Thomas Ricker is set to be appointed to the Executive Board with effect from January 1, 2012. www.krones.com Orders up at Erema Erema, the Austrian manufacturer of plastic recycling systems, reported improved sales performance for fiscal year 2010/2011, which ended March 31, 2011. The Erema Group is comprised of Erema Engineering Recycling Maschinen und Anlagen Ges.m.b.H., Ansfelden; Erema North America Inc., located in Ipswich/ MA; and 3S-GmbH of Roitham, Gmunden, Austria Consolidated sales across the Group were €95 million, with order intake at €127 million, compared with €75 million in 2009/10. Erema attributes its growth to further developments of its plant and process technologies, positive market developments, increased orders from existing accounts and the attraction of new customers. The company’s headcount increased to 335. www.erema.at","@ID":8} "23 Single stage machinery Readers will recall that, in our last issue, we discussed at some length the single stage process and, in addition to this issue (page 27), we will be highlighting this topic in two further issues when we shall also be exploring the technologies in more detail. The annual market survey with classic suppliers is the perfect supplement to our single stage feature in this issue. We are pleased to report that, along with Nissei, Sipa and Automa, Aoki is also back with us this year. Although the publishers have made every effort to ensure that the information in this survey is up to date, no claims are made regarding completeness or accuracy 07+08/11 MARKETsurvey Bottle-to-bottle recycling plants Conveyors for preforms and empty bottles Caps and closures Preforms Perform moulds and SBM moulds Single stage machinery 2-stage SBM machinery Compressors Filling equipment Resins and additives","@ID":25} "REGIONAL MARKET REPORTS 11 PETplanet insider Vol. 12 No. 07+08/11 www.petpla.net SOLO-MAS technology and savings Sacmi Filling S.p.A. Via E. Ferrari, 1 40026 Ramoscello di Sorbolo (PR) Italy Tel. +39 0521 695 411 - Fax +39 0521 695 401 E-mail: [email protected] www.sacmi.com SOLO-MAS is a modular and compact system which, thanks to a new patented technology, sets higher standards for filling accuracy, cleanliness, quality and safety of the product. The flexible software, the user-friendly operator interface and the reduced maintenance allow simplified and economical operation. SACMI Filling complete solutions for the beverage industry. Reg i ona l mar ke t repor t Finland part 2 - Issue 09/2011 Around half of packaged beverages relate to the alcohol segment (beer, cider, long drinks); the other half to the non-alcoholic sector. In Finland per capita consumption in the non alcoholic sector is at 104l. This represents only around 1/3rd of the comparable consumption of, for example, Germany or Italy (in each case just under 300l per capita). The reason for this could be the much shorter summer season (three months) for non-alcoholic beverages, and the outstanding quality of the municipal drinking water. Of significance is the rise of the Lidl chain in the Finnish market. With its imports, the German chain has successfully built up a 10% market share in CSD, and an impressive 33% in the case of water. In addition Lidl’s sales of own brand products, supplied by Finnish companies, means that their market share could well be higher. Table 2 Market share water in million litres 2004 2005 2006 2007 2008 2009 2010 Lidl Imports 6 11 23 31 30 29 31 Panimoliitto 63 63 68 69 64 59 65 Market share % 9 15 25 31 32 33 32 Table 3 Market share CSD/Tea etc. in million litres 2004 2005 2006 2007 2008 2009 2010 Import Lidl 25 28 42 40 45 37 34 Panimoliitto 275 273 282 278 269 267 263 Market share % 8 9 13 13 14 12 11 According to Canadean, in the water sector, 92% of all water is packaged in PET. In the CSD sector the proportion is likewise approaching 95% (Source: Canadean). Recycling A deposit is levied on all packs of beverages made from glass, metal and PET in Finland; up to 1l this amounts to 20 Eurocents and above that it is 40 Eurocents. Unsurprisingly with such a large deposit required, there is a very high rate of return in Finland. Some 13,000t of PET bottles find their way home from the end consumer (every year).","@ID":13} "BOTTLE MAKING 27 PETplanet insider Vol. 12 No. 07+08/11 www.petpla.net Single stage feature part 2 - a visit at PET Power in the Netherlands Single-stage converters In developed markets, single-stage processes are primarily used for commodities such as containers for the pharmaceutical, cosmetic and food sectors. In the emerging markets such as in Asia, South America and Africa there is considerable single-stage activity, including packaging for the beverages sector. Looking more closely at Europe the single-stage converter business is in the hands of a colourful mixture of small size, medium size and large companies – with a noticeable trend to consolidation from smaller to larger, the larger ones usually simultaneously engaged in numerous other diversified business activities. experience.Their facility is located in the industrial zone of Etten Leur near Breda, in the West of the Netherlands at the hub of land and sea transport facilities. Not far away is a major competitor, Graham packaging. Both companies have common historical roots here in the Netherlands. The company and its history The company was founded in 1995 by management of the former Skill Pack. Premises of PET Power are located just a few hundred metres away and today the original Skill Pack company is operated by competing Graham Packaging. In 2004 the US American John Raymonds bought PET Power and still is 100% owner. His commitment: “All we earn remains in the company and is invested to propel our growth.” We visited PET Power in the Netherlands, in order to gain a close insight into a single stage converting company. PET Power, the Netherlands We met Marcel Schröder, Managing Director:“We are scrupulously open in our approach to singlestage and two-stage technologies…. for our projects so far we have not yet decided in favour of two-stage.” Of the converters listed above we have selected PET Power to visit and to learn about their business – for various and sound reasons: PET Power’s only business is to manufacture PET containers for the pharmaceutical, cosmetic and food industries using single stage technology. No diversification, no resorting to other materials. PET Power is specialised, PET is core. The company is considered to be amongst the top 10 of European single-stage converters, and may even be amongst the top 3 considering the variety of PET containers on offer. Moreover, PET Power was recommended for a visit by both suppliers of single-stage equipment, namely by Aoki as well as by Nissei ASB. Here - at PET Power - both brands consider that their designs are shown to best advantage. Managing Director Marcel Schröder – we noticed from the first telephone contacts – was open minded, spontaneous and willing to share with us his knowledge and Aoki machinery for cleanroom applications by Wolfgang von Schroeter","@ID":29} "BOTTLE MAKING 19 PETplanet insider Vol. 12 centre of the lower antenna is used to distribute the gas inside the bottle. In order to enhance the ion bombardment on the interior bottle wall during the deposition process, a negative bias is applied on the bottle by means of a metallic bottle cage. There are various methods to extract the ions from plasma and to enhance the bombardment onto the substrate. DC bias for example can only be used for conductive substrates or films, and is therefore not suitable for polymer substrates. Since a charge accumulation does not occur for RF substrate bias, it is applicable to PET bottles. Substrate biasing can be used with the new reactor by electrically isolating the substrate holder from the chamber walls and placing a radiofrequency (RF) biased electrode (bottle cage) on it. This additional plasma source (RF source, Advanced Energy, Filderstadt, Germany) can be ignited independently from the MW source allowing three different operation modes: MW-, RF-, and dual mode. Developing a new coating process, the aim of this project was to study the effect of the substrate bias on the coating performance. A process that was developed in earlier studies was chosen. Hydrocarbon films (a-C:H) were deposited using acetylene (C 2 H 2 ) as layer forming precursor and a two staged pulsed plasma process with a fixed set of process parameters, which are shown in Table 1: Parameter Value Microwave frequency 2.45GHz Microwave power input: 1500W RF frequency 13.56MHz Pressure 20Pa ton (MW pulse duration) 5ms toff (MW interpulse period) 25ms Table 1: Fixed set of process parameters used for deposition of a-C:H films on PET bottles Are your standard PET preform molds making you as much money as they should? Ask how MPET with iFlow technology improves production and achieves greater quality results. Innovation doesn’t happen in isolation. It happens when blue-sky thinking meets down to earth knowhow and exceptional supply chain execution. The sort of innovation that Mold-Masters is known for, now applied to PET tooling for industry-leading results. Introducing MPET – the new PET preform tooling solution designed for the standards of tomorrow. Mold-Mastersand theMold-Masters logo are trademarksofMold-Masters (2007) Limited. © 2011Mold-Masters (2007) Limited.All rights reserved. Think about it. moldmasters.com/thinkaboutit [email protected] The deposition process consists of a pre-treatment of the polymer in an oxygen plasma and the final deposition of the barrier layer. The corresponding set of process parameters is shown in Table 2: Stage Parameter Value Pre-treatment Oxygen flow rate 60sccm Treatment time 0.5s Barrier layer C 2 H 2 flow rate 40sccm Argon flow rate 400sccm RF bias 0 – 80V (20V steps) Coating time 5s Table 2: Set of process parameters used for deposition of a-C:H films on PET bottles sensitive BEVERAGES","@ID":21} "PREFORM PRODUCTION 15 PETplanet insider Vol. 12 5. Reduce the initial mould opening speed (for the first few mm only) or increase the mould break valve to minimize the stress when the preform is released from the cavity. 6. Check that the hold (packing) time isn’t too short for the preform being moulded. Increase as necessary to improve solidification. 7. Check that the hold (packing) pressure isn’t too high to cause excessive swelling, especially in the last zone. Reduce as necessary. 8. Check that transition position is set to about 13% of shotsize + cushion. Lower values may result in overfilling. 9. Check all temperature readings and correct if necessary. PET resin should be melted at about 280ºC (536ºF) +/- 10ºC (18ºF). Minimize as necessary to reduce cooling requirements. 10. Check that the decompression (pullback) time and position is not too little. This should be set high enough to ensure the melt pressure is being released, yet as low as possible to minimize the risk of drawing in air. Typical settings for valve gated moulds are: Time = 0 – 1sec; Distance = 0 – 10mm. Non-valve gated moulds may require higher values to minimize gate stringing. 11. Check the valve gate close delay timer and decrease as low as possible to restrict any melt backflow into the nozzle tip area. 12. Check that the mould core half (moving platen side) doesn’t drop slightly during the unclamp and initial mould open sequence. This could scratch the bottom surface of the preforms. 13. Check that no anomalies are present on the moulding surfaces and robot cooling receptacles. Repair if necessary. 14. Ensure the mould / robot alignment is accurate. 15. Check hardware for worn, damaged or failed components, specifically the mould cavities, and clogged neck insert, cavity and robot receptacle cooling channels. www.petpla.net","@ID":17} "MARKET SURVEY 25 Automa SPA Aoki Technical Laboratory, Inc. Via Chiesaccia 38 40056 Crespellano -Bologna, Italy +39-051-739597 www.automaplast.com - www.automaspa.com Mr. Stefano Elmi Technical Manager +39-051-739597 - EXT.209 +39-051-739578 [email protected] 4963-3 Minamijo, Sakaki-Machi, Hanishina-Gun, Nagano-KEN 389-0603, JAPAN +81-268-82-0111 www.aokitech.co.jp Hiroshi Chino President Office +81-268-82-0111 +81-268-82-3699 [email protected] ECS FX 20 (6 models) ECS HS 12 (8 models) NSB 50 SH -3-stations-machine SBIII-500LL-50 From 0.25 to 3.8l From 0.25 to 7l 0,015 to 5l 0.25l to 2l Up to 80 Up to 40 1 to 12 9 ~ 16 cavities Up to 40 Up to 20 1 to 12 9 ~ 16 cavities 46.50g for the 80 injection cavities 37.50 g for the 40 injection cavities 4,5 to 105g 30 ~ 50g 36,000 b/h 18,000 b/h 1800 pcs/h. Approx. 5,485 27,100 b/h 13,600 b/h 1660 pcs/h Approx. 3,600 13,500 b/h 9,500 b/h 1200 pcs/h. Approx. 3,360 on different model (Please contact Aoki.) 700 pcs/h. Approx. 2,400 on differerent machine model (Please contac Aoki.) 4800 pcs/h. Approx. 2,000 ~ 4,000 400 pcs/h. 6.38 x 3.55 x 3.49 (m) Lightweight containers asymmetrical containers off-centred neck hot fill containers pasteurizable containers aseptic PET containers for cold filling ultra clean pet containers Lightweight containers big size containers(up to 30 l) asymmetrical containers off-centred neck hot fill containers pasteurizable containers aseptic pet containers for cold filling ultra clean PETcontainers 5,5 x 1,9 x 3,3 500 kN 510 mm 400 kN 220 mm NSB 80 - 4-stations-machine 0,030 to 5 1 to 16 1 to 16 5 to 105 grams 2400 pcs/h. 2200 pcs/h. 1900 pcs/h. 1000 pcs/h 6800 pcs/h. 500 pcs/h. 800 kN 630 mm 550 kN 220 mm Hybrid System\" for high quality, high cycle & energy efficient molding.","@ID":27} "BOTTLE MAKING 29 PETplanet insider Vol. 12 No. 07+08/11 www.petpla.net PET Power’s policies Asked about PET Power’s policies, Marcel Schröder quotes: “We are scrupulously open in our approach to single-stage and twostage technologies. First we monitor the market and listen to the client’s request – then we consider the necessary investment to satisfy the demand – then we decide about the machine platform – whether single or two-stage technology is the preferred option. Certainly, the decision is dependent on the volume of bottles to be moulded. In our view the issue should not be handled dogmatically or ideologically. The markets of single-stage and two-stage processing communicate with each other, supplement each other. At times products are developed using single-stage and when they reach higher volumes, they could well be processed in two-stage equipment with small cavitations. We also know that some products – for edible oil for instance – are well converted in both technologies.” So far we have confined ourselves to an annual volume of 10 million units per product type and stayed with single-stage processing. For our projects so far we have not yet decided in favour of two-stage. But for the future: We would never exclude two-stage processing in principle.” Fundamentals of company strategy On basis of the existing singlestage platform - as available for business today and for the foreseeable future – PET Power has formulated some fundamentals of company strategy: Operating in Europe only – from Portugal to Russia, from Scandinavia to Italy Aiming for business up to max. 10 million units per annum Solid packages/bottles/containers only Complete packages including labels, sleeves, prints and caps / closure systems, where desired Subsidiaries to be established – where transport especially of large bottles is a negative cost factor. Asked about the foreseeable future Marcel Schröder – low key and modest, but also engaged and ambitious: “Business is very competitive today. PET Power is a decent and respected enterprise within Europe. Our principles in doing business are open communication and fairness to our business partners – clients as well as suppliers. Our slogan “packaging your brand” communicates that we are part of a supply chain. In five years time either we will lead the market or we will be part of a large EU group – as a consequence of consolidation of our single-stage markets. Here in-house in Etten Leur we are still able to expand. But singlestep conversion is geographically a regional business. One needs subsidiaries in distant markets. Europe is PET Power’s home selling market. We are currently experimenting in China with some moulds for new product development and small containers. The world is opening up, also within PET Power”. Bottle range made of preforms of the same size In forthcoming issues of PETplanet: PART 3: Single stage machinery makers Nissei PART 4: Single stage machinery makers: Aoki Sipa","@ID":31} "MARKET SURVEY 24 MARKETsurvey 07+08/11 Company name Nissei ASB Machine Co., Ltd. Sipa SPA Postal address Telephone number Web site address Contact name Function Direct telephone number Fax E-Mail 4586-3 koo, Komoro-shi, Nagano-ken, 384-8585 JAPAN +81-267-23-1565 http://www.nisseiasb.co.jp/en Mr. Katsuo Ishiguro Section Manager, Sales Coordination Team +81-267-23-1565 +81-267-23-1564 [email protected] Via Caduti del Lavoro 3 31029 Vittorio Veneto, Italy 00390438911511 www.sipa.it Machinery Division Director 00390438911511 00390438911694 [email protected] Single stage ISBM machines Machine model / number ASB-50MB, ASB-12N/10, ASB-15N/10E, ASB-70DPH, ASB-70DPW, ASB-150DP, ASB-150DPW, ASB-650EXHS, ASB650EXHD, PF8-4B, PF6-2B, PF4-1BH, PF3-1BH, PF3-1BHLL ECS HS 6 (6 models) Bottle volume (from/to in litres) 0.003 (3ml) - 20l From 0.25 to 10l Number of preform cavities 1 - 36 Up to 20 Number of stretch blow mould cavities 1 - 36 Up to 10 Max. preform/bottle weight in grams for the stated number of cavities 3 grams - 800g 75.00g for the 20 injection cavities Hourly output based on: 0.5 litre container 1,200 -7,000bph 8,000 b/h 1 litre container 720 - 5,300bph 7,200 b/h 1 litre wide neck container up to 5,300bph 4,600 b/h 2 litre wide neck container up to 2,000bph other (e.g. containers for personal care products...) up to approx. 6,000bph Machine footprint / space requirement (LxWxH in metres) 3.56 x 1.14 x 2.73 (ASB-50MB) 7.66 x 3.12 x 3.89 (ASB-650EXHD) Special features (short description/keywords) Moldable resins include PET, PP, HDPE, LDPE, PLA, PES, PPSU, PC and others. Lightweight containers Big size containers(up to 30l) asymmetrical containers off-centred neck hot fill containers pasteurizable containers aseptic pet containers for cold filling ultra clean PET containers","@ID":26} "BOTTLE MAKING 18 PETplanet insider Vol. 12 No. 07+08/11 www.petpla.net New coating technologies for beverage packages Barriers without frontiers* The Institute of Plastics Processing (IKV) at RWTH Aachen University, Germany, is currently investigating a process to improve the barrier performance of plasma polymer layers using a substrate bias. Here are some results of the study. Since the last developments in light weighting and barrier coatings, PET bottles have become a serious alternative even in applications in which classically glass is used. PET bottles have never been more compelling for beer bottling; convenient, shatterproof, material and energy efficient. The forecasts promise an increased consumption of up to 5.3% to 7.7 billion packaging units worldwide until 2015 [1]. An essential aspect in further development, in order to widen the scope of application not only for PET, but also for materials such as polylactide (PLA), is to enhance the low permeation barrier of plastics. For certain applications plastics in packaging do not provide a sufficient permeation barrier for gases. To overcome this weakness, innovative technologies have been developed. Besides the use of monolayer-blends, the plasma coating process is increasingly attracting attention due to its cost attractive and effective barrier enhancement. It consists of the deposition of a thin barrier film (20-100nm) on the surface of the bottle. This film is obtained by exciting a monomercomposed gas with microwave energy under low pressure. To meet the challenges and rising demands of modern packages on excellent barrier properties for a high shelf life of the packaged good, increasing effort is made to further enhance the performance of modern plasma coating processes. At this, not only existing processes are optimised, but new process variants and new coating systems are evaluated. First key experiences come from coating of plastic foils. It was discovered that a substrate bias leads to a significant increase in the barrier properties because the negative effect of layer defects is reduced by ion bombardment during film deposition. Extensive studies on its suitability targeted at bottle coating cannot be found in literature. Interior coating of PET bottles using a substrate bias Within the development of a suitable coating reactor to investigate the interior coating of PET bottles using a substrate bias, strong emphasis has been placed on investigations concerning different bottle shapes and materials. Fig.1 shows the plasma polymerisation reactor used for coating thin films. The design of the used microwaveinduced plasma reactor consists of a stainless steel cylindrical tube using a microwave (MW) driven plasma source. Microwaves, generated from a magnetron (2kW, 2.45GHz, IBF Electronic, Ober-Ramstadt, Germany) are coupled into the processing chamber using a coaxial waveguide system which is arranged in the lid. Under certain circumstances, including the overall gas flow into the chamber, the amount of microwave energy and pressure condition (2-100 Pa), the microwaves create and maintain a low pressure plasma. The reactor used is of in-plasma type i.e. the substrate to be coated is inside the plasma volume. Therefor the vacuum chamber contains a socket to hold the sample. Other periphery like vacuum pumps, a pressure controller and four gas flow controllers correspond to the standard design. In order to excite a plasma and deposit a coating on the interior of the bottle the upper antenna is used to conduct the pulsed microwave energy into the chamber, while the isolated hollow Figure 1: Plasma reactor for substrate biased coating of bottles sensitive BEVERAGES","@ID":20} "BOTTLING / FILLING 30 PETplanet insider Vol. 12 No. 07+08/11 www.petpla.net PET-Asept D Compact – the aseptic solution from Krones for the low output range* Krones has developed and field-tested a compact-sized PET aseptic filler, for mid-tier companies. Demand on the market is already high, since this provides bottlers with an option for handling even relatively small batches in aseptic mode while retaining viable cost-efficiency. Aseptic PET filling on a compactly dimensioned aseptic line facilitates the change-over from carton packages to PET, which is more popular with consumers, or quite generally getting started with PET-filling of sensitive beverages without any preservatives. The option for lightweighting bottles by using a nitrogen droppler renders this technology more than equal in terms of cost-efficiency to the linear machines in the cartoning field. The PET-Asept D Compact technology is based on a line acceptance-tested by the American Food and Drug Administration (FDA). No sterile-water UHT unit is now required to operate it. Containers and isolator are sterilised using gaseous hydrogen peroxide. The machine itself is cleaned using caustic and acid. This means that peracetic acid and foam cleaning products are no longer required on the system. Its small footprint on a minimised floor area is comparable to that of linear machines. The output range extends from 6,000 to 12,000 containers/h. The machine can be installed in a stand-alone configuration or also as a monobloc with a stretch blowmoulder. In the core zone, the machine concept is restricted to an area of 6 x 2m. Here, the containers are passed by a gripper conveyor system first through a pre-warming zone before proceeding to gaseous H 2 O 2 sterilisation and the blow-out section of the steriliser, and finally being filled and closed. The heightadjustable conveyor is already insulated from the sterile zone, thus enabling minimised change-over times without any handling parts to be achieved. PET-Asept D Compact is an authentic aseptic solution for mid-tier companies. The containers, closures and the isolator are dry-sterilised using H 2 O 2 , thus ensuring container reduction rates for interior decontamination of as much as log 5, and for exterior decontamination of log 4. The H 2 O 2 residue is assured at ≤ 0.5 ppm. Container shrinkage is likewise very low, at ≤ 0.5%. The PET-Asept D Compact can handle containers with heights of 120 to 350mm and diameters from 50mm, plus neck finishes of 28 to 38mm, as well as flatcaps and sportscaps as closures. The gentle H 2 O 2 process enables lightweight containers, e.g. 13-to-14g preforms for a 330ml container, to be handled. There is also an option for dosing liquid nitrogen in order to reduce oxygen Compact and dry *Based on an article by Roland Laumer, Krones AG, Neutraubling sensitive BEVERAGES","@ID":32} "BOTTLES 37 PETplanet insider Vol. 12 No. 07+08/11 www.petpla.net Juice drink for children Czech drinks company Mattoni has recently launched a new juice drink for children, named Aquila Bimboo Frutta, which is available in three flavours and was developed in cooperation with Czech paediatricians. Labelling on the 33cl PET bottle features popular movie characters such as Shrek and Captain Jack Sparrow. The high-fruit drink has no added sugars and is filled on a Krones aseptic filling line. The package is completed with a standard Original 30/25 sport cap from Aptar. Mattoni has a long-standing relationship with Aptar and has been using the 28mm Original sport cap on its leading brands for several years. www.mattoni.cz www.aptar.com Fine food German retail giant Metro is selling milk in a one litre PET bottle under its own premium label, Fine Food. The tall, easy grip bottles have a shrink sleeve label with a nature-orientated design and a 32mm screw cap with tamperproof seal. The shelf life of the low-fat UHT milk and UHT full-cream milk is six months if kept in cold storage. www.metrofinefoods.com Slimming without tears 750ml sugar-free fruit drink for slimmers is being marketed by the French company Juvaligne of Paris in a distinctively shaped, red PET bottle. The waisted bottle features front and rear labels adapted to suit the shape and a screw cap with tear-off tamper-proof seal. Its bright red, strident colour and its waisted shape ensure that it stands out at the POS. www.juvaligne.com Lightweight hotfill bottle in SE Asia PT Ultra Prima Plast, a manufacturer of VC shrink film and injection-moulded products in Jakarta, Indonesia, has entered the growing PET packaging business in SE Asia with a new lightweight 500ml bottle, which is being used for FitActive, a house brand for distribution in supermarkets and local retail stores in Jakarta. The new product is intended to satisfy demand for affordable, quality packaging for new dairy-based nutritional drinks with real fruit juice, delivering quality packaging and reducing waste. The company worked with Sidel to develop a customised solution. The project’s aim was for a 20% weight reduction and savings on manufacturing costs. Sidel conducted design and feasibility testing at its Packaging & Tooling Center (PTC) in Shanghai and developed a 22.5g 500ml square-section hotfill PET bottle with a filling temperature of 89°C. Good high-temperature and mechanical performance is delivered by special panels. www.sidel.com","@ID":39} "BOTTLE MAKING 28 PETplanet insider Vol. 12 No. 07+08/11 www.petpla.net Nissei ASB machinery with capacities of 3,000 to 5,000bph Marcel Schröder – a MA economist by education – took over as the Managing Director in 2006. Under him he has a team of five directors for production, finance, quality assurance, sales and business development. Head office and production site are located in Etten Leur, the Netherlands. PET Power has enjoyed steady growth: Sales of €32 millions in 2006 Sales of €38 millions in 2009 Sales of €40 millions in 2010 In 2010 industries suffered under the financial and economic crisis. But the year also brought the Mexican ‘flu’. Bad enough for those affected , it was a “blessing in disguise” for the pharmaceutical industries and their suppliers including PET Power. In total PET Power supplied over 30 million units to package for the Antibacterial Gel (normal annual supply 3 to 4 million packages) and this helped the company to weather the crisis. In 2011 further growth in sales is expected, especially in foods (spices, peanut butter, spreads, dressings, etc.) where PET is increasingly replacing glass. But as the markets grow, results and profits – according to Marcel Schröder - will presumably be under pressure. Markets PET Power serves the three following trading branches: Pharmaceutical, exclusively for extreme clean room production, cosmetics and foods. Pharmaceutical is core business.Substantial growth is expected in foods. In plastics production even the smallest metal fragments can have far-reaching consequences. Total machinery protection guarantees high productivity and optimizes machine utilisation. Foreign body detection and separation for production and recycling S+S offers comprehensive separation and sorting solutions for the entire PET product life cycle: for the protection of injection moulding machinery for preforms and closures as well as for separation or material sorting – from systems for whole bottle sorting to highly sensitive PET particle separation. All about PET S+S Separation and Sorting Technology GmbH Metal Detectors Metal Separators Magnetic Separators Sorting Systems www.sesotec.com/pet Products Trends in single stage conversion are the same as for two stage conversion: Light weighting to safeguard resources Utilisation of recycled PET for cosmetics and foods (for pharma packaging no recycled resin permitted). Energy saving All the above should reduce carbon print for a sustainable package production. Facts and figures Approx. 220 employees A multifunctional machine platform with 52 systems, including Aoki 250, Nissei ASB-70DPW and ASB150DP, with capacities between 3,000 and 5,000bph. Aoki’s and Nissei’s are both considered to be very versatile and well suited for continuous operation. Both seen as the BMW and Mercedes of this industry, market demand determines which platforms best to use Between 5,500 and 8,000t/a PET conversion More than 240 preform moulds. Between 300 and 500 million containers/a More than 1,200 types of products. For fast delivery, cost and price consideration: there is always a family of formats from which to select, shapes in different sizes. More than 100,000 pallets handled annually Storage space available for more than 20.000 pallets. Average turn around stock every 2 months depending on season Number of customers: 2,000 Points of sales in 19 European countries – sales by in-house staff, agents and distributors with licence agreements Show piece of the clinically clean PET Power production is the clean room area, where currently 10 machines produce for the pharmaceutical industries. After single stage moulding bottles are tightly wrapped with several layers of plastic foils – without manual intervention – thus taking care of the delicate filling afterwards.","@ID":30} "BOTTLE MAKING 20 PETplanet insider Vol. 12 No. 07+08/11 www.petpla.net As substrate PET bottles with a volume of 0.5l, uniform neck geometry and a standard PCO28mm thread were used. Results and discussion For the measurement of the deposition rate, an adhesive tape is applied on the bottle surface before the coating process permitting the determination of the layer thickness by means of atomic force microscopy (AFM). Therewith the deposition rate can be determined by measuring the step height between coated and uncoated regions (Figure 2 and Figure 3). Using this method, coating thickness was determined to 90nm resulting in a deposition rate of 18nm/s. It was found, that the deposition rate is not influenced by a variation of RF bias. The surface morphology was analyzed simultaneously with regard to the roughness of the coatings. Evaluations show, that there is no obvious change in the average surface roughness with R a values between 7.1nm for coated samples without the use of a substrate bias and 3.8nm with an 80V RF bias applied. This confirms the assumption, that an applied RF bias does not change the morphology of the coatings significantly. Furthermore it could be observed, that the coatings show a good adhesion to the substrate. This can be concluded as no obvious delamination could be observed during the investigations carried out. The barrier properties of the deposited coatings were evaluated by measuring the carbon dioxide permeation rates through both coated and uncoated PET bottles using a gravimetric method. The bottles were filled with a specific amount of dry ice and sealed with an aluminium closure. After evaporation of the dry ice, an internal pressure of 2bar was reached. The prepared bottles were stored at 23°C and a relative humidity of 40% rh. The barrier improvement factor (BIF) against carbon dioxide permeation is then calculated by the weight loss of the uncoated bottles compared to coated ones. Preliminary results, due to limited number of samples, showing the best achieved barrier improvement are depicted in Figure 4. The achieved BIF values for a biased deposition seem to be higher than without. Although the results of the AFM measurements show, that the morphology of the coating surface does not change significantly. This clearly indicates changes in the layer structure itself. The results furthermore suggest a linear dependency between the applied RF bias and the achieved BIF value. This has to be investigated more closely with a higher number of samples and a wider range of the RF bias variation, since the experiments carried out so far do not show any sign of a saturation level. Conclusions A new reactor for plasma coating of plastic bottles has been designed allowing a future investigation of the influence of an applied RF substrate bias on the performance of plasma polymer barrier coatings. The presented results show that it is possible to achieve adhering coatings with enhanced CO 2 barrier properties on PET using a substrate bias. Besides the performance also the flexibility of the coating has to be taken into account. The influence on the strain tolerance is crucial for the success of this technology. For applications such as carbonated soft drinks a high strain tolerance is necessary, since the internal bottle pressure leads to a stretching of the bottle. Using coatings with a low strain tolerance, stretching of the bottle leads to a cracking of the barrier coating and thereby to a reduction of the barrier performance. In a next step, a transfer of the biased coating process to other materials such as polylactide (PLA) is targeted. This will show influences of different substrate materials on the plasma process and thereby on the structure of the plasma polymer layers and the result of the biased barrier coating. Acknowledgements The research project (No. 16306 N) of the Forschungsvereinigung Kunststoffverarbeitung has been sponsored as part of the “Industrielle Gemeinschaftsforschung” (IGF) by the German Bundesministerium fürWirtschaft und Technologie (BMWi) due to an enactment of the German Bundestag through the AiF. Fig. 4: Best measured CO 2 -barrier improvement varying substrate bias *contributed by Ch. Hopmann, W. Michaeli, K. Bahroun, H. Behm Institute of Plastics Processing (IKV) at RWTH Aachen University, Germany Fig. 2: AFM-image of a a-C:H coated PET bottle without substrate bias Fig. 3: AFM-image of a a-C:H coated PET bottle with substrate bias applied (80V) 2,5 2,0 1,5 1,0 0,5 0,0 0 40 80 60 RF Bias [V] CO 2 -BIF [-] References [1] N. N.: http://www.kiweb.de/Default. aspx?pageid=199&docid=219491. [2] S.-M. Baek, T. Shirafuji, S.-P. Cho, N. Saito, O. Takai, Japanese Journal of Applied Physics, 49, (2010), 08JF10-08JF10. [3] A. Grüniger, A. Bieder, A. Sonnenfeld, P. R. Von Rohr, U. Müller, R. Hauert, Surface and Coatings Technology, 200, (2006), 4564-4571. sensitive BEVERAGES","@ID":22} "TRADE SHOW REVIEW 35 PETplanet insider Vol. 12 4-colour offset printing machine for closures The company Wutung Holding Co., Ltd. (Hongkong) has exhibited its high-speed 4-colour automatic offset printing machine WT-3025 for closures.The automatic feeding system is made of aluminium and stainless steel, the conditions of the feeding tracks are monitored with sensors. Any dust on the caps surfaces is removed by means ofstatic bars before printing. The heart of the machine is two sets of colour offset printing heads equipped with magnetic print rollers. Each print head can be individually adjusted to different directions. In order to have a better shining effect on the cap surface, a varnishing unit with anilox rollers is employed. The caps are automatically unloaded, with counting and placing them into the carton system. The whole printing system can be operated via a user-friendly touch screen display. The WT-3025 is suitable for the caps sizes 28-38mm, with a maximum printing area of 34mm and a capacity 90,000 pcs/h. Smaller units with less capacity are also available. www.wutung.com.hk KraussMaffei and Netstal subsidiaries to merge in China In parallel with the merger in Brazil, the KraussMaffei Group is also bundling its activities in China. In the future a single subsidiary will market the products of all three brands, namely KraussMaffei, KraussMaffei Berstorff and Netstal. The new KraussMaffei Group subsidiary in China merges two existing Chinese subsidiaries into Shanghai KraussMaffei Machinery Co. Ltd., located in Shanghai. It started operating on July 1, 2011. Managing Director of the new, larger subsidiary in China is Harald Schweitzer. Each brand will continue to operate independently in the market. www.kraussmaffei.com Organoleptic HDPE grade for caps and closures Organoleptic properties are important requirement for materials used in water packaging as they ensure the high quality of the water. Sabic HDPE CC862 injection moulding grade is targeting the Caps & Closures (C&C) segment for qualitative still water packaging with high demands on organoleptic properties. This grade counts with the approval of triangular test NF V09-013 and has several key advantages that include being odourless, tasteless, easy to process with good mechanical properties, ESCR and high impact strength. During manufacturing, the process ensures no contamination with any foreign materials which makes Sabic HDPE CC862 suited for caps used in the packaging of still water. www.sabic.com","@ID":37} "PETbottles 36 PETplanet insider Vol. 12 No. 07+08/11 www.petpla.net Original cocktail Under its own ”Rioba“ label Metro Cash & Carry is marketing a range of alcoholic cocktails in specially designed 0.2l PET bottles. The round-bellied bottle is decorated with a silver-coloured shrink sleeve label and sealed with a black aluminium screw cap with a tearoff tamper-evident guarantee. The product supplier is MCC Trading Deutschland GmbH of Düsseldorf. www.metro24.de A taste of wine The French company Chamarré based in Paris is marketing red wine from Bordeaux in a 0.75l PET bottle. At first sight the dark bottle featuring an indented base and resembling glass is not readily identifiable as a PET bottle. It is fitted with a screw cap, the surface area of which is extended downwards so as to form a type of collar and labelled in the same way as a conventional wine bottle. A sticker affixed to the top serves as a tamper-proof guarantee; this splits when the cap is screwed open, thus providing a reliable indication that this is the first time the bottle has been opened. www.chammare.com Naturally cloudy The Jacoby Kellerei in Auggen, Germany is marketing its naturally cloudy apple juice under the brand name of “Schwarzwaldhof“ in a 1l PET bottle. The somewhat squat moulded bottle sports informative labels both at the neck and at the base and is fitted with a large 32mm diameter opening for dispensing the contents. The colour-matched plastic screw closure is equipped with a tear-off tamper proof seal. www.schwarzwaldhof.de Juicy quality 250ml orange juice, brand name “Sunny Delight“, is available in France in a 250ml PET bottle. The small, handy bottle features an easy to peel-off all-round film label and a screw cap which is large by comparison with the container format, having a diameter of 32mm and an integral tamper-proof seal. Stabilising crosswise elements in the base and central section are of considerable help in ensuring that the bottle is safe when placed in the upright position and in providing assurance of stability. www.sunnydelight.fr","@ID":38} "REGIONAL MARKET REPORTS 10 PETplanet insider Vol. 12 No. 07+08/11 www.petpla.net When, in 2008, the changeover took place from the highly robust PET refillable bottles to the lighter weight disposable bottles, the bottlers made their decision in favour of similarly robust yet disposable bottles. Weights for 0.5l bottles averaging 26g or an average of 43g for the 1.5l bottle are therefore the norm in Finland. Format changes need to be slick and all the bottlers are using the single section PCO 28. Cap weights of the bottles averaged around 2.9g. This weight matches the internationally determined mean weight for these caps. For the likes of Pepsi Cola and Coca Cola and their own brands the bottlers sometimes use the same preform weights. Generally speaking, suppliers of preforms to Finland are Putoksniks or Retal Europe, both from Lithuania. Logistics In addition to the large number of products that form part of the repertoire of every bottler, they also run a storage and retrieval operation, despatching a large proportion of their goods directly to the supermarket. So it is not difficult to amass up to 500 different products from cans to glass to PET for handling. Because labour costs are high in Finland, all breweries feature practically the same fully automatic storage facilities and storage retrieval/order picking arrangements. The basis for this very high level of automation is re-usable hard trays made from plastic which are here known as ”Displays“. For each type of drinks packaging there are special country-wide standardised displays that are loaded by robots directly at the end of the filling lines and collected on pallets (Fig. 1). In the case of PET bottles, there are 3 different types: one for the 0.5l bottle, one for the 1 litre and another for the 1.5l bottle. This fully automatic set-up leaves no room for any individuality. Fig. 2 shows, for example, how the cap on the overlying bottle supports the superimposed display pack. If the shorter PCO1881 cap were used instead of the PCO28, it would involve a radical re-design of the existing display pack. Nevertheless we heard time and time again that one or the other bottler was working on finding a solution to the problem. With around 500 million filled PET bottles in Finland it is not a difficult matter to quickly work out when the reorganisation has paid for itself. The two preform suppliers are already offering the weight-optimised preforms for the short cap. Fig.1: At the end of the filling lines, robots collect the bottle trays. After that, the trays are collected on pallets. One possible way forward would be to introduce the 1881 for the (likewise) standard Sixpacks that are not supplied in displays. Against that, however, is the fact that up to 2/3rds of the bottles reach consumers via displays, so this solution would incur additional expenditure on set-up in the bottling plants. Nevertheless the consumer is already buying the 1881. The discount chain from Germany, Lidl, has a big presence in Finland. They market their own brands that are bottled in Finland, although Lidl also imports a large number of soft drinks into Finland from Germany. Here the extremely light weight bottles for which Lidl is well known are fitted with the optimised 1881 cap. Since Lidl, as is customary in international markets, offers the bottles heat sealed on to pallets without any displays, the lightweight cap can be used here without any problems. Fig.2: Tray supported by the bottle cap Beverages consumption It’s always the same, you ask three different market researchers a question and you get five different answers. We asked three respected organisations, Canadean, the Finnish Panimoliitto Federation and the Federal Statistics Office in Germany for reliable data about the Finnish market. Although the figures (see Table 1) are not 100% complete, they are sufficient for us to attempt a reasonably comprehensive market analysis. Table 1: Breakdown by type of beverage packed 2010 Overall consumption of beverages in Finland 2010 Source: Panimoliitto PETplanet estimates Federal Statistics Office Members Smaller fillers Lidl imports Total Litres per capita % in million litres Beer 395 0 0 395 76 39 Cider 31 0 0 31 6 3 Long drinks 41 10 0 51 10 5 CSD/Tea etc 263 100 34 397 76 39 Water 65 50 30 145 28 14 Total 795 160 64 1019 196 100 Total as per Canadean 1200","@ID":12} "TRADE SHOW REVIEW 34 PETplanet insider Vol. 12 No. 07+08/11 www.petpla.net Chinaplas 2011 – Bigger than ever This year was the 25th Chinaplas jubilee and more than 2,200 exhibitors from around the world presented their products under the theme “Green Plastics – Our Goal – Our Future” to made efforts to promote environmental friendly technologies, recyclable plastics and bioplastics. It was the largest show scale ever with 21 exhibition halls and a total exhibition area reaching 180.000m². Conferences and more than 40 technical seminars accompanied the show. 94,084 visitors (thereof 20.3% from overseas) visited the 4-day exhibition. It is estimated that in 2010 the Chinese plastics industry consisted of 95,000 companies which produced more than 58 million tons of plastic products, an impressive average annual growth of 20%. Herewith also the plastics machinery sector experienced strong growth and produced 300,000 sets of machines with a total value of RMB 42 billion (€ 4.5 billion), thereof RMB 6 billion (€ 650 million) for export. China-made plastic machinery keeps its share of around 80% in the domestic market. The PET activities of the exhibitors were mainly focused on PET recycling and PET preform production. Leading PET machinery suppliers such as Husky or Sidel were not present. While some local Chinese companies wanted to show how much they have advanced in the fields of preform injection moulding machines and moulds others have simply focused to offer the lowest possible price. One of the local Chinese companies for instance stated that a complete 5 gallon PET bottle production line (from preform manufacturing to bottle manufacturing) would only cost about USD 52,000 –58,000. The finishing of the displayed moulds and machines was from rather modest to pretty good. Some local Chinese companies claim that they can produce up to 96 cavities and use highest-quality steel such as S420 material (Sweden ASSAB) for their moulds. However, highly polished moulds with “Please No Pictures” signs attached are no indication for good performance in the production environment. Extended range of clamping-forces with hybrid drive At the Chinaplas 2011 the hybrid version of Netstal’s Elion range was represented by a model with 2800 kN clamping force. This Elion 2800-2000 machine uses a 96-cavity mould of the Swiss mouldmaker Corvaglia and an HDPE of Ineos to mould light closing caps. It is said that with the new models Elion 2200-2000 and Elion 28002000 it is possible to achieve energy savings of up to 30% compared with conventional drives. Production at the show took place at a cycle of less than 2.5s. Directly after moulding all parts passed through a visual inspection station for quality control purposes. This inspection system was from the German Intravis company and the raw material feeding devices from the company Piovan. www.netstal.com Light closing caps produced on a Elion 2800-2000 machine Preform equipment from local suppliers Several local companies also presented their injection moulding machines for PET preforms. Haitian Plastics Machinery (www.haitian.com), the worldwide largest manufacturer of injection moulding machines, has no dedicated PET machine in its product range. But the company stated, that there are several customers in China and overseas that are using Haitian “standard” machines for PET preforms. Chen Hsong Group (www.chenhsong.com.hk), the number two injection moulding machinery manufacturer in China, has a special PET machine. The so-called ChenPET is a complete preform system (injection moulding machine, hot-runner system, mould and robot) which is able to work with moulds up to 72 cavities and a maximum output of up to 16,000 preforms per hour, according to the company. However, this machine was not on display this time. One of the most pro-active PET preform approaches was done by the Chinese company Yizumi Precision Machinery (www.yizumi-group.com.hk) who displayed a servo-driven high-speed PET preform injection moulding machine. According to the company the largest machine is able to hold 96 cavities moulds. Unique is the dualscrew design and synchronous plasticizing unit which is used to achieve higher plasticizing capacity. Yizumi can offer turnkey, i.e. injection moulding machine, moulds and robots and has a special focus on markets outside China: the company just purchased the intellectual property of bankrupt American plastics machinery maker HPM and is moving ahead with plans for a service operation for HPM machines and for a technical centre in the USA.","@ID":36} "MATERIAL / RECYCLING 13 PETplanet insider Vol. 12 The use of the original UV blocker was no longer an option, as it could not reach this level of protection within its normal use level range without creating issues in processing. ColorMatrix Ultimate UV390 was introduced to obtain the higher specification in the new container. UV modelling and internal light sensitivity testing on various bottle contents allowed accurate determination of the required protection. Not only could the use level be reduced to 0.11% for less sensitive products (a reduction of 66%), but for high sensitive products, the use level was reduced from 0.7% to 0.13% – a reduction of more than 80% (see fig.1). The visual impact of Ultimate UV390 used in combination with recycled content was minimised by the use of a specifically developed toner package, also used in other ColorMatrix additive solutions. Lean and green The implementation of Ultimate UV390 reduced overall packaging costs by 16%, and the total additive costs by 30% (see fig.2). It allowed Colormatrix to produce two different packaging solutions with one single product, without impacting the visual appearance, the manufacturing process or the mechanical properties of the container. Reducing materials usage not only reduces cost, but also contributes to the overall environmental impact of the process. These environmental benefits remain further down the line into the recycling stream, as the European PET Bottle Platform (EPBP) has recognised the recyclability of ColorMatrix’s Ultimate UV technologies by concluding that they will have “no negative impact on current European PET recycling.” www.colormatrix.com Performance Filling & Capping Labelling Blowing Fig. 1: Use level difference between standard UV blocker and Ultimate UV390 for low and high sensitive products. Fig. 2: Total resin & additive cost index before and after the introduction of Ultimate UV390. hours UV / Ultimate UV390 0.8% 0.6% 0.4% 0.2% 0% Low (380mm) High (390mm) 100 80 60 40 20 0 Before After Resin / Additive sensitive BEVERAGES","@ID":15} "REGIONAL MARKET REPORTS 8 PETplanet insider Vol. 12 No. 07+08/11 www.petpla.net Finland New start in 2008 They call it the land of a thousand lakes. It’s also the land of the 3 big bottlers. Between them, they control 80% of the soft drinks market, including the Pepsi and the Cola licences. When the Finnish government abolished the tax on one-way bottles in 2008, all the bottling plants began investing in new PET disposable systems. The most important criterion here is flexibility as this is where up to 50 different products are actually bottled. Since the investments are relatively new and the logistics are adapted to suit them, the Finns are running the PCO 28 (1810). Discussions on the 1881 are taking their time to get underway. Regardless of the specific field of analysis, in 2008 the additional tax on one-way drinks containers was abolished with the result that consumers naturally opted for disposable cans and PET bottles. PET refillables disappeared and refillable glass also dropped back dramatically. One glass plant after another was shut down in Finland. At practically the same time, all the bottlers were ordering stretch blow moulding and filler plants from the manufacturers. Although the basic preconditions were the same as far as everyone was concerned, the bottlers that we visited ordered different plants from different manufacturers. Having said that, all the fillers were satisfied with their decision at the time. Three breweries dominate the market, controlling 80% of the soft drinks market between them, including the Pepsi Cola and Coca Cola licences. In addition to beer (unfortunately not in PET) all three also bottle their own brand of soft drinks. They don’t, however, rest on their laurels: in addition to classic sectors like water and CSD they are producing energy drinks, cider and juices. Each bottling plant will feature at least 50 different products. Finland enjoys a comparatively brief summer, and hence the packaged drinking season is short, some three months. So the bottling plants need to be extremely flexible in producing the various formats required. Two of the major breweries have two production lines, one for formats of up to 1l and the others for formats in excess of 1l. by Alexander Büchler Regional market reports Finland","@ID":10} "PETbottles 38 PETplanet insider Vol. 12 No. 07+08/11 www.petpla.net Personal Care Total care out of a bottle The German marketing partner for Listerine anti-bacterial mouth rinse, Messrs. McNeil Consumer Healthcare based at Neuss in Germany, has recently launched its latest creation – 6 in 1 Protection “Total Care” in the typical 0.5l PET bottle. According to the manufacturer, Total Care reduces dental plaque, strengthens the teeth, keeps gums healthy, stops calculus from reforming, ensures fresh breath and effectively combats harmful bacteria. The product, which has a slight dark red colour, is packaged in a transparent bottle and a high gloss, metallised front label enhances the impression of a quality rinse as well as superior packaging. The screw cap, which is childproof, also acts as a dispensing unit and is secured by means of a printed shrink label. www.listerine.de Mickey mouse fragrance for the bath Spanish company Air-Val International based in Gava has enlisted the help of the licensed character “Mickey Mouse” to assist with marketing its 750ml fragrance “Colonia Splash Colonia“ in an attractively designed PET bottle. The front of the bottle sports a coloured, “non-label look” label, whilst colour printing on the inside of the rear label gives it an original appearance, attractive to children, that catches the eye at the POS. The finishing touch to the packaging is a snap-on lid, locked when in the open position, that can be operated using one hand only. www.air-val.com Body oil 150 ml gentle body oil with sea buckthorn and wild rose oil is being marketed by Berlin Cosmetics under the brand name “Indra Natural Cosmetics“ in an appropriately designed PET bottle. The bottle is decorated with front and rear labels adapted to its shape; the colour of the body oil is tinged with blue and the final crowning touch to the packaging is a screw-on, green hinged lid. www.berlin-cosmetics.de Soap bubble bath 200 ml soap bubble bath, the first children’s bath product that can also be used to blow soap bubbles, is being marketed by Messrs. Hipp from Pfaffenhofen/Germany in a transparent PET bottle. On the front the bottle sports a transparent, “non-label look” label giving a clear view of the screwin bubble blowing wand which is combined with the dispensing beaker. This ph-neutral skin care bath has no mineral oils, is soapfree and particularly gentle on the eyes. www.hipp.de Equine ointment Dr. Jacoby Vital GmbH based in Lahnau, Germany are marketing, under the brand name of “Apothekers Original“ a 250ml sports gel equine ointment in a PET bottle for relaxing the whole of the musculature. The packaging features an informative non-label-look label and a screw-on push-pull mechanism for ease of application prior to massage. www.pferdesalbe.com","@ID":40} "imprint EDITORIAL PUBLISHER Alexander Büchler, Managing Director HEAD OFFICE heidelberg business media GmbH Landhausstr. 4 69115 Heidelberg, Germany phone: +49(0)6221-65108-0 fax: +49(0)6221-65108-28 [email protected] EDITORIAL Doris Fischer [email protected] Michael Maruschke Ruari McCallion Ilona Trotter Wolfgang von Schroeter Anthony Withers MEDIA CONSULTANTS Ute Andrä [email protected] Martina Hischmann [email protected] Ursula Wachter [email protected] phone: +49(0)6221-65108-0 fax: +49(0)6221-65108-28 France, Italy, Spain, UK Elisabeth Maria Köpke phone: +49(0)6201-878925 fax: +49(0)6201-878926 [email protected] LAYOUT AND PREPRESS Exprim Kommunikationsdesign Matthias Gaumann | www.exprim.de READER SERVICES Kay Krüger [email protected] PRINT Chroma Druck & Verlag GmbH Werkstraße 25 67354 Römerberg Germany WWW www.petpla.net | india.petpla.net PETplanet insider ISSN 1438-9459 is published 10 times a year. This publication is sent to qualified subscribers (1-year subscription 149 EUR, 2-year subscription 289 EUR, Young professionals’ subscription 99 EUR. Magazines will be dispatched to you by airmail). Not to be reproduced in any form without permission from the publisher. Note: The fact that product names may not be identified as trade marks is not an indication that such names are not registered trademarks. 3 PETplanet insider Vol. 12 No. 07+08/11 www.petpla.net Go to Brau Beviale! Our Regional Reports are proving to be a big hit both with you, our readers, and with the companies we visit. The basis of our Regional Reports is simple: we visit PET users worldwide and invite them to tell us about the PET business in their countries. In this issue we have headed north to the Baltic for the first of our reports into the PET business in Finland. It proved to be an interesting visit. Following the government’s decision to drop the tax on one-way packaging, Finnish consumers have now regained their appetite for it. Within months of the announcement, PET refillables had vanished from the market whilst glass refillables continued to lose market share. Unsurprisingly perhaps, purchases of new PET filler equipment showed a dramatic increase. Our reports are authoritative and wide-ranging and we thought it would be an excellent idea to encourage readers’ participation in them. So, with the imminent opening of the Brau Beviale exhibition, we are inviting our readers to visit PETpoint to share with us all the news and views from the market. Our Editourmobile will be setting out from Nuremberg on October 3, 2011 and will be travelling through Austria, Slovenia, Croatia, Serbia, Bulgaria, Turkey, Armenia, Azerbaijan, Romania and Hungary. In Azerbaijan, we will be interviewing the winners of the Eurovision Song Contest Ell and Nikki who will be taking time out to sample their favourite drinks in PET bottles. There will be a regular blog to help you get really involved and – of course – you will be able to see the filler plants we visit. We return to base in time for Brau Beviale and, in addition to the vehicle, you will also be able to admire the bottles we have brought back and to talk shop directly with the editors. Subsequent issues will feature a full version of our comprehensive Regional Report as usual. Come on board with us and enjoy a trip through some very exciting PET markets. Yours, Alexander Büchler EDITORIAL dear readers, EDITORIAL","@ID":5} "BOTTLING / FILLING 32 PETplanet insider Vol. 12 No. 07+08/11 www.petpla.net KHS says that its new-generation Innosept Asbofill ABF 611 and Innosept Asbofill ABF 711 twin aseptic linear fillers offer high speed and flexibility for a range of drinks and liquid pharmaceutical products. The machines can handle both PET and HDPE bottles without conversion. The primary target market for the ABF 711 is also carton packaging businesses. It is hoped that the ABF lines will persuade businesses that have up to now used carton packaging to change to plastic bottles. The new Innosept Asbofill linear fillers can process up to 12,000bph. Innosept Asbofill ABF 611, the standard model, fills 0.1 to 0.75l bottles; the ABF 711 model can fill 0.25 to 2.1-l units. In the twin version the 711 can handle 24,000bph. The machines are designed to handle non-carbonated beverages, including milk, yogurt drinks, fruit juices, and fruit juice drinks. KHS says they are suitable for filling liquid pharmaceutical products, such as health drinks or products for enteral feeding. The machines’ integrated neck handling enables them to process novel designs, such as rectangular and square bottles, and they can fill either PET or HDPE bottles without conversion. Operators can thus consider diversification of their product range while still using the same equipment. Bottles and closures are sprayed with a hydrogen peroxide (H2O2) aerosol in a dry sterilisation process. H 2 O 2 reacts on the surfaces and is then dried by hot air. Whatever the size or shape of the bottles being processed, all surfaces are sprayed evenly. KHS says that the machines need only a very small sterile zone; the area required for the Innosept Asbofill ABF 711 – the larger of the two – is 1.5m³ (about 53 cu ft) and the Innosept Asbofill ABF 611 needs just 0.9m³ (32 cu ft). The bottles are conveyed through all the processing stages in just one holder, eliminating critical mechanical transfers. KHS launches dual-concept aseptic fillers The next generation F.l..: Bernhard Hinken, Eckes Granini Deutschland GmbH and Thomas Niehr, Director / Competence Centre Aseptic Filling Technology, KHS F.l.: Paul Winterhoff - Director Con- struction / Competence Centre Aseptic Filling Technology, KHS, Mike Herrmann - Sales KHS Germany, Berthold Burgmeier - Molkerei Gropper GmbH & Co. KG Filling is by two-stage free-flow filling valves, which means that bottles never come in contact with the valves themselves. Precise volumetric filling is delivered by magnetic inductive flowmetering. Options include integration of pulp jets into the filling valves; and nitrogen flushing before the filling process and head space nitrogen flushing afterwards, which reduces the amount of oxygen remaining in the bottle. Placing of a drop of liquid nitrogen in the headspace of filled plastic bottles is also available as an option – the first time this feature has been offered for linear fillers. This facility both displaces headspace oxygen and also helps to improve lightweight bottles’ stability, which can help achieve savings in materials. All options can be integrated either at installation or subsequently. Bottles filled by the new machines can be sealed with either aluminium seals or plastic screw-on caps. The two distinct processes of placing the caps on the bottles and then screwing them tight are carried out in entirely separate sterile chambers, which removes risks associated with the rotary capping motion. In anticipation of the forthcoming drinktec 2013, the company has announced an extensive update of the higher capacity aseptic rotary fillers. www.khs.com Innosept Asbofill ABF 711 twin aseptic linear filler sensitive BEVERAGES","@ID":34} "NEWS 7 PETplanet insider Vol. 12 No. 07+08/11 www.petpla.net A global player with special focus on health - 80 years of natural food ingredients Wild was founded in 1931 as a family business, when company founder Rudolf Wild was working on the revolutionary idea of producing soft drinks without the addition of synthetic ingredients. In 1951, he achieved a breakthrough with “Libella”, the first ever carbonated soft drink made entirely of natural ingredients. The product portfolio was extended to fruit preparations, fruit flavours, and later also natural colours, herbal, tea and plant extracts. This year Wild is celebrating its 80th anniversary; the company employs around 530 staff worldwide and is one of the world’s leading manufacturers of natural ingredients for the food and beverage industries. Products for a healthy diet The global trend towards natural foods is on the rise. Food constituents that can improve productivity and health will play an important role in future. Around a decade ago, the company was one of the first companies to introduce products offering additional health benefits, like antioxidants which, in high doses, are known to boost the immune system. Their health-promoting effects have been scientifically proven in clinical tests. The company’s portfolio also includes other plant extracts and substances which support the different metabolic processes. The gains must be measurable In future it will be essential to convince the consumer about a healthier nutrition. It is not enough for aAny new food or drink merely to promise to be health-promoting. The company is convinced that there has to be a proven, measurable effect. Wild has come up with a new tagline “Measurable Health”, and this will serve as a basis for research and development of verifiably healthy foods. The company is now working with researchers from various colleges and universities to investigate the effects of promising substances. In China for instance, the company is testing the high potential of “Traditional Chinese Medicine” (TCM) at its own production site. Stevia – the natural sweetener from South America The use of natural sweeteners which can be extracted from Stevia rebaudiana is also currently under investigation at Wild. Commonly known as sweetleaf and sugarleaf, this South American plant provides an extract that is several times sweeter than sugar. Stevia has a long tradition of use as a sweetener in Asia but in the European Union, with minor exceptions, its use is banned. However, the positive rating by the food safety authorities suggests that approval for use in the EU is on the horizon. The product developers at Wild have already created various concepts based on stevia, and the company is ready to serve the market as soon as approval of the natural sweetener has been given. www.wildflavors.com DAK Americas acquires Wellman PET business in USA DAK Americas LLC has announced that it will be acquiring the PET business of Wellman, Inc. for approximately US$ 185 million, including a cash payment and the assumption of certain liabilities. The acquisition is expected to complete in the second half of 2011, pending regulatory approval. The acquisition includes Wellman’s production facilities in Bay St. Louis, Mississippi, which has a production capacity of approximately 950 million lbs/a (approx 430 million kg/a) of PET resin and a workforce of approximately 165 people. DAK Americas, headquartered in Charlotte, NC, is wholly owned by Alfa S.A.B. de C.V. of Monterrey, Mexico. It is one of the largest integrated producers of PET Resin in the world and the main producer of polyester staple fibre in the Americas. www.dakamericas.com Appe invests £1.5 million in Krones ProShape Appe, the packaging division of LSB, is seeking to increase its output and flexibility, following its investment of around £1.5m in the newly-developed ProShape production process from Krones. Appe is the first operator to install ProShape. The machine is now in operation at Appe’s site at Gresford, UK, which supplies clients in the household and personal care sectors. The new ProShape module is integrated into Krones’ current Contiform series and combines its established blow-moulding technology with a new module for orientation and selective temperature control of the preforms. ProShape is claimed to offer an optimised production process for oval or asymmetrical containers, as well as the potential for light-weighting of oval packs and the production of unusual designs. Krones says that ProShape’s output is around 40% higher than standard blow moulding machines. The Contiform S8 installed at Appe’s plant has eight cavities with an output of up to 2,000 bottles/hr each, depending on container design and complexity. The system can be switched from the preferential heating and neck orientation process to a standard blowing mode. www.krones.com Repi opens Russian subsidiary Italian company Repi S.p.A., which produces liquid colorants and additives for plastics and polyurethanes, has opened its own company in Moscow, Russia. The company has had a presence in the Russian market for 12 years and its own representative office in the country for the past five years. Repi supplies customers in Russia with colorants and additives for PET preforms, as well as promoting its basic colorant technology for the extrusion of PVC profiles and panels, and other polymer-related activities. The new company will provide the growing market in Russia with local service, technical support and just-in-time deliveries from its Moscow warehouse. www.repi.ru","@ID":9} "BOTTLES 39 PETplanet insider Vol. 12 No. 07+08/11 www.petpla.net IN EVERY BOTTLE THERE IS ALL OUR KNOW HOW. RESEARCH & DEVELOPMENT A constant projection towards the future oriented to search not only for new materials but also new PET technologies of transformation and innovative materials. CONSULTANCY A concrete answer to all your questions. We put at your disposal all our know-how for every single requirement. PROTOTYPATION Prototypes of containers and innovative preforms in record times: you will be able to touch with your hands the bottles within a short time after approval of the design. DESIGN Creativity in search of elegance and refinement. Innovative designs, ergonomic structures, eye-catching and functional containers. We give a true shape to your product! Shower gel The cosmetics manufacturer Beiersdorf of Hamburg is marketing the “Nivea” brand shower gel ”Sensitive Balance“, 250 ml, in a transparent PET bottle. The packaging features a ’non-label look’ label on the front and, at the back, a white plastic label that emphasises the product’s transparency at the POS. A snap-on, two-colour lid which is locked in place in its open position to enable the contents to be dispensed more easily, puts the finishing touches to this attractive cosmetics packaging. www.nivea.com Baby’s first body oil The Germany company, Bübchen-Werk Ewald Hermes based in Soest is marketing its sensitive body oil, which is free of any perfume or preservatives, under the brand name of “Bübchen“ in a transparent 150ml PET bottle. The packaging includes informative front and rear labels and the company cites a positive classification in an eco-test by way of an additional incentive to purchase. The colour-matched, snap-on hinged lid remains stable in the open position and is combined with a self-closing silicon valve. www.buebchen.de Nievina gel fresh The Spanish company, Lab Vigmar, based in Real de Montroy, is marketing 250ml gel fresh in a transparent PET bottle under the brand name ”Nievina“. The product has a light blue hue and the packaging features printed “non-label look” labels to front and rear. A clear, screw-on hinged cap which can be relied upon to stay in place in the open position, puts the finishing touches to the product’s appearance. The company markets many kinds of cosmetics articles under the brand name “Nievina“, which is very similar to a well known German brand name article (Nivea). www.cosmeticosvigmar.com Green tea bath salts 1.3kg of green bath salts with green tea additives by way of active ingredient are being marketed in a transparent, round PET jar by the French company Laboratoires Sarbec based at Neuville en Ferrain. The paper label encircling the jar contains information in a number of languages. The shape and appearance of the plastic screw cap are based on a twist-off metal screw cap. www.corinedefarme.com","@ID":41} "Vol.6 PETplanet print PREFORM PRODUCTION 14 PETplanet insider Vol. 12 No. 07+08/11 www.petpla.net Parting Line Deformation The rapid guide to perfect preforms - part 22 Troubleshooting guides have suffered in the past from being locked away in offices and not being available to the people that actually need them. Considering the high cost of machine and tools high scrap rates can be a costly proposition eating away at already tight margins. PETplanet’s “Rapid Guide to Perfect Preforms” takes a different approach. Bound in laminated paper that is easy to clean off, the small format of the book of 108mm by 151mm (4.25” by 6”) allows easy storage in back pockets or tool boxes. It has been written for the people on the floor of injection moulding companies to support their daily work in making the best preforms possible. The product of two industry experts, Rick Unterlander and Ottmar Brandau, it gives concrete advice on 35 of the most common problems in preform manufacture, most illustrated by pictures. From high AA levels to wavy bodies processors can find help when they need it. Read chapter 22 of the guide. Symptom: A wavy or slightly wrinkled section near the neck insert/cavity parting line. Cause: The shrinkage rate on the exterior surface of the preform between the neck inserts and the cavity is significantly different. This is amplified when the preform remains on the core (out of the cavity) for a long time period. Table of Contents i........................ About the Authors ii.................................Introduction chapter 1.............................. AA Level High 2........................ Accordion Preform 3....................... Air hooks / Streaks 4............................... Black Specks 5...................................... Bubbles 6..................................Burn Marks 7...........................Colour Streaking ................................... /Peeling 8..................................Crystallinity 9.................................Drool Marks 10.......................................... Flash 11......................... Gate Depressions 12............................... Gate Peeling 13..................Gate Voids / Pin Holes 14......................... Internal Gate Sink 15................................Internal Sinks 16........................................ IV Loss Solutions: 1. Check water cooling temperature. This should be 7 – 10ºC (45 - 50ºF) for optimum cooling. 2. Check water cooling flow to mould and robot receptacles. This should be at the mould manufacturers rating (for a given preform size and cavitation). 3. Check that the cooling time is sufficient for the preform being moulded. This typically ranges from about 1 to 3sec depending upon the preform wall thickness. Add time if necessary to improve solidification and increase shrinkage for better release. 4. Ensure preforms are ejected from the cores and transferred into the robot cooling receptacles as soon as possible. Minimize any delays and ensure robot entry speeds are maximized. 17............................ Long Gate Nub 18...............................Milky Preform 19............................ Moisture Marks 20................Neck Finish out of Round 21....................... Parting Line Crease 22.................Parting Line Deformation 23......................... Preform Yellowing 24.................................. Short Shots 25.......................................... Sinks 26......................................... Splay 27........................... Stretched Necks 28..................................... Stringing 29......................... Surface Blemishes 30......................... Thread Flow Lines 31...............TSS (Top Sealing Surface) ......................................... Sink 32.......................................Unmelts 33.................Wall Thickness Variation 34.................................Wavy Body 35.................................. Weld Lines","@ID":16} "REGIONAL MARKET REPORTS 9 PETplanet insider Vol. 12 No. 07+08/11 www.petpla.net The three breweries are Hartwall, part of the Heineken Group, which has the Pepsi Cola licence; Synebrychoff, which belongs to the Carlsberg Group, bottles Coca Cola. Finally there is Olvi, the smallest of the Big Three, which is a wholly independent Finnish brewery. All three companies have already installed plants from Krones and KHS in the glass and cans sector. To handle PET containers, the three companies have each taken an individual approach. The minnow of the three, Olvi has installed a Corpoplast stretch blow moulder with a KHS bottling plant. This is designed for 18,000bph, and can handle a number of different formats. Olvi’s subsidiary company, A le Coq, based in Estonia, uses the same configuration, and produces a similar number of products. Over the season this means 40% is spent on format changeover. Hartwall took a slightly different tack. They have two plants and this significantly reduces the time taken to change formats. Between the Sipa stretch blow moulder and the Krones filler there is a conveyor with several minutes’ installed buffer-capacity. The plants operate at a maximum output of up to 44,000bph. Perhaps the neatest solution is the one adopted by Synebrychoff. They purchased each of the system components from a different supplier and thus succeeded in putting together the best system configuration for them at the time. For example, they opted for bottle silos as buffers between the Sidel stretch blow moulding and the Krones filler. This has enabled them to create buffers of up to one hour which gives them the opportunity to convert the stretch blow moulding to other formats. The maximum output of the two plants is 36,000 bph in each case. Macro-economic data Area 538,144 km² Population 5,4 millions (2010) GNP US $ 239 billions MHT MOLD & HOTRUNNER TECHNOLOGY Dr. Ruben-Rausing-Str. 7 | D-65239 Hochheim/Main Tel. +49(0) 6146-906-0 | www.mht-ag.de Make the most of your machine – with a mold from MHT! For many machine types, we supply the mold with the highest cavitation, thereby enabling optimum preform output. For the Husky HyPET machine, we offer an upgrade set for 33% more preforms, without refitting on the machine! • 60 cavities for Netstal PETline 2000 • 96 cavities for Husky HyPET 300 • 112 cavities for KraussMaffei 350 Engineering made in Germany Patent pending: MHTcoolMAX® post mold cooling Weight saving We have used our comprehensive bottle database PETplanet Zoom to evaluate the bottles currently on the market in Finland, which has enabled us to document precisely the shifts in weight. With the changeover to the one-way deposit system an enormous potential for savings in terms of preforms has been opened up, not only in relation to the bottles themselves, but also in the weight and therefore in the consumption of raw materials. In the case of the 0.5 litre bottles it was noted during the evaluation that a broad range of weights is possible. Among these are lightweights weighing no more than about 21g, going up to bottles that tip the scales at up to approx. 36g. Compared to refillable refillable refillable bottles – which weigh anything from 53 to 57g, weight savings of up to 63.5% are now achievable. Similar savings are possible in the 1l bottle, with reductions of up to 2/3 of the weight of the refillable bottles. The largest bottles in the study (with a 1.5l fill volume) weighed in at anything from 37g to around 48g. Here the savings potential by comparison with the refillable bottle at around 121g was just under 70%. These savings are good for sustainability, and the environment, but it also demonstrates how flexible plastic can be in terms of usage and strength.","@ID":11} "BOTTLE MAKING 21 PETplanet insider Vol. 12 No. 07+-08/11 www.petpla.net Some of the major machinery suppliers offer new bottle solutions for hot-fill applications Bottle developments for sensitive beverages The PET Keg revolution for beer Siapi was involved in the realization of an application for the beer sector: a coloured 4l PET Keg that was launched on the Benelux market with the Amstel brand by Heineken this past April 15, 2011. The weight of the KEG is 112g. The PET Keg is suitable for use at home, as it can be kept in the refrigerator and is extremely practical. The container has a built in tapping and dispensing system. The Amstel Tapje is available in most supermarkets, wine shops, liquor shops and at top wholesalers. Heineken recognized the high level of the application also from a technical point of view. In fact, Siapi contributed in the development of the PET Keg starting from the coloured preforms that, as is known, require specific decisions about heating the container body and, at the same time, cooling the neck. Siapi, leader in the stretch blow-moulding market for PET containers from standard to large capacity formats, has obtained considerable experience with PET Kegs - from 4l to 40l – for the beer sector, which replace the traditional steel kegs. This application is attracting a considerable amount of interest both among major international beer producers as well as among microbreweries and promises important developments for the future. The PET keg is produced on Siapi machines (EA2) with Siapi’s linear stretch blow-moulding technology. www.siapi.it Nitrofill 15.5 hotfill bottle Krones’ NitroHotFill 15.5 is a new, lighter PET bottle for hotfill, which weighs in at 15.5g in the 500ml size and is suitable for filling temperatures up to 87°C. The sportscap closure was developed by Aptar and successfully tested at Krones. The neck finish weighs 1.3g. The company says that the result has a ‘casually elegant’ visual appearance and a reduced CO 2 footprint. Process control for NitroHotfill is based on the relax-cooling concept in the blow-moulding machine. After filling, an injection of nitrogen just upstream of the capper creates a positive pressure of 1.5 to 2bar inside the bottle. This pressure compensates for product volume shrinkage downstream of the recooler and is claimed to prevent bottle deformation from underpressure. The bottle does not have expansion panels. The process can be used for producing bottles in the Contiform H, enables the use of aluminium moulds, and reduces the machine’s air consumption. Wall thicknesses are less than 1mm but can withstand internal nitrogen pressure of 1.5bar. www.krones.com Getting a handle on hot-fill Sipa has developed a new technology to allow users of its standard equipment to produce large hot-fill PET containers with handles. The technology uses a separatelymoulded polypropylene handle that is automatically inserted into the container between the blowing and filling stages. It has already been deployed on an industrial scale on lines bottling vegetable oils in handled containers. Sipa says that the process is suitable for hot-fillable containers upwards of 3l for such products as fruit juices, iced tea, lemonade, apple cider, juice cocktail and blends. The PP handle typically weighs around 9g. It needs to be designed for the specific bottle, which the company can help with as part of an overall bottle feasibility study. Sipa further claims that the technology’s key advantage is that it works with its standard bottle blowing machines, such as its SFL linear blow moulding machine and ECS integrated system. www.sipa.it sensitive BEVERAGES","@ID":23}]}}
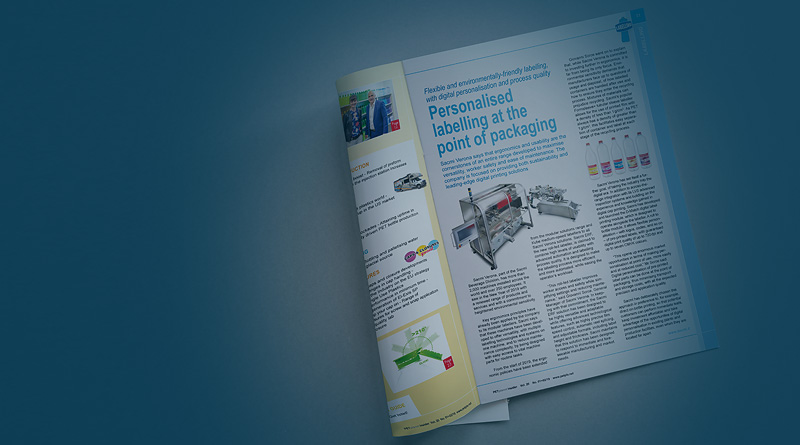