"PREFORM PRODUCTION 10 PETplanet insider Vol. 13 No. 01+02/12 www.petpla.net Netstal’s ‘LightBase’ process reduces weight while improving material distribution across PET bottles Ace of base Netstal has now introduced enhancements to its Calitec technology that are aimed at increasing process efficiency and reducing material usage, leading to lighter weight containers. Presented under the brand of LightBase, the new developments introduce different base geometries for preforms, which improve the blow-out behaviour of bottle bases. Netstal says that these modified base geometries optimise preform surfaces for the subsequent heating process in the blowing machine so that they are better able to absorb the thermal energy from the UV lamps. The company claims that this enables the base to be heated to optimum temperature later in the blowing process and blown out to produce thinner walls. Improved material distribution reduces the weight of the base and prevents build-up of material with consequent high level of crystallisation, which means that the base cannot crack as easily as in earlier methods. The process is claimed to deliver material savings accompanied by improved bottle strength. Netstal says that these developments enable the complete removal of unnecessary base material. Preblow for thinner walls Netstal’s patented ‘preblow’ process blows out the base area of the preform immediately after the injection moulding process. It says that this enables adjustment of both the base outline and surface dimensions. Enlarging the base outline reduces wall thickness in the base, which makes it possible to heat the area in the subsequent blowing process more precisely and efficiently, as a larger surface with a lower wall thickness requires less heating from the UV lamps in the blowing machine. Cutting 1l juice bottles produced by the new process reveals a wall thickness curve without any material build-ups in the base area; the cut surface runs evenly over the sprue point. The weight of the bottom section on the test bottle, for which the preform was not designed, was 0.6g. Testing found that it is possible to achieve a weight reduction of more than 1g, relative to the preform. Lighter but stronger bottles The LightBase test bottle demonstrates other properties as a result of better material distribution. Overall wall thickness can be increased, as shown in Fig. 4. Analysis of the LightBase bottle using 16 wall measurement points positioned axially on top of each other determined that the material taken from the base area Fig. 1: Depiction of the preblow process Lightweighting SPECIAL","@ID":12} "REGIONAL MARKET REPORTS 16 PETplanet insider Vol. 13 No. 01+02/12 www.petpla.net enjoyed success due to low price and excellent distribution. Premia and other private label products are forecast to expand production in the coming years in Serbian bottled water. After two difficult years of decreasing volumes, stagnation in terms of new product launches and a period of unit price decrease, 2011 is expected to bring a recovery to the Serbian bottled water market. Having shifted downmarket during this period, consumers are expected to gradually return to their favourite brands and this should help the unit price move upward again. However, caution is needed: prices are unlikely to rise as rapidly as before the crisis, since increasing competition in the sector may see a reduction in profit margins for producers. Source: Euromonitor Borverk Eurotrade We met: Predrag Radovančević Predrag Radovančević in front of his Netstal line A family firm 65km to the south of Belgrade lies the family-run firm Borverk Eurotrade. The company processes just under 12,000t of PET into standard preforms for the Serbian and neighbourhood markets. This represents slightly more than 25% of the overall market. Launched in 1997, the company today works on five Netstal lines with 48 and 72 cavities and a Krauss Maffei line with a 96-compartment mould. Director Predrag Radovančević manages the company. His wife, father, sisters and, naturally, his brotherin-law are closely involved and together they ensure that the lines never come to a standstill. “We developed fast in the first 10 years, while in the last couple of years we have been strategically planning for the future. These days margins are so narrow that we need to make highly precise calculations“ explains Predrag. The fact that they are not yet on the breadline is demonstrated by their consistent zeal for new investment. The new warehouse has just been completed; it won’t be long now before the new office building is also finished. New standard “Global packaging and packaging materials, BRCiOP ver.4” is being implemented. Perhaps it is typical for a family firm to tend to err on the side of caution. “What good to us are customers who don’t pay their bills?“ says Predrag and as a result he would rather forgo a contract than forgo the money. He intends to use this strategy to tide him nicely over the coming year – no expansion for the sake of expansion. As regards 2012 production, he envisages a resurgence of the 600 million preforms that he also produced in 2011. Out of these 65 % is channelled into the CSD and water market, 3 % into beer, 5 % into edible oil, 22% into milk and dairy produce and 5% into others. www.borverk.rs Knjaz Miloš We met: Mrs. Zorica Vukčević Kljajić, COO Milan Vujović, Marketing Director Goran Savović Production Manager The gradual installation of the 1881 will commence at the start of 2012, says Zorica Vukčević Kljajić, COO 200 years young In 2011 Knjaz Miloš celebrates the bi-centenary of its founding. Ranking as one of the largest bottling enterprises, this company, which supplies water from the spring, boasts a market share of 37% carbonated water, 20% still water as well as a 60% share of the market for energy drinks in Serbia. It features ten bottling lines for mainly glass and PET bottles. There is only one line for 0.25l energy drinks where cans are used in the filling operation. Two of the lines are deployed for water in demijohns and glass bottles are used in filling operations on Three lines. Here the company employs disposable as well as reusable bottles. Since 1989 PET bottles have been used for the most important brand “Knjaz Miloš“, a carbonated mineral water. In 1996 they launched still water on the Serbian market for the first time, naturally also in PET bottles. Hitherto consumers in Serbia had only been familiar with still water that came from the tap. At less than 400mg minerals/litre this represents a balanced mineral water that tastes not too tangy but not too bland either. Whereas, up to five years ago, the proportion of PET compared to glass was around 50/50, today there are four PET lines taking care of 76% of filling operations.","@ID":18} "REGIONAL MARKET REPORTS 19 PETplanet insider Vol. 13 No. 01+02/12 www.petpla.net ately, and by pressing a button he has every bit of information at his fingertips, accurate down to the last minute. “In the old days we used to sit down together and discuss production planning; today we make use of meetings to optimise our production” is how he describes the advantages of the new system. There is still only one database for the whole of the factory, the interface problems between the individual items of software are yesterday’s news. Preform capacity amounts to more than 800 million preforms/a In total six Netstal and one Husky systems are in operation on the factory floor. Capacity amounts to a total of more than 800 million preforms a year altogether although, in reality, they actually manage 500 to 600 million. The reason for this is the constant changes of colour. How to ensure that the right colours from light to dark run one after the other on the right machine in each case so that the colour change operation can proceed as quickly as possible is, so to speak, Energo PET’s corporate secret. In this way the company has made a name for itself, even outside Serbia, as a specialist in coloured preforms. “However, despite the multitude of colours, the future is not looking rosy“ says Miroslav. He goes on: “These are not good times for adventurers“. Nevertheless, they are planning a further production facility for the future as well as an extension to the warehouse. Everything is in place for the economic upturn which all hope is coming soon. www.energopet.net Coca Cola HBC Serbia We met: Martin Schacht, Plant Manager Moving from 1818 to 1881 With four Sidel filler plants for PET bottles, Coca Cola Hellenic is one of the market leaders in Serbia. The plant has a maximum capacity of 60,000 filling operations per hour. The company has been bottling the classic Coca Cola CSDs at its plant near Belgrade since 1968. Initially, of course, they used glass, but over the years they have increasingly come to use PET. In the meantime, alongside the filling operations, there is their own preform production. Coca Cola Hellenic has been performing injection moulding of the big, clear preforms on their own Husky installation since 2007. The Canadian machine produces 100 million preforms in a 3-shift operation throughout the year. This is around 60% of all the preforms required. They purchase coloured preforms and the nozzles on the free market during the season. There is space in the preform bay for a second installation, but Plant Manager Martin Schacht is taking a guarded approach - ”If we had two machines, it is unlikely that we would be able to utilise them to full capacity so it’s better at the moment if we buy in from outside” he tells us. It has been a year now since he switched his filling operations for the large 2l bottle to the weight-saving 1881 neck finish. Initially, the closures did not function as they should have done. “The closure applicators are arranged for the old 1810 tolerances; here you need a degree of patience to set them up for the narrower tolerances of the new closure“, says Martin. There were no problems with the new closure once it had passed out through the plant gates. Its sealing properties were of the same or higher quality as was the old closure. “You need to be more precise about closing the 1881, this has a positive effect as a better understanding of the cap application process results. At lower torques more bottles remain open than with 1810 cap“, Martin goes on. Customer feedback was that the 1881 was difficult to open. This can, however, only be subjective because the measured values for the old and the new closure are the same, could be associated also with the reduced surface area a customer has available. Martin has been able to reduce the weight of the 2l bottle from 47 to 45.7g. In the meantime he has also switched the remaining size 0.5l and 1.25l (planned Q1 2012) over to the lightweight version. Yes, you have read it right, 1.25l is a promotional campaign by Coca Cola Hellenic to mark the 125th anniversary of Coca Cola. The new format has been so well received by consumers that it has ousted the 1l bottle and it is anticipated that it will continue to be available into the company’s 126th year. www.coca-colahellenic.rs Minaqua We met: Zora Dankova, Marketing Manager Vinka Vujinović, Production Manager. A healing water In 1897, at a depth of 193m mineral water with a high level of naturally dissolved iodine was found in Novi Sad. The mineral water possessed significant healing properties. In 1911, it was was awarded “GRAND PRIX” prizes in to be continued on page 25","@ID":21} "MARKET SURVEY 22 PETplanet insider Vol. 13 No. 01+02/12 www.petpla.net MARKETsurvey 01+02/2012 Company name SMI S.P.A. GEA Procomac SpA KHS GmbH Postal address Telephone number Web site address Contact name Function Direct telephone number Fax E-Mail Via Piazzalunga, 30 24015 San Giovanni Bianco (BG), Italy +39 0345 40.111 www.smigroup.it Pietro Volpi Marketing Manager +39 0345 40.316 + 39 0345 40.209 [email protected] Head Office: Via Fedolfi 29, 43038 Sala Baganza, Parma, Italy GEA Procomac Packaging Division - Via Aldo Moro 1, 43044 Collecchio, Parma, Italy +39 0521 839411 www.procomac.it Fabio Borrini Product and Sales Manager Packaging +39 0521 839786 +39 0521 833879 [email protected] Juchostr. 20, 44143 Dortmund , Germany +49 231 569-0 www.khs.com Mattias Damm Head of Corporate Communication +49 231569-1718 +49 231569-1226 [email protected] Preform: from injection moulding machine into the box Box-filling system Yes No No Maximum drop from conveyor belt to base of carton (in cm) 120 In-line Control Yes Preform: from box into SBM Machine up to 60,000 preforms/h -Dumper Yes No Yes Conversion to different neck diameters(Mechanical / electrical) mechanical/electrical mechanical/electrical -In-line Control Yes Yes Bottle: From SBM to Filler, Air Conveyor Air Conveyor (incl. vertical) Yes Yes Yes Purity levels G3/F9/H14 99.99 DOP – photometric test method. Standard and hygenic Bottle format conversion Yes Yes, automatic Manual/automatic Conversion to different neck diameters Yes Yes, manual/automatic Manual/automatic Bottle storage systems Bottle up-ender Yes No No Buffer systems capacity (number of bottles from… to…) Depending on bottle diameter 100 - 10,000 Storage systems capacity (number of bottles from… to…) Depending on bottle diameter 100 - 10,000 Palleter and depalleter for empty PET bottles Yes Yes, depalleters Yes","@ID":24} "CAPPING / CLOSURES 33 PETplanet insider Vol. 13 No. 01+02/12 light-weighting closures for the new 26/21mm standard: its 26mm closure range for edible oil. The internal diameter of the 26/21 neck remains the same as on the traditional 29/21mm neck, which enables producers to keep the same filling nozzles. Only the external diameter – and therefore wall thickness – and the height of the neck have been reduced. While all the available new 29mm closure/ neck variants generate weight savings compared to their predecessors, the lightweight one-piece CTC 26/10 is another possible solution. Customers who prefer the two-piece, screwcap solution can be supplied with EV 26/18 closures equipped with a flow controlling marguerite; those who prefer a hinged closure can request the HC EV 26/18 one-piece closure solution. Customers looking for a cost efficient solution, while still wanting to have a pouring mechanism, could incline towards a two-piece CTC IP closure with an inserted pouring device. All these closure variants fit the same 26mm finish. www.Bericap.com Lightweight HexaLite 29/11 fitting on 30mm neck. One of the Bericap’s closure range for edible oil: Lightweight CTC IP 26/13","@ID":35} "REGIONAL MARKET REPORTS 15 PETplanet insider Vol. 13 No. 01+02/12 www.petpla.net holiday paradise and this has naturally led to increased demand for packaged drinks during the tourist season. This demand is being predominantly met by Serbian bottling plants making use of their own natural springs. As well as Montenegro, the other former Yugoslavian states are also an export target for Serbian producers. As far as preforms are concerned, larger operations such as Coca Cola or Minaqua produce a major part of their preforms in-house. However, the market is big enough to accommodate regional preform producers, and there is a growing export market for preforms in the former Yugoslavian states. The bottled water market in Serbia Bottled water posted a sales growth by value of 3% in 2010, totalling RSD 24 billion. Serbian bottled water is expected to achieve RSD 31 billion by 2015 As happened in all soft drinks categories, Serbian bottled water faced difficult times due to the economic crisis in 2009 and 2010. Whilst in 2009 the decrease in volume was 2%, in 2010 it fell by a mere 1%. The biggest category in Serbian bottled water is carbonated bottled water, accounting for 61% of sales by value of the whole sector and 72% of volume sales, which means that trends in carbonated bottled water clearly drive trends in the whole bottled water sector. Compared to the review period, 2009 and 2010 were poorer in terms of volume and value sales and, more significantly perhaps, in terms of marketing activities and number of new product launches. This is because the economic crisis forced Serbian consumers to reduce spending on bottled water as their household budgets were significantly squeezed. The key off-trade trends followed key trends in the category as a whole. These included a decrease in volume sales, a reduction in marketing activities, fewer new product launches and a decrease, in inflation-adjusted terms, of the unit price. Significantly, on-trade recorded a slightly faster decline of volume sales and constant unit price than the off-trade segment. With lower disposable incomes, Serbian consumers were clearly cutting back on discretionary expenditure, especially in 2009 and 2010. The leader in Serbian bottled water for decades has been Knjaz Miloš ad – a domestic producer of carbonated bottled water. In 2010, Knjaz Miloš ad held a 31% off-trade volume share of Serbian bottled water. The local bottled water industry fared better in the Serbian market in 2010, because there is a long tradition of bottling water that is available from natural springs nation-wide. This enables local producers to remain competitive, whilst foreign companies find it difficult to compete against them. In 2010 private label products were especially notable. One company, Premia, is found on the shelves of the country’s biggest retailer - Delta Holding doo. Premia bottled water is currently produced in 1.5l and 6l bottles and it has Serbia Coming from Bulgaria, I was very lucky with the Serbian transport network. The roads were excellent and there were no traffic jams. However, dense fog made the journey to Belgrade with the Editourmobil seem never-ending, and it was impossible to do much more than 50km / h. A combination of the fog and longer than expected visits to companies meant that my timetable went well and truly awry but thanks to different time zones and changes to daylight saving time everything just fell into place. It was fortunate I was not aware beforehand of all the time changes! So I managed to be reasonably on time for my appointments with Knjaz Milos and later with Borverk Eurotrade. I also discovered, luckily just in time, that appointments which I thought would be in the centre of Belgrade, were actually only head offices and that the production facilities were located out of town. On the way to Fruvita in the early morning of the following day I thought I would have an hour or so to spare before the factory opened. This turned out to be not the case, because my contact Mr Ivan Petrovic was ready and waiting for me at the factory gate, eager to show me the Krones aseptic line. No time for a lunch break today, instead of which I made my way to the other end of town for an appointment with Coca Cola. Finally there was a last visit later to the PET preform manufacturer Energopet. My eventful time in Serbia had come to an end, there was yet another meeting in my schedule, to the bottled water producer Minaqua in Novi Sad..And in the evening while I was sitting in the Editourmobil writing up my blog, my mind was already eagerly anticipating my upcoming visits to new countries.","@ID":17} "CAPPING / CLOSURES 30 PETplanet insider Vol. 13 No. 01+02/12 www.petpla.net Corvaglia drives for lighter one-piece caps and broader applications New caps for new markets Swiss closure system manufacturer Corvaglia continues its strategy of designing and manufacturing one-piece caps. It is developing new, lighter cap and neck designs, as well as combi-caps for still and carbonated beverages, hot-fill closures and economical flip-top caps. Since Corvaglia first opened its doors in 1991, it has focused on one-piece caps and closure systems. The company has been investing several million Swiss Francs annually developing optimised cap weight and efficient production processes. This year will see it introduce a number of new products, offering lighter weight, more applications, and taking it onto new markets. Combination caps for still water and carbonated beverages The company is close to launching a new combination cap for the 1881 short neck form. The ‘combiclosure’ has been developed for the demands of the carbonated beverages market, such as OPT and temperature cycle. But it goes further, by being intended to suit the needs of beverage fillers who, alongside carbonated beverages, also fill a rather smaller amount of still water; the closure is designed to meet other criteria, such as advanced tamper evidence. Caps for still water are usually lighter than those for carbonated drinks. Corvaglia’s new 1881 combi-closure has already demonstrated that it can meet both sets of requirements, under laboratory conditions, and at only 2.10g the company says it sets a record low weight for a carbonated drinks 1881 closure. In the pipeline: hot-fill closures and flip-top sportscap Corvaglia’s pipeline also contains a new range of hot-fill closures. During the development process it is looking at possible new neck forms as well as the optimisation of weight and performance. The company believes that the market will soon see one or two new hot-fill closures that will also meet the needs of still water and carbonated drink bottlers. A new type of flip-top sports cap for the 1881 neck form is reported to be at an advanced stage of development. With a light weight and thus lower cost, it is aimed at a wide range of products, such as low cost bottled water. Unusually for Corvaglia, it is a two-piece sports cap. It is designed to be visually attractive and to offer the possibility of combining different colours along with light weight. PCO 1881 combination cap New generation of hot-fill closures PCO 1881 In the pipeline: 1881 flip-top two-piece cap Lightweighting SPECIAL","@ID":32} "BOTTLING / FILLING 27 PETplanet insider Vol. 13 No. 01+02/12 www.petpla.net Stringent stipulations The initial talks with Krones started back in February 2009. The MEG laid down the following stipulations: the lightest possible weight, it must be possible to handle the bottles on all the machines installed in the MEG’s lines, use of recyclate possible up to 80%, a maximum CO 2 content of 8.0g per litre, trouble-free handling in reverse vending machines, the stability was required to be high enough to ensure that the bottle can also be run on older existing lines, passing the stress crack test, a tough burst test, low CO 2 losses during the specified shelf-life. New testing methods First of all, a series of internal tests was conducted on a total of four bottles currently on the market, each with different characteristics, so as to identify the status quo as a baseline. The ideal recessed-grip position was also determined here. This was followed by three different bottle designs, which were then tested in parallel. For all recessed grips, due to the smaller diameter involved in this area, thicker walls have to be provided when the bottle is being blow-moulded, for concomitantly enhanced stability. This enables the rest of the area to be maximally reduced in terms of wall thickness without any adverse effects on the functionality, e.g. the bottle will not crumple. The aim here is to dimension the recessed grip so as to ensure that the high internal pressure does not lead to subsequent expansion phenomena in the form of widening and stretching of the recessed grip. An ideal preform geometry also had to be designed for this job: using the test tool thus created, on an injection moulding line provided specifically for this purpose, Krones manufactured preforms for 1.5l containers in different weights and designs for testing, tipping the scales at 26.8, 28.5, and 29.7g. The sample moulds were then used in Krones’ pilot plant to make sample bottles, which were exhaustively tested against the client’s specification. Specially for this development project, Krones supplemented the tests with two additional methods: the touch-load test, which examines the bottle’s grip stability in the recessed grip area, and the tilting-force test, used to determine how much force is acting on the bottle, and how much is needed in order to pour a drink from it. These values are extremely important when, as in this case, the aim is to achieve an extreme reduction in the bottle’s weight. Scores in terms of technical values, bottle design and ergonomics Upon completion of all these tests, which extended over a period of several months, the bottle was presented to Lidl. It scored highly not only in terms of technical values, but also and crucially in bottle design and ergonomics. The newly created 1.5l bottle for Lidl, at 26.8g, is to our knowledge the world’s lightest CSD bottle for highly carbonated beverages. Meanwhile, all the lines at MEG have been modified, and the container has been well received on the market. The new bottle has replaced a host of different designs. As of now, all the products involved, namely water (still and carbonated) and soft drinks, are being filled in a single uniform bottle, and not in up to three different container shapes. This creates more efficiency when changing over to a different beverage on the production line. www.krones.com MHT MOLD & HOTRUNNER TECHNOLOGY Dr. Ruben-Rausing-Str. 7 | D-65239 Hochheim/Main Tel. +49(0) 6146-906-0 | www.mht-ag.de Make the most of your machine – with a mold from MHT! For many machine types, we supply the mold with the highest cavitation, thereby enabling optimum preform output. For the Husky HyPET machine, we offer an upgrade set for 33% more preforms, without refitting on the machine! • 60 cavities for Netstal PETline 2000 • 96 cavities for Husky HyPET 300, • 112 cavities for KraussMaffei 350 Engineering made in Germany 128 for HyPET 400 Booth 55009","@ID":29} "PETproducts 34 PETplanet insider Vol. 13 No. 01+02/12 www.petpla.net Cooling efficiency Sipa has launched a new range of solutions aimed at improving the cooling efficiency of PET preform moulds, under the CoolLife brand name. Sipa says that the system’s new layout provides better cooling performance at a higher water temperature, through improved distribution of the cooling channels to each cavity. It combines series and parallel distribution of the water to the cavities and effectively halves the amount of water required, while increasing water flow per cavity. The layout allows the permissible difference in the temperature (ΔT) of water flowing into and out of the cooling circuit to be 3°C, rather than the 1°C in existing systems. The CoolLife system allows input water temperature of 14°C rather than 8°C. With reduced water consumption, it is claimed that less expensive pumps are required, and higher input water temperatures lead to lower cooling capacity requirements. A ‘double-deck’ arrangement for the cooling channels around the preform neck increases the total channel surface area. The IceCool option has cooling channels that better conform to the geometry of the neck, have an even greater surface area and induce turbulent flow, to provide further optimised cooling when necessary. IceCool is claimed to save energy, cut cooling times by 25% and total cycle times by nearly 15%, while minimising preform distortion and reducing condensation. www.sipa.it Automatic leak detection American company Plastic Technologies, Inc. (PTI) is launching an upgraded version of its LeakMonitor device, which now has the ability to detect leaks at the production speeds achieved by contemporary blow moulding equipment. LeakMonitor uses an ultrasonic sensor to detect the noise that is generated by pressurised air passing through an orifice, and turning it into an electronic waveform. A deviation from pre-set parameters identifies defects in the product or machine components. During the production process, the LeakMonitor listens for leaky bottles, tracks them through the machine and triggers an eject mechanism when they are in the correct position. Routine background noise is also monitored and graphed and if it reaches an unacceptable level the ultrasonic sensor can trigger an alarm. The upgraded version features automated calibration, including a display of the relative severity of air leaks and where they are located on the blow wheel. As the percentage of rPET has increased, along with the trend towards lightweighting, the incidence of holes increased up to 1000 times, compared with virgin PET. PTI says that its LeakMonitor helps to ensure that rPET usage does not result in defective bottles leaving the operation. As well as bottles, it can identify and locate leaks from equipment such as valves, faulty lines, compensation gaskets, stretch rod seals and misaligned tooling. www.plastictechnologies.com Pre-glued, roll-fed labelling P.E.Labellers SpA, Italy, developed a labelling amchien called Adhesleeve system, which uses white or clear preglued roll-fed films with thicknesses lower than the films normally used on classic roll-fed labellers. The company says that the elimination of hot melt in its pre-glued film system offers a number of attractions, including a more sanitary and ecologically friendly working environment; the elimination of fumes; and complete recyclability. It is available with a thermal shrinking system and is claimed to be user-friendly in operation. It is also able to create a sleeve-type packaging with one labelling machine, by simply changing the type of film being used. www.pelabellers.it Slat lane dividers in-house After a period of analysis, design and development, end-of-line packaging machine manufacturer Cermex, part of Sidel, has been designing and manufacturing slat lane dividers totally in-house since the beginning of 2011. Twenty machine orders had been placed by the end of the year. The company says that it can supply its dividers either as standalone machines or integrated within a full packaging solution. The advantages Cermex claims for its new product line include alignment of management process for lead times and quality, and the ability to exercise greater control on the synergy between its machines and upstream operations. www.cermex.fr","@ID":36} "PREFORM PRODUCTION 11 PETplanet insider Vol. 13 No. 01+02/12 www.petpla.net during the blowing process distributed itself over the entire bottle. Thus, material taken from the base can be used to increase bottle strength, or it can be removed from the bottle altogether, resulting in material savings. Testing for maximum burst pressure also showed improvement. PET bottles have traditionally tended to crack in the sprue area, at an average pressure of approximately 10 to 11bar, due to the crystallisation of material build-up in the base area. The LightBase bottles reached pressures of 11.5 to 12.5bar before cracking, and the sprue was no longer the weakest point: the LightBase bottles cracked in the body section. Netstal’s testing program found these results in both juice and CSD bottles. www.netstal.com Fig. 2: Influence of different preform domes on bottle bases Fig. 3: Depiction of the measured weights of bottle sections Fig. 4: Bottle wall strength distribution Comparison of the LightBase and Cappello Design using the burst pressure test CCT Creative Competence Technology GmbH Idsteiner Strasse 74 D-65527 Niedernhausen, Germany [email protected] www.cct-systems.com Developments Type 2925-1,25g CCTsystem®-SBT CCTsystem®-slit-band technology Type 1881-2,1g CCTsystem®-SFBT CCTsystem®-slit-foldband technology All Closure types with CCTsystem®- BPT Best Performance Technology PET Molds Design and Patents Closure Molds Closure Systems Developments PET Systems","@ID":13} "21 PETplanet insider Vol. 13 No. 01+02/12 www.petpla.net Conveyors Bottle-to-bottle recycling plants Caps and closures Preform moulds and SBM moulds Preforms Preform and single stage machinery SBM machinery Compressors Filling equipment Resins and additives Suppliers of conveyors for preforms and empty bottles Preforms and empty PET bottles in a great variety of weights, shapes and sizes need to be transported gently and at high speed. This year the major suppliers of conveyors have contributed their data for our annual survey. These include GEA Procomac, Intec, KHS, Krones, Posimat, Sidel, SMI and Zecchetti. Suppliers in the preform conveyors sector include (from injection moulding machine into the box) Intec, SMI and in the sector ‘From the box into SBM machine’ KHS, Krones, Sidel, SMI and Intec. All the firms mentioned supply bottle conveyors. Whilst the publishers have made every effort to ensure that the information is up to date, no claims are made regarding accuracy or completeness. 01+02/2012 MARKETsurvey Company name Posimat Intec Solutions, Inc Postal address Telephone number Web site address Contact name Function Direct telephone number Fax E-Mail Avda Arraona 23 08210 Barberà del Vallès (Barcelona) Spain +34 93 7297616 www.posimat.com Cristina Fernández Sales Coordinator +34 93 7297616 +34 93 7188856 [email protected] 2382 Bolton Rd, Atlanta, GA 30318 +1 404-815-9983 www.intecsolutionsusa.com Arnold Manier General Manager +1-404-424-9454 +1-404-601-9778 [email protected] Preform: from injection moulding machine into the box Box-filling system Yes Maximum drop from conveyor belt to base of carton (in cm) In-line Control Yes Preform: from box into SBM Machine up to 60,000 preforms/h Dumper No Yes Conversion to different neck diameters(Mechanical / electrical) In-line Control Yes Bottle: from SBM to filler, air conveyor Air Conveyor (incl. vertical) Yes Yes Purity levels Hepa fillers DOP at 0.3 micros 99.99 effifiency Standard and clean filtration Bottle format conversion Yes CAM universal (multi position) side guide system for any type of bottles with one side guide Conversion to different neck diameters Yes Up to 2 positions Bottle storage systems Bottle up-ender Yes No, only bulk Buffer systems capacity (number of bottles from… to…) Tailor-made for any requested capacity From 0 to 15 -20,000 bottles depending on production rate and bottle size ) Storage systems capacity (number of bottles from… to…) Tailor- made for any requested capacity From 0 to 225,000 bottles for a 0.5l at 9g) Palleter and depalleter for empty PET bottles Yes Yes","@ID":23} "PREFORM PRODUCTION 12 PETplanet insider Vol. 13 No. 01+02/12 www.petpla.net Sipa’s latest processes for producing and handling lightweighting bottles Lighter PET bottle necks Sipa says that lightweighting PET bottles requires an holistic approach, which considers every aspect of design, development and engineering, preform injection moulding, bottle blow moulding, handling, filling and sealing. As well as lightening the container body, Sipa has been paying attention to reducing weight in PET bottle necks – which is where the bottle wall is at its thickest. Taking blow moulding to the extremes of its capability has already yielded results in producing very light containers, the thickness and weight of the neck is determined by the preform injection moulding process. Design and development In designing a lightweight neck, Sipa identifies a number of key issues. All areas relating to function and neck seal have to be maintained unchanged, so that the same closure can be used. Sipa has analysed the way the design performs all along the line, in order to minimise the need to change the configuration of the existing production operation – the blower, filling line, and so on. It has endeavoured to ensure that only the neck-ring needs to be changed, thus enabling the existing injection mould to be retained. It analyses how the neck performs during filling, in order to ascertain how much the wall thickness in the neck can be reduced. Where necessary, air vents and exhaust are optimised and treatments on the mould surface are considered. If it is possible, Sipa conducts industrial tests at the customer’s site, with the use of a single neck-ring installed on the existing mould. Injection moulding Moulding a lightweight neck can be challenging. The small quantity of PET resin used could cause the material to cool too quickly inside the injection mould, which may lead to a ‘short shot’; this occurs when too-cool resin is unable to fill the cavity all the way to the top of the neck. All factors are considered during development including resin viscosity, which may affect the process and its thermal profile inside the hot runner. Several tests are undertaken in order to ensure perfect neck injection: inclduing dimensional checks to verify the correct formation of the thread; pressure resitance and proper opening of the thread; chemical and/or biological contamination; and other physical and mechanical tests. The preference, when converting the injection mould to a lightweight neck, is to change only the lip – for example, when cutting weight from 3.9 to 3.2g. Reverse engineering limits the risk of creating defects in the final product and helps to ensure the correct mechanical matching and durability of the mould’s components. Sipa’s tool shops across the world are equipped to carry out the procedures. Lightweighting SPECIAL","@ID":14} "imprint EDITORIAL PUBLISHER Alexander Büchler, Managing Director HEAD OFFICE heidelberg business media GmbH Häusserstr. 36 69115 Heidelberg, Germany phone: +49(0)6221-65108-0 fax: +49(0)6221-65108-28 [email protected] EDITORIAL Doris Fischer [email protected] Michael Maruschke Ruari McCallion Ilona Trotter Wolfgang von Schroeter Anthony Withers MEDIA CONSULTANTS Ute Andrä [email protected] Martina Hischmann [email protected] Ursula Wachter [email protected] phone: +49(0)6221-65108-0 fax: +49(0)6221-65108-28 France, Italy, Spain, UK Elisabeth Maria Köpke phone: +49(0)6201-878925 fax: +49(0)6201-878926 [email protected] LAYOUT AND PREPRESS Exprim Kommunikationsdesign Matthias Gaumann | www.exprim.de READER SERVICES Kay Krüger [email protected] PRINT Chroma Druck & Verlag GmbH Werkstraße 25 67354 Römerberg Germany WWW www.petpla.net | india.petpla.net PETplanet insider ISSN 1438-9459 is published 10 times a year. This publication is sent to qualified subscribers (1-year subscription 149 EUR, 2-year subscription 289 EUR, Young professionals’ subscription 99 EUR. Magazines will be dispatched to you by airmail). Not to be reproduced in any form without permission from the publisher. Note: The fact that product names may not be identified as trade marks is not an indication that such names are not registered trademarks. 3 PETplanet insider Vol. 13 No. 01+02/12 www.petpla.net EDITORIAL EDITORIAL dear readers Emerald Christmas Tree 2011 Christmas may be well and truly over but I couldn’t resist a last backward glance at the festivities and in particular a stunning Christmas tree designed by Jolanta Smidtiene of Kaunas, Lithuania. 14 metres tall, fashioned from over 32,000 green plastic bottles, and containing 40,000 lights, the Christmas tree dominated the main square of this Lithuanian city. (http://www.tdg.lt/news/news-74/). “Each of us believed in miracles in childhood. But when we grew up we realised that we can create miracles by ourselves from the simplest of things. Of course, we don‘t have the power to turn water into wine. That’s what we expect from God. But still we are rewarded with many opportunities: imagination, diligence, love, dreams and the ability to create an environment which is full of creative things. The biggest miracle occurs when the ordinary is transformed into something better, something beautiful. All of this is the message of Christmas - miracle and hope. To manufacture this year’s Christmas tree we used green plastic bottles, because plastic is lightweight, transparent, easy to cut or connect to other materials. After two months of working, we finally made the Christmas tree, which stands 14m high: it is lit from the inside, creating a green glow that fills the town square. The tree is created by arranging giant orbs that decrease in size as the tree grows taller. The thousands of green bottles are placed with the nozzles facing out, and then fixed into place with the zip ties. The largest orbs, which sit on the ground, are over 1.5m in diameter.” Perhaps it is a challenge for us all to see things sometimes from a different angle and to do what we can to use things that are generally accepted as not so good for ends which are good. Perhaps in the same way as Jolanta Smidtiene has succeeded in creating a shining emerald from bottles. With this thought I wish you a good start to 2012. Yours Alexander Büchler","@ID":5} "REGIONAL MARKET REPORTS 17 PETplanet insider Vol. 13 All ten lines are made up of linked individual machines: three Sidel, one Krupp and one Sipa blower, fillers come basically from KHS although there is also a Procomac, labellers from a range of suppliers and the packer always comes from SMI. “Serbia has a very eventful past and as a result we have used a range of suppliers depending on the year and the underlying situation“ says Production Manager Goran Savović. He has been with the company for 20 years and loves all his machines whatever their pedigree and manages well with the colourful mixture of machines. The newest line is a Hotfill KHS line for 0.2l juice. This is fully automated including the syrup room. The largest PET line bottles 24 000bph of 1.5l still water. It is on to this line that Zorica Vukčević Kljajić, COO, is intending to introduce the lightweight 1881 at the start of 2012. “The other PET lines will follow bit by bit“ she states. This will mean that the weight will fall from 39g to 37g for 1.5l of carbonated water. They are not bothered about getting any more out of it. As regards the still waters, however, they are definitely keen to make more savings. Here they are looking at getting the weight of the bottle down from 37g to 30g˅. “We can only do this with a new design bottle that is at the same time still aligned to the design we have used hitherto” says Milan Vujović, Marketing Director. The preform and caps suppliers in Serbia already have sufficient capacity available to them for the new 1881. As a one-time market leader in the former Yugoslavia, the company still commands a high market share in Bosnia and Montenegro. It is the premium brand Knjaz Miloš that is doing very well in these countries. Still water there is exposed to strong local competitive pressures. In addition to this they supply to many other countries in the world, not always in large quantities but sufficient to make it worthwhile. A total of 67 different decorations are thus featured. www.knjaz.co.rs Goran Savovic Production Manager has been looking after the machinery at Knjaz Miloš for 20 years","@ID":19} "REGIONAL MARKET REPORTS 18 PETplanet insider Vol. 13 No. 01+02/12 www.petpla.net viable route. At the same time, with the help of the aseptic line, Fruvita have succeeded in tripling their turnover in just one year. www.fruvita.com EnergoPET We met: Miroslav Popović, General Manager Sasa Zdravković, Technical Director Nebojsa Tanasković, Production Manager Nenad Krstić, Head of Maintenance Department Nebojsa Tanasković, Miroslav Popović, Sasa Zdravković (F.l.t.r.) It’s the colour that does it Bottlers such as Coca-Cola produce clear standard preforms themselves in large-scale production. However, it is in coloured preforms where the real margins lie and but nobody really has much too confidence in them. Changes in colour can be both too time-consuming and too expensive. Here in Serbia the best in its class – even if not quite all the Balkan states – is EnergoPET. No colour is too outlandish for them. As is the case all over the world, earning money with standard preforms is difficult. A small fluctuation in material prices and bang goes the profit margin. Things are better where customer-specific preforms are concerned; here the quantities may be smaller but margins are better. And it is precisely here that Energo PET, located close to the airport in Belgrade, comes in. In addition to the “plain” preforms, everything at EnergoPET has its colour. And it’s not only blue preforms for the water bottles, coloured preforms for the CSD industry or brown ones for the beer either; here there is a preponderance of special colours in particular pouring off the conveyor belt. The milk industry demands white and pink-coloured preforms, other customers want red or green variations. One highlight just has to be the gold-coloured preforms that EnergoPET once produced for a particular marketing campaign using injection moulding. No colour is too outlandish to be used in a preform. Nevertheless, for Miroslav Popović, General Manager, standard preforms also represent an important arm of the business. “It ensures that we get basic capacity utilisation out of the equipment“ or so he contends. But because margins are generally tight, EnergoPET has introduced an extensive IT system. Everything is immediately registered everywhere, each octabin gets its own bar code, the material is booked out from the stores immediFruvita We met: Ivan Petrović, Maintenance Engineer Marjan Gavrilović, Mechanical Engineer Dragan Nikolić, Maintenance Manager Marjan Gavrilović, Ivan Petrović́, Dragan Nicoloic and Alexander Büchler (F.l.t.r.) Always fresh This is the way I imagine the land flowing with milk and honey. The area around Lunjevac resembles nothing so much as a constantly burgeoning fruit orchard. This is the fruit and vine cultivating region of Serbia and it was clear to Fruvita that this treasure chest of nature had to be got into a bottle. In order to extract the taste producing substances, Fruvita adopt an entirely aseptical approach to their filling operations. Both cartons and PET bottles are used. In the case of the carton, the Serbs have opted for the out-of-the-ordinary Tetra Gemina Aseptic gable-top packaging and, as regards PET aseptics, they have gone for KHS. Dragan Nikolic, Maintenance Manager, actually prefers to use PET bottles for his filling operations. These involve considerably less expense than carton packaging, plus the consumer can see what he is getting. For the 1.5l bottle they use a 39g preform. But the Serbs still have a soft spot for their cartons. When it comes to handling the top premium segment with 100% fruit, Fruvita have opted for a carton. However, the bulk then goes into the PET bottles. Here the company’s range includes juices with a 50% or a 15% fruit content. The moneyspinner here is the large 1.5l pack. In addition to the Tetra line with a capacity of 6,000l/h, the company also has an SIG Combibloc with a 5,000 cartons/h capacity for the 2l cartons. The KHS line is a smooth runner in the truest sense of the word. At the time of purchase the Serbs decided to go for dry sterilisation. This has made it possible to shrink the area covered by the clean room from 65m² (wet sterilisation) down to 15m². And here Maintenance Engineer Ivan Petrović is thinking ahead. He is dreaming of the aseptic linear KHS plant Innosept Asbofill, where the clean room is considerably smaller and constructed on a considerably more compact scale whilst maintaining the same capacity of 15,000bph. In total, Fruvita fill 6 million bottles per month using the KHS plant; when it comes to cartons, the total is 4.5 million and this total is on a downward trend. Fruvita are on their own in the region with their aseptic line. Other bottlers are still thinking about whether this represents a","@ID":20} "CAPPING / CLOSURES 31 PETplanet insider Vol. 13 No. 01+02/12 www.petpla.net About Corvaglia Corvaglia has been known as a supplier of ‘turnkey’ solutions for cap manufacturing systems since the early years of its existence. The first such systems were installed in 1993 in China and Korea, where at the time the majority of caps were being imported from Europe and there was a demand for local production capacity and expertise. Faced with competition from a new generation of very efficient compression moulding machines for two-piece caps made from PP with a PVC liner, Corvaglia strengthened its research function and focused on optimising the weight of one piece HDPE caps. Carbon footprint and sustainability programmes underpin the route of focusing on singlepiece closures. Romeo Corvaglia was among the first to experiment with new neck thread standards, which saved considerable amounts of material both in the cap itself and in the neck form of the bottle, as well offering certain technical advantages. Nestlé Italy set up the first line trials with the short neck design in 2004 and a new short and lightweight closure, suitable for water and carbonated products, was the result – PCO Corvaglia. This neck is still used on the majority of bottles in Italy. The ISBT’s a global standard that was, in its basic dimensions, very close to the Corvaglia solution, and led to a large number of weight optimisation programmes. Corvaglia was contracted to one of the water bottlers in the USA to develop further optimisations for bottling still water. www.corvaglia.ch Would you like your products to stand out from the crowd? Thanks to the technology of Holland Colours you can turn your PET bottles into almost any colour. Our outstanding experience and efficency in producing colouring additives guarantees that your product will differ from your competitors’. Would you like to renew your PET bottles with unique shades? We can provide the solution for your business success. Holland Colours European Division Halvemaanweg 1, 7323 RW Apeldoorn, P.O.Box 720, 7300 AS Apeldoorn, The Netherlands I Tel: 31(55)368 0700 I Fax: 31(55)366 2981 I E-mail: [email protected] SILK SCARVES? COLOURFUL BALLOONS? A MODERN STATUE PERHAPS? Or eye-catching PET bottles that are good to grab?","@ID":33} "MARKET SURVEY 23 PETplanet insider Vol. 13 No. 01+02/12 www.petpla.net Sidel Engineering & Material Handling Zecchetti Srl Krones AG Rue du Commerce, 67116 Reichstet, France +33 3 88 18 38 50 www.sidel-ec.com Michael Kropp Product Manager +33 3 88 18 39 51 +33 3 88 18 38 81 [email protected] Via Galileo Galilei, 1-1/A 42027 Montecchio E. (RE) - Italy +39 0522 867411 www.zecchetti.it Francesco Parma Sales Manager +39 0522 867411 +39 0522 866034 [email protected] Böhmerwaldstraße 5 93073 Neutraubling, Germany +49 9401 70-0 www.krones.com Reiner Kahl Vice President of Division Conveyor Technology +49 9401 70-3065 +49 9401 70-913065 [email protected] Yes No No No No No No Yes No Mechanical (step-less adjustment with hand crank ) No Yes Yes (no vertical) Yes Yes 3 air filtration levels: gravimetric (F5), opacimetric (F8), Hepa (H13) Various filtration degrees including Hepa 100 F5, F8, H13 (Hepa) Yes, automatic guide rails Quick change Automatic with multi position cylinders (up to 12 positions) Quick conversion thanks to \"any size driven units\" Automatic with 2 position cylinders No No Yes Customized according to bottle format and customer accumulation needs No No No No Yes Yes","@ID":25} "REGIONAL MARKET REPORTS 14 PETplanet insider Vol. 13 No. 01+02/12 www.petpla.net Serbia Difficult market but a high proportion of PET Although Yugoslavia has collapsed, politically speaking, into a number of different autonomous states, the individual countries of the former Yugoslavia live on in terms of their commercial complexity. We visited some of these states on our Go To Brau Beviale tour. Our regional reports from the Balkans kick off with Serbia. With a total of 7.5 million inhabitants, the country is one of the smaller countries of Europe. Its gross domestic product per capita is nominally around €4200 / year. In 2009 the average net wage was around €335 per person. Despite successful endeavours in the reconstruction sector after the NATO bombardment during the Kosovo Conflict of 1998/99, one in every seven Serbs is still living below the poverty line today. The worldwide economic crisis in 2009 did not have such a profound effect on Serbia as it did on other states, because the strict sanctions imposed by the Serbian National Bank and the absence of any attractions as far as speculative investors were concerned led to Serbia’s becoming one of the most highly capitalised and most stable banking markets. As might be suspected, the Serbian consumer does not place a high priority on packaged drinks. According to data obtained from Euromonitor, the market for packaged water in Serbia amounts to just €200m. That is a mere €21 per head per month. Despite these negative factors, a buoyant industry has developed in Serbia around beverages and PET. 90% of CSD and the same percentage of water is packaged in PET (source: Canadien). In the case of beer, the figure is likely to be in the region of 25%, and perhaps more. In addition to domestic consumption, exports are beginning to play a role, with Montenegro the principal outlet. Until 2006, the two countries were in a loose confederation. Montenegro has carved out a reputation as a summer by Alexander Büchler Regional market reports Serbia Part 1","@ID":16} "BOTTLING / FILLING 29 PETplanet insider Vol. 13 No. 01+02/12 www.petpla.net Energy reductions “We now demonstrably require 30% less energy than with our monoblocked InnoPET Blomax Series III“, Mr Richmond says. It is worth mentioning that the monoblock version put into operation in 2008 has a comparatively lower capacity of 43,200 0.5l PET bph. The actual performance is in particular attributed to the integration of a new heater module in the InnoPET Blomax Series IV, which roughly halves the heating time for the preforms in comparison to the InnoPET Blomax Series III. The preforms are heated using short-wave infrared radiation “Near Infra Red”. The preform heating process, which lasts only approx. 15s, the start-up time for the new InnoPET BIomax Series IV is extremely short. Filling still water without conductivity The Silver Springs company’s option was the stretch blow moulder InnoPET Blomax Series IV monoblocked filling system. Here the decision was made in favour of the same filler type as 2008. This is the electronically-controlled normal pressure filling system Innofill NV, on which the non-contact filling via a free-flow filling valve ensures microbiological and hygienic safety. The Innofill NV operates on the principle of volumetric filling. On the Innofill NV, impeller measurement is used instead of magnetically inductive flowmetering. The prime benefit of this measuring method is that Silver Springs can easily bottle even demineralised water which has no conductivity. Richmond: “Using this filling system, we are optimally equipped for all aspects of consumer requirements in terms of non-carbonated water. In addition, the filling system allows us to process other non-carbonated beverages such as fruit juice beverages, flavoured water etc....“. According to Richmond, the new InnoPET BloFill monoblock, which has been designed for all aspects of the production and filling of PET bottle sizes of up to 2l, will continue to process primarily the 0.5l PET bottle packaging preferred by the consumer. This supplements the KHS monoblock supplied in 2008, which is integrated into a KHS turnkey line. This line also features an Innopack Kisters TSP 080 tray shrink packer which is still doing the company proud. Richmond has ordered two further KHS turnkey lines. The first is to manage the filling and packaging of up to 72,000 0.5l PET bottles. The second has a capacity for up to 35,200 PET bottles, and is conceived as a multi-functional line for a wide range of PET bottle variants. Both are to be integrated into a new Silver Springs subsidiary in Pennsylvania. As background information: until now, the main distribution area of Silver Springs lay in the south-east of the USA and therefore runs from Florida to Pennsylvania. Deliveries are carried out through all distribution channels. This means that in addition to retail trade, products are supplied to the catering trade and to companies and households. In future, the intention is to expand distribution right up to the Canadian border. www.ssbwc.com www.khs.com The Silver Springs Bottled Water Company has achieved average annual sales increases of 20% within the past 10 years. 70% of the total PET bottle sales at the Silver Springs Bottled Water Company is achieved with the 0.5l bottle. Demineralised water which has no measurable electrical conductivity can be easily bottled. The Innopack Kisters TSP 080 packs 0.5l PET bottles in a wide range of formats. The standard format is 6 x 4.","@ID":31} "CAPPING / CLOSURES 32 PETplanet insider Vol. 13 No. 10+02/12 www.petpla.net Bericap has developed a range of solutions to match the drive for lighter bottles with slimmer closure systems Slimmer means fitter Competitive pressures in the food and beverage market compels companies to consider all possible cost reduction measures, one of which is lightweight packaging. As well as cutting the use – and therefore cost – of raw materials, lightweighting also helps to reduce a company’s CO 2 emissions. Lighter weight packaging is an important element in the carbon footprint improvement programmes initiated by many companies. PET bottles have significantly slimmed down over the last decade; the effort to save raw materials extends to closure systems and Bericap has developed a range of lightweight closures for food and beverages. PCO 1881 - Lightweight neck for 28mm CSD Probably the first and certainly the best-known lightweight neck standards is the 28mm PCO 1881, developed within ISBT (International Society of Beverage Technologists) for carbonated beverages, such as soft drinks or water. It delivers a weight saving of around 26%, compared to its predecessor. Bericap has, meanwhile, developed different DoubleSeal SuperShorty(DS SuS) variants: the DS SuS CSD and the DS SuS Eco, which are both suitable for carbonated beverages with up to 8g CO 2 /l. Both versions have variants for still beverages and water: DS SuS CSD Still and DS SuS Still. Bericap says that this provides the bottler with the ability to run two closure types, with two different weights, for different products but with the same chuck and helps to reduce costs for those bottlers filling, e.g. CSD and water on the same filling line. Depending on the filled product and related closure types, weight savings of up to 20% are feasible. All the company’s closure variants are equipped with the Bericap DoubleSeal system, which is designed to ensure a safe seal and to achieve very good CO 2 -retention. Still variants have an anti-sabotage feature. Water closures set light weight standards The highest weight savings over the last couple of years have been achieved in still water packaging. Both the bottles themselves and the closures have become significantly lighter. The 30/25 closure/neck combination is the main system used for still water in Europe and Asia. A 26.7mm closure type is mainly used in North America, but also in India and Italy. Bericap developed two alternative closure solutions in the quest for lightness. The HexaLite 29/11 FB fitting for 30mm necks offers a weight saving of around 30% for closure and neck, compared to the 30/25. These closures are in the roll-out phase in Europe, have already enjoyed significant sales in China and are now being launched into the Indian market. The HexaLite 26/10 FB together with the 26mm neck offers up to 41% lower weight for the 26.7mm closure and neck. The HexaLite 26/10 FB was introduced in partnership with a major global water brand in North America and China, some time ago. In Germany, the lightweight HexaLite closure was introduced to offer discount chains a cost-competitive alternative to the 26.7mm closure. The closure will be introduced to the Italian market during 2012 as a replacement for the 26.7mm system, with the offer of resin saving and reduced CO 2 consumption. The HexaLite 26 FB is also an alternative for bottlers currently using the PET 30/25 neck, over which it offers weight savings of around 50%. All HexaLite closures are equipped with a slit and folded safety band (flexband) for tamper-evidence and reliable performance, on high-speed lines. The sealing system has been designed for maximum tightness. For on-thego consumption, the light-weighted 2-piece Sportscap Thumb’Up for the either the 29/25 or PET 26/22 neck is available. Smaller diameters for ‘on-the-go’ packs The usual size of closure fitted to ‘on-the-go’ packs for fruit juice and energy drinks is 38mm. However, consumer studies have shown that smaller neck sizes, between 32 to 35mm, are more convenient for drinking. In response to pressure for greater consumer convenience and customers’ cost saving efforts, Bericap and various industry partners developed a lightweight 33mm neck along with the DoubleSeal 33screw cap. The neck/closure combination is claimed to offer weight savings of around 30%, compared to traditional solutions. DoubleSeal 33 is equipped with a folded tamper-evident band for safe opening, and a particular design of the sealing lip that is intended to ensure product integrity. It can be disinfected with all standard methods known for aseptic filling. Lightweight closure for edible oil New 26/21 neck finish and closures Most of the 1l PET bottles used by the edible oil industry have a standard 29/21 neck finish, weighing 2.74g. Bericap has been developing DoubleSeal 33 Lightweighting SPECIAL","@ID":34} "BOTTLES PETbottles 35 PETplanet insider Vol. 13 No. 01+02/12 www.petpla.net Oil and dressings UK company King’s Fine Foods specialises in luxury products such as caviar, smoked salmon, champagne, chocolates, handmade biscuits and hampers. It has selected M&H Plastics of Beccles, England, to manufacture PET bottles and caps for its new range of British rapeseed oil and apple balsamic dressing, which is being used by British Airways in-flight catering. M&H created new tooling specifically for the 12ml PET square bottle (Ref. 4172) with a 13mm screw cap. The company says that the bottle and closure is suitable for picnics, salads and lunch boxes, as well as in-flight catering. M&H has over 1,000 standard products plus a full custom moulding service for exclusive designs. It undertakes virtually all operations in-house, from concept design through toolmaking, production, artwork and decoration. www.mhplastics.com Pip-free Lemon Juice “Pip-free Lemon Juice“ is the additional name given by the Italian company B & G Srl to their no-added-sugar lemon juice extracted from fresh fruit and marketed under the “Limmi“ brand name. The transparent PET bottle is in a round body format and decorated with a shrink sleeve appropriate to the product. The screw-on cap is secured both by the shrink sleeve and by a tear-off guarantee strip. www.limmi.it Lemon Lychee in PET Pfanner, the Austrian beverages manufacturer, is launching an increasing number of new, multi-fruit drinks on the market, in some cases with exotic flavours and packed in made-to-match PET bottles. The latest example of this is the Lemon Lychee variant with added vitamins in a pale yellowish coloured PET bottle with a content of 1.5 litres. The bottle, with its easy-tohold waisted shape, sports a shrink sleeve label and is sealed with a yellow plastic screw closure complete with printing and tamper-proof guarantee. www.pfanner.com Double power in PET Gedima Soft Drinks GmbH from Hückelhoven in Germany is producing “Magic Man“, an energy drink that contains taurine as well as caffeine. By comparison to other drinks, the caffeine content is increased to 32mg per 100ml. Magic Man is bottled in a 500 ml transparent bottle made from PET with an all-round belly label made from paper. The bottle, which features diamondshaped indentations, is sealed with a tamper-proof screw closure. Freshly harvested juice from Valensina Since December 2011 Valensina GmbH has been selling 1l of freshly harvested pressed juice in a transparent PET bottle with a screw top and sealed for freshness. The available variants are Pink Grapefruit, Valencia Orange and Moro Blood Orange. The bottle features embossed brand name lettering and a transparent all-round belly label in plastic. The juice, made in each case from 2.5kg of hand-picked fruit, is carefully extracted shortly after harvesting, gently pasteurised and subsequently marketed in a closed cold chain so as to ensure optimum quality. www.valensina.de","@ID":37} "PETpatents www.verpackungspatente.de 36 PETplanet insider Vol. 13 No. 01+02/12 www.petpla.net Plastic bottle Intern. Patent No. WO 2011 / 024694 A1 Applicant: Yoshino Kogyosho Co. Ltd., Tokyo (JP) Date of application: 19.8.2010 The design and procedure for manufacturing a PET bottle are described. The bottle, which is manufactured using the biaxial stretch blow moulding process has defined strength / material values at the container opening. Plastic bottle Disclosure No. DE 102009038608 A1 Applicant: Krones AG, Neutraubling (D) Date of application: 26.8.2009 Thin-walled plastic bottle with sufficient stability to absorb the different pressures that occur during hot filling and the subsequent cooling process. In addition, this bottle has a sufficiently large surface to enable labels to be applied. Stackable bottle Europ. Patent No. EP 2292519 A1 Applicant: August Gysen, Gent (BE) Date of application: 8.9.2010 Set – consisting of at least two bottles which can be safely stacked thanks to top and bottom faces which fit into each other. For lighter weight and enhanced comfort when carrying, a folding handle is attached to the neck of the bottle. Optimised labelling Intern. Patent No. WO 2011 / 037762 A1 Applicant: Graham Packaging Comp., York (US) Date of application: 10.9.2010 A plastic bottle for hot filling with a corresponding compensating area to absorb the change in volume during cooling is specially shaped in the labelling area in order to improve the application and the appearance of the label. Indentation for drinking straw Intern. Patent No. WO 2011 / 023586 A1 Applicant: Innoprax AG, Meggen (CH) Date of application: 17.8.2010 This international application describes a plastic bottle featuring indentations which are incorporated in its curved surface area and which are designed as a zone for holding drinking straws. This enables a drinking straw to be sold along with the bottle so that it is secure and impossible to lose. Simple closure Intern. Patent No. WO 2011 / 026736 A1 Applicant: Nestec S.A., Vevey (CH) Date of application: 19.8.2010 Closure simply superimposed and placed directly on top of the container opening using high frequency, complete with tamper-proof seal and re-closable lid. The constructive closure can be manufactured at a favourable price.","@ID":38} "BOTTLING / FILLING 28 PETplanet insider Vol. 13 No. 01+02/12 www.petpla.net Silver Springs Bottled Water Company implements the InnoPET BloFill monoblock concept* Silver Springs strikes gold *Based on an article by Georg Zuzok1and Mike Brancato2 1 Head of Market Zone Americas, KHS GmbH, Bad Kreuznach 2 Vice President of Sales & Marketing, KHS USA, Inc. Silver Springs purchased the first monoblocked KHS stretch blow moulder/filler system InnoPET BloFill in 2008. Now this well-known beverage company has installed the KHS InnoPET BloFill monoblock with the new-generation stretch blow moulder InnoPET Blomax Series IV; the first ever to be used worldwide – in a high-performance version with an output of up to 72,000 0.5-l PET bph. The new monoblock is said to have led to significant energysavings in production and to an increase in the “lightweighting” of their PET bottle. Silver Springs is a source which has quite a history behind it. Native Americans in the 16th century held the superb water quality at Silver Springs, located in what is today the region of Ocala, Florida, in high esteem. When Hullam Jones developed the world’s first glass-bottomed boat in the 19th century and used it at Silver Springs to observe fish, turtles and century-old fossils, the source became more and more popular with the people of Florida. Today Silver Springs is known across the world. The breath-taking scenery provided by Silver Springs is used as a location in numerous films. The history of the Silver Springs Bottled Water Company dates back to 1886. The current owners Karl and Margaret Richmond bought the company in 1991. At that time, business with bottled water was not strong in the USA. However, this did not prevent the Richmonds from recognising its enormous future potential. At the start, a team of just six people were engaged to fill Silver Springs water into 5l gallons (an American gallon is the equivalent of 3.785l ); today, the company employs 150 workers and, in addition to large containers, fills numerous PET bottle variants, from 0.24l right up to 1.5l PET bottles. Kane Richmond, President & CEO of the Silver Springs Bottled Water Company, says “Since 2008, we have been able to achieve a weight reduction from 13.2g to 9.1g with our 0.5l PET bottle, using a twostep process. 70% of our sales are in the 0.5l PET bottle. We are working on further reductions in weight. Our next targeted objective is to achieve a bottle weight of below 9g, and we even have our eyes fixed on the 8g mark. We are also currently cooperating with KHS to check through our entire PET bottle series”. Material savings Silver Springs is hoping to reduce the weight of its 0.5-l PET bottles again. A key aspect in material savings using the monoblock concept in the production of plastic bottles is that lighter weight PET bottles can be used, since the transfer is much more gentle than if they are shifted via air conveyors. On the new InnoPET BloFill monoblock, this advantage is supplemented by the simplified blocking of filler and blow moulders in comparison to previous models. Here the functions for removing bottles from the blow station and adjusting the distance between finished PET bottles according to the configuration of the filling system is now handled by just one modular transfer wheel. If - as with the Silver Springs Bottled Water Company, which currently only fills still water - only non-carbonated beverages are to be bottled, the PET bottles are sent straight to the infeed star of the filling system after passing through the airlock. The servo motor-controlled stretching process on the new stretch blow moulder generation allows the use of light weighting preforms. Thanks to the servo-controlled stretching process on the InnoPET Blomax Series IV, when monoblocked with a filling machine the stretching movement can now always be carried out at the optimum speed – irrespective of filler speed – allowing reductions in material. Karl Richmond (left), purchased the Silver Springs Bottled Water Company in 1991, and it is today managed by his son, Kane Richmond (right), President & CEO of Silver Springs. Lightweighting SPECIAL","@ID":30} "PETnews 6 PETplanet insider Vol. 13 No. 01+02/12 www.petpla.net Husky completes sales reorganisation Husky Injection Molding Systems has announced that Gerardo Chiaia has been named Vice-President, Global Sales for Beverage Packaging and that Mike Urquhart has been named Vice-President, Global Sales for Packaging Systems. They will both continue as members of the company’s executive team. Husky says that these announcements complete the transition of its global sales force to a market-based organisation. Mr. Chiaia joined Husky in 1996 and served as its sales leader for Asia Pacific, Europe, the Middle East and Africa since January 2010. Mr Urquhart joined the company in 1980 and has been Vice-President, Americas Sales since 2010. www.husky.ca Polyester & PET Chain 2012 The 16th Annual Polyester and PET Chain World Congress takes place at the Swissotel, Zurich, Switzerland, from February 15-16 2012, with registration and a reception on February 14. Buehler, the producer of CP, SSP and RPET plants is offering a post-congress open house site visit on February 17. . Discussions will centre on strategies for coping with the uncertain global business conditions, future supply and demand challenges. A major focus will be the projected growth of world-wide polyester capacities in the various technologies and applications from the current level of around 64 million tons. The future availability of 100% bio-based PET resins will be discussed by Coca-Cola, while Appe will present on the protection of oxygensensitive food products with novel PET barrier materials. Possible migration of catalysts, additive and other resin residues will be reviewed by Fraunhofer. Further packaging presentations include PET colouring and reheat preform additives by ColorMatrix, recycling of PET film laminates by the Parc Corp, and the efficiency, quality, testing and economic enhancements for RPET with filtration and recycling by Chemspeed, Erema, Kreyenborg, Starlinger and others. PET reactor technologies and products and advances in the Russian markets will also be covered. www.mbspolymer.com/polyester New Artenius PET resin line combines virgin PET and rPET Artenius Elite is a newly-developed PET packaging material from Artenius, the PET division of La Seda de Barcelona, S.A (LSB). It combines virgin PET resin and post-consumer recycled PET (rPET) as feedstock. Its chemical process replaces conventional non-renewable petrochemical raw materials with recycled material, which reduces the use of natural resources and helps to cut the environmental carbon footprint. It is available in nine different kinds of resins, designed to meet various packing and moulding process needs. The Artenius Elite formulation has been specifically developed for beverage packaging, including both still and carbonated water, and soft drinks. The product is suitable for processing for stretch blow moulding in one- and two-stage processes, depending on the base resin employed. Artenius claims that all products in the Artenius Elite family of resins meet beverage package manufacturing demands in terms of mechanical strength, colour and transparency. The material is produced under a proprietary chemical recycling process, which begins when clean recycled PET is de-polymerized and mixed with standard virgin PET raw materials, integrating both types of compounds into the re-polymerization process. Decontamination challenge tests carried out by Fraunhofer Institute established that the production process results in resins as pure as 100% virgin resin, even under worst-case contamination scenarios. The European Food Safety Agency (EFSA) has ruled that the Artenius Elite process should not be treated differently from monomers manufactured by chemical synthesis. The process has also been approved by the U.S. Food and Drug Administration (FDA) through a nonobjection letter. Artenius Elite is currently produced in the Artenius Italia, S.p.A Italian factory. The factory at El Prat, Spain, will begin manufacture of the new product during Q2 2012. www.laseda.es Management changes at DAK DAK Americas LLC, of Charlotte, NC, USA, a whollyowned subsidiary of Alfa S.A.B. de C.V. of Monterrey, Mexico, has announced that Jorge Young has been promoted to the position of President and Chief Executive Officer. Young assumes the position of President and CEO with the retirement of Hector Camberos, who will be returning to Argentina and assuming the leadership of DAK Americas’ Argentina PET Business. Young has been with DAK Americas since it was established and has been serving as the Executive Vice President - PET Resins since 2007. DAK’s executive team is to be expanded and the following appointments were also announced: Jon McNaull, currently Vice President – Polyester Staple Fibers becomes Vice President – Resins at DAK’s PET Resins Business; Tom Sherlock, Business Director – PET Resins is promoted to Vice President – Specialty Polymers; and Mark Ruday, formerly President of the newly-acquired Wellman, Inc., will become Vice President - Fibers. DAK Americas’ production capacity is over 4.3 billion lbs/a(19 million t/a). www.dakamericas.com Creative Closure Technology becomes Creative Competence Technology Creative Closure Technology GmbH has been renamed, as at November 1st 2011 and is now known as Creative Competence Technology GmbH. Creative Closure Technology has been active in the market for 15 years, initially in the field of closures development and the marketing of patents for the beverage industry. In the subsequent years its markets, products, distribution channels and the company itself have changed. Creative Competence Technology now offers a wide range of new products within the scope of the beverage industry, from the development of closures and preforms through to supply of turnkey closure and/or preform production units. The change of name is accompanied by a change to the company’s logo and a new website, which will be available soon.","@ID":8} "BOTTLING / FILLING 26 PETplanet insider Vol. 13 No. 01+02/12 www.petpla.net Debut for lightweight PET bottle A lidl less weight* *based on an article by Heinrich Deyerl, Krones AG 26.8g, that’s what it weighs: the very latest 1.5l PET container for CSDs. designed by Krones for Mitteldeutsche Erfrischungsgetränke (MEG), a subsidiary of the Schwarz Group, Germany, which also owns the retailing chains of Lidl and Kaufland. Following successful testing, the new bottle can now be found in all of Lidl’s branches nationwide. It has saved a substantial amount of weight compared to the previous design, in conjunction with significantly improved grip stability. Lidl is today among the Top 5 of Germany’s food and beverage retailers, and in addition is one of the largest retailing companies in Europe. With more than 3,000 branches throughout Germany, Lidl is aiming to optimise the energyefficiency of its facilities, and to streamline its internal operations. 100% less energy for heating, 30% fewer CO 2 emissions, and 10% less electricity consumed in comparison to a conventional food and beverage company. The supply of merchandise to the branches nationwide is organised through various central warehouses in Germany. Saving energy – reducing weight Back in 2002, Lidl had already begun to put in place a series of measures for saving energy in its central warehousing operations. To ensure that the food arrives reliably every day fresh and in top quality for the customers, plus of course the consumer durables also on sale, Lidl likewise prioritises efficient logistics. Another major focus is the use of eco-friendly beverage packaging. Under the motto of “Do your own recycling”, early in 2011 Lidl launched a publicity campaign for full-coverage material recycling, more energy-efficiency and reduced packaging weights. The PET bottles for the firm’s own Freeway and Saskia brands are currently made more than 40% from recycled PET material. For this purpose, only the deposit bottles returned in Lidl’s own branches are recovered in a closed-cycle process. The MEG is currently increasing the proportion of recyclate from 40 to 50%. Krones has proved it possible to reduce the weight of the Freeway and Saskia PET bottles by almost 30% over the last few years, while still retaining and even improving their functionality and handling qualities. In conjunction with the proportion of recyclate involved, today only 42% of the fresh raw material quantity (38g) required three years ago for producing a bottle is needed, and in the future this figure will be a mere 35%. This amounts to just 13.3g for a 1.5l bottle. Compared to the situation three years ago, only 42% of fresh raw material quantities are required today for producing a PET bottle for Lidl, and in the future it will be a mere 35%. Lightweighting SPECIAL","@ID":28} "REGIONAL MARKET REPORTS 25 PETplanet insider Vol. 13 No. 01+02/12 www.petpla.net Rome, Paris and London for its exquisite quality. At that time, Minaqua was known as “Franz Josef’s water”. Soon after this discovery, a spa was built in the location where the water was found. It quickly attracted attracted over 1500 visitors per day. During the 20th century, the spa achieved fame far beyond the city boundaries of Novi Sad. The mineral water was used for therapeutic purposes as well as for drinking. After the Second World War the water was sold all over Yugoslavia under the name of “Mineral water of Novi Sad”. In 1972, the name “Mineral water of Novi Sad” was changed to “Minaqua”. In 1999, Minaqua was privatised. The new management team decided to implement new and efficient technologies, and to establish new company objectives and operating rules. Over the next five years, the new team succeeded in making Minaqua one of the strongest leaders in the bottling of mineral water in Serbia and Montenegro. The Editourmobile stops at the Minaqua bottling plant Since 2004 Minaqua have been producing mineral water only in PET bottles, although there are plans to purchase a production line for glass in the future. The complete bottling operations involve only PET. Preforms As the business was growing as well as the production capacity, the company’s managers decided to manufacture their own preforms. By doing this, the company was able to reduce costs and gain independence from other suppliers. The company has been manufacturing preforms since 2005 (the first Husky blow moulding machine was bought in 2005. Then in 2008 the company enlarged its capacity by purchasing a further Husky blow moulding machine. The total capacity of machines is 22,400bph. The present capacity is sufficient for the production of preforms to meet the company’s needs and there is no need to obtain preforms from other suppliers. Minaqua produces two bottle shapes: round (2l, 0,33l carbonated mineral water Minaqua Classic), square (2l, 0,33l still water Minaqua Life and 5, 75 l bottle still mineral Minaqua Life). The company was also able to reduce the weight of the preforms for the round bottle (2l capacity) from 45.3g to 41.5g in 2010. Current preform weights are as follows: 41.5g ( 2l round bottle ), 39g ( square 2l bottle ), 20.5g ( 0,33l round and square bottle ) and 90g ( 5.75l square bottle ). Stretch blow moulding and filling The production facilities of Minaqua consist of the following production and filling lines: Krones (Germany) capacity of 9,000 units of 2l bph; SIG (SIG Coproplast Germany and SIG Simonazzi Italy) capacity of 14,000 units of 2l bph Sidel (Italy) capacity of 16,000 units of 2l bottles/h; Thomason Machinery for producing 5l bottles with a capacity of 3,000 units/h (Cyprus); 3 blow moulding machines (SIG Corpoplast, 2 units, and Sidel, 1 unit, for PET bottle production of 2l , 0.5l and 0.33l). These machines have capacities of 16,000 bottles/h and 22,000 bottles/h respectively; Minaqua invested in an injection moulding system for the production of PET bottles. Two Husky Injection Moulding Systems have a total capacity of 22,400 units per hour. The production and filling lines for the PET industry are certified according to EU regulations. As stated above each line comes from one supplier and all filling lines are arranged in blocks. The final products are gathered in a shrink tunnel using a Dimac machine. At the end of 2008, a new warehouse with the innovative Radioshuttle System was installed. This equipment doubled the storage capacity of the company. The total number of euro pallets that can be stored with the System is around 5,390. In 2008 Minaqua doubled its storage capacity Products “Minaqua Classic” carbonated mineral water and “Minaqua Life ” still water have a high level of brand loyalty and enjoy a good competitive price. The water contains 0.94mg/l of iodine, and one glass of the water per day satisfies our daily needs for this element. Minaqua water contains a large amount of naturally dissolved iodine essential for brain development and concentration. It is the only mineral water in Europe with this specific property. In addition to the carbonated and still waters, Minaqua also produces a carbonated soft drink “Fructo”, in five flavours (Orange, Mandarin, Tonic-lemon, Tonic, Lemon and Cherry Cola). The company also produces “Jodi” designed for children and pregnant women. It is offered in two flavours (apple and cherry). The product incorporates a sport lock for ease of use. Minaqua’s current products are different from other soft drinks on the market. First Minaqua does not use any artificial flavours and second, all its products have naturally dissolved iodine. www.bbminaqua.com","@ID":27} "PREFORM PRODUCTION 13 PETplanet insider Vol. 13 No. 01+02/12 www.petpla.net The thread Sipa is studying further reductions in threads Still products Novembal 267 necks in still water bottles has already been reduced, from 3.6g to 2.6g: a saving of 27%. Special modifications on the line enable further reduction, to 1.8g – a total cut of 50% - which is already in use with Premium Water and other mineral water bottlers. A 3.9g Novembal 30/25 thread is widely used in non-carbonated drinks and a stripped-down version weighing 3.2g has already been used in several different projects. Towards Sipa the new trend in the global market is now Novembal 29/25 which is 2.5 g already adopted by several bottlers worldwide. Sipa is studying a further reduction of the new trend without any conversion to the cap and bottling line. CSD The PCO1881 standard, now widely adopted for carbonated drinks, weighs 3.7g, compared to 5g for the PCO1810; Sipa has already validated a 3.4g version and it says that is working to reach an extremely lightweight finish at 2.5g with the same performances of the existing necks on the market. Hot fill: It has already launched two lightweighted neck finishes for hot fill, which is marketed as the ‘HotLight 28’ and HotLight 26. Their weights are only 3.8g, which is 41% lighter than the standard neck finish’s 6.4g. Sipa describes the HotLight necks as an evolution of a traditional neck that is usually adopted for CSD. The company says that it does not compromise the bottle seal even if the filling temperature is 90°C (standard for RTD) and that it allows the production of hot fill and CSD containers on the same machine. It is being used by Universal Robina Corporation, Philippines and PT Mayora, Indonesia. Blow moulding and downstream Sipa’s rotary blow moulding equipment includes a system that enables the body to be reheated without deforming the neck. Preform loading now has a system that expels preforms that have become lodged one inside the other, as light preforms with small bodies have a tendency to stack together. The new system ejects them and enables loading rates of up to 48,000 preforms/h. The shape of the preform carrier in the SFR rotary stretch-blow moulding machine has been improved in order to ensure the stability of the preform during heating, and to keep the neck temperature as low as possible. Sipa has modified the ventilation modules in the oven, in order to facilitate processing of very light necks by improving cooling of the neck while increasing the capacity to heat the preform. The configuration of the infrared lamps has also been adjusted. Sipa’s ‘crocodile style’ vertical mould opening system is designed to keep centrifugal forces on preforms and bottles at a very low level. This means that the grippers do not have to pinch the necks to maintain the preforms and bottles in the correct position, which is important in handling easily deformable lightweight necks. Downstream, Sipa has modified filling and sealing procedures in order to minimise stress on the containers and has paid particular attention to lifting and contact forces. Lightweight necks need to be sealed using an axial load that may be as little as half that used for normal bottles. www.sipa.com","@ID":15} "NEWS 8 PETplanet insider Vol. 13 No. 01+02/12 www.petpla.net New KHS label lab KHS recently opened an in-house label lab at its plant in Dortmund, Germany, which analyses various properties of labels using state-of-the-art measurement devices. The lab is equipped for the study of all kinds of label, from conventional cold glue paper through self-adhesive to film and rollfed. All labels are tested in full detail under ideal test conditions, i.e. at a temperature of 23°C (+/- 1°C) and at 50% humidity (+/- 2%). The lab also checks whether newly-purchased machines and the ordered labelling technology are fully compatible with one another, and will provide advice on storage and processing conditions for the specified labels, including optimum humidity and air temperature in the plant. If the labels are changed during the service life of a KHS labeller, customers can refer their new label designs to the label lab at any time, for advice. Customers can also have access to a database, which is based on statistics collected from real-world experience and provides a resource for prognoses to be made as to the effect of certain label properties on quality. KHS says that it also maintains contact with various research institutes and label manufacturers with whom it constantly exchanges information and experience. www.khs.com Uhde Inventa-Fischer proves PLA process Uhde Inventa-Fischer has announced that it has proven the potential of PLAneo, its patented PLA (polylactic acid) technology, after an operating phase lasting several months. Its PLA pilot plant in Guben, Germany, has a production capacity of 500t/a of polymer granules. The company reports that testing covered the full functionality of the PLAneo process and that all achieved performance parameters were achieved. The process is claimed to produce PLA that is suitable for a range of applications including film and fibre, masterbatch base polymers, and various specialities such as PLA copolymers and stereocomplex PLA with increased heat resistance. Uhde Inventa-Fischer asserts that the continuous process is suitable for large-capacity industrial production plants. PLAneo uses commercially available lactic acid, which is converted to granules with a yield in excess of 95%. The company is part of Thyssen Krupp Uhde GmbH, which it says enables it to cover the entire process, from agricultural feedstock and lactic acid to the saleable granules. ThyssenKrupp Uhde is currently building a pilot plant in Leuna, Germany, for the production of lactic acid from glucose or saccharose. The plant is due to come onstream in the second quarter of 2012. www.uhde-inventa-fischer.com Fondo Italiano di Investimento buys into Amut SpA Fondo Italiano di Investimento (Italian Investment Fund) has contracted to buy shares in Amut SpA, headquartered in Novara, Italy. The transaction involves an overall investment in company equity of €10 million, giving Fondo Italiano di Investimento a minority share. Amut employs some 165 people and generates yearly revenues of approximately €47 million, 84% from sales outside Italy. Amut produces extruded profiles, pipes, sheets, and films that are used in a broad range of industrial applications. It also builds in-line and off-line thermoforming systems for the production of packaging materials (trays and tubs), and single-use articles such as plates and glasses. It began producing recycling plants for industrial and postconsumer plastics in the 1980s. Fondo Italiano di Investimento’s investment will support Amut’s future growth plans in all three of its business areas. CEO Mauro Drappo said that the investment will enable Amut to strengthen its position in foreign markets and provide resources to step up its research and development efforts in an increasingly complex and selective industry. www.fondoitaliano.it Appe awarded ‘Processor of the Year’ Nearly 800 plastic professionals and their guests at the 2011 Plastics Industry Awards ceremony saw convertor and PET preform manufacturer Appe named Processor of the Year in 2011. The company believes that becoming the first major PET producer to gain the BRC/IOP Global Standard for Packaging and Packaging Materials across all of its European plants was an important factor in winning the award. It was also shortlisted in two other categories: Best Business Initiative and Best Training and Development Programme. www.appepackaging.com Indian beverage industry discusses PET A pan-India seminar entitled “Unlocking the Value of Packaging for Liquor Business”, organised by Reliance Industries Limited (RIL) and other industry members, was held at the Hotel Westin in Pune, India, November 18 2011. Aimed at both domestic (‘country’) liquor manufacturers and imported beverage businesses, the half-day programme explored advantages of PET packaging, labelling, filling and shrink-wrapping systems, discussed emerging global trends in packaging, and addressed various technical and commercial issues. The Indian PET industry has identified alcoholic beverages as one of the key focus areas for development and promotion. PET bottles usage for alcoholic beverages in India is primarily in sizes up to 750ml, with larger pack sizes (2l and above) more popular in southern states. The use of PET for both imported beverages and country liquor is growing and gaining approval in progressively more states. Total usage in the sector has grown from 55kt in 2009-10 to 65kt in 2010-11. It is projected to reach 80kt in 201112 to grow at 20%/a in the next three to four years. The seminar followed similar exercises presented by RIL and partners for the pharma and edible oil sectors. It brought industry members together on one platform to “…network, brainstorm and establish PET as a solution provider” for emerging packaging opportunities, and to help manufacturers re-position their products by improving brand appeal and to become more competitive in costs. Presentations were made by RIL PET Division; Sunrise Containers Ltd; S S Packaging Industries; Swiss label printing machinery company Gallus; Avery Dennison; Maks Automation; Allied Blenders and Distillers; and Krishna Sahakari.","@ID":10} "PETcontents 01+02/12 4 PETplanet insider Vol. 13 No. 01+02/12 www.petpla.net INSIDE TRACK 3 Editorial 4 Contents 6 News 34 Products 35 Bottles 36 Patents REGIONAL MARKET REPORT 14 Serbia Difficult market with high proportion of PET MARKET SURVEY 21 Suppliers of conveyors for preformsand empty bottles PREFORM PRODUCTION 10 Ace of base Netstal’s ‘LightBase’ process 12 Lighter PET bottle necks Sipa’s latest processes for ightweighting bottles BOTTLE MAKING 26 A lidl less weight Debut for Krones lightweight bottle BOTTLING / FILLING 28 Silver Springs strikes gold Silver Springs Bottled Water company implements the KHS InnoPET BloFill monoblock concept CAPPING / CLOSURES 30 New caps for new markets Corvaglia drives for lighter one-piece caps and broader applications 32 Slimmer means fitter Bericap’ s range of slimmer closure system solutions Page 10 Page 26 BUYER’S GUIDE 37 Get listed! Page 30 Lightweighting SPECIAL","@ID":6}
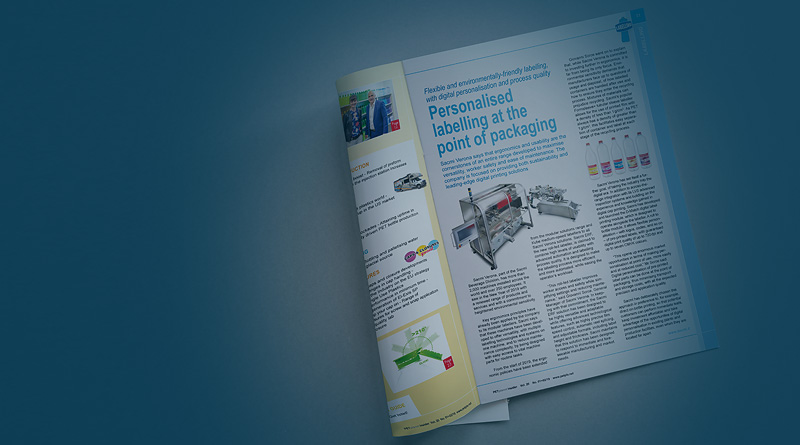