"TRADE SHOW PREVIEW 38 PETplanet insider Vol. 13 No. 03/12 www.petpla.net NPE Orlando, Florida, April 1 - 5, 2012 Breaking the mould on sustainability After 40 years in Chicago, IL, this year’s NPE will take place from April 1 to 5, 2012, at the Orange County Convention Center in Orlando, FL, USA. The exposition halls will be open April 2 to 5. The triennial international plastics exposition is organised by The Plastics Industry Trade Association (SPI). The trade show portion will include 1,800 companies exhibiting on 83,600m2 and is expected to be visited by industry professionals from over 100 countries. NPE can be seen as the largest plastics industry event in 2012 and targets plastics applications in building and construction, automotive, medical and consumer products and packaging. Highlights of specific interest to packaging professionals will include: Bioplastics and sustainability. These will be prominent themes throughout NPE2012, embracing not just a special multi-exhibitor Emerging Technologies Pavilion but developments highlighted elsewhere on the show floor and in many conference sessions. For example, these topics will be the focus of three sessions of SPI’s Business of Plastics conference, co-located with the trade show. 2nd International Plastics Design Competition. Categories open to entrants from around the world include packaging and sustainability. Entries may be submitted online at www.plasticsdesign.org. SPE Antec 2012, the plastics technical conference, will be co-located with NPE2012 and have multi-paper sessions dedicated to flexible packaging and bioplastics, respectively, as well as to key primary processes like blow moulding, extrusion, thermoforming, and other relevant sectors like thermoplastics raw materials, colour, and decorating. As readers of the magazine you will be particularly interested in PET, so our preview will give you a brief idea of what awaits you on the 83,600m² exhibition space in the field of PET . PETplanet will be on show at West Hall Level 2, Stand 3891. Full details on NPE are available at www.npe.org Servo stretch rods and flying head leak tester Amsler Equipment Inc. will demonstrate its latest reheat stretch-blow (RHB) moulding machines and auxiliary equipment. It will highlight the enhanced efficiency of servo stretch-rods for its RHB machinery and introduce a new single flying head leak tester, the latest addition to its line of quality inspection equipment. The stand will feature the company’s L32 convertible machine with servo stretch rods, a three-cavity all-electric unit designed to meet the high-output needs of custom blow moulders of PET containers with small to medium size requirements. The machine can be run with one, two, or three moulds. It will run an oval bottle production process without the complexity of a preferential heating oven system. Amsler says that servo-driven electric stretch rods offer more precise and better speed control and ramp up for better productivity, compared to pneumatics. The company will also introduce a high-speed single flying head leak tester, which has a relatively small footprint, a solid steel frame construction, and runs 50% faster than a stationary unit. www.amslerequipment.net Amsler West Hall | Booth 583 Injection stretch blow moulding Mould & Matic Solutions, part of the Haidlmair group, will be exhibiting its Blowliner, an injection moulding machine combined with a newly-developed automated blowing station. The Blowliner can produce a number of different plastic types and product shapes in volumes from 5 to 10,000ml, with output from 500 – 10,000pcs/h. The company says that its machine offers users short changeover times and servo engines for energy efficiency. Blowliner can be customised to customer requirements and can be offered as a turnkey solution for fillers. Mould & Matic will be on the Austrian Federal Economic Chamber stand in Hall F. www.mouldandmatic.com Mould & Matic Solutions Gmbh Hall F | Booth 9147","@ID":40} "imprint EDITORIAL PUBLISHER Alexander Büchler, Managing Director HEAD OFFICE heidelberg business media GmbH Häusserstr. 36 69115 Heidelberg, Germany phone: +49(0)6221-65108-0 fax: +49(0)6221-65108-28 [email protected] EDITORIAL Doris Fischer: [email protected] Michael Maruschke Ruari McCallion Ilona Trotter Wolfgang von Schroeter Anthony Withers MEDIA CONSULTANTS Ute Andrä [email protected] Martina Hischmann [email protected] Ursula Wachter [email protected] phone: +49(0)6221-65108-0 fax: +49(0)6221-65108-28 France, Italy, Spain, UK Elisabeth Maria Köpke phone: +49(0)6201-878925 fax: +49(0)6201-878926 [email protected] LAYOUT AND PREPRESS Exprim Kommunikationsdesign Matthias Gaumann | www.exprim.de READER SERVICES Kay Krüger [email protected] PRINT Louis Hofmann Druck- und Verlagshaus GmbH & Co. KG Domänenweg 9 96242 Sonnefeld/Oberfranken Germany WWW www.petpla.net | india.petpla.net PETplanet insider ISSN 1438-9459 is published 10 times a year. This publication is sent to qualified subscribers (1-year subscription 149 EUR, 2-year subscription 289 EUR, Young professionals’ subscription 99 EUR. Magazines will be dispatched to you by airmail). Not to be reproduced in any form without permission from the publisher. Note: The fact that product names may not be identified as trade marks is not an indication that such names are not registered trademarks. 3 PETplanet insider Vol. 13 No. 03/12 www.petpla.net EDITORIAL dear readers, EDITORIAL Husky or Netstal? This is the question the producers of preforms would ask themselves in most instances when they needed to buy a new preform installation. Again and again attempts have been made to penetrate the strong market position enjoyed by these two companies. Arburg or Engel come to mind. Finally, at the K-Fair, the gauntlet was thrown down by Mold Masters. This month two further companies keen to get involved in the high end – high volume segment - have appeared on the scene. These two companies have been well-known for a long time in the preform sector: their names are Sipa and Sacmi. In terms of technology, Sipa is certainly starting from an outstanding position as it has its own preform tool shop and many years of experience with its preform lines (see article p.14). The same applies to Sacmi, who are able to contribute extensive know-how as far as the preform is concerned (see article p.18). Common to both injection moulding plants is that they do not simply exist in the form of an idea but the Sacmi line can be viewed at the plant during Plast Milano, whilst the Sipa line is set to make its public debut at the NPE. Another common denominator is the fact that they are anxious to manufacture preforms more cheaply than the established machine manufacturers. In so doing they are looking at maintaining existing floor space requirements or even at reducing the existing footprint, not to mention lower investment costs. The difference from the established suppliers from Canada and Switzerland is that both Italians are designers and builders of preform tools, stretch blow moulding installations as well as bottling lines and are marketing these successfully. The presence of such knowledge from pellet to pallet is something that is not available in this distinctive form at Netstal and Husky. This may become a catalyst as far as the Italians are concerned: after all, in the last few years we have noticed that bottling plants are putting more effort into building up their own preform capacity. Netstal and Husky will need to go about winning the confidence of the bottlers here - Sipa and Sacmi already have at least one foot in the door. So, in the long term, the question is, who the new / old competitors are now poised to take market share away from: Husky or Netstal? Yours Alexander Büchler","@ID":5} "TRADE SHOW PREVIEW 39 PETplanet insider Vol. 13 No. 03/12 Vision inspection products for plastic containers Agr International, Inc. will be exhibiting an array of products for the quality management and testing of plastic containers. Pilot Vision is the company’s new vision-based inspection system. It mounts inside the blowmolder to provide detection of random occurring defects during the production of PET bottles. OptiCheck has a new multi-camera inspection and detection system for the entire bottle, including seal surface, sidewall, base and label defect, on the conveyor line. It is designed for a wide range of bottle shapes, sizes, materials and colours. Process Pilot automated blowmoulder control system, a real-time, process management program, works in conjunction with Agr’s PETWall Profiler system to automate the management of blowmoluder production. The program continuously monitors bottle material distribution and automatically adjusts blowmoulder operating parameters, without operator intervention. PETWall Profiler will also be on the stand, and the company will demonstrate several products for off-line or laboratory testing applications including the Gawis OD all-in-one laboratory test system; PPT3000 pressure tester; Combi tester; the new PG9800T Profiler Gauge; and MBT 7200/7400 wall thickness measurement gauge. www.agrintl.com Agr Interntional, Inc. West Hall | Booth 149 Improved closure production Netstal, the Swiss manufacturer of plastic injection moulding machines, will be exhibiting a process for more efficient beverage cap production. The Elion 2800 machine on the stand will feature electric form closure with energy recuperation. The machine will demonstrate production of PCO 1881 caps at a cycle of 3.5s using a 72-cavity mould made by z-mould, in combination with an Intravis optical quality control system. The hybrid Elion 2800 is equipped with the new aXos control, with enhanced operating panel and various new features. Netstal claims that its improvements can save operators several thousand USDollars/year in manufacturing costs. www.netstal.com Netstal Machinery West Hall | Booth 1903","@ID":41} "PETbottles 46 PETplanet insider Vol. 13 No. 03/12 www.petpla.net Personal Care Shower Gel with Micro-particles Under the brand name “Nivea for Men“, Beiersdorf AG of Hamburg are producing and marketing a shower gel in a PET bottle with a 250ml content. Featuring a slightly bluish tint and intended for both skin and hair care it has a screw-on, 2-colour hinged lid in PP. The micro-particles, transparent and orange, which are suspended in the viscous shower gel are “destroyed“ when they are massaged into the skin and, according to the manufacturer, will help to promote muscle relaxation as well as conveying a special feeling of freshness. A rear label with a reflective inner surface will ensure interesting light-play effects at the POS. www.nivea.de Easy opening thanks to two colours Under its Clearasil brand name, ReckittBenckiser is selling 200ml of skin clarifying toner for daily use in a transparent PET bottle with snap-on hinged lid. Thanks to the integrated recessed grip the 2-colour hinged lid can be opened with no problems using one hand only. The product has a slight bluish tint to it and the two self-adhesive labels in blue and white put the finishing touches to the product’s “clean” appearance. www.clearasil.de Grease Remover in PET The German pioneer of biocleansers, Erdal Rex of Mainz, has recently started marketing grease remover under the brand name “Frosch“ and featuring natural grapefruit extracts in a clear PET bottle with a content of 500ml. This product, specifically advertised for cleaning the oven and grill, is applied by means of a pump-action, screw-on spray attachment. Selfadhesive labels to front and rear convey all relevant retail information. www.frosch.de","@ID":48} "PET - THE NEXT GENERATION 37 PETplanet insider Vol. 13 No. 03/12 www.petpla.net starting with the North American International Auto Show (NAIAS), which took place in Detroit from January 9-10, and the International Consumer Electronics Show (CES) in Las Vegas from January 10-13. Global sustainability strategy Unifi says that the use of Repreve reduces energy consumption by offsetting the need to use newly refined crude oil for production. When full production of the Focus Electric is under way in March, the Focus Electric’s seat fabric could contain plastic bottles collected at NAIAS or CES. “Reduce, Reuse and Recycle” is part of Ford’s broader global sustainability strategy, which aims to reduce its environmental footprint while accelerating the development of advanced, fuel-efficient vehicle technologies. Ford vehicles are currently approximately 90% recyclable at end of life and it aims to raise that to 100%. In 2009, the company mandated its fabric suppliers to use a minimum of 25% recycled content for all 2009 and subsequent model year vehicles. Since then, 37 different fabrics meeting the requirements have been developed and incorporated into its vehicles. www.ford.com www.unifi.com www.repreve.com The seat fabric Repreve is made from a hybrid blend of recycled plastic bottles and post-consumer waste. The material is made by Unifi, Inc. From landfill to car seats: Two million post consumer PET bottles are given a new home in the new Ford Focus Electric CCT Creative Competence Technology GmbH Idsteiner Strasse 74 D-65527 Niedernhausen, Germany [email protected] www.cct-systems.com CCTsystems®-40 Cav. Mold ≥ 160 to Clamping force CCTsystems®-60 Cav. Mold ≥ 240 to Clamping force PET Molds Design and Patents Closure Molds Developments PET Systems Closure Molds All Closure types with CCTsystem®- BPT Best Performance Technology Closure molds","@ID":39} "BOTTLE MAKING 23 PETplanet insider Vol. 13 No. 03/12 www.petpla.net model, and by 32% compared to the 2008 version. The blowing wheel, two transfer starwheels, and the oven are each driven by an energy-saving servomotor. With Monotec drive technology, the total power consumption of these four motors is less than that of a single asynchronous motor. Again, if we compare a Contiform 316 with a vintage 2008, Generation 2 Contiform S18, it is claimed that savings of €24,000 per year can be achieved, assuming a production rate of 36,000 x 1.5l containers an hour, each weighing 28g, and 6,000 operating hours per year. The machine features a new casing, made of aluminium sandwich panels. The casing can be quickly cleaned both inside and out,. The lubrication-free electro-magnetic stretching system means that all lubrication points in the blowing wheel above the preform or container mouths have been eliminated. The use of heavy-duty plastic rollers at the transfer star-wheels and for locking moulds in place reduces the amount of grease required for the automatic central lubrication system. This new development halves downtime for cleaning and lubrication, as well as improving hygiene in the entire system. The use of actively controlled transfer clamps helps to reduce PET abrasion at the transfer of PET preforms or containers, and the concomitant risk of soiling the machine with PET dust. The Contiform 3’s touch-screen is installed on a swivel mounting at the machine. It has a new visualisation system that matches the control panel more closely to the needs and knowledge levels of the operating staff, as a central information and data entry unit. The system is designed to be easy to navigate; enabling all sequences to be handled with intuitive and unambiguous monitoring and control. The electro-magnetic stretching system enables the stretching distance to be set at the touch-screen for all blow-moulding stations, simultaneously. The optional MouldStar mould change trolley is claimed to provide ergonomical handling for rapid replacement. Contiform Generation 3 has been developed in sizes ranging from eight to 36 blow-moulding stations, enabling outputs of up to 81,000bph. The machine can also be directly blocked and synchronised with a filler or with both a labeller and a filler, in the ErgoBloc L. Heatset and small-cavity versions will be available from mid2012, which will also see the integration Contipure for preform decontamination. www.krones.com The Krones Contiform 3 has been developed insizes ranging from eight to 36 blow-moulding stations","@ID":25} "NEWS 8 PETplanet insider Vol. 13 No. 03/12 www.petpla.net New warehouse in Shanghai for KHS Corpoplast KHS Corpoplast has opened a spare parts warehouse in China at its site in Shanghai. The warehouse stocks spare parts to the value of over €1 million, including practically the full range of parts used in the InnoPET Blomax Series III and InnoPET Blomax Series IV generations of blow moulders. It is close to Shanghai Hong Qiao airport and the company says that its Chinese customers can be supplied with parts within 6 to 48 hours. KHS has entered into a cooperation agreement with China Air Express, one of the biggest air cargo services in China. The Chinese market is growing strongly and sales of KHS Corpoplast blow moulders have been strong as well. The company expects to see continued growth in the non-alcoholic beverage sector in the country and it intends to expand the warehouse in the next few years, with the aim of more than doubling its capacity. www.khs.com IV calculation app from PTI The PET Blend Calculator from Plastic Technologies, Inc. (PTI) is a free app designed to calculate the intrinsic viscosity (IV) of PET resin blends. It is available for iPhone/iPad and Android platforms. The calculation process goes through two stages. The first screen asks the user to plug in the volume percentage and IV for the rPET and virgin resins being processed. When the screen’s ‘submit’ button is pressed, the new IV, the molecular weight for each of the resins and the final blend is displayed. The user will then be directed to a second screen, which features a PET Hydrolytic Degradation nomograph, to input moisture information, as ppm. The blend IV number is plotted on the left-hand vertical scale; the user inputs moisture data by sliding a plot point on the right-hand scale. The intersection of those lines, on a third vertical plane located between the two, is the blended material’s final IV. Release of the PET Blend Calculator follows PTI’s launch in early 2011 of a standalone PET Hydrolytic Degradation nomograph. www.plastictechnologies.com Management changes at Mold-Masters Mold-Masters has announced a number of changes to its management structure and personnel. Three international area presidents, reporting directly to President and CEO Bill Barker, will oversee business in the Americas, Europe and Asia. Prior to joining Mold-Masters, Barker held leadership positions at Rexam, OEA Automotive Safety Products, and the Commercial Solutions Group of Textron Fastening Systems. He also serves on the board of directors of Huhtamäki, a major consumer packaging company. Ms. Ling An-Heid, President, Mold-Masters Asia, is responsible for China, Singapore, Japan, Korea and South Asia. After working at the company’s Canadian facility she relocated to China, becoming General Manager of the Kunshan facility. Patrick Bennett is President, Mold-Masters Europe, which also includes responsibility for the Middle East, Africa, and India. He was formerly Executive Vice President, based in Canada. Mike Cybulski, President, Mold-Masters Americas, is responsible for North and South America. He was formerly President and CEO of Festo USA, a global automation supplier. The European team acts as the Global Engineering headquarters. Hans Hagelstein, President, Global Engineering, assumes responsibility for a new product management project that will provide global CAD/CAM standards project. He was previously General Manager of Mold-Masters Germany. The manufacturing and service team in Baden-Baden is to be expanded to include new machinery and production cells for hot half plates and auxiliary equipment. Further investments are planned for Mold-Masters China, including machinery upgrades intended to meet capacity requirements for the local Asian market. The company has also redesigned its website. www.moldmasters.com PET Conference South Americas 2012 June 11/12 Sao Paolo, Brazil South America is one of the fastest-growing markets for the polyester industry and for PET packaging. ABIPET (Brazilian PET Industry Association) and Dr. Thiele Polyester Technology (organisers of the Polyester Recycling Forum) are to jointly host the PET Conference South Americas 2012 – PETtalk and PRF on June 11 and 12, 2012, in Sao Paolo, Brazil. Among the sponsors and participants are Amcor, Husky, Petroquímica Suape, Buhler, Plastipack, M&G, Gneuss, Herbold, Aquafil, Se-So-Tec and Hosokawa Bepex. Further information and updates are available at the websites: www.abipet.org.br www.polyester-technology.com www.polyester-recycling.com","@ID":10} "PREFORM PRODUCTION 17 PETplanet insider Vol. 13 be melted at about 280ºC (536ºF) +/- 10ºC (18ºF). Reduce as necessary. 8. Check that the decompression (pullback) time and position is not too little. This should be set high enough to ensure the melt pressure is being released, yet as low as possible to minimize the risk of drawing in air. Typical settings for valve gated moulds are: Time = 0 – 1sec; Distance = 0 – 10mm. Non-valve gated moulds may require higher values to minimize gate stringing. 9. Check the valve gate open delay timer and increase as necessary to release preform pressure. Typical settings are 0 – 0.3sec. This adjustment must work together with decompression (pullback) time. 10. Check that no debris, colorant buildup, or obstructions are on the cavity surfaces that may restrict preform release. Clean or repair as necessary. 11. Check hardware for worn, damaged or failed components, specifically the mould cavities, gate inserts, valve stems, and clogged cavity cooling channels. www.petpla.net PETplanet print vol.6 The Rapid Guide to Perfect Preforms machine no./name stretch-blow moulding and filling machines shrinkwrappers wrap-around casepackers conveyor systems palletisers SMI S.p.A. -Via Piazzalunga, 30 - 24015 San Giovanni Bianco (BG) - ITALY Tel. +39 0345 40111 - Fax +39 0345 40209 - [email protected] - www.smigroup.it ECOBLOC®PLUS integrated system Reduce the distances between preform and label! The integrated systems in the Smiform ECOBLOC® PLUS series bring together in a single machine the operations of stretch-blow moulding, filling, capping and labelling of PET containers and are the ideal solution for bottling lines of still and sparking soft drinks, milk and edible oil up to 36,000 bph. The ECOBLOC® PLUS systems stand out for their modular and compact structure and for the high technological content of the proposed solutions, which ensure high performance in terms of efficiency and operative flexibility, ease of running and maintenance, low energy consumption and maximum respect of the environment. ECOBLOC®PLUS SERIES: the “green” solution which saves you space and energy PETplanet print Vol. 6: The Rapid Guide to Perfect Preforms by Rick Unterlander and Ottmar Brandau fax: +49 (0) 6221-65108-28 [email protected] www.petpla.net Order your copy now! 1- 3 exemplar each 129,- € 4 - 10 exemplar each 99,- € 10 exemplar each 69,- € prices in EUR + VAT.","@ID":19} "EDITOUR REPORTS 33 PETplanet insider Vol. 13 No. 03/12 www.petpla.net way beyond the Slovenian market both in neighbouring countries and in the USA and Australia, most recently in Thailand and Russia and plans are afoot for India. This is something which is partly rooted in the fact that Slovenian expats have been enquiring about the product in their new homelands. In 1997 other types of beverages came on-board (see below). Since 2000 Radenska has been the leading manufacturer of natural mineral water and soft drinks. Pivovarna Lasko has become the biggest shareholder in Radenska. In subsequent years Radenska received multiple repeat accolades in respect of its products. For this reason the company has committed itself to sponsoring various types of sports such as ski jumping, volley ball, handball and football. From small beginnings an important bottler has developed in the meantime with 200 employees and premises extending to around 12 ha. With a total of nine highly mineralised springs available to it (Radenska has more than 100 approx., ranging from a depth of 60m to 300m, not all of which are in permanent use, however). Radenska is the only company in Slovenia producing mineral water with its own in-house produced CO 2 . The Radenska mineral water family comprises, in addition to the Classic line, a CO 2 -reduced ”Light“, a ”Natural“ as well as a functional water line known as ”Plus“. Further products include the flavoured water line Oaza, Radenska ACE drink, Radenska Iced Tea, the carbonated soft drinks brand Ora and a discounter lemonade called ”Stil“. By way of a side product there is also the sports drink “Sprint“ complete with sports cap. In the flavoured water sector, Radenska works with Wild, Döhler, Etol and other additives producers. By producing its own preforms on a Husky HyPET 225 and a GL 300 it is possible to influence subsequent bottle design on an individual basis. Thus both transparent as well as varicoloured preforms can be found here and these subsequently undergo further processing using the two-stage process. Bottle sizes of 0.33l, 0.5l, 0.75l, 1.5l and 2l are created on a Sidel blow moulding machine. The shape of the finished bottle, with the exception of the Pepsi bottles, consistently features characteristic sweeping indentations. All bottles, apart from Sprint, make use of the PCO 1810; however, a switch to 1881 is planned for the future. A total of 80 million bottles leave the plant each year; out of 100 million preforms produced, 20% are sold in addition to those that undergo further processing by the company itself. A proportion of the CO2 produced is also sold on. Plamegal Trio We met: Ivo Mrsic, Director Ivo Mrsic explains the production area Eisbär Material Drying PRODUCER MODEL LOW ENERGY CONSUMPTION LOW ENERGY CONSUMPTION LOWEST ENERGY CONSUMPTION ON THE MARKET RATING AAA Energy A Eisbär B C D E F G All the others A WWW.EISBAER.AT WUHRMÜHLE 22 / A-6840 GÖTZIS T +43 5523 55558-0 / [email protected]","@ID":35} "BOTTLES 47 PETplanet insider Vol. 13 No. 03/12 www.petpla.net Mouth Rinse in PET The Rewe Trading Group GmbH of Cologne is selling, under its own “Rewe“ brand name, 500 ml of antibacterial, alcohol-free mouth rinse with extract of sage and camomile in a transparent PET bottle. The bottle is sealed by means of a white screw cap which features a tamper-proof sticker. Self-adhesive labels to front and rear incorporate the consumer information for using the slightly bluish tinted product. www.rewe.de PET for Creme Oil Shower Gel The Creme Oil Shower Gel marketed by the Rewe Trading Group of Cologne under their own “Rewe” brand name is specially designed for dry skin. 200ml of the yellow-tinted oil is bottled in a transparent PET bottle with a snap-on hinged lid. A non-label look sticker at the front and a rear label that is also printed on the inside ensure interesting effects at the POS and convey the required retail information. www.rewe.de Top-Ups in PET A transparent inverted container in PET is used as a refill pack for the “Healthy Touch” no-touch soap dispenser available on the market under the brand name Sagrotan. The liquid soap which is available in several different fragrances – here ‘Pink Grapefruit’ – features front and rear labels to match the colour of the contents as well as a corresponding dispensing lid. Once a tamper-proof label has been pulled off, the 250ml content container is pressed into the separate dispenser with the lid facing downwards until a clicking sound signifies that it has locked into place. www.sagrotan.de Sustainable package for leading retailer’s toiletries RPC Containers Llantrisant (Wales) is producing a 300ml PET bottle for leading UK retailer Marks & Spencer’s (M&S) Essential Extracts personal care range, which incorporates 30% post consumer recycled (PCR) material. The company says that 30% PCR content is currently the optimum amount that can be incorporated while maintaining required performance. The bottles retain translucent clarity, which enables the product inside to be clearly visible. The M&S Essential Extracts range includes products such as handwash and hand & body lotion. The retailer is committed to increasing the amount of packaging made from more sustainable raw materials, such as recycled plastics. www.rpc-llantrisant.co.uk","@ID":49} "PETproducts 42 PETplanet insider Vol. 13 No. 03/12 www.petpla.net SBO Compact2 linear blow-moulder Sidel’s SBO Compact2 is claimed to deliver quality and performance levels equivalent to those of its SBO Universal blow-moulder range, and is more robust. With the installation of a servomotor and ball screw assembly, an electrical process has replaced the traditional pneumatic method. Sidel says that the new stretching console enables constant control of the stretching position and speed, which will deliver reliable repetition of the process. Production is also claimed to be more flexible; the machine has the capacity to cope with a variety of bottle sizes. Manual adjustment of pre-blowing and blowing start detectors during format changeovers is no longer necessary. Maximum stretching speed has been increased, from 1 to 1.3 m/s, which enables higher production speeds. Other developments are aimed at improving reliability and ease of operation. Sidel says that its longer orienting rollers secure preform stability and infeed fluidity, and that additional panel functions make the machines more ergonomically efficient for operators. Format changeovers are easier because the stretching parameters are managed directly from the HMI (Human Machine Interface), rather than within the machine. The SBO Compact2 can blow simple or standard shapes using either PET or other plastics, from 0.2 l to 10 l containers. It can also handle the blow-moulding of complex packaging, such as asymmetric shapes or flat containers, through the preferential heating process with a possible neck orientation. DeepGrip packaging, a box-conforming technology, is also supported by the SBO Compact2 platform. Sidel asserts that the range is suitable for water, CSD, juice, dairy, detergent and cosmetic packaging products at speeds ranging from 2400 to 7200 b/hr. Sidel is working to extend process capabilities to manage any type of container, including wide-mouth jars and heat resistant packages. More than 10 SBO Compact2 blowmoulders are currently being installed. www.sidel.com","@ID":44} "PET - THE NEXT GENERATION 36 PETplanet insider Vol. 13 No. 03/12 www.petpla.net Ford’s boost to PET reuse “Reduce, reuse and recycle” Auto manufacturer Ford Motor Company has announced plans to divert around two million postconsumer plastic bottles from landfill through the use of Repreve fabrics, made by Unifi Inc. The first Ford vehicle to feature Repreve will be the 2012 Focus Electric, which will be equipped with seat fabrics made from a hybrid blend of recycled plastic bottles and post-consumer waste. It is Ford’s first all-electric passenger car and started production in December 2011 at Michigan Assembly Plant in Wayne, Mich. The Repreve seat fabric is a polyester fibre made from a hybrid blend of recycled materials, including postindustrial and post-consumer waste. The technology meets Ford’s design and comfort requirements and the fabrics for each car will include about 22 recycled PET bottles. Ford says that it is committed to developing and producing vehicles with good fuel efficiency and, at the same time, aims to achieve at least 25% clean technology in interior materials, across its entire range. “The Focus Electric highlights this commitment as Ford’s first gasoline-free vehicle, and the first in the automotive industry to use Repreve branded fabric,” said Carol Kordich, lead designer of Sustainable Materials for Ford. However, the rate of PET bottle recycling in the USA is only 29%, which is less than half the European level. The two companies are addressing this issue by seeking to raise awareness and boost collections. They will collect bottles at various events throughout the year,","@ID":38} "TRADE SHOW PREVIEW 41 PETplanet insider Vol. 13 No. 03/12 www.petpla.net Co-injection technology Mold-Masters is partnering with other suppliers of plastics-processing technology in hosting a series of live demonstrations. It will be showcasing its new IRIS technology in a live workcell, producing HDPE closures in a 16-cavity, fast-cycling closure mould manufactured by F & S Tool, Inc.. The system incorporates Mold-Masters’ IRIS co-injection hot runner, an E-Multi secondary injection unit, and E-Drive servo driven valve gate control, all integrated into a single control unit. Using Mold-Masters new coinjection technology, the cap is moulded with a 3-6% EVOH barrier encased in its centre. The cap can be used directly and does not require a secondary operation to insert or mould a liner. IMD, from Brügg, Switzerland, provided testing equipment that can detect the presence, thickness, and location of clear barriers. The testing system is complemented with downstream equipment including an IMDvista INOX Line for cooling, sorting and packing. Engel Machinery, York Pennsylvania, provided the injection moulding machine.Polyone, of Cleveland, Ohio, supplied the HDPE material. The IRIS technology will also be shown moulding 0.5mm thick dairy containers in the JSW Plastics Machinery Inc. stand, number 463. Simultaneous injection of 3-6% barrier in each cavity is achieved with balanced filling and control of the melt streams. www.moldmasters.com Mold-Masters West Hall C | Booth 4463 Kreyenborg West Hall | Booth 7271 Premiere of latest backflush filtration techniques Kreyenborg Group is to unveil its latest development in backflush filtration at NPE 2012. The company says that the new machine will facilitate optimum performance, low backflush waste, low running costs and quick ROI. Also on the stand will be a range of the company’s screen changers and melt pumps, which are designed for operation in extrusion and reactor discharge, and its GPE-MB melt pump, which has been developed for quick colour and product changes. The BKG Bruckmann and Kreyenborg underwater pelletising systems, which are supplied with pelletiser, centrifugal drying, water system, and ready-to-use PLC control, are claimed to be suitable for production of all thermoplastic materials, including micro pellets. Throughput ranges from 2-80kg/hr (Labline 100) to systems capable of 35,000kg/h. BKG’s CrystallCut Inline Crystallization System undertakes pelletising and crystallisation in a single process step. The Kreyenborg IRD Infrared Drum uses infrared radiation for efficient drying and crystallization of PET in a continuous process. www.kreyenborg-group.com","@ID":43} "PETcontents 03/12 4 PETplanet insider Vol. 13 No. 03/12 www.petpla.net INSIDE TRACK 3 Editorial 4 Contents 6 News 42 Products 44 Bottles 46 Personal care 48 Patents EDITOUR REPORTS 24 Slovenia and Croatia Still waters run deep MARKET SURVEY 27 Suppliers of bottle-to-bottle recycling plants PET - THE NEXT GENERATION 36 “Reduce, reuse and recycle” Ford’s boost to PET reuse TRADESHOW PREVIEW 38 Breaking the mould to sustainability NPE, Orlando Florida, April 1 -5, 2012 MATERIAL / RECYCLING 10 The rPET market and its challenges Market perceptions of rPET do not reflect the true challenges of PET recycling says Appe 12 PET recycling at large Extricom offers recycling plants with capacities of up to 36,000t/a PREFORM PRODUCTION 14 A fast running workhorse Sipa to unveil all-new high-output PET preform moulding system 16 Stretched necks The rapid guide to perfect preforms - part 27 18 Addition to the family Sacmi makes a new start in the preform sector BOTTLE MAKING 22 Air on a 3-theme Contiform 3 claims major step-up in output, performance and energy efficiency Page 10 Page 24 BUYER’S GUIDE 49 Get listed! Page 42","@ID":6} "PREFORM PRODUCTION 19 PETplanet insider Vol. 13 No. 03/12 www.petpla.net the machine and cost-optimised production that the control can be operated even without a lengthy period of training. They have therefore developed a user interface where all the machine operator needs to do is input the preform geometry and the control sets all the process parameters automatically. In a second development stage the moulds will be fitted with a transponder to enable the machine to set itself automatically by recourse to the mould data. At the same time the material supply control system communicates with the machine control; here the current parameters are referred back to Material Control by the machine so that the temperature profile in the dryer can be adjusted accordingly. Preform discharge Similarly operator-friendly is the preform discharge. The standard procedure is for the handling system to transfer the preforms to a belt which then delivers the preforms into octabins. For start-up, the system ejects the preforms directly without unloading, two belts arranged in L-formation convey the startup preforms out of the machine. The machine is also able to accept single batches from the handling system via the same belt system and convey them to an automatic preform control quality unit. The unloading system is based on a concept by which the three postcooling stations are directly assembled on the take-out plate. The unloading robot has three offset pick-up stations with which it removes the preforms from the mould in a cyclical sequence, cools them over two further cycles and only then does it transfer them to the deposit station. This means that the hot preforms remain in the cooling station. It is only once they have cooled sufficiently that the deposit station picks them up. The take-out plate is driven by a linear motor (without gear box and belt) which converts the kinetic energy back into electrical energy at the deceleration stage. The unloading robot does not have a great deal of time because It is Sacmi’s intention, with the new IPS (Injection Preform System), to offer the converters and bottlers an alternative to other equipment currently on the market. ","@ID":21} "PETbottles 44 PETplanet insider Vol. 13 No. 03/12 www.petpla.net PET bottle and low-temperature sleeve for organic vodka brand Galatea, a Swedish beer and liquor exporter, is best known for its ‘Good Ol’ Sailor’ brand beer, which is sold across Europe, North America and the Caribbean. It has recently entered the vodka market for the first time, launching the product with a strong organic emphasis. The spirit is distilled from organic Swedish barley and the company has selected a recyclable PET 70cl bottle as the appropriate packaging, as its environmental footprint is less than that of glass. Galatea selected UK-based company CCL Label Decorative Sleeves, which is an established manufacturer of shrink sleeves for a range of market sectors, from food and beverage to cosmetic and household products. Its brief was to develop and deliver an eye-catching packaging treatment. The label features an original design by a leading Swedish tattooist, who created a ‘sailor’ theme with mermaids, roses and skulls, and a large sailing ship on the front. The label is a shrink-sleeve, providing an all-round visual projection. A particular challenge for CCL was to source a shrink-sleeve wrapping that would not damage the PET bottle, so a low-temperature solution was essential. CCL selected Eastman Embrace, a copolyester resin for shrink films from Eastman Chemical Company, which is designed to achieve a high level of shrinkage on the product but with a minimal shrink force. Another key parameter was the need for a high level of print definition, which would display the tattoo images on the shrink film to best effect. The eye-catching shrink sleeve, with its sailor tattoo and nautical theme, cover the bottle from neck to base. The entire packaging solution, with 100% recyclable PET, enabled Galatea to achieve its objectives in terms of a sustainable product. ‘Good Ol’ Sailor’ vodka, in its 70cl PET bottle, will be supplied to all 410 shops of Systembolaget, Sweden’s state-owned monopoly alcohol retailer. www.galatea.se www.ccl-lable.com/decorativesleeves Cordially yours Under the brand name “Yo“ Eckes-Granini Austria GmbH of St. Florian in Austria is marketing 700 ml elderflower cordial, without any artificial colouring and with no chemical preservatives, in a slim, transparent PET bottle with a red hinged lid. The hinged lid is fitted with a pouring spout and before opening for the first time a sealing membrane needs to be removed. www.yo-fruchtsirup.at Bio-honey 350g cold-pressed forest honey from New Zealand or Brazil, which originates from controlled ecology agriculture, is being marketed by Bio-Zentrale GmbH from the Ulbering region of Germany in a transparent PET inverted bottle with gold coloured closure featuring a selfsealing silicon valve. When the lid is opened for the first time a pre-perforated label is destroyed and it is easy to tell it has been opened. www.biozentrale.de Agave nectar In the wake of the Stevia licence, users are currently turning their attention to alternatives to sugar. One possibility is the sunshine alternative to sugar – agave nectar, or at least this how the message from the manufacturer goes. Messrs. CoSa Naturprodukte GmbH, based in Freiburg, Germany, is marketing 250ml agave syrup cultivated organically under the ”whole earth” logo in an upside-down PET bottle with an automatic closure silicone valve. A label stretched over the lid serves as a tamper-evident safeguard. www.whole-earth.de","@ID":46} "MARKET SURVEY 29 PETplanet insider Vol. 13 No. 03/12 www.petpla.net Amut S.P.A Erema Engineering Recycling Maschinen und Anlagen Ges.m.b.H. Extricom GmbH, Blach Extruder & Components Herbold Meckesheim GmbH Via Cameri 16 28100 Novara Italy +39 0321 6641 B7 www.amut.it Piergianni Milani President +39 0321 474200 [email protected] Unterfeldstr. 3, 4052 Ansfelden, Austria +43 732 3190-0 www.erema.at Christoph Wöss Vacurema Product Manager +43 732 3190-352 +43 732 3190-23 [email protected] Hoher Steg 10 74348 Lauffen a.N. Germany +49 7133 98 17 0 www.extricom.de Product Manager PET Recycling +49 7133 98 17 31 +49 7133 215 87 [email protected] Industriestr. 33 74909 Meckesheim, Germany +49 (0) 6226 932 0 www.herbold.com Mr. Siegfried Engel Vice President Sales +49 6226 932 0 +49 6226 932 495 [email protected] Yes, in cooperation with long-time partners (Agglomerate) up to 36,000 approx 1,000 approx 0.5 - 1 m³/t approx 545 kWh/t Basic flakes specifications: Higher contamination can influence pellet quality but are basically possible to process, after discussion and agreed by Erema. PET-Flakes FDA, EFSA (pending), ANVISA, ilsi, BGBI, brand owners Granulate with approvals up to 20,000 35,000 up to 13,000 t/a (1 unit) 200 approx. 64 FDA [cat. A-H&J]; efsa (pending); brand owners (conf.); some national approvals (Austria, CH, Zona Mercursur, etc.) FDA + various brand owner approvals Depending on application and technology type / closed loop system. 0,25 between 250 - 350 200 approx. 125 kWh/t Yes Yes, in cooperation with long-time partners Yes FDA [cat. A-H&J]; efsa (pending); with Multi Purpose Reactor (MPR) 3,600 - 45,000 up to 15,000 6,000 - 30,000t 1,500 - 3,000 between 20-40 1,000 - 3,000 FDA, efsa (pending) 1m3/t Closed loop system approx. 1 m³/t 250-300 100 approx. 450 kwh/t pre sorting system for mixed plastics PET bottle washing plants, turnkey systems, single components, size reduction components. Yes Yes: Vacurema inline sheet Yes Yes Yes: Vacurema inline fibre Yes Yes Yes: Vacurema inline strapping Yes","@ID":31} "NEWS 7 PETplanet insider Vol. 13 No. 03/12 www.petpla.net Mold-Masters and theMold-Masters logoare trademarksofMold-Masters (2007) Limited. ©2012Mold-Masters (2007) Limited.All rights reserved.17237 moldmasters.com Introducing IRIS Technology, barrier solutions for food and beverage containers. Break through the barrier and meet IRIS at NPE 2012, Mold-Masters booth 4463. At NPE 2012, Mold-Masters will unveil our new IRIS Co-Injection Technology. This revolutionary solution will forever change the way you make barrier closures and thin wall packaging. Husky sells Injectoplast to Alpla Husky Injection Molding Systems has announced that it has signed an agreement to sell Injectoplast, the former closure injection moulding operation of KTW, to Alpla Holding GmbH. Injectoplast was a division of KTW, a closure mould maker that Husky acquired in early 2011. Its intended disposal was announced at the time of the acquisition. The deal is anticipated to complete before the end of the first quarter of 2012. www.husky.ca Noventum offers business transformation services to PET market Noventum research has shown that as PET converters look at ways of avoiding being squeezed out of the value chain by brand owner’s insourcing manufacturing, many are offering services such as design consultancy or ‘hole-inthe-wall operations’ to develop closer partnerships with key clients. However this represents a significant shift in activity to business leaders who have established their careers in a plastics industry orientated around technology and manufacturing, according to service management consultants Noventum. Businesses can fail to appreciate that developing services requires a change in orientation of thinking from delivering ‘hard’ products to a more service-oriented activity. Noventum has identified five key steps that it says are essential to successful service transformation. First, get closer to key customers & take an ‘Outside-in’ approach; second, strengthen your service proposition; third, focus on high quality service delivery; fourth, use a service development process; and fifth, establish more effective remote support. Noventum says it can help PET Converters to speed up the transformation process by avoiding the pitfalls seen in other industries. www.noventum.eu Packaging prize for Krones’ FlexWave The German Packaging Institute has awarded Krones the German Packaging Prize for its FlexWave heating system. FlexWave, which is incorporated in Krones’ stretch blow-moulding machines, uses microwave technology to heat PET preforms. Krones says that this technology offers advantages over conventional infra-red heating methods in terms of sustainability, energy efficiency, flexibility and speed. The system allows the heating process to be individually set and monitored for each PET preform, enables the production of multicoloured bottles and requires only three seconds for heating up. www.krones.com","@ID":9} "EDITOUR REPORTS 24 PETplanet insider Vol. 13 No. 03/12 www.petpla.net Nuremberg Ljubljana Saedinenie Istanbul Yerevan Baku Beograd Novi Sad Subotica Cegled Dulo Selo Mirna Peˇc Radenci Gorica Svetojansk Plovdiv Gaziantep Ingöl Ploiesti Ankara Slovenia and Croatia Still waters run deep As part of the Go To Brau Beviale Tour in 2011, the PETplanet Insider team visited Slovenia and analysed this interesting, evolving beverage market, in particular the drastic changes that followed the break-up of Yugoslavia, and the impact these changes subsequently had on the economy and consumer demand. The Tour team also undertook a brief excursion to the neighbouring country of Croatia, visiting Plamegal and Jamnica. As far as the beverages market is concerned, when Slovenia won its independence from Yugoslavia the country made a successful transition from the previous predominant alcoholic beverages to non-alcoholic drinks. New markets and needs also saw the beginning of the PET success story. Still water, with and without flavouring, quickly became a best-selling product, both locally and on the export front. 0.5l PET bottles in particular are enjoying increasing popularity.","@ID":26} "PREFORM PRODUCTION 14 PETplanet insider Vol. 13 No. 03/12 www.petpla.net Sipa to unveil all-new high-output PET preform moulding system A fast running workhorse At NPE, Sipa will introduce a new system based around a machine capable of handling moulds with up to 128 cavities, which will be added to Sipa’s present PPS reange of preform injection moulding machines, with more than 300 systems installed. With this new development, the company is now tackling the high end and high output volume sector. The Italian company will have its new system running full-time throughout the show. Sipa says that the machine, with a very robust design developed with a primary partner, is built to last. It has a very solid, compact construction that is very low on maintenance. The company claims a TCO – Total Cost of Ownership – among the lowest in the industry. The icing on the cake is that it accepts moulds made not only by SIPA itself, but also by the sector’s other leading preform mould makers. This means that processors can install a SIPA system alongside its existing lines, and not have to worry about a major investment in new tooling. The machine is designed to run 24/7, and some people might call it a workhorse. But that could give the wrong impression, since workhorses are generally slow. This machine is fast. With a lock-to-lock time extremely fast, Sipa says that it can run quicker than some of its major competitors, without the minimum vibration. Mould change-over Time is also made up when the machine is not running, with mould change-over times said to be very short at less than three hours. This is helped by ease of access to the mould area, thanks to large tiebar distances. In addition, configuration changes to the preform post-moulding cooling robot system are relatively simple. This is because it is a single-stage system, which holds the preforms for six cycles. Sipa says it takes less than half an hour to change the cooling system. Sipa is already well-known for its low-maintenance preform tools. It has a patented system for blowing off dust from the mould, so that maintenance work on the hot side is only necessary after five million cycles. On the cold side the moulds exceed eight million cycles before The combined cooling and unload station of Sipa’s new preform system can be changed in 30 minutes","@ID":16} "MATERIAL / RECYCLING 11 PETplanet insider Vol. 13 No. 03/12 www.petpla.net in rigid PET packaging that can be recycled time and time again. The balance is used in applications such as sheeting, fibres and strapping, meaning that 78% of rPET is not returning to the closed-loop cycle. APPE believes that the biggest challenge of all is getting the brandowners and fillers to understand the huge complexities involved in processing rPET into new packaging while maintaining the necessary quality controls. Additional activities such as blending, process controls and changeovers all lead to increased costs. “The greatest contradiction faced by rPET producers and processors is that despite these complexities and their cost implications, the industry still expects rPET to be cheaper than virgin resin,” said Blanchard. He believed there are several potential solutions for the current Appe and Artenius APPE has already responded to the surge in demand for rPET by investing a further €10m at Beaune, increasing its output by 40% from 25,000 to 35,000 tonnes. Further expansion of the facility is now being considered; however this could be constrained simply by the lack of post-consumer PET for processing. Artenius, the PET division of LSB now offers a PET packaging material called Artenius Elite (see PETplanet insider issue 1+2/12, page 6). This material combines virgin resin and post consumer rPET. www.appepackaging.com www.laseda.es situation, from better consumer awareness and education in order to improve collection rates and sorting, to establishing a realistic vision of rPET content and enhancing bottle technologies to support the recycling stream. Conclusions “The challenges of stepping up rPET usage, which several brands are now driving, are clear and we feel it is important that the industry understands the full picture,” concluded Mr. Blanchard. According to Blanchard, the industry as a whole needs to look to the material collection systems to keep pace in order to satisfy customers’ requirements. “Increased regulation also has a part to play. Until then, the potential for bottleto-bottle rPET will always be limited by the amount of recycled material available.” Appe’s PET recycling plant in Beaune, France, has increased its output to 35,000t Frédéric Blanchard, Plant Manager at Beaune, France","@ID":13} "EDITOUR REPORTS 31 PETplanet insider Vol. 13 No. 03/12 www.petpla.net bottle volumes, these generally tend to be in the region of 0.33l to 2l. Particularly popular are single-serve PET bottles with a capacity of 0.5l. In the bottled water segment Pivovarna Lasko with its Radenska brand is the market leader with a market share of around 50%. Second place in market ranking in 2010 was held by Droga Kolinska with around 13% share followed by Uskok with approximately 5% (Source: Canadean). A significant level of demand exists in the flavoured waters sector, where natural additives such as fruit juice additives, for example, are used in the manufacturing process, which offers an interesting range of sweetened and unsweetened flavours. A glance into the future indicates that Slovenia is set to further extend its production of bottled water, probably by focusing on functional water and the export of local brands. Dana dd. Mirna, Slovenia We met: Mr. Mitja Majzelj, Production Manager Mitja Majzelj (left) with Kay Krüger (right) in front of the plan of the spring The chance discovery of the spring water Dana was launched in 1952 as a small schnapps distillery with the same company head office that is still occupied by the company today. With Slovenia’s declaration of independence in 1991 and the demise of the Yugoslavian market as its chief sales outlet, predominantly for alcoholic but also for carbonated drinks, the company changed direction and developed not only new brands, but also new markets. 1991 saw Dana using PET as drinks packaging for the first time; in 1995 came the first soft drinks and nectars, non-alcoholic in glass and Combibloc. A Sidel production line with a capacity of 9,200bph has been in use since 2001, with potential bottle sizes ranging from 0,33, 0,5, 1, 1,5 up to 2l. The largest bottle has a volumetric capacity of 18.9l. 2003 and a new chapter opens in the company history: Entirely by chance, when searching for cooling water for the existing machines, a very high quality spring water was discovered when drilling at a depth of 180m. This led to the decision to add an extra string to the company’s bow in the water bottling sector. The spring was situated in an ideal location directly on the company’s premises enabling processing to take place without having to adopt a circuitous route. Dana operates chiefly within a radius of approx. 400km, but is also active as a supplier in Germany, Austria, Netherlands, China, USA and Italy with a sales distribution of 80% for Slovenia and 20% for other markets. In addition to local shops Mercator, TUŠ, Spar, bottling operations are also conducted here for the major discounters e.g. Lidl , with annual sales totalling €12.7 million. Today Dana is able to offer around 300 different products, their main product being Dana Water, a pure and currently much in demand flavoured water with natural fruit additives which form part of its own manufacturing range. In addition, Dana also manufactures under licence from Sinalco. Bottle designs range from clear to coloured with partial sleeve and full sleeve for an enhanced marketing effect, in particular when it comes to the younger target group. Preform suppliers include Resilux, Putoksnis, Retal, GastroPET….. Dana claims to always have the most up-to-date machines in its repertoire for use in the sectors of blowing, filling and capping (Sidel) and labelling (Krones). As a result of continuous reinvestment on the part of the firm’s owner, Dana is constantly growing. Dana’s objective for the future is to focus more on the functional water sector. Pivovarna Union dd We met: Mr. Andrej Varsek, Technical Director Andrej Varsek (left) and Kay Krüger (right) backed by historic photographs of the brewery From beer and glass to water and PET The brewery Pivovarna Union d.d. is a company that was set up in 1864 in Ljubljana, as a small brewery producing beer and has since expanded to occupy company premises covering 37,000m². Also on site is a really impressive museum covering the whole of the company’s history which has also been singled out for an accolade. In addition to a wealth of information about the beginnings of beer brewing it is also here where the original machine parts, tools and bottles are exhibited. There is also a replica of a tavern here, constructed so as to be true to the original and dating back to those times. Up to 1991 when the country achieved its independence, the company produced only beer. This is still being brewed today using the natural spring water supplied from a total of six deep drilled springs. In consequence of the breakup of Yugoslavia a severe collapse in beer sales occurred with the result that the brewery was forced to perform a strategic realignment, expanding its product range with non-carbonated water and from then on (as of 1995) also using PET in its bottling operations with a KHS in the bottling and labelling sectors as well as a Sidel SBO 4 blow moulding machine.","@ID":33} "PETpatents www.verpackungspatente.de 48 PETplanet insider Vol. 13 No. 03/12 www.petpla.net Targeted liberation of carbon dioxide gas US - Patent No. US 2010 / 0104697 A1 Applicant: The Coca Cola Comp., Atlanta (US) Application date : 23.10.2009 The inside or the bottom of a bottle displays features in response to which the carbon dioxide gas forms (primarily) pearls or bubbles that rise to the top when the bottle is opened. This triggers the development of innovative optical effects. Optimised operation International Patent No. WO 2010 / 046568 A1 Applicant: Bericap, Longvic (FR) Application date: 22.10.2009 The individual sections of a push-pull closure for a beverage container are coordinated with one another in such a way that the forces applied are focussed on certain areas, thus improving function. There are integrated snap tabs to ensure better location of the closure in its end positions. Reduced risk of toppling over European Grant of Patent No. EP 2134612 B1 Applicant: The Coca-Cola Comp., Atlanta (US) Application date: 27.3.2008 Plastic container with a surface that prevents the container from toppling over. The bottle is designed for use on “sloping“ trade shelves where stocks are automatically replenished on removal of the first bottle by the bottles to the rear sliding forwards. Plastic container European Grant of Patent No. EP 1714887 B1 Applicant: Yoshino Kogyosho Co. Ltd., Tokio (JP) Application date: 25.1.2005 The structure and the process for manufacturing a threaded neck for a container are described. The neck and the thread are formed in such a way as to avoid any material fatigue / incorrect material accumulation. At the same time operational reliability is increased. Plastic bottle International Patent No. WO 2010 / 064749 A1 Applicant: Kyung Il Jung, Gyeonggi-do (KR) Application date: 9.12.2008 The neck area of a bottle is fitted with embossed sections that project into the internal space and in this way act to modify the flow behaviour of the beverage as it exits the bottle. Large bottom indent US - Patent No. US 2010 / 0140278 A1 Applicant: Paul V. Kelley, Wrightsville (US) Application date : 8.12.2008 Here the forming operation and the process for manufacturing a container with a “large“ bottom indent. The container is suitable for hot bottling and is manufactured from a preform. The bottom indent absorbs the change in volume during hot bottling.","@ID":50} "PREFORM PRODUCTION 15 PETplanet insider Vol. 13 No. 03/12 www.petpla.net Panoramic view of the Sipa preform system any need for refurbishment. The robust design of the clamp unit leads to low mould wear too, while a similarly robust platen design minimizes deflection. There are numerous other maintenance-friendly details on the machine too. Plastication Much attention has gone into the plasticating and injection system, based on a classical continuously-running extruder/shooting pot configuration. The extruder operates efficiently at low revs, without the need for a static mixer. It can also handle up to 50% regrind without the need for special screw. The system is kitted out with auxiliaries from Piovan (PET dryer) and Eisbär (dry air system). Machine cooling is said to be highly energyefficient. www.sipa.it 1050mm clearance between tie bars provides space between Sipa and competitors moulds ABC COMPRESSORS NEW PET RANGE THE MOST PROFITABLE AIR Safe Investment RELIABLE BEYOND LIMITS www.abc-compressors.com · Up to 5 years guarantee. · Special financial terms. · Plug&Play. Complete set on base frame. · Up to 6.080 m3/h with a single compressor. · Built-in quality. The only manufacturer machining, mounting and testing the 100% of its bare compressors in Europe. · Proximity. Whole packages delivered through our sites in Europe, America and Asia. Efficient Consumption Total energy savings over 50% · ABC guarantees up to 15% saving thanks to our efficient design. · Save 50%of compression energy thanks to air reinjection in our 4 stage machines. · Additional 15% savingscoming from perfect adaptation to frequency converters. · Energy-audits to demonstrate it. UPAKOVKA: Moscow (Russia), 24th – 27th of January. STAND 21D10 FISPAL: Sao Paulo (Brazil), 12nd – 15th of June. STAND M099 NEFTEGAZ: Moscow (Russia), 25th - 29th of June. STAND 21D18 EXPOPACK: Mexico City (Mexico), 26th – 29th of June. STAND 3906 RIO OIL&GAS: Rio de Janeiro (Brazil), 17th – 20th September. STAND 241 DRINKTEC: Mumbai (India), 6th – 8th November CBB: Beijing (China), 19th – 22nd September MinimumMaintenance · 8.000 hours of operationwithout any additional maintenance. · Life cycle services. From express spare parts delivery to special maintenance contracts and machine refurbishing. · 24Hx365D available worldwide for any service through our web platform. · More than 25 technical service hubs around the world to be closer. EXHIBITIONS 2012. Visit our stand at: NPE Orlando (USA), 1st – 5th of April. STAND 8584","@ID":17} "Vol.6 PETplanet print PREFORM PRODUCTION 16 PETplanet insider Vol. 13 No. 03/12 www.petpla.net Stretched necks The rapid guide to perfect preforms - part 27 Troubleshooting guides have suffered in the past from being locked away in offices and not being available to the people that actually need them. Considering the high cost of machine and tools high scrap rates can be a costly proposition eating away at already tight margins. PETplanet’s “Rapid Guide to Perfect Preforms” takes a different approach. It has been written for the people on the floor of injection moulding companies to support their daily work in making the best preforms possible. The product of two industry experts, Rick Unterlander and Ottmar Brandau, it gives concrete advice on 35 of the most common problems in preform manufacture, most illustrated by pictures. From high AA levels to wavy bodies processors can find help when they need it. Read chapter 27 of the guide. Symptom A section of the neck finish has been drawn out to increase in length. Cause The preform neck finish is deformed during the initial mould opening sequence (core side separating from cavity side) due to the preform not releasing freely from the cavity. Typically occurs with moulds that have the neck insert / cavity parting line on the support ring of the preform. Table of Contents i........................ About the Authors ii.................................Introduction chapter 1.............................. AA Level High 2........................ Accordion Preform 3....................... Air hooks / Streaks 4............................... Black Specks 5...................................... Bubbles 6..................................Burn Marks 7...........................Colour Streaking ................................... /Peeling 8..................................Crystallinity 9.................................Drool Marks 10.......................................... Flash 11......................... Gate Depressions 12............................... Gate Peeling 13..................Gate Voids / Pin Holes 14......................... Internal Gate Sink 15................................Internal Sinks 16........................................ IV Loss Solutions 1. Check water cooling temperature. This should be 7 – 10ºC (40 – 50ºF) for optimum cooling. 2. Check water cooling flow to mould. This should be at the mould manufacturers rating (for a given preform size and cavitation). 3. Check that the cooling time is sufficient for the preform being moulded. This typically ranges from about 1 to 3sec depending upon the preform wall thickness. Add time if necessary to increase shrinkage for better release. 4. Check that the hold (packing) time isn’t excessive for the preform being moulded. Reduce as necessary to minimize swelling. 5. Check that the hold (packing) pressure isn’t too high to cause excessive swelling, especially in the last zone. Reduce as necessary. 6. Check that transition position is set to about 13% of shotsize. Lower values may result in overfilling. 7. Check all temperature readings and correct if necessary. PET resin should 17............................ Long Gate Nub 18...............................Milky Preform 19............................ Moisture Marks 20................Neck Finish out of Round 21....................... Parting Line Crease 22.................Parting Line Deformation 23......................... Preform Yellowing 24.................................. Short Shots 25.......................................... Sinks 26......................................... Splay 27........................... Stretched Necks 28..................................... Stringing 29......................... Surface Blemishes 30......................... Thread Flow Lines 31...............TSS (Top Sealing Surface) ......................................... Sink 32.......................................Unmelts 33.................Wall Thickness Variation 34.................................Wavy Body 35.................................. Weld Lines","@ID":18} "MATERIAL / RECYCLING 10 PETplanet insider Vol. 13 No. 03/12 www.petpla.net Market perceptions of rPET do not reflect the true challenges of PET recycling says Appe The rPET market and its challenges The lack of high quality food-grade rPET material is hampering the aspirations of brand owners and fillers to increase the amount of rPET used in their packaging portfolio, according to APPE, the Packaging Division of LaSeda de Barcelona (LSB). APPE and its sister company Artenius manufacture PET preforms and containers, and virgin PET resin, as well as recycling food-grade PET recycler in Europe, with extensive experience and expertise in remanufacture with rPET. This position has given the company a detailed perspective of the challenges facing the recycling market. The company supplies global brands, some of which are driving the demand for greater rPET usage as they seek to reduce the environmental impact of their packaging, in line with the industry’s drive for sustainability, reduced carbon footprint and also consumers’ increasing awareness of environmental issues. Availability and quality of rPET In a presentation ‘The Challenges of Recycling for Food-Grade Application’ by Frédéric Blanchard, Plant Director of APPE’s dedicated recycling plant in Beaune, France. Mr. Blanchard was addressing delegates at the PETnology Europe 2011 conference held in Nuremberg, Germany prior to the Brau Beviale exhibition. Blanchard said that brand owners perceive rPET as a solution to their sustainability objectives and a way to communicate environmentally friendly credentials to consumers. However, some also incorrectly perceive it as a cost-reduction initiative. “Two of the major challenges facing rPET recycling for food-contact applications are the availability and quality of bale feed-stock,” explained Mr. Blanchard. “European reclamation capacity is increasing through the entrance of new but inexperienced recyclers into the market, but the collection of suitable material is not rising at the same pace. This imbalance of demand and supply is causing the price of the raw material – post-consumer PET bales – to rise to record highs, albeit recently price levels have dropped significantly as such high price levels were unsustainable. Longer term prices are set to rise once again and to track virgin PET pricing.” Specifications for rPET production While stringent technical specifications have been put in place for the supply of virgin resin, comparable requirements have not been established for rPET. APPE has implemented its own highly demanding specifications for rPET production, but other inexperienced food grade rPET producers have not yet introduced such measures. In order to maintain quality and safety, food-contact end-use customers must therefore adopt high-quality standards and ensure that closed-loop food-grade rPET is truly food-approved. In addition, only 22% of rPET produced in Europe is currently reused","@ID":12} "EDITOUR REPORTS 35 PETplanet insider Vol. 13 No. 03/12 www.petpla.net The specialists inplastic recycling systems. VACUREMA® – PETextrusion technologies million litres, to all intents and purposes omnipresent and not only in the territory of the former Yugoslavia. In total, 500-600 million PET bottles are filled each year in all three plants. There are other plants situated in Bosnia and Herzegovina and Hungary. The filling lines handle exclusively own brand products. Jamnica’s bottling history begins on 18th October 1828, although the spring itself has been in use for hundreds of years and, in the year 1772, as a result of analyses undertaken on behalf of the Empress of Austria, it was declared so pure that it was included in the Austrian register of mineral waters. Prior to the War of Independence, competition in the Yugoslav market was strong due to successful water brand names such as Radenska and Knjaz Milos, whilst, by contrast, Jamnica maintained a presence principally in Croatia. Following the granting of independence and with its flexible approach to new requirements, Jamnica was able to assert itself further in the marketplace and to strengthen its position. The natural mineral water “Jana“ introduced in 2002 provided added impulse for the water market and since that time has come to occupy a position where it accounts for a more than 50% market share in the non-carbonated water sector in Croatia. The main product – “Jana“ – bottled here, a naturally non-carbonated spring water extracted from a depth of 800m, reaches the surface here with a high level of inherent pressure. On the company site, which covers around 20,000m2. there are five GEA lines, two of which are aseptic lines and two ultraclean lines. By contrast to the Jamnica water, Jana is non-carbonated. Furthermore, in addition to the still water a range of different flavoured waters is manufactured whose natural additives are sourced from Döhler, Wild and Symrise. The flavoured waters differ both in terms of bottle design and as regards the cap (sports cap). Jamnica, as Croatia’s primary bottler, has also used sports caps which can also be found in Jamnica Iced Tea, which is also produced at the Jana plant. All caps used for the different applications are obtained through Bericap. PCO 1881 is not yet in use but is already at the tentative planning stage. The juicy fruits line, again in a different design bottle, rounds off the range of beverages featuring added vitamins. For bottle sizes 0.25l, 0.5l, 1.0l, 1.5l and 5l, the preforms used are sourced fromAlpla together with a proportion from Resilux and local suppliers. ’As regards Jana exports, the company delivers supplies to the USA (Jana was the official water at Madison Square Garden), Hungary, Bosnia, Serbia, Slovenia, Macedonia, Romania, Slovakia, Czech Republic, Portugal, Russia, UAE, Australia and Japan. Plans are afoot to branch out into Austria and Switzerland. A further glance into the future reveals that Jamnica is focusing on extending its export business as well as expanding its product range by adding functional water. In addition, particular attention is paid to the environment and to protecting it. www.jamnica.hr","@ID":37} "MARKET SURVEY 28 PETplanet insider Vol. 13 No. 03/12 www.petpla.net MARKETsurvey 03/2012 Company name Gneuss Kunststofftechnik GmbH Starlinger & Co. Ges.m.b.H. Postal address Telephone number Web site address Contact name Function Direct telephone number Fax E-Mail Mönichhusen 42, 32549 Bad Oeynhausen, Germany +49 5731 5307 0 www.gneuss.com Andrea Kossmann Marketing +49 5731 5307 10 +49 5731 5307 77 [email protected] Sonnenuhrgasse 4 1060 Wien +43 1 59955-0 http://recycling.starlinger.com Elfriede Hell, MBA General Manager Division Recycling Technology + 43 1 599 55 241 + 43 1 599 55 180 [email protected] Bottle to granulate 4 models: recostar PET FG, FG+, PET iV+, PET iV+ Superior Input variable: collected pressed bottles, various colours Engineering of washing lines and / or a turn-key project with components and technologies available in the market Output: Granulate with approval Yes (decontaminated for food-contact, IV increased, AA 1ppm, lowest VOC level) Capacity[t/a] 6.000 - 26.000 t / a rPET pellets Floor space [m²] Depending on design Which approvals Several USA / FDA (C-H), Austria, Germany BfR, Ilsi, France / AFSSA, Finland, Australia, Bolivia, Canada, Switzerland, Peru (pending); follows EFSA requirements; brand owners Fresh water consumption per tonne output [m³/t] Depending on design Consumption kWh per tonne output [kWh/t] Depending on design Flakes to granulate 4 models (see above) Input variable: Flakes, coloured proportion max 5%, not much chlorine Output: Granulate with Approval Yes (decontaminated for food-contact, IV increased, AA 1ppm, lowest VOC level) Capacity[t/a] 200 - 17,000 1,500 - 26,000 (6 extruder sizes) Floor space [m²] 30 - 80 130 - 540 Which approvals FDA Several USA / FDA (C-H), Austria, Germany BfR, Ilsi, France / AFSSA, Finland, Australia, Bolivia, Canada, Switzerland, Peru (pending); follows EFSA requiremens; brand owners Fresh water consumption per tonne output [m³/t] 0 approx. 0,15 Consumption kWh per tonne output [kWh/t] 350 approx. 410 (depending on design) Bottles to flakes Input variable: collected pressed bottles, various colours Engineering of washing lines and / or a turn-key project with components and technologies available in the market Output: Flakes with/without approval Yes (decontaminated for food-contact, IV increased, AA 1ppm, lowest VOC level) Capacity[t/a] 3,700 - 10,500 (5 sizes) Floor space [m²] approx. 150 Which approvals FDA (hot-fill), follows EFSA requirements Fresh water consumption per tonne output [m³/t] Consumption kWh per tonne output [kWh/t] 120 - 250 (incl. Bottle washing to SSP) Miscellaneous Company also offers systems for Bottle-to-film Yes Yes Bottle-to-fibre Yes Yes Bottle-to-strapping Yes Yes","@ID":30} "27 PETplanet insider Vol. 13 No. 03/12 www.petpla.net Conveyors Bottle-to-bottle recycling plants Caps and closures Preform moulds and SBM moulds Preforms Preform and single stage machinery SBM machinery Compressors Filling equipment Resins and additives Suppliers of bottle-to-bottle recycling plants This year nine companies took part in the poll for the bottle-to-bottle recycling plants market survey. The following were represented: Amut, Erema, Extricom, Gneuss, Herbold, Krones, Sorema, Starlinger and Zheijang Boretech. Extricom is a newcomer this year. PTI, who were present in 2010 and 2011, intend to take part again next year. Although the publishers have made every effort to ensure that the information in this survey is up to date, no claims are made regarding completeness or accuracy. 03/2012 MARKETsurvey Company name Krones AG Sorema division of Previero N.srl Zhejiang Boretech Co.,Ltd Postal address Telephone number Web site address Contact name Function Direct telephone number Fax E-Mail Böhmerwaldstraße 5 93073 Neutraubling, Germany +49 9401 70-0 www.krones.com Peter Hartel Sales Dept. PET-Recycling + 49 9401 70-5448 + 49 9401 70-91-5448 [email protected] Via per Cavolto 17 22040 Anzano del Parco, Italy +39 031 63491250 www.sorema.it Dario Previero Sales Manager +39 031 63491250 +39 031 63491217 [email protected] 19k-1 Economic Development Zone, Pinghu City, Zhejiang Province, China 86-573-85136190 www.bo-re-tech.com Alan Ou Marketing Manager 86-13575797979 86-573-85113959 [email protected] Bottle to Granulate Input variable: collected pressed bottles, various colours Output: Granulate with approval Yes Capacity[t/a] 3,500 to 20,000 Floor space [m²] 800 - 2000 Which approvals FDA - LNO, EFSA, various others Fresh water consumption per tonne output [m³/t] 1,0 m³/t - 2,5 m³/t Consumption kWh per tonne output [kWh/t] Flakes to Granulate Input variable: Flakes, coloured proportion max 5%, not much chlorine Output: Granulate with Approval Yes Capacity[t/a] 3,500 to 20,000 Floor space [m²] 800 - 2,000 Which approvals FDA - LNO, EFSA, various others Fresh water consumption per tonne output [m³/t] 1,0 m³/t - 2,5 m³/t Consumption kWh per tonne output [kWh/t] Bottles to Flakes Input variable: collected pressed bottles, various colours Output: Flakes with/without approval with/without approval Capacity[t/a] 3,500 to 20,000 5,000 - 45,000 0.5t - 6t Floor space [m²] 800 - 2,000 800 - 5,000 600-1500 Which approvals FDA - LNO, EFSA, various others not applicable Fresh water consumption per tonne output [m³/t] 1,0 m³/t - 2,5 m³/t 1-3 2-3m³/t Consumption kWh per tonne output [kWh/t] 0,22 - 0,27 90-110kw/t Miscellaneous Company also offers systems for “Super-PET”: integrated process from bale to preform Bottle-to-film No Bottle-to-fibre Yes Bottle-to-strapping No","@ID":29} "BOTTLES 45 PETplanet insider Vol. 13 No. 03/12 www.petpla.net Sweet PET solution for Heritage Foods Heritage Family Specialty Foods Inc., based in south-west USA and a supplier of speciality food products for retail and food service markets, is now using 50g, 32oz decanter-size PET bottles from Amcor Rigid Plastics for its Brack Ranch Sweet Pepper Glaze. The product is co-branded with Country Living magazine’s Country Living Specialty Food Collection. Heritage Family says that the stock PET bottle offers a premium look, sustainability, cost advantages and improved manufacturing efficiencies. The move to PET has enabled Heritage Family to gain entry into the club store market segment. It launched late in 2011 at Costco’s locations throughout the Southwest. The 32oz PET container has also enabled the company to achieve packaging advantages. Serving this particular market in its previous packaging format would have required two shrink-wrapped 16oz bottles, which would have added cost and increased production time, according to Heritage Family. The PET containers are seamlessly integrated into existing glass filling lines with minimal adjustment. Amcor’s 32oz ambient fill (up to 140°F/60C) and hot fill (up to 185°F/85C) decanters are particularly targeted at barbecue sauces, salad dressing, and other sauce products. The sweet pepper glaze bottle extends Amcor’s presence in the food category. www.hfsfoods.com. www.countryliving.com www.amcor.com 6-fruits nectar Rewe Markt GmbH based in Cologne is marketing a litre of still mineral water with six additional fruit juices and a total minimum 60% fruit content in a PET bottle with an easy-to-handle shape. The bottle is fitted with helixtype reinforcement grooves in the neck area and, in the waist area, with reinforcement grooves arranged horizontally. An all-round paper body label and a yellow screw top with tamper-evident strip complete the packaging. www.rewe.de","@ID":47} "EDITOUR REPORTS 34 PETplanet insider Vol. 13 No. 03/12 www.petpla.net Wide variety under a small roof A small company servicing a very wide range of different needs: that is Plamegal Trio. Some time after the company’s establishment in the vicinity of Zagreb in 1991, Plamegal Trio was to be found initially specialising in the manufacture of COEX- and PE bottles and cans in the agro-chemicals und mineral oils sectors. However, the up-and-coming market in the still young and independent state of Croatia quickly convinced the company that it needed to embark on a significant expansion of its product range as well as making some changes to its products. It was here that, in 2005, they first launched production of PET bottles, jars and cans. Touring the production area at the rear of the company building, Mr Mrsic explains that Plamegal Trio has opted for machines from ASB, four examples of which, namely two each NB10LCs and ASB-50MBs, are currently in service. The container and bottle sizes vary depending on the ml range and culminate in volumetric capacities of up to 5l. What the company is really interested in are the possibilities for manufacturing a wide range of products as well as product flexibility, wholly as defined by the respective customer requirement. And, despite the fact that the different applications derived from the foodstuffs and chemicals industries only account for small quantities, the company’s annual output is approximately 20 million units plus, of which around 60% are PET products. Today Plamegal Trio supplies Italy, the Czech Republic, Slovenia and Macedonia in addition to the Croatian market and neighbouring countries. www.plamegal-trio.hr Jamnica We met: Mr Darko Vernik, Plant Manager, Mr Mario Kernjus, Representative of GEA Procomac (from left to right) Darko Vernik, Mario Kernjus and Kay Krüger in front of the Editourmobil Water from Croatia The Jamnica plant is situated south-west of Zagreb, at the “Jana” company premises. This plant is one of a total of three Jamnica group plants situated in the surrounding area and was established in 2002. The first and oldest of these plants is the Jamnica plant which has its headquarters in Pisarovina. In all plants high quality natural mineral water is bottled, both with and without CO2, but more of this later. However, by now we have already placed on record that Jamnica is, with a market share of 80% in Croatia and an export volume of approx. 100 My port of call was Ljubljana, where my first interview is with the bottler Mirna Dana to learn about the varied tastes of the market and the company’s product portfolio. Many years ago the company discovered a spring in its grounds and they have used the water for bottling ever since. I then visit Pivovarna Union in the city centre. They have been producing beer since 1864, and since the collapse of the former Yugoslavia, they have marketed bottled water in a variety of flavours. After an interesting tour of the plant, including the factory museum, I have to get to my next appointment one hour away at Pivovarna Lasko, the main shareholder of Pivovarna Union. Sadly, due to heavy traffic, I was late and my interview partner Mr. Miro Firm had to leave, so I had to content myself with a few photos of the plant. My next objective is Radenci, where I have a meeting with Radenska, also part of the Pivovarna group. The following day Mr. Martin Lah, Technical Department Manager of Radenska, gives me an interesting exposition on the traditions and widespread popularity of bottled water here. My visit is all too short as I have to move on to Croatia, where I have two appointments at Plamegal Trio (Zagreb) and Jamnica, their Jana plant. Plamegal trio Director Mr Ivo Mrsic gives me a rapid tour of the factory including the PET production line. My next stop is at water bottlers Jamnica, where I meet GEA representative Mario Kernjus and Mr Darko Vernik, plant manager. Jamnica and Jana have a large catchment area which is undoubtedly reflected in the size of the factory. A few final pictures of the Editourmobil and I set off for Sofia. - Kay Krüger -","@ID":36} "PETnews 6 PETplanet insider Vol. 13 No. 03/12 www.petpla.net Scott Steele becomes Plastic Technologies President Scott Steele has been appointed President of Plastic Technologies, Inc. (PTI), which specializes in package development and design, rapid prototyping, and material evaluation engineering for plastic packaging. Steele will be responsible for global operations and will report to the company’s board of directors. He had been Vice President of PTI since 1995. Dr. Tom Brady, founder of Plastic Technologies, will continue as Chairman. He joined Plastic Technologies in 1987 as one of the company’s first employees and is the author of 11 U.S. and international patents. Steele began his career at OwensIllinois as a member of the team that developed and commercialized the world’s first successful PET carbonated soft drink container. He has served in numerous positions within the Society of Plastic Engineers and is the past Chairman of the Blow Molding Division board. www.plastictechnologies.com Coperion takes majority stake in PELL-TEC On January 1, 2012, Coperion GmbH, Stuttgart, acquired a majority stake in Pell-Tec Pelletizing Technology GmbH, Niedernberg, Germany. The two companies have been working together for a number of years. Pell-Tec supplies pelletizing systems to customers in the plastics processing and recycling industry. Its product portfolio covers the entire process from melt discharge through to ready-to-use pellets and offers systems with output rates of up to 6,000kg/h. Coperion says that the acquisition strengthens its competence as a systems supplier and it is now able to supply tailor-made pelletizing solutions for small and medium-sized extruders. www.coperion.com Refresco France, PepsiCo France and Sidel jointly receive award for efficient and clean technology Refresco France, PepsiCo France and Sidel have been jointly awarded first prize in the category of “Efficient and Clean Technology” at the Prix Entreprises et Environnement (Enterprise and Environment Awards) in France. The award has been given every year since 1987 by the ADEME, part of the French Ecology ministry, with the support of Orée, a non-profit organization that specialises in environmental management with businesses and local authorities and Credit Cooperative. Sidel’s main contribution to the award was the installation of its latest dry-decontamination technology for bottling beverages, the Combi Predis/Capdis FMa, at Saint-Alban-Les-Eaux, a Refresco France plant where Lipton Ice Tea drinks are bottled for PepsiCo France. The award also embraces the ecological design of the bottles used by Refresco France, especially its choice of using 50% recycled PET. As a result of all these innovations, the Refresco France plant is now saving more than 1,700 tons of CO 2 equivalent, 38,000m³ of water, 2.5 million kWh of energy and more than 400t of virgin PET every year. Sterilant usage has also been reduced from 42t of Peracetic Acid (or Peroxyacetic Acid: PAA) to 6.7t of H 2 O 2 . Significant cost savings have also occurred as a result. Throughout the project the quality of the bottled Lipton Ice Tea product was a non-negotiable priority. www.sidel.com. Polyone acquires Colormatrix Polyone Corporation has completed its acquisition of Colormatrix Group, Inc., the manufacturer of speciality additives, liquid colorant and dosing technologies for markets such as rigid beverage and food packaging, performance moulding and fibre. ColorMatrix has an intellectual property portfolio of 162 patents and 107 pending applications worldwide. Colormatrix is a leading provider of colorant and additives for fluoropolymers, as well as custom colour dispersions used in silicone processing for a range of medical, consumer and automotive applications. The acquisition is part of Polyone’s strategy to become a global company with a suite of additive technologies and a strong market position in liquid colorants. In connection with the acquisition, Polyone secured a new $300 million Term Loan B with a coupon of 5%, which replaced its expiring facility. Polyone Corporation had revenues of US$2.6 billion in 2010. www.polyone.com","@ID":8} "BOTTLE MAKING 22 PETplanet insider Vol. 13 No. 03/12 www.petpla.net Contiform 3 claims major step-up in output, performance and energy efficiency Air on a 3-theme Krones has announced the commercial launch of Contiform 3, its latest generation stretch blow-moulding machine. The Contiform 3 uses less compressed air and is more energyefficient, while increasing productivity to 2,250 containers/ cavity/h The blow-moulding module has been entirely redesigned and Krones says that the long-established linear oven of its Contiform S/H series has been enhanced and optimised for energy consumption. The design and development of the Contiform 3 was undertaken in compliance with a brief that required increased output per blow-moulding station; reduced air and energy consumption; improved hygiene; shorter changeover times; and easier operation in use. Increased output The Contiform 3 has a redesigned blow-moulding station, which is intended to enable reliable and consistent production of plastic containers at speeds up to 2,250 containers/cavity/h. The new design has enabled reduction in size of the machine at the same output level, compared with predecessors – for example, an output of 36,000 containers/h requires only 16 cavities on the Contiform 3, rather than 18, as previously. The blow-moulding station has a flexible electro-magnetic stretching system. The required machine speed can be precisely matched to a stretching speed. The integrated Monotec drive uses servomotors and operates synchronously continuously, in order to ensure accurate transfers. The servomotors have enabled the elimination of transfer belts. The new platform, which is based on existing platform construction, uses actively-controlled transfer clamps to minimise the forces acting on PET preforms and to provide precise transfer at high speeds. Quicker changeover and improved flexibility Krones says that Contiform 3’s fewer cavities for the same total output already leads to quicker changeover times. The option for integrating a MouldXpress system cuts mould replacement time to less than one minute per blow-moulding station. Complete mould-change takes around 16min. If PET preforms with a different neck finish are to be run, the quick-change handling parts (also available as an optional extra in the oven of the Contiform 3) enable reduced machine standstill times for a changeover routine. Compressed air consumption cut 33% The Contiform 3 series have a number of functions and features that help to reduce compressed-air consumption. Electro-magnetic stretching of the preforms using a linear drive instead of a pneumatic system eliminates compressed air from that part of the process. The Air Wizard Plus compressed air recycling system (internal to the machine) is now fitted with an intermediate blow pressure stage (Intermediate Pressure). This not only automatically sets the optimum proportion for recycling in each case but also reduces compressed air usage. This means the machine’s total air consumption has been reduced by a third, an achievement directly mirrored in the lower energy consumption of the compressor required, and the concomitantly downsized energy and operating costs. If we compare a Contiform 316 with a Generation 2 Contiform S18, evidence emerges that savings of €46,000 per year can be achieved, for example with a production rate of 36,000 x 1.5l containers/h, blow moulded at 30 bar, and 6,000 operating h/a. Less energy overall A new heating case configuration in the infra-red oven leads to savings in direct energy costs. With a shorter distance between the IR lamps and the ceramic reflectors, energy consumption of the Contiform 3 series has been reduced by an average of 15%, compared to the 2010 oven","@ID":24} "PREFORM PRODUCTION 18 PETplanet insider Vol. 13 No. 03/12 www.petpla.net Sacmi makes a new start in the preform sector Addition to the family Sacmi has developed a completely new preform injection machine. Against the backdrop of the Plastmilano exhibition in May, the Italians, in addition to a new 24-cavity compression line for closures, will be showing off to the public the newest addition to their family of preform manufacture, sporting 48 cavities and with a clamping force of 220 t. IPS, which stands for Injection Preform System, is the name calculated to give the established competition a headache. The unloading system is built up by a three-stage post cooling station Five years ago was the last time Sacmi captured the attention of the market with its idea of manufacturing preforms using compression moulding techniques. The PAM system, as it is known, processes high viscosity material (IV 1,15). In this way considerably more robust bottles can be produced with further reductions in wall thickness. And, with compression moulding, there is no need to focus too much on the geometric preform requirements of injection moulding; random bottom geometries, with optimised wall thickness profiling, should not pose a problem. Thus preforms promise to become very lightweight. The IPS preform system Sacmi’s present aim is not only to generate attention by means of a new technology, but also to develop a new injection moulding machine for PET preform named IPS. Although Sacmi, along with its subsidiaries BMB Biragi, Negri Bossi and Oima, has had preform injection moulding machines in its range, the solutions had, nevertheless, always been based on standard machines, adapted where necessary to make them suitable for PET and this is reflected in performance and costs. Moraldo Masi, Head of the PET BU summarised the situation as follows: ”We found ourselves with a jigsaw of variations but no clear strategy“. Two years ago the Italians changed all this. Starting from scratch, they drew up a specification sheet taking into account all the requirements, both on the part of the customer and those stipulated by the internal company departments. Masi continued: “Naturally, we are helped by the fact that we are very well aware how an optimum preform and its production should look, based on our closure business, our Laboratory and R&D and our beverages division which features stretch blow moulding and filling systems. There are hardly any market protagonists who have at their disposal such a wealth of knowledge which has been collected over what is now a period of 20 years“. The established preform system manufacturers from Canada and Switzerland have set themselves up as the benchmark when it comes to minimum cycle times and manufacturing reliability. On the other hand, as far as the converting (transformations) costs are concerned, Sacmi is anxious to close the gap on the market leaders. Their intention is, with their 48-compartment mould, to achieve the low production costs that are the hallmark of a very fast mould change. The result is a system that is peppered with interesting details. Let’s start with the control. The outcome of the Sacmi analyses was that it is important as regards the reliability of","@ID":20} "EDITOUR REPORTS 32 PETplanet insider Vol. 13 No. 03/12 www.petpla.net The cold aseptic installation used was a first for Europe, later a second one arrived from KHS. In addition to beer in glass bottles and cans, the annual production and filling operations in the PET bottles sector amount to around 70 million units and bottle sizes of 0.5 and 1.5l for the products Za (flavoured water), Zala (natural mineral water) and Sola (iced tea, multivitamin, still lemonade). As a result of the addition of natural fruit juices only and under a cooperation agreement with Wild, the flavoured water products have become very popular. The Slovenian beer customer is still not interested in PET as a packaging material for beer. The breakdown of distribution of PET bottles for beer, soft drinks and water is 80% for Slovenia and 20% for export. Caps are sourced via local producer T plast Mengeš (no PCO 1881s have so far been used and all closures are in principle suited to carbonated products), the preforms are supplied by subsidiary companies Radenska and GastroPET. In terms of design, all PET bottles stand out due to their square shaped bottles and a zigzag pattern in the lower third which is repeated both on the 0.5 litre bottles as well as on the 1.5 litre bottles. As regards the Slovenian market, Pivovarna Union retains 50% of the market share of beer and water, whilst a proportion of the beer bottling activities are also carried out for discounters such as Mercator and Spar. As far as the future is concerned, they are thinking about possibly converting to PCO 1881 and changing over from sugar to stevia. Radenska We met: Mr. Martin Lah, Technical Department Director Martin Lah (right) and Kay Krüger für PETplanet (left) in front of the Krones filler The (three) hearts of Radenska The history of Radenska goes back to 1833 when a Styrian medical student on his way through Slovenia happened to chance on mineral water springs. Decades later he returned and, in consequence, the year 1869 was the first time mineral water was filled into bottles under the brand name of Radenska. In 1923 the water was credited with health benefits. Shortly afterwards the Radenska logo – the three hearts – emerged and this is still used today. Just under 70 years later Radenska clinched a deal to act as a bottler under licence to Pepsi in Slovenia. However, the Radenska water was and still remains the main product right up to today, despite major slumps in sales as a result of the breakup of Yugoslavia. Today Radenska “Classic“ water has for years been marketed","@ID":34} "TRADE SHOW PREVIEW 40 PETplanet insider Vol. 13 No. 03/12 www.petpla.net MHT Mold & HoTrunner TecHnology Dr. Ruben-Rausing-Str. 7 | D-65239 Hochheim/Main Tel. +49(0) 6146-906-0 | www.mht-ag.de Make the most of your machine – with a mold from MHT! For many machine types, we supply the mold with the highest cavitation, thereby enabling optimum preform output. For the Husky HyPET machine, we offer an upgrade set for 33% more preforms, without refitting on the machine! • 60 cavities for Netstal PETline 2000 • 96 cavities for Husky HyPET 300, • 112 cavities for KraussMaffei 350 Engineering made in Germany 128 for HyPET 400 Booth 55009 Moretto SpA Hall D | Booth 6485 Compact minidryer Italian company Moretto S.p.A. will present new versions of its X Dry-Air minidryer, which is equipped with an OTX hopper and has a compact design. The company guarantees performance up to –72°C of dew point. Two models are available: XD0, with a 1.5dm3 hopper and processing capacity of 0.5kg/h; and the larger XD1, which has a 6.0dm3 hopper and hourly throughput of 2kg/h. Both models are available in a ‘Mirror’ version with a Pyrex OTX hopper, which is aimed at the medical and optical sectors. Standard equipment includes an integrated Venturi control; touch screen control; automatic airflow; Antistress system; USB port; and Mowis control system. www.moretto.com New features in extrusion lines, filtration and measurement Gneuss will be showing a complete MRS 130 extrusion line with a Multi Rotation System extruder, an RSFgenius 150 fullyautomatic filtration system with the option for an automatic backflush material ejector, and a VIS online viscometer. The company says that the main advantage of the MRS extruder is that it permits the processing of PET or PLA without pre-drying. The Filtration Technology division will present its Rotary Melt Filtration Systems, with various new features. An SFXmagnus 90, an RSFgenius 75 and an RSFgenius 200 will be displayed. The Measurement Technology division will show a new multipoint calibration system, with measuring accuracies of 0.15% in specific applications and the facility to set the sensor’s maximum accuracy individually to the operating range. A harder membrane coating, suitable for very abrasive media such as WPC (Wood Plastic Composite), is now available. A high-accuracy melt temperature sensor has been added to the existing range and a photo-eye option is available for the auto-zero function for sensors with integrated amplifier (4-20 mA; 0-10 V output). www.gneuss.com Gneuss, Inc. West Hall | Booth 6685 Engel Hall A | Booth 943 All-electric for high precision and short cycle times Engel’s e-cap 3440/460 US, on display on its Packaging Business Unit stand, will be demonstrating cap production with cycle times of less than three seconds and injection speeds of 450mm/second. The capacity of the unit is notable because it is claimed to reach levels previously possible only with accumulator machines and the e-cap 3440/460 US is an all-electric moulder. The company says that its machine is designed to achieve both high output and process stability, while saving both energy and cooling water. The machine uses fully electric drive technology combined with an injection unit and a rapid clamping drive. Alongside the e-cap display will be an electric e-motion 740H/310W/180 T combi machine, which will demonstrate production of thin-wall caps for a new range of ice-cream boxes, using two-component injection moulding with in-mould labelling. www.engelglobal.com","@ID":42} "PREFORM PRODUCTION 20 PETplanet insider Vol. 13 No. 03/12 www.petpla.net with the preform loading system this makes 11m. Orders for the first four machines have already been placed by the customer. By way of an extension to the series Masi has already announced a 72-cavity version with a capacity of 300t. The machine is likely to be almost the same length. www.sacmi.com the Sacmi development engineers have reduced the lock to lock time to less than 2.5s. Here an optimised design toggle arrangement ensures rapid opening and closing and minimum dry run times. If the control system is told that the machine is to produce a long preform, it moves the toggle unit with the movable mould plate so as to achieve an optimum lock to lock time once more. The machine is capable of producing 190mm long preforms - more than are needed in most cases. The movable plate looks like a lifebelt with two thick legs. “This layout was the result of extensive FEM analyses; we have left out any material which does not enhance rigidity and this leaves us with a weight-optimised plate which needs less energy for acceleration than classic concepts“ says Masi. The ejection hydraulics have not been able to elude the optimisation process either. The choice was a 2-stage system with a large ram that first of all supplies the necessary initial force required for removal from the mould, whilst a second, smaller ram subsequently ensures that the entire length of the preform is quickly taken care of. This has made it possible to reduce the amount of hydraulic oil required and this also contributes towards increasing the speed of the system’s motion sequences. The mould The actual heart of the plant, the mould, is located between the plates. Here Sacmi’s primary interest was to ensure that tool changing is carried out as quickly as possible. Rapid operation clamping devices are used to ensure that location in the exact position takes place within the shortest time possible. The utilities supply (energy, air and cooling water) then link up automatically. The overall time required for the mechanical change (including new unloading robot plate) should not be more than an hour. The mould as well as the hot runner originates directly from the company’s own mould fabrication plant; however, at a later date, there are plans to adapt moulds from other manufacturers for use on the machine. The PET is delivered by a 100mm injection moulding unit using a Shooting Pot. The power for the injection moulding is supplied by a hydraulic piston drive, whilst plastification is carried out by means of an electric drive. The cooling system for the machine, mould and postcooling is guaranteed by integrated pumps and temperature control system, which leaves only the cold water feed and discharge systems to be supplied by the plant. This simplifies the water piping required and assures the best cooling performance in each part of the moulding process. Despite all this efficiency, the machine when constructed is very long for this clamping force category and this is due to the use of a rapid-acting type of toggle switch. Edge to edge it spans 9.5m. Together Go for growth Vezio Bernardi, who took over as Managing Director (MD) of the Sacmi Group’s Beverage Division on November 1, 2011, outlined an ambitious growth plan for the company under the banner of ‘Objective 200’. The strategy includes a doubling of total plant output within three years, with the intention of taking total beverage business sales to €200 million. Vezio Bernardi was previously CEO of Sacmi Filling and will continue his role as sales manager at Closures&Container. Bernardi took over as Beverage Division MD from Pietro Cassani, who remains General Manager of the Sacmi Group and Sacmi Imola. Bernardi observed that the goal of becoming a complete plant provider has, as regards PET, already been fully achieved, with Sacmi now providing complete, integrated solutions. Applying the same approach to the rest of its product range is the ongoing task, which Bernardi revealed the Group aims to complete in the near future. “By 2012 we will be raising output and expanding the product range,” he revealed. “For example, we’ll be launching a new ‘super-Combo’ that combines the preform-making technology of the PAM, which we were the first to develop, with the latest generation of blow moulders. We already have a supply agreement with one of Italy’s biggest bottlers”. The core of the company’s R&D activities will remain in Imola, where its first blow-moulder was developed. Production will be moved to Sacmi Filling in Parma, with the intention of creating new synergies between fillers and blow moulder. At Sacmi Verona, product research is under way on labellers, from the new range of modular labellers to laser sealing systems and new self-adhesive applications. Group sales currently stand at approximately €150 million. However, the proportion represented by complete plants is below €50-60 million. Bernardi’s stated challenge is to double this in three years, which will enable Sacmi Group to achieve €200 million. Achieving that goal will mean reaching many new customers, in a number of emerging markets. The opportunities are seen in the Russian market, for example, where hot filling technology has shown itself to be a sound replacement for aseptic technology. There are also new developments in ‘traditional’ PET business - water and CSDs - where the biggest opportunities for market penetration appear to lie in North America and North Africa. Moreover, Bernardi observed that the Middle East also appears to be very receptive to this type of product. www.sacmi.com Two pumps take care of two cooling circuits, one for the mould, the other for the postcooling","@ID":22} "PRODUCTS 43 PETplanet insider Vol. 13 No. 03/12 www.petpla.net Naturally light MarketResearch.com estimates that the demand for eco-packaging will grow 6%/year until 2015 and companies, to meet this demand, will have to reconsider their own packaging and their own productive system in the light of eco-sustainability. The project of 5l LW, developed by P.E.T. Engineering in collaboration with Novapet, Spain and Side, Spain, makes it possible to turn a market trend into a business opportunity. The companies in the team have developed the 5l LW as an alternative to those bottlers who have a significant proportion of their turnover devoted to the manufacture of 5l containers. This has made those companies reduce the process of lightweighting even though they have concerns about the environment. The 5l LW container has been developed in two main versions, one to be filled up with nitrogen which weights 60g, and another one without nitrogen with a weight of 64g. The mechanical performance is equal to the 5l bottle weighing 74g and 78g currently in the market, due to the particular structure of the bottle. Ultra-light containers of big formats need special solutions to avoid the phenomenon of over-stretching and its consequent opaque effect in the base. Novapet, Spain, is the supplier of the material and has permitted the prototyping of preforms, together with the preform design of P.E.T. Engineering. The X_TREME resin, which is able to achieve a good level of stretching up to 22 instead of 14, like in standard PET, is designed for the manufacture of lightweight bottles. The combination of P.E.T. Engineering technology and Novapet’s lightweighting PET resin makes it possible to produce a container which is claimed to be 18-23% lighter than the rest of the products currently on the market. According to P.E.T. Engineering the process of stretch-blowing the performs with the Novapet material provides an energy saving up to 23% compared to the blowing of preforms made with standard PET. The containers have been blown on the Side TMS 2002e-G, latest generation Side machine. www.petengineering.com www.novapet.es www.side.es","@ID":45} "MATERIAL / RECYCLING 12 PETplanet insider Vol. 13 No. 03/12 www.petpla.net Extricom offers recycling plants with capacities of up to 36,000t/a PET recycling at large The goal for every recycling company is to implement an economical system and deliver high product quality for the final application. Since 1998, the RingExtruder RE developed by German company Extricom has been used for the bottle-to-bottle recycling of PET. The post-consumer waste is transformed into high quality raw materials approved for food contact. Capacities of up to 4,500kg/h rPET (36.000 t/a) can be achieved with the RingExtruder RE7 XPV. The requirements of an economical extrusion concept are varied and must be analysed on an individual basis. One focus is on energy consumption, disposal costs (e.g. vacuum slurry, screen cake, start-up material), plant availability and maintenance costs. These running costs are evaluated on a continuous basis and incorporated in the plant concept and design. Technology The process section of the RingExtruder RE mainly consists of 12 co-rotating and tightly intermeshing screws orientated in a fixed ring. The adjacent screws constantly wipe each other’s surfaces as well as the outer barrel and the stationary centre core. Stagnant areas are therefore eliminated inside the process section and deposits on surfaces are efficiently prevented. This arrangement results in a distribution of the depending on customer requirements and the final application for the produced material . Bottle-to-bottle application Both of these features lead to the high degassing efficiency of the RingExtruder RE. Thus, PET bottle flakes can be extensively decontaminated without pre-drying at high throughputs. In addition, the gentle treatment of the melt and the high ratio of heat transfer surfaces to volume allow for an accurate control of the material temperature. Plant availability Plant availability is a key factor in the design of the Extrusion System. For example, maintenance or cleaning work can be carried out without interrupting the extrusion process, since there is a dual filter/separator system, incorporating parallel circuits in the vacuum unit. According to Extricom, more than 260,000t/a of bottle-grade PET regranulate are produced with the RingExtruder RE. The increase in PET collection rates in various countries make high-duty plants over 20,000t/a very attractive. Extricom’s PET recycling plants cover a throughput range between 2,800 and 36,000t/a. www.extricom.de Extricom’s RingExtruder RE7 XPV melt flow into multiple small portions providing an effective surface to volume ratio. Furthermore, the twelve intermeshing areas create a unique flow pattern with a high rate of melt surface renewal. Setup of extrusion system Extricom is continuously developing the RingExtruder RE to create a complete turnkey concept. The focus of the development was always on a high level of flexibility, productivity and profitability and this has also resulted in the ecological efficiency of the system. The complete Extrusion System is based on the careful selection of every single component. Every module, e.g. gravimetric feeding, vacuum system, melt pump and filtration, pelletiser and crystallisation is tailor-made and optimised for PET recycling. Different kinds of pelletising and SSP systems can be integrated","@ID":14} "EDITOUR REPORTS 25 PETplanet insider Vol. 13 No. 03/12 www.petpla.net Beverage non-alcoholic % Consumption in 2010 Packaging types by percentage share CSD 49,52 PET 84.3, Glass 10.2, Metal 5.4, Other 0.1 Water 26,43 PET 86.7, Glass 13.3 Dilutables 14,03 PET 36.8, HDPE 18.2, Glass 5.55 Foil 38.9, Other 0.55 Juice & Nectars 10,02 Carton 87.9, PET 6.6, Glass 5.4 Overall consumption of beverages in 2010: 411,3 million litres The welcoming country of Slovenia, which borders on Italy, Austria, Croatia and Hungary, leaves a host of different impressions. With a relatively small population of around 2 million inhabitants, the Slovenian beverages market is well-known and respected far beyond the frontiers of its own country for its diversity, flexibility and quality. Prior to the break-up of the former Yugoslavia, demand was overwhelmingly dominated by alcoholic beverages. Having achieved its independence, Slovenia saw itself confronted not only with the new markets created following the break-up, but also with the much bigger competitors on the European market. The small country has made a superb job of mastering this balancing act. By means of continued commitment, a wealth of ideas and great flexibility in meeting new requirements and finding new sales markets, it has proved possible in the long term to compensate for the loss of the markets in the former Yugoslavia. The most striking thing here is the shift in focus from alcoholic drinks to a range of waters and juices. According to UNESDA, the per capita consumption of non-alcoholic drinks rose between 2005 and 2010 from 195.5 litres to 203.1 litres with a total consumption of 411.3 million litres as against 391.3 litres. Talks conducted with various bottlers have clearly shown a consistent rise in the use of PET as beverages packaging to meet the particular needs and applications of the water and soft drinks sector. However, in the case of alcoholic drinks (here, primarily) beer, customers tend to prefer their tipple packaged in the classic glass bottle or can. By contrast to some other central European markets, the interest in CSd is marginal in the Slovenian market and so, apart from bottling activities licensed from the big brand names such as, for example, Pepsi Cola or Sinalco, there is a general predominance of non-carbonated drinks. Likewise noticeable is the widespread use of the PCO 1810 closure, although a major proportion of the bottling firms are now thinking about converting to PCO 1881. As regards kronesFlexiFruit – doses fruit chunks as if they’re hand-picked. www.krones.com Anuga FoodTec 2012 Cologne, 27 – 30 March Hall 6.1, Stand B020/C029","@ID":27}]}}
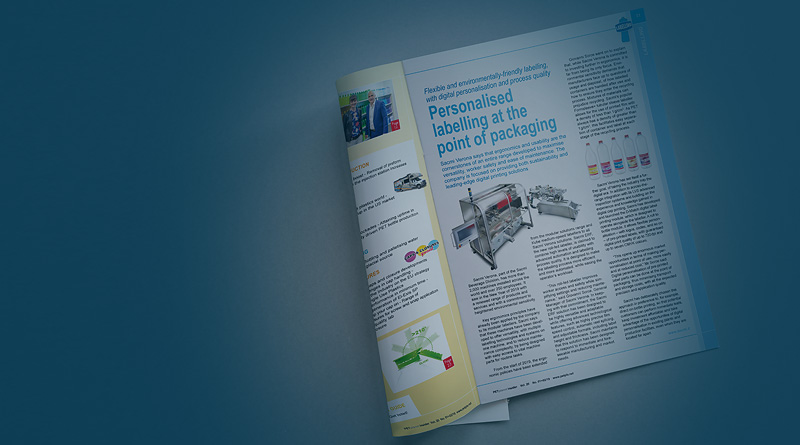