{"pages":{"page":[{"#text":"NEWS 8 PETplanet insider Vol. 13 No. 09/12 www.petpla.net Husky’s HyPET wins Ringier 2012 Technology Innovation Award Husky Injection Molding Systems has been recognised with the Ringier 2012 Technology Innovation Award for its HyPET HPP (High Performance Package) injection moulding system and its contributions to the packaging industry in China. The award was presented to Husky representatives in a special ceremony during the ProPak China 2012 tradeshow in Shanghai. The Ringier Technology Innovation Awards are presented by Ringier Trade Media Ltd.’s International Packaging News for China. The awards were launched in 2005 and are evaluated by a panel of ten judges against several criteria, including impact on the marketplace, inventiveness, financial results and the degree to which the innovation solves a customer need. www.husky.ca Starlinger has opened representative office in Uzbekistan As of May 2012 Starlinger & Co. GmbH, Austrian manufacturer of machinery for woven plastic packaging production and plastics recycling, has opened a representative office in Tashkent, Uzbekistan. The office is headed by Yuldosh Kazakov, who joined Starlinger in 2009 and is the chief representative for the region of Uzbekistan, Kazakhstan, Turkmenistan, Tajikistan and Kyrgyzstan. In addition, a locally based technician is available for immediate customer care and troubleshooting in case of machine problems. Strong economic growth in Central Asia in recent years has also had a positive effect on the textile packaging industry. Starlinger sees a strong potential for growth in this region – comparable to Russia, where seven new customers have been acquired within the past 18 months. Central Asian companies and governments are also beginning to recognise the economic potential that lies in reprocessing and reusing plastic waste as valuable secondary resource. Starlinger has sold their first PET bottle-to-bottle recycling line in Uzbekistan which is currently being installed in Tashkent. The rPET produced is supplied to the beverage bottling industry in the region and will be used in the production of preforms. www.starlinger.com New president for Conair Auxiliary equipment supplier Conair has announced that Larry Doyle, Vice President of Global Sales & Marketing, has been promoted to President of the company. The announcement was made by previous incumbent Chris Keller, who is also President and CEO of Conair’s parent company, IPEG. Doyle has been with Conair for six years and previously worked with Demag Plastics Group (now Sumitomo Demag) and Autojectors, which is now part of Milacron, Inc. Doyle also serves on the Equipment Council of the Society of the Plastics Industry and chaired the Sales & Marketing Committee for NPE 2012 and NPE 2009. www.conairgroup.com","@ID":10} "PETnews 6 PETplanet insider Vol. 13 No. 09/12 www.petpla.net Elasto Müller Kunststoffe and EPS come together After several years of co-operation between Müller Kunststoffe and EPS, the two companies have agreed a deal that brings them together in a new Caps and Closures division within Elasto Müller Kunststoffe. EPS specialises in the development of compounds for caps and closures. Raymond Exon, CEO at EPS, will remain as Caps and Closures Product Manager for Elasto Müller Kunststoffe. Elasto parent company Hexpol AB announced the acquisition of Horst Müller Kunststoffe in December 2011. www.elastotpe.com UK’s Lotte Chemical orders Uhde MTR plant KP Chemical Corporation of Korea subsidiary Lotte Chemical UK Ltd., a producer of PTA and PET, has commissioned a new plant from Uhde Inventa-Fischer for its production facility near Middlesbrough, NE England. The plant will have a production capacity of 200,000t/a, using the company’s patented Melt-To-Resin (MTR) technology. Resin made from this process is used, among other applications, as feedstock for the production of water and CSD bottles. Lotte Chemical UK Ltd produces pure terephthalic acid (PTA), at the site and will supply it directly to the new plant via pipeline. Uhde Inventa-Fischer will provide basic and detail engineering, supply of all plant components and supervision of the construction and commissioning activities, and will also train operating personnel. ThyssenKrupp Uhde and Uhde India will provide the civil and steel structure engineering. www.uhde-inventa-fischer.com Krones signs up to UN Global Compact Krones AG signed up to the United Nations (UN) Global Compact in May 2012, which it says is in line with its view of its social responsibilities as fundamental elements of its corporate culture. UN Global Compact signatory companies are obliged to comply with the global guidelines covering human rights, labour standards, environmental protection and combatting corruption. www.krones.com Agr offering Six Sigma Agr International has announced that its process consulting services for PET blowmoulding operations utilise a Six Sigma-based process evaluation. The Six Sigma methodology is a well-established process improvement toolbox widely used in manufacturing and product design, as well as complicated technical process management. Six Sigma is based on five steps; define, measure, analyse, improve and control, which are backed by a broad array of proven statistical tools. This is augmented by the use of Agr’s measurement tools specifically designed for the PET bottle industry. Agr uses the Six Sigma process to conduct a practical analysis of the blowmoulding process in a given manufacturing facility. The analysis includes the identification of the KPIs that should be measured and controlled to optimise the process. Agr’s consulting personnel work directly with process engineers and plant floor personnel to solve problems such as managing light weight applications and quality issues, as well as a range of process improvement efforts that lead to improved pack rate. www.agrintl.com PTi sells sheet extrusion system to Aserpet Sheet extrusion machinery manufacturer Processing Technologies International (PTi) has announced the sale of a new sheet extrusion system to Aserpet, of Gaziantep, Turkey. The recently completed sale is PTi’s first in Turkey. Aserpet, a recycler of PET flake for the packaging industry, purchased its first sheet extrusion line to help support the company’s entrance into the packaging industries. The PTi coextrusion system, which runs 750 kg/hr of PET, also includes a roll stand, winder, and stacker. The machine has been installed and is now operating at the customer’s facility. PTi sold the machine through its agent Kerem Anil with Plast-teknik in Istanbul. The company is exploring other business opportunities in Turkey, targeting PET, PP, PS, and barrier sheet extrusion systems for the packaging industry. www.ptiextruders.com IVL closes Indonesian PET deal Indorama Ventures Public Company Limited (IVL) has completed the acquisition of the PET assets of PT Polypet Karyapersada in Indonesia. The deal, which the company first announced in March 2012, provides IVL 100,800t of PET capacity adjacent to the PTA assets of PT Indorama Petrochemicals (formerly known as PT Polyprima Karyesreska) at Cilegon, West Java, which IVL acquired under a joint venture in 2011. Mr. Aloke Lohia, Group CEO of Indorama Ventures, said, “Indorama Ventures has pursued an integration strategy of our PET and PTA businesses in Thailand, Italy (under a joint venture) and The Netherlands and earlier announced upstream integration into MEG (Monoethylene Glycol) in North America. The acquisition of PT Polypet Karyapersada creates synergies due to it being co-sited with our PTA plant PT Indorama Petrochemicals in Indonesia, making it a strategic investment in the most populous country in ASEAN.” www.indorama.net","@ID":8} "CAPPING / CLOSURES 40 PETplanet insider Vol. 13 No. 09/12 www.petpla.net Co-injection keeps oxygen at bay Barriers under control Fig. 1.: This 38mm hot fill polypropylene (PP) beverage closure includes a tamper-evident band at the bottom, a locking band, bottle support on the sides, a plug seal, and a co-injected 0,1mm oxygen and CO 2 barrier layer made of EVOH (illustrated here in blue). This barrier has 30 times more resistance to permeation than a monolayer polypropylene cap. The new approach produces a single piece cap ideally suited for products like carbonated beverages, juices, water and tea that need oxygen or CO 2 barrier protection. The cap also has a tamper evident band compatible with current market bottle finishes. This tamper evident band features a continuous conical locking band with ribs to position the locking band on the bottle finish. Design by purpose These co-injection results are obtained by precise, integrated control of dosing, flow and pressure of the two melt streams. Balanced filling of 3-5% barrier-layer material into all parts equally is achieved using proprietary iFlow manifold technology, precise control of the E-Multi unit, and the positioning of the valve pins using the E-Drive actuation system. The single integrated Iris control system controls the E-Drive pin positioning, hot runner heaters, and the barrier injection flow to ensure that the elements of the system work together in harmony. The E-Multi auxiliary injection unit also allows moulders to revitalise existing machinery by converting a mono material machine into a multi-material application. The proprietary and patentpending Iris co-injection system design moves the melt simultaneously in the primary and secondary injection flow paths and delivers it through a single gate (Figure 2). The Iris nozzle design merges the two melt paths together and allows for on-the-fly control of the barrier position both in the direction of flow and in the cross section of the part. With a single integrated controller, the moulder can observe and control what is happening in the melt streams to a greater degree than ever before. Beverage barrier closures A recently showcased 16-cavity mould (Figure 3) produces the parts that are a tamper evident, liner-less, hot fill HDPE cap for a beverage container with an integrated oxygen and CO 2 barrier. The patent pending, tamper evident band is compatible with current market bottle finishes. The band features continuous conical locking, with ribs to position the locking band on the bottle finish. The co-injected barrier material is EVOH. Using Mold-Masters new Iris co-injection technology such caps are moulded with barrier technology encased in its centre. This results in a simpler cap design that can be used directly as opposed to needing a secondary operation to insert or mould a liner. The simultaneous injection of 3 to 4% barrier into the 16 cavity production mould is resulting in a very balanced thin layer. Fig. 2: The Iris co-injection system: The Iris nozzle design merges the two melt paths together and allows for on-thefly control of the barrier position both in the direction of flow and in the cross section of the part. Fig. 3: The 16-cavity Iris system for 38mm hot fill polypropylene (PP) closure produces co-injected parts at a cycle time of less than 5s. The permeation of oxygen into beverage containers or carbon dioxide out of carbonated products has a negative impact on product quality and shelf life. There has been considerable emphasis and development on beverage containers in recent years to reduce this permeation. Mold-Masters’ latest co-injection development now enables caps to be produced with a co-injected barrier (Figure 1).","@ID":42} "MARKET SURVEY 29 PETplanet insider Vol. 13 No. 09/12 www.petpla.net Dodhia Techno Engg. PVT. LTD. Urola S.C. Beutelspacher S.A. DE C.V. Nissei ASB Machine Co., Ltd. Mega Chum Power Machinery Corp. 69/3 Pervin Mansion, Sion West, Mumbai - 400022, INDIA +91 22-24030034, 66662110 www.dodhia.com Bipin Dodhia Managing Director +91 22-24082792 [email protected] Urola Kalea s/n, PO Box 20230 Legazpi, Spain +34 943 737003 www.urola.com Iñaki Unanue +34 943 737144 [email protected] Venados No 52, Col. Los Olivos, Tláhuac, Mexico D.F. +55 58404562 www.beutelspacher.com Ing. Sergio Beutelspacher Director +55 58404562 +55 58451053 [email protected] 4586-3 Koo, Komoro-shi, Nagano-ken 384-8585, Japan +81 267 23-1565 www.nisseiasb.co.jp/en/ Mr. Katsuo Ishiguro Manager - Sales Coordination Team +81 267 23-1565 +81 267 23-1564 [email protected] 47-8 # Huangzhou RD, Huangyan, Zhejiang provice, China +86-576-84020122 www.megamachinery.com Simon Cai Sales Manager +86-576-84020122 +86-576-84020107 [email protected] No. 688-1, Section 3, Zhong Shan Road, Wuri Township, Taichung, Taiwan +886 4 23388289 www.chumpower.com Grace Lee General Manager +886 4 23388289 #1200 +886 4 23380219 [email protected] FlexiPET -6000 AutoPET - Duo Urbi-2, Urbi-4, Urbi-6, Urbi-8; Urbi-2L, Urbi-4L SB 3002 HSB-4N, HSB-6N, HSB-6M 10 L series 0.01 - 6 0.1 - 2 25l 0.1 - 2 3 up to 0.6 ** up to 2.5 0.060 - 2 up to 10 3 up to 2 ** up to 25 4 - 20 16 5 2 8 2 6 up to 16 12 1 to 2 4 1 4 up to 2 4 1,500 1,200 -1,800 1,000** 1,500 1,700 360 1,400 1,500 1,200 -1,800 1,400 1,500 300 1,250 1,600 700 - 800 1,300 1,500 300 1,250 1,200 700 - 800 600** 150 550- 1,000 400 up to 6000 ml 500ml jars at 970bph/cav **data is for double blow-heat-set filling for hot fill containers. Can also be used for regular blowing at higher outpits 2 x 3 x 2 3.5 x 3 x 2 Smallest: 2.32 x 2.2 x 2.0; Largest: 5.9 x 4.35 x 2.3 2 x 3.8 x 2.5 6.7 x 2.0 x 3.2 Depending on machine model 7x2.02x3.5 KHS Corpoplast GmbH Sidel Group Meiendorfer Str. 203 , 22145 Hamburg, Germany +49 40 67907 -0 www.khscorpoplast.com Marco Boehnke Product Manager Blomax +49 40 67907 - 483 +49 40 67907-9483 [email protected] Avenue de la Patrouille de France, Octeville-sur-Mer, BP 204, 76053 Le Havre Cedex, France +33 2 32 85 86 87 www.sidel.com Dominique Martin Blowing & Coating Product Management Director +33 2 32 85 88 45 [email protected] Contiform Medium H; 8 (7) models available Blomax , Series IV SBO Universal 2eco 20 models (rotary blower) SBO Highspeed eco 2 models (rotary blower) SBO Compact2 3 models (linear blower) SBO Compact2 PH (Preferential Heating) 3 models available (linear blower) SBO Universal eco PH (Preferential Heating)/; 8 models (for flat and SBO Universal eco HR (Heat Resistant) /11 models (for hot fill) 0.1 - 2.0 0.2 - 3.0 0,25 - 3 0,2 - 0,7 0,25l - 10 0,25l -10 0,25 - 3,3 0,25 - 3 up to 10 up to 10 24 (26) 36 30 34 4 4 20 30 3 3 2,000 (aluminium moulds) 2,200 2,000/1,800 for SBO 30 2,000 1,600/1,200 for SBO2XXL 1,400/1,200 for SBO2XXL 1,400 1,800/1,700 for SBO 30 2,000 (aluminium moulds) 2,200 2,000/1,800 for SBO 30 1,600/1,200 for SBO2XXL 1,400 /1,200 forSBO2XXL 1,400 1,700 2,000 (aluminium moulds) 2,200 2,000/1,800 for SBO 30 1,600/1,200 for SBO2XXL 1,400/1,200 for SBO 2XXL 1,400 1,500 1,800 (aluminium moulds) 1,100 - 1,500 1,600/1,200 for SBO2XXL 1,400/1200 for SBO 2XXL 1,200 1,100 1,000 1,000 from 6.9 x 4.4 x 4.5 to 11.2 x 6.8 x 4.5 13,3 x 7,0 x 3,5 from 7.1 X 3.3 X 3.8 to 18.8 X 6.6 X 3.9 from 11.3 X 4.9 X 3.9 to 13.1 X 4.9 X 3.8 5.1 X 2 X 3.4 5.1 X 2 X 3.4 from 6.7 X 3.3 X 3.8 to 10.6 X 4.9 X 3.9 from 7.1 X 3.3 X 3.8 to 18.8 X 6.6 X 3.9","@ID":31} "PETpatents www.verpackungspatente.de 48 PETplanet insider Vol. 13 No. 09/12 www.petpla.net PET containers International Patent No. WO 2012 / 009156 A1 Applicant: Graham Packaging Comp., York (US) Date of Application: 28.6.2011 Extrusion blow moulded bottle in PET with integrated handle. The design of the chamfers and radii is shown. Additional security International Patent No. WO 2012 / 012715 A1 Applicant: Abbott Laboratories Abbott Park (US) Date of Application: 22.7.2011 In order to provide better protection for the use-by dates applied to the container, the sleeve label is subsequently pulled over it. This means that the information, which is applied using ink, cannot be readily wiped off or manipulated without previously destroying the label. Container fabrication International Patent No. WO 2012 / 013188 A2 Applicant: KHS Corpoplast GmbH, Hamburg (D) Date of Application: 26.7.2011 The design and the procedure for manufacturing a blow moulded container with specially shaped grip area are described. Multi-stage opening International Patent No. WO 2012 / 017934 A1 Applicant: Tetra Laval Holdings & Finance S.A., Pully (CH) Date of Application: 29.7.2011 The top side of the packaging for a beverages carton incorporates a closure with a multi-stage opening facility. A small opening can be selected for a straw or a large one for pouring out the contents. Angled neck using cap International Patent No. WO 2012 / 022475 A1 Applicant: SHB GmbH, Crailsheim (D) Date of Application: 17.8.2011 The manufacture of PET bottles with a curved external shape (e.g. for WC cleaners) is time-consuming and hence associated with increased production costs. In order to reduce these, mounting an appropriately curved adapter on a “straight” bottle is suggested, on which the screw closure is fitted. Closure system Disclosure No. DE 102009002074 A1 Applicant: Henkel AG & Co. KGaA, Düsseldorf (D) Date of Application: 1.4.2009 Design and operation of a container closure which combines the advantages of a screw closure with those of a snap-on cap are described. Mechanical mounting of the closure is easier and faster and does not present any disadvantages when being handled by the consumer.","@ID":50} "EDITOURS REPORTS 34 PETplanet insider Vol. 13 No. 09/12 www.petpla.net Bulgaria blog Finally I reach the Bulgarian border. Inevitably, there are queues of vehicles and endless hold-ups at the crossing point. Once arrived in Sofia, I manage to locate a suitable place to bed down for the night at a supervised car park near the airport. Slashed tyres on some of the other vehicles testify to the quality of supervision. The narrow, crowded roads of the city are not really suitable for the Editourmobil so I decide to hire a car, and the first task is to find a Wi-fi hotspot. Shattered after the long and tiring drive, I decide to call it a day, and go to bed early. Refreshed after a good night’s sleep, I prepare for my two appointments at Gotmar and index-6. To get to them is a 150km drive, and progress is not helped by the fact that it is bucketing down with rain, the road is under water, and there’s no sign of the weather improving. Both appointments more than make up for the pseudo-monsoon however. It is 10 o’clock at night when I finally pull up beside the Editourmobil. I am asleep practically before my head touches the pillow. The next day brings some new challenges. For starters, I have a lot of writing to catch up on, and more importantly, I need to get the windscreen repaired. The man in charge at Iveco Sofia is Victor, who cannot do enough for me. Without so much as a by your leave, I change Victor’s reception area into my temporary mobile office. He plies me with food and drink and even makes the Wi-fi access available. Victor, I can’t thank you enough for your hospitality. I leave Sofia and set off in the direction of Turkey. Victor had kindly allowed me to stay a second night at the Iveco premises which was handy as it is conveniently placed for the motorway to Istanbul. The sun is shining, and all is well with the world. Before long the temperature will hit 20 degrees and more. At the last petrol station, just on the border, the Editourmobil quenches its thirst. Turkey, here we come! - Kay Krüger - Romania blog After my brief sojourn in Turkey, Romania is next on the agenda with a detour via Bulgaria, where Kay has already interviewed two major companies. The roads in Bulgaria are in an awful state, so I am extremely relieved when, on Sunday evening, I reach my destination and my appointment with Bericap in Ploiesti, where I am to meet Tiberiu Bako, the General Manager. Together we spend a convivial evening at his local hostelry, where, over a pleasant meal and a bottle of the local wine, the conversation turns to a philosophical discussion about whether Count Dracula really did exist. - Alexander Büchler - In 2010 the figures shown in chart 1 emerged for the consumption of non-alcoholic beverages: CSDs 24.1%, water 26.9%, cordials, juices and sports drinks 9.7%, iced tea 1%, milk and dairy drinks 6.7% and, for hot drinks, 5.1% (coffee 3.9%, tea 1.2%). As regards the alcoholic beverages sector, beer takes a clear lead with 19.6% whilst wine and spirits accounted for a mere 4.3% and 2.6% respectively (Source: Gotmar). As far as market size is concerned chart 2 shows that there have been no significant changes in the various segments in the last four years. Categories 2008 2009 2010 2011 Alcoholic drinks in million litres 683.6 689.4 680 682.9 Hot drinks in tonnes 17,684.60 17,538.70 17,643.50 17,836.60 Soft drinks in million litres 1,385.90 1,368.70 1,315.70 1,337.50 Chart 2: Market size / total volume over the past years (Source: Euromonitor International) Gotmar From drawing board to finished product (from left to right) Dimo Golev, Kay Krüger, Zdravko Kormevski and Lidija Velcheva with the Go to Brau Beviale banner Chart 1: Overall consumption of beverages in 2010: approx. 2560.2 million litres (Source: Gotmar)","@ID":36} "PRODUCTS 43 PETplanet insider Vol. 13 No. 09/12 www.petpla.net Preblow process for reduced cycle times Netstal has announced a further development of its the PET-Line Calitec system, with the extension of the cooling phase with a blow-out process in the base area. The company says that this process, named Preblow, helps to reduce cycle times and improve moulding quality. During the Preblow process (which is the subject of a patent application) the preform is blown out in the base area directly after the injection moulding process. This means that both the base contour and, thus, the surface area can be changed for the first time. By increasing the size of the base contour through the blowing process, a thinner wall can also be obtained in the base area. Netstal claims that, during the subsequent blowing process, this effect can be used to heat the base area more specifically and more efficiently. With a larger surface area, the UV lamps in the blowing machine have to heat a thinner wall. During development, Netstal says that its technicians have exerted more influence and improved wall thickness and material build-up. Initial tests with 1l juice bottles achieved a weight reduction of more than 1g. The company presented a system at Chinaplas that produced a still water preform weighing 15.8g, in a 128cavity machine at a cycle time of around 7.2s. www.netstal.com Drying and material handling solutions Polymer dryers, including the EnergySmart SingleStage (ES-1) drying systemfrom Conair are available for throughputs between 182kg/h and 2273kg/h (400lbs/h and 5000lbs/h). In the so-called Optimizer Mode, the new TouchView dryer control (Siemens platform) regulates not only air temperature, but also dew point and air flow based on data from the Conair Drying Monitor. Just enough heat energy is added to the bed of material in the drying hopper to maintain optimum conditions while saving energy and producing highquality finished products more efficiently. The controls maintain a stable temperature within the drying hopper regardless of throughput changes or variations in material temperature or ambient conditions. Settings can also be stored in memory for instant recall. Other Conair drying solutions include the SlimLine compressed-air dryers. Targeted at drying applications requiring throughputs under 22.5kg/h (50lb/h), these easy-to-use dryers require 220v power and filtered compressed air, so they consume far less electricity than most conventional dryers. With no desiccant or moving parts, they require virtually no maintenance. To operate it, the user simply adjusts the air regulator, flips a switch, and sets the processing temperature. www.conairgroup.com Longskirt dispensing closure Bericap’s established Galileo moulded hinge closure technology is the base for the company’s new LSK EV 29/44 long-skirt dispensing closure, designed to fit to a Verplast 29/21 neck finish. The new design, which is aimed at premium edible oil, vinegar and traditional syrups markets, is also suitable for syrups aimed at children and young adults. It maintains the traditional Galileo look but also allows large-surface printing, as well as efficient tamper-evidence performance. It features post-opening breaking bridges and a tear-off membrane below the overcap. Bericap claims that the new product offers an attractive and functional design to brand owners; simple conversion of existing equipment for the new line, for bottlers; and an easy opening and closing to the consumer. www.bericap.com Centralized off-line blending TSM ’s multi-blend system TSM3000 allows the end user to centrally locate the blending of all materials and recipes in a high throughput gravimetric blender. This gravimetric blender can handle up to 12 individual material components and can supply any number of machines at any given time with total automatic cleaning between recipes. The design offers several advantages such as the use of centralised offline blending to feed multiple machines. This has many cost advantages as gravimetric blenders for each machine are no longer necessary. Individual material recipes are simply entered into the TSM central blender control panel. When a machine requests a material fill, the TSM blender prepares the required job recipe, mixes the material, before conveying it off to its respective machine. Another feature is the blender’s automatic self-cleaning feature which is initiated in anticipation of the next fill request or masterbatch change. All material consumptions are logged for traceability and accountability purposes, which contributes further to the overall production efficiency. www.tsmcontrols.com Loss-in-weight controlling technology Wuxi K-Tron colormax Co., Ltd. offers a feeding solution led by loss-in-weight controlling technology. This system includes single, twin screw, liquid, micro and vibratory lossin-weight feeders and weigh belt feeder. It is able to feed various materials such as pellets, powder, or the mixture of pellets and powder with a feeding accuracy of +/-0.5%. The loss-in-weight feeders can input the feeding set value on the WKC-HMI or input the technological recipe of the multi- feeders through this operator interface. The patented bowl hopper has been applied to all screw feeders of K-Tron Colormax. It allows the material to flow evenly from all directions to the screw and effectively avoids material build-up. All of the contact parts of the feeders are made of stainless steel material. The Wuxi K-Tron Micro Loss-in-Weight feeder is designed to provide high accuracy to loss-in-weight feeding of pellets, granules, free flowing powders and other bulk materials in the lower output range. Feeding rate can be 1-30 L/H with accuracy ≤+/-2%. www.ktroninternational.com","@ID":45} "Tradeshow preview 42 PETplanet insider Vol. 13 No. 09/12 www.petpla.net KHS South Hall 812 Roll-fed labeller KHS AG will be presenting its Innoket 360 roll-fed labeller. Focus of the machine is on ergonomic and cleaningfriendly, hygienic design on which all machine parts are easily accessible for operators: changeover and maintenance times are thus reduced to a minimum. Significant features are cutting technology with self-sharpening cutter, segmented vacuum drum and a gluing system based on the principle of induction. At one of its first reference customers, the Heil- und Mineralquellen Germete GmbH (spa and mineral springs), the Innoket 360 has labelled more than 20 million bottles since 2008. www.khs.com AGR South Hall 661 New inspection capability Agr International, Inc. has expanded its OptiCheck product line to include a sidewall module specifically designed to meet the inspection requirements of PET and transparent containers. This system takes into consideration the day-to-day variations in the production of plastic containers while maintaining the versatility to deal with frequent product change-overs and limited line space. The transparent sidewall module utilises four cameras that are strategically located to facilitate full 360° imaging of round and non-round containers in a range of sizes. LED back lights, in combination with high precision cameras, provide clear images for analysis. The OptiCheck system is also available with modules for finish measurement and gauging, seal surface inspection, sidewall and label inspection, and base inspection of opaque containers. The modular approach permits Agr to configure the OptiCheck system with the appropriate combination of modules to meet the inspection needs of a specific production line in the most economical manner. www.agrintl.com CSI South Hall 1566 Capping solutions In addition to a number of capping equipment products, Closure Systems International will be featuring several caps and closures, including (but not limited to) the lightweight Extra-Lok V 38mm OD and SP38D-ML Xtra-Lok mini S 28mm and Econo-Lok mini 28mm . Xtra-Lok mini ‘S’ 28mm closure for the short-height carbonated soft drink bottle finish features a lightweight design that delivers improvements in packaging cost and sustainability, CO 2 performance, and impact resistance. Econo-Lok mini is an ultra-lightweight 28mm linerless closure with 1881 short neck finish designed for use on both CSD and bottled water. This closure is engineered to meet all standard performance requirements for CSD and bottled water applications, while weighing less than 2g. It can be used on PET package sizes ranging from 250ml to 3l bottles. The cap is made of organoleptic resin material that meets sensory protocols for sparkling beverages and waters. It has a robust seal that meets all CO 2 performance requirements and has a patented secure tamper evidence system. The 38mm aseptic SP38D-ML closure is designed for the dairy market which can be applied either to 1842 HDPE bottle finish or 1845 PET bottles. This closure has a moulded in-shell liner which eliminates the need to use an induction foil seal and also provides excellent liquid reseal after the product is opened for the first time. www.csi Gernep Booth E-7717 Labelling combinations Gernep, supplier of rotary labelling machines, offers various labelling systems which can be combined on one Gernep machine.The rotary labeller Labetta-SK has special servo drives located at the self adhesive dispenser Innovative and exclusive label designs as well as no-label-look and water resistant plastic labels can be processed. Compared to wet glue labelling systems changeover times, as well as cleaning and maintenance works are obviously shorter. For wet glue labelling Gernep provides the labelling machine of type Labetta. The overlay gear of the wet glue aggregate allows precise label adjustment along with individually adjustable glue segments. With the Combi series, due to the compact arrangement of several different labelling systems, almost every label outfit can be realized. Labetta and Combi can be equipped with mechanical or photo electronical container orientation systems. The machines can additionally be equipped with (wet glue or self adhesive) guarantee seal labelling in L- or U-shape. Alternatively, all types of Gernep labelling machines can be equipped with servo driven bottle plates for labelling of various container formats. The servo controlled bottle rotation offers an especially high flexibility. www.gernep.de October 28 -31, 2012 Chicago, Illinois","@ID":44} "PETcontents 09/12 4 PETplanet insider Vol. 13 No. 09/12 www.petpla.net INSIDE TRACK 3 Editorial 4 Contents 6 News 42 Products 44 Bottles: Beverages 46 Bottles: Home and personal care products 48 Patents EDITOUR REPORTS 32 Bulgaria’s bounty from a single source BEVERAGE INGREDIENTS 38 The taste of nature New ways to beverage concepts at drinktec 2013 CAPPING / CLOSURES 40 Barriers under control Co-injection keeps oxygen at bay REGIONAL MARKET REPORT 10 China - Part 2 BOTTLE MAKING 22 Stack, rack and roll Sidel and Siapi launch multi-layer stacking systems for PET bottles 24 Multi-component bottles Coloured PET bottles on standard SBM machines MARKET SURVEY 23 Suppliers of two-stage SBM machinery BOTTLING / FILLING 31 Water from the foothills SMI line for still and sparkling water BUYER’S GUIDE 49 Get listed! Page 40 Page 20 Page 44 Page 31","@ID":6} "NEWS 9 PETplanet insider Vol. 13 No. 09/12 www.petpla.net Krones unveils half-year figures and confirms targets for 2012 With the figures for the first half of 2012, Krones is improving its consolidated earnings. Sales in the first six months of 2012 were up by 2.6% on the preceding year’s equivalent figure, from €1,257.5 to €1,289.7 million. Sales growth is predicted to accelerate during the year’s second half. Whereas sales in Europe fell slightly, the company’s turnover outside Europe rose by 8.6% on a like-for-like basis. In all, during the first half of 2012, Krones achieved just under 62% of its consolidated sales outside Europe. From January to June 2012, Krones received orders worth €1,327.8 million, up by 0.3% on the preceding year. Orders on hand effective 30 June, 2012 totalled €980.4 million (preceding year: €974.6 million). Earnings before taxes (EBT) were after six months down on the preceding year’s high level, decreasing by 7.5% from €69.2 to €64.0 million. The EBT margin came to 5.0% during the year’s first half (preceding year: 5.5 %). After taxes, during the first six months of 2012 Krones earned €44.2 million, 10.2% less than in the preceding year’s equivalent period. Earnings per share fell from €1.62 to €1.47. About 60% of the company’s consolidated turnover comes from emerging markets. On the basis of trends in the company’s markets and the uncertain macro-economic prospects, Krones anticipates that its turnover will rise by up to 4% in 2012 compared to the preceding year’s figure. Krones is aiming in 2012 for a substantial increase in consolidated earnings compared to the previous year. According to Krones, earnings in the second half of 2012 are set to significantly exceed the preceding year’s figure for July - December. The EBT margin should exceed 5% over 2012 as a whole (preceding year: 3.0%). www.krones.com Manjushree Technopack sets up 3 MW wind power plant in Karnataka Bangalore based packaging major Manjushree Technopack has set up a wind power plant, in Chikkodi town, Belgaum, Karnataka. The 3 MW plant is fully operational and is Manjushree’s first investment in a power project. The company has invested Rs. 20 crore (US$ 3.58 million) in this project. Wind energy company Gamesa is responsible for the construction and maintenance of the project. Karnataka holds the third favourable position in the country for wind based power projects. Speaking about the wind power project, Managing Director, Mr. Vimal Kedia said, “We plan to increase the capacity to 8 MW by next year and 20 MW in the next five years.” Currently the power generated is being used for captive consumption. Manjushree Technopack Ltd crossed the Rs. 300 crore (US$ 53.8 million) mark in the year 2011-2012, closing with a turnover of Rs. 310 crore (US$ 55.6million). The company has also committed investments of Rs.150 crores (US$ 26.9) for two new greenfield facilities, at Bidadi and Harohalli industrial areas, in Bangalore. The facility at Bidadi is under construction and will be operational by October 2012. www.manjushreeindia.com","@ID":11} "MARKET SURVEY 28 PETplanet insider Vol. 13 No. 09/12 www.petpla.net 09/2012 MARKETsurvey Company name Siapi SRL Kosme GmbH Wei Li Plastics Machinery (H.K.) Limited Postal address Telephone number Web site address Contact name Function Direct telephone number Fax E-Mail Via Ferrovia Nord, 45 31020 San Vendemiano (Tv), Italy +39 0438 4096 www.siapi.it Maico Zanco Sales Manager +39 0438 4096 +39 0438 401016 [email protected] - [email protected] Gewerbestrasse 3 2601 Sollenau, Austria 0043 2628-411-0 www.kosme-austria.com Johann Gugler Managing Director +43 2628-411-125 +43 2628-411-4125 [email protected] Room 1212, Fo Tan Ind. Centre, 26-28 Au Pui Wan St., Fo Tan, N.T. Hong Kong +852 2690 2368 www.weiliplastics.com Maggie Chau Business Manager +852 2690 2368 +852 2690 2380 [email protected] 1. Machine designation / model number S (3 models) SC series (7 models) SE series (13 models) SD series (6 models) Linear machines (6 models) Rotary machines (4 models) MP Series (Mini, StandardI-IV, Medium I-IV, Large I-II, Ex-Wide) 2. Bottle volume (from/to in litres) a) Standard machines 0.1 - 6 0.1 - 5 0.1 - 5 0.1 - 3 l 0.05 - 3 0.05 - 3 0.015 - 10 b) Machines for large containers up to 12 up to 10 up to 10 0.5 - 30 0.5 - 6 10 - 20 3. Maximum number of stretchblow moulds (units) a) Standard machines 2 3 - 5 5 - 10 12 -16 4 6 1 - 4 b) Machines for large containers 2 2 3 - 4 2 - 4 6 1 - 2 4. Output per stretch-blowmould for: a) 0.5 litres CSD bottle (units / hour) 1,500-1,800 1,500-1,800 1,500-1,800 1,500-1,800 1,700 2,000 800-1,000 b) 1 litre CSD bottle (units / hour) 1,500-1,800 1,500-1,800 1,500-1,800 1,500-1,800 1,650 2,000 800-1,000 c) 1.5 litres still mineral water bottle (units / hour) 1,500-1,800 1,500-1,800 1,500-1,800 1,500-1,800 1,600 2,000 800-1,000 d) Large capacity container 1,250-1,300 1,250-1,300 1,250-1,300 1,250-1,300 up to 1,250 for 5l; 350 for 30 l 1,250 500-650 for 5-10L; 100-120 for 20L e) Other 350-400 for 500ml PP Fridge Bottle 5. Footprint / space requirement (L x W x H in metres) 2,9 x 2x 2,2 5 x 2,2 x 2,55 7,3 x 3,1 x 2,4 7,3 x 3,1 x 2,4 min. 4.5 x 1.83 x 3.1; max. 5.1 x 1.85 x 3.1 (without preform feeding system) 6.05 x 3.85 x 3.25 (without preform feeding system) depending on machine model Company name TechnoPET Machineries Sipa Krones AG Postal address Telephone number Web site address Contact name Function Direct telephone number Fax E-Mail 14/15, Shree Naman Plaza ,S.V Road Kadivali (W), Mumbai-400 067 Maharashtra India +91 22-28610828 www.technopet.in Mr. Vineet Bannore/ Mr.Sunil Bharkhada Technology +91 982034656/09821040637 +91 22-28061410 [email protected] Via Caduti Del Lavoro 31029 Vittoria Venoto (TV), Italy +390438911511 www.sipa.it Antonio Narder Industrial Division Director +39 0438911511 +39 0438912273 [email protected] Böhmerwaldstr. 5 93073 Neutraubling, Germany +49 9401-70-0 www.krones.com Peter Christiansen Sales Manager +49 9401 70-4980 +49 9401 70-914980 [email protected] 1. Machine designation / model number Pauto 1200/1800 Pauto 2x2x5 AutoPET-T1 TPS-20L 5 Gallon jar TP-Beer For Beer/Liquore Rotary blowmoulders ; SFR 6 EVO, SFR 8 EVO, SFR 12 EVO, SFR 16 EVO,SFR 20 EVO,SFR 24 EVO, SFR 9/27 (7 models) Linear blowmoulders ; SFL 2/2,SFL 2/1,SFL 4/2,SFL 4/3, SFL 4/4, SFL 6/2, SFL 6/3, SFL 6/4, SFL 6/6 (9 models) Contiform Medium 11 models available Contiform Small 4 models available 2. Bottle volume (from/to in litres) a) Standard machines 0.05 to 2 0.10 to 5 0.10 to 2 0.2 to 2 0.25 - 3.3 0.25 - 3.0 0.1 - 3.0 (3.78 i.e. 1 gallon) 0.1 - 0.7 b) Machines for large containers 5 to 20 4 - 30 3. Maximum number of stretchblow moulds (units) a) Standard machines 1, 2, 4 2 2 1 1, 2, 4 24 6 28 36 b) Machines for large containers 1 1 6 4. Output per stretch-blowmould for: a) 0.5 litres CSD bottle (units / hour) 1,200 1,100 1,600 500 up to 2,000 up to 1,800 2,250 2,250 b) 1 litre CSD bottle (units / hour) 1,200 800 1,500 600 up to 2,000 up to 1,700 2,250 c) 1.5 litres still mineral water bottle (units / hour) 800 1,400 700 up to 2,000 up to 1,800 d) Large capacity container 500 100 1,250 for 5l; 800 b/c/h for 30l e) Other Hot-fill and wide mouth:450 Jars 800 1,5001,600 300 Combo filling 5. Footprint / space requirement (L x W x H in metres) 4x4x3 3x5x6 6x4x7 5x4x3.5 4x4x3 various 5,8x2,2x2,1m from 6.5 x 5.4 x 4.6 to 11.7 x 7.6 x 4.6 from 10.7 x 6.2 x 4.6 to 14.4 x 7.6 x 4.6","@ID":30} "BOTTLE MAKING 25 PETplanet insider Vol. 13 No. 09/12 www.petpla.net cation refers to the SBM process where the preform is partially moulded with a minimum of two components and then blow moulded in a second stage. The other patent application refers to the single-stage process to produce multi-component plastic containers by injection blow moulding. Licensee Gizeh The plastic packaging specialist Gizeh, Bergneustadt, Germany, is one of the first companies to employ this new technology and to produce multi-coloured PET bottles on conventional SBM machines. After an extensive development and testing phase, the company is now offering this technology to its customers worldwide. This technology opens up new horizons for PET bottles as regards visual and haptic design potential. It is possible to produce the bottles in various colour combinations by blow moulding or in combinations of transparency and colour. Handling elements such as soft or anti-slip gripper zones are currently being developed. In addition new possibilities are emerging on the technical front. On request an antibacterial inner wall coating can be applied which will increase the shelf life of the filler product. It is also possible, by means of concealed injection security pigments, to provide enhanced protection for the brand name and the product. Gizeh has experimented with various design options and achieved some good results. The product offers major potential, in particular for customers from the food and drinks industry, but also for cosmetics, domestic and technical fluids, says Daniel Rüth, Head of Gizeh PET GmbH. The new PET bottles can be obtained from Gizeh. About Gizeh Gizeh Verpackungen GmbH has its headquarters in Bergneustadt. It is one of the leading companies offering complete solutions for rigid plastic packaging in Europe. The company designs, produces and decorates innovative plastic packaging for products from the foodstuffs industry as well as for bodycare and cosmetic products. The GIZEH Group, headquartered in Bergneustadt, employs around 560 staff at five locations in Germany, France, Poland and Switzerland and generates annual sales of approx. €100m. www.gizeh.com www.gizeh-pet.com www.inotech.de","@ID":27} "BOTTLES 45 PETplanet insider Vol. 13 No. 09/12 www.petpla.net New shape bottle The Austrian company, Vöslauer Mineralwasser AG, showcased a special version of its 1l PET bottle for sparkling mineral water in a promotional campaign timed to coincide with a fashion fair. The unusual shape, light blue tinted bottle sports an all-round paper label which is printed so as to resemble a belt. Featured as a closure is an easy to hold tamperproof screw cap that makes for easy opening. www.voeslauer.com Special edition drinks The drinks industry is constantly developing and producing new variations on the theme of taste in what are sometimes compositions featuring an exotic appeal. These beverages, which are marketed as limited or special editions and subject to restrictions in terms of time or quantity are calculated to awaken the curiosity of the consumers and entice them to buy. Current examples of this are the well-known 1.5l PET bottle from Volvic in lime and coconut flavour and the Pfanner Ice Tea with strawberry and vanilla flavour in the waisted, 1.5l PET bottle with the shrink sleeve label stretched over the top half of the bottle and sporting coordinating printing. www.pfanner.com www.volvic.de Sports drink To support a balanced diet, performance sportsmen and –women need additional protein. Under the brand name of “Champs Sportsline“, Aktivkost GmbH of Hamburg are marketing a chocolate flavoured high protein drink with a 55g milk protein content. The product is intended to promote physical regeneration after sport. The fat- and gluten-free product is packaged in a waisted PET bottle with a 500ml content. A shrink-wrap sleeve label and a blue screw cap round off the presentation at the POS. www.champ-sportsline.de “Functional“ drink Packaged in a 500ml PET bottle are 500ml of “ganicwater” - a lowcalorie soft drink – available in plum flavour, with additional vitamins and health-promoting additives such as Aloe Vera and Taiga Root. The bottle containing the slightly tinted product features a paper body label, a transparent screw cap with tamperproof seal, reinforcing grooves and an embossed seal incorporating the brand logo. www.ganicwater.com","@ID":47} "REGIONAL MARKET REPORTS 17 PETplanet insider Vol. 13 No. 09/12 www.petpla.net waste recycling, energy saving, water saving, heat insulation, use of recycled material) – thus being an asset in terms of Sidel’s image in the country. Products and production Universal blowers are assembled using a conveyor assembly facility, the compact blowers on trolleys in three stations, likewise on an assembly line. A just-in-time approach is used for the placement of materials and subgroups on the assembly stands. For final assembly of the combis, blowers and fillers are put together, integrated and tested at specially created locations. While we were there, four combis were undergoing a test run. “At some stage“ – says Laurent Bousselet – “when the production processes have stabilised and become a routine operation, and once our employees have been trained to the desired and required level, we will assemble blowers and fillers at the end customer’s premises and in this way create more capacity at the Beijing plant“. Under the same massive roof in one and the same factory tools for the installations are manufactured as well as conveyor systems. The manufacture of steel components from stainless steel is currently (March) being set up. Since October 2008, more than 250pcs of equipment comprising the following have been manufactured in Beijing (Sidel figures): SBO universal blow moulder (large capacities) SBO compact blow moulders (small bph, small cavities, large bottles) CSD filler Aseptic filler Combi machines and equipment such as conveyors and other standalone equipment The SBO compact blowers are based on the former Malaysian design and are manufactured using locally sourced Chinese components. Also for the remainder of Sidel products, in particular for the classic and traditional SBO universal blower, a process of localisation and personnel training was initiated resulting in local content continually increasing. Laurent Bousselet – Product Supply Manager of the Beijing plant said: “There should be no difference either in the specifications or in the quality of a Sidel machine whether made in Europe or in China.” Our References In Shanghai we are talking to Marilyn Chua, for four years Communications Director of Sidel for Greater China Zone Market Operation. Marilyn Chua has been doing the job since the foundation stone was laid for the new Sidel factory in Beijing. She has been in charge of the project since 2008 and was, and Lead Sponsor www.petnology.com Conference Organiser PETnology/tecPET GmbH P.O. Box 120 429 D-93026 Regensburg, Germany Phone: +49 941 870 23 74 Fax: +49 941 870 23 73 [email protected] Get ahead with PET: versatile, sustainable and flexible November 12-13, 2012 Nuremberg Congress Center Nuremberg (CCN East) Prior to Brau Beviale 15th Strategy and Technology Conference for the PET Packaging Industry More Information PETnology Europe 2012:","@ID":19} "We met Dimo Golev, Production Manager Preforms Sector, Lidija Velcheva, Assistant Zdravko Kormevski, responsible for the production of plastic parts for industry and household equipment Gotmar was established in 1992, quite close to its present location at Saedinenie. The company moved here for reasons of expansion. Looking at what is actually a showroom and a meeting room at the same time, you will quickly realise that Gotmar is an absolute all-rounder when it comes to matters of plastics processing. “The Bulgarian market is something really special in relation to the demand for packaging“, explains Mr. Golev, glancing in the direction of the array of glass display cases with their product samples. In addition to the production of practically any bottle format you can possibly imagine, the company also goes in for the manufacture of high quality preforms and caps for a wide range of sectors, as well as water, CSD/ non-CSD, dairy products, beer and spirits, plus nonfood, such as e.g. cosmetics packaging, cosmetics jars and containers. And, as if that wasn’t enough: other departments at Gotmar are engaged in the precision manufacture of moulds for packaging and technical plastic components as well as manufacturing the technical plastic components themselves e.g. micro parts for electronic switches or large parts for (e.g.) refrigerators using materials such as PS, PA 6 and PA 66, ABS, SAN, TPE, PP and HDPE. Gotmar’s launch in 1992 began with the production of edible oil in PVC and PVC bottles. With the move and the 1997 expansion, the company added other departments to its existing portfolio. In 1998 PET preform production (in those days still on a machine from a Chinese manufacturer), the manufacture of bottles for household and cleaning preparations in 2002 and, in 2005, the division for manufacturing engineering components for well-known manufacturers like ABB, Liebherr, Schneider Electric etc. Innovation, taking into account cost structures, has been a guiding principle for Gotmar right from the beginning. In 2000 Gotmar was the first supplier in Bulgaria to produce 5l bottles from a preform that was, in those days, of a similar size. In 2002 the company developed a method for reducing the weight of the bottom section of preforms whilst retaining existing stability and quality levels. In the PET sector the company has today arrived at a manufacturing bandwidth featuring 5g to 670g preforms and manufactures 0.025l bottles for the hotel sector right through to 19l containers. Similarly impressive is Gotmar‘s array of machines, consisting of global players such as Netstal, Biraghi, Engel and Krupp. In preform manufacture, tools from Hofstetter and Sipa are used. Around","@ID":37} "REGIONAL MARKET REPORTS 15 PETplanet insider Vol. 13 “Proximity to customers, reduced lead times, speed to the market, localisation of product and fully trained personnel.” We met at Sidel Shanghai: Marilyn Chua,Communications Director Lenny Xuan, Design & Development Manager We met at Sidel in Beijing: Laurent Bousselet, Product Supply Manager Marilyn Chua, Communications Director Population of Sidel equipment in China Sidel in China is a long and successful story with more than 2,000 machines installed in China (Sidel count 03/2012), including blow moulding machines, fillers, labellers, conveyors and end-of-line, etc. It is well-known that the market trend as regards to blowing and bottling activities is moving in the direction of combination machines. Approx. 200 Sidel blowers and fillers are installed and running jointly in block combi lines. Organisation As a result of production activities in Beijing, staffing levels have more than doubled since our last visit in 2006. In Shanghai: Shanghai mouldshop with 120 blue- and white-collar workers. In Beijing: Beijing multi-product plant with 400 blue- and white-collar workers. Added to this is the company’s presence in Hongkong and on Taiwan. Manufacturing in Shanghai Here in Shanghai mould manufacturing starts with the development of the local bottle based on the characteristics of Chinese products. Laurent Bousselet at the Sidel Beijing plant","@ID":17} "REGIONAL MARKET REPORTS 11 PETplanet insider Vol. 13 No. 09/12 www.petpla.net the trend for brand owners to incorporate blowmoulding PET bottles into their production lines and, now, to start taking responsibility for the injection moulding of preforms in-house as well. As a consequence, the converters, having first lost the business of supplying the bottles, are now also potentially losing a piece of their preform supply business – to their own customers. An estimated 70% of mould cavities are today in the hands of the brand owners and only 30% are still with the converters. The fact that these converters are still not complaining is due to the phenomenal growth in the beverages market. We put some questions to Arthur Liu: PETplanet: How are you coming to terms with the migration of your core business? Arthur Liu: The Chinese beverage market is driven by huge volume but low margins. As a company specialised in packaging solutions, we have to adapt and change. We have a strategic phased plan that we follow – in several phases. Our target is to transform the business from a production-based model to one where we focus on creating value and bringing customised services to our customers. PETplanet: Could you explain what you mean by this transformation? Arthur Liu: Looking back at the development of the beverage industry in the last few years, we can summarise them in three phases. In order to remain competitive, we have to continually adapt our business model and adjust our strategy. PETplanet: Phase 1 (before 2005) Arthur Liu: Before 2005, the beverage industry value chain was conventionally a buyer-seller relationship. Supplying good quality products with a competitive pricing strategy was key to gaining more market share. During this time, we established one of the earliest ‘inline’ production models with our customers. Over the years, we successfully helped customers to reduce their logistics cost, improve product safety whilst continually raising the bar for our own operations. But no business model is sustainable forever (buy and sell is out). With the growing competitiveness of the market and the pressure to reduce cost, we need to re-invent our business model. Husky machinery at the Zi Jiang plant PETplanet: Phase 2 (2005 to 2010) Arthur Liu: From 2005 to 2010, the Chinese beverage market was growing at more than 25% annually. International players such as Coca-Cola and Pepsico were aggressively expanding their China operations and this brought about increased demands on cost optimisation. By end 2005, Coca-Cola BIG acquired bottler Kerry Beverages, and bought their first blow moulding machine F.l..: Wolfgang von Schroeter, Liu Tie Feng and Wang ZhenHui","@ID":13} "BOTTLES 47 PETplanet insider Vol. 13 No. 09/12 www.petpla.net bottle finish PCO1881 for HR neck PCO1810 neck O1 neck finish neck bottle finish PCO1881 for HR neck GDXL Bio-dishwashing liquid in PET 500ml dishwashing liquid scented with apple blossom and manufactured using sustainable raw materials is being sold by the Müller drugstore chain, packaged in a green PET bottle under the brand name ”Bio Blink“. A screw-on, green hinged lid with an opening for dispensing the product makes for easier handling and an all-round plastic label gives details relating both to the product and the quantities in which it is to be dispensed. www.mueller-blink.de Foot deodorant Under the brand name Laboratoires Mercurochrome, the French company Laboratoires Juva Santé is selling a 150ml content freshness spray to combat foot odour in a transparent PET bottle with a translucent spray device. Plastic labels to front and rear convey the retail information and a matching coloured cap protects the sprayer against faulty operation. www.mercurochrome.fr Nurturing soap with Ginkgo 300ml of nurturing soap with Gingko and extracts of olive (brand name “natuderm botanics“) is being marketed by the German company Mann & Schröder GmbH in a clear PET bottle complete with screw-on pump dispenser. The transparent pump dispenser features a rotating interlock and enables an optimum view of the flow of product during the dispensing operation. A decorative feature of the packaging is a matching shrink sleeve label. www.natuderm-botanics.de","@ID":49} "EDITOUR REPORTS 37 PETplanet insider Vol. 13 No. 09/12 www.petpla.net Don’t call it hopper. Auxiliary equipment for plastics processing. This is your hopper internal material flow, don’t worry, we’ve got the solution. Conventional Drying system 7EV The hopper has become a machine, it is able to control the process according to the result to be obtained. Now we know what happens inside the hopper and we have improved the material flow inside it, fixing the exact treatment time for a polymer. 7 patents for unlimited advantages: the choice is yours. Original Turbo eXchanger www.moretto.com MATERIAL FLOW designed by Moretto HALL 7A STAND 519 Bericap Romania Double digit growth We met: Tiberiu Bako, Managing Director Bericap Romania is just four years old. The company is a 100% -owned subsidiary of Bericap Hungary. As a birthday present to the new company, Bericap Hungary also made it a gift of the customers located in Romania. This marked the launch of Bericap’s latest baby in 2008. Since then it has also been successful in acquiring some new customers in the country, although there continues to be an absence of one major brand or another. “The major brands award their contracts over several years which means that it is only now, because we are locally placed, that we are really in a position to offer competitive tenders along with the others. Multinational soft drink bottlers and beer producer are already in portfolio.” says Managing Director Tiberiu Bako. Despite the company being in its infancy, Bericap Romania already has a leading market share under its belt for edible oil closures and a significant market share for water and CSD caps. Plus, where beer is concerned, the company has also worked hard to acquire a respectable share of the market. Starbev, URBB and Albacher are some examples. Due to the global presence of Bericap the national company can also offer closures sourced from the remaining locations. As far as this is concerned, a particular feature in Romania is the engine oil caps. Although the market for beverages is slightly depressed in Romania, the plant has succeeded in recording strong double digit growth rates every year. Because of the high market shares already achieved to date, it may be anticipated that this growth will slow down. In any event, the connections for further machines are already in situ in the machine hall. In January two moulds for the lightweight 1881 closure have been arrived. The contracts have already been negotiated so the Romanian market will soon be getting its first glimpse of lightweight bottling. As a special service, Bericap maintains an on-site advice and consultancy through its technical service team for its customers, if they wish to switch to the 1881. Since the introduction of the PCO 1881 neck and the Bericap DoubleSeal SuperShorty closure range more than 120 lines have been converted globally by the Bericap Technical Service to the advantage and satisfaction of the customers. www.bericap.com The Editourmobil in the land of Count Dracula, here against the backdrop of the Bericap Romania Plant","@ID":39} "REGIONAL MARKET REPORTS 18 PETplanet insider Vol. 13 No. 09/12 www.petpla.net still is, responsible for the company’s public image – something which she does very well. Laurent Bousselet, the Product Supply Manager for the past 18 months is an experienced and perceptive manager. Laurent Bousselet gave us a comprehensive presentation of Sidel’s Beijing Plant – all the way from initial concept to today’s reality. He took us through the production side, explaining procedures expertly. We were impressed with his professionalism as well as his sensitivity towards the situation in China, to the mindset of the employees and the fact that the patience and perseverance are necessary for implementing European goals and ideas. His knowledge of manufacturing is at the same high level as his motivation. Husky Injection Moulding Systems, Shanghai F.l.t.r.:John Zhang, Lesley Chen and Joe Man “Make sure your customer is profitable. We met: Joe Man, Consultant, Beverage Packaging Asia Pacific John Zhang, General Manager China South PET&Packaging, Huksy Injection Molding Systems (Shanghai) Lesley Shen, Communication Manager Husky (Injection Molding Systems (Shanghai) Impressions Outside: Green open park land, a large pond with fish and waterfall, a place to relax, overlooking the campus are large buildings with facades of clean concrete, glass and dark coloured windows. Inside: Widely spaced open offices, with people in visual contact, provided they are not otherwise engaged or occupied by their computer, a large cafeteria, a softly furnished breakout room for brainstorming and innovative ideas, on the walls photographs of Canadian Aboriginal Peoples, landscapes in autumn, bears, both polar and grizzly. No doubt, you have entered Husky territory, recognisable all over the world, including here in Shanghai. Our visit marked a return to Husky after 6 years. The Shanghai Technical Center has developed into a well organised, mature manufacturing location to assemble Husky injection moulding machines - located still on the same site within the Shanghai bonded, tax free, industrialised area. A view of the Husky Shanghai Technical Center Products All Husky products for beverage packaging, thinwall packaging, and for making caps and closures, medical and consumer electronics – are assembled in the Shanghai plant. This includes the complete suite of Husky systems ranging from the HyPET, HyCAP, HyPAC and base Hylectric systems, to the integration of the all-electric line that includes H-PET AE and H-MED AE. Husky places importance on the statement: All Husky machine products are made from globally sourced components. All components are identical whether assembled in Bolton, Canada or Shanghai, China. According to Husky the Shanghai location is capable of producing several hundred systems annually. In addition, Husky also manufactures hot runners locally to provide reduced lead times to the Asia market. Outside of the industrialised zone in a separate specialised facility, Husky refurbishes and in particular converts moulds, for PET preforms – an activity which has grown into a very good business due to the trends towards lightweighting. Market presence In the Chinese market of today more cavities are supplied to brand owners rather than to converters in China: According to PETplanet’s estimates, the overall market consists of 70% to brand owners, 30% to converters. And the percentage shift from converters to brand owners continues – a factor which we had already noted when visiting Zi Jiang. We estimated the general population of PET systems in China to be as high as 520 to 560 systems. We also estimate Husky’s market share amounts to approximately 80% of systems in China. Annual addition of systems is solely for the expansion of PET markets. By contrast, replacement of PET systems is practically unheard of. Brand owners normally do not replace","@ID":20} "EDITOURS REPORTS 36 PETplanet insider Vol. 13 No. 09/12 www.petpla.net 40% of Gotmar’s products are supplied to the bottler Nova Trade, located on the same site, with the remaining 60% being spread over both inland and foreign customers such as (e.g.) countries of the former Yugoslavia, Greece and Turkey. As far as the future is concerned, according to Mr. Golev, the company is targeting a new lightweight preform which will mean considerable cost savings as far as the customer is concerned. And, otherwise, Gotmar intends to remain true to its precept: it is the customer who comes up with the idea, Gotmar transforms it into a product. www.gotmar.com Index-6 Perpetual motion Dimitar Spasov on the stairs in front of the Index-6 Slogan We met: Petar Spasov, CEO Dimitar Spasov, Project Manager I have been invited to the town of Plovdiv for Machine maker Index-6. CEO Mr. Petar Spasov who escorts me into a large conference room where, a short time later, I am introduced to Mr. Dimitar Spasov in his capacity as Project Manager. Later that afternoon I get to know a great deal about this family operation which has experienced tremendous growth. Since its establishment in 1990 it has been a trailblazer in a number of areas, both in the machine building sector and in matters relating to sustained corporate development, evidence of which is forthcoming in the shape of various ISO certifications of Quality Management, integrated Management System and environmental protection. A high level of commitment to health and safety at work plays a significant part. For this reason the Index-6 motto “Always in Motion“ is, if anything, more than appropriate. Mr. Dimitar Spasov applies this maxim not only to the company but also to the machines themselves. Index-6 has specialised in the production of complete filling and closure lines right through to the labelling line, the PET sector playing a decisive role here, not only for beverages and food but also for non-food items. With six employees and starting with the design and manufacture of machines for the preserves industry, Index-6 has, in the meantime, built up a workforce of more than 180 employees and occupies factory premises with an area of around 20,000m2. On my way around the premises it is immediately clear that the team demonstrates a clear commitment and that the staff enjoy their work, something which is also an integral part of the company philosophy, i.e. happy, motivated employees. At Index-6 they do a lot to promote this, for example by taking suggestions for improvements on board and they give due credit to the staff and reward achievements. I find myself in front of CNC machines, tools of every sort and am totally fascinated by a large Lasermax cutting machine which has been subsidised by the EU and which is capable of cutting steel up to a maximum thickness of 15mm. Later I am shown into a kind of oversized showroom, a production hall in which some of the production lines are set up for both testing and display purposes. Dimitar Spasov tells me that Index-6 focuses mainly on export, this is where 90% of the company’s workload lies. And, as a result of Bulgaria’s admission to the EU in 2007, extra time savings are possible as regards the handling of import and export procedures for machine parts. Glimpse of Index-6 Showroom When I subsequently catch sight of a world map sporting pennants, I am unsurprised by the fact that, out of the exported machines, a considerable number go outside Europe and, while I am still inspecting the markings, I am proudly informed of a plant that is currently being installed in Bangalore. It is the company’s first line in India and will doubtless not be the last. What really makes a striking impression is all that has happened here since the sale of the first machine to Turkey over 15 years ago and the story continues. Since then Index-6 has gone on to be represented in 32 countries. The company’s vision of its corporate future envisages consistently very high machine quality and sustainability, as well as healthy growth and a continuous increase in efficiency. The Spasovs are paying particular attention to the promotion of an extremely high quality yet nevertheless well-priced ultra-clean line. True to their motto: “Always in motion“. www.index-6.com","@ID":38} "REGIONAL MARKET REPORTS 13 PETplanet insider Vol. 13 No. 09/12 www.petpla.net kronesFlexiFruit – doses fruit chunks as if they’re hand-picked. www.krones.com PACK EXPO 2012 Chicago, October 28th – 31st South Hall, Booth 2466 Leveraging on new technologies, beverage producers were able to increase efficiencies, reduce energy consumption while staying competitive. Quite frankly, we were trying to come to terms with the way the market had evolved during this phase. We believe that the Combi works well for running high volume productions for a single product. However, for lower volumes and multi-product line, the demands on customisation are high. That is why at Zi Jiang, we focus on creating value for our customer through technological development, innovations, developing key competences, etc, in order to help customers generate higher returns. Products of Zi Jiang In 2011 200,000t of PET resin converted Total output over 6.5 bn preforms, of which 5 bn are blown into bottles and 1.5 bn are supplied as preforms Target for 2012 – irrespective of trends and strategy - Total output: more than 7.3 bn preforms Clientele As a key supplier to the beverage packaging industry, Zi Jiang supplies to major brands such as Pepsi, Coca Cola, Uni-President, Danone, Nestlé, C’est Bon, etc. Out of Pepsi’s 24 bottling plants in China, Zi Jiang has placed their in-house equipment in twelve Pepsi plants. New customers, new applications, new commodities are Zi Jiang’s prime targets. A significant breakthrough was recently achieved with an order for non-beverage packages, i.e. 12,000bph for 1.9l of soya sauce. The technology was developed jointly and in cooperation with the local Sidel packaging team. Equipment installed in all plants Husky injection moulding systems: more than 70 systems; most of them 96 cavities; latest models with 144 cavities. Sidel blow moulding machines: more than 70 units; the biggest for 52.000bph. Production of Zi Jiang Zi Jiang produces in more than 30 factories geographically spread across China. In order to drive customer proximity and reduce logistics costs, all preform production is centralised in Zijiang’s Shanghai plant, Arthur Liu says:","@ID":15} "PREFORM PRODUCTION 38 PETplanet insider Vol. 13 No. 09/12 www.petpla.net New ways to new beverage concepts at drinktec 2013 The taste of nature New beverage concepts The Special Area is a separately designated and designed area located in the exhibition section featuring raw materials, additives and agents. Beneo, manufacturer of functional ingredients, will be demonstrating ideas for a better balance in energyboosting products: “Consumers are increasingly focusing on drinks concepts that release a steady supply of energy, avoiding the so-called ‘boost and crash’ effect. It is ingredients like ginseng or Palatinose (Isomaltulose) that rate highest on this criterion, as they are natural products that also offer nutritional benefits,” explains Jens Böhm, Marketing Manager for Beneo. The area has its own catering area enabling on the spot sampling of innovative drinks. Sweet = Good A good taste has always been the supreme imperative governing the development of beverages and liquid foods. But what exactly do we mean by ‘tastes good’, or indeed by the word ‘taste’ itself? The tongue can distinguish precisely five types of taste: sweet, sour, bitter, salty and satisfyingly meaty. Everything else about ‘taste’ comes from the eyes and the nose, which are incomparably more sensitive. All these sense impressions trigger emotions or memories, which our brain processes into an overall judgment. It’s because of the emotions that taste becomes a complex matter after all. For example, ‘sweet’ stands for ‘good’, and probably has done ever since our primeval forebears came out of East Africa. Sweet foodstuffs thus almost automatically trigger that “I like it” response, deep inside us. However, partly as a result of changing consumer lifestyles, new requirements keep emerging, as do new concerns motivating alternative approaches. These concerns come with category labels such as obesity, dental health, diabetes, glycaemic index or ‘natural’. These subcategories represented in Hall B1 range from calorie-free sweeteners through natural and almost blood sugar-neutral substitutes for sugar, special sugar combinations for sports use and classics like sucrose all the way to brand-new alternatives. The EU approval of steviol glycosides as a food additive (E 960) first and foremost enables the sweetening of drinks using new concepts based on stevia. Obtained from the leaves of a plant named stevia rebaudiana, steviol glycosides are up to 300 times sweeter than sugar, and calorie-free. At drinktec 2013, taking place at Munich´s trade fair centre from September 16 to 20, 2013, there will be a special exhibition area dedicated to New Beverage Concepts: the “Special Area New Beverage Concepts” in Hall B1 drinktec in cooperation with Dr. Harnisch International Publications, Nuremberg. We would now like to take a look at some of the trends that may feature as far as the flavours and beverage ingredients are concerned.","@ID":40} "BOTTLE MAKING 22 PETplanet insider Vol. 13 No. 09/12 www.petpla.net Siapi and Sidel launch multi-layer stacking systems for PET bottles Stack, rack and roll While PET has continued to demonstrate many advantages over other packaging materials for some time and in a number of applications, one area that has found the material at a disadvantage against its traditional competitors has been stacking. Heavier and more rigid materials tended to have the advantage but that may be changing, with the simultaneous launches of stacking systems by Sidel and Siapi. The two businesses have developed solutions aimed at different markets but claim similar benefits, including convenience, improved environmental performance and reduced CO 2 emissions. Stack & Pack In the mid-size category, Sidel says that its stackable bottle concept, Stack & Pack, is the first stacking solution of its kind for bottle capacities from 250ml up to 1l. A deeperthan-usual concave indentation at the base of each bottle enables efficient stacking. The neck of the bottle below fits into the base of that above, which reduces the required amount of stacking space and eliminating the need for interlayers. Once the bottle is filled and capped, a stretch sleeve is wrapped around to form a pack of six bottles. The stack can rise to ten layers, rather than six, and increases the number of bottles that can be fitted onto a standard Europallet by 40%. Stack & Pack is claimed to be suitable for sensitive products like juices and liquid dairy products. Sidel says that the commercial advantages include elimination of interlayers, which cuts immediate costs and reduces waste; optimisation of storage space; less shelf restocking; and fewer pallets for the same volume of bottles. The reduction of blowing pressure using the stroke base solution during production offers the potential for energy savings, as well as eliminating crushed bottlenecks. Sidel says that the technology is now in operation at its production facility and ready for field tests at customers’ plants. www.sidel.com Stack Lock Siapi has introduced a line of stackable containers with capacities of 10, 16 and 20l, with the brand name Stack Lock. The company initially developed them for the North European market but they have attracted interest from Central and North America as well. Containers of this size are used primarily in the foodoil sector, as well as in the chemical industry. The company recently converted a container for environmentally friendly fuel from HDPE to PET, which is claimed to have achieved a reduction of 50% of the original weight. The specially-designed container has a handle inserted into the neck and is stackable up to four layers. The weight reduction and strength of the material offer the potential to achieve lower-impact environmental solutions, including reduction of CO 2 emissions during road transport. www.siapi.it Stack & Pack is the brand name forSidel’s stackable bottle concept for 250ml to 1l Siapi’s stackable container with capacities of 10, 16 an 20l is named Stack Lock","@ID":24} "REGIONAL MARKET REPORTS 10 PETplanet insider Vol. 13 No. 09/12 www.petpla.net China The second part of our Regional Market Report on China is dedicated to the interviews with Zi Jiang, Sidel and Husky. We met: (Arthur) Liu Tie Feng, Zi Jiang Enterprise Group Container Packaging Unit General Manager Wang ZhenHui, Zi Jiang Enterprise Group Container Packaging Unit Technical Director Sun Bin , Zijiang Enterprise Group Container Packaging Unit Technical Centre Manager Together with Marilyn Chua, Communications Director of Sidel Visit to Zi Jiang and discussions represent the status of our visit in March 2012: Zijiang Enterprise is one of the largest manufacturers of PET packages in China and can look back on turbulent times in terms of its development over the last several years. The annual growth in the number of PET preforms and PET bottles and the resultant explosion in sales, in each case of the order of double digit growth, must surely be a source of elation and satisfaction for the people responsible. Not necessarily, in the view of General Manager Arthur Liu of Zi Jiang, who – although outwardly confident and delighted about what has been achieved – nevertheless does not shy away from the problem that is worrying all converters in the big markets. This has been caused by Zi Jiang Enterprise Group “No business model is sustainable forever. You need to re-invent your business continuously.” Liu Tie Feng, Zi Jiang Enterprise Group Container Packaging Unit General Manager by Wolfgang von Schroeter Regional market reports China Part 2","@ID":12} "REGIONAL MARKET REPORTS 19 PETplanet insider Vol. 13 No. 09/12 www.petpla.net In issues 10 and 11 you can read interviews with issue 10: KHS, KraussMaffei and Netstal, Yinglu , SOE issue 11: Krones, Sipa, Wahaha, Bericap CCT Creative Competence Technology GmbH Idsteiner Strasse 74 D-65527 Niedernhausen, Germany [email protected] www.cct-systems.com PET Molds Closure Molds Developments PET Systems Closure Systems ComPETCap® Designs powered by CCTSystems ® for further information please contact us Design and Patents CCTSystems®3025 for still water CCTSystems®1810 for CSD (carbonated soft drinks) current design CCT design 5,05g 4,10g 3,92g 3,05g current design CCT design old systems with new systems. They often have a sentimental attachment to their early investments. Converters would be more conscious of cost, more sensitive to fluctuations, more flexible. Referring to the latter converters, John Zhang – Husky’s Sales General Manager - maintains: “Make sure your customer is profitable. He loves you for the highest quality, lowest cost preform.” The major Chinese converters as well as the big brand owners are on Husky’s customer list. Organisation Husky has more than 900 team members in Asia Pacific. According to Joe Man, whom we had met six years ago: “We have built upon what you saw six years ago, when PETplanet visited, but doing more and better”. The manufacturing area is convincing proof of the statement. Manufacturing The amazing, eye-catching part of Husky Shanghai is the manufacturing area – with 13 clearly defined areas for final assembly and acceptance testing plus three more areas, where injection moulding machines are customised, integrated with complementary equipment, tested, and completed. Husky began manufacturing at this location in 2006. Strategy Despite their industry-leading position in global markets “Husky has always strived to develop innovative technology to help customers to be more profitable and grow their businesses. This is in large part due to the collective work of Husky’s strong team” (Husky claim). Customer satisfaction remains the ultimate target to be achieved. John Zhang – 17 years with Husky – started in Bolton as commercial manager, was assigned in 1998 to China for Sales Beverage & Packaging China South. John Zhang sums it up: “A local presence together with a complete system approach, combined with the size and scale of the operation, and of course, including the dedication of all Husky personnel, all are essential if we are to satisfy customer requirements. This is why customers continue to work with us. We have everything the customer needs – we are geographically close to them, we understand their culture and their requirements, we provide support in after sales and training for the entire system, and we do prototyping.” Joe Man adds: “And by assembling injection moulding systems in Shanghai, manufacturing hot runners in Shanghai, as well as refurbishing and converting moulds in Shanghai, we have indeed increased our speed to market.” Seniority, experience and respect for the wisdom of their elders are generally appreciated in this part of the world – more than in Western societies. Joe Man is a living example – being loved and honoured by his former team and by his clients. Joe Man was Vice President Asia Pacific until January 2012 and still occasionally acts as a consultant to the China, as well as the Asia Pacific operations. As active as ever, he was, still is and remains the well-known face of Husky in the market he knows best.","@ID":21} "46 PETplanet insider Vol. 13 No. 09/12 www.petpla.net PETbottles Home + Personal Care Maag Group is the innovative solution provider for pump, pelletizing and filtration systems. We deliver high-quality components and complete systems, from extruder tips to pelletizers. In addition to our primary locations in Switzerland and Germany, we have eight sales and service offices around the globe to provide our customers with full service par excellence. Automatik Plastics Machinery GmbH Ostring 19 ß 63762 Grossostheim ß Germany ßT +49 6026 503 0 ß [email protected] brands of maag group Maag Pump Systems AG Aspstrasse 12ß8154 Oberglatt ßSwitzerlandßT +41 44 278 82 00ß[email protected] www.maag.com Exotic shower gel Palmolive are expanding their range of shower gels by a variation with more exotic appeal. The shower gel, scented with Indian mulberry and lotus flower, is offered to the consumer in a waisted, tear-drop shaped PET bottle containing 250ml of product. The tinted product, the two-tone closure and the multi-lingual label design lend the package just the right look. www.palmolive.com Scent of spring Products scented according to the season are an effective way of increasing sales. One example is the spring edition of Pril washing up liquid which is scented with magnolia and apple blossom. By way of a container for the slightly purplish-coloured product, the well-known, transparent 600ml PET bottle with its shiny silver push-pull dispensing cap is used. A non-label look label on the front and a paper label at the back take care of the retail information. www.pril.de Dishwashing liquid in moulded PET bottle Under its own-label Auchan brand, the French chain Auchan is selling dishwashing liquid with grapefruit and vinegar additives packaged in a 500ml PET bottle which, despite its original shape, is still user-friendly in terms of handling. With a bit of imagination, the shape of the bottle resembles the bird in the lettering which makes up the brand name. A push-pull device, coloured pink, matches the colour of the slightly tinted product. The bottle features just one label on the front incorporating additional information on the inside. The back of the bottle has only a barcode label. www.auchan.fr","@ID":48} "NEWS 7 PETplanet insider Vol. 13 No. 09/12 www.petpla.net stretch-blow moulding and filling machines shrinkwrappers wrap-around casepackers conveyor systems palletisers PET collection rates up Petcore and EuPR have announced that European post-sorting PET collection reached 1.59 million tonnes in 2011, an increase of 140kt (9.4%) over 2010 and a record of 51% of all PET bottles in the market. Total mechanical reclamation capacity in the EU27+4 countries is estimated at around 1.9 million tonnes. Growth in collection across the EU27 is stable at 2%. Collection rates of over 70% are being recorded by about a third of the countries surveyed and all but three have a collection rate above the 22.5% target rate for plastic recovery set by the Packaging Waste Directive. More than 50% of the rPET produced in 2011 was used to make containers or sheet for new packaging applications. The 2011 share of fibres as an end use for rPET flake remained at 39%. The strapping market increased to just over 100kt. Net exports of PET bales to the Far East fell, for the third year running. www.petcore.org www.plasticsrecyclers.eu KHS supports Blue Competence initiative KHS GmbH has formally and publicly announced that it supports the VDMA Blue Competence Initiative, a growing European commitment by engineering companies aimed at improving environmental responsibility. The Blue Competence Initiative started in Germany. It covers the entire mechanical engineering industry and is operated by VDMA, the German Engineering Federation, under the slogan ‘Engineering a better world’. The industry has agreed on common principles and procedures which participating companies will follow, in order to achieve reduction of resource and energy use and implement improved management systems for handling waste and recycling, as well as implementation of sustainability principles in its own production. The organisation says that “…Blue Competence defines credible and resilient sustainability criteria and standards that all those who join the initiative must meet”. Among the developments that KHS highlighted in connection with Blue Competence were its new Innofill Glass DRS-ZMS pressure filling system; Innopack Kisters packaging machines; InnoPET Blomax Series IV stretch blow molding machines; and Petainer Kegs. All are claimed to offer reduced energy consumption, increased recyclability, improved material usage, or a combination. www.khs.com","@ID":9} "EDITOUR REPORTS 33 PETplanet insider Vol. 13 No. 09/12 www.petpla.net only include the design and development of PET packaging throughout the entire production process right through to bottling and palletising; often much is offered from a single source, or, in other words, by just one company. This means that it is possible to make a rapid response to changes or requirements. Bottle blowing is carried out by preform manufacturers, they may also create caps and closures, for example, or look after the labelling side. In addition to these possibilities, when it comes to complete solutions, the products created in the various processes can also be marketed separately. And all of this applies both to beverages and food, as well as to beauty and health care. The economy of Bulgaria has taken an interesting turn, especially in the wake of the country’s recent accession to the EU. Quite a few global players have expanded their business relationships with Bulgaria as far as import and export activities are concerned and are contributing to market activity in this region. In terms of beverage consumption, the population’s focus is on CSD and water, both of which are still way ahead of juices, for example. One special feature is that packaging manufacturers do not simply limit themselves to individual aspects of beverage packaging, but instead offer all-round solutions. Here the customer can count on the services of one and the same company, from the emergence of his idea right through to placement of the goods on the supermarket shelf. Consumption on the part of the Bulgarian population unequivocally favours CSD and water. In addition to beer in PET (which is available here in practically every supermarket in up to 3l bottle sizes) the demand for carbonated lemonade and water is relatively high. Of course, natural water without CO 2 also has a role to play, but tends to fall away when it comes to a comparison of consumption trends. The discounter range also offers, in addition to standard size bottles, significant quantities of container bottles with a volumetric content of ten or more litres, predominantly in the water and beer sectors. The specialists in plastic recycling systems. VACUREMA® – PET extrusion technologies Choose the Number One. One of the many display cases in the Gotmar showroom","@ID":35} "BOTTLING / FILLING 31 PETplanet insider Vol. 13 No. 09/12 www.petpla.net Water from the foothills A new SMI SACS (Stella Alpina Cost Saving) line for still and sparkling water at Stella Alpina’s plant in Mojo de’ Calvi, Bergamo, Italy, was devised, designed and created by SMI over a surface area of just 800m2. It produces up to 14,400bph. The new line is made up of just two integrated machine blocks, which enable lower costs and energy consumption. The first block consists of the Ecobloc Plus primary packaging unit, which is an integrated system of stretch-blow moulding, filling / capping and labelling. Downstream equipment comprises a Pack Bloc packaging unit, a shrink-film packaging system that features high levels of integration between the shrinkwrapper and palletiser. This solution has a much smaller footprint than usual, because the number of conveyors connecting them has been reduced. Reduced packaging material The system has reduced both primary and secondary packaging material. PET usage has been reduced by up to 30% with the introduction of new “ultra-light” containers. The 500ml bottle weighs 11g, the 5l version weighs 23g. Savings of up to 50% in thermo-shrinkable film have been achieved by equipping the shrinkwrapping machine with a new knife, which uses with a motorized blade controlled by digital servo-drivers. This allows shrink film with a thickness less than 30 microns to be used, as against the 50-60 micron previously used by Stella Alpina for the 3x2 format of 0.5l bottles. Reduced water and energy use The plant’s cleaning water consumption has been cut by 90% with the application of “baseless” technology to the filler. This allows the base of the machines to be “freed” from moving components and mechanical parts, where dirt and waste from the production process usually accumulates. Energy consumption of the entire production line has been reduced by 15%, through the adoption of a number of measures. The compact footprint of the bottling line requires less conveyor belts for the connection of a low number of single modules; the air recovery system enables a 40% reduction in the use of high pressure compressed air. Heat recovered from the blow moulder and air compression systems is partly used for pre-heating the preforms and partly discharged to the shrinking oven in the end-of-line shrinkwrapper; and lighter preforms and thinner shrink films require less heat from IR lamps and electricallyheated resistances. The number of moving parts has been reduced, the line is made of more resistant materials and high energy-efficiency motors are used on the conveyors. In the end an overall reduction in CO 2 emissions of 50% along the complete line has been achieved. www.smigroup.it SMI SACS line Stella Alpina produces still and sparkling water The Stella Alpina bottle logo PET bottles are packed on trays at the end of the line","@ID":33} "REGIONAL MARKET REPORTS 12 PETplanet insider Vol. 13 No. 09/12 www.petpla.net and injection moulding machines, as part of their efforts in integrating their production operations. At the same time, Wahaha, Ting Hsin were also charting their growth and adopted the business model of in-house manufacturing. This changed the dynamics of the beverage packaging industry. Zi Jiang not only has to be competitive amongst its competitors but also its customers. Leveraging on industry know-how and strong customer relationship, Zi Jiang established both joint-venture (JV) and JV-like business models, partnering with equipment suppliers and downstream suppliers to increase line efficiencies and achieve greater resource optimisation. PETplanet: Please explain what the joint-venture business model is about? Arthur Liu: A JV business model builds on the strong relationship between the stakeholders where both parties establish common interests such as return on investment, cost optimisation, etc. However, this form of strategic alliance has its limitations due to the nature of the long term equity investment. Zijiang then developed a JV-like business model and a deal was made with Swire under this arrangement. The basis of the JV-like formula is that both partners each make a separate investment – Zi Jiang, for example, in equipment for injection moulding and blow moulding in-house - and receive an agreed fixed amount by way of a return on investment. The costs incurred are separately recorded (open book) and split between the partners according to their investments. The commercial risk is jointly borne by the partners. In 2010, Zijiang was awarded ‘Coca-Cola best supplier’ for our outstanding efforts in creating value for Coca-Cola using this JV-like formula. Zi Jiang and Swire (Coca-Cola holding) currently have two JV-like partnerships which have been in operation for the last five years: Zheng Zhou plant: 200 million bpa; in-house: two blow moulding machines and two injection moulding systems Hanghou plant: 300 million bpa; in-house: two blow moulding and one injection moulding system. Zi Jiang is now working on adopting the same approach for Cofco, CCCIL and other customers. PETplanet: Five years from now, how do you think the beverage industry value chain will evolve? Arthur Liu: The rapid growth of China’s beverage market provides a unique development opportunity for equipment suppliers. When Sidel introduced the Combi (blower-filler-capper) to the Chinese market in 2008, major players such as Coca-Cola, Ting Hsin, Wahaha quickly warmed to it and the Combi soon became a trend in the market. I would categorise the period after 2010 as the Phase 3.","@ID":14} "EDITOUR REPORTS 32 PETplanet insider Vol. 13 No. 09/12 www.petpla.net We finish our Editour report from the Go to Brau Beviale Tour 2011 with the reports about Bulgaria (by Kay Krüger) and a step visit to Bericap Romania (by Alexander Büchler). In November, our Editour reports about the Go to Brau beviale Tour 2012 will start. is not long before you notice that there are hardly any big German companies that are not represented in this area. What does this mean as far as the drinks industry is concerned? Due to a significant reduction in complex bureaucracy, export and import activities in the injection moulding sector, filling lines, capping systems and entire PET product lines are, viewed from a time perspective, unquestionably enjoying some advantages. However, moving on to locally-established bottling companies or PET producers, the Bulgarian drinks market, by contrast to international retail chains or agencies representing major automotive concerns, displays a proprietary tendency. From discussions with a range of different firms it is evident that it is not essential, either in production or in PET processing, to be able to identify THE core market for just one product at any given time. Instead, people mostly approach the issue in a highly flexible and customer-orientated way, spreading their portfolio as wide as possible. The benefits for the customer are wide-ranging. These not Bulgaria Bulgaria’s bounty from a single source The Republic of Bulgaria, which has been a member of the European Union since January 2007, has 7.3 million inhabitants overall in a country occupying a total area of around 111,000km². 85% of these are Bulgarians whilst the remaining 15% is made up of Turks, Russians and Armenians as well as Wallachians and people of Romany origin. As a consequence of Bulgaria’s accession to the EU and the associated availability of subsidies, supply chains have not only undergone streamlining but have also been expanded correspondingly. For instance, mainstream export activities include the export of, for example, foodstuffs and machinery, together with chemical products. On the other hand, the country imports machines and machine components as well as consumer goods. Here the key role is played by Germany– altogether there are more than 5,000 German companies trading with Bulgaria, 1,200 of whom are represented locally; the volume of exports to the Balkans amounts to around €2.3bn whereas imports into Germany account for €1.4bn. Travelling through Bulgaria it Nuremberg Ljubljana Saedinenie Istanbul Yerevan Baku Beograd Novi Sad Subotica Cegled Dulo Selo Mirna Peˇc Radenci Gorica Svetojansk Plovdiv Gaziantep Ingöl Ploiesti Ankara","@ID":34} "PREFORM PRODUCTION 39 PETplanet insider Vol. 13 No. 09/12 www.petpla.net A further interesting option, on which visitors to drinktec can find out more at first hand, is the use of naturally sweet drink bases such as malt extracts or – distinctly more exotic – coconut water. But sweetness isn´t the whole story, as Caroline Sanders, Global Marketing & Communications Director, Tate & Lyle Speciality Food Ingredients, points out: “These days a whole variety of substances can be used or combined with each other to develop sweeteners and other sugar substitutes. As well as the property of sweetness, with sugar-free or sugar-reduced products we have to pay attention not only to the proper of sweetness, but also in particular to the sensory parameter of body/mouth feel.” Colouring from spinach and red cabbage Naturalness is also currently the headline theme dominating the world of flavours and colourings. Examples of well-known natural pigments include chlorophyll and carotene. It has also been found that Spirulina microalgae are a natural source of blue pigment. Other pigmenting extracts again are derived from beetroot, red cabbage, spinach or elderberry. Among natural flavours the trend is to concepts based exclusively on the source fruit or plant from which the aroma takes its name. However, it is worth remembering that, for very good reasons, some flavours do have to be made or harvested from other natural sources. For instance, the entire world harvest of strawberries would be nothing like enough to match the demand for natural flavours produced exclusively from strawberries. Also represented at drinktec will be natural ‘brown’ flavours like toffee, cappuccino, walnut, almond, caramel or nut. These are flavours of particular interest to the milk industry. Naturalness and technology The technological implications of the switchover to natural sourcing for flavours, colourings and key functional ingredients are far-reaching. Certain colours are just not provided by the natural environment, or substances used may prove less stable in terms of storage life, temperature or pH tolerance. The prerequisite for new developments is thus always a deep resource of specialist knowledge, built up through trial production runs, sensory analyses and, not least, representative keeping-quality tests. “Brilliance of colour, natural sourcing and stability were the objectives driving development of the new red tones from the black carrot,” says Christian Benetka, Senior Product Manager Colours for DöhlerGroup. “The pigmenting concentrates are now superior to other anthocyanin-based colourings in terms of stability. They also contain no sulphur dioxide.” www.drinktec.com","@ID":41} "imprint EDITORIAL PUBLISHER Alexander Büchler, Managing Director HEAD OFFICE heidelberg business media GmbH Häusserstr. 36 69115 Heidelberg, Germany phone: +49(0)6221-65108-0 fax: +49(0)6221-65108-28 [email protected] EDITORIAL Doris Fischer: [email protected] Michael Maruschke Ruari McCallion Ilona Trotter Wolfgang von Schroeter Anthony Withers MEDIA CONSULTANTS Ute Andrä [email protected] Martina Hischmann [email protected] phone: +49(0)6221-65108-0 fax: +49(0)6221-65108-28 France, Italy, Spain, UK Elisabeth Maria Köpke phone: +49(0)6201-878925 fax: +49(0)6201-878926 [email protected] LAYOUT AND PREPRESS Exprim Kommunikationsdesign Matthias Gaumann | www.exprim.de READER SERVICES Kay Krüger [email protected] PRINT Chroma Druck & Verlag GmbH Werkstr. 25 67454 Römerberg Germany WWW www.hbmedia.net | www.petpla.net PETplanet insider ISSN 1438-9459 is published 10 times a year. This publication is sent to qualified subscribers (1-year subscription 149 EUR, 2-year subscription 289 EUR, Young professionals’ subscription 99 EUR. Magazines will be dispatched to you by airmail). Not to be reproduced in any form without permission from the publisher. Note: The fact that product names may not be identified as trade marks is not an indication that such names are not registered trademarks. 3 PETplanet insider Vol. 13 No. 09/12 www.petpla.net As you do the weekly shop, do you ever find your gaze straying to the PET bottles on the shelf? The cap, the label, the size of the bottle and form of presentation all seem to induce a kind of fascination in me. The spell is even more pronounced as you stroll around the aisles of a foreign supermarket, admiring the exotic PET display. And after you return, what impressions will you have brought back? If your holiday involved a plane journey, you may well have spent some time eyeing up the PET bottles in the aircraft, perhaps reflecting on the manufacturing processes that ended with the bottles at 30,000 feet above ground. But have you ever asked yourself what happens to the bottles at the end of the flight? When you touch down, there will still be beverages containers in the trolleys, some of which will still be closed, others already opened and the rest empty. These need to be disposed of. It used to be only the sealed casks that were removed whilst the other containers had to be disposed of as expensive wet waste. LSG Sky Chefs, the catering arm of Lufthansa, has now addressed the problem. In association with a granulator manufacturer from Glandorf, they have developed a system that collects up the bottles and punches holes in them before compressing them slightly. Doing this means that the beverages packaging can be sent for recycling, thus avoiding expensive wet waste disposal. LSG service up to 350 flights, seven days a week. Not only that but the company packs 20,000l of beverages into 1,600 trolleys every day. In order to accommodate the returns, the granulator runs a 2-shift operation. This leaves 500kg of emptied containers and huge quantities of aromatized and sweetened liquids. However, as our magazine is principally addressed to producers we have in this issue also looked at beverage ingedients. The world of aromas and sugars and their processing in syrup and mixed rooms is now a regular part of PETplanet Insider. Yours Alexander Büchler EDITORIAL dear readers, EDITORIAL Right: the trolleys, in the middle the granulator; left the conveyor belt for the unopened faulty products- Emptying residual quantities at LSG Sky Chefs (photo Strautmann)","@ID":5} "at the viscotec open 2012 September 12-13, 2012 World premiere of PET sheet line viscoSHEET Starlinger & Co. Gesellschaft m.b.H.- viscotec - Adsdorf 38, 4113 St. Martin im Mühlkreis, Austria T: +43 7232 3817-0 - [email protected] - www.viscotec.at Food grade without compromise The decontamination of PCR PET for direct food contact reaches the highest level: As an integrated system it fulfills the worldwide strictest new EFSA standard for infants. Flexibility without compromise The conical twin screw extruder allows direct feeding of in-house skeleton or edge trim flakes and virgin/R-PET pellets up to 100% without predrying and guaranteed high iV levels. Thanks to the gravimetric dosing for up to 4 components, production issues during changing the material formulation are a thing of the past and can be done during full production of the line. Due to the short and defined residence time of the material melt in the extruder and the selfcleaning effect of the conical twin screw extruder, color changes are achieved within minutes, leading to an up to now unknown flexibility in production. Quality without compromise A fully integrated detection and documentation system shows failures in the sheet automatically. Parameters like iV or thickness and optical properties of the sheet such as color variation, black spots, fish eyes or holes are detected and documented instantly. Optionally these can be marked on the roll. Health and safety without compromise Despite the high operability and ease of handling, the roll stack and the fully automatic winder are setting new safety standards. In addition to recycled PET flakes, also sheet from recycled HDPE* (FDA LNO) and recycled PP*material for direct food contact can be produced on this line. *LNO is based on special limitations regarding the input material","@ID":25} "Vol.6 PETplanet print PREFORM PRODUCTION 20 PETplanet insider Vol. 13 No. 09/12 www.petpla.net The rapid guide to perfect preforms - part 32 32. Unmelts Troubleshooting guides have suffered in the past from being locked away in offices and not being available to the people that actually need them. Considering the high cost of machine and tools high scrap rates can be a costly proposition eating away at already tight margins. PETplanet’s “Rapid Guide to Perfect Preforms” takes a different approach. It has been written for the people on the floor of injection moulding companies to support their daily work in making the best preforms possible. The product of two industry experts, Rick Unterlander and Ottmar Brandau, it gives concrete advice on 35 of the most common problems in preform manufacture, most illustrated by pictures. From high AA levels to wavy bodies processors can find help when they need it. Read chapter 3” of the guide. Symptom Partially melted or totally unmelted resin pellets in the preform. Cause Unmelted pellets are present in the preform from insufficient melting of the PET resin. Solutions 1. Check dryer for alarms and correct as necessary. A high dewpoint (above –40ºC (–40ºF)) or low inlet resin temperature (should be minimum of 160ºC (320ºF)) may cause extrusion problems and must be rectified. 2. Check for adequate resin drying time in hopper (should be around 4h Table of Contents i........................ About the Authors ii.................................Introduction Chapter 1.............................. AA Level High 2........................ Accordion Preform 3....................... Air hooks / Streaks 4............................... Black Specks 5...................................... Bubbles 6..................................Burn Marks 7...........................Colour Streaking ................................... /Peeling 8..................................Crystallinity 9.................................Drool Marks 10.......................................... Flash 11......................... Gate Depressions 12............................... Gate Peeling 13..................Gate Voids / Pin Holes 14......................... Internal Gate Sink 15................................Internal Sinks at 175ºC (347ºF) and up to 6h at 160ºC (320ºF)) 3. Check all temperature readings and correct if necessary. PET resin should be melted at about 280ºC (536ºF) +/- 10ºC (18ºF). Increase as necessary. 4. Check throughput of plastic in system doesn’t exceed output of extruder screw. The processed kg/ hour of plastic should be below the manufacturers rating of the screw. Contact manufacturer for spec, and if exceeded, raise extruder temperatures and/or increase cycle time to compensate. 5. Check extruder throat cooling isn’t cooling resin pellets too much (should be minimum 160ºC (320ºF) inlet temperature). Restrict cooling as necessary. NOTE: Do not restrict when using colorants that are susceptible to jelling or coagulation. 6. Check extruder back pressure. This must be high enough for adequate mixing and shearing. Typical range is 15 – 20 bar (200 – 300 psi). 7. Check screw rpm. Screw speed may be increased to increase shear and improve melting. 8. Ensure PET resin pellets have not been degraded. This may raise the pellet crystallinity level and raise its melting point. Check with resin manufacturer for testing resin characteristics. 9. Check hardware for worn, damaged or failed components, specifically the resin in-feed line, and the extruder screw. www.petpla.net 16........................................ IV Loss 17............................ Long Gate Nub 18...............................Milky Preform 19............................ Moisture Marks 20................Neck Finish out of Round 21....................... Parting Line Crease 22.................Parting Line Deformation 23......................... Preform Yellowing 24.................................. Short Shots 25.......................................... Sinks 26......................................... Splay 27........................... Stretched Necks 28..................................... Stringing 29......................... Surface Blemishes 30......................... Thread Flow Lines 31........ TSS (Top Sealing Surface) Sink 32.. ...................................... Unmelts 33.................Wall Thickness Variation 34.................................Wavy Body 35.................................. Weld Lines","@ID":22} "REGIONAL MARKET REPORTS 14 PETplanet insider Vol. 13 No. 09/12 www.petpla.net “Assuring the efficiency of plant and equipment is high on the list of priorities and is my personal ambition.” The company is targeting efficiency of 97% for injection moulding and 95% for blow moulding. However, due to customer’s on-site management, utilisation and productivity at present is 85% for injection moulding and the utilisation of annual capacity for blow moulding machines is between 60 and 78%. Arthur Liu further claims: “In order to improve asset turnover rate we need to take several measures: replace older machines to increase productivity, adopt a new,planning module implement just-in-time production reduce inventory.” And returning to his favourite subject: “Europeans should not just consider a market in terms of product delivered. They need to recognise that the Chinese market has grown and matured in the last twenty years. China can also give lectures which Europeans should heed – how to add value to the business and how to grow jointly with your partner – local or international - into a new dimension. 20 years ago the emphasis was on selling production. Today our prime aim is to nurture talent and invest in R&D.” We at PETplanet Insider will certainly be keeping a close eye on developments at Zi Jiang in the years to come. Sidel China Marylin Chua, Marketing & Communications Director Sidel Greater China Zone The Shanghai free trade zone is the location from which Sidel runs part of its Chinese business and produces its moulds. Production and assembly of Sidel products takes place on the site in Beijing. The Shanghai office located within the free trade zone is just a few hundred metres away from Husky’s Center of Competence. Husky has been here since 1997, Sidel since 2004. Both companies have made their mark on China’s PET markets – in the early days, when PET almost exclusively represented a technological challenge – with deliveries from abroad, from far-away Canada and no less distant France. Those times have long gone. The competition has got its act together. The technical performance of the equipment is still important, but elements have been added in the battle for customers, namely commercial performance, on-site service and marketing. Nevertheless, both companies are clearly succeeding in maintaining their extraordinary position in the market. The majority of PET preform systems in the country bear the name of Husky, the majority of PET blow moulding plants come under the Sidel brand. (As regards the block lines for blow moulding / filling of PET bottles, Krones presents the strongest challenge; it is currently building up its order book and is certainly on an equal footing with Sidel). Apart from their strong market position, there is something else that both companies - Husky and Sidel – have in common: Both companies manufacture their PET machines for China and the adjacent Asian Pacific markets in China – with no compromises, in accordance with original designs and without accepting the slightest trade-off in terms of performance and quality compared with the original from abroad. There may well be differences as regards production methods and in terms of manufacturing penetration – as we will see – but once again common to both is the readiness to invest in China, with confidence in the sustainability of the Chinese market. Over and over again on our factory tours, we found ourselves hearing the same or similar statements as regards local Chinese production: “China’s manufacturing industry is currently in the second phase of globalisation. The expansion of international sales is now being followed by the development and expansion of global production”. Or: “China’s industries insist on the most modern technology. That is not possible with yesterday’s machines”. Or: “We are not prepared to compromise when it comes to product quality”. Or: “Customers in Asia expect excellent deliveries and the same service as in Europe”. And, again and again, the high concentration and the commitment of the Chinese workforce in the factories is mentioned – in particular that of the Chinese managers, their capacity for learning and their input as far as operational processes and the internal value chain are concerned. The Chinese – or so it seems – are unaffected by industrial traditions and pioneering achievements. A transfer of know-how in the opposite direction is taking place – in the direction of Europe – something that is likely to be a surprise for many Europeans.","@ID":16} "27 PETplanet insider Vol. 13 No. 09/12 www.petpla.net Conveyors Bottle-to-bottle recycling plants Caps and closures Preform moulds and SBM moulds Preforms Preform and single stage machinery SBM machinery Compressors Filling equipment Resins and additives Suppliers of two-stage SBM machinery This year, our annual market survey includes 16 global suppliers of twostage SBM machinery. In alphabetical order, these are: Amsler Equipment (USA), Beutelspacher (Mexico), Chum Power (Taiwan), Dodhia (India), KHS (Germany), Kosme (Austria), Krones (Germany), Mega Machinery (China), Nissei ASB (Japan), Siapi (Italy), Side (Spain), Sidel (France), Sipa (Italy), Technopet (India), Urola (Spain) and last but not least, Wei Li (China). These companies appear in the market survey in the order in which their details were received by the editors. Although the publishers have made every effort to ensure that the information in this survey is up to date, no claims are made regarding completeness or accuracy. 09/2012 MARKETsurvey Company name Side S.A. Amsler Equipment Inc. Postal address Telephone number Web site address Contact name Function Direct telephone number Fax E-Mail Pol. Ind. Monguit, C/Llinars, s/n 08480 - L'Ametlla del Valles (Barcelona) +34 938463051 www.sidemachines.com Josep Jiménez Global Export Manager +34 677551928 +34 938492211 [email protected] 1245 Reid St., Unit 1 Richmond Hill, Ontario, Canada L4B1G4 +1 905-707-6704 www.amslerequipment.net Heidi Amsler Sales and Marketing Manager +1 905-707-6704 +1 905-707-6707 [email protected] 1. Machine designation / model number Easyblow Maxiblow 1002e/ 2004e/ 2006e 2002e/ 2003e 5001 Maxi-W T-handle 1 / 2 / 3 Linear Series - 9 models Linear Widemouth Jar Series 2 models Linear Convertible Series 4 models Linear Large Format Series 5 models Rotary Series 2 models 2. Bottle volume (from/to in litres) a) Standard machines 0.1 - 2.5 0.1 - 11 0.1 - 2.5 0.1 - 11 1 - 40 0.1 - 11 1-4 0.05 - 5 0.1- 6 0.05 - 5 0.05 - 3 b) Machines for large containers 4 - 23 3. Maximum number of stretch-blow moulds (units) a) Standard machines 1 1 6 3 1 1 3 6 2 16 b) Machines for large containers 6 2 4. Output per stretch-blow mould for: a) 0.5 litres CSD bottle (units / hour) 1,500 1,500 1,500 1,500 1,500 1,500 1,000 1,800 1,800 1,500 b) 1 litre CSD bottle (units / hour) 1,500 1,500 1,500 1,500 1,500 1,500 1,000 1,400 - 1,800 1,400 - 1,800 1,250 - 1,500 c) 1.5 litres still mineral water bottle (units / hour) 1,500 1,500 1,500 1,500 1,500 1,500 1,000 1,400 - 1,800 1,400 - 1,800 1,300 - 1,500 d) Large capacity container 1,500 1,000 1,500 1,000 800 1,000 1,000 900(10l); 275(18.9l) e) Other 800 - 1600 3000(4l) 5. Footprint / space requirement (L x W x H in metres) To be determined. Taylored solutions for small areas. 4.0x1.8x2.4 to 4.3x3.7x2.5 3.9x2.5x2.2 5.7x2.0x2.4 to 4.3x3.7x2.5 3.9x3.8x2.7 2.7x2.2x3.1 to 4.2x3.0x3.2","@ID":29} "CAPPING / CLOSURES 41 PETplanet insider Vol. 13 No. 09/12 www.petpla.net Sustainable technology The elimination of secondary operations to insert or mould a liner results in a simpler, cost effective, robust cap design. The precise operation and control of the hot runner system produces a cap with the barrier only where it is needed. The barrier covers the top of the closure but does not extend into the threads. Tight integration of valve gate function, manifold heating and both injection units creates unprecedented precision and control of the barrier. To ensure that 100% of the caps have barrier all across the bottom an innovative barrier verification system is available to be integrated into the parts handling system. This coordinated design approach allows the closure systems to be optimised for lighter weight, fast cycles, quality and higher function. With the new technology, MoldMasters provides an alternative to multiple injection systems and postinjection application of barrier liners in closures by secondary processing equipment. It also eliminates the need to use thermoformed five- or sevenlayer structures that require tie layers and glues in thin-wall containers. The Iris co-injection system produces a Iris co-injection is achieved via the combination and integration of five key technology elements supplied by MoldMasters: Iris compact co-injection nozzle iFlowmanifold technology that combines melt streams and provides balanced fill E-Drive valve-gate control of the opening and closing movements of the servo-actuated valve-gate pins to achieve fast cycle times and precise cavity fill TempMaster M2 hot runner temperature control Mould mounted E-Multi auxiliary injection unit located close to the gates net-shape part with no web scrap. The advancement represents true simultaneous co-injection, different from sequential injection or multi-material injection. The combination of using the barrier technology with the efficient cooling technology makes it possible to have a greener production line, using less plastic, energy and water. Other typical co-injection application for the Iris technology include thin-wall, deep draw food containers with integrated barrier. Advantages over typical thermoformed thin-walled parts that have foil or label barriers is that with an injection moulded part and EVOH barrier the implementation is offering 30 times the protection against oxygen or other gases. The recyclability of the part is also improved due to elimination of tie layers and the low percentage of barrier (5%). The containers can be deposited into existing higher value recycling waste streams. Market potential The co-injection technology is well suited to producing hot filled beverage closures, packaging for food such as diced fruit and pudding, pet-food packaging, baby food, coffee beans, canned goods, and as a replacement for current packaging used for medical parts and other high-tech components. The Iris technology was introduced at the NPE show in early April this year. Moulders can now take their existing machinery capital and re-purpose it for much higher value applications. By combining five key technologies (melt distribution, nozzle design, portable auxiliary injection unit, temperature control and precise valve gate movement), the system provides the entire melt distribution and control system to implement co-injection on any modern injectionmoulding machine. Mold-Masters has also set a new pace by purpose engineering a beverage closures hot runner system for cycles between 3 and 6s. The Sprint system uses a unique nozzle tip design coupled with Mold-Masters iFlow manifold technologies. Sprint systems have 10% lower pressure drops, greater than 90% fill balance and 25% faster colour changes than comparable systems in the field. This allows moulders to reduce part weights and bring moulding costs down to new thresholds. www.moldmasters.com 1. System overview 2. E-Multi and E-Drive Integrated Control 3. Two melt streams 4. iFlow manifolds 5. Advanced cooling 6. Part improvements 7. Resin cost savings","@ID":43} "REGIONAL MARKET REPORTS 16 PETplanet insider Vol. 13 No. 09/12 www.petpla.net Lenny Xuan: “We approach clients before defining the product to be able to present the optimum solution for a sensitive product – utilising our global experience: In mould making speed to the market, rapid reaction to customer’s needs and time is of the essence. The design of the bottle is transferred directly to the tooling centre, where the mould is manufactured on Mazak tooling machinery. Thereafter the mould is assembled and tested – all within the space of 7 days.” Four designers, four process engineers, four laboratory engineers are servicing the market. Moulds for blowers are 100% made in the country. Manufacturing in Beijing We flew from Shanghai to Beijing, where we were anxious to visit Sidel’s “multi-product plant“, as it is known and for which the market and even competitors are full of admiration. The trip to Beijing turned out to be well worthwhile. For here, in a constantly developing industrial zone situated on the doorstep of the Chinese capital, is a modern factory for assembling all the products that form part of Sidel’s range – from blow moulding machines and fillers, supplied in combi format, in a block arrangement as well as standalone equipment. This lean factory could be anywhere, even in Europe, with its clear allocation of production space, with a well laid-out flow of materials, the KanBan systems for the smaller parts, the pre-assembled modules that are delivered just-in-time for final assembly. Sidel (or rather its Swedish holding company) have invested a total of € 45 million – Sidel’s “largest ever industrial investment” – in this impressive factory. It is “the first multi-product plant in Sidel’s global industrial set-up for making blowers, fillers, labellers, conveyors and end-of-line equipment”. Keywords from the vocabulary of Sidel Beijing and their message to the Chinese market: “Proximity to your customers, reduced lead times, speed to the market, localisation of product and qualified staff.” The factory is the expression of a commitment to the company’s customers locally and at the same time testifies to confidence in China’s future and to the assurance that the economic development of the last few years will be sustained. Equipment from France is still continuing to find its way into China, but only when the need arises – i.e. for reasons of technology and/or capacity. In terms of quality there should be no difference between products originating from European production plants and those that are produced in the Sidel plant in China. The Beijing plant Sidel’s factory in Malaysia has been closed and production relocated to Beijing/ China. The buildings here in Beijing came on stream in October 2008. The shop-floor covers an area of 38,000m2. The concept is intended to convey a professional and at the same time eco-friendly approach (light, water, landscape –","@ID":18} "PETbottles 44 PETplanet insider Vol. 13 No. 09/12 www.petpla.net Beverages + Food MHT MOLD & HOTRUNNER TECHNOLOGY Dr. Ruben-Rausing-Str. 7 | D-65239 Hochheim/Main Tel. +49 (0) 6146-906-0 | www.mht-ag.de Make the most of your machine - with a high cavitation mold from MHT! For many machine types, we supply the mold with the highest cavitation, thereby enabling optimum preform output. For the Husky HyPET machine, we offer an upgrade set for 33% more preforms, without refitting on the machine! • 60 cavities for Netstal PETline 2000 • 96 cavities for Husky HyPET 300, • 112 cavities for KraussMaffei 350 Engineering made in Germany 128 for HyPET 400 Patent pending: MHTcoolMAX® post mold cooling Romanian beer When Heineken enrolled PET Engineering in the re-launch of Silva, the best-known Romanian beer brand, the objective was to create a packaging with a premium identity, while retaining the essence of its land of origin. The new Silva is presented as a fusion of tradition and modernity, ‘made in Transylvania’. The connection with the history of the region can be seen in the main logo, which recalls a traditional bird-based coat of arms, which is complemented by the bottle’s distinctive and recognizable shape. The container is designed with a tapered centre, with labelling at the neck and towards the bottom of the bottle. www.petengineering.com Salad dressing UK supermarket chain Asda, part of US company Wal-Mart, is launching a new range of Chosen by You branded salad dressings in a new 250ml PET bottle, designed and produced by Appe. The new bottle is 90% lighter than the glass version it replaces, which represents a saving of around 200t/a of packaging and offers improved transport efficiencies, reduced costs and lower carbon impact in the logistics chain. Its high shatter resistance is claimed to eliminate breakages during filling and distribution. The bottle is the first of its kind for private-label salad dressings in the UK. It was designed at Appe’s design facility in Brecht, Belgium, and is manufactured by the two-stage process at the company’s Gresford factory, near Wrexham, N Wales. Appe’s technical team worked closely with the closure supplier in the development, piloting and testing of the design to deliver a complete solution to the customer. The dressings are being manufactured and packed by one of the UK’s leading suppliers of table sauces, salad dressings and chutneys. www.appepackaging.com Iced coffee from Müller The Alois Müller dairy has recently been selling a new product as part of its chiller range. The product, which is available in three variants, is made from milk with a shot of coffee. The caffeine content is equivalent to the taste of one to three cups of Espresso. Prior to consumption, the chilled product needs to be shaken until it foams. The product is packaged in a handy 250ml PET bottle. The sleeve-wrapped bottle is sealed with a colour-matched screw cap complete with tamper-proof strip. www.muellermilch.de","@ID":46} "BOTTLE MAKING 24 PETplanet insider Vol. 13 No. 09/12 www.petpla.net Coloured PET bottles on standard SBM machines Multi-component bottles Inotech Kunststofftechnik GmbH has developed a new technology to produce multi-component preforms which can be used for the production of bottles on standard SBM (Stretch Blow Moulding) machines. It enables individual colour and material combinations to be realised without any separate assembly steps. The security pigments (Securalic pigments) used for the multi-colour applications are based on a protected technology by Merck KGaA Darmstadt, Germany. From multi-coloured to demanding haptic applications Colourful PET bottles are only one of the possible applications. It is also possible to create multi-resin parts and assemblies for functionality such as transparent areas for windows and filling levels. A second material can stabilise the later bottle or haptic elements made of TPE can be incorporated. Another example is the muchdiscussed milk bottle: a black colour can protect the milk against UV light while another colour can be used as a design element. To solve functional problems without any additional assembly stage and to cover critical areas with another material open up a whole new world of possibilities. How is the preform produced? Multi-component moulding is a multi-stage moulding process that produces preforms with two or more integrated materials/components. In the first stage the resin A is shot into the injection mould. Then the mould, or part of the mould, is rotated in the machine. Resin B is then used in the second shot. The injection moulding machine needs to have two or more plastication/injection units (one unit for each different resin or colour). The machine’s multiple screws are usually arranged in a vertical position (90°). How are the preforms blown? These preforms can then further processed like standard preforms with standard IR or NIR heating systems. Minor adjustments have to be done on the process depending on the preform design, colour and shape. Some specific designs may only be possible to heat on a microwave system such as the Krones new FlexWave. The company actually has two patent applications to produce blown multicomponents containers. One appli-","@ID":26}
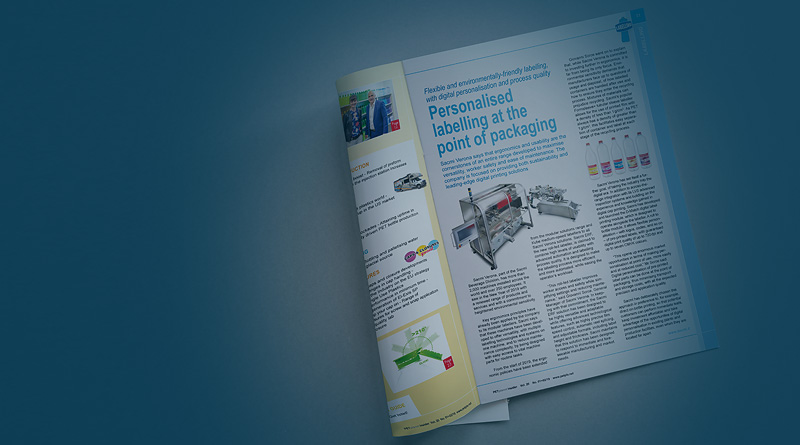