{"pages":{"page":[{"#text":"BOTTLE MAKING 30 PETplanet insider Vol. 14 No. 04/13 www.petpla.net Bottles, preforms and closures, 2nd Edition - part 2 Determination of bottle properties Ottmar Brandau has newly revised his book, “Bottles Preforms and closures” first published by hbmedia/PETplanetPublisher, and now to be re-issued under the Elsevier imprint. PETplanet insider will be publishing extracts from successive chapters in a series of articles in forthcoming issues. After considering the basic questions relating to bottle design in part 1, the second part talks about the determination of bottle properties. Based on the information collected in the discussions with the customer, as outlined in Part 1, the required properties of the planned container must be defined. Apart from dimensions such as diameter and height, plus the capacity and weight, these properties will form the starting point for a first draft design of the new bottle. Top load The required top-load properties can be derived from the desired or industry-specific stacking height. For this purpose, the number of bottles that will be stacked on a single pallet must be determined. In most cases, four bottles are normal, but this of course also depends on the height of the bottle. This figure is then multiplied by the number of pallets that the customer or the distribution chain will stack on top of each other. Usually the result of this calculation is further multiplied by a safety factor. The result will then be the total load to be supported by the lowest bottles on the pallet without deformation or failure. The bottles must not dent or collapse","@ID":32} "www.drinktec.petpla.net Supported by: Go With The Flow Tour South America here we come! Seeking to satisfy their thirst for knowledge, the PETplanet Insider team is about to set off on a new voyage of discovery. This – the longest tour by Editourmobil to date – will take our editors, split into four teams, through six countries in South America, starting in Lima, Peru. From there they will journey on to Uruguay, travelling through Bolivia, Chile and Argentina naries is a trip spanning three and a half months; a distance of more than 12,000 kilometres and the prospect of any number of exciting interviews with key players in the PET sector. And, once again, we will be giving you the opportunity of joining them – during the tour on our live blogwww.drinktec.petpla.net as well as after the tour on our trade stand at drinktec from 16th to 20th September 2013, Hall B3, Booth 501, when we shall be reviewing the tour for you. __________________________________________________ Sudamérica nos espera! nuevamente a un viaje de reconocimiento. La gira más larga hasta ahora con el Editourmobil lleva a nuestros editores, partiendo desde Lima, en cuatro equipos, por seis países sudamericanos: De Perú a Uruguay, pasando por Bolivia, Chile y medio, más de 12.000 kilómetros de recorrido y una gran cantidad de entrevistas fascinantes con lo más importante de la industria del PET están esperando a los expedicionarios. Y nuevamente, usted participará con ellos: Durante el Tour en nuestro blog en directowww.drinktec.petpla.net y después del Tour en nuestro puesto de la feria en el drinktec, desde el 16 al 20 de septiembre de 2013, Hall B3, Puesto 501, donde pasaremos revista al Tour para usted. __________________________________________________ AAmérica do Sul nos espera! A equipe da PETplanet Insider, sedenta de conhecimento, longa até a data com o Editourmobil leva os nossos editores, a partir de Lima, em quatro equipes, a seis países da América do Sul: desde o Peru através da Bolívia, Chile e Argentina meses e meio, um trajeto de mais de 12.000 quilômetros e muitas entrevistas emocionantes sobre o mais importante que so espaço na drinktec, de16 a 20 de setembro de 2013, salão B3, expositor 501, onde lhe mostraremos todos os detalhes da H[FXUVmR Go with the flow The South-America round trip with 18th February - 24th May, 2013 18 de febrero - 24 de mayo de 2013 De 18 de fevereiro a 24 de maio de 2013","@ID":30} "BOTTLE MAKING 33 PETplanet insider Vol. 14 No. 04/13 cally to give the KeyKeg resistance to higher internal pressures and very low deformation at high pressures. The company asserts that the one-way kegs will also be highly resistant to external influences, that they can withstand very high temperatures during transport in hot climates and are completely resistant to moisture. Its resistance to damage from outside influences makes the latest generation safer to use than its predecessors, Lightweight Containers says. The company further claims that it offers improved logistics performance, as the design enables 80 cylindrical KeyKeg20 units to fit onto a single pallet and its lower weight means that transport requirements are 65% less than equivalent steel and other kegs. The KeyKeg’s shell consists of 54% recycled PET, while the ergonomically-designed grip is made completely of recycled PP. Lightweight Containers says that the package is very stable, takes up less space than its predecessor and fits into existing cooling cabinets. Production The company manufactures the package on a fully-automated production line located in Den Helder, the Netherlands, which has a capacity of 400 kegs/h. The production line is just about ready for service. The first few hundred KeyKeg 20 cylinders have already rolled off the conveyor belt. After trialling in their own laboratories and with selected customers, Lightweight Containers will give the green light for the production of KeyKeg 20 cylinders. www.keykeg.com The KeyKeg Consortium Lightweight Containers is part of the KeyKeg consortium, which started production in 2006. The members of the consortium and their responsibilities are: Schoeller Arca Systems (production, assembly and stockholding); Scholle Packaging (inner bag assembly); Sipa (moulding machinery and tooling); m + f Keg-Technik (filling machines) and DSI (development and production of dispensing systems). Lightweight Containers itself is responsible for R&D, sales and marketing.","@ID":35} "EDITOURS REPORTS 18 PETplanet insider Vol. 14 No. 04/13 www.petpla.net Highly automated clean filling The flourishing Russian city of Lipetsk is located on the banks of the Voronezh River about 420km southeast of Moscow. Its population of 500,000 mainly works in heavy industry, with one steel plant alone employing 35,000. This means that air quality is an issue in Lipetsk and one reason why they put a special focus on cleanliness in production, as we learned from Vladimir Trofimov, a Director of Rosinka. Cleanliness is achieved with a high degree of automation; even the final stacking and wrapping of the PET bottle packs, completing the packing of the bottled water and juices is undertaken by robots. The company has been growing at about 15% annually, with Spritzer showing the highest growth rates. The product range extends to 55 drinks in total and consists of mineral water, tea, energy drinks (“Tornado” brand), Spritzer (with and without gas), and even an orange-flavoured cola drink distributed under its own brand name. Water comes from an underground spring about 100m deep (regular drinks) and up to 600m for the mineral water. Vladimir Trofimov says that the water reserves are huge and will last another 100 years. Current production is 62 million bottles for its own products and 43 million for co-packaging – 105 million in total. In winter the demand for its own drinks dips by 30-40%, while the demand for co-packing products such as energy drinks, for example, is quite stable. Co-packing also includes international companies like Coca Cola. Autumn will see the launch of a juice with pulp, which will require special filling and will be done by either Krones Ultra Clean or hot-fill. The company has three bottling lines in total: one Ultra Clean from Krones (installed last year with a capacity of 15,000bph, one hot-fill line from Berchi Group (10,000bph) and the newest installed CSD line from Kronos (22,000bph). They also have an old glass bottle line, which was acquired when the current owners purchased the company, about ten years ago, as well as a manual 5l filling station. Hotfill products are bottled in 330ml, 500ml and 1l sizes, while CSDs are produced in in 500ml, 1l and 1.5l. The same sizes are used for the Ultraclean line. Caps are purchased from Bericap, while preforms come from Retal and Resilux. By chance we learned from Vladimir that he has just finished his first Iron Man (4km swimming, 180km cycling, 42.2km running) and plans further starts, including an event in Sweden next year. While Iron Man and the bottling of water may appear to have nothing in common at first glance, the energetic approach and determination of the Iron Man can also be found in this company’s production. www.liprosinka.ru July, 26, 2012 Lipetskpivo We met: Vladimir Lyubanov, General Director Beer filling line at Lipetzkpivo The 30l PET beer keg Lipetskpivo was founded as a state-owned enterprise in 1977, and became apublic traded company in 2002. About 68% of production goes into beer; 14.5% is lemonade and soft drinks; 13% water; and 4.5% to Kwas, the unofficial Russian national beverage. The company’s52 different drinks are filled in 0.5, 1.5 and 2.5l bottles; 1.5l is the most popular size and carries about 50% of production. The company employs Sidel filling and closing monoblocs for 0.5l (12,000bph), 2.5l (9,000bph) and1.5l (24,000bph)and stretch blow moulders from Italian company SMI to produce the 0.5, 1.5 and 2.5l sizes. Lipetskpivo employs about 1,500 people, about 650 of them in production. Its latest innovation is the production line for 30 litre PET kegs, the Innokeg Till PETLine F8. The preform design was created by Czech company Petainer; preforms are supplied by KHS, who also supplied the fully automated filling equipment. Production capacity on this line is 240bph. An integrated scavenger material prevents oxygen penetration, while nylon particles protect the beer from CO 2 loss. Shelf life of the PET kegs is nine months. During the discussion Vladimir Lyubanov explains the advantages of PET, compared to conventional steel kegs. The PET kegs are non-returnable containers and 100% recyclable. The complete PET keg, including fittings, weighs about 400 gr (preform weight: 320g) compared to 6 - 7kg of its metal counterpart. Lower weight alone allows more kegs to be delivered per truck/vehicle, which means that logistics costs can be 20-30% per hl lower. In addition they do not generate costs for returning the kegs to the brewery, saving storing, cleaning and possible repairing costs.","@ID":20} "PREFORM PRODUCTION 20 PETplanet insider Vol. 14 No. 04/13 www.petpla.net Preform machines of Athena Automation Ltd. Ontario Canada – An interview with Robert Schad 84, and still going strong! By Waldemar Schmitke, Editor at large, PETplanet Robert Schad, who founded Husky Injection Molding Systems in 1953, is once more building injection moulding machines in Vaughan, ON, Canada. Now a sprightly 84 years of age, he has apparently lost none of his passion for injection moulding machines. With the establishment of Athena Automation Ltd., a privately owned company, he has the freedom to implement ideas which are the culmination of his decades-long experience. He is able to focus on the essentials rather than getting bogged down in big company bureaucracy. Working with Sipa Italy, global supplier of end-to-end PET solutions, gives Athena the opportunity to explore the possibilities of their machine for PET preform applications. requirements and applications. Robert Schad is convinced that this is the way forward, and to back up his belief he cites the many discussions he has had with leading players in the market. For PET applications, however, further steps are required. In particular, a significant element involves the development of PET-specific machines and system components coupled with the need to integrate the system with preform tools and peripherals. Having done all this, a global sales structure needs to be put in place, supported by a comprehensive after-sales and application-specific service. Exclusive partnership between Athena Automation and Sipa It was at this juncture, at the end of 2012, that an exclusive partnership was sealed between Athena Automation and Sipa. This collaboration is far-reaching and extends from the joint development of machine elements, screw geometries, unloading and post-mould cooling techniques, and right through to a common purchasing strategy. Both are privately run companies that adopt a flexible approach to development and rapid implementation. These are the cornerstones of the partnership. F.l.t.r.: Enrico Gribaudo, General Manager Sipa Italy and Robert Schad, Chairman Athena Canada Athena Automation has a total of 60 employees, of whom more than 90% are engineers and technicians. From scratch they have developed a line of two-platen hybrid injection moulding machines with clamping forces of 150 and 300t using a hybrid machine concept, which, for Athena, is the key to the market, in conjunction with a clearly configured, modular and accessible structure. This enables the company to react rapidly to changing market","@ID":22} "CAPPING / CLOSURES 36 PETplanet insider Vol. 14 No. 04/13 www.petpla.net 38mm neck finishes and corresponding closure designs in the market are certainly economical (i.e. light-weight) solutions. However, the combination of these necks and closures does not create a very stable packaging, especially against high temperatures, but even at room temperature also. This can be visualised when pinching a bottle with a 38mm ACF neck finish which results in severe ovalisation (c.f. Fig. 1). Fig 1: Bottle with a 38mm neck finish (inner bore diameter of 33.4mm), pinched at the middle part, resulting in severe ovalisation of the neck. The ratio of wall thickness (WT) to inner bore diameter (IBD) is being used as a measure of the stability of the neck. If we compare the situation of the 38mm neck finish to a 26mm neck finish customised by Corvaglia for flat water applications, we arrive at a much more favourable ratio for the flat water neck finish than for the sensitive beverage neck finish. The difference, as depicted in Fig. 2 is roughly 40%. In other words, the most expensive and sensitive drinks today are shipped in the cheapest packaging available. Additionally, for packages as unstable as the 38mm ACF example, a safe packaging is only created by the mutual stabilization of closure and neck in a tightly screwed state. Once partly unscrewed, this stability is lost and the product safety of a sensitive drink can no longer be guaranteed. Another interesting point to note is the fact that these ‘weak’ necks are better stabilised by one-piece than by two-piece closures. The reason for this is that the liner in two-piece closures only acts from above the neck, providing no horizontal guidance, whereas common one-piece closures do provide this guidance. Now, what happens if the tight combination between closure and neck is loosened? For the sealing parts of the closure we are talking about rather small HDPE components, where relatively small temperature variations resulting in small dimensional changes can have a relatively large effect on the sealing behaviour in such a delicate stabilising combination. Sidel (2) recently proposed a qualification test for packages filled under aseptic conditions. When it comes to product and PET packaging, the company’s Product Package Interaction laboratory assesses whether the products are packaged aseptically in order to ensure that the properties of the product and its packaging are not altered in any way. In this respect, they are tested over time through physical and chemical testing as well as by sensory analysis. For the recent qualification test proposed by Sidel, half of the samples under evaluation are partly unscrewed leading to a breach of the package’s stabilisation. The test contains temperature cycles that are run to simulate filling and real-life conditions of the package. The combination of a ‘weak’ package like the 38mm ACF neck, breaching the stabilising effect of a tightly screwed closure and running temperature cycles with it poses a huge challenge to design a closure maintaining under all conditions the sealing performance of packages for sensitive drinks. For these kinds of packages the stability can only be guaranteed when neck and closure are tightly screwed together, partial unscrewing leads to a breach of stability. Currently, Corvaglia has taken on this challenge. In cooperation with the Zurich University of Applied Sciences (ZHAW) Institute of food and beverage innovation (ILGI) the company is in the process of improving current closure designs in order to guarantee product safety of sensitive beverages even under the worst conditions. www.corvaglia.ch Fig 2: Above: 38mm neck finish for aseptic cold fill applications as used for sensitive drinks (SD). The wall thickness (WT) is 1.3mm, the inner bore diameter (IBD) is 33.4mm resulting in a ratio of 3.9%. Below: Corvaglia Short Neck (CSN) 26 mm neck finish for flat water applications. The wall thickness (WT) is 1.2mm, the inner bore diameter (IBD) is 21.8mm resulting in a ratio of 5.5%. References: 1. H.-D. Belitz, W. Grosch, P. Schieberle: Lehrbuch der Lebensmittelchemie. 5th Edition, Springer, 2001, ISBN 3-540-41096-1, p. 509. 2. Presentation by A. Maurey, Food Scientist, Sidel, held at CE.T.I.E. PET working group meeting on April 24th 2012 in Paris (France).","@ID":38} "PETproducts 38 PETplanet insider Vol. 14 No. 04/13 www.petpla.net Extended keg range Italian company PolyKeg s.r.l. launched a 16l version of its PolyKeg PET one-way kegs. The new size is available in all three variants of the package: BT, T and H. The BT type operates to a higher working pressure, offers good handling and ‘stackability’, and is claimed to be highly resistant to shocks. It incorporates a high-barrier polymer blend for long shelf-life, which is common to all three PolyKeg types. ‘O 2 -free’ versions are available on demand and all are compatible with existing filling lines and dispensing systems. The packages are suitable for beers, wine, cider and soft drinks and hold EU and FDA approval for food use. The weicht of the PolyKegs is amounting to just 5% of total filled weight. The H type range is the lightest, with the 16l version tipping the scales at 0.65kg. The equivalent T type weighs 1.15kg; the BT 16l keg is 1.6kg. All three are available in 16, 20, 24 and 30l sizes. The largest BT Polykeg weighs 1.85kg; the 30l H type is less than half as heavy, at 0.83kg unfilled. PolyKeg one-way kegs are fully recyclable. www.polykeg.it Aseptic filler for ESL beverages The KHS linear aseptic filling system Asbofill ESL has been developed for the bottling of extended shelf life or ESL beverages for the cold chain: Milk, mixed milk, coffee and yoghurt beverages, fruit juices and teas. It can also process products containing pulp and/or chunks. Different forms of plastic containers with identical neck rings can be filled. There are two types of machine available. The Innosept Asbofill ESL 611 is designed for bottles of 0.1 and 0.75l and has a throughput of up to 12,000bph. The Innosept Asbofill ESL 711 fills 0.25 to 2.0l bottles at the same rate. Both machines can be supplied in the twin version. In the twin version many of the components central to the systems are implemented just once. The sanitary room of the Innosept Asbofill ESL measures 0.7m³ in the ESL 611 and 1.2m³ in the ESL 711. The sterilization, filling, and sealing processes take place in different housings, with a partition separating the different areas. Bottles and caps are sterilized according to the process of dry sterilization. The bottles are filled using two-stage, free-flow filling valves, by the principle of volumetric, electromagnetic induction flow-metering into which pulp nozzles can be integrated. If products containing chunks are to be processed, a separate dosing unit can be incorporated. Both seals and screw caps can be applied as closures. www.khs.com Labeller Ocme, which specialises in the design, development and production of supply of secondary packing systems, has recently introduced some upgrades and improvements to its complete packing line management. Vela is described as a ‘new generation labeller’ and has various features that are claimed to improve efficiency and reduce cost of ownership by up to 99%. The standard Vela machine is equipped with double-reel support powered by servo motors. Ocme says that this arrangement means that film can be pushed rather than pulled, which helps to prevent excessive stretching and yield and thus reduce stoppages and enables the machine to process a wider range of materials. A servo motor-powered cutting drum is positioned above the support and is synchronised with the main machine drive. The drum incorporates a rotating blade which contacts the static blade and creates a “scissors” effect, which is intended to provide both a precise cut and up to 200,000 cuts between blade changes. The glue roller, which is also powered by a servo motor and is synchronised with the main machine drive, is fixed on a horizontal slide and moves forward and backward, rather than rotating. The roller is designed for fast changeover and simple maintenance and the glue tank has a new filtering system, which prevents film pieces from reaching the tank. The motorised tooth-belt and centred platform design are also designed for ease of service and maintenance. Reel supports can be loaded vertically. Ocme says that the servomotor on the labelling station delivers precisely-tensioned film, which is unwound, cut and transferred to the container using vacuum technology. The hot melt glue is spread on the leading and trailing edge of the label by a stainless steel glue roller. Ocme maintains that Vela can process up to 50,000bph. www.ocme.it Anti-loss screw cap Polish company Unicom International Ltd., based in Warsaw, has announced the launch of its patented antiloss 30/25 screw cap. Unicom claims that this cap is the first of its type to the market. When the cap is unscrewed, it remains attached to a secondary part of the neck ring, which means it will not drop off or accidentally fall away. The company says this feature also helps to keep the caps of opened containers clean. It is suitable for packaging of water, soft drinks, juices, milk, detergents, chemicals, pharmaceuticals and other products. www.unicompackaging.eu","@ID":40} "PETcontents 04/13 4 PETplanet insider Vol. 14 No. 04/13 www.petpla.net INSIDE TRACK 3 Editorial 4 Contents 6 News 38 Products 40 PET bottles for beverages and liquid food 42 PET bottles in health and beauty care packaging 44 Patents BOTTLE MAKING 30 Determination of bottle properties Bottles, preforms and closures, Part 2 32 Double walls, doubled resistance New generation one-way PET KeyKeg launched by Lightweight Containers CAPPING / CLOSURES 34 Sense and sensitivity Caps and closures for sensitive soft drinks – the Corvaglia approach EDITOUR REPORT 14 From Jekaterinenburg to Ukraine Russia Part 4 MARKET SURVEY 23 Suppliers of preform systems / single stage machinery BUYER’S GUIDE 45 Get listed! Page 29 PREFORM PRODUCTION 20 84, and still going strong! Preform machines of Athena Automation Ltd. 22 A breath of fresh air in emerging markets Husky’s focus on emerging markets 24 Performance boost for installed preform systems Mold-masters: From hotrunners to preform moulds PET - THE NEXT GENERATION 29 Eight bottles, one Jean Levi’s launches Jean genius containing PCR PET Page 32 Page 24 Page 20 Page 22","@ID":6} "MARKET SURVEY 26 PETplanet insider Vol. 14 No. 04/13 www.petpla.net 04/2013 MARKETsurvey Preform equipment Single stage machinery Company name Cypet Technologies Ltd Nissei ASB Machine Co., Ltd. Mould&Matic Solutions GmbH Postal address Telephone number Web site address Contact name Function Direct telephone number Fax E-Mail Lefkosias 45, 2540 Dhali, Nicosia, Cyprus +357 22 610 700 www.cypet.eu Constantinos Sideris Director +357 99 693 923 +357 22 610 800 [email protected] 4586-3 koo, Komoro-shi, Nagano-ken, 384-8585 Japan +81-267-23-1565 www.nisseiasb.co.jp/en Katsuo Ishiguro Section Manager, Sales Coordination Team +81-267-23-1565 +81-267-23-1564 [email protected] Ziehbergstraße 2 4563 Micheldorf, Austria +43 7582/61760 - 0 www.mouldandmatic.com Gerhard Zdebor Head of Division +43 7582/61760-408 +43 7582/61760-42 [email protected] Single stage ISBM machines Machine model / number K 16 K 28 K 53 ASB-50MB, ASB-12N/10, ASB-12M, ASB-15N/10E, ASB-70DPH, ASB70DPW, ASB-150DP, ASB-150DPW, ASB-650EXHS, ASB-650EXHD, PF8-4B, PF6-2B, PF4-1BH, PF3-1BH, PF3-1BHLL, PF24-8B(24), PF248B(12), PF24-8B(12H) 1050H-100/40-R2 Bottle volume (from/to in litres) 0.1 - 5 0.1 - 15 0.5 - 30 0.003 - 20 0,1 - 10 Number of preform cavities 1, 2, 4, 8, 12 1, 2, 4, 8, 12, 16 2, 4, 6, 8, 12, 16, 18, 24 1 - 36 1 - 32 Number of stretch blow mould cavities 1, 2, 4, 8, 12 1, 2, 4, 8, 12, 16 2, 4, 6, 8, 12, 16, 18, 24 1 - 36 1 - 32 Max. preform/bottle weight in grams for the stated number of cavities 200, 100, 50, 25, 16g 600, 300, 150, 75, 50, 36g 800, 400, 260, 200, 130, 100, 85, 65g 3 - 800g 500 - 150g Hourly output based on: 0.5 litre container 1,800 2,600 4,800 1,200 - 9,000 5,000 1 litre container 1,000 2,600 4,800 720 - 8,500 2,500 1 litre wide neck container 800 1,600 3,000 Up to 5,300 Ø70mm/12cav: 2,800 2 litre wide neck container 400 800 2,000 Up to 2,200 Ø70mm/12cav: 2,800 Other (e.g. containers for personal care products...) 900 1,700 3,200 Up to 6,000 Machine footprint / space requirement (LxWxH in metres) 5.2 x 1.4 x 3.4 6.8 x 1.9 x 3.7 10.3 x 2.2 x 4.4 3.56 x 1.14 x 2.73 (ASB-50MB) 8.95 x 2.15 x 3.25 (PF24-8B) 7,4 x 2,4 x 4 Special features All-electric versions of K 16 and K 28 ASB-12N/10: can operate in IBM or ISBM mode. ASB-12M: servo driven hydraulics. ASB-15N/10E: all-electric PF Series: lower blow mould cavitiation and blows multiple times per cycle PF24 models: outputs up to 9,000bph for smaller bottles / 2,500bph for 5l bottles. Vertical injection moulding machine fully servo-electrically driven strech blowmachine integrated leak tester system customized packing system customized blow liner configuration possible Company name Netstal Maschinen AG Postal address Telephone number Web site address Contact name Function Direct telephone number Fax E-Mail Tschachenstrasse 8752 Näfels, Schweiz +41 55 618 6111 www.netstal.com Stefan Bock Manager Application Technology +41 55 618 6156 +41 55 618 6070 [email protected] Preform injection moulding systems Netstal brand: PET-Line KraussMaffei brand: PETForm Machine model number / name PET-Line 2000-3700R (95) PET-Line 3500-3550R (110) PET-Line 3500-6600R (135) PET-Line 3500-6600R (150) PET-Line 6000-6600R (2x110) KM1751900CV KM1753500CV KM3203500CV KM3204500CS KM3206100CS KM3503500CV Number of cavities (min/max units) 32 - 60 64 - 128 72 - 128 72 - 128 128 - 192 8-60 8-60 32-96 32-96 32-96 32-112 Maximum individual preform weight 9 - 86g 9 - 86g 9 - 86g 9 - 86g 9 - 86g 30-228g 58-442g 36-110g 42-128g 71-215g 31-94g Max resin through-put (kg/h of PET) 560 740 1,050 1,350 1,400 380 600 600 800 1,050 600 Standard features Complete system including material preparation, take out robot post cooling Options / special features Suitable for hotfill materials, wide mouth and big size preforms *Calitec: intensive post cooling and shaping of produced preforms to reduce cycle time and increase productivity *Preblow: optimized preform design and post moulding process to reach thinner bottle bottom design and save material (light weighting preforms) *= available at PET-Line only","@ID":28} "PETpatents www.verpackungspatente.de 44 PETplanet insider Vol. 14 No. 04/13 www.petpla.net New lamps for old bottles Utility Model DE 202012005412 U1 Applicant: Kin Tec Technology Corp., Taipeh (TW) Date of Application: 1.6.2012 With a view to reducing the proportion of refuse accounted for by PET bottles, this application proposes re-using /recycling bottles in the form of lamps. To do this a lighting unit is inserted in the top and a water battery between the bottle top and the body of the bottle. Threadless top Intern. Patent No. WO 2011 / 048017 A1 Applicant: Nestec S.A., Vevey (CH) Date of Application: 15.10.2010 A PET / PEN container is sealed / provided with a closure and a lid is inserted into a partial recess in the container and this connects with the container by the action of external forces. Preform with pourer Europ. Grant of Patent No. EP 2346739 B1 Applicant: Procter & Gamble Comp., Cincinnati (US) Date of Application: 5.11.2009 A preform for manufacturing a PET bottle already incorporates an integrated pourer. The preform is also provided with an opening in the pourer which enables the recirculation of the product from the pourer back into the inside of the container. Plastic container Europ. Grant of Patent No. EP 2248728 B1 Applicant: Yoshino Kogyosho Co. Ltd., Tokyo (JP) Date of Application: 14.1.2009 A container made from PET is designed for hot filling. In order to enable absorption of the reduction in volume which occurs during the subsequent cooling process, the bottle is provided with a number of compensation panels. Improved screw thread Disclosure No. DE 102011015004 A1 Applicant: E-proPlast GmbH, Schmalkalden (D) Date of Application: 25.3.2011 The flanks on the external thread of a plastic container are moulded so that even just a ”light“ screwing action will create an anti-rotation element. Screwing the cap as far as the stop will in turn result in a considerably stronger antirotation element. Angled bottle opening German Grant of Patent No. DE 102011118950 B3 Applicant: Jörg Haberland. Uchte (D) Date of Application: 21.11.2011 The top edge / spout of a glass or plastic bottle is located at an angle to the central axis and incorporates a spherical extension. This extension ensures greater ease of handling during the pouring operation – without any ”gurgling“.","@ID":46} "EDITOUR REPORTS 15 PETplanet insider Vol. 14 No. 04/13 www.petpla.net SDWHQWV UHVHDUFKHUV DQG WHFKQLFLDQV LQVWDOOHG SODQWV EUDQFKHV ZRUOGZLGH ,I ZH KDGQêW JRQH VR IDU ZH ZRXOGQêW EH VR QHDU RXU IXWXUH VHHQ IURP QHDU Beauty in the bottle Russian Company Bering was established in the premises of a former Russian scientific company, in 1999, starting with the production of PE bottles for pharmaceutical products. However, the market for pharmaceutical bottles is considered to be conservative and is strongly regulated by the Russian authorities. “Concern Kalina”, a leading Russian cosmetics company, took Bering in a new direction and in 2007 Bering started using PET to meet the requirements of its cosmetics customer. It has passed several quality audits since then, including assessments by Henkel/Schwarzkopf and L’Oreal. Today the company employs 112 people and its product range includes bottles for cosmetics, pharmaceuticals, detergents, liquid soap, and others. The PET, PE and PP bottles range from 5ml to 1l in size and are supplied all over Russia, to key accounts such as “Pharmstandart” (pharmaceuticals) and “Faberlic”, “Krasnaya Liniya” and “Unicosmetic” (all cosmetics), as well as smaller companies. Caps, measuring cups and tubes are produced on injection moulding machines from Demag (100-400 Viva and 125-600 Extra) and Arburg (420C 1000-290). Blowmoulding machines from Bekum (BM-104D and H-121-1) and Italian company Automat (AT 2 DS) are used to blow PE/PP bottle and jars from 10ml up to 1l. Sterile production of pharmaceutical bottles is also possible. PET bottles and jars in sizes from 5ml to 250ml are manufactured on several Nissei machines (ASB 50MB). Tooling for bottle blow-moulding and injection moulding of the caps (up to 24 cavities) is produced either in-house on Mitsubishi E8A and Deckel Maha 63V cutting machines, or purchased from Nissei ASB (Japan), Pentag Stampi (Italy) or Woosung Tech (Korea). The factory closes for ten days each year for general maintenance and repair. According to Ildar Gafiyatullin, there is a general tendency to pack cosmetics, detergents and liquid soaps supplements in visible packaging. The strongly-growing market for cosmetics in Russia, in particular, requires PET bottles and containers. Gafiyatullin is strongly convinced of the superior properties of PET containers for cosmetics and pharmaceuticals, from their shiny appearance on store shelves to their advantages during transportation: PET is more suitable than any other material to be transported in a huge country, where temperatures range from -35 to +35°C degrees. With increasing demand from the cosmetic markets, Bering has found itself experiencing seasonality, as well. New cosmetic collections tend to be launched in spring and autumn, with production peaking as a consequence. And the same occurs at New Year, also.","@ID":17} "EDITOURS REPORTS 14 PETplanet insider Vol. 14 No. 04/13 www.petpla.net real boom in Russia. At that time most of the closures were being imported from the Ukraine. The amount produced by Bericap today is considerable: around 4billion closures per year, exactly double the output of 2008. Litskevitch is coy about revealing details on the machines in use, but he does let slip that there are currently 40 of them and ”the majority of systems are from Netstal“. All available space in the production hall is used in the most efficient way possible. The company premises cover 35,000m² and it currently employs 160 people. With such impressive capacity, it is hardly surprising that product is now being delivered beyond the borders of Russia as far as Belarus and the Ukraine. The list of customers is long and features many of the major players. At present there are 25 different types of closure produced in neck sizes 28 to 55mm. Litskevitch reports that Bericap was the very first company in Russia to start producing the PCO 1881 – on demand from Coca-Cola und Pepsi. Three to four months later competitors followed suit. Subsequently the first CocaCola and Pepsi bottles with the new, more lightweight closure, could be found lining the shelves in in 2011, followed in 2012 by any amount of B-Brands. Today the PCO 1881 is Bericap‘s best seller. Nevertheless, concedes Litskevitch, the manufacturers tend to be somewhat conservative here generally speaking. As long as the technology keeps going, nothing would change in a number of places, which is also the reason why a large number of BPF and PCO 1810 closures were circulating in the market. “The specific use of PCO 1810 will presumably continue for the next three to four years before the equipment is changed here too. Many companies do not have the necessary liquidity at their disposal to change from the material-saving neck finish, opting to modify the preform in some way as a cost-saving measure.“ What does the future hold? As Litskevitch sees it, the trend from oversize PET bottles to small, single-serve bottles on the beer market is discernible, especially in the major centres of population where higher earners are likely to reside. www.bericap.com By Kay Krüger July 21, 2012 Bering We met: Ildar Gafiyatullin, General Director Raoul Khasano Raoul Khasano (right) of Bering with Michael Maruschke Russia Tour Blog – around Moscow Friendly stewardesses, continually dripping teapots, passenger queues for the toilets, and no beer being served. The Transaero flight from Bangkok is heading to Moscow, fully booked and crowded with tired tourists. While most passengers will end their long journey in the Russian capital, for me it is only a transit point en route to Yekaterinburg, to explore the world of PET beyond the Ural Mountains. After taking over the Editourmobil from Kay, I continue the Go to Brau Beviale Tour as the second team. The first stop after Yekaterinburg is Ufa. We are welcomed to the premises of a former Russian scientific research company by Ildar Gafiyatullin, the General Director and perfectionist of Bering, and learn more about the PET bottles used for cosmetic products and the popular Lalinka beauty brand. After a friendly discussion and a factory tour we carry on to Kamenka brewery. There, we are brought to the company-owned pond in the middle of nowhere and experience “virgin nature” and Russian hospitality. We and the Kamenka guys pass the time fishing, cooking, having long conversations about PET. Long after midnight we go to sleep, and wake up the next morning to witness Kamenka’s time-honored brewing processes, including coal-fired heating and hand-filled bottles. A few days later we arrive at Lipetsk, a centre of heavy industry and a city of half a million people, for an appointment with Vladimir Trofimov of Rosinka. Air quality issues stemming from the city’s steel plants are one reason for them to put a special focus on cleanliness in production, which they achieve by a high degree of automation: Even the final stacking and wrapping of the PET bottle packs, the completion of the packing of the bottled water and juices, is done by robots. At very short notice we visit Lipetsk Pivo, right next to Rosinka. They produce a unique 30l beer “keg” – of course, made of PET. We need three days to get from Lipetsk to Rostov, the green city on the Don, and our final destination. We head to Aqua Don, the regional market leader in mineral water, where we learn more about bottled water in Russia, visit the production lines and have an extensive discussion with director Sergey Zaichenko. Finally, we have a meeting with the Russian beer giant Baltika, now part of the Carlsberg Group. This is one of the most modern European breweries, and we learn about Baltika’s preparations for the anticipated sales ban of beer in PET. We select a beautiful white downtown river beach for the night, but it soon turns out that it’s occupied by a hip party crowd. In our search for a more peaceful place for rest we drive out of town altogether.","@ID":16} "MARKET SURVEY 27 PETplanet insider Vol. 14 No. 04/13 www.petpla.net Sipa SPA Automa SPA Aoki Technical Laboratory, Inc. Via Caduti Del Lavoro 3 31029 Vittorio Veneto Italy +39 0438911511 www.sipa.it Machinery Division Director +39 0438911511 +39 0438911694 [email protected] Via Chiesaccia 38 40056 Crespellano -Bologna,Italy +39 051 19933740 www.automaplast.com - www.automaspa.com Stefano Elmi Technical Manager +39 051 19933740 - Ext. 209 +39-051-739578 [email protected] 4963-3 Minamijo, Sakaki-Machi, Hanishina-Gun, Nagano-Ken 389-0603, Japan +81-268-82-0111 www.aokitech.co.jp Hiroshi Chino President's Office +81-268-81-1368 +81-268-75-8114 [email protected] 650H - 60/20 - R2 ECS FX 20 (6 models) ECS HS 12 (8 models) NSB 50 SH -Three stations machine NSB 80 - Four stations machine SBIII-500LL-50 0,1 - 5 0.25 - 3.8 0.25 - 7 0,015 - 5 0,030 - 5 0.25 - 2 1 - 16 Up to 80 Up to 40 1 to 12 1 to 16 9 - 16 1 - 16 Up to 40 Up to 20 1 to 12 1 to 16 9 - 16 300 - 18g 46.50g for the 80 injection cavities 37.50g for the 40 injection cavities 4,5g with 12 cav. 80g with 4 cav. 5g with 16 cav. 87g with 6 cav. 10 - 50g 1,700 36,000 18,000 1,800 2,400 8,300 1,700 27,100 13,600 1,660 2,200 3,600 Ø60mm/6cav: 1,400 12,300 4,200 1,200 1,900 3,360 Ø60mm/4cav: 900 9,600 3,000 700 1,000 2,400 18,000 9,000 0.02l: 4,800 5l: 400 pcs/h. 0.03l: 6,800 5l: 500 pcs/h. 2,000 ~ 5,000 6,5 x 2,4 x 4 5.5 x 1.9 x 3.3 6.38 x 3.55 x 3.49 Lightweight containers asymmetrical containers off-centred neck hot fill containers pasteurizable containers aseptic PET containers (cold filling) ultra clean PET containers Lightweight containers large size containers wide mouth asymmetrical containers off-centred neck pasteurizable containers aseptic PET containers (cold filling) ultra clean PET containers Hybrid machines with “Direct Heatcon Molding System” for reduction of cycle time and energy Husky Injection Molding Systems Sipa SPA 500 Queen Street South Bolton, Ontario, Canada L7E 5S5 +1 9059515000 www.husky.ca Craig Reynolds Director +1 9059515000 [email protected] Via Caduti Del Lavoro, 3 31029 Vittorio Veneto, Italy +390438911511 www.sipa.it Stefano Baldassar Preform System Global Sales Manager +390438911511 +390438912273 [email protected] KM3504500CS KM3506100CS HPET 180 AE HyPET 230 AE HyPET 120 HyPET 225* HyPET300* HyPET400* HyPET400S** HyPET500* XForm 150 XForm 300 XForm 500 32-112 32-112 24 - 32 24 - 48 2 - 32 6 - 48 8 to 72 12 - 96 96 - 112 16 to 144 from 2 to 48 from 2 to 96 from 48 to 128 36-109g 60-184g 889*** 1448*** 2200*** 3344/2750*/*** 5770/4910*7*** 5770/4910*/*** 4910**/*** 8048/8030*/*** 1508/62 2885/60 125/47 800 1,050 221 334 500 720/1010* 1050/1260* 1200/1450* 1450** 1400/1700* 560 960 1,200 * Also available with High Performance Package (HPP 4.0) ** Only available in HPP 4.0 Special machine sizes and cavitations available upon request ***maximum shot capacity of PET in grams XForm 150: hybrid machine, servo-driven clamp, can install legacy tooling, servo-driven hydrauic pumps for low energy consumption, wide-mouth capability; XForm 500: low-maintenance toggle design, can install legacy tooling, fast mould changeover Special machine sizes and cavitations available upon request XForm 150: servo-driven screw, Duo I & Duo II ‘PostMold’ Cooling, Energy Meter; XForm 500: LongLife, ultra-thin preform injection capability, iFlow hot runner","@ID":29} "EDITOURS REPORTS 16 PETplanet insider Vol. 14 No. 04/13 www.petpla.net July 24, 2012 Kamenka Brewery We met: Alex I Golovachev, Ilya Golovachev, Development Manager and the whole Kamenka family Alex I Golovachev and his team Time stands still in Kamenka brewery The Kamenka brewery was established in 1968, with the help of Czech Engineering. When it was scheduled for closure 40 years later, due to unprofitability and mismanagement, former Soviet Army pilot Mr. Golovachev took it over in 2008. Prior to the acquisition, Mr. Alex I Golovachev has been the distributor of various beer brands, including Kamenka and Baltika. The whole upper management was changed and replaced by people from different regions. At that time the Kamenka beer was solely distributed in kegs; Mr. Golovachev came up with the idea of bottling it in distinctive barrel-shaped 1.5l PET bottles, weighing 32g and incorporating a handle, which made them easy to carry and easy to store in the refrigerator. One litre (32g) and 3l (51g) followed. When the season changes from UV-intensive summer to winter, the bottles follow suit and change their colours from brown to clear, while retaining their guaranteed shelf-life of 30 days. Preforms and caps are purchased locally from the region. Blowing of PET preforms to bottles is partly manual;. they are placed onto a conveyor chain by hand, before being heated during a circuit of the oven. The preforms are then removed from the conveyor chain, again by hand, and placed in a blowing device consisting mainly of mould and compressed air. The company is able to produce up to 180,000 bottles per month by this process. While PET processing and filling is not a bottleneck in the plant. Mr. Golovachev wants to increase overall capacity; not least because, in summer, demand is three times the plan’s actual production capacity. Kamenka has a population of about 25,000 people and, today 119 of them are employed at Kamenka Brewery, which makes it one of the biggest employers in the city. With the exception of a change in malt supplier from a local source to a more stable malt from Belarus, the entire brewing process and equipment dates back to the plant’s foundation, in 1968; the factory remains coal-powered. Mr. Golovachev is proud to be one of the few regional brewers who do not use any pasteurisation, preservatives or chemicals (mostly forbidden in Western Europe) as many larger breweries do in order to increase the shelf life of the PET beer bottles to 6-12 months. “Even if we wanted to, we could not use pasteurisation or chemicals as our equipment is too old”, Mr. Golovachev states with a smile. The fact that the beer is 100% natural but still affordable are the main sales points. When he emphasised this by putting an additional “100% natural” label on the bottle, sales increased immediately by another 14%. According to Mr. Golovachev beer in Russia is packed to about 73% in PET, 16% glass, 7% kegs and 4% cans. From 1996 to 2001 the beer market was solely in the hand of multinational companies. And even today, about 98% of the produced beer is sold by global businesses like Heineken or Carlsberg, which also owns the Baltika brand. The average beer consumption in Russia is about 42l per person/per year. Manual preform converting: Heating and blowing go hand in hand at Kemenka July, 26, 2012 Rosinka We met: Vladimir Trofimov, Board of Directors Vladimir Trofimov at his office","@ID":18} "PRODUCTS 39 PETplanet insider Vol. 14 No. 04/13 www.petpla.net Storage gets makeover The storage department may not be as visible as other functions and can be overlooked, which means that there may well be opportunities for improvement in this area, in order to raise consistency in the end-to-end management of plastic processing. Moretto says that it has dedicated a part of its research and development activity to enlarge its product range to include storage and the development of new, integrated solutions, based on the application of higher technology. Its Silcontrol solution is described as an integrated storage department management system, which synchronises material arrival with sorting to silos and helps to reduce human error. Entry material is identified by a bar code control and is automatically despatched to the identified silo. Silcontrol manages the tank truck connection to the silo loading pipe and verifies the exact connection. The process is displayed on a control panel that shows silo loading level. It also identifies any anomalies and allows operations on individual devices connected to each silo. A luminous signal indicates the system operating status, on the control panel and the silos’ main valves. Moretto says that Silcontrol can also be integrated in its Mowis supervising system. www.moretto.com Water treatment system Krones AG offers water treatment systems for the food and beverage industries. The systems incorporate individual units that can be used with fresh water from wells, tap water, or surface water. They also include media filtration with multi-layer or activated-carbon filters for removing sand, oxides, manganese, iron, flavourings etc., as well as ultra-filtration for decontamination and reverse osmosis for demineralisation. Customised systems can be created from the individual units. Krones claims that energy consumption is up to 20% lower than with conventional systems. They have been designed to consume less electricity and compressed air and to produce minimal wastewater quantities of concentrate. Frequency-controlled pumps prevent water hammers during start-up and shut-down and the reverse-osmosis membranes are rinsed with permeate, for protection against uncontrolled furring. Rinsing in ultra-filtration is performed using filtrate and the activated-carbon filters are sanitised with hot water, rather than steam. The standard resourceosmosis unit is made of a combination of stainless steel and GRP but can be made entirely from stainless steel and sanitised with hot water, for protection against microbiological contaminations. www.krones.com","@ID":41} "PREFORM PRODUCTION 22 PETplanet insider Vol. 14 No. 04/13 www.petpla.net Husky’s focus on emerging markets A breath of fresh air in emerging markets Husky’s announcement that in 2013 they have decided not to participate in the two major plastics fairs, K’ 2013 in Düsseldorf or at Drinktec in Munich, has caused a considerable stir, to say the least. Reason enough, then, to ask what lies behind the surprising decision and learn more about Husky’s growth strategy. Waldemar Schmitke, Editor-at-large for PETplanet, talked with Jeff MacDonald, Husky’s Vice President Marketing. The world market leader in PET preform systems has reported encouraging growth in emerging markets that has been accompanied by increased demand for lower volume preform systems in the 48-and fewer cavities sector. Jeff MacDonald began by stating that Husky has sold 50 preform systems in the H-PET All-Electric (AE) series since its launch in 2010, which has proven to be an ideal solution for customers in emerging markets: “It was only relatively recently that we started to realise just how much opportunity this market presents and how demand for two-stage preform systems is growing steadily.” “The question we have to ask,” MacDonald went on, “is what are our customers’ expectations? It seems to us that customers in this lower volume segment want to put themselves in a competitive situation by supplying a premium quality preform, while minimising production costs, and at the same time reducing investment risk.” Surprisingly, the dominant commodities in these emerging markets, even with lower volume systems, are for mineral water and CO 2 applications. While there has been global interest with orders for lower volume applications in mature markets, 90% of orders for the H-PET AE system have come from emerging economies. MacDonald explained that the lower volume H-PET AE range is a dominant force. Once again, it is not a question of all-electric versus hybrid machines. That is part of the key decision criterion, but it is important to look at the system’s total performance to determine what technology will work best to meet a customer’s production and application needs. What about established customers? Where are they heading? According to Jeff MacDonald, many are focusing on household and food packaging applications up to 48 cavities. Their objective is to enter new markets and extend their product range. Following years of increases in the average number of cavities for preform systems, it appears the demand has peaked for now and there seems to be little scope for further growth in cavitation. The average number of cavities per preform system supplied is currently between 72 and 96 cavities, which is now showing a decline. The basic reason for this is, “better technology equals improved performance per cavity.” Husky is also seeing established customers purchasing 144-cavity systems for very high volume production of the most highly standardized products. This leads us into an interesting discussion about Husky’s future projects. MacDonald was clear about where the priorities lie. In regards to PET, Husky is concentrating on its HyPET and H-PET AE preform systems, both now and in the immediate future. Husky’s next generation HyPET system was officially launched in November 2012. The system incorporates proven technology from Husky’s High Performance Package (HPP) system to enhance productivity and performance. We asked about the recent acquisition of the KTW mould making facility. MacDonald stressed that the acquisition is relevant to the company’s beverage strategy. “We will now be able to supply the complete HyCap injection moulding system, including machine, mould, hot runner and controller, from a single source. It means that we no longer have to use third party moulds, thus streamlining integration and enabling us to more effectively measure and deliver results. But the real benefit,” he concluded, “will be the impact on our customers’ total cost to produce through leveraging and improving on the closure mould as part of the complete system. For example, our HyCap HPP system offers an up to 20% increase in productivity, and energy savings of up to 20% over the previous generation product. This is only possible through the complete system approach and Jeff MacDonald, Vice President Marketing, Husky Injection Molding Systems Waldemar Schmitke, Editor-at-large for PETplanet insider","@ID":24} "NEWS 11 PETplanet insider Vol. 14 No. 04/13 www.petpla.net SIPA S.p.A. - Via Caduti del Lavoro, 3 - 31029 Vittorio Veneto (TV) - Italy Tel. +39 0438 911511 - Fax +39 0438 912273 - e-mail: [email protected] www.sipa-xform.com NEW PREFORM SYSTEM Designed to adapt. Built to last. Imagine using any preform mold in one system. Now you can. The new XFORM PET preform system gives you unprecedented flexibility combined with the highest running efficiency: it accepts the mostly used molds (old and new generation) present in the market. So you can feel free to innovate and grow without penalizing your existing assets. Chinaplas 2013 Chinaplas 2013 will be staged at China Import and Export Fair Complex, Pazhou, Guangzhou, May 20-23, 2013. The organisers say that the exhibition will showcase diversified solutions, new plastic materials and technologies, along with lower energy consumption. d by Saudi Basic Industries Corp (Sabic), uses new types of plastic materials with high light transmittance features. Eleven specific ‘zones’ cover a range of plastics applications, including film technology, moulding, plastic packaging and blow-moulding machinery. The exhibition area will exceed 220,000m², covering 25 exhibition halls located at zone A and B of the exhibition complex. More than 2,800 exhibitors from 36 countries together with 14 pavilions from Austria, Canada, France, Germany, Italy, Japan, Korea, PR China, Taiwan, Singapore, Swiss, Turkey, UK and USA, will be present. Over 115,000 visitors from 150 countries and more than 100 buyer groups are expected to attend. Free tickets can be obtained via the website. An app and website for mobile devices have also been launched. www.ChinaplasOnline.com K Show 2013 K 2013, the International Trade Fair for Plastics and Rubber, will be held in Düsseldorf, Germany, October 16 -23, 2013. The new website is now open and provides information surrounding the trade fair, news from the industry, research and science as well as advice for visitors. The exhibitors’ database is now online and serves as the virtual catalogue of the K trade fair. The “Companies and Products” area of the portal enables visitors to search for individual companies or compile a list of companies offering specific services or from selected countries and download them, and create a personalised exhibition catalogue. A “matchmaking” function is an internet networking service and the K App provides mobile access for Android and Apple systems. Tickets can be bought online and printed out from the end of March 2013; e-tickets are offered at a discount. As in 2010, the K ticket includes the use of buses and trains of the public transport system in Düsseldorf and the immediate region. Ticketholders can also benefit from special prices on rail travel from all German cities to Dusseldorf. The Dusseldorf Messe website provides lists of hotels in the area. www.k-online.de","@ID":13} "PREFORM PRODUCTION 21 PETplanet insider Vol. 14 No. 04/13 www.petpla.net Sipa handles worldwide sales, system integration and service for Athena-based preform systems. The 500t XForm preform system in horizontal construction introduced by Sipa is complemented by the Athenabased 300-tonne XForm with up to 96 cavities and the 150-tonne XForm with up to 48 cavities. According to Robert Schad, plans for machines in other sizes are underway. The first deliveries of Athena-based preform systems are expected in the second half of 2013. The preform systems feature: Hybrid construction Horizontal 2-platen machine, with electrically operated clamp stroke Various screw diameters on single and two-stage injection units Electric extruder screw-drive with two servo-motors. Central energy supply for entire system Lateral preform unloading and postmould cooling integrated in machine base Horizontal preform transfer with up to six cooling positions Recycling line recoSTAR PET iV+ Starlinger Head Office: Sonnenuhrgasse 4, A 1060 Vienna T: +43 1 59955-0, F: -180 [email protected] www.recycling.starlinger.com A member of Starlinger Group Visit us at: Chinaplas 2013, Guangzhou, May 20 - 23 Hall 9.2, Booth A41 Recycle, Refine, Reuse: Through upcycling, PET waste becomes a valuable secondary resource, substituting virgin resin at up to 100% According to Enrico Gribaudo, General Manager, Sipa Italy, the partnership represents a further step towards technological market leadership in the PET market. In so doing Sipa is not only showing a commitment to machine technology but is also driving forward the development of the PET bottle. Gribaudo says: “Through our portfolio and our own in-house expertise, we monitor bottle development from preform manufacture right through to the filling stage. This means that we are able to offer a customised solution for any packaging problem.” The next stages of PET bottle weight reduction The next generation of neck finishes and screw closures is under development and will be introduced shortly. Here the focus lies on further weight optimisation of the neck finish. “The potential for savings in the 1881 closure, for example, is something of the order of 40%. This means a further 1.8g reduction in weight. The bottom section offers further potential for weight reduction and we are currently working on this. The relevant technological solutions will be introduced shortly“, says Enrico Gribaudo, “and will undoubtedly feature at Drinktec and the K-Show later in 2013”. www.athenaautomation.com www.sipa.it F.l.t.r.: Enrico Gribaudo, Robert Schad, Waldemar Schmitke. In the background: Athena’s long time test PET preform machine 150t 48 cavities 360°","@ID":23} "imprint EDITORIAL PUBLISHER Alexander Büchler, Managing Director HEAD OFFICE heidelberg business media GmbH Häusserstr. 36 69115 Heidelberg, Germany phone: +49(0)6221-65108-0 fax: +49(0)6221-65108-28 [email protected] EDITORIAL Doris Fischer: [email protected] Michael Maruschke Ruari McCallion Waldemar Schmitke Ilona Trotter Wolfgang von Schroeter Anthony Withers MEDIA CONSULTANTS Ute Andrä [email protected] Martina Hischmann [email protected] Roland Loch [email protected] phone: +49(0)6221-65108-0 fax: +49(0)6221-65108-28 France, Italy, Spain, UK Elisabeth Maria Köpke phone: +49(0)6201-878925 fax: +49(0)6201-878926 [email protected] LAYOUT AND PREPRESS Exprim Kommunikationsdesign Matthias Gaumann | www.exprim.de READER SERVICES Shiraz El Goudi [email protected] PRINT Chroma Druck & Verlag GmbH Werkstr. 25 67454 Römerberg Germany WWW www.hbmedia.net | www.petpla.net PETplanet insider ISSN 1438-9459 is published 10 times a year. This publication is sent to qualified subscribers (1-year subscription 149 EUR, 2-year subscription 289 EUR, Young professionals’ subscription 99 EUR. Magazines will be dispatched to you by airmail). Not to be reproduced in any form without permission from the publisher. Note: The fact that product names may not be identified as trade marks is not an indication that such names are not registered trademarks. 3 PETplanet insider Vol. 14 No. 04/13 www.petpla.net EDITORIAL dear readers, Every so often we come across extraordinary new ways of re-using empty PET bottles that go way beyond the usual recycling process. For the most part these are highly unorthodox ways of transforming PET bottles into cones or strips which can then be woven into bags. It is quite rare for bottles to be taken up by designers. We have discovered this web page which we think might be of interest: http://www.designboom.com/contemporary/petbottles.html Here a few creative heads have got together to come up with novel ways of re-using empty PET bottles. We were particularly taken with the watering can and the clothes hanger. The only question that comes to mind is whether these two designer objects have been produced with the PCO 1810 or the PCO 1881. It should work with either of them. Yours Alexander Büchler Hanger, design by: Xuan Yu from USA Designer’s own words: The product turns two plastic bottles into a clothes hanger by screwing the bottles into the hook. By the concept that reuses empty plastic bottles, I am trying to present to consumers a realistic idea of environmental realities with the hope that it will encourage the reuse of already “consumed” items to form a new functional product. The design incorporates the following features that make it practical and appealing to both producers and consumers: • Low cost, realistic commodity • The shape of the bottle provides more fit support for the shoulder of clothes than traditional ones • Inspire the interest of users: the concept will attract consumers and inspire a rethinking of consumption habits. Watering can, design by: Nicolas le Moigne from Switzerland Designer’s own words: The idea consists in re-using PET and glass bottles. A PET closing piece is able to fit different shapes of bottles and change it into a watering can.","@ID":5} "BOTTLES 43 PETplanet insider Vol. 14 No. 04/13 www.petpla.net The natural look Latvian company Helen Herber has launched a new range shower gels formulated to cleanse and protect the skin without the use of harsh chemicals, and has selected M&H Plastics to help create their new packaging. Helen Herber Shower Gels contain natural ingredients including rose, melon, sweet plum, coffee and cornflower and were created without the use of what the company describes as ‘harsh chemicals’, such as SLS, PEG and Parabens. Their laboratory and manufacturing complex has been certified to ISO 22716 and HACCP standards and the raw materials have obtained ECOCERT certification. The company selected M&H’s 250ml Tall Square PET bottle (Ref. 4089) from its standard products range, topped off with a gloss black pump. M&H has over 1,200 standard products offering cost-effective solutions plus the ability to custom mould exclusive designs in house. www.mhplactics.com Easy grip The French trading group “System U“ of Rungis have their 2.25 litre liquid detergent “Aktiv 4“ on retail shelves in a PET bottle moulded into a shape that is particularly easy to grip. The square bottle features a particularly large gripping area designed with a roughened surface and with additional grooving. The contents of the bottle and the size call for a secure grip in order to ensure safe and secure handling of the gel. The labels to front and rear which are adapted to the shape of the packaging convey the retail and consumer information. www.magasins-u.com 1-2- spray from the handle Vileda GmbH of Weinheim, a subsidiary company of the Freudenberg Group, is offering a floor cleaning system with a spray action device incorporated in the handle. In this system the floor cleaner is integrated in the handle and is applied directly to the floor by means of a lever mechanism and a valve. A small PET bottle with a content of 275ml is fitted to the handle as part of the basic equipment although the 750ml re-fill bottle has to be purchased separately. Non-Label Look labels complete the packaging design. www.vileda.de Foam bath in designer bottle Lidl, the Neckarsulm, germany, discount chain, is selling, under its own brand name “Cien“, a 2-phase foam bath and shower gel in an unusually shaped, extrusion blow-moulded PETG bottle with a content of 400ml. The bottle is shaped like a segment of a sphere with a slightly concave front. The two phases that only the foam bath has enable the user to distinguish between shower gel and foam bath. The retail information is printed directly on the container. The fact that the bottle is tinted gives the product its name. www.lidl.de","@ID":45} "NEWS 10 PETplanet insider Vol. 14 No. 04/13 www.petpla.net BERICAP the plastic closure company committed to your success www.bericap.com Research and Development Developing closure solutions to meet your specific requirements Mould Technology A detailed understanding of mould design with in-house mould making facilities in Hungary and Germany Global Presence Local production in 21 strategically located factories. An on-going strategy of stregthening our global presence Capping Technology and Know-How Special advice on capping technology with on-going technical support Innovation and Flexibility Our broad range of plastic closures is the basis for generating new innovation. Our expertise covers aseptic, hot fill, barrier, anti-counter- feiting TE-systems, consumer convenience and child resistance Extricom: solid start to 2013 PET recycling plant manufacturer Extricom GmbH, of Lauffen am Neckar, Germany, started 2013 with orders in place for 400,000t/a of recycling capacity. Once installed, the plants will use ringextruder technology to turn postconsumer PET flakes into FDA and EFSA-compliant pellets. The company also reported strong demand for bottle-to-bottle PET recycling plants; a segment it currently serves this segment with standard plant capacities of up to 4200kg/h or 100t/ day. Existing orders means that Extricom will be supplying plants to customers in Europe, Asia and South America during 2013. In Belgium, engineering company Uhde Inventa-Fischer’s Melt-To-Resin (MTR) plant in Geel, Belgium, includes a continuous Flakes-To-Resin (FTR) recycling line with a capacity of 54,000t/a and will add a portion of rPET flakes straight to a virgin PET reactor. www.extricom.de IVL reports solid 2012, growth in 2013. Indorama Ventures Public Company Limited (IVL) has reported that its 2012 revenues amounted to US$ 6.78 billion in 2012; a rise of US$ 678 m over 2011. 2012’s EBITDA is reported as US$ 453 million; consolidated net profit after tax and minority was US$ 148 million; consolidated operating cash flow was US$ 471 million; and consolidated return on average net operating capital employed was 7%. Consolidated EBITDA declined by 19%, which the company ascribed to continuing oversupply of PTA in Asia and weakness in the commodity polyester value chain. IVL generated US$ 471 million of net cash flow from operations in 2012, compared to US$ 334 million in 2011. Net operating cash flow grew in line with investments. IVL says that operational improvements, a brownfield PET capacity addition at Rotterdam, the acquisition of FiberVisions’ global hygiene business and the addition of the Indorama Ventures (Oxide and Glycols) business in North America have potentially offset weak polyester chain margins in Asia. The Company has recommended a final dividend of THB 0.18 for 2012, making THB 0.36 for the full year. IVL expects revenues and EBITDA to grow in 2013 by 19% and 27%, respectively. www.indorama.net New CFO for Husky Husky Injection Molding Systems has announced the appointment of Mark Segal to the position of Vice President, Finance and Chief Financial Officer. Prior to joining Husky, he was Chief Operating Officer of outdoor clothing manufacturer Canada Goose Inc. He has also served as Chief Financial Officer of Spin Master Ltd. and as Vice President, Corporate Treasurer of Norigen Inc. He was previously with Husky as Director, Treasury and Finance from 1997 to 2000. Mr. Segal officially joined Husky on March 4, 2013, replacing George Halatsis, who retired as CFO at the end of 2012 and has joined Husky’s Board of Directors. www.husky.ca","@ID":12} "MATERIAL / RECYCLING 29 PETplanet insider Vol. 14 No. 04/13 www.petpla.net Levi’s launches Jean genius containing PCR PET Eight bottles, one Jean The Levi’s brand has been synonymous with denim jeans since the copper-riveted, hard-wearing work trousers were first put on sale in San Francisco, CA/USA in 1873. The company is now steering a new, trendsetting course with the launch of its WasteLess line. The distinct characteristic of these jeans is that their denim is made of more than cotton. Each pair incorporates recycled post-consumer PET bottles and food trays – a minimum of 20%, which works out as eight 12 to 20 fl oz (40 to 75cl) bottles per pair. The announcement of WasteLess is the latest – and most visible – manifestation of Levi’s policy commitment to sustainable design. In 2009, Levi Strauss & Co. introduced “A Care Tag for our Planet,” an education initiative intended to teach consumers methods of clothes cleaning with less environmental impact. It also encouraged donation of jeans they no longer wanted to recycling projects, rather than disposing of them. This was followed up by the development of WaterLess, a finishing technique designed to reduce the use of water. It is reported to have saved over 360 million litres during 2012. The company is also part of the Better Cotton Initiative. In short, Levi Strauss & Co now has an established history of commitment to improved environmental performance, so the WasteLess line will not be a completely unfamiliar venture. Through the company’s partners, PET bottles including brown beer bottles, green soda bottles, clear water bottles and black food trays – are collected through municipal recycling programs across the United States. The bottles and food trays are first sorted by colour, before being crushed into flakes and converted into a polyester fibre, which is blended with cotton fibre and woven with traditional cotton yarn by Cone Denim to create the fabric used in the WasteLess brand clothing. The colour of the bottles used is claimed to add a distinctive undertone to the denim fabric and to create a unique finish in the final product. The WasteLess line is available to both men and women and was commercially launched as part of Levi’s Spring 2013 collection. By adding value to waste, we hope to change the way people think about recycling, ultimately incentivising them to do more of it,” said James Curleigh, global president of the Levi’s brand. “This collection proves that you don’t have to sacrifice quality, comfort or style to give an end a new beginning.” The Spring 2013 collection uses more than 3.5 million recycled bottles. The men’s products will be available globally and will feature 511TM Skinny jeans, redesigned 504 Straight Fit jeans and the well-known Levi’s Trucker jacket. Women in the US and Europe will have the option of Levi’s Boyfriend Skinny jeans in a progressive fit. The WasteLess products are available in Levi’s stores and on Levi.com since January 2013. www.levistrauss.com","@ID":31} "25 PETplanet insider Vol. 14 No. 04/13 www.petpla.net Caps and closures Bottle-to-bottle recycling plants Preform and single stage machinery Preforms Preform / Stretch blow moulds Two-stage SBM machinery Filling equipment Resins / Additives Compressors Closure systems Preform and single stage machinery This issue features two market surveys; the first covers preform systems, the second relates to single stage machinery. The companies appear in the order in which their details were received by the editors. In alphabetical order they are: For preform systems: Husky, Netstal (including the Krauss-Maffei range), Nissei ASB, Olicorp, Sacmi and Sipa For single stage machinery: Aoki, Automa, Cypet, Mould&Matic, Nissei, Sipa. Although the publishers have made every effort to ensure that the information in this survey is up to date, no claims are made regarding completeness or accuracy. 04/2013 MARKETsurvey Preform Equipment Company name Nissei ASB Machine Co., Ltd. Sacmi Imola Olicorp Postal address Telephone number Web site address Contact name Function Direct telephone number Fax E-Mail 4586-3 koo, Komoro-shi, Nagano-ken, 384-8585 Japan +81-267-23-1565 www.nisseiasb.co.jp/en Mr. Katsuo Ishiguro Section Manager, Sales Coordination Team +81-267-23-1565 +81-267-23-1564 [email protected] Via Provinciale Selice 17/a 40026 Imola (Bo), Italy +39 0542 607111 www.sacmi.com Moraldo Masi B.U.PET - Beverage Division +39 0542 607888 +39 0542 642354 [email protected] rue de Montbrillant 26 1201 Geneva, Switzerland +41 223091540 www.olicorp.ch +41 443553820 [email protected] Preform injection moulding systems Machine model number / name PM-70/65NII, PM-70/111N, PM-170/111M IPS220 HSPI Series Number of cavities (min/max units) 6 - 48 48 16/48 Maximum individual preform weight 240g 60g 55g Max resin through-put (kg/h of PET) 250 (approx) 625 1,000 Standard features Vertical clamping built-in preform after-cooling stations injection cylinder (shooting pot) Rotary injecion compression machinery Options / special features Outputs are tailored to ASB's own range of two-step blowing machines for hot fill application. PM-170/111M designed for bottle and jar preforms with capability of neck size up to 120mm. Electrical drive for plasticizing screw; T-belt for preforms extraction; robot with three postcooling stations on take out plate; HMI with control of all auxiliaries; digital valves for each actuator; water unloading system prior to mould changing; fast change over system with plug-and-play mould fixing system; plug-and-play take out plate fixing system; energy recovery system on robot linear motor; belt free robot linear motor; water pumps for mould cooling assembled on main machine platform; double cylinder for preform ejection; secondary belts system for an easier collection of preforms; quality control vision system with multiple camera","@ID":27} "EDITOUR REPORTS 12 PETplanet insider Vol. 14 No. 04/13 www.petpla.net Time stands still in Kamenka. And from a long subsequent discussion we learn more about the Russian beer and PET market, and why Kamenka is one of the few breweries in the region that does not use any chemicals or preservatives during the brewing process. After Kamenka we pass over to Lipetsk, the flourishing Russian city of 500,000 people living mainly from the heavy industry and one steel plant employing 35,000 people alone. Because of this, air quality is an issue in Lipetsk as we learn from Vladimir Trofimov of Rosinka company and one reason why they put a special focus on cleanliness in production which in turn is realized by a high degree of automation. After that, we are getting a new appointment on a very short notice at Lipetsk Pivo, the manufacturer of the unique 30l beer keg made of PET. The company is located directly next to Rosinka and the 182 different drinks of Lipetsk Pivo get water from the same underground spring. Lipetsk was the last station of the Russian part of the Go to Brau Beviale Tour. We had several very interesting discussions and learned a lot about the Russian PET market and its specific characteristics. However, it is time to pass over to the Ukraine. Russia After taking over the Editourmobil, we continue the Go to Brau Beviale Tour as the second team. We drive from Jekaterinburg all the way into Ukraine. The first stop after Yekaterinburg is Ufa, the once booming Soviet industrial city, which is a great distance of 480km away. This city is getting a new modern touch, endless new buildings and can be proud to have already the third highest density of retailers in all Russia. Here, on the company ground of a former Russian scientific research company, we visit the Bering company and learn more about PET bottles used for cosmetic products and the popular Lalinka beauty brand. After a friendly discussion and a factory tour we receive a message from the Kamenka Brewery inviting us to visit their company to speak about PET and enjoy the “virgin nature” over there. We are pleased to confirm and head toward Kamenka town. Here we witness how the beer is brewed since more than 40 years in the Kamenka factory: coal-fired heating supply for the brewing process, unique manual PET converting and hand-filled bottles. by Michael Maruschke Part 4 From Yekaterinburg to Ukraine Nuremberg Nizhny Novgorod Kazan Perm Yekaterinburg Chelyabinsk Yaroslavskaya Moscow Ufa Samara Saratov Volgograd Rostov-on-Don Dnipropetrovsk Kiev Warsaw Novgorod Saint Petersburg Gatchina Fryazino Kamenka Lipetsk Zaporishsha Mykolaiv Kharkiv Chernihiv Kalinovka Lübeck","@ID":14} "PREFORM PRODUCTION 24 PETplanet insider Vol. 14 No. 04/13 www.petpla.net Mold-Masters: From hot runners to preform* Performance boost for installed preform systems by Waldemar Schmitke, Editor-at-large for PETplanet insider The PET market overall is showing cautious growth. Only in the emerging markets and specialist niches is there evidence of higher growth rates. In the niche markets, small and medium capacities of up to 48 cavities seem to be the predominant features. However, there does seem to be an increasing demand for the refurbishment of existing PET installations in the preform mould sector. According to estimates, the volume is higher today than the current demand for original equipment. The reasons for this may be traced to the continuously shrinking life cycle of preform geometries as a result of lightweighting and the need to make more flexible use of existing equipment in response to pressure from the market (more preform formats with no corresponding increase in volume). Mold-Masters entering in the PET market Mold-Masters is a specialist in hot runner technology. The company has been involved for more than 50 years in the building and development of hot runners for the plastics industry. Asked why Mold-Masters has become involved in such a specialised market as PET, Mr. Richard Sieradzki responded as follows: PET represents a very interesting market for Mold-Masters, In particular, the high population of preform systems and their requirement for refurbishment. However, the PET mould-making industry is relatively small and exclusive. The potential for supplying hot runners only to PET mould-makers is limited because the majority of suppliers have their own hot runner technology, consequently, the only way into this market is by way of a complete preform mould incorporating a competitive technology. It was this that led to the acquisition of Abba Canada, a long-term manufacturer of insert components for PET preform tools. The mould integration and the performance test take place at Mold-Masters in Georgetown, Ontario, Canada. iFlow and iCool Technological features include iCool for the cold half of the mould and iFlow for the hot side of the mould (the hot runner). The PET activities are brought together globally in MPET. The emphasis is on the two-stage market, but there is also a requirement in the single-stage market, although here demand is limited to hot runners. The performance package is made up of mould and hot runner conversions and refurbishments for 2 to 144 cavity preform moulds. Interface adaptation is taken care of and conversion kits include preform unloading plates that are available for all preform systems currently established on the market. This doesn’t just include the exchange or replacement of moulds or insert components but also improves the performance of existing preform systems in terms of energy requirements and capacity. This is possible because of the iCool and iFlow technology, says Richard Sieradzki and this means a further competitive option for the industry over the OEMs. In addition, there is the possibility of integrating moulds with a higher number of cavities into existing preform machines and thus achieving a considerable increase in output, providing other peripheral activities are in place. Co-Injection For co-injection PET applications there is a proprietary hot runner development that can also be adapted to existing cold sides. This applies both to 2-stage and single-stage systems. The incorporation of an all-electric injection moulding unit up to 55mm screw diameter (which can be supplied) turns a mono-application into a coinjection system. www.moldmasters.com Richard Sieradzki, Global Vice President MPET, Mold-Masters Richard Sieradzki Global Vice President MPET, left, and Waldemar Schmitke Editor at large PETplanet Some years ago, Mold-Masters made a decision to invest in the PET market. Richard Sieradzki, Global Vice President MPET at Mold-Masters, explained to PETplanet insider, why Mold-Masters has become involved in such a specialized market. *The interview with Richard Sieradzki took place one week before the news of the Milacron and Mold-Masters merger broke. Mold-Masters announced on March 28 the completion of the acquisition of Mold-Masters by Milacron LLC.","@ID":26} "PETbottles 42 PETplanet insider Vol. 14 No. 04/13 www.petpla.net Home + Personal Care Getting a grip on car care One problem with many thinwalled PET bottles is that you have to compress them slightly when lifting them in order to hold them securely. This often means that, if the product has been opened, one has to contend with the risk that the product may accidentally gush out. Cue for Sonax GmbH‘s bottle containing their car care product “Wash & Wax“ to come to the rescue. The red PET bottle has an indentation in the grip area and this indentation also incorporates additional recesses for the finger tips. Additional grooves and embossing on the bottle lend it an air of technical sophistication. A screw-type dispensing cap with tamper-proof strip and two self-adhesive labels complete the packaging. www.sonax.com Multi-active cleaner For more than 100 years products marketed under the Sagrotan brand name have been a pioneer in the household hygiene sector. The formulas are being constantly improved and adjustments made to meet current requirements. One example of this is the Multi-Active Cleaner which removes limescale, grease and soap residue, together with 99.9 % of bacteria. The product is packaged in a PET bottle which is comfortable to hold and also has a raised finish in the area where it is held in order to ensure a tighter grip. The bottle contains 500ml and the product is applied using a pump dispenser which features a locking function. An adhesive sticker indicates not only the birthdate of the brand name but also its mission to promote health. www.sagrotan.de 28 washes in one bottle Henkel France has in its range a detergent concentrate with the fragrance ”Savon d’Alep“. The product comes in a stylish PET bottle with a content of 925ml which the company is marketing under the “Le Chat“ brand name. The product, which is sufficient for 28 washes, is dispensed via a hinged lid with a snap-on, transparent lid incorporating markings. The bottle is decorated with a partially printed shrink sleeve label featuring a scale in the side section from which the user can easily read off how many washes are left in the bottle. According to the manufacturer, the bottle is made from recycled PET and the active washing substances (Tensides) are bio-degradable. www.henkel.fr Fun soap dispenser Erdal Rex of Mainz, Germany, are showcasing their original Froggy children’s soap dispenser in attractive packaging at the PoS. The 300ml content PET bottle is refillable and there is a frog clinging to the feed tube. The product, which is specifically adapted to children’s sensitive skin, is dispensed via a pump dispenser. A window on the front of the outer packaging and a coordinated printed section on the inside together give a fun, 3-dimensional impression. www.erdal-rex.de","@ID":44} "EDITOUR REPORTS 13 PETplanet insider Vol. 14 No. 04/13 www.petpla.net July 13, 2012 Bericap We met: Mr Sergey Litskevitch, General Director Bericap’s range of closures The only plant operated in Russia by the closure manufacturer Bericap is located around 450km from Moscow in Bor, close to the picturesque town of Ninzhniy Novgorod. We are in a meeting with Sergey Litskevitch, the company’s General Director. Since the late 1990s the Russian market had been serviced from locations in Hungary and subsequently also from Poland. This meant that there was already regular business with what was still, at that time, a packaging market for liquid food that was still pretty much in its infancy. Finally, the management of the German company realised that rapid growth in beverages in plastic packaging was occurring which would necessitate a reorganisation and re-structuring of the company. This led them to set up their own operation in Russia in 2002, and of course the emergence of a significant market was the reason behind this decision. Litskevitch himself was at the time not yet on board, joining the company only in 2008. An appropriate location to build the Bericap plant was ultimately identified in Bor in fields formerly used for growing potatoes. These days, says Litskevitch, Moscow is not really a viable option. Land prices, energy and personnel costs are too high which have made the city increasingly unattractive as far as big companies are concerned. Companies who were located in the capital have mostly decamped to the surrounding area. A decision that Bericap does not now have to face. Following the purchase of the plot in Bor the plant was established in 2002 and went into production for the first time in 2003. Subsequently, another storage facility was added. Initially, the only machines operating here were a handful of injection moulding machines and the closures produced were sold chiefly in the edible oils sector which was then experiencing a Sergey Litskevitch and Kay Krüger in front of the Bericap showcase in the meeting room","@ID":15} "NEWS 9 PETplanet insider Vol. 14 No. 04/13 www.petpla.net Are your standard PET preform molds making you as much money as they should? Ask how MPET with iFlow technology improves production and achieves greater quality results. Innovation doesn’t happen in isolation. It happens when blue-sky thinking meets down to earth knowhow and exceptional supply chain execution. The sort of innovation that Mold-Masters is known for, now applied to PET tooling for industry-leading results. Introducing MPET – the new PET preform tooling solution designed for the standards of tomorrow. Mold-Mastersand theMold-Masters logoare trademarksofMold-Masters (2007) Limited. © 2013Mold-Masters (2007) Limited.All rights reserved. Think about it. moldmasters.com/thinkaboutit [email protected] Döhler gets Egyptian Delta DöhlerGroup, of Darmstadt, Germany, has acquired the Fruit Processing and Flavour Unit of Delta Aromatic (Delro), a 25-year-old specialist in fruit and vegetable ingredients based in Egypt. Delro’s “Fragrance” and “Agriculture” business units are not part of the acquisition agreement. The name of the unit will be changed to Döhler Egypt and the production site in Cairo will be known as Döhler Egypt for the Production of Natural Fruit & Beverage Ingredients S.A.E.. The existing management of Delro will remain in place. DöhlerGroup’s technology-based natural ingredients, ingredient systems and integrated solutions for the food and beverage industry includes flavours, colours, speciality & performance ingredients, cereal ingredients, dairy ingredients, fruit and vegetable ingredients to ingredient systems. Döhler Egypt is the company’s first production site in Africa. Egypt is a member of the Comesa (Common market for Eastern and Southern Africa) and Gafta (Greater Arab free trade area) free trade zones. www.doehler.com CBE starts production in China Corpoplast Beverage Equipment Co., Ltd. (CBE), which was founded in 2012 by KHS, has formally opened its newly acquired production building on Suzhou Industrial Park, Suzhou, Jiangsu, which is about 100km north of Shanghai in China. Nearly 100 guests from various beverage companies in Asia attended the official event. The tour of the factory included a presentation on CBE’s Aquabloc blow moulder/filler/capper monobloc machine, which has been specially developed for the Asiatic market. Its outputs range from 24,000 - 48,000 PET bph, in sizes ranging from 200ml to 2l (see PETplanet insider 10/12, page 17). www.cbechina.cn Clariant breaks ground in Poland Speciality chemicals producer Clariant has held a groundbreaking ceremony at its new plant in Konstantynów Łódzki, Poland. The CHF11.3 million modern plant will commence production of colour concentrates for producers of plastic materials in March 2013 and will double Clariant’s masterbatch production capacity in Poland. The 6,800m² facility will include a new production site, laboratory, warehouse, and offices. Clariant has had a presence in Poland for 22 years. www.clariant.com","@ID":11} "CAPPING / CLOSURES 34 PETplanet insider Vol. 14 No. 04/13 www.petpla.net Caps and closures for sensitive soft drinks – the Corvaglia approach* Sense and sensitivity *based on an article by Dr. Michael Krueger, CTO Corvaglia Group The risk of contamination is especially critical for sensitive beverages. As a company specialising in providing technologies for soft drink closure solutions, Corvaglia’s primary goal has to be to avoid penetration of particles or other foreign matter into the bottle under any conditions. In this article Corvaglia presents its approach of taking all types of effects into consideration in the cap/closure design. Effects of pre-treatments Sensitive beverages can be affected and contaminated by external influences like light, temperature, oxygen or micro-organisms to name only a few. It is quite clear that by far the most amount of light or heat will enter through the bottle and not through the closure. Sensitive drinks are usually pre-treated and/or bottled using a filling method that either creates or maintains the sterility of the bottle’s contents in order to increase the shelf-life of the drinks by killing potential micro-organisms. Both pretreatments and filling procedures have an impact on the performance of the package. Hence the package design has to take these effects into account. Table 1 summarises some of the types of treatment typically used prior to filling to sterilise or clean beverages. Effect of filling methods Similarly, filling processes can create exactly the same challenges as pre-treatments since the same methods of sterilisation are used for both (c.f. Table 2). Obviously, challenges can vary significantly for the same treatment or filling types depending on implementation. For instance, whether an aseptic cold filling is done ‘dry’ or ‘wet’, dipped into a bath or sprayed on the product can make a difference: for dry aseptic procedures where hydrogen peroxide steam is used for sterilisation, the temperature of the closures can still be as high as 45°C when arriving at the chuck. This changes elasticity and consequently its capping behaviour. Using wet aseptic procedures, closures arrive at Temperature Radiation Filtration Pressure Chemicals Pasteurization Magnetic pulsation 5μ, 1μ, 0.2μ UHP Ozonation UHT UV Reverse osmosis Sulfuration Electron beam GAC Preserving agents Ultrasonic pasteurization Multimedia filtration Electron beam Table 1: Examples of types of treatment that can be used prior to filling in order to sterilise or clean beverages. UHT = Ultra high temparature; UHP = Ultra high pressure; UV = Ultraviolet radiation; GAC = Granular activated carbon. Temperature Radiation Filtration Pressure Chemicals Hot fill Plasma - - Addition of preservatives (e.g. E242 ‘Velcorin’) Tunnel pasteurization UV Aseptic cold fill Table 2: Examples of filling processes that can be used to sterilise beverages or maintain sterility. UV = Ultraviolet radiation Temperature Radiation Filtration Pressure Chemicals Change of material properties Change of inherent material properties - - Change of organoleptic properties Change of shapes of packages Remains of treatment chemicals Table 3: Potential hazards associated with pre-treatment types and filling procedures that have to be accounted for when designing closures the capping chuck with a lower temperature. Effects of temperature and chemical treatments When designing a package or closure, the effects of temperature and chemical treatments must be primarily taken into account. The former can for instance change the sealing performance by changing the material properties. The risk associated with the A Corvaglia 33mm hotfill closure on a sport drink","@ID":36} "BOTTLE MAKING 32 PETplanet insider Vol. 14 No. 04/13 www.petpla.net New generation one-way PET KeyKeg launched by Lightweight Containers Double walls, doubled resistance Lightweight Containers has announced the launch of KeyKeg20, the first of a new generation of KeyKegs. The cylindrical container, which will be available from Q1 2013, is claimed to offer improved logistics practicality, lighter weight and better resistance to both internal and external pressures. At its launch event at Brau Beviale 2012 in Nuremberg, Germany, representatives of Lightweight Containers said that the new KeyKeg20 (for 20l) has been developed in response to customer demand for one-way, lightweight packaging that could be used for highly-carbonated beverages, is robust enough to withstand hot climates and long journeys, is moisture-resistant, makes use of recycling technologies and is safe, as well as logistically effective. The company maintains that the market share of one-way kegs containing CSD, still soft drinks and carbonated alcoholic beverages will grow in years to come and that its new package is an important step along the way. “We have worked continuously for two years to develop the Double Wall technology and the cylindrical KeyKeg20,” said Bert Hanssen, R&D director of Lightweight Containers. “We have wanted to make a cylindrical keg for a long time, but we couldn’t get it to meet our high requirements for deformation, resistance to damage and high internal pressure. Newly developed PET-processing technologies like laser cutting and ultrasonic welding suddenly brought the cylindrical shape within our reach.” Key features The core innovation featured in the new package, called Double Wall technology, actually constructs a “cylinder within a cylinder”. When the product is seen unfilled, the appearance is of a rigid outer cylinder with a bag inside. Once filled, the two walls are claimed to work together dynami-","@ID":34} "NEWS 8 PETplanet insider Vol. 14 No. 04/13 www.petpla.net Amcor flourishes in Florida Amcor Rigid Plastics has announced a $20 million expansion of its southeastern U.S. bottle manufacturing operation in Orlando, Florida. The move comes in response to strong market demand for beverage and pharmaceutical packaging. Amcor says the investment will also enable the centralisation of preform manufacturing and warehousing while improving logistics and shipping efficiencies. The company recently relocated from an existing 15,000m² plant near the Florida Turnpike to a new, leased 45,000m² facility within the Airport Industrial Park of Orlando, just a few miles from the former location. The multi-milliondollar investment enabled the conversion of an unfinished shell structure into functional space for manufacturing, warehousing and offices. The new facility is already operational, producing hot fill and cold fill PET bottles for beverages such as sports drinks and orange juice, along with PET carafes for citrus beverages and HDPE pharmaceutical containers. Amcor will manufacture a majority of its preforms in house at Orlando and the new facility will eliminate the need for three offsite warehousing sites. The site has room for future expansion. www.amcor.com Breathe easy Plastic Technologies, Inc. (PTI) has launched a free app, which calculates the oxygen permeation of food and beverage packaging structures and containers. The PackLifeO2 app is based on the M-Rule model and is available on iPhone/iPad and Android platforms. It has been designed as a handy calculator for specific materials and combinations and is not presented as an absolute decision-making tool. The app contains five input sections – material, layers, concentration, conditions, results – that are designed to help the user quickly input data and obtain oxygen permeation results for their specific container. Simple touchscreen procedures cover package dimensions; materials – including PET, PP, PE, PC and nylon 6 – and their thickness; initial parameters; and period of time for study. Results are displayed on a graph. PTI describes PackLife02 as suitable for pretty much everyone involved in the package selection process. The new app is in addition to existing PTI apps: the PET Hydrolytic Degradation Nomograph and PET Blend Calculator. They are all available from the iTunes app store and Android Play Store. www.containerscience.com www.plastictechnologies.com","@ID":10} "PREFORM PRODUCTION 23 PETplanet insider Vol. 14 No. 04/13 www.petpla.net the system demonstrates that much of this new customer value is delivered directly from the mould and how it works together with the machine.” Husky debuted its new HyCap HPP system at Chinaplas 2012. The official launch is taking place in mid2013 and the first systems will be shipped this year. World Tour 2013 We asked Jeff MacDonald about the company’s courageous (or, some would say, risky) decision not to participate in the K-2013 and Drinktec fairs in Düsseldorf and Munich in 2013. He explained that Husky may still choose to attend tradeshows in the future, but for the products the company is launching in 2013, having more focused, local customer events was a more effective approach. “We believe that we can use our resources more effectively to develop closer links with customers across our core markets, both new and established,” he said. “What we are aiming to do,” he continued, “is to bring the newest Husky technology closer to today’s and tomorrow’s customers in our facilities in an interactive way, which will help us to gain a deeper knowledge of the market and of our customers’ requirements. And, we’ll be able to significantly increase the number of interactions we will have with customers throughout the year and in more locations than ever before.” The Husky World Tour 2013 will incorporate a series of customer events in the Americas, Europe, the Middle East and Asia Pacific. It has already been kicked off with a Beverage Packaging Day in Korea. China Any discussion with the key players inevitably comes to the “China question.” MacDonald is emphatic: “Our strategy as far as China is concerned has basically not changed. Machinery and hot runners are built in China. The mould insert groups come from Luxembourg or Canada. Prior to delivery to customers in China, we have the people and facilities in place to oversee final integration, testing and training. This allows us to deliver the same Husky value with competitive lead times and local support.” And the market? There continues to be a demand for high performance systems featuring 96 cavities and higher. “Even with the youngest fleet of equipment in the world, customers are demanding our latest technology advancements to continue improving their quality and lowering their production costs.” How will Husky maintain its position in the market in the coming five years? According to Jeff MacDonald, Husky is planning to become further involved in total solutions for beverage packaging. On-going development will be geared to increased efficiencies leading to lower risk and lower total cost to produce for its customers. MacDonald concluded by stating his belief that there is still enormous potential for reducing the manufacturing costs for preforms and closures without sacrificing quality. www.husky.ca 90% of orders for the H-PET AE preform system have come from emerging economies Husky debuted its HyCap HPP system at Chinaplas 2012 A HyPET system with 96 cavities","@ID":25} "BOTTLE MAKING 31 PETplanet insider Vol. 14 No. 04/13 www.petpla.net at any point on the shoulder or the lateral surface nor must the bottom zone be compressed or crimped under load. Particularly if low-cost bottles with very thin walls are used, it must be ensured that enough material is provided in the base zone to prevent such bottom failures. Internal pressure For the determination of the required internal pressure performance, the contents are the principal determining factor. Will the bottle be used for still liquids or is it intended for carbonated products? In the latter case, the amount of dissolved CO 2 must also be taken into account. Also to be considered are the temperature and humidity environment in which the filled bottles will be positioned to sterilize the headspace and the cap. The contents will generate a vacuum when they cool down. This vacuum condition must not result in the bottle collapsing inward. For this purpose special hot-fill panels can be incorporated in the bottle design, which counteract the tendency of the bottle to collapse. Handling stability The handling or gripping stability is a rather subjective parameter. The customer should have an opportunity to handle similar products so that he can decide which level of grip he desires. Premium products will certainly require a higher handling stability than low-cost products. For certain lightweight containers, e.g., for edible oils, the handling stability can be improved by horizontal ribs. Depending on the design, however, this may result in a “concertina” effect, which would compromise the top-load properties. Also the presence of certain design elements, such as logos, recessed handles, etc., can have a positive as well as negative effect on the handling stability. Stress cracking Especially if exposed to alkaline solutions, PET tends to stress crack when a certain level of stress is Please order your copy at the PETplanet insider book shop: Bottles, Preforms and Closures A Design Guide for PET Packaging Second Edition by Ottmar Brandau 115,00 € 180 pages © Copyright Elsevier 2012 applied. Such stress cracking mostly occurs near the moulding gate. In the case of bottles for carbonated drinks in particular, this may have a significant impact on the quality of the bottle base. Such alkaline solutions promoting stress cracking not only are encountered in the rinsing processes for returnable bottles but are also components of many of the lubricants used for conveyor belts. Although modern belt lubricants are acid based, the stress cracking test has proved to be a good method of evaluating the quality of a container. The stress cracking behaviour of the bottle may also depend on the selected preform and has an influence on the geometric design of the base as well as on the parameters of the stretch blow moulding process. Barrier Depending on the contents, the bottles may need certain barrier properties to ensure the required shelf life for the contents. For example, bottles used for CSDs, sparkling mineral water, or beer may require a barrier against the loss of CO 2 . On the other hand, fruit juices, mixed milk drinks containing fruit juice, or beers must be protected against the ingress of O 2 to prevent premature deterioration as a result of oxidation. Sometimes a barrier against water vapour may also be required, for example, in the case of bottles used for edible oils. The barrier problem is more pronounced with smaller bottles because here the surface/volume ratio of the container is rather high, which is a drawback of smaller containers. Although larger bottles for mineral waters and CSDs will have a sufficient barrier as a result of the biaxial stretching of the PET material, single-serve bottles, which are increasingly replacing beverage cans, will require additional barrier enhancements such as multi-layer constructions or coatings. Ultraviolet (UV) radiation is detrimental to dairy products and beer. As a rule, such products will require collared bottles or the use of preforms made from specially formulated resins with UV blockers. Yet, apart from the bottle size, the required barrier properties do not have an influence on the bottle design. They can, however, have an influence on the selection of the preform (colour, multilayer) (see Chapter 2). Problems of delamination in multilayer bottles, which occurred a year or two ago with certain bottle designs, have now largely been eliminated through modifications in preform production and by running preforms on the low temperature side of the process window. *This article was published in Bottles, Preforms and Closures, Ottmar Brandau, Chapter 1.2., Copyright Elsevier 2012","@ID":33} "BOTTLES 41 PETplanet insider Vol. 14 No. 04/13 www.petpla.net CCT Creative Competence Technology GmbH Idsteiner Strasse 74 D-65527 Niedernhausen, Germany [email protected] www.cct-systems.com PET Molds Closure Molds Developments PET Systems Closure Systems ComPETCap® Designs Design and Patents CCTSystems®BPF for CSD (carbonated soft drinks) current design CCT design 6,26g 4,32g CCTSystems®3025 for still water 3,92g 3,05g current design CCT design CCTSystems®38-2-3S for non CSD, Milk or Juice 4,38g 3,83g current design CCT design CCTSystems®1810 for CSD (carbonated soft drinks) current design CCT design 5,05g 4,10g Caffeine, taurine and vitamins Vitamizzer, a low-calorie soft drink without any artificial colorants or preservatives is available in four variants - Energy, Chill, Active and Absolute – each featuring different additives. The Energy variant contains, in addition to caffeine and taurine, a range of vitamins and tastes of pomegranate, cranberry and acai berries. The drink is packaged in a handy PET bottle with a content of 500ml and a sufficiently large drinking aperture. An opaque screw cap printed on the top and complete with tamper-proof guarantee seals the container and a plastic label serves to convey information. www.vitamizzer.de Fanta in a limited edition Under the Fanta brand name endorsed by the suffix “Beaches of the World“, Coca-Cola Erfrischungsgetränke GmbH of Berlin is marketing a succession of new and exotic tastes which are available in retail outlets for a limited period only. The range is currently featuring a sugar-free Red Kiwi Mix ( strawberry / kiwi), which can also be distinguished from the other Fanta variants by its colour. The variants are bottled in the familiar packaging sizes – the photograph shows the 1l returnable bottle with matching paper label and printed tamper-proof screw cap. www.fanta.de Fine sauce ingredients Right on time for the Christmas market Moreno GmbH of Bornheim in Germany, with an eye on impulse purchases in the retail trade, launched, under the brand name of “Marqués Campoalto”, its range of different port wines, sherries and fortified wines for adding a touch of extra refinement to meals. A number of product variants were grouped together in big cardboard displays. The small, handy PET bottles, which come with a shiny black finish, contain 100ml. Paper labels to front and rear transmit the necessary information and a black screw cap with a tamper-proof guarantee serves as a closure for the ensemble. www.moreno.de Decorated lemonade bottle Gerolsteiner is selling 500ml orangeade with natural ingredients and aromas in a 500ml content PET bottle sporting an elegant shape. The bottle features specially arranged reinforcing grooves that wind their way around the bottle prior to exiting in the form of embossed sections reminiscent of carbonated bubbles floating upwards. A plastic label around the circumference and a screw cap complete with embossed section and tamper-proof closure round off the appearance. www.gerolsteiner.de","@ID":43} "PETnews 6 PETplanet insider Vol. 14 No. 04/13 www.petpla.net Innovative packaging materials at drinktec 2013 drinktec 2013, takes place at the Messe München exhibition centre from September 16 to 20, 2013. drinktec 2013 has set itself the goal of promoting and facilitating the dialogue between the technical people and the marketing professionals by setting up the Innovation Flow Lounge at the West Entrance. Its motto is: ‘Technology meets Marketing’. Petra Westphal, Messe München´s Exhibition Group Director with responsibility for drinktec, explains: “We are not simply leaving that dialogue between technicians and marketeers to chance – instead we are providing a structured forum in which this can happen. Among the many events, for example, are chaired panel discussions.” “Focus on Packaging and Marketing” is the title of a forum event on Thursday afternoon (September 19) in Hall A2. Rising trend: QR codes A key trend that is becoming ever more important in this context is the digitalisation of marketing communication. QR codes on packaging are spreading rapidly. In autumn 2013 drinktec will also be the place for visitors to find out about these new techniques and technologies. PET continues to gain ground Glass and metal are well established, well researched packaging materials. With the tremendous global success of PET bottles, themes like barrier effect have emerged. Much innovative research is being carried out to develop ever more effective barrier layers. This is an important theme, because PET is becoming more and more popular. Of around 785 billion litres of filled beverages in 2010, worldwide around 35% were filled into PET containers, according to PETnology Europe. That made PET the No. 1 packaging material in the segment of non-carbonated water and it is increasingly being used in the filling of alcoholic drinks like beer, wine and spirits. By 2014, according to the forecasts, PET containers will account for a market share of 43%, beating cans as a packaging material for non-alcoholic beverage refreshments into second place. Also the PET beer keg market is gaining ground. With the general tendency towards smaller and lighter-weight pack sizes and the increasing problem of theft of the traditional stainless-steel kegs (because of its valuable raw material), lightweight disposable beer barrels are now attractive. www.drinktec.com Constar cuts CSD US company Constar International LLC, a global producer of plastic containers for food and beverages, has announced that it is reducing its exposure to the highvolume ‘commodity’ carbonated soft drink (CSD) market, which is shifting to self-manufacturing with widely-available machine technology. On January 1, 2013 Constar’s largest supply contract for CSD plastic packaging expired without renewal. Operations at Jackson, MS, and Havre de Grace, MD, which were dedicated to that contract, are being cut back. The Jackson plant at the end of January 2013. The Havre de Grace plant, which has a full range of injection and speciality blow moulding operations, will concentrate operations into the larger of its two buildings. CEO Andre Laus said that the company will now direct its efforts and resources to specific opportunities in packaging markets for hotfill beverage, food, barrier, short-run and specialty products, as well as new applications. www.constar.net CCL buying Avery Denison label business Canadian company CCL Industries Inc., which makes speciality packaging solutions for the consumer products and healthcare industries, has signed a binding agreement to acquire the Office & Consumer Products and Designed & Engineered Solutions businesses of Avery Dennison, on a debt-free basis for $500 million cash, subject to customary closing adjustments. A syndicate of banks has committed to provide debt financing to close the transaction. The two businesses had combined revenues of approximately $910 million with an estimated adjusted EBITDA of $110 million in calendar year 2012. The transaction requires regulatory approval and subject to receipt of that is expected to close by mid-2013. www.cclind.com New members for restructured Corvaglia Board With effect from March 25, 2013, Swiss closure specialist Corvaglia Group has enlarged its board of directors from two seats to five plus Secretary, and appointed a total of four new members. Three new members and a secretary joined the Group’s Board at the end of March 2013. Romeo Corvaglia, company owner and CEO, has moved to the position of Vice Chairman and will continue as CEO. New member Hans Peter Locher has assumed the position of Chairman. The other members are Martin Vogel (Corporate Finance); Barbara Gölz (Human Resources); Franco Bischof (volume production and Markus Alder (Secretary to the Board of Directors). Corvaglia says that all the Board members, existing and new, have experience in family-run companies. www.corvaglia.ch","@ID":8} "CAPPING / CLOSURES 35 PETplanet insider Vol. 14 No. 04/13 www.petpla.net latter is a degraded organoleptic performance and may also lead to a need to eliminate pockets, dead volumes or similar traps for deployed chemicals. Radiation can be an obstacle as well, since, depending on energy and intensity, electro-magnetic radiation can lead to changes to the inherent material properties, for example by cross-linking of polymer chains. An overview of potential hazards per type of treatment can be found in Table 3. The main difference between the effects of pre-treatments and the effect of filling methods on the packaging is that the former risks are merely carried over from the pretreatment whereas the latter risks are applied directly to the package. For example, beverages treated by a UHT process are usually cooled down significantly from the initial temperature of up to 150°C (1) once packaged, whereas the heat applied from tunnel pasteurisation acts directly on the package. Neck standardisation and its limits Beverage packaging is a high volume business which is one reason why standardisation is a very helpful tool within the industry. There is no doubt that standardisation allowed for fast development cycles and lead times since one could rely on an 1881 neck always being an 1881 neck for instance. But the idea of standardisation has its limits. In the early days of PET necks, it seemed like a good idea to take neck designs used for glass bottles and use them unchanged for the plastic bottles. These neck designs have proved to work well for many years. But obviously plastic and glass are significantly different materials. Bearing in mind the different types of treatment described above, it becomes immediately clear that resistivity against high temperatures, for example, has never been a problem with glass bottles while for plastic bottles the very opposite might be the case. Let us take a 38mm neck finish for aseptic cold fill (ACF) applications as an example of issues when adopting unchanged the glass necks. Bottles with 38mm ACF necks and closures are usually used as packages for sensitive beverages. The SINGLE STAGE ISBM MACHINES FOR PET BOTTLES & JARS MORE CAVITIES LESS INVESTMENT PATENTED TECHNOLOGY www.cypet.eu 10 & 12.5 Ltr bottles 2 Cavities MachineModel K 28 100ml Bottles 16 Cavities Model K 28 5 Ltr Bottle 80mm Jar 2 CavitiesModel K 16","@ID":37} "PETbottles 40 PETplanet insider Vol. 14 No. 04/13 www.petpla.net Beverages & Liquid Food New twist for spirits Amcor Rigid Plastics has expanded the use of its roll-on pilfer-proof (ROPP) finish design for aluminium screw-cap PET bottles to meet growing market demand in the wine and spirits segments. It already offers aluminium screw-cap containers in the wine market and has entered the spirits category with new 1.75l and 750ml stock PET bottles. Amcor Rigid Plastics, worked with its sister company, Amcor Flexibles Capsules Group, in transferring the successful wine bottle aluminium closure design to PET bottles. The ROPP finish design is available in 30-mm by 60-mm finish (750ml) and 36-mm by 52-mm finish (1.75l). Amcor asserts that the ability to use the same aluminium closure for glass on PET bottles offers brand owners lower-cost changeovers. The ROPP finish containers are designed to withstand the top load required for aluminium cap applications. The PET bottles meet all required testing to ensure a secure seal with the aluminium closure. A standard plastic anti-spillage pour restrictor typically used for glass bottles is incorporated inside the 1.75l stock bottle neck to prevent spillage. Various decorating options including custom printing and embossing are available. www.amcor.com Dispensing made easy Recently Sara Lee Coffee & Tea Germany GmbH has been marketing “natreen Classic Liquid“ in a handy PET bottle with a content of 125ml and featuring shrink-wrap sleeve label. The transparent, waisted bottle and the screw cap with tamper-proof dispensing lip help to ensure that the liquid sweetener is accurately dispensed down to the last drop. Eight drops have the equivalent sweetening power to that of a single teaspoon of sugar. For measuring out larger quantities of sweetener, a dispensing cap is mounted on the screw closure with a scale showing the corresponding amounts of sugar. www.natreen.de Three in a row The Italian company Casa del Dolce is featuring a strawberry flavoured soft drink for children in its range. Three small bottles made from PET in a novel shape, each with a content of 70ml, are linked by means of a common cardboard connecting strip. The screwed on, pink-coloured drinking fixture is protected by means of a tamper-proof cap. The transparent cap incorporates a depression which interlocks with a detachable segment on the drinking fixture via a keyed connection. www.trinketto.it Elegance in blue San Benedetto of Scorze in Italy has a PET bottle in an elegant blue PET bottle containing 1.5l of carbonated mineral water destined for retail shelves. The unconventional shape of the bottle features lengthwise grooves which are twisted in the waisted area into a helical shape. The tamper-proof (likewise blue) screw cap is only 16 mm tall. A transparent plastic foil label completes the look. www.sanbenedetto.it","@ID":42}
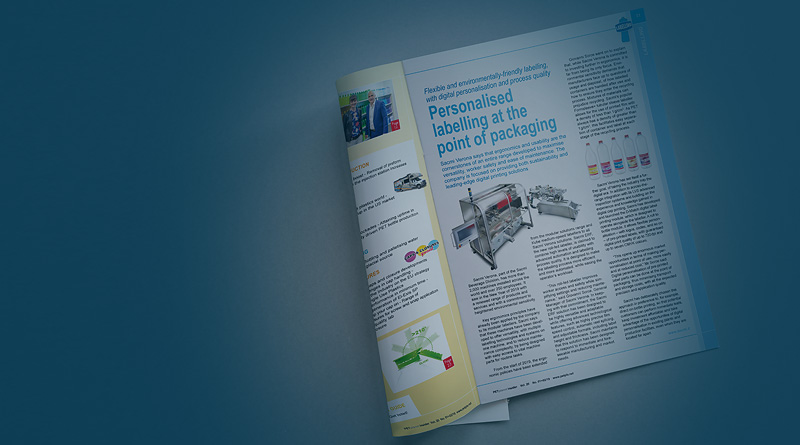