"MATERIAL / RECYCLING 23 PETplanet insider Vol. 14 No. 06/13 Recycling PET bottles at work When it comes to PET recycling, there are predominantly two companies that enjoy a good reputation with the Japanese public: Suntory Holdings Ltd. and Kyoei Industry Co. Companies made a concerted initiative to establish a “bottle to bottle” cycle, where bottles collected are recycled into a new PET bottle, the driving force being the technology of mechanical recycling ( in contrast to chemical recycling, where the bottles are broken down chemically to the molecular level. Used PET bottles, mainly collected from households, are sorted in Kyoei’s plant and processed, including being crushed into small pieces, washed with alkaline fluids and cleaned of impure substances. Chemicals and other substances are totally removed from the resin, which is then recycled into high quality material suitable for new bottles. The equipment used comes from Europe. Since 2011, Suntory’s Haruna Plant has started on a test basis using the recycled resin. The plant uses a blend of 50% Kyoei’s resin, which is mechanically recycled, together with 50% of chemically recycled resin - to produce 2l PET bottles for tea. It was Japan’s first major step into mechanical material recycling. Suntory has said in future it wants to establish a new resource recycling system together with consumers. Suntory plans to use 100 mechanically recycled materials in order to further minimise the quantity of new petroleum required and also cut carbon dioxide emissions. Conclusions The Japanese Packaging Recycling Law which is laid down by Government Ministries in combination with the voluntary obligation among PET bottle manufacturers, users, consumers and municipalities is considered effective. It can be said, that the collection rate is high – the bale quality is high – the high export of PCR to China is seen as a long term problem. Mechanical BtoB was started to economise processes. The voluntary action plan for 3R promotion is widely accepted and effective, in respect of higher collection, increased knowledge, insight and experience as well as in material savings. Sources: CPBR: Council for PET Bottle Recycling JCPRA: Japan Containers & Packaging Recycling Association Suntory – Corporate Message GEA Procomac S.p.A.Hall A4 Stand 314","@ID":25} "TRADE SHOW REVIEW 36 PETplanet insider Vol. 14 No. 06/13 petpla.net Chinaplas, Guangzhou, May 20 - 23, 2013 Dynamic development With its rapid economic growth, China has become the most influential country in the plastics markets worldwide. Last year, the total output of plastic products in China reached 57 million tons, representing a growth of 9% compared to 2011. And the total sales value of plastic products was about RMB 1,600 billion, a 15% growth compared to 2011. Once again, Chinaplas 2013 reflected this dynamic development. 2,900 exhibitors from 38 countries shared a total area of 220,000m². More than 3,200 sets of machines were on display in 25 exhibition halls. The four-day show’s 114,000 visitors (not including exhibitor staff and media) represented an increase of approx. 4% compared to the Chinaplas 2012 show in Shanghai. The international component of Chinaplas also continues to grow, with visitors from outside China increasing to 27%, up from 25% at the previous Shanghai show. Chinaplas is certainly no longer a “Chinese Affair”, but the meeting point of suppliers and customers from the West, Asia and Middle East. Not much has changed over the previous years. New Chinese machinery manufacturers appear virtually out of nowhere and present working machines, while other companies from previous years disappear. Although the organiser is keen to expand the show by another day to five days, some participants question the logic of an annual show which incurs significant costs, especially when machines are exhibited or in operation. Some PET technology leaders, such as KHS, Sidel and Husky, did not take part this year. The copying of other company’s technologies is still wide-spread and common. Visitors, equipped with digital cameras and iPhones, not only take pictures of every part of the machines, some even crawl directly into the clamping unit of the machine in order to snatch a close-up view. Stand personnel had to push back the crowds. Some companies (e.g. Akei) frantically erected additional barriers only a few hours after the show started. Some companies relied on external security guards. One of the hottest topics of the exhibition this year: compression moulding machines for the production of PE closures. Sacmi set the benchmark, Chinese machinery manufacturers follow and copy. And the quality and performance of the machines from the different manufacturers vary. Most machines were equipped with 48 cavity moulds (please note: the stated outputs vary and cannot be confirmed by us). Sacmi sets the benchmark Sacmi still sets the benchmark when it comes to compression moulding of single-piece caps used for CSD, mineral water, hot filling and cold aseptic filling. The compression moulding machine at the company’s booth produced up to 96,000pph with just 48 moulds (previous machines achieved this output only with 64 cavity moulds). The CCM48 on display featured a mould for the production of S29W-3 HDPE (high density polyethylene) caps with a diameter of 29mm, weighing just 1.25g. Besides Sacmi Imola’s Closures & Containers Division, the booth was shared with Sacmi Automation & Inspection Systems, Sacmi Hong Kong, Sacmi Nanhai, Sacmi Shanghai and Negri Bossi. Sacmi Automation & Inspection Systems, for instance, presented several inspection solutions, the most important being the new CHS cap quality control vision system, a high speed machine that sorts and inspects caps. CHS series machines were developed for the installation downstream from compression and injection production lines and provide the possibility for complete cap inspection, both inside and outside. They are particularly suited for inspection after slitting and printing or before packing. Thanks to its modular structure, the CHS machines can be set-up according to the customer’s specific quality control needs. Sacmi does not want to rely on compression moulding alone. Heavily promoted, but not on display was the IPS220 preform injection moulding machine which was officially launched in 2012. Called IPS (Injection Preform System), this system has been designed for the production of preforms and is currently available with a clamping force of 2,200kN and 48 cavity mould. Sacmi mentioned the company Gardaplast as a reference . Here a similar preform injection moulding system has been running in continuous production for more than 10 months now and has achieved very good results. www.sacmi.it The closure corner Cap making at Chinaplas","@ID":38} "imprint EDITORIAL PUBLISHER Alexander Büchler, Managing Director HEAD OFFICE heidelberg business media GmbH Häusserstr. 36 69115 Heidelberg, Germany phone: +49(0)6221-65108-0 fax: +49(0)6221-65108-28 [email protected] EDITORIAL Doris Fischer: [email protected] Michael Maruschke Ruari McCallion Waldemar Schmitke Ilona Trotter Wolfgang von Schroeter Anthony Withers MEDIA CONSULTANTS Ute Andrä [email protected] Martina Hischmann [email protected] Roland Loch [email protected] phone: +49(0)6221-65108-0 fax: +49(0)6221-65108-28 France, Italy, Spain, UK Elisabeth Maria Köpke phone: +49(0)6201-878925 fax: +49(0)6201-878926 [email protected] LAYOUT AND PREPRESS Exprim Kommunikationsdesign Matthias Gaumann | www.exprim.de READER SERVICES Heike Fischer [email protected] PRINT Chroma Druck & Verlag GmbH Werkstr. 25 67454 Römerberg Germany WWW www.hbmedia.net | petpla.net PETplanet insider ISSN 1438-9459 is published 10 times a year. This publication is sent to qualified subscribers (1-year subscription 149 EUR, 2-year subscription 289 EUR, Young professionals’ subscription 99 EUR. Magazines will be dispatched to you by airmail). Not to be reproduced in any form without permission from the publisher. Note: The fact that product names may not be identified as trade marks is not an indication that such names are not registered trademarks. 3 PETplanet insider Vol. 14 No. 06/13 petpla.net EDITORIAL dear readers, Wherever you are in the world, there’s more than a fair chance that the machinery, PET and cap materials used in PET bottle production and bottling will be pretty much the same. There’s a logic to this - at the end of the day the line manufacturers and raw materials producers are supplying their products all over the world. So it is not altogether surprising that any preform or filler line will look more or less the same and operate in more or less the same way. If this was really the case, surely all we would have to do is to produce a single report about a particular bottler or processor and claim that this represents the entire world of PET. So why exactly do we at PETplanet insider spend so much time travelling the world, interviewing bottlers and producers in situ, reporting on their concerns, investigating their markets? Yes, the machines might be identical, but their factories are not. Geography is important too: in hot regions thirsts are quenched throughout the year, whereas in places like Finland, the season lasts a mere two months or so. Every country has its own local taste: Russians quaff their beer from a PET bottle. Germans like nothing better than drinking highly carbonated water in PET. We could go on. Suffice it to say, people are different, markets vary, production and distribution are tailored to the local market. The machines might be the same, but people are individuals and markets have to adapt to local conditions. And this is why we will continue to visit you in our Editourmobil, we will listen to what you have to say, we will learn about what makes your market tick, and faithfully report our findings. It never ceases to amaze and delight us just how forthcoming and cooperative our interviewees can be, and for this please accept our grateful thanks. This issue and issue 7+8 contain the final reports from our comprehensive tour of Eastern Europe, the finals will make the reports of Poland in issue 7+8. One of the highlights of the next issue of PETplanet insider will be the reports from our latest adventure in Latin America. At PETpoint drinktec you will be more than welcome to visit us to view at first hand some of the products we brought back from that most fascinating of continents. We look forward to seeing you there. Yours, Alexander Büchler","@ID":5} "EDITOURS REPORTS 14 PETplanet insider Vol. 14 No. 06/13 petpla.net As the market for juice declined, Pepsico took over Sandora, adding iced tea filling on a Procomac installation, in addition to the standard CSD portfolio on two KHS installations. This new (at least for the Ukraine) taste won over consumers. Egorenko therefore switched one aseptic line over completely from juice to iced tea, leaving the other to carry on supplying the juice market. Iced tea production is now around 35 million litres. Andrey Makovyenko, Head of Production (left), and Waldemar Schmitke discussing packaging details With iced tea, Egorenko has discovered a way to keep the company on an even keel in the short term but he also has a medium term strategy. “We have to make it clear to the consumers that our juices are completely natural without any chemical additives. Juices are healthy!” As a result he has extensive marketing campaigns running to get the message through to the consumer. “We need to be open and reassure consumers that we are not hiding anything from them“, continues the Director. Mr Egorenko was keen to stress that he is always happy to take students and other groups round the plant so that he can show them everything. There is also his long term plan. Sandora is launching itself in the baby food market. “As manufacturers of baby foods, consumers will place more trust in us than if we are simply a producer of fruit juices. And once you have grown up with Sandora, from the baby stage and continuing through childhood, we hope that as an adult, you will remain loyal to the brand. “ says Egorenko. This strategy calls for new investments in beakers and glass equipment. A common feature of all his strategies is his appreciation of the importance of customer service. His maxim is “We need to listen to the customer, listen to what he wants and not force our products on the consumer!“ www.sandora.ua September 7, 2012 PET Technologies Chernihiv Ukraine We met: Aleksandr Suvorov, Proprietor Maxim Poliansky, Commercial Director Proprietor Aleksandr Suvorov( left) with his Head of Sales, Maxim Poliansky European standards and Austrian know-how Hidden behind ancient walls we discover a high-tech company that develops and builds, in accordance with European standards and Austrian know-how, stretch blow moulding machines for PET applications. For over ten years now, PET Technologies has been marketing semiautomatic stretch blow moulding machines and selling fully automated systems, in addition, for the past four years it has also been introducing new line of machines with output standard 1,500bph from one mould cavity. Capacity today is six stretch blow moulding machines a month, 100 blow moulds for their own stretch blow moulding machines as well as third party products. As regards fully automatic operation, the customer can choose from three models with capacities ranging from 3,000 to 6,000 PET containers per hour with a container volume of up to 2l. A special model with a capacity of 1,600 PET containers per hour for volumes of up to 10l is also part of the range. With the development of its special model, PET Technologies has targeted the special requirement of the Ukrainian market for 5-10 litre capacity drinking water bottles. The background to this is the poor supply of drinking water in the South of the country. Customers who value a simple operation and who need only relatively small capacities have the choice of three semi-automatic stretch blow moulding machines capable of up to 800 PET containers per hour. The 500 machines on the market are characterised by their simplicity of operation.","@ID":16} "BOTTLE MAKING 31 PETplanet insider Vol. 14 No. 06/13 petpla.net situations such as these the process commences with scanning the existing bottle using a 3D laser scanner. In a so-called “reverse engineering” procedure a surface reconstruction is then carried out, which will result in a new CAD data record for the bottle to be produced. Creation of a new design Based on the information gathered in the discussions described in section 1.1, the designer will generate a first design concept for the new bottle on a CAD system. This process is called design engineering and results in an exact bottle geometry on the basis of the intended “look” of the bottle, using appropriate design elements, such as logos, waistlines, decorative elements, etc., and also taking into account the technical requirements described in section 1.2. In this process, the designer will also ensure that the outer contour of the bottle is designed for manufacture. For example, undercuts and sharp edges combined withnextremely thin walls and high machine outputs should be avoided to prevent the material from tearing at these spots. If sharp edges are explicitly desired, e.g., for design elements such as logos, these may not be achieved by milling. In such cases, techniques such as laser engraving should be applied. The output of this design engineering stage is a 3D CAD data record that describes the outer contour of the bottle, initially without wall thicknesses. State-of-the-art CAD systems allow visualization of the container as a 3D free-form surface model that can also include class-A surfaces. Class-A surfaces are surfaces that model not only tangentially steady (or G2-steady) transitions but also curvature-steady (or G3-steady) transitions. Such systems, which are commonly used in the automobile industry, even permit a visualization of the gloss or the refraction of light. Ideally, CAD systems that support the process approach are used, such as Unigraphics NX. These integrated systems also include other performance features that go beyond the mere capturing of the bottle geometry, i.e., the mere constructive design of the bottle. Apart from the output of millPlease order your copy at the PETplanet insider book shop: https://petpla.net/books Bottles, Preforms and Closures A Design Guide for PET Packaging Second Edition by Ottmar Brandau 115,00 € 180 pages © Copyright Elsevier 2012 ing data for CAM, examples include the simulation of the mechanical behaviour of the bottle through finiteelement method (FEM) analysis (see also section 1.5). Because Unigraphics NX, as our example, is a knowledgebased system, the expertise referred to above can be incorporated in “digital process assistants.” These systems are thus not only suitable for a description of the cavity but also allow the design of the complete mould with all its components and the related cooling. One important aspect of the CAD output is the visualization of the bottle design in various forms for the approval process. The simplest case is a digital mock-up or photo rendering. In this case, the finished bottle, sometimes even with its label, is displayed in a photorealistic 3D view. This is possible on the monitor with various levels of quality (e.g., with or without transparency effect), both statically and dynamically. The bottle can be rotated against various backdrops (showroom effect). Customers who cannot attend the presentation in person, can be supplied with the dynamic photo rendering in the form of a digital video, e.g., in the Quick-Time or AVI format. A more demanding visualization is the output of the bottle geometry in a real, true-to-measure model, e.g., through stereolithography. For this purpose, a laser beam or UV light is used to harden a special resin in layers from the bottom upward so that a complete model of the bottle is generated. As a rule, this process can be completed in several hours or a single day. To get an even better impression of the optical appearance of the bottle, a 1:1 model made of solid polymethyl methacrylate can be produced. This process will take significantly longer because the model bottle is first milled on the basis of the CAD data and then has to be polished with a great deal of manual effort. On the other hand, the optical appearance of the acrylic model will be very close to that of the final bottle. High-end CAD systems are also able to map textures such as orange peel, condensed water droplets, or even animal skin, flake structures, or technical grains. Such textures, which have long been used in the automobile industry, are now increasingly finding their way into consumer goods. Often they not only result from aesthetic considerations but also have clear marketing reasons. For example, such graining may lead the consumer to grip the bottle exactly at predefined zones. Major mould makers usually have a large stock of different textures so that the customer can use sample bottles to see, touch, and select the desired effect. Of course, customerspecific ideas for the texture can be implemented as well. A high-contrast black and white picture in good quality will, as a rule, be sufficient input for the incorporation of a texture into the bottle design. If the customer is happy with the visual appearance of the container, the next step in the process can be taken, which is the transfer of the design features into a bottle design that are safe for the process. If not, the container geometry will be optimized in iterations until both the customer and the supplier are satisfied. *This article was published in Bottles, Preforms and Closures, Ottmar Brandau, Chapter 1.2., Copyright Elsevier 2012","@ID":33} "TRADE SHOW REVIEW 37 PETplanet insider Vol. 14 No. 06/13 petpla.net Securing value for a strong future www.krones.com Rigao Technology: Compression moulding, hard and loud According to Taizhou Huangyan Rigao Machinery Technology Co., Ltd. its range of different compression moulding machines can be equipped with up to 48-cavity moulds. When producing caps with a diameter between 20-50mm, the output is up to 34,500pph (+/- 20%). However, the machine running at the booth was shaking so heavily during production, that vibrations could be felt several metres away. www.rigaotech.com Huang Guan: Up to 42,000pph Shaoxing Huangguan Machinery Co., Ltd. claims to be the first manufacturer of cap compression moulding machines in China. The machines are offered with moulds from 16 to 48 cavities. The maximum outputs are 36,000-42,000 caps per hour. The company also offers cap folding (20 cavity mould, up to 45,000pph), cap slitting machines (up to 22,000pph) and cap lining machines. www.bottlecapmachine.com Minfeng: Compression moulding and cap lining Taizhou City Huangyan Minfeng Bottle Cap Machinery Factory offers 16, 24, 32, 36 and 48 cavity cap compression moulding machines. The main cap diameters are between 26-38mm, but diameters of up to 60mm are possible. The biggest machine equipped with 48 cavity mould, the MF-40B-48, is able to reach 25,000-27,000pph. The company also offers cap lining machines to produce the sealing gasket of the bottle caps with a maximum output of up to 12,000pph. www.tzminfeng.com Jin Kun Mould: Specialised in closure moulds The company Dongguan Chang Ping Jin Kun Precision Mold Factory specialises in the design and production of cap moulds and hot runners for injection moulding. The moulds, made of imported S136 steel, can be produced in up to 48 cavities and cover the entire application range including caps for mineral water, CSD, edible oil and five gallon containers. Caps can be made of PP, HDPE, LDPE or even a combination of HDPE and PP.","@ID":39} "TRADE SHOW REVIEW 38 PETplanet insider Vol. 14 No. 06/13 petpla.net Preform & blow moulding corner Akei: Fully automatic EBM machine for 25l containers Akei (Akei Plastic-Machine MFY. LTD.), founded by Dr. Banny Tam in 1974 in Hong Kong, can be considered as one of the most advanced EBM machinery manufacturers when it comes to the one-step process and the blowing of larger bottles and containers. The different business units include EBM machine manufacturing, EBM mould manufacturing and injection mould manufacturing. This year the company again put its focus on containers of 20 to 30l volume, which are widely used in the food and chemical industry. These containers are usually produced using single station, manual or semi-automatic blow moulding machines which can be slow and inefficient. With the introduction of the extrusion blow moulding machine LIN-90-TSI, the company is aiming to change the rule of the game. The machine, fully automatic with two stations, can be configured to a single or double head for the production of 20 to 30l industrial drums in single, double or three layers with view strip. The production output of a three layer, 20l drum at double head configuration is claimed to be 260cph. The clamping force is at 50t, clamping stroke 460-820mm and carriage stroke 900mm. This machine is also equipped with servo pump actuated hydraulics. www.akei.com.cn Intravis: Inspection of PET preforms and closures The German company Intravis GmbH presented new developments in optical inspection systems for closures and preforms, namely the Sample-PreWatcher, CapWatcher II and SpotWatcher. The Sample-PreWatcher is a system for the detailed inspection of preforms. Placed directly behind the injection moulding machine, the system measures length, diameter and ovality with a standard deviation of less than 0.02mm. In addition, the system recognises core shift as well as form changes and simultaneously checks the preform for material defects. The CapWatcher II is able to inspect up to 144,000pph for practically all measurements and visible defects. The system inspects the complete inside of the closure and checks the diameter and ovality of both, the tamper band and bore seal. Contamination on the inside of the head plate, colour deviations and flow lines are also detected. And the company’s SpotWatcher system checks the entire circumference of the plastic container for material errors, such as pin holes, burn spots, material inclusions and colour smears. Structures that are desired in the plastic material, such as edges or imprinting are not considered as errors by the evaluation system. According to the company, several machinery manufacturers have equipped their machines with inspection systems from Intravis during the Chinaplas, both local and international companies. www.intravis.de Netstal: 25 PET systems supplied last year Netstal sees itself well positioned in Asia, especially in the growing beverage market in countries such as China, Thailand and Indonesia. At the exhibition Netstal stated that the company is reaping the rewards from its two PET systems: the PET-Line from Netstal and the PETForm from KraussMaffei. More than 25 PET-Line systems were supplied to various local preform manufacturers in the past year. Business is also currently on the rise in Thailand and Indonesia. www.netstal.com Yizumi: Preform system Guangdong Yizumi Precision Machinery Co., Ltd. ran an injection moulding machine to produce PET preforms (18g, 500ml water, 28mm PCO) with 72 cavities. The “daily output” is claimed to be 565,560ppd. The machine was running with a self-developed servo driven, three station extracting robot. The 72-cavity mould was provided by the Chengdu Lianyu company. www.yizumi-group.com ZQ Machinery: Stretch blow moulding with a patent Zhejiang East Zhouqiang Plastic & Mould Industry Co., Ltd. had two stretch blow moulding machines running, both equipped with 2-cavity moulds. The ZQ-B2000-2 was producing 20l containers with 600-800bph, and the ZQ-B2500-2 produced 2.5l bottles with 900-1,200bph (2 cavities). This machine is also able to produce handled bottles in a fully automatic process: preforms are loaded and positioned with the help of a servo-motor device, before the handle is positioned accurately into the mould. The company mentions that the heating system is special: a patent light box provides an even temperature whereby the lamp distance is about 101mm rather than the 240mm offered by competitors which is said to save power by up to 50%. The company claims that the machines equipped with eight cavity moulds can reach outputs up to 9,000bph (2.0l bottles) and up to 11,000bph (0.6l). www.cnziqiang.com The automatic 25litre blow moulder of Akei attracted the visitorsitor","@ID":40} "PETcontents 06/13 4 PETplanet insider Vol. 14 No. 06/13 petpla.net INSIDE TRACK 3 Editorial 4 Contents 6 News 42 Products 44 PET bottles for beverages and liquid food 46 PET bottles in health and beauty care packaging 48 Patents WATER TREATMENT 34 Of the first water Water treatment and water management at drinktec 2013 TRADESHOW REVIEW 36 Dynamic development Chinaplas, Guangzhou, May 20 - 23, 2013 EDITOUR REPORT 14 Ukraine Part 2 RECYCLING SPECIAL 18 Challenges of PET recycling Positive EFSA opinions for Starlinger PET iV+ process 20 3R: Reduce, reuse, recycle in Japan PET bottle recycling global and local - initiatives and associations - Part 1 24 Playing it cool! Phoenix Technologies introduces new food-grade rPET BUYER’S GUIDE 49 Get listed! Page 24 BOTTLE MAKING 26 Generating the first design in CAD Bottles, preforms and closures - Part 3 MARKET SURVEY 23 Suppliers of mould tools for PET bottle production BOTTLING / FILLING 32 Ghana gets straight to the point Krones PET line with 40,000bph at Kasapreko, Ghana Page 36 Page 33","@ID":6} "MARKET SURVEY 27 PETplanet insider Vol. 14 No. 06/13 petpla.net Preform Moulds Caps and closures Bottle-to-bottle recycling plants Preform and single stage machinery Preforms Preform / Stretch blow moulds Two-stage SBM machinery Filling equipment Resins / Additives Compressors Closure systems Suppliers of preorm moulds/ stretch blow moulds Our annual overview of the market on the topic of mould tools for PET bottle production introduces you to the manufacturers of preform moulds and stretch blow moulds. The following manufacturers of preform moulds are listed: Electra, Husky, MHT, Mold-Masters, Otto Hofstetter, Steelmades. The manufacturers of stretch blow moulds listed here include: Awanti, Comep, Garrtech, KHS, Kiefer, Krones, Moldintec, PET Engineering, PET Technologies, Röders Tec, Sidel, SMT, Technopet, Vitalii, Wentworth. Then, there are also the companies who are active in both sectors: Nissei ASB, Petka, R+D/Leverage, Sacmi, Simex, Sipa, TPS. The companies are listed above in alphabetical order; in the tables they appear in the order in which their details were received by the editors. Although the publishers have made every effort to ensure that the information in this survey is up to date, no claims are made regarding completeness or accuracy. 06/2013 MARKETsurvey Company name Mold-Masters Europa GmbH Otto Hofstetter AG Husky Injection Molding Systems Electra Form Industries Steelmades MHT Mold & Hotrunner Technology AG Postal address Telephone number Web site address Contact name Function Direct telephone number Fax E-Mail Neumattring 1, 76532 Baden-Baden Germany +49 7221 5099-0 www.moldmasters.com Manfred Lausenhammer Director, Operations, Eng. & Bus. Dev. MPET Europe +49 7221 5099-0 +49 7221 53093 [email protected] Zürcherstrasse 73, 8730 Uznach Switzerland +41 55 285 22 11 www.otto-hofstetter.com Stefan Zatti Div. Manager Sales &Marketing +41 55 285 22 09 +41 55 285 22 44 [email protected] 500 Queen Street South, Bolton,Ontario, L7E 5S5, Canada +1 905 951 5000 www.husky.ca Robin Lovell Product Manager +1 905 951 5000 [email protected] 852 Scholz Dr. Vandalia Ohio 45377, USA +1-937-898-8460 www.electraform.com Brian Karns Vice President and General Manager +1-937-898-8460 ext:201 +1-937-898-1750 [email protected] B/ 14 & 26, Ghatkopar Indusrtial Estate, Off. LBS Road, Ghatkopar (W), Mumbai 400086, India +91 22 25007774, 67550450 Vipul Mehta Managing Director +91 22 40110450, 093239 07774 +91 22 67969001 [email protected] Dr. Ruben-Rausing-Str. 7, D-65239 Hochheim/Main, Germany +49 6146-906-0 www.mht-ag.de Volker Jährling VP of Sales and Service +49 6146-906-122 +49 6146-906-399 [email protected] Preform moulds Horizontal opening Number of cavities 2 to 144 2 to 192 2 to 196 2 to 96 48 cavities 2-192 cavities Preform sizes Up to 5gl / 20l Up to 500g All - accomodated preform lengths from 28mm to 310mm 17g to 349g, 18mm - 77mm 19mm to 120mm neck, Up to 600g, for bottles up to 30l Moulds already built for (makes) All major brands of PET systems Netstal, Arburg, BMB, Husky H-PETAE, HyPET, HyPET HPP, HyPET RF Husky, Cincinnati Milacron, BMB, Engel, Sumitomo Cold halves for Husky, MoldMasters, Yudo & Full Moulds Netstal, Husky, Engel, Arburg, Cincinnati, SIG, BMB Vertical opening Number of cavities Up to 96 2 up to 96 1 to 12 2 - 112 cavities Preform sizes Up to 5gl / 20 l Up to 500g 12g - 50g, 1 8mm -110mm up to 600g, for bottles up to 30l Moulds already built for (makes) All major brands of PET-systems Arburg, Krauss-Maffei Aoki, Nissei, Krauss Maffei, Engel, KraussMaffei Do you produce single stage tooling sets? Hot runners for single stage IBM, ISBM & Sipa machines No No No No No Other 96 drop moulds for 300t machines iFlow hotrunner systems, to reduce pressure drop and achieve better balance; quick change preformmoulds ; iCool conformal mould stack cooling technology for improved cooling; iFlow inside hot runner manifold upgrade program for better melt operation; hot runner refurbishing and upgrade programs Multilayer moulds up to 72 cav moulds for PP moulds for thinwall packaging moulds for cartridges and tubes Wide mouth, high performance moulds, up to 8 gallon, trigger moulds, moulds for vacuum blood test tubes","@ID":29} "MATERIAL / RECYCLING 20 PETplanet insider Vol. 14 No. 06/13 petpla.net Reduce Reuse Recycle PET bottle recycling global and local – initiatives and associations – Part 1 Recently recycling has become a topic of major importance, both strategically and existentially, as far as the plastics producing and plastics processing industries are concerned. For this reason we have decided to devote a series to this topic in which we will be describing the international recycling scenarios, the local recycling structures that vary from one country to another, the facts, differences in terms of consciousness and awareness plus the conclusions to be drawn from these factors and any measures adopted. We shall be starting with Japan, a country that embraced the topic of recycling at an early stage and which, in our opinion, provides the character of a model. by Wolfgang von Schroeter 3R i n Japan Plastics represent one of modern life’s key players; they are what make affordable products possible in the first place. Nevertheless plastics are objects of public criticism, including and more particularly PET. The subject of complaint is the “intolerable” pollution of the environment. Recycling is the response to be addressed to the critics, i.e. recirculation and re-use of the plastics in new products. As a result: a lessening of the burden on the environment whilst at the same time protecting oil as a resource, this being the basic raw material used in plastics. We at PETplanet Insider have in the past run reports about recycling processes on numerous occasions. Japan is one example of the successful social process of recycling. At the same time, the process is without doubt enhanced by the character-based features of the Japanese as a nation; that is, by an ability to conduct an unemotional analysis, to take decisions objectively and as a community and to implement them logically. Everyone within a society needs to take part and the Japanese do take part, at the same time offering commitment and discipline. These are optimum pre-conditions for successful recycling. The fact that decisionmaking processes in Japan take a long time due to the involvement of a large number of bodies is surely not a disadvantage here. Japanese cities are clean. In recent years, a typical district area in Japan makes at least twelve distinctions between types of waste – among which bottles, PET bottles, other plastics are three of the major categories. Much of Japan’s waste is picked up by waste trucks. Littering is an offence, but much more than that: littering causes a loss of face, if for","@ID":22} "BOTTLE MAKING 26 PETplanet insider Vol. 14 No. 06/13 petpla.net Bottles, preforms and closures, 2nd edition - part 3 Generating the first design in CAD Ottmar Brandau has newly revised his book, “Bottles, preforms and closures” first published by hbmedia, and now to be re-issued under the Elsevier imprint. PETplanet insider is publishing extracts from successive chapters in a series of articles in forthcoming issues. After the determination of bottle properties, the next step in product development is the generation of a bottle design in a CAD system or the digitising of sample bottles and moulds. The route taken depends on whether the bottle design already exists or whether a new design is to be created. The bottle design already exists Sometimes a customer changes his or her mould supplier or requires a new set of moulds for a blowmoulding machine of a different make. In such cases, moulds are needed for an already-existing bottle design. Yet, this does not automatically mean that the related 3D CAD data on the bottle are also available in a usable form. As a rule, the engineering know-how will remain with the original mould supplier, who will not always be willing to hand over CAD data to customers. In","@ID":28} "BOTTLE MAKING 35 mmm$he[Z[hi$Z[ Y O U R PA R T N E R F O R B L OW MO U L D S . STEPS TO THE PERFECT BOTTLE. rating off this resource from the waste water flows produced, and returning it to the cycle. Here also more and more membrane systems are being installed, but this, according to Professor Schildbach, gives some cause for concern: “In the recycling of waste water from production there have been many R&D projects in recent years yet still the biggest problem of premature membrane blocking has not been solved comprehensively. But we are also seeing, in the increasing number of membrane systems being used, that in individual cases very successful water recycling is being implemented. In future we will be finding out a lot more about this.” From biogas to natural gas Membrane systems are not only being used to recover water from the flows of waste water. Other resources, too, are being recovered, in particular in the optimization of biogas yields from the organic load. For as an “energy drink”, waste water can contribute quite considerably towards regenerative coverage of electricity and heat needs. The efficiency of this process can be improved still further using a membrane process system which involves continuous separation of the CO 2 content in the biogas. This gives rise to natural gas which firstly has a higher calorific value and secondly can be used in standard boilers. *Cost-efficient use of the resource of water will be a common theme covered right through the exhibition halls at drinktec 2013, in particular at the booths of the exhibitors in Halls A3, A4 and B2. www.drinktec.com PETplanet insider Vol. 14 No. 06/13 petpla.net","@ID":37} "MARKET SURVEY 28 PETplanet insider Vol. 14 No. 06/13 petpla.net Preform Moulds & SBM Moulds 06/2013 MARKETsurvey Company name Simex Petka Mold Industry TPS - Tooling Preform Systems Nissei ASB Machine Co., Ltd. Postal address Telephone number Web site address Contact name Function Direct telephone number Fax E-Mail Via M.Biagi e M.D'Antona ,5 60025 Loreto (AN) Italy +39 071 7500214 www.simexitaly.it Graziano Giuggiolini Sales Manager +39 071 7500214 +39 071 7501958 [email protected] Yeşiloba Mah.46075 Sok. No 8 Seyhan, Adana,Turkey +90 3224286400 www.petkamold.com Tarık Sivri General Manager +532 5248990 +90 3224282303 [email protected] C. Houtmanstraat 42, 7825VG Emmen, The Netherlands +3 591 679768 www.tps.nl Richard Tempel Sales Manager +31 6 25041136 +31 591 630616 [email protected] 4586-3 koo, Komoro-shi, Nagano-ken, 384-8585 Japan +81-267-23-1565 www.nisseiasb.co.jp/en Mr. Katsuo Ishiguro Section Manager, Sales Coordination Team +81-267-23-1565 +81-267-23-1564 [email protected] Preform moulds Horizontal opening Yes Number of cavities up to 144 cavity 2 - 96 96 Preform sizes All sizes and all finish 14mm -110mm neck finish up to 50l Moulds already built for (makes) Mineral water /milk /oil /beer etc. Husky, Netstal, KraussMaffei, Sipa Husky, Netstal Engel Krupp Battenfeld Demag etc. Vertical opening No Number of cavities 96 96 8 - 32 Preform sizes Up to 50l Up to 180g Moulds already built for (makes) Krauss Maffei Nissei ASB machines only Single stage tooling sets (Preform moulds AND blow moulds) Yes Yes, moulds for single stage machines (Nissei ASB, Aoki) No Yes - main business is single stage Other Injection preform moulds for PE/PP Large preforms / also PP Preform moulds Stretch blow moulds Bottle size (max.) (in litres) 20 (5 gallon) 0,1 -19 50 22 Moulds supplied directly to blowing machine manufacturers Yes No Only for own machines Do you supply retrofit moulds for existing SBM machines? Yes Yes Yes Only for own machines For which bottle makes have you already produced moulds Sidel, Krones, Kosme, Blomax, SMI Sipa, Siapi, MAG, Combi Various Moulds are customized for each customer Bottle design service Yes Yes Yes Specialities PET containers for mineral water, CSD, milk, edible oil, wine, beer, cosmetics etc Supply of bottle prototype Large containers Handled, non-round, wide-neck, hot fill, non-round neck, offset neck, heavy weight cosmetic, etc. SBM Moulds Company name Röders Tec Moldintec SRL Wentworth Mold Ltd. ST Vitalii and Son Awanti Polymoulds PVT. Ltd. Sidel Blowing & Services Postal address Telephone number Web site address Contact name Function Direct telephone number Fax E-Mail Scheibenstrasse 6, 29614 Soltau, Germany +49 5191 603 53 www.roeders.de Friedo Böhling Sales Manager +49 5191 603 53 +49 5191 603 36 [email protected] Lamadrid 501 - Pque Ind Tigre - Tigre -Bs As Argentina +54 11 6632 9999 www.moldintec.com.ar D.I. Jorge Pucci Commercial Director +54 911 4146 9594 [email protected] 566 Arvin Ave., Stoney Creek, ON, Canada L8E 5P1 +1 905-643-9044 www.wentworthmold.com Tar Tsau General Manager +1 905-643-9044 ext. 311 +1 905-643-5406 [email protected] 9009; City Varna; #276; bul. Vladislav Varnenchik Bulgaria +359-887-978757; www.vitaliiandson.eu Vitaliy Marinyak Executive Manager +359-888-518782 +359-52-510168 [email protected] 25/5A/1/2, Nanded, Near Sawali Dhaba, Sinhagad Road, Pune - 411 041, India +91 020 24392225 www.awantipolymoulds.com Shirish Kshirsagar Managing Director +91-020- 24392225 +91 98220 40771 [email protected] Avenue de la Patrouille de France, Octeville sur Mer, BP 204, 76053 Le Havre cedex - France +33 2 32 85 86 87 www.sidel.com Laurent Charrier Tooling Product Manager +33 2 32 85 80 63 +33 2 32 85 81 69 [email protected] Stretch blow moulds Bottle size (max.) (in litres) 10 20 10 Up to 20 Up to 20 From 0.2 to 10 Moulds supplied directly to machine manufacturers Yes Sacmi No MAG; ADS; Sipa, Siapi, SMI;SIG;Krones;Sidel Sidel, Mag, Global PET, Technopet, Shyam Plastic Machinery, Polytech Yes Retrofit moulds for existing SBM machines? Yes Yes Yes, also multi-platform compatible mould systems Yes Yes Yes, moulds and personalized parts, repairs and refurbishment Moulds for bottle makes already produced Sidel, KHS Corpoplast, Krones, Sipa, Kosme, ADS, Nissei and other Coca-Cola , Danone, Nestle waters, Pepsico For all blow moulding machine platforms. e.g.Sidel, Krones, KHS, Sipa, etc. Karlsberg Bulgaria; Quadrant Beverages; Obolon; Cetec Sidel, Sig, Krones, Nissei, Mag, Kosme, Chum Power, Shyam Plastic, Urola, Wei Li, etc. Sidel, Krones, KHS Corpoplast, Sipa Bottle design service Yes: bottle design and development, test blowing, full laboratory available Yes Yes. Also prototype sampling and bottle performance tests Yes Yes Yes, design, prototypes, blowing samples, bottle performance tests, sensitive products Specialities Mould solutions compatible for different machine types, RMC-system for quick mould change, single stage tooling sets Industrial design, lightweighting, low pressure blow moulding for CSD bottles (20bar) Hot-Fill/Heat-Set moulds and multi-platform interchangeable quick mould systems Designing, prototyping Designing, prototyping, Unit Cavity Testing Packaging design, preform and bottle lightweighting development, blow mould and personalization. parts engineering, line conversion, etc.","@ID":30} "PETbottles 46 PETplanet insider Vol. 14 No. 06/13 petpla.net Home + Personal Care CanNeed Instrument(HK)Limited Tel: +86-758-2788469, Fax: +86-758-2782729 E-mail: [email protected] Web: www.canneed.com PET B ments ottle & Preform Instru Meet us at 16~20 September 2013 drinktec Booth: A3507 Magnetic Bottle Thickness Gauge Secure Seal Tester PET Bottle Pressure Tester ( Burst ) Hot Wire Bottle Cutter M+H shows off its curves M&H Plastics has added a brand new PET bottle to its portfolio of standard products, in the form of a 25ml curved container. The company says that the gently curved shape of the bottle, which takes a screw-on cap is suitable for a wide range of market sectors and that its 25ml size is appropriate for use as a samples, travel or hotel amenities pack. www.mhplastics.com w Brightly coloured blubber shower gel The German drugstore discounter dm is marketing 250ml of shower gel in a transparent bottle made from PET under the brand name of “SauBär“. The lustrous green product is specially geared to sensitive children’s skin and incorporates a visually interesting design featuring bubbles of entrapped air and small, coloured floating balls for the specific target group. A 2-colour, snap-on hinged lid closure with easy identification of the opening side together with self-adhesive labels put the finishing touches to the packaging. www.dm.de Neat Appearance Colgate Palmolive has bottled its “Total Pro Zahnfleisch“ (Total Pro Gum) mouthwash, which contains fluoride but is free of any alcohol, in a transparent cylindrical PET bottle containing 400ml of product. The product, which is slightly violet-tinged, the body label which has been kept white and the white screw cap complete with tamper-proof guarantee and a dispensing function lend an aura of “clinical purity” to the product on the shelf. www.colgate.de","@ID":48} "NEWS 9 PETplanet insider Vol. 14 No. 06/13 petpla.net We feel steel. Always with quality from the start. S+BIGROUP www.dew-stahl.com Plastic mould steels. We use them every day: PET bottles, caps, plastic packaging and other plastic parts. But scarcely anybody is aware that these products are manufactured in a tool or a mould made of specialty steel. Our plastic mould steels are easy-tomachine, corrosion-resistant, clean and wear-resistant – depending on what is required of them during use. That guarantees long tool service life, high productivity and efficiency. Which steel do you need? Husky’s leadership changes Husky Injection Molding Systems has announced a number of changes in its global leadership team, with the intention of providing more focused customer service and support in its core markets of hot runners and beverage packaging. Gerardo Chiaia will take on the new role of President, Hot Runners, which has now been set up as a standalone business. Keith Carlton has been named Vice President, Global Sales, Beverage Packaging. They will both continue as members of Husky’s executive team. Robert Domodossola, now appointed Vice President, Engineering and Business Development and to the executive team, will be leading a newly-created team responsible for the development, refinement and launch of new products. Gerardo Chaia joined Husky in 1994 and was appointed Vice-President, Global sales, in December 2011. Keith Carlton has been with the company since 1999 and has been Chief Operating Officer since 2008. Mr. Domodossola has been Director, Development Engineering since December 2008, having joined Husky ten years earlier. www.husky.ca Low Acid validation for ABF GEA Procomac has announced that the ABF (Aseptic Blow Fill) machine has successfully passed the LA (Low Acid) microbiological validation making it suitable to fill milk and milk based products. The Low Acid validation was structured to challenge the decontamination capabilities of the machine in different crucial areas. A production test with Culture Broth was carried out on three batches of 10,000 bottles. The result was zero defects on the 30,000 bottles produced. The accepted standard for this kind of text is of max 1:10.000 defects per batch. GEA Procomac ABF has passed all the steps to be suitable for the production of LA products. A new stretch rod system in the ABF includes a magnetic joint that allows movement inside the aseptic housing and makes sure that, after sterilisation with Hydrogen Peroxide, the stretching rod remains sterile. www.gea.com","@ID":11} "EDITOUR REPORTS 13 PETplanet insider Vol. 14 No. 06/13 decline. Five years ago the volume of the juice market was 750 million litres and we sold 500 million litres. Today the overall market is just 500 million litres, the same as we were bottling five years ago on our own“, he explains. Even so, the future had looked rosy. Sandora, once in private Ukrainian hands, has its own plant which processes all kinds of fruit and vegetables into juice and juice concentrate. The main proportion, at 30,000t/a, is made up of apples and tomatoes; bringing up the rear and a long way down the line are carrots (10,000t/a carrots) and other fruits (5,000t/a). Within 24 hours of harvesting everything is packed into aseptic tanks and drums. Together with other fruit preparations from other countries, the aseptically bottled juices come rolling off the production lines in the Mykolayiv plant. The company supplies both the economy as well as the premium segment with various brands. Originally all the juices were produced on Tetrapack installations. Once their competitor, Biola, had invested in aseptic PET in 2004 and immediately registered a market share of more than 15% in the Ukraine, Sandora followed suit. In 2006 the Ukraine company built a new plant in Mykolayiv and put two aseptic Procomac (Gea) systems into the plant along with two Sipa blowers. Designed for 20,000bph, the intention was likewise to ensure growth in juice production. But the world economic crisis put a spanner in the works. Juice became too expensive for the Ukrainians. Sandora was unable to halt the fall in volume, even with its economy brands. Juice in PET also lagged behind expectations. Here, because PET bottles do not incorporate any barriers, (usual in the Ukraine), some UV-sensitive juices were becoming discoloured within a period of four weeks. As a result, more consumers were opting for Tetrapak containers. This meant that the 25 Tetrapak installations were going at full steam packaging juices in cartons. Today, in the market for juices, their cartons have a share of 45% whilst juice in PET is treading water with a roughly 1% share. However, Biola was unable to maintain the original level of 15% and is now significantly below 10%. We are naturally interested in which type of packaging now represents better value for money – the carton or the aseptic PET bottle. “From the point of view of purely material and personnel costs and depreciation, the monolayer PET bottle is ahead, but if you take into account the resources such as energy consumption, together with the chemicals required for disinfection purposes etc., then the PET bottle comes out slightly more expensive than the carton”, was Mr Egorenko’s verdict.","@ID":15} "NEWS 8 PETplanet insider Vol. 14 No. 06/13 petpla.net petengineering.com [email protected] P.E.T. Engineering: the one-stop shop for beverage packaging. Technology excellence, captivating design, ergonomic shapes: a product developed by P.E.T. Engineering is easily recognizable. Its technical know-how and experience have made of it a leader brand in the sector of PET containers. Design, prototyping, laboratory tests and the production of blow moulds: P.E.T. Engineering is the perfect partner, holding itself all the possible solutions. PACKAGING. EVERYTHING YOU NEED DESIGN The perfect shape for an easy handling. PROTOTYPING Bottles available just a few hours DIWHU WKH ȴQDO GHVLJQ RESEARCH AND DEVELOPMENT New materials, innovative solutions and cutting edge technologies. PRODUCTION AND CUSTOMISING OF THE MOULDS High quality blow moulds for every kind of container and any type of blowing machine. STARTUPASSISTANCE AND TRAINING Supporting the client during the whole project. Visit us at Drinktec 2013 Hall B3, Booth 309 Munich – Germany 16-20 September 2013 M&G opens N American plants and signs license with Alpek Italian PET producer M&G Group has announced the signing of a Licensee Agreement with Alpek, S.A.B. de C.V. for IntegRex PTA technology, which will be used in the construction of M&G’s 1,200,000t/a PTA plant at Corpus Christi, Texas. M&G has also revealed that Alpek has purchased a multiyear sourcing agreement covering rights to 400,000t/a of PET (made with 336,000t/a of integrated PTA). The purchase price of the agreement was US$350 millions. M&G will fully own and independently construct and operate both the PET and PTA plants and will also use the vast majority of their output to supply its North American PET clients and to maintain control of sourcing of its other PTA requirements in North America. The two plants are expected to begin production in 2016. Other terms and conditions of the agreements were not disclosed. www.gruppomg.com Mocon and Inspection Systems tie up in Australia Minneapolis company Mocon, Inc., and Inspection Systems, Melbourne, Australia are working in partnership to establish a certified lab for permeation, seal strength and leak detection testing for food and pharmaceutical packaging structures. Inspection Systems has created IS Laboratories, Melbourne, as a separate entity to support the partnership, which is aiming to provide food and pharmaceutical companies with fast and affordable testing services using Mocon instrumentation. IS Laboratories is the first Mocon-certified test facility in Australia and the eighth in the world. Its capabilities include: oxygen, water vapour and carbon dioxide permeation testing; burst and pressure strength testing; and pressure decay. www.islaboratories.com www.mocon.com Sidel revives Gebo for integration The launch of GeboCermex, which was announced in April by Sidel, revives the Gebo brand in the beverage world. It is combined in the new company with Cermex, which specialises in secondary packaging and end-of-line equipment. Sidel says that the new company remains part of the Sidel Group but has the freedom to focus on engineering, line-integration and end-of-line packaging for a range of industries beyond beverages. Sidel will continue to provide packaging design, blowing, filling and labelling equipment, and offer its beverage customers complete line solutions for PET, can and glass across all categories. GeboCermex will offer beverage customers line integration and engineering services, including its standalone equipment (conveying and feeding systems, tunnels, overwrapping, packing and palletising). GeboCermex will be Sidel’s exclusive partner for can and glass lines, and a key partner for PET lines. www.gebocermex.com","@ID":10} "MATERIAL / RECYCLING 24 PETplanet insider Vol. 14 No. 06/13 petpla.net Phoenix Technologies introduces new food-grade rPET Playing it cool Phoenix Technologies, a long-time producer of recycled polyethylene terephthalate (rPET), is announcing the launch of LNO w resin, a new food-grade, melt-extruded rPET pellet for ambient/cold/frozen applications. Phoenix Technologies Phoenix Technologies produces clean, consistent and highgrade rPET resin pellets from post consumer recycled plastic flake shipped from all over the world. Phoenix Technologies is a member of Plastic Technologies, Inc., Holland, OH family of companies. For more information: www.phoenixtechnologies.net The new rPET product targets both blow moulded and thermoformed applications for water, coldfilled beverages, deli trays, fruit tubs, etc. LNO w resin is designed for packages which are not subjected to heat (either in the filling process or during consumer usage) or need the rigorous performance attributes required by certain food applications. Phoenix Technologies claim that the material can be used at levels up to 100%, or blended with virgin PET. Additionally, the resin is suited for personal care packaging applications which can benefit from foodgrade rPET attributes which align with corporate philosophy and marketing objectives. LNO w resin complies with the Food & Drug Administration’s letter of no objection issued to Phoenix Technologies for the following conditions of use: E. Room temperature filled and stored (no thermal treatment in the container). F. Refrigerated storage (no thermal treatment in the container). G. Frozen storage (no thermal treatment in the container). “As you expand your conditions of use, the decontamination process gets more rigorous. These cold-filled, frozen or ambient-use applications do not involve a thermal process. That means they can use a resin that has been produced under milder processing conditions. LNO w resin combines material properties and desirable cost attributes for these applications,” said Lori Carson, Director of Commercial Operations, Phoenix Technologies. LNO w is said to be 5 - to 8% less expensive than Phoenix’s rPET grades used for containers that are subjected to thermal situations. (Pricing is dependent on fluctuations in raw material costs.) The new grade is the third product in Phoenix’s LNO rPET line. LNO w resin joins the company’s food grade LNO p and LNO c resin, plus the non-food grade NLP resin. The LNO process is based on Phoenix’s patented “small particle size” technology. The particle size is directly related to decontamination efficiencies usually resulting in faster output and significant energy savings.","@ID":26} "MARKET SURVEY 29 PETplanet insider Vol. 14 No. 06/13 petpla.net SBM Moulds R&D/Leverage Sacmi Imola Sipa Molds Solent Mould Tools Ltd & SMT Americas Inc. Kiefer Werkzeugbau GmbH Leverage House, Hamilton Road, Sutton in Ashfield, Nottinghamshire, NG175LD, United Kingdom +44 1623 556287 www.rdleverage.com Damon Sykes Sales Manager +44 1623 552240 dsykes @rdleverage.com Via Provinciale Selice 17/a 40026 Imola (Bo), Italy +39 0542 607111 www.sacmi.com Moraldo Masi B.U.PET - Beverage Division +39 0542 607888 +39 0542 642354 [email protected] Via Caduti del Lavoro 3 31029 Vittorio Veneto, Italy +390438911511 www.sipa.it Franco Porracin Molds & Hot Runner Division Manager +39 0438911511 +39 0438911694 [email protected] Relay Road, Waterlooville, Hampshire, PO7 7SB United Kingdom +44 23 9223 9950 www.solentmouldtools.com Mark Sim Managing Director +44 23 9223 9950 +44 23 9223 9951 [email protected] Steinhäldenstraße 11, 74193 Schwaigern, Germany +49 7138-9732-0 www.kiefer-mold.de Jörn Herget Project Manager +49 7138-9732-70 +49 7138-9732-90 [email protected] 1 - 96 Up to 72 Up to 144 24mm - 63mm neck, 12g - 350g. Up to 60g - 160mm length Up to 30l Husky, BM Biraghi, Milacron, Engel, Krupp, Krauss-Maffei Husky, Netstal, Krauss-Maffei, Krupp, BMB Up to 96 Up to 10l Husky Standard and custom; Sipa, Krauss-Maffei Yes No yes, for Sipa machines Air recovery systems, rotary blowmoulder and filling lines, spare parts 30 3,3 30l 5 10 Yes No Yes Yes Yes Yes Yes Yes, all platforms Yes Sidel, SIG, Krones, Side, Chumpower Still water, CSD, Oil Sidel, Krones, KHS/SIG/Krupp, SMI, Siapi, Kosme, Side Sidel, Krones, KHS, Sig, Siapi,Aoki, NisseiASB, Krupp, Mag, etc; Yes Yes: brandbuilding, product repositioning, marketing design, packaging engineering, lightwiegtening of exhisting bottles, etc. Yes and rapid prototyping of marketing mockups Yes Large volume capability Wide mouth, large sizes (up to 30l), asymmetrical, nitrogen hot fill, containers with handles, HDPE to PET conversions. Mould and change-parts packages supplied; support available across N.America and Europe for pilot and production moulds Lightweight design, special design for functional drinks, juices and household products Comep SAS PET Technologies P.E.T. Engineering Srl Garrtech Inc. KHS Corpoplast GmbH Krones AG Technopet Machineries, India. ZAE Du Pont Neuf, 16 130 Salles D'Angles (Cognac) France +33 5 45 36 63 50 www.sa-comep.fr Christophe Amarant CEO +33 5 45 36 63 50 +33 5 45 32 08 08 [email protected] Prof. Dr.Stephan Koren Str.10, 2700 Wr.Neustadt, Austria +43 720 902 169 www.pet-eu.com Maxim Poliansky Commercial Director +43 720 902 169 [email protected] Via Celtica 26/28 San Vendemiano Treviso, Italy +39 0438 403069 www.petengineering.com Elisa Zanellato Mark. & Comm. Manager +39 0438 403069 +39 0438 408420 [email protected] 910 Arvin Ave, Stoney Creek, ON, L8E 5Y8 Canada +1 905-643-6414 www.garrtech.com Donna Watson Sales Account Manager [email protected] Meiendorfer Str. 203, 22145 Hamburg, Germany +49 40 67907 -0 www.khscorpoplast.com Otto Krumeich Head of Modernization +49 40 67907 -360 +49 40 67907 -9360 [email protected] Böhmerwaldstr. 5, 93073 Neutraubling, Germany +49 9401 70-0 www.krones.com Peter Christiansen Sales Director Blow Moulding +49 9401 70-4980 +49 9401 70-914980 [email protected] Industrial sector 1-S, road no e, Plot no 40, New Panvel. Navi Mumbai. 410206, India. +91 9820346565 www.techno-pet.com Vineet Bannore +91 22 28610828 [email protected] 35 30 10l 6 Up to 8 3 50ml to 20l Yes Yes Yes Yes Yes No Yes, repairing of machines on site, supply and set up spare parts, Yes Yes Yes Yes Yes Sidel, Krones,SIG, ADS, Sipa, SMI, Sacmi, Serac, Agami, Tecsor ADS, Dynablow, KHS, Kosme, Krones, Siapi, Sidel, Sipa, SMIForm, etc. Nestlé Waters, PepsiCo, InBev, Ferrero, Carlsberg, Efes Food & beverage, household, personal care; all technologies and mould types. Mainly for KHS Corpoplast InnoPET Blomax SBM Krones, Kosme, Sidel, Sipa, KHS (SIG) Corpoplast Bislari, Bailley, Maza Dubai, Reliance, King fisher, CSD, Hotfil Yes Yes Yes: Design matched to industrialization Yes Yes (‘Bottles & Shapes’ programme) Yes Yes, prototype trial, bottle blow simulation, thermal flow analysis, FEM bottle blow simulation. lightweight design support, preform design Complete bottles projects Library of over 6,000 PET bottle shapes, 3D, 2D drawings, mockups and pre-series bottles blown in-house. Bottle design, prototyping, laboratory tests, blow moulds production, auxiliary parts and mould repair Neck finish conversion, Upgrading of existing blowing machines (Polaris Project), Moulds Restyling (I.S.O.S.) ‘Bottles & Shapes’ programme; light-weight design and special applications Bottle development services, preform-and bottle lightweighting developments for standard- and heat-set process, \"Mould Quick-Change\" solutions .","@ID":31} "44 PETplanet insider Vol. 14 No. 06/13 petpla.net PETbottles Beverages & Liquid Food White tea with Acai Teeküche GmbH based at Kempten in Germany are selling 1l of quality manufacture, refined white tea flavoured with cranberry/acai in a transparent PET bottle. The bottle, with its individual shape, incorporates reinforcement grooves under the all-round paper label and, in the neck area, embossing in the shape of a tea leaf. A tamper-proof screw closure in green completes the packaging. www.ti-erfrischungstee.de Form and function come together Sipa developped a ketchup bottle that stays in shape after filling. Numerous computer simulation tests provided accurate predictions of bottle design behaviour after the bottles have been hot-filled. The problem normally encountered with hot filling plastic bottles, particularly those with long necks sometimes used for ketchup, is that, when the contents cool, their volume reduces and creates a partial vacuum. The bottle walls collapse, and the label becomes partly or completely unstuck. To stop the vacuum effect which ruins the package, Sipa’s designers took an existing ketchup bottle design, shortened the neck and softened the angles around the bottle body to prevent the collapsing and provided an attractive appearance. This bottle can be filled between 85 and 90°C, stays in shape afterwards, and prevents “label crinkling. It can be produced on Sipa’s SFR rotary stretch-blow moulding systems equipped with an oven intended for heatset and oval containers. Making this type of bottle does require a special PET resin suitable for the heat setting process used for hot-fill containers.The resin also needs to contain an oxygen scavenger to stop the ketchup oxidising and discolouring over time. With a suitable scavenger, the container can have a shelf life of at least 12 months. Sipa has already carried out successful tests using Amosorb, which is produced by ColorMatrix, a member of the PolyOne group. www.sipa.com Clean dispensing For its sauces sold under the Knorr brand name, Unilever Germany has fitted its squeeze bottles made from PET with an improved dispensing cap. A 2-colour hinged lid incorporating a tapered inner section and a silicone valve is screwed on to the upright bottle which has a content of 250ml. One part of the transparent segment is flipped open by means of a hinge and held in this position. Product is expelled by applying pressure to the bottle and the valve is locked in its rest position once pressure is removed and the lid snapped shut. Prior to initial opening a sealing membrane needs to be removed. www.knorr.de BERICAP the plastic closure company committed to your success www.bericap.com Research and Development Developing closure solutions to meet your specific requirements Mould Technology A detailed understanding of mould design with in-house mould making facilities in Hungary and Germany Global Presence Local production in 21 strategically located factories. An on-going strategy of stregthening our global presence Capping Technology and Know-How Special advice on capping technology with on-going technical support Innovation and Flexibility Our broad range of plastic closures is the basis for generating new innovation. Our expertise covers aseptic, hot fill, barrier, anti-counter- feiting TE-systems, consumer convenience and child resistance","@ID":46} "MATERIAL / RECYCLING 19 PETplanet insider Vol. 14 No. 06/13 petpla.net Step 2: The contaminated flakes (washed or unwashed) are processed at a rate of 100 % without dilution (i.e. adding non-contaminated flakes) – no mixing of flakes or homogenisation, In order to prove FIFO (first-in, first-out) processing, contaminated flakes have a different colour, in this case green. To be able to run a small challenge test batch (about 80 – 100kg) the pilot plant also has to process a certain amount of clean flakes to allow stable production. Those flakes are transparent so that at Challenge test results unwashed flakes, washed flakes in comparison with the EFSA threshold The EFSA evaluation procedure According to a the Commission Regulation (EC) No 282/20084 of 27 March 2008 on recycled plastic materials intended to come into contact with foods and amending Regulation (EC) No 2023/20065, the EFSA is requested to evaluate recycling processes of plastic waste. EFSA evaluations only concern the safety of mechanical recycling processes in which used consumer plastics are collected, ground into small flakes and decontaminated before being processed into new materials for use in the food packaging chain. Collected plastics used in mechanical recycling could be contaminated with chemicals that are not suitable for food contact applications. Consequently, recyclers are required to demonstrate that their process can reduce chemical contaminants in the recycled plastic to such a level that potential migration of any residual chemicals does not pose a risk for human health. Detailed specifications for the input materials are provided for each of the submitted recycling processes; the amount of PET from non-food consumer applications should be below 5% for all of them. www.efsa.europa.eu the end the pellets produced from contaminated flakes (green) can be distinguished from those produced from clean flakes (transparent). No dilution: only pellets produced from contaminated flakes (green) are used for analysing the quantity of residual surrogates or calculating the cleaning efficiency. Step 3: Analysis of super cleaned rPET pellets. Relevant are results regarding residual surrogates (ppm) and decontamination efficiency (%) relative to input contamination. In both scenarios the recoStar PET iV+ process reached the required EFSA cleaning efficiency according to the defined criteria (Criteria for safety evaluation of PET recycling processes, published 2011: Contamination concentration in the PET flakes are modelled corresponding to a migration after 365 days storage at 25°C. Not exceeding dietary exposure of 0.025μg/kg body weight/day The most conservative default scenario for infants is used for modelling (migration of 0.1μg/kg) www.recycling.starlinger.com Molecular weight Required cleaning efficiency EFSA Cleaning efficiency recoStar PET iV+ Cleaning efficiency recoStar PET iV+: (g/mol) 100% unwashed flakes 100% washed flakes Toluene 92.1 97.34 % 99.9 % 99.9 % Chloroform 119.4 96.67 % 99.9 % 99.9 % Phenyl Cyclohexane 160.3 95.57 % 99.9 % 99.9 % Benzophenone 182.2 94.87 % 98.5 % 99.8 % Lindane 290.8 89.67 % 90.9 % 99.9 %","@ID":21} "EDITOUR REPORTS 17 PETplanet insider Vol. 14 No. 06/13 petpla.net Ukraine Tour Blog A longish stretch of the tour of 350km or so guides us to the beverage company Sandora in Mykolayiv. Progress is deadly slow, and after 3 hours, having covered a mere 100km, we decide to put back the interview to the next day. Once again, the wonders of satellite navigation let us down and we are forced to fall back on good old paper maps, and some helpful members of the local constabulary. Thanks to this old-fashioned “technology”, we find ourselves by evening at the factory gates, looking forward to enjoying a peaceful night’s sleep. The interview on the following day with manufacturing director Volodymyr Yehorenko is, to our delight and astonishment, virtually “print-ready”. So much information, we hardly need to ask any questions. The next stretch is a daunting 600km north to Chernihiv. No traffic or satnav issues today and by evening we have already reached our destination. Ably assisted by significant quantities of the amber liquid and lashings of good food, we easily rise to the challenge of solving all known preform and bottle production problems. Suitably fed and watered, we retire to our beds for an excellent night’s sleep. Thanks to the punishing hours and hours of brainstorming which kept us awake till the wee small hours, getting up proves to be something of a challenge. Nonetheless, we arrive brighteyed and bushy-tailed at our appointment with PET Technologies. Here waiting for us was a machinery manufacturer created out of nothing a mere 15 years ago. We want to make good use of our evening here to have a good look around Kiev. We manage to find a superb camp site situated on an island on the Dnieper. Even better, it is linked directly to the city centre by means of a convenient wooden footbridge. by Alexander Büchler Save RAW MATERIALS reduced plastic volumes Save ENERGY less energy consumption Save TROUBLE more quality and higher performance, guaranteed by a sole supplier Full INSPECTED online quality control / stand alone With Sacmi, the beverage specialists are always at your side. With our unbeatable technological know-how and continuous research we are creating new containers and closures designed to ensure outstanding performance. The new IPS injection system for preforms, the CCM compression press for caps and the quality control systems fully designed and built by Sacmi, allows for large-scale production with considerable advantages in terms of efficiency and flexibility. The outcome? Reduced plastic volumes, less energy consumption and lower running costs.All in a bottle: the one you’ll soon be making. Preform & Closure technologically together HALL C 134","@ID":19} "NEWS 11 PETplanet insider Vol. 14 No. 06/13 petpla.net moldmasters.com Mold-Mastersand theMold-Masters logo are trademarks ofMold-Masters (2007) Limited. ©2013Mold-Masters (2007) Limited.All rights reserved. Rely on our global support network for fast service and parts. North America 1-800-387-2483 | Europe 49 (0) 7221 5099-0 ALWAYS INNOVATING. ONE SHOT. MULTIPLE LAYERS. REDUCED COSTS. Produces barrier packaging parts at lower costs by using existing machinery and standard molds. + Replaces glass, can and multi-layer thermoforming parts at up to 50% cost savings + Simplifies packaging operations + Integrated process controller for flexible barrier placement + Economical solution that uses less plastic, energy and water for greener, cost-effective production IBWA accentuates the positive for Earth Day 2013 Substantial reductions in plastic use and significant increases in recycling rates make bottled water packaging a `face of positive change´ the International Bottled Water Association (IBWA) claimed in its promotions for Earth Day 2013 (April 22). A study from the National Association for PET Container Resources (NAPCOR) shows PET water containers are the single most recycled item in the USA’s kerbside collection programmes. The country’s recycling rate for single-serve PET bottled water containers is now 38%; more than double that of 2005. A life cycle assessment conducted by Quantis in 2010 found that bottled water´s environmental footprint is the lowest of any packaged beverage. The Beverage Marketing Corporation (BMC) reports that, between 2000 and 2011, the average weight of a 16.9-ounce (500cc) PET water container declined 47.8%, saving 3.3bn pounds (1.5bn kg) of PET resin. The proportion of rPET is up to 100% in some cases. NAPCOR states that 1.5bn pounds (0.7bn tonnes) of PET were recycled in 2010; producing new products from rPET uses 66% less energy than production from virgin materials and also reduces greenhouse gas emissions. The US Environmental Protection Agency (EPA) reports that plastic water bottles make up less than 0.33% of the US waste stream. IBWA’s Material Recovery Program (MRP), a collaborative venture between businesses and government, actively seeks to improve recycling and waste education, and to collection efforts for all packaged goods. www.bottledwater.org Serac Asia appoints new general manager Philippe de Sarrazin, former Vice President of Sidel South East Asia Pacific and former CEO of Sidel Russia-CIS, has been appointed General Manager of Serac Asia. He replaces Wilfrid Marie, Vice-President of Serac Group, who was acting in an interim capacity and will now focus on Serac Group new business development. Philippe de Sarrazin joined the Serac group in January 2012 as Sales Director in charge of Asia Pacific. www.serac.fr","@ID":13} "BOTTLING / FILLING 33 PETplanet insider Vol. 14 No. 06/13 petpla.net “The aphrodisiacal effect, by the way, is not just psychological, but actually does work”, emphasises Managing Director Martyn Mensah. “Until 2010, we had been advertising the product with the slogan ‘It’s a great tonic especially for men’. But since then we’ve stopped making this sort of claim on the label and in our advertising.” Success bred imitators: today, there are more than 200 relatively small herbal bitters producers in Ghana. But Kasapreko remains the front-runner on the spirits market, with a share of almost 50%, four times as much as the next-biggest producer. “By 2013, we aim to have doubled the output to ten million cartons”, says a confident Martyn Mensah. PET line for spirits In order to reach this target, Kasapreko commissioned two new Krones lines in December 2012. Hitherto, the bottling operation featured a relatively small glass line rated at 8,000bph, a Chinese PET line dating from 2004 for 12,000bph, a pre-owned 10,000bph PET line, plus an English line installed in 2011 as an interim measure in rapid response to rising demand and rated at around 9,000 round bph. “For all these lines, it wasn’t always easy to plan the spares and the service, which was a bit of a handicap”, comments Martyn Mensah. Kasapreko had been planning a major expansion thrust ever since 2007, because it was at this time that exports to Nigeria, Togo, Benin, Burkina Faso, Liberia and Sierra Leone began to take off. The company first had a new cantilever hall built for the new lines, measuring 100 x 44m. Here, Krones has installed a returnable-glass line rated at 30,000bph, and a non-returnable PET line for 40,000bph – the fastest PET spirits line Krones has installed so far. Both lines are mainly used to bottle Alomo Bitters, plus Dry Gin, Kasapreko Brandy and other herbal bitters. The PET line also bottles the Lime Cordial soft drink in 0.75l containers. In 2013, moreover, Kasapreko intends to launch further alcoholic ready-to-drink beverages. Container: convex at the front, concave at the back The PET container is concave at the front and convex at the back, which means it can be packed with particular space-economy. The design had previously won an award for successful packaging. Since the front and back are different in design, the bottles have to be appropriately orientated so as to ensure that in actual fact only their fronts are labelled. Installation of the line finally began on uly 15, 2012. Both lines started operation early in December 2012. The high-speed PET line is supplied with containers by a Contiform S24 blow-moulding machine, which is set up for transparent, flat 0.2l, blue 0.5l, plus round 0.75l containers made of green and blue material. An AirCo conveyor feeds them to the rinser-filler monobloc, which features a gravimetric filler in the shape of a Sensometic VP-GW-PET to ensure accurate fill levels. The fill level is additionally verified by a Checkmat F-G. A Solomatic labeller dresses the bottles at the shoulder using a coldglue station. A Linaglide then distributes the containers among up to six lanes. At the same time, two Variocart carton erectors unfold the carton blanks. In a Linapac II, the cartons and the bottles are then brought together, whereupon the cartons are sealed by a Variocol, and palletised by a Modulpal 2AC. The same type of palletiser is directly adjacent, and is tasked with palletising the bottles from the glass line. The returnable glass is fed into the line by hand in the basement. Global market ahead The company had already begun exporting to South Africa and Tanzania in 2012. In 2013 Kasapreko aims to be selling its products in East Africa as well, with Kenya, Tanzania, Uganda, Ruanda and Burundi, a market with 210 million people. “Our most important sales market at present remains West Africa, where we still have a lot to do. Besides tapping into the mar kets of South Africa and West Africa, we’ve long since had a presence among the Ghanaian and Nigerian communities in the global diaspora, not only in Europe, but also in the USA and in Asia”, explains Martyn Mensah, “In five years’ time, we aim to be an internationally respected spirits producer on the global market.” The first step has been taken. Nigeria is the second-biggest market for Kasapreko, with almost 40% of its sales finding their way over the borders. This, too, is why Kasapreko is planning to build a production facility of its own in Nigeria. But for the time being the herbal bitters continue to trundle over the trans-African highways. www.krones.com www.kasaprekogh.com Precise fill levels are obtained by the weighing-cell filler with neck-handling Kasapreko commissioned two new Krones lines in December 2012. The company first had a new cantilever hall built.","@ID":35} "MATERIAL / RECYCLING 22 PETplanet insider Vol. 14 No. 06/13 petpla.net PET resin for bottles produced and sold in 2011: 605,000t Recycling of PET bottles: Target of 3R for PET bottles Collection rate target more than 75% Promotion of mechanical BtoB instead of re-use Bottle weight reduction target more than 10% Obligation of PET bottle manufacturers and users Plastic closures: must be made of PE or PP (aluminium not permitted). Bottles: must be made of clear PET only (no colour). When using multilayer/ coating for barrier, evaluation of recycling performance must be made. Labels: must easily be removable by hand Bale quality: Obligation for consumers and municipalities in 2011 Collected bottles are compressed into bales. The very high percentage of high quality clean post consumer PET in bales - suitable for high quality BtoB processing - reflect the self-regulated, self- imposed discipline of Japanese consumers and municipalities. Rank A: 88% collected clean, suitable to be processed for BtoB Rank B: 10% collected, suitable to be processed into low spec. products Rank C: not applicable to PET Rank D: 2% collected and waste Collection status of PET bottles in 2010 and 2011 PET bottle sales in 2010 595,000t (see above) Collection rate72% (target more than 75%, see above) = 430,000t PET bottle sales in 2011 605,000t (see above) Collection rate in 2011 79,6% (above target) = 480,000 tons Comparison of collection rate with Europe (48% of sales) and USA (28% of sales). The above PET bottles are recycling designed PET bottles only: Bottles of soft drinks, liquor, soya sauce included in the above and designated for recycling; bottles for pharmaceuticals, cosmetics, detergents, edible oil, seasoning excluded in the above (not designated for recycling). Voluntary PET collection in Japan approx. 22% of total. Municipality PET collection in Japan approx. 50% of total Reuse Collection and recycling channels In 2011 approx. 230,000t of post-consumer PET materials were collected and reused and reprocessed in Japan, the biggest portion of recycled PET flakes was used for sheets (42,4%) and fibres (42%), but already approx. 11% for bottles. The remaining balance of total PET bottle collection is exported from Japan to China. PET bottle to bottle recycling processes - history 2004: Chemical bottle to bottle recycling was approved by the Food Safety Commission. 2006: Start of the 1st Voluntary Action Plan for 3R Promotion For safety reasons, chemical PET bottle recycling (PET Polymerisation) was for many years the only recognised technology as far as BtoB was concerned. Materials recycling for BtoB was already state-of-the-art technology in Europe when Japan made its first hesitant move in the direction of the new, less expensive technology. 2011: The 2nd Voluntary Action Plan for 3R promotion is started for Mechanical BtoB Recycling. Guidelines for use of recycled PET in food packaging were laid down by the Ministry of Health, Labour and Welfare – defining standards for source, testing, evaluation, safety and process quality control. Reduce At the same time – through their efforts aimed at achieving a plastics-free environment and returning PET for re-use within the processes – Japanese PET processors, bottlers and brand owners have reached agreement as follows on targets for less PET per bottle for lighter bottles: Average weight in 2004 100% Average weight reduction, 2010 minus 3% -97% Average weight reduction, target 2015 minus 10% -90% Outstanding examples of weight reduction achieved Kirin Beverage “Pecology Bottle”: from 2l hot fill to 2l aseptic from 63g/b to 38g/b Coca Cola (Japan) “Eco-ru-Bottle: Shiboru”: from 500ml aseptic to 520ml aseptic from 20.5g/b to 12g/b Suntory (Pepsi) “Hybrid (multilayer) Bottle”: from 500ml CSD to 500ml CSD from 31g/b to 24g/b","@ID":24} "EDITOUR REPORTS 15 PETplanet insider Vol. 14 No. 06/13 However, at the heart of the company is its own tool manufacturing facility for blow moulds. These are fabricated not only for the company’s own blow moulding machines but also for all established suppliers of rotary stretch blow moulding machines. This means that PET Technologies is always up to date and in touch with the latest trends in the PET market. Around 80% of production is exported, predominantly to Eastern Europe, CIS countries and Middle East. The sales and service network that has been built up is also enabling the company to open up new markets. To cope with the increasing demand, a new factory with a 3,000m² production and assembly area is currently under construction next door, and will be capable of manufacturing up to twelve stretch blow moulding machines a month. Asked about the secret of the company’s success, Mr Poliansky responded: “With the exception of bought-in parts, PET Technologies manufactures all the machine components itself, from the machine framework right down to final painting. In our view this is the only way to provide a guarantee of quality”. PET Technologies offered us this perspective of the Ukrainian market. Target customers are medium-sized enterprises that have a capacity requirement of up to 12,000 PET containers per hour. There are some 50 to 60 of these companies in the Ukraine. In this sector the proportion up to 10l capacity PET bottles for drinking water is 85%, a proportion that has shown a steady increase since 2008, in particular the 5-6l bottles. PET milk packs have a 15% share of the market and are showing slight growth whilst edible oils are flatlining at around 10%. Machines for other PET applications such as, for example, household packs, is a sector that PET Technologies sells to only infrequently. Another special feature of the Ukrainian market is the consumption of fresh fruit in August and September over the harvest period. In these two months the consumption of bottled drinking water falls dramatically. This also has an impact on the utilisation of capacity in engineering plants, and this provides an opportunity for PET technology to explore new markets, offering clever solutions to problems. www.pet-eu.com","@ID":17} "BOTTLES 45 PETplanet insider Vol. 14 No. 06/13 petpla.net Upbeat protection Upbeat drinks, recently launched by the Good Whey Co, part of British family-owned business, Volac, are the result of intense research and development intended to create a tasty dairy drink that is also full of essential protein, the company says. Good Whey wanted the packaging for the 250g servings to project a premium image and, at the same time, provide effective protection from UV light degradation. The company selected a custom-designed PET bottle with a tapered waist; CCL Decorative Sleeves developed a full-body shrink sleeve label in white cavitated PET, to ensure opacity. The sleeves are printed with a UV absorbing lacquer, wrap tightly around the contours of the bottle and are flexo-printed in nine colours. CCL Decorative Sleeves was selected for the project because of its technical knowledge and its ability to provide customer support during product development. www.ccllabel.at Rice wine The Korean company Koreawine is packaging 1l of rice wine with a 6% alcohol content in a whitetinted, waisted PET bottle. The opaque bottle protects the product from light, thus increasing the possible storage times. Before enjoying the wine, the bottle must be shaken well so that the heavy constituents are mixed with the rest of the product. A white foil label in the middle of the bottle and a screw cap (also white) with tamperevident strip round off the appearance. www.koreawine.co.kr","@ID":47} "MATERIAL / RECYCLING 18 PETplanet insider Vol. 14 No. 06/13 petpla.net Positive EFSA opinions for Starlinger PET iV+ process The challenges of PET recycling In issue 10/12 of PETplanet insider, we reported on how the EFSA evaluates the recycling processes for PET used in food contact applications. The preliminary results of these tests were published by the EFSA in August 2012. December 2012 saw the publication by the EFSA of further results. These revealed positive evaluations for all recycling companies which produce recycled PET pellets from PET materials and articles using the Starlinger recoStar PET iV+ technology or the recoStar PET FG technology. We had a closer look on how the EFSA test procedures work. The challenge test results for the cleaning efficiency of the Starlinger PET recycling process involving the five specified surrogates toluene, chloroform, phenyl cyclohexane, benzophenone and lindane came out well above the thresholds specified by EFSA. This means that the process is considered not to give rise to safety concerns if operated under welldefined and controlled conditions. The recycling companies who took part in the tests were: Preformia (Finland), STF (Germany), MPTS (Poland), PET to PET (Austria), Eco Plastics (UK), BtB (Germany), PRT (Austria), Valplastic (Italy), Fellinger B (Austria), BariQ (Egypt) Conditions of the process The evaluation of the process is based on data obtained in challenge tests carried out using Starlinger recycling technology. The same data were also used in 2007 for obtaining the Non-Objection-Letter from the US FDA. Challenge tests are usually carried out with washed flakes, Starlinger, however, performed them under socalled “worst case” conditions. In the 4-step recycling process heavily contaminated unwashed PET flakes were processed. Despite the high contamination the process achieved a cleaning efficiency exceeding the EFSA thresholds (Graph 1). For comparison Starlinger also carried out a challenge test with contaminated flakes that were washed before being processed, which is the input material recyclers usually deal with. In this case, four out of five surrogates showed a cleaning efficiency of 99.9 %. Even lindane (non-volatile/non-polar) showed a cleaning efficiency of 99.9 % where the EFSA threshold requires 89.67 % (Graph 2). Both challenge test results show the decontamination capacity of the recoStar PET iV+ technology. Specifications of the challenge test The challenge tests are carried out by independent test facilities such as the Fraunhofer Institute, Germany, TNO, Netherlands, or OFI, Austria, who are commissioned by the technology provider and/or the recycling companies. The results obtained are forwarded by the respective applicants as part of the request to the EFSA for evaluation. Test procedure for the recoStar PET iV+ technology Step 1: Conventionally hot washed flakes are contaminated with the surrogates Normal case scenario – contaminated flakes are washed again Worst case scenario – contaminated flakes are processed unwashed 0,8 0,6 0,4 0,2 0,0 0 100 200 300 400 500 molecular weight [g/mol] Cp,O [p pm] 100 90 80 70 60 50 0 100 200 300 400 500 molecular weight [g/mol] cleaning efficiency [%] Graph 1: Results of the challenge test under worst case conditions Graph 2: Results of the challenge test under normal conditions 0,8 0,6 0,4 0,2 0,0 0 100 200 300 400 500 molecular weight [g/mol] Cp,O [p pm] 100 90 80 70 60 50 0 100 200 300 400 500 molecular weight [g/mol] cleaning efficiency [%]","@ID":20} "PETnews 6 PETplanet insider Vol. 14 No. 06/13 petpla.net Indian summer for Cermex French company Cermex, part of the Sidel Group, has announced the opening of a new plant in Pune, India. The facility will initially assemble three machine models, one from each major product line family and including a machine that was designed in India. They are: the vertical Pick & Place Packer; an automatic shrink-wrapper with sealing bar; and a P9 four-axis gripping/transfer palletiser, which has been developed for local industry needs. Cermex says that its 15-person Indian team, which was established in 2011, will now be able to create end-of-line packaging machines that are specifically adapted for the local market. As it has its own design capacity, can handle assembly of existing machines and has the capacity to accept further technology transfers from France, the team is expected to expand as business develops. The company intends to open additional sales offices in India, which will be in addition to offices in Vietnam and Indonesia. www.cermex.com Husky World Tour makes stop in Austria and Brazil The Husky World Tour 2013 touched down in Austria in April for a two-day Speciality Closures Conference at the company’s Technical Centre in Waidhofen. Representatives from across the packaging industry saw presentations on the latest trends and developments in closures manufacturing, including Husky’s speciality closures manufacturing technology. The event included tours, case studies, demonstrations, discussions and presentations from Husky and other industry experts. Topics included advanced mould technologies, complete speciality closure systems, a presentation from Joseph Everard, Senior Manager, Mould Management from Unilever, and a demonstration of Husky’s Easycube mould technology. The next event on Husky’s World Tour was the South American Beverage Packaging Conference in São Paolo, Brazil in May 2013. On May 14, 2013, Husky hosted its first South American stop on the Husky World Tour 2013 – a Beverage Packaging Conference at its Technical Center in São Paolo, Brazil. More than 130 business leaders representing over 70 different companies gathered together to learn about the latest innovations and challenges in the beverage packaging industry. The one-day event included networking opportunities and presentations from Husky and industry experts, including guest speakers Paulo Villas, Packaging Supply Chain Manager and Lucas Amendola, Chemical Engineer from Coca-Cola Brazil, highlighting current and upcoming industry trends. Husky also presented its comprehensive range of products and services. Some of the key products highlighted include Husky’s H-PET AE system for lower volume preform manufacturing, HyCAP system for the high output production of beverage closures, as well as mould conversions and aftermarket services to help preform manufacturers keep their operations running at peak efficiency. South America has long been an important market for Husky. Recent investments to enhance regional support include increased accessibility to service specialists, as well as the addition of local PET experts.To further reduce customer downtime, Husky is working to improve spare parts ordering and delivery by increasing inventory in the region. The Husky World Tour 2013 is a series of global customer events taking place throughout the year in the Americas, Europe, the Middle East and Asia Pacific. Several events are being held throughout the month of June, including a North American Caps and Closures Conference at Husky’s global headquarters in Bolton, Ontario, Canada, a Beverage Packaging Conference in Istanbul, Turkey and a Hot Runners Conference in Chicago, United States. www.husky.ca Resilux reports resilience Resilux NV has reported 2012 unit sales volumes 2% higher than 2011’s, with the strongest increases being seen in East and Central Europe, and Switzerland. Poor weather conditions in Northern Europe and the economic crisis in Southern Europe had negative effects. Revenues fell, by 2.6% to €279 million, which the company attributed to decreased prices for raw materials. Resilux has agreements to pass on raw material price fluctuations to customers. “Added value” (total revenues less trade goods, raw materials, services and other goods) increased by 0.8%, to €56.3 million. EBITDA, however, fell 7.6%: from €28.28 million to €26.14. The company reported that a stronger Swiss Franc and US $ led to an increase in remuneration costs, in addition to indexation of salaries and wages. Non-personnel cash costs in 2012 increased 8.7% compared with 2011, which was attributed to variable production costs arising from increased volumes, as well as repair, maintenance and R&D outlay. Operational non-cash costs declined by €1.1 million, to €12.5 million, while depreciation costs increased by a similar amount. Pre-tax profit in 2012 was €12.1 million, an increase of 10.6% over the previous year’s €10.9 million. After-tax profit was reported as €10.1 million (2011: €9.1 million). The Board of Directors has proposed a gross dividend per share of €1.65 – unchanged from 2011. Resilux says that it expects to see a similar outturn of EBITDA in 2013 The AiroLux AG joint venture is not expected to make a positive contribution in 2013. www.resilux.com","@ID":8} "EDITOUR REPORTS 12 PETplanet insider Vol. 14 No. 06/13 petpla.net Surviving in a shrinking market Fruit juice manufacturer Sandora, a 100% owned subsidiary of Pepsico, is battling in the Ukraine against the shrinking juice market. With iced tea, Sandora has identified a potential means of keeping the company on a secure footing. The market for fruit juice in the Ukraine has undergone a rapid decline. The reasons are many and diverse. On the one hand, the Ukraine is an agricultural country in which a number of juicy fruits such as melon and peach grow and naturally, people prefer fresh fruit to packaged juices. On the other hand, Ukrainians perceive the weakness of the euro and the uncertainty about the future this brings with it. Saving spare cash for a rainy day is the paramount concern. In the beverages sector that means cutting back on packaged juices. We meet Vladimir Egorenko, in Mykolayiv, not far from the Black Sea coast. He is the head of all five Sandora plants in the Ukraine and it is he who has to cope with this Ukraine September 16, 2012 Sandora, Mykolayiv We met: Vladimir Egorenko, Plant Manager Sandora Vladimir Egorenko, Plant Manager Sandora by Alexander Büchler Waldemar Schmitke Part2 We rounded off our journey through the Ukraine with interviews at the soft drinks bottling company Sandora and at PET Technologies, manufacturers of bottling and packaging systems, moulds and peripherals. We caught up on the interview with OldiPET after the tour. In the next issue we shall be concluding our tour in Poland and going straight on to our tour of South America this year. Nuremberg Nizhny Novgorod Kazan Perm Yekaterinburg Chelyabinsk Yaroslavskaya Moscow Ufa Samara Saratov Volgograd Rostov-on-Don Dnipropetrovsk Kiev Warsaw Novgorod Saint Petersburg Gatchina Fryazino Kamenka Lipetsk Zaporishsha Mykolaiv Kharkiv Chernihiv Kalinovka Lübeck","@ID":14} "TRADE SHOW REVIEW 39 PETplanet insider Vol. 14 No. 06/13 petpla.net Demark Machinery: from preforms to stretch moulding With a history going back 20 years, Zhejiang Demark Machinery Co., Ltd is a very well-known supplier of PET preform injection moulding systems (16-96 cavities, 50ml to 2l), stretch blow moulding machines and PET preform moulds. The equipment is used to manufacture a wide range of bottles and preforms for beverages, but also containers for food, automotive components, and consumer electronic parts. The 50,000m² manufacturing facility is located in Huangyan, Zhejiang (China). Recently the company introduced its DMK series rotary blow moulding machines which can achieve a capacity of 5,000 to 22,000bph. The subsidiary company Demars Mould Co., Ltd. specialises in designing and manufacturing PET preform moulds and was one of the first companies to adopt needle valve of nocutting and hot runner system. The blowing moulds can also be equipped with other blow moulding machines such as from Sidel, Krones and Sipa, the company states. www.demark-pet.com Tech-Long: Public listed and multinational customers Tech-Long Packaging Machinery Co., Ltd. is one of the few public listed company in the liquid packaging machinery business and can be considered, together with its several subsidiary companies, as a leading supplier in this field. The product portfolio includes both beverage and beer packaging lines, preform injection moulding machines, PET stretch blow moulding machines, filling machines and labellers, among others. The company supplies several multinational companies including Coca-Cola, Pepsico, Danone, Nestlé Waters and Procter & Gamble. www.tech-long.com Sanxinghuifeng Machinery: 3-in-1 machines Zhangjiagang City Sanxinghuifeng Machinery Co., Ltd. specialises in 3-in-1 machines (washing, filling, capping). The largest machines can achieve a capacity of up to 36,000bph (500ml). In addition the company offers production lines for 3 and 5 gallon barrels, drink mixers, sterilisation machines and small injection moulding and blow moulding machines. At the exhibition they demonstrated a blow moulder with a capacity of 5,000 to 8,000bph. www.sxhfjx.com","@ID":41} "MATERIAL / RECYCLING 21 PETplanet insider Vol. 14 No. 06/13 petpla.net example bags are not tied properly and rubbish is not disposed of in an orderly way. In 1995 the Container and Packaging Act was established to meet the increasing need to reduce the volume of waste and make use of recyclability. The “Receptacle Packaging Recycle Law” in 1997 had placed the responsibility for the recycling of PET bottles, glass bottles, paper and plastic packaging on the manufacturer. The cost of waste disposal was divided amongst companies, consumers and municipalities. Consumers were required to pre-sort their waste at designated municipality pick-up areas, where it is collected by the manufacturer for recycling. In 2000 the “Fundamental Law for Establishing a Sound Material-Cycle Society” was enacted to serve as the basis for a comprehensive and systematic approach to waste and recycling. CHOOSE THE NUMBER ONE. TOTHE NEWDIMENSION K 2013 / 16 - 23 October 2013 Düsseldorf / Germany / Hall 09, Booth C05 On an international level, Japan proposed the “3R Initiative” at the G8 summit in 2004. Approved by the G8 nations, this initiative seeks to promote globally the 3R project (i.e. Reduce, Reuse and Recycle) with the objectives of reducing the amount of waste created, reusing the material, where possible, and then recycling, if these materials cannot be re-used. Organisations Two organisations play major roles in Japanese recycling: JCPRA: Japan Containers & Packaging Recycling Association, a government-designated organisation responsible for coordinating government, municipalities, consumers, specified entities, recyclers and manufacturers, who use recycled goods in their products – in accordance with the Containers and Packaging Act established in 1995. CPBR: The Council for PET Bottle Recycling: CPBR members include the Associations for Soft Drinks, Fruit Juices, Soya Sauce, the PET Bottle Recycling Association and the PET Bottle Association. The obligations voluntarily assumed by the Council and its members are: promotion of PET bottle recycling - research, study and advice – establishment of guide lines for PET bottle recycling - as well as cooperating with related recycling organisations and associations. The implementation of 3R in Japan in relation to PET is a programme and is an obligation on both organisations. Many of the guidelines und obligations defined are voluntary, but nevertheless are considered binding for all - companies, consumers and municipalities. PET data and targets PET resin market 2010 in total (PET resin processed in Japan) 1,750,000t PET resin for bottles produced and sold in 2010 595,000t i.e. 34.1% of total.","@ID":23} "PETproducts 42 PETplanet insider Vol. 14 No. 06/13 petpla.net Form-fitting flexibility Italian company Sacmi claims cost savings and flexibility with roll-fed tubular sleeves methodology from its new, modular Formsleeve+ machine Sacmi says that its new Formsleeve+ modular labelling machine allows the creation and application of tubular sleeves created on the machine from roll-fed film stock. The sleeve is made on a series of motorized mandrels through the use of vacuum technology and sealed with a laser source controlled by a high speed scanner, and then applied to the container. A tunnel positioned at the outfeed of the labeller completes the shrinking process. The creation of the sleeve is integrated into the labelling process and Sacmi claims that this leads to savings of up to 20%, compared to traditional shrink-sleeve solutions. The company further assets that its roll-fed technology allows a great deal of machine autonomy and, in addition, that it can be adapted to different film types. Furthermore, the laser welding process does not produce toxic gases such as ozone, dioxin or chlorine, in contrast to processes such as hot melt, ultrasound welding or chemical solvents. The Formsleeve+ labels printer can print in machine direction orientation (MDO), which allows more lanes of graphic on the same web and helps to improve efficiency. MDO shrink roll feed can produce 20,000 (or more) impressions per roll, which is between three and four times as many labels per roll as the shrink-sleeve process. It has no need for tube formation and seaming, which helps to eliminate splitting seams and thus increase process speed. MDO shrink rolls are stacked and palletised, which leads to lower costs of packing and transportation, because more impressions per pallet can be carried. Savings in personnel and space can be achieved as the MDO method enables labelling speeds of up to 50,000bph on one machine. Formsleeve+ can work with several film types, including PET, which offers good shrinkage percentage and is adaptable to irregularly-shaped containers; PO and OPP for easier recycling and low film density; PVC for highquality finish; PLA, which is an eco-friendly product with biodegradability; and OPS, for good printing quality and stable shrinkage. The Formsleeve+ can be equipped in different configurations and combinations, for full or partial-body cover, for example. This layout optimisation enables smaller machine dimensions and thus make installation easier. At the same time, Sacmi says that the machines are designed to facilitate excellent accessibility for changeover and for cleaning and maintenance. The “Plug and Label” system enables each labelling station moving cart module to be easily connected and disconnected from the machine base frame and replaced by other modules of different technologies and performances, according to need. www.formsleeveplus. sacmi.com Low-output solution for aseptic production Sidel recently launched a new low-output integrated aseptic blow-fill-cap solution. This low-output aseptic Combi Predis/Capdis FMa is based on the dry-preform and cap decontamination technology.With a standard output of 12,000bph for a 1l bottle, the new low-output solution can accommodate high- and low-acid products packaged in all common bottle volumes required by the market – between 0.2l and 2l, with outputs of up to 16,000bph. The new version is based on Sidel’s dry-preform and cap-decontamination system - Predis and Capdis. Attention has specifically been paid in the design of the low-output Combi Predis/Capdis FMa to accommodating it easily into new or existing plants through its ultra-compact footprint (up to 30% reduction in the footprint compared with existing linear solutions). Its linear design also allows for parallel packaging machines, a typical layout in the milk industry. With its special ‘plug and play’ conception, on-site installation is simpler and faster and can be managed in ‘hidden time’ while installing the rest of the line. Despite its compact design, the platform remains ergonomic and straightforward. Accessibility to the machine’s key components has been ensured, allowing operators to maintain and manage it easily. Low-output production can also be a practical solution in regional markets which require smaller product volumes. In the dairy industry, low-output packaging solutions are common, particularly in UHT milk production. The new line is designed for markets and applications where smaller batches or smaller product volumes are required. www.sidel.com","@ID":44} "PETpatents www.verpackungspatente.de 48 PETplanet insider Vol. 14 No. 06/13 petpla.net Closure with valve Disclosure No. DE 102011101109 A1 Applicant: 4Pack GmbH, Wolfsburg (D) Date of Application: 10.5.2011 Closing and opening device with a pressure relief valve for a container to accommodate a liquid. Pressure on the centre area allows the lid to “flip open“, thus releasing the opening. Pressure on the edge allows the lid to “snap back” so that the closure is sealed. Folding container Intern. Patent No. WO 2012 / 154713 A2 Applicant: Amcor Limited, Hawthorn (AU) Date of Application: 8.5.2012 This international application relates to a PET container with one or more edges permitting controlled and even compression. This also improves emptying any residual product in the container. Preliminary spot treatment Intern. Patent No. WO 2012 / 162132 A1 Applicant: Procter & Gamble, Cincinnati (US) Date of Application: 18.5.2012 In many instances, where soiled clothing is concerned, it is sufficient for the soiled part to undergo “preliminary treatment“ by applying the normal washing medium and then to put it in the washing machine. To this end this container cap is being patented with a special surface for rubbing into the soiled area. Hot fill bottle European Award of Patent No. EP 1688354 B1 Applicant: Yoshino Kogyosho Co. Ltd., Tokyo (JP) Date of Application: 24.11.2004 This European Award of Patent describes the shape of a plastic bottle suitable for hot fill. In addition, there are sufficient pressure compensating areas distributed over the surface of the container. Pack manufacture Disclosure No.DE 102011102683 A1 Applicant: KHS GmbH, Dortmund (D) Date of Application: 20.5.2011 Device and procedure for manufacturing a pack made up of a number of containers. Following removal of one container the pack can be securely reassembled by adjusting the pack holder. Bottle pack Intern. Patent No. WO 2013 / 004339 A1 Applicant: KHSGmbH, Dortmund (D) Date of Application: 15.6.2012 Construction of a pack that is fixed during transport and storage in such a way that the individual holders stay in the same order even after some of them have been removed.","@ID":50} "NEWS 10 PETplanet insider Vol. 14 No. 06/13 petpla.net Milacron appoints Chief Operating Officer Milacron LLC, a global plastics industry company that offers a range of plastics processing equipment, technologies and services, has named Ron Krisanda to the newly created position of Chief Operating Officer (COO). He will be responsible for manufacturing, engineering, technology, research and development, quality, continuous improvement, environmental health and safety for Milacron’s global businesses. He will report directly to Tom Goeke, Chief Executive Officer, and will be based in the UK. Before joining Milacron, Krisanda was COO of Edwards Group Limited, a UK manufacturer of sophisticated vacuum pumps and abatement systems and a portfolio company of affiliates of CCMP Capital Advisors, LLC. He has previously held senior management positions with Tyco International, Motorola and Ford Motor Company. He holds a BS degree in mechanical engineering from Clarkson University in New York and an MS in manufacturing systems from Lehigh University in Pennsylvania. Milacron LLC is owned by affiliates of CCMP Capital Advisors LLC. www.milacron.com Mocon reorganises global business structure Mocon, Inc., headquartered in Minneapolis, USA, which is described as a manufacturer of package integrity instrumentation, has created four global business units, with the intention of providing better support to its international operations. The units are: Permeation (based in Minneapolis); Package Testing (Ringsted, Denmark); Industrial Analyzers (Lyons, Colo.); and Microbial Detection (Minneapolis). Over the past 15 years, Mocon has acquired companies including Microanalytics, Round Rock, Tex.; Baseline, Lyons, Colo.; Lippke, Neuwied, Germany; and PBI-Dansensor, Ringsted, Denmark. The company has grown from a manufacturer of permeation equipment for packaging applications into providing products and services for food safety, medical device, pharmaceuticals, mud logging, gas monitoring, aroma/odour analysis and more. Permeation offers instruments for analyzing film structures and packaging for oxygen, CO 2 and water vapour transmission, as well as testing for organic compounds and hazardous material transmission rates. Package Testing includes headspace analysis instruments (oxygen, CO 2 and CO), leak detection, package integrity, seal and burst testers, modified atmosphere gas analysis, in-line gas blenders and leak detectors. Industrial Analyzers business unit offers gas chromatography and continuous environmental air and water quality monitors; the Microbial Detection unit is based on the GreenLight food safety product line. www.mocon.com Sidel celebrates Chinese five years Sidel has marked its five years of manufacturing in China with an event attended by customers, employees and senior representatives of the company’s management team. The plant has received considerable investment over the period, which has led to significant increases in the number of employees, production capacity and overall capabilities. Sidel has been operating in China for over 20 years, with offices in Shanghai, Beijing and Guangzhou. Its main Beijing manufacturing plant was opened on March 21, 2008 and now occupies some 40,000m². Recent additions include the creation of a training centre, a mould shop and a product care facility. Production of labellers at the site is scheduled to begin in 2014. Among the guests were Ms Zhao Yali, Head of the China Beverage Industry Association and Mr Zhu Hua Xu, CEO of Tingyi-Asahi Beverages Holding. www.sidel.com CCT Creative Competence Technology GmbH Idsteiner Strasse 74 D-65527 Niedernhausen, Germany [email protected] www.cct-systems.com PET Molds Design and Patents Developments PET Systems Closure molds Closure Molds Closure Systems at the drinktec in Munich (Sept. 16-20), booth B3/414 at the K in Düsseldorf (Oct. 16-23), booth 1/1A40","@ID":12} "PRODUCTS 43 PETplanet insider Vol. 14 No. 06/13 petpla.net Label remover upgrade Herbold Meckesheim GmbH has announced a new range of label remover machinery that enable more efficient handling of contemporary PET bottles. The company has identified a number of specific developments in bottle design that make the task of recycling PET bottles more challenging. They include labels that cover the whole surface of the bottle, which are an obstacle to optic sorting; and labels made of PVC, which can compromise quality. The new equipment deals with these materials and also effectively removes paper labels, which helps to improve recyclate quality. The Herbold label remover undertakes a preliminary treatment of the bottles before size reduction. It makes use of friction and in a way that avoids breakage to remove and separate paper labels while still dry, which makes separation of remaining paper fibres easier. Full-cover shrink-fit labels can be almost completely removed and separated, which helps to prevent sorting errors. The friction process also helps to remove other contaminants from the surface, such as sand and foreign bodies, which helps to extend the lifetime of cutting blades. The technique also helps in the removal and separation of obstructive bottle caps and silicone sealants. www.herbold.com Crusher press combination for PET recycling Frickinger, manufacturer of bale presses, PET solutions, document shredders and cutting machinery, has recently introduced the crusher press combination HSM PET CP 4988. According to the manufacturer, the PET recycling system reduces the volume of empty PET bottles by up to 90% in a single operation and generates compact bales of raw material from them. A throughput of up to 4000 1l bph is made possible thanks to a reliable input system based on a dispenser shaft incorporating a number of paddles. The filling operation can be carried out either manually or automatically. The drainage system specifically ensures that any residual fluids are discharged prior to pressing. In the downstream bale press (which has a pressing force of 11t) the crushed bottles are compressed into triple strap bales of raw material weighing up to 100kg. Reliable removal of the compressed plastic bottles from the crusher rollers which are made from specially hardened and ground steel is ensured by means of a stripper system. www.hsm.eu September 15th-17th, 2013 Munich, Germany, in parallel to Drinktec PETnology/tecPET GmbH P.O. Box 120 429 D-93026 Regensburg, Germany Phone: +49 941 8702374 [email protected] connecting comPETence More information PETnology Europe 2013: Lead Sponsor Sponsor S e n s o r s y s t e m e G m b H","@ID":45} "The lines are mainly used to bottle Alomo Bitters, said to have an aphrodisiacal effect. BOTTLING / FILLING 32 PETplanet insider Vol. 14 No. 06/13 petpla.net Krones PET line with 40,000bph at Kasapreko, Ghana Ghana gets straight to the point based on an article by Horst Meixner, Krones AG, In the West African nation of Ghana the privately owned enterprise Kasapreko commissioned Krones’ fastest PET bottling plant in December 2012. Two lines, to be precise: a returnable-glass line rated at 30,000bph, and a PET line rated at 40,000bph. The lines are mainly used to bottle a herbal bitters product, said to have an aphrodisiacal effect. Almost every day, in the courtyard of Kasapreko’s facility in Ghana’s capital Accra, stands a heavy goods truck from Nigeria with an open, overlength trailer. Early in the morning, three men begin to load the truck, carton by carton, each packed with 24 0.2l flat PET containers, filled with the herbal Alomo Bitters, with each carton weighing 5.2kg. By the afternoon, the workers will have loaded precisely 10,000 cartons, for a load weighing 52t. The vehicle will be on the road for almost four days, always along the coast, and crossing three frontiers on its way: first to Togo, then to Benin, and finally Nigeria. Dr. Kwabena Adjei was supporting himself and his family as a small-scale trader. Towards the end of the 1980s, the time of revolutions in Ghana was finally over and business life was gradually returning to normal. There were already, of course, a whole series of spirits producers back then. But almost everyone was buying the flavourings from the same supplier, with the result that everything somehow tasted more or less the same. Dr. Adjei found a producer whose gin flavour accentuated the taste of juniper rather more vividly. In his garage in Accra’s suburb of Nungua, he teamed up with four employees to launch a small-scale bottling operation. In his ancient Volvo, he drove from bar to bar, and offered the proprietors his “Kasapreko Dry Gin” on a commission basis. This triggered a boom in demand. Up till then, the Ghanaians’ high expectations for taste, quality, safety and packaging had had to be met with costly imported goods. “Good quality doesn’t necessarily have to be expensive”, to quote Dr. Kwabena Adjei. Kasapreko was the first local producer to put in place a modern-day form of quality control and a product development lab, and to introduce an individualised bottle. Today, Kasapreko Dry Gin is the market leader in Ghana’s gin segment. With this vision, he kept on searching for new products. Traditionally, the Ghanaians marinate fresh herbs and spices in alcohol for extraction, and use this form of bitters as a medicine to cure stomach problems or fever. Many small private producers also swear that their secret recipes have an aphrodisiacal effect. Dr. Adjei gave considerable thought as to how this secret could be industrially packaged in bottles. He consulted Africa’s leading research institute, which has specialised in tropical medicine, and had a recipe developed for a new kind of herbal spirit. He gave it the name of “Alomo”, a word from the widely used Ghanaian dialect Twi, which means roughly “my romantic interest” or simply “desire”. The word “Kasapreko” also comes from the Twi language: it’s the form of address for a tribal chief, and can be translated as “speaking with authority” or “getting straight to the point”. The eponymous chief, by the way, sits on Kasapreko’s supervisory board. At the beginning, Dr. Adjei was still using all sorts of different bottles, and even pre-owned cartons from other producers, which he turned inside out so as to conceal the printing. Professional-style bottling began in 1997. Alomo Bitters were thus the first Ghanaian herbal bitters to be produced on an industrial scale, and proved to be a great success. Kasapreko sold five million cartons in 2012, 70% of which were bitters with 43% abv, using a 96% base alcohol.","@ID":34} "WATER TREATMENT 34 PETplanet insider Vol. 14 No. 06/13 petpla.net Water treatment and water management as key themes at drinktec 2013* Of the first water All the major international brewing and soft drinks groups have long since formulated ambitious goals for reducing their ‘water footprint’, none of which would be achievable without in-company water recycling. Water treatment and water management will be key themes at drinktec 2013 in Munich, between September 16 and 20, 2013. “Sustainability most certainly also affects the subject of water processing. Savings that only a few years ago were considered too small and not cost-effective to implement, are now becoming ever more interesting. I am thinking here, for example, of the processing of water from filter backwash and of further increasing the yield in reverse osmosis plants. Also, intelligent control and monitoring strategies will start to become more important.”, this is how an expert, Professor Dr. Stefan Schildbach from the University of Fulda, Germany, Dept. of Food Technology, describes the current situation. The membrane trend What, then, does this mean for the separation technology being used? “For some years now the trend has been clearly towards membrane separation. That applies both to reverse osmosis for desalination of water as well as to the area of filtration,” explained Wolfgang Winkler, Technical Managing Director at EUWA H.H. Eumann GmbH. There are good reasons for this development: Membrane systems operate fully automatically and continuously, they need virtually no chemicals and the waste water from water preparation has no added salt from regeneration media. Added to this is the fact that the membranes have become cheaper and more effective and the necessary pressure and therefore energy input is now much lower. Ion exchangers and lime precipitation still have a place However, there are still applications in which the ion exchanger or even the most traditional of all preparation methods – lime precipitation – will be fully justified, as Winkler points out: “Lime precipitation has very low operating costs and very low wastage given, for example, the right composition of untreated water. In water treatment plants with a standard 20-year lifespan, these two factors are of considerable importance. In addition, lime is a natural product. Lime precipitation can therefore be an attractive alternative for businesses following strictly organic guidelines, or for tradition-conscious craft breweries. Until now, however, the vessel sizes necessary for lime precipitation have been a disadvantage, in particular in view of current steel prices. We have therefore combined lime precipitation with membrane filtration, so do not need these vessels and we operate fully automatically.” Regenerating with the sun Experts continue to see potential in electrodeionisation (EDI) which is currently being used, for example, in semiconductor production as the final polishing stage in the preparation of ultrapure water. In the EDI process the ions in the drinking water are separated off via an exchange resin system. At the same time a DC voltage is applied, which gives rise to H 2 O+ and OH- ions which continuously regenerate the resin. This regeneration is also the reason why it is believed the process will soon find new applications. Because the DC voltage needed for regeneration can be generated easily with photovoltaics, this represents a further step in the direction of autonomous production. Membranes also at the “end-of-pipe” Modern water management does not only mean ensuring enough fresh water is prepared. It also means sepa-","@ID":36} "TRADE SHOW REVIEW 40 PETplanet insider Vol. 14 No. 06/13 petpla.net Yusheng Mold & Machinery Hotrunners and PET preform moulds Yusheng Mold & Machinery Manufactory is a Chinese manufacturer of hot runners and moulds for PET preforms (up to 96 cavities) and caps (72 cavities). The company also supplies blow moulding and preform injection moulding machines and BOPP moulds (72 cavities). The company was founded in 1988 and currently employs 350 people. According to their own account, they have supplied moulds to customers in more than 60 countries. www.cn-yusheng.com Material handling solutions Automatik Plastics Machinery: Strand pelletiser for PET Automatik Plastics Machinery displayed its Baoli 200 strand pelletiser which is locally manufactured at Maag’s brand new Shanghai facility. The Baoli series is available in three basic machine sizes with operating widths of 100mm, 200mm and 300mm. The cutting tools employed ensure both a long equipment lifespan as well as very high throughput rates, for example up to 3,000kg/h for PBT or PET compounds. Additional features such as quick product changeovers come from the feed rollers and cutting tools being readily accessible, making them easy to clean or exchange. According to the company, the system combines a high quality standard with a competitive price. The company has more than 500 references for the Baoli system in China alone. www.automatikgroup.com Translucent sofa made of recycled PET bottles","@ID":42} "BOTTLES 47 PETplanet insider Vol. 14 No. 06/13 petpla.net A TURN AHEAD TO MORE EFFICIENCY. Thanks to their high performance and constant mode of operation, our technologies developed for the plastics-processing industry increase the cost efficiency of every production process. Your production line benefits from maximum availability while at the same time guaranteeing optimum product quality, even when using 100 % recycled material. With Gneuss you are always a decisive turn ahead! www.gneuss.com a turn ahead Technology made by Gneuss: • Filtration • Extrusion • Processing K‘ 2013 16.10.-23.10.2013 Duesseldorf, Germany Hall 9, Stand 9A38 Sun spray for kids A recent introduction to the market is Nivea’s moisturising sun spray “Sun Kids“ in a triggerstyle bottle containing 300ml of product. The blue-tinged PET bottle is moulded so that it is easy to grip and the sunshine yellow trigger makes the important and essential task of applying sunscreen a doddle. Before the bottle is opened for the first time an actuation lock (coloured red) that can be folded up again for transporting the spray in a bag needs to be folded down and when the trigger is operated for the first time a pre-weakened part breaks off so that it is possible to see at first glance whether any previous actuation has occurred. www.nivea.de The raspberry kiss Following the first time listing of the brand name Treaclemoon by Tesco in England in 2007 it has now developed there into a fixed variable in the sphere of bodycare. 2013 has seen the launch of the brand name in Germany with three shower creams in vivid colours and packaging guaranteed to catch the eye. One variation is “the raspberry kiss“, a shower cream characterised by its raspberry scent. The stand-up, transparent PET bottle with a content of 500ml is sealed with a black, screw-type hinged lid. The transparent plastic labels incorporate retail information and notes on manufacture and use all couched in a jokey format. www.treaclemoon.de Spray with push-up effect 150ml volume spray for use with a hair dryer and incorporating a push-up effect due to collagen is being marketed by Schwarzkopf under the brand name ”3-Wetter Taft“ (3-weather spray) in a transparent PET bottle with a pump atomiser. The product is applied to toweldried hair and distributed through it. A transparent cap provides protection against erroneous operation and there are two shaped labels to convey the retail information. www.taft.schwarzkopf.de","@ID":49} "EDITOURS REPORTS 16 PETplanet insider Vol. 14 No. 06/13 petpla.net Oldi PET Preforms, Vasyhcheve History, markets and future UAB Putoksnis in Lithuania is your parent company. How did Oldi PET Preforms come to be established in the Ukraine? Was part of the reason the fact that they were looking for a location outside the EU? The reason for Oldi’s opening in Ukraine was not to sell Lithuanian preforms in other European markets but to start production with the aim of selling to the local market. It was the first step in enlarging the business to exploit other markets. How many injection moulding machines have you installed in the Ukraine and how many preforms did you produce in 2011? Currently we have five injection moulding machines of which three are Husky and two Krupp machines. In 2011 Oldi produced about 400million preforms 100% of which were sold. What are your main preforms (beverages, water, etc?) Our main customers are producers of mineral water and carbonated drinks, some companies bought our preforms for beer production. What is the proportion of preforms produced with the 1881 neck finish? At present we are producing preforms with the PCO neck finish only. We plan to start producing preforms with the 1881 neck finish next year. Do you produce any other products in addition to preforms (bottles, closures etc)? No, we produce only preforms. Bottles are generally blown by the factories producing mineral water and carbonated drinks. How much of your production stays in the Ukraine, how much is exported? All we produce we sell in the local market. We don’t therefore need to export. In 2013 we plan to enlarge our MHT MOLD & HOTRUNNER TECHNOLOGY Dr. Ruben-Rausing-Str. 7 | D-65239 Hochheim/Main Tel. +49(0) 6146-906-0 | www.mht-ag.de Make the most of your machine – with a mold from MHT! For many machine types, we supply the mold with the highest cavitation, thereby enabling optimum preform output. For the Husky HyPET machines, we offer upgrade sets for up to 50% more preforms, without refitting on the machine! • 60 cavities for Netstal PETline 2000 • 96 cavities for Husky HyPET 300, • 112 cavities for KraussMaffei 350 Engineering made in Germany 128 for HyPET 400 + 1/C35 Booth B3/441 production and to set up two more Husky machines. This will require us to find additional markets and this we are planning to do with the help of exports. The market for beverages in the Ukraine has stagnated over the past few years. Have you been able to achieve growth in spite of this or have you been part of the sideways movement of the market? No, we have not achieved any growth, we are producing at approximately the same volumes: in the peak season our loading is 100%, at other times about 80%. Did Euro 2012 stimulate business as far as you are concerned? No, Euro 2012 didn’t bring us any additional business, but fortunately we did not bank on any stimulus from the event. We are already selling all that we produce. What are you looking at achieving in the future (new markets, lighter preforms etc)? In the near future we are planning to set up two more Husky machines on our factory, so as to commence production of the 1881 neck finish as standard. We are also planning to enlarge our portfolio of preforms with light weights and to start exporting to neighbouring countries. In 2011 Oldi produced 400 million preforms.","@ID":18} "TRADE SHOW REVIEW 41 PETplanet insider Vol. 14 No. 06/13 petpla.net Polyone / Colormatrix: Improved clarity in PET packaging Colormatrix, a subsidiary of Polyone Corporation and supplier of liquid colour and additives for plastics, launched Amosorb Plus, an oxygen scavenging solution for PET packaging. The material offers enhanced container clarity to help customers achieve aesthetic and recyclability goals. Because it is based on a previously approved technology, Amosorb Plus does not require the complex regulatory approval procedures of a completely new material, allowing customers to improve speed to market. Amosorb Plus is a crystallised PET-based concentrate with a built-in catalyst to promote oxidation. It offers product protection for non-carbonated foods and beverages for up to six months or longer, depending on the container design. Customers can tailor shelf life while reducing container weight for raw material and transportation savings. www.polyone.com ProTec Polymer Processing: Bottle-to-bottle recycling technology ProTec Polymer Processing, making its inaugural appearance as an exhibitor at Chinaplas, presented its technology for the improvement of polymer properties, especially polyesters and polyamides. The technology includes vacuum reactors with varying frame sizes to complete turn-key manufacturing lines for the recycling of polymer materials, such as the bottle-to-bottle recycling of PET. An important system component in this multistage process is the Ohl tumble reactor, a rotation reactor that can be heated and evacuated. The PET treatment process involves purging (decontaminating) the repellets inside of any volatile pollutants, while at the same time allowing post-condensation (increasing the intrinsic viscosity IV) to take place. The rPET produced by the OHL process has an acetaldehyde content of ≤ 1ppm and exhibits material properties just like virgin PET material. The Non-Objection Letter from the US certification authority FDA (Food and Drug Administration) verifies the safety of the PET recyclates produced in this way with regard to direct contact with foodstuffs. In addition, the company also provided information on the Somos range of systems for material handling during injection moulding and extrusion which includes powerful and energy-efficient dryers, conveyors and precise dosing systems for all free-flowing types of plastics. Through the precise control of the parameters temperature, vacuum and time, the pellets in the Ohl tumble reactor, recyclates or also virgin material, are individually processed to the required quality based on technical requirements. In this way, during the post-condensation of polyesters even IV values of ≥ 1.2dl/g as required in technical applications, for example, can be achieved. As well as treating PET both for the production of high-quality rPET and for the postcondensation of new PET product, the Ohl tumble reactor is used in equal measure to carry out decontamination and post-condensation. www.sp-protec.com Kreyenborg: From pelletiser to Infrared drum Kreyenborg displayed a continuous screen changer, two melt pumps for different applications, an underwater pelletiser and the underwater pelletising system Optigon. The underwater pelletising systems of the company are supplied with drying, water system and control ready for use and are suited for all thermoplastic materials, also for the production of micro pellets. As for throughput, the scope ranges from 2-80kg/h (Labline 100) to systems with 35,000kg/h. For particularly economic processing of PET, the company has developed the inline crystallisation system CrystallCut. With this system, pelletising and crystallisation are effected in one process step, without the supply of additional energy. The Infrared Drum IRD is of special interest for PET recycling: by means of infrared radiation an extremely efficient drying and crystallisation of PET in a continuous process is guaranteed. In principle it is also suited for the thermal treatment of almost all free flowing bulk goods. www.kreyenborg.cn","@ID":43}]}}
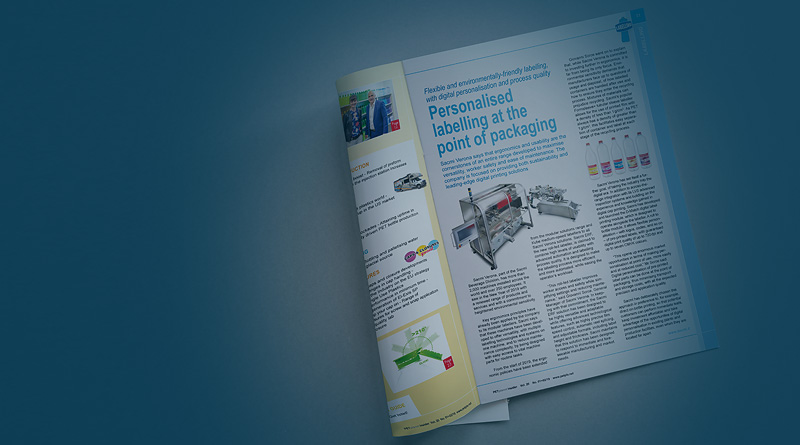