"MARKET SURVEY 30 PETplanet insider Vol. 14 No. 07+08/13 petpla.net 07+08/2013 MARKETsurvey Company name Technopet Machineries 1 Blow Sidel Group Postal address Telephone number Web site address Contact name Function Direct telephone number Fax E-Mail Office: 14/15, Shree Naman Plaza, S.V.Road, Kandivali(W), Mumbai- 400 067, India +91 22-28610828 www.technopet.in / www.techno-pet.com Vineet Bannore/Sunil Bharkada Director +9820346565/09821040637 +91 22 - 28061410 [email protected]; [email protected] 35 rue de la Ravine de Glatigny 95280 Jouy Le Moutier, France +33 9800 820 70 www.1blow.com Olivier Perche Sales Director +33 9800 820 75 +33 9800 820 71 [email protected] Avenue de la Patrouille de France, Octeville-sur-Mer, BP 204, 76053 Le Havre Cedex, France +33 2 32 85 86 87 www.sidel.com Damien Fournier Blowing Product Management Director +33 2 32 85 88 15 +33 2 32 85 81 16 [email protected] 1. Machine designation / model number Pauto 1200/1600 Auto 1800 Auto TSBM Pauto 2X2X5 TPS 20L 5 Gallon Jar TP-Beer For Beer/ Liquore/ Hotfill 1XL / 1XLab / 2L / 4L Matrix Blower 20 models available by end of 2013 SBO Universal 2eco; 39 SBO Highspeed eco 2 models 2. Bottle volume (from/to in litres) a) Standard machines 100ml to 2l 100ml to 2l 100ml to 2l 100ml to 5l 200ml to 2l 0,2 to 2,5l 0,1l to 3,5l 0,25l to 3l 0,20l to 0,71l b) Machines for large containers 5l to 20l 0,2 to 12l 3. Maximum number of stretchblow moulds (units) a) Standard machines 2 2 2 2 1 1,2,4 4 34 30 24 and 34 b) Machines for large containers 1 1 1 4. Output per stretch-blowmould for: 0.5 litres CSD bottle (units per hour) 1,200/1,600 2,000 2,200 1,000 500 2,000 2,300 2,200 2,100 1 litre CSD bottle (units per hour) 1,200/1,600 2,000 2,200 800 600 1,800 2,250 2,200 1.5 litres still mineral water bottle (units per hour) 800 1.600 1,800 600 700 1,700 2,250 2,200 Large capacity container 500 100 1,000 Other 1,600 800 300 combo filling 5. Footprint / space requirement (L x W x H in metres) 2,1 x 1,6 x 2,4 from 11.3 x 4.9 x 3.9 to 13.1 x 4.9 x 3.8 Company name Wei Li Plastics Machinery (HK) Ltd Mega Machinery Mould Co., Ltd. Beutelspacher S.A. DE C.V. Side S.A. Postal address Telephone number Web site address Contact name Function Direct telephone number Fax E-Mail Room 1212, Fo Tan Ind. Centre, 26-28 Au Pui Wan St., Fotan, N.T. Hong Kong +852 2690 2368 www.weiliplastics.com Maggie Chau Business Manager +852 2690 2368 +852 2690 2380 [email protected] 47-8 Huangzhou road, Huangyan, Taizhou city, Zhejiang province, China +86-576-84020122 http://www.MegaMachinery.com Cai Jiahan(Simon) Assistant to GM +86-13586002000 +86-576-84020107 [email protected] Venados No 52, Col. Los Olivos, Tláhuac, Mexico D.F. +52-55 58404562 www.beutelspacher.com Sergio Beutelspacher Director +52-55 58404562 +52-55 58451053 [email protected] Pol. Ind. Monguit, C/Llinars, s/n 08480 - L'Ametlla del Valles (Barcelona) +34 938463051 www.sidemachines.com Josep Jiménez Global Export Manager +34 677551928 +34 938492211 [email protected] 1. Machine designation / model number MP Series (Mini, Standard-I-IV, Medium I-IV; Large I-II, Ex-wide & Ex-Large) RB,EB,SS,E,SA total 5 series SB 3002 Easyblow Maxiblow 1002e/ 2004e/ 2006e 2002e/ 2003e 5001 T-handle 1/2/3/4/6 2. Bottle volume (from/to in litres) 0.1 - 25l 0,1 - 2,5 0,1 - 11 0,1 - 2,5 0,1 - 11 1 - 40 1-4 a) Standard machines 0.015-10l 0.30 - 2.5l 3l b) Machines for large containers 10-20l 25l 3l 3. Maximum number of stretchblow moulds (units) 1 1 2 - 4- 6 2 - 3 1 from 1 to 6 a) Standard machines 1-4 16 2 X X X X X X b) Machines for large containers 1-2 6 1 4. Output per stretch-blowmould for: 1,700 1,500 1,700 1,500 1,500 1,200 0.5l CSD bottle (units per hour) 8,00-1,000 1,700 1,200 to 1,800 1,700 1,500 1,700 1,500 1,500 1,200 1l CSD bottle (units per hour) 8,00-1,000 1,400 1,200 to 1,800 1,700 1,500 1,700 1,500 1,500 1,200 1.5l still mineral water bottle (units per hour) 8,00-1,000 1,200 700 to 800 1,700 1,000 1,700 1,000 800 1,200 Large capacity container 500-650 for 5-10l; 100-120 for 20l 900 700 to 800 Other 350-400 for 500ml PP Fridge Bottle 5. Footprint / space requirement (L x W x H in metres) Depending on machine model 5.7 x 1.8 x 2.2 2 x 3.8 x 2.5 Depending on machine models. Taylored solutions for small areas","@ID":32}, "EDITOURS REPORTS 34 PETplanet insider Vol. 14 No. 07+08/13 petpla.net February 27, 2013 Industrias Lara Bisch S.A., La Paz Manufacturer of labels and foil pouches Roberto Renjel Doria Medina (Managing Director) February 27, 2013 Cerveceria Boliviana Nacional S.A., La Paz Bottlers of beer and CSDs Ibo Blazicevic (General Director CBN)(r) and (Cristina Montilla, Director CSD)(l) February 28, 2013 Embol S.A., Santa Cruz CSD bottler (Coca-Cola) Roberto Francino in his office holding 190ml Coca Cola bottle February 28, 2013 Empacar S.A., Santa Cruz Bottle-to-bottle recycling, manufacturer of preforms and bottles The Empacar team March 04, 2013 Surena, Sucre Brewer and beer bottler Surena’s filling section Chile March 13, 2013 Embosur S.A., Concepión Bottler of CSDs (f.l.t.r.) David Fierro Salazar (General Manager), Kay Krüger and Sergio R. Valenzuela (Controller) Peru February 18, 2013 San Miguel Industrias PET S.A., Lima Bottle to bottle recycling, preform and bottle manufacturers Sven Broderson (CEO) (l) and Alexander Büchler (r) February 25, 2013 UCP Backus y Johnston S.A., Lima Bottlers of beer, CSDs and water In the Backus production area with Maria Contreras (l) and Jorge Ayestas (r) Bolivia February 26, 2013 Ecovecindarios, Swisscontact, La Paz Waste separation (NGO) A member of the Ecovecindarios team sorts PET bottles 360° 360° 360° 360° 360° 360° 360° All the companies we visited will feature on our PETplanet booth 501, hall B3","@ID":36}, "imprint EDITORIAL PUBLISHER Alexander Büchler, Managing Director HEAD OFFICE heidelberg business media GmbH Häusserstr. 36 69115 Heidelberg, Germany phone: +49(0)6221-65108-0 fax: +49(0)6221-65108-28 [email protected] EDITORIAL Doris Fischer: [email protected] Michael Maruschke Ruari McCallion Waldemar Schmitke Ilona Trotter Wolfgang von Schroeter Anthony Withers MEDIA CONSULTANTS Martina Hischmann [email protected] Roland Loch [email protected] phone: +49(0)6221-65108-0 fax: +49(0)6221-65108-28 France, Italy, Spain, UK Elisabeth Maria Köpke phone: +49(0)6201-878925 fax: +49(0)6201-878926 [email protected] LAYOUT AND PREPRESS Exprim Kommunikationsdesign Matthias Gaumann | www.exprim.de READER SERVICES Heike Fischer [email protected] PRINT Chroma Druck & Verlag GmbH Werkstr. 25 67454 Römerberg Germany WWW www.hbmedia.net | petpla.net PETplanet insider ISSN 1438-9459 is published 10 times a year. This publication is sent to qualified subscribers (1-year subscription 149 EUR, 2-year subscription 289 EUR, Young professionals’ subscription 99 EUR. Magazines will be dispatched to you by airmail). Not to be reproduced in any form without permission from the publisher. Note: The fact that product names may not be identified as trade marks is not an indication that such names are not registered trademarks. 3 PETplanet insider Vol. 14 No. 07+08/13 petpla.net dear readers, Sustainability is about communication: this was one of the messages to emerge from the platform discussion on the occasion of the trade press conference at drinktec PETpoint on Lake Spitzing. A lively exchange of views on the subject ensued between machine manufacturers and processors. Karl Klein, of the Gropper Dairy, expressed it like this: “For many people, doing things in a sustainable way is quite normal. It’s just that they don’t realise it.” This, perhaps, was the phrase that characterised the whole event. Sustainability has always been in the DNA of the drinks industry but only now is it slowly coming to be recognised as a potent marketing tool. The discussion then turned to where sustainability is possible. Suddenly, the general view seemed to be that they are all, in fact, sustainable in everything they do. The big machine manufacturers are not only building sustainable machines and equipment that consume less energy, water or material; no, they are also sustainable in relation to their own production and, it goes without saying, also in terms of personnel development. Again Mr Klein chipped in with a comment about personnel development: he found it worrying that some new developments came from designers who had never actually been at the coalface, which meant that, often, the “improvements” ignored the needs and requirements of the producers. Professor Niemeyer interposed with a contrary view, emphasising to the participants that “In our company the young engineers are sent out to meet customers face to face to ensure that they understand these important factors.” So could there be a breakdown in communication here? Actually, if anything, sustainability arguably represents just a different form of communication. Once again it was Mr Klein who put it in a nutshell: “Media, Non-Government Organisations (NGOs), customers and even governments,” he said, “ask specific questions that companies need to answer – questions which may be related to factors such as water, packaging, CO 2 footprint as well as about the production of raw materials.” Karl Klein does not accept that such questions are a burden. For him, they constitute one of the ingredients of success. “If sustainability is genuine, the consumer will also accept it. And, more importantly, it will also be profitable. For instance, I would never have thought that we, as a specialist in discount products, would today find ourselves occupying the position of a leader in the manufacture of bio-products“. So how can we summarise the discussions? Sustainability has always been part and parcel of the drinks industry, but as a topic for communication, it has been seriously neglected. And not just within companies themselves but in the various sectors and even amongst consumers. Where is the best place for the industry to talk about this? The answer is at drinktec/PETpoint. Yours Alexander Büchler Round table discussion moderated by Kilian Reichert. From left to right: Volker Kronseder, Chairman of the Board of Krones AG, Prof. Dr.-Ing. Matthias Niemeyer, Chairman of the Board of KHS GmbH, Christian Frahm, Director Business Line Beverage and Dairy, GEA Westfalia Separator Group GmbH, Dr Klaus Peter Stadler, Director Environment & Water Resources, Coca-Cola Europe, Peter Peschmann, Divisional Director Production and Management Engineering, Veltins Brewer and Karl Klein, Director of Production and Technology at the Gropper Dairy","@ID":5}, "NEWS 10 PETplanet insider Vol. 14 No. 07+08/13 petpla.net Sidel, SBA renew partnership Sidel has announced that it is renewing an agreement with long term partner SBA, with whom it has worked closely since 1999. The collaboration is intended to improve access to local resources for Sidel customers in East Africa, Ethiopia, West and Central Africa. SBA has offices in Nigeria, Kenya, the Ivory Coast and Congo, along with subsidiary operations in the DRC (Democratic Republic of Congo), Cameroon and Angola. www.sidel.com Engel turns over a new record Engel, the Austrian packaging machine manufacturer, has reported record revenues of €950 million in financial year 2012/2013. This is a 14% increase over the previous year and an overall increase of 165% since 2009/2010. Engel says that it expects to generate further growth of about five per cent for each of the next three years. The company increased its market share across the world and now claims 10% of the Asian market for European and Japanese technology; 18% in America and 30% in Europe. It reports that more than half of all its hydraulic machines are now equipped with ecodrive. Around 12% of injection moulding machine sales in Europe are to customers in the packaging sector, with a rising number of large machines, able to work with a high number of cavities, being sold in the region. A total of 65% of the company’s total revenues are generated in Europe, with approximately 20% of global turnover coming from Germany. Turkey and Russia follow, in terms of sales volume, with American and Asian markets responsible for 17 and 18%, respectively. Revenues from Asia were €145 million, another new record, and the company has tripled turnover in SE Asia over the past two years. Sales to India are expected to increase in the short term. Engel has invested over €57 million in various sites during 2012/13 (see separate story). www.engelglobal.com Döhler expands in Brazil DöhlerGroup, an international producer of technology-based natural ingredients, systems and technologies headquartered in Darmstadt, Germany, has invested in additional capacity at its Döhler América Latina plant in Limeira, Brazil. The company says that the site’s new, multipurpose distillation columns will allow greater production flexibility and enable it to broaden its citrus keys portfolio, as well as expanding capacity. Natural Isolates and keys such as octanal, decanal, linalool, valencene, ethyl-butyrate, sinensal, hexanal and others derived from oranges are processed at Döhler América Latina. Tailormade Isolates can be processed and directly supplied from the plant, which was chosen as Döhler’s Centre of Excellence Citrus because of its location in the heart of Brazil’s citrus-growing area. All relevant technologies for its Natural Flavour extract portfolio are available at the site, which exports direct to customers around the world. www.doehler.com SGT goes three up in Algeria Société Générale des Techniques (SGT), which specialises in the manufacture of PET preforms for packaging liquids, has opened a new factory in Sétif, Algeria, to meet increasing market demand. The company already has a plant in Rouïba, Algeria, and its original facility in Rezé, France. SGT says that the new plant will enable it to provide more local service and effective response to its customers in the region. The factory is equipped with three types of 72-cavity moulds and nine presses. It has the capacity to produce 2 billion preforms/a; with the 15 presses at the Rouïba site, production capacity is now 3.8 billion preforms/a. The new facility now has 175 Algerian employees and is already operational. The official inauguration will be in September 2013. www.sgt-pet.com ProTec gets new MD ProTec Polymer Processing GmbH, of Bensheim, Germany, has appointed Peter Theobald (54) to the position of Managing Director. His experience includes technical and sales positions with leading manufacturers of pumps and fittings, machine tools and plastics engineering companies in Europe, China and Asia. He joins Christian Bennhold and Alfred Kimpel on the company’s management team. www.sp-protec.com","@ID":12}, "NEWS 13 PETplanet insider Vol. 14 No. 07+08 Alpla and Avantium team up for PEF Avantium, a renewable chemicals company, and Alpla Werke Alwin Lehner GmbH, plastic converters, have announced that they have entered into a Joint Development Agreement for the development of PEF bottles. Alpla becomes the third company – after Coca-Cola and Danone – to collaborate with Avantium on PEF, a bioplastic based on Avantium’s YXY technology. The goal of the collaborations is to bring 100% biobased PEF bottles to the market by 2016. Alpla will develop PEF bottles for personal care and home care applications, such as cosmetics and detergents, and for food applications such as sauces, dressings, baby foods and edible oils. The two companies also announced their intention to work on the development of bottles for beer and other alcoholic beverages. Avantium is currently supplying its development partners with PEF manufactured from material produced at its Geleen pilot plant. Avantium is planning a 50,000t commercial plant, which is projected to be operational in 2016. The YXY technology and further details of PEF were described in detail on p11 of PETplanet Insider issue 6/2012. www.buhlergroup.com No more Fear DAK Americas LLC (DAK) has announced that it will be closing all its operations at its Cape Fear Site, near Wilmington, North Carolina. The closure is expected to be completed by September 2013. The site was built in the late 1960’s and acquired by DAK Americas in 2001. Approximately 600 staff are employed on the site in the production of PTA, PET resins and polyester staple fibres. DAK says that it will supply the majority of its current Cape Fear customers from other North American facilities. www.dakamericas.com","@ID":15}, "PRODUCTS 47 PETplanet insider Vol. 14 No. 07+08 Screw-fed granulators Herbold Meckesheim SB Series Granulators’ patented screw-feed mechanism is claimed to make them quieter and more efficient than gravity-fed size-reduction equipment for pulverizing PET bottles and other recyclable plastics. The SB Granulator is suitable for either wet or dry operation and is claimed to be able to process up to 7t of plastic per hour. Materials to be granulated are delivered from the unit’s hopper to the cutting chamber by one or more conveyor screws mounted at an angle (45° to 90°) to the rotor axis. The screws maintain a steady feeding pace, even if the plastic is a mixture of sizes and shapes, with throughput at 30% to 50% above that of gravity-fed machines with cutting chambers of the same size. Herbold also maintains that the machine uses less power, has no fly-back, reduces wear to the cutting blades, and the shorter time that granulated particles spend in the chamber leads to less fines and dust. These granulators can also be used for secondary size reduction of pre-shredded plastics. www.herboldusa.com Oil goes PCO1881 Bericap has announced the development and commercial launch of its EV 28/26, a press-on closure designed to suit the lightweight PCO1881 bottleneck. It is equipped with a screw-closure opening and contents are protected with a non-drip function to eliminate spillage. It can be supplied either with or without a flow regulator. The EV28/26 has been designed to enable producers in the edible oil market to take advantage of the PCO1881 lightweight standard. It can also be used with products such as sauces, dressings, syrups and other similar products. www.bericap.com","@ID":49}, "TRADE SHOW PREVIEW 39 PETplanet insider Vol. 14 No. 07+08/13 petpla.net drinktec + PETpoint, September 16 -20, Munich, Germany PET trends bundled At drinktec + PETpoint manufacturers and suppliers from all over the world meet up here with all sizes of producers and retailers of beverages and liquid food products. They will present the latest technology for processing, filling, packaging and marketing all kinds of beverages and liquid food – raw materials and logistics solutions included. The themes of beverages marketing and packaging design round off the portfolio. drinktec 2013, which takes place at the Messe München exhibition centre in Munich, from September 16 to 20, 2013, is expected to attract over 1,400 exhibitors from over 70 countries and approximately 60,000 visitors from more than 170 countries. All the trends in PET manufacture and bottle design will be on show at PETpoint, the PET segment within drinktec 2013, mainly in hall B3. The enormous quantity of PET bottles produced each year (in 2010 worldwide around 500 billion) highlights the importance of increasing energy and resource efficiency in bottle manufacture. A key factor is the weight of the PET bottles – up to 70% of the costs of a bottle are accounted for by the materials, preform manufacture and bottle production each account for only around 15%. For every 100 million PET bottles produced, roughly 100t of material could be saved by reducing the weight of each bottle by just 1g. In the process of heating preforms and in the use of compressed air, there is untapped potential for saving energy, and the new generation of stretch blow molders is achieving impressive reductions in energy consumption. Drinktec 2013 will be showcasing the latest results of the manufacturers’ R&D efforts, the focus being on optimizing strength, faster processing, heat-tolerance and cleanliness. According to Markus DalPian, Head of Business Units PET, CAP and PAC at Netstal-Maschinen AG, Switzerland, developments in the market are focusing ever more on the overall view of packaging production and ways to optimize the entire value-added chain: “This means even closer integration and a more efficient grouping of the stages in the process. Production and process efficiency are the key concerns that we are hearing from our customers. These requirements can no longer be met by injection moulding machines alone. What´s needed is a more comprehensive system approach, taking into account the entire value chain as well as the requirements of the end product. Part of the answer lies in turnkey system solutions tuned precisely to the needs of the user and optimized machine technology to help reduce the overall weight of packaging. Further efforts are concentrating on reducing processing costs through the use of efficient energy systems which incur very low costs on operation and maintenance.” Visitors can also look forward to some new ideas and solutions from the manufacturers in the area of multilayer bottles. Today all kinds of PET bottles – multilayer, blend or no blend – have established themselves as suitable packaging for a wide range of beverage types. Optimizing the characteristics of these barrier coatings is one of the biggest challenges in opening up new markets. As regards the main trend in PET, which continues to be weight reduction, there will be a lot to see at drinktec, as there is still much potential here to be exploited. In this first show preview we gathered some of the PET highlights at drinktec. www.drinktec.com Light as a feather Sipa is planning to unveil a machine that enables further bottle lightweighting. Dubbed “Xtreme”, the new equipment is claimed to treat material very gently and to significantly reduce the rate of acetaldehyde generation and consequent loss of bottle performance. The company’s preform system range has been expanded with the Xform 150, developed in partnership with the Canadian company Athena Automation Ltd. It is designed to offer the capacity to cope with a range of applications, from narrow necks through to wide mouths, and will accept legacy moulds. Also on the stand will be Flextronic, a new multifunctional volumetric electronic filler platform. Sipa will be demonstrating its flexibility with the Isotronic Evo valve configured in XFill version, integrated with the Massblend mixer. The valve is capable of placing carbonated, still and hot fill products, with or without pulp, into different type of containers on the same line. The company will also be exhibiting Cinetic, its new generation of space-saving pallet stretch-wrapping equipment. www.sipa.it Sipa Hall A5 Booth 303 PE Labellers Hall A5 Booth 315 Enhanced safety, more modularity, hot glue shuffle Italian company PE Labellers has reserved a 300m² area on which it will be showing its complete range of labellers for the beverage industry. The company says that its latest machines have been designed for higher safety and even claims zero workplace accidents. Its modular labeller is designed to be scalable to cope with present and future needs and its Adhesleeve technology is claimed to be the only way to turn a hot-glue machine into a self-adhesive machine. PE Labellers’ Rollmatic rotary and Roll-Line linear roll-fed machines will also be on display. www.pelabellers.it","@ID":41}, "NEWS 11 PETplanet insider Vol. 14 No. 07+08/13 petpla.net Electrification of industry American plastic closures manufacturer Weatherchem Corporation, which was recently acquired by Mold Rite Plastics, has added an Engel e-motion 550 US injection moulding machine to its production capacity. Weatherchem says that the machine provides it with a combination of high efficiency and low energy consumption. Engel has installed a total of nine all-electric e-motion injection moulding machines at Weatherchem’s 45,000 square foot plant in Twinsburg, Ohio, in sizes ranging from 310 to 550 US tons. Weatherchem decided to change from hydraulic to allelectric injection moulding machines in 2008 and adopted a partnership approach with Engel. Comparative internal testing with one of their applications, first on a hydraulic press and then on the Engel e-motion, demonstrated energy savings of over 70%. www.engelglobal.com www.weatherchem.com Manjushree’s money Manjushree Technopack Ltd, has registered a growth of 17% in its consolidated revenue for the year ended March 31, 2013 at Rs.36,122 lacs (€500 million/ US$650 million) as against Rs. 30,978 lacs (€428 m / $557 m) for the same period last year. Profit Before Tax (PBT) grew by 25% and Profit After Tax (PAT) by 18%. The fully diluted earnings per share (EPS) for the quarter stood at Rs17.82 (€0.23 / $0.30) as against Rs.15.13 (€0.20 / $0.26) for the same period last year. Exports rose up by 55% during the financial year. The company has committed to investments totalling Rs150 Crores (€2.1 million / $2.7 million) for two new green-field facilities in Harohalli and Bidadi. The Bidadi facility is the single largest PET preform manufacturing plant in South Asia and was commissioned during the year 2012-13. It has raised the company’s total capacity from 50,000t/a to 80,000t/a – equivalent to 15% of total PET consumption in India. Manjushree Technopack manufactures speciality plastic packaging products for domestic and export markets and supplies companies in the FMCG, pharma and food & beverage sectors including Coca Cola, PepsiCo, GSK, Nestle, Unilever, Pfizer, DelMonte, Tata Tea and Mondelez International (formerly known as Cadbury). The company has expanded into the liquor, personal care, dairy and edible oils segments. Companies including United Spirits, Reckitt Benckiser, Bacardi, Diageo and Big Cola have been added to the client portfolio for the PET Bottles and PET Preforms businesses. www.manjushreeindia.com Mitsubishi sets higher PET barrier Mitsubishi Plastics, Inc. has announced that it is to establish a new production line for high-barrier PET bottles at its plant in Hiratsuka City, Kanagawa Prefecture, Japan. The intention is to meet a growing demand for the highbarrier PET bottles that are increasingly being used for packaging alcoholic beverages, cooking oils and seasoning agents. The new production line is expected to begin operation by November 2013 and will more than double the plant’s production capacity. The Company will be investing approximately one billion yen (€7.7 million / US$10 m) in the project. High-barrier PET bottles developed by Mitillionsubishi Plastics are based on the diamond-like carbon (DLC) technology, which deposits a thin carbon film on the inner wall of the PET bottle. This is done by placing the bottle in a vacuum, filling it with acetylene gas and generating a plasma. The process significantly increases the ability of the wall to prevent permeation of gases such as oxygen by a factor of 10, compared to standard bottles. The process also makes the bottles seven times better at preventing carbon gas penetration, and five times better at inhibiting water permeation. Mitsubishi’s production of highbarrier PET bottles is currently conducted at its Azai Plant in Nagahama City. www.mpi.co.jp Bühler sells thermal processing unit Swiss private equity firm Cross has acquired a majority holding in Bühler Thermal Processes AG (BPAG), which was spun off into a separate company by Bühler in October 2012. The sale contract was signed on June 4, 2013 and is subject to the approval of the competition authorities and other agencies and interested parties. The new majority shareholder is taking over Bühler Thermal Processes with its management team and all its employees at its present location in Oberbüren and will add other industry experts to its Board of Directors. Bühler retains its link with the company through a substantial minority holding. BPAG focuses on multifunctional large-scale plants and is a leader in post-condensation technology for PET, mainly used in food packaging and technical yarn. It designs and manufactures plant and equipment for the heat treatment of a variety of polymers, which are mainly used for the processing of PET. BPAG’s product range also includes plants for recycling used PET into materials for direct food contact. It employs around 80 staff and achieved revenues of CHF 88 million (€71.4 million / US$93 million) in 2012. Cross’ mission is stated to be the support of sustainable development of mid-sized companies in Switzerland, Germany and Austria through equity capital, industrial expertise and an extensive relationship network. www.buhlergroup.com","@ID":13}, "EDITOUR REPORTS 33 PETplanet insider Vol. 14 No. 07+08/13 petpla.net This year’s roadshow, in collaboration with drinktec/ PETpoint, took us to the distant lands of South America. After the PETplanet Team’s successful tour to Russia, Ukraine and Poland, we began planning our most ambitious undertaking so far: nothing less than a detailed examination of the South American PET market. Of course we are not on our own in this endeavour. We have the wholehearted help and support of numerous industry colleagues both here in Europe and over in South America. Above all, we have the backing and encouragement of our friends at drinktec, arguably the world’s leading beverages exhibition. Before us lay a gruelling expedition, our biggest tour yet. The route would take the PETplanet teams from the start point in Peru, across Bolivia, Chile, Argentina and Uruguay and finally to Brazil. As with our previous tours in 2012, we are using three Editourmobil teams for the different sections of this daunting journey, some 13,000km in total length, and including the breathtaking landscapes of the Andes, 4,000m above sea level. The first stage of the adventure was to ship the Editourmobil to Montevideo, and from there drive to Lima, the actual start of the tour. The first team, consisting of Alexander Büchler and Rolf Sinkovec, interviewed companies in Peru and Bolivia and drove the vehicle to Chile. Here, in Santiago de Chile, team two, consisting of Kay Krüger Go with the flow Tour 2013 on drinktec and Shiraz el Goudi, took over the reins but immediately found themselves forced to book the vehicle into a garage, where, as would become apparent later, the Editourmobil was destined to remain for quite some considerable time. During the first section of the tour, the fine sand of the Atacama Desert had damaged the gears of the Editourmobil, and this had meant that the itinerary had to be rapidly revised. Thus it was that Kay and Shiraz were obliged to fly to their appointments whilst the vehicle was being repaired, and this considerably reduced the number of companies they were able to visit. However they managed to cover Argentina and Uruguay. Subsequently, once the vehicle had been successfully repaired, the final and longest section of the tour could begin, taking the Editourmobil and team three through Brazil. The team consisted of Waldemar Schmitke and Florian Roscheck. In the course of the 14 weeks, from mid-February to the Feiplas Fair in late May, we visited numerous players in the beverages sector, some large, others exploiting niche markets. In this issue we give you a preliminary overview of the companies involved and the interviews in chronological sequence of visits. For more information visit: www.drinktec.petpla.net PETplanet visits bottlers, processors and recyclers in South America - Peru, Bolivia, Chile, Argentina, Uruguay and Brazil Lima Santiago La Paz Buenos Aires Montevideo Progresso São José dos Pinhais Sao Paulo Rio de Janeiro Lindóia Santa Cruz Sucre Quilmes Pilar Jaú Concepción Santa Fe Barueri Jundiai Sorocaba Amparoa Limeira South America by Kay Krüger Part1","@ID":35}, "PETcontents 07+08/13 4 PETplanet insider Vol. 14 No. 07+08/13 petpla.net INSIDE TRACK 3 Editorial 4 Contents 6 News 46 Products 40 PET bottles for beverages and liquid food 48 PET bottles in health and beauty care packaging 50 Patents PET - THE NEXT GENERATION 28 Ready, steady, bowl! Salad packaging production to Use More than 56,000,000 recycled PET bottles TRADESHOW PREVIEW 39 PET trends bundled drinktec PETpoint, Munich, September 16 - 20, 2013 EDITOUR REPORT 14 Poland: Go to brau tour - Last part 33 South America - introduction Go with the flow tour 2013 MARKET SURVEY 29 Two-stage stretch blow moulding machinery BUYER’S GUIDE 53 Get listed! Page 24 PREFORM PRODUCTION 20 Reduced electricity consumption in the preform oven Bottles, preforms and closures - Part 4 BOTTLE MAKING 22 Air back KHS claims compressed air savings of up to 40% with Airback Plus 24 Bright idea ATMI develops BrightPak for speciality and sensitive liquids BOTTLING / FILLING 26 Putting the fizz into Santiago Coca-Cola installs 7,200bph SMI production line in Cape Verde Page 46 Page 26","@ID":6}, "PREFORM PRODUCTION 21 PETplanet insider Vol. 14 No. 07+08/13 petpla.net contents, base shape, etc. (see Sections 1.1 and 1.2 of the book). The output of the preform design is usually a 2D drawing that includes all required dimensions and designations according to international standards. This ideal preform geometry is then the benchmark for the real preform. Here, two fundamentally different approaches can be taken. Standard preform In most cases, the ideal preform is used as a reference to select a standard preform from the catalogues of PET converters. Although this will always involve a certain degree of give-and-take, the technical advice from the manufacturers or external consultants can help reduce the inevitable compromise to a minimum. Purpose-made preform Depending on the bottle design and its performance requirements, it may be necessary to create a special preform with the ideal geometry for the bottle to be produced. This may, for instance, be considered if particularly a lightweight container is required or if the container is to be produced in large numbers for a very long period such that the investment in injection moulds permitting an optimum preform geometry will be economically viable. In Chapter 2, this will be discussed in greater detail. At this stage, the real preform geometry for the subsequent design steps has been defined. The bottle geometry and the preform geometry, and in particular the preform weight, now permit a direct calculation of the average wall thickness. Bottle design for a dependable process Making the bottle design totally suitable for the process requires its adaptation to possible constraints by the downstream equipment, which may even result in a deviation from the initial ideal shape. Aspects to be considered and clarified include: The transport of the bottle downstream of the blow moulding machine may require special design features. If an air conveyor system is used, a certain neck height below the neck ring may have to be provided. Please order your copy at the PETplanet insider book shop: https://petpla.net/books Bottles, Preforms and Closures A Design Guide for PET Packaging Second Edition by Ottmar Brandau 115,00 € 180 pages © Copyright Elsevier 2012 The contents as well as the type of filler may have an influence on the design of the shoulder geometry and in particular on the shoulder profile and the diameter in the transition area between the neck and the shoulder. For example, if a spreader or rotating filler head is used, it must be ensured that the flow of the contents is not interrupted during filling and that no excessive foaming occurs. After filling, the bottles are transported on conveyor belts. This requires an examination of the behaviour in bottle-to bottle contact. It must be ensured that the bottles do not tip over if jams occur. Also the “bouquet effect,” which may be produced by strongly clubshaped bottles, should be avoided. It should also be remembered that filled bottles should have as few friction points as possible. Ideally, just one such point or line of contact (contact ring) is specifically arranged above and below the labelling zone. When roller conveyors are used, the feet of petaloid bases must be designed such that the bottles do not become stuck between the rollers, preventing rotation. Unsuitably designed petaloid bases will also promote tipping over of the bottle when negotiating curves. The feet should not be too narrow or sharply angled. In this context, the tipping angle of the filled bottle as a function of base geometry and conveyor speed must be determined and optimised by modifying the bottle geometry to ensure that the bottles do not tip over during transport. The tipping angle should not fall below the minimum values indicated below for the stated base geometries and conveyor speeds. The design of the bottle geometry should also ensure that the required filling level for the volume is reached. In particular for aseptically filled contents, this filling level should be as high as possible to minimise the remaining headspace. It may be zero for hot-filled bottles. For the labelling zone, it is important that the bottle is designed such that major variations in diameter are avoided. This is particularly important for wraparound labels, which in many cases are no longer glued in an overlapping fashion but with a butt joint. In particular, for bottles filled with carbonated products, which generate an internal pressure, certain minimum wall thicknesses must be observed, and/or the bottle has to have a high orientation (see Chapter 2). These are just some of the aspects that must be considered when designing the bottle for a reliable production and filling process. Depending on the contents and other details of the respective line, a large number of other aspects will have to be taken into account. Further input on the wall thickness distribution will be available to the bottle designer from the expert knowledge of the process engineers. Such knowledge can either be based on experience or, ideally, can be retrieved from the databases of expert systems during the CAD phase. *This article was published in Bottles, Preforms and Closures, Ottmar Brandau, Chapter 1.4., Copyright Elsevier 2012","@ID":23}, "BOTTLES 51 PETplanet insider Vol. 14 No. 07+08/13 petpla.net Hair care Under the brand name Deliplus – well-known in Spain for quality at a low price – Messrs. Laboratorios Maverick based in Ulldecona are offering 200ml of hair care product in a waisted PET bottle. The gold coloured bottle with a basic rectangular shape varies in terms of its form and becomes oval in the area of the shoulder. The packaging incorporates a screw-on hinged lid with a dispensing opening and two transparent self-adhesive labels. www.laboratoriosmaverick.com Rotary switch closure The Spanish cosmetics manufacturer Laboratorios dermatologicos Kinesia is marketing After-Shave Lotion in a 300ml oval PET bottle under the brand name Kinesia Artic. The greenish tinged bottle is fitted with a closure which is opened by turning the switch through 90° (towards the back of the container). At the same time a section of the closure is raised by means of an internal thread, so releasing a discharge opening. Turning the switch back so as to re-close the pack triggers an audible sound when the switch engages via a catch mechanism in the shiny silver sub-section of the closure. www.puig.com Moisturising under pressure The French company Laboratoires Klorane has various products based on marigold (Calendula) in its range for gentle and caring cleansing and treatment of sensitive baby skin. The alcohol- and paraben-free cleanser is fitted with an innovative dispensing system. The transparent, 500ml PET bottle is combined with a closure which, when a pad of cotton wool is placed on it followed by depressing the plunger, moistens it. Prior to initial opening the reclosable hinged lid is secured by means of a sleeve label. www.clubmamansklorane.com","@ID":53}, "MARKET SURVEY 29 PETplanet insider Vol. 14 No. 07+08/13 petpla.net Caps and closures Bottle-to-bottle recycling plants Preform and single stage machinery Preforms Preform / Stretch blow moulds Two-stage SBM machinery Filling equipment Resins / Additives Compressors Closure systems Suppliers of two-stage stretch blow moulding machinery This year’s participants in our market survey are shown below in alphabetical order. 1Blow (France), Amsler Equipment (USA), Beutelspacher (Mexico), KHS (Germany), Kosme (Austria), Krones (Germany), Luxber (Spain), Mega Machinery (China), Nissei ASB (Japan), Sacmi (Italy), Serac (France), Siapi (Italy), Side (Spain), Sidel (France), Sipa (Italy), SMI (Italy), Technopet (India), Urola (Spain), Weil-Li (Hong Kong), The companies are shown in the table in the order in which their details were received by the editors). Although the publishers have made every effort to ensure that the information in this survey is up to date, no claims are made regarding completeness or accuracy. 07+08/2013 MARKETsurvey Company name Amsler Equipment Inc. Luxber, S.L.U. Serac Group Postal address Telephone number Web site address Contact name Function Direct telephone number Fax E-Mail 1245 Reid St., Unit 1 Richmond Hill, Ontario, Canada L4B1G4 +1 905-707-6704 www.amslerequipment.net Heidi Amsler Sales and Marketing Manager +1 905-707-6704 +1 905-707-6707 [email protected] Av. De Azorin, 34-36 03440 Ibi (Alicante), Spain +34 965 553 853 www.luxber.com Mr. Jose S. Mira General Manager +34 965 553 583 +34 965 553 861 [email protected] 12, route de Mamers, BP 46, 72402 La Ferté Bernard Cedex, France +60 378472228 www.serac-group.com Philippe de Sarrazin Managing Director - Asia Pacific +60 378472228 +60 378471208 [email protected] 1. Machine designation / model number Linear Series - 9 Models: L12, L15, L22, L32, L407, L42, L515, L615 Linear Widemouth Jar Series - 2 Models: L16J,L25J Linear Convertible Series 4 Models: L32C, L42C, L515C, L615C Linear Large Format Series 5 Models: L110, L210, M120, LM120, L120C Rotary Series 2 Models: APT10,APT16 Tecnopet 1000, 2000, 4000, 6000 & 8000 SBL Series (Linear) 2. Bottle volume (from/ to in litres) a) Standard machines 50ml to 5l 100ml to 6l 50ml to 5l 50ml to 3l 0.1 to 3l 0,05 to 5l b) Machines for large containers 4l to 23l 0.1 to 10l 3. Maximum number of stretch-blow moulds (units) a) Standard machines 6 2 16 1, 2, 4, 6 and 8 8 b) Machines for large containers 6 2 1, 2 and 4 2 4. Output per stretchblow mould for: 0.5l CSD bottle (units per hour) 1,800 1,800 1,500 1,600 1,800 1l CSD bottle (units per hour) 1,400 - 1,800 1,400 - 1,800 1,250 - 1,500 1,500 1,800 1.5l still mineral water bottle (units per hour) 1,400 - 1,800 1,400 - 1,800 1,300 - 1,500 1,700 1,800 Large capacity container 900( 10l); 275( 18.9l) 1,200( 5l), 1,000 (8l), 850 (10l) 1,300 (5l) Other 800 - 1,600 3,000 (4l) 5. Footprint / space requirement (L x W x H in metres) 4.0 x 1.8 x 2.4 to 4.3 x 3.7 x 2.5 3.9 x 2.5 x 2.2 5.7 x 2.0 x 2.4 to 4.3 x 3.7 x 2.5 3.9 x 3.8 x 2.7 2.7x2.2 x3.1 to 4.2 x 3.0x3.2 5.1 x 6.3 x 2.5 5,3 x 2 x 2,1","@ID":31}, "PREFORM PRODUCTION 20 PETplanet insider Vol. 14 No. 07+08/13 petpla.net Bottles, preforms and closures, 2nd edition - part 4 From shape to fully-fledged design for a dependable process Ottmar Brandau has newly revised his book, “Bottles, Preforms and Closures” first published by hbmedia/PETplanetPublisher, and now to be re-issued under the Elsevier imprint. PETplanet insider is publishing extracts from successive chapters in a series of articles in forthcoming issues. Once the initial outer appearance of the bottle has been visualised and agreed upon, the shape must be implemented in a bottle design that ensures a high level of process dependability and will also include the wall thickness and its distribution. The first step in this stage is the design of the preform. From the ideal to the real preform Based on the dimensions of the bottle (height, diameter, capacity, and desired weight) and the selected or required neck design, the ideal preform geometry for the bottle is determined. This can be done either “manually” using the experience of a product developer or by applying the defined rules of a computer-aided expert system as described in Part 1. An example of such rules is as follows: The shoulder zone requires 20% more material than the labelling zone, and the bottom zone requires 50% more material than the shoulder zone. The exact values for these rules will be derived from the bottle requirements defined at an earlier stage of the development process, such as","@ID":22}, "BOTTLE MAKING 22 PETplanet insider Vol. 14 No. 07+08/13 petpla.net KHS claims compressed air savings of up to 40% with Airback Plus Air back Based on an article by Frank Haesendonckx, KHS Corpoplast KHS Corpoplast developed the Airback Plus system for the InnoPET Blomax Series IV stretch blow moulder. More compressed air from the stretch blow moulding process can now be reused than was previously the case, says KHS Corpoplast. The InnoPET Blomax Series IV cuts its use of compressed air by a targeted redesign of the valve block, among other factors. Depending on the bottle volume, between five and 15% of compressed air is saved, compared with the Series III. At the same time, the dead space volume (the volume of air which is applied at high pressure but which does not help to form the PET bottle) has been reduced by 25-30%. KHS Corpoplast claims that bottles can be manufactured from a pressure of 28bar upwards. Reuse of air A minimum of compressed air is consumed per bottle. A big target is to reuse as much of the air digested in the system as possible, again reducing the amount of compressed air required by the stretch blow moulder. Hitherto, KHS Corpoplast satisfied this market demand with its Airback I and Airback II systems. During the stretch blow moulding process the pre-blowing phase (PI phase), which takes place at low blowing pressure, is then followed by the blow moulding of the bottles at high pressure (PII phase), after which the pressure is then reduced. In Airback I some of the compressed air present in the newly produced bottle is fed into a ring line located at the centre of the blowing wheel. From there it passes directly to the next preform to be blown. The preblowing phase thus makes use of the existing compressed air. About 10% of the compressed air used for stretch blow moulding can be saved with Airback I alone. Airback II builds on the Airback I process by feeding more of the compressed air present in the finished bottle into a second ring line. This sends the compressed air through a rotary distributor out of the stretch blow moulder and straight into the compressor. It then uses its energy to prepare air for the PII phase, increasing the pressure from 28 to 40bar. Where Airback II is incorporated, up to 20% of the energy consumed during the process is saved. Reduction of compressed air Airback Plus no longer reduces the energy in the compressor but instead directly reduces compressed air consumption itself. The system works as follows: the reusable compressed air present at the end of the Airback I process in the newly produced bottle Airback Plus air reovery system by KHS Corpoplast: 40% internal high-pressure air recycling","@ID":24}, "TRADE SHOW PREVIEW 44 PETplanet insider Vol. 14 No. 07+08/13 petpla.net CanNeed Instrument(HK)Limited Tel: +86-758-2788469, Fax: +86-758-2782729 E-mail: [email protected] Web: www.canneed.com PET B ments ottle & Preform Instru Meet us at 16~20 September 2013 drinktec Booth: A3507 Magnetic Bottle Thickness Gauge Secure Seal Tester PET Bottle Pressure Tester ( Burst ) Hot Wire Bottle Cutter Printing, filling, hygiene and service KHS’ 4,200m² stand will be showcasing the company’s latest developments in stretch blow moulding, filling, and labelling technology. The new generation of Innoprint machines offers capabilities for printing directly onto PET bottles, eliminating the need for labels. HD digital print images can be sent directly from the computer to the machine’s control unit. The machine is capable of processing bottles ranging from 0.33 to 1.5l, with diameters from 40 to 120mm. The Innoprint is designed for a capacity of 36,000bph. KHS will also exhibit its Innosept Asbofill ASR, a new generation of aseptic rotary machine technology with linear and rotary systems that offers a complete aseptic program. A number of components and processes from the ABF range have been incorporated into the new rotary machine series, including an aerosol and heating system. The company’s new ultraclean concept is integrated into a mini hygiene housing, which completely isolates the filling area and requires up to 40% less space in the bottling shop. Monoblocking the filler-capper area with an InnoPET Blomax Series IV stretch blow moulder is prerequisite for the new KHS ultra-clean system. The volumetric Innofill DRV-UCF filling system optionally fills PET bottles with carbonated and non-carbonated beverages. The system is able to process up to 60,000bph with volumes ranging between 0.1 and 3l. KHS will also be presenting a comprehensive package of services at drinktec. www.khs.com KHS Hall B4 Booth 328 Sacmi Hall B5 Booth 302 End-to-end solutions Sacmi will be presenting an ‘automated magazine’ for preforms and caps, which it says is a world first and completes its turnkey plant engineering range that extends from raw material intake to end-of-line solutions. It integrates cap (CCM 48SC) and preform production (IPS 220B) with the bottling line (Combo EWE 10/15/15 + Formsleeve+), via an automated buffer (CPB Link). Visitors will be able to see the entire production line in action. Sacmi’s 1,000m2 stand encompasses product and packaging material analysis in a dedicated R&D area, a beverage plant and a workshop, which will feature solutions for filling and cap/preform production. The workshop area will also house IPS 220B injection press for preform production, which incorporates the SBF 410’s doublecavity stretch blowing technology. The company’s latest high-tech filling valves will also be on display, as will an all-new aseptic filler from the Bag-in-Box range and Formsleeve+ roll-fed labellers. www.sacmi.it","@ID":46}, "EDITOURS REPORTS 16 PETplanet insider Vol. 14 No. 07+08/13 petpla.net Maintaining the company’s competitiveness and margins is the first priority, especially in a stagnating market such as Poland. Here Alpla makes use of the strength of the enterprise as a whole, together with its long years of experience in PET processing and product development, to retain its position as market leader. However, if sales are to be increased, other sectors of the market need to be opened up. For this reason, the investment in PET recycling systems represents a logical step towards further extending business activities in relation to PET within Poland. In addition Alpla sees the increased usage of recycled PET as their contribution to sustainability and protection of the environment, both topics in line with Alpla’s company strategy. www.Alpla.com September 11, 2012 Hanex Dabrowa Gornicza Poland We met: Dr. Dariusz Lizak Vice President (from left to right) Dr Dariusz Lizak and Alexander Büchler From seasonal PET business to all the year round capacity utilisation. Hanex is one of the established PET processors in the Polish market. Since 1992 Hanex has been offering its customers PET preforms, PET bottles and since 1997 PET film. 50% of turnover is accounted for by the sales of preforms. Continuous expansion of preform capacity to 1 billion preforms a year has today secured a market share of over 20% for Hanex. Production is carried out on twelve Husky PET injection moulding systems. “A highly competitive market calls for constant innovations“ says Dr. Lizak. What he means by this is not only optimisation in the machinery sector but also own development preforms. HDN stands for“ Hanex Drink Neck“, a development by Hanex themselves featuring reduced preform weight on the neck finish. Whilst maintaining the same function, the “ HDN“ neck finish weight is, at 3.2g, 0.7g lighter than the standard 1810 version. A new development, featuring a further weight reduction on the neck finish to 1.6g, is being prepared for release. However, the high season as far as beverages in Poland are concerned is short and highly dependent on the weather. In addition the current market is close to saturation. The plant cannot run at full capacity on preform production alone. Here Hanex has opted to manufacture PET containers for applications which display a uniform consumption trend over the course of the year. These are predominantly containers for milk, ketchup, mayonnaise, cosmetics and household products. Production is carried out on 13 single-stage PET machines from Nissei ASB, 2 Mag and 1 Sipa. The annual manufacturing output in this division of the company is 100 million PET containers, corresponding to 20% of the company’s turnover.","@ID":18}, "PETproducts 46 PETplanet insider Vol. 14 No. 07+08/13 petpla.net Automatic burst expansion tester Versatile says that its JJ139 automatic PET burst expansion tester. increases testing frequency while reducing labour costs significantly. It is equipped with a 16 head load and performs automatic testing of hold, expansion percentage, expansion ml/cc, and burst pressure, which means that operators do not need to spend hours in front of manual gauges. The company claims that data output quality is also improved by the JJ139’s automation of the entire measurement test cycle, which means that data is completely free from operator influence. Other features of the machine include ethernet, usb and RS232 port for program updating/ data exports, a 15” colour LCD touch screen and a ruggedised V2 embedded microprocessor, which requires no PC. Coca-Cola Amatil in New Zealand has installed Versatile Technology’s JJ139 www.versatiletechnology.com.au SFR Evolution The latest rotary stretch-blow moulding machines from Sipa are claimed to be faster, more versatile and more efficient than their predecessors. The SFR EVO3 model range is available in versions with 6, 8, 12 and 16 cavities. A new 10-cavity platform and larger units, with 20 and 24 cavities, will be launched later in 2013. Developments in the machines include new designs in the clamp unit and in the cams, which help to achieve a maximum output rate of 2,250bph/cavity. The more compact blowing valve block has 35% less “dead air” volume. Mechanical compensation is also available in the blowing process. In traditional pneumatic compensation, the total stroke is made with high pressure blowing air; the new new mechanical system uses high pressure blowing air only on the final fraction of a millimetre. The company says that this leads to a major reduction in air consumption, particularly with smaller bottles. The SFR EVO3’s ‘green’ ovens offer reductions in electrical consumption of up to 40%, compared with previous generations. Process conditions are kept stable by new lamps, along with special materials and coatings for the reflectors. Electricallydriven stretching rods are also available. Sipa asserts that they are more versatile than pneumatic drives in finetuning the process. Stretch rod timing, speed, acceleration and distance are all controlled from the machine controller (HMI). Electric drives also enable the company’s Sincro Bloc integrated blowing and filling system to match blowing operations to different filler speeds and to eliminate the need for a stretch rod decelerator and stretching cam, which helps shorten changeover times. These are also cut by a new mould changeover system. Sipa claims that the SFR EVO3 is now easier to convert from production of hot-fill to cold-fill containers because the cooling circuit is now built into the cavity. www.sipa.it Green light for GreenLyte US company Portola Packaging, Inc., has announced the introduction of GreenLyte plug-seal, high-density polyethylene (HDPE) 38mm closures for single and multiserve, hot-fill and aseptic beverage packaging applications. Portola claims that its new product presents a cost-effective alternative to traditional two-piece PP closures typically used for juices, ready-to-drink teas, isotonics, enhanced waters, low-acid nutraceuticals, and aseptic-filled beverage products. The company asserts that the one-piece design reduces cost through lightweighting, liner elimination and the lower cost of the material itself. The liner has been eliminated through a change in design. Portola Packaging says that it is among the first North American manufacturers to commercially produce linerless closures that can meet the requirements of hot-fill, extended shelf life and aseptic applications. www.portpack.com DryBlock final packaging Italian packaging specialist Ocme says that its DryBlock integrated final packaging system offers a solution that takes up less space than its predecessors, and eliminates synchronisation problems associated with bottle in-feed at shrinkwrapping machines and at palletiser infeed. The system takes up less space because it requires fewer conveyors, less accumulation and eliminates the need for dividers. It is capable of handling either cylindrical or non-cylindrical bottles, including square packages, as well as being able to deal with different quantities. Outfeed can be on single or double lanes and a single operator can run a line for 36.000bph. It can be delivered completely assembled ready to be installed. www.ocme.it Dehumidifier Moretto’s OTX Spyro hopper features a number of changes from previous models. The new shape is designed to solve falling flow problems and is claimed to allow more efficient management and control of the drying process. The company says that it provides a stable airflow and even temperature, leading to optimal treatment of each granule and enabling significant energy savings, compared to conventional hoppers. The new hopper features ‘shockproof’ Spyro finishing, which is claimed to improve damage resistance. www.moretto.com","@ID":48}, "EDITOUR REPORTS 35 PETplanet insider Vol. 14 No. 07+08/13 petpla.net HOLLAND COLOURSEurope BV | Halvemaanweg 1 | 7323 RW Apeldoorn | P.O. Box 720 7300 AS Apeldoorn | The Netherlands | T +31(0)55 368 07 00 | F +31(0)55 366 29 81 [email protected] | www.hollandcolours.com Thousands of colour shades, a variety of product forms and a dedicated team at YOUR SERVICE to assist toYOUR SUCCESS. é Protective colourants with specific light and UV absorbance é Functional colourants for Oxygen Scavengers é High opaque white for dairy é AA Reducer é Tintmask-neutralising off-colour regrind é Blowing Aid é Optical Brighteners é Slip Additives é Matting Agents Visit us at: Hall B3 / Stand: 103 March 21, 2013 Bericap S.A., Pilar Cap manufacturer Gonzalo J. Frejenal (Sales Manager, Plastics Division) and Kay Krüger Argentina March 21, 2013 Refres Now S.A., Buenos Aires Bottler of CSDs (f.l.t.r.) CEO Walter Canido, Laura (linguistic support ) and Kay Krüger April 16, 2013 Plasco Fabrica De Envases Plasticos S.A., Santiago Manufacturer of preforms, bottles and caps Marco Dall’Olio, (CEO of Plasco), shows his company’s preforms, caps and bottles.","@ID":37}, "EDITOUR REPORTS 17 Market share in this segment is around 50% and is, according to Dr. Lizak, showing encouraging growth rates. In milk packaging in particular, consumption is growing at the rate of 8% a year. A third string to the company’s bow when it comes to smoothing out capacity utilisation over the year is the production of PET film. This consists of an annual manufacturing output of 30,000t. This sector of the company is exhibiting pleasing growth rates and today corresponds to 30% of turnover . According to Dr Lizak, its special feature lies in the processing of PET flakes. In each case the 3-ply PET film produced is made up, as far as the internal and external layer are concerned, of a thin layer made from virgin PET material and, in the middle, a thicker layer made from R- PET. Hanex compound PET flakes, obtained from Germany, in their own factory and process the R-PET material, together with waste from the total production, in the middle shift. At the heart of the system are four film extrusion installations; in addition to these a fifth installation is available externally for use if required. Mainly Reifenhäuserfilm extrusion systems are installed. Market share in Poland is 48% and 30% of sale volume is exported, and this is expected to increase. According to Dr. Lizak, the concept is bearing fruit. Ultimately, PET film can be used for a range of diverse applications in the packaging industry and is not subject to seasonal fluctuations. This means that the company can count on guaranteed uniform capacity utilisation throughout the year www.Hanex.com.pl Cisowianka , Naleczow Pure mineral water! Cisowianka is a mineral water from a region with a unique geological structure – the Nałęczowski plateau, rich in loess, marl and limestone. The water is drawn from the same groundwater sources used medicinally in the Nałęczów spa, famous for the treatment of cardiac diseases. The source of water is located up to 100m below ground, and it can take up to 100 years for the water to percolate down to the source. Cisowianka is classified as a medium-level mineralised water, low in sodium. Share of the bottled water market in Poland: Żywiec Zdrój 23.6% Cisowianka 8.5% Nestlè Waters 7% Coca-Cola 3.1% Others 57.8% (source: Rzeczpospolita, 07.09.2012) Respecting values in effective dialogue www.krones.com","@ID":19}, "BOTTLE MAKING 24 PETplanet insider Vol. 14 No. 07+08/13 petpla.net ATMI develops BrightPak, a two-part liquid ‘next generation’ containment system for speciality and sensitive liquids Bright idea BrightPak, developed by ATMI, Inc, Danbury, CT, USA, features a collapsible rigid PEN liner inside a PET bottle and is designed for handling sensitive chemical and other products. ATMI worked with Plastic Technologies, Inc. (PTI) to overcome a number of challenges, including structural and production problems, on the way to commercialisation. create the rigid, three-dimensional collapsible interior “liner”, which actually holds the chemicals. The liner has to be able to collapse at low pressures without tearing in order to be compatible with various chemicals, and to be able to dispense 99% of its contents. The UVresistant amber-coloured external PET bottle has to withstand six times the dispensing pressure (greater than 90lbs/sq in) to provide an additional safety cushion. The system also needs to withstand shipping and storage conditions including temperature as low as -20°F (-73°C) and also block out 99.9% of light in the 190-425 nanometre UV-visible light range. One of the biggest issues was the “ship in a bottle” challenge of placing the rigid inner PEN liner into the outer PET bottle. PTI found a proprietary solution. The two-piece assembly fits into a third component - a blow-moulded, full-body PET base cup, which also provides a stable base for the bottle’s slightlyrounded bottom. The bottle and rigid liner are created in a proprietary blow moulding process. The base cup, handle and closure are assembled in a clean room environment in order to meet the high purity requirements of ATMI’s semiconductor food, beverages and others. The resin used for each layer can be adjusted for particular performance requirements. The company is actively seeking licensing opportunities. Challenges The BrightPak system’s primary components are created from two separate preforms. The PET preform is blowmoulded to create a bottle with a capacity of 4.6l. The second preform, made from PEN, is used to Applications ATMI says that its objective in developing BrightPak was to create a commercially effective alternative to large glass bottles and other systems that have been used to store and dispense photolithography chemicals used in the manufacturing of semiconductors, LEDs and flat panel displays. ATMI believes its BrightPak liquid delivery system is suitable for applications beyond those originally intended, including adhesives, pharmaceuticals, The BrightPak system’s primary components are created from two separate preforms","@ID":26}, "TRADE SHOW PREVIEW 45 PETplanet insider Vol. 14 No. 07+08 Strong fresh air for PET-bottle industry Glide intoa new eraof air-cooled, oil-free, and cost-efficient high pressure Time to gain new heights. The highly energy efficient ZD compressor, with superior screw and booster technology, offers Class Zeroquality air and is extremely silent with no vibrations. Theair-cooledZD provides you anexceptional reliability, no water consumption, while driving down investment and installation cost. It all adds up to sustainable productivity for today’s challenging low carbon economy. This new ZD is The answer for all your high pressure 40 bar applications. For more information, visit www.atlascopco.com/petcompressors CCL Label Hall B5 Booth 326 Super stretch sleeve Austrian company CCL Label Völkermarkt GmbH will be showing its Triple S Super Stretch Sleeve. The company says that it opens up a number of opportunities, as well as supporting a sustainable recycling process. Its high elasticity, along with stretchable inks specifically developed for this application, allows individual designs, including adaptation to unusually-shaped containers. Its material stretch of up to 54% enables it to cope with bottles with variations in diameter of up to 35%, as well as squeezable bottles. Its capacity for reverse printing protects the bottle’s graphics from scuffing; it does not require glueing; enables clean separation from PET for ease of recycling; the material can itself be recycled; requires no shrink tunnel; and uses little energy in production. CCL further claims that the Triple S system requires only half as much material as comparable shrink sleeves. www.cclbeverage.com Low pressure, high output Krones AG will be showcasing its full range of corporate capabilities for beverage filling and packaging technology. The emnphasis this year is on solutions that are sustainable, energy-saving, cost-effective and optimise resource usage The exhibits on show at drinktec include high-performance lines and monobloc solutions for filling and packaging applications, new developments in labelling technology, and its latest developments in process technology. Krones is also showcasing innovations for small and mid-tier bottlers. www.krones.com Krones AG Hall B6 Booth 100","@ID":47}, "PET - THE NEXT GENERATION 28 PETplanet insider Vol. 14 No. 07+08/13 petpla.net California-based Ready Pac is a producer of convenience fresh foods including freshcut produce. With its rPET salad bowl, the company is celebrating yet another achievement on its bowl salad line. In 2012 the company launched Ready Pac Bistro Organic bowl salads, new items for the conventional line, and new private label bowl salads. Now the company has tallied up the effects of on-going efforts to improve the sustainability of the product packaging and determined that the Ready Pac Bistro Bowl Salads line is on track to use more than 56,000,000 recycled plastic beverage bottles this year. “When Ready Pac created the bowl salad line our first requirement was that the packaging used would deliver the necessary shelf life to meet or exceed our customers’ requirements, and the second was to make it easy for a consumer to see how fresh the product is,” says Tristan Simpson, Director of Marketing and Communications, Ready Pac Foods. “Since then, we have made continuous improvements over time to create a more sustainable bowl salad package, and the net effect is we’re making a significant contribution to helping the environment.” Each Ready Pac bowl salad package, including the insert that separates protein ingredients and condiments from the salad greens, contains 60% post-consumer recycled content. That works out to slightly more than one recycled 500ml beverage bottle per package. The salad bowls and inserts are produced in plants powered by 50% solar energy. Combining the energy savings of using recycled PET bottles and the solar energy savings versus conventional power, each Ready Pac bowl salad package saves about 1,000BTUs or 0.30khh of electric power. Theses energy savings are enough to run a traditional 100W light bulb for about 3h, or an energy-saving 26W/ 1300 lumen bulb for 26h. www.readypac.com Salad Packaging Production to use more than 56,000,000 recycled PET bottles Ready, steady, bowl!","@ID":30}, "PETpatents www.verpackungspatente.de 52 PETplanet insider Vol. 14 No. 07+08/13 petpla.net Oxygen scavenger Europ. Patent No. EP 2527268 A1 Applicant: Colormatrix Holdings Inc., Wilmington (US) Date of Application: 24.1.2008 The material of a PET bottle has been so modified that it will, together with the lid and the additives contained therein, absorb or convert the air in the bottle headspace. This means that product quality is maintained. Coated preform Europ. Patent No. EP 2532600 A1 Applicant: Kuraray Europe GmbH, Hattersheim (D) Date of Application: 6.6.2011 The preform for manufacturing a pack is coated inside and out so as to minimise any risk of oxygen or carbon dioxide leakage. In addition, the inner coating improves pouring behaviour and the external coating prevents the formation of any unsightly scratches on the outside of the container. Individual bottles pack Intern. Patent No. WO 2013 / 004337 A1 Applicant: KHS GmbH, Dortmund (D) Date of Application: 15.6.2012 In order to improve the appearance of a pack made up of individual bottles, a proposal is being made to align the bottles in accordance with certain characteristics and to subsequently fix them by means of a peripheral strap or by applying adhesive and linking via a carrier plate. Fixed capsule Intern. Patent No. WO 2013 / 009202 A1 Applicant: Bahus Doo, Paracin (RS) Date of Application: 26.1.2012 The walls of a PET container are fitted with a recess into which a small receptacle can be inserted and “wedged in”. Lid with membrane Intern. Patent No. WO 2013 / 006927 A1 Applicant: Resilux, Wetteren (BE) Date of Application: 9.7.2012 In order to enable better absorption of the differences in volume that occur during hot filling and subsequent cooling, the screw closure is fitted with a membrane which “bulges“ inwards during cooling. An opening takes care of the pressure equalisation between membrane and the head space in the lid. Non-drip bottle opening Intern. Patent No. WO 2013 / 015006 A1 Applicant: Toyo Seikan Kaisha Ltd., Tokyo (JP) Date of Application: 28.5.2012 An edge section is located between the end of the thread and the edge of a plastic bottle which affects water as a fluid medium during the pouring operation in such a way that any dripping / residual dripping is avoided.","@ID":54}, "TRADE SHOW PREVIEW 40 PETplanet insider Vol. 14 No. 07+08/13 petpla.net Blowmoulders with new technologies SMI Group of Italy will premiere a number of new developments and technological steps forward at drinktec 2013. Its stand will feature blow-moulding, packaging and end-of-line machinery. The company says that its new machinery has been designed with high efficiency, low power consumption and reduced running and maintenance costs in mind, and are the product of an intense period of R&D activity over the past few years. www.smigroup.it SMI Hall A6 Booth 303 Dairy blow-moulding, filling and capping The Serac Group will be unveiling its new, fully integrated Combox ultra-clean blow moulding-filling-capping line. Specifically designed for dairy bottle production at rates below 12,000bph, Combox incorporates the H2F (Highly Hygienic) filler, which meets the hygiene requirements of cold chain dairy products. The focuses in the machine design phase were to integrate the company’s latest aseptic filling developments and to control cost. Serac says that Combox answers the needs of developing countries using PET, as well as the low volume and high value-added product segments. www.serac.fr Serac Hall A6 Booth 334","@ID":42}, "EDITOURS REPORTS 38 PETplanet insider Vol. 14 No. 07+08/13 petpla.net May 13, 2013 Grupo Ravi, Barueri Cap manufacturer Aurelio Silva (Director) showing a typical plastic closure produced by the company May 13, 2013 Amcor Rigid Plastics South America, Jundiai Preform and bottle manufacturer Ruben Melara (General Manager) May 14, .2013 Husky Injection Molding Systems, Jundiai Manufacturer of injection moulding machinery (f.l.t.r.) Keith Carlton (Vice President Global Sales) and Waldemar Schmitke (PETplanet) at the Husky World Tour 2013 in Jundiai May 15, 2013 Bericap do Brasil Ltda., Sorocaba Cap manufacturer The Editourmobil at the entrance to the Bericap factory in Sorocaba May 21, 2013 Ecoplaca, Sorocaba Processor of recycled PET Ferdinando Roberto Carvalho (Commercial Director) stands in front of his promotion wall which shows objects made from recycled PET May 23, .2013 Krauss Maffei do Brasil Ltda., Feiplastic, Sao Paulo Manufacturer of injection moulding machinery Klaus Jell (CEO KraussMaffei do Brasil) in front of the machine on the stand at Feiplastic Sao Paulo SP. On show, a Netstal Elion 3200 72 cavity injection moulding machine for plastic closures. May 24, 2013 Otto Hofstetter AG Feiplastic, Sao Paulo Mould manufacturer, particularly preform moulds Harry Kleiner (Area Sales Manager PET, Otto Hofstetter AG, left) Stefan Zatti (Division Manager Sales & Marketing, Otto Hofstetter AG) at the Feiplastic Fair in São Paulo May 16, 2013 Ambev, Sao Paulo Brewer and drinks bottler Ricardo Rolim (Director of Social and Environmental Affairs and Communications) May 17, 2013 Logoplaste Shefa, Amparo Manufacturer of PET milk preforms and bottles – milk bottler Paulo Vitor R. Mendonca of Shefa standing in front of his Krones labelling machine for 1l PET milk bottles May 20, 2013 Döhler América Latina, Limeira Manufacturer of concentrates and flavours for drinks (f.l.t.r.) Waldemar Schmitke (PETplanet), Jane Vieira (Marketing) and Martin Tolksdorf (General Manager) All the companies we visited will feature on our PETplanet booth 501, hall B3","@ID":40}, "BOTTLE MAKING 25 PETplanet insider Vol. 14 customers. The PET bottle’s structural panels present challenges for labelling, so the textured full body cup is designed to provide branding options. Its amber colour provides another layer of UV and shipping protection. The BrightPak package dispenses liquids using either pressure (direct or indirect) or pump systems. It is specifically designed to eliminate the sources of bubble formation and particle defects caused by pump and vacuum delivery containers. Drive gas can be applied between the rigid liner and the bottle; the pressure from the gas in the space squeezes the rigid liner, causing it to collapse and force the chemical out of the bottle, through a sealed pathway from the liner to the dispense tool. Positive gas pressure protects the bottle’s chemical contents from external contamination. The rigid liner eventually collapses fully, which helps to greatly reduce the quantity of residues for disposal. Properties of the container ATMI claims that the BrightPak doublecontainment technology offers users around 21% additional volume compared to the typical onegallon glass bottle used in lithography applications today. The higher fill volume does not affect the labelling surface, handle location or physical dimensions of storage and usage locations. The additional volume is available because comparable glass containers usually have thicker sidewalls and longer necks. The BrightPak system is made from shatter-resistant plastic resins, which should minimise the chance of chemical spills and production shutdowns. The company maintains that it also provides high levels of chemical protection from environmental factors. Filled BrightPak containers have successfully passed drop tests ranging between four and eight feet (1.3 – 2.2m). Recycling ATMI have developed a tool for the separation of the PEN from PET at the end of the container’s life. While the PET content is expected to be recycled, its colorant content means that reuse will be limited to recycled raw materials like rugs. The PEN with chemical residual content will be thermally recycled and used for its energy value. www.atmi.com www.plastictechnologies.com","@ID":27}, "EDITOUR REPORTS 37 CHOOSE THE NUMBER ONE. TOTHE NEWDIMENSION K 2013 / 16 - 23 October 2013 Düsseldorf / Germany / Hall 09, Booth C05 May 08, 2013 Coca-Cola Industrias Ltda., Rio de Janeiro Bottler of CSDs Lucas Angelo Amendola (Especialista de Embalagens SR) May 10, 2013 Lindoyana de Aguas Minearis Ltda., Lindóia Drinks bottler (f.l.t.r.) Giao Andre Arlotti (Marketing Manager) and Julio Almeida (Administration Director) May 09, 2013 Andina Rio de Janeiro Refrescos Ltda., Rio de Janeiro Drinks bottler (l) Ana Carolina (Almeida Industrial Supervisor) and (r) Andre Braga (Production Director Sopro/TPM)","@ID":39}, "MARKET SURVEY 31 PETplanet insider Vol. 14 No. 07+08/13 petpla.net Sipa Urola S.C. Siapi Srl a socio unico Nissei ASB Machine Co., Ltd. Via Caduti Del Lavoro, 3 - 31029 Vittorio Veneto, Italy +39 0438911511 www.sipa.it Pietro Marcati Blowmolding Systems Sales Director +39 0438911511 +39 0438912273 [email protected] Urola Kalea s/n, PO Box 20230 Legazpi, Spain +34 943 737003 www.urola.com Iñaki Unanue +34 943 737144 [email protected] Via Ferrovia Nord, 45 31020 San Vendemiano (Tv), Italy +39 0438 4096 www.siapi.it Fabio Paron Commercial Director +39 338 6789217 +39 0438 401016 [email protected] 4586-3 Koo, Komoro-shi, Naganoken 384-8585, Japan +81267 23-1565 www.nisseiasb.co.jp/en/ Katsuo Ishiguro Manager - Sales Coordination Team +81 26723-1565 +81 26723-1564 [email protected] SBO Compact2 6 models Rotary systems (7models): SFR 6 EVO3, SFR 8 EVO3, SFR 10 EVO3, SFR 12 EVO3, SFR 16 EVO3,SFR 20 EVO,SFR 24 EVO (7 MS) Linear systems (15 models): SFL 6/6 SS, SFL 6/6 XXL,SFL 6/4 XL, SFL 6/4 XXL , SFL 6/3 XL , SFL 4/4, SFL 4/3 XL, SFL 4/2 XL, SFL 2/2, SFL 2/1 , SFL 4/4 WM, SFL 4/3XL WM, SFL 4/2XL WM URBI-2, URBI-4, URBI-6, URBI-8 URBI-2L, URBI-4L Standard Machines: S2 SC2 SC3 SC4 SC5 SE4 SE5 SE6 SE7 SE8 SE9 SE10 SD8 SD10 SD12 SD14 SD16 SD18 SD20 for wide mouth: SW1 SW2 SW3 SW4 SW2-3-4 SW40 for large containers: S2M S1X SX1-K SX2 SX3 SX4 SX5 SX Super Flexible SX 5 - 3 SF HSB-4N, HSB-6N, HSB-6M (The HSB Series data is for double blow heat-set moulding of bottles and jars giving up to 95°C filling temperature for hot fill) 0,25l to 10l 250ml to 3l 250ml to 3l 100ml to 2l up to 0.6l 10l 4l to 30l up to 10l 0,25-6 l; 5-40 l up to 2l 0,25- 12 l (neck finish diameter up to 180mm) up to 4 24 6 8 20 6 up to 3 4 4 4 4 1,800 2,250 1,500 1,000 1,800 2,250 1,500 1,800 2,250 1,600 1,350 for SBO 3 XL / up to 1,200 for SBO 2 XXL 1,200 600 500ml jars at 970bph/cav 5.1 x 2 x 3.4 2.32 x 2.2 x 2 to 5.9 x 4.35 x 2.3 6.7 x 2.0 x 3.2 SMI S.p.A. Krones AG Kosme Gesellschaft mbH Sacmi Imola KHS Corpoplast GmbH Via Piazzalunga, 30, 24015 San Giovanni Bianco (BG), Italy +39 0345 40.111 www.smigroup.it Mr. Pietro Volpi Marketing Dept. Manager +39 0345 40.316 +39 0345 40.209 [email protected] Böhmerwaldstr. 5 93073 Neutraubling, Germany +49 9401-70-0 www.krones.com Peter Christiansen Sales Director +49 9401 70-4980 +49 9401 70-914980 [email protected] Gewerbestrasse 3 2601 Sollenau, Austria +43-2628-411-0 www.kosme-austria.com Johann Gugler Managing Director +43-2628-411-125 +43-2628-411-4125 [email protected] Via Provinciale Selice 17/a 40026 Imola (Bo), Italy +39 0542 607111 www.sacmi.com Moraldo Masi B.U.PET - Beverage Division +39 0542 607888 +39 0542 642354 [email protected] Meiendorfer Strasse 203 22145 Hamburg, Germany +49 40 67907-0 www.khs-corpoplast.com Marco Böhnke Product Manager +49 40 67907-0 +49 40 67907-100 Marco.Bö[email protected] SR series / 8 models (6 for standard capacity containers and 2 for high capacity containers) Contiform 3 11 models available Contiform 3 SC 4 models available Contiform 3 H 8 models available Rotary Machines 6 models Linear Machines (7 models) SBF InnoPET Blomax Series IV 0,25 to 10l 3,1l 0,25 to 3l 0,05 - 3,0 0,05 - 3,0 Yes 0,2-3,0 4 to 10l 0,1 - 3,0 (max. 3,78 i.e. 1 gallon) 0,1 - 0,7 0,1 - 2,0 0,5 - 6,0 0,5 - 30,0 up to 5,0l 20 20 6 4 18 (in double cavity - 48.600bph up to 0,6L) 36 6 28 36 26 6 2 8 1,800 - 2,000 2,000 1,700 2,700 up to 2,250 1,800 - 2,000 2,250 2,250 2,000 2,000 1,650 1,800 up to 2,250 1.800 - 2,000 2,250 2,000 2,000 1,600 1,800 up to 2,000 1,100 - 1,200 2,250 1,800 1,250 up to 1,250 for 5,0 l; 350 for 30,0 l up to 1,000 3.7 x 4.4 x 3.5 (SR 4HP /SR 6HP) to 4.8 x 8.8 x3.5 (SR20) from 6,5 x 5,4 x 4,6 to 11,7 x 7,6 x 4,6 from 10,7 x 6,2 x 4,6 to 14,4 x 7,6 x 4,6 from 6,9 x 4,4 x 4,5 to 11,2 x 6,8 x 4,5 6.05 x 3.85 x3.25 (without preform feeding system) 4.5 x 1.83 x 3.1 to 5.1 x 1.85 x 3.1 (without preform feeding system) 12 x 5,5 x 3,8 (SBF618) approx. 13,3 x 7 x 3,2 (Blomax 36S)","@ID":33}, "EDITOURS REPORTS 36 PETplanet insider Vol. 14 No. 07+08/13 petpla.net March 22, 2013 Reciclar S.A., Buenos Aires PET recycling Erwin Auspitz (Commercial Director, left)) with Kay Krüger March 22, 2013 Andina Empaques Arg. S.A., Buenos Aires Preform and bottle manufacturer Packing the printed bottles March 25, 2013 Cervecería y Maltería Quilmes S.A.I.C.A. y G., Quilmes Bottler of beer (f.l.t.r.) Kay Krüger, Juan Pablo Zug (Packaging Development Manager for Latin America South) and Pablo Heras (Packaging Engineer) Brazil April 30, 2013 Mineracao Campo Branco Ltda., Progresso Bottler of mineral water In front of Mesal Maquinas (Brazil) filling line, (from l to r) Nestor Jose da Silva (Production Manager), Erminio Virian (General Director), Diego Pellenz (FD) and Waldemar Schmitke (PETplanet) May 03, 2013 Hugo Cini S.A., Sao José dos Pinhais Bottler of soft drinks Filling Cini Laranjinha soft drinks in 600ml PET bottle on a KHS filling machine May 07, 2013 Ind. Zugliani de Refrigerantes e Bebidas Ltda., Jaú Bottler of mineral water (f.l.t.r.) Jose Guilherme Zugliani (Gerente Administrativo), a staff member, Sidney Angelo Zugliani (Director Industrial), in front of a Brazilian filling machine for soda drinks in 250ml PET bottles April 22, 2013 Estambul Industria Sodera S.R.L., Santa Fe Bottler of mineral water Estambul has been filling mineral water in PET siphon bottles for some time. April 23, 2013 Druetta Hnos S.R.L., Santa Fe Bottler of mineral water and CSDs Andres Druetta is making a name for himself in the region with his mineral water Uruguay April 25, 2013 CristalPET S.A., Montevideo Preforms, bottles and caps Production Manager Fernando Moreira has been looking after preform production at CristalPET in Montevideo since 1994. All the companies we visited will feature on our PETplanet booth 501, hall B3","@ID":38}, "BOTTLE MAKING 23 PETplanet insider Vol. 14 No. 07+08/13 petpla.net is collected and the pre-blown bottle fed with compressed air at a pressure higher than the pre-blowing pressure (intermediate pressure stage). In the Airback Plus system the rotary distributor is thus omitted, which reduces system complexity and results in lower maintenance and spare part requirements. Furthermore, the fact that Airback Plus directly transfers compressed air into the bottle reduces consumption by up to 30%. This means that, where Airback I is used in conjunction with Airback Plus, the consumption of compressed air is reduced by up to 40%. It is also possible to prepare air intended for reuse with sterile filters and the procedure becomes essential when a supply of clean ambient air cannot be guaranteed on site. A certain amount of pressure is lost during filtration, meaning that the amount of compressed air saved in such a case would be 35% maximum. Savings potential The following example illustrates the potential cost savings achievable with the use of Airback I and Airback Plus. A beverage bottling plant produces 35,200 1.5l PET bph (2,200bph/cavity) on a 16-station InnoPET Blomax Series IV 16 S stretch blow moulder. The blowing pressure for bottle production is 28bar. The amount of air usually needed in the above circumstances Want the real secret to bottle light weighting? Measurement and process control systems for the packaging industry Process Pilot® automated blowmolder control system can make the difference between a modest attempt at light weighting and a truly successful program. Process Pilot works with your blowmolder to continually monitor and maintain material distribution on every bottle to an unmatched degree of accuracy. Featuring automatic adjustment and 24/7 control, Process Pilot can facilitate even the most aggressive light weighting program while ensuring the highest quality and performance! Not convinced? See us at the drinktec and K shows to set-up a trial. BOOTH: B3/332 BOOTH: 11B40 is 1,680m3. A saving of just 36% of compressed air results in around 600m3/h less air is used. This means that 600m3 of air per hour less has to be compressed to high pressure. Assuming that 0.2KWh of energy is required for one 1m³ of air, this would save 121KWh/h. E.g. for 5,000 production hours, this would lead to a total reduction in energy requirement of 605,000KWh. These figures become even more interesting when smaller bottles are manufactured. As a general rule, the smaller the bottle, the greater the probability of achieving the aforementioned 40% saving. A much lower compressor output is needed for the stretch blow moulding process, and thus, the compressor can be of much smaller size. In the above mentioned example, a compressor with a maximum power of 1,320m3/h can be selected, in place of one with an output of up to 2,100 m3/h – saving up to €7,000. Significant reductions in annual running costs – in the region of €4,000 – are also claimed, thanks to the reduction in spare part requirements and the amount of maintenance necessary. Retrofitting possible Airback Plus is available both for new equipment and for retrofitting of existing InnoPET Blomax Series IV and Series III stretch blow moulders. Return on investment is achieved in 1½ years maximum. As no additional rotary distributor is required for Airback Plus, this retrofit is quick to implement; it takes about a day. A new ring line will be fitted and the valves and valve switching will be adapted to the new production environment. After conversion, the machine implements three different stages of pressurisation during bottle manufacture: applying pre-blowing pressure; intermediate pressure, and high pressure. Whether as part of a new investment or a retrofit, KHS claims that with Airback Plus the quality of the produced bottle is identical to that of bottles manufactured using traditional compressed air preparation. The output of the stretch blow moulder, up to 2,250bph/cav for the InnoPET Blomax Series IV, is also maintained. KHS Corpoplast is expecting that Airback Plus will become very important in countries where the amount of energy provided each day is subject to a specific quota. Energy quotas are already in force in some Asian and Arabic countries, for example. www.khscorpoplast.de","@ID":25}, "NEWS 12 PETplanet insider Vol. 14 No. 07+08/13 petpla.net Gesellschaft Wärme Kältetechnik mbH Friedrich-Ebert-Str. 306 · D-58566 Kierspe Tel. +49 2359 665-0 · www.gwk.com Perfect cooling and temperature control You will feel better having made the right decision. Reduce your energy consumption. Tailor made solutions Energy saving cooling systems Temperature controllers Chillers System solutions Water treatment Cooling technology Mould inserts Temperature control technology KHS Corpoplast inauguration of new production facility On June 13 and 14, 2013, a total of more than 100 participants celebrated the official opening of the new production facility of KHS Corpoplast, Hamburg, Germany. Enhancing the event in terms of its content were talks on new technological developments from KHS Corpoplast. (A more detailed report will be included in Issue 9 of PETplanet insider.) The new production facility, with an assembly area of approx. 2,500m2 , was completed in November 2012. This has provided the KHS Corpoplast plant in Hamburg with an assembly area covering approx. 11,000m2, a logistics area of approx. 3,500m2 and office accommodation amounting to some 6,500m2. Plans are afoot for a further increase in 2015 which will extend the assembly area by about 2,500m2. www.khs-corpoplast.com Siapi on the road in emerging markets Siapi, the Italian PET container blow moulding machinery manufacturer, is to continue and extend its programme of symposiums and events abroad aimed particularly at emerging markets. The most recent conference, organised by Siapi and Siapi Africa, was held at the Carthage Thalasso Resort hotel, Gammarth, Tunisia, in February 2013 and presented a range of solutions and applications available to the African market. The afternoon debate focused on the pursuit of quality in blow moulding processes for PET bottles and containers. The next symposium is scheduled for September 2013 and be held in Mexico. Along with issues specific to the local markets, Siapi is highlighting its development of lighter packages, such as its 330g 5 US gal watercooler bottle, and improved energy efficiency through technology such as its blow air recovery system and energy-efficient ovens. www.siapi.it LSB, Artenius, Appe insolvency La Seda de Barcelona, S.A. (LSB) has filed a petition for declaration of voluntary insolvency with the Commercial Court of Barcelona, in compliance with a resolution adopted by the Board of Directors. The petition also includes Artenius España, S.L.U.; Artenius Green, S.L.U.; Industrias Químicas Asociadas LSB, S.L.U.; Artenius Italia, S.p.A.; Artenius Hellas Holding, S.A.; Inmoseda, S.L.U.; Appe Benelux, N.V.; Appe Deutschland, GmbH; Appe UK, Ltd; Appe France, SAS; Appe Iberia, S.A.U. and Appe Polska Spolka Z Ograniczona Odpowiedzialnoscia. The Board has also agreed to file for insolvency (or local legal equivalent) proceedings for Group subsidiaries based in Morocco (Artenius Pet Packaging Maroc,) and Turkey (Artenius Turkpet, A.S. and Appe Turkpack, A.S.). The appointment as insolvency manager of Mazars Financial Advisory SL on July 15, was subject to confirmation. www.laseda.es","@ID":14}, "TRADE SHOW PREVIEW 42 PETplanet insider Vol. 14 No. 07+08/13 petpla.net P.E.T. Engineering Hall B3 Booth 309 Feasible light weighting P.E.T. Engineering’s ultra lightweighted projects will be the core of its stand at drinktec. It will be showcasing developments in preform designs that are ultra-light, economical, environmentally friendly and, at the same time, easy to implement effectively on filling lines. EvoLight, in 500cc format, weighs just 7.5g; 31.5% less than the average of bottles currently on the market. The bottle utilises a new Husky 26/22 neck finish; the award-winning Swerve Neck solution; and Sunbase patented bottom. Versions of EvoLight in 1.5l (suitable for CSD as well as still drinks), 1.0l (suitable for milk) and 75cl (juices) versions will also be on display. Moreno Barel, CEO of PET Engineering, will be among the speakers at PETnology. The projects on display have been developed with the support and collaboration of Husky Injection Molding Systems and with resins specialist Novapet. www.petengineering.com Management, measurement and quality Agr International says that the centrepieces of its stand will be Process Pilot and the Dimensional Sampling Gauge. Process Pilot provides material thickness distribution management on PET bottles along with hands-off blowmoulder control and the ability to reduce bottle weight while ensuring appropriate distribution of material. Benefits claimed include elimination of section weights; reduced scrap; improved overall bottle performance and quality; and less downtime. The Dimensional Sampling Gauge is a vision-based precision dimensional measuring system for glass, plastic and aluminium bottles. It provides repeatable and comprehensive measurement of critical bottle dimensions including weight, push up and ID. Configurations are available for automated laboratory applications or as part of an automated sampling station. www.agrintl.com AGR International Hall B3 Booth 332 New PET lines Netstal, the Swiss machine manufacturer, will be presenting two new machines at drinktec. It will demonstrate the manufacture of a 500ml lightweight PET preform on the PET-Line 2400 and will also offer exhibition visitors the chance to see its new PET-Line 4000 on site at its factory in Näfels. Fellow Swiss company Otto Hofstetter provided the mould. The preform is produced in a total cycle time of just 5.4s, using a 72-cavity mould. Italian company Piovan is responsible for the material processing and the air dryer. Equipment from ef-cooling, another Swiss enterprise, provides cooling services. Netstal says that both new machines have been designed with production and energy efficiency in mind. Hydromechanically driven axes with advanced valve and control technology, along with further increases in the throughput performance of the injection unit, have enabled further reductions in cycle times and, consequently, capacity. Netstal claims that its “Eco Powerunit” drive technology can help achieve energy savings of up to 10%. The parts-removal unit with the 2,400kN and 4,000kN clamping force variables of the PET-Line series has been reworked and further optimized This now also offers exchange sets compatible with PET-Line 3500. The company further claims that refinements to its Calitec cooling system help to optimise preform cooling. This cooling system supports the preform cooling process by exerting internal pressure in the preform. Preblow extends this cooling phase with a blowing process in the base area. Netstal experts expect an additional savings potential of approx. 2% on the bottle. www.netstal.com Netstal Hall B3 Booth 339 Finding solutions R&D/Leverage Europe has announced the full commissioning of an Aoki 250LL-75S moulding machine, which has been added to its Product solutions Laboratory (PSL), which joins its range of ISBM single stage sampling machines. The company’s stand at PETpoint at drinktec will showcase on its capabilities in unit tool development; production tool sampling; resin development; and colour trials. www.rdleverage.com R&D Leverage Hall B3 Booth 303","@ID":44}, "BOTTLING / FILLING 26 PETplanet insider Vol. 14 No. 07+08/13 petpla.net Coca-Cola installs 7,200bph SMI production line in Cape Verde Putting the fizz into Santiago Coca-Cola was first produced in the islands of the Republic of Cape Verde in 1997. The Equatorial Coca-Cola Bottling Company (ECCBC) itself, along with linked businesses, now occupies a prominent position in the local economy. It directly employs over 100 people at its Cavibel plant in Praia, the capital and main city of the Republic of Cape Verde, located on the island of Santiago. The new line has been installed in response to continually increasing demand and will package Coca-Cola and Fanta brands in PET bottles. ECCBC operates 14 factories in 13 countries, with a total production volume of about one billion litres. It started its production business in Africa in 1989 with just six people and a production volume of about 300.000l; today, it is a joint venture between Cobega and The Coca-Cola Export Co. and has 6,263 people on the payroll. Cobega, the largest business unit of the Spanish group of the same name, includes bottlers and distributors of Coca-Cola products in Catalonia, Aragon, Balearic Islands, Canary Islands and Portugal. In addition to Cavibel in the Republic of Capo Verde, the ECCBC business unit includes production facilities in Central and Northern Africa: Morocco, Algeria, Mauritania, Gambia, Guinea Conakry, Guinea Bissau, Sierra Leone, Liberia, Ghana, Equatorial Guinea and São Tomé y Príncipe. Filling line for ginger drinks","@ID":28}, "BOTTLING / FILLING 27 PETplanet insider Vol. 14 No. 07+08/13 petpla.net CCT Creative Competence Technology GmbH Idsteiner Strasse 74 D-65527 Niedernhausen, Germany [email protected] www.cct-systems.com PET Molds Developments PET Systems Design and Patents Closure Systems at the drinktec in Munich (Sept. 16-20), booth B3/414 at the K in Düsseldorf (Oct. 16-23), booth 1/1A40 CCTsystems®-SST Standard Slider Technology 1 Closure Type 3 Technologies CCTsystems®-SFBT Slit Fold Band Technology Design and Patents Closure Molds CCTsystems®-SBT Slit Band Technology Adding modern technology to the mix Cobega seeks to reduce production costs and improve efficiency by investing in continuous improvement of processes and structures in addition to equipping its facilities with advanced technologies. This strategy has helped Cobega Group companies to expand their production capacities and increase their market shares. The recent expansion of the Cavibel ECCBC plant in the Republic of Cape Verde, which is part of this process, has involved the installation of a complete new line, provided by SMI. It has been set up to manufacture and fill PET bottles of sizes ranging from 0.33 to 2l with Coca-Cola and Fanta branded products. The new plant, which has a capacity of 7,200bph, includes a Smiform SR4 rotary stretch-blow moulder, a rinse-fill-cap monobloc and relating premixer, a rotary reel labeller, a Smiflexi LSK 35F shrinkwrapper for filmonly packaging of 0.33, 0.35 and 0.5l bottles in 4x3 arrangement, and 1, 1.5 and 2l bottles in the 3x2 and 2x2 configurations. SMI also provided all the conveyor belts for the loose containers and the packaged products, as well as the control and electrical distribution systems. Energy savings along the line During the project study stages, SMI designers performed a thorough analysis of product build-up, distribution and handling dynamics to ensure fluid and constant production flows as well as maximum operating flexibility in the installed machines. Today, the line engineering solution designed by SMI allows the Cavibel ECCBC plant to manage complete product flows. The automation and control system, which involves the use of sophisticated sensors positioned in the line’s most strategic points, allows the maintenance of high levels of operating efficiency during all production cycle phases. All the machines provided by SMI are electronically controlled and have been designed in full compliance with the environmental policy of the CocaCola Group. To reduce energy consumption, all the motors are equipped with inverters. The Smiform SR 4 stretch-blow moulder is equipped with a system that recovers the compressed air used during the blowing process and Smiline conveyor belts are lubricated with silicone material, which allows considerable saving of water and reduced release of organophosphates in the drains. Further, the air conveyors between the blow moulder and the filler have filters designed to prevent contamination of the conveyed empty bottles. www.smigroup.it Sprite is also being filled at Cavibel Cavibel staff in front of the SMI line","@ID":29}, "TRADE SHOW PREVIEW 41 PETplanet insider Vol. 14 No. 07+08 Shrinks Just a few months after the Gebo Cermex merger, Cermex will be exhibiting upgraded versions of its VersaFilm machine range, as well as a new machine equipped with a new vacuum infeed table and multichannel shrink tunnel. The company says that it has completely re-engineered its vacuum table to make film handling more fluid and to facilitate maintenance on high-speed lines. The cutting module is equipped with Dual Injection System (DIS) and is completely separate from the vacuum module for film infeed. Reel changeovers can be made without stopping the machine and it is designed to cope with different film grades, including recyclable or biodegradable polyethylene film, at higher output rates. A new generation of tunnels features hot air circulation that can be adjusted based on the specific product format: height, collation and number of lanes. The tunnel is fully modular and can operate with single, dual or triple lanes. Cermex is planning to offer additional new functions to the market in Q3 2013. www.gebocermex.com Gebo Cermex Hall A6 Booth 340 Triple inspection launch Trac Measurement Systems will be launching a brand new range of plastic bottle inspection machinery. Three machines will be exhibited, covering bottle wall thickness measurement, burst testing and automatic preform measurement. The new Trac Bottle Wall Thickness gauge uses advanced non-contact sensor technology to accurately measure bottle wall and base thickness from outside the bottle. It offers traceable measurement to UKAS standards, linearity over the entire sensor range and external measurement without having to enter the neck of the bottle. The sensor can also be rotated to suit a range of types and sizes of bottle design. Surface angles and base thickness can be measured without any need to cut the bottle. The Bottle Burst Testing system can be used in the laboratory or alongside manufacturing lines. The preform measurement gauge uses vision-based technology to check all industry standard dimensions, including neck finish, body diameters, height and internal neck diameter in a matter of seconds. www.trac-group.com Trac Hall B3 Booth 135","@ID":43}, "TRADE SHOW PREVIEW 43 PETplanet insider Vol. 14 No. 07+08/13 petpla.net Plast Engineering Knauff Hall B3 Booth 413 Low pressure, high output Plast Engineering Knauff will be exhibiting its complete PET manufacturing line that can be installed in a standard 40 foot HC transportation container. The Econ-PETblow A4C inside manufactures up to 2,800 0.5 – 1.5l PET bph from PET preforms, with air pressure of only 15bar. The fully-automated system disinfects the bottles with UV radiation, labels them and transfers them directly to the filling station where they are filled and then sealed with UV-radiated caps. The filled and finished bottles leave through a window in the container wall as ready-for-sale PET drinking water bottles. An EC connection for electrical power and a two-inch pipe coupling for drinking water, are mounted on the outside of the container. The system’s modular design allows additional functions to be added. www.pet-equipments.de Sealed and delivered Bericap will present a blend of existing products, upgrades and new features. It has already converted a large portion of its beverage closures into lighter weight versions. Its 33mm closures are now available for hot fillings in flat screw and ‘PushPull sport’ versions. The PushPull does not require any aluminium foil for safe sealing. The DoubleSeal 33mm is equipped with a cut and folded tamper-evident slit band. The bottleneck and closure can be as much as 40% lighter than existing 38mm closure systems. A new HexaLite closure being presented at drinktec fits the PET 29/25 neck but is slightly higher compared to the current 29/11 closure. The HexaLite closure types are suitable for N2 dosing. BericapValve is a dispensing valve that is bi-injected to offer tightness, the company says. It is manufactured from TPE material in order to avoid contamination of the PET recycling stream. It is currently used for applications such as ketchups, chocolate sauces, products containing pieces and bodycare products and in the pharmaceutical industry. www.bericap.com Bericap Hall B3 Booth 502","@ID":45}, "PETbottles 48 PETplanet insider Vol. 14 No. 07+08/13 petpla.net Beverages & Liquid Food Boston plays Snap PET Power is expanding its existing Boston Round family to include a new standard neck finish, in addition to the existing SP410 and 415 designs. As its name suggests, the Boston Snap has a snap-neck finish. It is available in three different volumes: 500, 250 and 100ml. The specific snap expansion was primarily developed for products requiring a tamper-evident closure. PET Power has also developed a matching flip-top cap with a tamper-evident tab, which is removed by the first user. The company says that the new caps are suitable for cosmetic and pharmaceutical products for which tamper evidence is required. The bottle and the matching closure are available in any colour and the coloured bottles can be printed. Other decoration options include sleeves or labels. www.petpower.eu Ready to drink tea PT ABC President, a joint venture between PT ABC Central Food Indonesia and Uni President Enterprise Corp. of Taiwan, has adopted Bericap’s DS SUS 28/16 7085 SFB CSD3 closure system for its extended “Nu” range of ready-to-drink tea. The company has been producing ready-to-drink tea since 2005, initially using a hot fill PCO 1810 closure system. Since 2010 the company has been closing PCO 1881 bottles filled on a Sidel aseptic line with Arol cappers. The Bericap closures now being deployed are produced under license in Indonesia on a 96-cavity mould with an annual capacity of about 500 million units. The new closure is a one-piece DoubleSeal SuperShorty screw closure with a 120-knurl design. It is fitted with inner and outer sealing lips for a tight seal on 28mm PET one-way bottles with PCO 1881 neck. The slit flex band provides tamper evidence. The closure is suitable for aseptic, cold and hot filling technology. www.bericap.com Brightly coloured trio The German discount chain Lidl is selling, under the name of “The Cool 3“, three fruit nectars each with a 50% proportion of fruit in a colourful design, waisted PET bottle. The 300ml content bottles, designed with an adolescent target group in mind, are fitted with a screw closure with a pushpull operation and tamperevident strip. Prior to opening the push-pull facility is protected by a tamper-proof snap lid. Coloured sleeve labels serve as a vehicle for information. Tea hectagon Thailand company Oishi Trading is selling 500ml black tea flavoured with lemon in a hexagonal bottle made from PET. The tea is free of colourants and preservatives. The bottle is decorated with a shrink sleeve label with an exotic design. A small shrink label is attached to secure the screw cap and this can be removed by tearing along dedicated perforations. www.oishigroup.com Marinade in moulded bottle Korean company Sempio is marketing 300g Bulgogi Marinade for Korean-style BBQ-ing in an original design bottle made from PET. The slimline bottle features two constrictions in the neck area that give the packaging an original appearance. Underneath the screw cap the bottle is protected against manipulation by means of a sealing membrane. An all-round paper label in the body area conveys the necessary retail information. www.sempio.com","@ID":50}, "BOTTLES 49 PETplanet insider Vol. 14 No. 07+08/13 petpla.net BERICAP the plastic closure company committed to your success www.bericap.com Research and Development Developing closure solutions to meet your specific requirements Mould Technology A detailed understanding of mould design with in-house mould making facilities in Hungary and Germany Global Presence Local production in 21 strategically located factories. An on-going strategy of stregthening our global presence Capping Technology and Know-How Special advice on capping technology with on-going technical support Innovation and Flexibility Our broad range of plastic closures is the basis for generating new innovation. Our expertise covers aseptic, hot fill, barrier, anti-counter- feiting TE-systems, consumer convenience and child resistance Chinotto and ginger The Italian manufacturer of Aqua Minerale San Benedetto are marketing under their own label two soft drinks with an unusual taste in identically shaped PET bottles containing 1.5l. One of the drinks tastes of ginger while the other has a flavour of the bitter orange Chinotto and is reminiscent of Cola. Both bottles are fitted with colour-matched film labels and tamper-proof screw closures reduced in height. www.sanbenedetto.it Rough finish for lemon syrup Italian company General Fruit of Credaro is bottling 750ml of lemon syrup in a PET bottle which feels unusual to the touch. The bottle, which is shaped so as to enable it to be gripped easily, is designed to give special stability in some areas and the exterior of the bottle is reminiscent, in terms of roughness and appearance, of the surface of a lemon. There is a pourer inserted into the neck of the bottle and a screw closure with tamperevident strip closes the orifice. Two self-adhesive labels are attached in the body area of the bottle. www.generalfruit.com Vitafit spring edition Lidl, the German discount store is marketing, under the brand name of “Vitafit“, directly pressed fruit juice in a waisted PET bottle containing 750ml of product. As part of the promotional activity, the product range, manufactured by the Gropper Dairy, is being extended with seasonal fruits aimed at awakening the curiosity of the consumer. Recently a spring edition featuring apple and strawberry limette and an apple and rhubarb variant were launched. The bottles are transparent, they feature reinforcing grooves in the grip zone, are decorated with a sleeve-type label and are sealed with a screw cap complete with tamperproof guarantee. www.lidl.de www.gropper.de Direct oranges New variations on well-known drinks are aimed at enticing the customer to buy. Valensina is extending the selection of its gently pasteurised ”100% direct juice” series by a number of interestingsounding variations such as Orange and Kiwi or Orange and Raspberry. These juices are bottled in 1l content PET bottles. The transparent bottles feature embossing with the brand name logo, a body label in plastic (also transparent) and a screw cap with a seal of freshness stuck to it. The entire contents are visible through the entirely transparent bottle. www.valensina.de","@ID":51}, "NEWS PETnews 9 PETplanet insider Vol. 14 No. 07+08/13 petpla.net Husky world tour stops at global headquarters Husky Injection Molding Systems brought its World Tour home when it hosted its North American Caps and Closures Conference at its global headquarters in Bolton, Ontario, Canada, June 11-12, 2013. The two-day event was attended by more than 85 business leaders from around the world and showcased the company’s range of solutions for beverage and specialty closure manufacturing. Attendees were given unprecedented access to Husky’s facilities, labs and technology development programs and were able to learn how the company is improving the performance and capability of plastic closure manufacturing through the introduction of new technologies. “We are investing in resources to move our products and services forward, and improve our customers’ total cost to produce,” said John Galt, Husky’s President and CEO. “We find that events like our Caps and Closures Conference help support this goal and allow us to learn as much from our attendees as they do from us.” The event included networking opportunities, product demonstrations and presentations from Husky and industry experts. Keynote speaker Bill Hall, Executive Vice President of Manufacturing from Niagara Bottling, LLC, delivered a presentation on managing rapid growth in beverage manufacturing. Key presentations by Husky experts covered the topics of improving specialty closure quality with hot runner technology, specialty closure mould technologies for complex applications, beverage packaging industry trends and the role of equipment in the reduction of variability. Attendees toured Husky’s testing and validation facilities and company specialists demonstrated the company’s refurbishment capabilities, enabling customers with an aging asset base to bring their operations up to the latest generation performance and production standards. The event also saw the North American debut of Husky’s HyCap High Performance Package (HPP) system for high output beverage closure manufacturing. The system was producing a 1.2g 29/25mm lightweight water closure running a 1.9s cycle time on a 72-cavity mould, with complete downstream IMD vision inspection system. A Hylectric 300 specialty closure system producing a 3.5g sport cap running a 12.5s cycle time on a 24-cavity mould was also demonstrated. The system used in-mould closing technology with downstream part handling from MMC Packaging and resin supplied by Nova Chemicals. www.husky.ca New director for PETcore PETcore Europe, the new association that has replaced the former Petcore (PET COntainer REcycling), has announced the appointment of Patrick Peuch as its new Executive Director. He has professional experience in polymers and chemicals through business, environmental affairs, advocacy, recycling and product regulatory management in Europe and beyond. The membership of PETcore Europe is made up of four leading industry sector European associations: CPME (the PET manufacturers); EuPC including Forum PET Europe, and EuPET (the converters); EuPR (the recyclers); and several individual companies involved in the value chain. PETcore Europe says that it will be the voice of the PET industry in Brussels, communicating with European institutions about the importance of the PET value chain, ensuring that PET is positioned as a sustainable packaging material, and responding to any concern or issue. It held its first board meeting in Brussels on April 23. 2013. www.petcore-europe.org Weener absorbs Plasticum Weener Plastic Packaging Group, of Weener, Germany, has announced a restructuring operation that will see Dutch operation Plasticum Group, B.V., of the Netherlands integrated into the Weener Plastic Packaging Group as a subsidiary. Weener Plastik GmbH will continue under a restructured management. Plasticum manufactures standard (large production run) plastic caps and closures for personal care, food and home care products in four plants located in Tilburg (NL), Ede (NL), Waldkirch (D) and North Walsham (UK). Weener is largely concerned with customised packaging projects. Roel Zeevat has been appointed CEO of the group. Other management changes include the appointment of Gerhold Flockenhagen as Chief Technical Officer (CTO); Ralf Sonnenberg as CSO for branded articles; and Ben Mennink as CSO for standard products. Former Weener CEO Johann Meinders will leave the management team but remain connected to the company as consultant. Weener and Plasticum were both acquired by Lindsay Goldberg LLC (private equity fund of New York) in 2012. It is represented in Central Europe by Lindsay Goldberg Vogel GmbH. www.wppg.com","@ID":11}, "EDITOUR REPORTS 14 PETplanet insider Vol. 14 No. 07+08/13 petpla.net Poland is the happy recipient of excellent water flowing directly from the Carpathian Mountains which separate Poland from the Czech Republic and Slovakia. Which explains precisely why so many breweries and water bottlers have established themselves in the region. And of course where there are bottlers, can preform producers be far behind? In the ten years since Poland joined the EU, the country has prospered. Nevertheless sales of packaged beverages have been stagnating for a number of years. Preform production is currently running at some 5bn per year, yet companies are continuing to expand their capacities. Alpla reckons there is a 30% or so overcapacity in the preform sector. Even last year, when the Ukraine co-hosted Euro 2012, there was no additional demand for PET packaging. The strategy of those involved in the market varies from company to company. Alpla lost its top dog status with its standard portfolio of specialities and recycling; preform producer Hanex by contrast tried to hedge its bets with innovative closure design and film manufacture. Meanwhile preform manufacturer Oldi, a subsidiary of UAB in Lithuania is adopting a much more relaxed stance and is even contemplating investing in new capacity. Poland A stagnating market with too much capacity In the final stage of our tour of Eastern Europe, we cross Poland from the Ukraine, skirting the Carpathian mountains, and then heading south of Warsaw before making our way back to Germany. by Alexander Büchler Waldemar Schmitke September 11, 2012 Alpla, Zywiec We met: Stanislaw Biernat Plant Manager Stanislaw Biernat (Plant Manager, left)) and Waldemar Schmitke (right) Nuremberg Nizhny Novgorod Kazan Perm Yekaterinburg Chelyabinsk Yaroslavskaya Moscow Ufa Samara Saratov Volgograd Rostov-on-Don Dnipropetrovsk Kiev Warsaw Novgorod Saint Petersburg Gatchina Fryazino Kamenka Lipetsk Zaporishsha Mykolaiv Kharkiv Chernihiv Kalinovka Lübeck","@ID":16}, "EDITOUR REPORTS 19 PETplanet insider Vol. 14 No. 07+08/13 petpla.net Poland Tour Blog We are en route to Kiev. As we head westwards, the roads become ever more splendid. We are approaching the border with Poland, our next destination. Our departure from Ukraine goes off smoothly, which is more than can be said for our entry into Poland. Still, the tedious wait at the border crossing does give us the opportunity to catch up on our report writing. Finally, they let us through and we set off in search of a suitable parking place after a gruelling 14 hour drive. We awake next morning to brilliant sunshine and in great good humour we set off for Krakow and the water bottlers Zywiec Zdroji. We have a little bit of time to spare before our appointment so we use it to look for a campsite in the beautiful countryside. The interview is interesting albeit rather short, because everything has to be submitted to Danone, the owners, for their approval. The campsite is next to a small hotel where we are able to take advantage of their facilities. It makes a change to be able to luxuriate in the shower without having to watch how much water we use. The hotel also boasts Wi-Fi access which means that we can send our reports and photos back to base. First on the agenda on the following day is a visit to preform manufacturer Alpla. Stanislaw Biernat welcomes us and we learn, among other things, that the company is planning to install a bottle-to-bottle recycling plant. Our next appointment is in Dabrowa Gornicza, a two hour drive away, where we visit Hanex, a direct competitor of Alpla, and meet Dr Dariusz Lizak, who, in his varied product portfolio, has preforms lighter than the PCO1881 finish. The next appointment is in Warsaw but we are so far behind schedule that we are forced to postpone it. The weather has taken a turn for the worse, and the rain is bucketing down. It’s time for us to be making tracks again for Germany – the final stage of this year’s Go To Brau Beviale tour is at an end with our last stop here in Poland. It’s been a wonderful experience and thanks to everyone for making it so enjoyable! by Alexander Büchler","@ID":21}, "EDITOURS REPORTS 18 PETplanet insider Vol. 14 No. 07+08/13 petpla.net Cisowianka’s bottling plant The Drzewce bottling plant produces Cisowianka Perlage and Classique. The water is offered in various types of packaging PET, glass und cans. The manufacturing plant is equipped with eight production lines with an output varying between 12,000 to 20,000bph. Six of the lines have an output of 20,000bph. One of the lines is the universal line dedicated to the production of 0.7l PET bottles, 0.3 and 0.7l glass bottles and 0.33l cans. The water filled on this line uses a patented saturation method called “perlage”. This saturation device enables a maximum of 17,500 bottles and 12,000 cans per hour to be produced. The logistic centre is able to load up to 200 trucks per day. For the preforms they work with various suppliers WIP, Hanex, Alpla and with Bericap, Mika, Aptar and CSI Closures for caps, O-I for glass bottles and Ball Packaging for cans. Cisowianka uses the following equipment for bottling - KHS, Sidel, Krones, SMI, CFT. Perlage mineral water (available in PET, glass and now in cans) is - carbonated with CO 2 of natural origin. Last year (2012) Cisowianka presented a new idea in water packaging, Perlage in cans with temperature indicator. According to Emanuele Piva, Sales Manager at the CFT, responsible for installing the bottling line at Cisowianka “the market perspectives for canned water are very promising, there has been a 5% increase in the global market during the past year. One of the advantages of this packaging made from aluminium is that it is completely recyclable. The can also is more suitable for cooling the water to the appropriate temperature, especially important in the summer. It is also very convenient - easily fits in the pocket, handbag and is light and unbreakable. Even more important, the can is opened and consumed “at once” which makes it especially suitable for a variety of social events. www.cisowianka.pl","@ID":20}, "PETbottles 50 PETplanet insider Vol. 14 No. 07+08/13 petpla.net Home + Personal Care Protection from heat for the hair Protection from heat up to 200°C: this is the promise of the protective hair spray available under the dm label Balea in conjunction with the auxiliary product Trend it up. The product is sprayed on to the hair when wet and protects it from any damage from hair straighteners, hair dryers or curling tongs. The product is packaged in a black PET bottle with a volume of 200ml and a screw-on trigger in signal colours complete with a disable function. An allround label explains how to handle the product. www.dm.de For bouncy curls More bounce for curly hair plus an anti-frizz effect, that is the promise of Nivea’s “Curl Balm - flexible curls“. A PET bottle with a content of 150ml serves as packaging. The bottle, which is moulded to give a ripple pattern on the side and which incorporates an easy grip facility, is tinged light blue and decorated with transparent selfadhesive labels. The screw-on pushpull comes in two colours and can be used without any tamper-proofing or protective cap. The brand name logo has also been converted to the new, round, unified look. www.nivea.de Shower gel in pink Cien Bodycare - an own label of the German discount store Lidl – are selling a specially put together shower gel with Patchouli oil in a transparent 300ml bottle made from PET. The curved bottle fits neatly in the hand and the tinted product is easy to dispense via the snap-on hinged lid closure. Shaped labels to front and rear convey the consumer information. www.lidl.de White teeth for longer The alcohol-free Colgate Max White One mouthwash promises white teeth for longer, in addition to the well-known advantages provided by a mouthwash if used regularly. A white PET bottle with a screw cap contains 250ml of product. The screw cap serves as a dispensing cup and features a sleeve label pulled over the lid and the neck of the bottle which acts as tamper proofing. Perforations make it easy to remove the protection element. A metallised label on the front and a label on the back complete the packaging. www.colgate.de Attractive sleeve packaging Korott, a Spanish cosmetics manufacturer based in Alcoy, is selling a 500ml pack of mouthwash in a transparent, bulbous PET bottle. The bottle is decorated with an attractive design sleeve label incorporating a transparent zone in the area of the base. The label is pulled over the screw cap (which also acts as an aid to dispensing) and can be removed easily by means of vertical and horizontal perforations. www.korott.com","@ID":52}, "EDITOUR REPORTS 15 PETplanet insider Vol. 14 No. 07+08/13 petpla.net A Pioneer in the Polish PET Market expands his business In Radomsko Alpla are setting up a new plant for the manufacture of 1,000 to 1,200t R-PET per month. 2013 is the scheduled start of production. The basic material for production is used PET bottles from the Polish market. The returns quota for PET bottles today is around 40 % and these are separated out mainly from domestic waste. As far as the future is concerned, Alpla are banking on the statutory regulations envisaged by the EU and at the same time on significantly higher rates of return. More than 20 years ago Alpla started up in Zywiec with the production of PET bottles. Today Alpla operates four plants in Poland for the manufacture of packaging. PET is processed at the Zywiec, Radomsko and Ostrow plants: manufacture of preforms and bottles in Zywiec and Ostrow, preforms in Radomsko.In Poland, sales of PET bottles within the beverage sector are becoming less and less important. Bottling plants are already operating their own stretch blow moulding machines starting from minimum fill capacities of 3 to 4 million PET bottles per month. At the same time, Alpla is concentrating its PET processing activities on preform manufacture. The preform business accounts meanwhile for the major part of annual turnover. Zywiec features two production facilities which are situated two kilometers apart. In the first of these facilities there are Husky preform systems in operation, in the second Netstal preform machines and several linear stretch blow moulding machines. The stretch blow moulding machines produce PET containers for milk, edible oil, cosmetics and household packaging and have a total production capacity of approximately 30 million containers per year and per machine. The plant in Radomsko operates simultaneously Husky and Netstal preform machines. The total preform production at all plants was more than 2,3 billion preforms in 2011. The total requirement for Poland is estimated at more than 5 billion preforms per year, of which about 300 million preforms originate from the bottlers’ own production. This gives Alpla a solid market share in this highly competitive market. The annual consumption figures fluctuate, but are to a major extent dependent on economic data and weather conditions. n addition, the main season of the year is only five months long and there are no transition periods worthy of mention. According to Mr Biernat, the seasonal requirement can only be met by exercising a high level of flexibility i.e. keeping capacity in reserve. Mr Biernat is assuming a preform overcapacity of 30% in Poland. In 2011, for example, consumption of beverages fell as a result of the influence of economic and weather factors by comparison to the previous year. As a result of the better summer weather, it is anticipated that 2012 may just end up nudging the level achieved in 2010. Full inspected! PVS-2 in line or off-line Sampling Quality Inspection System for PET preform PVS-2 is capable to detect all the possible defects that could appear during preforms production, reading the cavity number and weight all the preforms. All the data are filed in a SQL data base that can be shared over a LAN. PVS-2 can be connected to any type of injection moulder or used as a standalonemachine for the quality lab. The system can run at the speed of 1.100 preforms/hour. VISIT SACMI B5 - 302","@ID":17}]}}
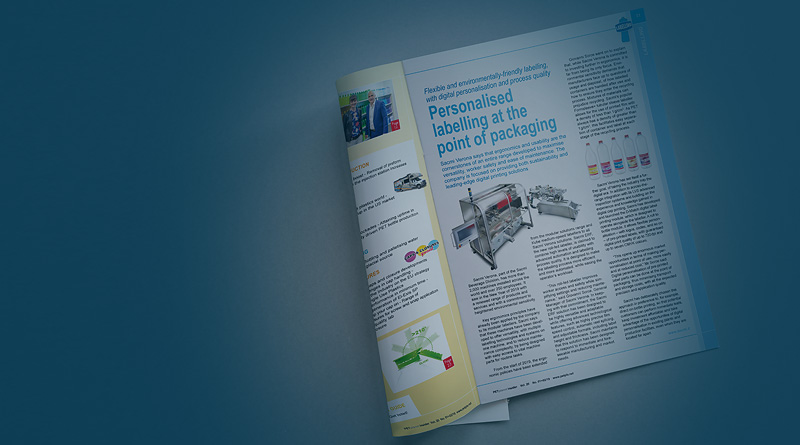