"EDITOUR REPORT 11 PETplanet insider Vol. 15 No. 09/14 petpla.net 2.8% (or 2.9% harmonised Eurostat value) in 2011. It was noticeably lower in 2013 at 1.2% (or 1.3% harmonised Eurostat value). The crisis also affected the unemployment rate, which currently stands at 12.9%. Numbers at work remain comparatively low at 55.3% (January 2014) compared to the mean annual rate in 2013 of 55.6%. There also continues to be a marked imbalance between the regions. The effect of (youth) unemployment in the south is significantly more noticeable than in the north. Italy depends significantly on imports for its energy (79%). Approx. 36% of the demand is met by crude oil, 35% by gas, 15% by renewable forms of energy, 9% by solid fuels and 5% by imported electricity. Renewables (solar and wind power) are expected to play an increasing role over the next few years. The reintroduction of nuclear energy was decisively rejected in a referendum held on June 12-13, 2011. PET industry In the context of our Mediterranean market tour, Italy is particularly interesting because here, in a single country, the whole of the PET industry is represented. Thus we visited a broad spectrum of manufacturers and bottlers: raw material manufacturers, machine manufacturers for preforms and PET bottles (both the 1- and 2-stage process), manufacturers of plastic closure cap machines (injection and compression moulding), manufacturers of injection/blow and compression moulds, manufacturers of filling machines (rotation and linear), and finally, manufacturers of downstream equipment and peripherals. In the processing sector, we met converters for preforms, PET bottles and closure caps as well as bottlers, but also complete in-house production, from the preform right through to the filled bottle. Despite all this, it is a fact that the economic downturn has weakened the beverages market, and this presents a stern challenge for producers: how to find a way out of the crisis. High energy and transport costs (the highest in the EU) do not help matters either, as all the businesses we visited were quick to point out. Reducing the cost of energy and raw materials thus becomes a prime concern. Progress is being made as can be seen in preform production. Around 10 billion preforms a year are used in Italy, yet materials usage is falling by between 5 and 8% a year. There is a similar situation in plastic closures. Beverages and drinks packaging market The market for beverages in Italy has been static for years and may even be going slightly backwards. Amongst non-alcoholic beverages, for example, mineral water, with around 11bn litres in 2013, was the dominant force, followed by CSD, milk and other beverages such as juices and iced tea. Consumption of beverages in 2013 in terms of millions of litres of non-alcoholic drinks (information compiled from the various companies visited) Macro-economic data (Source: Germany Trade & Invest, as at May 2014) Area 30134 km² Population 60 million * Population density 199.1* inhabitants per km² Population growth 0.3% Age structure 0-14 yrs: 13.8% 15-24 yrs.: 9.8% 25-54 yrs.: 43% 55-64 yrs: 21% 65 yrs and older: 20.8% Raw materials Agrarian Fruits, vegetables, potatoes, sugar beet, soya beans, corn, olives, beef, milk products, fish Mineral Coal, mercury, zinc, potassium chloride, marble, baryte, asbestos, pumice, fluorite, pyrite (sulphur), natural gas and crude oil reserves, arable land Gross Domestic Product (GDP, nom. ) Billion € 2013: 1,560.0 2014: 1,592.4* 2015: 1,634.3* Billion US$ 2013: 2,072.0* 2014: 2,171.5* 2015: 2,263.5* GDP per inhabitant (nominal) € 2013: 26.138 2014: 26.456* 2015: 26.968* US $ 2013: 34.715 2014: 36.216* 2015: 37.577* Economic growth Gross Domestic Product (change in % actual) 2012: -2.4% 2013: -1.9% 2014: 0.6%* 2015: 1.2%* *estimated Mineral water 11,400 CSD 3,800 Milk 1,000 Nectar juice (40 to 100% proportion fruit) 430 Iced tea 420 Still drinks (0 to 40% proportion fruit) 190 Sport/energy-drinks 90 Total 17,330 million litres In the drinks packaging sector PET is the dominant commodity and the trend is upward. Drinks packaging (overall) 2013 in millions of units (Euromonitor International) PET bottles 10,640 Glass bottles 4,330 Metal beverage cans 1,750 Brick liquid cartons 1,010 Flexible packaging 800 Miscellaneous 1,500 Total 20,000 units","@ID":13}, "BOTTLE MAKING 29 PETplanet insider Vol. 15 No. 09/14 petpla.net Recycling line recoSTAR PET substituting virgin resin at up to 100% Offices in: Brazil, China, India, Indonesia, Russia, South Africa, USA, Uzbekistan, and agents in over 130 countries worldwide textile packaging consumer bags Visit us at: Equiplast 2014, Fakuma 2014, moulding wheel, you are talking about a fill volume of up to 1kg in one cavity. Does this have an effect on the process? Ms Ann O’Hara: We have been and will continue to be making some appropriate adaptations to the machine technology so as to avoid any problems in this regard. PETplanet: So does the high filling speed for all the products bottled also apply to CSD? Ms Ann O’Hara: In principle, yes. Our vision is that all the liquids for bottling you can think of will be packaged using this technology. Whether it’s cleaning agents or water. When it comes to CSD we do in fact have to modify the system and have a design to accommodate the carbonation process, so yes, we believe it can be done. PETplanet: What additional benefit is incorporated in your new technology? Ms Ann O’Hara: We are thinking about aseptic filling in particular. By combining the moulding and filling processes, we can significantly reduce the size of the aseptic chamber and required clean room. PETplanet: Liquiform is a 50/50 JV between Amcor and Sidel. Will the technology be exclusively for Amcor? Ms Ann O’Hara: Our JV has decided to commercialize this technology as an industry platform, so with this announcement we invite competitors, regardless of whether it is on the machine building or the processor side, to become a licensee. Our aim is to implement a new technology for the PET sector, as broadly based as possible, and therefore look forward to additional licensees. PETplanet: Ann, thank you very much. Ms Ann O’Hara: Thank you! www.liquiform.com","@ID":31}, "TRADE SHOW PREVIEW 48 PETplanet insider Vol. 15 No. 09/14 petpla.net Volufill The Volufill is the new Kosme filling machine, designed for noncarbonated filling products, conductive filling products free of pulp and fibres. In this electronic full-jet volumetric filling system all functions are controlled electro-pneumatically. This permits a quick and individual adjustment of the filling steps to the different combinations of product and containers. The filler has two filling speeds, the filling volume is defined by an inductive flow meter. The machine is cleaned in a closed circuit. The filling is processed contact-free in full-jet process with gas lock. This ensures a high micro-biological safety as the return gas has no contact with the product. The safe conveyance of the containers is ensured by active neck handling. The advantages claimed for the system include micro-biological safety, hygienic filling, short change-over times, as well as ease of servicing and maintenance. www.kosme.com Bericap presents innovative products on drink technology India Booth I59 During the drink technology India trade fair Bericap will be showcasing new types of closures for still waters, as well as closures for aseptically filled products and hot filled beverages. The company will also be presenting new developments for the sparkling products market. HexaLite 26 and 29 mm – new variants Bericap has developed a lighter weight closure, known as the HexaLite 29/11. It fits a 29/25mm neck size – the weight saving compared with the previous 30/25 neck and closure combination is as much as 33%. Also new is the HexaLite 29/13. The height of 13mm allows the same grip height already familiar from the previous generation of 30/25mm closures. The HexaLite 29/13 fits the lightweight 29/25 neck. The weight difference compared with the HexaLite 29/11 closure and neck combination is negligible. In addition, the German company has developed a new HexaLite 26/13 closure for the 26mm lightweight neck. It can be applied onto the lightweight 26mm neck and the closure itself is only slightly heavier than the HexaLite 26/10 introduced 3 years ago. Both HexaLite 29/13 and 26/13 closures are equipped with a slit flexband. Nitrogen dosing is possible where bottlers wish to use lightweight bottles and need to add nitrogen to stabilise the bottle. Both 29/25 and 26/22 neck types are standard necks approved by Cetie. New closure solutions for aseptic filling 38mm closures for aseptic filling are predominant mainly in Europe. Variants for this size will be on show at drink technology India, both for double and for triple thread necks. By introducing the 33/15mm closure for aseptic filling with the same gripping height of 15mm, as used with the 38mm cap, a significant weight saving of up to 30% can be achieved, according to the company. The 33mm opening allows convenient drinking, especially with small-size containers. For on-the-go-consumption the company offers the 38mm sport closure PushPull Next Generation. This closure can be used both for wet and for dry sterilisation and does not require any aluminium foil. A sport closure variant is also available for the PCO 1810 thread. Adapting to other threaded neck sizes is possible. www.bericap.com Booth L35 Intralox layout optimization At drink technology India, Intralox will be demonstrating the advantages of the Activated Roller Belt (ARB) technology, which has been on the market for more than 10 years now. The US based company pioneered the first modular plastic belting back in 1970. Today there are more than 4000 ARB installations worldwide. ARB technology brings the benefits of modular belting to complex processes like sorting, merging, and switching. In 2012, Intralox opened its assembly centre in Bangalore, India. This facility increases Intralox’s worldwide presence to eight facilities and is now providing support for their local customers’ conveying requirements. www.intralox.com Booth H51 High Performance liquid colours, additives and dosing systems for Packaging Italian company Repi S.p.A., manufacturer of high performance liquid colours, additives and dosing systems will be showcasing the complete product portfolio for packaging at drink technology India. At Stand H51, exhibition visitors will learn more about Repi’s extensive range of liquid colours and additives as well as demonstrating the U2011 liquid colour dosing equipment and the Light Meter. Repi headquarters are located in Northern Italy. Distribution worldwide is provided through own organisations in Europe, Russia, North and South America, and the global sales network. www.repi.com","@ID":50}, "PETnews 6 PETplanet insider Vol. 15 No. 09/14 petpla.net Sidel appointments in senior positions Sidel has made two appointments in senior positions. Pavel Shevchuk becomes Zone Vice President for Europe and Central Asia, heading up the team at the recently opened regional headquarters in Frankfurt, Germany. Alessandro Paini has been appointed Vice President of Product Management at Sidel’s global headquarters in Switzerland. Ukrainian born Pavel Shevchuk was previously Managing Director at Sidel Vostok, the company’s base for operations in Russia, having also spent twelve years at Sidel sister company Tetra Pak where he held leadership roles in both Ukraine and Indonesia. Alessandro Paini has over 20 years experience with Sidel, bringing extensive management knowledge to his new role as Vice President of Product Management. In 2008 he was appointed Zone Vice President for Western Europe and Africa, before taking up his most recent position as Zone Vice President for Europe and Central Asia, the role now fulfilled by Pavel. www.sidel.com Doehler and Afriplex form joint venture for integrated ingredients Doehler is expanding in South Africa and has founded a joint venture with the food and beverage division of Afriplex. Located in Paarl, South Africa, Afriplex is one of the market leaders in natural extracts in Africa. Alongside its core competence in the field of manifold high-quality botanical extracts, Afriplex also provides emulsions and compound solutions for national and international customers in the food and beverage industry. The common goal of the joint venture is to deliver integrated ingredients that are tailored to the needs of Southern African markets in terms of taste preferences and technological and regulatory requirements. Doehler has been active in South Africa with its own sales office since 2009. The joint venture is expected to have multiple synergies for both of the companies. Thanks to an own application centre in Paarl, Doehler is now able to develop region-specific solutions and deliver customised product samples within a very short time. Afriplex produces more than 100 different plant extracts. Backed by its own cultivation technology, the company produces a variety of indigenous plant extracts, with a focus on rooibos, honeybush, hoodia, pelargonium, buchu, baobab and a selection of African aloe species. Making use of the Doehler Group’s supply chain network and distribution channels, customers of the food and beverage industry all around the globe will have access to this extraordinary extract portfolio. www.doehler.com China Brew & Beverage 2014 China Brew & Beverage (CBB), the international exhibition for brew and beverage processing technology, will take place on October 13-16, 2014 in Beijing. The exhibition is regarded as the most important event for this sector in China and Asia. More than 700 exhibitors are expected to attend on a hall space of 80,000m2. Messe München International, the organiser of drinktec, has been a co-organiser of CBB since August 2011. The close cooperation between drinktec and CBB has achieved a great success in 2012. Compared with CBB 2010, the number of international exhibitors and exhibition space grew by 17.2% and 40% respectively. Exhibitors from 22 countries attended CBB 2012 to display their latest products and technologies for the beverage and liquid food industry. Six halls were occupied at the New CIEC exhibition centre, using a total of 70,000m2. 51,428 visitors from 74 countries attended CBB 2012. www.chinabrew-beverage.com/english Indorama Ventures sees strong year-on-year growth H1 2014 Indorama Ventures Public Company Limited, a vertically integrated polyester value chain producer, saw total revenues of THB125.7 billion in the first half of 2014, a 12% rise over the same period in 2013, with Core EBITDA growing 44% to THB 10.2 billion. Net profit correspondingly grew by 163% to THB 1.8 billion over 2013. According to Indorama, the Chinese PTA overcapacity continues to depress the company’s feedstock segment but is optimistic that the bottom has been reached with most producers operating at below cost over the last two years, which has led to industry restructuring and better producer discipline. 2014 has been positive for all segments of the business and especially the focus on High Value Add (HVA) products continued to gain traction and are now contributing to about 40% of the core EBITDA. The company also announced that it has started PET packaging business in the Philippines and Nigeria. www.indoramaventures.com PET Network Day Petcore Europe, the Brussels based European PET value chain association, will hold the annual PET Network Day conference on October 9, 2014 in Brussels. The event is supported by eight leading European associations representing manufacturers, converters, packers, fillers, and recyclers. Last year’s event showed a strong and growing interest in PET value chain issues with over 100 participants from across Europe. Building upon that experience, this year the conference will discuss whether PET as a packaging material could impact its future and ongoing success. www.petcore-europe.org PETnology, PET Arena and Passion for PET The first “PET Passion Week” will combine the PETnology Conference (10-11 November 2014) and PETarena exhibition at Brau Beviale 2014. Presented by PETnology/tecPET GmbH, the industry meeting is aimed at all suppliers and customers involved with PET value chain. www.pet-arena.com www.petnology.com","@ID":8}, "PRODUCTS 49 PETplanet insider Vol. 15 No. 09/14 petpla.net PETproducts New gravimetric blender by Piovan Quantum is the name of the new range of gravimetric blenders designed by Piovan, a leader in the production of auxiliary equipment for the plastics processing industry. The blender embodies innovations that are claimed to change the way injection moulding machines and extruders are fed with blends of materials (virgin, recycled, masterbatch and additives). The innovations are said to help increase the efficiency of production, and feature improved design together with innovative technologies and high performance components, which, according to the company, offer concrete advantages for the user. The Quantum blender can be used in all application environments such as Packaging, Automotive, Industrial and Electronics, Building and Construction, Textile, Furniture, Toys and Housewares, Medical and Pharmaceutical, Recycling and Compounds. It features two distinctive characteristics. The first is that all surfaces that come into contact with the process material are manufactured from stainless steel, which can be used in critical environments such as the medical and food & beverage sectors. The second characteristic is that every blender comes with up to six dosing stations, which can easily be removed, for emptying or cleaning. Each dosing station is dedicated to a single ingredient-be it principal or additive; easy removal therefore aids material changes and enables optimal operating conditions to be immediately resumed without contamination from powder or residue. These interventions do not require the blender to be dismantled and can be done manually by an individual operator. The dosing stations can be used across all Quantum blenders in a factory. The weighing pan is mounted on two load-cells, even on the more compact Quantum model. Shock absorbers, between weighing pan and load-cells, filter all possible machine vibrations to enable the load-cells to weigh the material with greater precision and mechanically protect the data transmitted to the control unit. The entire batch is transferred from the weighing pan to the mixer by the dump flapper, which opens and closes pneumatically. The mixer is spherical and the mixer blade is round to fit its geometry and prevent material stagnation problems. Its strength lies in an intelligent sensor that employs the surface of the mixer as a sensitive element, needing no adjustment caused by powder, electrostatic charges, or changes in material and blend density. The sensor is an integral part of the mixer’s design. The interface is designed to maximise intuitive use. The control The Eureka moment Moretto’s advanced drying system can process up to 12,000kg/h of PET, efficiently Ancillary equipment specialist Moretto SpA, headquartered in Massanzago, Italy, has launched Eureka, a new version of its drying system. It consists of a Flowmatik airflow management and distribution system; OTX hopper drier; and X Max drier. The company claims that it can process up to 12,000kg/h of material while consuming up to 56% less energy, compared with traditional drying systems. The X drier incorporates a multi-bed single molecule sieve desiccant system and provides a constant –65°C to –85°C dew point. It is larger than conventional beds, works without requiring cooling water or compressed air for the changeover valve and recovers heat during bed cooling. Its multi-stage centrifugal blower was developed in co-operation with Padua University. Up to ten X Max driers can be combined at once, offering 20,000 m3/h airflow. The Flowmatik airflow management unit matches unit usage to demand and shares air with up to 32 truncated cone shaped OTX (Original Thermal Exchanger) hopper driers. The OTX is available in 28 sizes and has internal geometry designed for even material and airflow. Moretto says that it consumes as much as 40% less energy than conventional hoppers. www.moretto.com panel, with an 8” touch screen, shows the operator the actual configuration of the equipment in real time, without showing redundant or unused elements. Depending on the type of production, the control system calls up the corresponding recipe and the blender automatically configures accordingly. The control system is designed for integration with WinFactory, the industrial supervisory software operating by application licence developed by Piovan, the outcome of consolidated knowledge in various application environments. WinFactory can interface all Quantum blenders in the factory for: sharing recipes, managing material and production batches, and tracking raw materials; these are fundamental data for product certification, in particular in food & beverage and medicalpharmaceutical environments. Piovan has filed a patent application for the two more complex parts of Quantum: the dosing device and the mixer unit. The blenders are designed to be produced at all Piovan plants in the world and are part of the “High Efficiency Line”, comprising all products guaranteeing maximum energy and operational efficiency. www.piovan.com","@ID":51}, "BOTTLING / FILLING 17 PETplanet insider Vol. 15 No. 09/14 petpla.net Kumla: the paradise of fruit and berries Beverages made from fruit, fruit syrups, blueberry creams, fruit purees, juices... any product the basic ingredient of which is a fruit or a berry comes from the Procordia plant in Kumla. This is where Ekströms, Felix, Bob, Fun Light-branded food & beverages and many others are packaged, the main ingredient of which is fruit. In particular, the “Fun Light” product line is characterised by the continuous launch on the market of new products with innovative tastes, which often are created by unusual combinations of different types of fruit. With an annual consumption of around 60 million units, “Fun Light” is now the leading brand in Sweden in the fruit juice-based beverage sector and in the beverage field in general. www.smigroup.it G sensitive BEVERAGES A fruitful affair Procordia in Sweden has expanded its filling capacity by the Ecobloc from SMI. According to the Company, what goes into this are “products with a unique flavour“. Procordia, a leading company in the production, marketing and sale of a wide variety of well-known food and drink brands, has encapsulated its vision in the slogan: “our love for food & beverage will conquer the hearts of people”. This Scandinavian company has production units based throughout Sweden, which every day produce foods & beverages with a distinctly national flavour. For example, in their facility in Kumla, a small town in southern Sweden known as “the paradise of fruit and berries”, Procordia produces fruit juice based beverages. Here, the Swedish company recently installed a 14,400bph production line, implemented by SMI, which includes a Smiform Ecobloc 8-42-8 VMAG model integrated system for stretchblow moulding, filling/capping. It is equipped with an air recovery system and does not need a rinser. The dry part is a Smiflexi SK 350 T model shrinkwrapper and bottle handling conveyor belts. The compact Ecobloc fills and caps two different types of 0,5l PET bottles, one 0,95l PET bottle and one 1l PET bottle at the maximum speed of 14,400bph; bottles are filled with numerous types of juice without pulp marketed under the Bob and Fun trademarks. The 0,95l bottles were redesigned by SMI who came up with a container with a higher top-load value, therefore more resistant. More specifically, the “restyling” primarily involved the “shoulder” of the bottle while the bottle’s body and bottom parts remained substantially the same. The secondary packaging consists of the tray + film in the 4x3 collation packed by a Smiflexi SK 350 T model shrinkwrapper, which groups the PET bottles arriving from the blow filling station in packs of twelve. The 0,5l bottles are packaged in trays with smooth edges while the larger 0,95l and 1l bottles are packaged in trays with edges of different heights.","@ID":19}, "BOTTLES 53 PETplanet insider Vol. 15 No. 09/14 petpla.net Smooth orange juice from France On its home market, the French juice manufacturer “Fruite“ is marketing a litre of smooth orange juice “Douceur d’Orange“, which contains less citric acid and is therefore easy to tolerate, in a white PET bottle with a large opening of adequate proportions. The bottle incorporates horizontal reinforcing grooves in the body area; these also keep the shrink sleeve label in place as well as helping to fix it in position. The bottle is sealed by means of a screw closure with tamper-proofing. www.fruite.fr Safety dispensing Aptar Food + Beverage present its latest development with France’s leading concentrate brand Teisseire. Aptar and Teisseire, a Britvic Group plc company, have teamed up to develop a customized dosing system which allows consumers to safely and intuitively dispense concentrate. This dispensing pump, based on Aptar’s HiFlow platform, is an ideal solution for children. The easy to use dispenser delivers a precise 4ml dose of concentrate with each actuation and ensures no leaks or spills, to the delight of parents, and prevents any crystallization in the dispensing mechanism. www.aptar.com 18,9l of water-gallon implemented with new design The latest project from Kiefer was the redesign of the 18,9l water gallon for Side. The challenge was to realize an optimal insertion of the handle. In this realized mould linear type the shape is blown around the handle. Kiefer also designed change inserts without screws, implemented for a quick change of font inserts. As an independent mold maker Kiefer manufactures blow moulds made of aluminium for all rotary blow molding machines from Krones, Sidel, KHSSig, Sipa, SMI and linear blow moulding machines of ADS, Bekum, Kosme, MAG, Tetra Pak and Arcor. www.kiefer-mold.de","@ID":55}, "PETpatents www.verpackungspatente.de 56 PETplanet insider Vol. 15 No. 09/14 petpla.net Container Bottom Section European Award of Patent No. EP 2396246 B1 Applicant: Sidel Participations, Octeville sur Mer (FR) Application Date: 8.2.2010 A European patent is to be awarded to a plastic container (PET bottle) where the bottom section incorporates a curved stable base. Tamper-proofing European Award of Patent No.EP 2424789 B1 Applicant: Krones AG, Neutraubling (D) Application Date: 19.2.2010 A bottle made from glass or plastic is closed by means of a simplified screw closure which is secured by affixing a seal. When the lid is unscrewed this seal is irreversibly destroyed. This version permits dispensing with a guarantee strip which, in turn, results in a reduction in the material used. Bottom Section Moulding International Patent No.WO 2014 / 004919 A1 Applicant: Plastipak Packaging Inc., Plymouth (US) Application Date: 27.6.2013 In the interests of improving the appearance of a plastic bottle for carbonated products or those intended for hot filling, compensation for the change in volume is undertaken from the bottom section. This needs to be specially moulded in order to do this so that it can absorb these forces elastically. This outside section of the bottle may be designed so that it incorporates a smooth surface. Carbonic Acid in the Bag International Patent No. WO 2014 / 006776 A1 Applicant: Hikarimirai Co. Ltd., Tokyo (JP) Application Date: 12.11.2012 A bag is placed in a liquid container with carbonated contents. This bag releases carbonic acid over an extended period of time and thus keeps the product inside at a specific carbonic acid level. Dispensing cap International Patent No. WO 2014 / 005845 A1 Applicant: Obrist Closures Switzerland GmbH, Reinach (CH) Application Date: 20.06.2013 Dispensing cap optimised for products such as mustard, ketchup or similar which are capable of flowing. Discharge is via a “long” route through the cap, which results in better mixing of the product. Taking pressure away from the container reduces the amount left in the cap. High Volume PET Bottle Patent No. WO 2014 / 013470 A1 Applicant: PET Engineering S.p.A., San Vendemiano (IT) Application date: 18.7.2013 The international application describes the requirements in respect of a bottle manufactured from PET with a content of approx. 5 litres. The preform must be specially moulded.","@ID":58}, "EDITOUR REPORT 12 PETplanet insider Vol. 15 No. 09/14 petpla.net If we look at Italy from the point of view of drinks packaging overall, it is not surprising to find that the dominant proportion of PET bottles, amounting to approx. 75%, is to be found in the non-alcoholic drinks sector. It is only when it comes to juices with a proportion of fruit in excess of 40% that the brick packaging tends to dominate. Now, however, in 2014, the first aseptic filling line for PET bottles is being put into operation. Italy as a market for mineral water With mineral water consumption amounting to 11.4 bn litres and a per capita consumption of 190l per year, the mineral water market is the pillar of the Italian beverages market. Although the mineral water market has been saturated for years, the market remains an important economic factor in Italy. Mineral water prices are very low by comparison to other European countries and so, for reasons of cost, imports are virtually invisible in the market. As a result competition tends to be local and almost exclusively related to price. Hence the trend goes towards private labels for discounters because the premium brands are losing share. For instance, within the bottling plants (numbering in excess of 140), there are more than 250 different brands. Although this development has to do with the economic situation of the country, the purchasing mindset of the Italians is also a factor. The Italians buy approx. 70% of their drinks in supermarkets along with their groceries. 2/3rds of the drinks consumed are still mineral water, with a geographical distribution from northern/central Italy to southern Italy of 75/25%. When it comes to packaging there is a preponderance of 80% PET bottles incorporating bottle sizes with contents ranging from 0.25 to 2l. As regards the distribution of bottle sizes, we find that the 1.0/1.5/2l sizes account for more than 75% with the smaller content bottles (0.25/0.33/0.5l) bringing up the rear at around 25%. The most significant companies on the Italian water market in terms of size are: San Pellegrino San Benedetto Norda+Gaudianello Rocchetta/Uliveto Ferrarelle Spumodor Lete These eight businesses represent some 70% of the market for bottled water in Italy. Interviews on the Italian Tour In the interests of doing justice to the water market in Italy we focused on this segment. In the mineral water bottlers sector we visited the following firms: Acqua Nepi in Nepi (VT) Ferrarelle in Riado (CE) Fonti di Posina in Posina (Vi) Fonti di Pineta in Clusone (Bg) San Pellegrino in San Giorgo in Bosco (PD) Tavina in Salo (Bs) We were able to conduct interviews with the following: PET machine manufacturers CFT in Parma. Manufacturers of PET bottling machines for special applications Sacmi in Imola (Bo). Manufacturers of preform and closure cap machines.The closure cap machines based on the compression process. Siad in Bergamo. Manufacturers of air compressors for PET stretch blow moulding machines with the Vito brand name. Sipa in Vittorio Veneto (TV). Manufacturers of PET preforms and stretch blow moulding machines and bottling lines. PET preform and bottle converters Alpla in Tortona (AL). Manufacturers of PET preforms and bottles Garda Plast in Polpenazze (BS). Manufacturers of PET preforms Plasco in Anangni. Manufacturers of PET preforms Retal in San Dona Piove (Venice). Manufacturers of PET preforms Sicon in Giammoro (ME) on Sicily. Manufacturers of PET preforms. Manufacturers of additives Repi in Lonate Ceppino (VA). Manufacturers of additives for PET tints and barriers. Recycling Recycling policy tends to vary with country, and Italy is no exception. Costs and individual national regulations may mean that the price of rPET is higher than new material. We shall be interviewing Messrs. Cier in Castellato (TE) with a view to probing such matters more deeply.","@ID":14}, "BOTTLE MAKING 28 PETplanet insider Vol. 15 No. 09/14 petpla.net Liquiform, one step bottle forming and filling by Alexander Büchler The 50/50 Joint Venture between Amcor and Sidel Liquiform has seen the development of a bottle forming and filling technology which makes forming and filling bottles possible in a single step. This means that the energy-intensive compressed air conditioning process can be dispensed with, along with some of the transfer and/or logistics steps in the process. We spoke with Ann O’Hara, President, LiquiForm. In the classic process, the preform is initially heated in a furnace before being placed in the mould and then the actual liquid or whatever product is to be bottled is forced at pressure into the preform, moulding it into the bottle shape. This results in a filled bottle, ready for capping and labelling. PETplanet: Hello Ann, is it your aim, with your new Liquiform hydroforming technology, to revolutionise the stretch blow moulding and filling sector? Ms Ann O’Hara: We think it makes sense to mould the preform into a bottle by means of the end product instead of using compressed air. In this way we not only save on the filling machine but primarily also on the air compressor and hence any amount of energy. Beyond the primary benefits, there are secondary opportunities to leverage the “nonair” process for its additional benefits – smaller clean rooms for aseptic filling, more ambitious designs given the more precise forming, potential elimination of the stretch rod, reduction of waste given the increased accuracy of filling volume, etc. And in the end, the step change in efficiency, combined with the additional benefits, will revolutionise the container forming market. PETplanet: If I understand the system correctly, the preform is traditionally heated in an oven, goes into a normal stretch blow moulding machine and your process involves initial stretching and then moulding the walls with the product liquid. Does the liquid not immediately cool the inner wall of the heated preform and at least make it difficult to shape the bottle correctly? Ms Ann O’Hara: Our trials have shown that this is not the case. On the contrary. The liquid is so fast that the cooling of the bottle wall only happens at the wall of the mould. In a similar way to blow moulding, we go into the cavity at a pressure of 14bar. And in fact, after the bottle is formed, there is a benefit of the liquid cooling in that the newly formed container does not need to be held in the mould very long and much less than in air blowing where there is a designed in “hold time” to allow for that cooling. To take advantage of that speed improvement we are working on offtake processes and technologies. PETplanet: Is the process slower? In the case of traditional stretch blow moulding / filler lines there are around six filler valves serving one stretch blow moulding cavity. Do you only mould at a stretch blow moulding speed of 1/6? Ms Ann O’Hara: No, the speed of the stretch blow moulding cavity stays the same.The filler process is considerably. The LF process can form and fill a 2l container in less than 0.3s compared to over 10s on conventional filling systems. PETplanet: Up to now we have only had one empty bottle, perhaps with 30g, in one cavity. Now, with the high rotational speeds of the blow Ann O’Hara President at LiquiForm","@ID":30}, "CAPPING / CLOSURES 26 PETplanet insider Vol. 15 No. 09/14 petpla.net Closures flash sterilisation by Claranor Flash sterilisation of packaging materials in sensitive beverages Flash Sterilisation technology uses the bactericidal effect of ultraviolet rays contained in intense flashes of white light emitted by Xenon lamps. Compact and efficient, pulsed light is well suited to integration on industrial production lines, with investment and operating costs matching current business constraints. Save the date Petcore Europe, the Brussels based European PET value chain association, is organizing the annual PET Network Day conference on 9 October this year. The event is supported by eight leading European associations representing the manufacturers, converters, SDFNHUV DQG ÀOOHUV DQG WKH UHF\\FOHUV The success of last year event showed the continuous and growing interest in PET value chain issues. Building upon that experience with the participation of over 100 participants from across Europe and beyond, this year the conference will discuss whether the very success of PET as the packaging material of choice could impact its future and ongoing success. The conference will take place on the 9 of October 2014 in Brussels and will gather the worlds of the PET industry & European institutions together. Do not miss the opportunity to be updated and informed on the latest aspects of PET and to network with a wide range of key actors across Europe. P E T N E T WO R K D A Y 2 0 1 4 The essent ial PET event to at tend in Brussel s 9 October 2014, Brussels For more information about the speakers and agenda, please visit our website: www.petcore-europe.org Do not miss this opportunity and register now to the PET NETWORK DAY 2014! More information, contact [email protected] Claranor, a young company located in the south of France, has developed various industrial applications of Flash technology for food products, packaging materials and for medical applications. The focus of the company’s latest developments is on food packaging material sterilisation systems. It installed its firstever closures sterilisation unit in 2004 and has subsequently supplied equipment to major companies in the beverage industry across the world, including Nestlé Waters in France, Saudi Arabia, USA, and Mexico. The company has now widened its range of solutions with the development of integrated decontamination systems for preform necks, cups, and lids. Industrial enterprises are constantly struggling to improve their productivity and, at the same time, have to comply with regulatory constraints and increasing pressure to adopt sustainable production practices. Disinfection with pulsed light has the capacity to replace chemical or radiation-based technologies. It is dry, compact, easy to integrate on new or to retro-fit on production lines and offers limited running costs. Furthermore, Claranor’s technology does not require operators to learn a new set of specific hazard management procedures. Claranor’s market targets are industrial plants of international groups in the beverage and dairy sectors, as well as smaller industrial actors, on a worldwide scale. Around 90% of its 2013 turnover was generated outside of France. The","@ID":28}, "EDITOUR REPORT 13 PETplanet insider Vol. 15 Strapping instead of shrink wrap by Waldemar Schmitke Accompanied by executives from Siad’s Vito Division, we arrive at the premises of the beverages bottler Fonti Pineta in Clusone (BG) where we meet Luca Bordogna, Managing Director and Cristian Magoni, Technical Director. Here we not only have the opportunity to view the prototype of Siad’s latest blowing air compressor from its Vito range of models but also an up-to-the-minute blowing and bottling operation, kitted out with machinery and equipment in compliance with the latest technical specifications. Fonti Pineta pumps and bottles mineral water out of its own five springs. In addition to these there are soft drinks in eleven different flavours that are bottled exclusively in glass. The company operates at two locations, one of which is here in Clusone, and from its other site in Zogno (BG). The two sites are not too far distant from each other. Their own brand names are Pineta and Bracca and sport supplementary private labels for supermarket chains, such as, for example, Flavia, Blues und Presolana. Today the company’s total bottling capacity is 450 million litres a year (including the new PET bottling line from Sidel) and is divided up into 410 million litres in non-returnable PET bottles and 40 million litres in reusable glass bottles. Capacity utilisation is currently (March 2014) still around 280 million litres which corresponds to the level of the previous year. PET bottle sizes filled are 2.0, 1.5 and 0.5l. Glass bottle sizes filled are 1.0, 0.75 and 0.5l (deposit bottles). Glass bottles are stagnating. The filler units are broken down into two for PET and one for glass per location. What if you could redefine shelf life? You can — when you work with PolyOne. Our PET barrier solutions enable effective and precise shelf life management to oxygen sensitive foods and beverages preserving freshness. Visit www.colormatrix.com/PETbarriersolutions to make it possible. Always active barrier High performance light & gas barrier protection Assured container clarity","@ID":15}, "PREFORM PRODUCTION 35 PETplanet insider Vol. 15 No. 09/14 petpla.net Two-stage Process Injection Moulding, part 14 Preforms for Single – and Two-stage Processing Preforms for these two processes are quite different, and one made for one process will not work in the other. The reason for this becomes clear when we look at what is actually happening to the preform just prior to stretch blow moulding. PETplanet insider is publishing extracts from successive chapters of Ottmar Brandau’s “Bottles, Preforms and Closures”, which was first published by hbmedia. A newly revised version is reissued under the Elsevier imprint. Two-stage process injection moulding To guarantee optimal flow of the moulten PET into the injection cavities, designers use ratios of gate wall thickness to body wall thickness. Ideally, one would want to keep the gate wall thickness as low as possible as this part of the preform does not generally participate to a large degree in the stretching process and stays as an often wasteful, thick disc in the centre of the bottle. (In CSD bottles however, a thick centre disc is required because a thinner, amorphous centre would not be able to withstand the considerable","@ID":37}, "BOTTLING / FILLING 23 PETplanet insider Vol. 15 15,000 1.5l bph; up to that time, Pfanner had contracted-out the filling of smaller numbers of PET packages. Demand for PET grew so that, in 2011, Pfanner installed a second Krones bottling line, rated at 13,500 1.5l bph, at its Enns plant. This was a PET-Asept L, a wet-aseptic line with peracetic acid as the sterilisation medium. This monobloc is suitable for filling still, low-acid beverages with a guaranteed germ reduction of log 5. Pfanner now fills all its still fruit-juicebased beverages in 1.5l PET bottles on this line. In 2013/2014 Pfanner boldly ventured where it had never gone before, by taking the leap to decontaminating the preforms, rather than the blow-moulded containers. This itself was a first for the sector but, in addition, the machine incorporates a new filling valve that can also handle carbonated beverages. The company replaced its existing rinserfiller monobloc and Contiform blow-moulder (linked by means of air conveyors) which dated from 2003, with a Contiform Bloc with Contipure. The new preform infeed is now located directly at the Contiform Bloc, which comprises a heater module, the Contipure preform-decontamination unit (using H 2 O 2 ), a conventional Contiform S8 blowmoulder module, an isolator with base cooling, an aseptic Volumetic filler with capper, and a height-adjustable discharge conveyor, which was incorporated in order to match different container sizes. This technology enables high-acid beverages (with pH-values smaller than 4.5) such as ice teas, juices and squashes, as well as carbonated spritzer drinks to be filled aseptically with a decontamination rate larger than log 4. In the Contipure process, both the outside and the inside of the hot preforms are simultaneously sterilised with gaseous hydrogen peroxide: an H2O2-air mixture is injected The biggest drying system for plastic materials ever installed in the world, 6,000 kg/h PET. www.moretto.com Drying Revolution designed by Moretto STAND 3208 HALL B3 into the preforms from above, through a central manifold, The preforms are located in a space with an H 2 O 2 atmosphere, which ensures that their external surfaces are also decontaminated. As the preforms are treated downstream of the oven, re-contamination risk is reduced. The outstanding new feature in this system is the combination of Contipure preform decontamination and the use of a new filling valve, which is able to handle both still and carbonated beverages. The valve has a base that can be magnetically extended and retracted as required; when carbonated products are being filled, the base is extended and pressed against the bottle’s neck finish. With still beverages, in contrast, it is retracted, thus keeping the valve at a distance from the bottle and ensuring full-jet filling for the still products. “There used to be general agreement that aseptics were only suitable for still beverages. An aseptic line fill-","@ID":25}, "PREFORM PRODUCTION 36 PETplanet insider Vol. 15 No. 09/14 petpla.net pressure.) However, to make sure that PET can enter the cavity without too much shear stress, a ratio of 72–80% is used in most cases. This means that a preform with a 3mm body wall thickness will have a gate wall thickness of 2,16–2,34mm. The exception to this rule is a preform with a body wall thickness less than 2,5mm. These have become quite popular with lightweight water bottles as a lower preform wall thickness reduces cooling requirements and speeds up cycle times. There is a minimum gate wall thickness of about 1,8–2mm, and gate to body wall thickness ratios of up to 100% may become necessary for these preforms. Two-stage process blow moulding All preforms are at the same temperature when they are fed into the blow moulding machine. In the heating section they spin on mandrels while infrared heaters bring them to blowing temperature. This virtually guarantees that all preforms are at the same temperature circumferentially. One limitation of the process is that, in order to protect the neck finish, the first lamp in the oven section has to have a certain distance from the neck finish that is protected by a sheet metal shield. Therefore, the preform section below the neck support ring cannot be heated to the degree that proces¬sors would want to. The material in this section forms the shoulder of the bottle, where less material is needed, and it is beneficial for overall weight savings to pull material out of this area. Preform designs for the two-stage process take this into account by bringing the thinner neck section down to a point where material is then needed to form the wider body of the bottle. When reheating preforms in a good blow moulding machine, knowledgeable processors can actually bring the inside temperature of the preform to a higher level than the outside, achieving the optimal temperature profile through the wall. They do this by using high lamp settings and enough venting air in the oven to keep the oven temperature below blowing temperature. A longer equilibration time after heating is also helpful for this purpose. This is beneficial because the inner surface material of the preform has to stretch further than the outer one. By changing lamp heater outputs, oven fan cooling, and preform throughput, operators can precisely adjust the temperature to an optimal level. For these reasons high blow up ratios up to twelve are possible in the two-stage process, resulting in very good properties such as carbonation retention for CSD bottles. Single-stage process In this process preforms and bottles are manufactured in the same machine. After injection moulding, the preforms stay in the neck inserts and are shuttled to a conditioning station in some machines or directly blown in other machines. At this point in time the preform has only partially cooled down from the melting temperature of around 250°C (482°F). The cooling of the preform comes from inside (injection core) and outside (injection cavity) during injection, resulting in the centre of the preform wall staying warmest. This residual heat makes preforms from the single-stage process on average warmer than their two-stage counterparts. Because the last part of the preform to receive hot material is toward the gate area, this part of the preform is always warmer than the area underneath the neck. Processors are therefore limited in how they can process these preforms. Designers compensate for this in two ways. They use a lower gate to body wall thickness ratio, usually between 58% and 66%. This reduces wall thickness in the gate area, allowing faster cooling. They also tend to have the greatest body wall thickness underneath the neck if possible. Quite contrary to intuition, a thicker wall in the PET preform in this process leads to a thinner wall in the corresponding bottle wall thickness. This is true because a thicker wall retains more heat and will then subsequently stretch so much more that a thinner bottle wall. Nonetheless, when the blow moulding process is the slave of the injection process, process capabilities diminish. Another limitation of the singlestage process is viscous heating. To understand this process we have to examine what happens inside the molten resin during injection. PET flows through the barrel, hot runner channels, and nozzles in a laminar fashion like honey flowing through a squeeze bottle nozzle. This flow is characterized by the highest shear rates occurring at the channel walls, whereas there is much less shear at the centre directly adjacent to the runner walls as the speed drops to zero (Fig. 2.19). Figure 2.19 Friction just off the channel walls causes viscous heating Shear deformation causes internal friction between adjacent entangled polymer chains, which results in shear heating. As a result of the laminar flow there is an elevated temperature in the ring-shaped area just off the channel wall (Fig. 2.20). Figure 2.20 Calculated temperature spike in area adjacent to channel wall Most hot runners for single-stage machines are designed in a way that one large channel diverts into two smaller channels that come in at 90° (Fig. 2.21). Figure 2.21 When one channel intersects at 90°, the result is a skewed temperature profile.","@ID":38}, "BOTTLING / FILLING 24 PETplanet insider Vol. 15 No. 09/14 petpla.net Pad Printing Machines ALFALAS® Laser Systems Automations PAD PRINT ING & LASER MARKING FOR CAPS AND CLOSURES Made in Germany: TAMPOPRINT® machines decorate 50 million bottle caps per hour worldwide ■ Highest efficiency ■ Best quality ■ Newest technology ■ Fastest service www. tampopr int .de ing both still and carbonated products was regarded as problematic. The Contipure system has, in my view, changed things here”, explains Günter Feusthuber. “The Contipure’s big advantage is that it’s the preform that is sterilised, which means the bottle shape isn’t important any longer. This also means that it’s not necessary to validate every new bottle shape. The system is resource-economical. Because no liquid chemicals are used, no sterile water is required for spraying the bottles, which consequently reduces amounts of wastewater,” he continues. “What’s more, less time is needed for make-ready at bottle changeovers than with wet aseptics, thanks to neck-handling throughout and the lowerable discharge conveyor.” Since both cleaning and sterilisation times are significantly shorter, the Contipure’s overall equipment effectiveness is correspondingly higher. Last but not least, the Contipure system has a smaller footprint: “We’re talking about nine by nine metres here, while the figure for a wet-aseptics system (including all peripherals) would be around 14 by 18 metres.” “As far as continuous running time is concerned, the two lines score more or less the same: both the PETAsept L and the Contipure line can be run without any interruptions for 120h,” he concludes. “In my view, the wet-aseptic system retains its justification for still products. This is despite the additional outlay involved and is because it offers a higher degree of safety, especially for more sensitive, low-acid products, with a germ reduction of log 5. But I see the Contipure system as the more future-compatible option both for still and carbonated products. In our case, the Contipure is absolutely sufficient for 90% of all articles we’re filling, and it’s more affordable and resource-economical into the bargain.” www.pfanner.com Pfanner replaced the existing rinser-filler monobloc and Contiform blow-moulder, linked by of air conveyors to a Contiform Bloc with Contipure.","@ID":26}, "TRADE SHOW PREVIEW 43 PETplanet insider Vol. 15 No. 09/14 petpla.net Coca-Cola India Pvt. Ltd. Mr Chandra Mohan Gupta (Supply Chain Director) Coca-Cola in India offers a range of healthy, safe, high quality, refreshing beverage options to consumers. The Company along with its bottling partners, through a strong network of over 2.2 million retail outlets, touches the lives of millions of consumers. With 59 bottling plants in the country and a journey spanning over 20 years now, we are happy to have the opportunity to provide hydration choices to our consumers. I am looking forward to Drink Tech and sharing experiences and insight from CocaCola India and also learn how other industry players are innovating. Bisleri International Pvt Ltd. Mr K. Ganesh (General Manager, Technical North) The bottled water industry in India witnessed a boom in the late 1990s soon after Bisleri launched its packaged drinking water in the country. This significant growth was fuelled by a surge in advertising by the industry players that “bottled water was pure and healthy”. Today, with a rise in health awareness, poor quality of tap water, and the ease of availability of bottled water, the per capita consumption of bottled water in India is on the increase. The total market was valued at Rs.60 billion in 2013, of which the top five players accounted for 67% of the market share .This market is expected to grow at a CAGR of 22%, to reach Rs.160 billion in 2018. Maximum sale of bottled water comes from the retail sector; but this is changing with demand coming from social functions and corporate events, especially for bulk water or bottled water cups. With the aim to capture all the segments of society, players have started foraying into packaged drinking water with small pack size. I am looking forward to discuss this with the other market experts and the audience during the Roundtable Talk at drink technology India. FlavorActiV Ltd. UK Dr. Binod K. Maitin (Spirit Beverages Consultant) Now an independent consultant, Dr Binod K. Maitin, a doctorate in Analytical Chemistry, has spent his career in the area of Sensory Sciences. For many years he was Head of the Technical Centre at United Spirits Ltd, of Bangalore, (UB Group), where, amongst other responsibilities, he conducted research into cross-cultural aroma and taste perceptions amongst consumers. Dr. Maitin has worked with various academic and industrial organisations, and was, for 20 years, a member of the Indian National Food & Drink Standards Committee. In 2008 he was appointed a Fellow of the Royal Society of Chemistry UK. As a consultant with FlavorActiV, UK, he is now able to offer the fruits of his experience and expertise, and in the Round Table talks he will be highlighting the importance and applications of sensory evaluation techniques for quality, shelf life, consumer insights for innovative NPD and their significance for products’ appreciation and marketing. He will also explain the benefits of outsourcing intensive sensory training. Discussion partners at DTI Round Table Talks Time Company Speaker Topic September 27, 2014 11:00 am - 11:30 am Block 5 - Machinery and systems engineering for food production 11:00 am - 11:30 am Siemens AG Mr Pratish Sheth (Marketing Manager) & Mr Annamitra Mahanty (Senior Executive) Plant-wide-automation for dairy industry / Integrated filling & packaging lines for reduced life cycle costs 11:30 am - 12:00 am Block 6 - The right food packaging 11:30 am - 12:00 am Beta-Pak Mr Turgay Gezer (General Manager) & Mrs Sonay Celebi (Export Responsible) High standards thermoforming and special packing machines Data are subject to change. Final version expected for 15.09.2014","@ID":45}, "PREFORM PRODUCTION 37 PETplanet insider Vol. 15 No. 09/14 petpla.net Smarter Compressor Technology HIGH PRESSURE SOLUTIONS Belliss & Morcom offers a complete range of solutions, delivering the highest quality, oil free compressed air for all your needs. Talk to our experts today. Exceptional Performance, with Lowest Life Cycle Costs, Guaranteed. Belliss&Morcom is a brand of Gardner Denver Your Ultimate Source for Vacuum and Pressure Gardner Denver Ltd – Belliss & Morcom Claybrook Drive, Redditch, Worcestershire B98 0DS UK T: +44 (0) 1527 838 600, F: +44 (0) 1527 838 630 E: [email protected] W: www.gdhighpressure.com","@ID":39}, "PREFORM PRODUCTION 39 PETplanet insider Vol. 15 No. 09/14 petpla.net As you can see from Fig. 2.22, there is a tendency for the cooler material from the centre of the channel to flow toward the far side of the intersecting channel, whereas the hotter material flows to the near side. While intermixing and subsequent temperature homogenization is happening, it is in many cases (depending on hot runners used, material properties, temperature, pressure, speed, and shot weight) not enough to prevent the hotter resin from being injected into the side of the cavity that faces the back of the machine, whereas cooler material is injected in the front. Because PET is very sensitive to even small temperature fluctuations, processors often fight uneven bottle walls with thinner sides toward the parts adjacent to the back of the machine (Fig. 2.22). Figure 2.22 Hotter material may be pushed to the nearer side of the secondary runner. Uneven heat of the melt also causes the melt to move at different speeds into the cavities. This can be established by doing a so-called “short shot” where an insufficient amount of material is injected (or the injection is interrupted at some point). It can then be clearly seen if all cavities are filling at the same speed. Uneven filling means that the heat profile in each preform is slightly different, which always results in wall thickness differences of the blown bottles (Fig. 2.23). Figure 2.23 Actual infrared photograph of preforms after injection. Large sideto side temperature variation is clearly visible. There is however a way to improve on some of the inadequacies of this process. I should mention here that uneven filling is also a problem in twostage injection moulding. Although it does not affect bottle properties, uneven filling and with it cooling can lead to gate and packing problems in some cavities. This is because the material in the cavities that are filled first cools down quicker and increases in viscosity earlier compared with the late-filling material. This may lead to a situation where the fast-filling cavities are overpacked and the slow-filling ones are underpacked. The preforms from the former may be hard to blow, and preforms of the latter could show flow lines or sink marks. The degree to which this happens and how much preforms will be affected depends on the particular preform geometry and process conditions but will be a factor when the fastest cycle time is the primary goal. One way to improve on this is to change the way the melt changes direction in the hot runner. Instead of changing in hard right angles, a brazed, rather than drilled, hot runner plate allows the gentle curving of the directional changes, leading to less of a melt separation by temperature. In brazing the hot runner plates, two individually milled plates are fused together after milling, allowing curved melt paths (Fig. 2.24). Figure 2.24 Lower temperature variations and more equal flow are the advantages of brazed hot runner plates that allow curved paths. (Diagrams courtesy of Mold-Masters) For cavitations other than multiples of two, the path width has to be adjusted to achieve a similar result. In practice, these manipulations often work well for a certain gram weight but fail to deliver balanced flow with others. In PET injection moulding for the two-stage process, only certain cavitations are used in order to prevent a departure from a naturally balanced design. In most hot runners here, one flow is divided into three and that is the reason for the 48, 72, 144, and so on cavitations. In the one-stage process, just about any number of cavitations between one and 16 has been built. This is because converters want to use a given machine frame to the maximum cavitation available for a bottle application. This has forced hot runner manufacturers to come up with different approaches to still deliver good flow behavior (Fig. 2.24). An excellent way of measuring the performance of any hot runner is to perform a short shot. The operator interrupts the injection about midway or dials in the shotsize so that only half of the resin necessary to fill the cavities is available. The machine is then stopped and the half-injected preforms are numbered for identification and weighed. It is not unusual to find a 50% variation at the 50% injection mark, i.e., preforms may weigh between 14 and 21 g, for example. This uneven development leads to different cooling times and incorporated stresses in the preforms. Roundedpath hot runners have proven to significantly ameliorate this situation (Figs 2.25 and 2.26). Figure 2.25 Equal-length paths to each cavity are critical for balanced hot runners. (Drawing courtesy of Huangyan Yusheng Polyester Mold Factory) Figure 2.26 Very even injection development is apparent by the even length of the shortened preforms. (Picture courtesy of Mold-Masters)","@ID":41}, "EDITOUR REPORT 16 PETplanet insider Vol. 15 No. 09/14 petpla.net We feel steel. Always with quality from the start. S+BIGROUP www.dew-stahl.com Plastic mould steels. We use them every day: PET bottles, caps, plastic packaging and other plastic parts. But scarcely anybody is aware that these products are manufactured in a tool or a mould made of specialty steel. Our plastic mould steels are easy-tomachine, corrosion-resistant, clean and wear-resistant – depending on what is required of them during use. That guarantees long tool service life, high productivity and efficiency. Which steel do you need? The PET lines are of traditional construction based on unit machines. Both lines start with a Sidel SBO II: the variable line with 14 cavities, the 1.5l line with 16 cavities. Output on the 0.5 litre variable line reaches a maximum of 21,000 bph, on the other it is 22,400 bph. Buffer segments lead on into the Gea Procomac rinser/filler/capper combination. Krones Contirollers apply the label. The dry stretches are equipped with Italian machines, including from Acmi. In the near future Tavina is intending to expand its production. Two PET lines and a glass line are planned to ensure continued growth. They are also looking at incorporating soft drinks into their range. www.tavina.it Mr. Carlo Andreotta, Plant Manager, next to Dr. Brunella Vetturi, Head of Quality Management, standing in front of the Procomac bottling line which is just bottling the 1.5l “Sankt Emilia” bottle for the German market.","@ID":18}, "EDITOUR REPORT 14 PETplanet insider Vol. 15 No. 09/14 petpla.net As regards the six-packs, we were amazed to find that there is an alternative here. A Krones packing / strapping machine for six packs has been in operation here for the past two years. The line was installed here even before its official launch. The six-packs are no longer shrink-wrapped but held together by means of strapping, as it is called. According to Luca Bordogna, the savings in PVC foil amount to 28g in weight when replaced by the strapping, which weighs a mere 2g. In addition, combination options of this type enable the bottles to be arranged differently and at the same time permit 15% more bottles to be accommodated on the same pallet. This means that, instead of 504 1.5l PET bottles, 576 bottles can now be accommodated on one pallet. The preforms come predominantly from Garda Plast Italy and the one piece plastic caps from CDS Holland. Plastic closure weights For still water 2.0g For sparkling water 2.5g Preform Weights 0.5l still water 12g 1.0l CO 2 and still water 22g 1.5l CO 2 and still water 27g Finally, we take a look at the new Vito 1920 compressor in operation. Two old compressor lines, each with a capacity of 1260m3/h were shut down.The Vito compressor, with a capacity of 1920m3/h, has now taken over the job of supplying two Sidel stretch blow moulding machines with compressed air and has so far been running for 1,500h. The stretch blow moulding machines are supplied via a 3,000l pressure accumulator. We noted that the system pressure shown in the in the accumulator was 24bar and that the blow moulding machines are supplied at a working pressure of only 20bar; this saves energy. You learn something new every day. We took our leave of all participants and resumed our journey in the direction of Lake Garda. www.siadmi.com www.fontipineta.it Here in Clusone we find the new Sidel line arranged in block format. What this means is that the stretch blow moulding machine and filler units are directly connected to one another without buffers. The stretch blow moulding machine has twelve blow stations and transfers the 0.5l PET bottles for still water to the filler module on completion of the blow moulding operation. The blowing pressure is only 20bar at a blowing temperature of 120°. For this reason and in the interests of enhanced stabilisation, the bases of the PET bottles are cooled from the outside with water during transfer into the filler module. The filler module itself has 72 filler valves and a filling pressure of 3bar. The line capacity is 27,000 PET bottles per hour. The downstream equipment comprises an Arol capping machine, a labeller from Krones. The shrinking tunnel and the palletiser are sourced from Acmi Italy. All the remaining PET lines are a combination of Sidel stretch blow moulding machines with 14 blow stations and Simonazzi filler machines, likewise with capacities of 27,000 PET bottles per hour. After filling the PET bottles are packaged in PVC shrink foil with a handle made from PET material. Six-pack 1.5 and 0.5l PET bottles Twelve-pack 1l PET bottles 24-pack 0.5l PET bottles F.r.t.l.: Luca Bordogna, Managing Director, Silvia Sangiorgi, Customer Relations Manager Siad, Cristian Magoni, Technical Director, Manuela Teocchi, Market Analyst & Head of Project Development, in front of the Krones packing / strapping machine with a six-pack of 0.5l water bottles in their hands.","@ID":16}, "BOTTLES 55 PETplanet insider Vol. 15 No. 09/14 petpla.net High-performance pampering oil from Diadermine Schwarzkopf & Henkel is marketing, under the “Diadermine“ brand name, a smoothing, nourishing and skin-enhancing high-performance pampering oil under the name of “N° 110“ and packed in a shapely PET bottle with a content of 100ml. The number 110 refers to the addition of 110 drops of a multi-correcting elixir as well as the 110th birthday of the brand in 2014. The droplet-shaped bottle which is slightly tinged with colour and which has a content of 100ml, features thicker walls stimulating the impression of appealing, high quality haptics with a stable effect. The lettering is applied direct and a matching screw closure rounds off the appearance of superior quality. The bottle can be identified at the PoS by the folding box with gold printing which likewise gives an impression of quality. www.diadermine.de Embossed PET bottle for shower gel Arthes Parfums from France is distributing on its home market and under the name of “Jeanne en Provence“ 250ml a shower gel scented with apricot and peach in a striking, transparent PETG bottle. This has longitudinal grooves running round it and features an embossed brand name logo in the front section. Smooth surfaces enable labels designed to match to be affixed to front and rear without wrinkling. The screw-on, shiny silver closure can be opened and subsequently re-closed by activating a tilt function. www.jeanne-en-provence.com Duo-effect care from Garnier Garnier have re-designed the packaging of its range of care products “Garnier Fructis Oil Repair 3 Duo Effect Care“ for dry and stressed hair. Instead of what has hitherto been an elongated bottle slightly tapered towards the top, the second stage product, consisting of nurturing milk and repairing shine serum, is now packaged in a droplet-shaped PET bottle containing 150ml. A screw-on pump dispenser with a removable protective cap enables the product (shake slightly before use) to be sprayed on to either damp or dry hair. www.garnier.com","@ID":57}, "PETcontents 9/14 4 PETplanet insider Vol. 15 No. 09/14 petpla.net INSIDE TRACK 3 Editorial 4 Contents 6 News 49 Products 50 On site 52 PET bottles for beverages and liquid food 54 PET bottles for home care and beauty care products 56 Patents MARKET SURVEY 31 Compressor manufacturers PREFORM PRODUCTION 35 Preforms for single- and two-stage processing Bottles, preforms and closures, part 14 TRADESHOW PREVIEW 42 The trade show double feature International PackTech India and drink technology India BUYER’S GUIDE 57 Get listed! sensitive BEVERAGES Page 16 Page 28 EDITOUR REPORT 10 Italy- Part 1 13 Strapping instead of shrink wrap A vistit at Fonti Pineta 15 Own brands for export A visit at Fonte Tavina BOTTLING / FILLING 17 A fruitful affair Procordia in Sweden 22 PET nibbles away at cardboard packaging 28 Liquiform, one step bottle forming and filling BOTTLE MAKING 18 New PET bottle design for beer based on Bulgarian & Northern Irish technology CAPPING / CLOSURES 20 Three steps to refresh… Vicap Systems connects packaging and delivery system in one cap 25 Thinking caps on Reuseable caps for PET bottles 26 Flash sterilisation of packaging materials Closures flash sterilisation by Claranor Page 53","@ID":6}, "PETbottles 52 PETplanet insider Vol. 15 No. 09/14 petpla.net Beverage + Liquid Food Vöslauer with fruit juice The Austrian company Vöslauer Mineralwasser AG of Bad Vöslau/ Austria has expanded its product range of mineral waters and flavoured waters to include a variant with 7% fruit juice. Up to now there have been two variations available – Vöslauer Balance Juicy Pink Grapefruit and Lemon. The products’ colouring comes from the fruit juice; they are low in calories and free of artificial colourants and preservatives. They are bottled in the familiar 750ml PET bottles which are made from 100% recyclate. The closure is a coloured, easy-to-handle screw cap complete with tamper-proof guarantee. www.voeslauer.com An agonising choice Standing in front of a shelf in a French retail store consumers is likely to find themselves faced with the agony of choice. Lesieur, the specialist in edible oil, is marketing its rape seed oil using two different packaging concepts. One is a green headstand bottle made from PET with a content of 675ml and a hinged lid closure with an automatic closure silicone valve. Prior to initial opening the lid needs to be unscrewed and a membrane removed. Two studded segments at the sides mark the pressure points for dispensing the product. There is also an elegant, fluted bottle in green PET containing one litre of product. The oil is dispensed via a screw-on, 2-colour dispenser cap. Once the tamper-proof strip has been removed, the two sections of the closure can be twisted in opposite directions, thus making a variable flow rate possible. www.lesieur.fr Müller Milk for the Football World Cup Within the framework of a promotional campaign, the Alois Müller Dairy of Aretsried in Germany is distributing its well-known Müller milk products as part of a special series featuring specially designed sleeve labels. The white PET bottles, each of which contains 400ml are printed with comic-style characters and the rear of the bottles also depicts the backs of the characters’ heads complete with their names. The bottles are closed by means of tamper-proof screw closures. www.muellermilch.de Raspberry syrup in PET Under its own label “Fruchtstern“, the German discounter Netto is marketing 500 ml of raspberry syrup for long drinks, alcoholfree mixed drinks or for mixing with water or soda in a ratio of 1:7, in a transparent PET bottle with all-round grooves emanating from the body area which is decorated with an adhesive label. The screw closure with tamper-proof band also matches the screw closure.","@ID":54}, "CAPPING / CLOSURES 21 PETplanet insider Vol. 15 Short cycle times, high shot-to-shot quality, low energy consumption and maximum flexibility. The new XFORM 300 with its unique 6-position post-mold cooling system boosts your output performance for the widest range of preforms. Cooling preforms faster and better, the 96-cavity platform is ideal for large runs and quick mold changes. And it lets you run any mold you want, old or new, OEM-built or not, in total freedom. From ultra-thin walled (with proprietary XMould™ technology) to wide mouth. XFORM 300, low transformation cost, high value. SIPA S.p.A. - Via Caduti del Lavoro, 3 - 31029 Vittorio Veneto (TV) - Italy Tel. +39 0438 911511 - Fax +39 0438 912273 - e-mail: [email protected] www.sipa-xform.com Designed to adapt. Built to last. The new XFORM 300 IMAGINE THE LOWEST TRANSFORMATION COST. IN TOTAL FREEDOM. bottling and sleeves, and initial customers Dr. Jan Berentzen with Powerlook from Germany and Printer & Long with Ink from Norway. Since the launch of the first Vicap in 2012, interest in the Vicap has grown exponentially: 0.5 million Vicaps in 2012, 1.5 million Vicaps in 2013, 10 million Vicaps in 2014, and growing. In a first expansion step and to cope with fast growing demand, Vicap Systems AG and its partners are installing further capacity to deliver up to 60 Million caps by 2015. www.vicapsystems.com The Vicap is used at Powerlook, which is filled into 0,25l PET bottles","@ID":23}, "MARKET SURVEY 33 PETplanet insider Vol. 15 No. 09/14 petpla.net PETStar – Booster / PS-2B 1250, 1470, 1980, 2290, 2840, 3340, 3850 PETStar –4 – 1500, 1700, 1900, 2100, 2300, 2500, 2800, 3000, 3300 7 8 (9 new models optimized for 28 bar pressure) based on an inlet pressure of 8 bar-g: PS-2B 1250 [1195}, PS-2B 1470 [1397], PS-2B 1980 [1881], PS-2B 2290 [2198], PS-2B 2840 [2727], PS-2B 3340 [3206], PS-2B 3850 [3696] PS-4 1500 [1497m3/hr], PS-4 1700 [1691 m3/hr], PS-4 1900 [1884 m3/hr], PS-4 2100 [2102 m3/hr], PS-4 2300 [2308 m3/hr], PS-4 2500 [2501 m3/hr], PS-4 2800 [2793 m3/hr], PS-4 3000 [2986 m3/hr], PS-4 3300 [3298 m3/hr] primary booster system 4-stage from atmosphere reciprocating to 40 Bar available oil free 2-stage screw or 3-stage centrifugal two stage reciprocating booster oil-free oil free horizontal PETStar-4 is a balanced horizontally opposed layout Petstar Primary + Booster is a 4 or 5 stage design. 2-3 stages Primary + 2-stage booster PETStar-4 has 4-stages of compression all double acting no no water water Direct Driven primary Booster is belt driven belt Boge Kompressoren Siad Macchine Impianti Otto Boge Str. 1-7, 33739 Bielefeld, Germany +49 5206 601 0 www.boge.com Mr Klaus D. Korzeng Business Unit Manager- PET +49 5206 601 200 [email protected] Via Canovine, 2/4, 24126 Bergamo, Italy +39 035 327611 www.siadmi.com Mr Giovanni Brignoli Compressor Division, Food & Beverage Product Leader +39 035 327609 +39 035 327694 [email protected] Boge BS Line Boge SRHV Booster System Vito BS Line 8 (BS 14-0 to BS 38-0) 4 (SRHV 170-10 to SRHV 470-10) 20 19 150 m3/h to 3000 m3/h range - singles or unlimited 94 m3/h - 274 m3/h range singles or multiples thereof 300 - 5500 1.000 – 6.000 high pressure blowing air (up to 40 bar) Oilfree SO range - fixed speed or frequency controlled 10 bar screw compressors S or SLF range - fixed speed or frequency controlled oillubricated 10 bar screw compressors low pressure screw Oilfree booster range 40 bar fixed speed or frequency controlled SRHV oil-lubricated booster range 40 bar piston high pressure piston (booster) Oilfree LP air with oilfree HP air as fully frequency controlled modular system Separat prepressure compressor with HP base frame solution oil free oil free Oilfree Class 1 - optional Class 0 by BC Converter oil free oil free Oilfree Class 1 - optional Class 0 by BC Converter oil free oil free Oilfree Class 1 - optional Class 0 by BC Converter yes yes Individual system components custom designed system layout Skid mounted fully wired, piped and factory tested base frame solution v v LP two stages HP two stages - system four stages Two system stages 3 2 screw + 2 booster= 4 total no no no no water air cooled or water cooled water water belt drive direct belt or direct direct drive belt belt belt drive belt and direct belt and direct","@ID":35}, "BOTTLING / FILLING 22 PETplanet insider Vol. 15 No. 09/14 petpla.net PET nibbles away at cardboard packaging Pfanner, the Austrian fruit drinks manufacturer, is increasingly coming to rely on PET. Until now, only about 1/5th of its beverages have been packaged in a PET bottle but a new Krones Contipure aseptic line with preform sterilisation for still and carbonated drinks is set to change all that. It replaces an Ultraclean line that dates back to 2003 and will be able to package up to 90% of all Pfanner products, including iced tea and fruit juices. “The Contipure´s big advantage is that its the preform that is sterilised, which means the bottle shape is not important any longer. This also means that its not necessary to validate every new bottle shape“ says Günter Feusthuber who is responsible for engineering and production at all the firm´s plants using the new line, together with managing partner Hermann Pfanner. The company currently fills more than half of its production output in soft packages. About a quarter goes into cans, which are predominantly contract-filled. Around a fifth of sales leave the plants in PET bottles, while glass containers account for just 4-5% of the total. “PET is increasingly driving soft packages off the market even though, in the fruit-juice market in particular, the soft package definitely has its legitimate place”, Günter Feusthuber comments. “But PET is nibbling away at the soft-packed product’ market share.” In his eyes, there will probably be no end to further design enhancements in the field of aseptics. “We could well imagine a faster change-over from the 28-mm to the 38-mm neck finish in the future, for example, but as things stand now, the Contipure constitutes a very sophisticated state-of-the-art machine for filling still and carbonated beverages, one that is highly future-compatible, into the bargain.” According to Canadean, the market research institute, the Austrian Pfanner brand is the Number two among Europe’s ice-tea brands. PET-bottled ice tea must be filled aseptically, if it is to be sold without preservatives. But ice tea is just one drink out of the many that contribute to Pfanner’s continuing success. The family firm, which is in the safe hands of the clan’s fifth generation, is one of Europe’s biggest fruit processors: apples, pears and red fruit form the foundation for fruit juices, fruit squashes, fruit-juice-based drinks, and ice teas. Total production output amounted to around 450 million litres in 2013. Traditionally, consumers know that Pfanner products come in 1l and 2l beverage cartons. For quite some time, the gable-top carton had been something of a hallmark for Pfanner’s portfolio. But that was changed, step by step, after the installation of the Krones UltraClean PET bottling line in 2003. Its first PET line was rated at Pfanner’s Enns plant now has a Krones Contipure system with preform sterilisation installed.","@ID":24}, "PETbottles 54 PETplanet insider Vol. 15 No. 09/14 petpla.net Home + Personal Care Fa. Vitamin & Power Schwarzkopf & Henkel is packaging 250ml of its new, invigorating shower gel “Fa vitamin & power“ incorporating vitamin C and pink grapefruit in a slim, transparent PET bottle. The snap-on hinged lid closure reflects the colour of the product and an adhesive sticker draws attention to the innovative factor. A transparent film label to the front and a printed label on the back convey user information. www.fa.com Facial cleanser in PET The Spanish supermarket chain Mercadona markets a very wide range of skin care products under its own brand “deliplus”. For example, a cleansing lotion for sensitive skin in a slim, blue-tinged bottled made from PET with a content of 200ml. The product is discharged via a screw-on, 2-colour closure. Pressing down on one side activates a pivot point which lifts the other side, thus opening up a dispenser channel. Pressing down right to the point of engagement re-closes the bottle which is decorated with no-label look labels. www.consejosmercadona.es/deliplus/ Rinse aid from Claro 500ml of bio-degradable rinse aid for pouring into the rinse aid compartment is being marketed by Claro Products GmbH of Mondsee in Austria in a transparent bottle made from PET. The rinse aid eliminates any water and limestone marks and assists with the drying process for the dishes. A snap-on hinged lid complete with integrated silicone valve assists with pouring into the machine. Two self-adhesive labels explain all about the product and its application. www.claro.at Rinsing balsam with sea buckthorn Frosch, who have been active pioneers in matters related to environmentallyfriendly cleaning materials since 1986, are consistently resorting to nature and discovering new cleansing and nurturing product additives. The latest example is their rinsing balsam with extract of sea buckthorn. Frosch are packaging 500ml in a transparent PET bottle with a recycled proportion in excess of 80%. There is a screw-on push-pull closure for simple dispensing of the contents. Two shaped labels round off the appearance at the PoS. www.frosch.de","@ID":56}, "TRADE SHOW PREVIEW 42 PETplanet insider Vol. 15 No. 09/14 petpla.net International PackTech India and drink technology India The trade show double feature To meet the requirements of the market, drink technology India and International PackTech India will be undertaking a joint presentation of the complete value chain for food processing, liquid food, beverage and packaging technology under one roof from September 25 to 27 in Mumbai. Messe München International for drink technology India and Messe Düsseldorf for International PackTech India expect about 260 exhibitors from all over the world and around 8,500 trade visitors from India and neighbouring regions. Currently India’s drink consumption amounts to 22 billion litres. The lion’s share goes to soft drinks (bottled water is the best seller) which recorded an increase of 23% between 2010 and 2013. Juices are also popular, with growth of 20% a year. Experts in the beverages sector are anticipating a rise to 38 billion litres in 2017. This year both exhibitions will be extending their portfolio by also covering the food sector. Currently the value of the packaged food industry is US$39.7bn and this is forecast to increase to US$65.41bn by 2020. With a sales volume of 30 million tonnes in 2013, India is one of the largest markets for packaged food in the world, figure which is poised to increase to 37 million tonnes by 2017. Just under 70% of the population of India live in rural areas, a gigantic market that an increasing number of beverages and food manufacturers are looking to develop. An overview of India´s beverage and food industry including statistics of machinery imports and exports is available at: www.drinktechnology-india.com Time Company Speaker Topic September 25, 2014 01:00 pm - 01:30 pm Block 1 - Preform & closure manufacturing – technologies and innovations 01:00 pm - 01:30 pm Sacmi Engineering (India) Pvt. Ltd. Mr Sachin S. Gije (Manager Sales & Marketing – Closures & Containers) & Mr Satish Kanaghinhal (Area Sales Manager-Beverage) Sacmi – Complete solution to beverage industry: focused on closures, preforms, containers 01:30 pm - 02:30 pm Block 2 - The latest technologies and trends in the Indian drinks and beer industry, Part 1 01:30 pm - 02:00 pm KHS Corpoplast GmbH Mr Amos Lopez (Area Product Manager) New technologies in stretch blow moulding 02:00 pm - 02:30 pm Intralox LLC Mr Scott Shannon (Packaging Industry Team Leader) Change in package type - Challenges - Conveyance optimization 02:30 am - 04:00 pm Block 2 - The latest technologies and trends in the Indian drinks and beer industry, Part 2 02:30 pm - 03:00 pm FlavorActiV Ltd. Mrs Evelyne Canterranne (Global Sensory Manager) The value of sensory in global beverages 03:00 pm - 03:30 pm Pentair Haffmans B.V. Dr. Roland Folz (Director Technology & Innovation Food & Beverage) Holistic R&D approach of a global company, shaping the brewing & beverage future 03:30 pm - 04:00 pm Institute Of Brewing & Destilling Mr Simon Jackson (Executive Director) The importance of technical education September 26, 2014 11:00 am - 12:00 am Block 3 - Aseptic filling 11:00 am - 11:30 am KHS Corpoplast GmbH Mr Amoz Lopez (Area Product Manager) Preform sterilization: Reliable protection for the sterile manufacture and filling of your PET bottles 11:30 am - 12:00 am Sidel India Pvt. Ltd. Mr Max Duclot (Business Development Director Sensitive Products) Aseptic 12:00 am - 01:00 pm Lunch Break 01:00 pm - 01:30 pm Block 4 - Milk and milk products 01:00 pm - 01:30 pm Krones AG Mr Paul Schönheit (Project Engineer Aseptic Technology, Filling Technology) Krones solutions for milk filling and processing 01:30 am - 01:45 pm Short Break 01:45 pm - 03:15 pm Round Table Talks - dti panel discussion Bisleri International Pvt Ltd., Mr K, Ganesh (General Manager, Technical North), discussing market growth in water segments and competition Coca-Cola India Pvt. Ltd., Mr Chandra Mohan Gupta (Supply Chain Director), discussing market growth in the individual beverages and food segments FlavorActiV Ltd. UK, Dr. Binod K. Maitin (Spirit Beverages Consultant, former Head of Technical Centre, United Spirits Ltd., UB Group), discussing sensory approaches to consumer-centric innovation in alcoholic beverage industries Marico Ltd., Mr Prabodh Halde (Head Regulatory, Marico R&D), discussing regulatory aspects ActiveSolutions, Mr Subba Bangera (President), discussing foreseen Indian specific demand for food & beverage packaging Data are subject to change. Final version expected for 15.09.2014","@ID":44}, "NEWS 8 PETplanet insider Vol. 15 No. 09/14 petpla.net CCL Industries signs binding agreement to acquire Bandfix AG in Switzerland CCL Industries Inc., a global manufacturer of label and packaging products, announced that it has signed a binding agreement to acquire Bandfix AG, located near Zurich, Switzerland. Bandfix is a privately owned label company increasingly focused on European specialty customers with estimated sales for the calendar year of 2014 of USD47 million and anticipated adjusted EBITDA of approximately USD3,5 million. The agreed debt and cash free enterprise value is USD18,0 million subject to customary closing adjustments. CCL also announced that the operation will change its trading name post close to CCL Label, Switzerland. CCL Industries employs approximately 10,100 people and operates 97 production facilities in 27 countries on five continents with corporate offices in Toronto, Canada, and Framingham, Massachusetts. CCL Label is the world’s largest converter of pressure sensitive and extruded film materials. www.cclind.com Plastic Technologies, Toyo Seikan enter into PET bottle technology agreement for the U.S. market Plastic Technologies, Inc. (PTI), a global player PET package development, announced that it has entered into a representation agreement with Toyo Seikan Co., Ltd., Tokyo. PTI will be the exclusive U.S. agent responsible for the sales and licensing of several new Toyo Seikan PET bottle processing technologies for packaging applications. One of the areas that the two companies will be working together on is new foamed PET bottle technology which produces lightweight containers with good barrier attributes and special visual/tactile attributes. The companies are expected to unveil more details about the new technology, and its potential impact on beverage packaging in the United States, in the coming months. “PTI has been a developer and integrator of new packaging technologies for many well-known brands in the United States. Due to our compatible areas of interest and ongoing working relationship, it was logical to take the relationship to a more formal level. PTI’s extensive PET expertise and long-standing client relationships will be a big asset in helping us commercialize our proven technologies in the U.S. marketplace,” said Toshio Sue, deputy head of technical headquarters, Toyo Seikan. www.toyo-seikan.co.jp/e/ www.plastictechnologies.com Husky World Tour makes stop in Mexico and holds specialty closures conference In June 2014, Husky Injection Molding Systems hosted the first event of its Husky World Tour for 2014, a specialty closures conference at its technical center in Cuajimalpa, Mexico. This event featured in-depth presentations and discussions with nearly forty attendees, made up of both current and prospective customers. The one-day event included networking opportunities and presentations from industry experts, including Greg Lathrop from Unilever, Anthi Balafoutis from MMC Packaging, and Javier Ortiz from IHS Chemical, discussing current trends in the design and manufacture of specialty closures. Highlights from the event included technical presentations from Husky subject matter experts, covering topics such as specialty closure mould technologies for complex applications and using process and productivity monitoring to improve plant efficiencies. The Husky World Tour 2014 is a series of global customer events taking place throughout the year, in various locations across the globe. With multiple events spanning multiple locations, the tour gives companies more direct access to Husky’s latest technologies at a local level. Other Husky World Tour events are scheduled for 2014, including a specialty closures conference in Bangkok in November and a beverage packaging conference in Casablanca in November. www.husky.ca The plastic closure company committed to your success BERICAP Technology Research and Development Mould Technology | Global Presence Capping Technology and Know-How Innovation and Flexibility www.bericap.com","@ID":10}, "TRADE SHOW PREVIEW 44 PETplanet insider Vol. 15 No. 09/14 petpla.net One trade platform The ”who’s who” of two industries Contact drink technology India MMI India Pvt. Ltd. [email protected] | www.drinktechnology-india.com Phone+91 22 42554710 | Fax++91 22 42554719 Contact International PackTech India Messe Düsseldorf India Pvt. Ltd. [email protected] | www.messe-duesseldorf.de Phone+91 11 26901600 | Fax+91 11 26971746 NEW in 2014: Features Food Processing www.drinktechnology-india.com drink technology India 2014 International trade fair for the beverage and food industry 8th International Exhibition and Conference for Processing, Packaging and Printing www.packtech-india.com September 25–27, 2014 Bombay Convention and Exhibition Centre Mumbai/India Presented by Forum organizer Supported by Supported by Supported by and conference organizers Partner German Engineering Federation Subba Bangera 1973 Senior Research Chemist with Polychem Ltd. Garware Plastics& Polyesters Ltd, Technical Marketing Executive polyester film division ABS Plastics Limited Head of Product Development Managing Director of Sidel India Pvt Ltd from 1998 to 2006 After his retirement, Mr Bangera acted as business advisor to several key plastic processing industries and beverage industries. He is also advisor to a number global company in various business sectors. In 2014, India showed to the world what democracy really means. By electing a new Government with a clear majority, the 1.2 billion population of India showed the politicians that voters in India are not sleeping. Enough has already been written about India’s young population, aspirational India, urban growth and rural purchasing power etc. and I have no intention of repeating all that. But, let me say, in the context of drink technology India that India’s demographics require a very different approach from that which is adopted in Europe or China. The Taste of India varies from region to region for food products and beverages. While pizza, Coke, Pepsi are accepted throughout the country, it is not the same when it comes to juices, flavoured milk and food products. What is popular in the north of India may not be so successful in the south. The growing vegetarian population is demanding more variety in the products, and this cannot be achieved by simply copying what is done in Europe. After having been associated in this industry for 15 years as Managing Director of Sidel India, I retired in June last year. Over the past year, I have met many local brand owners, and I have seen their plans for the future. The rate at which they are growing clearly shows that a Chinese type revolution in food and beverage Industry will also happen in India. This brings into to focus the increasing number of Indian brands in the beverage and food industry. Roadside food and drink stalls still offer good freshly squeezed juices with a variety of spicy additives, but hitherto very few","@ID":46}, "CAPPING / CLOSURES 27 PETplanet insider Vol. 15 company has established partnerships with a number of packaging plant suppliers who are interested in integrating Claranor technology into their offers, in place of hydrogen peroxide or continuous UV treatment units. Around 80 sensitive beverage filling lines worldwide are now equipped with Claranor cap sterilisation units. Sensitive beverages, such as fruit based drinks with low preservative content, low carbonated soft drinks, flavoured waters, drinkable yoghurts and other drinks filled in ultra-clean conditions are very much aware of the need for packaging decontamination. Enterprises in these markets that have chosen pulsed light solutions include Hansa Heemann in Germany, which recently installed its fourth pulsed light cap sterilisation unit on a KHS new line, and Vilsa Brunnen, which has three lines equipped with the Claranor solution. The technology The use of flash UV lights for microbiological decontamination was first developed in Japan in the 70’s and has since been widely tested in laboratory situations. Ultraviolet rays contained in intense flashes of white light emitted by Xenon lamps have been demonstrated to be effective as decontaminants against a wide range of microorganisms: bacteria, moulds, viruses, etc. The UV part (200 – 400nm) of the radiation included in the flash, brings about the destruction of microorganisms present on the product under treatment by a combination of a photothermic effect and a photochemical reaction. The absorption of UV rays by DNA provokes its modification, leading to the death of the microorganism. The decontamination level obtained depends on the number and power of the flashes applied and the nature of the surface being treated; it ranges from simple logarithmic reduction to complete sterilisation. PROVEN COST SAVINGS PERFORMANCE moldmasters.com Mold-Mastersand theMold-Masters logoare trademarksofMold-Masters (2007) Limited. ©2014Mold-Masters (2007) Limited -AMilacronCompany.All rights reserved. Rely on our global support network for fast service and parts. North America 1-800-387-2483 | Europe 49 (0) 7221 5099-0 Asia 86 512 86162882 ALWAYS INNOVATING. + More efficient use of platen real estate increases the cavitation for a given machine size: s 72 vs. 48 Cavity with a 28mm finish in a 225T s 72 vs. 48 Cavity with a 38mm finish in a 300T s 96 vs. 72 Cavity with a 28mm finish in a 300T s 128vs. 96 Cavity with a 28mm finish in a 400T + Proprietary iFLOW and iCOOL technology reduces cycle times while improving balance, lowering injection pressure and increasing dimensional repeatability + Tooling solutions to revitalize, recapitalize and rev up existing systems Get 50% more output from the same machine 96-CAVITY MICRO PITCH MOLD FOR 300T MACHINES Contact us today at: [email protected] Pulsed light is purely a surface treatment; only those areas directly illuminated by the lamps’ rays or the reflectors are decontaminated; shade phenomena impair the treatment’s efficacy, which is the main limit to the technology. The treatment equipment is composed of two main parts: An electronics bay, which generates high power impulses from mains energy, through a capacitor. A control panel is used for observation and control of the process; An optical cavity located in the optical cabinet, fitted with one or several lamps and aluminium reflectors, specifically designed to homogenize and focus the light ray on the surface under treatment. An additional cooling system enables the regulation of the temperature of the lamp’s water. www.claranor.com","@ID":29}, "TRADE SHOW PREVIEW 45 PETplanet insider Vol. 15 No. 09/14 petpla.net attempts have been made to bottle this taste for the panIndian market. Now we see this happening. Local flavours, local colas, local pizzas with different add-ons are on the rise. The style of packaging may be copied from multinational brands, but the product has a distinctively Indian flavour. It is predicted that India will consume 20million metric tonnes of plastics by 2020, up from the present level of 8 million. The bulk of that growth in plastic consumption is predicted to come from the food and beverage industry. Demographically the growth will shift to the rural areas. The potential growth will be in the 7000 or so small cities contributing over 40% of growth in consumption. Where does the growth come from? Every day, Indians buy 10 million cinema tickets, 100,000 air tickets, around 3000 cars, and more than 5 million condoms. Add to these figures the large number of rail and bus travellers and look at the consumption pattern. Each one of them is almost certainly carrying a packet of food and is definitely carrying bottled water or other beverages. The growth in food and beverages is linked both to demographic change and infrastructure development which allow the faster movement and migration of people. The present Government is aware that the man or woman in the street is watching closely the promises made and promises fulfilled. To survive from five years to ten years, the minimum comfort level of ordinary people has to be improved. That is when growth will soar dramatically. In summary, having a stable government, an ability to market in smaller cities and rural markets, the capability to develop acceptable taste, an improved infrastructure and more importantly the availability of disposable income of the ordinary citizen will all combine to grow the packaged food and beverage industry in India. India is most definitely the country to watch in next 20 years.","@ID":47}, "BOTTLE MAKING 18 PETplanet insider Vol. 15 No. 09/14 petpla.net BOTTLE MAKING 18 Based on Bulgarian and Northern Irish technology New PET bottle design for beer The emerging company Vitalii and Son was given the complex task of exploring the opportunity to develop new PET bottle designs for the beer market. The Bulgarian company Carlsberg wished to change the size (diameter) of their bottles but to keep the volume of 2l and 3l. Reducing the bottle diameter meant that more bottles could be placed on each level on a standardized pallet thus increasing the efficiency of each pallet. From a technical point of view, it was important to investigate how the bottle behaves in the production process – more specifically if the bottle would resist carbonation at 5.6 CO 2 /l. The second task was to examine whether the bottle would be able to handle both the logistic and the filling/capping issues upstream; this involved analysing the pressure and top load deformation. Vitalii and Son developed three new designs of 2l and 2,3l bottles for Pirinsko and Shumensko Carlsberg Bulgaria. Those designs differed from each other in diameter, label area size and bottom petaloid configuration. The complexity of the task was intertwined with the aesthetic appearance of the bottle i.e if the engineers reduced the diameter the bottles would become taller and asymmetric. However, for marketing reasons, the lines and surfaces of the bottles had to be kept distinctive. Dr. Gary Menary, of Queen’s University in Belfast, simulated the required tests such as pressure and top load, material thickness and weighting. Following these detailed tests and investigations, involving applied numerical technologies for packaging innovation and performance, the conclusions about the 2l Pirinsko and Shumensko bottles, and the Pirnsko 2.3l bottle can be summarised as follows: Sports Closure Hot Fill SimpliSqueeze® valve SensitiveBeverage Dosing Aseptic Pouches Flip-Top Meet us at Hall 4 Stand 4-336 BrauBeviale 2014 Nov. 11-13, Nürnberg sensitive BEVERAGES","@ID":20}, "imprint EDITORIAL PUBLISHER Alexander Büchler, Managing Director HEAD OFFICE heidelberg business media GmbH Häusserstr. 36 69115 Heidelberg, Germany phone: +49 6221-65108-0 fax: +49 6221-65108-28 [email protected] EDITORIAL Heike Fischer Gabriele Kosmehl Kay Barton Michael Maruschke Ruari McCallion Waldemar Schmitke Ilona Trotter Wolfgang von Schroeter Anthony Withers MEDIA CONSULTANTS Martina Hirschmann [email protected] Roland Loch [email protected] phone: +49 6221-65108-0 fax: +49 6221-65108-28 France, Italy, Spain, UK Elisabeth Maria Köpke phone: +49 6201-878925 fax: +49 6201-878926 [email protected] LAYOUT AND PREPRESS Exprim Kommunikationsdesign Matthias Gaumann | www.exprim.de READER SERVICES Till Kretner [email protected] PRINT Chroma Druck & Verlag GmbH Werkstr. 25 67354 Römerberg Germany WWW www.hbmedia.net | petpla.net PETplanet insider ISSN 1438-9459 is published 10 times a year. This publication is sent to qualified subscribers (1-year subscription 149 EUR, 2-year subscription 289 EUR, Young professionals’ subscription 99 EUR. Magazines will be dispatched to you by airmail). Not to be reproduced in any form without permission from the publisher. Note: The fact that product names may not be identified as trademarks is not an indication that such names are not registered trademarks. 3 PETplanet insider Vol. 15 No. 09/14 petpla.net This spot in the magazine normally features my views of the PET world and their suppliers. This is time I would like to give our friends in the PET industry itself the opportunity to have their say on PETplanet Insider and the Editour Roadshows: dear readers, „Aseptic bottling is no longer simply a question of marketing promotions, we are actually installing a number of lines in newly industrialised and developing countries as well. Here the PETplanet Insider tours are helping us to demonstrate, from a neutral editorial viewpoint, how successfully the technology is being used there. For us, this is a vital component in our marketing mix.“ Silvia Armanetti, Marketing Manager GEA Procomac S.p.A. “We at Sipa are a unique enterprise supplying the entire PET world chain, from mould making to preforming, SBM and filler lines and culminating in the pallet stage. PETplanet Insider magazine has the unique ability to depict this chain in its entirety and thus succeeds in achieving comprehensive coverage of all participants in the market. The editorial team make their own particular contribution towards reinforcing this coverage through their worldwide Editourmobil trips that take them to the furthest corners of the globe where they visit our customers and report on our technologies”. Martina Bottarel, Communication Manager Sipa S.p.A. “The PETplanet tour provides Husky with a great opportunity to get closer to our customers, something we find extremely valuable. It allows us to build on our meaningful relationships by meeting people in our markets locally, all over the world.” Joanna Ford, Marketing Specialist, Husky Injection Molding Systems Ltd. „Reports from actual customers make much more of an impact amongst our own customers than other more traditional articles. For us at Erema, the PETplanet Roadshows represent an innovative B-to-B cross-marketing tool thanks to the mix of editorial presence in both print and online versions. The Roadshows help bring us closer to our customer base and customer support, and finally offer an exhibition presence on completion of the tour.“ Dr. Gerold Breuer, Head of Marketing & Business Development Erema Engineering Recycling Maschinen und Anlagen Ges.m.b.H „The PETplanet tour was a great experience; an important occasion to spread our name and launch in the market our new product. Networking with key customers and industry experts has allowed us to better tune our sales and marketing strategies for the coming years.” Manuela Teocchi, Market Analyst & Projects Development Leader Siad Macchine Impianti S.p.A. “We greatly value the work of hbmedia under the leadership of Alexander Büchler. Each month, his team offers a magazine with diverse articles and reports in and around the PET world. In our view, the quality of this magazine and the focus on our market is unique. The Editourmobile travels across the continents and the resulting Editour reports generate unique insights into the world of our customers. These live reports attract our closest attention. For these reasons, we are proud to support the Editours and hope that many more are planned.“ Stefan Zatti, Division Manager Sales & Marketing / Member of Management Otto Hofstetter AG Yours Alexander Büchler","@ID":5}, "ON SITE 51 PETplanet insider Vol. 15 No. 09/14 petpla.net Thai newcomer chooses Sidel for country’s first high-speed aspetic line Sidel has installed its first complete aseptic production line in Thailand. The installation was for a new company set up to serve the whole southeastern region of Asia. When Thai businessman, Pongsakorn Pongsak established the General Beverage Company Limited in his home country, he was entering the beverage industry for the first time. In doing so, he turned to Sidel for the first time too, for the supply of a turnkey aseptic PET packaging line. Founder and owner, Kitti Pongsakdi (Pongsakorn’s father), originally established the textile company Suwan Spinning and Weaving which is today one of the top producer of yarn and fabric in Thailand. Following a visit to the Sidel’s exhibition stand at Anuga in Germany in 2012, senior managers from General Beverage were introduced to Sidel technology and witnessed aseptic filling for the first time ever. They became keen on Sidel’s aseptic filler and the company’s overall technology capabilities. Several project discussions and meetings were conducted with Sidel. General Beverage wanted a supplier able to supply a turnkey installation to produce a broad range of beverages like coffee, tea, milk and fruit juices. The Thai producer decided in favour of Sidel. As a result, Sidel designed, manufactured, supplied, installed and commissioned the entire bottling line. The plant, located in the Sam Phran district of Nakhon Pathom, is being built at a cost of nearly EUR 120 million (USD 160 million) in three distinct stages. The first stage, already completed, features the country’s fastest production line for PET aseptically filled bottles and includes a Sidel SBO20 Universal2eco blow moulder equipped with the Ecoven. The production line has a capacity of 40,000 bottles per hour and is the most-advanced, eco-friendly manufacturing system in the region, according to Sidel. For the first time ever, the aseptic filler is able to handle “particulates” of up to 5 x 5 x 5mm in size. The filler is connected to an Aidlin Eco cap feeder. The line can handle high volumes of high quality beverages of low or high acidity, including the most sensitive products. The line is currently set up to produce a nutritional drink with high dietary fibre (white grape juice with pieces of aloe vera), yoghurt and milk in a 280ml format, with green tea and juice in the larger 350ml format. Being new to the beverage industry, the company’s decision to bottle such sensitive products was a bold move as it requires special knowledge to set up and maintain the most stringent standards of food safety. The factory’s second stage follows in mid-2014, while the third and final stage is scheduled to be finished over the following five years. General Beverage is offering its services for aseptic PET filling as a co-packer to major players in both domestic and nearby international markets. The company performed roadshows across the country and other South East Asian countries to announce its presence as the supplier of various packaged products including coffee, tea, milk and fruit juices covering over 20 local and overseas brands. Within the South East Asia Pacific (SEAP) region, the juice drinks, teas and sports drinks sector is forecast to grow by 4% per annum over the next four years, with the market share of PET bottles in this sector to grow by 6% as consumers increasingly recognize the material as more convenient and lighter than glass, and more hygienic than HDPE. www.sidel.com Prepare for Life. From preform to bottle. We ensure a perfect process. www.prewatcher.com","@ID":53}, "MARKET SURVEY 31 PETplanet insider Vol. 15 No. 09/14 petpla.net Caps and closures Bottle-to-bottle recycling plants Preforms Preform and single stage machinery Preform / stretch blow moulds Two-stage SBM machinery Compressors Resins / additives Filling equipment Closure systems Compressors Compressors-not often in the spotlight perhaps, yet a vitally important component of the PET bottle production, and with significant potential in energy-saving. Our annual Market Survey takes a closer look at these unsung heroes of the PET industry, featuring six compressor manufacturers and their product range (in alphabetical order): Atlas Copco Crépelle, Boge Kompressoren, Gardner Denver Ltd, Ingersoll Rand Company, Kaeser Kompressoren SE, Siad Macchine Impianti. In the table the suppliers are listed in the order in which their details were received by the editors. Although the publishers have made every effort to ensure that the information in this survey is up to date, no claims are made regarding completeness or accuracy. 09/2014 MARKETsurvey Company name Atlas Copco Crépelle Kaeser Kompressoren SE Postal address Telephone number Web site address Contact name Function Direct telephone number Fax E-Mail 2 place Guy de Dampierre, PB 29 59008 Lille Cedex, France +33 3 59 01 05 02 www.atlascopco.com Ms Sabine Wagnon Communications +33 3 59 01 05 02 +33 3 20 53 76 51 [email protected] Carl-Kaeser-Str. 26, 96450 Coburg, Germany +49 9561 640 0 www.kaeser.com Mr Wolfgang Hartmann Marketing Manager +49 9561 640 252 +49 9561 640 890 [email protected] 1. Machine designation / model number ZD ZD VSD P-compressors DX/DN 2 stage booster DX/DN 1 stage booster Sigma PETAir 2. Number of models in range 23 6 6 1 16 6 15 5 25 3. Output in m³/hour 792 - 4108 FAD 702 - 1177 FAD 529-1152 FAD up to 15843957 FAD 626 to 1119 FAD 163 to 786 FAD 890 to 1372 FAD 792-4108 FAD 5300 (9,5 to 30b) 336 - 2772 4. Compressor type Low pressure air screw screw variable speed drive screw variable speed drive screw screw screw High pressure blowing air (up to 40 bar) piston piston variable speed drive piston variable speed drive piston piston piston Integrated system piston piston piston 5. Lubricated or oil-free Low pressure compressor oil-free oil-free oil-free oil-free oil-free lubricated Booster compressor oil-free oil-free oil-free oil-free oil-free oil-free oil-free lubricated Integrated system oil-free 6. Machine layout horizontal horizontal horizontal horizontal horizontal horizontal horizontal horizontal V (2 cylinder), W (3 cylinder) 7. Number of compressor stages 2 and 2 2 and 2 2 and 2 2 and 2 3 3+1 1+2 1+2 1+1 8. Are special foundations required ? no no no no no no no no no 9. Cooling system water air water air water water water water air (water option) 10. Belt or direct drive Low pressure compressor direct drive direct drive direct drive direct drive direct drive direct Booster compressor belt drive belt drive belt drive belt drive belt drive belt drive belt drive belt Integrated system belt drive","@ID":33}, "PREFORM PRODUCTION 40 PETplanet insider Vol. 15 No. 09/14 petpla.net Please order your copy at the PETplanet insider book shop: https://petpla.net/books Bottles, Preforms and Closures A Design Guide for PET Packaging Second Edition by Ottmar Brandau € 115,00 180 pages © Copyright Elsevier 2012 Hot runner controls In order to keep temperatures in the hot runner and the injection nozzles stable, companies go to great lengths designing control algorithms that not only react to temperature variations but also are able to predict them and compensate for them before any fluctuations may occur. To do this, temperature is measured up to 20 times per second and controllers change heating current by very small amounts when variations of as little as 0.1°C are detected. Control loops measure the rate of change and adjust the necessary current changes continuously. Melt temperatures may change when operators change dryer settings or screw speeds, for example, and hot runners must be able to cope with these in order to deliver stable injection profiles (Fig. 2.27). Figure 2.27 Sophisticated control algorithms and an easy-to-use interface are characteristics of modern hot runner controllers. (Picture courtesy of MoldMasters) Gate mechanism There are two ways to separate the hot melt coming through the hot runner from the cooled preform: thermal and mechanical. Thermally gated hot runners are most prevalent in the one-stage process, whereas the mechanical ones are most prevalent in two-stage injection moulding. In a thermally gated hot runner the break point between the hot and the cold melts is controlled by temperature alone. As seen in Fig. 2.28, the temperature difference between the cold cavity and the hot melt is substantial at around 255 °C (491 °F). A suitable insulation made from stainless steel or any other material with insulating properties separates the two sections. When the machine ejects the preforms, the melt breaks at the point where the cold gate vestige connects with the hotter material inside the nozzle. This material is already partly cooled down and so has a higher viscosity than melt. This prevents it from seeping into the cavity or leads to “stringing,” a common defect where small strands of PET from the melt stream are pulled out with the preform during ejection. An air gap may also assist in the separation process. (Fig.2.28) Figure 2.28 The temperature difference between the cold cavity and the hot melt is used to break the preform free off the melt. (Diagram courtesy of Synventive Molding Solutions) Valve-gated hot runners (see also Chapter 3.2.7) use a mechanical seal between the hot and cold areas by means of a pin called the valve stem. Usually around 3mm (1/8 in) to 5mm (0.2 in) in diameter, this pin moves back allowing melt flow into the cavity, stays back during hold time, then moves forward controlled by a timer that energizes with the end of hold time. Gate vestiges made with valve-gated hot runners are on average shorter than those with thermally gated ones, and the cutoff is more precise. Properly operated they also tend to give less problems with stringing and gate crystallinity. Disadvantage of valve gates is the higher maintenance requirement for the pins and air cylinders driving them (Fig. 2.29). Figure 2.29 Typical difference in length of gate vestige between preforms of thermally gated (left) and valve-gated (right) hot runners. * This article was published in Bottles, Preforms and Closures, Ottmar Brandau, Chapter 2.5. Copyright Elsevier 2012","@ID":42}, "MARKET SURVEY 32 PETplanet insider Vol. 15 No. 09/14 petpla.net 09/2014 MARKETsurvey Company name Ingersoll Rand Company Postal address Telephone number Web site address Contact name Function Direct telephone number Fax E-Mail 800 D Beaty Street, Davidson, North Carolina, USA +1 704 655 4000 www.ingersollrandproducts.com Mr George Mankos Product Management +1 704 655 4311 +1 704 655 4039 [email protected] 1. Machine designation / model number Centac C750-18, C750-20, C750-21, C1050-36 2. Number of models in range 7 (3 standard models, 2 models optimized for 28barg pressure, 2 models for 20barg pressure) 3. Output in m³/hour C750-18 [3,085 m3/hr], C750-19 [3,220 m3/hr], C750-20[3,398 m3/hr], C750-21[3,568 m3/hr], C1050 – 36[6,360 m3/hr] 4. Compressor type Centrifugal design / 4-stages from atmosphere to 40 bar Low pressure air High pressure blowing air (up to 40 bar) Integrated system 5. Lubricated or oil-free oil-free Low pressure compressor Booster compressor Integrated system 6. Machine layout horizontal 7. Number of compressor stages 4-stage from atmosphere design 8. Are special foundations required? no 9. Cooling system water 10. Belt or direct drive Low pressure compressor Booster compressor Integrated system direct drive Company name Gardner Denver Ltd Postal address Telephone number Web site address Contact name Function Direct telephone number Fax E-Mail Claybrook Drive, Redditch, B98 0DS Great Britian + 44 1527 838 600 www.gdhighpressure.com Mr Trevor Perry Director, High Pressure Sales +44 1527 838 601 +44 1527 838 630 [email protected] 1. Machine designation / model number VH7 VH9 VH12 VH15 VH18 VH21 VH25 WH28 WH29 WH35 WH40 WH45 WH50 2. Number of models in range 13 3. Output in m³/hour 420 580 729 916 1116 1402 1500 1680 1800 2100 2300 2700 3200 4. Compressor type High pressure blowing air (up to 45 bar) Low pressure air High pressure blowing air (up to 40 bar) Integrated system 5. Lubricated or oil-free oil free Low pressure compressor Booster compressor Integrated system 6. Machine layout Reciprocating V Reciprocating W 7. Number of compressor stages 3 8. Are special foundations required ? no 9. Cooling system water 10. Belt or direct drive direct drive Low pressure compressor Booster compressor Integrated system","@ID":34}, "ON SITE 50 PETplanet insider Vol. 15 No. 09/14 petpla.net Five caps production lines of Sacmi installed in Vitaqua GmbH, Breuna At their major facility in Breuna, Kassel region, Viatqua GmbH has installed five of Sacmi’s Continuous Compression Moulding (CCM) lines, manufacturing caps with a diameter of 28mm (standard 1881) and a weight of about 2g, with per-line output rates of approximately 1,500pcs/min. More significantly, as Mr. Reinhold Juelg, R&D Manager at Vitaqua, points out, “the advantages associated with this technology, compared to injection, allow us to work at lower extrusion temperatures with significant energy savings”. For Vitaqua, that advantage is enhanced by the fact that water cooling flow rate temperature is in the range of 20-25°C, meaning, according to Juelg, that “the water in the circuit only needs cooling in the summer months. Sacmi technology, used in conjunction with the correct masterbatch, minimises waste and gives the line overall efficiency: on the basis of random testing effected on a 10-hour production run, 900,000 caps were produced and only 35 faulty ones rejected. Average cap weight is consistent. In the bottling line, since the caps production equipment has gone online, the percentage of bottles with caps incorrectly applied due to dimensional variations has dropped from up to 0.5% to below 0.02%”. “That was one of the decisive criteria”, says Mr. Juelg. Since the installation of the caps production lines, the number of complaints received from the three German plants belonging to the Beverage Group since start-up in March 2013 until today has been reduced to zero. www.sacmi.it PETnology/tecPET GmbH | Regensburg, Germany Phone: +49 941 870 23 74 | Fax: +49 941 870 23 73 [email protected] PET Passion Week2014 NUREMBERG, GERMANY ˎ 129(0%(5 &21)(5(1&( 129(0%(5 www.petnology.com Supported by: Lead Sponsor: 3(7 $7 %5$8%(9,$/( 129(0%(5 www.pet-arena.com ONsite","@ID":52}, "CAPPING / CLOSURES 25 PETplanet insider Vol. 15 No. 09/14 petpla.net Reuseable caps for PET bottles Thinking caps on Clever Pack’s new bottle cap is reusable and designed to be easy to use even by those who find bottles hard to open, such as those afflicted with arthritis. Clever Caps, which were created by two Brazilian inventors and are being marketed by a company named Clever Packs, are designed to be ‘compatible with building blocks available on the market’ – Lego-style blocks, in short. They are also compatible with commercial bottle necks including the PCO 1881 standard - but many other sizes and shapes are in the development pipeline. The novel caps are clearly bigger than conventional caps, which may seem strange when the trend is towards lightweighting. “Recycling is good. Reusing is even better,” said Cláudio Patrick Vollers, inventor and Clever Pack CEO. He maintains that Clever Caps incorporate the “three Ecodesign sustainability pillars” (ecologically sound, socially just and economically viable) but they go further, by incorporating the concept of immediate reuse. “There is no need to recycle Clever Caps. They can have an immediate ‘second life’, without additional energy consumption, nor the emission of polluting gases and residues.” The first and clearest reuse is by linking them with building blocks, which greatly extends their range of subsequent uses and also reduces the risk that they would become a passing trend or a piece of junk that people will keep for a while and then throw away. They can be turned into works of art, SmartPhone stands, light shades or even children’s toys. However, if they did not have immediate benefits then they could be viewed as a bit gimmicky. The inventors say that Clever Caps are more “friendly” to the elderly, children and physically disadvantaged. The larger diameter and the rings, or “ears” at the base offer a slightly greater leverage for rotating the tops to open or close bottles. They can also be connected to a second Clever Cap, which doubles the radius in relation to the rotation axis and dramatically reduces the force needed to rotate the bottle top. This makes them easier and more accessible to the elderly, those suffering from arthritis or similar impairment, or to children. The producers claim that Clever Caps are also safer than standard closures, which are 31mm diameter; Clever Caps are 31.8mm and the four ”ears’ take their operational width to over 40mm. This enables them to pass the standard “Choke Test”, which uses a cylinder 31.7mm diameter. In their first version, the caps are made of PP, but according to the developers, PE is also possible. Clever Caps were nominated by the London Design Museum as one of the 76 “Designs Of The Year”, were recognised with two IF Packaging Design Awards in Germany, and two Embanews Awards in Brazil. Clever Pack intends to expand through licensing its portfolio of patents and industrial designs to national and foreign companies. Clever Caps were launched in the bottled water sector. www.cleverpack.com.br In their first version, the caps are made of PP but an implementation in PE is also possible The reusable bottle caps are compatible with commercial bottle necks including the PCO 1881 standard. The Clever Packs are designed to be compatible with most popular building blocks available on the market.","@ID":27}, "EDITOUR REPORT 15 PETplanet insider Vol. 15 No. 09/14 petpla.net Welcome to visit TECH-LONG CHINA BREW CHINA BEVERAGE 2014 No. 23 Yunpu 1 Road, Luogang District, Guangzhou, 510530, China Tel: +86 20 62956800 Fax: +86 20 82266913 www.tech-long.com E-mail: [email protected] TECH-LONG PACKAGING MACHINERY CO., LTD. BEVERAGES HOUSEHOLDS CONDIMENTS DAIRY BEER Booth: E2C67 Date: 2014 10.13-16 Add: New China International Exhibition Center, Beijing,China Own brands for export by Waldemar Schmitke In Italy’s stagnating water market, all the bottlers want to find and then a particular segment of the Tavina in Salo, situated on beautiful Lake Garda, has found its own particular niche in export. Almost 40% of the total 190 million litres of water it bottles are sold abroad. Interestingly, it is not their own local brand that they are exporting. The guys from Salo have developed specific brands for each market . For example, in Japan their water goes by the name of “Fontana“, in Germany ”Sankt Emilia“ or in Australia ”St. Victoria”. In Italy they have three brands: Fonte Tavina, Linda and Allegra. The proportion of returnable glass depends on the particular brand. In the premium restaurant segment for example, they have developed a non-returnable glass bottle marketed under the brand name “Tavina Elegantia“. Tavina envisage further potential for growth in the local market. A total of four bottling lines are in operation at Tavina, two glass, two PET. The PET lines bottle 150 million litres whilst the two glass lines produce a total of 40 million litres. One of the PET lines fills the 1.5l containers, the other line handles all the other sizes. The pivot point is the 0.5l bottle.Tavina goes in for very lightweight bottles; in the case of the 0.5l bottle, it is 11g for still and 13.5g for carbonated water. The 1.5l bottle weighs 25g for still and 27g for carbonated water.","@ID":17}, "BOTTLE MAKING 19 PETplanet insider Vol. 15 1) All three bottle designs met the technical requirements, and principally the resistance to carbonation (5.6g CO 2 /l which corresponds to ~2.5bars inside the bottle). 2) In relation to the Pirinsko and Shumensko 2l bottles - they behave in the same way against pressure load so Carlsberg preferred the design that mostly saves space on the pallet. 3) Opportunity to improve the technical performance through thickness profile optimisation. 4) Regarding the Pirinsko 2.3l bottle good performance at 51.5g and 50g. The lighter preform could be used in the production of beer bottles. After extensive work good results were achieved, testimony to experience and years of hard work. Thanks to this development Carlsberg is now able to put up to 14.28% more bottles on a pallet than previously. Vitalii and Son is delighted to have helped their clients and is keen to pursue future projects. www.vitaliiandson.eu","@ID":21}, "EDITOUR REPORT 10 PETplanet insider Vol. 15 No. 09/14 petpla.net Italy Part 1 by Waldemar Schmitke The Editourmobil Go to BrauBeviale 2014 Western Mediterranean tour reaches Italy. From Bergamo in the north the route takes us as far south as Sicily and then back again, the objective being to give our readers an understanding of the beverages packaging market in Italy. The majority of the Italian Republic, and the capital city of Rome, lies on the Apennine Peninsula, surrounded by the Mediterranean Sea and the Plain of the River Po, as well as within the southern section of the Alps. It covers a distance of approx. 1,200km from north to south. The national territory of Italy borders on France, Switzerland, Austria and Slovenia. The micro-states comprising the Vatican City and San Marino are completely surrounded by Italian national territory. In addition to the larger islands of Sicily and Sardinia there are a number of groups of islands situated off the coast. The climate is sub-tropical, sometimes with highly pronounced differences from one region to another. In the north the winters are cool and the summers long and hot with high atmospheric humidity; in central Italy it is considerably milder as a result of the influence of the Mediterranean and, in the south, there is a hot Mediterranean climate all the year round with temperatures that exceed the 40° mark in the summer. With 60 million inhabitants, Italy is the fourth largest country in Europe after Germany, France and the United Kingdom. The bulk of the population is concentrated in the larger towns and cities and their immediate surroundings. Only six cities have a population of more than 400,000. In order of size these are: Rome, the capital, with 2.72 million (3.6 million if greater Rome is included), followed by Milan, Naples, Turin, Palermo and Genoa. With Milan and Naples and surrounding areas each having a population of 3.6 to 4 million, this means that approx. 20% of the population of Italy live in the three cities of Rome, Naples and Milan alone. Economically speaking there is a pronounced divide between the prosperous north and the less developed south of the country. The principal commercial hub of the country centres within the Milan - Turin - Genoa triangle with its high population density. Economy (Foreign Office – Economics, March 2014 ) Following the collapse of its gross domestic product following the 2008-9 financial crisis, Italy experienced weak growth (+1.7%) in 2010 and 2011. This did not last and in 2012, the economy contracted (-2.4%), and by 2013 the country was once again in recession. The collapse affected domestic demand in particular. By contrast, exports fared better, and by 2011 were registering an 11.4% increase rising by a further 3.7% in the following year. In 2013 they appeared practically static overall (-0.1 %). Imports in 2013 declined by 5.5%. In 2012 inflation rose to 3.0% (or 3.3% harmonised Eurostat value), from Nuremberg Milan Rome Naples Palermo Tunis Algiers Rabat Casablanca Marrakech Seville Madrid Lisbon Bologna Monastir Agadir Tangier Valencia Cordoba Bilbao Oporto Andorra La Vella Venice Turin Florence Messina Barcelona Zaragoza","@ID":12}, "CAPPING / CLOSURES 20 PETplanet insider Vol. 15 No. 09/14 petpla.net CAPPING / CLOSURES 20 Vicap Systems connects packaging and delivery system in one cap Three steps to refresh… *based on an article by Roger Franz Wilfinger, CEO Vicap Systems AG Scan & Measure Oxygen Ingress & Transmission Rates www.PreSens.de/ Fibox4 Fibox 4 Stand-alone fiber optic oxygen transmitter The Vicap is a novel closure developed by Swiss food technology company Vicap Systems. While looking like a normal sports cap the Vicap also serves as packaging and delivery system for liquid and powder content, offering a solution for functional beverages. If mixed with water or getting exposed to sunlight, most potent active ingredients as marketed in functional beverages lose their efficacy within just a few days. By the time the functional beverage has finally reached the consumer, active ingredients are mostly lost and advertised functions become questionable at best. The Vicap’s packaging and release properties enable separation between vital ingredients such as vitamins, minerals, antioxidants and carrier elements like water, milk and soya until the moment of consumption. In this way, Vicap powered products evade loss of efficacy by taking the act of mixing ingredients and exposure to sunlight directly to the consumer, respectively to the moment of consumption. Expensive functional ingredients stay protected and with a single push the consumer can activate the desired effect. The cooperation partners from Vicap Systems AG that played a vital role in the development of the Vicap are plastics and injection moulding specialist Montfort Kunststofftechnik from Austria, Germany’s DMK subsidiary Humana Pharma International from Italy for testing, ingredients, Separated active ingredients, protected from sunlight have to be mixed before consumption","@ID":22}]}}
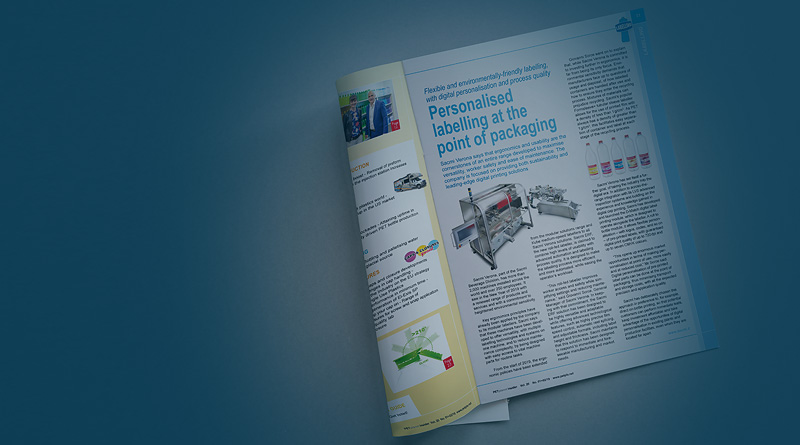