"NEWS 8 PETplanet insider Vol. 16 No. 01+02/15 petpla.net Corvaglia Group: Romeo Corvaglia found his successor The Corvaglia Group, with around 250 employees at locations in Switzerland and Mexico, has grown constantly over the course of the past few years. Company founder and owner Romeo Corvaglia began adapting internal structures early on in order to respond to the challenges associated with the growth. The Board of Directors grew from two to six members in March 2013, and was divided up into different areas of expertise. Romeo Corvaglia has been working on finding his successor as Group CEO for several years. As of January 1, 2015, group operational responsibility will be handed over to Michael Krueger (36, Dr. rer. nat.). Michael Krueger began working for Corvaglia as Chief Technology Officer three years ago. One year later, he was given the additional responsibility of overseeing operations and managing around 100 employees at Corvaglia Mould AG. Romeo Corvaglia will work in a more withdrawn role over the next one to two years, and will only carry out operational duties in a supportive capacity. He plans to completely withdraw from operational duties by 2016, but will retain his position on the Board of Directors. www.corvaglia.ch Amcor acquires Chinese flexible packaging company Amcor announced an agreement to acquire Zhongshan Tian Cai Packaging Company, a Chinese flexible packaging company for EUR29 million. The purchase price represents 7.1 times EBITDA. Tian Cai has one plant located in Zhongshan and sales of approximately EUR39 million p.a. The business produces flexible packaging products for the food, beverage and pharmaceutical end markets and supplies leading local and multinational customers. Amcor is currently the market leader in Southern China, with three flexibles packaging plants, including one plant in Zhongshan. This acquisition will complement the existing food and beverage business and broaden Amcor’s capabilities within the South China region to include pharmaceutical packaging. www.amcor.com Start of preparations for Drinktec 2017 With the appointment of the Advisory Board, preparations for Drinktec 2017 have now begun. Volker Kronseder, Chairman of Krones AG and President of the Advisory Board so far, was confirmed in office. The Advisory Board represents the interests of the companies exhibiting at Drinktec. The dates for the next edition of the “World´s Leading Trade Fair for the Beverage and Liquid Food Industry” are September 11-15, 2017 in Munich. In their review of Drinktec 2013 the board members all drew positive conclusions. They were all agreed that the last Drinktec had been a great success. In particular they praised the international character of the event and its outstanding role as an ideas platform and innovations driver. Volker Kronseder pointed out that many of the innovations presented at Drinktec 2013 were now reaching the market. According to Beatrix Fraese of the VDMA, Drinktec will continue to have an effect for a long time and in 2015, too, it will have a positive influence on business for the German machinery and plant manufacturers. Drinktec 2013 attracted 66,886 visitors, of which 62% were from outside Germany, reflecting a rise of 14%. Beatrix Fraese reported in the meeting on the current economic situation in the engineering sector. The segment that is relevant to Drinktec, namely food processing and packaging machinery, saw growth of 4% in 2014, with production volumes rising to EUR13 billion. Strong domestic demand played a large part in this. For 2015 the machinery manufacturers are upbeat, because demand from other EU countries is rising again, the economy in China is also picking up and the industrial policies in the US are creating a favorable climate for investment. As well as for Drinktec 2017, preparations are also underway for the Drinktec offshoots outside Germany, all of which are taking place in 2016: Drink Technology India (provisionally April 28-30), Food & Drink Technology Africa (September 14-16) and China Brew and China Beverage (October 13-16). www.drinktec.com Interactivity is key at international Knowledgeshare Live forum Knowledgeshare is a beverage industry forum comprising a digital community of senior industry players and thought leaders. In association with Sidel, Knowledgeshare Live takes these discussions from online to the stage and will take place in Dubai on February 10 - 11, 2015, providing a neutral setting to discuss where the beverage industry is heading and how it will handle the challenges and opportunities. The two days in Dubai will feature keynote presentations, thought-provoking panel discussions, as well as the opportunity for all delegates to get involved and make an active contribution to the dialogue. Before and after the event in Dubai, the experts will share their knowledge and opinions online (blog.knowledgeshare.com) where everyone is welcome to join in the discussions. This blog is a platform that provides opportunities to continue the ongoing discussions between the knowledgeshare Live events. The Dubai event will build on the success of previous Knowledgeshare Live events, staged in Frankfurt, Germany, and Sanya, China, in 2013 and 2014. blog.knowledgeshare.com Polyester recycling forum informs about latest developments The upcoming polyester recycling forum in Bad Oeynhausen on March 3 – 4, 2015 will provide conference participants with profound market information and the possibility to collect knowledge about the latest technical and technological status of regeneration and processing of the PET wastebottle stream. Several companies from all areas of polyester recycling will present their latest developments. www.polyester-recycling.com","@ID":10}, "PETbottles 42 PETplanet insider Vol. 16 No. 01+02/15 petpla.net Home + Personal Care Floral edition of Pril How many of us still remember the floral adhesive stickers that achieved cult status at the start of the 1970s: they decorated the tiles lining the kitchen walls in the homes of countless mothers, grandmothers and greatgrandmothers? In remembrance of those times, Henkel has been selling its Pril Power Gel in a floral edition with the adhesive stickers familiar from the old days on the backs of the bottles. The PET bottles are brightly coloured and filled with 500ml Power Gel or Power Gel Lemon. The labels to front and rear are decorated to reflect the flowery look and, at the rear of each, are three adhesive labels to peel off. The bottles are sealed with the familiar screw closure with angled pourer incorporating a push-pull function. www.pril.de Palmolive goes anti-bacterial In the highly competitive liquid soaps market the selection of products for all types of usage is correspondingly large. Following the Sagrotan advertisement for a product with 99.9% germ destruction capability, not to be outdone, their competitor ColgatePalmolive also launched a product of this kind on the market. “Palmolive antibacterial“ is said to provide protection against bacteria over a lengthy period of time and, at the same time, gently care for the hands. Packaged in the waisted PET bottle typical of the brand, in this case in a “clean“ white emphasising the hygienic aspect. The soap is discharged by way of a transparent, slightly greenish-coloured pump dispenser with locking function. www.colgate-palmolive.de 5 in 1 Cleaner from Pronto SC Johnson are selling, under the “Pronto“ brand name, a 5 in 1 multi-surface cleaner in a PET bottle coloured blue with a content of 500ml. When reaching for the bottle, the user’s hand and fingers quickly locate in just the right position for activating the screw-on trigger. This is designed in two colours and features a rotatable lock / spray jet setting. Colourmatched self-adhesive labels to front and rear take care of product and retail information. According to the manufacturer, the eco-friendly product contains bio-alcohol obtained from sustainable raw materials. www.scjohnson.com Ajax with essential oils The ColgatePalmolive Group is selling, under its own brand name “Ajax“ and the product tag “Aroma Sensations“, a household cleaner with natural, essential oils designed to ensure a long-lasting fragrance. The violet-coloured product with lavender and magnolia fragrance is packaged in a 1l rectangular bottle. Underneath the all-round plastic label the bottle incorporates reinforcing grooves. For sealing purposes the bottle is fitted with a coloured screw cap with dispensing function. An additional self-adhesive sticker at the front advertises the advantages of this innovative product. www.colgate-palmolive.com","@ID":44}, "ON SITE 41 PETplanet insider Vol. 16 No. 01+02/15 petpla.net ONsite Gea Procomac ABF is first low acid plant in Asia A Gea Procomac ABF (Aseptic Blow Fill) system is now producing low acid products at Pokka Singapore Corporation’s new plant in Johor Bahru, Malaysia. It is the first system of its kind in Asia. Pokka Singapore, part of Pokka Sapporo Food & Beverage Group of Japan, manufactures and markets a wide range of beverages under the Pokka brand name. The company exports to more than 60 countries around the world and says that its leading position in its markets is driven and sustained by a continuous focus on quality improvement and implementation of innovative systems and processes, along with extensive experience in the food and beverage industry. An opening ceremony in Johor Bahru, Malaysia, saw Pokka Singapore celebrate the launch of Jasmine green tea, Chrysanthemum, Oolong tea, Premium milk coffee and Premium milk tea, which are produced on a new PET Aseptic line supplied by Gea Procomac from Italy. The low acid bottles, which are extremely microbiological sensitive, are produced with a 14 cavities Gea Procomac blow moulder at a rate of 28,000 single-serve bph and 13,000 1.5l bph. The Gea Procomac ABF is composed of a rotary aseptic blow moulder with an integrated aseptic filler and capper. It uses dry H 2 O 2 (hydrogen peroxide) preform sterilisation, which it says offers maximum effectiveness in processing both high acid and low acid beverages. The system uses a flow of vaporised H 2 O 2 at controlled temperature, concentration, contact time and flow rate to achieve an effective Log 6 sterilisation of the preform at the exit of the oven. After the sterilisation phase, the preforms enter a microbiological isolator, which encloses the blowing wheel. The stretch-blow machine is the first truly aseptic blow moulding system and it is an integral part of the ABF. All non-cleanable components, such as electrical and mechanical items that require lubrication, are located outside the sterile zone. All surfaces within it are accessible and can be cleaned by automatic foaming and sterilised by an automatic sterilisation cycle with VHP. Sterilisation is performed before every production cycle. The system has undergone and successfully completed a sequence of rigorous decontamination tests on all microbiological isolator surfaces, including the blower, filler and capper, and on preforms and caps both internally and externally, reaching up to 6 Log reduction on target microorganism (on B.atrophaeus). To enter into commercial production however, the ABF has also had to pass a “broth filling test”, a production filling test with a specific and very sensitive LA product. It demonstrated complete control in terms of critical control points and possible microbiological risk. Over a run of more than 30,000 bottles, the Gea Procomac ABF delivered zero contaminated bottles and thus proved to be a robust and reliable system. www.procomac.com","@ID":43}, "imprint EDITORIAL PUBLISHER Alexander Büchler, Managing Director HEAD OFFICE heidelberg business media GmbH Häusserstr. 36 69115 Heidelberg, Germany phone: +49 6221-65108-0 fax: +49 6221-65108-28 [email protected] EDITORIAL Heike Fischer Gabriele Kosmehl Kay Barton Michael Maruschke Ruari McCallion Waldemar Schmitke Wolfgang von Schroeter Anthony Withers MEDIA CONSULTANTS Martina Hirschmann [email protected] Johann Lange-Brock [email protected] phone: +49 6221-65108-0 fax: +49 6221-65108-28 France, Italy, Spain, UK Elisabeth Maria Köpke phone: +49 6201-878925 fax: +49 6201-878926 [email protected] LAYOUT AND PREPRESS EXPRIM Werbeagentur Matthias Gaumann | www.exprim.de READER SERVICES Till Kretner [email protected] PRINT Chroma Druck & Verlag GmbH Werkstr. 25 67354 Römerberg Germany WWW www.hbmedia.net | petpla.net PETplanet insider ISSN 1438-9459 is published 10 times a year. This publication is sent to qualified subscribers (1-year subscription 149 EUR, 2-year subscription 289 EUR, Young professionals’ subscription 99 EUR. Magazines will be dispatched to you by airmail). Not to be reproduced in any form without permission from the publisher. Note: The fact that product names may not be identified as trademarks is not an indication that such names are not registered trademarks. 3 PETplanet insider Vol. 16 No. 01+02/15 petpla.net Our reports from Italy and Spain are still appearing in the current issues, but already, since the beginning of the year, the Editourmobil has been girding up its loins for another major tour, this time destination North America. In cooperation with our colleagues at the NPE in Orlando we will be visiting the PET industry in North America. The tour actually begins in Canada, at the docks in Halifax, Nova Scotia, where we are confidently expecting to be greeted with temperatures of minus 20, plus plenty of snow. Getting the Editourmobil suitably equipped to cope with these Arctic conditions has been a major task for us in Germany: anti-freeze to cope with temperatures at minus 30, snow chains, jump leads, jump start spray all packed. Hopefully all this will see us safely through. I will be in charge of operations as we negotiate the snow drifts and the freezing temperatures. Watch this space for our reports. Our first appointments are in the Greater Toronto area. From there Waldemar Schmitke will be travelling down the eastern side of the USA and steering a consistent course in the direction of the NPE in Florida. With every mile covered in the southerly direction we can look forward to warmer weather where we can hopefully ditch the winter clothes and start unpacking the T-shirts. Once at the NPE we shall be looking forward to your visiting us in the South Hall. It is here that you will have the opportunity to experience our Editourmobil live, to have a look at the mementos we have gathered from our visits to date and, of course, have a chat with us, the people we have met and the things we have seen during our tour. In the summer and the autumn we shall be continuing the tour in the direction of the west coast, returning to base before the winter really sets in. Come and experience with us the Canada and USA PET world! Yours Alexander Büchler dear readers,","@ID":5}, "PRODUCTS 39 PETplanet insider Vol. 16 No. 01+02/15 petpla.net Milliken & W R Grace launch next-generation catalyst and additive technologies W. R. Grace & Co. and Milliken & Company say that their latest generation advanced technologies offer polypropylene (PP) with the ability to develop new and differentiated resin portfolios featuring enhanced clarity, cleanliness, processability and mechanical performance. Grace’s Consista C601 PP catalyst is the first sixth-generation non-phthalate-based catalyst and a drop-in solution for the Unipol PP process. Grace says that it enhances the performance and processing of homopolymers, random copolymers and impact copolymers. The company claims that random copolymers made from Consista catalysts, combined with Milliken’s next-generation Millad NX 8000 clarifier, offer glass-like transparency and faster cycle times. Ella Chen, Unipol PP licensing global marketing director asserted that the companies’ solutions together address a broad spectrum of resin manufacturers’ requirements, ranging from higher melt flow to lowertemperature processing for cycle time reduction. Consista C601 catalyst imparts a balance of impact and stiffness that facilitate lightweight, thin-wall designs. The technology is claimed to enable the production of random copolymers with improved taste and odor performance for food contact applications. It is further maintained that the Consista catalyst enables faster cycle times by increasing melt flow rates and that its broader molecular weight distribution improves mechanical and processing attributes for a variety of applications. When Millad NX 8000 clarifier and Consista catalyst are combined in random copolymers with a high melt flow rate (MFR), up to 36% reduction in haze over previous generations is claimed, which enables high transparency, bright appearance and high gloss in moulded parts. The Milliken additive also allows PP to be processed at temperatures of 190°C to 200°C, a reduction of up to 40 degrees compared to other clarifiers. Cooler temperatures shorten cooling times and can increase productivity by facilitating mould release. www.milliken.com www.grace.com","@ID":41}, "NEWS 9 PETplanet insider Vol. 16 No. 01+02/15 petpla.net V I S I T U S A T B O O T H W 2 4 8 9 W W W . I N T R A I S . C O M Constantia Flexibles sold to investment firm One Equity Partners (OEP) and the H. Turnauer Foundation have agreed to sell their 100% stakeholding in Constantia Flexibles to the Wendel Group. Constantia Flexibles is one of the world’s leading manufacturers of flexible packaging products and labels. Constantia Flexibles supplies its products to multinational and local companies in the food, pet food, pharmaceuticals and beverage industries. The company employs over 8,000 people in almost 80 Group companies and delivers to over 3,000 customers worldwide. In 2013, the company achieved sales of EUR 1.63 billion and earnings (EBITDA) of EUR 233 million. OEP acquired the company in 2009, when it took over the majority of Constantia Packaging AG, and holds 75% of Constantia Flexibles. 25% belong to the H. Turnauer Foundation. The new owner Wendel Group is known to invest internationally in companies that can be described as leaders in their fields, such as Bureau Veritas, SaintGobain, Materis Paints, Stahl and IHS in Africa. The transaction is subject to approval from the relevant antitrust authorities and is expected to be closed in the first half of 2015. www.cflex.com Official tradeshow introduction to Husky’s barrier solution at NPE 2015 Husky Injection Molding Systems will be showcasing its latest technologies for the beverage packaging, medical and hot runner markets at NPE 2015. The company will a HyPET HPP5 system running at its booth, a fully integrated injection moulding system for PET preform manufacturing. The system will be running Shotscope NX, the company’s integrated process and production monitoring system that provides a real-time snapshot of information to help optimize overall factory efficiency. NPE will also serve as the official tradeshow introduction to Husky’s barrier solution, built on the HyPET HPP5 platform. The PET preform barrier module offers manufacturers new possibilities to use PET as a packaging material for beverages, sauces, and other food products. The company will also showcase its latest hot runner and controller systems, including UNIFY pre-assembled manifold systems, Altanium Matrix2 hot runner and mould controllers, and its next generation valve gate nozzles. Its Altanium controllers are built on a software platform that allows for greater integration with other Husky products, providing a foundation to support total mould control with mould servo-controlled actuation, in addition to valve gate and temperature control. www.husky.ca Read more News: petpla.net","@ID":11}, "www.npe.petpla.net , / 0 Premium Sponsor Sponsors Toronto Québec New York Atlanta Orlando Chicago Denver Las Vegas Seattle Calgary Montréal Los Angeles San Francisco Vancouver Dallas New Orleans Phoenix Washington, D.C. Boston Detroit Halifax Kansas City Oklahoma City Albuquerque NPE 2015 - The North American Road Show The survey of PET markets worldwide by our Editourmobil is moving into the next phase! This year we find our team of intrepid adventurers from PETplanet landing on the North American continent. The Columbus PET Bottling Team under Captain Alexander Büchler, First Mates Kay Barton and Waldemar Schmitke, together with Second Mate Anatol Hanau, will first of all be steering a course for the east coast of Canada and then tacking southwards via the east coast of the USA as far as Orlando, Florida, where the NPE 2015will be waiting. Here, on the PETplanet exhibition stand (S21189 in the South Hall) between 23rd and 27th March, the crew will be displaying all the PET treasure collected to date. After the NPE comes the second section of this research expedition and the team will be exploring the markets of the west coast of the USA followed by the west coast of Canada. The figures relating to this tour speak for themselves: a distance of around 17,000 km and approximately six months of this exciting adventure will be waiting for you! And, as always, you will have the chance to accompany the crew interactively. Follow the complete tour on our weekly travel blog under npe.petpla.net and contact us for an editorial walk on the wild side around your own bottling plant, PET processing plant, closure cap production facility, material manufacturing or recycling plant. It is YOU who are our story. Cast off ! Part 1 The worldwide round trip with","@ID":26}, "PETnews 6 PETplanet insider Vol. 16 No. 01+02/15 petpla.net Sipa acquires Automa PET bottle production activities Sipa has officially acquired all activities related to the production of injection-stretch-blow moulding (ISBM) equipment at Automa S.p.A. The acquisition represents an important strategic move for Sipa. It will enable the company to extend its existing offering in single-stage ISBM systems and to gain a stronger position in the market for equipment producing specialty products, such as containers for pharmaceuticals, cosmetics, personal care products and spirits. And it is in line with Sipa’s objective of becoming a leader in the development and supply of complete solutions for filling and packaging. Automa ISBM machines are designed for the production of containers in smaller lots than Sipa’s existing units, with features that enable quick change-overs between diffferent product configurations. The machines are also characterized by their compact layouts and high energy efficiency. The three-station ISBM 50SR unit, for example, with a 500-kN injection clamp force, has a rated power consumption of just 18.5 kW/h for the machine, hot runner system and PET loader. The 800-kN ISBM 80SR, which has four stations (separate stations for stretch-blow and discharge), consumes 20 kW/h. Enrico Gribaudo, General Manager of Sipa, says the company intends to maximise synergies between Sipa and Automa’s ISBM operation, in three areas in particular: in packaging development, in research and development of the ISBM process and containers, and in technical support, which Sipa now provides through 18 branch offices and 23 technical assistance centers worldwide. www.sipa.it Bottled water consumption projected to be the number one packaged drink by 2016 Information presented by the Beverage Marketing Corporation (BMC) during the International Bottled Water Association (IBWA) Annual Business Conference in Dallas, Texas, points to bottled water’s growing share of the packaged beverage market.While other beverages struggle to gain or maintain market share, bottled water is expected to have a 7.4% increase in 2014. Every segment of the bottled water industry is growing and bottled water can be considered to be the most successful massmarket beverage category in the U.S. In fact, single serve PET plastic bottled water outperformed all other beverage categories, posting an increase of 8.4%. Sales of bottled water in 2014 are expected to grow to $13 billion, an increase of 6.1% from 2013. Reflecting a clear trend of consumers increasingly choosing healthy, convenient, zero-calorie bottled water, BMC reported that over the past five years alone, bottled water has increased its “share of stomach” of the overall beverage market from 14.4% in 2009, to 17.8% in 2014. With 20.9%, carbonated soft drinks currently holds the number one position. However, BMC now predicts that by 2016 bottled water will be the number one packaged beverage sold in the United States. Even with this continuing growth and increased consumption, bottled water still has the smallest water and energy use footprint of any packaged beverage. The results of a recent benchmarking study show that the amount of water and energy used to produce bottled water products in North America is less than all other types of packaged beverages. On average, only 1.32l of water (including the liter of water consumed) and 0.24MJ of energy are used to produce one liter of finished bottled water. www.bottledwater.org PTI expands PET bottle testing to Southeast Asia via Hemetek partnership Companies in Southeast Asia will now have access to state-of-the-art polyethylene terephthalate (PET) package and bottle evaluation services. The new capability is a result of a partnership between Plastic Technologies, Inc. (PTI) and Hemetek Techno Instruments, Mumbai. An open house was planned for January 20th, after which the facility will be accepting bottle performance projects. The expansion into the region has been driven by brand owner requests for PTI to establish a local resource to help them determine if their preforms and bottles are meeting performance parameters. Up until now, companies were forced to send these components to laboratories in other parts of the world or rely on limited internal capabilities. PET resin, preform and bottle testing will include solution intrinsic viscosity, acetaldehyde and moisture content, finish dimensions and bottle expansion and burst. The new capability will be based out of Hemetek’s expanded testing facility in Baroda, located in the Gujarat state in western India. www.plastictechnologies.com www.hemetek.com Read more News: petpla.net","@ID":8}, "MARKET SURVEY 27 PETplanet insider Vol. 16 No. 01+02/15 petpla.net EKG Group Corvaglia Closures Uner Plastik Ravibras Embalagens Da Amazonia Ltda Alpla Werke Alwin Lehner GmbH & Co KG Njegoseva 10 34220 Lapovo, Serbia +381 34 61 000 11 Mr Dragan Miljkovic General Manager +381 34 61 000 11 +381 34 61 000 12 [email protected] Hörnlistrasse 14 8360 Eschlikon, Switzerland +41 71 973 77 77 www.corvaglia.ch Mr Bernardo Osés Managing Director Closure Division +52 712 2839181 +52 712 2839185 [email protected] Gebze Plastikciler OSB, 1.Cadde, 11.Sokak 41400 Gebze/Kocaeli/Turkey +90 262 751 34 00 www.uner.com.tr Mr Cumhur Filik Sales and Marketing Manager +90 530 265 0663 +90 262 751 21 25 [email protected] Av. Andrômedra, 855 – 1º andar, Cj 114 – Alphaville, 06473-000 - Barueri - SP, Brazil +55 11 4689 6500 www.gruporavi.com Mr Aurelio Silva Gerneral Director +55 11999 808 645 [email protected] Mockenstraße 34, 6971 Hard, Austria +43 5574 602 0 www.alpla.com Ms Gabriele König Sales Assistant Injection Molding +43 5574 602 555 [email protected] PCO 28mm 1881 & 1810 ; 38mm 3 start ; 48 mm and handle all in HDPE Yes, HDPE Yes, PCO-1810 and PCO-1881 Yes, HDPE Yes, HDPE No No No Yes, PP No 28mm for carbonated drinks and juice, 38 mm juice CSD, water, juice, milk, isotonic, aseptic fill and hot fill CSD, water, edible oil, beer CSD and Isotonic CSD, water, juice and milk 1810, 1881 CSN26,27mmAlaska,28mm 1810, 28mm 1881, 28mm PCO Corvaglia, 29/25 , 30/25,33mm HF, 37mm HF, 38mm 3 start, 38mm 2 start, 48mm 29/25mm, 30/25mm, 38mm 3-start/2-start, PCO-1810, PCO-1881, 29/21 and 32/28 edible oil, 48/41mm, 55mm HOD and handles for 48/41mm and 55mm HOD bottles 28mm, 33mm, 26mm 1881, 1810, 38mm 2 starts, 38mm 3 starts, 48mm, Alaska, Glass, SPI-necks No ut logo yes Yes Yes, up to 3 colours Yes, 4 colours & 1 Coloar Yes Yes Yes Yes Yes Yes No No No Yes No Yes No Yes Yes On request Closures for all major beverage brand owners, customized closures (e.g. for medical applications) 37mm Snap on caps especially designed for lemonade products. 26 mm 1g for water; 28mm 2,45g and next year 2,15g for CSD, 33mm with alluminiun foil for hot fill and Sport Cap 33 mm with aluminium foil 2-chamber caps; bi-and multicomponent injection, co-injection, custom made closures Yes but, till Q2/2015 the project is confidential, will be revealed in Q2. Aptar Food + Beverage Silgan White Cap Belgium Europlast Affaba & Ferrari S.r.l. 36-38 rue de la Princesse 78430 Louveciennes, France + 33 1 30 87 19 80 www.aptar.com Fabriksstraat 25, 2547 Lint Belgium +32 3 460 13 91 www.silgan-closures.com Mr Hans Van Baekel Business and Technical Development Manager +32 475 81 64 85 [email protected] Novopresnensky Lane 7, 123557 Moscow, Russia +7 495 777 888 7 www.europlast.ru Ms Natalia Selezneva Marketing Director +7 495 777 888 7 ext. 1220 +7 495 745 88 82 [email protected] Via Don Luigo Sturzo, 2 26851 Borgo San Giovanni (LO) - Italy +39 0371 213021 www.affabaferrari.com Ms Silvia Ferrari Sales & Marketing Director +39 0371 213030 +39 0371 97031 [email protected] Yes, PP & PE. Yes in PE and PP Yes, HDPE and PP Yes, 38mm caps in HDPE, 48mm caps in HDPE and PP Yes, PP outer shell with comfortable PE drinking spout Yes , 38 mm PP for hotfill with TPE liner Yes, HDPE and PP Yes, 38mm caps with IHS liner and Oxygen Scavener liner - 28mm and 38mm 2-pc flip top caps available, as well Beverages and liquid food applications Yes Milk, still water, favoured water, juice, CDS, smoothies, agrochemicals, mineral oils 28mm 1881, 28mm 1810, 30/25H, 33mm, 38mm. 28 mm- 30/25 - 38 mm sportscaps range / 38 mm 2 and 3 th caps / multitreads PCO 1810, PCO 1881, 38 mm, 47 mm food & beverage : 28mm: PCO1810, BPF, BPF light, 1881, 3-start (Alaska) - 38mm: 1-start, 2-start for aseptic, 2-start for hot fill, 3-start pitch 9, 3-start pitch 8 Various custom decorative closure options including hotstamping. Yes - 4 colour tampo print and promotional laser printing Yes Yes Yes Yes Yes Yes Yes No No Yes Yes, only flip-top Sport caps. Yes both Yes, Sport Caps Yes All dispensing solutions including new water enhancers closures with performing SimpliSqueeze(R) Valve technology and also pumps, sprays and pouch fitments with valve. Carton fitments , 5 gallon caps PCO 1881 28 mm - 2,15 g (one-piece closures) 28mm 1-pc and 2-pc flip top closures, 38mm 2-pc flip top closures, caps for agrochemical products, mineral oils and lubricants, caps for technical gases. Tailor made soultions according to customer's needs. BAP technology (Bonded Aluminium to Plastic) process to seal a closure to a container. A&F own many patents and utility models","@ID":29}, "BEVERAGE INGREDIENTS 17 PETplanet insider Vol. 16 No. 01+02/15 petpla.net BEVERAGE INGREDIENTS 17 Symrise unlocks the Code of Nature. A new dimension in naturalness for beverages Fruits, roots, seeds, rinds, herbs, blossoms and nuts. Nature is brimming over with ideas for inspiring drinks concepts, whether it’s lemonades, teas, juices or alcoholic drinks. Customers love the taste of nature. It has become a global trend in both developed and emerging markets. Symrise has brought together its collected expertise in its strategic Code of Nature programme to develop beverages concepts that complement the idea of naturalness. In particular the company has focused on naturalness from a number of perspectives: customer requirements, expert knowledge, modern technologies. To understand better what consumers think of when they think of naturalness, Symrise conducted a detailed survey of consumers in five countries, as well as consulting industry experts. The questions in the survey covered a wide range of topics associated with the concept of naturalness, its role in consumer thinking, the type of packaging considered appropriate. Analysis of the study helped the company to understand consumer expectations of how a beverage should taste, together with other characteristics that reinforce the impression of naturalness. From this, the company can begin to develop successful drinks concepts. For decades the company has been a significant force in matters of extraction, distillation and separation, making use of traditional methods as well as employing the most up to date technology. Based on knowledge obtained from the Code of Nature, the company has developed two product portfolios namely, Botanical Essentials and Fruity Essentials. Botanical Essentials The aromas are 100% natural. Beverages manufacturers can choose from the Botanical Essentials which consist of roots, seeds, rinds, nuts, blossoms and herbs. These are suitable as a basis for alcoholic and alcohol-free beverages that are popular everywhere. One in every two beverages includes herb and spice components, such as the classic gin and cola.","@ID":19}, "MARKET SURVEY 26 PETplanet insider Vol. 16 No. 01+02/15 petpla.net 01+02/2015 MARKETsurvey Company name Closure Systems International RETAL Sarl SBECM Postal address Telephone number Web site address Contact name Function Direct telephone number Fax E-Mail 7702 Woodland Drive, Suite 200 Indianapolis, IN 46278 USA +1 317 390 5082 www.csiclosures.com Mr Juanjo Martinez Business Development Manager (EU) +34 93 891 78 08 +34 93 891 78 00 [email protected] 1643 Luxembourg +352 20 605 555 www.retalgroup.com Mr Jean-Noël Boursiez Closure Sales Director +33 6 238 30 427 +352 20 605 555 [email protected] Rue de la plaine 47230 Lavardac, France +33 5 53 97 41 00 www.sbecm.com Mr Jean-Luc Didouan General Manager +33 5 53 65 85 97 [email protected] Product Range One-piece closures for beverages (Yes /No -If Yes, please specify material) Yes HDPE, PP, Copolymers, etc. Yes - HDPE Yes - HDPE, LDPE or PP Two-piece closures for beverages (with liner) (Yes / No -If Yes, please specify material) Yes, plastic & aluminum closures No No Applications relevant to PET containers (e.g. CSD, water, juice, beer, etc.) Carbonates, water, juice/fruit drinks, sports drinks, teas, energy drinks, liquid dairy, beer, liquor, wine, food, automotive fluids, etc.; cold-fill, hot-fill, & aseptic-fill applications CSD, water, juice, beer, dairy, beer, oil Water, CSD, juices, dairy products, any liquid or solid products Neck finishes available as standard short-height/lightweight and standard neck finishes for 26mm, 28mm, 29mm, 30mm, 33mm, 38mm, 43mm, and other bottles (e.g., 1881, 1873, 1810, 1716, 1914, 1901, 1844, 29/25, 30/25 Haute, 1851, 1874, 1875, 1876, 1842, 1843, 1845, 1799, 1814, 1841, etc.) complete range: 1810, 1881, 38mm, 48mm, 29/21mm, etc 30/25 high and low, 29/25 light, PCO 28 (1810, 1881, BPF), 38mm, 48/41 Printed caps available (Yes / No) Yes Yes No, but embossed Colour matching service (Yes / No) Yes Yes Yes Child-proof closures (Yes /No) Yes No On request Push-Pull / sports caps (Yes / No) Yes Yes On request Special comments/special closures (e.g. flipt-tops, drinking spouts, lightest cap for 28mm PCO, 26mm for water etc including non-beverage closures...) High speed capping equipment and expert technical services Handles for 5 liters, overcaps Special patented closures or marketing features Many patened safety and design features across a wide range of closures Several patents Company name Bericap GmbH & Co.KG ViCAP systems Europa Asia Ltd. Intergulf Ltd Euro-Plast LCC Postal address Telephone number Web site address Contact name Function Direct telephone number Fax E-Mail Kirchstrasse 5, 55257 Budenheim, Germany +49 6139 2902 0 www.bericap.com Mr Volker Spiesmacher Director +49 6169 2902 0 +49 6139 2902 188 [email protected] Oetenbachgasse 26, 8001 Zürich, Switzerland +41 79680 2271 www.vicapsystems.eu Mr Roger F. Wilfinger Ceo +41 79680 2271 [email protected] Po box No.6131 Sharjah,UAE +971 65029 284 www.empol.com Mr Vikram Singh Sales Manager +971 65029 330 +971 65285 720 [email protected] 230005, Gorkogo str. 95, pre. 1, Grodno, Belarus +375 152 45 04 51 www.euro-plast.by Mr Aleksander Hombak Leading Sales Manager +375 152 45 03 56 +375 152 45 07 59 [email protected] Product Range caps and closures One-piece closures for beverages (Yes /No -If Yes, please specify material) Yes, DoubleSeal for PCO 1810, DoubleSeal SuperShorty for PCO 1881(for CSD, aseptic and hot fill), HexaLite for PET 29/11, 29/13 and PET 26/10, 26/13, DoubleSeal 38 for 38mm 2-start and 3-start neck finish; DoubleSeal 33mm 2-start for aseptic filling and hot filling No Yes,HDPE Yes, PE virgin raw material Two-piece closures for beverages (with liner) (Yes / No -If Yes, please specify material) Yes, Liner Seal, SuperShorty for PCO 1881 No Yes,PP Yes, PP virgin raw material Applications relevant to PET containers (e.g. CSD, water, juice, beer, etc.) CSD, Still Mineral Water, HOD and Bottled Water, Beer, JETS (Juices, Energy Drinks, RTD, Teas, Syrups), for hot fill and aseptic application, Edible Oil, Sauces and Dressings, Dairy Mineral water, CSD, edible oil, juice, hotfill & barrier applications - Neck finishes available as standard PCO 1881, PCO 1810, PET 26/22, PET 29/25, PET 26/21, 38mm 2-start, 38mm 3-start, 33mm 2-start aseptic, 33mm 2-start HF 38mm 1810,1881,30/25,38mm 3 start, 38mm 2 start, 29/21, 36/29, 45mm 3 start PCO 28mm, Bericap 38mm Printed caps available (Yes / No) Yes, up to 3 colours No Yes upto 4 colours Yes, 3-colours Colour matching service (Yes / No) Yes Yes No No Child-proof closures (Yes /No) Yes No Yes No Push-Pull / sports caps (Yes / No) Yes, 3-piece Push-Pull and 2-piece Thumb'Up Yes No No Special comments/special closures (e.g. flipt-tops, drinking spouts, lightest cap for 28mm PCO, 26mm for water etc including non-beverage closures...) 3-piece Push-Pull for aseptic and hot filling without aluminium foil with high flow rate; Special closure solutions for lightweight necks Valve Closures for Food and Beverages and Health/Body-Care Sports Cap with a Size: 38mm, 3 starter thread, content: 12.5ml liquid / 7g powder, recycled: 100%, shelf life: depends on content 29/25 PCO 1881 28mm Special patented closures or marketing features Thumb'up screw closures for easy opening and drinking, PushPull sports closure for hot fill application without aluminiuim foil, PushPull sports closure for aseptic application without aluminiuim foil Fully Top","@ID":28}, "EDITOUR REPORT 11 PETplanet insider Vol. 16 No. 01+02/15 petpla.net All Netstal preform machines produce with Otto Hofstetter moulds.The total capacity in this hall is 2,925mill preforms per year. In the second hall older preform systems for special preforms are used with 48 and 56 cavities: 3 x Sipa 1 x BM Biraghi 1 x Netstal HP The total capacity of this hall is 455mill preforms per year. Giuseppe Silveri explains: “This variety of preforms means huge investment in injection moulds and in the procurement of raw materials. But this means that our business model works well with client materials and preform moulds. In approximately 50% of cases it is our client who supplies the raw materials and occasionally the moulds as well. R-PET is not used, simply because R-PET prices in Italy are significantly higher than new material.” Paolo Vittori takes up the story: “A very significant proportion of our deliveries, some 1,500mill annually, consist of preforms with a 38mm neck finish. In addition to juices and hot-fill with a 38mm neck finish, the fresh milk market is very important for us in Italy. The market size for milk in PET bottles amounts to 1,000mill litres in 1l PET bottles with a 38mm neck finish, split between 800mill litres of fresh milk and 200mill litres in UHD. The special feature here is the use of transparent PET bottles for fresh milk without any further barrier. For this application, we produce here at Anangni 140mill preforms per year on four preform machines (2x72-cavity, 2x96-cavity). In contrast to other customers we supply here mainly the smaller milk bottlers, because the big milk bottlers in Italy have their own preform capacity as a rule. Otherwise, our customers include the large blow moulders and bottlers. The 10 largest customers of Plasco account for 75% of production.” Due to the high transport costs the domestic market accounts for 95% of production. The remaining 5% is spread across Greece, Cyprus, Serbia, Spain and Belgium. Paolo Vittori again: “In Greece, we have a cooperation agreement with EP SA and have installed two preform systems there. A 48-cavity Sipa and a 48-cavity Biraghi produce preforms with 38 and 48mm diameter neck finish for the Greek market. In 2013, another plant was built in Atella, Italy for mineral water preforms near the Coca Cola bottling plants. Three preform machines (Netstal 72-cavity and 96-cavity and one Sipa 48-cavity) produce preforms here with the Alaska finish. The advantage for us is that we are here close to our customers with the consequent reduction in transport costs.” According to Giuseppe Silveri, “We are constantly facing the challenge, in what is a stagnant market Italy with its myriad of product variants, of competing with the fillers and converters themselves. We have to seek out markets in which we can grow, such as the market for the 38mm neck finish applications where we have specialised, and to use other cost saving measures both in production and on products ie preforms themselves. For example, we can look to weight savings projects for preforms in cooperation with our customers and partners, so that, with the same preform volumes as 2012 (70,000t), it proved possible to make savings in PET material of a total of 5,000t of PET material up to 2013 (65,000t). With regard to energy savings we have for example installed a gas powered dryer in the preform production and some of our energy needs are met via solar cells. Equipment upgrades and process optimisation are a further area to consider to reduce costs and increase productivity. We have ambitious plans on the table. We thank our hosts for the informative discussions, and prepare ourselves for the most gruelling section of our journey which will take us from here to Sicily. www.plascospa.it f.l.t.r. Waldemar Schmitke, PETplanet, Paolo Vittori, Sales Manager in the main preform production hall in Anangni. f.l.t.r. Giuseppe Silveri, Vice President, Paolo Vittori, Sales Manager, Waldemar Schmitke, PETplanet at the entrance to the Plasco Plant in Anangni Italy.","@ID":13}, "EDITOUR REPORT 10 PETplanet insider Vol. 16 No. 01+02/15 petpla.net The 38mm neck finish is important for us by Waldemar Schmitke Novembal, 38 mm - Bericap, A & F and Hotfill and last but not least a special finish without support ring for San Benedetto. Our most recent variant is the Hexalite finish for CO 2 drinks.” Giuseppe Silveri went on to discuss the preform market: “Our markets for preforms are the packaging and filling industry for fresh milk, carbonated beverages, drinking water, edible oils and juices, and mainly in Italy.” The factory area covers 50,000m2, of which 6,000m2 is dedicated to production and 13,000m2 warehouse space for preforms (in octabins), as well as loading platforms for trucks. For the raw material supply hoppers are available with a total capacity of 1,200t plus enough space for deliveries in bags and a bag storage area. Preform production is carried out in two halls. 4 x Netstal 72-cavity 7 x Netstal 96- cavity (a preform system is being converted to 128-cavity) 1 x Netstal 128- cavity 2 x Sipa 72- cavity 1 x Sipa 48/56 - fold 1 x Husky G-Line Plasco S.p.A. Our next stop takes us to Plasco in Anangni. Plasco is specialised in the manufacture of PET preforms and with a capacity of 3,380mill preforms per year, is amongst the market leaders in Italy. Here in Anangni we meet Giuseppe Silveri, Vice President, Paolo Vittori, Sales Manager, at Plasco Spa. The history of the family business began in 1995 here in Anangni with the production of PET preforms and bottles. Over the years, Plasco came to focus solely on preform production. The site was chosen centrally (near Rome) for purely logistical reasons, because transport costs in Italy are extremely high compared to the rest of Europe. Giuseppe Silveri takes up the story: “We were able to develop very quickly. From 300mill preforms delivered in 2003, we have grown to 2,500mill preforms in 2013. However, the Italian market is very diverse in PET bottle sizes and shapes, weights and neck finish. The consequence for us was that in our portfolio more than 80 preform geometries with more than 12 different neck finishes. The variants range from BPF L and S, PCO - 21, 19, and Corvaglia 1881, Crown Obrisk, Nuremberg Milan Rome Naples Palermo Tunis Algiers Rabat Casablanca Marrakech Seville Madrid Lisbon Bologna Monastir Agadir Tangier Valencia Cordoba Bilbao Oporto Andorra La Vella Venice Turin Florence Messina Barcelona Zaragoza ITALY Part 5","@ID":12}, "MARKET SURVEY 25 PETplanet insider Vol. 16 No. 01+02/15 petpla.net Caps and closures Bottle-to-bottle recycling plants Preform and single stage machinery Preforms Preform / stretch blow moulds Closure systems Two stage SBM machinery Compressors Resins / additives Filling equipment Suppliers of caps and closures for PET bottles Our annual Market Survey on the subject of manufacturers of caps and closures for PET bottles this year clocks up to 16 firms, active both locally and globally. They are (in alphabetical order): Affaba & Ferrari, Alpla, Aptar, Bericap, Closure Systems International, Corvaglia, Ekg, Europlast Russia, Europlast Serbia, Intergulf Ltd, Ravibras, Retal, S.B.E.C.M., Silgan Closures, Uner Plastik and ViCap systems. The companies are listed in the table in the order in which their details were received by the editors. Although the publishers have made every effort to ensure that the information in this survey is up to date, no claims are made regarding completeness or accuracy. 01+02/2015 MARKETsurvey","@ID":27}, "BOTTLING / FILLING 30 PETplanet insider Vol. 16 No. 01+02/15 petpla.net The InnoPET Blomax Series IV The first station in each line is an InnoPET Blomax Series IV equipped with six blowing stations, each of which is able to produce 2,250 PET bottles per hour. “What we appreciate about this stretch blow moulder is not only that it produces the high quality PET bottles we require, but also its economical principle of operation, coupled with a high efficiency of 98%,” says Gökhan Doganay, Doganay’s general manager. An important highlight of the machine that specifically reduces energy consumption is the heater area. The preforms are heated using short-wave, near infrared radiation that intensively penetrates the preform walls. This effect is heightened yet again by guiding the preforms through a surrounding reflective heater chamber and the very short distance between mandrels (minimum pitch) of only 37.7 millimeters. A servomotor-controlled stretching process ensures that the bottles are produced with utmost precision. Stretch speed does not depend on the output speed of the machine. The machine quickly adapts to changing filler capacities. Using servotechnology also makes it possible to optimize the preforms down to the last tenth of a gram of PET material. “What counts for us more than anything else is always the quality aspect, says Remzi Doganay. He is very happy with the strech blow moulder. InnoPET Plasmax – “Technology of the future” Air conveyors transport the freshly produced PET bottles to the InnoPET Plasmax. The insides of the PET bottles are coated with a Plasmax barrier coating made of pure glass, which provides even the most sensitive of beverages with optimum protection against loss of quality. This is because the ultra-thin coating of glass prevents the exchange of carbon dioxide, oxygen, and flavours between product, packaging, and the environment. “Here, we combine the advantages of a glass bottle with the lightweight handling of PET bottles the consumer values so highly,” Remzi Doganay explains. “It’s no wonder that they are so well accepted. For our Limonata in the coated bottle, we currently guarantee a shelf life of nine months, but would soon like to increase the shelf life to one year.” Bottling water in Campet bottles already planned Because the glass coated PET bottles are fully recyclable, plasmax coating complies with sustainability requirements. Rafet Doganay says, “When we heard about this machine, we contacted KHS directly and got Ten plastic bottles are conveyed in each cell support bar of the Innosept Asbofill ABF 711, which holds them by their neck rings and guides them through all processing stages of the machine. Only the bottle necks are contained inside the particularly small sterile zone. Sterilization of bottle exteriors is therefore not necessary. The bottle interiors like the caps are sterilized with H 2 O 2 aerosol. Air conveyors convey the PET bottles produced by the InnoPET Blomax Series IV to the InnoPET Plasmax that applies a coating of pure glass to the inside surfaces that provides optimum protection against loss of quality for even the most sensitive of beverages.","@ID":32}, "INSPECTION SYSTEM 23 PETplanet insider Vol. 16 No. 01+02/15 petpla.net Feasibility analysis In certain cases, a feasibility analysis is an appropriate way to find out how the customer’s requirements are met best. “Sometimes a producer asks us for inspecting objects with a standard system we haven’t done before yet”, explains Klaus Schönhoff. “In this case we have to gather more detailed information concerning the feasibility to make reliable statements, just as the customer expects from us quite rightly. In this case, it is necessary to create a feasibility analysis in advance. Sometimes the analysis takes up a lot of resources as there are complex experimental assemblies to be made. However as soon as the order for the system follows, the costs can be accounted.” A finished analysis makes decisions easier and gives both parties a good basis for the cooperation. It might even save costs for the system itself when it turns out that other or less components like cameras or inspection modules are needed than originally planned. Experience has shown that the best results are obtained when the internal customer’s departments like the head of quality management, production and purchasing department define the specifications together. When the system is in use in the field, the user should not exceed the limits of the system agreed upon in the specification due to new requirements. Otherwise, this might bring negative consequences like malfunctions and breakdowns. To avoid this, one should contact the expert team of Intravis who will help to readjust the system to the new requirements. Well maintained specification book As a central document, a specification book is normally compiled by Intravis. It exactly defines the range of performance of the inspection system. Among other things, it contains a precise listing of all samples and of all defect classifications. Furthermore, it provides an overview of the system structure and gives many technical details about measurements and the technical execution. Finally, it comprises the requirements to the production processes such as object gap and speed as well as the temperature and humidity of the entire environment. Finding a vision inspection system – proposal for the customer Bring a reference object as well as several bad parts with various defects. This will reduce costs and time for a consultancy service Find out together if other defect types have to be specified to have a complete coverage It is advisable not to exceed the limits agreed upon in the specification when the system is in use in the field as errors might occur or the reliability of the system might suffer Take care of a well maintained specification book that has been agreed upon by all relevant internal departments to avoid ill-defined criteria. The best is to come to an internal agreement within the customer’s company in advance. In this regard, a well maintained specification book is a good guideline. “The specification books are more precise and detailed than a few years ago”, says Klaus Schönhoff. “Not only technical drawings are added but there are more drawings overall. They replace text passages as they define more clearer the object areas to be inspected.” In general: The more precise and comprehensive an inspection is, the more extensive and costly it will be – the best reason to focus on the relevant inspection criteria and to narrow the defect definitions. www.intravis.com To define precise inspection requirements, complex experimental assemblies are necessary In the application laboratory, the self-developed software IntraVision helps to find bad parts in every object area","@ID":25}, "PREFORM PRODUCTION 37 PETplanet insider Vol. 16 No. 01+02/15 petpla.net Please order your copy at the PETplanet insider book shop: https://petpla.net/books Bottles, Preforms and Closures A Design Guide for PET Packaging Second Edition by Ottmar Brandau € 115,00 180 pages © Copyright Elsevier 2012 * This article was published in Bottles, Preforms and Closures, Ottmar Brandau, Chapter 3.2. Copyright Elsevier 2012 pressures will require longer dwell times. A good starting point is 0.5 s. After the dwell timer has timed out the shut-off nozzle that is situated between the extruder and the hot runner closes allowing transfer (shooting pot system) or recovery (reciprocating system). 3.2.6 Cooling time At the same time that the screw decompresses the melt, the cooling timer starts. During cooling time the preform cools down further so that: It can be properly ejected. Gate crystallinity is minimized. The preform shrinks away from the cavity to allow easy removal from the cavity when the mold opens. Minimum cooling time is about 0.5 s to give the valve stems enough time to properly close. Recommended cooling times depending on pre-form wall thickness are on the graph in Fig. 3.12. 3.2.7 Gating Most modern tools control the opening to the cavities with a cylindrical piston called valve stem. This stem is connected to a pneumatic cylinder that moves it back into the open position and forward into the closed position (Fig. 3.13). Molten material surrounds the valve whose housing (the nozzle tip) is temperature controlled by either a percentage heater or a thermocouple. The valve stem must be open during injection, hold, and decompression but is otherwise controlled by timers that may delay the opening and closing actions. The valve stem open delay timer can be activated from a number of cycle steps such as mould open (before ejection) or mold starts to close (after ejection). While the valve stem is in the closed, forward position, it touches the cold mould wall. If it stays there too long it may cool down too much and the material around it will crystallize. The valve stem is therefore opened well before it has to be open, i.e., when injection starts. When the valve stem is opened too early, molten material may enter the cavity as drool while the mold is open. This is especially a danger with low IV resins, with insufficient decompression, or when high temperatures have to be used. The valve stem close delay timer is triggered from the end of hold time. The timer needs to be set as a minimum, the same as the pullback dwell time, to allow the pressure to dissipate. A short delay time cools the preform nub sooner, whereas a longer time gives the nozzle tip heater time to transmit heat into the nub area. The operator has to judge from the appearance of the gate which way is better. The goal is to achieve the least amount of gate crystallinity and properly form the preform nub. The maximum time that can be entered for this timer is 0.4s shorter than cooling time. This will ensure that the valve stem has enough time to close before the mold opens. Process conditions such as melt temperature, injection and hold pressures, as well as the resin all have to be taken into account when adjusting this timer. Figure 3.12 Recommended cooling time versus preform wall thickness Figure 3.13 The vertically shown valve stem opens and closes material access to the cavity at the bottom. (Diagram courtesy of Mold-Masters). Figure 3.14 Three-station servo robots carry water-cooled take-out plates with three times the number of injection cavities. (Photograph courtesy of SIPA)","@ID":39}, "PETcontents 01+02/15 4 PETplanet insider Vol. 16 No. 01+02/15 petpla.net INSIDE TRACK 3 Editorial 4 Contents 6 News 38 Products 41 On site 42 PET bottles for Home + Personal care 43 PET bottles for Beverage + Liquid food 44 Patents INSPECTION SYSTEM 22 Towards optimal inspection systems MARKET SURVEY 25 Caps and closures for PET bottles BOTTLING / FILLING 28 On the road to crystal-clear success Turkish Doganay bottling operation invests BUYER’S GUIDE 45 Get listed! Page 22 EDITOUR REPORT 10 The 38mm neck finish is important for us Plasco S.p.A. 12 New challenges s.i.con s.r.l. 13 25 Years in the service of the environment Cier s.r.l. SPECIAL FOCUS 16 Beverage ingredients Naturalness and energy PREFORM PRODUCTION 20 Netstal completes PET-Line family on a high 35 Practical Guide to Injection moulding of Preforms Bottles, preforms and closures, part 17 Page 43 BEVERAGE +ingredients Page 28","@ID":6}, "INSPECTION SYSTEM 22 PETplanet insider Vol. 16 No. 01+02/15 petpla.net Vision inspection system solutions To ensure a complete and precise inspection of their products, many producers and customers choose an inline or offline vision inspection system. But what has to be considered after the decision about this investment has been made? First of all, the customer must specify the inspection requirements of his future system. What sounds obvious is often an obstacle when it comes to a cooperation. “Most customers have a clear idea of what is a good product and a bad product”, says Klaus Schönhoff, Technical Director at Intravis GmbH, producer of vision inspection systems for the plastic packaging industry. “Our task is to define it together with them. It sometimes can get challenging when a bad part is to be defined in comparison with a reference sample. The goal is to specify valid rules that have been unambigously agreed upon and are understood by both parties. Our task is in the next step to put these rules into inspection algorithms.” Intensive consulting in advance To receive a vision inspection system that exactly meets the needed inspection requirements, an intensive information exchange between provider and customer is necessary, including valid reference samples. Klaus Schönhoff: “Ideally, we receive several numbered bad parts with an informative classification list of defect types as well as reference samples of exactly the same colour and size.” As a counterperformance, it is an important consultancy service of Intravis to tell the customer if a request cannot be fulfilled the intended way. If this should be the case, the team provides alternatives. Indirect measurements A good example: A producer wants the wall thickness to be inspected in a product region that cannot be pictured entirely by cameras. In this case it might be a possible solution to measure the wall thickness in other regions of the cap or preform. As for every product the same amount of material is used, in this case the wall must be thicker in those other regions. Here it might be useful to define a thicker wall as a defect criterion. But this makes a deep knowledge about the production process on both sides inevitable – another evidence of how important an intensive communication is. No difference at first view: Good parts and bad parts with different defect specifications Intravis vision systems Towards optimal inspection systems The requirements of producers in the plastic packaging industry have been increasing for years. On the one hand, thinner walls, caps, closures and bottoms lead to maximum savings and sustainability. On the other hand, from the customer’s point of view, a constantly high level of material stability and product quality must be ensured. Moreover, the quality management has to be able to provide a complete documentation. Particular defect types also require a manual measurement to define the bad part range","@ID":24}, "PREFORM PRODUCTION 21 PETplanet insider Vol. 16 No. 01+02/15 petpla.net PREFORM PRODUCTION 21 whereas the energy costs are reduced by 9.4%. Assuming that the price of electricity is 0.12 euros per kilowatt hour, the annual saving amounts to a figure of 120,000 euros. When it comes to the economic success of a company, the operating costs for the machinery are therefore considerably more important than their purchase price. Comfort and convenience in operation have been considered by the developers either. They have come up with something new and fitted the PET-Line 5000 with the DSP6, a further development of the tried-andtested DSP control (Digital Signal Processing). This offers even more possibilities for remote maintenance and diagnosis and fits in particularly well with the new digital control technology. In the interests of optimum preform quality and maximum flexibility, the PET-Line 5000 is presented in the form of a modular structure: the injection moulding and clamping units are accommodated on a dual section bed which makes optimum layout possible to suit the requirements of the individual project. The plasticising and clamping units are each available in three different sizes – thus making it possible to ”mix and match“. For example, if you wish to produce extremely lightweight preforms in a 144-cavity mould, it may be sensible, in the interests of working in a way that ensures greater savings in relation to materials, to combine enhanced clamping force with a smaller injection moulding unit. The minimum throughput will then be less, the time the PET melt spends in the machine will be shorter and the resulting Acetaldehyde (AA) level will be lower. With its speed and high output quantity, the PET-Line 5000 has established itself in the top segment of the market. Reto Bamert, sales manager BU PET, sees the target markets as tending to lie outside Europe. “We think primarily of the USA and China, because it is here that they demand very big output figures. Our customers there are, as a rule, large bottling plants that need a manageable number of varieties of bottles but in such large quantities as to make investment in a 144-cavity preform mould worthwhile. Here our equipment is horizontally integrated into the production process; so our product stands right next to a blow moulding machine”. www.netstal.com","@ID":23}, "BOTTLING / FILLING 28 PETplanet insider Vol. 16 No. 01+02/15 petpla.net Turkish Doganay bottling operation invests in three KHS aseptic lines with integrated Plasmax technology Campet marketing campaign captures positive consumer response On the road to crystal-clear success According to Remzi Doganay (CEO, production manager) who, together with his brother Rafet Doganay (managing board, marketing and sales manager), owns Doganay, the Turkish fruit and vegetable beverage producer located in Adana, Turkey, “Only the very best quality for consumers,” is one of the key aspects of the company’s philosophy. able to meet the growing demand for Limonata bottled in GlasPET (Campet in Turkish) exceptionally well. A third KHS aseptic line, also equipped with an InnoPET Plasmax machine, has already been ordered from KHS and is scheduled to go into operation before the beginning of the 2015 season. This line will enable the company to fill all of the other fruit and vegetable beverages in the company’s range of products into Campet bottles without adding any preservatives. Rafet Doganay says, “And this is exactly what we have planned in our next step.” Based on this, we’re expecting enormous growth in sales of all of our products in the future, even in exports.” Rafet Doganay says, “When we heard about the InnoPET Plasmax, we directly contacted KHS and got straight to the point and said that we wanted to buy it. It wasn’t until later that we asked about the price and examined the machine in practical operation.” “In addition to using excellent raw materials and outstanding technical systems, we also make high demands of our distribution partners and our marketing concept,” explains Remzi Doganay. Rafet Doganay adds, “For this reason, we are also regarded as a provider of premium products within Turkey and in the many countries to which we export.” The company just recently caused quite a stir within their own country with a very special television campaign that conveyed that the still Limonata lemon soda pop is now available bottled in a particularly high-quality bottle known as GlasPET- which is coated on the inside with pure glass. With this TV campaign, Doganay is the first beverage company in the world to specifically communicate the benefits of KHS Plasmax technology to consumers. “The response to our advertising message was even more positive than we expected,” says Rafet Doganay. “This is indicated by the tremendous increase in website traffic as well as the number of more than a hundred thousand followers on Facebook and Twitter in the meantime,” Remzi Doganay adds. “We’ve also registered a significant increase in sales volume since our TV advertising was launched.” With the two new KHS aseptic lines, each equipped with integrated KHS Plasmax technology, Doganay is Doganay offers a wide selection of products today, from Salgam, lemon sauce, lemon juice, grape, apple, and balsamic vinegar, pomegranate syrup, Limonata, up to and including orange juice. Future plans include expanding the range of products significantly.","@ID":30}, "BOTTLES 43 PETplanet insider Vol. 16 No. 01+02/15 petpla.net Beverage + Liquid Food PETbottles The plastic closure company committed to your success BERICAP Technology Research and Development Mould Technology | Global Presence Capping Technology and Know-How Innovation and Flexibility www.bericap.com Stackable bottles for edible oil The French company Lesieur is marketing three different edible oils in transparent PET bottles. The bottles, with a content of 150, 250 and 500ml, vary only in terms of their height, whilst the top and bottom surfaces are coordinated so that they interlock and can be stacked safely. This enables them to be deployed in the kitchen without taking up a great deal of space. The bottles feature an embossed diamond (the company trademark) on the side. The bottles are decorated with selfadhesive labels and a snap-on coloured screw closure with detachable tamper strip puts the finishing touches to this clever concept. www.lesieur.fr Bulbous bottle for Chino San Pellegrino is marketing its Italian answer to Cola – Chino, a caffeine-free lemonade with the sharp taste of the Chinotto bitter orange - in a black PET bottle with a content of 500ml. The actual bottle has been kept completely black, it is of bulbous design, decorated with a sleeve label and sealed by means of a tamper-proof screw closure. Earlier versions still showed images of the oranges used in the product, but today the company has dispensed with these and it is only at the first sip that the interesting flavour of bitter orange becomes apparent. www.sanpellegrino.com Crazy Tiger in PET Crazy Tiger, on its own admission the market leader in France in the energy drinks sector for 1l and 0.33l packs, is packaging its triple-variation energy drink– Regular, Apple and Orange – in stable, rather squat, white-tinged PET bottles. The retail and product information is provided on an all-round plastic label and the bottle is sealed by means of a tamper-evident screw closure. www.crazytiger.fr","@ID":45}, "PETproducts 38 PETplanet insider Vol. 16 No. 01+02/15 petpla.net Modular central chillers from Conair offer process cooling up to 960t Conair’s new ESE Series EarthSmart central chillers are claimed to offer more accurate temperature control and longterm reliability. Their modular design enables plastics processors to start with just one chiller and expand to a plantwide multiple chiller system, operated by a single controller, the company says. ESE chillers are available with integrated pumps and fluid reservoir or as a standalone chiller to supply a separate pump tank system. Systems can be water cooled, using tower water, or can be installed in a remote-air-cooled condenser configuration. The range extends to 12 different sizes, from 10 to 160t. Single refrigeration circuits are available on units from 10 to 80t capacity, with dual refrigeration circuits on 20 to 160t machines. Each refrigeration circuit has two Copeland scroll compressors, which is designed to enable the system to stay up and running even if one of the compressors has to be shut down for maintenance. Users can install one or more ESE chillers and then add more modules up to a total of six for cooling capacity to 960t. Up to 12 refrigeration circuits can be connected to a single control interface using twisted-pair wiring, allowing centralised control. The standard Panasonic PLC control operates with proprietary programming developed specifically for the ESE chillers. The LCD touch-screen user interface is designed to facilitate quick monitoring and control, using a clear, simpleto-understand display. All circuits are controlled using readings from a common manifold-mounted temperature sensor. Conair says that this helps to avoid blending and temperature drift that can occur when individual supply and return sensors are used. Electronic expansion valves compensate automatically for load variations and ambient conditions. The condenser-water regulating valve is also electronic. Extensive temperature and pressure displays, trending screens and efficient diagnostic tools are intended to make commissioning and fine-tuning easy. Conair claims that service and maintenance personnel typically do not need separate meters or gauges. ESE chillers, which are built in an ISO 9001:2008-certified facility, use standard direct-drive scroll compressors. Conair claims that these are inherently more reliable than most other designs and are hermetically sealed in order to minimise maintenance requirements. Remote air-cooled models have corrosion-resistant brazed-plate, stainless-steel evaporators. Water-cooled units feature a shell-and-tube condenser and a filtration system to keep out debris and prevent clogs. Chillers with integral stainless-steel reservoir and pumping system are delivered piped, wired and ready for installation. www.conairgroup.com RPC creates narrower jar for Tangerine Confectionery RPC Containers Ltd, which is based in Blackburn, England, has created a new, narrower jar for Tangerine Confectionery Ltd, an independent UK manufacturer of sugar confectionery and branded popcorn, based in Pontefract, England. RPC was asked to create the new pack as a result of its long-term supplier relationship with Tangerine Confectionery.The 3.6l injection-moulded PET jar, made in a custom mould, is the same height as a 4l version. RPC asserts that this means that it maintains the same onshelf presence. Tangerine has switched its Taveners “traditional sweet shop range” and Jameson’s high-quality chocolate-covered confectionery to the new, classic-style container, which has been specifically developed for Tangerine’s cash and carry customers. Its glass-clear appearance is designed to highlight the colourful product within. The wide neck, which is designed for easy dispensing, uses a 105mm black cap supplied by RPC Halstead. www.rpc-blackburn.co.uk www.tangerineuk.net","@ID":40}, "EDITOUR REPORT 14 PETplanet insider Vol. 16 No. 01+02/15 petpla.net covered area totalling 12,000m2. The first building houses the manufacture of bottle to bottle pellets R-PET IV( FDAapproved). Installed inside is a complete Erema extrusion line which handles the whole of the processing cycle as far as the in-line crystalliser with a capacity of 1,800kg/h. The second building is given over to the manufacture of PET Flakes R-PET for fibres and packaging not in contact with foodstuffs. Installed here are two Sorema washing and sorting lines for two colours at the same time, with an overall capacity of 5,000kg/h. The third building is where the post-consumer HDPE and LDPE treatments are accommodated, with washing and crushing lines as well as extrusion lines with a total capacity of 6,000kg/h. Production is on a 24/7 basis. The basic material for the PET treatment is postconsumer bottles that are sourced in colour-sorted and pressed bales. These bales come predominantly from Corepla Italy with a smaller proportion (high transport costs) from Belgium (transparent material only). Corepla is a national consortium handling the collection and recycling of used plastic packaging. It was established in 1997. Within the communities (more or less) used plastic packaging is collected and brought to collection stations that can be found distributed throughout Italy. Here the plastic packaging is then separated from the rubbish and streamed into various categories such as, for example, film, PE or mixed plastic bags. From these latter, PET containers are then separated into three colour categories, light blue, mixed and transparent. Once pressed into bales, authorised recyclers throughout the EU will then be able to purchase the bales at auctions which are held on a monthly basis. Cier only purchase light blue and transparent. The quality of the baled material is, however, not good enough which means that Cier need to instigate their own sorting and separating measures. In addition, Italian legislation will only allow 95% of the post-consumer material for PET to come from foodstuffs packaging. The material from the bales is washed on two lines, one for transparent and one for light blue. Paper, closures and bottles with PVC labels are sorted at the same time (partly by hand). After this comes crushing to form flakes in sizes ranging from 2 to 8mm. Subsequently the flakes go through another separating station designed to separate out any further label residue or other contaminants. These processing stages take place in parallel on both lines, with a sorting rate of 25%. These flakes (R-PET) in light blue and transparent are the basic commodities that undergo further processing into film, fibre and PET packaging without any contact with foodstuffs. For Bottle to Bottle Quality, however, the customers demand 100% pure goods and a higher IV. For this only transparent flakes undergo further treatment in a heat process. On an Erema extrusion line with subsequent granulation, crystallisation and IV enhancement in a high vacuum, pellets emerge (R-PET IV) that are FTA-approved for the manufacture of PET beverage bottles and cosmetics. The overall quantities are divided up as follows: 75-80% in R-PET flakes, 15-20% in R-PET IV pellets and approx. 5% in PE. Coming back to the point about excessively high prices in Italy mentioned at the beginning of this article, Palmino Di Giacinto’s reaction is one of bitterness. “Italy is not in a position to monitor the quality of the post-consumer material. Neither is the government in a position to support firms in the chain from user to pressed bale by means of standardised regulations. We can also purchase post-consumer material abroad but the trucks have to be driven by Italian drivers and a permit is required. Transport costs in Italy are higher here than anywhere else in Europe, due to high wage and fuel costs. Then, on top of this there are the high energy costs of electricity and gas. All in all, Italy is not competitive anywhere in Europe in this market.” Palmino Di Giacinto continued: “The Italian baled material is becoming ever more expensive. Currently it is costing around €500 a tonne. In addition to this the poor quality of the material means that we are obliged to invest in our own sorting and separating lines so that we can guarantee the required quality and consistency for our customers. Flakes in R-PET quality in light blue f.l.t.r.: Sandra Di Giacinto, Financial Manager and Palmino Di Giacinto, Sales Director of Cier with Alexander Büchler and Waldemar Schmitke of PETplanet on the Cier forecourt in front of the Editourmobil","@ID":16}, "BOTTLING / FILLING 34 PETplanet insider Vol. 16 No. 01+02/15 petpla.net the same type of filling system with identical filling valves, implements the room-in-room concept, and is fitted with the same model of valve manifold. Another important identical item: similar to the ABF series, only the cones of the capping heads are contained inside the aseptic zone of the new ASR technology. The ASR utilizes a new innovative drive concept for all of the capper head drives which are located outside the aseptic zone, that carries out all rotational and lifting movements using servo technology. Sterile air enters the aseptic zone of the Innosept Asbofill ASR between the drying and filler wheel. Here again, a positive displacement current prevents germs from entering the aseptic process. “Because we are going to continue to grow significantly, we are planning to invest in tailored KHS aseptic systems in the future,” says remzi Doganay. Step by step on the road to success as an international brand Future goals are ambitious, but nevertheless can be summarized in one sentence: Doganay plans to become an international brand. “With this goal in mind, we intend to integrate more products into our product range, open up new sales channels, and expand our distribution network to an even greater extent,” says Rafet Doganay. “We are currently looking for interested distribution partners and are also planning to establish bottling operations outside Turkey.” www.khs.com f.l.t.r.: Remzi Doganay, Doganay’s owner also in charge of technology, Jörg Niehus, KHS service site manager, Hasan Doganay, Doganay’s export manager, Gökhan Doganay, Doganay’s general manager and Vedat Güler, KHS Sales, Turkey.","@ID":36}, "BOTTLING / FILLING 32 PETplanet insider Vol. 16 No. 01+02/15 petpla.net is sprayed on the caps, allowed to take effect, and subsequently subjected to a drying process. The screwcaps are placed on the bottles by a suction unit. The reason for this is that this method protects the filled product against external influences when the caps are screwed on in a separate sterile chamber in the next step. Closures are then subjected to a final optical closure inspection. A gripper system then removes the bottles from the cell support bars and places them on a conveyor, after which they pass through a leak check. Gökhan Doganay explaines “For safety reasons, we test our products filled by the Innosept Asbofill ABF 711 more often than prescribed, and they meet all requirements every time.” Innoket 360 roll-fed and selfadhesive labeling in practise The bottles are labeled by an Innoket 360 which is fed containers from both lines. Each bottle is dressed with two labels. While roll-fed labels decorate the middle of the bottles, selfadhesive labels are applied to the neck area. The purpose of the neck label is to convey the message that the Limonata bottle is a container with ‘glass on the inside and PET on the outside’. The roll-fed labeling process in brief: the label web is fed from a roll by a controlled feed mechanism to the labeling station, where it is cut exactly to length according to markings printed on the web. One of the real highlights of the Innoket 360 type labeler is the cutting unit with a self-sharpening cutter. The labels are cut to size and then fed to a vacuum drum that glues them to the bottles with hot melt. The slip-free design of the vacuum drum eliminates any label soiling. The gluing roller shell is equipped with induction heating that operates especially energy efficiently. Heat is generated exactly where it is needed, in the roller jacket to be exact, thereby protecting the internal components such as bearings and sensors. Temperatures are controlled very accurately with deviations of less than one degree Celsius. By simply turning a crank, the labeling station of the Innoket 360 family of labelers can be swiveled out to make mismatch overlap corrections during the ongoing production process. The ergonomic design of the machine in addition to the easy accessibility in all areas contributes yet again towards great ease of operation. The Innoket 360 applies self-adhesive labels following the roll-fed labeling process. Reversing rollers feed the label materials to the peeling edge. A sensor determines the exact timing for dispensing the label. Gökhan Doganay says, “Our Innoket 360 operates highly efficiently and with utmost precision. At the same time, it is designed for exceptional ease of operation and adapts to new situations exceptionally quickly thanks to the integrated automatic height adjustment.” Great flexibility is also a hallmark of the Innopack Kisters SP Basic shrink packer.","@ID":34}, "EDITOUR REPORT 12 PETplanet insider Vol. 16 No. 01+02/15 petpla.net New challenges by Waldemar Schmitke s.i.con. s.r.l. Following a rather adventurous journey in our 8.4m long and 3.9m high Editourmobil through small Sicilian towns, we arrive at Giammoro (Me) in Sicily. Here in Giammoro we visit s.i.con. s.r.l. where we are introduced to Dr Fabrizio Quagliuolo, Management Representative, and the regional Husky representative, Fausto Guerra. s.i.con. is a manufacturer of PET preforms and has been active in this market since 1983. Originally preforms and PET bottles for soft drinks and drinking water were produced at other locations in Italy, but, after the takeover of parts of the firm by Coca Cola Hellenik Bottling in 2011, s.i.con. continued to focus exclusively on preform manufacturing. There are five Husky preform machines installed here on site: In 2007 1 x Hypet 300 72-cavity In 2012 2 x Hypet 400 HPP 96-cavity In 2013 1 x Hypet 400 HPP 4.0 96-cavity In 2014 1 x Hypet 300 HPP 4.0 72-cavity Total production amounted to 600mill preforms in 2013 and 650mill in 2014. Breakdown of deliveries: 350mill preforms for Hellenik Bottling Italy 150mill for Nestlé Italy 30mill preforms for export to Coca Cola Malta 30mill for Sibeg authorised Coca Cola bottler for Sicily 90mill preforms for local customers The range includes the following neck finishes: PCO 1881 and 1810, Alaska, Hexalite 26-22 For supplies to Coca Cola, the raw material is purchased and processed on behalf of Coca Cola. The preform geometries are specified in advance by Coca Cola and the preforms called off as required. For example, the 0.5l preform shipped in summer has a weight of 22.7g whilst the winter preform weighs 20.7g. The raw material is provided by Nestlé. This also includes R-PET of Spanish manufacture. Up to 25% R-PET is added in pellet form for Nestlé. Deliveries are made within a radius that extends only as far as Rome, due to the high transport costs in Italy. “The Italian drinks packaging market,” says Dr Fabrizio Quagliuolo, “consistently confronts us with new challenges. Overall there is zero growth and, in the individual segments such as, for example, soft drinks, the trend appears to be going backwards. The drinking water market is stable, but is showing no growth potential. “ He went on: “There are still niche markets such as fresh milk in PET bottles or PET packaging in the food, household and the bodycare sector that have a certain growth potential as a result of removing plastic, glass and metal in packaging. Further potential is demonstrated by juices, aseptically bottled in PET bottles.” Although the soft drinks market is in decline in terms of consumption, there is, from the point of view of one preform manufacturer, growth in the 0.5 and 2l bottles sector. The reasons for this lie in the divergent drinking mindsets that exist in the north, as opposed to the south of Italy. In the north it is the 1.5l bottle that dominates whilst, in the south, people are tending to go more and more for the 2l and 0.5l bottle, which means an increase in quantities. Otherwise there is only the cutthroat competition left. Dr Fabrizio Quagliuolo continues: “Competition in the market is getting harder and harder and we will face stiff challenges. We are well-prepared with modern machinery that is up to date in terms of energy usage and optimised process sequences in our company with a high level of automation. We have installed a photovoltaics plant on the roof and we already produce 400 000 KW/yr., 5% of our energy requirement, ourselves. Together with Husky we are working on further weight optimisations in the preform sector. As part of this collaboration we have been among the first to launch a weight-optimised Hexalite 26/22 version on the market for plan and slightly carbonated beverages with a carbon dioxide content of up to 3.5% by volume. Here the positive characteristics of the Alaska and PCO Corvaglia neck finish are united in a weight reduced version.“ We extend our thanks for the frank interchange and set off in a northerly direction on our return trip. www.sicon.org/en www.husky.ca Dr Fabrizio Quagliuolo, Management Representative","@ID":14}, "PREFORM PRODUCTION 35 PETplanet insider Vol. 16 No. 01+02/15 petpla.net Injection parameters, part 17 Practical Guide to Injection moulding of Preforms PETplanet insider is publishing extracts from successive chapters of Ottmar Brandau’s “Bottles, Preforms and Closures”, which was first published by hbmedia. A newly revised version is reissued under the Elsevier imprint. 3.2.3 Transition Point As discussed in Chapter 2.4.2 the purpose of the injection phase is to fill the cavity with molten material, at which point the machine switches over to hold (also called packing). The point at which this happens is called the transition point. During the hold phase the material cools and shrinks, thereby changing density. Density is a measure of mass per volume and is dependent on how energetic molecules of a given material are under given circumstances. For plastics (and most other materials) density changes with temperature. At higher temperatures plastic molecules take up more room and density decreases. As the plastic cools down, the opposite happens and the material shrinks. Typical melt density for PET is 1.15g/cm3, whereas For PET, only the last option is used as it has been proven that it leads to the most stable process. Once the operator has established the injection parameters, the transition point is calculated as follows: TP =(SS - CU) × 13% + CU where TP = transition point, SS=shotsize, and CU = cushion. SS - CU is the distance the screw actually travels, 13% of it should happen after injection and during hold. The cushion has to be added at the end as the transition point is a fixed value. solid, amorphous density is 1.335g/ cm3 with solid crystalline density being slightly higher. At around 100°C (212 °F) demolding temperature density is about 1.3g/cm3. The difference between the melt and the demolding density is about 13%. This means that 87% of the injection stroke should happen during injection and 13% during the subsequent hold phase. The machine does not set the transition point automatically. Instead, it gives the operator three choices at which point hold should begin: When the pressure reaches a certain value After a certain injection time When the screw reaches a certain position","@ID":37}, "BEVERAGE INGREDIENTS 16 PETplanet insider Vol. 16 No. 01+02/15 petpla.net Doehler launches natural herb & spice extracts and natural blossom flavours on the market Trend: Naturalness and Energy What is the trend in beverages likely to be this year? This is a question that concerns not only you as a filler/bottler, but of course the laboratories of the aroma manufacturers too. Döhler and Symrise have pinpointed naturalness as a likely flavour of the year. The flavour of herbs, roots or spices is there to attract consumers. Growth is particularly spectacular as far as the energy drinks are concerned. This sector has managed to persuade not only younger but also older customers of the merits of the “in” drinks. Doehler is meeting the increasing demand for botanical flavours in the food and beverage industry with a new portfolio of natural herb and spice extracts and natural blossom flavours. Although herbs and spices are found in every kitchen these days, they still offer plenty of scope for new and attractive taste creations. That is why herb and spice notes are becoming popular in every segment of the food and beverage industry – including some previously untouched ones – and top the list of trendy flavours. As a provider and producer of natural ingredients and ingredient systems, Doehler has proved this with a whole series of innovative application examples. The wide variety of products ranges from still drinks with a strawberry-basil taste to refreshing aqua fruit beverages with a fine rosemary note. “It is easy to explain the reason behind the success of these flavours. For instance, cardamom from the Himalayas, oregano from Italy or coriander from Morocco all transport consumers to far-away worlds of taste. This results in both interesting taste combinations and great product positionings,” says Daniel Courtehoux, Head of Business Unit Flavours at Doehler. However, not every type of herb and spice is suitable for producing authentic, natural extracts and flavours - no matter how tasty they may be when fresh. At its own facilities, the company thus obtains a wide range of premium quality extracts characterised by a particularly pure and intense taste. The portfolio contains FTNS (from the named source) flavours from oregano, rosemary, coriander, caraway, cardamom, marjoram, chilli, pepper, sage, thyme and basil. The new Doehler botanical range also includes a selection of natural blossom flavours such as rose, violet, lavender, lotus blossom and hibiscus. In many cultures, flowers are a symbol of beauty, naturalness and health. In the past, it was predominantly the cosmetics, fragrance and pharmaceuticals industries that knew how to use these properties for emotional product positionings. Blossoms have recently been rediscovered for culinary indulgence – and not only in haute cuisine. Food and beverages with a hint of rose, lavender or hibiscus are all real trendsetters today. 2013 saw around 70 new soft drinks with the taste of rose alone, introduced to the global market (Döhler Market Research) – an increase of over 100% compared to the previous year. Hibiscus and elderflower have enjoyed similar success. “Blossom flavours also unlock exciting product concepts – and not only in the wellness segment or in products targeted at women. As a provider of integrated solutions, Doehler has developed inspirational product concepts for the beverage and food industry. The company’s product developments are always built around a multi-sensory product experience,” explains Daniel Courtehoux. Thanks to many years of experience in food and beverage applications, Doehler has a deep understanding of how flavours behave alongside other ingredients in a wide range of applications, packaging types and production processes. This means that they know how to formulate flavours so that your product tastes perfect, along the shelf-life – even under stressful situations such as heat, light and challenging pH values. www.doehler.com BEVERAGE +ingredients","@ID":18}, "PETpatents www.verpackungspatente.de 44 PETplanet insider Vol. 16 No. 01+02/15 petpla.net 2-chamber bottle International Patent No. WO 2014 / 062071 A1 Applicant: Sub Zero International Ltd., Hamilton (NZ) Date of Application: 17.10.2013 2-chamber bottle for storing in the refrigerator / freezing compartment. The products are only mixed at the time of opening / shortly before opening due to a difference in the pressure generated and, resulting from this, the opening up of a diaphragm / narrow point. Versatile label International Patent No. WO 2014 / 060930 A2 Applicant: PET Engineering S.R.L., San Vendemiano (IT) Date of Application: 14.10.2013 The application relates to a number of variations on a sleeve label featuring straps which may be used, for example with straps which can be used, for example, as a carrying strap by pulling over the closure. Closure cap International Patent No.. WO 2014 / 057054 A1 Applicant: Capartis AG, Schaffhausen (CH) Date of Application: 10.10.2013 The international application relates to a screw closure with tamper-proof strip. Improvements have been made to the closure with regard to identifying an opening already made. It can also be applied without any problems to bottles with a shortened neck area. The bottle neck is designed so that it visibly “destroys” the guarantee strip when it is first opened. High volume bottle Disclosure No.DE 102012019629 A1 Applicant: Herzberger Bäckerei GmbH, Fulda (D) Date of Application: 6.10.2012 In order to be able to handle plastic PET bottles with a content of up to 2 litres using one hand only and to be able to accommodate them in the inside compartment on the refrigerator door, a specially shaped bottle is proposed. The front of the bottle is designed to give it a concave curve. Switchover from glass to plastic Utility Patent DE 202012012232 U1 Applicant: Gizeh PET GmbH, Bergneustadt (D) Date of Application: 21.12.2012 Switching over from glass to plastic packaging and any requirement to maintain the external size or the fill quantity calls for a cavity to be incorporated in the container. This cavity may be used to improve stability and be shaped correspondingly. Double wall preform International Patent No. WO 2014 / 077681 A2 Applicant: Heineken Supply Chain B.V., Amsterdam (NL) Date of Application: 13.11.2013 Double-wall preform for generating a highvolume container (content of more than 3 litres). More than 2 materials can also be processed, e.g. coloured layers or layers with a blocking effect aimed at preventing the migration of gases.","@ID":46}, "36 PETplanet insider Vol. 16 No. 01+02/15 petpla.net In our example TP should be (assuming a 5-mm cushion): (65 -5) × 13% +5 = 12.8 or 13mm This is a good starting point that may need adjustment to account for changes in temperature or viscosity. If the transition point value is set too high, the cavity is not filled when the machine goes into hold. This could result in sink marks or even short shots as there may not be enough resin in the mold to account for subsequent shrinkage during hold. If the transition point value is set too low, the cavity is completely filled during injection and the pressure will rise steeply as the resistance of the material in the cavity increases. This could lead to overpacking of the cavity and gate problems. Very thin (2.5mm) and very thick (4.5mm) preforms deserve special considerations. Melt injected into thin mold channels cools down quicker than when it is traveling in thicker channels. Therefore, its density increases during injection and the transition point for these preforms should be set much lower, as far down as 6–8%. Very thick preforms show the opposite behavior. They cool down very slowly and must therefore be run with a transition point set at a higher percentage, up to 18%. When in doubt it helps to study the injection graph (or watch the injection pressure gauge) and note the point at which the pressure increases. This is the point when the cavity is filled and where the transition point should be. 3.2.4 Hold time and pressure During the hold or packing phase the material shrinks and density increases. If no more material was added after injection, this shrinkage would result in voids that are called sink marks. The operator has full control over the pressure, whereas the machine adjusts to a low speed setting without operator input. Hold time is dependent on the wall thickness of the preform and temperature of the melt. The chart in Fig. 3.10 gives values for different melt temperatures. This chart assumes certain cooling water conditions that may not be available on every machine. It should therefore be taken as a starting point only. Most machines feature three hold times, and the overall time should be equally divided among them. Also available are three hold pressures. The first is used to pack the material in the neck finish area. The material has had longer time to cool, and its viscosity has therefore increased. It requires the highest hold pressure. The second controls the body of the preform and is set to a lower value. The third controls the gate area and may be again lower but features the largest difference in possible values because wall thickness in the gate area, gate diameter, and gate cooling all come together to demand a particular setting for optimal gate uniformity and appearance. The maximum injection pressure can be read either on the screen or on a gauge mounted on the injection cylinder. It can be used to calculate hold pressures 1, 2, and 3 as 60%, 50%, and 40% of this pressure, respectively. These values should only be used as starting points and may need adjustments to overcome sink marks or gate problems. 3.2.5 Decompression In either injection system, whether reciprocating screw or shooting pot, the pressure that is present in the hot runner and the cavities must be relieved when hold is finished to allow easy demolding and prevent the material to drool into the cavity once the preform has been removed. This is done by moving the screw or shooting pot backward (“screw pull-back” on the screen) and leaving it there for a period of time (“pullback dwell time”). A distance of 10mm is usually enough, whereas the time depends on the last hold pressure used. Higher Figure 3.10 Recommended hold times versus performed wall thickness. Figure3.11 This machine uses a graphical user interface for the control of injection parameters. (Picture courtesy of Netstal-Maschinen AG).","@ID":38}, "EDITOUR REPORT 15 PETplanet insider Vol. 16 A tonne of virgin material from South Korea costs around €1,000 euros on the market. A tonne of R-PET IV costs €1,200 euros. Enough said.” Palmino Di Giacinto summarised the current position: “The only way we can get round this problem of price is by supplying material of perfect quality, ensuring we have the most modern machinery and investing heavily in a comprehensive range of laboratory equipment. Only by doing all this can we offer our customers maximum support.” www.cier.vomano.com Short cycle times, high shot-to-shot quality, low energy consumption and maximum flexibility. The new XFORM 300 with its unique 6-position post-mold cooling system boosts your output performance for the widest range of preforms. Cooling preforms faster and better, the 96-cavity platform is ideal for large runs and quick mold changes. And it lets you run any mold you want, old or new, OEM-built or not, in total freedom. From ultra-thin walled (with proprietary XMould™ technology) to wide mouth. XFORM 300, low transformation cost, high value. SIPA S.p.A. - Via Caduti del Lavoro, 3 - 31029 Vittorio Veneto (TV) - Italy Tel. +39 0438 911511 - Fax +39 0438 912273 - e-mail: [email protected] www.sipa-xform.com Designed to adapt. Built to last. The new XFORM 300 IMAGINE THE LOWEST TRANSFORMATION COST. IN TOTAL FREEDOM.","@ID":17}, "PRODUCTS 40 PETplanet insider Vol. 16 No. 01+02/15 petpla.net Fogg twins filling bowls for higher productivity Fogg Filler, a specialist in the design and manufacture of rotary filling systems for the liquids industry, has developed a filler that features two filling bowls on a single base, with one capper. The company claims that this combination offers lower initial investment, lower ceiling height, less floor space, and more manageable maintenance. Fogg says that the high capacity filling requirements of slow filling bottles, such as 28mm glass, 750ml wine or spirits packages, can lead to the requirement for one very large filling bowl and a very large capper to match the geometry. However, the capper will run at only about 50% capacity, which means that the other 50% is wasted, simply because of the size requirements of the large filling bowl. Fogg’s solution is to offer the option of twin smaller bowls. It claims that they will fill faster than a single, large filling bowl and utilise 100% of the capper’s capacity, at the same time. The company asserts that this arrangement offers savings of 10-40% in initial investment. Fogg further claims that the twin filling bowls reduce wastage rates. Two F6.2 filling bowls have a combined maximum capacity of 340 US gallons (approx.1300l) while large fillers can exceed a capacity of 400 gallons (c.1550l). This reduction of 15%-20% in volume is claimed to be helpful in maintaining temperatures and in flavour changes. Fogg says that CIP (clean in place) savings can also be achieved with twin F6.2 bowls, compared to a single, large unit. In terms of footprint, the twin bowl layout is approximately 600mm (two feet) narrower and around 1300mm (four feet) shorter than a comparable single bowl machine. Fogg asserts that the smaller floorspace will facilitate more manageable installation into an operating plant and its existing piping, wiring, elevated walkways, other height restrictions and width constraints between other adjacent installed equipment. The twin bowl arrangement also enables two operators can simultaneously work on the filler’s changeover and maintenance. According to Fogg, change parts will be considerably smaller and more manageable. Fogg has a track record and proven technology within its field, which the company asserts helps to reduce operating costs while providing high standards of reliability. www.foggfiller.com","@ID":42}, "BOTTLING / FILLING 29 PETplanet insider Vol. 16 No. 01+02/15 petpla.net 95% market share with Salgam Doganay was founded in 1997. The aim was to fill Salgam, an exceptionally popular juice made of fermented red turnips known then only in the southern part of Turkey, in bottles and make it popular throughout the entire country. Previously, it was common for Salgam to be produced only in households for personal use. We launched a number of sampling campaigns, but during the first few years we were just not able to exceed the annual sales figure of 150,000 liters,” says Rafet Doganay. The bubble burst in 2002. Sales virtually exploded to two million liters. By 2004, sales had already climbed to 5 million liters, then to 15 million liters in 2008, on to 27 million in 2013, and then hit the 40 million mark in 2014. This rapid success led to more companies ‘jumping on the Salgam bandwagon’. Nevertheless, Doganay continues to hold a 95% share of the market. The company benefits from the excellent product quality and the clear leader status. Numerous other products integrated into the product range With a share of 70% share of total sales, Salgam remains the star product of the company’s variety of products. Today, Doganay also offers lemon sauce, lemon juice, grape, apple, and balsamic vinegar, pomegranate syrup, Limonata, and orange juice. This range of products is not to remain the same however. Plans for next year alone include incorporating the production of iced tea and expanding the variety of juices by introducing grape, pomegranate, apple, and mandarin juices. Other new products are planned for the years to come. As for the present products, the company expects considerable sales growth. Five times the current sales figure expected in 2015 for Limonata in GlasPET While Limonata currently ranks second at Doganay with sales of about 15 million liters in 2014, sales figures of at least 80 million liters are expected in 2015 - which would equal five times the current sales figure. Sales of more than 150 million liters are expected in 2015 right from the start for iced tea. For 2015, liter sales in the upper double-digit million range are planned for juices, which according to Remzi Doganay are made from 100% freshly squeezed juice and can be stored bottled aseptically in GlasPET without refrigeration for nine months thanks to a secret, sophisticated production process. 70% of sales in exports by 2020 planned “35% of our sales were already in exports in 2014,” says Rafet Doganay. By 2020, we plan to realize 70% of our sales with exports and to act globally.” “In our opinion, the Campet bottle and KHS aseptic lines play a decisive role in this planned success story,” Remzi Doganay adds. Investment in a second production site In order to expand their production capacity, Doganay just recently invested in a second production site in Adana. In a first step, the two KHS linear aseptic lines, which have been operating to the great satisfaction of Doganay since they were commissioned, have been integrated into the newly constructed production facility. The upcoming third KHS system includes innovative KHS aseptic rotary technology. The first two systems share a common packaging area Each of the existing lines is comprised of an InnoPET Plasmax machine, an InnoPET Blomax Series IV stretch blow moulder, and an Innosept Asbofill ABF 711 aseptic linear filling machine. They share the packaging area. The capacity of both lines is 24,000 bottles/hr. 0.25- and 1-liter size containers are currently being processed. Next year, the 0.75liter version is to be integrated into the container portfolio as well. The still Limonata lemon soda pop is the company’s first product to be aseptically bottled in CAMPET (Turkish for GlasPET). The benefits of this style of container were communicated through TV commercials and are clearly indicated on the neck label. This has already resulted in a large group of GlasPET bottle enthusiasts.","@ID":31}, "BEVERAGE INGREDIENTS 18 PETplanet insider Vol. 16 No. 01+02/15 petpla.net Wild’s innovations for energy drinks. Trendy flavor combinations Fruity Essentials You can get 100% authentic and natural fruit essences with the Fruity Essentials, the second level of the Code of Nature. Included in the portfolio are red fruits, garden fruits, exotic types of fruit and citrus fruits. These are suitable for declaration-free juices and manufacturers can promote naturalness, for example, in beverages containing fruit as well as near-water drinks. “The Code of Nature embraces the full spectrum of our cumulative expertise in matters of naturalness,“ is how Cornelia Weiblen, Marketing Director BU Beverages EAME at Symrise, describes their approach. “At the same it is especially important to us to begin with the customer and the demands of the market. Armed with this knowledge and on this basis we develop beverages concepts that precisely meet the requirements of our customers.” www.symrise.com/de/code-of-nature Energy drinks are making their way into countless new consumption situations and are continuing to drive the market for non-alcoholic beverages forward, thanks to the wide variety available and customized concepts. More and more often, they are being sold as an alternative to classic soft drinks because of their added value and the many different flavors and options to choose from. Wild has developed new cross category concepts and several innovative flavors. Growth in the energy drink sector is still going strong: the market research company Canadean has stated that in 2014, energy drinks will achieve a market volume of 2.4 billion liters in Europe, corresponding to a 5.5% increase versus 2013 figures. The steady growth means that these beverages are moving from being a niche product to a mainstream lifestyle item. A broad target group and multiple usage situations At the same time, energy drinks are making their way to additional target groups and are bringing new life into the market. Energy drinks are not only something that teenagers enjoy: those who have to drive, study or work also appreciate the invigorating effects of these beverages. The new taste generation in particular is interested in appealing flavor sensations above and beyond the standard classics. The trend is leaning more and more towards fusions which combine energy drinks and other segments from the food and beverage sector. Wild’s portfolio includes classic flavors as well as blends with juice and flavored drinks. Wild has expanded its energy range to include the product groups Energy Carbonates and Clear Energizers. From an impulse purchase to a daily thirst quencher With Wild’s new Energy Carbonates concept, energy drinks really allay people’s thirst every day. This new category offers the effervescence of a classic soft drink combined with the invigorating effect of an energy product. Merging these segments allows manufacturers to win over new target groups and generate attention on supermarket shelves. The flavors apple, lemon and cherry cola will draw consumers who want something other than traditional energy drink flavors. Wild’s innovative Clear Energizers range focuses on new target groups and consumption situations. It brings stimulating flavors such as lemon and pink grapefruit to the near water and energy drink segments. Sour and refreshing flavors Throughout Europe, the Energy Plus Flavor category has remained in strong demand, with year-on-year growth of 7.1%. Wild is solidly positioned here with popular flavors such as cranberry, blueberry and lime. Something new in the product palette is the Sour Energy range: Wild has taken up the fusion trend by blending energy drinks with other segments from the food and beverage market. The result: energy products with tart notes such as apple. Sour Energy will not only win over people who love tangy tastes: it will also draw in consumers who look for alternatives to classic energy drinks but still want a stimulating boost. Juice as popular as ever With an increase of 6.5% versus 2013 figures, the category Energy Plus Juice is still going strong in Europe. Their refreshing flavor lets these products stand out from classic energy drinks, making them attractive to new target groups as well. Wild has energy drink concepts in its portfolio which include different juices or juice blends. The juice content can be customized to each beverage manufacturer’s individual specifications. Wild is presenting its refreshing fruity flavors featuring watermelon and lime. Watermelon is a popular flavor in the food and beverage sector. All of Wild’s energy drink options offer manufacturers major potential for further growth throughout Europe, thanks to its creative ideas and well-designed concepts. www.wildflavors.com The trend among energy drinks is towards products which overlap with other beverage segments such as near waters. BEVERAGE +ingredients","@ID":20}, "PREFORM PRODUCTION 20 PETplanet insider Vol. 16 No. 01+02/15 petpla.net New PET Line 5000 for up to 144 cavities Netstal completes PET-Line family on a high Up to ten percent less energy consumption compared to the previous model and even up to 20 percent compared with the competition. One year after the launch of the new model series with PET-Line 2400 and 4000, Netstal is presenting its new PET-Line 5000 for moulds with up to 144 cavities. Testimony to the fact that the company is actually completing its PETLine family on a high. The “Big Boy“ has been developed specially for markets with extremely high output quantities and is designed for moulds where the number of cavities ranges from 96 to 144. Like the smaller models, it offers a number of new developments in the energy consumption, closed loop technology and machine control sectors, including, for example, an energy-efficient adaptive drive unit. This no longer operates at a constant pump pressure but instead can be flexibly adapted to the requirements of applications and cycles. In addition, all the electrical drive motors on the machine are combined within an intermediate circuit so that the braking energy arising during operation can be used elsewhere. Altogether the savings amount to around ten percent of the power requirement compared to the previous model. Of the total costs of a preform, around 80 to 85% represents the price of the raw material for the material processed. Because it is not possible to influence this variable, optimisation as regards the machine operating costs are the medium of choice for converters and bottlers to enable them to remain competitive at an international level. As a result it pays to be energy efficient. The same applies to speed. In the case of the new PET-Line 5000, the lock-to-lock time from opening the mould, taking into account the time needed to remove the preform prior to re-locking, is up to half a second faster than it was previously. For standard applications with cycle times of less than ten seconds, this means an output of ten thousand more preforms per day. This has been made possible thanks to new closed loop technology: this involves the installation of exclusively digital controllers, combining them with the most modern valve technology. The effect of shorter reaction times and higher oil displacement is to bring about faster movement of the mould and to reduce the duration of the machine drying cycle. The drive to achieve greater speeds has also resulted in the incorporation of a robot developed by themselves which is capable of dynamic travel into the mould, even if it has yet to be opened to its fullest extent. It has to be possible to calculate efficiency. In the pilot model for the machine series, the PET-Line 2400 has given Netstal the economic advantage. In the case of one sample application involving a 25g preform fabricated in a 72-cavity mould, the output per hour increases by 13.6%,","@ID":22}, "BOTTLING / FILLING 33 PETplanet insider Vol. 16 Compelling packing and palletizing technology Gökhan Doganay is delighted with the Innopack Kisters SP Basic shrink packer: “It offers us tremendous flexibility and allows us to run production with many different types of packaging with a minimum amount of changeover time.” After robot grouping, the formed shrink packs arrive at the Innopal PBL1NH - a palletizer equipped with level compensation which makes it possible to feed the packs at any height. Each layer is centered from all sides prior to discharge onto the pallet. This results in perfect layer patterns and a high overall stability of the pallet load. The pallet liner inserter goes into action automatically after each layer is discharged. A pallet wrapper located downstream of the palletizer secures the pallet loads. Perfect interaction Remzi Doganay is glad about the way the different machines interact. “For us, this means a high line efficiency of more than 90%. We are already looking forward to our third KHS aseptic line particularly in view of the positive experience we have gained with the installed KHS linear aseptic lines.” Expected soon: the new generation of KHS aseptic rotary technology The new KHS generation of the Innosept Asbofill ASR aseptic rotary machine technology is to be implemented in addition to the already existing machines - albeit mostly in a larger version than in the past because of the up to 36,000 bottleper-hour line capacity. Gökhan Doganay explains that the proven components and methods of the ABF series will be used for the Innosept Asbofill ASR. “This gives us the security we need,” he asserts. For example, the Innosept Asbofill ASR utilizes an aerosol and heating system which is identical to the one found in aseptic linear filling technology, adopts the sterilization principle used here, uses","@ID":35}, "BOTTLING / FILLING 31 PETplanet insider Vol. 16 No. 01+02/15 petpla.net straight to the point and said that we wanted to buy it. It wasn’t until later that we asked about the price and examined the InnoPET Plasmax in practical operation.” It is interesting to note the enthusiasm of the consumers, who learned of this new technology from TV commercials, was so great that many of them have already asked why Doganay doesn’t consider filling water in the Campet bottle as well. Thus, a decision was recently made to launch still water filled in the GlasPET bottle to the market and to purchase a water bottling plant near Istanbul. “We will be starting operations there in 2015 and then also begin exporting in this segment starting in 2016,” Rafet Doganay elaborates. “We are reckoning with sales of approximately 300 million water bottles by as early as 2015.” Innosept Asbofill ABF 711 FS The next station in the line for the coated PET bottles is the Innosept Asbofill ABF 711. Gökhan Doganay says, “This is an excellent machine that enables us to bottle our Limonata completely free of preservatives. With the help of this aseptic system we are able to reliably ensure a long shelf life of products filled in GlasPET bottles.” “It is especially important that the natural taste and flavor of each bottled beverage are retained, as well as the vitamins,” Remzi Doganay adds. The sterile product is stored in an upstream aseptic buffer tank from where sufficient amounts are supplied to the linear machine through a sterile valve manifold connection. This product connection to the linear filler ensures a safe supply of product free of recontamination. A multi-strand CIP system makes sure that the sterile tank, the sterile process engineering equipment, and the linear filler are properly sanitized at the end of production. The product preparation and system cleaning facilities were also supplied by KHS. Ten plastic bottles are placed in each cell support bar of the Innosept Asbofill ABF 711, which holds them by their neck rings and guides them through all processing stages of the machine. Only the bottle necks are contained inside the particularly small 1.5-m3 sterile zone of the Innosept Asbofill ABF 711. Sterilization of bottle exteriors is therefore not necessary. Sterile air is blown permanently into the aseptic zone area and discharged downward by what is known as a positive displacement current via a perforated plate which separates off the aseptic zone. From there it enters the machine room where it is specifically extracted. Dry sterilization is used for interior sterilization. This process involves injecting H 2 O 2 aerosol into each of the plastic bottles through a lance that ends just below the bottle neck. The aerosol is distributed evenly throughout all areas so that even the ribbed areas of the Limonata bottles are reliably reached. The system is excellently suited for sterilizing all bottle sizes and shapes. Even embossed and square bottles and bottles with very structured surfaces are reliably sterilized. “All options for new bottle designs remain open for us in the future,” Remzi Doganay comments. To ensure the greatest possible safety, the H 2 O 2 aerosol is injected into bottles in cycles each in two stations. The displaced gas is able to escape past the lance located in the center of the bottle. Two further cycles are necessary to allow the sterilant to take effect. The bottles dry free of residue after four cycles. A partition separates the area where drying takes place from the actual sterilization process. Another partition is located between the drying and filling processes. The bottles are filled by two-stage, free-flow filling valves. The advantage: maximum aseptic safety, as there is absolutely no contact between the bottle and the filling valve during the filling process. Using the volumetric filling process by means of electromagnetic inductive flow metering ensures exact fill volumes. The filling and capping processes are also separated by another partition through which the bottles pass after filling. The caps, like the bottles, are sterilized with H 2 O 2 aerosol which An Innosept Asbofill ABF 711 is in operation in each of the two linear aseptic lines.","@ID":33}, "EDITOUR REPORT 13 PETplanet insider Vol. 16 25 Years in the service of the environment by Waldemar Schmitke Cier s.r.l. During our meetings with PET processors on our Italy trip the topic “Use of R-PET” tended to be rapidly dismissed with the words “too expensive in Italy”. Reason enough, therefore, to pay a visit to the largest recycling business in Italy with an annual capacity of 30.000t, namely, Messrs. Cier in Castellato (TE). Here in Castellalto we meet Palmino Di Giacinto, Sales Director and Sandra Di Giacinto, Financial Manager. Cier‘s story starts in 1998 with the treatment of PVC post-consumption packaging material (no longer processed today). Then, in 2000, came the launch of HDPE and LDPE post-processing and afterwards, in 2006, the breakthrough into PET postconsumer processing for R-PET flakes. Rounding off the treatment of consumer PET in 2009 was the company’s investment in an extrusion line with IV upgrade and crystalliser for generating R-PET IV pellets for use in contact with foodstuffs. At the site here in Castellalto we find three buildings together with a","@ID":15}]}}
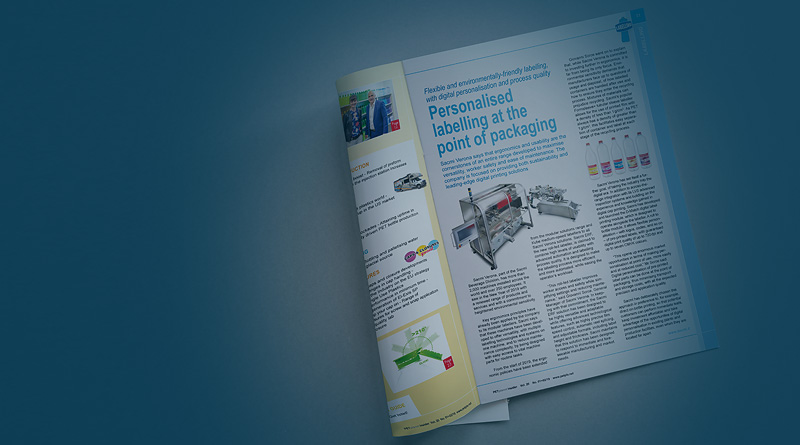