"TRADE SHOW PREVIEW 49 PETplanet insider Vol. 16 No. 03/15 petpla.net West Hall Level 2, Booth:W5673 Capacity expansion and latest developments for recycling Erema North America, Inc., a subsidiary of Erema Engineering Recycling Maschinen und Anlagen Ges.m.b.H., has announced that it is to expand its facilities at Ipswich, Mass, from 1000m² floorspace and three recycling systems to 2400m², and will add an INTAREMA 1108 TVEplus with Laserfilter system to the existing equipment. It will demonstrate the new system on its stand at NPE. The company says that the Laserfilter is particularly suitable for the processing of materials with a high degree of contaminants such as wood, paper, aluminium or copper. Its INTAREMA 605K fully automatic edge trim system, which is aimed at the in-house recycling sector, will be demonstrated at the show as well. The INTAREMA K is described as an intelligent in-house recycling solution that can maintain consistent end product quality, while saving production and labour costs. The new, fully automatic processing system, designed especially for the recycling of PE edge trim, is the successor to the KAG system. www.erema.at Your UV invisible protection our tailor-made UV blockers Booth S26167 High Performance Liquid Colours and Additives repi.com crystal clear 300 to 400nm West Hall Level 2, Booth:W903 Thin-wall drinking vessels Netstal will be demonstrating production of 44oz (1.3 ltr) “stadium” cups with IMLs on a hybrid ELION 3200-2900. The company points out that the production of drinking vessels is highly complex and when producing thin-walled packaging, the ratio of flow path to wall thickness (F/W) demonstrates increasing difficulty as the ratio rises. For the 44 oz cup, the ratio is 300:1. Any slight core shift, i.e. the lack of concentricity between the mould, which forms outer contour of the cup, and the core, which forms the inner contour, has a direct impact on product quality. Netstal says that its best practice, called thin-wall centring, centres the core by means of rheological flow paths and varying melt pressure levels. www.netstal.com","@ID":51}, "MATERIAL / RECYCLING 23 PETplanet insider Vol. 16 No. 03/15 petpla.net What technical innovations can be found inside the SW RTF melt filters? Christoph Wöss: First and foremost the very large active filter areas and the patented partial surface backflush screen changers. These screen changers feature a fully automatic self-cleaning system which, despite extremely fine filtration of 32 μm, allows low pressure losses, high filter capacity and long filter service life. These factors play a considerable part in the outstanding efficiency of the systems and the result is extremely clean recycled pellets. What is the additional benefit for the users as a result? Christoph Wöss: Here it is worth noting in particular the fact that our customers save costs which are often necessary in the case of other manufacturers’ systems due to expensive special filters. Which application fields are recommended in particular for SW RTF melt filter systems? Christoph Wöss: The Erema highperformance filters can be connected directly to the extruder outlet and have been so successful especially for large area ultrafine melt filtration in the production of flat film that other manufacturers of film plants now use the EREMA piston screen changer for melt filtration as standard. I would like to emphasise the process stability to be achieved here. Thanks to the large filter surface and pressure-stable single-screw extruder, unequalled pressure stability upstream of the flat die can be reached compared to other processes, despite a higher level of contaminants in the input material. Together with the patented pre-treatment of the PET flakes this results in an end product with top-quality reproducibility and stability in terms of viscosity, colour and purity. This is why so many of our SW RTF filters are also used successfully for optically ultraclean film applications and have proven their merits even in inline applications which require a stable and smooth process for clean results. These are available in a variety of sizes and output levels, up to the sixpiston system with twelve parallel filter screens. www.erema.at product development caps & closures design high cavitation moulds multi-component moulds closure production systems after sales service competent – professional – inspiring Hoechster Strasse 8 | 6850 Dornbirn | Austria | www.z-moulds.com NPE 2015 March 23rd-27th meet us at booth S24138-04","@ID":25}, "PREFORM PRODUCTION 42 PETplanet insider Vol. 16 No. 03/15 petpla.net Injection parameters, part 18 Practical Guide to Injection Molding of Preforms PETplanet insider is publishing extracts from successive chapters of Ottmar Brandau’s “Bottles, Preforms and Closures”, which was first published by hbmedia. A newly revised version is reissued under the Elsevier imprint. 3.2.8 Postmold Cooling Devices The outside skin of preforms must be cooled to about 50 °C (122 °F) before they can fall onto a conveyor belt. Higher temperatures lead to unsightly blemishes or even deformities. Preforms can however be taken out of the preform tooling at much higher temperatures, up to 100 °C (212 °F). At temperatures above this value, preforms may buckle during ejection. Postmold cooling devices with three or up to six stations take the ejected preforms and cool the outsides with water-cooled take-out tubes. In a typical three-stage robot machine,","@ID":44}, "TRADE SHOW PREVIEW 53 PETplanet insider Vol. 16 No. 03/15 petpla.net IMAGINE FILLING MULTIPLE PRODUCTS ON THE SAME LINE…NOW YOU CAN! Water, juice and soft drinks, all on a single machine? The Flextronic modular platform adapts effortlessly to still or sparkling, clear or pulpy and hot or cold-fill, and easily switches from one bottle neck-size to the other. A revolutionary filling technology that gives you extreme operational flexibility with minimal product loss and downtime at flavor switch. Clean, safe and versatile. Welcome to the new generation of fillers. carbonated still hot-fill cold-fill pulp non-pulp water juice soft drink SIPA S.p.A. - Via Caduti del Lavoro, 3 - 31029 Vittorio Veneto (TV) - Italy Tel. +39 0438 911511 - Fax +39 0438 912273 - e-mail: [email protected] www.sipa.it West Hall Level 2, Booth: W1523 Project part samples with MuCell technology Trexel’s stand will feature a variety of project part samples that use MuCell technology, including examples such as running shoes, packaging and automotive and a new automotive oil pan made with impact resistant BASF PA 6. It is claimed to offer significant cost and weight savings while maintaining the dimensional stability required for a perfect seal against the engine block. The show will see the global premiere of Trexel’s T-100 Series SCF (Super Critical Fluid) Delivery System, which is dscribed as a state-of-the-art gas delivery and dosing system. The system is specifically designed for small shot size moulding applications of 140gr. / 5oz. Small injection moulded parts are typically used in complex mechanisms, electrical connectors or other applications requiring a high level of precision. Visitors will also be able to see demonstrations of MuCell technology in action on a number of other manufacturers’ stands. Examples on display will include a coffee maker panel; automotive centre console with thin-walled parts; a gear cam for bowling sweeper application; light-weighted automotive bezel; and oPTI process lightweight foamed PET bottles. www.trexel.com","@ID":55}, "PET TOP TALK 29 PETplanet insider Vol. 16 No. 03/15 petpla.net You count 5 preforms in 2 . 5 seconds . I guess . PreWatcher I I I count s 50 preforms in 2 . 5 seconds . inspects i know. W W W . I N T R A V I S . C O M / P R E W A T C H E R W A T C H I T A T B O O T H W 2 4 8 9 “Using hydrogen peroxide mist, Predis removes the need for any water and uses only small amounts of chemicals. It is both cost-effective in providing complete decontamination and also offers significant environmental benefits. The systems in use worldwide contribute to sustainability initiatives, with more than 2 billion litres of water already saved compared with traditional aseptic filling systems since their use began.” When it comes to aseptic and ultra clean production, the Combi Predis FMa ensures total sterilisation of the packaging in a single machine offering a competitive production alternative to protect the integrity and safety of any beverage of either high or low acidity distributed at ambient temperatures. Beverage producers can calculate the potential cost savings that could be achieved in producing their beverage in PET on Sidel’s Combi solution with dry preform decontamination. The online calculator is available at www.sidel.com/save-in-aseptic. By selecting the following criteria - production type currently used, the quantity of bottles to be produced per year and the bottle format and weight - the savings can be calculated in terms of PET usage, electricity, water and chemical consumption. Freedom in bottle design With decontamination taking place at the preform stage, the resulting blown bottle has not undergone any thermal stress. This makes it possible for the designers to have total freedom when designing the bottle and allows almost any type of intricate bottle shape - round or square, small or large, in different sizes from 0.2l to 2l, at production rates from 10,000 up to 52,000bph. The continuous by-the-neck transfer of the bottles and the absence of thermal stress also mean there are fewer restrictions in terms of bottle lightweighting. Different typs of caps can be used for bottles, flat and sports caps. The aseptic Combi solution with dry preform decontamination is designed to ensure food safety while being simple to operate and also maintain the flexibility and simplicity required by bottlers. The mantra “Make it simple, keep it simple” comes from the fact that the best warranty for food safety is simplicity, because operators have to run and maintain the line with the relevant and simple Good Manufacturing Practices (GMP). This is why complex configuration or sterilisation is not required at the blowing stage because the preform is decontaminated with hydrogen peroxide (H2O2) before being heated in the oven to activate the H2O2 through the existing preform-heating stage. This results in a reduced risk of peroxide residue remaining within the preform. This efficient solution, including only a few technical features, such as filtered air treatment, UV-c and surface decontamination into the blowing stage, is well-proven in several production facilities with product safety and quality. www.sidel.com","@ID":31}, "EDITOUR REPORT 17 PETplanet insider Vol. 16 Paradiso S.p.A. by Alexander Büchler The first step is always the hardest, so runs the proverb. This is a lesson that Paradiso had to learn when, in 2003, the company, at the time a newcomer to the beverages market, was launched with 2 PET water lines. In the first few years the company relied on attractive prices to sell its products, in the interests of gaining market share. There is no money to be earned through selling “value” water. In 2006 the company decided to enter the highpriced restaurant water market with a glass line and, in 2011, supplemented this with an aseptic line from the manufacturer Procomac so as to be able to supply drinks which enjoyed higher margins. As the consumer is unwilling to accept price increases for “value” water, the company has now established its own higherpriced water brand in the market place. The price for the “value” water is still at rock bottom. Today, in addition to water, Paradiso also supply CSD, juice, iced tea and isotonic drinks under their own brand name and also as private labels. In the water sector, you find yourself with 300 competitors to battle with, in the aseptic sector; by contrast, it is a mere four or five, explained Mr Luca Ravetti plant manager. Along with the filling/bottling plants, Paradiso has also expanded its beverages development activities. This enables the company to react very quickly and flexibly to market conditions. In particular when new flavours from the big brands make an appearance on the market, the private labels are keen to have similar products on the shelves. Unless they develop their own drinks, where new flavours can be launched without delay, creating new flavours with the syrup manufacturers would take too long. www.acquaparadiso.it","@ID":19}, "PREFORM PRODUCTION 46 PETplanet insider Vol. 16 No. 03/15 petpla.net Temperature therefore plays a more important role in AA generation. To keep temperature at a minimum, processors should follow these procedures: Maximum heater adjustment should be 290°C (554 °F). If there are percentage controlled heaters such as those com¬mon for injection nozzles, they should be set at a minimum and only raised for start-up. All thermocouples need to be firmly inserted into the respec¬tive machine parts to avoid false (too low) readings. Injection time should correspond to 10–12 g/s per cavity, i.e., a 15g preform should inject in 1.5–1.8 s to avoid shear stress. Back pressure should be set to a minimum, again to avoid shear stress. The typical range is 15–20 bar (200–300 psi). Screw speed should be set to a minimum. This can be done by measuring the time that the screw is not recovering (turn¬ing) during the automatic cycle. This time should be between 1 and 2 s. If it is longer, screw rpm can be reduced. Copolymers have a lower melt temperature than homopolymers (see Chapter 3.1) and should be exclusively used for the production of preforms for water bottles. Another resin feature should be low IV because high IV increases the melt viscosity of the resin, requiring higher injec¬tion force and thereby increasing shear stress. Typical IV values for water bottle preforms are 0.72–0.76. 3.6.2 AAinWater Bottles The process by which AA may be released from the bottle walls into the beverage is quite complex and both humidity and temperature play a role over time besides the initial AA level in the bottle. Taste tests have shown that consumers can detect a level of 20 to 40 parts per billion (ppb) of AA in their drinks. Starting with the lowest possible AA level is paramount to delay this point in time as far out as possible. Therefore, the initial level should be as small as possible. Experiments have shown that the 40 ppb threshold is reached after 350 days when the initial level was 2.5 ppm but as quickly as 120 days when that level was 3.5 ppm to begin with. Temperature also plays a role. The above numbers were obtained by keeping the product at 22°C (72 °F). Raising it to 29°F (84 °F) reduces the time to get to 40 ppb from 120 to 70 days while keeping the temperature as low as 15°C (59 °F) would extend it to 250 days. This effect can easily be experienced by leaving a water bottle Figure 3.19","@ID":48}, "EDITOUR REPORT 16 PETplanet insider Vol. 16 No. 03/15 petpla.net Piovan S.p.A. by Alexander Büchler “The material used in the manufacture of one in two PET bottles flows through a Piovan dryer.” This is the claim of Giorgio Santella, Chief Marketing Officer for Piovan. And to ensure that this continues to be the case, the company is researching and developing special solutions for the PET industry. The market for the supply of PET material has undergone a fundamental change over the past few years. Previously, 1, possibly 2 different materials were used, but today just one unit needs to be able to handle a very wide diversity of materials. This could mean different types of new products for water, CSD or milk or a very broad range of R-PET as well as new materials such as PLA. Despite the fact that only a short time ago the maxim “the dryer, the better” still applied, AA-critical packaging still demands a certain minimum moisture level; material that is too dry allows the AA content of the preform to increase. This calls for systems that are essentially more flexible than ever before, equipped with more extensive control systems. Here, Piovan is able to draw on its vast reservoir of experience encompassing 10 different application sectors within the plastics industry. Here up to 200 different types of plastics can be accommodated on one machine. However, this experience is only the start point. “No other plastics sector is as demanding as the PET industry. Guaranteeing 98% efficiency of operation, if not more, is not exactly common in any other sector of the industry,“says Giorgio Santella. Piovan guarantees this high level of availability by means of 120 field engineers who, together with a 24/7 service facility, ensure that granulate flows permanently wherever it is required in the world. In addition to increasing flexibility and the high level of availability, the world of PET has for quite some time been keeping a weather eye open on the issue of energy saving. To address this new demand, Piovan launched the Genesys generation of dryers in 2010. This enables average savings of 50% to be achieved compared to similar systems. To meet the growing demand for blenders demonstrating high levels of accuracy for mixing R-PET and virgin PET, Piovan are now offering their new gravimetric blender marketed under the Quantum brand name. This new machine can also be used for mixing PET materials of various densities. The company is also nurturing some new ideas for the dryer. Until now, filters and sieves at the top infill area have been required to ensure dust-free granulate in the dryer, but now a new loading system, PureFlo, ensures that all the dust collects centrally in the filter on the vacuum pump, thus eliminating the laborious maintenance and cleaning of filters in the production hall. www.piovan.com Alimpet S.r.l. by Alexander Büchler Alimpet in Borgolavezzaro processes PET bottles into flakes and granulate. Like all the recyclers in Italy they buy in the bottles collected and pre-sorted through the National Consortium of Plastic Recyclers (CO.RE.PLA). This consortium only sorts on the basis of colour without taking into account previous contents of the container. As a result it may well happen that bottles that formerly contained foodstuffs are included in the pressed bales. Current legislation in Italy, however, decrees that any packaging used for foodstuffs must be derived from packaging previously used for foodstuffs. This legislation has to be strictly observed. Advances in processing technology now mean that high quality drinks bottles can now be manufactured from recycled PET shampoo bottles. For Alimpet, this means that they produce only PET material for non-food applications even though they have had the appropriate certificated Erema foodgrade equipment in their portfolio for the past 4 years. Luca Bozzalla, Quality Manager, is hoping for a change in the legislative position, but this can take some time in Italy. www.aliplastspa.com","@ID":18}, "EDITOUR REPORT 19 PETplanet insider Vol. 16 market. After the introduction of the PET-Line 2400, there was an increase in questions from customers using 48 cavity preform moulds on old HP preform machines about compatibility with the new preform system. Otto Hofstetter’s response was: “OK, we will create the necessary interfaces for operation on a PET-Line 2400.” China The service unit in China with its complement of at the moment 5 employees has now been in operation for a year. The work carried out here consists primarily of hot runner overhauls for the Chinese market and spare part deliveries out of the Chinese warehouse. The parts are all produced in Switzerland. There are no further steps envisaged towards localised manufacture of moulds and mould components. Thinking is along different lines. According to Otto Hofstetter: “We are looking to produce the frame moulds here in Switzerland in advance and ship it to our warehouse in China by sea fright. Once the order from the Chinese customer is placed, we will produce the insert groups here in Switzerland and fly the parts out to China. Then, we complete the whole preform mould at our facility in Shenzen and deliver it to Netstal Haiyan or direct to the customer. In this way we safeguard the level of quality implied by ‘made in Switzerland’ and do not experience any disadvantages in terms of delivery time by comparison to local suppliers.” To conclude our visit, Otto Hofstetter proudly shows us the award certificate for second place in this year’s competition between businesses in eastern Switzerland issued by the Swiss Venture Club (SVC). 150 medium-sized companies (primarily family-owned companies) in eastern Switzerland were assessed on the basis of their products and innovations, their company culture and quality of employees and management as well as their sustained success. And the jury’s main reason for awarding second place out of 150 companies was the outstanding performance of Otto Hofstetter AG in doing successful international business for almost 60 years as well as the company has trained hundreds of apprentices over all the years. Otto Hofstetter AG knows how to position itself in the face of powerful major concerns and, despite a share of exports of more than 95%, is continuing to manufacture in eastern Switzerland. We express our thanks for the meeting and resume our journey home. www.otto-hofstetter.ch","@ID":21}, "EDITOUR REPORT 14 PETplanet insider Vol. 16 No. 03/15 petpla.net Additives AA Reducer, specially for mineral water UV Absorber, UV radiation absorption up to 300-400nm IV Enhancer, improves the mechanical characteristics of a bottle made with R-PET Anti Yellow, reduces the yellow haze in preforms, extruded sheets and R-PET Blowing Additives, improve blowing characteristics and allow energy saving especially for thick-walled preforms Optical Brighteners, improve the brilliance of PET bottles and sheets Process Aid, allow process enhancement, better preform quality and storage optimisation. Colour Barriers Protect the contents against UV radiation, visible light degradation and the negative effect of oxygen. PET packaging applications for beer, juices, wine, food, and milk. Equipment Dosing units for dispensing and flow control of Repi products Light Meter, for light transmission measurement on opaque, semi-transparent and transparent preforms, before the blowing stage. This allows a more scientific alternative to the visual control in all coloured preform ranges. We extend our thanks for this interesting overview of the PET market from the point of view of a colours and additives supplier. www.repi.it f.l.t.r.: Filippo and Ferruccio Angiolini in front of the Editourmobil Nuova S.A.MI.CER. S.p.A. by Alexander Büchler The Sem Group operates a total of 4 water bottling plants in Italy. We visited the Fonte Ventasso facility situated in the heart of the mountains. This is a small operation that bottles some 110 million litres of water per year, using approx. 75 million bottles. In order to be able to survive in the tough Italian water market, the company operates a strategy of cost optimisation. As part of this strategy they have reduced the weight of the 1.5l bottle from 32 to 23 grams over the last 17 years. f.l.t.r.: Giovanni Brignoli, Siad Compressor Division Food & Beverage Product Leader and Marco Bassi, Siad Compressor Division Food & Beverage Application Engineer in front of the Vito compressor One special feature of the operation is the production of water bottles for use in vending machines. Some 50% of production finds its way to the consumer via automatic machines. These bottles are not only designed like normal bottles to withstand being stacked one on top of the other (top-heaviness); they also need to be able to withstand a certain stacking pressure when in the horizontal position. The attention focused on reducing the weight of the bottle has to be balanced by giving a more in-depth consideration to this stacking pressure. Optimisation is ongoing in bottle design, and the company has also been looking at the potential for savings in the production process. With the modern Procomac and Sipa block-format filling plants with a capacity of 16,000 b/h, the lightweight bottles can be reliably produced and filled. The company has uncovered potential for savings in energy consumption. The biggest consumer of energy on the production front is the compressor. For this reason they have now adopted the new Siad Macchine Impianti Vito compressor with which they have","@ID":16}, "TRADE SHOW PREVIEW 48 PETplanet insider Vol. 16 No. 03/15 petpla.net NPE Orlando, Florida, March 23-27, 2015 For the second time, after 40 years in Chicago, IL, the NPE will take place from 23-27 March, 2015 at the Orange County Convention Center in Orlando, FL USA. The triennial international plastics exposition is organised by The Plastics Industry Trade Association (SPI). Covering an area of about 1 million m2, the exhibition will be showcasing the market leaders in the industry. In addition to about 600 items of equipment, 400 exhibits will be showing off their paces. With 60,000 industry professionals expected, the exhibition is something of a barometer for the recovery in the US economy. NPE can be seen as the largest plastics industry event in 2015 and target plastics applications in building and construction, automotive, medical and consumer and packaging. As readers of the PETplanet Insider you will be particulary interested in PET, so our preview will give you a brief idea of what awaits you on the 1 million m2 exhibition space in field of PET. We will be delighted to welcome you to the Editourmobil at our booth South Hall – S21189! www.npe.org West Hall Level 2, Booth: W618 Light weighting and quality control Agr International will display its latest developments aimed at achieving aggressive lightweighting goals while maintaining high quality. The Pilot Profiler with Process Pilot automated blowmoulder management system interfaces with the blowmoulder to provide precise material thickness distribution management and defect detection for PET bottles, while offering hands-off blowmoulder control. The company says that the system offers bottle producers the ability to aggressively reduce bottle weight while ensuring that the material is distributed appropriately. Agr claims that the Process Pilot system enables the consistent production of high-quality bottles regardless of operator skills, environmental changes and preform variations. Pilot Vision, Agr’s vision-based inspection system that mounts inside the blowmoulder, is designed to offer manufacturers a means to critically evaluate even the lightest preforms and blown bottles for defects that may compromise the quality of the finished product. OptiCheck, a compact and powerful vision system that is designed to manage quality on HDPE and similar containers, features a new level of vision-based quality management for rigid plastic containers transported on a tabletop conveyor. The system can be configured with up to 12 cameras and can provide comprehensive inspection for the entire container, including seal surface, sidewall, base and label defect detection as well as laboratory-precision finish gauging. OptiCheck is designed for manufacturers that produce bottles in a wide range of shapes, sizes, materials and colours. www.agrintl.com West Hall Level 2, Booth: W2143 “Next-generation” material handling, processing and proofing Conair will unveil several brand-new products at NPE 2015, including a “next generation” system that uses machine vision to help prevent material contamination due to operator error. Material Vision Proofing (MVP) includes a motorized camera that automatically confirms that the connection between material sources and destinations has been made correctly and conveying can begin. Users of the new modular ESE Series EarthSmart central chillers can install a single chiller initially and then add up to a total of six modules, for cooling capacity of up to 960 tons. All units – up to a total of 12 refrigeration circuits – can be connected to a single control interface. Systems can be water or air-cooled. Process fluid for EarthSmart Adiabatic Cooling Towers circulates in a closed loop through tubing in the tower and is thus isolated from contamination and evaporation. Eleven models are available to handle nominal flow rates, from 45 gal/min (170 l/min) up to 510 gal/min (1930 l/min) of process fluid (35% ethylene glycol). Conair says that its MicroWheel Desiccant Dryers are the smallest desiccant-wheel dryers available and offer an alternative to compressed-air dryers and small twintower units. The company asserts that they are particularly suitable for medical processors and others running small quantities of expensive engineering resins. They are available in two basic models: MW1 and MW2. They make use of brushless blowers with speed control built in in porder to facilitate the right process air flow for different resin volumes. Each model is available with several different hopper capacities. The MW1 units can support hoppers of 0.2-cu-ft (5.7-l), 0.5-cu-ft (14.2-l) and 1.0-cuft (28.5-l) capacity. Including the hopper, they range in height from 19.5 in (495mm) to 27.7 in (704mm); the largest weighs 106lb (48kg). www.conairgroup.com","@ID":50}, "www.npe.petpla.net , / 0 Premium Sponsor Sponsors Toronto Québec New York Atlanta Orlando Chicago Denver Las Vegas Seattle Calgary Montréal Los Angeles San Francisco Vancouver Dallas New Orleans Phoenix Washington, D.C. Boston Detroit Halifax Kansas City Oklahoma City Albuquerque NPE 2015 - The North American Road Show The survey of PET markets worldwide by our Editourmobil is moving into the next phase! This year we find our team of intrepid adventurers from PETplanet landing on the North American continent. The Columbus PET Bottling Team under Captain Alexander Büchler, First Mates Kay Barton and Waldemar Schmitke, together with Second Mate Anatol Hanau, will first of all be steering a course for the east coast of Canada and then tacking southwards via the east coast of the USA as far as Orlando, Florida, where the NPE 2015will be waiting. Here, on the PETplanet exhibition stand (S21189 in the South Hall) between 23rd and 27th March, the crew will be displaying all the PET treasure collected to date. After the NPE comes the second section of this research expedition and the team will be exploring the markets of the west coast of the USA followed by the west coast of Canada. The figures relating to this tour speak for themselves: a distance of around 17,000 km and approximately six months of this exciting adventure will be waiting for you! And, as always, you will have the chance to accompany the crew interactively. Follow the complete tour on our weekly travel blog under npe.petpla.net and contact us for an editorial walk on the wild side around your own bottling plant, PET processing plant, closure cap production facility, material manufacturing or recycling plant. It is YOU who are our story. Cast off ! Part 1 The worldwide round trip with","@ID":43}, "MATERIAL / RECYCLING 21 PETplanet insider Vol. 16 No. 03/15 petpla.net then rinsed twice with fresh water, dried to less than 50ppm moisture and injection moulded into 3mm thick plaques. Samples of flake from each of the exposure time periods was measured for IV (intrinsic viscosity) to determine if Solar UV caused any loss in molecular weight. The moulded plaques were also measured for IV, colour and haze. The data clearly shows that exposure to UV radiation was very damaging. Sample flake was measured for colour before and after the 12-month exposure to determine if any obvious yellowing occurred and it was found that the level of yellowing was not significant. It became so only after the weather-exposed PET had been subjected to the melting required for moulding the plaques. PET reclaimers extrude washed and cleaned flake into pellets, not plaques. If their bottles are stored outside and exposed to UV radiation, an increase in yellowness resulting from the extrusion process can be expected. Further yellowing will occur when pelletised rPET is blended with virgin PET resin and melted again, during preform manufacture. Sunlight exposure effects on the IV of PET Measurement of the cleaned and washed flake samples found decline in IV of about 0.04 dL/g over 12 months. This same molecular weight loss was seen when the weathered flake was injection moulded into the 3mm plaques. The degree of IV loss increased to ~0.06 dL/g when flake was melt-processed into 3mm plaques. Effects of sunlight exposure on PET colour and haze L* indicates the lightness of the sample: 100 is very white and 0 is black very dark. The injection moulded plaques made from weathered bottles show a definite reduction in L* over time. Virgin PET bottles will typically have L* values ranging from the high 80s to the low 90s. Bottles made with weather-exposed recycled PET will show a reduction in L* values; they are less clear to the eye and look duller. The diamonds on the graphs show the effect of two months’ exposure to fluorescent light, after the bottles were moulded into plaques. While they exhibited a measureable decrease in L*, direct sunlight had a much more significant and pronounced effect. 1 D. Hayward, The Effect of Contaminants on Yellowness in Recycled PET, APR presentation, Feb., 16, 2006 3 Jovan Radulovic, Degradation of Polyethylene Terephthalate in Natural Conditions, Scientific Technical Review, Vol. LVI. No. 2, 2006 4 S. Venkatachalam, Shilpa G. Nayak, Jayprakash V. Labde, Prashant R. Gharal, Krishna Rao and Anil Kelkar, Degradation and Recyclability of Poly(Ethylene Terephthalate), Reliance Technology Group, Reliance Industries Limited, B4, MDIC Industrial Area, Patalganga, Raigad District, Maharashtra State, India 5 Yu. S. Akishev, M.E. Grushin, A. I. Drachev, V.B. Karalnik, A.V. Petryakov and N.I. Truskin, The Open Plasma Physics Journal, 2013, 6,(suppl 1: M4) 19-29 b* denotes the degree of chromaticity from yellow (+b*) to blue (-b*). The increase in yellowness on moulded plaques was very significant after only one month of exposure. Beyond three to four months the effects of UV, while still significant, were not as dramatic as during the initial months. As was the case with L*, yellowness development was not as significant from the fluorescent light. The effect of the sunlight exposure on the haze of the molded plaques was minimal. The control plaque showed haze values of 9.9%, while the 12 month weathered PET haze dropped only to 9.5%. This study demonstrates that exposing bottles to sunlight in a humid environment can have a severe effect on the L*, b* and IV properties of recycled PET. Exposure to UV radiation, whether in external bale storage or even through exposure to fluorescent lighting in retail stores, should be considered as another contributor to rPET quality degradation. www.plastictechnologies.com","@ID":23}, "MATERIAL / RECYCLING 20 PETplanet insider Vol. 16 No. 03/15 petpla.net Shedding more light on rPET Yellowing by Dr. Francis M. Schloss and Ms Julie Brown, Plastic Technologies, Inc. The amount of recycled PET (rPET) used in rigid packaging applications is limited because of the yellowness it causes. The source of the rPET has an influence on yellowing; depositgrade materials typically suffer less than kerbside-grades. Residual levels of nylon trapped in PET flake after washing and cleaning cause considerable yellowing when the rPET is extruded and additives such as ultraviolet (UV) light blockers, slip agents and acetaldehyde and oxygen scavengers can all contribute to yellowing as the rPET is subjected to additional melt processes. A study by Phoenix Technologies LLC into the effects of label adhesives found that they also could be a significant contributor, if not effectively removed from the flake during the cleaning process1. The effect of UV radiation, however, has not been widely addressed. PET is sensitive to UV light, especially at elevated temperatures, under high humidity, and in the presence of oxygen-all of which are present when PET bottles are exposed to the weather. UV radiation is found in the electromagnetic spectrum at wavelengths from below 100 up to 400 nanometres (nm); the UVA segment of the spectrum represents the greatest amount of UV radiation that penetrates the atmosphere and reaches the Earth’s surface. This long-wavelength UV radiation is strong enough to cause chemical reactions and is responsible for the damage plastics experience when exposed to the elements. Free radicals created by UV within the plastic cause degradation that is compounded by the presence of oxygen in the air leading to polymer chain breakage. The result is discolouration, embrittlement and cracking. The addition of antioxidant and UV absorbers can help to stabilise and prolong the material’s useful life but PET bottles do not normally contain these additives. Published papers that describe the degradation effects of UV light on PET3-5 have focused on the degradation in the article being studied, not what happens to PET’s properties when recycled. UV radiation above 320 nm will pass through unprotected PET. Products that need protection will either have UV-blocking full-sleeve labels or will have UV absorbers added during manufacture. Only a small number of PET bottles in the market contain UV absorbers. While PET bottles and their contents do not experience significant exposure to sunlight, bottles under storage after manufacture as well as product-filled bottles sitting on a store shelf can be exposed to artificial light sources that can also emit low levels of ultraviolet light. Exposure of PET bottles to sunlight is most likely when bales of PET bottles are stored outside, awaiting recycling. This study, which used two-litre commercial-grade PET bottles, was undertaken to understand the effects weathering would have on PET bottles exposed to Toledo, Ohio weather for one year. This resin used to make the bottles did not contain any UVabsorbing additives. Virgin bottles were crushed, stacked five to six deep and placed in uncovered open-sided crates, to afford maximum exposure to the elements. The crates were placed on the roof of the Plastic Technologies, Inc. building in early January. Every three months, the bottles were agitated so that those on the bottom were able to move to the top or outside edges. Another set of bottles was stored indoors approximately 18-inches under a fluorescent light source for two months. A control set was stored and protected from light exposure. Throughout the year, bottles were periodically taken off the roof to study the effects of sunlight and weathering. Each set of bottles was ground through a 3/8” screen into flake, which was then aggressively washed at 88°C for 15 minutes in a solution of 0.3% Triton X-100 and 1.0% caustic (NaOH). The flake was","@ID":22}, "TRADE SHOW PREVIEW 51 PETplanet insider Vol. 16 No. 03/15 petpla.net West Hall Level 2, Booth:2703 Increased speed for PET and PP production Milacron will be presenting its range of products and brand portfolio on a single, 2323m² stand, which will showcase technology from brands including Machinery, Mold-Masters, Uniloy, DME and Cimcool. Milacron says that its new servo-hydraulic M-PET 300 offers higher speed, greater flexibility and lower energy consumption than its predecessors. In the production of PET and PP preforms. The system operates with Milacron’s Preform Tooling, as well as with existing industry tooling solutions. The company will be giving the American premiere of its Klear Can product line, which it claims offers plastic storage solutions for food and beverage packaging previously dominated by metal and glass products. Milacron’s new Ferromatik 580 machine is available in nine sizes, from 120 to 650 metric tons of clamping force. The Ferromatik machine platform has options for single-component, multi-component, mono-sandwich, co-injection and cube moulding with electric, hydraulic and hybrid drive options. The modular design offers a wide range of customized solutions. The Roboshot 165 LSR moulding cell is the company’s injection moulding solution for multi-material moulding of both thermoplastic and thermoset materials using an Electric machine, an E-Multi secondary injection unit and a Varian rotary turntable. The new, all-electric system uses a combination of nylon injection with liquid silicone rubber (LSR) over-moulding for precise shot-to-shot repeatability. The Summit-Series is Mold-Master’s new, premium hot runner line. The series offers new valve gating methods using servo controlled actuators. SmartMold technology enables moulders to see more mould details than were previously possible. Contactless wet cycle counting, uptime and cycle time sensing, as well as variations from standard specification can all be sensed and recorded. Milacron stand will also showcase products and technology for PE pipe, large mould bases, quick-change insert moulds and automotive product lines www.milacron.com [email protected] Tel: +90 212 695 50 00 Fax: +90 212 694 97 24 .com Caps & Closures West Hall Level 2, Booth: W643 New closure solutions Sacmi will be displaying a fully functioning, optimised version of its CCM 48 continuous compression moulding machine, fitted with the COOL+ mould for the manufacture of one-piece CSD caps. The company says that this solution offers reduced energy consumption and very low cycle times as well as optimum cap size and weight. The machine can produce up to 2000 light caps/hr, in mineral water configuration. The new COOL+ mould features a modified liquid coolant circuit inside the mould, which is claimed to significantly reduce total cycle time. The CCM48 will be demonstrated with Sacmi’s one-piece HDPE neckfinish 1881 CSD cap, which will be produced at a cycle time of less than 2.4 seconds, allowing output rates of 1200 caps/min. www.sacmi.com","@ID":53}, "PETpatents www.verpackungspatente.de 64 PETplanet insider Vol. 16 No. 03/15 petpla.net Opaque, multi-layer container European Award of Patent No. EP 2641837 B1 Applicant: Sociedad Anonima Minera Catalano-Aragonese, Zaragoza (ES) Registration date: 20.3.2012 Design and process for preparing an opaque multi-layer PET container from a preform. The different positions allow for the selective blocking of light on different wavelengths. Sprayer with lock European Patent No. EP 2735526 A1 Applicant: TECHNIMA, Nersac (FR) Registration date: 25/11/2013 The spray head of an aerosol incorporates a lower section which, by deploying a twisting action relative to the upper section, prevents any possibility of the actuating button being pushed downwards. In this way accidental operation during storage/transport can be prevented. Plastic Containers International Patent No. WO. 2014/082696 A1 Applicant: Alpla Werke Alwin Lehner GmbH & Co. KG, Hard (AT) Registration date: 17/10/2013 The base form of a plastic PET bottle for containing a carbonated beverage or a product that is filled under slight excess pressure needs to be specially shaped. If there are any deformations they must not be permitted to affect robustness or stability. Bottom shape of a PET bottle International Patent No. WO. 2014/083255 A1 Applicant: Sidel Participations, Octeville sur Mer (FR) Registration date: 11/13/2013 The bottom of a PET bottle requires a special shape in order to ensure its ability to achieve optimum accommodation of the deformation forces that occur as a result of increases or reductions in pressure and also its ability to deform appropriately without any loss of stability or robustness. Aseptic closure International Patent No. WO. 2014/088811 A1 Applicant: Abbott Laboratories, Abbott Park (US) Registration date: 11/20/2013 Screw cap for mounting on a plastic container for products which are preserved by heating. The closure is not damaged by heat and retains its properties. Dual-removal facility International Patent No. WO. 2014/086719 A1 Applicant: L’Oreal, Paris (FR) Registration date: 02/12/2013 The closure of a cosmetic container not only allows extraction via a kind of pipette but the contents can also be discharged using the container as a hand-operated pump sprayer.","@ID":66}, "PREFORM PRODUCTION 47 PETplanet insider Vol. 16 No. 03/15 Please order your copy at the PETplanet insider book shop: https://petpla.net/books Bottles, Preforms and Closures A Design Guide for PET Packaging Second Edition by Ottmar Brandau € 115,00 180 pages © Copyright Elsevier 2012 * This article was published in Bottles, Preforms and Closures, Ottmar Brandau, Chapter 3.2. Copyright Elsevier 2012 on the dashboard of a car for a few weeks during the summer months. The water in this bottle will taste stale and have a light, unpleasant sweetness to it. Water bottlers have decreased the amount of AA they accept in their bottles. While 10 years ago 6 ppm was widely accepted some companies now demand levels as low as 1.5 ppm. Machine manufacturers have responded by fine-tuning screw and hot runner design and are able to deliver preforms at those levels. Besides the previously mentioned design optimizations a resin inlet temperature at the extruder throat of the injection machine is also important. Best results are achieved by having the resin at 164 °C (327 °F) at the inlet. Because resin in the lower part of the dryer is some¬what cooler than resin in the upper parts, and may also cool down on its way from the dryer to the extruder throat, the dryer should be set to 170°C (338 °F). Ideal placement of the dryer is directly above the extruder rather than standing beside the machine. This will minimize the cooling down effect during transport. 3.6.3 AA-level Measurements There are two ways to measure AA level. Most common is the groundcomparison method, bottles, or resins are cut into small pieces and ground up toparticles smallerthan 1mm. Inorderto avoidcreatingAAduringgrinding, specimens are cooled down with liquid nitrogen before entering the grinder. The ground material is then placed in a closed glass vial and heated to 150°C (302 °F) for 30minutes. The thus-prepared sample now contains headspace withAA in it, and it is this gas that is being measured in a gas chromatograph. The other method uses blown bottles. These are purged with nitrogen and stored for 24hours.Then a fixed gas volume is extracted with a syringe and measured in the gas chromatograph. It is apparent that both procedures are cumbersome and timeconsuming. With the development of 144-, 192-, and even 216-cavity preform injection tools, it is outright daunting in its scope.A more efficient method is to check only the so-called “hot cavities.” In Chapter 2.5.3 the mechanics of viscous heating has been explained, the fact that the resin heats up unevenly as it moves through the barrel and hot runner channels. Although this has undesired effects in injection stretch blow molding with respect to the bottles, in injection molding the effect is that the preforms in some cavities are always warmer than the majority of the others. This higher temperature also increases the AA level in the affected cavities, and fortunately it is always the same cavities that show this behavior. After establishing the performance of all cavities, labora¬tory personnel can concentrate on the “hot cavities” and still make valid assumptions about the AA level of the entire tool.","@ID":49}, "TRADE SHOW PREVIEW 54 PETplanet insider Vol. 16 No. 03/15 petpla.net designed by Moretto West Hall Level 2, Booth:7371 Plastics processing ancillary equipment Italian company Moretto S.p.A. has established a new North American subsidiary, based in Columbus, Ohio. Its stand at NPE 2015 will be focused on the company’s Eureka processing system, which will consist of its Flowmatik airflow management and distribution system, OTX hopper drier and X Max drier. Moretto says that the system can process 10,000 to 12,000 kg/h of material in compounding, extrusion and PET processing. The core X Max drier incorporates a multi bed single molecular sieve desiccant system providing constant –65°C to –85°C dew point. The machine on show will incorporate a multistage centrifugal blower, developed in cooperation with Padua University. Up to 10 X Max driers can be combined to provide up to 20,000 m3/h airflow rate. The Flowmatik airflow management unit manages demand across the entire bank of driers as well as sharing air with up to 32 truncated cone shaped OTX (Original Thermal Exchanger) hopper driers. The OTX hopper drier is available in 28 sizes. www.moretto.com","@ID":56}, "EDITOUR REPORT 18 PETplanet insider Vol. 16 No. 03/15 petpla.net f.l.t.r.: Stefan Zatti Divisional Manager Sales & Marketing, Waldemar Schmitke, PETplanet, Otto Hofstetter, Managing Director, in front of the Editourmobil on the forecourt of Otto Hofstetter AG in Uznach Switzerland PET is for us the past, present and future by Waldemar Schmitke Otto Hofstetter AG Having crossed the Alps on our way back from Italy in the Editourmobil, we make a stop for what will for the time being be our final meeting on this section of the tour - at Otto Hofstetter AG in Uznach in Switzerland. This family concern is one of the pioneers in PET mould making. PET moulds have been built here in Switzerland for more than 35 years using mould and mould construction technologies that have themselves existed for over 50 years. level of capacity on a country-specific basis and, secondly, the company’s partner on the machine front, Netstal, who have, with their PET-Line 4000, a machine system with competitive potential in this segment.” He went on: “30% of mould deliveries are handled through Netstal systems business and the remaining 70% are direct customers.” With the new PET-Line 2400 from Netstal, Hofstetter are expecting a significant increase in competitive capability in the 72 cavity sector. The 72 cavity preform mould developed specially for this machine is in accordance with the latest state-of-the-art technology and the insert groups are designed to be compatible with the 128 cavity mould. An expansion of the horizontal preform machines tailored to a 48 cavity preform mould would be desirable. However, Netstal are using a Krauss-Maffei “PETform” vertical machine for this. Nevertheless, there are currently no plans at Hofstetter for vertical construction preform moulds. The service sector, made up of overhauls, refits and upgrades, is showing encouraging growth. Citing Russia as an example, Stefan Zatti reported that BPF neck finishes are still a predominant feature of the market. Conversion to the more lightweight finish is only a gradual process. But instead of using the lightest version, PCO 1881, the choice tends to be predominantly in favour of PCO 1810 because the further processing lines are not yet being designed for this. Hence there is still major potential for refits on the Here we meet Otto Hofstetter, the Managing Director and Stefan Zatti, Division Manager Sales & Marketing. The company employs 200 people and has a turnover of approx. 52 million CHF. Of the 200 employees, 23 are apprentices, as Otto Hofstetter is at pains to emphasise: “Everybody is looking for skilled personnel but only a few are prepared to train them; the training of young people is part of our company culture and at the same time it also helps to safeguard long-term quality within the company“. Hofstetter have specialised in moulds for packaging products in the high-performance segment and PET preform applications. Here the PET moulds dominate with a total share of 70% of turnover. The company’s capacity is approx. 50,000 mould inserts per year. The fact that Hofstetter will also be opting for PET in the future is reflected in their most recent investments. It is impressive to see how the site has changed and not only as a result of the construction works; the fleet of production-machines has gradually been extended to provide a higher level of automation. Otto Hofstetter continued: “With our investments in machinery we have not only increased the degree of automation, but also our in-house manufacturing.“ He went on: “Slide bars and hot runner parts used to be bought in; nowadays we make them ourselves. In addition, we have extended the frame - mould manufacturing facility even further. All in all, this is increasing our flexibility and helping to keep the know-how in the company.” The risk is, of course, problems with capacity which could result from a change to the market, but Hofstetter continue to have faith in the PET market and in their own performance capability. The company has already experienced this in 2013. Deliveries to China fell between 2012 and 2013 more than 50%. Since then, by the first quarter of 2014, the shortfall had been compensated by markets such as Russia and Middle East by increasing operational group deliveries to major customers. Preform Moulds As far as the new moulds are concerned, today it is the 96-128 cavity models that dominate with a share of 80%. Stefan Zatti takes up the story: “The reasons for this can be found firstly in the beverages market that is geared to this","@ID":20}, "PET TOP TALK 28 PETplanet insider Vol. 16 No. 03/15 petpla.net Dry preform decontamination technology Growing forward… A Predis review After a good trading year 2014 three companies talking about their new and approved technologies. Here are the exciting growing strategies and product developments for 2015 of Sidel, GDXL and Piovan. Worldwide sales in 2014 of Sidel’s Predis dry preform decontamination were doubled, compared to the 2013 figures. In this growth, Predis has supported produce beverages safely while reducing the costs and improving the environmental performance of the bottlers who have invested in it. Fifteen years ago, Sidel recognised that it was simpel and safe to decontaminate the preform, being smaller and having a single straight surface, rather than the bottle. Sterilising the preform is an appoved method for producing sensitive products safely. When the dry preform decontamination solution was launched in 2006, the market was dominated by traditional solutions based on wet bottle decontamination. Predis became the accepted standard for the beverage industry and Sidel has took a leading position in beverage production technology and solutions for liquid packaging. The near doubling of sales compared with the previous confirmed an endorsement of this technology by beverage and dairy companies, many of which are producing leading brands. Sidel’s Vice President of Product Management, Alessandro Paini, comments: “With over 40 years’ experience in aseptic beverages and dairy bottling solutions, Sidel enjoys a leading position in production technology and solutions for liquid packaging. Predis protects brands, ensuring complete product integrity and safety. It can also assist in the more natural reformulation of sensitive products that previously required the addition of preservatives to maintain food safety. It is the ideal solution for products distributed at ambient temperature and, when products are refrigerated during distribution, can actually extend shelf life.” It is a success that the technology has already brought to bottling lines by complying with the hygienic design requirements for safe beverage and liquid dairy production. With around 19 billion safe bottles produced worldwide to date and more than 90 production lines equipped with preform decontamination, Sidel reached a high level of customer satisfaction that is an indicator of the reliability of the technology. In 2014, the investments in Predis came from throughout the world, from China to South East Asia, from Europe to the Americas. Proven environmental and cost benefits As fully dry systems, Predis and Capdis enable the 100% decontamination of all types of preforms and caps within an integrated blowfill-cap solution. Mr Arnaud Poupet, Sidel Product Manager for Predis: Food safety for beverages applications The Sidel Predis systems sold in 2014 will be used in the bottling of a very wide range of products, from juice and ready-to-drink beverages, isotonics and functional drinks, mineral, flavoured and coconut waters, to liquid dairy products including UHT white milk. This demonstrates the production versatility of this dry preform decontamination in terms of applications, whether it is used in aseptic or ultra clean bottling facilities. It may also be combined with Sidel Capdis™ for the sterilisation of caps. To provide the flexibility to meet many varied applications, Sidel Predis has been sold in various equipment configurations last year, mainly in the Sidel integrated aseptic blow-fill-cap Combi Predis FMa.","@ID":30}, "imprint EDITORIAL PUBLISHER Alexander Büchler, Managing Director HEAD OFFICE heidelberg business media GmbH Häusserstr. 36 69115 Heidelberg, Germany phone: +49 6221-65108-0 fax: +49 6221-65108-28 [email protected] EDITORIAL Heike Fischer Gabriele Kosmehl Kay Barton Michael Maruschke Ruari McCallion Waldemar Schmitke Wolfgang von Schroeter Anthony Withers MEDIA CONSULTANTS Martina Hirschmann [email protected] Johann Lange-Brock [email protected] phone: +49 6221-65108-0 fax: +49 6221-65108-28 France, Italy, Spain, UK Elisabeth Maria Köpke phone: +49 6201-878925 fax: +49 6201-878926 [email protected] LAYOUT AND PREPRESS EXPRIM Werbeagentur Matthias Gaumann | www.exprim.de READER SERVICES Till Kretner [email protected] PRINT Chroma Druck & Verlag GmbH Werkstr. 25 67354 Römerberg Germany WWW www.hbmedia.net | petpla.net PETplanet insider ISSN 1438-9459 is published 10 times a year. This publication is sent to qualified subscribers (1-year subscription 149 EUR, 2-year subscription 289 EUR, Young professionals’ subscription 99 EUR. Magazines will be dispatched to you by airmail). Not to be reproduced in any form without permission from the publisher. Note: The fact that product names may not be identified as trademarks is not an indication that such names are not registered trademarks. 3 PETplanet insider Vol. 16 No. 03/15 petpla.net dear readers, As previously mentioned by Alexander Büchler in issue 01+02 of 2015, we face major challenges in the course of our 2015 North American tour. At time of writing, we have already successfully completed two of our appointments in the Toronto region, but other unexpected and unpredictable setbacks have occurred. This has a little to do with the very cold weather, but a great deal to do with problems with the Editourmobil. The situation is requiring some flexibility and a lot of ingenuity. Notwithstanding all the difficulties, we will be continuing the tour as planned, temporarily without the Editourmobil. Our reports will continue in the usual way. We have finished our tour of Canada and we are now heading for the US, where we are looking forward to visiting new destinations in Ohio, Michigan and Wisconsin. An interview from the tour in Canada with Husky, the world leader in PET preform systems will be published in this issue. On March 23 2015, the doors will open on one of the world’s largest plastics exhibitions, the NPE in Orlando, Florida. Covering an area of about 1 million m2, the exhibition will be showcasing the market leaders in the industry. In addition to about 600 items of equipment, 400 exhibits will be showing off their paces. With 60,000 industry professionals expected, the exhibition is something of a barometer for the recovery in the US economy and for Orlando, hosting the NPE for the second time. We will be delighted to welcome you to the Editourmobil, where we will present information on the visits we have made, giving you the opportunity to take part in the tour. Also in this issue, you will find a new 2015 market survey on bottle-to-bottle recycling plants. PET recycling the number one issue in the PET world. Yours Waldemar Schmitke","@ID":5}, "MATERIAL / RECYCLING 25 PETplanet insider Vol. 16 No. 03/15 petpla.net RECORD BREAKING SPEED IN CLOSURE PRODUCTION The world’s fastest plastic closure folding and slitting machine capable of more than 60 parts/second, designed and built using Swiss precision technology. Slitting tamper evident bands is more efficient and accurate than molding bridges in the mold Multiple injection molds processed on one folding/slitting machine possible Higher efficiency and faster cycle times Lower energy consumption on a small footprint PackSys Global – a cut above the rest, easily meeting the performance demands of the beverage industry. PackSys Global AG T +41 55 253 3700 [email protected] @packsysglobal PackSys Global designs and builds full lines for manufacturing: Laminate, extruded and aluminum tubes Plastic beverage caps Monobloc aerosol cans Decorating aluminum screw caps PackSys Global now comprises three other Swiss companies in the industry: Combitool, Madag Printing Systems and Texa Packaging. www.packsysglobal.com A Member of Brückner Group","@ID":27}, "THE NORTH AMERICAN ROAD SHOW 40 PETplanet insider Vol. 16 No. 03/15 petpla.net New hot runner Husky has recently announced the development of a new beverage packaging hot runner that features a new melt delivery system. The company says that this provides benefits in part weight, cycle time, part tolerances, and package design. Mould alignment Husky’s tooling capabilities include enhanced mould alignment features, including integrated alignment technologies that work together to decrease wear and extend mould life. Three sets of sensors are used to detect the position of the core plate relative to the cavity plate; the HMI displays the mould position and provides instructions to resolve any misalignment with the mould positioning device, allowing the user to align the mould using the adjustment mechanism. These sensors are also used to optimise the injection process to improved cycle time and part quality. Multi-layer barrier technology Barrier technology is also an important feature in the company’s roadmap. Robert Domodossola observed that the recent trend towards smaller PET bottles may cause issues with shelf life in certain environments; it seemed that the time was right for Husky to launch its barrier module. Built on the HyPET® HPP5 platform, the co-injection unit is claimed to be able to produce multilayer preforms with a wide range of barrier content, while delivering up to 50% savings on material costs and providing more precise control for the barrier layer. A system for beverage closure manufacturing Husky’s latest HyCAP system, launched in late 2012, has become one of the leading beverage closures injection moulding systems. It incorporates new technologies that are intended to simplify operations and extend mould life, and to offer additional energy savings over previous generations of the system. It also delivers improved cycle time and useability. We thanked our hosts for their hospitality and detailed discussions, and prepared ourselves for the inhospitable Canadian cold. We agreed that one consolation is that we will enjoy warmer temperatures when we meet again, in Orlando. f.l.t.r.: Wesley Grove, Manager – Advanced Engineering Process & Technology, Robert Domodossola, Vice President, Engineering & Business Development, Roman Pirog, Director, Development Engineering","@ID":42}, "PET TOP TALK 33 PETplanet insider Vol. 16 No. 03/15 petpla.net PET TOP TALK 33 Save RAW MATERIALS reduced plastic volumes Save ENERGY less energy consumption Save TROUBLE more quality and higher performance, guaranteed by a sole supplier Full INSPECTED online quality control / stand alone With Sacmi, the beverage specialists are always at your side. With our unbeatable technological know-how and continuous research we are creating new containers and closures designed to ensure outstanding performance. The new IPS injection system for preforms, the CCM compression press for caps and the quality control systems fully designed and built by Sacmi, allows for large-scale production with considerable advantages in terms of efficiency and flexibility. The outcome? Reduced plastic volumes, less energy consumption and lower running costs.All in a bottle: the one you’ll soon be making. Preform & Closure technologically together PROPAK E. AFRICA, 17/19.03.15 - #A3 24 - Nairobi KENYA ENOLITECH, 22/25.03.15 - #F VIC M7 - Verona ITALY NPE, 23/27.03.15 - #W643 - Orlando USA ANUGA, 24/27.03.15 - #7 B051/A050 - Koeln GERMANY AUSPACK, 24/27.03.15 - #323 - Melbourne AUSTRALIA Energy efficiency and product development The plan, which has led to the development of products that offer maximum energy efficiency, began in 2006 and resulted in the launch of the first High Efficiency Line products in 2010. In this field Piovan’s most striking achievement has been improving energy efficiency by optimising the operational parameters of its machinery: energy efficiency is achieved by making its systems extremely efficient across the board. The validity of this approach is confirmed by the number of orders received from the many brand leaders that have purchased solutions from Piovan in recent years. The Genesys drying system, for the PET bottle sector, is one of the clearest examples: the development of this ambitious project was kick-started by applications used in the packaging sector as this accounts for about half of all plastic materials in production around the world. A machine such as Genesys may be more expensive than a more conventional system, but the world’s leading beverage producers lost no time in adopting this new solution as the optimised production parameters it offers ensure a constantly high level of quality and production. www.piovan.com Piovan do Brasil, Osaco","@ID":35}, "PETnews 6 PETplanet insider Vol. 16 No. 03/15 petpla.net Sacmi at Propak East Africa Propak East Africa is the biggest event for the manufacturing industry in East Africa. The last edition saw over 2,000 visitors flock to Nairobi from all over Africa and the rest of the world to see more than 60 exhibitors from over 15 countries. This latest edition will once again be held in Nairobi, Kenya, from 17-19 March, 2015. At this year’s edition, the company Sacmi will present a series of new developments for the beverage & closure industry. There will be a focus on compression technology for the production of plastic caps featuring the Cool+ enhanced cooling system which reduces both process times and energy consumption. According to Sacmi the Cool+ system can increase productivity by up to 50%. The company will also present its IPS, the injection-technology preform production machines, characterised by a series of energy recovery and energy saving systems. At the preform outfeed station, for instance, kinetic energy of the slide is recovered during deceleration, and then reconverted into electricity. Other machines include the labellers made by Sacmi Verona. The latest edition, the Formsleeve+, was first presented last March offering greater flexibility in the choice materials. According to Sacmi, the machine is so efficient that it is able to reduce plastic costs by up to 20%. www.sacmi.it Save Food meeting at Nestlé Following the second Save Food congress held alongside interpack in May of last year, the joint initiative of the FAO, UNEP and Messe Düsseldorf is now charting the course for further development in the coming years. From now on it will be holding additional meetings in the years between interpack editions, with the events being hosted by brand manufacturers in the food industry. The first such meeting will take place on 11-12 May, 2015 at the headquarters of Nestlé in Vevey, Switzerland. The Save Food Meeting 2015 will be a gathering point for companies and organisations from the industry, who now total more than 120, and the approximately 230 NGOs and research establishments that are registered with the FAO. Beyond this, the Meeting is open to attendance by all companies interested in the issue of food waste and loss. The aim of the Meeting is to stimulate dialogue between representatives from industry, science and research, policymakers and persons from civil society and so to provide the impetus for launching (pilot) projects. www.save-food.org/sfm15 Sidel sponsors Bevtec Asia Sidel will be exhibiting at Bevtec Asia 2015 in Bangkok and will be Gold Sponsor of this year’s biennial exhibition and conference. The bottled drinks industry in Thailand, to include bottled flavoured drinks, water and minerals waters, have reached a market value of EUR 535 million (Baht 19.882 billion), according to the National Food Institute under the Ministry of Industry. The industry is divided into 3 categories with bottled water and mineral water valued at EUR 383 million (Baht 14,178 million), functional beverages (excluding functional essence or shot) has a market capitalisation of EUR 151 million (Baht 5,602 million) and the flavoured carbonated drinks’ market value stands at EUR 2.8 million (Baht 102.4 million), representing a combined market value of more than 15% of the non-alcoholic drink sector with the growth rate to the current market levels. The functional beverage is the key driver of the growth at 33.25% for the period since 2010. The 3 day biennial event will be held at BITEC from 6-8 May, 2015. Bevtec Asia 2015 is the region’s only dedicated drink manufacturing exhibition and conference with over 100 of the world’s leading product, machinery and technology suppliers. www.bevtecasia.com www.sidel.com Fi-Cell PET bottle representation agreement expanded Plastic Technologies, Inc. (PTI), a global leader in PET package development, announced that its representation agreement with Toyo Seikan Co., Ltd., Tokyo, has been expanded. PTI has been named the exclusive agent in Europe for the sales and licensing for Toyo Seikan’s FiCell foamed PET bottle processing technology for packaging applications. Last year, the company announced its exclusive representation of Fi-Cell technology in the United States. The Fi-Cell foamed PET bottle technology produces lightweight containers with good barrier attributes and very good visual/tactile attributes. Monolayer bottles feature a smooth inner and outer wall surface. Other foamed bottle technologies usually require an overmolded bottle to achieve a similar result. The introduction is particularly significant for carbonated beverage applications that require a smooth inner wall for an accurate fill. www.toyo-seikan.co.jp www.plastictechnologies.com","@ID":8}, "THE NORTH AMERICAN ROAD SHOW 38 PETplanet insider Vol. 16 No. 03/15 petpla.net John Galt, President & CEO, described Husky’s development and future direction, from a company specialising in injection moulding machines and tools, to an integrated and innovative technology and systems solutions provider. “This focus on innovation ensures we continue to progress in the market by specialising in highly technical areas, but we are also expanding our portfolio in order to capitalise on new opportunities,” he explains and says that Husky has invested in order to better understand and respond to customers’ production issues and needs. He cited as an example the interface Toronto Québec New York Atlanta Orlando Chicago Denver Las Vegas Seattle Calgary Montréal Los Angeles San Francisco Vancouver Dallas New Orleans Phoenix Washington, D.C. Boston Detroit Halifax Kansas City Oklahoma City Albuquerque The North American Road Show between the PET bottle and the closure. “With some specifically targeted research, along with investment in test equipment, we have learned a great deal about the neck finish of the PET bottle and how its interaction with the closure during filling and capping can be optimised.” Husky believes that improved insights have generated significant improvements in the efficiency of filling lines. “We have invested in analysis, testing and validating our technologies, and will continue to focus on this in the future.” Husky’s business philosophy is to work collaboratively with its customers in order both to identify new market The North American Road Show has started: PETplanet Insider meets Canada and USA Husky: Innovation is key by Waldemar Schmitke opportunities and to reduce the total cost of production, in a variety of ways. Its acquisition of KTW in Austria and Schöttli in Switzerland, two specialist companies, has enabled it to build a better tooling business, for example. “The acquisition of KTW enabled us to become a global presence in the closures market, and the largest supplier of injection moulding equipment for closure manufacturing,” Galt says. Along with its established presence in the PET preform business, he maintains that Husky now has a more complete offering and has been able to make inroads into the consumer packaged goods, household products and food packaging industries. The acquisition of Schöttli, which provides precision, high-quality moulds to the medical application industry, has opened up a third market, alongside preforms and closures, and brought additional expertise in select medical applications and the medical tooling market. PET markets John Galt believes that the market with the greatest growth rate for Husky is, currently Africa. “In spite of some political uncertainties, the market is growing and absorbing preform systems in all capacity sizes,” he says. “It is important for our customers that we have a presence here, and that we have an effective service organisation.” Preform systems Eighty per cent of Husky’s preform applications are in three segments: CSD, water and sensitive PETplanet Insider’s North American Road Show kicked off at Bolton, Ontario, global headquarters and Canadian manufacturing campus of Husky, the leading PET preform systems company. The icy wind and temperatures of minus 11 degrees Celsius were offset by the warm welcome Waldemar Schmitke and Theo Busch of PETplanet Insider received from the team responsible for business development and engineering: Robert Domodossola, Vice President, Business Development & Engineering; Roman Pirog, Director, Development Engineering; and Wesley Grove, Manager – Advanced Process Engineering & Technology.","@ID":40}, "MATERIAL / RECYCLING 22 PETplanet insider Vol. 16 No. 03/15 petpla.net Key function High-performance filtration The trend in plastics recycling of being able to produce even higher quality end products is relentless. The amount of processed plastic waste is growing all the time and there are signs of an additional challenge, especially in the postconsumer field: innovations continually reduce the portion of plastics in packaging while the impurities present in the recycling process are increasing proportionately. In order to be able to achieve consistent quality results nevertheless, high-performance filtration is emerging more and more as a key function in plastic recycling systems. Erema’s melt filters offer efficiency solution. There is no overlooking the trend towards high-performance filtration systems. Recyclers around the world are showing ever increasing interest and the number of new investments and retrofits is soaring. Increasing impurities are not always attributable to the likewise increasing quantities of the processed plastic waste; continuous advancements – such as in packaging materials in the food sector (bottle lightweighting) – are also a factor. Bottles are produced with ever thinner walls to reduce the weight of the end products and thus protect resources. By comparison, however, the absolute amount of impurities such as labels, lids, can parts and metal parts from spray bottles remains the same. It is a fact that the relative/percentage portions of plastic in the waste material is falling and the level of impurities is rising. To meet the requirements for the production of these further developed plastics in recycling, however, the quality of the pellets has to rise even further for the plastic recycling loop to close again. Ultraclean results Erema high-performance filter systems have proven their worth over a number of years in an extremely wide variety of applications. While the recently modified Laserfilter system delivers high quality in film production with a filtrated impurity level of up to 5%, the SW RTF melt filter systems with partial-surface backflushing ensure clean results with a filtered impurity level of up to 0.2%. Eremas Business Development Manager Christoph Wöss explains in short the highly efficient Erema melt filters: Christoph Wöss, Erema Business Development Manager Appilication Bottle Erema SW 12/170 RTF melt filter with six carrier pistons (12 screen) for heavily contaminated polymers","@ID":24}, "EDITOUR REPORT 10 PETplanet insider Vol. 16 No. 03/15 petpla.net Nuremberg Milan Rome Naples Palermo Tunis Algiers Rabat Casablanca Marrakech Seville Madrid Lisbon Bologna Monastir Agadir Tangier Valencia Cordoba Bilbao Oporto Andorra La Vella Venice Turin Florence Messina Barcelona Zaragoza ITALY Part 6 One division, two product groups by Waldemar Schmitke Netstal-Maschinen AG En route to Italy, we now stop off in Näfels, Switzerland, situated in the mountainous canton of Glarus, where we visit Netstal, part of the Krauss Maffei Group Munich. Surrounded by 2,400m high peaks, Netstal manufactures and installs injection moulding machines and system solutions in the high-performance segment for the beverages, packaging and medical equipment sector. This visit has particular resonance for me as I worked here for 15 years, and had the great good fortune during this time to build up and lead the PET Preform Systems division. It is a real pleasure not only to see again my former colleagues and employees, but also exciting to see how the division has evolved from a structural point of view. I am especially delighted to meet once more my former colleague, Markus Dal Pian, now Netstal’s Vice President of Sales and Marketing. In addition to his current responsibilities, he also heads up the management of the PET (preforms), CAP (caps machines) and PAC (packaging applications) business units. Markus Dal Pian is thus directly responsible for the PET preform and caps machines of Netstal, bringing both product groups under one management. Preform systems The preform system portfolio includes the horizontal and vertical clamping unit injection moulding machines and the Prelactia range, special machinery division for two-layer preforms. PET-Line In the classic horizontal Netstal PET Preform systems division, PET-Line, we find today two new models, PET-Line 2400, which supersedes the PET-Line 2000, and PET-Line 4000. PET-Line 2400 covers preform applications up to 72 cavities and the PET-Line 4000 to 128 cavities. The PET-Line 6000 preform system (up to 192 cavities) is no longer offered and is no longer part of the preform machine portfolio. A 144 cavity solution will be introduced in the market soon and will complete the range for high volume markets. According to Markus Dal Pian, “With the three PET-Line systems we are now strongly positioned in the current preform market place, and well-placed to meet customer requirements.","@ID":12}, "THE NORTH AMERICAN ROAD SHOW 39 PETplanet insider Vol. 16 No. 03/15 petpla.net beverages (juices, sports drinks and tea), and it claims that is experiencing positive growth rates for most of these markets. Its all-electric preform system, H-PET™ AE, is an evolution of its entry-level system. It continues to be a popular choice in the market for certain applications and is making inroads in niche, low-volume markets such as consumer packaged goods, niche beverages and packaged foods. Husky’s “renewal cycle” for novel technologies and products is 18 to 24. It maintains that it is continually looking for opportunities to eliminate waste and to boost consistency in the injection moulding process. The latest version of the HyPET® HPP5 is claimed to significantly improve uptime and the user interface, as well as reducing maintenance costs and simplifying operations. Customers will be able to see for themselves when it is demonstrated at NPE in Orlando, Florida, in March. John Galt said that Husky has a healthy development pipeline, with new technologies and product features to come. A major feature of 2014 for Husky was its “World Tour” which, John Galt says, generated “very good feedback” from its customers. It will not be the last – a number of World Tour events are already planned for 2015, along with appearances at trade shows such as NPE 2015. “We strongly feel that a mix of Husky World Tour events and traditional trade shows works best to reach both current and potential customers,” he says. “The Husky World Tour allows us to bring our customers and subject matter experts from Husky and from other suppliers together to engage in deeper-level discussions, which can be difficult to have at busy industry tradeshows.” Business Development and Engineering We thanked Mr Galt for his time and joined the business development and engineering team of Robert Domodossola, Roman Pirog and Wesley Grove, who took us to the showroom and R & D area of Husky’s corporate headquarters. Robert Domodossola explained that Husky has developed a structured approach to innovation, which balances creativity and discipline and enables it to apply a proven method of solving problems and developing products that are designed to answer customers’ clearly identified needs. “We develop virtual models using computer simulations that provide clear insight into how a closure might be deformed during the ejection from a mould. These findings can then be used to optimize design features or functions in a development project before the actual prototyping begins.” Mr. Domodossola explained. f.l.t.r.: John Galt President & CEO, Waldemar Schmitke PETplanet","@ID":41}, "TRADE SHOW PREVIEW 50 PETplanet insider Vol. 16 No. 03/15 petpla.net Recycling line recoSTAR PET iV+ Sonnenuhrgasse 4, A 1060 Vienna substituting virgin resin at up to 100% Visit us at: NPE 2015, Plast Milan 2015, textile packaging consumer bags 1835 – 2015: HDUV West Hall Level 2, Booth:W151 Preform injection moulding and stretch-blow-moulding developments Sipa, will be showing one of its latest Xform preform injection moulding systems on its stand, along with its T80 single-stage injection-stretch-blow (ISBM) moulding system. Sipa is sharing its stand with Athena Automation, its partner in the development of the Xform 300 and the smaller Xform 150. The Xform 300 has an electrically-driven two-platen clamp unit and accepts moulds with up to 96 cavities. The demonstrator at the show will be equipped with a Sipa 72-cavity preform mould. Sipa says that the unit features advanced platen parallelism, wide tie bar spacing and sensitive mould protection, and accepts. legacy moulds from all leading mould manufacturers. It can also be fitted with a new post-mould cooling system that can cool the preforms for up to six cycles. The four-station Sipa T80 ISBM was originally developed by Automa, whose ISBM business was acquired by Sipa in 2014. It will be demonstrated with a six-cavity mould and will produce 500-mL asymetric PET bottles for household cleaning products. These ISBM machines are designed for production of containers in smaller lots than the company’s existing units. Sipa will also be presenting its latest developments in in production and refurbishing moulds and will present the latest innovations in packaging created by its own engineering and design staff. Sipa will be holding seminar presentations on its Sincro Xtreme technology for production of PET bottles using injection-compression-stretch-blow moulding (ICSBM). www.sipa.it","@ID":52}, "PETcontents 03/15 4 PETplanet insider Vol. 16 No. 03/15 petpla.net INSIDE TRACK 3 Editorial 4 Contents 6 News 58 Products 60 PET bottles for Beverage + Liquid Food 43 PET bottles for Home + Personal Care 64 Patents PREFORM PRODUCTION 26 Sipa synchronises light preform production 42 Practical Guide to Injection Moulding of Preforms Bottles, preforms and closures, part 18 PET TOP TALK 28 Growing forward... A Predis review Sidel Group 30 2015, reaching a step further GDXL Precise Machinery Co., Ltd. 32 2014: reporting growth for another year Piovan Group MARKET SURVEY 35 Suppliers of bottle-to-bottle recycling plants THE NORTH AMERICAN ROAD SHOW 38 A company driven by innovation Husky Injection Molding Systems Ltd. TRADE SHOW PREVIEW 48 NPE 2015, Orlando, Florida BUYER’S GUIDE 65 Get listed! Page 22 EDITOUR REPORT 10 One division, two product groups Netstal Maschinen AG 12 Liquid colours and additives only Repi S.p.A. 14 Nuova S.A.MI.CER S.p.A. 16 Alimpet S.r.l. 16 Piovan S.p.A. 17 Paradiso S.p.A. 18 PET is for us the past, present and future Otto Hofstetter AG MATERIAL / RECYCLING 20 Shedding more light on rPET yellowing Plastic Technologies, Inc. 22 High perfomance filtration Erema Ges.m.b.H. 24 PET recycling line requires less maintenance and improved quality Starlinger & Co Ges.m.b.H. Page 60 Page 10","@ID":6}, "TRADE SHOW PREVIEW 56 PETplanet insider Vol. 16 No. 03/15 petpla.net West Hall Level 2, Booth:W903 Three strong brands: KraussMaffei group KraussMaffei’s stand will include exhibits from all three of its brands: KraussMaffei; KraussMaffei Berstorff; and Netstal. Its established GX series will be presented in a new size (GX 900 – 8100) and as a multi-component machine (GXH 550 – 1400/1400). The CX series will round out the company’s presentation with a lightweight and a multi-component application. Netstal’s Elion 32002900A will produce 44-oz stadium cups, with IML decoration. An Evos 5500-2900 will demonstrate the production of 16oz containers. Also on the stand will be a KME 60 XS single-screw extruder for technical profiles as well as QuickSwitch technology for in-line dimension changes. The KM-3L RKW 74-250 IPC multi-layer pipe head is designed for the efficient production of multi-functional pipes with an internal pipe cooling system. A wide selection of ZE twinscrew extruders will be on show as well. www.kraussmaffeigroup.com West Hall Level 2, Booth:W1303 Injection moulding machines and systems Engel will be exhibiting eight applications appropriate for solutions to meet the requirements of five industrial branches—automotive, packaging, medical, teletronics and technical moulding. Engel says that it intends to show that increased competitiveness can be delivered by both customised, highly-integrated system solutions and flexible standard machines. Highlights will include the first composite brake pedal manufactured in a one-shot process; the new high-performance Engel e-speed machine, the particularly dynamic Engel e pic pick-and-place robot, as well as service tools for higher levels of process security and machine availability. The new e-speed 720 US injection moulding machine will be presented for the first time in North America at NPE2015. It combines the all-electric technology of the Engel e-motion and e-cap series along with the high injection speeds and energy efficiency of the Engel speed series. The electric clamping unit of the 720-ton hybrid machine features a completely new drive solution that uses a flywheel that acts as an electrical power reserve. It stores the braking energy from the platen movements and transfers it back to the motor when required. Any excess energy from the generator, beyond the storage capacity, is fed back into the grid. This allows the e-speed 720 US to run with a relatively low and constant connected load. The established Engel inline injection unit will be on display. It can reach injection speeds of up to 800mm per second. Engel says that its long opening stroke allows the new high-speed machine to work with large stack moulds. An Engel e-speed 720/90 US with a 4+4-cavity mould from StackTeck (Brampton, Ontario, Canada) will be producing 1.5 litre containers. With high-speed automation from CBW automation (Fort Collins, Colorado, USA) fitted the machine only needs 0.5 seconds to remove the containers from the mould. www.engelglobal.com West Hall Level 2, Booth:5945 Pumps, pelletisers and screen changers Maag Pump Systems and Maag subsidiary Automatik Pelletizing Systems will show an extrex 90 extrusion pump and a CSC 116-RS arched screen changer, along with its Primo 200E dry-cut cantilever design strand pelletizer and extrex GPD twin outlet gear pump. The GDP pump is capable of feeding constant-pressure melt to two different nozzle blocks. The extrex 90 extrusion pump will be shown feeding melt to the Sphero S underwater pelletiser. The system includes the CSC 116-RS screen changer with arched cavities, which allow the screen surface area to be up to four times larger than equivalent conventional designs. The Primo 200E from Automatik Pelletizing Systems is designed for compounding of thermoplastic masterbatches at throughput rates of up to 1.5 t/h. It is a singleside mounted dry-cut strand pelletizer with a cutting width of 200mm and is claimed to be able to quickly change pellet dimensions capacity. www.maag.com","@ID":58}, "EDITOUR REPORT 12 PETplanet insider Vol. 16 No. 03/15 petpla.net An example from production: Closure 29/25 Weight 1.4g Elion 4200-2000 Injection moulding mould, 96 cavity Cycle time 1.8sec China Market Finally, we must not neglect to mention a hotly contested market – China. Today China probably represents the biggest market for preform and closure cap machines and has the greatest growth potential in this sector, but it is also the market with the highest demands. In order to secure the market it is essential not only to demonstrate a local presence but also competence. In addition to machine technology, specialist support and the supply of tools are of very great importance. “With the plant in Haiyan, part of the KraussMaffei Group in China,” Markus Dal Pian is quick to point out, “we have created the preconditions necessary for this. We have not only been able to settle specialist personnel there but are also able to demonstrate the performance of a Netstal PET-Line to our customers and offer local training courses.” I extend my thanks for the interview and wish Markus Dal Pian and his team continued success. wwww.netstal.com Liquid colours and additives only by Waldemar Schmitke Repi S.p.A. Meanwhile, back in North-West Italy, we pay a visit to family-owned company Repi in Lonate Ceppino (VA), not far from Milan. Repi is a global supplier of colours and additives in liquid form for thermoplastics and polyurethanes. The company’s range comprises dosing units and measuring devices specifically developed by Repi for dosing liquid colours and additives. Here in Lonate Ceppino we met Ferruccio Angiolini, President, and Filippo Angiolini, Managing Director Thermoplastics division. The company can look back on a history spanning more than 40 years. Filippo Angiolini explained: “The company was set up in 1973. A start was made straight away with the production of liquid pigment and additive dispersion and solid masterbatch. Today the company has two production locations, one of which has its headquarters here in Lonate Ceppino and a further production site in Charlotte NC, USA.” Out of 100 employees divided between Italy, US and Russia, 80 work here in Lonate Ceppino and 18 of them are employed in the laboratory and R&D. Filippo Angiolini continued: “In 2013 we were able to supply a total of 4,000t of liquid colours and additives to 70 countries worldwide; this represents an increase of 10% compared to the previous year.“ Repi was keen to point out the significance of this: considering an average l.d.r. between 0.01% to approximately 2% of Repi products, it is ultimately possible to colour up to 800,000t of resins. Further milestones in the history of Repi are listed below: 1997: the company enters the PET market (PET preforms) 1998: relocation to this site with R&D, Production, Stores and Service 2011: expansion of the Lonate Ceppino site with focus on the laboratory Own branch office in Moscow with sales, technical service and stores 2012: Start of production, R&D and technical service in Charlotte NC, USA 2013: Solid masterbatch production was gradually phased out. “This“ explained Filippo Angiolini “was a milestone for us.” Colours and additives are readily available in granulate form (masterbatch). Repi also used to offer these additives in masterbatch as an option. However, for strategic reasons, Repi took the decision to offer colours and additives in liquid form only. Liquid additives call for sophisticated technology and consequently are able to yield higher margins. Masterbatch manufacturers are legion but there are just a few large companies that manufacture liquid additives. Repi’s argument is that it is possible to achieve better and more homogeneous colouring performance with liquid additives, at lower addition rates, making for savings in costs. Filippo Angiolini concluded: “40% of our total turnover in Italy is thermoplastics, of which the proportion in turn for PET applications is around 65%.” Repi aerial view Lomate Ceppino Italy","@ID":14}, "BOTTLES 61 PETplanet insider Vol. 16 No. 03/15 petpla.net Daily Nutella ration In some European countries, the customer has the option to purchase seven 30g Nutella containers, constituting a so-called “weekly ration”. These are packaged in a cardboard box and also feature a label that can be written on and which serves as a gift tag. At the end of 2014, Ferrero France were selling these little Nutella jars made from PET, each about 4cm high, individually as part of a promotional campaign. Each jar is sealed with a glossy lid made of PP, underneath which there is a tear-off freshness membrane attached to the rim of the container. On the top of the lid there is a transparent tape with perforations for hanging up the jar at the PoS or from fixtures at the breakfast buffet. The small containers, individually packaged, are ideal for hotels, or for those with a sweet tooth when travelling. Chiquita Organic Smoothie CBS GmbH & Co. KG of Geretsried Germany are selling a smoothie with an “organic” tag and a bio label under the brand name of Chiquita. According to the manufacturer, these smoothies consist of more organically sourced fruit, are free of sugar and are not made from concentrate. The six different varieties are packaged in 200 ml PET bottles whose labels are made from plain paper to emphasise the natural touch of the products. Different-coloured screw caps with tamperproofing plus an extra label pulled across the closure that features bio information, not to mention a prize competition, complete the packaging. www.chiquita.de","@ID":63}, "PETbottles 60 PETplanet insider Vol. 16 No. 03/15 petpla.net Beverage + Liquid Food Valensina Harvest-fresh – pressed and ready to go As part of its “Harvest-fresh – 100% direct juice pressed and ready to go” range Valensina GmbH, Mönchengladbach has recently launched its Valencia orange and orange/ mango/passion fruit varieties in 250ml packs. The packaging consists of a transparent, deposit-free PET bottle, reminiscent in terms of its shape of the familiar 1-litre Valensina bottles. The bottles are closed by means of a screw cap incorporating lateral grooves to give a better grip, together with a guarantee band by way of evidence against tampering. The bottle, decorated with a non-label-look bottle label, also features a paper sleeve in the neck area which is designed to draw attention to it in the refrigerated section. www.valensina.de Feel-good factor in a bottle Under the brand name “Inju”, Sportlernetzwerk GmbH of Berg in Germany are selling three different drinks preparations which are intended, by virtue of their formulation and the interplay of active ingredients and nutrients, to enhance the performance of the human body and thus improve feelings of well-being. “Balance” is designed to benefit the immune system and the organism as a whole, “Focus” to improve performance and reduce fatigue and, to increase performance, there is “Sport”. The products can be taken neat or mixed with water or juice. The liquids are bottled in amber-coloured PET bottles containing 30, 100 or 500 ml. The bottles feature brown selfadhesive stickers made of paper and a screw cap with a tamper-evident band. The colour of the anti-tamper strip is adapted to the primary colours of the three product variants. www.inju.com MHT MOLD & HOTRUNNER TECHNOLOGY AG Your Machine - Our Solution German Technology South Hall · S36088","@ID":62}, "TRADE SHOW PREVIEW 55 PETplanet insider Vol. 16 No. 03/15 petpla.net Respecting values in effective dialogue www.krones.com Anuga FoodTec 2015 Cologne, 24 – 27 March Hall 8.1, Stand A020/B039 West Hall Level 2, Booth:W643 Injection moulding machines Italian company Negri Bossi, through its subsidiary Negri Bossi North America, will be exhibiting four of its most popular injection molding machine models, along with several of Sytrama robots. The Vesta All Electric VE3301580 is equipped with a 4-cavity coat hanger mould with gas assist technology and features the new Sytrama Robot Model S9-L alongside. An ELEOS 65-210 will be shown running a single-cavity sunglasses case with live-hinge. This machine has a large tie bar space and a cantilever two-platen clamping unit. The new Sytrama Robot ONE-L Model will demonstrate automation of a standard injection moulding process with the robot configured for clamp end deposit of moulded part in a small footprint. The Canbio Evolution series, a core solution for general purpose moulding, will also be on show with an e3002100 running a specialised industrial part featuring MuCell microcellular foam injection moulding technology. The new Sytrama Robot Model S9T-L will complete the process. The fourth solution will be a Canbimat Multi-Material e210-850h320v with rotary mould table, which will produce a special two-colour decorative container. It will be complemented by the new Sytrama Robot S7-L with a special gantry mounting. www.negribossi.com","@ID":57}, "PETbottles 62 PETplanet insider Vol. 16 No. 03/15 petpla.net Home + Personal Care Thick-walled PET bottle for hair care As part of its “Acti Repair” range, the French manufacturer of hair care products, Activilong, is distributing a product based on olive and avocado oil. This is presented in a PET bottle containing 100ml of product. The bottle is made with thick walls which enhance the feeling of heaviness – and hence quality – reminding the user of a glass container when grasping and lifting the bottle. The product is applied via a screw-on pump dispenser which is protected by a transparent cap. Parts of the pump dispenser incorporate a metallised surface and decorated with an allround non-label look label. www.activilong.com Micelle cleansing wash from Garnier At the beginning of 2015, Garnier in Germany brought out a product for easy, gentle cleaning of the skin of the face as well as around the eyes and lips. Micelle cleansing wash is available in several versions suitable for different skin types. According to the manufacturer, micelles are cleansing agents that latch on to impurities and make-up whilst gently cleansing and conditioning the skin. The product is packaged in a transparent plastic bottle containing 400ml. The bottle is closed by a snapon hinged lid closure which, because of the way it is moulded, is easy to open. The back label features shiny silver printing on the inside and generates reflections under appropriate lighting conditions at the PoS. www.garnier.de Want the secret to bottle light weighting? Process Pilot® automated blowmolder control system takes the guesswork out of material distribution management and can help ensure the success of even the most aggressive light weighting program. Featuring 24/7 blowmolder control, the Process Pilot system continuously maintains material distribution, on every bottle, to an unmatched level of accuracy. With the Process Pilot system, you have the means to push light weighting to the limit without sacrificing bottle quality or performance. Not convinced? Talk to one of our specialists today to schedule a free seminar and evaluation of the Process Pilot system on one of your blowmolding lines. Web: agrintl.com Tel: +1.724.482.2163 E-mail: [email protected]","@ID":64}, "MARKET SURVEY 37 PETplanet insider Vol. 16 No. 03/15 petpla.net Gneuss Kunststofftechnik GmbH Starlinger & Co. Ges.m.b.H. Bühler Thermal Processes AG Krones AG Phoenix Technologies Intl LLC Mönichhusen 42, 32549 Bad Oeynhausen, Germany +49 5731 5307 0 www.gneuss.com Sonnenuhrgasse 4, 1060 Wien, Austria +43 1 59955-0 www.recycling.starlinger.com Ms Elfriede Hell, MBA General Manager Division recycling technology +43 1 599 55 1300 +43 1 59955 25 [email protected] Sandackerstrasse 24, 9245 Oberbüren, Switzerland 41 71 552 10 22 www.btpag.com Mr Karl Schoepf Product Manager Reycling +41 71 552 10 82 [email protected] Böhmerwaldstr 5, 93073 Neutraubling, Germany +49 9401 70-0 www.krones.com Mr Peter Hartel Sales Dept. PET-Recycling + 49 9401 70 5448 + 49 9401 70 91 5448 [email protected] 1098Fairview Ave, Bowling Green, OH 43402, USA +1 419 353 7738 www.phoenixtechnologies.net ms Lori Carson Director Commerical Operations +1 419 353 rPET +1 419 354 7738 [email protected] Engineering of washing lines with long term partners Four models: recoSTAR PET FG, recoSTAR PET FG+, recoSTAR PET iV+, recoSTAR PET iV+ Superior Starlinger recycling technology offers the engineering of washing lines and / or a turn-key project with components and technologies available in the market yes Yes (decontaminated for food-contact, IV increased, AA 1ppm, lowest VOC level) yes up to 17.000 6.000 - 26.000 t / a rPET pellets 24.000 t/a 3.400 t/a - 30.000 t/a Depending on design 5000 1000 - 6000 m² FDA, ESFA (pending), INTI, brand owners (conf.) USA/FDA (C-H), Austria, Germany/BfR, Ilsi, France/AFFSSA, Finland, Australia, Canada, Egypt, Japan, Switzerland, Latin American Countries; follows EFSA requiremens; brand owners FDA, EFSA, Brand owner FDA - LNO / EFSA - LNO Depending on bottle contamination Depending on design 2.15 m3/to Depending on input material Depending on design 580 KWh/to, 590 kg steam/to Four models: recoSTAR PET FG, recoSTAR PET FG+, recoSTAR PET iV+, recoSTAR PET iV+ Superior LNO yes, PVC less than 50ppm FDA, ESFA (pending), brand owners (conf.) Yes (decontaminated for food-contact, IV increased, AA 1ppm, lowest VOC level) yes yes 200-17,000 1.500 t / a - 26.000 t / a (5 extruder sizes) 12000 - 50000 t/a 3.400 t/a - 30.000 t/a 38, total plant capacity, 9K ton of LNO installed, with additions available of 9K tons 30 - 80, depending on size 130 m² - 540 m² 400 - 600 m2 800 - 3000 m² 1000 FDA, ESFA (pending), INTI, brand owners (conf.) USA/FDA (C-H), Austria, Germany/BfR, Ilsi, France/AFFSSA, Finland, Australia, Canada, Egypt, Japan, Switzerland, Latin American Countries; follows EFSA requiremens; brand owners FDA, EFSA, Brand owner FDA - LNO / EFSA - LNO FDA, Health Canada, EFSA no fresh water needed approx. 0,15 0.15 m3/to trace 350 approx. 410 (depending on design) 290 KWh/t 660 kwh/t Starlinger recycling technology offers the engineering of washing lines and / or a turn-key project with components and technologies available in the market Yes (decontaminated for food-contact, IV increased, AA 1ppm, lowest VOC level) with/without approval 3.700 - 10.500 (5 sizes) 24.000 to/a output 3.400 t/a - 30.000 t/a approx. 150 4500 m2 1000 - 4000 m² FDA (hot-fill), follows EFSA requirements FDA - LNO / EFSA - LNO N/A 2 m3/t 120 - 250 (incl. Bottle washing to SSP) 290 kWh/to, 590 kg steam/to yes, mainly thermoforming sheet lines in direct food contact yes yes, several lines under operation in Europe and America yes Yes yes","@ID":39}, "PREFORM PRODUCTION 44 PETplanet insider Vol. 16 No. 03/15 petpla.net Next the speeds have to be calculated by using the wall thickness of the different parts. Let us assume that the preform in our example has the following wall thicknesses: End cap: 2.8 mm Body: 3.4mm Transition: 2.5mm Neck finish: 1.5 mm Taking the body as 100%, i.e., the highest fill speed, it is now easy to calculate the other wall thicknesses as percentage of the maximum: End cap: 2.8/3.4 = 82.3% Transition: 2.5/3.4 =73.5% Neck finish: 1.5/3.4 =44.1% The maximum speed has to be determined by trial and error to get the desired injection time as outlined earlier. If it is 50 mm/s, the relevant values would be: End cap: 50 × 82.3% = 41 Transition: 50 × 73.5% = 37 Neck finish: 50 × 44.1% = 22 Speed: 22 37 50 41 mm/s Position: 23 32 40 101 120 mm 3.4 Cycle Time Calculations Preforms are molded with various machines and molds and of course they differ in weight, geometry, and wall thickness. Required cycle time for a particular preform and at a given machine is most dependent on wall thickness, not weight. It is easy to understand why this is so. At a recommended injection rate of 11g/s, the difference in injection time between 15- and 30-g preforms is only 1.4 s. However, the difference in process time between a preform with a wall thickness of 2.3 mm and one with a 3.3-mm wall is about 5–6 s. This is because it takes that much longer to cool down the center of the wall before the preform can be demolded. This in turn can be understood because PET, like most other plastics, is a good insulator, slowing down heat transfer from the center to the cold mold wall. Machinery also plays an important role. A 20-year old machine without postmold cooling (in what we call “freedrop”) may process a given pre-form in 24 s, whereas the same preform could be made on the latest high-speed machine with four postmold cooling stations in 10 seconds or less. 3.5 Challenges in Thin-wall Molding As preforms get lighter and lighter, their wall thickness becomes smaller as well. This leads to considerable challenges in the molding process as higher pressure is needed to push the material through thinner mold chan¬nels. This leads to increased shear, and because PET is shear sensitive, great care must be taken not to overshear the material with subsequent deteriora¬tion of the properties or the occurrence of defects such as yellowing. Thin walls are mostly used in the production of lightweight water bottles and feature body walls 2.2–2.4 mm thick. They are necessary to have adequate stretch ratios in these highperformance containers. As a windfall of this arrangement, extreme short cycle times as low as 6 s at the time of this writing are possible because it is mainly the wall thickness that controls cycle time. Although there are some preforms in the market with even lower wall thickness in the body, 2 mm and less, these lead to less operational efficiencies and are not recommended. Neck finish walls that are only 1mm thick are possible though. To visualize what happens inside the preform, it may be helpful to recall a diagram from Chapter 2.4 (Fig. 3.17). Figure 3.17","@ID":46}, "EDITOUR REPORT 13 PETplanet insider Vol. 16 PET Markets Filippo Angiolini then went on to give us his view of the current market situation. “Our most important PET markets are: Russia was our starter market for PET Colours and is still, despite the volatile political situation, a considerable source of revenue with its own branch office. All other European states are supplied and supported from Italy. The Italian market is characterised by dwindling purchasing power and the associated effort to reduce costs. On the one hand, the customer is anxious to use colour in order to stand out from the crowd and this encourages more colours to be employed, but at the same time, he wants to reduce the costs of colours for his product. This also applies to additives, e.g. for milk packaging in PET, where a 90-day shelf life is required (UHT milk). The USA is one of our growth markets and justifies the investment in own brand presence and production. The location has been chosen to provide potential for 4-fold expansion. This market is defined by massproduced items with less colour diversity. There is less demand for additives because, in PET, there is still a large number of coinjection barrier applications. In the Far East, we are represented by local partners (including technical service). We have decided not to invest in China because the risks are too high at for a mediumsized, family-run company. However, of interest to us are the Japanese and South Korean markets, which are very highly sophisticated in terms of technology and akin to our own set-up. In Africa, we are already present in few countries in South Africa as well as, Saharan and Sub-Saharan areas. Business in this area will probably grow for us in the coming years in terms of volumes and applications.” Summing up, Filippo Angiolini emphasised that “we have a product that can be shipped at reasonable costs and, because of this, we do not have to build production locations everywhere in the world.” Products The products are split into four categories for PET processing: Liquid Colours For PET application in injection moulding of PET preforms","@ID":15}, "MATERIAL / RECYCLING 24 PETplanet insider Vol. 16 No. 03/15 petpla.net Nordson Kreyenborg screen changer cartridge increases filter life by a factor of nine in a Starlinger recoSTAR line PET recycling line requires less maintenance and improved quality A Nordson Kreyenborg screen changer filter cartridge that was designed to resist deformation and enhance polymer flow has enabled the European operator of a Starlinger recycling technology high-throughput PET recycling line to reduce the frequency of filter replacement and improve pellet quality. A Starlinger recoSTAR PET 165 HC iV+ recycling line, installed in a “bottle-to-bottle” recycling line at a European company, includes a Nordson Kreyenborg K-SWE-4K-75/RS screen changer located between the extruder and the underwater pelletizer. The line, which operates “24/7/365,” converts PET bottle flakes to rPET with positive opinion by the European Food Safety Authority (EFSA) for re-use in bottles with adjustable IV (intrinsic viscosity) levels, depending on application. When Starlinger’s customer replaced a standard filter medium in the screen changer with the new Nordson Kreyenborg filter cartridge, the filter life was lengthened from eight to 72 hours, according to Christian Lovranich, head of process engineering at Starlinger recycling technology. Besides prolonging filter life, advances in specifications and design of the new filter cartridge also address the requirements of highthroughput systems, such as the 1400 to 1600 kg/h (3,086 to 3,527 lb./hr.) Starlinger line. “The larger filter area of the cartridge and the elimination of stagnation zones reduce pressure variations that can detract from pellet quality,” said Mr. Lovranich, who further asserts that there is less material lost in backflushing, and no metal impurities. As well as the increase in screen life, a 40% reduction of the backflush amount compared to the previous system (a conventional backflush filter) was achieved. The resulting waste reduction alone led to a short pay-back of the replacement investment. The available filter area is 1672 cm2 (260 sq.in.) and the filtration fineness is 50 m with the used screens. The structure of the new filter cartridge is intended to prevent pressure loss and deformation of the steel filter fabric, or screen medium, and to enable it to withstand the high mechanical stresses encountered during production startup, according to Christian Schröder, research and applications engineer for Nordson PPS GmbH. “Our new filter cartridge is an alternative to standard filter discs, in which surface area is increased through pleating of the filter fabric—that is, installation of the fabric in a wave or wrinkle pattern instead of being flat,” he said. “The pleating makes the fabric susceptible to mechanical stresses, which can reduce the efficiency of melt filtration by causing the pleated layers to be pushed together or squeezed during processing. This also reduces the working life of the filter.” Starlinger PET recycling systems produce food-safe rPET and are approved for use in food applications by many brand owners as well as various national and international authorities. www.starlinger.com","@ID":26}, "MARKET SURVEY 36 PETplanet insider Vol. 16 No. 03/15 petpla.net 03/2015 MARKETsurvey Company name Zhejiang Boretech Co.,Ltd. Sorema division of Previero N. Srl Amut S.p.A. Erema Engineering Recycling Maschinen und Anlagen Ges.m.b.H. Tecnofer Ecoimpianti SRL Postal address Telephone number Web site address Contact name Function Direct telephone number Fax E-Mail NO.888, Jiuliting Avenue, Caoqiao Street, Pinghu,Zhejiang, China +86 573 85120 186 www.bo-re-tech.com Mr Alan Ou Senior VP +86 573 85120 186 +86 573 8511 3959 [email protected] Via Per cavolto 17, 22040 Anzano del Parco (Co), Italy +39 031 6349 1250 www.previero.it - www.sorema.it Mr Dario Previero Sales Manager +39 031 63491250 +39 031 63491217 [email protected] Via Cameri, 16 28100 Novara, Italy +39 0321 6641 www.amut.it Mr Piergianni Milani President +39 0321 664941 +39 0321 474200 [email protected] Unterfeldstraße 3, 4052 Ansfelden, Austria +43 732 3190-0 www.erema.at Christoph Wöss Business Development Manager,Application Bottle +43 732 3190-352 +43 732 3190-23 [email protected] Via Calto 409 45030 Ceneselli (Ro) Italy +39 0425 849090 www.tecnofer.biz Mr Mauro Garbellini Sales manager +39 0425 849090 [email protected] Bottle to Granulate Input variable: collected pressed bottles, various colours yes Yes, in cooperation with long-time partners Output: Granulate with approval Questions: Capacity[t/a] 3.000 - 45.000 Floor space [m²] in function of size and stream quality Which approvals Fresh water consumption per tonne output [m³/t] depends on stream quality Consumption kWh per tonne output [kWh/t] 300-600 Flakes to Granulate Input variable: Flakes, coloured proportion max 5%, not much chlorine collected pressed bottles, various colours yes Basic flakes specifications: Higher contamination can influence pellet quality but are basically possible to process, after discussion and agreed by EREMA Output: Granulate with Approval Granulate with approval Questions: Capacity[t/a] 3.000 - 15.000 32000 Floor space [m²] in function of size and stream quality Depending on through-put and technology: 8 - 200 Which approvals FDA [cat. A-H&J]; efsa (postive opinion issued); brand owners (conf.);several national approvals (Austria, CH, Zona Mercursur, etc.) Fresh water consumption per tonne output [m³/t] 0,5 Depending on application and technology type but we have a closed loop system Consumption kWh per tonne output [kWh/t] depending on design 250 - 350 Bottles to Flakes Input variable: collected pressed bottles, various colours collected pressed bottles, various colours Yes, in cooperation with long-time partners Output: Flakes with/ without approval Flakes with/without approval FDA [cat. A-H&J]; efsa (postive opinion issued); with Multi Purpose Reactor (MPR) Questions: Capacity[t/a] 3300 t/a -39600 t/a 5.000 - 45.000 t/a 3.600-45.000 15000 3,000-25,000 Floor space [m²] 600 m²-2000 m² 800 - 5.000 m in function of size and stream quality 20-40 500-1500 Which approvals not applicable FDA, efsa (postive opinion issued) not applicable Fresh water consumption per tonne output [m³/t] 1.5 m³/t 1-3 1 m³/t closed Loop system 1,5-3 Consumption kWh per tonne output [kWh/t] 180 kWh/t-150 kWh/t 0,22 - 0,27 250-300 100 280-320 Miscellaneous Pre-sorting system for mixed plastics - Innovative de-labeller machine for sleeves, complete removal Company also offers systems for Bottle-to-film yes Vacumera inline sheet Bottle-to-fibre yes Vacumera inline fibre Bottle-to-strapping yes Vacumera inline strapping","@ID":38}, "PREFORM PRODUCTION 43 PETplanet insider Vol. 16 No. 03/15 petpla.net the water-cooled take-out plate carries three times the number of cavities and stops in three different positions to receive preforms. These stay in the plate for another 2.5 cycles before the plate turns and releases them onto a conveyor. The takeout can also be done by transfer into an intermediate plate. In a second step, preforms are then handed over into the actual cooling station on top of or beside the machine. The intermediate plate has the advantage that it can be very light and fast as it carries fewer cavities and/ or has no water cooling. The advantage of the direct approach is that it uses one handshake, i.e., transfer from one plate into another (Fig. 3.15). Figure 3.15 Blow tubes are used to further reduce cooling times by air cooling preforms simultaneously with water cooling. (Photograph courtesy of MHT AG). Patented devices also use tubes of one kind or another to blow air onto the preforms in various ways, further reducing cooling times. All mod¬ern machines feature servo motors that drive the take-out or intermediate plates, and postmold cooling stations can reduce overall cycle times by 20–40% and pay for themselves very quickly. Machines without these sta¬tions must use much longer cooling times, which increases the stress inside the preform walls. This is because during hold the shrinking material is replaced but during cooling time the preform shrinks onto the cores and encapsulates, thus incurring stresses. Figure 3.16 To better tailor the injection profile to the preform it is cut into sections. 3.2.9 Machine Cycle Improvements In order to produce more preforms in less time, machine manufacturers have changed tool actions from sequential to concurrent. An example is to start injection after the mold is closed but before it is clamped, i.e., under full clamp pressure. This is possible because the extruder injects into an empty cavity, thereby not applying any significant amount of pressure. This pressure is exerted during hold time when the cavity is full of the material. Similar improvements can be made during unclamping and in the timing of the movements of mold and take-out robot. Operators must be aware of the condition the machine is in as certain functions cannot be accessed when the machine is in “rapid” mode (Fig. 3.16). 3.3 Optimizing the Injection Settings Preforms can be divided into four sections (see Fig. 3.16): Gate area covering the hemispherical portion, also called end cap Body area Transition area where the thicker body merges into the thinner neck Neck area To keep shear constant and achieve a uniform preform temperature, the melt should move at a constant speed inside the cavity. However, the amount of material that fills each cavity section is not uniform because of the differences in wall thickness and diameter. Therefore, the fill speed should be adjusted to account for these differences. Here is how this is done. The first step is to cut the preform at the three places indicated in the drawing and weigh each piece, also noting its wall thickness. For the end cap and the transition zone, the wall thickness in the middle of each part should be noted. If only three speed and position settings are available, only two cuts are made, cap and body are weighed together, and the body wall thickness is used for the calculations. Next, each weight is calculated as a percentage of the total weight. The weight percentages are then transferred into position settings from shot-size to transition point and subtracted from the shotsize to yield the num-bers to enter on the screen. Let us look at an example: Shotsize: 120mm Transition point: 23 mm Distance between them: 97 mm Here are the weights and calculated results: Figure 3.16.1 Preform Weight (g) Percentage of Weight (%) Screw Distance (mm) Screen Values (mm) Cap 7.5 19.7 (7.5/38) 19.1 (97× 19.7%) 101 (120 − 19) Body 23.8 62.6 (23.8/38) 60.7 (97× 62.6%) 40 (101 − 61) Transition 3.2 8.4 (3.2/38) 8.1 (97× 8.4%) 32 (40 − 8) Neck 3.5 9.2 (3.5/38) 8.9 (97× 9.2%) 23 (32 − 9) Total 38 99.9 96.8 Figure 3.16.1","@ID":45}, "PETproducts 58 PETplanet insider Vol. 16 No. 03/15 petpla.net APPE launches SprayPET Reveal Packaging specialist APPE has launched its latest aerosol product ‘SprayPET Reveal’ at the recent Aerosol and Dispensing Forum in Paris. SprayPET Reveal is a fully see-through aerosol product providing complete product visibility. The product is the result of a cooperation between APPE and US-based Power Container Corp, a privately-owned developer and manufacturer of airless dispensing systems. SprayPET Reveal is the combination of APPE’s transparent SprayPET container with Power Container Corp’s Power Pouch dispensing system, a bag-on-valve, which is also transparent. A European-exclusive agreement between both companies means that SprayPET is the only plastic aerosol container that can be used with Power Pouch. Bag-on-valve pouches, usually opaque silver in colour, are flexible multilayer laminated bags, made from layers of nylon, polyethylene and aluminium. Power Pouch is manufactured from single-layer PET, yet retains all of the benefits of bag-on-valve technology. Unlike multilayer laminated pouches, Power Pouch is a seamless bag that provides inherent strength. Structurally and chemically robust, the SprayPET Reveal system operates with standard actuators, is environmentally friendly and easy to recycle through normal kerbside collection. The container and pouch can be clear or coloured, and both are fully food-approved for food-based applications. SprayPET containers have the ability to be printed or fully or part sleeved. www.appe.com www.powercontainer.com","@ID":60}, "PREFORM PRODUCTION 26 PETplanet insider Vol. 16 No. 03/15 petpla.net Sipa synchronises light preform production The production plant Mr Enrico Gribaudo, Sipa’s General Manager says: “One that is compact, flexible and easy to operate; which has very low energy consumption; which treats the PET as gently as possible to keep material highest quality; which provides perfect product handling without damaging the preforms in any way and which produces bottles with extraordinary performance, but which are lighter than anything available on the market thus reducing the amount of PET used.” Preforms are 10% lighter The preforms are 10% lighter than preform produced by conventional injection molding - without losing any key properties. Injection-compression molding overcomes the issue of filling moulds with very thin walls, by having the moulds slightly open when injection starts, and closing them as dosing finishes. Lower injection pressure can be used, lower clamp force is needed, reducing 10%. The integration of the preform injection-compression and the bottle blowing operations has a further effect. There is no need to cool down the preforms after molding, and the need to reheat them just before blowing is reduced. Mould change The SFR EVO3 has a new mould changeover system. It relieved to convert from production of cold-fill to hot-fill containers, too. This is because of the heating circuit remains in the shell holder; the cooling circuit is built into the cavity. Filling is fully integrated. Xtreme Sincro system can be directly connected to filling equipment developed and produced by Sipa. The Xtreme Sincro project is realized with the contribution of the Life financial instrument of the European Union. www.sipa.it Preforms transfer to conditionimg station there is less stress on the melt-acetaldehyde (AA) levels are reduced, and resin intrinsic viscosity (IV) falls less. Compact system The product changeover times are reduced. With its rotary configuration and its pneumatic actions, it fits into integrated preform molding and blowing operations. In the Xtreme Sincro, it is directly coupled to an SFR EVO3 next-generation rotary stretch-blow molding unit. Special features include new designs in the clamp unit and in the cams that help the SFR EVO3 to achieve a max. output rate of 2250 bph per cavity, putting it on the front line of the grid with the competition. The blowing valve block is more compact, it has 35% less dead air volume. The overall footprint is reduced and compact. Eenergy consumption The Xtreme injection-compression system uses lower temperatures than an injection molding system, energy The Xreme Sincro brings together in a single machine Sipa’s preform compression molding system with a high-speed stretch-blow molding unit.","@ID":28}, "PRODUCTS 59 PETplanet insider Vol. 16 No. 03/15 petpla.net Belgian milk bottle look in PET Asinerie du Pays des Collines and M&H Plastics cooperated to create a traditional Belgian milk bottle look for a unique bath cream range that uses asses milk as a core ingredient. M&H Plastics, part of the RPC Group of companies, has supplied the bodycare company with a range of clear bottles including a 400ml tall round and a retro ‘mushroom’ cap. The transparent, glass-like nature of PET was important since it highlights the rich, creamy texture of the product. To complement this look, M&H also supplied bottles for body milk, make-up remover and shower gel. The upmarket look is provided by the silver metallised screw and fliptop caps and serum pumps that complement the branding. www.mhplastics.com There is no challenge we will say no to. Because we know that with the widest range of products, technologies, expertise and services, there is no solution we can’t conceive. And this year at NPE 2015, you’ll see how our philosophy of Yes has reshaped the very fabric of our brand. Come explore all that’s possible with injection, extrusion, blow molding, co-injection, hot runner systems, mold technologies, process control equipment and fluids. Come by Booth W2703, March 23-27, to see our new line-up of products. Or visit One.milacron.com COME SEE WHAT YES BUILT. The new Milacron PET system can produce 10% more output. See it at NPE 2015.","@ID":61}, "PET TOP TALK 30 PETplanet insider Vol. 16 No. 03/15 petpla.net Growing strategies at GDXL 2015, reaching a step further Locating in the heart of China’s Pearl River Delta at themanufacturing center of Foshan, Guangdong Province, GDXL has been building a solid foundation of its expertise to be a trustfull engineering partner and service provider in the PET packaging industry since its establishment in 1993. For bringing out design and manufacture innovations of PET bottle, preform and cap, GDXL proudly deliver corresponding blow mould, preform mould, and closure mould, as well as implementation, optimisation and retrofit conversion solutions to production lines for PET containers. With strong technical capability, top-notch quality products and high efficient services, GDXL has successfully served more than 600 customers in over 40 countries and regions, combined with the endeavor from more than 430 professional employees including 100 engineers and technicians. GDXL’s Deputy General Manager, Mr. Xiaoping Jiang, introduced that GDXL offers mould products to major beverage brands and bottlers, which include preform moulds suitable for up to 144 cavity single-stage and twostage machines; blow moulds for high speed multi-cavity cold and hot filling blow moulding machines; closure moulds up to 72 cavity; and the corresponding components and parts. GDXL receives market recognition from being customer’s 360-degree partner of PET packaging solutions, Mr. Jiang elucidated, “GDXL owns a market share of more than 50% in China’s high-end blow mould market; and more than 60% of blow moulds current in use by high-end beverage brands are coming from us. These numbers for preform moulds are more than 35% and 40%, respectively”. Mr. Jiang appreciates that in 2015, GDXL’s action will further synchronising with the company’s vision, carrying out by two major strategic deployments of plant and network expansion. Opening of the new GDXL R&D and production base To strengthen the company’s core competences and to amplify its production capacity, GDXL has planned investment on equipment and machines to accelerate the automation and compound process with numerical control system. The new plant is locating in Foshan’s new district, Sanshan, with 33,337m² of land occupation and a workshop area measuring 33,400m², which is planned to be putting into operation by August this year. Nearly 300 million RMB (48.783.900 USD) capital fund is invested in making a smart and flexible PET mould R&D and production base. More than 80% of the equipment will be newly purchased; hardware and software will be upgraded to support and standardise the new rules: such as with compound flexible production line, five axis machining center, smart logistics system, information management system (i.e. ERP & PLM), emission reduction designs; 95% of the equipment will be digital controlled to achieve a full automation of the plant. Such initiatives will boost the company’s capacity in time phase Mr. Jiang explained: “The capacity will upsurge by 50% in 1 to 2 years, and doubles in the following year”. Consequently, the company’s current strong capacity will reach 30,000 cavities a year for blow mould; 20,000 cavities for preform mould and 6,000 cavities for closure mould in the third year. With such gain in production capacity, GDXL attaches equal importance to R&D innovations. The R&D capacity will be able to conduct 5,000 studies after moving, including 4,500 bottle studies, 1,000 preform studies and 100 closure studies. Mr. Jiang added that the new GDXL plant will evidentially help enhancing production quality and shortening delivery cycle with our","@ID":32}, "EDITOUR REPORT 11 PETplanet insider Vol. 16 No. 03/15 petpla.net New, continuous development of the two preform systems will naturally focus on increasing production efficiency and profitability.” Markus Dal Pian continued, “For example, in calculating the cost of a preform, energy costs come in second place (behind raw material costs), amounting to 40-45% of the pure production costs. Reason enough, if any were needed, to continue along this path,” concluded Markus Dal Pian. The hybrid drive concept, for example, has been further optimised by a variable-speed main motor with an appropriately adapted pumps array. In composite of the power converters, kinetic energy can be reclaimed and a melt treatment that has undergone further development not only saves energy but also improves melt quality. Closed loop control axes ensure rapid movements and transfers and the unloading device is not only compatible with 2400/4000, but also with the previous model PET-Line 3500. The Calitec (trademark) and Preblow (trademark) should not be omitted from consideration; they may contribute towards shortening the cycle time or reducing the weight of the preforms. Production example of a 0.5l still water preform: PET-Line 2400 Injection moulding mould, 72 cavity Hofstetter Switzerland. Cycle time 5.4sec. Key markets for PET-Line systems: China, Korea, Africa and the Middle East, Americas and Europe PETForm Today it is not only the project work for the PETForm preform system with a vertical clamping unit formerly marketed by Krauss Maffei that is carried out by Netstal together with the marketing, but the system is also assembled in Näfels. The range comprises two machine sizes with a 175 (up to 60 cavity) and 320 (up to 112 cavity) tonne clamping force. Dominating the sales figures is the PETForm 175 preform system. This system is a typical entry level system and is thoroughly at home in virgin markets. There is also a customer base that has been developed over a number of years and which remains faithful to the vertical system. A considerable number of PETForm preform systems supplied annually are distributed as follows: Eastern Europe, Thailand, Indonesia, Africa and India. Prelactia This technology-focus is on 2-layer preforms, manufactured using the overmoulding process known as PreLactia. The PreLactia preform system is used predominantly for UHT milk bottles in situations where a shelf life of more than 6 months is required. The range includes a 240t horizontal machine for operation with a 24 or 32 cavity mould. Markets: Mexico, France and Brazil. Machines for Plastic Closures In the caps and closures sector, Netstal has specialised in the one-piece version, for the PET beverages bottles sector, for multi-piece cardboard packaging (“bricks”) and speciality closures such as flip-tops or functionality closures. By contrast to the preform machines (systems), the closure caps machinery business commenced with the supply of injection moulding machines specially developed for the product, followed by a gradual but consistent transformation into complete system solutions. Systems business tends to converge more on specific countries although of course they are sold world-wide. The development of new closure geometries and weight optimisation makes very high demands on the injection moulding machines in terms of speed and precision without at the same time having a negative effect on energy consumption. For this reason, according to Markus Dal Pian, Netstal is opting for the Elion hybrid series, with a machine range from 2200kN up to 4200kN allowing the implementation of the most common mould sizes. The Evos series covers wide mouth closures up to 72 cavity and the high volume card-board closures whereas the Elion hybrid range is deployed in closures systems up to 96 cavities mainly for 26 to 32mm diameters and flip top closures where the free programmable aXos control can show all the advantages in programming complex mould movements.The standard beverage closures today are mostly produced on the Elion machines in a range between 48 to 96 cavities. f.l.t.r.: Waldemar Schmitke PETplanet and Markus Dal Pian, Vice President Marketing and Sales Netstal in front of the Editourmobil at the premises in Näfels Switzerland.","@ID":13}, "BOTTLES 63 PETplanet insider Vol. 16 No. 03/15 petpla.net Air bubbles ensure glitter effect The drugstore discounter dm is selling, under its own “Balea” brand name, 300ml of mild hand soap with the tag “Dreamflower” and scented with hibiscus and green tea in a stand-alone PET bottle. The consistency of the greenish-coloured product has been selected so that any air bubbles contained in the product “float” and, when exposed to light, produce a sparkling effect. The screwed pump dispenser, complete with activating lock, as well as the non-label look on the front are specially selected so as to be colour-matched to the content. www.dm.de Pantene Pro-V to tackle hair loss The Pantene Pro-V range from Procter & Gamble incorporates a hair strengthening tonic to combat hair loss due to breakage. Packaged in a transparent plastic bottle containing 95ml, the clear, slightly viscous product is applied by means of a spray pump to dry or damp hair. The gold-coloured pump sprayer features a separately manufactured component that prevents any downward pressure on the dispenser, thus avoiding accidental operation. A non-label look label explains the application and transmits the necessary trading information. www.pantene.de Hand wash with Tiger Grass and Ginkgo Under the brand name “Abbott & Broome”, Aldi Sued is marketing, in round PET bottles containing 300ml, four of the transparent hand soaps / hand lotions with Tiger Grass & Ginkgo and Amber Extract & Ylang-ylang manufactured by Dalli-Werke in Stolberg. The bottles feature transparent self-adhesive labels and lockable pump dispensers. www.aldi-sued.de","@ID":65}, "PET TOP TALK 32 PETplanet insider Vol. 16 No. 03/15 petpla.net Piovan 2014: reporting growth for another year As a result of its continuing international expansion, seven production facilities and 23 associated companies, the Piovan Group has been able to build up an articulated position in all main trading partner nations. This multinationalstyle of organisation is based on strong local representation and a close working relationship with the customer base in order to offer technical assistance in real time. The Piovan Group In 2008 the group began its mission to strengthen its position in the marketplace with its acquisition of Universal Dynamics (Una-Dyn), a US-based company specialising is the design and production of storage, handling, blending and drying systems. The Una-Dyn purchase was key to Piovan’s breaking into the American market. In the following six years the partnership with the Virginia-based company went from strength to strength and Una-Dyn is now a well-established member of the Piovan family fully on board with the group’s objectives in terms of product design, expansion and sales strategies. German company FDM, a leading name in blending systems for extrusion lines based in the town of Königswinter, joined the group in 2010. This was followed, at the end of 2014, by Penta, an Italian firm from Poggio Renatico, near Ferrara, that designs and produces large-scale systems for the storage and handling Piovan has been operating in the plastics sector since 1964: during these fifty years it has reached many important milestones. While in the beginning the company concentrated on the development of plastic processing technology, it later adopted a strategy of specialisation in conversion processes. Now it has extended its areas of expertise to include a number of sectors in which plastic materials are used. Ten years ago the company was divided into four divisions: Injection and Blow Moulding, Extrusion, PET Preforms and Optical Applications. At the beginning of 2013 there was a further re-organisation with the introduction of 10 application sectors that correspond with specific industrial segments and products that Piovan, together with other companies from the group, is able to supply in highly specialised formats: PET Preforms & Bottles, Rigid Packaging, Automotive Components, Medical Solutions, Technical Parts, Thermoforming & Technical Sheets, Flexible Film, Pipes – Profiles – Cables, Fibres & Strapping, Recycling & Compounds. Overall Piovan employs a staff of 900, including 106 Research and Development engineers, who are constantly at work to perfect the operational performance levels offered by the company’s products. The group also has 120 technicians who provide after-sales assistance to customers so they can be sure of a rapid, reliable and efficient response wherever their production may be based. of raw materials and ingredients in powdered form used mainly in the plastics and food and beverage industries. Aquatech, a new company founded to operate in the industrial refrigeration sector, opened its doors in January 2015 and represents a natural evolution of Piovan’s existing chiller department. Another member of the group, Energys, works mainly on the Italian market in the field of energy efficient industrial systems. Structur and organisation Piovan’s drive towards growth has been achieved using synergy and by continuing to integrate the know-how and business acumen each member of the group brings with it thereby creating closer ties within the group itself. This has allowed it to exploit to the fullest its high degree of specialisation in those fields of application where the group has now become a leading name and a recognised brand.","@ID":34}, "TRADE SHOW PREVIEW 57 PETplanet insider Vol. 16 No. 03/15 petpla.net South Hall Level 1,Booth:S32156 Mega Machinery: preform injection Chinese company Mega Machinery Mold Co., Ltd, will be exhibiting a 144-cavity preform injection mould. The preforms’ shape are CAD-designed to optimise bottle weights, the mould uses double taper locking technology and it is equipped with a similar needle valve hot runner system design to that deployed by MHT and Husky. Mega claims that the system, mostly designed by its own R&D department, assures balanced flow rate, no dead space, and low crystallization. The 144-cavity mould is designed for water bottle preforms with 30/25 necks. Preform weight is 20g and cycle time is 27 seconds in standard form but can be as low as 13 seconds when equipped with a threestage post-cooling system. Mega says that it will also present its broader range of services, including preform light-weighting or conversion and its capacity to produce core, lock ring, neck ring pair, cavity and all mould bases. In addition to its own products, Mega offer refurbishment or overhaul for hot runners from other leading mould makers. www.megamachinery.com West Hall Level 2, Booth:W1989 Amsler Equipment Inc presents: Amsler will be running their L32 Convertible PET Stretch Blow Molding Machine. Convertible means it can run one, two, or three cavities depending on the required bottle size, from two to five litres. Output ranges from 1100 five litre b/h to 4800 500ml b/h. Amsler will also demonstrate a new empty bottle Leak Tester. The upgraded unit, the fifth in its series, features a colour touch-screen interface, smaller footprint than competitive models, solid steel frame. It offers a top-load, wall-thickness, colour and vacuum leak testing options. www.amslerequipment.net","@ID":59}, "TRADE SHOW PREVIEW 52 PETplanet insider Vol. 16 No. 03/15 petpla.net South Hall Level 1, Booth:S28000 Injection mould making capabilities R&D/Leverage will be showcasing a range of its capabilities, services and achievements in precision injection moulds, preform tooling, injection stretch blow moulds, injection blow moulds and blow mould tooling. It will also be presenting the results of work with partners such as Replenish, who have created a new format for plastic spray bottles and injection moulded containers. R&D/Leverage’s injection mould making capabilities in the home and personal care, food and beverage, and medical/ healthcare market sectors. The company specialises in high precision, high cavitation, single face, two-shot, stack, units and prototype moulds and also offers full, in-house, sampling and qualification services. Visitors to the stand will be able to inspect precision injection moulds for the food and beverage, personal care, and healthcare markets as well as high performance preform moulds from 1–96 cavities in a variety of pitches, along with the design and manufacture of End of Arm Tooling. R&D/Leverage also provides refurbishment, restacking/product changes, and reverse engineering. R&D/Leverage claims to be the only mould manufacture to offer customers three options in manufacturing injection blow moulds: Traditional, Hybrid, or the Freedom System. It has now introduced a two-tiered mould maintenance program that delivers new levels of time and cost efficiencies for makers of a wide range of consumer products – whoever originally made the mould. www.rdleverage.com West Hall Level 2; Booth:4675 Large MRS extruder; rotary filtration for highly contaminated materials Gneuss’ Processing Technology division will show the latest generation of its Multi Rotation System extrusion technology. The MRS 160 is the biggest extruder Gneuss has ever brought to a show. After NPE 2015 closes, the MRS 160 and accompanying units forming a complete line will be delivered to a customer in Florida to process 3000 lbs/h of R-PET into a thermoforming sheet. Although it was originally developed specifically for PET, the MRS is now running in polyolefin and nylon applications. The MRS extruder enables the processing of PET without pre-drying by using a simple water ring vacuum system in order to process the material directly to high quality end products. The company’s Filtration Technology division will give its new RSFgenius M its North American debut. This is a new option in the fully-automatic, processconstant and pressure-constant Rotary Filtration System series. Gneuss says that the RSFgenius M is especially designed for highly contaminated materials, such as are found recycling processes, and that it can cope with higher contamination rates. The SFpvc is the latest addition to the Gneuss range of screen changers for PVC and is specifically designed for recycling highly contaminated PVC. The KR rotary filter is a discontinuous screen changer and is claimed to be particularly suited for fast colour changes. The Measurement Technology division will present its complete line of pressure transducers and transmitters, temperature sensors and accessories. www.gneuss.com","@ID":54}, "PET TOP TALK 31 PETplanet insider Vol. 16 No. 03/15 petpla.net commitment on the foci of surface coating, vacuum heat treatment, fine machining control and inspection reinforcement. Mr. Jiang further emphasised that the nearly 100 million RMB (16.261.300USD) investments on these state-of-the-art equipment would bring innovative changes to GDXL’s production mode. For example, GDXL will be the first mould company who owns a compound machine of lathing and grinding. “This set of equipment worths 7 RMB million alone. It will minimise the quality instability caused by human factor, maximise production efficiency and product precision, hence lower the cost,” said Mr. Jiang, “and we also adapted stereoscopic warehouse with AVG control system to certify better logistics and to escalate production speed”. GDXL take the opportunity of full upgrade, with forward-looking investment in the Sanshan plant. Progression on building the international presence and localisation of service The efforts made by GDXL in the domestic and international markets make the company stronger. Mr. Jiang is confident that the oversea markets’ prospects are bright: “Our majority sales are generated domestically, it would be well worth doing to expand possibilities abroad.” For new overseas expansion GDXL will set up multiple branches in commercial active countries and regions such as the United States, France, Dubai, etc. “We look forward to providing faster response and localised services to our overseas clients, it would be a great opportunity for us to build a marketing and service site network, too”. Mr. Jiang is looking to show that the sincerity and commitment from GDXL’s work should gain the company high trust from more markets. He affirmed that GDXL’s actions in 2015 are only a beginning step of steadily reaching further in the future. www.gdxl.com New GDXL R&D and production base","@ID":33}, "MARKET SURVEY 35 PETplanet insider Vol. 16 No. 03/15 petpla.net Caps and closures Bottle-to-bottle recycling plants Preform and single stage machinery Preforms Preform / stretch blow moulds Closure systems Two stage SBM machinery Compressors Resins / additives Filling equipment Suppliers of bottle-to-bottle recycling plants This year ten companies took part in the poll for bottle-to-bottle recycling plants market survey. The following are presented: Zhejiang Boretech Co., Ltd., Previero N. Srl, Amut S.p.A., Erema, Tecnofer, Gneuss Kunststofftechnik GmbH, Starlinger, Bühler Thermal Processes AG, Krones AG and Phoenix Technologies International LLC. Although the publishers have made every effort to ensure that the information in this survey is up to date, no claims are made regarding completeness or accuracy. 03/2015 MARKETsurvey","@ID":37}, "NEWS 8 PETplanet insider Vol. 16 No. 03/15 petpla.net Reconditioning of 192 cavity PET preform tool after ten years A reliable endurance runner: ten years ago, Western Container Corporation installed their first 192-cavity tool from MHT Mold & Hotrunner Technology AG, Hochheim a. Main, Germany. The tool was installed in a Netstal PET-Line 6000 system and has subsequently produced some 3 billion preforms. Roger Kerr, Vice President of Engineering & Manufacturing Technology at Western Container Corporation (WCC), is delighted with the tool-machine combination: “The availability of the system is very high, and with 192 cavities we have the large output volume we need for our business.” Western Container produces preforms for Coca-Cola with five sites in the US, and operates three of MHT’s 192 cavity moulds. MHT has a total of ten 192 cavity tools in the market worldwide. The original preform design is being superseded with a new lightweight design, and once again MHT has been selected to provide the tooling for WCC’s 192 cavity systems.The new 22 gram preform has a lightweight PCO 1881 thread finish, and MHT has built complete new cold halves incorporating the latest stack design technology. Although the first tool is now ten years old, it is technically completely up to date. Despite its size, the 192-cavity tool is surprisingly user-friendly in its start-up performance. Generally, the 3rd shot generates the needed preform quality. The MHT founder and longtime Technical Manager, Werner Plass, and his successor Christian Wagner came to visit the customer for the hand-over of the new moulds. The collaboration between MHT and Western Container goes back many years and covers tools for Netstal and Husky machines. www.mht-ag.de P.E.T. Engineering: sales up, two awards and major investment in 2015 15 years in business, 2014 marked by important goals and a new year full of promises: these few words sum up the past, present and future of a small company that, in a short period of time, has become an important player in the field of design and commercialisation of PET containers for international beverage brands. P.E.T. Engineering Srl closed 2014 with a turnover of EUR 7.5 million, consolidating the good results achieved in 2013, when the company recorded a 45% increase over 2012. With an increase by 45.3% over 2013, 20.5% of the company’s sales come from China. Due to the strong growth, the company also attended the China Brew China Beverage for the first time. And after Moscow, the company opened its second branch in the city of Shanghai. The ongoing commitment to research was recognised in Italy with the “Imprese per Innovazione – Andrea Pininfarina” award, with P.E.T. Engineering being entered among the 20 most innovative companies in Italy. The company also received the World Beverage Innovation Award in the “Best bottle in PET” category, with Devin – Crystal Line, a PET bottle with a premium appearance and imitation glass finish addressed to the Horeca sector. To better support team work, the company has also decided to invest, not only in the purchase of state of the art machinery and software, but also in its own technology centre. An investment of around EUR 2.5 million will provide the staff with new laboratories, larger prototype production and assembly areas, as well as relaxation areas with a fitted gym. www.petengineering.com Holistic packaging approach helps to streamline development process When it comes to plastic packaging development, companies can now benefit from a seamless structure-to-branding approach. The newly-announced alliance of marketplace leaders R&D/Leverage and Hughes Design Group offers packaging expertise across all key development phases, from consumer research, concept, brand development to go-to-market execution. The full-spectrum offering helps to streamline the development process and eliminates the costly, cumbersome, and frustrating package design silos that often throttle speed-to-market and yield sub-optimal packaging. R&D/Leverage USA, headquartered in Missouri, services the food and beverage, home and personal care, and healthcare industries. R&D/Leverage states that it is the only company to offer both structural brand development and mould manufacturing capabilities. Structural brand development includes upfront research such as retail audits that include trend and color study, ethnographic research, consumer focus groups, concept development, validation, and implementation. Mould manufacturing capabilities include full mould manufacturing for PET tooling, IBM tooling, injection moulds, as well as unit tool development, testing, validation, and training. Hughes Design Group is an award-winning strategic visual branding and packaging design firm headquartered in Norwalk, Connecticut. The company is sought out by leading national consumer package goods clients and ascending brands across many industries and categories, for its expertise in brand identity, packaging, merchandising and new product development. www.rdleverage.com www.hugheslink.com Read more News: petpla.net","@ID":10}, "PREFORM PRODUCTION 45 PETplanet insider Vol. 16 No. 03/15 petpla.net Experiments have shown that the boundary layer, shown here in light-gray, is about 0.25mm thick. In a 2.3-mm-thick body wall this leaves only 1.8mm for the material to flow through. In order to reduce complications, typically a preform of this type will have the same gate wall thickness as the body and the injection speed is controlled to move the material forward at a constant speed. When the melt front reaches the thinner neck area, the pressure behind it increases while the pressure in front decreases as in the case of any other liquid when faced with an orifice. Peak injection pressure will happen at this point, and values of 125 bar (1800 psi) may be neces¬sary to overcome the restriction. This is against the recommendation of a maximum of 100 bar (1450 psi) but unavoidable in this situation. A few measures can assist in injecting into these thin channels: Use of low IV resins: As shown in Chapter 2.3, the lower the IV, the lower the melt viscosity and therefore the lower the force required during injection. Increase temperatures to lower the IV of any material: This often does not work well because with higher temperatures, higher shear is also encountered. Increase the cooling water temperature especially during start-up. Increase clamp tonnage to hold the clamp closed during higher pressure hold times. This will lead however to more tool wear. Setting the transition point with these preforms can be a challenge. When it is set too high, underfills will occur, which may be difficult to see (when not all preforms have them) or may lead to machine stoppages because of problems in the postmold cooling area. When it is set too low very high pressures may be necessary, which may lead to shear stress. Operators are well advised to carefully control this parameter taking all elements into account. 3.6 Acetaldehyde in PET Bottles Acetaldehyde (AA) is a natural sweetener that is present in all citrus fruits and is often used as a sweetener in beverages. It is also a byproduct of heating PET, especially heating it to melt temperature. Its significance in the PET industry relates to the production of water bottles. Still water taste is very sensitive to even small AA concentrations, whereas the sugar content of carbonated drinks and juices masks any flavor contributed by AA com¬pletely. Producers of preforms for other beverages may still monitor AA content as a way of keeping track of the maintenance state of screw and bar¬rel, because when these parts wear, shear stress and AA creation increase. 3.6.1 AA Creation In the initial stages of PET resin manufacture, AA level may be as high as 150 ppm. What happens is that – OH end groups combine with water, glycol, or oxygen that may come in contact with the resin at this stage to form AA whose formula is CH3CHO. During solid-state polycondensa¬tion the material is heated and AA is removed by nitrogen gas to a level of 1ppm. Drying is again critical to AA generation during preform injection molding as moisture present in the resin will not only break the molecular chains but also create AA. A material temperature of 165°C (329 °F), as measured at the extruder throat of the injection machine, has been proven as optimal to minimize AA generation. Residence time and temperature are the other crucial factors (Fig. 3.18). The relationship between residence time and AA level is linear. For the preform molder this means that extruder size and preform weight should be closely matched. One intriguing detail of PET preform manufacture is that cycle times do not vary significantly depending on weight but rather on wall thickness. Two preforms with the same wall thickness where pre-form A is twice the weight of preform B may differ in cycle time by only 1 or 2 s. This means that the residence time of the lighter preform B is almost twice as long as that of preform A with corresponding effect on AA content. Over the past few years water bottles especially have become lighter with the negative effect that their residence time has increased if they are produced in the same extruders as they were before lightweighing. The relationship between AA generation and temperature is exponential (Fig. 3.19). Figure 3.18","@ID":47}, "NEWS 9 PETplanet insider Vol. 16 No. 03/15 petpla.net New Chief Sales Officer at Sumitomo (SHI) Demag Sumitomo (SHI) Demag Plastics Machinery GmbH announced that Gerd Liebig will become Managing Director (Chief Sales Officer) of the group. Gerd Liebig, 53, will take over full responsibility of all worldwide sales, after sales and marketing activities out of the company’s headquarter in Schwaig. He will also lead the worldwide sales subsidiaries and representatives. Gerd Liebig will join Sumitomo (SHI) Demag from April 1st 2015 with extensive experience in the plastic machinery business. Most recently serving as Group Marketing Director for an injection moulding machine manufacturer in Austria, Gerd Liebig has been engaged for 25 years in the injection moulding machinery business. Before joining the last position he spent 15 years at former Demag Plastics Group, now Sumitomo (SHI) Demag Plastics Machinery GmbH, as Marketing Director and later Chief Strategic Officer. www.sumitomo-shi-demag.eu The plastic closure company committed to your success BERICAP Technology Research and Development Mould Technology | Global Presence Capping Technology and Know-How Innovation and Flexibility www.bericap.com LDPET system revolutionises recycling of PET bottles Launched in 2014 after 5 years of research and development, the LDPET system by Sleever International can be considered as a major breakthrough when it comes to the recycling of PET bottles. The system allows bottles, decorated with either a total or a partial sleeve, to be treated and recycled to produce new bottles. The LDPET system was awarded with the “Oscar de l’Emballage” within the environment category at the recent Emballage 2014 packaging exhibition. Besides beverage, the LDPET sleeve also offers new opportunities to all manufacturers of household products, cosmetics and solid food products. Newly developed film and unique printing process make breakthrough possible. The LDPET system permits 100% recycling of sleeved bottles while producing a completely pure recycled resin, a prerequisite for the manufacturing of new bottles. Developed using several technological platforms of Sleever International, this breakthrough was made possible thanks to two major developments: The SI-TPEG/050 ZL film, which shows a spectrum recognized by infrared detection systems as being the same as PET, and a specific gravity below 1 which allows easy sorting via a floatation tank. A unique printing process, which ensures that the specific non-bleeding inks attach easily to the sleeve during separation processes. As a result, the LDPET sleeve allows to eliminate bottle rejection at the optical sorting stage, meaning that any bottle decorated with an LDPET sleeve, either total or partial, will be oriented, with no exception, towards the PET recycling channel. The LDPET sleeve also allows the production of a completely pure recycled resin. There is no more pollution risk due to ink migration or imperfect sorting. Inks remain trapped in the flakes of sleeve which float to the surface of settling tanks, while PET flakes sink to the bottom. With the LDPET sleeve, recyclers benefit for the first time from a system that allows the systematic bottle-tobottle recovery of PET bottles, according to the company. The LDPET sleeve is a step forward in terms of sustainable development for beverage manufacturers who can now produce new bottles from used ones, whatever the decorating solution chosen (partial or total LDPET sleeve). Although the LDPET sleeve can be integrated on existing equipment, its implementation with the so-called SleeverCombisteam-LDPET will offer higher production outputs. The SleeverCombisteam-LDPET allows total or partial decoration of bottles ranging from 20 cl up to 2 litres, with two models enabling to follow outputs between 8,000 and 12,000 or between 15,000 and 30,000 bottles per hour. The LDPET sleeve has just been approved by the APR (Association of Plastic Postconsumer Recyclers) to be used in the bottle to bottle channel. This highly demanding association represents today 90% of the North American recycling capacity. www.sleever.com","@ID":11}]}}
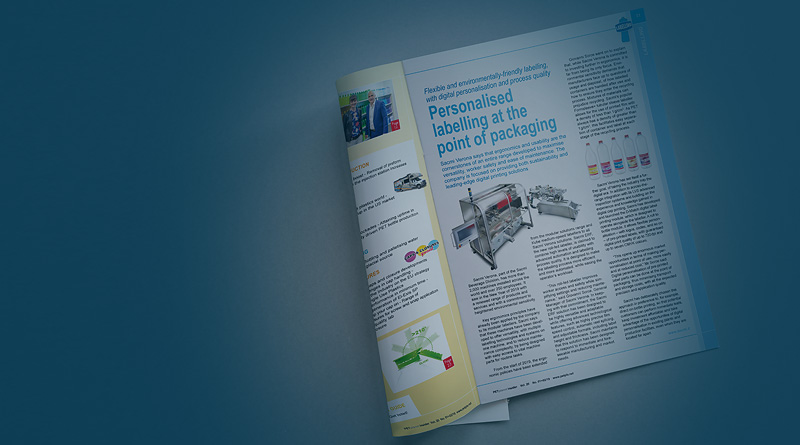