"BOTTLE MAKING 14 PETplanet insider Vol. 17 No. 01+02/16 petpla.net PET Technologies’ new Ukraine factory is up and running by Kay Barton Impression of the new manufacturing hall We met: Mr Maxim Poliansky, Commercial Director PET Technologies, the Austrian company headquartered in Neunkirchen, Austria, manufactures a wide range of semi and fully automated PET blow moulding systems as well as blow moulds for both its own equipment and for machinery from internationally known brands. The spectrum stretches from blow moulding systems for 0.2 to 2l PET bottles with capacities ranging from 3.000 to 12.000bph; PET containers from 3 to 10l with outputs of 1.600 to 2.500bph; and 20 to 30l containers produced at up to 220bph. We previously visited the company’s outsourced production facility in Chernigov, 140km to the north-east of Kiev, Ukraine, during our Editour trip through Eastern Europe in 2012 (see PETplanet Insider Issue 6/2013). At that time, construction had just begun on a factory extension; the new facility was intended to raise production capacity to 12 stretch blow moulding systems a month, which would enable the company to better respond to the growing international customer base. The new building was opened in February 2015 as part of PET Technologies’ 16th anniversary celebrations, which provided ample reason to talk to Commercial Director Maxim Poliansky about the new situation, to take a look back through the past and to venture a view to the future. It must be first noted that the new factory’s local market for PET products is actually declining. According to PET Technologies, around 3.5 billion preforms were manufactured in Ukraine in 2014 – around 18% less than in 2012 – and the forecasts for 2015 don’t look any better, with a further decline of 16% predicted. The primary reason for this downturn is the current political and economic situation in the country. The main local suppliers for preforms are Retal, which has 74% market share; Oldi with 10%; and Sirius with 8%. Preforms are also imported from Europlast, the Russian manufacturer and Belarusian company Mogilevkhimvolokno. Around 14% of the preform market is held by Ukrainian bottling companies that manufacturer their own preforms. 80% of PET bottle production is used for water, CSDs and beer; 10% for milk products, iced tea and juices; 7% for cooking oil and liquid food and 3% for non-food packaging, such as household cleaning products (data provided by Retal group). PET Technologies’ local share of sales in 2014 was 23%, while 77% was export business. The company expects local sales in 2015 to register a continuing decline, due to the ongoing situation in Ukraine, but growing demand from abroad will lead to a further increase in exports. “The initial idea of a new plant opening back then was to increase our production facility and extend our existing blow moulding machines range with new models, in order to meet the demand from growing markets, particularly in Europe and Asia,” says Poliansky. “The new manufacturing unit will deliver PET Technologies a considerable increase in production capacity and, consequently, minimise the cycle time between placing an order for a blow moulder and installation at the customer’s plant. Our new plant will also produce blow moulds for multi-cavity linear and rotary","@ID":16}, "PACKAGING 29 PETplanet insider Vol. 17 No. 01+02/16 petpla.net This is about to change – new beverage can by Kay Barton The idea of ringing in a new era in packaging in an aluminium-dominated world by producing the bulk of classic beverage cans in PET is not new – but nothing along those lines has yet entered the market. However, this is about to change. After more than ten years’ preparation Invento, a company based in Warsaw, Poland, opened a brand new, €11.7 million factory in Gryfino, 30km south of Szczecin, on September 24, 2015. It now produces Invento PET cans, which are currently patented in nearly 100 countries. Mr Łukasz Kręski, founder of the esky.pl travel portal, is Invento’s CEO; the President of the Board for Poland is Mr Jacek Gnich. The Invento story started in 2004, when the discussion during an informal meeting in a café turned to the high prices of aluminium and prompted the idea of a PET beverage can. Most of the time, such ideas remain hanging in the air and never take concrete form but, this time, the talk was quickly followed by action: the foundation of a company with the intention of making the idea a reality. Over the coming years, various designs of preforms for a wide variety of can applications and sizes were developed, along with the technology for integrating the lid into the PET container. It was intended that the lid would still be made from aluminium and thus would not visibly differ from traditional aluminium cans. In 2013, Invento looked to establish itself in the North American market pretty much from outset and established a facility in Sheboygan, Wisconsin. In the same year it produced its first PET cans in the Polish city of Gorzów Wielkopolski; it then determined to establish its own factory, with its own filling line. The Gryfino location was selected for its excellent transport infrastructure and connections between Eastern and Western Europe. The factory site extends to around 10,000m2; production and warehousing accounts for 3,000m2. The company employs 20 people at the site. Production is currently carried out on two blow moulding systems; two filling systems cater for hot and cold filling. The blow moulding machines come from Polish company TES; the filling systems are supplied by CFT in Italy and the labelling machines come from Dimac, another Italian company. Today, the company offers both empty and completely filled and labelled cans in sizes ranging from 250-500ml. Beverage flavours for complete products are determined individually with customers and developed both in the in-house laboratory and with the help of external partners. The current product range includes flavoured waters, soft drinks, juices, energy drinks and others, both carbonated and still. Labelling options are shrink sleeves and pressure sensitive labels. Invento says that it has capacity for 160 million cans/ yr, of which roughly 100 million/yr are for ready for sale products in Poland, and 80 million cans/yr for the USA site, which does not have in-house filling. The company also offers complete blow moulding systems and preforms for inhouse, on-site production by customers themselves. “The Polish market is quite conservative when it comes to beverage cans,” Marketing & Sales Specialist Marcin Hakowski told us, when we asked how the markets have reacted to the PET cans. “The majority of our customers are abroad. A large company from the States, for example, has ordered 160 million PET cans from us for 2016.” Invento says that the advantages of PET cans are clear. In-house production by the filler should make the production process considerably more cost-effective overall than aluminium, in terms of material, energy and transport expenditure. The machines are compatible with existing aluminium can lines and it should thus be possible to integrate without significant disruption. Storage capacity can be saved or optimised by storing preforms rather than finished cans. For the customer, the transparent body in various designs and colours presents the contents of the can and offers a wide variety of labelling options. There is currently no competition in this special packaging sector. Invento does not consider the local PET top dog Alpla as competition; it only takes can producers into account. “For now this is the beginning of a long road. It is hard to compete with companies like Ball Packaging, whose history dates back 170 years,” Mr Hakowski explains to us, and he clearly has a point! Nevertheless, the company confirms that international interest is high and is already making the first plans for new investments, such as increasing capacities, in order to meet rising demand. The workforce should also grow to 50. www.inventocan.com","@ID":31}, "INSPECTION 19 PETplanet insider Vol. 17 No. 01+02/16 petpla.net Figure 1 - Semi-Auto Preform Inspection Gauge with telecentric lens and collimated light source Precision is not accuracy Precision is the expected spread of results when a specific measurement is repeated under fixed conditions. Use of the word precision is discouraged by measurement institutes and standards authorities worldwide who instead entreat the use of defined terms such as capability, repeatability and reproducibility. The difference between accuracy, precision and resolution are illustrated in Figure 2. Figure 2 - Illustrative difference between accuracy, precision and resolution System repeatability Repeatability & reproducibility, often referred to as R&R, is a quantitative value representing the expected scatter of measurement results when the same test is performed multiple times. It is generically expressed by the equation where GRR is the calculated gauge R&R, EV is equipment variance (repeatability) and AV is appraiser variance (reproducibility). Repeatability, or equipment variance, is the contribution to overall R&R that comes from the instrument. Specifically, the range of obtained measurement results when a particular measurement is repeated with no external influence. Reproducibility, or appraiser variance, is the expected measurement change that can be attributed to operator influence. Contributing factors include operator training, loading factors, positional variation and misuse. Torus Measurement Systems’ R&R study is historically derived from the AIAG (Automotive Industry Action Group) MSA (Measurement System Analysis) and performed on all gauges prior to shipping. The study evaluates measurement results of 10 parts each measured three times by three individual operators, using a 5.15 sigma value to represent 99% of the area beneath the normal distribution curve. Subsequently, equipment and appraiser variation are evaluated by identifying trends present in control charts, see Figure 3, Figure 4 and Figure 5, for examples. Figure 3 - Points beyond either of the control limits # Figure 4 - Points consistently one side of the centreline Figure 5 - Points consecutively rising and falling Traceable standard Measurement quality is ascertained by comparison to a reference instrument of higher accuracy or to a master calibration. Either method must be certified, directly or indirectly, to a primary standard. The series of documented links between the highest level calibration and the final gauge accuracy is known as measurement traceability. The primary, or national, standard is defined by a country’s National Measurement Institute (NMI), see Table 1. They are responsible for providing guidelines, working practices and calibration services. By collaborating with other NMIs they ensure standards are internationally recognised and adhered. This means a traceable gauge accuracy is valid in many countries.","@ID":21}, "PETcontents 01+02/16 4 PETplanet insider Vol. 17 No. 01+02/16 petpla.net INSIDE TRACK 3 Editorial 4 Contents 6 News 30 Products 33 On site 34 PET bottles for Home + Personal Care 36 Patents INSPECTION 18 Base and wall thickness measurement, part 2 25 All lines on one display MARKET SURVEY 21 Suppliers of PET preforms CAPPING / CLOSURES 26 Bottles, Preform, Closures Closure for PET bottles - Different applications, neck finishes for various, part 5 PACKAGING 29 This is about to change - new beverage can BUYER’S GUIDE 37 Get listed! Page 15 MATERIAL / RECYCLING 10 From bottle to tile - A recycling idea beyond shopping bags and fleece pullovers COLOURING / ADDITIVE 12 Colour design BOTTLE MAKING 14 PET Technologies’ new Ukraine factory is up and running 16 Blow-fill-cap units for mid-size bottle producers Page 30 Page 12 CAPS & CLOSURES","@ID":6}, "MATERIAL / RECYCLING 11 PETplanet insider Vol. 17 No. 01+02/16 petpla.net MATERIAL / RECYCLING 11 BERICAP Technology The plastic closure company committed to your success www.bericap.com Research and Development Mould Technology | Global Presence Capping Technology and Know-How Innovation and Flexibility derly called Henry. Thomson put a stress on the manual operation in order to keep the machine affordable and easily replicable all over the world. The carefully designed bottle shape ensures the perfect crimping and exact fitting tiles. Henry does just the opposite of a blow moulder – it takes out the air of the bottle and folds it accordingly. The tile itself is filled with 200gr of an insulating and light weight mixture of concrete and paper which does not decompose and thus does not produce greenhouse gases. The colour of the filling can be individually chosen by the costumer and resembles exactly those of ordinary tiles. The tiles are attached on 3-foot wide and 12-foot long rolls and are only rolled out and fixed on the roof when installed. The water The water filling the Agua bottles has its origin in Parque National del Agua in the center of Costa Rica. Due to its geographical location and the rain and cloud forest the water is a resource of abundance. The quality is very high and was recently awarded at the International Termatalia Water and Wellness Convention to be the Best Testing mineral water. The water comes right from the well and is filled directly in the bottles. The filling line fills 10.000 bottles per day. Good story, good marketing Donald Thomson is very careful about to communicate the story behind the water brand Agua end-to-end not leaving any unanswered questions. The key to success: the supermarket chain Auto Mercado in Costa Rica developed an awareness campaign making sure that costumers are aware about the unique water brand. The costumers appreciate not only the fantastic water which recently won an award but also community and environment serving philosophy behind it. 15.000 bottles are sold per month right now but the project has only started. Due to successful marketing the numbers are expected to increase. www.crdc.green","@ID":13}, "ON SITE 33 PETplanet insider Vol. 17 No. 01+02/16 petpla.net ONsite Growth at United Caps: new factory in Schwerin Following the recent announcement of its new name and strategy (see PETplanet Insider 11/15), United Caps, the Luxembourgeois closure manufacturer, is seeking to further expand its reach and effectiveness in national and international business. After its 2013 acquisition of the Schwerin, Northern Germany-based SME Schoeller Cap Systems (SCS, €12 million turnover) Procap – as it was then named – undertook a series of meetings with authorities representing the city and Mecklenburg-Vorpommern state, the company commenced building a larger, more modern facility in April 2014. The premises first had to undergo a survey by a bomb disposal team, after it emerged that it was a former military exercise ground. The project was managed by Chief Project Officer Rony van Regenmortel and, on November 25, 2015, with the completion of the construction phase of its €26 million investment in the site, United Caps Schwerin GmbH opened its doors. It is now located on a new industrial estate that is also home to Nestlé’s Dolce Gusto capsules factory. “With this step, which is in line with our philosophy of customer proximity, we seek to strengthen our business in Germany and in Scandinavia and Eastern Europe,” says Managing Director Harry Briese. Aged 64, Mr Briese is an experienced hand in the plastics sector and has worked for United Caps and Procap for several years. He began his career as a plastics mechanical engineer, working at Plastmaschinenwerk Schwerin from 1971 to 1991. He became operations manager and then head of SCS and later Procap/United Caps, a position that he retains. The Schwerin factory includes two production halls extending to 10,000m² in total; another two are already planned. One of the existing halls produces standard sizes for water, carbonated soft drinks and juice bottles; the second is dedicated to the manufacture of two- and three-part closures for use in cartons of milk and fruit juice. United Caps says that the new factory, whose client list includes Wesergold and Darguner Brewery, could produce up to 2.5 billion closures annually; output of 5 billion units are forecast for 2016/2017. The company currently employs 58 people; it expects to double its workforce over time. The new building houses 19 machines, including Husky and Engel brands. Some systems are new; the other machines were brought over from the previous factory, according to Mrs Astrid Hoffmann-Leist, Director of Marketing & Communication. Material supplies are held in 12 x 800t silos. www.unitedcaps.com MHT MOLD & HOTRUNNER TECHNOLOGY AG Your Machine - Our Solution E1E59 1996-2016 20YEARS","@ID":35}, "MARKET SURVEY 22 PETplanet insider Vol. 17 No. 01+02/16 petpla.net 01+02/2016 MARKETsurvey Company name Plastipak Packaging PET-Verpackungen GmbH Deutschland Intergulf Ltd Empol LLC Empak (Africa) Ltd Postal address Telephone number Web site address Contact name Function Direct telephone number Fax E-mail Ellice Way, Wrexham Technology Park Wrexham LL13 7YL, Great Britian +44 1978 317 378 www.plastipakeurope.com Mr Mike Hanratty Commerical & Business Dev. Director +44 1978 317 366 [email protected] Gewerbegebiet 4, 98701 Großbreitenbach, Germany +49 367 8180 44 00 www.pet-verpackungen.de Mr Hubert Rebhan Head of Sales +49 367 81480 4453 +49 36781 480 4452 [email protected] PO.Box.6131,Sharjah UAE +971 650 29 284 www.empol.com Mr Vikram Singh Sales Manager +971 650 29 330 +971 652 85 720 [email protected] PO.Box.78174, Dubai UAE +971 650 29 284 www.empol.com Mr Vinod Kanchan Head of Sales +971 650 292 46 +971 652 857 20 [email protected] Warehouse No -7, Mer rouge, Free Port of Mauritius, Port Louis, Mauritius www.empak.com Preforms Multilayer preforms (Yes/No) Yes Yes No PEN prefoms (Yes/No) Yes Upon request No Preforms in alternative materials (PP/PLA/PEF) Which? Yes, PLA & PEF Upon request No Preforms incorporating rPET (rPET content in %) Yes, 1-100% Up to 100% Yes List of additives available All colourants and barrier technologies. Colours, oxygen scavengers, UV-blockers, slip-agents, AAscavengers, brighteners, PA-based barriers Oxygen Scavenger, AA, Slip Additive, UV Blocker Preform range Plastipak has a wide range of preform sizes and weights. Preforms for use in bottled water, CSD, food, dairy, home and personal care, alcohol, industrial and other applications. Complete range of standard preforms with 28mm PCO1810 & PCO1881 finish from 14.5 g (e.g. for 0.25l bottles) up to 54 g (e.g. for 2.0l bottles). Preforms with 28mm PCO1810 and PCO1881 PETCYCLE-finish. The product range includes 38mm 2-Start & 3-Start Bericap preforms for wide mouth applications as well as 29-21 finish for flip top caps. Preforms for hotfill applications in range from 23g up to 45g. For large containers 60g, 92g and 98g preforms with Bericap 48-41, customized preforms with weights up to 481g. If the product requires enhanced barrier protection, the majority of the preforms are also available as multilayer with tailor-made barrier properties. Neck Finish 30/25 (14g to 36g) 29/25 (12.3g, 12.5g, 30.2g) 28mm PCO 1810 (16g to 55g), 28mm PCO 1881 (14,76g to 51,6g), 38mm 3 start (16g to 91g), 29/21 Dropless (18g-36g), 36/29 Dropless (48g-69g), 38mm 2 start (25g & 30g), 45mm 3 start (85g), Ketchup M33SP 400 (25g-43g) Company name PET Prefroms Morocco SARL Gulf Packaging System Co. Société Générale des Techniques (SGT) Postal address Telephone number Web site address Contact name Function Direct telephone number Fax E-mail B 8-1 Zone Industrielle 13000 Benslimane, Morocco +212 5 23 29 88 78 www.petmorocco.com Mr Rachid Nourredine Managing Director +212 5 23 29 88 78 +212 5 23 29 88 67 [email protected] Industrial City Phase 5, P.O.Box 20266, Jeddah 21455, Saudi-Arabia +966 1263 60099 www.3p-gulf.com Mr Fyasuddin Dulvi Sales Manager +966 55 3002 399 +966 12 6352 111 [email protected] 3 Rue de l’Île Macé 44412 Rezé, France +33 240 0509 37 www.sgt-pet.com Ms Le Claire Sales Administration Manager +33 240 0502 88 +33 251 7001 55 [email protected] Preforms Multilayer preforms (Yes/No) Yes No Yes PEN prefoms (Yes/No) Yes No No Preforms in alternative materials (PP/PLA/PEF) Which? PLA No No Preforms incorporating rPET (rPET content in %) No No 0% to 100% (according to client request) List of additives available Barrier additive, colourants All colours, UV blocker, AA reducer, O2 & CO2 scavenger, reheat additive, white colour for UHT milk, gliding agent Preform range Sorf drinks/water PET Preforms Morocco, has Netstal machinery, a capacity of 200 millions units per year. Moulds supplied by Otto Hofstetter. For CSD preform are 28mm PCO 1810, 38g and 28g, still water 32g and 18g and 0.5 litres with 30/25 neck finish, hotfill preforms. Closures production for CSD and still water. For still water 7,9g - 200g (250ml - 12l), CSD bottles 21g - 23,5g (250ml - 2,5l), Neck finish: still water 29/25, 30/25, 28mm 3 start, CSD: PCO1810/1816, PCO1881, Juice and milk: 38mm 3 start, Closures for all the above NF available 30/25 high neck and low neck: 13g - 44g; 29/25 (without step): 8,6g - 35,8g; 29/25: 8,8g - 36g; PCO 1810: 16g - 52,5g, PCO 1881: 14,5g- 50g; 28 BPF: 20g -53g; 38mm: 14g - 44g; 38mm 43/36: 14g - 16g; 38mm 43/36,5 (without step): 26g - 32g; 38mm 43/36,5: 14g - 50g; 48/40: 77g -160g; 21/29: 20g - 52g; 28/22: 23g; 28/410:19,5g - 40g; 28/410 with anti back off system: 34g -40g; BVS 30 H: 40g - 53,5g; CRC63: 445g; 55mm:650g.","@ID":24}, "CAPPING / CLOSURES 28 No. 01+02/16 petpla.net Please order your copy at the PETplanet insider book shop: https://petpla.net/books Bottles, Preforms and Closures - A Design Guide for PET Packaging Second Edition by Ottmar Brandau € 115,00 180 pages © Copyright Elsevier 2012 * This article was published in Bottles, Preforms and Closures, Ottmar Brandau, Chapter 4.3 Copyright Elsevier 2012 4.3.3 Sports closures Consumers on the go are the main targets for closures that need not be unthreaded to gain access to the product. Unthreading requires two hands, and in many activities such as biking this can be cumbersome or even dangerous. The industry has addressed this need and invented a series of closures that offer improved ease of access. There are a variety of designs available, but the “push–pull” closure is most widely used (Fig. 4.16). These closures feature a threaded base fitted with a tamper-evident band. A protruding cylinder is part of the base onto which a hollow cylinder is fitted in a secondary operation. The liquid flows through the ringshaped area between these two parts when the outer part has been pulled open. The inner cylinder serves as guide for the outer part and forms a seal with it when the outer part has been pushed down. A dust cover, which could also feature a tamperproof device, goes on top of the spout. The consumer can, after removing the dust cover, pull the spout up and gain access to the drink. Figure 4.16 The push–pull closure is the most widely used sports closure in the market. (Picture courtesy of Bericap).","@ID":30}, "COLOURING / ADDITIVE 13 PETplanet insider Vol. 17 A further possibility is offered as regards the manufacture of injectionmoulded parts in the form of colour plaques or square parts that fit together to make a sort of cosmetic case. The surfaces of the cosmetic case have different textures, thus drawing attention to their particular effect on colour perception. Samples can also be viewed in a light studio where a range of different lighting sources can demonstrate how colour perception changes under different lighting conditions, e.g. in sunlight or on a shelf in a supermarket. Materials and applications HDPE 60% PET 35 % PP in small volumes for closures and engineering plastics PET products have increased significantly over the last few years and are continuing to make headway. As far as the PET sector is concerned, it is cosmetics applications that dominate here in the USA. Further potential has been identified in energy drinks and small mineral water bottles with colour intensifiers that are used as marketing tools to promote specific aspects. Lab The laboratory consists of five machines: Preform machine with a single cavity for preform samples Amsler stretch blow moulding machine with one blow mould and hand infeed Extrusion blow moulding machine, triple layer with one blow mould Extruder for masterbatch manufacture Injection moulding machine for the manufacture of injection moulded colour samples such as colour plaques and square cases with variations in surface finish on the side walls Following a tour of the plant, which included the concentrate manufacturing section, we leave Chicago and extend our thanks for an impressive meeting. www.clariant.com","@ID":15}, "MARKET SURVEY 23 PETplanet insider Vol. 17 No. 01+02/16 petpla.net Novapet S.A. S.B.E.C.M. PDG Plastiques Empacar S.A. UAB Terekas Paseo Independencia, 21 3º, 50001 Zaragoza, Spain + 34 976 216 129 www.novapet.es Mr Antonio Lázaro Preform Business Manager + 34 976 216 129 + 34 901 021 138 [email protected] Rue de la plaine 47230 Lavardac, France +33 553 9741 00 www.sbecm.com Mr Jean-Luc Didouan General Manager +33 553 9741 00 +33 553 6585 97 [email protected] ZI secteur 2 45330 Malesherbes,France +33 238 3461 95 www.pdg-plastiques.com Mr Francois Desfretier General Manager +33 238 3461 95 +33 238 3463 82 [email protected] Casilla de Correo 2865, Parque Industrial - 45, Santa Cruz de la Sierra, Bolivia +591 334 655 25 www.empacar.com.bo Mr Carlos Limpias General Manager +591 33465 525 +591 33461 883 [email protected] Vytauto g. 114 A Kretinga LT-97134, Lithuania +370 445 51 431 www.terekas.com Mr Gytis Sirvinskas Sales Manager +370 445 43 744 [email protected] No No No No No In project Yes Yes No No Wide PET resins portfolio According to the customer's needs PP, PE, BioPET No PP 10.0 to 25.0% 25% - 30% on regular request, could be 100% Yes up to 100% Yes 10% to 100%, own BTB EcoPET rPET, clear and coloured No Concentrates (for milk and light sensitive products) Colours, Lubricants, nucleants, under customer requirements AA scavengers, blockers, all colouring agents (liquid or masterbatch), O2 absorbers, additives, lubricants, blends, etc. Prelactia 100% light barrier for UHT steralized milk long shelf-life, Oxygen, UV, CO2 barriers, coloured preforms, Preblow technology All colours, Activer barrier, 02 scavenger UV protection, various colours, fast reheat, hot-fill 29/25 W (short neck) 330ml to 2.000ml (10g to 32g), 30/25 W (std neck) 330ml to 2.500ml (12.5g to 39g), 48mm W, 5.000ml to 10.000ml (77g, 82g & 98g), PCO 1810 (std neck) 500ml to 3.000ml (18.5g to 54g), PCO 1881 (std neck) 500ml to 2.000ml (19,5g to 38,7g) , 38mm, 500ml to 5.000ml (23g to 68g) Any other shape and weight:customer requirements Neck finish : 30/25 High and Low, 29/25, PCO 28 (1818, 1881), BPF, 38mm, 48/41, BVS, 21/29, 36/29, 28/400, 28/410. Preform weight : from 10 to 91g Possible neck finish adaptation and preform customisation. For any application and size: water, softdrinks (CSD), wine and spirits, oil, milk and dairy products, house and personal care, etc. 29/25 shorty: 8g to 28g, 30/25 high & low: 17,5g to 50g, 38mm 3 start: 28g to 50g, Prelactia 38mm 3 start: 17g to 38g, 48/40: 47g to 62g, 27/32: 6,5g dairy & smoothies, 25/20: 6,5g to 8g dairy, PCO 1810: 33,6g, PCO 1881: 32g, 29/23: 24g to 33g chemical, BVS 30H60: 50g Wine (high oxygen barrier), 22H30: 19g Wine (high oxygen barrier) ultra-lightweighting 2,4g preform standard & specific preforms for mineral water, dairy, juice, CSD etc. Overmoulding technology for 2 layers preforms Preblow technology for lightweigthing bottles PCO 1810 (17.5g to 64 g), PCO 1881 (20.6g, 23.1g, 46.6g, 54.6g), Bericap 38mm wide (70g,80g), Bericap 48mm wide (85g,94g), 700g preform for 5 gallon water bottle, 29mm edible oil : 18g, 21g, 24 g Neck/weight/application: 38mm, 30g, hot fill / 38mm, 28,8g, 33,6g, 19,5g milk and juice / 38mm, 61,5-66g, 5l 38mm, 73g, 5-7l 29-21mm, 20g, edible oil / 83mm, 47g, wide mouth jars UAB Retal Lithuania Retal Italia Srl Varioform PET Verpackung Ges.m.b.H. Alpla-Werke Alwin Lehner GmbH & Co. KG Fabriko str. 14 A Lentvaris, LT-25121, Lithuania +370 528 58 400 www.retal.lt Mr Rimvydas Bazinys Regional Sales Director Retal EU (PET) +370 528 56 444 [email protected] 30027 Via Giustinian, 1 San Dona'di Piave, VE, Italy +39 0421 320 678 www.retal.biz Mr Renzo Imperia General Manager +39 0421 320 678 +39 0421 320 678 [email protected] Industriestr. 5 3134 Reichersdorf, Austria +43 2783 7114 0 www.varioform.at Mr Werner Maurer General Manager +43 2783 7114 10 [email protected] Mockenstrasse 34 6971 Hard, Austria +43 5574 6020 www.alpla.com Mr Jens Seifried Global Sales Director +43 5574 602 518 +43 5574 62017 518 [email protected] Yes No Yes No No No Only PET Yes, any compound suitable for specific barrier projects Hot fill & barriere solutions Yes 0%-100% 0% - 55% Yes, on request Oxygene scavengers, UV blocker, AA blocker, slip agent, blowing additive, anti yellow additive etc. contact for further information all customary additives Neck finishes: PCO 1881, PCO 1810, 38 mm 2 starts, 38 mm 3 starts, oil, W 48/41, WM, HN, 30/25, 29/25, BPF, crown cork Retal Italy, with a wide range of preforms can fulfill requirements of the most common and modern neck solutions and weights: PCO1810 (24g to 52g) , PCO1881 (20,7g to 50,4g), PCO Corvaglia (15g to 26g), Alaska Novembal 267 (12g to 32g), Alaska lightweighted (30g to 31,5g) , OBRIST 19mm (21g to 23g) , OBRIST 26/22 (Gravity II) 1 Start (9,8g to 33g), HEXALITE 26/22 3 Starts (9,7g to 23,5g), 38 mm 3 Starts (17g to 19,5g) , oil 29/21 (21,8g to 27g), Affaba & Ferrari (21,7g to 48g), 48/40 (87g to 90,5g), 38mm Bericap (48g) , Oil 36/29 (48g),BPF Light (18g to 38g). Portfolio includes different preforms for the Beverage and Non Food.Preforms from 14,8g up to 54g with PCO 1810, PCO 1881 as well as Petcycle neck finishing. Different virgin resins as well as recyclates (up to 55%) or special materials (e.g. hot fill or barrier). Softdrink preforms, various neck versions (0.25l to 2.5l); Water preforms, various neck versions (0.25l to 19l); Edible oil preforms (0.5l to 10l); Milk preforms various neck versions (2-start, 3-start); Preforms for personal care, home care, lubricants various neck versions.","@ID":25}, "BOTTLE MAKING 15 PETplanet insider Vol. 17 equipment, and provide PET bottles testing services in our own laboratory, in addition.” PET Technologies currently employs 200 staff members, of whom 160 are already working in the new 4500m² factory. Once the capacity is fully used the company plans long-term development of the PET markets for food and non-food in North and South America, and in Africa and Asia. Among the patents PET Technologies holds is one for a mould closure method that it says is unique. It confidently asserts that its machines are energy-saving, easy to use and straightforward to integrate into existing production lines. Its blow moulding systems use a compressed air recovery process that can achieve savings of up to 25%. “The packaging industry currently has several hot topics, including the production of PET kegs, wide-neck jars or the ongoing trend in preform lightweight, for example,” Poliansky continues. “We will be able to present several innovations in these areas in the near future. Our investments include the modernisation and refurbishment of our factories and further automation of them. We are continuously working on the improvement of our tools and increasing their output. We have recently added new CNC machines to our range. A DMG Mori is in use in the new factory, and more will be delivered in this year. Finally, we have just approved the layout for a building extension near the new plant, which will include a procurement department and new office spaces.” www.pet-eu.com","@ID":17}, "INSPECTION 18 PETplanet insider Vol. 17 No. 01+02/16 petpla.net Part 2: Metrology principles for the PET packaging industry Base and wall thickness measurement by Chris Freshman MEng.(Hons) CEng MIMechE, Torus Measurement Systems, Telford, UK This article explores the PET industry’s changing requirements from process monitoring to ‘true’ measurement systems. The differences between accuracy, resolution, precision, repeatability, reproducibility and traceability are detailed and each clearly defined. It then demonstrates how discernible metrology is coupled with technological improvements, such as those described in part 1 (see PETplanet insider 12/2015), to produce the highest level of measurement systems. Quality control Process monitoring evaluates part to part variation, focusing on the difference between one result and the next as opposed to the determination of a ‘true’ value. The PET packaging industry, due to the initial requirement for stable production, originally implemented inspection systems based on process over metrology. This aided the creation of reliable manufacturing techniques with minimal variation, thus allowing performance optimisation, material resource reduction and design improvements. However, quality requirements are changing with the emphasis now on ‘true’ metrology. Recorded, traceable and accurate measurement results are essential to ensure parts are correct and consistent, regardless of the country of manufacture. There has also been an increase in the number and variety of measured features with a greater amount of the bottle and preform being inspected, calling for more sophisticated methods. An undesirable scenario If a batch of bottles were uncharacteristically splitting in the base area, it would be important to determine if they had been blown and stretched correctly. This could be assessed by checking the material thickness in that area. For example, captured data may indicate parts checked during that production period tested within tolerance and were verified against a reference sample. However, how do we know instruments accuracy it must first be quantified by using one of two methods. The first method, categorised as a ‘Type A’ evaluation, statistically analyses repeated measurements, often referencing values from equipment of a higher traceable accuracy. The second method, categorised as a ‘Type B’ evaluation, uses a calculated uncertainty value by following the ISO Guide to the Expression of Uncertainty in Measurement. Gauges supplied by Torus Measurement Systems, such as the B300 Wall Thickness, B303 Bottle Burst or B304 Top Load & Volume, are supplied with a proven accuracy, giving the end user confidence in their measurement results. This is determined through a Correlation study (Type A), where six parts are each measured five times and compared to the same number of measurements from a higher accuracy instrument. Resolution is not accuracy Resolution is defined as the smallest discernible change in the instrument or value of interest; a system may have a better resolution than accuracy. For example, the camera configuration used on Torus’ Preform Inspection Gauge, Figure 1 has a resolution equating each virtual pixel to a physical 17μm, but has a proven system accuracy of 30μm. Accuracy, as previously defined, is affected by factors such as lens aberration, calibration uncertainty, part variation, algorithm programming, view angle, and focal distance. the average thickness result reflects the physical size and has not been affected by linearity errors? Additionally, how do we know the reference standard used for setup is correct? Furthermore, how do we know, if re-checked, the results would repeat within an acceptable range? The answers to these questions define the fundamental differences between process monitoring and traceable measurement. Discernible metrology A measurement value can never be exact or perfect. There is always a degree of error associated with any type of inspection. Measurement is its own discipline with internationally recognised definitions, methodology and standards. Only through strict adherence to these rules and guidelines can quality of measurement be ascertained. Clearly defining terms such as accuracy, precision, resolution, repeatability and reproducibility, and their associated methodologies, is important for a fair comparison between systems. Additionally, tracing measurements back to reference instruments and international standards can ensure, for instance, that test results obtained in Brazil correlate to those obtained in Poland. System accuracy Accuracy is a qualitative term defined as the deviation between the measurement result and the ‘true’ value. In order to determine an","@ID":20}, "MARKET SURVEY 21 PETplanet insider Vol. 17 No. 01+02/16 petpla.net Preforms Filling equipment Resins /additives Preform / stretch blow moulds Caps and closures Preform and single stage machinery Bottle-to-bottle recycling plants Compressors Closure systems Two stage SBM machinery 01+02/2016 MARKETsurvey Suppliers of PET preforms 17 companies from 13 countries participated in this year’s market survey of preforms suppliers. They are shown in order in which their details were received by the editors. In alphabetical order there are as follows: Alpla (Austria), Amcor (USA), Empacar (Bolivia), Gulf Packaging Sytem (Saudi Arabia), Intergulf Ltd. (UAE), Manjushree (India), Novapet (Spain) PDG Plastiques (France), PET Preform Morocco, PET Verpackungen GmbH Deutschland (Germany), Plastipak (UK), Retal (Italy), Retal (Lithuania), S.B.E.C.M. (France), SGT (France), Terekas (Lithuania) and Varioform (Austria). Although the publishers have made every effort to ensure that the information in this survey is up to date, no claims are made regarding completeness or accuracy. Company name Amcor Rigid Plastics Amcor Rigid Plastics Manjushree Technopack Postal address Telephone number Web site address Contact name Function Direct telephone number Fax E-mail 2801 SW 149th Avenue - Suite 350, Miramar, FL 33027, USA www.amcor.com Mr João Lorenzoni Strategic Marketing, Beverage - Latin America +1 954 499 4863 +1 954 704 0443 [email protected] 935 Technology Drive - Suite 100, Ann Arbor, MI 48108, USA www.amcor.com Mr Frank Lin Director, Marketing & Strategic Business Dev. - Arpna Beverage Business Unit +1 734 358 1838 +1 734 428 4528 [email protected] 60 E, Bommasandra Ind. Area, Hosur Road, Bangalore - 560 099, India +91 80 43436 200 www.manjushreeindia.com Mr Rajat Kedia Director +91 80 43436 200 +91 80 27822 245 [email protected] Preforms Multilayer preforms (Yes/No) No No PEN prefoms (Yes/No) No No Preforms in alternative materials (PP/PLA/PEF) Which? No No Preforms incorporating rPET (rPET content in %) Up to 100% rPET depending on requirements/specs 10% and 25% List of additives available Colourants, barriers UV Blocker, oxygen scavenger, slip additive, anti yellow additive, AAA Preform range 26 - 43mm Cold fill preform solution for CSD, still & sparkling water, energy drinks, juices, dairy and nutraceuticals. PCO 1810: 12,4g - 48g, PCO 1881: 11,2g - 52,7g, PCO 1810 Thick Neck: 18.5g, 23.8 g, 27.0g & 47.0g, 3 Start Alsaska: 10,6g - 35,6g, 30/25 MM 3 Start: 20.5g, 22.0g, 29/25 MM 3 Start: 18,6 Manjushree producing 2.4 billion quality preforms per year in Bangalore, India. Approved by Coca-cola, PepsiCo, RC Cola & Big Cola. Over 65 varieties of PET preforms starting from 100ml upto 20l. Exporting preforms in over 20 countries across North America, Africa, Middle East and Oceania.","@ID":23}, "NEWS 9 PETplanet insider Vol. 17 No. 01+02/16 petpla.net Amsler designs a single-cavity machine Amsler Equipment Inc. has just completed and shipped its first next-generation single-cavity LM15X PET stretch blow moulding machine to R&D/Leverage in Lee’s Summit, Missouri. The requirement from R&D/Leverage for a machine to test and run moulds for various PET machines led to the development of the new series. The result is a smallfootprint fully-functioning, production-capable, single-cavity PET stretch blow moulding machine. It can be used in labs, for small production runs, pilot production, customer trials, mould run-offs, material testing and preform testing. The options of neck orientation, hot fill and preferential heating can all be included. The machine can make up to 11 million 500ml water bottles per year. Two bottle size ranges are available for the single-cavity machine: the L12X for bottles from 20ml up to 2l and the L15X for bottles from 20ml up to 5l. Neck sizes for both systems range from 18mm up to 63mm. Each size range has two versions: the semi-automatic with hand loading of preforms and the fully automatic version with an automatic preform loading system. The neck orientation system feature is unique in that it orks with standard preforms. The preferential heating option is designed for oval bottles and can help to open up the processing window. These options can be used separately or together using a simple bolt-on and -off installation system. www.amslerequipment.com www.rdleverage.com All about PET Petcore Europe is pleased to announce the new date for its annual conference: February 23rd, 2016 in Brussels, Belgium. Due to the exceptional situation in Brussels in November, Petcore had to postpone the conference. The topics Sustainability, European Circular Economy, Innovation and Globalisation will be discussed by 130 experts and leaders from the complete PET value chain in Europe and beyond as well as representatives from the European institutions. www.petcore.org With Sacmi, the beverage specialists are always at your side. With our unbeatable technological know-how and continuous research we are creating new containers and closures designed to ensure outstanding performance. The new IPS injection system for preforms, the CCM compression press for caps and the quality control systems fully designed and built by Sacmi, allows for large-scale production with considerable advantages in terms of efficiency and flexibility. The outcome? Reduced plastic volumes, less energy consumption and lower running costs.All in a bottle: the one you’ll soon be making. DRINKTEG ISTANBUL, 4/6.02.2016 - #E17 - Istanbul TURKEY PRODEXPO, 8/12.02.2016 - #7-HALL1-71C32 - Moscow CSI BEER ATTRACTION, 20/23.02.2016 - #A7-117 - Rimini ITALY PROPAK VIETNAM, 1/3.03.2016 - #K18 - Ho Chi Minh VIETNAM PROPAK AFRICA, 15/18.03.2016 - Johannesurg SOUTH AFRICA DJAZAGRO, 18/21.04.2016 - Alger ALGERIA CHINAPLAS, 25/28.04.2016 - #E2B51 - Shanghai CHINA","@ID":11}, "INSPECTION 20 PETplanet insider Vol. 17 No. 01+02/16 petpla.net Country National Measurement Institute United Kingdom National Physics Laboratory (NPL) United States National Institute of Standards and Technology (NIST) Japan National Institute of Advanced Industrial Science and Technology (AIST) Germany Physikalisch-Technische Bundesanstalt (PTB) Table 1 - A small selection of National Measurement Institutes from around the world Measurement competency is assessed and monitored by accreditation bodies. They ensure laboratories are capable of calibrating in accordance to the national standard. Torus Measurement Systems have an in-house measurement laboratory accredited by the United Kingdom Accreditation Service (UKAS), for internal and external calibration services. Specifying measurement performance The questions set-out at the beginning of this article can now be answered in reference to Torus’ B300 Wall Thickness Gauge. How do we know the measured value reflects the physical size and has not been affected by linearity errors? The gauge has a proven accuracy determined by performing a ‘Type A’ correlation study on a master artefact, see Table 2. In addition, 4 reference pucks of thickness 0.125mm, 0.250mm, 1.000mm and 1.500mm, are supplied with each gauge, verifying the system will remain linear through its measurement range. How do we know the reference standard used for setup is correct? The artefact and reference pucks are UKAS calibrated and traceable to a national standard for thickness measurement. How do we know, if re-checked, the results would repeat within an acceptable range? The gauge repeatability is confirmed by conducting a comprehensive R&R study, as previously detailed, see Table 2. Feature Accuracy +/- (mm) R&R (mm) Wall thickness 0.020 0.020 Base thickness 0.050 0.050 Overall height 0.025 0.050 Base clearance 0.025 0.050 Table 2 - Proven accuracy and repeatability values for the B300 Wall Thickness Gauge Beyond base and wall thickness measurement Torus Measurement Systems have produced a wall thickness gauge by combining new technology, sophisticated software and stringent metrology techniques. Enhanced bottle profiling and positioning has enabled shoulder, wall, base peak and base valley thicknesses to be inspected, as well as measuring Overall Height and Base Clearance. The new B304 Top Load & Volume Gauge has been developed by continuing to apply the above principles and innovation to further meet industry requirements, see Figure 6. Improvements include; integrated top loading and volume testing into a single station, removing the need to move the bottle between tests and reducing labour time and costs; a unique fill nozzle design that improves reliability and fill level repeatability; calibrated load cell and weigh scale traceable to national standards. The measurement principles, as outlined in this article, are currently being implemented on a new high-speed automatic preform measurement and inspection gauge. Figure 6 - B304 Top Load & Volume Gauge www.torus-group.com Cape Town Port Elizabeth Maseru (Lesotho) Durban Maputo (Mozambique) Pretoria Gaborone (Botswana) Johannesburg Hong Kong Chongqing Xi'an Taiyuan Shenyang Qingdao Nanjing Guangzhou Shanghai Beijing Jinan BE PART OF IT! petpla.net The South Africa Road Show The China Road Show April – October 2016 August – September 2016 The worldwide round trip with to to Powered by","@ID":22}, "imprint EDITORIAL PUBLISHER Alexander Büchler, Managing Director HEAD OFFICE heidelberg business media GmbH Bunsenstr. 14 69115 Heidelberg, Germany phone: +49 6221-65108-0 fax: +49 6221-65108-28 [email protected] EDITORIAL Kay Barton Doris Fischer Heike Fischer Gabriele Kosmehl Michael Maruschke Ruari McCallion Waldemar Schmitke Wolfgang von Schröter Anthony Withers MEDIA CONSULTANTS Martina Hirschmann [email protected] Johann Lange-Brock [email protected] phone: +49 6221-65108-0 fax: +49 6221-65108-28 FRANCE, ITALY, UK Elisabeth Maria Köpke phone: +49 6201-878925 fax: +49 6201-878926 [email protected] LAYOUT AND PREPRESS EXPRIM Werbeagentur Matthias Gaumann | www.exprim.de READER SERVICES Till Kretner [email protected] PRINT Chroma Druck & Verlag GmbH Werkstr. 25 67354 Römerberg Germany WWW www.hbmedia.net | petpla.net PETplanet insider ISSN 1438-9459 is published 10 times a year. This publication is sent to qualified subscribers (1-year subscription 149 EUR, 2-year subscription 289 EUR, Young professionals’ subscription 99 EUR. Magazines will be dispatched to you by airmail). Not to be reproduced in any form without permission from the publisher. Note: The fact that product names may not be identified as trademarks is not an indication that such names are not registered trademarks. 3 PETplanet insider Vol. 17 No. 01+02/16 petpla.net Dear friends of PETplanet insider, We are starting this year with a moderated knowledge management system. What is that? You may well be asking? Our aim is to try and show the PET world in a joined-up way. We’ll start at the PETcore Conference in Brussels on February 23, 2016, which focuses on PET recycling. Erema and Starlinger have already announced they will co-operate. We would like to invite you too – dear Reader – to join us. Design a tool to gather up-to-date information about the PET industry, its technologies, processes, applications, companies, events, all along the PET value chain. Our target is to offer organisations and suppliers a unique way to present themselves on an independent platform and for producers to find comprehensive information on their relevant topics. As an independent source of information the database is inviting all partners of the PET value chain to create the contents. In order to guarantee high quality of content, Doris Fischer, of the PETplanet editorial team, will moderate the content. One question that immediately springs to mind is this: what exactly do all these recycling terms actually mean? We are all familiar with PET recycling and down-cycling but where does PET bottle upcycling fit in? Our back story from Costa Rica may supply the answer. Donald Thomson the initiator and brains behind the scheme calls the idea REAP - Recover, Enrich, Appreciate and Prosper. This somewhat abstract concept became reality in the “bottle to tile” project. Before the bottles became a down-cycle product, or even worse, dumped in a landfill site with all the harmful environmental consequences, the bottles were enriched by transforming them into high quality tiles which were then used to improve housing for poor people. A win-win situation for recyclers, the environment and for people. The waste stream of the PET bottle has thus become the value stream for the roof tile. Thomson draws an infinity loop to outline the interdependence of input and output: “two intersecting cycles, synergistically co-nurturing a balanced and zero waste growth between themselves.” Yours Alexander Büchler","@ID":5}, "PRODUCTS 31 PETplanet insider Vol. 17 No. 01+02/16 petpla.net Amcor Rigid Plastics wins WorldStar 2016 Packaging Award for Hot-Fill PET bottle Amcor Rigid Plastics has been honoured with a packaging award at the World Star 2016 Packaging Awards Competition, sponsored by the World Packaging Organization (WPO). The award was in recognition of Amcor’s development of an ultra-lightweight, hot-fill PET container, which was designed exclusively for PepsiCoLipton’s tea drink brand in Central America. Competition winners were selected by representatives from 19 WPO member associations, who judged 293 packaging entries from 35 countries. Amcor’s Latin America design team, based in Miramar, Fla., worked in partnership with PepsiCo-Lipton to develop the new container, which gives regional consumers a lighter, more functional bottle. The 500ml package weighs 22g and utilises a 33mm finish that features a 50% reduction in material over a traditional 38mm finish. The leaf body panels have practical functions in supporting the vacuum and providing a gripping surface for the consumer, while offering aesthetic appeal by adding visual interest. Amcor says that the bottle enables manufacturers to achieve aseptic filling packaging weights without prohibitive investment, while offering a more eco-friendly option. Weighing in at just 22g, the new bottle is approximately 30% lighter than standard 500ml heat-set PET containers, which weigh about 34g. The material reduction increases the bottle’s recyclability, cuts the energy needed for its production and thus reduces its environmental footprint. Greenhouse gas emissions are cut by 26%, energy use is reduced by 23%, and water consumption is decreased by 24%. The new container also results in a 26% reduction in the amount of waste that could potentially end up in a landfill. The new hot-fill bottle is designed to run on existing filling lines with minimal changeover. Along with the ultra-lightweight container, Amcor and Bericap, in cooperation with PepsiCo, developed a 33mm, 3.7g tamper-evident finish/closure for hot fill. The new closure incorporates a built-in seal that eliminates rubber liners or induction seal foils, thus reducing overall materials use. It is made of HDPE rather than PP, as previously. The new product was initially launched in El Salvador and has since been introduced in Mexico and other Central American countries. In addition to the award for the PepsiCo-Lipton container, sister company Amcor Flexibles was recognised with three World Star awards for pharmaceutical, medical, and wine packaging solutions. www.amcor.com www.bericap.com [email protected] Tel: +90 212 695 50 00 Fax: +90 212 694 97 24 100815dmyR .com","@ID":33}, "CAPPING / CLOSURES 27 PETplanet insider Vol. 17 No. 01+02/16 petpla.net CAPPING CLOSURES 27 of the sheet material cannot be used and must be scrapped. Liners are compression moulded with the cap acting as the cavity. A very small drop of suitable plastic is placed directly into the cap and the resulting liner bonds with the cap material. This is the most cost-effective method but leads to a liner that moves with the cap during unscrewing. Small imperfections on the sealing area of the bottle neck may damage the liner and lead to problems. Liners can also be compression moulded outside the cap and then be inserted into it in the same machine. As a result, the liner can rotate freely inside the cap and eventually become stationary with respect to the bottle neck while still rotating with the caps. This has the advantage that different friction characteristics, as those for glass and PET, have no impact on the opening torque, allowing the use of the same liner for both bottle materials (Fig. 4.13). Advantage • Uniform opening torque • Proofed and well known design • Resistant to smaller inside and outside preform damages • Resistant to mechanical influences • Easy to sterilise Disadvantage • Sensitive for application torque • Releases pressure after few degree without tamper evidence • High production costs 4.3.2.1 In-shell moulded liner This liner is moulded right inside the cap in such a way that it forms a well into which the bottle neck fits. In a way, this is like the aforementioned triple seal with the majority of the work being done by the outside seal. The open structure poses no obstacles for sterilisation, and this seal is well suited for single-serve juice bottles. As with all liner seals, this design releases pressure after turning the cap only a few degrees and before the tamper-evident band makes it visible. You can easily try this out with a hot-filled product: the bottle expands visibly during turning of the cap as the vacuum inside the bottle is released and well before the tamper-evident band breaks (Fig. 4.13). 4.3.2.2 Out-shell moulded liner This liner has been molded outside the cap and is inserted in a secondary operation. It sits on a ridge inside the cap and is squeezed against the inside cap surface when the capper screws it onto the bottle. Contamination behind the liner cannot be reached by a sterilization procedure. Because the liner is made in a separate process, the cap can be printed inside, and this is the most widely used cap design for promotional initiatives that ask consumers to look behind the liner for a possible prize announcement (Fig. 4.14). 4.3.2.3 Co-injected liner This design takes the idea of lining the cap one step further. Both cap and liner materials are injected into the same mould via a co-injection process. A smaller, secondary extruder supplies the drop of liner material that is required for each cap. The seal is made in a manner similar to the in-shell design, but the cap construction is somewhat different. The cost of machinery and tool and the low output have never allowed a breakthrough for this solution (Fig. 4.15). Advantage • Uniform opening torque • Good seal Disadvantage • Sensitive for application torque • Releases pressure after few degree without tamper evidence • High risk for liner defects • World champion in terms of production costs Squeezing Drinking Pouring Pumping Meet us at February 24 & 25 Stand A61 NEC Birmingham","@ID":29}, "PETproducts 30 PETplanet insider Vol. 17 No. 01+02/16 petpla.net Frosch presents new designs with Gizeh When launching its natural cosmetic line “Frosch Reine Pflege” the company Werner & Mertz is focused on a natural appearance, also with regard to the packaging. In collaboration with the packaging specialist Gizeh the manufacturer established a new design line for his care products. The liquid soap bottle in a tear drop shape is subtly decorated with spring-like flowers, leaves and butterflies. It has a matt white shrink-sleeve with discreet appearance. The children´s series, on the other hand, is focused on high-gloss: The world of the little frog is presented in bright colours and details on the bottle. Gizeh produces the bottles for both series of PET. The 300ml soap containers are manufactured by single-stage injection stretch blow moulding and decorated with shrink-sleeves. Once the first common project is launched successfully in the market, the next joint development for the “Erdal” brand will arrive in stores within the next few weeks. www.gizeh-pet.com PET bottle is flavour of the month RPC Promens Consumer Innocan is launching a 750ml barrier PET bottle for flavoured syrups for cold drinks. The new bottle provides a more cost-effective, convenient and flexible pack format compared to the metal can which has traditionally been used for these products. For the consumer, the PET bottle’s lighter weight ensures ease of handling. For manufacturers, the bottles can be sleeved with individual branding and graphics as required, simplifying logistics and avoiding delays or unwanted stock as there is no need to buy-in and store pre-printed metal cans. The curved design of the PET bottle echoes the design of the metal can to help maintain brand familiarity and allows the bottles to be filled on existing lines and use the same cap. The multilayer construction incorporates a layer of oxygen scavenger (active barrier) and polyamide (passive barrier), which provide an effective barrier against oxidation to prolong the shelf life of the syrups. In addition, this helps to maintain the flavour of the syrups in the bottle for longer. www.rpc-promens.com SGT, naturally innovative The specialist in PET preforms and HDPE caps for over 30 years. +33 (0)2 40 05 09 37 /www.sgt-pet.com","@ID":32}, "BOTTLE MAKING 17 PETplanet insider Vol. 17 No. 01+02/16 petpla.net Serac Blow Linear (SBL) blowing units Having acquired state of the art skills in PET blow-moulding over the past few years, Serac started designing its stretch blow-moulding units. By concentrating on controlling the heating process of preforms and maximising time allocated to heating and blowing, Serac has been able to stretch lightweight preforms up to their limits with a homogeneous bottle thickness and without neck deformation. Ultimate control of the blowing process of SBL units has been achieved by integrating advanced technologies and proven, long-lasting devices. These include the new generation of NS-IRS heating boxes from Olicorp, Geneva, Switzerland, Seitz technology Wetzikon, Switzerland based solenoid pre-blowing and blowing valves and automation control from B&R, Eggelsberg, Austria. For example, Serac’s SBL 50g yogurt portion packages are presented in a fruit-shaped flask, blown from a PET preform of 2.3g and with nearly half of the mass concentrated in the neck. The fruit-shaped flask requires an expansion rate of 16 (four times in both length and width), which is remarkable in this industry. A preferential heating option is available to further enhance the versatility of the SBL blowing units. In contrast to standard processes, heat is not evenly distributed on the preform but is concentrated on two sides. Preferential heating is used to produce oval bottles (width/length ratio equal or higher than two), as well as square and complex-shaped containers. The main applications of this specific process are to be found in markets such as oils and sauces, dishwashing and surface care products, and hair and skin care products. Serac’s linear blowing units produce up to 12,000 1l bottles per hour, with an efficiency rate up to 98%. Combox: a single block blowfill-cap concept Under the name Combox, Serac is offering a single block blow-fill-cap element for a high precision blowing unit, with a rotary weight filler for low to medium outputs. The net weight filling technology, a specialty of the group for over 45 years, offers benefits in filling accuracy and reliability, Clean In Place (CIP) facilities and maintenance. Serac’s patented transfer system ensures that preforms and bottles are always positively transferred and move along the process without ever touching each other. This avoids jams, bottle drops and scratches. The transfer system converts the sequential motion of the linear blower into a continuous motion adapted to the rotary filler. It is associated with a special filling mode to ensure quick adjustment of the filler-capper to the blowing unit output. At the end of each production batch, both machines communicate with each other to ensure all remaining preforms in the blowing unit are used and properly filled and capped. Combox units help to cut downtime to a minimum, thanks to quick mould changeovers that will take a single operator 10 minutes to perform, as well as simplified maintenance operations and the elimination of production starts and stops often associated with accumulation systems. www.serac-group.com","@ID":19}, "PETbottles 34 PETplanet insider Vol. 17 No. 01+02/16 petpla.net Home + Personal Care Treasure trove from Garnier L’Oréal has launched a new product line under its Garnier brand name and the tag “Treasure Trove” which dispenses with parabens and reinstates the use of vegetable components to reinforce the cleansing and pampering effect when you wash your hair. Depending on your hair type and need, various combinations are used by way of active ingredients. For dry hair, for example, a shampoo with argan and camellia oil is recommended. This shampoo is packed in a coloured bottle with a content of 250ml. One striking feature of the packaging is the snap-on hinged lid with dispenser opening. In order to make it easier to open with one hand, even with wet hands, there is a built-in recess with grooving in the lid. The transparent front label enables the user to view the rear label which is printed on the inside. www.garnier.de Slim bottle for fragranced laundry “Denk mit”, an own label belonging to the discount drug store dm, has recently integrated a laundry fragrance into its range. The product, which is suitable for the washing machine and the washer/dryer, imparts an intensive fragrance to the laundry. 200ml of the product is packaged in a blue-tinted, slim bottle which is tapered towards the top. The dispensing aid in the bottle opening incorporates a recess to assist dispensing. The screw cap is easy to grip and open thanks to its rough surface. www.dm.de Foam bath in PET Manufacturers t e t esep t Pha rma GmbH, mainly known up to now for their health products and diet supplements, have now launched a life-style range of foam baths in four fragrance variants under their brand name “t:by tetesept”. According to the manufacturer, time out, pampering, winter and good luck ensure a new bathing experience as a result of long-lasting foam, natural aroma oils and gentle care. The appearance of the packaging has been designed to reflect the trendy, high-quality nature of the product. In each case 420ml of the foam bath has been packaged in elegant, white, stable PET bottles, each of which is decorated with a product-specific sleeve label. Rounding off the product’s presentation at the PoS is a shiny silvery screw cap which serves to draw the eye towards the item. www.t-by-tetesept.de Aqua citrus versus cigarette smoke Shoshu Riki, manufacturers of household cleaners from Japan, are marketing among other items room fragrance dispensers catering for a range of requirements. The illustration shows a room fragrance dispenser that claims to eliminate cigarette smoke in particular and keep the area fresh and smelling of lemons. The multi-compartment dispenser is filled with 400ml of liquid which is conveyed via an uptake pipe to an applicator pad where it evaporates. Prior to initial use a pre-perforated sleeve label, the cap and a screw closure need to be removed from the container. Subsequently the cap is replaced and the pad moistened via the uptake pipe.","@ID":36}, "PRODUCTS 32 PETplanet insider Vol. 17 No. 01+02/16 petpla.net New addition to Liese’s Flexximal family Liese GmbH’s Brau Beviale 2015 stand hosted the public debut of its new Hygienic clamping unit, the latest addition to its Flexximal range. The German manufacturer, based in Walzbachtal, says that the unit is intended for use in fillers, infeed, discharge and transfer starwheels. In common with other products in the Flexximal range, including “Crashsafe“ and “Light“, the Hygienic’s clamp is designed to work with a range of bottle forms, with diameters from 60-90mm. The unit operates independently of the rotation and running direction and can be controlled from both above and below. Ms Carmen Schreiber, Liese’s Marketing Manager, said that the clamper’s simple design has no complex contours or components, such as compression springs, it offers good access for cleaning as well as lighter weight and reduced wear characteristics. Its compact construction enables it to be installed and used in small spaces and is particularly appropriate for use in hygiene-sensitive areas, as its name indicates. Development of the Flexximal Hygienic was undertaken in accordance with guidelines from the European Hygienic Engineering & Design Group (EHEDG). Liese’s product portfolio includes capping machines, inspection machines and specialist label removers for returnable PET bottles and glass. Its 2014 takeover of the portfolio of Adelski, a mechanical engineering company based in Mannheim, enabled the company to expand its range of products and services to include capping systems for beverages and food applications, as well as to non-food industries. www.liese-gmbh.de Shrinking dispenser bottle Large PET dispenser bottles are often used for storing and dispensing water in the office or at home. Starting with five gallon glass-version weighted 20kg, the regular multi-trip PET dispenser bottle fitted on a dispensing unit has a weight of 650g. The next step was a single dispenser bottle, minimum weight 330g. This saves on materials, as well as on transport costs. Following the development Sipa engineered a new dispenser bottle collapsing on it selves as neatly as possible. Collapsing sequences were simulated using Finite Element Method (FEM) analysis to find the buckling mechanism that would best suit the client’s requirement. “FEM analysis accelerates the time of investigation and reduces the number of trials aiming at the correct solution,” says Dino Zanette at Sipa. “It also aids in determining a minimum weight at which the collapsing mechanism is still functional.” Different bottle shapes, square and round, were analysed along with the shape of the ribs and base. Graphs of volume vs. pressure and base center displacement vs. pressure, together with photograms of the simulation, helped the Sipa experts to understand the collapsing phenomena and how to modify the bottle structure to get the best performance. Physical prototypes were built to verify the “virtual” results. Trials have proven the reproducibility of the collapsing mechanism that was studied during the development stages. Now fully self-collapsible containers that require the application of no external mechanical forces to deflate are in industrial production at Sipa. Collecting for recycling or putting them in a recycling bin is simplified. www.sipa.it","@ID":34}, "CAPPING / CLOSURES 26 PETplanet insider Vol. 17 No. 01+02/16 petpla.net Different applications, neck finishes for various, part 5 Closure for PET bottles PETplanet insider is publishing extracts from successive chapters of Ottmar Brandau’s “Bottles, Preforms and Closures”, which was published by hbmedia. A newly revised version is reissued under the Elsevier imprint. 4.3.1.4 Double seal This seal is a combination of the plug seal and the second outside seal and shares their attributes. By having two equally engaging sealing lips, it can overcome preform damage to either the inside or outside wall of the bottle neck. Because two lips have to be engaged, the application torque of the capper is higher and so are mould costs (Fig. 4.11). • Medium removal torque • Resistant to smaller inside and outside preform damages • Good resistance to mechanical influences • Very good for CSD applications • Seal performance depends on application torque • High production costs • Higher application torque • Difficult to sterilise 4.3.1.5 Triple seal Here three sealing lips engage with the bottle neck using the inside, top, and outside. This method is most resistant to any preform damage but requires the highest application torque. Unscrewing this type of cap also requires extra torque (Fig. 4.12). • Medium removal torque • Resistant to smaller inside and outside preform damages • Good resistance to mechanical influences • Very good for CSD applications • Easy to sterilise • Higher application torque 4.3.2 Two-piece closures Although most end users would prefer one-piece caps, liners may be required for a variety of reasons. As discussed in Chapter 5.4, liners are always used with polypropylene (PP) closures. Other liner uses may enhance the functionality or shelf life of the package. The liner material must be soft enough to squeeze between the harder cap and bottle materials. Ethylene vinyl acetate (EVA) is commonly used but other materials may be chosen for specific applications. Caps made for use with liners feature a protrusion in the outer rim that holds the liner in place. The main seal is formed not at the top of the neck but rather on the outside seal area. This design better withstands top loads. Liners are made thick enough to overcome neck and bottle tolerances and minor surface damage. Liners can be inserted into the caps in three ways: Liner material is punched to the correct size and inserted into the cap, often in the same special-purpose machine. This is a relatively expensive operation because some CAPS & CLOSURES","@ID":28}, "PETnews 6 PETplanet insider Vol. 17 No. 01+02/16 petpla.net ChemChina to acquire Krauss Maffei Group The ChemChina - China National Chemical Corporation has agreed to acquire KraussMaffei Group, manufacturer of machinery and systems for producing and processing plastics and rubber, from Onex Corporation for a cash enterprise value of €925million. The transaction is subject to closing conditions including customary regulatory approvals. ChemChina together with Guoxin International Investment Corporation and Agic Capital will make this acquisition. “With ChemChina, we have found a strategic and long-term oriented investor who has been interested in our Company for many years,” said Frank Stieler, CEO of the KraussMaffei Group. The KraussMaffei Group will continue to operate in its current corporate structure. “We are strengthening our company with one of the leading global engineering groups, encompassing a 178-year corporate history. In doing so, we expect that KraussMaffei Group will maintain its identity and independence,” said Jianxin Ren, Chairman of ChemChina. “We are investing in the company’s strong management team and its technological expertise, which we believe will benefit our Chinese subsidiaries and position the chemical machinery business of ChemChina, which build and sell equipment for the rubber and chemical industry, to become a pioneer in achieving the “Made in China 2025” program which aims to enhance Chinese industry.” “Following Onex’s acquisition in late 2012 KraussMaffei Group has achieved strong growth and had a very successful year in 2015. As part of ChemChina, we expect to considerably accelerate our growth strategy, especially in China and Asia, and to further strengthen the Company in Germany and Europe,” Stieler explained. In China, the company is expected to benefit from the trend towards higher quality and sustainability. The machines and systems of the three brands - KraussMaffei, KraussMaffei Berstorff and Netstal - are suited to meet more challenging customer requirements. As a result of the transaction, the KraussMaffei Group will be able to accelerate its planned expansion in China. www.kraussmaffeigroup.com www.chemchina.com www.netstal.com Ultralight Demo collection Demo Design and Moulds debuted their Ultralight Demo collection, containers targeted mainly at the bottled water market with the aim of lowering environmental impact and saving energy. The company created a round shaped 1.5l bottle for still water with a short neck, weighting 21.7g and equipped with the light base. The container can be filled both in the traditional way, as well as with liquid nitrogen. The second product is a 0.5l bottle for sparkling water with a short neck, weighing just 9.7 grams. According to the company the C0 2 level inside the container is equal to that of heavier containers found on the market, and the grip shall provide a good handling even after the bottle has been opened. Both containers have been produced with preforms that can be found on the market, so customers could start a production right away. The adoption of the Ultralight Demo bottles must be accompanied by the conversion of the filling lines in order to use the short neck. Here the company can offer their support and install the entire conversion kit for the main filling lines on the market. www.designandmoulds.com Kosme 3 Bloc for PET The Krones subsidiary Kosme S.r.l., Roverbella, has now, in the shape of the 3 Bloc, presented a block configuration available in two different variants, for PET and for HDPE containers. The 3 Bloc for PET comprises three concatenated machines: blow-moulder, filler and labeller. The particular version of the Flexa labeller can vary, either featuring pressure-sensitive labelling with a Flexa Sensicol station or wrap-around labelling with a roll-feed capability. This version is suitable both for cylindrical and square PET bottles and also for containers with special shapes. The maximum speed is 16,000 bottles per hour. www.kosme.com www.krones.com F.l.t.r.: Ting Cai, Chairman and CEO of China National Chemical Equipment Co. Ltd. (CNCE), Dr. Frank Stieler, CEO of KraussMaffei Group and Chen Junwei, CEO of ChemChina.","@ID":8}, "MATERIAL / RECYCLING 10 PETplanet insider Vol. 17 No. 01+02/16 petpla.net A recycling idea beyond shopping bags and fleece pullovers From bottle to tile by Miriam Trotter This is the first time we report about someone who initially hated plastic and would not even drink out of a PET bottle, someone who fought against this in his former opinion environmentally harmful material. However, seeing the PET bottle industry growing he took the very inspiring decision “if you can’t beat it, join it.” This is how the Center for Regenerative Design and Collaboration (CRDC), the water brand Agua and the “bottle to tile” project were brought to life. The idea behind it The success story started in 2010 during a beach clean-up when the initiator and CEO of CRDC, Donald Thomson, saw children stomping down plastic bottles on a Costa Rican beach. At that very moment his idea of turning PET bottles into roof tiles was born. The concept is as simple as genius, specially designed water bottles are crimped into roof tiles for houses of the poorer population of Costa Rica where the Canadian-born entrepreneur has lived for the last 25 years. However, this is much more than just a recycling idea for PET bottles which might otherwise end up in the oceans - it is the unique idea of up-cycling a waste product. Thomson calls this idea REAP which is an abbreviation for Recover, Enrich, Appreciate and Prosper. Transferring this abstract concept of the specific “bottle-to -tile” project means recovering the empty water bottles before becoming a down-cycle product or even an environmental contaminant. Enriching them to a high quality product by making tiles out of them and appreciating the tiles by using them for housing for poor people guarantees prosperity to all stakeholders. The waste stream of the PET bottle has become the value stream for the roof tile. Thomson draws an infinity loop to outline the interdependence of input and output: “two intersecting cycles, synergistically co-nurturing a balanced and zero waste growth between themselves”. As binding element between input and output the company ensures balanced management and investment. Professional realisation Good ideas need professional realisation and that is what Donald Thomson - initially working in the real estate sector - was occupied with for almost five years. The design of the 700ml bottle was a hard task in order to meet the requirements for the crimping process. Many modifications led to the eye-catching rectangular shape combining in the end perfect crimping and also smooth blow moulding and the latter turned out to be a real challenge. The bubble on top creates a magnifying optical effect, an essential part of the unique bottle shape. It was initially not only a fancy detail to the bottle design but an indispensable element to fill the mould properly during the blow moulding process. Otherwise the material would collapse and the bottle’s shoulders were not shaped. In 2012 the bottle was finally patented. Donald Thomson orders the 32gr preforms from the Peruvian supplier San Miguel. Its comparatively heavy weight is necessary to make the bottle respectively the tile durable and strong enough to last about 50 years. Earlier the blow moulding was out-sourced as well but after frustrating experiences in India and a bankrupt company in Costa Rica Thomson decided to blow mould in-house. A Chinese double cavity manual mould, equipped with Costa Rican moulds and retrofitted by Nova Mart from Costa Rica, became a loyal companion. Moulding two bottles at once it produces 300.000 pieces per month as of now but bears the potential of doubling the amount. A crimping machine called Henry A crimping machine in the sense of Donald Thomson needs did not exist before. With the help of the Seattle University they developed a manual crimping machine ten-","@ID":12}, "INSPECTION 25 PETplanet insider Vol. 17 No. 01+02/16 petpla.net All lines on one display Screenshot of the board manu of the IntraVisualizer inspection system When it comes to quality control in the plastic packaging production, requirements have emerged during the last few years due to automation and digitalisation. Since one single operator has to be in charge of more production lines, the tool to control quality statistic has to become more powerful. It has to show several production lines at a glance and give early alarms and indicate an upcoming defect before it develops into a problem for the production plant. Moreover, it needs to be transportable and therefore has to be integrated in a portable device. At the same time a comprehensive quality management tool is a basis to document the production quality over a long period of time. Visualising error statistics The German company Intravis has developed the IntraVisualizer inspection system. To use it, the producer needs to connect a SQL server to his inspection system. It is a strong software that edits and visualises the performance data of the entire production. This is designed for a self-explanatory use. An intensive development phase has resulted in an easy-to-use software interface. The tool turns all relevant characteristic production numbers into significant visual diagrams. The IntraVisualizer is usable with a touchscreen as interface and a standard internet-browser, it can be used on a portable tablet device. By clicking the operator can choose the value he liked to be monitored such as ovality, surface, diameter and others. It is also possible to track single measurement readings. The user can set up the display according to his needs by adding or changing systems. It is also possible to add certain defects like cavity faults. The IntraVisualizer receives all needed data of several systems that are part of one production facility from the server. When the software accesses the data base, it can visualise different time periods like shifts, days, free date ranges and also batches. Trend statistics The software comprises a trend statistic that prevents the production of too many waste objects. To activate the trend statistic the user has to determine values for certain production parameters. These values may not deviate too much from the reference value. During production the software observes production parameters and analyses trends. As soon as a trend stabilises and may lead to a non-acceptable deviation within a certain period of time, it shows the trend on the screen or even sends an e-mail to the operator automatically. The operator has now the opportunity to correct the parameters. For this reason production errors are corrected before they really occur. The result is avoiding defects, saving material and high productivity. Mould diagrams The IntraVisualizer is able to generate mould diagrams to inform the operator about the current error rate of the cavities of a single mould. When using this mould diagram the user can choose a product, time period, product run and moulds on the interface and shortly afterwards he receives a diagram that tells him which production moulds will deliver a reliable performance. It shows the entire cavity or the single moulds as a 2D or even 3D diagram and it displays the statistics of the total number of objects, the incomplete evaluations and the defective objects. With this comprehensive knowledge about the actual performance of the production line, the production quality improves automatically. www.intravis.de","@ID":27}, "BOTTLE MAKING 16 PETplanet insider Vol. 17 No. 01+02/16 petpla.net Blow-fill-cap units for mid-size bottle producers Over the past few years Serac Group has acquired state of the art expertise in packaging manufacturing – in both food and non-food markets – and is now producing blowing units. Serac is convinced that the PET bottle is a packaging that is ripe for further development and, in addition, that fully integrated packaging lines can provide mid-size bottle productions with a long-lasting competitive edge. It is targeting these opportunities with its recently-launched Combox machine range, which is designed to link the group’s SBL linear blower with its rotary weight fillers, in a ‘smart’ manner. On-site “right sized” bottle manufacturing When a company decides to produce its own container it is natural for it to start with in-house packaging manufacturing, which enables it to capitalise on the range of benefits that emerge as volumes grow and the product portfolio expands. Purchasing plastic preforms instead of blown bottles reduces the transported volumes as well as the risk of having bottles scratched or distorted, while on-demand production avoids wasting money on storage. In-house manufacturing gives more flexibility on packaging lines, by enabling the production of different packaging shapes or sizes on the same line. Finally, in-house manufacturing provides higher protection against pollution or contamination, as the blown bottles go directly from the mould to the filling unit. Serac says that its SBL linear blowers offer all the benefits of onsite bottle manufacturing but in a machine specifically designed for low to medium outputs. The SBL range offers output rates up to 18,000bph, depending on the machine model and bottle size, which ranges from 50ml up to five litres. PET stretch blow-moulding for high quality bottles Bottles are strongly associated with quality, whatever the product (food or non-food) and the distribution channel. Consumers tend to prefer them because of the convenience they offer. Bottles are easy to handle, reclosable and shock-resistant, and so are naturally adapted to both household and on-the-go use. A bottle can enhance the on-shelf appeal of the product it protects, by enabling manufacturers to differentiate themselves from their competition by the use of original shapes and colours.Choosing the right material is essential in the planning of on-site production. While it was originally dedicated to water and drinks, PET is increasingly used to package products in the dairy, edible oil, household and personal care markets, because of the advantages it offers against glass or PVC, for example. These advantages can include production of transparent bottles with glossy appearance, novel shapes, better recycling properties, and the cost effectiveness of the PET bottle production line. When it comes to quality, PET has proven ideal for use in lightweight but highly resistant bottles. The material bi-orientation achieved through the two-step stretch blow-moulding process provides high levels of toughness and resistance to internal pressure, and enables thin bottles to be stacked as high as glass ones.","@ID":18}, "COLOURING / ADDITIVE 12 PETplanet insider Vol. 17 No. 01+02/16 petpla.net Tour Sponsors: Colour design by Waldemar Schmitke F.r.t.l.: Ms Adriana Rueda, Manager, Mr Len Kulka, Creative Director, and Ms Hsi Chen, Designer, in front of the lab. February 27, 2015 We met: Mr Len Kulka, Creative Director, Ms Adriana Rueda, ColorWorks North America Manager, Ms Hsi Chen ColorWorks North America Designer and Mr Thomas Schneider, representing Amsler Blow Molding Equipment. The plant here in West Chicago is also one of the production operations for masterbatches 80%, and liquid colourants 20%. It is also home to the North American ColorWorks,which is part of a global network of four such sites created to provide packaging and product designers with colour ideas and inspiration and technical guidance. Here we meet Len Kulka, Creative Director, Adriana Rueda, Manager, Hsi Chen, Designer and Thomas Schneider, a visiting representative of Amsler Equipment Inc. We not only receive a friendly welcome but are bowled over by what we see here. We hadn’t reckoned on finding premises that could keep pace with designer living space in the loft. Brightly-coloured bottle samples stand out impressively against a totally white environment. Separated off by window panes from where we are standing is the lab with machines for colour samples and prototyping. Adriana Rueda’s team consists of eight people here on site who are tasked with noting colour trends in the marketplace so that they can advise customers appropriately. “Design and colour are important elements in packaging and play a vital part in ensuring the successful marketing of products in line with market requirements”, says Adriana Rueda, and, she continues,” it is well known what colours can do if they are used with a specific aim in mind, this is something that branded products in particular rely on. This is what we want to achieve”. Although it can support the development of any plastic product, ColorWorks West Chicago specialises in working with packaging designers. “Here we are in a position where we can generate colour samples and sample packaging for our customers within a very short space of time,” Adriana Rueda explains, “and also demonstrate the colour effect in bottles and closure caps. Our laboratory facilities allow us to create individual colour concentrates in the form of masterbatches and to produce preforms and sample bottles.” It’s Friday and on our agenda for today is a visit to Clariant Masterbatches in West Chicago. Clariant Masterbatches is one of seven business units making up Clariant International, a company headquartered in Muttenz, Switzerland. In this division there are approximately 3,100 employees working on colour and additive concentrates and performance solutions for plastics in 50 production workshops worldwide.","@ID":14}, "PETpatents www.verpackungspatente.de 36 PETplanet insider Vol. 17 No. 01+02/16 petpla.net Bottle as component Intern. Patent No. WO 2015 / 044231 A1 Applicant: Martin Olivier, Paris (FR) Date of Application: 24.9.2014 In order to give a bottle made from plastic additional service life, even in countries with reduced recycling facilities or none at all, the application proposes to incorporate recesses with a thread in the surface of the bottle. Any number of bottles can be put together in this way e.g. as a component for creating a wall. Container with handle Intern. Patent No. WO 2015 / 053257 A1 Applicant: Nissei ASB Machine Co. Ltd., Nagano (JP) Date of Application: 7.10.2014 A high volume plastic bottle is fitted in the area of the side wall with an indentation and features that enable a separately manufactured handle to be fitted and secured. Waisted bottle Intern. Patent No. WO 2015 / 059381 A1 Applicant: Sidel Participations, Octeville sur Mer (FR) Date of Application: 6.10.2014 Waisted bottle manufactured from PET with rectangular/square base. The bottle, which is designed for hot fill applications, is equipped with specially moulded compensation areas. Plastic bottle Intern. Patent No. WO 2015 / 068763 A1 Applicant: The Coca-Cola Comp., Atlanta (US) Date of Application: 6.11.2014 A thin-walled, weight-reduced plastic bottle incorporates grooves and indentations for fingers in the waisted area which enable the bottle to be held and secured without the bottle “collapsing”. Base section Europ. Patent No. EP 2853501 A1 Applicant: Yoshino Kogyosho Co. Ltd., Tokyo (JP) Date of Application: 18.11.2009 The base section of a plastic bottle for product under pressure/hot fill product is specially designed. On reduction of the internal pressure/cooling, the base becomes distorted and changes to support points/support surfaces emerge. The bottle remains stable. Screw cap US Patent No. US 2013 / 0319968 A1 Applicant: Closure Systems International Inc., Indianapolis (US) Date of Application: 31.5.2013 In the interests of mounting a container closure securely on the container opening even under “high speed” conditions, the closure is fitted on the inside with a feature that is intended to prevent “incorrect mounting”.","@ID":38}, "BOTTLES 35 PETplanet insider Vol. 16 No. 11/15 petpla.net Room fragrance for the girls The Japanese company Kobayashi Seiyaku is marketing under its brand name “Sawaday Pink Pink” a room fragrance that is specially coordinated with the scents preferred by Japanese teenagers / young women. The multi-section containers, which are designed in an almost kitschy fashion, consist of a filled lower section, an upper section and an attachment with pads to enable the fragrance to evaporate. Prior to initial use the dispenser needs to be activated by opening the container and attaching the closure with the applicator pads. Once put together the components are secured in position once again. The fragrance can now escape over a specific period of time via the openings in the lid area. www.kobayashi.co.jp Easy combing for children’s hair The German manufacturer bebe is featuring in its bebe gentle care range a two in one product consisting of shampoo and conditioning rinse which is specially coordinated to suit the hair of babies and infants, makes the hair easy to comb and prevents tiresome “tangles”. The product contains argan oil but is free of soap and colorants and does not sting if it gets into the eyes. The 300ml pack includes a tinted PET bottle with screw-on hinged lid and dispenser opening. The lid can also be easily opened using one hand, even with moist fingers. Dropshaped self-adhesive labels at front and back convey retail information and instructions for use. www.bebe.de","@ID":37}]}}
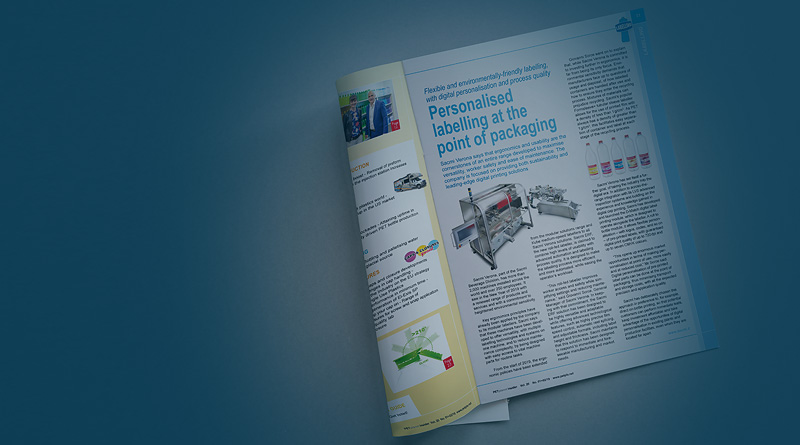