"MARKET SURVEY 25 PETplanet insider Vol. 17 No. 05/16 petpla.net 05/2016 MARKETsurvey Preforms Filling equipment Resins / additives Preform / stretch blow moulds Caps and closures Preform and single stage machinery Bottle-to-bottle recycling plants Compressors Closure systems Two stage SBM machinery Suppliers of preform moulds and stretch blow moulds Our annual overview of the market on the topic of mould tools for PET bottle production introduces you to the manufacturers of preform- and stretch blow moulds. Have a look at the new developments and results of the machine engineers. The companies participating at our market survey are listed in the order in which their details were achieved by the editors. We are pleased to show you an overview of 23 companies: Indus Moulding Solutions PL, Kiefer Werkzeugbau GmbH, PET Engineering, Kronce Enterprise Development Co., Ltd., Smargon Plastic Machinery Co., Ltd., R&D/Leverage, Simex srl, Hallink, Acme Die Systems Pvt. Ltd., Otto Hofstetter, Kosme, Nissei ASB, Demo Design and Moulds, Wentworth Mold Ltd., KHS, Moldintec, Awanti Polymoulds Pvt. Ltd, Solent Mould Tools Ltd, PET Technologies, Tooling Preform Systems BV, MHT Mold & Hotrunner Technology AG, Sipa S.p.A., Vitalii and Son and Sacmi Imola. Although the publisher have made every effort to ensure that the information in this survey is up to date, no claims are made regarding completeness or accuracy. SBM moulds Company name Indus Moulding Solutions PL Kiefer Werkzeugbau GmbH PET Engineering Kronce Enterprise Development Co., Ltd R&D/Leverage Simex SRL Postal address Telephone number Web site address Contact name Function Direct telephone number Fax E-Mail 51/54 Daman Industrial Estate, Daman 396210, India +91 22 28776984 www.petform.net Mr Shurid Mody CEO +91 9769758634 [email protected] Steinhäldenstraße 11, 74193 Schwaigern, Germany +49 7138 9732 0 www.kiefer-mold.de Mr Jörn Herget Project Manager +49 7138 9732 70 +49 7138 9732 90 [email protected] Via Celtica 26/28 San Vendemiano, Italy +39 043 840 3069 www.petengineering.com Ms Elisa Zanellato Marketing & Communication Man. [email protected] Room 06/07, Floor 35, 6088 Humin Road, Minghang District, Shanghai 201199, China +86 21 24202001 www.smargon.com Mr Andy Yang Deputy General Manager +86 15 000770587 +86 21 24202278 [email protected] Leverage House, Hamilton Road, Sutton in Ashfield, Nottinghamshire UK, NG175LD +44 1623 556287 www.rdleverage.com Mr Alan Tolley Managing Director +44 1623 552240 [email protected] Via M.Biagi e M.D'Antona ,5 60025 Loreto (AN) Italy +39 071 7500214 www.simexitaly.it Mr Graziano Giuggiolini Sales Manager +39 071 7500214 +39 071 7501958 [email protected] Stretch blow moulds Bottle size (max.) (in litres) 50 18,9l 10l 20l 5l 20l (5 gallon) Moulds supplied directly to blowing machine manufacturers No Independent mouldmaker Yes Yes No Yes Do you supply retrofit moulds for existing SBM machines? Yes No Yes Yes Yes Yes For which makes of bottle makes have you already produced moulds? Coke, Fanta, Sprite, Pepsi, Sidel, Krones, Sipa, Side, Chumpower yes Bottle design service Yes Yes Yes Yes Yes Specialities Lightweight design, special design for functional drinks, juices and household products Special design as European blow mould, to reach the fast action during the blowing stage Pet containers for mineral water, CSD, milk, edible oil, wine, beer, cosmetics and other Other Supplier for single stage, Injection Stretch Blow Moulding ISBM industry. In Product Solution Laboratory we can trial product, colour, materials plus qualify production tooling on Nissei and Aoki Injection SBM machines","@ID":27}, "COMPRESSORS 17 PETplanet insider Vol. 17 No. 05/16 petpla.net COMPRESSORS Efficient high pressure production at San Pellegrino´s Castrocielo plant Up to 80% energy savings Statement by Werner Hoffmann (Ing. grad.), Technology Center / Project Engineering, KHS Corpoplast GmbH, answering our question “What would your ideal compressor look like?” The ideal compressor When a compressor supplier advertises low energy consumption, they always refer to a specific operating point of the compressor. This is usually the highest output at a particular pressure. This approach however does not really help an operator. A customer can produce different products on a blowmoulding machine, with various bottle volumes, blow pressures or production performances, and so different compressor outputs become necessary. In these cases, the compressor with the highest air consumption is selected. If a smaller output is required, it will operate intermittently. This means that the idle times during which energy is used but no air is outputted becomes progressively larger – a compressor should however run energy-efficiently even under these operating conditions. An ideal compressor for me, would be able to be set to different outputs for which it would run virtually continually with a very small amount of idle time. For this purpose, there are possible solutions such as e.g. “a semi-load setting” that is achieved by switching off cylinders or pressure levels. In my view, this is however not yet sufficient. A speed control of a compressor would also not be a solution, as a frequency converter is always an electrical component which itself consumes additional electrical energy. Moreover, the compressors often cannot be regulated to the required levels, as a certain minimum compressor speed and thus a minimum output must be adhered to. www.khs.com The Spanish high pressure compressors manufacturer ABC Compressors launched its new Horizon PET range in 2015, in which the main technical developments are the combination of the optimised design of the horizontal-boxer type with double acting compressors and the directly coupled transmission. Its design is intended to improve previous standards by double digit percentage and to give the best flow/installed power ratio of the market. In a new green field project at Nestlé Waters / San Pellegrino, a compressor unit out of the Horizon range was selected for a new mineral water bottle plant in Italy. This compressor range can be upgraded with two energy saving features, with noticeable impact in the energy TCO category and environment care: The Variable Speed Drive (VSD) adapts, by means of a pressure transmitter, the compressor rotational speed to the real high pressure air consumption, maintaining at the same time the required working pressure in the pipe line. This reduces or eliminates the compressor idle operation and its wasteful energy consumption. On average it saves 20% of the Horizon-2400 in San Pellegrino’s Castrocielo plant: variable speed drive on skid close to the main cabinet and hot water outlets on the top of the coolers","@ID":19}, "PETbottles 42 PETplanet insider Vol. 17 No. 05/16 petpla.net Beverage + Liquid Food MHT MOLD & HOTRUNNER TECHNOLOGY AG Your Machine - Our Solution 1996-2016 20YEARS Booth 1C35 Low acid content thanks to a late harvest The German juice maker Valensina has extended its selection of juices by one more option that is to appeal to customers who prefer a low acid content in juices. Under the name “Late harvest – A lot of sun, little acidity”, 750ml of the 100% gently pasteurised, not from concentrate juice is bottled in a long-neck bottle, which is decorated with a diamond pattern and brand logo imprints on its neck area. A transparent film label and a freshness seal with guarantee strip that is guided across the screw cap complete the packaging at the top. “Late harvest” is available in five flavours and placed in the refrigerated shelf in supermarkets. www.valensina.de Smoothie with oats Juicy Production from Dordrecht in the Netherlands is marketing various smoothies with oats and flax seeds. The picture shows the varieties “Cherry-Strawberry” and “Mango-Coconut”. The not from concentrate produced juice is pressed cold and is not heated, which according to the manufacturer leads to a setting of the heavy constituents and makes shaking before consumption essential. 250ml of the product is bottled into a clear bottle with screw cap and guarantee strip. A self-adhesive label communicates the necessary notes to consumers. Fructiv as a limited summer edition The dairy producer Alois Müller brought two new Fructiv flavoured milks with the additive “summer multivitamin” to the refrigerated shelves in a limited edition. New juice combinations such as “Cherry-Coconut-Apple” or “Grapefruit-AppleLemon” are to arouse the curiosity of consumers and encourage them into buying. The well-known, easy-grip PET bottle with a 440ml/456g capacity is decorated with a suitably designed shrink sleeve. A colourful screw cap with a display of first opening completes the look. www.muellermilch.de Cool-fresh berries by Rewe Under its own brand “Rewe Beste Wahl” (Rewe best choice), the German Rewe group is offering several juices with a 100% fruit content. The juices are additivefree and are gently pasteurised, continually cooled and sold in the refrigerated shelves. The juice is produced by PL Drinks GmbH in Mönchengladbach. A clear PET bottle serves as packaging with a one-litre capacity, a printed film label and a screw cap secured for first opening.","@ID":44}, "COMPRESSORS 23 PETplanet insider Vol. 17 No. 05/16 petpla.net COMPRESSORS 23 Save RAW MATERIALS reduced plastic volumes Save ENERGY less energy consumption Save TROUBLE more quality and higher performance, guaranteed by a sole supplier Full INSPECTED online quality control / stand alone PROPAK ASIA, 15/18.06.16 - HALL101 A21 - Bangkok THAILAND FISPAL, 23/26.06.16 - K115 - Sao Paolo BRASIL SRI LANKA PLAST, 5/7.06.16 - Colombo SRI LANKA FOOD & DRINK Africa, 14/15.09.16 - Johannesburg SA PROPAK WEST AFRICA, 20/22.09.16 - Lagos NIGERIA Preform & Closure technologically together With Sacmi, the beverage specialists are always at your side. With our unbeatable technological know-how and continuous research we are creating new containers and closures designed to ensure outstanding performance. The new IPS injection system for preforms and the CCM compression press for caps, fully designed and built by Sacmi, allows for large-scale production with considerable advantages in terms of efficiency and flexibility. The outcome? Reduced plastic volumes, less energy consumption and lower running costs. All in a bottle: the one you’ll soon be making. Transfer of technical applications results in energy efficiency To concentrate on what matters For many years, rotary blowers were the preferred choice for applications involving the handling of powders and bulk goods. The new screw blowers of Kaeser Kompressoren featuring the renowned Sigma Profile prove that the technology which already powers Kaeser’s rotary screw compressor and delivers energy savings can also be successfully applied to the low pressure range. Kaeser offers a selection of these products. Kaeser said that the screw blowers deliver energy cost savings of up to 35% compared to conventional reciprocating blowers. To ensure that projected savings are actually delivered, Kaeser specifies the total power consumption as well as the actually usable flow rate as per ISO 1217 Annexes C and E. The integrated Sigma Control 2 controller ensures comprehensive monitoring and straightforward connection to communication networks via Ethernet or databus interfaces for example. The integrated web server enables clear visualisation of current machine status (e.g. process data) via Kaeser Connect. With software just for blowThe CSG-2 compressor powered by IE3 motors COMPRESSORS","@ID":25}, "Hong Kong Chongqing Xi'an Taiyuan Shenyang Qingdao Nanjing Guangzhou Shanghai Beijing Jinan Sponsors The China Road Show The worldwide round trip with www.china.petpla.net 2016 is both the Year of the Monkey in Chinese astrology and the occasion of our first Editourmobil quest to sample the far-eastern culture of China. Following our successful Editours in the past few years, our voyage into the Middle Kingdom begins in Shanghai in April. We are scheduled to cover a distance of approximately 7,000 kilometres between then and October, which will be covered is a series of stages in the eastern part of the People‘s Republic - and, as always, the whole distance will be travelled by road! During our trip, we will take in the entire PET process chain and discuss facts and trends with a great variety of users from the bottling, processing and recycling industries, as well as with suppliers, toolmakers and mechanical engineers. As always, reports and reviews of all of our visits and interviews with local and global players will be published in PETplanet Insider. We will keep you right up to date on our travel experiences through near-live event coverage on our Editourblog at www.china.petpla.net. Come and join us on an incredible exploration of the Chinese PET market, right from the start. As the saying goes: ॹ䠂ҁ㺂θခ᯲䏩сȾ (A journey of a thousand miles begins with a single step). April – October 2016","@ID":40}, "MATERIAL / RECYCLING 13 PETplanet insider Vol. 17 No. 05/16 petpla.net These first bottles contained an additional plastic component of HDPE in the bottle’s base, the so-called base cup, which in the second stage of the process was stuck to the actual PET bottle with a rounded bottle base, ensuring that it stood upright. Without this base cup, the bottles could not stand upright. The 80g light non-refillable bottles also caused quite a stir in Europe. In Germany for example, in 1980 the press were celebrating Coca-Cola’s market test of a PET bottle as “the perfect solution”. The recycling of PET At this time, the recycling of bottles was also in full flow. Only four years after the modification of PET for bottle production, the first bottles were recycled in 1977. Want the secret to bottle light weighting? Process Pilot® automated blowmolder control system takes the guesswork out of material distribution management and can help ensure the success of even the most aggressive light weighting program. Featuring 24/7 blowmolder control, the Process Pilot system continuously maintains proper material distribution, on every bottle, to an unmatched level of accuracy. With the Process Pilot system, you have the means to push light weighting to the limit without VDFULȴFLQJ ERWWOH TXDOLW\\ RU SHUIRUPDQFH Not convinced? Talk to one of our specialists today to schedule a free seminar and evaluation of the Process Pilot system on one of your blowmolding lines. Web: agrintl.com Tel: +1.724.482.2163 E-mail: [email protected] See us at booth 11B40 However, the HDPE bottle base added on proved to be inappropriate in the recycling process and it became redundant with the introduction of the Petaloid base. From now on, PET bottles could be produced as one piece and recycled at less cost. The associated patent “Bottom end structure for plastic containers” (published in 1971) was granted to the Continental Can Company. The first recycled bottles were turned into bottle base cups. Even today, a large part of the recycled material is used in areas of application beyond the production of new bottles, for example in the textile industry. At the start of the 1990s the first PET bottles with a recycling content came onto the market. In the bottle-to-bottle recycling process, the recyclate is used in the production of new PET bottles. Drivers of innovation Playing an even better part than the bottles in the recycling process is material which can be saved right from the start in production. Thus the PET sector has been continuously improving the bottles through to today – for example in relation to their weight in the area of material, preforms, closing systems and the bottle design. 0.5l bottles for still water can now be produced as ultra-light containers weighing less than 8g and in the hot-fill sector at under 60g. And even 1.5l bottles made from PET for mineral water have a weight of under 20g for still water and under 25g for carbonated. So that bottles do not deform on opening, the bottle designs must also be continually adjusted. One other innovation driver is the rise in the areas of application resulting from the continual improvements in the material. Barrier bottles for beer, juice, tea or wine were a massive step for PET. Aseptic filling, for example with milk, demands the most sophisticated technologies, including sterilising the preform or bottle and closing device, as well as sterile filling. Here there must surely be potential uses for the PET bottle which have not yet been exhausted. And PET bottles made from plant materials, such as the PET bottle introduced in 2015 by Coca Cola, made entirely from plant materials, point to further possibilities for improvement. Water is, as ever, the biggest market, with a continuing small rise in growth rates world-wide, whilst the CSD market, which helped PET to bloom as a drinks container, is seen as stagnating. The largest growth rate in terms of new developments for PET containers, comes from the dairy market. Geographically, key market drivers include rising incomes in developing markets of Asia Pacific, South and Central America and Central and Eastern Europe. In terms of geographical regions, Asia Pacific overtook both North America and Western Europe to become the largest regional market for PET packaging. www.forum-pet.de et al. Coloured PET bottles, manufactured on standard SBM machines (photo: Gizeh) 7.5g bottle for 0.5l of still water (photo: PET Engineering)","@ID":15}, "COMPRESSORS 24 PETplanet insider Vol. 17 No. 05/16 petpla.net ers, it is a powerful tool for boosting productivity and for achieving even greater energy savings. Sectors such as the food and beverage, pharmaceutical, chemical, pulp and paper, textile and construction materials industries and applications such as wastewater treatment, pneumatic conveying systems and power generation can benefit from this screw blower technology. The EBS blowers are easy to install, are highly reliable for continuous operation and provide outstanding strength and durability. The screw blowers feature an internal cooling concept that makes the energy-wasting use of an oil pump and oil cooler superfluous. They are designed with an effective sealing concept which ensures sealing over the long-term without the need for a vacuum pump. Dispensing with auxiliary equipment and oil lubrication also increases machine service life and reliability. For optimum cooling, cooling air is drawn in from outside the enclosure, which not only boosts performance. It provides greater usable air-mass flow for the same drive power. Rotary blowers available with Sigma Control 2 Kaeser completes its blower product portfolio with the BBC and FBC series. These compact rotary blowers could be connected with integrated mains power supply equipment and the proven Sigma Control 2 controller for comprehensive system monitoring and communication. The internal Sigma Control 2 controller makes blower mode selection, such as remote speed control or pressure control, by pushing a button. Performance parameters relevant for dependable blower performance are monitored by sensors, and warning or fault signals are automatically generated accordingly. Optional communication via databus (multiple databus systems can be connected) allows operational status read out and enables the machine to be remotely controlled. Kaeser’s rotary blower range covers air deliveries from 2 to 72 m³/ min at up to 1000mbar gauge pressure and 500mbar vacuums. Key applications for these blowers include pneumatic conveying and water treatment. The complete system packages are CE and EMC certified. The rotary blowers feature a high broadband sound and pulsation damping ensures quiet operation at all times, which applies to both the machine and the pipework. The blower block with its proven Omega profile rotors enhances operational reliability and uptime, whilst adaptive compression reduces energy consumption, and long bearing life minimises maintenance costs. Space-saving component layout results in a compact footprint. As these blowers were designed to allow the service to be carried out from the front of the unit, it is possible with star-delta equipped models to install several blowers side by side. Components such as control valves and exhaust silencers are integrated. Relevant factors for reducing operation cost are actual pressure and air demand, selection of appropriate and suitably matched blowers and drive systems, as well as tailored sequencing control. This is where an Air Demand Analysis (ADA) can prove invaluable: With help of detailed analysis it is possible to determine how compressed air demand varies over time, how efficiently a blower station is operating, and to what extent availability and efficiency can be further enhanced. The Kaeser Energy Saving System (KESS) is an optimisation tool. This specialised planning software enables different system variants to be simulated and compared with one another, and their respective potential savings to be calculated. Transparency of future servicing and maintenance costs is also essential when considering the total life cycle costs of both individual blowers and stations as a whole. The expanded dry-runner range The latest range of dry-running rotary screw compressors is the CSG-2 series. Available with drive powers ranging from 37 to 90kW, these two-stage machines provide free air deliveries from 5.4 to 13.1m³/min for pressures between 4 and 10bar (g). Together with the existing DSG-2 and FSG-2 series, Kaeser‘s dry-runner range covers free air deliveries ranges from 5.4 to 50.0m³/min, and 3.2 to 50.8m³/min for variable speed machines. One can choose between air- and water-cooled versions and have the option of SFC variable speed control for applications with fluctuating air demand. At the heart of these units lies a two-stage compressor airend. The rotors are equipped with “Ultra Coat”, which is resistant to temperatures up to 300°C. Because this cost-reducing coating is highly abrasion-proof, its sealing and protection performance remains virtually unchanged. As a result, compressed air delivery also remains consistent. Air-cooled systems designed for use in ambient temperatures up to 45°C are said to provide further potential for additional long-term savings. The CSG-2 systems are enhanced by the new PC-based Sigma Control 2 internal controller. A precision electronic pressure sensor keeps switching differential to a minimum thereby saving even more energy. It provides greater flexibility through its numerous interfaces and plug-in communication modules. The addition of an RFID reader ensures service continuity, increases security and significantly raises service quality. The Sigma Control 2 is also responsible for compressor monitoring. All CSG-2 compressors are powered by IE3 motors. Standard equipment includes ‘PT 100’ sensors for measurement and monitoring of the motor winding temperature. This enables full use of the maximum motor switching frequency and lower costly idling periods. The use of stainless steel rotors in the second compression stage helps guarantee compressed air quality and enhances service life. As air intake is regulated via a hydraulically operated inlet valve, there is no need for regular replacement of pneumatic diaphragms. This reduces both service costs and downtime. The use of fibre-free pulse dampers is said to keep pressure loss to a minimum, to maintain consistent air quality and to prevent contamination of the compressed air. These systems operate with minimal sound levels. www.kaeser.com","@ID":26}, "BOTTLING / FILLING 14 PETplanet insider Vol. 17 No. 05/16 petpla.net Machine and bottle ‘light-lifting’ Birštono Mineraliniai Vandenys (BMV) in Lithuania has followed the success of its original PET bottling Greenfield project in ordering a Sidel Combi FMc line. Sidel collaborated on the design of BMV’s eye-catching and product-differentiating PET bottle shapes to boost sales of the client’s water brands. The new design contributed to light weighting the bottles by up to 30%. High nature resources BMV is a well-known and leading provider of mineral water in the Baltic States. Its water, rich in beneficial minerals and known for its properties, and for the fact that it has the highest level of mineralisation in Europe, was first bottled on an industrial basis in 1924. Today BMV is a modern company using advanced technology and strict quality control methods to bring natural mineral water from its original source to the consumer in exactly the same form as enjoyed by the region’s ancestors. BMV is currently selling three water brands: Vytautas, Birute and Akvile, the latter is suitable for baby food. The company’s beverages are widely exported, including to neighbouring Baltic countries, as well as further afield including to the UK, the United States, China and the Gulf region. A successful greenfield project In 2008, BMV began bottling natural mineral water under the Akvile brand. Some years later, the company intended to update one of its production lines with new equipment. The Baltic producer asked Sidel to support with a technical and financial proposal for a new complete packaging line solution for bottling Akvile. This was a greenfield project to increase PET water production capacity to meet market demand. A Sidel team collaborated closely with the customer at the early stages of the company’s first complete water bottling line project. The team developed a complete project plan, selected the specific equipment, defined the floor layout and implementation plan and detailed a cost analysis and budget plan, including the management of third-party contributors. To make sure the line was ready for production, Sidel used the latest technology and methods including feasibility studies, simulation modelling and 3D animations to ensure that the line’s master plans were carefully constructed and perfectly controlled. Once the design for the new water line was established, it was implemented as rapidly and as efficiently as possible. It required thorough planning, management and follow-up, from start to finish. “We were particularly satisfied with the entire experience of dealing with Sidel and witnessing the benefits of the company’s engineering support experience was key in the success of this greenfield project and complete line solution”, explains CEO of BMV, Mr. Pranckus. Product safety and integrity were important priorities for the water producer. The original Sidel Combi FMc was perfectly matched with the producer’s expectations. Its single production enclosure - including the three main integrated functions configured with the positive, filtered air-pressure - ensures a hygienic and safe production environment. The hygienic design of the filling valve, with no mechanical parts in contact with the filled water and a filling process controlled by a pneumatic membrane valve, ensures safe filling. Additional hygienic options have been implemented in the Combi configuration to further optimise food safety, including air filtration and overpressure area protection. The magnetic flow meters, which control the filling volume, ensure an accurate dosing while the filling parameters of each filling valve are controlled directly from the operator panel. The automatic dummy bottles to close the filling circuit during the internal and external cleaning of the filling valves, cleaning in place, or ‘CIP’ as it is commonly known, contribute to fast and safe product changeover. Based on the performance of the newly installed bottling line producing Akvile, a second Sidel line was installed. The new bottle shapes were designed by Sidel to boost both the ‘Vytautas’ and ‘Birute’brands.","@ID":16}, "PRODUCTS 40 PETplanet insider Vol. 17 No. 05/16 petpla.net Minting the base Mint-Tec is a new technology to press the preform base into optimum shape for the subsequent blowing process. The effect is a reduced wall thickness of the preform base while the base surface is increased. As the warmest spot of a preform after injection moulding is the base, very little force is needed to bring the base into optimum shape. The special minting device shapes the conical or spherical base of the preform directly after injection moulding in the first heat. The Mint-Tec unit is designed to use the reheating effect directly after moulding to decrease the base wall thickness and increase the outer surface of the preform by means of a gentle, but fast minting process. At the end of the shaping process the preform is in contact with the cooling sleeve where cooling takes place very rapidly thanks to the reduced wall thickness and the increased outer shape. Main advantages of the Mint-Tec preforms are the lower wall thickness in the bottle base which leads to a faster cycle time of the blow moulding machine and the total PET bottle weight savings by 3-5%. www.mint-tec.com Block configuration featuring three machines The trend towards combining several units to form a single machine continues unbroken. In the shape of the 3Bloc, Krones’ subsidiary Kosme has presented its first concept for a block configuration featuring three machines available in two different variants: one for PET and one for HDPE containers. 3Bloc for PET containers consists of the three concatenated machines: the blow-moulding machine, the filler and the labeller. The labeller is constructed either for applying pressure-sensitive labels or for reel-fed wrap-around labelling. This configuration is suitable both for cylindrical or square PET bottles and for special-shaped containers. The maximum output is 16,000bph. The 3Bloc for HDPE containers consists of the following three concatenated machines: The unscrambler, filler and the labeller. The unscrambler is tasked with putting the already-blow-moulded HDPE bottles in an upright position before they reach the filler and here takes the place of the blow-moulder needed for PET containers. This 3Bloc variant can handle up to 25,000bph. It concept has been based on technically sturdy components, and when compared to a layout featuring individual machines scores in terms of its substantially lower energy consumption, its efficiency and its enhanced user-friendliness. The block configuration benefits the machine’s footprint, plus the capital investment and operating costs involved. For example, no intermediate conveyors are needed and the times required for format change-overs and maintenance routines are also shorter. www.krones.com PET bottle for pasteurised beer PET Engineering, the international company for the design and industrialisation o f PET packag i ng received the prestigious 2016 Packaging Oscar - Quality Design-category, at the headquarters of the Corriere della Sera in Milan, Italy. The winning packaging solutions were selected based on the ten principles of the Packaging Ethics Chart for a responsible, balanced, safe, accessible, straightforward, informative, contemporary, visionary, educational and sustainable packaging; a packaging that combines, on the one hand, practical functions such as preservation, protection, transport, accessibility and easy disposal, and on the other, its communication functions, transforming it into a tangible product capable of establishing a connection with the consumer. “9.3”, the 500ml PET bottle for pasteurised beer presented by PET Engineering, was designed according to such criteria. “9.3” stood out for its light weight, 26.3g compared to approximately 27.0g for a glass half-litre bottle for its material, which keeps the bottle safe and unaltered from high temperatures during the pasteurisation cycle, and for its Pelliconi pull-off cap, which not only facilitates the opening process, but also the disposal of the whole packaging in the plastic waste, since its label is also made of the same material. www.petengineering.com","@ID":42}, "TRADE SHOW PREVIEW 32 PETplanet insider Vol. 17 No. 05/16 petpla.net drink technology India (dti) 2016 It will soon be “that time” again. From December 15-17 this year the exhibition halls at the Bombay Exhibition Centre will, once again, be the venue for drink technology India (dti). The biennial trade show, now in its sixth incarnation and coinciding with International Packtech India, has developed over the years into an established institution of the entire local drinks industry on the Subcontinent, enjoying a steadily growing number of exhibitors and visitors. The PETplanet team has been part of it since the beginning and we continue support the events as a cooperation partner. The Indian drinks market is undisputedly one of the most exciting markets in the world. The burgeoning middle class, with its new-found purchasing power and growing awareness of hygiene and health, is steering the packaging industry and creating room for investments by machinery manufacturers and users alike. That is why we, as a publisher, regularly take editorial trips to India, speak with the important players in the market and present the trends and developments in the industry. Once again and in the context of this year’s dti, I went to visit and interview PET machine manufacturing, supplier and drinks companies across India. Over three dti specials spread through the year, we will be publishing the reports of these interviews together with helpful information about dti itself. Yours, Kay Barton Overview of the Food and Beverage Industry – Trends & Outlook Advantage India by Rajesh Nath The Indian economy – the “I” in BRICS – is one of the fastest growing in the world. It is currently ranked as the 7th largest, based on its 2015 GDP, in US Dollars. Food, food products and beverages are the largest consumption categories in India; with a population of over a billion and 300 million middle class consumers, it has an immense domestic market. Consequently, the Indian beverage and food processing industry is seen as a sunrise sector and has gained in prominence in recent years. Rising incomes are expected to further stimulate future sales growth. The opening up the multi-brand retail business for foreign direct investment (up to 51%), as announced in the country’s recent Budget statement, is also certain to pave the way for investment in supermarkets and hypermarkets. The Boston Consulting Group predicts an increase of expenditure in India for processed foods and beverages from $40 billion to $180 billion by 2020. Trends A wide array of products, coupled with increasing global connectivity, has led to a change in the tastes and preferences of domestic consumers. This trend has been supported by rising incomes, increasing urbanisation, a young population and the emergence of nuclear families. In addition, consumer preference is moving towards healthier drinks and snacks. Consumers have become aggressive in demanding better, safer and convenient beverage and food products and they are willing to pay a higher price for health and convenience. This creates opportunities in product innovation, specialised products and product extensions. Liberalisation and growth of organised retail have made the Indian market more attractive for global players. With a large agriculture sector, abundant livestock and cost competitiveness, India is fast emerging as a sourcing hub of beverages and processed food. Currently the international players in beverages market in India are Coca Cola, PepsiCo, Diageo, SAB Miller, Heineken and in the food processing area Danone, Nestlé, Kraft Foods, Mondelez International and Heinz. Strategic geographic location and ongoing increase in raw material production help India to supply cheaper products to other countries. This boosts India’s exports of processed food and related items, which rose at a CAGR of 23.3% during FY11–15. Companies like Haldiram’s and Bikanervala supply Indian snacks to over 70 countries. Beverages and food packaging has enabled today’s consumers to look for various options and to compare their value offerings, before making a purchase. Packaging has helped enhance the ‘carryability’ of products, while improving their shelf life at the same time. In a symbiotic relationship, rising demand for Food and Beverage boosts the packaging industry as well. Beverage industry Sales volume of total soft drinks and of the main product categories in India In litres mn 2013 2018 Growth rate 2013-2018 Soft drinks 11,755 22,937 95.1% Bottled water 8,197 16,957 106.9% CSD 2,352 3,465 47.3% Juice (fruit/vegetable) 1,132 2,413 113.2% Source: Euromonitor International 2014, VDMA Rajesh Nath, Managing Director at VDMA India","@ID":34}, "imprint EDITORIAL PUBLISHER Alexander Büchler, Managing Director HEAD OFFICE heidelberg business media GmbH Bunsenstr. 14 69115 Heidelberg, Germany phone: +49 6221-65108-0 fax: +49 6221-65108-28 [email protected] EDITORIAL Kay Barton Heike Fischer Gabriele Kosmehl Michael Maruschke Ruari McCallion Waldemar Schmitke Wolfgang von Schröter Anthony Withers WikiPETia.info Doris Fischer [email protected] MEDIA CONSULTANTS Martina Hirschmann [email protected] Johann Lange-Brock [email protected] phone: +49 6221-65108-0 fax: +49 6221-65108-28 FRANCE, ITALY, UK Elisabeth Maria Köpke phone: +49 6201-878925 fax: +49 6201-878926 [email protected] LAYOUT AND PREPRESS EXPRIM Werbeagentur Matthias Gaumann | www.exprim.de READER SERVICES Till Kretner [email protected] PRINT Chroma Druck & Verlag GmbH Werkstr. 25 67354 Römerberg Germany WWW www.hbmedia.net | petpla.net PETplanet insider ISSN 1438-9459 is published 10 times a year. This publication is sent to qualified subscribers (1-year subscription 149 EUR, 2-year subscription 289 EUR, Young professionals’ subscription 99 EUR. Magazines will be dispatched to you by airmail). Not to be reproduced in any form without permission from the publisher. Note: The fact that product names may not be identified as trademarks is not an indication that such names are not registered trademarks. 3 PETplanet insider Vol. 17 No. 05/16 petpla.net Dear friends of PETplanet insider, Sometimes, the world of terrorism encroaches on events in the otherwise tranquil drinks industry. The attacks of 9/11 and the subsequent paralysis of flight traffic remain fresh in the memory. Shortly after these attacks, drinktec with PETpoint took place in Munich. With few visitors coming from overseas, the event was sombre indeed. Terrorism casts a long shadow and can strike even closer to home. On the night of November 26, 2008, terrorists ranged through luxury hotels in Mumbai seeking out and killing foreigners. It was a tense situation, and the Indian authorities were unable to cope as the terror raged. No-one knew what was happening. No reliable information was forthcoming. After three days it was still unclear whether any of the attackers were still active. And throughout this time, we were holding our dti Conference in the Grand Hyatt, together with our colleagues at the Munich Trade Fair. We count ourselves lucky to have escaped unscathed. This year it was the turn of the PETcore Europe Conference. Initially, the event in Brussels was postponed following the Paris attacks on 13 November 2015 and the subsequent terror warning for Brussels. However the event passed off peacefully and successfully on 23 February (see report p.8-9). The threat of a terrorist attack had not in any way diminished and the situation in Brussels was still critical, a fact that became tragic reality almost exactly a month later in the attacks of 22 March 2016. Our sympathies go out to all the victims and their loved ones affected by these acts of inhuman violence. It is a sad fact but true that terrorism has now become almost a constant in our society and, despite everything being done to prevent it, there continue to be victims. Which makes it even more important that, despite the latent threat, we continue to meet, to exchange knowledge and not be cowed by the criminals. I therefore have the highest respect for the many who attended the PETcore Europe Conference – especially Eva Schneider and Patrik Peuch – for the fact that, despite the circumstances, the event ran safely. Yours, Alexander Büchler","@ID":5}, "MARKET SURVEY 27 PETplanet insider Vol. 17 No. 05/16 petpla.net Kosme Gesellschaft mbH Wentworth Mold Ltd. KHS Corpoplast GmbH Moldintec Brasil Vitalii and Son , ST Gewerbestr. 3, 2601 Sollenau, Austria +43 2628 411 0 www.kosme.at Mr Johann Gugler Managing Director +43 2628 411 125 +43 2628 411 4125 [email protected] 566 Arvin Ave., Stoney Creek, Ontario, Canada L8E 5P1 905-643-9044 www.wentworthmold.com Mr Tar Tsau General Manager +1 905 643 9044 ext. 311 +1 905 643 5406 [email protected] Meiendorfer Str. 203, 22145 Hamburg, Germany +49 40 67907 0 www.khscorpoplast.com Mr Dennis Jacobi Team leader modernisation +49 40 67907 225 +49 40 67907 210 [email protected] Av Brigadeiro Faria Lima 3729, 5 andar, Sao Paulo - SP, CEP 04538-905, Brazil +55 11 3443 6493 www.moldintec.com Eng. Thiago Tullio Country Manager +55 11 98815 3333 [email protected] №276, bul. Vladislav Varnenchik, 9009 City Varna, Bulgaria +359 8879 78 757 www.vitaliiandson.eu Mr Vitaliy Marinyak Executive Manager +359 8885 18 782 +359 5251 01 68 [email protected] 30 20l Up to 3,5l 20 Up to 20l No Yes Yes Yes Yes Yes Yes Yes Yes Kosme, Krones, Sidel and KHS For all blow moulding machine platforms, such as, Sidel, Krones, KHS,SIPA, Siapi, etc. Mainly for KHS Corpoplast InnoPET Blomax SBM Coca Cola, Pepsico, Danone, Nestle, Aje group certified mould supplier Carlsberg Bulgaria, Ecobottles Ltd, PJSC Obolon, IPR Ltd and Kelto Ltd Yes Yes, prototype sampling, bottle performance tests Yes (bottles & shapes) Yes Yes Bottle development service free of charge, if blowmoulds are ordered Hot-Fill/Heatset moulds with enery efficient system & multi-platform interchangeable quick mould systems Light-weight design and special applications. Bottles & Shapes programme, complete chain of competence from bottle design to perfect performance in filling lines Low pressure blowing 17bars for CSD bottles up to 3l Designing, Prototyping Enhanced cooling system NCBs propietary base for use of nitrogen and wide nitrogen operation range up to 30psi Solent Mould Tools Ltd PET Technologies Sipa Molds Sacmi Imola Relay Road, Waterlooville, Hampshire, PO7 7SB UK +44 23 9223 9950 www.solentmouldtools.com Mr Mark Sim Managing Director +44 23 9223 9950 +44 23 9223 9951 [email protected] 2 Shirokaya St., Chernigov, 14021, Ukraine + 380 43 720 902 169 www.pet-eu.com Mr Maxim Poliansky Marketing Director +380 43 720 902 169 [email protected] Via Caduti del Lavoro 3 - 31029 Vittorio Veneto, Italy +39 04389 11511 www.sipa.it Mr Franco Porracin PET Systems and Tooling BU Director +39 04389 11511 +39 04389 11694 [email protected] Via Selice Prov. le 17/A 40026 Imola BO, Italy +39 0542 607 111 www.sacmi.com Ms Valentina Gollini PR& ADV dept +39 0542 607 607 +39 02 57763006 [email protected] 5l 30l 30l 3.3l Yes Yes No No Yes - all platforms Yes Yes Yes Sidel, Krones, KHS, Sig, SIAPI, Krupp, Mag, etc. ADS, Dynablow, KHS, Kosme, Krones, Siapi, Sidel, SIPA, SMIForm, etc. Sidel, Krones, KHS, SIG, Krupp, SMI, Siapi, Kosme, Side Yes, full bottle design capability and rapid prototyping of marketing mock-ups Yes Yes, brandbuilding, product repositioning, marketing design, packaging engineering, lightweightening of existing bottles, etc. Sacmi Interface parts & carriers to allow different OEM moulds to be fitted in other machine platforms, e.g. Krones into Sidel, Sidel into KHS, etc. EBM moulds supplied for all platforms Bottle design, prototyping, laboratory tests, blow moulds production, auxiliary parts and mould repair, bottleneck standards conversion Wide mouth, large sizes (up to 30l), asymmetrical, Nitrogen hot fill, containers with handles, HDPE to PET conversions Double cavity mould on bottles with d73mm Processing support available across N.America and Europe for pilot and production runs Acme Die Systems Pvt Ltd Otto Hofstetter AG Nissei ASB Machine Co., Ltd. TPS Tooling Preform Systems MHT Mold & Hotrunner Technology Sipa Molds Sacmi Imola C207 Mayapuri Industrial Area Phase II, New Delhi 110064, India +91 11 47718888 www.acmedisys.com Mr Sukhbir Singh Dir. Mktg +91 9810418975 +91 11 47718888 [email protected] Zürcherstrasse 73, 8730 Uznach, Switzerland +41 55 285 22 11 www.otto-hofstetter.swiss Mr Stefan Zatti Division Mgr Sales &Marketing +41 55 285 22 09 +41 55 285 22 44 [email protected] 4586-3 Koo, Komoro-shi, Nagano-ken 384-8585, Japan +81 267 23 1565 www.nisseiasb.co.jp Mr Paul Atkin Sec. Manager Marketing Group +81 267 23 1565 +81 267 23 1564 [email protected] C Houtmanstraat 42, 7825VG Emmen, The Netherlands +31 591 679768 www.tps.nl Mr Richard Tempel Account Manager +31 6 25041136 +31 591 630616 [email protected] Dr. Ruben-Rausing-Str. 7, 65239 Hochheim/Main, Germany +49 6146 906 0 www.mht-ag.com Mr Carsten Lurz Vice President Sales, Marketing +49 6146 906 0 +49 6146 906 399 [email protected] Via Caduti del Lavoro 3 31029 Vittorio Veneto, Italy +39 04389 11511 www.sipa.it Mr Franco Porracin PET Sys.Tooling Director +39 04389 11511 +39 04389 11694 [email protected] Via Selice Prov. le 17/A 40026 Imola BO, Italy +39 0542 607 111 www.sacmi.com Ms Valentina Gollini PR& ADV Dept +39 0542 607 607 +39 02 57763006 [email protected] For preforms & caps For various applications Yes Yes 16-32-48-72-96-128 2-72 2 up to 192 96 2-192 cavities Up to 192 L 190mm Weight 4-750g & dia 12-150mm up to 500g Up to 50l Up to 700g, for bottles up to 30l Up to 30l Acme, MHT and Husky Netstal, Arburg, BMB and Husky Husky, Netstal, Engel, Battenfeld, Demag etc. Netstal, Husky, Sacmi, Engel, Arburg, Cincinnati, SIG, etc. Husky, Netstal, KraussMaffei, Krupp, BMB Not in range at present Yes Yes 2 up to 112 6 - 48 96 2-112 cavities Up to 96 up to 500g Up to 241g, necks up to 120mm diameter Up to 50l Up to 600g, for bottles up to 30l Up to 10l Arburg, Krauss-Maffei Supply for our own machines only Krauss Maffei KraussMaffei Standard and custom, Sipa, Krauss-Maffei No No Yes, main business is single stage. Preforms up to 800g, bottles up to 20l No No Yes, for Sipa machines No Multilayer moulds up to 72 cav., moulds for PP Specialised in large preforms, also double wall Wide mouth, up to 5 gallon, trigger moulds Air recovery systems, Rotary blowmoulder","@ID":29}, "CAPPING / CLOSURES 30 PETplanet insider Vol. 17 No. 05/16 petpla.net Interview with Dipl.-Ing. Christian Krautkrämer, Managing Partner, Bericap Think global, work local by Alexander Büchler Hardly any other company in the closure cap industry works locally to such an extent without neglecting its global company philosophy. We spoke with Christian Krautkrämer about rhinos, injection moulding machines, right weight, family, local markets and of course closures. A. Büchler: Mr Krautkrämer, here in Budenheim close to your headquarters, the 20 million year old “Budenheim Rhino“ was unearthed. According to Wikipedia, the “Rhino family“ is one of the most diverse and successful mammal species. Do I see an analogy to Bericap here? C. Krautkrämer: When I think about rhinos, I can only say that they are extinct in today’s Budenheim and I therefore don’t see any reference to a successful family saga. A. Büchler: How have your father Günter Krautkrämer, your brother Alexander Krautkrämer and yourself structured the management of the company? C. Krautkrämer: First we are not alone. We have also non-family members running Bericap group. Responsibilities are split between members of the management team according group functions like marketing, production, finances, quality assurance, etc. and geographical responsibilities. Far more important than the division of labour within the family and the entire management team is surely the structure of Bericap. We support local decentralised management which are supported by group functions. A. Büchler: This means that many decisions are taken directly on site? C. Krautkrämer: At each site, we have local management which speaks the local language, knows the market and acts independently to a large extent – but always within group guidelines. The local management is responsible for their market and has to act accordingly. We have clearly defined short communication lines to keep the decision making fast. A. Büchler: What then creates the characteristic Bericap flair, if all facilities are managed in such an individual way? C. Krautkrämer: Local management has to act like if it was their own company, act like entrepreneurs. This keeps teams motivated and allows to react fast and flexible. Our people will do the best for the customer. Nevertheless we have defined Best practices and group key performance indicators (kpis) to keep the group developing in one direction. For example we measure group wide energy efficiency as a figure of Kwh/kg of material. In this way we can guarantee our customers worldwide the same products and same services at best quality, but also adapt to regional peculiarities. A. Büchler: How do the company figures look like? C. Krautkrämer: In 2015 group revenue was €750m for 76bn screw caps. Altogether we employ 3,300 workers worldwide at 23 production sites. A. Büchler: With that, you are just below the score that your father predicted in the PETplanet Insider Interview in 2006. He foresaw a €1bn revenue target for 2016. C. Krautkrämer: If closures had still the same weight as 2006, we had passed the revenue of 1bln EUR. But revenue is only a figure, profitability, productivity and quality count. A. Büchler: Let’s stay with the family. In the same interview, he said: “Caps are central to my life”. How is that with you? C. Krautkrämer: I can’t escape my fascination of closures either. When I was only 14 years old, I was already going in and out of the Budenheim facility here. I have worked in many Bericap facilities worldwide and at night at home, closures remain the topic of conversation. As such, I can only concur with that. A. Büchler: The main cost factor for closures is the material. The developments for light weight closures clearly save material. Is the HexaLite “Correct weight” is a trend today, weight reduction was yesterday”, Christian Krautkrämer on today’s development of closures.","@ID":32}, "COMPRESSORS 21 PETplanet insider Vol. 17 Shaftless motor with direct drive When compared directly, a W-series machine from Belliss & Morcom, a Gardner Denver Group company, produced the best values. A type WH 29 3N oil-free piston compressor with a 325kW direct drive and a maximum volume flow of 1,800m3/h (at 40bar) was therefore purchased. One of the features of the W-series piston compressors is the special drive concept, which does not have a belt drive or gear and clutch. This direct drive is said to make for a high degree of efficiency, long service life and low space requirement. Half-load/full-load control The W-series piston machines are doubleacting: two suction and compression processes are performed per revolution. They are also easy to control, even with the basic version, because they can be operated with half load (50% of full load) by means of valve cut-off and even then they are efficient. As they are quiet, there is no need for foundations, and the precision guidance of the piston and piston rod according to the crosshead principle makes for a long compressor service life. Frequency-controlled drive Gropper opted for an even more efficient W-series version with frequencycontrolled drive. The piston compressor has a very large control range from 530 to 1,800m3/h (30 to 100%), so that even smaller quantities or lighter PET bottles can be produced equally as efficiently (although the plant mainly fills 0.9 to 1.35l containers they also fill 0.33l bottles). At the same time, there are hardly any off-load losses, as the pressure can be kept constant over a very narrow pressure range. The system is controlled via a Siemens S7 PLC, programmed by Gardner Denver, which controls the compressor according to demand (with the network pressure as the reference variable). In addition, the pressure can be specifically reduced below 30 bar if lighter bottles are being produced. This also helps to ensure economical, demand-based compressed air generation. The compressed air experts at Gardner Denver were tasked with the design of both the compressor and the controller. They worked on this together with Claus Meyer, Electrical Engineering Planner at Gropper. They also planned the user interface, which displays the operating states of the plant – which also includes an energy-saving refrigerant dryer with scroll compressor from the Gardner Denver range.","@ID":23}, "MATERIAL / RECYCLING 10 PETplanet insider Vol. 17 No. 05/16 petpla.net Improvements in the washing process of PETflakes A little bit more is always good? by Alexander Büchler The volume flows for bottle-to-bottle recycling are constantly increasing so that the corresponding plants have to grow with them. Polymetrix with its expertise in virgin PET is focusing its thoughts on these kinds of plants. We spoke to Martin Müller, Managing Director and Andreas Christel, Director Process Technology. Polymetrix, previously part of the Bühler Group, has received almost every order for the solid state process (SSP) in PET production over the last few years. The energy optimised EcoSphere SSP process in the stable Bühler process (see PP 3/2016, pp. 10) in particular has ensured this strong position with 90% market share. Polymetrix has developed an annual capacity of 19.8 million tonnes of virgin PET with 173 plants in total on the market. In the recycling segment it is no fewer than 21 lines with 400t annual capacity. The market share of new business is 40% here. “Besides the actual preparation of flakes into granules we mainly see considerable potential for development in the washing process,” says Martin Müller. “Above all we don’t need to clean the residue that we can remove during flake washing out of the exhaust air later on, cleaning the exhaust air is a much more complex process,” says the Director Process Technology Andreas Christel. What is meant here is not just the impurities that get back into processing with the bottle but also the previously rather neglected issue of washing substances. If the maxim of a little bit more is always good tends to apply today the washing agent residue in the exhaust air leads to considerably more cleaning work later on. Polymetrix sees its EcoSphere SSP as a key technology for energysaving processing for the other processing stages. As the IV only increases very late on the spherical granule the IV can be kept low throughout the entire process. As a result the moulding compound flows through the plant at much lower temperatures and there is no AA increase at all to the otherwise usual extent. As the spherical granule does not have any “corners” that might flake if they rub together the granule is also dust-free. A prerequisite for smooth processing in the preform process. www.polymetrix.com F.l.t.r.: Camille Borer, Team Leader Design & Test Center and Andreas Christel, Director Process Technology, during a tour through the test facility.","@ID":12}, "BOTTLES PETbottles 43 PETplanet insider Vol. 17 No. 05/16 petpla.net Home + Personal Care [email protected] Tel: +90 212 695 50 00 Fax: +90 212 694 97 24 100815dmyR .com Shampoo with coconut water The Ogx company is selling 385ml of their transparent shampoo “coconut water” in German-speaking countries in a similarly transparent PET bottle in the brand’s typical shape. The bottle is decorated on the front with a non-label-look label, whilst the back is covered with a folded plastic label with consumer instructions. The inside of the label facing the bottle has coconut designs printed on it that are visible from the front. A punched-on hinged lit with an opening for dispensing serves as closure. www.ogxbeauty.com Sweet apple pie hugs body milk The products of the “treaclemoon” brand, available in selected pharmacies, stand out with their novel fragrance varieties, fun product names and descriptions. The most recent example is a body milk for dry skin available under the name “sweet apple pie hugs” in a temporary promotional offer. This trial pack was on offer so that you did not need to reach for the 350ml bottle or in order to take a small bottle with you on your travels. 60ml of the light pink tinted substance was bottled in a transparent PET bottle with a screwed-on pump dispenser and an attached protective cap. www.treaclemoon.de Two-phase spray-cure by Guhl Guhl Ikebana in Darmstadt, Germany, is offering an intensive spray-cure with monoi oil for strained and damaged hair. 180ml of the two-phase product that is mixed by shaking before applying and massaging in, is bottled into a grip-friendly shaped bottle. Two non-label-look labels explain its application and an attached clear snap-cap protects the shiny silvery pump dispenser from malfunction. www.guhl.com Sidolin for many surfaces The new Sidolin streak-free multi-surface cleaner by Henkel is promising a 5x longer glow on all types of surfaces and an improved protection from water and dust. The easy-tohandle transparent trigger bottle with handle recess, anti-slip knobs for secure handling and a 500ml capacity make up the packaging for this blue tinted product. The lockable trigger produces foam or spray depending on its setting. The bottle is labelled with a partly transparent shrink sleeve. According to the manufacturer, the product impregnates the cleaned surfaces and protects them in this way from new adhesions. www.henkel-reiniger.de","@ID":45}, "TRADE SHOW PREVIEW 37 PETplanet insider Vol. 17 liquid food sector. He is consciously focusing on the growing demand for compressor technology in PET. “Things are looking positive in countries like Saudi Arabia, Nigeria and Mozambique,” Panchal says, as he outlines the firm’s current business. Altogether, around 250 compressors of every kind leave the plant every month. Of these around 40% are for export, to France, Australia, Dubai, Israel and Canada, some countries in Africa and many of India’s immediate neighbours. Ninetyfive employees ensure smooth production. In 2015 the company’s turnover was US$2.7 million; this figure which is set to increase to US$3.1 million in 2016. In the area of PET, blow-moulding machines are the leading market, followed by compressors for extrusion, printing, roto-moulding and injection moulding machines. The latest product is the oil-free high pressure compressor, which was introduced twoand-a-half years ago. It is available in eight versions with outputs of 25-42 bars and/or 187-688m3/h discharge flow for automatic blow moulding machines of high volume bottle production. “When we talk about India and the international markets, we also define ourselves by the good after-sales service provided by our service team here and our regional representatives on-site,” explains Panchal. “Our regular customers in France, Australia, Africa, Middle East, Israel and neighbouring countries buy compressors in quantity every quarter. In the future, we want to manufacture even bigger machines; our key goal is to focus on the area of energy saving more strongly with our new models. We are also considering expanding at the international level by opening a small office in the USA.” Indo-Air says that its activities and facilities definitely live up to the “Make in India” campaign launched by the Indian Government in 2014. www.indoair.com","@ID":39}, "BOTTLING / FILLING 15 PETplanet insider Vol. 17 Second complete PET line solution meets requirements of challenging installation BMV renewed its confidence in Sidel seven months after the order for the initial equipment, investing in this second Sidel complete PET bottling line solution to produce the ‘Vytautas’ brand at the Birštonas plant. This line features a very similar scope of supply, therefore ensuring that the advantages and benefits of the Combi would be realised again. However, the installation of this second line was more challenging because the footprint of the layout was 20% more compact than the original bottling line. Mr. Valentinas Lukosevicius, BMV’s Production Director at the Birštonas site, commented: “Installation of the second line was a big challenge - both for us and Sidel. This new Sidel line was substituting the old existing line and the constraints of the limited plant floor space were therefore an important consideration when designing the line layout. Sidel’s considerable project experience was therefore very important in achieving our goals.” The new complete line solution comprises: a Sidel Combi 8 FMc; a cap air rinser; UV lamps on the infeed rail of the preform feeding rail; a Sidel Rollquattro Evolution labeller; a cap feeder for sport and flat caps, coder, packer, handle applicator twin pack, bottle conveyor, pack conveyor, and palletiser. Strong re-branded PET packaging The new bottle shapes were designed by Sidel to boost both the ‘Vytautas’ and ‘Birute’ brands, with the ‘Vytautas’ bottle design targeted primarily at male customers and ‘Birute’ at female customers. With elegant curves and elongated shoulders, the body of the bottle is engraved with the brand logo and its mineral content. The same shape was adopted for both still and sparkling water, with just differences in the bases, and deployed for a complete family of four bottle formats. Although the main format produced on the line is the 1.5l bottle, the new line has the flexibility to produce either still or sparkling water in the four different PET bottle formats: 0.5,","@ID":17}, "NEWS 7 PETplanet insider Vol. 17 No. 05/16 petpla.net • 28mm, 33mm and 38mm screw closures • Robust and trouble free capping • Established DoubleSeal™ technology - for secure sealing performance - for better protection against micro-organisms • Slit FLEXBAND® band technology for enhanced tamper evidence • O 2 barrier and scavenging options for screw flat caps supporting longer shelf life and fresher taste • Sports closures for aseptic filling and hot filling without aluminum foil • Special closures for syrups and carton packaging Unique range of screw and sports closures designed for cold fill and aseptic application BERICAP Technology for juices, RTD teas, health drinks www.bericap.com Mpact Polymers unveils bottle-grade recycling plant On May 10, the Minister of Environmental Affairs Ms. Edna Molewa officially unveiled Mpact Polymers in Wadeville, Germiston, South Africa. The new bottle-to-bottle facility will produce recycled polyethylene terephthalate (rPET). The R350-million state-ofthe-art operation’s recycling process complies with European Union (EU) Food Safety Authority specifications and is the first in Africa to meet The Coca-Cola Company’s full certification for PET bottles to package the company’s soft drinks. The operation enjoys the backing of the departments of Environmental Affairs (DEA), Trade and Industry (DTI) and Economic Development (EDD) in promoting job creation, reducing waste to landfill and improving rPET production that will ultimately help to reduce the carbon footprint of the food and beverage industry. www.mpact.co.za ChemChina completes takeover of KraussMaffei Group China National Chemical Corporation (ChemChina) has successfully completed the acquisition of the KraussMaffei Group from Onex Corporation. All relevant regulatory approvals have been achieved. In the future, the KraussMaffei Group will be ChemChina’s principal business entity in the operating and managing of related machinery enterprises. According to Jianxin Ren, Chairman of ChemChina, the KraussMaffei Group will instill the German Industry 4.0 gene and the manufacturing tradition of craftsmanship into ChemChina’s advanced manufacturing segment, so as to provide integrated solutions to more customers around the world, especially in the emerging markets, thus complementing ChemChina’s shortcoming. “The transaction will enable us to gain stronger access to the market of the Greater China Region. We intend to accelerate our growth in Asia and particularly in China, which will also strengthen our company both in Germany and in the rest of Europe”, said Frank Stieler, CEO of the KraussMaffei Group. The acquisition of the KraussMaffei Group by ChemChina from Onex was announced in early January 2016. ChemChina effected this acquisition together with its partners CNIC Corporation Limited and AGIC Capital. ChemChina is China’s largest chemicals group. It generated revenues of around €42.3 billion in 2015 with approximately 140,000 employees, of whom 48,000 are located outside China. The group operates internationally with a global strategy, having acquired companies in France, Australia, the UK, Israel, Norway and Italy in the last few years with the most recent acquisition being the high-end tire manufacturer Pirelli. www.chemchina.com.cn/en www.kraussmaffei.de/en WikiPETia sorts things out Following the tremendous response to our open PETplanet insider archive, we have now begun to assemble articles according to company entries, and we have also sorted magazines by date of issue in WikiPETia. Participants in the PET value chain now appear on successive pages. Under the appropriate company name, you can then consult all contributions that have appeared in PETplanet insider from the relevant companies. Just click to special pages in the left menu bar www.wikipetia.info and then click List of all pages and you can browse the companies and their articles archived and linked in WikiPETia so far. We have started with the most recent issues, and the list will be continually updated. Many companies have already expanded their profile in Wiki. Companies who are not yet listed or who have made no new entries can easily do so. Simply ask us to open an account for you on WikiPETia. We look forward to your visit!","@ID":9}, "MARKET SURVEY 26 PETplanet insider Vol. 17 No. 05/16 petpla.net SBM moulds Preform moulds Company name Hallink RSB Inc. Nissei ASB Machine Co., Ltd. Demo Design and Moulds Postal address Telephone number Web site address Contact name Function Direct telephone number Fax E-Mail 284 Pinebush Road, Cambridge, Ontario N1T 1Z6, Canada +1 519 624 9720 www.hallink.com Mr Jason Warmington General Manager +1 519 624 9720 +1 519 624 9721 [email protected] 4586-3 Koo, Komoro-shi, Nagano-ken 384-8585, Japan +81 267 23 1565 www.nisseiasb.co.jp Mr Paul Atkin Section Manager - Marketing Group +81 267 23 1565 +81 267 23 1564 [email protected] Via Olivera 48, 31020 San Vendemiano, Italy +39 0438 409048 www.designandmoulds.com Michela Carrer Export Manager +39 346 7527625 (mobile) +39 0438 409046 [email protected] Stretch blow moulds Yes Yes Bottle size (max.) (in litres) 10l 22 0.25 to 20.0l Moulds supplied directly to blowing machine manufacturers Yes No, for our own machines only Yes Do you supply retrofit moulds for existing SBM machines? Yes Only for own machines Yes For which makes of bottle makes have you already produced moulds? Sidel, Krones, KHS, SIPA, Nissei ASB, Aoki, Kosme, SIAPI, SIDE, Urola, 1BLOW, W. Amsler, Chia-Ming, Aoli, etc. Mould designs are customised on a per customer basis Europe, Africa and Asia Bottle design service Yes, services include preforms & bottle design, rapid prototyping, bottle sampling on a lab stretch blow moulder & on-site process assistance Yes, complete design service from concept to finished moulds and machines Yes Specialities Manufacturing stretch blow moulds and change parts (aka personalisation parts, handling parts and/or product dependant parts) for any make of 2-stage stretch blow moulder, un-scrambler and blow/fill/cap system Handled, non-round, wide-neck, hot fill, non-round neck, offset neck, heavy weight cosmetic, PET, PP, PC, PES, PEN, PLA, etc. From bottle design to blow moulds installation. Training on-site - Change neck spare parts for bottling line Other Manufacturing descrambler, filler and capper change parts as well as blow mould/change parts custom tooling carts Specialised in lightweight bottle project and high design bottle for premium brands Company name Moldintec Argentina Awanti Polymoulds PVT. LTD. TPS - Tooling Preform Systems Postal address Telephone number Web site address Contact name Function Direct telephone number Fax E-Mail Lamadrid 501 - Los Troncos del Talar - Tigre - Buenos Aires, Argentina +54 11 6632 9999 www.moldintec.com D.I. Jorge Pucci Commercial Director +54 911 4146 9894 [email protected] 25/5A/1/2, Nanded, near Sawali Dhaba, Sinhagad Road, Pune - 411 041, India +91 20 24392225 / +91 8888 827595 www.awantipolymoulds.com Mr Shirish Kshirsagar Managing Director +91 20 24392225 / +91 8888827595 +91 20 24392225 [email protected] C Houtmanstraat 42 7825VG Emmen, The Netherlands +31 591 679768 www.tps.nl Mr Richard Tempel Account Manager +31 6 25041136 +31 591 630616 [email protected] Stretch blow moulds For mineral water, CSD, warm-and hotfill application, liqour, pharmaceuticals, edibile oil and wide mouth jars Bottle size (max.) (in litres) 20 Up to 20l 50 Moulds supplied directly to blowing machine manufacturers Yes Sidel India, MAG PlasticAsia, Shyam Plastic Machinery, Global PET No Do you supply retrofit moulds for existing SBM machines? Yes Yes Yes For which makes of bottle makes have you already produced moulds? Coca Cola, Pepsico, Danone, Nestle, Aje group certified mould supplier Sidel SBO & Synery series, KHS, Krones, Nissei, MAG, Kosme, Chum Power, Shaym Plastic, Urola, Wee Lei Various Bottle design service yes, pre series blowing service & bottle lab tests Yes Yes Specialities Low pressure blowing 17bars for CSD bottles up to 3l We are an end-to-end solution provider, from desinging of bottle, prototyping to unit cavity testing and final mould making Large containers Other NCBs propietary base for use of nitrogen and wide nitrogen operation range up to 30psi In house production equipment for preforms and containers up to 50l Company name Indus Moulding Solutions PL PET Engineering Kronce Enterprise Development Co., Ltd R&D/Leverage Simex SRL Postal address Telephone number Web site address Contact name Function Direct telephone number Fax E-Mail 51/54 Daman Industrial Estate, Daman 396210, India +91 22-28776984 www.petform.net Mr Shurid Mody CEO +91 9769758634 [email protected] Via Celtica 26/28 San Vendemiano, Italy +39 043 840 3069 www.petengineering.com Ms Elisa Zanellato Marketing & Comm. Mgr. [email protected] Room 06/07, Floor 35, 6088 Humin Road, Minghang District, Shanghai 201199, China +86 21 24202001 www.smargon.com Mr Andy Yang Deputy General Manager +86 15 000770587 +86 21 24202278 [email protected] Leverage House, Hamilton Road, Sutton Ashfield, Nottinghamshire, UK, NG175LD +44 1623 556287 www.rdleverage.com Mr Alan Tolley Managing Director +44 1623 552240 [email protected] Via M.Biagi e M.D'Antona ,5 60025 Loreto (AN) Italy +39 071 7500214 www.simexitaly.it Mr Graziano Giuggiolini Sales Manager +39 071 7500214 +39 071 7501958 [email protected] Preform moulds Horizontal opening Yes Number of cavities 144 cavities 4 1 to 72 1 to 96 up to 144 Preform sizes 5.5 to 160g 5g lotion bottle, 750g for 5l gallon bottle 24mm to 63mm neck, 12g through 350g All sizes and all finish Moulds already built for (makes) Husky, Netstal, Sipa, Arburg, Engel, SIG, Krupp Several formats Husky, BM Biraghi, Milacron, Engel, Krupp, Krauss-Maffei Mineral water, milk, oil, beer etc. Vertical opening No No Number of cavities 96 cavities Preform sizes Moulds already built for (makes) Krauss Maffei Do you produce single stage tooling sets? (Preform moulds AND blow moulds) Yes No Yes, we can make the moulds sets for AOKI, ASB Yes Yes Other Supplier for Single Stage, ISBM worldwide. Product Solution Laboratory Injection preform moulds for PE and PP SBM moulds","@ID":28}, "PETcontents 05/16 4 PETplanet insider Vol. 17 No. 05/16 petpla.net Page 19 Page 39 INSIDE TRACK 3 Editorial 4 Contents 6 News 39 Products 41 On site 42 PET bottles for Beverage + Liquid Food 43 PET bottles for Home + Personal Care 44 Patents MATERIAL / RECYCLING 8 PETcore Europe Conference 10 A little bit more is always good? Improvements in the washing process of PET flakes 12 75 years and big in business PET is now in its 75th year – and still revolutionising the drinks world BOTTLING / FILLING 14 Machine and bottle ‘light-lifting’ COMPRESSORS 17 The ideal compressor Statement by Werner Hoffmann, KHS Corpoplast 17 Up to 80% energy savings Efficient high pressure production at San Pellegrino’s Castrocielo plant 19 Coping with pressure Oil-free piston compressor “Vito” for Italian water brand Motette 20 Air for expansion Piston compressor as “energy source” for bottling not-from-concentrate juice 23 To concentrate on what matters Transfer of technical applications results in energy efficiency MARKET SURVEY 25 Suppliers of preform / stretch blow moulds BOTTLING / FILLING 28 A hot crate Upgrade improves heater box efficiency CAPPING / CLOSURES 30 Think global, work local Interview with Dipl.-Ing. Christian Krautkrämer, Managing Partner, Bericap TRADE SHOW PREVIEW 32 drink technology India (dti) 2016 32 Advantage India Overview of the Food and Beverage Industry - Trends & Outlook 34 PET from the heart of Bollywood Interview with Chemco Plastic Industries 36 Compressors from Ahmedabad Interview with Indo-Air Compressors BUYER’S GUIDE 45 Get listed! COMPRESSORS Page 42","@ID":6}, "MATERIAL / RECYCLING 8 PETplanet insider Vol. 17 No. 05/16 petpla.net PETcore Europe Conference by Alexander Büchler We often attend events, and sometimes we lose count, but the PETcore Event in Brussels, Belgium was different. Here there were heated discussions between the recycling industry and Eric Liegeois, Policy Officer, DG for Enterprise and Industry European Commission, on how the EU envisages recycling. The other presentation sessions also treated content and professional expertise. Roberto Bertaggia, President of Petcore Europe summarised the atmosphere thus: “This huge success of our annual conference outlines the importance of this event for participants from all sectors of the PET value chain.” The first session of the conference dedicated to Sustainability gave an outline of different EU projects. The Innovation session outlined the penetration of PET replacing conventional materials in new markets such as large volume water coolers and kegs, aerosols and novel recycling technologies for coloured PET. The last session on Globalisation was dedicated to the inter-connection of work including Napcor activities in the US as well as the marine litter issue presented by Waste Free Oceans. At its core however, the event focused on Eric Liegeois, Policy Officer, DG for Enterprise and Industry European Commission. He presented the status of the EU Action Plan for the Circular Economy to the audience. The core message was to achieve a high proportion of recycling from waste, thus ensuring a significant part of the EU’s demand for raw materials is covered, creating jobs and helping Eric Liegeois, Policy Officer, DG for Enterprise and Industry European Commission talking about concrete and ambitios actions.","@ID":10}, "TRADE SHOW PREVIEW 34 PETplanet insider Vol. 17 No. 05/16 petpla.net Interview with Chemco Plastic Industries We met: Mr Vaibhav Ram Saraogi, Director PET from the heart of Bollywood By Kay Barton Mumbai, the home of the Bollywood movie empire, plays host once again to this year’s dti drink technology India exhibition. Just a short distance down the Western Express Highway from the Bombay Exhibition Centre was the location for our meeting with Chemco Plastic Industries Pvt. Ltd., a multinational plastics manufacturing firm whose PET packaging segment accounts for around 75% of its total output. As well as its Mumbai facility, the familyowned business has production sites in the Indian cities of Silvassa, Daman and Vadodara, and in Bahrain and the United Arab Emirates. With an estimated market share of 17.5%, it is one of the leading manufacturers of preforms and bottles in India. The company is currently pursuing a range of different expansion projects as it responds to increasing demand in the packaging sector. At the same time as meeting local challenges it is seeking to maximise its international potential. There was, therefore, much in the way of both historic data and recent developments to discuss with company director, Vaibhav Ram Saraogi (29). “Although we’re one of the biggest converters in India our media presence hasn’t been so strong. That’s something we want to change,” says Vaibhav Saraogi, making clear that we definitely approached him at the right time. “My father, Ram Saraogi, my brother Gaurav Saraogi and I currently represent the company,” he explains. The Chemco story began in 1980, in Mumbai, with a few injection and single stage moulding machines for manufacture of baby feeding bottles (a product that continues today in the form of its own “Small Wonder” brand) along with contract manufacture for various international brands. “Our second plant, constructed in Daman in 1982, is focused primarily on storage and product containers for food, non-food and healthcare packaging. Our customers there include ITC, Parle Agro, Johnson & Johnson, Nestlé, Dabur, Reckitt Benckiser and many more. Our third factory was opened in Silvassa and is equipped with a highspeed preform machines from Krauss Maffei, Husky and ASB. Our manufacturing operations there consist of 80 systems and around 600 employees. The facility in Vadodara is our largest in terms of output and serves the packaging requirements of various beverage and water brands locally and internationally. It has won various awards. We have also recently added machines to manufacture multilayer shrink films.” Chemco’s India turnover in 2015 amounted to US$33.6 million and is forecast to be US$52.3 million in 2016. The forecast increase, of more than 50%, will be as a result of further expansion. The momentum for growth will continue to be maintained, with the planned opening in 2018 of an enormous new plant, which will be focused on beverages and household items. It will use many Husky preform systems and will primarily supply to major beverage brands alongside some local private labels. It will also produce shrink film. “Right now, PET manufacturing accounts for 80% of our plastic business in India,” Saraogi continues. “We currently have production space totalling more than 200,000m2 globally, and offer a four-figure choice of products. We are one of the biggest manufacturers in the country, in terms of output.” He explains that the company processes 200-220t of material per day, 340 days per year. In addition to PET, supplied by firms including Reliance and JBF, 15% of Chemco’s manufacturing is accounted for by PP and 5% by HDPE. The factories operate three shifts a day, 24/7. The expansion momentum is being maintained with new, Huskyequipped factories already planned for 2017/2018. The investment will total almost US$30 million over two years; they are planned to increase output by 35%. “Among the reasons why Gujarat is a good location is the constant supply of clean energy that’s available there,” explains Saraogi. “We have also made a point of looking for locations that are near our major customers so that we are able to respond to possible requirements at short notice, and control logistics costs.” Coca-Cola accounts for approximately 35% of Chemco’s PET business; it has won the CocaCola Gold Award for three years in a row. The new plants are planned to see the launch of the company’s in-house production of closures, safe guard envelopes, insulation roofing material and bubble film for packaging. Chemco is now opting to branch out to every segment of packaging, protection and some segments of construction. “With the growing potential and high movement in the e-marketing trade we feel it is important that we reach out into all segments of protection packaging”, says Saraogi. Chemco’s international operations have been no less busy. Its first international factory was opened in 2000, in United Arab Emirates (UAE), where the","@ID":36}, "MATERIAL / RECYCLING 9 PETplanet insider Vol. 17 No. 05/16 petpla.net the environment. More specifically, the rate of return of plastics is to rise from its current level of about 35%, to 55% in 2015. That is the theory. From the audience the questions came thick and fast: how exactly does the EU imagine the process of recycling plastics. The recycling industry is keen to invest the money, but as long as they are not clear on how to recycle, they are not going to throw money away. Eric Liegeois had no concrete answers to this. He admitted that so far implementation guidelines are missing and are not in sight but are going to come. He pointed to the national committees. This begs the question how the proportion of recycled material is to rise without investment into recycling. Elfriede Hell from Starlinger recycling technology pointed out how badly things can go wrong and particularly how long it can go on for, in her presentation “Implementing the food contact plastics recycling regulation in practice“. She clearly summarised the draft law that has been ongoing since 2008 on the demands of bottle to bottle (b to b) recycling. She tried to show the obstacles which lie behind the politically motivated requirement that only up to 5% of non-food bottles can be included in the recycling stream for the b to b. The recycling plants do technologically manage to generate food contact material from all PET bottles. She also showed how cumbersome the Compliance Monitoring Summery Sheet (CMSS) is which the EU requires, and that there still isn’t a final EU guideline for the implementation of the ordinance (audits) and therefore, as described above, the cat would seem to be chasing its tail. No guidelines, no investments, PET recycling stagnates. By their actions, the EU Commission has achieved the exact opposite of what it actually intended. And the great thing is, the PET industry recycles anyway. The conference was originally planned to take place in November 2015, but – due to the security situation in Brussels – had to be postponed to early 2016. The next Petcore Europe conference will be held in Brussels in February 2017. www.petcore-europe.org This is how the EU imagines recycling in the coming years. All of this is to be included in the Compliance Monitoring Summery Sheet (CMSS) by Elfriede Hell, Starlinger. Patrick Peuch, Executive Director of Petcore Europe. Eva Schneider, Communications Officer of Petcore Europe.","@ID":11}, "TRADE SHOW PREVIEW 33 Compared to other developing markets, the penetration level of soft drinks is still low in India. However, this offers a huge future potential for the beverage market. The sales volume of soft drinks is expected to rise with a growth rate of 95.1% from 11,755 million litres in 2013 up to 22,937 million litres in 2018. During this period, sales volume of soft drinks is forecast to increase by 19% annually. Increasing demand for healthy and hygienic products is expected to fuel the growth of the soft drink sector. Increasing penetration in rural areas will also contribute to significant sales increments. Sales volume of alcoholic drinks and beer in India In litres mn 2013 2017 Growth rate 2013-2017 Alcoholic drinks 3,847 5,152 33.9% Beer 1,837 2,599 41.5% Source: Euromonitor International 2014, VDMA India is one of the largest markets for alcoholic beverages in the world and the third largest in Asia, after China and Japan. Although its market has been dominated by rum and whiskey for a long time, beer is becoming increasingly popular – among the younger, affluent population in particular. The sales volume of beer amounted to 1,837 million litres in 2013; the annual growth rate is forecast to reach 9% by 2018. Sales volume of drinking milk products in India In 1,000 tons 2013 2018 Growth rate 2013-2018 Dairy products 14,457 18,479 27.8% Source: Euromonitor International 2014, VDMA Milk production in India is the highest in the world; 37% of the market is for processed product. Within the next few years the demand for packaged milk and milk products is expected to increase as the growing health-conscious middle class consumer segment turns towards the western way of life and demands more and more processed and packaged food in modern supermarkets. The availability of fresh/pasteurised and long life/UHT milk is increasing all across the country. Event Building on the momentum of the strong forecast on beverage and food processing industry in India, the dti (drink technology India) and PackTech India (International Packaging Technology Exhibition) exhibitions will be taking place at the Bombay Convention & Exhibition Centre in Mumbai between 15th and 17th December 2016. The trade fair duo, which will be held together for the fourth time, unite the interests of three industries under one roof: Beverages, Food and Packaging. The exhibition attracts international visitors and exhibitors from all relevant segments of the beverage, food and packaging industries and offers the Indian industry a good opportunity to learn about the latest technological developments, both domestically and around the world. www.drinktechnology-india.com PH.","@ID":35}, "BOTTLING / FILLING 16 PETplanet insider Vol. 17 No. 05/16 petpla.net 1.0, 1.25 and 1.5l, to a maximum production output of up to 16,000bph. This production level represents an output three times faster than the previous BMV line it replaced. This significant increase in production capacity assisted BMV in serving its national market, as well as providing opportunities for expanding exports in Poland and Russia. Lightweighting and recycling make contributions to BMV sustainability As a means of showing gratitude for the natural resource from which the company profits, together with a sense of responsibility to the environment, society as a whole and future generations, BMV is firmly committed to contributing to the maintenance of ecological balance. Consequently, the company determined to meet several sustainability targets and the introduction of the complete line, coupled with the new bottle designs made a significant contribution. One of the important environmental concerns is the amount of plastic used to produce the bottles and BMV is strongly committed to reducing this as much as possible. “The company became the first in Lithuania to reduce the amount of PET in its bottles, adopting a short-neck capping system and cutting the use of PET by up to 50t per year. The new bottles designed by Sidel also contributed to lightweighting the bottles by up to 30%,” comments Pranckus. BMV then took the decision to use only packaging that is recyclable in its bottling. Finally, the Baltic producer focused on improving its production equipment wherever possible in order to become even more environmentally friendly. The company intended to reduce the total amount of electrical power it consumes through the implementation of eco-friendly technologies. “The Sidel Ecoven used within the Combi configuration makes a big contribution to this target and both of the complete Sidel lines significantly reduce the company’s consumption of electricity,” concludes Pranckus. www.akvile.lt www.sidel.com The new line is flexible to produce four PET bottle formats: 0.5, 1.0, 1.25 and 1.5 litres, to a maximum production output of up to 16,000bph. At the end of the line the pack conveyer and pallatiser.","@ID":18}, "BOTTLING / FILLING 29 PETplanet insider Vol. 17 No. 05/16 petpla.net Mineralbrunnen Teinach GmbH is part of Mineralbrunnen Überkingen-Teinach GmbH & Co. KGaA. The regional brand company fills about 1.5 million bottles of non-alcoholic beverages a day. The mineral water bottling plant produces Teinacher and Hirschquelle Vital mineral waters, a curative Hirschquelle water and soda pops Teinacher Limo, Limo Light, ISO, ACE and Multi 10. Mineralbrunnen Teinach GmbH has 130 employees and is situated in Germany’s largest nature reserve, the Central/ North Black Forest Nature Park which covers approximately 3,750km2. Besides holding the Energy Management System Standard according to ISO 50001, ISO 500001 and IFS Food Version 6 2013 certificates, Mineralbrunnen Teinach GmbH was the first mineral water plant to be granted the Assured Sustainability – Investment in the Future seal of approval for sustainability in ecology, economy and social competence in 2013 by the private German Institute for Sustainability and Economy. Engineering Excellence Low production costs Maximum output At Netstal our aim is to help you produce the perfect PET preforms: at minimum cycle times you achieve maximum output with constantly high quality and energy efficiency. And that’s no coincidence: our team of experts are always there for you – with state-of-the-art systems. www.netstal.com demonstrates this outside the production shop, too, through its longterm cooperation with the Central/ North Black Forest Nature Park for the conservation of the unique local countryside, for example. Or with its system of energy management, certified according to ISO 50001. “We can simply read off the history of the heating costs for the modernised system on the electricity meter and document the significant savings,” he claims. Schanz adds that KHS converted the line quickly and competently without affecting system operation. Since the end of last year the revamped heater box has been running trouble-free. Through the amount of energy saved, investing in a modernisation of the InnoPET Blomax Series III pays off for users after one to three years depending on the line’s capacity utilisation and the price of electricity. KHS offers the conversion for both versions of the Blomax Series II: the modular or the compact. “For many companies, energy-optimised PET stretch blow moulders are an excellent way of reducing production costs,” says Goebel. He expects more orders for this sustainable KHS conversion product in 2016. www.mineralbrunnen-kgaa.de www.khs.com The heater boxes are distinguished by new reflectors made of modern ceramics and a precisely adjusted geometry.","@ID":31}, "PETnews 6 PETplanet insider Vol. 17 No. 05/16 petpla.net For the first time: motan innovation award “mia” Businesses, universities and employees of the motan group submitted their applications for the motan foundation’s first innovation award “mia” with a large spectrum of innovative solutions for Materials Handling. “Despite it being the first call and the comparatively short application deadline, we received an unexpectedly large number of applications”, explains Sandra Füllsack, Managing Director of motan. “And the breadth of topics was astounding.” Along with submissions for specific solutions in material supply, there were innovations for adjacent areas of the process chains in the plastics industry. Among the applicants were application specialists from plastic processors, employees of the motan group from all over the world, and applicants from universities and institutions. Independent industry and science experts nominated five potential winners after a detailed examination and assessment process. Aspects such as additional benefit for the processor increase in efficiency for processing, and effects of the proposed solutions on the environment were just some of the criteria. At the beginning of July 2016, these five innovations will be personally presented to the jury at motan-colortronic in Friedrichsdorf, Germany. The jury will decide on three finalists for the award. The prizes worth a total of over €20,000 will be presented during a special award ceremony during the plastics exhibition K 2016 in Düsseldorf. www.motan-colortronic.com Flavours with freshness Archer Daniels Midland Company’s (ADM) Wild Flavors and Specialty Ingredients business unit (WFSI) is expanding its portfolio to include new concepts featuring nuances of mint. On the one hand, it has been extremely popular and well-known around the world for centuries, and on the other hand it still has a very versatile character full of nearly inexhaustible potential for product innovations across all segments and categories. The flavourists at WFSI have developed two concepts for new still drinks and carbonated soft drink applications. Both of these creations are based on tropical fruits but are different in terms of their mint profile. Ginger ale, ginger beer and tonic are popular soft drinks in and of themselves, but they are favorites when it comes to mixing long drinks and cocktails. In the past five years, the number of new product launches involving ginger ale and similar products tripled (Mintel GNPD, 2016), thereby showing their increasing relevance on the European market. New impulses for this growing and diversifying segment come from “fresh” creations with mint. WFSI offers three new kinds of CSD: “Citrus & Mint,” “Ginger Ale & Mint” and “Tonic & Mint” can each be enjoyed straight up, on ice or as a mixer with vodka or gin. WFSI has developed colourful granulates which offer a burst of freshness. Manufacturers can work with “Spearmint Green” and “Peppermint Blue” in different applications to create a truly cool response to the ongoing demand for unexpected product innovations. All of WFSI’s mint concepts are characterised by well-balanced flavour compositions made of quality raw materials. WFSI is continuing to rely upon the Plant Science Program so it can also be a global technological leader in developing natural, GMO-free kinds of mint. With its expert knowledge of cultivating, procurement and processing mint, WFSI is able to produce high quality ingredients and flavours on a sustainable basis. www.wildflavors.com Chinaplas 2016 ended successfully The 30th edition of Chinaplas ended successfully. The fairgrounds in Shanghai were visited by the record number of 148,575 visitors which is an increase of approx.15% compared to last year’s Chinaplas in Guangzhou and a plus of 14% compared to the 2014 Shanghai edition. 27% of the visitors came from overseas, from 160 countries and regions. This also sets a new record for overseas visitors. In addition, the trade fair occupied an exhibition area of more than 240,000m2, gathering 3,335 exhibitors from 39 countries and regions - also a new record since the establishment of the show in 1983. 35% of the exhibitors came from overseas. Next edition of Chinaplas will return to Guangzhou and be held from May 16-19, 2017 at China Import & Export Fair Complex, Pazhou, Guangzhou, PR China. www.chinaplasonline.com","@ID":8}, "BOTTLING / FILLING 28 PETplanet insider Vol. 17 No. 05/16 petpla.net Upgrade improves heater box efficiency A hot crate Overheads for materials and the price of energy are among the biggest cost drivers in production. Mineral water bottlers Teinach GmbH have thus charged the KHS Group with the modernisation of their PET bottle filling line. In the course of the process the systems supplier improved the level of energy efficiency by optimising the heater boxes on the PET stretch blow moulder in particular. engineers from the mineral water company. The stretch blow moulder in Teinach has been in operation since 2007. “Over the last nine years the machine has given us wonderful service. KHS then showed us that with little effort we could improve further on our levels of energy efficiency,” Schanz explains. After a maximum of two days the machine would again be ready for operation, yielding savings of up to 50%. Heater box geometry with ceramic reflectors The upgrade primarily consisted of converting the heater box on the Blomax Series III Compact where the PET preforms are heated for the downstream stretch blow moulding process. Frank Goebel, head of Service Engineering at KHS, summarised the development of the past few years: “We have almost 600 Series II Blomaxes in operation worldwide. We aim to continue to support the operators of these durable machines even after many years of service.” At Teinach this means saving over 40% in energy by converting the heater box which KHS achieved by adding new reflectors made of modern ceramics to the heater boxes and precisely adjusting the geometry. Thanks to their special design the physical properties of the ceramic elements have a very positive impact on the energy distribution, resulting in less energy being needed to heat the preforms. The reflectors and infrared emitter are built that the sensitive bottle thread area is not unnecessarily heated. The amount of cooling in this area can then be reduced, thus saving Teinach even more energy. This higher efficiency makes it possible to shorten the heating segment, explains Goebel. If fewer heating elements are required in the heater, the infrared emitter consumption also drops as a result. KHS usually converts the heater boxes on all Series III Blomaxes in about two days. The process engineers make the fine and final adjustments during the startup phase so that disruption to production is kept short. Teinach’s head of Engineering is suitably satisfied with his company’s decision to invest in this new feature. “We’re always trying to save energy to cut costs and protect the environment,” states Schanz. The bottler The Teinach product range, filled in PET bottles. Non-alcoholic beverages in the Teinacher and Hirschquelle brand portfolio are the chief products for the company from the north of the Black Forest, Germany, which belongs to Mineralbrunnen Überkingen-Teinach KGaA. At its plant in Bad Teinach, the mineral water bottler achieves an output of about 150 million bottles of water and soda pop per year, a third of which are made of PET. Preform heating consumes a lot of energy and is a relevant factor when it comes to the operating costs incurred during the manufacture of PET bottles. One of Michael Schanz’s main tasks as Head of Engineering at Mineralbrunnen Teinach GmbH is to constantly monitor the energy efficiency of the lines. KHS analysed the savings potential of the reliable InnoPET Blomax Series III together with the","@ID":30}, "PRODUCTS 39 PETplanet insider Vol. 17 No. 05/16 petpla.net PETproducts More capacity for specialised preforms The specialist in PET preforms and bottles in France, PDG Plastiques, continues to increase its Prelactia preforms capacity with two new PETLines from Netstal. Prelactia PET preform is a two-layer preform which offers a 100% light barrier with low weight (38Ø, 24-28g), in order to preserve sterilised milk. Prelactia preforms are available for 0.25l to 1.5l milk bottles. PDG Plastiques is well known in France in the PET preform market for long shelf life milk. New preforms for mineral water with low weight and specific preforms for liquid soap bottles have been recently developed. PDG plans a new building for production and storage which will be completed before the end of 2016. www.pdg-plastiques.com www.netstal.com Preforms for the big one SGT specialist in PET packaging for liquids for human consumption is expanding its high volume range with a new preform with a 55mm neck to meet the market demands for water fountains. This 100% PET preform is entirely recyclable. It can be used for five gallon reusable bottles with or without a handle. SGT said that its special geometry and thickness give the preform more advantages than a standard one: an optimised blowforming process and a better distribution of the material, there is no crystallisation and it has a more innovative design. The costs are lower and there is less environmental impact. Robust, transparent and unbreakable, the PET bottles comply with new European legislation as they are certified free of bisphenol A. SGT is preparing its extended range with the 12l format, again in one-way or refill versions. www.sgt-pet.com","@ID":41}, "COMPRESSORS 18 PETplanet insider Vol. 17 No. 05/16 petpla.net consumed energy when running at half of the nominal air flow capacity. This achievement is feasible thanks to the balanced operational torques and absence of vibrations. The Heat Recovery System, where the generated heat during the compression is recycled to provide hot water (above 80°C) for the customers (allowing an extra amount of savings and reducing the CO 2 footprint). The system is said to recover up to 45% of the consumed energy by the compressor. After each compression stage, hot air enters a first phase cooling chamber where it is cooled down to 80-90°C. From the chamber ABC provides hot water to the customer while the air continues to the next cooling phase. Using double circuitsphase in all the compressor coolers not only provides water flow at high temperatures but delivers overall Δt of 6-8ºC for optimum compressor set thermodynamical efficiency. According to ABC, it is the only system on the market adapted to all the compressor inter and after coolers. Group’s multisourcing project in Italy. With the activation of the new Naturae source in Castrocielo, Nestlé Vera adds the third pillar to the virtuous triangle that the brand has outlined in Italy. It already has a source in the North in San Giorgio in Bosco, and one in the South in Santa Rosalia. The marketing plan for the Castrocielo plant, at operating speed, entails the production of approximately 220 million litres in the first year, with clear margins of growth in the following years. San Pellegrino´s Castrocielo plant is said to bring innovation to the mineral water bottling segment, both for the production and distribution model. In line with Nestlé’s commitments to environmental sustainability, the factory will only use green energy from renewable sources such as solar power. It will also incorporate LED lighting and systems for heat recovery and storage. With high pressure blowing air responsible for a large part of the botDirect coupling transmission detail with the gear box in between The compressor is said to achieve outstanding efficiency of 0.135kWh/m3 before considering VSD and hot recovery impact, thanks to the balanced compression ratios among stages, large cooling capacity and low transmission power requirements. According to San Pellegrino objectives, the Horizon-2400 compressor, fitted with additional energy saving devices, is said to achieve energy savings as follows: An average of 12% energy consumption reduction is granted by the adaptation of the Variable Speed Drive, reaching around 60% saving with low blowing air demand. 46% of the 355kW installed power is provided for other plant services in form of hot water at 80-90ºC. Overall, around 75-80% of the energy consumed for producing high pressure air in older traditional installations is saved or recovered for other applications by the new compressor. www.abc-compressors.com A new horizon for Nestlé waters Since its market kick-off many key players worldwide have trusted this new technology, either for new installations or for old machinery replacement. Among the ones who decided to install a Horizon unit in a new green field project are Nestlé Waters and its Italian subsidiary San Pellegrino. With an investment of 16 million Euros, San Pellegrino, Nestlé Waters, has started operation of its new mineral water bottling plant in Castrocielo, Italy. The plant will bottle Nestlé Vera Naturae mineral water, completing the Heat recovery system diagram tling line energy consumption, San Pellegrino trusted ABC Compressors to meet its costs and environment objectives. Starting with a bottle production for 220 million litres, growing in the coming years, the new Horizon-2700 was selected and installed. With a motor installed power of 355kW the compressor set produces a high pressure air flow of 2,440m3/h FAD. Supplied as self-contained package, even the ancillary equipment as electric cabinets, dryer, receiver, arrived installed on skid and interconnected. Being vibration free, due to the perfectly balance torques distribution, the skids are placed directly on the floor, avoiding vibration pads. Horizontal ABC arrangement at Castrocielo","@ID":20}, "MATERIAL / RECYCLING 12 PETplanet insider Vol. 17 No. 05/16 petpla.net PET is now in its 75th year – and still revolutionising the drinks world 75 years and big in business by Gabriele Kosmehl The synthetic material polyethylene terephthalate this year celebrates its 75th birthday. Originally developed as an alternative to the manufacture of textile fibres, the material is today one of the most important in the packaging and textile industries. Since the start of the 1970s, PET has revolutionised the drinks market. According to Krones, today every third drinks packaging in the world is a PET bottle, more than 500,000,000,000 bottles. The year is 1941. In the laboratories of the textile company Calico Printers Association in Accrington, UK, the Englishmen John Rex Whinfield and his assistant James Tennant Dickson produced a polyester from ethylene glycol and terephthalic acid. The material was intended to serve for the production of robust and cheaper textile fibres, as an alternative to Japanese silk and nylon. As the patent came during the Second World War, the invention was initially clothed in secrecy. The British chemical company ICI, asked by the British government to carry out further research, started a trial production of PET fibres in 1949, under the brand name “Terylene“. The production rights for the USA were acquired by DuPont. DuPont later branded the polyester fibres as “Dacron.” Triumph with the bottle format In 1967 Nathaniel Convers Wyeth, who joined DuPont in 1936 as a field engineer, asked himself whether the very popular carbonated soft drinks that came in heavy glass bottles could be stored in plastic bottles. After experimenting at home with a plastic detergent bottle that proved incapable of withstanding the forces of pressurised liquids, he realised that a much stronger material would be required. He initially experimented with polypropylene and transferred his knowledge about stretching polyamide 6.6 to PET. After thousands of attempts he succeeded with PET as the material, using compression-moulded preforms, and obtained the patent in 1973. From then on, PET could be transformed into strong but lightweight bottles. Also in 1973, Bill Gaiser, Founder of Broadway Industries, designed and built the first injection mould to produce a PET preform, and then used it to produce the first injection-moulded PET preform in the world and developed the process even further during the following years. Now that the pre-requisites had been set, Pepsi and Coca-Cola in particular set about conquering the world with the PET bottle. Since the 1960s both companies had been repeatedly trying to put their drinks into plastic bottles. There had been numerous tests with various types of plastic for the first PET bottles, of which only polyester and nitrile proved to have the necessary physical characteristics. Whilst nitrile proved to be unsuitable for contact with foodstuffs because of its toxicological characteristics - a plastic bottle with a high nitrile content launched by Coca-Cola in 1975 had to be withdrawn from the market because of health concerns - PET crystallised during processing and at high temperatures became cloudy. Wyeth’s invention solved these problems and PET bottles came onto the market quickly and in great numbers. Pepsi and Coca-Cola were pioneers in filling CSDs into PET bottles and in 1977 (Pepsi) and 1978 (CocaCola) launched 2 litre bottles onto the market. The PET plastic bottle soon became popular for numerous reasons: it does not break, it is re-sealable; it is lightweight and it is recyclable. One of the very first PET bottles for CSD (photo: Coca Cola)","@ID":14}, "TRADE SHOW PREVIEW 35 PETplanet insider Vol. 17 No. 05/16 petpla.net company manufactures packaging for well-known brands such as Mondelez, Reckitt Benckiser, Johnson & Johnson and others. The UAE production plant, whose key focus is on beauty, healthcare and household, is equipped with 30 machines for mixed applications from EBM, ISBM and IM. PET accounts for 30% of the production, followed by 30% for PP and 40% for HDPE. “Our business in UAE is worth US$14.5 million. Ten more machines are set to follow soon, and then we’ll hit the US$ 25 million mark,” Saraogi says. Chemco has also been making a big effort to conquer the market in Bahrain, where it has investments to the value of around US$20 million since 2014. Ten machines are operating on various applications, of which approximately 20% are PET, with PP and HDPE accounting for 40% each. Chemco exports about 25% of its manufacturing output, with products destined to more than 50 different countries worldwide. A new location for Global expansions is currently under discussion. Globally, 50% of its products are used in the drinks sector; 20% in food; and 30% in the non-food sector. Chemco Group has been showing a 25% growth rate with PET and has forecast global turnover of US$ 71million for 2016. Despite its many activities – or, perhaps, because of them – competition is not considered to be a serious issue. “There is no comparable operator in terms of the full range of products that we deal with,” Saraogi maintains. “In the sub-sectors relating to PET, however, we want to compete with companies and similar global players over the long term, and become more international.” The company also has commitments at the level of social responsibility. It is a founding member of PACE (PET Packaging Association for Clean Environment) and, in collaboration with the public authorities, it supports recycling and has also been working on a project for the installation of water filters throughout India, with a particular focus on rural regions. Part of the company’s profits are donated to Corporate Social Responsibility India, which supports a number of initiatives aimed at improving living standards. “A lot of things are going on here. We believe that, within five-seven years, there will be genuinely possible to able to supply everyone in India with clean water.” Chemco has pencilled in additional forward-looking projects for 2017, including its intention to move into “Chemco House”, an office in Fort, in the southern part of Mumbai, which is home to several well-known drinks manufacturers. In more recent developments, Saraogi adds: “We also believe there to be interesting possibilities in the area of 20l water coolers. The traditional polycarbonate coolers have been banned, which is another huge opportunity for PET.” Chemco as a corporation is destined for tremendous growth and is well set on the path of packaging excellence mirroring India’s entrepreneurial vision for local as well as global influence. www.chemcogroup.com Vaibhav Ram Saraogi (left), Director of Chemco Plastics Industries, with Kay Barton","@ID":37}, "COMPRESSORS 19 PETplanet insider Vol. 17 No. 05/16 petpla.net COMPRESSORS Oil-free piston compressor “Vito” for Italian water brand Motette Coping with pressure Motette’s products, widely distributed at regional and national levels, include the brand labels “Motette”, “Fonte Santa Chiara” and “Altea”. The products are ISO 9001:2008 certified, as well as being recognised by Italy’s Ministry of Health as recommended for preparing infant foods. The water comes in PET bottles ranging from 0.5l to 2l. In a small Italian village inside the Monte Cucco Natural Park, the “Motette” bottling company has been controlling and bottling mineral water since 1970. One of the two company owners Federico Stocchi explains how the investment in a Siad Macchine Impianti “Vito” compressor contributed to the company’s growth path. This new compressor range was specially designed for blow-moulding PET bottles. Assured by their customers’ feedback, Siad Macchine Impianti recently went into mass production. The mineral waters company “Motette” is blessed with water from an area rich in beneficial geological, natural and climatic characteristics, but another key element in maintaining its market positioning is technological innovation. Collaborating successfully with Siad Macchine Impianti since the 1990s, the company relies also on Siad Macchine Impianti ’s new range of the oil-free three-stage compression unit “Vito” when it comes to the blow moulding of its PET bottles. “Motette is always keen to be efficient in terms of innovation and of the quality of its services. By innovation I also frequency of maintenance operations. Before installing “Vito”, we had to programme twice-yearly maintenance services for our compressors, whereas today they’re checked after every 8,000 hours of use; which means roughly once every two years, depending on production.” said Stocchi. The savings achieved by the new compressor were invested in technology and marketing. www.siadmi.com Marco Bassi (left), Siad Macchine Impianti Compressors Division Food & Beverage Key Account / Italian Sales and Federico Stocchi, Owner of Motette srl The “Vito” compressor does not need special foundations. mean energy savings and the use of avant-garde machinery” states Stocchi, explaining their decision to invest in the new “Vito” compressor. He went on: “‘Vito’ compressors also have the advantage of not needing special foundations, not least because they are so finely balanced that vibration is reduced almost to zero.” Cost and energy savings “Thanks to the new compressor, installed in April 2015, our company has reduced its energy costs by 15-20%, and also reduced the","@ID":21}, "CAPPING / CLOSURES 31 PETplanet insider Vol. 17 No. 05/16 petpla.net Quality is Bericap’s top priority. 29/11 that you introduced last year the end of the story? C. Krautkrämer: For the HexaLite, its low weight is surely a decisive factor. But at some point, the consumer can no longer properly use the bottle. The various regions possess various acceptability limits for this, but the fact is that today, ONLY light weight is only one aspect amongst many. A. Büchler: Can you name examples? C. Krautkrämer: Take a look at the Asian market; consumers are highly sensitive towards counterfeit products. There, a closure has to have significantly higher requirements of genuineness i.e. Tamper Evidence, than in other regions. This is as true for the beverage industry as it is for example for the agricultural industry. The farmers want to be sure that the highly priced chemicals do actually contain the chemicals for which they have paid. But we do everything to stay ahead. A. Büchler: Let’s stay in Asia. In China you’re operating two facilities that we’ll visit on the coming Editormobil China Road Show. One near Shanghai, one near Shenzhen. What can we expect there? C. Krautkrämer: Actually, you only need to visit a single facility; both companies are managed by the same management team. Still it’s important in China – as with other countries of the world – that you have local people in the management. In the long term we are thinking of building one facility each for the north and the west, to strengthen the local presence, to be able to get a handle on the high cost of logistics in China, but also to be able to reflect the cultural diversity of China. A. Büchler: In Singapore, you have moved your facility to Malaysia. What were the reasons? C. Krautkrämer: We could no longer expand in Singapore and also, the infrastructure no longer conformed to our expectations. Now we have a facility according our best practice which allows us to fulfil requirements of specific markets which we could not guarantee before. For example the micro biological controlled production for the still water market. So we just went over the border with a new facility. A. Büchler: Your facilities are highly standardised. Worldwide you install the same machines. So far you have always had an impressive piping and supply infrastructure for the injection moulding machines in your facilities; in the new buildings this has now disappeared. Has this infrastructure not proven successful? C. Krautkrämer: Well, the global standardisation gives us the advantage to follow the best practice and same procedures for each product in every company. This enables us to offer the same product to one customer in various countries in the world. Further it provides us back up supplies and support within the team itself. Regarding the infrastructure itself, all new companies which are a green field project these installations are installed in the basement for better operation, cleanliness, micro biological controlled environment etc. A. Büchler: When touring your facilities, the significant portion of allelectric machines also stands out. C. Krautkrämer: We had already experimented with all-electric machines more than 20 years ago. Today, of our 900 injection machines, about half are all-electric. Once the all-electric machines are also commercially available at higher classes of clamping force, we will also try these out. A. Büchler: This brings us to the old discussion; why the focus on injection moulding and why not on also on compression moulding? C. Krautkrämer: Compression moulding is surely justified in many areas; we had nine installed systems ourselves. But about 15 years ago I personally advocated, that we concentrate ourselves on injection moulding. Our tools are suited for this; we have the same hole patterns on our machines worldwide so that all tools can run anywhere; all our staff members are trained for injection moulding, so we would have to put in a huge effort to operate a rotary machine just as efficiently. In the end the product is what counts, we need to supply best quality to our customers. We achieve this through the right combination of products, machines, and tools and a focus on customers A. Büchler: Thank you very much Mr Krautkrämer. www.bericap.com","@ID":33}, "ON SITE 41 PETplanet insider Vol. 17 No. 03/16 petpla.net ONsite Lightweight Containers has opened US keg production line Lightweight Containers has started up a new production line to make KeyKeg Slimlines and UniKegs. The new line is in Joliet, Illinois (USA). The fully automated computer- and robot-driven line can produce the entire Slimline and UniKeg series depending on demand. Logoplaste supports and oversees the line’s daily production. With the new line, Lightweight Containers is preparing for the rapid growth it anticipates in the United States. The new plant was designed in close collaboration with the manufacturing specialist Logoplaste. Logoplaste takes care of organising the line’s daily production. KeyKegs are now produced at three locations: Schwerin (Germany), Den Helder (the Netherlands) and Joliet (USA). A fourth production line in Germany will be opened in mid-2016. UniKegs will be produced in Joliet (USA). Producers and distributors of beer, wine, cider and soft drinks are making the switch to the kegs, which are now in use in over 180 countries. www.unikeg.com The Sample - PreWatcher. Any informat ion you ask for. Geometry & Material Faults Cavity Number Reading Thread Measurement Weight & Color Sealing Surface Injection Gate & Dome W W W . I N T R A V I S . C O M","@ID":43}, "COMPRESSORS 20 PETplanet insider Vol. 17 No. 05/16 petpla.net Piston compressor as “energy source” for bottling not-from-concentrate juice Air for expansion COMPRESSORS The focus was on energy efficiency and sustainable productivity during the planning of a new site for the Gropper group of companies. This site is used exclusively for the manufacture and bottling of high-quality not-from-concentrate fruit juice. The 40 bar compressed air for the PET blow-moulding machines is generated by a highly efficient piston compressor from Gardner Denver, which is optimally integrated into the processes at the new plant in Stockach, Germany. The Gropper group of companies, based in Bissingen, Germany, processed approximately 290 million kilograms of milk (of which 50 million was biomilk) in 2015 in order to create a variety of milk products. Gropper employs around 700 people, buys milk from 870 suppliers and in the last fiscal year they achieved a turnover of approximately 400 million euros. The company is continually expanding and in the last few years they began to manufacture smoothies and not-fromconcentrate fruit juices. And this has been a success: their annual production of these juices has already reached 80 million kilograms. To pave the way for further growth, Gropper opened a completely new plant in Stockach, Germany in autumn 2015. This plant will focus solely on the production of not-fromconcentrate juices, which require refrigerated transport and storage. Multi-stage piston compressors As the new plant was built from scratch, those responsible were able to fully exploit all the potential of modern factory planning – an area in which they have a great deal of expertise. Berthold Burgmeier, Head of Technology: “Basically, we plan and optimise our systems ourselves and efficiency, flexibility and economical energy consumption are extremely important to us.” For this reason, both the procurement costs and the life cycle costs are important when it comes to investments. This also applies in particular to the compressed air generation, which is required for the on-site supply for the PET bottle production. The preforms are blown up with a pressure of up to 40 bar and then filled. Those responsible for planning this system and associated peripheral equipment at Gropper were able to draw on existing experience: four PET blow-moulding machines and bottling lines are already in use in Bissingen. Thus Gropper had no doubt that multi-stage piston compressors would be the most economic way to generate this pressure level. Bottling plant for not-from-concentrate juices at the new plant of the Gropper group of companies in Stockach Type WH 29 3N oil-free piston compression with shaftless 325kW motor, direct drive and maximum volume flow of 1,800m3/h (at 40bar)","@ID":22}, "PETpatents www.verpackungspatente.de 44 PETplanet insider Vol. 17 No. 05/16 petpla.net Foamed screw cap Intern. patent no. WO 2015 / 128303 A1 Applicant: Obrist Closures Switzerland GmbH, Reinach (CH) Date of application: 24.2.2015 To make screw caps lighter, to save materials and costs, a closure consisting of several layers is proposed, whose middle layer is “foamed”. As with the properties of the closure, the inner and outer layers remain unchanged. Guarantee closure Intern. patent no. WO 2014 / 057054 A1 Applicant: Capartis AG, Schaffhausen (CH) Date of application: 10.10.2013 The application describes a container closure with a guarantee strip that was improved with respect to recognising an already completed first opening and which is suitable for “shortened” container necks in terms of applicability. The container neck must be shaped accordingly. Packs with handle Utility model DE 202015103378 U1 Applicant: Krones AG, Neutraubling (DE) Date of application: 26.6.2015 The utility model describes a repackaging for a number of individual packs. These are held together using shrink film and a handle. Dispenser with break element Europ. patent grant no. EP 2749502 B1 Applicant: Colgate-Palmolive Company, New York (US) Date of application: 21.4.2011 In the dispensing opening of a container for a product containing microcapsules, an insert is integrated that destroys the microcapsules upon dispensing of the contents. In this way, the best possible effect of the mixed product is achieved. Container manufacturing Intern. patent no. WO 2015 / 151559 A1 Applicant: Yoshino Kogyosho Co. Ltd., Tokio (JP) Date of application: 23.1.2015 The international application describes the moulding and the procedure for manufacturing a PET bottle with all-round wavy, reinforcing ribs, a reinforcement at the handle area and a bottom with stabilising struts. Closure without thread Intern. patent no. WO 2015 / 150661 A1 Applicant: Sidel Participations, Octeville-sur-Mer (FR) Date of application: 23.3.2015 A membrane is attached to the opening of a plastic container and then additionally fixed by pressing onto a matching counter piece. The container is subsequently tightly sealed. The container is lighter because threading is avoided.","@ID":46}, "COMPRESSORS 22 PETplanet insider Vol. 17 No. 05/16 petpla.net Roof-top cooler The cooling water for the Belliss & Morcom compressor is provided by a system which was also designed by Gardner Denver. A redundant arrangement of two energy saving pumps with just 5.5kW of drive power (with a cooling power of 300kW) is installed on a skid. An energy-saving roof-top cooler takes care of cooling with speedcontrolled fans driven via modern EC motors. These are regulated via the intake temperature and thereby adjust their power to the outside temperature. An automatic summer/winter control adjusts the intake temperature to the current climatic conditions. Heat recovery The optimum integration of the compressor in the temperature-controlled processes is crucial for the efficiency of the compressed air generation. The system in Stockach is said to ensure optimum conditions for this, as the entire plant was planned and built from scratch. Burgmeier explains: “The compression of the air produces waste heat, which we use for other processes.” Therefore, along with the piston machine, Gardner Denver supplied a heat exchanger. The volume flow can be adjusted via a control valve so that the discharge temperature is kept as high as possible, i.e., at approximately 50°C. The key component for heat recovery is a water tank with a capacity of 10m3, which can be used as a source of hot water or, as an energy reservoir via the heat exchanger. Both the cooling circuit and the heat recovery are also controlled via central PLC of the compressed air station. Networking The Belliss & Morcom machine is connected to the general 7 bar plant network at the Stockach plant via a pressure reducer, so that it can also feed into this network in the event of an emergency. The 40 bar network is also redundantly designed: shortly, Gardner Denver will be installing a second piston compressor of the same type together with the second bottling line at the Stockach plant. This will act as a backup system to safeguard the compressed air supply for the PET bottle production, and in the truest sense of the word, also supply sufficient air for future expansion. www.gardnerdenver.com/industrials F.l.t.r.: Robert Kupka and Dirk Tenbrink, Gardner Denver, plus Berthold Burgmeier, Gropper, in front of the new Belliss & Morcom piston compressor WH H3N at Stockach The most efficient version of the W-series, used by Gropper, has a control range of 530 to 1,800m3/h (30 to 100%). Energy-saving roof-top cooler with speed-controlled fans","@ID":24}, "TRADE SHOW PREVIEW 36 PETplanet insider Vol. 17 No. 05/16 petpla.net Interview with Indo-Air Compressors We met: Mr Kuntan Panchal, Joint Managing Director Compressors from Ahmedabad by Kay Barton The global compressor market, even in fast-growing and changing countries such as India, is a secure area of business – particularly in the context of continuously increasing demand from the construction and packaging sectors. We visited Indo-Air Compressors Pvt. Ltd., a company based in Ahmedabad, Gujarat and took a look at the opportunities available to the family-owned business. While it started out as a local supplier it is now constantly developing its national and international activities. Indo-Air is part of a family-owned and managed corporate group that also includes Manilal & Sons, IndoMac Engineers and Shree Chamunda Engineering Works. Its activities include the manufacture of machine parts, technology for plastic injection moulding machines and areas of relevance to plastic. Established in 1977 as a supplier of compressor parts, Indo-Air is now an established supplier to OEMs including Ferromatik, Negri Bossi, KHS, Shyam Plastic, Windsor, Nissei ASB, Sidel and Newamstar. Kuntan Panchal (26), Joint Managing Director and son of one of the company’s founder brothers, met us to answer our questions. “We come from this region; my family originally comes from the farming business,” Panchal replies, when asked about the company’s historic roots. “My father was a technician and designer. He started out designing and preparing compressor parts with a small machine because he saw that the market had a lot of potential. The actual compressor business, with machines that we developed and constructed inhouse, began in 1998. Starting out early with compressor parts production gave us an insight into compressor technology and its manufacturing”. Indo-Air’s current portfolio encompasses high-, medium- and lowpressure compressors for the bottling industry as well as rotary screw compressors and vacuum pumps. Its main market is in the construction industry; customers such as Ammann Apollo have been buying equipment from Indo-Air since 2001, when they were simply known as Apollo and a long time before they were acquired by Ammann, Switzerland. The plastics industry accounts for around one third of its main business; PET applications account for 20-25% of that. These figures could change quickly, however; Panchal believes there is considerable potential in the drinks and Kuntan Panchal sees the growing demand for compressor technology in PET.","@ID":38}]}}
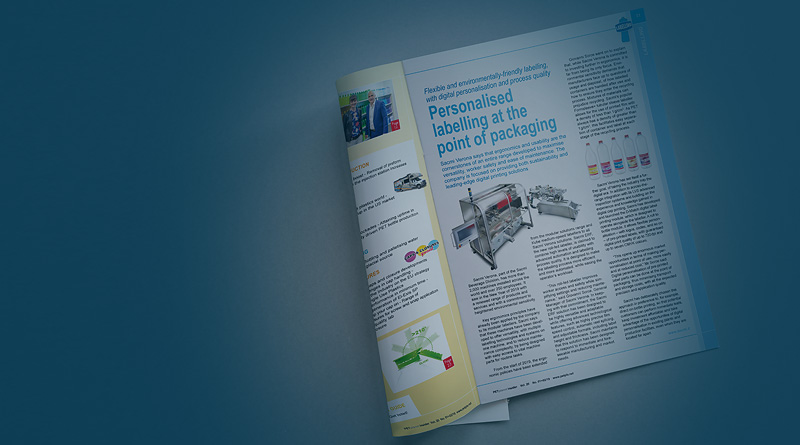