"MATERIAL / RECYCLING 33 PETplanet insider Vol. 17 No. 06/16 petpla.net CHOOSE THE NUMBER ONE. talk to EREMA! We need more performance! ON the WAY to the K careformance! DISCOVER more AT K2016 Hall 9 / Stand C05 too many risks, while another necessitated excessively high temperatures in the decontamination stage. The key criterion for placing the order with Krones was FDA approval, plus the system’s relatively favourable water and energy consumption. Krones was able to offer the PET recycling capability as a complete system, and not just delivering individual parts.” Stage 1: Front end In the facility’s courtyard, the PET bottles from the collection points are delivered in bales. The material is introduced to the front end, which opens them up in a bale-breaker to distribute bottles evenly on the conveyor. The first metal removal is performed using a permanent magnet to remove ferrous metal. The next unit is a ballistic separator, which in two stages removes flat contaminants like foils from the bottles, and lighter ones like dirt, dust and glass, etc. In the de-labeller unit, the containers are now fed between two drums, which mechanically remove labels, which are then separated out and disposed of in skips. A cascade-structured nearinfra-red (NIR) sorting station detects coloured PET bottles and foreign plastics, and ejects them. At the end of this cascade, only transparent and light-blue PET bottles are then passed to the downstream process. As part of a dual checking system, the NIR sorting stage is followed by a manual sorting station. At the grinders, the final station in the front end, the bottles are shredded into small flakes. Now that only a minimised proportion of contaminants remains, the downstream washing module can operate more efficiently. “Thanks to dry removal of labels and dry grinding, the washing process has significantly lower water and energy consumption, in fact the water consumption is running at approximately 2.5l/kg of rPET, In the de-labeller unit, the containers are fed between two drums, which mechanically remove labels, which are then separated out and disposed of in skips. A cascade-structured near-infra-red (NIR) sorting station detects coloured PET bottles and foreign plastics, and ejects them.","@ID":35}, "BOTTLE MAKING 44 PETplanet insider Vol. 17 No. 06/16 petpla.net Preferential heating on Serac Blow Linear (SBL) units Three steps to success Serac’s stretch blow moulding units, dedicated to on-site manufacturing of PET bottles, can now be equipped with a preferential heating module ideal for blowing new bottle designs used on the home care and personal care markets. This solution has already been adopted by the French leader of eco-friendly detergents products. Serac’s SBL technology is proposed as stand-alone machines as well as in single-block blow fills cap equipment, to cover manufacturing needs, from mass production of wide and deep product ranges to niche markets. Preferential heating offering many possibilities Selective heating of PET preforms is necessary to obtain homogeneous material distribution on flat and oval bottles as well as complex shapes. The preferential heating solution proposed by Serac has been designed as a complementary device that can be installed or removed without any tools, in short time. This way, manufacturers can produce round and complex bottles on the same equipment. After a continuous heating in the first oven, preforms enter the second oven where cams operate predefined discontinuous rotations. This way, some surfaces of the preform get hotter than others which results, at the blowing stage, in controlled uneven expansion into the mould. Integrated PET linear stretch blow moulding units Serac’s preferential heating solution benefits from the high-quality SBL linear blowing technology that can stretch lightweight preforms up to their limits with a homogeneous bottle thickness with no risk of neck deformation. Ultimate control of the blowing process is achieved through precise heat profile management and smooth transfer system. Flexibility is ensured through fast and effortless mould changeover, that takes minutes and helps manage wide product ranges with reduced downtimes. Serac Blow Linear serie for various kinds of production needs The SBL serie has been designed to produce bottles up to 5l at output rates up to 18,000bph. SBL machines can be integrated as stand-alone units to existing lines, or supplied as global blow fill cap equipment. Combox single-block blow fill cap units are becoming increasingly popular because of their cost-efficiency and flexibility. They represent a lower investment since they do not require peripheral devices such as silos, orientators and conveyors; they generate savings on maintenance operations with less devices and spare parts and can be driven by a single operator. They offer a higher OEE through a better integration of the different functions and much faster changeovers. With production outputs and price positioning optimised for small to medium-sized production batches, Serac’s SBL units equipped with the preferential heating option enable manufacturers are able to highlight their brand through new bottle designs and develop value-added market segments. www.serac-group.com PET bottles with complex shapes Used for beverages, PET is increasingly preferred on other markets for the benefits it offers in terms of raw material cost, energy-saving process and recycling properties. PET also enables to produce squeezable bottles, a must for highly viscous products such as shampoos, skincare creams or dish soaps. First, it allows many possibilities in terms of design, which is a major advantage for products which require eye-catching packagings that are also easy to hold and use. Second, when used crystal clear transparency reveals the product it contains (colour, texture) and thus allows to have a single bottle for a whole range. Third, the extremely precise neck finish offers perfectly tight closure for low viscous liquids and easy adaptation to different capping systems, the same bottle can be fitted with a spray gun for the first purchase and with a screwed cap for refills.","@ID":46}, "MATERIAL / RECYCLING 32 PETplanet insider Vol. 17 No. 06/16 petpla.net Installation of a complete Krones recycling system at Mpact Recycling South Africa recycles Based on an article by Peter Hartel, Krones AG RECYCLING S P E C I A L Mpact, one of South Africa’s leading paper and packaging producers, and its new division Mpact Polymers started operations in late 2015 with its MetaPure bottle-to-bottle PET recycling system. The plant was designed with a capacity to process almost a quarter of the PET bottles produced by the South African beverage industry into bottle-grade PET. Mpact uses the pellets itself for making its own preforms or sells them to converters or directly to the beverage industry. In Wadeville, about 60km east of Johannesburg, Mpact has inaugurated a new line of business. The MetaPure PET recycling system is the logical continuation of the recycling operations run by this listed South African company. According to Petco, the national Extended Producer Responsibility Organisation for the PET sector, the demand for PET in South Africa is growing by approximately 8% annually. In 2015, the total South African market for PET (virgin and recycled) was approximately 210,000t, close to 70% of which was processed into PET bottles, primarily for use in the beverage industry. More than 74,000t of PET bottles were collected for recycling in 2015, the majority of which were processed into polyester staple fibre, or recycled into bottle- and foodgrade recycled PET resin, thereby fully closing the loop in bottle-grade recycling. With the new Krones recycling system, Mpact can now process 29,000t of used PET bottles into 21,000t of rPET raw material. The choice of location was logical: Gauteng Province, in which the new system is operating, consumes a large majority of PET containers in South Africa. The recycling of PET bottles is, of course, primarily a high-volume business, which is why the collection points are mostly concentrated in towns and large cities. Nonetheless, Mpact is aiming to increase the collection from rural areas with carefully targeted projects. This is particularly important, not least, in the context of the high unemployment rate (25%) in the country, and the poor chances of being hired as a trainee here. John Hunt, Managing Director of Mpact Recycling, explains the reasons for opting for the Krones system: “We talked to operators of recycling systems, converters and beverage producers all over the world and looked at quite a few different models. But one process in our view entailed In the ballistic separator, in two stages flat contaminants like foils from the bottles, and lighter ones like dirt, dust and glass, etc. are removed","@ID":34}, "MARKET SURVEY 29 PETplanet insider Vol. 17 No. 06/16 petpla.net 06/2016 MARKETsurvey Preforms Filling equipment Resins / additives Preform / stretch blow moulds Caps and closures Preform and single stage machinery Bottle-to-bottle recycling plants Compressors Closure systems Two stage SBM machinery Suppliers of caps and closures for PET bottles Our annual market survey on the subject of manufacturers of caps and closures for PET bottles this year clocks up 16 companies, active both locally and globally: Corvaglia Mould AG, Intergulf Ltd, S.B.E.C.M., EKG, Uner Plastik, Bericap, HasPlastik A.S., Euro Plast Belarus, Aptar Food+Beverage, Silgan-Closures, ViCap, Retal Group, Novembal, United Caps Luxembourg, Gulf Packaging and Affaba & Ferrari S.r.l.. The companies are listed in the table in the order in which their details were received by the editors. Although the publisher have made evry effort to ensure that the information in this survey is up to date, no cliams are made regarding comlpeteness or accurancy. Company name United Caps Luxembourg Gulf Packaging System Co Postal address Telephone number Web site address Contact name Function Direct telephone number Fax E-Mail Zone Industrielle de Wiltz, B.P. 49 9501 Wiltz, Luxembourg www.unitedcaps.com Ms Astrid Hoffmann Chief Marketing and Communication Officer +352 95 05 50 +352 95 94 95 [email protected] Post Box 20266 Jeddah 21455, Saudi Arabia +966 12 6360 099 www.3p-gulf.com Mr Mohammed Najmuddin Operation +966 1 2 63600 99 Ext. 111 +966 12 6352 111 [email protected] Product Range One-piece closures for beverages (Yes /No - if yes, please specify material) Yes, HDPE / LDPE Yes, HDPE M80064 Two-piece closures for beverages (with liner) (Yes / No - if yes, please specify material) Only 1p closures Yes, PPBD950MO Applications relevant to PET containers (e.g. CSD, water, juice, beer, etc.) Water, NCS (non-carbonated beverages), CSD, dairy (milk & yoghurt drinks), juices Yes Neck finishes available as standard 28-1810, 28-1881, 30/25, 29/25, 38-2SOT, 38-3SOT 1810, 1881, 30/25, 29/25 Printed caps available (Yes / No) Yes Yes Colour matching service (Yes / No) Yes Yes Child-proof closures (Yes / No) Yes Yes Push-Pull / sports caps (Yes / No) Yes Yes Special comments/special closures (e.g. flipt-tops, drinking spouts, lightest cap for 28mm PCO, 26mm for water etc including non-beverage closures...) 29/25 Prospring (1p sports closure) Special patented closures or marketing features","@ID":31}, "MATERIAL / RECYCLING 37 PETplanet insider Vol. 17 MPR – Multi Purpose Reactor complements existing extrusion systems Gianfranco Zoppas emphasised the low pressure needed and the resulting gentle melt treatment. He spoke about a new era in PET recycling. This achievement enables direct and flexible processing of washed PET flakes to produce preforms. “We look forward to building the prototype in the first quarter 2017 at Sipa to start the test phase,” Christoph Wöss added. There is an interested party for the machine, but for the moment, this is a closely guarded secret. 1.2 million tonnes of PET recycled with Vacurema technology Some 1.2 million tonnes of PET are already recycled every year around the world with Vacurema technology for end products such as preforms for the beverage industry as well as for thermoforming sheet, fibres, strapping, etc. This shows that recyclers and producers can count on flexibility in their production processes to react to fluctuating economic factors. The claim of adaptability applies likewise to the efficient MPR which can be retrofitted to existing extrusion lines. Decontamination, drying, dedusting and crystallisation of different PET input materials are carried out in a single step. As a result, the washed PET material is already food contact compliant prior to extrusion. Vacurema technology offers a very high degree of flexibility in PET recycling which is enhanced even further through the successful collaboration between Erema and Sipa. www.erema.at www.sipa.it","@ID":39}, "PETcontents 06/16 4 PETplanet insider Vol. 17 No. 06/16 petpla.net INSIDE TRACK 3 Editorial 4 Contents 6 News 48 Products 50 PET bottles for Home + Personal Care 51 PET bottles for Beverage + Liquid Food 52 Patents CHINA EDITOUR 10 Red giant on the road to normality The Editourmobil goes to China 12 Compression moulding as the biggest competition 12 A man of many talents MATERIAL / RECYCLING 14 PET: The bottle and beyond 17 Revaluation to recycled PET Aesthetics and performance through Advanced Additives 18 Suitable storage solutions UV light exposure negatively impacts next generation PET bottles 20 Finding the optimal process Efficient chemicals and technologies for PET recycling 22 PET strapping Narrow straps for secure transport 24 Successful premiere of PET briquettes 26 A valuable raw material PET fines from recycled bottles 32 South Africa recycles Installation of a complete Krones recycling system at Mpact Recycling 35 Drink up and help the community GM recycles water bottles into engine components, air filters and sleeping bags 36 PET flakes for food contact compliant inline preforms in one processing step RECYCLING S P E C I A L MARKET SURVEY 29 Suppliers of caps and closures PREFORM PRODUCTION 38 Creating new markets for PET Novapet’s 5th edition of “Chips & Grapes” PET in the vineyards conference 41 “This is only the first phase” Retal opens plant in Luxembourg INSPECTION 42 Exact colour match Early preform quality inspection avoids waste BOTTLE MAKING 44 Three steps to success Preferential heating on Serac Blow Linear (SBL) units CAPPING/CLOSURES 45 Change of orientation and strategy From machine builders to part & solution experts BUYER’S GUIDE 53 Get listed! Page 42 Page 14 Page 44 The China Road Show","@ID":6}, "PETnews 6 PETplanet insider Vol. 17 No. 06/16 petpla.net PET recycling plant for MEG The soft-drinks producer Mitteldeutsche Erfrischungsgetränke GmbH & Co. KG (MEG) is part of the Schwarz Group that also owns the Lidl and Kaufland supermarket chains. The company is Germany’s second-largest beverage producer, with domestic sales of more than 25 million hectolitres, and also exports its wares throughout Europe. Since 2010, MEG has taken back the deposit-bearing, non-returnable bottles from the DPG system (German deposit system). MEG now uses PET bottles which are processed into regranulate at its own recycling plant and at various contract recycling companies. To increase regranulate quantities still further, MEG is building another recycling plant near Aachen, Germany. As part of this project, Krones AG was awarded the order for the installation of a module that grinds bottles into flakes, and a washing module. MEG also appointed Krones as the vendor responsible for the interfaces to the upstream and downstream process stages. www.krones.com Uptrend for South African PET recycling Plastics SA – the umbrella organisation representing the local plastics industry – has been measuring the recycling rate of plastics in South Africa. According to their latest survey, the recycling of PET has seen a strong and steady growth over recent years. While 30,690t of PET was recycled in 2011, last year, 2015, saw a recycling rate of 53,493t of PET. The recycling rate of other plastics such as PP, PE-HD or PVC has, however, shown a slight decrease. Plastics SA Director Anton Hanekom cites historically low oil prices which led to lower polymer prices. This in turn had a direct impact on the price of recycled material which resulted in minimal growth and a slowdown in the amount of plastics which could be diverted from landfill, says Hanekom. According to the latest Plastics SA figures, the lack of a consistent incoming stream of recyclables was the single biggest challenge plastics recyclers had to face during 2015. A large quantity of the materials that were made available for recycling, was recovered by waste pickers off landfill sites where they were contaminated and therefore of poor quality. According to Hanekom, there is the need for an effective separation-atsource infrastructure to be implemented throughout the country. www.plasticsinfo.co.za Change in management at Corvaglia Closures Mexico Bernardo Osés, Managing Director of Corvaglia Closures S.A. de C.V. (in Ixtlahuaca, Mexico), and Francisco González, Consultant, have left the company with effect from 1 June 2016. The Board of Directors and management expressed their regret at these departures, and would like to thank Mr Osés and Mr González for their many years of dedication to the company and wish them every success for the future, both privately and professionally. José Salame has been named new Managing Director of Corvaglia Closures S.A. de C.V. Salame boasts an exemplary service record and has many years of experience as a decision maker in the beverage-packaging industry in Mexico. www.corvaglia.ch PET recycling established in Europe - but with room for expansion PET accounts for almost 7% of total plastics consumption per year in Europe or about 3.1 million tonnes. Overall, the 30 countries of Europe achieve an average collection rate of 57%. In 2014, for example, 1.75 million tonnes of post-consumer PET wastes were collected. The collection rates vary greatly. While Germany, Italy and Switzerland collect about half of the total volume, some countries achieve a collection rate of only 10 to 20%. The PET sector is enjoying rising collection rates overall, which, according to PCI PET Packaging, Resins & Recycling Ltd., should increase by a further 3 to 5%/a by 2019. It is almost exclusively bottles that are collected, usually in dedicated collection schemes. Although it was originally the goal to return the collected bottle flakes to bottle production, the industry has sought and found customers in other areas. For film/sheet manufacturers, post-consumer bottle flakes have become increasingly interesting, and in 2014 they used the biggest share – 34% – of the collected residuals in their branch of industry. Almost 30% of the flakes were used in blow moulding applications, 26% in the fibre industry and the rest for packing straps and other products. www.k-online.com Husky and MHT settle long-standing dispute After many months of ongoing discussions, Husky Injection Molding Systems and MHT Mold & Hotrunner Technology announced that they have come to a joint agreement to settle all pending disputes regarding issues concerning trade secrets. After many years of litigation, Husky and MHT have decided to amicably resolve any differences relating to this dispute. The terms of the settlement are confidential and both Husky and MHT look forward to closing this chapter to continue focusing on their respective businesses. www.husky.co www.mht-ag.com José Salame","@ID":8}, "CHINA EDITOUR 11 PETplanet insider Vol. 17 No. 06/16 petpla.net Thus the Chinese beverage market can only grow organically as living standards improve. The potential is huge. Looking at the official economic forecasts, growth in the future is likely to be of the order of 5%, a third of the figure for previous years. The bottlers however relied on the usual 15% growth of the economy, and now find themselves with significant overcapacity, which will decrease only slowly over the next few years. For the Chinese bottler growth is now only possible through intense competition rather than by exploiting the potential of new regions. The result is a dynamic market, as is to be found everywhere else in the world. A bit of normality. Particularly hard hit in this context are the manufacturers of bottling machinery. In China at present the market is all but dead. Sales of machinery from all manufacturers can be counted on the fingers of two hands. The market is still in its infancy, so the replacement machine business is not mature enough to be able to deal with the brutal realities of the current situation. In the preform and cap area, the situation is somewhat different. While the multinational OEMs continue with their classic strategy, buying preforms and caps, local brands are producing their own packaging themselves, i.e. preforms, closures, labels etc. Here the machine manufacturers are now trying to win round the group of in-house producers and converters. To bottlers without their own packaging facilities they are proposing their own production, while on the other hand they are building converters, with the idea that the multinationals will buy, and the local bottlers will then follow suit. There is a lot of talk about this or that machinery, but market demand is not actually rising. The mould makers have come out best from the situation. Cut-throat competition amongst the bottlers calls for new designs, new caps. New moulds are therefore constantly required. A good example in this context is the light weighting in Coca Cola. In 1996, the 0.5l bottle came on the market, weighing in at 32g, in 2014 a landmark was achieved with 25.5g. For consumers this was just too thin, so Coca Cola increased the weight to today’s 28g. All the other market participants followed suit. Even the least expensive bottle today weighs in at 22g, a significant weight. China is not a lightweight country. A familiar problem in China is the copying of drinks. We have seen a number of interesting solutions to tackle the issue. On premium brand Red Bull, every packaging has its own QR code, and in addition the packaging is also marked with UV ink. Converters today supply caps with the individual QR code imprinted on the lid. The big trend at the moment is overcapping. A huge overcap is placed over the 28mm cap, giving it a classy appearance. The bottlers are currently displaying sports caps on their desks. Could this be the trend in the next few years? ","@ID":13}, "CAPPING / CLOSURES 45 PETplanet insider Vol. 17 No. 06/16 petpla.net From machine builders to part & solution experts Change of orientation and strategy by Alexander Büchler Michael Feltes, Vice President Business Unit Packaging at Engel Austria GmbH To successfully sell injection moulding machines for volume production of closures and caps on the market, it requires more than just a good machine. The head of the BU packaging at Engel, Michael Feltes, calls it parts expertise, which is needed in order to precisely meet customer requirements such as reliable quality, output, performance and energy efficiency. Feltes: Sometimes customers tell us what they want, not what they need. We have to listen very carefully to them to ensure we fully understand their requirements. In the past, customers came and bought a machine with such and such options and special features. Today, they want a good cap – the machine technology is just something that goes on in the background for them – and: it is a must-work expectation. Our job is to put together the right package and solution based on their specific application. PETplanet: Does this mean that it doesn’t matter to the customer whether they buy a hydraulic or allelectric machine? Feltes: If the performance data is the same, then they prefer nowadays the all-electric solution. Beverage closures aren’t low-cost parts anymore; they are no-cost parts. They have to be produced with an extremely high repeatability and accuracy, so that they will run problem-free subsequently at the bottling process. And here I see all-electric machines having a distinct advantage over hydraulic or hybride systems. All-electric machines can run the required process parameters with a very high repeatability, resulting in a considerably smaller tolerance range on the part. We therefore choose all-electric rather than hydraulic or hybride for the caps, even at 420t clamp tonnages and screw diameters of 70-80mm. We have also hybride variants of similar clamp tonnages in our machine portfolio available, but these are mainly used for other packaging solutions such as larger thin wall containers with extreme L/D ratios. PETplanet: But this is also true, in principle, for every all-electric machine type, even those of your competitors? Feltes: Not all competitors are offering all-electric machines up to 420t for caps production, but yes, in theory this applies to every all-electric type. You have to focus on the key aspects of performance, precision and energy efficiency in every single detail in the equipment, its components and its interfaces. PETplanet: How does it stand with the other classical arguments like speed and energy savings for the allelectric type? Feltes: Energy saving is clearly the big advantage for the all-electric machine type. We really do not need to argue any words on this today, it’s a given standard request from the market. But as for the speeds, especially injection and clamp movements, you have to delve a little deeper into the technology for that. The electrical and hydraulic type machines are becoming very similar in performance, which defines in the production environment the overall cycle time. However, more important than speed is acceleration. The difference with a hydraulic drive is the acceleration curve. Especially in cycle-times below 3s, the reaction time of a hydraulic system (hoses, valves, pumps, accumulators) is loosing ground. When you set a defined starting point to accelerate, the system will require a fraction of a second to start the steep acceleration curve with the accumulator pressure, but then accelerates extremely fast. This fraction of a second can increase ultra short cycles up to 5-10%. With a high performance servo-electric motor, the torque and acceleration results in a uniformly high pressure and speed throughout the whole injection time. This is specifically important on short screw strokes of 0,7 x D. PETplanet: With your 420t allelectric e-cap, you’re offering the biggest all-electric machine on the market. Your competitors on the market are at 280t.","@ID":47}, "MATERIAL / RECYCLING 22 PETplanet insider Vol. 17 No. 06/16 petpla.net Narrow straps for secure transport PET strapping Based on an article by Thomas Schwachulla, freelance journalist For end users they will probably just be consumables for packages; packaging experts however like them for their mechanical advantages and easy handling: PET straps. a stamping unit to an oven where the stressed material is relaxed. This is followed by a cooling station, the printing unit for individual labelling and the winders for packaging. The extrusion lines including the upstream and downstream peripheral equipment are almost completely redundant. This has the advantage that in case of failure of one of the plant components, e.g. a mixer, the switch to another mixer can be effected without stopping the extrusion line. A throughput of the extrusion lines of 450 to 600kg/h provides an idea of the required level of machine performance. PET is a difficult material At the start of its career as a strapping material, polyester was still considered an engineering plastic and therefore was expensive. It was not until the beginning of the 90s when PET beverage bottles conquered the European market that PET became a mass plastic. “The disposers and recyclers suddenly provided us with enough recycling material to be able to counter the high cost of virgin material,” recalls Bernd Causemann. “In those days we mostly used regranulate because the flakes usually were too much contaminated. In the mid-90s we then succeeded to use bottle regranulate for polyester strap production,” reports Causemann. Today, Cyklop hardly processes virgin material any more, but primarily regranulate and regrind (flakes) from DSD material, which comes washed from the recyclers. Virgin material is used only if transparent or white straps or special designs are ordered. PET belongs to the sensitive, highly hygroscopic polymers; it is very susceptible to hydrolysis and hence degrades under heat. This property is detrimental to the strength of the straps. The influence of humidity or the quality of PET can be assessed on the basis of IV value which is indicative of the mean molecular weight. “Regranulation of PET triggers some sort of “downcycling”, i.e. melt viscosity decreases due to the repeated thermal load. In the case of flakes, the bottles become thinner every time, leading to even more rapid degradation of the material. In 2004, we had IV values of 0.75-0.76dl/g for the flakes, today we are down to 0.690.70dl/g”, summarises Causemann. In other words a conflict of interest: Bottle manufacturers want to produce thin bottles and therefore need low IV values. Cyklop, on the other hand, needs high IV values for stretching. According to Causemann, the ideal IV value is 0.83-0.87dl/g. The material is stored in twinchamber silos from Zeppelin, nine for regranulate and three for regrind. Inside the silos, the chambers are separated by a centre cone and each chamber accommodates the load of one lorry. Batch separation has a practical background: All incoming material is subjected to an in-house IV test which lasts approximately 70-80min – no unloading permitted until after this test. If problems should still arise in spite of the test, the material can be removed from the chamber before it has mixed with the good material. Vacuum conveying is used to transport the material from the silos to the crystallisers. Before PET is processed, it must be dried at temperatures of 160-170°C to a residual moisture of approx. 0.2%. However, at about 80°C, the material reaches a glass transition range where the molecular structure changes from amorphous to partly crystalline. In this transition phase, the material becomes sticky and tends to clump together. For this reason, PET is first crystallised at 150-160°C, keeping it in constant motion to prevent clumping. After crystallisation – separately for the granules and flakes – the pre-dried material must be left to dry to its processing moisture level for a further five to six hours at a dry-air temperature of 160-170°C before it can be conveyed to the extrusion lines. The era of PET straps actually started in 1979 when the European company Cyklop GmbH in Cologne was the first to take up the issue and made it a success together with the Dutch raw materials manufacturer Akzo. Since then, Cyklop has been manufacturing over 60,000,000km of polyester straps which is equivalent to 1,500 times the circumference of the earth. The success of the polyester straps is based on their numerous advantages over steel straps. PET may not have the tensile strength of steel, but this is not what really matters in load securement. Much more important is the so-called shock reserve when sudden impact is to be absorbed. In addition, elasticity – up to 14% with Cyklop straps, depending on design is crucial to compensate for loss of tension in the case of shrinking packages. By contrast, steel straps only have an elasticity of 1%. What is more, PET does not corrode, the risk of injury is much lower, it can be used for sensitive packages, and it is much lighter than steel. Compared to PP strapping, the glass transition temperature of PET (60-70°C) has the advantage that the packages are held together firmly even under heat. Producing straps only appears to be easy In Cyklop´s Cologne factory, the extrusion lines plus downstream peripherals manufacture about 50 different PET straps with tensile strengths of between 2.000 and 13.000N depending on cross-section. The extrusion lines run with up to ten single strands of a length of 90-100m each, including upstream and downstream peripherals. After the straps have left the nozzle head, they are passed through a water bath to cool down and subsequently are stretched twice. Then they run through RECYCLING S P E C I A L","@ID":24}, "MATERIAL / RECYCLING 25 PETplanet insider Vol. 17 No. 06/16 petpla.net MATERIAL / RECYCLING 25 Uwe Lauf, operation manager Repasack www.bericap.com Unique range of light weight screw and sports closures for light weight PET neck standards for water • Closures for all common neck sizes 26/22, 28mm (PCO 1810, PCO 1881), 29/25, 30/25 • Light weight Hexalite range allowing light weight neck • Still water closures suitable for N 2 dosing • Sports closures fulfill BSDA requirements • Boreseal systems for excellent tightness • Consumer friendly opening forces BERICAP Technology for still water The counting centre in Oberhausen is one of the largest of its kind with 55 million containers per year (2014). In November 2014 in the former fertilizer warehouse, a milestone was reached of a total output of 500 million containers. The operator, Repasack, is a subsidiary of Interseroh, an environmental services provider active throughout Europe with one hundred sites. Repasack in Oberhausen has been counting packaging with deposits since 2006. Four presses stand in the hall; one of them was showing clear signs of ageing in 2014. The manufacturer ruled out of the possibility of repair and recommended buying a new model. During the search for alternatives, the recycling experts struck gold at HSM. The HSM BRP 4810, according to Lauf, gave a “completely different impression” at first sight and seemed “considerably more robust”. And then the testing started: the recycling experts went to Lake Constance with three hundred sacks of recycling material and tested the HSM machine. While whole bottles would crop up in briquettes made by machines from other manufacturers, HSM’s first test run went well, reported Uwe Lauf. But he agreed with HSM that the machine would have to be modified for the new press material. During a six month on-site trial at Oberhausen, the operators and the manufacturers optimised the press together. As a result of this, thicker plates were inserted, the gap dimensions were reduced and the software was enhanced. The operators and the manufacturers gave feedback throughout, HSM tailored the machine to their requirements for PET briquetting. Uwe Lauf: “It was a real win-win situation.” A further advantage of the HSM machine for the officials at Repasack is its ease of maintenance. The third stage of compression, the main stage of pressing, and therefore the part during which the most wear and tear occurs, is completely replaceable. This third stage, according to Uwe Lauf, also distinguishes the HSM machine from the products of other manufacturers, which operate in two stages. The results of HSM’s extra power: the machine spits out PET briquettes with a density of up to 400kg/m³ and tin can briquettes of up to 760kg/m³. The summary from Oberhausen: after six months of operations Uwe Lauf said that the investment had already paid off. There has been no record of wear and tear yet and no breakdown of the press. There was one case of a broken pressure switch and a cable was faulty, and then it became clear that the manufacturer’s after-salesservice at Lake Constance was also very good: “If you call them at midday, someone is here the next day at the latest” says the operations manager. He is pleased that, in future, HSM technicians will probably not need to come to Oberhausen, since he wants to make use of remote maintenance. Then he and his co-workers could even attach a webcam to the machine and show the manufacturer the problem. That is, if there are any. www.hsm.us www.interseroh.de","@ID":27}, "MATERIAL / RECYCLING 24 PETplanet insider Vol. 17 No. 06/16 petpla.net Successful premiere of PET briquettes based on an article of by Harry Weiland, freelance journalist RECYCLING S P E C I A L At the large counting centre for disposable packaging made from PET, aluminium and tin there was a positive summary regarding the first new HSM briquetting press. Despite some difficulties that had had to be overcome along the way. After the HSM BRP 4810 had been set up for testing in the counting centre in Oberhausen, Germany, the employees would only have used the new machine, although the old one could have been used in parallel, reported Uwe Lauf, the operations manager in the Repasack counting centre in Oberhausen. The new press works twice as fast as its predecessor and it compresses with much more power. “This machine works very well and very reliably”, concludes the operations manager after nine months, taking stock of the performance of the HSM press for PET bottles and cans for the first time. The new machine in Oberhausen also gave the employees a few surprises: the very first roll-off container, filled with briquettes from the new HSM machine, was too heavy. The successful outcome of the machine’s premiere in Oberhausen was by no means guaranteed: when, in September 2014, the briquetting press was set up in the counting centre in the Ruhr, this was the first time this type of machine had been used for the difficult task of pressing disposable packaging. HSM has a long history of manufacturing channel baling presses for the recycling industry, but for the disposal and compression of PET and tin needed by Repasack, baling is out of the question. So HSM developed the first briquetting press for heavyduty work in a counting house in close cooperation with the recycling experts from Repasack in Oberhausen. The advantage of briquettes: they are small and heavy and therefore fill transporters to their optimum load capacity. And they do not need strapping materials such as wire. The demand for a press for the drinks industry is therefore high: PET is a very abrasive substance, which can wear machines down badly. Thicker, premium quality types of sheet metal and steel are therefore a must-have - which is why the developers were delighted that HSM installs particularly wear-resistant steels as standard. PET can, moreover, be rather stubborn: an additional guide plate must be installed, because PET bottles manage to force themselves again and again between the plates and then pop up in places where they don’t belong. This must not happen, because pressing bottles and cans properly is practically a legal obligation for the machine, since disposable packaging is only regarded as disposed when it has been properly destroyed. A quality criterion, for which the counting centre must be certified once a year by the German Deposit Association. Unique threefold compression produces a PET briquette density of up to 400kg/m³","@ID":26}, "MATERIAL / RECYCLING 18 PETplanet insider Vol. 17 No. 06/16 petpla.net UV light exposure negatively impacts next generation PET bottles Suitable storage solutions A research study conducted by Plastic Technologies, Inc. (PTI) has found that exposing post-consumer bottles to ultraviolet (UV) light prior to recycling has a severe impact on the physical properties and visual attributes of next generation, recycled PET (rPET) bottles. However, the degree of yellowness can be decreased by using suitable storage conditions. Intrinsic viscosity, yellowing, haze are just some of the attributes that provide challenges when using rPET along with virgin material. rPET producers have engineered elaborate processes to minimise those characteristics in order to create material that provides the desired environmental attributes along with key visual and processing properties. One of the problems that limits the amount of recycled PET (rPET) used in rigid packaging applications is the degree of yellowness that it can cause. The more rPET that is added to virgin PET during bottle manufacture, the more yellow the resulting bottle tends to become. The source of the rPET used has a great influence on yellowing. Deposit-grade materials are in the greatest demand as they result in less yellowing than curbsidegrade material. Even virgin PET will discolour and yellow with each additional melting cycle. But there are many other causes that contribute to this problem. For example, it is known that low levels of nylon coming from multilayer bottles can remain trapped in the PET flake after washing and cleaning. This residual nylon will cause considerable yellowing when the rPET is extruded. But one cause of yellowing that has not been widely addressed is the effect that UV radiation from the sun, as well as that emitted by artificial sources, such as fluorescent lighting, can have on PET. PET is sensitive to UV light especially at elevated temperatures, under high humidity, and in the presence of oxygen - all of which are present when PET bottles are exposed to the weather. Free radicals form within the plastic that cause subsequent degradation. The degradation effects seen are also compounded by the presence of oxygen in the air. The free radicals created by the UV radiation react with this oxygen to form hydroperoxides that can result in polymer chain breakage. Thus the end result in many plastics, including PET exposed to an outdoor sunny environment, is that they will discolour, embrittle and crack over time. While antioxidant and UV absorbers can be added to the plastic to help stabilise and prolong the material’s useful life, PET bottles normally do not contain significant amounts of these additives. The Association of Postconsumer Plastic Recyclers (APR) notes in their model bale specification for PET bottles, that bales should not be stored outdoors uncovered for a period exceeding two weeks to prevent UV degradation. There have been many papers published that describe the degradation effects that UV light has on PET. But these papers have primarily focused on the degradation seen on the actual PET article being studied and not what happens to the properties of PET when it is recycled. While PET bottles and their contents do not experience significant exposure to sunlight, bottles under storage after manufacture as well as product-filled bottles sitting on a store shelf can be exposed to artificial light sources that can also emit low levels of ultraviolet light. But the most probable time that PET bottles might see significant exposure to the elements occurs when bales of PET bottles are stored outside while waiting to be brought into a reclamation facility to be ground into flakes, washed and re-pelletised for sale back into the industry. The study This study was undertaken to understand the effects weathering would have on PET bottles exposed to Toledo, Ohio weather for one year. 2l PET bottles produced using a commercial grade of PET were used for this study, not densely packed into large bales. The resin did not contain any ultraviolet absorbing additives. These virgin bottles were crushed, stacked five to six deep, and placed in uncovered open sided crates to afford maximum exposure to the elements. Sunlight could easily penetrate through the several layers of bottle sidewalls, even reaching the bottles located at the bottom of the open crate. These crates of bottles were then placed on the roof of Plastic Technologies, Inc. building in early January. Every three months, the bottles in the crates were agitated so that those on the bottom had a chance over time to move to the top or outside edges. Another set of bottles was stored indoors approximately 18-inches under a fluorescent light source. This light source was left on continuously, exposing the bottles for two months. A third set of bottles was stored and protected from light exposure for one year for use as a control. Periodically bottles were taken off the roof to study the effects of sunlight and weathering over the course of 12 months. Each aged set of bottles was ground into flake. The flake was then aggressively washed to remove accumulated surface dirt at 88°C for 15 minutes. Following the hot caustic wash, the flake was rinsed twice with fresh water, dried to less than 50ppm moisture and injection moulded into 3mm thick plaques. PET bottle bale RECYCLING S P E C I A L","@ID":20}, "MATERIAL / RECYCLING 35 PETplanet insider Vol. 17 No. 06/16 petpla.net RECYCLING S P E C I A L GM recycles water bottles into engine components, air filters and sleeping bags Drink up and help the community General Motors is giving its employees’ recycled water bottles a new life: noise-reducing fabric insulation that covers the Chevrolet Equinox engine. The bottles – collected from five of its Michigan facilities – are also being turned into air filtration components and insulation in coats for the homeless community. Recycling collaboration network Each partner engaged in this initiative brings specific capabilities. Hamtramck Recycling bales the plastic bottles collected from GM’s world headquarters at the Renaissance Center, Warren Technical Center and Orion Assembly, Flint Tool and Die and Flint Engine plants. Clean Tech Inc. washes the bottles and converts them to flake. Unifi, Inc. recycles the bottle flake into resin. Palmetto Synthetics processes the resin to create fibres and William T. Burnett & Co. processes the fibres into various forms of fleece, serving all three applications. Rogers Foam Corp. die cuts the fleece and Exo-s attaches it into the nylon cover for the Chevrolet Equinox V6 engine. Filtration Services Group works with New Life Center, a nonprofit jobs development and training mission in Flint, to make the panels for the air filtration fleece, which is then sent to 10 GM facilities. The coat insulation is sent to Carhartt, a workwear company established in Detroit in 1889, who cuts it to size for The Empowerment Plan. GM also is working with various organisations such as Schupan The empty water bottles collected at five locations of the facilities of General Motors are funnelled into the “Do Your Part” project, where 11 businesses collaborate to give the PET bottles a second life. After processing, the recycled PET is used for the manufacture of the Chevrolet Equinox V6 engine cover, a part which helps dampen engine noise to deliver a quiet ride. In addition, the recycled bottles are used for air filtration components which are used in GM facilities to protect air quality and insulation material that goes into coats that transform into sleeping bags. “Recycling is good, but viewing waste as a valuable resource that can be plugged into your operations or products is even better,” said John Bradburn, GM global manager of waste reduction. “It’s about rethinking the process and finding more sustainable ways to manufacture products and contribute to our communities.” GM pursued this project after analysing that sourcing recycled material costs the same as new material while saving energy and reducing waste. Also, the project helps to support local companies which are part of the recycle network. These bottles, emptied by GM employees, take on a new life as noise-reducing fabric insulations, air filtration components or coats insulation fabric for the homeless community. GM Global Manager of Waste Reduction John Bradburn demonstrates the Chevrolet Equinox engine insulation made from used water bottles from several GM facilities. Recycling in Flint to collect additional water bottles to plug into the project. Meanwhile, GM has 131 landfillfree facilities around the world and recycles the equivalent of 38 million garbage bags of byproducts each year. www.gm.com www.stf-group.de ENGINEERING WITH THE COMPETENCE OF THE RECYCLER •Complete Plastic Sorting and Washing Lines engineered by Europe’s largest PET Recycler •Bottle-to-Bottle rPET Recycling •More than 60 PET Recycling Lines installed worldwide","@ID":37}, "PREFORM PRODUCTION 38 PETplanet insider Vol. 17 No. 06/16 petpla.net Novapet’s 5th edition of “Chips & Grapes” PET in the vineyards Conference Creating new markets for PET by Gabriele Kosmehl Every two years the Spanish producer of PET, preforms und bottles Novapet opens the doors to its Chips and Grapes Conference, which established itself as an important venue for the European PET industry. This year’s fifth edition, however, unlike its predecessors, did not take place during the grape harvest in the wine region around Barbastro, but in April – for a good reason, since the launch of Novapet’s newly expanded injection plant was the centrepiece of the meeting. When Novapet entered the PET business about 20 years ago, there were hardly any customers in the beverage bottling industry who were interested in buying PET granules. Instead, the bottling companies demanded finished bottles which only had to be filled. But the market developed and demand for preforms among the bottling companies rose and rose, and, with increasing expertise among Novapet’s customers, so did demand for PET granules. “Now it is kind of a way back,” explains David González, Managing Director of Novapet when talking to PETplanet. “The market has changed again; the injection activity became more complicated. Years ago, a customer would produce a single bottle type without modifying or changing the mould during the whole process. Now the very same customer has to have a variety of bottles at hand, so he is outsourcing the injection activity.” Novapet recognised the need to provide the beverages market with the entire spectrum of the services associated with the material, preforms und bottles. “Our business is arranged in three divisions. We have our Polymers division through which we produce and distribute a wide range of specialised resins,” explains González. “The second division is Packaging, focused on preforms and bottles. The third division is specialised in Light barrier applications for the dairy market.” In order to offer its customers the full range of injection services, the plant in Barbastro was refitted in record time: in just five weeks, the injection plant was modified so that it can now be operated with a maximum of twelve injection moulding machines instead of the previous seven. The machine park was expanded by five new PET-line 96CV moulds machines from Netstal, complementing the existing Husky and Netstal injection moulding machinery. As Juan Antonio Cejalvo, Industrial Manager Novapet, explained in his speech at the meeting, the expansion was also accompanied by investments in quality assurance procedures as well as the installation of online preform control units in all IMM, the incorporation of a new artificial vision quality inspection unit for automatic preform control – with simultaneous reduction of CO 2 emissions by 50 % across the entire system. “The implementation of this project has had the difficulty that all new units had to be fitted within the original plant, which posed an engineering challenge.” explained Cejalvo. Trends on the PET market With this investment project and the positioning in the sectors raw materials, preform/bottle and light The conference participants of this year’s Chips & Grapes Conference","@ID":40}, "Hong Kong Chongqing Xi'an Taiyuan Shenyang Qingdao Nanjing Guangzhou Shanghai Beijing Jinan CHINA EDITOUR 10 PETplanet insider Vol. 17 No. 06/16 petpla.net SPONSORS The Editourmobil goes to China Red giant on the road to normality by Alexander Büchler grinds to a halt. The reason for this is complex. It is not simply a question of China’s moderate growth rate, the principal reason is probably down to the fact that the beverage industry is now serving all regions and therefore the market has become to a certain extent saturated. With a population of around 1.4 billion, China is clearly a huge market for beverages. People drink a lot of tea, which they brew themselves. At motorway services you would normally expect to find a cigarette machine, whereas in China a jug of 95°C hot water is made available free of charge for the tea drinker. Despite this, a healthy market for packaged beverages has rapidly developed. It is estimated to amount to some 116 billion litres. Ignoring beer and other alcoholic beverages this equates to a per capita consumption of 82l. Of this 33% is in water (28l), 22% in CSD (18l), 15% in juices (12l) and 10% in ready to drink tea (8l) (source: data from machine builders and our own research). In 2015 a total of 118 billion preforms were produced in China. Measured on an international scale, there is still considerable scope for significant per capita usage. Depending on who you speak to, average annual per capita consumption of bottled water is 65 bottles, i.e. an average of 0.43l (Mr Yin Zhipin, JiangSu Shen Qian Food Packaging) or 0.8l/PET bottle amounting to 35 bottles per capita (Mr George Wan, MHT). The truth probably lies somewhere between these two figures. The key point now is that in the last year (2015) the usual increase did not occur. On the contrary, the CSD sector declined and in the water sector there was a shift from cheap to premium. The minor reason for this may have been the chilly weather in 2015 but more likely is the fact that bottlers have been installing their filling lines in the westernmost tip of China, meaning that there are now no more blank spaces on the map. For years Western companies delivered machinery, equipment and moulds for the beverage industry to China, enjoying annual two-digit growth rates. Then suddenly it all The China Road Show","@ID":12}, "PETproducts 48 PETplanet insider Vol. 17 No. 06/16 petpla.net PETproducts Bericap’s light weight closure The last few years have seen a significant drive for reductions in the cost of packaging for all beverages alongside with an improvement in the carbon footprint of the package. But consumer convenience became more important, too. Reducing packaging weight and costs is important for bottlers selling their products either to discount markets or in countries with low purchase power. Responding to these market requirements Bericap developed an ultralight weight closure for the 29/25 PET neck finish (HexaLite 29/11 SFB UL 3T). Weight saving compared to former 30/25 neck/ closure combination reaches almost 38%. That lightweight closure variant has been introduced now successfully in Turkey and Egypt for more than a year. A new trend especially for brands puts consumer convenience more in focus again. A new closure type HexaLite 29/13 was developed by Bericap. That closure offers a superior grip experience to the consumer and allows easy handling when opening. The closure weight is only slightly higher compared to the standard HexaLite 29/11 closures. All HexaLite closures are designed with slit flexband supporting efficient application and reliable tamper evidence. Nitrogen dosing is feasible supporting light weight efforts of bottlers. www.bericap.com","@ID":50}, "MARKET SURVEY 31 PETplanet insider Vol. 17 No. 06/16 petpla.net S.B.E.C.M Bericap GmbH & Co. KG Has Plastik Co ООО Euro-Plast Rue de la plaine 47230 Lavardac, France +33 5 53 97 41 00 www.sbecm.com Mr Jean-Luc Didouan General Manager +33 5 53 65 85 97 [email protected] Kirchstrasse 5, D–55257 Budenheim, Germany +49 6139 2902 0 www.bericap.com Mr Volker Spiesmacher Director +49 6169 2902 0 +49 6139 2902 188 [email protected] Firuzkoy Bulvari No. 50, Avcilar Istanbul, Turkey +90 212 695 50 00 www.hasplastik.com Mr A. KerimAtas Operation Executive +90 212 695 50 00 +90 212 694 96 24 [email protected] ul. Gaspadarchai, 17A-1, Grodno, 230000, Belarus +375 152 4504 51 www.euro-plast.by Ms Galina Pocelyiko Commercial director +375 152 4503 56 +375 152 45 07 59 [email protected] Yes, HDPE, LDPE or PP Yes, DoubleSeal for PCO 1810, DoubleSeal SuperShorty for PCO 1881 (for CSD, aseptic and hot fill), HexaLite for PET 29/11, 29/13 and PET 26/10, 26/13, DoubleSeal 38 for 38mm 2-start and 3-start neck finish. DoubleSeal 33mm 2-start for aseptic filling and hot filling Yes HDPE: PCO 1810, 28mm; PCO 1881, 28mm, 2,15 g; PCO 1881, 28mm, 2,0 g; PCO 1881, 28mm, 1,95 g; No Yes, Liner Seal, SuperShorty for PCO 1881 Yes PP: PCO 1810, 28mm; Water, CSD, juices, dairy products, any liquid or solid products CSD, still mineral water, HOD and bottled water, beer, JETS (juices, energy drinks, RTD, teas, syrups), for hot fill and aseptic application, edible oil, sauces and dressings, dairy Yes HDPE: PCO Type 4, 38 mm; 30/25 high and low, 29/25 light, PCO 28 (1810, 1881, BPF), 38mm, 48/41 PCO 1881, PCO 1810, PET 26/22, PET 29/25, PET 26/21, 38mm 2-start, 38mm 3-start, 33mm 2-start aseptic, 33mm 2-start HF Yes No, but embossed Yes, up to 3 colours Yes 3 colour print Yes Yes Yes No On request Yes No No On request Yes, 3-piece push-pull and 2-piece Thumb'Up Yes No Handles for 5l, overcaps 3-piece push-pull for aseptic and hot filling without aluminium foil with high flow rate, 2-pieces Thumb'Up for aseptic filling, special closure solutions for lightweight necks, valve closures for food and beverages and health/body-care, customised closures Projects for customised closure available upon customer request Several patents Thumb'up screw closures for easy opening and drinking PushPull sports closure for hot fill application without aluminiuim foil, PushPull sports closure for aseptic application without aluminiuim foil Yes FullyTop Retal Baltics, Retal Luxembourg, Retal Balkans Novembal USA Affaba & Ferrari S.r.l. Vicap global ag Luxembourg, Vilnius (Lithuanie), Sliven (Bulgarie) www.retalgroup.com Mr Boursiez Jean-Noël Sales Director Closures +33 6238 30 427 [email protected] 3 Greek Lane, Edison NJ 08817, USA +1 732 847 9408 www.novembal.com Mr Don Thompson Commercial Director North America +1 480 677 9505 [email protected] Via Don Luigi Sturzo, 2, 26851 Borgo San Giovanni (LO), Italy +39 0371 21301 www.affabaferrari.com Ms Silvia Ferrari Sales & Marketing Director +39 0371 21301 +39 0371 97031 [email protected] Gewerbestraße 12, 8800 Thalwil, Switzerland +41 79 680 2271 vicapglobal.com Mr Roger Wilfinger CEO +41 79 680 2271 [email protected] Yes, HDPE Yes, HDPE 38mm flat caps, 1-start, 2-start for aseptic filling and hot filling, 3-start pitch 9 and pitch 8 (HDPE). 48mm flat caps (HDPE and PP). 28mm 1-pc flip top cap for 1881 neck finish (PP) No No No 38mm 1-start cap with IHS and liner 38mm 3-start cap (pitch 8 and pitch 9) with IHS and oxygen scavenging liner No CSD, water, juice (CF, HF, aseptic), beer, dairy Water cold fill, CSD and aseptic Still mineral water, flavoured water, milk and liquid dairy products, soft drinks, energy drinks, juices, teas, smoothies, mineral oil and agrochemical producs Water, juice and vitamin drinks 1881, 1810, 38mm, 48mm, 29/21, 29/25mm, 30/25mm BAG8148, BAG8210, PCO-1881, PCO-1810, BAG8155 and BAG8223 Food & beverage : 28mm: BPF, BPF light, PCO 1810, PCO1881, 3-start (Alaska) - 38mm: 1-start, 2-start for aseptic, 2-start for hot fill, 3-start pitch 9, 3-start pitch 8, 48mm; Agrochemicals : 45mm, 50mm, 63mm; Mineral oils and lubricants : 37mm, 38mm, 40mm, 41mm 38mm Yes No Yes No Yes Yes Yes Yes No No 28mm, 50mm and 63mm for agrochemicals No Yes No 3-pc 28mm sports closures for 1810, 1881, Alaska neck finish 3-pc 38mm 3-start sports closures Dispenser closure with push-pull system 26mm for water and various light weight options, 5 gallon PET closures and 43mm closures 1-pc 28mm flip top cap for 1881; 2-pc 28mm flip top cap for 1810 and 1881; lightweight 38mm 3-start flat cap (pitch 8 and pitch 9); 38mm 3-start flat caps from bio material (project in progress) ; 40mm and 41mm caps with pourer for mineral oil; caps for technical gases; tailor made solutions according to customer's needs Dispenser closure with container for vitamin and ingredients High grip All closures A&F owns many patents and utility models Worldwide protected","@ID":33}, "MATERIAL / RECYCLING 26 PETplanet insider Vol. 17 No. 06/16 petpla.net PET fines from recycled bottles A valuable raw material Today’s PET recycling facilities create high quality flake from post-consumer bottles. The process starts with automated sorting equipment which is used to remove unwanted products from the incoming material stream. After the bottles have been pre-sorted and the labels have been removed, they are visually inspected and sorted by polymer type and colour. Once separated into clear and coloured streams, the bottles are ground and washed. During this process, PET fines are generated and usually removed along with other residues. With a proper pre-screening system in place, combined with a dryer, extruder and continuous melt filter, customers can now create a useable product from these fines. The purity requirements of the final product made of recycled PET bottles vary depending on the end user. The following table represents the purity levels typically required for flake used to produce thermoform sheet. Clear PET, thermoforming sheet Metal: 10 ppm Paper: 50 ppm Polyolefins: 50 ppm Others: 25 ppm Coloured flakes: 500 ppm Light blue 50,000 ppm (5%) PVC: 10 ppm Adhesives: 400 ppm Additives: 1,200 ppm are separated during the screening and hot washing processes. This is precisely the reason why they are so difficult to utilise as a valuable raw material. Due to the small size of the PET particles, they have a larger surface area and hence absorb more moisture. Even with efficient degassing technology during the extrusion process, the IV values tend to drop significantly. Additionally, higher contamination levels block static screens quickly, making it a challenge to process this material, even with sophisticated back-flushing screen changers. As a result, a large majority of the PET fines are sold off at a very low price. When considering that even a small recycling facility can produce more than 20t of fines per month, finding a solution to filter this product could have a huge commercial impact on the bottom line. With a proper prescreening system in place combined with a dryer, extruder and continuous melt filter, customers can now create a useable product from these fines. The “Eco” continuous melt filter manufactured by Ettlinger Kunststoffmaschinen GmbH plays a major role RECYCLING S P E C I A L The final quality of the PET flake is dependent on the composition of the incoming bales as well as the sorting technology used in the recycling facility. This represents a daunting challenge for the melt filtration system in re-pelletising, thermoforming and packaging tape lines, especially if the aluminium fraction dramatically exceeds the specified 10ppm. The challenge is all the more intriguing when it comes to applications for the fines that are obtained when the PET bottles are ground. These fines contain a much higher percentage of contaminants because more paper, aluminium, and PCV","@ID":28}, "MATERIAL / RECYCLING 15 PETplanet insider Vol. 17 all the blow moulder’s sub-assemblies. The process and technical qualities of the package and the overall production environment in which the machine operates can then be measured to provide a comprehensive analysis from which a personalised action plan is developed. Through this, energy- and cost-saving targets can be identified, with ongoing monitoring of energy and utilities consumption put in place to see if those targets are being met. It also offers the opportunity for continuous improvement initiatives to be adopted, based on the strategic information supplied, to reduce waste and improve sustainability measures. Audits can often also highlight the potential for new technologies to be employed which can improve the energy performance of an existing line. Eco heating, adopting the use of energy saving lamps and ovens can bring substantial savings. Lamps can consume as much as 90-95% of the electrical power used by a PET blower so any focus here can bring substantial benefits. Eco ovens, which require fewer heating modules and lamps, can be installed on a blow moulder to reduce preform heating time and to ensure more efficient use of energy. Eco lamps are also available which themselves can offer significant savings. An example is a line producing 1.5 and 2l PET bottles for PepsiCo Deutschland which saw a target of 15% savings in energy by introducing Eco lamps. Results from the measurements taken showed that actual savings were as high as 19%. In addition to the in-house savings that can be achieved, there is also the wider environmental issues to consider. Reducing the demands on national power generation is a focus for many industries, including liquid packaging, particularly given the projections for energy demand increasing by 50% over the next 14 years. IMAGINE FILLING MULTIPLE PRODUCTS ON THE SAME LINE…NOW YOU CAN! Water, juice and soft drinks, all on a single machine? The Flextronic modular platform adapts effortlessly to still or sparkling, clear or pulpy and hot or cold-fill, and easily switches from one bottle neck-size to the other. A revolutionary filling technology that gives you extreme operational flexibility with minimal product loss and downtime at flavor switch. Clean, safe and versatile. Welcome to the new generation of fillers. carbonated still hot-fill cold-fill pulp non-pulp water juice soft drink SIPA S.p.A. - Via Caduti del Lavoro, 3 - 31029 Vittorio Veneto (TV) - Italy Tel. +39 0438 911511 - Fax +39 0438 912273 - e-mail: [email protected] www.sipa.it","@ID":17}, "MARKET SURVEY 30 PETplanet insider Vol. 17 No. 06/16 petpla.net Company name Corvaglia Closures Eschlikon AG Intergulf Ltd EKG Group Uner Plastik Postal address Telephone number Web site address Contact name Function Direct telephone number Fax E-Mail Hörnlistrasse 14 8360 Eschlikon, Switzerland +41 71 973 77 77 www.corvaglia.ch Mr Fredy Möckli Director Sales & Service +41 71 973 77 69 +41 71 973 77 78 [email protected] Po Box 6131, Sharjah United Arab Emirates +971 6502 9246 www.empol.com Mr Vinod Kanchan Head of Sales +971 50633 1295 +971 6528 5720 [email protected] Njegoseva 10 34220 Lapovo, Serbia +381 34 61 000 11 Mr Dragan Miljkovic General Manager +381 34 61 000 11 +381 34 61 000 12 [email protected] Gebze Plastikciler OSB, 1.Cadde, 11. Sokak No.3; 41400 Gebze, Kocaeli, Turkey +90 262 751 34 00 www.uner.com.tr Dr Cumhur Filik Sales and Marketing Manager +90 530 265 0663 +90 262 751 21 25 [email protected] Product range One-piece closures for beverages (Yes /No - if yes, please specify material) Yes, HDPE Yes, HDPE Yes , HDPE, LDPE or PP Yes, PCO-1810 and PCO-1881 Two-piece closures for beverages (with liner) (Yes / No - if yes, please specify material) No Yes, PP No No Applications relevant to PET containers (e.g. CSD, water, juice, beer, etc.) CSD, water, juice, milk, isotonic, aseptic fill and hot fill CSD, water CSD, dairy products, juices, water, beer CSD, water, edible oil, juice, beer Neck finishes available as standard CSN 25/22, CSN26, 27mmAlaska, 28mm 1810, 28mm 1881, 28mm PCO Corvaglia, 29/25, 30/25, 33mmACF, 33mm HF, 38mm HF, 38mm 3 start, 38mm 2 start, 1810, 1881 PCO 28 (1810, 1881), 38mm, 48/41, 30/25 high and low 29/25mm SFB, 30/25mm, 38mm 2/3 start, 28mm PCO1881/1810, 29/21 and 32/28 edible oil, 48/41mm 55mm HOD 5 gallon, lean handles for edible oil Printed caps available (Yes / No) Yes Yes Yes Yes, up to 3 colours Colour matching service (Yes / No) Yes Yes Yes Yes Child-proof closures (Yes / No) No No No No Push-Pull / sports caps (Yes / No) Yes No Yes No Special comments/special closures (e.g. flip-tops, drinking spouts, lightest cap for 28mm PCO, 26mm for water etc including non-beverage closures...) Closures for all major beverage brand owners, customised closures (e.g. for medical applications) On request Special patented closures or marketing features Company name Aptar Food + Beverage Silgan Closures Postal address Telephone number Web site address Contact name Function Direct telephone number Fax E-Mail 36-38 rue de la Princesse 78430 Louveciennes France +33 1 3087 19 80 www.aptar.com [email protected] Fabriksstraat 25, 2457 Lint Belgium +32 3460 1391 www.silgan-closures.com Mr Hans Van Baekel Technical & Commercial Sales Area Manager + 32 475 81 64 85 [email protected] Product Range One-piece closures for beverages (Yes /No - if yes, please specify material) Yes, PP & PE Yes , PE and PP Two-piece closures for beverages (with liner) (Yes / No - if yes, please specify material) Yes, PP outer shell with comfortable PE drinking spout Yes , PE & PP, flow in and elastomer liners, wads, induction heat seals Applications relevant to PET containers (e.g. CSD, water, juice, beer, etc.) Yes Neck finishes available as standard 28mm 1881, 28mm 1810, 30/25H, 33mm, 38mm, 29/25 38mm, 28mm 1810 - 1881, specific customer finishes Printed caps available (Yes / No) Various custom decorative closure options including hotstamping Yes, 4 colour tampo print and promotional laser printing Colour matching service (Yes / No) Yes Yes Child-proof closures (Yes / No) Yes No Push-Pull / sports caps (Yes / No) Only flip-top Sport caps, i.e. hinged Yes , both push-pull and flip-top Special comments/special closures (e.g. flipt-tops, drinking spouts, lightest cap for 28mm PCO, 26mm for water etc including non-beverage closures...) All dispensing solutions including liquide beverage, enhancers closures with performing SimpliSqueeze(R) Valve technology and also pumps, sprays and pouch fitments with valve 28 range of sportscaps and NCB flat cap in 1810 & 1881, 38mm caps in several configurations for cold, aseptic and hotfill. 5 Gallon water closures for HOD, gable top carton fitments Special patented closures or marketing features BAP technology (Bonded Aluminium to Plastic) process to seal a closure to a container Yes 06/2016 MARKETsurvey","@ID":32}, "MATERIAL / RECYCLING 19 PETplanet insider Vol. 17 No. 06/16 petpla.net Samples of flake from each of the exposure time periods was measured for IV to determine if the ultraviolet light from the sun’s radiation caused any loss in molecular weight. The plaques moulded from this flake were also measured for IV, colour and haze. The test results The IV results are quite interesting but not surprising in that the data clearly shows that exposure to ultraviolet radiation was very damaging to the PET material. Sample flake was also measured for colour before and after the one year exposure to determine if any obvious yellowing occurred. Surprisingly there was not a significant amount of yellowing seen in the colour of the bottle flake. The yellowing only became significant after the weather exposed PET had been subjected to melting required for moulding the plaques. PET reclaimers will take washed and cleaned flake and extrude it into pellets (not plaques). Thus if their bottles have been exposed to similar levels of ultraviolet radiation due to being stored outside, there would be an expected increase in yellowness resulting from the extrusion process. Further yellowing will then result when this extruded pelletised rPET is blended with virgin PET resin and melted yet again during preform manufacture. Thus the bottle production process will only further exacerbate the yellowing seen when this rPET is used. “What the average effect might be on an entire bale of bottles compared to what was seen in this study is a matter of debate. However one should consider all the potential causes of yellowing that can that limit the percentage of recycled PET that can be used. Exposure to UV radiation, whether it is from outside bale storage or possibly even exposure to fluorescent lighting in retail stores, should be considered as another contributor to rPET quality degradation,” explained Dr Frank Schloss, PTI vice president. The white paper with detailed research findings is available on the PTI website. www.plastictechnologies.com Shades of yellow – UV light exposure and its impact on rPET 19 SRI LANKA PLAST, August 05-07, 2016 | Colombo | Sri Lanka FDT, September 14-15, 2016 | Johannesburg | South Africa PROPAK WEST AFRICA, September 20-22, 2016 | Lagos | Nigeria PROPAK MYANMAR, September 22-24, 2016 | Yagon | Myanmar CBB, October 11-14,2016 | Shanghai | China K 2016, October 19-26, 2016 | Düsseldorf | Germany CIBUS TEC, October 25-28 | Parma | Italy With Sacmi, the beverage specialists are always at your side. With our unbeatable technological know-how and continuous research we are creating new containers and closures designed to ensure outstanding performance. The new IPS injection system for preforms, the CCM compression press for caps and the quality control systems fully designed and built by Sacmi, allows for large-scale production with considerable advantages in terms of efficiency and flexibility. The outcome? Reduced plastic volumes, less energy consumption and lower running costs.All in a bottle: the one you’ll soon be making. MATERIAL / RECYCLING","@ID":21}, "50 PETplanet insider Vol. 17 No. 06/16 petpla.net Ultimate blends for children by Garnier Garnier has extended its “Ultimate Blends” product range for a mild 2-in-1 shampoo made especially for children. According to the manufacturer, the paraben- and silicon-free shampoo with apricot and cotton flower extract does not burn in the eyes, does not tangle the hair and is gentle to the scalp. 250ml is bottled into a transparent, lightly orange tinted PET bottle. A brightly tinted hinged lid that is easily graspable even with wet fingers with an opening for dispensing seals the bottle. A transparent front label and a self-adhesive label on the back complete the scene on the store shelves. www.wahre-schaetze.de Kitchen cleaner with Clementine Method, a brand of the Ecover group, bases its cleaning and cleansing on natural ingredients. The products are packaged in clear packaging with reduced decorations to optimally present the colour of the product. The newest example of this is a PET bottle made out of 100% recycled material with 828ml contents that has rounded edges which converge to a round bottle shoulder at the closure area. The cleaner with its clementine cleaning power is dispensed by a screwed-on and lockable pump sprayer. Three transparent self-adhesive labels explain the product and its usage. www.methodhome.de Flattened bottle for shampoo The brand “Redken” belonging to L’Oreal, is marketing a 300ml “Diamond Oil - high shine shampoo” with glitter effect (shine sparkles) in a plastic bottle with a straight front face. It looks almost like a bottle cut in half. The bottle is equipped with grooves at the sides for easy gripping and holding. The sparkles in the product noticeably reflect light and make the packaging interesting for the observer. The hinged lid with the opening for dispensing is irremovably attached to the bottle. Transparent self-adhesive labels in conjunction with the straight front face, allow for a best possible view of the product. www.redken.com Moulded bottle for blow-dry lotion Bed Head Tigi’s hair care product packaging has a distinctly different shape and colour which are bound to prove eyecatching. A successful example is a waisted PET bottle with 250ml of content for a heat-activated blow-dry lotion with the name “Superstar”, which according to the manufacturer gives hair unparalleled volume. The bottle, dyed purple, is printed on directly and comes with a hangtag with additional information. A screwed on, metallic shiny push-pull closure serves as the dosing cap. www.bedhead.com .com 100815dmyL PETbottles Home + Personal Care","@ID":52}, "MATERIAL / RECYCLING 14 PETplanet insider Vol. 17 No. 06/16 petpla.net PET: The bottle and beyond by Nicholas Bloch, Executive Vice President for Communications, Sidel Adopting and developing a more sustainable approach throughout the supply chain is undoubtedly one of the biggest challenges faced by the packaging industry. In terms of beverages, there are many different materials employed, such as plastic, can, carton and glass, each with its respective advantages and disadvantages. Here, Nicholas Bloch, Executive Vice President Communications at Sidel, considers PET and its position as arguably the most sustainable package of choice. PET (sometimes also abbreviated as PETE) is a form of polyester and is one of the most widely used consumer plastics. Its importance to the beverage industry is highlighted by the fact that bottle production represents some 30% of its total use.1 The major benefits of PET as a packaging material are numerous: it is strong, shatterproof, lightweight, transparent, safe, and, importantly, recyclable, with an inherent barrier which makes it particularly suited to a wide range of food and beverage applications. It also offers significant design flexibility for brands that want to stand out on the supermarket shelf. In discussing what is meant by a sustainable package it is important to understand that its primary function must be to protect the food or beverage it contains, and deliver it safely to the consumer, surviving all the challenges of the supply chain. Beyond that, sustainability considerations include how the environmental footprint of the package can be minimised through reducing the use of raw materials and other resources; reducing energy use or employing renewable energy sources, especially during production and transportation; building recycling principles into the design stage; incorporating recycled content in the packaging; and adopting end-of-life options, including recycling. At the same time, for that product to remain sustainable it needs to be attractive to the consumer and so brand, design and consumer experience considerations are important also. Rightweighting As a lightweight material, PET already provides significant environmental advantages in terms of lower transportation costs and reduced fuel emissions. Its unique geometric properties and inherent barrier qualities, combined with innovative designs, have increasingly allowed manufacturers to use less plastic resin in the packaging process. There has been much research and development into how this can be further improved through lightweighting, a prime focus for the beverage packaging industry, whereby the amount of raw material required to produce a bottle is reduced through the bottle design process. At Sidel we have taken this a step further with RightWeight, a 0.5l PET water bottle which weighs only 7.95g and represents a 34% weight reduction compared to the average commercial bottle weight of 12g. We have used the ‘RightWeight’ name to highlight that lightweighting a bottle should not compromise the integrity of the bottle performance or the consumer experience, with a design which prevents the ‘over squeeze’ issue that can result in the spilling of contents unintentionally when using ultra-light bottles. By reducing the material content of the packaging, it offers environmental advantages on two fronts: firstly, the savings achieved in the PET resin raw material itself and, secondly, further reducing the impact of transporting the bottles throughout the supply chain. Modern bottle designs can lead to substantial savings for beverage producers worldwide. To make it as easy as possible to see the actual savings that can be achieved, Sidel has introduced a PET savings calculator, (www.sidel.com/ PET-savings-calculator). Optimising energy use Recognising that sustainability in beverage production is influenced by a number of different factors, one focus is how energy use can be optimised. Programmes are available which provide an initial audit to measure electricity consumption, along with influencing factors such as air pressure and leaks, with mechanical testing on Mr Nicholas Bloch, Executive Vice President for Communications at Sidel Collected and stacked PET bottles RECYCLING S P E C I A L","@ID":16}, "MATERIAL / RECYCLING 23 PETplanet insider Vol. 17 No. 06/16 petpla.net The perfect image Precision within seconds. Closure cap decoration with rotary pad printing machines. www.tampoprint.de Visit us at the exhibitions in Germany: K-2016, Düsseldorf, Hall 4, Stand 4C46 BrauBeviale 2016, Nuremberg, Hall 4, Stand 4-617 Optimisation engineering Most of the Cyklop production plants are configured by Causemann himself and are constantly being optimised. The most recent measure was the reconstruction of a production line to be able to process both granules and regrind at proportions of up to 100% each. “The individual configuration of the plants at Cyklop is a big challenge for us every time”, recalls Georg Flink of Kunststofftechnik Flink und Wortmann GbR, Burscheid, who was in charge of the project as a sales partner of Motan-Colortronic. In this particular case, the primary task was to integrate into the existing infrastructure a Luxor HDC 1800 crystalliser with agitator bin (capacity 2.500l), equipped with a Metro HCG 30 MG hopper loader suitable for flakes. In addition, the old dryer was to be supplemented by another drying bin from Motan-Colortronic with a capacity of 7.500l. Finally, a Gravicolor GC 600 dosing and mixing device of appropriate capacity needed to be integrated. Due to the available space and the already existing loader installed on the extruder, the Gravicolor had to be set up at the back of the extruder. From there, the material is collected by an Azo loader and transported to a 400l buffer container. Material conveying at Cyklop is handled completely with vacuum systems. Georg Flink continues: “Normally, system units are coordinated. Here, our application department primarily had to deal with adapting the different systems to each other. For example, the new drying bin had to be adapted to the blower of the already existing dryer. To do this, you need to know the type of blower, its dynamic pressure and characteristic curve, and the cross-sections of the available pipes. After all, the new bin should not use up too much air; otherwise the existing drying bin will stop working. The flow calculation was really tricky.” Another hurdle were the temperatures in the production environment. Particularly the machine-mounted Gravicolor devices are exposed to very high ambient temperatures (between 80 and 100°C) on the shop floor during full-load operation. To ensure that they work precisely and trouble-free, the pneumatic cylinders were equipped with special seals. The Gravicolor 600 devices installed at Cyklop are each equipped with four dosing units for granules, flakes, colour and masterbatch. In two of the lines, the dosing and mixing units as well as the 400l buffer containers were installed directly above the extruders, in spite of their size. According to Bernd Causemann, this layout helps to prevent rapid segregation of the material on its short way from the hopper to the inlet and thus leaves it more homogeneous. And he even sees another benefit: “For us, the buffer containers – whose contents is blanketed with dry air – serve as small silos. If a problem arises during production, the shift foreman has five to ten minutes to solve it without having to stop the plant. Minor problems in material supply can definitely be solved during this time”, he claims. In the third line, the Gravicolor was placed beside the extruder, away from the high-temperature area. Plant configuration – technology composed individually The know-how gathered by Cyklop over many years is the reason why they do not use ready-made production plant. Bernd Causemann configures, partly constructs and builds the lines according to his own ideas. This is why the plants incorporate extruders from Barmag and Reifenhäuser, melt filters from Gneuß and Kreyenborg, temperature controls from GWK, Trane and Weinreich, dryers, dosing devices and suction boxes from AZO, Zeppelin and Motan-Colortronic – to mention just a few. In-house developments, e.g. spooling devices or transfer points between the individual components, benefit from the fact that Cyklop do their own engineering. Even the central plant control has been configured according to individual requirements. Apart from the regulation and control options at the machines themselves, there is a central station in the office of the shift foreman where all data can be monitored. www.motan-colortronic.com www.cyklop.de","@ID":25}, "imprint EDITORIAL PUBLISHER Alexander Büchler, Managing Director HEAD OFFICE heidelberg business media GmbH Bunsenstr. 14 69115 Heidelberg, Germany phone: +49 6221-65108-0 fax: +49 6221-65108-28 [email protected] EDITORIAL Kay Barton Heike Fischer Gabriele Kosmehl Michael Maruschke Ruari McCallion Waldemar Schmitke Wolfgang von Schröter Anthony Withers WikiPETia.info Doris Fischer [email protected] MEDIA CONSULTANTS Martina Hirschmann [email protected] Johann Lange-Brock [email protected] phone: +49 6221-65108-0 fax: +49 6221-65108-28 FRANCE, ITALY, UK Elisabeth Maria Köpke phone: +49 6201-878925 fax: +49 6201-878926 [email protected] LAYOUT AND PREPRESS EXPRIM Werbeagentur Matthias Gaumann | www.exprim.de READER SERVICES Till Kretner [email protected] PRINT Chroma Druck & Verlag GmbH Werkstr. 25 67354 Römerberg Germany WWW www.hbmedia.net | petpla.net PETplanet insider ISSN 1438-9459 is published 10 times a year. This publication is sent to qualified subscribers (1-year subscription 149 EUR, 2-year subscription 289 EUR, Young professionals’ subscription 99 EUR. Magazines will be dispatched to you by airmail). Not to be reproduced in any form without permission from the publisher. Note: The fact that product names may not be identified as trademarks is not an indication that such names are not registered trademarks. 3 PETplanet insider Vol. 17 No. 06/16 petpla.net Dear friends of PETplanet insider, The Editourmobil goes to China I have just stepped out of the aeroplane on the first part of the “Editourmobil goes to China” tour. First impressions are varied, with much that is different from anywhere else. For example, the Chinese have come out against lightweighting. Compared to 2014, bottles have become 10 to 20% heavier. In the last year, the market has not maintained its enviable growth rate. For years Western companies delivered machinery, equipment and moulds for the beverage industry to China, enjoying annual two-digit growth rates. Then suddenly it all grinds to a halt. The reason for this is complex. It is not simply a question of China’s moderate growth rate, the principal reason is probably down to the fact that the beverage industry is now serving all regions and therefore the market has become to a certain extent saturated. The key point now is that in the last year (2015) the usual increase did not occur. On the contrary, the CSD sector declined and in the water sector there was a shift from cheap to premium. The minor reason for this may have been the chilly weather in 2015 but more likely is the fact that bottlers have been installing their filling lines in the westernmost tip of China, meaning that there are now no more blank spaces on the map. Manufacturers of stretch blow moulding machines and filling lines have been particularly badly affected. Business is practically at rock bottom. The situation is slightly better for some preform and cap producers. The mould makers have come out best from the situation. Cut-throat competition amongst the bottlers calls for new designs, new caps. New moulds are therefore constantly required. Thus the Chinese beverage market can only grow organically as living standards improve. The potential is huge. Looking at the official economic forecasts, growth in the future is likely to be of the order of 5%, a third of the figure for previous years. Yours, Alexander Büchler","@ID":5}, "PREFORM PRODUCTION 39 PETplanet insider Vol. 17 No. 06/16 petpla.net l l l consumer bags textile packaging recycling barrier, Novapet feels well prepared for demand on the market, as José Antonio Ramos, Head of Packaging Division Novapet, said in his speech: “New customer habits and preferences are challenging new opportunities for PET introduction because of its versatility, design possibilities and sustainability.” As far as current technical trends are concerned, Ramos listed the reduction of bottle weight, energy saving along the process chain and the launch of new resins and formats on new markets as well as an increase in stretching capacity, improvements of the bottles’ mechanical behaviour and thermal resistance as well as barrier effect. Tons (t) PET Preform Units Tons (t) PET Preform Units Total 2013 Total 2013 Total 2015 Total 2015 Water market 129.569 4.717 134.552 5.287 CSD market 91.584 2.416 93.746 2.484 others 52.443 1.488 64.743 1.601 Total production 273.596 8.621 293.041 9.372 Development PET used for preform production 2013/2015, Spain In an analysis of the Spanish PET market 2013-2015 in particular, Ramos associated the increasing demand for PET in the country primarily with an increased consumption of bottled water as well as growth of the detergent and cosmetics markets. The CSD sector on the other hand, stagnated. Lightweight water bottles as well as falling raw material prices (by 20% during the past two years) are among the other trends on the market, said Ramos.","@ID":41}, "BOTTLES PETbottles 51 PETplanet insider Vol. 17 No. 06/16 petpla.net Beverage + Liquid Food powered by International trade fair for the beverage and liquid food industry processing+filling+packaging+ logistics In conjunction with: Forum organizer: featuring dairy processing Waisted bottle for Pure Tea The consumer demand for unsweetened, natural beverages from organic farming is forcing the manufacturers to develop precisely those products and bring them to market. An example for this is the Pure Tea range of the brand Pfanner. The various tea-based beverages do not contain any forms of added sugars or sweeteners. According to the manufacturer, Pure Tea conforms to the zeitgeist – to drink adequately without compromising on taste and avoiding excessive sugar consumption. The packaging that is used is a strongly waisted transparent bottle with a 1l capacity that is labelled with a shrink sleeve and sealed with a screw cap. www.pfanner.com The lemonade with stimulant The German Eckes-Granini GmbH has extended its “die Limo” (the lemonade) product line that so far consisted of three varieties, and added a fourth variant with a stimulant. Whilst the varieties so far targeted consumers that do not want sweet but refreshingly bittersweet beverages, “die schwarze Limo” (the black lemonade) with blackcurrants is combined with guarana – a product that is to keep people awake. Fitting to this is its advertisement with the slogan “The first lemonade that keeps your eyes open”. 1l of the beverage is bottled into a slim, transparent PET bottle that has a surface texture typical of the Granini brand. The shrink sleeve contains a prize code for a collector’s edition of the European Football Championship 2016 in France. www.dielimo.de","@ID":53}, "MATERIAL / RECYCLING 27 PETplanet insider Vol. 17 in processing highly contaminated feed streams. The central component of the Eco melt filter is a rotating, cylindrical filter screen with millions of conical holes that can be supplied with a wide variety of screen sizes. When melt flows through the filter, contaminants are retained on the outside of the screen – in addition to solid contaminants such as aluminium and black specks as well. High-molecular and cross-linked fractions which arise due to high temperature stresses are separated from the melt stream along with gels. The cleaned melt on the inside of the drum is supplied to the downstream die via a system of flow channels. The contaminants are wiped clean from the filter surface after each rotation of the screen. They are then discharged from the unit by means of a discharge shaft. If contamination levels spike causing the pressure to rise, the drum automatically increases speed. This is said to ensure a steady pressure at all times. Unlike many backflush systems, the purge from the Eco contains a high percentage of contamination. The interval between screen changes can last several weeks or even months depending on the material and level of contamination. During this time, the melt pressure is said to remain stable. The unit is designed to remove contamination levels as high as 1.5% by weight. Two sizes are available depending on the capacity requirements: The Eco 200 is for throughputs up to 1,500kg/h and as the Eco 250 for a maximum of 3,000kg/h. In addition to polyolefin melts, it is also suitable for filtering easyflowing materials such as PET or PA. With their compact design Eco melt filters can be retrofitted in existing extrusion lines. www.motan-colortronic.co.uk www.ettlinger.com Ettlinger Kunststoffmaschinen GmbH was founded in 1983. The German company has its headquarters in Königsbrunn, not far from Augsburg. Its core competency is the development and manufacture of injection moulding machines and high performance melt filters for continuous filtration of heavily contaminated feedstock. Contaminants like paper, aluminium, wood, silicones, or high-melting polymer composites can be removed from all standard polymer materials. Ettlinger’s new agent in the UK and Ireland is Motan Colortronic Limited of Chesterfield.","@ID":29}, "MATERIAL / RECYCLING 16 PETplanet insider Vol. 17 No. 06/16 petpla.net Recycling rates – good but not good enough The recycling of PET is certainly crucial in enhancing its position as a sustainable material. Producing virgin PET requires the use of resources which are finite so adopting processes which allow it be 100% recycled are key. Analysis has shown that recycling of PET uses two-thirds less energy than that required to manufacture virgin PET, demonstrating the clear environmental benefits of the process.2 In principle, all PET bottles could be manufactured using recycled PET (rPET). This is because, as long as the resulting rPET is approved for food contact, which it easily can be through the regulatory environment that is in place, then it can be used for this purpose. However, there are sometimes issues in the take-up of rPET. This is largely in terms of marketing since the slight discolouration that can result from employing rPET does not impact in any way on the bottle’s performance. By far a greater barrier to the adoption of rPET is the lack of availability of quality rPET. Currently the demand for rPET outstrips supply. This is due in part to the traditional mechanical methods of recycling PET bottles in which it was previously difficult to efficiently separate the contaminants, particularly dyes, from the plastic. Collection rates of recycled bottles are also an issue, with highly fluctuating rates across different regions. While global recycling rates continue to improve, there is still much work to be done in post-consumer PET packaging. Leading the way in terms of recycling is Asia with a rate of almost 80%, whereas in Eastern Europe only 12% of bottles are collected and recycled.3 However, it is important to qualify those figures and recognise that in many developing countries, a discarded PET bottle has a greater intrinsic value. For those living in poverty, the collection of discarded bottles from households or open landfill sites provides a revenue stream and this is one contributory factor in the high recycling rates of certain regions. The emphasis on collecting bottles needs to continue, with commitments to further improving collection rates. The technological advances being made to optimise the use of those bottles also needs to be encouraged, building on the new filtration processes being adopted to generate PET flakes in a way which is both more eco-friendly and more cost 1 www.benefits-of-recycling.com 2 www.sidel.com/about-sidel/sustainability-/reuse-recycle 3 PCI, PET Packaging, Germany effective. This will enable the production of more new bottles from rPET, and also allow the recycled PET flakes to be used in a wide range of other applications. Despite the challenges of sourcing rPET, many of the major beverage brand owners are committed to increasingly adopting it in their bottling processes, with some already achieving usage levels in excess of 50% for certain product lines. Meeting future demand The focus on sustainable methods of production is a feature in many industries and in packaging it is particularly acute. This is highlighted by a comment from Dr James Bellini, a futurologist, who said at a dedicated event for the beverage industry: “Food and beverage is very much at the top of the agenda. There are probably three big issues that we have to crack this century: one of them is health and wellbeing, one is sustainability and the third one is food and beverage.” Forecasts for 2030 suggest that demands for energy will have increased by 50%, food by 50% and water by 30%, alongside the additional pressures brought about by an increasingly urban population. This means that finding ways to optimise the planet’s resources in meeting those demands will only intensify and with it the need to ensure that the packaging we employ can contribute to that sustainability agenda. PET has a vital role to play. The responsible use of virgin PET across the supply chain can bring immediate and significant sustainability benefits. Extending that beyond the virgin resin, in its recycled form PET can be reused time and time again, reducing consumption of what is a finite resource. Already the most widely recycled plastic in the world, through initiatives to further improve collection rates and the methods of recycling, PET can further strengthen its position as the sustainable package of choice. It is about taking what is currently in the waste stream and putting it in the resource stream, reaching for the ultimate objective of a closed-loop sustainable packaging supply chain. www.sidel.com RECYCLING S P E C I A L","@ID":18}, "NEWS 9 PETplanet insider Vol. 17 No. 06/16 petpla.net Brau Beviale 2016 BrauBeviale 2016 will be opening from November 8-10 again after two successful events, before it closes its doors for the scheduled break next year. Last year this Nuremberg trade show welcomed almost 1,100 exhibitors and over 37,000 visitors from 131 countries. Brau Beviale is covering all aspects of the beverage production process chain, from raw materials, technologies, up to logistics solutions and creative marketing ideas. The supporting programme includes, among others, the Craft Beer Corner where beverage experts will be presenting special tasting sessions for specialist retailers, caterers, producers and all other interested trade fair guests as well as the European MicroBrew Symposium, which for the fifth time, is taking a very close look at markets, trends and technologies. Parallel to this, for the first time, there will be a training event for European distillers and representatives from the spirits industry: the 1st European MicroDistilling Symposium. Also featured is the international beer competition European Beer Star, the popular tradition at BrauBeviale is the selection of the Consumers’ Favourites in Gold, Silver and Bronze. On all three days of the fair, there will be presentations and discussions held by experts for experts at the Forum BrauBeviale. The range of themes extends from design right up to the beverage container issue, from packaging up to Creative Beverage Culture or training in the beverage industry. PET @ BrauBeviale Covering all aspects of the beverage packaging theme, BrauBeviale is presenting a diverse range: packaging materials and packing supplies – from glass, through to cans up to kegs or barrels – sealing systems – bottle caps, swing tops, twist-off caps, corks and more, along with packing ancillaries. In addition to this, PET@BrauBeviale is offering solutions for the entire PET value-added chain. In the PETarena – connecting competence, companies will be presenting a diverse PET range of services for small and medium-sized companies and global players. The international, two-day congress PETnology Europe, which is being held directly in the run-up to the fair, will open PET Passion Week. www.braubeviale.de A survey of surveys Every year Petplanet publishes comprehensive overviews of the various sectors of the PET market. If you wished to consult any of these specialist subject areas, you had to go through the booklets one by one to find what you were looking for. A cumbersome process. To make things easier, we have now clearly listed all our market overviews on WikiPETia.info on one page. One click will take you to your desired page. For any other information, simply go to the www.WikiPETia.info page, via the market surveys, and on to the pdfs of the relevant issues. To date, we have linked the subject areas there with the pdfs of the issues in which the relevant market overview was published. But we won’t be stopping there: we are also gradually converting the surveys from the booklet into sortable wiki tables. This will then allow you to sort the tables according to the parameters most important to you, thus enabling you to access relevant information easily and quickly. Currently, the following topics are available in sortable wiki tables: Additives, Resins, Compressors. And if you would like to have your details in the table, but are not included as yet, you can as always contact PETplanet’s editorial office in confidence. MHT MOLD & HOTRUNNER TECHNOLOGY AG Your Machine - Our Solution 1996-2016 20YEARS Booth 1C35","@ID":11}, "PRODUCTS 49 PETplanet insider Vol. 17 No. 06/16 petpla.net PreWatcher I I I . Essent ial when you use rec yc l ed mater ial . W W W . I N T R A V I S . C O M / P R E W A T C H E R Replacing of paper labels by Direct Print technology For the launch of its beer brand “Dagschotel”, Martens Brouwerij based in Bocholt, Belgium, decided to inject some fun in the digitally printed PET bottles. Using a specially-designed smartphone beer application, the characters printed on the bottles deliver a rather special performance when brought together. The PET bottles filled with “Dagschotel” beer show a well-known group of Belgian TV sitcom actors, “F.C. Kampioenen”. When two bottles are brought together, a smartphone app sets off a dialogue between the characters. The bottles appear to “talk” to each other. It was the KHS Direct Print process that made this possible. The process prints all information straight onto the bottle in true colour. It was the first industrial-scale introduction of this digital printing process where low-migration UV cure inks provide a food-safe solution for PET bottles. Recently, Martens is again leveraging this printing technology by eliminating labels altogether, this time to renovate the look and feel of their Pils beer. The required print image is transferred straight from the computer to the labeller’s control unit. The cloud-based Direct Print software platform links a headquarters-based sample printer for 1-to-1 proofing and artworks design approvals, linked via the cloud with the workflow of the production site based Direct Print industrial printer. The industrial scale Direct Print equipment is capable of printing variable, high quality images on each bottle in PET filling and packaging lines running at 12,000 / 24,000 / 36,000bph. As no time-consuming label printing processes or shipping distances for label materials are necessary, the process offers a high level of flexibility. Graphics can be changed in hours instead of weeks. One crucial aspect of this process is that PET bottles printed on the KHS-Innoprint are suitable for bottle-to-bottle recycling. Hardened inks can be completely removed from the flakes. The Direct Print team at KHS will soon be bringing new technical features to their next version equipment – bringing even higher quality decorations and the capability to individualise each bottle with variable image capability. www.khs.com","@ID":51}, "CHINA EDITOUR 12 PETplanet insider Vol. 17 No. 06/16 petpla.net SPONSORS The China Road Show May 20, 2016, Husky Beijing Compression moulding as the biggest competition We met: Bin An, Regional Manager, China North & South (in the middle) Husky, with a 880 preform systems and 100 closure systems is the market leader in China. The organisation is managed from Shanghai. This is also where the mould shop is located (see PETplanet Insider 4/2007). The Canadians have divided the country into the south, east and northwest areas, in order to reach customers in the most efficient way possible. Unlike in other countries, the Chinese owners want to create brand value at their own companies as far as possible. This results in their producing the preforms and closures themselves. The converter only plays a subordinate role in this. In the closure sector, compression moulding is the biggest competition. As the onepiece closures have already replaced two-piece closures throughout China, an increasing number of processors are also switching to injection moulding technology there. Husky developed wide ranges of beverage closure applications for Hot Fill, Aseptic, CSD and Diary etc. New customers are attracted especially when there are no significant alternative suppliers, and Chinese technology is also growing up very fast. www.husky.co/ZH-CN May 17, 2016, Delvron Aman of many talents We met: Mr Jock C. Lim Jock C. Lim is sitting at the table in the conference room, talking about his extraordinary career. Born 70 years ago in Malaysia and migrated to Singapore at the age of 2, he first gone into the plastics industry 45 years ago and later decided to move his factory to China. There he continue in his Electronics, Plastic Injection and Tool making. The factory was re-located to Tianjin and started preform production facility. He sold his preforms and bottles all over the world, except China. The reason is that it costs very little more to ship a container overseas than it does to move it within China. Hence he shipped containers and preforms to Canada and North America, for the household, chemicals, pharmaceuticals and spirits sectors. What propelled his business at the outset – inexpensive shipping costs – turned sour in recent years. Shipping costs rose relentlessly until it became uneconomic to continue exporting preforms. But Jock would not be Jock if he let this get him down. His solution is to supply bottles direct to the customer in the shape of a one-stage system. Together with two friends from Canada, he is close to being able to launch the machine on the market. It is a hybrid system, in which the hydraulic part exclusively supplies the screw. The remaining part is operated by servomotors. 2 to 12 cavities fit into any station of the rotary plate. First, the screw injects. The plate rotates 90 degrees. All preforms are conditioned simultaneously. The plate rotates forward a quarter turn and it is blown. In the last stage, the product is ejected. Throughout the process, the neck is contained within grippers, and goes through the entire machine in this way. For the principal components, such as the spindles, Jock uses branded products rather than local alternatives. Nevertheless, the complete system costs only US$110,000 including a first set of tools and all ancillary units. An ROI in 18 months would therefore be feasible. For the hydraulic part of the plasticising unit, he already has ideas about making it fully electric. And as if that were not enough, we see in the yard another invention of his, which is destined for the water sector. He was unwilling to divulge any details, but no doubt he will, when the time is right. As a memento of our visit we were presented with two 6 gallon containers for the Editourmobil – naturally, they are made out of PET and water purified in-house by portable solar powered system. We wish Jock every success. www.delvron.com F.l.t.r.: Nicolas Kuhr, PETplanet; Jock C. Lim, owner and founder Delvron; Alexander Büchler","@ID":14}, "PREFORM PRODUCTION 41 PETplanet insider Vol. 17 No. 06/16 petpla.net Retal opens plant in Luxembourg “This is only the first phase” by Kay Barton Retal Group is a multinational preforms, closures, resin and films manufacturer that can truly be described as a ‘giant’. It has a 22-year history and currently owns 19 plants in 12 countries and cooperates with five further partner plants in four additional countries. It can claim to have the biggest footprint in terms of outputs, local supply and “Who’s Who” customer base in Eurasia. The raw numbers are pretty impressive: it produces about 18 billion performs, up to 11 billion closures and 50 million containers annually. We meet with Mrs Valérie Mure, General Director of the new plant and also General Director of Retal France to discuss Retal’s strategy. “2003 I started working for Sodripack France as Financial Manager. 2009, two years after Sodripack has become Retal France, I became General Director there and 2015 also for our Luxembourg plant. If we see the past three years, Retal has grown at an average of more than 10% anually. We would like to continue this trend further being closer to customers and partners, offering new products and enter new markets. When we thought of Luxembourg as the best place we wanted to strengthen primarily our market positions in Benelux, Germany and France. But moreover we will sell our products also in other European countries like Spain, UK and Greece plus some parts of Northern Africa. Talking about the closure business we are planning with 20% exports in the first year and an increase for 2017.” It bears mentioning that from starting the plant from the scratch until now it took only twelve months of time, thanks to a lot of governmental support. With its start the capacity is going to reach about 350 million preforms and 1.5 billion closures per year and Retal plans to increase the capacity further in the near future. The available equipment contains two preform and three closure production lines from Husky and in terms of closures equipped with Corvaglia Moulds. “We traditionally start with the production of preforms and caps for the beverage and food industry and cosmetics and technical industries as well. There are plans to add new products and services in the near future”, explains Mrs Mure. At the moment the company employs 20 people and the next steps have been announced as well: “With regard to Luxembourg, this is only the first phase. We are confident that soon we will expand our production. We focus on dynamic growth. In terms of our global expansion Retal will open its first plant in Pittsburgh, USA in autumn 2016.” Certainly enough events to discuss again in the near future! www.retalgroup.com Ribbon-cutting ceremony with General Director Valérie Mure and Anatoliy Martynov, Chairman of the Board At the end of May 2016 the company opened its new Retal Luxembourg plant, which has a 4,000m2 production area equipped with the latest technologies, along with a dedicated R&D area. The project includes significant investment in energy saving and ecofriendly technologies including dryers with heat pumps, advanced chilling systems and machinery with electric clamps. Want the secret to bottle light weighting? Process Pilot® automated blowmolder control system takes the guesswork out of material distribution management and can help ensure the success of even the most aggressive light weighting program. Featuring 24/7 blowmolder control, the Process Pilot system continuously maintains proper material distribution, on every bottle, to an unmatched level of accuracy. With the Process Pilot system, you have the means to push light weighting to the limit without VDFULȴFLQJ ERWWOH TXDOLW\\ RU SHUIRUPDQFH Not convinced? Talk to one of our specialists today to schedule a free seminar and evaluation of the Process Pilot system on one of your blowmolding lines. Web: agrintl.com Tel: +1.724.482.2163 E-mail: [email protected] See us at booth 11B40","@ID":43}, "MATERIAL / RECYCLING 36 PETplanet insider Vol. 17 No. 06/16 petpla.net PET flakes for food contact compliant inline preforms in one processing step In 2011 Erema launched its open house events. Now something of a tradition, the 4th Discovery Day took place at Ansfelden, Austria on June 1, 2016, featuring some new highlights. For the first time partners of Erema such as Redwave, Unisensor or STF had the opportunity to show their technology to visitors on booths located directly in the event room. From sorters and washing plant manufacturers to downstream producers, fillers and brand owners, representatives from the entire PET recycling value chain were present at the Erema headquarters. Around 250 international guests were present at the launch of a new system: Xtreme Renew. This new system enables the direct processing of PET flakes for food contact compliant inline preforms in one processing step. For this new recycling system Erema collaborated with Sipa, the Italian PET packaging specialist. The expectations of the interested attendees were high as, with the oil price at its current low level, it could be thought that PET recycling is not profitable at the moment. “In my experience with customers, the reason why a producer decides in favour of a major investment in a recycling solution is based on a broad-view, entrepreneurial approach. Only those companies which are willing and able to adapt will remain in the constantly fluctuating plastics industry in the long term. Thanks to the collaboration with Sipa we are making it possible for plastics producers to demonstrate the necessary flexibility,” says Christoph Wöss, Business Development Manager for Bottle Applications at Erema. The cooperation between two significant players in the plastics industry made it possible to develop a direct processing solution which stands out through better preform quality characteristics when using rPET. “Two years ago,” explained Manfred Hackl, CEO of Erema, “we started thinking about this technology and after some discussions with a number of companies found the perfect partner in Sipa. Our project was perfectly realisable with the Extrem technology line of Sipa.” The food contact compliant melt produced by Vacurema runs when hot and thus without the otherwise usual, intermediate cooling stage in pellet production. It is then fed directly into the Xtreme production process developed by Sipa to make preforms in a single step. The benefit of this direct processing, therefore, is an enormous boost in energy efficiency plus considerably lower thermal damage to the PET material. Enrico Gribaudo, Sipa General Manager, notes: “We are proud to have developed such a sustainable product together with Erema. Sustainable for the company and sustainable for the environment. In addition, the processing offers unrivalled benefits in logistics. Xtreme Renew not only saves space, CO 2 and energy, it also reduces costs.” Presentation of Xtreme Renew (f.l.t.r.): Gianfranco Zoppas, Chairman Sipa/Zoppas Industries; Manfred Hackl, CEO Erema; Klaus Feichtinger, CEO Erema; Marc Jacobs, CEO Marc Jacobs Consulting; Christoph Wöss, Business Development Manager Application Bottle Erema; Enrico Gribaudo, General Manager Sipa RECYCLING S P E C I A L","@ID":38}, "PETpatents www.verpackungspatente.de 52 PETplanet insider Vol. 17 No. 06/16 petpla.net PET aerosol can Intern. patent no. WO 2015 / 155424 A1 Applicant: Farvea, Savigny le Temple (FR) Date of application: 9.4.2015 The material specifications, the moulding and the process for manufacturing a PET aerosol can are described. The can is able to withstand increased internal pressures. PET container made out of 100% recycled PET Intern. patent no. WO 2015 / 160902 A1 Applicant: S.C. Johnson & Son Inc., Racine (US) Date of application: 15.4.2015 An easy-grip container that is made out of nearly 100% recycled PET. The manufacturing process and the material requirements for the trigger bottle are described. Integrated tamper-proof closure Europ. patent grant no. EP 2001766 B1 Applicant: Léon Ribi, Vérossaz (CH) Date of application: 22.3.2007 The European patent describes a plastic bottle made out of PET or other plastics with an integrated tamper-proof display at the container wall. When filling and sealing, a depression “snaps” outwards due to the increased internal pressure. On first opening, this surface snaps back inwards and thus an already completed opening becomes recognisable. Plastic bottle Europ. patent grant no. EP 2662297 B1 Applicant: Yoshino Kogyosho Co. Ltd., Tokio (JP) Date of application: 18.11.2009 Plastic bottle with a special outer shape to stabilise the bottle when it is gripped and a bottom that absorbs the vacuum forces that occur after hot-filling. The bottom deforms towards the inside of the bottle and in this way reduces its volume and the negative pressure. Packs Disclosure no. DE 102014104643 A1 Applicant: Krones AG, Neutraubling (DE) Date of application: 2.4.2014 To be able to combine several identical bottles equipped with a RFID label into a pack using an adhesive application, a special procedure is necessary. The design and the procedure to manufacture the packs are disclosed. Foldable bottom Europ. patent no. EP 2933206 A1 Applicant: Yoshino Kogyosho Co. Ltd., Tokio (JP) Date of application: 24.12.2009 The European application describes the structure of a plastic bottle with a bottom that is folded “inwards” only after manufacturing, and thus allows for a sufficiently stable bottom and stand. The deepest point of the container is at the centre of its bottom – good emptying of residues.","@ID":54}, "CAPPING / CLOSURES 47 PETplanet insider Vol. 17 No. 06/16 petpla.net DRYING HAS NEVER BEEN THIS EFFICIENT: ETA plus® LUXOR A 80-2400 Now available with ETA plus ® ETA plus ® considerably reduces energy consumption and protects materials. When it comes to drying, saving energy is a key concern. We have developed a system that combines airflow regulation with a temperature adjustment feature – that can be disabled if required – and efficient waste heat recovery. The result? A drying system that cuts energy consumption by up to 64%: ETA plus ® . motan-colortronic gmbh [email protected] www.motan-colortronic.com iQ weight control keeps the injected melt volume and the viscosity constant throughout the entire injection moulding process the new iQ clamp control software determines the mould breathing to continually readjust the clamping force. As mould temperature control also affects efficiency and quality, Engel is now going one step further for K 2016. The electronic temperature-control water manifold Engel e-flomo and the temperature control unit merge at controller level to form a single unit. With the help of the new iQ flow control software, the pump speed is adapted automatically to current requirements based on the measurement values determined by Engel e-flomo. Whereas Engel e-flomo increases the process stability and therefore lowers the reject risk, the automatic speed adjustment ensures that temperature control requires less energy. A second innovation I’d like to mention here is the Engel e-connect monitor, which analyses the condition of process-critical machine core components – such as the screw – in the live operation and reliably predict the risk of default. The condition-based, predictive maintenance makes it possible to exploit the service life of critical machine parts to the full and avoid any unplanned equipment stoppages that occur in spite of this. PETplanet: Your CV is greatly varied. From tool makers, to stamping technology, right up to electronics in China, you have been in a few businesses. For 2 years you have now been responsible for the packaging area at Engel. Why Engel exactly? Feltes: Well, firstly, the company structure fascinates me. Engel is a family company with a long-term strategic direction and short decision making pathways. This is not just me, but also the customers in the packaging industry that have the same impression and expectations to their suppliers. The successful ones focus on long-term partners and strategies. Moreover, since Engel started in the cap business relatively late compared to others, it is important to provide a great customer experience, support and satisfaction right away with the first machine or system delivered. This resulted in an elevated increase of market potentials worldwide. That is a very appealing task for me in the years to come in a leading position at Engel. PETplanet: In conclusion: Where do you see the closures in the coming years? Feltes: I think weight reduction has reached its limits. With the recently introduced closures of 0.8g, we are much more like a thin-wall injection part and hardly closure technology anymore. Also, the switch-over from twopiece closures with liners to a one-piece closure of large brand-owners like Pepsi Cola, Coca Cola and others will be interesting and exciting especially in countries with difficult logistics and climates. There is a great potential for long-term changeover from compression to injection moulding. Yes, and if we continue to work with the customers and our partners like the tool makers, the magical 2s limit for a continuous operation for closure production systems is also going to drop off at some point. PETplanet: Thank you very much. www.engelglobal.com","@ID":49}, "MATERIAL / RECYCLING 17 PETplanet insider Vol. 17 No. 06/16 petpla.net Aesthetics and performance through Advanced Additives Revaluation to recycled PET The use of recycled material in PET preform and sheet production is growing rapidly and gaining an ever larger market share. The aesthetic features of the final product, which can be liable to degrade using rPET, often do not satisfy customer specifications. Recycled PET is generally characterised by a yellowish shade and a lower and irregular Intrinsic Viscosity, which influences the mechanical properties of the final package. Cielab. An additional aim is to influence and balance the level of grey (L value) and green, so to improve the value “a” coordinates Cielab. The key to obtaining successful formulations of Anti Yellow is the extensive knowhow on the different processes involved. These differ in the case of the injection of preforms, the extrusion of sheets, and the production of rPET chips). A further issue is how not to interfere and modify process parameters while working, even with high vacuum levels. The Anti Yellow additives line developed by Repi has seen its number of formulations approved and used not only in all injection and extrusion processes, but also in the various PET recycling technologies, where a number of issues related to the vacuum and the sensitivity of the filtration and cleaning, require special attention. The very low addition rates in use have also required the optimisation of the dosing systems: Repi claims that their dosing units on the market today can guarantee a constant dosage to an accuracy of 0.004%. To illustrate the behaviour of the company’s Anti Yellow additives, the graphs show lab values on two main applications, PET sheet and rPET resin. High performance additives Among the high performing additives by Repi, an interesting role is also played by the “no cross link” Intrinsic Viscosity Enhancer (IVE), added during the processing in order to improve the molecular weight (MW) and the mechanical properties. After the reaction takes place, the chain extender is physically bonded into the main PET backbone. The reaction can continue to 100%, according to the temperature and the residence time available and the chain extender cannot be released from the polymer. The link established between the PET and the chain extender is stronger than the ester bond and is not subject to further hydrolytic scission. The molecular weight (MW) and the mechanical properties increase accordingly. The chain linearity reduces the risk of creating gels. In the production of rPET resin and preforms, this additive helps to improve the physical and mechanical characteristics of the final product. In PET sheet extrusion, it enables a better thickness distribution, as well as an optimisation of the process parameters (pressure in the melting pump increases significantly). Calenders will get less dirty, substantially reducing the need for cleaning. www.repi.com Special additives are required in PET performs, in the production of rPET resin as well as in the extrusion of PET sheets. Repi, global supplier of high performing liquid colours and special additives began working on rPET in 2007. The result has been a series of advanced additives able to correct the shade and to improve IV parameters of rPET, whatever the end-product is. Today a variety of innovative solutions is undergoing constant improvement for each specific family of products made from rPET. This is in parallel with the on-going developments in recycling technologies and the introduction of different grades of rPET, whose use is growing, in percentage terms, relative to the total quantity of resin. The principal reasons are firstly to improve the aesthetics and secondly to increase the performance of the final product, be it for PET preforms, PET sheet or rPET resin. Anti Yellow additives Repi‘s Anti Yellow additives are formulated so to be able to modify the main required parameter, namely to correct the yellowish shade with an action on the value of “b” coordinates RECYCLING S P E C I A L Effect of Remap AY on rPET chips 100% 50% 0% -50% -100% REMAP AY@0,03% none REMAP AY 00015@0,03% Performance PET sheets db dL da REMAP AY @0,005% none REMAP AY 00090@0,005% Performance on R-PET resin 100% 50% 0% -50% -100% dL da db","@ID":19}, "PREFORM PRODUCTION 40 PETplanet insider Vol. 17 No. 06/16 petpla.net We asked David González how important these trends are going to be for the future positioning of Novapet. “We respond with very well balanced resins to the lightweight requirements of the bottle market. But the mission of our R&D is not to push boundaries even further, but to create new markets. We have more than 20 resins: crystallised PET for high temperature trays, we have resins for direct injection which require no blowing at all, we have PET resins for extrusion blow moulding with which you can make bottles with handles for detergents or the edible oil market which usually are made from polyolefins (PE),” the Managing Director explains and identifies four markets on which he sees good growth potential: detergents and household products, cosmetics and personal care, non-liquid food, and dairy products. “The dairy market is dominated by a single carton company but it is a very clear trend that customers ask for more consumer-friendly packaging nowadays. So the dairy market is of high potential in terms of growth and in terms of value,” González continues and admits that switching from a typical carton line to PET requires a high level of investment. “But it is a very fast growing market and a very important development.” In 2005, Novapet launched its PET dairy resins. The light-blocking additive DCU (Dairy Concentrate Ultra) protects the product contained in monolayer PET bottles against degradation caused by light radiation. For the current year, González expects a turnover of €15m in the sector light barrier applications. This is accompanied by expected turnovers of €190m in the polymers division and almost €30m in the packaging division. What exactly is Novapet expecting for the upcoming years apart from that? González has specific plans: “Right now, we are serving 30 different countries on four continents with David González, Managing Director Novapet Novapet, S.A. is a Spanish producer of PET grades for packaging applications, preforms and bottles with three PET plants in Barbastro, Huesca and a total annual capacity of 260 ktn/year and more than one billion preforms for food and beverage containers. Its portfolio is characterised by its variety and adaptation for each of the applications in its final uses. The company offers packaging products for food, CSD, mineral water, still drinks, fruit juices, beer, carbonated drinks and dairy products. It also provides technical and industrial services. The company was incorporated in 2004 and is based in Saragossa, Spain. Novapet operates as a subsidiary of the Spanish Grupo Samca SA, holding activities in mining, agricultural, energy, plastics, synthetic fibres and real state promotion, with an annual turnover of nearly €850m. Plant tour of the refitted injection site Juan Antonio Cejalvo, Industrial Manager Novapet Antonio Ramos, Head of Packaging Division Novapet our products. And we have concrete plans for expansion, not in the resin production which remains bundled in Barbastro, but for our packaging division with which we will expand in other European countries.” www.novapet.es","@ID":42}, "MATERIAL / RECYCLING 34 PETplanet insider Vol. 17 No. 06/16 petpla.net RECYCLING S P E C I A L which is about 40% lower than the industry’s standard figure,” explains Ronald Fairbanks, General Manager Mpact Polymers. Stage 2: Washing module The shredded flakes are conveyed to a silo of the washing module, and then precleaned in a dry mixer and the downstream zigzag sifter, to remove light-weight fractions like dust or label residues. They come into contact with water for the first time in a pre-washer, where they are treated at moderate temperatures. Jets and mechanical friction remove any ingrained dirt particles. In the downstream caustic bath, any remaining labels and adhesives are detached in a mixture of hot water and caustic. The caustic solution used is prepared in a two-stage caustic treatment system featuring the Parcival filtration system, enabling it to be subsequently re-used in consistent quality. Then, the polyolefins are removed from the flow as well, that is the material of the bottle closures. This is accomplished using a sink-float process in a density separator: the polyolefins float to the top, while the heavier PET falls to the bottom. This is said to ensure very good flake quality. These PET flakes are then rinsed again with hot water in several stages and mechanically and thermally dried using hot air. Finally, in the washing module, any remaining residues of metals are separated. At the same time, the flakes are sorted by size using three sifters, and any flakes that are too small will be rejected. Stage 3: Decontamination module In this step, the sorted and washed flakes are treated to create bottlegrade recyclate. The decontamination modules are, for reasons of hygiene, located in a separate room with a positive air pressure. From a buffer silo, the washed flakes are first of all pre-warmed in the first heating worm, then dried in the second worm, and brought up to process temperature, which is well below PET’s melting temperature. This is followed by the heart of the decontamination module: the vacuum reactor, where migrated constituents are expelled from the materials and the intrinsic viscosity (IV value) is increased. After this treatment, food-grade PET flakes are now ready for use. It is precisely this stage that accounts for the recycling system’s relatively low energy consumption because, in comparison to other recycling processes, the decontamination module is said to work swiftly, and therefore to require less energy. In the downstream extruder, the flakes are melted, extruded through a melt filter and pelletised. There, too, the energy consumption is lower in relative terms, because the flakes are already warm and dry from the decontamination process. The crystallisation of the pellets also utilises the residual heat, and does not require any additional energy input. Once the products have cooled down, they are packed in big bags, and undergo extensive and thorough quality checks Pellets instead of flakes There were several reasons why Mpact opted for producing pellets instead of flakes as the end-product. “Flakes require higher capital investment for the preform production operation: the pre-dryers need to be duplicated for equal thermal treatment compared to pellets. Furthermore, pellets are more compact than flakes, which means lower transportation costs. When new technologies like recycling are introduced, of course you’re looking to avoid all possible risks. These advantages, particularly the lower logistical costs, offset the higher energy costs entailed by producing pellets,” explains Hunt, and Fairbanks adds: “What’s more, rPET pellets behave better than rPET flakes when mixed with virgin PET.” www.krones.com The polyolefins are removed from the flow as well, that is the material of the bottle closures. This is accomplished using a sink-float process in a density separator: the polyolefins float to the top, while the heavier PET falls to the bottom. The heart of the decontamination module: the vacuum reactor, where migrated constituents are expelled from the materials and the intrinsic viscosity (IV value) is increased.","@ID":36}, "INSPECTION 42 PETplanet insider Vol. 17 No. 06/16 petpla.net Early preform quality inspection avoids waste Exact colour match Due to colour deviations in preform production, large amounts of waste can be produced as the quality inspection is done mostly at the end of the production line and deviations are detected at this late stage. As a result, entire batches can turn out to be unusable or are substandard when delivered. In the worst case, a product recall can happen, causing substantial costs and seriously damaging a company’s image. An exact and objective inspection of preforms is necessary, ideally immediately after the production of the product. The space in the production line is however very limited and for an additional inspection system there is little or no floor space. A manual inspection is not possible either as the usual gauges are not suitable for use in the production environment. An option to meet inspection requirements at this stage however is the use of the ColorWatcher Integrated. The newly developed inspection system of the German company Intravis is made to detect and display exact and reliable data about the colour deviations of the preforms immediately after their production. The ColorWatcher Integrated is a measuring and warning system that inspects transparent and translucent preforms. It does not require its own floor space but instead is integrated into the injection moulding machine, inspecting every shot. Its camera is located above the tooling plate where the preforms are cooled down directly after the injection process. Here, it takes images of the top row of preforms. The steady position of the inspection objects ensures an exact and reproducible measuring condition and accordingly exact measurement. The L*a*b* values of the images are calculated and immediately compared to the existing reference data indicating if they deviate from that reference colour. The values are indicated before the next shot is produced. This is a clear benefit for users: they can intervene in the production process before more shots with defective preforms are produced. With many vision based quality inspection systems, the user has to program the software to adjust it to their own requirements. This, in turn, requires a deep understanding of the system, resulting in an undesirable interruption to daily production. This step is unnecessary with the ColorWatcher Integrated through its userfriendly and self-explanatory software. Preventing defects For years, the goal of quality inspection in the plastic packaging industry was to sort good parts from bad parts and eject the latter. Delivering flawless quality meant setting the sorting loop in a way that all defective objects were ejected. But the more inaccurate a sorting system works, the wider the setpoint has to be chosen. Consequently, more and more objects are sorted out that would still be defined as good by the human eye and definitely could be sold. Especially when good-bad-decisions are made upon a small amount of data resulting from insufficient camera resolution, the ejection might reach a high rate. Today’s inspection systems go a step further: They create extensive statistics and display them. The collected data is not displayed in pure numbers but visualised in clear diagrams. Deviations and the most frequent defect types of the specific production lines are apparent at a glance. This reveals a lot about how defects develop and where they most occur. But a basic problem remains: Defects still occur and flawless batches are only possible if bad parts are ejected. To avoid this, the ColorWatcher Integrated has the goal of preventing product defects from occurring in the first place. Its software gives a warning signal as soon as a predefined limit in the colour range is reached or When it comes to preforms, even the smallest defects and deviations might have a fatal outcome when the preform is processed into its final product. To avoid this from the start, a thorough inspection is essential. Among the most obvious product characteristics to be inspected is the colour. A newly developed inspection system by German company Intravis detects colour deviations immediately after the preform production. The ColorWatcher Integrated is implemented directly into the production machine, inspecting preforms immediately after they are produced.","@ID":44}, "MATERIAL / RECYCLING 20 PETplanet insider Vol. 17 No. 06/16 petpla.net Efficient chemicals and technologies for PET recycling Finding the optimal process CHT/Bezema Group has nearly 2,000 staff members employed by 20 companies and was established at Tübingen, Germany more than 60 years ago. The group has focused on special chemicals. Since 2008, the know-how and years of experience in textile finishing have been successfully transferred to mechanical PET recycling. The recycling business of CHT/ Bezema Group has become an established player worldwide in the interesting PET recycling market in supporting the PET recycling process with sustainable and efficient process aids. Intelligent process aids for quality improvement and process optimisation The consistently high quality of a recycled product as well as optimisation throughout all process stages are crucial pre-requisites for a successful PET recycling company. The requirements differ from country to country and from recycler to recycler. Finding the optimal process solution is a challenge every day. Bottles from a deposit system Dirty bottles (no deposit system) Cleaning that is visible The cleaning additives of the Tubiwash range remove adhering soilings and prevent deposits from sticking to machine parts in the aqueous cleaning stage of PET recycling. In addition, Tubiwash is able to reduce the consumption of energy and caustic soda in the cleaning process. PET-flakes after roasting test (220°C, 30min) cleaned without Tubiwash/with Tubiwash (right) Reduced foam formation leads to better machine operation In the recycling process of PET there is mostly a foam formation which prevents an optimum machine operation. Therefore a defoamer is often indispensable and helps by diffusing into the foam lamellae in order to destabilise and finally destroy them. The applied quantity can, however, be reduced to a minimum by using the effective products of the Tubifoam range. They inhibit foam occurring in the various process stages ensuring thus an optimum machine operation. Product solutions for water recycling such as e.g. ultrafiltration also belong to the groups’ portfolio. Perfect separation helps to recycle the different polymers effectively In the PET recycling process the PET needs to be separated from other polymers such as e.g. PP or PE. This procedure is mostly done by means of flotation where air inclusions on the PET flakes may be dramatically impaired this separation. Specialised flotation auxiliaries, namely Tubiwet products, supersede the air adhering to the flakes and facilitate thus a sinking of the PET flakes in the flotation bath. Thus the different polymers can be recycled separately with a high varietal purity. Some of the defoamers of the Tubifoam range are not only used for inhibiting foam but also as flotation auxiliaries. This helps reduce the number of products used in the PET recycling process. Air adhering to the PET-flakes Cleaning and more The consistently high quality of a recycled product as well as optimisation throughout all process stages are crucial pre-requisites for a successful recycling company. Therefore besides a broad product range of intelligent cleaning additives for quality improvement and process optimisation CHT/Bezema offers several measuring methods for controlling the quality of cleaned PET flakes. It is a valuable part of the service to support the PET recyclers worldwide by well-qualified technical service team. CHT/Bezema focuses on producing sustainable process aids. Products of the CHT/Bezema Group used in the recycling process can be eliminated from the wastewater and are thus environmentally friendly. www.cht.com RECYCLING S P E C I A L","@ID":22}, "CAPPING / CLOSURES 46 PETplanet insider Vol. 17 No. 06/16 petpla.net CAPPING / CLOSURES 46 E n g i n e e r i n g 4 . 0 For machinery and equipment manufacturers the score is 4:0. The 4th industrial revolution is on the world’s digital agenda. Laying the foundations of plastics production in the future. Aiming for one goal: to network and interlink production processes. With some 3,200 exhibitors in 19 exhibition halls on more than 171,000 sqm of exhibition space, the world’s premier trade fair for the plastics and rubber industry will once again be presenting the entire range of products and services that the industry has to offer. Everything that will move the world in the future. Plan your visit now. Y o u r K e y t o t h e F u t u r e k-online.com Messe Düsseldorf GmbH P.O. Box 101006 40001 Düsseldorf _ Germany Tel. +49(0)211/4560-01 Fax +49(0)211/4560-668 www.messe-duesseldorf.de Feltes: That is true. We are setting today a benchmark on larger all-electric injection moulding machines. Technically we could also offer up to 650t for fast-cycling packaging applications, except that the components then become so expensive that it would become uneconomical. Therefore we are using a hybride concept for such applications on the same machine basis as the all-electric ones. PETplanet: Well alright, if you have the allelectric technology at your company, you can just upscale the system relatively easily, can’t you? Feltes: We also thought this seven or eight years ago, but the durability of the machine comes into play here. All components must be matched to the greater power requirements. And it is an exponential increase, especially the generation of heat in the whole power train. For example, the ejectors could run hot during continuous operation on fast cycling caps – this requires special attention to the cooling and configuration of the choosen motors, spindles and drives. PETplanet: Why should I buy an Engel machine rather than a competitor’s? Feltes: As already mentioned, it is the parts and application expertise first of all. Together with our tool making partners, we analyse very accurately the needs and requirements of customers. We have to think in a parts-orientated way and only secondarily in terms of the machine. As the machines are fully flexible and configurable, the actual part and mould defines the machine and system solution. PETplanet: And from a technological point of view? Feltes: It’s the level of detail you are prepared to put into your development work. For the toogle levers and in the entire machine, we have closedloop lubrication systems. This always guarantees a permanent and optimal lubrication situation of bearings, spindles and joints and it is a guarantee for constant low energy usage at lowest possible friction and wear. Or, specifically at the spindles, the ball bearings have an outstanding efficiency factor of 90%, which eliminates friction and reduces the energy needed on each motion significantly. Overall, a state-of-the-art all-electric moulding machine from Engel can reduce energy consumption for cap production by at least 20-30%, compared to hybride ones. PETplanet: And what new things will we see at your e-cap and K-show? Feltes: At K show, we will further complete our system solutions with industry 4.0 technologies. inject 4.0 – this is Engel’s answer to the challenges of the Fourth Industrial Revolution. Engel already has solutions within the range today to support processors to enable their processes to tackle the new challenges. For example, the iQ software products continually analyse critical process parameters in order to identify and immediately compensate for deviations even before rejects are produced. While","@ID":48}]}}
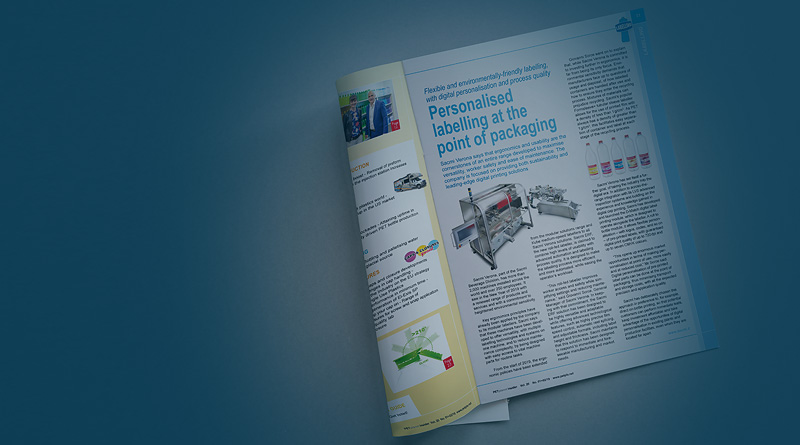