"38 PETplanet insider Vol. 17 No. 07+08/16 petpla.net .com 100815dmyL PETbottles Beverage + Liquid Food Landliebe in PET The German Landliebe Molkereiprodukte GmbH in Heilbronn has brought to the market several beverages based on milk or yoghurt. The products named Trink-Joghurt (drinking yoghurt) or Landmilch (country milk) are bottled in newly designed, polygonal PET bottles with a 350g capacity. Decorated with shrink sleeves, the bottles of the Landmilch variety are equipped with a new screw cap that removes the freshness membrane attached to the bottle top on its first unscrewing and securely holds it to the inside of the closure. www.landliebe.de Extended product range The brand “Vio” of the Coca-Cola group that created a lemonade range some time ago under the name “Vio Bio-Limonade,” has extended this to one new variant. The organic lemonade with15% fruit content contains lemon, currants, and grapefruit pink and white. The fruits come from 100% organic controlled cultivation. The lightly tapered PET bottle with grooves running around it consists of 14% renewable raw materials, 35% recycled plastic, and is 100% recyclable. A matching colourful screw cap with a guarantee strip and a sleeve label complete the packaging. www.biolimo.vio.de/produkt.html Organic caramel sauce The German company KHS-Food GmbH is marketing 300g of an organic caramel sauce in German supermarkets; it is free from fat and gluten, avoids artificial colours and conservatives, and does not use any industrial sugar. The product uses high quality agave and rice syrup and is thus healthier with respect to sugar metabolism. The manufacturer is the French company St. Dalfour. The sauce is filled into a sleek, clear squeeze-bottle with selfadhesive form labels at the front and back. Before first use, the hinged lid with its integrated silicon valve has to be screwed off and a freshness membrane must be removed. www.stdalfour.com www.khs-food.de","@ID":40}, "TRADE SHOW PREVIEW 32 PETplanet insider Vol. 17 No. 07+08/16 petpla.net either. The equipment from China was cheap but its results were very patchy, and half of the preforms were rejects. After talking to the bottler I took management of the situation, and contacted the local representative of Husky in Ahmedabad, who invited me to the K’ trade fair in Düsseldorf to take a look at their fully electrical 32 cavity H-PET AE 180.” The in-depth inspection of the machine at the trade fair stimulated the idea of independent manufacturing of preforms. Ahimsa and Husky agreed to install the machine in India but the project encountered some initial problems. Fully electrical systems were, at the time, new to everyone, including Husky. The difficulties were rooted in the reality that a machine that had been developed under European or Canadian conditions was suddenly exposed to the 45 degree heat and 95% air humidity of Gujarat. The Husky team that had developed the machine, consisting of Alex Chen, Mark Lee as well as some technicians and software developers, came to the Ahimsa plant and spent two weeks solving the problem, with a software patch. This patch eventually resulted in savings of almost 80% in worldwide service costs, Mr Gandhi was advised. Manufacturing started in October 2011, initially with an Alaska Mould for standard 28mm neck, 19.6g preforms for 1l PET bottles. “The 21g preforms were popular here at the time, which is why we caught the market’s attention. Our slightly different design raised our profile in the lightweight sector, although we had begun manufacturing in something of an unconventional way,” he recounts. “I didn’t have a particular customer in mind when I started; I just started production. The basic idea was and remains that, as a matter of principle, we want to be able to deliver the volumes the customers want, no matter how small.” It was clear to them from the start that it wasn’t going to be comparing itself with the big competitors. Coca-Cola, PepsiCo and so on already had suppliers, so Ahimsa’s declared focus, from the start, was on the market for the B and C brands. The concept proved to be successful. “I approached small companies with my preforms by cold-calling them and, in the summer of 2012, we had completely sold out. People appreciated our products, as the ability to access preforms made on Husky machines in such unit volumes was new for this group of customers. In addition to this, approaching the decision-makers was easier when compared to the global brands. I ultimately registered my own brand label, with the name Greenpet.” Over time, the customers for smaller-volume bottle sizes have come to include bottlers such as Bisleri and Rail Neer, the brand of water sold on the Indian Railways. After ten months of successful production Mr Gandhi opted to add a second Alaska Mould for 9.7g preforms for 200 ml bottles, which saw the company extending the scope of its operations to include all of India. “We wanted to continue supplying everyone without entering into a fixed contractual partnership,” explains Gandhi. “A meeting with the then Vice President of Reliance led me to doubt my project briefly, however, because he told me that soon I wouldn’t even be able to pay my electricity bills without fixed contract partners. Luckily, he proved to be wrong.” In 2013, Ahimsa invested in another Husky H-PET AE 230 and began extending its customer portfolio to include OEMs. In addition to water and CSD bottlers, Ahimsa currently supplies producers of fruit juices, dairy products, alcoholic drinks, cooking oils and pharmaceutical products with preforms in sizes including 28 mm PCO1810/1881, CTC29/21, 38 mm multilayer, and so on. India’s trend towards small bottles of up to 600 ml in the drinks segment is stronger than ever and currently accounts for around 75% of the market; volumes from 750 ml to 2 l are only estimated to have a 10% share. Looking at the trends, Mr Gandhi is certain of one thing: “We can see a change taking place in the Indian market right now, with the major PET manufacturers recognising their potential and becoming increasingly open to focusing on the smaller brands more strongly.” www.greenpet.in","@ID":34}, "CHINA EDITOUR 9 PETplanet insider Vol. 17 No. 07+08/16 petpla.net SPONSORS The China Road Show Stretch blow moulding and filling machines Assembly line production May 19, 2016, Sidel, Beijing We met: (f.l.t.r.): Laurent Bousselet, Industrial Operations Director; Alexander Büchler, PETplanet; Tammy Li Vice President of Sales, Greater China and Marilyn Chua, Communications Director. Sidel owns two production sites in China. Shanghai is the home of the mould shop together with the packaging design team (see PETplanet Insider 5/2007) whilst Beijing is the group’s China headquarters with the machine production halls. In addition, there are other sales offices throughout China. We visited the facilities in Beijing. Sidel’s buildings are located directly next to its sister company Tetrapak. 40.000 m² halls have been in operation since 2008 to produce the product range for PET machines by Sidel and Gebo Cermex. In China, Sidel constructs machines and systems exclusively in accordance with European standards. The company deliberately does not use specialist Chinese machines that have an inferior design. Industrial Operations Director Laurent Bousselet shows us the most advanced stretch blow moulding production line in the world. Here, the machines are constructed on an assembly line. As the machine base moves through the production line on the sliding platform in stages, more leaving the plant are Combi machines. Occasionally single machines are produced. In total, there are more than 300 Sidel complete lines in China, ⅔ of which bottle water. In recent years, Sidel has installed a few noteworthy systems in China, such as for example a CSD complete line for Coca Cola capable of 55,000 bph. In addition, over 70 aseptic lines by Sidel are running in the region. In the hot-fill sector, in addition to its usual 20,000bph capacity, the company is now also offering 48,000 bph. As the hot-fill bottles have over time also become lighter, hot-fill is becoming competitive once more to aseptic processing. One of the biggest problems in China is food safety. Thus, Sidel is anticipating a decisive market advantage for the coming years with Predis, the dry sterilisation of preforms for aseptic machines. Using no water and almost no chemicals, the technology not only protects the integrity and safety of the end beverage product, it generates substantial cost savings as well. The usual wet sterilisation areas with their high water consumption will no longer be needed. The company also wants to enter the market in the next year with a technology for edible-oil bottles of 1 to 3l, for which the handle will be integrated and the expensive manual grip attachments will no longer be needed. Sidel too is coming to terms with the stagnating beverage market in China. Its strategy is a strong local service team aimed at providing good customer care and helping the customer to continue to bring in innovations to counter the increasingly tough market conditions. www.sidel.com components arrive from the right and left until the machine is completed. In 2012 Sidel invested in a heavy parts centre, in order to be able to produce large formatted parts inhouse. Thus machine frames and carousels up to 6 m in diameter are now produced in the factory. Previously, these components had been delivered from France or ordered from suppliers in the region. A few key components are still produced in France. Relatively new for Sidel in China is the retrofitting of machines. Laurent has allocated a separate area in the hall for this purpose, in which older machines of the first or second generation are refurbished. Tammy Li told us that around 99% of the machines","@ID":11}, "PETpatents www.verpackungspatente.de 40 PETplanet insider Vol. 17 No. 07+08/16 petpla.net Level indicator Europ. patent no. EP 2927141 A1 Applicant: Yoshino Kogyosho Co. Ltd., Tokio (JP) Date of application: 30.11.2013 The structure, design and process of manufacturing a preform and a PET bottle with an integrated opaque or transparent window for the level indicator is described. It is manufactured by the process of biaxial stretch blow moulding. Plastic container Swiss patent no. CH 707262 A2 Applicant: Alpla Alwin Lehner GmbH & Co. KG., Hard (AT) Date of application: 5.3.2013 Plastic container with a base that is designed and formed especially for products with only slight excess pressure. Form of base Intern. patent no. WO 2014 / 083255 A1 Applicant: Sidel Participations, Octeville-sur-Mer (FR) Date of application: 13.11.2013 To ensure stability of a plastic bottle whilst saving material at the same time, the form of its base is of critical importance. Several grooves, depressions, graduations allow this actual contrast. Grip for bottle Intern. patent no. WO 2015 / 166046 A1 Applicant: SIPA, Vittorio Veneto (IT) Date of application: 4.5.2015 Separately moulded, two-part grip that is placed and fixed round the tampering of a large volume plastic bottle in order to improve the handling of the bottle. Plastic bottle Intern. patent no. WO 2015 / 166619 A1 Applicant: Yoshino Kogyosho Co. Ltd., Tokio (JP) Date of application: 2.3.2015 The base of a plastic bottle for hot filling / products with excess pressure is designed in such a way that it deforms towards the inside of the container when the internal pressure is reduced. Bottle with facets Intern. patent no. WO 2015 / 187761 A1 Applicant: Procter & Gamble Comp., Cincinnati (US) Date of application: 3.6.2015 Plastic bottle with a number of facets at the surface. The outer shape of the bottle immediately attracts attention on the shelf due to its reflective properties. However, the label or the printing can be easily read upon closer inspection.","@ID":42}, "BOTTLING / FILLING 27 PETplanet insider Vol. 17 No. 07+08/16 petpla.net V I S I T U S A T 2 0 1 6 H A L L 1 1 , B O O T H A 5 8 W W W . I N T R A V I S . C O M Integrated Inspection for the Plastic Packaging Industry. LabelWatcher® Inspects the entire label for presence, identity, position and quality CapWatcher® Inspects the quality of the caps after production or before capping Inspects for the correct placement of closures Inspects bottles inside the stretch blow molding machine CrownWatcher® PetWatcher® Mac Bullet Valve manifold drop in solution in situ (in black on the picture) maintains low leak rates (1 cc/min), can manage different gases and liquids; and provide high flow in a compact footprint. Mac Valves further asserts that it will deliver consistent pulse performance over cycle life; accurate liquid dispensing; and good dosing repeatability. As well as its main facility in Michigan, Mac Valves has sales and manufacturing facilities in a further four locations, in Europe, Asia and New Zealand. MDN (Mac Distributor Network) services customers all over the world. www.macvalves.com","@ID":29}, "BOTTLING / FILLING 18 PETplanet insider Vol. 17 No. 07+08/16 petpla.net Decentralised drive solutions in beverage production Energy efficient drive technology Based on an article by Gunthart Mau, trade press officer, SEW-Eurodrive FILLING SPECIAL At Hansa-Heemann’s beverage bottling site in Bruchsal, Germany, SEW-Eurodrive decentralised drives take on a wide range of transporting tasks. For a planned increase in capacity, the bottling plant decided on MGF..-DSM integrated gear motors from the Movigear mechatronic drive system product family. The water bottled by Hansa-Heemann AG comes from 140 to 150 m deep wells which go back 6,000 to 8,000 years, an important criterion for its purity. “We’re supplying the water at about 13.5 °C,” explains Thomas Herzog, head of the HansaHeemann plant in Bruchsal. “It retains its temperature throughout the whole process chain up until bottling.” The water is filled into 1.5 l and 0.5 l PET bottles. “On our production lines, we produce mineral water and refreshing drinks – lemon and orange lemonade, cola, cola-mix, and apple spritzer,” Herzog continues. The production runs in a three-shift operation. During one of the 52 weeks of the year, the planned maintenance of each bottling line is carried out. The prerequisite for this high capacity production is the drive technology from the drive supplier SEW-Eurodrive. The relationship between HansaHeemann and SEW-Eurodrive is longstanding. The collaboration began in 2006. In March of 2007, the first lines were fitted with Movimot decentralised drive units. SEW-Eurodrive was one of the first companies to build these AC induction motors with integrated frequency inverters. This decentralised SEW technology has proved its worth to date. These drives have been in operation now for eight years, and that around the clock. That is up to 8,000 operating hours a year. When converted to a one-shift operation, this is equivalent to a running service of 24 years. A few years later, production was to be extended. Thanks to the good experiences with the decentralised technology, Hansa-Heemann stipulated SEW-Eurodrive drive technology at the call for bids for the new bottling lines. The first preliminary talks occurred at drinktec 2013. In the same year the project was assigned. And since March 2014 the new lines are running with MGF..-DSM integrated gear motors from the Movigear family in combination with a control cabinet converter. This system is especially suited for use in beverage transport systems and already meets the requirements for the current highest class of energy efficiency for IE4 motors today. Since 2014 the new lines are running with MGF..-DSM integrated gear motors from the Movigear family in combination with a control cabinet converter. The water is filled into 1.5 l and 0.5 l PET bottles. The MGF..-DSM integrated gear motors from the Movigear family meet the requirements for the current highest class of energy efficiency for IE4 motors.","@ID":20}, "BOTTLING / FILLING 22 PETplanet insider Vol. 17 No. 07+08/16 petpla.net FILLING SPECIAL MHT MOLD & HOTRUNNER TECHNOLOGY AG Your Machine - Our Solution 1996-2016 20YEARS Booth 1C35 Preform & closure decontamination Thanks to an integrated blow module, the containers and the products are aseptically treated throughout the entire process. After preform decontamination by means of gaseous hydrogen peroxide, the block produces the containers and fills them in aseptic mode. When compared to a conventional aseptic filling line, this line also dispenses with a sterilewater UHT and a hygiene centre, and does not consume any water in production mode. With the aid of evaporated hydrogen peroxide, the closures are sterilised in next to no time, and then passed through double sorters. After that, they are run through an inspector featuring high-resolution camera technology. A downstream closure buffer then ensures sufficient buffering capacity. This is followed by a hygienic-design aseptic closer, in which every closing element has its own separate servo-drive. Finally, the bottles leave the Contiform AseptBloc via a transfer tunnel. Aseptic filling system for still and carbonated beverages The filling valve possesses a magnetically extendable base, which is pressed onto the bottle’s neck finish when carbonated products are being filled. With still beverages, the base is retracted, the valve is kept at a distance from the bottle and the still beverage concerned is filled in full-jet mode. The valve guarantees accurate fill quantities plus a high degree of microbiological safety, and is very gentle on the product. Little time and energy are needed for the cleaning routine. VFJ stands for volumetric filling (V) with accurate control of the inflowing quantities of liquid by means of an inductive flow meter (F) in full-jet mode (J). Non-contact, centred filling in fulljet mode enhances the filling procedure’s microbiological safety. Two different filling speeds are said to guarantee an optimum flow behaviour. Switching from one speed to the other is performed using membrane valve technology, which means it is turbulence-free. the start. It now bottles up to 15 different products per week. Its maximum speed is 36,000 containers an hour. A choice of six mould sets are available, for blow-moulding both round and square containers. Five of these (in sizes of 1.00l, 1.5l and 2.0l) have been designed for still beverages, and one mould is used specifically for blow-moulding a bottle later to contain carbonated beverages. But not every product change-over inevitably necessitates an intermediate rinsing routine. Although the continuous running time has been acceptance-tested at 120h, in the case of the shell-and-tube heat exchanger JFA performs an intermediate cleaning routine after 72h, just to be on the safe side – especially when products with a pulp content are being handled. www.krones.com www.jusdefruitsalsace.fr Daniel Eva (right), who was the longserving factory manager in Sarre-Union, and Jérôme Buhler (left), his successor and likewise a long-term member of the JFA team concur: “For us, dry aseptics are the process of the future.”","@ID":24}, "CHINA EDITOUR 8 PETplanet insider Vol. 17 No. 07+08/16 petpla.net SPONSORS The China Road Show Year by year in China May 25, 2016, Demag Plastic Group, Beilun We met: Stephan Greif, Vice President China Demag in China has been producing injection moulding machines since 1999. At that time, Stephan Greif set up production close to Ningbo. Despite Demag’s many takeovers in the last sixteen years, Stephan is still holding the reins today and is continually developing the Chinese business for Demag. capacity for up to 1,500 machines a year. At the moment, 500 machines a year go through the production halls. “We were the first European injection moulding machine manufacturers to set up machine production in China” says Stephan, “Continuity is our recipe for success.” In addition to continuity, the transformation of the Chinese plastics industry is playing into the hands of the Nurembergers. The high-end segment, the high quality area with customised machines, is increasingly getting bigger at the expense of the low-end high volume machines. Of the 45,000 machines that were sold in the year in China, 6,000 of them constitute the high-quality segment. With the production of the hydraulic machines, Demag is hitting exactly this area. Customers can order any machine with different special features just as they are accustomed to do in Europe. Up until 2009, only 4% of the Demag machines were made for the packaging sector, such as caps, cups, or handles for oil bottles; today that trend has increased to14% i.e. 70 machines. “We are offering the fully-hydraulic version up to about 5s cycle time - for everything below this, we recommend the El Exis SP high speed machines from Germany,” says Stephan. For packaging applications, Demag China is now offering a system with a bigger hydraulic pump and hydraulic accumulators in order to be able to achieve faster injection times. An all-electric machine from Beilun is not on the cards for the foreseeable future. In contrast to the parent plant in Schwaig, Beilun is an assembly only facility. There are 42 injection moulding machine manufacturers in the region, so Demag can fall back on the well-equipped supplier industry. Stephan for instance purchases moulding parts and has them processed by the 100% Sumitomo subsidiary NSJ. The quality is so good that Demag China also purchases a few moulding parts for Demag Germany. www.sumitomo-shi-demag.eu “We have always been too far away and too small to be a major target in the takeover game,” Stephan assumes this is the reason for Demag China’s independence. Only last year he had inaugurated a new plant for the fourth time with 27.000m² of production space, paid for by their own funds, without financial support from Germany or Japan. This provides Stephan Greif (right) and Alexander Büchler in front of a Systec 650 C 3300 with a flip cap tool and a parts removal system by Pushmold.","@ID":10}, "LABELLING 29 PETplanet insider Vol. 17 No. 07+08/16 petpla.net Three Soluta labellers installed Recently Gernep installed three Soluta machineries at Hela Gewürzwerk Hermann Laue GmbH in Ahrensburg, Germany. Gernep provided Hela with a full sales and commissioning service, from bottle conveyancing right up to the filler. Thanks to the close cooperation between Hela and Gernep engineers, the line start-up was rapid and problem-free. Internationally-known brand Hela is famous for its best-selling spicy ketchup. Fo r t he na t i ona l and international market 28 million units per year are produced. In Germany Hela is the market leader in this segment. Hitherto, printed plastic bottles were used by the manufacturer in Ahrensburg, but this incurs high warehousing costs due to the variety of bottles used for the different products. There were also high material costs because of the print process used by the bottle maker. This prompted the company to switch to blank bottles which would then be labelled during the production process. to the production hall in Barbing, Hela ordered three machines in June 2015. These machines were delivered on the 15th of October 2015 and gradually installed and commissioned by the 3rd of November 2015. A Gernep engineer then remained for a further week to ensure the machines were correctly levelled and to provide on-site training for the Hela operators. Alexander Stag felt very comfortable with the way the project was handled. Minor difficulties and problems were quickly and efficiently resolved by the Gernep engineers. Production process Empty bottles are orientated for labelling by a mechanical process controlled by a cam. Transparent plastic wrap-around labels were used. Two adhesive stations on each machine ensure that operations are not interrupted whilst the empty label roll is exchanged. The switchover process is fully automatic. The rotation of the bottle plate is controlled by servo drive, for which Gernep is well-known. In the frame of the labellers there is a high definition camera integrated to check the quality of the wrap-around labels. Any faulty bottles are ejected at the machine outlet. From the Soluta machine the labelled bottles are transported to the filler. When different bottle formats are required, Hela will be supported by a technician on site. In addition the Soluta machine is connected to a remote maintenance and control system which is controlled by Gernep to provide direct support. Space-saving The round design of the machine table is comfortable for the operator. It not only saves space, but it is also easier for the operator because the self-adhesive stations can be removed completely. www.hela.eu Out of five competitors, the Barbing-based specialist manufacturer of labelling machinery was selected. Hela ordered three Soluta 12-784 2SK SD machines for the ketchup production line. All the machines have the same design and are capable of handling formats from 300 to 800 ml. Capacity ranges from 7,000, 10,000, or 12,000 bph depending on product type. Project timeline Alexander Stab, Technical project manager at Hela takes up the story: “We were introduced to Gernep by an independent machinery salesman. We opted for Gernep machinery because of the excellent customer service offered by the German machine manufacturer.” After a test phase, including a visit Alexander Stab, Technical Project Manager at Hela: “We opted for Gernep machinery because of the excellent customer special services offered by the German machine manufacturer.”","@ID":31}, "MARKET SURVEY 23 PETplanet insider Vol. 17 No. 07+08/16 petpla.net Preform equipment 07+08/2016 MARKETsurvey Preforms Filling equipment Resins / additives Preform / stretch blow moulds Caps and closures Preform and single stage machinery Bottle-to-bottle recycling plants Compressors Closure systems Two stage SBM machinery Preform and single stage machinery This issue features two market surveys: the first covers preform systems, the second relates to single stage machinery. Please have a look at the company’s new developments! The participants are: Cypet Technologies, Unique Injection Molding Systems Co., Nissei ASB Machine Co., Sacmi Imola, Milacron MoldMasters Europe GmbH, Sipa SPA, Husky Injection Molding Systems and Netstal-Maschinen AG. Although the publisher have made every effort to ensure that the information in this survey is up to date, no cliams are made regarding comlpeteness or accurancy. Company name Cypet Technologies Ltd Unique Injection Molding Systems Co., Ltd. Nissei ASB Machine Co., Ltd. Milacron Postal address Telephone number Web site address Contact name Function Direct telephone number Fax E-Mail Lefkosias 45, 2540 Dhal Nicosia, Cyprus +357 22 610 700 www.cypet.eu Mr Constantinos Sideris Director +357 99 693 923 +357 22 610 800 [email protected] No. 19 Shenzhou Road HuangPu District, GZ, China +86 20 8226 5488 www. unique-pet. com Ms Corrine Chen Marketing Manager +86 20 8226 5488 817 [email protected] 4586-3 koo, Komoro-shi Nagano-ken, 384-8585 Japan +81 267 23 1565 www.nisseiasb.co.jp Mr Paul Atkin Section Manager, Marketing Group +81 267 23 1565 +81 267 23 1564 [email protected] 428 Newburyport Turnpike Rowley, MA 01969, USA +1 978 238 7100 www.milacron.com Mr Sam Michael Director of Sales - Systems +1 978 238 7167 +1 978 238 7171 [email protected] Preform injection moulding systems Machine model number / name PC-S-2 PC-S-4 PC-S-6 PC-S-8 UPET500 PM-70/65NII, PM-70/111N, PM-170/111M M-150 PET M-300 PET M-500 PET Number of cavities (min/max units) 2 4 6 8 6 to 144 6 to 48 Up to 60 Up to 96 Up to 160 Maximum individual preform weight 750 750 500 375 55G 240g Max resin through-put (kg/h of PET) 75 150 175 200 860 250 approx. 675 1,150 Standard features (short description / keywords) Preform moulding systems with intensive post-cooling Efficient, energy saving and high precision Vertical clamping, built-in preform after-cooling stations, extremely compact Complete high performance preform moulding systems, hybrid design for energy savings, compatibilty with legacy moulds, fast cycle times and low operating costs, monolayer and multilayer preforms Options / special features (short description/keywords) Ideal for thick-wall preforms for large bottles 5-30 l High performance and stably produced Outputs are tailored to ASB's own range of 2-step blowing machines for hotfill application; PM-170/111M is designed for bottle and jar preforms with capability of neck size up to 120mm iCool & iFlow technologies","@ID":25}, "BOTTLING / FILLING 13 PETplanet insider Vol. 17 XFORM 500 ENTERS ITS THIRD GENERATION Imagine using any preform mold in one system. At the fastest speed. The new XFORM 500 GEN3 PET preform system gives you unprecedented flexibility combined with the fastest speed and the highest running efficiency: it accepts the widest range of legacy tooling present in the market. So you can feel free to innovate and grow without penalizing your existing assets. We made it happen. Designed to adapt. Built to last. At the fastest speed. SIPA S.p.A. - Via Caduti del Lavoro, 3 - 31029 Vittorio Veneto (TV) - Italy Tel. +39 0438 911511 - Fax +39 0438 912273 - email: [email protected] www.sipa.it for PET bottles. “The technology required for this is more sophisticated,” says Nagiah. Following a carefully considered consultation process Coca-Cola Canners decided to go for a system manufactured by KHS. Especially the hot fill technology for hygienic bottling combined with an output of up to 48,000 bph had those responsible convinced. “For this demanding project we developed a system which is precisely tailored to meet Coca-Cola’s specifications,” declares Philipp Casparby, project manager for KHS Manufacturing (South Africa) (Pty) Ltd., KHS’ South African subsidiary. Like other KHS block systems, the new line covers all stages in production from stretch blow moulding through filling to labelling, packaging and palletising. The key is in the detail, however; the line also processes fruit juices with a percentage of fruit pieces. These fruit chunks must not be damaged during filling; at the same time the low filling dosage tolerances must be adhered to. The company designed a line with two precision volumetric fillers. On this the fruit pieces are first bottled with a little juice before the second filler tops up the bottles with the rest of the juice. The entire filling process makes use of hot fill technology where the content is heated to over 100 °C and then filled at a temperature of about 83°C. This ensures that microorganisms are safely eliminated. With the new line Coca-Cola Canners is able to fill up to 48,000 bph holding between 0.3 and 1.50 l. After almost two years the customer’s summary is a positive one, not just with respect to the sustainable technology but also regarding the service provided 24/7. Nagiah reveals, “we thus recently ordered two more KHS packaging machines.” www.khs.com","@ID":15}, "CAPPING / CLOSURES 34 PETplanet insider Vol. 17 No. 07+08/16 petpla.net Different applications, neck finishes for various, part 7 Closure for PET bottles & Resins PETplanet insider is publishing extracts from successive chapters of Ottmar Brandau’s “Bottles, Preforms and Closures,” which was published by hbmedia. A newly revised version is reissued under the Elsevier imprint. 4.4.2 Pilfer-proof rings and their construction 4.4.2.2 Folded band The folded pilfer-proof ring has become famous together with the development of CM machines. Because closures are already orientated after the CM process, the pilfer-proof rings can be slit and folded immediately after this operation. The IM process made this kind of construction inefficient because closures have to be unscrambled and orientated for this second operation. Nevertheless, mould costs seem to put a limit for this solution because prices for closures have become very competitive. 4.4.2.1 Preshaped band The preshaped pilfer-proof ring has become the most common one for single-component closures. This is because it is easy to produce and has a low maintenance cost on the mould. There is no limit in production speed because of the pilfer-proof ring. Such moulds can run up to 5 years without changing inserts in the moulds. The disadvantage of this construction is the limited safety in terms of resistance to tampering. Nevertheless, latest developments show good improvements also in this respect. 4.4.2.3 Inserted band The inserted pilfer-proof ring has the maximum safety in terms of tampering. This is because it obviously can be produced in a different material than the closure shell, which is optimally designed for the function of the ring. This type of pilfer-proof ring was developed for the aluminium roll-on closure and later used also for a similar construction of lined plastic closures. This three-component closure became too expensive in a very early stage and has almost disappeared in the plastic closure market.","@ID":36}, "BOTTLING / FILLING 26 PETplanet insider Vol. 17 No. 07+08/16 petpla.net PETplanet Insider takes a closer look at the Mac range of valves Filling and bottling solenoid valves from Michigan by Kay Barton FILLING SPECIAL Mac Valves, Inc, based in Wixom, MI, USA, has been developing solenoid valves since it was founded in 1948. It has had a strong focus on innovation since its inception and has amassed now over 90 patents. It began to bring solutions to converters and bottlers about 20 years ago. More recently, the company has been focusing on particular concerns of the drinks industry: reducing over and underfilling, increasing output, and cutting downtime in the filling lines. The magnetically-operated Bullet Valve generation is designed for precision actuation, in response times and flow control. Adjusting the poppet allows individual coordination of flow and uniformity in the filling process. Mac Valves says that every single valve is fully tested, in order to guarantee consistent response times and flow. Other features of the valve include minimised friction, high shifting forces and a patented balance design, to control and compensate for fluctuations. “Solenoids offer better response times and work more accurately. The sum of a few wasted millilitres for each single bottle that is over or underfilled is financially significant at the end of the year,” said Vincent Flagothier, Filling Industry Coordinator EMEA, Russia and India, who is in Belgium. “In some cases, propsays. “Updates from manufacturers often require additional modifications to the machine; these are not required for our solutions.” Mac Valves offers suitable alternatives to OEM standard components in the blow moulding and preforming sector, also. It promises greater volumetric air flow in otherwise unchanged conditions with its Iso 2 Blow Mould valves, for example. The company says that one test at a bottle-blowing plant delivered an airflow increase of 40%, with exactly the same setup. For the preformer, the 57, 67 and 92 series of valves are claimed to be reliable and can be changed without removing the distributor. Measured flow values reach up to 20,000 Nl/min. Mac Valves recently introduced a solenoid that is designed to manage both fluids and liquids: the Double Diaphragm Bullet Valve, which features Mac “lifting” solenoid technology. This configuration’s claimed unique feature is that the valve maintains a balanced design: shifting forces are consistently high and response times are repeatable regardless of inlet pressure fluctuations. Two-way and three-way configurations of the BV cartridge (9 mm, 10 mm, 14 mm, and 21 mm) are available. The company says that its D-Flex Double Diaphragm technology erly working valves ultimately ensure better output over the same amount of time.” Mac has published a case study of a CSD bottling plant that achieved savings of just under €78,000 per year, following an investment of around €59,000 in modernising its filling carousel. The savings break down as operating costs (€6,720), fifty fewer standstills due to faulty valves (€22,100), reduced syrup and water overfilling (€34,705.12) and reduced rejects due to overfilling (€14,354.55). The technical change alone thus generated savings of €71,159.67 and full return on investment (ROI) in about nine months. “The equipment can be replaced 1:1 for the existing equipment, meaning no modifications are required to the machine itself,” Vincent Flagothier 16 Stations Bullet Valve manifold drop in solution for volumetric fillers Liquid Bullet Valve 214 including D-Flex technology","@ID":28}, "TRADE SHOW PREVIEW 30 PETplanet insider Vol. 17 No. 07+08/16 petpla.net TRADE SHOW PREVIEW 30 Interview with Ahimsa Industries Ltd. March 1, 2016 We met: Mr Ashutosh Gandhi, Managing Director Mr Sanjay Agrawal, CEO Mrs Sneha Balpande, Marketing Specialist From specialist consultant to preform brand by Kay Barton Gujarat, in north western India, offers a range of support to national and international companies interested in establishing a presence in the state, and works to attract manufacturing companies in particular with attractive tax regimes. As a consequence, the state is characterised by a high density of mechanical engineering firms and PET processing companies, at both the start-up and expansion ends of the investment spectrum. The Plast India trade fair, which recently relocated from Delhi to Ahmedabad, has had the effect of greatly strengthened the regional economy. After an hour’s travel from Ahmedabad city centre we met for a scheduled interview with Mr Ashutosh Gandhi, Managing Director of Ahimsa Industries. Ahimsa has developed a business specialising in the production of preforms in small units for brands outside the realms of the multinational bottlers. A degree-educated Plastics Engineer, Mr Gandhi is the first entrepreneur in a family of academics. He began his career as a consultant to the manufacturing","@ID":32}, "MARKET SURVEY 24 PETplanet insider Vol. 17 No. 07+08/16 petpla.net Preform equipment Company name Sipa SPA Husky Injection Molding Systems Postal address Telephone number Web site address Contact name Function Direct telephone number Fax E-Mail Via Caduti Del Lavaro 3 31029 Vittorio Veneto, Italy +39 04389 11511 www.sipa.it Mr Stefano Baldassar Preform System Global Sales Manager +39 04389 11511 +39 043891 2273 [email protected] 500 Queen Street South Bolton, ON, L7E 5S5, USA +1 905 951 5000 www.husky.co Mr David Matts General Manager, PET Systems +1 905 951 5000 x 5092 [email protected] Mr Sean Hoy Director, Business Development, Beverage Packaging +1 905 951 5000 x 5148 [email protected] Preform injection moulding systems Machine model number / name XFORM 150 XFORM 300 XFORM 500 GEN3 H-PETAE HyPET Number of cavities (min/max units) 2 to 48 2 to 96 48 to 144 2 to 48 6 to 144 (in standard matrix) Maximum individual preform weight 1508/62 3000/60 156/52 Dependent on number of cavities and preform design 83g, dependent on number of cavities and preform design Max resin through-put (kg/h of PET) 580 900 1,400 448 1,470 Performance enhancement, energy efficiency, system robustness, faster controls. Standard features (short description / keywords) XFORM 500 GEN3: Reduced lock-to-lock; full legacy tooling compatibility; reduced energy consumption Cost effective, all-electric, complete preform moulding system (machine, mould, robot, full auxiliaries). Low system energy consumption, capable of ≤20,000bph depending on preform design, simple factory installation, up to 3 stage cooling take-off plate, auto lubrication, three year limited warranty Adaptive post-mould cooling, performance packages. Options / special features (short description/keywords) XFORM 500 GEN3: LongLife, XMold for ultra-thin preform injection capability, long preforms capability Integrated auxiliary controls through single machine HMI, quick mould change with split gate & magnetic platen option, stripper ring mould technology for wide mouth applications, able to produce from 30mm to 180mm neck finishes as standard 07+08/2016 MARKETsurvey Single stage machinery Company name Cypet Technologies Ltd Postal address Telephone number Web site address Contact name Function Direct telephone number Fax E-Mail Lefkosias 45, 2540 Dhal Nicosia, Cyprus +357 22 610 700 www.cypet.eu Mr Constantinos Sideris Director +357 99 693 923 +357 22 610 800 [email protected] Single stage ISBM machines Machine model / number K 12 K 16 K 28 K 38 K 53 K 12E K 19E K 30E Bottle volume (from/to in litres) 0.05 - 1 0.05 - 5 0.05 - 50 0.2 - 60 0.5 - 100 0.05 - 1 0.05 - 10 0.05 - 50 Number of preform cavities 1 - 12 1 - 12 1 - 16 1 - 16 1 - 24 1 - 12 1 - 16 1 - 24 Number of stretch blow mould cavities 1 - 12 1 - 12 1 - 16 1 - 16 1 - 24 1 - 12 1 - 16 1 - 24 Max. preform / bottle weight in grams for the stated number of cavities 200 - 12 280 - 16 760 - 38 1,300 - 70 1,600 - 65 140 - 12 360 - 18 760 - 32 Hourly output based on: 0.5 litre container 1,000 1,800 2,600 3,400 4,800 1,000 2,600 3,400 1 litre container 500 900 2,600 2,600 4,800 500 1,700 2,600 1 litre wide neck container 400 800 1,600 1,600 3,000 400 900 1,700 2 litre wide neck container 400 400 1,600 1,600 3,000 400 800 1,700 other (e.g. containers for personal care products) 500 900 1,700 2,200 3,200 900 1,700 1,700 Machine footprint / space requirement (LxWxH in metres) 4.9x1.5x3.6 5.3x1.7x3.8 8.0x2.0x4.0 8.8x2.2x4.2 9.7x2.3x4.3 5.4x1.6x3.7 5.5x1.9x4.3 7.4x2.4x4.5 Special features (short description/keywords) K 12, K 16, K 28 K 38 & K 53 are servo-hydraulic, energy-saving models K 12E, K 19E & K 30E are all-electric","@ID":26}, "BOTTLING / FILLING 14 PETplanet insider Vol. 17 No. 07+08/16 petpla.net A single system for blowing and filling bottles for CSDs and hotfill products Flexible filling Around the world, many PET bottling companies are handling both carbonated soft drinks and hotfill drinks such as fruit juices, isotonic sports drinks and teas. To do this, they generally choose lines that are configured for one type of product or the other. But they don’t have to. Italian company Sipa has for some time been offering filling lines that can handle both types of product, with change-over times of just a very few hours. The third-generation SFR Evo3 rotary stretch-blow moulding machine and the Flextronic C multi-product volumetric filling monobloc are designed to offer more added-value than ever. According to Sipa, the ability to blow and fill diverse types of container on a single line has been made without compromising any performance characteristics of the line. The latest generation unit is said to be fast, flexible and cost-efficient and to be easier to convert from production of hotfill to coldfill containers than its predecessors. The Flextronic C is suitable for filling CSDs, still and sparkling mineral waters, cold- and hotfill juices. The principal differences between the lines for producing and filling the products lie in the bottle blowing unit, in the filling station and in the unit that prepares the product prior to filling. Blowing equipment There are important differences in the designs of CSD and hotfill (HF) drinks bottles - and hence also in the way they are produced. HF bottles are heavier than CSD bottles, since the vast majority incorporate special panels to stop them distorting as internal pressures change when the product cools down. They also tend to use wider necks: 38mm rather than 28mm. The two bottle types also differ in the base, with CSD variants generally having a petaloid base that better resists the pressure from the carbon dioxide in the drink. The blow moulds on HF lines need to be heated so that bottles can be heat-set to increase the crystallinity of the PET and thermal stability; and also reduce internal stresses and the tendency to distort. For more than ten years now, Sipa has pioneered electrical resistance heating, which makes it easier to pass from one configuration to another and which is also more energyefficient, easier to customise to different bottle shapes, more precise and responsive and safer to use, according to the company. The electrical heating circuit is incorporated into the mould shell holder; cooling water runs through circuits within the cavity walls. It is said to be easy to change moulds on the SFR Evo3 from CSD to HF and vice-versa. With new striker plates that allow rotation of the shell inside the shell holders, and with a “no tool” quick-change system for the mould base, the time needed to change each mould is little more than one minute. Furthermore, the system for changing neck size is claimed to be faster than rival systems, with “no tool” quick change spindles a standard feature. It takes only two minutes to change the neck section on each mould. “Green” ovens on the unit are big energy savers. Compared to earlier generations of oven, they could reduce electrical consumption by up to 40% while keeping process conditions stable, thanks to the use of new lamps and special materials and coatings for the reflectors. Also available are electrically driven stretching rods, which brings more versatility in fine-tuning the process compared to pneumatic drives, “green” ovens which are energy savers and Sipa ARS+ air recovery system. Filling equipment CSD filling lines require contact filling and a CO 2 circuit to pressurise the empty bottle, so that isobaric filling can be carried out. HF systems, on the other hand, work with gravity fill and there is no need to control the pressure in the bottle during filling, which takes place at atmospheric pressure. What they do require, however, is tight control over the filling temperature: recirculation through the filling valve is needed to reach and maintain the correct temperature prior to filling and during line stops, by means of a separate recirculation circuit. All valve components are designed to withstand temperatures of up to 100 °C. With the Flextronic C filling valve, the company believes it has achieved the task of combining all the requirements for CSD and HF drinks filling into a single, compact design. This provides the user with a considerable extra level of flexibility in their filling operations. A further advantage of the filling valve is its ability to handle pulpy products, not only in single stream configurations but also in double stream, for higher fibre and pulp contents that require the use of piston fillers. FILLING SPECIAL","@ID":16}, "TRADE SHOW PREVIEW 33 PETplanet insider Vol. 17 No. 07+08/16 petpla.net Interview with Shyam Plastic Machinery March 2, 2016 We met: Samir V. Khakharia, CEO, Shyam Plastic Machinery Chetan V. Khakharia, CEO, Shyam Plastic Industries Keeping up with the customers by Kay Barton Samir V. Khakharia in front of one of his newly assembled machines Ahmedabad-based machine-building firm Shyam Plastic Machinery has been active in the development of plastics processing technology since the early 1990s. Over this time it has experienced consistent growth at rates matching those of its regular customers. As we were interested in finding out more about its past and its plans for expansion, we met with this family-owned company in its home city. Mr V. A. Khakharia is the original founder and the father of our interviewees: Samir V. Khakharia, CEO of Shyam Plastic Machinery, and Chetan V. Khakharia, CEO of Shyam Plastic Industries. The company started out in 1993 at an 800m2 site with the construction of extrusion lines for PVC hoses, with which it remains involved to this day. It started its second line of business in PET machines in 1997, in response to the then dramatic fall in the price of PET, whose attractiveness as a material was already clear. Shyam started by developing and constructing hand-operated two-cavity PET blow-moulding machines with a maximum blowing pressure of 10 bars and a capacity of 500-600 bph. This was followed, from year 2000 onwards, by the development of the company’s first semi-automatic machine, which also had two cavities but achieved double the output capacity. The following year saw the development of its first four-cavity machine, which boasted an output of 2,800 bph; Shyam’s current four-cavity machines have an output of 5,400bph. The company’s product range also includes the semi-automatic SP 500 H blowing machines for 40 ml to 5 l bottles with a 20mm-120mm neck; the SP 25000 H for 20 l bottles; the SP 5000 H-HF for hot-fill applications from 0.1 l to 5 l; and two fully-automatic PET blowing machines with two or four cavities. Shyam has also developed an all-electric blowing machine, which will produce bottles in the 9,000 to 12,000 bph range. This machine is currently the fastest to have been designed and manufactured entirely in India. “In 2016 we will manufacture around 60 fully automatic machines. We are currently growing at an average rate of 25%, and this year, we appear set to surpass 35%,” Samir Khakharia says. “Our primary customer group is the drinks industry. We also have customers in the area of liquid food, however, including cooking oil bottlers.” The company’s key customers include Bisleri, Parle Agro and Manpasand Beverages. While the company’s sales focus is primarily on India, recent years have seen exports to the Gulf States and African countries account for around a third of its turnover. “Around two thirds of all our orders go to our regular customers, which means that our growth very much depends on their growth,” Samir V. Khakharia explains. “To all intents and purposes we grow with them, which means we don’t necessarily have to acquire new customers.” In 2015, Shyam’s turnover hit US$ 3.85 million; in 2016, it is set to reach US$5.64 million. “We have sold 100 semi-automatic machines since April 1, 2015, of which 30 are to be used for wide-mouth jars.” Shyam Plastic Machinery currently employs 140 members of staff, of whom eight work in its development division. It completes all of its work in house. The current company premises occupy a 3,400m2 site, and multi-phase expansions are planned for the next two to five years. In two to three months’ time, production is also set to start at a second, 1,000m2 leased plot, situated 500 m away. “Although we have been presenting our firm at the K trade fair in Europe since 2004, Europe isn’t our biggest market because requirements are different here in India. A few of our machines are being used there but the numbers are very low. Nevertheless, it could still be a market for the future. Our existing customers value our service very highly, which is certainly one of the main reasons why we see our long term business here.” www.shyamplastic.com www.shyamplastic.in","@ID":35}, "imprint EDITORIAL PUBLISHER Alexander Büchler, Managing Director HEAD OFFICE heidelberg business media GmbH Bunsenstr. 14 69115 Heidelberg, Germany phone: +49 6221-65108-0 fax: +49 6221-65108-28 [email protected] EDITORIAL Kay Barton Heike Fischer Gabriele Kosmehl Michael Maruschke Ruari McCallion Waldemar Schmitke Wolfgang von Schröter Anthony Withers WikiPETia.info Doris Fischer [email protected] MEDIA CONSULTANTS Martina Hirschmann [email protected] Johann Lange-Brock [email protected] phone: +49 6221-65108-0 fax: +49 6221-65108-28 LAYOUT AND PREPRESS EXPRIM Werbeagentur Matthias Gaumann | www.exprim.de READER SERVICES Till Kretner [email protected] PRINT Chroma Druck & Verlag GmbH Werkstr. 25 67354 Römerberg Germany WWW www.hbmedia.net | petpla.net PETplanet insider ISSN 1438-9459 is published 10 times a year. This publication is sent to qualified subscribers (1-year subscription 149 EUR, 2-year subscription 289 EUR, Young professionals’ subscription 99 EUR. Magazines will be dispatched to you by airmail). Not to be reproduced in any form without permission from the publisher. Note: The fact that product names may not be identified as trademarks is not an indication that such names are not registered trademarks. 3 PETplanet insider Vol. 17 No. 07+08/16 petpla.net Dear friends of PETplanet insider, Today, we would like to make an announcement on our own behalf. Elisabeth Maria Köpke left us on June 28, 2016. The “mother” of the publishing company died after bravely fighting a serious illness. Since PETplanet’s founding 17 years ago, she has been a true stalwart of the company. Initially she campaigned tirelessly for subscribers. No-one can forget how – at drinktec 2001 – she fought her way up all the way to the board of exhibitors in order to bring subscriptions to everyone. She was always friendly and full of empathy in her approach to people. Seven years ago, she took over ad sales for the Mediterranean in her typical warm-hearted fashion. With customers, she was helpful and caring, handling any complaint with a smile and expressing delight at every order. But woe betides any customer reluctant to advertise, because then Elisa could be very demanding indeed. At the company, she was there at all times, day or night, and not only to discuss professional problems: many of us also trusted her with personal issues. These were – as everything else – in very capable hands with Elisa. In the mornings, a single look from Elisa was enough to tell her whether one was doing well or not. In this way, she not only became a good friend, but also the mother of the publishing company. Our thoughts are now with Elisa’s family, especially her children Patricia and Karsten and their families. Dear Elisa, To the very end you battled with courage and kindness, always with a smile on your face, exactly as we will remember you over all the years. Very often, you showed us the way. We will carry you in our hearts. We miss you. Farewell.","@ID":5}, "CAPPING / CLOSURES 35 PETplanet insider Vol. 17 Please order your copy at the PETplanet insider book shop: https://petpla.net/books Bottles, Preforms and Closures - A Design Guide for PET Packaging Second Edition by Ottmar Brandau € 115,00 180 pages © Copyright Elsevier 2012 * This article was published in Bottles, Preforms and Closures, Ottmar Brandau, Chapter 4.4 Copyright Elsevier 2012 You make a great product – why hide it? We’ve seen the future of canning and it’s Klear. Milacron’s Klear Can technology gives manufacturers a cutting-edge, cost-competitive alternative to metal cans for fruits, vegetables, soups, meats and other products – and it’s transparent, so you can show off your goods. Using the same machinery as metal cans, going Klear requires minimal investment. With the option to use colored plastic cans, in-mold labels, or standard labels, the possibilities are endless. Ready to see what you can do? Contact us or visit www.Milacron.com to learn more. 4.5 Resins There are mainly two resins used for closure production: PP and high-HDPE. Liners for oxygen-sensitive products contain other components (see chapter 4.3). In some applications either material may be used but others are suitable for just one. There is little price difference between the two. It is therefore important to understand the differences between these two materials for those applications where a choice exists. Both materials belong to the group of plastics known as polyolefins. They are thermoplastics, which means that they deform with the application of heat. Both materials consist of long chains of carbon and hydrogen atoms. To obtain good flow in the IM process, the weight distribution, i.e., the difference between the shortest and longest chains, is kept narrow. Both materials form a crystalline structure that must be completely melted by frictional heat in the extruder. 4.5.1 Polypropylene PP is the most widely used thermoplastic with excellent availability in every part of the world (Fig. 4.30 and 4.31). Figure 4.30 PP structure as monomer (on the top) and polymer Figure 4.31 The PP molecule","@ID":37}, "BOTTLING / FILLING 19 PETplanet insider Vol. 17 Comprehensive energy management The bottling plant’s energy management system monitors the entire energy consumption, including the processing technology in the boiler house, the cooling system and compressors, the building technology such as light and ventilation, and not least the drive technology as well. Apart from the MGF..- DSM units, bevel gear drives and worm drives with DR.. brake motors are used to drive inclined belt systems. Kuka robots are at work in the area of packaging. The drive technology in this area in turn comes from SEW-Eurodrive: planetary servo gear units, bevel gear units, and CMP.. servomotors, that are controlled by Movidrive single-axis servo inverters. In total, about 800 SEW drives have been installed at this site. For so many installed units, an effective customer service is highly important. SEWEurodrive has a comprehensive store of spare parts for service emergencies. Within a few hours, 98% of all drives can be made available from this within the shortest time. www.sew-eurodrive.de DR.. brake motors with bevel gear drives or worm drives are used to drive inclined belt systems. The drive technology in the area of packaging also comes from SEWEurodrive: planetary servo gear units, bevel gear units and CMP.. servomotors, that are controlled by Movidrive singleaxis servo inverters. Bertwin Ley, Client Advisor at SEWEurodrive (left), in talks with Thomas Herzog, Head of the Hansa-Heemann plant in Bruchsal -*5 RTGHQTO UVGTKNK\\CVKQP KP VJG +PPQ2'6 $NQƂNN 1RVKOWO NQY IGTO EQPFKVKQPU HTQO VJG RTGHQTO VQ VJG ƂNNKPI XCNXG Guards against all types of intrusion Q Minimum use of H 2 O 2 media Q 2QUKVKQPGF KP VJG JGCVKPI RTQEGUU HQT GZEGNNGPV GHƂEKGPE[ Q 2TGHQTO CPF DQVVNG EQPXG[KPI RTQVGEVGF WR VQ VJG ƂNNKPI XCNXG Learn more at www.khs.com or scan the QR code.","@ID":21}, "BOTTLING / FILLING 21 PETplanet insider Vol. 17 No. 07+08/16 petpla.net ment, we knew already that Krones was at that time developing the new process of a 100% aseptic block. The Contiform AseptBloc system premiered at the drinktec 2013 ultimately proved persuasive for us, not least in comparison to other vendors. For me personally, when it came down to it, the aseptic process from Krones was more important than the price.” Jérôme Buhler gives his reasons: “Dry preform sterilisation with hydrogen peroxide in combination with the aseptic blow-moulder – that’s simply irresistible. And besides the top-notch microbiological safety levels it provides, it also scores highly in terms of cost-efficiency: there’s no longer any need to rinse the bottles before filling them, so we save on water, chemicals and energy. In our view, dry aseptics is the process of the future.” And there was yet another plus. With the newly developed valve (see Thanks to an integrated blow module, the containers and the products are in the Contiform AseptBloc aseptically treated throughout the entire process. Variopac Pro TFS packer for 6-, 8- and 12-container film-wrapped trays, or for film-wrapped packs BOTTLING / FILLING 21 • 28mm, 33mm and 38mm screw closures • Robust and trouble free capping • Established DoubleSeal™ technology - for secure sealing performance - for better protection against micro-organisms • Slit FLEXBAND® band technology for enhanced tamper evidence • O 2 barrier and scavenging options for screw flat caps supporting longer shelf life and fresher taste • Sports closures for aseptic filling and hot filling without aluminum foil • Special closures for syrups and carton packaging Unique range of screw and sports closures designed for cold fill and aseptic application BERICAP Technology for juices, RTD teas, health drinks www.bericap.com box page 22), the filler is able to bottle both still and carbonated beverages in aseptic mode. So far, JFA has made use only of the option for filling still NFC juices, concentrate-based juices, squashes and vegetable juices in PET containers with a 38 mm neck finish. Now it still has an option available for likewise producing carbonated drinks with a fruitjuice content in future and filling these in containers with a 28 mm neck finish. It was not least for this purpose that JFA had a VarioAsept shell-and-tube heat exchanger installed, for flash-pasteurising soft drinks with a fruit-juice content, plus a second disinfection unit for 28 mm closures. Three-shift operation The new line has been working in three-shift operation right from","@ID":23}, "NEWS 7 Polymetrix seeks strategic buyer The shareholders of Polymetrix plan to sell their shares in Polymetrix and combine the company with a strategic buyer who would be able to contribute significant synergies and support Polymetrix’s development into the next growth phase, expanding its technology and service portfolio and securing sustainable business advantages. Following the spin-off from the Swiss-based Bühler Group and rebranding as Polymetrix AG in 2015, the company is ideally positioned for growth in connection with the blossoming packaging and speciality plastics market. Polymetrix will also focus on supplying technologies and integrated plants for recycling of post-consumer plastics. Outlining their decision, the shareholders of Polymetrix, the Swiss-based financial investor Cross Equity and Bühler Holding AG, stated that they have jointly decided to sell all shares in Polymetrix to an international industrial partner. Under new ownership, Polymetrix would then be able to fully exploit its values and competencies, and to benefit from a dedicated strategically oriented business environment. The shareholders are committed to selling Polymetrix to an industrial owner with a strong financial back-ground and a leading international position in the relevant market segments. Financial investors have been specifically dissuaded from bidding. Qualified investors with an interest in the acquisition of Polymetrix are therefore requested to submit their rationale and strategic fit within their business portfolio along with their bidding inquiry. In 2016, Polymetrix expects to achieve a turnover of approximately CHF55 million at sustainable double digit EBITDA margins. Polymetrix employs an international engineering workforce of more than 70 specialists. www.polymetrix.com PETplanet insider Vol. 17","@ID":9}, "Hong Kong Chongqing Xi'an Taiyuan Shenyang Qingdao Nanjing Guangzhou Shanghai Beijing Jinan Sponsors The China Road Show The worldwide round trip with 2016 is both the Year of the Monkey in Chinese astrology and the occasion of our first Editourmobil quest to sample the far-eastern culture of China. Following our successful Editours in the past few years, our voyage into the Middle Kingdom begins in Shanghai in April. We are scheduled to cover a distance of approximately 7,000 kilometres between then and October, which will be covered is a series of stages in the eastern part of the People‘s Republic - and, as always, the whole distance will be travelled by road! During our trip, we will take in the entire PET process chain and discuss facts and trends with a great variety of users from the bottling, processing and recycling industries, as well as with suppliers, toolmakers and mechanical engineers. As always, reports and reviews of all of our visits and interviews with local and global players will be published in PETplanet Insider. We will keep you right up to date on our travel experiences through near-live event coverage on our Editourblog at www.china.petpla.net. Come and join us on an incredible exploration of the Chinese PET market, right from the start. As the saying goes: (A journey of a thousand miles begins with a single step). April – October 2016 www.china.petpla.net","@ID":30}, "PETnews 6 PETplanet insider Vol. 17 No. 07+08/16 petpla.net Otto Hofstetter AG considers expansion into the international market Otto Hofstetter AG has been operating with great success since 1955, and today is one of the leading providers of injection moulding tools for the production of PET preforms and packaging. In order to consolidate this position in the market and to remain successful as a family-owned enterprise, Otto Hofstetter AG is committed to continued development. Against this backdrop, Otto Hofstetter is keen to explore new opportunities and perspectives in the global plastics market. To this end, Otto Hofstetter AG has signed a letter of intent with Korean family-owned enterprise Yudo. This agreement is intended to enable research into how and in which business areas closer collaboration could improve the position of both companies in the international business world. www.otto-hofstetter.swiss Agr International opens centre in Italy April 30, 2016 officially marked the opening of a newly expanded sales, training and service facility in Montecchio, Italy of Agr International, Inc. This grand opening event was attended by a number of Agr customers and a large representation of business associates and other key players within the Italian packaging industry. In addition, management from Agr International’s USA corporate headquarters took part in this event. Marco Palma, the director of Agr Europe S.R.L. hosted the ceremonies, featuring an extensive tour of the facility and an overview of the new capabilities and services that will be provided at this location. According to Palma, increased business in the region, especially North Africa and the Middle East, required Agr to consider additional space to handle their operations. The 1,100m2 facility includes 900m2 dedicated to service and support operations for Agr equipment and another 200m2 housing the sales offices, conference area and training centre. The centre also includes a demonstration show room that showcases Agr’s newest and most popular products, facilities for component/small equipment repair, a section for refurbishment and re-manufacturing of legacy equipment, calibration and re-certification, equipment training and an expanded parts warehouse. The opening of the new expanded service centre in Italy is one more segment of Agr’s programme to provide accessible and responsive worldwide support for Agr testing and quality management equipment. The Agr headquarters and main manufacturing facility is located in Butler, PA, USA. www.agrintl.com Athena – Husky legal battle ends Husky has abandoned its appeal of the judge’s decision released April 2016 and paid a cost settlement to the defendants – Robert Schad, Athena, Stephen Mason (former General Manager of Niigon), and Sipa. Further, Husky has agreed that it will not contest the judgement. Originally, Husky had claimed that Athena misused confidential information in designing their injection moulding systems, resulting in a patent dispute. Athena currently builds 150, 300, and 450 metric ton injection moulding machines. A new 14,400 m2 plant for just-in-time manufacturing of machines is ramping up operations. The existing 3,700m2 building houses the head office including sales and customer services. The simple and flexible machine platform is said to feature energy efficiency, process repeatability and reduced space requirements. It is built for customisation with options such as a stack mould carrier, multi-material injection, rotary table, cube, and integrated robot and hot runner controller. www.athenaautomation.com The future of plastics packaging EuPC Packaging (European Plastics Converters) is organising a conference on “The Future of Plastics Packaging”. It will take place on September 20, 2016 in Brussels, Belgium. The event is intended to bring together the plastics industry, brand owners, research centres, the European Institutions and media to interchange during presentations by industry leaders, debates on potential challenges and working groups. www.eupc.org","@ID":8}, "MARKET SURVEY 25 PETplanet insider Vol. 17 No. 07+08/16 petpla.net Netstal-Maschinen AG Sacmi Imola Mr Sean Hoy Director, Business Development, Beverage Packaging +1 905 951 5000 x 5148 [email protected] Tschachenstrasse 1 8752 Näfels, Switzerland +41 55618 6111 www.netstal.com Mr Reto Bamert Head of Business Unit PET +41 55 618 61 11 [email protected] Via Provinciale Selice 17/A Italy +39 0542 607111 www.sacmi.it Mr Moraldo Masi Director of Business Unit PET +39 0542 607888 +39 0542 642354 [email protected] HyPET HPP5 PET-Line, PETForm IPS220 IPS400 48 to 144 (in standard matrix) 12 to 144 16 to 72 48 to 128 102g, dependent on number of cavities and preform design ~450 140 140g 1,700 Performance package, increased uptime & tooling life, reduced maintenance package with alignment features and self-cleaning technology, reduces maintenance time from four hours to eight seconds, preform sampling, AltaniumTM inside, system integration, auxiliaries integration, ease of use enhancements, system-based HMI, CoolPik DH2 1,350 625 1,250 Flexibility package, high cavitation option, compatibility packages, 30mm performance package, injection completion during power outage Engineering excellence, lowest energy consumption, lowest AA values, sustainable, etc Injection cylinder (shooting pot); electrical drive for plasticizing screw, T-belt for preforms extraction, belt free robot linear motor with KERS, take out plate with 3 postcooling stations, HMI with control of all auxiliaries, double cylinder for preform ejection, double cylinder for preform ejection, digital valves for each actuator, water unloading system prior to mould changing. Injection cylinder (shooting pot): electrical drive for plasticizing screw, direct preforms unloading from gripper plate, belt free robot linear motor with KERS, take out plate with four postcooling stations, HMI with control of all auxiliaries, boosters on moving platen for first phase ejection, digital valves for each actuator, water unloading system prior to mould changing Calitec, preblow, fast cycle time, intrusion system, etc Fast change over system with plug-and-play mould fixing system; plug-and-play take out plate fixing system; water pumps for mould cooling assembled on main machine platform; secondary belts system for an easier collection of preforms sampling; quality control vision system with multiple camera Mould interchangeability with most common existing solutions; boxes located in robot cabinet (less handling and contamination); water pumps for mould cooling assembled on main machine platform; on demand sampling system (up to four shots); quality control vision system with multiple camera Nissei ASB Machine Co., Ltd. Sipa SPA 4586-3 koo, Komoro-shi Nagano-ken, 384-8585 Japan +81 267 23 1565 www.nisseiasb.co.jp Mr Paul Atkin Section Manager, Marketing Group +81 267 23 1565 +81 267 23 1564 [email protected] Via Caduti Del Lavaro 3 31029 Vittorio Veneto, Italy +39 04389 11511 www.sipa.it Mr Pietro Marcati ISBM - Global Sales Manager +39 04389 11511 +39 04389 11694 [email protected] ASB-50MB, ASB-12M, ASB-15N/10E, ASB-70DPH, ASB-70DPW, ASB-150DP, ASB-150DPW, ASB-650EXHS, ASB-650EXHD, PF8-4B, PF6-2B, PF4-1BH, PF3-1BH, PF3-1BHLL, PF24-8B(24), PF24-8B(12), PF24-8B(12H) ECS FX 20 (6 models) ECS HS 12 (8 models) 3ml - 20 liters 0.25 to 3.0l 0.25 to 7l 1 - 36 Up to 80 Up to 40 1 - 36 Up to 40 Up to 20 3 - 800 46.50g for 80 injection cavities 37.50g for 40 injection cavities 1,200 - 9,000 36,000 18,000 720 - 8,500 27,100 13,600 up to 5,300 12,300 4,200 up to 2,200 9,600 3,000 up to approx. 6,000 18,000 9,000 3.56x1.14x2.73 (ASB-50MB) (smallest) 8.95x2.15x3.25 (PF24-8B) (largest) ASB Series can mould a range of resins including PET, PP, HDPE, LDPE, PLA, PES, PPSU, PC etc.; Several models using servo driven hydraulics for energy efficiency. ASB-15N/10E is an all electric 1-step ISBM machine. PF Series uses lower blow mold cavitiation and blows multiple times per cycle for excellent efficiency. PF24 models offer outputs up to 9,000 bph for smaller bottles and 2,500 bph for 5 liter bottles. Wide mouth, oval & asymmetrical, Off-centred neck, hot fillable & pasteurisables, aseptic & ultraclean, lightweight","@ID":27}, "PETcontents 7+8/16 4 PETplanet insider Vol. 17 No. 07+08/16 petpla.net Page 18 Page 39 Page 29 INSIDE TRACK 3 Editorial 4 Contents 6 News 36 Products 37 On site 38 PET bottles for Beverage + Liquid Food 39 PET bottles for Home + Personal Care 40 Patents CHINA EDITOUR 8 Year by year in China 9 Assembly line production Stretch blow moulding and filling machines BOTTLE MAKING 10 14g PET bottle for edible oil BOTTLING / FILLING 12 Hygienic bottling thanks to hotfill technology 14 Flexible filling A single system for blowing and filling bottles for CSDs and hotfill products 18 Energy efficient drive technology Decentralised drive solutions in beverage production 20 Designed to be aseptic After glass and carton: aseptic filling system for still and carbonated juices in PET 26 Filling and bottling solenoid valves from Michigan PETplanet Insider takes a closer look at the Mac range of valves MARKET SURVEY 23 Suppliers of preform and single stage machinery LABELLING 29 Three Soluta labellers installed TRADE SHOW PREVIEW 30 From specialist consultant to preform brand Interview with Ahimsa Industries Ltd. 33 Keeping up with the customers Interview with Shyam Plastic Machinery CAPPING / CLOSURES 34 Bottles, Preforms and Closures Closure for PET bottles & Resins - Different applications, neck finishes for various, part 7 BUYER’S GUIDE 41 Get listed! The China Road Show FILLING SPECIAL","@ID":6}, "BOTTLING / FILLING 20 PETplanet insider Vol. 17 No. 07+08/16 petpla.net FILLING SPECIAL After glass and carton: aseptic filling system for still and carbonated juices in PET Designed to be aseptic Based on an article by Laurent Olivier, Krones SARL On the fruit-juice market, especially when it comes to large container sizes sold at food retailers, the soft-carton package still has a special justification – for the time being. But PET is visibly catching up and nibbling away at the carton’s market. This development made the French producer of fruit and vegetable juices Jus de Fruits d’Alsace (JFA) sit up and take notice, triggering the fruit-juice producer’s decision to enter the PET bottle market. They invested in a new bottling line in fully aseptic design from the blow-moulder to the filler. JFA had been founded back in 1956, originally as a marketing initiative for the regional apple-growers. Over the decades, the company then changed hands internationally several times, until the French family firm LSDH (Laiterie de Saint-Denis-del’Hôtel) integrated JFA into its group of companies in 2008. Since then, around 40 million euros have been channelled into the facility in the Alsatian village of Sarre-Union. One major focus was the installation of a highbay warehouse, supplied by Krones in 2012 complete with the building that houses it, which provides space for 35,000 pallets. Laser-controlled robot vehicles, each able to carry four pallets, constitute the link to the filling hall. The second major investment was channelled into a new syrup kitchen, and finally, the third modernisation step, taken in April 2015, covering a new aseptic line from Krones for filling PET containers. Market shift to PET Up until then, JFA had been concentrating its filling operations on soft packages. On 15 cartoning lines, the company produced around four fifths of its output, with a non-returnableglass line supplementing the production kit. So the mix, until that time, comprised 80% carton, 20% glass. The LSDH Group was, of course, aware of the market shifting away from the carton and towards PET: it had been filling PET containers for several years already in another plant. What was now involved at JFA, however, was a strategic decision. Daniel Eva had been the long-serving factory manager in Sarre-Union and was crucially involved in the installation – although retired but still playing a role in the “aseptic PET line” project. “The aim here was to optimise the production operation logistically,” he says. “JFA’s plant is situated in the vicinity of the German border and the Benelux countries, a fact that offers us good opportunities for the future. Its geographical location predestines it for expansion north- and eastwards.” Hitherto, LSDH had been supplying its PET products almost exclusively to French customers. Two thirds of JFA’s output are dealer’s brands for the major players on the French retail market, and about 20% are well-known fruit-juice brands that the company produces under licence. The rest consists of contract-filling and a small number of own-brand products such as the LSDH brand Cidoux. With the new aseptic line for PET containers, a second major investment target was achieved: “We can now optimise the container mix for our key accounts. Because we have an option for providing products in soft packages, glass and in PET in a single truck consignment,” explains Jérôme Buhler, Daniel Eva’s successor. “The third goal was to be able in future to fill not only dealer’s brands but branded products as well into PET, thus boosting the latters’ acceptance among consumers,” adds Daniel Eva. Dry aseptics – process of the future There is a basic principle at the parent company LSDH when it comes to sensitive beverages: either aseptic, or in the cold chain. So it was one of these two, and nothing else, for JFA as well. “Hotfill has never been a viable alternative for us,” emphasises Daniel Eva. “Aseptic filling is quite simply more gentle on the products. When we were considering our investDry preform sterilisation with hydrogen peroxide in combination with the aseptic blow-moulder","@ID":22}, "BOTTLING / FILLING 12 PETplanet insider Vol. 17 No. 07+08/16 petpla.net Hygienic bottling thanks to hotfill technology Around the globe consumers are finding that juices and sports drinks are a healthy alternative to what are often rather sugary soft drinks. Bottlers who want to muscle in on this growth market have to satisfy the special technical demands made of the process and filling technology for such products. For its juice and sports beverages Coca-Cola Canners in South Africa has now opted for a high-performance hot filling line from KHS. “The entire fruit juice and sports drinks segment is growing all over the world as health awareness increases among many consumers,” states Steve Nagiah, plant manager at Coca-Cola Canners. It was decided to extend the company portfolio in the long term in order to develop this growth area. With its four canning and two PET lines the production site in Wadeville just outside Johannesburg is one of the largest of its kind in the world. 320 employees working round the clock make sure that around 350 million litres of near-water beverage Glacéau, sports beverage Powerade and the Coca-Cola, Sprite and Fanta brands leave the factory every year. Coca-Cola now bottles iced tea, sports drinks and juices with and without fruit chunks on the new line. The new pulpy beverages could not be bottled on the two existing lines Coca-Cola Canners in South Africa bottles a range of soft drinks in PET. KHS has developed and installed a complete new line for the site in Johannesburg. Total flexibility: Coca-Cola Canners fills up to twenty different beverages into eight different bottle formats on the KHS line. FILLING SPECIAL","@ID":14}, "ON SITE 37 PETplanet insider Vol. 17 No. 07+08/16 petpla.net ONsite Retrofitted stretch blow moulder goes to San Salvador Amsler Equipment Inc. has refurbished, retrofitted and delivered its first PET blow moulder to Poliflex S.A. de C.V in San Salvador, El Salvador. Poliflex S.A. de C.V. is a custom blow moulder serving the pharmaceutical, cosmetic, beverage, household goods and food products industries. Founded in 1992, the company operates both injection-stretch moulding and two-step blow moulders to produce a wide variety of jars and bottles. Poliflex is currently updating their plant to meet ISO 22000 food safety standards. Poliflex needed a modern single-cavity PET stretch blow moulding machine to replace an older machine. Small footprint, machine performance, low tooling costs and easy supplier communication were important in selecting a replacement. Amsler was able to supply a used single-cavity machine that was originally installed at a US-based customer. The L12 had been outgrown and was traded in for a new three-cavity L32C. The L12, which was manufactured in 2007, was retrofitted with a preferential heating oven, which was a Poliflex requirement. The machine was completely refurbished and full warranty was provided by Amsler. Poliflex was able to start up the machine and begin production in their plant themselves and it is currently running four days a week. The company is in the process of acquiring new moulds and converting their existing moulds to run on the Amsler L12. This small fullyautomatic single-cavity machine can make bottles from 50ml up to 2l in capacity with neck sizes from 18mm to 63mm. The L15 version of the machine is available to make bottle sizes up to 5l. The options for these machines include neck orientation, hotfill, and preferential heating. www.amslerequipment.net www.poliflexsa.com","@ID":39}, "TRADE SHOW PREVIEW 31 PETplanet insider Vol. 17 No. 07+08/16 petpla.net industry. In 1990, he supported the paint manufacturing project of a corporate group from Gujarat, which had locations in the East African cities of Nairobi, DarEs-Salaam and Kampala. The plan was to facilitate a changeover from packaging in metal cans to HDPE containers. “The group invested in the appropriate equipment and was looking for a specialist; it actually got in touch with me on the basis of a recommendation,” Mr Gandhi recalls. He decided to join the project on-site as a consultant and supported it for around one and a half years. “When I got there they were still using old Windsor machines, the oldest of which dated from 1963. Part of my work involved buying spare parts from India, because Windsor UK was long since defunct. The group subsequently bought around 45 machines for the individual locations, and the project gave me a good insight into the African market. On returning to India in 1992, I decided to use the experience that I had gathered to start up my own business.” Initially, Mr Gandhi continued to work as a consultant. Recognition of his work, a growing reputation and the increased demand eventually led to the foundation of Ahimsa Industries in January 1996. In addition to consulting work, the new company got involved with the production of injection moulds. It initially focused on exporting to Africa and on specialist projects in plastics processing there. From 1996 to 2010, it undertook projects in practically every country in Africa, usually in collaboration with a supplier from India. The projects included installation of moulds, machinery or auxiliary products for injection or extrusion moulding, as well as recycling projects for the sugar and sweets industries. Between 2004 and 2005 Ahimsa acquired a 49% stake in General Additives, the Mumbai-based flavourings manufacturer for the food & pharmaceuticals sector. The company moved into PET in 2010. “I was approached by a private label bottling company from Zambia,” Mr Gandhi explains. “They had bought some equipment from China and weren’t happy with the performance of the compressor. Ingersoll Rand were already active in the Indian market so I recommended their compressors, and managed the installation on-site. It then transpired that my customer wasn’t satisfied with the preforms that they were producing, 31 TRADE SHOW PREVIEW (f.l.t.r.:) Ashutosh Gandhi with Sanjay Agrawal","@ID":33}, "BOTTLE MAKING 10 PETplanet insider Vol. 17 No. 07+08/16 petpla.net 14gPET bottle for edible oil Sidel has collaborated with Algar Agro to produce the lightest 900ml PET bottle for edible oil. A large player in the Brazilian market, Algar Agro worked with Sidel to reduce the total weight of its finished bottle from 18 to 14g, a reduction of 22%. The bottle was redesigned without any obvious changes to the customer in its well-established external appearance. By using the lightweighting expertise of Sidel, Algar Agro was able to achieve the significant saving in weight and in raw material used. It has a substantial impact in minimising the cost to produce, package and transport the finished product, along with lowering the total cost of ownership (TCO) of the production equipment itself. Proposals for the bottle’s packaging optimisation were put together by Sidel, who carried out feasibility tests for the new design at its Packaging & Tooling Centre in Guadalajara, Mexico. Sidel was chosen over the competition because of its experience and expertise, as well as the actual proposals presented to Algar Agro during initial discussions to lightweight the bottle. Edney Valente Lima Filho, Project Manager with Algar Agro, explained: “We put together the best industry suppliers and this is reflected in the project results. The success of Sidel was assured by the know-how demonstrated during the negotiation to propose and ensure the new bottle for vegetable oil - the lightest in the world.” With the acquisition of two Sidel Matrix blowers, one at each of its production plants, Algar Agro believes it is the first oil producer in Brazil with integrated injection and blowing in its PET production process. The Sidel machines were installed in bottling lines producing 25,000 PET bottles of vegetable oil per hour. The installation","@ID":12}, "BOTTLE MAKING 11 PETplanet insider Vol. 17 followed a two year investigation and feasibility study into the integration process for the production and packaging of vegetable oils. Modular blowing for significant benefits The Sidel Matrix blower is a modular blow moulding system that delivers very fast changeover times, lower environmental footprint, higher oven efficiency, and greater uptime, all contributing to a lower TCO. With up to 200 possible configurations, it offers quality and consistency across all of them giving producers the flexibility to pick a size and shape that best fits their needs. Three sizes of blowing stations make it possible to produce an almost limitless variety of distinctive bottle shapes for singleserve, up to 750ml, multiserve, up to 2l or extended bottles family, up to 3.5l. The machine is equipped with electrical stretching for better control of material distribution and the embedded machine intelligence increases self-monitoring and automation of processes to achieve safe packaging. Specially designed to reduce scrap, the Sidel Matrix blower can also automatically detect and eliminate bottle process deviations. Sidel currently operates seven Packaging & Tooling Centres around the world: two in China and one each in France, India, Brazil, the USA and the one in Guadalajara. The facility in Mexico’s second largest city demonstrates the company’s focus on transferring its global knowledge to producers at a local level and, in doing so, helping to meet the growing demand in this market. From bottle design to line engineering and complete life cycle management, producers need optimised solutions and service with greater flexibility, reactivity, interaction and increased cooperation. Oil products produced from two sites Algar Agro is a privately-held company producing, processing and marketing soybean and its derivative products. The company’s food product lines include soybean oil, as well as olive oil, composite oil, tomato extract and sauce, some produced in partnership with other companies. It supplies both the domestic and external markets. The company’s crushing, refining and packaging activities for the soybean oil, are concentrated in two advanced industrial complexes located in Uberlândia, in the Triângulo Mineiro region of Brazil, and Porto Franco, in the south of the State of Maranhão. www.sidel.com www.algaragro.com.br","@ID":13}, "BOTTLING / FILLING 16 PETplanet insider Vol. 17 No. 07+08/16 petpla.net Blowing and filling in a monobloc The Italy-based company says that more advantages could accrue for the user when the filling valve system is built into their Sincro Bloc, a monobloc with integrated bottle blowing and filling. This incorporates a star-wheel system for transferring the bottles from the blowing station to the filling station, which enables a rapid change-over of the grippers that grab the bottle necks. In fact, rather than the pincers being changed one at a time, they are changed in groups, each making up a semi-circle around the wheel, in a single and simple operation - all without the need for any special tooling. This is said to be an advantage in the case of the use of two neck sizes (ie 28 and 38mm) typical of hotfill and CSD mixed lines. Together with all the other quickchange solutions of the Sincro Bloc, the neck change is straightforward, according to Sipa. Units are capable of producing and filling up to 1,800 HF bottles per hour per blow moulding cavity, and as many as 2,250 CSD bottles. Hygiene in product preparation In the product preparation area, Sipa has extended its offering with a series of machines that, together, provide an increased high level of flexibility and customisation. The deaeration, carbonation, blending and pasteurisation stages can all be configured exactly to the specific needs of the customer and their products, whether they are CSDs or HF types. In this area of the line, the main focus is on the flexible pasteurising unit, suitable for handling both HF and CSD products. The ability to control this part of the overall process in such a flexible and product-specific way, together with the use of advanced filling technologies, also means that it is possible to carry out CSD filling operations without the need for any preservatives. Furthermore, it is possible to fill CSDs at ambient temperature (up to 20 °C), which could provide appreciable energy savings. The idea of being able to do away with preservatives for drinks is one that has always generated a lot of interest in the food and beverage industry, as well as among consumers, that are looking for more “natural” food products. The company has been studying various aspects of its filling line equipment that will facilitate the elimination of such preservatives. On systems with integrated PET preform production, for example, various options are now available to maintain the cleanliness of the preforms between the injection moulding machine and the stretchblow moulding unit: the collection hopper, lift and slide can all be enclosed and subject to over-pressure to keep out dust; Want the secret to bottle light weighting? Process Pilot® automated blowmolder control system takes the guesswork out of material distribution management and can help ensure the success of even the most aggressive light weighting program. Featuring 24/7 blowmolder control, the Process Pilot system continuously maintains proper material distribution, on every bottle, to an unmatched level of accuracy. With the Process Pilot system, you have the means to push light weighting to the limit without Not convinced? Talk to one of our specialists today to schedule a free seminar and evaluation of the Process Pilot system on one of your blowmolding lines. Web: agrintl.com Tel: +1.724.482.2163 E-mail: [email protected] See us at booth 11B40 preforms can be treated to eliminate any possible contamination; preforms de-dusting with ionised air; special ventilation filters can be installed in the reheat oven area. The valves use PTFE bellows that protect all moving parts, meaning that virtually nothing adheres to them, no matter how sugary and sticky the product is. The complete units are also designed to be easy to clean using Clean in Place (CIP) and Clean out of Place (COP) washing systems. Another important feature is the use of a microbiological isolator around the immediate filling area, which enables a reduction in the space that needs to be kept under control, making it possible to use cost-effective sanitising systems. Furthermore, contamination of the bottle closures can be minimised with the use of a peroxide washing tunnel. A complete package Sipa also takes full responsibility for all aspects of the line. So, the company is able to provide its customers with its skills in development and design of all types of PET containers, however they are filled. The company has also produced designs of lightweight hot-fill bottles with ribbing that adds to the stability of the bottle but also to the aesthetic qualities of the bottle. The company has also developed a squeezable bottle that withstands the hotfilling process. www.sipa.it","@ID":18}, "PETproducts 36 PETplanet insider Vol. 17 No. 07+08/16 petpla.net Light blocking technology for liquid dairy packaging PolyOne announced that its ColorMatrix business has licensed the right to manufacture, market and sell a highperformance light blocking technology for liquid dairy packaging from leading PET resin and concentrate manufacturer Novapet. Novapet’s Dairy Concentrate Ultra (DCU) additive protects liquid dairy products packaged in monolayer PET bottles from degrading due to light radiation. Novapet has already established DCU additive as a reliable light-blocking solution, and will retain commercial and manufacturing responsibility for the product in France, Italy, Portugal and Spain. PolyOne will manufacture, market and sell the product as ColorMatrix, Lactra SX Light Blocking Additive in all remaining markets. Traditionally packaged in laminate paper cartons or multilayer HDPE bottles, Ultra High Temperature (UHT) milk products are popular in Europe and have been growing in popularity in Asia and Latin America. As the market expands, dairy processors are looking for ways to differentiate their packaging to engage consumers. Switching to DCU additive-modified PET gives processors this ability, in addition to reduced weight and other cost advantages, because it allows lighter weight, monolayer PET bottles to preserve liquid dairy products. ColorMatrix Lactra SX is supplied as a solid masterbatch, and provides the ability to tailor the level of light protection by adjusting the dosage (%) to match the needs of each individual product. As an alternative to multilayer preforms, this additive can easily be added to PET using a single-stage process that gives identical light blocking performance at a lower machinery cost. The simpler injection process can also lead to reduced production waste, while lightweighting lowers production costs per bottle. www.polyone.com www.novapet.es Bottle Green Drinks extends into PET M&H Plastics has recently completed production of a new 50ml bottle for SHS Drinks’ brand, bottlegreen. Initially produced to allow added value as an inclusion of a 50ml cordial serve in a twin pack of 750ml glass sparkling pressés for Waitrose meal deals, the use of these new plastic bottles has opened up a range of benefits to the company. The PET bottles were developed, tooled, moulded and finished by M&H Plastics at its Beccles plant, working closely with SHS Group’s fillers and marketing department. An exceptionally fast turnaround enabled SHS Group to benefit by getting the product to market in short time. Alongside this, SHS found that, as the company was now using lighter plastic for the bottles, more could be put on pallets, reducing distribution and logistics costs. An added benefit to using plastic for this product has meant that new markets are opening up in foodservice, transport markets (especially aviation) and on-thego. Commenting on the new bottles and the service received, Amanda Grabham Marketing Director, Soft Drinks from SHS Drinks said: “M&H has shown that it is really on top of the game with our project. Not only has its team performed superbly with the market-beating turnaround for the product, they have kept us informed and advised us throughout the process. The new markets that this bottle has opened up will mean that bottlegreen will continue to benefit from an expanded market without sacrificing any quality or production and marketing issues.” www.bottlegreendrinks.com www.mhplastics.com","@ID":38}, "BOTTLES PETbottles 39 PETplanet insider Vol. 17 No. 05/16 petpla.net Home + Personal Care Bath elixir in PET Under the Dermasel brand name, the German company Fette Pharma AG is marketing exclusively through pharmacies a Dead Sea elixir with algae extracts and an aquatic scent in a clear bottle with 150ml contents. The thick-walled bottle for the light blue shimmering liquid salt concentrate is about 170mm tall and is reminiscent of a preform for manufacturing plastic bottles that has not been processed further. The product amount is sufficient for about 3-5 bubble baths.The handy packaging is sealed with a shiny silvery metal screw cap. www.dermasel.com Dishwashing liquid with Aloe Vera The German pioneer of ecological detergents and dishwashing liquids Frosch, has launched in Germany a dishwashing liquid for hand washing in an optically responsive and functional packaging. The times when dishwashing liquids were filled into only rather functional bottles and hidden away under the sink during non-use are over. Today’s bottles are shapely, functional, and almost collectable. Frosch is filling 400ml of dishwashing liquid containing Aloe Vera into a bulbous, stable bottle, decorated with sleeve labelling. A screwed on push-pull closure serves as a dosing cap and a glued on miniature fold label that does not disturb the look, make the packaging into an eye-catcher at the kitchen sink. www.frosch.de","@ID":41},
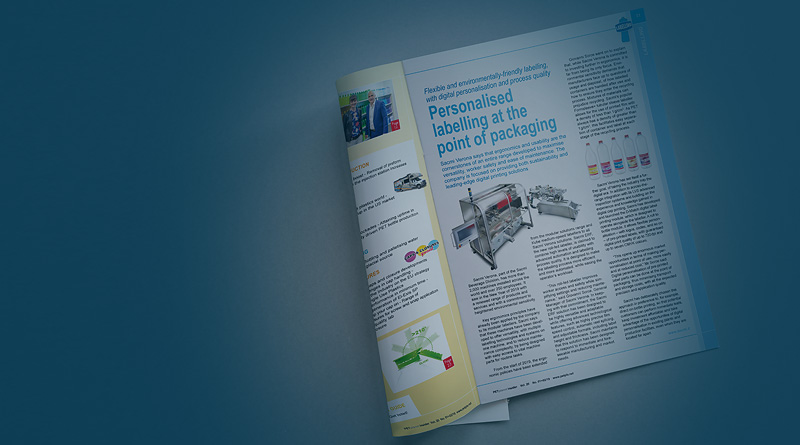