"BOTTLING / FILLING PETplanet Insider Vol. 18 No. 01+02/17 petpla.net 12 BOTTLING / FILLING 12 Sensitive beverages are only as good as the bottle they come in Trends in aseptic and hot filling When you are dealing with sensitive beverages such as fruit juice, tea, sports drinks or dairy products, all is about filling under the most rigorous hygiene conditions, preserving the packaged goods. And this while operating as sustainable and costefficiently as possible. But which is the most appropriate filling method to meet the growing demand for natural and health-sensitive beverages? The traditional answer to this question is hot filling – heating the product before filling until sterile and then filling it into a non-sterile container which has to withstand temperatures up to 92°C. Current developments around hot filling include, amongst other things, reducing the weight and thus the costs of the relatively heavy container. Expanding the design options for the bottles by, for example, removing panels and at the same time preventing vacuum distortion of the bottles when cooling down, or improving the blowing process, i.e. by rapid electrical heating of the moulds up to 140°C are also at the focal point. By contrast, with aseptic filling, the attention is on the container, whose sterility as a preform or a blown bottle, either by a wet solution or a dry solution using paracetic acid and/or hydrogen peroxide (H 2 O 2 ), is guaranteed. Above all, we see the trends are towards reducing the chemicals needed for sterilisation or eliminating them, i.e. by using pulsed light for decontamination. Flexible designs for the filling machinery, which makes cycle times obsolete and yet guarantees thoroughly hygienic filling are other topics on the spotlight. Whether you are going for hot fill or aseptic solutions – the manufacturers are offering a huge variety of choices, tailored down to the specific product. The following pages of our special feature give you an update on current trends and developments. PRODEXPO, 6/10.02.2017 - HALL6#6C35 | Moscow CSI IPF BANGLADESH, 15/18.02.2017 - #635 | Dhaka BANGLADESH ENOMAQ. 14/17.02.2017 - HALL4 #A-B/1-4 | Saragoza SPAIN NONALCOHOLICBEVERAGECONGRESS,15/16.02.2017 |BarcelonaSPAIN MEAPET CONFERENCE, 21/22.02.2017 | Dubai UAE PROPAK EAST AFRICA, 7/9.03.2017 | Nairobi KENYA PROPAK VIETNAM, 21/23.03.2016 | Ho Chi Minh VIETNAM With Sacmi, the beverage specialists are always at your side. With our unbeatable technological know-how and continuous research we are creating new containers and closures designed to ensure outstanding performance. The new IPS injection system for preforms, the CCM compression press for caps and the quality control systems fully designed and built by Sacmi, allows for large-scale production with considerable advantages in terms of efficiency and flexibility. The outcome? Reduced plastic volumes, less energy consumption and lower running costs.All in a bottle: the one you’ll soon be making. ASEPTIC HOT FILL SPECIAL","@ID":14}, "BOTTLING / FILLING PETplanet Insider Vol. 18 No. 01+02/17 petpla.net 21 BOTTLING / FILLING 21 Aseptic bottling of all soft drinks on one machine without line shut downs One machine fills all In the last ten years global consumers have increasingly looked for healthier, naturally-positioned beverages including milk-based products, juices (with and without fibres), RTD (Ready To Drink) teas and functional or energy drinks. This need to produce a wide range of drinks has created a demand for multi-functional equipment, hence the Fillstar CX EVO. Gea has recently launched this latest development of its Fillstar aseptic bottling technology for carbonated products. The new counter-pressure, volumetric electronic filling head has the ability to fill all types of soft drinks – high acid, low acid, still, carbonated and those containing fibres and fruit pieces up to 3mm diameter x 20mm long without any mechanical adjustment of the machine or loss of sterility during changeover. This is intended to provide the instant flexibility demanded by manufacturers who wish to bottle a range of products on a single machine. Product switch without downtime Previous generations of machines had to be shut down for mechanical adjustment when changing from a ‘noncontact’ filling process for still drinks to a ‘contact’ process for carbonated drinks. This was time consuming – more than three hours to stop, adjust, clean and restart – and the machine lost sterility during the process. The new Fillstar CX Evo, While global consumers are increasingly looking for trendy beverages such as ‘food in a bottle’, manufacturers are in need of multi-functional equipment that can switch smoothly between products and bottle types in a single aseptic machine: Gea’s new Fillstar CX Evo is claimed to give them this flexibility in an efficient way. www.bericap.com Unique range of light weight screw and sports closures for light weight PET neck standards for water • Closures for all common neck sizes 26/22, 28mm (PCO 1810, PCO 1881), 29/25, 30/25 • Light weight Hexalite range allowing light weight neck • Still water closures suitable for N 2 dosing • Sports closures fulfill BSDA requirements • Boreseal systems for excellent tightness • Consumer friendly opening forces BERICAP Technology for still water ASEPTIC HOT FILL SPECIAL however, can seamlessly switch between products, adjust bottling speed and handle different cap and bottle sizes without losing sterility or interrupting the process. The new bottling parameters are simply programmed through the machine’s control system. When integrated with an aseptic piston doser the system can also fill products that contain fibres or fruit pieces of up to 10mm3. Meeting the challenges of a diverse market The global market for soft drinks has changed in recent years. The need for high production of standard products has diminished in favour of increased variety that requires dynamic manufacturing systems that can meet the demand for ‘food in a bottle’ that has become popular, especially for the Far East market. Products include high and low acid drinks, still, carbonated and slightly carbonated products that are becoming the ‘fizzy’ alternative to conventional still drinks. All these drinks are presented in a range of PET bottle sizes that provide both practicality and marketing inspiration. Gea’s intention was to bring this whole capability together into a single aseptic machine. The company has already received advance orders for high speed machines (up to 54,000bph) fitted with the Fillstar CX Evo and aseptic piston doser technology for HA/LA products (High Acid/Low Acid) which are planned for delivery to the Far East during the first half of 2017. www.gea.com","@ID":23}, "imprint EDITORIAL PUBLISHER Alexander Büchler, Managing Director HEAD OFFICE heidelberg business media GmbH Bunsenstr. 14 69115 Heidelberg, Germany phone: +49 6221-65108-0 fax: +49 6221-65108-28 [email protected] EDITORIAL Kay Barton Heike Fischer Gabriele Kosmehl Michael Maruschke Ruari McCallion Waldemar Schmitke Anthony Withers WikiPETia.info Doris Fischer [email protected] MEDIA CONSULTANTS Martina Hirschmann [email protected] Johann Lange-Brock [email protected] phone: +49 6221-65108-0 fax: +49 6221-65108-28 LAYOUT AND PREPRESS EXPRIM Werbeagentur Matthias Gaumann | www.exprim.de READER SERVICES Till Kretner [email protected] PRINT Chroma Druck & Verlag GmbH Werkstr. 25 67354 Römerberg Germany WWW www.hbmedia.net | petpla.net PETplanet Insider ISSN 1438-9459 is published 10 times a year. This publication is sent to qualified subscribers (1-year subscription 149 EUR, 2-year subscription 289 EUR, Young professionals’ subscription 99 EUR. Magazines will be dispatched to you by airmail). Not to be reproduced in any form without permission from the publisher. Note: The fact that product names may not be identified as trademarks is not an indication that such names are not registered trademarks. 3 PETplanet Insider Vol. 18 No. 01+02/17 petpla.net Dear friends of petPLANET insider, Today, for the first time, I have swapped the upper and lower case letters in our name. I think it has to be done. After the many regional, nationalist movements, the USA now has a president who sees only himself and his country. This one-sided view of things gives him many plus points with his voters but there can little more behind this than posturing. We live in a networking, work-sharing world, with finance flowing across the world and so it will be fascinating to see how the new president can harmonise all of this with his populist utterances. Our PET branches alone show how networked we are, how we purchase machinery, tools and materials across continents and how regional bottles and products are adapted to the needs of local markets. And will American citizens then even be able to buy their drinks with their conscience clear? From preform machines in Canada, Switzerland or Italy, from stretch-blow moulding machines in France, Germany or Asia? And how many Americans actually have shares in drinks manufacturers? We at petPLANET see the whole picture, the whole planet. And to keep it that way, in February I’ll be flying off again to take our antinationalist Editour further. China isn’t quite fixed up yet so for me it means three weeks in Indonesia. Thailand, Laos, Cambodia, Malaysia and Singapore will follow in the summer. For a quick look at our preparations, please read from page 30 onwards. Your petPLANET publisher,","@ID":5}, "MARKET SURVEY 26 PETplanet Insider Vol. 18 No. 01+02/17 petpla.net Company name Torus Measurement Systems Sacmi Imola S.C. IMD Ltd Pressco Technology Inc Agr International Inc. Postal address Telephone number Web site address Contact name Function Direct telephone number Fax E-Mail Torus House, Nedge Hill Science Park, Telford, Shropshire, TF3 3AJ, Great Britain +44 1952 2100 20 www.torus-group.com Mr Spencer Whale Technical Sales Manager +44 1952 2100 20 [email protected] Via Selice Provinciale 17/A 40026 Imola (BO), Italy +39 0542 607111 www.sacmi.com Mr Stefano Severi Sales Area Manager +39 335 6594236 [email protected] Moosweg 1 2555 Brügg, Switzerland +41 32 366 80 66 www.imdvista.ch Mr Martin Gerber CSO of IMD Ltd. +41 32 366 80 66 +41 32 366 80 69 [email protected] 29200 Aurora Road Cleveland, OH, USA +1 440 498 2600 www.Pressco.com Mr Tom O'Brien VP, Marketing, Sales & New Business Development +1 440 498 2600 [email protected] 615 Whitestown Road Butler, PA, USA +1 724 482 2163 www.agrintl.com Ms Karen Marcellus Marketing Coordinator +1 724 482 2163 +1 724 482 2767 [email protected] Preform Inspection Systems B305 Automatic Preform Inspection System, B301 Semi-automatic Preform Gauge PVS-2 PVS-3 Preform Vision Gauge (PVG4100) Gawis OD Inspection speed 8-10s Up to 1200 parts per hour Up to 72,000 parts per hour Up to 1,500 pieces per minute or 90.000 pieces per hour Up to 2,500/min 1 preform/minute depending on measurements 45 preform/hour depending on measurements Inspected parameters: Geometry / Body Contamination, length, diameter, short shots, gate length, bubbles, burning, wall thickness, stringing Contamination, shape, diameter, ovalization, wall thickness, crystallisation, contamination, unmelts, bubbles, water marks, black specks, gate length, opacity, colour variations, scratches Contamination, shape, diameter, wall thickness, crystallisation, contamination, unmelts, bubbles, water marks, black specks, gate length, opacity, colour variations, scratches Black dots, burn marks, contamination, bended body, bubbles (air pockets), crystallised body, scratches, non-visible flow structures (low pressure while injection), total lenght, colour and colour deviation, long injection, unmelts Unmelts, heat splay, burn marks, water spots, bent/ warped preforms, contamination, carbon streaks, bubbles/blisters, colour, crystallinity & clarity/hazing, gate length Length, body diameters, lean Body diameters Thread area 19 dimensions (absolute measurement) Contaminations, cavity number recognition, diameters, flashes Contaminations, cavity number recognition, flashes Flashes on neck/ thread, scratches on neck area, support ring deformation, missing material on support ring Contamination, flash, dimensions, pulled threads Finish dimensions ( A, T, E, F, D, S, H, L, W, K, B, X ) T, E, A, NR, H, L/D, ovality Mouth / Sealing surface Diameter, internal diameter, roundness Diameters,ovality, thickness,scratches,short shots,flashes,notches, contaminations Diameters,ovality, thickness,scratches,short shots,flashes,notches, contaminations Ovality,diameter,flashes,shorts shots,flashingonparting line, deformationofsealingarea, coulorandcoulordeviation Contamination, ovality and diameter, dirt & debris in the preform, nicks, gouges, short shots & dips Finish bore/ID measurements, OD measurements No Gate / Dome Burning, contamination, tearing, stringing, cracks, voids Crystallisation, contaminations, unmlet, bubbles, grooves, holes, cracks, position of the injection point Crystallisation, contaminations, unmlet, bubbles, grooves, holes, cracks, position of the injection point Gate defects, gate length (long gates), holes in gate and gate area, gate deformation, cracks in gate area, injection point out of centre, drip marks Bent/warped preforms, dirt/ debris, cracked gates Gate length No Colour LAB Measurement, UV (coming soon) Colour deviations, intensity deviations, LAB measurement Colour deviations, intensity deviations, LAB measurement Colour and colour deviation Colour variations, incorrect colour No No Cavity number Cavity number, cavity related statistics, preform sorting according to cavity number or weight or severity of failure Cavity number recognition, cavity related statistics, sorting by cavity number Cavity number recognition, cavity related statistics, sorting by cavity number Cavity reading, self-learn cavity function for several cavity/templates, cavity related statistics and alarms, rejection of x cavity number, possibility to share information with injection moulding machine based of cavity number No No No Further criteria Weight, stress test (polarisation) Weight, patented grid inspection for detection of defects usually visible with polarised light Patented grid inspection for detection of defects usually visible with polarised light Non-visible flow structures (low pressure while injection) on body, extreemly compact layout, less than 7m2 Additional inspection modules include: Neck support ring, inner barrel Preform weight No Measurement of absence or presence of barrier material Future development No No IMDvista BTIR Barrier Testing System Yes No No Layer thickness & position measurement at distinctive points Future development No No IMDvista LAYER Testing System No No Comprehensive thickness (monolayer) at any location over preform sidewall Layer thickness & position measurement at the complete body by scanning No No IMDvista LAYER Testing System No No No Features: Installation: Stand-alone Yes Yes Inline after injection moulding machine; before blowing and filling machine/line; complete line after injection and before blowing/filling. Production monitoring by IMDvista PECO LUX Mounting and installation inside major OEM blowmoulding machines Yes Yes Installation: Inline Yes Yes Options available for standalone and inline systems Side camera for cavity recognition Yes Yes No, patent pending cavity recognition with top camera 4 cameras with our NEWEST intelligent software technology No Method: destructive / non destructive Non destructive Non destructive Non destructive Non-destructive vision inspection Non destructive Non destructive Non destructive Data base connection Suitable data output for Excel, statistical process control SQL database, possibility to extract data in XLS format, possibility of connection to ERP system SQL database, possibility to extract data in XLS format, possibility of connection to ERP system IMDvista Portal, connect all system on one central processing unit (operator panel) Yes Industry standard Industry standard","@ID":28}, "MATERIALS / RECYCLING PETplanet Insider Vol. 18 No. 01+02/17 petpla.net 10 A wide variety for food and non-food packaging Heat resistant PET polymers by Kay Barton Ester Industries, which is headquartered in Gurgaon (Gurugram), Haryana State, India, recently announced the commercial launch of a series of speciality polymer resins for packaging of beer, other beverages, liquid food and non-food items. produced by conventional ISBM or EBM processes on existing machines without any need for special heat set blow moulding processes, which means that there is no need for high levels of investment in special equipment, nor is there any requirement for additional operating or material cost. ESPET HR products can be used for manufacturing containers which can be hot filled at 84°C to 90°C, facilitating extended product shelf life. Ester claims that the material has a brilliant look and is suitable for food and beverage hot fill applications such as sauces, jams, condiments, juices, etc. It is completely recyclable under RIC code 1. Ester has an HR series grade that is suitable for manufacturing four to five gallon containers that are typically used for packaging of water. They can be hot washed at 70°C for 35-40 cycles. The company has also announced a newly-developed co-polymer for its HR range that has improved thermal, mechanical and optical properties, as well as good CO 2 and O 2 characteristics. It is heat resistance of up to 55°C and is particularly suitable for companies using PET for beer packaging. It uses Ester’s modified PBN polymer, which is blended with its HR-01A and is claimed to offer better transparency and recyclability than nylon-MXD6. Packaging beer in containers made of this grade provides beer with a shelf life of more than nine months. Ester says that its ESPBN (clear modified PBN) is transparent, has good thermal, mechanical and barrier properties, and is suitable for food contact application and packaging. It can be used both in monolayer and multilayer applications. Its barrier properties are not adversely influenced by temperature or humidity. It has good adhesion to PET, as it is a polyester with the same glass transition temperature as PET; there is no delamination in multilayer containers. No tie layer is required, which means to lower cost. www.esterindustries.com Ester’s heat-resistant PET, which can be produced using conventional ISBM or EBM manufacturing processes, can be filled with products at temperatures up to 90°C without vulnerability to deformation or destruction of the bottle, keg or other container. Its clear, modified PBN (polybutylene naphthalate), which is transparent and has good barrier properties, can be used in the preparation of both monolayer and multilayer containers. Ester has three business divisions: BoPET Films; Engineering Plastics; and Specialty Polymers. Their production capacities are 57,000t/a; 26,000 t/a; and 47,0000t/a respectively. Specialty Polymers includes the development of newly polymers for the PET industry. Ester says that its ESPET HR heat-resistant PET resin series can cope with filling temperatures above commonly used methods. Containers made with HR-03 resin can be Material bales waiting for further procedure at Ester’s premises in Gurgaon, India","@ID":12}, "BOTTLING / FILLING PETplanet Insider Vol. 18 No. 01+02/17 petpla.net 15 BOTTLING / FILLING 15 oil, accurately providing the correct temperatures from the very first bottles produced. This results in a blowing process which is uniform between blowing stations, ensuring high bottle quality and consistent performance in the hands of the consumer. Compared with Sidel blowers that used traditional heating with oil, this electrical mould heating and the proven Sidel Matrix blower technologies are said to offer together energy savings of up to 45%. A further saving of 25% could be achieved with Sidel Matrix Ecoven, which uses infrared lamps with ceramic instead of metal reflectors. A reduction by up to 45% of air consumption is said to be possible by implementing Sidel’s air recovery option, AirEco2. Hot filling of beverages with or without pulps To meet the production demands of sensitive and natural beverages, the Sidel Matrix hot filler – SF700 FM can be hygienically used for a variety of sensitive beverages, with or without pulps. Beverages containing particles up to 10 x 10 x 10mm can also be handled with a double stage filling. It is suitable for PET bottle sizes ranging from 200ml to 3l. Operating at production rates ranging from 6,00060,000bph, it features electronic filling valves equipped with individual flow meters that ensure precise filling volumes while minimising product wastage. Its operation of contactless filling - where there is no contact between the filling valve and the bottle neck - optimises product safety throughout the whole process. Additionally, by integrating of the electrical HR blowing and hot filling technologies in one single controlled production environment, the Sidel Matrix Combi Hot Fill eliminates conveying and allows hygiene and food safety to be maintained, says the company. Beverage safety Once the beverage is filled and the bottle capped, beverage safety and consistency are ensured by sterilising the head-space and cap with the Sidel cap steriliser. It controls this process by tilting the bottle at a precise angle, temperature and contact time. This step puts all internal surfaces and air space in contact with the hot beverage, eliminating microorganisms and extending product shelf life. Sidel’s cooling system cools the product while avoiding thermal stress and preserving organoleptic properties, taste and colour, for a great consumer experience. The modular cooling configuration can be easily upgraded to match the production needs. Additionally, the advanced engineering allows a precise sizing of the cooler with a 20% reduced footprint and minimal water consumption compared with traditional solutions. Line integration with Tetra Pak Processing Systems can also lead to energy savings of up to 45% by recovering, for example, warm water from the cooler for pre-heating at the pasteuriser. www.sidel.com Filling valves The cooling system reduces the liquid beverage’s temperature while avoiding thermal stress and preserving organoleptic properties. [email protected] Tel: +90 212 695 50 00 Fax: +90 212 694 97 24 100815dmyR .com","@ID":17}, "Sponsors asia.petpla.net 2017 is Drinktec year! All over the world, the beverage and liquid food industry is preparing for the next edition of the great event, held once again in Germany. A new year also means a new road show - and a very special one. PETplanet is again partnering with Drinktec and we will be bringing our crew to South East Asia, under our new slogan: Go with the flow – South East Asia Road Show. From the end of January our editors Kay Barton and Alexander Büchler, along with “Flowy“, the Drinktec mascot, will be investigating the latest market-specific characteristics of distant countries as well as following welltrodden oaths, as always. With various “Editourmobil” vans we will travel to Thailand, Vietnam, Cambodia, Malaysia, Singapore and Indonesia. As our valued reader, you will once again get insider information and insights from the PET beverage and supplier industries, published regularly in PETplanet Insider. You can get even closer to the Tour experience by following us live on our travel blog at asia.petpla.net. Drinktec awaits us at journey‘s end. When we get there we will be presenting factsheets and product samples of all the companies we visited. We hope you enjoy “keeping up with the PETplanetarians“. We look forward to welcoming you on board once again! January – July 2017 Cambodia Laos Thailand Indonesia Vietnam Malaysia Singapore The worldwide round trip with Go with the flow. South East Asia Road Show powered by","@ID":11}, "BOTTLING / FILLING PETplanet Insider Vol. 18 No. 01+02/17 petpla.net 27 filling line. We paid the company a visit in order to better understand the technology as well as the company philosophy. Janyce Franc, R&D Manager at Claranor, explained the company’s history: “We were founded in 2004 and worked on sterilisation with impulse lamps for years, originally for caps in ozone free water filling of water. This is therefore the area that we are mainly known for. Later, the importance of the treatment of preforms became a priority for us and we began to develop the appropriate systems for it. In 2013, we installed the first equipment for the decontamination of preform necks. The idea is that it offers a clean alternative to the chemical-based sterilisation method, which is well-established in the beverage production process. It is widely known that consumer expectation of ‘naturality’ of the products is increasing; that should begin with the packaging. For the producer, the use of our equipment should be cheaper, in comparison with other methods.” The idea of using pulsed light technology for decontamination at the microbiological level is not new. Field tests in Japan in 1970s were followed by a patent in 1984, in which xenon light is named as a method of decontamination. The 1990s saw further research in the area but, while the positive effect of xenon light could be demonstrated, the precise parameters – including the most appropriate and effective voltage, power, duration of flash and so on – could not be established in a way that provided reliable, commercially-acceptable results. It took Claranor a few more years and a lot more effort, both on its own and in collaboration (especially with INRA, the French Institute for Research in Food and Agriculture through a common PhD work), to arrive at the effective solution. “In our own research projects, together with those we conduct in cooperation with the Fraunhofer Institute for Process Engineering and Packaging, we verified various effects under a range of parameters and can Chemical-free decontamination for preforms and closures integrated into the filling line Pulsed light sterilisation by Kay Barton Claranor is based in Avignon, France, about an hour’s drive north of Marseilles. A small company with just 30 employees, it develops inline equipment for the decontamination of preforms, caps, cups and lids in the beverage and milk sectors. We met: Mrs Janyce Franc, R&D Manager Mrs Isabelle de Forsanz, Marketing Manager Mr Pierre Lalubin, Mechanical Project Manager Mr Alain Berberian, Microbiology Manager Mrs Magali Bry, Microbiologist The special feature of Claranor’s process is that it uses no chemicals to destroy the microorganisms that adhere to the inner and outer surfaces of the preform or closure. Instead, Claranor uses a xenon impulse flash lamp producing an intense flash of white light containing a high quantity of UV, which verifiably kills mould and bacterial spores. In addition to environmental aspects, this method is claimed to offer efficiency and total cost of ownership advantages when the equipment is integrated into the Claranor’s technician at work with Janyce Franc (left) and Isabelle de Forsanz (right) Sterilisation of caps ASEPTIC HOT FILL SPECIAL","@ID":29}, "BOTTLING / FILLING PETplanet Insider Vol. 18 No. 01+02/17 petpla.net 16 Handling high-acid products Fruitful alliance Based on an article by Roland Scheuing, Krones AG Ten years ago, the Gropper dairy company started a production operation for fruit smoothies as dealer’s brands, and has for seven years now also been making NFC juices. Currently, juices and smoothies account for over a quarter of total sales. Buoyant growth over recent years was the reason that Gropper had come up against the limits of its capacities at its headquarters in Bissingen, Germany. The obvious option was to erect a new filling plant next to the Dreher facility in Stockach, with Innocent as a long-term partner for contract-bottling, and with Dreher as the NFC-juice supplier next door, so to speak. The production operation in Stockach is focussed on cooperation with Innocent, a British producer of juices and smoothies. The plan is that in future Gropper will here be filling the vast majority of refrigerated NFC juices of the Innocent brand for continental Europe, but no smoothies. In Stockach, Gropper fills NFC juices for which cooling is mandatory not only in this strategic alliance but also for customers from the retailing trade. The fresh juices from Innocent, first and foremost NFC apple juices, but also various blends like apple-mango, apple-berry or apple-peach-pear juices, are delivered by the neighbour Dreher – through a pipeline. Thanks to the short distance involved, heating up the juices a second time can now be eliminated. This sort of flash pasteurisation had hitherto been necessary following tanker-truck transit. Now, the interface is located directly in the filling line. This is also the reason that Gropper does not need its own process technology for juices in Stockach. Two filling lines featuring the UltraClean process The result was that Gropper had to build a bottling hall “merely” 2,500m2 in size, plus an adjacent warehouse for coolants, raw, processing and operating materials. For this purpose, the newly founded company Gropper Fruchtsaft GmbH has invested around 30 million euros, 20 million euros of this in new machinery alone. The cold-storage warehouse, cooled down to 3-6°C and equipped with automated narrow-aisle forklift trucks, serves as a buffer store. The finished products are kept here for one to two days. This fast turnover rate, however, also increases the pressure on the filling operation to provide a sufficient number of packaged products at any given time. For its filling operation, Gropper opted for two lines installed in parallel, each rated at 25,000 1l containers an hour, which are largely identical in their layouts. The divergences are due ASEPTIC HOT FILL SPECIAL In Stockach on the shores of Lake Constance, the German Gropper dairy had in mid-2015 opened its second facility, which fills NFC juices (not-from-concentrate juices) in PET containers. Two can-do alliances were instrumental in achieving this: one of them is a cooperative arrangement with the English vendor of smoothies and NFC juices, Innocent, and the second is with Dreher Spirit of Fruits, a company producing NFC juices, purees and concentrates. Two Krones filling lines featuring the UltraClean process are bottling the juices under safe microbiological conditions. The high H 2 O 2 concentration, in conjunction with the hot preforms, provides preform decontamination inside and out. Berthold Burgmeier (right), Technical Manager at Gropper, with Gerd Schanzenbach, Gropper Plant Manager at Stockach","@ID":18}, "BOTTLING / FILLING PETplanet Insider Vol. 18 No. 01+02/17 petpla.net 20 disadvantage is that it requires a large amount of the recycling disinfectant to be used, and sterile water is necessary to rinse the cap and wash away the residual disinfectant in the cap. High water consumption is thus the biggest disadvantage of the wet sterilisation process. Following research and analysis, Newamstar has released the combined scenarios by using middle pressure UV sterilisation and H 2 O 2 dry sterilisation. The sterilisation scenario is divided into two steps due to the special internal structure of the cap. The first step is to sterilise the cap by using the middle pressure UV lamp, which de-activates the bacteria, virus, spores and other pathogenic bacteria. The effect of the sterilisation can reach ≥3log. Then the second step is to use the spraying gaseous H 2 O 2 to sterilise the cap, which takes the sterilisation effect to ≥5log. By this method, only a little disinfectant is used and without the consumption of water. However, a thorough sterilisation can be achieved. For an aseptic production line with 36,000bph, more than 5,000l/hr water can be saved in the cap treatment stage alone. Empty bottle dry sterilisation technology Currently, lactobacillus milk stored at low temperature is becoming more and more popular with consumers, not only because of the high nutrition of the product itself but also to some extent it can improve the physiological function of the body. The dilemma is how to capture market share by extending the shelf life of the product, whilst ensuring that product quality is guaranteed. Using the empty bottle dry sterilisation and sterile hot wind decomposition technology can be applied to cold chain filling production. This ensures that the packaging is thoroughly sterilised, whilst guaranteeing the quality and safety of the lactobacillus beverage and high & low acid beverage in low temperature. The gaseous H 2 O 2 will be sprayed into the bottle evenly; the log level of the sterilisation can be achieved after the microorganism is rendered inactive through the condensing procedure. Afterwards, the sterile hot wind system rapidly decomposes the H 2 O 2 to ensure that no residuals are passed to the filling procedure. The sterilisation can be used for all kinds of bottle shape (square bottle, round bottle), bottle size 0.2-1.5l. By using this sterilisation method, for one 36,000bph filling production line, 5,000-10,000l/ hr rinsing water can be saved whilst guaranteeing effective sterilisation. The dry sterilisation technology developed by Newamstar is already widely used in all kinds of the system and production lines, and has received widespread customer approval. The technology can make the product safe and at the same time the energy consumption will be reduced, bringing considerable economic benefits. www.newamstar.com","@ID":22}, "39 BOTTLES PETplanet Insider Vol. 18 PETbottles Home + Personal Care Scented washing liquid from Denk mit “Denk mit”, an own brand from the German discount stores dm, reacted to the new product from the big brands and brought its own scented washing liquid onto the shelves. Put a larger or smaller quantity, depending on the desired level of scent, of the scent pearls, or granular components, into the still empty washing machine, then fill the washing machine with water, pour in washing liquid and softener. The product is available with two different scents – “Fresh” and “Sweet”. The packaging is a stable clear bottle which contains 275g of scent pearls. The screw cap fits over the bottle neck and a clear window in the sleeve label allows a direct view of the product. www.dm.de Slim bottle for conditioner The 150ml spray conditioner for fine flat hair with no volume is filled by Balea – a dm own brand – into a slim, attractive green PET bottle. The silicone-free product makes hair easy to comb, gives it volume and moisturises it. It is dispensed via a screw-on pump which is protected against damage by a snap cap. www.dm.de","@ID":41}, "BOTTLING / FILLING PETplanet Insider Vol. 18 No. 01+02/17 petpla.net 13 Bottles and jars for hot filled beverages Standing the heat PET bottles can be considered heat-resistant once they are able to pass a filling temperature of 85°C. This can be achieved with a special heating, crystallisation and blowing process. In the process of blowing hot fill bottles, a number of technological specifications are required: for example in order to reheat the preforms for the hot fill bottles to be blown properly, the temperature has to be 10-15°C higher than would be used for the same preform/bottle combination for a cold fill. Terekas Sweden AB supplies both the stretch blow moulding systems and dedicated PET preforms for hot-fill bottle production. carbonated soft drinks. A standard bottle shape without panels is also an option which requires liquid nitrogen dosing equipment due to the vacuumation effect that begins when liquid is cooling down. Nitrogen helps counteract this effect so as to sustain the correct bottle shape. The nitrogen replaces the oxygen in the headspace, warms up, and fills in the amount lost during the shrinkage. It thereby increases the pressure inside the bottle just after the filling and may thus reduce or equalise the vacuum acting on the bottles. In addition, an option of rounded bottles with heavy ribs secures the maximum hot fill bottle strength. Finally, bottles of a squarish/oval design form are also available and well-liked by bottlers although the bottle base length can only be up to two times larger than the width. It also requires nitrogen dosing equipment when filling. The bottles are popular amongst bottlers producing freshly squeezed fruit or vegetable juices, mixtures, syrups or any other healthy drinks that require a filling temperature up to 85°C and from 250ml to 1l in size, says Terekas. A major benefit of PET hot fill bottles is that a fill temperature of 85-93°C is already a healthy option, since all non-carbonated drinks containing sugar are sensitive to microbial contamination and therefore require a sterile container. For the most part, the temperature is sufficient to eliminate the need for preservatives to be added to the product, making it healthier and extending the product shelf life, and, as a result, preserving the same taste for a longer period of time. Thus, hot fill bottles have a wider 38mm neck opening in comparison with cold fill PET bottles, making the bottle design highly attractive to juice lovers. Furthermore, when it comes to considering the investment in filling equipment, there could be significant cost savings for bottlers to use a hot fill PET bottles line rather than an aseptic filling line. Thus, compared to a closed environment carton tetra pack line, the advantage of having a hot fill is that it has virtually unlimited design possibilities. www.flexblow.com ASEPTIC HOT FILL SPECIAL The blow moulds that are used during the blowing process have to be heated up to 120-140°C rather than being cooled as in the case of cold fill bottles production. This measure is necessary for the crystallisation process to be performed. In addition, high crystallinity levels increase the thermal resistance, minimising the risk of bottles being distorted. Depending on the filling temperature as well as the size and wall thickness, Terekas offers several bottle design options. To begin with, there is a standard rounded bottle with collapsible panels that work as the absorber of vacuum so that the bottle walls do not collapse after cooling down. Additionally, in order to withstand the thermal load, such bottles are significantly heavier compared to bottles for water or","@ID":15}, "BOTTLING / FILLING PETplanet Insider Vol. 18 No. 01+02/17 petpla.net 18 Application of dry sterilisation technology in filling production line To reach for low temperature Beverage producers increasingly focus on achieving ultra-high line speeds, lightweighting, and reducing energy costs. Thus, demand for high-end technology equipment to meet changing market conditions is becoming more and more urgent. Newamstar, the liquid product packaging machinery supplier in China, was one of the first companies to develop the dry sterilisation technology, using H 2 O 2 and peracetic acid. The system has already been operating in the Combi production line and aseptic cold filling production line, for PET bottled water, beverages and dairy products. The application of dry sterilisation technology can reduce the consumption of chemical products and the water used in bottle rinsing, and can achieve the same sterilisaASEPTIC HOT FILL SPECIAL tion effect under the low concentration compared with wet sterilisation. Newamstar aseptic technology is being continuously updated and improved, in addition to the VHP and HPV systems, developed by the company to sterilise packaging materials. In cooperation with Jiangnan University, a series of theoretical sterilisation intensity figures are being collected to verify the microorganism in the laboratory. This technology has been successfully applied on the non-ozone mineral water Combi production line, aseptic cold filling and cold-chain filling production line etc. The low concentration 1-3mg/l, low temperature 20-50°C gaseous H 2 O 2 , rapidly achieves the sterilisation level ≥5log. Preform dry sterilisation technology The dry gas spray device is installed before the preform enters the heat oven, gaseous H 2 O 2 is evenly sprayed to the internal surface of preform. The H 2 0 2 will be activated by the heating process in the heat oven and the sterilisation effect will be intensified, resulting in a reduction in the numbers of bacteria in the preform. The H 2 0 2 will be evaporated by decomposition instantaneously by the means of high temperature heating after the preform is sterilised by H 2 O 2 . The whole technical process design is simple and reliable. The technology not only reduces the risk of an H 2 O 2 residual inside the preform, but also achieves the high hygienic safety level target. Cap dry sterilisation technology The traditional cap sterilisation technical process normally uses the wet sterilisation type that uses disinfectant to soak the cap for certain time. The advantage of this method is that the intensity of the sterilisation is high, stability and reliability are good but the","@ID":20}, "PETplanet Insider Vol. 18 No. 01+02/17 petpla.net 33 TRADE SHOW REVIEW over time. Via the latest version of the Efficiency Improvement Tool (EIT) for example, it is possible to capture production data and to put in place comprehensive line monitoring. The toll allows also an accurate detection of the causes of unplanned stoppages, and contributes to increase operators’ awareness and responsiveness. A counterpart to EIT, the Equipment Smart Monitoring (ESM), is a performance analysis tool which operates at individual machine level. The production data are then sourced and transferred to the Gebo Cermex experts, who can analyse them and make recommendations for improving performance at all levels. Additionally, Remote Video Assistance uses video, audio and augmented reality technology to optimally link the line operator and the Gebo Cermex specialist, for effective and connected maintenance and troubleshooting. This reduces costly downtime, particularly given the increasing sophistication of packaging lines. 4) Eco-friendly factory: Philosophy of sustainable production Gebo Cermex focuses on sustainability through “Smart Energy Management”. Agility 4.0 programme encompasses energy and water consumption reduction, use of new materials as well as 3D-printed components. The “Line Energy Simulation” software is able to link energy consumption and line performance taking into account the utilities involved in food and beverage applications, as electrical power, compressed air, steam and condensation, water and CO 2 . A special water management diagnostic tool identifies out-of-the-ordinary water consumption and guides operator whilst at the same time resolving the issue. This improves the sustainability of the Gebo Cermex Swing pasteurisers and bottle discharge temperature control on the bottle washers. 5) Extended factory: Total mastery of extended factory Agility 4.0 includes a new approach to traditional packaging line and factory concepts the so called “Dematerialised layout”. By linking small specific production islands with automatic guided vehicles, production can be customised on a mass scale without changing costs, yet increasing flexibility. This is at the core of intralogistics. These vehicles are intended for finished goods and consumables to support between-the-lines materials handling, eliminating need for repacking and reducing storage and waste. Developing bottling and canning plants to meet distributors’ requirements is a lengthy and complex process which can be greatly aided by the Agility 4.0 programme. As explained, simulation is at the core of it: for example the system allows for accurate simulation of daily operations in a production plant, and therefore developing and testing new production models. The “Line Energy Simulation” tool can be used to audit existing installations or to assist in the design of new ones. It enables beverage producers to test a wide range of possible configurations, validate design variants and optimise energy saving proposals. In a nutshell, the programme increases the chances of a successful implementation of a project, while minimising the spending, as customers can tailor their investments. In recognition of its efforts to introduce, develop and implement Industry 4.0 initiatives, Gebo Cermex has recently received the official mark “Vitrine industrie du futur” (Industry of the future), awarded by the Alliance Industrie Du Futur (AIF). On receiving the award, the company highlighted the importance of investing in Industry 4.0 possibilities to build long term competitive advantage in the packaging industry. This mark is awarded by AIF to companies that implement new tools such as digital data exchange and advanced robotics to drive the transformation of business models and organisations as well as design and marketing methods. www.gebocermex.com PROCESS PILOT® makes producing a better PET bottle as easy as 2 3 1 MEASURE CONTROL OPTIMIZE every bottle for changes in material distribution process variation, inside the blowmolder material utilization and orientation to achieve maximum bottle performance CONTACT US TODAY TO LEARN MORE! AGRINTL.COM | +1.724.482.2163 | [email protected]","@ID":35}, "TRADE SHOW REVIEW PETplanet Insider Vol. 18 No. 01+02/17 petpla.net 35 Growth of dti, PackTech and FoodPex reflects societal and economic change in India India trade shows set new record This is the fourth time that dti and PackTech India were held within the scope of a combined event. However, an additional element was added in 2016: FoodPex India is a new exhibition that focuses on processing and packaging solid foods of all kinds. As a result, the three Indian exhibitions depict sectors that revolve around three main themes, i.e. packaging and related processes, beverage technology and liquid food and food processing and packing. Economic growth in India stimulates exhibition The 2016 exhibition was larger than ever, occupying 14,000m2 of space. Bhupinder Singh, CEO of Messe München India, explains: “The driving force behind this growth is societal change and significant economic growth.” And Thomas Schlitt, Managing Director of Messe Düsseldorf India, elaborates: “The growing middle class is increasing demand for hygienically processed foods, dairy products and packaged beverages. Producing these products calls for suitable plants and machinery that are on display here.” Supporting programme The Packaging Design, Innovation and Technology (PDIT) Conference that was organised together with partner IPPStar and held in conjunction with International PackTech India and FoodPex India for the first time ever, was well received among visitors. The central theme of the conference was SAVE FOOD, addressing the problem of food losses and food waste. Among other things, it focuses on ways that the packaging industry can use its know-how to improve the situation. For the first time ever, the results of a field study on food losses in India were presented at the conference. The conference programme was rounded out by topics such as improving efficiency, sustainability, traceability and intelligent packaging. The programme of events also allowed visitors attending dti to gather information about trends in the food, beverage and liquid-food industry and about packaging and related processing technology in general. The roundtable talks, which were booked to capacity on both days, were very well received. Notable representatives of the beverage and liquid-food industry made presentations on the topic “Beverage manufacturing, food processing and product packaging in India: Lifestyle, trends, challenges and future concepts.” Dr Keshab Nandy from Tilaknagar Industries Ltd. summed up the results on behalf of the other participants: “The roundtable talks at dti 2016 were extremely well organised. The experts’ professional presentations also verified that fact. I was particularly impressed by the quality of the audience members. They discussed important challenges and issues facing the food and beverage industry in India with great intensity and presented solutions.” Attendance at the dti Exhibitor Forum was very high. Exhibitors presented their product solutions for the beverage and food market in India. Both the Exhibitor Forum as well as the roundtable talks were organised by PETplanet. Other new items on the agenda included buyer-seller meetings and the MicroBrew Symposium India, which is organised by the Research and Teaching Institute for Brewing in Berlin. dti is organised by Messe München India, a subsidiary of Messe München. International PackTech India and FoodPex India are organised by Messe Düsseldorf and its subsidiary Messe Düsseldorf India. The VDMA Food Processing Machinery and Packaging Machinery Association, a proven partner to drinktec in Munich and to interpack in Düsseldorf, was also involved in the three shows. The next edition of the Indian exhibitions will take place at the Bombay Convention & Exhibition Center in Mumbai from October 24 to 26, 2018 - as a quartet together with IndiaPack, the trade fair for packaging materials and packaging-material production in India. In that quartet, International PackTech India will be replaced by pacprocess India. IndiaPack and pacprocess will be held for the first time in New Delhi in October 2017. www.drinktechnology-india.com www.packtech-india.com www.foodpex-india.com Panel discussion experts at drink technology India 2016 The fourth and so far the largest event consisting of drink technology India (dti), PackTech India and FoodPex India welcomed nearly 12,100 visitors at the Bombay Exhibition Centre in Mumbai, an increase of more than 18%. A total of 298 exhibitors (2014: 231 exhibitors) presented the latest technologies and solutions for the Indian market on more than 40% more exhibition space on the three-day event.","@ID":37}, "MARKET SURVEY 24 PETplanet Insider Vol. 18 No. 01+02/17 petpla.net Company name PDG Plastiques Hodmeter Resilux ALPLA-Werke Alwin Lehner GmbH & Co. KG Retal Industries LTD Postal address Telephone number Web site address Contact name Function Direct telephone number Fax E-mail ZI secteur 2, 45330 Malesherbes, France +33 2 3834 6195 www.pdg-plastiques.com Mr Francois Desfretier General Manager +33 2 3834 6195 +33 2 3834 6382 [email protected] 140, rue Louis Pasteur 76160 Darnétal, France +33 950 373 373 www.hodmeter.com Mr Antoine Brémilts Sales & Marketing +33 684 633 154 +33 955 373 373 [email protected] Damstraat 4 9230 Wetteren, Belgium +32 9365 7474 www.resilux.com Mr Philippe Blonda Marketing & Business Dev. Dir. +32 9365 7476 +32 9365 7475 [email protected] Mockenstrasse 34 6971 Hard, Austria +43 5574 6020 www.alpla.com Mr Jens Seifried Global Sales Director +43 5574 602 518 +43 5574 62017 518 [email protected] Epimitheos St. 6, Industrial Area A, Limassol, 3056, Cyprus +357 25 270 500 www.retalgroup.com Mr Milos Kuzman Chief Sales Officer +357 25 270 500 [email protected] Preforms Multilayer preforms (Yes/No) No No Yes Yes Yes PEN prefoms (Yes/No) No No No No No Preforms in alternative materials (PP/PLA/PEF) (Which?) PP - PE - BioPET No Yes, on request Yes applicable Preforms incorporating rPET (rPET content in %) Yes, up to 100% No Yes, according customer wishes Yes, on request Yes, rPET content 10-100% List of additives available Prelactia 100% light barrier for UHT steralized milk long shelf-life; oxygen, UV, CO2 barriers, coloured preforms, Pre-blow and Mintec technology No Oxygen barrier: ResiOx; CO2 barrier: ResiC; oxygen and CO2 : ResiMid, ResiMax; light barrier: ResiBlock All customary additives CO2 scavangers; AA reducers; slip agent; UV blockers; brighteners; nylon Preform range 29/25 shorty:8-28g; 30/25 high:17.5-50g; 30/25 low:17.5-50g; 38mm 3 start:28-50g; Prelactia 38mm 3 start:17-38g; 27/32: 6.5g dairy & smoothies; PCO 1810: 33.6g; PCO 1881: 32g; 29/23: 24 -27-33g chemical; BVS 30H60: 50g Wine (high oxygen barrier);22H30: 19g Wine (high oxygen barrier) ultra-lightweighting 2.4g preform; overmoulding technology for 2 layers preforms; Preblow and MintTec technology for lightweigthing bottles 55mm neck for 5 gallon water bottle; 700g (refillable application); the PET preform is injected to blow refillable water bottle from 10l to 5 gallon format with a 55mm neck available with optional ring for handling. Its specific design brings best biaxial orientation with the high planar stretch ratio for a 5 gallon bottle. Juice, milk: 38mm 2 start, 3 start; CSD, water: 28 PCO 1810 & 1881 water: 29/25, 30/25; water, oil: 48/40; oil: 29/21, 39/21, 45/34; detergents: DIN28/410 Softdrink preforms: various neck versions 0.25-2.5l; Water preforms: various neck versions 0.25-19l; edible oil preforms: 0.5-10l; milk preforms: various neck versions (2-start, 3-start); preforms for personal care, home care, lubricants Around 800 different preforms designs with different weight (9.7-485g) and neck (PCO 1881, PCO 1810, PET cycle Pco 1810, High PCO 1810, PCO HYBRID, BPF, 30/25, 29/25, Hexalite 26/22, Obrist, 34/29, 38 mm, 29/21, 28/410, etc. Company name Chemco Plastic Industries PVT. LTD. Varioform PET Verpackung Ges.m.b.H. Retal Iberia SLU Postal address Telephone number Web site address Contact name Function Direct telephone number Fax E-mail 1412, 14th Floor, Maker Chamber 5, Jamnalal Bajaj Marg, Nariman Point, Mumbai 400021, India +91 2222 821 777 www.chemcogroup.com Mr Vaibhav Saraogi Managing Director +91 2222 821 777 [email protected] Industriestr. 5 3134 Reichersdorf Austria +43 2783 7114 0 www.varioform.at Mr Werner Maurer General Manager +43 2783 7114 10 [email protected] Industrial Estate Gaserans, Ctra. C-35 Km. 66,147 Sector 2 Parcela 5, 17451 Sant Feliu de Buixalleu, (Girona), Spain +34 9728 657 30 www.retalgroup.com Ms Raquel Oller i Bosch Commercial Manager +34 9728 657 33 +34 9728 657 31 [email protected] Preforms Multilayer preforms (Yes/No) Yes No No PEN prefoms (Yes/No) Yes No No Preforms in alternative materials (PP/PLA/PEF) (Which?) Yes, PP PLA PEF Hot fill & barrier solutions No Preforms incorporating rPET (rPET content in %) Yes, depending on customers' requirements 0-55% Yes, % requested by client List of additives available All, as per customers' requirements please contact for further information Colourants, UV, scavengers, carbon black Preform range Chemco is multi-national manufacturer & exporter of preforms. It has a large range of preforms. Chemco has five FSSC certified manufacturing facilities (3 in India 2 in the Middle East). Varioforms preform portfolio includes different preforms for the beverage and non food usage. Preforms from 14.8g up to 54g with PCO 1810, PCO 1881 as well as Petcycle neck finishing are available. Varioform uses different virgin resins as well as recyclates (up to 55%) or special materials (e.g. hot fill or barrier). Neck 29/25: 9.3-29.5g; Neck 30/25:11.539g; Neck Bericap 38/33: 64g; Neck Bericap 48/40: 77-100g; Neck BPF: 26-50.5g; Neck Obrist: 23g; Neck PCO 1810: 20.5-50.5g; Neck PCO 1881: 23.7-45.7g Preform inspection As part of a holistic approach to quality control in preform production PETplanet Insider showcases for the first time an overview of preform inspection systems. Even the smallest faults in PET preforms have a significant impact in bottle production and bottle quality. In the most severe cases, faulty preforms can even lead to malfunctions in the blow moulder. With ever increasing outputs in the blow moulding systems, perfect preforms are indispensable. This is where preform inspection systems come in: preform inspection systems check the preform’s quality and reject faulty preforms immediately from the production line. Thus preform inspection becomes an essential part of process quality control. The companies participated were listed in order in which their details were received by the editors: Intravis GmbH, Torus Technology Group, Sacmi Imola S.C., IMD Ltd. and Pressco Technology Inc. Although the publishers have made every effort to ensure that the information in this market survey is up to date, no claims are made regarding completeness or accuracy.","@ID":26}, "PETcontents 01+02/17 4 PETplanet Insider Vol. 18 No. 01+02/17 petpla.net INSIDE TRACK 3 Editorial 4 Contents 6 News 36 Products 38 PET bottles for Beverage + Liquid Food 39 PET bottles for Home + Personal Care 40 Patents MATERIAL / RECYCLING 8 The big challenge of waste plastic Synergy effect by combining expert’s technology 10 Heat resistant PETpolymers A wide variety for food and non-food packaging BOTTLING / FILLING 12 Trends in aseptic and hot filling Sensitive beverages are only as good as the bottle they come in 13 Standing the heat Bottles and jars for hot filled beverages 14 Protecting sensitive beverages Complete line solutions for hot filled beverages 16 Fruitful alliance Handling high-acid products 18 To reach for low temperature Application of dry sterilisation technology in filling production line 21 One machine fills all Aseptic bottling of all soft drinks on one machine without line shut downs 27 Pulsed light sterilisation Chemical-free decontamination for preforms and closures integrated into the filling line MARKET SURVEY 23 Suppliers of PET preforms & preform inspection systems GO WITH THE FLOW - EDITOUR 30 South East Asia Road Show Overheard: views on the South East Asia Road Show, three weeks befor the start TRADE SHOW REVIEW 32 What’s new about Industry 4.0? A smart step forward with Agility 4.0 34 Filling while forming and forming while filling Dr Christian Compera, Head of Bottling Technology at Krones, on the advantages and current status of liquiform technology 35 India trade shows set on record Growth of dti, PackTech and Food Pex reflects societal and economic change in India BUYER’S GUIDE 41 Get listed! ASEPTIC HOT FILL SPECIAL Page 13 Page 16 Page 18","@ID":6}, "MARKET SURVEY 23 PETplanet Insider Vol. 18 No. 01+02/17 petpla.net 1+2/2017 MARKETsurvey Preforms & preform inspection Recycling plants & washing units Palletising & shrink film machinery Caps & closure systems & CC inspection Labelling & marking systems Recycling: Cutting plants Filling equipment & filling inspection Resins, additives Compressors SBM machinery & quality inspection Suppliers of PET preforms 18 companies from 11 countries take part in this year’s market survey of preform suppliers. They are shown in order in which their details were received by the editors: PET-Verpackungen GmbH Deutschland, Empacar S.A., Société Générale des Techniques (SGT), Etalon Group, S.B.E.C.M., PDG Plastiques, Hodmeter, Resilux Belgium, Alpla, Retal Cypres, Terekas Sweden AB, Terrachim 97 AD, Novapet S.A., Plastipak, Manjushree, Chemco Group, Varioform PET Verpackung Ges.m.b.H and Retal Iberia. For the first time we have extended our market survey preform production with a new and special feature for you: One page is reserved to show preform inspection systems to complement this topic! Although the publishers have made every effort to ensure that the information in this survey is up to date, no claims are made regarding completeness or accuracy. Company name PET-Verpackungen GmbH Deutschland Empacar S.A. Société Générale des Techniques (SGT) JSC Etalon-Plastservice S.B.E.C.M. Postal address Telephone number Web site address Contact name Function Direct telephone number Fax E-mail Gewerbegebiet 4, 98701 Großbreitenbach, Germany +49 36781 48044 00 www.pet-verpackungen.de Mr Hubert Rebhan Business Development/Key Account +49 36781 48044 53 +49 36781 48044 52 [email protected] Casilla de Correo 2865, Parque Industrial 45, Santa Cruz de la Sierra, Bolivia +591 334 655 25 www.empacar.com.bo Mr Carlos Limpias Genreal Manager +591 334 655 25 +591 33461 883 [email protected] 3 Rue de l’Île Macé, 44412 Rezé, France +33 2 4005 0937 www.sgt-pet.com Mrs Le Claire Sales Administration Manager +33 2 4005 0288 +33 2 5170 0155 [email protected] Avtomobilistov St.12, Michurinsky Settlement, proezd, 630526 Novosibirsk, Russia +7 383 334 71 55 www.etalon-group.ru Mr Petr Durnov Main engineer +7 913 912 84 16 +7 383 334 64 70 [email protected] Rue de la plaine, 47230 Lavardac, France +33 5 5397 4100 www.sbecm.com Mr Jean-Luc Didouan General Manager +33 5 5397 4100 +33 5 5365 8597 [email protected] Preforms Multilayer preforms (Yes/No) Yes No Yes No No PEN prefoms (Yes/No) Upon request No No No Yes Preforms in alternative materials (PP/PLA/PEF) (Which?) Upon request No No No Possible Preforms incorporating rPET (rPET content in %) Up to 100% Yes (10% - 100% rPET, clear and coloured) 0% - 100% (according to the client request) 1.5% 5% to 30% on regular production, possible to 100% List of additives available Colours, oxygen scavengers, UV-blockers, slip-agents, AA-scavengers, brighteners, PA-based barriers Activer barrier, 02 scavenger All colours, UV blocker, AA reducer, O2 scavenger, CO2 scavenger, reheat additive, white colour for UHT milk, gliding agent Energy-consicious and A/A absorber AA scavengers, blockers, all colouring agents (liquid or masterbatch), O2 absorbers, additives, lubricants, blends, etc. Preform range PET-Verpackungen provides standard preforms with 28mm PCO1810 & PCO1881 finish from 14.5g to 54g. For German market, preforms with 28mm PCO1810 & PCO1881 PETCYCLE-finish. 38mm 2-Start and 3-Start Bericap preforms for wide mouth applications as well as 29-21 finish for flip top caps. Preforms for hot fill applications, for large containers 60g, 92g and 98g preforms with Bericap 48-41. Enhanced barrier protection, the majority of the preforms are available as multilayer with tailor-made barrier properties. PCO 1810 (17.5-64 g), PCO 1818 (20.6-58.6g) Bericap 38mm wide (70 & 80g) Bericap 48mm wide (85 & 94g) 700g preform for 5 gallon water bottle 29mm edible oil : 18,21,24g Neck finish: 27/31, 45g; 55mm, 650g; 55mm S, 650g; 30/25 High neck and Low neck: 13-44g; 30/25 BB Light, 22,50-28g; 29/25 (without step): 9.3-35.8g; 29/25, 9.536g; 28 PCO 1810, 16-52.5g; PCO 1881,14.4-50g; 28 BPF, 20.5-53g; 38mm 42/36, 14-44g; 38mm 43/36, 14-16g; 28/410 anti back off system; BVS 30 H, 40-53.5g; CRC63, 400-450g PCO: 20.5, 22.0, 24.0, 26.0, 36.0, 39.0, 39.5, 41.55, 52.0g BPF: 21.0, 23.4, 24.0, 30.0, 32.0, 34.5, 42.0, 51.5g Bericap 38: 18.0, 24.5, 25.5, 27.0, 64.0g Bericap 48: 86.0, 89.0g; Oil: 23.3, 25.5g Neck finish : 30/25 High and Low, 29/25, PCO 28 (1810, 1881), BPF, 38mm, 48/41, BVS, 21/29, 36/29, 28/400, 28/410…. Preform weight: 10-91g Possible neck finish adaptation and preform customisation for any application and size : water, soft-drinks (CSD), wine and spirits, oil, milk and dairy products, house and personal care, etc.","@ID":25}, "37 PRODUCTS PETplanet Insider Vol. 18 Abbey Well Spring Water launches new look ‘twist’ bottle and label for recycling ease Coca-Cola European Partners (CCEP) has launched a new ‘twist’ bottle format and label for its Abbey Well Spring Water, designed to be more environmentally friendly and encourage consumers to recycle more.The innovation from British designers was enabled following a £14m investment at CCEP’s bottling facility in Morpeth, Northumberland. The bottle is claimed to require less energy to make, transport and recycle. The new design uses up to 32% less plastic than in the previous bottle design, depending on the bottle size. As well as the bottle itself being more environmentally friendly, it also encourages consumers to recycle, featuring a new label with the wording ‘Recycle Me’ on the outside of the bottle and a prompt to ‘Peel Me Here!’ The reverse side features further information about the brand and the new lightweight bottle including the percentage of less plastic used vs the previous bottle and a ‘Recycle It!’ call to action image. To guide consumers on twisting their bottles for ease of recycling after use the plastic bottle features arrow contouring in two different directions as part of the design. The new bottle is 100% recyclable, aligned with CCEP’s initiative to minimise the environmental impacts of its operations. Bottled water recycling is becoming increasingly important, with the category growing rapidly, according to a Nielsen study. The new bottle will be introduced for Abbey Well Still 500ml, 750ml Sports Cap, 250ml Sports Cap and Sparkling 500ml. CCEP’s Morpeth site is the only source of Abbey Well Spring Water, and the only Coca-Cola water site in Great Britain. The water is bottled at source from a natural spring in Morpeth, with each drop having been filtered through water bearing white sandstone for at least 3,000 years. www.cokecce.co.uk","@ID":39}, "BOTTLING / FILLING PETplanet Insider Vol. 18 No. 01+02/17 petpla.net 14 Complete line solutions for hot filled beverages Protecting sensitive beverages With 45 years of experience in hot filling and over 1,000 pieces of equipment for hot fill packaging installed worldwide, Sidel is highlighting how beverage producers can safely handle sensitive and natural beverages such as juices, teas and sports drinks from the preform to the bottled product. features of the customer’s packaged beverage, the company’s solutions employ the processing equipment and capabilities from Tetra Pak Processing Systems, to ensure processing and filling systems are seamlessly combined to reduce downtime, consumption and costs. Based on control and regulation systems, producers can increase performance and make more informed decisions, ensuring hygiene, efficiency and safety throughout the supply chain, says Sidel. Lightweighted HR PET bottle In terms of hot fill, the temperature of the beverage heating process is as high as 80-92°C which is above the normal thermal resistance of conventional PET bottles. “This requires specific packaging and equipment to allow PET to resist the hot filling temperature. In 1986, Sidel pioneered the heat-resistant (HR) stretch blow moulding process to allow PET bottles to withstand these high temperatures, since when the company has driven PET’s transformation into the flexible packaging solution it is today.” explains Gabriele Gatti, Sidel Filling Product Manager. Today, Sidel has reduced the weight of HR bottles while retaining their durability and increasing the bottle design opportunities. This latter achievement is due to the elimination of vacuum panels - previously a design necessity to absorb the variations in volume that the HR bottle and contents undergo passing from hot to cold conditions, and also to the efficient electrical mould heating and accurate material distribution. Responsive mould heating Traditionally, PET bottles for hot filling are produced via the heatresistant stretch blow moulding process at 120°/140°C - a temperature usually attained by circuits of hot oil. By using electricity instead to heat the mould for the PET bottle body, the Sidel Matrix eHR blower enhances operator safety preventing hazards caused by oil leakages, such as operators’ slipping and product contamination. Probes are directly located in each mould shell to regulate the temperature as closely as possible to the PET bottle as it is formed. The process is very responsive, heating at a rate three times quicker than by ASEPTIC HOT FILL SPECIAL Complete hot filling line According to the market research company Euromonitor, the annual market growth of 6% for the consumption of sensitive drinks such as juices, nectars, still drinks, isotonics and teas presents significant business development opportunities for beverage producers worldwide. To accommodate the demand of packaging solutions using hot fill technology, Sidel is offering a complete hot fill solution that is intended to expand packaging opportunities. Fully integrated and flexible, the company’s PET hot fill packaging solutions are claimed to provide reliable and safe production. By taking a holistic view of the production cycle and line performance, Sidel’s intention was to optimise uptime and operating costs. Focusing on the specific Sidel is using electricity instead of oil to heat the mould. Sidel Matrix Combi","@ID":16}, "BOTTLING / FILLING PETplanet Insider Vol. 18 No. 01+02/17 petpla.net 29 anticipated customer base. As well as high speed lines, it also aims it’s the company maintains. While a replacement for a worn xenon lamp costs more than USD $1,000, the manufacturer guarantees 100% effectiveness for up to 10 million flashes, enabling the treatment of 50 million caps with 30mm diameter, or 40 million caps with 40mm diameter. Claranor has sold more than 200 systems to date. While the majority have been installed in Europe, it also enjoys healthy sales in the USA, Middle East and Asia. In 2016, turnover was US $4.5 million. The devices are still exclusively produced at the Avignon location and shipped worldwide. Eighteen distributors globally take care of local sale and support. At present, Claranor works with local technicians, who visit customer facilities and provide on-site support. Over the medium term, the goal is to create a network of completely self-sufficient dealers. Its customer base includes machine manufacturers Serac, Krones and KHS, Sidel, and CFT; among its customers are numbered Nestlé Waters, CocaCola, Danone and Unilever. Inactivation profiles of A. brasiliensis, B. subtilis, B. pumilus, B. atrophaeus depending on medium Fluence Results obtained by C. Levy, PhD student, on Claranor 3 lamp pilot equipment, 2008 “We may develop sterilisers for the food industry in the future but, at the moment, our chief goal is to achieve a higher degree of name recognition for our preform treatment technology. To do so, we are planning a lot of participation at trade fairs in 2017. Among others, we will be present at Interpack, of course, and at Drinktec later in the year,” Mrs Franc concludes. www.claranor.com Chart of xenon lamp emission spectrum and absorption by DNA and proteins","@ID":31}, "MATERIALS / RECYCLING PETplanet Insider Vol. 18 No. 01+02/17 petpla.net 8 Synergy effect by combining expert’s technology The big challenge of waste plastic Waste plastic is an enormous challenge worldwide. Yet, as production continues to increase, just 5% of waste plastic is recycled effectively. Bühler is addressing this global challenge with a tailored PET recycling solution, capable of improving yields by 30%. A strategic partnership with US-based National Recovery Technologies (NRT) allows the company to offer plastics recyclers a complete solution for plastic bottle and flake sorting. Plastic production is increasing massively and has become a severe ecological challenge. Plastic production has increased 20-fold since 1964, to some 311 million tonnes in 2014 and the numbers are expected to double again in the next 20 years and quadruple by 2050, according to a report produced by the World Economic Forum and the Ellen MacArthur Foundation. The report also found that just 5% of waste plastic is recycled effectively. Assuming the recycling rate remains unchanged at just 5%, the report warns of alarming consequences – that there will be more waste plastic in the sea than fish by 2050, if the world doesn’t make significant changes. Collecting and recycling PET plastic has the potential to reduce millions of tonnes of waste each year. It can be reused to manufacture a wide range of consumer products, as well as food and drink packaging. Bühler accounts for 25% of the rPET recycled stream in Europe and approximately 10% of the global market. The company is now helping PET recyclers with a twomachine process solution that delivers bottle-to-bottle grade rPET flakes. and flake sorting, with NRT specialising in bottle sorting, combined with Bühler’s expertise in flake sorting. Matthias Erdmannsdoerfer, President of NRT, says: “This significant partnership agreement is further acknowledgement of our commitment to supply and service leading plastics recyclers with a full portfolio of leading bottle and flake sorting equipment. We’re excited to bring the industry’s first complete offering to market that doesn’t require a plastics recycler to compromise on bottle or flake sorting performance and provides high-quality, local support.” Bühler’s PET recycling solution also reinforces its sustainability strategy. Bernhard Gabauer, Segment Development Manager for Plastics at Bühler said: “Sustainability is increasingly vital in the food industry. Our new flake sorting technology enables our customers to recycle more plastic, more efficiently and to a higher grade. It is a perfect fit with Bühler’s environmental goal of a 30% reduction in energy, water, and resources in all core processes by 2020.” As a result of the new offering, global OEM and leading PET recycler STF recently switched to Bühler’s new process solution and was able to increase its yield of bottle-to-bottle grade rPET flakes by more than 30%. Mr Josef Söllner, managing director at STF, is convinced by the new technology: “We choose to use Bühler’s Sortex technology, as it is the best flake sorter on the market. We undertook several industry trials to evaluate other technologies, but discovered that Bühler provided the best solution – first class machine results combined with impressive customer service,” he said. www.buhlergroup.com www.nrtsorters.com www.stf-aicha.de The two-machine solution incorporates the Sortex A ColorVision, which delivers high quality colour sorting thanks to its use of three visible wavelengths, allowing a detailed colour detection. When combined with enhanced InGaAs camera technology (infrared detacting), an advanced inspection system and SmartEject technology, the sorter efficiently removes challenging foreign material from clear, blue, green and jazz applications. Then the Sortex E PolyVision employs a polymer sorting process, using a unique combination of transparent and reflective sorting, simultaneously. This identifies invisible and same-colour polymer contaminants by their unique chemical signature, successfully separating clear polymers from clear PET. This combination delivers higher grade rPET flakes that exceed the minimum standards for re-use. Furthermore, Bühler’s partnership with NRT establishes the two companies as first-choice technology partners for plastics recyclers. Together, they offer plastics recyclers a complete solution for plastic bottle Two-machine process solution delivering bottle-to-bottle rPET flakes.","@ID":10}, "TRADE SHOW REVIEW PETplanet Insider Vol. 18 No. 01+02/17 petpla.net 34 Dr Christian Compera, Head of Bottling Technology at Krones, on the advantages and current status of liquiform technology Filling while forming and forming while filling by Gabriele Kosmehl and Kay Barton In the late summer of 2016 it became known that Krones, as a licence holder, was entering the world of liquiform technology. This form and fill technique brings together both stages of the process for shaping a pre-form and filling in one process stage. PETplanet went to BrauBeviale to meet the person with overall responsibility for bottling technology, Dr Christian Compera, and spoke to him about the potential of the new technology. PETplanet: Dr Compera, can you give us a brief outline of the reasons why Krones has got into liquiform technology as a licence holder? Compera: Bottle filling technology is our core business and liquiform has the potential to increase our core technology. Undertaking the forming of the plastic bottle to match the product that goes in it is actually obvious, as it brings many advantages with it, in terms of economy and efficiency. Users then experience a functional integration between the two stages of forming and filling in a single process. We look at liquiform as a sensible expansion to our portfolio and think that the classic two-stage and liquiform will exist alongside each other for a long time. PETplanet: Can you explain the advantages of liquiform in a bit more detail please? Compera: Firstly, the process brings cost savings. Compressed air is very expensive and, because of the compressibility, it cannot be used as exactly as liquids. We also have savings in the electricity and energy areas. Depending on the use, production costs can definitely be brought down by about 10-20%. A second important advantage in addition to the costs structures is product flexibility with the starting material. In addition to PET, the shaping of HDPE containers would definitely be possible. Even rPET can be considered. The limits here must be explored in more detail. Another advantage lies in the fact that additional functionalities can be shaped which, for example, lie in the area of mechanical characteristics such as robustness. All in all, preliminary consultations look very promising. PETplanet: Can you say something about output figures? Compera: In general they will fall within the current levels. Right now we are filling water, for example, about 81,000bph. We won’t start with that but basically there’s based on our current knowledge nothing to prevent this figure being achieved or even surpassed. PETplanet: Do you see water as the main application for the liquiform process? Compera: Yes. It’s here that the process initially enables a huge leverage. In the water sector, clients are up against low margins and are seeking for further TCO reductions to have a profitable business. The advantages of liquiform mentioned above are directly reflected here. At the same time, bottling water undoubtedly poses the fewest challenges compared with CSD or aseptic filling, where the complexity is greater. For that reason, in the drinks segment we shall probably start with water. PETplanet: To date the process is still in development. Are customers already showing any interest? Or do they have reservations? Compera: The brief announcement we made a few months ago publicising our liquiform licence caused something of a stir, to an extent that took us by surprise (see PETplanet Insider No. 09/2016). Client interest is definitely there. Nor has the sector expressed any reservations. There may be some concern amongst consumer groups that the taste of the product may be affected by using it to form the preform under high pressure. As a result, a number of extensive studies were carried out to allay these concerns. All the studies showed that consumer concerns about the taste being affected were completely unfounded. PETplanet: With all the interest – when will we see the technology on the market? Compera: At the moment we are still developing the process and it would be too early to throw an exact date into the discussion. To get a next update, drinktec 2017 would be good event. PETplanet: Dr Compera, thank you very much for talking to us! Compera: Thank you for your interest! www.krones.com Dr Christian Compera, Krones, with Kay Barton (left) and Gabriele Kosmehl (right)","@ID":36}, "PETpatents www.verpackungspatente.de PETplanet Insider Vol. 18 No. 01+02/17 petpla.net 40 PET bottle base shape Intern. Patent No. WO 2015 / 114330 A1 Applicant: Petainer Large Container IP Ltd., London (GB) Application date: 28.1.2015 The special base shape for a weight-reduced, stable PET bottle with a petaloid base is shown. Pack Intern. Patent No. WO 2015 / 121023 A1 Applicant: KHS GmbH, Dortmund (DE) Application date: 19.1.2015 Several of the same bottles can be joined together with an adhesive application on certain contact surfaces into one pack with a handle. Plastic bottle Intern patent no. WO 2015 / 188515 A1 Applicant: Sidel Participations, Octeville-sur-Mer (FR) Date of application: 9.6.2015 To give stability to a lightweight PET plastic bottle against bursting or other stresses, forming and stiffening the base is especially important. The application describes a particular design for the base. Variable base Intern. patent no. WO 2015 / 192918 A1 Applicant: Sidel Participations, Octeville-sur-Mer (FR) Date of application: 3.12.2014 A PET bottle for hot filling / carbonated products is equipped with a base that equalises the changes in pressure that occur more effectively than previous forms for bases. Aerosol container made of plastic Europ. patent no. EP 2763908 B1 Applicant: Procter & Gamble Comp., Cincinnati (US) Date of application: 16.4.2013 Container for holding and dispensing an aerosol. The container is made out of a mix of PET and PEF to increase stability and resistance to cracks. Form of base Intern. patent no. WO 2014 / 113371 A1 Applicant: Graham Packaging Comp., York (US) Date of application: 14.1.2014 The international application describes several forms for the base of a plastic bottle filled with hot products. The base deforms elastically in a predetermined way for volume reduction.","@ID":42}, "EDITOUR PETplanet Insider Vol. 18 No. 01+02/17 petpla.net 30 Overheard: views on the South East Asia Road Show, three weeks before the start South East Asia Road Show With preparations for the coming South East Asia Road Show well underway, the PETplanet offices are buzzing with excitement – and a little apprehension! The publishers have divided the tour into four parts, specifically so that they could also visit the up-coming Propak fairs in Vietnam and Thailand. Part 1 of the tour will take the editors to Indonesia, part 2 Cambodia and Vietnam, part 3 Malaysia and Singapore and finally part 4 will be covering Thailand and Laos. We thought it would be interesting to eavesdrop on the discussions in the office between tour organiser Kay Barton and publisher Alexander Büchler. It soon became clear that time is rapidly running out and some appointments are still very much in the air. Will the tour go ahead as planned, nevertheless? Alexander Büchler: In three weeks I fly to Indonesia and I still haven’t booked the flight. Kay Barton: Ok, we need to get a move on. We ought to be finished with the tour by summer, before the rainy season starts. And then, at drinktec, we aim to do a presentation on all the companies visited. Alexander Büchler: Yes, but as usual with our tours, not all appointments have yet been confirmed. In Indonesia we’ve got tentative appointments with Indo Tirta Abadi, Indo Kompresigma, Dynaplast, Namasindro Plas and Production Recycling Indonesia. How are things going with the vehicle marking? Kay Barton: The layout has been begun, but we are designing it so that sponsors who come in late will still be able to come on board. My worry at the moment is driving in these countries. Our contacts are saying that we would be well advised to use a local driver rather than doing it ourselves. Alexander Büchler: I think I’ll trust my instinct. Satay kebabs on banana leaves and platefuls of rice will be our guiding beacons. Kay Barton: Yes, and you won’t be sweating with panic as happened in Peru during our Latin America tour of 2013 when you came down with severe cramp after negotiating those serpentine mountain bends. Alexander Büchler: Indeed. Now, how are you getting on with your part of the tour to Cambodia and Vietnam? Kay Barton: After my experiences in India, I’m immune to any kind of traffic situation. Besides, Rolf* will be organising for me a Satnav that works. The trick is to drive defensively and then it’ll be fine. I just hope the vehicle can take it. Alexander Büchler: Do you remember that gear damage in Latin America, the broken windscreen during the Russia tour and the engine breakdown in the USA? The good thing is that South East Asia is famous for its generous hospitality so if there is a problem, we should be able to count on getting help from the companies we visit. Kay Barton: So maybe we should ask these companies to be ready and waiting with a box of tools! Actually, joking apart, we’ve had great support on our tours with the problems we have encountered, so I’m confident all will be well this","@ID":32}, "TRADE SHOW REVIEW PETplanet Insider Vol. 18 No. 01+02/17 petpla.net 32 A smart step forward with Agility 4.0 What’s new about Industry 4.0? The beverage market is changing fast. With distribution looking for more customised delivery methods and increased responsiveness, and with people showing different consumer behaviours that influence their purchase decisions, the packaging industry needs to find new ways to improve line operations in terms of speed, efficiency, flexibility and versatility. To move toward the era of Industry 4.0, the concept of the smart factory has become an important and much-discussed topic in manufacturing, highlighted by the trend for an increasing use of automation, cyber-physical equipment and computerised systems for the acquisition and processing of data. At BrauBeviale 2016, Gebo Cermex showcased their advancedproducts system programme called Agility 4.0 which is a vehicle aimed at helping producers achieve all the benefits of Industry 4.0. PETplanet Insider took the opportunity of talking with Ludovic Tanchou, Vice President of Strategy, Products and Innovation of the Sidel Group business unit, Gebo Cermex, who has worked in the group for 16 years. With Agility 4.0 Gebo Cermex is bringing the smart factory to life. This programme incorporates all the essential elements required to build up or improve a plant in accordance with Industry 4.0 opportunities. A series of live demonstrations to highlight the different elements that collectively help producers to shift from mass production to mass customisation were shown on the company’s booth at BrauBeviale 2016. An expert guide was available to drive visitors through the Agility 4.0 programme that as Ludovic Tanchou explained is based on five pillars. 1) Virtual factory: From initial virtual design right through to logistics With virtual reality customers have the opportunity not only to simulate but also to model their own production concept which is a key to controlling costs. Customers need the ability to both visualise and forecast, so that they can make all the right decisions and thus keep their Operating Expenditure (OPEX) to an absolute minimum. With this tool it is possible to optimise capital expenditure (CAPEX) and return on investment (ROI). Additionally, the “Asset Utilisation” ensures - via simulation - that the system can be optimally put into operation. This increases the chances of a successful project execution, as well as improving safety, operability and ergonomics. 2) Smart factory: Machine, system and data intelligence including robotics and communicating hardware The second pillar is about implementing “Smart technologies” to obtain a more agil production model. With Agility 4.0, Gebo Cermex provides a range of advanced solutions aimed at improving performance of equipment and packaging lines, as well as operators’ safety and efficiency in the long term, including easy to use robotics and cobotics, together with a new cognitive Human Machine Interface (HMI). 3) Connected factory: State-of-the-art digital connectivity and simulation With the Gebo Cermex Agility 4.0 the connected factory has become reality as the programme delivers a highly flexible model of operations which ensures high performance Ludovic Tanchou, Vice President of Strategy, Products and Innovation of the Sidel Group business unit, Gebo Cermex","@ID":34}, "7 NEWS PETplanet Insider Vol. 18 For the second time: Beviale Moscow 2017 On February 28 until March 2, 2017, the Beviale Moscow will take place at the Crocus Expo in Moscow. As the big sister BrauBeviale at Nuremberg, Germany, the Beviale Moscow is the equipment show in Russia that covers the entire beverage production process chain: raw materials, technologies, logistics and marketing. Dairy products, beer, wine and sparkling wine, mineral water, juices and soft drinks will be covered, as well as liquor and spirits. The special thing about Beviale Moscow is that there will be a firm Eastern European perspective in 2017. Exhibitors and trade visitors will be discussing solutions specifically for the Russian and Eastern European beverage industry – and how these countries can benefit from internationally successful technologies. www.beviale-moscow.com Agthia acquires water bottling plant in Saudi Arabia Agthia Group, a food and beverage group in the UAE, has signed a purchase agreement for 100% of the shares in the water business of Delta Marketing Company, based in Jeddah, Kingdom of Saudi Arabia producing “Al Ain” brand water. The transaction is expected to be completed by Quarter 1, 2017, following regulatory approvals and other closing conditions. The acquisition enables Agthia to enter the Saudi market for the first time with its Al Ain water brand, the leading bottled water brand in the UAE, reflecting the Group’s strategy to expand in the GCC and become a region-wide player. Delta’s water business has been present in Saudi Arabia for three decades and is a growing and cash-generating operation. The transaction is said to help to fast-track Agthia’s objective of establishing a fully-fledged water production presence in KSA. DWFC has three water brands: Delta Water, a premium product available in large size dispenser bottles of 5 and 6 gallon; Al-Ain, its largest selling brand produced in a range of sizes from dispenser bottles, regular PET bottles and cups; and Bambini the first water in the Middle East specifically designed for the preparation of baby food and available in regular PET bottles. The company also operates a bulk water activity which is mainly targeted for large industrial processing companies. Agthia reported net profit of AED 200 million for the period ended September 30, 2016, an increase of 12% from the previous year, with net revenues increasing by 11% to AED 1.52 billion. Its water business represented 32% of net revenues, and grew 27% against the same period in 2015. www.agthia.com ","@ID":9}, "PETnews 6 NEWS PETplanet Insider Vol. 18 No. 01+02/17 petpla.net Chinaplas 2017 This year’s Asia’s No. 1 plastics and rubber trade fair, is an end-user-oriented trade fair focusing on “Intelligent Manufacturing, High-tech Materials and Green Solutions”. It will take place from May 16-19, 2017 at the China Import and Export Fair Complex, Pazhou, Guangzhou, PR China. Green packaging to be on stage Environmentally friendly packaging is a global hot topic when talking about sustainable development. The packaging industry tends to adopt lightweight, thin films, degradable materials, and package constructions that resist water, oxygen, air and ultraviolet rays. Exhibitors at the show will be displaying examples of all such materials for the packaging industry. In addition, packaging related machinery and automation equipment will be centre stage, to include injection moulding and extrusion technologies that deliver high-barrier end products, automatic detection equipment and multilayer film technology. Other topics at the show are a showcase for highperformance automotive materials; advanced materials for the embrace building & construction industry, plastics and 3D printing to promote medical industry and multifunctional plastics for electrical & electronics products. www.chinaplasonline.com PET omnipresent at drinktec 2017 When drinktec 2017 opens its doors for trade visitors from all over the world from September 11-15, 2017, PET will be almost omnipresent in the limelight, says the organiser. While the demand for CSD is rather stagnating from a global perspective, bottled water in PET continues to boom. Many new developments of PET containers are also used in the dairy industry now. Consequently, drinktec has created a separate exhibition area with PETpoint in line with its importance for bottlers, which is dedicated exclusively to PET technology and presents all innovations with relevance for PET. drinktec shows the entire value chain of PET in this area. The exhibitor group on the subject of PET includes manufacturers of injection moulding machines to produce preforms and stretch blowing systems for plastic containers, among others, but also filling machines for plastic bottles. Representatives are also suppliers of raw materials and auxiliary materials for the manufacture of plastic containers as well as the producers of plastic bottles made from PET, PEN, PP, PE, HDPE or other plastics. Machines and systems for recycling PET bottles and closures are on the other end of the life cycle of PET containers. In advance of the trade fair, the “Go with the flow. Southeast Asia Roadshow” is starting, a collaboration between drinktec and PETplanet (see page 30). Energy and resource efficiency are especially important for the bottlers in manufacturing PET containers. Visitors can obtain information concerning this in the context of the focus topic water, energy management and recycled PET at drinktec. www.drinktec.com Preform inspection systems in WikiPETia Are you looking for the right quality control tool for preform inspection? This year, for the first time, we are publishing a market survey listing suppliers of preform inspection systems (see page 26). In addition, you will find lots of information about each vendor collected on our wiki pages. Go to the preforms homepage: https://petpla.net/wiki?title=Preforms and at a glance you have all the companies listed in WikiPETia for preform inspection systems. From there, simply click on the company profile. Would you like to create a page yourself? Then contact us: [email protected] www.WikiPETia.info Corvaglia Closures Eschlikon AG has a new General Manager The former General Manager of Corvaglia Closures Eschlikon AG, Franco Bischof, has gone into retirement at the end of 2016. His successor, Reto Graf, has been Manager IT & Controlling at the Corvaglia group until now. Corvaglia would like to thank Franco Bischof for many successful years and for his great dedication to the company. He managed both Closures plants in Mexico and Switzerland, and played a major role in ensuring that both business segments grew to become successful market players. In 2012, he was elected to the Board of Directors of the corvaglia group. Franco Bischof will retain this position at the company also in future. Corvaglia is pleased to have found an internal successor for the position of General Manager. Reto Graf has been part of the Corvaglia team since 2013. Thanks to his previous experience, he is already familiar with the key areas of Corvaglia Closures Eschlikon AG. www.corvaglia.ch New General Manager of Corvaglia Closures: Mr Reto Graf.","@ID":8}, "MARKET SURVEY 25 PETplanet Insider Vol. 18 No. 01+02/17 petpla.net UAB Terekas / Terekas Sweden AB Terrachim 97 AD Novapet, S.A. Plastipak Packaging Manjushree Technopack Ltd Vytauto g. 114 a, Kretinga LT-97134, Lithuania +46 700 189 133 www.flexblow.com Mr Gintautas Maksvytis Head of the Export Department +370 698 22 961 [email protected] 21 Bodra Smiana str. 5300 Gabrovo, Bulgaria +359 2 955 6322 www.terrachim.com Mr Lyuben Dryankov Supply Manager +359 8 8799 7336 +359 2 955 63 25 [email protected] Paseo Independencia, 21, 3rd floor., Zaragoza 50001, Spain +34 976 21 6129 www.novapet.es Mr Antonio Lázaro Preform Business Manager + 34 976 216 129 +34 901 021 138 [email protected] Ellice Way, Wrexham Technology Park, Wrexham LL13 7YL, Great Britain +44 1978 317378 www.plastipakeurope.com Mr Mike Hanratty Commerical & Business Dev. Dir. +44 1978 317 366 [email protected] 60 E, Bommasandra industrial Area, Hosur Road, Bangalore - 560 099, India +91 80 43436 200 www.manjushreeindia.com Mr Rajat Kedia Director +91 80 43436200 +91 80 27822245 [email protected] No No No Yes No No No In project Yes No PP No PET resins portfolio by Novapet Yes, PLA, PEF No Yes, up to 100 % 10-15% 10.0-33.0% Yes, 1-100% 10% and 25% Heat-resistance, UV blocker, any colour colourants, amosorb, anti yellow, UV blocker Concentrates (for milk and light sensitive products); colours, lubricants, nucleants, under customer requirements All colourants and barrier technologies UV blocker, oxygen scavenger, slip additive, anti yellow additive, AAA Custom design: any geometry, material, colour and quantity; preforms: ultra light preforms for 5-7 L: 61-73 g. Hot fill preforms for juices: 30g. Metal twist of jar preforms: 47g. PP preforms for candles: 20g. 10.5-128g Ø 29/25 W (short neck) 330ml to 2,000ml: 10-32g Ø 30/25 W (std neck) 330ml to 2,500ml: 11.6-47g Ø 48mm W from 5,000ml to 10,000ml: 77g, 82g & 98g Ø PCO 1810 (std neck) 500ml to 3,000ml: 18.5-54g Ø PCO 1881 (std neck) 300ml to 2,000ml: 18-38.7g; etc. Plastipak supplies preforms for use in bottled water, CSD, food, dairy, home and personal care, alcohol, industrial and other applications. PCO 1810: 12.4-59.5g; PCO 1881: 11.2-52.7g; PCO 1810 Thick Neck: 18.5-47g; 3 Start Alaska:10-35.6g; 30/25 MM 3 Start: 15-31.5g; 29/25 MM 3 Start:17.1-18.6g; PCO 1881 Thick Neck: 22.4-45.7; 26mm Novel Short Neck:8-18g; 28 MM ROPP with NSR: 47g; 32 MM:23g; 38 MM 3 Start twist off: 29g; 55 MM 5 Gallon water. Company name Intravis GmbH Postal address Telephone number Web site address Contact name Function Direct telephone number Fax E-Mail Rotter Bruch 26a 52068 Aachen, Germany +49 241 9126 0 www.intravis.de Markus Juppe Director Sales & Marketing +49 241 9126 0 +49 241 9126 100 [email protected] Preform Inspection Systems PreWatcher III Sample-PreWatcher ColorWatcher Integrated LayerWatcher Inspection speed Up to 72.000 objects/hour Up to 1.200 objects/hour 8 preforms within 0.25s Up to 144 objects/hour Inspected parameters: Geometry / Body Contamination, length, diameter, shape, short shots, gate length, unmelted material, bubbles, oil & water marks, burn spots Contamination, length, diameter, shape, short shots, gate length, unmelted material, bubbles, oil & water marks, burn spots, wall thickness, inner wall damage, core shift Presence of barrier layers, thickness of barrier layers, position of barrier layers, structure of barrier layers, position of barrier leading edge, position of barrier trailing edge Thread area Contamination, thread dimensions, defects at the neck support ring, flash Contamination, thread dimensions, defects at the neck support ring, flash Mouth / Sealing surface Diameter, ovality, flash, scratches and notches on the sealing surface Diameter, ovality, flash, scratches and notches on the sealing surface, inner mouth wall inspection Gate / Dome Contamination, grooves, holes, cracks, crystallisation Contamination, grooves, holes, cracks, crystallisation Colour Colour and intensity deviations (ΔL*, Δa*, Δb*), presence of UV blocker, nylon blocker and IR absorber Colour and intensity deviations (ΔL*, Δa*, Δb*), presence of UV blocker, nylon blocker and of IR absorber Colour and intensity deviations (ΔL*, Δa*, Δb*), presence of UV blocker, nylon blocker and of IR absorber, detection of trend of colour deviations Cavity number Cavity number reading, cavity related statistics, preform sorting according to cavity number Cavity number reading, cavity related statistics, preform sorting according to cavity number, enables collection of reference samples Cavity related statistics Further criteria Stress test with polarised light, high precision weight measurement Early warning stage, fast reaction time because inspection results available parallel to preform cooling Visualisation of barrier layers in 3D images Measurement of absence or presence of barrier material Yes Yes Yes Yes Layer thickness & position measurement at distinctive points No No No Yes Layer thickness & position measurement at the complete body by scanning No No No Yes Features: Installation: Stand-alone Yes Yes No Yes Installation: Inline Yes Yes Yes, integrated into injection moulding machine No Side camera for cavity recognition Yes Yes No No Method: destructive / non destructive Non destructive Non destructive Non destructive Non destructive Data base connection Yes Yes Yes Yes","@ID":27}, "PETproducts 36 PETplanet Insider Vol. 18 No. 01+02/17 petpla.net Fogg Filler enclosure wash options for hot and cold fill machines Fogg has improved enc l osure wash i ng processes by offering multiple wash down options. These options can be implemented on Fogg fillers for either hot or cold fill applications. Fogg Filler offers three different wash systems to easily and effectively clean filling machinery. The first is the enclosure wash. The cleaning solution sprays from the top of the enclosure, sanitising the walls and everything in them. It is a great choice to keep the enclosure wet for easier, occasional light hand cleaning. This system conserves water, the process completes in about a minute. The second wash down option is the ultra-wash: This wash system allows a more targeted flow customisable to the machine to hit the most difficult areas. This option takes about three times as long as the enclosure wash because there are three zones spread through the top, middle, and bottom of the machine. There is an enhanced option for the ultra-wash that allows the user to sanitise with foam (caustic, rinse, and acid sanitiser). The foam sanitising option allows for a more consistent level of cleaning. It is computer controlled and reduces the manual cleaning requirements. Additionally there will be a foam box and the foam pumping unit to complete this system. www.foggfiller.com 38mm closure for aseptic applications To respond to increasing demand for higher performance and convenience in the beverage industry, RPC Obrist Madrid has launched a new 38mm closure specifically developed to be compatible with aseptic filling lines. Aseptic filling processes are becoming increasingly important to brand owners in order to eliminate product contamination. RPC Obrist Madrid has therefore expanded its standard range of 38mm closures with a new 3-thread aseptic cap, which is claimed to be ideal for a wide range of drinks including juices, nectars, teas, sport drinks, and dairy products. The new consumer and sterilisation-friendly screw cap has been designed for wide mouth bottles. As well as being easy to apply on the filling lines and open by consumers thanks to its reduced torques, the closure also meets the rigorous requirements of aseptic applications. In addition, the cap weight has been reduced to 2.80g while still providing good sealing and safety performance for product integrity, quality and freshness. The new RPC Obrist Madrid 38mm cap is produced in Spain for the European and African markets. www.gcs.com www.rpc-group.com W W W . I N T R A V I S . C O M Sample-PreWatcher® Comprehensive sampling analysis inline and offline High speed 100 % inline and offline inspection Color inspection right above the tooling plate Non-destructive layer inspection PreWatcher® III ColorWatcher® Integrated LayerWatcher® Preform Inspection Today.","@ID":38}, "PETplanet Insider Vol. 18 No. 0/17 petpla.net 38 PETbottles Beverage + Liquid Food Fruit Sensation from Rewe Un d e r i t s l a b e l “Rewe Beste Wahl” (Rewe Best Choice), the German trading company sells several refreshing drinks with about 12% fruit content. 750ml of the Orange with Grapefruit Raspberry flavour or AppleKiwi with Sweet Lime flavour fill clear, square bottles. The bottles have sideways grooves, in order for them to be easy-to-grasp and more stable when lifting, opening and drinking from them. In the neck area there are four embossed brand names. Colour-matching screw caps with the product name have a guarantee band and a sleeve label to make them ready for sale. www.rewe.de Milk from peas The American company Ripple Foods makes a milk substitute product from peas, sunflower oil, algae oil and other plant-based ingredients. The 100% vegan product is free of lactose, nuts and gluten. The image shows the sugar-free variant, with 12fl.oz or 335ml filled into a clear bottle made entirely from 100% recyclate which is 100% recyclable. It closes with a screw cap with first opening security. A matt sleeve label with partially shiny printing explains the contents and how to use this product which catches the spirit of the moment. www.ripplefoods.com","@ID":40}, "PETplanet Insider Vol. 18 No. 01+02/17 petpla.net 28 now fulfil customer wishes in a purposeful way”, says Alain Berberian, “In our own research projects, together with those we conduct in Institute for Process Engineering and Packaging, we verified various effects under a range of parameters and “These light pulses achieve denaturing and complete destruction of DNA, proteins and enzymes in a sustainable way,” explains Mr Berberian, while Mrs Magali Bry, his microbiologist colleague, is preparing preforms inoculation with Bacillus atrophaeus for a challenge testing. “It is quite possible, today, in the beverage industry to come across such inline continuous UV light treatments, but exclusively in the form of lower-intensity prolonged exposure, not as an intense light pulses,” says Mrs Franc. “That is where the difference lies. In order to achieve decontamination, a high-voltage pulse is created which, upon discharge, spikes the xenon lamp to a 1MW output for 0.3ms. The flash of light created by this covers the entire spectrum of white light, 20% of which is in the UV range and has a high amount of UVC. The treatment reaches the range of 1kW/cm² of UV light whereas normal continuous UVC operates in the W/cm² range or even lower. For pulsed light treatment in continuous use, the emission of energy is high, but thanks to the patented water cooling system, the temperature of the complete equipment is kept at around 35°C. Depending on which customer product it is dealing with, other factors, such as the design of the reflector around the lamp, the optimal distance of the product from the light pulse or the number of flashes per treatment also play a decisive role in achieving the desired effect, too.” “We come into play, above all, when bottling sensitive beverages and liquid ZZZ IOH[EORZ FRP )OH[%ORZ 8OWUD )OH[LEOH 3(7 6WUHWFK %ORZPRXOGHUV :LGH 0RXWK -DUV +RW )LOO &RQWDLQHUV 2YDO %RWWOHV /DUJH 6L]H &RQWDLQHUV &KRLFH E\\ 3DFNDJLQJ 3URGXFHUV 21( IRU $// food,” Mrs Franc adds. “We also have customers who are active in the area of water, with the issue of removing ozone. In fact, the number of enquiries that we receive for this technology is constantly rising. Due to the architecture of our equipment, we are increasingly having more to do with established filling line OEMs. The interest is growing there as well.” Claranor currently offers the beverage industry a preform steriliser of up to 50mm diameter and with outputs up to 90,000 units per hour, as well as three capping sterilisers for 28-55mm and outputs of 16,000, 60,000 and 90,000bph. This range enables the company to cater both to existing and Preforms treatment at Nong Shim, Korea can now fulfil customer wishes in a purposeful way”, says Alain Berberian, the company’s Microbiology Manager. In the case of preform decontamination, the results of a study conducted in 2016 show that pulsed light treatment of a preform heated up for the blowing process leads to improved destruction of microorganisms on the body of the preform, compared to treatment prior to heating. The company works closely together with the INRA Institute on its testing regime. The Institute undertakes research in the areas of agriculture and food safety, among others, and is located close by; this was the main reason for Claranor’s choice of location for its current headquarters. It maintains a laboratory on site at INRA, where equipment and effectiveness are continuously tested. Its tests show reduction of Aspergillus brasiliensis as well as Bacillus subtilis, B. pumilus and B. atrophaeus by close to 5log. Modelling of cap optical reflector Modelling of preform optical reflector","@ID":30}, "EDITOUR 31 PETplanet Insider Vol. 18 Kay Barton: Yes, that makes sense. I must say that I’ve become more laid back over the course of the many trips. On many things, there is a steep learning curve, especially with areas like bureaucracy and customs formalities. And that’s not forgetting the language barrier, which is a constant feature of our tours. But coping with crossing borders can certainly be a positive experience! Alexander Büchler: Great, and definitely something to look forward to again! Meeting people, new experiences and stimuli! I’d better get my first flight booked... *Editor’s note: Rolf, IT Specialist und Commercial Director at PETplanet time. In the seven years we have been doing these tours, we have got to know more than 250 customers, and they were all willing to lend us a hand when needed. Alexander Büchler: Seven years of tours already? We must be mad! Kay Barton: Too true. If I could have just one wish, it would be for a few more appointments with endusers. Alexander Büchler: But suppliers with on-site facilities are also important. They create a high market transparency. On the other hand, it is always exciting to see how users from different regions make use of similar equipment. Kay Barton: Quite so. And if we do that we get a real feel for any special regional features in product design, finding out what works with the end client and why. Alexander Büchler: Yes, for example, the large PET bottles for beer in Russia, the small 0.25l Coca-Cola bottles in India or the extremely light bottles for water in North America... Do you think there are going to be differences between Cambodia, Thailand and Laos? Kay Barton: To find that out we have to go there and plan to be at the Propak fairs. As far as Thailand is concerned, I do have real concerns about the security situation. Alexander Büchler: I’m reasonably relaxed about it. If we contact our office in Bangkok and our clients, we can always keep ourselves updated about the current security situation.","@ID":33}, "BOTTLING / FILLING PETplanet Insider Vol. 18 No. 01+02/17 petpla.net 17 checks the bottles’ top and base. Especially as the preforms for the Innocent containers are supplied from the UK, meaning they have travelled a long distance, it is necessary to check the containers for neck finish ovality. After the square containers have been stretch-blow-moulded, they are orientated by magnetically springloaded fingers. This is necessary in order to ensure dependable closing of the containers later on. The Modulfill VFJ machine fills the products volumetrically in full-jet mode by means of an inductive flow meter, which is said to be product-friendly and to guarantee a high degree of microbiological safety and accurate fill quantities. “Each line has been connected to its own CIP module, which means cleaning and disinfection times are extremely short, coming to a mere two and a half hours approximately,” says Berthold Burgmeier. “This short time is due not least to dry sterilisation of the isolator with H 2 O 2 . We were worried that in view of the complicated container shapes we’d have to manually intervene more frequently in the isolator, which is why we were keen to have additional wet sterilisation of the isolator with peracetic acid. This kind of intermediate disinfection routine is then completed within 15 minutes,” explains Berthold Burgmeier. However, for the intermediate-disinfection routine with peracetic acid, the line also needs sterile water in order to rinse off the acid. To obtain this, Gropper does not use an elaborate UHT system, the company just filters the sterile water. www.krones.com to the different filling portfolio each of them has to handle, which on Line S1 are square bottles for Innocent NFC juices (0.9l, 1.35l and 1.5l) and round bottles for NFC-juice dealer’s brands (1l and 1.25l). On Line S2 specialshaped square bottles (0.33l, 0.5l and 0.9l) and Round bottles (1l) are being handled. To match these different containers, the lines have been appropriately equipped in terms of closers: Line S1 handles flatcaps and the large Innocent closure, Line S2 likewise processes flatcaps, plus the large and the small Innocent closures. Besides the Innocent products, the two lines also fill a variety of NFC juices for retail customers. While there is a format change-over only every one day or two days, the product itself is changed two to three times a day. Almost from the start, both lines have been working in three-shift operation. Each of the lines features an identical Contiform Bloc, which in this configuration permits filling with the UltraClean process. This is the major difference as compared to the PETAsept D block with H 2 O 2 decontamination in use at the Gropper Bissingen plant. Since both high-acid products, such as NFC juices and smoothies, and dairy products are filled there, aseptic filling was imperative. Not so in Stockach. “Here, we’re filling exclusively high-acid products. In order to market these, whether inside the cold chain or out, the UltraClean process suffices,” explains Berthold Burgmeier, Technical Manager at Gropper. “I like Krones’ top-down approach to the filling of sensitive beverages. It means that the aseptic machine is matched to the UltraClean process, and not the other way round. In the final analysis, we’re running an aseptic line here, only it isn’t called that, but it invariably gives us that reassuring feeling of being on the safe side.” Container orientation feature integrated After the preforms have been preheated, they are decontaminated in the Contipure system and transferred to the blowing wheel. This is followed by the PET-View inspector, which The Contiform Bloc with the UltraClean process is composed of: Contipure preform decontamination system with H 2 O 2 and isolator Contiform stretch blow-moulding machine Isolator CIP module Closure decontamination unit Modulfill VFJ filler Closer Contipure decontaminates the preforms by means of gaseous hydrogen peroxide within just a few seconds – in a treatment chamber between the linear oven and the blow module. The high H 2 O 2 concentration, in conjunction with the hot preforms, is intended to guarantee an excellent decontamination rate for the preforms both inside and out. The risk of subsequent recontamination has been reduced to a minimum. Treating the preforms, instead of the blow-moulded bottles, is claimed to make for savings in energy and media consumption. For its filling operation, Gropper opted for two lines installed in parallel, each rated at 25,000bph. The screw-caps for the Innocent containers taper downwards, so neck-handling is ruled out for this container variant.","@ID":19}]}}
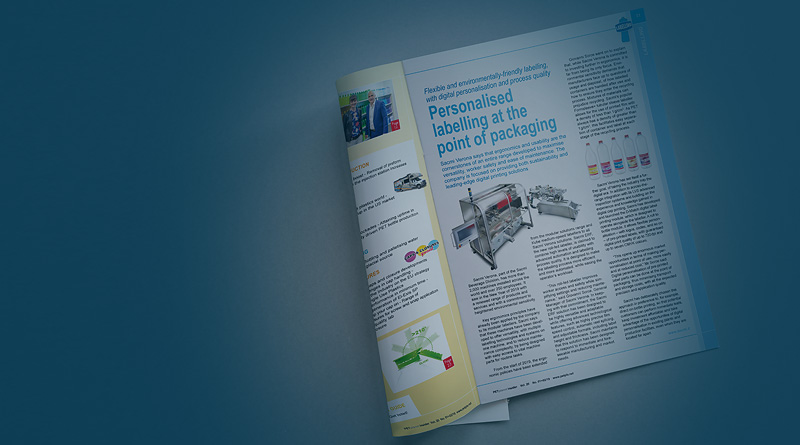