"45 PRODUCTS PETplanet Insider Vol. 18 No. 05/17 petpla.net IM capability for prototyping and sampling of preforms Brand owners interested in conducting package validation testing (performance, filling line, shipping, etc.) and small test market distribution before committing to a wider launch now have access to a cost-effective alternative. Additionally, converters needing development and production support also can tap into a new resource. Plastic Technologies, Inc. (PTI) has added new injection moulding capability for prototyping and sampling of preforms which reduces cost and lead time and improves speed-to-market. PTI has added Husky’s Adapt tooling capability to its new all-electric Arburg injection moulding machine. The mould base features a valve-gated hot runner which allows one to four cavities to be moulded per cycle. If desired, a single cavity can be built for the initial development, and then scaled up to four cavities for larger sampling requirements. “This multicavity preform approach is ideal for supporting smaller product launches. These quantities are much smaller than those required by nationally-distributed brands which can be upwards of 5 million units,” said Chris White, supervisor, injection moulding services. “Further, because of our 30-year track record in PET development and preform production, PTI can cost-effectively produce the preforms.” In addition to PET, polypropylene, polylactic acid, polyethylene, bio-based polymers and other materials can also be injection moulded via the new tooling. www.plastictechnologies.com Sangemini’s new “sporty” water bottle PET Engineering continues to work with Acque Minerali d’Italia. After launching ‘Exclusive’, the new range of bottles for the professional catering industry from Norda, the Group’s leading brand, Sangemini Sport – a “sporty” bottled water – is being released. PET Engineering’s bottle is therefore designed to be immediately recognised by its target audience, by athletes and, more in general, by anyone who exercises. That’s why this design takes its inspiration from the shape, strength and compactness of the flasks used by cyclists and marathon runners. The open/close cap has a drip-proof valve, the squeezegrip makes it practical to use even when running, and the carbon-look knurled pattern is inspired by the material used to make sports bikes, all of which make the new Sangemini packaging considerably technical and particularly well suited to its role as “Official Water” for the 2017 Giro d’Italia. www.petengineering.com PolyOne presented Lactra SX update PolyOne has presented an update for its high-performance light blocking technology for liquid dairy packaging. Lactra SX light blocking additive, which is marketed by PolyOne’s ColorMatrix business, protects liquid dairy products packaged in mono-layer PET bottles from degrading due to light radiation. Since the launch of Lactra SX last year, and as part of a planned testing protocol, PolyOne has carried out a series of comparative laboratory tests to the light-blocking additive to understand specific performance levels. ColorMatrix Senior Product Manager Azam Khan has presented the findings of these new test results at the Dairy China Summit: a best light blocking at lower usage, a low density leading to lighter weight bottles, a high top load performance, the best burst pressure in bottles and PolyOnes leading position in class for mono-layer PET bottles for light blocking in UHT milk bottles. UHT dairy products require special packaging consideration for long ambient shelf life, which ColorMatrix Lactra SX Light Blocking Additive can provide as a high-performance light blocking product. www.polyone.com","@ID":47}, "TRADE SHOW REVIEW PETplanet Insider Vol. 18 No. 05/17 petpla.net 40 Plastics Recycling Show Europe, Amsterdam, NL 2017, part 1 Creating a sustainable recycling society by Heike Fischer The statement plastics recycling first by Ton Emans, President of Plastics Recyclers Europe was a striking, persuasive comment on the importance of the all-embracing Plastics Recycling Show Europe, held for the first time in Amsterdam, Netherlands in March 2017. PRS Europe 2017 featured over 80 exhibiting companies, heard more than 40 conference speakers giving imaginative and inspirational presentations and had a total footfall close to 1,400 over two days. Exhibitors and visitors attending the show were a good representation of the whole value chain of the plastics industry including among others: recyclers, machine producers, raw material producers, converters, waste management companies and brand owners. It resembled something of a family affair as Gerben-Jan Gerbrandy, member of Parliament (MEP) and committee member for the Environment, Public Health and Food Safety opened the event at the RAI Amsterdam, where he urged the European Commission to take plastics recycling seriously in its Plastics Strategy report due to be published later this year. He also took the opportunity to call for action to increase the reuse and recycling of plastics. “We can show the world that it makes economic sense to recycle plastics, that it has a huge environmental benefit, but first of all it has huge economic benefits,” Gerbrandy said at PRS. The two-day conference program was divided into three parts: materials focus sessions, plastics recycling industry challenges and the plastic recycling process. The PET session was opened by Casper van den Dungen, Vice President and PET WG Chairman at Plastics Recyclers Europe. His question to the audience was: How can we develop PET recycling further in Europe? In his presentation, he promoted the mission of Plastics Recyclers Europe: The important point is to create conditions which enable profitable and sustainable business, and this, he stated, should be by initiating recycling projects to promote the use of recycled plastics. Additionally, he underlined the importance of offering a service platform to inform the industry and their customers in detail. He showed the current status of use of virgin and rPET in different applications: for sheets, preforms, additives and machines. The use of virgin PET per year in different application he mentioned amounted to 3,000kt, whilst the use of rPET per year was 1,200kt. In the end, the collection rate of material from virgin PET is 1,700kt, and for rPET 50kt, which equates to a percentage of 57%. Den Dungen pointed out that the feedstock status for bottle collection is close to saturation based upon current infrastructure. The sheet and tray collection is still in the start phase and needs infrastructure adaption. The washing lines of bottle recycling plants were busy at 30%, with a capacity average of 20-25tk input. To meet the Commission’s new proposal that recycling volume should be doubled by 2025, den Dungen spoke of the need for a change in outlook. The circular economy, especially in PET recycling is an important component as is the deposit refund scheme also. He considered that there is and will be a volume growth of plastics use but profitable growth would be limited if there are no changes. For him the deposit refund scheme would be like motorway tolls. The major changes for him have to be an adaption of infrastructure to increase the collection rate. He further suggested using as much collected PET as possible to program new business models to finance the higher targets. According to him the new recycling capacities need to be adapted to future collection facilities. To program future values, it is also good to know the history of the product which has to be recycled, he added. He concluded by saying that the successful past history of rPET is preparing for a transition for the next level. The leading recycling rate of 52% will move up if higher targets for plastics are required. New deposit bottle and new tray, and non-food packaging collections are new infrastructure developments which can be expected at a level of more than 500kt. In his summary, he stated that a high collection rate will result in higher cost but that these costs would be absorbed in the value chains. There is the need for new business models to secure investment as well as the absorption of this new volume in the market, he concluded. A number of PET experts then proffered their own views on new developments and projects in the PET recycling business. PET recycling competence (f.l.t.r.): Casper van den Dungen, Vice President, PET WG Chairman at PRS, Board Member of PRS Paolo Glerean and Olivier Vilcot, Vice President at SRP","@ID":42}, "PREFORM PRODUCTION 37 PETplanet Insider Vol. 18 No. 05/17 customer gets a high-quality feel from the product. Over 20 Netstal facilities with Otto Hofstetter moulds ensure everything keeps running smoothly. “We have to keep on making products – downtime costs money and we wouldn’t be able to maintain our current prices if we had to constantly service our facilities and equipment,” explains Yanto. In the preform division, the flow of materials is organised efficiently, as expected. From supplying raw materials through to the production process, all the way to storing products in the warehouse and the shipment process. On the other side of the factory, there is another division that also delivers products to the dispatch centre, where seals come from many, many Sacmi compression facilities. And needless to say, this is also well organised. The caps are in acclimatised clean rooms and packed in plastic bags in the most hygienic way. These are then sent onto a separate warehouse specifically for the seals. Only then will both divisions join up and the products can be loaded onto the lorries and dispatched – depending on customer requirements, preforms or seals can be dispatched separately or together. His newest business has been running for four years and produces water beakers. Do I need to say it? Yes, this production process is also very well organised. Granular material arrives at sheet extruders from SML and is then mixed with grinded, recycled lead frame. The sheet then runs on the production line into the Kiefel thermoform unit which deep draws and stamps out 54 beakers per 3.1g. As a result, Yanto now produces all the bottles that the Indonesian water industry needs. He supplies multinational companies, such as Danone and Coca-Cola, national brand names, such as Club, Sosro and Viro, as well as over 700 more bottling companies, some which are very small regional businesses. He wants to use the experience he has gained to advise bottling companies should they encounter difficulties. Whether they have packaging or technical problems, or questions regarding water sources, Namasindo Plas can help in what I suspect will be a very organised manner. www.namasindoplas.com A look inside one of the clean rooms where caps are produced","@ID":39}, "MARKET SURVEY 29 PETplanet Insider Vol. 18 No. 05/17 petpla.net Sumitomo (SHI) Demag Plastics Machinery GmbH Husky Injection Molding Systems Ltd. +49 911 5061 0 www.sumitomo-shi-demag.eu Mr Arnaud Nomblot Director - Business Development Packaging +49 911 5061 625 +49 911 5061 96 625 [email protected] 500 Queen St S Bolton, ON, CAN L7E 5S5 +1 905 951 5000 www.husky.co Mr Michael White Business Manager, Beverage Closures +1 905 951 5000 ext. 2913 [email protected] 500 Queen St S Bolton, ON, CAN L7E 5S5 +1 905 951 5000 www.husky.co Mr Henry Zhang, Director of Business Development, Medical and Specialty Packaging +1 905 951 5000 ext 5196 [email protected] El-Exis SP HyCAP4 225t RS50/50 | RS60/60, HyCAP4 300t RS50/50 | RS60/60 | RS70/70, HyCAP4 400t RS60/60 | RS70/70, HyCAP4 500t RS70/70 HyperSync Injection Moulding Injection achieved by a direct drive reciprocating screw Injection achieved by a direct drive reciprocating screw 150 - 750t 225t (2,250kN) | 300t (3,000kN) | 400t (4,000kN) | 500t (5,000kN) 26mm: 2,800 caps/min Varies depending upon application Varies depending upon application 29mm: 2,300 caps/min PCO 1881: 1,650 caps/min Hybrid Clamp stroke achieved by a servo driven ball screw 0.40 - 0.50 Varies depending upon application Varies depending upon application Z-Moulds / Plastisud Husky Husky Mould Identification (ID) ready; Mould Alignment ready large 19\" intuitive touch screen HMI for simple operation eIMC servo-driven in-mould closing technology Mould Identification (ID) ready; Mould Alignment ready Sacmi Imola S.C. IMD Ltd Pressco Technology Inc Via Selice Prov.le 17/A 40026 Imola - BO - Italy +39 0542 607111 www.sacmi.com Mr Stefano Severi Vision System Sales Area Manager +39 3356594236 [email protected] Moosweg 1, 2555 Brügg - Switzerland +41 32 366 80 66 www.imdvista.ch Mr Martin Gerber Sales Director IMD Ltd. +41 32 366 80 66 +41 32 366 80 69 [email protected] 29200 Aurora Road, Cleveland, OH USA +1 440 498 2600 www.pressco.com Mr Tom O'Brien VP, Marketing, Sales & New Bus. Develp. +1 440 498 2600 [email protected] CHS IMDvista Closure Vision Inspection High-speed Vision System Up to 4,000 pcs/min Up to 4,000ppmin/ 240,000pph (depending on customers request and product) up to 3,600 ppm Interior, exterior, sidewall In- or off-line solution, downstream solution by IMDvista - from undermould conveyor (UMC) to cooling conveyor (CCS) in the feeding system (WFS) up to the vision inspection (CLCO) and packaging station (BS), integrated as OEM systems in any kind of machine Plastic caps having diameter up to 43mm One piece closures, assembled closures, doy pack closures, oil closures, sport caps, aluminium (longskirt) closures, rubber parts, coffee cups, coffee filters, shampoo closures, medical closures, lens container, pouches, food container Food, beverage, pharma, specialty, dispensing, sport, plug seal or liner, injection or compression moulded Yes, complete (ovality, colour variations, contaminations, black specs, liner or plug seal…) Short shots, overfill & flashs, contamination, seal defects, colour & colour changes, deformations, diameter & ovality, laser marking inspection Yes Yes, complete (includes decoration inspection) 360° outside view, colour and colour changes, contamination, height measurement Yes Yes, complete (diameters, height) Geometry measurements upon request Yes Yes, it can read any type of character font through a smart learning procedure Easy teach in function, cavity recognition, cavity related statistics, cavity related alarm No Yes, through a spark tester device IMDvista Spark for pinhole detection No Cut and bridges of tamper evident band Upon request Wide range of insert types and materials Sidewall can be inspected by means of a peripheral lens or through Sacmi CVS360-3D inspection module; CVS360-3D consists of a sert of four cameras capable to acquire the 360° of the sidewall, making a compensation of any possible deformation that may stem from perspective, lens and spatial position IMDvista BTIR barrier testing system IMDvista Layer testing system Colour, UV, print/deco, liner/wad, caps on filled containers Yes Flexible In-Line or Off-Line system solution available Yes Yes Yes Correlation defect/cavity number; Through a special software developed by Sacmi R&D, the four images are used to precisely reconstruct the 3D sidewall on a 2D image. Such reconstruction allows to operate on a perfect 2D image carrying out special inspections like TEB band cuts and bridges. IMDvista V5 - newest intelligent software technology. IMDvista Portal, connect all system on one central data base (HMI for fast and transparent production overview) Real-time trend data, last 100 images, defective image database/archive, remote access, biometric user login, customisable reports, OPC connectivity","@ID":31}, "BOTTLE MAKING 33 PETplanet Insider Vol. 18 No. 05/17 custom phase, where it is further developed with specific attention to graphics, aesthetics, practicality, cost and ergonomics. Only when the client gives approval will the project then advance to the final phase: creating the mould that will bring the physical prototype of the new container to life. Moulds and testing A great design on its own is not enough to make a great looking bottle. Something that will offer shelf appeal and attract consumers also depends on the accuracy and precision with which the moulds used to produce it are made. In order to ensure that customers will receive the highest quality containers, SMI has created a department dedicated to the production of special aluminium and steel alloy moulds, suitable for use in its own stretch-blow moulders, as well as those of other manufacturers. The quality of the moulds is assured by employing an FMS line, consisting of 12 CNC machining centres. These are technologically advanced, fully automated, unmanned machine tools that run nonstop, 24/7, following computer-aided manufacturing (CAM) programs. Research and development are constantly in the foreground at SMI. Its labs are able to deploy a range of resources for testing new technologies and applications, especially in the stretch-blow moulding of preforms made of PET and other materials. Its sophisticated equipment allows sophisticated and highly accurate testing of the customer’s preforms: thickness, for example, is measured by cameras linked to parameterisation comparison software; polarised light equipment analyses polymer homogeneity. SMI’s prototyping facility is equipped to provide rapid quality sampling. The creation of a “pilot” container gives shape to the design, providing a physical product for testing and inspection. The SMI laboratories check its mechanical, physical, and functional characteristics and determine whether these are consistent with the customer’s expectations. SMI’s range of up-to-date testing equipment includes the AGR International PPT3000 tester, which tests the quality of the bottles created by the SMI R&D Centre and ensures that they meet pressure resistance and volume expansion specifications. With its modern CAD centre, equipped with the latest generation of design tools, SMI is able to design and decorate a large variety of PET bottle and containers shapes, both simple and complex, with functional and custom designs. www.smigroup.it We do more. The factory of the future starts now drinktec 2017 Munich, 11 – 15 September Hall B6","@ID":35}, "PETpatents www.verpackungspatente.de PETplanet Insider Vol. 18 No. 05/17 petpla.net 48 Bottle with variable volumes Intern. Patent no. WO 2016 / 132469 A1 Applicant: Viewtec Japan Co. Ltd., Kanagawa (JP) Application date: 18.2.2015 A bottle for containing a carbonated drink can have its volume reduced by a device in order to “gas out” the residue and thus improve product quality. Plastic bottle Intern. Patent no. WO 2015 / 032962 A1 Applicant: S.I.P.A. S.p.A., Vittorio Veneto (IT) Application date: 9.9.2014 Plastic PET bottles designed for hot filling with compensation surfaces for equalising the pressure and volume differences after cooling. In order to bring the contents out via an ejection port or a closing device, the bottle can be used as a squeeze bottle by applying pressure to the compensation surfaces. Bottle with a grip Europ. Pat.issue no. EP 2471718 B1 Applicant: Yoshino Kogyosho Co. Ltd., Tokyo (JP) Application date: 20.8.2007 The outer wall of a large-ish plastic bottle is given a shape which is proposed as the holding device for a separately-made grip. The grip is sealed against being lost when putting it on and turning it. Linear mouth area Europ. Patent no. EP 2679507 A2 Applicant: Krones AG, Neutraubling (DE) Application date: 1.7.2013 The mouth area of a PET plastic bottle must be particularly designed in order to avoid the content frothing during filling. The radii of the inside are designed in such a way that the liquid at best runs along the inside of the bottle and not direct to the base with excessive frothing. The matching filling process is also described. Base for a plastic bottle Europ. Pat. Issue No. EP 2619097 B1 Applicant: Red Bull GmbH, Fuschl am See (AT) Application date: 21.9.2011 Design and process for producing a reduced-weight PET bottle which can also resist a raised internal pressure and can be developed optically, as any deformation can be taken up by the shape of the base. Foamed containers Europ. Patent No. EP 2993144 A1 Applicant: Toyo Seikan Group Holdings Ltd., Tokyo (JP) Application date: 25.4.2014 It is proposed to integrate air bubbles into the preform / wall of a plastic bottle. The air bubbles stabilise the bottle and can be used in a targeted way to influence the transparency of the bottle.","@ID":50}, "MATERIALS / RECYCLING PETplanet Insider Vol. 18 No. 05/17 petpla.net 25 degassing-free and highly robust 3S bimetal single screw extruder in L/D 26.5. Reciclar sees the years of reliability of the overall Vacurema concept with low maintenance at the same time as clearly confirmed. Increasing challenges in PET recycling The situation for plastics recyclers around the world has changed, also for Director Sergio Martin and his stage washing process and sophisticated pre- and post-sorting. The main investments here were ultramodern automatic flake sorting plants from leading manufacturers. With this recycling concept the Argentinian company can supply high-grade PET flakes and PE and PP recyclates, mostly independent of the quality of the input materials. www.erema.com www.sima-ds.com www.reciclarindustrial.com.br team in Buenos Aires. The PET postconsumer bottle market – not only in Argentina – consists of a growing number of extremely lightweight bottles and has proportionately considerably more contaminants such as full-body-sleeve labels made of BOPP, PE, PLA, PET or PS. The ISO-9001 certified company Reciclar reacted early on and, besides the most efficient extrusion technology, was soon committed to a multiple Thanks to the recycling and extrusion systems Reciclar produces high-quality end products such as strapping bands from post-consumer PET bottles. The recycling and production hall at Reciclar","@ID":27}, "imprint EDITORIAL PUBLISHER Alexander Büchler, Managing Director HEAD OFFICE heidelberg business media GmbH Bunsenstr. 14 69115 Heidelberg, Germany phone: +49 6221-65108-0 fax: +49 6221-65108-28 [email protected] EDITORIAL Kay Barton Heike Fischer Gabriele Kosmehl Michael Maruschke Ruari McCallion Waldemar Schmitke Anthony Withers WikiPETia.info [email protected] MEDIA CONSULTANTS Martina Hirschmann [email protected] Johann Lange-Brock [email protected] phone: +49 6221-65108-0 fax: +49 6221-65108-28 LAYOUT AND PREPRESS EXPRIM Werbeagentur Matthias Gaumann | www.exprim.de READER SERVICES Till Kretner [email protected] PRINT Chroma Druck & Verlag GmbH Werkstr. 25 67354 Römerberg Germany WWW www.hbmedia.net | petpla.net PETplanet Insider ISSN 1438-9459 is published 10 times a year. This publication is sent to qualified subscribers (1-year subscription 149 EUR, 2-year subscription 289 EUR, Young professionals’ subscription 99 EUR. Magazines will be dispatched to you by airmail). Not to be reproduced in any form without permission from the publisher. Note: The fact that product names may not be identified as trademarks is not an indication that such names are not registered trademarks. 3 PETplanet Insider Vol. 18 No. 05/17 petpla.net Dear friends of PETplaner Insider, B-to-I (Bottle-to-Island) PET recycling is always a hot topic for us. It includes collecting, sorting, washing, preparing, granulating etc. Bottle-to-bottle recycling in particular has really caught our fancy. In addition, we also talk a lot about bottle-to-film or -thread. But today I’d like to talk about the second life of a PET bottle. For those who do not know, an old PET bottle can become a car oil bottle in the garage, or the bottle with fine holes in its lid becomes a spritz bottle for ironing or watering plants. We have found PET bottles used as spaghetti storage jars and much more. We would like your help to report on these other uses in the PETplanet Insider from time to time. For every one published, we will donate 20 euros to a good cause. Send us your examples of similar ingenious second uses of the PET bottle! I would like to start the series with an incredible B-to-I project, an island on around 150,000 PET bottles. The first PET bottle island, “Spiral Island” conceived by British artist Richart “Reishee” Sowa was washed up on the beach by hurricane Emily. In late 2007 and 2008, Sowa built a replacement for Spiral Island in the waters of Isla Mujeres, the “Island of Women”, also near Cancun. He filled nets with empty discarded plastic bottles to support a structure of plywood and bamboo, on which he poured sand and planted numerous plants, including mangroves. The new island was initially 20 metres (66 ft) in diameter, which has since expanded to 25 metres (82 ft), and plants and mangroves are already growing on it. The new island has three beaches, a house, two ponds, a solar-powered waterfall and river, a wave-powered washing machine and solar panels. Volunteers helped with the project. Sowa will continue to make improvements to the Island, so it will always be a work of art in progress. www.youtube.com/watch?v=El6AU3riRI8 No need to be shy; we would love to hear about your projects, which do not, of course, need to be quite so ambitious! Yours Alexander Büchler","@ID":5}, "MATERIALS / RECYCLING PETplanet Insider Vol. 18 No. 05/17 petpla.net 10 PET, rPET, bio-PET and more Multiple choice Since the invention of PET in 1941, the material revolutionised the drinks market with approximately every third beverage packaging today filled in PET. From the start, research has constantly focused on improving the materials’ properties, and an entire industry has since been developed also around the recycling of the post-consumer bottles. But besides making bottles of virgin or bottle-grade rPET, bio-PET is also a growing segment. On the following pages, we highlight some recent developments in the resin and processing sector. The worldwide market for virgin PET is expected to grow +/-5% this year (PCI Wood Mackenzie). The highest proportion of the consumption is in bottle-grade resins for water and CSD, with a rising number of oxygen sensitive beverages. Improving the shelf life of the products is a constant struggle for the industry. As consumer habits change, so material development must keep pace. Additives and special solutions for PET packaging help meet the needs of the market. For example, bottles in which juices and smoothies are filled, require a reliable UV protection to ensure the shelf life of the contents. This is not only true for beverages packaged in PET but also for the Health and Beauty Care market where consumers shun products whose contents are loaded with UV stabilisers to products where the protection is guaranteed by the improved package itself. In addition to UV shielding additives, these include anti-yellow solutions, IV enhancer for rPET or additives for easier processing of the material. Even the unintended off-taste of water bottled in PET can be eliminated by the right choice of additives. Bioplastics currently still represent a small share of the global plastics packaging market, of which bio-PET bottles are part. According to a new report from Smithers Pira, global demand for bioplastics for the packaging industry is forecast to grow from 2017–2022 at an annual average rate of 17% amounting to a market value of almost $7.2 billion. Most successful will be those who identify opportunities where a premium can be expected for a naturally sourced product. This will help in counteracting the uncompetitive cost of biopolymers compared to petro-polymers, a factor brought about by falls in world crude oil prices since mid-2014. Furthermore, in packaging applications where it is technically possible for bioplastics to replace oil-based polymers, suppliers will also have to manage the problems of higher production costs, capital availability, and limited availability of bio-based feedstock over the coming years. However, it is expected that future biopolymers will offer improved rates of bio-renewability and bio-degradability, as this rate is an important factor in achieving market acceptance. In 2017, non-food is the largest area of application for bioplastic packaging, accounting for almost 46% of global consumption. Food is the second largest end-use sector, followed by beverage bottles. Bioplastic beverage bottle consumption has grown dramatically since 2012, following the introduction of bio-derived PET for soft drinks bottles, and will account, according to the report, for almost 22% of bioplastics for packaging consumption in 2017. Different PET from numerous sources are available today, each requiring different processing or preparation conditions to be adequately and efficiently transformed into the perfect preform/bottle. www.smitherspira.com www.woodmac.com MATERIALS Special Photo: Starlinger","@ID":12}, "MATERIALS / RECYCLING PETplanet Insider Vol. 18 No. 05/17 petpla.net 17 PETplanet: What about future developments, are there any you can discuss? Cécile Bourland: We have a number of new developments that have just been launched or will be available within the next months and will support areas of potential growth. PoliProtect K: for kegs, aimed at the CEE market (including Western Europe) and Central/South America, this will be used by premium breweries. Currently, many bars, pubs and restaurants are not returning the metal kegs used to distribute beer from the breweries; this could be for a variety of reasons, but it remains a big problem. A plastic keg can help alleviate these problems by being less expensive to produce and ship. Lost or unreturned kegs would be less of an impact to the brewers’ bottom line. Historically, one of the difficulties has been making a strong barrier resin that can sustain specific mechanical properties of the keg. Now there is a solution. rPET: M&G is able to use its proprietary Bico PET technology in order to produce PET (standard or barrier) including 10-20% recycled PET in the resin core. The fact that the M&G rPET is encapsulated in the core of the PET pellet is a key benefit that allows us to overcome the limitations of rPET currently available on the market. In fact, the current available rPET flakes are not consistent in quality and lead to questions from producers about whether it is food approved and colour consistent across the whole product; what impact the grade will have on bottle appearance; and how to guarantee barrier performances. With its BicoPET technology allowing the insertion of rPET into the core of the PET chip, M&G will be able to offer a highquality, consistent, food-contactapproved resin. W W W . I N T R A V I S . C O M For all Specialty Closures like flip top or push-pull closures as well as dosing inserts and sports caps CapWatcher® SC Closure Inspection Today. Gentle and safe high speed inspection, including cavity number reading CapWatcher® III PETplanet: Finally, what would be your key message to the beverage producers? Cécile Bourland: We are investing in PET production technology in order to build the most cost-efficient and state of-the-art PET plants (M&G is currently building the largest PET plant in the world in Corpus Christi, Texas, with start-up scheduled for Q3 2017). In addition, we continue to invest in and improve speciality products. In recent years, a number of our developments have been created through collaboration with converters and brand owners. By continuing to have an open dialogue with end users on their needs, M&G can continue to drive investment and development in resin manufacture and produce the best possible product for their ongoing requirements. PETplanet: Thank you very much for talking to us! www.gruppomg.com/en","@ID":19}, "MATERIALS / RECYCLING PETplanet Insider Vol. 18 No. 05/17 petpla.net 12 Also in the field of plastics processing, manufacturers are looking for the possibility of lowering the costs of materials and processing, while maintaining the highest quality for their products. In the production of PET preforms, for example, work has long Additives for more efficient and economical PET-packaging by Lucia Buffoni, Marketing Manager at Repi One of the main tasks facing the world today is how to save the resources of our planet, including all types of natural raw materials and energy, which allows us to live on a level of comfort, which we have become used to, and from which, more and more, we depend. been going on to reduce the weight of the preforms. At the same time, machines yield a higher productivity: cycle times have been reduced, while the quantity of preforms in one shot has increased. In this context, Repi is established with a series of liquid additives and special solutions for PET packaging, as a support to the market needs. The fastest growing Repi additive family is the one of Anti Yellow. These additives in liquid form are dosed from 0.005% to 0.05% both in the rPET resin production and in the rPET packaging injection moulding process. If we consider PET produced on bottle-tobottle recycling lines, these additives are able to perfectly make up the preforms since this material has the characteristics of virgin PET, with one exception, namely that the rPET has a slight yellow or grey shade, which is successfully “cancelled” by using the additive. Enhancer for optimising process parameters In the field of rPet, Repi IV Enhancer is widely used both in injection moulding, where it enhances the physical and mechanical characteristics of the bottle and in the extrusion of rPET sheets for thermoforming, where it optimises the process parameters, enables better thickness distribution and allows for a less frequent cleaning of calenders. The above mentioned process additives are closely followed by others no-less successful, the first one being Repi Blowing Additive. This product is able to improve and control the absorption of infrared in the blowing stage, giving customers the possibility of reducing blowing temperatures. At the same time, the blowing equipment works in a smoother way, without unplanned stops, and the productivity of blown bottles per hour is increased. From the aesthetic point of view, this additive hardly affects the colour of a transparent preform. It even happens that customers who have access to Fast Reheat PET resin, prefer to work with standard PET and blowing additive, since they enjoy the flexibility in production having the freedom to modify the addition rate of the additive themselves. Repi offers also the option of colour with additive inside: popular ones are not only dark amber and dark green for beer preforms, but also blue for mineral water preforms, and even a white colour developed for milk monolayer preforms. Repi Process Aid is another additive positively acting at the blowing stage by reducing sticking between one and other of preforms and bottles. This product creates a better slip effect between preforms and as a result up to +10% of preforms can be stored in a box, with consequent advantages in terms of transport and storage costs. Preforms maintain a better visual aspect, remain more transparent and clear, with fewer scratches. The recommended dosage is from 0.12% to 0.2%. Also here “all-in-one” solutions of colour and additive are often demanded by customers. MATERIALS Special Repi Anti Yellowing additive for rPET","@ID":14}, "MATERIALS / RECYCLING PETplanet Insider Vol. 18 No. 05/17 petpla.net 16 New developments of PET resin in the beverage sector The PET resin of choice Polyethylene terephthalate (PET) is the choice of industry heavyweights for bottling the world’s favourite brands of water and soft drink. In addition, its behaviour in recycling systems allows easy conversion into a versatile material for use in textiles, carpets and new bottles. PETplanet Insider sits down with M&G Chemicals marketing manager Cécile Bourland to find out more about developments in PET resin. One of the biggest challenges for beverage manufacturers is continually improving the barrier to extend the shelf life and quality of products as diverse as beer, juice and carbonated water. Players in the sector’s value chain argue that this gives PET extended environmental benefits that competing plastics cannot offer. Brand manufacturers across the beverage industry are putting their weight behind sustainable technologies that are commercially feasible, socially acceptable and ecologically sound. Combined with the move towards lightweighting bottles without sacrificing the integrity or quality of the barrier, this has led these manufacturers to meet M&G chemicals. PETplanet: What is the share in the PET resin market, and where do you see the real growth? Cécile Bourland: The current market for PET resin in packaging applications is about 20 million tons, of which about 80% is for beverage applications. We expect the market to grow in volume by 7.5% annually over the next few years. Currently, the largest applications by volume are in water and carbonated soft drinks (CSDs), but we are increasingly seeing growth in a large number of oxygen-sensitive beverages such as beer, juices and dairy. Europe, Latin America, the Middle East and warmer areas in Asia tend to have need for the strongest barriers in PET packaging and are an area of potential growth. The main end markets that M&G covers with its resins are CSD, water, beer, wine, juices, dairy (milk, soy, vitamin-enhanced and yoghurt), energy drinks and coconut water. PETplanet: What are the main challenges you see as a resin producer? Cécile Bourland: In beverages, there is an increasing desire to extend shelf life. If one talks about a CO 2 barrier, the average shelf life offered by all technologies is about six months. Improving CO 2 barrier performances is therefore a constant challenge for the industry - to optimise all available parameters: resin performances, preform and bottle design, and process conditions. Regarding O 2 barrier, PoliProtect resin offers the strongest barrier providing the longest shelf life (more than a year and a half on average), and fully satisfying market needs. By extending shelf life, companies are able to better manage their exports (avoiding the risk of their beverage being unfit for sale before it reaches the consumer in a faraway country). In addition to being able to go through logistics, extending the product’s shelf life means reducing overall supply chain costs – generating further savings for the brand. The size of the bottle can also impact the shelf life, or the barrier required. A smaller container exerts a greater pressure on the surface of the bottle, which will require a stronger barrier to protect it. This is also true when a company lightweights its bottle. Even if the bottle is the same size, less material means a thinner bottle wall and an improved barrier is required. PETplanet: What is M&G’s offer to address these challenges? Cécile Bourland: We have developed three different grades of PoliProtect to cover the different barrier needs in the industry, and they are as follows: APB: a CO 2 /O 2 barrier of the strongest grade, used primarily by brewers and also by producers of premium 100% juice. JB: a medium O 2 barrier mainly for products where the makeup is not 100% juice. It can be used for wine, vitamin-enhanced waters and flavoured milk. PB: a strong CO 2 barrier used mainly for CSD and sparkling water. MATERIALS Special","@ID":18}, "BOTTLING / FILLING PETplanet Insider Vol. 18 No. 05/17 petpla.net 35 Tour Sponsors: Japan in Indonesia! by Alexander Büchler PT Hokkan Indonesia, Bogor, February 18, 2017 We met: Mr Nasruddin Suyuti, Marketing & Sales There are two aseptic facilities at Japanese company PT Hokkan Indonesia’s site in Bogor. The first began as a Sidel wet aseptic facility in 2012 with 600bpm, the other started as a dry aseptic in 2015, also by Sidel and also with 600bpm. Hokkan does not use its own brand in its Indonesian facilities, rather it is purely a bottling company for other OEMs, focusing on manufacturing RTD coffee and tea with milk. My first meeting on the tour was not in the factory, rather, I was invited to the Old Town Café in Bogor shopping centre. I was greeted by Mr Nasruddin Suyuti who works in marketing & sales for Hokkan. We chatted about the various products bottled in PET and the characteristics of the Indonesian market. But first of all, we talked about Hokkan. Both facilities fill bottles between 200 and 500ml in size. The new plant operates seven days a week, whereas the earlier plant only operates five days a week at the moment. Hokkan Indonesia is able to draw on the extensive expertise of their parent company in the field of packaging and beverage production, a fact which does not go unnoticed by their customers. Two years ago, Hokkan started a small test centre in Bogor in order to speed up their production processes; this centre manufactures pre-production batches within the space of a day in order to perform durability tests, as well as other similar checks. Nasruddin calls what they offer to their customers a ‘Total Packaging Solution’ (TPS). For example, if a customer comes to them with a new recipe or product, Hokkan analyses the recipe and tries to achieve the same flavour by using less expensive ingredients. What makes Hokkan stand out from the crowd is that they produce their own preforms. They have also installed Husky preform equipment in both their aseptic facilities; the earlier plant has 72-cavity equipment, while the newer plant is equipped with 96-cavity moulds. They manufacture a single preform size of 17 grams which can be used for all bottles with volumes ranging from 200 to 500ml. They’re also considering the possibility of using a slightly lighter preform for bottles 330ml and smaller in the future. But moulding aseptic bottles is a lot more complex than the moulding process for bottles in the water industry, as any attempt to save on materials might turn out to be detrimental. In total, there are 35 different products from 14 different brand-owners in production across both facilities and besides tea and coconut water, they mainly produce coffee with milk and sugar. Hokkan regards itself as a pioneer for beverage production in Indonesia and the locals regard their products as energy drinks: if you drink coffee with milk when you are driving, you won’t get tired. Meanwhile, RTD coffee with milk has captured 1% of the entire drinks market in Indonesia. So that was all the theory we discussed over coffee. Then off we went to the supermarket, where Nasruddin showed me the special characteristics of the market first hand - with regards to an overwhelming amount of bottles. First of all, he pointed out Indonesia’s price-sensitivity. A product is classified as affordable if it costs under 6,000 Indonesian Rupiah (IDR) (40 cents). And in fact almost all the products are under this threshold. Newcomers to the market, as well as any products rapidly gaining popularity, cost under 3,000 IDR. Anything costing over 6,000 IDR is regarded purely as a luxury product. The shapes of RTD coffee and tea bottles vary from the classic curved forms to angular shapes, all the way to bottles which have lumps and bumps. Some bottles are even shaped to look like animals or dolls. It is obvious which designs have been victims of material conservation. And there is RTD coffee and tea on every shelf. The product display areas in the supermarket do not reflect the market shares of individual kinds of beverages. Water and CSDs are almost drowning in a sea of tea and coffee. Nestlé is the only brand to offer RTD, in an attempt to capture the market for themselves with cans or cartons. www.hokkan.co.id Nasruddin Suyuti, Marketing & Sales, PT Hokkan Indonesia, in front of supermarket shelves with two of their customers’ products in his hands Go with the flow. South East Asia Road Show","@ID":37}, "MATERIALS / RECYCLING PETplanet Insider Vol. 18 No. 05/17 petpla.net 23 Tour Sponsors: Post-consumer PET bottles without labels or stickers by Alexander Büchler PT. Production Recycling, Karawang, Indonesia. February 16, 2017 We met: Susan Hueber, Director Joseph Soesilo, General Manager In emerging nations, recycling mostly means collecting by hand – which is also the case in Indonesia. We visited PT. Production Recycling Indonesia ( PT. PRI ) in Karawang and were able to learn that collecting by hand leads to an extremely high proportion of PET in waste bales and simplifies the processing of bottles. In Indonesia, people throw their rubbish onto the side of the road. The rain will wash it away or someone will remove it. Whilst a few years ago, the rain was doing most of the work, today, people are finding out that there is money hidden amongst the rubbish. This provides sufficient income especially for those in the population who are at the lower end of the earnings scale. So alongside certain materials, used PET bottles are collected from the rubbish by hand and brought to buyers. They press the bottles into bales and sell them to recycling plants such as PT. Production Recycling Indonesia in Karawang. Because they are collected by hand, the bales contain a high percentage of PET bottles which have been well sorted. Joseph Soesilo, Managing Director at PT. PRI, has also instructed buyers to remove labels and caps from the bottles before pressing them into bales. A novelty for waste bales. Thus PT. PRI can get up to 90% PET flakes out of a bale. Despite having been very well sorted, a manual sifting for incorrect materials takes place at the start, which looks for PVC in particular. After shredding, the PET is put into a bath of hot alkaline solution twice to completely remove the sticky remains of labels in particular. After being washed in cold water and dried, the flake sorters start working and pick out everything that has sneaked through in the processing. What remains is sorted flakes with levels of purity which are suitable for foils, sheets and fibre production. Production is rare in the 50ppm sector – flakes for bottleto-bottle recycling. “Our clients mostly come from the fibre and sheet sector and we have exactly the right products for them,” said Susan Hueber, Director at PT. PRI. Currently, light blue is very popular; this composition is in great demand in China in particular. However, PT. PRI does not just deliver to China; alongside Asia, they also deliver to the rest of the world. To prevent all the washing water from making its way into the water cycle, PT. PRI processes its water. As a closed cycle, only a small amount of fresh water has to be added. LPG heats the water for washing. Founded in 2011, PT. PRI is considering the possibility of installing a second line in the near future, one that is bigger than the current line. Post-consumer bottles are also available. It seems that PT. PRI can successfully brace itself for the pricing pressure of the currently cheap PET virgin material. “We need to connect with our suppliers; it’s a kind of marriage”, said Susan speaking of the secret of her success. “If a partner does not have a bale press machine, we install one, which makes a really good connection.” That way, PT. PRI receives a constant stream of PET bottles which have been very well sorted. www.pt-pri.com It’s hard to believe, but the bales arrive at the plant with the labels and caps of the bottles removed. Both run the business: Susan Hueber, Director and Joseph Soesilo, Managing Director Go with the flow. South East Asia Road Show","@ID":25}, "PREFORM PRODUCTION PETplanet Insider Vol. 18 No. 05/17 petpla.net 36 Tour Sponsors: PT Namasindo Plas, Bandung, Indonesia, February 17, 2017 We met: Mr Herman Neo, Executive Vice President Mr Yanto Widodo, Director High-tech for affordable products by Alexander Büchler Affordable preforms and caps in a logistically complicated setting that can even measure up to the high technical demands of international brand names, as demonstrated by Mr Yanto Widodo, founder, owner and director of PT Namasindo Plas in Bandung. His secret? Standardisation, effective organisation, cleanliness and high-tech machinery. After coming off the motorway and driving for half an hour along stretches of bumpy roads, past plain and simply constructed residential and industrial areas, it’s quite a shock when the entrance to the PT Namasindo Plas factory appears on the horizon. From the outside all you can see are walls, no sign of the company’s name. Then the factory opens its gates and a sense of therapeutic order instantly washes over you – lorries come and go in an orderly manner, streets and squares are clearly structured, buildings are wellmaintained. What kind of owner builds such an oasis in the middle of a region which had previously been the epitome of disorder? It was Mr Yanto Widodo who founded the business in 2001 by producing 5 gallon PC water bottles. Since then, his company has expanded to include 13 factories across Indonesia, which not only produce PC gallons, but also seals, preforms, bottles, caps and deep-drawn beakers. But the apple of his eye is a PET processing plant for bottle-to-bottle grades. “It’s extremely important for us to think about the environment when we manufacture our products, so PET recycling is effectively a must-do.” The goal is to be the best integrated plastic company in Indonesia. The key product is light blue and forms 10% of the product used in the preforms for his principal customer Danone. His emphasis has always been on state-of-the-art technology, and so the granulation equipment processing 10,000t/a comes from Erema, and he sources post-condensation technology from Bühler. The problem is that customers in Indonesia are rather price-sensitive. “It’s fair to say we have the lowest preform prices in the world here in Indonesia,” Yanto surmises. On the other hand, he supplies Danone and Coca-Cola, companies who are not prepared to compromise on their quality. What’s more, he has to factor in the risks associated with foreign exchange rates: raw materials are generally bought in US $, but packaging is paid for in Indonesian rupees. Furthermore, the expensive transport in Indonesia drives up costs; transport links are inadequately developed and there are several ferry connections to take in order to reach the island. He has addressed these issues in the orderly fashion that is also evident on his business premises: he has limited production to a few standard preforms with longnecks (CSD) and shortnecks (water) and manufactures very high quantities. Shortnecks weigh 9.7g for 330ml, 12.5g for 600ml and 26.15g for 1,500ml. Longnecks in the same sizes are between 1-1.3g heavier. The market is satisfied with these three sizes. Smaller bottle volumes are simply produced using larger preforms. CC fills a 600ml preform with 390ml and at AJE the 535ml bottle is also produced from a 600ml preform. In this way, bottles are stronger and the PT Namasindo Plas have over 20 Netstal facilities across Indonesia which produce preforms. Yanto Widodo, company founder and classic car enthusiast Namasindo Plas started off producing 5 gallon PC water bottles, then the company grew and grew. Go with the flow. South East Asia Road Show","@ID":38}, "PETplanet Insider Vol. 18 No. 05/17 petpla.net 46 PETbottles Beverage + Liquid Food Fruit 2 go in bright green The German drinks’ manufacturer Franken Brunnen is expanding its Fruit 2 go product range (with or without carbonic acid) to produce new and different taste varieties that stand out by their colour. Fruit combinations such as grapefruit, raspberry, maracuja and lime or lime and pineapple sound a little unusual and might well arouse the consumer’s curiosity and tempt them into buying. In the picture, you can see the lime and pineapple combination in a waisted 750ml bottle. The product is classed as a soft drink with around 10% fruit content. The bottle is stabilised through a number of elongated embossments extending across the label area. A screw top with tamper-proof strip and sleeve label completes the colourful picture. www.frankenbrunnen.de Hohes C (High C) plus antioxidants Eckes-Granini has high hopes for its two new juice creations with extra functions that are being advertised with the slogan “Immer im Plus” (“Always on the plus side”). One product is a 100% juice made from the aronia grape and strawberries, including antioxidants, while the other is an orange maracujakaki juice with added Vitamin D. “Satisfaction or your money back” is the advertising slogan on the product in the picture. The benefits of the drink for active cell protection and the fact that it is made with no added sugar makes the product interesting for the consumer. This is a stand-out juice product which has an eye-catching mat red sleeve label stretched across a recognisable, brand typical and deposit-free bottle. The label explains the benefits to be derived from the juice and how people can be reimbursed if dissatisfied with the product. www.hohesc.de Aldi South’s Super Fruit The range of South Aldi’s specially installed refrigerated shelves for high quality, more unusual consumer products is being further extended. The latest line in 100% fruit juices as part of the “rio d’oro” brand is the socalled “Super Fruit” juice with a new fruit combination. According to the manufacturer, the pineapple, apple, guava and baobab fruit juice has special qualities. All the constituent juices are carefully treated and pasteurised only for a short time. The juice comes in a clear, deposit-free 750ml bottle with a narrow neck which should be shaken before opening. The screw top and tamper-proof strip complete the whole packaging. www.aldi.de Relaunch of “Late harvest” Valensina has redesigned and streamlined the packaging of its smooth fruit juices from the “Late harvest” product range. “Late harvest” is particularly renowned both for the harvesting of its perfectly matured fruit, which is freshly pressed, gently pasteurised and constantly chilled, and its taste. In order to avoid confusion with other “non-refrigerated” Valensina fruit juices, the shape of the 750ml bottle has been altered and now resembles the embossed Valensina bottle of its chilled sibling brand. The freshness seal has also been designed in the shape of a leaf imprinted with the words “contains 100% fruit”. The label showing stylised sun rays will remind the customer of the time it takes for the fruit to fully mature in the sun. www.valensina.de","@ID":48}, "MARKET SURVEY 27 PETplanet Insider Vol. 18 No. 05/17 petpla.net 05/2017 MARKETsurvey Preforms & preform inspection Recycling plants & washing units Palletising & shrink film machinery Caps & closure systems & CC inspection Labelling & marking systems Recycling: Cutting plants Filling equipment & filling inspection Resins, additives Compressors SBM machinery & quality inspection Suppliers of systems and moulds & inspection systems for caps and closures For this issue 5/2017 PETplanet Insider interviewed the market participants in the system for the production of closure sector. It includes both: The machine manufacturers and the mould suppliers. We also add as a new special feature a survey reading closure inspection systems! Intravis GmbH, Netstal, Corvaglia, Sacmi Imola, IMD Ltd., Milacron c/o Mold Masters, Sumitomo (SHI) Plastics Machinery, z-werkzeugbau-GmbH, Husky Injection Molding Systems and Pressco Technology Inc. Although the publishers have made every effort to ensure that the information in this survey is up to date, no claims are made regarding completeness or accurancy. Closure moulds Company name Corvaglia Mould AG z- Werkzeugbau Husky Injection Molding Systems Ltd. Postal address Telephone number Web site address Contact name Function Direct telephone number Fax E-mail Hörnlistr. 14 8360 Eschlikon, Switzerland +41 71 973 77 77 www.corvaglia.ch Mr Albert Brunner Director Sales & Service +41 71 973 77 52 +41 71 973 77 51 [email protected] Dr.-Walter-Zumtobel-Strasse 9 6850 Dornbirn, Austria +43 5572 7272 0 www.z-moulds.com Mr Michael Fink VP Sales & Marketing +43 5572 7272 610 [email protected] 500 Queen St S Bolton, ON, CAN L7E 5S5 +1 905 951 5000 www.husky.co Mr Michael White Business Manager, Beverage Closures +1 905 951 5000 ext. 2913 [email protected] Mr Henry Zhang, Dir. of Bus. Devlp., Medical & Specialty Packaging +1 905 951 5000 ext 5196 [email protected] Filling good - beverages Carbonated soft drinks and non-carbonated pressurised & non-pressurised beverages including water, juices, teas, milk/dairy, coffee, beer, isotonics, energy drinks, etc. Carbonated and non-carbonated drinks, water, juices, etc. Screw-on beverage closures for water, carbonated, hot-fill and aseptic beverage types Specialty closures including flip-top for personal care, sports caps, detergent, edible oil, carton closures and pouch fitments - other Edible oil, detergents, other filling goods possible upon request Edible oil, dairy, beer, etc. - individual cap solutions Possible upon request Personal care and household products Closure -type Flat top & sports closures for beverages from 26 to 48mm neck finishes, e.g. Alaska, 1810, 1881, 29/25, 30/25, 33 HF, 33 ACF, 38 HF, 38 ACF All single-piece standard closure dimensions for all neck finishes, sports closures, flip-tops, pushpulls, multi-component closures… Screw-on (moulded-in TE band), Screwon (Post-mould slit TE band) Specialty closures including flip-top for personal care, sports caps, detergent, edible oil, carton closures and pouch fitments -material HDPE (PP for transparent parts) HDPE, LDPE, PP, TPE, … HDPE -weight Starting from 0.8g Lowest from 0.8g 0,7g Moulds Clamping dimensions/cavities 24 - 96 cavities 16 - 128 cavities Standard cavitations = 32cav - 96cav, 594mm x 1,045mm - 695mm x 1,050mm Custom cavitations depending on customer need and application being moulded; capability for high cavitation moulds Preferred hot runner suppliers Various Mold Masters Husky Husky Special features Closure design approvals from all major beverage brand owners; most economical closure designs for private labels Several patented technologies for most efficient closure production Horn-pin less design for high output, simple, & robust operation; integrated cooling manifolds for balanced flow & pressure (quick connect/disconnect) HT-S6 hot runner for optimal gate quality / minimal flow lines / fast colour change eIMC in-mould closing technology for flip-top closures; part optimsation and fast prototyping capabilities","@ID":29}, "PETplanet Insider Vol. 18 No. 05/17 petpla.net 41 TRADE SHOW REVIEW 41 TRADE SHOW REVIEW PETplanet: You were also present as exhibitors: what innovations did you or were you able to present at the conference? Laux: Since we act as an auxiliary supplier in this value-added chain, we have introduced, in addition to our tried and tested, new product systems, such as, for example, the cleaning agent Tubiwash Top and the combination product for process optimisation Tubifoam KE 100. PETplanet: A topic that excites many of our readers: Are there any new developments at CHT in the PET recycling sector? Laux: At present, we are active around the world and are therefore confronted with and challenged with the most diverse requirements. Together with our research department, we are constantly developing new and market-adapted products and systems. For example, we now offer combination products that allow our customers to reduce the number of products. PETplanet: Was the conference successful for you? Laux: Yes, PRS Europe was a great success for us, so we’ll be back again next year. A word of praise must go to the organisers, who have done a great job in bringing together all the exhibitors and speakers, and making all this possible. In addition to interesting discussions with recyclers and machine manufacturers, PRS has also produced a few new customer projects for us. What was striking and fascinating was that there was a real sense of motivation from all participants to work together towards a “clean” future. PETplanet: Thank you for your time and the pleasant conversation. www.prseventeurope.com www.cht.com After the presentation visitors had the opportunity to go around to talk with the exhibitors. PETplanet Insider met Sebastina Laux of CHT Group for a rapid impromptu interview after the show: PETplanet: What were the reasons for the participation of CHT Group at this conference? Laux: First of all, we wanted to introduce ourselves as a customer-oriented foundation with our facilities for the cleaning process of plastics and sustainability. We have had interesting discussions with customers by participating and from this projects may materialise. PETplanet: Did you meet many customers here? Laux: We had many visitors yesterday, whereas today it is a bit quieter, but we do certainly expect the number of customers to increase in the coming years. But numbers were satisfactory considering this is only the first occasion that the PRS has taken place. We had visits from existing customers, as well as interesting potential customers, and this has already resulted in some exciting projects. PETplanet: Is it a conference where you can exchange views? Laux: Definitely. We met representatives of the entire value-added chain in the plastics recycling sector. We were able to discuss various types of plastics, e.g. from PET to PE and on to PVC. In addition, there was mention of current topics in recycling, such as the problems the opaque PET brings with it in the recycling process and how they could be solved. [email protected] Tel: +90 212 695 50 00 Fax: +90 212 694 97 24 100815dmyR .com Sebastian Laux Technical Service Recycling at CHT Group","@ID":43}, "MATERIALS / RECYCLING PETplanet Insider Vol. 18 No. 05/17 petpla.net 21 MATERIALS / RECYCLING 21 • 28mm, 33mm and 38mm screw closures • Robust and trouble free capping • Established DoubleSeal™ technology - for secure sealing performance - for better protection against micro-organisms • Slit FLEXBAND® band technology for enhanced tamper evidence • O 2 barrier and scavenging options for screw flat caps supporting longer shelf life and fresher taste • Sports closures for aseptic filling and hot filling without aluminum foil • Special closures for syrups and carton packaging Unique range of screw and sports closures designed for cold fill and aseptic application BERICAP Technology for juices, RTD teas, health drinks www.bericap.com PET fusion jar made up of a main jar, small jar main cap and small cap. Paints The Relpet team is proud to be associated in the development of 1l and 4l transparent PET for water based paints jointly with one of the major PP container suppliers to paint industry. PET packaging is cost-competitive along with improved physicals. Nerolac Paints launched one of their paint variants in PET in 2015-16 and there is latent potential with other paint majors. Barrier PET is used for enhancing shelf life of contents in bottle and thermoformed packages. RIL has developed Relpet B9845 barrier resin with an active oxygen barrier and an passive barrier to carbon dioxide. Typical applications are ketchup, beer, wine, mayonnaise and juice variants. Both opaque barrier PET and transparent barrier PET with shrink sleeve are being used. Non-bottle applications It includes thermoformed APET trays/blisters, PET strapping, wires, mono filaments, blood collection tubes, injection moulded items among others. Niche PET grades In addition, there are other special PET grades like thin wall injection moulding PET and extrusion blow moulding PET, which are slowly getting evaluated for niche uses in India. Recycling and sustainability It is important to note that PET remains eco-friendly throughout its life cycle. The recycled PET bottles are used as raw material in textiles, like blankets, T-shirts, pillows, etc. and strappings in India. The recycling rate for PET is as high as up to 90% in India. RIL itself recycles 50 KTPA of PCR PET bottles to value-added products. PET bottles are thus proving to be the perfect ecofriendly and circular economy pack for planet earth in this part of the world, as globally, according to Reliance. The reverse vending machines for PCR PET which are now being installed in India rewards consumer with discount coupons/vouchers, runs advertisements and have static advertisement on machine body thus further engaging the consumer. PET usage thus results in reducing the carbon footprint and leading to a cleaner and greener world for coming generations in India! Indian PET market: The road ahead! The PET packaging market in India has grown exponentially and will continue to expand further into newer areas. In 2007-08, PET usage was 210 KTA and in 2015-16 it was 820 KTA, a growth of 300% in nine years. Reliance is proud to be a part of this success journey and continues to strive jointly along with other stakeholders to co-develop niche resins and packaging solutions. India is now all set to cross mile stone of 1mn TPA of PET consumption in 2018-19! www.ril.com","@ID":23}, "PETplanet Insider Vol. 18 No. 05/17 petpla.net 47 BOTTLES PETbottles Home + Personal Care Refill for Sagrotan kids The “Sagrotan” brand, which is owned by ReckittBenckiser, has launched the no-touch liquid hand soap dispenser in Germany which has been specially adapted for use by children. The dispenser itself can be personalised with funny adhesive stickers, while the hand soap has a smiley face on it. The hand soap does not contain alkaline, silicone, parabens or mineral oil and comes in a recognisable, clear, stand on its head bottle. The bottles are closed with a normal top that fits easily into the dispensing mechanism. A hinged label on the reverse side explains the various handling and safety instructions. www.sagrotan.de Fairy as an active foam In some countries, Fairy is available as a foam for cleaning dishes and packaged in a strong, typical market brand 375ml liquid green bottle. The foam is dispensed and produced by an easy to grip pump dispenser with locking function which can also be used with wet hands. By exerting downward pressure, the washing-up liquid mixes with the air to produce a foam. The bottle is also commercially available without a pump and is designed as a cheap and environmentallyfriendly refill. Just unscrew the pump dispenser from the empty bottle and simply screw it onto the refill bottle. www.pg.com Schauma depends on nature The trend towards natural and well-known active ingredients in personal hygiene products cannot be denied. One example of this is Schwarzkopf’s latest “Schauma Nature Moments” product. There are currently four hair shampoos that have 100% natural essences, according to the manufacturer. The “Schauma Nature Moments” product shown in the picture is designed to enhance the hair’s suppleness and freshness and contains green apple and stinging nettles, with no silicone or artificial dyes. It comes in a distinctive 250ml green bottle which can be closed with the aid of a green hinged cap with dispensing spout. www.schwarzkopf.de Two stage hair repair “Therapy Repair-in-Oil-Spray Fibre” is a new product from Schwarzkopf’s Gliss Kur range for reconstructing hair fibres that have been damaged by using dyes and through excessive heat during styling. It also helps to enhance hair shine and suppleness. The product is made up of two phases which have to be combined by shaking just prior to the operation of the pump for application to the hair. It should be rubbed into slightly damp hair but not washed out. It comes in a slim, easy to grip and clear 100ml bottle which is embellished with two embossed labels, while there is a folded label on the reverse side so that additional information can be added. The pump dispenser is protected at point of sale by a cap to prevent damage or misuse. www.schwarzkopf.de","@ID":49}, "PETproducts 44 PETplanet Insider Vol. 18 No. 05/17 petpla.net Sipa upgrades ECS SP injection-stretch-blow moulding line Sipa has made some important improvements to its ECS SP range of medium-sized single-stage injection-stretch-blowmoulding (ISBM) machines. These units, which complement Sipa’s larger single-stage ECS FX and ECS HS systems, were added to the Sipa portfolio when it acquired some of the activities of Automa, another well-known PET processing equipment supplier, in late 2014. Sipa says that its ECS SP system is ideal for the production of speciality containers for pharmaceuticals, cosmetics, personal care products and spirits, particularly (but not exclusively) in sizes between 20 and 50ml. Two models are available: the ECS SP 50 with a 500kN injection clamp force, and the 800kN ECS SP 80. The latest ECS SPmachines feature an upgraded user interface (HMI), as well as improvements to the injection system, preform conditioning and bottle blowing. The machines can now also accept a wider range of legacy moulds. Sipa has replaced the original thermal gating in the preform injection hot runner systemwith needle valve gates. Because these new gates can be purged much more quickly, the time taken to get the machine up and running is notably shorter. Injection point quality has also been improved, thanks again to the valve gate system, and with much less risk of gate stringing or incidence of off-centred injection points. The number of tasks that the operator needs to carry out every time the machine stops and restarts has been reduced, and the more straightforward geometry of the gates enables a simpler solution for clearing the hot runner system. There was a redesign of the preform conditioning system on the ECS SP. The company says that higher power heaters have been developed, along with the new approach, offering customers a wider process window and the option of internal conditioning. The process is now more energy efficient and each individual cavity can be provided with its own conditioning parameters, determined according to the design of the preform. Numerous changes have been made to the bottle blowing section on the ECS SP, with the result that the process is now more stable and energy-efficient. Laurent Sigler, Head of Innovation at Sipa explained that Sipa used the knowledge that it built up with its original ECS series to enable blowing conditions in each cavity to be managed separately, in order to ensure that every bottle is perfect. This upgrade means that different blowing parameters can be set for every single blowing cavity, so that the blowing pressure in each mould can be accurately and individually fine-tuned. A special “compatibility kit”, now available for the ECS SP, makes it much easier to accept major competitors’ moulds, which were originally intended to run on single-stage ISBM machines. It is now possible to quickly adjust the vertical position of an extruder according to the mould, without having to use the previous, rather less robust, adaptor solution. www.sipa.it Volumetric dosing unit with flexible exchange system Whether powder, pellets, regrind, granulate, flakes or fibres, the new Spectroflex V of Motan is a volumetric dosing unit for continuous processes, designed for many different applications. Should material colour, flow properties or grain size change, than motan´s exchange system offers a simple way to swap materials without the need of tools in under a minute. The single- and double-screw exchange modules as well as the easy-to-clean supply hopper allow for fast and easy material changes and so reduces production downtime. The material loader mounted on the cover of the supply hopper does not have to be removed during the material change, resulting in higher efficiency and shorter downtimes in your production. Thanks to the function of the massage-rollers, even nonfree flowing and fragile materials are no longer a problem. Powered by an independent motor and designed for 48 different settings, Spectroflex V offers high dosing accuracy for a wide range of materials - even for small dosing quantities. The special design of the oscillating elliptical rollers extends the service life of the polyurethane dosing hoppers. The Spectroflex V is equipped with an intuitive touch screen for trouble-free and simple control. The integration into an existing motan Controlnet network is possible via an Ethernet interface, as an option the conveying control can also be integrated. www.motan-colortronic.com","@ID":46}, "MATERIALS / RECYCLING PETplanet Insider Vol. 18 No. 05/17 petpla.net 14 PETplanet: Piovan’s Genesys system delivers PET-resin drying with energy consumption 55% lower than today’s conventional resin-drying systems. GenesysR is a new product – how does it build upon this energyefficient profile? Piovan: Reactor drying is a new technology, combining the benefits of rapid heat up of the PET with a new control of the residual moisture of the resin. Piovan was a supplier of small scale vertical tower SSP systems, a range of products that would find use in the late 80’s, early 90’s, that allowed us to learn in depth about the physical phenomenon taking place in the vertical tower (reactor) while rapidly increasing the polymer temperature. SSP takes place at temperatures of 220°C and in absence of oxygen. GenesysR operates at regular drying temperatures (170 to 180°C) in a dried air environment and, differently from what happens in an SSP process, it does not increase IV and reduce the drying time from 7 hours to 5 hours. The energy efficiency is further increased by 10Wh/ kg, it will ensure savings in the range of 60% and beyond when compared to a conventional drying system. Piovan holds the only patent ever released for high efficiency system for dehumidifying and/or drying plastic materials. PETplanet: Is the high productivity of the Genesys maintained? Piovan: The GenesysR line is particularly suited for high productivity applications, where the benefits of having a very low energy utilisation and a highly stable process are exploited in the highest degree. GenesysR benefits of a new control of the residual moisture in the PET, namely AIPC. AIPC stands for Automatic Injection Pressure Control. Any GenesysR system can be connected to the preform injection moulding machine and by reading the injection pressure in real time it has the capability of stabilising to the desired value. A new algorithm specifically developed for the AIPC can constantly adjust airflow, temperature and dew-point of the process air, so that the injection pressure be kept at the highest possible level of constancy. This feature is particularly valuable today as the new preform formats require thinner walls and therefore controlled conditions of moisture and injection pressure. AIPC is a patent pending new invention. PETplanet: How will the GenesysR support beverage packaging manufacturers regarding high quality and constancy of physical characteristics? Piovan: GenesysR is the only auto-adaptive drying system available in the market that is capable of determining a condition of energy balance in the PET resin between drying and injection processes. The reason why energy balance is key for the production of a preform, and subsequent bottle, resides into the physical and mechanical characteristics of the bottle itself. The best processing condition for the PET resin is obtained when the lowest possible temperature increase, or energy addition, must be performed by the injection unit, or extruder. GenesysR is capable of measuring the quantity of energy released to the PET, to feed the injection unit with material having the highest possible mass temperature. The energy addition at the injection unit is a very critical parameter, as it determines the IV drop of the PET: the lower is the energy addition the lower is the IV drop. The auto-adaptability feature of GenesysR benefits the bottle characteristics from two main perspectives: highest IV of the PET, obtained by the energy balance capability, and lowest AA level, obtained by the AIPC feature. PETplanet: How did you develop the new product, and will it ultimately replace Genesys? New reactor drying technology by Piovan Low temperature and constant viscosity GenesysR, the new generation of reactor drying systems by Piovan officially launched at the PETnology Forum in Nuremberg 2016. Naturally, PETplanet Insider was keen to find out more. MATERIALS Special New reactor drying technology for PET","@ID":16}, "9 NEWS PETplanet Insider Vol. 18 No. 05/17 petpla.net Greiner Packaging: joint venture in Russia Greiner Packaging is establishing a joint venture with the Russian company Plastic System which serves the market under the Souzpromplast brand. Under the name Greiner Packaging System, the joint venture – located in Noginsk – will be driven by a focus on IML, direct printing and larger packaging containers primarily in the food and non-food sector in Russia. Greiner Packaging will be holding the majority of the shares of the new company. The goal of the joint venture is to reinforce activities in Russia and to drive the market through new innovations. The offerings for the Russian market can be expanded through the site. In particular, the competence in the IML and direct printing sector will be strengthened and the product portfolio expanded to larger packaging units. Synergies with the existing plant will be exploited and new options developed. “The Russian market offers great potential and, together with our experienced partners, we expect a significant growth spurt. The joint venture will allow us to expand our product portfolio and strengthen our market position as well,” stresses Manfred Stanek, division head of Greiner Packaging International. The formal closing of the joint venture was in March, with both partners currently working on the implementation of the agreed-upon integration measures. www.greiner-gpi.com Amcor opens on-site PET bottle manufacturing at Campbell’s plant Amcor Rigid Plastics expands its relationship with long-time customer Campbell Soup Co. with the opening of an on-site bottle manufacturing operation in Paris, Texas, USA. Amcor’s new in-line operation is expected to produce approximately 50 million hot-fillable PET bottles each year. Amcor invested $7 million to re-purpose 6,000 sq ft of the Paris manufacturing facility. The on-site operation will produce 46oz and 64oz PET containers for a variety of V8 vegetable juice products. At the Paris site, on-site production of hot-fill PET bottles will keep over 2,000 truckloads of containers off the road each year and eliminate over 376 metric tons of carbon dioxide emissions which are equivalent to 901,246 miles driven annually by an average passenger vehicle, according to Amcor. Previously, Amcor supplied Campbell’s with PET containers from its Fort Worth, Texas manufacturing plant. Since 2004, Amcor has operated an on-site blow moulding operation at Campbell’s beverage production plant in Napoleon, Ohio where it produces 150 million hot-fill PET containers annually. www.amcor.com An April 20, a ribbon-cutting ceremony officially marked the opening of Amcor Rigid Plastics’ new on-site bottle manufacturing operation at Campbell’s beverage production facility in Paris, Texas, USA.","@ID":11}, "BOTTLE MAKING 32 PETplanet Insider Vol. 18 No. 05/17 petpla.net Using tattoo design as a promotional tool for Papua New Guinean bottle “Starting from sketch” The distinctive feature of SMI’s bottle design for Paradise Food in Papua New Guinea (PNG) is its beautiful stylised decoration, which covers a large part of the container. Starting from an existing design and drawing on PNG’s tradition of tattooing, SMI designers and the customer worked together to create a custom version of beverage containers for Paradise Food’s “Tru Tru Wara” brand. When SMI’s designers and Paradise Food began working on new 0.5l and 1l containers for Paradise’s Tru Tru Wara brand, an important objective identified early in the process was that it should be easily recognisable on the supermarket shelf. The team decided to go right back to basics and start from the original bottle sketch. The decoration, which is based on traditional PNG culture, looks almost like a real tattoo on the upper part of the bottle. This project was a major challenge for SMI designers – the complex decoration work especially. It is wrapped around the entire surface of the bottle, which made it necessary to perfectly align both ends of the tattoo. SMI was able to realise the design within the mould; its technical department designed the bottle and then manufactured the mould for the blow moulding machine. The creation of a PET bottle After a thorough analysis of clients’ needs and requests, SMI designers usually develop one or more ideas for the container and produce three-dimensional simulations of it, to present to the customer. These virtual prototypes vary in appearance, shape, size, external appeal, etc., and provide different visual interpretations of the parameters specified by the client during the project development process. As well as the restrictions imposed by the product to be bottled (soft drinks, water, oils, foods, detergents, cosmetics, etc.), SMI’s designers must also take into account the technical specifications of the preform to be blown, the characteristics of the production line, and so on. After the preliminary stages the bottle design then moves on to the The “Tru Tru Wara” brand from Paradise Food, Papua New Guinea, comes with a 360° tattoo design. The bottle designing team mastered the challenge of the 360° decoration where the starting and the final points of the “tattoo” have to coincide perfectly.","@ID":34}, "MATERIALS / RECYCLING PETplanet Insider Vol. 18 No. 05/17 petpla.net 24 Reciclar advances from PET flake producer to high-end producer Argentinian recycling pioneer The Argentinian company Reciclar is continuing its success story in South America in 2017. Following the established business fields of PET flakes and PET recyclates the company has now invested in what is currently the most modern recycling technology: the direct processing of PET flakes to PET strapping band. Since the company was founded in 1994, Reciclar has specialised in the production of washed polyolefin and PET flakes. In 2010, Director Sergio Martin decided to expand the portfolio by adding the production of meltfiltrated recycled PET pellets. After comparing globally established recycling technologies he decided for the Austrian plant manufacturer Erema in 2011. The plan was for 7,500t of rPET pellets per year with the Vacurema Basic 1714-T for the thermoforming, packaging and fibre industry. 1,100 kilos per hour – production expectations fulfilled A delighted Sergio Martin confirms that the Vacurema Basic has already surpassed the contractually agreed performance for the sixth year in succession by 10% and delivers a stable IV value of the pellets in the process. Thanks to the optical transparency, the reliable colour values and the comprehensive FDA A-H and J approvals, Reciclar can take on shortterm orders from new customers. “We are proud to have received the Exporting Excellence Gold Award only recently for our achievements,” states Sergio Martin. PET inline strapping – from recycler to a producer At the beginning of 2017, the company added the production of PET strapping to its portfolio featuring the production of PET flakes and recyclates. The Argentinians once again chose Erema as the general contractor for a Vacurema 1510-T inline strapping system in combination with a Tight Strap 550 from the Italian manufacturer Sima (Dietze + Schell Group). The direct processing of washed PET flakes to high-strength PET strapping with an annual capacity of around 4,000t was realised. The downstream strapping system from Sima receives the IV-stable melt in an absolutely consistent process directly from the latest generation Vacurema system. The homogeneous melt is routed to the extrusion head double spin pumps, scaled as required and wound into high-performance PET strapping. Flexibility is one key feature of Vacurema: the input materials are washed PET flakes, plus PET recyclates and ground production waste from thermoforming plants, for example. The materials are processed at Reciclar also in a mixed state in crystalline or amorphous form and have large, real density differences (down to 150kg/m³), input moisture (up to 1%) and PET fines. The patented vacuum reactor/extruder series masters the difficult input spectrum with considerably reduced energy consumption compared to conventional PET processing systems. This pretreatment enables the use of a F.l.t.r.: Daniel Cappeletti, Fernando Gomes Veiga, Luis Dallacqua and Clemens Zittmayr in front of the Vacurema system at Reciclar","@ID":26}, "PETplanet Insider Vol. 18 No. 05/17 petpla.net 43 TRADE SHOW REVIEW cling landscape is to be affected by new legislation – in particular the enhanced manufacturer responsibility – and how the industry should react. “Producers of packaging should understand that they have responsibility,” states Melanevskaya. As a concrete example, he mentioned the establishment of independent infrastructure as a strategy for stimulating the recycling market, as well as encouraging young people in particular to be aware of recycling, not to mention exerting pressure on the bottle manufacturing industry to place the focus of manufacturing on bottles that are easy to recycle. Technologies Various company representatives presented solutions in the recycling field. Danil Polyakov, Head of Sales von Polymetrix presented their FDA and EFSA compatible process for the manufacturing of bottle-grade rPET. Post-consumer PET bottles undergo grinding, surface cleaning and sorting in PET wash plants. The resulting PET flakes are the input material for the Polymetrix bottle-to-bottle rPET process. The process consists of an initial extrusion step with melt degassing and melt filtration and is followed by pelletising and a decontamination step in an SSP under nitrogen. A feature of this process is the reduced use of detergents and water. Procedures for the further processing of PET bottles are also offered by Viscotec, part of the Starlinger Group. Representative Gerhard Ossberger explained how post-consumer recycled PET flakes can be both dried and decontaminated using the Decon decontamination dryer in accordance with EFSA and FDA standards prior to the extrusion process. Their Viscosheet line is designed for the production of 100% food grade PET sheet. It can process up to 100% of undried material with minimised IV decrease. Christoph Wöss, Business Development Manager Erema then presented the company’s Vacurema System. The patented pre-treatment of PET flakes at raised temperature and in high vacuum before the extrusion process removes moisture and migration materials from the feedstock. Thanks to the vacuum treatment, stable IV values can be achieved even in the case of varying moisture levels and different IV values in the input material. To counteract loss of material in the recycling process, Erema follows the zero waste approach. In recent times, PET rejects from metal detection have also been considered through improved filtration as well as fines, which were previously thrown away as material loss from the washing centrifuge. The PET proportion here makes up around 25% – accordPROCESS PILOT® makes producing a better PET bottle as easy as 2 3 1 MEASURE CONTROL OPTIMIZE every bottle for changes in material distribution process variation, inside the blowmolder material utilization and orientation to achieve maximum bottle performance CONTACT US TODAY TO LEARN MORE! AGRINTL.COM | +1.724.482.2163 | [email protected] see us at Booth A4-336 ing to Wöss an important starting point for the recycler to establish himself more reasonably in the economically difficult rPET segment. Conclusion The day confirmed what Sergey Stolyarov, Managing Director of the Creon Group had said in his opening address: That in terms of recycling, Russia is “not in the leading group”. The lack of an infrastructure of collection systems - many conference participants saw a government obligation here - hampers recycling efforts and makes recyclate more expensive. The economically difficult environment currently does little to stimulate the industry to invest in modern recycling systems. But the page can turn quickly with far-reaching legislation and suitable currency situations, which could make the recycling market in Russia very attractive - assuming that consumers play their part. www.creonenergy.ru","@ID":45}, "PETcontents 05/17 4 PETplanet Insider Vol. 18 No. 05/17 petpla.net Page 45 Page 38 Page 35 INSIDE TRACK 3 Editorial 4 Contents 6 News 44 Products 46 PET bottles for Beverage + Liquid Food 47 PET bottles for Home + Personal Care 48 Patents MATERIAL / RECYCLING 10 Multiple choice - PET, rPET, bio-PET and more 12 Additives for more efficient and economical PETpackaging 14 Low temperature and constant viscosity - New reactor drying technology by Piovan 16 The PET resin of choice - New developments of PET resin in the beverage sector 18 Indian PET packaging - Growth journey and beyond 22 Thinking outside the bottle - Sea-weed based packaging for water 23 Post-consumer PET bottles without labels or stickers 24 Argentinian recycling pioneer - Reciclar advances from PET flake to high-end producer MARKET SURVEY 27 Suppliers of caps & closures systems and cap inspection systems BOTTLE MAKING 31 PET fusion jar - Indian double package for Tata tea 32 Starting from sketch - Using tattoo design as a promotional tool BOTTLING / FILLING 34 Big player in CSD - Peruvian concern bottles 300,000bph in Indonesia 35 Japan in Indonesia! PREFORM PRODUCTION 36 High-tech for affordable products CAPPING / CLOSURES 38 New ideas for more performances TRADE SHOW REVIEW 40 Creating a sustainable recycling society Plastics Recycling Show Europe, Amsterdam, NL 2017, part 1 42 A sector in its infancy - Third rPET & recycling plastics conference in Moscow, part 2 BUYER’S GUIDE 49 Get listed! MATERIALS Special","@ID":6}, "CAPS & CLOSURES 38 PETplanet Insider Vol. 18 No. 05/17 petpla.net New ideas for more performances The sportscaps market has been a tough competitive environment from the start. In recent years, participants have been focusing on the effectiveness of their productive systems to secure a competitive edge. The goal has been to produce more parts per minute from within the same installation area. One solution has been pursued by Contexo, the machine builder from Winterbach in Germany. Contexo’s engineers have integrated comprehensive quality-control and TE-proof feeders into compact continuousmotion systems. Their machine can be directly chained with an injectionmoulding machine, and moments later pack the finished and fully inspected cap. This means high output rates are now possible on a small installation area. “The challenge was to build an exceptionally reliable and fast assembly machine on a small footprint”, recounts Jürgen Müller, CEO of Contexo. “In our opinion, continuous motion combined with feeders for warm-moulded parts, and with direct inline inspection of those parts is the most effective solution.” Contexo is currently using this technology to build a machine for one of the largest beverage-closure manufacturers. It counts as the third Contexo machine ordered by the client this year. This means that production at the company will be state of the art. Machine tests confirm expectations: 1.3 million parts per day with 100% reliability. One sportscap is assembled, folded and inspected against 13 quality-control criteria every 6-hundredths of a second. Higher capacity through innovative feeding, fast assembly and inline control Contexo reaches these high speeds using continuous-motion technology. A central tower with 36 tools assembles the parts, feeder satellites guide the parts at a perfectly controlled speed. This means each part experiences minimal stress and wear during assembly. Contexo has been investing in continuous-motion technology for over ten years, and in that time further developed it. “When we started with continuousmotions systems over ten years ago, we were one of the fastest at 300 parts per minute. Now we are three to four times faster,” explains Jürgen Müller. However, assembly speed is only one condition required for high, market-conform output rates. The market now expects zero defects. End products have to be 100% flawless. This is why many producers have launched additional inspection machines in recent years. But they The highest speeds: almost 1,000 parts per minute are fed to the main tower by a satellite.","@ID":40}, "PETnews 6 NEWS PETplanet Insider Vol. 18 No. 05/17 petpla.net United Caps to open manufacturing facility in Malaysia United Caps announced an investment in the development of manufacturing capabilities in Malaysia. The company will be building a state-of-the-art manufacturing facility to meet increasing customer demand in the region for its advanced caps and closures. “We are experiencing significant growth in South East Asia,” said Benoît Henckes, CEO. “In keeping with our ‘Close to You’ strategy, this expansion of manufacturing capabilities allows us to continue to capitalise on the dynamic growth opportunities in the region and better serve our local customers. Localising production of our pioneering closure technologies in the South East Asian marketplace is the next logical step in our business expansion.” United Caps conducted an extensive search and determined that property in the Kulim High Tech Park provided an optimum location for the new manufacturing facility, expected to be fully operational in the first quarter of 2018. “This investment will initially create more than 20 new jobs in the region,” Henckes added, “and enable the local production of about 300 million closures in the first year. We are excited about the opportunity to bring our advanced technology to the new facility, and also to support the local community with jobs and other opportunities.” www.unitedcaps.com R&D/Leverage promotes Mike Stiles to CEO April 26, 2017 R&D/Leverage, headquartered in Lee’s Summit, MO, USA announced the promotion of Mike Stiles to CEO. Stiles joined the company in 2000 as an Account Manager and was promoted to Director of Sales in 2015. He has been instrumental in helping to grow R&D/Leverage to a globally recognised manufacturer of precision injection and injection stretch blow moulds, and structural brand development for Fortune 500 customers in the rigid packaging, consumer products and healthcare markets. According to Stiles, the process of becoming more than just a mould maker over the past decade involved understanding the customers’ requirements and collaborating with them to solve their challenges and problems. Structural Brand Development is a valueadded proposition that R&D/Leverage implemented to help customers. While that part of the Company’s business doesn’t come into play on every project, Stiles noted that many of R&D/Leverage’s customers depend on this expertise that includes market research and trends, and other branding considerations. For those who come with the upfront structural branding & design work completed, R&D/ Leverage puts every project that comes through the doors through a risk analysis process. Stiles sees good things for R&D/Leverage’s future. “I see us continuing with what is currently our biggest growth segment, which is high quality, high cavitation, ultra-precision injection moulds that are required for the medical and packaging markets. These are areas where we currently have a large and stable customer base. We are recognised as industry innovators when it comes to implementing some of the latest direct side-gate or direct angled-tip hot runner systems for injection moulds and this is producing many opportunities. Additionally, we have plans in place to increase our global footprint in the injection blow mould and injection stretch blow mould segment – stay tuned.” R&D/Leverage is hosting their tri-annual Open House this September 20-22, where new developments will be presented and demonstrated during plant tours and presentation series. The theme of the event is “Breaking Down The Silos In Plastic Packaging” featuring Keynote speaker, Gerry O’Brion “What Big Brands Know”. www.rdleverage.com Beverages-related joint venture in Singapore Sumitomo Heavy Industries, Ltd. (“SHI”) and its subsidiary Izumi Food Machinery Co., Ltd. have established a beverage machinery related joint venture company with Germany-based Krones AG to develop the Asia region. Through the establishment of this joint venture company, SHI Group aims to capitalise on the know-how and supply chain of Krones and accelerate the development of its beverage machinery business in the Asia region. Under the name Krones-Izumi Processing Pte. Ltd., the joint venture which will be located in Singapore, targets facilities that manufacture soft drinks, juice, tea, coffee, water, milk, soy sauce and other beverages (excluding food, ice cream and alcoholic drinks) in the Asia Pacific region, excluding Japan, China and India. The Memorandum of Understanding was finalised on April 25, 2017. Operations are expected to start in June this year. www.shi.co.jp WikiPETia.info New contents at wikipetia.info","@ID":8}, "Sponsors asia.petpla.net 2017 is Drinktec year! All over the world, the beverage and liquid food industry is preparing for the next edition of the great event, held once again in Germany. A new year also means a new road show - and a very special one. PETplanet is again partnering with Drinktec and we will be bringing our crew to South East Asia, under our new slogan: Go with the flow – South East Asia Road Show. From the end of January our editors Kay Barton and Alexander Büchler, along with “Flowy“, the Drinktec mascot, will be investigating the latest market-specific characteristics of distant countries as well as following welltrodden oaths, as always. With various “Editourmobil” vans we will travel to Thailand, Vietnam, Cambodia, Malaysia, Singapore and Indonesia. As our valued reader, you will once again get insider information and insights from the PET beverage and supplier industries, published regularly in PETplanet Insider. You can get even closer to the Tour experience by following us live on our travel blog at asia.petpla.net. Drinktec awaits us at journey‘s end. When we get there we will be presenting factsheets and product samples of all the companies we visited. We hope you enjoy “keeping up with the PETplanetarians“. We look forward to welcoming you on board once again! January – July 2017 Cambodia Laos Thailand Indonesia Vietnam Malaysia Singapore The worldwide round trip with Go with the flow. South East Asia Road Show powered by","@ID":32}, "MARKET SURVEY 28 PETplanet Insider Vol. 18 No. 05/17 petpla.net Systems for caps Company name Netstal-Maschinen AG Milacron c/o Ferromatik Milacron GmbH Postal address Telephone number Web site address Contact name Function Direct telephone number Fax E-mail Tschachenstrasse 1 8752 Näfels, Switzerland +41 55 618 6111 www.netstal.com Mr Michael Birchler Marketing Manager +41 55 618 6772 [email protected] Riegeler Str. 4, 79364 Malterdingen, Germany +49 7644 78 0 www.milacron.com Mr Stéphane Grossnickel Director International Accounts & Intercompany +49 7644 78-0 +49 7644 6885 [email protected] Systems for cap/closure production Model Elion Evos Ferromatik Electric Procession technology Injection moulding Injection moulding Injection moulding Clamp force 175 - 420t 300 - 550t 1,500 - 6,500kN Cycle time (guaranteed 98% closure system efficiency for): 2.0s 2.3s - High speed production: closure type/weight/cavities: caps/min \"29/25\"/1.2g/96/2880 \"29/25\"/1.2g/96/2504 1881/1.6 - 1.9 g/ 2.9 seconds +/- 5% - Individual cap solution: closure type/weight/cavities: caps/min Drive concept hybrid / electric hydraulic / hybrid Electrical Energy consumption (kwh/kg) 0.48 0.73 Under 0.20 kWh/kg (based Ferromatik Electric with 48 cavity mould) Preferred mould makers various Special features Dedicated CAP Systems including mould and all peripheral equipment; air condition, conveyors, cap cooler, chute, quality vision, box changer etc. Special ejector design dedicated for caps, modular machine concept, high level of customisation Closure insection Company name Intravis GmbH Postal address Telephone number Web site address Contact name Function Direct telephone number Fax E-Mail Rotter Bruch 26a, 52068 Aachen, Germany +49 241 9126 0 www.intravis.de Mr Markus Juppe Director Sales & Marketing +49 241 9126 0 +49 241 9126 100 [email protected] Inspection system CapWatcher III CapWatcher SC (Specialty Closures) Integrated CapWatcher Systems Inspection speed Up to 252,000 objects / hour Up to 62,000 objects / hour Up to 79,200 objects / hour Inspection method Non destructive Non destructive Non destructive Inspected objects Standard closures: carbonated & non carbonated beverage, single- or multithread, with TE band, one-piece Specialty closures: flip top, sports caps (incl. push-pull), tube, for chemical industry, assembled closures Inserts: dosing inserts, liners, child protection Standard closures: for carbonated & non carbonated, onepiece, single- or multithread, with TE band, specialty closures: sports caps Inspected parameters: -Inner inspection Spots & contamination on the inside of the head plate, colour deviations, flow lines, liner inconsistencies Contamination, colour deviations on the inside, flow lines Contamination, colour, brightness, spots -Outer inspection Contamination on the side wall and on the head plate, colour, dark & bright spots on the outer wall, flow lines and printings on the head plate, printed image, registration shifts, position (printed image) Contamination on the outer wall, colour, scratches & pressure marks Contamination, colour, spots, brightness -Geometry Diameter, diameter & ovality of TE band and ovality of seal cone, closure height, gate, gate length, horizontal &vertical long shots, open & closed short shots, curvature of head plate, missing or damaged TE band, damaged flaps, turned up flaps, damaged seal cone, slitted & folded closures Diameter and ovality (e.g. closure, seal cone): closure height, assembly faults, missing components, damaged components, damaged seal cone, vertical long shots, open & closed short shots, horizontal/radial long shots, missing or damaged TE band, damaged flaps, turned up flaps, damaged pull tabs and missing or damaged quality seal Diameter and ovality, rotational position, outer dimensions, short shots, long shots, long shots at the mouth, contour deviations, contour & surface defects of the mouth ring, missing or damaged TE band, handle fold, open closure -Cavity number reading Cavity number reading, cavity related statistics (also for microhole defects), closure sorting according to cavity number, automatic selection of cavity fonts Cavity number reading, cavity related statistics, closure sorting according to cavity number, automatic selection of cavity fonts Cavity number reading, cavity related statistics, closure sorting according to cavity number, automatic selection of cavity fonts -Microhole inspection Microholes in the area of the injection gate (inspected with HV) -Additional inspection criteria for inserts Missing components, closure height (only metering inserts), diameter & ovality, flow lines Further inspection options Installation: Stand-alone (offline) Yes Yes Inline Yes Yes Yes, CapWatcher technology integrated into assembly machine Software features: Data base connection; reject rate monitoring; production monitoring with IntraVisualizer; integrated control of up- and downstream equipment; integrated trend statistics with pre-warning; ColorCameras Data base connection; reject rate monitoring; production monitoring with IntraVisualizer; integrated control of up- and downstream equipment; integrated trend statistics with pre-warning; ColorCameras Data base connection; reject rate monitoring; production monitoring with IntraVisualizer; integrated trend statistics with pre-warning; ColorCameras","@ID":30}, "No.05 2017 petpla.net D 51178; ISSN: 1438-9452 22 . 05 . 17 PETplanet is read in more than 140 countries MAGAZ I NE FOR BOT T L E R S AND BOT T L E - MAK E R S IN THE AMERICAS, ASIA, EUROPE AND ALL AROUND THE PLANET MARKETsurvey Suppliers of systems and moulds & inspection systems for caps and closures Page 27 MATERIALS Special Page 10 Go with the flow. South East Asia Road Show Page 23","@ID":3}, "MATERIALS / RECYCLING 15 PETplanet Insider Vol. 18 No. 05/17 Piovan: GenesysR is the evolution of Genesys and represents a further step towards optimisation and perfection of the bottle manufacturing process. The development of this new category of drying systems, the new “reactor drying systems”, was not performed in a one, two or three year program, it is the outcome of research and development in PET drying systems of Piovan knowledge management. GenesysR is not available in all the configurations of Genesys. The two product lines will coexist. PETplanet: How have you tested and certified it? Piovan: Ten GenesysR beta installations have been functioning for the latest nine months and the first GenesysR systems will be made industrially available in the first quarter of 2017. PETplanet: Piovan first introduced an auto-adaptive system, able to adjust the functioning mode of the drying system to the industry in 2009. What makes auto-adaptability so advantageous, and how does the technology work in your new product? Piovan: GenesysR features the highest degree of autoadaptability. If such function was valuable back in 2009, it has become indispensable today. Auto-adaptability allows the use of multiple grades of PET, from different suppliers and produced in different processes. PET is today available in the so called water grade (0.72 IV) and bottle grade (0.82 IV), however it can be produced by utilising very new and innovative processes of polymerisation and solid state post condensation, along with older production systems. Different PET from numerous sources are available today, each requiring different processing or preparation conditions to be adequately and efficiently transformed into a preform/bottle. GenesysR is a first milestone of Industry 4.0 in the rigid packaging industry, as it is a concrete example of how an Industry 4.0 compliant system, the so called Cyber Physical System, is configured to operate for the objective of achieving: a high constancy of production, high preform and bottle quality, stable injection moulding and blow moulding machine operation, a reduction of scrap rate to zero and an energy efficiency of the preform system. PETplanet: We thank you so much for this interesting discussion! www.piovan.com The GenesysR system for optimising the bottle manufacturing process SIPA S.p.A. - Via Caduti del Lavoro, 3 - 31029 Vittorio Veneto (TV) - Italy Tel. +39 0438 911511 - Fax +39 0438 912273 - email: [email protected] We make it happen. www.sipa.it Imagine taking your operating costs at the lowest level. Designed to adapt. Built to last. Preform Systems MAINTENANCE COST i stment Less than1%of the capital nve","@ID":17}, "MATERIALS / RECYCLING PETplanet Insider Vol. 18 No. 05/17 petpla.net 20 Pharma What started in the early ‘90s for a few pharma products, PET is today used for all major cough syrups, anti-acids, vitamins etc. PET use is catching up for packaging of more and more pharma products, making it easy to be handled by all age groups. Edible oil PET has clearly established itself in 0.1l to 5l packages in India. There is a growing interest now in 2l PET packages with handles and 5l opaque PET. The 2l PET bottle with pinch grip has also been launched by RR Omerbhoy among others and is widely used with CTC neck throughout India. In view of its price-competitiveness, there is growing awareness for possible use of PET in 15l packages and it will be soon launched by one of the edible oil majors in India. The 15l package has been designed for improved physicals with respect to requirements of top load for stacking and good supply chain management (SCM). In order to improve shelf life and mechanical strength, liquid nitrogen can be introduced in headspace just after filling. It was launched for edible oil by one of the edible oil majors in India. It enhances product appeal, market reach and makes shifting to lighter PET packs a reality. A stackable 15l PET container have been developed to reduce logistics cost. Country liquor in PET has been another unique India-centric application supported by the RIL team. Today the majority of states are using PET bottles from 90ml to 750ml pack sizes, resulting in overall savings to brand-owners. The shatter-proof economical option of PET packaging is the buzz word today in liquor segment. There is an opportunity to save on SCM cost by shrink-sleeved filled PET bottles. Indian-made foreign liquor (IMFL) PET bottles are extensively used for Indian-made foreign liquor (IMFL) and the growing trend is to further shift to PET for more liquor variants. The use of PET bottles in liquor has seen emergence of niche shapes and effects. A 1l frosted PET bottle is used for vodka packaging and a 2l PET bottle with externally fitted handle for whisky, both by UB group. It has led to enhanced product appeal and increased sales for the said liquor variants in PET packs. Beer SAB Miller in India is using 1l barrier PET bottles for some of their brands with a shelf life of two months. They are filled on a Sidel’s combi line (blowing and filling). Wine Sula Vine yards and UB among others are using PET in pack ranges of 187ml and 375ml. There is a growing interest for light-weight and cost-competitive packaging and thus there is potential interest in PET. The stackable PET wine bottles and APET glasses as used abroad will see a similar trend soon in India. Lube oil It was launched in 2007 in transparent PET, to made product visible and to reduce packaging cost. PET bottles made by ISBM process are leak-proof. The ‘Lal Ghoda’ brand in PET developed for HPCL uses 0.5l and 1l packs. It has potential to snowball with another oil major soon, who will start using PET for one of their lubricants. It is an interesting development with potential for the neighbouring countries, too. PET cans Today cans are used both for solid and liquid packaging due to the visibility of contents and lower cost when compared with metal. Dry fruits, spices, CSD and auto parts are already available in PET cans in India and slowly juices and other major segments are going to be packed in PET cans. The Indian government has allowed bulk export of selected edible oils. (photo by: www.business-standard.com)","@ID":22}, "MATERIALS / RECYCLING PETplanet Insider Vol. 18 No. 05/17 petpla.net 22 ”Have you eaten your water package yet?“ could be the question being asked if you are resorting to an Ooho instead of a PET bottle to hydrate. The spherical flexible packaging Ooho is the first product of Skipping Rocks Lab, a start-up based in London. Their goal is nothing less than a revolution of the water-on-the-go market. The scientists are pioneering the use of natural materials extracted from plants and seaweed, to create packaging with low environmental impact – and afterwards, you can actually eat it! brown algae and calcium chloride in a specific proportion in order to generate a gelification on the exterior of the liquid. The final package is a simple, cheap, resistant, hygienic, biodegradable and even edible water blob. It also requires less CO 2 , energy and money to produce than an equivalent PET packaging. The seaweed being used for the bite-sized packages has several advantages: besides being fast growing and available all over the globe, the packaging membrane – if not being eaten but peeled off – is biodegradable within four to six weeks. Since the scientists set up the company in 2014, they have been improving the properties of the mateMATERIALS Special rial and developing the technology for which they filed a patent application. At the moment, Oohos come in different flavours and three sizes (20ml, 55ml and 150ml) and are mostly being sold at public events and private functions. A wider audience will be targeted in 2018. To achieve this, the team is preparing to get their fullyautomated production machine up and running: “As a part of this scaleup, we are developing a manufacturing machine that will produce Oohos automatically” explains Rodrigo García González. Skipping Rocks Lab is part of the Climate KIC start-up acceleration program founded by the European Institute of Innovation & Technology (EIT), and the scientific team is based in Imperial College London. The start-up just closed their first investment round via crowdcube with £850,000 raised and 904 investors. www.skippingrockslab.com www.climate-kic.org Ooho team from left: Manuel López Romero, Chemical Engineer, Lise Honsinger, COO/CFO, Pierre-Yves Paslier, Co-founder & Co-CEO, Rodrigo García González, Co-founder & Co-CEO, and Eugenio Perez de Lema Bühl, Industrial Prototyping Inspired by the way nature encapsulates liquids using membranes, the architect Rodrigo García González and packaging engineer Pierre Paslier have come up with Ooho as an alternative to established beverage packages. After experimenting with the culinary technique of spherification with different ingredients, proportions and dimensions, a recipe was found to create Ooho with a double gelatinous membrane in different sizes. The technique applies sodium alginate from the Sea-weed based packaging for water, soft drinks, spirits and cosmetics Thinking outside the bottle","@ID":24}, "BOTTLE MAKING 31 PETplanet Insider Vol. 18 No. 05/17 petpla.net PETplanet: What is the jar’s size and capacity? Ankit Kedia: The size of the top jar is 55.5mm high with a 25g capacity; the lower jar is 132.5mm high with a capacity of 225g. PETplanet: Presumably you will be relying on single stage technology for production? Or are you in fact using two stage equipment? Ankit Kedia: We use ASB 70DHP single stage technology with SP400 neck finish, 73mm neck diameter for the bottom container and 56mm for the top container. The moulds used are from ASB, too. PETplanet: The tea jar has been on the market for a year now. Where can you actually obtain it? Ankit Kedia: Currently you can find it in supermarkets all over India. PETplanet: Thank you very much, Mr Kedia! PETplanet: Mr Kedia, how did the idea of this double jar come up? Ankit Kedia: The idea came up after the customer gave us the brief that they wanted to pack two types of tea in one container, so that the customer can blend both the tea varieties to create a unique beverage. PETplanet: What role exactly did Tata Tea play in this development? Ankit Kedia: The Tata Tea team was instrumental in giving us valuable consumer insights which we were able to incorporate in the overall design of the final packaging. PETplanet: Okay, but of course such packaging could pose particular problems in production. Did you face any difficulties while designing and modelling prototypes? Ankit Kedia: During the prototyping phase, we faced various challenges especially in making the packaging tamper-evident. The top container is fixed on the top of the lower container making it vulnerable to pilferage or tampering on the retail shelf. We overcame this by interlocking the top container firmly to the cap of the lower container. Ankit Kedia, Director Manjushree Indian double package for Tata Tea PET fusion jar by Kay Barton Manjushree Technopack from Bangalore, India, has developed, as the first converter in the country, a PET fusion jar made up of a main jar, small jar main cap and small cap. The advantage is that the main cap and the small jar have a locking mechanism which interlock to form a single component. The two jars cannot be separated without breaking the locking mechanism. Thus the consumer can access two very different taste enhancers which can be blended to create a unique brew. The fusion jar has been on the market since 2016. In conversation with Director Mr Ankit Kedia, we learned interesting details about this unusual packaging.","@ID":33}, "BOTTLING / FILLING PETplanet Insider Vol. 18 No. 05/17 petpla.net 34 Tour Sponsors: Peruvian concern bottles 300,000bph in Indonesia Big player in CSD by Alexander Büchler AJE, Bekasi, Indonesia, February 14, 2017 We met: Joe Miranda, Maintenance Chief AJE got big with the motto “Think BIGGER”. Now, it operates in 23 countries and is the fourth biggest CSD producer worldwide. We visited the bottling plant in Bekasi in Indonesia. The Peruvian worldwide concern AJE operates six bottling lines for CSD and isotonic beverages in Indonesia. We visited maintenance chief Joe Miranda at the plant in Bekasi. It is the first of three AJE plants in Indonesia. It started manufacturing there in 2010. In the plant there is a bottling facility which handles 70,000 bottles per minute and a Sacmi bottling machine which handles 35,000 bottles per hour. In the neighbouring plant which is only a few kilometres away, Netstal and Sipa facilities have been manufacturing preforms since 2014 and Sacmi compression lines produce the caps. As the latest acquisition, a hot fill facility is in operation for isotonic beverages. In total, all six bottling facilities together have a capacity of 300,000bph. Home brand Big Cola is bottled in an unusual size of 535ml. Other sizes are 300ml, 425ml, 1.8l und 3.1l. AJE was founded on June 23, 1988, a creation of Kola Real in Peru by the Añaños family. The Peruvian region of Ayacucho was devastated by the Shining Path guerrilla conflict, leading major beverage suppliers to pull out of business there. Noting this gap in the market, the Añaños family started to produce carbonated beverages under the “Kola Real” brand, starting with an orange-flavoured drink. They focused their business on selling drinks to segments of the population neglected by the leading brands, which were focused only on consumers with the highest purchasing power. Today, AJE is present in over 23 countries in Latin America, Asia and Africa. Annual sales volume amounts to 3.6 billion litres. Globally AJE is the 10th largest soft drink company in sales volume and the 4th largest producer of carbonated soft drinks (source: Euromonitor, 2011). And the 3rd in carbonated drinks in those countries where it operates (source: Canadean Annual Soft Drinks – Wisdom – 2014). AJE has a broad portfolio of products, with BIG Cola as its flagship brand. AJE produces carbonated soft drinks, water, juices, isotonic and energy drinks. AJE sells its products directly or through distributors in 23 countries throughout Latin America, Asia and Africa: Bolivia, Brazil, Colombia, Costa Rica, Ecuador, Egypt, El Salvador, Guatemala, Honduras, Réunion Island, Mexico, Nicaragua, Nigeria, Panama, Peru, Venezuela, India, Indonesia, Thailand and Vietnam. AJE products are also exported to and distributed in Cambodia, Malaysia, Myanmar and Laos. AJE has 32 manufacturing facilities with 89 bottling lines, 20 injection lines for the production of plastic bottles and 10 cap compression lines installed throughout its operations around the world. www.ajegroup.com Our Editourmobil at AJE Maintenance Chief Joe Miranda AJE in front of a picture of the founders Mr & Mrs Añaños AJE trusts on the SMI packager in the drying line. Go with the flow. South East Asia Road Show","@ID":36}, "MATERIALS / RECYCLING 19 PETplanet Insider Vol. 18 No. 05/17 1l transparent PET for fresh milk with a shelf life of four days in refrigerated conditions. PET for fresh milk by Gowardhan was launched more than a decade back. (photo by Parag Dairy) Amul, the Indian milk major, uses 1l plain PET for pro-biotic milk (Chaas) and uses PET for fresh milk (A2 milk) in 500ml transparent PET bottles. Amul started aseptic filling of Lassi and flavoured milk in 200ml plain PET bottles in 2013 with shelf life of four months and six months resp. It received good market response, so two more PET aseptic filling lines were installed. The launch of the energy drink ‘Stamina’ in PET also received good market response. The UHT milk of Amul is packaged in 200ml opaque white bottles made from Relpet OP5821 resin. PET for different milk variants and dairy products has shown good growth. Reliance’s Relpet grade PET resin bottles are used in full range of milk variants. It includes fresh milk, flavoured milk, buttermilk, UHT milk and these milk variants are filled in more than ten locations across India. PET is catching up fast for ‘Farm Fresh’ milk in India. The Indian milk majors are studying use of PET bottles and jars for packaging of different milk variants and VADP’s to improve product’s appeal and to hasten inorganic growth of their dairy products. In addition, APET trays, glasses, cups and lids are slowly gaining acceptance in the Indian dairy sector due to enhanced clarity, improved physicals and also lowest embrittlement temperature. Sweetened syrups Relpet bottles were developed for Rooh afza in 2013 after a two year long test process where upcon Hamdard have now shifted totally to PET. This shift received good market response and pack size also increased from 700ml to 750ml PET. Rooh afza has been also test launched in 250ml and 1.5l PET. They are now working on more PET conversions for the other products. 6JG -*5 U[UVGO HQT GHƂEKGPV 2'6 DQVVNKPI .KIJVYGKIJV 2'6 1WT NKVGT 2'6 DQVVNG HQT JKIJN[ ECTDQPCVGF DGXGTCIGU YGKIJU LWUV ITCOU s YKVJQWV EQORTQOKUKPI KVU UVCDKNKV[ 6JKU KU C YQTNF TGEQTF s QPG YG YCPV VQ DGCV CU UQQP CU RQUUKDNG /QTG KPHQTOCVKQP QP VJG CFXCPVCIGU QH NKIJVYGKIJV 2'6 ECP DG HQWPF CV YYY MJU EQO HE LIGHT PET BOTTLE IN THE WORLD IS STILL TOO HEAVY FOR US. drinktec 2017 September 11–15 Hall B4 | Booth 328 (photo by: vataworld.files. wordpress.com)","@ID":21}, "MATERIALS / RECYCLING PETplanet Insider Vol. 18 No. 05/17 petpla.net 18 Indian PET packaging - Growth journey and beyond By Rajesh K. Gera, Reliance The move to PET packaging in India began in the mid 1980’s. With the introduction of PET bottles for household containers (jars) and edible oil (EO). In moving away from conventional use, PET packaging in India started with PET jars and kitchen wares aided with spices, pickles, edible oil, etc and kept the PET packaging market trickling. The market expanded to include bottled water, CSD, alcoholic beverages, fruit drinks, wellness drinks, personal care, agro-chemicals in the 1990s. The next decade saw energy drinks, fortified water and RTDs added to the PET packaging portfolio. PET moved forward through healthcare to personal care, confectionary, alcoholic beverages and non-alcoholic beverages. Today all the milk variants (fresh, flavoured, UHT, Chaas, Lassi) and beer are also packaged in PET in India. Indian PET evolution India’s specific PET evolution began in the 1980s. The use of PET for health care, alcoholic beverages especially for mass class segment were growth drivers in the non-CSD market, which otherwise was growing organically. PET growth got reinforced with personal care and confectionary using more PET. Water was picking up (mushrooming local brands), so even non-CSD kept PET package primed up. A clear shift to PET in beverages is continuing as a primary driver even today. The emerging PET applications in India include fresh/ flavoured milk, chaas, beer, paint, bulk edible oil packs. In addition to the sparkling clear packs, opaque PET use is also growing due to glossy pack finish in the edible oil and other sectors. Value-positioning is today shifting more literage in PET and gave opportunity for non-Cola beverages on health-wellness platform resulting in the introduction of variants of fruit drinks, flavoured water, nimboo paani and other beverages in PET. Soft drinks Indian consumption is moving from ‘class to mass’, resulting in a boom for PET demand. Coke has launched CSD in a 250ml barrier PET bottle for the first time in India. There is a growing interest in small size PET packs by regional majors in PET who successfully launched 250ml and 300ml packages across India. The Indian 250ml PET coke bottle with an internal coating of Plasmax by KHS Juices The trend for health and fitness is catching up fast and is buoyed by growth of juice drinks in PET bottles. There is now a growing interest in PET for 100% juices and increased awareness among potential end-users on economic aseptic filling systems primarily to suit Indian market requirements. Water This sector has the maximum PET usage in India (200KTA) with increased usage in bulk water too. The latent potential for regional water variants is leading to new usages. Different sizes of PET water bottles available in the Indian market Milk The success story of PET packaging for milk in India is driven by brandowners and supported by RIL jointly with machinery suppliers. Gowardhan Dairy, a leading Indian dairy is using MATERIALS Special","@ID":20}, "8 NEWS PETplanet Insider Vol. 18 No. 05/17 petpla.net Single stream recycling system in Buenos Aires The City of Buenos Aires, in partnership with San Diegobased CP Group, opened an advanced recycling system in Argentina. The new 10t/h residential single stream recycling system began running last October in Villa Soldati, a neighbourhood of Buenos Aires. Since then it has helped the city achieve its sustainability goals. “It’s the most modern recycling center in Argentina,” announced the Head of Government of Buenos Aires, Horacio Rodríguez Larreta, at the inauguration of the plant in October 2016. “The city has improved a lot in the separation and treatment of recyclable waste,” he continued. “Four or five years ago nothing was separated. Today, this system is recovering 400t of dry materials per day, and that amount is expected to double to 800t per day in 2019.” The system features CP separation equipment, including the CPScreen for 2D/3D separation, MSS Aladdin optical sorter, CP Metering Drum, CP OCCScreen, and CP Glass Breaker Screen with patented Cam-Discs. The recycling system is part of the city’s Green Center, a program involved with recovering recyclable materials and providing education about waste treatment processes and its importance in Buenos Aires. “Throughout the entire process, the City of Buenos Aires has demonstrated environmental leadership as well as a long term commitment to developing a sustainable solution for capturing the valuable recyclables and diverting them from the landfill,” says Dirk Kantak, International Sales Director for CP Group. The materials recovery facility (MRF) began running October 2016. During the training and commissioning period, CP Group worked closely with the Spanish-speaking local staff to operate and maintain the MRF. www.cpgrp.com Eight new members join Petcore Europe Petcore Europe, the Brussels based association representing the PET value chain in Europe, welcomes eight new members in 2017: Hordijk, Sukano, Pellenc ST, M&G, SUEZ, Plastipak, Sidel and L’Oréal. “Gaining additional support from these eight leaders in their respective market sectors is a real asset for Petcore Europe,” outlines Christian Crépet, Executive Director of Petcore Europe. “It clearly reflects how our association aligns the complete PET value chain in Europe in order to work together and speak with one voice.” Hordijk Verpakkingen is designing and producing plastic packaging for various national and international company branches and has specialised in the packaging for food products and personal care products. Sukano is a leader in the development and production of additive and colour masterbatches and compounds for polyester and specialty resins. Pellenc ST designs, produces and sells optical sorting equipment for waste treatment and the recycling industries. The Mossi Ghisolfi Group is a leading name in the application of innovation to the sectors of PET, engineering and renewable chemical products derived from non-food biomass. As industrial services and solutions company specialising in sustainable resource management, SUEZ supports towns and industries in the circular economy to maintain, optimise and secure the resource essential for our future. Plastipak Packaging, Inc., a wholly-owned subsidiary of Plastipak Holdings, Inc., is a leader in the design and manufacture of high-quality, rigid plastic containers for the food, beverage and consumer products industries. With 30,000 machines installed in more than 190 nations, Sidel has been helping producers fill beverage bottles for over 80 years, blow them for more than 50 years and label them for more than 35 years. Sidel has 40 years of aseptic packaging expertise, and was one of the first companies to introduce PET bottles to the beverage industry over 30 years ago. L’Oréal has devoted itself to beauty for over 100 years. With its international portfolio of 34 diverse and complementary brands, L’Oréal is present across all distribution networks: mass market, department stores, pharmacies and drugstores, hair salons, travel retail, branded retail and e-commerce. Petcore Europe membership is open to all interested companies involved in the PET value chain. www.petcore-europe.org","@ID":10}, "TRADE SHOW REVIEW PETplanet Insider Vol. 18 No. 05/17 petpla.net 42 Third “rPET & recycled plastics” conference in Moscow A sector in its infancy by Gabriele Kosmehl Part 2 On February 16 and 17, the “PET 2017” and “rPET and recycled plastics 2017” conferences, organised by Inventra, part of the Creon Group, took place in Moscow, Russia. During this annual meeting point of experts from the Russian PET industry, major trends and projects were the subject of lively discussion about the worldwide market and for the Russian market in particular. The latter is showing a promising development for PET (see PETplanet 04/2017) while there is still a lot to do as far as the recycling business is concerned. The “rPET and recycled plastics” topic day was introduced with a general worldwide market overview presented by Helen McGeough, PCI Wood Mackenzie. Defined as key drivers of the bottle recovery market are sustainability, waste management, in particular the lack of space for disposal in landfill, and economics. Asia is the worldwide market leader with a PET bottle collection rate of 55%. The reason for these high rates is the high demand for PET in the fibre industry that makes the collection of PET bottles into a lucrative source of income constituting an independent line of business. In Western Europe, the region with the second highest collection rate (17%), legislation is the main driver behind the return rates. The motivation for a market to move towards high return rates can vary dramatically. For example in South Africa, McGeough showed that industry initiatives can also be very successful. The end of the talk indicated that the key issues for Eastern Europe are the establishment of a collection system together with finding suitable motivation for the market to set the system in motion. Domestic processing capacities should be created alongside this. Eastern Europe currently exports the majority of material it collects. As regards price trends, a rise in the prices of rPET has been seen worldwide in recent years, attributable primarily to the crude oil situation. As it is usually expected by consumers that recycled products must be cheaper than virgin material, a lower oil price and therefore a lower virgin PET price restricts further developments of the rPET market. This point was also confirmed for other plastic types by subsequent speaker Kaspars Fogelmanis, Chairman of the Board at Nordic Plast. His talk illuminated in particular the situation for plastic recycling generally in the Baltic region, whereby he indicated both the trend of recent years from landfill to collection and reprocessing and the current challenges facing the industry. Konstantin Rzaev, Chairman of the Board, Ecotechnologii, brought the issue of currency into play. The exchange rate of the weak rouble against the dollar had made it more difficult for recyclers to establish themselves economically in the market. Recently however, the rouble has rallied significantly and in February/March the rate was again 57RUB = 1US$. This trend is linked to the oil price, which has risen again after many months on the decline. PET collection rates are estimated to be stable at 160,000t for 2016. For 2017, Rzaev expects a cautiously optimistic scenario with further stabilisation of the rouble, growing PET bottle collection rates and a single digit growth rate in the demand for rPET. This is an increasing tendency, although with somewhat marginal numbers, which has also been recognised by Victor Kernitskiy, President of Arpet. From a collection rate of 115,000t in 2015, he reckons on growth to 147,000t in 2016. Besides the price trend, he defines the negative attitude of consumers to recycled materials to be the critical point. Lyubov Melanevskaya, Managing Director of RusPEK Association, described how the recyFrom left: Danil Polyakov, Polymetrix, Kaspars Fogelmanis, Nordic Plast, Nikolay Asatiani, Inventra and Helen McGeough, PCI Wood Mackenzie","@ID":44}, "MATERIALS / RECYCLING PETplanet Insider Vol. 18 No. 05/17 petpla.net 13 MATERIALS / RECYCLING 13 Protecting the inside As far as the packaging content is concerned, some additives offer valid protection enabling brands to preserve taste and aesthetics of its products on the shelves. On the one hand, SenzAA acetaldehyde reducers act to avoid the unpleasant off-taste of waters bottled in PET. The reduction performance goes up to nearly 85% allowing measuring a AA value of less than 1ppm. On the other hand Repi UV Absorbers create a barrier to the harmful UV-rays and visible light, which when passing through bottles and jars wall, can damage the product inside. Like the others, also this additive is liquid, and here, too, the dosage, from 0.1% to 0.2%, is significantly lower, than for its solid masterbatch alternatives, while obtaining equal or better final results. It is used especially for transparent preforms meant for sensitive liquids like vitaminic waters, juices and sauces in the food industry as well as for fabric conditioners, detergents and household products. The world of packaging is under unceasing innovation from each point of view and we as colorants and additives producers are proud to play a leading role and to be involved in this virtuous process, offering smart solutions where nature and production processes do not come yet. www.repi.com METPACK, 2/6.05.2017 – #1E12 / #1E16 | Essen GERMANY INTERPACK, 4/16.05.2017 - #4G20 | Duesseldorf GERMANY CHINAPLAS, 16/19.05.2017 - #C41 HALL4.1 | Guangzhou CHINA IRAN FOOD + BEV TEC, 23/26.05.2017 - HALL 38B | Tehran IRAN PROPAK ASIA, 14/17.06.2017 | Bangkok THAILAND EXPO PACK MEXICO, 13/15.06.2017 | Guadalajara MEXICO FISPAL TECNOLOGIA, 27/30.06.2017 | Sao Paolo BRASIL With Sacmi, the beverage specialists are always at your side. With our unbeatable technological know-how and continuous research we are creating new containers and closures designed to ensure outstanding performance. The new IPS injection system for preforms and the CCM compression press for caps, fully designed and built by Sacmi, allows for large-scale production with considerable advantages in terms of efficiency and flexibility. The outcome? Reduced plastic volumes, less energy consumption and lower running costs. All in a bottle: the one you’ll soon be making. Preform & Closure technologically together Save RAW MATERIALS reduced plastic volumes Save ENERGY less energy consumption Save TROUBLE more quality and higher performance, guaranteed by a sole supplier Full INSPECTED online quality control / stand alone","@ID":15}, "CAPS & CLOSURES 39 PETplanet Insider Vol. 18 No. 05/17 petpla.net can only inspect the assembled parts after the production process. This results in a larger installation area and slower completion times – and a finished closure cannot be illuminated with full reliability. Inline inspection before and after assembly For this reason, Contexo has adopted a different method for quality control: the individual components are inspected before assembly, the finished closure is inspected after assembly. For this to work, the inspection systems are integrated, inline, into the assembly machine and work in sync with it. The endeavour is a cooperation between Contexo and Intravis, a German supplier of vision inspection systems for the plastics packaging industry. “As the output rates of continuousmotion technologies improved, we quickly noticed limits to its speed in the area of part inspection. We have found a great partner in Intravis, who provides us with exactly the support we need in the integration of inline inspection systems into our highspeed systems”, explains Müller. Contexo has fully integrated the Intravis CapWatcher system into their machine concept. The additional system enables the comprehensive inspection and evaluation of all of the sportscap’s features. Before assembly the spout is for example checked for geometrical characteristics such as diameter or ovality, contour defects as well as a flawless plug seal. After assembly the whole closure is inspected for assembly faults, defective or missing tamper evident bands, contour and geometrical defects of the body and even if the closure is opened. Chained TE-proof feeding with injection-moulding machines At high assembly speeds, reliable feeding is the primary and largest challenge. These performance rates can be too much for existing feeder technologies. At high speeds, they cause pearlescence and other damage to the fed-in parts. Contexo therefore had to develop their own TE-proof vibration feeder. To ensure continuous flow, the solution is an especially stable unit capable of 80% overcapacity and can process warm-moulded parts directly from the system. This means sportscaps machines can be directly chained with the injection-moulding machine and feed in the parts without human logistics or contamination. The key to success: Continuous motion, vibration feeding and inline vision inspection The expansion of the purely continuous-motion unit into an inspection instrument and injectionmoulded-parts feeder appears to be a trend-setting step towards higher effectiveness. The concept tackles the most severely limiting factors of sportscap production. By chaining injection-moulding machine, assembly unit, vision inspection system and packaging system, Contexo offers a space-saving and effective alternative for manufacturing sportscaps. www.contexo-gmbh.de www.intravis.de Full inspection: the closures are examined from all sides on an inspection belt. Quality control of individual parts: the parts are first inspected before assembly for any defects that would be difficult to detect in the finished closure. ZZZ IOH[EORZ FRP )OH[%ORZ 8OWUD )OH[LEOH 3(7 6WUHWFK %ORZPRXOGHUV :LGH 0RXWK -DUV +RW )LOO &RQWDLQHUV 2YDO %RWWOHV /DUJH 6L]H &RQWDLQHUV &KRLFH E\\ 3DFNDJLQJ 3URGXFHUV 21( IRU $//","@ID":41}]}}
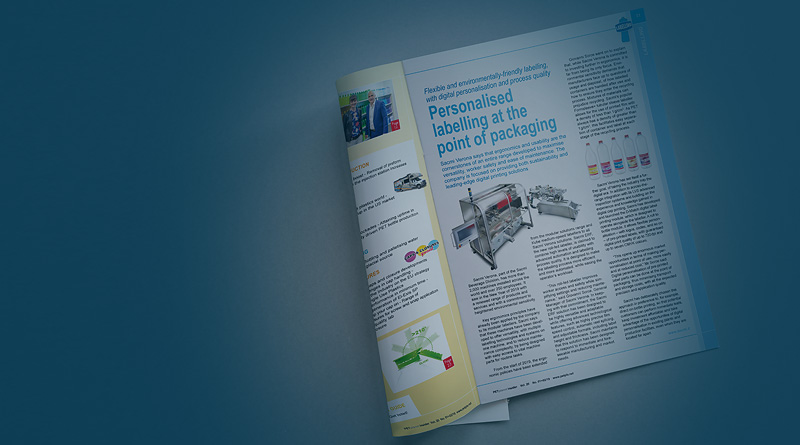