"MARKET SURVEY 29 PETplanet Insider Vol. 19 No. 01+02/18 petpla.net Resins Company name M&G Polimeri Italia Invista Resins & Fibers GmbH NEO GROUP Reliance Industries Limited Postal address Telephone number Web site address Contact name Function Direct telephone number E-Mail Via Morolense Km 10 Italy +39 0775 84 221 www.mg-chemicals.com/en Ms Marilena Grecchi Area Sales Export, Marketing Itelli. Exp. +39 0282 273 242 [email protected] Philipp-Reis-Strasse 2, 65795 Hattersheim, Germany +49 69 305 6025 www.polymers.invista.com Mr Achim Heyer Business Director PET Resins +49 69 305 6025 [email protected] Industrijos str. 2, Rimkai LT-95346, Klaipeda district, Lithuania +370 464 66 710 www.neogroup.eu Mr Gediminas Paulauskas Sales Manager +370 464 66 711 [email protected] PET Business, Build. No. 8, B Wing, 1st Floor, Thane Belapur Rd, Ghansoli, Navi Mumbai, 400701, Maharastra, India +91 22 4477 0000 www.ril.com Mr Rajesh K Gera Asst. Vice President - Business Development +91 2244 7814 26 (D) [email protected] RESINS 1. Brand name of the resins Cleartuf Polyclear PET, PolyShield Resin, XPure Polyester NEOPET Relpet and Relpet Green 2. IV Range a. of Homo-Polymers 0.60 - 1.0 0.56 - 0.82 0.76 b. of Co-Polymers 0.76 + 0.95 0.81 - 0.87 0.76 - 0.84 0.59 - 1.00 3. Speciality resins CSD Cleartuf Ultra Polyclear PET 1101 NEOPET 80, NEOPET 82 Relpet G5841 Water Polyclear PET 1101 Aqua NEOPET 76, NEOPET 78 Relpet G5761 Beer Cleartuf P76-P82 PolyShield Resin 2300 and Masterbatch 2520 NEOPET 80, NEOPET 82, NEOPET 84 Relpet B9845 Edible oil Polyclear PET T94N Wine / Liquors Poliprotect Polyclear PET T94N, 1101, PolyShield 2300, 2520 NEOPET 80, NEOPET 82 Relpet B9845 / Relpet G5801 Personal care / Pharmaceuticals Cleartuf 82 Polyclear PET 1101, T94N NEOPET 80 Relpet G5801 Slow crystallisation Polyclear PET T94N, XPure Polyester Relpet S5841 (5 Gallon returnable, thick sheet and moulded articles) Hotfill Cleartuf P85 HF NEOPET 82 HF Relpet H7761 Pre-coloured Fast reheat Cleartuf Ultra Polyclear PET 1101 NEOPET 82 FR, NEOPET 84 FR Relpet QH5821 Other 1) Barrier resins (i.e. Poliprotect) 2) Cleartuf T95 (high viscosity) main application: trays Ultra NEOPET Relpet F7600 (film/fibre products), Relpet IM5900 (thin wall & injection moulded products), Relpet OP5821 (UHT milk-aseptic filling) 4. Increased barrier properties Yes, with Poliprotect PolyShield Resin 2300 and Masterbatch 2520 Relpet B9845 barrier grade has active oxygen barrier & passive carbon dioxide barrier. 5. PEN mixes available 6. Recycled blends available Relpet Green (100% PCR) 7. Special comments Next generation catalyst polymer series Xpure Customised grades (Thin wall/EBM) available on request Company name Indorama Ventures Ltd Postal address Telephone number Web site address Contact name Function Direct telephone number E-Mail 75/102 Ocean Tower 2, 37th Floor Bangkok 10110, Thailand +662 661 6661 www.indoramaventures.com Mr W.G. Hoenderdaal Technical Marketing Manager +316 51809942 [email protected] RESINS Europe USA/Canada Latin America Asia 1. Brand name of the resins RamaPET, PlantPET Polyclear PET, Oxyclear Barrier PET, Oxyclear Shield PET, Preformance PET, FuTuRe-PET Resin, PlantPET Resin Polyclear PET, Oxyclear Barrier PET, Oxyclear Shield PET, Preformance PET, FuTuRe-PET Resin, PlantPET Resin RamaPET, Afron 2. IV Range a. of Homo-Polymers IV 0.58 - 0.95 IV 0.58 - 0.95 IV 0.74 - 1.25 IV 0.50 - 1.08 b. of Co-Polymers IV 0.58 - 0.84 IV 0.58 - 1.25 0.58 - 1.25 IV 0.58 - 1.08 3. Speciality resins CSD R1, R182C, R180 ES11, ES11 (A)-R10, 1101 1101, 1111 S1, S2, R1, N1S Water N180, W176, W170, N1, N1(S) N2R, N2R (A)-R10, N2R-Ti, 3301 3301 N2, N1 Beer N1, N1(S), N180 Oxyclear Shield PET 2310 Oxyclear Shield PET 2310 N1 Edible oil Wine / Liquors N1, N1(S), N180 Oxyclear Barrier PET 3500, PolyClear EBM PET 5505, 5507; 1708CC, 3302 Oxyclear Barrier PET 3500, Polyclear EBM PET 5505 and 5507 N1 Personal care / Pharmaceuticals N1, N1(S), N180 Polyclear EBM PET 5505/5507 Polyclear EBM PET 5505/5507 N1, G1 Clear Slow crystallisation P184 T-94 T-94 G1, G1AS (scratch resistant version) Hotfill R1, HF 2201, 1708HS 2201 H1 Pre-coloured None Fast reheat R1, R182C, R180 ES11, 1101 R1, R2, ES11 Other PlantPET R182C PlantPET Resin (Bio-MEG), High IPAmodified resins, BOPET Grades PlantPET Resin (Bio-MEG) L1 (high flow blood tubes), film grades, low melting resins & silica masterbatches 4. Increased barrier properties Oxyclear Barrier PET 3500, OxyClear Shield PET 2310 Oxyclear Barrier PET 3500, OxyClear Shield PET 2310 5. PEN mixes available Co-polymers; Homo Polymer PolyClear Heat 2222, 2224, 2226, PEN PolyClear Heat 2222, 2224, 2226, PEN 6. Recycled blends available r-PET flake and granulate FuTuRe-PET Resin, PolyClear Conserve PET FuTuRe-PET Resin, PolyClear Conserve PET 7. Special comments RamaPET L1 for injection thin walled articles Polyclear EBM PET for extrusion blow moulding; Low IV and functionalised copolyester N2G (Germanium based PET); HPC Grades for crystal clear bottles/articles, BioPET based on BioMEG","@ID":31}, "imprint EDITORIAL PUBLISHER Alexander Büchler, Managing Director HEAD OFFICE heidelberg business media GmbH Bunsenstr. 14 69115 Heidelberg, Germany phone: +49 6221-65108-0 fax: +49 6221-65108-28 [email protected] EDITORIAL Kay Barton Heike Fischer Gabriele Kosmehl Michael Maruschke Ruari McCallion Waldemar Schmitke Anthony Withers WikiPETia.info [email protected] MEDIA CONSULTANTS Martina Hirschmann [email protected] Johann Lange-Brock [email protected] phone: +49 6221-65108-0 fax: +49 6221-65108-28 LAYOUT AND PREPRESS EXPRIM Werbeagentur | exprim.de B. Gaumann, M. Gaumann READER SERVICES Till Kretner [email protected] PRINT Chroma Druck & Verlag GmbH Werkstr. 25 67354 Römerberg Germany WWW www.hbmedia.net | petpla.net PETplanet Insider ISSN 1438-9459 is published 10 times a year. This publication is sent to qualified subscribers (1-year subscription 149 EUR, 2-year subscription 289 EUR, Young professionals’ subscription 99 EUR. Magazines will be dispatched to you by airmail). Not to be reproduced in any form without permission from the publisher. Note: The fact that product names may not be identified as trademarks is not an indication that such names are not registered trademarks. 3 PETplanet Insider Vol. 19 No. 01+02/18 petpla.net PETplanet is back once again after its usual winter break. Two press releases have appeared on our desk in recent weeks that show almost in textbook fashion the difference between strategic and financial investors. First, Husky has been passed from one financial investor to another and, second, there has been a change at the top of KHS management. First the financial investors. Their business model is to buy a company then sell it on after a few years for the greatest possible profit. Berkshire Partners LLC and the private equity arm of Ontario Municipal Employees Retirement System (Omers) have sold Husky to financial investor Platinum Equity. In August 2017, the news agency Reuters reported the company was seeking US$4bn with an estimated profit before tax, interest and depreciation of around US$350 million. It is unlikely that investors were able to complete the purchase at the asking price, but the general direction is clear. In 2011, Berkshire and Omers acquired Husky from Onex Corp for US$2.1bn. Investors have moved on but the boss remains a constant. Platinum Equity has reacted positively to John Galt, who has been CEO at Husky since 2005. He is therefore one of the longest-serving CEOs in the sector and so ensures the necessary consistency at Husky. Consistency is an attribute more frequently associated with family businesses and strategic investors. This is the case at Salzgitter, which purchased KHS in 2007. Here, it was the investors that stayed and the boss who left. This was Prof. Dr.-Ing Matthias Niemeyer, who came to KHS in 2011 through Salzgitter as Chair of the Board of Directors. The Supervisory Board thanked him expressly for significantly increasing turnover but there was no mention of the profit increase in the press release. According to a report by Salzgitter AG, the 2016 profit was around 2%, while competitor Krones achieved 7% with a similar product range. This shows that Salzgitter stands by its investment and prefers to work on the foundations. For a transition period, the interim Chair is former Managing Director of Finance at KHS, Burkhard Becker. He also comes from Salzgitter but has been part of Krupp Kunststofftechnik since 1998, to which at that time belonged also Corpoplast, which is today part of the KHS Group. How’s that for consistency!? Yours, Alexander Büchler Dear friends of PETplaner Insider, Consistency: One way or another... Husky sold, KHS under new management","@ID":5}, "CAPS & CLOSURES 20 PETplanet Insider Vol. 19 No. 01+02/18 petpla.net New solutions for premium products Cap-preform combination Sustainability, low weight, advanced cap-bottle design solutions and consumer services: Sacmi is responding to the latest market trends with a range of solutions co-developed with its own research facility. CAPS & CLOSURES On the beverage market where environmental sustainability and cost reduction go hand in hand with the request for new solutions that give consumers new designed, high-value products, Sacmi continues to demonstrate a capacity to respond to such needs with a lot of new solutions. The aspect of weight reduction has been merged with new cap features to ensure new consumer needs are met with appropriate, up-to-theminute solutions. For example, for Asian markets (ASEAN and China, but also including Africa) where the use of tall caps is still quite common, Sacmi has developed a cap and neckpreform solution that retains its ergonomic grip and smart shape yet cuts weight by some 30% without affecting performance. The ability to provide advanced cap-preform combinations has led to the development of a cap weighing just 1.55g. This will soon be launched in South East Asia together with a preform with a 30-25mm neck finish that weighs just 3.3g. Sacmi is also equipped to grasp another recent market trend: this concerns the ever-sharper focus on the marked functional design differentiation that accompanies premium products aimed at HoReCa segments and other market niches. While such items use PET bottles, their distinctiveness is entrusted to the plastic or metal closure. In this field, Sacmi can provide complete lines that make both plastic and metal caps; such lines are perfect for the development of these product lines. Two key examples being the highly popular pull-ring cap (as shown on the picture), and the aluminium screw cap in all its variants. Thanks to the expertise in the slitting and folding of both flat-top and sport caps, Sacmi is able to provide technical solutions to produce patented tamper evident bands; in addition to responding to advanced performance requisites, these feature further characteristics that respond, for example, to the need to keep the cap connected to the container once it has been opened. The Sacmi slitting-folding machine creates a stable connection between band and cap. The solution, attainable with a Sacmi slitting-folding machine, allows for the creation of a stable connection between band and cap. This ensures the latter is not dispersed in the environment; however, if the consumer so desires, the cap itself can nevertheless easily be torn from the band to allow more traditional utilisation. A practical advantage is that in this case, combined with a potential environmental advantage as the entire cap-container system - with the anti-tamper band thus connected - is easier to introduce into the recycling system. The Group prides itself on its innovative strategy, in responding to the new trends in the beverage sector, focusing on efficiency and cost-effectiveness. Sacmi works closely with its customers to design and manufacture the most suitable cap and preform solutions to meet the needs of the consumer, whilst observing environmental and green concerns. www.sacmi.it For example, for Asian markets (ASEAN and China, yet also Africa) the use of tall caps is still quite common. Sacmi cuts weight by some 30% without affecting performance.","@ID":22}, "CAPS & CLOSURES 26 PETplanet Insider Vol. 19 No. 01+02/18 petpla.net Convenient caps and differentiation on the shelf are the keys Facing customer and market challenges With a broad range of products, Bericap, one of the leading plastic closure manufacturers, focuses with its products on consumer convenience as well as on sustainability. Nevertheless meet the producers’ expectations towards weight-optimised packaging. CAPS & CLOSURES “In recent years there has been a strong trend to light weight closures which serve the functionable purposes in the field of PET containers, but are difficult and inconvenient to handle by consumers” says Christoph Thünemann, Group Director Communications and Marketing at Bericap. “With the latest product innovations and modifications, Bericap pays more attention on convenience aspects for consumers and differentiation on the shelf.” Consumer-convenient closures for all major PET containers Bericap offers closure solutions for all major PET neck finishes for carbonated soft drinks, mineral water, juices and dairy products. The latest product innovation is Bericap Neo 30/17, a weight-optimised closure for the well-known neck finish PET 30/25. Bericap Neo provides easy application, a good grip, safe tamper evidence and low, consumer-convenient removal torques – attributes that make it a closure with positive package experience for the consumer. Neo 30/17 For bottlers who want to take advantage of the light weight neck PET 29/25, but still lay their focus on consumer convenience, Bericap developed the closure HexaLite 29/13. It is available with rounded as well as straight knurls, which states a clear advantage for shelf differentiation with different outside designs. Bericap has added a hinge cap for small sized bottles for still water to its product portfolio: the SnapCap 26. A hinge cap pressed on a light weight PET 26/21 neck. The closure allows opening the bottle by simply clipping back the hinged lid by 180°. Bericap ScapCap 26 recloses safely with a click sound. SnapCap 26 A newly designed sports cap Bericap Crystal has a transparent closure body and coloured insert. It is available with a tear strip for visible tamper evidence or with bridges which break at first opening. Most PET bottles used for juices or dairy products a 38mm neck finish. But from the consumers’ point of view drinking from a 33mm neck is much easier. Bericap offers a 33mm closure that can be used for cold, cold-aseptic or hot filling and provides less weight for both closure and neck. New closures for the food market Since PET is used besides the beverage market also for the food market, Bericap additionally provides a wide range of closure solutions for all major neck finishes for edible oil, vinegar, soya sauce, ketchup and other spreadable products. For liquid food products, like edible oil or vinegar, Bericap developed the new 2-Flow closure. This is a shaped pouring orifice which allows pouring a wide flow from the large and a well-controlled reduced flow from the small orifice. From the consumers’ point of view this is of interest when – for instance – edible oil is used with a large flow for cooking or with a small flow for salad dressing. For spreadable food products like ketchup, mayonnaise or chocolate sauce, Bericap’s portfolio contains hinge closures with a dispensing valve. Serving sustainability aspects, Bericap Valve is made from TPE, allowing separation of the valve from PET during the recycling process. The Bericap Valve is food approved also for fatty products. In mid-2018, Bericap will open a new production site north of Mexico City, Mexico. In Nairobi, Kenya, a new warehouse was recently put into operation in order to react quickly and flexibly to customer requirements and wishes with a local focus on Kenya, Uganda and Somalia. “All our production sites and subsidiaries all over the world guarantee a competent technical customer service, supporting our clients with the effective application of our closures. Based on our vast know-how, we help our customers with safe applications, increased line efficiency and a smooth integration of our products”, concludes Thünemann. www.bericap.com 2-Flow EV 21/20 for edible oil, soya sauce and vinegar","@ID":28}, "MATERIALS / RECYCLING PETplanet Insider Vol. 19 No. 01+02/18 petpla.net 11 PET recycling in Thailand by Kay Barton Recycling is still in its infancy in Thailand. Royal Interpack has made it its mission to recycle post-consumer PET bottles and to use the resulting materials in-house, as up to 50% of flakes for rPET food packaging using an FDA approved super clean sheet extrusion process. This is no easy task; not only is there the lack of the necessary infrastructure for the proper collection, sorting and processing of the plastic waste, there is also the lack of any genuine awareness of the importance of recycling and the value of resource recovery. Above all, there is an especially urgent need for action outside the major conurbations. Royal Interpack, one of the first recyclers of this size in Thailand, processes its products with turnkey recycling equipment from STF Germany. Royal Interpack Co., Ltd., June 21, 2017 We met: Mr Visanu Chawla, CEO Mr Marcel Rauser, Plant Manager Chonburi Province, located some 130km south-east of Bangkok, is where Royal Interpack is heaquartered and where we met to discuss the market situation and equipment with company CEO Visanu Chawla, and Plant Manager Marcel Rauser. The company began thermoforming and extrusion operations in 2010, and decided to build a recycling plant for PET bottles in 2012. The STF recycling line now in use was the first that had been designed with a label scraper, for the removal of full PVC sleeve labels. The focus on automated and optical sorting of both bottles and flakes was still quite unusual in Asia, back then. “The turnkey, fully integrated recycling, extrusion and thermoforming plant represented a total investment of US$40 million”, says Mr Chawla. “Of course, given the current levels of awareness of recycling, it will take some time for the investment to pay off.” The plant’s capacity totals 1.8t/h of material processing. Inadequate local collection and availability means that the dirty-looking bales of bottles are even more likely to be imported from overseas than sourced in Thailand. Inside the recycling plant, the system works fully automatically; the facility needs a total of just 15 employees, who alternate in shifts. After the removal of labels, sorting takes place in a two-stage process, according to foreign materials and colour, followed by another mandatory manual sorting process before the bottles are then grinded. The material is then conveyed through two hot-steam washing stages before the PET and PP Tour Sponsors: Inside Royal Interpack: recycling equipment from STF The Editourmobil in front of Royal Interpack’s main entrance are separated via a separating tank and centrifuge. In the next stage, the material enters a cold wash, before moving to the flake sorter to remove any remaining foreign materials. www.royalinterpack.com","@ID":13}, "TRADE SHOW REVIEW PETplanet Insider Vol. 19 No. 01+02/18 petpla.net 40 World premieres and digitalisation solutions for the beverage filling and packaging sector Digitalisation and flexibility The major focus of Krones presentation at Drinktec was on solutions that on a smaller footprint enable the same output to be achieved, provide ever higher levels of individualisation and flexibility, and impart additional sustainability to the production operation – with digitalisation playing a key role. Concept study: Bottling on Demand Is Batch Size 1 a realistic option on a bottling line? And if so, can it ever be commercially viable? If you ask the development people at Krones, then in both cases the answer is yes. In order to substantiate this assertion, they were at the Drinktec showcasing the Bottling on Demand concept study, which explores the limits of practical flexibility. Its core elements include a newly developed filling valve. But what differentiates this filling valve from the others is its versatility. The water is supplied through the main pipe into the valve, each of the individual flavour components is dosed to the correct amount and added through the secondary pipes. Thus, soft drinks and other mixed beverages can be produced individually and directly in the filler itself. There’s also an option for feeding in different final syrup variants via the valve’s secondary channels. This enables the client to switch back and forth between different products without a make-ready routine being required. For everyone who wants to exploit product individualisation to the full, the system features an additional option: it is possible to provide different components via the valve’s secondary channels, and to determine individually the precise composition of the beverage for each bottle. “Here we’re thinking primarily of the premium or luxury segment at brand owners,” explains Stefan Pöschl, Head of Technology Development at Krones. “It would be conceivable, for instance, to adapt the recipes of sport or medicinal drinks to precisely suit the consumer’s needs and preferences.” This does not entail any problems in terms of evidencing the constituents involved: direct printing on each bottle enables the client to individually identify what recipe the consumer ultimately holds in their hands. How specifically the principle of Bottling on Demand is implemented in a line will depend upon many different factors, particularly the products and goals of the plant concerned. Dynafill Dynafill had been originally invented for the filling of beer. This filling process enables the bottle to be filled with beer within just 0.5s. If you add in the crowning operation, then the entire process takes 5s. The number of filling valves is reduced from 100 to 66, and this while retaining a rating of 36,000 containers per hour. The CO 2 consumption is claimed to be 20% lower than with conventional systems. The Dynafill can handle beverages in both coldfill and warmfill (temperatures of up to 30°C) modes – the process duration is in both cases less than 5s. The filling process remains stable. Digitalisation & digital direct printing Overall, the combination of machines and lines, clouds and data, played a paramount role in Krones’ presence at the fair. With cloud computing, big data, smart data, the internet of things and much more. The digitalisation solutions from Krones provide data, know-how and fast communication. Designed to upgrade still further the efficiency of the lines concerned to make comprehensive use of all potentials along the entire value creation chain. Thus enabling genuine added value to be generated in the In the Dynafill, beer bottles are filled in 0.5s.","@ID":42}, "9 NEWS PETplanet Insider Vol. 19 No. 01+02/18 petpla.net Kick-off for K 2019 Starting now, exhibitors from all over the world can register for the world’s No. 1 trade fair for the plastics and rubber industry. A print version of the exhibitor invitation has been sent to all participants in the prior event K 2016 and further interested parties. The registration forms can be found at the website. The deadline for registration is 31 May 2018. Messe Düsseldorf, the event organiser, is expecting a very large number of registrations. The range of exhibits at K 2019 spans the categories of machinery and equipment, raw materials and auxiliaries, semi-finished products, technical parts and reinforced plastics. K 2016 was characterised by the good global business climate in plastics and rubber and the industry’s positive future prospects. A total of 232,000 trade visitors from 161 countries received a warm welcome over the eight days of this Düsseldorf event. Their lively interest in the innovations shown and their ready willingness to invest generated an excellent mood among the more than 3,200 exhibiting companies. K 2019 will take place from 16 to 23 October 2019 at the Düsseldorf exhibition centre. An extensive supporting programme supplements the exhibitors’ presentations. Especially noteworthy are the special show titled “Plastics shape the future” and the Science Campus as the forum for exchanges on science and research. www.k-online.com Global plastic caps & closures market study With gains boosted by continued growth in bottled water, demand for plastic caps and closures is expected to increase 4.1% per year to nearly 1.9 trillion units in 2021. Growth in the pharmaceutical market will be above average. Value gains will be driven by a shift to dispensing and other closures that offer improved performance characteristics, while unit volume will continue to be dominated by low cost commodity caps. These and other trends are presented in the new study ‘Global Plastic Caps & Closures’ from the Freedonia group. This study analyses the global plastic caps and closures market. It offers historical demand data (2006, 2011, 2016) plus forecasts for 2021 by product (threaded, unthreaded, dispensing, child-resistant) and by market, including beverages (bottled water, CSDs, milk, other), food, pharmaceuticals, and other (household cleaning products, personal care products, etc.), as well as by global region. The study also assesses industry competitors worldwide, including Albéa, Amcor, AptarGroup, Bericap, Berry Global, Closure Systems International (Reynolds Group), Dätwyler, RPC Group (GCS), Scholle IPN, Silgan, and West Pharmaceutical Services. Some of the questions addressed in the study are: How will regulatory concerns influence the product mix for childresistant closures? Will plastic bottles and closures outgrow their niche status in the global beer market? How will changes in the global wine packaging mix affect the outlook for synthetic corks and other plastic closure types? www.freedoniagroup.com","@ID":11}, "BOTTLE MAKING 15 PETplanet Insider Vol. 19 No. 01+02/18 petpla.net Growing PET market in India for edible oil by Kay Barton India’s market for PET bottling of edible oil has been booming, across the country, for over five years. More and more brands in this segment are investing in PET packaging, both from outset in new sites and in conversions from other packaging types. PET preform and bottle giant Manjushree Technopack, from Bangalore, already cooperates with leading local edible oil players and sees significant growth in PET market share, from its current 25% level up to 30-40% in the near future. As well as being India’s only national producer of a two-litre bottle with handle for edible oil, the company is working hard on material reduction, new designs and cost optimisation. We discussed market trends and emerging developments for edible oil in India with Manjushree’s Managing Director Mr Vimal Kedia, who gave us an impression of the current and future shape of this segment of India’s food market. PETplanet Insider: Mr Kedia, apart from the attractive appearance of PET bottles, what are the main reasons PET is becoming more and more popular in the edible oil segment? Vimal Kedia: PET bottles have been popular in the last five years because of evolving consumer preferences, the growth of retail industry, the eco-friendly nature of PET bottles, and government regulations that will ban multilayer pouches in the coming years due to problems in the recycling streams. PETplanet Insider: The overall share of edible oil packaging for Manjushree is 10% of its turnover. What does this mean in terms of current outputs of preforms and PET bottles produced by Manjushree for this segment, and how many tonnes of PET are converted for this? Vimal Kedia: Edible oil is a very important section for Manjushree as it is one of the fastest-growing markets in the industry. Our production of edible oil packaging is currently 5,000t/a; we have been investing in new moulds and machines for providing various types of rigid packaging for the edible oil industry and we estimate that this will form a significant part of our production capacity. PETplanet Insider: Which equipment do you primarily use for the production of preforms, bottles and closures? Vimal Kedia: We use multi-cavity moulds from ASB and Husky platforms to produce PET preforms for the edible oil industry. We use ASB machines like PM 70 with 24 cavities and Husky 48 cavity all-electric machine to produce the preforms. We also use injection moulded machines to produce larger size preforms, including 5l, 20l, and so on. We also make injection moulded closures for CTC caps. Manjushree has developed a patented super-short neck preform for edible oil packaging, which can be very economical for that market. The super-short neck preform in 26mm, which can be used in a 1l pack, can weigh as little as 18g. The closure for this, a single piece compression moulded cap, can bring about substantial savings in weight of both preform and cap. The design of the neck, which is suitable for various shapes and designs of bottles of 200ml, 500ml and 1l capacity, was a result of Manjushree’s strong focus on research and development – as well as fire in the belly for innovation and cost consciousness! Our capacity for production is 300 million super-short neck preforms and caps, in highspeed ASB and Husky systems. PETplanet Insider: Smaller volumes, like 500ml or 1l, are becoming more and more popular. How is the market structure in terms of edible oil PET bottle volumes and what are the overall shares in India today? Vimal Kedia: The edible oil market in India is estimated at 7.66 million tonnes, according to GGN International, one of India’s largest research firms. Presently, PET packManjushree’s MD Vimal Kedia","@ID":17}, "MATERIALS / RECYCLING PETplanet Insider Vol. 19 No. 01+02/18 petpla.net 10 Amut Group and CarbonLite working together to improve bottle recycling A new recycling plant for Dallas The new CarbonLite recycling facility, located in Dallas, Texas, USA started operations in September 2017, as per the schedule. The washing line supplied by Amut has state of art of technology and is the second plant of this size in operation in the USA, capable of producing over 12,000 pounds per hour of high-quality PET from MRF post-consumer bales. This 250,000ft2 bottle-to-bottle PET recycling plant processes more than 100 million pounds plastic bottles annually and the Amut washing section is capable of reaching 6t/h and permits the transformation of old plastic bottles into PET resins, flakes and pellets that can then be used to produce new beverage bottles and other sustainable products. Thus, the Dallas facility will double the company’s annual capacity of foodgrade PET. “We are glad to have scored another top reference in the Northern America plastic recycling market. The CarbonLite PET recycling project comes after the two mega PET recycling plants that Amut supplied in North America to Unifi in Reidsville, North Carolina, and to Petstar Coca-Cola Mexico” stated Mr. Piergianni Milani, the President of Amut Group. According to Mr. Leon Farhanick, President of CarbonLite, the company is very satisfied with the quality, punctuality and technology provided by the Amut technology. Anthony Georges, President of Amut North America, stated: “CarbonLite management has over a decade of experience in PET wash lines and selected the Amut solution to face the new challenges in the market conditions for their Dallas operations. Considering that Amut is one of the major OEM supplier for their system, we integrated our De-Labeller, Amut’s patent technology, and as well the wet whole bottle pre-wash.” Awarded De-Labeller The Amut De-Labeller won the prestigious Plastic Recycling Innovation Award from the APR (Association of Plastic Recyclers) in 2017. Georges states: “When you are dealing with comingled MRF bottle bales you need to be able to detect and remove all nonPET and colour PET containers prior to entering the final washing process. By utilising our double stage we perform with the first De-Labeller the dry-cleaning action able to detach most of the shrink sleeve labels, while the second unit is a wet De-Labeller process to pre-wash the whole bottles and reduce wear effect on grinders blades. This wet bottle washing technology utilises the filtered recycled flake washing water therefore it does not increase the consumption of fresh water used in the complete cleaning process, and contributes to the elimination of outside dirt as well as remaining labels on the whole bottles”. Critical to the Amut technology is that the bottles stay intact through these two machines and are not damaged during the actions of De-Labeller therefore improving efficiency and the functionality of the following automatic sorting equipment so that the nonPET and colour PET can be easier removed from the clear PET bottle stream. The clear PET bottles will be washed directly in the Amut wash flake system. Amut scope of machinery & technology supplied includes as well, the wet grinding system to turn bottles into flakes, along with two of the Amut patented Flake Friction Washers, and two of their newest advance technology ‘Sink-Float’ separation machines, which are able to capture the polyolefin caps so that these cleaned caps can also be valued. The whole process is engineered to increase the grade quality of the clear PET flakes which comply with the most demanding bottle-to-bottle applications, optimising the value of every bale, while minimising operational costs, fresh water usage, energy and cleaning agents. www.amutgroup.com","@ID":12}, "PETplanet Insider Vol. 19 No. 01+02/18 petpla.net 47 BOTTLES Sleeve with Playmobil motif In Spain, Nestlé sells natural mineral water in a 330ml person-shaped clear bottle with the brand name Aquarel. In collaboration with Playmobil, the bottles narrow in two places and are decorated with person-shaped sleeve labels that look like the famous Playmobil figures. The sleeve label is drawn up over the screw seal as an additional tamper-evident seal and can be easily removed using the two perforations in this area. www.nestleaquarel.es Sauce in contoured upturnable bottle In its domestic market, the Spanish sauce manufacturer Chovi sells different sauces in contoured and polygon squeeze bottles. The bottles contain between 280 and 300g of product and are sealed with a screwed on hinged cap with a dosage opening and a selfsealing valve. There is a seal membrane under the lid that must be removed before first use. A sleeve label shows directions for use and inverted printing around the base makes the sauce bottle easy to identify when stored on its head in the cupboard. www.chovi.com PETbottles Beverage + Liquid Food","@ID":49}, "PETproducts 34 PETplanet Insider Vol. 19 No. 01+02/18 petpla.net Solutions for high volume caps and speciality closures Lightweighting is the industry trend, and the caps and closures section is no exception. 1810 closures with their heavy w e i g h t a n d bulky designs can compensate for some variability in the manufacturing p r ocess , ye t their lightweight successors (e.g. 1881 or 26mm CSD) require tighter process control to achieve the targeted ‘cap on bottle’ performance and day to day production stability. Milacron/Mold-Masters is providing solutions for high volume beverage caps as well as speciality closures. Mold-Masters patented iFlow manifold technology comes with 30+ years of experience and is claimed to ensure uniform fill from cavity to cavity, shot after shot – highly critical for lightweight caps. A slight imbalance during filling in combination with top panels as thin as 0.4mm and cycle times <2.2s will slow down the melt front within some cavities and impact shrinkage. This can be one of the causes of dimensional and performance variation. Reducing this variability factor and improving part quality is one of the key benefits leading closure converters are looking for. iFlow manifolds provide advanced technology combined with an optimised thermal profile via brazed heater elements. This minimises changes of melt viscosity that are typically seen with traditional manifold designs. These are key factors in increasing the process window. Plus one of the untapped potentials of this technology is the ability to increase output per machine. “The main reason for the cavitations we know today (48, 64, 72, 96, etc.) is the aim of naturally balancing the hot runner to secure good cavity to cavity consistency. Many machines in our industry could take a few cavities more without being tie bar, tonnage or injection capacity limited,” said Thomas Bechtel, Sales Director Packaging at Milacron Mold-Masters. The channel designs of iFlow are milled and not gun drilled which allows a “creative” routing of the melt maintaining a uniform shear distribution. One of the recent successes was an 80 cavity system operated on the same machine the customer previously ran a 72-cavity system. There was no impact on cycle time or part quality. The productivity increase was confirmed to be 11%. www.milacron.com Push Cap provides a fresh way to infuse nutrients The Push Cap is a delivery system that can infuse either powdered or liquid ingredients into almost any substance. Beyond vitamins, the prospective uses for the Push Cap include workout formulas, nutrient supplements, immunity boosting extras and weight loss additives encompassing any composite of superfoods, probiotics, amino acids, fibres, and/or proteins. The possibilities are virtually limitless. Moreover, the cap allows infusion of these ingredients into practically any liquid – including but not limited to – water, juices, tea, coffee, etc. In an attempt to reach beyond mainstream beverages, KarmaCap is in negotiations with pharmaceutical companies for collaborations in creating ready-to-drink over the counter (OTC) beverages. With the Push Cap, active ingredients are mixed only seconds before consumption, the ramifications of which are substantial. The Push Cap facilitates portion control and the ability to separate ingredients that are not shelf-stable. Other advantages are that the consumer can actually see the powdered additives in the Push Cap, so they are assured that the purported nutrients are there, as well as intuitive and easy use. A hermetic seal maximises quality, freshness, and performance. The cap and seal are durable, standing up to extreme temperatures, exposure to light, and the shock from loading, unloading, and transportation, according to the company. The Push Cap is made of recyclable material, and its design and production are FDA approved with statistical quality control that meets Six Sigma standards. www.karmacapco.com Whistle Cap The Whistle Cap from South Korean company Kwang Dong Pharmaceutical Co., Ltd. has been awarded at the WorldStar Packaging Awards in the category Beverages. The Whistle Cap enables the user to make sounds easily from 360 degree (all directions) either for self-protection or for the purpose of playing. The acoustic sound is generated by differently sized holes in the mouthpiece and integrated channels for the air flow. www.worldstar.org CAPS & CLOSURES","@ID":36}, "BOTTLE MAKING 17 PETplanet Insider Vol. 19 No. 01+02/18 petpla.net BOTTLE MAKING 17 With Sacmi, the beverage specialists are always at your side. With our unbeatable technological know-how and continuous research we are creating new containers and closures designed to ensure outstanding performance. The new IPS injection system for preforms, the CCM compression press for caps and the quality control systems fully designed and built by Sacmi, allows for large-scale production with considerable advantages in terms of efficiency and flexibility. The outcome? Reduced plastic volumes, less energy consumption and lower running costs.All in a bottle: the one you’ll soon be making. SAVE THE DATE http://www.sacmi.com/en-US/Events/Packaging CTC neck and precisely fitted polypropylene handle, for easy dispensing. However, market demand is currently very low. The positioning of this pack can be improved as most of the households use approximately 2l/month and providing them with a single pack that can last them for one month is a convenient option. Marketing and positioning by brand players will play a critical role in this pack size. PETplanet Insider: Thank you very much for the interview, Mr Kedia. www.manjushreeindia.com","@ID":19}, "CAPS & CLOSURES 22 PETplanet Insider Vol. 19 No. 01+02/18 petpla.net Collaborative action to clarify cap ovality issues Round table for oval caps The lightweighting of plastic caps for PET bottles necessarily involves compromises for both application and functional performance of the closure. One consequence of lower rigidity is the increased risk of deformation of the caps during transport and storage, compounded by the effect of higher capacity bulk storage bins. This deformation is characterised by an ovalisation of the cap body which may cause blockage of the cap infeed to the capper and resulting line jams. The Cetie PET Finishes working group thus identified the need to set up a specific group dedicated to cap ovality, and this new working group recently held its first meeting in Cetie offices in Paris. As the contribution to ovalisation depends on conditions encountered by the caps after leaving the cap production site, the manufacturer is not in a position to guarantee a given low ovality for caps as received. Generally, cap suppliers’ ovality specifications will thus be wider than those given by the capping machine supplier for trouble free operation. In addition, although the principle is understood, there is no single recognised definition of cap ovality as a quantity and how it should be measured. Moreover, as avoiding jams is a prime concern for bottlers, optical inspection equipment is increasingly favoured on incoming caps streams to reject, in particular, those whose ovalisation is detected as potentially line-blocking. Line jams may be particularly penalising for aseptic filling if sterility is broken and involves a 3-hour plus production stop. However, in the absence of a clear understanding of the extent to which the capper can accept a degree of ovality, appropriately setting the criteria for rejection remains a recurrent difficulty, as this will depend for example on the cap design. Inspection thus may result in high cap reject rates if restrictive ovality reject criteria are favoured. Cases are reported where unacceptably high reject rates for lightweight caps have led the bottler to revert to heavier caps even for lines otherwise designed for lightweight versions. Although blockage on the cap infeed is the principal issue, there is apparently little known on the extent to which ovalised caps may also affect cap application and subsequent functional performance. It is generally considered that once inserted in the capping chuck the cap will be forced to recover its initial roundness, and after capping the correct shape maintained by the finish. However, there might be cases where for example the correct positioning on the finish of the sealing feature or the tamper-evident band be affected by residual ovalising forces. The issue is thus complex and no single actor in the value chain – cap supplier, capping equipment supplier, optical inspection equipment supplier or filler/brand-owner currently has the means to ensure that the adoption of lightweighted caps might not be jeopardised by problems attributed to cap ovality. This is typically an area where it is beneficial for the actors concerned to participate in a collective action to exchange industrial experience and develop appropriate guidance for the industry based on objective shared knowledge. Cap ovality working group Cetie is an inter-professional association dedicated to producing technical reference documentation - best practice, recommendations and specifications - for the bottling industries. It provides facilities to enable such collaborative initiatives for the development of authoritative reference documents by the technical experts from its member companies, within working groups either dedicated to general themes or to specific subjects. The Cetie PET Finishes working group thus identified the need to set up a specific group dedicated to cap ovality, and this new working group CAPS & CLOSURES","@ID":24}, "45 PETplanet Insider Vol. 19 No. 01+02/18 petpla.net 45 PETproducts [email protected] Tel: +90 212 695 50 00 Fax: +90 212 694 97 24 100815dmyR .com Aseptic soft drink bottling without changeover time GEA has launched the Fillstar CX EVO. The usual product changeover times of approximately three hours are claimed to be a thing of the past as the new system eliminates changeover times thanks to the integrated control unit merely requiring reprogramming. The changeover from contact filling to non-contact filling is fully automated. The system sterility is thus not interrupted. Aseptic filling for a wide range of beverages The Fillstar CX EVO can handle high and low acid beverages, as well as aseptic soft drinks with varying carbonation levels, to ensure complete sterility. The Fillstar CX EVO can fill products with fibres up to 2mm long and with diameters of 3mm; when integrated with an aseptic piston doser the system can fill even fruit pieces with a volume of up to 10x10x10mm. Bottle sizes and shapes – which is just as important for producers to attract consumers’ attention – can be easily changed. In the second half of 2017, it delivered a Fillstar CX EVO with an aseptic piston doser to a company in South East Asia, where trendy beverages, such as “food in a bottle” and organic teas, are very popular and new creations are welcome. The high-performance system will have a capacity of 54,000bph. www.gea.com Pretium Packaging’s launched SureHandle The PET container with an integrated handle has received validation that it can be used for high-pressure processing (HPP) food and beverage applications. Because HPP does not rely on heat for pasteurisation, this validation opens the door for products that are using the cold processing pasteurisation to go to market in an equally new, disruptive container which will protect their nutritional and flavour profile. The cold processing enables the use of less expensive, linerless plug-seal style closures. The stock SureHandle bottle is currently available in a 64-ounce, 38-400mm finish. This disruptive commercialisation gives brand owners significant shelf differentiation, plus handling convenience and aesthetics that were not previously possible. HPP is a cold pasteurisation technique which introduces filled and sealed packages into a vessel and subjects them to high water pressure. The high pressure at ambient temperature deactivates bacteria, virus, mould, yeast, etc., making the food product safe and extending product shelf life. Because heat is not involved, the organoleptic and nutritional attributes of the product are not altered. The container is easier to handle for both younger children and older adults, and those with physical challenges, compared to pinch grip or straightsided alternatives. The handle not only provides carrying advantages, but also improved pouring control. www.pretiumpkg.com PRODUCTS","@ID":47}, "44 TRADE SHOW REVIEW PETplanet Insider Vol. 19 No. 01+02/18 petpla.net TRADE SHOWreview First KeyKegs made from used KeyKegs Lightweight Containers has been developing new recycling technologies for KeyKegs along with technology institutes and partners in the recycling industry. The company announced that it has started several pilot projects for collecting used KeyKegs. At Drinktec in Germany, Lightweight Containers presented the first KeyKegs made from 10% used KeyKegs and a total of 40% recycled materials. This percentage will rise rapidly as the collection of used KeyKegs expands. Collection as a service As Chief Commercial Officer Anita Veenendaal, explains: “The logistics are a challenge. After all, you want to set up the logistical process so that you have fewer trips and thus minimal CO2 emissions from transport, and at the same time you want the recovered material to cover the costs of processing. We have worked out several models and are testing them now. We’re testing two of them in Amsterdam; one through beverage distributors who collect the empty kegs during their rounds and the other once they’ve been separated out of the garbage after collection by the city. The KeyKegs are then compressed and brought to our recycling sites, thousands at a time. The beverage distributors see it as a service for their customers, and the bars and restaurants are happy to cooperate. Although it’s just a pilot, all the signs are that it will be a great success. We expect to start a similar pilot in the United Kingdom, a large and growing market for us. Lastly, we’re also testing various collection methods at beer and music festivals. We expect that this will give us a set of collection methods that we can implement in other cities and countries.” www.keykeg.com The first circular KeyKegs are now ready to be filled, transported, used and reused for new KeyKegs again. Smart packaging innovation On 14th September 2017 the annual World Beverage Innovation Awards took place at Drinktec in Germany as part of the 15th Beverage Awards. The judging panel considered 227 entries from 33 countries in 25 categories.“World Beverage Innovation Awards really showcase some of the most ambitious new products and developments of the year, from a wide range of companies all over the world, both large and small. Keep an eye on the latest entries to spot the upcoming trends.” stated FoodBev Media marketing director Isabel Sturgess. PET Engineering received during the ceremony its third World Beverage Innovation Award in the category “Best Bottle in PET” for FonteVita, the new PET premium bottle developed in collaboration with Husky Injection Molding Systems and LaBrenta. FonteVita is part of PET Engineering’s new Luxo line that redefines the boundaries of “Premiumness” for the Horeca sector through new shapes, new finishes and LuxCap, a new PCO 1881 cap which is entirely customisable. This line, based on the extensive experience of the Packaging Innovators, has three different versions: FonteVita, Queen and Erawan with a 0.75l capacity. PET Engineering has already made a name for itself both in Italy and abroad having won two ‘Packaging Oscars’, two ‘World Star Awards’ and two ‘World Beverage Innovation Awards’ thanks to its elegantly designed, sophisticated PET bottles dedicated to the food service industry. FonteVita is a a 39g bottle with a shade created using multilayer Husky technology, LuxCap developed in collaboration with Labrenta, and a shape that brings to mind a flower slowly blossoming. www.petengineering.com FonteVita bottle with LuxCap from the Luxo line of PET Engineering","@ID":46}, "CAPS & CLOSURES 31 PETplanet Insider Vol. 19 No. 01+02/18 petpla.net [email protected] MATTHEWBARBER GLOBAL POLYMER GROUP EVENT SUPPORTERS: PRSEVENTEUROPE.COM PLASTICS RECYCLING AWARDS EUROPE 2018 THE DEDICATED PAN EUROPEANEXHIBITIONAND CONFERENCEFOR THE PLASTICS RECYCLING INDUSTRY. INTRODUCING ORGANISERS: BOOK YOUR STANDTODAY: +44 (0)1622 370570 Industry 4.0: Simplified injection moulding based on intelligent connectivity “We are constantly looking at how we can further optimise the manufacturing process. Our vision is an intelligent injection moulding machine that communicates with connected peripherals and coordinates adaptively with them,” said Schmid. With cycle times already impressively fast, the key to success is the connectivity within a production line and the intelligent use of data and consequent major simplification of operation and control. In collaboration with the image processing specialists Intravis, at Drinktec 2017 in Munich, Netstal presented an Intravis CapWatcher III system connected to a Netstal Elion 2200. The CapWatcher III continuously sent key parameters of currently inspected closures to the machine via the control circuit. “This was a major milestone for us because we were able to deliver real-time proof to an audience of trade visitors that under specific conditions an injection moulding machine could independently control itself,” asserted Schmid. Data generated by the CapWatcher III quality inspection is sent to the Netstal injection moulding machine via an OPC UA interface, providing it with a continuous flow of key closure parameter information. Upon registering a sustained deviation from the presets, on the basis of the data received the machine controller automatically readjusts its corresponding settings. The closures are promptly produced again within the applicable quality parameters without any loss of efficiency or productivity. Netstal’s high level of precision made visible “As a result of comprehensive integration into our aXos controller, we can even specifically change certain product characteristics within the process window with a single entry,” said Schmid. The operator is able to adjust the outer diameter of the closures upwards and downwards in size by up to one tenths of a millimeter. The machine operator achieved this by simply entering a single value and confirming it with a click of a mouse. Accordingly, any further settings required to carry out the desired diameter change were adjusted fully automatically by the machine controller. The commensurate change could then be visually observed and checked on the displayed main CapWatcher diagram, which illustrated each closure as a point. “With the outer diameter of the closures produced on the Elion moving along the preset target value within a span of a half tenth of a millimeter, the demonstration perfectly illustrated the high level of precision and repeatability of our controller technology. In actual fact, deviations of up to one tenth upwards or downwards were within the tolerance limits,” explained a delighted Peter Schmid. The value added for users is obvious in that the manufacture of plastic closures is less resource-consuming and more efficient than ever before. www.netstal.com Up to 1.4 billion of lightweight 29/25 closures can be manufactured on a single Netstal injection moulding machine per year.","@ID":33}, "PETplanet Insider Vol. 19 No. 01+02/18 petpla.net 46 PETbottles Home + Personal Care New brands on the market So that they can compete better with the growing number of new, small and trendy brands in the body care sector, large companies have reacted by introducing into new markets regional or country-specific brands with a traditional history from their own brand portfolio. This is how in late 2017, the “Barnängen” brand, which has been well known in Sweden for over 140 years, came to be introduced by Schwarzkopf & Henkel onto the German and European markets. The brand represents the Swedish “Lagom Stil” – a relaxed, peaceful and nature-loving lifestyle. An example from the product range is this Sauna Relax shower gel & bath foam with birch extract. A clear PET bottle holds 400ml of the light green shimmering liquid. This is dispensed via a screwed-on, metallic shining disc-top seal. www.barnangen.de Limited edition from Ecover Ecover has given the name “Ocean Bottle” to its clear 500ml PET bottle for Handwash with Seagrass & Orange. The drop-shaped bottle consists of 50% plastic waste that has been collected on the beaches of Rio de Janeiro, and 50% recycled material from other sources. In some areas, the surface features raised bubbles. The packaging is presented at POS with a screw-on hinged cap seal with dosage opening and two self-adhesive labels, the rear of which is printed on the inside. A folded paper sheet secured around the bottle neck gives information about the Ocean Bottle and other environmental activities by Ecover. www.ecover.com Family packaging for Ariel 3in1 pods The success of 3in1 pods for washing detergent, so far available mostly in small packs of less than 20 pods, and the associated competition from providers, has demonstrated the need for an attractively priced large pack. Procter & Gamble now sells the Ariel 3in1 pods in round plastic boxes containing 47, 58 or 80 pods. The green coloured container is manufactured from PETE with two grip dimples and is combined with a snap-on lid with screw seal. The screw seal with a large diameter ensures increased child safety. This can only be removed from the container by pressing simultaneously on two opposing, specially marked places on the oval lid and twisting it. Several foldable adhesive stickers give information about the hazards of the pods for children, the correct handling of the pods and the new packaging features. www.ariel.co.uk Designer dispenser for hand soap The German pharmacy chain dm launched in its branches a shapely dispenser for liquid hand soap under its own brand “Balea”. The dispenser is designed to stand upside down. The c on i c a l bo t t l e i s comb i ned wi t h a thick-walled, twistable, transparent collar with a wavy edge. After removing the transportation security, the self-closing silicon valve seal that is screwed on to the container threading is ready to use. Product is dispensed by squeezing the container; releasing the pressure reliably stops the flow of product. The wavy collar protects the seal from dirt and ensures sufficient ventilation when the product is stored upright in the bathroom. A removable adhesive sticker explains how to use the liquid soap. www.dm.de","@ID":48}, "CAPS & CLOSURES 30 PETplanet Insider Vol. 19 No. 01+02/18 petpla.net Caps 4.0: smart and efficient injection moulding by Michael Birchler, Head of Marketing and Communication at Netstal Netstal injection moulding solutions provide users with reliably functioning closures at a minimum cost per unit. Simultaneously, the current trend is towards increasingly more intelligent machines that, assisted by data, are capable of independently regulating connected peripheral systems. At Drinktec 2017, Netstal highlighted the advantages of the injection moulding process and demonstrated how production operation and monitoring will be significantly simpler in future. CAPS & CLOSURES Many contemporary closure designs distinctly favour injection moulding over compression moulding. “Injection moulding especially comes into its own in the production of lightweight and thin-walled standard closures, where cleanly moulded thickness geometries can be manufactured in huge numbers with a high level of reliability,” explained Stefan Müller, Sales Director Asia Pacific at Netstal. In contrast, the material volumes used for these closures are much too small for the compression process. Quality problems may arise because the plastic cools off too quickly in the cavity before it can be formed in the mould. Contrastingly, boasting short cycle times, a high number of cavities and low power consumption, a high-performance injection moulding system from Netstal’s Elion series offers a high level of productivity. As an example, an Elion 4200-2900 equipped with a 96-cavity mould can produce around 170,000 type 29/25 closures per hour. At an overall availability level of 95%, the annual output of a single line would be approximately 1.4 billion units. Low cost per unit on the basis of state-of-the-art hybrid technology The optimised energy efficiency of injection moulding machines has played a decisive role in reducing unit costs. “Hybrid systems in operation today often only consume around half the power that their fully hydraulic predecessors used,” declared Müller. In the case of the aforementioned 29/25 closure, the electricity consumption of the entire system is a mere 0.56kWh per kilo of material. An additional plus point is the comparatively small footprint required by an injection moulding system. “Every injection process on an injection moulding machine produces finished closures complete with fully functional tamper-evident bands. This eliminates the need for separate process stages such as the cutting and folding of tamperevident bands,” explained Peter Schmid, Netstal’s Applications team leader. Injection moulded lightweights with precisionformed lip seals First a closure must fulfill one primary and decisive task: reliably seal the bottle. The contents should not run out and outside impurities must not pass into the beverage. This is achieved by lip seals located on the inside of the closure. Particularly in the case of very thin lightweight models, the forming of these lip seals is extremely challenging as a result of the brief process window and minimum material volume. Injection moulding enables the manufacture of a reliable seal even with these closure models. “The principle advantage of the injection moulding process on high-precision Netstal machines is that depending on the application and closure type, the material is injected at processing temperature in less than 0.2 of a second. This enables moulding and shaping of the finest lip seals that later reliably protect the bottled beverage,” said Schmid. The high-performance Elion 3200-2000 machine from Netstal shown at the Drinktec 2017","@ID":32}, "BOTTLE MAKING 16 PETplanet Insider Vol. 19 No. 01+02/18 petpla.net aging of edible oil stands at seven lac [700,000] tonnes; the most popular format is 1l, followed by 500ml and then 200ml. The market is dominated by companies like Adani Wilmar, Ruchi Soya, Marico, Emami and other national and regional players. Within the PET packaging segment, the 1l PET bottle has 60% market share; 500ml has 30% and 200ml 10%. The market for bulk packs of 5l is primarily in HDPE and is mainly for institutional or bulk requirements. While that market is currently dominated by HDPE cans, many companies are actively trying to convert to PET. One of the main challenges with PET is the non-availability of a handle, which is possible in HDPE. The 20l market is in tins, but Manjushree has developed and patented a 20l pack that is stackable and has a unique inter-locking system that makes it possible to stack up to five jars. This jar also comes with a special cap with a handle that is capable of carrying a fully-filled 20l oil bottle. The design of this jar has a very special rib structure, designed in our studio. A pilot exercise was done to ascertain top load, rigidity and overall performance compared to conventional tin containers. These 20l PET jars are 30-40% cheaper than tin containers. PETplanet Insider: What are the special requirements for edible oil PET packaging in India with regard to design, appearance and shelf life, considering long transportation and very high/low temperatures? Vimal Kedia: PET bottle packaging of edible oils is an evolving market. The customer continually strives to stand out with their packaging and to ensure a strong visual appeal on retail shelves. Customers require features like easy grip, easy dispensing and FMOT (First Moment of Truth) in all their design choices. The bottles have to withstand long journeys from the manufacturers, as the oil market is concentrated primarily in eastern India, north west and south. The versatile nature of PET enables it to withstand various types of climatic conditions. PETplanet Insider: Let’s talk about other packaging materials as well. Can you give us an idea of the shares for PET, pouches, tins, PVC, PP and glass, for example, in the edible oil market? Vimal Kedia: The current packaging of edible oil in India is largely dominated by five-layer flexible pouches, consisting of an LLDP and nylon combination. While this is the most economical way to package oil it is also highly non-environment friendly. Its multilayer structure and the use of nylon as a material perform very poorly in the recycling stream and creates havoc in the recycling system. The current distribution of edible oil packaging is 60% pouches, 25% tin, 7% HDPE, 5% PET and the rest are other materials. PETplanet Insider: What is your impression of consumer behaviour? Do they currently prefer more expensive edible oil brands over cheaper brands that provide discounts? How price sensitive are the people? Vimal Kedia: Since edible oil is a widely used commodity, an everyday home requirement, it is a highly cost sensitive product. Most of the cooking in Indian households is done in oil as it is the most economical medium to cook food. Other value-added products like ghee (clarified butter), olive oil, flaxseed oil and other products have a niche market and audience. In the premium edible oil space, mustard oil is widely used in Northern and Eastern India. Apart from domestic premium oil brands like Marico, which produces Saffola and Saffola Aura edible oil, there are also imported brands, such as Hadsun, Figaro, Delmonte and so on. Many stores also sell organic oil but these have a very limited market. Our manufacturing plants in Pantnagar, Guwahati and Bangalore are strategically placed to cater to the oil hubs of the country like Rajasthan, West Bengal, Andhra Pradesh, and Telangana among others. PETplanet Insider: What are the three most important and influential edible oil brands in India today and how are they ranked? Vimal Kedia: The top three brands in the country are: Adani Wilmar’s Fortune; followed by Nature Fresh, from Cargill and Mahakosh’s Ruchi Soya ranked third. The precise market share across the country varies, depending on the states in which these brands have a strong presence, but these are the top three industrial manufacturers of edible oil. PETplanet Insider: Manjushree is the first company to produce a 2l bottle for edible oil. Is this 2l package the next market trend? And what other trends can be seen in the near future? Vimal Kedia: The market for 2l bottles in India is very small and faces both pricing and dispensing challenges. Manjushree has developed special 2l packaging with a 36mm","@ID":18}, "PETplanet Insider Vol. 19 No. 01+02/18 petpla.net 39 TRADE SHOW REVIEW Energy savings through control The control system, based on a Siemens Delta S4, features a sophisticated compressor management system that allows data visualisation of each single compressor. It is able to implement any of the above-mentioned energy saving devices; allows the automatic selection of the most suitable compressor (or compressors) to meet fluctuating air demands and/ or air blowing requirements. For example, when the first preforms enter the oven and needs to be blown at 40 bar, the blow moulding machine sends a signal to the compressor’s control system to start the compressor. Once started and in the correct status the compressor sends a signal to the blow moulding machine to start the blowing process. This not only reduces off load time but also prevents preform waste, as sufficient air pressure to blow the preforms is always provided. A smooth start-up with no stress on the belts is assured. Pressure settings can also be adjusted to a certain bottle type. The operator simply changes the bottle type in the control of the blow moulding machine; it then sends a signal to the compressor, which selects the appropriate pressure table. Example: Bottle 1 blown at 35 bar: Pressure table 1►Pmin = 35 b, Pmax = 37 b Bottle 2 blown at 28 bar: Pressure table 2►Pmin = 28 b, Pmax = 30 b Bottle 3 blown at 22 bar: Pressure table 1►Pmin = 22 b, Pmax = 24 b www.afcompressors.com Working Principle of the Heat Recovery System 90°C and the compressor itself runs with a smaller water cooling system. Potential savings with this heat recovery system are significant: A 200kW compressor running 6,000h/a, with energy priced at 0.05€/kWh can achieve savings of 48,000€. AF Compressors offers an external skid heat recovery system for the 40°C range. It includes a dismountable, stainless steel plate exchanger and a 500l water receiver; it is delivered ready to use. The skid system comes with plug and play fittings for easy connection to the customer’s water circuit.","@ID":41}, "PETcontents 01+02/18 4 PETplanet Insider Vol. 19 No. 01+02/18 petpla.net Page 44 Page 24 Page 12 INSIDE TRACK 3 Editorial 4 Contents 6 News 45 Products 46 PET bottles for Home + Personal Care 47 PET bottles for Beverage + Liquid Food 48 Patents MATERIAL / RECYCLING 10 A new recycling plant for Dallas Amut Group and CarbonLite working together to improve bottle recycling 11 PET recycling in Thailand PREFORM PRODUCTION 12 Sustainable preforms guarenteed Facing the challenges of circular economy: Alpla joints the RAL quality association BOTTLE MAKING 14 Local sales and support for machines and moulds 15 Growing PET market in India for edible oil 18 A reunion with a booming company CAPS AND CLOSURES SPECIAL ICON 20 Cap-preform combination New solutions for premium products 22 Round table for oval caps Collaborative action to clarify cap ovality issues 24 Rapid colour change Fighting contamination with purging compounds 26 Facing customer and market challenges Convenient caps and differentation on the shelf are the keys 30 Caps 4.0: smart and efficient injection moulding 32 Shaking the market Dispensing caps enable consumers to mix drinks on the go 34 Caps and closures products CAPS & CLOSURES MARKET SURVEY 28 Suppliers of resins and additives PACKAGING / PALLATISING 36 Good service means rapid service TRADE SHOW REVIEW 38 Ways and means of saving energy 40 Digitalisation and flexibility 42 Three modules, one block 44 First KeyKegs made from used KeyKegs 44 Smart packaging innovation BUYER’S GUIDE 49 Get listed!","@ID":6}, "TRADE SHOW REVIEW PETplanet Insider Vol. 19 No. 01+02/18 petpla.net 42 New system for still water in single-serve formats Three modules, one block With its InnoPET TriBlock Aqua M the KHS Group was presenting a compact, powerful block system for single-serve formats at Drinktec. The high-performance unit is specifically geared towards the growth segment of water in single portions. It processes container sizes of between 250 and 800ml at a rate of up to 50,000bph. The new system blocks the further developed Blomax Series IV stretch blow moulding module, a labelling module and the Innofill PET NV filler. Together they form a unit which is claimed to be perfectly suited to the application on hand, manufacturing bottles from preforms and then labelling, filling and capping them. Further advantages of the machine according to Arne Andersen, global product account manager for the TriBlock at KHS, are its hygienic design and optimised housing. The machine is centrally controlled by the improved HMI (human machine interface) on a clear 21.5-inch monitor with full HD resolution for detailed visualisation of the process graphics. Another aspect which is important for practical operation is the consistent drive and operator concept with which KHS aims to boost effectivity and the level of convenience. The individual modules on the TriBlock promise optimum performance at every stage in the process. Compared to the previous model, the further developed Blomax Series IV has blow stations on which small bottles with a maximum diameter of 75mm can be blown. The low level of noise pollution also deserves a mention here, this ensured by the InnoPET Silent TipTainer (see PETplanet 7/2017); with its closed system and lower PET preform drop height the latter are fed especially gently and thus less noisily to the sorting unit. The labelling module is distinguished by its robust design and thus a high degree of reliability and availability. A special vacuum system permits materials of a very low thickness to be used for the bottles and thus helps to cut costs. In addition, the top-drive technology, which consistently feeds the bottles through the TriBlock by their neck rings, also has many benefits: it is gentle on the PET bottles, minimises downtimes and is advantageous Hall 2H · Booth 2P07 German Technology when making lightweight containers as these are no longer exposed to any compression force in the labeller. Low maintenance effort cuts costs A new generation of valves in the filler shortens the filling time so that fewer valves can be used for the same total filling capacity. By focusing on smaller bottles and through the subsequent reduction in pitch, the diameters of both the filling wheel and ring bowl have been decreased. This makes both the filler and the TriBlock as a whole more compact. Users profit from a reduced maintenance effort and cuts in maintenance costs. www.khs.com","@ID":44}, "MARKET SURVEY 28 PETplanet Insider Vol. 19 No. 01+02/18 petpla.net 01+02/2018 MARKETsurvey Resins & additives Preform machinery Preform production Preform inspection SBM 2-stage Compressors Filling equipment & filling inspection Caps & closures and inspection Palletising & shrink film machinery Recycling Additives Suppliers of resins & additives There is rapidly increasing demand for packaging materials that give even greater protection to their contents. Functional additives and resins are an important technology in meeting this demand for greater product protection in the plastic packaging market. A functional additive modifies the properties of packaging to impart desirable or beneficial functions. That is why we decided to start in 2018 with an overview of resins and additives. These companies participated: Reliance Industries Limited - PET Division, M&G S.p.A., Invista Resins & Fibers GmbH, Penn Color International B.V., Repi S.p.A., Indorama Ventures, Neo Group and Clariant Plastics & Coatings. Although the publishers have made every effort to ensure that the information in this survey is up to date, no claims are made regarding completeness or accurancy. Company name Invista Resins & Fibers GmbH Penn Color International B.V. Repi S.p.A. Clariant Plastics & Coatings GmbH, BU Masterbatches Postal address Telephone number Web site address Contact name Function Direct telephone number E-Mail Philipp-Reis-Strasse 2, 65795 Hattersheim, Germany +49 69 305 6025 www.polymers.invista.com Mr Achim Heyer Business Director PET Resins +49 69 305 6025 [email protected] Smakterweg 31 5804 AE Venray, Netherlands +31 478 55 4000 www.penncolor.com Mr Scott Stamback Business Director +31 478 55 4000 [email protected] Via B. Franklin 2 21050 Lonate Ceppino VA, Italy +39 0331 81 9511 www.repi.com Ms Lucia Buffoni Marketing Manager [email protected] Am Unisys-Park 1 65843 Sulzbach am Taunus, Germany +49 6196 757 60 www.clariant.com/masterbatches Ms Severine Wild Marketing Europe +49 6196 757 6276 [email protected] Additives and Colours for PET Liquid colours Pennacle - L Yes Yes Microgranule colours Pennacle Yes Masterbatch colours Pennacle Yes UV protection additive (solid) Yes Yes UV protection additive (liquid) Yes Yes Yes AA reduction (solid) No Yes - SenzAA Yes AA reduction (liquid) No Yes - SenzAA Yes Oxygen scavenger (solid) OxyClear Additive, PolyShield Masterbatch No Yes Oxygen scavenger (liquid) No No IV enhancer Yes Yes (solid) No Reheating Yes Yes Blowing additive No Yes (liquid) No Slipping agent Yes Yes (liquid) Yes Other PET additives: Slip; AntiBlock; High Opacity Dairy; Laser Marking; Frost; Mould Release; IV Enhancer; Flow Modifier; Reheat Anti Yellow (liquid); Process Aid (liquid); Optical Brightener (liquid); Colours for Barrier Solutions (liquid); Whites for monolayer UHT Milk (liquid) Matting agent, surface modifier and special effect","@ID":30}, "CAPS & CLOSURES 25 PETplanet Insider Vol. 19 No. 01+02/18 petpla.net pound grades are either GRAS (Generally Recognised As Safe) or compliant with direct or indirect food contact according to the U.S. Food and Drug Administration’s 21 CFR regulations. They are also European Plastics Regulation-compliant (No 10/2011). Purging compounds improve efficiency Purging compounds can be an integral element in optimising output of injection moulded caps and closures. Use of the right compound is not simply about cleaning; it becomes a key part of the preventive maintenance regime too. With proper regular use, purging compounds reduce carbon buildup from thermo-sensitive resins, working to preserve equipment and prevent wear caused by steel oxidation. This saves valuable time and cuts the incidence of ‘black specks’ during start up. Maintenance Chem-Trend offers injection moulders a range of products that ensure their caps and closures’ capacity remains optimum. Mould maintenance products like lubricants, anti-corrosion agents and cleaning materials all come with NSF registration; they are completely safe for use in food and beverage packaging. Its range of cleaning agents easily remove resin, pigment deposits and contaminants from mould surfaces. High-performance lubricants resist the extreme pressures and loads intrinsic to the moulding process, remaining temperature- and viscosity-stable under typical thermoplastic moulding parameters. They are designed to stay in place where they were applied, thus preventing through-vent migration. Even moulds in storage can be effectively protected against rust. Using anti-corrosion agents with NSF registration ensures that injection moulding machines create blemish- and defect-free parts from every shot. www.chemtrend.com INSPECTED BY COL LECT ING GU I DANCE TO PRODUC ING QUAL I TY DATA & TRENDS W W W . I N T R A V I S . C O M V I S I T U S I N O R L A N D O | M A Y 7 - 1 1 | B O O T H # W 3 3 9 1 INTRAVI S IMM PRODUCTS By using a suitable purging compound neither flushing (picture on the top) nor short shots (picture below) will occur.","@ID":27}, "PETpatents www.verpackungspatente.de PETplanet Insider Vol. 19 No. 01+02/18 petpla.net 48 A stackable container European Patent Application No. EP 2861499 B1 Applicant: Sidel Participations, Octeville-sur-Mer (FR) Registration date: 06.06.2013 A plastic container with a top side which can be pushed in reversibly for better stackability. Three stable positions are preset. A coated preform Internal Patent Application No. WO 2017/ 072040 A1 Applicant: Kuraray Europe Ltd., Hattersheim (DE) and Container Corporation of Canada, Richmond Hill (CA) Registration date: 21.10.2016 The application describes a method for coating a preform/container with a substance that improves the gas tightness/gas permeability of the container. A base design Internal Patent Application No. WO 2017/ 076617 A1 Applicant: Sidel Participations, Octeville-sur-Mer (FR) Registration date: 17.10.2016 A firm plastic bottle with an “internal” foldable compensation area for produced deformation energy resulting from hot filling or pressure differences. The bottle’s robustness is unaffected. An easily separable container Internal Patent Application No. WO 2017/ 094273 A1 Applicant: Sheng Fang, Hyogo (JP) Registration date: 09.05.2016 A PET bottle that has several strips that are integrated within the container wall. By pulling on the strip, the bottle can be broken down into several parts once empty, making it suitable for low volume recycling. A multi-part drinks’ container Internal Patent Application No. WO 2017/ 100285 A1 Applicant: Plastipak Packaging Inc., Plymouth (US) Registration date: 07.12.2016 A PET drinks’ container with enhanced barrier properties for accommodating a carbonated product. The approximately 50mm diameter container has a pin its lower half for adjusting into a type of base. It is secured by a screw top. A container for liquid detergents Application No. DE 102014212601 A1 Applicant: Henkel AG and Co. KgaA, Düsseldorf (DE) Registration date: 30.06.2014 A specially designed container for liquid detergents with a means of dispensing the detergent in measured amounts.","@ID":50}, "TRADE SHOW REVIEW PETplanet Insider Vol. 19 No. 01+02/18 petpla.net 38 Energy and cost savings in PET compressor installations Ways and means of saving energy Sufficient and reliable compressed air supply is one of the main requirements for running a modern blow moulding operation. Liftetime costs for high-pressure, oil-free, multiple-stage piston compressors are dominated by energy, which accounts for 80% of the total, dwarfing the outlay for capital investment and maintenance (based on a 10-year life cycle). AF Compressors claims that its latest range of oil-free PET compressors improve efficiency and generates costs savings through improved control, regulation and heat recovery. Energy savings through regulation of motors and air flow SIS: Smart Inverter Starter Induction motors, as used in compressors, have a very high starting current; often many times the nominal current. This can cause problems with plant power networks if, for example, several motors in the factory start at the same time. Using standard electric motors, AF Compressors addresses this problem with its SIS (Smart Inverter Starter). Developed by Ateliers François Liège, this inverter system for starting purpose only, ensures that the starting current never exceeds the nominal current and that the full load power never exceeds 100%. There is no need for additional shielded cables, line filters or other protection devices. This innovation on the market comes along with the adjustment of air flow, the AFS System. Adjustment of air flow Another way to save energy is to adjust the air flow in cases where less than full air capacity is needed. AF’s Adjustable Air Flow System (AFS) does this by deployment special working protocol around the acting compressor cylinder. Normally, when full air capacity is required, a 1st stage double acting cylinder raises atmospheric air from 1 to 4 to 5 bar. At full load, the 1st stage double action cylinder produces 100% of rated capacity and provides of required 100% air to the blow moulding machine. When full air capacity is not required: the 1st stage cylinder compresses atmospheric air only on the upward stroke of the piston. Shown: 50% on the very top and 75% below. In circumstances when full air capacity is not required, the system around the acting cylinder works in a different way: the 1st stage double acting cylinder compresses air upward only. The system automatically unloads the lower part of the cylinder and delivers the air flow required in the system. AFS is available on new units and can also be retrofitted. Frequency Inverter Alternatively, depending on the specific PET bottling production profile, a classical frequency inverter can also be a good choice to increase efficiency and decrease power consumption. AF Compressors also offers conventional Variable Frequency Drives which are based on Siemens Sinamics. A pre-lubrication oil pump, a specific motor and other special device such as shielded cabling are included in the package offered by the company. Heat recovery system Energy savings through heat recovery Efficient heat recovery can also achieve significant cost savings. AF offers two basic systems: one for higher water temperatures – around 90°C – and the other for temperatures around 40-45°C. The heart of the “Heat Recovery System 90°C” is a special double cooler, for the 2nd and 3rd stage. In this system, the compressor can run with a smaller water pump equipped with a frequency inverter","@ID":40}, "BOTTLE MAKING PETplanet Insider Vol. 19 No. 01+02/18 petpla.net 14 BOTTLE MAKING 14 Local sales and support for machines and moulds by Kay Barton After a visit to marketing manager Roberta Gualtieri at the Sipa booth at Propak Asia and a first meeting with Mr Weera Eiamrattanawong, branch director with responsibility for South East Asia for Sipa S.p.A., the Italian PET machineries and filling lines provider, we arranged to visit the local representative office in Watthana, Bangkok. The SE Asia sales office has been in existence for 15 years and is a hub for all of South East Asia. Together with filling and packaging systems from mechanical engineer Berchi, which was taken over nine years ago by Sipa, the company currently has more than 300 machines in the region, from where it coordinates 20 engineers. Sipa S.p.A., June 26, 2017 We met: Mr Weera Eiamrattanawong, Bangkok branch director Mr Weera Eiamrattanawong opens the glass doors of the Sipa office on the third floor of the MSC Tower and guides us past some of his colleagues, who are busy at their desks, and into the meeting room where, of course, genuine Italian espresso is available. He has been with the Italian company for nine years and he’s responsible for both sales and the deployment of his service team in cases of equipment maintenance. “Main converters and brand owners have Sipa PET injection systems on an average market share of 15%” he says. “With our local base here in Bangkok, our spare parts stores and our strategically distributed service technicians, we are able to carry out maintenance and repairs within one to two days.” Sipa’s Thai customers include Klintpac, Precision Plastic, HSK, Petpack and Imco, while Sipa is also working with many South East Asian Brand owners as URC, which has operations in the Philippines and in Vietnam, Mayora, Suntory, THP. “All main converters in Thailand have minimum one Sipa SFL linear blowing system that increase the market share in this specific technology. In the moulds segment, the biggest sales in Thailand are the injection moulds. Our tooling run both Sipa and competitors’ equipment.” Mr Eiamrattanawong identifies Myanmar and Cambodia as the largest growth markets. “Over the past two years we have seen a number of investments and joint ventures from producers such as Coca-Cola, Pepsi and Nestlé, especially in Myanmar, and processors are also playing an increasing role in the market. Here in Thailand, the trend for beverage is still hot fill and aseptic bottling. Sipa can provide both, and in case of aseptic filling we partner with Gea Procomac”. www.sipa.it Tour Sponsors: www.bericap.com Unique range of light weight screw and sports closures for light weight PET neck standards for water • Closures for all common neck sizes 26/22, 28mm (PCO 1810, PCO 1881), 29/25, 30/25 • Light weight Hexalite range allowing light weight neck • Still water closures suitable for N 2 dosing • Sports closures fulfill BSDA requirements • Boreseal systems for excellent tightness • Consumer friendly opening forces BERICAP Technology for still water","@ID":16}, "BOTTLE MAKING 18 PETplanet Insider Vol. 19 No. 01+02/18 petpla.net A reunion with a booming company by Kay Barton It is more than eight years since we last spoke with Imco Food Pack; the opportunity to do so again was very welcome. The family-owned company is part of the Imco Group, which also includes Combipack (for (LD)PE extrusion tubes); Imco Label; and Imco Pack, which is active in PP and (HD)PE packaging of non-food products. Sixty percent of its conversion work is in processing of PET, with the balance (40%) being PP. During our previous visit, in 2009, the company had placed its trust in high-quality equipment for sustainable growth (see PETplanet Insider 09/2009). At that time, the forecast by company manager Kriengsak Panrattanamongkol - the son of founder Vibul Panrattanamongkol - was for growth of around 10% for the 2009 financial year. He confirmed to us that the company’s overall growth has remained pretty constant, at between 8-10% through all the years to this day. Imco Food Pack Co., Ltd., June 21, 2017 We met: Mr Kriengsak Panrattanamongkol, Managing Director Mr Thanakrit Kongkorawit, QMR & QR Manager drive from central Bangkok, towards Rayong. Mr Panrattanamongkol and QMR & QR Manager Mr Kongkorawit welcomed us to the meeting room. The photos from then and now reveal very little change in the appearance of the company’s director. “Imco has been going for a long time; the company was officially registered as a business in Thailand back in 1967”, says Mr Panrattanamongkol. “My father started with extrusion, an important part of our business, and one that still exists today. 2003 saw the start of our Imco Food Pack business. We began with PP thin-wall products before moving into PET, three years later.” Today, Imco produces 30-40 million preforms, 40 million closures and 20 million bottles a month. Ninety percent of the PET stays in Thailand, leaving around 10% for export. The majority of the PET bottles are used for water and aseptic packaging. “The market here has moved strongly away from hot-fill”, says Mr Panrattanamongkol. The machines have partly been expanded and some new ones have been added. Its three Husky HyPET systems have been upgraded from 48 to 72 cavities; two more HPP4 4.0 machines, each with 96 cavities, have been added, along with a Sipa PPS 300. An Intravis Prewatcher has been installed for product testing. Imco’s bottle portfolio ranges from 13.5g to 37.5g, with PCO 1881, PCO 1810, 29/25, 30/25 or 38mm neckfinishes, as well as crystallised. Four Sidel systems - an SBO 8, SBO 10, SBO14 and SBO 16 - and two Sipa SFL linear blowing lines are to be found in the blowing area. The bottles range from 280ml to 1.5l. Imco uses Sacmi compression lines and a Netstal Elion for the production of the closures. There is also a Nissei ASB 8-cavity machine and four Netstal Synergy 5000 units for the PP thin-walled cups, and a Synergy 3500. Tour Sponsors: Managing Director Kriengsak Panrattanamongkol at Imco’s entrance area In the PET segment alone, Imco recorded a 10% annual increase, and has expanded its previous machinery park and activities in order to cope with demand. It now has a total of five locations, which are mostly located around Bangkok plus some in-house production facilities at bottlers. In 2016 it opened a new plant in Indonesia for the production of HDPEextruded packaging. Imco Food Pack is located in the Bangpakong district, about an hour’s","@ID":20}, "8 NEWS PETplanet Insider Vol. 19 No. 01+02/18 petpla.net WikiPETia.info New contents at wikipetia.info PlasticsEurope’s reaction to Europe’s Plastics Strategy PlasticsEurope welcomes the publication by the European Commission of “A European Strategy for Plastics in a Circular Economy”. PlasticsEurope supports the creation of a joint vision for a truly circular and resource efficient Europe, the promotion of actions aimed at tackling plastics leakage into the environment, increasing recycling and re-use and boosting innovation. The Strategy calls for the adoption of harmonised rules to ensure that by 2030 all plastic packaging placed on the EU market can be reused, recycled and are not littered. “We, the European plastics manufacturers, are committed to ensure high rates of reuse and recycling with the ambition to reach 60% for plastic packaging by 2030. This will help achieve our goal of 100% reuse, recycling and recovery of all plastics packaging at European level by 2040”, said Karl-H. Foerster, Executive Director of PlasticsEurope. In order to support the ambitious recycling goals, the Strategy for Plastics stresses the need to discourage the landfilling of plastics waste and recognises that effective waste management systems are key to avoid littering and ensure that collected waste finds its way to proper treatment. In this context, PlasticsEurope is thrilled to announce the publication of its “Plastics 2030 - Voluntary Commitment”, which contains a set of ambitious targets and initiatives representing the plastics industry contribution to achieve a fully circular and resource efficient Europe. This voluntary commitment focuses on (1) increasing re-use and recycling (with the ambition to reach 60% for plastics packaging by 2030), (2) preventing plastics leakage into the environment, and (3) accelerating resource efficiency. By mid-2018, PlasticsEurope will set up concrete action plans and time-based performance indicators which will be used to evaluate the achievement of these objectives. The results will be monitored by an independent committee, made of representatives of academia, the European Commission, the European Parliament, civil society and PlasticsEurope. Also, from 2019, an annual progress report will be published. www.plasticseurope.org State of the US Market: Bottling According to analyses of Perc Pineda, Chief Economist, Plastics Industry Association, recent data continue to underscore the vitality of the U.S. as a market for plastic bottles. Businesses that use plastic bottles showed an uptick in sales in December. Retail sales at food and beverage stores rose 0.5% in December - a 4.5% increase from December 2016. Healthcare and personal care stores’ sales rose 0.4%, increasing 3.6% year over year. With the U.S. economy operating at full capacity, it can be expected that the demand for goods and services using plastic bottles will continue to increase as well. Beverage and food manufacturing continue to be the largest market segments for the plastic bottles market, and will probably not change dramatically this year and the next. Last year, estimates showed that beverage and food bottle usage held the largest share of the market at 42% and 16%, respectively. Not only is the U.S. an important market for plastic bottles, it is also a viable plastic bottle manufacturing base. U.S. imports of plastic bottles far exceed its exports. Advanced estimates show that last year, the U.S. exported $597 million and imported $930 million worth of plastic bottles. The trade deficit proves a robust U.S. market and suggests room for domestic plastic bottle manufacturing to grow. Low manufacturing costs are also influencing growth, with U.S. cost advantages coming as a result of an abundance of natural gas, which is keeping feedstock prices for polyethylene production low. Plastic bottle manufacturing technology and innovation will be part of the main showcase at NPE2018 (May 7-11, 2018 in Orlando, FL, USA). Technology for plastics bottle manufacturing including caps and closures, from the simple twist caps to more sophisticated dispending pumps and safety closures, will be on full display in the Bottle Zone at the show with supporting partners PETplanet, drinktec and the International Society of Beverage Technologists (ISBT). The zone’s more than 80 companies within more than 5,300m2 on the show floor will promote the latest advancements and trends in bottling and container manufacturing for this booming sector of the plastics industry. Additionally, the Bottle Zone Technical Forums will provide industry insights and innovation Monday-Thursday of the show. With higher consumption of bottled products and low cost of materials, and now that investments in capital equipment can be immediately and totally expensed by companies as a result of newly-approved U.S. tax bill, now is the time and the NPE Bottle Zone is the place for manufacturers and suppliers to explore ways to incorporate new technology, supplies and equipment into their manufacturing processes. www.npe.org/bottlezone","@ID":10}, "PACKAGING / PALLETISING PETplanet Insider Vol. 19 No. 01+02/18 petpla.net 36 Good service means rapid service by Kay Barton Engel Machinery (Thailand) Ltd., June 27, 2017 We met: Mr Romain Reyre, President South East Asia Engel, the mechanical engineering firm headquartered in Schwertberg, Austria, is established as one of the leaders in the world’s injection moulding market. Founded over 70 years ago, the family business has grown into a global network, with representation in more than 85 countries. Its revenues totalled more than US$1.5bn in financial year 2016/2017. Engel sees great potential for growth in South East Asia, and is increasingly focusing on local presence and corporate development there. With this in mind, the Group established the position of President South East Asia. Fifty-year-old Romain Reyre, who has 25 years’ experience in plastic processing, focusing on packaging technology, was appointed to the post in October 2016. As part of the Go With The Flow Tour, we met him in Bangkok, the home of Engel’s local representation and spare parts warehouse. In what tends to be the conservative environment of mechanical engineering, Romain Reyre stands out somehow; at least, he does on the interview date with PETplanet Insider. When this married father of one greeted us at a table in the Chatrium café, he had his motorcycle helmet by his side; in this city, you can simply get around faster on two wheels. His jobs have already taken this native Frenchman halfway around the world over the course of his career; he and his family have been living in Bangkok since 2015. Mr Reyre’s employment with air conveyor manufacturer NTS France in the early 1990s led him to forge a close cooperation with Sidel, who became his new employer which is why he went to the USA in 1998. At the beginning of the 2000s he moved back to France, working as sales director central Europe alongside Dominique Lipinski, Vice President for the zone and now CEO of TechLong Europe. With the takeover by Tetra Laval in 2003 Mr Reyre’s role in the company took him to Austria for over four years, then for another two in the USA where, among other tasks, he managed the Coca-Cola Atlanta account for Sidel. He then returned to France, where he spent three years with key clients such as Alpla, Unilever and Danone before moving to Mexico in late 2011 where he was responsible for marketing and business development for Latin America. “After a total of 19 years at Sidel, it was time for me to do something new, so I decided to take over the responsibility as President South East Asia for Engel.” This new position is integral to the future strategy of the plastic injection machine manufacturer in South East Asia, which, among other things, intends to carry out a broad optimisation of its service provision. Mr Reyre coordinates 40 specialists and is responsible for the current complement of 30 sales and service staff across the region. “Service is the most important thing for our customers and we aspire to be the leading supplier in this field,” explains Mr Reyre. “For this purpose, we have appointed Mr Dave Lock, as Regional Service Director. He has been exclusively responsible for the service division since April and reports directly to me. Michael Hofstaetter is our plastic processing expert. He is also based in Bangkok and his solid know-how helps our customers reduce energy consumption, optimise cycle times and improve parts quality.” Engel currently has around 3,000 machines in the South East Asian market; Bangkok will now become the central hub for the entire area. At the moment, spare parts worth around US$8 million are in storage near the airport, Mr Reyre explains that the company is striving to provide sameday shipment across the region. A 1,000m2 complex is planned to be built by the end of 2018 and it will become the headquarter for Engel SEA, as well as accommodating a showroom and a training centre for Engel customers and staff. The company’s sales figures for packaging applications in SEA are in double digits, amounting to about 30 units, mostly for caps and thin wall containers with IML. “The market is developing towards more performance-driven machines, with high cavitation and a big focus on energy efficiency. In terms of services our customers are more and more looking for process support, service proximity, and we have started receiving a lot of inquiries on industry 4.0 for multi machines and multi-site management. “We are also monitoring trends for lightweight caps in the beverage industry very closely,” Mr Reyre says, and concludes with a smile: “I am definitely very happy about my new job.” www.engelglobal.com Tour Sponsors: Mr Romain Reyre, President South East Asia at Engel Machinery Thailand","@ID":38}, "PETplanet Insider Vol. 19 No. 01+02/18 petpla.net 41 TRADE SHOW REVIEW filling plants of the beverage and food industries. While Krones at the last Drinktec exhibited a prototype of the DecoType family, meanwhile the digital direct printing machine has attained product maturity. The DecoType Select prints on both special-shaped and cylindrical containers made of PET, HDPE and glass; capabilities for handling metal containers and other plastics like PP are currently under preparation. In contrast to traditional labels, moreover, direct printing can also be applied selectively to grooved and relief structures. This opens up new opportunities for consumer products, to differentiate them distinctively from the mass of competing articles – e.g. by creating 3D effects on their packaging or simulating the look of different materials. At the same time, the print height of up to 205mm still leaves sufficient space for accommodating not only elaborate designs, but also detailed textual information on the packaging. In conjunction with external partners, Krones has created an ink composition for PET that has been confirmed as recyclable in laboratory tests and also meets the hygiene standards of the packaging industry. When it came to the colour space, the R&D people at Krones opted for the established CMYK model which can be extended to the hexachrome model, or alternatively special inks (spot colours) can be used. The associated printing heads operate using the drop-on-demand principle, where each drop of ink is not created until immediately before it is actually used. An automatic cleaning system for the print heads assures optimal print quality and high machine availability. www.krones.com Form and fill technique Liquiform - an update Dr Christian Compera, Head of Bottling Technology Krones in conversation with Gabriele Kosmehl, PETplanet Insider. PETplanet: Dr Compera, when last we spoke at the Brau Beviale 2016, you mentioned a new milestone in in-house developments in Liquiform technology that was expected to be reached by the time of Drinktec (see PETplanet 1+2/2017). How have your expectations been met thus far? Compera: We took control of the Liquiform technology, assimilated it and have now developed the first prototypes which are being used to fully groundtruth the technology and test its robustness. At this stage, it is important for us to identify potential pitfalls and explore system responses before deciding which direction we should take. Naturally, the risks to customers who acquire the technology will be kept to a minimum. So far, we have not encountered any insurmountable difficulties and overall everything is extremely positive. PETplanet: You were originally thinking of still water in PET or HDPE as the initial application of form-fill technology. Which elements have you been able to successfully road-test so far? Compera: The drinks’ industry is naturally uppermost in our thoughts but it is conceivable that we could explore other lines of business. The form-fill of liquid food and healthcare products as well as water using the Liquiform process is a very feasible option. However, we would need to discuss this with the customer. Decisions will be taken on this over the next few months. Plans for packaging sizes ranging from 250ml to gallons in PET, HDPE or PP for a variety of applications using the Liquiform process at Krones are being made. PETplanet: What is currently getting in the way of using the process in series production? Compera: Our next major challenge is the closure of full bottles. Given that it takes less than 100 milliseconds to form and fill a 0.5l bottle, we naturally do not want to limit the advantages brought about by this enormous speed for the capping. We are deriving positive benefits from using our Dynafill system where the one step filling and closure of bottles in a filling carousel only takes a few seconds. The exact dosage in terms of filling capacity is a tricky question. If the stretching rod is pulled in shaping and filling, the displacement volume of the rod for each product needs to be taken into account in order to reach the precise filling level. PETplanet: Mr Compera, many thanks for these new insights!","@ID":43}, "BOTTLE MAKING 19 PETplanet Insider Vol. 19 Imco produces 30-40 million preforms a month: this is possible because of the upgrade of its three Husky HyPET systems, two more HPP4 4.0 machines, each with 96-cavities along with a Sipa 300 system. “Our customers in the drinks sector include Singha, Chang, Redbull and Oishi. The trend for the use of PET in household or beauty products is developing slowly and we are following it accordingly, step by step”, says Mr Panrattanamongkol. Imco has a share across its markets of around 20%. Its competitors include Precision Plastic, Petform (Indorama), Srithai and Taiwan Hon Chuan. From idea to realisation “The reason why our customers find us interesting, despite all the other companies”, says Mr Panrattanamongkol, “is the fact that we have a separate division for product conceptualisation, planning and design, in addition to the actual products. Essentially, the customer simply needs to come to us with just one idea. Another reason in our favour is our long-standing company philosophy, in which we make quality our priority. This is supported by all the employees here.” Imco Food Pack has been ISO 22000 certified since 2014. www.imcofoodpack.com repi.com A COLOUR IDENT I TY LIQUID COLOURS AND ADDITIVES FOR CAPS AND CLOSURES NPE - Orlando, FL - South Hall - Level 1 - Booth S19103","@ID":21}, "CAPS & CLOSURES 24 PETplanet Insider Vol. 19 No. 01+02/18 petpla.net Fighting contamination with purging compounds Rapid colour change Injection moulding machines’ cleaning regime should always include the use of purging compounds to ensure the highest standards of performance. Cleaning screws, barrels and gates is fairly straightforward but the buildup of resin in hotrunners can be more problematic. Contamination in the form of resin buildup in machine’s tooling or hot runner system is often responsible for spoiling new caps or closures, when it lingers for prolonged periods into new colour production runs. Even the tiniest streaking, hang ups and black specks in a new production schedule can render thousands of caps or closures unfit for sale. Carbon buildup and contamination can lead to downtime, excess scrappage and, in the end, decreased profitability. Efficient purging at shutdown or prior to difficult colour changes is key to increasing productivity. Some specialised purging compounds have been specifically developed for high MFI applications and are compatible with polyolefins in injection moulding machine processing. Ensuring a smooth-running hot runner system Not all purging compounds are suitable for cleaning the entire equipment in one go. While some can be processed through hot runners into the open mould, this might cause contaminations in the mould; however, specialised compounds have been developed that are suitable for use in these situations. Ultra Purge 1001 is designed for thin-walled packaging applications like multi-cavity or stack mould processing systems. Neither flushing nor short shots, which would put demoulding at risk, will occur. Incorporating a suitable purging compound into an injection moulding machine shutdown processes and colour changes will be faster and more efficient; also hang up spots and streaking that show up in newly moulded parts will be prevented. As a suitable and effective cleaning regime helps maintain machine cleanliness, downtime for unplanned stoppages will be greatly reduced or even eliminated altogether. Some of Chem-Trend’s purging compounds have been designed specifically for use through hot runners. They have been shown to actually pull chunks of carbon from the machine, and to extract residues from previous production runs even weeks after a colour change. Extended machinery life cycle Some specialised purging compounds, including several within Chem-Trend’s portfolio, are comprised of highly-efficient cleaning additives that trigger a chemical reaction, softening accumulated residues. Mechanical purging compounds – when they can be run through moulds at all – are known to be hard on the CAPS & CLOSURES barrel, screw and mould and can damage mould cavity surfaces, leaving imperfect finishes on new parts. In the worst of these cases, the moulds needed to be replaced, adding cost and increasing production downtime. Chem-Trend’s speciality additives do not contain damaging abrasives at all, says the company. Seamless colour changes Processing natural resin through an injection moulding machine will, eventually, flush out loose material. However, a purging compound can dislodge and flush out material that has built up in a machine’s void or “dead spots”, resulting in a clean, contamination-free system many times faster than can be achieved with natural resin. Undertaking a colour change without using a purging compound will simply layer new material residue on top of the buildup that was already there. A recent trial of a grade of Chem-Trend’s purging compounds at a bucket manufacturing plant showed the product went beyond extracting deposits left by the immediately prior production run; it extracted the colour used in the previous run as well. Switching a moulder directly from one colour to another without using a purge compound will see colour resins from the previous run caught up in the machine’s dead spots. The new production resins will, without warning, push the old colour into new caps and closures. Contaminated products will end up in the scrap bin. Food contact application safe Some of Chem-Trend’s purging compounds have been classified to be compliant with U.S. and European food legislation, meaning there is no risk to your finished moulded parts. Every element of those purging com-","@ID":26}, "PREFORM PRODUCTION PETplanet Insider Vol. 19 No. 01+02/18 petpla.net 12 Facing the challenges of the circular economy: Alpla joins the RAL quality association Sustainable preforms guaranteed by Heike Fischer Sustainability is an important part of a large company’s corporate identity. However, its various definitions and applications in terms of practical implementation can sometimes seem confusing. Fortunately, there are now some very specific factors at play in the PET industry, generally recognised systems that enable particular contributions to the circular economy and sustainability to be observed. The establishment of a RAL quality association for the PET drinks’ packaging value chain goes back to the year 2014. The goal of the RAL quality association is to sustainably promote, with respect to ecological factors, the further evolution of PET beverage bottles, and to make a positive contribution to resource efficiency and environmental and climate protection. A high level of consumer protection and the optimisation of the interfaces between the levels of the supply chain are guaranteed through the use of standard guidelines for members, which are specified in the RAL quality and testing regulations. The RAL quality association spans supply chains and sectors. The list of members includes: Recyclers that manufacture PET recyclates (food-grade) Preform producers and Beverage producers (bottle-fillers) - Mineral water and soft drinks The members of the quality association gain the right to use the recognised RAL certification mark by voluntarily submitting to the testing criteria of the RAL quality assurance process. A consulting committee safeguards the high quality level of the work done by the quality committee. The quality criteria are audited and then certified by a recognised testing institute. We spoke to Georg Pescher, the Quality Association’s Deputy Chair and Alpla’s Operations’ Manager since 2009. He is responsible for Alpla’s site in Exter as well as various other plants in Germany. Preforms are produced in Exter according to Quality Association’s criteria. Prior to joining Alpla, Mr Pescher worked in the packaging industry (production and decoration) for CCL and occupied a senior position dealing with production and developmental issues in Germany, France and the USA. On finishing his studies, he joined Procter and Gamble where he worked in R&D for 10 years. PETplanet: You have been working for Alpla for eight years now. What is happening at the Exter plant under your watch? Pescher: We make bottles and preforms at our Exter site which was established back in 1974. Bottles are produced from PET and polyolefins using extrusion and stretch blowmoulding techniques. Here at Exter, we newly started making wide-neck jars with an injection-moulded neck and tubes using the extrusion blow-moulding process. Alpla produces up to 1.5 billion preforms and 300 to 350 million bottles per year at the Exter site. 60% of preforms go to local customers working in the beverage sector, with the remaining 40% blown into bottles at either the company’s own premises or at Alpla’s sister plants. Preforms in the plant are produced with up to 100% PET reycling material. PETplanet: How did the collaboration with the RAL quality association come about and what is the extent of Alpla’s involvement? Pescher: The German Association for Plastics Packagings and Films, IK, approached Alpla to ask if any interest had been expressed in working with the RAL. Alpla has been involved with RAL from the very beginning. Quality and associated test guidelines and methods were jointly discussed and agreed during the course of several working sessions with other funding members and experts from the industry. Commitment to the certification makes sense for Alpla as it is consistent with the company’s sustainability goals and we are convinced that the use of high-quality PET recycling material represents a sustainable and viable product concept. For us, the RAL certification mark is a clear sustainability statement. For that reason, we, along with a number of plants working in preforms (Berlin, Exter) and in recyclate production (PRT Wöllersdorf), have RAL certification. PETplanet: How does application of the certification mark criteria affect the production process? Georg Pescher, the Quality Association’s Deputy Chair and Alpla’s Operations’ Manager Examples of preforms and bottles with 80% rPET content. Quality according to RAL requirements, produced by Alpla","@ID":14}, "The North American Road Show Toronto New York Atlanta Orlando Denver Las Vegas Seattle Los Angeles San Francisco Vancouver Dallas New Orleans Phoenix Washington, D.C. Boston Detroit Kansas City Oklahoma City Albuquerque Milwaukee Chicago Minneapolis Charlotte Ottawa Montreal Quebec www.npe.petpla.net March – August 2018 The North American Road Show - Bottle Zone on tour PETplanet has successfully deployed its “Editourmobil” Road Shows across the world for seven years now. This is in addition to traditional forms of reporting; we have found that travelling by road enables deeper insights into markets; interviews with bottlers, suppliers and manufacturers can be conducted with greater exibility, both in cities and in more rural areas. The appearance of the Editourmobil has created quite a stir in several countries - in addition to the impact of the interviews and meetings themselves. The Editourmobil is to return to North America once again, in cooperation with the NPE trade show (May 7 – 11, 2018 in Orlando, Florida). From March through August 2018 - three years after our last tour in 2015, which proved to be very successful - the PETplanet team will, once again, visit a variety of locations across the USA and Canada. The “Editour“ journeys will take in professional discussions and interviews with market leaders from the West to the East Coast. We will be stopping o at the NPE show itself, where the PETplanet and Editourmobil team will present initial reports of our visits and interviews. We will be part of the new Bottle Zone, which will be a rst for us as well! Make sure you’re on board with us when we set o again. Get ready for in-depth analyses of the special features and trends in the bottles and beverages sectors of North America! All aboard! Premium Sponsor to date Sponsors to date The worldwide round trip with","@ID":45}, "35 PRODUCTS PETplanet Insider Vol. 19 Closure technology for bottled waters Silgan Closures has developed a plug and play system for the bottled water market. The K-Seal offers improved operation and hygiene combined with valuable sustainability benefits for five gallon containers. The closure features Silgan’s Probe+ system, suitable for a wide range of water coolers. This enhances overall easeof-use by ensuring full plug engagement to the cooler spike with minimal risk of misapplication and detached plugs. The K-Seal also retains the overall height of a traditional five gallon closure, meaning it can run on existing lines with little or no adjustment to filling or capping equipment. Hygiene levels have been improved thanks to the reformulated Flow Seal material which reduces the ability for microbes to attach themselves to the material surface and survive. In addition a reduction in pigment usage further minimises the risk of taste or odour issues. To meet growing demands for more sustainable packaging solutions, use of the latest manufacturing techniques, along with a new resin and low-power consumption during production, reduce the closure’s carbon footprint. All materials used in the manufacture of the closure are fully approved for direct food contact and meet relevant EU directives and FDA (Food and Drug Administration) requirements. www.silgan-closures.com SIPA S.p.A. - Via Caduti del Lavoro, 3 - 31029 Vittorio Veneto (TV) - Italy Tel. +39 0438 911511 - Fax +39 0438 912273 - email: [email protected] We make it happen. www.sipa.it Imagine taking your operating costs at the lowest level. Designed to adapt. Built to last. Preform Systems MAINTENANCE COST i stment Less than1%of the capital nve","@ID":37}, "CAPS & CLOSURES 23 PETplanet Insider Vol. 19 recently held its first meeting in Cetie offices in Paris. The description of the different aspects of the problem as above summarises some of the initial input from the industry experts in the meeting, representing the main industrial sectors concerned. The group aims to propose a definition for ovality with the corresponding measurement method, and recommendations for industrial best practice, taking into account “total cost of ownership” aspects for cap lightweighting options. As for all Cetie documentation, these will be established on a consensual basis and subjected to enquiry within wider Cetie membership before publication. Cetie membership is open to all stakeholders - companies or professional federations. Another example of the work done in Cetie are the recently published recommendations for Index Marks on PET finishes and caps (reference FS18), available from the Cetie website. Work on a revised and extended PET Closure Qualification Test Manual is also in final stages of preparation, in collaboration with ISBT, for publication by both organisations in the course of 2018. www.cetie.org Cetie is an inter-professional association dedicated to producing technical reference documentation for the bottling industries - best practice guides, recommendation data sheets, industry standards, test methods, etc. The objectives shared by its members, companies from the complete value chain, is to contribute to consistently high quality levels for bottled products - foods and beverages, cosmetics, personal care, perfumes, home care, pharmaceutical products, etc.","@ID":25}, "CAPS & CLOSURES 32 PETplanet Insider Vol. 19 No. 01+02/18 petpla.net Dispensing caps enable consumers to mix drinks on the go Shaking the market The main characteristic associated with the dosing cap is the separate storage of dry or liquid supplements from the water, allowing the ingredients to form a vitamin or energy drink, even a medicinal drink, when the supplement is released from the bottle. The demand for simple and convenient ready-to-go products is increasing, particularly where it concerns food, sports drinks and vitamin products. A novel cap design is enabling consumers to mix their own drink – on demand. The Incap is claimed to be an easy-to-use dosing cap that fits on any standard bottle, and adds another benefit to the beverage producers equation: maximum freedom of product design, along with additive options that can be tailored to individual consumer requirements. Catering to an emerging trend for beverages enriched with vitamins, minerals or probiotics, dry or liquid additives are stored in a separate chamber within the cap, eliminating the need for preservatives and extending the shelf life of the drink itself. The user simply twists the cap to release the additive, triggering the mixing process when the product is ready for consumption. “A beverage is so much more interesting if consumers can prepare their very own, special drink,” Co-Owner and European Director of Incap, Axel Hauck, commented. “Consumers using our product feel that they are contributing to their health and wellbeing. They also regard this cap as a fun novelty item, as they allow them to add the ingredients themselves and watch them dissolve in their beverage.” The cap offers beverage manufacturers a host of new product and growth opportunities, he explained. Liquid or granule additives can be stored within it, and these can be mixed with cool, hot, still or carbonised bottled beverages. Because the bottom of the cap is hermetically sealed, it can be sold alongside the beverage or as a standalone refill product. “Athletes can conveniently carry their additives in their gym bags, children can mix in apple or orange flavours while travelling – there is no end to the creative potential of this innovative product,” he added. On the basis of end use, the dosing caps market is segmented into beverages, food, healthcare, cosmetics & toiletries, and chemistry. Dosing caps – market data According to Transparency Market Research, the market research and business intelligence company, the global dosing caps market is expected to witness a significant CAGR (compound annual growth rate) over the period 2016-2024. APAC dominates the global dosing caps market and the trend is expected follow the same over the forecast period due to growing food & beverages market in this region. The evolution of the retail sector in growing economies such as India & China is expected to further boost sales of dosing caps in Asia Pacific by the end of the period of 2016-2024. Europe is expected to follow APAC in dosing caps market over the forecast period, while rest of the world is expected to witness a steady growth. www.incap.hk CAPS & CLOSURES","@ID":34}, "PREFORM PRODUCTION PETplanet Insider Vol. 19 No. 01+02/18 petpla.net 13 Pescher: Daily production procedures are not significantly changed as a result. Extra effort goes into ensuring that both preforms and material are properly controlled as the requirements go beyond the legally prescribed level. PETplanet: Which criteria have to be used? Pescher: There is an increased focus on quality control for the incoming PET recycling materials. There are higher expectations in regards to volatile organic compound (VOC) parameters to be controlled more frequently (per batch) on the supplier site. The same more detailed testing is done with the preforms that we produce in house and in addition we control the quality of the PET recyclates in more depth and more often. PETplanet: Are the criteria applicable to every preform? I am thinking here of, say, multi-layer? Pescher: All types of monolayer preforms are suitable for preforms into which the desired combination of new material and recyclates are added. Multi-layer preforms can be produced according to quality criteria in exceptional circumstances but they represent a niche. The problem with multilayer preforms is that, depending on the barrier material used, the preforms cannot be recycled. The materials that can be added are defined within the quality criteria. Specifically, a multilayer preform with a polyamide barrier would not be so recyclable as to maintain an acceptable quality in the material/product cycle. Consequently, this preform is not suitable. PETplanet: RAL is Alpla’s certificate as well as an international company. Are the guidelines for the certification mark being adopted at international plants? Pescher: The certificate standards can be met at any site. In all our sites we follow the general quality requirements set by ISO 9001 and ensure conformity to EU-VO 10/2011. For applying the RAL certification mark there has to be a commitment to sustainable actions on the part of both customers and retailers. Alpla is more than willing to support partners throughout the whole food and beverage industry by supplying produce fulfilling the RAL certification mark guidelines. www.alpla.com www.wertstoff-pet.de Depiction of the PET drinks’ packaging value chain MANAGE PREFORM VARIANCES CONTACT US TODAY TO LEARN MORE! AGRINTL.COM | +1.724.482.2163 | [email protected] 1MEASURE 2CONTROL 3OPTIMIZE Blowmolder management easy as . . . PROCESS PILOT® Automatically manage preform variations to produce better, more consistent PET containers.","@ID":15}, "PETnews 6 NEWS PETplanet Insider Vol. 19 No. 01+02/18 petpla.net PET collection and recycling rates in Europe increased in 2016 Out of 3.147.000 tonnes of PET bottles and containers placed in the European market in 2016, a remarkable number of 59.8% - in total 1,880,900 tonnes - were collected and of these 1,773,200 tonnes were mechanically recycled. These conclusions come from the annual PCI Wood Mackenzie PET recycle survey for Western Europe in 2016, commissioned by Petcore Europe. It shows that the collection rates increased by 7.4%, while the recycling rates also grew by 7.3%. In 2016, that resulted in 129,400 tonnes more collected and 120,000 tonnes more recycled PET compared to 2014. “These PET collection and recycling rates are unreached in the plastics packaging industry while it is worth mentioning that PET recyclers still have unexploited capacities for recycling,” states Paola Arlotti from Equipolymers, Petcore Europe President. “The figures clearly outline the crucial role of PET in a Circular Economy and for reaching the plastics recycling targets currently discussed on EU level.” When it comes to more country specific figures, the survey reveals that the combined volumes reported for France, Germany and Italy represent 47.9% of the total volume collected in the region, continuing the gradual decline in the top three’s share (48.5% in 2014 and 53.3% in 2011). These three largest countries in terms of collection volumes are now joined by two other countries that contribute a significant proportion of the regional total, namely Spain and the UK. The combined total share of these five countries in the overall EU collection accounts for 70.9%. The survey outlines a slightly more positive picture on the clear bottles amount compared to the previous years. Clear bottles accounted for 17.3% of the complete stream revealing an increase of 2.1% on the 2014 share and the first increase in share in five years. “This is an encouraging sign for recyclers and hopefully this increased share is set to continue,” outlines Christian Crepet, Petcore Europe Executive Director. “However, the quality of bales with additionally a total share of 26.4% clear/light blue bottles, 25.5% mixed colours including green/brown bottles, and 30.8% of unspecified mixed colours clearly continues to challenge the recycling industry. Therefore, we believe that there is a vital need for a detailed analysis of the unspecified waste stream which will be part of the 2018 study commissioned by Petcore Europe.” “As regards the quality of the bales, a shift to more highquality markets also requires a stable and high level sorted input,” states Casper van den Dungen, Petcore Europe VicePresident. “The survey confirms an increased waste ratio at the recycling stage. Therefore, efficiency increase in collection and sorting is needed and would also contribute to the cost reduction of the total system in the long term.” With 38% the major market for rPET in 2016 remained sheet, followed by blow-moulding applications with 26% and fibres with 24%. The remaining just over 11% are used for strapping and other applications. www.petcore-europe.org Platinum Equity to acquire Husky International Platinum Equity announced that it has signed a definitive agreement to acquire Husky Injection Molding Systems from Berkshire Partners and OMERS Private Equity for $3.85 billion. The transaction is expected to close during the second quarter of 2018. John Galt, who has served as Husky CEO since 2005, is staying on to lead the business. He and other members of Husky’s management team will remain substantial investors in the company. Over the last several years, Husky has worked with its investors to successfully advance stateof-the-art manufacturing equipment, which it delivers to its wide range of customers in various end-markets across the globe. Berkshire Partners LLC and Omers acquired Husky in June of 2011. Demand for Husky’s products and services is primarily driven by growth in the beverage packaging segment, as well as in plastics consumables. Husky is a global enterprise with approximately 75% of its sales generated outside North America. In addition to complete injection moulding solutions, Husky provides aftermarket services and parts to a large and growing installed base of systems globally. “In Platinum, Husky has found a partner that brings a wealth of experience, a highly capable team, and a shared enthusiasm for building great companies. I am confident that by working together we will find new and exciting ways to serve our customers,” said John Galt, Husky’s President and CEO. www.husky.co GEA closes acquisition of Vipoll GEA completed the acquisition of Vipoll, headquartered in Križevci pri Ljutomeru, Slovenia, which was signed in November 2017. With the acquisition, GEA has added to its group a manufacturer of filling technologies for soft drinks, beer and fresh milk products into glass bottles and cans, as well as PET bottles. “This acquisition will support our position as a leading global supplier of complete solutions for the beverage industry. The complementarity to our products provides an excellent opportunity to fill a white spot”, explained Jürg Oleas, CEO of GEA. Vipoll employs more than 100 employees. In 2016, it generated sales of approximately EUR 20 million. Both companies have agreed to keep the purchase price confidential. Vipoll adds filling and bottling equipment, container conveyors and comprehensive engineering solutions for low and mid speed lines to GEA’s downstream process chain competencies. Vipoll’s customers are mainly in Europe which should lead to sales synergies from marketing its technology globally and increasing the share of services through GEA’s existing sales & service network. www.gea.com","@ID":8}]}}
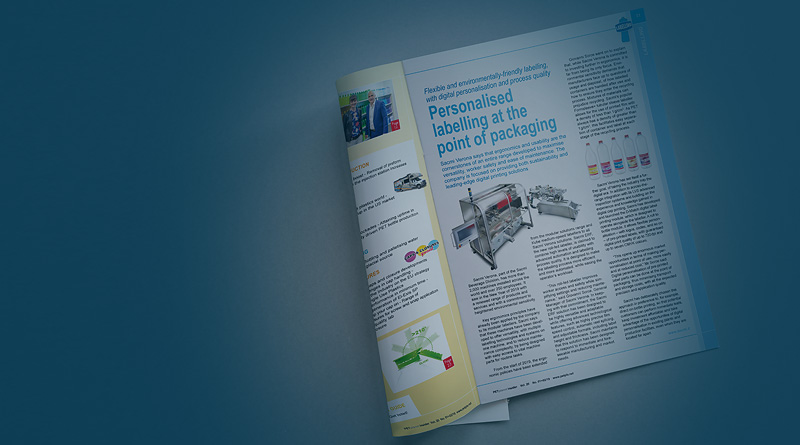