EDITOUR PETplanet Insider Vol. 19 No. 04/18 petpla.net 12 Don’t talk, listen! Has been the motto of John Galt, President and CEO of Husky for many years. We spoke with him on a variety of topics covering Husky’s change of ownership, new technologies, competition, history and about what the future holds. All of these themes are part and parcel of John’s and therefore Husky’s focus on customer requirements. PETplanet: Hello John: Husky is now 65 years old and has had two Presidents in that time. You have been its second since 2005. Such continuity is unique in the PET machine building world. Do you find such continuity more stressful or does it just spur you on? John Galt: The role of CEO is stressful, but that continuity helps. It helps to create an opportunity to learn. Being at Husky for so long has given me an opportunity to learn about our industry, try things and learn from my mistakes. PETplanet: Continuity is not always visible to the owner. Onex bought out Husky for just under one billion dollars in 2007. Two years later, Onex sold Husky to Berkshire for more than two billion dollars and this year we are witnessing the takeover of Platinum Equity for nearly four billion dollars. What is your secret given the fact that the new owners are prepared to pay around twice the previous purchase price? John Galt: We have continuity in our approach. What works for us is listening to our customers, developing solutions to their unmet needs and then delivering great products that operate with less waste and higher effectiveness. We invest in changes that take not only us, but the industry forward. First thing I learned is to listen and not talk. What are our customer looking for? What is the market looking for? Let’s try to give them what they want. PETplanet: In a PETplanet Insider interview back in 2010, you said that “ownership, leadership and strategy are aligned on where we are talking business”. Is that still the case? John Galt: Absolutely. It’s been that way for years. The alignment of these three principles has and will continue to be a winning formula for us. PETplanet: A large proportion of Platinum’s purchase price is based on future expectations. What can we expect from Husky in four years’ time? More sales of preform or closure systems, the strengthening of other business areas such as hot runners and packaging, or completely new commercial areas? John Galt: We see PET developing within, but also beyond Beverage Packaging to service the needs of new markets. We are looking for new potential applications, like food, personal care and home care. We will also continue to invest in Closures, Packaging, Medical and Hot Runners. PETplanet: For many years, the preform machine business was clearly split between Canada and Switzerland. Over the past decade, we have seen many injectionmoulding manufacturers come and go who wanted to gain a foothold in the preform sector by employing various strategies. Only our Italian colleagues with their considerable number of machines were able to achieve this, mainly because they can supply the preform machine and mould from a single source. How does Husky deal with this new market competition and do preform machine suppliers without moulds still have a future in the market in the long run? John Galt: Competition makes us stronger. It helps us to develop. It helps us to grow. Technology is the catalyst. We focus on how we can tailor our systems to the product. At the core of that strategy is our Tooling, Systems and Services. We believe in the value that can be generated by offering a complete, integrated system solution. Our ability to innovate at this higher level is limitless. PETplanet: Sipa and Sacmi go one step further and tell you if you have the whole production chain from pellet to pallet in house, and by looking closely at all the information, optimal products can be produced at each stage. At AMC, Joachim Niewels showed us a KHS stretch-moulding machine and Krones filler. Is this heralding a long-term entry into the business of stretch-blowing machines and filling lines? John Galt: We learn from what our competitors are doing, but we have no plans to offer stretch blow machines or filling lines to the market. We focus on our customers, who produce preforms, either standalone or in line with downstream technologies. The preform moulding stage must be done well in order to get a good final product. That being said, we may consider injection and blowing together for small volume production. PETplanet: A big step for Husky was the acquisition in 2011 of KTW, which meant it could dispense with its long-standing closed mould Tour Sponsors:,@ID:14}, 9 NEWS PETplanet Insider Vol. 19 No. 04/18 petpla.net Where next for bottled water? The report ‘Where Next for Bottled Water?’, published by the Beverage Research Company Drink Sector presents information on the latest research and events in the global beverage industry and outlines the key consumer trends and innovation opportunities within the bottled water category. According to their research, health & wellness is considered to be the most influential factor for consumers when purchasing soft drinks. Around 60% of consumers globally say that how the product impacts their health and wellbeing always (33%), or often (27%), influences their purchases when choosing a non-alcoholic beverage. Bottled water has a high inherent health appeal, given that water is crucial to staying hydrated and supporting the function of every bodily system, including the brain, heart and muscles. The study also finds that consumers are looking to remove high-sugar beverages, such as carbonates, from their diets and replace them with low-sugar alternatives which they perceive to be healthier, such as bottled water. Also, consumers are more willing to experiment with conventional beverages, such as coffee, tea and bottled water, than they are with functional beverages such as energy or sports drinks. The report identifies five key innovation opportunities within the packaged water space: Functional waters: A proactive approach to health is steering consumers towards enhanced water products that address specific health needs and offer more functional benefits. Outside the bottle: Plastic water bottles are a major contributor to plastic waste, so more sustainable packaging alternatives are needed to combat the growing plastic waste issue. Hybrid waters: Hybrid products such as energy waters, sports waters and juice-infused waters represent a major opportunity in the soft drink market as they are seen as healthier than conventional soft drink beverages. Alternative waters: The plant water trend has expanded to include maple, cactus, birch, aloe vera and even honey water, driven by health-conscious consumers seeking beverages that provide natural hydration and other functional health benefits. Premium waters: Premium waters hold potential in the market, leveraging high-quality claims and sustainability credentials to differentiate themselves in the highly competitive bottled water market. Companies mentioned in this report: Reliant Recovery, Kirin, Suja, Giant, Box Water, Just Water, Memobottle, CanO Water, DASH Water, Hint Water, Gatorade, Go Water, Bee’s water, Water Works, Green Beverages, Alnatura, Naeve, VOSS, O Pure Water, Life Water, Aquiem, Ecomo, Ooho! www.drinksector.com Indorama Ventures to acquire PET business in Brazil Indorama Ventures Public Company Limited (IVL), a global chemical producer, has announced that it has entered into an agreement to acquire M&G Polimeros Brazil S.A. in Ipojuca Brazil. The plant is the largest PET facility in Brazil, with capacity of 550,000t/a. This plant is strategically located and benefits from virtual integration with a manufacturer of Purified Terephthalic Acid (PTA), a key feedstock to PET. The transaction is expected to be completed in second quarter 2018, subject to regulatory approvals. This acquisition in Brazil is in line with the company’s strategy to further extend its market position, and expand its global footprint in key markets with high growth potential. This strategic position is intended to allow Indorama Ventures to deliver products to key customers in Brazil and elsewhere in a cost-effective and efficient manner. Indorama Ventures is well positioned to service its current global client base and M&G’s existing customers once this acquisition is complete and the plant is fully operational. The company expects immediate incremental revenues and cost synergies, driven by a substantial volume increase and potential value add through backward integration. SouthAmerica is an important emerging market with domestic demand for PET growing at around 5%. Today’s per capita consumption of PET is comparatively low at 2.8kg and has potential for growth. Brazil also has strong underlying fundamentals, supported by government policies to stimulate economic growth and strengthen the domestic market. Indorama Ventures continues to be on a transformational journey aimed at accretive growth and sustainable value creation, while maintaining financial discipline. In its latest financial disclosure of 20 February 2018, the company announced its record EBITDA of US$ 1 billion for 2017 which was a growth of 30% on a year-onyear basis. Significant improvement in the PET and feedstocks business environment also enabled its net profit to grow by 68% on a year-on-year basis. This acquisition will significantly advance IVL’s strategy in its Necessities business, where the company aims to deepen its global footprint and build scale in key markets. HSBC is serving as financial advisor, KPMG is serving as finance and tax due diligence advisors, and Mattos Filho & Lowenstein Sandler is serving as legal advisors. www.indoramaventures.com,@ID:11}, BOTTLE MAKING 28 PETplanet Insider Vol. 19 No. 04/18 petpla.net Stretch Blow Molding, part 8 Machine details - Oven section by Ottmar Brandau Ottmar Brandau has newly revised his book “Stretch Blow Molding”, first published by hbmedia/ PETplanet Publisher, and now re-issued in a third edition under the Elsevier imprint. PETplanet Insider is publishing extracts from successive chapters in a series of articles. 4.1 Oven section The importance of a properly designed oven section cannot be overstated. This refers to both the overall layout and the design of the actual ovens. Ovens must: impart the correct temperature profile into the bottle wall give processors flexibility in heating sections of the preform to the best temperature for even bottle wall thickness distribution have large enough blowers to control heat buildup inside the ovens protect the neck finish of preforms cool the infrared lamps for maximum life-span cool the reflectors opposite the lamps leave room for sufficient equilibration time be sized for the correct throughput at a given preform wall thickness. It is apparent from this list that oven design has attracted a great deal of engineering effort and modern achines feature excellent systems that are able to deliver lightweight bottles conforming to ever-increasing specifications. Layout As previously mentioned preforms may travel through the oven system neck-up or neck-down. As long as heated air is efficiently vented out of the system both methods work well. Figure 4.1 Layout of infrared oven. Diagram courtesy of Krones AG. There are usually eight or nine infrared lamps spaced vertically at a distance of 15–19mm (5/8–3/4in). Close spacing is necessary in order that the corresponding sections of the preform can be heated exactly to the point where the best bottle wall thickness distribution is achieved. Older designs incorporated larger or twin lamps that did not offer processors enough flexibility and these systems are no longer being manufactured. Lamps should be adjustable horizontally. This allows the processor to move them closer into areas that need the most heat. This is usually the section immediately below the neck. This area requires more heat as it is adjacent to the cooler (unheated) neck, and also because the shoulder of the bottle requires less material in most cases. Failure to heat up this section sufficiently results in a ring of thick material in the bottle that is both unsightly and leaves less material for the rest of the bottle where it is needed. Lamps are,@ID:30}, PETnews 6 NEWS PETplanet Insider Vol. 19 No. 04/18 petpla.net PET upcycling of fibre reinforced industrial plastic A recently launched research project “UpcyclePET” is developing an innovative process for high-grade recycling of PET. This will enable PET waste from used drinks’ bottles to be recycled as an industrial plastic, thereby reducing the use of new plastic based on polyamide. The project team comprises the Fraunhofer Institute for Structural Durability and System Reliability LBF, the Institute for Applied Ecology and Easicomp Ltd. As the project coordinator, Dr Volker Strubel, explains “In this upcycling project, we are using recycled PET to produce new lightweight reinforced glass fibre components, thereby reducing the use of polyamides in the production of automotive parts such as engine mounts and mounting supports”. The UpcyclePET project is harnessing its partners’ expertise in material and process development to create an integrated manufacturing system for the production of reinforced glass fibre PET components. In this case, a pultrusion technique is used to reinforce the PET plastic with long glass fibres and is technically evaluated as part of the process. Such an approach combines the mechanical advantages of the particularly robust long glass fibres with the special properties of PET which include low swelling capacity and dimensional stability. “The distinctive feature of this approach is that it combines two process phases that are decoupled in modern day practice and specifically customises the properties of the recycled PET used by means of additives and modification”, explains Dr Frank Schoenberger of Fraunhofer LBF. The fact that all the necessary process steps are undertaken at just one plant makes production particularly cost-effective. Using the lightweight component from the car industry as an example, the project team assesses the potential for the technical replacement of the material and identifies possible environmental and economic benefits. Easicomp Ltd is a manufacturer of reinforced long glass fibre thermoplastics using pultrusion techniques and is responsible for the large-scale application of reinforced long glass fibres under UpcyclePET. As part of the project, Fraunhofer LBF is using its considerable expertise in the field of additives, modification and processing of industrial plastics in its customised material and process development. The Institute for Applied Ecology is conducting environmental and economic analyses of important sustainability impacts (savings in resources, energy and CO 2 etc.). The Federal Ministry of Education and Research is supporting the project as part of its “Innovative SMEs” funding programme. www.lbf.fraunhofer.de www.oeko.de www.easicomp.de WIkiPETia – The online PET knowledge platform More than 240 suppliers at a glance More than 240 companies along the PET value creation chain are already registered on the moderated knowledge management system WikiPETia. At www.wikipetia.info, there are profiles, products, technologies and other valuable information about companies in the materials, PET recycling, preform production, bottle making, filling, capping and labelling sectors. Each company profile has direct links to posts and reports relating to it in PETplanet Insider. All important information is available at a glance! Is your company listed yet? Would you like to add more information? We would be happy to set up an account for you and you can amend your details yourself. Simply contact us at [email protected]. www.wikipetia.info UK water drinks approach 4,000 million litres UK consumption of water drinks rose 7% in 2017 to nearly 4,000 million litres, with a retail value of £3.1 billion, according to a new report from global food and drink experts Zenith. Sales of plain bottled water in retail packs increased by 8% to over 3,100 million litres, while volume through bottled water coolers grew a more modest 2% to 310 million litres. This marks a slowdown in growth from the preceding four years, partly as a result of poor summer weather. Conversely, sales of flavoured, functional and juicy waters, which increased by 2% in 2016, advanced by 5% in 2017, after more strong branded players entered the market. Plain bottled water, with average annual consumption of 54l per person, strengthened its market dominance in 2017 to account for 87% of total sales. Flavoured water’s share of the market fell to 11% volume share, with juicy and functional water making up the remaining 2%. In terms of water types, still water drinks accounted for 83% of total volume in 2017, with sparkling water drinks contributing 17%. The top 5 UK plain water brands - Highland Spring, Evian, Buxton, Nestlé Pure Life and Volvic - are collectively responsible for 30% of total water drinks sales, whilst the top 5 water plus brands - Volvic Touch of Fruit, Calypso Clear, Trederwen Essence, Drench Juicy and Perfectly Clear - account for 5%. “Environmental concerns have grown, but are being tackled by lighter bottles with more recycled content and by new packaging formats as well as recycling initiatives,” commented Zenith Chairman Richard Hall. Zenith forecasts that, by 2022, the total market for UK water drinks will reach 5.3 billion litres, 32% above 2017 levels. Plain bottled water is set to lead this advance, with average growth of 6% per year. Flavoured, functional and juicy waters are forecast to expand more slowly. www.zenithglobal.com,@ID:8}, BOTTLE MAKING 30 PETplanet Insider Vol. 19 No. 04/18 petpla.net www.npeguestpass.org/588580 Visit us at Booth S15089 Free Ticket at: Infrared lamps The lamps themselves consist of tungsten filaments sealed in quartz tubes. Quartz is transparent to infrared radiation and can withstand the high temperatures that the lamp generates. The filament temperature determines the wavelength emitted (Table 4.1). The tubes are filled with halogen and an inert gas to avoid oxidation and blackening of the tube as well as lowering the operating temperature to about 800°C (1472°F). Lamp emission peaks at 1200nm, which is the optimum for PET processing (Chapter 6) (Fig. 4.4). Figure 4.4 Typical infrared lamp. Photo courtesy of Philips. Pinch sections of the lamp, where the tungsten filament connects to the electrical supply, must be kept below 350°C (662°F), otherwise the molybdenum film at the contacts starts to oxidise and the pinch may actually crack, causing the lamp to leak. Most ovens have blowers at the back of the lamps accomplishing this task and also monitor the temperature with special thermocouples. Operating Percentage Respective Voltage (V) Temperature (K) Temperature (°C) Temperature (°F) 40 88 1800 1527 2780 70 154 2000 1726 3140 100 220 2600 2327 4220 Table 4.1 Relationship between operating percentage, used Voltages, and temperature output of a typical infrared lamp,@ID:32}, 66 TRADE SHOW PREVIEW PETplanet Insider Vol. 19 No. 04/18 petpla.net Closures on top Corvaglia, a leading supplier of closure solutions for PET bottles, will be present at the NPE2018. A team of experts will be delighted to discuss possible solutions with visitors at the company’s booth. Corvaglia offers a great variety of closures, closure designs and closure moulds for the PET bottle sector. Recent innovations are claimed to contain a better to grip 1881 slitted/folded closure. It has a reduced weight of 25% compared to other 1881 closures while coming back to the consumer comfortlevel of 1810 closures 20 years ago due to its higher grip-area. Compared to 1810 closures this design saves around 40% of weight. For the non-carbonated water segment, Corvaglia introduced an “Aqua 2522” closure. This closure, also designed for pressurised or nonpressurised packages, impresses with its light weight of 30% less than a typical 29/25 closure yet still meeting the most stringent requirements of bottlers. At NPE sales managers for all regions of the world will be present at Corvaglia’s booth. Among them representatives that are able to provide visitors with first-hand information about the upcoming market launch of Corvaglia Closures USA, Inc. with a closure manufacturing facility in the Southeastern USA. www.corvaglia.ch Booth 2P07 German Technology Booth S21085 Time to freshen up: odour reduction A circular economy in plastic packaging is currently on everyone’s agenda. Clearly, the recycling of packaging saves raw material and reduces waste as well as CO2 emissions. Starlinger will present two technologies that help advance closed loop packaging. Recycling is key in achieving a circular economy. But in order to be fit for reuse in production, recycled material needs to match the quality of virgin resin. The removal of well-known contaminants such as ink is only the beginning; any migrated substances or residues of monomers or decomposition products have to be eliminated as well. For materials that are prone to suffer from unpleasant smell (e.g., polyolefin containers that were filled with detergents, cleaners, or cosmetics, but also polyolefin film with organic contamination), Starlinger developed a technology that neutralises odours on a permanent basis. This technology has just been nominated for a Plastics Recycling Award Europe in the category “Best Technology Innovation in Plastics Recycling”. The three-step procedure (material preparation, degassing, and post-treatment) works without the use of additives and removes even deeply embedded odours. At NPE, visitors are invited to take a sniff of the input material and the smell-improved regrind at a laboratory table with sample stations. Production in a closed loop is also a hot topic in the area of FIBCs and consumer goods packaging. Thanks to Starlinger’s PET technology, customers starting to use rPET flakes as input material for their tape extrusion lines. The excellent recyclability of PET comes in handy: (big) bags can theoretically be recycled indefinitely. Two types of packaging that are made from 100% rPET bottle flakes will be on display, too: an rPET FIBC for large product volumes as well as rPET PP*Star pinch bottom bags for dry bulk goods. The rPET PP*Star has recently won a WorldStar Award in the category “Packaging Materials and Components” and is on the short list for the sustainability award. Another application for rPET is sheet production: the Starlinger viscotec solution deCON / viscoSHEET can process 100% rPET, in-house waste, and virgin material at guaranteed IV levels for direct food contact. Customers benefit from the flexibility and low energy consumption; the final product has a high-quality appearance as well as good mechanical properties. www.starlinger.com Visitors may take a sniff at the laboratory table. South Hall 36150 West Hall 6885,@ID:68}, TRADE SHOW PREVIEW PETplanet Insider Vol. 19 No. 04/18 petpla.net 72 Gneuss Processing Unit (GPU) for 2,000lbs/h of rPET Filtration, extrusion and measurement technology Gneuss Extrusion Technology will show a Gneuss Processing Unit (GPU) including a Multi Rotation System MRS 130 extruder, a fully automatic melt filtration system RSFgenius 150 and an online viscometer VIS, for the processing of 2,000lbs/h of undried and uncrystallised polyester (PET). West Hall 6473 Sheet extrusion line with Multi Rotation Extruder MRS, Rotary Filtration System RSFgenius, Online Viscometer VIS and PET foam module The Gneuss Processing Unit (GPU) has been available for several years now and has proven itself for the reprocessing of bulky PET waste without pre-drying. A Gneuss Processing Unit consists of a Gneuss MRS extruder with its unmatched devolatilisation and decontamination performance in combination with a highly-efficient Gneuss Rotary Filtration System and an online viscometer VIS for intelligent dynamic viscosity control. The line in Orlando will be delivered to a customer in the U.S. after the show to process 2.000lbs/h of rPET into a thermoforming sheet. Although originally developed specifically for PET, the MRS is now also running in polyolefin and nylon applications, and being tested on a range of other materials and applications. Thanks to the patented combination of single screw extruder with a multiple screw section, the extruder is sturdy and well suited for recycling applications. The MRS extruder permits the processing of PET without pre-drying by using a simple water ring vacuum system to process the material directly to high quality end products. This is achieved by means of its unique and patented processing section. Based on a conventional single screw extruder, the Multi Rotation Section is a drum containing eight satellite single screws, driven by a ring gear and pinion transmission. The “barrels” cut into the drum are approximately 30% open and provide optimum exposure of the melt. Thanks to this design, the devolatilising performance is approximately fifty times greater than that of a conventional single screw extruder – and this at a vacuum of only 25 to 40mbar. By avoiding the need for a deep vacuum system and pre-drying, the MRS is an economically alternative to conventional technologies. Further arguments besides energy savings are the simple and rugged design, small footprint, its ease of operation and low maintenance, processing flexibility and the melt quality and homogeneity. One area this technology has been especially successful is in PET sheet extrusion. Besides producing high quality rigid sheet, Gneuss now also offers the option for its PET sheet extrusion lines to quickly and flexibly switch to producing physically foamed PET sheet with the addition of the new PET foam module. Foam sheet with a weight reduction of 50% can be extruded (depending on the process) with a consistent foam structure and mechanical properties. And this from up to 100% post-consumer material. Strong and consistent growth in North America has allowed the company to move forward with an expansion of its US facilities in Matthews, NC. The larger facilities offer a larger laboratory as well as more space for spare parts. www.gneuss.com,@ID:74}, TRADE SHOW PREVIEW PETplanet Insider Vol. 19 No. 04/18 petpla.net 52 FTR technology from Uhde Inventa-Fischer Towards the circular economy in PET packaging based on an article by Dr Christopher Hess and Martin Hittorff, Uhde Inventa-Fischer Market and societal pressures are driving the plastic packaging industry towards a real circular economy (CE). How can the competing interests be met that plastic producers - of PET resin in particular – are challenging? The tightening of European and German legislation, which sets high targets for the recycling of packaging material, is a recent manifestation of increased public awareness on packaging. The German law, passed in March 2017, requires that the recycling rate for plastic packaging in the dual system must rise from 36% in 2017 to 58% in 2019 and go on to reach 63% by 2022. The global collection rate of PET reached 55% in 2017 (see diagram 2), with some local collection systems achieving over 90%. The total PET collected is expected to reach 12m t in 2017. However, recyclate content in PET packaging is around six to seven per cent globally; with local exceptions, such as approximately 24% in Germany. A major portion of collected, used PET bottles end up as feed to staple fibre production; effectively, a down-cycle of valuable packaging material. The key question is: how can the rPET content in PET packaging be increased, to achieve real recycling, rather than down-cycling? The most frequently observation made by big brand owners, producers and broader market participants is that all available recycling technologies have to be combined and Hall 7.2 Booth K25 Diagram 1: Triangle of interests influencing the PET resin industry (source: PCI Wood Mackenzie 2017) Diagram 2: PET Resin and rPET, the global view (source: PCI Wood Mackenzie 2017) 2016 actual 2017 provisional 2022 projected 1.8 2.8 2.4 10 12 17 21 22 29 8.6 9.2 14 0.8 0.9 2 0.30.3 1 50% 55% 58% 5% 6% 10% PET consumption [mio t/a] PET resin consumption PET bottle collection Process losses PCR flakes available Bottle food contact Bottle nonfood contact PET bottle collection rate rPET content of bottles,@ID:54}, MARKET SURVEY 44 PETplanet Insider Vol. 19 No. 04/18 petpla.net 04/2018 MARKETsurvey Resins & additives Preform machinery Preform production Preform inspection SBM 2-stage Compressors Filling equipment & filling inspection Caps & closures and inspection Palletising & shrink film machinery Recycling Suppliers of PET preforms To complement this exciting trade fair issue of PETplanet Insider we choose to present you the state of the art preform manufacturers with their product range and innovations! 17 companies from 13 different countries taking part: PET-Verpackungen GmbH, Hodmeter, National Group, SGT, PDG Plastiques, Resilux, UAB Terekas, Plastipak, Empacar S.A., Alpla, Novapet, Hokkan Indonesia, Köksan PET Preform Industry, Gulf Packaging Systems-3P Gulf Group, Energo PET,Retal Group and Chemco Plastics Industries. Although the publishers have made every effort to ensure that the information in this survey is up to date, no claims are made regarding completeness or accuracy. Company name PET-Verpackungen GmbH Deutschland Hodmeter National Polyplast (India) Ltd Société Générale des Techniques (SGT) Postal address Telephone number Web site address Contact name Function Direct telephone number E-mail Gewerbegebiet 4 98701 Großbreitenbach, Germany +49 36781 48044 00 www.pet-verpackungen.de Mr Hubert Rebhan Business Development/Key Account +49 36781 48044 52 [email protected] 140 rue Louis Pasteur 76160 Darnétal, France + 33 950 373 373 www.hodmeter.com Mr Antoine Brémilts Director + 33. 684 633 154 [email protected] 44, Pantheon Road,Thiru, Compelx, 2nd Floor, Egmore, Chennai - 600 008, India +91 44 434043 40 www.nationalgroup.in Mr Alok Parakh Director +91 44 434043 40 [email protected] 3 Rue de l’Île Macé 44412 Rezé, France +33 2 40 05 09 37 www.sgt-pet.com Mrs Le Claire Sales Administration Manager +33 2 40 05 02 88 [email protected] Preforms Multilayer preforms (Yes/No) Yes No No Yes PEN prefoms (Yes/No) Upon request No Upon request No Preforms in alternative materials (PP/PLA/PEF) - Which? Upon request No Upon request No Preforms incorporating rPET (rPET content in %) Up to 100% No No From 0% to 100% (according to the client request) List of additives available Colours, oxygen scavengers, UV-blockers, slip-agents, AA-scavengers, brighteners, PA-based barriers Colours, Oxygen scavengers, UVblockers, slip-agents, AA-scavengers, brighteners, PA-based barriers All colours, UV blocker, AA reducer, O2 scavenger, CO2 scavenger, reheat additive, white colour for UHT milk, gliding agent Preform range PET-Verpackungen provides standard preforms with 28mm PCO1810 & PCO1881 finish from 14.5g to 54g. For German market, preforms with 28mm PCO1810 & PCO1881 PETCYCLE-finish. 38mm 2-Start and 3-Start Bericap preforms for wide mouth applications as well as 29-21 finish for flip top caps. Preforms for hotfill applications, for large containers 60g, 92g and 98g preforms with Bericap 48-41. Enhanced barrier protection, the majority of the preforms are available as multilayer with tailor-made barrier properties. 700g for 5 gallon bottle with 55mm neck Specially designed for 5 gallon bottle with a stretch ratio of 7,3; injected with a dedicated PET material made in Europe; with a 55mm neck with optional ring for some automatic line; we are also injecting PET side handle for related bottle PCO1810 (23.5 to 56g); PCO1881 (11.4 to 54.7g); 30/25 (22g); Novembal 267 (10.6 to 21g); 38mm Bericap for milk Neck finish: 27/31, 45g; 55mm, 650g; 55mm S, 650g; 30/25 High neck and Low neck: 13-44g; 30/25 BB Light, 22,50-28g; 29/25 (without step):9.3-35.8g; 29/25, 9.5-36g; 28 PCO 1810, 16-52.5g; PCO 1881,14.4-50g; 28 BPF, 20.5-53g; 38mm 42/36, 14-44g; 38mm 43/36, 14-16g; 28/410 anti back off system; BVS 30 H, 40-53.5g; CRC63, 400-450g.,@ID:46}, MARKET SURVEY 46 PETplanet Insider Vol. 19 No. 04/18 petpla.net Company name MHT Mold & Hotrunner Technology AG Postal address Telephone number Web site address Contact name Function Direct telephone number Fax E-Mail Dr. Ruben-Rausing-Str. 7, 65239 Hochheim/Main, Germany +49 6146 906 0 www.mht-ag.com Mr Carsten Lurz Vice President Sales, Service, Marketing +49 6146 906 0 +49 6146 906 399 [email protected] Preform moulds Horizontal opening Yes Number of cavities 2-192 cavities Preform sizes Up to 700g, for bottles up to 30l Moulds already built for (makes) Netstal, Husky, Sacmi, Demark, Engel, Arburg, Cincinnati, SIG, BMB, Sumitomo, Unique Vertical opening Yes Number of cavities 2-112 cavities Preform sizes Up to 600g, for bottles up to 30l Moulds already built for (makes) KraussMaffei Do you produce single stage tooling sets? (Preform moulds AND blow moulds) No Other Wide mouth, up to 5 gallon, trigger moulds, moulds for vacuum blood test tubes Company name Köksan Pet Preform Industry Gulf Packaging System, 3P Gulf Group EnergoPET d.o.o. Chemco Plastic Industries Pvt. Ltd. Postal address Telephone number Web site address Contact name Function Direct telephone number E-mail 4.org.san.bolg. 83422 nolu cad. no:10, Sehiykamil, Gaziantep, Turkey +90 53269 655 86 www.koksan.com Mr Serhat Tumer Export Sales Manager +90 5326 965 586 [email protected] P.O.box #20266, Indus. City Phase 5, Jeddah 21455, Saudi Arabia +966 12 6360099 www.3p-gulf.com Mr Shadi Khan Key Accounts Executive, International Sales +966 547492027 [email protected] Bulevar Mihajla Pupina 12 11070 New Belgrade, Serbia +38 1222 391 334 www.energopet.net Mr Miroslav Popovic General Manager +38 1222 391 334 [email protected] 1412, Maker Chamber 5 Nariman Point, Mumbai 400021, India +91 2222821777 www.chemcogroup.com Mr Amitabh Agrawal Executive Director +91 2222821777 ext 230 [email protected] Preforms Multilayer preforms (Yes/No) No No No PEN prefoms (Yes/No) No No No Preforms in alternative materials (PP/PLA/PEF) - Which? No No PP Preforms incorporating rPET (rPET content in %) No On the customer request Customer defined List of additives available Colourants, AA reducers, barrier additives Yes Customer defined Preform range Water: 29/25 neck: 9-30g, 30/25 neck: 14-39g, 38/33 neck: 57-62.5g PCO, 48/41 neck: 67.5-130g PCO,33mm, Hot fill neck: 15-42g, 55mm neck 5 gallon: 300-330g PCO, PETKEG S.ON 405g CSD: 1881 neck (28mm) 12-52g PCO, 1810 neck (28mm) 15-54g PCO Edible Oil: 31/21 neck (28mm) 26.5-49g PCO, 34/27 neck (32mm) 23-25.9g PCO, 35/27 neck (32mm) 25.5-27g PCO 7.9 to 30g, 29/25: 200 to 2,000ml for still water 10.9 to 39.2g,30/25: 330 to 2,500ml for still water 69g, 38mm for 5l still water 78g, 82.5g, 90.3g, 48mm for 5l still water 16g to 53.5g, PCO 1881 for CSD 18g to 55g, PCO 1810/1816 for CSD 13.5g, 18g, 38mm for juice and milk We also produce all types of closures for the above preforms. 900 millions preforms; EnergoPET is specialised in manufacturing of PET preforms, used for bottling of mineral water, soft drinks, beer, milk, chemical products etc. The products include preforms with neck finishes: PCO 1810, Bericap 38mm, TwistOff 30/25, Twist-Off 29/25 and PCO 1881. Our equipment enables us to manufacture quality products that conform to the highest standards. We've implemented one of the GFSI - FSSC 22000. Alaska PCO 1881 PCO 1880 29 - 25 30 - 25 38mm (2 Start) 38mm (3 Start) 48mm 25mm ROPP 26/29 CTC 36/29 CTC 55 mm 28 mm hot fill 1810 28 mm hot fill 1881 9.5g to 42g 12g to 52g 13.5g to 54g 10.4g to 35.7g 12g to 37.2g 22.63g to 30.7g 12.5g to 35g 78g, 82g and 90g 10.2g to 14g 15g to 26g 48g to 67g 270g to 700g 23.5g to 48g 22.4g Suppliers for preform moulds Resins & additives Preform machinery Preform production Preform inspection SBM 2-stage Compressors Filling equipment & filling inspection Caps & closures and inspection Palletising & shrink film machinery Recycling,@ID:48}, 50 TRADE SHOW PREVIEW PETplanet Insider Vol. 19 No. 04/18 petpla.net Mixing and dosing In the field of auxiliary equipment, Eisbär manufactures systems to improve quality and productivity for the plastics industry focusing on syst ems t o av o i d condensation on moulds, cap cooling, drying of plastic resin, processing PET flakes, crystallisation as well as mixing and dosing. The E i sbä r mixing and dosing unit for high material throughputs is a tailor-made system solution for accurate mixing and dosing of materials and additives. Amongst the many features of the system is a high throughput (up to several tons per hour), high accuracy, since each component has its own weighing system. Hot material can be processed and mixed simultaneously. Stored recipes allow reproducibility. The unit has 100% network connectivity and a final feature is that no pre-mixer is required. How the unit operates The principal materials and additives are supplied and filtered using optional grating filters. The weighing and dosing hoppers are filled accurately by means of screw conveyors, and can be continuously discharged for further processing. The unit is capable of accurately mixing and dosing different materials and additives, and offers a visual and graphic overview of the various dosing units and the set recipes. www.eisbaer.at Mould making, refurbishing and conversion services The advantage of mould conversion over buying a brand new mould lies in the lower capital investment involved. SIPA’s mould refurbishing and conversion services in China are an important element of its PET preform and bottle mould offering.The existing mould shoe is reused, and return of investment is faster. Customers can choose which is best for them by having a mould audit carried out by SIPA experts. The state of wear of mould components can be assessed in their own plant, and different options on refurbishing or conversion can be proposed. The mould refurbishing and conversion services complement SIPA’s in-house capability to develop and produce high performance moulds and hot runners in-house. The hot half of each SIPA mould requires maintenance only after five million cycles, and it is possible to maintain components such as piston, flange O-rings and pin valves without opening the whole mould. The company’s range of solutions benefits from SIPA’s special focus on reducing energy consumption. With better distribution flow and a higher water temperature (14-15°C instead of 8°C), water consumption is minimised and performance in terms of condensation reduction is improved. The smooth, polished, rounded profiles on SIPA hot runners reduce stress on material, resulting in better preform quality and a reduced acetaldehyde (AA) level. Mould systems also exhibit enhanced cooling performance, resulting in high quality preforms, maximum productivity and reduced production costs. SIPA’s service center in Hangzhou, China, in operation since 2004, complements two others in Italy and the USA. www.sipa.it Hall 2 Booth B51 Hall 4.1 Booth C71 inject 4.0 With intelligent assistance systems such as iQ weight control, Engel makes it easy for its customers to ensure consistently high product quality, even without specialist knowledge. The iQ systems continually analyse critical process parameters and readjust them automatically, shot for shot. The result is a self-optimising injection moulding machine. The growing intelligence of the machine control is a key feature of the smart factory, the goal of Industry 4.0. Networking of production systems and systematic use of machine, process and production data additionally help to raise the productivity, quality and flexibility of manufacturing. Under the name of inject 4.0, Engel already offers a series of mature products and solutions for digitalising and networking injection moulding production that have proven themselves in practice many times. These generate considerable benefits both in isolation and as part of a digitalisation strategy encompassing the entire production operation. Engel is demonstrating the potential of the inject 4.0 solutions in the production of inject 4.0 logos on a tie-bar-less and fully electric e-motion 80 TL injection moulding machine. The CC300 machine control is capable of simulating process fluctuations so that the automatic readjustments by the intelligent assistance systems can be tracked on the display. While iQ weight control maintains consistent injected melt volume throughout the injection moulding process, iQ clamp control monitors the mould breathing in order to calculate and automatically adjust the optimal clamping force. www.engelglobal.com Hall 5.1 Booth E71,@ID:52}, 60 TRADE SHOW PREVIEW PETplanet Insider Vol. 19 No. 04/18 petpla.net Technical Forum at NPE 2018 hosted by PETplanet Insider On this year’s Technical Forum NPE 2018 - taking place for the first time - you will learn about new and emerging technologies, about market trends and new directions proven business strategies working today. These are the experts talking about their experience and strategies of their every days challenges and future trends. Exhibiting Company Session Title Speaker(s) ABC Compressors HORIZON 2019 Richard Zhang Agr International, Inc. PET Process Automation - Easy as 1-2-3 David Dineff Conair Capture the future of PET: What will drying technology look like in 5 years? Chris Weinrich Dow Chemical Company Caps and Closures Trends for 2018 Mandy Craig and John Sugden Frigel North America High Efficiency Process Cooling Lou Zavala Husky Injection Molding Systems Unlocking opportunities with next generation engineered PET packages Sean Hoy Improving Overall Efficiency – How Close Collaboration and Focus on the Right KPIs Can Generate Dramatic Results John Quail How Multi-Layer Technology is enabling growth in PET packaging Dave Morton Inherent Closure Features that Enhance Closure Performance and Appeal Mike White ISBT Trends in Beverage Plastic Packaging Ron Puvak ISBT’s Online Beverage Institute Sara Shumpert Lanfranchi North America Switch to PET: The Best Solution for Most of Your Packaging Lucia Comper and Giovanni Renati Moretto USA LLC EUREKA PLUS: Modular, Energy-Saving, Resin Dehumidification System for PET Eugene “Gene” Flockerzi Nissei ASB Containers for Hot Filling and Pasteurizing- A Full Overview of the Challenges and ASB’s Solutions Speaker tbc ASB Technical Support Center Capabilities Speaker tbc Guidelines and Constraints for Optimal ISBM Container Design Speaker tbc One Step ISBM 101 Speaker tbc SIPA The Importance of a Fast and Cost-Effective Response in Plastic Industry Morris De Marchi PET Preform Manufacturing in the Era of Circular Economy Enrico Gribaudo Tech-Long Packaging Machinery Preform and Bottle Manufacturing – A turnkey approach from Tech-Long Keith Boss and Fred Pinczuk W. Amsler Equipment Linear Blow Molding of Non-Conventional Barrier Containers Bruce Coxhead,@ID:62}, BOTTLE MAKING 29 PETplanet Insider Vol. 19 No. 04/18 petpla.net also often pushed outward to heat the gate area of the preform from above. In this case the lamp may be rotated in order that it points downward. Another design feature is the use of tubes with a higher linear watt density in the first (or the first two) row of lamps. Wattages range from 1000 to 3500W. Figure 4.2 Easy access to the infrared lamps is another important design feature. Courtesy of Krones AG. The stack of lamps must also be adjustable in the vertical direction to allow them to be aimed at the exact location in preforms that may vary with the type of neck finish used (Fig. 4.2). Opposite the lamps are the reflectors. These are, of course, made from highly reflective material and contribute up to 40% of preform heating. Polished aluminium has proven to be the most economical material to use. To prevent oxidation, reflectors must be cooled either by air or water and both methods are in use. Tarnished reflectors must be replaced or resurfaced, otherwise energy consumption will increase and/ or bottle quality will suffer. Protecting the neck finish from infrared heat is another crucial part of oven design. Polyethylene terephtalate (PET) starts getting soft at temperatures above 65°C (150°F). If necks soften they are subject to deformation under the impact of hoop stress, that is, the force of the air pressure against the inner neck walls or through handling inside the machine. Neck finishes are protected with one or several metal shields that are either air or water-cooled. Hoop stress increases with the diameter of the neck. Therefore widemouth bottles are exposed to higher hoop stress. Air cooling may be sufficient for a 28mm neck but water cooling may be necessary to protect a neck of 63mm. Figure 4.3 An infrared temperature sensor is mounted before the blowing section monitoring preform temperature. At the end of the oven track, just before preforms enter the blow station or blow wheel, a single infrared thermocouple provides information on preform skin temperature (Fig. 4.3). It should be noted that the thermocouple by its nature cannot provide information on temperatures underneath the preform skin. Depending on preform thickness and equilibration time the sensor might report the same temperature for very different preform conditions. Since it is only monitoring one specific location, the reading will only change when the particular lamp or lamps that are affecting this spot are changed. This can lead to confusion and operators should take note which lamp is affecting the part of the preform that the sensor is monitoring. However, the reading is very useful in monitoring the process once it has been established and machines allow the setting of upper and lower tolerances and will alert operators to deviations. Some machines also close-loop the preform temperature with the lamp output thus reducing the impact of changing environmental conditions. Because of complex interrelationships, algorithms employed on some older machines do not always result in the most stable process and many operators choose not to use this option. product development caps & closures design high cavitation moulds multi-component moulds closure production systems after sales service competent – professional – inspiring Dr.-Walter-Zumtobel-Straße 9 | 6850 Dornbirn | Austria | www.z-moulds.com CHINAPLAS April 24th-27th meet us at booth 2B53 Mould at CHINAPLAS 28mm 1881 FlipTop @KraussMaffei at booth 2T01,@ID:31}, TRADE SHOW PREVIEW PETplanet Insider Vol. 19 No. 04/18 petpla.net 71 Add filling and capping module for an integrated Ecobloc The company further maintains that combining the Ergon EBS machine with a filling and capping module, to form an integrated Ecobloc Ergon K system, integrating the three main wet area operations into a single bloc, helps to achieve optimum performance at reduced costs for the production, filling and capping of rigid containers of up to three litres. This solution does not require connecting conveyors between the stretch-blow moulder and the filler and, in most cases, does not even require a rinser, as the empty bottles are blown, filled and capped on the same machine, thus eliminating risk of contamination from the external environment. Various models of Ecobloc Ergon K systems are available for use on bottling lines of still water (EV) and edible oil (EM). The electronic control of operations provided a filling technology that uses high-efficiency valves, controlled by flow meters, is designed to ensure a very precise and fast process. Preparation times for the machine wash cycle have been reduced by integrating dummy bottles into the valve. The filling and capping module, a new design featuring a modular, seamless frame, is equipped with access doors made of highly resistant and durable tempered glass. The transmission system of the filling module utilises independent axes, using brushless ICOS motors equipped with an integrated driver. The automation and control system, equipped with a very simple and intuitive human-machine interface, permits operation by a single line operator. SMI says that the new EBS K Ergon series of rotary stretch-blow moulders offer attractive quality/price ratios. The system’s compact design means that the machines can be installed in as little as one day, thus offering further savings on installation and start-up costs. www.smigroup.it PET-HIGH PRESSURE LOW PRESSURE A new is coming DOUBLE ACTING DIRECT COUPLED MOTOR HEAT RECOVERY SYSTEM HORIZONTAL OPPOSED PROPAK VIETNAM (Saigon) 20–23 March NPE 2018 (Orlando) 7-11 May PROPAK ASIA (Bangkok) 13–16 June DRINK JAPAN (Tokyo) 27– 29 June GASTECH (Barcelona) 17– 20September CBB (Shanghai) 23-26 October BRAU BEVIALE (Nuremberg) 13-15 November,@ID:73}, TRADE SHOW PREVIEW PETplanet Insider Vol. 19 No. 04/18 petpla.net 54 What makes the FTR process unique? PCR flakes used as feed to the FTR unit can replace up to 50% of PET raw materials, such as PTA, PIA and EG. It can be used to boost capacity of exciting polycondensation units, without changing reactor cascades upstream of the Finisher (Discage reactor, in the case of MTR). The carbon footprint is cut to a fraction, compared to full virgin PET polycondensation. A significant reduction of production cost in the PET manufacturing process can be achieved, depending on the price and availability of PCR-flakes. The needs of brand-owners, NGOs and legislators for a ‘greener’ PET resin, containing a high level of recycled material, is fulfilled by FTR. Uniform product quality is achieved with defined levels of PCR content, as blend uniformity of FTR resins is superior to mixtures of virgin and recycled pellets. UIF FTR technology offers PET producers the following features: it adds a ‘green’ label by producing PET resin with a high content of PCR-flakes it considerably reduces PET resin’s carbon footprint it reduces production cost, by replacing expensive raw material with PCR flakes it is integrated into UIF’s MTR technology to produce PET resin it produces virgin-like PET resin it is approved by FDA and EFSA for food-contact applications it reduces additional efforts at preform manufacturing (logistics, handling, mixing etc.) it is a patented, proprietary technology What will come next? In most industrial scale applications of FTR technology, 10–15% PCR flake content has been found to strike a good balance between plant capacities and local availability of high quality flakes. Commercially operated MTR/FTR units have been proven to run well with levels of 25% PCR in the final chips and to yield a product with properties as good as virgin PET. Requirements for use of higher levels of PCR in all kinds of packaging, including food-contact applications, are expected to become a reality soon; PCR levels of 50% or more in PET chips will be required. Besides improved cleaning efficiencies (degassing, filtration etc.) the whole process has been optimised for a simple and highly efficient production. It also allows relaxation of quality requirements for PCR flakes by integrating pre-sorting directly upstream of the feed to the melting extruder. Tolerance of inferior flake quality means that the FTR process will become even more economical and will lead to a bigger pool of potential suppliers of flakes. www.thyssenkrupp-industrial-solutions.com FTR recycling integrated into MTR technology,@ID:56}, PETplanet Insider Vol. 19 No. 04/18 petpla.net 77 BOTTLES Bio rose blossom water in PET The German discount pharmacy dm is selling 100ml of bio rose blossom water for the cleansing and care of dry skin under its own brand “alverde” in a light pink coloured bottle with a screw-on pump dispenser – also pink. The product can be applied directly to the face and/or body either by spraying directly or by moistening a cotton pad and smoothing over skin. Storing in the fridge is recommended to improve its effectiveness. The label gives details of content and application. www.dm.de Washing up liquid with floating pearls In a promotion for the start of spring, the German discount pharmacy dm is showcasing various cleaning products for all kinds of housework. These “Fleck Weg Editions” are presented in its stores in suitable displays. The products differ from typical cleaning products with their amusing names or an altered appearance. One example from the promotion is a washing up liquid for dishes from the own brand “Denk mit” with tiny beads in different colours that seem to float in the product. The clear product is available in a bulbous 500ml bottle with the slogan “I just want to wash up”. It has a screwed-on hinged cap seal with dosage opening. www.dm.de,@ID:79}, MATERIALS / RECYCLING PETplanet Insider Vol. 19 No. 04/18 petpla.net 18 A far-reaching European enactment – what about the industrial solution? “Plastic packaging never returns into waste” by Heike Fischer It was perfectly timed; doubtless this was planned, shortly after the statement of the European Union presenting their Strategy Paper for Plastics in a Circular Economy, released in January 2018, the entire PET value chain meets in Brussels for the annual Petcore Europe Conference. On February 7-8, 2018 more than 200 delegates from Europe and beyond gathered in Brussels discussing the “Strategy for PET in the Circular Economy”. A comprehensive conference programme included a number of the leading players in the sector: Christian Crepet, Executive Director of Petcore Europe and Paola Arlotti, President of Petcore Europe: speakers from the European Commission (DG GROW), the Ellen MacArthur Foundation as well as PCI Wood Mackenzie who all shared their thoughts on the PET market as well as the plastics industry in the European Circular Economy. The topic for the first day can be summarised in the title: Trends in PET collection, recycling & sustainability, and perspective & strategy from the PET value chain. Helen McGeough from PCI Wood Mackenzie gave an overview of the 2016 PET collection and recycling rates as well as the key drivers of the market. According to her “economics is still a key driver of the PET market, however, sustainability is moving up the agenda.” With Alessandra Funcia, Head of Marketing at Sukano, one of the most frequently raised topics was introduced: The new recycling material challenges and opportunities of PET thermoforms and ODR (opaque and difficult to recycling PET) containers. Alessandra referred to the working group of Sukano and Petcore. The working group defined the recycling guidelines for ODR containers and disseminates to promote them throughout the value chain: Improve sorting and establish suitable end applications for recycled material. In addition, the image of ODR containers and PET should be improved to help maintain and even increase post-consumer recycling performance as new applications are unveiled. For this to happen, new technical solutions have to be found in a fast-growing market of ODR PET bottles. The end of life status has also to be defined and the validating accepted standards conditions to streamline existing and future developments. This will endorse the EU action plan of ensuring that all plastic packaging is recyclable by 2030. As a preliminary conclusion, the working group raised some of the problems currently facing recyclers: a difficult economic situation due to low oil prices, the increasing presence of contaminants in bales, decreasing quality and finally production yield. There is the need to increase recycling rates in the short term to add value to PET chain and the EU economy. The existing technology tackles ODR bottles today but volumes remain relatively low. Higher expectations for additional ODR business would give the right recycling conditions and directions. Incentives to include recycled materials in new product design would boost the demand for recycled plastics. The group recommended a standardisation in the waste stream across the EU, an agreement on bale requirements and quality will directly and positively impact the market. But investing in expansion and modernisation of sorting and recycling capacity are lagging behind due to uncertainties concerning market outlets and profitability. The compounders are ready to consume coloured PET bottle flakes to provide it as mono-material. After this introduction, experts from the PET value chain gave a detailed market overview. First, Antonello Ciotti, President of CPME, spoke about perspectives for European PET manufacturers. In his view, “the circular economy directive requires a major modification in the actual packaging chain. That is why CPME members are introducing and supporting innovative and sustainable packaging solutions in PET.” Antonello was followed by representatives from the PET converting industry. First, Ana Fernandez from Klöckner Pentaplast stressed the importance of sustainability when it comes to PET thermoforms: “We need to design packaging for the circular economy. PET has an excellent environmental profile due to its lightweight and recyclability.” Ana also emphasised that “end-users have to be better informed since they represent the first step in the recycling process.” Paulo Correia, CTO Eric Liégoise, member of the EU comission, presented the EU Plastic Strategy paper for the first time in public. Paola Arlotti, President and Christian Crepet, Executive Director welcomed their guests in Brussels.,@ID:20}, 47 TRADE SHOW PREVIEW PETplanet Insider Vol. 19 No. 04/18 petpla.net TRADE SHOW preview Chinaplas 2018 This year’s Chinaplas will be held for the first time at the National Exhibition and Convention Center (NECC) in Hongqiao, Shanghai, PR China, on April 24-27. The exhibition area is expected to exceed 320,000m2 - 30% more exhibition space than that of the 2016 edition of the show in Shanghai. Chinaplas will bring together 4,000 exhibitors from 40 countries, who will be allocated over a series of well-organised theme zones. New theme zones To ensure a welcoming and pleasant visitor experience, the show organiser is rearranging the overall theme zone layout. Extrusion-related technology will be in the eastern part of the NECC, injection moulding technology will be in the west, and blow moulding technology will occupy the southern part of the complex. Adsale is also arranging exhibits of the same category in nearby locations, for example, “film technology and plastic packaging machinery” and “injection moulding technology and smart manufacturing equipment” etc. And different European pavilions, which were scattered among different halls in the past, will be gathered in Hall 2H. “3rd Industry 4.0 Conference” Industry 4.0 solutions facilitate business transformation. Chinaplas began organising a conference on this topic two years ago and received enthusiastic feedback. With continuing support from VDMA, the German Engineering Federation, the “3rd Industry 4.0 Conference” will take place at the show. Drawing on an accumulation of Industry 4.0 experience among global enterprises, the topics of this conference will be far-reaching and practical. Participants can expect plenty of industry 4.0 factory case studies and in-depth application discussions. The conference is scheduled on April 24-25 (afternoon) and April 26 (morning). “Tech Talk” The organiser introduced “Tech Talk” last year to enrich the technology content of Chinaplas, creating a platform for international exhibitors to launch their state-of-the-art products. It also featured more than 30 talks, which provided visitors with valuable knowledge. This year, “Tech Talk” will shed light on a wide range of topics, including: “Smart Manufacturing”, “Innovative Materials” and “Green Solutions”. “Tech Talk” is scheduled on April 24-26, in both Hall 4.2 and Hall 8.2. More than 80 technical seminars In addition to the events highlighted above, more than 80 technical seminar sessions will take place during Chinaplas 2018. These include “Application of Plastics in Transportation Protection Packaging Technology Summit”, and much more. www.chinaplasonline.com Hall 8.1 Booth B03 Swiss Made | www.imdvista.ch S-11057 NPE2018: The Plastics Show, May 7th -11th, visit IMD @ Inspection Systems for the Plastic Packaging Industry IMDvista BTIR & LAYER IL Barrier Inspection high speed. Layer Measurement Inline (NEW). Easy integration. IMDvista PECO V3 Preform Inspection. Less than 7mƹ and up to 90’000 pph. Cavity reading. IMDvista PECO LUX Preform Monitoring shot by shot. Requires no additional floor space. No preform orientation. The PETplanet Insider team is looking forward to meeting you in Shanghai! You are assured of a warm welcome in Hall 8.1 stand B03!,@ID:49}, BOTTLING / FILLING PETplanet Insider Vol. 19 No. 04/18 petpla.net 32 Mastering liquid food manufacturing Something to eat or drink? The worldwide beverage market is forecast to grow to USD 1.9 trillion by 2021, which is great news for manufacturers. What’s slightly trickier is what consumers are actually asking for: a variety of high quality hybrid products which are also produced sustainably. So the question is: How can we help manufacturers to create a wide range of beverages as efficiently as possible? Following the process of bottling liquid food as described here, GEA believes that aseptic dual-fill technology will play a decisive role here. Demand is growing for beverages that include solids, such as fruits, fibres, nuts and cereals. Acting as stand-in meals, “liquid food” has become increasingly popular as a result of people’s busy lifestyles and unwillingness to compromise on nutrition or mealtimes just because “time is of the essence.” However, traditional single-line pasteurisation systems are unable to process products with a solid content of more than 5–10%. The challenge then for manufacturers is to treat the products in way that ensures product safety and shelf life requirements, while maintaining taste and texture. Likewise, processors need to have the flexibility to optimise the volume of solids in the products to meet increasing customer demands for a greater variety of ingredients. Getting it right from the start – prep and pasteurisation Manufacturers must accommodate the different requirements of liquids and solids throughout the entire manufacturing process because each product requires a different level of heat treatment to achieve bio-stability. In order to prevent damage to these products and to achieve the best possible product quality – as well as minimising energy consumption – it is necessary to precisely balance the levels of heat used throughout the process. Solid ingredients are generally delivered as compote in a carrier fluid or in pieces. If delivered dry, they must first be mixed with a carrier liquid before further processing can take place, such as pasteurisation or aseptic filling. Liquids on the other hand, are often prepared in advance, having already undergone deaeration, and may have already had ascorbic or citric acids added to them or even undergone homogenisation. Next, each component must undergo pasteurisation. For a long shelf life, microorganisms – including dormant spores – must be killed or inactivated. And while the application of heat destroys harmful bacteria and spores in foods, it can also adversely affect both the taste and texture of products. Using unnecessary heat is also expensive and wasteful which is major concern as companies strive to reduce their consumption and emissions. For fruit juices, pasteurisation at a minimum temperature of 85° Cel-,@ID:34}, PACKAGING / PALLETISING PETplanet Insider Vol. 19 No. 04/18 petpla.net 43 , / 0 Toronto New York Atlanta Orlando Denver Las Vegas Seattle Los Angeles San Francisco Vancouver Dallas New Orleans Phoenix Washington, D.C. Boston Detroit Kansas City Oklahoma City Albuquerque Milwaukee Chicago Minneapolis Charlotte Ottawa Montreal Quebec www.npe.petpla.net March – August 2018 The North American Road Show - Bottle Zone on tour PETplanet has successfully deployed its “Editourmobil” Road Shows across the world for seven years now. This is in addition to traditional forms of reporting; we have found that travelling by road enables deeper insights into markets; interviews with bottlers, suppliers and manufacturers can be conducted with greater flexibility, both in cities and in more rural areas. The appearance of the Editourmobil has created quite a stir in several countries - in addition to the impact of the interviews and meetings themselves. The Editourmobil is to return to North America once again, in cooperation with the NPE trade show (May 7 – 11, 2018 in Orlando, Florida). From March through August 2018 - three years after our last tour in 2015, which proved to be very successful - the PETplanet team will, once again, visit a variety of locations across the USA and Canada. The “Editour“ journeys will take in professional discussions and interviews with market leaders from the West to the East Coast. We will be stopping off at the NPE show itself, where the PETplanet and Editourmobil team will present initial reports of our visits and interviews. We will be part of the new Bottle Zone, which will be a first for us as well! Make sure you’re on board with us when we set off again. Get ready for in-depth analyses of the special features and trends in the bottles and beverages sectors of North America! All aboard! Premium Sponsor to date Sponsors to date The worldwide round trip with,@ID:45}, INSPECTION 40 PETplanet Insider Vol. 19 No. 04/18 petpla.net Intravis presents Industry 4.0 applications Smart factories are becoming a reality By displaying a Closed Loop link between an injection moulding machine and a vision inspection system, Intravis GmbH demonstrated the benefits of its Industry 4.0 solutions. Specifically, the specialist in quality control for the plastics packaging industry is showing how the combination of high precision inspection system and analysis software can minimise scrap by using an intelligent approach. Industry 4.0 remains the buzzword in manufacturing. In the production of plastic packaging, it stands for a fusion of the most modern IT benefits with current production technologies. The goal is to achieve improved time and cost efficiencies in production while not compromising product quality. Intravis has been focusing on the latter for years by combining state-ofthe-art inspection technology - with hardware and software. By using its vision systems to not only inspect but to improve production, Intravis is becoming “the eyes of Industry 4.0”. “Closed Loop” realised At last year’s Drinktec in Munich, Intravis presented their vision of the future for quality control for the plastic packaging industry. Together with Netstal, a functioning Closed Loop link between an injection moulding machine and a vision inspection system was presented for the first time. Every part being manufactured has its quality parameters inspected by the vision inspection system. The resulting data is analysed and summarised into trends. This precise data powers the Closed Loop’s effectiveness. The data generated during the quality control is transmitted to the injection moulding machine, relaying detailed information about the parameters of the object within a short time. With this constant information interchange, operator interventions are reduced to a minimum. On the basis of the analysis results, the injection moulding machine automatically regulates its corresponding settings. This Closed Loop relies heavily on the precision of the measurements performed; the more precise the quality control, the better the data, the better the analysis and the more successful the regulation of the manufacturing process. Intravis demonstrated the functionality of the Closed Loop link by means of the diameter inspection of beverage closures produced at the trade show. “By changing individual settings on the injection moulding machine, a deviation of the diameter from a predetermined tolerance range was deliberately created - the simulation of an external influence”, says Dr Gerd Fuhrmann, CEO of Intravis GmbH. “Our high-precision vision inspection system, a CapWatcher III, directly determines the continual deviation of a parameter, in this case the diameter. It immediately reports this deviation back to the injection moulding machine via an OPC UA interface. Based on the transferred data, the injection moulding machine starts a self-correction process and produces closures within the tolerance limits within a very short time. After a few production cycles, everything is back within the tolerance range.” Advantages of a Closed Loop The advantages of such a fast self-regulation are obvious: Less scrap and rejects are manufactured. This increases the effectiveness of a line and its yield. In addition, the manual intervention of an operator is reduced significantly, which makes the production less susceptible to improper operation. This means energy savings and improved sustainability. The use of a Closed Loop link is not limited to the production of closures. It can also be integrated into other plastic packaging manufacturing processes. Diagram of a closed loop link between an IMM and an Intravis vision system,@ID:42}, TRADE SHOW PREVIEW 69 PETplanet Insider Vol. 19 Fastest neck change In the highly saturated market of PET SBM machines one need to possess a competitive advantage against other manufacturers to gain customers’ attention and trust. FlexBlow claims that the latest 2018 two cavity FlexBlow2 model is the most universal 2-stage PET SBM machine on the market. It enables the production of wide range of PET containers possible on one piece of equipment with necks ranging from 18mm up to 110mm and bottle volumes from 50ml up to 6,000ml. Changing the bottle format including moulds, neck and gripper parts, and fine-tune the machine afterwards takes no longer than 30m, according to FlexBlow Marketing Manager Gytis Sirvinskas. There is a number of developments that FlexBlow has added to their new machine in 2018 to stretch the ease of use and flexibility even further. To begin with, their dedicated Siemens control panel now has several new functions to make the experience of operating the machine intuitive. There is an integrated operator’s manual that guides the user along every step of operation to make it repeatable and minimise the impact of human factor. There is also an integrated catalogue to achieving top PET bottle quality with pictured troubleshooting guide, not to mention the machine production and efficiency statistics for performance tracking. The challenge of automatically loading a range preforms with significant differences in neck diameter from narrow neck to wide mouth has been tackled by the use of dual preform loading system. When it comes to minimising the support ring, FlexBlow uses the precision adjustable feeding slides that allow loading preforms with support ring starting from 0.8mm. Inversed preforms with body wider than support ring is also compatible with FlexBlow universal feeding system due to innovative gate-like structure that opens slightly at the end of preform slide to allow the thicker preform body to come out. The company plans to bring equipment for wide-mouth jar production, SBM machine for cosmetic bottles and a PET blower for large size bottles – all in one machine. Live changeover shows will take place daily to demonstrate the process of switching between wide mouth jar and cosmetic bottle production. www.flexblow.com South Hall 10196,@ID:71}, TRADE SHOW PREVIEW PETplanet Insider Vol. 19 No. 04/18 petpla.net 58 ASB to demonstrate one-step high output triple row moulding Moulding live on stage cavities. At a cycle time of 7.5s the ASB-150DPX will achieve a production rate in excess of 17,200bph. Even if a container design such as this could be moulded by re-heat blow moulding, the required floor area for a similar capacity two-step production unit would be three to four times greater, Nissei ASB says. The onestep solution is claimed to provide technical superiority and enhanced quality, in a significantly reduced production space. The recent rise in prices of PE/PS materials means that demand for PET conversion of this type of small container is increasing. The company has received a number of specific inquiries from major food manufacturers and is confident of good demand for this new model. Nissei ASB’s stand will, in addition, host demonstrations of a full range of compatible moulding ancillary equipment, including a resin dryer, chiller, mould dehumidifier and mould temperature controllers. An in-house custom-designed pick and place takeout unit with conveyor system will also be on show. www.nisseiasb.co.jp Hall 8.1 Booth D75 Nissei ASB will be holding live moulding demonstrations on its 210 square metre booth, along with a display of some of its most interesting recent updates in injection stretch-blow moulded packaging technology. The company’s triple row, high output ASB-150DPX model for small bottle production will be making its regional debut. Visitors will be able to see live demonstrations of the complete moulding system, every day. The new machine expands the company’s ASB-150 based models to three variants: The ASB-150DP offers single row moulding up to 16 cavities and is designed for very large bottles and jars; the ASB-150DPW double row model moulds medium sized bottles and jars up to 32 cavities. The new ASB-150DPX offers triple row, small bottle moulding in 24, 36 or 48 cavities. The three models are built on common architecture so factory layout, key functions, spare parts, maintenance and operator training are the same across the range. The newly added DPX model has specific design features to maximise efficiency in small container moulding. The injection clamping stroke is optimised for short cycle small containers and its upgraded hydraulic components provide a faster injection clamping cycle while maintaining smooth machine movement; servo hydraulic pumps, which are fitted as standard offer, up to 30% reduction in energy consumption. Its blown air circuit is optimised for small container production. Nissei ASB says that it consumes up to 50% less air than standard systems. While these features were introduced for the ASB-150DPX, all but the small bottle-optimised clamping stroke are planned to be made available on future updates of its range-mates. Nissei ASB says that one-step, triple row injection stretch blow moulding is a “global first” for the company. Several areas of the machine design are already patented or have patents pending. At Chinaplas, the ASB-150DPX will be conducting daily moulding demonstrations of a 180ml, 11.4g yoghurt drink container, with a standard 38mm neck. This lightweight container design requires a very short preform that would be impossible to handle and re-heat in a two-step system, so the one-step moulding process, where the container is formed directly from resin within one machine and held securely by its neck throughout, is the only practical choice. The smaller the container is, generally the more advantageous it is for production on a large one-step machine with high outputs. The demonstration machine’s triple row moulding layout has 36 blow,@ID:60}, PETplanet Insider Vol. 19 No. 04/18 petpla.net 76 PETbottles Home + Personal Care Environmental awareness from Aldi Under its own brand “Zekol”, Aldi Süd is launching a particularly environmentally friendly kitchen cleaner with scent of orange blossom and the endorsement “Environmentally Aware”. According to the printed statement, the light orange coloured product contains a plant-based surfactant of European origin that conforms to the requirements of the EU Ecolabel (www.ecolabel.eu). It is also stamped with the “Blue Angel” seal for ecological products. The clear, easy-grip bottle is made from 100% recycled plastic, holds 750ml and is combined with a screwed-on lockable trigger. www.aldi-sued.de “The General” as spray cleaner Recently, the well-known all-purpose cleaner “The General” from Henkel has become available in a spray variety. The product is advertised with the description “Spray – Wipe – Done” with the first wipe. The white easy-grip bottle of the “Mountain spring” scent has the pump spray often used by Henkel. It clips on to the opening and features improved function and handling. The spray head is locked and unlocked by twisting it 180° and the white lateral slider enables switching between spray or foam. www.henkel.de Suprême Perfume Pearls from Vernel Following the trend for washing scents, an increasing number of washing detergent and fabric softener manufacturers are launching granulated or pearl-shaped additives under their own brand names to keep laundry scented more intensively for longer. Under the brand “Vernel” and the name Suprême Perfume Pearls, Henkel is selling three differently scented varieties that promise fragrance for up to 20 weeks in a clear, easy-grip, contoured PET bottle that holds 260g. The container is sealed with a screw cap with two small openings, allowing the consumer to smell the scent in store on the shelf without taking this off. There is also a protective cap that functions as a dosing aid. Aromatic air is released from inside when the bottle is pressed. The bottle is decorated with a full sleeve label. www.vernel.de,@ID:78}, TRADE SHOW PREVIEW PETplanet Insider Vol. 19 No. 04/18 petpla.net 53 technology co-operation has to be fostered, in order to raise PET packaging’s recylclate content. The PET recycling technologies currently available are detailed in Table 1. The table shows that only Uhde Inventa-Fischer’s (UIF) FTR technology can produce high quality, virginlike PET resin, economically, at high production capacities, claims the company. Since UIF introduced its proprietary, FDA-approved FTR in 2007, several FTR units have been brought into production at PET manufacturing sites in the US, EU and Asia. Units are designed to be attached to newlyinstalled PET manufacturing plants but they can also be integrated into existing plants using MTR (Melt-toResin) technology, as well as conventional SSP lines. What does the FTR process look like? Post-consumer recycling (PCR) flakes undergo a two-step process. First, impurities are removed; then, the PCR material is remanufactured to a virgin-like, bottle-grade resin. The PCR flakes are fed into an extrusion unit, where they are gently transferred into the melt phase. The first deconFTR technology by UIF Physical recycling Chemical recycling to raw material Description Partly glycolysis and feed before Finisher Reactor (when combined with MTR, Discage reactor) Bottle to bottle process with pre- or post-treatment for decontamination and viscosity adjustment of flakes/pellets Mostly catalytic break-up of PET by Hydrolysis, Glycolysis or Methanolyis Product Virgin-like PET resin with adjustable rPET content rPET, to be mixed with virgin PET at preform making Raw Material PTA & EG, or DMT & EG, or intermediate product BHET. By-products are challenging De-contamination steps Including pre-washing: 4 steps. Most powerful de-contamination in Finisher. Including pre-washing: 3 steps Complete de-polymerisation Filtration Fine filtration of glycolysed melt at low viscosity Filtration at high viscosity Complete de-polymerisation Sensitiveness to PRC flakes quality Sensitive, pre-sorting can be integrated Sensitive Not sensitive CAPEX & OPEX Medium-Low Medium Very high Proven technology Yes Yes Only Methanolysis has been operated for some time. FDA approved EFSA approved Yes up to 50 % PCR flakes Yes, ruled as chemical recycling Yes Yes Methanolysis: yes, other no, but approval is no issue Table 1: Survey of PET recycling technologies MTR is UIF’s proprietary Melt-to-Resin technology. It produces high viscosity PET resin in an integrated process, without a Solid State Postcondensation (SSP) unit. tamination is performed by applying vacuum to the melt, with low boiling components like water or acetic aldehyde being effectively removed. At the same time the PET is partly glycolysed, by feeding a defined amount of ethyleneglycol (EG), so as to achieve the same intrinsic viscosity (IV) as virgin pre-polymer. EG dosing is controlled by an on-line viscosimeter. The melt is passed through a highly efficient filtration system, for removal of solid impurities like traces of paper, coatings, dirt, etc. Finally, it is combined and admixed to the virgin pre-polymer stream from the polycondensation plant, before the final stage in the polycondensation reactor (Discage). Cleaning in the Discage reactor is under high temperature and high vacuum conditions, which allows the removal of even very high boiling contaminant. The reactor also increases the viscosity of the polymer melt to the required final level. The melt leaving the reactor is subject to a final filtration, where any remaining impurities are removed. An underwater pelletising system converts the PET melt into pellets. The final step is the removal of acetaldehyde in a conditioning silo, operated at mild temperature and with air atmosphere. Diagram 3: FTR concept with part depolymerisation and feed into virgin PET-prepolymer stream,@ID:55}, PREFORM PRODUCTION PETplanet Insider Vol. 19 No. 04/18 petpla.net 24 Constant quality in the preform production process Automatic control of injection pressure Process control, stable product characteristics and improved energy efficiency: Piovan claims that these aims have now also been achieved in PET treatment thanks to its Automatic Injection Pressure Control (AIPC) Technology. AIPC is the new Piovan patentpending technology which enables the injection moulding machine to “guide” the Genesys drying system so that it operates with a constant injection pressure around a customer-defined set point. In a conventional PET preform production system, the resin drying phase is not connected to injection and preform production: therefore, the pressure does not always fall within a predetermined range of values which could ensure a constant product quality throughout the cycle. On the contrary, the pressure fluctuates continually, causing possible variations in the characteristics of the PET products. Injection pressure Injection pressure is a fundamental process parameter, because it is directly dependent on the amount of water left in the PET after the drying process. Keeping it constant ensures that the preforms produced always have the desired properties and physical characteristics. Prior to the introduction of automatic pressure control, Genesys dryer’s performance was optimised using the AECS algorithm, based on measurement of the weight loss of the dried material. Equipped with a state-of-the-art control, Genesys is a “self-adaptive” system: it automatically, continually manages the quantity of air to be introduced into the production process; further, it allows reductions of 35% to 55% in electricity consumption, independently stabilises the air flow in the drying hopper and recovers energy for sieve regeneration, creating additional savings compared to the conventional systems currently used for PET processing. Although precise, injection pressure monitoring is one-way and takes place on a feedback basis; in addition, the graph of this essential parameter shows significant variations. Now, Piovan has researched and with AIPC developed an innovative system for minimising them. With AIPC, the IMM itself supplies the data necessary for process management, ensuring that the degree of drying is really suitable for the type of preform to be produced. With the aid of a signal transducer, the injection pressure is continually measured at the extruder and sent to the Genesys dryer. The dryer continually adapts its operation even more effectively in order to keep it within a working range suitable for the type of production, with variations not exceeding ±2 bar throughout the cycle. Equipped with automatic pressure control as well as with selfadaptation functions, Genesys gains the capacity to operate constantly in line with the IMM. The machine supplies continuous reading of the injection pressure and the dryer adapts its action on the basis of this uninterrupted data exchange. The result is shown on the control screen: the graph remains stable within ± 2 bar of the operator’s chosen set point. The advantages claimed for the system include: the injection pressure remains stable: rejects are reduced. The cycle time is improved thereby increasing efficiency and electricity consumption is optimised. Advantages The injection pressure remains stable around the optimal value set on the basis of the product’s required characteristics. AIPC Technology allows to determine, in a precise and accurate way, the preform properties that depend on the injection pressure value. Keeping this value constant ensures that the intrinsic viscosity (IV) and acetaldehyde (AA) values do not vary during the production process: the quality of the result remains unchanged. Reduction of rejects The total synchronisation between dryer and IMM during the production of the actual preform improves the cycle time and increases the productivity of the whole system. The dryer’s electricity consumption is optimised, maximising the energy efficiency of the entire system and reducing waste and costs. www.piovan.com,@ID:26}, 63 TRADE SHOW PREVIEW PETplanet Insider Vol. 19 No. 04/18 AF Compressors shows off its leadership qualities After having partnered with eight of the leading blow moulder manufacturers in drinktec 2017 in Munich, AF Compressors will be providing high-pressure compressor air for the Bottle Pavilion at the NPE Show. AF will be operating the AF models L5B and L6B compressors for a total air capacity of 3,850m³/h to supply air to six blow moulder manufacturers (Nissei ASB, Tech Long, Serac, SMI, Sipa, and Meccanoplastica). www.afcompressors.com New technologies for optimising plastics to increase sustainability and cost savings Vertellus, a leading global supplier of additives to the plastics and polymer industries, will introduce two new technologies for driving increased use of recycled polyester in nylon resins (creating alloys) and enhancing the benefits of rPET. By enabling new alloys and compounds containing these recycled resins to deliver improved properties and processability, Vertellus’ new additive solutions will help compounders and OEMs boost sustainability and control costs without sacrificing performance. Vertellus will also showcase a novel, patent-pending technology for upgrading recycled PET and, potentially, bio-plastics such as polylactic acid (PLA). This new additive is expected to deliver higher clarity and better performance at lower dosages. www.vertellus.com South Hall 16053 South Hall 10155 Preform moulds PETform, India, a manufacturer of two stage & single stage moulds for PET packaging, will show a 72-cavity preform mould for a Netstal PETline machine. It will also display a preform moulding solution for heavy thick walled preforms with an innovative postcooling system that functions without the use of a robot. The technology is based on empying an additional set of cores and two sets of aluminium sleeves to provide post mould cooling for approximately one additional machine cycle of cooling on the core and two additional machine cycles of cooling in the sleeves. It allows for earlier de-moulding compared to conventional outside mould cooling systems. These are currently being used in the industry but do not have the ability to control preform ovality if the preform is de-moulded too soon, says the company. www.petform.net South Hall 15087,@ID:65}, 51 TRADE SHOW PREVIEW PETplanet Insider Vol. 19 No. 04/18 petpla.net Advanced pelletisers Maag, a leading global manufacturer of gear pumps, pelletising and filtration systems as well as pulverisers for challenging applications, is highlighting pelletising systems for plastic producers, compounders and recyclers. Chinaplas is also Maag’s first joint appearance with Ettlinger, a manufacturer of high-performance melt filters for recycling applications which was acquired by Maag since the beginning of the year. The pelletising systems presented at the show focus on the Zhuli, Pearlo, Baoli and M-USG series. Maag’s Zhuli underwater pelletising system was expanded with the new Zhuli MAP, building upon the ZHULI SLC (SLC stands for Spring Loaded Cutters) which was introduced in 2017 and is the cost-effective basic system for numerous standard applications with low to medium throughput. While the knives in the SLC type are pressed against the die with a permanently selected spring pressure, the pressure of the knives against the die in the new MAP type (Manual Adjustable Pelletiser) is variably adjustable. This option extends the application range by making it possible to adapt to the relevant process parameters. Pearlo is the high-performance underwater pelletising system from Maag for making spherical pellets. It combines technologies from the previously independent companies Gala and Automatik for efficient and flexible use in challenging applications with throughput of up to 36,000kg/h. Compact and modularly designed, it requires only a very small footprint in production. Electronically controlled EAC technology guarantees precise feed of the pelletising knives during operation, thereby ensuring long runtimes free of interruptions with consistently high pellet quality. Baoli dry-cut pelletisers for compounding and recycling hard and soft materials are available at Chinaplas in the 3rd, completely revised generation. With working widths up to 300mm, they are designed for processing up to 75 polymer strands into cylindrical pellets from 1.5mm to 5mm in length. Their advantages compared to previously available versions include the more compact design and good accessibility for cleaning as well as variable height adjustment and control elements optionally positioned on the left or right side for added operational flexibility. The M-USG underwater strand pelletisers are the flagship of Maag pelletisers for making raw plastic materials such as PET, PA and PC. With throughputs of up to 20,000kg/h, they stand for consistent pellet quality, high system availability due to the quick-change cutting head, a high level of automation, long service life of the wear-resistant cutting tools and good accessibility for convenient operation and maintenance, says the company. www.maag.com SDWHQWV UHVHDUFKHUV DQG WHFKQLFLDQV LQVWDOOHG SODQWV EUDQFKHV ZRUOGZLGH ,I ZH KDGQêW JRQH VR IDU ZH ZRXOGQêW EH VR QHDU RXU IXWXUH VHHQ IURP QHDU Hall 2 Booth P83 M-USG underwater strand pelletiser,@ID:53}, CAPS & CLOSURES 38 PETplanet Insider Vol. 19 No. 04/18 petpla.net 25 people are currently employed at the factory, working on a two shift system. If orders demand it, 24/7 operations are also possible, Michael Van Dord told us. As well as straightforward manufacturing, the company also works with customers to develop appropriate closures for their specific needs, supporting them throughout the process, from idea to production prototypes. Its standard portfolio ranges from 22mm to 83mm, with demand for large diameter closures being particularly big. During our visit, closures for PET honey pots were leaving the conveyor belt; they are an important current growth market. Compared with competitors like giant-sized packaging firms Visy or Orora, Caps & Closures sees its strengths to be in areas in which a high degree of flexibility and the appropriate outputs are required in the low cavitation segment. “Of course, we can also manufacture high volumes if required but our size gives us the ability to respond at short notice and to address our customers on an individual basis“, says Brendon Holmes. In the drinks segment, Caps & Closures manufactures for Asahi, Schweppes, fruit juice manufacturers and the discount brands of supermarket chain Coles, amongst others. The focus is on the Australian market; its exporting business is limited but it has plans to expand to Asia, to China in particular, where Australian products are generally highly regarded. The company estimates that around half of its sports drinks closures are sold throughout Asia. In the future, the company wants to gradually increase its market share in the high cavitation market, whose biggest segments are food, beverage and pharmaceuticals. This is another reason for its investment in the most recent new additions to its machine park, including two Netstal Synergy systems. Caps & Closures has plans to expand the plant in the local industry park and to launch new products. “We have recently developed a new form of dispensing closure which we are presenting in this interview for the first time,” Michael Van Dord says. The new product retains the twist-pull concept on the neck of the bottle; depending on the application, whether dosing opening or drink opening, it is opened and closed by twisting. The closure is currently intended for HDPE bottles but Brendon Holmes tells us that it could be very interesting for PET bottles. “We are also working on a new technology for product traceability using microchips,” he continues. “This would be of interest for products in the higher priced segment, for example, in which counterfeiting is an issue.” In response to the question of what makes Caps & Closures the company it is, Brendon Holmes says: “Our creative teams, consisting of engineers, designers and specialists, are exceptionally hard working and transfer their dedication to our products. We work for our customers on a global basis; we want to develop excellent new technologies and bring them onto the market in collaboration and partnership with them.” www.capsandclosures.com.au Brendon Holmes and Michael Van Dord (left) in the company’s foyer,@ID:40}, CAPS & CLOSURES 36 PETplanet Insider Vol. 19 No. 04/18 petpla.net Closures from Melbourne by Kay Barton Australian company Caps & Closures’ manufacturing facility is situated in Dandenong South, to the south east of Melbourne, the capital city of the state of Victoria. The company’s name perfectly describes its main activity: it manufactures plastic closures locally for domestic and foreign manufacturers. Its products are used across a wide range of business areas, including the food and beverages industry and almost every conceivable area of non-food. For managing director Brendon Holmes, who is also the company owner, PET plays an essential role; a growing trend towards this material as the preferred packaging is clearly evident in the market. Caps & Closures intentionally focuses on smaller manufacturing volumes and specialist solutions but it also intends to secure a stronger presence in the high-cavitation market in the future. February 15, 2017 We met: Brendon Holmes, Managing Director Michael Van Dord, Technical & Design Engineer Bruce Langlands, Head of Sales We were greeted at Number 1 Quality Drive, the headquarters of Caps & Closures, by Bruce Langlands, Head of Sales. He escorted us past the manufacturing facility on the ground floor and upstairs to the company foyer, which features a large, eye-catching logo on the wall and hosts recessed cabinets, displaying a variety of the company’s closures. To the left in the offices section towards the rear is the meeting room, which is adjacent to co-founder, owner and managing director Brendon Holmes’ office. Large-size paintings hang on the walls, which we later find out were painted by Mr Holmes himself. We discussed the company’s key cornerstones with Mr Holmes, Bruce Langlands and Technical & Design Engineer Michael Van Dord, who has been with the company for three years. “We view our young and innovative team as a strength; we want to offer our customers flexibility,” Mr Holmes says. The company was originally founded in the early 1990s, as Tec Caps, and adopted its current name a few years later. Mr Holmes – along with his family – acquired it in 2004; he has been sole owner since 2017. Surprisingly, his professional background is from a completely different sector. He’s an enthusiastic golfer, a musician and a painter. He brings his passion for artistic creativity into his business, which is reflected in the corporate style. “We started off with eight injection moulding machines from Battenfeld and manufactured for all of the areas in which closures were required,” he explains. “That included drinks, food, cosmetics, pharmaceuticals and medical products, lubricants, agricultural products and much more.” Today the company has 22 machines with clamping forces ranging from 35t to 240t, including Nissei and Netstal equipment in addition to Battenfeld. Creative paintings of Brendon Holmes (F.l.t.r.) Brendon Holmes and Michael Van Dord,@ID:38}, EDITOUR PETplanet Insider Vol. 19 No. 04/18 petpla.net 14 History of Husky Husky is founded in 1953 and was initially a small machine shop with no ties to the plastics industry. Husky Injection Molding Systems Ltd. is a publicly traded company from 1998 to 2007. On December 13, 2007, the Canadian private equity investment firm Onex Corporation completed a friendly buy-out of Husky for $960 million. On May 26, 2011 Husky announced it completed the acquisition of KTW of Waidhofen, Austria, recognised as a global leader in closure mould making. Berkshire Partners LLC and Omers Private Equity Inc. announced on June 30, 2011 the successful closing of their previously announced acquisition of Husky International Ltd for $2.1 billion. On December 19, 2013 Husky announced completion of the acquisition of the Schöttli Group of Diessenhofen, Switzerland, recognised as a global leader in medical and closure mould making. In 2018 global investment firm Platinum Equity signed a definitive agreement to buy Husky for $3.85 billion. John Galt CV John Galt is President and Chief Executive Officer of Husky, having been appointed in September 2005. He joined Husky in 1985 and during his 33 years with the company has held a number of progressive positions in the areas of engineering, manufacturing and customer service. John holds a Mechanical Engineering Degree from Ryerson Polytechnic University in Toronto. Louis Samson, a Platinum Equity partner on John Galt (2017): “John Galt and his team have built one of Canada’s most successful enterprises and a truly world-class industrial company.”,@ID:16}, INSPECTION 41 PETplanet Insider Vol. 19 No. 04/18 petpla.net INSPECTION 41 Increased efficiency Even though the widespread use of self-regulating production lines is in its infancy, Intravis’ products provide valuable insights that enable machine operators to make qualified decisions for regulating the system in a shorter time. The IntraVisualiser software transforms and measured results of Intravis systems into easy to read graphs. The user can monitor all equipped lines easily and simultaneously. Customisable time periods such as batches, shifts, or days can be visualised. If necessary, the IntraVisualizer also creates trend statistics with additional calculation of future trends, which helps to minimise the reject rate. The IntraVisualizer analyses the progress of the measured results of selected product parameters and predicts when a value will permanently deviate from the desired nominal value. The value Estimated Time to Failure (ETF) is then displayed or communicated via email alert. Now the alerted operator has the opportunity to intervene before the tolerance limit is exceeded. This avoidance of rejects creates material savings, higher productivity and efficient maintenance. Intravis continues to expand its vision system offerings to stay on the leading edge of “Industry 4.0”. The IntraVisualizer, in combination with Intravis vision inspection systems on each production line, provides comprehensive insights into the production process, including Estimated Time to Failure (ETF) analysis. Furthermore, the Closed Loop link makes it possible to detect and correct certain process drifts within an incredibly short time. Intravis remains strongly committed to making its vision equipment the “eyes of Industry 4.0” for the plastic packaging market. www.intravis.de The CapWatcher III Print as part of a Closed Loop link at the booth of Netstal !!!! ! \# $ ! \\% %$ & '( ) * ) + , -,@ID:43}, 62 TRADE SHOW PREVIEW PETplanet Insider Vol. 19 No. 04/18 petpla.net Solutions and complete turnkey operations for the bottle blow moulding industry Among the highlights which will be shown at the And & Or booth will be the bagging machine: Today Bagging is one of the most popular ways of packing bottles around the world, offering a wide range of benefits in the packing process: a significant cost saving compared to traditional corrugated box and tray. It often allows more bottles per layer, thus increasing the number of bottles packed in a pallet. The improved hygiene in products, being the bottles protected from human manipulation or cardboard contamination, of special importance in applications such as pharmaceutical, cosmetic and food bottles. The automatic bagging machines producing selfmade bags from rolls of thermo-shrinkable film (no need for preformed bags). With a small footprint, it is usually installed after the blower and the leak tester and finally it automatically arrays bottle layers and packs them into bags, by means of automatic film supply (rolls) without the need of an operator intervention. Quality control And & Or are also presenting the leak detection technology which is available with models that process from 1,000 up to 32,000bph for containers from 150ml to 20l. Great versatility, high sensibility and automatic calibration has made And &Or systems a market reference. The LS Series a conveyor mount design can be integrated over the existing line conveyor. It is supplied with one or more heads, fix or mobile, depending on the production line output and bottle size. Optionally weight control or camera vision built-in systems can be included in the leak testing machine. www.andyor.com All-electric e-cap live on stage Highest degree of efficiency with the best quality and shortest cycle times: this is the daily challenge that the manufacturers of beverage caps face. For the production of 26mm caps with tamper-proof bands made from HDPE, Engel is presenting a state-of-the-art solution. At the core of the highly-integrated solution is an all-electric e-cap 2440/420 US injection moulding machine, equipped with a 96-cavity mould by z-moulds (Austria). On the periphery, Engel integrates a dryair system by Eisbär Trockentechnik (Austria), and an optical inspection system by Intravis (Germany) into the overall concept. To combine minimal energy consumption with process consistency and precision in the production of beverage caps, Engel relies on the all-electric high-performance machines of the e-cap series, which, with clamping forces of 120 to 460 US tons, were developed specifically for this market segment. With their high-performance servodrives, the e-cap machines ensure the required plasticising capacity and maximises part production quality even when using the new high-strength HDPE materials with an MFI significantly lower than 2 or even 1g/10min. In spite of its impressive performance, the e-cap uses very little power and cooling water, even at high speed. The increased ejection and clamping forces help to achieve very short cycle times. www.engelglobal.com www.bericap.com Unique range of light weight screw and sports closures for light weight PET neck standards for water • Closures for all common neck sizes 26/22, 28mm (PCO 1810, PCO 1881), 29/25, 30/25 • Light weight Hexalite range allowing light weight neck • Still water closures suitable for N 2 dosing • Sports closures fulfill BSDA requirements • Boreseal systems for excellent tightness • Consumer friendly opening forces BERICAP Technology for still water South Hall 19097 During the NPE, an all-electric e-cap injection machine equipped with a 96-cavity mould will be producing 26mm caps with tamper-proof bands in a cycle time of less than 2s. West Hall 3303,@ID:64}, TRADE SHOW PREVIEW PETplanet Insider Vol. 18 No. 0/17 petpla.net 68 Recycling in greater demand than ever Quality in plastics Top process and quality standards guarantee the decisive edge in the recycling of clean production waste, with post-consumer material and in PET processing. The trend towards the sustainable handling of plastics combined with the right technology is responsible for the continuing upswing of recycling in the U.S. plastics industry. IMPROVE LINE EFFICIENCY by 10% OR MORE CONTACT US TODAY TO LEARN MORE! AGRINTL.COM | +1.724.482.2163 | [email protected] 1MEASURE 2CONTROL 3OPTIMIZE PROCESS PILOT® Blowmolder management easy as . . . The potential of plastics recycling in the USA has never been as big as it is today. The reason for this is the interplay of several factors: the significant reduction of post-consumer plastics waste imports by China, the growing circular economy movement and the ambitious targets of major brand article manufacturers and other producers to increase the amount of recyclate in their products. “If I had to describe the current situation of the plastics industry in the USA in just one word, ‘dynamic’ would probably be the most appropriate,” says Martin Baumann, Vice President Sales of Erema North America. “Above all, China no longer being an international customer for postconsumer waste plastic is a dramatic development. But since, unlike waste plastic, high-quality recycled pellets can still be exported to China, this represents a potential opportunity for plastics recycling in the USA and Canada. This is why Erema North America has added an Intarema TVEplus with Laserfilter to its Technical Centre for customer trials especially for the recycling of postconsumer materials with a high degree of contamination. This system typically processes film waste with paper labels from commercial waste or washed film from curbside waste to make film-grade pellets. Trade fair attendees will receive information about the Erema melt filters directly from the Erema business unit Powerfil which will be represented at NPE for the first time. The proven filter systems are available as individual components for extrusion plants from other suppliers. “Plastics recycling is more an opportunity than an alternative with regard to sustainability and against the backdrop of increasing prices for landfilling. The focus of our technical developments lies quite clearly on increasing the quality of recyclates. It is precisely for this reason that we have developed the new ReFresher anti-odour technology which enables us to open up completely new application opportunities for plastics recycling,” says Mike Horrocks, CEO Erema North America. Additional highlights More and more producers of plastic products are counting on reducing their manufacturing costs through the recycling of clean production waste, as Martin Baumann explains: “Our sales in the recycling of clean production waste are constantly growing. We put this down largely to the increasing demand for high-quality film products and the associated expansion of production capacities,” says Martin Baumann. An Intarema T 1108 will be in action live at the booth, processing clean LDPE production waste direct and without pre-shredding to make high-quality recyclates. Additionally, Erema will be providing details on the world’s first rPET Inline Preform system at its booth. Sipa, a leading manufacturer of PET packaging solutions from Italy, joined forces with Erema to develop a flexible, direct processing solution to make food-contactcompliant preforms from rPET flakes – in a continuous process. For PET processors the pioneering system has both economic and ecological benefits: energy savings, lower logistics and process costs and higher profitability. The Inline Preform system is in full line with the global trend of processing post-consumer PET flakes direct to make sheet, strapping or end products. www.erema-group.com West Hall 1249,@ID:70}, 11 NEWS PETplanet Insider Vol. 19 No. 04/18 petpla.net Beviale Moscow: closing report At the trade fair Beviale Moscow, held from 27 February to 1 March 2018, 146 exhibitors (2017: 130) showed their products and solutions relating to beverage manufacture and marketing to more than 5,300 visitors (2017: 4,000), in an exhibition area of about 2,000m2 (2017: 1,600m2). New elements this time were the programme points covering wine and soft drinks, which were very positively received, says the organiser. “For its third edition, Beviale Moscow made an excellent and significant step forward,” says Thimo Holst, project manager for Beviale Moscow. “Not only was it much larger, but it was also much better.” This was partly a reflection of the positive atmosphere in the halls, which were full for all three days of the event, reflects the organiser. The quality of the stands was better, and the visitors themselves had come well prepared to take part. The all-encompassing approach adopted by Beviale Moscow – covering the entire beverage industry – was adopted again in 2018, and showed the extent of the market potential the event offers. The supporting programme on industry topics of current interest was aimed at decision-makers in the beverage industry. This was the first time the Russian wine industry exhibited at Beviale Moscow. The subject of soft drinks also premiered at Beviale Moscow this year, in the form of the “Production of non-alcoholic beverages in Russia” conference, held in association with the Union of Producers of Soft Drinks and Mineral Waters. In view of the positive response, this collaboration will be taken further next year. The Craft Drinks Corner, where visitors were able to taste craft beverages in the presence of the respective manufacturers, also proved very popular. The tasting zone was a collaborative effort with partner entity Association of Beer and Beverage Market. Craft beers were also the focus of the two-day VLB Seminar for Modern Brewing Technologies, organised by the Versuchs- und Lehranstalt für Brauerei Berlin (VLB, Research and Teaching Institute for Brewing, Berlin). PETarena powered by PETnology offered attractive solutions for the entire PET value chain – a topic that is of strong current interest in the Russian market. The next edition of Beviale Moscow will once again be held at Crocus Expo, Moscow, on 19-21 February 2019. www.beviale-moscow.com,@ID:13}, 67 TRADE SHOW PREVIEW PETplanet Insider Vol. 19 No. 04/18 petpla.net W. Amsler to launch next-generation four-cavity stretch blow machine W. Amsler Equipment Inc., a leading supplier of all-electric linear PET stretch blow moulders, will introduce its nextgeneration four-cavity all-electric reheat stretch blow moulder. The company will also exhibit its newly-enhanced leak tester that inspects bottles from 10ml-23l and its standalone spin trimmer for both stretch- and extrusion-blown containers. W. Amsler also announced that General Manager Bruce Coxhead will give a presentation entitled “Linear Blow Molding of Non-Conventional Barrier Containers” at NPE’s Bottle Zone Technical Forum on Wednesday, May 9, at 10.45a.m. The L42X all-electric reheat machine offers several new features including preferential heating, neck orientation, and hot-fill capabilities. “For custom blow moulders, the next-generation four-cavity machine provides versatility to enable PET bottle production in a range of configurations and sizes,” said Heidi Amsler, sales and marketing manager for W. Amsler. The new machine makes up to 2l containers at a rate of 6,500/hour in four cavities. It can also be used to run two-cavity moulds for production of larger containers up to 5l. Neck finishes range from 18mm to 70mm. The L42X reheat machine has four parallel heating ovens, one for each cavity. It comes equipped with 12 Bosch-Rexroth servo motors, compared to three servos for the previous model. The extra servos provide more repeatability, lower energy consumption, and require less wiring, resulting in easier troubleshooting, according to W. Amsler. The machine also has a 40t servo-driven mould clamping system. Servo systems are used to control preform loading, preform transportation through the machine, rotation through the ovens, stretch rod actuation, motion towards the moulding station and clamp opening, closing, and bottle unloading. Other key features include agitated preform infeed to prevent bridging, preform temperature sensing prior to blow, pre-blow flow control for each cavity, water-cooled neck shields, and a large touchscreen operator interface. Servo-driven stretch rods are 14mm with 10mm and 12mm options. T h e L 4 2 X c ome s equipped with a large touchscreen operator panel from Wonderware. It has a Windows-based human machine interface (HMI) with full access to assembly drawings, bills of materials (BOMs), set-up guides, troubleshooting, and training videos. The four-cavity system is commercial and W. Amsler has already sold a machine to a custom blow moulder. www.amslerequipment.net South Hall 21067,@ID:69}, PETpatents www.verpackungspatente.de PETplanet Insider Vol. 19 No. 04/18 petpla.net 80 Thin-walled container European Patent issue No. EP 2938547 Applicant: Societe Anonyme des Eaux Minérales d’Evian (FR) Application date: 28.12.2012 Thin-walled, large-volume container to hold drinking water. The container is placed upside down in a water cooler and collapses in accordance with the structure and ridges. Reduced-weight container International Patent No. WO 2017 / 136584 A1 Applicant: Niagara Bottling LLC., Ontario (CA) Application date: 2.2.2017 To further reduce the weight of a plastic bottle, changes to the preform in the area where the bottle opens are required, as a great deal of material accumulates there. The patent describes this possibility. Bottle for chicken egg whites European Patent No. EP 3208204 A1 Applicant: Pumperlgsund GmbH, Munich (DE) Application date: 15.2.2017 Plastic bottle with a concave base to hold liquid chicken egg whites. The bottle must be specially shaped so the product can be distributed in a non-chilled condition. Optimised plastic container European Patent issue No. EP 3068696 B1 Applicant: Sidel Participations, Octeville-sur-Mer (FR) Application date: 23.10.2014 The European patent describes the procedure for manufacturing a reduced-weight plastic bottle with a petaloid base. The injection moulding capabilities of the bottle have been improved. Bottle for water cooler International Patent No. WO 2016 / 050977 A1 Applicant: S.I.P.A., Vittorio Veneto (IT) Application date: 2.10.2015 Described here is the composition and handling of a large volume plastic bottle made from PET for placing upside-down in a water cooler. Container for hot filling International Patent No. WO 2016 / 060680 A1 Applicant: Amcor Ltd., Hawthorne (US) Application date: 17.10.2014 Reduced-weight wide-neck container made from PET with special shaping in the base to enable the optimal equalisation of the vacuum forces arising through hot filling and subsequent cooling, without deforming the outer wall of the container.,@ID:82}, 61 TRADE SHOW PREVIEW PETplanet Insider Vol. 19 No. 04/18 petpla.net Colours, additives and equipment For the second time Repi LLC will be exhibiting at the American’s leading plastics trade show. Located immediately over the Bottle Zone, Repi will presenting the entire range of liquid colours, additives and equipment for all plastics and their disparate applications. The portfolio comprises speciality additives for the packaging industry, which ranges from anti-yellow and IV enhancers for rPet processing, moving to UV additives and special UHT milk - barrier whites, which preserve the content from light damages, to anti-block, blowing agents and process aids which improve the production process and protect containers from scratches and damages. Industrial applications are as well a target of Repi’s liquid technology, with products dedicated to PC, PMMA, PVC, HDPE, PP, ABS which offer good dispersion and respect the technical requirements (like light diffusion targets). A special mention goes to Repi’s Xpansor, the foaming agent for PVC in liquid form, able to lighten the sheet and make the surface smooth. Among Repi’s ancillary equipment, the Light Meter Plus is the new entry. In the perspective of offering an all-round solution rather than just a product, Repi has been working over the years next to its customers building ties with them as partners. In this scenario, not only is the colour and additive formulation important, but also the availability of accurate dosing and analysis instruments to rely on for measuring the real presence and properties of the colour/additive in the final product. This is what the Dosing Unit U2011 and the Light Meter are able to offer, and its latest version offers the user dramatic advantages in this direction. www.repi.com Process Pilot, 3-step approach for PET bottle manufacturing process and automated laboratory Agr International offers a number of products that are designed to aid bottle manufacturers achieve their most aggressive light weighting and sustainability goals while maintaining the highest quality. Agr products are designed to assist container producers, converters and fillers stay competitive while meeting the increased quality demands of today’s changing world. Process Pilot automated blowmoulder management system with individual mould control, is designed to help PET bottle manufacturers measure, control and optimise their bottle blowing process in order to produce the highest quality, best performing bottles possible while maximising production efficiency. The Process Pilot system interfaces with the blowmoulder to provide precise material thickness distribution on a per bottle basis while managing to eliminate the effect of process and environmental variables that impact bottle material distribution throughout the production cycle. The Process Pilot system offers a simple three-step approach towards PET blowmoulder management: First it measures material distribution and pearlescence on every bottle, secondly it controls the blowmoulder to overcome process variation and maintain on-target material distribution and finally at last it optimises the process to suit the product, application or business objective of the production facility. Automated laboratory system is a solution that offers a precision pick & place industrial robot to select, handle and transfer PET container and preform samples through multiple thickness and dimensional tests. Integrated with Agr’s Gawis container measurement system, comprehensive measurements, including thickness and critical dimensional measurements can be performed without operator intervention. The tests are fully optimised and performed quickly and efficiently through the handling of the multi-axis robot and the fast throughput of the Gawis measurement device. Test results are compiled with data correlated by sample and consolidated in a single test report. The system offers a number of benefits including hands-free, walk-away operation, efficient management of samples, testing operations and documentation of results, and an improvement in testing throughput. In addition to the Gawis measurement system, the automated laboratory system can be configured to incorporate Agr devices for top load, volume and pressure measurements, providing a complete laboratory automation solution to meet the challenges of over-worked testing labs and the ever increasing demand for testing to manage quality and support ongoing production. www.agrintl.com South Hall 19103 South Hall 16045,@ID:63}, MATERIALS / RECYCLING PETplanet Insider Vol. 19 No. 04/18 petpla.net 17 and suppliers to benefit from more stable prices and encourage investment in equipment and capacity, both in the MRFs and in users. Next steps The recommendations from RSS and Closed Loop Partners are, in summary: Capital investments in new technologies at MRFs and reprocessors. Improving packaging design-forrecyclability. Creating more reliable agreements among parties. On the design side, recycling would be made easier by adoption of the following measures: Avoid using metal with PET packaging. Use pressure sensitive film labels that meet APR Critical Guidance Test Criteria, including use of conforming substrates, adhesives, and inks. Use shrink sleeve labels that meet APR Critical Guidance Test Criteria, or which have been evaluated within APR’s Responsible Innovation Program. Avoid use of paper labels. If used, conduct lab testing to select paper labels that have negligible impact on colour and haze of recycled PET. Avoid using PETG in packaging. RSS says that, if these interventions are implemented together, then MRFs, reprocessors, and end users could lower costs by 10%, improve yield by 21%, and create other system benefits. If they are implemented at scale, the national recycling rate of PET could increase by 6%. It further observes that value creation opportunities exist throughout the supply chain, and notes that lessons learned in the PET recycling initiative could be transferable in considering solutions for polypropylene (PP) and polyethylene (PE). www.closedlooppartners.com NO. ONE-WAY PRODUCTION. YES. TOP QUALITY RECYCLING. How can your recycled product meet permanently increasing demands? With the CHT range of high performance process solutions with environmental relief for the wet chemical cleaning. We support you directly on site and ensure your quality controls in our laboratories with state-of-the-art equipment. Thus, your strong position in the growing market is confirmed day by day. More about us at www.cht.com PLASTIC RECYCLING SHOW | 24 – 25 April 2018 RAI Amsterdam | stand E5 Interventions can have impact across the system (Closed Loop Partners),@ID:19}, MATERIALS / RECYCLING PETplanet Insider Vol. 19 No. 04/18 petpla.net 15 Cleaning the rPET stream U.S. PET Recycling A new report calls for investment in recycling infrastructure to raise rates from less than 30% and to develop pathfinding closed loop systems to recycle an additional 80 million lbs (36.4 million kg) of PET bottles each year. Towards the end of 2017, the publication of a study entitled “Cleaning the rPET stream”, conducted by Closed Loop Partners with Resource Reycling Systems, Inc (RSS), drew attention to major gaps in PET bottle recycling in the United States of America. RRS researched and compiled 12 years of data on U.S. pricing trends and cost structures for both virgin and recycled PET (rPET), including sorting, processing, contamination levels, and yield loss. It also evaluated multiple interventions that could improve the cost structure for rPET with implementation by materials recovery facilities (MRFs), reclaimers, reprocessors, and end users. “We believe there are investable opportunities that benefit municipalities, the PET recycling industry, and end users by making rPET a more desirable material that competes with virgin,” said Ron Gonen, Closed Loop Partners managing partner. Before the industry in the country gets to that positive state, however, there are several major issues that need to be addressed. Use of virgin PET has grown but recycling rates are low Less than 30% of the PET used in bottles and jars is recovered in the U.S., and just 6% is re-used as rPET in new bottles. This is despite the fact that PET is the most common resin type used in plastic packaging and the most universally accepted plastic in U.S. municipal recycling programmes, and the recycling infrastructure for post-consumer PET is also the most mature. The report found that, in the past decade, virgin PET consumption has grown, which is the common experience across most – if not all – of the world. In the USA, production has been consolidated among a few, privately-held market players, such as DAK and Indorama. Virgin PET is produced at scale by combining raw material inputs (PTA, MEG) in a polymerisation process. Post-consumer rPET, in contrast, must travel from consumer to MRF (material recovery facility) to reclaimer/reprocessor to end user. There is potential for yield loss and inefficiency at each stage. Cost considerations These two, very different, processes result in quite divergent cost structures. At the time of the study, the estimated average cost to produce virgin PET was $0.52-0.56 per lb ($1.14-$1.23/kg), while the cost to process and produce rPET was estimated at $0.60-0.65/lb ($1.32-$1.43/ kg). The existence of this cost differential means that it is not surprising to find that end users tend to opt for virgin PET. If rPET is ever going to be competitive with virgin at scale, ways have to be found to make improvements, across the system. Supply and demand; capacity excess The price of rPET closely follows that of virgin PET, which has seen considerable volatility, along with global oil prices, over the past 10 years. Through all this volatility, the national recycling rate for PET has hovered around 30%; this tends to reflect an inelastic supply, the report says. Over the same period, capacity for processing post-consumer rPET has also fluctuated. The recent closure of a number of facilities removed 400 million lbs (182 million kg) of capacity. Although at least 350 million lbs of new PET processing capacity is expected to come online in the next few years and the total is expected to return to about 2 bn lbs/ year (910 million kg) by 2018, existing facilities are operating at only around 75% capacity. Convertors and bottle manufacturers will be inclined to increase the amount of rPET they use in bottles and containers only if that material is price-competitive with virgin, and of appropriate quality specifications. The U.S. doesn’t seem to have a collection problem; it has a usage problem. In 2016, 1,753 million lbs (796 million kg) of PET was collected for recycling but only 370 million lbs (168 million kg) of rPET was reused for food and beverage bottles. Ideally, demand pull from end users should encourage the recovery and reprocessing of post-consumer recycled PET; however, the market is constrained by the ability of suppliers to offer rPET at prices that can compete with virgin PET resin. rPET versus virgin PET production processes (Closed Loop Partners),@ID:17}, 64 TRADE SHOW PREVIEW PETplanet Insider Vol. 19 No. 04/18 petpla.net .com 100815dmyL Moretto USA will present Eureka Plus at the NPE Bottle Zone Technical Forum 2018 On Monday 7th May at 10.45a.m., Moretto USA will proudly take part in the Bottle Zone Technical Forum, presenting a background and overview of the Eureka Plus drying system. Motivated by success with a growing list of USA customers, Moretto USA will exhibit prominantly at NPE2018 with two booths: The first, W8545, located in the West Hall, will present innovative solutions for any processor in need of conveying, drying, additive feeding, blending, temperature control and supervisory control products and systems. The second Moretto booth, S17095, is located in The Bottle Zone of the South Hall, an area dedicated to innovations targeted for the critical PET sector of the plastics industry. Particular attention will be dedicated to the resin-drying process: Mr Gene Flockerzy, Moretto USA General Manager, will presents to the Bottle Zone Technical Forum’s audience the new drying system Eureka Plus. Eureka Plus is a modular, self-adjusting, energy-saving dehumidification system. It is comprised of four Moretto-patented technologies: Moisture Meter Manager, an in-line resin moisture sensing and drying control, the X Max, a high performance, multi-bed dryer with consistant dew point, the Flowmatik, a dynamic airflow management device, and the OTX, drying hoppers with superior mass flow drying characteristics. The Eureka Plus system effectively closes the loop on resin drying by in-line measurement of each granule’s moisture content and applying this data to the adaptive drying system. Ever-responsive, the system essentially provides “drying on demand”, based on the real drying needs of the polymer at any given time. Managing drying functions in direct response to environmental variables that typically interrupt predictable polymer moisture levels, the Moretto drying system can guarantee production certification and maximum energy efficiency. www.moretto.com South Hall 17095 A thorough, yet delicate, clean for many applications Cold Jet, a manufacturer of high performance, reliable dry ice cleaning and production equipment will demonstrate its MicroParticle technology. MicroParticle technology is used heavily in the plastics industry to clean moulds, deflash and deburr parts and for surface preparation prior to painting. The technology allows companies to clean moulds at operating temperature and in place and does not generate any secondary waste or leave any residue behind. This patented MicroParticle technology shaves dry ice into sugar-sized particles. This allows more media to strike the surface per second than traditional methods, which results in an increased coverage area and a faster and more even clean. ”The MicroParticles will enter the hardest-to-reach places in complex geometry moulds, including vents, and are small and delicate enough for a thorough clean without worry of damaging the mould surface or changing dimensions, improving product quality, lowering costs and increasing productivity,” said Steve Wilson, Global Business Unit Manager Plastics, Rubber & Composites. The i3 MicroClean, which utilises MicroParticle technology, is used heavily in the plastics industry and features dry ice shaving technology. The MicroClean is claimed to be a lightweight, compact, single-hose low pressure blasting system that uses less compressed air and less dry ice than similar machines. It is also quieter than traditional machines. “When companies introduce the i3 MicroClean into their cleaning process, it extends the running time of their molds by 200-500%,” said Wilson. “It saves them from cooling the mould down, removing it, disassembling it, reassembling it, putting it back in and heating everything back up. That is a lot of time and risk for damage.” www.coldjet.com West Hall 483,@ID:66}, MATERIALS / RECYCLING PETplanet Insider Vol. 19 No. 04/18 petpla.net 16 RRS maintains that the stark underperformance of PET recycling can be addressed and improved, through investment in solutions that will provide long-term benefits to the overall system. Initiatives and interventions An analysis conducted by Closed Loop Partners with RRS identified a suite of interventions that would greatly improve the cost structure of rPET and benefit MRFs, reprocessors, and end-users. RRS claims that, if these measures were implemented nationally, the rate of PET recycling could be increased by 600 basis points (six per cent, from 30 to 36%) and close the loop on nearly 80 million pounds of PET bottles each year – all without putting a single new collection cart on the street. The focus of the strategy on bottleto-bottle processes identified several measures that effectively improve yield from residential kerbside collection by more than, 20% and lower costs of rPET processing by 10%. By targeting action and investment, MRFs, reclaimers, reprocessors, and end-users could realise value for themselves and across the system, RSS asserts. The cost structures for producing rPET and virgin PET are very different; rPET is a highlight distributed, mechanical process, involving policydriven supply and market-based demand. Consumer access to, and participation in, convenient recycling schemes and systems determines the supply of PET. Supply is not influenced by price or demand, as demonstrated by the excess of material collected over that used; rather, supply is a function of municipal and state policies that determine material recovery, and consumer behaviour. Quality and quantity Collections infrastructure and policies influence how much material is available for reprocessing. “Bottle bill states” – those that have legislated to charge consumers a deposit on packages – typically see higher value in collected bales than are found in pure kerbside collections. The premium ranges from $0.05 - $0.15/lb ($0.11- $0.33/kg) over the typical kerbside price of $0.17/lb ($0.374/kg). The estimated average yield of PET in a kerbside bale is 62%; there is potential to recover more PET than is collected today. It is estimated that another 17% of PET that travels through a MRF is not captured in the PET bale. For the reclaimer, the adjusted yield price is $0.31/lb ($0.68/ kg). Contaminants contribute to this yield loss, such as caps, labels, nonPET material, ‘fines’, and moisture. Mechanical processing of the PET bale and subsequent conversion to flake drives costs by an estimated average of $0.19/lb ($0.42/kg). Contamination issues arise partly because of MRF inefficiencies in sorting and partly as a result of brand owners’ design decisions that are incompatible with or inconvenient to – and therefore costly for – the recycling process. Whether kerbside or ‘bottle bill’ collected, the quality of rPET can vary with little warning. This can make it difficult for end users to maintain a consistent quality specification. Commodity prices can vary, suddenly and significantly; rPET is typically purchased on the spot market. Longerterm contracts would enable buyers STAND S10196 – ONE for ALL Capacity of U.S. PET infrastructure (Closed Loop Partners),@ID:18}, 75 PRODUCTS PETplanet Insider Vol. 19 No. 04/18 petpla.net Made out of waste?! Transforming marine plastic litter into sustainable packaging Commitment to sustainable packaging Waste Free Oceans has announced a new partnership with Henkel to remove plastic waste from oceans and rivers and transform it into over a million bottles used for the Lovables laundry brand. The collaboration is the largest that WFO has agreed so far and will run for at least three years. Together, the partners aim to remove enough plastic from rivers, lakes, seas and oceans to produce 100t of usable recycled material each year. The partnership between Henkel and Waste Free Oceans will begin by collecting plastic waste from the Danube River in spring 2018. Activities will target locations ranging from Bulgaria through to Hungary and Romania that were selected based on a detailed analysis of the way the currents and geography of the river cause plastic to accumulate at certain points. Volunteers will gather plastic waste from the river banks and beaches, while teams of fishermen will trawl the river using a special device that removes floating plastic waste from the water. The trawlers are able to collect between 2 and 8t of marine litter on each journey. The collections along the Danube will be followed by activities at several locations in the Mediterranean Sea during the summer. Once recycled, the plastic will be included in bottles for the Lovables laundry brand. Launched in 2018, Lovables offers special gentle cleaning that preserves consumers’ favourite clothing by protecting the quality of the fabrics and colours. Lovables bottles are made from 100% recycled material – and the brand aims to include recycled marine plastic litter from Waste Free Oceans in over a million bottles. “Our partnership with Waste Free Oceans is another step forward in our commitment to promoting sustainable packaging and recycling,” says Prof. Dr Thomas Müller-Kirschbaum, Head of Global Research and Development in Henkel’s Laundry & Home Care business unit. Henkel’s commitment to sustainable packaging follows three focus principles: less packaging and waste, better packaging, and enabling a circular economy. In 2017, Henkel used recycled plastic in the packaging for more than 1.2 billion detergent, household cleaning and beauty care products globally. This new partnership with Waste Free Oceans builds on the company’s existing activities related to sustainable packaging and recycling, such as its partnership with the social enterprise Plastic Bank. www.wastefreeoceans.org l l l consumer bags textile packaging recycling rECO,@ID:77}, 8 NEWS PETplanet Insider Vol. 19 No. 04/18 petpla.net Industrial Solutions for Polymer Plants MTR® Melt-To-Resin PET resin technology developed by Uhde Inventa-Fischer for all your packaging needs Opt for superior quality resin with our proven MTR® technology that eliminates SSP (solid-state processing). The MTR® process is based on our advanced, proprietary 2-Reactor high i.V. melt technology. Reduced thermal stress and soft reaction conditions, combined with minimum raw material consumption and an economical investment will highly improve your profitability – 30% less conversion cost is feasible. www.uhde-inventa-fischer.com,@ID:10}, BOTTLING / FILLING PETplanet Insider Vol. 19 No. 04/18 petpla.net 35 FDA approval of Sidel’s Aseptic Combi Predis blow fill seal filler for low acid product manufacturing in the U.S. UHT liquid dairy products in PET Sidel has received Food and Drug Administration (FDA) approval for its Aseptic Combi Predis FMa blow fill seal filler following tests run at a dairy customer in North America. This means that the Sidel Aseptic Combi Predis FMa PET filler is validated for low acid manufacturing and commercial distribution in the United States market. The Sidel Aseptic blow fill seal solution is claimed to be the world’s first aseptic PET filling equipment with dry preform sterilisation approved by FDA. The FDA approval officially qualifies the Sidel aseptic solution with dry preform sterilisation technology to produce and distribute shelf-stable low acid products in PET bottles for the U.S. market. The Process Authority for the Sidel aseptic filler was Dover Brook Associates (DBA). DBA applied their 30 years of professional experience in sterile processes to validate the scheduled processes of the Aseptic Combi Predis. Using a scientific-based approach of specific tests and acceptance criteria, DBA was able to prove that the scheduled processes were in compliance with the predicate rules and expectations of the FDA so that the equipment could produce a commercially sterile low acid product. The Sidel patented technology is said to be safe for the packaging of UHT milk, soymilk, coconut water, or teas in PET bottles, sold through the am- bient chain market in the US and the rest of the world. Merging dry preform sterilisation with aseptic functions The Sidel Aseptic Combi Predis merges dry preform sterilisation with aseptic blowing, filling and sealing functions within a single production enclosure and respects the fundamental concept which underpins state-of-the-art aseptic packaging rules: producing a commercially sterile product, filled in a sterile zone, in a previously sterilised package. It differs from traditional aseptic technology because the package sterilisation takes place at the preform rather than at the bottle phase. DBA conducted a detailed review of the design, critical factors, and the sterile zone boundaries. The stringent validation tests were performed on a commercial filler producing aseptic UHT milk, and all the tests were successfully passed. “We accumulated more science from these tests performed with DBA. They challenged and validated the process and the technology itself”, explains Arnaud Poupet, Aseptic Product and Platform Manager at Sidel. DBA concluded that the minimised sterile zone provided a safe and successful aseptic process that produced a commercially sterile, hermetically sealed bottle. “DBA’s testing demonstrated that the sterile zone during the blowing process was the critical component, not the blow-moulding zone itself, which was due to the Sidel patented dry-preform sterilisation technology”, comments Poupet. The scheduled processes require minimal critical factors, which have to be monitored during the production, cleaning and sterilisation phases of the aseptic process. The critical parameters are continuously monitored to ensure full production sterility, beverage integrity and food safety. “Our best warranty for food safety is simplicity, because a line with a small sterile zone and minimal critical factors is managed more safely, easily and effectively,” continues Poupet. “We partnered with one of the major dairy producers in North America who was confident of the safety and efficiency of the Aseptic Combi Predis. He invested in the solution to introduce new UHT liquid dairy products in PET bottles. Under the coordination of DBA, we went through a rigorous FDA qualification process at the FDA registered customer site”, explains Poupet. The Aseptic Combi Predis approved by the FDA is very similar to the existing machines installed for aseptic production in customers’ plants worldwide. www.sidel.com,@ID:37}, BOTTLING / FILLING PETplanet Insider Vol. 19 No. 04/18 petpla.net 34 fully automated without compromising system sterility. This new technology uses a counter-pressure, volumetric electronic filling valve and is suitable for a wide range of applications, including high and low acid beverages and aseptic soft drinks with varying carbonation levels, all the while ensuring complete sterility. It can fill products with fibres up to 20mm long and with diameters of 3mm. Bottle size and shape – which are just as important for attracting consumer attention – can be easily adapted. The ABCs of ABF The GEA aseptic dual filling process can be applied to any beverage filling platform but achieves maximum flexibility when used in conjunction with an Aseptic Blow Filling (ABF) line. The key principle involves sterilising the preforms (as opposed to the bottles) with hydrogen peroxide as they exit the oven. The bottles are then blown using sterile air in a sterile environment, which is maintained from filling to capping. Sterilising the preform instead of We care about your performance. CAREFORMANCE STAY FLAKESIBLE. DIFFERENT INPUT. STABLE OUTPUT. VISIT US: CHINAPLAS, Shanghai / China 24 – 27 April 2018 Hall 2H, Booth 2B59 NPE 2018, Orlando / USA 7 – 11 May 2018 Booth 1249 ACUREMA® Inline Sheet and Preform Flexible for sure: from varying wall thicknesses, IV values and input materials such as PET bottle flakes, skeleton waste, edge trim or mixtures of them directly to the end product in stable, top quality. Food contact compliance included. That’s Careformance! the bottle reduces the amount of sterilising agent required since the preform is smaller and has a simpler shape. And because the preform is made of thicker material than the bottle, it’s possible to increase the temperature of the treatment without the risk of shrinkage. This means the bottle weight can be kept to an absolute minimum. Ultimately, this GEA development means manufacturers can experiment and be more creative with bottle designs, making them more ergonomic or visually attractive, which is a win-win in the cluttered retail environment. Ready to cap At the end of the filling cycle, the containers must be sealed before exiting the controlled environment to avoid recontamination. Cappers are therefore integrated into the microbiological isolator and specifically designed for aseptic applications. Aseptic dual fill technology can be used with the entire range of GEA filling/capping systems including GEA’s Sterilfoil VHP L closure system. Flexibility for efficient production The rising consumer demand for more sustainably produced, diverse liquid food choices, shows no sign of waning. Luckily, today’s manufacturers have access to superior pasteurization and aseptic dual fill technologies which allow for gentle processing while extending product shelf life, without the need for preservatives. These new advances make experimentation more affordable and ensure products get to market more quickly. And the improvements in the overall efficiency of the process means both manufacturers and consumers can feel better about these time-saving products. www.gea.com,@ID:36}, MOULD MAKING PETplanet Insider Vol. 19 No. 04/18 petpla.net 20 Bonaqua Argentina switches from glass to PET for the on-premise water market Less material, more content, lighter weight Bonaqua is the spring water of The Coca-Cola Company in Argentina. Traditionally bottled in a premium glass bottle for the on-premise market the company was keen to create a premium glass-like PET bottle designed to meet the longhaul transportation in this huge country. The Coca-Cola Company (TCCC) serves the Argentinian market with a premium spring water from Coca-Cola Andina’s plant in Cordoba. Located at a central province in this huge territory, Bonaqua has to transport its products more than 700km, and this is what motivated the company to redesign the packaging with the twin aim of cost efficiency and a reduction in the carbon footprint. The development of the new premium packaging was entrusted to the blow mould manufacturer Moldintec. The Moldintec’s industrial design team worked closely with bottler’s engineers and TCCC’s technical, marketing, and operations team to meet its branding requirements and operational efficiency of the existing bottling line. With the focus on keeping the premium look of the bottle, the main shape was preserved while also satisfying the mechanical requirements for a highspeed blowing-filling blocked hybrid glass/PET type line. Many other savings were secured by this master design principle due to the existing bottle tooling being adapted to the novel PET bottle. Even the paper labeller kits work perfectly with the new bottle, according to the Industrial Director of Coca-Cola Andina Argentina based in Cordoba. Bonaqua’s drop shape, combined with the water, creates a magnifying effect, intended to make the bottle shine on the table. The same effect was reached using a high gloss polished blow mould, smooth surfaces, and a perfect material distribution during the blowing process. A MonoBloc Shell mould type was chosen for this application. The lubrication free concept of MonoBloc Shell contributes to avoiding any contamination of the bottle surface so that it keeps its clear and shining look. A HexaBase was specially developed by Moldintec for a perfect match keeping in mind the water drop shape. The base design accomplishes all physical requirements from TCCC for both CSD and NCB because Bonaqua has a sparkling version or has a nitrogen headspace for still water. The BaseMAX technology applied to these high-efficiency bases has the capability to copy a sharper geometry in the container while reducing the blowing pressure. It improves the reliability of the bottle due it six stand planes that support the top load even at the low inner pressure on still. HexaBase delivers a more stable container and less susceptible to falling on the line even at high line speed and reduced stand diameter. Less material, more content, lighter weight Moving from a glass bottle to PET blow-fill process immediately translates into a multiplicity of savings. Starting with a lower bottle weight per unit, 24g on the PET version versus 263g of a glass bottle. The company also took advantage of this weight reduction increasing the bottle capacity by 100ml. The result is a lighter pallet with more liquid on it. The total full loaded Bonaqua on-premise truck weight was reduced 18% while the water payload is increased by 20% now, according to Eng. Daniel Rodriguez, Technical Director of Cola-Cola South Latin Business Unit. The extra 100ml also differences Bonaqua with a new 600ml packaging from its competitors which mainly deliver 500ml to consumers. The operation was also a winner during the improvement process. Many of their tasks were eliminated or improved. From no more glass bottle reception from the manufacturer, warehousing space for empty bottles, depalletising at the line inlet and many others savings were captured by bottler engineers to cut product cost. www.moldintec.com.ar Lubrication free MonoBloc Shell for a shining look 24g PET version versus 263g glass bottle,@ID:22}, BOTTLE MAKING 31 PETplanet Insider Vol. 19 No. 04/18 petpla.net BOTTLE MAKING 31 Please order your copy at the PETplanet Insider book shop: petpla.net/book3 Stretch Blow Molding Third Edition by Ottmar Brandau € 130,00 374 pages © Copyright Elsevier 2017, 2012 Unique technologies, innovative solutions, comprehensive technical support, high expertise in all kinds of plastics applications. In others words: typical Gneuss. The Big Cleanup 'HʏEKGPV &GEQPVCOKPCVKQP MRS Extrusion gneuss.com NPE Stand W6473 Plast Stand 15 / B11 Plastic Recycling Show Stand B10 Chinaplas Stand 2J31 Bare hands should never touch lamp surfaces, as oil can be transferred on them that leads to burn marks. Should it happen, lamps should be wiped off with alcohol. When it comes to selecting lamps from different suppliers one important detail is how much of the applied energy is actually converted to infrared radiation. This has a significant impact on energy consumption and buyers should carefully scrutinise data supplied by manufacturers. Halfround reflectors at the back of the lamps have proven to be a significant improvement in this respect. It should also be noted that athough these lamps emit a wide spectrum of light waves, only some of which are optimal for PET (Chapter 6). Near-infrared (NIR) heaters concentrate more of the output in the 1000-nm range, which is especially suitable to penetrate preform walls. Ovens with these heaters can reduce heating time, space requirements, and energy costs, and manufacturers have started to equip their ovens with them.,@ID:33}, PETcontents 04/18 4 PETplanet Insider Vol. 19 No. 04/18 petpla.net INSIDE TRACK 3 Editorial 4 Contents 6 News 73 On-site 74 Products 76 PET bottles for Home + Personal Care 78 PET bottles for Beverage + Liquid Food 80 Patents EDITOUR 12 Don’t talk, listen! Interview with John Galt, CEO Husky MATERIAL / RECYCLING 15 U.S. PET Recycling 18 “Plastic packaging never returns into waste” MOULD MAKING 20 Less material, more content, lighter weight PREFORM PRODUCTION 22 Wherever possible, get ahead; make the competition follow 24 Automatic control of injection pressure BOTTLE MAKING 26 PET blow moulding machines made in Thailand 28 Machine details - Oven section Stretch Blow Molding, part 8 BOTTLING / FILLING 32 Something to eat or drink? Mastering liquid food manufacturing 35 UHT liquid dairy products in PET CAPS AND CLOSURES 36 Closures from Melbourne INSPECTION 40 Smart factories are becoming a reality PACKAGING / PALLETISING 42 Alamo Red Salsa in PET jars MARKET SURVEY 44 Suppliers of PET preforms TRADE SHOW PREVIEW 47 Chinaplas 2018 preview 52 Towards the circular economy in PET packaging 56 Drying on demand 57 2,000 caps per minute 58 Moulding live on stage 59 NPE 2018 Bottle Zone floor plan 60 NPE 2018 Technical Forum 61 NPE 2018 preview 68 Quality in plastics 69 Fastest neck change 70 SMI embraces Eco & Industry 4.0 72 Filtration, extrusion and measurement technology BUYER’S GUIDE 81 Get listed! Page 58 Page 36 Page 61,@ID:6}, TRADE SHOW PREVIEW PETplanet Insider Vol. 19 No. 04/18 petpla.net 57 Sacmi to showcase its full range of caps & closures and services 2,000 caps per minute Sacmi Imola’s stand at Chinaplas, which will occupy 300m2 of display space, will feature its full range of cap manufacturing and quality control technology. Its compression press range now benefits from the company’s new cap-preform integrated design services. It will also showcase closure handling inspection systems for cap quality control and the advanced Sacmi line supervisor, which manages orders and monitors all plant performance parameters, even remotely. Hall 2H Booth B61 The company’s range of CCM (continuous compression moulding) compression presses are claimed to offer the lowest cycle times in the industry. Production output is up to 2,000 caps/minute from 48 mould units. Offering intrinsic advantages in terms of productivity, energy savings and reliability, compression technology operates at lower temperatures, which reduces on-material stress and extends the working life of both machine and plant, Sacmi says, and adds that the technology has the capacity to manufacture lighter, better-performing caps, compared to other solutions, such as injection moulding. Weight and other parameters can be modified via the operator interface. Sacmi CCM machines can manufacture caps of different designs using the same mould and provide a large variety of designs. The company also offers integrated cappreform design services that can combine weight and cost reduction, along with innovative design solutions. It can provide targeted consultancy services right from the product design stage. One of the flagships of the Sacmi range is a slitting machine series that is specifically designed to manage every aspect of cap finishing, even where caps are manufactured using non-CCM presses. Sacmi’s CHS (closures handling system) works alongside the compression presses to provide a total, in-line high-speed cap inspection. The latest CHS version to reach the market can perform comprehensive cap inspection through 2D reconstruction of the 3D perimeter. This solution, which was developed by Sacmi Automation & Inspection Systems Division, uses the advanced algorithms already successfully implemented on labelled container, preform and decorated metal cap inspection systems. Both machine and inspection system can be controlled remotely using the advanced Sacmi line supervisor, which allows real-time monitoring of plant performance and management of production orders by interfacing directly with the customer’s ERP. Sacmi has been based in China, offering its advanced technology and efficient after-market assistance, for over 30 years. www.sacmi.it,@ID:59}, PREFORM PRODUCTION PETplanet Insider Vol. 19 No. 04/18 petpla.net 22 PET processing on high-quality equipment from Europe Wherever possible, get ahead; make the competition follow by Kay Barton Precision Plastics has two plants in Thailand. The first that we visited is located around one-and-a-half hours’ drive north of Bangkok, close to the historic city of Phra Nakhon Si Ayutthaya, the former capital of the Kingdom of Siam. The company has been manufacturing PET preforms, bottles and closures since 2001 but its story actually began another two hours’ drive further north, in Nakhon Sawan, where its original site is still located. Precision Plastic has relied on innovative technologies and high-quality equipment from Europe, right from the day it entered the PET processing market, and it still does so today. Precision Plastic Co., Ltd., June 24, 2017 We met: Mr Somsak Sutharoskajornchai, President Mr Komsorn Vipudhamorn, Plant Manager Ms Jidapha Sutharoskajornchai When Precision Plastic was founded, in 1990, it specialised in the manufacture of HDPE bottles. “With our entry into the PET business at our plant in Nakhon Sawan, wonderful opportunities opened up for us”, said company owner and President Mr Somsak Sutharoskajornchai. Plant Manager Komsorn Vipudhamorn pointed to the building and explained: “We built this new site here in Phra Nakhon Si Ayutthaya in 2011, in order to expand our capacity. Regrettably, in the same year, we were hit by the flood disaster and the new plant was flooded on the ground floor.” This had to be cleared up before any further work could be done. Total production area here now extends to around 40,000m2; the original factory is about half this area but both sites employ 250 employees, in two-shift operation. Total investment across the two sites amounts to almost US$ 60 million. As well as its two main sites, Precision Plastics operates a number of smaller, in-house production departments at bottlers. Total revenues for 2016 were just under US$ 59 million. “We have always tried to be innovative and to supply a certain quality”, said Mr Somsak. “We were probably the first in the market to, for example, produce a one-piece closure for hot-fill applications.” Before we could enter Production we had to change and have an air shower. One of the customers is Ichitan, the RTD tea manufacturer, whose aseptic closures were coming off the production line as we arrived. The storage area is gigantic, and pretty much full. The company produces over-whelmingly for local demand; only 6% is exported, and mostly to customers in neighbouring countries, such as the Lao Brewery in Laos, who we also visited and whose senior management we interviewed. Precision Plastics buys material mostly from Indorama and Shinkong. Ninety per cent of its preforms are produced in MHT moulds; the remaining 10% are made in GDXL, among others. A brand new Netstal PET line was delivered just three weeks before our visit, during which we saw Krauss Maffei and MHT service employees engrossed with the test run of the new system. Tour Sponsors: Welcoming the Editourmobil and PETplanet editor Kay Barton (right): Somsak Sutharoskajornchai with his wife Jidapha Precision Plastics’ President Somsak Sutharoskajornchai,@ID:24}, MARKET SURVEY 45 PETplanet Insider Vol. 19 No. 04/18 petpla.net Company name PDG Plastiques Resilux Flexblow UAB Terekas Plastipak Packaging Postal address Telephone number Web site address Contact name Function Direct telephone number E-mail ZI secteur 2 45330 Malesherbes, France +33 2 383461 95 www.pdg-plastiques.com Mr Francois Desfretier General Manager 33 2 38 34 61 95 [email protected] Damstraat 4 9230 Wetteren, Belgium +32 93657474 www.resilux.com Mr Philippe Blonda Marketing & Business Development Director +32 93657476 [email protected] Vytauto g. 114 a Kretinga, Lithuania +370 445 51431 www.flexblow.com Mr Gytis Sirvinskas Marketing Manager +370 620 115 28 [email protected] Ellice Way, Wrexham Technology Park, Wrexham LL13 7YL, UK +44 1978 317378 www.plastipakeurope.com Mr Mike Hanratty Commerical & Business Dvlp. Director +44 1978 317 366 [email protected] Preforms Multilayer preforms (Yes/No) No Yes No Yes PEN prefoms (Yes/No) No No No Yes Preforms in alternative materials (PP/PLA/PEF) - Which? PP - PE - BioPET Yes, please contact us Yes - PP Yes, PLA, PEF Preforms incorporating rPET (rPET content in %) Yes up to 100% Yes, according customer wishes Yes, up to 100% Yes, 1-100% List of additives available Prelactia 100% light barrier for UHT sterilised long shelf-life milk, oxygen, UV, CO2 barriers, coloured preforms, pre-blow technology, Mint-Tec technology Oxygen barrier (ResiOx), CO2 barrier (ResiC), oxygen and CO2 (ResiMid, ResiMax), light barrier (ResiBlock) UV blocker, oxygen blocker, slipping agent All colourants and barrier technologies Preform range 29/25 shorty: 8-10.5-11.7-18.7-21-22-23-23.5-24.528g 30/25 high: 17.5-24.5-26-28-31-33-36-39-50g 30/25 low: 17.5-24.5-26-28-31-33-36-39-50g 38mm 3 start: 28-33.5-35-44-50g Prelactia 38mm 3 start: 17-24-28-38g 48/40: 47-55-62g 27/32: 6.5g dairy and smoothies 25/20: 6.5-8g dairy PCO 1810: 20-33.6g PCO 1881: 18.5-30-32g 29/23: 24-27-33g chemical BVS 30H60: 50g wine (high oxygen barrier) 22H30: 19g wine (high oxygen barrier) ultra-lightweighting 2.4g preform Juice, milk (38mm 2 start, 3 start), CSD, water (28 PCO 1810), CSD, water (28 PCO 1881), water (29/25), water (30/25), water, oil (48/40), oil (29/21), oil (39/21), oil (45/34), detergents (DIN28/410) We specialise in manufacturing customised preforms in small batches: any neck, shape, weight, colour. 1. Light preforms for edible-oil bottle production: 20.5 g, 29/21 neck 2. Preforms for hot-fill bottles: 30g, 38mm neck 3. Wide-mouth preforms: 47g, 82mm neck 4. PP preforms for candle jars: 20g, 63mm neck 5. Preforms for juice and milk bottle production: 19,5–28g, 38mm neck 6. Ultra-light preforms for large-size bottles (5-7l): 61-73g, 38mm neck As the largest suppliers of preforms in Europe, Plastipak has a wide range of preform sizes and weights too numerous to list. Plastipak supplies preforms for use in bottled water, CSD, food, dairy, home and personal care, alcohol, industrial and other applications. Company name Empacar ALPLA-Werke Alwin Lehner GmbH & Co. KG Novapet S.A. Hokkan Indonesia Retal Postal address Telephone number Web site address Contact name Function Direct telephone number E-mail Parque Industrial - 45, Santa Cruz de la Sierra, Bolivia +591 3 3465 525 www.empacar.com.bo Mr Carlos Limpias General Manager +591 3 3465 525 [email protected] Mockenstrasse 34 6971 Hard, Austria +43 5574 602 0 www.alpla.com Mr Jens Seifried Global Sales Director +43 5574 602 518 [email protected] Paseo Independencia 21, 3rd floor, Zaragoza 50001, Spain +34 976216129 www.novapet.com Mr Antonio Lázaro Preform business manager +34 976 216129 [email protected] Jalan Raya Ciawi Sukabumi (Bitung Sari), Km. 3, Ciawi, Bogor, Jawa Barat, 16720, Indonesia +62 2518243555 www.hokkan.co.id Mr Nasruddin Suyuti Marketing & Sales Manager +62 8128047966 [email protected] Epimitheos St. 6, Industrial Area A, Limassol, 3056, Cyprus +357 25 270500 www.retalgroup.com Mr Milos Kuzman Vice President Sales & Service +357 25 270500 [email protected] Preforms Multilayer preforms (Yes/No) No Yes No No Yes PEN prefoms (Yes/No) No No No No No Preforms in alternative materials (PP/PLA/PEF) - Which? No Yes, PEF under devolpment No No Possible Preforms incorporating rPET (rPET content in %) Yes (10% to 100% rPET content, clear and coloured) Yes, up to 100% rPET Yes, from 10-50% Not available Up to 100% List of additives available Activer barrier, 02 scavenger All customary additives Concentrates (for milk and light sensitive products), colours, lubricants, nucleants, under customer requirements Just colourant/masterbatch CO2 scavangers; AA reducers; slip agent; UV blockers; brighteners; nylon, coatings, CO2 barrier, oxygen scavenger Preform range PCO 1810 (17.5, 21, 22, 24.5, 28, 34, 36, 37, 48, 50, 52, 54, 56, 58, 60, 64g) PCO 1881 (20.6, 23.1, 42.5, 43.3, 46.6, 52.5, 54.6, 56.6, 58.6g) Bericap 38mm wide (70.8g) Bericap 48mm wide (85.94g) 700g preform for 5 gallon water bottle 29mm edible oil: 18, 21, 24g Softdrink preforms: various neck versions (0.25 to 2.5l), water preforms: various neck versions (0.25 to 19l), edible oil preforms (0.5 to 10l), milk preforms: various neck versions (2-start, 3-start), preforms for personal care, home care, lubricants: various neck versions Ø 29/25 W short neck - 330ml to 2,000ml (10 to 32g) Ø 30/25 W std neck - 330ml to 2,500ml (11.6g to 47g) Ø 48mm W 5,000ml to 10,000ml (77g, 82g & 98g) Ø PCO 1810 std neck - 500ml to 3,000ml (18.5g to 54g) Ø PCO 1881 std neck - 300ml to 2,000m (18g to 38,7g) Ø 38mm 500ml to 6,000ml (27g to 75g); any other shape and weight 17g, 14.3g (understudy) with PCO 1881 Hokkan Indonesia is 100% OEM company for RTD with aseptic filling system. We don’t have our own brand, and produce the preform in-house. We have mixing tank, blending tank, UHT, combi machine for blowing and filling, and automatic packaging system. We may support our customers to develop the recipe in our own mini laboratory, with aseptic system as well. More than 800 different preforms designs with different weight (9.7-485g) and neck (PCO 1881, PCO1810, PET cycle PCO 1810, High PCO 1810, PCO HYBRID, BPF, 30/25, 29/25, HEXALITE 26/22, Obrist, 34/29, 38mm, 29/21, 28/410) Can produce any other type of preforms,@ID:47}, 65 TRADE SHOW PREVIEW PETplanet Insider Vol. 19 No. 04/18 “When you are playing an exhibition, you are kind of letting everyone get an opportunity” This year for the first time PET Technologies bring advanced technology to Orlando and showcase it at NPE2018. Blow moulds produced by PET Technologies will furnish showcases. The company will share their experience in the field and discuss further projects. On the other hand, the guests will see automatic PET stretch blow moulding machine APF-3002 with output of 3,000bph, 0.2-2.0l. This model has high demand among PET bottles manufactures in Europe, Asia, North and Latin America due to its technical characteristics. The APF3002 blow moulder mould quick change permits to start another bottle volume in just a half an hour. Preform intensive heating system with eight temperature regulation zones and air cooling system provide uniform preform heating. It is easily possible to blow mould asymmetric bottles with an original design. What is the fourth generation of PET Technologies equipment? The company presents last generation of PET stretch blow moulders APF-Max with output up to 14,000bph to produce 0.2-3.0l bottles. Its flexibility permits to form bottles with neck finishes of 18-48mm at the same machine. New NIR heating system and modular systems that gives the possibility to increase the blower output after certain period of operation are among the highlights. The new series is user-friendly and easy to operate due to PLC that stands alone from the machine, electric cabinet backside and all the communications connection from the top. Visitors at the PET Technologies booth will get familiar with several generations of stretch blow moulding machines to choose the best option. They will see blow moulds that the company’s R&D and production area implements into reality. Guests will be among the first to find out what other new products PET Technologies will launch soon! www.pet-eu.com South Hall 10057,@ID:67}, imprint EDITORIAL PUBLISHER Alexander Büchler, Managing Director HEAD OFFICE heidelberg business media GmbH Bunsenstr. 14 69115 Heidelberg, Germany phone: +49 6221-65108-0 fax: +49 6221-65108-28 [email protected] EDITORIAL Kay Barton Heike Fischer Gabriele Kosmehl Michael Maruschke Ruari McCallion Waldemar Schmitke Anthony Withers WikiPETia.info [email protected] MEDIA CONSULTANTS Martina Hirschmann [email protected] Johann Lange-Brock [email protected] phone: +49 6221-65108-0 fax: +49 6221-65108-28 LAYOUT AND PREPRESS EXPRIM Werbeagentur | exprim.de Matthias Gaumann READER SERVICES Till Kretner [email protected] PRINT Chroma Druck & Verlag GmbH Werkstr. 25 67354 Römerberg Germany WWW www.hbmedia.net | petpla.net PETplanet Insider ISSN 1438-9459 is published 10 times a year. This publication is sent to qualified subscribers (1-year subscription 149 EUR, 2-year subscription 289 EUR, Young professionals’ subscription 99 EUR. Magazines will be dispatched to you by airmail). Not to be reproduced in any form without permission from the publisher. Note: The fact that product names may not be identified as trademarks is not an indication that such names are not registered trademarks. 3 PETplanet Insider Vol. 19 No. 04/18 petpla.net It is that time again. In conjunction with the NPE, the Editourmobil will be visiting companies across North America. It starts with an interview with John Galt, only the second CEO at Husky since the company was formed 65 years ago. We asked him about the changes in ownership during his tenure, about new technologies, the competition and the secret of his success. He has a simple yet clear answer: “Don’t talk, listen!”. The Editourmobil is currently heading along the west coast from Seattle to San Diego. Here on the west coast, the severe drought of recent years has significantly altered the people’s relationship with and understanding of water. Packaged water is currently experiencing something of a boom. Every child in California now knows that drinking a glass of water from the tap uses three times as much water as drinking the same glass out of a PET bottle. However, it is not just ordinary, low-priced packaged water, but particularly premium water, which is in increasing demand. While premium water came from abroad a few years ago, a significant group of local waters has now emerged, with 100 new brands being added each year, only 5% of which are likely to survive in the market. Although the focus of this and future editions is and will be on North America, I would just like to mention Chinaplas. Chinese trade fairs are leading the way in Asia which is reason enough for us to be there. Yours Alexander Büchler Dear friends of PETplaner Insider, The Editourmobil is back on the road!,@ID:5}, PETproducts 74 PETplanet Insider Vol. 19 No. 04/18 petpla.net PET for pets Moderna Products nv are known for creating smart plastics for happy pets. Their designs and accessories are used by pets everywhere, from bowls and cat toilets to carriers and gravity feeders and waterers. Their newest design is a gravity fed waterer with a difference: together with the team from PET Technologies, Moderna have worked hard to create a feeder that utilises a blow-moulded jar. Through the specially modified, semiautomatic blow moulder UPF-30 they can now create jars with a neck diameter of 120mm and a volume of 0.5 or 1 gallon. By combining this new technology with their existing injection moulded bases, they have created the perfect gravity-fed watering system. What’s more the PET jars are fully recyclable. So one jar creates another, helping the planet for future pets and owners alike. The UPF-30 was installed at the company’s American plant in Gaffney, South Carolina to run along-side their existing machines there. PET Technologies technicians were on hand to commission the new machine and to give first-hand tuition to the new operators. The new machine is now fully operational. A second installation at their headquarters in Belgium is already pencilled-in for the future. www.pet-eu.com Wide-neck containers: KHS presents individual PET systems for the food sector There is a definite trend towards PET and ever larger bottle neck openings: in the food sector, where to date glass filling was standard, manufacturers are increasingly favouring lightweight plastic. Not only are individual bottle and packaging designs in demand but also wide-neck containers for sauces, dressings and dairy products. In order to give bottlers in this field a great possible flexibility, KHS has further developed its InnoPET Blomax stretch blow moulder. The systems supplier is also extending its Bottles and Shapes program for distinctive bottle design. PET and wide-neck containers are becoming more important to the food industry in particular, with this type of packaging steadily growing in popularity for products such as sauces, dressings or dairy products. To quote Haesendonckx, “PET has a number of advantages over glass, such as its unbreakability and low weight.” Another plus point is that sensitive products can also be filled into transparent plastic packaging thanks to KHS’ FreshSafe PET coating method. Already tried and tested many times over in the beverage industry, this process finishes the inside of the PET bottle with a wafer-thin layer of pure silicon oxide. “This barrier gives products a shelf life which is comparable to that of glass. This latest improvement enables preforms measuring up to 70mm in diameter to be processed,” says Frank Haesendonckx, head of Sales and Technology at KHS Corpoplast in Hamburg, Germany. The machine is available as a modular design with an output of up to 2,500 PET bottles per hour and station. the stretch blow moulder can be blocked with other KHS systems – not just with the InnoPET Plasmax for container coating but also with the Innosept Asbofill for the hygienic filling of sensitive products, for instance. The new KHS chunk dosing unit for flexible product design, which adds fruit, vegetables or cereals, can also be integrated into the system. www.khs.com,@ID:76}, PACKAGING / PALLETISING PETplanet Insider Vol. 19 No. 04/18 petpla.net 42 Ecommerce-friendly packaging project launch Alamo Red Salsa in PET jars Houston, Texas-based contract food packager Consolidated Mills wanted a better way to bring their Alamo Red branded products to consumers. After being frustrated with the normal retail model which relies on distributors to manage the distribution channel to the retailer and ultimately to the consumer, owners and brothers Keith and Scott Vrana, decided that they needed to have more control over this process. Consolidated Mills, Inc. is a Houston, TX based food contract packaging company that specialises in dry blending, processed foods, and flavour concentrates. Since 1962, Consolidated Mills has offered custom blending and packaging solutions for spices, salsas and sauces, flavour concentrates, and non-alcoholic cocktail mixers. Alamo Red is a Consolidated Mills brand that features Texas Crafted recipes for Fire Roasted Salsas, Bloody Mary Mixes, Spice Blends, BBQ Sauces, and Margarita Mixes. Alamo Red can be found in Spec’s Liquor locations around Texas. “Our ultimate goal was to control our brand including how we supply the product to our consumers and how we continue to support our community,” said Keith Vrana. In addition to launching their Alamo Red Foods website, in which consumers can order their family of products, Consolidated Mills has partnered with its local school district, and has launched an additional website to promote “buying local”. Parents can go to this website, select the school or school’s organisation that they associate with, and then order a custom case of salsa. Consolidated Mills will donate $5.00 per case to the school or organisation that the customer has chosen. There are three salsa SKUs: Medium Heat Fire Roasted Salsa, Hot Heat Fire Roasted Salsa and Black Bean, and Corn Fire Roasted Salsa. Ecommerce-friendly solution To provide a better ecommerce solution to the standard glass jar, Consolidated Mills needed a more durable and lighter alternative.“After seeing a sample of the new Apex jar, I knew this would be a game changer for the ecommerce industry,” said Keith Vrana, Owner, Consolidated Mills. At this point, David Parker, packaging consultant and the TricorBraun team, were asked to step in to facilitate the process for commercialisation. TricorBraun partnered with Consolidated Mills and the manufacturer of the Apex jar, to trial a hot fill PET jar. According to Vrana, “TricorBraun was instrumental in helping us realise our objective.” Consolidated Mills wanted to be able to fill the PET jars with their current equipment line used to fill glass jars. “We wouldn’t have done this if a large financial investment was needed to change the set up and the equipment,” explains Vrana. The main goal of the trial was to set up the production line in the same way that it would have been for the glass container to properly cap, using a steam injected capper, and label the new PET jar. Technicians were on hand from the enclosure and capper manufacturer to help fine tune the cap application. “Because we do not have a cooling tunnel, we allow the jars to naturally cool in the shipper box after being filled and labelled...so our main concern was how the labels would react to the PET material. We did see some problems initially, but our label supplier recommended a new material that corrected the issue,” explains Vrana. PET versus glass The advantages of PET versus glass are numerous. “Using the PET jars greatly reduces the decibel levels during production, and we don’t have to worry about broken glass shutting down the line. Our cases weigh three pounds less now, reducing our freight cost, and because we are now shipping plastic containers, we are able to eliminate the extra packaging costs needed for ecommerce,” according to Vrana. “Our goal is to get all of our salsas plus our other Alamo Red products, Blood Mary mixes and barbeque sauces, into hot fill PET jars,” explains Vrana. He goes on, “We will also encourage our private label customers to switch to PET as well.” Vrana describes working with TricorBraun this way, “Every time we discuss a project or idea with TricorBraun, both Scott and I feel that they are truly engaged in what we are trying to accomplish. David and the rest of the TricorBraun team understand where we wanted to go, and offered ideas to help us achieve our mutual goals. We’re poised for growth and TricorBraun is helping us get there.” According to Parker, “We’re thrilled to be helping Consolidated Mills with this ecommerce-friendly project launch...now consumers accustomed to the quality look and feel of a glass jar with a metal lug closure will enjoy the same quality experience with a lightweight, shatter-proof PET jar. It’s a win-win.” www.tricorbraun.com www.alamoredfoods.com,@ID:44}, TRADE SHOW PREVIEW PETplanet Insider Vol. 19 No. 04/18 petpla.net 56 Focus on smart factory Drying on demand The Chinese plastic industry market has huge potential and is increasingly sensitive to new technologies. At Chinaplas, the Italian company Moretto presents solutions, know-how and service for material handling, drying, blending, heat transfer and size reduction equipment, able to respond to the needs of Chinese customers. At Chinaplas the spotlight will be focused on Eureka Plus and Moisture Meter Manager. Eureka Plus is a modular, energy-saving, low consumption resin drying system. A project born from over 15 years of studies, simulations and experiments and which continues to evolve including new tools and applications. Eureka Plus is comprised of four Moretto-patented technologies: X MAX high performance, modular multi-bed dryer with consistent dew point, combined with Flowmatik, a dynamic airflow management device, OTX drying hoppers with superior mass flow drying characteristics and now Moisture Meter Manager, an in-real and real-time moisture analyser. Moisture Meter Manager measures in-line the actual residual moisture content in the granule and checks that the polymer is adequately dehumidified immediately prior to the transformation process. The delta measurement between the initial and final moisture content of the pellet, at the hopper inlet and outlet, allows Moisture Meter Manager to automatically manage the dryer working conditions and to adapt the process on the fly defining process parameters for proper drying and energy efficiency. This process allows the dryer to operate based on the condition of the polymer at any given time, providing a real “drying on demand.” By acquiring the initial data of the material and knowing the final moisture requested, the solution holds a complete control over the process and manages all the process variables (type of material, final moisture set, hourly production, treatment temperature, specific airflow). Moisture Meter Manager closes the loop on resin drying by integrating the dryer in an adaptive system as requested by the smart factory, says the company. The right amount The DGM Gravix series gravimetric dosing units are high-tech machines, conceived by Moretto not only for ensuring precise levels (0.001%) but also for interchanging data with the possibility to be networked, for remotely managing the machine parameters and performing statistics on production, consumption and costs. Gramixo is available in various specific models for different sector applications. These dosers are characterised by a double eyelid system, a free weighing hopper, vibration immunity system, a Touch View interface and a connection to the Mowis supervision system. TE-KO is Moretto’s temperature control series, available in pressurised water and oil versions, designed to ensure efficiency and precision in automatic temperature control even in the most difficult conditions, whether they are dedicated to injection moulds or extruders. Mowis (Moretto Object Windows Integrated Supervisor) is the integrated self-configurable supervision system with intuitive object programming, developed for the machine’s connection and the control of the whole automation chain in the plastics processing plants. The company states that Mowis adapts to the needs and the qualitative, productive and managerial objectives of every customer. With Mowis the integrated process control can be managed from any location, on-site or remote. Built on Scada system Mowis make safe and immediate the exchange of data between standard modules, tailormade modules and the customer management system. The Moretto’s smart factory is where machines are interconnected with each other and with the company management software, a system that is able to acquire large amounts of data from all the actors of the production process, elaborate, share and use them to achieve higher levels of efficiency. The project aims to obtain plants that are able to automatically adapt output to the market needs, predict breakages or machine stops in advance and have a real-time remote support. www.moretto.com Hall 2 Booth C61,@ID:58}, PETplanet Insider Vol. 19 No. 04/18 petpla.net 78 PETbottles Beverage + Liquid Food Frying oil from Italy Olitalia, the manufacturer of a wide variety of cooking oils, has developed a special oil suitable for the high temperatures generated during deep frying. The oil does not contain palm oil and through the addition of rosemary extracts contains healthy antioxidants and has a Mediterranean aroma. The oil, which can be used in temperatures up to 230°C, comes in a 1l, slightly contoured bottle with ridges to increase its stability. The circulating sleeve label has a viewing window to check fill level and to estimate usage; the product packaging is finished with a sunshine yellow screw cap with a ring-pull seal. www.olitalia.com Fruit juice drinks trending Still mineral waters with a juice content of up to 50% are trending as perfect thirst quenchers. The vegan, glutenfree drinks from German drinks manufacturer Rapp’s contain only the sugar naturally present in the fruits. They are free from artificial aromas, colours and preservatives. The ratio of 50% water to 50% juice halves the sugar consumption for the same volume of drink, fitting perfectly into discussions about a low sugar diet. “Rapp’s Naturell” juice drinks are available in two varieties, Apple-Cherry and Apple-Lemon, and come in disposable contoured bottles with sleeve labels and a screw cap with guarantee band. www.rapps.de,@ID:80}, 48 TRADE SHOW PREVIEW PETplanet Insider Vol. 19 No. 04/18 petpla.net High quality injection moulds Following the successful trade fairs of previous years, the Swiss firm Otto Hofstetter has its own stand this year, where it will be presenting its products and services. Otto Hofstetter will be showing customers their complete portfolio of high quality injection moulds. In addition to their well-known high-quality injection moulds, Otto Hofstetter will be on hand to advise customers on the complete moulding process, beginning with the basic idea for a product, leading to consultations over the design, and once the mould has been built, the entire project is completed with a comprehensive after sales service package. Otto Hofstetter is well known for PET preform moulds from 2 up to 192 cavities, as well as for injection moulds for thin walled packaging application and In-Mould Labelling solutions. Otto Hofstetter will be presenting products for the thin-walled packaging sector as well as demonstrating the company’s competence in supplying complete systems for producing PET preforms. Therefore Otto Systems AG is present on the same stand. www.otto-hofstetter.swiss Solutions for quality recycled pellets in demand Visitors to the Erema trade fair stand will find out how, using the right technology, they can process not only clean production waste but also even heavily contaminated postconsumer materials to make new raw material. In combination with Erema’s smart digital solutions, this is intended to set a new standard in terms of quality and processes in plastics recycling. The potential of plastics recycling in China can be tapped even further, says James Qiu, CEO of Erema China. To support this development from the technological side, Erema developed the Intarema TVEplus system especially for the processing of post-consumer materials. The company says that the combination of Intarema TVEplus and Erema Laserfilter is particularly suitable for material with a high degree of contamination, when conventional melt filters can no longer offer the necessary cleaning efficiency. For processors, Erema offers the technical answer to the question of how the production waste which accumulates can be used as efficiently as possible. Interested attendees can see the production quality of the Intarema TVEplus 1007 for themselves at the Erema booth. The system will be processing production waste from polypropylene big bag bulk containers (FIBCs) live to make high-quality recyclates – direct and without any pre-shredding. Equipped with an Erema Laserfilter, the Intarema TVEplus system can even recycle heavily contaminated or heavily printed post-consumer bulk bags. Erema’s smart factory package is intended to represent another boost in quality. Recyclers and producers can equip their Erema systems with online quality measuring equipment to record the MVR and colour values of the recyclates at the machine during processing – as opposed to later on in the laboratory. Additionally, the re360 Manufacturing Execution System (MES) enables you to transfer production and machine data from one, two or dozens of systems – also at different locations – directly to the computer in real time. www.erema-group.com Hall 5.2 Booth J05 Hall 2 Booth B59,@ID:50}, TRADE SHOW PREVIEW PETplanet Insider Vol. 19 No. 04/18 petpla.net 70 Internet of Things (IoT) connectivity for productions of up to 8,800bph SMI embraces Eco and Industry 4.0 SMI has announced the extension of its Ergon EBS (Electronic Blowing System) range of stretch-blow moulders with the launch of the Ergon EBS K and Ecobloc Ergon 4-12-4 K EV models. New new models offer advanced technology in a compact modular footprint. The machines were presented for the first time at Interpack 2017 and will make their North American debut at NPE. The K designation in the new series stands for the German word “Kompakt”, which means the same as it sounds in English: compact. The design of the new machines builds on the advances and innovations introduced with the original Ergon EBS range. Available in two, three and four-cavity versions, they can produce bottles of up to 3l in capacity. Bottles of 500ml capacity can be produced at a rate of 2,200bph; maximum output for smaller packages is 8,800bph. Efficient preform heating The preform-heating tunnel module is integrated with the stretch-blow moulding carousel into a single, very compact module. SMI says that this allows the machines to be installed even in small bottling lines. The tunnel has a horizontal preform feeder chain and an optimised ventilation and aeration system and its infrared heating units have a system of thermo-reflective panels, made of highly energyefficient composite material and located both in front of and behind the lamps. These are designed to facilitate high levels of heat reflection and thus achieve more uniform temperature distribution over the entire surface of the preform. The inside of the module is also equipped with an aluminium diffuser, to provide optimal temperature control and prevent overheating. The machine frame that contains the tunnel and blowing-wheel features slightly rounded safety doors. These provide a wide opening, enabling easier access to the interior of the machine for cleaning and maintenance operations. Electric motors for efficiency and accuracy The stretch-blowing wheel is equipped with motorised stretch rods, controlled by electronic drives. The elimination of mechanical cams enables precise control of the stretch rod’s path and position, and energy savings as well. The stretchblow moulding system itself uses high-performance, low dead-volume valves that reduce pre-blowing and blowing times. This is designed to improve both machine efficiency and finished bottle quality. Because it is equipped with its own motorisation, the mould’s mechanical assembly is able to ensure high standards of precision for both the up/ down motion of the mould base, and the opening and closing of the mouldholder unit, the company states. Automation for cost savings The Motornet System, which provides control and automation, is designed to ensure the constant maintenance of optimum processing parameters throughout the entire manufacturing cycle, as well as the direct modification of machine settings. These features help to simplify format changeover operations. SMI says that the automatic adjustment of blowing pressure, according to bottle format, offers significant advantages over comparable manual adjustment solutions employed on other linear blow-moulders operating in the same market segments. The new machines also come with a two-stage air recovery system as standard. South Hall 16085,@ID:72}, 10 NEWS PETplanet Insider Vol. 19 No. 04/18 petpla.net Tech-Long partners with Unique Injection Molding Systems LTD. Tech-Long Americas has announced its partnership with Unique Injection Molding Systems, Ltd. The addition of injection moulding to Tech-Long’s product line portfolio offers customers a complete turnkey solution – from the making of PET preforms, through to complete liquid filling packaging lines. Fred Pinczuk, a twenty-two year veteran of the beverage and packaging industries has joined Tech-Long as Business Development Manager for Unique Injection Systems and TechLong Packaging Machinery, where he will lead marketing, sales and service efforts. Unique Injection Molding Systems based in Guangzhou, China, is located within minutes of Tech-Long’s global headquarters. Founded in 2007, Unique Injection Molding Systems provides PET preform manufacturing solutions that promote energy savings, ease of use and environmental sustainability. The company’s product lines include injection moulding machines with take-off robots, PET preformmould and auxiliary equipment such as drying systems, dehumidifying systems, chiller water systems, air compressors and preform conveyors. Injection moulding machines use optimised machine design and major components sourced from leading suppliers around the world. Exceptional system performance and reliability has resulted in the company quickly gaining significant market share in Asia and abroad. Tech-Long USA is a wholly owned subsidiary of Guangzhou Tech-Long Packaging Machinery Co., Ltd. Established in 1999, the company supplies equipment and services to the beverage and non-beverage filling and packaging industries including: preform injection moulding machines; water treatment systems; beverage processing systems; PET bottle blow-moulding machines; filling machines; labellers and secondary packaging equipment. With over 2,500 production lines globally, Tech-Long has systems operating in more than 80 countries. www.tech-long-intl.com Joint Venture to acquire bankrupt M&G USA PTA-PET plant in Texas Corpus Christi Polymers LLC (“CC Polymers”) - a newly formed joint venture between Alpek, S.A.B. de C.V., Indorama Ventures Holdings LP, a subsidiary of Indorama Ventures Public Company Limited, and Far Eastern Investment (Holding) Ltd. - has entered into an asset purchase agreement with M&G USA Corp. and its affiliated debtors. CC Polymers will acquire the integrated PTA-PET plant currently under construction in Corpus Christi, Texas, certain M&G intellectual property, and a desalination/boiler plant providing water and steam needs to the Corpus Christi Project. The purchase agreement provides M&G with a binding bid of $1.125 billion in cash and other capital contributions. The Corpus Christi Project is an integrated PTA-PET plant currently under development that, when completed, will have nominal capacity of 1.1 million and 1.3 million metric tons per year of PET and PTA, respectively. The plant is expected to be the largest single line vertically integrated PTA-PET production facility in the world and the largest PTA plant in the Americas. Pursuant to the terms of the newly formed joint venture: The parties will provide resources to CC Polymers to complete the project in the most efficient and cost effective way. A timeline for project completion will be communicated at a later stage. Each of Alpek, Indorama, and Far Eastern will have the right to receive one-third of the capacity of PTA and PET produced at the Corpus Christi Project upon completion. Each party will independently procure its raw materials and will independently sell and distribute their corresponding PTA and PET. The closing of the transaction is subject to conditions precedent including approval by the bankruptcy court and applicable governmental authorities. PJT Partners is serving as financial advisor and Weil, Gotshal & Manges LLP is serving as legal advisor to Alpek. HSBC is serving as financial advisor and Lowenstein Sandler LLP is serving as legal advisor to Indorama. Morgan Stanley is serving as financial advisor and Duane Morris LLP is serving as legal advisor to Far Eastern. www.indorama.net,@ID:12}, MATERIALS / RECYCLING PETplanet Insider Vol. 19 No. 04/18 petpla.net 19 at Logoplaste fully agreed with Ana during his presentation on PET bottles. For Paulo “design for recycling is key in a circular economy”. At the conclusion of day one, Casper van den Dungen and Herbert Snell from Plastics Recyclers Europe (PRE) gave their view on PET recycling. The two experts emphasised the importance of optimising the value of collectables. To achieve this optimisation PRE will focus on collecting, sorting and recycling standards. Casper ended the presentation with a call to the entire industry: “Don’t ask what PET can do for you but ask what you can do for PET.” The second day of the conferencebegan where the first left off: with a room full of representatives from the PET value chain - ready for the morning session on the European Circular Economy. Eline Boon from the Ellen MacArthur Foundation presented the “new plastics economy”. According to Eline there is “a global momentum to rethink the plastics system”. However, it is not about “doing without plastics, but doing things differently”: “We need a new plastics economy where packaging never turns into waste.” One highlight of this year’s conference was the presentation of the EU Plastics Strategy by Eric Liégoise from the European Commission - DG GROW, who emphasised that there is finally a concrete strategy on the table for plastics in the circular economy: “Our plan should bring not only economic but also social and environmental growth while boosting the competitiveness of Europe’s plastics industry.” The presentation stressed the fact that an industrial commitment to use more recycled plastics as well as global action is essential. After explaining the strategy developed in detail by the EC, Eric Liégoise took the time to thank Petcore Europe for its voluntary commitment to 65% recycling and reuse of PET packaging material collected by 2030. Trends and solutions in PET collection and recycling After an informative Q&A session, the focus of the conference shifted to trends and solutions in the PET postconsumer collection. First, Gian de Belder from Procter & Gamble presented the Holy Grail project on markers and digital watermarks. Gian gave an interesting overview of the five pillars for a circular economy: design for recycling, access to collection, participation/ education, separation and product innovation. Gian was followed by Clarissa Morawski from Reloop, who compared deposit versus non-deposit collection. Even though there are still many issues with post-consumer waste collection, Clarissa sees a positive development: “I have seen more activity from the industry and governments in the past year than in the previous 20 years.” The last presentation of the collection focused session was delivered by Carlos de los Llanos and Vincent Colard from CITEO and focused on the development of opaque PET bottles and PET thermoforms collection in France. To introduce the topic of PET post-consumer collection, Antonio Furfari from PRE gave his presentation on design for recycling. Antonino presented RecyClass, an online tool that ranks the recyclability of a plastic package, as well as the European PET Bottle Platform (EPBP) providing design guidelines for recyclability. After Antonino’s introduction, Francois Lagrue, plant manager at Wellman gave an overview of the state of the art in the collection, sorting and recycling technologies of PET thermoforms. Even though the recyclers face a number of problems in this area Francois is more than positive about the future: “The PET bottle recycling is a success story, but it did not happen with a click of the fingers. It needed some time, as it will still need some time for the thermoforms. If the entire value chain works together we will have another success story around PET.” DuPont, for example, is already working on solutions to increase the recyclability of PET thermoforms. Heiko Schenck presented the challenges the company and industry are facing, and more importantly, possible solutions to overcome these challenges. Full body sleeves on PET bottles represent another challenge for recyclers. An Vossen gave an exciting overview of the current situation and presented a possible solution: easily removable labels as well as end-consumer education and engagement. Chemical or back-to-monomer recycling The last session of this year’s Petcore Europe Conference focused on chemical recycling which was generally seen as one of the long-term solutions for a circular economy. Wim Hoenderdaal from Indorama Ventures Europe kicked off the session with a general overview and stressed the following points: Chemical recycling is complementary to mechanical recycling and should recycle PET thermoforms, opaque bottles and other difficult to recycle PET products. The whole supply chain needs to invest and bridge the initial higher cost associated with the development and up-scaling of the new technologies. For Wim, chemically recycled or as he calls it “circular PET feels like a dream that is close to reality.” After Wim’s introduction, Martin Stephan from Carbios and Maurizio Crippa from gr3n presented two chemical recycling projects in detail to conclude the second day of the conference. Whereas the project of Carbios relies on enzymes to rethink the lifecycle of plastics, the EU funded project Demeto with the technology of gr3n uses microwaves for de-polymerisation. Both projects are in progress at this moment and have to be finalised but they are excellent examples that the PET industry is focusing on further developments and innovation in order to tackle the challenge of the circular economy today. It was not only the final session devoted to chemical recycling but the entire conference was a vivid demonstration of why it is so vital to bring together every year all the players in the PET value chain for the annual meeting - to take the PET industry on to the next stage. www.petcore-europe.org Wim Hoenderdaal states: “Circular PET feels like a dream that is close to reality!”,@ID:21}, EDITOUR PETplanet Insider Vol. 19 No. 04/18 petpla.net 13 maker partner Corvaglia and supply its own tools for HyCAP. Joachim Niewels showed us in AMC, Bolton how you approached this issue strategically and still do. The “We will give it a go” era has given way to a strategic analysis of the individual process steps. What concrete results have emerged from this strategy? John Galt: The acquisition of KTW and then Schöttli has allowed us to take a big step forward in the Medical and Closures sectors. We are a global leader in specialty closure and medical mould production today. We are doing some great work now where we are combining our mould expertise in these areas with Multi-Layer system level technologies to open up new markets for the company. PETplanet: At the moment, you are placing great emphasis on Multi-Layer Technology. You are now dealing more effectively with previous market barrier systems, such as additives, new material coatings and classic Multi-Layers thereby achieving cost savings, and above all making machine control extremely user-friendly. Should new technology replace existing processes or should the market be expanded for barrier PET bottles? John Galt: Multi-Layer Technologies have been tried before, but they’ve never realised their full potential. They’ve either been handicapped by issues with material degradation, by lower overall output in efficiency, or by significant compromises in cycle time. These factors have created an obstacle to achieving a balance between enhancing package performance, while maintaining a lower part cost. We believe entirely new markets for injection moulded plastics and PET can be developed through this approach. We believe we can demonstrate that two materials, properly positioned in the container, with no loss in productivity over the mono-layer solution, is a game changer. We have applications that deliver greater barrier performance, new product decoration solutions, and the solution even has the potential for smart packaging. There are just so many uses if you can master the process and encourage resin producers to expand the range of materials and additives they provide. PETplanet: You won the PETplanet Award Service Performance, Developing Countries Group Preform Machine Builder Customer Survey in 2014. You nailed points such as Competence or Technician Categories Close to My Plant. Only on point pricing and volume discount on aftermarket products are you well below the industry average. If the survey was to be repeated today, would the outcome be any different? John Galt: Naturally we are very proud of the award, but the outcome for today would be something our customers should decide. We continue to invest in Aftersales Services and the only way to find out if this is the right decision is to ask our customers. The proof is in the pudding, as they say. Our goal is to invest in Services that are invaluable to our customers and that help them make good returns on the investments they make with us. PETplanet: John Galt. Thank you very much for your time. I have one final question I would like to put to you. Looking ahead into the world of PET, what topics do you think we will be discussing in PETplanet Insider 10 years from now? John Galt: I can only tell you what I am observing. The future is going to be revolutionised by digitization. It will influence what consumers buy, how it is delivered and how we communicate. It will result in entirely new products. Lower volume, shorter life cycle products will also be a far more significant market as young consumers demand more variety and are constantly looking for new things. We will need to have moved forward dramatically on the environmental front to create a truly efficient, circular economy for plastics. This last one is a big issue for our industry. Technology exists or will exist. What doesn’t exist is the way we work together to close the loop from production, to recovery, to reprocessing, to reuse. These factors will become a big part of how we design new technology. We have to come together as an industry and I hope that is a part of how we operate 10 years from now. www.husky.co,@ID:15}, 73 ON SITE PETplanet Insider Vol. 19 No. 04/18 petpla.net Nanjing Ziquan installs second Sidel complete hot fill line Nanjing Ziquan, one of China’s leading co-packers, has turned to Sidel to increase its hot fill production capacity of Mizone, a functional drink brand popular in China and packaged in PET, for which consumption is growing. The new line - running at a speed of 36,000bph - follows positive feedback on a similar complete hot fill PET line installed by Sidel in 2013. Nanjing Ziquan is a member of The Shanghai Ziquan Beverage Company Limited, one of the country’s leading OEM companies. Established in April 2004 and located in the Nanjing Hi-tech Industrial Development Park, the company bottles products in PET on behalf of leading brands such as Danone, Coca-Cola and others for distribution in Greater China. With a production capacity of 490 million standard bottles (500ml or 600ml) per year, Nanjing Ziquan is a key OEM company in the region. “The earlier Sidel line had been maintaining an operating efficiency of 95%+ and has even been upgraded recently, so that its output speeds for the 600ml bottle format increased from 30,000bph to 34,500bph,” comments the management team of Nanjing Ziquan. “As a result of the excellent and reliable performance of this first complete hotfill line, we were happy to award the project for a similar solution once again to Sidel.” Both Sidel lines comprise a Sidel SBO Heat Resistant blower with 20 blowing stations, Sidel Matrix SF700 hot filler, conveyors, labeller and packer. In 2013, when Nanjing Ziquan installed the first Sidel complete hot fill PET line - which featured the very first Sidel Matrix hot filler ever in Greater China - the functional drinks market was increasing. The first line was installed to increase production capacity for the co-packer, and the most recent line was intended to meet the continuing market growth in Greater China for functional drinks, forecast at a CAGR of 15% from 2016-2020 (Euromonitor). This second line, used exclusively to bottle the Mizone functional drink, was installed in anticipation of substantial market growth for the product. The Sidel Matrix hotfiller, the SF700, featured by the second line, meets the production demands of a variety of beverages, such as teas, isotonics and juices, with or without pulps or particles - in formats to match production needs. www.sidel.com ONsite stf·sorting line stf·washing line professional plastic recycling solutions – made in germany The stf· group is the leading manufacturer of plastic sorting and washing machinery, especially for PET post-consumer bottles, with more than 60 turn-key plants and several single machines delivered worldwide. stf·group Industriestr. 1-3 94529 Aicha v. Wald – Germany fon +49 8544 960-110 mail [email protected] web www.stf-group.de scan for vCard stf ·group,@ID:75}, PREFORM PRODUCTION 23 Phra Nakhon Si Ayutthaya Injection moulding: 7 Krauss Maffei PET mould, 96 and 112 cavities 1 Netstal PET Line, 96 cavities Closures: 2 Krauss Maffei, 60 cavities Compression moulding: 6 Sacmi, 32 and 48 cavities Blowing: 2 Sidel, SBO 16 and SBO 20 Nakhon Sawan Injection moulding: 5 Krauss Maffei PETmould, 72 and 96 cavities Closures: Compression moulding: 4 Sacmi, 32 and 48 cavities Blowing: 4 Sipa 1 Sidel SBO 10 3 ADS Linear Overall outputs Preforms: 1.2 bn p.a. Closures: 2.6 bn p.a. Bottles: 57 million p.a. PETplanet Insider Vol. 19 No. 04/18 “85% of our preforms go to aseptic filling, mostly for RTD tea and still water,” said Somsak Sutharoskajornchai. “12% is hot-fill, the rest is for other applications.” Sacmi compression lines are mostly used for aseptic closures, while two Krauss Maffei injection moulding machines produce closures exclusively for non-CSD beverages; mainly for water. “In terms of competition, our customers are basically our main competitors now, because the fillers now often produce the bottles themselves. Good examples of how the market has changed in this respect, are Oishi and Semsurk, who have become independent,” he concluded. www.preciplas.com Test run of the new Netstal PET line Introducing the latest innovation in Tech-Long’s complete line of liquid packaging solutions: the CPX2 PET Stretch BlowMolder – featuring rotary processing performance in a stationary design. • Compact design, 2-cavity solution • Servo stretch • High performance, low energy usage • High versatility • Standard, oval shaped bottles • Application range from150ml to 1 gallon • Easy access to reducemaintenance time and allowquickmold changeover,@ID:25}, BOTTLING / FILLING PETplanet Insider Vol. 19 No. 04/18 petpla.net 33 sius for 20 to 30s is ideal. Less acidic liquids, such as vegetable juices, need to be heated to higher temperatures. Finally, both solid and liquid ingredients pass through an aseptic balance tank before filling. This step prevents re-contamination and eliminates the need for further pasteurisation. Pasteurisation solutions for liquid food GEA’s Asymmetric Two-Stream Pasteuriser brings together two separate processing lines to manufacture a single product. An aseptic product holding tank is placed at the head of each line. The tank containing the solids uses a slow-moving agitator to ensure the consistent fluidisation of the product and a modified atmosphere, either nitrogen or aseptic air, to prevent bacterial infection and oxidation which adversely affect taste and product appearance. The flash pasteuriser system on each line features GEA’s Varitube tubular heat exchangers; these comprise a patented deflector at the inlet which creates a powerful vortex and prevents the formation of deposits. Large radius bends in all the pipework also prevent dead areas and the accumulation of product. Product changeovers in just 20 minutes Treatment of the relative product in each line is based on exact specifications to minimise holding times and the detrimental effects of heat. Pressures within the system are kept below 4bar to limit structural damage to product fibres or particles and both heating and post-holding cooling is optimised to ensure product quality and stability. Fluctuations in the pasteurisation units are prevented via a self-adjusting feedback system which continually monitors, analyses, and adjusts the process to make it more efficient and reduce product losses. In-place cleaning or sterilisation is quick and efficient, requiring a minimum of energy and water. Added up, all these efficiencies mean products can be switched out in just 20min, thereby reducing downtime. After the appropriate heat treatment, the products are gently combined in a small, aseptic mixing tank before going on to aseptic or hot-fill bottling. Customers are able to manufacture products that contain up to 30% particles. 87% of heat recycled In addition to minimising the energy used within the system, the GEA Asymmetric Two-Stream Pasteuriser incorporates a GEA heat recovery system which recoups up to 87% of the thermal energy, minimising the steam network load requirement and reducing energy costs. This significantly reduces the Total Cost of Ownership (TCO) of the system over the lifetime of the plant and contributes to the overall sustainability of the process. GEA’s dual fill solutions within aseptic production To achieve the quality and variety demanded by consumers, GEA believes that a filling system needs to be both dual fill and aseptic: dual fill technology uses an aseptic piston doser to very accurately add the pieces of fruit in a separate process from the liquid beverage, which is filled in a second step with a volumetric electronic filler. This is very difficult to achieve in a single stream process as the solid product tends to settle and separate from the liquid phase within the system. Keeping the product in a constant state of agitation to maintain the homogeneity is likely to cause product stress and loss of quality. Kept in suspension in this way pieces can also bridge with each other and clog making them hard to process. And although the technology is more widely available today, GEA was the first manufacturer to supply dual fill technology as part of an aseptic, cold fill process. As with all aseptic processes, dual fill bottling takes place within a controlled microbiological environment that maintains sterility throughout the process. This approach can accommodate a wide range of drinks, including complex liquid foods such as yoghurt, liquid breakfasts and juices that contain pieces of fruit and fibre - whether high or low acid, still or carbonated. Likewise, different products can be run on the same machine, and automatic sterilisation-in-place (SIP), which uses overheated water, allows for quick product changeover while eliminating any chance of cross contamination. The GEA aseptic dual fill system complies with the most stringent microbiological validation protocol specifications worldwide, including Europe, the Far East and the United States. All sanitation and sterilisation cycles are automatically controlled at all critical points. The system can maintain a production level of over 50,000bph. Aseptic dual fill is also claimed to be the most flexible PET bottle filling system available for beverages containing pieces, largely because the aseptic process doesn’t require the application of heat. This means PET bottles can be much lighter, resulting in both material and manufacturing cost savings, as well as reducing the impact on the environment. Dosing valve fills accurately A benchmark in the industry, GEA’s system achieves high filling accuracy and allows for pieces of fruit or cereals up to 10 x 10 x 10mm. This precision is thanks to a unique dosing valve, the GEA Piston Doser PX, which uses an accurate, camdriven piston to draw the prescribed volume of solid particles into the cylinder before injecting them into the PET bottle. A hygienic seal around the piston maintains the aseptic integrity of the doser by preventing product leakage. The dosing volume can easily be regulated from 15 to 150ml by changing the dosing value on the HMI (Human Machine Interface). The stroke of the piston is automatically adjusted by a linear motor, which provides adequate dosing for most products in PET bottles up to 2l. Smaller or larger dosing volumes can be achieved by simply adjusting the cylinder diameter. Seamlessly switching between different liquids Following the dosing phase, a standard volumetric electronic filler, such as the GEA Fillstar CX EVO, is used to add the liquid part and to complete the aseptic filling process. The Fillstar CX EVO is a multi-functional system that allows customers to seamlessly switch between different types of products, from still to carbonated aseptic beverages and vice-versa. Product changeover times are significantly reduced as the integrated control unit can easily be reprogrammed. The changeover from contact filling to non-contact filling is,@ID:35}, BOTTLE MAKING 26 PETplanet Insider Vol. 19 No. 04/18 petpla.net PET blow moulding machines made in Thailand by Kay Barton Mahatanee machine manufacturer, headquartered in the Bang Bon district in Bangkok, has been operating in Thailand for 25 years and remains a family-owned and managed company. Initially established as a classic bottle-maker, over the course of time and with growing technical understanding of the machinery it began, in 1997, to develop and construct PET bottle making machines for small and medium quantities. This makes Mahatanee unique in Thailand, because this type of equipment has normally been imported. In 2000, it opened a production area for blow moulds and now offers a range extending from 30ml to 20l bottles. The company is run by joint Managing Directors and brothers Mr Yick Yu Lam and Mr Metee Nilparak. “When our father started the company in 1992, we were producing on Chinese machines. After two years of development, we created our own blow moulders for first time, with a cavity for 800ml wide-mouth cans,” said Mr Lam. “In the early 2000s we did not sell more than perhaps ten machines a year; PET was still something really new then. Things really got going after the flood disaster of 2011, when the supply chain to beverage fillers collapsed and more and more bottlers decided to mould their own bottles, or found that they had to.” By 2014 annual machinery sales had more than doubled; they have doubled again since then. For 2017 Mr Lam is expecting to sell 50-60 machines; 80% will go to water bottlers, the rest to CSD, edible oil, food, and non-food packers. A small number of customers are active purely in bottle supply. “Due to the special situation of non-existent competition we are of course in a good position”, Mr Metee Nilparak said, and laughed. “Nevertheless, we regard ourselves as competitive, both locally and at international level.” He described the 40% export share that the company is aiming for in 2017. Exports are mostly concentrated in Vietnam, Myanmar and the Philippines. “We use high-quality components, such as servo systems and Siemens control”, Metee explained. Turnround time is, on average, eight weeks from enquiry to the machine being ready for dispatch. The brothers are forecasting revenues of US$ 3.5 million for this year. The long-term objective, they say, is US$ 6 million in machine sales alone; revenues from the mould business, which currently account for around 20% of overall sales, would be on top of that. In 2016, Mahatanee sold 200 moulds, all made in Swiss aluminium alloy; in 2017 it expects sales to total 250. The current company value is around US$ 7 million. www.great-pet.com Tour Sponsors: Staff working on new moulds MDs and brothers (f.l.t.r.) Yick Yu Lam and Metee Nilparak Mahatanee Industrial Co., Ltd., June 24, 2017 We met: Mr Yick Yu Lam, Managing Director Mr Metee Nilparak, Managing Director Mahatanee’s factory in Samutsakorn is brand new; the company moved here only six months ago. As well as the production facility the 8,000m2 plot of land also accommodates the residences of joint Managing Directors Yick Yu Lam and Metee Nilparak and their families. To the front right of the main building itself are the offices, covering two floors; the rest is a workshop and divided up into the areas of machine construction, CNC machining and mould assembly. To the rear are found the shop floor itself, along with work materials and replacement parts stores. Mahatanee’s workforce totals 80. During our visit, there was still plenty of space in the hall for additional equipment or more warehouse area for preorders. Machine shipment packaging at Mahatanee’s workshop,@ID:28}, PETplanet Insider Vol. 19 No. 04/18 petpla.net 79 BOTTLES “Naked” smoothies in Germany In cooperation with PepsiCo and following success in America, the German Uplegger Food Company is bringing the smoothie brand “Naked” to German chiller shelves. Under the names Red Machine, Blue Machine and Green Machine, the juices with high apple juice content are combined with ingredients such as linseed, spirulina, spinach, wheatgrass and other vegetables and vitamins. The square, clear and sturdy bottles with rounded corners hold 450ml, are decorated with a transparent foil label and are sealed with a tamper-evident screw cap with brand name embossing. www.nakedjuice.com 100% NFC juice from Aldi Süd In a promotion, Aldi Süd is bringing two new NFC juices onto its chiller shelves under its own brand “rio d’oro”. The vegan juices Apple/ Raspberry/Chokeberry and Orange/Mango consist of 100% NFC juice and are available in clear 1l bottles. The matt printed paper label has a rough easy-grip surface; in this area, the thin-walled bottle has reinforcement ridges for stabilisation. The generous opening is sealed with an opaque screw cap with guarantee band. www.aldi.de [email protected] Contact Shaping the future powered by Messe Münchendrinktec food and drink technology Africa is the premier platform for the Southern African food, beverage, and packaging industries. The established event serves as a trade fair, top-selling market place and future-oriented knowledge center. food & drink technology Africa 2018,@ID:81}]}}
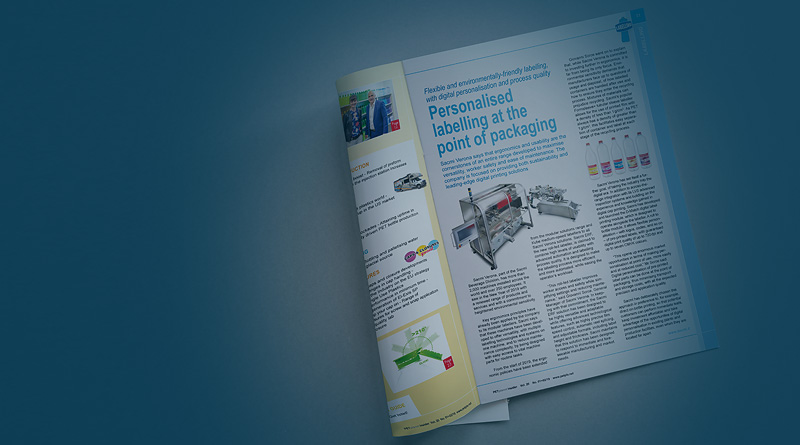