INSPECTION 38 PETplanet Insider Vol. 19 No. 06/18 petpla.net Toronto New York Atlanta Orlando Denver Las Vegas Seattle LosAngeles San Francisco Vancouver Dallas New Orleans Phoenix Washington, D.C. Boston Detroit Kansas City Oklahoma City Albuquerque Milwaukee Chicago Minneapolis Charlotte Ottawa Montreal Quebec , / 0 The worldwide round trip with The North American Road Show - Bottle Zone on tour PETplanet has successfully deployed its “Editourmobil” Road Shows across the world for seven years now. This is in addition to traditional forms of reporting; we have found that travelling by road enables deeper insights into markets; interviews with bottlers, suppliers and manufacturers can be conducted with greater flexibility, both in cities and in more rural areas. The appearance of the Editourmobil has created quite a stir in several countries - in addition to the impact of the interviews and meetings themselves. The Editourmobil is to return to North America once again, in cooperation with the NPE trade show (May 7 – 11, 2018 in Orlando, Florida). From March through August 2018 - three years after our last tour in 2015, which proved to be very successful - the PETplanet team will, once again, visit a variety of locations across the USA and Canada. The “Editour“ journeys will take in professional discussions and interviews with market leaders from the West to the East Coast. We will be stopping off at the NPE show itself, where the PETplanet and Editourmobil team will present initial reports of our visits and interviews. We will be part of the new Bottle Zone, which will be a first for us as well! Make sure you’re on board with us when we set off again. Get ready for in-depth analyses of the special features and trends in the bottles and beverages sectors of North America! All aboard! Premium Sponsor to date Sponsors to date from those products must go through a series of tests to ensure they can be processed with high performance and meet the required specification. The Gawis system is used again to verify the thickness distribution and dimensional accuracy of the actual bottles produced in the moulds and provides a final confirmation of the concept. Sipa has relied on the Gawis measurement technology since 1999 when they purchased their first system. They have been using that system continuously to this day. A growing business and increased testing demands necessitated additional measurement capabilities. “When it came time to procure an additional measurement system to expand our measurement capability, we reviewed other offerings in the market and, in the end, came back to the Gawis because of its flexibility and precision. The Gawis can measure both preforms and bottles, offers comprehensive and precise thickness and dimensional measurements including finish areas, all in one operation”, explained De Luca. When asked about the fate of the original Gawis system, De Luca responded, “It still works fine after 19 years. There are no immediate plans to retire it.” The same lab that houses the two Gawis test systems is also host to several other Agr test devices including a new PPT3000 pressure tester. The PPT3000 also figures prominently in the bottle design qualification program. “We pressure test CSD and noncarbonated pressurised bottles”, De Luca explained. The reasoning behind pressure testing of those containers is because bottles are subjected to pressure from a range of sources, including nitrogen dosing, filling operations (where volume expansion also plays a role) and palletising where bottles encounter a combination of pressure and increasing loads. Burst strength is an important attribute along with the location of the burst during the test. “A burst in the base area is an alarm signal of potential issues during industrialisation so it is important to note where burst takes place”, explained De Luca. The PPT3000 is claimed to offer the versatility necessary for measuring pressure strength and volume expansion on a range of bottles. And, unlike other pressure testers, the PPT3000 actually simulates the pressures that a bottle will incur during the filling process. In addition to the PPT3000 and Gawis testers, the Sipa design, testing and qualification laboratory also includes an Agr Combi tester for volume and topload tests and an Agr Vacuum tester for qualifying vacuum strength of hot fill containers. Sipa states that it has developed their business based on its extensive experience, high-quality products and a focus on building long-term business relationships. In support of this business model, De Luca explained that “it is our fundamental process to use Agr test machines with every design. Agr is very well known and the industry recognises the quality of the test that Agr equipment provides.” www.agrintl.com www.sipasolutions.com,@ID:40}, PETcontents 06/18 4 PETplanet Insider Vol. 19 No. 06/18 petpla.net INSIDE TRACK 3 Editorial 4 Contents 6 News 51 On-site 52 PET bottles for Beverage + Liquid Food 54 PET bottles for Home + Personal Care 56 Patents MATERIAL / RECYCLING 10 Sorting things out in Alabama 11 PET strapping tapes made of bottle flakes 12 South Africa hits new recycling high 14 China stirs up the markets 16 A sharp eye on sorting 19 Dream, fiction or reality? - Circular economy of PET waste by loop recycling 25 Hot PET recycling topics 26 Growing number of recycling projects in China and abroad 28 Recycling products MARKET SURVEY 31 Suppliers of 2-stage stretch-blow moulding machinery PREFORM PRODUCTION 35 The sum of little things INSPECTION 36 ‘Feel free to imagine, we make it happen’ - Pressure testing ensures produces bottles to meet customer expectations BOTTLE MAKING 39 0.66l water bottle 40 PET in paradise BOTTLING / FILLING 42 Rising demand in liquid dairies 44 Setting trends with ready-mixed drinks TRADE SHOW PREVIEW 46 Bringing know-how to emerging markets - Interview with Petra Westphal, Exhibi- tion Group Director Messe München TRADE SHOW REVIEW 47 Chinaplas 2018 review, part 1 BUYER’S GUIDE 57 Get listed! Page 35 Page 36 Page 39 12 RECYCLING S P E C I A L,@ID:6}, MATERIALS / RECYCLING PETplanet Insider Vol. 19 No. 06/18 petpla.net 19 Circular Economy of PET waste by loop recycling Dream, fiction or reality? by Dr. Ulrich Thiele, Polyester Technology During the past 20 years the polyester recycling industry has grown to become a multimillion-ton business; it enjoys an above-average growth that continues today. According to recent publications the amount of PET recycled in 2017 was about 10 million tons. Most of this rPET is generated by mechanical recycling processes, in which PET bottles are collected, intensively sorted, cleaned, ground and then converted, either to polyester intermediates or re-pelletised. There have been many attempts to establish chemical recycling processes on an industry-scale, with the target of producing PTA or BEHT and MEG from polyester waste during the past 10 years. Some of the more recent developments are described below. 1. New chemical recycling processes under development A relatively small portion of PET bottle waste (less than 5%) is converted by means of chemical recycling back to polyester raw materials: PTA (Purified Terephthalic Acid) and MEG (Mono Ethylene Glycol). Patent literature has a large number of patents dealing with the chemical PET recycling, mainly based on hydrolysis to produce PTA, and glycolysis to produce BEHT or methanolysis to produce DMT. Hussain Al Ghatta of former M&G group developed a process whereby PET waste is hydrolysed by concentrated acetic acid under pressure, to generate PTA and MEG. The advantage of this process is the fact that the resulting terephthalic acid is dissolved in acetic acid, which is then diluted with water as the medium of further purification and trans-crystallisation. Unfortunately, the process did not go beyond the pilot stage. For full details see: US2002077500 (A1) ― 2002-06-20 “Recovery of dicarboxylic aromatic acids from polyester-resin contained in articles for recycling”. In 2005, Fraunhofer developed the “Crea Solve” process. The key step of this technology is the use of a blend of selective solvents to dissolve the PET waste, with removal of impurities by filtration, precipitation by a non-solvent and separation of the purified polyester. The invention relates to a method for recycling polyesters or polyester mixtures from polyester-containing waste. According to this method, the polyester or polyester mixture is dissolved in a solvent, whereupon free-flowing particles thereof are precipitated with the aid of a precipitating agent. The precipitating agent is selected so that the precipitating agent and the solvent can later be separated in a simple manner. This process has not progressed beyond pilot stage up till now. Canadian company Loop Industries recently published a new PET recycling process on its website, based on solvent supported alkaline hydrolysis of PET waste. The publication made public that Loop Industries is investigating this process along with Danone and Coca-Cola. Intensive public patent research brought the result that this process is most likely based on the invention of Hatem Essaddam, inventor of PET US Appl. 20170008826 and 20170152203, and USP 9,550,713, dated 27.01.2017. At the heart of this process is the treatment of PET flakes with a solvent mixture of methanol and dichloromethane, in the presence of equimolar amounts of potassium hydroxide. Provided the input material is standard bottle PET, the resulting solution contains terephthalic acid 2-4% isophMechanical vs. chemical recycling: The figure illustrates the complexity of the chemical process, with the most important being that the raw materials produced by recycling have to be reconstituted into polymers. RECYCLING S P E C I A L,@ID:21}, INSPECTION 36 PETplanet Insider Vol. 19 No. 06/18 petpla.net INSPECTION 36 Pressure testing ensures produced bottles to meet customer expectations ‘Feel free to imagine, we make it happen’ Sipa S.p.A. recently added its second Agr Gawis allin-one measurement station and a PPT 3000 pressure testing system to its design, testing and qualification laboratory. The Gawis systems and PPT 3000 are used to verify the quality of bottles and preforms produced with Sipa moulds. In addition, the systems are integral to the final qualification of entire preform or bottle production systems manufactured at this facility, on behalf of Sipa customers during factory acceptance tests. Sipa mould department - Sipa operates the second largest PET mould manufacturing operation in the world. Sipa, with headquarters in Vittorio Veneto, Italy, is no novice when it comes to providing packaging solutions. Dating back to its entry in the PET container market in 1986, Sipa has grown its brand from a manufacturer of PET preform and bottle production equipment, to a one stop shop for the complete production line - from resin to finished product, including preform manufacturing, bottle design and production, filling, capping and palletising. A core aspect of their business is to understand their customer’s needs and provide flexible, high-value, top performing solutions over the complete PET packaging line. One very important segment of Sipa’s business is mould and bottle design. According to Martina Bottarel, Communications Manager, Sipa operates the second largest PET mould manufacturing www.bericap.com Unique range of light weight screw and sports closures for light weight PET neck standards for water • Closures for all common neck sizes 26/22, 28mm (PCO 1810, PCO 1881), 29/25, 30/25 • Light weight Hexalite range allowing light weight neck • Still water closures suitable for N 2 dosing • Sports closures fulfill BSDA requirements • Boreseal systems for excellent tightness • Consumer friendly opening forces BERICAP Technology for still water,@ID:38}, 51 ON SITE PETplanet Insider Vol. 19 No. 06/18 petpla.net From bottle bales to egg packs with Amut technology Global Plastics is a well-known Californian manufacturer of PET packaging made entirely from post-consumer bottles. The company recycles approximately four million bottles a day, which are sorted by colour, ground and washed. The company then pelletises the flakes and extrudes the sheet for final use in thermoforming. The entire process is performed by Amut Group machines and complies with FDA certification regulations for packaging suitable for direct food contact applications. Hickman’s Family Farms is a significant producer of eggs and has launched into the market an egg container made entirely from post-consumer PET soda and water bottles. The partner for this project is Global Plastics. This eco-friendly container takes about five bottles to make an 18-count egg pack and about three bottles to make one of 12-count egg. A 24-egg carton will be coming to shelves very soon. Hickman’s Family Farms is also starting its own inhouse thermoforming business with ACF920 model branded Amut-Comi. The newly developed software named Easy is intended to simplify machine running, and is particularly suitable for companies entering the market. ACF is the Amut-Comi series that was launched at K 2016: in two years several machines have already been installed worldwide. The ACF model has now also penetrated the North American market. www.amut.it ONsite stf·sorting line stf·washing line professional plastic recycling solutions – made in germany The stf· group is the leading manufacturer of plastic sorting and washing machinery, especially for PET post-consumer bottles, with more than 60 turn-key plants and several single machines delivered worldwide. stf·group Industriestr. 1-3 94529 Aicha v. Wald – Germany fon +49 8544 960-110 mail [email protected] web www.stf-group.de scan for vCard stf ·group,@ID:53}, BOTTLE MAKING 40 PETplanet Insider Vol. 19 No. 06/18 petpla.net Preforms, bottles and closures from Plastiserd, Tahiti PET in paradise by Kay Barton French Polynesia is probably the ultimate travel destination for holidaymakers. Some of the world’s best (and most expensive) hotel chains and resorts attract around 200,000 sun-seekers a year to the endless sandy beaches and the innumerable islands and atolls. The island of Tahiti, with its capital Papeete, serves as a base for some and the key transportation hub for many more; it is from there that tourists fan out to visit world-famous dream islands such as Bora Bora and Moorea. The 4,000,000km2 of water over which the islands are distributed compares with a terrestrial area of just 4,000km2. Geographically it is in the centre of the Pacific Ocean, between Australia and South America. The islands are extremely isolated but have become noteworthy for the development of their self-contained economy. Group Martin is believed to be the biggest local employer. Its “Brasserie de Tahiti” Group includes “Plastiserd”, the plastics processing division. It produces PET preforms, PET bottles and closures in numerically small production runs – the ideal setup for the local market. Its other divisions produce a variety of containers for food and nonfood, as well as extrusion-moulded products for home and garden, and the construction sector. Brasserie de Tahiti uses PET bottles produced by Plastiserd in bottling operations for Coca-Cola, and for packaging its Eau Royale and the hi-level brand “O Tahiti” water product. These all added up to an excellent series of reasons for PETplanet to make a somewhat unconventional journey to the other side of the world, to meet General Manager Bruno Bellanger for an interview and to tour his company. Bruno Bellanger is practically part of the furniture in Plastiserd. He first joined the company in 1988 as a first job after engineering school, then worked in the quality management division and has been the company’s Managing Director since 1996. Group Martin, its parent, is 100% family owned and is currently managed by its President, Jean-Pierre Fourcade, the grandson of founder Emile Martin. It began its life in the power generation sector. Brasserie de Tahiti is divided into three companies. “Jus de fruits de Moorea” produces juices (also from locally produced fruits, such as as pineapple) and rum; “SDA” produces premium water in 5 gallon containers, sells Nespresso capsules and Polynesian food products; and Plastiserd, the location for our interview. As well as processing plastics, Plastiserd, under Tahiti Sign brand manufactures advertising media such as signs and banner prints and, under the Tahiti Access brand, makes entrance and garage doors from aluminium. “In January this year (2018) the group completed the acquisition of Pearl Beach Group, the local resort chain”, Mr Bellanger said, indicating a collection of photos of over-water bungalows on his screen. “We were already shareholders. Here in French Polynesia it is extremely important to remain flexible, which is why we operate in so many different areas”, he continued. “Taxes on imported products are kept intentionally high, in the interests of boosting local manufacturing and creating jobs, which would probably not otherwise occur because of our remote geographical location and the low local population.” The region is generally expensive, even away from the glitzy world of the high-end resorts. Energy costs are huge; Plastiserd currently pays approximately €1.4 million per year for energy, we were told. The company was founded in 1977 and produced PVC bottles until 1980/1981. That was the year it produced its first PET bottles, on new blow moulding equipment under license from French company Carnaud-Kerplas. In In discussions with MD Bruno Bellanger Closure testing in the laboratory,@ID:42}, BOTTLING / FILLING 43 PETplanet Insider Vol. 19 No. 06/18 offered by monolayer and multilayer preforms in competitive supply chains across the world. Switching to PET, or starting anew Sidel presented the conference with examples of its ability to support dairy players in the introduction of a new product, or in switching their product from another packaging material to PET. Sidel has been providing aseptic packaging systems for 50 years and maintains that it offers fully integrated and technically advanced solutions for the liquid dairy sector, employing the processing equipment and capabilities of Tetra Pak Processing Systems (TPPS). The two companies have, so far, worked together on more than 100 complete line projects. Sidel highlights its 40-year experience as a basis for working with customers in designing unique, ergonomic bottles in line with dairy brands’ needs. Ms Boutroy highlighted the company’s Aseptic Combi Predis as an example of Sidel’s expertise in aseptic applications. This solution integrates dry preform sterilisation with aseptic blowing, filling and sealing functions within a single production enclosure. It fully recognises and complies with the fundamental concept that underpins state-of-the-art aseptic packaging rules: producing a commercially sterile product, filled in a sterile zone, in a previously sterilised package. It differs from traditional aseptic technology in that package sterilisation takes place during the preform phase, rather than the bottle phase. The company says that the benefits its solutions offers include safety and simplicity, cost-effectiveness, no water, and very little use of chemicals. Sidel was pleased to confirm that the systems recently received Food and Drug Administration (FDA) approval for its Aseptic Combi Predis blow fill seal filler, making the solution the world’s first aseptic PET filling equipment with dry preform sterilisation validated for low acid manufacturing and commercial distribution in the United States. www.sidel.com Naima Boutroy, Global Packaging Technical Support Sidel,@ID:45}, BOTTLING / FILLING PETplanet Insider Vol. 19 No. 06/18 petpla.net 44 44 less sunny, which means that the fruits are less sweet when they ripen, than in the warmer north. But the juice obtained from these oranges scores highly in terms of taste, precisely because of this lesser sweetness and its vibrant, intensive colour. Sr Ricardo Ermirio de Moraes’ company was the first to export NFC (Not From Concentrate) juices from Brazil - a decision that has turned out to be quite visionary. He was ahead of where the market was trending. Natural One was also ahead of the game in 2014, when it became the first firm in Brazil to bottle 100% NFC juice in PET containers. By the autumn of the same year, it had sold out its stock completely. The company responded to this unexpectedly high demand by ordering a new aseptic line from Krones. By early 2016, it was installed and in production. “This technology has enabled us to translate our idea of natural juices into fully functional reality”, according to Valdenir Soares, of Natural One’s New Business Brasilian fruit juice grows market share by using Krones aseptic PET bottle filling Setting trends with ready-mixed drinks Ricardo Ermirio de Moraes, the founding father of Citrovita and, subsequently, the long-serving President of Citrosuco set up a new company, Natural One, about ten years ago. The company’s first products were ready-mixed vodka-based fruit juice mixtures, bottled in PET. In 2012 he decided to launch pure fruit juices on the market, with the slogan “pura verdade” (“pure truth”); the Natural One pura verdade drinks are 100% juice; they contain no concentrate or cordial, no added sugar and no preservatives. It was the first company in Brazil to offer such products packaged in PET bottles. Valdenir Soares, head of the new business development department, Natural One Natural One’s juice comes primarily from its own oranges. Mr de Moraes arranged for five million new orange trees to be planted on a farm measuring 2,800km2 (280,000ha; 1,081mi2). This “fazenda” is located in the cooler south of São Paulo state. This looked strange because the area is BOTTLING / FILLING,@ID:46}, BOTTLING / FILLING PETplanet Insider Vol. 19 No. 06/18 petpla.net 42 Sidel encourages switch to PET packaging at global Dairy Innovation Summit Rising demand in liquid dairies The use of PET as a packaging material within the liquid dairy sector is forecast to grow by 9% (according to Euromonitor) over the period 20182020, which means demand rising from today’s 13.7 billion package units today to 14.9 billion in 2020. Regionally, growth is expected to be particularly strong in Europe and in Central Asia, with a 7.5% forecast. The trend towards PET packaging for dairy products began in Europe more than ten years ago and has spread worldwide. It has been widely adopted for chilled and ambient distribution, UHT milk, flavoured milk or soya milk. “Onthe-go” formats have been particularly well received, according to Naima Boutroy, Global Packaging Technical Support at Sidel. Driven by health The liquid dairy market, traditionally in carton or HDPE containers, is driven by the burgeoning consumer demand for more functional and health-oriented drinks. This is the driver behind product diversification. The large number of product launches means that dairy players are under pressure to differentiate their brand; at the same time, they have a more flexible and cost-effective production. PET offers a number of attractive features as a packaging material in this market. A range of variables can influence the quality of packaged milk and liquid dairy beverage, especially microorganisms, light, oxygen and temperature. Perfectly defined liquid recipes and processing methods, combined with the right PET bottle and aseptic packaging solution, can ensure maximum product integrity along the supply chain for liquid dairy products, while optimising uptime and costs. “It is important to remind the dairy industry players how they can easily benefit from PET in terms of marketing opportunities, as well as flexible and cost-effective production”, Ms Boutroy said, as she addressed the conference. “The PET package fully ensures product integrity and safety with the right barrier performance for protection from light and oxygen, facilitating extended shelf life. This has been demonstrated across the world.” She also highlighted the advantages At the Global Dairy Innovation Summit 2018, held in Amsterdam from April 11-12, leading industry professionals discussed a range of challenges facing today’s dairy sector, and a number of novel approaches and innovations to overcome them. Sidel highlighted reasons to switch liquid dairies’ production to PET bottles for marketing and for costeffective, flexible production.,@ID:44}, MATERIALS / RECYCLING PETplanet Insider Vol. 19 No. 06/18 petpla.net 15 from other countries that now have to establish their own recycling cycle.” Low supply, high demand But establishing a recycling flow takes its own time. Driven by the high demand, the focus in China in the short term is the import of already recycled top-quality fibres or of virgin PET. This is according to a Chinaplas exhibitor from a German company that manufactures parts for recycling systems. “The flakes on our stand have been made up purely for demonstration purposes, but it is these that are arousing the greatest interest with the Chinese customers. Most just want to know whether they can obtain large quantities of flakes from us quickly.” According to figures from the China Chemical Fibre (CCF) Group, in 2016 China imported 2.64 million tonnes of PET waste, which now leaves a sizeable hole. “The market has certainly become more competitive since no more postconsumer bottles are being imported,” reports Ralf Altepeter, Regional Sales Manager from Gneuss. “The bottles that are collected are often of relatively low quality but are to be transformed into high-quality end products. That’s why the focus this year at Chinaplas has also been on complete turn key lines lines for PET recycling.” The reason why the collected bottles are of low quality is that there is no officially organised collection system but an informal one chiefly carried out by garbage pickers, who, however, obtain a very high collection rate of 90%. But since this is not enough to fill the gap, another approach to secure an additional source of post-consumer bottles is to open up landfill sites to the garbage pickers. However, the bottles thus collected will be of a lot poorer quality making them more difficult to recycle. The Chinese market has already reacted to the shortages with price increases in the virgin PET grade area and delivery delays. “The price rise is a worry for many processing companies. In the next 3-5 years, many fibre converting companies will almost certainly have to close”, says Yiming Fan from Zhangjiagang Gangying Industry, a staple fibre machine manufacturer. Reduced exports are in turn affecting the countries that have previously obtained their virgin PET from China. China was the largest supplier of PET for Japan until the import ban increased prices and reduced availability. The American market is stepping in and is driving the expansion of PET and MEG facilities, which should be operational in 2020/2021. According to market experts from ICIS, the new capacity is less for the local market and more for export to Asia. Effects outside China Meanwhile, in other countries the rubbish tips are piling up. For example, the USA was one country that previously relied on exporting its post-consumer bottles rather than comprehensively expanding its recycling network. But Japan, Australia, New Zealand and the UK, among others, are also facing their own rubbish mountains. The background to this is that recycling the material was not economic, especially when raw material prices were low. The necessity of investing in expensive recycling works was not a consideration from an economic point of view. But the U-turn in Chinese import behaviour could force the industrialised nations to make changes as well. This is already visible in cash flow. In Australia, for example, many companies paid councils to take their recyclable waste for selling on to China; now these councils must find the money themselves to start up a collection. Not the most sustainable but the simplest solution is to export the material to other countries. Shipments of plastic waste have actually already increased to South-East Asian countries like Malaysia, Indonesia, Vietnam and Thailand. For example, New Zealand’s exports to Malaysia in April were five times as great this year as in the comparable period in 2017. Not everyone views this positively. “Every country should recycle its own waste itself”, says Alan Ou from Boretech. In China, our government campaigns fiercely for environmental issues and other countries should do this too.” Kurt Pichlmann, Erema, is equally impressed by this initiative from the Chinese government. “I am convinced that the import ban is the way forward. Because of increasing labour costs and environmental impacts, China cannot produce cheaply in the long term. The import ban is simply a catalyst.” Oct. 24-26,2018, Mumbai German Technology,@ID:17}, PREFORM PRODUCTION PETplanet Insider Vol. 19 No. 06/18 petpla.net 35 The sum of little things In the middle of ‘Husky Land’ there is a company which has nicely positioned itself to meet the potential challenges of the future - Western Container Corporation. Accompanied by its Director of Engineering, Darrel Smith, we visited one of their plants in Tolleson, Arizona. Western Container is unique in the United States in that they run Netstal machines on nine of the eleven preform lines at this plant. Tour Sponsors: Interview with Western Container Corporation April 2, 2018 We met: Darrel Smith, Director of Engineering The Western Container Tolleson facility, located just outside the city of Phoenix, supplies 11 Coca-Cola bottling outlets within a 500-mile radius in several western states and produces around two billion preforms and 500 million bottles annually. Western Container is a model example of a company that has successfully adapted to changes in technology, market conditions, and customer demands in order to meet its mission of “maximising value to our Coca-Cola bottler shareholders by providing lowest cost, highest quality and service, and assurance of supply.” To meet the mission requirements on a daily basis, Darrel relies heavily on Swiss technology, utilising Otto Hofstetter as his primary tool supplier since 2016. Installed on a Netstal 5000 machine, an Otto Hofstetter mould generates 500 million preforms per year. Darrel sees the mould’s operational longevity as its major asset. He estimates 10 million shots for an Otto Hofstetter mould as opposed to the usual 6 million. The hot runner is capable of up to 6 million cycles which is about twice as long as other types. While the service life of the mould is remarkable, it is the extraordinary customer service that particularly impresses Darrel. The exceptional training that Otto Hofstetter provides to the Western Container maintenance teams allows them to perform any necessary maintenance inhouse. This increased skill competency and autonomy improves performance, leads to higher levels of member engagement, and positively impacts the program’s ROI. The injection moulding machines, however, are only one piece of the continuous improvement process at Western Container. The Western team are continually looking at all areas where improvements can be made, and advances in automation technology make implementation a more viable business proposition than in past years. The plant currently uses automatic guided vehicles to move preforms within the plant, and other areas of material handling have been identified which would likely benefit from automation making the process safer, more efficient, and cost effective. The plant layout is impressive and the movement of material extremely smooth. The design of the injection area allows overhead cranes to get to any part of the machines, which allows mould handling to be done smoothly, efficiently, and safely. The plant layout also allows the Netstal machinery with its overhead action to be perfectly positioned. The fact that this machinery is more compact than its Husky counterpart with lateral draw-off enables more lines to fit next to one another. Preforms from the injection systems are discharged into plastic foldable boxes which are then transported via automatic guided vehicles to the storage area. A bin erecting robot automaticly assembles the flattened boxes ready for use. It is interesting that empty preform boxes that come straight from the blow moulding department are not collapsed down, but filled again straight away with preforms which saves time in folding and erecting boxes. The production process continues in the blow moulding process where two KHS Blowmax systems operate alongside two Series 2 Sidels. Both the Sidel and KHS lines use the same preforms for the same bottles. The control room, or Quality Assurance Centre as Darrel likes to call it, is situated in the heart of the plant where a large monitor shows camera shots of all the key parts of the facility. At the same time, machine operators have a wide range of quality instruments at their disposal on-site which are used to accurately check size, weight etc. and to make system improvements where necessary. A Zecchetti handling system collects the bottles and palletises them on reusable plastic pallets which are then loaded onto large American trucks; just one pallet can hold 3,168 bottles of 20oz. As Western Container prepares for the many challenges that the future will hold, they are well aware that it is the work of the whole plant as well as the corporate support staff that ultimately determines whether they will achieve their mission goals. Indeed, it is the sum of many little things. www.westerncontainercoke.com Darrel Smith, Director of Engineering, Western Container Cooperation, Tolleson, Arizona, standing in front of the 11 preform lines,@ID:37}, PETplanet Insider Vol. 19 No. 06/18 petpla.net 52 PETbottles Beverage + Liquid Food NFC juice from Hohes C For a short while now, the classic brand Hohes C belonging to Eckes-Granini has been selling four different 100% NFC juices under its own brand name. Alongside a red, yellow and white multi-fruit juice there is also AppleRaspberry-Pomegranate. The directly squeezed juices feature on the chiller shelves and come in clear, easy-grip 0.8l bottles. The no-deposit bottles consist of 25% recycled PET. A freshness seal is additionally adhered over the screw cap with guarantee band. The transparent sleeve label contains details of the ingredients and information for consumers. www.hohesc.de Cold pressed from Aldi Süd Under the motto “cold pressed, never heated”, the discount supermarket Aldi Süd is offering several multi-fruit juices on the chiller shelves in a limited sales campaign under its own brand Rio d’Oro. The name describes the manufacturing process and Aldi hints at the natural mixing of the juices and expressly suggests shaking the bottle before consumption. The slim, clear bottle holds 500ml, is decorated with a plastic label and is closed with a screw cap with a tamper-evident seal. www.aldi-sued.de [email protected] Contact Shaping the future powered by Messe Münchendrinktec food and drink technology Africa is the premier platform for the Southern African food, beverage, and packaging industries. The established event serves as a trade fair, top-selling market place and future-oriented knowledge center. food & drink technology Africa 2018,@ID:54}, 49 TRADE SHOW REVIEW PETplanet Insider Vol. 19 No. 06/18 petpla.net Single camera system and compact inspection systems Intravis GmbH, a market leading manufacturer of vision inspection systems, highlighted the new “Intra One!” smart camera solution at its booth at Chinaplas - a premiere at an Asian trade fair. This single camera system can be used for the inspection of closures, preforms, bottles and containers as well as for decorations and labels. The system is unique in that it comes with purpose-dedicated, ready-to-use software as on Intravis’ full scale systems. Therefore, the customer does not need a vision expert and an extended learning curve to become successful with the technology, as is the case with traditional smart cameras. “To the Intra One! we’ve had very good feedback from visitors, as it exactly meets the needs of the market“, says Intravis CEO Dr Gerd Fuhrmann. Collaborating with its long-term partner Guangzhou Wutung Engineering Co., Ltd., Intravis showcased even more of its high-end technology. At the Wutung booth two Print Watcher displayed Intravis’ broad range of vision inspection systems for printed and decorated objects. The first system was integrated into a printing machine and provides a 360° inspection of the entire print on the body of transparent bottles, using a single integrated line scan camera. The second system was used for the inspection of prints on closures. As another highlight, Intravis’ proprietary vision inspection software Intra Vision was presented, of course, with a user interface in Chinese language. “We are happy to display this highly developed system, together with Wutung, to our Chinese customers”, said Sonja Rademacher, General Manager of Intravis Co., Ltd. “Especially encouraging for us is the fact that we have had many requests for systems like these in the last months from various customers all over the country. We are very optimistic that our Print Watcher will even exceed their expectations.” Another focus was on the Spot Watcher S, a compact bottle inspection system for extrusion blow moulded bottles. “Chinese customers are showing great interest in this solution, which requires less than 1m2 of floor space“, explains Fuhrmann. “Despite this compact design, it offers a variety of inspection options, from material inserts and defects to dimensional accuracy.” The system is designed for bottle diameters between 30 to 100mm and heights between 30 and 200mm. www.intravis.de SIPA S.p.A. - Via Caduti del Lavoro, 3 - 31029 Vittorio Veneto (TV) - Italy Tel. +39 0438 911511 - Fax +39 0438 912273 - email: [email protected] We make it happen. www.sipa.it Imagine taking your operating costs at the lowest level. Designed to adapt. Built to last. Preform Systems MAINTENANCE COST i stment Less than1%of the capital nve,@ID:51}, MARKET SURVEY 34 PETplanet Insider Vol. 19 No. 06/18 petpla.net l l l consumer bags textile packaging recycling rECO Company name Amsler Equipment Inc. 1 Blow Newamstar Packaging Machinery Co., Ltd. Postal address Telephone number Web site address Contact name Function Direct telephone number E-Mail 1245 Reid St., Unit 1 Richmond Hill, ON, Canada L4B1G4 +1 905 707 6704 www.amslerequipment.net Ms Heidi Amsler Sales and Marketing Manager +1 905 707 6704, +1 905 707 6707 [email protected] 23 Chemin de Gerocourt 95650 Boissy L'Aillerie, France +33 9800 820 70 www.1blow.com Mr Olivier Perche Sales Director +33 9800 820 75 [email protected] East Xinjing Road, Zhangjiagang Economic & Technological Development Zone, Jiangsu 215618, P.R. China +86 512 5869 1111 www.newamstar.com +86 512 5867 3920 [email protected] 1. Machine designation / model number Linear (6 models): L12, L15, L22, L32, L407, L42, L42X Linear Widemouth JAR (2 models): L16J, L25J Linear Convertible (2 models): L32C, L42C Linear Large Format series (3 models): L110, LM120, L120C, LS230 Rotary series (2 models): APT10, APT16 1XXL / 1XXLN / 1XL / 1XL Lab / 2L / 2LN / 2LO / 2LHF / 2XLS / 4L / 4LN / 4LO / 4LHF / 5M / 6MO RBM2D / RBM4D / RBM6D / RBM8D / RBM8M / RBM8 / RBM10 / RBM12 / RBM12M / RBM14M / RBM16M / RBM20 / RBM20M / RBM24 / RBM24M / RBM26 / RBM30S / RBM40S 2. Bottle volume (from/to in litres) a) Standard machines 0.05-5 0.1-6 0.5-5 0.1-12 0.25-2.5 b) Machines for large containers 4-30 5-30 3-20 3. Max. number of stretch-blow moulds (units) a) Standard machines 4 2 16 6 8-40 b) Machines for large containers 6 2 1 6 4. Output per stretch-blow mould for: 0.5l CSD bottle (units/hour) 1,800 1,800 1,500 2,000 8,000-80,000 1l CSD bottle (units/hour) 1,400-1,800 1,400-1,800 1.250-1,500 1,800 4,000-40,000 1.5l still mineral water bottle (units/hour) 1,400-1,800 1,400-1,800 1,300-1,500 1,700 4,000-40,000 Large capacity container 300 (18.9l) 1,000 for 5l ; 600 for 20l 6,000 Other 800-1,600 3,000 (4l) 5. Footprint / space requirement (L x W x H in metres) 4.0x1.8x2.4 to 4.3x3.7x2.5 3.9x2.5x2.2 5.7x2.0x2.4 to 4.3x3.7x2.5 3.9x3.8x2.7 2.7x2.2x3.1 to 4.2x3.0x3.2 2.1x1.6x2.4 6. Special features (short description/keywords) Accepts MAG & other moulds; all servo-electric, servo stretch rods; hotfill, neck orientation, preferential heat; air recovery system, handle insertion Accepts MAG & other moulds, automatic loading of preforms, up to 120mm neck size; hot fill Accepts MAG & other moulds / hot fill / necks up to 70mm; flexible cavitation - run 1, 2 or 3 cavities in one machine; Accepts MAG & other moulds; L120C capable of 1, 2 or 3-cavity; configuration and sizes from 4-30l Hot fill; PP Preferential heating (oval bottles); neck orientation (with standard preforms); hot fill; compatible with Sidel, Krones, KHS, Sipa, Side moulds; recovery of blowing air; power recovery; 5M-C available as a Combi in cooperation with Ermi and Synerlink Efficient single mould capacity, perfect security system, quick-replaceable moulds, long-term continuously-running, energy-saving and lower consumption, capable for multi-type bottles, information processing system, remote monitoring and service module,@ID:36}, 48 TRADE SHOW REVIEW PETplanet Insider Vol. 19 No. 06/18 petpla.net Range of materials for the Freeformer continues to expand Arburg was demonstrating the current status of Arburg Plastic Freeforming (APF), with which functional components can be additively manufactured using original materials. Visitors were able to see a Freeformer, numerous sample components and an interactive station where they could test the quality of selected functional components themselves. Among the samples on display were PP closures for shampoo bottles. At Chinaplas, a Freeformer used PP and the associated water-soluble support material Armat 12 to produce functional cable clips. The delicate yet durable structures have the click effect typical of injection moulded parts. Due to the very positive response, this semi-crystalline material has now been included in the Arburg Prototyping Center. A total of seven Freeformers for the production of sample parts from qualified and certified original materials are available in Lossburg, each of which is equipped with a different material and produces sample parts for potential customers. The APF process is not only suitable for prototyping, but also for the industrial additive manufacturing of functional components in particular. One of the major advantages is that Freeformer customers can use the open system to qualify their own original materials and optimise the freely programmable process parameters specifically for their respective application. All of this process data can be stored and analysed and designs can be optimised in a short time to produce prototypes and functional components quickly and economically using the Freeformer. Mechanical stress tests show that adapted process control can achieve component densities of up to 95% and tensile strengths of up to 97% compared with injection moulding. www.arburg.com Granulators for preforms and more Granulators for numerous applications were presented by the German company Tria. The Tria 42 Series granulators for example are available in fully sound proofed execution and designed to cater to a variety of feed methods from manual to fully auto turn key systems. In granulation of preforms, the production output is about 1,000-1,200kg/h. Features include standard grinding chamber in anti-wear steel to 750 Vickers, high level of safety switches, rotary discs as standard as well as a constant cutting geometry. www.triaplastics.de NO. ONE-WAY PRODUCTION. YES. TOP QUALITY RECYCLING. How can your recycled product meet permanently increasing demands? With the CHT range of high performance process solutions with environmental relief for the wet chemical cleaning. We support you directly on site and ensure your quality controls in our laboratories with state-of-the-art equipment. Thus, your strong position in the growing market is confirmed day by day. More about us at www.cht.com PLASTIC RECYCLING SHOW | 24 – 25 April 2018 RAI Amsterdam | stand E5,@ID:50}, MATERIALS / RECYCLING PETplanet Insider Vol. 19 No. 06/18 petpla.net 13 been paid by contracted recyclers to collectors for baled bottles, with a total of 609,306t of PET recycled to date. This has saved more than 900,000t of carbon and almost four million cubic metres of landfill space. End use markets From the amount of recycled bottles, 38% went to bottle-to-foodgrade and bottle-to-bottle applications i.e. for use in bottles and PET thermoforms like sandwich trays or cake trays. 58% went into polyester fibre applications. This includes the manufacture of pillows and duvets, some apparel and roof insulation, amongst others. It further includes “geo-textiles” which are liners for dams, roads and landfills. Only 4% was exported as either baled bottles or flakes for recycling in other countries. This low figure is regarded positively because it means 96% of bottles collected were recycled and directly used in South Africa, states the organisation. www.petco.co.za Petco is responsible for fulfilling the PET plastic industry’s mandate of Extended Producer Responsibility (EPR). About Petco: Petco (the PET Plastic Recycling Company NPC) works to fulfil the South African PET industry’s role of Extended Producer Responsibility (EPR). EPR promotes the integration of environmental costs associated with PET products throughout their life cycles into the market costs of the products and shifts responsibility for the used packaging from government to private industry. They are financed by a voluntary recycling fee paid by converters on PET resin purchased, and grants from brand owners, resin producers and retailers.,@ID:15}, TRADE SHOW PREVIEW PETplanet Insider Vol. 19 No. 06/18 petpla.net 46 Interview with Petra Westphal, Exhibition Group Director Messe München Bringing know-how to emerging markets PETplanet: How long have you been working for Messe München, what is your professional background and what fascinates you about the trade fair business? Petra Westphal: I started at Messe München in 1993, and since 1995 I have been working for Drinktec and since 2003 as project manager. Since 2010, I have been the project group leader for all Drinktec events. These include our international fairs Drink Technology India (dti), Food & Drink Technology Africa (fdt) and China Brew China Beverage (CBB). In concrete terms, Drinktec, for example, I think it’s terrific that we offer the beverage and liquid food industry a marketplace and bring it all together in one place over five days. With Drinktec Worldwide, our industry events around the world, we are also offering a tailor-made meeting place for local markets. PETplanet: How exactly do you have to imagine “Drinktec Worldwide” and how did it start? Petra Westphal: Drinktec Worldwide stands for a global network, but always with an eye to local markets, offering a meeting place for local industry. It combines Drinktec with dti, CBB and fdt. The events are international and provide a networking opportunity for industry around the world. With Drinktec we had already established a strong brand in Munich. Our goal was to bring the know-how of the exhibitors additionally to emerging markets. We started our foreign activities in 2007 with dti in Mumbai. Since 2011, we have co-organised CBB to further expand our market position in China. In 2014, we further expanded our portfolio in the promising market of Africa with fdt. In doing so, we build up the expertise of Drinktec in key markets, but we also offer tailor-made platforms for the regions. PETplanet: China, India and Africa: three large and multi-layered countries. How do you currently assess the market potential for the industry? Petra Westphal: The forecasts are positive for all three countries. The economy of South Africa is one of the strongest on the African continent. In particular, the food and beverage sectors are developing well. An attractive market also for international companies. In the Indian market, the soft drinks and alcoholic beverages sectors in particular are growing at extraordinary rates of increase in sales. With our current three locations in India - in Mumbai, New Delhi and Bengaluru - we are superbly positioned on the subcontinent. In China it is similar, the beverage industry is developing dynamically. Solutions in the area of packaging and PET are hot topics in the Chinese market. PETplanet: Which of the three markets is currently the most exciting for you? Petra Westphal: You can’t put it in such simple terms. All three markets bring exciting opportunities and challenges. What I find particularly remarkable is how fast the markets in the countries are developing. So we are constantly refocusing ourselves to take account of local conditions. In China, PET is currently of particular importance. The industry is looking for concrete solutions. We are meeting this with, among other initiatives, the introduction of PET Talks, a new framework program for this year’s CBB, which PETplanet is also co-organising. Another example is our event in India, where we are not simply rotating annually, but also changing venues between Mumbai, New Delhi and Bengaluru. In the future, we will be able to reach even more targeted relevant visitor groups in the metropolitan regions. PETplanet: How do you and your team manage to organise so many fairs in such a short timescale? Petra Westphal: That is indeed a challenge. Three fairs in two months! But our teams in Munich, Mumbai, Johannesburg and Shanghai are well positioned here. The Drinktec Worldwide Team in Munich is in constant and close contact with our colleagues on site. Together we develop the strategy, the supporting program and the communication. Our subsidiaries are essential to the success of the events, because they are in close contact with local industry and are the country’s experts. It would not work without them! PETplanet: What goals have you set for the three fairs this year? Petra Westphal: Our goals are first and foremost satisfied exhibitors and visitors. Positive feedback after the show is always a confirmation to us that we have taken the right path. PETplanet: Let’s imagine it’s the end of 2018. What would you say in retrospect, and also with regard to 2019? Petra Westphal: At the end of the year, we’ll be saying to Drinktec Worldwide: after the show is before the show. We will then be looking back on three successful events and we’ll already be getting ready for our first dti at Bengaluru, which will take place there at the end of February. And preparations for fdt Africa will also be well underway. And this is because in 2019, the fair will be taking place for the first time in July as a co-location with two other events of Messe München, the Analytica Lab Africa and the IFAT Africa. PETplanet: Could there be other regions in the world in the future where you could imagine a local Drinktec? Petra Westphal: As a matter of principle, we keep an eye on market developments and react accordingly, after consultation with the industry. It is quite possible that the Drinktec family will grow in the future. PETplanet: Thank you very much!,@ID:48}, MARKET SURVEY 31 PETplanet Insider Vol. 19 No. 06/18 petpla.net 06/2018 MARKETsurvey Resins & additives Preform machinery Preform production Preform inspection SBM 2-stage Compressors Filling equipment & filling inspection Caps & closures and inspection Palletising & shrink film machinery Recycling 2-stage SBM machinery What all types of 2-stage stretch blow moulding machines do have in common is that prior to the stretch blow moulding process, preforms have to be injection moulded in a separate machine. However, there are a diverse range of models to choose from in 2-stage stretch blow moulding. Our market survey allows you to compare specific parameters of these stateof-the-art machines from some of the market leading manufacturers. Companies included in the survey: Luxber S.L.U., Flexblow (UAB Terekas), SMI S.p.A., Kosme Gesellschaft mbH, Tech-Long Europe GmbH, Sipa, KHS GmbH, Krones AG, Newamstar Packaging Machinery Co. Ltd., Lanfranchi S.r.l., Amsler Equipment Inc., Sacmi Beverage, 1 Blow, Technopet Machineries, Side S.A., Sidel Group Although the publishers have made every effort to ensure that the information in this market survey is up to date, no claims are made regarding completeness or accuracy. Company name Luxber S.L.U. FlexBlow (UAB Terekas) Sacmi Beverage Lanfranchi S.r.l. Postal address Telephone number Web site address Contact name Function Direct telephone number E-Mail Av. de Azorin, 34-36 03440 Ibi, Spain +34 96 555 3853 www.luxber.com Mr Ricardo Sanchez Export Manager +34 606 964 907 [email protected] Vytauto g. 114 a, Kretinga, Lithuania +370 620 115 28 www.flexblow.com Mr Gytis Sirvinskas Marketing Director +370 620 115 28 [email protected] Via Enzo Ferrari, 1 43058 Ramoscello di Sorbolo, (PR), Italy +39 0521 6954 11 www.sacmifilling.it Mr Lorenzo Casadio Head of Technical Dep. +39 0542 6071 11 [email protected] Via Scodoncello, 41 43044 Collecchio (PR), Italy +39 0521 5410 11 www.lanfranchigroup.it Mr Mihai Burlea Sales Department +39 0521 541011 - 150 [email protected] 1. Machine designation / model number Tecnopet 2000, 4000, 6000 FlexBlow1 FlexBlow2 FlexBlow3 FlexBlow4 FlexBlow6/4 FlexBlow4 Hybrid FlexBlow6 Hybrid FlexBlow8 Hybrid Combo 18/120/30 LG2 / LJ2 2. Bottle volume (from/to in litres) a) Standard machines 0.1 up to 10 0.05-2 0.05-2 0.05-2 0.05-2 0.05-2 0.05-2 0.05-2 0.05-3 0.2-3 0.25-12 b) Machines for large containers 0.05-10 0.05-10 0.05-10 0.05-6 0.05-6 NA 5-30 3. Maximum number of stretch-blow moulds (units) a) Standard machines 2, 4 and 6 1 2 3 4 4 4 6 8 18 8 b) Machines for large containers 1 1 2 2 4 NA 2 4. Output per stretch-blow mould for: 0.5l CSD bottle (units/ hour) 2,250 1,600 2,600 4,800 6,400 6,000 6,400 9,000 12,000 4,500 12,000 1l CSD bottle (units/hour) 1,900 1,500 2,400 4,500 6,000 5,600 6,000 8,500 11,400 2,250 12,000 1.5l still mineral water bottle (units/hour) 1,800 1,400 2,400 4,200 5,600 5,200 5,600 8,000 10,800 2,250 10,500 Large capacity container 1,000 1,000 3,000 2,000 4,000 2,000 NA 250 Other 5. Footprint / space requirement (LxWxH in metres) 14.3x8.3x3 8x3x3 6. Special features (short description/keywords) Preferential heating; air recovery system Fast bottle format changeover, production flexibility; possibility to produce hot-fill containers, oval-shaped bottles, wide-mouth jars, deep-grip bottles and large size containers Suitable for continuous bottle production; fast and easy mould change Double cavity concept (blower); not contact filling valves Keg manufacturing; handle insertion; preferential heating,@ID:33}, MATERIALS / RECYCLING 27 PETplanet Insider Vol. 19 No. 06/18 to add additional value from waste. The line has been completely manufactured and will be exported to the customer by the end of May, for installation and testing, prior to acceptance. Bottle-to-fibre engineering plant Anshun Pettechs Fibre Co., Ltd., a subsidiary of Boretech Group, has been involved in the production of recycled polyester fibre for more than 20 years. Boretech itself has extensive fibre production experience and processing skills, and owns advanced technology for recycled PSF fibre production. Boretech provided an Indian customer with a complete bottle-to-fibre plant as long ago as 2010. At the end of 2016, the company determined to integrate the upstream and downstream industries of PET bottle recycling technology in order to offer customers complete bottle-to-fibre solutions. Its main bottle-to-fibre production lines now include 15-100 T/D flexible fibre line, hollow conjugate line, dope dyed fibre line and spinning grade line. Boretech has already provided six different specifications of fibre production lines to a customer in Uzbekistan. Bottle-to-bottle engineering plant Bottle-to-bottle PET recycling process plants and equipment have been supplied by European and U.S. enterprises for a long time, almost exclusively. However, Boretech officially launched its small capacity bottle-to-bottle plant engineering services to the market in 2017. The complete, integrated and economic bottle-to-bottle solution, aim at emerging economies in Africa and around the world, was developed jointly with established equipment suppliers in Asia. The solution includes PET bottle washing, pelletising and solid-state polymerisation (SSP). European screw technology was added in 2018 and launched a complete food-grade bottle-to-bottle recycling plant that does not require SSP to achieve increased IV. The complete line can obtain FDA/EFSA certification, Boretech says, and further asserts that the total cost for the whole line is less than 2/3 of that for equivalent European equipment.,@ID:29}, PETplanet Insider Vol. 19 No. 06/18 petpla.net 54 PETbottles Home + Personal Care Private Spa from Litamin Create a luxury spa in your very own bathroom! This trend is supported by most manufacturers with own-brand, top-quality products for bathing and showering and ensures that there is always something new on offer from well-known brands. Amost recent example is a range of six differently scented and coloured aromatic oil foam baths called “Private Spa” from the well-known brand Litamin. The 400ml PET bottles are oval shaped and clear with no-label-look labels on front and rear. The shiny gold-coloured screw cap has a “New” adhesive sticker to reinforce the newness of the product. www.litamin.de Mouthwash for children GSK Consumer Healthcare has revised and improved its mouthwash for children under the OdolMed 3 brand. On the packaging, the manufacturer advertises fluoride protection against sugar acid on the teeth particularly for children aged 6 to 13. The clear bottle contains 300ml of the slightly coloured liquid. The sleeve label is drawn up as a tamper-evident seal over the screw cap with dosage function. Suitable perforations in the seal area simplify removal of the sleeve so the screw cap can be removed. www.odol-med3.de,@ID:56}, MATERIALS / RECYCLING PETplanet Insider Vol. 19 No. 06/18 petpla.net 11 Production without pre-drying or crystallisation with MRS technology of Gneuss installed in Dubai PET strapping tapes made of bottle flakes Consent Plastic produces his own flakes out of collected PET bottles and uses these flakes to manufacture polyester strapping tapes with a high tensile strength. These tapes are sold also to countries beyond the Middle East. A wide range of high-quality polyester tapes are offered under the trademark PET Band. In the course of further capacity expansion, the Arabian company purchased a new production line for the manufacture of PET strapping tapes made of 100% non-dried postconsumer bottle flakes. Further, the line can process shredded preforms and shredded straps or a mixture out of these materials. It was the avoidance of the time and energy intensive drying and crystallisation of the PET flakes which convinced Consent Plastic of the Gneuss MRS extruder. Compared to Consent’s previous production line including a single-screw extruder, crystallisation and drying processing steps, the footprint of the line could be reduced by 12% and the energy requirement by 20-25%. Further, the strapping tape produced with the MRS extrusion line is of much better quality in terms of tensile strength, stretch and splitting. This is a result of the intensive mixing effect of the MRS in the degassing section and the high degassing efficiency. Further, there is no need for work-intensive maintenance of the drying and/or crystallisation system, which was necessary with consent’s previous line, so that the resulting machine downtimes are avoided, too. The line reacts to a significant extent automatically to quality fluctuations in the input material without causing production interruptions. “Here in Dubai, we operate the world’s first and only line for the production of PET tapes made of bottle flakes without a complicated pre-drying or crystallisation process”, explains Maheshwar Akkala, the Division Manager-Plastic Products at Consent. “This has already got around in this sector. Some of our competitors have already asked us about this technology.” The throughput rate of the new Consent line amounts to maximum 700kg/h, the vacuum of the installed water ring pump is around 25mbar. The pressure-constant and process-constant rotary filtration system uses filtration finenesses of down to 56μm, to make sure that all foreign particles are removed which could cause breaking points later on during stretching. The die group consists of 4 pumps, which can produce a total of 8 straps with a dimension of 9.5 x 0.6 up to 32 x 1mm. The stretching ratio is around 1 to 8, the haul-off speed can be up to 160m/min. An embossing unit or a wax adding unit, as required, is used for manual or automatic packing. Further, an accumulator compensates the reduced haul-off speed when rolls are changed. Maheshwar Akkala states: “We have been in a position to improve our product qualities even more and reduce our costs with this new strapping tape line based on the Gneuss MRS Extrusion System.” www.gneuss.de RECYCLING S P E C I A L Maheshwar Akkala in front of his new line; Consent Plastic is a leading producer of strapping tapes and PET flakes in the Middle East.,@ID:13}, MATERIALS / RECYCLING PETplanet Insider Vol. 19 No. 06/18 petpla.net 21 useful as “drop-in” replacements for the usual market commodity qualities. But this question is not as simple as it seems; it took the polyester industry decades of time and lots of money during its development phase in the last century to establish raw material qualities that are taken for granted today. And now, added to the word “Quality” comes the demand for “Quality consistency”. Polyester continuous production plant capacities are within a range of 500-1,500t/d today; lines of smaller capacities have been and are being shut down one by one. As a consequence, consistent quality of PTA is crucial to making the running of plants of such capacity stable and successful. When we look for publicly-available PTA product specifications it is striking that there is no or very little information on basic details, like grain size, grain size distribution, flowability or shelf life in big bags. The right grain size of PTA, which is within the 40-240μm range, at an average of 150170μm is a basic property that governs reactivity, flowability and, together with moisture of less than 0.1%, the guarantee of flowability in silos and pneumatic conveying systems, as well as shelf life in big bags, over many years. This means of achieving this feature is, for example the recrystallisation of crude TA under pressure in water or diluted acetic acid, centrifugation and subsequent drying. Because of the high corrosive internal environment of recrystallisation and drying, this equipment is made of titanium or titanium lined stainless steel. Another basic question appears to be: how to separate TA from IPA. Recrystallisation in diluted acetic acid or organic solvents is required for this operation. Such essential chemical operations are, for any investor and in terms of process economy and profitability, meaningful only at capacities commonly used in basic material chemistry. Using the PTA quality specification in Figure 1 as example, and looking at the control of metal content (10ppm for Mg, Ca, Na, K, and Al together) it becomes obvious that recycling processes that use as hydrolysis aids large quantities of alkaline like NaOH or KOH, will need highly sophisticated purification and recrystallisation technology to achieve 10ppm metal content. One way of avoiding high expenses for purification and finishing of PTA, IPA and MEG is described by an EU-registered patent (EP2838941 A1) in which PET waste glycolysis is done by MEG, fine filtration of the solved PET waste and direct reuse of the glycolate blend as 20-100% raw material replacement in a running PET filament plant. Similar approaches are also described in Chinese patent literature. 2.2 What shall the PET waste input quality be? While PET bottle waste which is the most common input material for polyester recycling, there is a broad range of quality in the market. All kinds of material are available, from baled bottles of 80 95% PET, or PET flakes up to 99,9% purity with variation in colour and transparency. The vital question is: what level of purity is feasible for the chemical recycling process? It becomes obvious immediately that high impurity waste streams, such as unsorted household packaging waste, presorted polyester textiles or polyester-cotton blend textiles, which would otherwise be used as waste incineration power plants fuel, are useful in terms of economy and CO 2 footprint. As soon as waste of purity levels 80% PET is used for chemical recycling, this input is competing with mechanical recycling where a large number of well-established, optimised and low cost processes are available. When considering the CO 2 footprint of PET chemical recycling, it is frequently forgotten that the rPTA, rIPA and rMEG produced are converted to polyester again, with known conversion costs (energy, investment, labour). In simple terms, chemical recycling to produce PTA, IPA and MEG must use crude waste instead of crude oil. 2.3 What is the minimum feasible and economical plant capacity of such a chemical recycling project? This is the most crucial question. Current PTA and MEG plant production capacities are within the 0.6-1.2mt/a or 1.6-3.3kt/d range, which is beyond all current recycling capacity. Let us consider a very simple example; producing PTA and MEG of bottle or fibre grade market quality and assuming a PET waste input of 200t/d and purity of 70% PET. Provided the PET fraction could be converted with 90% yield to crude PTA and 90% yield to MEG, final products are estimated as following: Example: input waste should contain 70% PET The 140t PET contained within the 200t waste is theoretically converted to 119.8TA + 44.6t MEG. Rectification and recrystallisation losses are estimated at 10%; products resulting from 200t waste are therefore: 107.8t PTA and 40.2t MEG. Non-PET waste is 60t, plus 16.4t production waste; 76.4t waste in total. This example project would produce ~110t PTA, 40t MEG and 76t non-PET wastes per day. The equipment these amounts of PTA and MEG will cover the size of a small pilot facility; it will cleave away from common polyester raw material production capacities in economical size. The simple conclusion is – ignoring imponderables – the production of market standard PTA and MEG from PET waste based on a green field investment is not commercially viable within an input capacity range of 50-200t/d. Common production capacity of PTA from PX is 1.2mt/a. “Small” plants have a capacity of 600,000t/a. Old-fashioned PTA plants have a capacity range of 200,000-400,000t/ a. Another interesting figure: downsizing capacity from 100 to 50% still requires 70% of the investment! 2.4 Are there existing chemical PET recycling processes on an industrial scale? It is surprising that, while newer processes of chemical recycling are invented, there are a number of wellfunctioning and commercially-proven recycling processes on an industrial scale already available. RECYCLING S P E C I A L,@ID:23}, MATERIALS / RECYCLING PETplanet Insider Vol. 19 No. 06/18 petpla.net 10 Recycling of post-consumer and post-industrial PET in a challenging environment Sorting things out in Alabama by Valentin Trotter The manufacture of a bottle made of rPET consumes 40% less energy than one made of virgin PET. This competitive edge in ecology is why Byron Geiger, President of Custom Polymers PET, Athens, Alabama, is dedicated to further invest in recycling. This endeavour is especially challenging in the United States – a country ranking amongst the lowest of the Western hemisphere with a recycling rate of PET bottles of only 28.4 %, according to the Recycling Report published in 2016 by “The Association of Plastic Recyclers” and the “American Chemistry Council”. Interview with Custom Polymers PET, April 2, 2018 We met: Byron Geiger, President As a consequence of this, Byron needs to import the pre-sorted raw material from 20 different US states in order to keep the plants working to capacity. Thereby, he receives around 81,000 metric tonnes annually from communal collections, so-called material recovery facilities and other recycling processes. The purity of the collected material is with only 80% in poor condition - the European standard in comparison is of 99% - which makes the recycling process more extensive. After different processing steps 54,000t of recycled PET flake is generated, and in addition around 13,600t of FDA approved granulate. This granulate is manufactured by an Erema plant. The majority of the latter is sold to PET bottle manufacturers. In total Custom Polymers PET recycles approximately 5% of the overall 795,000t recycled PET bottles in the USA, making it one of the leading PET recyclers in North America. The recycling process starts with the plastic bales being broken down. A system then sorts the plastic waste into PET bottles and other objects like cans, HDPE, PVC and household waste, even glass sometimes remains in the feedstock. Byron still uses such foreign material for example by sorting out and selling polyethylene bottles as a sought-after recycling material. Further, a shredder grinds the PET bottles into flakes. This allows a more thorough separation of the component parts. After passing through a water bath, all materials of a different density than PET are sorted from the flakes, such as the lighter HDPE and paper labels or the higher density sand. In order to sort out PVC which has the same density than PET, an optical sorter from NRT identifies such flakes by near infrared spectrometry and ejects them by compressed air. A second optical sorter of the same kind identifies and removes remaining foreign bodies, including metal parts, fibres or other plastics. The remaining PET flakes need to be separated by residual colours for different applications. The green ones go into fibre manufacturing. Only the transparent and blue ones go on for further production. After cleaning, drying and packing these flakes are either directly sent on to the processing industry or are being regranulated for the bottle production. For this, the flakes are dried once more to remove any residual moisture. After this, they are melted down and pressed through a fine sieve to remove the last of any impurities and to make it FDA-approved. The now liquid PET is extruded. After hardening in water, the PET strands are chopped into granulate. The clear granulate becomes opaque due to recrystallisation. New bottles entirely made from this granulate without adding any resin can be made. According to Byron, an important step forward to elevate the rate of recycled PET bottles to a comparable level would be long-term investments in sorting technologies for PVC labels and lighter bottles. Up to now, air is used to separate lighter PVC labels from PET flakes. This technology, however, bears the disadvantage of blowing away flakes from thin-walled PET bottles too which will then end up as fuel for electricity generation – a rather inefficient way of sorting. Nevertheless, the separation process is indispensable since Byron needs to assure that the material is PVC-free which is reassured through frequent sampling in the laboratory. www.custompolymerspet.com RECYCLING S P E C I A L Tour Sponsors: Custom Polymers PET is the only recycling company in Alabama. (F.l.t.r.) Byron Geiger and Valentin Trotter,@ID:12}, BOTTLING / FILLING PETplanet Insider Vol. 19 No. 06/18 petpla.net 45 45 Development Department.“The aseptic process was the best choice for a company like us, which looks to the future. Consumers want products that are of high quality and maximised purity.” Krones wasn’t the cheapest vendor but, Soares maintains, it did have the best technology. Its Contipure Asept Bloc DA aseptic blow-moulder/filler block for highly acidic beverages offers stretch blow-moulding and filling on a single machine. Until the end of 2016, Natural One was the only fruit juice producer in Brazil using this technology and thus the only one able to offer fruit juices in the cold chain with a shelf-life of eight months. The quality and support provided by Krones’ technical staff was also an important factor. Natural One today draws a distinction nowadays between products in the cold chain, where it began operations, and its ambient temperature products. These newer products already account for around a quarter of total sales. The high level of the Krones technology had an effect on outsourced parts, such as preforms or labels, too. “We decided to meet the world’s most stringent requirements, of the kind taken for granted in Japan, Europe and the USA, for example”, Soares explains. This will be a help when in exporting to those countries but the new line also made things easier in other ways. Its fast output meant that night shifts and Sunday working could be dispensed with. Its original, small line, rated at around 7,000bph needed twelve operators. The new line, which can handle 24,000 900ml bph, needs only four. The aseptic line passed its acceptance test with an efficiency level of 96%. Natural One says is can see fruit juice as a third major softdrink segment alongside water and CSDs, and regards 100% natural purity as the basis for rising consumer demand. Natural One is now aiming to promote this feature in neighbouring South American countries, in Japan, South-East Asia, Europe and in the USA. It has set itself an ambitious target: to raise the aseptically bottled NFC juices from their present-day two per cent to around a quarter of total exports – more than a 12-fold increase – and in just one year. Product development Paola Toller is responsible for R&D at Natural One. She has developed five product lines and is pursuing the idea of using many different kinds of fruit to create new categories in the market. More new product categories are under preparation, including “spa waters”: water mixed with coconut water and with a fruit juice content of 10-20%; and smoothie-like beverages featuring sweet potatoes, for example. “There are thousands of fruits and combinations of them”, says Paola Toller. “The background to our efforts, of course, is the general ongoing trend: away from solid food and towards liquid food. For many consumers, it’s more convenient to enjoy liquid foods when they’re travelling. Needless to say, healthy fruits are a preferred option here. In this context, it’s essential to find the right technology for processing the fruits. It’s not easy, for instance, to make a good watermelon juice: the product’s shelf-life is very limited, and the freshness starts to decline after a few days. But I guess it’s only a matter of time before we find a solution there as well.” www.krones.com Paola Toller, responsible for R&D, has developed five product lines. Aseptic blow-moulder/filler block for highly acidic beverages BOTTLING / FILLING [email protected] Tel: +90 212 695 50 00 Fax: +90 212 694 97 24 100815dmyR .com,@ID:47}, MATERIALS / RECYCLING PETplanet Insider Vol. 19 No. 06/18 petpla.net 25 New potential, new processing, new challenges Hot PET recycling topics The second PRS Europe show held in Amsterdam in April this year was a great success, featuring over 100 exhibiting companies and more than 40 conference speakers who gave informative and inspirational presentations and which attracted more than 2,400 visitors over the two days. The show will move to a bigger exhibition hall in the RAI next year to enable a greater number of exhibitors to show more machinery in their booths. The 2018 conference programme caught the attention of a great many visitors. Ton Emans gave a warm welcome to decision-makers from the plastics recycling industry sitting in the audience. Not only European companies attended the show as the name of the event itself would imply. International visitors from China, Japan and the USA were also present to take part in discussions on current hot recycling topics in Europe and beyond. The opening conference session highlighted the great potential of PET recycling. Casper van den Dungen, Petcore, Johan Kerver, CEO of Fili Grade and Jean-Loup van de Wiele, Commercial Director and Owner of 4 PET Recycling, gave three interesting and forward-looking presentations on PET recycling. Casper van de Dungen asked the audience: “What can we expect from rPET towards 2025?” First of all, he provided figures on current PET recycling rates in Europe. PET recycling capacity rests on the shoulders of 115 PET recyclers with a total output of 2,000kt per year. Germany produces the highest volume of 500kt per year, followed by France and Italy with 300kt, and Spain with about 200kt. The UK and the Republic of Ireland together have a capacity of 90kt, and Poland 80kt a year. For the 2016 market status of bottle mass, this means that total consumption is around 3.1million tons. 1.9mt were collected. 0.1mt have been used in direct net trade and 0.5mt gets lost in the process. In the end, 1.3mt were available as flakes. The majority of flakes are used for sheets and in the blow-moulding process, followed by fibre and strapping (Source: PCI Wood Mackenzie). For Casper, the key market developments needed to achieve greater potential involve the implementation of a bottle deposit system as, for example, in the UK. He explained the challenges involved in the collection of trays and nonfood packaging - in this case, markers and tracers need to be found to programme their road value. Both are required to achieve higher plastic recycling targets. Casper expects a potential increase of more than 1,500kt in the years to come. He also highlighted the need to develop different facilities for bottle, tray and chemical recycling. Casper’s concluding remarks led neatly into the next speaker: Johan Kerver, CEO of Fili Grade. The company’s new product is the socalled watermark. This technology, introduced in the Holy Grail project Gian de Belder, P&G, at this year’s Petcore Europe Conference held in Brussels, is designed to make the sorting of plastics waste as simple as possible. This means that plastic packaging has its own unique fingerprint which makes it easily identifiable in all sorting systems. The fingerprint is visible for the machines but not to the end-consumer. Cameras used during the sorting process identify the inscribed watermark. The watermark is engraved directly into the mould. Every producer can have his own unique watermark. This system has many advantages for producers. They know full well where their products are sold and how they are regarded by consumers. Furthermore, they can add many functions to the watermark for end-consumers, as well as an already established app. In addition to educating consumers who use the app to scan the product, it also gives them more information, for example, on the product or the company. For the sorting process, the watermark can help, for example, in identifying food grade or non-food plastics. Jean-Loup van de Wiele, explained the initial steps that are being taken in tray-to-tray recycling and identified three main areas: input, washing and repelletising. A quality sorting process is required for the input section to identify colour, multilayer and lids sealed on the trays, as well as sorting adhering pollution and absorbent pads. Organic pollution, labels and adhesives can be found in the washing process. There will also be a high percentage of fines (2mm) that need to be cleaned. The repelletising section covers filtration, the increase of the IV and food grade guarantee. 4 PET Recycling has taken matters into their own hands working with Sorema and Erema to develop the first trays’ recycling process. The company started feasibility trials at the end of 2014 which have proved to be successful. Sorema washing technology has developed a specific washing process for trays, as well as a PET fines’ washing line. Eremas Vacurema technology is used in the extrusion process converting fines into food grade pellets. By restoring the IV, the food approval is guaranteed. Preparatory work to install the equipment in Duiven, NL, already began in April and May 2018, with the start of trays’ recycling planned for June/July 2018. An update on the projects and technologies will be given in Amsterdam in 2019. www.prseventeurope.com RECYCLING S P E C I A L Ton Emans, President, Plastics Recyclers Europe by Heike Fischer,@ID:27}, 47 TRADE SHOW REVIEW PETplanet Insider Vol. 19 No. 06/18 petpla.net TRADE SHOWreview Chinaplas 2018 & the Chinese beverage market Records were shattered at the 2018 Chinaplas: 180,701 visitors attended the four-day event, which was held for the first time at the new exhibition venue in Shanghai. Since Shanghai’s former venue was no longer able to cope with capacity, the show moved to the world’s largest purpose-built facility, the National Exhibition and Convention Center (NECC). The exhibition covered an area of 340,000m2, an increase of 100,000m2 compared to the Shanghai edition two years ago. Some 3,948 market leaders exhibited and brought cutting-edge solutions to the visitors from 150 countries during the show period. While occasionally Chinese company brochures with advertising imprints such as “the largest European moulds copying manufacturer in China” caught the eye of western visitors, reactions were generally positive, particularly on visitor numbers and, above all, on the technological advances amongst the local exhibits. Chinaplas 2019 will rotate to Guangzhou, running from May 21-24, 2019. The Chinese beverage market Beverages in PET are on an upward trend in China. According to data from Euromonitor, since 2013 the market has increased by just under 12% (96,338.5 million units) to 107,787.8 million units. For 2017, the experts of Euromonitor expect a further increase of almost 6% compared to the previous year to 114,118.3 million units. While sales of bottled water fell from 5% in 2015 to 4.2% in 2017 and are expected to dip further to 2.8% by 2021 (see PETplanet 5/2018, page 9), China still remains one of the biggest bottled water markets globally with a wide choice of brands and wells. Especially waters with an extra, such as added minerals or purification are what Chinese customers are willing to pay for. Growth markets for PET are also seen in the juice segment as well as in dairy products like yogurt drinks, as Jerry Yang, Sales Director for Greater China from Sipa tells: “Today Chinese customers are much more health conscious as they were a few years ago. For the beverages segment this means that less sugar products are preferred by the Chinese market. And also dairy drinks are becoming more and more popular; this at the same time represents a growth opportunity for PET. The big dairy company Yili already invested in PET filling lines for their products and likely others will follow.” Looking ahead, market researching company Mintel forecasts the dairy market to grow at a 6.6% CAGR (compound annual growth rate) in value, to reach RMB349.7 billion (US$54.4 billion) in 2022. Despite consistent sales growth, Mintel Market Sizes data shows that annual per capita volume consumption for major dairy products remains low compared to other countries. For example, per capita volume milk consumption in China is 14.3l, compared to 36.8l in Japan and 51.7l in the U.S.; per person consumption of yoghurt in China is 3.43kg, 4.92kg in the U.S. and 9.66kg in Japan. Summer Chen, senior food and drink analyst at Mintel, said, “Dairy consumption in China is still low when compared to Japan, where consumers share a similar dietary tradition to China. Mintel research indicates that China’s dairy market growth will be driven by increased consumption, resulting from the expansion of consumption occasions, a value increase due to the rising price of raw milk, and consumers trading up to more premium options. When we look specifically at the yoghurt market, thanks to the recent fad for ambient yoghurt, the category is now leading not only in China’s dairy market, but among all food and drink products.” IMPROVE LINE EFFICIENCY by 10% OR MORE CONTACT US TODAY TO LEARN MORE! AGRINTL.COM | +1.724.482.2163 | [email protected] 1MEASURE 2CONTROL 3OPTIMIZE PROCESS PILOT® Blowmolder management easy as . . . part 1,@ID:49}, PETplanet Insider Vol. 19 No. 06/18 petpla.net 53 BOTTLES „Natürlich mild“ from Valensina Valensina is offering vegan from four different, freshly harvested and especially mild fruits that have been squeezed and gently pasteurised. Each bottle contains around 1.8kg of fruit, is chilled and is to be consumed within three days of opening. The nodeposit bottles feature several brand logos and contain one litre of juice. A transparent foil label around the bottle belly, a gold-coloured screw cap with guarantee band and an additional freshness seal complete the packaging. www.valensina.de Individual Mattoni water bottles Founded in Kyselka in 1873, the mineral water manufacturer Mattoni is selling 500ml PET bottles in various shapes in its home nation, the Czech Republic, alongside the larger sized products also available in Germany. Mattoni is part of Karlsbader Mineralwasser AG. The bottles are coloured differently depending on the product and also differ in features around the neck area. The otherwise smooth surface of the still water bottle features one stylised eagle, while the bottle with pomegranate flavour has pimples and three smaller embossed areas with stylised eagles. The bottles all have a transparent label around the middle and a transparent screw cap with tamper-evident seal. www.mattoniwasser.de Big Shock! in contoured bottle Big Shock!, an energy drink from the Czech Republic, has revised the 1l bottle available in its home country and updated it to suit the times. The former pot-bellied bottle has become a tall, slim, contoured bottle decorated with a full-bottle label. The consumer can view the product only through the base. It is sealed with a lightweight screw cap with guarantee band. www.bigshock.eu,@ID:55}, MARKET SURVEY 33 PETplanet Insider Vol. 19 No. 06/18 petpla.net KHS Corpoplast GmbH Krones AG Side S.A. Meiendorfer Str. 203 22145 Hamburg, Germany +49 231 569 0 www.khs.com Mr Marco Böhnke Product Manager +49 40 67907 483 [email protected] Boehmerwaldstr. 5 93073 Neutraubling, Germany +49 9401 70 0 www.krones.com Mr Peter Christiansen Head of Sales Blow Moulding Techn. / Block Techn. +49 9401 70 498 0, +49 9401 70 91 4980 [email protected] Pol. Ind. Montguit, C/Llinars s/n 08480 L'Ametlla del Vallès, Barcelona, Spain +34 938 463 051 www.sidemachines.com Mr Josep Jiménez Sales Manager +34 677 551928 jose.jimé[email protected] InnoPET Blomax Series IV SR Contiform 3 Pro (11 models) Contiform 3 Pro SC (4 models) Contiform 3 Pro H (11 models) Maxiblow 1002e 2004e 2006e 2002eG 2003eG 5001e 0.1-3.0 0.1-3.5 0.1-0.7 0.1-2.0 0.25-2.5 0.25-3 0.25-2.5 up to ca. 5.5l 0.25-10 0.25-10 0.25-10 up to 50 4-36 28 36 28 2 4 6 4-8 1 2,500 2,500 2,500 2,000 1,500 3,000 7,000 10,000 2,600 3,600 2,500 2,500 2,000 1,500 3,000 7,000 10,000 2,600 3,600 2,500 2,400 1,800 1,500 3,000 7,000 10,000 2,600 3,600 ca. 1,000 1,500 10,000 2,600 3,600 950 - in Multiprocess config. max. 2,500 6.1x4.7 - 11.1x7.1 6.5x5.4x4.6 to 11.7x7.6x4.6 10.7x6.2x4.6 to 14.4x7.6x4.6 from 6.9x4.4x4.5 to 11.2x6.8x4.5 5.8x5.3x2.9 7x4.75x3.33 6.90x10.15x3.65 6.3x10x3.65 7.54x10x3.33 10.48x6.65x3.65 5.8x5.3x2.88 Clever-Loc mould hanger (for larger process angle & less complexity); focus heater for better material usage & bottle light weighting; InnoPET Silent TipTainer for preform scrap- & noise reduction Bottle design and mould manufacturing; nitro-hotfill; air-recycling systems for standard- and heat-set machines; rapid product change-over systems (MouldXpress); integrated preform- and bottle inspection; ContiformBloc (blower-filler-block); Contiform Bloc BL(blower-labeler-block); Ergobloc Land LM (blowerlabeler-filler-block); ContipureAsept Bloc with integrated preform decontamination, ProShape (non-round bottle production) Preferential oven; neck orientation; T-handle system; PP preform blow moulding; on-line remote device; 5 gallons returnable / one way; beer kegs; asymetric / oval botlles; air recovery system Sidel Group Kosme Gesellschaft mbH www.sidel.com Mr Stéphane Ménard, Mr Mathieu Druon Blowing Product Management Directors +33 2 32 85 86 87 [email protected]; [email protected] Gewerbestrasse 3 2601 Sollenau, Austria +43 2628 411 0 www.kosme.at Mr Johann Gugler Managing Director +43 2628 411 125 [email protected] Sidel Matrix Blower (101 models) Sidel Matrix eHR (heat resistant) blower (35 models) Sidel Matrix PH (Preferential Heating) blower (18 models) Sidel Matrix Blower Predis (50 models) Rotary machines (10 models) Linear machines (7 models) 0.25-3.5 0.25-2 0.25-2 (upon bottles dimensions) 0.25-2 0.05-3.0 0.05-3.0 up to 5 up to 3.5 up to 3 (upon bottles dimensions) not applicable 0.5-6.0 0.5-30.0 from SBO 6 to SBO 34 (three frames, three oven pitches) from SBO 6 to SBO 28 from SBO 6 to SBO 22 from SBO 6 to SBO 26 (one frame, two oven pitches) 8 4 from SBO 6 to SBO 14 (one frame, three oven pitches) from SBO 6 to SBO 14 from SBO 6 to SBO 14 not applicable 6 3 2,500 (XS mould size), 2,400 (Mmould size), 2,250 (Lmould size) 2,000 (L mould size) 2,000 (L mould size) 2,500 (XS mould size); 2,400 (M mould size); 2,250 (L mould size) 2,300 1,700 2,400 (M mould size), 2,250 (L mould size) 2,000 (L mould size) 2,000 (L mould size) 2,400 (M mould size); 2,250 (L mould size) 2,300 1,650 2,400 (for M mould size), 2,250 (L mould size) 2,000 (L mould size) 2,000 (L mould size) 2,400 (M mould size); 2,250 (L mould size) 2,200 1,600 up to 1,800 (L Jumbo mould size) 1,800 (L Jumbo mould size) 1,800 (L Jumbo mould size) not applicable 1,250 up to 1,250 for 5l; 750 for 15l; 700 for 20l; 350 for 30l 2,000 (L eHR mould size for hot fill) 2,000 (L mould size) For juices, tea, sport drinks, milk-base products MM model: 7.9x4.6x3.7 / GM model: 9x5x3.7 / LM model: 13.7x7x3.7 MM model: 7.9x4.6x3.7 / GM model: 9x5x 3.7 / LM model: 13.7x7x 3.7 MM model: 7.9x4.6x3.7 / GM model: 9x5x3.7 MM model: 7.9x4.6x3.7 6,050 x 3,850 x 3,250 (without preform feeding system) min. 4,500x1,830x3,100; max.5,100x1,850x31,00 (without preform feeding system) Maxi output smaller model / larger model: for XS mould (up to 0.75l): 45,000-82,000bph; for M mould (up to 2l): 14,400-67,200bph; for L mould (up to 3.5l): 13,500-63,000bph; for L Jumbo mould (up to 5l): 10,800-25,200bph Maxi output smaller model / larger model: for L eHR mould:12,00056,000bph; electrical mould heating instead of oil mould heating Maxi output smaller model / larger model: 8,400-36,000bph; for flat and complex containers Maxi output smaller model / larger model: for XS mould (up to 0.75l): 45,000-82,000bph; for M mould (up to 2l): 14,400-67,200bph; for L mould (up to 3.5l): 13,500-63,000bph; dry preform decontamination, Predis, for aseptic bottling with no blower sterilisation Active neck cooling; patented modular oven (low energy consumption); block version with fillers available; ProShape technology available for oval bottles (up to 2,000bph/cavity) Air recycling system; mould shells of linear machines are compatible with rotary machines; fast semi-automatic mould change within 10m; preferential heating,@ID:35}, imprint EDITORIAL PUBLISHER Alexander Büchler, Managing Director HEAD OFFICE heidelberg business media GmbH Bunsenstr. 14 69115 Heidelberg, Germany phone: +49 6221-65108-0 fax: +49 6221-65108-28 [email protected] EDITORIAL Kay Barton Heike Fischer Gabriele Kosmehl Michael Maruschke Ruari McCallion Waldemar Schmitke Anthony Withers WikiPETia.info [email protected] MEDIA CONSULTANTS Martina Hirschmann [email protected] Johann Lange-Brock [email protected] phone: +49 6221-65108-0 fax: +49 6221-65108-28 LAYOUT AND PREPRESS EXPRIM Werbeagentur | exprim.de Matthias Gaumann READER SERVICES Till Kretner [email protected] PRINT Chroma Druck & Verlag GmbH Werkstr. 25 67354 Römerberg Germany WWW www.hbmedia.net | petpla.net PETplanet Insider ISSN 1438-9459 is published 10 times a year. This publication is sent to qualified subscribers (1-year subscription 149 EUR, 2-year subscription 289 EUR, Young professionals’ subscription 99 EUR. Magazines will be dispatched to you by airmail). Not to be reproduced in any form without permission from the publisher. Note: The fact that product names may not be identified as trademarks is not an indication that such names are not registered trademarks. 3 PETplanet Insider Vol. 19 No. 06/18 petpla.net If you have ever experienced the ineptitude of American Airlines then you will empathise with our team and our nightmare journeys to and from NPE. The saga began with PETplanet staff Valentin T. on May 5, whose flight from Frankfurt never left the ground. After 4 hours sitting on the aircraft, all passengers were asked to disembark and the flight was cancelled. Luckily Lufthansa saved the day and Valentin managed to get on a flight to Orlando that very day. I wasn’t quite so lucky. Booked onto the same American Airlines flight I wasn’t even able to board the fated plane as my passport was supposedly ‘too worn out’. “You won’t get into the States with this, pal”, was the sneering advice. The fact that I had flown to Hawaii only a few days earlier with the same passport, and that neither the carrier nor the immigration authorities had found anything wrong with it seemed to cut no ice with American Airlines. I never got to NPE. American Airlines sank to new depths on Valentin’s return flight. His first connecting flight was delayed due to technical problems, which meant he arrived at the departure gate for the Frankfurt flight just five minutes before final boarding. The Gate had closed. A bad tempered customer service assistant rebooked him via Dublin, arriving 12 hours later than scheduled in Frankfurt. Valentin’s harmless comment about Lufthansa getting him there quicker soon escalated into the assistant saying she felt “under personal attack”. And the American Airlines saga does not end there. Kay Barton drove to Atlanta in the Editourmobil to catch an American Airline’s flight to Frankfurt. No surprises that the first connection to Philadelphia was delayed and then cancelled. Amazingly a re-booking was made on an alternative AtlantaDallas-London-Frankfurt flight on the same day. However, this flight to Dallas was also delayed, resulting in a re-booking for the next day and an unintended overnight stay at the airport. The following day, an announcement at the departure gate confirmed that this flight was also delayed and therefore cancelled. Finally, the only way that American Airlines could get Kay back to Frankfurt was to re-book him on a direct flight with one of their competitors, Delta. Having spent 30 hours in Atlanta, Kay was finally able to get a return flight to Frankfurt, with no hitches... Thanks to American Airlines, two of my colleagues spent over 24 hours in airports and I never even got to fly. Needless to say we’ve had no acknowledgement of our emails of complaint... I should just mention that other colleagues did manage to fly to NPE without a single problem thanks to Lufthansa and Delta. Yours, Alexander Büchler Dear friends of PETplanet Insider, Never Ever American Airlines,@ID:5}, BOTTLE MAKING 41 PETplanet Insider Vol. 19 No. 06/18 petpla.net BOTTLE MAKING 41 1984/1985, with two Nissei ASB 250, 0.33l PET bottles were produced for Coca-Cola Tahiti for the first time, followed by 1.5l bottles in 1987/1988. The following year, another five new models for Coca-Cola brands, ranging in size from 0.5l to 2l were added. In 1996, the company made its own preforms on Husky 16-cavity equipment for the first time. Sidel SBO1 and SBO4 blow moulding machines were added over the following two years. In 2004, it made its first closures for water bottles, on Corvaglia moulds; since 2015, one-piece PCO 1810 CSD closures have been produced on z-moulds under license of Universal Closures Ltd. “PET processing and production accounts for roughly 45% of our business at Plastiserd, and closures, about 3%”, he explained. At present, Plastiserd uses two Husky HyPET 120 systems and one HyCap 160. Three 24-cavity moulds are used for the production of 26g, 44g and 52g CSD preforms, as well as 16g and 27g preforms for water. “We currently use moulds from Husky and GDXL as well”, Mr Bellanger continued. “The quality here is extremely good and we are very enthusiastic about the Chinese alternative. We previously used moulds from China for production back in the noughties, and that is certainly one of the reasons why we proved to be so successful over the years. With our low rates of output, depending on the application, these moulds constitute an ideal investment.” Further preform processing takes place at Plastiserd’s second site, which is situated roughly 14km away and which we also visited. This facility is home to a range of blow moulding equipment, including two Sidel SBO4 and SBO1 machines. The bottles produced here are sent across the road – quite literally – to a Brasserie de Tahiti plant, which bottles Coca-Cola products; completing the circle. www.plastiserd.pf Plastiserd’s blown PET bottles Bottle production for the Brasserie de Tahiti bottling plant,@ID:43}, 29 PRODUCTS PETplanet Insider Vol. 19 No. 06/18 petpla.net The vertical baler HSM V-Press 860 P presses PET bottles The V-Press series from HSM GmbH + Co. KG, the German manufacturer of baling presses, PET solutions and document shredders, is claimed to be a combination of the quality requirements of the HSM environmental engineering and high profitability. With their performance and long service life they are an economic disposal solution. The bales have ideal dimensions to achieve a perfect utilisation of the trucks, which saves handling costs and increases the marketability of the bales. The vertical baling press HSM V-Press 860 P is especially designed for the compression of opened or perforated PET/UBC bottles. With a pressing force of 434kN and a low-noise and energy-saving technology, this baler is the economic and environmentally sound solution for all tasks of disposal. With the rapid motion technology developed at HSM, the power consumption and drive power are significantly reduced and, at the same time, the throughput rate increases, says the company. This special design with twice the number of retaining claws, compared to the HSM V-Press 860, optimises the compaction of the material to be pressed and reduces the number of filling processes. The pressing process, which starts with closing the door, proceeds automatically. A comfortable membrane keyboard including text display comprehensively informs the user about the state of affairs. After the end of pressing, the sliding door is opened automatically. A fourfold wire banding ensures the shape of the bale with a weight of up to 230kg. The maximum bale size amounts to 1,200 x 780 x max. 1,200mm. Taking out the bale is said to be easy and can be removed on a pallet. The inclination of the pressing plate is continuously monitored in all directions thanks to the special HSM TCS (Torsion Control System). It prevents one-sided Ioads, optimises the pressing process and ensures a long service life. With these balers, the volume of the packaging material can be reduced by up to 95% directly on site. www.hsm.eu RECYCLING S P E C I A L A COLOUR IDENT I TY LIQUID COLOURS AND ADDITIVES FOR PACKAGING repi.com,@ID:31}, MATERIALS / RECYCLING PETplanet Insider Vol. 19 No. 06/18 petpla.net 26 PET recycling developments Growing number of recycling projects in China and abroad The Chinese government’s announcement of a ban on the import of waste plastics material has had a profound impact on the country’s recycling industry. A programme of strict environmental inspections and enforcement has led to the closure of a large number of small workshops and low-efficiency factories. At the same time, it created a favourable business climate for large-scale PET bottle recycling projects. The rise in demand for its range of large-scale recycling equipment has seen Zhejiang Boretech Environmental Engineering Co., Ltd. (Boretech) complete a growing number of projects, for both domestic and international customers. Activity in China Zhejiang Boretech Environmental Engineering Co., Ltd. (Boretech) has more than 20 years of experience in PET bottle recycling. It deploys its own technology in processing postconsumer PET bottles for a range of customers. The company has been specialising in the research and development of large-capacity, high-grade PET bottle recycling equipment. It is able to offer complete production lines, complete with intelligent control systems and on-line pollution, contamination and waste treatment. Boretech successfully completed commissioning work of a large-scale PET bottle recycling line for a wellknown Chinese group in May 2018. The project comprised two complete 6,000kg/h PET bottle washing lines, and an additional 3,000kg/h mixedcolour bottle washing line. The plant, which is designed to cope with waste bottle material with high impurity content and multiple colours, was equipped with four optical bottle sorters, four colour sorters, and an on-line waste treatment system that achieves zero sewage discharge, in compliance with China’s latest, very strict domestic environmental protection standards. Boretech expects to build more than 20 similar-scale PET bottle washing line projects in the next 3-5 years. A first in Eastern Europe In December 2017, Boretech signed a contract with a Polish organisation to provide a 1,500kg/h bottle-to-bottle grade PET bottle recycling washing line – its first in Eastern Europe. This project represents a major upgrade to the company’s existing cold-wash line, enabling it to expand operations into new markets and products. This line in Poland features improved appearance, equipment quality, safety in operation and spare parts specifications, compared with equipment previously exported, mainly to the Southeast Asian market. The equipment complies with CE standards. Despite its relatively low capacity, the line is equipped with an automatic bottle sorter and a flakes sorter. It has the ability to remove metal, to reject non-PET materials, and to undertake colour sorting. The crusher’s forced feeding system manages and controls output. The on-line labels packaging system is designed RECYCLING S P E C I A L,@ID:28}, BOTTLE MAKING 39 PETplanet Insider Vol. 19 No. 06/18 petpla.net The new 0.66l Chiarella bottle is a genuine innovation in the national and international Ho.Re.Ca (Hotel/Restaurant/Café) market sector, being positioned halfway between the 0.5l bottle, which is ideal for on-the-go consumption, and the 1l package. Acque Minerali Val Menaggio suggests that restaurants that replace the 1l format with the 0.66l bottle could increase their margins and units sold. The shape of the bottle is simple and linear. It is smooth, decoration and texture free, and without embellishment or obvious design features – which is itself a feature that sets it apart from all competitor products. There is no other 0.66l water bottle on the market; all these features are intended to add up to a product that is immediately recognisable, by its dimensions, proportions and appearance. The standard label features an image of Lake Como but is designed to be ‘infinitely customisable’. The concept of the label is by internationally acclaimed contemporary artist Fabrizio Musa. It is part of the Sympòsion project, with which Chiarella invites exponents of the art world to connect with each other, through the reduced space of the label, on the theme of ‘Excellence of Nature and Man’. The deceptively simple label design is intended to be well-suited to customisation. Early editions of the new bottle featured limited edition labels that were produced to pay tribute to the architect and designer Achille Castiglioni (Feb. 16, 1918 - Dec. 06, 2002) on the occasion of the centenary of his birth. The Limited Edition project was managed by public relations agency Comunity Lab’s media partner Design Street. “Zero 66 Castiglioni” was launched during Design Week and will be sold throughout 2018. As well as packaging design and engineering services, PET Engineering supplied Acque Minerali Val Menaggio with a series of production moulds for its Krones blowing machines, for use in production. The company, which has won four ‘Packaging Oscars’ and two World Star Awards, has brands such as Pepsi Co, Nestlé Waters, Carlsberg, Heineken, Coca-Cola, AB Inbev and Ferrarelle among its customer base. www.petengineering.com New bottle for Chiarella, the ‘Ambassador of the Lake Como Lifestyle’ 0.66l water bottle Acque Minerali Val Menaggio, S.p.A., of Plesio, Italy, has been working with Treviso-based PET Engineering, which specialises in packaging design and manufacture for the food & beverage sector, to develop a new and original format for packaging Chiarella water, which is marketed as the “Ambassador of the Lake Como lifestyle”. Swiss Made | www.imdvista.ch IMDvista INOX Line Closure Inspection – 100% inline. Robust, compact and very flexible. One control center (HMI) for the whole line. IMDvista PECO V3 Preform Inspection. Less than 7m² and up to 90’000 pph. Cavity reading. IMDvista PECO LUX Preform Monitoring shot by shot. Requires no additional floor space. No preform orientation. Inspection Systems for the Plastic Packaging Industry,@ID:41}, PETnews 6 NEWS PETplanet Insider Vol. 19 No. 06/18 petpla.net PET Engineering wins the Golden A’ Design Award PET Engineering has announced that the packaging design Fonte Vita has been awarded the coveted Golden A’ Design Award. In the Packaging Design Category, Fonte Vita has been chosen as the winner by the distinguished panel of the A’ Design Awards & Competitions from the thousands of submitted designs. Elisa Zanellato, Marketing & Communication Manager at PET Engineering says “Fonte Vita redefines the boundaries of premiumness for the HoReCa sector using plastic packaging with an eye-catching shape rather than traditional glass packaging, creating a new style of decoration. A shade is made possible thanks to an original use of the multilayer technology by Husky Injection Moulding Systems and its easy colours dosing process, eliminating the need for a full sleeve label. On the top there is Lux Cap, developed with La Brenta, the very first premium PCO 1881 cap, which is entirely customisable in colours, finishing and printing options. Fonte Vita, a 39g bottle, is the alternative to glass with a host of other benefits such as unbreakability, lightweight and low cost.” Entries to the A’ Packaging Design Awards are peer reviewed and anonymously judged by an expert jury panel of prominent academics, influential press members and experienced professionals. www.petengineering.com Mould & Matic expanding in Micheldorf, Austria Mould & Matic Solutions GmbH, a specialist in tool and plant engineering for the packaging industry, on May 2, 2018, launched the expansion of the site in Micheldorf, Austria. Completion is scheduled for May 2019. Generously proportioned assembly halls for the construction and commissioning of plastics processing machines are being built on a total area of approx. 3,355m2. Additionally, a new customer centre and office space for engineering, international sales and project management will be built and the technology centre expanded. A great deal of importance was placed on an optimal balance of sustainability, energy efficiency and maximum flexibility for the technical building equipment. Therefore, for example, compressed air, cooling water and electricity are supplied through floor channels of the facilities. Mould & Matic has been part of the Kiefel GmbH, Freilassing, Germany group since 2016. The newly created assembly areas and the focus on the cup and bottle market segment technologies reflect the consistent growth and competence of the automation technology and tool specialists in cooperation with Kiefel as Kiefel Packaging. Mould & Matic Solutions GmbH has 155 employees in Micheldorf, including 22 apprentices. The expansion is expected to increase the number of employees to 250 over the next few years. www.kiefel.com US$180 million turnover barrier broken The Erema Group closed the 2017/18 fiscal year at the end of March with double-digit growth of over 10 per cent. The companies integrated in the Group have achieved a new turnover record with consolidated sales reaching US$180 million for the first time. “The past financial year made one thing clear to us as the Group: with our quality-oriented recycling solutions, we are exactly in tune with the times. The end of China as an international customer for post-consumer plastic waste, the strategy for plastics presented by the EU Commission and initiatives such as the Ellen MacArthur Foundation are just some examples of the current period of strong change for the plastics industry. One of the reactions – among others – to this is the increasing willingness of raw material manufacturers, international producers and recyclers to invest in modern and quality-oriented extrusion technology”, says Manfred Hackl, Erema Group CEO. This development is reflected in the sales figures of the entire Group. The plastics recycling machine manufacturer Erema Engineering Recycling Maschinen und Anlagen Ges.m.b.H increased its turnover compared to the previous fiscal year, generating sales of US$167 million. According to Manfred Hackl the positive development is thanks to an increase in sales in all three recycling markets – Post-consumer, Inhouse & Industrial and Bottle Recycling – throughout the world. www.erema.com New owner for Polymetrix Polymetrix is now owned by Sanlian Hope with 80% of its shares. The Bühler Group remains a minority shareholder with 20% of the Polymetrix shares. The sale of 80% of the shares of Polymetrix from the Bühler Group to Sanlian Hope has been successfully closed on March 22, 2018. The direct buyer is Sanlian Material Science S.à.r.l. in Luxembourg, a subsidiary of Beijing Sanlian Hope Shin-Gosen Technical Service Co. in China. Polymetrix remains a Swiss entity and continues to operate under the existing management and the existing employees. The new board of Polymetrix now consists of five directors with representatives of both shareholders. The company’s legal name and the address remain identical and are expanded with the following suffix: “Polymetrix, a Sanlian-Bühler Company”. www.polymetrix.com,@ID:8}, MATERIALS / RECYCLING PETplanet Insider Vol. 19 No. 06/18 petpla.net 24 The new TEM machine offers new possibilities for slitting or slitting and folding of tamper evident bands for specialty caps. The TEM, a highly versatile machine for beverage, food, beauty & home, chemical and other products. Modular design machine for slitting/folding or folding/slitting of tamper evident band Large variety of cap dimensions, including sport caps All size parts located in the outside for easy adjustment and changeover Heating system for the blade. Blade position sensor Servo-driven infeed star wheel, integrated cap stop and sensor controlled upside down closure detection Operator friendly interface Match the output of associated moulding and downstream machines Easily integrated into any production line due to independent control and optional vision inspection system PackSys Global and its affiliated companies offer a wide product portfolio: Complete lines for laminate, extruded and aluminum tubes Plastic closures slitting and folding machines Cap printing lines Monobloc aerosol can lines Hot stamping solutions from Madag Printing Systems Tube, aerosol can and cartridge packing solutions from Texa Packaging Highly skilled R&D and production teams ensure constant development and integration of the latest technology on our equipment. We stand for Swiss engineered innovation and performance. Creating Packaging Technology. PackSys Global AG T +41 55 253 38 31 [email protected] www.packsysglobal.com A Member of Brückner Group SPECIALTY CLOSURES TAMPER EVIDENCE,@ID:26}, Recycling products 28 Vol. 19 No. 06/18 petpla.net Retal converts rPET for Nestle Retal’s major investment in state-of-the-art equipment at its facility near Pittsburg has enabled this leading packaging manufacturer to deliver preforms to make the ‘glass-like look’ of PET using recycled PET (rPET). It is with pride that Retal can confirm that its rPET preforms have been chosen by Nestle North America for its Pure Life Purified Water 700ml bottles. Admir Dobraca, General Manager Retal PA, said: “Every aspect of Retal’s rPET converting is under strict control - that is how we can be sure that our preforms offer that glass-like look of PET but with the environmental advantages of using 100% recycled PET. We process using superior injection and drying equipment, making Retal rPET preforms perfect for mineral water applications like Nestle Pure Life.” Nestle Waters North America said in a statement, “We work with a number of strategic suppliers, including producers of food-grade, post-consumer recycled PET. We are expanding our roster of suppliers to purchase even more recycled plastic, which we plan to use in our other bottled water brands across the country.” The confirmation that Nestle Pure Life Purified Water 700ml bottles are made from Retal rPET preforms is a great illustration of Retal’s ongoing dedication to developing and delivering sustainable packaging solutions and highlights the flexibility in its production processes as an added value to customers. www.retalgroup.com RECYCLING S P E C I A L,@ID:30}, PETpatents www.verpackungspatente.de PETplanet Insider Vol. 19 No. 06/18 petpla.net 56 Seal for keg British Patent No. GB 2532223 A Applicant: Petainer Large Container IP Ltd., London (GB) Application date: 11.11.2014 To protect a plastic keg from damage caused by the effects of various forces, the proposal is to install this in a protective cover consisting of base, cap and cover. Multi-layer container International Patent No. WO 2017 / 176859 A1 Applicant: Amcor Ltd., Hawthorne (AU) Application date: 5.4.2017 The application describes a multilayer preform for creating a PET bottle intended for hot filling. The bottle must fulfil certain properties in terms of heat resistance. PET bottle without foaming International Patent No. WO 2017 / 189334 A1 Applicant: Niagara Bottling LLC., Ontario (CA) Application date: 20.4.2017 The upper side / circulating edge of a PET bottle is equipped with two notches, which the applicant suggests will prevent unwanted foaming when the bottle is opened. Bottle in dumbbell shape Utility model DE 202017004295 U1 Applicant: Klaus Kling, Kirchheim (DE) Application date: 16.8.2017 Specially shaped plastic bottle for wide variety of drinks. After removal of the drink, the bottle can be individually filled with products of different densities and used as a dumbbell. Plastic bottle European Patent No. EP 3225562 A1 Applicant: Yoshino Kogyosho Co. Ltd., Tokyo (JP) Application date: 23.2.2017 The outside of a plastic bottle designed for hot filling is smooth and furnished with a defined area for affixing a label. The base absorbs the vacuum forces arising after hot filling preventing a negative change to the bottle shape by distortion. Wrap with handle International Patent No. WO 2016 / 096619 A1 Applicant: Nestec S.A., Vevey (CH) Application date: 10.12.2015 To enable easier carrying of several bottles in a wrap, a foldable handle construction of cardboard/corrugated cardboard is proposed, which is folded out of the wrap for carrying.,@ID:58}, 8 NEWS PETplanet Insider Vol. 19 No. 06/18 petpla.net Prof. E.h. Dr.-Ing. Johann Grabenweger is leaving KHS KHS in Dortmund, Germany, part of the Salzgitter Group’s high-growth technology business unit, has announced changes to the KHS Executive Management Board concerning the Sales and Service division. As part of its Strategy 2021 program Salzgitter AG plans to further expand its technology business unit. In order to follow KHS’ own growth strategy while strengthening its inner performance KHS is implementing its KHS Future action plan. As part of the KHS realignment process Prof. E.h. Dr.- Ing. Johann Grabenweger, is leaving the company by mutual consent after 13 years of successful work in Production, R&D and, most recently, Sales and Service which has grown by about a third in the last few years. Until a final decision has been reached regarding the appointment of a successor, Management Board responsibility for the Sales and Service Division will be assumed by the chairman of the KHS Executive Management Board, Burkhard Becker. www.khs.com European bottled water producers make major pledges towards circular economy by 2025 The European Federation of Bottled Waters (EFBW) announced four industry-wide pledges that aim to increase the collection of PET bottles and the use of recycled PET. This will accelerate the shift towards a more circular European economy. EFBW is therefore announcing the following pledges to be implemented by 2025: Collect 90% of all PET bottles by 2025, as an EU average. Ensuring PET bottles are collected means that they can be used to produce new bottles or for other products. EFBW will be a driving force alongside all actors involved in the waste management process; Collaborate with the recycling industry to use at least 25% recycled PET (rPET) in its water bottles by 2025, as an EU average. To increase the use of rPET into new bottles, natural mineral and spring water producers require a consistent supply of high-quality recycled material; Innovate and invest further in eco-design and research on non-fossil based plastic materials. The bottled water industry has always had sustainability at its heart, and is continuously investing in packaging R&D. This includes optimising its packaging design through light-weighting, eco-innovation, and research on plastics from renewable origin; Engage with consumers who play a key role in preventing littering. The industry will support initiatives which encourage the proper sorting and disposal of packaging. To ensure that its members can deliver on the new pledges, the EFBW intends to work with all relevant stakeholders, including Plastics Recyclers Europe (PRE). In order to guarantee transparency and accountability, EFBW will report regularly on progress of the pledges announced. www.efbw.org Husky announces organisational changes to align with market demands and consumer trends Husky Injection Molding Systems has announced organisational changes to proactively realign its business to support customers in response to evolving market trends and changing consumer demands. Husky has taken the step of combining its Beverage Packaging business and Specialty Packaging business under one new consolidated business called Rigid Packaging. This change will allow the company to offer a wider range of solutions and services to both Consumer Packaged Goods brands and plastics processors. Robert Domodossola will lead Husky’s new Rigid Packaging business. Mr Domodossola was formerly President of Husky’s Medical and Specialty Packaging Systems business and was appointed to this position in April of 2017. Since joining Husky in 1996, he has progressed through a number of design and engineering management roles. Bringing these two businesses together under Robert’s leadership will enable Husky to be more nimble in responding to market needs and better help its customers to be more competitive. Gerardo Chiaia, Husky’s former President of Beverage Packaging, is leaving the organisation to dedicate more time to his family. This comes after an outstanding 24-year career with the company. www.husky.co SMI chosen as ‘National Winner’ of the European Business Awards SMI has reached the Grand Final of the European Business Awards, after being chosen as a ‘National Winner’ by independent judges from a list of almost 3,000 businesses. The European Business Awards created the list after a review of over 110,000 European companies. At the final in Warsaw, Poland, in May, for the first time in the Awards’ 11-year history, each finalist had a stand to display their notable success, and 55 business experts come from across Europe to decide the winners of the Awards’ 12 categories. In this final stage of the competition SMI has represented Italy in the category “Awards for Innovation” with the project of the EBS K stretch-blow moulding machine. This latest development is the results of an even more compact, ergonomic, eco-friendly machine. www.smigroup.it,@ID:10}, MATERIALS / RECYCLING PETplanet Insider Vol. 19 No. 06/18 petpla.net 22 Teijin Eco-Circle Process: Teijin is playing a pioneering role in Chemical Polyester Recycling (CPR). It builds on the experience of methanolysis of polyester waste, which has been operated by polyester manufacturers for many years. Together with Teijin’s existing equipment for the production of DMT and PTA, a robust process for the chemical recycling of polyester waste has been developed during the last 15 years. The initial production of PET resin for bottle making (B2B) was changed several years ago to the manufacture of all types of textile fibres and filaments, for profitability reasons. Teijin now works with more than 150 apparel and sportswear manufacturers worldwide to develop and manufacture products made from recyclable materials, as well as to collect and recycle these products at the end of their useful lives.Zhejiang Jiaren New Materials Co., Ltd. operates a chemical recycling plant of 70t/d capacity on a Teijin license; a new 440t/d plant of is under construction. Polygenta Re New process: “Polygenta’s proprietary, commercially proven technology Re New that produces polyester filament yarn from post-consumer waste PET bottles, is executed at 10,000t/a recycling facility in Nashik, India. The Re New process is a trailblazer technology given its ability to recycle dirty clear and coloured PET bottles in a cost effective manner as well as significantly reducing the use of virgin petrochemical feedstock and delivering superior quality products”. The basic principle of the Re New process is the washing of the PET bottle flakes with glycol; glycolysis of the flakes; fine filtration of the glycolysate; removal of the excess glycol; and polycondensation of the glycolysis product thus obtained. Simon West, the father of this process, started its development in the 1990’s; Polygenta completed the technical process development over three years, from 2010 to 2013. Today, POY filaments are produced by direct spinning from 100% recycled material. Aquafil Engineering: Aquafil’s process approach is similar to the Polygenta Re New process and based on mild glycolysis, purification of the glycolysate and direct repolycondensation by a polyester polycondensation plant. Chinese approaches: Substantial industry development and R&D work towards of new PCR-technologies are underway in China. The major target is the development of recycling processes using polyester textiles as input material. Preferred processes are methanolysis and glycolysis, combined with the direct consumption of the recycled materials in polyester production lines. The latest news about this processes will be presented during the next polyester recycling conference in China. 2.5 What to be done with the resulting non-PET-waste? Looking at a chemical PET recycling plant with an assumed capacity of 400t/d rPET and an input purity of 70%, 170t non-PET wastes are produced daily. This means that, as well as the chemical recycling plant, a waste treatment plant of this capacity will be required. In this context, the construction of a CHP (combined heat and power) waste incineration plant would be sensible, with the majority of the heat produced being used for the recycling plant. 3. Conclusion In summary, it is becoming obvious that the main problem is not the lack of a chemical recycling process but the solution of logistical, capacitive and financial issues of a large-scale plant for PET recycling. To simplify process chemistry and purification of the monomers, polymer destruction should refrain as much as possible from the use of catalysts, additives, solvents and process aids like KOH, NaOH, HCl or H 2 SO 4 and favour heat and pressure, along with process friendly chemicals like water, methanol or glycol. All that is added must be removed, up to a purity 99,99%! There are several industry proven chemical recycling processes for licensing available in the market. In view of the useful capacity of a recycling plant and its complexity, the cooperation of major polyester manufacturers, such as Idorama or Reliance, along with major consumers such as Coca-Cola, Nestlé, Danone, Lidl or P&G, will be essential for polyester to make a successful entry into the chemical recycling www.polyester-technology.com,@ID:24}, PETplanet Insider Vol. 19 No. 06/18 petpla.net 55 BOTTLES Transparent sun protection spray Garnier Ambre Solaire is selling 150ml of UV water, a transparent sun protection spray invisible on the skin but with a refreshing effect, in a light blue, dropshaped bottle. The two-phase product, which must be shaken before application, contains aloe vera from a fair trade source. The UV water is applied via a screwed-on pump dispenser with a removable protective cap. The transparent self-adhesive labels on the front and rear present information about the product and enable a clear view of the waterproof, non-greasy product. www.garnier.de Plant-based hand soap Method – a manufacturer of ecological cleaning products – is selling 354ml of plant-based liquid hand soap in a clear, pot-bellied bottle with a decorative sleeve label. The label for the “Mimosa Sun” soap is printed with animal motifs. The manufacturer does not use any animal-based ingredients and it indicates this expressly on the hang tag attached to the bottle. A lockable pump dispenser, which is also transparent, enables easy application of the liquid soap. www.dm.de New range from Nivea Glow is the name of the new Nivea face care range from Beiersdorf. It includes a twophase eye make-up remover with the additive Happy Shake. According to Nivea, this removes even waterproof eye make-up. Before application, the two phases must be mixed by shaking, which creates a slightly milky, pink-coloured liquid. There is a dose dispenser pressed into the bottle opening to simplify application of the product onto cotton wool or a cleaning pad. The 125ml bottle is decorated with two transparent self-adhesive labels. www.nivea.de Via Scodoncello n° 41/E - 43044 Collecchio (PR) - Italy - Tel.: +39 0521 541011 Everything and more... cooperating together global solutions for containers in PET and other plastic materials Design, construction & installation of: • Systems for handling & storing all types of plastic containers • Linear blow molders for PET bottles LANFRANCHI S.r.l. www.lanfranchi.it innovation plastic container Design, industrialization, blow molds & prototype sampling for PET containers IPC S.r.l. www.ipcsolution.it,@ID:57}, MARKET SURVEY 32 PETplanet Insider Vol. 19 No. 06/18 petpla.net Company name SMI S.p.A. Tech-Long Europe GmbH Sipa S.p.A. Postal address Telephone number Web site address Contact name Function Direct telephone number E-Mail Via C. Ceresa, 10 24015 San Giovanni Bianco (BG), Italy +39 0345 40 111 www.smigroup.it Mr Pietro Volpi Marketing Dept. Manager +39 0345 40 316 [email protected] Cobenzlgasse 32/7 1190 Wien, Austria +43 1 320 10 41 www.tech-long-intl.com Mr Dominique Lipinski Managing Director [email protected] Via Caduti del Lavoro, 3 31029 Vittorio Veneto (TV), Italy +39 0438 911 511 www.sipa.it Mr Paolo De Nardi Project leader/Stretch-Blow Molders Development +39 0438 91 1624 [email protected] 1. Machine designation / model number EBS (Electronic Blowing System) Ergon series (10 models): N°7 models (4-16 cav); N°3 HC (3-6 cav); EBS K (Electronic Blowing System Kompact) Ergon series (3 models) (2-4 cav) Rotary blow molders CPX Rotary Blowmoulders Xtra (4 models); SFR Evo Cube: (3 models) Linear Blowmoulders SFL 6 (5 models); SFL 4 (3 models); SFL 4 wide mouth (3 models); SFL 2/2 & SFL 1 (2 models) 2. Bottle volume (from/to in litres) 0.10-10 a) Standard machines 0.10-3 0.25-3.3 0.25-3.5 0.25-3 b) Machines for large containers 3.5-10 up to 20 5-30 3. Max. number of stretch-blow moulds (units) a) Standard machines 16 26 24 8 b) Machines for large containers 6 10 2 4. Output per stretch-blow mould for: 0.5l CSD bottle (units/hour) 2,100/2,200 (depending on the bottle features) up to 2,250 2,550 - up to 54,000 1,800 1l CSD bottle (units/hour) 2,000/2,100 (depending on the bottle features) up to 2,200 2,550 1,600 1.5l still mineral water bottle (units/hour) 2,000/2,100 (depending on the bottle features) up to 2,400 2,550 1,650 Large capacity container 1,100/1,200 (depending on the bottle features) up to 1,400 650 Other up to 2,000 5. Footprint / space requirement (LxWxH in metres) Standard models: min 4.2x3.5x2.75 / max 6.8x3.9x2.75; K models: 2.32x3.28x2.3; HC High Capacity models: min 4.45x3.46x2.57 / max 5.55x3.46x2.57 6. Special features (short description/keywords) Compact space-saving frame; ergonomic and functional design; new preform-heating module (horizontal frame); heat-reflecting and energy-efficient composite panels; low dead volume valves system; motorised stretching rods; mould-holder opening/closing/locking system operated by brushless motor; minimised maintenance; ReduxAir optional kit; air recovery system; MotorNet System technology; quick changeover and mould replacement. Up to 50% high pressure air recycling; low pressure; servo motor driven stretching; all key components form international OEM; low TCO and maintenance cost; efficiency at 97% min. Output 2,550 bph/cav. with best process angle: easy to blow; reduced TCO: lower air and energy consumption (again -25%); quick mould changeover time, simple use & maintenance. Bottles for water, oil, CSD, heat resistant, oval simmetric and asimmetric, with preferential heating, neck orientation, with handle, wide mouth (up to 130mm NF), large size (up to 30l), in OPP and PLA Company name Technopet Machineries Postal address Telephone number Web site address Contact name Function Direct telephone number E-Mail Office: 14/15, Shree Naman Plaza, S.V. Road, Kandivali (W), Mumbai 400 067 Factory: Plot No. A-40, Sector-1 S, CIDCO Industrial Estate, New Panvel, Navi Mumbai 410 206, India +91 022 28610 828 www.technopet.in / www.techno-pet.com Mr Vineet Bannore / Mr Sunil Bharkada Business Partner +91 98 20346565 / 98 21040637, 022 28061 410 [email protected] / [email protected] 1. Machine designation / model number Auto OL 3000-2C TP-OL-2400-2C PDW-1800 Bottle & Jar / P-Auto 2X2X5 Jar 20 lit /TPS-20L 2. Bottle volume (from/to in litres) a) Standard machines 0.2-1 0.2-1 0.2-2 b) Machines for large containers 0.5-5 10-20 3. Max. number of stretch-blow moulds (units) a) Standard machines 2 units 2 units 2 units 2 units b) Machines for large containers 1 unit 1 unit 4. Output per stretch-blow mould for: 0.5l CSD bottle (units/hour) 3,000 2,400 1,800 1,000 1l CSD bottle (units/hour) 3,000 2,400 1,800 800 1.5l still mineral water bottle (units/hour) 1,800 600 Large capacity container 400jph/c 200jph/c Other Neck diameter 19-28mm 19-28mm 19-28mm 28-120mm 46-120 5. Footprint / space requirement (L x W x H in metres) 2.2x2.0x2.5 1.5x1.1x2.5 2.1x1.5x2.2 2.1x2.0x2.5 3.1x2.5x3.0 6. Special features (short description/keywords) Low air consumption at 20bar; low conversion cost as minimum PCD of preform 36mm in oven for effective heating; rotary oven with frictionless movement of preform; neck down IR isothermal relaxation with intermittent heating; robotic servo movement for preform transfer; 360° neck protection for low weight thin short neck bottle; easy mould change system with lifting arrangement; orient preform in neck up position than bottle for online facility. Economical and compact automatic hand feed; servo driven online machine; neck-up-top blowing system; rotary oven with neck down IR isothermal relaxation with intermittent heating; servo control with 360° neck protection for low weight thin short neck bottle. Neck-up-top blowing system; neck down IR Isothermal Relaxation with intermittent heating, 360° neck protection for low weight thin short neck bottle with offline system. Low cost; auto ejection semi auto; 2 gallon; 28-120mm neck for versatile bottle and jar for different sector like water, oil & confectionary. New patented technology of preform heating up to 12mm thickness for 5 gallon jar with 46-120 mm neck. 360° preform neck protection system; blown air reclamation system; centralised lubricating system.,@ID:34}, MATERIALS / RECYCLING PETplanet Insider Vol. 19 No. 06/18 petpla.net 14 The effects on the PET chain of China’s import ban on plastic waste China stirs up the markets by Gabriele Kosmehl The Chinese fibre industry is the market leading processor of rPET. In the local market, and in the markets of trade partners, the import ban on plastic waste imposed by the Chinese government has been received with mixed feelings. At Chinaplas in Shanghai, PETplanet captured a few opinions about the current situation. For many years, it has been a win-win situation for many: Western countries rid themselves of their plastic waste by shipping their used material to China by the container-load, earning hard cash and sugar-coating their recycling statistics. In turn, China, which has the highest demand for polyester fibres in the world, got its hands easily on millions of tonnes of recyclable plastic waste – most recently around seven million tonnes annually – which did not arise in sufficient quantities within China itself. But in the middle of last year, the Chinese government announced a halt to this procedure that had been operating since the 1980s. The halt manifested itself as the import ban that came into force at the beginning of this year. Announced for the end of this year is an enhancement of the ban to include post-industrial scrap plastics including production scraps, off-cuts and regrind. The background to this is the government’s struggle against industrial environmental pollution, says the Ministry of Ecology and Environment. In order to cover the demand for PET fibres, for example for the country’s strong textile industry, the country is now relying on the expansion of the recycling industry. The funding options made available are benefitting both local and Western companies. In all provinces, recycling centres have been and will be established, and these are equipped with state-of-the-art European and Chinese technologies. “The PET recycling industry is getting bigger and bigger. What we are seeing now are many Chinese players with professional equipment but also increasing collaboration between European and Chinese companies”, explains Ted Park, Regional Director Asia from Tomra. Kurt Pichlmann, Head of Sales China at Erema confirms this remark. “The government has already invested a great deal and at Erema we are certainly feeling the benefit”, he says. But the Chinese themselves have big players in the market who demonstrate increasing professionalism, have good contacts and applications for the bottle industry.” However, smaller recycling companies, who no longer have access to affordable raw materials are threatened with going under as the profit margin on high-end starting products is no longer sufficient for them. Nevertheless, Alan Ou, Senior VP from Boretech sees the trend in a more positive light. “It’s true, all raw material costs have increased by 10-15%. In Hangzhou City we are operating our own fibre factory. Before the import ban, imported goods made up 80%; due to the new policy, we are now processing 100% local material. But the import ban has initiated some big projects; we have orders from our own country and also RECYCLING S P E C I A L Source: iStockphoto ©Young777,@ID:16}, MATERIALS / RECYCLING PETplanet Insider Vol. 19 No. 06/18 petpla.net 20 thalic acid (IPA), monoethylene glycol, 1-2% diethylene glycol (DEG), and, depending on input source, also 1-3% cyclohexane dimethanol (CHDM) as well. The mother liquor is treated with equimolar amounts of sulfuric acid in order to pseparate the acids from the glycols and precipitate them. The papers do not describe how to separate TA from IPA. The process leaves substantial amounts of potassium sulphate left, insoluble impurities with adhering solvents, a blend of terephthalic acid and isophthalic acid, and, finally, the solvent containing MEG, DEG and maybe CHDM. These fractions have to be separated one by one to get PTA (purified terephthalic acid of 99.9-99.98% and 0.15% humidity), purified IPA, EG fibre grade, DEG and/or CHDM at the end. The methanol and dichloromethane solvents must be completely removed from the insoluble waste, like caps and labels, and purified quantitatively by distillation or other means. Swiss company Gr3n has published a European project under the nameDemetowhich focuses on the chemical recycling of coloured PET bottles. Maurizio Grippa, CEO of Gr3n and one of the major stakeholders, is inventor of the process patent WO2013014650 (A1) - 2013-01-31, which seems to describe the technology of the new recycling process. The key element of this process is a microwave reactor, in which the hydrolysis of polyester waste, intermingled with MEG and water, takes place in the presence of alkaline-like sodium hydroxide (NaOH) or potassium hydroxide (KOH) to generate terephthalic acid alkaline salt and glycols. After the removal of insoluble waste by filtration the terephthalic acid is precipitated by neutralisation under addition of hydrochloric acid (HCl). The process by-products, sodium chloride (NaCl) or potassium chloride (KCl), are converted to NaOH or KOH by applying chloralkali electrolysis. Chlorine (Cl 2 ) and hydrogen (H 2 ) gases recovered are reacted to form HCl, which is reused in the process. This means that the hydrolysis agents - NaOH or KOH - are recirculating as process aids. The process patent WO2013014650 does not disclose how the usual comonomers like IPA, DEG or CHDM are separated from each other and purified to get the PTA and MEG (or their separated co-monomers) in commercial, industrial standard quality. The use of HCl raises some questions because the finished PTA, IPA, MEG and DEG must be completely free of chlorine ions. The companies Ioniqa and Accenture advertised their new polyester recycling process in 2016, thus: “Ioniqa invented a Magnetic Smart Process to recycle all kinds of colored PET polyester waste into ‘virgin quality’ raw materials, competing with oil-base PET in both quality and costs (….). In the last weeks (Oct 2016) the recycling process was scaled up successfully to a volume of 1,000l. This brings the world closer to an economical viable solution for tens of millions of tons of PET Polyester waste, currently down cycled, dumped or incinerated.” According to Ioniqa’s patent publications the core of its recycling process is the application of a new generation of ionic liquids as decomposition catalysts, where the magnetic properties of the catalyst enable its removal by means of magnetic fields. This means that the catalyst can be repeatedly used in the decomposition process. The US patent 2018037710 (A1) - 2018-020 describes the theoretical background of the hydrolysis process catalysed by ionic liquids. Basic technical details such as how to separate the common bottle PET co-monomers, or how to remove the adhering ionic catalyst from the solid waste filtrates, are not covered in the publication. That is a short summary of some recently published activities and projects to establish circular manufacturing approach to PET waste by chemical loop recycling. 2. Which route leads to industrial scale plants? Looking at these new processes and considering a production of PTA, MEG and PET resins on an industrial scale raises some questions. The most obvious are: 2.1 What will the final PTA, MEG, IPA product quality be? 2.2 What will the PET waste input quality be? 2.3 What is the minimum feasible and economical plant capacity of such a chemical recycling project? 2.4 Are there any existing industrial scale chemical PET recycling processes already available? 2.5 What is to be done with the resulting non-PET-waste? 2.1 What will the final PTA, MEG, IPA product quality be? Everyone will, of cause, answer: “PTA, MEG and IPA will be produced in fibre or bottle grade quality”, meaning that these PET raw materials are Quality characteristics Specification 1 Apperance White crystalline powder 2 Colour, Hazen unit 10 Max 3 Colour index b 2.5 Max 4 Acid number, mg KOH/g of product from 673 to 677 inclusive 5 4-Carboxybenzaldehyde content, μg/g 25 Max 6 para-Toluic acid content, μg/g 150 Max 7 Benzoic acid content, μg/g 100 Max 8 Water content, % 0.2 Max 9 Ash content, μg/g 10 Max 10 Metals content*, μg/g - Fe, Mo, Cr, Ni, Mn, Co, Ti - Mg, Ca, Na, K, Al 3 Max 10 Max 11 Iron content, μg/g 2 Max 12 Particle size distribution, % - under 40 μm - over 250 μm 30 Max 18 Max * At the customer´s request Figure 1: PTA quality specification from SIBUR (Google: SIBUR+ terephthalic acid + specifications, 4th answer),@ID:22}, 50 TRADE SHOW REVIEW PETplanet Insider Vol. 19 No. 06/18 petpla.net Improved HDPE for caps and closures At Chinaplas, the Korean chemicals group LG Chem presented its HDPE range for closure solutions for the PET bottle sector. LG’s proprietary Metallocene catalyst technology allows the design of a unique material architecture at a molecular level of the HDPE, making it possible to tailor physical, mechanical and processing properties of products. The advantages of this catalyst include low content of volatile organic compounds (VOCs) which can affect the beverages’ taste as well as the processing performance: As the fluidity of the grades is enhanced, the injection moulding temperature could be reduced by around 5~20°C. This results not only in energy cost savings but also in a reduced cycle time of 10% and a better output regarding problems like burn marks or flow marks. Compared to conventional catalysts, Metallocene is also claimed to provide better environmental stress cracking resistance (ESCR) when converted into closures. Where conventional HDPE pellets lose ESCR properties when moulded, the Metallocene-based HDPE is said to keep its already higher ESCR level. LG Chem markets the bottle cap HDPE under the names SM 800 for still mineral water, SM 250 for juice, CSDs and carbonated water, and SM100 for CSD with high level of CO2 . Caps manufactured with LG Chem’s HDPE have a shiny and premium appearance, says the company. www.lgchem.com Flip-top closures Z-moulds from Austria presented its know-how in high cavity injection moulds, especially for closure production systems. With the patented Z-slides technology Z-moulds claims to offer better output per capita compared to common injection and compression moulds. This technology ensures the efficient production of lightweight closures with fast cycle times. The company also offers a patented Z-cube technology for multi-component (plastic parts with varying materials or colours) injection moulds. The Z-cube moulds offer easy accessibility for maintenance and a better flexibility for machine use than other known technologies for multicomponent closures, says the company. On top of that, the company also featured a tool: together with its partner Krauss Maffei, the closure specialist presented a 6-cavity HDPE flip-top. “One-piece sport closures are next to lightweight closures a trend in China”, said VP Sales & Marketing Michael Fink. The 28mm PCO 1881 fliptop was produced on Krauss Maffei’s all-electric PX with a cycle time of 9.0s. www.z-moulds.com motan-colortronic gmbh - [email protected] www.motan-colortronic.com ETA plus® considerably reduces energy consumption and protects materials. Drying has never been this efficient: ETA plus® LUXOR A,@ID:52}, MATERIALS / RECYCLING PETplanet Insider Vol. 19 No. 06/18 petpla.net 12 65% recycling rate on a par with international standards South Africa hits new recycling high The 2.15 billion bottles or 93,235t of collected PET exceeded the industry target of 58% for the year 2017 and created 64,000 incomegenerating opportunities for waste pickers, collectors and recyclers, saving 578,000m3 of landfill space and 139,000t of carbon in the process. Petco said the 3% year-on-year increase in tonnage (versus 90,749 tonnes in 2016) was particularly significant against the backdrop of the political and economic instability, volatile exchange rates and industrial strike action, which had affected some of the major industry players in 2017. Member-funded recycling fee According to the organisation, water shortages in the Western Cape had seen an increased consumer demand for bottled water during the latter part of the year, which grew the waste volumes available for recycling in this region. Petco chief executive officer Cheri Scholtz said the organisation was thrilled with the latest figures, which demonstrated both the industry’s commitment to recycling and the economic value of post-consumer PET in the circular economy. “Through the remarkable network of people, companies and organisations we work with, 5.9 million PET bottles were collected for recycling across South Africa every day during the course of 2017, creating thousands of incomegenerating opportunities for small and micro-collectors, and changing their lives and those of their families in immeasurable ways.” Scholtz said Petco members paid a voluntary recycling fee on every tonne of raw material purchased, which funded their efforts and supported a sustainable recycling industry. Since the organisation’s incorporation in 2004, a total of R2.3 billion (US$182.7 million) has RECYCLING S P E C I A L Despite tough trading conditions and a 13% fall in the total PET market, the South African plastic industry recycled a record 2.15 billion PET plastic bottles in 2017, setting a post-consumer recycling rate of 65% to put the country on a par with international standards. This was announced by national industry body Petco, which is responsible for fulfilling the sector’s mandate of Extended Producer Responsibility (EPR). PET collector Violet Selota of Thinana Cooperative surveys a mountain of PET plastic bottles collected on behalf of Petco, the national body responsible for PET plastic recycling in South Africa. Phillip Julius (front) and another Cannibal Glass employee prepare to process post-consumer PET plastic bottles. According to national industry body Petco, a record 2.15 billion bottles were collected and recycled in South Africa in 2017, which equates to 65% of all those produced.,@ID:14}, MATERIALS / RECYCLING PETplanet Insider Vol. 19 No. 06/18 petpla.net 16 Separating single layer PET trays from PET bottles A sharp eye on sorting Tomra Sorting Recycling has introduced a new technology called Tomra Sharp Eye, which makes it possible to separate single-layer PET trays from PET bottles. This enhances the previous capability of Tomra’s Autosort machine to separate multi-layer trays. The step-by-step process, which concludes with the separation of single-layer PET trays and PET bottles, is seamless and flexible. During the preparation for sorting mixed plastics into different polymers, packaging material collected or pre-sorted from municipal solid waste (MSW) first runs through a mechanical treatment process which reduces voluminous materials, mainly soft items such as plastic, film, and non-plastic products. To then separate mixed PET into different polymers, Autosort functions as a combined system, detecting material and colour in combination with grain size. With a very mixed material input, this process achieves an impressive sorting efficiency of 95% or greater. More than a million plastic bottles are bought around the world every minute and within the next five years this number is expected to increase by a further 20%. In response, EU regulations are tightening and organisations such as Plastics Recyclers Europe are instigating recycling guidelines for PET trays. This will encourage separate sorting streams to enable PET tray recycling and to develop markets for this packaging product. www.tomra.com/recycling RECYCLING S P E C I A L About Tomra Sorting Recycling Tomra Sorting Recycling designs and manufactures sensor-based sorting technologies for the global recycling and waste management industry. Over 5,500 systems have been installed in 80 countries worldwide. Tomra Sorting Recycling is part of Tomra Sorting Solutions which also develops sensorbased systems for sorting, peeling and process analytics for the food, mining and other industries. Tomra Sorting is owned by Norwegian company Tomra Systems ASA, which is listed on the Oslo Stock Exchange. Founded in 1972, Tomra Systems ASA has a turnover of around US$870,8 million and employs more than 3,500 people. This system is said to be commercially significant, because small but critical differences in the chemical properties of PET food trays and PET bottles mean that they have to be separated for equivalent-product recycling. In addition to this, artificial intelligence embedded in Tomra systems enables seamless analysis of sorted products, making the future plants even smarter. Valerio Sama, Tomra Sorting Recycling Product Manager, commented: “We expect our new Tomra Sharp Eye technology to be welcomed by collection-and-sorting plants and by PET regeneration centres. Demand for this is likely to grow, because the widening international adoption of on-the-go lifestyles is pushing-up the use of plastic drink bottles and plastic trays used for fruit, vegetables and other foodstuffs.” The key to this is an enhancement of Tomra’s Flying Beam technology, which is already a well-known sensor technology on the market. As the first near-infrared (NIR) scan system with point-scanning (and no need for external lamps), this focuses only on the area of the conveyor belt being scanned. Allowing a wide range of calibration possibilities, this can distinguish even the finest molecular differences in materials flowing down the recycling line - and now that Tomra Sharp Eye introduces a bigger lens for higher light intensity, it is possible to detect the most difficult-to-distinguish properties. Simplified Flowchart - Bottle versus Tray sorting,@ID:18}, INSPECTION 37 PETplanet Insider Vol. 19 No. 06/18 petpla.net INSPECTION 37 operation in the world, with over 5,000 bottles designed by Sipa engineers to date. “We focus on a ‘design to production’ philosophy to make sure bottles not only look good on the shelf but also are able to be produced without difficulty, while giving due consideration to sustainability and light weighting.” To support their ‘design to production’ philosophy, Sipa has invested in a comprehensive prototyping area that supports the tooling operations. In this section, they have all of the appropriate laboratory and design equipment present to develop light weight efforts, produce new preform or bottle design prototypes and thoroughly test them. “This is a capability that is especially valuable to Sipa’s ability to supply complete systems”, explained Ms Bottarel. “There are not many companies that know both preforms and bottles. Sipa can provide design services for preforms and the bottles as well as the equipment to make them. Our customers can come to us for everything.” Agr Gawis test systems play a critical role in the qualification process of moulds and machines for both bottles and preforms that are produced. “The Gawis systems are used in several stages as Sipa’s ‘design to production’ Agr Gawis test systems play a critical role in the qualification process of moulds and machines for both bottles and preforms that are produced at the Sipa facility. CSD and non-carbonated pressurised bottles are tested with the Agr PPT3000 as part of the design qualification process. process is implemented on a given project”, noted Roberto De Luca, QC Lab Manager at Sipa. Early in the bottle design process, when there is a focus on creativity and the bottles have been evaluated via FEA analysis, pre-production prototypes of the bottles are produced for analysis and performance testing of the designs prior to the cutting of the final moulds. During this testing phase comprised of various analyses, there is particular emphasis on thickness distribution. Top load strength is very important for the performance of the bottle, and collapsibility is directly linked to the thickness. As explained by Mr De Luca, “According with the bottle shape, Sipa’s qualification process may require up to 50-60 different thickness measurements over the entire bottle to be documented to verify that material is properly distributed when the bottle is produced. The Gawis system is used to provide these measurements. A complete scan of the bottle, using the Gawis system, takes on average 2-3 minutes to fully profile the bottle for thickness and finish dimensions. Manually, this would take at least double the amount of time.” Additionally, the Gawis is very helpful in automating dimensional measurements, especially in certain tests like thermal stability for CSD and distortion in hot filling applications, where the behaviour of the packaging is evaluated by the comparison of the dimensions measured before and after the thermal treatment. Once the bottle design is fully established, and the final set of moulds is produced, another round of testing is performed on the production bottles. Before a mould or a complete blowing line is released to a customer, the bottles or preforms produced TUNING UP YOUR PRODUCTION Mould & Matic Solutions GmbH Ziehbergstraße 2 4563 Micheldorf AUSTRIA T +43 7582 617 60-0 VѝJL'TV\\SKHUKTH[PJ JVT www.mouldandmatic.com BLOWLINER Injection Stretch Blow Moulding – customised to your needs,@ID:39}]}}
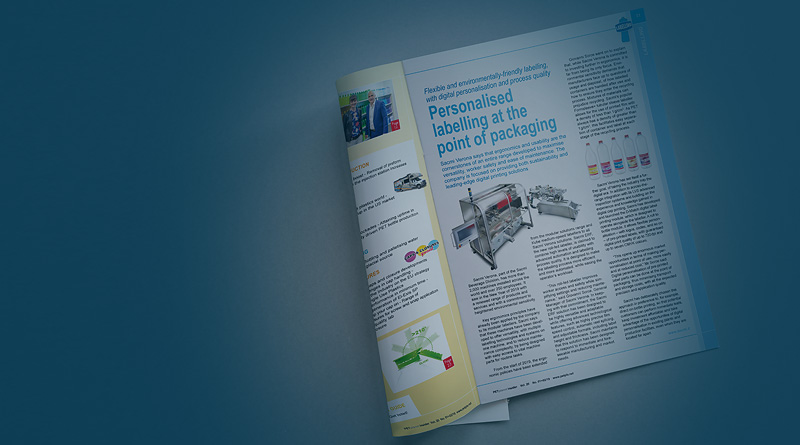