"PETplanet Insider Vol. 19 No. 07+08/18 petpla.net 47 BOTTLES Vöslauer cherry in two sizes Vöslauer Mineralwasser AG from Vienna, Austria, is expanding its Vöslauer Flavours range with two new varieties – lemongrass and cherry. The image shows the cherry variety in the unusually shaped bottles that are typical of this range. The calorie-free drink does not contain animal products and is 100% vegan. Alongside the 1 l bottle, a 0.5 l bottle in the same shape has also been launched. The slightly blue-coloured bottles are up to 60% recycled PET with a circulating label and have an easy-grip screw cap. www.voeslauer.com D 16. – 20. OCTOBER 2018 a FRIEDRICHSHAFEN The Entire World of Plastics International trade fair for plastics processing @www.fakuma-messe.com B g +49 (0) 7025 9206-0 [email protected] Organizer: P. E. SCHALL GmbH & Co. KG 26th Fakuma ! More than 1700 exhibitors from all over the world will present global offerings for technologies, processes and products made of plastic, as well as equipment and tooling for plastics processing, in 12 exhibition halls. You’ll be awaited by flexible, individualised solutions for current and future challenges faced by the automated, globalised economy. 4 Injection moulding machines 4 Thermal shaping technology 4 Extrusion plants 4 Tool systems 4Materials and components","@ID":49}, "37 INSPECTION PRODUCTS PETplanet Insider Vol. 19 No. 07+08/18 petpla.net Inspecting diameters Torus Measurement Systems have recently released the latest gauge in their line of inspection equipment for plastic containers. The B309 internal diameter gauge offers noncontact internal diameter measurements in a single operation with industry leading measurement range. Tests are carried out using 4-axis motion control without the container being touched, completely eradicating any operator influence. The integrated vision package is claimed to provide an intelligent neck centralisation function for a miniature confocal white light sensor to enter the container neck and carry out the measurement process. This newly developed gauge offers customers unprecedented improvements to accuracy and repeatability, whilst reducing the time and labour costs associated with common manual quality control checks, says the company. The state of the art gauge has the ability to measure internal diameters at multiple heights (from TOF), mapping the internal diameter profile in a series of radial movements. The gauge is housed in a robust, floor standing industrial enclosure making the B309 suitable for both laboratory and shop floor production environments. The semi-automatic system can be supplied as standalone or integrated into a multiple module Torus system. As with all the Torus range, the B309 is fully traceable and certified to UKAS standards, comes with CE certification and utilises Torus’ own windows-based software GaugeXplorer, which allows customers to switch between language options at the touch of a button.","@ID":39}, "MAINTENANCE PETplanet Insider Vol. 19 No. 07+08/18 petpla.net 19 How investing in new technology can reduce cost, time and environmental impact. Component cleaning: the end of high-cost headaches? Most businesses in the polymer industry have the headache of dealing with filter and component cleaning and rejuvenation. This often involves lengthy down times while contaminant polymer is removed in a messy and costly process which, all too often, leaves components damaged and in even worse condition and less suitable for future use. Precious financial resources may have to be allocated for new filters on a regular basis and may even be accepted as an unavoidable cost of production. There are many technologies available that are capable of cleaning woven steel mesh filters and other complex components used in polymer production. However, these technologies involve harsh solvents, chemicals or burning, all of which are capable of damaging the components they are supposed to be rejuvenating. Longworth began cleaning highly engineered components for the polymer-melt industry in 1976. As the environmental and economic impacts of oil-based solvents have become clear, the company has invested heavily in R&D. Its investment has achieved the development of Deecom, a low energy and low cost alternative to conventional cleaning materials and methods. Environmental performance The patented Deecom system uses only steam as a cleaning medium. The complete absence of air and chemicals removes the risk of burning and consequent degrading and ‘pitting’ of steel. Longworth claims an impressive list of positive environmental characteristics for Deecom, including low energy, reduced off-line time and even the ability to reclaim previously scrapped components. Efficiency and costs The current practice during production is for molten polymer to be filtered through layered steel mesh. Food and medical grade polymer products require highly effective filtering and, consequently, very small orifices, down to as small as five microns. The high process pressures and temperatures required in the manufacturing process push and compact contaminants deep into this mesh, making it difficult to return filters to full efficiency. Recent developments to Longworth’s technology include reduction in the number of cleaning steps, as well as a process that permits full cleaning without stripping units down to competent parts. Both these developments help to save time and cost. Trials are ongoing to assess the retrofitting of Deecom technology to polymer-melt production lines, reducing the need to remove, cool and strip down items for cleaning, even on existing equipment. The company says that its equipment has been proven in use in the production of CSD packages such as Cola and Lucozade bottles; water bottles for still, carbonated and other products; and PP milk bottles. Waste reduction Longworth has also patented Deecom applications in waste reduction and repurposing. Independent analysis by Clemson University, South Carolina, USA, has shown that the technology is capable of reclaiming carbon fibres in near-virgin conditions. Reclaimed fibres have high tensile strength and good length. Deecom is also claimed to be capable of repurposing segregated household waste into low-grade products with some value or processing waste into something less unpleasant and of lower volume. Plastic waste can be processed into a low-grade filler and mixed food waste can be processed into a clean, dry pellet with a calorific value. The process heavily reduces off-gassing and limits problems with vermin and odours at landfill sites. www.bmlongworth.com Typical filter stacks before (left) and after processing by Deecom","@ID":21}, "INSPECTIONproducts 36 PETplanet Insider Vol. 19 No. 07+08/18 petpla.net Inspecting PET preforms Sacmi offers three inspection systems for PET preforms, designed to respond to specific production needs and to meet any type of production requirement in this field. The PVS-2 Plus was created for the specific purpose of supporting the quality control laboratory in carrying out sample checks on individual preform batches. At inspection rates of up to 1,200 pph, the system is able to carry out a complete set of checks, including dimensional, weight and cavity number reading checks. The PVS-5 system is a high-performance, compact machine designed to operate in line with the press, at speeds up to 60,000pph. The design stands out for its reduced footprint and increased efficiency, and integrates a centrifugal positioner to ensure correct preliminary positioning of the preforms before 100% production inspection. Both designs, intended for different and complementary production fields and requirements, are completed by PVS-01, the new Sacmi machine allowing for off-line linear inspection of potentially defective preform batches. Replacing traditional carousels with side belts and conveyor belts results in a considerably simplified machine - making format changeover totally automated. Thanks to the self-adjustment features ensured by brushless motors, the system makes it possible to carry out real-time inspections of composite batches - with preforms of different sizes and diameters. In this case, too, the customer can equip the machine with a roller positioner - also fully automated. As a result, with PVS-01 the customer can set an inspection recipe and the machine autonomously adjusts itself to it - without any need to replace mechanical parts. Designed for off-line inspection of up to 36,000 pph, PVS-01 is equipped with a backlighting system which, like other proposed solutions, uses the innovative “grid” method to detect defects otherwise only visible with polarised light, such as any sign of stress on the resin derived from the cooling process and/or water present in the moulds (the so-called “watermark”). All Sacmi preform inspection systems designed by the automation & inspection systems division are also suitable for advanced management of statistical data and for interfacing directly with the customer’s ERP. Thanks to the CVS 3000 2.2, a 64 bit software, interoperability between machines is guaranteed via a direct system interface with the Sacmi supervisor Human Expertise for Reactive Engineering (H.E.R.E.) and with the possibility of monitoring, even remotely, all the efficiency parameters of a single machine, department, or multiple interconnected production units. www.sacmi.it Inspecting bottles for leakages And & Or releases complete inspection s y s t ems w i t h l e a k tester and artificial vision integrated. This system is said to be reliable, sensitive and accurate for productions from 1,000 bph (linear machines) up to 55,000 bph (rotary machines). Having a wide range of models in between low speed and high-speed productions. The leak tester allows the detection of micro leakages, with a sensitivity of 0.2mbar (pores up to 0.1mm). If there are several consecutive faulty bottles, it is detected and a light warning alarm will go off. This system is said to be reliable and to avoid manual calibration. The leak tester calibrates automatically according to external condition changes, such as temperature, pressure, etc. In addition to leak testing through pressure decay method in empty bottles, it also offers: Leak testers through vacuum decay method: used to detect leaks in hermetically sealed bottles; Leak testers in caps through squeezing method: used to detect the correct hermetic closure of the cap in a filled bottle. The idea to integrate vision in the leak tester happened because of space optimisation needs in factories, as well as joining several pieces of equipment in one and optimising investment costs (fewer conveyors, fewer additional structures, etc). The system includes the detection of leaks (pressure decay method), contamination measurements, ovality, colour, injection point positioning. The incorporation of several pieces of equipment in one can be offered in different applications in the And&Or machine portfolio: Take out robot + integrated leak tester; Lost dome trimming machine + integrated leak tester. www.andyor.com INSPECTION S P E C I A L","@ID":38}, "PETcontents 07+08/18 4 PETplanet Insider Vol. 19 No. 07+08/18 petpla.net INSIDE TRACK 3 Editorial 4 Contents 6 News 45 PET bottles for Home + Personal Care 46 PET bottles for Beverage + Liquid Food 48 Patents MATERIAL / RECYCLING 10 The future of circular economy - New technologies and effective strategies BOTTLE MAKING 12 “Smart” bottling lines to be more competitive 15 Increased investments in the local service MOULD MAKING 17 Diverse markets offer new potential - Expansion of services for German moulds and hotrunners in the USA CAPS & CLOSURES 18 Swiss closures in Newnan, GA - Corvaglia’s strategy for the American market MAINTENANCE 19 Component cleaning: the end of high-cost headaches? LABELLING 20 For every kind of label - Flexible labelling solution can be equipped with up to four different labelling technologies 24 Labelling in small capacities - Compact labelling machine for the beverage and food industries 26 Labelling products MARKET SURVEY 28 Compressors INSPECTION 31 Impurities detected - Manufacturing image processing & inspection machinery 32 The next step in preform inspection - Inline and offline use of the new PreWatcher 4 35 First total bottle inspection solution at the NPE 2018 36 Inspection products TRADE SHOW REVIEW 38 Chinaplas 2018 review, part 2 41 NPE 2018 review, part 1 BUYER’S GUIDE 49 Get listed! Page 22 Page 36 Page 41 15 INSPECTION S P E C I A L","@ID":6}, "PETplanet Insider Vol. 19 No. 07+08/18 petpla.net 46 PETbottles Beverage + Liquid Food Fruit juice drink from Aldi Süd In a limited campaign, Aldi Süd sold different fruit juice drinks for children in colourfully designed bottles. The juice drinks from the “rio d’oro” brand were manufactured from fruit juice concentrate and pulp and had a fruit content of over 68%. The contoured, transparent, no-deposit bottles were decorated with sleeve labels and held 300ml of juice. The seal was a screwed-on push-pull cap with a transparent cap as a tamper-evident seal. www.aldi.com “die faire Limo” in PET Under the logo “Für”, the endorsement “Good drink – Good deed” and the description “die faire Limo”, the German juice and smoothie manufacturer Voelkl GmbH has recently started selling several types of organic lemonade made from organically cultivated NFC juice and Fairtrade raw cane sugar in a slim long-necked bottle holding 0.43 l. The transparent bottle emphasises the product colours, a paper label provides retail information and an appropriately coloured screw cap with guarantee band completes its appearance at POS. www.sei-mit-uns-fuer.de Twisted Bottle for Fanta The Fanta brand, which belongs to the Coca-Cola Group, has reworked the shape of the 500 ml bottle to make it more attractive to the younger target audience. The contouring of the bottle moves towards the base of the bottle, giving the impression that it has been created by twisting the bottle from top to bottom. The bottle also features embossing in bubble shapes in this area. The larger volume is found above the contouring, making the bottle look somewhat unstable. Depending on the Fanta variety, the bottle is clear or coloured, decorated with an appropriate label and is sealed with a tamperevident screw cap. www.cocacola.de Cocoa powder in PET The German company TSI GmbH & Co. KG, specialist for retail brands, own brands and high-quality products at low prices, is selling 500 g of drink powder containing cocoa under the brand Oprima. It contains 10 vitamins, calcium and glucose and is available in a slightly contoured pack made from light brown PET. The bottle is easy to grip and has a seal membrane as a tamper-evident seal. A complete sleeve label provides retail information and ingredients. www.tsi.de","@ID":48}, "BOTTLE MAKING 16 PETplanet Insider Vol. 19 No. 07+08/18 petpla.net The Sidel EvoDECO labelling solutions, available either as a modular, multi-technology or as dedicated-technology equipment, offer customers total flexibility and performance, fulfilling any need to meet today’s demands within labelling. They deliver great efficiency and low Total Cost of Ownership with high output, 30% faster changeover time, 40% less maintenance time and 40% less electrical consumption compared to the previous generation. With EvoDECO Multi you can easily change from high-performance cold glue, Pressure Sensitive Labels, or roll-fed, to hot melt modules and quickly ramp-up your production. Find your labelling solution at sidel.com/labelling DESIGNED FOR TOTAL FLEXIBILITY OPTIMISED FOR UNMATCHED PERFORMANCE SIDEL EVODECO LABELLING SOLUTIONS","@ID":18}, "INSPECTION 32 PETplanet Insider Vol. 19 No. 07+08/18 petpla.net Inline and offline use with the new PreWatcher 4 The next step in preform inspection No blind spots in the quality control-up to 100,000 tested preforms per hour and orderly outlet for further processing. These are some of the highlights of PreWatcher 4, the new preform inspection system from Intravis GmbH presented at the NPE show 2018. With the new adjustment concept, which eliminates the need for any change parts, it is now possible to set the PreWatcher 4 to a new type within a few minutes, and therefore not lose valuable time by long conversion. Speaking of time savings: One can also achieve this with a test performance of up to 100,000 preforms per hour. “Currently, the PreWatcher 4 is the fastest, turnkey inspection system for preforms on the market,” reports Klaus Schönhoff proudly. With all these features, the PreWatcher 4 is an optimal solution for offline use, states Intravis. Inline use also possible While the PreWatcher 4 was designed with the idea of offline use in mind, it can also be used inline, i.e. in front of a SBM machine. Again, this system has some innovations to offer. The most important novelty in this context: an outlet rail, which, for the first, allows an orderly and direct further processing of the preforms after the test. So what is offered in addition to a hardware saving is that downstream handling accessories are no longer necessary. This benefit also offers time saving possibilities since the preforms no longer need to be stored and transported. The PreWatcher 4 can also be integrated very flexibly. Intravis offers the system as standard with a corresponding feeder. However, the company emphasises that their system can also be used with any other preform feeder on the market. Customers therefore have the freedom to choose whether “If one of the world’s largest beverage bottlers comes to you and says he’d like to have a new preform inspection system, then you’ll just ask when it’s needed,” Gerd Fuhrmann, CEO of Intravis GmbH, says, as he describes the first steps taken towards the PreWatcher 4. The Aachen, Germanybased provider of vision inspection systems, which is one of the world market leaders with its systems for quality control of plastic packaging, caused quite a stir at this year’s NPE. Many innovations and, above all, the focus on delivering added value to the customer, have also been very popular. No blind spots What makes PreWatcher 4 different from other systems on the market Mr Klaus Schönhoff, CTO of Intravis explains it this way: “First of all, we have no blind spots in the test. We have always kept it this way. We think that a 100% inspection has to mean that you are really testing the complete preform.This,” says Schönhoff, “can be achieved by resorting to innovative possibilities during the transport. The 17 cameras in total, of which 13 check in colour, therefore consistently have an optimal view of the preform.” “The increasing use of opaque preforms worldwide, for example for milk bottles, has also been taken into account,” said Schönhoff. Thanks to a switchable illumination one can switch between white and infrared light – the PreWatcher 4 is able to test transparent, strongly coloured and also opaque preforms. This makes it the first inspection system that can control opaque preforms inline. Benefits of offline usage Furthermore, the setting concept has changed and thereby a short changeover time is achieved. Dr Gerd Fuhrmann reports from practical experience “In offline mode, an inspection system is often used to sort stock. It can happen that you drive several different types of preforms within a day.” INSPECTION S P E C I A L","@ID":34}, "BOTTLE MAKING 15 PETplanet Insider Vol. 19 No. 07+08/18 petpla.net Sipa’s Italian way in North America Increased investments in the local service by Kay Barton Italian machine and bottling lines manufacturer Sipa’s North America branch office is based at a facility located near Atlanta airport, Georgia. As well as refurbishment and routine spares and replacement parts services provided by the company’s 40-member on-site team for its customers across North America, prototyping and testing are available at the in-house test centre and laboratory. The spare parts warehouse, located at the airport, is managed and organised by Sipa with the support of a partner company, can supply customers in North and South America with scheduled and routine spare parts and provide components at short notice, if needed for repairs. Key Account Director Antonio Orru explains why the location is so important to Sipa. Interview with Sipa North America, Inc. May 17, 2018 We met: Mr Antonio Orru, Key Account Director Mr Morris De Marchi, Vice President Operations “We have a considerable interest in consistently improving the service to our customers,” Mr Orru declared. “We are making strong and steady investments in the interest of achieving this goal. It is clear to us that highquality equipment is in demand – and European and American technology continues to predominate over equipment from Asian manufacturers.” Sipa North America was founded in 1996 in Campreek, GA, about 20 minutes from its current site, where it moved in 2012 for the additional space available. Antonio Orru has been working for the company since the autumn of 2012. He previously worked in areas such as bottles leak testing, bottling lines and plastic bottles storing and conveying systems, so he knows the different facets of the industry from deep, personal experience. “The refurbishment business accounts for a significant part of our service activities here on site,” he continued. Without mentioning specific figures, he confirms that North America is currently home to a significant number of Sipa machines. The largest share is accounted for by linear blow moulding and single stage injection blow moulding equipment, in addition to complete lines, injection machines and moulds. “All in all, the market today is characterised by two stage processes,” Mr Orru said. “The trends here in the USA continue to show that lightweight remains a key topic. In the area of supply, the in-house manufacturing of preforms Antonio Orru (left) and Morris De Marchi in Sipa’s foyer and closures has also increased.” Sipa expects further growth both in the beverage and specialties sectors and further believes that hot-fill and aseptic bottling will slowly but steadily expand. www.sipa.it Tour Sponsors:","@ID":17}, "MOULD MAKING PETplanet Insider Vol. 19 No. 07+08/18 petpla.net 17 Expansion of services for German moulds and hotrunners in the USA Diverse markets offer new potential by Kay Barton Three years after our last visit, the PETplanet team returned to Peachtree City in Georgia, USA. In 2015 we travelled 50 km south-west of the city of Atlanta to visit the sales and service centre of MHT Mold & Hotrunner Technology, the German mould manufacturer from Hochheim, Germany. Back then, we talked about the importance of a local presence for North and South America (see PETplanet Insider 10/2015). As part of the new North American Road Show, we wanted to find out what has happened over the past three years and how the marketing and business strategies of the company have developed further. Interview with MHT, USA, LLC May 15, 2018 We met: Mr Andreas Krampe, CEO Ms Patricia Ortega-Chagoyan, Business Administrator Mr Christopher D. Brown, Project & Sales Engineer CEO Andreas Krampe, chemical engineer, formerly of North Germany but now settled in as an Atlanta local, welcomed us into the office section of a building complex, where MHT USA and several other companies have their headquarters. MHT USA has been resident here since 2006, with a workshop and a spare part storage facility alongside its offices. The need for company representation in this precise location was voiced by Western Container, the Coca-Cola packaging supplier and key client, who wanted to have an MHT contact person in their area. Service for the North American market was then later extended to include the South American market. Mr Krampe has been working here since 2010, with a break in 2015, while he went on a short excursion to an injection moulding system supplier. He returned to MHT after a year and a half away, with a clear vision: to establish a local “Centre of Excellence”, with customer service and technical know-how the top priorities. The company seems to be on the right path. As well as being able to deliver spare parts quickly, overnight, his current four-person service team can fully rework or repair moulds and hotrunners manufactured by MHT and by external manufacturers and can also carry out modifications for existing applications or install new ones. “We receive a mould here for reworking every four to six weeks,” Andreas Krampe said. “In addition, we work with various strategic partners, particularly in South America, whose injection moulding systems we can use for our moulds or prototypes. That brings us closer to our respective customers.” He estimates that there are, currently, around 200 MHT moulds in operation in the American market. “If you compare customer behaviour in the PET market in the past to the behaviour we see today, then the willingness to invest in other systems and moulds besides those which are well-known in North America is much higher than before,” he said. “The market has become very diverse and so offers much new potential. Along with providing a good service and fact-based solutions, we want to respond to this in a short period of time.” For the Centre of Excellence, Andreas Krampe plans to use additional members of staff and extra opportunities to be able to offer customers straightforward assistance with all problems that may arise. “We want to become THE consultant for PET for these markets,” he added. The company plans to increase MHT’s overall revenue from North and South America by a third, within the next two to three years. usa.mht-ag.com The Editourmobil at MHT USA with (f.r.t.l.) Christopher D. Brown, Patricia Ortega-Chagoyan, Andreas Krampe, Kay Barton and Heike Fischer Tour Sponsors: PETplanet in discussions with CEO Andreas Krampe MHT’s workshop","@ID":19}, "INSPECTION 35 PETplanet Insider Vol. 19 No. 07+08/18 petpla.net First total bottle inspection solution at NPE 2018 Air Logic Power Systems (Alps) has joined forces with Swiss company IMD Ltd. to provide the blow moulding industry with the first total bottle inspection solution. Alps, the recognised leader of high-speed leak testing equipment has combined its leak testing technologies with IMD’s state of the art IMDvista Vision Inspection Systems. By integrating both leak testing and visual inspection methods into one machine, the new total bottle inspection solution provides a range of quality-control checks, including the detection of leaks, contamination, cosmetic defects, measurement, ovality or other material issues. The combined and linear system can be integrated directly into the production line and enables containers that pass the set criteria to continue down the conveyor, while defective bottles will be rejected into a separate chute. Michael Lawson, General Manager of Alps is thrilled about the partnership “In IMD Ltd. we have found a partner that will take our equipment to the next level. We can now offer our customers an integrated system containing the latest technologies for their leak test and inspection requirements. The total bottle inspection solution will save space as multiple technologies can be combined in one machine, enabling blow moulding operations to be even more efficient’’. Flex Pitch: multi-moving head leak tester with integrated visual inspection The Alps Flex Pitch is a fast, toolless, multi-moving head leak tester with the flexibility to test a wide range of empty containers. The maximum speed with two heads is 150 bpm, with three heads 185 bpm and with four heads 250 bpm, depending on bottle size. The machine operates without a timing screw, reducing cost for tools and changeover time radically. The new design maximises flexibility as test heads can be pre-set to the required pitch enabling fast changeover between containers of varying diameters. The built in visual inspection unit enables customers to inspect the bottles at the same time, providing more efficient quality control checks. It is ideal for more difficult containers including shingling, reverse-taper and small bottles. Matthias Hermle, CEO IMD Ltd. adds “It is an exciting time for IMD to team up with the Alps team and see our bottle vision inspection solution integrated in the Flex Pitch machine. Our system has unique self-learning tools that make it intuitive and easy to use. This really differentiates it from the other offerings in the market. As quality control in the plastic industry is becoming more and more imperative, we see great potential for the future in our partnership with Alps and an excellent value for customers’’. IMD Peco V3 preform inspection system for inline inspection or resorting There was the U.S. début of the new IMDvista Peco V3. It has a very compact, yet robust design (taking up less than 7m2 including the sorter), a high output speed of up to 90,000 pph, cavity detection and easy product change without costly replacement of matched parts. This testing system is well adapted for fully automated and optimised preform production processes in the plastics packaging industry, where the early detection of any impurities or faults is becoming more and more important. Peco Lux fully integrated monitoring system for preforms The Peco Lux was also shown at the NPE. With just a few modifications, the Peco Lux can be integrated into all existing production lines without taking up any extra space. The IMDvista V5 software is said to be easy to operate and gives a continuous overview of production quality, as well as any colour variations and issues a warning immediately if anything is running slightly askew. This means that production reliability is guaranteed. Every shot is tested. With Peco Lux, IMD offering a monitoring system to incorporate into all preform production facilities. www.alpsleak.com www.imdvista.ch F.l.t.r.: Michael Lawson, General Manager of Alps, Matthias Hermle, CEO of IMD and Heike Fischer, PETplanet Insider, at the Alps booth in the Bottle Zone at NPE 2018 INSPECTION S P E C I A L","@ID":37}, "8 NEWS PETplanet Insider Vol. 19 No. 07+08/18 petpla.net Engel is further expanding its world-wide mould technology Engel is establishing a decentralised network of mould experts in its sales regions. Around the world, demand for integrated system solutions from a single source is rising. Alongside automation and other peripherals, the mould is part of the overall set-up in more and more cases. It all starts with China. Davy Kong, head of the new department, and Ian Wang are the Mould Managers advising Engel customers in China on mould projects while developing mould solutions precisely tailored to products and manufacturing processes in partnership with a mould producing partner. “Injection mould technology calls for a great deal of coordination and close cooperation between ourselves, as the system solutions provider, and the plastics processors. That’s why it is so important to establish mould technology expertise close to our clients and have contact persons who speak their language,” says Dr Christoph Steger, CSO of the Engel Group. “These two factors simplify project management and speed up the start-up of a new manufacturing solution.” The two Mould Managers at Engel Machinery Shanghai underwent intensive training at the headquarters in Austria. They now work closely with other mould technology staff in Austria as well as the business units and application technology departments in Austria and Asia. Engel will continue to strengthen its mould technology division in Shanghai in order to be able to offer its services from Shanghai to customers in other Asian countries in the future. In the course of the next year, mould managers will also be deployed to the production plant in York, PA in the USA serving the North American markets. Developing customised injection moulding solutions presupposes a thorough understanding of available technologies and product specifications as well as sector-specific requirements and regional characteristics. As production solutions become ever more complex in the face of advancing process integration, for example, these aspects will become all the more important. Over the past four years, Engel has been continually expanding a decentralised network of specialist experts in its sales regions in order to keep pace with this trend. The first step was to establish its own automation centres in America and Asia while introducing a business unit structure. In establishing further teams for mould technology, Engel has reorganised another strategically important area on a global scale. www.engelglobal.com All 4 Pack Paris 2018 The international trade show All 4 Pack Paris, taking place November 26-29, 2018 at Villepinte in the North of Paris, France, will bring together 87,000 professionals for four days of exchange, demonstrations, innovation and presentations from sectors such as food, beverages and liquids, cosmetics and toiletries, healthcare and pharmaceuticals, retail, e-commerce, consumer goods and capital goods. All 4 Pack offers a comprehensive range which addresses the integration strategy witnessed by the market, shining a light on the innovation capabilities of the packaging ecosystem: raw materials, process, packaging and packing machines, marking and coding, packaging solutions and containers, pack printing and labels, secondary, tertiary and shipping packaging machines. It also addresses the intralogistics sector: continuous handling, automated systems, logistics services and IT systems, storage and warehouse facilities, lifting, forklifts. The 2018 marketing strategy is inspired by a drive upmarket and the targeting of buyers with high investment potential. All 4 Pack Paris carefully studies their expectations in order to streamline and optimise their meetings with exhibitors whose range corresponds to their plans. In addition to this supply/demand matchmaking and the business meetings which will be arranged, a specific programme is also being organised for a selection of 1,500 top European and top African buyers. As a tradeshow, All 4 Pack Paris has a role as a business accelerator but also as a community facilitator, and the 2018 edition will feature a wide variety of exclusive content and events. Several events within the event are scheduled, dedicated to innovation. www.all4pack.fr Udo Stahlschmidt, Head of Mould Technology at Engel Austria, (centre) shares his expertise related to moulds with Davy Kong, Head of Mould Technology in China, (left) and Ian Wang (right), Mould Manager at Engel Machinery Shanghai United Caps unveils extended R&D centre in Messia, France United Caps, an international manufacturer of caps and closures, hosted an open house celebrating the opening of its extended R&D facility in Messia, France, on June 21. In order to continue to provide a high level of service and to maintain the 50/50 split between standard and bespoke product development, the caps and closure manufacturer has extended its R&D centre located in Messia. With the addition of 200m2 of floor space, an increase of 30%, the facility now is comprised of 600m2. This was accompanied by a 30% increase in staffing, the addition of a 3D printer for fast prototyping, and a restructuring of the R&D organisation to be more responsive to market needs. The end result is an average decrease in development time of 10-20%. www.unitedcaps.com","@ID":10}, "PETplanet Insider Vol. 19 No. 07+08/18 petpla.net 43 TRADE SHOW REVIEW Liquiform technology is in the starting blocks for drinks bottling Liquid soap: just the beginning by Kay Barton 43 TRADE SHOW REVIEW Liquiform’s concept of consolidating the forming and filling process has caused quite a stir globally. The presentation of the technology with the new KHS FormFill machine at the KHS stand at the latest Drinktec 2017 has made clear that this could herald a revolutionary process for the drinks and PET-processing industry. At NPE in Orlando, we spoke extensively with Vice President and General Manager Ashish Saxena, as well as with Technical & Commercial Director Richard Sieradzki, about the current state of the technology and upcoming developments. Liquiform’s small stand at NPE seemed unimposing for such a revolutionary technology, whose licensees and cooperation partners include companies such as Amcor, KHS, Krones and Sidel. Its principle was explained by a video presentation, including a highspeed recording of the fill-form process, on quite a modestly sized screen. Vice President and General Manager Ashish Saxena reached over to the presentation shelf beside him and set down the bottle filled with water in front of us. “Form-fill is taking on concrete form,” he began. “Now that liquid soap has been successfully bottled using the Liquiform principle and is now on the supermarket shelves, we can successively advance into the drinks sector.” Of course, in the months between the announcement and the presentation, a crucial question had been repeated from all sides: the technology works, but as well as the non-food sector can it also be applied to food and drink, without food becoming contaminated? “We can now answer with a clear yes,” said Mr Saxena. “In addition to beauty care, detergents and engine oil, we have also carried out successful tests for water and ice tea in various, in some cases complex bottle forms, with fill quantities of 200ml to 2l, bottled both cold and hot. No adverse effects were found. Further smaller and larger volumes are planned.” The process works equally well with PET and HDPE material or preform. In addition to considerable energy saving offered by the combination of blow moulding and filling, compressor output and space requirements are reduced as well. Furthermore, comprehensive testing demonstrated improved material distribution in the bottle wall compared to traditional stretch blow moulding, and top load capacity increased by up to 20%. “Additionally, thanks to the direct forming by liquid, we achieve a more detailed, finer and more defined structure for graphic applications on the bottle surface, compared with conventional blow moulded ones, and the fill level variation is less than 0.5 %,” he said. A further saving, in maintenance, is also expected to become apparent, due to the omission of a production step. However, another question that Liquiform is frequently confronted with is: what about the cycle time? “If we take the time for stretch blow moulding and filling per unit as a basis, we already have similar values in terms of time.” Liquiform has confirmed that the technology can be integrated into existing fill lines and that only small alterations become necessary in the areas of hygiene and downstream handling. www.liquiformgroup.com","@ID":45}, "The whole world of Congresses PET symposiums and lectures WikiPETia.info PET knowledge management system Pulse The monthly PET price index Worldwide PET magazine Social Media Connecting worldwide No.4 2016 ZZZSHWSODQHW ' ,661 25.04.16 PETplanet LVUHDGLQPRUHWKDQ 140FRXQWULHV MAGAZINE FOR BOTTLERS AND BOTTLE-MAKERS IN THEAMERICAS,ASIA, EUROPEANDALLAROUND THE PLANET BEVERAGE +ingredients Page 10 MARKETVXUYH\\ 6XSSOLHUVRI UHVLQVDGGLWLYHV Page 27 petpla.net D 51178; ISSN: 1438-9452 No. 9 2016 PETplanet is read inmore than 140 countries MAGAZINE FOR BOTTLERS AND BOTTLE-MAKERS IN THEAMERICAS,ASIA, EUROPEANDALLAROUND THE PLANET 07.09.16 MARKETsurvey Bottle-to-bottle recycling plants Page 41 TheChinaRoadShow Page 12 bottlemaking Page 21 Page 52 PETplanet is read in more than 140 countries News Daily PET business news Editours Worldwide editorial reporting petpla.net WHY PETPLANET? For more than 19 years, PETplanet Insider has been the world’s leading magazine for the PET bottling and bottle-making industry, bringing together machine manufacturers and their customers – directly, with up to date on-site reports at customer plants, providing first hand information on the latest developments and trends. Our market reports and surveys, along with interviews with the major players in the industry give our readers an excellent overview of what is happening in the world of PET. PETplanet Insider continues to be the highly specialised source of information for more than 10,000 readers in over 140 countries and the ideal publication for advertisers who wish to target decision makers in this sector. Events Fairs, open houses, on-site sessions ...","@ID":32}, "INSPECTION 33 PETplanet Insider Vol. 19 No. 07+08 to buy a new feeder or use an existing feeder to save money. Collecting reference samples also makes PreWatcher 4 easier. Thanks to the installation of a second ejector unit, the tedious search of good parts can be eliminated. If the first station is always used to sort out the parts qualified as faulty, then the second station basically has various possible uses. Most important, however, is certainly the collection of reference samples. And what about the megatrend Industry 4.0? The PreWatcher 4, like all Intravis systems, is also future-proof and Industry-4.0-ready. By using standardised interfaces, it can be easily integrated into existing lines and provides quality-relevant information for improving and stabilising the processes. Conclusion And how satisfied was the customer, one of the world’s largest beverage bottlers? “By the end of March 2018, the system had arrived at the customer site. And after the first months in action, the customer is absolutely thrilled,” says Gerd Fuhrmann. “And we are also very satisfied. With all the innovations for inline and offline use, we can safely claim that we’ve achieved our self-imposed goal: The PreWatcher 4 is the next step in the preform inspection!” Via Scodoncello n° 41/E - 43044 Collecchio (PR) - Italy - Tel.: +39 0521 541011 Everything and more... cooperating together global solutions for containers in PET and other plastic materials Design, construction & installation of: • Systems for handling & storing all types of plastic containers • Linear blow molders for PET bottles LANFRANCHI S.r.l. www.lanfranchi.it innovation plastic container Design, industrialization, blow molds & prototype sampling for PET containers IPC S.r.l. www.ipcsolution.it The new PreWatcher 4 - the next step in the preform inspection","@ID":35}, "INSPECTION 34 PETplanet Insider Vol. 19 No. 07+08/18 Three questions for Dr Gerd Fuhrmann, CEO of Intravis GmbH PETplanet: How was the NPE show 2018? Fuhrmann: “NPE 2018 was a huge success for Intravis. We generated hundreds of leads from our booth as well as from our partner booths at Engel and Sumitomo-Demag. Activity was high – we finalised purchase orders for five systems during the show, including inspection systems for bottles, preforms and closures (our major markets).” PETplanet: You displayed a new preform inspection machine – the PreWatcher 4. How was the resonance? Fuhrmann: “The PreWatcher 4 was the highlight of our display. Customers were really intrigued by such a comprehensive number of inspections available within an affordable system requiring no change parts. One customer gave us a letter of intent to purchase immediately after seeing the system and followed-up with an order the next week. A number of projects became active and are expected to evolve into business in the third quarter.” PETplanet: Where do you see potential for inspection in the American market? Fuhrmann: “Our major American customers continue to invest in equipment to inspect bottles, closures, preforms and decorations, with no slowdown in sight. The market where we expect the most growth to emerge near term is preform inspection. The major suppliers are planning investments for lab, offline sorting, and inline inspection equipment.” www.intravis.de F.l.t.r.: CEO Dr Gerd Fuhrmann and Scott Heins, Director of Sales & Marketing at Intravis, in front of the new PreWatcher 4 at NPE 2018.","@ID":36}, ", / 0 Toronto New York Atlanta Orlando Denver Las Vegas Seattle Los Angeles San Francisco Vancouver Dallas New Orleans Phoenix Washington, D.C. Boston Detroit Kansas City Oklahoma City Albuquerque Milwaukee Chicago Minneapolis Charlotte Ottawa Montreal Quebec www.npe.petpla.net March – August 2018 The North American Road Show - Bottle Zone on tour PETplanet has successfully deployed its “Editourmobil” Road Shows across the world for seven years now. This is in addition to traditional forms of reporting; we have found that travelling by road enables deeper insights into markets; interviews with bottlers, suppliers and manufacturers can be conducted with greater flexibility, both in cities and in more rural areas. The appearance of the Editourmobil has created quite a stir in several countries - in addition to the impact of the interviews and meetings themselves. The Editourmobil is to return to North America once again, in cooperation with the NPE trade show (May 7 – 11, 2018 in Orlando, Florida). From March through August 2018 - three years after our last tour in 2015, which proved to be very successful - the PETplanet team will, once again, visit a variety of locations across the USA and Canada. The “Editour“ journeys will take in professional discussions and interviews with market leaders from the West to the East Coast. We will be stopping off at the NPE show itself, where the PETplanet and Editourmobil team will present initial reports of our visits and interviews. We will be part of the new Bottle Zone, which will be a first for us as well! Make sure you’re on board with us when we set off again. Get ready for in-depth analyses of the special features and trends in the bottles and beverages sectors of North America! All aboard! Premium Sponsor to date Sponsors to date The worldwide round trip with","@ID":46}, "MATERIALS / RECYCLING PETplanet Insider Vol. 19 No. 07+08/18 petpla.net 10 New technologies and effective strategies The future of the circular economy More than 1,000 guests invited by Erema made their way to Ansfelden, Austria, for the Discovery Days June 27-29, 2018. Well-known companies from the plastics sector, such as Borealis, Engel, Greiner, Haidlmair and Henkel gave participants an insight into their view of working with plastics in a sustainable way. With this year’s Discovery Days Erema staged a multi-company event to inspire its attendees together to address what is without doubt the most talked about topic in the plastics industry: how the amount of recycled material and the recyclability of end products can be increased. At the beginning of the conference Manfred Hackl, Erema Group CEO, summed up the challenges facing the industry as follows “To reach the new European recycling goal of 55% by 2030, more than 10 million tonnes of recyclate has to be used in the end markets. Compared to 2014, this corresponds to more than double the amount of recycled material. To achieve this, we as raw material manufacturers, producers, processors and recyclers together have to identify new markets, make use of previously untapped sources of plastic and implement an even stronger design for recycling in the long term.” The presentation of concrete lighthouse projects in the post-consumer and production waste recycling sectors showed how advanced the technical recycling solutions are already. For them to become a fixed part of the solutions of tomorrow, everyone involved in the entire plastics chain must have an intensive exchange of experience. “As a producer of brand articles we work systematically together with our partners on optimising our packaging. In doing so we rely on small amounts of material which are made with recyclate and, at the same time, are recyclable. Resource efficiency and premium products are not a contradiction in terms in our view,” says Thorsten Leopold, Head of International Packaging Development Home Care at Henkel. Attendees were shown how far-reaching the product range of such end products made of recyclate already is today at the accompanying product exhibition at the Erema headquarters. From pipes for the construction industry and lifestyle products such as sunglasses to coffee machines – products containing recycled material have been part of daily lives for quite some time. High-quality recyclate is essential here. Visitors were able to see a total of ten recycling machines from Erema and its sister company Pure Loop were live in action around the clock. Communication as the key to the circular economy The presentation of selected pioneer projects made it absolutely clear that the plastics chain can only grow through communication. Engel with injection moulding and Haidlmair in the tool making sector, for example, showed that it is not automatically necessary to develop existing products even further in order to use recycled pellets, often all that is needed in the first step is knowledge transfer between producers and recycling specialists. New and further developments by mechanical and tool engineers aim more at increasing process consistency when using recycled pellets in order to use them in an even broader spectrum. The idea of the LIT Factory, a public 4.0 pilot facility under the leadership of the Linz Institute of Technology (LIT) at the Johannes Kepler University, showed how production could be in the future. Local companies will be able to try out digitalised Dr Gerold Breuer, Head of Marketing & Business Development at Erema guided the visitors through a three days program with interesting speeches and panel discussions. F.l.t.r.: The raw material producers Anton Wolfsberger, Head of Marketing Consumer Products and Pipe at Borealis, and Alexander van Veen, Managing Director / Commercial, Procurement & TS&D at Braskem Netherlands, gave insights into their view of a sustainable plastics industry in a discussion, moderated by Steven Chaid.","@ID":12}, "MARKET SURVEY 28 PETplanet Insider Vol. 19 No. 07+08/18 petpla.net 07+08/2018 MARKETsurvey Compressors Compressors - not often in the spotlight perhaps, yet a vitally important component of PET production, and with significant potential in energy-saving. Our annual market survey takes a closer look at these unsung heroes of the PET industry, featuring five compressor manufacturers and their product range: ABC Compressors, AF Compressors - Ateliers François, Kaeser Kompressoren SE, Siad Macchine Impianti and Gardner Denver Ltd. Although the publishers have made every effort to ensure that the information in this survey is up to date, no claims are made regarding completeness or accuracy. Company name ABC Compressors AF Compressors - Ateliers François S.A. Kaeser Kompressoren SE Postal address Telephone number Web site address Contact name Function Direct telephone number E-Mail Pol. Ind. Azitain 6, 20600 Eibar, Spain +34 943 820 400 www.abc-compressors.com Mr Gonzalo Gabarain Sales & Marketing Manager +34 647 413 760 [email protected] Rue Côte d'Or 274 4000 Liège, Belgium +32 4 229 70 10 www.afcompressors.com Mr Pascal Heyden Marketing Manager +352 26 95 66 28 [email protected] Carl-Kaeser-Str. 26 96450 Coburg, Germany +49 9561 640 0 www.kaeser.com Mr Wolfgang Hartmann Marketing Manager +49 9561 640 252 [email protected] 1. Machine designation / model number Horizon & Horizon LP AF Range (PET compressors 20-40bar) ; OPC Range (LP compressor 6-15bar) Sigma PETAir 2. Number of models in range 30+ models 30 for PET compressors; 22 for low pressure compressors 25 3. Output in m³/hour 425-6,000 From 150 to 3,300m³/h for PET compressors From 432 to 3,480m³/h for LP compressors 336 - 2,772 m³/h 4. Compressor type Oil-free reciprocating piston compressor \"allin-one\" skid Low pressure air Low pressure piston compressor Yes Screw type High pressure blowing air (up to 40 bar) High pressure piston compressor (up to 40bar) Yes Piston type Integrated system Yes (including VSD with huge regulation range from 20% to 100% of the capacity) Yes 5. Lubricated or oil-free Oil-free (lubricated on demand) Oil-free Low pressure compressor Oil-free (lubricated on demand) Piston compressor Lubricated Booster compressor No Lubricated Integrated system Yes (including VSD with huge regulation range from 20% to 100% of the capacity) Yes 6. Machine layout Horizontal opposed cylinders, forces balanced and virtually no vibrations L shape, 3 stages, 3 cylinders for PET compressors L shape, 2 stages, 2 cylinders for LP compressors \"V\" (2 cylinder), \"W\" (3 cylinder) 7. Number of compressor stages 3-4 3 for PET compressors; 2 for low pressure compressors 1+1 8. Are special foundations required ? No No No 9. Cooling system Water Yes Air (water option) 10. Belt or direct drive Direct drive Belt for PET compressor Low pressure compressor Belt for LP compressor Direct Booster compressor No booster Belt Integrated system Yes (including VSD with huge regulation range from 20% to 100% of the capacity) Belt","@ID":30}, "PETpatents www.verpackungspatente.de PETplanet Insider Vol. 19 No. 07+08/18 petpla.net 48 Bottle with light Intern. Patent No. WO 2017 / 207923 A1 Applicant: Société Anonyme des Eaux Minérales D’Evian et en Abrégé, Evian les Bains (FR) Application date: 31.5.2017 To create special optical effects with a bottle, it is proposed to implement a light source at the opening that illuminates the inside of the bottle. A special design of the sleeve label enables three-dimensional views, e.g. if the label is designed as an aeroplane hull, the lighting shows a view of inside the aircraft. Sheathing for bottles Intern. Patent No. WO 2016 / 102581 A1 Applicant: Area S.R.I., Rho Mi (IT) Application date: 22.12.2015 Improved wrap around packaging with handle to package several individual bottles together. Bundle with carry handle Intern. Patent No. WO 2016/ 113118 A1 Applicant: KHS GmbH, Dortmund (DE) Application date: 7.1.2016 The application describes how several plastic bottles are bound together with different “strong” adhesive points. The bundle is equipped with a carry handle and individual bottles can be removed easily from the adhesive points. Stackable bottles Intern. Patent No. WO 2017 / 205946 A1 Applicant: Marcelo Perucci, Campinas (BR) Application date: 1.6.2016 The base of a plastic bottle is shaped so that the top of a bottle stacked underneath fits inside. This saves space when the bottles are stacked, which can lead to lower logistics costs. There is also no need for cardboard inserts. Coated plastic container Europ. Patent No. EP 3072825 A1 Applicant: Takemoto Yohki Co. Ltd., Tokyo (JP) Application date: 30.10.2015 The application describes a plastic container and the procedure for coating a plastic container with a metal oxide layer to improve the barrier properties of the container. Improved contact surfaces Intern. Patent No. WO 2016 / 123423 A1 Applicant: The Coca Cola Comp., Atlanta (US) Application date: 29.1.2016 The application proposes that the touch points on a multi-use plastic bottle be specially designed to maintain the attractiveness of the bottle, even towards the end of its useful lifespan.","@ID":50}, "TRADE SHOW REVIEW PETplanet Insider Vol. 19 No. 07+08/18 petpla.net 42 New Viper granulator product line At NPE 2018, Conair officially launched its entirely new portfolio of Viper granulators with standard features that include improved sound insulation, hardened and water-cooled cutting chambers on most models, as well as bigger screens for increased throughput compared to the company’s previous offerings. Seven different models have been shown on display at the show, in configurations for injection moulding, blow moulding, and both pipe/profile and film/sheet extrusion. From small press-side units to large, central granulators, the new Viper product line includes 14 different models with rotor diameters of 140, 200, 300, 420, 570, 810 and 900mm. The maximum throughputs are from 80 lb/hr (36 kg/hr) to 13,200 lb/hr (6,000 kg/hr). Tangential-feed cutting chambers are standard on smaller grinders, while large units come in a super-tangential configuration to facilitate feeding of large and bulky scrap. Three-blade open rotors are also standard, and other rotor designs are available. More standard features “The design of our new Viper granulators has been totally customerdriven,” Sam Rajkovich, VP, Sales & Marketing, said. “Our objective was to develop a straightforward, uncomplicated suite of Conair-designed machines, suitable for most applications. We also wanted to make standard as many popular features as possible. I think we have done just that and very successfully. This may well be the largest product launch at NPE 2018 and it certainly is one of the most exciting.” Amongst the benefits and advantages the company claims for their range of granulators, the following are key. The operation is said to be quieter thanks to full sound insulation. Wear is reduced on the cutting chambers by the use of abrasion-resistant steel. The system has water cooling. Larger screens allow more granulate through the cutting chamber. Other benefits claimed by the company include easier cleaning, low energy consumption and rapid knife changes. Feeding and discharge Every one of the new Viper granulators can be configured for the safe and convenient feeding of scrap in a wide range of shapes and sizes. For basic hand feeding, an upturned feed tray accepts most parts and/or runners. A similar feed-tray configuration suits robot feeding and front-facing hopper opening accepts metered feeding of scrap via conveyor. Conveyor speed can be automatically regulated to prevent excessive loads on the granulator drive motor. For reclaiming film scrap, the granulator infeed can be fitted with feed rollers (slaved to drive motor amps) that draw film from large rolls. A relief head can be mounted on top to receive blown-in edge trim. When small parts, blow-moulding tops and tails, or pre-shredded scrap is fed by a blower, a cyclone can be fitted to the top of the hopper. And, for long pipes and profiles, an angled side feed chute is used. For other unusual applications, custom infeed configurations can be engineered. Several evacuation options are also available, including self-powered vacuum motor loaders that draw granulate out of the catch bin and deposit into a Gaylord or bin. Compressed air evacuation via venturi can be used to move regrind to a Gaylord or barrel, which can be fitted with flexible covers to minimise dusting. Finally, multiple granulators can be emptied by a central vacuum system to a common collection bin or box. Each granulator is equipped with a vacuum pick-up tube and a material line valve, sequenced by a central loading control like the Conair FLX-128 Plus. In each of these cases, evacuation can be set up to convey continuously, on a timed basis or a signal from a level sensor in the catch bin. Blower/cyclone evacuation systems, including back filters when needed are also available. www.conairgroup.com","@ID":44}, "imprint EDITORIAL PUBLISHER Alexander Büchler, Managing Director HEAD OFFICE heidelberg business media GmbH Bunsenstr. 14 69115 Heidelberg, Germany phone: +49 6221-65108-0 fax: +49 6221-65108-28 [email protected] EDITORIAL Kay Barton Heike Fischer Gabriele Kosmehl Michael Maruschke Ruari McCallion Waldemar Schmitke Anthony Withers WikiPETia.info [email protected] MEDIA CONSULTANTS Martina Hirschmann [email protected] Johann Lange-Brock [email protected] phone: +49 6221-65108-0 fax: +49 6221-65108-28 LAYOUT AND PREPRESS EXPRIM Werbeagentur | exprim.de Matthias Gaumann READER SERVICES Till Kretner [email protected] PRINT Chroma Druck & Verlag GmbH Werkstr. 25 67354 Römerberg Germany WWW www.hbmedia.net | petpla.net PETplanet Insider ISSN 1438-9459 is published 10 times a year. This publication is sent to qualified subscribers (1-year subscription 149 EUR, 2-year subscription 289 EUR, Young professionals’ subscription 99 EUR. Magazines will be dispatched to you by airmail). Not to be reproduced in any form without permission from the publisher. Note: The fact that product names may not be identified as trademarks is not an indication that such names are not registered trademarks. 3 PETplanet Insider Vol. 19 No. 07+08/18 petpla.net Let me start today with a quote from the successful American merchant John Wanamaker, the “pioneer in marketing”: “Half the money I spend on advertising is wasted; the trouble is, I don’t know which half.” As PETplanet, we live by advertising and we make every effort to be in the half that John Wanamaker would consider useful. We cannot prove it, of course, no magazine can. The advertising industry simply puts their trust in us. We do everything not to disappoint their confidence in us, making regular follow-up calls to subscribers to ensure we are getting things right is just one tiny building block. A rather bigger building block was certainly the Bottle Zone at the NPE, where, together with the Plastics Industry Association, we brought together all the PET-active people in the exhibition hall. Still more building blocks undoubtedly came by the truckload with our “editours” around the regions. These involve visiting and filing firsthand reports on both the big and small players in the PET world. There cannot be in the specialist magazine sector – and even beyond the world of plastics – any other magazine which offers such a wealth of in-house researched on-site stories. We are now running around sixty such reports every year. For us the important thing is to be out and about on the street. Driving advertising throughout the country with the Editourmobil. Being seen and delighted to be recognised. Exactly what happened on the final stage of our North America tour, when we were overtaken on the highway by Agr: “We were EXCITED to see you on the road yesterday… hoping you would see the “Agr” sticker on the rear window of my truck and “recognise us back”! We were convinced that you did, because we saw you SMILING when you passed us :)” - Henry Dimmick, CEO Agr International. I believe John Wanamaker– had he been working in the PET world - would have had every confidence in advertising with us. Yours, Alexander Büchler Caught in the act Dear readers, The Editourmobil caught the eye of Agr CEO Henry Dimmick, jr. (left) and his team on the highway 80 to Ohio .","@ID":5}, "LABELLING PETplanet Insider Vol. 19 No. 07+08/18 petpla.net 24 Compact labelling machine for the beverage and food industries Labelling in small capacities With the Innoket Roland 40 the KHS Group has launched a compact labeller to market. The KHS Innoket Neo’s little brother has a capacity of 2,500 to 25,000 containers per hour (cph) and is thus specifically tailored to the requirements in the low capacity range. The Innoket Roland 40 can be fitted with various labelling stations and is characterised by its ease of use, states KHS. “The machine is specially geared towards lines with a low output,” explains Cornelius Adolf, labelling product manager at KHS. During development particular attention was paid to simple operation and a high degree of economy. The table machine is not only of interest to craft breweries but also to companies in the food sector, such as manufacturers of canned food, sauces or dressings. In its standard version the Innoket Roland 40 comes with two cold glue stations. This allows shoulder and neck labels to be applied at two levels by the first station, for instance, with the second station affixing back labels to the bottles. Alternatively, self-adhesive stations, a combination of cold glue and self adhesive technology and hot melt labelling processes can be used. Proven components from the high capacity range Inside the Innoket Roland 40 are countless quality determining components taken from the established high performance KHS Innoket Neo labelThe Innoket Roland 40 is the little brother of the Innoket Neo, suitable for outputs of between 2,500 and 25,000 containers per hour.","@ID":26}, "INSPECTION 31 PETplanet Insider Vol. 19 No. 07+08/18 petpla.net Manufacturing image processing & inspection machinery Impurities detected For the Propak Asia, held from June 13-16, 2018 in Thailand, members of P&S Technology were assembling the latest preform inspection machine (PS-21GP S2W) and the new concept centrifugal preform feeder brought directly from Korea in order to promote them on overseas markets. P&S Technology is a company specialised in the manufacturing of image processing and inspection machines. Since 1997, the company has focused on developing and manufacturing image processing and impurities inspection machine independently.Since 1999, the company has run a technology research centre consisting of researchers with MD and PhD degrees. It has been releasing inspection machines for preform and glass bottles for the food and beverages sectors, alcoholic drinks, and automatic inspection instruments for the inside and outside of can and bottle lids. Also, machinery for the inspection of instruments for pharmaceutical vial bottles & pills, cosmetics containers, filled and empty bottles, straw inspection machines, vision inspection machines etc. based currently on around twenty patented technologies. The company is equipped with the small quantity batch production system to develop customised products tailored to customers’ needs. Its impurities inspection machine acquired the ISO9001 certification and can accurately detect impurities and defects on the inside and outside of cans and bottles. In particular, its (PS-21GP) preform inspection machine is said to thoroughly inspect the whole surface of the preform by applying a rotary type mirror tracking system, can overcome the limit in utilisation of space with its built-in gate cutting device and also is reasonable in terms of price. Its vision inspection machine can automatically inspect 800 PET and glass bottles per minute, 1,600 cans a minute and 3,000 per minute in case of the surface and side of bottle lids at high speed. P&S Technology has also developed an image processing-based software, a smart camera, various controllers and control systems and in addition, has recently developed an inspection machine fitted with a special lens and lighting. Cosmetics manufacturers are showing huge interest in this instrument because it can carry out the inspection of the surface of cosmetics containers and check printing quality as well as inspecting impurities on the inside and outside of containers simultaneously, says the company. For the last 10 years, the company has received tremendous attention from buyers in industrial exhibitions in China, Japan and Thailand and it accounts for a high share of the domestic market with its policy of high quality, high performance and reasonable price. In addition, it has 12 overseas agencies which are in active operation and is gearing up for establishing a service centre and an instrument production factory in Bangkok for the South East Asian customers by 2020. Further to this, in order to explore Europe, Middle East and African emerging market, it continues to expand its overseas sales area. www.pnstech.co.kr INSPECTION S P E C I A L","@ID":33}, "BOTTLE MAKING 12 PETplanet Insider Vol. 19 No. 07+08/18 petpla.net “Smart” bottling lines to be more competitive Italian company SMI S.p.A.’s latest range of bottling and packaging machines are equipped with Internet of Things (IoT) and Industry 4.0 (4IR) compliant technologies. The intention is to enable customers to install “smart” solutions that will help to improve production efficiency, operational flexibility, energy saving and ease of use and control. Its EBS K Ergon rotary stretch blow moulder and Ecobloc K Ergon integrated system feature a compact footprint, which bring advanced solutions within reach of smaller bottling plants. The EBS K project has won a number of awards for SMI from Italy and across Europe. An example from the range will be showcased at the Brau Beviale exhibition, to be held in Nuremberg, November 13-15, 2018. The new rotary blow moulder is available in 2, 3 and 4-cavity models and is suitable for manufacturing PET containers up to 3 l with a capacity of 1,000-9,000 bph. SMI says that it combines the advantages of rotary technology with speeds usually associated with linear stretch blow moulders. Compact and integrated The letter ‘K’ in the EBS K Ergon range title comes from the German word “kompakt” and highlights the machine module’s reduced dimensions. The preform heating tunnel is integrated with the stretch blow moulding blowing wheel in a single, very compact module, which can be installed in even the smallest bottling lines. The tunnel features a horizontal preform feeder chain and optimised ventilation and aeration system. The infrared (IR) lamp heating units are equipped with thermoreflective panels made of a highly energy-efficient composite material, mounted both in front and behind them. This solution ensures more effective reflection of the IR lamps’ heat and, consequently, a more uniform distribution of heat over the entire surface of the preform. The inside of the tunnel is also equipped with an aluminium diffuser, to provide optimal temperature control and prevent overheating problems. The machine frame containing the tunnel and the blowing wheel is equipped with safety doors that are slightly rounded, providing more space inside the machine to perform cleaning and maintenance tasks easily and safely. Electronic power for precision The stretch blowing wheel is equipped with motorised stretch rods, controlled by electronic drives. They do not require mechanical cams. SMI says that this solution ensures precise control of the stretch rod’s path and position, as well as saving energy. This technology makes it possible to change the stretching speed without switching cams and greatly reduces vibration stress on the blowing wheel, compared to traditional solutions. The Ergon range has a completely electronic production process and transmission system, using brushless motors equipped with integrated digital servo-drivers. This design is said to be offering customers low operating and maintenance costs, low energy consumption and eco-friendly processes. The stretch blow moulding system uses high-performance, low-dead volume valves. This facilitates shorter preblowing and blowing times, boosting machine efficiency and bottle quality. The system’s control and automation is by the established MotorNet System, which ensures the maintenance of processing parameters throughout the entire manufacturing cycle and enables the direct modification of machine settings, thus simplifying format changeovers. Blowing pressure is automatically regulated according to bottle format, completely eliminating manual adjustments. The new machine has a two-stage air recovery system as standard.","@ID":14}, "LABELLINGproducts 26 PETplanet Insider Vol. 19 No. 07+08/18 petpla.net APR-recognised wash-off film labels with recycled liners UPM Raflatac has developed a range of wash-off film labelling solutions for a variety of end uses that can help brands create a circular economy and also meet or even accelerate their ambitious sustainability targets. These clear, white and metallised film label stocks – featuring UPM Raflatac’s RW85C wash-off adhesive and a PET liner made from 90% postconsumer recycled (PCR) content – have been recognised by the Association of Plastic Recyclers (APR) as exceeding their strict standards for recyclable label products. Now available in the Americas and Asia Pacific market regions, the labels are intended for labelling PET containers in the food, beverage, home care and personal care segments. Thanks to the RW85C wash-off adhesive, the labels are able to undergo common PET recycling processes without contaminating any of the PET flake by-products. During the caustic washing process, the polypropylene labels easily separate from PET containers and float, allowing more highvalue, clean PET flakes to be recovered. The clean flakes can then be converted back into PET containers, which promotes a circular economy and reduces the amount of plastic pollution in landfills and the environment. www.upmraflatac.com Recycle-friendly PETG shrink sleeves Sun Chemical has launched its SunLam de-seaming adhesive for shrink-labelled containers. This de-seamable adhesive is intended to help recyclers improve rPET yield without process changes. Developed in partnership, Sun Chemical and Eastman extensively tested SunLam on labels made with Eastman Embrace LV copolyester. It has received a “Responsible Innovation Acknowledgment” by the Association of Plastic Recyclers (APR) after passing stringent testing outlined by the APR. By changing from a traditional solvent to SunLam deseaming adhesive, shrink labels de-seam and release during the whole bottle wash step of the wet recycling process, without sacrifice of label performance. The label removal occurs prior to colour, infrared and manual sorting, thus preventing shrinklabelled PET bottles being removed from the rPET stream due to misidentification. The efficacy of SunLam de-seaming adhesive was tested on bottles with shrink sleeves made from Eastman Embrace LV copolyester. The tests utilised whole bottle wash equipment at commercial recycling facilities and yielded results of greater than 95% label removal, with results typically exceeding 99%. By using SunLam de-seaming adhesive, brand owners need not sacrifice full-body shrink sleeve label coverage, shrinkage or quality, says Eastman, but can continue to use full-body shrink labels on their containers. An additional 20% of label surface area is regained with full-body shrink labels, compared to the portion of the bottle that must be left uncovered to avoid near-infrared or colour mis-sorting, as bottles with full wrap shrink sleeves could get rejected by the NIR or colour automated sorting equipment. www.sunchemical.com www.eastman.com Oct. 24-26,2018, Mumbai German Technology","@ID":28}, "9 NEWS PETplanet Insider Vol. 19 No. 07+08/18 petpla.net Clariant breaks ground on JV production site in Cangzhou, China Clariant, a world leader in speciality chemicals, and Beijing Tiangang Auxiliary Co., Ltd (Tiangang), conducted a ground-breaking ceremony in Cangzhou (China), just over 200 km south of Beijing. The ceremony marked the start of the construction of a world-class production facility for stabilisers for plastics and textiles that will form the heart of the joint venture between both parties. The event was marked by a special event with representatives from both companies, as well as local officials. The joint venture between Clariant and Tiangang was established in September 2017, and combines the technology and production knowledge of both companies to provide even better process and light stabilisers for various growing industries in China, including automotive and textiles. China is a key market for Clariant high-end process and light stabilisers, which include the state-of-the-art Nylostab S-EED chemistry – invented by the company – a unique multifunctional hindered amine light stabiliser, or HALS. Tiangang, which was founded in 1991, is already an important manufacturer of light stabilisers and UV absorbers, with two plants in China backward integrated with production of key intermediates. During the ceremony, Clariant Global Business Unit Head of Additives, Stephan Lynen, said “This new facility enables the successful implementation of our joint venture, and we are excited about the improved proximity to customers and raw material suppliers.” Mr Gang Liu, Deputy General Manager of Tiangang announced “We look forward to the facility coming on-stream in the first half of 2019 and start serving the growing demand for high-end additives solutions in Asia even faster. The Cangzhou National Coastal-Port Economy & Technology Development Zone is an ideal production base for additives, with very good access to necessary raw materials and other support.” The ground-breaking took place just one day after Clariant officially opened wholly-owned plants for Ceridust micronised waxes and AddWorks synergistic additive solutions in Zhenjiang, 1250km further south. Lynen added that “Clariant is committed to sustainable growth in China and therefore continues to invest across the country to increase its local production capability and competitiveness. I am proud to announce these two instances of the Business Unit Additives making progress on this expansion strategy in such short succession and look forward to leveraging this new capacity towards achieving sales growth supported by new and sustainable developments.” www.clariant.com Brau Beviale 2018 Brau Beviale will open the exhibition halls in Nuremberg November 13-15, 2018. A comprehensive supporting programme aims to provide impetus for addressing all the challenges that the beverage sector is currently facing. The Export Forum German Beverages with high-calibre speakers and networking opportunities at the forum will help manufacturers to make decisions about exporting their products. The European Micro Brew Symposium hosted by the Berlin-based Research and Teaching Institute for Brewing (Versuchs- und Lehranstalt für Brauerei, VLB) is intended for international craft brewers and brewpub operators. Another hot topic among brewers worldwide is heirloom brewer’s barley. This will be the focus of the Heirloom & Terroir Barley and Malt Symposium hosted by RMI Analytics. The Brau Beviale Forum will once again take place on all three days of the exhibition. The proven blend of talks, presentations, panel discussions and award ceremonies invites visitors to become informed about raw materials, technologies, entrepreneurship and marketing. The diversity of beverage specialities can be experienced in the Craft Drinks Area. With a total of around 7,500 participants over the three days of the last event, it represents a logical development of the Craft Beer Corner from the last trade fair cycle. The European Beer Star, which has been part of Brau Beviale since it was “born” in 2004, will also be awarded again at the event. In 65 categories, breweries from all over the world can submit their beers for inclusion in one of the most important beer competitions worldwide. Various themed pavilions will present themselves as the focal point for certain issues tailored to specific groups of visitors, as the Artisan and Craft Beer Equipment and brau@home for micro-breweries and hobby brewers, or the “Sustainable Water Management in the Beverage Industry” pavilion - an issue that affects all drinks manufacturers and is becoming increasingly important at a time when raw material resources are becoming scarcer. At the Special Show Innovative Beverage Packaging interesting examples of packaging innovations will be provided by the winners of the World Packaging Awards that will be presented from the World Packaging Organisation. PET continues to be a topical and important issue. The quality association Wertstoffkette PET-Getränkeverpackungen e.V. will cover various approaches and present ideas and solutions for PET recycling. www.braubeviale.de WikiPETia.info New contents at wikipetia.info","@ID":11}, "PETplanet Insider Vol. 19 No. 07+08/18 petpla.net 45 BOTTLES 45 BOTTLES PETbottles Home + Personal Care Pril Sensitive Henkel has revised the appearance of Pril washing up liquid at POS. A while ago, the push-pull cap was replaced by a two colour screw-on hinged cap seal; now Henkel has made the shape of the previously rather thickset bottle slimmer and taller and has amplified the contouring. The fill quantity has been adjusted to 600ml. The two self-adhesive labels provide handling and safety information. www.pril.de New fabric conditioner from Unilever “Comfort intense” is the name of a new laundry care range from Unilever consisting of fabric conditioner and laundry scent. The fabric conditioner is available in the varieties Fresh Explosion, Fuchsia Passion and Pure. According to the manufacturer, the ultra-concentrated fabric conditioner promises threefold aromas - from the dryer, from the cupboard and when wearing. The drop-shaped bottles hold 960ml and have partial reinforcement ridges on the front and rear. This quantity is sufficient for 64 wash loads. The fabric conditioner is applied using a screw cap with dosage chamber that is integrated into the packaging design. The bottle has a plastic sleeve label, which gives information about the advantages of the new design and explains the dosage. www.comfortintense.de The scent of summer Those desperate for a beach holiday, or keen to enjoy the scent of summer, or even the smell of sun cream on the skin, can find the perfect solution with Nivea shower gel “Welcome Sunshine” from Beiersdorf. The shower gel smells like the original Nivea sun cream and brings that summer holiday feeling straight back. A slightly coloured bottle holds 250ml and is sealed with a two-colour hinged cap with a dosage opening. To avoid any possible confusion, Nivea explains on the rear that this shower gel does not contain any sun protection and does not protect against UV radiation. www.nivea.de braubeviale.de MAKING YOUR BUSINESS SUCCESSFUL. BrauBeviale is where you cultivate success – in dialogue as an equal partner, with experts in the sector, with innovations that give you a competitive edge. Everything you need for tomorrow – in a single venue. For exhibition highlights and important information for your visit: braubeviale.de/Your-Success Good business. Good conversations. Nuremberg, Germany | 13 – 15 November","@ID":47}, "CAPS & CLOSURES 18 PETplanet Insider Vol. 19 No. 07+08/18 petpla.net CAPS & CLOSURES 18 Corvaglia’s strategy for the American market Swiss closures in Newnan, GA by Kay Barton In February of this year, Swiss cap producer Corvaglia made a statement that caught the attention of the bottling industry: 2018 will see it open a new plant in the USA, serving the North American market and a strategic addition to its current location in Ixtlahuaca, Mexico. A few months before the plant’s official opening, scheduled for early November, we met James B. Fischer, the company’s new President and GM, to find out more about the project. Interview with Corvaglia Closures USA Inc. May 17, 2018 We met: Mr James B. Fisher, President & General Manager The new plant at Coweta Industrial Park in Newnan, Georgia is still a major construction site, so we met for the interview with Mr Fisher in his temporary office, not far from the future high-end location. Mr Fisher has now been with Corvaglia for a year and is able to look back on 30 years of experience in the plastics industry. He got a call from Corvaglia one day and was on board more-or-less immediately. It is evident that he’s a positive thinker and doer, and someone who looks forward to everything that’s on the horizon. “We’re talking about a $25 million investment here,” Mr Fischer said. “The future site, covering approximately 9,300m², is currently being equipped with completely new injection moulding and digital printing equipment, and will also include expansion options for the future.” When the plant opens, its initial focus is set to be on one-piece, flat-cap closures. Over the medium term other standard models will be added, which will be particularly relevant to CSD or hot-fill products. In addition to PCO 1881 or 38mm closures, the share of PCO 1810 in the local market, for example, is still relatively high. “The new plant will enable us to optimise our after-sales activities, in addition to time-saving local manufacturing for customers in the USA and Canada,” Mr Fisher added. “Between 40 and 50 employees are planned for the new plant, which will operate using highly automated technologies.” There is a particularly strong market trend and focus in the USA on energy drinks and fruit juice. He explained: “The market for packaged water is also big, however, and is set to continue to grow in the future. Single serve also remains popular with American consumers, especially the small 8 oz bottles (approx. 0.23 l).” www.corvaglia.ch Tour Sponsors: James B. Fisher (left) with Kay Barton in front of the Editourmobil .com 100815dmyL","@ID":20}, "39 TRADE SHOW REVIEW PETplanet Insider Vol. 19 Round three for the Eco PET preform machine from China Improvement of cycle time by Kay Barton Demark presented the third generation of its Eco 300/2500 injection moulding machine, which has been on sale since October 2014. The company, which is based in Huzhou, China, is again focusing on further development in the field of energy efficiency and closing times. “We are achieving closing cycles that are about 30-40% faster,” said Jason Xue, Manager of Marketing and Sales at Demark. The “Pressure Hold Valve”, which keeps the plastination requirement constant with a non-stop working screw conveyor, is also new. Clamp force is between 260t for the smaller model and 300t for the larger model, with a maximum of 4.4kg PET injection and up to 72 cavities for 15g preforms, in the case of the Eco 300/3500 model. The machine was demonstrated at Chinaplas with a 48-cavity mould and a single screw, at an energy consumption rate of approximately 400kW/t. “We have enjoyed a successful launch with the latest generation of Eco 300/2500 and we have now received a confirmation of acceptance from CocaCola for the machine,” said Xue. The manufacturer now wants to expand its existing presence in the international market; Jason Xue estimates that some 50-60 machines have already been installed in overseas markets. At its second trade fair booth, Demark presented its IPP 300 injection moulding machine for thin wall products and closure caps. “We can see a large target Meeting the 3rd generation of Demark’s Eco 300/2500 with (f.r.t.l.) Jason Xue, Martina Hirschmann (Media Consultant PETplanet) and Kay Barton market in PET bottle applications, especially for closures,” explained Xue. Four models, from a shot volume of 325 up to 1,212cm3 and a clamp force of 200 to 400t, were on show at Chinaplas 2018. www.demark-pet.com","@ID":41}, "PETplanet Insider Vol. 19 No. 07+08/18 petpla.net 41 TRADE SHOW REVIEW Colour & effects for PET bottles Penn Color’s specialist Penneffex design team, which was established in Q4 2017, brings together employees from North America, Europe and Asia, who have combined to influence the company with packaging ideas and design trends from around the world. Penneffex is currently focused on developing colour & effect concepts for both mono- and multi-layer PET bottles and is adding HDPE extrusion blow moulding prototyping capabilities, which will further extend its concept, design and development expertise and resources. At NPE, the Penneffex team demonstrated a range of bicolour, thermochromic and phosphorescent PET bottles, specifically aimed at and designed for the beverage market. Overcoming challenges The presentation demonstrated how Penn Color’s specialists have overcome three main challenges associated with special effects pigments in PET bottles, which are: Special effect pigments can degrade at the high process temperatures required for PET, causing the bottle to lose its eye-catching effect. They are not always approved for food contact. This has tended to limit applications to non-food contact applications like Homecare and Personal Care. Special effect pigments are generally expensive, which makes them potentially prohibitive for massmarket applications. The Penneffex team overcame these challenges by designing a proprietary special effect compound, to be used in the mid-layer of a multilayer PET bottle. The multi-layer hot-runner was able to process the Penneffex compound in the mid-layer at lower temperatures than the inner and outer layers. This served to significantly reduce the impact of thermal degradation and allowed the special effects to maintain their full effect in the finished bottle. Within the structure of the bottle, an inner layer of food grade PET can effectively create a functional barrier between the mid-layer and the food or beverage content. The Penneffex compounds were specifically tailored to be dosed in high concentrations and in minute amounts, in the preform’s mid-layer. Even in these minute amounts, the pigments can achieve their targeted special effect, which helps to deliver a meaningful reduction in the total production cost of the finished bottle. Successful collaboration and future developments The bottles demonstrated at NPE were developed in collaboration with Husky Injection Molding Systems and designed and engineered by PET Engineering. Penneffex intends to proceed with a series of launches of new colours and effects developed specifically for the packaging market. Penn Color is establishing a new Research & Design Center, which is scheduled for completion in Q4 2018. It will be located in Hatfield, PA, USA, which is 30 miles from Philadelphia, PA, and 90 miles from New York City, NY. The new Center will showcase Penneffex concepts. Penn Color is actively encouraging converters, brand owners, package designers and equipment manufacturers to visit the center and to continue to push technical limits in the possibilities and applications of packaging colours and effects. www.penncolor.com www.petengineering.com www.husky.co At NPE 2018 Penn Color’s Penneffex design team, in association with Husky Injection Molding Systems and PET Engineering, demonstrated a range of its new colour and finish effects, created using advanced techniques and technology. Room temperature Frozen","@ID":43}, "TRADE SHOW REVIEW PETplanet Insider Vol. 19 No. 07+08/18 petpla.net 38 Eight years market presence and customers in more than 30 countries Blow moulding machines from South China by Kay Barton Friend Machine, based in Zhongshan, between Guangzhou and Macau in southern China, has since 2010 been developing blow moulding plants that produce PET bottles and jars for packaging drinks – including mineral waters and hot fill products – edible oils, cosmetics, personal care, medicines and more besides. The company was founded by James Zhang, who currently holds he position of General Manager. It is focusing on global growth and is a regularly presence at Asia’s key trade fairs. At Chinaplas, Friend presented its 10 cavity FR-L10E model, which has an output of up to 18,000 bph. Its capabilities were demonstrated with the production of 500ml milk bottles, with the growing international market for PET packaged dairy products in the single serve segment very much in mind. “James Zhang’s vision when he founded the company was to promote bottle blowing technology in China,” says Mrs Bonney Zhao, Zhang’s wife. The company founder had previously worked as Director of Sales at a mechanical engineering firm located in Taiwan that made blow moulding equipment and recognised the growing demand in China for locally-produced machinery in this sector. Friend now produces about 100 linear blow moulding machines and components every year, has roughly 50 patents and installations in more than 30 countries; exports account for roughly 30% of the company’s total output. “We want to continue growing overseas and to develop our international customer base in particular,” said Mrs Zhao. Half of the company’s machines end up in the edible oil segment, followed by water (30%). Juices and cosmetics applications currently share the balance of customers, with 10% each. In China itself, the firm’s customers include influential brands like C’estbon, Watsons Water, Red Bull, Yanjing Beer and Lee Kum Kee. The Friend factory floor space totals 10,000m2, 6,000m2 of which is used by the production function, and accommodates roughly 80 employees. Friend Machine has been recognised as a “Key Project for Equipment of Zhongshan City”; it is the only machinery producer of its type in Zhongshan. It is also officially recognised as a “Guandong Province High Technology Enterprise”. “Our equipment is modularly integrated into the production line at the customer’s and is both energy-efficient and quiet,” Mrs Zhao explained. “It is easy for machine personnel to operate and to maintain, and the installed components guarantee bottling companies consistent quality for PET containers. We want to continuously improve our technology in future, particularly in terms of speed and consumption.” www.friend-machine.com L IGHTWE IGHT WI TH CONF IDENCE CONTACT US TODAY TO LEARN MORE! AGRINTL.COM | +1.724.482.2163 | [email protected] PROCESS PILOT® Blowmolder management easy as . . . Highly accurate material distribution guarantees that even WKH OLJKWHVW FRQWDLQHU PHHWV \\RXU VSHFLȴFDWLRQV","@ID":40}, "LABELLING PETplanet Insider Vol. 19 No. 07+08/18 petpla.net 22 With an integrated glue tank, patented vertical melter and heating control, glue is melted on demand and circulated always at a precise temperature and in smaller quantities, increasing the label quality application. This allows for reduced consumption of glue and avoids glue degradation, glue filament, and glue splashing, for better overall quality and improved sustainability. Adhesive labeller The adhesive labeller is designed to apply labels at high speed. It can be equipped with six different carousel sizes, up to five labelling stations and 36 configuration possibilities. Able to apply plastic or paper pressure sensitive labels (PSL), it has been optimised to suit the needs of beer, water, food, home and personal care producers. The advanced unwinding, feeding and peeling control, through efficient servomotors, enables greater stability and precision in the labelling process, says Sidel. This allows the machine to handle also ultra-thin labels, down to 25 μ, at speeds of up to 66,000 cph. It also delivers the flexibility that manufacturers need in applying labels to a variety of containers of different shapes and sizes. The adhesive labeller is equipped with brushless motorisation of the bottle platforms to smoothly handle round and shaped bottles. A vision system can be added for accurate bottle orientation and label positioning. With its stainless-steel structure and components, the EvoDeco Cold Glue labeller is hygienically designed and fully washable","@ID":24}, "PETnews 6 NEWS PETplanet Insider Vol. 19 No. 07+08/18 petpla.net Alpla and Fromm cooperate in PET recycling Alpla, the Austrian packaging solutions specialist, and Fromm (Switzerland) have agreed on a collaboration in relation to PET recycling. Both companies operate recycling plants for PET bottles, thus ensuring the necessary supply of materials for their own production facilities. The goal of the collaboration is the further optimisation of the recycling rates for PET as well as a significant reduction in CO 2 emissions through saved transport. There are also further benefits for the partners, such as simplified access to markets in the respective countries. “The requirements at our production sites complement one another very well. At Alpla, we mainly need clear, food-grade pellets. Fromm processes coloured flakes for the strapping bands,” explains Georg Lässer, Head of Corporate Recycling Services at Alpla. “The collaboration between our recycling facilities will ensure the necessary quantity and quality of materials for production for both sides.” “The three recycling plants are integrated in various procurement markets and complement one another ideally in the procurement of raw materials,” highlights Reinhard Fromm, owner of the family-run Fromm Group. The PET recycling team plants in Wöllersdorf (Austria) and Radomsko (Poland) are part of the Alpla Group. These recycling facilities have an annual capacity of approximately 45,000 t of food-grade rPET produced from post-consumer materials. The PET recycling company Texplast in Wolfen (Germany) has been a subsidiary of Fromm Plastics GmbH since 2004. Texplast produces PET pellets and PET flakes. Fromm uses these for its own production of strapping bands and also supplies manufacturers of beverage bottles, thermoforming sheets and fibres. The contract partners have agreed not to disclose the details of the cooperation. Further possibilities to extend the cooperation are to be explored. www.alpla.com www.fromm-pack.com www.texplast.de South Africa: beverage and food industry focuses on resource conservation and energy efficiency The Food & Drink Technology Africa (FDT) positions itself as a forward-looking platform for the industry. Water is the decisive element in the food and beverage industry, whether as an ingredient or in production and cleaning. The demand is correspondingly high while at the same time the scarcity of this precious raw material is steadily increasing. At FDT Africa, the focus will therefore be, among other things, on solutions for water and energy management. Companies are looking for new approaches to an efficient resource and energy management, from reliable, environmentally-friendly and energy efficient pumping of water from company-owned wells to appropriately treated process water that can be used for irrigation or equipment cleaning the starting points for solutions are many and varied. Local and international exhibitors such as Dematech, Ecolab, Ningbo Lehui, Pall and Praj Industry will present their ideas and products from this field at FDT, taking place from September 4-6, 2018. Visitors will receive a comprehensive overview of water treatment and water recycling as well as possibilities for reducing water consumption. Water and energy management will also play an important role in the supporting programme. The FDT speakers corner offers a three day platform for the exchange of experiences and practical solutions for the food and beverage industry. In her presentation, “How technology contributes to saving water and energy in beverage production, food processing and packaging”, Vera Fritsche from the VDMA Food Processing and Packaging Machinery Association, will give an initial overview of the respective technologies. Further presentations on hygiene and energy saving are currently being planned. The supporting programme thus responds precisely to the needs of the local industry, creating a definite added value, both for exhibitors from the segment and for exhibition visitors. Consequently, FDT Africa 2018 will once again show what is technically feasible for local industry today and what could be possible tomorrow. www.fdt-africa.com Avery Dennison Label and Graphic Materials names Pascale Wautelet Global Vice President, R&D Ave r y Denn i son Co r po r a t i on announced the appointment of Pascale Wautelet as the Global Vice President of Research and Development (R&D) for its Label and Graphic Materials Group, effective immediately. She succeeds Hassan H. Rmaile, who was promoted earlier in the year as Vice President and General Manager for Global Graphics and Reflective Solutions and Vice President, Global Technology and Ventures for Avery Dennison. As Global VP for R&D, Pascale will lead Label and Graphic Materials’s global R&D network, including oversight of the seven regional R&D centres and teams. Along with a team of 300+ scientists, Pascale will continue to build the future pipeline products and solutions for this materials science company. Pascale joined Avery Dennison in July 2017 as Vice President, Label and Graphic Materials for Europe, Middle East and Africa. She has more than 20 years of domestic and international experience across multiple functions in the chemical, petrochemical and plastics industry, including flexible packaging and labelling. Prior to joining Avery Dennison, Pascale was Global Technology Director at Jindal Films, overseeing corporate innovation and research and development across Europe and North America. Pascale earned her PhD in Materials and Polymer Chemistry and Physics, and received a Masters degree in Polymer Chemistry from the University Louis Pasteur of Strasbourg, France. She graduated with a Bachelor of Science, Chemistry from the University of Louvain-La-Neuve, Belgium. www.averydennison.com","@ID":8}, "","@ID":23}, "LABELLING PETplanet Insider Vol. 19 No. 07+08/18 petpla.net 23 LABELLING 23 An air-dancer and a push-pull system ensure that the labels are not under any stress at any point, to avoid labels web liner breakage, and to ensure the correct alignment with the containers being labelled for a flawless “no-label” look. Users can configure the labelling module with either two reels - both engaged, applying two different labels - or a master-slave non-stop labelling, applying the same label without production downtime during reel changeover. The machine can apply up to ten different labels to the same bottle while a highly efficient auto-splicer changes reels without any reduction in production speed. The automatic opening and closing of the protection window, a Sidel patented solution, makes it possible to engage or disengage modules for changeover or maintenance. Cold glue labeller The cold glue labeller is available in six carousel sizes and can feature up to five labelling stations, making it easy to configure according to bottle size, output need and product type. Capable of generating outputs of up to 81,000cph, the solution handles partial pre-cut paper labels, as such it is particularly suitable for the beer, food, home and personal care markets. It comes with a fully washable stainless-steel structure and components: this, together with an automatic cleaning system, dedicated to all the parts that come into direct contact with the glue, is claimed to ensure top levels of hygiene. The easy-to-operate labelling station features quick-release tool-less label pallets for quick change-over time, while consistent uptime is ensured by the automatic label magazine loading system. www.sidel.com The EvoDeco Adhesive labeller achieves speed of up to 66,000bph.","@ID":25}, "LABELLING 25 PETplanet Insider Vol. 19 SIPA S.p.A. - Via Caduti del Lavoro, 3 - 31029 Vittorio Veneto (TV) - Italy Tel. +39 0438 911511 - Fax +39 0438 912273 - email: [email protected] We make it happen. www.sipa.it Imagine taking your operating costs at the lowest level. Designed to adapt. Built to last. Preform Systems MAINTENANCE COST i stment Less than1%of the capital nve ling machine. These include the carousel, infeed and discharge stars, folding doors, installation and format parts and guides, and on the cold glue station the gripper cylinder and label magazine. The Innoket Neo servo feed screw has also been applied and integrated here, permitting gentle bottle stops. Plenty of upwards scope The KHS development also provides many different opportunities for extension to cater for individual labelling tasks. It is possible, for example, to equip the Innoket Roland 40 with the KHS VarioDrive electronic bottle plate control system. Other options include mechanical alignment by side notch in the infeed star and the fitting of travelling applicators, the latter used for cap or lid labels. U-shaped labels – as tamper evident seals for twist-off caps, for instance – can also be labelled and rolled on. Optional sensors check for the presence of labels at certain points, for example in the label magazine or on the glueing roller, and for other factors such as broken bottles. With its many expansion options the KHS Innoket Roland 40 is thus suited to cater for all requirements in the low capacity range, says the company. www.khs.com Cornelius Adolf, Product Manager Labelling at KHS","@ID":27}, "MARKET SURVEY 29 PETplanet Insider Vol. 19 No. 07+08/18 petpla.net Resins & additives Preform machinery Preform production Preform inspection SBM 2-stage Compressors Filling equipment & filling inspection Caps & closures and inspection Palletising & shrink film machinery Recycling Siad Macchine Impianti Gardner Denver Ltd - Belliss & Morcom Via Canovine, 2/4 24126 Bergamo, Italy +39 035 327611 www.siadmi.com Mr Giovanni Brignoli Compressor Division, Food & Beverage Product Leader +39 035 327609, +39 035 327694 [email protected] Claybrook Drive, Redditch B98 0DS, United Kingdom +44 1527 838 601 www.gdhighpressure.com Mr Trevor Perry Sales Director +44 1527 838 601 [email protected] BS Line Vito VH & WH Series 19 models 21 13 1,000 – 6,000 250 - 5,500 400 - 3,220 High pressure blowing air (up to 40bar) Oil free water cooled reciprocating piston Low pressure screw High pressure piston (booster) piston 3 stage oil-free - 18 - 45bar Oil-free Oil-free Oil-free Oil-free Yes Yes V V V & W cylinder configurations 2 screw + 2 booster = 4 total 3 3 No No No, all compressors are dynamically balanced Water Water Water Belt drive Direct drive using zero loss high efficiency shaftless motor Direct drive Belt drive • 28mm, 33mm and 38mm screw closures • Robust and trouble free capping • Established DoubleSeal™ technology - for secure sealing performance - for better protection against micro-organisms • Slit FLEXBAND® band technology for enhanced tamper evidence • O 2 barrier and scavenging options for screw flat caps supporting longer shelf life and fresher taste • Sports closures for aseptic filling and hot filling without aluminum foil • Special closures for syrups and carton packaging Unique range of screw and sports closures designed for cold fill and aseptic application BERICAP Technology for juices, RTD teas, health drinks www.bericap.com","@ID":31}, "MATERIALS / RECYCLING PETplanet Insider Vol. 19 No. 07+08/18 petpla.net 11 production technologies in this test lab and develop business models parallel to them. Exchanging experience today leads to the solutions of tomorrow The discussion between raw material producers confirmed once again that sustainability is playing an increasing role in company visions. The title of this particular discussion was “Circular economy and raw material producers – parallel worlds or a complementary concept?” which enabled participants to outline their own respective strategies for the future. The result: recycling is not a contradiction in terms, it is an asset in raw material production. Sustainable end products call for the know-how of raw material producers in combination with the experience of recycling specialists. The remarks of Plastics Recyclers Europe (PRE) focused on European initiatives such as EuCertPlast and RecyClass which aim to drive uniform quality standards in the use of plastic materials and design for recycling. The European recycling industry can already turn to a wealth of experience in the field of innovative circular economy and has a significant lead as a result, according to Manfred Hackl “The circular economy is not only an ecological must, it also gives Europe the chance to position itself as a pioneer of the green economy.” Attendees received an insight into the activities of plastics companies among the value chain in parallel event and company visits to Engel and Greiner Packaging. Borealis also invited Discovery Day participants to their Innovation Headquarters in Linz on day two. In a Science Walk through the company’s application hall the focus was on the processing of recyclable polyolefins and recycled pellets. The third day was dedicated to trends in the reprocessing of production waste. Speakers from SML and Brückner confirmed that more and more packaging manufacturers already count on a combined production and recycling solution when investing in new equipment. “Erema began manufacturing recycling systems for production waste 35 years ago. This division now accounts for over 50% of our turnover and we are proud that more and more international packaging producers place their trust in our quality,” said Manfred Hackl. Comprehensive recycling concepts through recycling technology Erema was already committed to quality and process transparency at an early stage. The ReFresher in combination with the Intarema, for example, ensures the thermal-physical odour minimisation of recyclates. This considerably broadens the field of application for recyclates from post-consumer material. In the smart factory area, Erema offers online quality monitoring of colour and MVR value already while processing. The Manufacturing Execution System re360 gives a digital overview of production data. This is not only for Erema machines, it can also be used for a company’s entire range of machinery – ideally from plastic bales to recyclate. To meet the demand for comprehensive recycling concepts Erema, using its knowhow, added the business unit KeyCycle to its portfolio only recently. This means that the Erema Group can now also offer complete engineering and integration services for plastics recycling systems. Furthermore, customers are already supported in the early planning stage with specific consulting and, if required, feasibility studies to integrate the appropriate recycling solution for their use. Besides the technical and strategic answers presented by Erema with regard to plastics recycling, there was an extensive array of perspectives on the topic of the plastics industry – the circular economy. The conclusion of the conference: only more intensive collaboration within the industry can collectively develop the required technologies which will meet the recycling targets and thus see more recycled pellets used in end products. www.erema.com Thorsten Leopold, Head of International Packaging Development Home Care at Henkel Manfred Hackl, Erema Group CEO, summed up the challenges facing by the industry. Peter Hartel, Head of Sales PET Recycling at Krones, presented bottles with a diffrent amount of rPET at the Erema Discovery Day 2018.","@ID":13}, "BOTTLE MAKING 13 PETplanet Insider Vol. 19 No. 07+08/18 petpla.net SMI says that the EBS K Ergon rotary stretch blow moulders can be installed and started up in a single day. In addition to the features of the standard model, the Ecobloc K Ergon rotary “combi” machine includes advanced solutions based on IoT and 4IR parameters and is an ultra-compact system for high performance stretch blow moulding, filling and capping PET containers up to 3 l, SMI says. The systems are suitable for bottling lines for milk and still water (EV models) and edible oil (EM models), at rates of 1,000-9,000 bph. The EBS K Ergon stretch-blow moulder was named one of 11 national winners from 189 businesses representing Italy for The European Business Awards, Europe’s largest business competition. SMI was chosen by a panel of independent judges including senior business leaders, politicians and academics as the best in Italy in the category “Awards for Innovation”, and represented Italy in this category in the final stage of the competition. Easier cap positioning SMI’s new Easy-Cap gravitational cap grabber takes caps from the hopper, gives them the desired orientation and moves them into the bottling line. It features integrated motorised hopper for loose cap loading; elevated cap handling conveyor; and an outfeed cap discharger linked to the cap channel. It allows the passage only of correctly positioned caps; others are gravity-fed back to the hopper. The compact machine is made of AISI 304 steel and features a “userfriendly” operator interface, for ease and efficiency. www.smigroup.it","@ID":15}, "LABELLING PETplanet Insider Vol. 19 No. 07+08/18 petpla.net 20 Flexible labelling solution can be equipped with up to four different labelling technologies For every kind of label It has never been more important to stand out from the crowd than in today’s competitive beverage market. Labels are key components of any brand marketing mix, allowing manufacturers to differentiate their products and give end consumers the information they need and increasingly expect. The Sidel EvoDeco solutions, available either as a modular, multi technology or as dedicated technology equipment, are designed to meet today’s demands within labelling. Precise application of high quality labels typically contributes to an excellent brand experience. At the same time, a growing variety of beverage types and bottle formats has made labelling increasingly challenging. More than ever, flexibility has become a valuable benefit to beverage producers. For them, top priorities today are faster product and format changeovers, simple operations and optimised processes that use the same equipment for different label types, still ensuring consistent uptime. In order to meet these demands, Sidel has introduced the EvoDeco labelling solutions. Based on a common core and optimised design, they enable producers to deliver different stock keeping units (SKUs). They might either include several labelling applications in one multi-technology machine or a single labelling application through dedicated equipment, for optimised uptime, reduced footprint and low total cost of ownership (TCO). The EvoDeco platform is built using the latest technologies regardless of model or configuration. This gives beverage producers the ability to choose solutions based on their specific labelling needs and output levels, without compromising on flexibility, efficiency or sustainability, says Sidel. Sidel’s most flexible labelling solution to date, the EvoDeco Multi offers a standardised carousel that can be equipped with up to four different labelling technologies: roll-fed, self-adhesive, cold glue and hot melt. This allows manufacturers to set up the machine for their unique labelling needs, as they can apply several types of labels to different types of containers and packaging materials (PET, HDPE, glass), of varying formats and dimensions (from 0.1 l to 5 l), on a single machine at speeds from 6,000 up to 81,000 containers per hour (cph). Roll-fed labeller Boasting four carousel sizes, up to three labelling stations and 24 configurations, the Roll-fed can generate outputs of up to 72,000 cph (or - when integrated in the Sidel Super Combi - of up to 81,000 bph) at an efficiency rate of 98%. It is particularly suitable for water, carbonated soft drinks (CSD), juices and dairy producers. Using hot glue to apply wrap-around plastic labels, it can handle lightweight containers and ultra-thin labels, yet allowing for better glue control and distribution, together with reduced consumption. The ergonomics of the solution have been optimised for performance and efficiency as reflected by the linear design of the roll-fed station, with all main components fully visible and accessible during production or maintenance. Cleaning can be carried out automatically during production by a system installed on the vacuum drum, which removes any glue residual for higher performance. It can also be equipped with an automatic label extraction system (Sidel patent), ensuring no downtime occurs due to labels being not properly applied on the bottle or no bottles being present, for a smooth and consistent flow of production. The label application is carried out with a pad-to-pad transfer, leading to a stable and accurate process, even at high speeds. Furthermore, the reels auto-splicing system can be activated at high speeds of up to 30,000 cph resulting in improved productivity. The solution can be controlled and adjusted via a human-machine interface (HMI) which is integrated within the labelling station. Additionally, the vacuum drum is built in light-weight sectors for easy and quick replacement, without disengaging the station, and also features newly patented adjustable pads for longer production time and less time needed for maintenance.","@ID":22},
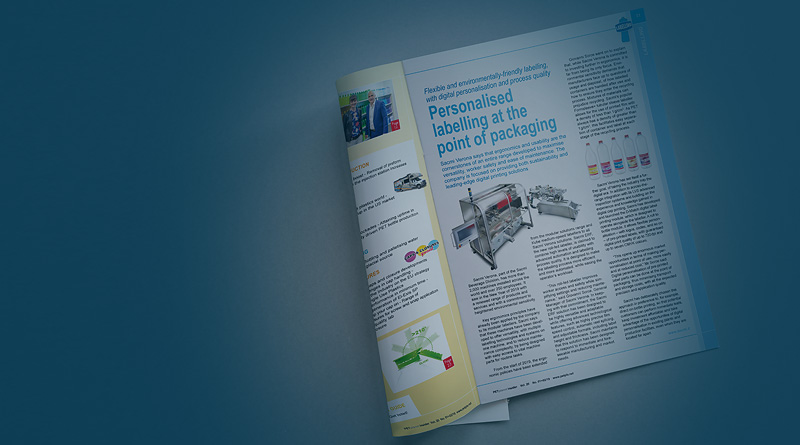