CAPS & CLOSURES 26 PETplanet Insider Vol. 19 No. 10/18 petpla.net “The issues we faced were: cost; the global shortage; high prices, including the cost of transportation; and long lead times,” said Grant. These issues were also affecting the ability to supply markets such as Russia and Africa. PSD had all the resources it needed when it came to production of preforms and flat cap closures but the manufacture of sports caps was a different scenario. Utilising internal technical knowledge and Coca-Cola Amatil selecting the right external partners for the project was paramount. “The company could have gone in for a ‘me too’ like-for-like product, as The Coca-Cola Company owns the intellectual property (IP) for the Mercury caps it uses, but Coca-Cola Amatil wanted to turn necessity into an opportunity, to take the product forward,” said David Chalmers. This included addressing some issues with the existing design, which was not totally reliable with warm-fill nitro dose technology; sealing; and historic tamper evident (HTE) features” said Chalmers. Added security The sports cap is a three-piece closure, comprised of the base, slider and overcap. The external base tamper band is located at the bottom of the thread and there is a second tamper feature where the overcap joins the base. Closures used for products in the Coca-Cola System need to pass their “Tamper Evident Testing”, known as “Historic Tamper Evidence” (HTE) testing. The design is the first-of-its-kind to be approved by The Coca-Cola Company. At the same time as addressing the issues of security and performance, especially in extreme temperatures and with nitro dosing, the opportunity was taken to address the issue of materials. The presence of two complicates recycling and adds an additional layer to the manufacturing process, so the decision was made to go with just one: HDPE. Its strength and rigidity characteristics are different from PP, which meant that attention had to be paid to structural integrity during the design process. Weight was not so much of an issue, as the sports cap is a premium product. “We didn’t have an end weight target; our priority was the design features,” said David Chalmers. “We were prepared to add weight to achieve quality and security approval from Coca-Cola; we could have gone more aggressive in regard to light weighting but then we would have been in the same position as our existing suppliers. We knew what was required and undertook design and safety iterations ourselves, until we were confident this cap would pass the tests. We became the first company within the Coca-Cola organisation to pass the HTE and Packaging approvals, in the first attempt.” The design process: two years and multiple iterations There were plenty of challenges along the way, including getting the slider to perform its functions properly, and to feel right while doing it. The spout itself had to dispense at the right flow rate and achieve the right ‘drip performance’. It took a total of two years, plenty of human resources and numerous iterations of the design until it was right. We were fortunate to be joined by Michael Fink, Vice-President Sales and Marketing with z-Moulds; Michael Ludemann, General Manager of Husky Injection Molding Systems ANZ Pty Ltd; and Rod Druitt (CEO) and Michael Furlong, of Universal Closures Ltd (UCL), which is based in Tewkesbury, England, as well as Wahroonga, Australia. Mischa Bechtolsheimer, International Sales Manager with Eckel & Sohn, was also present for the launch ceremony. UCL was briefed to improve the existing cap design and to ensure approval for the tamper-evident features – a major consideration, according to Rod Druitt. “The existing designs only had provisional approval,” he explained. “Our brief was to ensure that the whole closure would be approved by The Coca-Cola Company. Not just the base – the cap as well. We were also tasked to come up with a design that could be assembled satisfactorily, would deliver ‘drinkability’, would protect the product and would cope with warm fill.” Along with the requirement to shift from two materials to one, while keeping familiar ‘feel’ and visible features, it was quite a challenge. UCL, Husky and z-Moulds collaborated closely in developing the finished product. F.l.t.r.: CCA managing director Alison Watkins and David Chalmers, Operations Manager, CSD, at the official opening of the SyLon Mercury sports cap production line at Eastern Creek, New South Wales, Australia Final assembly of the SyLon Mercury sports cap. Finished units can be seen on the conveyor visible through the lower part of the window just right of centre. Explaining how the SyLon Mercury sports cap is put together A view of the Sylon Mercury sports cap production line, including raw material storage bottom right.,@ID:28}, ONsite 53 ON SITE PETplanet Insider Vol. 19 No. 10/18 petpla.net Piovan announces new headquarters in North America Universal Dynamics, Inc., a company of the Piovan Group, completed its move from Woodbridge to Fredericksburg Virginia, USA in July of 2018. The newly outfitted structure, which occupies 110,000 square feet (10,000 square meters), was designed with lean manufacturing practices in mind, and will allow the company to double its production capacity. The new premises are also the new headquarters of the Piovan Group in North America. Storage, conveying, blending, drying and size reduction equipment, along with supervisory software solutions, are now being produced in the new factory. In 2019, the new facility in Fredericksburg will also become the manufacturing center of Aquatech process water-cooling equipment, imported for about three years now from Aquatech Italy. Aquatech is the Piovan Group company that supplies process water solutions and temperature control systems to the industries Piovan serves. With its Aquatech production, Universal Dynamics will become the first manufacturer of high efficiency adiabatic fluid-coolers in the USA. With the factory in full production, a grand opening event has been held on October 4, 2018 at its new location. With visitors from Canada, USA and Mexico, the event included an address from multiple industry leaders, live demonstrations of new technologies, plant tours demonstrating manufacturing capabilities, as well as an official ribbon cutting ceremony. www.piovan.com SDWHQWV UHVHDUFKHUV DQG WHFKQLFLDQV LQVWDOOHG SODQWV EUDQFKHV ZRUOGZLGH ,I ZH KDGQêW JRQH VR IDU ZH ZRXOGQêW EH VR QHDU RXU IXWXUH VHHQ IURP QHDU,@ID:55}, 44 TRADE SHOW PREVIEW PETplanet Insider Vol. 19 No. 10/18 petpla.net TRADE SHOW preview China Brew China Beverage 2018 The 13th international Brew and Beverage processing technology and equipment exhibition China Brew China Beverage 2018 (CBB) will be held at the Shanghai New International Expo Center (SNIEC) from 23 to 26 October. The trade fair covers the whole process chain of the beverage and liquid food industry, including related processing technology, packaging, raw materials, logistics, equipment and components. CBB offers a variety of activities for visitors alongside the displays of new products from around 850 exhibitors and the latest technologies showcased on site. Visitors can join seminars, attend new product release conferences, visit forums or take part in end-user enterprise visits, amongst others. www.chinabrew-beverage.com Booth 2C64 in Hall W2 Dispensing solutions Aptar Food + Beverage will showcase a wide range of dispensing solutions and technologies that have been designed to bring differentiation, safety, convenience, and superior functionality to consumers. As an example, Aptar will introduce the new Guardian Light. With an ergonomic and lightweight design, this non-detachable tamper evident closure is leading the way in sustainable solutions for on-the-go beverage consumption. www.aptar.com motan-colortronic gmbh - [email protected] www.motan-colortronic.com ETA plus® considerably reduces energy consumption and protects materials. Drying has never been this efficient: ETA plus® LUXOR A Please visit us: Hall B1, Stand B1-1111,@ID:46}, MOULD MAKING PETplanet Insider Vol. 19 No. 10/18 petpla.net 18 MOULD MAKING 18 Moulds for beverageclosures lines From cap to preform and stretch-blowing, Sacmi acts as a one stop shop for every stage of the beverage production process. Their services aim to make a difference - against a backdrop of progressively shorter average product life cycle and customers’ demands for minimal lead times for new caps and formats - by providing consultancy and customer support right from the design phase. Sacmi’s strategic decision to act as both supplier of moulds and machines as well as cap designer in the beverage-closures industry ensures they make the very most of technologies, such as compression. “In the closures field”, states Davide Penazzi, Technical Manager of Moulds & IPS, “Sacmi leads the way in the manufacture of flat-top caps with compression technology.” On average, Sacmi produces and supplies 8-9,000 moulds a year for compression moulds for caps. There are two reasons behind this: the first dates back to the end of the 1980s when Sacmi decided to invest in compression as the technology of choice for switching from crown cap to plastic cap production. The second relates to more recent mould configuration developments. These range from the Cool+ boostedcooling system, which comes as-standard on the continious compression moulding (CCM) machine range, and increases production by 50% without compromising performance, to the complex light weight developments that are steadily evolving every design aspect of the cap-preform-bottle system. “In itself”, explains Penazzi, “compression technology is better suited to the manufacture of very thin caps. This is because it is a particularly stable technology that operates at lower temperatures than injection does. It also allows independent control of every single cavity-mould, thus ensuring perfect process repeatability whatever the production conditions”. As the Technical Manager of Sacmi Moulds & IPS reveals, “ More and more customers request in-depth cap design consultancy as well as machine consultancy. It’s here that the ‘mould factor’ comes into play. The operating parameters of the mould play a crucial role in finished product quality, which allows us to supply distinctive services to our two main customer groups: converters and bottlers”. MOULDspecial mmm$he[Z[hi$Z[ Y O U R PA R T N E R F O R B L OW MO U L D S . STEPS TO THE PERFECT BOTTLE. YZV 9Zh^\\c IZX]cdad\\n BVcj[VXijg^c\\ 8bem CekbZ &%% HZgk^XZ Meet us at Brau Beviale in Nuremberg - Hall 7A / 7A - 301,@ID:20}, MOULD MAKING PETplanet Insider Vol. 18 No. 0/17 petpla.net 13 “Our customers come to R&D simply because we are one of very few companies – maybe the only one in the world – that can offer the whole range. We can assist with the upfront evaluation. We will tell them what cavitation they could run and on what machine. We’ll give them all the technical specification and if there are any potential issues, we will tell them and what they have to change.” R&D Leverage can produce a single-cavity pilot tool should the customer require this or it is seen to be required by R&D to “This year, we are about 40% up on sales. Revenues were over a million Pounds in February, in March and probably April, too. It’s great but all of a sudden, we’re creaking at the rafters,” he said, with a laugh. Success brings its own challenges; absolute profit margin has been trimmed because of the need to ensure delivery of the new orders, on time and in full – which means more staff, more subcontractors and more expense. But they are challenges he is happy to take on. The fall in the value of Sterling has been a help. “We still have to be competitive but people recognise that our tools are very good.” There will always be someone who will offer to do the job cheaper but Tolley is prepared to say ‘no’ to unprofitable work; R&D Leverage’s reputation is for quality and reliability, sustained by a strategy of investment and a clear focus on excellence. www.rdleverage.com prove the quality or supply bottles or jars for filling, labelling, capping line trials, from this point to production tooling. The customer can come in with an idea and, ultimately, leave with a finished product and the tooling to produce it in commercial quantities. Inside R&D’s UK site Besides tools for a range of one stage ISBM, R&D has also a wealth of experience in two-stage blow moulds or hot runner manifolds.,@ID:15}, TRADE SHOW PREVIEW PETplanet Insider Vol. 19 No. 10/18 petpla.net 50 l l l consumer bags textile packaging recycling rECO October 24, 2018 - Focus on trends in packaging and recycling in India Company Speaker Topic All India Platics Manufacturers’ Association (AIPMA) Mr Akhilesh Bhargava, Chairman of Environment Committee EPR - Opening a new window of opportunities for the plastic recycling industry Bisleri International Pvt. Ltd. Mr K. Ganesh, Head - Sourcing & Vendor Management and Packaging Development Packaging trends and technologies, e.g. convenience packaging and small bottles Food Safety and Standards Authority of India (FSSAI) To be confirmed To be confirmed PET Packaging Association for Clean Environment (PACE) Mr Rajesh Kumar Gera, PACE Member PET recycling focusing on packaging developments and trends in the PET packaging for dairy and beverage industries Reliance Industries Mr Rajesh Gauba, Recycling & Sustainability To be confirmed RJ Corp., Varun Beverages Ltd. Mr Prabal Chakraborti, Asst. Vice President, Packaging Operations Advancements in active and intelligent packaging vis-a-vis face and role of packaging online Round Table Talks organised by PETplanet Insider Drink Technology India Supporting Programme October 24-25, 2018, 2.00 - 4.00 pm, Hall 1 (attendence for dti visitors free of charge) India's beverage market: Trends in drinks, packaging and recycling,@ID:52}, CAPS & CLOSURES 24 PETplanet Insider Vol. 19 No. 10/18 petpla.net Coca-Cola Amatil breaks new ground with fully recyclable sports cap All-HDPE sports cap by Ruari McCallion Ruari McCallion visited Coca-Cola Amatil’s plant on the outskirts of Sydney, Australia, for the official opening of the company’s new sports cap production line and spoke to senior executives about innovation and market trends ‘Down Under’. Eastern Creek is supposed to be half an hour’s drive from Downtown Sydney, Australia, but heavy traffic and construction work on a new highway meant that the journey took closer to 60 minutes than 30. Luckily, we had set off in plenty of time for an important event: the official launch of the SyLon top, Coca-Cola Amatil’s new sports cap. The company’s managing director and senior management were all on hand to see the culmination of two years’ hard work, with the very first production run. The Coca-Cola Amatil Packaging Services Division at Eastern Creek, Sydney is quite extensive and houses all of the equipment and manufacturing lines needed for the production of preforms and closures for Coca-Cola, Fanta and a range of other drinks. It serves a market that extends beyond Australia’s shoreline, to New Zealand and South-East Asia. The new sports cap is something of a breakthrough: it is made entirely of HDPE (high density polyethylene), rather than the traditional mix of HDPE and PP (polypropylene). Being made entirely of one type of plastic means that it is much easier to recycle; the cap can be disposed of by the consumer into the same waste collection and recycling stream as the PET bottle. With the world becoming more and more conscious of the need to recycle, this is an idea whose time has definitely come. As well as recycling, a single material means more effective use of raw materials, and a simpler production process. After the official opening ceremony, performed by Coca-Cola Amatil managing director Alison Watkins along with representatives of the Eastern Creek facility’s management and workforce, we were able to sit down and discuss the processes involved in designing a new closure system. First, we spoke to Coca-Cola Amatil executives David Grant, Supply chain director; David Chalmers, Operations Manager, PSD; and Martin Orzinski, General Manager, Operations. A history of innovation Coca-Cola Amatil is no stranger to innovation. The SyLon 1881 ‘shorty’ cap was invented here, as were Coke Zero, Ginger Coke, Coca-Cola Orange No Sugar, the Australian Packaging award-winning ‘easy crush’ bottle, warm-fill nitro (nitrogen) dose technology which replaced the original hotfill production and the ‘personal names’ “share a Coke” bottle campaign. “We are always thinking about innovation – we have a hunger to do things right,” said Martin Orzinski. “In order to be successful, we recognise that we continually have to be driving forward.” Coca-Cola Amatil’s innovative culture is driven partly by necessity. Australia is geographically large but it is a long way away from the big, established markets of Europe and North America, and pretty far away from the fast-growing markets of China, India and South-East Asia, as well. It has to be self-reliant. Security of supply “We imported sports caps from Switzerland and Spain, from Bericap and Corvaglia, for years,” said David Grant. Its share of the total global market escalated way beyond original expectations. “Out of 358 million sports cap units a year used by CocaCola worldwide, Coca-Cola Amatil uses 120 million. We first undertook a feasibility study into making caps here at Eastern Creek in 2013.” The time was not right then but growing demand, added to a global shortage of production capacity, raised the pressure to ensure continuity of supply. Having considered other possibilities, the decision was made to look more closely into the commercial feasibility of making their own caps. Coca-Cola Amatil’s new SyLon Mercury sports cap is made entirely of HDPE – a world first The heart of the production line for CCA’s Mercury sports cap,@ID:26}, MATERIALS / RECYCLING PETplanet Insider Vol. 19 No. 10/18 petpla.net 11 CarbonLite processes PET fines with Starlinger recycling line PET recycling all-in-one CarbonLite Industries LLC recently installed a recoStar PET 125 HC iV+ bottle-to-bottle recycling line from Austrian manufacturer Starlinger recycling technology at its plant in Dallas, Texas. At this 23,000m² facility with an annual recycling capacity of well above 45,000 t of bottles, CarbonLite recycles not just clear PET bottle flakes, but also more challenging material streams such as coloured material as well as so-called PET fines. PET fines are small particles of 1-3mm in size (bottle flakes have a size of 3mm) that are a by-product of washing and grinding. These fines tend to show higher surface moisture and have a lower intrinsic viscosity (IV) than regular bottle flakes, and they typically contain a larger amount of contaminants such as paper, glue, metal, or PVC. As a result, many recyclers do not process the fines together with PET bottle flakes, but instead sell them off for use in different applications. The desire to use this waste in a more profitable and sustainable way prompted CarbonLite to investigate recycling options. Starlinger recycling technology offered an all-in-one solution that can operate with PET fines as well as PET bottle flakes, or with a mixture of both. The line consists of the main stages pre-drying, extrusion, degassing, melt filtration, pelletising, crystallisation, and solid-state polycondensation. Due to the special characteristics of PET fines, the steps that require particular attention are melt filtration and decontamination as well as IV increase during solid-state polycondensation. Continuous melt filtration with power backflush To extract the high amounts of contamination, the recycling of PET fines calls for a melt filter with a large surface area and a special self-cleaning mode. The MPB1940P supplied by Starlinger recycling technology is a continuous melt filter with a unique design for the removal of solid contaminants. Two pistons that carry eight screens provide a total open filter surface of 1,940cm². When the surface of a screen becomes clogged, the backflush function cleans it fully automatically: the contaminants are flushed out through pressure build-up and a reversal of the melt flow. The melt filter is equipped with hydraulic power backflush. The high pressure involved in this auto-cleaning process leads to short backflush cycles and thereby keeps melt loss to a minimum. Unlike conventional backflush filters, the power backflush works with two additional pistons that generate extra backflush pressure independently of the melt pressure that builds up in front of the pelletising head. Through filtration under constant pressure, a consistent pellet size is achieved during the backflush process. The lifetime of the filter screens is longer, which lowers operating and maintenance costs. During a screen change, the recycling machine does not have to be stopped, as the remaining screens take over and filter the entire melt stream. IV increase Another important aspect in fines processing is intrinsic viscosity (IV). Due to their higher surface moisture and level of contamination, fines tend to lower the IV of the recycled material; consequently, it has to be raised to the required level. To accomplish this, CarbonLite operates a Starlinger solid-state polycondensation reactor for high IV increase and superior colour values. Decontamination for direct food contact The cleaning efficiency of the Starlinger PET iV+ recycling process guarantees the requirements of national and international food safety authorities such as FDA or EFSA. The bottle-to-bottle recycling line from Starlinger recycling technology holds a letter of non-objection by the FDA for 100% rPET – this means that the recycled material is food-safe and can fully replace virgin pellets in the production of PET bottles. The recycling line at the CarbonLite Dallas plant is highly versatile: It can produce rPET for a variety of applications, as the material is suitable for direct food contact with or without treatment in the downstream solid-state polycondensation reactor. The Starlinger recycling line was installed in Dallas in June/July 2018. The installation and start-up posed a challenge insofar as the schedule outlined by the customer was exceptionally tight. „CarbonLite asked us to install the line without interrupting their daily operations, which left us with a short time frame,” says Stefan Obermüller, Head of Project Management at Starlinger. “But only six weeks after delivery of the line, it was already running three shifts and producing material with the agreed specification.” The line achieves a throughput of 950-1,050kg/h and allows CarbonLite to process a maximum of PET waste that it obtains from materials recovery facilities. “We initially approached Starlinger for a solution for our PET fines,” states Leon Farahnik, Chairman and CEO of CarbonLite Industries. “But the longer we discussed the project with them, the more Starlinger customised the recycling line, giving us maximum flexibility to process a great variety of input streams into highend rPET pellets.” www.recycling.starlinger.com,@ID:13}, MARKET SURVEY 31 PETplanet Insider Vol. 19 No. 10/18 petpla.net 10/2018 MARKETsurvey Suppliers of systems, moulds and inspection systems for caps & closures For this issue 10/2018 PETplanet Insider interviewed the market participants in the system for the production of closure sector. It includes both: The machine manufacturers and the mould suppliers. We also add as a new special feature a survey reading closure inspection systems. Intravis GmbH, Corvaglia, Sacmi Imola, IMD Ltd., Husky Injection Molding Systems, Sumitomo (SHI) Plastics Machinery, z-werkzeugbau-GmbH and Pressco Technology Inc. Although the publishers have made every effort to ensure that the information in this survey is up to date, no claims are made regarding completeness or accurancy. Resins & additives Preform machinery Preform production Preform inspection SBM 2-stage Compressors Filling equipment & filling inspection Caps & closures and inspection Palletising & shrink film machinery Recycling Closure moulds Company name Corvaglia Mould AG z-Werkzeugbau Husky Injection Molding Systems Ltd. Postal address Telephone number Web site address Contact name Function Direct telephone number Fax E-mail Hörnlistr. 14 8360 Eschlikon, Switzerland +41 71 973 77 77 www.corvaglia.ch Mr Albert Brunner Director Sales & Service +41 71 973 77 52 +41 71 973 77 51 [email protected] Dr.-Walter-Zumtobel-Strasse 9 6850 Dornbirn, Austria +43 5572 7272 0 www.z-moulds.com Mr Michael Fink VP Sales & Marketing +43 5572 7272 610 [email protected] 500 Queen St S Bolton, ON, CAN L7E 5S5 +1 905 951 5000 www.husky.co Mr Michael White Business Manager, Beverage Closures +1 905 951 5000 ext. 2913 [email protected] Mr Henry Zhang, Dir. of Bus. Devlp., Medical & Specialty Packaging +1 905 951 5000 ext 5196 [email protected] Filling good - beverages Carbonated soft drinks and non-carbonated pressurised & non-pressurised beverages including water, juices, teas, milk/dairy, coffee, beer, isotonics, energy drinks, etc. Carbonated and non-carbonated drinks, water, juices, etc. Screw-on beverage closures for water, carbonated, hot-fill and aseptic beverage types Specialty closures including flip-top for personal care, sports caps, detergent, edible oil, carton closures and pouch fitments - other Edible oil, detergents, other filling goods possible upon request Edible oil, dairy, beer, etc. - individual cap solutions Possible upon request Personal care and household products Closure -type Flat top & sports closures for beverages from 26 to 48mm neck finishes, e.g.Alaska, 1810, 1881, 29/25, 30/25, 33 HF, 33ACF, 38 HF, 38ACF All single-piece standard closure dimensions for all neck finishes, sports closures, flip-tops, push-pulls, multi-component closures… Screw-on (moulded-in TE band), Screw-on (Post-mould slit TE band) Specialty closures including flip-top for personal care, sports caps, detergent, edible oil, carton closures and pouch fitments -material HDPE (PP for transparent parts) HDPE, LDPE, PP, TPE, … HDPE -weight Starting from 0.8g Lowest from 0.7g 0,7g Moulds Clamping dimensions/cavities 24 - 96 cavities 16 - 128 cavities Standard cavitations = 32cav - 96cav, 594mm x 1,045mm - 695mm x 1,050mm Custom cavitations depending on customer need and application being moulded; capability for high cavitation moulds Preferred hot runner suppliers Various Mold Masters Husky Husky Special features Closure design approvals from all major beverage brand owners; most economical closure designs for private labels Several patented technologies for most efficient closure production Horn-pin less design for high output, simple, & robust operation; integrated cooling manifolds for balanced flow & pressure (quick connect/disconnect) HT-S6 hot runner for optimal gate quality / minimal flow lines / fast colour change eIMC in-mould closing technology for flip-top closures; part optimsation and fast prototyping capabilities,@ID:33}, Round Table Talks The dynamic development of the Indian food and beverage market is reflected at dti: The exhibition area will be expanded by 18 percent compared to the previous event in Mumbai in 2016. The exhibitors at dti cover the entire value chain of the beverage and liquid food industry. This offers visitors a comprehensive overview of the latest developments and solutions. Supporting programme: What is moving the Indian market, now and in the future? The place2beer celebrates its premiere at this year’s drink technology India. The networking platform with sensory tasting, panel discussions and brewery supply displays, was first introduced at drinktec in Munich in 2017. Another novelty at dti is the Oiltech Forum which will take place for the first time as part of the Oiltech Pavilion, powered by oils+fats and supported by the Oil Technologists’ Association of India (OTAI). The topic of the half-day seminar is: ‘Challenges in packaging of edible oils and other related products’. The exhibition is thereby responding to the increasing importance of the topic of oils and fats for the Indian market. Current and forward-thinking topics for the entire Indian beverage and liquid food market are addressed during the Round-Table Talks (see p.50 f). Trends with regard to beverages, dairy, packaging and recycling are on the agenda. Among other things, experts will discuss which social developments the industry is currently dealing with, such as the increasing health awareness of the consumers. Further panel discussions will be dealing with, among other topics, packaging trends or new concepts in the dairy industry. The buyer-seller meetings offer additional benefits to exhibitors and visitors by bridging the gap between exhibitors and top managers. www.drinktechnology-india.com indiapack pacprocess,@ID:51}, 40 TRADE SHOW PREVIEW PETplanet Insider Vol. 19 No. 10/18 petpla.net 40 TRADE SHOW PREVIEW • 28mm, 33mm and 38mm screw closures • Robust and trouble free capping • Established DoubleSeal™ technology - for secure sealing performance - for better protection against micro-organisms • Slit FLEXBAND® band technology for enhanced tamper evidence • O 2 barrier and scavenging options for screw flat caps supporting longer shelf life and fresher taste • Sports closures for aseptic filling and hot filling without aluminum foil • Special closures for syrups and carton packaging Unique range of screw and sports closures designed for cold fill and aseptic application BERICAP Technology for juices, RTD teas, health drinks www.bericap.com Moretto presents his concept of Efficiency 4.0 For almost 40 years, Moretto has been researching, developing and producing automations for plastics processing. Injection, extrusion and PET processing are characterised by specific complexities and high levels of performance, in which production and energy efficiency play key roles. In order to remain competitive, plastic processors need to equip themselves with high performance plants in terms of energy efficiency and quality of the final product. Moretto’s goal, declared by the new pay off Empowering Plastics (that means “infuse more power to plastic”), is to help the industry make a difference through know-how, innovation and high-precision machines. At Fakuma 2018, Moretto presents his concept of “Efficiency 4.0”, essential for the factory of the future. For Moretto, “Efficiency 4.0” means a plant made up of advanced machinery and solutions, connected and integrated with each other by a supervision system that guarantees total control of the process. With a broader view, Moretto aims to support customers by providing experience, technologies and services which meet the needs of the global market. On the 4.0 factory, machines can be remotely managed, they are able to supply and exchange information, to self-programme and to provide frequent reports on production. The data obtained are used to modify the process parameters and to monitor the performance of the machines, thus optimising the efficiency of the entire plant. The Moretto’s 4.0 automations, drying solutions and the Eureka Plus System will be shown with new highlights. www.moretto.com Hall B3, booth 3208 Hot runner, controller and moulding solutions at two booths Husky Injection Molding Systems, an industrial technology provider to the plastics processing community, will participate in Fakuma with two separate booths in Hall A6. Husky’s exhibition features a space dedicated to its hot runners and controllers technology (booth 6222), as well as a booth focused on its packaging and medical moulding solutions (booth 6401-1). At booth 6222 Husky’s hot runners and controllers business will be showcasing its Ultra Helix valve gates, with over 4000 nozzles installed. Husky offers the Ultra Helix valve gate to provide moulders with quality and reliability. At the show, Husky will be demonstrating several new products, including its Altanium Valve Gate Sequencer, an easy-to-use single unit that combines temperature and servo control, ideal for filling large, multi-gated parts. As well, the booth will be displaying Husky’s new Altanium Matrix5 and Altanium Delta5 mould controllers. The company will also showcase its new Ultra SideGate Inline, providing 18mm gate spacing for small parts and ideal for compact moulds. At booth 6401-1, Husky will be displaying a variety of injection moulding solutions for the medical and packaging markets. Under the Schöttli brand name, Husky manufactures precision, highly-engineered tooling for the production of plastic medical applications. On display will be a variety of target medical parts that Schöttli manufactures moulds for, showcasing the company’s ability to mitigate risk in the manufacturing process. Husky will also highlight its range of tooling and system capabilities for the manufacture of packaging, including closures and thinwall packaging, as well as its Multi-Layer technology for packaging applications. www.husky.com www.schoettli.com Hall A6, booth 6222 & 6401-1,@ID:42}, MARKET SURVEY 32 PETplanet Insider Vol. 19 No. 10/18 petpla.net Closure inspection Company name Intravis GmbH Postal address Telephone number Web site address Contact name Function Direct telephone number Fax E-Mail Rotter Bruch 26a, 52068 Aachen, Germany +49 241 9126 0 www.intravis.de Mr Markus Juppe Director Sales & Marketing +49 241 9126 0 +49 241 9126 100 [email protected] Inspection system CapWatcher III CapWatcher SC (Specialty Closures) Integrated CapWatcher Systems Inspection speed Up to 252,000 objects / hour Up to 62,000 objects / hour Up to 79,200 objects / hour Inspection method Non destructive Non destructive Non destructive Inspected objects Standard closures: carbonated & non carbonated beverage, single- or multithread, with TE band, one-piece Specialty closures: flip top, sports caps (incl. push-pull), tube, for chemical industry, assembled closures Inserts: dosing inserts, liners, child protection Standard closures: for carbonated & non carbonated, onepiece, single- or multithread, with TE band, specialty closures: sports caps Inspected parameters: -Inner inspection Spots & contamination on the inside of the head plate, colour deviations, flow lines, liner inconsistencies Contamination, colour deviations on the inside, flow lines Contamination, colour, brightness, spots -Outer inspection Contamination on the side wall and on the head plate, colour, dark & bright spots on the outer wall, flow lines and printings on the head plate, printed image, registration shifts, position (printed image) Contamination on the outer wall, colour, scratches & pressure marks Contamination, colour, spots, brightness -Geometry Diameter, diameter & ovality of TE band and ovality of seal cone, closure height, gate, gate length, horizontal & vertical long shots, open & closed short shots, curvature of head plate, missing or damaged TE band, damaged flaps, turned up flaps, damaged seal cone, slitted & folded closures Diameter and ovality (e.g. closure, seal cone): closure height, assembly faults, missing components, damaged components, damaged seal cone, vertical long shots, open & closed short shots, horizontal/radial long shots, missing or damaged TE band, damaged flaps, turned up flaps, damaged pull tabs and missing or damaged quality seal Diameter and ovality, rotational position, outer dimensions, short shots, long shots, long shots at the mouth, contour deviations, contour & surface defects of the mouth ring, missing or damaged TE band, handle fold, open closure -Cavity number reading Cavity number reading, cavity related statistics (also for microhole defects), closure sorting according to cavity number, automatic selection of cavity fonts Cavity number reading, cavity related statistics, closure sorting according to cavity number, automatic selection of cavity fonts Cavity number reading, cavity related statistics, closure sorting according to cavity number, automatic selection of cavity fonts -Microhole inspection Microholes in the area of the injection gate (inspected with HV) -Additional inspection criteria for inserts Missing components, closure height (only metering inserts), diameter & ovality, flow lines Further inspection options Installation: Stand-alone (offline) Yes Yes Inline Yes Yes Yes, CapWatcher technology integrated into assembly machine Software features: Data base connection; reject rate monitoring; production monitoring with IntraVisualizer; integrated control of up- and downstream equipment; integrated trend statistics with pre-warning; ColorCameras Data base connection; reject rate monitoring; production monitoring with IntraVisualizer; integrated control of up- and downstream equipment; integrated trend statistics with pre-warning; ColorCameras Data base connection; reject rate monitoring; production monitoring with IntraVisualizer; integrated trend statistics with pre-warning; ColorCameras Systems for caps Company name Sumitomo (SHI) Demag Plastics Machinery GmbH Husky Injection Molding Systems Ltd. Postal address Telephone number Web site address Contact name Function Direct telephone number Fax E-mail Altdorferstr.15 90571 Schwaig Nürnberg, Germany +49 911 5061 0 www.sumitomo-shi-demag.eu Mr Arnaud Nomblot Director - Business Development Packaging +49 911 5061 625 +49 911 5061 96 625 [email protected] 500 Queen St S Bolton, ON, CAN L7E 5S5 +1 905 951 5000 www.husky.co Mr Michael White Business Manager, Beverage Closures +1 905 951 5000 ext. 2913 [email protected] 500 Queen St S Bolton, ON, CAN L7E 5S5 +1 905 951 5000 www.husky.co Mr Henry Zhang, Director of Business Development, Medical and Specialty Packaging +1 905 951 5000 ext 5196 [email protected] Systems for cap/closure production Model El-Exis SP HyCAP4 225t RS50/50 | RS60/60, HyCAP4 300t RS50/50 | RS60/60 | RS70/70, HyCAP4 400t RS60/60 | RS70/70, HyCAP4 500t RS70/70 HyperSync Procession technology Injection Moulding Injection achieved by a direct drive reciprocating screw Injection achieved by a direct drive reciprocating screw Clamp force 150 - 750t 225t (2,250kN) | 300t (3,000kN) | 400t (4,000kN) | 500t (5,000kN) Cycle time (guaranteed 98% closure system efficiency for): 26mm: 2,800 caps/min Varies depending upon application Varies depending upon application - High speed production: closure type/weight/cavities: caps/min 29mm: 2,300 caps/min - Individual cap solution: closure type/weight/cavities: caps/min PCO 1881: 1,650 caps/min Drive concept Hybrid Clamp stroke achieved by a servo driven ball screw Energy consumption (kwh/kg) 0.40 - 0.50 Varies depending upon application Varies depending upon application Preferred mould makers Z-Moulds / Plastisud Husky Husky Special features Mould Identification (ID) ready; Mould Alignment ready large 19\ intuitive touch screen HMI for simple operation eIMC servo-driven in-mould closing technology Mould Identification (ID) ready; Mould Alignment ready,@ID:34}, BOTTLING / FILLING PETplanet Insider Vol. 19 No. 10/18 petpla.net 23 Flexibility in the pasteurisation process Microbiological safety With the Innopas SX KHS GmbH provides a tunnel pasteuriser in a modular design. The systems supplier from Dortmund, Germany has optimised spare part management for this flexible machine. The beverage market is facing increasing levels of dynamic competition, with new flavours in new packaging formats hitting supermarket shelves at ever shorter intervals. Flexibility is thus becoming more of an issue when it comes to filling. The necessary pasteurisation of filled and sealed beverage containers for longer shelf lives is a decisive factor. The completely modular KHS Innopas SX tunnel pasteuriser is intended to satisfy these demands for PET and glass bottles and cans. Dynamic adaptation to line behaviour The basic functions of the Innopas SX are initially identical to the triedand-tested tunnel pasteuriser systems already provided by KHS. The dynamic pasteurisation unit or PU control system reacts variably to changes in conditions. If, for example, a fault occurs during the pasteurisation process, the process temperatures are kept under control in the hot zones of the tunnel pasteuriser to ensure both product safety and flavour stability. New features on the KHS Innopas SX include extended functions in the dynamic PU control system which result in greater flexibility and yield savings in energy and media. Much of this is attributable to the optional speed regulation function. The individual zone temperatures are automatically raised or lowered depending on the conveyor speed. “This allows the pasteuriser to dynamically adjust to match the line behaviour within a range of 50 to 105% of the nominal capacity for most processes without making any drastic changes to the pasteurisation units and maximum product temperature,” states Knut Soltau, product manager for Bottle Washers and Pasteurisers at KHS. This prevents the corresponding consumption of media and at the same time has a positive impact on the behaviour of the entire line. With a new program for PU control the customer can independently adapt the pasteurisation unit setpoint for a specific container type. Here, the full functionality of the PU control unit is maintained. “In this way subsequent product changes or new products can be easily made or introduced at any time,” says Soltau. “Bottlers can thus react quickly to changes on the market and product trends.” Improved design KHS has also made several improvements to the design of its Innopas SX, with emphasis on easy operation. The tunnel pasteuriser is clearly structured; optimum access simplifies the maintenance and cleaning of the system. For this reason, parts of the process engineering, such as the heat exchangers and media supply, have been relocated on the machine as modules in order to further improve servicing and machine safety. Spare part management for the KHS Innopas SX has also been optimised. The number of components the customer is required to keep in stock has been reduced while the delivery times for spare and wear parts have been shortened, meaning that functions can also be simply retrofitted as an option. www.khs.com The Innopas SX tunnel pasteuriser product development caps & closures design high cavitation moulds multi-component moulds closure production systems after sales service competent – professional – inspiring Dr.-Walter-Zumtobel-Strasse 9 | 6850 Dornbirn | Austria | www.z-moulds.com FAKUMA 2018 October 16th-20th meet us at booth A7-7502 Mould at FAKUMA 26mm 3-start water, 72-cavity @ENGEL, booth A5-5204,@ID:25}, MOULD MAKING PETplanet Insider Vol. 19 No. 10/18 petpla.net 16 Bottle base for highly carbonated beverages in ultralight bottles A base for bubbly beverages The Sidel StarLite family of bottle base solutions is expanding through the StarLite UltraLight for carbonated soft drinks (CSD). As the name suggests, this design allows for a lighter bottle than the existing solutions in the beverage marketplace. By lowering the product costs while maintaining the expected level of carbonation, this solution addresses the discount chains’ needs for more affordable products while ensuring a good product quality. The Sidel StarLite UltraLight base has been designed for highly carbonated beverages with a short distribution stream. “As such, it lends itself perfectly to CSD and sparkling water - CSD containing up to 8.4 g of CO 2 /l; sparkling water typically containing 3.2 g CO 2 /l - and is sold in countries with a more temperate climate through hard discount supply chains, applying regular stock rotation,” explains Laurent Naveau, Packaging expert at Sidel. Just like the other propositions in the Sidel StarLite range, the new base design decreases the amount of raw material needed to produce PET bottles. “The optimum bottle base design results in a staggering 25% lighter bottle weight compared to a traditional CSD bottle at around 13.5 g, contributing as a whole to reduced production costs while maintaining carbonated beverage quality,” adds Laurent. Whereas a traditional 0.5 l CSD bottle weighs 13.5 g, the very lightweighted StarLite UltraLight CSD only weighs 10.5 g. When it comes to the 1.5 l bottle, it now weighs 24 g rather than a traditional bottle, which is normally at 28 g. The innovative CSD bottle neck design features a 26/22 neck finish with a weight of 2.3 g, a thread diameter of 26mm, an inner diameter of 21.7mm, and a height of 13mm. Referenced at CETIE (the International Technical Center for Bottling and related Packaging), the bottle neck can be combined with the new Novembal cap, the Novasoda 26/22 for carbonated beverages. Robust and tight to preserve the beverage quality, this one-piece closure is easy and safe to apply, open, and reclose, says Sidel. By optimising the amount of PET required to manufacture the bottle, the new Sidel StarLite UltraLight CSD base offers a substantial reduction in Total Cost of Ownership (TCO). For example, for a 0.5 l bottle the total yearly production PET savings for the new base combined with the new neck would be at € 1,125,000, states the company. Looking at the 1.5 l bottle, the yearly production PET savings would amount to a total of € 1,530,000. This cost estimation is based on a bottle production on a Sidel SBO 20 blower, running at 2,400 b/h/m, 5,000 h/a, for a PET cost of € 1,580/ton (source PCI - April 2018). The bottle featuring the StarLite UltraLight CSD base also includes a patented design, which combines the base with an optimal body shape. It is intended to offer functional benefits without compromising on attractiveness and brand differentiation potential. “When opening the bottle with a firm hand grip, there is no splashing due to the rigid waist embedded in the structured bottle design,” comments Laurent. Additionally, the good base seating surface eliminates any risk of bottle base distortions, as such contributing to perfect bottle stability. Moreover, production speed can reach up to an output rate of 2,500 bphm. www.sidel.com MOULDspecial,@ID:18}, MOULD MAKING PETplanet Insider Vol. 19 No. 10/18 petpla.net 20 A petaloid mould base for CSD Almost a year after the commercial launch of BaseMax, Moldintec’s bases for CSD PET bottles, two new releases have evolved that use laser machining technology and a proprietary software development for freeform laser metal ablation. Testing takes place in customer plants as well as with manufacturers of OEM blowing machines. The blowing of CSD beverage bottles is increasingly challenging in terms of speed, energy consumption and the unprecedented lightweighting possibilities. As far as bottle bases are concerned, Moldintec’s engineering team used the BaseMax original mould design as a starting point to redefine the cooling circuit, improving the heat transfer for reduced contact time between the PET and the aluminium base. The blower operating as a standalone machine emphasises the cooling of the mould as no water jets, spray or air cooling after blowing are permitted for global bottling systems. The geometry of the BaseMax petaloid is designed to be copiable even at extremely low pressures, but the pushup-less design requires that the mould accurately controls the material cool down even at 2,550 b/m/h. The design and manufacturing of these two test base sets involved the integration of a multiplicity of resources. The first version is a mono-material BaseMax laser, which evolved by applying a freeform venting frame machined by laser. The 5-axis laser ablation capability enables Moldintec’s engineers to design the venting channels freely, ensuring that the pressure between the preform and the mould always remains low, even on the complex shape of a BaseMax petaloid surface. The patented continuous venting concept provides a solution to extracting the air exactly where it is pushed by the preform during the blowing stage. The laser ablation creates a singular shape without the limits of small milling tools. “electrical discharge machining (EDM) is not an option for us”, says Diego Taboada, CTO of Moldintec “due to the extra delivery time and costs that are related to EDM. A laser offers unique technology to go from CAD to the part in a single step.” The second version is a BaseMaxHybrid solution. This mould concept combines the Moldintec technology of 3D continuous venting, thermal isolation from multi-material construction and the innovative laser manufacturing process. This hybrid concept is under development mainly for large-sized containers, where the thermal control of the cavity is critical to improving the stress cracking performance. The manufacturing concept allows optimal cooling of the amorphous zone while the energy from the oven is retained to improve heel formation. Test run under real plant conditions Reducing the final blowing pressure immediately translates into a multiplicity of savings. These include a lower consumption of electrical energy, less maintenance of the air compression equipment, less equipment investment and the consequent MOULDspecial,@ID:22}, CAPS & CLOSURES 30 PETplanet Insider Vol. 19 No. 10/18 petpla.net laboration that led us to develop the three grades of Lucene we have.” He described SM100 as a leading candidate for light weighting of applications. “What we are doing is striving to deliver the optimum solution for the market. HDPE made with metallocene catalysts produce a lower proportion of volatile components during polymerisation. That means they are cleaner while, at the same time, providing a good match for lighter caps.” The lower VOC (volatile organic compound) content has already been put to good use, in the automotive industry, where they enable OEMs to produce interiors that meet ROHS (restriction of hazardous substances) standards more easily. Testing for perfection Bae and Joon led a tour of some of the testing facilities at the Daejon complex. As well as the molecular structure, LG tests the material it produces on the same types of machines that its customers use. “We test mechanical properties, as well as resistance to environmental, heat and pollution factors,” said Bae. We put our compounds through a range of tests that demonstrate to our customers that they will do the job they want. We have had to invest in up to date testing and metrology machinery, both to measure what we have done and to understand customers’ needs. We test integrity, leakage under different conditions, stress resistance and performance with water, CSDs, juices, dairy, edible oils and the whole spectrum of products.” For LG Chem, consistency and a worldwide distribution network are crucial. Its customers, such as closure system manufacturers, and worldclass producers of popular CSDs, dairy and other drinks, are global companies themselves. “We produce in Korea but we export across the world. We have customers in Korea and Japan who are conservative in their approach to subjects such as light weighting; while those in the USA and Italy, for example, are rapid adopters,” said Joon. “The brands want to maintain the same product quality, worldwide. LG Chem is driving to be recognised as a global leader. We can supply the same materials everywhere, from Europe to Asia, North America to India and Africa. Wherever our customers are, we can deliver – both traditional products and groundbreaking new materials, such as Lucene.” www.lgchem.com LG Chem’s Convergence R&D Complex, the LG Sciencepark,@ID:32}, PETpatents www.verpackungspatente.de PETplanet Insider Vol. 19 No. 10/18 petpla.net 56 Preform Intern. Patent No. WO 2018 / 020817 A1 Applicant: Yoshino Kogyosho Co. Ltd., Tokyo (JP) Application date: 30.5.2017 A specially designed preform is described for manufacturing a bottle that is formed by unscrewing a cap and filling with a liquid. Superimposed base Intern. Patent No. WO 2018 / 025032 A1 Applicant: PET Engineering & Services Srl., Bergamo (IT) Application date: 2.8.2017 On the base of a plastic keg, a bell-shaped base is applied and fixed. The type of fixing/connection of keg and base has been improved. Sturdy light bottle Intern. Patent No. WO 2018 / 037052 A1 Applicant: Krones AG, Neutraubling (DE) Application date: 23.8.2017 The international application describes the shaping of a lightweight plastic bottle made from PET, which offers sufficient stability during handling, even after opening and despite reduced material use. This is achieved by a shape with crossing straps. Plastic container Europ. Pat.issue No. EP 3048059 B1 Applicant: Krones AG, Neutraubling (DE) Application date: 1.7.2013 A European patent is issued for the filling procedure and shaping of a plastic bottle with a straight-lined mouth area. Container with handle Intern. Patent No. WO 2018 / 050376 A1 Applicant: Krones AG, Neutraubling (DE) Application date: 11.8.2017 Design, mechanism and procedure for manufacturing a container for several bottles. Plastic bottle surface Intern. Patent No. WO 2018 / 051509 A1 Applicant: Suntory Holdings Ltd., Osaka (JP) Application date: 16.9.2016 The surface of a PET bottle features specially formed patterns / indentations / embossing of 1-100mm2 to improve stability, handling and appearance.,@ID:58}, MOULD MAKING PETplanet Insider Vol. 19 No. 10/18 petpla.net 12 Solution provider for the single stage market Leveraging advantage by Ruari McCallion R&D Leverage in Sutton in Ashfield, near Nottingham, England, is the European site of an Anglo-American enterprise that uses its knowledge, experience and expertise to provide unusual and often unique solutions to customers in a range of businesses. Its ‘one-stop shop’ offer, from idea to commercial tooling, has enabled it to survive and prosper as an independent toolmaker and contractor through some challenging business periods. While it makes conventional stretch blow-mould equipment, its focus on single-stage technology sets it apart from most businesses in the field and has helped it to generate market-leading levels of growth. It is always interesting to speak to Alan Tolley, Managing Director of R&D Leverage in Sutton in Ashfield, UK, because there always seems to be something new going on. Our last site visit, three years ago, was to the official opening of its Product Solutions Laboratory (PSL), a facility dedicated to taking customers’ ideas and turning them into market-ready solutions. It was quite groundbreaking at the time – but time moves on. As we pass the bottle / jar inspection area, Mr Tolley points out a machine that still has the aura of newness about it, “That’s our new Torus. It measures everything: wall thickness, finish, body internal dimensions, height – everything,” he said. He indicates another recent addition: a drop test, then there’s a vacuum machine; a shadowgraph for measuring threads; a hydrotracer for making sure that all the material is dry. A vacuum machine and an oven and climate simulator. “We ship across the world, from South Africa to Russia, to Indonesia and to China. We have customers who will want a bottle inspected after it has been sitting for 50 hours at 40 degrees Celsius,” he continued. “In Russia, bottles or preforms might be sitting for months in a warehouse in sub-zero temperatures, so this machine is a fridge as well as an oven. You can put the bottles in there at below freezing or halfway to boiling point, leave them for however long, then bring them out and inspect them, to see how they’ve performed.” There is a lightbox that uses polarised light to detect faults in preforms; it is only a month old. All this equipment is new since our last visit. “We also added two CMMs (coordinated measuring machines) about 18 months ago in the tool manufacturing site, along with camera technology measuring equipment. They physically measure metal, the tools, the components of them, to qualify and validate that everything is to specification. If ever there is a query from a customer, we can pull up all our records and make sure we have delivered what they asked for. “The company has to invest heavily,” Tolley said. It is essential; the customer base is expanding and it is also demanding. “Our commitment to investment in technology has taken us from where we were, in a niche market, to where we are now. We are not simply a general engineering company; we are a Global solutions provider.” While it can work with preforms, two-stage manufacture and with a range of packaging materials – including recycled PET - the UK operation has maintained its focus on single stage tooling production. It has been rewarded with remarkable levels of sales growth. Core business: Tooling “Our core business is tooling and I think we are now being recognised as the leaders in our field,” he said. The company’s salespeople speak nine different languages, reflecting the global nature of its customer base. MOULDspecial R&D Leverage’s core business is tooling.,@ID:14}, MOULD MAKING PETplanet Insider Vol. 19 No. 10/18 petpla.net 19 Cap-mould design Integrating cap-mould design with machine development, as well as consultancy offers big advantages in terms of a longer mould lifespan. Final performance is guaranteed thanks to the careful selection of materials and linings and the mechanical precision of components. “We should bear in mind that the cost of raw materials accounts for 50 to 70% of all finished closure costs. That’s why the development of lighter caps and preforms, together with guaranteed process repeatability makes all the difference, both with customers who operate directly on consumer markets and those companies which, in turn, have to supply large beverage groups according to well-defined design specifications”. Davide Penazzi, who is responsible for closure moulds as well as IPS (injection preform system) preform moulds explains, “Generally having in-depth experience with closures ensures we are well recognised and respected with converters. Even in the most competitive markets, customers will tend to evaluate solutions offered by Sacmi as we have a reputation as a reliable partner, from project to product and after-sales service”. The machine size has shifted towards 72 and 96-cavity solutions, with parallel development of the Sacmi range in terms of both machines (IPS 400) and the relative moulds. “Increasing the number of cavities per machine”, illustrates Penazzi, has brought significant economic savings”. Sacmi has achieved this by decisively developing their processes (i.e. through automatic preform handling to reduce the risk of deformation, contamination or breakage as well as the capacity to ‘go light weight’ by proposing integrated cappreform solutions). For some time now, Sacmi has invested in new plant engineering to make a progressive reduction in medium sizes (with the dual-cavity SBF stretch-blower range). It has done so by simultaneously improving the mould concept as well as the process to guarantee a more assured finished product performance (in the plant, during transport, on shelves, in storage). “The blown bottle”, explains Lorenzo Casadio, technical manager of Sacmi Beverage, “is a delicate, complex product in which the most important competitive factor is the capacity to provide the customer with a complete service, from bottle design (and, consequently, mould design) to guaranteed technical performance of the product in terms of resistance to impact, falls and temperature variation etc.” Sacmi also engages in numerical simulation that uses finite element analysis techniques: “These techniques”, states Casadio, “make it possible to simulate product performance without costly lab testing and provide solid guarantees on the subsequent industrialisation phase.” With regards to the required technological characteristics of the mould, Sacmi has designed and patented a system that lets manufacturers blow bottles at low pressure. It provides system airenergy savings and it downsizes the line compressor. “A third, often forgotten advantage, is longer-lasting mechanical machine and mould components as the lower pressure means they are subject to less stress”, observes Lorenzo Casadio. The challenge being faced by stretch-blowing – similarly to developments taking place in the closures field – consists of the shorter on-shelf life-cycle of the bottle and ever-greater demand for weight reduction. “That’s why” concludes Casadio, “the Sacmi solution focuses on reducing line set-up times and numerical simulation techniques. Having a set of machinemoulds with automatically set recipes at your disposal makes start-ups much faster. A complete solutions provider is able to govern all these aspects much more accurately. And that’s the approach we want to take: to extend our current range to include production areas and formats that go beyond those where Sacmi already enjoys outstanding market recognition”. www.sacmi.it Oct. 24-26,2018, Mumbai Hall 1, Booth K35 German Technology Moulds for the CCM Sacmi machinery,@ID:21}, CAPS & CLOSURES 28 PETplanet Insider Vol. 19 No. 10/18 petpla.net LG Chem introduces Lucene HDPE for caps and closures Customised caps and closures by Ruari McCallion The Korean giant LG Chem is positioning itself as a “solution partner” and collaborator, rather than just a supplier of commodity plastic raw materials. Ruari McCallion visited the company headquarters in Seoul and its polyolefin R&D facility at Daejon, South Korea. LG Chem, headquartered in Seoul, South Korea, is a world-class supplier of polymers, which generated sales of US$17.8bn in 2016. It employs 26,660 people across the world; it has 14 manufacturing subsidiaries, located in China, Korea, Hong Kong, Japan, India, SE Asia, USA and, since 2005, at a site in Wroclaw, Poland. While its principal markets have, for historical reasons, been primarily in the Far East it is eager to sell its products all across the world. In its drive to forge a strong presence in a competitive market, it is seeking to prove itself as a solutions provider, a company that understands customer needs and designs products to suit. Its recent launch of Lucene, an HDPE (high density polyethylene) based on LG’s own metallocene catalyst technology, is part of this strategy. LG started producing lowdensity polyethylene (LDPE) in 1991, when it manufactured a total of 150,000 t. The first shipments of HDPE followed a year later. Its vertically-integrated production operation refines crude oil into naphtha, which is then used to produce a range of petrochemicals including ethylene and propylene. The company’s total output of EVA, PP, POE, LDPE and HDPE now exceeds 1,460 kt, of which approximately one-third is HDPE. Growth in future is expected to come from specialist, higher value areas. “We are focused on virgin PE (polyethylene), including HDPE, which we sell to all sizes of companies,” said Mr Kim Ji Hun, known as “Joon”, Sales Manager with the PO (polyolefin) Overseas Sales Team. “The HDPE market is very big but it is also commoditised. By focusing on bottle caps. We are able to concentrate our efforts on a premium, higher-technology and sophisticated market.” Production facilities The polyolefin production complexes are located at Yeosu, on the southern coast of the country and was opened in 1976; and Daesan, on the west coast, which opened in 2005 and is the primary manufacturing site for LDPE and HDPE. It is about 90 minutes’ drive from Seoul. The advantages for food and beverage packaging of PEs, both low and high density, are well known and also extend to pharmaceutical and personal care applications. LG produces the full range of standard HDPEs for food and beverage package closures. It makes a feature of very good organoleptic properties and can remove small-molecule hydrogen in order to prevent negative effects on taste. The launch of Lucene The primary reason for visiting LG Chem was to learn about Lucene, the company’s HDPE based on its propriFrom left: Joon Kim (Sales Manager, LG Polyolefin Overseas Sales Team), Ruari McCallion (PETplanet) and Jo Han Bae (Professional, LG Polyolefin TS Team),@ID:30}, MOULD MAKING PETplanet Insider Vol. 19 No. 10/18 petpla.net 21 reduction of the carbon footprint and its impact on the environment. Collaboration with Sipa was crucial when conducting a real operational test with a 1,500 ml CSD bottle at 2,550b/m/h, says Moldintec. Last September, a test lasting three full days was carried out in the Sipa headquarters laboratory facility. It demonstrated the high process capabilities of the blower and pushed the Moldintec bases to their limits. The first test day was fully dedicated to BaseMaxLaser; the advanced geometry of the BaseMax petaloid is perfectly copiable although at extremely low pressures. Test runs have shown 100% copying of the standing and heel area, obtaining successful results when running at the maximum machine speed of 2,550 b/m/h @24bars. The primary objective was a perfect and smooth material distribution for a 7g base. The second day offered the opportunity to test BaseMaxHybrid. Starting from 2,000b/m/h @20bars up to the peak speed of 2,550b/m/h, it used several processing options like variable blowing timing, heating, stretch rod speed and base weight. “The super flexible process control of the Xtra allows us to emphasise the BaseMax capabilities, producing many material distribution profiles. The Xtra oven offers a bonus when BaseMax requires heating on a specific zone of the preform to go down with the pressure”, says Engineer Nicola Brugnera, head of Sipa’s advance processing team, which took charge of all the testing. The laboratory controls were all passed in accordance with global bottlers’ standards to ensure that the final process will be replicable under real plant conditions. Easy to implement and to retrofit, Moldintec’s new BaseMax solution is said to be fully compatible with new and existing moulds, even if they have been manufactured by another tooling supplier. PLUG & DRY • SCREW ON, PLUG IN AND START • ELECTRIC POWER SUPPLY ONLY • LOWEST ENERGY CONSUMPTION • NEARLY SERVICE FREE • HIGHEST AVAILABILITY • WLAN CONNECTIVITY TO YOUR MOBILE DEVICE EISBÄR TROCKENTECHNIK GMBH WUHRMÜHLE 22 / A-6840 GÖTZIS T +43 5523 55558-0 / F -50 [email protected] / WWW.EISBAER.AT MATERIAL DRIER AS ALL IN ONE UNIT FOR 50 TO 200 KG/H VISIT US AT FAKUMA IN FRIEDRICHSHAFEN BOOTH A7-7312 “Over the last nine months, we have had the opportunity to collaborate closely with one of the leading blowing machine manufacturers in the world to improve our technology. The results encourage us to continue our research to keep us on the blowing edge. We are very grateful to Sipa, especially Engineer Paolo De Nardi, who coordinated and observed these tests”, says Moldintec’s CCO D.I. Jorge Pucci. www.moldintec.com,@ID:23}, TRADE SHOW PREVIEW PETplanet Insider Vol. 19 No. 10/18 petpla.net 51 C L O S U R E I N S P E C T I O N October 25, 2018 - Focus on trends and developments in alcoholic beverages in India Company Speaker Topic Bohemia Beer Pvt. Ltd. Mr Rakesh Dhawan, Director The trends in the beer industry Boroton Research Centre Pvt. Ltd. Mr Yogesh R. Bhandane, CEO Trends and needs in the wine industry Carlsberg India Pvt. Ltd. Mr K. N. Gopalakrishnan, Head Brewery & Processing India’s beer industry: current trends and challenges John Distilleries Pvt. Ltd. Vijay Kauthekar, Head Sales & Marketing Consumption trends in the alcobev sector in India Sula Vineyards Pvt. Ltd. Mr Gorakh Gaikwad, Associate Vice President & Sr. Winemaker Overview of Indian winemaking The Biere Club (Elite India Constructions Pvt. Ltd.) Mr Rohit Jairam Parwani, Head Brewer Micro breweries in the world of macro breweries and the importance to brew with local ingredients Tilaknagar Industries Ltd. Dr Keshab Nandy, Director The right drink in the right place: alcoholic demands of different target groups and occasions in India Vbev Mr Sumedh Singh Mandla, CEO Trends in the Indian alcobev industry,@ID:53}, TRADE SHOW PREVIEW PETplanet Insider Vol. 19 No. 10/18 petpla.net 47 TRADE SHOW PREVIEW 47 Each of the two process has its own merits depending on the market volume and end-use of the bottle. As the world’s leading one-step machine manufacturer, ASB recognised the merits of each system and combined them into a moulding system that became known as 1.5-step moulding. In this process, preforms are injected in a greater number of cavities, partially cooled to maximise stability then temperature conditioned before being passed to a blow mould containing 1/3 the number of cavities of the preform mould. Since it normally takes around three times longer to injection mould a preform than to blow a bottle, this means that each part of the machine is now operating at maximum utilisation. The result is a very compact bottle moulding machine that operates at high efficiency and yet can produce the highest quality of finished bottle because, as in the onestep system, preforms are never released so there is no risk of scuffing or neck deformation. In order to achieve the same output by two-step moulding at least 2-3 times the factory floor area would be required, and the container visual and neck quality would be significantly lowered. Additionally, by moulding the preform within the same machine that the bottle is blown, the hygiene of the preform and finished bottle is of the highest possible level making the machine ideally suited to an in-line filling operation for beverage products, states the company. At China Brew & Beverage 2018 the machine will demonstrate live moulding twice daily and the booth will include a wide range of samples and displays of other specialised technologies fromASB. The booth will also be exhibiting a full line of matched moulding ancillary equipment that ASB is able to supply, such as resin dryers, chillers, mould dehumidifiers and mould temperature controllers. www.nisseiasb.co.jp ! ! \ #$% %% &''% (((( #$% $(%%)*$%+$ #$% $(%)),&,+' - ! ! Vertical injection mould in a compact 3-row layout (PF36/36-600) PF36 1.5-step operation principle, blow station has 1/3 the number of injection cavities and operates three times per injection cycle,@ID:49}, 52 PETplanet Insider Vol. 19 No. 10/18 petpla.net 52 PETproducts Moulds for linear and rotary machines Awanti Polymoulds is a manufacturer and exporter of PET blow moulds for various product applications, such as packaged drinking water, carbonated soft drinks, warm-fill and hot-fill juices, edible oil, pharmaceuticals and liquor. In the Awanti facility in Pune, India, moulds are manufactured for linear machines (up to 9 cavity in-line moulds for 200bpm line) and for rotary machines (up to 720bpm), including high-speed lines and Combi lines. The facility is equipped with CNC machines, special purpose machines, advanced CAD-CAM software and a world-class blowing machine for mould testing. There is also an international-standard laboratory with high-precision instruments for conducting over 15 different quality tests, such as stress crack tests, burst tests, thermal tests, top load tests or material distribution tests, amongst others. In addition to moulds, Awanti also manufactures auxiliary parts, such as shell holders for rotary machines, base cooling plates or cooling connectors. www.awantipolymoulds.com braubeviale.de MAKING YOUR BUSINESS SUCCESSFUL. BrauBeviale is where you cultivate success – in dialogue as an equal partner, with experts in the sector, with innovations that give you a competitive edge. Everything you need for tomorrow – in a single venue. For exhibition highlights and important information for your visit: braubeviale.de/Your-Success Good business. Good conversations. Nuremberg, Germany | 13 – 15 November PETproducts Rotary mould for 600bpm line MOULDspecial,@ID:54}, TRADE SHOW PREVIEW PETplanet Insider Vol. 19 No. 10/18 petpla.net 43 China’s beer and beverage market Round Table Talks This year’s Round Table Talks focus on trends, technologies, market demands and future outlooks of China’s beer and beverage market. On October 24-25, 2018, 2.00 pm - 5.00 pm., visitors of China Brew China Beverage are invited to join the Round Table Talks free of charge. ADHESLEEVE® TECHNOLOGY THE BEST SOLUTION FOR ROLL-FED LABELLING EVEN ON CANS! CHINA BREW CHINA BEVERAGE OCTBER 23 – 26, 2018 SHANGHAI, CHINA HALL W2 | BOOTH # 2-A62 BRAU BEVIALE NOVEMBER 13 - 15, 2018 NUREMBERG, GERMANY BOOTH # 7-315 PACK EXPO INTERNATIONAL OCTOBER 14 – 17, 2018 CHICAGO, USA BOOTH # S-3620 ProMachBuilt.com | PELabellers.com LABELS APPLICATION WITHOUT HOT MELT GLUE. EASY LIKE SCOTCH-TAPE! EVEN MORE! The first eco-friendly linerless labeller using pre-glued films. 100% ecologic and recyclable product. Also for empty containers. Adhesleeve + thermal-shrinking system. More than a valid alternative to the sleeve application. organised by PETplanet Insider Company Panelist Topic Demag Plastics Machinery (Ningbo) Co., Ltd. Mr Alan Min, Key Account Manager Packaging Efficient closure systems in focus Engel Machinery (Shanghai) Co., Ltd. Mr Kurt Hell, Director Business Unit Medical/Packaging Challenges in producing light weight caps and closures GDXL Precise Machinery Co. Ltd. Mr Patrick Lam, Sales Director Product shelf life extension – A review on ideal solution Jiangsu Newamstar Packaging Machinery Co., Ltd. Mr Wesley Yin, Head of Marketing Packaging trends and technologies for beer and beverages Shanghai Beverage Association Dr Chen Jie, Vice President Globalisation and tendency of beverage development Suntyech Process Engineering (Shanghai) Co., Ltd. Mr Shao Jinrong, CEO Traditional flavours translated to modern products and packaging trends Voss (Hubei) Water & Beverage Co., Ltd. Mr Xia Jinshun, General Manager Water and packaging trends for bottled water in China Programme extract as of September 27, 2018,@ID:45}, PETcontents 10/18 4 PETplanet Insider Vol. 19 No. 10/18 petpla.net INSIDE TRACK 3 Editorial 4 Contents 6 News 52 Products 53 On site 54 PET bottles for Home + Personal Care 55 PET bottles for Beverage + Liquid Food 56 Patents MATERIAL / RECYCLING 10 Flakes flying by - Sorting solutions for bottles as well as for flakes 11 PET recycling all-in-one - CarbonLite processes PET fines with Starlinger recycling line MOULD MAKING 12 Leveraging advantage - Solution provider for the single stage market 14 192 cavities evenly filled - Keeping balance with ultra-high-cavitation hot runner systems 16 A base for bubbly beverages - Bottle base for highly carbonated beverages in ultra light bottles 18 Moulds for beverage-closures lines 20 A petaloid mould base for CSD BOTTLING / FILLING 23 Microbiological safety - Flexibility in the pasteurisation process CAPS AND CLOSURES 24 All-HDPE sports cap - Coca-Cola Amatil breaks new ground with fully recyclable sports cap 28 Customised caps and closures - LG Chem introduces Lucene HDPE for caps and closures MARKET SURVEY 31 Suppliers of caps and closure moulds, systems and inspection TRADE SHOW PREVIEW 35 Fakuma 2018 42 China Brew China Beverage 2018 49 drink technology India 2018 BUYER’S GUIDE 57 Get listed! Page 12 Page 36 Page 54 24 MOULDspecial,@ID:6}, 38 TRADE SHOW PREVIEW PETplanet Insider Vol. 19 No. 10/18 petpla.net 38 TRADE SHOW PREVIEW Smart operation advances injection moulding Netstal will be introducing the Smart Operation control option. With its new operating philosophy, the new option for the aXos machine controller offers a sensible separation of the development of applications and the subsequent operation of the machine in the production environment. The benefit is the increase of the effectiveness of the production plants. High-performance injection moulding machines are complex systems. The wide range of applications requires a high degree of individualisation when developing applications. In a production environment, however, it’s all about a control concept that is as intuitive and safe as possible. Netstal’s answer to this requirement is called “Smart Operation” and will be in action at Fakuma for the first time. An Elios 4500 will be in operation at the Netstal booth. Guided and safe operation The aXos controller offers high flexibility when it comes to programming a wide range of injection moulding applications. Based on the application, all processes can be flexibly defined by in-house experts. Smart Operation provides users with an innovative operating concept to be used in a production environment. It consists of four new buttons, the so-called Smart Buttons, as well as a pre-configurable dashboard on the main screen for the illustration of relevant process information, situational interaction notifications as well as application-specific instructions. Smart Operation builds on the concept of clearly defined machine conditions. The new Smart Buttons trigger status transitions during the production process. This means that with the push of just three buttons, the machine can be turned on, prepared for production and begin production. Once the production can be ended, the machine turnes off just as quickly, easily and safely. Improved safety and effectiveness Thanks to the safe and guided operation, the high availability of the Netstal machine is increased even further. Incorporating handling guidelines into the machine controller, coupled with the guided operation, is an effective way to prevent operator errors, states the company. “Through Smart Operation, we are helping our customers achieve their effectiveness goals over the long term by keeping unit costs low while maintaining a consistent quality”. Smart Operation is available now as an option on all Netstal machines of the Elios and Elion series. Existing plants that use an aXos controller can be retrofitted. www.netstal.com Hall A7, booth 7303/7304,@ID:40}, MATERIALS / RECYCLING PETplanet Insider Vol. 19 No. 10/18 petpla.net 10 Sorting solutions for bottles as well as for flakes Flakes flying by Do you remember Byron Geiger, a PET recycler from Alabama we reported on in PETplanet Vol. 06/2018 who is really struggling with poorly sorted PET material? His problems could be solved by the sorting technologies presented by National Recovery Technologies (NRT) which promise sorting rates higher in speed and efficiency as well as less human interference in the sorting process itself. Interview with National Recovery Technologies (NRT) April 4, 2018 We met: Mr Travis Curtis, Outside Sales Manager NRT, located in Nashville, Tennessee, is an equipment manufacturing and engineering company specialised in sorting solutions for the recycling industry. The merger with Bulk Handling Systems (BHS) in 2012 now allows NRT to offer fully integrated solutions for the sorting of waste, from household single stream waste to precisely sorted components. Sorting bottles In order particularly to improve the recycling of PET, NRT developed an advanced infrared sorting system, NRT SpydIR, which separates numerous polymers and composite materials from a mixed stream. In this process NRT uses its In-Flight Sorting technology, one of its numerous patents in this field. Typically, the items are carried over a belt. Once they pass the end of the belt the ejection system of compressed air ejects foreign items. The difference between ordinary overthe-belt sorting and In-Flight Sorting is the point in time of detection through near infrared spectrometry. As already indicated by the names of the technologies, this happens either on the belt or directly in flying motion immediately before the ejection. The latter technology allows for a significant improvement in the sorting result due to the decreased time gap between detection and ejection. Hence, the risk of unpredictable movements of the items between these two steps and errors associated is thereby reduced. Furthermore, interferences on the belt no longer have any impact on the detection performance. Last but not least, In-Flight Sorting enables not only reflective but also transmissive detection allowing for the detection of thin-wall, wet and full-sleeve labelled PET. In order to enhance this effect NRT SpydIR is additionally equipped with the PET Boost technology using algorithms to boost weak detection signals. Sorting flakes Additionally, since 2015, NRT and Buhler Sortex, a member of the Bühler group, have joined forces in order to combine top-notch expertise in the field of optical flake sorting technologies. This summited in the development of Sortex A. Sortex A is a high speed PET and HDPE flake sorting solution which provides a throughput of 5 t/h – the highest throughput in the industry. Foreign items are detected with help of high-definition colour cameras and broadband LED lightning. In order to elevate the targeting result tiered chutes accurately separate the flakes from each other. Unwanted flakes are then ejected by the SmartEject system located directly under the chute. Depending on the desired result – either high output or high purity – of the separated flakes the algorithm`s sensitivity of the SmartEject can be adjusted. Latest development The Max-AI AQC (for Autonomous Quality Control), NRT’s latest development, is able to take multiple sorting decisions autonomously. With the help of a machine vision system to see and artificial intelligence to identify different materials only by form and to target and to prioritise, a robot then picks items correspondingly. The advanced system can be further trained in accordance with changing waste streams. The Max-AI AQC capability of up to 65 picks per minute exceeds such of humans. Installed in combination with an NRT optical sorter human contact to waste can even be eliminated entirely. www.nrtsorters.com NRT has integrated the company’s SpydIR optical sorter with Max-AI technology. The SpydIR technology uses near infrared light (NIR) detection to identify materials by type; Max-AI technology uses artificial intelligence (AI) to identify materials using a camera and neural network algorithm (NN). Unifi, Inc.’s Repreve Bottle Processing Center in Reidsville, N.C. features the latest in separation technologies from the BHS family of companies, including NRT. The Editourmobil at NRT in Nashville, Tennessee Tour Sponsors:,@ID:12}, PETplanet Insider Vol. 19 No. 10/18 petpla.net 55 BOTTLES PETbottles Beverage + Liquid Food Jelly Beans in a miniature bottle The American manufacturer Jelly Belly is packing 42 g of jelly beans into clear miniature bottles. The bottle is sealed with a simple, push-on hinged cap. The sleeve label is drawn up over the cap and protects the Soda Pop Shop products, which are reminiscent in taste to well-known drinks like 7Up or A&W. www.eu.jellybelly.com Canada Pure in a blue bottle The Canadian manufacturer Canada Pure is selling its eponymous, lightly carbonated drink in a blue 445ml bottle. The drink is slightly sweetened with sucrose and one bottle contains 90kcal. No sweeteners or artificial flavours are used. The bottles are decorated with a transparent foil label around the body and the different flavours can also be easily identified by the colour of the tamperevident screw cap. www.canadapure.com Bottles designed by artists Under the name “Arto Lift WTR”, the brand belonging to PepsiCo has enabled as-yet unknown artists to design bottle labels. The “Purified Water, pH Balanced & Electrolyte for Taste” is bottled in clear PET bottles holding 700ml. The transparent, self-adhesive labels are printed with the motifs of each artist and offer colourful variety on the shelves. Each edition is available for a limited time only and is replaced by a new art edition. The seal is a screw cap with a tamper-evident seal. www.lifewtr.com,@ID:57}, 45 TRADE SHOW PREVIEW PETplanet Insider Vol. 19 No. 10/18 petpla.net Booth 1B31 in Hall W1 Agility 4.0 programme Sidel and Gebo Cermex will be showcasing the Group’s commitment to future-proof solutions with the Agility 4.0 programme, which is intended to bring smart factories to life and to create a world of greater choice and unique consumer experience. Also featured will be performance-based services, which focus on maximum equipment availability and a shorter time-to-market. Both Sidel and Gebo Cermex are showcasing their new modular maintenance agreements at CBB 2018: the ‘Time & Material’ agreement for tailored preventive maintenance and the ‘Fixed Price’ agreement for condition-based maintenance at a fixed cost. These new additions are specifically designed to strengthen the Group’s Services portfolio through a holistic approach to preventive maintenance, helping customers to maintain performance at an optimum level throughout their production. An additional highlight at the show will be the Sidel Services Online platform, a user-friendly web interface for fast and easy ordering of original spare parts, options and upgrades. Other market-tailored solutions highlighted at the show include the Sidel Aseptic Combi Predis, an integrated blow-fillseal-filler solution with dry preform sterilisation, the new patented base mould system Base OverStroke System (BOSS) and the Sidel Super Combi, which integrates five process steps into one single system: preform feeder, blowing, labelling, filling/ capping and cap feeder. www.sidel.com www.gebocermex.com Via Scodoncello n° 41/E - 43044 Collecchio (PR) - Italy - Tel.: +39 0521 541011 Everything and more... cooperating together global solutions for containers in PET and other plastic materials Design, construction & installation of: • Systems for handling & storing all types of plastic containers • Linear blow molders for PET bottles LANFRANCHI S.r.l. www.lanfranchi.it innovation plastic container Design, industrialization, blow molds & prototype sampling for PET containers IPC S.r.l. www.ipcsolution.it,@ID:47}, 39 TRADE SHOW PREVIEW PETplanet Insider Vol. 19 No. 10/18 petpla.net From raw material production through to recycling systems For the first time at Fakuma, Maag will be sharing a stand with filter manufacturer Ettlinger, which joined the group in January this year. As a result, Maag will be offering products for applications from raw material production, through compounding, to recycling, all from a single source. The range of products shown will encompass a gear pump for high pressures, a dry-cut strand pelletiser as well as an underwater pelletising system for the production of spherical pellets finishing with a high-performance melt filter with an extra-fine filtration grade for bottle-tobottle PET recycling. The Eco 200 high-performance melt filter from Ettlinger being presented at Fakuma 2018 is – like the larger Eco 250 version – designed for very free-flowing materials such as PET and PA with pollution severities up to 1.5 %, but is also suitable for polyolefins and polystyrenes. Typical applications are compounding and filtration of gels and agglomerates, in particular of aluminum, paper, silicone or PVC constituents from recycled PET bottles. The now available extra-high filtration grade of 60 μm is stated to be ideal for bottle-to-bottle recycling. Thanks to their efficiency, the Eco melt filters can be integrated directly into PET thermoforming lines, where their throughput rates of up to 1,000 kg/h (type 200) and 3,000 kg/h (type 250) help to improve machine availability and enhance cost-effectiveness. www.maag.com Hall A6, booth 6202,@ID:41}, PETnews 6 NEWS PETplanet Insider Vol. 19 No. 10/18 petpla.net PepsiCo to more than triple rPETcontent to 50% in the EU by 2030 PepsiCo announced its goal to achieve 50% recycled plastic (rPET) in its bottles by 2030 across the European Union, with an interim target of 45% by 2025. Through this target, the company will more than triple the amount of recycled plastic it uses, equating to over 50,000 t of rPET. The announcement comes in support of the European Commission’s voluntary recycled plastics pledging campaign to ensure that by 2025, ten million tonnes of recycled plastics are used to make new products in the EU market. PepsiCo’s goal covers all countries expected to be members of the EU in 2025 (with the UK covered through a signature on the UK Plastics Pact), and all the company’s beverage brands in PET including Pepsi, Pepsi MAX, 7Up, Tropicana and Naked. PepsiCo is already a significant user of food grade rPET in the EU, using approximately 13% rPET in its EU beverage operations in 2017. Silviu Popovici, President ofPepsiCo Europe & Sub-Saharan Africa commented: “Developing an effective, long-term approach to sustainable packaging requires a multifaceted effort, and PepsiCo is committed to collaborating with the many stakeholders involved to ensure it succeeds in developing a Circular Economy for plastics into the future. With serious under-capacity in the supply of affordable recycled plastics suitable for food packaging, we call on public and private stakeholders in the recycling system, including the European Commission, to join us and make the needed investments to expand recycling capacity. Provided the right progress is made on increasing packaging recovery rates, and improving reprocessing technology, we will look to go even further than our current commitment.” A critical part of increasing the availability of recycled plastics, suitable for re-use in packaging, is ensuring that bottles are placed in the recycling system, rather than littering the environment. In addition to participating in Extended Producer Responsibility (EPR) schemes across the EU, PepsiCo is partnering on programmes to increase recovery and recycling rates. www.pepsico.com Evian to host 15th Global Bottled Water Congress The 15th Global Bottled Water Congress will be held from October 22-24 at the Evian brand in France. Highlights will include a focus on sustainability, hydration, innovation, marketing and water stewardship, capped by the 2018 Global Bottled Water Awards at a Gala Industry Dinner. Participants of the congress will feature Chief Executives and Directors from many national market leaders as well as a majority of the top global producers. Speakers already confirmed include Danone, Gerolsteiner, Nestlé and PepsiCo as well as Bisleri from India, Niagara from the United States and the Alliance for Water Stewardship. A keynote address on sustainability will be given by Maurizio Patarnello, Chief Executive of world market leader Nestlé Waters. The Congress already has strong supplier sponsorship support with Ardagh Group as platinum sponsor, Bericap, Sidel and Tetra Pak as gold sponsors, and ICE Water Engineering as a silver sponsor. The programme includes an opportunity to visit both the Evian water factory and ICE Water Engineering. “Everyone wants a healthier society and a healthier planet,” commented Richard Hall, Chairman of Zenith, who are organising the event, as well as providing global food and drink consulting expertise. “Bottled water has a growing role to play in sustainable hydration and this Congress is designed to help the industry meet that challenge more effectively.” www.zenithglobal.com/events,@ID:8}, CAPS & CLOSURES 27 PETplanet Insider Vol. 19 Smoother, simpler, easier to maintain “Our responsibility was to provide a machine that would put the plastic through at the right rate,” said Michael Ludemann. “In the design phase, we worked with both PP and HDPE, in parallel, until the decision was made on which material was chosen.” The reality of Australia’s geographical position meant that there was also pressure to produce moulding equipment that would be easy to use and to maintain. “We tried to bring in existing concepts and, finally, we managed it,” said z-Moulds’ Michael Fink. “We simplified the technology. Moulds like that used for the overcap and base have been in the market for 20 years. We sought to simplify how it moves and how many parts it has. The fewer parts are involved, the easier the machinery is to maintain.” Ease of maintenance also means that it will be easier to use in practice. It was kept as simple as possible. All of the partners agreed that the development of the SyLon cap was a success because, although it incorporated and built on existing ideas and experience, there was willingness across the board to consider it as something brand new; it was actually a ‘clean sheet’ project. “It’s very much because of the attitude of CocaCola Amatil, which we have seen from the flat cap (FC) 1881 onwards. They really are driving to be the best in the world,” said Druitt. All of them agreed that the project, while demanding, had been a pleasure to be involved with. “It was not easy; it has been a complex project,” said Husky’s Ludemann. “We have been through some tough times but we The team responsible for getting the Sylon Mercury sports cap from idea to reality at the official line opening. have built stronger relationships out of it.” So: will there be time for a celebration, now that the SyLon cap is successfully launched, and we have seen it produced from pellets to finished product? “No, we haven’t stopped to celebrate,” Furlong laughed. “There’s always something else to be doing.” www.ccamatil.com Contiform 3 Pro #GermanBlingBling #Contiform3Pro We do more. China Brew China Beverage 2018 Shanghai, 23 – 26 October Hall W1, Booth 1Y631,@ID:29}, imprint EDITORIAL PUBLISHER Alexander Büchler, Managing Director HEAD OFFICE heidelberg business media GmbH Bunsenstr. 14 69115 Heidelberg, Germany phone: +49 6221-65108-0 fax: +49 6221-65108-28 [email protected] EDITORIAL Kay Barton Heike Fischer Gabriele Kosmehl Michael Maruschke Ruari McCallion Waldemar Schmitke Anthony Withers WikiPETia.info [email protected] MEDIA CONSULTANTS Martina Hirschmann [email protected] Johann Lange-Brock [email protected] phone: +49 6221-65108-0 fax: +49 6221-65108-28 LAYOUT AND PREPRESS EXPRIM Werbeagentur | exprim.de Matthias Gaumann READER SERVICES Till Kretner [email protected] PRINT Chroma Druck & Verlag GmbH Werkstr. 25 67354 Römerberg Germany WWW www.hbmedia.net | petpla.net PETplanet Insider ISSN 1438-9459 is published 10 times a year. This publication is sent to qualified subscribers (1-year subscription 149 EUR, 2-year subscription 289 EUR, Young professionals’ subscription 99 EUR. Magazines will be dispatched to you by airmail). Not to be reproduced in any form without permission from the publisher. Note: The fact that product names may not be identified as trademarks is not an indication that such names are not registered trademarks. 3 PETplanet Insider Vol. 19 No. 10/18 petpla.net Yet again, it is not just the plastics industry that suffers great losses due to fire or water. And as with all disasters, those most affected are often the least prepared. In 1998 disaster struck the production facilities of the BIG company, known for its Bobbycar. 2002 saw devastating floods at Engel in Schwertberg, which left the factory under two meters of mud, water and boulders. These are just two spectacular examples of natural calamities affecting the plastics industry. On Monday, September 10, Herbold, based in Meckesheim, Germany was hit. A huge conflagration devastated the warehouse and an outdoor storage area, leaving both burnt-out shells. Firefighters managed to salvage the production areas and offices, but the spare parts warehouses and the logistics facility were completely destroyed. Fortunately, there were no casualties, either here, or in the Austrian and German disasters described above. Werner Herbold, one of the two managing directors at the site, estimated the total damage at five to ten million euros. But is there another side to the story apart from the physical damage caused? The two “historic disasters” described above have shown that catastrophes can sometimes generate a hopeful new beginning. Outdated structures can be replaced without any ill effects. Staff come together in a mood of positive cooperation, teams are rebuilt, and suppliers make the impossible possible. At a speed no-one would believe possible, machines and components are quickly replenished, so that everything is up and running. Customers rally in support of the affected company. A year from now, let’s hope that Herbold and all their staff can look back with satisfaction and say: “We’ve done it. The scars left by the fire have now been healed.” For our part, we wholeheartedly wish them every success. Yours, Alexander Büchler PS: Shortly before closing this issue for printing Herbold Meckesheim officially stated: In the second half of October, Herbold Meckesheim will once again be producing at the same level as before the fire, with the additional expenditure covered by business interruption insurance. Dear readers,,@ID:5}, MARKET SURVEY 33 PETplanet Insider Vol. 19 No. 10/18 petpla.net – ONE for ALL STAND E-11019 STAND D05:20 STAND: 6 D 055 Sacmi Imola S.C. IMD Ltd Pressco Technology Inc Via Selice Prov. 17/A 40026 Imola - BO, Italy +39 0542 607111 www.sacmi.com Mr Stefano Severi Vision System Sales Area Manager +39 3356594236 [email protected] Moosweg 1, 2555 Brügg, Switzerland +41 32 366 80 66 www.imdvista.ch Mr Martin Gerber Sales Director IMD Ltd. +41 32 366 80 66 +41 32 366 80 69 [email protected] 29200 Aurora Road, Cleveland, OH, USA +1 440 498 2600 www.pressco.com Mr Tom O'Brien VP, Marketing, Sales & New Bus. Develp. +1 440 498 2600 [email protected] CHS (inspection machine for plastic & aluminium caps) CVS (vision system for plastic & aliminium caps) IMDvista Closure Vision Inspection High-speed Vision System Up to 4,000 pcs/min (CHS), up to 6,000 pcs/min (CVS) Up to 4,000ppmin/ 240,000pph (depending on customers request and product) up to 3,600 ppm Interior, exterior, sidewall In- or off-line solution, downstream solution by IMDvista - from undermould conveyor (UMC) to cooling conveyor (CCS) in the feeding system (WFS) up to the vision inspection (CLCO) and packaging station (BS), integrated as OEM systems in any kind of machine Plastic caps having diameter up to 43mm One piece closures, assembled closures, doy pack closures, oil closures, sport caps, aluminium (longskirt) closures, rubber parts, coffee cups, coffee filters, shampoo closures, medical closures, lens container, pouches, food container Food, beverage, pharma, specialty, dispensing, sport, plug seal or liner, injection or compression moulded Yes, complete (ovality, colour variations, contaminations, black specs, liner or plug seal…) Short shots, overfill & flashs, contamination, seal defects, colour & colour changes, deformations, diameter & ovality, laser marking inspection Yes Yes, complete (includes decoration inspection) 360° outside view, colour and colour changes, contamination, height measurement Yes Yes, complete (diameters, height) Geometry measurements upon request Yes Yes, it can read any type of character font through a smart learning procedure Easy teach in function, cavity recognition, cavity related statistics, cavity related alarm No Yes, through a spark tester device IMDvista Spark for pinhole detection No Cut and bridges of tamper evident band Upon request Wide range of insert types and materials Sidewall can be inspected by means of a peripheral lens or through Sacmi CVS360-3D inspection module; CVS360-3D consists of a sert of four cameras capable to acquire the 360° of the sidewall, making a compensation of any possible deformation that may stem from perspective, lens and spatial position IMDvista BTIR barrier testing system IMDvista Layer testing system Colour, UV, print/deco, liner/wad, caps on filled containers Yes Flexible In-Line or Off-Line system solution available Yes Yes Yes Correlation defect/cavity number; Through a special software developed by Sacmi R&D, the four images are used to precisely reconstruct the 3D sidewall on a 2D image. Such reconstruction allows to operate on a perfect 2D image carrying out special inspections like TEB band cuts and bridges. IMDvista V5 - newest intelligent software technology. IMDvista Portal, connect all system on one central data base (HMI for fast and transparent production overview) Real-time trend data, last 100 images, defective image database/archive, remote access, biometric user login, customisable reports, OPC connectivity,@ID:35}, TRADE SHOW PREVIEW PETplanet Insider Vol. 19 No. 10/18 petpla.net 46 ASB to demonstrate new & upgraded “1.5-step” moulding and advanced control systems Extended ISBM range The Nissei ASB Machine Co., Ltd., booth (W2-2B36) at China Brew & China Beverage exhibition will feature live demonstrations of the latest and most advanced versions of its machines for injection stretch blow moulding of PET and other plastics. It will also be exhibiting recent updates in its injection stretch-blow moulded packaging technology. ASB says that the PF36 series extends the range and capabilities of the PF platform, first shown as the PF24-8B 1.5 step injection stretch blow moulding machine at K2013 in Düsseldorf. The latest version is claimed to provide higher productivity and greater efficiency. The model on the stand will be the PF36/36-600. The designation identifies it as being able to mould 36 preforms per cycle, producing bottles of up to 600ml capacity. Blow moulding is carried out by an integrated 12-cavity linear blow system that operates three times per injection cycle. PF36/36-600 has a footprint 30cm longer than its predecessor but is claimed to offer productivity increase of 50-80%, to 14,000-17,000bph, subject to container specification. The machine will be demonstrated moulding a 500ml, 8g water bottle with a 26mm threaded neck, which is currently the lightest practical weight in this class of container. Other models on the same platform currently available are: PF36/24-1500 (24 preforms and 8 blow cavities up to Faster response & communication speed than dedicated PLC systems enhances machine cycle efficiency and control precision. PC based system makes it flexible in use and compatible with the Industrie 4.0 standard for enhanced factory networking into the IIoT (Industrial Internet of Things). Larger, 18.5 inch easy to read panel provides easier access to relevant information without changing pages. Most manual operation switches are replaced by touchscreen operation. Improved operator feedback improves troubleshooting response time and minimises down-time. Internal hard wiring is reduced. Major machine functions can be added or updated via software installation only. Easier & faster service support. Standardised interface planned across the model range assists in operator training. 1.5-step moulding method The 1.5-step moulding method is a unique process originally developed by ASB in 1995, that has since been utilised in a wide range of machine models sold by the company resulting in significant sales revenue and growth. Before its introduction all PET bottles had either been moulded using the one-step or two-step process. In the one-step process, PET resin is moulded directly into the finished container in one machine using residual preform heat from the injection process to enable blow moulding of the bottle into an equal number of blow cavities. In the two-step process, preforms are injection moulded on dedicated machines then stored or transported before being re-heated and moulded into container on a dedicated stretch-blow moulding machine. 1,500ml); PF36/18-2000 (18 preforms and 6 blow cavities, up to 2,000ml); and PF36/12-5000 (12 preforms and 4 blow cavities, up to 5,000ml). ASB says that further models based on the same mechanical function and footprint are currently under development, which will enable high commonality of machine parts, potentially reducing parts inventory across multiple machines; reduced manufacturing cost and competitive purchase price; and simplified operator training and troubleshooting. While injection moulding is carried out hydraulically, all downstream systems are fully electric including the blow mould clamping and servo-driven stretch rods. Next-generation advanced control system At China Brew & Beverage, the PF36/36-600 being exhibited is utilising ASB’s all new advanced control system. This industrial PC based system provides a long list of advantages for potential users of the PF36 series: Temperature optimised preforms are seen just before transfer into the PF36/36-600 blow station Overview of PF36/36-600 1.5-step injection SBM machine,@ID:48}, CAPS & CLOSURES 29 PETplanet Insider Vol. 19 No. 10/18 petpla.net CAPS & CLOSURES 29 etary metallocene catalyst technology. Metallocene polymerisation produces PE with a much higher molecular weight than that made by the ZieglerNatta recipe; indeed, some have claimed that PE made using metallocene methods can be a better material than Kevlar for making bulletproof vests. However, that level of strength is not what LG Chem is focused on. “We have three Lucene ranges: SM100; SM250 and SM800,” said Joon. “The metallocene catalyst process enables us to produce HDPEs with excellent mechanical, processing and organoleptic qualities. They are very suitable for high performance caps and closures applications; they have very high ESCR (environmental stress-cracking resistance) characteristics and offer excellent ‘flowability’ in processing.” SM100 is very suitable for lightweight CSD closures, such as the PC 1881; it and SM250 are both suitable for aseptic fill water and tea; and SM800 is the grade for sports closures, as well as CSD and edible oils. Lighter weight without black spotting “Lucene products offer customers a number of features and advantages,” Joon continued. “They can be processed at lower temperatures, which means less energy consumption as well as less incidence of ‘black spot’ and flow marks. The improved ESCR characteristics offer potential for light weighting, and they also present an excellent appearance, with high gloss and good whiteness.” Light weighting and lower energy consumption are two ‘hot button’ issues for manufacturers across the world. But it is one thing saying these characteristics can be delivered; it is another to see them confirmed in practice. In order to see first-hand what LG is doing in order to ensure it is meeting customer needs, we took a drive down to the R&D facility at Daejon. We travelled in the thick of the typhoon season, so the trip took rather longer than would normally be the case – 2.5 hours by road, through wind and streaming rain. The rain had eased by the time we arrived at the plant but its effects were obvious, both inside and out. But LG’s staff weren’t about to let water ingress and other inconveniences stop research, development and production. A key question is: how does Lucene retain strength while achieving weight reductions to below 2 g for CSD caps? The people with the answers were Yo Han Bae, Professional at the Tech Center, in the PO TS Team; and In-Gyu (“Joseph”) Park, General Manager and Team Leader. Designing the future “Our technicians amend and control the molecular structure of Lucene during the metallocene process, in order to retain the required qualities of rigidity, ESCR and so on,” Bae explained. “It is a question of achieving balance. If the material is made very stiff, its ageing and processing performances may not be as strong.” “It was difficult to determine the design,” Joseph said. “The minimum density and melt index are vital in determining the quality of the material. We worked with a leading closure system manufacturer, who took soundings from their customers on their reaction to different formulations. It was that [email protected] Tel: +90 212 695 50 00 Fax: +90 212 694 97 24 100815dmyR .com In 2017, LG Chem spent a total of 841US$ on R&D.,@ID:31}, 35 TRADE SHOW PREVIEW PETplanet Insider Vol. 19 No. 10/18 petpla.net TRADE SHOWpreview FAKUMA 2018 Fakuma will take place in Friedrichshafen Exhibition Centre from 16th to 20th October 2018. More than 1,900 exhibitors will present their international offerings at this technical event for industrial plastics processing. Attention will be focused on the latest technologies which promise advantageous benefits, as well as processes and tools for efficient plastics processing by means of injection moulding, extrusion, thermoforming and 3D printing. Fakuma sees itself as the number one technical event for injection moulding. The injection moulders with flexible options and ever more efficient processes are clearly in the majority as compared with 3D printing, foaming, extruding and thermoforming. The trade fair, which is seeing continuous growing international recognition, attracts numerous exhibitors who want to take advantage of the fair to unveil their new products to a broad-based audience for the first time. www.fakuma-messe.de Fast cap production At the Fakuma trade fair, Engel will demonstrate a further reduction in cycle times for the production of caps. An all-electric Engel e-cap 2440/380 will be used to produce 26mm caps, including tamper-proof bands made of HDPE, at a cycle time of under 2 seconds under realistic manufacturing conditions. The optimised movement of profiles allows an increased output. The Engel e-cap 380 with 3,800 kN of clamping force can provide a dry cycle time of 1.4 s. This e-cap machine is the only cap machine on the market providing all-electric operation with a clamping force range as high as 4,200 kN. The e-cap, due to be showcased at Fakuma, needs around 0.4 kWh of electricity to process a kilogram of plastic granulate. Integrated systems solution to unlock full potential A 72-cavity mould from z-moulds (Dornbirn, Austria) will be used at the trade fair. The exhibit will also include a dry air system from Blue Air Systems (Kundl, Austria) and a camera inspection system from IMDvista (Brügg, Switzerland). As a system solutions provider, Engel delivers fully-integrated and automated manufacturing cells around the world from a single source. Efficiency potential is maximised and overall energy consumption is kept to a minimum as the injection moulding machine, mould and peripheral systems are properly coordinated from the start of the project. Alongside energy efficiency, the all-electric e-cap machine’s main feature is extreme precision. This ensures the greatest possible number of good parts, even in the production of demanding lightweight caps. www.engelglobal.com www.imdvista.ch www.z-moulds.com Innovative recycling technology The focus of Erema Group´s trade fair appearance at Fakuma is technologies that aim to further improve the quality of recyclates. These include: the recycling and compounding technology Corema ReFresher (together with the proven Intarema TVEplus machine) - an anti-odour technology for odour-optimised premium recycled pellets directly from contaminated postconsumer material QualityOn for continuous quality monitoring of colour and MVR values Re360 - the Erema Manufacturing Execution System for real-time production and machine data Erema´s business unit Powerfil, presenting the Erema filter systems, that are also suitable for existing extruders Pure Loop, presenting ISEC evo, the integrated shredderextruder combination. www.erema-group.com Hall A5, booth 5204 Hall A6, booth 6314,@ID:37}, 41 TRADE SHOW PREVIEW PETplanet Insider Vol. 19 No. 10/18 petpla.net Just published Birkner’s Beverage World, the print edition 2018/2019 More than 20.000 company profiles from 199 countries. Additionally in web and mobile: Current news and industry information. • Unlimited research for producers, raw material suppliers, merchants, service companies and suppliers • Search for management, machines, raw material, brands and products • Easy data export for enhancement of own customer and serial letter files Registration for the professional access: +49 40 800 80 1777 or E-Mail [email protected] Puts the beverage world in motion. from 199 countries 20.000 company profiles Professional access with unlimited research and data export + business information current news www.beverage-world.com,@ID:43}, 9 NEWS PETplanet Insider Vol. 19 No. 10/18 petpla.net 1,600 participants at 3rd Food & Drink Technology Africa The third edition the Food & Drink Technology Africa (FDT Africa) trade fair for the food, beverage and packaging industry in South Africa has now firmly established itself on the market. Around 1,600 participants from 81 countries attended the international event, which took place in Johannesburg on September 4–6. As a networking opportunity, it offered a platform for the industry to exchange views on current and future trends. A total of 111 exhibitors represented the entire process chain of the food, beverage and liquid food industry. According to the Mechanical Engineering Engineering Industry Association (VDMA), South Africa has the most diverse economy in Sub-Saharan Africa, and the food and beverages industries are key pillars of the country’s economy. Over the last ten years, the value of the food and beverages produced annually has almost doubled, reaching a value of ZAR392 million (€26 million) in 2017. The VDMA further states that South Africa – whose population’s median age is just 27 – also has a growing and increasingly consumerist middle class, gradually becoming established in the major cities of Johannesburg, Cape Town and Durban. This emerging middle class requires an increasing amount of food and beverages, prepared and packaged using the latest technology, for which most of the appropriate mechanical equipment is sourced from beyond its borders – and even from beyond Africa entirely. The value of imports of food and packaging machinery in South Africa totalled € 331 million in 2017, of which € 168 million was spent on packaging machinery alone. The trend towards increased imports appears set to continue over the years to come. According to Euromonitor International, beverage sales reached a volume of 11 billion litres in 2017 and are expected to increase by about 18% to 13 billion litres by 2022. The next edition of FDT Africa is already planned and scheduled for 2019 – next year – which is outside the regular two-year cycle of the event. From next year, FDT Africa will be co-located fair with analytica Lab Africa and IFAT Africa. Petra Westphal, Exhibition Group Director of Messe München, said: “Going forward, we will offer exhibitors and visitors of FDT Africa the opportunity to obtain even more comprehensive and cross-thematic information on trends and innovations from the environmental, beverage and food industries, as well as analytics. Together, the co-located trade fairs ensure the best possible knowledge transfer for all industries.” The first analytica Lab Africa, FDT Africa and IFAT Africa joint event will take place at Gallagher Convention Centre in Johannesburg, July 9-11, 2019. www.fdt-africa.com Demeto announced that The Coca-Cola Company will join its industrial advisory board Demeto (Modular, scalable and high-performance DEpolymerisation by MicrowavE TechnolOgy) is a European Project financed by the European Community within the framework of the Horizon 2020. The partners of the consortium are working to bring to reality a revolutionary new way to chemically recycle PET, invented by gr3n, which is both sustainable and profitable. The Industrial Advisory Board (IAB) of Demeto is a committee of stakeholders external to the project that will interact with the partners of the consortium to follow its public developments and, most of all, provide feedback and comments to steer the direction of its business development activities. The IAB already consists of 16 companies involved in the complete PET/polyester value chain at different levels, including: top brands of home textile, sportswear textile, fashion textile, home and personal care and drinks, as well as plastic converters, waste collectors and recyclers. Demeto and The Coca-Cola Company share a common interest in closing the loop of the Plastics Circular Economy. As one of the largest beverage producers worldwide, The Coca-Cola Company relies on PET in various applications, from transport to packaging, and has long been recognised as an industry leader in supporting and enabling PET recycling. By joining the advisory board of Demeto, The Coca-Cola Company supports the first European Project to build an industrial plant for chemical recycling of PET. Unlike mechanical recycling, Demeto’s technology allows a complete recovery of PET without any degradation of the material. Thanks to its innovative technology, Demeto will be able to return postconsumer PET into its basic components, Ethylene Glycol (EG) and Terephthalic Acid (PTA). The process is enhanced by microwave radiation to speed up the reaction time and to make it suitable for industrial application. Since the resulting PET is designed to be competitive to virgin PET in both quality and costs, DEMETO offers a serious alternative source of raw materials to the plastics industry, and aims to enable up to 100% recycled content in packaging at parity cost to virgin resin. www.demeto.eu,@ID:11}, PETplanet Insider Vol. 19 No. 10/18 petpla.net 54 PETbottles Home + Personal Care Shower gel with avocado oil Henkel has launched a number of skin products under its new “Nature Box” range which are based on the many small brands that have made sustainability and the rejection of certain product groups central to its philosophy. For example, a vegan shower gel made from 100% cold-pressed avocado oil is now available in the shops under the “Nature Box” brand which gently soothes the skin, making it soft to the touch. The product comes in a strikingly shaped, clear green 385ml bottle and is dispensed using a screwed-on hinged press-down lid with dispensing spout. A dark self-adhesive label with shiny gold lettering, in combination with the green bottle, makes the product immediately noticeable on the shelves. www.natureboxbeauty.de Raspberry-flavoured mouthwash The German drugstore, dm’s, own brand “Dontodent” is launching a limited product edition, Raspberry Splash, a mouthwash that offers seven-fold protection, including protection against cavities and tartar, protecting gums and tooth enamel, as well as providing long-lasting breath freshness. It comes in a lightly coloured, tapered bottle with side embossing in the neck area, and is secured by a tamper-proof screw cap with dispensing spout. Two adhesive labels provide product information and instructions on how it should be used. www.dm.de Aloe Vera Gel by Jean and Len A 100ml soothing and cooling Aloe Vera gel to soothe stressed skin, especially after being out in the sun, is being sold by the German company, Jean and Len Limited, which is renowned for its commitment to health and wellbeing. The product comes in a slightly opaque plastic bottle with a screwed-on pump dispenser for applying the gel. A cap protects the pump dispenser from damage and dirt. The vegan product does not contain parabens, silicones or nanoparticles. The manufacturer recommends the product be kept refrigerated in order to enhance the cooling effect of the aloe vera. www.jeanlen.de #ALL4PACK INSPIRE SHARE ACCOMPLISH (*) The new name of EMBALLAGE & MANUTENTION 26-29 NOV 2018 PARIS FRANCE Get your badge with the code PPPA4PALL WWW.ALL4PACK.COM,@ID:56}, MOULD MAKING PETplanet Insider Vol. 19 No. 10/18 petpla.net 14 Keeping balance with ultra-high-cavitation hot runner systems 192 cavities evenly filled Mould making has always been a brew of engineering expertise and artistry. That is especially so in the world of PET preforms, where customers want something that can be turned into a product – the bottle – that combines beauty and strength. Can this observation be extended to hot runner systems? After all, hot runner design is very much a case of form following function and obtaining that functionality is very much in the hands of the engineers. Hot runner systems for preform moulds holding close to 200 cavities are delicate to handle. At high speed, many cavities have to be filled identically, without excessive force. Underlining its engineering expertise, the Italian company Sipa has just conceived, designed, built and delivered a preform mould with 192 cavities to one of the world’s leading PET container makers, based in North America. Sipa’s XFlow melt distribution system, which is now available for use on GEN 3 (third generation) XForm 350 and 500 high-performance injection moulding machines, incorporates an innovative hot runner manifold design that has been engineered to provide an excellent balance of melt distribution. As Sipa states, it exhibits the lowest pressure drop ever measured. That is one reason why the maintenance interval can be extended, since wear and tear is reduced. An additional benefit, according to the company, is that any maintenance required is easy to carry out. A tooling and hot runners R&D team member from Sipa explains “XFlow technology, which is unique to Sipa, allows us to create very highcavitation systems without having to compromise on balance, pressure losses, and the formation of acetaldehyde due to polymer degradation. It goes without saying that XFlow can also be applied to moulds with more modest levels of cavitation with equally impressive results. XFlow is extremely efficient and it is scalable according to customer needs.” Everything in the melt flow Over the course of the last five years, Sipa has made great efforts in hot runner technology. The first generation of their hot runners depended on a purely mechanical technology for balancing melt flow. Then in 2013, the company introduced a new generation of hot runners, which marked a turning point in the approach to flow balance. This is when XFlow first came onto the scene. The XFlow solution applies advanced concepts of polymer fluid dynamics to hot runner engineering. By taking melt rheology aspects into account, it became possible to obtain balancing results quite beyond those of traditional systems, states Sipa, halving the imbalance in melt flow compared with the first generation. In a next step, third generation hot runner systems - introduced soon after the second generation – are claimed to incorporate a further evolved version of XFlow that benefits from a total overhaul of the cylinder units, valve guides and nozzles. “When we design XFlow hot runner systems, we now take fully into consideration the rheological properties all along the many flow paths to the individual cavities,” says a Sipa team spokesperson. “This is really important, given that these days we are increasingly working on projects where preform walls are thinner than ever before. This means that it is critical for the hot runners to consume as little energy as possible so that the injection unit can push the molten polymer as quickly and efficiently as possible into all the cavities.” And continues “Use of rheological rather than mechanical balancing translates into minimum energy demand and a very low pressure drop. XFlow can be applied to any application to provide the best solution for high-speed injection of critical preforms. Without XFlow, such results are impossible to achieve.” www.sipa.it MOULDspecial,@ID:16}, 37 TRADE SHOW PREVIEW PETplanet Insider Vol. 19 No. 10/18 petpla.net IML technology Sumitomo will be exhibiting their ElExis SP 200 with highspeed IML application. “The fourth generation El-Exis SP is still the fastest injection moulding machine in the world,“ states Arnaud Nomblot, Director Business Development Packaging at Sumitomo (SHI) Demag. Two years after its launch, he is still happy with the machine’s performance. From the very beginning, the machine concept has been designed to guarantee high performance in conjunction with availability and reliability, says Nomblot. Thanks to its dynamic hybrid drive and intelligent accumulation control, the El-Exis SP is claimed not only to deliver a good performance in terms of acceleration, mould movement and deceleration but also process constancy and precision paired with an energy efficient production. The live demonstration at Fakuma will highlight the complex packaging processes: a production unit with a high-volume output, low part weight, in-mould labelling and cycle times below 3 s. In a four-cavity mould (Simon), this system produces decorated food cups from polypropylene (Borealis). It also comes equipped with an automation solution (Beck Automation). A high-speed side-entry robot places the labels (Verstraete) into the fixed mould half, while removing the finished cups from the moving mould half and stacking them. www.sumitomo-shi-demag.eu Processing solutions Piovan Group will feature its Piovan, Aquatech and Fdm brands. While Piovan and Fdm are both specialised in material handling systems and advanced solutions for plastics processing, Fdm are more focused on the extrusion process. Aquatech specialises in industrial cooling and temperature control technology. The Friedrichshafen’s exhibition will be the platform to present Easytherm by Aquatech. This is the new temperature control line, “Industry 4.0 ready” thanks to the integrated OPC-UA protocol, which includes a range of versatile units allowing smart energy use management. Another solution from Aquatech is Flexcool, a system which allows utmost efficiency and flexibility predominantly in the thermochiller application, DigitempEvo. Piovan will show its Winenergy and Winfactory 4.0 supervision software which will be featured on touchscreens. Winenergy is the energy use monitoring and analysis system comprising proprietary software that is connected to a series of measuring devices. These devices acquire data about a variety of physical parameters including power, electricity, thermal energy and temperature. It can be installed on its own or in combination with Winfactory 4.0, to maximise system control and efficiency. Also by Piovan is the ideal solution for the fully automatic material supply to the processing machines. Featured at the fair will be the model EL20 of the Easylink+ line, characterised by a state-of-the-art pipe cleaning procedure, which guarantees the absence of cross-material contamination. Easylink+ will be in operation together with the Modula series auto-adaptive dryer and the Pureflo filterless granule receivers. For the first time at Fakuma, the Piovan Quantum E gravimetric batch blender with continuous extrusion control will be exhibited, equipped with its 15” touch-screen panel control. A big-size granulator will complete the product display under the Piovan brand. Fdm will showcase a gravimetric dosing system from their GDS series, featuring a Siemens control unit, designed for the needs of pellet, flakes, regrind, additives and powder treatment. www.piovan.com YOUR PARTNER FOR TECHNOLOGY MACHINERY AND MANAGEMENT www.sorema.it FOR INTERNATIONAL SALES: 7 NEWS PETplanet Insider Vol. 19 No. 10/18 petpla.net Start up: All4Pack Paris 2018 The international trade showAll4Pack Paris, taking place from November 26 to 29, 2018 at Paris Nord Villepinte, France, will bring together 87,000 professionals for four days of exchange, demonstrations, innovation and presentations from sectors such as food, beverages and liquids, cosmetics and toiletries, healthcare and pharmaceuticals, retail, e-commerce, consumer goods and capital goods. From raw materials to end-of-line and intralogistics, the packing and packaging world is a global, innovative and totally connected production chain and a sector undergoing deep transformation, fuelled by opportunities offered by Industry 4.0 and by the new requirements of omni-channel B2B and B2C trade. Prior to the show a press conference took place on 28th of August in Frankfurt, Germany, welcoming the international press to present the new key facts in the concept of the upcomingAll4Pack. Véronique Sestrière, Director of Comexposium, talked about the new hall 7 where for the first time the All4Pack Startup Lab will be shown. In this hall, 15 startups will present themselves and demonstrate over four days their innovation during live pitch sessions. Also in hall 7, the Creativ Lounge, with awarded company in the packaging and intralogistic area, will entertain the visitors. This fairground is in addition to the new communication space with conferences, debates, key-note speeches and awards. All4Pack Paris offers a comprehensive range which perfectly addresses the integration strategy witnessed by the market, shining a light on the innovation capabilities of the packaging ecosystem: raw materials, process, packaging and packing machines, marking and coding, packaging solutions and containers, pack printing and labels, secondary, tertiary and shipping packaging machines. It also addresses the intralogistics sector: continuous handling, automated systems, logistics services and IT systems, storage and warehouse facilities, lifting, and forklifts. www.all4pack.fr UNITED CAPS ZI de Wiltz, BP 49, 9501 Wiltz, Grand-Duchy of Luxembourg T +352 95 94 94 1 I F +352 95 94 95 www.unitedcaps.com LET’S CREATE NEW GOLDEN MOMENTS... The best parts of life reveal themselves in the Golden Moments. For UNITED CAPS those moments exist when we work with great brands like Nescafé to reach new technological peaks and our closures enable differentiating total packaging solutions. Moments like that are possible when we combine our 79 years plastics experience with your brand. They start with a conversation. Lets create some new Golden Moments together. Get in touch below. www.unitedcaps.com ©2018 UNITED CAPS group. All rights reserved. Amcor announces appointment of Eric Roegner as president of Amcor Rigid Plastics Eric Roegner will succeed Mike Schmitt in this role in mid-November. Eric will be based in Ann Arbor, Mich., in the United States. Eric brings significant experience leading and growing large-scale multiregional businesses, including 12 years of executive leadership roles with Arconic Inc., previously known as Alcoa Corporation. Most recently, Eric was Executive Vice President and Group President of the US$6 billion Arconic Engineered Products and Solutions business. Earlier in his career, Eric was a partner at McKinsey & Co. Eric holds a master’s degree in Business Administration from Case Western Reserve University in Cleveland, Ohio, and a bachelor’s degree in Aerospace and Mechanical Engineering from Princeton University. Mike Schmitt has led Amcor Rigid Plastics through a period of strong growth since his appointment in June 2011, significantly increasing profitability and successfully integrating several strategic acquisitions. Following the transition period, Mike will become Executive Vice President, Amcor Limited. In this role, Mike will continue to manage the Bericap North America joint venture, remain executive sponsor of certain Amcor global customer relationships and, importantly, support the integration of the previously announced Bemis acquisition to leverage his prior 25 years of flexible packaging experience. Mike and Eric will report to Ron Delia, Amcor Chief Executive Officer, and serve on Amcor’s Global Management Team. www.amcor.com,@ID:9}, 36 TRADE SHOW PREVIEW PETplanet Insider Vol. 19 No. 10/18 petpla.net The new TEM machine offers new possibilities for slitting or slitting and folding of tamper evident bands for specialty caps. The TEM, a highly versatile machine for beverage, food, beauty & home, chemical and other products. Modular design machine for slitting/folding or folding/slitting of tamper evident band Large variety of cap dimensions, including sport caps All size parts located in the outside for easy adjustment and changeover Heating system for the blade. Blade position sensor Servo-driven infeed star wheel, integrated cap stop and sensor controlled upside down closure detection Operator friendly interface Match the output of associated moulding and downstream machines Easily integrated into any production line due to independent control and optional vision inspection system PackSys Global and its affiliated companies offer a wide product portfolio: Complete lines for laminate, extruded and aluminum tubes Plastic closures slitting and folding machines Cap printing lines Monobloc aerosol can lines Hot stamping solutions from Madag Printing Systems Tube, aerosol can and cartridge packing solutions from Texa Packaging Highly skilled R&D and production teams ensure constant development and integration of the latest technology on our equipment. We stand for Swiss engineered innovation and performance. Creating Packaging Technology. PackSys Global AG T +41 55 253 38 31 [email protected] www.packsysglobal.com A Member of Brückner Group SPECIALTY CLOSURES TAMPER EVIDENCE,@ID:38},
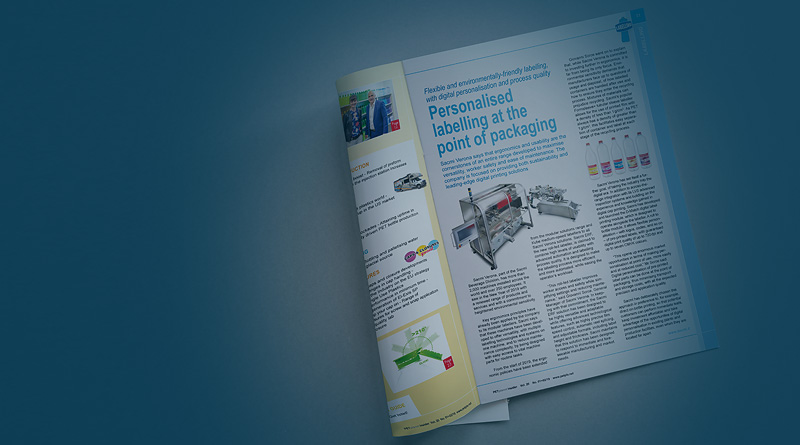