"43 TRADE SHOW PREVIEW PETplanet Insider Vol. 20 / 4.0 solutions for plastics processors Injection, extrusion and PET processing are characterised by specific complexities and high levels of performance, in which production and energy efficiency play key roles. Moretto’s goal is to provide exclusive technologies and automations maximising the production efficiency of these processes, by furnishing plastics processors with customised solutions and services. The impression of Industry 4.0 is evident on all product lines, Moretto offers smart and automatic machines able to automatically adapt the output to the needs of the market predict in advance breakages or downtime and have a support in real time remotely. These smart machines are required mainly by sectors such as automotive, medical and packaging, where Moretto records his better performance. Shown at Chinaplas 2019 is Moisture Meter Manager. This device reads in-line the moisture content of the granule, manages and controls in close loop the drying process guaranteeing product certification and energy savings. Moisture Meter Manager is equipped with the sensor MM Crown for measuring the moisture of the granule when it enters the hopper; this detection allows the system to accurately predict the drying process that the dryer must handle. The dried material exiting by the hopper is further analysed by the MM Box sensor that, thanks to the exclusive Power-Peak technology, measures the exact content of water present in the polymer with an extraordinary precision (up to 15ppm, with a temperature range of 20÷180°C). The range between initial and final moisture levels allows Moisture Meter Manager to automatically manage the dryer working conditions and to maximise process performances only using the strictly necessary energy. This creates a perfect close loop that integrates the dryer into a fully automatic adaptive system. Moisture Meter Manager is intended to mark a revolution on the traditional drying concept and create a perfect “drying on demand”, based on the real drying needs of the polymer, able to manage the internal and environmental variables that interfere with the polymer’s moisture level. www.moretto.com MORETTO Hall 4.1 Booth C45","@ID":45}, "MARKET SURVEY 28 PETplanet Insider Vol. 20 No. 05/19 petpla.net Preform Moulds Company name R&D/Leverage Sipa SpA Husky Injection Molding Systems Postal address Telephone number Web site address Contact name Function Direct telephone number E-Mail Leverage House, Hamilton Road, Sutton in Ashfield, Nottinghamshire, United Kingdom, NG175LD +44 1623 556287 www.rdleverage.com Mr Alan Tolley Managing Director +44 1623 556287 [email protected] Via Caduti del Lavoro 3 - 31029 Vittorio Veneto, Italy +39 0 438911 511 www.sipa.it Mr Stefano Baldassar Sales Director, Preform Systems & Tooling +39 0 438911 511 [email protected] 500 Queen Street South - Bolton, ON L7E 5S5, Canada +1 905 951 5000 www.husky.co Mr Raphael Juvan Business Development Leader, PET Tooling [email protected] Horizontal opening Number of cavities 1 through 96 Up to 192 6 to 144 Preform sizes 24mm through 63mm neck, 12g through 350g weight Up to 750g Threads up to 100mm in diameter and up to 205mm in length Moulds already built for (makes) Husky, BM Biraghi, Milacron, Engel, Krupp, Krauss-Maffei Sipa, Husky, Netstal, Krauss-Maffei Moulds to support all preform designs and output requirements; moulds for preforms with a thread diameter up to 120mm and lengths over 400mm long Vertical opening Number of cavities up to 96 Preform sizes up to 10l Moulds already built for (makes) Standard and custom Sipa, Krauss-Maffei Do you produce single stage tooling sets? (Preform moulds AND blow moulds) Yes Yes, for Sipa machines Husky does not currently produce blow moulds Other We are one of the worlds leading tooling suppliers for single stage, injection stretch blow moulding ISBM. Product Solution Laboratory with Nissei and Aoki machines for product, colour, material trials plus production tool qualification Husky's HyPET preform injection moulding systems deliver reduced variability and increased part quality; and the lowest energy consumption per part produced. Backed by Husky's more than 35 years of preform equipment experience, our preform systems offer industry-leading technology that is proven and reliable. Stretch Blow Moulds Company name Kosme Gesellschaft mbH SMI S.p.A. Sipa S.p.A. Sacmi Beverage Röders TEC Postal address Telephone number Web site address Contact name Function Direct telephone number E-Mail Gewerbestr. 3, 2601 Sollenau, Austria +43 2628 411 0 www.kosme.at Mr Johann Gugler Managing Director +43 2628 411 125 [email protected] Via C.Ceresa, 10 24015 San Giovanni Bianco (BG), Italy +39 0345 40 111 www.smigroup.it +39 0345 40111 [email protected] Via Caduti del Lavoro 3 - 31029 Vittorio Veneto, Italy +390 438911 511 www.sipa.it Paolo De Nardi Product Manager SBM +39 0438 911511 [email protected] Via Selice Provinciale 17/a, 40026 Imola (Bologna) Italy +39 0 542607 111 www.sacmi.it Scheibenstraße 6, 29614 Soltau, Germany +49 5191 603 53 www.roeders.de Mr Steffen Lühning / Mr Jani Rickert Sales Manager +49 5191 603 822 / +49 5191 603 340 [email protected] Stretch blow moulds Bottle size (max.) (in litres) 30 10 30 12 20 Moulds supplied to blowing machine manufacturers/ converters Kosme, Krones, Sidel, KHS Yes, up to now, SMI engineers have designed about 1,700 containers, featuring from the most simple to the most sophisticated shape. Sidel, Krones, KHS,SIG, Krupp, SMI, Siapi, Kosme, Side Yes Yes, Sidel, KHS Corpoplast, Krones, Sipa, Kosme, ADS, Nissei, Chumpower, Terekas, 1 Blow and other major machine types Do you supply retrofit moulds for existing SBM machines? Yes Yes Yes Yes Yes Bottle design service Yes Yes Yes: brandbuilding, product repositioning, marketing design, packaging engineering, lightweightening of existing bottles, technical feasibility, etc… Preform, cap and bottle design service Bottle design development: quick and flexible bottle sampling and qualification in Röders laboratory with certified equipment Specialities Bottle development service free of charge if blow moulds are ordered The moulds are manufactured using a special aluminium alloy. SMI relies on a special laboratory for the production of moulds and mechanical components, equipped with an FMS line consisting of 12 CNC machining centres: highly automated machines, running 7 days a week round the clock, even operator-less, according to pre-set production programmes (CAM). Wide mouth, large sizes (up to 30l), asymmetrical, Nitrogen hot fill, containers with handles, HDPE to PET conversions, pharma & cosmetics Other The 12 machining centres can achieve an output of more than 15,000 moulds per year; they are equipped with linear motors with a speed rate up to 80 meters per minute and mandrels achieving a speed rate of 30,000 rounds per minute.As a result, top-level quality standards are constantly provided. Solutions for compatibility of moulds between different machine types, new Röders RMC-system for quick mould change to reduce changeover times and cut mould costs","@ID":30}, "MATERIALS / RECYCLING PETplanet Insider Vol. 20 No. 05/19 petpla.net 10 Novel mobility aid masterbatch improves PET bottle production efficiency More clarity, fewer blockages Sukano launches a novel masterbatch that allows bottle makers and brand owners to run conveyor belts and robots at maximised speed, increasing productivity and yields. Using this mobility aid additive masterbatch, problems like release, scuffing, and sticking will be a thing of the past. Sukano, a global leader in the development and production of additive and colour masterbatches and compounds for polyester and speciality resins, announced the launch of a new mobility aid additive masterbatch for injection stretch blow moulded (ISBM) PET bottles. This new additive masterbatch allows bottle makers and brand owners to run their conveyorbelt systems and production robots without the need for a spray coating. Bottles must rotate freely as they pass through the production conveyor, as forced rotation caused by friction can lead to a blockage on the line. The new Mobility Aid solution, believed to be the first commercially available for this application, is provided as a solid PET masterbatch that is blended with virgin PET or rPET material during moulding or processing. Even at low concentrations, the masterbatch disperses consistently through the PET material, reducing its coefficient of friction (COF), and modifying the surface texture with a microstructure. This new masterbatch produces a silicone-like mobility aid effect in PET material, yet has been engineered to preserve material clarity with minimal impact on haze. It is well suited to clear, translucent, and coloured bottles produced for personal care, household and cleaning, cosmetics, as well as food and beverage applications. It is also widely applicable, as PET material containing the new masterbatch can be run on existing ISBM bottle production equipment without modification. Sukano is currently assisting a customer in the U.S. optimise its production process. “Our customer, a key and leading global player in the consumer goods industry, reported that PET bottle mispicks by their production robot decreased sixfold when using our Sukano Mobility Aid masterbatch,” stated John Price, director of technology and operations in the U.S. The consistency and even distribution of the masterbatch lead to improved performance. The additive masterbatch preserves secondary processing steps that require adhesion, like labelling and printing. It also helps eliminate the cost and cleaning requirements associated with spray coatings, which leave a waxy residue on bottles and packaging equipment that must be removed through regular cleaning. Additionally, the masterbatch is claimed to avoid the potential risk of microbiological contaminations of bottle surfaces by aqueous-based coatings, which may require additional additives or application in a cleanroom environment. Formulated according to EPBP guidelines Circularity as a decisive design criterion to Sukano’s products placed in the market; PET recyclability is essential in an increasingly environmentally conscious world — and Sukano’s mobility aid is claimed to make no compromises in this area, as it is formulated according to the European PET Bottle Platform (EPBP) guidelines. These enable the industry to innovate and bring new PET bottle packaging solutions to the market without disrupting the existing clear PET recycling value chain, with special focus on bottle-to-bottle recycling. The company’s vision is that the new mobility aid supports the PET value chain to keep and further enhance its circularity goals to meet the voluntary pledge of exceeding the Plastics Strategy targets for recycled PET rates by 2025. www.sukano.com","@ID":12}, "COMPRESSORS 33 PETplanet Insider Vol. 20 KRONES Recycling Solutions #GermanBlingBling #KronesMetaPure We do more. PROPAK ASIA 2019 Bangkok, 12 – 15 June Hall 103, Stand BR01 compression system will automatically reduce or stop the first stage inspiratory volume, thereby reducing energy consumption. Constant pressure Constant pressure control mode currently standard in the air compressor market is constant pressure control: a PLC (programmable logic control) adjusts the compressor speed according to the pressure value, to achieve a constant outlet and supply air pressure. Nanjing Shangair has also developed a smart flow control: the air compressor is equipped with a flow meter and the PLC adjusts the air production capacity of the compressor to more accurately meet demand. This dual mode control has helped to improve energy saving. Nanjing Shangair says that its M-type symmetric balanced water-cooled oil-free air compressor has quickly gained a leading role in its market because of its reliability and superior energy performance. The company’s after-sales service that uses advanced IoT (Internet of Things) technology to help customers to monitor machinery performance 24 hours/ day. Data is analysed in real time, to help improve equipment performance and maintenance. Abnormalities are notified to customers immediately; energy consumption is calculated and maintenance reminders are generated automatically. www.shangair.com Interface of Shangair's DCC system","@ID":35}, "PETproducts 48 PETplanet Insider Vol. 20 No. 05/19 petpla.net Software creates virtual bottle PET and rPET packaging producer Retal’s latest development supports its focus on creating lighter, stronger bottles that meet the precise performance and sustainability goals of brand owners. Retal worked together with Dassault Systemes to add several plug ins to its Abaqus software product that provided an exact 3D modelling. The bespoke simulation software now in operation at Retal’s R&D Centre means that it is able to create precise information regarding performance relating to the distribution of the thickness and stretch ratio of the bottles without needing to produce a physical product. Designer Andzejus Buinovskis explains, “With the 3D model of the preform and bottle, we can simulate different temperatures, movements, pressures and pre-blow and blow variations. It’s a powerful tool that saves the considerable time and money associated with prototyping; in one case, two bottles of the same weight but different geometry showed that one had a better stretch ratio, making it stronger.” Physical tests can be conducted for the most optimal model, avoiding the cost of testing all intermediate versions. Investing in this complex software makes it faster, cheaper and easier for its global brand customers to choose the precise bottle for their food and beverage applications. www.retalgroup.com HyPET HPP5e – refinement on proven preform moulding system At the heart of the platform is an intelligent, adaptive technology that uses feedback from pressure and actuator sensors to determine the optimum pressure required to effectively and efficiently mould every application. This smart system monitors and automatically adjusts for optimal energy consumption without impacting system capability, cycle time or part quality. A number of modifications have been made by Husky to make HyPET HPP5e more robust and reliable. New conveyor technology significantly reduces preform bounce when parts are ejected from the CoolPik unit to the exiting conveyor. This bounce reduction results in improved part quality, reduced scrap, more streamlined operation and decreased cycle interruptions. Enhanced mould alignment software supports faster system set-up and troubleshooting. Other advancements include new robot linear bearings to maximise longevity, upgraded Altanium 2/2 Inside ICC cards for more integrated, accurate temperature control and a new nozzle shut-off cylinder to promote component longevity. HyPET HPP5e has adopted new intelligent features and real-time control enhancements to simplify operation and optimise the moulding process. By integrating more intelligence into the system, operators of all skill levels are able to achieve maximum productivity and part consistency. HMI screen upgrades, software updates and improved EtherCAT diagnostics promote user friendliness, making the system easier to navigate, convenient to set-up and issues faster to troubleshoot. www.husky.co Sigma Air Manager 4.0 Kaeser Kompressoren is presenting the latest generation of SAM 4.0, the master control system for compressed air production and treatment components. It optimises pressure values, automatically adjusts compressor system air delivery to accommodate fluctuating pressure demand and optimises system efficiency based on control losses, switching losses and pressure flexibility. Moreover, the SAM 4.0 enables your compressed air station to take advantage of future services such as Sigma Smart Air, for predictive maintenance. All of these features not only boost operational reliability and efficiency, but also significantly reduce energy costs. This is in no small part made possible by Kaeser’s adaptive 3-D advanced Control, which takes into account additional factors, aside from switching losses (start/ stop), that affect compressed air system energy efficiency. These include control and idling losses, frequency converter operation and pressure flexibility (average increase above required pressure). The patented optimisation method predictively calculates the optimum achievable configuration and adjusts the connected components accordingly – all based on the specific pressure required by the user. The SAM 4.0 supports operation in 30 languages, while the easy-to-use 12-inch colour touchscreen shows at a glance whether the station is operating in the ‘green zone’ from an energy management perspective. Operating status, pressure history, free air delivery, power consumption, as well as maintenance and any error messages can be easily displayed and analysed – both in real-time and retroactively. Using a PC and network connection, this data can be accessed conveniently from anywhere, not just at the machine itself. This not only gives users peace of mind and lays the foundation for digital products in the pipeline, it also enables energy management in accordance with ISO 50001. www.kaeser.de","@ID":50}, "42 TRADE SHOW PREVIEW PETplanet Insider Vol. 20 No. 05/19 petpla.net Focus on post consumer recycling In Asia the recycling industry is becoming increasingly quality conscious. Countries that used to export plastic waste to China are now stepping up their own recycling activities. In China as well, high-quality recycling of post-consumer waste is becoming more and more important. The plastics recycling expert Erema will be making the most of this development during the Chinaplas trade fair. They will demonstrate that not only the hollow body of PET bottles, but also PP bottle caps and LDPE films can be recycled to produce high-quality pellets and that the plastic loop of this typical post-consumer waste can be closed 100 percent. For these demonstrations, an Intarema TVEplus system equipped with an Erema laser filter will be in operation at the trade fair stand. This combination is particularly suitable for materials with a high degree of contamination, when conventional melt filters can no longer achieve the necessary cleaning efficiency. Innovative ideas for products made from recyclate The range of products that are manufactured partly or entirely from recycled materials now extends from everyday consumer items to lifestyle goods. With a display of selected products, Erema provides an overview of the myriad possibilities for the use of recyclates. One example is the skateboards made by Bureo. What is special about this Chilean-based company’s innovative idea is that disused fishing nets, which would otherwise end up in the sea as waste, are collected, recycled using Erema technology and processed into cool products. From the collection of fishing nets to the production of new consumer goods, this is one of many successful lighthouse projects for the implementation of a circular economy and the avoidance of ocean plastics, both of which are topics that are also driving plastics recycling in the Chinaplas catchment area. www.erema.com EREMA Hall 9.2 Booth A41","@ID":44}, "40 TRADE SHOW PREVIEW PETplanet Insider Vol. 20 No. 05/19 petpla.net The new TEM machine offers new possibilities for slitting or slitting and folding of tamper evident bands for specialty caps. The TEM, a highly versatile machine for beverage, food, beauty & home, chemical and other products. Modular design machine for slitting/folding or folding/slitting of tamper evident band Large variety of cap dimensions, including sport caps All size parts located in the outside for easy adjustment and changeover Heating system for the blade. Blade position sensor Servo-driven infeed star wheel, integrated cap stop and sensor controlled upside down closure detection Operator friendly interface Match the output of associated moulding and downstream machines Easily integrated into any production line due to independent control and optional vision inspection system PackSys Global and its affiliated companies offer a wide product portfolio: Complete lines for laminate, extruded and aluminum tubes Plastic closures slitting and folding machines Cap printing lines Monobloc aerosol can lines Hot stamping solutions from Madag Printing Systems Tube, aerosol can and cartridge packing solutions from Texa Packaging Highly skilled R&D and production teams ensure constant development and integration of the latest technology on our equipment. We stand for Swiss engineered innovation and performance. Creating Packaging Technology. PackSys Global AG T +41 55 253 38 31 [email protected] www.packsysglobal.com A Member of Brückner Group SPECIALTY CLOSURES TAMPER EVIDENCE","@ID":42}, "COMPRESSORS PETplanet Insider Vol. 20 No. 05/19 petpla.net 20 COMPRESSORS Atlas Copco’s new ZD line has been developed specifically for PET bottle blowing (see issue 12). The company took a fresh look at some other aspects of a PET compressor, which had previously been regarded as unalterable characteristics of a 40 bar system: A first in PET compressor design is the piston compressor’s integral concrete base plate which eliminates the need for special foundations of any type and allows the compressor to be picked up and moved by fork-lift. The baseplate absorbs all of the vibration, with no transmission to the ground. The base plate also includes buffer capacity for 10 bar air - no need for a separate 10 bar receiver. In combination with a newly developed silencer housing it is now possible to locate the compressor in close proximity to the blowing machine. 2005 1998 saw the introduction of the LMF EcoPET range of compressors with smooth speed regulation. Seven years later we reported in issue 9 on the extension of some models (from 950-2,700 m³/h) and the development of Eco-SpeedControl for efficient use of compressed air. A single-stage, oil-free, rotary blower is used as what LMF call their booster (the term booster normally being applied to the latter, i.e. piston stages of a multi-stage system). Its strong point lies in its ability to compress large quantities of air at low pressures. To cater for the periods under partial load, typical of a blowing air compressor, LMF developed and introduced the EcoSpeed-Control. The advantage of this system is that only the booster (rotary blower) is controlled by a frequency converter that matches it to the final pressure of the unit as a whole. This means that the piston compressor downstream is fed with less air, so reducing its power requirement proportionally. PETpoint exhibition in September 2005 saw the unveiling of Atlas Copco’s latest compressor system ZD, developed specifically for PET bottle blowing (see also 12/2004). 2006 In issue 11+12, LMF Austria discussed the topic of air recovery and demonstrated the possible savings if the compressed air is fed directly back into the blowing compressor using the patented EcoPET C.A.R. (Compressed Air Recovery) after the stretch blowing process. The pressure level of the return air, which is available for further use, is between 6 and 18 bars, and the amount of air fed back into the compressor can be between 0-80%. This optimised air control system is made possible by the use of “smart” valves integrated in the compressor control circuit. 2008At the 2008 edition of Brau Beviale, Kaeser Kompressoren featured a powerful booster used to deliver air at up to 45 bar as well as the compact “Sigma PET Air” complete compressed air system for stretch blow moulders. Also on show was the Kaeser screw compressors and the “Sigma Air Manager” which controls and adjusts the flow and pressure from several compressors for maximum economy and efficiency (issue 10) 2009Gardner Denver Ltd used Drinktec to show its new VH25 oil-free compressor for PET bottle blowing and a new, low-maintenance, shaftless and water-cooled motor, as reported in issue 10. In common with other compressors in its VH range, the VH25 features its AirPET air recovery system, which is designed to accommodate a returned pressure from the blow moulding machine that can be recycled back through the compressor. At PETpoint, Kaeser Kompressoren exhibited its new dry-running rotary screw compressors and the ‘Airbox Centre’ – a compact compressor system offering all-in-one compressed air production, treatment and storage. The compact system is an all-in-one solution for compressed air production, treatment and storage, with a dry-running industrial reciprocating compressor at its core, providing free air delivery of 0.9 cubic metres (issue 9, photo above right). 2011Compressor coordination and regulation: In issue 4, ABC Compressors presented its works on savings in compressor central units and made recommendations to guide distribution line set-up. Coordinating the work done by all the compressors together helps to provide energy savings in a number of ways: it minimises the number of compressors running idle and the number of start-ups; it helps to stop machines that are not required and identify which compressors should be adapted to total air demand at any time; and covers possible compressor stoppages due to maintenance requirements or breakdowns. 2014The name is Vito. In PETplanet 1+2 we introduced Siad’s new compressor technology, the result of a complete re-think both of the design and production of an entirely new compressor concept. The new model should be suitable for all performance categories above 1,200m3/h, with variable speeds to ensure flexibility in production. Covering all performance ranges with just one compressor generates cost savings in the manufacturing process: a number of identical parts can be used. This of course includes the pistons, piston rod and crankshaft.","@ID":22}, "MARKET SURVEY 27 PETplanet Insider Vol. 20 No. 05/19 petpla.net Stretch Blow Moulds 05/2019 MARKETsurvey Resins & additives Preform machinery Preform production & inspection Preform & SBM mould manufacturer SBM 2 stage Compressors Filling equipment & inspection Caps & closures & inspection Palletising & shrink film machinery Recycling Suppliers of preform and SBM moulds In this issue of PETplanet we are very glad to present you an update of mould manufacturing for performs and SBM mould production. Please have a close look at the companies showing their newest developments: Demo-Design and Molds, Wentworth Mold Ltd., Electra Form Ind., UAB Terekas, R&D/ Leverage, PET Technologies, Kosme Gesellschaft mbH, SMI S.p.A., Sipa S.p.A., Sacmi Imola S.C., Husky Injection Molding Systems Ltd., MHT AG, Otto Hofstetter AG, Röders GmbH, Sidel and Krones. Although the publishers have made every effort to ensure that the information in this survey are up to date, no claims are made regarding completeness or accuracy. Company name Demo Design and Moulds Wentworth Mold Ltd. FlexBlow R&D/Leverage PET Technologies Postal address Telephone number Web site address Contact name Function Direct telephone number E-Mail Via Olivera, 48, 31020 - San Vendemiano (TV), Italy +39 0438 409048 www. designandmoulds.com Mr Carlo Boscolo Sales Manager +39 338 630 1522 [email protected] 156 Adams Blvd Brantford, ON, Canada +1 519 754 5400 www.wentworthmold.com Mr Tar Tsau General Manager +1 519 754 5400 ext 611 [email protected] Vytauto g. 114a, Kretinga, Lithuania +370 445 51431 www.flexblow.com Mr Gytis Sirvinskas Marketing Director +370 620 11528 [email protected] Leverage House, Hamilton Road, Sutton in Ashfield, Nottinghamshire, United Kingdom, NG175LD +44 1623 556287 www.rdleverage.com Mr Alan Tolley Managing Director +44 1623 556287 [email protected] Grünlandgasse 5/1/12 2620 Neunkirchen, Austria +43 720 775 196 www.pet-eu.com Mr Maxim Poliansky CEO +43 720 902 169 [email protected] Stretch blow moulds Bottle size (max.) (in litres) 40 10 12 5 40 Moulds supplied to blowing machine manufacturers/ converters Yes Yes, for all blow moulding machine platforms, e.g. Sidel, Krones, KHS, Sipa, etc. Sipa, Sidel, Krones, Kosme, 1 Blow Sidel, Krones, Sipa, Side, Chumpower Yes, Sidel, KHS, Krupp, Sipa, SMI, Krones, Kosme, Siapi, Mag Plastic, ADS, Lonza, Side Do you supply retrofit moulds for existing SBM machines? Yes Yes, also manufacture multi-platform compatible mould systems Yes Yes Yes Bottle design service Yes, for flat-sparkling water, CSD, wine, dairy, edible oil, detergency Yes, container design, prototype sampling and bottle performance tests Yes Bottle design, 3D models, prototyping, bottle sampling, PET containers laboratory tests Specialities Blow moulds, modification of blow moulds Hot fill, heat-set moulds with energy efficient system and multi-platform interchangeable quick mould systems Hot fill, wide mouth, oval shaped R&D/Leverage are recognised as a world leading tooling supplier for the single stage, injection stretch blow moulding ISBM industry. In our Product Solution Laboratory we can trial product, colour, materials plus qualify production tooling on our Nissei and Aoki injection stretch blow moulding machines. Water, CSD, dairy, bottles for chemicals and detergents, 20-40l containers, hot fill, wide neck jars, lightweight designs, laboratory tests Other Joint development projects for special applications and new blow mould development We can make and test any type of PET blow mould in-house with our universal PET SBM machine FlexBlow1 - compatible with blow moulds from different original suppliers Short Lead Time","@ID":29}, "8 NEWS PETplanet Insider Vol. 20 No. 05/19 petpla.net Nampak Inspection & Coding Systems new partner of Sesotec in South Africa Since June 1, 2018 Sesotec GmbH has a new partner in South Africa with Nampak Inspection & Coding Systems. The partnership relates to the “Inspection Division” and primarily concentrates on the food sector, but it is also planned to utilise the existing potential in the plastics industry and to conquer regional markets with active campaigns. At the ProPak Africa trade fair that was held in Johannesburg from March 12-15, 2019 Sesotec presented the Varicon+W metal detection system with Intuity metal detection coil, and the Raycon EX1 X-ray scanner at the Nampak trade fair stand. In addition to sales and distribution, Sesotec states that service is another strong point of Nampak, which is why Nampak also will perform local service for Sesotec metal detection and X-ray systems. www.sesotec.com Simon Euler, Account Manager Division Product Inspection of Sesotec GmbH (fourth from left) was present at the ProPak Africa trade fair stand of Nampak Inspection & Coding Systems Pilot plant to turn sugarcane waste into bottles Researchers of Queensland University of Technology and Mercurius Australia have commenced work on a pilot plant to prove the economic viability of turning sugarcane waste into either jet and diesel fuel or chemicals that could be used to make plastic soft drink and beer bottles. Dr Darryn Rackemann, Senior Research Fellow from QUT’s Centre for Tropical Crops and Biocommodities (CTCB), is leading the program at the Gladstone pilot plant. The patented Reach technology, developed by US parent company Mercurius Biorefining, is claimed to have the potential to convert sugarcane bagasse and other biomass into cost effective drop-in biofuels and bio-chemicals, as alternatives to fossil fuels. Dr Rackemann said the pilot plant would have a flexible technology base that would allow targeting production of renewable fuels and green chemicals. He said the work by QUT researchers proved the system worked in producing grams of chemical and fuel samples, while the pilot plant this year would be able to demonstrate the viability of manufacturing kilograms of chemical and fuel samples. While the initial focus of the pilot plant is investigating the conversion of biomass into fuel, Professor Doherty said the technology had the potential to create chemicals that could be used to make polyethylene furanoate (PEF), a completely bio-based polyester used to make bottles, films and fibres as an alternative to PET produced from fossil fuels. Mr Seck said the pilot plant would be testing sugarcane residue, but the process could work with other plant crop wastes. Based on the successful completion of the pilot project, Mercurius Australia is planning to build a larger demonstration plant, which could scale up production of biofuels and biochemicals. www.qut.edu.au","@ID":10}, "COMPRESSORS PETplanet Insider Vol. 20 No. 05/19 petpla.net 24 COMPRESSORS (SIS) significantly reduces the starting current and keeps it low. Variable Speed Drive packages adjust compressor operating speeds to meet actual production needs. A fully integrated system is capable of recovering up to 80% of the input shaft heat produced by a reciprocating compressor and recycling it to supply water at up to 90 °C. Further savings can be found by decreasing the size of the cooling system needed to maintain water temperatures to the compressor. “Automation 4.0” boosts customer ability to control, manage, and monitor equipment, and optimise efficiency. AF’s DX1 and DXB PLCs use Siemens S7 controllers and HMI interface for local control, which enable operators to manage multiple compressors within specific installations, modify pressure settings from the blow moulding machine, and allow remote monitoring of the system from anywhere in the world, via 3G/4G. Giovanni Brignoli, Compressors Division Food & Beverage Product Leader, Siad Macchine Impianti S.p.A.: Currently, and much more than in the past, the air demand is not constant but highly “intermittent” due to the influence of many factors: change in bottle sizes; change of production rate – thus blowing speed; the possibility of having different blowing machines working together; the possibility of relocating the blowing facility to a different site, with different conditions. Given this, it is imperative that the compressor should be flexible in the compressed air production rate, in order to be able to constantly follow the ever-changing air demand. A compressor with a variable speed drive (VSD) , also known as VFD (Variable Frequency Drive) or frequency converter, or inverter system, could drastically reduce the waste of energy given by the traditional “load/unload” compressor working mode, used in the past as the only way to face this changing compressed air request and adapt its working mode (and consequent energy consumption) to the real-time air demand, without any waste. Furthermore, the continuous reduction of the “dead volume” of the blowing machine, combined with increased air recovery, can significantly reduce the air rate requested. It means, in practical terms: a smaller compressor with consequently lower energy consumption. Gonzalo Gabarain, Sales & Marketing Manager, Arizaga, Bastarrica y Cía, SA (ABC): As I mentioned in the above question, installing a VSD helps to avoid the off-loading situation (where you consume energy but don’t compress any air). It even allows to have different pressure set points in order to be ready any time to blow at the correct pressure and the requested flow. In the above mention Etherplus Package we added the e-ntelligent system, which allows to install more than one VSD at the same time (1 VSD per compressor) in order to reach the best energy performance. Installing also a compressor manager for the whole compressor room to drive it properly and decide automatically which compressor should be running is also a must, and we are working on that. Compressor must be linked to blowing machines and technology allows us to do so. Communication between each other is out of question and we are working it to be standardised. Do you see energy savings potential among your customers that are already possible but often remain unused? Trevor Perry, Sales Director, Gardner Denver (Belliss & Morcom): We regularly witness inefficiencies on customer’s sites, however we are quick to support, advise and recommend improvements that can be made to the complete compressed air system, (LP and HP) such as optimum control of the compressors through reduced pressures, reduction in no load running time, all with the introduction of our AirPET Control Systems, installation of our new VP Valves in to the compressors that can reduce energy consumption by up to 20%, combinations of utilising VSD (where it makes sense to do so) to again reduce energy consumption through optimising the load patterns and reduced pressure set points and differentials. Pascal Heyden, Marketing Manager, AF Compressors: For the most part, we actually see just the opposite. With the technological advancements made on our current compressors, customers are now coming back to us to see what improvements could be made to older compressors to increase their efficiency. Years ago, AF developed the “L-series” with an improved and more efficient cylinder design that can be adapted to older units in the field. By upgrading to the new “eco-cylinders”, customers can see immediate benefits. Furthermore, existing compressors can be retrofitted with our Adjustable Air Flow System (AFS) and Smart Inverter Starting (SIS) options to further reduce operating costs. Older PLC controllers can be converted to the newest DX1 or DXB PLC’s to ensure proper monitoring and control of the system. The fact that our customer’s see a huge benefit with the upgrades available for older machines has led AF to create a new department to work with customer’s wanting to improve their total cost of ownership by enhancing their older compressor with the latest energy saving equipment and automation that is available to them.","@ID":26}, "9 NEWS PETplanet Insider Vol. 20 No. 05/19 Institute of Scrap Recycling Industries names Nestlé Waters North America as Recycling Award Winner In recognition of its innovative use of recycled plastic, and its product design centered on recycling, the Institute of Scrap Recycling Industries (ISRI) names Nestlé Waters North America as its 2019 Design for Recycling (DFR) Award winner. The DFR Award is ISRI’s most prestigious award given annually to the most innovative contribution to products designed with recycling in mind. Nestlé Waters has received the award specifically for the design of its Nestlé Pure Life 700ml bottle made from 100% recycled PET plastic (rPET). In addition to the bottle being made entirely from rPET, its design also takes into account end-of-life processing. For instance, the bottle features a state-of-the-art, pressure-sensitive label. Unlike traditional adhesive labels that may not release from the PET flakes during the recycling process, potentially damaging the recycling stream, these new labels are claimed to release easily during the wash stage of the recycling process so the material can be used to make new bottles again. www.nestle-watersna.com Atlas Copco: Acquisitions Atlas Copco has acquired PSI Compressors of Brockville Incorporated. The company is a distributor of compressors in the south-eastern part of Ontario. PSI Compressors is located in Brockville, Ontario, Canada and sells, services and installs compressors and related ancillaries. The company’s main focus is general industrial manufacturing, food and beverage, agricultural, government and educational institutions. PSI Compressors of Brockville Incorporated will operationally become part of the Compressor Technique service division. Earlier in April, Atlas Copco has acquired S.A.S. Air Diffusion. The company is a distributor of compressors for Atlas Copco. Air Diffusion is located in St. Etienne in the southern part of France. The company has around 15 employees. Air Diffusion has a diverse group of small to medium-sized customers in workshops and in the manufacturing, food and beverage, wood, plastic and foundry industries. Air Diffusion is acquired by Exlair S.A.S., which is part of Atlas Copco Holding France. www.atlascopcogroup.com","@ID":11}, "COMPRESSORS PETplanet Insider Vol. 20 No. 05/19 petpla.net 37 AF Compressors launches new compressor range Low pressure, high savings AF Compressors considers the trend towards more sustainable machinery and presents its new oil-free 58m3/min OPC45-355 range, developed in response to customer demand. The trends towards cleaner manufacturing solutions are driving demand for compressed air machinery that is free from contaminants, including oil, with low dewpoints and achieving foodlevel Class 1 ISO8573-1 standards. Levels of sustainability in compressed air installations have to be higher than in the past. Key performance indicators include: energy consumption across full and partial loads and the full range of conditions, wastage, equipment lifetime, and machinery disposal. Oil and oil-free Oil-injected and oil-flooded compressors produce waste in the form of oil vented into the air, contamination of filter cartridges, and polluted condensate. Individual components wear out in use and tend to be disposed of, rather than recycled. Rotary compressors require comprehensive compressor block overhaul every two to five years; centrifugal machines need major core overhaul every five years. Useful life is 10-15 years. As refurbishment costs are high, operators tend to dispose of existing machinery and replace it entirely. Oil-free compressors, which are available in industrial piston, rotary, and centrifugal forms, produce less waste. Their condensate is pure water, there is no oil to contaminate filters and they obviously do not require oil changes. Cost, compliance and maintenance Increasing complexity, raw material costs and legislative compliance are driving up the cost of compressed air. Energy prices are on an upward trend for a number of reasons, including rising demand, more expensive resources leading to supply constraints, and the cost of compliance with climate change regulations. Maintenance costs can spiral upwards as well. Energy Electricity accounts for the overwhelming majority - around 80% - of the running cost of compressed air systems. While optimal usage is achieved at near full load, very few compressors run at that level. Variable-speed drives help reduce consumption but do not eliminate losses completely; partial loads deliver less than maximum efficiency. Running at varying loads and speeds also raises the risk of expensive breakdowns and reduces the life of electronic components. Extending range AF’s introduction of advanced technology into its standard 6-15 bar oil-free applications has helped to boost energy efficiency and reduce maintenance requirements. They offer longer working lifetimes even under extreme environmental conditions, such as ambient temperatures in excess of 50 °C and high humidity. At idle, the OPC90-132’s specific energy consumption is below 7 kW/ m3/min. It is claimed to be one of the most energy-efficient compressors under full load conditions, consuming just 5.5 kW/m3/min at 8 bar. This is 29% below BAFA (German organisation for subsidising Energy projects) minimum requirements. AF Compressors claims that its new range offers savings of up to € 10,000 a year, depending on machine size and usage. The new dual flow adjustable airflow system (AFS) digital control on the OPC90132 does not need a frequency converter, cutting costs and eliminating the need for expensive, frequently replaced electronics. Extending service intervals and reducing waste The OPC90-132 has been designed to minimise component wear, lubrication, waste and maintenance requirements. Service intervals have been extended: second-stage seals must be replaced and valves refurbished every 8,000 hours; first-stage seals and valves require service at 16,000. Extending compressed air system lifetimes The OPC90-132’s designed lifetime is 40 years – four times the length of current systems. It should require no major overhaul during its working life; just normal maintenance, supported by approved, genuine parts. The company says that the new OPC range offers a substantial carbon footprint reduction, compared with previous models. www.afcompressors.com COMPRESSORS 10bar compressor OPC200 AF 10 bar oil free compressor at CocaCola Al Ain in the UAE","@ID":39}, "COMPRESSORS PETplanet Insider Vol. 20 No. 05/19 petpla.net 18 COMPRESSORS A review of PET compressor developments A large amount of air is needed to blow PET preforms into bottles. The compressors that compress atmospheric air into compressed air must withstand extreme conditions such as high pressures, heat and continuous operation. But the success of the blowing process depends on a consistent and clean flow of air regulated at a specific pressure. The first models of compressors constructed for the bottle-making process appeared on the market when the PET bottle industry took off in the late 1970s and early 1980s. Reciprocating piston compressors are the most common type in the stretch blow moulding field. Since the early 2000s, centrifugal compressors have also been found on the PET bottling market. Centrifugal compressors provide 7-13 bar air, which is compressed to the desired pressure by a booster. This type of compressor requires less maintenance than equivalent models of reciprocating compressors as there are fewer inbuilt sliding parts. Disadvantages are the amount of floor space and the need for two units to do the work. With piston compressors, the air becomes ever more compressed in different cylinders and then is cooled again. After opening the suctions valves, atmospheric air is fed into the cylinder through an air filter and is compressed for example to 4-5 bar when drawing back the piston to the cylinder head, and this warms it up. The compressed air is pushed out of the cylinder through a delivery valve and is cooled in an inter cooler. Moisture is removed. In the next step, compression, for example, to 15-17 bar is achieved. The air is cooled again and dehumidified before compression, for example, to 40 bar is achieved. The required pressure depends to a certain extent on the container’s design and its wall thickness. Thick walls and sharp edges require higher pressures than simpler shapes and thinner walls. As a general rule, the stretch blow moulding process works with a pressure of 10-25 bar for preblowing and a maximum of 40 bar for the bottle blowing process. A pressure of 7-10 bar is needed to actuate pneumatic equipment. For most water or CSD lines, a maximum output of around 3,000m3/h is sufficient; for plants with particularly high compressed air consumption, for example for hot filling, models with an output of around 6,000m3/h are available. Depending on the layout of the cylinders, designs include L-shape; Y-shape; V-shape; or M/W-shape, horizontally opposed design. Is the air clean? The purity of the air is essential for the stretch blow moulding process. Water, dust and oil are the typical particles that must be cleaned from the air before bottle production by a separate air purifier system. Some compressor manufacturers rely on oil-free systems. However, because of the lack of lubricant, these can more easily generate abrasion particles, making it necessary to filter out these typically larger particles. In order to recycle the compressed air after blowing the bottle, it can be captured using an annular pressure vessel and is fed back into the network using an air recovery system. A bundle of energy Manufacturing PET bottles is an energy-intensive process. As the PET market has matured, plant engineers have come to realise that their choice of certain compressor models affects the profitability of the overall system. Ultimately, the compressors are the largest individual energy user in the system, taking around 50% of the total energy expenditure. To save costs and also because of rising environmental awareness, more and more companies are paying close attention to the calibration of the air pressure they actually require. As mentioned above, a pressure of 40 bar is the maximum required to manufacture standard PET bottles. Each reduction brings energy and cost savings, which explains the trend towards lower pressure settings. Depending on bottle volume and production performance, analysis is performed to establish which blowing pressure is needed for which product. Compressors for PET bottle manufacturing – some highlights 1999 to 2019 as reported in PETplanet 2000The very first article on compressors in PETplanet Insider came from LMF Austria (issue 1/2000). The company had developed and brought onto the market a new compressor design, delivering from 353-1,413 cfm (600-2,400m³/h FAD). The basic aggregate consists of either a 3-stage VC type compressor for 353 cfm (600m³/h) or a VCL type for 706 cfm (1,200m³/h). Its total capacity can be doubled by adding a Roots blower as a booster. It is possible to adjust the blower motor capacity via a PLC control system to produce exactly the amount of air required at any one time (e.g. when the size and/ or number of bottles per hour is not constant). Belliss & Morcom supplied their first PET compressor system in 1978, when PET bottle manufacture was still in its infancy. In 1995 the company merged with Hamworthy and became part of the Powell Duffryn group. The merger provided the newly-named company, Hamworthy Belliss and by Gabriele Kosmehl","@ID":20}, "BOTTLE MAKING 12 PETplanet Insider Vol. 20 No. 05/19 petpla.net Stackable packaging solutions with integrated handles The PET-in-Box concept Cypet Technologies delivered its first machine for 18 l stackable PET bottles for edible oil packaging in 2015. Since then, several additional machines for this application have been delivered, for bottle sizes from 9-25 l, also featuring integrated handles for convenience, lower cost and easy recycling. But Cypet’s design and development team did not stop here. Now it has designed an alternative PET packaging solution for higher stackability, resulting in the PET-in-Box concept. Cypet Technologies Ltd is located in Nicosia, Cyprus and manufactures single-stage machines for the production of a large range of containers sizes. Installed Cypet machines are producing from 20ml miniature bottles to the world’s largest PET container, a 120 l open mouth drum, with 400mm neck diameter, says the company. For comfortable handling and emptying of the bottles, Cypet machines can produce bottles with an innovative strong integrated handle, which eliminates the need for additional and costly production steps of producing a handle separately and then fitting it on the bottles. The single-stage technology used is capable of producing with 4 cavities, up to 25 l stackable bottles with integrated handles. The company states that their one-piece stackable PET bottles with integrated handles offer an environmentally friendly packing solution, by saving up to 40% raw material compared to HDPE jerry cans, with a corresponding saving in raw material cost. In addition, the PET bottles offer better gas barrier, impact strength and stress crack resistance. PET-in-Box Cypet’s new packaging solution for higher stackability comes with many functional features. The PET-in-Box concept consists of a lightweight PET container with an integrated handle in a carton box. While the box is providing the required stackability, a cut-out in the carton top face exposing neck and handle, enables carrying and pouring of the contents without the need to open the carton. Another cut-out in the base with recess on the container enables tilting the package for convenient pouring of the contents. Because of an off-centre neck, easy pouring can be also realised from the side. A 4-cavity single-stage Cypet system now in production, is making the world-first PET-in-Box solution, for a 15 kg (16.5 l) application in Asia. Both Cypet solutions for stackable PET packaging can be applied to packaging sizes from 8-25 l capacity. According to the company, they are very well suited for the commercial packing of edible oils, household cleaning chemicals, personal care products, kerosene and many other liquids. www.cypet.eu Stackable PET containers with handles The lightweight container with handle comes in a carton box. A cut-out in the box enables pouring the contents without the need to open the carton.","@ID":14}, "41 TRADE SHOW PREVIEW PETplanet Insider Vol. 20 No. 05/19 petpla.net Sacmi takes five Italian packaging machinery manufacture Sacmi offers five reasons for visitors to Chinaplas to visit its stand. It will be displaying a CCM 48 SD continuous compression moulding press, one of 23 solutions recently supplied to Hebei Red Hat Plastic Co., Ltd, the Chinese packaging giant. The company will be showcasing its end-to-end solutions for entire beverage lines, in the shape of its advanced IPS platform for the manufacture of PET preforms along with a full range of filling, labelling and bottling solutions. CBF machinery uses compression technology for making containers especially for the dairy and pharma industries. The fourth area of focus is quality control, including camera inspection systems to maximise the performance of every single machine. Chinaplas will see Sacmi present its CHS (capsule handling system), part of a range of vision systems developed by the Group’s Quality & Process Control Division. Sacmi’s hand is completed by its Customer Service Division, which works in close concert with the Sacmi Global Network. Its suite of aftersales support includes advanced remote assistance services including e-learning training and production management support through Sacmi S.P.A.C.E. (Sacmi Portal for Aftersales and Customer service Excellence). www.sacmi.it Vision inspection systems Intravis GmbH, a manufacturer of vision inspection systems for the plastic packaging industry, will show its new systems in hall 5.1, booth J09, in the German pavilion. This year’s highlight will be the IntraOne smart camera solution, inspecting various plastic packaging products. Intravis will also showcase its PrintWatcher at a partner booth. “In the last years we have seen a rapidly increasing demand for vision inspection systems in the Chinese plastic packaging industry. Therefore, Chinaplas is one of the most important trade shows for us,” says Dr Gerd Fuhrmann, CEO of Intravis GmbH. “Furthermore, it’s also a delight to meet so many of our long term partners and customers again.” The highlight at the Intravis booth will be the IntraOne, a smart camera solution. This single camera system can be used for the inspection of closures, bottles and containers as well as for label inspection. The IntraOne offers a wide range of inspection possibilities and comes with Intravis’ well-known, user-friendly and purpose-dedicated IntraVision software. Collaboration with Wutung extended Intravis, collaborates with its long-term partner Guangzhou Wutung Engineering Co., Ltd. Together the two companies will exhibit a PrintWatcher at the Wutung booth (4.1 K01) to display Intravis’ broad range of vision inspection systems for printed and decorated objects. The system is integrated into a Wutung printing machine and provides a 360° body inspection of transparent bottles, using a single line scan camera. Another highlight at this year’s show is the presentation of Intravis’ own user-friendly vision inspection software IntraVision. Of course, with a user interface in Chinese. “We are happy to display this highly developed system to our Chinese customers this year”, says Ms Sonja Radermacher, Intravis Sales Manager for South East Asia. “Typical printing defects like print offset as well as defects at the label joint are easily picked up by the Intravis inspection system. The PrintWatcher is the comprehensive result of many years of experience in the printing industry.” During the show international sales managers from the German headquarters as well as CEO Dr Gerd Fuhrmann will be happy to meet new and existing customers. At both, the Intravis and the Wutung booth, the international team will provide comprehensive demonstrations and presentations of the technology made in Germany. www.intravis.com Gneuss rotary filtration systems The patented Rotary Filtration Systems are characterised by the filter disk on which the screen cavities are located in a ring pattern and which is completely encapsulated by the two filter blocks. Screens can be inserted into the cavities by opening a small hatch door giving access to the cavities while the production process continues to run without any interruptions or disturbances. All models have been completely revised in the last years. Modifications to the screen changer housings permit operation on a wider range of applications at higher pressures, whilst offering enlarged active filtration areas. Components and modules have been commonised in order to offer shorter delivery lead times and lower costs. The SFXmagnus series operates automatically as well as process and pressure constant. It is suitable for a wide range of applications. This series is characterised by an extra large active screen surface area, its compact design, as well as easy operation. Screen changes do not have any influence on the product quality. Gneuss’ top model, the RSFgenius, operates with an integrated self cleaning system for very demanding applications and highest quality requirements. Screens can be automatically re-used up to 400 times and filtration finenesses below 10 microns/1200 mesh are available. The KF range of continuous filtration systems is designed specifically for applications with frequent material type, grade or colour changes as well as for high pressure applications like blown film. The KF screen changers are claimed to be especially compact and to offer excellent value for money while permitting simple and quick screen changes on the fly. www.gneuss.com SACMI Hall 4.1 Booth C41 GNEUSS Hall 5.1 Booth J36 INTRAVIS Hall 5.1 Booth J09","@ID":43}, "BOTTLE MAKING 17 PETplanet Insider Vol. 20 No. 05/19 petpla.net BOTTLE MAKING 17 Excellent distribution and control of the barrier layer allows us to accurately dose the barrier and place it where it is needed to minimise the use of the barrier material; which is typically more expensive than the skin material. It also allows the customer to light-weight the container knowing the barrier will be accurately distributed where you need it, to achieve the shelf life requirements for the application. We are also seeing a lot of interest in co-injection for UV light blocking applications like in dairy applications (i.e. milk preform- and bottles). In this case we can replace an injection over inject system with a coinjection system and automatically double the cavitation yields since we will be injecting simultaneously. The Klear Can is another area where we are seeing a lot of interest with customers asking about different size cans to substitute the metal can by a clear plastic container (Klear Can), which is already in stores. PETplanet: Recyclability is a big topic in the plastic and packaging industry. Where do you see future development? Milacron: We see two big areas in the future: One is on material development and the other one is introduction of PCR due to the directives e.g. from the European Union. Biodegradable skin and core materials are currently already being used in our systems. We are studying these materials and working with materials suppliers to test them, on customers’ specific applications. We are also working with the University of Massachusetts Lowell to see how these materials perform. We are getting a lot of requests to co-inject a high core content of PCR into what would be normally a monolayer part. We have done this for industrial segment and showcased this at NPE a few years back. Now we are getting the same requests from packaging applications. We believe the European directive is driving a lot of this. By 2030 all plastic packaging should be designed to be recyclable or reusable. By 2040 USA and Canada are proposing complete recyclability and/or recovery of plastic products. As a result we are getting a lot of requests for co-injecting large percentages of low-cost PCR. At the end we can reduce the consumption of virgin resin, by substituting it with recycled material, in the inner layer. This is fully supported with our technology and realised already. As an example, we have moulded a 5 g pail, with 50% scrap material in the inner layer. Similarly we can apply this in packaging. PETplanet: Thank you very much. www.milacron.com Ms Cheryl Sayer, Director of Engineering at Mold-Masters Americas Mr Oliver Lindenberg, President Mold-Masters Americas","@ID":19}, "BOTTLE MAKING 14 PETplanet Insider Vol. 20 No. 05/19 petpla.net 64oz PET barrier-container with handle for the craft beer market Easy to handle W. Amsler Equipment Inc., a leading supplier of all-electric linear PET stretch blow moulders, has launched a new 64-oz PET growler jug that aims to emulate the traditional format and provides barrier protection for extended shelf life. The PET container is believed to be the first in the industry to include a handle and provide barrier protection. A growler is a jug commonly sold at breweries and brew pubs as a means of selling take-away craft beer. The significant growth of craft breweries and the growing popularity of home brewing have also led to an emerging market for the sale of growlers. The amber PET container is manufactured by W. Amsler at its Bolton, Ontario, facility on behalf of JMS International Packaging, a leading packaging solutions provider, on a W. Amsler all-electric linear series stretch blow moulder. The PET barrier container weighs 106 g compared to 1.2 kg for the glass version, thus resulting in reduced shipping costs. It is also event-friendly, unbreakable, and 100% recyclable, according to Heidi Amsler, sales and marketing manager for W. Amsler. “We’re proud to be part of this highly collaborative effort that has resulted in a breakthrough in PET barrier containers for the craft beer market,” said Amsler. “We’ve set a new benchmark in terms of shelf life and provided craft brewers a highly viable alternative to the standard glass container.” Unbreakable and portable PET growlers provide an entry into such venues that do not allow glass because of the potential for breakage and other security requirements. The 64 oz, 106 g container was designed by W. Amsler with standard preforms supplied by Preform Solutions Inc., Sioux Falls, S.D. The PET growlers have a flat champagne base rather than a carbonated base design and withstand 15 psi of pressure. PET growler with an HDPE handle W. Amsler made the announcement April 8-11 at the Craft Brewers Conference & BrewExpo America in Denver. For the conference, W. Amsler selected a barrier with a monolayer structure which includes a Sherwin Williams’ barrier additive. The barrier prevents oxygen ingress and egress and loss of CO 2 , thus providing a 120-day shelf life compared to 48hrs for standard PET growlers. This monolayer barrier solution is compatible with existing recycling streams. The high-density polyethylene (HDPE) handle, designed by JMS International Packaging, is produced separately and attached to the container via a secondary process. The PET container comes with a 38mm finish. The amber colour for the 64oz barrier bottle is supplied by Penn Color. New patented PET grade In the future, the JMS production bottles will be manufactured with a new patented PET plastic (PETB1) that has been developed by JMS International Packaging Inc. The new patented plastic (PETB1) offers the best barrier to CO 2 plus oxygen egress and ingress on the market. This unique material also protects the product from UV rays and is available in transparent or opaque versions. The product is claimed to resist impact and ensure a certain economy compared to glass. The formula has enabled JMS to obtain a recycle code 1. It has strong resistance to hot filling and is much lighter than glass. The PET plastic growlers are also available in a clear colour with or without barrier protection for ciders, craft sodas, craft cocktails, and liquor. Pressure-sensitive labels can be applied and a screen-printing process can also be used. W. Amsler has focused new resources and expanded its participation in the beer packaging market. The company sees significant opportunities in glass conversion applications where barrier PET bottles have a strong fit due to their light weight and portability. The company introduced 12 oz barrier PET bottles in a longneck style with a crown cap at NPE 2018. Subsequently, a second 12 oz format with a slightly different design and label panel was launched. www.jmsintpackaging.com www.amslerequipment.net","@ID":16}, "PETplanet Insider Vol. 20 No. 05/19 petpla.net 47 BOTTLES Dextro energy drink The drinks’ manufacturer, Columbus Drinks Ltd, has developed a “D by Dextro Energy” drink under licence from Dextro Energy, a classic brand with emphasis on fast-acting energy intake in the form of dextrose which is currently being sold on retail shelves. This carbonated and caffeine-free soft drink with extra energy is suitable for vegans, as well as being gluten-free and enriched with various vitamins. The three different flavours come in transparent, slightly tapered 500ml bottles and have a sleeve label typical of the brand. It is secured via an embossed red screw cap and tamper-proof strip. www.columbus-drinks.com [email protected] Tel: +90 212 695 50 00 Fax: +90 212 694 97 24 100815dmyR .com An organic smoothie In an advertising campaign lasting only a few days, the German discount outlet, Aldi South, introduced several smoothies under its own organic brand onto refrigerated shelves. The picture shows pear, orange, kiwi and passion fruit varieties. The fruits are grown in an organically controlled environment, then gently heated and cooled. They come in handy, transparent 200ml bottles with an amusing film label, screw cap and freshness seal. www.aldi-sued.de AdeZ plant drinks Since taking over the plant-based fruit drinks’ manufacturer “AdeZ” around two years ago, Coca-Cola has had a presence nearly everywhere on smoothie refrigerated shelves. The pictures show two different varieties: “Magic almond with mango and passion fruit” and “Happy oats with strawberry and banana” which come in slightly tapered 250ml bottles. These “plant bottles”, which have eye-catching sleeve labels and consist of 30% of renewable raw materials, are secured via a screw cap and tamper-proof strip. The top side of the screw cap has the name of the brand embossed on it. www.coca-cola-deutschland.de Rauch tea with juice The Austrian juice manufacturer, Rauch and Co. Ltd KG, has a variety of tea-juice combinations on offer under the name “Rauch Juice Bar” which include a herbal tea with pear and lime, and a hibiscus tea with blueberry and raspberry. The freshly prepared drink contains no added sugar and comes in a clear, slim 500ml bottle. The conveniently sized spout is secured via a printed screw cap with tamper-proof strip. A partially transparent, large, dark sleeve label conveys all the relevant product information. www.rauch.cc","@ID":49}, "COMPRESSORS PETplanet Insider Vol. 20 No. 05/19 petpla.net 34 Answers to advances PET bottle blowing Evolving compressed air requirements By Jared Link, Global Product Manager - Large Reciprocating Compressors, and Michael Nicholl, Industry Manager - Plastic Blow Moulding, Ingersoll Rand Over the past two decades several advances have been made in container design, blowmoulding machinery, and bottle processing that have significantly changed the requirements for high-pressure compressed air in the PET bottle blowing industry. Despite significant increases to machine cavitation and bottle speeds, high-pressure compressed air consumption has decreased. Firstly, light-weighting efforts aimed at reducing the PET raw material requirements for packaged containers had the unanticipated benefit of allowing for effective blow moulding at reduced pressures. This had an impact on both compressed air flow usage and corresponding energy consumption. In addition to the more obvious benefit associated with the reduced energy consumption to generate lower system pressures, the more impactful benefit was the reduction in actual air flow consumed for the blowing process. This is often referred to as “artificial demand” in which an excessive amount of compressed air is utilised to blow and subsequently exhausted as a function of the elevated feed pressure. Secondly, design improvements in blow moulding machinery have eliminated the waste of compressed air and optimised air recovery technologies. As an example, several manufacturers have reduced the ‘dead space’ within their valve blowing blocks and eliminated excess compressed air that previously filled larger chambers and was effectively wasted in the process. In another example, air recovery technology improvements allow for the capture of blowing air exhaust at a higher pressure (20 bar) which enables recycled compressed air to be utilised for pre-blow. These developments have further reduced the air flow requirements of high-pressure compressed air systems. Lastly, packaging equipment manufacturers have simplified blow moulding machinery and bottle COMPRESSORS manufacturing processes so that more customers are embracing vertical integration and the self-manufacture of PET containers. The trend towards multiple smaller capacity systems, as opposed to larger centralised container manufacturing operations, has resulted in lower capacity high-pressure compressed air systems. This also impacted the financial viability (ROIC) of installed redundancy as a typical design best practice and placed a premium on air compressor uptime availability. Answers to the variability in demand for compressed air Ingersoll Rand’s PET*Star is a 4-stage compression technology that is claimed to provide an inherent efficiency advantage when compared to 3-stage competitive alternatives. Depending on the size of the air compressor, the 4-stage design translates into an efficiency benefit of anywhere from 10-15%, states the company. In addition, PET*Star can operate at air discharge pressures ranging from 350 PSIG to 610 PSIG to meet the specific requirements of a given system. Operating at lower pressures directly correlates to reduced energy consumption and improved air compressor efficiency. With the trend toward smaller capacity systems, there also tends to be greater variability in demand for high-pressure compressed air. Therefore, it is increasingly important for air compression technologies to deliver efficient part load performance. As a result, Ingersoll Rand’s PET*Star technology features 3-step capacity control to achieve optimal performance under any load condition. 3-step capacity control leverages the double-acting stage design coupled with simplified valve controls to allow for unloaded, 50% load, or full load operation without the additional electrical componentry and cost associated with a variable speed drive (VSD). Ingersoll Rand PET*Star-4","@ID":36}, "44 TRADE SHOW PREVIEW PETplanet Insider Vol. 20 No. 05/19 petpla.net High quality injection moulds and PET Systems Following the successful trade fairs of previous years, the Swiss company Otto Hofstetter is present with its own booth showing the products and services this year. Otto Hofstetter is a producer for PET preform moulds from 2 up to 192 cavities, as well as for injection moulds for thin walled packaging applications and IML solutions. Otto Hofstetter will inform customers regarding the complete portfolio of high quality injection moulds. Besides the well-known high quality injection moulds, Otto Hofstetter‘s strength is the full portfolio around the plastic article, which starts with an idea for a product, followed by the competence to consult and design the product. Once the injection mould is built, the after sales service will round up the complete package. Otto Systems AG specialises in conceiving, planning and implementing first-class systems to produce PET preforms. Experienced experts uncompromisingly tailor high-quality components to specific customer need to create optimal, top-performing systems. www.otto-hofstetter.swiss OTTO HOFSTETTER Hall 4.2 Booth J41 Automation of caps production Switek Technology Automation Co., Ltd. has been working with a number of customers to improve productivity through the automation of closure manufacture, inspection, sorting and packing. It recently helped the closure production operations of DongPengTeYing, producer of the number two (after Red Bull) energy drink in China, to cut labour costs, optimise production processes, improve packing and boost just-in-time delivery to world-class standards. Switek’s R&D team has been working on a new lids automation system, which is expected to be premiered at Chinaplas 2019. The company claims that the new system, which includes IML unit, spoons assembly unit, CCD inspection unit, lids auto-sorting units and auto-packing, will increase productivity by 30%. www.switekautomation.com SWITEK Hall 12.1 Booth R21 l l l consumer bags textile packaging recycling rECO","@ID":46}, "COMPRESSORS PETplanet Insider Vol. 20 No. 05/19 petpla.net 25 COMPRESSORS 25 Giovanni Brignoli, Compressors Division Food & Beverage Product Leader, Siad Macchine Impianti S.p.A.: We completely see this potential and, to exploit it, the customers need to be more and more informed and educated about all the different means of reducing energy consumption. Indeed we, normally, suggest and provide the basic step to reach such a target, which is the Energy Audit. Sometimes the improvements that need to be carried out are really simple: for example, defining the right priority for compressor usage represents the basic step to exploit the compressor network in an efficient way. In other cases, tangible energy saving results can be achieved by adopting a dedicated control system that can automatically manage the compressor’s operational parameters in function of the air request, or simply by installing a VSD (Variable Speed Drive), thanks to a simple retro-fit. Our offer for the optimal management of energy is called “Energy Saving Pack” (ESP): from the initial assessment, provided by the energy audit, we are able to suggest to our customers the best way to manage their specific requirements related to power savings, using one (or more) of the solutions defined above. Last but not least: the customers today are also interested in receiving a proposal for a global saving, related to their whole plant installation, and not just limited to the power consumed by air compressors. Again, we are able to suggest and obtain energy consumption reductions even in this field, by exploiting the thermal energy of the hot water coming from the compressor’s cooling water circuit, energy which can be re-used for different purposes, such as feeding the factory’s heating system. Gonzalo Gabarain, Sales & Marketing Manager, Arizaga, Bastarrica y Cía, SA (ABC): One of them is again the VSD. Some customers don’t know all the potential they have with the VSD and keep it just to avoid the pick of the start-up, but they don’t regulate. We are now trying to be more “consultants” in order to help them saving energy. Another one which in most cases unused is the HRS (Heat Recovery System). Thanks to our superb large intercoolers, we can recover hot water at around 80-90 ºC that mean around 50% of the energy consumption. This hot water can be used for the plant heating, showers, plant cleaning, etc. However, we realise that many customers have requested it, have it installed but remains unused. We are also working on this to give them a solution for them to be something more easily useful.","@ID":27}, "COMPRESSORS PETplanet Insider Vol. 20 No. 05/19 petpla.net 19 Morcom with the backing of a powerful industrial group. In issue 7 they announced three new versions of their oil-free PET system compressors range. LMF’s development of a logic controller to control the pressure and flow rates of several compressors delivering air for PET bottle blowing is also a topic in issue 7. The company saw that many of their customers were using more compressors, or more compressor capacity, than was really necessary for the job being done. The first installation was realised at Coca Cola in Austria. 2001 In issue 4+5 AF Compressors explains why they chose an L-shape design for their compressors. The “L” shaped layout makes it possible for the number of moving parts to be reduced to a minimum. There are only two cross-head assemblies with two piston rods and associated bearings. The fact that the pistons at stages two and three are single-acting also means that a minimum number of valves are required. Having pistons 2 and 3 on the same piston rod means that the 40 bar stage (piston 3) does not require piston rod air packing seals between the 40 bar compressed air and atmosphere. In issue 11+12 we report about the joint forces of Boge and Siad in the field of oil-free compressors. The oil-free system, called the Superflow, makes use of an oil-free screw compressor from Boge and an oil-free piston booster made by Siad. The whole unit can be supplied completely skid mounted, complete with driers, receivers, water coolers and control panel. The range of installations offers 19 different options, with blowing air outputs from 1,150-3,000 Nm3/h. 2002When Atlas Copco introduced their Petpack compressed air system in 2000 they took a novel approach by combining oil-free screw and piston technologies. In issue 4/2002 the company announced a new standard in cost effective bottle blowing with the introduction of Petpack VSD. The Variable Speed Drive technology in both the screw compressor and the piston booster introduces power savings. 2003Kaeser has created a system solution to satisfy the requirements for control and blow-moulding air at different pressures with the “Sigma PET Air” system, which consists basically of a low pressure stage (at least one fluid-cooled rotary screw compressor with a refrigeration dryer for the control air) and a high pressure stage (at least one booster with a high pressure refrigeration dryer) plus the necessary filters and condensate treatment equipment (issue 12). The screw compressors are fitted with modulating control, which ensures that the compressor’s air delivery always matches the air demand from the blow-moulding machine. 2004A centrifugal compressor for PET bottle blowing was highlighted as a world first in issue 1+2. It is Ingersoll Rand who make compact centrifugal compressors available for PET bottle blowing at 40 bar. Reasons for that were their long life, due in part to an inherently simple and rugged design (there are only four basic moving parts - a bull gear and three rotating impeller assemblies); the dynamic compression process in which the air is compressed by converting velocity energy, imparted by the impeller, to pressure energy without any contact between mechanical components, ensuring oil and particle free air; the energy efficiency through the use of multiple stages in conjunction with constant pressure control operation. In Issue 9, we presented an alternative approach to compressed air: renting rather than purchasing a reserve compressor minimises capital outlay and the maintenance costs associated with a unit that may not be utilised year-round. All the plant manager has to do is to provide level ground and a power source. Swiss Made | www.imdvista.ch Inspection Systems for the Plastic Packaging Industry IMDvista INOX Line Closure Inspection – 100% inline. Robust, compact and very flexible. One control center (HMI) for the whole line. IMDvista PECO V3 Preform Inspection. Less than 7m² and up to 90’000 pph. Cavity reading. IMDvista PECO LUX Preform Monitoring shot by shot. Requires no additional floor space. No preform orientation.","@ID":21}, "PETcontents 05/19 4 PETplanet Insider Vol. 20 No. 05/19 petpla.net INSIDE TRACK 3 Editorial 4 Contents 6 News 46 PET bottles for Beverage + Liquid Food 48 Products MATERIALS / RECYCLING 10 More clarity, fewer blockages - Novel mobility aid masterbatch improves PET bottle production efficiency BOTTLE MAKING 12 The PET-in-Box concept - Stackable packaging solutions with integrated handles 14 Easy to handle - 64oz PET barrier container with handle for the craft beer market 16 Get connected - Co-injection for absolute flexibility COMPRESSORS 18 A review of PET compressor developments 30 Two-in-one compressor - Low pressure from the second stage and high pressure from the third stage 31 Award-winning design - Nanjing Shanghair Machinery Manufacturing changes the shape of air compressors in China 34 Evolving compressed air requirements - Answers to advances PET bottle blowing 37 Low pressure, high savings - AF Compressors launches new compressor range MARKET SURVEY 27 Suppliers of preform and SBM moulds TRADE SHOW PREVIEW 38 Chinaplas 2019 BUYER’S GUIDE 49 Get listed! Page 36243612 Page 34 COMPRESSORS Page 38","@ID":6}, "MARKET SURVEY 29 PETplanet Insider Vol. 20 No. 05/19 petpla.net MHT Mold & Hotrunner Technology AG Wentworth Mold, Electra Form Ind. Otto Hofstetter AG GDXL Precise Machinery Co., Ltd. Dr. Ruben-Rausing-Str. 7, 65239 Hochheim/Main, Germany +49 6146 906 0 www.mht-ag.com Mr Carsten Lurz Vice President Sales, Service, Marketing +49 6146 906 0 852 Scholz Dr. Vandalia OH 45377, USA +1 937 898 8460 Mr Brian Karns V.P. & G.M. +1 937 475 5189 [email protected] Zürcherstrasse 73, 8730 Uznach, Switzerland +41 55 285 22 11 www.otto-hofstetter.swiss Mr Stefan Zatti Division Manager Sales & Marketing +41 55 285 22 09 [email protected] No. 18 Changjiang Road, Guicheng, Nanhai, Foshan city, Guangdong Province, China. Postcode: 528251 +86 757 8677 7168 www.gdxl.com Mr Billy Ay Marketing Specialist +86 757 8677 7168 [email protected] 2 to 192 cavities 2 cavity up to 72 cavity 2 up to 192 From 32 to 144 cavities up to 700g, for bottles up to 30l 9g up to 350g Up to 500g Various neck finish standards including 1810, 1881, 30/25, 29/25, 26/22, 38mm, etc. Preform size ranges from pharmaceutical/cosmetic bottle to 5-gallon keg applications (approx. weight from 3.5g to 750g) Netstal, Husky, Sacmi, Demark, Engel, Arburg, Cincinnati, SIG, BMB, Sumitomo, Unique Husky, Niigon, Netstal, Milacron, others Netstal, Arburg, BMB, Husky More than 35,000 cavities have been fabricated and applied to various reowned injection machines for applications including beverages, food, home and personal care products. 2 to 112 cavities 16 cavity up to 32 cavity 2 up to 112 From 16 to 96 cavities up to 600g, for bottles up to 30l 24g up to 66g up to 500g Various neck finish standards including 1810, 1881, 30/25, 29/25, 26/22, 38mm, etc. Preform weight up to 69g KraussMaffei Krauss Maffei Arburg, Krauss-Maffei More than 2,000 cavities have been fabricated and applied to various reowned injection machines for applications including beverages, food, home and personal care products. No No No Wide mouth, up to 5 gallon, trigger moulds, moulds for vacuum blood test tubes - Multilayer moulds up to 72 cavities - Moulds for PP - Moulds for thinwall packaging - Moulds for cartridges and tubes Sidel Krones AG GDXL Precise Machinery Co., Ltd. Kiefer Werkzeugbau GmbH P.E.T. Engineering S.r.l. Avenue de la Patrouille de France, 76930 Octeville-sur-Mer, France +33 232 8586 87 www.sidel.com Mr Guillaume Leroux Moulds and Line Conversion Product Manager [email protected] Böhmerwaldstrasse 5 93073 Neutraubling, Germany +49 9401 70 0 www.krones.com Mr Moritz Vowe SA LCS Retrofits and Products +49 9401 70 5250 [email protected] No. 18 Changjiang Road, Guicheng, Nanhai, Foshan city, Guangdong Province, China. Postcode: 528251 +86 757 8677 7168 www.gdxl.com Mr Billy Ay Marketing Specialist +86 757 8677 7168 [email protected] Steinhäldenstraße 11, 74193 Schwaigern, Germany +49 7138 9732 0 www.kiefer-mold.de Mr Maik Weber Sales & Project Manager +49 7138 9732 70 [email protected] Via Celtica 26/28, Zona Industriale Ungheresca Sud, 31020 San Vendemiano (TV), Italy +39 0438 403 069 www.petengineering.com Ms Elisa Zanellato Marketing & Communication Manager +39 0438403069 [email protected] 5 5 5 30 10 To beverages, food, home care and personal care products manufacturers, as well as to converters (bottles manufacturers) Yes, Krones, Kosme, Sidel, Sipa, KHS (SIG) Corpoplast etc. Yes, various bottlers which supply bottles to beverage brands such as Coca-Cola, Pepsi-Cola, Danone, Nongfu Spring, etc. Kosme, Krones, Sipa, Sidel, ADS, Sacmi, KHS, Bekum, TetraPak, Side, SMI, MAG No Moulds retrofit/modification, repair and refurbishment Yes Yes, we supply moulds applicable to various renowned brands of SBM machines Yes Yes Brand design, creative packaging design, technical packaging design, packaging validation for industrialisation, bottle sampling, product and package interaction evaluation, packaging audit Yes Design bottles according to customers' requirements on technical performance and market appeal Yes Yes Aluminium and stainless steel moulds for rotative and linear blowing machines. Five mould shops located worldwide: France (Octeville-sur-mer), China (Shanghai), US (Atlanta), Mexico (Guadalajara), India (Pune) Bottle development customised to filling and packaging lines with performance commitments; preform-/bottle light weighting for standard- and heat-set process; low blowing pressure mould design; \"Mould quick change\" systems; automated mould change-over systems Bottle design optimisation for light-weighting, optimised CSD base, etc. Lightweight design, special design for functional drinks, juices, oil and vinegar, household chemistry, dairy products, cosmetic industry, petrochemical industry","@ID":31}, "COMPRESSORS PETplanet Insider Vol. 20 No. 05/19 petpla.net 23 COMPRESSORS 23 to compress at 40 bar. The lower the pressure, the bigger the dryer, and more over-dimensioned is the compressor. We are working on that to manufacture a compressor according to the industry. Beside this, the gases from the refrigeration dryers has become a concern for the major players and even though the price of a desiccant one, nowadays, is considerably higher, we are now implementing them when requested. This is something coming and will be a must in the future. The other most important point is the energy consumption. Most of the customers are requesting now Frequency Converters to be installed with the compressor. That’s why we developed our Etherplus Package, the better energy saving solution in the market. Topic energy savings: Besides the current trend of lower blow pressure, what are the parameters you still see to ensure a consistently low energy consumption with the production of different bottles, bottles volumes and production capacities? Trevor Perry, Sales Director, Gardner Denver (Belliss & Morcom): Efficiency of the compressor is vital, from low pressure drops across the compressor to the utilisation of the most energy efficient drive motors without the need for any belt drives or couplings, we at GD Belliss & Morcom are the only compressor manufacturer to offer a truly direct drive solution with “zero” drive losses utilising our unique “shaftless” motor solution. In addition to adding our VSD and half load system we can achieve a 30% to 100% load variation whilst still maintaining optimum drive efficiency to accommodate fluctuating demands for air as a result of variable bottle sizes, whilst maintaining stable output pressures. Pascal Heyden, Marketing Manager, AF Compressors: AF can offer potential energy savings through regulation, recovery, and “Automation 4.0”, which utilises IT based control and management. Regulation savings can be achieved by a Prestart Module or a Variable Pressure Setting Module, which allows blow moulding machine operators to alert the compressor with the specific pressure needs for production of particular containers. An Adjustable Air Flow System (AFS) automatically optimises compressor load ratios by 100, 50, and 0%, depending on requirements. Where power companies penalise peak electrical usage, Smart Inverter Starter www.sacmi.com SACMI manufacturing technology: the advanced solution,from single machines to complete lines Product design Product development Product validation Industrial production plant Process & quality control On-site and start-up assistance After-sales and Customer service SACMI 4.0 THE COMPLETE CLOSURE, PREFORM AND CONTAINER SOLUTION FOR YOUR SMART FACTORY Your Smart Factory will be child’s play. sculpture by Antoine Geoffrion / bottlerobot.com Products created using SACMI compression technology can be made from PCR polymers too.","@ID":25}, "PETplanet Insider Vol. 20 No. 05/19 petpla.net 46 PETbottles Beverage + Liquid Food A healthy shot of ginger juice In what proved to be a short promotion campaign, Aldi South sold an apple and lemon juice called “Ginger Shot” under its “rio d’oro” brand. This was an enjoyable, healthy beverage with 35% ginger content which could be drunk between meals. The clear, refrigerated 150ml bottle had a reasonably sized spout with screw cap and tamper-proof strip. A surround glossy film label provided all the relevant product information. www.aldi-sued.de Vöslauer with less sugar The on-going debate about the amount of sugar that is added to food can be heard in almost every sector these days. The beverage manufacturer, Vöslauer Mineral Water Ltd, is promoting its “Balance Juicy Lemon” soft drink on a label highlighting the fact that the product contains “only 13 calories per 100ml”. It also has an adhesive sticker that includes the words “significantly reduced sugar content (30% less)”. The drink comes in a clear 0.75 l bottle and has a smooth surface around the label area. It has a screw cap with tamperproof strip and vertical grooves on the outside of the bottle for easy handling. www.voeslauer.com bioPAC bioplasticsMAGAZINE presents: Conference on Biobased Packaging 28 - 29 May 2019 - Düsseldorf, Germany Gold Sponsor Silver Sponsors Coorganized by supported by www.bio-pac.info #biopac Media Partner 1st Media Partner TECHNICALMAGAZINE -ARGENTINA Editorial EmmaFiorentino","@ID":48}, "COMPRESSORS PETplanet Insider Vol. 20 No. 05/19 petpla.net 22 COMPRESSORS addressed this problem in issue 1+2 with its SIS (Smart Inverter Starter). Developed by Ateliers François Liège, this inverter system for starting purpose only, ensures that the starting current never exceeds the nominal current and that the full load power never exceeds 100%. Another way to save energy is to adjust the air flow in cases where less than full air capacity is needed. AF’s Adjustable Air Flow System (AFS) does this by deploying a special working protocol around the acting compressor cylinder. In Issue 8, Atelier Francois announced improvements to its “L-shape” design compressors: the compressor cylinders themselves have been redesigned, new piston ring technology has been introduced, and improvements to the interconnecting pipework and intercoolers have increased air capacity and output. In the same issue, Bellis & Morcom explained the advantages of the shaftless motors, which are built directly onto the compressor crankshaft to ensure direct transfer of the power into the running gear. Kaeser Kompressoren demonstrated in the same issue possible energy savings that can be realised through analysis by its energy saving system, KESS. Air treatment systems, which recycle the warm exhaust air from the compressors, were also presented. Compressors – Voices from the industry What developments in bottle processing over the past two decades have been particularly influential to you as a compressor manufacturer and have most influenced your R&D work? And what trends do you expect in the coming years? Trevor Perry, Sales Director, Gardner Denver (Belliss & Morcom): Air Recovery back from the bottle blowers has been a significant initiative from the SBM’s (Stretch Blow Moulders), in addition to the reduction in blowing pressures required, these changes have seen us develop our own solution for accommodating air recovery back to the compressor, in addition to us installing new materials for prolonged life of wearing parts, leading to both energy reductions and a lower cost of ownership for the end user. For the coming years we see a continuation in the drive to lower energy costs through more efficient use of both LP and HP compressed air and the recovery of the heat generated, we have further developed a heat recovery system that will add to the customers savings of potentially 20% to 30%. Pascal Heyden, Marketing Manager, AF Compressors: Between 1999 and 2009, AF saw a rise in compressed air requirements due to an increase in cavitation and speed of the SBM machines. Some of the larger production lines had such large air consumptions, that the customer often placed orders for “twin’’ or “tandem’’ compressor units, capable of providing up to 5,200m³/h to satisfy the needed air demands. At the time, a great majority of these projects also required pressure setting between 35 and 40 bar. As a result, AF reached a total order intake of 449 units in 12 months during 2011 due to the markets high demand for compressors. In recent years, the R&D of blowing technology has reduced air requirements by reducing the weight of the container. The light weighting of the containers has led to a significant reduction in blow pressures. Today, some applications require pressures below 25 bar thus having a huge impact on capacity requirements. Furthermore, the SBM machine manufacturers developed air recovery systems to recapture the air during the blow process to further reduce demands. The direct effect was a reduction in the size and quantity of compressors needed for current blow moulding applications. Giovanni Brignoli, Compressors Division Food & Beverage Product Leader, Siad Macchine Impianti S.p.A.: The daily research in terms of efficiency improvements made by the SBM producers had a high impact in our compressor R&D activity. The continuous reduction of the “old” blowing pressures (which were, until a few years ago, up to 42 bar) to lower values and the reduction of the dead volumes inside the blowing machines finally led to a reduction of the size of the compressors and to the optimisation of all components of a compression line, in order to perform properly at a lower pressure. We expect in the next few years an even greater pressure reduction that will result in one radical redesign of the high pressure compressor. Siad Macchine Impianti is already prepared to face such a challenge with its innovative solutions. Another important efficiency improvement required by blowing machine producers is the reduction of stops and the increase of the mean time between maintenances. Nowadays, an extremely reliable compressor, easily maintained (in terms of easiness and rapidity of operation and maintenance ergonomic features), and with a very long time between maintenances, is the market standard. Gonzalo Gabarain, Sales & Marketing Manager, Arizaga, Bastarrica y Cía, SA (ABC): Clearly one of the most important development has been the new moulding designs that allow the blowing machine to use a much lower pressure. Our machines are prepared","@ID":24}, "BOTTLE MAKING 16 PETplanet Insider Vol. 20 No. 05/19 petpla.net Co-injection for absolute flexibility Get connected Kortec (now Milacron Co-injection) is a leading supplier of co-injection solutions to the plastics and especially packaging Industries. The company’s systems are used to produce high-barrier multi-layer containers featuring three-layer construction that optimises clarity and strength while maximising the shelf-life of the end-use products. PETplanet talked to Mr Oliver Lindenberg, President Mold-Masters Americas, Ms Cheryl Sayer, Director of Engineering about their systems and future developments in the plastic packaging industry. PETplanet: When and why was Kortec or Co-Injection Milacron founded? What was the decisive point of this system to market? Milacron: After almost 20 years of developing technology for plastic packaging by Kortec, Milacron decided to acquire this compelling technology and technologically driven company (first system shipped in 1999) to complete our offering to the injection world and pursue a growing and wide range of opportunities. PETplanet: How has this brand developed under the Milacron umbrella since its inception? Milacron: We have integrated Kortec under Mold-Masters, as coinjection is the knowledge of the melt distribution of the different melt layers (process) and the molding process, which is the core competency of MoldMasters. Mold-Masters has over 50 years of knowledge and expertise with our hot runner and controller history to drive this technology to the next level, enter new markets and enable our customers to differentiate and be prepared for the future. PETplanet: Where do you see particularly lucrative future markets for this system? Milacron: The market drivers are part cost reduction, product differentiation, sustainability and increased shelf life and the percentage of injected scrap material, which can be added to reduce virgin plastic consumption. The main markets as of today are single serve coffee capsules, where we are the market leader, as well as in pet food containers with approximately 30-40B units, and general canned food, like soups, veggies with 80+ bill units, with our Klear Can co-injection solution as well as the beverage closure market. PETplanet: Where and how is the co-injection system used? Milacron: Co-injection is the simultaneous injection of two materials. Material A is the skin and Materials B is the core, where the core B is fully encapsulated by the skin A. Because they are injected simultaneously so there is no cycle time penalty. Coinjection is used typically to introduce a barrier, for example, to block transmission of CO 2 , O 2 , light. But it can also be used for introducing a high-volume low-cost core (PCR), mechanical advantages (injecting a core material of a different durometer) for a sealing application, and for the aesthetics for on the shelf differentiation. PETplanet: What are the key benefits of the system? (Especially for PET applications) Milacron: Milacron’s Kortec technology is the industry leader in barrier distribution and control. The system delivers excellent leading-edge control and barrier core weight control from shot to shot, run to run. It is world class due to its barrier distribution capabilities. A monolayer machine can easily run as co-injection process with Kortec Connect. This enables the machine to be used for multiple purposes, one day it can be used for co-injection molding, the next day it can be used for monolayer moulding. Because Kortec Connect enables customers to make better use of their existing assets; it is the most cost competitive entry to coinjection on the market! PETplanet: How much weight is gained by the co-injection process e.g. saved in comparison to other multilayer preforms? Milacron: Weight is not gained, in fact, since for example in a PET barrier application, the core material has 10 times better permeation rates than PET, the part is typically lightweighted with the introduction of a barrier layer. The Kortec Connect system (MM-co-injection hot runner + controller + auxiliary injection unit) enables customers to upgrade their existing injection machine (all major brands) from mono-layer to multi-layer (co-injection). This helps to minimise the investment costs for the moulder and enables them to re-use existing equipment for a new purpose. by Heike Fischer","@ID":18}, "38 TRADE SHOW PREVIEW PETplanet Insider Vol. 20 No. 05/19 petpla.net Chinaplas 2019 Locally manufactured moulds PET bottle production equipment specialist Sipa is coming to Chinaplas to demonstrate its solutions for packaging that combine high performance with low weight. Sipa produces machinery and moulds for injection moulded PET preforms and for stretch-blow moulded containers, in sizes from the smallest miniatures all the way through to large bottles for water coolers. It also provides design services that help customers create products that stand out from the competition. Headquartered in Italy and with manufacturing units in several countries, Sipa has operations in China for preform and bottle mould production, refurbishing and conversion. This makes it the only European firm providing its Chinese customers with locally designed and produced moulds for preforms and bottles, states Sipa. Its experts in Hangzhou can design moulds, preforms and bottles, and perform a wide range of laboratory tests. The mould refurbishing and conversion services in China are an important element of the total PET preform and bottle mould offering. They provide customers with the option of having some components replaced by new ones in order to improve preform quality (refurbishment), or having the mould converted to produce a completely new (and quite often lighter) design of preform. The advantage of mould conversion over buying a completely new mould lies in the lower capital investment involved. The base (or “shoe”) of the existing mould is retained and reused, accelerating return on investment. Customers can choose which alternative works best for them by having local Sipa experts come and carry out a mould audit. They will assess the state of wear of the various mould components on the spot, and propose different options for conversion and/ or refurbishing, according to the customer’s request. These services complement Sipa’s inhouse capability to develop and produce complete brand-new high-performance moulds including, in the case of preform moulds, hot runners – also developed and produced by Sipa. The hot half of each of their moulds requires maintenance only after five million cycles, and it is possible to carry out maintenance on components such as piston, flange O-rings and pin valves without taking the whole mould apart, states the company. Sipa’s service centre in Hangzhou, China, has been operating for 15 years. In that time, its facility has grown rapidly. The Hangzhou operation can now produce 300 cavities a month for blow moulding and 800 cavities for injection moulding. With local mould plate manufacturing as well, a 144-cavity cold half can be created in eight weeks. www.sipasolutions.com Chinaplas 2019 will take place on May 21 – 24, 2019 in China Import & Export Fair Complex, Pazhou, Guangzhou, PR China, with “Smart Manufacturing”, “Innovative Materials”, and “Green & Circular Solutions” being the show focuses. Building on the success achieved in the last edition of Chinapls in Shanghai, Chinaplas 2019 will continue to showcase innovative technologies and solutions for different sectors, such as automotive, building materials, E&E, medical, and packaging, etc. There will be a wealth of advanced exhibits, of which more than 140 technologies shown are newly announced to the globe or Asia. The advanced exhibits together with a series of concurrent events will demonstrate the theme of “Innovation is Key to the Future”. The packaging industry is playing an increasingly critical role across various sectors. Brands are looking for crowd-pulling customised packaging. Whether packaging can serve as the driving force behind a brand and how it becomes an important means for enterprises to implement their business strategies are currently hot topics in the industry. Compared to Europe, the US, Japan, and other countries, China is a late starter in the packaging industry, which, however, has grown to a fairly large-scale industry over the past few decades. And thanks to China’s 40 years of reform and opening-up, the income and living standard of people in the country have improved significantly. As a result, the market has a rising demand for technology that helps deal with small and customised orders in a precise, quick and flexible manner, and brands are going through substantial upgrades with unprecedented frequency. The importance of packaging to products is growing exponentially. PETplanet picked out some relevant innovations. www.chinaplasonline.com SIPA Hall 4.1 Booth B55","@ID":40}, "COMPRESSORS 21 PETplanet Insider Vol. 20 2015With the launch of a new machine, the WH35 high-pressure reciprocating compressor, the celebration of Gardner Denver’s 45-years anniversary festivities at its Redditch, UK site, hit its peak, as we reported in issue 9. The oil-free system offering 2,120m3/hr at 40barG was claimed to bridge the gap between their WH29 model, with its output of 1,800m3/h and the WH40, with its output of 2,300m3/h. 2016 Improved volumetric design and optimally balanced compression ratios were introduced in issue 3 by ABC Compressors and their Horizon models’ cylinders. To avoid losing energy in the transmission between the electrical motor and the compressor shaft, a direct coupled configuration has been constructed. Reducing the moving parts of the cylinders by 33% also affects the maintenance costs in a positive way. Issue 5 highlighted two energy saving features, the Variable Speed Drive (VSD) and the Heat Recovery System fromABC Compressors. The VSD adapts, by means of a pressure transmitter, the compressor rotational speed to the actual high-pressure air consumption needed, maintaining at the same time the required working pressure in the pipe line. This reduces or even eliminates the compressor idle operation and the resultant wasteful energy consumption. The Heat Recovery System recycles the heat generated during compression to provide hot water (above 80°C) for the operation, allows extra savings and reduces the CO2 footprint. After each compression stage, hot air enters a first phase cooling chamber from where hot water can be provided while the air continues to the next cooling phase. For the Gropper Group, Gardner Denver installed a piston compressor with a focus on energy efficiency. This included a roof-top cooler and a heat recovery system (also issue 5). Also in Issue 5, we reported on tools from Kaeser Kompressoren that aim to increase energy efficiency: the integrated Sigma Control 2 controller ensures comprehensive monitoring and straightforward connection to communication networks via i.e. Ethernet or databus interfaces. The integrated web server enables clear visualisation of current machine status (e.g. process data) via Kaeser Connect. 2018 Induction motors, as used in compressors, have a very high starting current; often many times the nominal current. This can cause problems with plant power networks if, for example, several motors in the factory start at the same time. Using standard electric motors, AF Compressors","@ID":23}, "COMPRESSORS PETplanet Insider Vol. 20 No. 05/19 petpla.net 30 Low pressure from the second stage and high pressure from the third stage Two-in-one compressor ABC Compressors, a family owned company founded in 1943 in Eibar, Spain, is one of the world’s leading PET compressor companies. In the early 1980s it developed the first 40 bar compressor for PET blowing machines. Today’s technologies have moved on from those days – and tomorrow’s machines will be even more advanced. ABC Compressors’ R&D team, consisting of more than 10 engineers and doctors, has made sure that compressor development is the daily focus within the company. More than 10% of revenues are reinvested in R&D, every year. ABC’s successful Horizon range, first released at the end of 2015, has helped it grow by more than 20% over the past 3 years. But the market demands new developments and features to reduce cost, energy consumption and blowing pressure. During the last Brau Beviale exhibition in Nuremberg, in November 2018, ABC released Etherplus in response to market demands for energy savings. The Etherplus system integrates a number of new features to reduce energy consumption, in the compressor and in the VSD (Variable Speed Drive). They seek to eliminate off-load running, improve the speed regulation range beyond current limits and extend component life cycles. The initial capital cost (CapEx) of a compressor represents just 10% of its Total Cost of Ownership (TCO) through its lifetime. Maintenance and support add up to another 10%. The remainder – fully 80% – is accounted for by the cost of energy. A water plant with several blowing lines and several compressors consumes thousands of Euros in electricity per month. Almost 50 % of that consumption is accounted for by the compressor room. Focusing on saving energy in the compressor room offers the opportunity to make significant savings in electricity usage, and the cost of buying it. There are different ways, all valid and none of them exclusive. ABC says that the Etherplus package delivers to users: E-limitless: A VSD without any extra consumption and full regulation capacity E-ntelligent: Install several VSDs (one per machine) to synchronise all of them and get the perfect energy consumption E-wide: Reach the longest regulation capacity avoiding any off-loading situation E-control: Enlarge spare parts lifecycle over limits and get full control of maintenance. The latest moulds on the market operate at 15-18 bar. ABC’s R&D team is working to develop a compressor capable of blowing at this pressure, with its lowest-ever energy consumption. The newest Horizon models are the only compressors currently available with the following premium features as standard: Direct couple motors (7% energy savings over belt-driven motor) Double-acting cylinders (20% energy savings over single acting) Horizontal opposed cylinders (no vibrations, longer machine life) Longest intercoolers to decrease air temperature at maximum ABC is about to release its latest and most advanced solution, which it is calling Horizon Duo. It is described as a ‘two-in-one’ compressor, which will be able to provide 100% high pressure, 100% low pressure - or both at the same time. The Horizon Duo delivers low pressure from the second stage and high pressure from the third stage, at the same time. According to ABC, that new machine offers: Immediate CapEx savings – operators don’t need to buy two compressors Time savings on maintenance Space savings – the footprint is the same as a single high pressure compressor Simplified spare parts inventory. ABC says that Duo technology is retrofittable, in many cases. ABC Compressors’ R&D team is now working on the development of a completely new range of compressors, which will be focused on even higher energy savings. www.abc-compressors.com COMPRESSORS","@ID":32}, "PETnews 6 NEWS PETplanet Insider Vol. 20 No. 05/19 petpla.net Logoplaste announces new CEO Logoplaste announced the appointment of Gerardo Chiaia as the Group’s new CEO (photo). Roberto Villaquiran, Logoplaste’s current CEO will be leaving his position for family reasons, and to pursue other activities. The company states that over the past two years, Roberto has been instrumental in implementing a new management structure, focusing the organisation on operational excellence, building a strong world-class team and creating a platform for future growth. The Board of Directors, and the Logoplaste team, are grateful for his contribution and wish him the best for his future plans. Incoming CEO Gerardo joined the management team in October 2018 as CEO Europe & Asia, after many years of having a very close trusted relationship with Logoplaste as a key partner. Gerardo has made a strong contribution to the European Business operations, commercial opportunities and strategic focus. He has 24 years of deep experience in the plastic industry, having worked at Husky in various positions from technical service, to operations, and sales. In recent years, he served as President of a number of different business units including the Beverage Packaging, the Hot Runner and Controllers Businesses. During his time at Husky, Gerado spent five years in China developing the regional business. www.logoplaste.com New COO for the Motan group From April 1st, 2019, Michael Tregner (photo) took on responsibility for Motan Gmbh as Managing Director and for global Motan production units as COO (Chief Operating Officer). He takes over for Ulrich Eberhardt, who is going into well-deserved retirement after 40 years of service for the Motan group. Michael Tregner (52 years old) has been responsible for the future of various manufacturing industrial companies as Managing Director for nearly 20 years. He is a qualified specialist for operational excellence and lean management. “The corporate growth of the past years confronts us with new strategic and organisational challenges,” explains Sandra Füllsack, CEO of the Motan group. “With Michael Tregner we have gained an outstanding expert who will advance the Motan group and its development and will advance the implementation of a global production and procurement strategy.” Michael Tregner says, “I look forward to having the chance to implement my integrated understanding of operative excellence into a medium-sized company and further to supporting the Motan group with their growth strategy.” www.motan-colortronic.com Drink technology India South premiere show Drink technology India South (dtiSouth), which took place for the first time in Bengaluru from April 10 - 12, has established a strong position on the South Indian market. With more than 90 brands, 6,481 visitors and an extensive supporting programme, the dti family further expands its footprint to the southern region of India. The local approach is intended in particular to address those sectors that are represented locally. Bhupinder Singh, CEO of Messe Muenchen India, explains “In this region of India, non alcoholic beverages as well as beer are predominant segments. Key exhibitors addressing these sectors, such as Ambicon Breweries, DVKSP, Goma Engineering and Hilden Packaging, presented their solutions and were able to get the most out of the visitor potential in the metropolitan region.” From trends and ingredients for brewing to craft beer variations: In addition to the Buyer-Seller Meetings, the place2beer and the Brewer World Seminars provided insights into future topics of the industry. Representatives of microbreweries, mediumsized and industrial breweries as well as suppliers for the brewing industry used the place2beer for networking and knowledge exchange. In addition to this platform, where even Indian beer was tasted, the Brewer World Seminars took place on the first and second days of the trade fair. There, experts discussed topics such as quality assurance of raw materials and ingredients and global trends in beer brewing. Dti-North Dti-North will take place in New Delhi December 12-14, 2019 in conjunction with pacprocess and food pex India from Messe Düsseldorf India. www.drinktechnology-india.com","@ID":8}, "45 TRADE SHOW PREVIEW PETplanet Insider Vol. 20 No. 05/19 petpla.net German Technology May 21-24, 2019, Guangzhou Hall 5.1, Booth S27 New lower volume PET preform system The PET bottle global market has been transforming from high output demands to more personalised packaging solutions. To address this new market, Guangzhou Huayan is introducing at Chinaplas the Econ PET preform system, a cost effective solution for low volume production, especially suited for small brand owners and converters with many different products. A 48 cavity system for a 12 g water bottle will be running at Chinaplas. Huayan is a leading supplier of PET preform systems in China, with over 850 systems running today up to 176 cavities in more than 50 countries on four continents. The new Econ system is built from the well-received Ecoys platform with independent servo plasticising and optimised PET screw designs, resulting in lower AA and IV drop as well as reduced energy consumption. The 220 t clamp machine accommodates moulds up to 48 cavities. The three position take off units minimise cycle times. Huayan produces their own precision PET moulds. They offer a wide range of application knowledge from the many Huayan preform moulds in operation worldwide as well as extensive prototyping capabilities. This provides small converters the ability to create a wide variety of preform designs for smaller production volumes at an attractive price. The Huayan Econ line provides high quality, reliable low cavitation preform systems at a price that results in the lowest cost of ownership, states the company. www.gzhuayan.com/en www.mymoldingsolutions.com Amut presents food-grade rPET solutions Having achieved a high profile after regularly collaborating in China National Building Waterproof Association events, Amut will be exhibiting a concept for processing 100% post-consumer bottle flakes into food grade single layer foil. The process, which was developed in partnership with plant and equipment manufacturer Erema, has already received FDA and EFSA approval and has been adopted by a number of European companies. Technology for waterproofing membrane production also on show Amut’s recycling division has been busy with the development of a Delabeller-PreWasher, which uses a dry process for both label removal and initial cleaning action. The Turbo Washer and Friction Washer carry out intensive cleaning, to remove all fine pollutants and even glue. These machines and the processes have demonstrated outstanding results even in the cleaning of highly polluted bottles. Fresh water usage is reduced to the minimum through continuous filtration, which enables it to be re-used through the whole process. Energy and cleaning agent consumption are also kept as low as possible. www.amutgroup.com AMUT Hall 4.1 Booth C55 HUAYAN Hall 3.1 Booth K31","@ID":47}, "COMPRESSORS PETplanet Insider Vol. 20 No. 05/19 petpla.net 32 Less speed, less strain Despite a higher rotational capability, the M-type air compressor actually has lower piston speed. This means that lower pressure-volume (PV) values put less strain on bearings, bushes and other components, which helps with reliability, machine life and energy consumption. Core parts, like piston rings and packings, are from specialist manufacturers and designed to cope with 24/7 continuous operation. The maintenance cycle is over 8,000 working hours; normal service warranty is five years. New compressors for VV VV Group had been using two sets of L-type compressors at its headquarters in Xuzhou City. Its problems with noise, vibration and unreliability lead them to seek alternatives. After a comprehensive review and analysis of the domestic and international air compressor market, VV Group adopted a 16m³/min Shangair M-type air compressor for a PET bottles blowing and filling production line at its plant in Wuxi city, Jiangsu province. It was put into operation on August 8, 2018 and the experience was sufficiently good that the company decided, at the beginning of 2019, to replace the two sets of L-type air compressors, with total installed power of 550kW, in its Xuzhou headquarters facility with two Shangair 26m³/min machines. The customer reported that it expects to save approximately CN¥ 500,000 (~€66,000) in electricity costs per year. Energy savings in practice Anhui Yingjia Group expressed doubts as to whether the frequency conversion range and energysaving effect of the M-type air compressor could be as claimed but it replaced its old screw-booster type air compressors with Shangair equipment in 2017. In October that year, a survey of the energy consumption of the whole plant found that air pressure consumption had decreased by 36.24%, compared with the same month a year earlier. The Shangair M-type air compressor frequency conversion system uses an AC/DC/AC generalpurpose inverter: the standard fixedfrequency AC power of the grid is converted into DC power through the thyristor, and then inverted into frequency-controllable AC. Variations in pressures are automatically controlled, keeping output pressure constantly around the set value and balancing air production precisely with consumption. This is of particularly significance for large compressors that supply air to a pipe network; a stable supply pressure means that product quality will also be improved. The M-type air compressor features advanced residual gas recovery and injection boosting functions, which are of particular benefit to the PET industry, especially hotfilling and blowing operations. If the user chooses the residual air recovery and then injects the boosting function, along with appropriate modifications to the blow moulding machine and mould system, the Shangair compressor can re-inject a large amount of residual air recovered from the blowing bottle, into the compressor’s third-stage. The Two new compressors in VV group headquarter New compressors in VV group Wuxi branch Shangair’s DCC app for mobile phones","@ID":34}, "imprint EDITORIAL PUBLISHER Alexander Büchler, Managing Director HEAD OFFICE heidelberg business media GmbH Bunsenstr. 14 69115 Heidelberg, Germany phone: +49 6221-65108-0 fax: +49 6221-65108-28 [email protected] EDITORIAL Kay Barton Heike Fischer Gabriele Kosmehl Michael Maruschke Ruari McCallion Waldemar Schmitke Anthony Withers WikiPETia.info [email protected] MEDIA CONSULTANTS Martina Hirschmann [email protected] Johann Lange-Brock [email protected] phone: +49 6221-65108-0 fax: +49 6221-65108-28 LAYOUT AND PREPRESS EXPRIM Werbeagentur | exprim.de Matthias Gaumann READER SERVICES Till Kretner [email protected] PRINT Chroma Druck & Verlag GmbH Werkstr. 25 67354 Römerberg Germany WWW www.hbmedia.net | petpla.net PETplanet Insider ISSN 1438-9459 is published 10 times a year. This publication is sent to qualified subscribers (1-year subscription 149 EUR, 2-year subscription 289 EUR, Young professionals’ subscription 99 EUR. Magazines will be dispatched to you by airmail). Not to be reproduced in any form without permission from the publisher. Note: The fact that product names may not be identified as trademarks is not an indication that such names are not registered trademarks. 3 PETplanet Insider Vol. 20 No. 05/19 petpla.net Compressors and stretch blow moulding systems are two things that go hand in hand in the world of PET. However, an independent sector has developed just for PET compressors. These are still bought-in parts for complete system providers and filling operations. These bought-in parts have been treated as a secondary consideration for many years. It was only when the first lightweight water bottles came onto the market that the efficiency of compressors came into focus. Competition to build the most efficient compressors erupted and remains strong to this day. Each manufacturer uses his own measurement methods and in 20 years of PETplanet, we have never managed to make direct comparisons. Meanwhile, information has become more harmonised but the devil is in the detail. Much has happened, particularly on the stretch blow moulding machinery side, that makes comparing efficiency quite difficult on paper. SBM no longer just runs uniformly; high product variety requires retooling times without compressed air consumption. Systems require high pressures for classic bottles and low pressure for lightweight bottles. The modern compressor is therefore flexible and within certain parameters can be adapted to fluctuating compressed air requirements by controlling the speed. Join us from page 18 on a tour through 20 years of compressor history. Yours Gabriele Kosmehl Dear readers,","@ID":5}, "39 TRADE SHOW PREVIEW PETplanet Insider Vol. 20 No. 05/19 petpla.net Zero cooling Japanese company Nissei ASB Machine Co Ltd (ASB) will be exhibiting for the first time at Chinaplas its new and innovative Zero Cooling technology, which was announced in 2018. The company says that developments introduced in this new series enable significantly faster moulding cycles, along with improved product quality. The reduced injection cycle times are made possible by ASB’s proprietary fourstation, one-step moulding methodology, which allows virtually all preform cooling to be moved away from the injection station and into the second, conditioning station. The Zero Cooling moulding method eliminates any need for thin, non-optimised preforms, which are susceptible to several quality related problems such as “fisheye”, “body ring” and “orange peel”. This means that designers can create shorter preform designs with thicker wall sections, thus enabling the optimisation of stretch ratios, improved quality and increased productivity. ASB says that there is no need to conform to the traditional need to compromise between cycle time and container quality. The new, advanced cooling method also permits moulding of heavyweight premium cosmetic containers in very short cycle times, without haziness, using standard PET grades. The latest version of the mid-range ASB-70DPH one-step injection stretch blow-moulding machine will be demonstrated for the first time. Regular technology updates have kept it at the forefront of its class, in terms of efficiency and productivity. The version being shown at Chinaplas, a pre-production model of the next generation, will showcase a range of updates and options that improve flexibility and productivity, especially for smaller containers. Among the improvements are: a revised clamping hydraulic circuit; adjustable stroke in all clamping stations; and adjustable daylight, which allows for longer preforms. A fully-revised blow station is claimed to cut index time, simplify mould changeover and reduce maintenance. The new model is compatible with existing ASB-70DPH moulds. ASB says that these features cut indexing time 40%. A 30ml container using a short preform can be moulded up to 2.2 seconds faster; this is in addition to reduced cycle time obtained from the use of Zero Cooling technology. The new technologies will be joined on ASB’s stand by a range of sample packaging technologies and a full line of ancillary equipment. www.nisseiasb.co.jp Agr’s patented control technology precisely manages material distribution in PET containers to produce more consistent NISSEI ASB Hall 11.1 Booth R21 Multilayer co-injection solution GDXL Precise Machinery Co., Ltd.’s multilayer co-injection solution allows a gradual colour change along the preform, enriching the possibilities for product designs. The solution can be achieved by modifying an existing injection equipment into a co-injection system to achieve multilayer manufacturing. It enhances the insulation of containers and extends their durability to the maximum extent (about 200% of those packed in monolayer containers). This technology is applicable to the packaging markets of beverage, food, cosmetics, and even pharmaceutical products. www.gdxl.com GDXL Hall 9.1 Booth J01","@ID":41}, "COMPRESSORS PETplanet Insider Vol. 20 No. 05/19 petpla.net 35 Ingersoll Rand has identified additional energy savings opportunities through the implementation of ‘system level controls’. This is an important component of any system including multiple high pressure air compressors. Unmanaged systems are inherently inefficient as air compressors operate independently and often ‘against’ one another. System level controls provide intelligent load sharing in multi-compressor environments including systems featuring machines of different sizes, compression technologies, and control methodologies. By utilising system level controls, customers can optimise the efficiency of the ‘supply side’ (compressed air equipment) of the system to match the ‘demand side’ (blow moulding operations) load profile. Energy savings within a typical high-pressure compressed air system can easily exceed 10 % when system level controls are implemented. Rugged reliability With customers focused on increased uptime availability and with fewer systems designed to include installed redundancy, reliability by design has become paramount. The conservative design of the PET*Star technology delivers reliability, as Ingersoll Rand states. Design features that illustrate the conservative design approach include the following: Low air compressor operating speeds (RPM) - results in reduced wear of piston rings, rider bands, and packing materials as well as fewer open/close cycles on compressor suction and discharge valves. Rugged frame and running gear co-developed with Dresser Industries – design includes a unique single piece 4-Throw crankshaft as part of an ‘H’ cylinder arrangement configuration, an additional outboard bearing to bolster crankshaft support, and an auxiliary oil pump to ensure continuous running gear lubrication. Premium suction and discharge valve technologies – carefully selected valve designs inclusive of PEEK composite materials to ensure extended run life (24,000 hours of operation) between required rebuilds. Conservative drive motor configuration – slow speed (1,200RPM) duty rated motor selection ensures peak horsepower requirement is below nameplate rating and that motor never operates in the service factor. All motors feature TEFC enclosures. Comprehensive service plans In order to achieve maximum compressor availability and minimise downtime (scheduled and unplanned), customers are increasingly interested in comprehensive service plans to complement the compressor design reliability. This has become even more important as customers today are less likely to have in-house maintenance resources that are capable and/or comfortable working on high-pressure compressed air systems. In response to this need, Ingersoll Rand developed their PackageCare program to provide proactive service intervention and leverage predictive and analytical tools to help prevent unexpected interruptions. PackageCare delivers cost certainty and risk transfer while driving maximum asset availability. Remote monitoring Ingersoll Rand anticipates that the trend toward asset availability will result in customer expectations for uptime availability guarantees. To that end, the company is developing and implementing remote monitoring functionality on the PET*Star that facilitates real-time asset health assessment and predictive analytics to support rapid troubleshooting and to determine appropriate service interventions. As the remote monitoring program evolves, they expect to acquire machine learnings that enable them to understand the correlation of particular data to potential failures better and to improve the predictive service execution so that strenuous uptime availability expectations can be met. www.ingersollrand.com","@ID":37}, "COMPRESSORS PETplanet Insider Vol. 20 No. 05/19 petpla.net 31 Nanjing Shangair Machinery Manufacturing Co., Ltd. is dedicated to developing advanced, effective and productive air compressors, with a particular focus on improvements in energy consumption. It describes itself as a high-tech enterprise that develops, manufactures and sells Shangair brand piston air compressors. It has more than 20 years of experience in blow moulding machinery and air source leak detection. It holds a number of patents in its areas of operations. The company designed and developed the “intelligent” horizontal symmetric balanced PET air compressors, which it says fill a gap for Chinese-origin, high-performance air compressors dedicated to PET blow moulding. The company has sold products to more than 60 countries and regions. It has provided systems and equipment to a range of beverage manufacturers in China, including Mengniu Dairy, Anhui Yingjia, Guangxi Shibu Dairy and VV Group. China’s only award-winning compressor design Shangair’s M-type symmetric balanced water-cooled oil-free air compressor is claimed to consume up to one-third less energy than traditional angle-type oil-free compressors, and 5-10% less than European and American equivalents. It is the only air compressor product to have won the China Industrial Design Award. Traditional design The company states that traditional L-type machines can have a number of disadvantages, which the M-type is designed to overcome, and continues that L-type compressors can suffer from strong vibration, and be very noisy. Even when equipped with variable speed drives (VSDs), it can be hard to operate them in an energy-efficient way. High failure rates and a short maintenance cycle, which interferes with production and leads to financial underperformance, can also be an issue. According to Shangair Machinery, these issues appear to be quite common in the L-type design, which features a vertical first-stage cylinder, with horizontal cylinders in the second and third stages. This means that inertial forces are difficult to balance and lead to vibration and associated noise. When unbalanced, the design limits maximum speed and normal lubrication processes so that speed cannot get too low, which makes the speed range narrow. Even a VSD controller could then be unable to achieve any energy saving. Better by design Shangair claims that its M-type design overcomes these problems. In its design, the crankshaft crankpin has an angle of 180°, and the corresponding pair of crankpins sit at 90°. The dynamic balance design make the first-order and second-order inertial forces of each column completely balanced. The resultant force is zero, which means that the M-type compressor has very little vibration in operation. The first-stage suction port is equipped with patented suction buffer tank and suction noise filter technologies, which greatly reduce low-frequency noise, keeping them below 85 decibels. The equal-pressure ratio fourstage compression design is stated to help the M-type compressor to be more energy-efficient. This, along with its structural stability, enables it to achieve higher rotational speed. A wider speed range means that the VSD can deliver real energy savings. In daily use, M-type can be more than 15% energy-efficient than L-type compressors. Nanjing Shangair Machinery Manufacturing changes the shape of air compressors in China Award-winning design Among the biggest challenges for beverage manufacturers to overcome are: reliable operation of production lines, with no breakdowns or unscheduled stoppages, and energy consumption. Compressed air is an essential element in manufacturing, production of PET bottles in particular. Air compressors have long been known to be significant consumers of energy and they are a focal point in operations; and their reliability is critical. If they fail, the consequences – such as delivery failures and quality problems – can be very significant and expensive. Hall 9.2 booth K71 COMPRESSORS M-type balanced structure Shangair’s M-type compressors for Anhui Yingjia Old screw-booster compressor of Anhui Yingjia","@ID":33}]}}
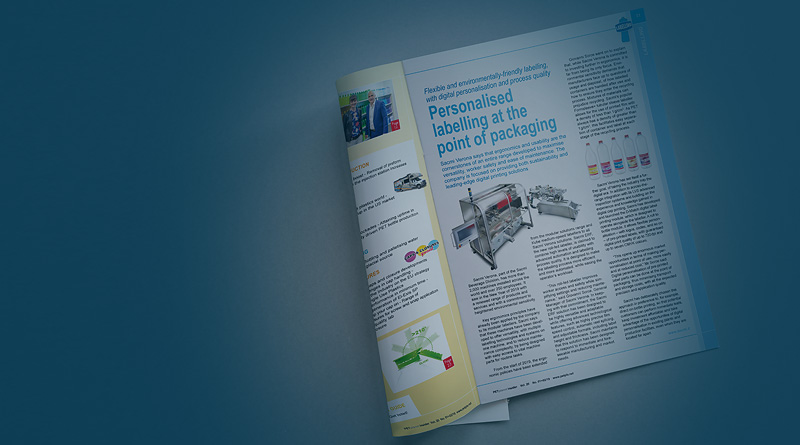