"PREFORM PRODUCTION PETplanet Insider Vol. 19 No. 09/19 petpla.net 48 Niigon PET preform machines Prepared for the future Tour Sponsors: F.l.t.r. Rob Sicilia, Niigon VP PET Preforms and Harold Luttmann, Niigon CEO In the last part of our North American Road Show the way led us to good friends. At Niigon (formerly Athena) in Ontario we were warmly welcomed by Harold Luttmann, CEO Niigon, and Rob Sicilia, VP PET preforms. Niigon is an Aboriginal word meaning ‘for the future’. Robert Schad chose this name to emphasise that this company is prepared for the future. We were very impressed with the new 155,000 square foot production hall. The plant was opened in 2016 and provides an energy efficient and automated infrastructure. It features geothermal heating and cooling, daylight harvesting LED lighting, automated high density part storage and state of the art inspection equipment. “In 2010 we started to build rugged two platen injection moulding machines with two models, 150 t and 300 t,” explained Harold. “Preengineered options for stack and cube, two colour, unscrewing and PET provided proven performance and fast delivery for a wide range of applications. All machines come with a five year warranty. In 2017 we extended the product line with our first 500 t machine.” At the time of our visit there were three stack machines on the production floor, each with two injection units, one at each end. “For PET preform applications, you can run two standard 96 cavity moulds in a 300 t stack machine” said Rob. “The two moulds can run different preforms, in different colours, at the same cycle at the same time. It is very flexible. You can shut one mould down and service it while the other mould is running.” At the far end of the production hall is the Lightsout operation. Here two PET systems run production for Canadian customers. A 150 t machine runs four different 24 cavity moulds all with a 38mm finish for Salbro, a food and beverage packaging company. The 300 t machine operates a 72 cavity 16g preform. “The Lightsout program enables us to run fully equipped production preform systems unattended to monitor and improve our designs to ensure we can provide our PET customers the lowest cost of ownership” explained Rob. “The energy consumption of our 150 t 24 cavity machine, robot, conveyors and dehumidifier today is 0.204Kwh/kg. The 300 t 72 cavity uses 0.189Kwh/kg. We are constantly looking at ways to reduce this even further.” Other development projects include one hour mould change time, a 50% reduction in cooling water flow and automated mould vent cleaning. Both of these PET systems use Yudo moulds. These moulds incorporate Yudo’s latest developments include diffusion bonded stack components incorporating conformal cooling to improve cycle time and preform dimensional accuracy. In the hot runner, diffusion bonding technology has shown significant reductions in cavity-to-cavity weight variations, pressure drop and AA. “PET is the fastest growing segment of our business“ says Harold. “We welcome anyone in the PET preform business to visit Niigon and see these systems in operation for yourself.” www.niigonmachines.com www.yudo.com","@ID":50}, "MATERIALS / RECYCLING PETplanet Insider Vol. 19 No. 09/19 petpla.net 33 MATERIALS / RECYCLING 33 the DAK Americas Group, as we reported in the same issue. The special iPET architecture simplifies and eliminates several production stages in the manufacture of PET resin, such as omitting solids polymerisation. Annual sales back then were 540 kt. At Fakuma, Finke presented its granulated masterbatches and pigment powders, liquid dyes and colouring pastes. The masterbatches can be tailored according to customers’ requirements and include i.e. UV protection. 2016 In issue 3 we reported about the EcoSphere technology from Polymetrix. Among the key features of this bottle grade virin PET production is the link between melt phase and solid phase polymerisation which allows the recovery of energy. In Issue 5 we celebrated 75 years of PET. Invented in 1941, it took until 1977 until the first commercially available bottles were available on the market. Also in issue 5 we reported about Chemco Plastics whom we visited in Mumbai. As one of the biggest converters in India, back then, 200-220 t of material were processed every day. A series of additives able to correct the shade and to improve IV parameters of rPET were being introduced by Repi (issue 6). The degree of yellowness of rPET can be decreased by using suitable storage conditions, as Plastic Technologies Inc (PTI) showed also in issue 6. Issue 9 saw the Editour report of Far Eastern Industries, China. With 1.3 million tonnes worldwide, it occupied the fifth place among PET bottle grade manufacturers. The portfolio was partly made up of faster reheat resin which saves up to 20% energy when heating up. Also in the context of the China Road Show we learned about colourants for CSD or water PET bottles when visiting Holland Colours in Shanghai (issue 9). Introduced at K was the new alternative to amorphous PET pellets, called PET CrystalBatch. In a new process developed by cpc, the material is directly post-crystallised and thereby subjected to less thermal stress, retaining its cylindrical shape. The Melt to Resin (MTR) technology by Uhde InventaFischer is an integrated one-step process, providing bottle grade IV PET melt directly from the Discage reactor. In issue 10 we compared several aspects with those of SSP. Karl Finke GmbH was presenting a range of colourings with a focus on effect pigments and new additives for irreversible laser marking. During K 2016, Polyone unveiled colour concentrates to enhance PET packaging with an ultra-glossy metallic effect – processable on standard injection stretch blow moulding machinery (issue 12).","@ID":35}, "EDITOUR PETplanet Insider Vol. 19 No. 09/19 petpla.net 16 Upward trends and opportunities for PET Returning briefly to the milk market, material manufacturer Reliance Industries says that PET packaging used for milk and dairy products, including ghee (which is packaged in PET jars) currently accounts for around 1.2-1.5 % of all PET used in India; this figure is expected to grow by 10% annually. If one considers the huge share that pouches have in this segment – around 29 billion units sold in 20181 and with average growth of over 5% total consumption. Approximately 6% of PET resin in India is used in APET sheet, strapping, injection moulding, monofilaments and masterbatches. The current installed capacity for material production is 2 million tonnes per year. The biggest private company in the country, Reliance Industries, manufactures 1 million tonnes, while IVL Dhunseri Petrochem Industries, the local base of Indorama Thailand, makes approximately 700,000 tonnes. Another 150,000 tonnes of PET are imported, mainly from China. Both Reliance and IVL Dhunseri plan to counter import levels with growth. The industry is expecting a steady rate of PET growth of 8-10%, with the growth market of eastern India expected to grow by as much as 15-20% as stated by visited companies such as e.g. Epitome and Indoplast from West Bengal state. According to Reliance, between 2018 and 2019 the magic threshold of one million tonnes of PET consumption in India was breached; the domestic market in India reported a growth rate of 13% in 2019 (financial year ending March 2019), compared with the previous year. 1 Figures by Market Research Company Euromonitor International since 20161, it becomes clear that we are looking at a correspondingly large potential for PET, one that is yet to be tapped. Although single-serve, PETpackaged milk products have been established on retail shelves for some time, sales volume figures have not yet been independently audited by the well-known research companies, due to a lack of volume. The “PET-packaged milk” description includes fresh, flavoured and UHT. In the non-bottle applications of PET, APET (amorphous PET) lids are being used selectively for some ice cream brands, as its embrittlement temperature is the lower than other polyolefins and styrenics that have been used. The proportion of PET in beverage packaging for water, CSDs, fruit juices, alcoholic beverages, hot beverages and syrups as measured by retail sales was 46% in 20181, more than 15% higher than the figure for 20171. The strongest growth in the sector was recorded by water, with almost 20%1. In a direct comparison with total PET consumption, the beverage packaging component accounts for an estimated 50%. This includes water, CSD and fruit juices. The majority of the preforms and bottles manufactured on the market, approximately 60%, are now lightweight. In non-food areas, such as personal care and health care, we can also assume that PET accounts for some 15-20% of Retail units (Source: Market Research Company Euromonitor International)","@ID":18}, "PETplanet Insider Vol. 19 No. 09/19 petpla.net 51 OPEN HOUSE PET bottle-to-bottle recycling the focus of attention at Sipa Open House Circular economy in action At an Open House in Vittorio Veneto, Italy, Sipa and its partner Erema demonstrated how their co-developed Xtreme Renew technology converts post-consumer PET bottle scrap into food-grade preforms and bottles with excellent properties and colour. A unique example of closed plastic loop. “Xtreme Renew is the first system in the world to produce food-grade preforms from 100% washed post-consumer recycled PET – rPET – flakes in a single thermal cycle,” says Gianfranco Zoppas, Chairman of Sipa parent company Zoppas Industries. “It is both costeffective and highly energy-efficient.” When PET bottle preforms are produced from recycled material using previously developed rPET processes, the amount of carbon dioxide created is already 60% lower than when using virgin PET. With Xtreme Renew, these emissions are cut by an additional 25%, and 30% less electricity is consumed, thanks to the integration of the various phases of the complete process into a single plant, states the company. Erema technology incorporated into Xtreme Renew converts conventional washed bottle flakes into decontaminated PET food-grade melt with an increased viscosity (IV). The melt is then immediately fed to the Sipa section of the plant, which creates preforms using the new injection-compression moulding technology. Because the recyclate is put through a single thermal cycle, the overall quality of the preforms is higher than with other systems in which the recyclate is granulated and then re-melted. This is most evident in terms of aesthetics: the preforms are less yellow and more transparent. Preforms produced using Xtreme Renew are up to 10% lighter than traditional injection-moulded preforms. According to the company, Xtreme Renew can also reduce logistics and transportation costs by 20% and the Total Cost of Ownership by 15%. Sipa also offers the option of directly connecting Xtreme Renew to its stretchblow moulding equipment for production of finished bottles – several months ago, the company unveiled a new generation of very high-speed rotary SBM equipment called Xtra – as well as filling lines, which it also manufactures in various versions according to the type of beverage to be bottled. “I believe it is vital that a circular economy is implemented as quickly as possible, or our industry risks becoming a victim of its own success,” Zoppas says. “Without it, the levels of plastics packaging re-use will not be enough for a fully sustainable packaging sector. I hope and trust that our actions will provide an important boost in making PET packaging sufficiently sustainable for its future success.” Xtreme Renew technology found its first commercial application late last year: Erema and Sipa collaborated with two Japanese partners – Kyoei Industry (a major recycling company) and Suntory (one of the largest beverage producers in the world) on an installation in Kasama in Japan. The system can produce over 300 million rPET containers per year. The Japanese companies have already ordered the second Xtreme Renew line. www.sipa.it www.erema.com Xtreme Renew processes washed flakes to food-grade preforms in a single cycle. Gianfranco Zoppas, owner and founder of Sipa during the Open House From 100% flakes to food-grade bottles","@ID":53}, "MATERIALS / RECYCLING PETplanet Insider Vol. 19 No. 09/19 petpla.net 42 Time to increase the rPET content The chemical industry must play a key and decisive role in the plastics recycling revolution, states Sukano. With the expertise it has at its disposal, the Swiss company says it can support efforts to deliver innovative and collaborative products and services for the concept of circular economy. Sukano is launching a global campaign to lead the #wearepartofthesolution platform to deliver improved social standards demanded by consumers and society, by proven scientific performance and technology. Recovering original PET properties After collection, post-consumer PET is purchased by reclaimers who wash, grind and further process PET containers to produce a recycled resin ready for reuse in a variety of end products. For a long time, the reuse of PET was limited to applications like fibres, because the process of recycling shortens polymer chains and makes processing more difficult for production of high-quality packaging or bottles. Sukano Melt Enhancer Masterbatches are designed to enable upcycling instead of just recycling. The solution ensures uniform cell structure, improving mechanical performance and processing stability enabling recycled PET use in bottles or trays packaging. As different end applications require different product performances – and processing technology is not uniform – company specialists are available to help develop the most accurate and appropriate reactive chemistry for customers’ needs. Increasing rPET content As demand for rPET grows, bale quality is decreasing. The lack of bale standardisation also does not help and brand owners have set up their own individual corporate goals for recycling content, providing convertors and the plastics value chain with an additional challenge. Sukano’s masterbatches, such as Anti-Yellowing Masterbatches, neutralise the visual effects of heat history and impurities from contaminated, low quality bales and recycled PET, improving optical clarity and appearance. Impact Modifier Masterbatches enable producers to include a higher dosage of rPET in the core layer of the end application, while maintaining or improving cost base and film performance. MATERIALS The circular economy operates system-wide to redefine products and services, to design out waste and pollution, keep products and materials in use longer, and regenerate natural systems. Plastics recycling and energy recovery account for over 70% of post-consumer plastic treatment in the EU; since 2006, the EU as a whole has managed to reduce landfilling by more than half, while nearly doubling recycling. As far as PET is concerned, there is a growing trend in the collection of PET materials for specific recycling activities. Sukano states that nonetheless, more work must be done. Besides separate collection and proper sorting various, design for recycling is a must for the company.","@ID":44}, "7 NEWS PETplanet Insider Vol. 19 No. 09/19 petpla.net New leadership team for Messe Muenchen Shanghai A fresh start for Messe Muenchen Shanghai Co., Ltd.: Xu Jia is to be the new Chief Executive Officer (CEO) and General Manager of Messe Muenchen Shanghai. Together with Deputy General Manager Stephen Lu as Chief Operating Officer (COO) and Deputy General Manager Candace Hua as Chief Financial Officer (CFO), Xu Jia will form the Management Board of Messe Muenchen Shanghai, responsible for the organisation and execution of trade fairs in China. Beyond their functional roles, all of the management board members will be in charge of operational business areas. Xu will be responsible for the capital goods trade fairs. She has more than ten years of experience in the Chinese trade fair business. Among various roles, Xu was the Group Project Director and Deputy Managing Director of Messe Muenchen Shanghai. She has been Chief Operating Officer (COO) for Messe Muenchen Shanghai since 2013. As the new COO, Lu will be responsible for new technologies, product marketing and communication, business development and M&A, as well as collaboration with IMAG. Until recently he was the Group Project Director of Messe Muenchen Shanghai. Hua will start as Chief Financial Officer (CFO) at Messe Muenchen Shanghai on October 1. She is an internationally well-rounded manager with previous experience as CFO in China and France. Most recently, the U.S. American was the Financial Director for Risk, Compliance & Commercial Lending for the Boston-based technology company FIS (previously known as Sunguard). She brings with her a wealth of commercial know-how, which will strengthen the further growth of Messe Muenchen Shanghai. www.messe-muenchen.de Reliable high quality in plastic recycling thanks to HERBOLD Meckesheim’s modern washing systems www.herbold.com The increasing amount of plastic waste worldwide, along with legally stipulated recycling quotas, is making great GHPDQGV RI WKH LQGXVWU\\ (I¿FLHQW technical solutions are therefore needed. The quality of the recyclate produced must be just right, so that it can be used in as many branches of industry as possible. HERBOLD has improved all process stages: Visit us at the K 2019 trade fair in Düsseldorf Hall 09, Stand 9B42 Pre-crushing The new EWS 60/210 shredder has been designed for both dry and wet operation, and delights thanks to its high capacity and maintenance-friendly design. The pre-wash unit helps protect the subsequent machines and provides capacity for more material. Hydrocyclone separation stage: HERBOLD has optimised density separation in the hydrocyclone stage over the course of many years. Hydrocyclones achieve significantly better separation results than float/sink tanks. Hot washing (optional) With optimised temperatures and dwell times, and with the use of suitable cleaning agents, hot washing achieves better cleaning results compared to pure cold washing. HERBOLD has refined this process step, which has long been standard for recycling PET bottles, for use with PO film. The combination of hydrocyclone separation and hot washing forms the basis for quality levels never achieved before. Candace Hua Xu Jia Stephen Lu","@ID":9}, "PETplanet Insider Vol. 19 No. 09/19 petpla.net 62 PETbottles Beverage + Liquid Food Rice syrup in upturnable bottle German discount retailer Aldi Süd had two naturally based sweeteners available in a sales promotion: rice and date syrup. The viscous organic products were available in 250ml/350 g transparent dispenser bottles. These were designed as transparent upturnable bottles with hinged cap seals and silicone valves. When first opening the lid, the original seal connecting the lid and lower part of the cap was changed irreversibly and came away from the bottle. www.aldi-sued.de Red Miso Soup in PET Under the brand name “Organic Ville”, American company Sky Valley is selling 345 g of gluten-free soup concentrate for making red miso soup. The concentrate enables up to 19 soups to be prepared or the product can be used for marinating or giving meals a special finish. It is packaged in a clear bottle with a hinged cap and a tamper-evident seal. The label is designed appropriately for the soup and has a perforation for removing the label from the bottle. An integrated viewing window with a scale makes portioning easier. www.innit.com","@ID":64}, "EDITOUR PETplanet Insider Vol. 19 No. 09/19 petpla.net 25 and rightly so, considering the opportunities and possibilities in this huge country, whose efforts in recycling and sustainability of packaging waste are pretty much in their infancy. “I am convinced that the victory procession of recycled PET can only be guaranteed by a law that obliges manufacturers to use a specific share of rPET in their products. The money is there; you could even say that it’s the rubbish (actually money) on the streets,” he said, emphatically. “Also, over the coming years, continuing high demand seems set to increase the price of rPET, which means we need to think about ways to recycle and use existing materials sensibly, with technology and legislation being required that allow the use of rPET. Creative is at the forefront of this innovation and I am excited to see where we can take this technology in the next five years. Our ultimate mission is to ensure that we leave a better world for our children than the one we found.” he concluded. www.creativeplasticindia.com Creative Plastic’s entrance area with (f.r.t.l.) Surendra Agarwal and Kay Barton","@ID":27}, "BEVERAGE INGREDIENTS PETplanet Insider Vol. 19 No. 09/19 petpla.net 26 “Naturalness”, healthy added value and unique taste experiences Beverage trends in India Exotic or traditional: New taste sensations While the classic cola, citrus, lemon-lime, mango, mixed fruit and apple beverage flavours continue to be the most popular and dominant in the Indian market, curiosity for “something different” is starting to make an impact. Regional flavours, in particular, are on the rise; they enjoy high consumer recognition and reflect the Indian tradition and lifestyle, “with every sip”. Doehler, the global producer, marketer and supplier of technologydriven natural ingredients, systems and integrated solutions for the food and beverage industry, offers both classic nectars and juices featuring popular flavours, along with a new range of typically Indian fruit flavours, such as falsa and bael or sugarcane, to reflect regional taste preferences. Simple and tasty: Nature at its best The trend for natural food and beverages is growing worldwide and extends across all food and beverage categories. It is therefore no surprise that fruit juices are more popular than ever and that they and juice drinks are increasingly recognised as a convenient lifestyle product, one that supports a balanced diet, even “on the go”. As well as classic fruit juices and nectars, more and more consumers are looking for exciting concepts that provide authentic taste and healthy added value. Doehler is tapping this trend by developing innovative solutions with premium quality NFC (Not From Concentrate) juices that deliver naturally fresh tastes and provide inspiration for healthy and fashionable product positioning. One of the hottest trends is for cold-pressed, non-heated NFC juices, produced using state-of-the-art gentle processing methods. This preserves the best nature has to offer, from the fresh taste of the fruits and vegetables to their valuable ingredients. Fruits are the classic basis but NFC juices with fresh vegetable ingredients such as beetroot, carrot and mixed vegetable are also becoming more popular. They may be the next healthy beverage trend in India, because of their delicious flavour and vitamin content. Doehler, which has its own fruit and vegetable processing at the point of origin and state-of-the-art blending facilities worldwide, offers a diverse range of high-quality raw juices for different product concepts. Another emerging ‘natural’ trend is for malt beverages. These sweet and non-alcoholic alternatives to beer, which have a long history in the Middle East especially, are also becoming visible on the Indian market. Doehler’s range of malt beverages is designed to meet the demands of target groups looking for novel sensory experiences; the young, particularly. The natural raw material provides a range of B vitamins, key minerals and trace elements and are thus a base with a positive image as a natural source of energy, while containing nutritional elements. Flavours such as mango and mixtures featuring strawberry and lime offer modern positioning opportunities. ‘Natural’ meets healthy nutritional value Today’s consumers are increasingly health-conscious. They believe that quality of life is as important as longevity and they are prepared to invest time and money to achieve both. Health has become one of the most important mega trends in India. Increasing numbers of people in India are striving to pursue a healthier and more natural lifestyle. As well as the overall multi-sensory impression, a product’s healthy nutritional values and the sources of its ingredients also need to impress the customer. Doehler’s research and development process embraces both aspects while ensuring that the product contributes to a healthy diet. Michaela Schmidt-Meier / pixelio.de","@ID":28}, "59 TRADE SHOW PREVIEW PETplanet Insider Vol. 19 No. 09/19 petpla.net Milacron launching new and upgraded Mold-Masters Solutions Milacron will be displaying its Advanced Plastics Processing Technologies (APPT) featuring Milacron and Ferromatik product branded injection, and extrusion offerings, as well as Milacron’s Melt Delivery and Control Systems (MDCS). Displays will feature Milacron’s product brands: Mold-Masters, DME, Tirad, and CimCool. Milacron will present its ThinPak-Series, a Hot Runner system for thin wall is specifically engineered for producing exceptionally high-quality thin wall packaging products and offering a wide process window. Incorporating new MasterShield technology, ThinPak-Series has the strength and durability to mould with complete reliability in high-pressure applications up to 2,800bar. ThinPak-Series is compatible with all common packaging resins. Its new Centi Nozzle Size broadens ThinPak’s part weight application capacity and includes everything from small in-mould labelled containers to large pails. Milacron says that the stack mould capabilities increases productivity and profitability. Mold-Masters Co-Injection, formerly Kortec will also be on display at K-Show. Mold-Masters Co-Injection Technology is used for placing barrier layers in a wide range of parts including coffee capsules, beverage containers of all kinds, preforms and more in a single step. These high-performance barriers extend shelf life by up to five times, lower production costs and offer greater design flexibility. The Mold-Masters Co-Injection Connect unit on display allows moulders to quickly and easily convert their existing single-shot injection machine to allow for co-injection capabilities. The simplest package Milacron offers includes a Mold-Masters Co-Injection hot half, E-Multi Auxiliary Injection Unit and E-Multi Co-Injection Controller. This package has the potential to reduce capital investment requirements by up to 84% says Milacron. www.milacron.com www.sacmi.com Product design Product development Product validation Industrial production plant Process & quality control On-site and start-up assistance After-sales and Customer service SACMI 4.0 THE COMPLETE CLOSURE, PREFORM AND CONTAINER SOLUTION FOR YOUR SMART FACTORY 30 years of putting things together perfectly to create ƤVWX GPEWW TVSHYGXW les 4 With 30 years of experience and 15,000 stacks a year, SACMI is the world’s biggest producer of moulds for the beverage industry. Product design, mould development and direct testing on SACMI machines ensure an all-round service of unrivalled quality. Hall 1 Milacron Booth C05","@ID":61}, "MATERIALS / RECYCLING PETplanet Insider Vol. 19 No. 09/19 petpla.net 28 PET - A review of material developments A desire for a plastics-free world has been identified by market research company Euromonitor as one of the top ten global consumer trends of 2019. In relation to PET however, the facts tell a different story: around 80% of the PET resin market still goes into more than 500 billion bottles worldwide annually, and PET remains the beverage packaging material with the strongest growth rates and prospects. And this is with good reason. Alongside advantages like rupture safety, resealability and recyclability, the life cycle assessment of PET bottles can be impressive. Following our reviews of the achievements in stretch blow moulding and filling (issue 3/2019), recycling (4/2019) and bottle making (issue 6/2019), we will now take a closer look at developments on the materials side. Like most polyesters, PET is manufactured in a multi-stage procedure. The first step is an esterification based on the monomers purified terephthalic acid (PTA) (70%) and monoethylene glycol (MEG) (30%) at 220-260 °C. The components can also be substituted with bio-based variants, such as from sugar cane. The precondensate this creates is reconstructed through polycondensation into long-chain PET. The result is a polyester that can be used to make films and fibres. To obtain bottle grade PET, this polyester subsequently undergoes solid state polycondensation (SSP) to achieve higher molar masses. The long chains, indicated by this high molar mass, are reflected in the intrinsic velocity (IV) values, which are around +/- 0.80 for bottle grade PET. Because of the pressure, carbonated soft drinks require a high viscosity (0.80-0.88) but for still water, a lower IV value is sufficient (0.70-0.80). Alternatively, MTR technology (Melt to Resin) eliminates the step of solidstating; during melt polycondesation, by means of a special high-viscosity finishing reactor, high-molecular PET material with almost the required IV can be obtained. Co-monomers are required as catalysts for these processes and these can constitute up to 10% of the weight. Their purpose is to optimise the bottle grade PET with regard to properties like colour, melting temperature or crystallinity. 1941 to today PET can be traced back to an invention by John Rex Whinfield and James Tennant Dickson. In 1941 they applied for a patent for the “highly polymeric substance” they had developed for the textile industry in the laboratories of the English company Calico Printers Association as a cheap alternative to silk or nylon. The chemical company ICI bought the world manufacturing rights in 1947 and began full-scale commercial production in 1955 under the name “Terylene”. The PET yarn was found to be strong and moisture-resistant, and therefore became a popular fibre for use in manufacturing shirts. It took until the end of the 1970s (see PETplanet 06/2019) until its modification and use in bottle production. Since then, the material has continually been adapted to suit the requirements of the sector. There can be great differences depending on the type of product to be bottled and the processes used to do this. Still waters for example require a high level of transparency and a low proportion of acetaldehyde; sensitive beverages require an effective UV barrier; carbonated drinks require an increased gas barrier. The properties can be adapted precisely to suit the requirements profile by modifying the material or dosing tailored additives. The type of further processing must also be considered: the lower the degree of crystallinity, the less heat is necessary for melting the resin, while the higher the degree of crystallinity, the more heat is required. A reduction of crystallisation speed (achievable through co-monomers or additives) is of little significance in a single-stage process but is of much greater significance in a two-stage process where the preforms must be cooled quickly so that no crystallisation takes place. Enjoy our overview of 20 years of achievements in bottle grade PET - as reported in PETplanet Insider! MATERIALS by Gabriele Kosmehl","@ID":30}, "EDITOUR PETplanet Insider Vol. 19 No. 09/19 petpla.net 12 The average population density in India is 430 people per km2, with the distribution varying widely throughout the country. Its headcount of more than 1.3 billion is only just behind that of China – for now. Forecasts are that it could overtake China within the next two to three years, although China is now increasing, slightly, following the abolition of the one-child policy. In India, advancements in education and growing per capita income have led to a decline in the rate of growth for some years. While the population grew by 1.8% 20 years ago, today’s rate of growth is roughly 1.3%. Traditionally, the fertile regions have been populated much more densely than areas with little rainfall or parts of the Indian Himalayan region. This makes the current situation in the conurbations and metropolises far more extreme. The Dharavi district of Mumbai, for example, has one of the highest population densities in the world, with an estimated 600,000 to one million people living in an area of just two km2. However, cities only account for about one third of the total population; most still live in rural areas. India is a “young” country. The average age recorded in 2015 was 27.6 years; a third of its people are less than 15 years old. In 2018, Indian gross domestic product (GDP) was US$ 2.7 billion. Real GDP is growing, albeit at a slower pace than in the past, at around 7% a year. This makes the country one of the fastest-growing economies in the world. Inflation is 3.5 percent. Per capita income, meanwhile, is rising steadily and is expected to reach around US$ 2,200 this year. While this is more than 30% higher than 2015, it demonstrates the inequality with which India must contend. Although the country has more billionaires and millionaires than ever before, the majority of the population remains on the poverty line. The huge economic growth between 2011 and 2014 led to an even greater income disparity between the emerging middle class in the metropolitan areas and the rural population, which accounts for almost 70% of all the people but makes almost no contribution to economic growth. Although some 50% of India’s total labour force is employed in agriculture, their share of economic output is declining steadily due to a lack of income. Subsistence farming is widespread. The winner is the services sector, which contributes more than 50% of GDP but employs a relatively small proportion of the people. The majority – something like 90% of the population – has no access to health and accident insurance or to any social services. To counteract this, over the long term, the government wants to bring unskilled and low-skilled workers into work, mainly in the manufacturing industry. The extent of this mammoth project becomes clear when one takes into account the fact that just five per cent of all potential employees are qualified for any job at all. A considerable investment in the education and healthcare sector will be required in order to achieve a broad impact. A number of projects are currently up and running, including some with support from Europe. In the medium term, direct investments aim to increase the share of GDP accounted for by manufacturing industry, through the large-scale “Make in India” campaign, for example. The progressive privatisation of state-owned organisations is also driving economic growth. In the cities and conurbations, economic growth has led to considerable infrastructural challenges, for many years. The bureaucracy in India is notorious, frequently inefficient and rarely transparent, which slows business processes down. Corrup-","@ID":14}, "EDITOUR 23 PETplanet Insider Vol. 19 No. 09/19 petpla.net BOTTLE MAKING 23 Until now, it has been the injection and cooling times of preforms at the first station of the process that have determined the cycle time for single-stage machines. To reduce cycle time, past practise within the industry has been to make the preform as thin as possible resulting in an elongated design necessary to incorporate the PET mass for the bottle. This, in turn, led to low stretch ratios at stretch-blow mould resulting in less orientation. Using this new moulding method, preforms are designed much thicker and therefore shorter while cooling is virtually eliminated from the first station and now occurs at the second station in combination with preform conditioning. With the Zero Cooling system, there is ample time to cool the thicker walls of the shorter preforms, and the revised geometry provides improved stretch ratios, resulting in bottles with better orientation. Blow moulding at the third station is already shorter than the required injection time so has no influence on cycle time. The final result is an average reduction of 30% on overall cycle time. The end result: significantly shorter cycles combined with a greatly improved product. Machine testing area at ASB Thane","@ID":25}, "MARKET SURVEY 36 PETplanet Insider Vol. 20 No. 09/19 petpla.net Filling Equipment Filling Equipment Company name SMI S.p.A. KHS GmbH Newamstar Packaging Machinery Co., Ltd. Fogg Filler Postal address Telephone number Web site address Contact name Function Direct telephone number E-Mail Via Carlo Ceresa, 10, 24015 San Giovanni Bianco, Italy +39 0345 40111 www.smigroup.it Mr Pietro Volpi Marketing Dept Manager +39 0345 40316 [email protected] Juchostraße 20 44143 Dortmund, Germany +49 231 569 0 www.khs.com Mr Manfred Härtel Product Manager Filling +49 231 569 0 [email protected] East Xinjing Road, Zhangjiagang Economic & Technological Development Zone, Jiangsu 215618, P.R. China +86 512 5869 1111 www.newamstar.com +86 512 5867 3920 [email protected] 3455 John F Donnelly Dr. Holland, MI 49424 USA +1 616 786 3644 www.foggfiller.com Ms Susan Lamar Media Ralations Manager +1 616 786 3644 [email protected] 1. Machine designation / model number Blowing, filler and capping machine in Ecobloc configuration; rinser, filler and capper machine in Monobloc configuration Innofill PET DRV-VF Innofill PET NV XGF F series 2. Number of filling heads (range: from/to) 9-126 48/216 32/144 12-120 1-120 3. Min. to max. bottle contents (in liters) 0.25-10 0.1/3.0 0.1/3.0 0.25-15 0.05-5l 4. Filling speed: output (bph) (min. to max.): 1,000-68,100 Up to 82,000 Up to 82,000 1,200-81,000 specifiy: 1l bottle / still water (bph) Up to 68,100 Up to 82,000 Up to 82,000 Up to 48,000 0-60,000 1l bottle / CSD (bph) Up to 36,800 Up to 72,000 Up to 36,000 0-60,000 1l bottle / Milk (bph) Up to 36,000 Up to 50,000 Up to 36,000 0-60,000 1l bottle / Juice (bph) Up to 36,000 Up to 60,000 Up to 60,000 Up to 36,000 0-60,000 5. Filling process Pressureless (still drinks) Yes Yes Yes Yes Yes, gravity, non-contact Pressure filling (carbonated drinks) Yes Yes Yes Yes Hot filling Yes Yes Yes Yes, gravity Cold aseptic filling Yes Yes Yes Cold extended shelf life, gravity Juices with high pulp content Yes Yes Yes, gravity 6. Type of filling valve and metering system Electronic volumetric filling valves Flowmeters (metering system) Volumetric filling system; pneumatic cylinder; MID (inductive flow meter); mass-flow (Coriolis) Water valve, hot filling valve, isobaric valve, electronic valve; Flowmeter, weight liquid level inspection No metering system- gravity filling vales (to a level) 7. Special features (short description/keywords) Compact modular frame, with a wide choice of customisation options; operating and maintenance costs dramatically cut; easy and quick format changeover, with no need to replace mechanical components; high hygiene and easy maintenance and cleaning CSDwarm-filling up to 24 °C; simple filling valve; compact unit; slow & fast-filling; gentle filling with low foaming; no beverage loss during production; PTFE-sealing technology prevents aroma transfer Contact-free filling Intelligent factory management platform Rinsers, fillers, cappers, cap sorters, sanitisers, skids Company name Sidel Postal address Telephone number Web site address Contact name Function E-Mail Via La Spezia 241/A, 43126 Parma, Italy +39 0521 9991 www.sidel.com Mr Stefano Baini Filling Product Manager [email protected] 1. Machine designation / model number Sidel Matrix SF 300 FM Sidel Matrix SF 100 FM Sidel Matrix SF 700 FM Sensofill FMa / FMac 2. Number of filling heads (range: from/to) 32-216 24-120 32-108 27-150 3. Min. to max. bottle contents (in liters) 0.2-3.0 0.2-3.0 0.2-2.0 0.2-3.0 4. Filling speed: output (bph) (min. to max.): 4,000-81,000 (18°C) 5,000-81,000 6,000-60,000 6,000-60,000 specifiy: 1l bottle / still water (bph) 80,000 70,000 1l bottle / CSD (bph) 68,000 (18°C) 36,000 1l bottle / Milk (bph) 48,000 1l bottle / Juice (bph) 48,000 48,000 5. Filling process Pressureless (still drinks) Yes Yes Yes Yes Pressure filling (carbonated drinks) Yes Yes Hot filling Yes Cold aseptic filling Yes Juices with high pulp content Yes Yes Yes Yes 6. Type of filling valve and metering system Electropneumatic volumetric filler with flowmeter volume control Electropneumatic volumetric filler with flowmeter volume control, with no bottle/valve contact Electropneumatic volumetric filler with flowmeter volume control Electronic volumetric filler magnetic filling valve 7. Special features (short description/keywords) Fully automatic operating computer control, external beverage tank (no ring bowl) For mineral and demineralised water ie R.O. (Reverse Osmosis) water, fully automatic operating computer control, external beverage tank Quick changeover procedure, fully automatic operating computer control, food safety due to recirculation and CIP (Clean In Place) minimum flowrate control during operation Up to 60,000 bph (500ml bottle format), 200 production hours without cleaning/sterilisation, flexible aseptic filling for a wide range of beverages, including still water, still and carbonated drinks","@ID":38}, "EDITOUR PETplanet Insider Vol. 19 No. 09/19 petpla.net 18 From magnetic tape manufacturer to PET all-rounder Machines, moulds, preforms and containers from Mumbai The Bahubali Group, which is based in Khar West, Mumbai, is a good example of the importance of diversity in India. Initially operating in a completely different business division, in the early 2000s, the company’s “Bahubali PET” division turned its focus onto PET processing, and the construction of machines and moulds. In addition to its own PET products, equipment manufacturing has contributed significantly to the company’s current success. It is planning to expand its machine segment in a progressive, incremental way. We talked to Director Sangeet Jain about current and future developments. We met: Mr Sangeet Jain, Director Since its foundation in 1990, the Bahubali Group has been active in a variety of segments, including agriculture; processing of marble; and hotel management. It has always focused on the manufacturing and processing of products, not least because of the technical background and expertise of the company’s management team, which consists of three members of the Jain family, who also own the company. “In the 1990s, we were one of the leading manufacturers of magnetic tape in India. When the PET trend gradually reached the country, in 2002, we decided to enter the production of PET preforms and PET moulds,” explained Sangeet Jain. “The logical next step was to add the production of PET bottles. In 2003, we started to develop and build automatic blow moulding machines on a large scale. We now have a good position in the market, particularly with these machines.” Bahubali’s business model employs its own distribution network; it does not use distributors. Countrywide, there are 200 employees in the Bahubali team and sales offices in Mumbai, Delhi and Ajmer. Amjer, situated in Rajasthan, is also home to its plastics processing operations; all products are manufactured in-house. Some 12 production lines are installed here, ten for preforms, with neck sizes of 19mm to 120mm and grammage of 7g to 140g representing 40% of output (600 million units per year). Twenty per cent of total output is accounted for by the production of 40 million bottles, in sizes ranging from 10ml to 10 l. In terms of machine and equipment, according to the company’s figures, it has so far manufactured approximately 200 machines and 1,500 blow moulds, with 250 machines and 300 moulds now being added every year. The product range also includes 32-cavity injection moulds; so far, Bahubali has 120 units in the market, with 20 being built this year. In total, machinery and moulds account for 35% of the business. Turnover in 2018 was estimated at USD14 million. “We are in direct competition with Sunpet and Pearl PET,” Mr Jain said. “As our auto blow moulding machines business thrives, in the future, we are planning to increase our investments in this area for new equipment and moulds.” www.bahubaligroup.com Tour Sponsors: Director Sangeet Jain at his desk Production hall with Ferromatik Milacron injection moulding equipment","@ID":20}, "EDITOUR PETplanet Insider Vol. 19 No. 09/19 petpla.net 15 EDITOUR 15 erages, the following years saw the well-known brands joined by carbonated and non-carbonated beverages from manufacturers such as Parle Agro, Dabur, Bisleri and Coca-Cola, for example. They frequently have a higher fruit content than the required 5% – and the demand is rising. Tax incentives for these beverages and education and awareness campaigns for a more health-conscious diet are driving the trend forwards. Also CocaCola recently launched three new varieties of its long-running Minute Maid, to which minerals and vitamins have been added. In 2019, according to research company Statista, the revenue in soft drinks in India amounts to US$4.3 billion and the annual market growth could amount to 8.1%. Things are also happening with dairy products. The packaging market for milk, which is still dominated by pouches, has grown strongly in recent years in the single-serve segment, where the bottlers rely on PET packaging. What started with flavoured milk drinks from Amul, the biggest milk processor, is paving the way for a wide range of dairy products from different manufacturers. In addition to flavoured drinks, fresh and UHT milk, as well as chaas and lassis are also included. Today, fresh milk in India, including A2 type milk, is being packaged in PET bottles. It typically has a shelf life of 4-7 days, depending on the packaging conditions. The famous ‘Pride of Cows’ milk is packaged in 1 litre PET bottles and has a shelf life of one week. Of course, fresh milk packaged in PET has to be transported and stored in refrigerated conditions. It is interesting to note that, today, chaas and lassi packaged in PET each have shelf lifes of 15 days, in refrigerated conditions. While the beverages are produced locally, around two-thirds of the country’s cooking oil is imported. Ten years ago, imports were just one-third of the total. The divergence is because India is growing too rapidly and there is insufficient local agricultural and technical capacity for cooking oil production. As well as production capacity constraints, lower monsoon rainfall in large parts of the country in recent years has caused crop failure, and led to an estimated increase in additional imports of more than seven per cent, according to the Economic Times of India. www.sacmi.com THE COMPLETE CLOSURE, PREFORM AND CONTAINER SOLUTION FOR YOUR SMART FACTORY Product design Product development Product validation Industrial production plant Process & quality control On-site and start-up assistance After-sales and Customer service SACMI 4.0 GOOD GOOD GOOD GOOD BAD %VXMƤGMEP -RXIPPMKIRGI and Polarised Light: automatic quality control made perfect By using polarised light and numerous, fully automated AI-controlled scans, the SACMI vision system learns LS[ XS VIGSKRMWI ERH GSVVIGX ER] TVSHYGXMSRɅƥE[W","@ID":17}, "55 TRADE SHOW PREVIEW PETplanet Insider Vol. 19 No. 09/19 petpla.net PET processing solutions, preform moulding and sustainability goals Focused on a wide range of plastic applications within a variety of markets, including food and beverage packaging, general plastic packaging, medical, automotive, and home, beauty and personal care, Husky will demonstrate its injection moulding solutions helping their customers to find ways to better respond to changes through the development of digitalised end-to-end manufacturing processes, flexible, scalable moulding solutions and more sustainable packaging options. Husky will run its new HyPET HPP5e system, delivering better energy savings, system reliability, preform quality and user friendliness. The system will be producing preforms made from 100% rPET. New tooling technologies including Husky’s new NexPET Mould, which is a flexible mid-volume tool for shorter production runs and frequent changeovers. Introduction of a versatile, energy-efficient platform of PET preform moulding solutions to handle any application and production need. A preview of Husky’s Next Generation Operating Model (NGOM) digitalised end-to-end manufacturing system that offers enhanced capabilities to enable customers to more quickly respond to changing consumer trends. Husky highlights to support the circular economy and customers’ sustainability goals. Husky is committed to developing sustainable packaging solutions in aligning the goals of sustainability with the many positive attributes of plastic packaging. Spotlight on the latest hot runner and controller developments, including Ultra Helix 250 T2 valve gates, which are designed to improve part quality and maintain superior gate quality for millions of cycles for small parts with difficult to access gate locations. Also displayed will be the latest family of Altanium Mould Controllers, providing accurate temperature, integrated servo and valve gate control. Introduction of Husky’s new online spare parts ordering portal, which will be available for a demonstration on the booth. www.husky.co Product Solutions Lab R&D/Leverage Europe offers full-service manufacturing, sales and service from its state-of-the-art facilities in the UK. During K-Show R & D Leverage will be highlighting their expertise in single stage blow mould tooling, product evaluation, tooling design and its manufacturing and technical service assistance programs. A key highlight will be its Product Solutions Lab (PSL). With a reputation in the packaging world as a company that will consider challenging bottle designs to create brand owner success, visitors can come and learn how the PSL can be utilised for material trials, tooling qualification and process validation for single stage blow moulding programs. The PSL provides a secure research and development working environment to confirm the feasibility for bottle/jar shape, market evaluations, short-run production for line, filling, labelling and capping trials. The company also has on-site capabilities offering pilot tooling, material trails, colour trials, and production tool qualification. From concept to market, R&D/Leverage Europe is one of the leading providers of complete solutions to the single stage blow moulding industry for a wide range of consumer products. www.rdleverage.com Hall 14 R&D Leverage Booth B64 Hall 13 Husky Booth A61 Precision, power and productivity to plastic moulders Sumitomo (SHI) Demag Plastics Machinery GmbH will introduce its fastest, most energy efficient, sustainable, and data driven integrated machine line-up. Presenting five machines, the company is continuing its staunch focus on delivering precision, power and productivity to plastic moulders globally. Consuming up to 20% less energy than its predecessors, Sumitomo (SHI) Demag is bringing two energy-enhanced ElExis SP machines to K 2019, a large and a smaller version. Catering specifically to the packaging moulding markets, the ultra-high speed range ensures manufacturers no compromise on quality, production efficiency or sustainability, says Sumitomo. Central to the machine’s fast cycle time is the hydraulic accumulator, which achieves injection speeds of up to 1,000mm/s. This enables moulders to produce even thinner packaging items. The range is also one of the fastest machines in the market for injection dynamic, “The combination of speed with high quality moulding repeatability helps to minimise packaging production waste,” explains Arnaud Nomblot, Director Business Development Packaging at Sumitomo (SHI) Demag. www.sumitomo-shi-demag.eu Hall 15 Sumitomo Demag Booth D22","@ID":57}, "MARKET SURVEY 35 PETplanet Insider Vol. 20 No. 09/19 petpla.net 09/2019 MARKETsurvey Resins & additives Preform machinery Preform production & inspection Preform & SBM mould manufacturer SBM 2 stage Compressors Filling equipment & inspection Caps & closures & inspection Palletising & shrink film machinery Recycling Supplier of filling equipment and filling inspection systems It’s time to present some state-of-the-art filling equipment and filling inspection systems in our annual market survey. Please have a look at the up to date technical details provided by: Sacmi Imola S.C., Filtec S.A., SMI S.p.A., Sipa S.p.A, Pressco Technology Inc., Sidel, KHS GmbH, Heuft Systemtechnik GmbH, Krones AG, Newamstar, Fogg Filler and Serac Group. Although the publisher has made every effort to make sure that the information in this survey is up to date, no claims are made regarding accuracy and completeness. Filling Equipment Company name Sipa Postal address Telephone number Web site address Contact name Function Direct telephone number E-Mail Via Caduti del Lavoro n. 3 31029 Vittorio Veneto (TV), Italy +39 0438 911 511 www.sipasolutions.com Mr Matteo Tagliaferri Marketing and Communication +39 0438 911 511 [email protected] 1. Machine designation / model number Isofill P Stillfill EVO Flextronic C Flextronic SE Flextronic S Flextronic W Bigfill 2. Number of filling heads (range: from/to) 20-160 20-120 50-180 20-180 20-180 20-96 12-24 3. Min. to max. bottle contents (in liters) 0.125-3 0.125-3 0.125-3 0.125-3 0.125-3 0.125-3 3-20 4. Filling speed: output (bph) (min. to max.): specifiy: 1l bottle / still water (bph) 60,000 62,000 60,000 62,000 63,000 36,000 16,000 (3l) 1l bottle / CSD (bph) 51,000 (CMW) 55,000 (CMW) 1l bottle / Milk (bph) 62,000 62,000 36,000 1l bottle / Juice (bph) 53,000 60,000 59,000 62,000 62,000 36,000 5. Filling process Pressureless (still drinks) Yes Yes Yes Yes Yes Yes Yes Pressure filling (carbonated drinks) Yes Yes Hot filling Yes Yes Cold aseptic filling Juices with high pulp content Yes Yes 6. Type of filling valve and metering system Isobaric mechanical level filling Mechanical gravity filling Isobaric volumetric filling valve Gravity volumetric filling valve Gravity volumetric filling valve Electronic weight filler Gravity volumetric filling valve 7. Special features (short description/ keywords) AISI 316L SS valve, product deflection without deflector on the filling tube, quick changeover for different neck diameters, automatic dummy bottle insertion, mobile vent tube, centralised remote fill level adjustment AISI 316L SS valve, product deflection without deflector on the filling tube, quick changeover for different neck diameters, seperated bottle air return, hot fill kit for product recirculation, constant and controlled recirculation rate in bottle, centralised remote fill level adjustment no bottle no fill system AISI 316L SS valve, product deflection without deflector on the filling tube, quick changeover for different neck diameters, automatic dummy bottle insertion, magnetic flow meter product control, filling speed control, XFill configuration without tank on board, dry pressurisation separated bottle air return AISI 316L SS valve, no contact between valve and bottle neck, quick changeover for different neck diameters, ultra clean version available, magnetic flow meter product control, filling speed control, automatic dummy bottle insertion, XFill configuration without tank on board AISI 316L SS valve, no contact between valve and bottle neck, quick changeover for different neck diameters, ultra clean version available, 3 positions membrane valve filling speed control, automatic dummy bottle insertion, XFill configuration without tank on board AISI 316L SS valve, no contact between valve and bottle neck, quick changeover for different neck diameters, load cell integrated in the bottle neck support, 3 positions membrane valve filling speed control, automatic dummy bottle insertion AISI 316L SS valve, no contact between the valve and the bottle neck, quick changeover for different neck diameters, ultra clean version available, 3 positions membrane valve filling speed control, automatic dummy bottle insertion, high flow performance","@ID":37}, "60 TRADE SHOW PREVIEW PETplanet Insider Vol. 19 No. 09/19 petpla.net 2019 March - December Powered by The worldwide round trip with Thanks to our sponsors and partners for your support Vacunite – new bottle-to-bottle technology meets highest specifications The Vacunite bottle-to-bottle recycling technology from the Austrian recycling machine manufacturer Erema is known for high-efficiency decontamination, best colour values, top IV stability, and low energy consumption during the entire process. Its compact design meets high demands in the production of food-grade rPET pellets. The Vacunite process is based on the combination of Vacurema technology which has been proven over many years and has been further developed for this application together with newly patented vacuum-assisted Solid State Polycondensation (SSP). Polymetrix developed this SSP for Erema especially for the demanding application. What makes this combination special is that all thermal process stages take place in a nitrogen and/or vacuum atmosphere, largely eliminating undesirable flake and pellet discolouration and reliably removing additives which could lead to unfavourable reactions in the melt. The nitrogen used in the SSP is cleaned and can be fed back into the previous processing stage so that nitrogen consumption is reduced as a result. To increase the transparency of the preforms, the pellets are dedusted again before filling. Overall, the technology requires 40% fewer components, making the plant more compact at the same time as consuming up to 36% less energy than comparable systems on the market. The end product is rPET pellets of unique quality which, in terms of food contact compliance, exceed both the current legal requirements and the even higher requirements of leading brand owners, says Erema. www.erema.com Hall 9 Erema Booth C05 High cavitation closure mould For the first time z-moulds will be present during the Kshow with its own booth. After showing high efficient closure moulds during the last couple of years together with different injection moulding machine partners, z-moulds will this year join the show for the first time as an official exhibitor. Together with the drying specialist Eisbär, z-moulds will share a twofloor booth. Also this year z-moulds will be displaying one of its high cavitation closure moulds, running with the patented z-slides technology at a cycle time below 2 s, on a Sumitomo Demag machine in hall 15 booth D22. www.z-moulds.com www.eisbaer.at www.sumitomo-shi-demag.eu Hall 10 z-moulds Booth H48","@ID":62}, "PETplanet Insider Vol. 19 No. 09/19 petpla.net 63 BOTTLES 63 BOTTLES Drink from Reishi American company Reishi is selling various drinks with unusual ingredients that come from organic farming in structurally weaker countries. The plant-based drinks come in slim, transparent 354ml/12fl oz bottles. The variety shown in the picture is “Reishi Cold-Brew Coffee + 7 g Coconut MCTs” and claims to boost health. A bottle also contains 140mg of caffeine. The bottle is decorated with a naturally held sleeve label. www.rebbl.co Summer edition of Valensina Consumer desire for something different and special treats ensures plenty of work in the laboratories of juice manufacturers. This is why Valensina brought a juice innovation onto chiller shelves under the name “Summer Edition”. The NFC juice is 100% made from fruit and contains approx. 65% orange, pineapple and lime juice. Mango pulp and mint round off the new variety, which – according to the manufacturer – should appeal to consumers between 18 and 39. One litre is available in a bottle made from up to 50% recyclate with brand embossing, a green screw cap and a freshness seal as an advertising surface and a tamper-evident seal. The transparent sleeve label ensures a full view of the product from all angles. www.valensina.de Good conversations. braubeviale.de CONNECT WITH THE FUTURE Over 1,000 exhibitors and more than 40,000 trade visitors all have exactly one goal in mind: To drive progress for the beverage production of tomorrow, so that new solutions can be used to market better products. Sound exciting? Find out more: braubeviale.de/next Good business. Nuremberg, Germany | 12–14 November","@ID":65}, "MATERIALS / RECYCLING PETplanet Insider Vol. 19 No. 09/19 petpla.net 32 At K, Chroma was exhibiting its new range of frosted PET colour concentrate additives, designed to achieve the look of glass in PET containers (issue 10). According to the company, processors save up to 90% by eliminating spray-painting. In issue 11, Uhde Inventa Fischer compared its Melt to Resin (MTR) technology to the polymerisation process where Solid State Post condensation (SSP) is required and referred to energy efficiency of PET production by about 40%. During K, Polyone launched its OnColor liquid colourant system. It has been designed to help converters and OEMs reduce costs and eliminate waste by optimising colourant use and handling (issue 12). 2011 In a case study presented in issue 7+8, Colormatrix pointed out how the implementation of their UV protection Ultimate UV390 addresses issues of costs or visual impact. At Brau Beviale, Repi was present with their Remap Liquid Colours with a broad range of colour shades and effects, and the Remap Additives for protection of packaging content (issue 11). 2012 Artenius FastFlow+ was introduced in issue 4. The new material was stated to capture the heat energy of the blowing process more efficiently, leading to energy savings of up to 20% compared to standard PET resins. Americhem added a PCR renewal additive to its range, masking yellowness and improving the L-value (issue 5). The cylindrical pellets have been introduced at NPE. Issue 6 highlighted Coca-Cola’s extended range and collaboration of PlantBottle packaging, made from 30% plant-based MEG and 70% PTA. The company underlined its aim to use PlantBottle packaging the company’s entire virgin PET supply by 2020. Artenius had developed a new PET resin that combines virgin PET and PCR PET as feedstock in the polymer production process. The result was an energy-efficient food-safe resin called Artenius Unique (issue 7+8). To increase the viscosity, the material undergoes a polycondesation melt phase, completing the removal of any contamination which might be present. 2013 Novapet had pioneered the development and delivery of solutions in PET resins and concentrates for long life dairy packaging, as we reported in issue 1+2. This includes besides the “Dairy” resins also DCU concentrates for opaque bottles and the Luz range of concentrates for transparent or translucent PET bottles. During our Editour through Russia, we visited the resin producer Senege, part of Europlast Group. Back then, they were discussing an alternative to oil-based PET and were looking into the possibilities of bioPET (issue 3). In issue 5 we reported about what we learned at the PET 2013 Conference in Moscow where a shortage of feedstock (both therephthalic acid and MEG) in the Russian PET market concerned the sector. Phoenix Technologies was launching LNO w resin, a new food-grade, melt-extruded rPET pellet (issue 6). The company stated that it could be used at levels up to 100%, or blended with virgin PET. Joncryl ADR is an additive introduced by BASF Plastics Additives at K. It was claimed to help recyclates to achieve high performance characteristics, superior even to virgin products. This is possible as the molecular chains produced can even be longer after adding the additive (issue 10). 2014 Catalytic Technologies Ltd (CTL) had developed a new titanium catalyst technology which eliminates the use of the heavy metal catalyst antimony oxide in PET production. The new technology has been tested by major industry players around the world. The company has announced the ambitious business target of taking over 50% of the PET resin and sheet market within the next five years, as we reported in issue 5. Acetaldehyde (AA) can affect the taste and smell of carbonated and still mineral waters. In issue 8, we were comparing two currently used AA scavenging additives, an anthranilamide and a polyamide-based AA system, that help reduce the negative taste and odour effects of AA migration. The level of AA (ppm) was reduced by both formulations, but results demonstrated that the anthranilamide solution performed better, particularly at lower addition rates up to 0.15%. 2015 Sukano’s latest introduction to the PET portfolio included an impact modifier for transparent applications, reducing brittleness (issue 7+8). Also in issue 7+8, Holland Colours launched a new series of liquid colourants: HolcoPET. Improved processability regarding slip, retention of mechanical properties and colour distributions were claimed to be the benefits. In issue 9 we introduced NGR’s LSP process. Standing for Liquid State Polycondensation, the PET recycling process combines increased IV and decontamination properties with low energy consumption. IntegRex PET (iPET) was the main driver in the programme of","@ID":34}, "MARKET SURVEY 38 PETplanet Insider Vol. 20 No. 09/19 petpla.net Filling inspection systems Company name Sacmi Imola S.C. Filtec Europe GmbH Pressco Technology Inc Heuft Systemtechnik GMBH Krones AG KHS GmbH Postal address Telephone number Web site address Contact name Function Direct telephone number E-Mail Via Selice Prov.le 17/A Imola (BO) Italy +39 0542 607111 www.sacmi.com Mr Stefano Severi Sales Area Manager +39 0542 607553 [email protected] Osterrade 56, 21031 Hamburg +49 40 7393 350 www.filtec.com Dr Joachim von Meyer Director +49 40 7393 350 [email protected] 29200 Aurora Road, Cleveland, OH USA +1 440 498 2600 www.pressco.com Mr Tom O'Brien VP, Marketing, Sales & New Business Development +1 440 498 2600 [email protected] Am Wind 1, 56659 Burgbrohl, Germany +49 2636 56 0 www.heuft.com Sales requests +49 2636 56 0 [email protected] Böhmerwaldstr. 5 93073 Neutraubling, Germany +49 9401 70 0 www.krones.com Juchostraße 20 44143 Dortmund/Germany +49 231 569 0 www.khs.com Mr Helmut Schmitt Project Man. & Production Man. Inspection Techn. +49 231 569 10124 [email protected] Fill level control Complete range of fill level inspectors Infrared No Filtec 3 No Yes Yes X-ray No Filtec 3XR No Yes Yes Yes Gamma No Filtec 3G No No Yes Camera Yes Visiontec Yes and high frequency fill level control Yes Yes and high frequency Yes and high frequency Contamination control No Intellect+ Vision No Foreign object detection, low & high density, all types of foreign detection, unique pulsed X-ray & camera combined in one system Foreign substance inspection (sniffing) for empty Ref PET bottles Closure inspection Intellect+ Vision Presents of cap Yes Yes Yes Yes Yes Yes Crooked cap Yes Yes Yes Yes Yes Yes Lifed cap Yes Yes Yes Yes Yes Yes Wrong cap Yes Yes Yes Yes Yes Yes Tamper evident band control Yes Yes Yes Yes Yes Yes Camera: 360° / sensor Camera with special peripheral lens to control 360° of the sidewall, real 3D technology for 360° precise inspection Yes Yes Yes Yes Yes, both Label inspection Intellect+ Vision Torn label Yes, +/- 1° Yes Yes Yes Yes Vertical / horizontal misalignment Yes, +/- 1mm Yes Yes Yes Yes Yes Best-before date control Presence / absence if printed in inkjet, OCR if laser printed Yes No Yes Yes Code presence inspection Camera: 360°/ sensor Camera 360° with real 3D technology Yes Yes Yes Yes Camera and sensor Pressure leak detector No AURAtec No Yes Yes Squeezer Applicable bottle type 100-3,000ml Diameter Up to 150mm All standard sizes can be handled Up to 150mm 30 -80mm 50-105mm 40-110mm Height Up to 340mm All standard sizes can be handled Up to 400mm 100-350mm 60-340mm & closure diameter 27-46mm 150-360mm Rejecting bottle Single or multi push devices Yes, different reject systems available Push reject and diverter reject options available Yes Yes, without air consumption Into bin and onto collecting table Inspection speed Up to 72,000bph Up to 1,200bpm Over 3,000ppm Up to 72,000bph Up to 84,000bph PET: up to 86,000bph Monitoring Panorama supervisor Yes Filler valve, capper head correlation Filling valves, closer heads, continous bottle tracking Yes Filler-/sealer management","@ID":40}, "MATERIALS / RECYCLING PETplanet Insider Vol. 19 No. 09/19 petpla.net 44 Reduce, reuse, recycle - refit! Author: Lucia Buffoni, Marketing Manager Repi Plastics attract a lot of blame for pollution but the negative image ascribed to them (often erroneous) is the key challenge that players in the plastics industry need to address, to prove the contrary. Repi, a supplier of colours and additives to the plastic packaging industry for years, is among them. Research and development of plastic packaging has been increasingly driven by the desire to actively contribute in creating packaging that is environmentally friendly and highlights the unique properties of plastics in packaging, including single-use. It is worth retracing once again some of the reasons why plastic is so successful in packaging: It preserves food from degradation and makes transglobal transport convenient and safe. It is lighter than any other packaging. It is convenient for consumers. Plastic packaging helps reduce CO 2 emissions, especially when recycled. Plastics Europe reported that the recycling rate of 5 million tonnes of plastic packaging would cut CO 2 by 7 million tonnes, corresponding to 2.4 million cars less on streets. Bottles made of 50% rPET have lower environmental impact than glass (whether single use or reusable) or cans. That includes contribution to climate change and smog as well as water consumption. Single use glass is the least environmental. Recycling is crucial. Plastic is too valuable to be thrown away; it must be reused and recycled. The “3-R” statements adopted by many plastics stakeholders clearly summarise where we need to move: Reduce the quantity of plastic put on the market (by lightweighting, e.g.); reuse when feasible; and recycle. Refit: acting responsibly towards sustainability Repi’s 4th “R”: Refit, represents its approach towards sustainable growth. It involves internal processes, from choice of suppliers, through tuning low energy production cycles, to the use of renewable energy sources for its facilities, and separate waste collection; all before production. Now coming to products, Repi specialises in additives and colours for recycling and offers broad-spectrum support in aesthetics enhancers and mechanical boosters for rPET, Anti Yellow (AY) additives and IV enhancers. rPET colour varies between suppliers and even batches. Depending on the ratio of virgin and recycled PET used, results can range from grey or pale yellow to blue or greenish. The higher the recycled content, the darker the resulting colour. Mechanical issues include a drop in Intrinsic Viscosity (IV). This happens because PET, after several production cycles, due to degradation processes, shows a reduction in the molecular weight: its chains are shorter and mechanically the final product is weaker. Repi’s R&D laboratories mould preforms and bottles and experiment with colours and additives using rPET pellets and flakes mixed in different percentages. The Anti Yellow liquid additives range balances inconsistent material appearance and enables brightness to be regained, as well as correcting green or grey tones. The IV enhancer combines shorter molecular chains to longer ones, thus increasing the IV of the material. Colours can help, too! The use or rPET presents a challenge to brand owners who are not ready to sacrifice packaging aesthetics and brand recognition. When a very dark rPET is used, AY additive may not be enough. Repi’s Fumè colour range can give packaging a premium and elegant look, masking the rPET colouring effect. It is used at very low dosages, down to 0.05%, and therefore does not impact the recycling stream because it is read as a transparent light colour. The range goes from light amber to light blues, greys, aquamarine and antique rose. Moving towards a circular economy is not simple but solutions are already in place to help sustainability from branding, aesthetic and technical perspectives. www.repi.com MATERIALS One single shade starting from two different rPET variations","@ID":46}, "MATERIALS / RECYCLING PETplanet Insider Vol. 19 No. 09/19 petpla.net 41 motan-colortronic gmbh - [email protected] www.motan-colortronic.com ETA plus® considerably reduces energy consumption and protects materials. Drying has never been this efficient: ETA plus® LUXOR A Please visit us: Hall 9, Stand C64 16 - 23 October 2019 About Avantium Avantium is a leading technology development company and a forerunner in renewable chemistry that develops novel technologies based on renewable carbon sources as an alternative to fossil-based chemicals and plastics. The company currently has three technologies at pilot and demonstration phase. The most advanced is the YXY plant-to-plastics–technology that catalytically converts plant-based sugars into a wide range of chemicals and plastics, such as PEF. Avantium has successfully demonstrated the YXY Technology at its pilot plant in Geleen, the Netherlands. Its Dawn Technology converts non-food biomass into industrial sugars and lignin. In 2018, Avantium opened a DAWN pilot biorefinery in Delfzijl, NL. Mekong, the third technology, catalytically converts industrial sugars to plant-based MEG (mono-ethylene glycol). www.avantium.com PET-PEF-PET multilayer When gas barrier requirements for small CSD bottles are too high for PET to meet alone, currently, a PA barrier layer can be added to achieve the required performance. A potential solution for this is a PET-PEF-PET multilayer structure, creating a product that will be recyclable in current PET waste streams. The amount of PEF will be diluted so much that its concentration will be far below the threshold whereby it may cause detectable differences in the properties of rPET. PEF also has potential in high-barrier flexible packaging. Currently, such films consist of many layers, composed from different types of polymers. PEF can be bi-axially oriented to form BO-PEF (same as BO-PET). This film has the potential to simplify existing structures, combining different functionalities, such as gloss, strength and barrier, in one polymer layer. Although recycling of such films is still in its infancy, one can make the general statement that a simpler structure will result in a simpler, more easily recyclable film. Summary PEF is a very versatile and promising polymer for the future. Avantium and several other companies are working on processes to make it commercially viable. The company states that it is only a matter of time until its entry into the market as the benefits are too many and too obvious for it to fail; it fits perfectly alongside PET as a recyclable raw material in the bio-based economy.","@ID":43}, "MATERIALS / RECYCLING PETplanet Insider Vol. 19 No. 09/19 petpla.net 39 Consistent preform wall thicknesses for large-volume containers Optimising with nanoparticles by Gabriele Kosmehl In a joint project, the Institut für Kunststofftechnik (IKT) in Stuttgart, Germany, Fricke und Mallah Microwave Technology GmbH and Spritzguß Müller GmbH are researching the manufacturing of plastic containers with volumes greater than 30 l in stretch blow moulding procedures. PETplanet talked to Head of the IKT Institut für Kunststofftechnik, Prof. Christian Bonten and his academic co-worker in processing technology, Ms Laura Klis, MSc, about the results that they are hoping for from nanoscale fillers as regards improved wall thickness homogeneity of the parts due to an adjusted warming process using microwave radiation. The objective of a new project by the IKT and two partner companies is to design thick-walled preforms in such a way that, from the very start, consistent heating takes place before the stretch blowing process and a consistent result can be generated. “In the stretch blowing process for large-volume containers, even greater challenges must be overcome that relate to the warming process with infrared (IR) emitters,” explains Laura Klis. “Preforms with inconsistent wall thicknesses sometimes aren´t heated homogeneously by IR radiation. This might cause a polymer film tear in the tool or poor mechanical properties of the end product.” Therefore, Head of Institute Prof. Bonten’s team is working on optimising the materials and is planning to compound special fillers into the plastic before using it in the injection moulding process. By means of the special and well distributed fillers, the preforms are warmed, not using traditional IR but microwave energy. “The fillers work as small hot spots in the material and allow for a homogenous warming,” explains Klis. During the research project, which is scheduled to last three years, different materials are to be tested with different filler types and filler contents. Besides PET with and without a proportion of rPET, bio-based and biodegradable plastics like PLA will also be used. As the compounds need to be well suited for warming with semiconductor-based microwave techniques, the decision was made to use carbonbased fillers. “Carbon nanotubes or graphene are very small and – if well distributed - have a great surface to volume relation, ,” says Prof. Bonten. “Precisely in relation to PET, this offers the advantage that they can also be used even in transparent containers.” Good results are expected even from a filler content of around two percent by weight. “We will certainly also be testing less expensive fillers such as magnetite or carbon black, which might allow costwise to use even ten percent by weight. Perhaps we may also be able to generate the best results with particle mixes – ultimately, we will find it out in large-scale tests,” says Klis confidently. Expertise in tool construction and injection moulding comes from Spritzguß Müller GmbH. There, work is currently in progress on the construction of an injection moulding tool and ultimately, the optimised preforms will also be stretch blow moulded there. An (optical) retail-typical microwave is used as a cavity for microwave irradiation. Project partner Fricke und Mallah Microwave Technology GmbH is contributing to the innovative microwave source. Their technology enables to generate microwave radiation no longer by magnetrons, but by semiconductors. Hence, scientists at IKT are expecting a higher effieciency in heat input, better controllability, and focussing of the heat sources, which is supposed to result in a more homogenous warming than in the IR procedure. The extent to which microwaves will lead to shorter heating times compared to IR and therefore to gains in energy efficiency could be a welcome additional finding of the project. www.ikt.uni-stuttgart.de MATERIALS The semi-conductor-based microwave radiation is generated by a generator.","@ID":41}, "61 PRODUCTS PETplanet Insider Vol. 18 No. 0/17 petpla.net PETproducts Near-infrared masterbatch for recycling black and coloured plastics Plastics´ recycling in the EU has increased by almost 80% since 2006. During the same period, landfill disposal has significantly declined by 43%. The problem when it comes up to recycling is the fact that some black and coloured plastic items do not get recognised by detecting or sorting machines. That is why these pieces are still disposed as landfill or incinerated to produce energy. So the common use of carbon black still issues the big challenge with it. The reason resides in the fact that sorting machines usually work with near-infrared (NIR) sensors. However, plastics items that contain carbon black absorb the light signal instead of reflecting it, and the product is not detected, thus not sorted and end up its service life as landfill mass or as an incineration mass. Gabriel-Chemie introduces a professional solution for NIRdetectable and sortable thermoplastic masterbatch colours. The NIR reflective masterbatch is made by using special pigment formulations which enable the correspondent sorting and recycling, is food contact approved and laser markable. The masterbatch can be extruded, blown or moulded by injection, compression, etc. Solutions made with GabrielChemie’s NIR masterbatch have no lower mechanical properties than products made by carbon black based products. The masterbatch is a solution for plastics that are intended to be reused or recycled. They can be produced applying the ISO norms 9001, 14000 (environmental management), 22000 (food contact materials) and 13485 (medical devices). www.gabriel-chemie.com www.bioplastics-breakfast.com Register now B3 BIOPLASTICS BUSINESS BREAKFAST 17. - 20.10.2019 Messe Düsseldorf, Germany PLA, an Innovative Bioplastic Bioplastics in Durable Applications PHA, Opportunities & Challenges Bioplastics in Packaging At the World‘s biggest trade show on plastics and rubber: K‘2019 in Düsseldorf, Germany, bioplastics will certainly play an important role again. On four days during the show bioplastics MAGAZINE will host a Bioplastics Business Breakfast: From 8am to 12pm the delegates will enjoy highclass presentations and unique networking opportunity. The trade fair opens at 10 am. Media Partner 1st Media Partner TECHNOLOGIE & MARKETING Getränke! KOREAPACKAGINGASSOCIATION INC. Supported by organized by Gold Sponsor MATERIALS","@ID":63}, "58 TRADE SHOW PREVIEW PETplanet Insider Vol. 19 No. 09/19 petpla.net Future-oriented extruder machine design The design is eye-catching with modern colours and shape is more functionality with improved ergonomics. Among the practical extras are, for example, the large-scale safety gates and integrated variable colour LED signal lights that indicate operating status and simplify required maintenance. One feature is the optional magnetic quick mould change system. Mould change-over is accomplished in 15 minutes per clamping unit – without tools or a special mould cart. Moulds and blow pins are always changed from the front side of the machine. The new generation of high-output extruders of the future packaging machine line distinguish themselves through processability, high maximum throughput, and excellent melt homogeneity. Bekum places particular importance on energy efficiency when developing extruders. Bekum extruders use energy efficient motors and drives, which are important to achieve high energy efficiency. (Class 10 as described in Euromap 46.1). Bekum extrusion heads in either mono- or multi-layer technology are designed to achieve precise flow guidance, short colour change times and uniform wall thickness throughout the article for all extrusion blow mouldable plastics. The modern machine design of the future machine series will be enhanced via a portrait-oriented, generously dimensioned 24-inch operator panel and a new, intuitive touchscreen called Bekum Control 8.0. Visualisation of throughput values and energy consumption on the multi-touch operation panel is provided as well as the display of power, water, air consumption, and the pressures of all supplies process utilities. Remote on-line service: with permission of the owner, Bekum service technicians can log in to machine controls and carry out function tests and perform software updates. Bekum is engaged in the circular economy. Its Bekum 3-layer heads, offers a solution for costs-effective recycling of single-origin PE of PP plastic scrap. Thanks to Bekum’s tri-extrusion technology, recycled material (PCR) can be embedded between layers of virgin plastic materials. The use of PCR in the middle layer can permit a cost-reduction in the manufacture of containers. Bekum is presenting the Concept 808 show machine with a multi-cavity three-layer application. www.bekum.com corner Amut Group carries on with the motto “Go Green” firstly launched during Chinaplas 2019 edition and offers several solutions to support the circular economy. The friction washer, patented machine exhibited, performs intense PET/HDPE/LDPE washing and pollutants removal action. Thanks to the strong cleaning force of the friction washer, the outgoing flakes have the quality required to be re-used in many applications. Amut also proposes the line concept for Bottle to Packaging application developed in collaboration with Erema. The extrusion line is designed to process 100% post-consumer PET bottle flakes into single layer foil certified food grade thermoforming foil, with a direct FDA extrusion process. The line has a net width from 1,000-2,000mm, configuration with one layer, three layers or up to five layers upon request. The thickness is from 0.15-2mm and the output is up to 2,000 kg/h. www.amut.it Hall 14 Bekum Booth C03 Hall 16 - Booth A05 Amut Hall 3 - Booth B92 15min for a mould change","@ID":60}, "imprint EDITORIAL PUBLISHER Alexander Büchler, Managing Director HEAD OFFICE heidelberg business media GmbH Bunsenstr. 14 69115 Heidelberg, Germany phone: +49 6221-65108-0 fax: +49 6221-65108-28 [email protected] EDITORIAL Kay Barton Heike Fischer Gabriele Kosmehl Michael Maruschke Ruari McCallion Waldemar Schmitke Anthony Withers WikiPETia.info [email protected] MEDIA CONSULTANTS Martina Hirschmann [email protected] Johann Lange-Brock [email protected] phone: +49 6221-65108-0 fax: +49 6221-65108-28 LAYOUT AND PREPRESS EXPRIM Werbeagentur | exprim.de Matthias Gaumann READER SERVICES Till Kretner [email protected] PRINT Chroma Druck & Verlag GmbH Werkstr. 25 67354 Römerberg Germany WWW www.hbmedia.net | petpla.net PETplanet Insider ISSN 1438-9459 is published 10 times a year. This publication is sent to qualified subscribers (1-year subscription 149 EUR, 2-year subscription 289 EUR, Young professionals’ subscription 99 EUR. Magazines will be dispatched to you by airmail). Not to be reproduced in any form without permission from the publisher. Note: The fact that product names may not be identified as trademarks is not an indication that such names are not registered trademarks. 3 PETplanet Insider Vol. 20 No. 09/19 petpla.net This year’s K trade fair in Düsseldorf will open its doors from 16-23 October. Machine and raw material producers traditionally use this event to showcase innovations and cultivate customer contacts. This will be the case again this time. However, business discussions are likely to be overshadowed by the global economic situation. Brexit will happen shortly after the trade fair ends if the EU and UK are unable to reach an agreement. How detailed cooperation will be handled from 1 November is still unclear. Key global economic indicators are flatlining and contribute to lively discussions on whether the world is slipping into recession, or just taking a breather following many years of growth. A recession is looking increasingly likely if the USA and China continue with their imposition of protective tariffs. But it is not just the economic figures which are open to broad interpretation. What the global environmental community failed to achieve over many years, Greta Thunberg has managed to accomplish with her Friday movement in just over 12 months. Climate change and sustainability are now at the top of everyone’s list of priorities and dominate discussions at political level and within industry. Alongside current discussions on sustainability, environmental pollution caused by plastics has become a major issue. Concrete solutions have not amounted to much thus far. Dr Oliver Möllenstädt, Executive Director of the German Association of Plastics Converters (GKV), summed up the current dilemma as follows: “The European Commission and individual national Governments are attempting to respond to consumer concerns with symbolic gestures such as restricting the use of single-use plastics and plastic bags. While this approach might reassure the public in the short term and give them the impression that much is being done, such actions will not have the desired effect in terms of environmental protection and sustainability”. One such example is the EU Directive on restricting the use of single-use plastics, adopted by the European Parliament in March and which is expected to be implemented in Member States by 2021. The Directive covers 10 common items found on EU beaches. Measures being introduced include a ban on a number of single-use plastic products to which the market can offer sustainable alternatives. These items include cotton buds, cutlery, plates, straws, drink stirrers, cups, expanded polystyrene (EPS) food containers, all products made from oxo-degradable plastic, together with balloon sticks. The Directive also sets a 90% collection target for plastic bottles by 2029 (77% by 2025). The Directive also introduces design requirements for attaching caps to bottles, as well as setting targets for recycled plastic content. All PET bottles are to consist of 25% of recycled material by 2025 and all plastic bottles to comprise 30% recycled content by 2030. As well as going to Düsseldorf with a large budget, we will also be taking a number of creative and innovative ideas with us to the Rhineland. Your PETplanet Insider Editorial Team Dear readers,","@ID":5}, "MARKET SURVEY 37 PETplanet Insider Vol. 20 No. 09/19 petpla.net Filling Equipment l l l consumer bags textile packaging recycling rECO Company name Krones AG Serac Group Postal address Telephone number Web site address Contact name Function Direct telephone number E-Mail Böhmerwaldstr. 5 93073 Neutraubling, Germany +49 9401 70 0 www.krones.com Mr Philipp Schön Product Manager Filling Division +49 9401 4567 [email protected] 12, route de Mamers, BP 46, 72402 La Ferté Bernard, Cedex, France +33 2 4360 2828 www.serac-group.com Mr Roland Nicolas Dairy & Aseptic Business Development Director +33 2 4360 2832 [email protected] 1. Machine designation / model number Modulfill Serac Aseptic System 5 (SAS 5) 2. Number of filling heads (range: from/to) 16-216 8-90 3. Min. to max. bottle contents (in liters) 0.1-5 0.05-2 4. Filling speed: output (bph) (min. to max.): 6,000-48,000 specifiy: 1l bottle / still water (bph) Up to 72,000 1l bottle / CSD (bph) Up to 65,000 1l bottle / Milk (bph) Up to 60,000 6,000-48,000 1l bottle / Juice (bph) Up to 60,000 6,000-48,000 5. Filling process Pressureless (still drinks) Volumetric & net weight filling system contactless filling; height filling system with short or long tube Electronic net weigh filling Pressure filling (carbonated drinks) Volumetric filling system with short tube, net weight filling system contactless, height filling system with short or long tube Hot filling Volumetric & net filling system contactless filling, height filling system with short or long tube Electronic net weigh filling Cold aseptic filling ContiformAseptBloc L, contactless with wet bottle sterilisation, Contiform AseptBloc D contactless with dry bottle sterilisation, ContiformAseptBloc DN/ DA contactless with dry preform sterilisation Electronic net weigh filling Juices with high pulp content Height filling system with long tube, pre-dosing system aseptic mode with dosing into filling valve, pre-dosing system hot mode: full bore filling, contactless, for pulp, fibres or fruit pieces Electronic net weigh filling 6. Type of filling valve and metering system Volumetric filling system: inductive and mass-flow meter, net weight filling system with weighing cell and height filling system with electronic fill height measuring Electronic net weigh filling, Multiflow (patented) magnetic valves with flow monitoring during filling process, pressure filler tank sterilisable with over-pressured water 7. Special features (short description/ keywords) Monotec (starwheel columns with servo drives), cap disinfection (UV light / PAA / H2 O2 , optional), clean room cover, foam cleaning system, nitrogen injection system, automatic CIP-cups, capcade, Bloc solutions SAS 5 generation of aseptic filler with liquid PAA, dry controlled H2 02 or e-beam packaging sterilisation; bottle filling-closing with hygienic definition: Filling: Upfill: net weigh filler; Capping: Upcap brushless screw-capper for plastic caps; Sealing: E-Sealer electrical heat-sealer for aluminium foil caps, isolator with unidirectional sterile air flow","@ID":39}, "EDITOUR PETplanet Insider Vol. 19 No. 09/19 petpla.net 20 Turnkey from India High-end preform systems June 2019 We met: Mr Shurid Mody, CEO of PETform, Daman Must it always be a new turnkey preform system? Everyone who deals intensively with TCO asks themselves this question. On the one hand, complete systems like Husky or Nissei ASB promise high availability but they do require an enormous capital investment. Shurid Mody, CEO from PETform Technologies, Daman, has taken up this issue and has come up with an interesting solution. He offers reworked used systems with individual new moulds. His primary business is the development and construction of complete preform tools produced in-house and refurbishment sets for all tool and machinery providers. Whether for the Husky or the MHT principle, he supplies up to 144 cavities. He prefers the hot runner design from Otto Hofstetter. “Their runner system uses fewer elements, where the valve stem is always concentric with the gate regardless of being in cold or hot condition. This allows the use of larger manifolds and fewer points of melt transfer, making it less prone to melt leakages. Also, the complete valve stem assembly can be replaced without opening the hot runner. We take this concept to a higher level by improving the insulation between the hot and cold side reducing energy consumption significantly. Most processors in India using local equipment are not aware that their energy wastage in the hot runner is around 30% of their overall energy consumption!” says Mr Mody. “Most Indian mould designers come from simple moulds for the Milacron systems and have less experience with high-tech moulds,” he continues. “Most mould makers in Asia tend to respond to their domestic markets with a focus on reducing cost per cavity. They then cut corners by using cheaper materials and less precise metal cutting machinery, and inspection equipment. This affects the preform quality, cycle time and life of the tool adversely. We use only high quality European manufactured steels that are alloyed more homogenously and include less impurities. We also use exotic materials such as titanium and ceramic in our hot runners to improve insulation between hot and cold side, saving the user thousands of dollars in energy costs per year while putting less load on the hot runner controllers, heaters and chilling plants. We understand the fundamental science of high end tool making, machining & metrology and are not just another copy-paste mould manufacturer from Asia.” He also supplies tools for Nissei ASB systems using higher quality steels vs the OEM. All critical moulds elements (wherever possible) are manufactured from corrosion resistant European manufactured stainless steels that are harder and tougher. The market for high end moulds like this in India is small so he exports the tools and sets throughout the world, with a focus on the North, Central & South American & European markets. Here, he has former Husky employers, who install, run in and maintain the moulds on site. Five years ago he began by reworking Husky and Nissei systems. “The mechanics of the systems are usually in order but the controls and the hydraulics need some exchanges,” explains Mr Mody. For the controls he relies on B&R but the hydraulics he exchanges completely. “Servo pumps are used here, which make the old system energy efficient and are up to 10% faster and more accurate,” reports Mr Mody. He includes the unencrypted software alongside. The hydraulic components come from the catalogue so the customer can re-order cost effectively if necessary and is not reliant on expensive original replacement parts. With many years of experience in mould building, he can now carry out turnkey projects. Customised preform moulds are made on reworked systems. This enables PETform Technologies to guarantee high availability at quick cycles, individual moulds and reduced maintenance costs at low investment. A dream from any TCO point of view. In his factory, he can run up to 48 cavities and he is currently waiting for a larger machine so that he can test up to 96. All mould surfaces are cut to size; tolerances are around 3-4 microns. The second string to his bow is the production of special preforms for export. Wide mouth preforms are a speciality of his factory. www.petform.net Hot and cold sides stand ready for delivery. A tool set for Nissei ASB can be seen in the background. Tour Sponsors:","@ID":22}, "PETpatents www.verpackungspatente.de PETplanet Insider Vol. 19 No. 09/19 petpla.net 64 Plastic bottle base shape Intern. Patent No. WO 2018 / 228921 A1 Applicant: Nestec S.A., Vevey (CH) Application date: 7.6.2018 Weight-reduced plastic bottle with a base that has been optimised in terms of manufacturing, weight and stability. Pressure compensation areas US - Patent No. US 2017 / 0225863 A1 Applicant: PepsiCo. Inc., Purchase (US) Application date: 9.2.2016 Contoured bottle with specially shaped compensation areas for the optimum absorption of the forces arising when pressure differences occur. Aerosol can made from plastic FR - Patent No. 3047234 B1 Applicant: L’Oreal S.A., Paris (FR) Application date: 2.2.2016 Application is made for the shaping and structure of a pressurised aerosol bottle made from plastic. Plastic container Intern. Patent No. WO 2019 / 003637 A1 Applicant: Yoshino Kogyosho Co. Ltd., Tokyo (JP) Application date: 7.5.2018 Design and procedure for manufacturing an easily collapsible container. The base and side walls are specially shaped for this. Plastic container Intern. Patent No. WO 2019 / 003810 A1 Applicant: Yoshino Kogyosho Co. Ltd., Tokyo (JP) Application date: 7.5.2018 Design and procedure for manufacturing an easily collapsible but stable container. The base and elastically mouldable side walls are specially shaped for this. Bottle Europ. pat.issue No. EP 3138782 B1 Applicant: Yoshino Kogyosho Co. Ltd., Tokyo (JP) Application date: 12.2.2015 A plastic bottle with circulating reinforcement ridges and a special base for pressure equalisation has been issued a European patent. The bottle stands on the base with a circulating edge piece. The appearance of the bottle on retailer shelves is improved.","@ID":66}, "MATERIALS / RECYCLING PETplanet Insider Vol. 19 No. 09/19 petpla.net 43 MATERIALS / RECYCLING 43 Detectable black Black may be the absence of visible light, but that should not make it undetectable. In fact, black can – and should – be detected by sorting equipment. In strict compliance with EPBP (European PET bottle platform) design guidelines, Sukano successfully submitted a black masterbatch portfolio to the sorting machine technology leaders in France to certify the portfolio for detectability. Pioneering work in silicon free denesting Sukano pioneered a slip/antiblock masterbatch for PET to reduce the coefficient of friction (COF) of films and cut sheets. This allows deep drawn applications to demould and denest much more easily; films have less tendency to stick during winding and unwinding, and thermoformed parts are destacked without surface abrasion. The masterbatch also helps improve processing, printability and transparency. Convertors can ensure higher yields and lowest waste generation. In addition, Sukano has designed processing aid masterbatches that allow customers to enjoy the original cycle times and productivity of virgin PET. Sukano combi mix Sukano offers help in the recycling of all types of plastics. [email protected] Tel: +90 212 695 50 00 Fax: +90 212 694 97 24 100815dmyR .com tomers advise the company which polymers are being wasted or do not have an ideal end of life and the company offers technical suggestions on reuse. Tracking packaging Smart packaging can help recyclers to understand the composition and origin of their packaging waste, which will help boost recycling rates and improve yields and purity. This will enable the plastic industry to become less dependent of virgin material, with the ultimate aim of neutrality. The plastics industry is deeply committed to Circular Economy goals and challenges and has been working to address different issues related to production, consumption and end-of-life management. The Plastics 2030 Voluntary Commitment sets out a series of ambitious targets for 2030 and outlines future initiatives that will be undertaken by the industry, in partnership with others. The focus is on three key areas: increase re-use and recycling, prevent plastics leakage into the environment, and accelerate resource efficiency. Prevention, re-use, collection and recycling should always be the first choice. Achieving the goals of a circular economy will require commitment from all parties to responsible use, recover and re-use. www.sukano.com","@ID":45}, "PETnews 6 NEWS PETplanet Insider Vol. 19 No. 09/19 petpla.net PET Engineering celebrates 20th anniversary in the business of PET packaging PET Engineering celebrates its first 20 years of activity even if its history began in 1986 when Moreno Barel, former owne r and CEO, started acquiring the technical skills and know-how that have become the sturdy foundations of the company since 1999. PET Engineering is now a well-known specialist in packaging design of PET containers worldwide and counts brands such as Pepsico, Nestlé Waters, Carlsberg, Heineken and Coca-Cola among its global customers. This result was possible thanks to its innovative approach which integrates design, engineering and industrialisation making the company obtain 18 awards for its creative and fully feasible packaging. This unique approach generated the interest of Sidel Group that finalised the acquisition in October 2018. So, PET Engineering celebrates its 20th anniversary as part of one of three business groups of Tetra Laval, with 40,000 machines in operation in 190 countries and 170 years of experience and innovation, and it’s ready to live the coming years bringing to the Group more business opportunities, offering customers a single interlocutor for any need related to food & beverage packaging design and development. www.petengineering.com Petcore Europe launches special industry group “PET Monomer Recycling” Petcore Europe, the industry organisation representing the whole PET value chain, launched the “Special Industry Group – SIG” to establish a strong and sustainable value chain in the development of re-using the monomers from PET waste. Bringing the PET bottles and food containers as well as polyester textiles back to its constituents, monomers or low molecular weight components that allow purification means in principle endless re-use of these PET building blocks. This will improve the circularity of PET since colours, additives and other polymers in multi-layer constructions will be from now on fully recyclable. Monomer recycling is claimed to help solving the waste problem by giving all PET waste value. Christian Crépet, Executive Director of Petcore Europe explains: “The mission of this new group is to facilitate a platform to position PET monomer recycling as a viable addition to the established mechanical recycling process, enhancing the circularity of PET.” The SIG will use the networking and outreach of the Petcore Organisation to interact with legislators, regulators, NGOs and other stakeholders to ensure chemical recycling of PET is an acceptable business and fulfils the future requirements of business environment. The Group will work to ensure health and safety aspects as well as product acceptance is achieved. www.petmonomerrecycling.org Drink Japan 2019 Japan’s largest B2B trade show Drink Japan, specialised in beverage/liquid food development and manufacturing will be held from November 27-29, 2019 at Makuhari Messe, Japan organised by Reed Exhibitions Japan Ltd., co-organised by Japan Soft Drink Association. The fourth edition of the international Beverage & Liquid Food Development/Manufacturing Expo is gathering more and more attention from the industry where investments on cutting-edge technologies for facilities are increasing dramatically. In parallel to the exhibition, a conference will be held during the three-day show period. This edition’s programme covers hot topics in the industry such as Factory IoT and AI. In addition there will be sessions regarding waste reduction, recycling and sustainability. This edition will be concurrently held in conjunction with Japan’s Food Export Fair. www.drinkjapan.jp","@ID":8}, "BEVERAGE INGREDIENTS PETplanet Insider Vol. 19 No. 09/19 petpla.net 27 As well as the pharmaceutical, cosmetics and sports industries, the food and beverage industry is keen to take advantage of this by introducing relevant product developments. Doehler offers a variety of ingredients that are tailor-made for functional beverages for healthy and active lifestyles, such as well-known vitamin and mineral blends, fashionable plant-based proteins, and exotic botanical extracts. All provide improved nutritional value and a selected taste profile. With these, the company can support diverse positionings such as digestive health, bone and joint health, the immune system, mental health and energy. Less is more: fewer calories and free from artificial ingredients To accommodate the demand for beverages with reduced sugar, Doehler offers a broad range of MultiSense Flavours and sweetening solutions that allow sugar reduction of up to 100%, while improving the taste and organoleptic feel of reduced-sugar beverages and dairy and plant-based drinks, without the need for sweeteners. India’s increasing health awareness is reflected in the number of new products that are free from artificial ingredients. This trend is associated with growing demand for ‘clean label’ products, which contain minimal even zero additives. This means foregoing preservatives and environmentally-critical ingredients, such as palm oil. Doehler offers its customers a large number of natural ingredients, from natural flavours and natural colours to natural fruit concentrates and numerous clean label concepts, as well as supporting them in all questions regarding claims and legal constraints. www.doehler.com 1st Aseptic blower FDA certified in USA ABF 1.2 is the Aseptic Blow-Fill system featuring the very first sterile aseptic blower approved FDA. The GEA ABF 1.2, installed and successfully validated in the USA, obtained the FDA certificate for shelf-stable, low acid beverages produced and distributed in the USA. Thanks to ABF 1.2 each single step of the sterilization process is monitored, whilst the aseptic blower, housed inside a microbiological isolator, avoids any potential risk of recontamination. Another milestone for GEA 10 years after the first FDA certificate received for its PAA based sterilization system.","@ID":29}, "MATERIALS / RECYCLING PETplanet Insider Vol. 19 No. 09/19 petpla.net 46 rPlanet Earth sets up recycling plant in California Closed-loop recycling Usually, when someone decides to launch a startup company, they start small. But not Bob Daviduk and Joe Ross. When they established rPlanet Earth, they set up a company that recycles post-consumer PET containers and converts the flakes into food-grade preforms, extruded sheet, and thermoformed packaging in a single, closed-loop process. Bob Daviduk and Joe Ross envision a world without plastic waste. “It’s a very ambitious goal, but you have to aim high from day one,” explains Bob Daviduk. Plastic is a valuable resource, but only around nine per cent gets recycled worldwide. The rest lands in incinerators, landfills, or worse – the environment. Daviduk and Ross both hail from the United States, where daily consumption of single-use plastics is staggering: there’s coffee in to-go cups, disposable cutlery, and even peeled hard-boiled eggs in plastic containers. But when it comes to recycling these products, things look pretty grim: “In terms of sustainability, the US is an emerging market. We recycle one in five bottles give or take. In Europe, it’s closer to five out of ten. In Germany, it’s over 90 per cent because of the deposit,” says Daviduk. In the US, only one-fifth of the states have adopted a deposit and redemption system for PET and glass bottles and cans. But where there is a system in place, it works, as these statistics show: while the collection rate averages only about 30 per cent nationally, the ten states with bottle deposits have raised their collection rates to an average of over 70 per cent and as high as 92 per cent. Growing demand for rPET packaging But returning bottles for recycling is just one (extremely important) part of a functioning recycling process. Of course, the goal is to ultimately make the best possible use of the post-consumer PET and convert it back into high-quality products. And that is where rPlanet Earth comes in. The company’s two founders have recognised the market’s enormous potential. “I have been in the plastics industry for over twenty years. Unfortunately, most people don’t give any thought to what happens to plastic once it’s been used. So, our goal is to produce plastic packaging for a broad array of consumer packaged goods (CPG) companies and then be able to take that used plastic and turn it right back into the same product,” explains Joe Ross. Bob Daviduk adds: “There is strong demand for rPET across almost every CPG company, but not enough material. The market is growing fast. A few years ago, most companies were satisfied if their preforms had 25 per cent recycled content, and now many are saying they want 100 per cent. Many brand owners see that as their contribution to protecting the environment and promoting sustainability,” says Bob Daviduk. And that is why the two entrepreneurs decided to start up a company that converts used PET containers back into new food-grade packaging – an ambitious project for a start-up. Once they had secured financing, Daviduk and Ross began to look at technology and equipment in earnest. And it was purely by coincidence that rPlanet Earth found Krones: “I was looking for equipment suppliers and was just googling around when I found Krones – and the German company sounded interesting to me,” explains Daviduk. “Six years ago, Krones wasn’t really known in the PET recycling field. But my business partner Joe and his brother were both in the packaging industry and, of course, knew Krones. So I called – and was immediately put in touch with the right people; first in Neutraubling, then here in their Franklin, Wisconsin, office.” Joe Ross adds: “What started as doing some research turned into some really tight relationships with everybody from the Manual pre-sorting process in the front end Decontamination module MetaPure S","@ID":48}, "57 TRADE SHOW PREVIEW PETplanet Insider Vol. 19 No. 09/19 petpla.net High-precision laboratory thickness and dimensional measurement system Agr will display several new product developments as well as an array of quality management and process control equipment for plastic containers. Pilot Vision+ is Agr’s latest and most powerful in-the-blow moulder vision system. This system is positioned for the quality management of bottles with high percentages of rPET. Designed to work in conjunction with today’s high speed reheat stretch blow moulding equipment, the Pilot Vision+ system offers a modular approach to defect detection that works within the blow moulder. The open architecture of this system allows for simultaneous management of up to six cameras, in multiple locations. Some of the features of this system include colour preform cameras for managing colour variations, simple configuration and operation, largescreen user interface and defect categorisation by mould/ spindle and defect type. As part of Agr’s Process Pilot family of products, Pilot Vision+ can be combined with Process Pilot for a total bottle management solution, providing the ability to detect random occurring defects as well as manage the process to maintain precise material distribution, even with the lightest and/or most difficult-to-process bottle design. The Process Pilot system with advanced thin-wall capability is ideally suited for the production of ultra-light bottles. It provides the added precision and blow moulder control necessary to produce very light bottles, with consistent quality, in order to ensure proper performance on the production line and throughout the distribution chain. The Process Pilot system works in conjunction with the blow moulder to continuously measure material distribution on every bottle, and proactively manage the blow moulders to maintain optimal material distribution. Since the Process Pilot system manages the blow moulder based on actual bottle measurement, it is an ideal tool that can be used to overcome many of the issues that compromise bottle manufacture and filling line productivity such as process and environmental variables, increased levels of rPET and preform variability. www.agrintl.com Hall 11 AGR Booth B40 Agr’s Pilot Vision+ system is designed to meet the inspection challenges of PET bottles made with higher percentages of rPET.","@ID":59}, "EDITOUR PETplanet Insider Vol. 19 No. 09/19 petpla.net 24 How a leading converter in India is positioning itself on recycling Bottles, containers and closures for non-food applications March 2019 We met: Dr Surendra Agarwal, Founder Tour Sponsors: The Creative Plastic Group, which is based in Mumbai, looks back on 30 years of experience in plastic conversion. Since the launch of its first plant in 1986, the company has paid consistent attention to sustainable management as an essential part of its corporate philosophy. The founder and head of the packaging company, Dr Surendra Agarwal, provided us with a detailed explanation of the importance of dealing with waste and emotional attachment in everyday business. The Creative Plastic Group, one of the country’s leading plastics processing businesses, has 14 plants in India and employs around 1,000 people. The company is also scaling operations in global markets including the UK and UAE, with additional plants planned in other markets such as Indonesia, USA, Germany, South Africa, etc. It manufactures more than 3.65 billion containers a year, easily enough to be classified as a largescale producer in any market. The distribution of its production facilities across India enables it to deliver its strategy of serving its clientele quickly. Its conversion processes include injection moulding, injection blow moulding, extrusion blow moulding, injection stretch blow moulding, labelling and printing. In total, Creative Plastic operates between 300 and 400 machines; the set-up of the equipment is almost identical at all of the plants and includes suppliers like Husky Injection Molding Systems, Krauss Maffei and Ferromatic Milacron for injection moulding. “We are in the fortunate position of being able to partner with companies who share our mindset of creating and building long-term win-win relationships. We have been privileged to work with a select roster of global clients, many of whom we have worked with for upwards of 25 years.” explained Dr Agarwal. Over the years, the company has invested heavily in research and development. Its current customers include Unilever, Procter & Gamble, Marico and Johnson & Johnson. Of all the plastics processed, PET accounts for approximately 30% of the total volume, with the remaining 70% being equally divided between HDPE and PP. The materials come from Reliance or Dow, for example. Creative Plastic likes to keep its finer details private and rules out factory visits, with the company preferring to operate outside the media hype so as to protect its suppliers, customers and operational processes. Dr Agarwal says that the company takes human resources very seriously. “We very much consider our employees to be our company’s greatest asset,” he said. “Interpersonal relations here are informal; things have always been like that here, and they will stay that way.” The founder of the company isn’t able to hide his enthusiasm for the subject of packaging, and above all else, for sustainability. In conversation, it quickly becomes clear that he lives what he loves and vice versa. Dr Agarwal explained that under the protocol of the Carbon Disclosure Project (CDP), an NGO for the evaluation of corporate emissions, Creative achieved a score of 99% in the ecology category in 2017 and now “Leadership A”. Descriptions of ways to deal with post-consumer waste that he proactively initiated accounted for more than half the total time of his interview with us. He mulls things over a lot - Meeting Creative Plastic’s founder Surendra Agarwal (right)","@ID":26}, "52 TRADE SHOW PREVIEW PETplanet Insider Vol. 19 No. 09/19 petpla.net TRADE SHOWpreview K’ SHOW 2019 Plastic processing for a circular economy A science campus for discussions, new PET processing technology: What the trade fair and the exhibitors at K’ show 2019 will be presenting, part 1: From October 16-23, 2019 more than 3,000 exhibitors from 60 countries will be exhibiting in Düsseldorf. The K’ trade fair will occupy the entire Düsseldorf exhibition ground, and 200,000 trade visitors from all over the world are expected. The hot-topics are sustainable plastic development and circular economy. New supporting programme Plastics shape the Future: Podium for conscious use of resources The podium ‘Plastics shape the Future’ aims to provide solutions and answers to current social trends and discussions. Topics such as packaging waste, marine litter and climate change on the one hand and resource conservation, energy efficiency and recycling on the other are discussed in detail. ‘Plastics shape the Future’ not only aims to provide international information and networking platform, but also to increasingly integrate politics and socially relevant groups with keynote speeches and speed talks. The Science Campus: Expert discussion area about sustainability and recycling management The Science Campus of K’ 2019 stands for dialogue between science and industry, in which sustainability and recycling management are intensively examined. As a highlight, the joint appearance of the VDMA (Verband Deutscher Maschinen- und Anlagenbau - German Engineering Federation) and its member companies will also be dominated by the topic of circular economy. State of the art PET processing technology PETplanet Insider has picked out PET relevant exhibits from the entire value chain of PET processing. Of course, the companies introduced will be presenting a lot more of their production range. We wish you an interesting and successful K’ show 2019! See you in Düsseldorf! Smart compressed air Every part of a compressed air station, whether it is the compressors, compressed air treatment components or distribution system, should operate as efficiently as possible. These components are not individual players; they have to work as a team which is perfectly coordinated. Kaeser presents its Sigma Air Manager 4.0 (SAM 4.0) compressed air management system that performs this particular function. At the heart of the service package lies the Sigma Air Manager 4.0. Serving as the central intelligence core within the compressed air station, it assumes control duties and provides data-streaming to the Kaeser Plant Control Center. Process data are encrypted and transferred in real-time via a radio modem, ensuring reliable and efficient operation of the compressed air station throughout its whole life cycle. With the new Sesotec TG series, Kaeser extends its range of energy-saving refrigeration dryers to accommodate flow rates up to 98m³/min and offers a choice of air or water-cooling. This compact powerhouse ensures stable pressure dew points with maximum reliability and minimal life cycle costs, even under the toughest of operating conditions. www.kaeser.com Three precision high-tech injection moulds StackTeck Systems Ltd., a global manufacturer of multi-cavity, highvolume production moulds for packaging, pails, thin-wall packaging, closures, PET preforms, medical, and mould bases, will be showcasing three of its precision, high-tech moulds running in several booths of high-performance machinery manufacturers. These include: Small and large cavitation moulds for round and rectangular containers featuring ultra-light weight TRIM (Thin Recess Injection Moulding) panels. In-Mould Labelling technology for a round thin-wall lid. Static displays in the StackTeck booth will showcase the latest technologies in its booth with plastic parts and steel components. Some of these include: PET preform technologies, servo driven technology for different applications, coinjection, multi-material, specialty coating, KoolTrack, TRIM (Thin Recess Injection Moulding), IML and closure technologies. www.stackteck.com Hall 1 StackTeck Booth C29 Hall 11 Kaeser Booth G59","@ID":54}, "PETcontents 4 PETplanet Insider Vol. 20 No. 09/19 petpla.net 09/19 INSIDE TRACK 3 Editorial 4 Contents 6 News 61 Products 62 PET bottles for Beverage + Liquid Food 64 Patents THE INDIA ROAD SHOW 10 India - A place of limitless potential 18 Machines, moulds, preforms and containers from Mumbai - From magnetic tape manufacturer to PET all-rounder 20 High-end preform system - Turnkey from India 22 Doubling capacity; one third less cycle time 24 Bottles, containers and closures for non-food application BEVERAGE INGREDIENTS 26 Beverage trends in India - “Naturalness” added value and unique taste experiences MATERIALS / RECYCLING 28 PET - A review of material developments 39 Optimising with nanoparticles - Consistent preform wall thicknesses for large-volume containers 40 PEF and PET, side by side 42 Time to increase the rPET content 44 Reduce, reuse, recycle - refit! 46 Closed-loop recycling - rPlanet Earth sets up recycling plant in California MARKET SURVEY 35 Suppliers of filling equipment and inspection systems PREFORM PRODUCTION 48 Prepared for the future - Niigon PET preform machines OPEN HOUSE 51 Circular economy in action - PET bottle-to-bottle recycling, the focus of attention at Sipa Open House TRADE SHOW PREVIEW 52 K’ show 2019 - Plastic processing for a circular economy BUYER’S GUIDE 65 Get listed! Page 52 Page 36243610 Page 40 MATERIALS","@ID":6}, "8 NEWS PETplanet Insider Vol. 19 No. 09/19 petpla.net Suntory aims to use fully recycled or plant-based materials for all PET bottles by 2030 Suntory Group’s new company-wide policy focuses on implementing sustainable plastic that promote a recycling-oriented and decarbonised society. Based on this Plastic Policy, Suntory will aim for fully sustainable plastic bottles by expanding “FtoP production” capability and switching to recycled materials or plant-based materials for all PET bottles used globally by 2030. FtoP production, “FtoP Direct Recycle Technology”, has been introduced by Suntory last year. It is a first-of-its-kind PET preform manufacturing technology that streamlines the recycling process of making PET bottles out of used PET bottles which is useful in decreasing environmental impact while improving supply chain efficiencies. Suntory also is the first company to use plastic caps made of 100 percent plant-based materials for its beverage product and Suntory’s efforts go beyond for realising PET bottles made of 100 percent plant-based materials. Suntory will continue its effort for developing PET bottles with less environmental impact and for contributing to build an efficient recycling system. Through these initiatives, Suntory Beverage & Food Ltd, a beverage company of Suntory Group will increase usage of recycled content in its PET bottles to over 50 percent in Japan by 2025 as mid-term goal. www.suntory.com Giulio Mengoli is the new General Manager of Sacmi Group Since June 1st, Giulio Mengoli has been the new General Manager of the Sacmi Group. His appointment was made official by the Board of Directors of the parent company, Sacmi Imola. A native of Padua, 49 years old, Giulio Mengoli has a long international experience, having held top positions in France, the United States, Brazil, Sweden and Italy. With great international experience, Mengoli spent five years with General Electric and was 15 years at the top levels of Tetra Pak. The meeting with Sacmi came in November 2018 and for seven months Mengoli acted as General Manager of Sacmi Business Units, immediately working alongside the present management to define the governance and strategic planning of the Group. Giulio Mengoli takes over from Claudio Marani, who has led the Sacmi Ceramics Division since 2000 and has been the Group’s General Manager since 2016. In the medium term, in addition to the development of core sectors, Sacmi’s priorities include the issues of digital transformation and the circular economy, “to offer products and services that are increasingly customised and in line with the real needs of production and of the market”. www.sacmi.com Sidel acquires Comep On July 18, Sidel announced the acquisition of Cognac Moules Emballages Plastiques (Comep), a French producer and designer of moulds for PET, adding further strength to the group in the manufacturing of moulds and tooling. Comep was created in 1998 to focus on the design and manufacturing of moulds for PET bottles. Based in Sallesd’Angles, France, with more than 20 years of experience in this industry, Comep produces over 4,000 moulds per year for customers around the world. With around 60 employees, they were a first mover in the low blowing pressure technologies. Comep and Sidel state that they will remain set on their current focuses with a strong, adapted go-to-market strategy to leverage their respective capabilities, while offering a full set of packaging services to companies bottling their products in PET. Comep will represent a separate channel to market for moulds and tooling. This means that both companies will take distinct commercial approaches while sharing best practices and capitalising on efficiencies whenever possible. www.sidel.com","@ID":10}, "MATERIALS / RECYCLING PETplanet Insider Vol. 19 No. 09/19 petpla.net 29 PET bottle material – some highlights 1999-2019 as reported in PETplanet Insider 1999 When PETplanet was launched in 1999, PET prices were hitting the floor due to world-wide overcapacity, and the enthusiasm to invest in the business was damped. Manufacturing costs for small scale plants were just below the market price. In an article in our first issue we summarised the world-wide market situation. 2000 In issue 1 Wilson Color business of M. A. Hanna Company was serving the particular interest to make PET bottles looking like glass bottles with its FX range of frosted colours. The article also points out that - under some circumstances - a UV barrier or stabilisation function may be desired; this was why combined formulations were being developed. (Ed., in 2001 M.A. Hanna merged with Geon Corporation and formed PolyOne.) Eastman Chemicals has developed a number of different PET grades for specific purposes, including PET for beer bottles and PET for water bottles. The Eastapak Aqua range was designed specifically to meet the stringent standards of optical clarity and taste established by the major international water companies and regulatory bodies (issue 7). How to keep the taste of beer in PET bottles was a question answered by a resin from Darex. The Dareval oxygen barrier resin enables multi-layer PET bottles to have glass-like oxygen barrier capabilities (issue 12). 2001 In issue 8, Polyone gave an insight in the development work of its Technical Centre and the growing need for precise colour matching. At the Centre in Georgia, USA the company had more than thirty standard colours, effects and additives available for PET, as well as offering a bespoke colour matching service. 2002 The range of colours used for beverage bottles had, hitherto, in most cases remained fairly conservative and marketers have had stuck to tradition: amber for beer, blue for water. As PET continues to find applications in an ever-wider range of product sectors, colour additives offering almost unlimited options to the packaging designer, and protecting the contents of the container are accelerating. In issue 4, we were reporting on the Macrolex colour additives which were supplied in the form of micro-granules by Bayer. In issue 6+7 we discussed with M&G the uses of PET and how the end use application drives the resin attributes required. Different requirements for CSD, water, beer or juice were examined. Issue 8 took a look at some of the functional additives available from ColorMatrix Europe. Besides their range of acetaldehyde scavengers, UV absorbers or reheat performance additives, the company forecasted a barrier additive that should significantly improve the barrier performance of single layer PET bottles. 2003 Acetaldehyde can be a particular problem in water bottles, which is why PET resin producers such as Voridian were tackling it head on with specifically-tailored resins, as we reported in issue 1. The first step to reduce AA levels is choosing the right PET resins with an IV. The low IV minimises AA generation during melt-processing. The resins can be combined with an AA scavengers which react or combine with AA to ‘lock’ it into the polymer matrix so that it cannot migrate into the product. A new resin range developed by M&G, ActiTUF, contain barrier properties within the resin in the form of an oxygen-scavenging additive. As reported in issue 3, M&G believed that, by eliminating the risk involved in selecting a specific barrier technology, more brand owners could be encouraged to convert to PET. ColorMatrix tackled the wine market with a pallet of PET colourants familiar to the wine industry (issue 4). Having recognised the potential and the technical demands the company announced it was working on a range of additives for mono-layer PET packages, that would complement existing multilayer solutions. 2004 Using accelerated UV exposure testing in refrigerated UV chambers, Milliken scientists simulated retail store environments and explored the impact of UV light on beverages at various levels of light exposure and various levels of UV protection. These research studies have been instrumental in the development of ClearShield, a homogenous polymer additive that provides UV protection at the 390 level (issue 3). In issue 5, M&G’s International Marketing Manager, David Swift explained the differences in the needs of customers in specific regional markets. So the European market had not generally moved towards darker resins for faster reheat of preforms to speed bottle blowing operations, whereas the US market had placed less emphasis on grades that are specifically designed for still mineral water. At a press conference in September, Eastman Chemicals announced that they had developed a new way of making PET and will build their largest ever plant based on this technology. Named ‘Integ-Rex’, the new technology promised four times the space efficiency, lower energy requirements, and overall lower costs (issue 10). New brands and products introduced on the market in PET had heightened the need for product protection","@ID":31}, "EDITOUR 22 PETplanet Insider Vol. 19 No. 09/19 petpla.net Doubling capacity; one third less cycle time June 2019 We met: Kota Aoki, Director of Nissei ASB, Japan at ASB Thane Nissei ASB Machine Co., Ltd., together with its wholly owned subsidiary of ASB International in India, has introduced an innovative “Zero Cooling” process in which cycle time in single-stage machines can be significantly reduced, whilst at the same time improving preform geometry and with it, quality. The company has also invested in two new factories that have more than doubled its manufacturing capacity in Japan and India over the past 12 months with the result that up to 700 machines could now leave its plants every year. However, the focus of this increased capacity is mould making where the goal is to reduce delivery times and raise the number of moulds produced to 1,500 per annum. We spoke to Kota Aoki, Director of Nissei ASB, Japan at the company’s Indian plant. PETplanet: Mr Aoki. Can a twofold increase in capacity in just one year be seen as beneficial? How will you utilise this additional capacity? Mr Aoki: We have significantly increased our capacity both here and in Japan which is in response to the constant high demand for our single-stage machines. However, our emphasis is very much on mould making, which is an area where we want to improve delivery times and output. This, of course, will be driven by our new patented Zero Cooling technology. PETplanet: You reduce cycle time and at the same time improve bottle quality? Mr Aoki: Our main focus is on reducing the amount of cooling time in the injection moulding stage, hence the term “Zero Cooling”, enabling us to make thicker-walled preforms which ultimately results in better quality bottles. PETplanet: Your machines are principally used for pharma, household, liquor and wide-mouthed bottles. Everything that is, apart from beverages. Do you want to use this new technology in the drinks sector? Mr Aoki: Our machines definitely have some beverage applications and I see some opportunity with the new technology in the drinks sector in the future. However, our current efforts for now will concentrate on the non-beverage areas you have already mentioned. Here, we also see great opportunities in moving from glass and PP to PET. Mould & process engineering will be our primary focus in the coming years. PETplanet: And where would you want to sell your additional machine output? Mr Aoki: It is noticeable that a lot of companies here which previously have only operated in India using our machines are now on the lookout for lucrative markets outside of the subcontinent, particularly in Africa, using proven technology from us of course. Many Indian firms have expanded overseas and established production facilities in the USA and elsewhere. Our machines are also used there. PETplanet: In India, there is an anti-dumping tax on preform machines (injection-moulding) coming from China. Does this also apply to single-stage systems which also produce preforms? Mr Aoki: No. This affects facilities that only produce preforms. However, I do not see any real competition here either. I have just come from Chinaplas where I saw exact replicas of our machines. These are purely mechanical duplicates - our cycle times and bottle quality cannot be achieved using replicas. Our mould making & processing expertise gives us a major advantage in this respect. PETplanet: Which completes the circle again. Thank you Mr Aoki for sparing the time for this interview. www.nisseiasb.co.jp/en Tour Sponsors:","@ID":24}, "MATERIALS / RECYCLING PETplanet Insider Vol. 19 No. 09/19 petpla.net 47 recycling experts in Germany to the local people in the US and even the directors. We’ve gotten to know the Krones family very well and we consider them friends.” Krones served as one of the general contractors, integrating the front end for sorting and shredding the post-consumer PET containers, its own cleaning and decontamination modules, and all pneumatic material conveyance. The line processes approximately 6,600 pounds of PET per hour. “Before we decided on Krones, we looked at some projects around the world that were already using Krones equipment. We were quite impressed by how mechanically sound the equipment was and how little manual labour was involved,” says Ross. Daviduk adds: “We believe that Krones offered the most comprehensive and the best recycling system in the world. And we fully expect Krones to live up to that.” Bob Daviduk (l.) and Joe Ross, the two founders of rPlanet Earth Krones as one of the general contractors Of course, a plant of this size needs a lot of space. rPlanet Earth found that space in Vernon, California, about five miles southeast of Downtown Los Angeles. Vernon is an industrial city with its own power company, which provides competitively priced electricity. The facility sits on a 657,000 square-foot property (about 15 acres) that houses a logistics yard for truck traffic, a covered collection area for PET plastic bale receiving and storage, and the 302,000 squarefoot plant at the heart of it all. The plant itself consists of three different sections: In the front end, the feedstock is debaled and sorted using multiple technologies. When the sorting is complete and only PET plastic containers remain, they are then shredded. The resulting flake enters a MetaPure W wash line, which removes any remaining contaminants and foreign matter and cleans the flakes in several stages. Another sorter at the end of the wash line ensures that only PET flakes move on to the next processing stage. In the MetaPure S decontamination reactor, the flake is heated to around 390 degrees Fahrenheit (200 degrees Celsius) – depending on the target application – under a vacuum. Flake that has passed through this step is safe and approved for direct food contact packaging. The rPET flake continues right on to one of the plant’s plastics processing lines, where it is converted into preforms or extruded sheet. The latter is also used as the basis for producing thermoformed containers downstream. This closed loop is both extremely compact and highly complex and is ultimately what sets rPlanet Earth apart. “The setup was important for us for a couple of reasons. One is because, as far as we know, it gives us the lowest carbon footprint for packaging worldwide,” explains Bob Daviduk. “Another is that it just made sense for us to have everything under a single roof because it’s a more efficient process. At rPlanet Earth, our goal is to have the lightest possible impact on the environment, on our planet Earth.” Skipping the pellets The PET material recycled in rPlanet Earth’s new plant goes directly into the production of preforms, sheet, and thermoformed containers. The decision to produce precisely these three products was based on logical criteria: the primary use for recycled PET is bottle production. In the US alone, the market for PET beverage and food bottle production is some 6 billion pounds a year. For that reason, preforms make up around 35 per cent of the rPlanet Earth plant’s output. Thermoformed containers make up around 50 percent. Sheet extrusion makes up about 15 per cent of the product mix. rPlanet Earth can produce all three packaging types with up to 100 per cent recycled content, depending on customer specifications. www.krones.com Float-sink tank in the washing module MetaPure W","@ID":49}, "53 TRADE SHOW PREVIEW PETplanet Insider Vol. 19 No. 09/19 petpla.net New filtration and extrusion technology Gneuss Filtration Technology will be exhibiting different models of the patented Rotary Filtration Systems. These continuous filtration systems are characterised by a filter disk on which the screen cavities are located in a ring pattern. Screens can be changed on the part of the filter disk that is not active in the melt channel, while the production process continues to run without interruptions or disturbances. The new model SFneos offers a constant pressure during screen changes. It is suitable for most types of polymers and viscosities and it has a compact design thanks to an enlarged active screen area (up to 2,370cm2). The SFneos is a filtration system for applications that benefit from a continuous, pressure and process constant screen changer, but that do not require back-flushing. The SFneos 90 on display has an active screen area of 260 cm2. Gneuss’ top model, the RSFgenius, operates with an integrated self-cleaning. Screens can be automatically re-used up to 400 times and filtration finenesses below 10 microns/1,200 mesh are available. There will be different sizes on display. Gneuss will show a Processing Unit (GPU) including a second generation Multi Rotation System MRS110 extruder, a fully automatic melt filtration system RSFgenius 90 and a new style online viscometer VIS, for the processing of 600 kg/h of undried and uncrystallised polyester (PET). At the K show the second-generation design will be on display. The enhanced drive design is more robust to handle even more demanding recycling environments. Thanks to several changes in the MRS drum and screw design the IV retention has been further improved, while continuing to eliminate pre-drying. The MRS extruder permits the processing of PET without pre-drying by using a water ring vacuum system to process the material directly to high quality end products such as packaging sheet, strapping tape or filaments. This is achieved by its patented processing section. Based on a conventional single screw extruder, the Multi Rotation Section is a drum containing eight satellite single screws, driven by a ring gear and pinion transmission. The “barrels” cut into the drum are approximately 30% open and provide high exposure of the melt Thanks to this design, the devolatilising performance is about fifty times greater than that of a conventional vented single screw extruder – with a vacuum of 25 to 40mbar. While other dryerless technologies are promoting partial pre-drying, the MRS extruder can process rPET with up to 1% moisture content. By avoiding the need for a deep vacuum system and pre-drying, the MRS is an economically efficient alternative. Further arguments in its favour besides energy savings are the simple and rugged design, small footprint, its ease of operation and low maintenance, processing flexibility and its melt quality and homogeneity. A Letter of Non Objection (LNO) from the FDA, EFSA conformity and several local approvals in Latin America confirm the decontamination efficiency of this technology. www.gneuss.com Hall 9 Gneuss Booth A38","@ID":55}, "EDITOUR PETplanet Insider Vol. 19 No. 09/19 petpla.net 11 potential Indian customers, it usually requires a longer familiarity phase – a personal getting-to-know-each-other phase, whose outcome is decided over time and by one’s gut feeling. Then there is, regrettably, a complex administrative bureaucracy, which regularly tests the patience of both companies and their employees, and includes an uncertain outcome. As a former expat for our part-time local PETplanet representation in India, I know what I’m talking about. To counteract this, almost all foreign companies that are active in India also rely on local agents so as to be closer to the people, markets and authorities from the cultural perspective, and to thus reduce the communication difficulties to the minimum – and not just those of a linguistic nature. Showing interest, regular conversation and the willingness to allow time for all these prerequisites, are key. Hurdles of the India Road Show In the India Road Show, we have embarked on our most challenging tour to date. The progress so far is both highly informative and promising but it is also a genuine challenge, in terms of the on-the-ground implementation. When we were told long before the start of our tour that the Indian parliamentary elections would be taking place in the year of the tour we did not, admittedly, quite realise the extent to which this would be relevant to the tour. We know now. Every time one enters a new state there is a lot of bureaucracy, the design of the vehicle has to be approved all the time (even our lettering in national colours has resulted in long discussions), and one finds oneself being checked almost daily by the police. This inevitably leads to many a delay to the schedule. Our editor, Michael Maruschke, who was responsible for the north-east and the north on the tour, was obliged to switch to transport by bus, train and taxi for a short time, because the local authorities prevented the Editourmobil from being driven through their area. This year has seen incredible heat and drought, which affects not only us editors but also large sections of the population and which, here and there, is causing the public supply of drinking water to collapse. Water reservoirs dry out at temperatures close to the 50 degree Celsius mark; the groundwater level sinks and, in many places, mobile drinking water tankers have to supply the people with rationed water. Measurements taken in the Editourmobil show that, depending on the region, the temperature inside the vehicle has consistently hovered between 40 and 50 degrees Celsius, despite the air conditioning system! This has sometimes forced our editors to stay in hotels and guest-houses for the night. Altogether, this year’s tour is certain to lead the field of the most difficult overland editorial journeys undertaken by PETplanet. Macro-economic data India 2016 2017 2018 Population (billions) 1.3 1.32 1.33 Population growth p.a. 1.3% 1.3% 1.3% GDP (current prices, billions) US$ 2.29 US$ 2.65 US$ 2.72 GDP growth rate (real) 8.2% 7.2% 7.1% GDP per capita (current prices) US$ 1,762 US$ 2,014 US$ 2,036 Import (billions) US$ 361,2 US$ 443.0 US$ 513.3 Export (billions) US$ 264,1 US$ 296.2 US$ 320.1 National debt of GDP 69.0% 69.8% 69.8% Unemployment rate 2.7% 2.6% 2.6% Inflation 4.5% 3.6% 3.5% India’s Economy & Infrastructure With just under 3.3 million km2, India is the seventh-largest country in the world. With its particular location, nestling between the Himalayan region and largely surrounded by water, much of India enjoys a subtropical-continental climate all year round; the high regions in the north and certain coastal regions are the obvious exceptions. The south experiences pretty high temperatures year round, without pronounced fluctuation; by contrast, the northern part of the country can see temperatures range from 10 degrees Celsius in the winter up to 50 in the summer. When the monsoon arrives, between the middle of the year and autumn, there is, depending on the region, abundant rainfall. It regularly leads to flooding and causes densely populated areas and cities, in particular, to become submerged in water, as occurred last year in the metropolis of Mumbai. The country is divided into 29 federal states and seven union territories. The capital and the seat of government is the city of New Delhi in the north. It is part of the Capital Territory of Delhi, which is divided into nine districts; the conurbation’s total population is over 16 million, just behind the business centre of Mumbai.","@ID":13}, "MATERIALS / RECYCLING PETplanet Insider Vol. 19 No. 09/19 petpla.net 40 PEF and PET, side by side Polyethylene 2,5-furandicarboxylate (PEF) is a novel polymer with a chemical structure that highly resembles PET. It is produced by polycondensation of FDCA (2,5-furandicarboxylic acid) and MEG (mono-ethylene glycol) monomers, analogous to the polycondensation of raw materials used to produce PET. The PEF polymer itself has been known for a long time but has never been produced at large scale or applied commercially, as there were no economically viable production routes to manufacture FDCA. Avantium (and other companies) are working on new methods of producing FDCA that will enable PEF to become a widely used polymer in the future. Basic properties The Furan ring in this polymer introduces a ‘kink’ into the polymer chains that makes them less mobile than the straighter chains of PET, affecting its properties significantly. The dipole in the ring introduces attraction forces between the molecules, further reducing mobility. Some of the resulting effects are a higher glass transition temperature and higher modulus, relative to PET, and a higher barrier against gases, which makes PEF very interesting for packaging applications. Property1 2 3 PET (amorphous ) PEF (amorphous) Molecule Density 1.36 g/cm3 1.43 g/cm3 Tm 250-270 °C 210-230 °C Tg ~76 °C ~88 °C E-modulus 2.1-2.2GPa 3.1-3.3GPa Yield strength 50-60MPa 90-100MPa O 2 permeability 4.7–7.4 cc*mm/(m2*24h*bar) 0.4–0.7 cc*mm/(m2*24h*bar) CO 2 permeability 20–30 cc*mm/(m2*24h*bar) 1–3 cc*mm/(m2*24h*bar) Many, if not all, the relevant manufacturing processes under development aim at using plant-based resources (e.g. fructose) as a feedstock. When plant-based MEG is used with FDCA, PEF is a fully bio-based polymer and thus a good candidate for the bio-based economy. In many regions around the globe, recyclability of everyday materials is of prime interest and industry and government organisations are setting high recycling targets. By 2030 the EU requires all beverage bottles to contain at least 30% recycled material. High quality PET waste is essential to achieve those recycling targets but is notoriously difficult to obtain. One of the main challenges is that most polymers used in combination with PET hamper its recyclability. In a multilayer bottle that uses polyamide (PA) as a barrier layer, the PA disturbs the output of a mechanical recycling process and induces haze in the rPET. Less than 2% of PA in a PET waste stream can cause enough haze to render rPET unusable; a higher percentage of bottles with a 5% PA barrier layer is considered unrecyclable in mechanical bottle to bottle recycling processes. PEF is chemically so similar to PET that it blends well during the recycling process, forming a copolymer and thus causing very little disturbance in the resulting rPET; a PET/PEF mixture will stay almost completely transparent with up to 5% PEF. This makes it highly suitable for combinations with PET and, as a polyester, it can itself be recycled by the same technology used for PET. MATERIALS","@ID":42}, "EDITOUR PETplanet Insider Vol. 19 No. 09/19 petpla.net 10 INDIA – A place of limitless potential by Kay Barton Starting at the beginning When one thinks about India or talks about the country, there seems to be neither a beginning nor an end. From a global perspective, this multi-ethnic and multi-religious state is undoubtedly the greatest degree of adventure, mystery and chaos brought together in an almost unbelievable nation – from every respect. As a confirmed fan of India and after several stays in various regions on the subcontinent, only one thing seems to repeat itself: a subjective strategy of integration and allowing things to happen, which can develop on the basis of experience, understanding and confrontation with the country and its people – or, indeed, not. After all, it isn’t without reason that one hears time and again that India divides opinions all over the world. “Either you love it or you don’t” is a typical quote which almost everyone has probably heard before. I can say quite clearly that I belong to those who love it. India has become a kind of second home for me. I have worked here, lived here and made friendships here that have lasted for many years. I never suffered from the much-quoted “culture shock” but, during my initial visits, I did experience difficulties with the local customs and impressions of chaos to which I wasn’t yet accustomed. Today and every time I return to this country, I see again and again what is possible, how this great nation with its 1.3 billion people is developing and the opportunities that are emerging in it, especially at the global level. Emotionality and, of course, spirituality are omnipresent here. This is certainly a major difference from western countries, where people’s business and personal lives overlap as little as possible. In India, in one’s personal life and in everyday business life, culture dictates that it is the subjective feeling that is the decisive building block for the success or failure of a business relationship. Many of our readers who know India, who work and do business there or have local representative offices there, know that almost nothing works without that typically Indian gut feeling. If, for instance, the European plant- and equipment supplier interacts with","@ID":12}, "EDITOUR PETplanet Insider Vol. 19 No. 09/19 petpla.net 17 Environment, sustainability and recycling The use of rPET is expected to grow by around 20%. Sufficient quantities of post-consumer PET bottles are available and, although large parts of the country have no infrastructure whatsoever for the disposal, let alone separation of waste, some functional methods for further use have developed over time. The majority of plastic waste currently ends up unsorted in unregulated landfill sites, discarded in the open country, by the roadside or individually incinerated. Some discarded waste is collected by self-organised collectors, mostly from the lower social classes, before being taken to collection centres for a small amount of money per kilo. The bottles are sorted there and can be added to the recycling stream. For the collectors this is often their only regular source of income. A proportion of PET bottles is reused for private purposes. Families use them again and again for their own needs by, for example, refilling them with water or tea. Another popular pursuit is for the PET bottles to be filled with petrol before being sold by the roadside or simply emptied into the fuel tank of a motorised two-wheeler and refilled again – a behaviour frequently encountered in Asia, which increases the availability of fuel. While recycling for plastic waste generally is abysmal, that for PET is, by contrast, exceptionally high, at over 85% and therefore leaves quite a few regions in the world far behind. “Producers should take responsibility for collecting and recycling as per EPR laws”, said Mrs Wilma Rodrigues, Founder & CEO of Saahas Zero Waste, a waste management firm from Bangalore. “PET in India has a formal recycling backend compared to other streams of waste. The economic value is low for other streams of plastic, such as PS and PP, on account of which they most often are dumped or burned. The end destinations and recyclers for other plastics are also far less developed and mostly informal, compared with PET.” Mrs Rodrigues added that a study undertaken by the Federation of Indian Chambers of Commerce and Industry said that the plastic processing industry is forecast to grow to 22million tonnes a year by 2020, from 13.4 tonnes in 2015. Nearly half of this growth is in single-use plastic. What does not yet exist is a local bottle-to-bottle system, which means that the PET flakes used for manufacture by the recycling companies are not recycled into food or beverage packaging, but primarily “downcycled” into the textiles sector. The self-administration by the collectors also affects other recyclable materials. The proportion of waste that is not sent for recycling cannot be ignored, however. A single glance at the landfill sites, littered rivers or even backyards in conurbations is enough. The government is attempting to counter this situation with the support of numerous associations and NGOs. The objective is to achieve a sea change in the attitude of the general public towards the correct handling of waste. The major players in the beverage and plastics processing industry, whose products find their way onto the market in large quantities, have been taking an increasing degree of responsibility, conveying important knowledge about the value of used plastic packaging and the reasons why discarding waste is bad for the environment. A public awareness campaign of this kind is currently being implemented by preform giant Manjushree Technopack. The company, which processes some 110,000 tonnes of material in India per year with a PET share of 82%, is currently building its “Reuseum”, a 1,800m2 complex that includes an education contract, directly adjacent to its plant in Bidadi, Bangalore. The project, which is to be completed at the end of the year and which has also had input from Coca-Cola, aims to serve as a universal information platform for all types of recycling, to be accessible to all, and to convey the topic of handling and value creation on an holistic basis with exhibitions, workshops, lectures, etc. Sources: German Ministry of Foreign Affairs, IMF (International Monetary Fund), Market Research Company Euromonitor International, Netscribes, Nielsen, Reliance Industries Limited, Sahaas Zero Waste, Statista, WKO (Austrian Economic Chambers), World Bank","@ID":19}, "MATERIALS / RECYCLING PETplanet Insider Vol. 19 No. 09/19 petpla.net 30 and longer shelf life. Container manufacturers were constantly required to create innovative packaging with diversified colours and new properties, in support of this huge market expansion. In support of this, Clariant Italia developed a colourful new range of masterbatches (issue 10). 2005 In issue 1+2 M&G reported that they were building the world’s biggest virgin PET plant with an output of 450,000 t/a in Brazil. Strong opaque colours for PET were growing in popularity. Holland Colours was comparing the pros and cons of liquid colours and solids in the same issue. One of the biggest brewing and bottling plants in Russia and Europe has extended the shelf-life of a popular beer by six months. To achieve this, they were using Amosorb, a polyester based active oxygen scavenger by ColorMatrix. The first PLA bottles popped up in issue 5. The Nature Works article on the PLA material appeared in issue 6+7. Clariant Italia compared the UV transmittance of PET bottles with a wall thickness of 300 μ with and without UV absorbers or amber shade in issue 9. In issue 11, Zimmer presented the latest generation of PET solid state polycondensation equipment. Döhler commented on the challenges of filling dairy products in PET. They define oxygen-free bottling as of major significance (issue 12). 2006 At K 2004, Croda was launching IncroMax PET 100. In issue 2 the company showed a friction reduction of up to 60% when using the product,without affecting the physical properties or colour of the polymer. Every new application brings a new challenge. In the case of beer for the Russian market, ColorMatrix has been asked for a new generation of liquid colourants with the ability to remain stable if subjected to ambient winter temperatures of -40 °C (issue 3). In issue 4 Holland Colours showed how adding colour to PET that already contains an oxygen scavenger compound can have the undesirable effect of partially or totally destroying the action of the oxygen scavenger. Holland Colours developed a special high gloss white colourant for use on monolayer PET UHT milk packaging, named Holcomer (issue 9) 2007 Issue 3 and 4 featured a presentation on PET catalysts, including non-antimony alternatives. A major hurdle was that a new catalyst must have an activity comparable to that of antimony, both in the melt phase and also in the SSP. Possible NACs (nonantimony catalysts) are based on titanium, magnesium, silica or aluminium. We were identifying milk as the emerging market for PET in issue 3. ColorMatrix explained why white alone might not be the right option for PET packaging in this sector. According to their explanation, it is impossible to obtain a complete light barrier with white only. The suggestion: A multilayer bottle with a black light absorbing layer in the middle. In issue 11, PETplanet reported that DAK Americas has completed work on its Cape Fear site near Wilmington, USA, adding 204,000 t of PET resin capacity. The plant uses MeltTek, Uhde Inventa-Fischer’s process, eliminating solid stating. The process allows the addition of various amounts of copolymers, to develop resins with improved properties. 2008 We were presenting solutions for sensitive beverages in issue 3. Colormatrix pointed out how additive blends can be tailored for convenient handling and ease of dosing. In an interview with PETplanet, Neo Group’s Managing Director Linas Bulzgys reported on how 2007 was very difficult for everyone involved in the European PET industry, caused by a significant over-production and bad weather conditions (issue 4). 2009 In issue 2+3 we reported that the price of virgin PET had steadied again after a dramatic fall. At PETpoint, ColorMatrix was launching Amosorb SolO2, designed to ensure extended product protection and longer shelf-life in oxygen-sensitive beverages. It is claimed to delay CO 2 egress by up to 30 days and protect from O 2 ingress for up to four months longer than PET with standard Amosorb. Rieter Automatic and Buhler developed a combi-crystal-PET (CCPET) process which uses direct crystallisation to deliver dust-free, stable PET and crystallisable polyester. It combines pelletising, drying and crystallisation into a single process (issue 12). 2010 A new masterbatch additive for UV protection launched by Ampacet was claimed not to cause discolouration. CrystalClear achieves a clear nonyellow package with protection up to 380 nm (issue 7+8). In the same issue we reported on the launch of Atmer 7510, a slip concentrate by Croda Polymer Additives. It should reduce surface friction by up to 60% without an adverse effect on PET.","@ID":32}, "56 TRADE SHOW PREVIEW PETplanet Insider Vol. 19 No. 09/19 petpla.net German Technology Oct 16-23, 2019 Hall 1, Booth C42 Entering the single-stage market with new Beauty Series machines FlexBlow has been producing most flexible two-stage stretch blow moulding machines since 1994. To celebrate its 25th anniversary, FlexBlow is launching a special Beauty Series – a bespoke two-stage response to changing industry needs. On top of zero-scratch philosophy, the cosmetic market requires an increasing variety of container shapes, colours and necks - in ever decreasing batch sizes. FlexBlow has developed an integrated solution, which enables complete changeover from oval narrow neck cosmetic bottles to shallow wide-mouth jars within 30 minutes. Cosmetic jars: FlexBlow’s pick-and-place solution allows in feeding of any wide-mouth preform, including shallow shapes, and direct integration with parallel injection system, all-to minimise scratches on the preforms. Because in cosmetics elegance is everything, the Beauty Series machine comes in aesthetic white colour and premium exterior design. www.flexblow.com Hall 1 FlexBlow Booth A09 Versatile cleaning application Cold Jet, specialised in dry ice technology, will be presenting its new PCS 60. The PCS 60 features Cold Jet’s patented Particle Control System (PCS). The PCS precisely cuts dry ice into diamond shaped particles in the exact dimensions chosen by the operator (3mm to 0.3mm and 28 sizes in between). This allows the user to have versatility options in their cleaning applications. With the PCS, a plastics processor can use one machine to clean many types of surfaces, such as the surface of injection moulds, deburring and deflashing, to cleaning injection screws. With a 7” LCD colour screen and digital controls, the PCS 60 provides an intuitive display that allows the user to easily view and adjust blasting parameters and machine settings. The machine features programmable and password-protected application recipes. This feature allows users to set and save blasting parameters, such as blast pressure, particle size and feed rate, which increases efficiency and ensures the right settings for each individual application. A plastics processor can save one application recipe for one of their moulds and another application recipe for a separate mould. This prevents user error and ensures the right parameters are used for each unique application. The optimised design, including a “straight through” air system and redesigned SureFlow feeding system, minimises air pressure loss and dry ice sublimation within the machine. This allows the user to maximise air supply yield and reduce dry ice waste. The PCS 60 is IoT enabled via Cold Jet’s Industry 4.0 solution, Cold Jet Connect. The system provides remote monitoring and diagnostics while allowing users to collect and manage data and employ tools for optimum performance and productivity. www.coldjet.com Hall 10 Cold Jet Booth D48","@ID":58}, "EDITOUR PETplanet Insider Vol. 19 No. 09/19 petpla.net 14 plus growing health awareness. PET packaging’s biggest market in terms of penetration is in one-litre bottles, with around 42% market share in 2018, followed by 0.5 and 0.25 litre bottles. The consumer swears by still water. Carbonated water is a long way behind and has only a niche presence. The major bottled water brands operating in India are Bisleri, Kinley (Coca-Cola) and Aquafina (PepsiCo). With an estimated market share of around 60% in the branded category (according to their own figures), water giant Bisleri is clearly in the lead and is well-positioned nationwide with a total of 51 bottling companies. The extent to which the Indians have integrated Bisleri into their daily lives is demonstrated by the fact that well over 90% of Indians have heard of the company; “Bisleri” is often used as a synonym for water in restaurants and shops, regardless of where you are in the country. The brand is one of the products that is genuinely available everywhere. Apart from Bisleri, CocaCola and Pepsi the rest of the water market is accounted for lower sales volumes from big brands (e.g. UB Group, Danone, IRCTC or Tata Beverages), or smaller, local brands. Until a few years ago, the wellknown soft drinks from the multinational brands hardly made a profit, according to industry figures. Sales in these areas are now increasing strongly, due both to growing personal income and to ‘fashion’ - and Coca-Cola leads in all of them. A strong characteristic of the Indian market is the strong focus on local tastes and market preferences, even by the multinational major players like Coca-Cola and Pepsi, who are prepared to adjust their product portfolio and recipes to suit established regional and even state-based consumer tastes, demands and preferences. The conurbations in which the majority of the population with disposable income lives, are catering for a gradual turnaround in the rates of beverage consumption. In addition to regular soft drinks and water, and driven by a growing awareness for health and well-being, beverages with functional additives and juices are now widely available as well. With the request made by the government in the year 2014 for the inclusion of a fruit content of at least 5% from local fruit farmers in the production of bevtion remains widespread, although efforts are under way to bring this to an end, if the government is to be believed. The energy supply and its network are frequently unable to cope with the soaring demand, leading to frequent power cuts. The road network, especially in the cities, is completely overloaded and often in a terrible state. Just half of the road network is asphalted. Metro systems, such as those in Delhi, Mumbai or Bangalore, only relieve the traffic situation to a limited extent. On the other hand, India is highly technologically developed, especially in terms of communications networks and, according to the CIA World Factbook, ranked second behind China in 2016, with 89 mobile phones per 100 inhabitants. The market for beverages, milk and cooking oil Over 5,500 different water brands demonstrate that India is clearly a Mecca for water. In West Bengal alone, in the region surrounding Calcutta, there are some 1,500 bottlers; there are over 1,000 water brands in Tamil Nadu. According to a report by market research company Netscribes, the bottled water market in India could reach US$5.6 billion by the end of 2023, from a current value of US$2.2 billion. This equates to annual growth of more than 20%; volume is also forecast to grow, by more than 18%, to nearly 35.53 billion litres in 2023. Reasons for a steady growth are often a lack of clean drinking water,","@ID":16}, "MATERIALS / RECYCLING PETplanet Insider Vol. 19 No. 09/19 petpla.net 34 Holland Colours featured its LightGuard series of UV and light absorbers, providing specific protection from 370-400 nm in the UV range, and from 400-700 nm for light-sensitive products. If only UV protection was required, this can be combined with any colour. Achieving the delicate balance of costs-in-use without sacrificing final product integrity while keeping aesthetics and packaging communication for consumers is a topic Sukano addressed in issue 12. In the same issue, EnerPlastics, UAE, introduced its range of additive masterbatches. Blocking UV light from 300-370 nm, their UV barrier masterbatch is claimed to maintain a very high clarity. 2017 We visited Ester Industries in Gurgaon, India for issue 1+2. The heat-resistant PET which can be produced using conventional ISBM or EBM manufacturing processes can be filled with products at temperatures up to 90 °C, facilitating extended product shelf life. In the field of rPET, yellowing is a blemish to be avoided. In our issue 5/2017, Repi presented a solution in additive form, namely its Anti Yellow liquid additive family with which a yellow or grey shade can be eliminated. (see photo next column on the top) Also in issue 5/2017, three new grades to cover barrier needs were presented by M&G Chemicals, from a very strong CO 2 /O 2 barrier for brewers and juice producers over a medium O 2 barrier mainly for vitamin-enhanced waters to a strong CO 2 barrier for CSD and sparkling water. Outside of the box: Ooho is not made from PET but from sea-weed. The edible package from the British start-up company Skipping Rocks Lab is the result of aiming to create a packaging with low environmental impact (issue 5). At Interpack 2017, Milliken Chemical demonstrated how its ClearShield colourless UV absorbers are protecting UV-sensitive contents from degradation while maintaining the packaging’s clarity and transparency (issue 6). During our South East Asia Roadshow, we visited Indorama Ventures in Thailand, as reported in issue 11+12. Their global PET market share to this date was 20%. 2018 Uhde Inventa Fischer featured its optimised FTR (Flakes to Resin) technology at Chinaplas. This fully integrated process of PCR PET directly onto polymerisation of virgin like rPET resin material is claimed to allow the replacement of up to 50% of raw material without affecting food approvals from FDA and EFSA for the final product (issue 4). In issue 5, Repi reported on progresses in liquid technology of colours and additives where bright shades can be combined with UV protection, blowing additives, IV enhancer and more. Consent Plastic, based in Dubai, UAE, produces its own flakes out of collected bottles to manufacture polyester strapping types with a high tensile strength (issue 6). A Gneuss MRS extruder helped to reduce the line’s footprint by 12% and the energy requirement by up to 25%, compared with a previous production line including an extruder, crystallisation and drying processing line. At NPE 2018 Penn Color’s Penneffex design team, in association with Husky Injection Molding Systems and PET Engineering, demonstrated a range of new colour and finish effects (issue 7+8). The special effects pigments designed a proprietary special effect compound to be used in the mid-layer of a multi-layer bottle such as thermochromic, phosphorescent or bicolour effects.","@ID":36},
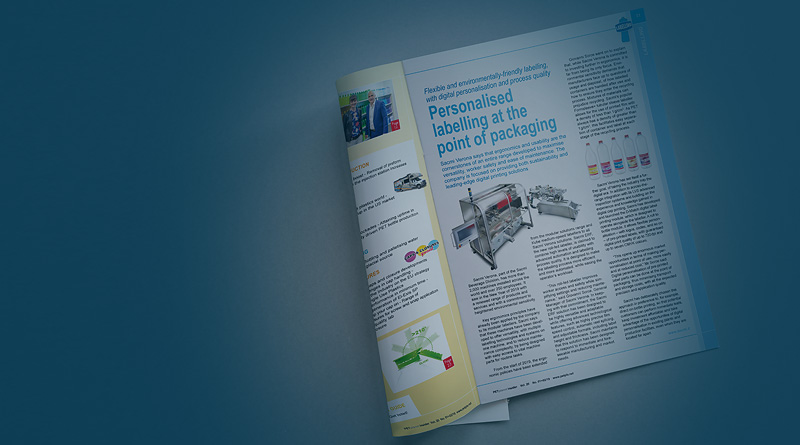