"MATERIALS / RECYCLING PETplanet Insider Vol. 21 No. 07+08/20 petpla.net 27 out. However, the performance is still comparable against films made from UV masterbatch, checked by various parameters such as tensile strength, transmittance and optical properties. The competition between PET resin producers and masterbatch producers in processing will be interesting, states Chitec. Chiguard as a powder form used during PET processing is claimed not to affect IV or other mechanical properties. Some liquid UV absorbers are considered quite difficult to handle when a biaxial extension is applied for the production of film. In a recent study, 200um PET films were produced aiming for a 400nm sharp cut-off. Transmittance at 390nm, 400nm and 410nm was monitored initially and then after 500hr Xenon Arc lamps exposure. Transmittance (%) PET without UV absorber With 1.5% Chiguard 0hr 500hrs 0hr 500hrs at 390nm 77.1 39.4 0.1 0.2 at 400nm 77.6 67.5 0.1 3.6 at 410nm 78.1 72.0 3.1 28.8 With a 1.5% dosage of Chiguard, a complete UV blocking effect is claimed to be easily achievable and performance is maintained after 500hrs QSUN keeping transmittance at less than 10% at 400nm. Optical properties with Chiguard addition are also maintained as shown below: L a* b* Blank PET 92.82 0.05 0.56 With Chiguard 92.76 2.28 4.93 It is also possible to combine other UV absorbers to reach moderate UV coverage for various end usages. Synergy between two benzotriazole compounds was reported in US patent number US2006/0083940A1. The studies demonstrated that UV coverage using a combination of benzotriazole (UV-234 and UV-326) was much better than using each separately either in the same layer or in a multiple film structure. It still allowed a 12% transmission at 390nm by combining two UV absorbers, for the thermoplastic films with 66um thickness and 1.2% total dosage. Chitec Technology would like to find more potential applications developed with this new Chiguard product which other UV absorbers are not always able to achieve. For instance, it is possible to make one thin PET film to greatly reduce the harmful blue light from LCD screens, thus improving the reading experience. Safety of use is the first consideration in considering the potential for food packaging and cyanoacrylate compounds are not new faces in PET industries. A preliminary study of potential migration of Chiguard from PET film was conducted with a 1,400 ppm dosage. Chitec states that they were unsurprised to find no detectable (ND) results, and they did not see any trace of Chiguard in simulants applied for extraction under 60°C over a period of ten days. The results are given in the table below: Blank Chiguard in simulant 10% ethanol ND ND 3% acetic acid ND ND Vegetable oil ND ND More studies are to be undertaken after these promising results so as to comply with food packaging regulatory requirements in the near future, states the company. Another example is given in a 80um PET film with a 2% dosage of Chiguard, exposing the bottles of various colours to sun light for 48hrs. Yellow, orange, red and blue diluents are made by crocin dyes, natural colours easily degraded by UV. The glass bottles under the sun on the right show significant colour fade. The bottles on the left covered by the UV blocked PET, show great colour stability in comparison, especially for yellow and orange. Glass and PET bottles of different colour shades and their degradation by UV (glass on the right, PET on the left of each colour) The studies are supported by the Industrial Technology Research Institute in Taiwan with a team experience in handling PET resins, twin screw extruder and film making equipment. www.chitec.com","@ID":29}, "9 NEWS PETplanet Insider Vol. 21 No. 07+08/20 petpla.net South African plastic industry announces positive PET recycling rate Despite global market contractions, and now the rolling economic impact of Covid-19, South Africa’s PET plastic recycling value chain has kept its wheels turning, delivering another positive annual recycling rate while creating thousands of jobs for informal reclaimers who returned to work under level three of the national lockdown. According to new statistics released by the PET Recycling Company (Petco), which is the producer responsibility organisation for the sector, 62% of all PET beverage bottles placed on the market in 2019 have been recycled – a trend which is in line with global PET recycling rates. This amounts to 95,879 t of postconsumer PET bottles collected, which would otherwise have occupied 594,448 cubic metres of landfill space and produced 144,000 t of carbon emissions. Aside from these environmental benefits, PET recycling also generated 65,900 income-earning opportunities among informal reclaimers and SMMEs, with R1.1 billion injected into the downstream economy via the manufacturing, distribution and sale of products made from recycled PET (rPET). Petco chief executive officer Cheri Scholtz said while the overall 2% yearon-year decrease in volume was disappointing, it was as good as could be expected, given the significant loss of installed capacity following the closure of one of the country’s six PET recyclers. “The closure of Mpact Polymers had a significant impact on our capacity to recycle, with the remaining recyclers unable to pick up the slack as they were already operating at maximum capacity in the fourth quarter.” On a positive note, Scholtz said the tonnage of rPET sold in South Africa – more than 23,904 t – was similar to 2018, reflecting both the improving output at the remaining recyclers, as well as the increasing demand for rPET. www.petco.co.za Acquisition of PET recycling facility in Brazil Indorama Ventures Public Company Limited announced that it has, through its indirect subsidiary Indorama Ventures Polimeros S.A., acquired 100% equity stake of AG Resinas Ltda., a limited liability company incorporated under the laws of Brazil and completed the transaction on June 8, 2020. AG Resinas is a PET recycling facility in Juiz de Fora, Brazil and processes postconsumer PET into recycled PET flakes and pellets with a combined capacity of approx. 9,000 t/a. The facility is in close proximity to a large supply of recovered PET bottles, bringing the advantages of logistical benefits. This acquisition is strategically in-line with the IVL’s long-term sustainability objectives and will complement IVL’s PET business in Brazil and provide a unique opportunity to create an immediate recycling presence with opportunities for further expansion. The value of the above acquisition, calculated in accordance with the regulations of the Capital Market Supervisory Board and the Stock Exchange of Thailand, as prescribed by the regulations of the Stock Exchange of Thailand Re: Disclosure of Information and Other Acts of Listed Companies Concerning the Acquisition and Disposition of Assets, 2004 (as amended), is less than 15 per cent and the total size of all transactions in the past 6 months also does not exceed the 15 per cent threshold limits as prescribed in the regulations. www.indoramaventures.com/en Tshidi Ramogas, Petco board chair BevTech EU 2020 in digital format The International Society of Beverage Technologists (ISBT) is an impartial organisation that deals with all technical and scientific aspects of beverages. Next to providing forums for scholarly discussions, publishing of “voluntary” technical guidelines and best practices, the annual BevTech meetings are a widely recognised activity of the ISBT. These meetings are held in the US, in Europe, Latin America, Canada and India. The current challenges caused by the Covid-19 pandemic have made ISBT all the more conscious of the need to ensure the wellbeing of attendees and presenters. As a result of these concerns it was decided to move the 2020 BevTech Europe meeting from a face-to-face in Amsterdam, The Netherlands, to an online meeting. The date of the BevTech EU 2020 webinar is September 10th from 2 pm to 6 pm Central European Time. On the agenda are five presentations of 20 min followed by 10 min Q&A each. The speakers are specially invited to present their experience in managing their business during the Covid-19 pandemic. Other subjects are welcome such as: Sanitation of fountain systems in a retail environment Global quality standardisation vs. regional approach Smart use of manufacturing and quality data Quality and safety management The need to launch new products/ applications/packaging quickly versus proper testing. The webinar will conclude with a 50 min online live panel discussion by some of the most influential specialists in the industry. The panel discussion will highlight the experiences gained from managing Covid-19 impacts at different stages of the supply chain. www.bevtech.org","@ID":11}, "INSPECTION 22 PETplanet Insider Vol. 21 No. 07+08/20 petpla.net Meeting on-line rPET inspection challenges when producing PET bottles The Pilot Vision+ system, Agr’s latest generation of vision-based inspection systems, is designed to work in conjunction with today’s high-speed reheat stretch blowmoulding equipment. As part of Agr’s Process Pilot family of products, it is designed be used as a stand-alone system or in conjunction with Agr’s Process Pilot automated blowmoulder management system. INSPECTION The combination of Pilot Vision+ and Process Pilot provides bottle producers with the ability to detect random occurring defects, manage the process to maintain precise material distribution, even with the lightest and/or most difficult-to-process bottle design. Modular design The compact design of cameras and lighting components, and an operating speed of up to 100,000 bph, make the Pilot Vision+ compatible with most blowmoulder models and brands. The open architecture of this vision-based inspection system can manage up to 6 cameras in multiple locations. The modular design makes it possible for cameras and lighting components to positioned at optimal locations within the blowmoulder in order to facilitate the most effective inspections. Typically, units are configured in four separate inspection stations; preform inspection in the oven area, and then immediately after mould takeout for bottle seal surface, base and sidewall inspection. Special attention to preforms, colour and rPET Agr states that the preform inspection module of the Pilot Vision+ system makes it possible to identify defects that are visible in the preform, before the bottle is blown. Multiple colour cameras provide the imaging for 360° preform sidewall inspection as well as end cap and gate. Optics, LED illumination and image analysis routines are optimised to identify preform defects that impact bottle integrity, particularly the black specs and particle contamination sometimes associated with recycled PET (rPET). With the increased use of rPET, challenges related to colour consistency are an issue. In the Pilot Vision+ system, the colour preform cameras can be used to monitor the colour of preforms entering the blowmoulder and ensure that colours are consistent and within acceptable ranges. This feature is particularly valuable with the variations in colour that can typically occur when higher percentages of rPET are used. Additionally, the Pilot Vision+ system incorporates another tool to help address rPET related colour issues. This tool provides the capability to learn multiple reference image sets for colour inspection. With this, it is possible to process a preform supply with slight colour variations and manage the range of colour by accepting those that match the reference images, while rejecting those that do not match.","@ID":24}, "BOTTLING / FILLING PETplanet Insider Vol. 21 No. 07+08/20 petpla.net 46 There is a place in Amazonia... In the city of Leticia, the most southern in Colombia, in the area of “Tres Forest”, surrounded by the undisputed force of luxurious nature and where the intense green of the jungle, populated by sloths, parrots, monkeys and many other species of animals is interrupted for a brief spell to give home to Gaseosas Leticia S.A., the smallest bottling plant within the Coca-Cola Company circuit. It is a bottling plant with great strategic importance for Amazonia, the heart of the jungle; it generates work for over 500 people directly and indirectly and in five years, has seen an annual growth of between 8% and 11%. The Colombian company, which, currently has four bottling lines, decided to automate the production of Coca-Cola bottles in PET and therefore, installed a new ultra-compact rotary stretch-blow moulder from the SMI EBS K Ergon range. “Gaseosas Leticia – as confirmed by the company CEO Mr Hauptman Puentes – began its activity 50 years ago with just six employees and a small production of 25 cans of soft drinks per day (around 625 cans per month), while today they sell 2,000 per day (50,000 cans per month). Over the years, the company has evolved constantly, and if we consider the last five years, the annual growth has fluctuated between 8% and 11%”. The Gaseosas Leticia S.A. plant is situated in a strategic point, from where it is possible to distribute the production of its soft drinks all over the Colombian Amazonia. The Colombian company also produces beverages such as flavoured water, carbonated water, fruit juices with guarana, grapes, oranges, citrus, lemons, etc. Through this latest investment, Gaseosas Leticia aims to widen its production capacity by bottling soft drinks. The EBS 4 K Ergon stretch-blow moulder produces 0.5l and 2l bottles in PET, with a maximum speed of 8,800bph (0.5l containers). Inspired by the principles of industry 4.0 and the Internet of Things (IoT) it satisfied the requests in terms of productivity, operation flexability, energy savings, simple management and monitoring of the entire bottling line. The stretch-blowing system is equipped with motorised stretch rods (commonly used for high speed production) controlled by electronic movements. This solution guarantees precise cycle of the stretch rods. The ultra-compact structure results from one single structure which groups the section that heats the preforms with the one which stretch-blows. The production process is completely electronic, with brushless motor transmission and equipped with an integrated servo driver. There is a reduced blower energy consumption, thanks to the preform heating module. This is equipped with IR lamps, and to the stretch-blowing module equipped with dual air recovery system that allows the reduction of energy costs tied to the production of high pressure compressed air. The stretch-blowing system has high performance valves with low deadvolume, which reduce the length of time for pre-blowing and blowing. It is ensuring greater machine output and a higher quality of bottles produced. The machine geared to be placed in the Ecobloc version together with filler and a capper. The soft drink market in Colombia Data from statistics from the second quarter of 2018 elaborated by the main international financial institutions, that consider the GDP and the sensibility of consumer purchase, have shown that the Colombian economy performed well. The soft drink industry was one of the most dynamic sectors, with the companies who are part of the Coca-Cola group in the lead for volume of sales. In answer to the request in growth, The CocaCola Company recently strengthened its investments in production plants in Colombia, with the aim to reinforce and increase its share in this region’s market and produce more efficiently, using less energy and less water during all the bottling and packaging process. www.smigroup.it The Gaseosas Leticia S.A. workforce in its plant which is situated in a strategic point from where it is possible to distribute the production of its soft drinks all over the Colombian Amazonia. The SMI EBS 4K during processing","@ID":48}, "INSPECTION 16 PETplanet Insider Vol. 21 No. 07+08/20 petpla.net Digital control system for PET bottle production Even on the most advanced machine there can be discrepancies in the distribution of PET bottle material in the stretch blow moulding process. This has an impact on the bottle quality and production efficiency. In order to optimise these parameters KHS developed Unit Mold Control in cooperation with US company Agr International inc. (Agr). INSPECTION This digital, automated process control system, connected with the KHS controller, individually regulates the respective blow stations in KHS’ InnoPET Blomax series, thus minimising fluctuations in quality during stretch blow moulding. This results in improved bottle stability coupled with lower preform weights. This had proved something of a challenge to date, especially where containers with a high recycled PET content are used. On a stretch blow moulder the amount of wear on the individual blow valves used can vary. This means that the bottles blown with them also change throughout the service life of the stretch blow moulder depending on the station used. In the production process this can cause discrepancies in the distribution of material and thus to differing thicknesses of bottle wall. To date parameters could only be adjusted for the entire machine and not for each individual station. With the new digital Unit Mold Control system manufacturers optimise their blow moulding process by making individual settings for each station. “This enables material distribution to be more precisely controlled per station, thus minimising variations in the wall thickness from mould to mould by more than 30%,” explains Frank Haesendonckx, head of Technology at KHS Corpoplast. Unit Mold Control To this end, Unit Mold Control inspection technology constantly measures the material distribution in each bottle and adjusts the settings for optimisation fully automatically. “With this system deviations in the individual mould stations are identified. By applying an algorithm the degree of variability is reduced without operator intervention and possible incorrect settings are avoided,” states Haesendonckx. Furthermore, the data captured from the individual mould stations provides valuable information for the condition-based maintenance of valves, stretching systems or mould shells, for instance. Unit Mold Control yields further benefits with regard to the growing percentage of recyclate used in PET bottles in particular. “Process accuracy reaches its limits with containers such as these,” Haesendonckx says. “As the material quality varies when recycled PET is used, the bottle becomes less and less stable the less the preform weighs or manufacturers have to use heavier preforms to ensure stability.” With the new system weights can be reduced while retaining bottle stability, claims Haesendonckx. “Unit Mold Control effectively compensates for discrepancies by identifying any unwanted material displacement during wall thickness inspection and automatically counteracting this.” Partner Agr is also convinced by the joint new development. “Our commitment to the global beverage market is to provide innovative process control solutions for the factory floor,” says Robert Cowden, COO of Agr. “In doing so we’re helping to constantly optimise processes and improve production line efficiency and productivity by reducing unplanned downtime, labor content per produced container and energy costs.” Unit Mold Control is available as an option for KHS InnoPET Blomax Series IV and V stretch blow moulders and has already successfully proved itself on the market several times over. Furthermore, the new system – whose industrial property rights are held by KHS and Agr – can be retrofitted into existing plant machinery. www.khs.com www.agrintl.com “With the new system weights can be reduced while retaining bottle stability. Unit Mold Control effectively compensates for discrepancies by identifying any unwanted material displacement during wall thickness inspection and automatically counteracting this,” explains Frank Haesendonckx, head of Technology at KHS Corpoplast. The new technology minimises any fluctuations in quality during stretch blow moulding. This results in improved bottle stability coupled with lower preform weights.","@ID":18}, "INSPECTION 15 PETplanet Insider Vol. 21 No. 07+08/20 petpla.net Sacmi presents four AI-equipped preform vision systems Preform quality control Sacmi says that its new preform computer vision systems make extensive use of artificial intelligence (AI) concepts at a specific stage of the production process. This is to deliver easier quality control and format changeover tasks, even for workers who have not been specifically trained on the machine, plus changeover times of less than one minute, compared to about an hour on traditional systems. The PVS10 off-line preform quality control machine, which is equipped with the new CVs20 (Computer Vision software 2020) app, features an HD camera vision system that performs polarised light inspection and automatic size changeover control both on the machine and on the preform sorter/ feeder. This replaces the previous grid system and uses AI algorithms to simulates the behaviour of human eyes. The company says that the system is capable of identifying any sort of defect, over the entire preform, whether transparent or opaque, faster and more accurately than conventional technologies. It is designed to perform off-line inspection of lots or sample checks on output and enables manufacturers inspect every aspect of the preform, from body to bottom. It can read the cavity number and inspect the thread area. Eliminating manual input errors CVs20 control software incorporates the Sacmi Drive and Recognise through Intelligent Vision Algorithms, (DRIVA) platform. Sacmi says that this enables autonomous format change-overs and thus makes the machine much easier to operate, even by non-specialised workers. The operator submits the preform to the system, which uses a photograph of the object to recognise the format, including colour and dimensions. It then makes any necessary adjustments - not just to the inspection machine but also the preform feeder. This cuts change-over times to less than a minute and eliminates any chance of error due to manual intervention. The new system performs targeted checks on preform dimensions, such as top seal diameter and ovality, and offers offline inspection rates of up to 72,000 pph. New production control systems PVS3, which is equipped with CVs20 software, has a compact footprint and is designed to operate either off-line or in-line, with new or existing presses. It uses AI algorithms to provide the same inspection quality off or on-line, at rates in excess of 70,000 pph. The smaller PVS5, with a footprint of just 4.5 m2 , including sorter/feeder, can also be installed on existing systems. Its centrifugal positioner enables speeds of up to 55,000 pph. The range is completed with PVS2, which is designed to carry out in-line or off-line sample checks or provide additional quality control lab support. It runs a full check by taking diameter measurements of the top seal, of three or more points on the body, of the thread zone and by measuring wall thickness and perpendicularity, at rates of up to 1,100 pph. PVS-2 uses cavity recognition to produce a comprehensive set of preform measurement and weight data, by cavity number, while calculating minimum, maximum, average values and standard deviation for each measured parameter. The PVS-2’s CVs20 AI algorithms include polarised light inspection. All data is saved on SQL databases and made available via HTML pages that can be consulted on any fixed or mobile device with access to the corporate network, including smartphones. The new AI algorithms simplify quality control management and minimise production downtimes associated with changeovers and management of new materials, such as recycled PET. Advanced software and user interfaces enable production of targeted statistical reports on each stage of the process, which can be made available via the corporate network. www.sacmi.com INSPECTION","@ID":17}, "INSPECTION 25 PETplanet Insider Vol. 21 No. 07+08/20 petpla.net Closing the PET cycle with sorting and material analysis systems Europeans produce 25 million tonnes of plastic waste every year. Worldwide, 78 million tonnes of plastic waste are produced annually. The world as a whole must react to this global problem, because so far recycling rates are at a low level everywhere: in Europe at 30%, in China at 25% and in the USA at only 9% (plastic waste statistics 2017). INSPECTION Large parts of the alleged waste are still being incinerated or end up in landfills and in the environment, thus posing risks to water, air, animal life, health and the food chain. In order to achieve a circular economy, Sesotec states that it is important that all players make their contribution to this task: from product design and manufacture by the plastics industry, through conscious use and waste avoidance or waste separation by consumers, followed by proper recycling and sorting by the waste and recycling industry, to conversion into high-quality secondary raw materials and their use in the manufacture of new products. A prime example that already shows how a recycling economy can function is PET. Bottle sorting system PET recyclers face the challenge that the quality of the input material varies greatly. Poor material quality often leads to reduced throughput, higher loss of good material, poor purity of the sorted fractions and frequent plant downtimes for cleaning and maintenance. Each of these factors has a negative impact on the efficiency and thus the profitability of sorting and recycling processes. Variosort+ sorting systems detect and sort plastic types, colours, shapes, metals and other foreign objects from the product stream. The material throughput is up to 8 t/hr. Thanks to the intelligent machine design, cleaning work can be carried out quickly and maintenance requirements remain low. Flakes sorting PET flakes can still contain metal particles, colour impurities and foreign plastics such as PVC, which are then recycled during further processing. If these recyclates are used the impurities can get into the melt and be the cause of costly breakdowns, e.g. during injection moulding of preforms. Incorrectly coloured particles impair the colour of the “new” bottles, thus protecting processing machines from damage and ensuring perfect product quality. Quality analysis of PET flakes For manufacturers and processors of plastic flakes, ensuring high material quality is a decisive factor for profitable sales and use of recycled plastic. Depending on the use of the recyclate, and to evaluate the recycling sorting process, the quality of material batches often has to be assessed with elaborate manual, visual or thermal random sample analyses. This causes additional effort, high costs, loss of time and a low representativity of the random samples. With the material analysis system Flake Scan, the plastic flakes quality can be precisely determined according to plastic types, off-colours and metal foreign bodies, done in a few minutes. The automatic and reproducible analysis of material samples is carried out by up to three integrated sensors: colour sensor, NIR sensor, metal sensor. The effort for manual, visual and thermal analysis can be reduced and a fast and resilient decision can be made about the profitable use of plastic flakes. Furthermore, conclusions can be drawn about the recycling process and the function of various components. Michael Perl, Group Director Sales Division Sorting Recycling at Sesotec, says: “Recycling management is a complex task. Our sorting solutions and material analysis systems are indispensable building blocks for recycling companies to produce highquality secondary raw materials. In this way, we are helping to move one step closer to the goal that sustainability, profitability and environmental protection go hand in hand”. www.sesotec.com With the flexible Variosort+ sorting systems, products made of PET and other (plastic) materials are said to be sorted efficiently, flexibly and profitably.","@ID":27}, "CAPS & CLOSURES 49 PETplanet Insider Vol. 21 No. 07+08/20 petpla.net Special thanks must go toDavid Chalmers ofCoca-Cola Amatil who spoke to us from Sydney at ten o’clock in the evening. He highlighted the perspective of the user. Although the use of tethered caps is not yet mandatory in Australia, David wants to be prepared because it is only a matter of time until they are introduced there. Amatil is also developing new packaging of its own and preparing case studies, in particular the challenge regarding lightweight bottles and closures. He also showed us how the process influences cap design. German Technology PETinars - specialist webinars created by and for the PET sector! We are bringing together experts and key figures from across the sector. Topics will be chosen based on particular PETplanet Insider focus themes, with participation free of charge for our readers. Using the example of caps used by Amatil up until now (PCO 1881, Hotfill PET 26/22 and 38mm aseptic), he showed us how they envisage the tethered cap. Based on the PCO 1881, which has been in use since 2012, the idea is to merely replace the slitting sides in the mould in order to produce a tethered cap. This would be the equivalent of around 10% of a new mould. This is different with PET 26/22 which needs completely new cavities and amounts to around 70% of the original mould investment. On the other hand, it is sufficient to change the slitter with the 38mm aseptic and 1881 Hotfill. Using the example of the 600ml Powerrade Hotfill, Chalmers showed us the specifications of the 1881 Hotfill. He also briefly explained the manufacture and assembly of the three-part closure, slider and overcap. He has no tethered solution for the overcap as yet. The presentations are available at petpla.net","@ID":51}, "INSPECTION 24 PETplanet Insider Vol. 21 No. 07+08/20 petpla.net Automated pull-off tester While the majority of plastic beverage closures undergo quality inspection by inline camera systems, optical inspection does not discover all potential functionality errors that can affect performance during or after the application to the bottle. Industry standard practice for checking closure functionality is batch sampling: periodically taking a selection of caps to a laboratory for analysis. As this is time consuming, it is done only a few times each day. If defects are discovered, all closures produced since the previous check will usually be scrapped. This can mean the scrappage of in excess of a million closures. With CapLab, PackSys presents an automated TE-band quality inspection system which inspects samples according to a freely definable frequency. Inline TE band inspection The CapLab system offered by PackSys is an inline, automatic integrated unit for testing the functionality of a closure’s tamper evident (TE) band. It takes samples from the slitting/ folding machine outfeed and measures inline the pull-off strength of the closure’s TE band. It can, optionally, be combined with an optical inspection system that can select closures by cavity number. Test frequency can be set by quantity – e.g. every 100,000 caps – or by time: every three hours, for example. Sampling can be selected randomly, according to the spindles of the slitting machine, or by cavity number of the production mould and by quantity. Test sequences can also be triggered manually, e.g. at the start of a production shift. CapLab can also be connected inline to systems producing closures with moulded, rather than slit, TE bands. Automated adjustment The values found by CapLab inspection may indicate the need for corrective action. Temperatures of knives used by slitting machines to form bridges, for example, can be monitored and changed to keep values within target range, in a fully automated process that will maintain cap quality over the lifetime of a knife. Communication to the moulding machine and mould will enable the line to be stopped in the event of a major quality defect. Where the root cause of unacceptable TE band performance can be linked to a specific cavity on a mould or spindle on a slitting machine, the operator will be informed to address the root cause directly. Data management The CapLab system has its own screen for operation and data analysis. The database can be transferred easily to onsite production data monitoring or QC systems. Customised screens showing the measurements per cavity can be accessed directly at the user interface of the injection moulding machine. The flexible interface allows various layout options. PackSys says that CapLab’s compact design enables integration onto existing lines with existing optical inspection systems. www.packsysglobal.com INSPECTION CapLab is an inline, automatic integrated unit for testing the functionality of a closure’s tamper evident (TE) band.","@ID":26}, "PETplanet Insider Vol. 21 No. 07+08/20 petpla.net 54 PETbottles Beverage + Liquid Food Smoothie with hemp And the wheel just keeps on turning – after smoothies made from fruit, vegetables, ginger, turmeric and combinations of all these ingredients there now comes one containing hemp. The German company “Rewe” has brought out a “Good Vibes Hemp Smoothie” with extract of hemp seeds as part of its “Rewe to go” series. The product also contains apple juice, pineapple juice and pulp from apples, bananas, melons, passion fruit and goji berries. No additional flavours, concentrates or sugar have been added by the manufacturer. The smoothie comes in a clear 250 ml bottle with sleeve label and an opaque screw top with tamper-proof strip. www.shop.rewe.de Drink Pink Being invited for a “Drink Pink!” or “Drink Orange!” is also an invitation to have a drink. The German retail group, Rewe, has brought out three different 100% fresh juices containing a variety of ingredients under their “Rewe to go” series. The picture shows that the juices have had “energy” and “immunity” added to their names. “Pink” contains, among other things, grape juice, lychee and dragon fruit pulp, while “Orange” consists of goji berry pulp, coconut and passion fruit juice. The products’ “loud” colours are particularly striking in the refrigerated section. The drinks come in clear 750ml bottles, fitted with a transparent screw top and tamper-proof strip. The bottles are made from 50% recycled material with a non-label-look label printed in a colour that matches the contents of the products displayed on the shelves. www.rewe.de “Vio Bio Limo Light” with ginger This product contains 50% less sugar than standard lemonades in Germany. This is how Coca-Cola’s Vio brand promotes its lemonades. Its packaging design and brand identity have been revamped, with the picture showing the ginger-flavoured variety. The product also contains 4% apple, 3% red grapefruit and 3% lemon juice, i.e. 10% total fruit content. Each tapered disposable bottle with surrounding reinforcement grooves contains one litre of lemonade. The transparent sleeve label is appropriately printed with various ginger images. The colours of the caps have been individualised in order to differentiate them more clearly from other company products. www.cocacola.de Apple lemonade from Gerolsteiner Gerolsteiner’s apple lemonade with 15% fruit content comes in a tapered and clear 750 ml disposable bottle of brand-typical design. As well as its well-known mineral water with natural carbonic acid, the slightly cloudy lemonade contains 4% lemon juice and 11% apple juice, both made from concentrates. A sleeve label in matching colour and a green, easy-to-grip screw top displaying the brand’s logo and tamperproof ring complete the packaging. www.gerolsteiner.de","@ID":56}, "CAPS & CLOSURES 50 PETplanet Insider Vol. 21 No. 07+08/20 petpla.net Portfolio of caps and closures for edible oils and vinegars Closures that flip, click, switch and flow United Caps, an international manufacturer of caps and closures, reported that, following the acquisition of Spanish firm Embalatap, the company has completed a period of consolidation and integration, resulting in an enhanced portfolio of caps and closures for edible oils and vinegars. “The United Caps new Edible Oils and Vinegars line of products features significant innovation packed with small details that make them a portfolio built for life in the kitchen,” said Benoit Henckes, CEO of United Caps. “They include differentiated design, smart security and affordable sustainability, and are true to our principle of ‘Less is More,’ reducing the need for range complexity.” Caps and closures in the Edible Oils and Vinegars portfolio are available in a wide variety of colours for on-shelf standout and a premium look with optional tamper evident and tear-off membrane security features. The portfolio contains closures that flip, click, switch and flow. It offers a variety exemplified by a range with maximum and minimum pour options. The Edible Oils portfolio includes: A new United Caps 26 Family of lightweight closures designed to enable brands to maximise weight saving potential without impacting the end customer experience. These caps are the lightest products in the company’s Edible Oils portfolio, weighing in at less than one gram. A new United Caps 29 Click TE cap with a premium look, tear-off membrane and tamper evident (TE) band flip top closure suitable for use with PET and glass bottles for both Edible Oils and Vinegars. The 29 Doubleflow caps are claimed to be a popular offering within the Edible Oils portfolio, offering a variety of pouring options and good control thanks to its droplet shape. It is lightweight and keeps the bottle dry with spill-free performance. Doubleflow weighs three grams and is designed to perform reliably on the production line with no line modification. A product developed especially for large containers (2 to 5 litres), the 42 Sun snap-on closure is also available with an ergonomic “Porter” handle for ease of use. In addition to the 29 Click TE cap described above, the enhanced company’s portfolio for vinegars includes: 29 Vinjet, a best-selling product in Southern Europe with vintage appeal for vinegar, sauces and dressings. Caps for white and red vinegar have one hole for pouring, while caps for sauces, dressings and balsamic vinegar feature four holes. The United Caps 36 Pro2P is an easy-to-use product for glass and PET Edible Oil and Vinegar bottles. This snap-on two-piece closure features an anti-drop system and unique pouring shape for good control and a content-preserving tearoff membrane. www.unitedcaps.com Caps and closures in the Edible Oils and Vinegars portfolio are available in a wide variety of colours for on-shelf standout and with optional tamper evident and tear-off membrane security features. The 29 Doubleflow offers a variety of pouring options and good control thanks to its droplet shape.","@ID":52}, "TOP TALK PETplanet Insider Vol. 21 No. 07+08/20 petpla.net 10 “More intelligent elements will be incorporated in future plant designs” by Heike Fischer PETplanet Insider talked with a spokesman of the management team of GDXL about the company’s experience during the Covid-19 pandemic and the PET market in China. We thank the GDXL team very much for their assessment of the situation on site. PETplanet: China was the first country to be hit hard by the Covid-19 pandemic. Looking back at the beginning of this year what have been challenges for GDXL? And how did you manage them? GDXL: During February, China was hit hard by the pandemic and daily new confirmed infection reached its peak. Some of our colleagues had returned home during LNY and were stranded in pandemic-stricken provinces. So our workforce was not in full. Since it was uncertain when lockdown would be relieved and there were accumulated orders and deliveries to complete - upon full consideration of safety - we decided to resume operation in mid-February, around a week delay from the original schedule. We stayed highly cautious. To ensure hygienic safety we applied stringent measures including frequent temperature check, daily report of travel history and body conditions, quarantine measures in company’s canteen and dorm, rationing of masks, etc. We also maintained good communications with government officials and strictly followed their rules and guidelines. Logistic service was affected in the beginning by quarantine measures but just to a limited extent. In general, we were able to arrange deliveries of samples and finished products on time. PETplanet: Upon completion of the lockdown how did you start running the business again? GDXL: Since we resumed operation relatively early, we had more time to react and prepare. Our sales team checked the situations in every region, and maintained good communications with overseas colleagues, agents and customers. We accessed their business needs and adjusted R&D and production plans accordingly, so as to minimise the impact on our projects. PETplanet: How do you assess the situation in the PET industry in China today? What will be the challenges in the near future? GDXL: Although the pandemic has suppressed consumers’ sentiment, the demand for PET packaged products has been steadily growing in China in long run. The pandemic has shown the hygienic advantages and convenience of plastic packages, which supports its demand as a necessity during difficult times. Surviving the crisis and getting well prepared for future regional and global economic recovery are the main tasks to be fulfilled. During the lockdown there were accelerated development and utilisation of online sales outlets, either selfdeveloped or from third party, by brand owners. They also provided different levels of assistance and credit relieve measures to their employees, suppliers and retailers, so as to maintain product supply chains as intact as possible. GDXL headquarter in Foshan, China","@ID":12}, "PETplanet Insider Vol. 21 No. 07+08/20 petpla.net 55 BOTTLES PETbottles Home + Personal Care Face care from Levera Levera Natural Cosmetics has brought out a vegan facial hair spray called “Hydro Sensation”, containing organic algae and natural hyaluronic acids. It comes in a 100ml bluish coloured bottle with a screw-on pump sprayer and clear protective cap. Two self-adhesive labels describe how the product should be applied, together with information on the ingredients and highlighting the manufacturer’s commitment to protecting the environment through its various eco-brands. www.lavera.de Easy-to-grip liquid soap from Cien The German discount outlet, Lidl, is selling a number of liquid soaps under its own Cien brand. They come in clear bottles with two specially shaped sidewalls. The walls are cushion-like in design, resulting in an enhanced appearance and improved grip on the 500ml bottle. The product containing elderberry scent shown in the picture is applied by a transparent pump dispenser and has a lock function. Two clear self-adhesive labels have been placed on front and back of the bottle. www.lidl.de Extra Listerine content For some time now, the German company, Johnson and Johnson, has been promising its German customers 20% extra content in the added glossy gold-coloured printed area on the front label. This square-edged bottle with its firm top has increased in volume from 500-600ml. The screw-on black cap, which also serves as a dispenser, has been retained. It is secured with a pre-perforated shrink film prior to the first removal. The “Total Care Sensitive” product with its “6 in 1” effect for pain-sensitive teeth is slightly bluish in colour and is said to have a mild taste. www.listerine.de Sundowner shower gel with mango extract Treaclemoon, a brand of the German company, Vendoleo Ltd, a specialist in trendy shower and bathtime products, is bringing out a shower gel with mango extract for the summer months and comes in a 375 ml bottle. The bottle is made from 25% (without cap and label) recycled material, is CO2 neutral, has vegan content and has been dermatologically tested. As with all the brand’s products, it always has something amusing or informative printed on the label. In this case, a recipe for an alcohol-free “Passion fruit Sundowner” cocktail. www.treaclemoon.de","@ID":57}, "53 PRODUCTS PETplanet Insider Vol. 21 No. 07+08/20 petpla.net A new closure for edible oils Maestro is Aptar’s new solution that is intended to give consumers an easy-toopen, portion control, and drip free benefits. Maestro is designed to allow brands to stand out from the competition, while also staying aligned with e-commerce and sustainability trends. Giving consumers an enjoyable cooking experience is the core mission of Maestro. Maestro’s wide finger recess allows consumers to easily open the lid with one hand, and the raised spout was thoughtfully designed to let consumers decide which flow to pour with. The pouring lip also promotes a clean product cut-off, keeping drips, spills, and messes under control. In the kitchen, on the table, or even outdoors, Maestro delivers an easy, controlled pour, states Aptar. Maestro’s appearance brings a fresh, modern look to edible oil packages. The coloured spout paired with a translucent over cap allows brands to select colours to match each product’s identity. This trendy design helps draw the attention of consumers not only on stores shelves, but in the e-commerce sector as well. The premium look and feel of Maestro lends itself to fit seamlessly into the modern lifestyle of today’s consumers. A notable feature of Maestro is its fully recyclable composition. With its tethered cap, non-detachable parts, and 100% recyclable material, Maestro enables brands to meet their sustainability goals, and appeal to environmentally conscious consumers. www.aptar.com 7-8 October 2020 Messe Essen, Germany The international exhibition for plastics recycling technology Exhibitors include: 200+ EXHIBITORS 4 EXHIBITIONS 5 CONFERENCE THEATRES 1 FREE TICKET REGISTER FOR FREE TODAY Co-located with: www.ami.ltd/essen-prwe","@ID":55}, "INSPECTION 18 PETplanet Insider Vol. 21 No. 07+08/20 petpla.net The IMDvista Boco Scan Today’s next generation bottle inspection For more than a decade bottle vision inspection systems have been stagnant. Bottle manufactures have been forced to use systems with limited capabilities, which still required increased manual inspection costs. Systems were not capable inspect clear and opaque bottles on the same system. Measurements were not accurate enough for injected finish bottles and systems were difficult to change over. INSPECTION In 2017, IMD Ltd. took up the challenge to address these difficulties and began engineering the next generation in bottle inspection system named the IMDvista Boco Scan. During the next two years, IMD engineers began designing new lighting techniques, new algorithms and new hardware. Market research was performed to understand the requirements of potential customers. Different types of bottles were collected and an improved R&D was done on these bottles. This resulted in an advanced bottle inspection system including calibrated measurements, unique in the market today. Major challenge The first major challenge was the ability to inspect multiple different types of bottles using the same system; transparent, natural, opaque, shiny, flat, smooth and structured. Each of these types of bottles requires different lighting and camera techniques to achieve optimal inspection results. For example, a customer may run a clear PET bottle and a white shiny PET bottle on the same line. Traditionally this would require two completely different designs of hardware configurations; backlighting for clear and front lighting for opaque as well as different camera angles due to the clear bottles. The shiny white bottles would cause multiple lighting reflections causing a limited side inspection for contamination, scratches or burn marks. The Boco Scan has the capability of inspecting all of these bottles within a compact single module. Using four special high-resolution cameras (12.5 megapixels) and proprietary lighting configuration most complex bottle designs are capable of inspection. IMDvista Neuron Additionally, using Artificial Intelligence (AI) the system can learn and easily distinguish a good bottle from a defective bottle. Most bottles have some natural defects to them, especially extruded bottles. These defects do not affect the integrity or performance of the bottle. Many vision systems cannot tell the difference between these natural process driven bottle marks and actual defects. This is alleviated with the use of AI, the Boco Scan gets smarter over time. This is useful with bottle with strong structural features. Accurate measurement The second major challenge was the ability to perform extremely accurate measurements on the finish. Many bottle manufacturers still resort to pulling bottle samples and performing measurements in the quality lab. This still allows for some error depending on the operators level of experience. IMD took on the challenge to introduce lab quality measurements in an automated online inspection system. By imple-","@ID":20}, "TOP TALK 11 PETplanet Insider Vol. 21 PETplanet: What is the feedback of your customers? Are you able to support them? Do they have special needs - different needs - since the pandemic? GDXL: Our worldwide customers have been affected to different extents according to their regions. Due to border control we support overseas customers through online means, logistics or local representatives. Their needs are somehow as usual which include shortening delivery time, fast trouble-shooting response, etc. PETplanet: What about machine manufacturing: do you think that the running systems worked well during the Covid-19 period? Can on-site service continue despite high demands? GDXL: Plants with high degree of intelligent control and automated development may suffer less in production. Safe and reasonable work shift adjustments can also help maintain normal running of production systems as far as possible. It is less feasible to provide on-site service in person especially for overseas customers. Providing technical support through online means or local professional resources may help. PETplanet: What outcomes and experiences of the crisis will be incorporated in future overall plant designs? GDXL: In our opinion, more intelligent elements will be incorporated in future plant designs. Application of unmanned infrastructure, software and IOT systems can improve productivity and precision. It also reduces close human contact, lowering contagious risks. The crisis may accelerate such development. Such experience may also be considered in designing employees’ amenities. For instance, more spacious and hygienic facilities may be applied. But perhaps the post-crisis improvement will be more reflected in plant management. We will see more sophisticated safety precautions, flexible work shift arrangements and employees’ training. PETplanet: What will be the future strategy of GDXL? Is there anything special you would like to tell our readers, your customers? GDXL: Throughout the years we have evolved from merely a mould manufacturer to an engineering partner providing complete solutions for PET packaging. Since 2018, together with our partners, we have launched complete preform production systems with optional multilayer capabilities. This opens opportunities for our customers to keep up with the forefront of market trends. www.gdxl.com","@ID":13}, "BOTTLING / FILLING PETplanet Insider Vol. 21 No. 07+08/20 petpla.net 47 Gea’s Whitebloc Filling System Aero New filling technology for ESL beverages During the recent years, a key trend in the market for dairy products has resulted in the demand and consequent development of a wide range of high-quality dairy beverages with a prolonged shelf life compared to fresh products, with an increasing request in both developed and emerging markets. Compact design Sensitive, milk-based ESL beverages need special requirements to preserve their shelf-life and organoleptic properties. As such, container decontamination is an essential part of the process to ensure an effective and reliable extended shelf-life in cold chain distribution. The Gea Whitebloc Aero’s design is optimised for the treatment time required in ESL applications; this allows bottle decontamination with dry H2O2 and subsequent activation with warm air to be performed on a single carousel which keeps the layout as compact as possible. The decontamination, filling and capping processes are performed in a simple hygienic cabin with a top-down laminar flow of sterile air with a slight overpressure to maintain a clean and protected environment. Machine efficiency The ESL market frequently requires producers to run small batches and fill a variety of products on the same machine. The Whitebloc Aero offers the typical production rate of fresh and ESL applications, using both PET and HDPE containers with plastic caps or aluminium foil closures and using neck or base handling. The machine can be supplied in a standalone configuration or, for PET bottles, combined with a stretch blow moulding machine. The Whitebloc Aero can achieve a wide range of decontamination targets depending on the required level of product sensitivity and shelf-life for both high and low-acid products. Equipment cleaning is fast, cost-effective and flexible thanks to the possibility to choose between the integration of customers’ existing fluid cleaning system or a dedicated cleaning process skid unit embedded with the Whitebloc Aero. A built-in product recovery system eliminates product waste during the start-up cycle, at the end of production and during changeovers. Filling valves can be equipped with a load cell (weight filling) or flow meter (volumetric filling) to meet the various requirements of the liquid dairy product market. Environmentally sustainable No water is used in the process so producers can be confident that production is not wasting scarce natural resources. Both bottles and closures are treated using the same chemical for maximum convenience and consistency. Filling system As part of the Aero platform, Gea has developed a dedicated filling system designed specifically for fresh beverages, the Aerobloc Fresh. This is a hygienic filling platform for milk and liquid dairy products with a short shelf-life, without requiring any container decontamination. Its versatile, modular design allows the option of adding a synchronised stretch blow moulding machine or an air rinser and/or a neck trimmer to meet the specific requirements of the product and container material. Together, the Whitebloc Aero and the Aerobloc Fresh completes the range of advanced filling equipment for ESL and fresh beverages from Gea as end-to-end dairy processing single-source supplier. Gea states that with its global service support and local technical team, customers can feel confident that their processing and manufacturing infrastructure will work to help ensure their continued business success. www.gea.com Decontamination module as option according to the required product shelf life","@ID":49}, "INSPECTION 19 PETplanet Insider Vol. 21 No. 07+08/20 petpla.net menting telecentric camera, telecentric lighting and new algorithms, the result is a fully calibrated measurement system capable of measuring to an accuracy of +/- 5μm (T/E) on 100% of the bottles. Certified calibration Each system is calibrated during installation using a certified calibration tool. This tool is manufactured and certified though a 3rd party company, which specialises in measurement certification, and a letter of certification is supplied with each tool. For companies requiring annual certification, IMD can provide a visit to recalibrate and certify the Boco Scan or the tool is available for customers to perform the calibrations and certification themselves. IMDvista Portal Through the IMDvista Portal Software, these measurements can be saved and exported directly to the quality management systems, freeing up valuable time for quality department to perform other tasks. IMDvista login Security is a priority: The system includes a state-of-the-art vein scanner. This hardware features uses an infrared sensor to “scan” the blood veins in the operators hand. Each person’s blood veins are unique to that person only. This method is far more secure than traditional methods of fingerprints or RFID tags. Unlike tags and passwords, veins cannot be shared with others. With three levels of access to the system, the vein scanner will automatically log each person into the level of access they have been granted. Quick and automated changeover IMD has developed the Boco Scan to be easy to operate. The system can inspect and measure a large range of bottle sizes without the need for any changeover parts, reducing the operating cost and risk of lost changeover parts. Additionally the most important cameras, such as the measurement and top cameras positions are automated for reliable and repeatable results. Complete inspection solution To round-out the system additional inspections are available: Thin wall inspection and material flow 360° IR control for monitoring of heat profile. Prevention of deformation after cooling of the bottle Base control - panel inspection Parting line (also in the handle area) Neck inside inspection (choked necks) Thread inspection. www.imdvista.ch +44 (0) 1254 584210 [email protected] petmachinery.com Active for over 25 years, our global network and specialist knowledge makes us the go-to company for the sale or purchase of a PET machine. Commercially savvy, we work closely with our customers and our global network, to make sure everyone gets the best deal. Providing comprehensive advice throughout your sale or purchase; we can arrange dismantling, loading, packing, shipping, specialist insurance and commissioning. If you have amachine to sell or you’re looking to purchase, please get in touch. THE INDUSTRY EXPERTS","@ID":21}, "BOTTLE MAKING 41 PETplanet Insider Vol. 21 No. 07+08/20 petpla.net Ecology and economy Over the years, the company has developed a number of sustainability concepts. It has been able to reduce the use of material in PET bottles by 12%, and by 15% for HDPE and PP closure caps. The company is keen for the issue of post-consumer-waste to be taken seriously. “Companies that bring plastics into circulation are being held more accountable,” Ms Chauhan said. “As part of the Extended Producer Responsibility Programme (EPR), we have joined forces with associations such as the Indian Pollution Control Association and with waste management companies such as Nepra, Shakti Plastic Industries and Ramky Enviro Engineers.” The EPR programme is targeting the collection and recycling of some 3.1 billion PET bottles per year in India alone, equivalent to 50,000t of PET waste. Recycling machines have been set up for the collection of empty PET bottles. Additional partnerships have been launched with Action Alliance for Recycling Beverage Cartons (AARC) and Packaging Association for Clean Environment (PACE). “We need sensible approaches for making use of the waste that we have here,” Ms Chauhan continued. “Last October, our employees conducted coaching sessions for 15,000 students in 13 states on how to manage waste correctly. We repeat this every six months; we see it as part of our responsibility.” www.parleagro.com State No. of plants Uttarakhand (Sitarganj) 1 Uttar Pradesh (Varanasi, Ghaziabad) 2 Madhya Pradesh (Bhopal + Gwalior) 1 + 1 planned Odidha (Khordha) 1 Maharashtra (Patalganga) 1 Karnataka (Mysore) 1 Telangana (Hyderabad) 1 Andhra Pradesh (Vijayawada) 1 planned Tamil Nadu (Chennai) 1 Parle Agro’s 160ml bottle development Developments and innovations Parle Agro today packages its products in PET and cartons and, to a limited extent, also in cans and glass bottles. Its output is split approximately 66% for juice and 34% for water. Its pioneering tradition remains strong: it was one of the first producers in India to use a 180-cavity mould. Schauna Chauhan explained how the company is positioned in terms of production technology. “In addition to nine company-owned bottling plants, we have four franchise bottling plants nationwide for fruit juice and water, 63 additional franchise plants for bottling water and five plants that fill in returnable glass bottles only,” she explained. “We also have three preform production facilities: in Sitarganj, Uttarakhand; in Khorda, Odisha; and in Silvassa, Gujarat.” Two more companyowned plants – one in Andhra Pradesh and one in Madhya Pradesh – are soon to be added to the current nine. Production output, employment and resources Parle Agro consumes around 47,450t of PET annually in producing 116 million preforms and bottles. Preforms, which range from 8.5g to 46.4g, are made on 13 machines from Husky, Sipa and Krauss Maffei, with a total of 1,280 cavities. The company relies on equipment from Sidel, Newamstar and Tech-Long for bottle blowing; filling is undertaken on KHS, Hilden, Newamstar, Tech-Long, Hymech and Jieh Hong machinery. The PET bottles are designed to contain 690 million litres of water, 13 million litres of Appy Fizz and 12 million litres of Frooti. Final packaging of the bottle cases is done with SMI, Newamstar and Tech-Long equipment. Packaging sizes across its full product range extend from 65ml up to 20l. These numbers mean that the company is counted among India’s top three leading beverage players. Water products are packaged in bottles with TSSN (two start short neck) finishes; PCO1881 necks are used for fruit juices and CSDs. It also uses proprietary, in-house developed bottle, neck and closure systems, such as a 19g short-neck preform for 1l bottles and 9.6g preform for the 160ml Appy Fizz bottle. A completely new, Parle Agro-designed and developed, 25/19mm closure for small beverage containers is a world’s first. The company currently employs roughly 4,500 people; headcount is set to increase as the sales department expands. Parle Agro says that its market share in India for fruit juice drinks in the FFSD (fruit flavoured still drink) category is 25%, with a PET/carton packaging ratio of 61/39%. Revenues in 2019 amounted to US$700 million. While it is a forward-looking and innovative company, its corporate strategy is firmly based on backward integration. “We are one of a few beverage makers in India that designs and produces its own preforms,” Ms Chauhan explained. The 160ml bottle is one of those in-house developed bottles. “We are continuously developing our packaging and can match designs and weights on an optimum basis in terms of yield ratios for the respective applications.” Closure cap production, by contrast, is not part of Parle Agro’s operations. It is supplied with compression moulded closures by OCL, Hitesh Plastics, Secure Seal, Plenco and Algo.","@ID":43}, "MOULD MAKING PETplanet Insider Vol. 21 No. 07+08/20 petpla.net 30 Expansion of established two-stage business with single-stage moulds Production of new moulds accelerates by Kay Barton Moulds manufacturer Acme Disys, based in Delhi, has been designing two-stage moulds for well-known machine brands for more than 18 years. The business is flourishing and now serves an international customer base in the medium cavity segment. In October 2017, the company expanded into the field of single-stage moulds. The decision proved to be strategically beneficial, as a large proportion of its existing customer base uses both types of conversion technology. Acme Drinktec Solutions (ADS), which was established specifically to develop these products, has been making its mark on the market for 18 months. Managing Director Mr Sukhbir Singh and his Head of Operations, Mr Ramesh Desale, shared details of the project with us when we met during the India Editourmobil Roadtrip. Interview with Acme Drinktec Solutions LLP (ADS), January 2020 We met: Mr Sukhbir Singh, Managing Director Mr Jasvinder Singh, Head of Design, R&D Mr Ramesh Desale, Head of Operations “The idea for ADS emerged in October 2017; in response to our customers’ requests,” said Mr Sukhbir Singh, who is a graduate mechanical engineer with an advanced degree in mould design and manufacturing. He brings 30 years of expertise in the plastics industry to his role and led the Acme Disys team, and now the ADS team, right from the start. He is ably supported by Mr Jasvinder Singh, who has 25 years’ experience in the area. “It was a logical decision for us to expand into the single-stage segment with ADS and the existing set-up,” explained Mr Singh. Setting up the new company involved an investment of US$4 million. “After a nine-month development phase, we went live with the company and manufactured the first moulds. Since then, we have invested a further US$2.5 million in machinery and equipment, including brands such as Mazak, Doosan and SIG. We employ 60 people on an area of approximately 1,800m2 . Our objective is to provide customers with a customised and economical solution at a competitive price.” Initial capital investment is usually around 10-15% lower than that for original equipment, with a higher number of cavities at the same time. ADS says that it has built more than 100 single-stage moulds since it was launched. Current capacity is ten moulds per month but is set to double by 2022. It estimates that its market share of the single-stage segment in India already amounts to 10% and it expects to achieve a turnover of US $ 2.5 million in the current financial year. Although the company initially focused entirely on India, exports are also expected to grow in the future. It has already acquired some new customers in the USA and the UAE, through recommendations from Indian clients. “We estimate that about 5-10% of our moulds are used in the beverages and liquid food packaging sector,” Sukhbir Singh explained. “About 25-30% are destined for use in the production of liquor packaging. Non-food accounts for the rest, with 25-30% for cosmetics and beauty products and 25-30% for healthcare. In the long term, we consider our primary market to be in the liquor and pharmaceutical sectors,”. www.acmedrinktec.com Tour Sponsors: The ADS team with Jasvinder Singh (front left) and Sukhbir Singh with Ramesh Desale (both in the middle) Sukhbir Singh (second from left) discussing bottle and mould designs","@ID":32}, "MOULD MAKING PETplanet Insider Vol. 21 No. 07+08/20 petpla.net 36 High resolution 3D bottle surface decoration via laser machining Label-less design Moving a step forward in its environmental efforts to reduce the impact of all single-use PET bottles, the blow moulds manufacturer Moldintec has developed the technology to design a label-less bottle by taking advantage of the Advanced Laser Decoration. The label is the primary way of communication for the marketing team when designing a new package, but generally, they are limited to cylindrical panels. Applying a label on a PET container implies the use of equipment, tooling, and adhesive in addition to the label itself. Successive technological advances to improve labelling or direct printing on the blown bottle indisputably create packages of bright and attractive colours, even on-demand. Now, what is the role of bottle morphology in this seduction game to achieve commercial success? What else can industrial designers offer to differentiate and change the way a brand sticks in the consumer’s mind? Moldintec is known for its developments of tooling for blowing PET bottles, in which it emphasises the efficiency of the manufacturing process and how it affects the environment. The mould manufacturing industry is technologically dynamic from its genesis. PET blow moulds are metalmechanic assemblies that combine engineering solutions, industrial design, and manufacturing technology to achieve high dimensional precision that later translates into a stable, efficient, and energy-saving blowing process. Advances in mould making equipment face us with new challenges but also opportunities. “This was the case of the arrival of the very first laser machining equipment in our company in 2016”, says Diego Taboada COO of Moldintec. Initially intended for the simple task of texturing surfaces replacing obsolete chemical methods, the laser sparked initiatives within the company at an early stage. The R&D + I team quickly saw the potential for ablation. Historically limited by cutting tool diameters and spindle RPMs, the light beam changed the rules and freed designers from previous limitations. This paradigm change required hundreds of design hours, as well as programming to create software plugins capable of generating 3D geometry wrapped on the skin of the bottle with complex surfaces without distortion. The etching is nothing more than 2D patterns that cover a cavity at a constant depth in general, but the R&D team expected much more. NoLabel development NoLabel has evolved over the last two years. More than 60 pilot cavities were tested, taking advantage of the MultiFlexM platform, Moldintec’s quickchange cavity inserts system. “Today","@ID":38}, "52 PRODUCTS PETplanet Insider Vol. 21 No. 07+08/20 petpla.net Complete concept for wastewater recycling Between one and three litres per litre of beer or soft drinks, two litres per kilo of PET – during a production operation, very substantial quantities of wastewater are created. For precisely this reason, not only beverage and liquid-food producers, but also recyclers are continually seeking solutions for downsizing this wastewater incidence. Since Krones has already optimised its individual machines for enhanced efficacy, the complete-system vendor has now expanded the horizons of its corporate capabilities to factory level: a treatment concept has been developed for converting wastewater from the production operation into new process water. This covers all the process steps involved that give rise to wastewater in production. From effluent to process water In this concept, all the process wastewater from the production operation is passed through the existing network of gullies into a central storage basin. From there, any solids it contains are sieved out, whereupon the wastewater is neutralised in a collecting tank. The next step in the process, depending on the size of the system concerned, is traditionalstyle water treatment. If very sizable quantities of wastewater are involved, it is expedient to use an anaerobic stage: this will then produce biogas, which can be re-used in a unit-type cogeneration plant, for example. Once all the residues have been removed from the wastewater, it needs to be treated to make it suitable again for use as process water. This is where Krones’ Hydronomic water treatment systems come into play. By means of ultra filtration and reverse osmosis, even the tiniest particles like micro-organisms or salts are filtered out of the water. Following the subsequent admixture of chlorine dioxide in order to disinfect and stabilise the water, it is ready to be used again in the production process. The closed-circuit concept enables the water consumption in the production operation to be substantially reduced: up to 80 per cent less water is now required – which of course has a perceptible effect on both the company’s water costs and its environmental performance balance. The system can not only be installed in new factories, it can also be retrofitted in existing plants. www.krones.com Sustainable label collection CCL Label offers a sustainable label collection including recycling-friendly solutions like EcoStream and EcoFloat, technologies like ultra-thin films, adhesives with specific functionalities or materials from renewable resources but also label innovations using recycled content such as rPET from post-consumer recycling (PCR). Permanent and WashOff labels with rPET content Permanent self-adhesive labels based on PET are available with up to 70-90% recycled content from PCR. WashOff labels allow the clean removal of labels from returnable glass bottles in typical industrial washing processes. Compared to paper wet-glue labels they also help save water and energy and do not contaminate the washing bath. WashOff labels are currently available with 30% rPET from PCR – even higher percentages of recycled materials are currently being tested for the future. Liner solutions with rPET content Liners are the carrier sheet for the label and adhesive. Release Liners for both label solutions made from 30% recycled materials are available. 30% rPET content reduces the carbon footprint by 24% CO2 equivalent emissions, 70% rPET content by 56%. Sleeve solutions with recycled content This solution, a medium shrink transparent PETG film for sleeves with approx. 30% recycled material (post-industrial), is claimed to offer good performance in steam and hot air applications. It is suitable for gravure, flexo and rotary offset printing. Thanks to the sophisticated chemical recycling process, the post-consumer recycled plastic from PET bottles is of highest quality and safe to use on food and beverage packaging, states CCL Label, and continues that the functionality and performance of the labels with rPET share are not distinguishable from those made from virgin raw material. www.ccllabel.com","@ID":54}, "Out of shredded and cleaned packaging waste from the Yellow Bag (left), The Green Dot produces recyclates (centre) that go into the production of new bottles for cleaning products from Werner & Mertz (right). The recyclates – although significantly more environmentally friendly – are more expensive than comparable new plastic. MATERIALS / RECYCLING PETplanet Insider Vol. 21 No. 07+08/20 petpla.net 28 The Green Dot, Werner & Mertz and the German Association for the Waste, Water and Raw Materials Industries demand financial incentives and commitment from German government Is this the end of high-quality plastic recycling? Plastic waste in private households increased by 10% in recent months as the numbers of home offices and internet orders went up and the demand for recyclates – recycled plastic from plastic waste – decreased dramatically. What appears at first glance to be a paradox can be attributed to one cause – oil prices. The corona pandemic brought about a sharp fall in the price of oil. Cheap crude oil lowers the cost of producing new plastic and thus reinforces new plastic’s privileged legal status in Germany as it is exempt from petroleum tax and EEC levies. In comparison, the material recycling of used plastic packaging is economically even less attractive. Many manufacturers which previously used recyclates for products and packaging are now switching back to new goods. That means not only substantial losses for the recycling industry and a giant step backwards for climate and environmental protection, but also a huge blow to the circular economy. Consumers long ago feared a danger. Surveys show that consumers see plastic as the greatest (environmental) problem. They expect solutions in favour of a sustainable economy and that has not been changed by the coronavirus. The solution to the plastic pollution of our environment has been known for some time. Used plastic from post-consumer waste collections like the Yellow Bag can now be recycled at such a high quality that it fulfils strict requirements for use in cosmetic packaging. Plastic remains in a closed cycle, where it becomes valuable raw material instead of polluting waste. The technology of material recycling, however, is still pushed aside because the use of new plastic is cheaper in comparison. That’s why three representatives along the supply chain have issued a joint statement in which they demand that the German government use the impending transformation of the economy to establish a sustainable circular economy in general and the reuse of recyclates from used plastic in particular. Peter Kurth, President ofBDE (German Association for the Waste, Water and Raw Materials Industries), appeals to the role model function of public procurement for sustainable management: “The decline in oil prices intensified the already difficult circumstances for many plastic recyclers. Expensively produced recyclates find no takers; investments in better recycling are put off or cancelled because refinancing appears impossible. Given the lack of political action, plastic recycling is threatened with severe damage. Anyone who wants a successful, sustainable economy has to employ suitable instruments that have been known for a long time. An altered procurement process that takes ecological aspects seriously should be at the top of the agenda.” Reinhard Schneider, Reinhard Schneider, owner of the cleaning products companyWerner & Mertz and winner of the German Environmental Award 2019, provides","@ID":30}, "PETnews 6 NEWS PETplanet Insider Vol. 21 No. 07+08/20 petpla.net Clariant completes sale of its masterbatches business to PolyOne for approx. USD1.6 billion Speciality chemical company Clariant completed the sale of its entire masterbatches business to PolyOne. The enterprise value of the sale, which consists of separate transactions for Clariant’s global masterbatches business and its masterbatches business in India, amounts to approximately USD 1,560 million which is equivalent to c. 12.2 times the last twelve months reported EBITDA (ending September 2019). “With this completed transaction, Clariant takes another significant step towards becoming a pure-play speciality chemical company. By focusing on its three core Business Areas, Care Chemicals, Catalysis and Natural Resource, Clariant intends to deliver above-market growth, higher profitability and stronger cash generation. Having successfully sold masterbatches and healthcare packaging, our target is now to progress with the divestment of our Pigments business,” said Hariolf Kottmann, Clariant’s Executive Chairman ad interim. As a consequence of the completed divestment of the masterbatches business, as well as the anticipated divestment of the Pigments business, Clariant will now proceed as soon as practicable with an extraordinary cash distribution of CHF 3.00 per share to its shareholders. Clariant’s Board of Directors has set the ex-date to 6 July 2020, the record date to 7 July 2020, and the payment date of the extraordinary distribution to 8 July 2020. As previously announced, remaining net proceeds from the intended divestments will be used to invest in innovations and technological applications within the core Business Areas and to strengthen Clariant’s balance sheet. www.clariant.com www.polyone.com Chinaplas moves to Shenzhen for 2021 debut The 34th edition of Chinaplas has been rescheduled to April 13-16, 2021, at a new venue – Shenzhen World Exhibition & Convention Center. This will be the first time for Chinaplas to be held in Shenzhen. The trade fair will alternate between Shenzhen (odd years) and Shanghai (even years) in the future. The 400,000m2 Shenzhen World Exhibition & Convention Center has been classified as an ideal venue for a world-class trade show as all of the 19 exhibition halls feature column-free structures and are located on the first floor, which is claimed to be suitable for displaying large-scale machines, and easy for visitors to navigate. The advanced hardware features and supporting services are to provide exhibitors and visitors a convenient and refreshing experience. In a press conference held on June 23, Chinaplas organiser Adsale explained that the Greater Bay Area is not only an international centre of scientific and technological innovation, but also the most concentrated region for plastics processing in China. Shenzhen was made a Pilot Demonstration Area in 2019, as well as being one of the core engines of the Greater Bay Area. In 2018, the total industrial added-value of the Greater Bay Area reached 2.82 trillion RMB (about US$399 billion), of which Shenzhen accounted for the lion’s share of 32.3%. “Technology + Innovation” is Shenzhen’s business profile, with more than 3 million companies located there. As far as the pandemic situation is concerned, Adsale states that combined with continually emerging new trends and opportunities, all signs currently point to a positive outlook for the Chinese plastics industry. In the first quarter, as a result of the coronavirus pandemic, business shutdowns, the Chinese New Year off-season and other factors, China’s plastic products output dropped 22.9% from the same period last year. Production resumed in April in an orderly way, and industries’ supply chains gradually returned to normal operations. In April, the year-on-year decline in the total output of plastic products narrowed, achieving a recovery of 8.6% from the previous month. In the battle against the pandemic, plastics played a key role in the production and supply of vital healthcare materials, personal protective equipment, medical supplies, and medical facility construction. The pandemic also fuelled the rapid growth in demand for takeaway service, fresh meal delivery, express delivery, convenience foods, household electronic products, medical supplies and fitness equipment. The post-pandemic era is seeing the acceleration of next-generation 5G wireless technology, artificial intelligence (AI), autonomous vehicles, high-end medical products, antibacterial and antimicrobial surfaces for use in everything from cars to appliances, and more. Demand is expected to remain strong for new materials and technology, including those for key medical applications, safe and protective packaging, and digital production, as well as for recycled and recyclable materials. www.chinaplasonline.com","@ID":8}, "PREFORM PRODUCTION PETplanet Insider Vol. 21 No. 07+08/20 petpla.net 38 Preform production solution Each year, Milacron India, produces around 2,000 injection moulding machines with 50-3,200 tonnes of locking force for all applications. Of these, 130 to 140 are fully Hydraulic Toggle dedicated preform Mmachine PET series suited for 16 to 48 cavities. Also, Milacron offers high speed closures / cap injection moulding machines for various types of closures from 16 to 144 cavities. Milacron India, June 2019 We met: Umesh Pareek, Vice President – Sales Ankur Agarwal, Manager – Marketing Communications The technology is well engineered and customised to offer complete solutions to the Indian, Middle East & African customers. The preform system cools the preform within the tool, which is little higher in cycle time as compared to high end preform systems with take-out robots. However, the preform quality in terms of its dimensional accuracy is at par with any high-end system. The value preposition is that it gives the highest output / capital investment for the given capital invested. The resultant benefit to the customer is the industry lowest cost per preform. “While high-end systems are bought as a system together with their tools, the Milacron India systems go to the customer just as machines. The customer buys the tool separately in most cases,” says Umesh Pareek, Vice President – Sales. The systems go into sectors such as the local water providers, jars, pharma, edible oil and spirits. Growth in these segments is between 8 and 10% per year. www.milacronindia.com Tour Sponsors: F.l.t.r.: Umesh Pareek, Vice President – Sales; Ankur Agarwal, Manager – Marketing Communications Building the future in every moment of your business 40 Bar Oil-Free Piston Compressors for PET Applications. hertz-kompressoren.com","@ID":40}, "INSPECTION 12 PETplanet Insider Vol. 21 No. 07+08/20 petpla.net What to expect when you’re inspecting by Christoph Wynands (Product Manager) and Malte Nitz (Marketing), Intravis In recent years, the demands and challenges in the production of preforms have grown steadily due to needs for increasing material savings and the expanding use of recycled materials. The demands on inspection solutions for preforms have also risen to the same extent during this period. More and more inspection systems and concepts have entered the market. INSPECTION When do you use an offline system and when is a monitoring system the better choice? Or perhaps it is best to have both together? What are the differences between 100% inline inspection and a laboratory system for random sample inspections? And how can you get even more out of your existing inspection solutions with the appropriate software? Despite the current prevailing mood in the media that plastic packaging is responsible for all of the ills in this world, the number of drinks that have been filled in PET bottles continues to increase in recent years. Ever lower manufacturing costs, safer transportability, increased recyclability and low weight are just some of the positive characteristics that explain the increasing share of PET packaging. Due to these advantages, the spreading use of PET bottles has increased significantly. Let’s take the developments in Germany as an example. The market share of PET bottles was still around 30% in 2003. This is when the deposit on nonrefillable bottles was introduced and the share then increased to almost 72% by the end of 2017. In line with this development, which can also be observed in many other countries around the world, more and more companies are starting to produce PET preforms or expanding their capacities in this area. Due to these changes, indispensable elements in modern production lines now include inspection systems. They guarantee consistently high product quality and offer their users clear competitive advantages. Increasing requirements With the increase in the number of preforms produced, new requirements and expectations for inspection systems have arisen on the production side. Because the market requirements are very different and sometimes incompatible, various system types were developed over time. Whereas years ago, suppliers often only offered one “system for preform inspection”; today they often offer four or five different solutions - some of which are still adapted to meet specific customer requirements. As a result, this means an ever increasing range of systems for different situations. The customer rarely knows exactly what the best solution is for their production from the beginning without consultation. Critical applications = 100% inline testing Choosing which inspection system is the right solution depends first and foremost on the customer’s requirements. So he must ask himself the following questions: How demanding is my product? Which risk factors can influence product quality? How important is the job that I produce on this machine? Do I produce for a demanding customer or critical market to which I only want to deliver perfect quality? If so, even one bad preform can lead to the rejection of a delivery or, in the worst case, the end of a partnership. Accordingly, a 100% inline inspection solution is the best choice for such cases. Systems such as the PreWatcher Inline from Intravis inspect all preforms directly after an injection moulding machine and sort out the defective ones. The PreWatcher Inline inspects up to 72,000 pph with a precision that is pixel accurate for a total of 25 criteria - including the reading and correlation of data to the cavity number. In-house production = monitoring may be sufficient Machine downtimes due to bursting preforms in the blow moulder, responsibility for the entire supply chain and short distances in-house are more forgiving than an external customer who suffers a production stoppage and complains about an entire delivery. Due to this lower risk, 100% inline inspection may not be required. In this case, many customers rely on the results of a lower cost production monitoring system. When embedded in a production line, these systems do not achieve 100% inspection; but offer a good compromise in terms of up-front costs, space requirements and inspection performance. Also, monitoring systems can achieve the same accuracy as the more expensive and required larger Monitoring, inline, offline and laboratory systems complement each other with different strengths within a preform production.","@ID":14}, "BOTTLING / FILLING PETplanet Insider Vol. 21 No. 07+08/20 petpla.net 44 Edible oil in PET The Mega Factoryby Michael Maruschke There is a widely-held view that edible oil factories tend to caution in the adoption of new PET production technologies. However, this preconception is overturned on our visit to B.L. Agro Industries’ Mega Factory in the city of Bareilly, 252 km East of New Delhi, in the state of Uttar Pradesh. B. L. Agro Industries Ltd. May 2019 We met: Ashish Khandelwal, Executive Director Ramneek Vats, Founder & CEO B.L. Agro Industries has a 60-year history and is a household name in edible oil. It imports about twothirds of its edible oil supplies, which matches the proportion across India generally. Incoming supplies offloaded at Kandla Port, Gujarat, are transported to Bareilly by railway to its own siding at its refinery at Jauharpur, in Bareilly. Total edible oil supply capacity is 225,000 t/a. 70% packed in PET B.L. Agro’s flagship brand is “Bail Kolhu” mustard oil. It also supplies sunflower, soyabean, palmolein, rice brand and canola edible oils to the Northern part of India. About 70% is packed in PET; the rest goes in tins and pouches. PET capacity is about 1,250 t per day and accounts for about 60% of sales; the most popular bottle sizes are 2 and 5 litre. All preforms and caps are supplied by Balaji Polymers, who also collaborate with B.L. Agro in developing new bottle designs and sizes. Major machinery upgrade Ashish Khandelwal joined his father’s business in the late 1990s, bringing new marketing concepts and production innovations with him. The edible oil packaging operation was founded in 1999; a major machinery upgrade was carried out in 2014, when new Sidel machines were installed. This upgraded what had been a relatively low-output facility into one of the most advanced and automated PET production plants in Asia. A linear two-stage stretch-blow moulding, filling and capping line produces 6,000 five-litre bottles per hour. A Sidel Combi line makes and fills 200ml, 500ml and 1 l bottles at a rate of 24,000 bph. The popular two litre package is produced, filled and capped on its own dedicated line at 14,000 bph. There is essentially no human involvement from the moment the preforms and caps enter the factory to when they leave as finished, filled bottles, packed in cardboard boxes. Every step is automated, including the high-speed, in-line insertion of HDPE handles into the five litre PET containers, a function performed by a specially-made machine supplied by Spanish machinery manufacturer And & Or. The conveying and storage system, supplied by Japanese company Daifuku, is also highly automated; the similarity to an Amazon Production area Tour Sponsors: F.l.t.r.: Amit Arora, Ramneek Vats, Michael Maruschke, Ashish Khandelwal and Amit Kumar Namdeo (Husky Injection Molding Systems)","@ID":46}, "MOULD MAKING PETplanet Insider Vol. 21 No. 07+08/20 petpla.net 37 MOULD MAKING 37 we have the technical and creative skills to tattoo the full skin of the container. Laser machining allows us to stamp the bottle with brand logos at high resolution, HD pictures converted into 3D surfaces to decorate without limits. Essentially, it is not an offset of the primitive surface only. The decoration is entirely 3D,” explains Eng. Juan Manuel Colmenares, who interacts with clients to transform labels into the new bottle skin. NoLabel entirely eliminates the use of labels. That is a considerable challenge for marketing people who have to change the way they communicate without using multiple colours, shines, and shades from a printed label. On the other hand, they get absolute freedom of form; it is no longer mandatory to have a cylinder in its geometry to apply a wraparound or a full-body label. NoLabel is being implemented for water containers to create clean morphology and more environmentally friendly packaging. In addition to cost-savings, the PET is free of other materials such as the label itself or the adhesive, which means better PCR. From a photograph with 3D information to perfectly legible characters, anything can be stamped from the mould, even when the preform is transparent, without any additional cost beyond the initial investment. As economies recover from the pandemic, markets will face challenges and consumers will demand solutions that protect the environment, states the company. “We are confident that NoLabel will serve a niche for products that connect to the consumer in a more responsible way, where less is more,” explains Ing Thiago Tullio, Moldintec’s Brazil Country Manager. A video can be found at www. youtu.be/MflZFSoZOI4 www.moldintec.com ENDLESS INNOVATION SINCE 1919","@ID":39}, "BOTTLING / FILLING PETplanet Insider Vol. 21 No. 07+08/20 petpla.net 45 Not round, not oval and not square format: a special design of a 5 litre edible oil bottle warehouse operation has not gone unremarked. Discovery Channel paid a visit to the company to film an episode of its Mega Factory series here. The high level of automation is also reflected by the payroll. In 2013 the factory employed around 2,100 people; today’s headcount is just 250. www.blagro.org Conveying system to the storage area","@ID":47}, "CAPS & CLOSURES 48 PETplanet Insider Vol. 21 No. 07+08/20 petpla.net An opportunity for compression and injection moulding? PETinar: Tethered caps At the second PETplanet PETinar in which 248 attendees took part, Andreas Brem, Group Sales Director of Food and Drink at Bericap; David Chalmers, Operating Manager, Packaging Services Division at Coca-Cola Amatil and Iacopo Bianconcini, Marketing Manager at Sacmi under the chairmanship of Ruari McCallion, PETplanet, spoke about current developments and the potential for tethered caps. Andreas BremfromBericap started off by explaining the legislative timeline. The SUP Directive came into force nearly a year ago and new caps should be available on the market by 2024. Technical requirements, transposition into national legislation and, of course, the introduction of technology with experimental moulds will all have taken place in the intervening five years. Andreas highlighted potential solutions for the three elements of noncarbonated drinks (press-on hinge and screw caps), aseptic and carbonated bottles. Here, I would like to mention a very instructive video that was included in the presentation. Of the many options shown is the clip aside screw cap. Here, he demonstrated its intuitive opening and closing and its prominent position when opened which allows for hassle-free drinking and which meets the requirements of the CEN Regulation (25N pull-off resistance, opened 15 times and closed without rupturing). The new cap must be suitable for all standard neck finishes. Consequently, there will probably be one for the traditional PCO 1881, as well as for PET 26/3T; PET 29/25; PET 30/25; PET 33 2T etc. This means that no new neck geometries are needed and that the bottler will not have to adjust his lines, except for the capper. In order to answer the question as to whether injection moulding with or without slittering is the preferred choice, Andreas showed us an impressive mould flow video. Whereas the melt flow in injection moulding with slitting flows evenly into the outer area, it is not suitable for injection moulding without slitting (i.e. injecting the perforation) as the perforation has to be washed around the mould, resulting in two flow lines for each perforation which then come together again behind the perforation. The flow lines can cool down which creates cold seals and with it fracture lines when they come together. This has no effect in the laboratory but slittering causes far fewer problems when it comes to 24/7 production. The latest development is the approval of closure design, with market tests for different designs planned for next year. Questions were asked about cap material, whether there are likely to be any changes and what recyclability will look like. Iacopo Bianconcini fromSacmi also showed an instructive video that highlighted a number of solutions his company has in mind for the tethered cap. Common to all solutions is that slitting occurs after compensation moulding. Iacopo also told Andreas that new caps are not an investment for bottlers, that no approval for new packaging is necessary and that they could be brought in very quickly. The situation is somewhat different for snap-on caps in which both the cap and preform manufacturer must invest in new moulds. The bottler must also make adjustments to his processes and machines. Iacopo again pointed out that the melt index range is wider for compression moulding than for injection. Implementation of subsequent slitting and process control solutions ensures that new caps are of consistent quality. PETinar Andreas Brem, Group Technical Sales Director Beverage and Food, Bericap David Chalmers, Operations Manager Packaging Svcs Div. Coca-Cola Amatil Iacopo Bianconcini, Marketing Manager Sacmi by Alexander Büchler","@ID":50}, "empowered by Drinktec New Zealand Australia Philippines Taiwan South Korea Japan Let Your Inspiration Flow. )URP 'RZQ 8QGHU WR -DSDQ G’day and Konnichiwa! Editour Road Show goes virtual This year’s Editour Road Show was planned to be our next big international editorial project. That is now impossible. For the safety of others and our own, we are all working from home during the lockdown period. But it’s still time for the Editour Road Show to hit the road – it’s just that we won’t be doing so physically, not at the moment. The start of the new decade will see us undertaking a trip starting in Australia, moving on to New Zealand and then Japan, via the Philippines, Taiwan and South Korea. With support from Drinktec, the world’s biggest beverages show, we will be ‘virtually’ shooting off to Australasia in April. The first weeks will see us interviewing PET companies along the route via Internet and phone. These encounters will appear not only in PETplanet Insider but also in a completely new way – new to us, anyway: as podcasts on our website, for the first time ever! We will keep monitoring the situation closely to decide if, how, when and where we can still go personally with our Editourmobil, later in the year, while complying with governmental rules. We will present a comprehensive review of our Tour experiences both at China Brew China Beverage in Shanghai, China, in October and at Drink Technology India in Mumbai, India, in December 2020. Make sure you’re on board when we set off on our next adventure and get ready for in-depth analyses, special features and reports of trends in these bottle and beverage sectors! Enjoy our first-ever Virtual Editour! Stay safe and healthy! Interested in being interviewed? [email protected] April - December 2020 Powered by","@ID":42}, "8 NEWS PETplanet Insider Vol. 21 No. 07+08/20 petpla.net Starlinger introduces measures in the field of corporate social responsibility Corporate Social Responsibility (CSR) is becoming increasingly important. With Clarissa Graf, the Austrian mechanical engineering company Starlinger has hired a Sustainability Manager to address this essential task; since autumn 2019, she has been actively defining CSR measures for the internal and external implementation of the company strategy. One of these measures is the membership in respACT, Austria’s leading corporate platform for responsible business practices. “My task is to devise and implement a company-wide CSR strategy,” says Starlinger Sustainability Manager Clarissa Graf. “This strategy is being developed internally – for example in workshops – and is constantly extended through the participation in external events designed to promote an exchange of experiences as well as further training in the field of sustainability.” Through her studies in the field of environmental management and ecosystem research, Graf combines her knowledge of natural cycles with business objectives and economic processes. In doing so, she relies on existing resources and a lively exchange with the entire group of employees as well as other companies. This year, Graf has applied for membership in respACT, Austria’s leading business platform, which supports companies in practicing business responsibly and thus works towards a sustainable and futureoriented economy. This is accomplished through providing assistance in the area of sustainability, through clear communication of existing guidelines in the course of reporting as well as through networking events such as the annual CSR day. “Sustainable business management has been a focus of our activities for many years,” emphasises Starlinger Managing Partner Angelika Huemer. “In doing so, closed production circles and plastics recycling are key priorities. With the appointment of a Sustainability Manager and the membership in respACT, we will be able to address this topic even more intensively.” The activities of respACT follow the principles of the worldwide initiative UN Global Compact as well as the UN Sustainable Development Goals – SDGs for short. www.respact.at www.unglobalcompact.org www.starlinger.com Erema Group looks back on a successful financial year The financial year 2019/20, which ended on 31 March, marked a special milestone in Erema’s corporate history. For the first time the group of companies generated a consolidated total turnover of more than EUR 200 million and, with its recycling technologies and professional services, underlined its position as a technology leader and driving force in the implementation of a circular economy for plastics. Then along came the Corona pandemic and the impact it made on everyone’s private lives and the economy. Within a very short period of time, Erema implemented numerous measures to protect the health of employees, to continue business operations and to continue to meet the needs of customers as best they could. As Manfred Hackl, CEO Erema Group GmbH says, “We are proud of our achievements in the past financial year and how we have handled the special challenges presented by the corona pandemic so far.” A total turnover of more than EUR 200 million represents an increase of more than 10 per cent compared to the financial year 2018/19. The number of employees also increased again. More than 600 people now work for the group of companies consisting of Erema Group GmbH and its subsidiaries Erema, Pure Loop, Umac, 3S, Keycycle and Plasmac. CEO Hackl names as success factors the innovative and diverse recycling technologies of the subsidiary companies as well as their comprehensive consulting, service, engineering and planning services. That is how Erema Group was once again able to set new standards in the past financial year. In the in-house and industrial sector, Erema GmbH launched the new Intarema ZeroWastePro system as a compact solution that is precisely tailored to the requirements of recycling production waste. Pure Loop, a subsidiary in the shredder-extruder technology segment, added the ISEC evo series to its product range, which enables output rates of more than 1,500 kg/h to be achieved for the first time. The range of products for in-house applications is rounded off by the Plasmac range of solutions especially for straightforward applications at low throughput rates such as in the blown film sector. Outlook The company states that the past financial year was an intensive and successful year with many highlights for the Erema Group, followed by the unforeseeable outbreak of a pandemic. “Corona is likely to remain with us for some time, but that will not diminish the significance of our mission: Another Life for Plastic. Because we care,” says Manfred Hackl. On the contrary, the group of companies is looking to the future with confidence over the long term, even though recent developments have led to a very tense situation for plastics recyclers. The unanimous opinion is that sustainability and consequently plastics recycling will continue to be important issues for society and industry, possibly even gaining in significance as a result of the lessons learned from this crisis. At the moment, the economic impact of the Corona crisis on the recycling industry requires that decision-makers at national and international level ensure that recycling know-how and the requisite recycling systems acquired over the years are maintained and further developed to meet EU recycling targets. www.erema-group.com Clarissa Graf, Starlinger Sustainability Manager Manfred Hackl, CEO Erema","@ID":10}, "INSPECTION 13 PETplanet Insider Vol. 21 No. 07+08/20 petpla.net footprints of inline and offline 100% inspection systems. One of the latest monitoring systems on the market is the PreMon. Due to its new transport technology it inspects up to 70% of preform production, and costs only one fifth the price of a 100% inspection system. Therefore, it offers the optimal compromise by having a fast ROI, small space requirements and still delivers the security of high product quality. PreMon special features include an optional ejector that sorts out defective preforms. It offers grading statistics in which the system collects and visualises real-time data, as well as, the most important information of the last 24 hours and assigns the information to the corresponding packaging units (octabins). By indicating the error rate, the corresponding error images and the corresponding evaluation statistics; the PreMon provides a stable foundation for making the right decision on whether or not an octabin meets quality requirements with certainty. With this information, the producer can reliably decide how to proceed with an octabin: recycle the entire packaging unit, send the octabin into storage and re-sort it with offline inspection, or release it for sale or for further processing. Offline re-sorting systems When an octabin lands in the blocking warehouse, the hour strikes for an offline inspection system. On one hand, these systems are characterised by higher inspection speeds and on another hand they are so flexible that they can be converted from one preform design to another very quickly. Compared to 100% inline inspection systems, offline inspection systems often offer a similar scope of inspection capabilities. Laboratory systems support analysis and reporting For comprehensive quality audits, preform producers require extensive reporting on the quality of the preforms that are made. If a company wants to offer its customers the highest possible level of detail in this area, it will use a laboratory system such as the Sample-PreWatcher. It is common practice to sort out the first and the last complete shot of a shift and to subject it to a precise inspection in the laboratory. The Sample-PreWatcher with its circa 30 inspection criteria replaces the laboratory. It offers an additional weight check, and a higher precision during inspection compared to an inline or offline vision system. Other capabilities include a polarisation test with which stress points in the preform can be detected. As far as speed is concerned, it must be considered in a differentiated way. Compared to an inline, offline or monitoring system, a laboratory system with up to 1,200 tested preforms per hour is considerably slower. However, a comparison with conventional test methods within a laboratory is more appropriate. Here, the laboratory system offers a higher test performance with up to 30,000 individual quality data points collected per hour; it gives a decisive advantage of an objective and reproducible test situation. The “human” influence factor is thus reduced from quality control and has no influence whatsoever on the accuracy of the measurement results. In addition, the measurements of the laboratory system can be output directly as a report with one click, thus providing comprehensive support for laboratory personnel. Data summary and optimisation with software All inspection systems whether they inspect inline or offline, 100%, or only partially, have one thing in common. They produce a very large amount of product-related quality data. With the right tool, a comprehensive analysis software, important insights can be drawn from this collected data. With the help of these findings, producers can then optimise their processes and compare at a glance which lines and settings may require changes for improvement. As an example of a benefit of data collection, the mould diagram function of the IntraVisualizer analysis software is described here. This feature uses the cavity numbers of preforms to create a three-dimensional graphic of the distribution of a defect within the mould for each individual defect type. Based on this graphic representation it is possible to see that the clamping force of the mould needs to be adjusted because defects such as long shots (flash) occur more frequently in one area of the mould. The benefits of timely information and findings such as these can demonstrably increase the performance of a production line and result in a large savings of material and time. Conclusion In summary, given the large number of different inspection solutions available, each has its own advantages and could be the best choice for certain situations and requirements. For future production, which is increasingly controlled and optimised by data and information, a combination of different system types together with additional analysis software is the best choice. If a company is aware of the accuracy and speed required for its needs and to fill its orders, the optimal quality inspection concept can be found for every producer. The right quality information can help to identify production advantages and provide a decisive competitive edge in the global preform market. www.intravis.com Monitoring systems like the PreMon are the latest development in the field of preform inspection.","@ID":15}, "BOTTLE MAKING 42 PETplanet Insider Vol. 21 No. 07+08/20 petpla.net rPET in stretch blow moulded bottles The first PETinar attracts more than 200 participants by Alexander Büchler The first PETinar organised by PETplanet Insider took place on the 28th of May 2020. PETplanet invited three specialists to discuss the topic of manufacturing and processing rPET right through to a blown PET bottle. Mr Stefan Bock, CEO of RedupPET, expert in the field of preform production, moderated the discussion. The first presentation was delivered by Mr Christoph Wöss, Business Development Manager, Bottle Application at Erema Group. Christoph introduced the new bottle-to-bottle recycling technology Vacunite from Erema. He was followed by Mr Arne Wiese, Product Manager Bottles & Shapes at KHS. Arne described and analysed the processing from an rPET preform to a blown rPET bottle. Christoph Wöss, Erema began his presentation with a brief overview of PET recycling. Most of the 268 PET food-grade machines sold worldwide have gone to the bottle-to-bottle sector (95 units), closely followed by the bottle-to-sheet sector (77 units). The remainder went to other areas including PET palletising fibre. The systems have a total capacity of 2.3 million tonnes per annum. Christoph spoke of a most recent development, the Vacunite recycling system, which has already got off to a good start with 11 machines planned worldwide. Compared to Erema’s earlier bottle-to-bottle systems, the idea of working with vacuum and nitrogen is still in its early stages. Vacunite is a combination of the proven Vacurema technology and an assisted SSP (Solid State Polycondensation) at reduced pressure under nitrogen, patented and designed by Polymetrix. In the Vacunite system, the extruder is short with backward degassing at the melting zone. For a higher degree of crystallisation, a new, compact inline crystallisation system was added. It shows no sticking behaviour because the shift of low melting peak is above drying temperature. The technology reduces yellowing due to vacuum and N2 and generates a reliable decontamination, which is FDA & Efsa approved. The low IV decrease in the vacuum reactor enables a high increase of the IV in the SSP. The IV increase is determined by the process temperature (190-210 °C) and pressure (100-200mbara). Christoph concluded that the Vacunite technology is a well-controlled thermal process, has very high energy efficiency and is officially food contact approved. It has an output from flake to pellet up to 0.35 kWh/kg. The participants were chiefly interested in some technical details about the system, together with the stability and quasi-quality of rPET. Arne Wiese, KHSexplained the material difference between PET and rPET. While colour variation, IV and IV variation are all pretty similar, rPET is slightly darker and much more expensive (1EUR to 1.25EUR/kg). The factor that most strongly represents a variance to virgin PET is the colour and the cost of the recycled material. The impact on the blowing process is based on experiences with an InnoPET Blow Moulder Series V PETinar Arne Wiese, Product Manager Bottles & Shapes KHS Christoph Wöss, Business Development Manager, Bottle Application Erema Stefan Bock, CEO RedupPET","@ID":44}, "MARKET SURVEY 33 PETplanet Insider Vol. 21 No. 07+08/20 petpla.net Company name Siad Macchine Impianti Hertz Kompressoren GmbH Nanjing Shangair Machinery Manufacturing Co., Ltd. Postal address Telephone number Web site address Contact name Function Direct telephone number E-Mail Via Canovine, 2/4, 24126 Bergamo, Italy +39 035 327611 www.siadmi.com Mr Giovanni Brignoli Compressors Division, Food & Beverage Product Leader +39 035 327609 & +39 035 327694 [email protected] [email protected] +49 951 9643 13 88 www.hertz-kompressoren.com Mr Ercan Asmaz Sales Manager / Europe +49 533 962 64 22 [email protected] No.1, Xiyan Road, Binjiang Economic Development Zone Jiangning District, Nanjing, China +86 25 86408239 www.shangair.com Mr Edward Zhou Overseas Sales Manager +86 1519595 1347 [email protected] 1. Machine designation / model number Vito BS Line Pet Master VSD 180 (PET Master Series & PET Master VSD Series) WM 2. Number of models in range 32 19 PET Master 50/75/100/125/150/18 0/220/270/300 & PET Master VSD 75/125/180/220/300 2 3. Output in m³/hour 100 - 6,000 1,000 – 6,000 810 60 ~ 72 4. Compressor type High pressure blowing air (up to 40bar) High pressure blowing air (up to 40bar) Low pressure air Low pressure screw High pressure blowing air (up to 40 bar) Piston High pressure piston (booster) Reciprocating Integrated system 60m3 /min, 72 m3 /min, air tank 150 l 5. Lubricated or oil-free Oil free Oil-free (high pressure compressor) Oil splash lubricate Low pressure compressor Oil free 30bar Booster compressor Oil free Integrated system Yes Yes 6. Machine layout V and H (horizontal) V 4,192 x 1,977 x 2,814 7. Number of compressor stages 3 2 screw + 2 booster = 4 total 3 2 8. Are special foundations required ? No No Yes No 9. Cooling system Water Water Water-cooled Air cooling 10. Belt or direct drive Belt drive Belt Low pressure compressor Direct drive Belt Booster compressor Belt drive Integrated system Dimensional and thickness measurements for plastic containers and preforms. • Repeatable • Accurate • Precise • Fast GAWiSD +1.724.482.2163 AGRINTL.COM SEE GAWIS4D IN ACTION","@ID":35}, "INSPECTION 17 PETplanet Insider Vol. 21 No. 07+08/20 petpla.net Inline leak testing of colourful PET bottles Detecting pre-defects Allvig says that it provides its customers with advanced and sophisticated optical control systems for inline quality assurance in manufacturing. Allvig has many years’ experience in quality assurance. Its systems for inspecting transparent lenses, shrinksleeves in the shape of plastic cups, PET bottles and caps now include artificial intelligence capabilities that operate in ways similar to human cognition. The company says that its combination of “innovative optical technology and tried-and-tested proprietary software” enables it to deliver reliable systems tailored to customers’ specific needs. Inline leak testing of colourful PET bottles Its recent “Inline leak test of colourful PET bottles” project, which was designed to facilitate production process optimisation, incorporated the company’s ‘double level inspection’ quality control strategy. The first step covers inspection and rejection of defective parts; the second is preventive investigation: one of Allvig`s strengths is the detection of low-contrast and intricate defects by finding them at the beginning phase of the production process, tracking down and detecting defects before they arise. The system searches for areas or tiny spots that indicate anomalies, even before dents or scratches become visible. When such a pre-defect is detected, the operator receives an alert and can calibrate the production machine to prevent the accumulation of additional defects. This strategy helps to reduce waste and save production costs. Allvig says that its systems, equipped with proprietary optical inspection technology, help manufacturers overcome one of their biggest contemporary challenges: reliable defect detection while minimising pseudo-rejections. This helps to reduce waste to a minimum which benefits the environment and also results in substantial production cost savings. Allvig systems can be integrated in any existing production machine, on conveyer belts or into handling and robot systems. Bespoke modifications available range from process speed and product size to specific contrast detection. Statistical data are automatically logged during processing to establish traceability. The user interface is claimed to be easy to use and available in customer languages. The company’s turnkey solution includes a personal access service, with 24/7 technical support. www.allvig.com INSPECTION","@ID":19}, "MARKET SURVEY 32 PETplanet Insider Vol. 21 No. 07+08/20 petpla.net 07+08/2020 MARKETsurvey Resins & additives Preform machinery Preform production & inspection Preform & SBM mould manufacturer SBM 2 stage Compressors Caps & closures & inspection Filling equipment & inspection Recycling Palletising & shrink film machinery Compressors Compressors – not often in the spotlight perhaps, yet a vitally important component of PET production, and with significant potential of energy saving. Our annual market survey takes a closer look at these unsung heroes of the PET industry, featuring six compressor manufacturers and their product range: ABC Compressors, Kaeser Kompressoren SE, Siad Macchine Impianti, AF Compressors - Ateliers François S.A., Hertz Kompressoren GmbH and Nanjing Shangair Machinery Manufacturing Co.,Ltd. Although the publishers have made every effort to ensure that the information in this survey are up to date, no claims are made regarding completeness or accuracy. Company name ABC Compressors Kaeser Kompressoren SE AF Compressors, Ateliers François S.A. Postal address Telephone number Web site address Contact name Function Direct telephone number E-Mail Pol. Ind. Azitain 6, 20600, Eibar, Spain +34 943 820 400 www.abc-compressors.com Mr Gonzalo Gabarain Sales & Marketing Manager +34 647 413 760 [email protected] Carl-Kaeser-Str. 26, 96450 Coburg, Germany +49 9561 640 0 www.kaeser.com Mr Henry Beyer Produkt Manager Kolbenkompressoren +49 9561 640 5017 [email protected] Ateliers François, Rue Côte d'Or 274, Liège B-4000, Belgium +32 4 229 70 10 www.afcompressors.com Mr Pascal Heyden Marketing Manager +352 26 95 66 28 [email protected] 1. Machine designation / model number Horizon | Horizon LP Sigma PETAir CE & L (high pressure) OPC (low pressure) 2. Number of models in range 30+ models 25 30 high pressure, 24 low pressure 3. Output in m³/hour 250 - 6,000 336 - 2,772 150 - 3,300 (high pressure); 432 - 3,480 (low pressure) 4. Compressor type Oil-free reciprocating piston compressor \"all-in-one\" skid Low pressure air Low pressure oil-free piston compressor Screw type 7 - 10bar High pressure blowing air (up to 40 bar) High pressure oil-free piston compressor (atmospheric up to 40bar) Piston type 20 - 40bar Integrated system Atmospheric compressor including VSD with largest regulation range from 20% to 100% of the capacity All in one system, high & low pressure simultaneously 5. Lubricated or oil-free 100% oil-free compressor class 0 Low pressure compressor 100% oil-free compressor class 0 Lubricated Oil-free 6 - 15bar Booster compressor Not needed Lubricated Oil-free 0 - 40bar Integrated system Atmospheric 100% oil-free compressor class 0 6. Machine layout Horizontal opposed cylinders, forces balanced and virtually no vibrations \"V\" (2 cylinder), \"W\" (3 cylinder) L shape 7. Number of compressor stages 2 for LP and 3-4 for HP 1+1 3 (20 - 40bar) or 2 (6 - 15bar) 8. Are special foundations required ? No, virtually no vibrations No No 9. Cooling system Water cooled (closed cooling tower or aerocooler) Air (water option) Evaporative or radiator system 10. Belt or direct drive Direct drive V-belt transmission Low pressure compressor Direct drive Direct V-belt transmission Booster compressor Not needed Belt 0 - 40bar, V-belt transmission Integrated system Direct drive","@ID":34}, "INSPECTION 23 PETplanet Insider Vol. 21 No. 07+08/20 petpla.net Inspecting the base with liquid lens technology The base inspection on the Pilot Vision+ system incorporates a powerful set of inspection algorithms that identify the smallest defects and anomalies regardless of base size, shape or design. The base inspection features a liquid lens that adjusts focus for bottle heights from five to sixteen inches, without mechanical components. This feature eliminates the need for mechanical lens adjustment when changing between containers of different heights. Focus settings are saved with each job and focus is automatically adjusted to accommodate new container heights. This saves changeover time and ensures a clear, high-resolution image of the base at the start of production. The highresolution imaging is important when managing bottles with high percentages of rPET where the presence of small particle contaminants can increase the incidences of holes in To the colour preform cameras and liquid lens technology for base inspection, the Pilot Vision+ offers features that include: Large, touch-screen user interface with all data accessible from the main screen Compact LED light panels Pre-built tool sequences provided for each inspection type Flexibility to adjust parameters using live and history images during production Full-colour preform imaging for colour management Active cooling for high temperature operation Sealed components to prevent damage from fluids and moisture the highly stretched regions of the foot and base. The Pilot Vision+ system offers a number of tools to assist operators with setup and job management. These include adjustable ROI tools, digital image filtering, zone scaling and the ability to display live and historical inspections images that can be used for evaluation or setup purposes. To aid operators in monitoring line status and assessing production trends, detailed defect and reject information and production-run data summaries are continuously updated. Defects are correlated to the mould/ spindle to easily identify the source of a defect. Defects are categorised using colour codes for quick and easy identification of offending characteristics. The Pilot Vision+ system is another segment to Agr’s Process Pilot family of products, designed to provide comprehensive material distribution monitoring, automated blowmoulder management and vision–based defect detection. Agr International Inc., develops and manufactures a full line of laboratory and on-line testing/quality control devices for containers and similar products www.agrintl.com compatible with all range Ask more information about HORIZON DUOO to our commercial department:","@ID":25}, "SURVEY PETplanet Insider Vol. 21 No. 07+08/20 petpla.net 34 Focused on feedstock affordability and low-margin converting Russian PET market by Maria Dimenko, Alina Ilyicheva, Creon Market Monitor The 15-20% increase in demand for plastic packaging in March and April has revived the PET market, and in May Russian feedstock producers raised the prices. Since then, many converting companies switched to more affordable supplies from China; the local PET market became loose. The bottle-grade PET accounts for about 94% of virgin PET market volume in the consumption structure of the Russian market, and the remaining 6% belong to fibre, sheet and film-grade PET. Currently, the total capacity for PET production in Russia is 635,000 t. In 2019, 602,000 t of virgin PET was produced. That was slightly lower than in 2018, and was caused by the unplanned turnaround at Polief plant. Market participants interviewed by Creon said that due to self-isolation and rainy season, the sales of PET-bottled soft drinks had dropped by more than 25% compared to the same period of previous year. At the same time, Russian producers of feedstock raised the spot prices in March and April anticipating increased consumption. After that in May, converting companies switched to lower-priced virgin PET from China, where the output grew since the quarantine had been lifted. This situation led to the stocked warehouses and oversupply in the market. “Russian producers of feedstock raised the price too high, and converters started imports from China, so the import share in the PET segment was large in the first five months. By the end of May, Russian producers lowered the prices, and locally produced PET will be back in demand again gradually. The situation was disturbing, as this was the way to lose your clients; suppliers’ strategy was wrong as they expected the short-term profit”, said the source in the market. Indeed, in the first week of June, the spot prices of Russian producers fell from 80,000 rubles per ton [992 EUR] to the level of contract prices at 72-74,000 rubles per ton [893-918 EUR]. Decline in soft drinks, growth in packaging Consumption of carbonated soft drinks has suffered most notably, first of all in the premium segment. “Consumers started cutting expenses, and the premium segment was affected the most. Roughly speaking, children would get their soda, but in a cheaper category”, said one of the sources in the market. The PET demand saw changes in the bottling size in favor of larger volume: while 0.33 l bottles were more popular earlier, the trend is now shifting towards larger bottles, 1 l to 5 l. However despite a significant reduction in the demand in May, the PET converters are expecting recovery this summer, assuming hot weather. “We expect to be revived when the heat comes”, the expert says. “If we compare monthto-month data, the market is down, but if we compare the period of January-May, we see an increase of about 10%”. Experts also noted the increase in demand for PET packaging: “We see that plastic is back, it’s everyone’s good friend again”, says the manufacturer of PET packaging equipment. In March/April, the demand for food-grade plastic packaging grew sharply. However, already in May, this segment lost 75%, since street trade was suspended and restaurants were closed. “Overall, consumption patterns have changed a lot: “eat-togo” has gone completely, although earlier it was developing rapidly. Restaurants are closed, people are sitting at home. For example, demand for sunflower oil went up first, and then it fell. We can’t compare 2020 and 2019 data, as they are radically different”, - said the major producer. Where does the market go Market participants are cautious in long-term forecasts. However, new production lines, equipment and recycling projects are being planned, and new players are emerging. “This year we are not expecting large investments, but the overall trend is towards investing in production, converting and recycling. And this is real money”, says the industry expert. To date, pharmaceutical and food sectors remain the most demanded, showing an increase of about 20% since March due to the explosive demand for personal protective equipment and online delivery services. Russian converters also increased output of PET sheets during pandemic, as these are now widely used in shops, banks, gas stations, and other places where physical contact between people needs to be prevented. Ekopet company has increased daily production by 4.5% and, according to Alexander Anikeev, general director, at the moment the operation rate stands at 109%. Overall, experts agree that the packaging market will continue to grow, but its focus will shift towards cheaper and lower-margin packaging. “We still believe that new capacities for PET production and converting in Russia are needed, as the demand will recover, and the lobbyist attempts to restrict plastic packaging have gone quiet. Globally, PET is oversupplied, so the import alternative will remain affordable, but for the Russian market to develop, it needs locally produced granules, preforms, and converted products even more. Moreover, I hope that the share of recycled PET will increase and find its demand”, said Nikolay Asatiani, CEO of Creon Energy Asia. www.creon-conferences.com/en","@ID":36}, "PETpatents www.verpackungspatente.de PETplanet Insider Vol. 21 No. 07+08/20 petpla.net 56 Bottle pack Internal Patent No: WO 2019/241246 A1 Applicant: Jeffrey Meyer, Pormona (US) Date of application: 11.6.2019 The front and rear of the drinks’ bottles feature a kind of dovetail arrangement. Bottles can thus be easily attached to one another without any additional fitment or worn on a belt with a corresponding clip. Bottle as a mobile phone support Internal Patent No: WO 2019/237895 A1 Applicant: Zhu Lou, Liaoning (CN) Date of application: 22.5.2019 Casually watching a video on a smartphone with both hands free is possible with this specially shaped bottle. The phone can be placed horizontally into the base and slotted in at an angle in the corresponding recess. Compensation surface shape European Patent No: EP 3564141 A1 Applicant: Suntory Holdings Ltd, Osaka (JP) Date of application: 25.12.2017 A weight-reduced PET bottle with improved durability achieved through the special shape of its base and compensation surfaces. Along with the extra stability, the compensation areas also enhance the bottle’s appearance. Moulded plastic bottle shape European Patent No: EP 3564142 A1 Applicant: Suntory Holdings Ltd, Osaka (JP) Date of application: 22.11.2017 A plastic bottle with a base mould shape which retracts in a particular way when reacting to changes in pressure. Various straight and curved areas are provided in the base area for this purpose. Light but sturdy bottle Internal Patent No: WO 2019/228741 A1 Applicant: Société des Produits Nestlé, S. A., Vevey (CH) Date of application: 2.5.2019 A weight-reduced PET bottle, the outside of which is shaped to meet supply chain demands. The grip area is specifically designed to avoid giving way when held. Monitoring re-use Internal Patent No: WO 2019/246342 A1 Applicant: Amcor Rigid Plastics, LLC., Delaware (US) Date of application: 20.6.2019 A QR code is incorporated within the surface of this reusable plastic bottle enabling it to be identified and in so doing keeping track of its history.","@ID":58}, "51 PRODUCTS PETplanet Insider Vol. 21 No. 07+08/20 petpla.net PETproducts Non-nylon based PET oxygen scavenger with lower haze and less impact on recycle stream Avient announced the launch of ColorMatrix Amosorb 4020G, a non-nylon based, low-haze oxygen scavenger for PET rigid packaging. The new 4020G grade offers up to 50% lower haze and reduced impact on the PET recycle stream compared to previous grades, while maintaining the same reliable active oxygen scavenging performance, as the company states. Additives are often included in PET packaging to help protect contents and extend shelf life, but they can decrease packaging clarity. This in turn affects consumer perceptions of product appearance and brand value. To support the move toward a circular economy, governments are legislating increased levels of recycled material in single-use packaging. For example, an EU directive for use of rPET in beverage bottles will increase from 25 per cent in 2025 to 30 per cent in 2030. As a result, brand owners need to ensure the oxygen scavengers used in their PET bottles maintain efficacy as increasing levels of rPET are introduced. Avient testing shows that ColorMatrix Amosorb 4020G is a robust oxygen scavengers for PET rigid containers, with negligible effects on efficacy for the rPET grades tested, while other competitive materials lost almost all oxygen scavenging ability with rPET content as low as 20 per cent. ColorMatrix Amosorb 4020G is available with applicable regulatory approvals. www.avient.com New application for trinamiX NearInfrared Spectroscopy: plastic sorting trinamiX GmbH, a wholly owned subsidiary of BASF, announced it has developed a new application for its mobile Near-Infrared (NIR) Spectroscopy Solutions related to plastic sorting and recycling. Using trinamiX technology, the diverse compositions of different plastics can now be precisely determined and thus distinguished via the simple use of a portable handheld device that combines trinamiX data analysis with a mobile app, states the company. NIR spectroscopy is a proven technology and used in laboratories around the world – the innovation is the portable format of the spectrometer and the sophisticated data analysis that can now be processed in the field via wireless cloud uploading. Slightly larger than a mobile phone, the spectrometer has nearly universal use cases. With the help of trinamiX NIR Spectroscopy Solutions, all common plastics are said to be now identified within seconds. The spectrum ranges from classic polyolefins such as PE, PP and PVC to PET. In addition, technical plastics such as or PA can also be correctly identified in the field (especially in blends with other plastics). trinamiX can integrate additional materials according to customer requirements. The company states that wherever quick identification has an advantage, the trinamiX solution is a good decision aid. In recycling, for example, it is aimed at companies that do not need a large, stationary sorting plant, but a flexible and mobile solution. Examples include recycling yards and plants as well as manufacturers of recycled goods. The solution is also interesting for decommissioning companies and large dealers. www.trinamiXsensing.com","@ID":53}, "BOTTLE MAKING 43 PETplanet Insider Vol. 21 No. 07+08/20 petpla.net from KHS. Arne stated that the colour variation results in more heat absorption, and this means more material in the shoulder area of the preform. The pyrometer at the end of the oven can only adjust an average of the preform temperature. If the quality of the bottle is not sufficient during this phase, additional hardware can help, added Arne. With the process pilot and mould control the machine can react much faster on colour variations in the preform. The Process Pilot can improve CPK (process stability) by 28%, the Unit Mould Control can improve CPK by 16%, and the overall CPK is thus improved by 28%+16% = 44%. Another important question is the impact on the IV. During the heating process and the material distribution there was no difference compared to the virgin material measured. Differences could be measured on bottle performance due to the different IV´s of the material. Arne’s suggestion here is to ensure that the IV never drops below the critical level. Arne’s conclusion on the quality of an rPET bottle: There can be variations of material distribution and the IV, but problems only occur if minimal requirements are no longer met. The rPET bottle helps to close the loop for recycling. Switching from PET to rPET should not just be about a change in material. It also makes sense to improve bottle design in terms of less weight. The questions that followed centred mainly on possible applications of rPET in various filling products. The proportion of rPET and its resulting appearance was also discussed. The main topic in the Q and A session was the comparison between rPET and brand-new bottles. Are mechanical properties such as top load, stress crack results etc comparable? The audience also wanted to know which countries allow rPET in food and whether biograde or rPET is the better option in terms of sustainability. We thank the speakers and the numerous participants for their interest and the exciting discussions! Both presentations can be found at: petpla.net Tour Sponsors: The man behind the seams Mr Mundhra has been producing PET cans for three tennis balls since 1988. The cans are sealed with a fully opening aluminium lid. Inside the can, there is an excess pressure of around 1 bar, so the packaged tennis balls do not lose their internal pressure. To maintain this internal pressure, the rim of the PET can must be very precise. The aluminium lid is attached in two steps with a lock seam, like a classic metal can. The can has a champagne base, which is able to equalise the internal pressures inside the can. Transpet Jaipur, June 2019 We met: Mr. S.K. Mundhra, B.E. Elect. Director Over the course of the last 30 years, many offshoots have developed from the tennis ball can. Cans without internal pressure are among his bestsellers. He offers a standard range for bulk materials, such as seasonings. These always come with a suitable lid and, when required, also an appropriate seal. Alongside his standard range, he develops customer-specific applications, which might be cans for CSD or cans for ball bearings. Mundhra builds his own tools for this that are then passed on to the customer. Embossing is also an option. Common to all cans is the absolutely precise rim, onto which standard removeable aluminium or tin plate lids are crimped. The bases are different depending on whether the filler is under pressure (pressure equaliser base) or whether the filler is in the can without excess pressure. His vision is to develop a can in the near future, which can be hotfilled with juice. www.transpetcans.in From left to right: 200ml can filled with screws. This protects the screws from corrosion. 330ml can for CSD with standard drinks lid, customer based in Dubai; it all started with the three-tennis ball can; the small can is oil-proof packaging for ball bearings; The bestseller from the standard range is the can for dry food.","@ID":45}, "MATERIALS / RECYCLING PETplanet Insider Vol. 21 No. 07+08/20 petpla.net 26 Cyanoacrylate UV blocker promises good processing features and long wavelength coverage A new UV blocker for PET PET as a substrate, made in films or containers, provides great transparency, atmosphere barrier and mechanical strength for various applications. An addition of UV blocking is necessary everywhere where UV sensitive ingredients such as vitamins, colourants or fragrances have to be protected from degradation. PET films completely covering 400nm or beyond are allowed more potential usage to protect human eyes from frequent usage of 3C devices. Chitec Technology has filed a patent for its first cyanoacrylate UV blocker and launched Chiguard GA403 at K2019, aiming for good processing possibilities and long wavelength coverage. UV is commonly considered a radiation from the sun, and organic UV absorbers are recognised for prolonging polymers service life, retaining colour stability, gloss and mechanical strength and so on. Commercially available UV absorbers developed from various compounds such as benzophenones, benzotriazoles, hydroxyltriazines, cyanoacrylates and others are each having its unique absorption ranges and limitations. These chemicals are recognised as being highly efficient at absorbing high energy UV light and dissipating it as heat which is then released. Chitec Technology has been heavily involved in organic UV absorber studies for decades, and pushed for long wavelength absorption especially suitable for PET substrates. When it comes to PET, many UV absorbers are not considered suitable because they cannot meet the required temperature of 230°C or higher. Amongst the choices available, many benzotriazoles, benzophenones are regarded as being unsuitable because of their low decomposition temperature and often cause yellowing. Amongst the most popular UV absorbers used in PET resins are 2-(2H-Benzotriazol-2-yl)-4,6-bis(1methyl-1-phenylethyl)phenol (CAS no. 70321-86-7) 2-(4,6-diphenyl-1,3,5-triazin2-yl)-5-[(hexyl)oxy]-phenol (CAS no. 147315-50-2) or 2,2 ′ -(1,4-Phenylene) bis[4H-3,1-benzoxazin-4-one] (CAS no. 18600-59-4), all of which are able to sustain processing temperatures above 300°C. Of the organic UV absorbers available, many have peak absorptions around 330~350nm but when bottle producers require a 380nm~400nm cut off, very few UV absorbers can be used. Cyanoacrylate chemistry has been selected as industrially approved safe for food packaging usage with superior long wavelength coverage. This is essential to protect nutrition ingredients or retain colourants stability, which are sensitive to UV. Chitec studies have shown that absorbing blue light ranges up to 410nm is also achievable. This unique performance is all the more interesting as we are surrounded in our daily life by mobile 3C devices with large LCD screens. One of the critical breakthroughs of this new compound is the peak absorption at 363nm as shown in Fig. 1. When long wavelength coverage is considered, especially 380nm or above, peak absorption wavelength plays a decisive role in efficiency. From an organic chemistry perspective, however, attempts to redshift 5 or 10nm from any existing chemicals are not easily achievable. With some dosage options in 1mm thickness PET specimen, Chiguard provides complete coverage of the UV spectrum from 400nm and below as shown in Fig. 2. To achieve the same performance with other UV absorbers, a much higher dosage is required, which then has the possible side effects of yellowing or blooming. Chiguard has a 10% weight loss at temperatures above beyond 350°C, which is manageable for PET compounding process. Thermal stability of UV additives is recognised as another important factor. Chitec states that Toray’s study (extracted from US20150183957A1) gives a good understanding of the benefits of using UV absorbers during the polymerisation process compared to commercially available UV masterbatch. At a temperature of 280°C maintained for several hours, there is an inevitable loss of UV absorbers when polymerisation is carried Fig. 1 Fig. 2","@ID":28}, "BOTTLE MAKING 39 PETplanet Insider Vol. 21 No. 07+08/20 petpla.net From beverage manufacturer to market leader Fruit juices for India and further afield by Kay Barton In the Andheri East district of Mumbai, near the airport and the key Western Express Highway transport artery, is the headquarters of the beverage and preform manufacturer Parle Agro. The company, which is owned and managed by the Chauhan family, has 84 production facilities and has a strong claim to being the biggest bottler of beverages in India. Its main lines are Fruit Flavoured Still Drinks (FFSD), along with sparkling fruit drink and packaged drinking water. Parle Agro also supplies preforms and beverages of various types to the local market and more than 50 countries worldwide, including the UK, USA and Canada, Australia, various countries in Africa, the Gulf region, and in Asia. Interview with Parle Agro Pvt. Ltd December 2019 We met: Mr Prakash Chauhan, Executive Chairman Ms Schauna Chauhan, CEO The company has responded to the trend for smaller beverage volumes with a 200ml PET bottle, which has been very well received, and is following up that success with a newly-developed 160ml bottle. We visited the company in the home city of Bollywood and talked to Executive Chairman Prakash Chauhan and his daughter Schauna Chauhan, the current CEO, about market demands and developments, and why success isn’t possible without taking risks. From the beginning… The history of the Parle Agro Group goes back some 90 years. The company primarily operated in the confectionery business; its beverages line was launched in 1959 by founder Jayantilal Chauhan. The business really began to take off with the 1985 launch of “Frooti”, a mango fruit juice drink, under the leadership of now-Chairman Prakash Chauhan. It was joined a year later by “Appy”, an apple-flavoured alternative. Both were packaged in Tetrapak beverage cartons. “At that time, I was the first person to bring Tetrapak to India. Amajor share of our best-selling beverages are packaged in cartons but PET is clearly the leader in all of our segments, now,” Mr Chauhan explained. The company installed its first PET line in 1996, centred around a 48-cavity Husky LX system and Sidel blow moulder. Parle Agro was among the pioneers of PET in a packaging market that was, at that time, dominated by PVC. “We started by converting the PVC bottles for “Bailley”, our water product, to PET,” he explained. “The Bailley brand had been on the market for three years by then. In 2002, we made Frooti the first fruit juice to be packaged in PET in India. In 2005, we introduced a sparkling fruit drink version of Appy, “Appy Fizz”. Tour Sponsors: Parle Agro’s CEO Schauna Chauhan Executive Chairman Prakash Chauhan","@ID":41}, "INSPECTION 20 PETplanet Insider Vol. 21 No. 07+08/20 petpla.net Automated pressure testing For many years there has been a requirement for pressure testing on PET containers. The required test procedures are often driven by the brand owners creating consistent standard from customer to customer. Given the obstacles faced in recent months, maintaining high levels of production and quality control with existing manpower is a huge challenge. How can more testing take place as production levels increase, design parameters change, or insufficient manpower levels are present? INSPECTION Torus’ answer is automation. Providing more autonomous production and inclusion of industry 4.0 concepts is a target for most manufacturers, a direct payback on the investment of efficient production equipment is easily justifiable in terms of increased sales, reduced scrap, and/or better efficiency. When it comes to container quality control, there has not been a viable fully automated solution on the market. There are still large variations in container testing methods, ranging from completely manual checks such as hall effect thickness gauging and Vernier callipers, to faster vision systems and advanced sensor technologies which have created that next step in terms of efficient and repeatable processes. Pressure testing in simple terms is carried out by displacing the air inside a container with water, pressurising that water and recording the expansion and pressure to yield. Incorrect process control can cause failures in the base of the container creating a package that is more suspectable to failure at low pressures. This testing process is accepted and sufficient to feedback data to production and therefore make process changes where required. Development of new quality control equipment has been a focus for Torus Measurement Systems. Whilst reviewing all aspects of quality in rigid plastic packaging it was evident that having an operator stand and load containers into a burst tester, wait for 60-120 sec. for the test to complete before loading the next container was an efficiency problem for most manufacturers. In addition to this, blow moulding machines are getting faster and cavitation is growing, which is expected to continue as production equipment suppliers develop and look for improvements. If automation in production is demanded, then quality control should follow suit. Torus have developed their TQ-Lab, which offers automated quality control for dimensions, thickness, internal diameter, top load, volume capacity, weight, to now include automatic burst pressure and volume expansion. This ‘all in one’ total quality machine can handle up to 50 cavities in one batch providing reliable statistics without operator intervention. Data handling processes can be streamlined by connecting the machine to the factory network and reporting directly into an ERP or SPC package. The system configuration is modular allowing customers to choose their level of automation. If the requirement is purely to automate the burst test function, then a single module system can be offered. Blanks can be provided for future expansion of the system giving the customer future flexibility to include other important tests without having to invest again in another full system. www.torus-group.com","@ID":22}, "MATERIALS / RECYCLING 29 PETplanet Insider Vol. 21 concrete solutions to balance out the existing financial disadvantage between the use of post-consumer recyclates (PCR) and of new goods in Germany. “The ecological differential in the purchase prices could be incorporated in the Packaging Law in Paragraph 21 in the form of a fund to which all producers would have to contribute. Only those who use recyclates should receive reimbursement. Additionally, a plastic tax could be introduced which would apply only to new goods, something Italy plans to do. That corresponds to cutting the subsidies for the manufacture of new goods in that the exemption from mineral oil tax and EEC levies no longer apply. The debated minimum utilisation rate makes sense only when combined with incentivisation for exceeding the minimum rate.” Michael Wiener, CEO of The Green Dot , says specifically about minimum utilisation rate: “The potential of the circular economy for climate protection, especially for plastic, has not yet been exhausted. We are missing out on the economic opportunities the circular economy offers. A circular economy that earns the name creates jobs and brings urgently needed added value into the European Union. Instead, we are experiencing a complete market failure. Recycled plastic saves up to 50% in greenhouse gas emissions generated by new plastic, but that is not reflected in the price. Politicians have to set defined recyclate utilisation goals for certain product groups in order to promote the creation of sustainable recyclate markets and provide the necessary investment security. In July 2020 the federal government will take over the EU Council Presidency – a good opportunity to advance relevant measures.” A stronger focus on sustainability in public procurement, a fund system, a new plastic tax for new goods and a clearly defined minimum rate for the use of recyclates combined with financial incentives are instruments that will save plastic recycling from extermination and, after the corona crisis, will ensure a stable, sustainable circular economy as an important contribution to climate protection. www.werner-mertz.com","@ID":31}, "imprint EDITORIAL PUBLISHER Alexander Büchler, Managing Director HEAD OFFICE heidelberg business media GmbH Vangerowstraße 33 69115 Heidelberg, Germany phone: +49 6221-65108-0 fax: +49 6221-65108-28 [email protected] EDITORIAL Kay Barton Heike Fischer Gabriele Kosmehl Michael Maruschke Ruari McCallion Waldemar Schmitke Anthony Withers WikiPETia.info [email protected] MEDIA CONSULTANTS Martina Hirschmann [email protected] Johann Lange-Brock [email protected] phone: +49 6221-65108-0 fax: +49 6221-65108-28 LAYOUT AND PREPRESS EXPRIM Werbeagentur | exprim.de Matthias Gaumann READER SERVICES Till Kretner [email protected] PRINT Chroma Druck & Verlag GmbH Werkstr. 25 67354 Römerberg Germany WWW www.hbmedia.net | petpla.net PETplanet Insider ISSN 1438-9459 is published 10 times a year. This publication is sent to qualified subscribers (1-year subscription 149 EUR, 2-year subscription 289 EUR, Young professionals’ subscription 99 EUR. Magazines will be dispatched to you by airmail). Not to be reproduced in any form without permission from the publisher. Note: The fact that product names may not be identified as trademarks is not an indication that such names are not registered trademarks. 3 PETplanet Insider Vol. 21 No. 07+08/20 petpla.net Our first PETinar on rPET took place at the end of May with 216 people attending. Our second event had 248 participants. While the issue of rPET attracted global attention (almost half of the active 216 participants came from Europe, with nearly 40% from Asia including Australia and 15 from North America), tethered caps were of particular interest to the 80% of attendees who came from Europe. 10% of those taking part were from America or Asia. This was followed by a lively internal discussion. How should the PETinar be structured? How long does it keep you glued to your monitor? Are you distracted by e-mails, questions from staff or telephone calls? Is having a lot of speakers in groups like a normal conference or focusing on two or three experts giving short presentations the right way to go? We decided on the latter. Participation was constant throughout the first PETinar which lasted for an hour. The same was true for the first hour of the second event. However, just 30 minutes later there were around 200 attendees online compared to the original 248 which suggests that an hour is a reasonable amount of time to set aside for such events. The worldwide response has shown that our approach was the correct one. Questionnaires issued after the event to attendees elicited a constructive yet diverse response for which we are very grateful. However, all were agreed on one point, namely that they would be taking part in the next PETinar. The PETinar’s conclusions can be found on pages 42-43 & 48-49. Yours sincerely Alexander Büchler Dear readers,","@ID":5}, "PETcontents 4 PETplanet Insider Vol. 21 No. 07+08/20 petpla.net 7+8/2020 INSIDE TRACK 3 Editorial 4 Contents 6 News 51 Products 54 PET bottles for Beverage + Liquid Food 55 PET bottles for Home + Personal Care 56 Patents TOP TALK 10 “More intelligent elements will be incorporated in future plant designs” - Interview with GDXL INSPECTION 12 What to expect when you are inspecting 15 Preform quality control - Sacmi presents four AI-equipped preform vision systems 16 Digital control system for PET bottle production 17 Detecting pre-effects - Inline leak testing of colourful PET bottles 18 Today’s next bottle inspection - The IMDvista Boco Scan 20 Automated pressure testing on PET containers 22 Meeting on-line rPET inspection challenges when producing PET bottles 24 Automated pull-off tester 25 Closing the PET cycle with sorting and material analysis systems MATERIAL / RECYCLING 26 A new UV blocker for PET - Cyanoacrylate UV blocker promises good processing features and long wavelength coverage 28 Is this the end of high quality plastic recycling? Demanding financial incentives and commitment from German government MOULD MAKING 30 Production of moulds accelerates - Expansion of established two-stage business with single-stage moulds 36 Label-less design - High resolution 3D bottle surface decoration via laser machining MARKET SURVEY 32 Suppliers of compressors 34 Russian PET market - Focused on feedstock affordability and low-margin converting PREFORM PRODUCTION 38 Preform production solution BOTTLE MAKING 39 Fruit juices for India and further afield 42 The first PETinar attracts more than 200 participants - rPET in stretch blow moulded bottles 43 The man behind the seams BOTTLING / FILLING 44 The Mega Factory - Edible oil in PET 46 There is a place in Amazonia... 47 New filling technology for ESL beverages CAPS & CLOSURES 48 PETinar: Tethered caps - An opportunity for compression and injection moulding? 50 Closures that flip, click, switch and flow BUYER’S GUIDE 57 Get listed! Page 18 Page 44 Page 56 INSPECTION","@ID":6}]}}
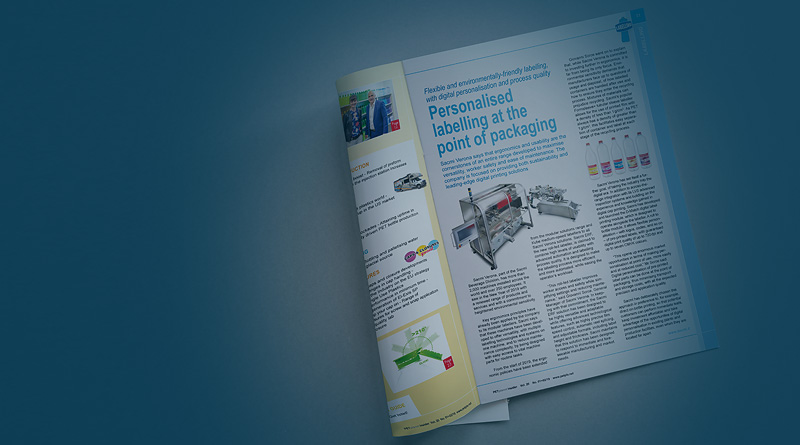