"imprint EDITORIAL PUBLISHER Alexander Büchler, Managing Director HEAD OFFICE heidelberg business media GmbH Vangerowstraße 33 69115 Heidelberg, Germany phone: +49 6221-65108-0 fax: +49 6221-65108-28 [email protected] EDITORIAL Kay Barton Heike Fischer Gabriele Kosmehl Michael Maruschke Ruari McCallion Waldemar Schmitke Anthony Withers WikiPETia.info [email protected] MEDIA CONSULTANTS Martina Hirschmann [email protected] Johann Lange-Brock [email protected] phone: +49 6221-65108-0 fax: +49 6221-65108-28 LAYOUT AND PREPRESS EXPRIM Werbeagentur | exprim.de Matthias Gaumann READER SERVICES Till Kretner [email protected] PRINT Chroma Druck Eine Unternehmung der Limberg-Druck GmbH Danziger Platz 6 67059 Ludwigshafen, Germany WWW www.hbmedia.net | petpla.net PETplanet Insider ISSN 1438-9459 is published 10 times a year. This publication is sent to qualified subscribers (1-year subscription 149 EUR, 2-year subscription 289 EUR, Young professionals’ subscription 99 EUR. Magazines will be dispatched to you by airmail). Not to be reproduced in any form without permission from the publisher. Note: The fact that product names may not be identified as trademarks is not an indication that such names are not registered trademarks. 3 PETplanet Insider Vol. 21 No. 11/20 petpla.net Nothing is the same as it was before the virus and this is especially true for trade fairs. The China Brew China Beverage (CBB) event recently came to a close. Due to entry restrictions into China, this year’s fair was a local event. It is hard to believe that drink industry representatives from all over Asia used to meet up there in years gone by. But the good thing is that the CBB was able to take place – one small step back to normality. However, the situation is quite different in Europe where the Brau Beviale trade fair in Nuremberg has been cancelled due to the increasing number of coronavirus cases. There had been plans to restrict the event to a few exhibition areas but it will now take place digitally. Here, a return to normality is still some way off. And what has the supply industry been up to? Trade fairs are always seen as an ideal opportunity to showcase new innovations and to chat to customers. Nowadays, communication is largely digital, with new developments being promoted, for example, in our PETplanet Insider magazine. In our last issue 10/2020, we featured the new Netstal line and Sipa injection compression moulding machine. Here, our focus is on digital printing of caps using CAPrint. All these technologies would normally have been the highlights of a trade fair’s exhibition. We hope that next spring’s trade fairs such as Interpack in Düsseldorf at the end of February and the NPE event in Orlando in May can be a step back to normality. It will be interesting to see just how much further ahead the Chinese are by then which we will see for ourselves at the Chinaplas trade fair in Shenzhen in April 2021. Let us all look forward to the time when bustling trade fairs with face-to-face contact are able to take place again. Yours sincerely Alexander Büchler Dear readers,","@ID":5}, "CAPS & CLOSURES 39 PETplanet Insider Vol. 21 No. 11/20 petpla.net PETplanet: These are the facts. But when listening to the industry, I hear general reservations being expressed about the value of digital printing, despite the fact that a number of companies have been trying to digitally print PET bottles on a commercial basis for years. Maibach: Printing on a bottle is more difficult to achieve over large areas. You have a 3-D rotation body which has relatively high geometric tolerances. This makes the printing technology and with it the machine extremely complex. The caps have an advantage in that only the upper surface is printed, essentially a 2-D print which you will recognise from your office or home printer. A sealing cap is also made within very tight geometric tolerances which means that the surface to be printed is always positioned directly under the printing head. In addition, our printer does not use mechanical holders for the closures, so there is no risk to damage the parts inside where the sealing is located. PETplanet: As a new company, how do want to go about making yourselves known to your customers? Maibach: Evolution over the last 5 years has taken place at IMDvista. The fact that the success of the technology has now been recognised by customers has enabled us to spin-off this business to CAPrint in 2020. This means that we can benefit from the developmental know-how and production potential of IMD Ltd while at the same time trading on the market as an independent company where we are setting up our own sales and service structure. CAPrint CAPrint 1.0 printing system is an digital printing system that uses CMYK colours. Hapa supplies the printing engine. White is also used to produce light print images on dark caps. Firstly, pre-treatment of the caps which reduces the surface tension of the plastic closure. Caps are then passed underneath the printing heads which are put in place in a row. Imaging how precise this movement must be, it is not surprisingly that this was one of the most difficult hurdles to take. Finally, curing takes place using UV LEDs. The configurated system is set up to produce printing speeds of up to 90,000 caps/hour, depending on size of the closures. The cap is moved on a conveyor belt underneath the printing heads. There is no manual handling, thereby avoiding any potential physical damage. The User Interface simplifies the use of the system and makes it an easy to run solution. CAPrint Ltd has been officially trading on the market since this summer and is a sister company of IMD Ltd. Matthias Hermle is President of both companies. www.caprint.ch Michael Krueger by the CAPrint system, examining printed cap. CAPrint system motan-colortronic gmbh - [email protected] www.motan-colortronic.com ETA plus® considerably reduces energy consumption and protects materials. Drying has never been this efficient: ETA plus ® LUXOR A","@ID":41}, "PETplanet Insider Vol. 21 No. 11/20 petpla.net 43 TRADE SHOW REVIEW tions. He expects that demand for PET bottles will remain tighter, and lower than the past, also in 2021. The audience again questioned whether consumers would be willing to pay a higher price for rPET. But all bottlers underlined that price was not a factor, but the culture and education on recycled materials. Eventually prices will be only be slightly affected or not at all. The final round table looked at environmental issues. Mr Hans van Bochove , VP Public Affairs EU, Coca-Cola, underlined that the movement towards sustainable packaging is facing hurdles with many regulations coming from governments. The media also criticised plastic heavily during 2019, but now the situation is changing. Packaging is 50% of CocaCola’s carbon footprint, hence its huge importance in the Group strategies. Mr Hikoji Kosaka , CEO of Toyotsu PET recycling systems, Japan, explained that his company was created by Toyota in July 2020, and the group intends to invest in a new production of 40.000mt/a of rPET, which will be starting operations in 2021.The availability of recycled materials is not sufficient, and more investments will be needed, not only in Japan but world-wide. Mr Renato Zelcher , CEO and President EuPC, was representing the European converters, who employ more than 1.6 million people. The packaging sector showed big resilience, as consumers returned to plastic, because of its image of safety and hygiene, and this led to increasing purchases of packaged food and beverages. On the other hand, a dramatic downturn was seen in the automotive and building sectors. Plastic tax may be kill off a significant part of this industry, since companies are uncertain whether investment in plastics in still worthwhile. Mr Antonello Ciotti , VP Corepla, attacked the concept of the plastic tax in Europe, which is to be applied at the beginning of 2021, but only in some countries. Nobody knows yet how it will be implemented and collected. There is huge uncertainty, and a total lack of harmonisation. Mr Werner Bosmans , EU Commission, tried to counter critics explaining that what EU commissioners are doing is to accelerate the birth of a circular plastic economy. It is necessary to find solutions against plastic littering, upstream and downstream. Already the measures against single-use plastics are in force, and soon measures to avoid dispersion of microplastics will come. EU is aiming therefore at recyclability and reducing marine litter (estimated 29 million tonnes in 2030). Mr Philippe De Baere , Partner of Van Bael & Bellis, focused on international trade measures. The main thing today is that duties will be abandoned to make way for trade measures on social environments. EU will move the playing field more aggressively into the suppliers’ environment, so affecting other areas around the world. That will influence social activities, job safety, pollution, recycling, and environmental activities in other continents, pushing exporters to the EU to comply with clear and sustainable behaviours within a wider social and environmental agenda. Discussions then became more heated as Mr Zanchi stressed that education is the key to reducing plastic pollution in the oceans and more should be invested in this. The plastics industry could invest any amount of money but if one don’t educate the consumer, the money would be wasted. Mr van Bochove agreed with this, claiming that it is also a problem of infrastructure: one cannot blame the plastic industry for littering. It is the litter that must be addressed. Finally, Mr Bosman acknowledged that educating the consumer is a huge and continuing task. In his closing address, Mr Zanchi thanked all the panellists for the excellent presentations and discussions, and wrapped up this special webinar edition of PET Day 2020 by underlining how all people are really in an era of huge transformation. “We have all to realise we are in a global village, one entity. Covid has greatly enhanced this concept. We have to achieve a circular economy but we also have to introduce a social circularity by supporting the poorer areas of the world that Covid is making even poorer. And this can be done by helping these areas to help themselves, and thus discourage people abandoning their homelands to face a sometimes perilous future.” www.gsiplastic.com","@ID":45}, "EDITOUR PETplanet Insider Vol. 21 No. 11/20 petpla.net 25 Young people make up the majority of the Philippines’ population. In 2019, the largest group (62.5%) were 15 to 64-year olds, followed by 32.7% under the age of 15. The average age of the population in 2016 was 23.4. More than 180 different languages are spoken, with Filipino based on the standardised version of Tagalong and English being the country’s official languages. The Philippines is one of the emerging economic nations in SouthEast Asia, although the gap between rich and poor is still very wide. There is also a strong north-south divide as development, modernity and economic activity are concentrated on the island of Luzon, while those in southern Mindanao are often poor by comparison and make their living through farming. The service sector is the main force that drives the economy, contributing around 60% of total GDP. The manufacturing industry makes up 30%, followed by agriculture, forestry and fishing. The rise of a more prosperous middle class is closely associated with the service sector. Traditional telephone services in which countries like India have long been dominant are being replaced by Philippine call centres. This is because of the availability of excellent American-English language skills, which are vital in providing telephone services for the US market. Software development, online services and tourism also play significant roles in the economy. The Philippines is facing a severe recession this year as a result of the pandemic. Years of stable economic growth of around 6.4 % up until 2017 have been followed by a 7.3 % fall in GDP as was predicted by the Asian Development Bank in mid-September. A weakening in the demand for exports to the country’s main trading partners, China, USA and Japan, disrupted Makati City’s economic and financial centre in Metro Manila","@ID":27}, "TOP TALK PETplanet Insider Vol. 21 No. 11/20 petpla.net 13 A. Funcia: At Sukano we work mainly in partnership with customers, developing dedicated product performance according to their specific needs. We certainly see a bright future, and we dedicate a lot of attention and work on products that support alternative ends of life, such as mechanical recycling and organic recycling (certified compostable), depending on what the end application of the final article and geographical location requires. Through masterbatch formulation, we design products that our partners can use to go monomaterial in PET, for instance our transparent impact modifier for cold application, which enable replacement of GAG films by fully recyclable PET designed trays, or our compostable certified PLA and PBS masterbatches portfolio for food packaging applications. In addition and aligned to the EU Green Deal strategy and recovery plan, we also have NIR detectable and certified blacks, colours and white masterbatches for bottle-to-bottle closed loop applications in PET dairy food. One of our key and most challenging projects is working in partnership with leading companies such as Gneuss and Illig, along with the support of Veolia, to supply the recycled PET flakes from the German yellow bags, to prove and manufacture thermostable CPET trays from recycled PET non-clear bottles. This is our vision: a world with dedicated economically viable PET waste streams to enable PET plastic parts to circulate, keeping them in the economy and out of the environment. PETplanet: Fortunately, when producing masterbatches and additives today, we also automatically think of recycling. You are very familiar with the topic of recycling. You lead the working group recycling of opaque and functional PET bottles at Petcore Europe. What are your tasks there and what results have you achieved in this working group? A. Funcia: Sukano is an active member of Petcore and I am the company´s representative at the association. Earlier this year I was kindly invited to take the role of Chairwoman of the Opaque and Functional PET bottles as Gian de Belder from P&G was assigned to another role. As a representative of the PET value chain players, PETCore focuses on ensuring that all PET article is responsibly placed in the EU market, so once it is collected, it can also be effectively recycled and returned into the economy or remain in the economy as long as possible. The overarching goals of our actions at Petcore are that all PET products meet European Regulations, meaning essential requirements to be fully recyclable. Specifically, to our opaque and functional bottles working group we have: MISSION- Identify, foster, communicate and promote outlets/end applications for non clear (opaques), sleeved and functional rPET bottles. And our Vision is “All opaque and functional bottles (and trays) are recyclable, collected and recycled”. We were already able to identify and quantify the amount of white opaque PET bottles available today in the market, per key EU member states, and we are now focusing via four task forces activities within the WG, in viabilising the effective recycling of white PET opaque containers using different business models, according to the infrastructure of each country identified as major consumers of white PET opaque. PETplanet: One last question for you: Where do you see the plastics processing industry in 10 years? - Besides Covid-19, what about the EU Plastic Strategy, the recycling industry and the trend towards a sustainable lifestyle? A. Funcia: At Sukano #wearepartofthesolution, all our action plans and strategic activities boil down into the same basket. We walk the talk, therefore we are confident that the world can and will co-exist sustainably with plastics. Not all plastics, that is clear. Not all formats and designs we live with nowadays. We believe in science! A rational and scientific based approach for a selection of the material and product design/structure will lead us positively into the direction of a waste-free and circular material environment where the society can benefit responsibly and jointly with the industry and government. PETplanet: Thank you very much! Read more about antiviral masterbatch solutions of Sukano: www.sukano.com/en/company/ news/sukano-masterbatches-demonstrate-long-term-antiviral-effect","@ID":15}, "MATERIALS / RECYCLING PETplanet Insider Vol. 21 No. 11/20 petpla.net 14 NGR’s LSP technology has proven itself worldwide Rapid IV build-up Austrian company Next Generation Recyclingmaschinen GmbH (NGR) has been implementing sustainable recycling systems for PET since 2014. The core of the technology is polycondensation in the liquid phase along with highly efficient decontamination, rapid IV build-up and stabilisation of the IV value. In contrast to conventional systems, such as solid state polycondensation (SSP), NGR uses P:React liquid state polycondensation (LSP), which can process up to 3,000kg/h. The process utilises PET’s tendency to rapidly condense in the melt phase, so that the IV value increases quickly and in line with requirements. The process begins with the PET scrap being melted in a standard extruder, such as NGR’s own P:Gran. From there it is delivered to the P:React reactor vessel, where the melt is purified and decontaminated under high vacuum with a controlled residence time. Different modular filtration technologies are used according to the degree of particle contamination. In the reactor vertical section the melt is divided into numerous individual strands, which then drop through the high-level vacuum, with an extremely high surface area exposure. The increase in surface area allows the contaminants to be quickly removed. The melt collects in the horizontal section, where it remains for up to 30 minutes. A slow rotating augur further creates surface area exposure to the vacuum, where polycondensation is completed. An example concept of a complete solution: Fig. 1 LSP schematic diagram NGR’s high-level vacuum removes nearly 100% of all critical impurities found in PET waste. The filtered-out substances are collected in a redundant filter system, where they can be cleaned out without interrupting operations. The LSP’s decontamination performance makes it open to a wider range of applications than other processes. The P:React has been successfully used in the film and fibre sector for several years already and NGR has installed several operating systems across the world for bottle-to-bottle recycling. More systems continue to being commissioned, as major beverage brand owners test, veryify and approve the LSP process for recycling post-consumer waste. LSP has also received food certifications such as FDA and EFSA. The main qualification that rPET must meet to achieve food-grade status is the extensive removal of all contaminants in a continuous process. The graph in fig. 2 shows that the decontamination levels achieved by the LSP exceed FDA requirements in all areas. This ensures that both post-consumer and post-industrial PET waste is transformed into valuable rPET, with consistent IV value and consistent food safety, in the shortest possible time. The importance of quality and IV value of the input material is minimised as the LSP can achieve up to 30% IV increase. The entire process takes only minutes, rather than the hours required by conventional SSP methods. Fig. 2 Decontamination performance, certified for 100% food contact Consistent output IV and melt quality is achieved with two control parameters: 1) Vacuum pressure and 2) Residence time in the reactor. LSP production is a continuous (rather than batch) process and requires no process aids, such as nitrogen gas. Taking advantage of the energy efficiency associated with such a short residence time, while avoiding the high costs of nitrogen supply, helps to achieve very low overall operating costs. Increased demand and the sensitive price structure of input materials, such as bottle flakes, require that continuous process, along with a high flexibility in the technology. The SSP process is generally used to produce batches whose quality depends essentially on the input material. Analyses have shown that, within any given batch of post-consumer bottle flake, there is considerable variation in IV level and degree of impurity. RECYCLING","@ID":16}, "MARKET SURVEY 32 PETplanet Insider Vol. 21 No. 11/20 petpla.net Company name Starlinger recycling technology Gneuss Kunststofftechnik GmbH Sorema Div. of Previero Srl. Postal address Telephone number Web site address Contact name Function Direct telephone number E-Mail Furtherstrasse 47, 2564 Weissenbach, Austria +43 2674 808 3101 www.recycling.starlinger.com Mr Paul Niedl Commercial Head - Division recycling technology +43 2674 800 3100 [email protected] Mönichhusen 42, 32549 Bad Oeynhausen, Germany +49 5731 5307 0 www.gneuss.com Via Per Cavolto 17, 22040 Anzano del, Parco (CO) - Italy +39 031 63491 250 www.sorema.it Mr Dario Previero General Manager +39 031 63491 250 [email protected] Bottle to granulate Four models: recoStar PET FG, recoStar PET FG+, recoStar PET (HC) iV+, recoStarPET (HC) iV+ Superior Input variable: collected pressed bottles, various colours Starlinger offers the engineering of washing lines and / or a turn-key project with components and technologies available on the market Engineering of washing lines with long term partners Variable quality of input material integrating bottles sorting Output: Granulate with approval Yes (decontaminated for food contact, IV increased, AA 1ppm, lowest VOC level) Yes Engineering and system integrated for complete system Capacity [t/a] 6,000 - 26,000t/a rPET pellets Up to 17,000 Up to 10,000kg/h Floor space [m²] Depending on design According to sizes of plants and customer buildings Which approvals Several USA/FDA(C-H),Austria, Germany/BfR, Ilsi, France/AFFSSA, Finland,Australia, Canada, Egypt, Japan, Switzerland, several LatinAmerican Countries (Bolivia, Brazil, Chile, Colombia, Ecuador, Guatemala, Peru); follows EFSArequiremens; several brand owners FDA, ESFA, INTI, brand owners (conf.) Depend on customer specifications Fresh water consumption per tonne output [m³/t] Depending on design Depending on bottle contamination Depend on input quality Consumption kWh per tonne output [kWh/t] Depending on design Depending on input material Depend on sizes and plant configuration Flakes to granulate Four models: recoStar PET FG, recoStar PET FG+, recoStar PET iV+, recoStar PET iV+ Superior Input variable: flakes, coloured proportion max 5%, not much chlorine Output: Granulate with approval Yes (decontaminated for food-contact, IV increased, AA 1ppm, lowest VOC level) FDA, ESFA(pending), brand owners (conf.) Capacity [t/a] 1,500t/a - 26,000t/a (7 extruder sizes) 200 - 17,000 Floor space [m²] 130m² - 540m² 30 - 80, depending on size Which approvals Several USA/FDA(C-H),Austria, Germany/BfR, Ilsi, France/AFFSSA, Finland,Australia, Canada, Egypt, Japan, Switzerland, several LatinAmerican Countries (Bolivia, Brazil, Chile, Colombia, Ecuador, Guatemala, Peru); follows EFSArequiremens; several brand owners FDA, ESFA (pending), INTI, brand owners (conf.) Fresh water consumption per tonne output [m³/t] Approx. 0.15 No fresh water needed Consumption kWh per tonne output [kWh/t] Approx. 410 (depending on design) 350 Bottles to flakes Input variable: collected pressed bottles, various colours Starlinger offers the engineering of washing lines and / or a turn-key project with components and technologies available on the market Variable quality of input material integrating bottles sorting Output: Flakes with/without approval Yes (decontaminated for food contact, IV increased, AA 1ppm, lowest VOC level) Engineering and system integrated for complete system Capacity [t/a] 3,700 - 10,500 (5 sizes) Up to 10,000kg/h Floor space [m²] Approx. 150 According to sizes of plants and customer buildings Which approvals FDA (hot-fill), follows EFSA requirements Depend on customer specifications Fresh water consumption per tonne output [m³/t] 1 - 2.5m³/t Consumption kWh per tonne output [kWh/t] 120 - 250 (incl. bottle washing to SSP) 220 - 270kWh/t Kind and quantity of detergents Confidential Removal of the organic residuals up to which size [ μm] Best results in industry. Values according to standards. Presetting residence time in the process Confidential Company also offers systems for: Bottle-to-film Yes Yes, mainly thermoforming sheet lines in direct food contact Engineering and system integrated for complete system Bottle-to-fibre Yes Yes, several lines under operation worldwide Bottle-to-strapping Yes Yes, several lines under operation worldwide Engineering and system integrated for complete system","@ID":34}, "EDITOUR PETplanet Insider Vol. 21 No. 11/20 petpla.net 26 Dimensional and thickness measurements for plastic containers and preforms. • Repeatable • Accurate • Precise • Fast GAWiSD +1.724.482.2163 AGRINTL.COM SEE GAWIS4D IN ACTION supply chains, strict lockdown measures, a decline in tourism, reduced income being sent home by Filipinos working abroad and lower consumption rates are all exacerbating the current situation. However, the economy should return to pre-Covid levels in 2021. The drinks’ world and PET There is one thing that has remained constant since our 2017 market report. Carbonated soft drinks (CSD) are still way out in front when it comes to consumption of nonalcoholic drinks in the Philippines. According to a report by Euromonitor in late June, CSD sales in 2019 comprised 4.86 billion litres, followed by bottled water (in 8 l packs) which comprised 2.86 billion litres. This is just what market experts had expected to happen here during our last on-site visit. Consumption of water is increasing as are non-CSDs, albeit on a smaller scale. Along with new market products and taste varieties, the industry reacted to the introduction of the sugar tax in 2018 by downsizing product content to minimise sugar tax impact, using different ingredients and producing healthier drinks which created markets in nearly every area. And these are almost literally catching on with customers. Changes in consumer trends in favour of online shopping, together with the building of new retail channels such as modern supermarkets, convenience stores and shops outside cities are ensuring ever-increasing outreach to the general population. According to a Euromonitor forecast for the rest of this year, there will only be a slight change in consumption of all non-alcoholic drinks. In terms of growth figures for individual drinks’ ranges this means a modest decline in CSDs, bottled water, ready-to-drink (RTD) tea, sports and soy drinks. Consumption of energy drinks is expected to remain at a steady level, with RTD coffee likely to increase by a few percentage points. The reusable glass bottle is still a firmly established feature in the Philippines unlike in many other countries. For CSDs in particular it is expected to have a 66% share of the packaging market in 2020, ahead of PET with 31%. However, according to Euromonitor, this could change again in favour of the PET bottle at some point as use of PET is anticipated to grow by 11%. For the water market, 98% is in plastics packaging which is mostly PET and 2% in glass. Here, the increase in PET use would be 12% and 9% for glass. PET bottles are almost exclusively used for RTD teas and coffees, i.e. 95% and Rice farmers at work Philippines bottled water packaging split (retail/off-trade unit volume) (Source: Market Research Company Euromonitor International)","@ID":28}, "BOTTLING / FILLING PETplanet Insider Vol. 21 No. 11/20 petpla.net 30 German Technology Innovative hotrunner optiRun The new Krones line is composed of: Contiform Bloc with Contiform 3 Pro blow-moulder, Modulfill filler and capper, directly block-synchronised with: a Prontomodul labeller featuring two cold-glue stations for paper labels Carboflow carbonator Two Variopac Pro packers, each one for shrink-packs and trays Robobox layer preparation unit Modulpal 2AC palletiser Kit system, the line’s efficiency and availability can now be verified in realtime as well on a smartphone or an iPad. “The organisational structure of Krones France means closer service support proximity and faster response times, really an excellent support. The supply of spare parts is very efficient, thanks to the nearby warehouse in Germany. What’s more, Krones’ online shop makes it easier for us to place an order and gives us a good overview of what spare parts are available,” explains Lilian Oyhenard. Open to new markets – despite the regional focus In 2015, the Ogeu Group has founded two small breweries in Hapchot and Belharra. “Craft beer fits in very neatly with our strategy of regional products. We entered this market at an early stage, because in France the craft beer is only just getting started,” explains Jean-Hervé Chassaigne. The capacity of the two breweries will shortly be doubled. Likewise since 2015, Ogeu has also been represented in Singapore through a joint venture with the French sea container group CMA CGM. “Ogeu itself has been operating in Asia for more than 15 years now. The internationalisation of our brands is the second major thrust we’re working on. Here we can build upon the globally excellent reputation of French mineral waters,” says JeanHervé Chassaigne. “But the group’s domestic sales are still preponderant, at around 85 per cent.” For the future, too, Ogeu has fully-formulated plans: the next stage on the roadmap is to expand the facility in Var for bottling private-label products; the family firm also intends to broaden its own product range, and is open for further acquisitions – less in its home market The Robobox grouping station and the Modulpal 2AC palletiser make sure that the pallets are properly stacked. of France than in Asia. Moreover, further subsidiaries in China, Japan and India are also being planned. www.ogeugroupe.com/en www.krones.com","@ID":32}, "51 ON SITE PETplanet Insider Vol. 21 No. 11/20 petpla.net Burkasan has chosen Tomra’s sorting technology Turkish company Burkasan is using Tomra Recycling’s sorting machines in its new plastic recycling plant. The plant, equipped with Tomra’s Autosort and Autosort Flake, is capable of sorting 5 t/h of waste (including PET, HDPE, PP), enabling them to be brought back in the loop and the economy for further usage. The new plastic recycling plant established by Burkasan with an investment worth TL 50 million (€5.4m) is the first recycling plant in Turkey which processes mixed plastic containers using an advanced sensor-based sorting solutions from Tomra Sorting and Recycling for the production of PET flakes and HDPE granules. Vedat Kılıç, Chairman of the Board at Burkasan, stated that with the investment in this new plant, all the facilities operated by Burkasan now process a total volume of about 15,000 t of materials per month. Detailing the operation in the new plant he added: “We are planning for our new plastic recycling plant to process 2,500 t of waste material per month and to thus obtain a minimum of 1,500 t of high purity PET flakes and HDPE granules. It is utterly impossible to achieve the same level of capacity and purity with manual sorting, regardless of the number of workers. Especially during the current pandemic and the need to adhere to strict social distancing guidelines, manual sorting turns out to be a very challenging and costly method and product quality cannot be guaranteed.” Tomra’s Autosort is located right at the beginning of the plant, following the pre-sorting operations which takes out fines, metals and 2 D materials. In the first steps of the process, machines such as a bale opener, magnet, eddy current and ballistic separator go into action and are followed by the main sorting operation which is performed by the Autosort machines. Only later in the line does Tomra’s Autosort Flake take over the task of burr removal, sorting material by colour, metal and polymer type. It can even detect the smallest pieces of foreign substances in the material mix. Vedat Kılıç said that mixed plastic bottles are sorted based on their polymer structure: ”For instance, when using conventional methods, PET and HDPE are transported on conveyor belts and sorted by manual sorters. However, it is not possible to consistently achieve the same capacity, quality and cost of product with manual sorting. By employing Tomra’s sensor-based sorting machines, PET and HDPE products are separated from other materials and subsequently sorted by colour. Using this automated process, recycled raw materials can be generated that have the same quality as the original ones. This automated bottle-to-bottle recycling process is being carried out for the first time in Turkey and it enables us to supply global brands, which are increasingly focusing on their environmental credentials and the use of resources, with high-quality products.” Upcoming plans: production of PET granulates Asked about future plans, Vedat Kılıç responded: ”Initially, we are focusing on obtaining high density polyethylene granulates and PET flakes, but our aim is to make an additional investment to produce PET granulates. In the medium-term, we plan to achieve ’bottle to bottle’ recovery. If the Turkish Food Codex gives its consent, we’ll target the production of raw materials for making PET bottles that can also be used in the beverage sector.” www.tomra.com ONsite RECYCLING +44 (0) 1254 584210 [email protected] petmachinery.com Active for over 25 years, our global network and specialist knowledge makes us the go-to company for the sale or purchase of a PET machine. Commercially savvy, we work closely with our customers and our global network, to make sure everyone gets the best deal. Providing comprehensive advice throughout your sale or purchase; we can arrange dismantling, loading, packing, shipping, specialist insurance and commissioning. If you have amachine to sell or you’re looking to purchase, please get in touch. THE INDUSTRY EXPERTS","@ID":53}, "CAPS & CLOSURES 40 PETplanet Insider Vol. 21 No. 11/20 petpla.net Interview with Michael Krueger, CEO, Corvaglia at the site of Corvaglia, Eschlikon PETplanet: You operate two CAPrint units in Switzerland and one in the USA. Is yours the showroom for the good people of Brügg? Krueger: Oh, good grief, no, despite it being close nearby! In our Swiss plant we have not manufactured a lot of printed caps until maybe 3 years ago. Before that we had focused on plain flat caps without any printing and sports caps in this location. Having agreed a targeted strategy to achieve significant growth in the caps market, we have done an assessment of printing technologies to evaluate which technology will help us better to achieve our growth plans. (Interview with Michael Krueger discussing the cap business, see p. 36) PETplanet: Why then a new technology system such as CAPrint rather than a commercially successful model that has been around for decades, such as pad printing? Krueger: We knew very well the pros and cons of ‘conventional’ cap printing technologies from our Mexican cap production site, where we manufacture printed caps since about 15 years. In Switzerland we have automated our entire cap production process which allows us to produce significantly more caps without increasing the number of employees on the shop floor. This is a MUST do in such a high wage country like Switzerland in order to ensure our competitiveness in the market. We could not afford a pad printing or offset system that typically require more manual interaction during operation. PETplanet: Does that mean that automated production was a major factor in your investment decision? Krueger: Unlike other users of the technology that might use digital printing predominantly for special images, we are also printing classic motifs that would also have been possible using other systems. Here we have an example of a pure white image on a cap without any gradations or even multicolours. So, yes, the ability to operate the printing technology in our automated production environment indeed was a major factor in our investment decision. However, we see the flexibility and quality that comes with this new technology as an additional benefit for sure. PETplanet: Has the new technology met your expectations? Krueger: There is always a risk that unexpected issues may arise when you walk new paths. But it is the only way to succeed to embrace the unexpected and solve the problems. The same was true here when we used a new technology as a workhorse in a high output 24/7 production. There were some initial problems, of course. But CAPrint did everything they could to solve the issues with an outstanding effort. We are still sure we have taken the right decision by investing in digital printing. www.corvaglia.com www.ngr-world.com The next dimension of PET recycling. Fully iV-controllable and 100% food-safe. It will not only satisfy, but also inspire. MEMBER OF NEXT GENERATION GROUP :REACTLIQUID STATE POLYCONDENSATION (LSP by NGR) PET in – Future out","@ID":42}, "BOTTLING / FILLING PETplanet Insider Vol. 21 No. 11/20 petpla.net 28 A new Krones PET bottling line replaces two existing ones at the Ogeu Group’s site in Quézac, France, with a customised block solution provided for the cold-glue labelling specified by the client. One of the last European’s wild corners Ogeu’s history began almost 200 years ago in the heart of the French Pyrenees. In 1820, a spa resort centre was set up around the spring in the eponymous town of Ogeu-les-Bains, followed later on by a bottling plant. The group itself was then formed after the Second World War, and has been family-owned ever since. Today, CEO Jean-Hervé Chassaigne and his sister Pascale Lapassade are carrying on the family tradition in the third generation. Ogeu’s market strength is a result of water brands from different regions – a segment in which the group nowadays is the market leader in France. “In view of the fierce competition, it doesn’t really make sense to try and establish a national brand,” says Jean-Hervé Chassaigne. Facilities all over the country The family firm fills water from and in a hugely diverse array of the country’s landscapes: from the Atlantic coast of Brittany in the north through the heartlands of the country with the Ile de France, all the way to the French Alps, the lavender fields and Mediterranean beaches of Provence, and the mountain ranges of the Pyrenees in the south. With a series of new acquisitions and start-ups, Ogeu has expanded the number of its springs, and nowadays operates six facilities for bottling mineral water. With a payroll of 200, the Ogeu Group achieves a turnover of around 80 million euros, from overall sales of 350 million litres. For this purpose, it operates 18 lines, eight of them for PET containers. It was back in 1971 that the group had commissioned its first PET bottling line. Now it has for the first time opted for a complete line from Krones. This was installed at the facility in Quézac, which Ogeu had taken over from Nestlé. It is located in the heart of the French Cevennes National Park, only around 100km away from the Mediterranean coast. This oasis of natural splendour is often referred to as one of Europe’s last remaining “wild corners”: the scenery is characterised by high mountains, deep ravines, tenebrous grottoes, untamed rivers, isolated mountain villages and uninhabited plateaus. New format, less weight Already before the take-over, the plant was filling carbonated mineral water in 0.33 and 1.15l PET bottles on two lines. One of the first goals of the new proprietor family was to replace the ailing small format by a 0.5l container and to fill both sizes on a single line. At the same time, the client wished to retain the design of the popular 1.15l customised bottle, and the paper labels as well – a rather unusual choice for PET containers. Ogeu also wanted to save weight at the preforms. So the group got in touch with Krones: the new line was supposed to be able to fill and package both formats cost-efficiently under the specified preconditions. Initially, Ogeu was thinking of an ErgoBloc L, in which the labeller is located between the blow-moulder and the filler: “Krones is the only vendor on the market that has mastered this technology,” comments Jean-Hervé Chassaigne. Because of the cold-glue labelling, however, Ogeu and Krones then opted for a Contiform Bloc with a directly coupled modularised labeller downstream of the filler. “We nonetheless achieved our goal of running the wet end with just a single operator,” explains Jean-Hervé Chassaigne. Together with the people at Krones’ container design team Ogeu took a long hard look at the 1.15l container, and at the base and the neck finish reduced the weight from 34 to 30g. The change-over to a short-neck closure produced additional savings. Short manufacturing and installation times After three months of manufacturing time, installation of the new line had already begun. “A mere three weeks later, the line was ready for commissioning,” explains plant manager Mickael Ferreira, and Jean-Hervé Chassaigne CEO Jean-Hervé Chassaigne is carrying on the Ogeu Group’s family tradition in the third generation.","@ID":30}, "MATERIALS / RECYCLING PETplanet Insider Vol. 21 No. 11/20 petpla.net 16 Recycling systems and auxiliary equipment Making the most of recycling material As recycling post-consumer plastics has become more important, Eisbär has developed systems to handle these materials’ special requirements, including equipment for processing flakes and cleaning different materials, leading to a higher quality of regranulated plastics. Eisbär Trockentechnik GmbH, which is headquartered in Gotzis, western Austria, around 30 km north of Liechtenstein, manufactures systems and auxiliary equipment that is designed to improve quality and productivity in the plastics industry. It has a particular focus on products intended to eliminate condensation on cooled moulds and during the drying phase of plastic resin manufacture. Its systems have high throughput capability, of up to 5,000 kg/h. The recycling range includes: Crystalliser The use of a crystalliser is essential in processing amorphous PET flakes. Eisbär’s crystalliser first puts flakes into a hopper, where they are subject to rotation mixing at temperatures of 130-140 °C for one to three hours, depending on the degree of crystallisation. The flakes are then ready for the next production step – usually, drying. Dryer GDS Drying of recycled flakes or granules is essential, in order to achieve a particular level of residual moisture, to clean the material or to reach a dealdehydisation. This process is an important step in meeting the requirements necessary to achieve food standards approval from FDA (U.S. Food and Drug Administration) or EFSA (European Food Safety Authority). Eisbär dryers are also used to remove contaminations from recycled plastics. The dryer is equipped with a slowly rotating adsorption wheel with a multitude of honeycombed, axially aligned tunnels and uses a continuous drying process to achieve residual moisture of 30ppm. Mixing and dosing units Eisbär mixing and dosing units are available in gravimetric or volumetric versions and in different sizes. They are especially suitable for recycled materials converters who often mix virgin and recycled materials to get the best results. Conveying systems Flakes and recycled granulates’ levels of bulk, density, flow properties and dust content extend across a wide range. Whatever the content, concentration and quantity, Eisbär equipment can process any and all free-flowing materials at rates up to 5,000 kg/h. Test centre Eisbär’s test centre, located at its headquarters, enables customers to undertake a range of different tests, with granules or flakes. The plastics are processed in a material dryer for a predetermined period of time and at preset temperatures. After completion the materials are ready to be analysed for any sort of contamination, in a chemical institute of their own choosing. Experience and knowledge Eisbär regards its experience, practical knowledge and clear focus on understanding customer needs as its core strength. The company presents itself as a flexible and reliable partner for new, competitive and energy-efficient tailor-made and bespoke system solutions. Digitalisation is one of its key competences; it employs clearly structured visualisation as well as operational data connectivity for efficient management, control and maintenance. www.eisbaer.at Eisbär crystalliser Mixing and dosing unit RECYCLING","@ID":18}, "PREFORM PRODUCTION PETplanet Insider Vol. 21 No. 11/20 petpla.net 22 We also developed an 8-cavity mould for an ergonomic grip over the same period”. Other machines were acquired over the next few years, e.g. from Sidel and the Indian machinery builder, SAP Blowtek. Integrated Plastics also signed a partnership agreement with the wellknown former boss of Sidel India, Mr Subba Bangera. Finally, from 2016 onwards, the company moved into increasingly competitive markets in terms of its production capacity by developing bigger cavities such as a 16-cavity mould for 2 l IMH bottles and the use of a rotary blower developed together with South Korean machine builder, SDB. Mr Mellen went on. “We applied for several patents after 2012 but kept our marketing and public relation plans on hold until 2018 to ensure we were able to enter the market with a technology that was proven to meet customer need, as well as being environmentally-friendly. In 2018, we finally acquired B&R Industries and Sangraal, Australia who were the original developers of early integral handle patents giving us 100% control of all patents, designs and prior art globally. We then launched the technology worldwide.” “Although licensing and development are Integrated Plastic’s two main business areas, in-house production currently also contributes 80% of the company’s overall turnover. Over time, the bottles came to the attention of decision-makers in Europe, Asia and the Middle East which culminated in all international patent rights being agreed in 2018. Since then, the company has held all the technology’s global patents, some of which date back to the 1990s.” The technology, process and application The exact process remains a company secret but according to Integrated Plastics, IMH preforms can be produced either on existing equipment with uncomplicated conversion achieved by simply changing the mould, or by purchasing a new injection moulding machine for dedicated IMH production systems. “Conventional PET injection moulding machines are standard here, while compatible preform moulds can be bought from our licence partners, Classic Tools, GDXL, Husky Injection Moulding, Kisan and Sipa. A special machine developed in partnership with the South Korean firm, SDB, is now used in the blow moulding process”, said Mr Mellen. “Two-stage ISBM machines can be fitted with 1, 2, 4, 6 or 8-cavities and can produce around 4,000 1 l bph in a 4-cavity configuration using the rotary system. A 12-cavity mould is currently being developed.” The standard portfolio range includes more than 25 different bottle types for the drinks, catering and non-food industries. PET and rPET can be processed equally well within an intrinsic viscosity range of 0.76 to 0.84 decilitre/gram, including hot-fill and fast reheatable varieties. Savings of up to 30% should be possible as a result of high production capacity compared to other processes. The fact that the handle has already been moulded during preform production should make it easier to optimise wall and handle thickness. “A 2 l IMH bottle can weigh anywhere between 69 g and 75 g, whereas the weight of the extrusion area and the subsequent handle attachment can be between 80 g and 96 g, not forgetting the generally lower PET price compared to HDPE. Logistics for the converters are also made easier given IMH preforms are made centrally and can be blown either in-house or at outsourced bottle filling plants. The shape is typically based on the usual customer bottle design to minimise costs that might be incurred for any modifications made at the plant. As well as designs developed in-house, licensees can also use standard and customer bespoke bottle shapes internationally. The number of bottle designs within the IMH family is constantly expanding thanks to the efforts of everyone involved. Present and future developments In Australia, the company currently has a 57% market share in the sector which, according to Mr Mellen, continues to grow steadily. “While 1 l and 2 l are the country’s most popular bottle sizes, other potential markets are on the lookout for 1.5 l to 4 l bottles with their own special design. Without saying too much about which companies are involved, the efforts of Managing Director Nicholas Mellen","@ID":24}, "empowered by Drinktec New Zealand Australia Philippines Taiwan South Korea Japan Let Your Inspiration Flow. G’day and Konnichiwa! Editour Road Show goes virtual This year’s Editour Road Show was planned to be our next big international editorial project. That is now impossible. For the safety of others and our own, we are all working from home during the lockdown period. But it’s still time for the Editour Road Show to hit the road – it’s just that we won’t be doing so physically, not at the moment. The start of the new decade will see us undertaking a trip starting in Australia, moving on to New Zealand and then Japan, via the Philippines, Taiwan and South Korea. With support from Drinktec, the world’s biggest beverages show, we will be ‘virtually’ shooting off to Australasia in April. The first weeks will see us interviewing PET companies along the route via Internet and phone. These encounters will appear not only in PETplanet Insider but also in a completely new way – new to us, anyway: as podcasts on our website, for the first time ever! We will keep monitoring the situation closely to decide if, how, when and where we can still go personally with our Editourmobil, later in the year, while complying with governmental rules. We will present a comprehensive review of our Tour experiences both at China Brew China Beverage in Shanghai, China, in October and at Drink Technology India in Mumbai, India, in December 2020. Make sure you’re on board when we set off on our next adventure and get ready for in-depth analyses, special features and reports of trends in these bottle and beverage sectors! Enjoy our first-ever Virtual Editour! Stay safe and healthy! Interested in being interviewed? [email protected] April - December 2020 Powered by","@ID":52}, "PETplanet Insider Vol. 21 No. 11/20 petpla.net 55 BOTTLES Liquid soap with grapefruit oil An antibacterial liquid soap containing natural grapefruit oil with added “Stop kitchen odour” is being sold in a robust 300 ml PET bottle under the German company Lornamead Ltd.’s “Handsan” brand, which is well-known for its hand care products. The clear bottle contains t he s l i gh t l y co l ou r ed , soap-free product, which is applied via a lockable pump dispenser. A wrap-around self-adhesive label provides information on the contents and how the product should be used. www.lornamead.com Curved soap bottle In Italy, “Spuma di Sciampagna” is selling a liquid soap containing almond milk and shea butter, which comes in a curved and coloured 400ml bottle. This antibacterial product is said to gently cleanse and moisturise the surface of the skin. Either a pump dispenser or hinged lid with dispensing spout can be screwed into the opening. Two embossed, clear self-adhesive labels provide commercial and product information. www.spumadisciampagna.it Tapered detergent bottle The Bolton Group via its subsidiary in Italy is selling a concentrated liquid detergent in gel form, suitable for both hand and machine washing as part of its “Omino Bianco” brand. The product comes in a strikingly shaped, clear 900ml bottle with a sleeve label which is perforated, making it easy to remove for waste sorting and disposal purposes. The part of the eye-catching shaped screw-top that protrudes into the inside of the bottle is designed as a dispensing cap. www.ominobianco.com","@ID":57}, "7 NEWS PETplanet Insider Vol. 21 No. 11/20 petpla.net drink technology India will take place in an online format Due to the rampant spread of Covid-19 in the country and the consequent travel restrictions imposed by the Government of India, show organiser Messe Muenchen India has announced the postponement of the Mumbai edition of drink technology India to October 20-22, 2021. To meet business networking requirements, an online exhibition and conference platform is scheduled for December 9-11, 2020. The trade fair on site was also scheduled from December 9-11, 2020 at Bombay Exhibition Center, Mumbai. However, considering the safety of the stakeholders, exhibitors and visitors, the show organisers have rescheduled the trade fairs. The decision of postponement is also based on industry feedback received through the extensive survey conducted by the organiser. Mr Bhupinder Singh, CEO, Messe Muenchen India explains, “Owing to the restrictions enforced by the Government of India on travel and massgatherings, December is no longer a viable option to organise drink technology India.” Mr Singh added that, “Health and safety of everyone involved in the trade fairs is our prime concern. For the upcoming edition we will strictly follow government directives and standard operating procedures to ensure a safe environment to conduct business at our trade fairs. To meet our customers’ business networking requirements, we are holding an online exhibition and conference platform on the originally scheduled date of December 9-11, 2020.” The online exhibition and conference platform of drink technology India offers a business opportunity to global customers while protecting data and providing a real-time dashboard view on their engagement with buyers, a conference program, and buyer-seller meetings. Participants can also make use of synergies with other shows in the Messe Muenchen India portfolio, such as analytica Anacon India & India Lab Expo, IFAT India, MatDispens, Pharma Pro&Pack Expo, PackMach Asia Expo, World Tea & Coffee Expo and The Smarter-E. www.drinktechnology-india.com Kick-off to the next K show The first meeting of the exhibitors’ advisory board had marked the kick-off to the next ‘K’ in Düsseldorf, to be held from October 19 to 26, 2022. The body of experts has met now to chart the course for the trade fair and to enter into the concrete planning stage. The exhibitors’ advisory board supports Messe Düsseldorf in the preparations for K2022 and provides consulting on basic conceptual and organisational issues. Here particular attention is paid to considering current developments as well as to the global economy and the discussion of forward-looking trends and technologies. The invitations to exhibitors will be sent out in early 2021. www.k-online.com","@ID":9}, "PETplanet Insider Vol. 21 No. 11/20 petpla.net 41 TRADE SHOW REVIEW PET Day 2020 - the webinar edition Since 2003, top managers, professionals and entrepreneurs in the international polyester industry have met in the Villa Medicea of Artimino, Tuscany, in Italy for the international PET Day. In April 2020, Mr Francesco Zanchi, CEO of GSI and organiser of the annual event, recognised that this year it would not be possible to hold the event as normal. So the team at GSI organised the 18th PET Day, to be known as the first webinar PET Day, held on October 1st , 2020. The morning session started withMr Paul Hodges , Chairman of International eChem, who gave his general overview of economic trends and offered some food for thought as to what might happen to our world after the pandemic. He drew a picture of wealthy western world getting older and this means that consumption is decreasing dramatically. The proportion of the population over 55 years old will increase to more than 50% in 2030. Russia and China are poorer but they too are ageing societies. Consumption, in future, could grow fast mainly in Africa and South America, butfirst they need money to spend. Hodges then compared the current economic downturn to that of 2007. “Today the economy reacts much more slowly, because it was slowing down even before Covid-19 hit,” he stated. Now, the behaviour needs to change in response to the pandemic. The polyester industry must follow. There is a the need to move away from providing ‘stuff’ and focus more on sustainability and affordability, for example intelligent and reusable packaging, cleanliness, renewable items and overall showing moreflexibility and leadership focused on stimulating creativity. The ‘economic super cycle of the baby Boomers’ is well and truly over; and the ‘New Normal’ is a demand-led, solutionoriented cycle. Mr Francesco Zanchi , praising Mr Hodges’ presentation, underlined the fact that it is a huge change we are going through, with refineries disappearing now and in the immediate future. Zanchi laid particular emphasis on the great social responsibility that entrepreneurs and managers must shoulder in these difficult times. He then gave his in-depth analysis of the polyester industry and its status in the Covid era. Capacity utilisation rates are low right through the polyester chain. Whether it’s PX or PTA or PSF, the situation is bleak. A number of new plants will begin operations throughout the chain creating an even bigger overcapacity in China and all over the world in 2021. Only one point is clear: that rPET will get bigger in this market because of regulations; all the major beverage and food brands are going at full speed to expand into re-usable packaging. Textile demand, which accounts for 70% of all world polyester, is down at least 30% since 2019, and that brings us to the question: when will raw materials producers finally cut their output in line with actual market demand? Looking to the future, in 2021, in the hope that a vaccine for Covid-19 will be available, it is foreseeable that economies will return to some sort of normality in the second semester. Oil is likely to remain at the current levels, but we should expect PX, PTA and also PET to recover some ground and margins eventually. The afternoon session of the webinar opened up with a round-table discussion among polyester producers. Mr Hemant Sharma , COO of Polyester Reliance Ind., India, gave a picture of how Reliance coped with the virus emergency in India, where they had to send home some 25,000 workers. They had to face major logistic problems around their country, with different states enforcing different pandemic measures. Business however continued, and it did well, especially in oil (Reliance is fully integrated), pharma and films, all increased by 20% by June 2020, in comparison to 2019. Mr Jon McNaull , Global VP Polyester of Alpek, USA, indicated how during the spring, in the US, grocery business increased 12% while fresh food services shrunk dramatically. Consumers showed a much bigger need of packaged food. Textile and apparel shrunk by a dramatic 35%, as Americans switched consumption to home appliances and furnishing. In June sales of beverages got back to normal. It is difficult today to predict what might happen in 2021. Mr Sam You ZhenYi , Yisheng PET Sales Director, China, said that","@ID":43}, "PETcontents 4 PETplanet Insider Vol. 21 No. 11/20 petpla.net 11/2020 TOP TALK 12 ”We provide a safe environment that enables us to focus our energy on our daily operations” - PETplanet talked to Alessandra Funcia, Head of Sales & Marketing at Sukano MATERIAL / RECYCLING 14 Rapid IV build-up - NGR’s LSP technology has proven itself worldwide 16 Making the most of recycling material - Recycling systems and auxiliary equipment 18 Making recycling work MOULD MAKING 20 The smart guardian - Monitoring the efficiency of mould operations PREFORM PRODUCTION 21 PET bottle handles produced during the preform phase EDITOUR 24 The Philippines drinks’ market - Sugar tax, Covid-19 and modest PET growth BOTTLING / FILLING 28 One of the last European’s wild corners - A new Krones PET bottling line replaces two existing ones at the Ogeu Group’s site in Quézac 35 Bottling Fruiticana juice drinks - Sipa bottling technology at Big Tree Beverages: fast and flexible MARKET SURVEY 31 Suppliers of recycling plants and washing units CAPS & CLOSURES 36 Boosting business - Michael Krueger, CEO Corvaglia, on strategies to be well positioned in a competitive market 38 Digital printing of closures operating 24/7 TRADE SHOW REVIEW 41 PET Day 2020 - the webinar edition 44 China Brew China Beverage, part 1 - A strong signal for the beverage industry 46 Market-tailored, agile solutions and sustainability in the spotlight - Sidel at Propak Asia 2020 BUYER’S GUIDE 57 Get listed! Page 35 Page 12 Page 38 INSIDE TRACK 3 Editorial 4 Contents 6 News 48 Products 51 On site 52 PET bottles for Beverage + Liquid Food 54 PET bottles for Home + Personal Care 56 Patents RECYCLING","@ID":6}, "11 NEWS PETplanet Insider Vol. 21 No. 11/20 petpla.net 11 NEWS BERICAP Tethered Cap Solutions • Easy& intuitive handling • 180° opening • No change to - Neck finish - Capper - Filling line Approved and ready for line trials now! Obituary for the founder of the Dr Gupta publishing house: Dr Heinz B. P. Gupta has passed away at the age of 88 On September 30, 2020, Dr Heinz Bijoy Prosad Gupta (*1932 in Calcutta, India) passed away in Ratingen, Germany, at the impressive age of 88. He was founder of the Dr Gupta Verlag (today Dr Gupta Verlags GmbH), for many years’ editor-in-chief of GAK Gummi Fasern Kunststoffe and until 2019 publisher of various national and international specialist journals for the rubber, polyurethane and TPE industries. Heinz Gupta studied chemistry at the University of Bonn, Germany, where he also received his doctorate. After graduating, he worked for Kabelwerke Duisburg and Paguag (Pahlsche Gummi- und Asbest-Gesellschaft) in Düsseldorf. From 1970 he was consultant to various manufacturers of tyres, moulded articles and sponge rubber products. In 1972, he assumed additional responsibilities as editor-in-chief of GAK, which had been published since 1948 by Gentner Verlag, then still under the name of Gummi-AsbestKunststoffe. His work in industry and as a consultant provided an excellent basis for this journalistic role and encouraged him to found Dr. Gupta Verlag in 1993 and to continue to run GAK himself. He remained true to GAK’s declared goal of providing technical information that is both scientifically sound and comprehensible to the practitioner. Raw materials, machines, products, processes and their scientific backgrounds were the focus of this important source of information for technicians, engineers and chemists in the rubber industry. However, relevant economic and legal news was not ignored either. The magazine was given a special note by its unique editorials, in which Heinz Gupta questioned current events, sometimes critically, sometimes benevolently, sometimes argumentatively, but always humorously and thoughtfully. He spoke his mind, and he did not care whether it was appropriate. Over the years Heinz Gupta broadened the portfolio of his publishing house. At K 2001, he launched PU Magazin, a new trade journal for the polyurethane industry. PU Magazine International followed in 2004 as an English-language edition. In 2006, GAK was expanded to include an English edition, RFP Rubber Fibres Plastics, and in 2009 the English-language TPE Magazine International was launched. Most importantly, Dr Gupta worked tirelessly to maintain and improve the image of the industry, whose well-being was so close to his heart. His passion was the rubber industry. For decades, he was regarded as the “rubber man” who was a sought-after discussion partner at all important trade fairs, conferences and industry meetings. Often it was he who asked the first – usually well-intentioned – question after a lecture, just to break the ice. In 2006 his lifetime of service to the field was awarded with the plaque of the German Rubber Society for special achievements in research, technology and business as a mark of gratitude for his great commitment.","@ID":13}, "MATERIALS / RECYCLING PETplanet Insider Vol. 21 No. 11/20 petpla.net 18 Making recycling work What Invema Group, a Honduran-based waste recycler with a sister company in El Salvador, has achieved in economic, environmental and social terms is nothing short of remarkable. It’s successful story is an example for a highly sustainable business. Starting in the early nineties with two employees and the collection of aluminium beverage cans, Invema has consequently been growing. Today, it is the largest recycler in Central America, and the only producer of food grade recycled PET resin and packaging approved by Coca-Cola, Pepsi, and Nestlé in Central America. Invema currently employs 400 people and recycles all kinds of non-organic waste. 12,000 t of waste is processed each month, a sixth of it being PET bottles. Invema sells the produced rPET to various national and international customers but also uses it to produce 100% food grade rPET sheet for thermoform containers which it is marketing under the brand name “lu’um”. Recycler in Central America trusts in Starlinger technology In 2016 Invema invested in a Starlinger recoStar PET 125 HC iV+ bottle-to-bottle line with a production output of 8,000 t of regranulate per year. “Provide our suppliers with the best market for their scrap and deliver to our customers eco-friendly products on time with quality they can trust.” is George Gatlin’s, General Director of Invema Group, daily goal. That important brand-owners rely on rPET pellets from Invema proves that the investment in the Starlinger bottle-tobottle line was the right decision to fulfill this objective. As second part of the investment, George Gatlin opted for the production of food grade rPET sheet and added a viscoSheet rPET extrusion line with a deCon flake decontamination reactor for producing 100% food grade rPET sheet. “We strive in investing in the most modern technology to be able to process and trade scrap in the most efficient way”, says Gatlin. As the company is expanding rPET production due to increased demand, they have purchased a second recoStar PET 125 HC iV+ from Starlinger which will be delivered in March 2021. Environmental protection and social responsibility In order to get input materials Gatlin built up a national collection network where people of any age, level of education or gender are compensated equally and fairly. “In Honduras, recycling is a way of living, and it provides a way of living for thousands of people. We have a lot of poverty here and recycling is a solution for the people” he says. Because of Gatlin and his efforts the collection rate for PET bottles in Honduras has reached 84%. This is much higher than the European average. But not only PET is collected; Invema collects all types of plastics as well as metal, paper, and electronic scrap through approximately 20,000 suppliers. Considering that each supplier gathers waste from about 40 people, it means that as much as 800,000 people directly benefit from recycling. Invema has a monthly education program for suppliers where they can learn financial stability, thus guaranteeing their continued growth. Invema also runs one of the largest solar power systems in Latin America, producing about 2 megawatts of electricity through 5,600 solar panels, which is approximately a 40 % saving in their electric consumption. For waste water, the company set up a treatment plant that recycles it for further use. The right thing to do “We’ve gotten ourselves into a situation where we need to make a change – and that starts by taking recycling seriously”, says George Gatlin. In summer 2020 Invema, together with their business partner Lacerta Group, Inc. based in Mansfield, USA, have launched a striking video clip in which George Gatlin and Lacerta Principal Mostafa Lotfi explain how recycling works and lay out their vision of how a vertically integrated business model can lead the way in the packaging industry. “The most important thing is to believe in technology and not to be afraid to invest. Technology today allows us to recycle plastic infinite times”, George Gatlin points out. “If the consumer is conscious, if the industry is conscious, if we invest in the equipment, in the processes in the right way there is no doubt that recycling can work. But it has to be a team effort”. The video can be viewed by clicking https://vimeo.com/439786636 www.invemagroup.com www.starlinger.com/en A waist-high sea of collected PET bottles at Invema Invema production hall with Starlinger recycling technology RECYCLING","@ID":20}, "47 TRADE SHOW REVIEW PETplanet Insider Vol. 21 a 220ml water bottle with a targeted weight of just 5 g. It is blown from 100% rPET preforms and comes with a snap-on tethered cap to additionally reduce plastic pollution. The bottles’ distinguished V-shape offers innovative packaging alternatives in terms of compactness and reduction of secondary and tertiary packaging materials wellsuited to optimise logistics. Improving performance over time Moreover, as a part of the service portfolio, Sidel showcased its remote video assistance at Propak Asia. Leveraging this tool, especially during the Covid-19 pandemic and the ensuing travel restrictions, the company has well demonstrated its capability to secure and improve the performance of its customers’ equipment throughout their entire asset lifecycle. “Propak Asia remains one of the most important trade fairs for Sidel. We have been participating for many years now as the show brings us together with important contacts from the packaging industry as well as visitors and customers across the SEAP region. We are looking forward to present our latest innovations and service solutions again in Bangkok this year and gather valuable feedback to see whether our portfolio and our roadmap anticipate Asian producers’ needs to stay abreast of ever-changing market demands,” concludes Dominique Martin, Sales Vice President South East Asia & Pacific at Sidel. www.sidel.com","@ID":49}, "PETnews 6 NEWS PETplanet Insider Vol. 21 No. 11/20 petpla.net New hot washing system at Herbold’s test centre The plant manufacturer Herbold Meckesheim will expand its test centre with a new hot washing plant by the end of the year as a consequence of the fastgrowing demand for superior recycled plastic (aim: “similar to virgin”). For several years, Herbold has been operating a washing test centre on an industrial scale in which customers, potential buyers, planners and researchers can test and simulate recycling processes way beyond laboratory level. This plant is to be expanded by a suitable hot washing step. It allows customers to test the treatment of rigid plastics and films with an output of up to 1,000 kg/h also in the hot washing system. The plant has been designed for continuous operation and operates in line with the existing hydrocyclone washing plant. It can be verified whether and how an improvement of the final product is achievable. Especially common in the PET recycling, the hot washing system was traditionally used to remove adhesives with which labels were glued on bottles. The hot washing system is on its way to an essential process step in the recycling of polyolefin and other plastics; anywhere where complicated residual material, heavy contamination, persistent odours are to be treated or just simply highest quality is demanded. www.herbold.com Resilux and RCS build partnership to achieve full circularity in PET production PET bottle and preform producer Resilux and recycling management company RCS are working together to achieve complete circularity for their PET products. By combining RCS’s waste collection and Resilux’s production capabilities, the two companies will be able to offer 100% traceability in the recycled PET produced. This growing partnership will help them and their customers to comply with the EU’s directive on plastic products which states that all PET bottles should contain at least 25% recycled PET material by 2025. Resilux and RCS have agreed to enter into a partnership which will involve the sharing of knowhow and usage of each other’s resources. This will enable Resilux to source high quality recycled base material produced from German waste collection expert RCS. The combination of the two companies’ capabilities means Resilux and RCS will create a complete sustainability loop. In other words, there will be an unbroken recycling chain stretching from waste PET collection to making food-grade recycled pellets or flakes right through to the production of brand new preforms and bottles using the recycled base material. By securing an additional dependable supply of recycled base material, Resilux is well placed to meet the requirements of the EU directive for 2025. It will also be able to offer its customers 100% traceability information in order to verify the source of its recycled material. Today it is increasingly important for both RCS and Resilux customers to know the precise origin of the recycled material in their preforms or bottles so they can demonstrate compliance with the new directives. RCS has more than 40 years’ experience in the waste disposal industry while Resilux has over 25 years’ experience in preforms and bottles. Through this long-term partnership, the two companies will pool that knowhow to reinforce the investments they are both making in recycling technology. www.resilux.com Engel’s live e-xperience with several thousand participants Several thousand customers, partners and interested parties from 90 countries took part in the Engel live e-xperience in mid-October 2020. The keynotes, expert talks, one-on-one meetings and machine exhibits in the virtual showroom were very well attended throughout all four live days. All presentations are still available from the media library. “Even though no classic trade fairs are taking place, and restrictions apply to personal meetings, we still want to exchange ideas with our customers, partners and interested parties and present our solutions and innovations. After all, Covid-19 does not mean that we are slowing down our development activities”, says Dr Christoph Steger, CSO of the Engel Group. Against this background, the injection moulding machine manufacturer developed a completely new virtual and interactive trade fair concept. Seven machine exhibits, an online specialist congress and one-on-one meetings with familiar local contacts and other experts ensured that the Engel live e-xperience was on a par with a physical trade fair. Many customers booked appointments in advance and were guided through the virtual showroom during the meetings. Engel provided insights into the new machine solutions and process technologies via video streams. www.engelexperience.live www.engelglobal.com","@ID":8}, "PETproducts 48 PETplanet Insider Vol. 21 No. 11/20 petpla.net Intellect filler management inspection solutions Filtec, a global provider of inspection solutions for the food and beverage industries, showcases its Intellect Filler Management Solutions for both cans and bottles. Correctly filled containers maximises product quality, reduces waste and product give-away, increases the efficiency of the downstream processes and delivers a high return on investment (ROI). Intellect Filler Management Solutions are available for glass and PET bottles, plus metal cans. They use either vision or photon inspection technologies following the seamer and closer operations to check each container for underfill and overfill. The Vision Filler Management Solution for bottles offers even greater results from a wide range of optional inspection applications including slosh compensation, foam measurement, closure colour detection, pattern detection, closure defects, vent tube detection, pressure integrity and date code detection. There is also a compact Intellect photon solution that inspects the fill level of cans between the filler and seamer for true fill level measurement, avoiding potential content spillage errors prior to the seamer. Central to the Intellect Filler Management Inspection are its family of analytics applications that give a detailed visual insight for each container and filler valve. For example, the fill level application checks each container against underfill and overfill threshold limits and presents the information on an operator trend display. This is complemented by the filler and closer application that tracks each container to provide a graphic and numeric defect count display for each filler valve. Finally, a quantitative analysis application gives a complete statistical analysis of the entire filler process showing fill level distribution histograms for each filler valve to support preventative maintenance programs to ensure that each filler valve runs at its highest efficiency. Filler management inspection join Filtec’s suite of Intellect non-contact in-line solutions that utilise measurement, inspection and control technologies to examine each container with speed and precision that elevate both quality achievement and production performance. www.filtec.com Husky releases award-winning Ultra Helix 250 T2 nozzle for small parts Husky Injection Molding Systems announced the release of the newest addition to the Ultra Helix Valve Gate nozzle lineup, the Ultra Helix 250 T2. The advanced design of Ultra Helix nozzles minimises wear, providing industry leading gate quality and longevity. The award-winning Ultra Helix 250 T2 was specifically developed to extend the benefits of the Ultra Helix technology for small part weights with difficult to access gate locations. Direct gating for small parts With a 12mm nozzle bore, the Ultra Helix 250 T2 allows for direct gating in locations not achievable with larger nozzles. The pitch spacing down to 15mm enables the highest cavitation density and smallest mould footprint, states Husky. Reduced maintenance The new nozzle’s extended maintenance interval PX actuation is designed for applications with leakage prone resins like TPE and PE. The addition of a stem seal paired with enhanced thermal management heater technology is intended to improve performance and to significantly optimise maintenance requirements. This results in lower risk and cost of ownership. Three actuation options available The Individual Pneumatic option offers pitch spacing down to 25.4mm, providing ease of access for maintenance with the ability to individually access valve stems without removing the backing plate. Both the plate actuated UltraSync-P or servo driven UltraSync-E options can achieve 15mm pitch spacing. Producing part weights of less than 0.1g Husky’s global customers are already taking advantage of the Ultra Helix 250 T2’s performance to make high quality precision parts from medical barrier closures and flow regulation valves to personal care products, food and beverage packaging and flip top closures. The part weights being produced range from less than 0.1 g to over 4 g and are being made from resins that are prone to leakage like PP, HDPE, LDPE, TPE and TPV, in both single injection and multi-material applications. The Ultra Helix 250 T2 is already demonstrating its performance for small part weight with difficult to access gate location applications in both Individual Pneumatic and UltraSync actuations. The extended maintenance interval for leakage prone resins is providing additional value for the customer. Award winning technology The new nozzle received an award at the 2020 Plastics Industry – Ringier Technology Innovation Awards in the Mold and Component category. Contending products were evaluated based on their ability to improve product efficacy through technological innovation or provide new business opportunities for the market. Winners were selected by professionals from industry associations and scientific research institutions. The features of the Ultra Helix 250 T2 make it the ideal solution for specialty and flip-top closures, small medical parts and multi-material parts with limited gate access, says Husky. www.husky.co","@ID":50}, "PETplanet Insider Vol. 21 No. 11/20 petpla.net 54 PETbottles Home + Personal Care Natural cosmetics from Dove “Powered by Plants”, which is part of the trademark “Dove” brand, is a new, official natural cosmetics line from Unilever. The products contain 98% naturally active ingredients while the perfume is 100% natural. One example from the line is a eucalyptus shower gel, which is specially designed to care for and moisturise soft skin. The 250 ml bottle made from 100 % recycled material contains a slightly greenish coloured product, which is dispensed via a screw-on disc-top cap. www.dove.com Mouthwash with tea tree oil Mann and Sc h r öde r ’ s “Alkmene” brand has been using natural ingredients and active substances in the manufacture of body care products for nearly 50 years. Among these is a mouthwash that contains Australian tea tree oil. As a 6-in-1 product, the mouth rinse protects teeth against decay and the build-up of tartar. According to the manufacturer, 98% of the ingredients are of natural origin, while the remaining 2% is added for safety and taste. The clear product comes in a transparent, slightly tapered 500 ml bottle with a screw-on, grooved cap with dispensing function. www.alkmene-teebaumoel.de","@ID":56}, "BOTTLING / FILLING PETplanet Insider Vol. 21 No. 11/20 petpla.net 29 adds: “This was important, because we had a fixed deadline for market-launching the 0.5l bottle. I was very happy with Krones’ punctuality. This could be achieved only because we had chosen Krones as our single-source vendor. I was also very impressed by the training our staff received from Krones during the commissioning phase,” he says. This short erection time was likewise favoured by the fact that the new line was being installed in an emptied storage area, while the older lines next to it were able to continue operating until the new line was up and running. So now the new Krones non-returnablePET line is the sole bottling line at the facility in Quézac. It is rated at 27,000 containers per hour, referenced to the 1.15l container, and runs in three-shift operation, round the clock from Monday to Friday. Carbonated water only At this facility, Ogeu bottles only carbonated water, and thus – despite the focus on regional roots – ranks fifth for this market segment in France. Carbonated mineral water is more of a niche product there, with a market share of around 15 per cent; the French mostly consume still water. The mineral water bubbles up from a spring 200m away, with a natural carbon dioxide content of 2g per litre. Before being bottled, it is carbonated in the Carboflow to 5.5g per litre. As with the filling operation, the variants are manageable in terms of packaging as well. Both container types are each formed into six-bottle shrink-packs by a Variopac Pro FS. Afterwards, the 0.5l containers are then grouped together to form 24-bottle trays in a second Variopac Pro TFS. “One weak point in many lines is layer preparation upstream of the palletiser,” comments Jean-Hervé Chassaigne. “The elegant solution with the Robobox was another important criterion that tipped the scales in favour of Krones.” High OEE Three staff suffice for operating the entire line: one for the wet end, one for the dry end, and a fork-lifttruck driver. “The line achieves a high OEE of 86 per cent,” says the Ogeu Group’s Technical Director Lilian Oyhenard. With a retrofitted ReadyThe mineral water bottler’s plant is located in the heart of the French Cevennes National Park.","@ID":31}, "PREFORM PRODUCTION PETplanet Insider Vol. 21 No. 11/20 petpla.net 23 PETcast In our new Road Show podcast, PETplanet meets industry experts from Down Under to Japan and talks with them about their successes, decisions and current developments. Listen to the full conversation atwww.bit.ly/2HVwbAd bottlers worldwide to achieve sustainability, recycling and ergonomics will result in IMH bottles appearing more and more on international shelves during 2021.” New global bottler distributors will be coming on board from February 2021, with several currently in the pipeline. According to Mr Mellen, Tru Blu Beverages’ sales are expected to increase by 50% in 2021. Tru Blu as the main local customer is involved in nearly all of the soft drink markets with 25 brands, as well as being the country’s largest privately-owned drinks’ producer. Tru Blu has successfully distributed more than 100 million IMH bottles on the Australian drinks’ market since 2018, including several OEM brands for retail chains such as Woolworth Coles, Aldi and IGA. Integrated Plastics use virgin PET material purchased from Reliance Industries in its preform production, while rPET is obtained from the Martogg Group. The licence partner and material manufacturer, Sabic, supplies the Middle East region, while SDB uses local manufacturers in South Korea. “Tru Blu are currently expanding their production capacity and, with our help, are adding two inline blow moulding machines for IMH hot-filling applications, as well as increasing their annual output to 50 million bottles. We are also in the process of building new capacity with extra production space set aside in Sydney for prototyping. We want to open a plant in India with centralised production of IMH preforms for the local market”, said Mr Mellen. The company currently employs around 20 full-time development and production staff at its Villawood facility and has a current turnover of US$ 5 million. “Fortunately, Australia is coping pretty well with the Covid pandemic compared to other countries”, said Mr Mellen. “This year, we have been focusing increasingly on digital conversation, teamwork and remote management which, while progressing well, are certainly no substitute for face-to-face meetings. We are therefore looking forward to hopefully travelling abroad again soon.” www.integratedplastics.com.au","@ID":25}, "CAPS & CLOSURES 38 PETplanet Insider Vol. 21 No. 11/20 petpla.net Digital printing of closures operating 24/7 IMDvista visit/CAPrint, Brügg/Switzerland We met: Martin Gerber, CSO, IMD Matthias Hermle, CEO, IMD Fridolin Maibach, CEO, CAPrint After five years in development, CAPrint is showing that its system for digitally printing caps has finally risen to the challenge and is now in production around the clock. The first units have now been delivered to customers. We were able to take a look at two of them at the Corvaglia cap plant. We spoke to Fridolin Maibach, CEO of CAPrint and Michael Krüger, CEO, Corvaglia. Interview with Fridolin Maibach, CEO, on the site of CAPrint Brügg PETplanet: Mr Maibach, printing can hardly be said to be a lucrative business. In most cases, the cap manufacturer must literally put printing on the top. What makes you think there is a market for such sophisticated technology? Maibach: Our CAPrint 1.0 system makes a significant difference in terms of cost reduction and marketing possibilities by using state-of-the-art quality prints. Digital printing opens up a new world in terms of printing excellence. Compared to pad printing, digital printing allows multi-colour and shading, which allows us to create realistic-looking pictures and graphics on the cap. We can go even further by creating an optical 3-D image or metallic looking effects by using smart processing. High gloss printing is also achievable. In the past, this would only have been possible with an additional label. PETplanet: Realistic illustrations and different design motifs reflect the marketing aspects. Are there also arguments in favour of your technology in terms of cost? Maibach: Our cost advantages clearly lie in logistics and operation. Customers do not need specific staff, nor specific infrastructure. The overall energy consumption is also significantly below a mechanical printing solution. It is key to understand that our customers have almost no start up and exchange costs. The cap manufacturer can store larger quantities of closures and, if necessary, process the closure for the bottler as required. The switch from one design motif to another takes place via the push of a button one piece at a time during the production process. This avoids lengthy switchover times and different caps being warehoused by the manufacturers. By taking this one stage further and setting up the printing system with the bottler, we will be able to simplify logistics and storage issues even more. Another issue is automated operation of the system compared to the labour-intensive pad printing process. The classic method involves ink being refilled and printing positions constantly readjusted. Even changes in design require a certain set-up time. Ours is an automated system, which gives us advantages over the cap manufacturer – it’s unmanned. Plus the print is 100% repeatable over time and place – receiving same results at different locations, avoiding any operator misuse. CAPrint 1.0 leads to less costs and comprehensive cost control which is key in our industry as you mentioned. Fridolin Maibach, CEO CAPrint Individual closures with printing","@ID":40}, "PETplanet Insider Vol. 21 No. 11/20 petpla.net 53 BOTTLES Kalinka Kefir in an angular bottle German dairy Alois Müller GmbH & Co. KG is selling some new products - Ayran and Kalinka Kefir - in bottles that are very different to those of other Müller products, especially in the shape around the shoulder area. The bottle shoulder is angular and the base shape has also been changed and is better integrated into the packaging design. The white bottles have three circulating ridges around the middle, contain 500 g of product and are decorated with a sleeve label. The sufficiently wide white screw cap has a tamper-evident seal. www.muellermilch.de Bulbous bottle for iced tea The Rewe own-brand “Rewe to Go” is selling 500ml of iced tea in a bulbous transparent bottle. This is made from 50% recyclate. As with many other products on the market, there is a note to indicate that the recycled proportion does not include the cap. The iced tea is made from freshly brewed tea and tastes of mint and lemon. It should be shaken well before consumption. A transparent sleeve label makes the product easily visible and provides all product information. The opaque screw cap has a tamper-evident seal. www.rewe.de Innocent up to 100% recyclable Innocent, the specialist for smoothies and juices, is promoting an improvement to the recycling quotient on its smoothie bottles and asks that the consumer actively participates. The bottle is made from 50% recyclate and 15% plant-based PET. After consumption, the lid should be screwed back on and the bottle placed in the nearest recycling bin. The products bear striking names like “Kiwi Wonder” and “Granatenstark” [Pomegranate Power] that reveal the fruit varieties in the bottles. Transparent self-adhesive labels explain environmental considerations and a screw cap with a freshness sticker seals the bottle. www.innocentdrinks.de","@ID":55}, "TRADE SHOW REVIEW PETplanet Insider Vol. 21 No. 11/20 petpla.net 46 Sidel at Propak Asia 2020 Market-tailored, agile solutions and sustainability in the spotlight At Propak Asia 2020, from October 20th to 23rd , Sidel presented its newest agile and markettailored innovations at booth AD01, in Hall 1010 at the Bangkok International Trade & Exhibition Centre (BITEC), Thailand. Placing a special focus on line design and its compact, high-performance equipment and service solutions, the company exhibited its latest sustainable end-to-end packaging innovations, designed in the spirit of circular economy. One company – many future-proof solutions At this year’s trade show, Sidel especially highlighted its competencies in line design, presenting market-tailored packaging innovations and new agile solutions, designed to increase sustainability, reliability and performance as well as flexibility throughout the entire production process: The next generation Super Combi Compact allows for a footprint reduction of up to 30% compared to the previous Super Combi model. At the same time, this new solution also excites with its efficiency enhancement for still drinks production thanks to the new filling technology of the Sidel EvoFill HS Still, which is claimed to guarantee a 30% faster filling performance. Super Combi Compact integrates five process steps – preform feeder, blower, labeller, filler/capper and cap feeder – into an all-in-one, compact and smart system that delivers continuous top-level performance of up to 54,000 bph. Furthermore, the new EvoFill HS Still filler comes with proportional filling valves, controlled by electro-magnetic actuators, ensuring the best hygiene and control of the complete filling cycle. The Combi BD (Blowing and Decoration) marks another new and compact solution by Sidel that allows producers to deliver perfect empty, labelled PET bottles. The system incorporates features of the modular Sidel EvoBlow and EvoDeco technologies with the advantages of an integrated configuration for fast, safe manufacturing and decoration of premium and/or lightweight PET packaging at up to 48,000 bph. Accordingly, the Combi BD stands for optimum packaging quality and integrity: Dispensing with the need for conveyors significantly reduces the risk of bottle damage. Also, having no infeed screw on the labeller – which accommodates roll-fed or pressure-sensitive labels (PSL) – ensures that the labelling will leave no marks on the bottles, even on specially shaped ones. Another big company highlighted the Sidel Aseptic Combi Predis, the integrated blow-fill-seal-filler solution with dry preform sterilisation, which is intended to ensure an aseptic production that is flexible, cost-effective and safe. Sidel was the first company to receive the United States Food and Drug Administration’s (FDA) approval for this patented technology. The solution sits among the many innovations across the line and beyond that champions Sidel’s commitment to help producers reduce their environmental footprint because the dry preform sterilisation technology does not require any water and uses only minimal amounts of chemicals in the production process. New “end-to-end” eco-packaging alternative for still water Beyond the mentioned solutions, visitors to Sidel’s booth could also have a first-hand experience of the new, prize-winning eco-packaging concept Aya, which reinforces the company’s commitment to sustainability, offering a new “end-to-end” packaging alternative for still water. Aya – which has already been awarded with the prestigious World Food Innovation Award (WFIA) in the category “Best Drink Packaging Design” this year – is","@ID":48}, "TRADE SHOW REVIEW PETplanet Insider Vol. 21 No. 11/20 petpla.net 45 the Guangdong Beer Association. 418 Chinese exhibitors and 101 international companies presented their innovations and products – with the latter largely represented by their subsidiaries in China. International industry giants such as ABC Compressor, Alfa Laval, Anton Paar, Arol, Atlas Copco, Barth Haas, Endress+Hauser, Fermentis, GEA, Heuft, Kalsec, KHS, NORD, ocme, Pall, Pentair, Pressco, Schneider, SEW Eurodrive, SMI, Yakima Chief Hops and Ziemann Holvrieka were represented across 60,000m2 . There, a German Pavilion was set up for companies such as BBull, Hottinger Baldwin, Jasbos, Lechler, ProLeit, WiKa and Xispek. Among others, the national exhibitors included Best Crown, Diron, E-STAR, GDXL, GsPak, HGM, Kelang, Lehui, Newamstar, Precise, Talos, Tech-Long, Tiantai, VANTA, YoungSun, YueDong, ZhongChen and Zhongya. Valuable platform for business opportunities The exhibitors were relieved that CBB was able to offer them an efficient platform again. Ivan Liu,General Manager of Beverage and Filling Technology, Gea China, states: “CBB is an influential large-scale exhibition for the beverage industry in Asia. It has greatly contributed to the liquid food processing and packaging industry in China. Although the current market is unsteady owing to the Covid-19 pandemic, we still decided to take part in this exhibition as scheduled. The prevention measures and exhibition preparation work are very impressive and professional. The results have exceeded our expectations.” Christian Blatt, General Manager of Ziemann Holvrieka Asia Co., emphasises: “This year our business was also affected by the Covid-19 pandemic, but CBB was a big help for our communication with Chinese customers. Since CBB moved to Shanghai, the show facilities have highly improved, and it is also very professional. I hope that in two years’ time, once the international situation has changed, CBB will continue to bring new opportunities for the liquid and beverage industry in other countries and regions.” Varied supporting program The supporting program offered an attractive knowledge platform. During the “CBB International Forum” organised by Doemens e.V. for example, experts spoke about trends, requirements and challenges in the South Asian beverage and liquid food industry, while visitors had the opportunity to taste different beers under the guidance of a beer sommelier during the “Doemens Tasting Class.” www.chinabrew-beverage.com EISBÄR TROCKENTECHNIK GMBH / Wuhrmühle 22 / A–6840 Götzis / T +43 5523 55558-0 / F –50 / [email protected] / www.eisbaer.at RECYCLING Conveying Drying Crystallizing Mixing&Dosing Decontamination Testing","@ID":47}, "MOULD MAKING PETplanet Insider Vol. 21 No. 11/20 petpla.net 20 Monitoring the efficiency of mould operations The smart guardian Otto Hofstetter showcased its OH Xport at the K2019 trade fair. This allows mould data to be gathered autonomously from the preform mould. In particular, it continuously gathers information on mould breathing as an important feature of mould condition. The first machines are now being deployed. We spoke to Stefan Zatti and Markus Feldmann, Otto Hofstetter, Switzerland. PETplanet: Mr Zatti, injection moulding machines document a large number of parameters during production. This allows conclusions to be drawn about the quality of the preforms. Why is your new OH Xport box needed? Stefan Zatti: The idea behind it is that we measure the mould breathing during the cycle. This is normally around 25 .. 30 micrometer. If the value drifts away from the target, it is a sure sign that something is not right, long before the quality of the preforms drops. No machine controls record this value. If the value changes, it is high time to recondition the mould. PETplanet: Your moulds have a reputation for having the longest tool life on the market anyway. Why do you need more measurements? Stefan Zatti: Mould breathing is a crucial factor. This enables mould lifetime to be increased even further and plan intervention when parameters start to develop in the wrong direction, long before preform quality is affected. Next to mould breathing, a variety of other sensors analyses the operating conditions. The hot runner is monitored in order to protect against leakage, and the cold half is monitored for condensation, with alarms possible via twitter. The stop reason evaluation allows tracking error causes, error times and frequency, which are important information when improving plant efficiency. PETplanet: Do the machine controls not record these values as well? Stefan Zatti: To some extent, yes. However, for the cooling water flows, the machines often regard the mould as one unit. For example, and in the case of the hot runner starting to clog, the cooling water bypasses via the cold sign and the problem becomes visible only at a later state of the process. By close-look monitoring, OH Xport monitors those mould components which are really the critical ones, and any issues which arise are detected much earlier. PETplanet: This means that the efficiency of the mould increases, as any possible causes of parameter changes can be rectified during routine downtimes? Stefan Zatti: Yes, OH Xport monitors the efficiency of the mould operation, thus measuring the overall uptime efficiency of the entire injection system. PETplanet: Why do you not integrate this measurement recording and log into the machine controls? Stefan Zatti: We offer a system which runs independently from all other controls and customer networks. Plug and play, so to speak. OH Xport works regardless of the machine installed. We don’t have to adjust to other systems, we do, however, offer compatibility with various centralised production control software systems. PETplanet: Are devices already being installed in the field? Stefan Zatti: Yes. A couple of systems are running in Europe and Asia, with others being commissioned soon. PETplanet: Thank you very much! www.otto-hofstetter.swiss OH Xport The standalone device collects measurements of mould breathing, coolant parameters, hotrunner temperatures and downtimes from up to 10 preform moulds per machine. Data is stored and computed within a cloud-based data engine. A web-based Visualization Dashboard provides the evaluation results. OH Xport can be installed on site within 2-3 hours. A 72 cavity side entry mould 144 cavity working horse for 12-16 million cycles before refurbishment, now being converted into a side entry mould F.l.t.r.: Stefan Zatti and Markus Feldmann","@ID":22}, "MATERIALS / RECYCLING PETplanet Insider Vol. 21 No. 11/20 petpla.net 15 Since melting and decontamination happen in separate steps in the SSP process, the final IV result cannot be influenced during decontamination if the quality of the input material is not consistent. In fact, the detailed result is only known after the entire process has been completed. In contrast, P:React carries out the entire decontamination in the liquid phase, so that the control parameters described above can directly control the IV increase. If, for example, the input IV value drops, the vacuum level is automatically increased without operator intervention, keeping the output IV value very stable. This is particularly important because the IV value is first reduced in the extrusion process. The course of IV loss in the extruder, subsequent increase in the reactor and output stabilisation is shown below: Fig. 3 IV value development The stabilisation of IV value, which is not possible using solid state methods, allows other solutions for integrated processes. P:React has been used as upstream equipment for some time now and is directly coupled to the production of semifinished products such as films, fibres and preforms. This results in further advantages and efficiencies on the manufacturer side. Energyintensive heating and re-melting of rPET pellets is no longer necessary. More importantly, the recycling process does not need to overshoot IV buildup to account for subsequent IV loss in the re-melt step. As a result, the PET material is less stressed and the entire process is simplified in terms of costs and production time. A further advantage of the LSP process is its ease of use and high process stability. On the one hand, a standardised extruder without vacuum, but optionally with degassing stages, is used, and on the other hand, production interruptions do not affect the quality of the starting material. Since the vacuum is reduced when the material remains in the reactor for a longer period of time, the IV value remains constant at the desired level even during longer downtimes. In order to help operating personnel and to achieve a constant IV value, NGR has integrated an online viscometer. The measurement results are constantly reported to the plant control system. If minor deviations occur, the required control parameters are immediately adjusted to stabilise the output IV. Specifications of the input material thus take a back seat and manual intervention by operators is no longer necessary. A constant granulate quality with consistent IV value and the feeding of a constant melt specification into subsequent processes is guaranteed. It is possible to supplement the input material with additives or colour masterbatches, in order to optimise the output material. Corresponding feeding and dosing devices can be provided as an option at any time. NGR operates a special PET pilot plant, with a fully instrumented test laboratory on site, where clients work alongside with NGR’s own experts to design their ideal process. Customers’ own material is processed in the required quantity and then subjected to a detailed properties analysis. In summary, NGR’s LSP process represents a major step in the ongoing struggle for sustainability. PET waste from both post-consumer and post-industrial resources can be reprocessed quickly and cost effectively. LSP can also be used to reprocess PET/PET-G or PET/PE composites, which have, previously, presented problematic challenges. In today’s commercial environment, where many countries are establishing deposit and collection systems, PET reprocessing is already of special importance but it must also overcome economic hurdles and perform at high commercial levels. For this reason, numerous recycling companies and globally active producers of semi-finished products already rely on the NGR P:React series. All these companies can take advantage of the benefits for themselves and, simultaneously, reduce their CO2 footprint. www.ngr-world.com Fig. 4 P:React","@ID":17}, "MARKET SURVEY 31 PETplanet Insider Vol. 21 No. 11/20 petpla.net 11/2020 MARKETsurvey Resins & additives Preform machinery Preform production & inspection Preform & SBM mould manufacturer SBM 2 stage Compressors Caps & closures & inspection Filling equipment & inspection Recycling Palletising & shrink film machinery Suppliers of recycling plants and washing units This time we close our annual market survey with a deeper look at suppliers of recycling plants and washing units. Find out more about new developments of the participating companies: Krones AG, Starlinger Recycling Technology, Boretech Environmental Engineering Co.,Ltd., Gneuss Kunststoff GmbH, Previero N.-Sorema, Reciclar S.A., Erema Group, Tecnofer and Empacar SA. Although the publisher have made every effort to ensure that the information in this survey is up to date, no claims are made regarding completeness or accuracy. Company name Krones AG Boretech Environmental Engineering Co., Ltd. Postal address Telephone number Web site address Contact name Function Direct telephone number E-Mail Boehmerwaldstr 5, 93073 Neutraubling, Germany +49 9401 70 0 www.krones.com Mr Peter Hartel Head of Sales - Recycling Solutions +49 9401 70 5448 [email protected] No.888, Jiuliting Ave., Caoqiao Street, Pinghu, Zhejiang, China +86-573-85120186 www.bo-re-tech.com Bottle to granulate Input variable: collected pressed bottles, various colours Yes, post-consumer or post-industrial material PET Collected pressed bottles, various colours Output: Granulate with approval Yes Yes, for food grade, IV increased, AA 1ppm, lowest VOC level Capacity [t/a] Output between 7,000t/a and 42,000t/a Up to 36,000 Floor space [m²] 3,000m² - 8,000m² Depeding on design Which approvals FDA, EFSA, various brands Flakes and Granulate FDA approval Fresh water consumption per tonne output [m³/t] 1.5 - 2.0m³/t 1.5 Consumption kWh per tonne output [kWh/t] Designed to fit the needs of the customer; depending on the scope of supply 550 (including washing, pelletising, SSP) Flakes to granulate Input variable: flakes, coloured proportion max 5%, not much chlorine Yes, e.g. hot washed flakes from Krones MetaPure W Flakes, coloured proportion max 5%, not much chlorine Output: Granulate with approval Yes Yes Capacity [t/a] Output between 7,000t/a and 42,000t/a 8,000 - 20,000 Floor space [m²] 1,500m² - 5,000m² (no frontend sorting and grinding) 300-500, depeding on design Which approvals FDA, EFSA, various brands Granulates with FDA approval Fresh water consumption per tonne output [m³/t] 1.5 - 2.0m³/t No fresh water needed Consumption kWh per tonne output [kWh/t] Designed to fit the needs of the customer; depending on the scope of supply 150-300, depending on design Bottles to flakes Input variable: collected pressed bottles, various colours Yes, post-consumer or post-industrial material Collected pressed bottles, various colours Output: Flakes with/without approval Yes, both; hot washed flakes or foodgrade flakes depending on customers needs Flakes with FDA approval Capacity [t/a] Output between 7,000t/a and 42,000t/a 4,000 - 72,000 Floor space [m²] 3,000 - 8,000m² 800 - 4,500 Which approvals FDA, EFSA, various brands CE Fresh water consumption per tonne output [m³/t] 1.5 - 2.0m³/t 1.5 Consumption kWh per tonne output [kWh/t] Designed to fit the needs of the customer; depending on the scope of supply Kind and quantity of detergents Depending on infeed quality; caustic soda: 8.0 - 12.0ml/kg output; additives: 0.5 - 1.0ml/kg output; acid for neutralisation: 1.2 - 1.8ml/kg output NaoH (2-3kg per tonne output), and brand detergent (1-1.5l per tonne output) Removal of the organic residuals up to which size [ μm] Water filtration up to 1μm Presetting residence time in the process Yes, according to desired final product quality Company also offers systems for: Bottle-to-film Yes, with partner Bottle-to-fibre Yes, with partner Yes, one stop solution from post-consumer bottles to PSF, POY and FDY Bottle-to-strapping Yes, with partner","@ID":33}, "CAPS & CLOSURES 36 PETplanet Insider Vol. 21 No. 11/20 petpla.net Michael Krueger, CEO Corvaglia, on strategies to be well positioned in a competitive market Boosting business Corvaglia is well known as a mould and cap manufacturer. For a while now, the company has been aiming to increase its cap production. We met Michael Krueger, CEO of Corvaglia and asked about his strategy. Other topics included tethered caps and of course the coronavirus. PETplanet: Hello Michael. In my view, cap production has always been something of an afterthought to mould making. Now you want to build up this area? Michael Krueger: It has always been our strategy to produce and sell caps. Now we want to boost business and have expanded our production to do so. Two years ago, a new factory was constructed in the USA. But we have expanded our capacities here in Switzerland too. PETplanet: Is it not difficult when you sell moulds and caps at the same time in the same market? Don’t your mould customers give you competition? Michael Krueger: In mould making, we work closely with regional partners. We do not go into those markets with our caps. We only overlap in Europe to a certain extent, but we have been able to manage it so far. And for the bottlers and brand owners it is certainly no disadvantage to have options. In the USA, we had only built moulds for bottlers’ inhouse production so here the market is completely open for us. And we are producing and manufacturing beverage caps in Mexico for 17 years now. PETplanet: Caps are a highly competitive market, the margins are low and you want to supply Europe from a high-wage country like Switzerland? Michael Krueger: We have greatly automated our cap production here in Eschlikon. Using an intelligent transport system, we can carry the caps from the machines and send them for further processing or for packing. The manpower we free from such intralogistics duties is used to expand production. After investing in automatisation, we produce more caps with the same amount of people on the shop floor. PETplanet: Why did you want to manufacture so much more caps than before in Switzerland? Michael Krueger: Previously, we had focussed on production of sports caps and unprinted flat caps in Switzerland. That was a contrast e.g, to our Mexican operations, where we are producing significantly higher volumes since a long time. As we were successful in Mexico, we wanted to proof a couple of years ago that it is possible on our ‘home turf’, too. PETplanet: Did you encounter challenges along the way? Michael Krueger: Extending the flat cap portfolio was the easy part as we utilise our own closure designs and mould technology. The harder part was that we had to scale up printing capabilities in parallel. Similar to the decision to automate, we decided to go a bit of a new route by utilising digital printing technology in both our Swiss and US operations. (See article CAPrint page 38) PETplanet: Have you been able to achieve your own targets? Michael Krueger: Of course, coronavirus has also presented us with several challenges. Supporting our customers with technical expertise on their bottling or injection lines is part of our business model. It was very hard for a couple of months to just travel to our customer’s sites to do that. In the meantime, we have been able to implement projects both remotely and on site. PETplanet: A bit more about coronavirus. How has it affected the cap industry overall? Michael Krueger, CEO of Corvaglia Small section of the fully automated cap production","@ID":38}, "PETplanet Insider Vol. 21 No. 11/20 petpla.net 52 PETbottles Beverage + Liquid Food Power Shot from Innocent Innocent, one of the trailblazers of the smoothie movement, is continuing to broaden its range of healthy juices and other related products. One such example is the two Energy Shots: Ginger Power and Ginger Turmeric Power, both of which are designed to provide a quick boost between meals. In addition to the ingredients mentioned in the products’ names, the juices contain apple and lemon or apple and carrot. The small, compact 100ml bottles have additional labels on the transparent screw cap which make it easier to spot a particular variety on the shelves or in the refrigerator. www.innocentdrinks.de Caffeine-free iced tea for children In its home country of Italy, drinks manufacturer San Benedetto is selling 250ml of iced tea for children in easygrip squeezy bottles with a drinking cap. The decaffeinated tea is available in lemon flavour and peach flavour. The container is sealed with a screwed-on push-pull cap in a colour matching the product; this is protected before first opening with a transparent cap. The transparent cap is removed from the lid by twisting and the guarantee band is fixed to the cap. The bottle is decorated with a sleeve label. www.sanbenedetto.it Bottle with sharp contouring Glance down the colourful drinks shelves in an Italian supermarket and the sharply contoured bottles of the “SanTHE” product range from drinks manufacturer Sant’Anna will catch your eye. The decaffeinated version, which is aimed especially at children and parents, is available in a sharply contoured bottle. It holds 250ml of lemon-flavoured tea. A circulating label is applied around the contoured area and embossing ensures a good grip. The drink comes out through a two-colour, resealable drinking cap with a tamper-evident seal. www.santanna.it Mountain in bottle base The “Levissima” brand, which belongs to Nestlé or San Pellegrino, is selling 600ml of natural mineral water with different additives like magnesium or zinc in eye-catching bottles. On front and back, there is a square indentation into which the labels are affixed. The brand logo is worked into the side walls as a large embossing. A particular feature of the transparent bottle is the base formation. The place where the base protrudes into the bottle is shaped like a mountain. www.levissima.it","@ID":54}, "TOP TALK PETplanet Insider Vol. 21 No. 11/20 petpla.net 12 PETplanet Insider talked to Alessandra Funcia, Head of Marketing and Sales at Sukano “We provide a safe environment that enables us to focus our energy on our daily operations” PETplanet: In this series of interviews, the first mandatory question we ask is: Where are you right now? From where are you answering us? A. Funcia: I am answering from our Sukano headquarter office in Switzerland (with a view to the lake and another to the Alps). PETplanet: Switzerland, the headquarters of Sukano, is now also affected by a second wave of the coronavirus. In mid-October, the Swiss Federal Council decided on more stringent measures for the cantons. Despite the restrictions, it should be possible to continue economic and social life. How are you experiencing the situation at Sukano? A. Funcia: These are strange times for all of us. The “enemy” is around the corner and yet we can’t see it. The current exceptional situation regarding the coronavirus (2019nCoV) demands action and solidarity all over the world. The safety of our employees, customers, and society at large is of the highest priority to Sukano. The crisis management action plan drawn up by Sukano Management, which is in place since earlier this year, concentrates on the maintenance of operational activities (Business Continuity Management). It also enables certain employees to work from home or to provide a single office to each employee when necessary, in addition to the use of masks and the disinfection of all shared areas in the company. This allows us to both guarantee our ability to fulfil our customer´s needs reliably and with the quality our customers are experienced with Sukano, under the safety and preventive requirements the situation demands, while still ensuring the health and wellbeing of our employees. Our team spirit attitude and practices have been excellent and we are experiencing the highest level of mutual collaboration and special dedication and attention from our own colleagues, as well as from our partners! We are all one and we are all in the same boat. One infected person could bring the disease to the company, to our collaborators and to our families. At Sukano, our campaign has never been so in line with our needs and actions: #wecare, #wetakeactions, #wearepartofthesolution. PETplanet: What did Sukano learn from the pandemic? What are the consequences for production, customer service and working methods? A. Funcia: We provide a safe environment that enables us to focus our energy on our daily operations. In close consultation with the public health authorities, we take a 4 pillar approach to ensure our safety at work. The cornerstones of our approach are: Personnel Management: minimum number of people in face-to-face meetings when digital communications can be applied Engineering controls: ensuring continuous, and periodically intensifying, clean environments through facilities management Administrative controls: managing and controlling the use of offices and common zones Personal protective equipment made fully available Additionally, we further intensified the synchronisation of our daily operations by splitting our company into four independent teams. One of these four groups works from their home office. This ensures that no one in one group has physical contact with anyone from another in our daily activities. So in case of an infection, the home office team can come back to the production site and take over for the team that would need to go into quarantine, and operations will continue. During an unprecedent crisis like this, there are big threats, but there are also opportunities. Through this tragedy, we have been given an enormous opportunity to reimagine what this world and society can be, and it will be on our hands to take this opportunity and build an even better future. We stringently protect ourselves to be able to look into the opportunities from a safe atmosphere and still work on relevant and upto-date needs through innovative technologies, such as the recently launched antiviral masterbatches. Our R&D team identified this at an early stage, and then tested it in a specialised microbiological lab, where the performance of our products against Feline Coronavirus in PET and PA was positive. PETplanet: In which area of masterbatch or additive development do you see the future? Which areas are worth special attention? Are there any planned projects at Sukano? Alessandra Funcia, Head of Marketing and Sales at Sukano by Heike Fischer","@ID":14}, "MARKET SURVEY 33 PETplanet Insider Vol. 21 No. 11/20 petpla.net Reciclar S.A. Erema Engineering Recycling Maschinen und Anlagen Ges.m.b.H. Tecnofer Ecoimpianti SRL Empacar S.A Heredia 3220, Sarandi, Buenos Aires, Argentina +54 11 4205 0102 www.reciclarsa.com.ar Mr Nicolás Pell Richards Director +54 11 4205 0102 [email protected] Unterfeldstraße 3, 4052 Ansfelden, Austria +43 732 3190 0 www.erema.com Mr Christoph Wöss Business Developm. Manager, Application Bottle +43 732 3190 0 [email protected] Keycycle GmbH member of Erema Group GmbH Mr Michal Prochazka Managing Director +43 732 3190 545 [email protected] Via Calto 409 45030 Ceneselli (Ro), Italy +39 0425 849090 www.tecnofer.biz Mr Mauro Garbellini Sales Manager +39 0425 849090 [email protected] Parque Industrial 45, Santa Cruz de la Sierra, Bolivia +591 3 34655 25 www.empacar.com.bo Mr Carlos Limpias Elío General Manager +591 3 34655 25 [email protected] Yes, washing done in cooperation with long-time partners or Keycycle 18,000 tons/year 9,600 tons/year 25,000 tons/year of flakes 22,000 m2 FDA, Local for food contact Vacunite-and Vacurema-technology, specification of input flakes: higher contamination can influence pellet quality but is basically possible to process, after discussion and agreed by Erema PET flakes 10ppm, PVC max content FDA, efsa (positive opinion issued), ANVISA, ilsi, BGBI, brand owners Yes: EFSA and FDA approved technology Up to 42,000 8,000 Depending on through-put and technology: 50 - 600 3,000 FDA (cat. A-H&J); EFSA (positve efsa opinion issued); brand owners (conf.); several national approvals (AUSTRIA, CH, Zona Mercursur, etc.) Coca-Cola , Pepsico, local government Closed loop system depending on application & technology type 1.5 Between 250 - 350 333 Specification of input flakes for MPR; higher contamination can influence flake quality but basically possible to process after discussion and agreed by Erema Pressed and loose bottles, clear, green and blue FDA (cat. A-H&J); EFSA (positve efsa opinion issued); with Multi Purpose Reactor Up to 20,000 Amin. output capacity of 1,000kg/h up to 4,000kg/h 12,000 Between 20 - 60 Min. floor space from 700 - 800m² onwards, depending on layout type and hourly capacity 3,000 FDA, EFSA (positive opinion issued) Respect the food grade parameters of the equipment dedicated to their use for food contact applications. Coca-Cola , Pepsico, local government Closed loop system Approx. 2.5 - 3l/kg (2.5 - 3m³/t), but it depends on layout type and production capacity 1.8 100 Between 0.58 - 0.62kWh/kg (580 - 620kWh/t), but it depends on layout type and production capacity 350 Detergent of different suppliers; quantity in function of the detergent 0.4 kgrs/t Erema RTF automatic backflush filter: 25μm; Erema continuous laserfilter: equals to 50/250 mesh 1,000μm or 30 Mesh Vacumera series: 1.5 - 3h; MPR series: 1 - 2h; Vacunite series: 7 - 15h To be defined in function of the contamination of the material 360 - 400 min in SSP @ 200-210°C Yes, Vacurema Inline Sheet Each washing line is customised as per customer’s final applications, so our lines can be applied and customised to each of the listed applications. Yes Yes, Vacurema Inline Fibre for Staple Fibre, BCF and POY No Yes Yes, Vacurema inline strapping or monofilament Yes, 100% rPET strap 8 -20mm width; yes, 700mm width, 0.1-1.5mm thickness","@ID":35}, "BOTTLING / FILLING PETplanet Insider Vol. 21 No. 11/20 petpla.net 35 Sipa bottling technology at Big Tree Beverages: fast and flexible Bottling Fruiticana juice drinks New Fruiticana fruit juice drinks from Big Tree Beverages are free of preservatives, thanks to Sipa filling technology. A new fully integrated blowing and hot-filling line was commissioned by Sipa at Big Tree Beverages’ main plant in Lusaka, Zambia, at the end of last year, and the drinks have been booming into market since then. Big Tree Beverages took advantage of Sipa’s skills in bottle design to create new shapes with wrap-around labels for the Fruiticana juice bottles. These come in several sizes and innovative flavors. All hot fill bottles have a 1881 neck finish that works with standard 1881 closures. The new line starts with a rotary stretch-blow moulding unit equipped with 12 cavities, which feeds bottles directly to a Flextronic SE 36/9 filling monobloc. This is electronic volumetric gravity filler, designed for hot fill applications in ultraclean configurations. It is capable of running Nitro Hot Fill, in which a small amount of nitrogen gas is injected into the top of the filled bottle to stop it from deforming as the contents cool (the Flextronic can also be used for standard hot fill and cold fill). That’s followed by a cooling tunnel, labeller, and finally a shrink wrapper. The flexibility of the Sipa line was an important factor in Big Tree Beverages’ choice for its latest investment. It means that changing from one product to another is quick and easy. Moulds can be changed quickly, so it is easy to move from one bottle size to another (and in the future, possibly change bottle designs while processing the same size of preform). On top of that, Sipa has provided a system that gives the output Big Tree Beverages needed – the line runs at high speed. Plus, there was Sipa’s ability to create a new bottle design in line with the customer’s concept for the Fruticana brand. Sipa’s Sales Manager for Southern Africa highlights further advantages of the system. “Consumption of air and energy is low, and Nitro Hot Fill helps further in containing costs compared to standard hot fill,” he says. “Finally, the whole line fits into a relatively small space.” Big Tree Beverages is one of the largest beverage companies in SubSaharan Africa, offering a broad portfolio of beverages at a very affordable price point in over 10 countries. The product range includes energy drinks, cola, various carbonated beverages, juices, cordials, and many other type of beverages. The portfolio is constantly changing thanks to the visionary approach of the family that leads the company, in line with the company’s goal to keep offering products that fulfill changing consumer demands and provide with best in class refreshments. Big Tree Beverages, which employs more than 5,000 people in Zambia and adjoining countries, is a part of Trade Kings Group, the largest FMCG Company in Sub-Saharan Africa. www.bigtreebev.com www.sipa.it","@ID":37}, "TRADE SHOW REVIEW PETplanet Insider Vol. 21 No. 11/20 petpla.net 42 today all economic activity in the country is now at 90% of normal. In Q1 of this year they also had major logistic issues, like India. Now production is at a reasonably high level, and more capacity is coming onstream in the polyester chain. They see tougher competition inside China, while exports are still lagging. Following questions from the audience, all the producers indicated how seriously they are investing in rPET lines, and are keeping their options open in using either chemical or mechanical recycling systems. The round table went on with the participation of a number of important PET converters expressing their point of view. Mr Christian Mayr , Global Purchasing Dir. of Alpla, said how quickly his Group reacted to the Covid threat, having been well informed in advance by their China office. He also noted that the image of plastic dramatically improved in the eyes of the final consumers, as they now appreciate better food wrapped in a plastic film, as it promotes the idea of better protection and cleanliness. Mr Paolo Cescutti , CPO of AMB SpA, stated that, as his group was fully involved in the packaging business, they had made enormous efforts to cope with the surge in demand from supermarkets and food chains during the spring. People now realise the importance of plastic packaging in preserving food, and the industry should take every opportunity of reminding consumers of this vital fact. Mr Massimo Cutolo , CEO of Gardaplast & IFAP, explained the early difficulties they encountered in the battle against Covid inside the company, with no masks or hand sanitisers available at the beginning. They hope that in 2021 economy will recover, and the arrival of a vaccine will help greatly. He also pointed out that there is the big question mark on the Plastic Tax both in Italy and Europe. Mr Mathieu Haels , Strategic Business Dev. at Plastipak, is convinced that the impact of the Covid issue on the economy will last for years. He also expressed the fear that there will be other virus pandemics, causing even larger problems to the world economy and to people’s behaviour. Mr Jonathan Glickfeld, GM of Visy Trading, Singapore, stated that he had not noticed any movement in PET demand which remained flat, same as 2019. On the other hand, his company saw a surge of 20% in the use of aluminium cans and canned food, like fruits, beans and also spaghetti. Consumer behaviour has changed in a significant way; people are cooking more at home as they are now working from home. Responding to several questions on rPET, the above converters agreed that the public will embrace it, and will be ready to pay more for more recycled material. However, there is not enough rPET in the market, so it will be necessary to push harder on collection activity around the world. The webinar gave the platform to the opinion of the bottlers, with some big names participating. Mr Malik Bechar , Global Procurement, Coca-Cola, explained that Covid affected more the hospitality sector, while supermarkets were less hit. That caused a fall in PET use, both virgin and rPET. Some recovery will be seen but only at the end of 2020. Coca-Cola is already using less and less virgin, while increasing the use of recycled material. Mr Carlo Pontecorvo , President of Ferrarelle, Italy, said that the pandemic had not affected his company unduly sales volumes were 4% higher than in 2019. It was true that sales to the hospitality sector dropped dramatically, and it was only in August and September that there was some normal activity in this sector. Ferrarelle has its own recycling plant, and all their bottles are made of 50% rPET. Mr Coert Michielsen , CPO of Refresco Holding, stated that even during the pandemic they kept their 60 plants open and working, in safe condi-","@ID":44}, "8 NEWS PETplanet Insider Vol. 21 No. 11/20 petpla.net 2nd CSR Report shows progress from Retal Global plastic packaging manufacturer Retal has published its 2019 Sustainability Report, proudly highlighting improvements across its ambitious CSR goals. In this second annual Sustainability Report Retal lays out its Circular Economy Strategy as integral to the business which revolves around increasing recycled material uptake, promoting Design for Recycling (DfR), and plastic pollution awareness and education. Sustainability Director and author of the report Emmanuel Duffaut adds, “The report shows our first steps in the three axes of our strategy with heavy investment in our processing capacity of rPET, engagement with our customers on recyclability guidelines and cleanup activities with our local communities”. The 2019 Sustainability Report from Retal also includes particular progress in its climate change action, with a major reduction of greenhouse gas emissions (down 17% from its 2018 base year), which contributed to its B score in the Carbon Disclosure Project (CDP). Duffaut explains, “Our management of climate change is a real success story, and we intend to continue mitigating our impact by continuously increasing our consumption of renewable energy and improving our energy efficiency across the whole company. A B-score from the CDP for our first evaluation show that we are on the right track, so we’re motivated to carry on and keep pushing boundaries.” Labour Practices, Human Rights, and Sustainable Procurement are also strongly addressed in the report, with, for example, the launch of an internal project to globally rollout an ISO 45001 certified Occupational Health & Safety management system. www.retalgroup.com Coca-Cola European Partners has made a non-binding proposal to acquire Coca-Cola Amatil Limited Coca-Cola European Partners plc (CCEP) announces that it has made a non-binding proposal to acquire Coca-Cola Amatil Limited (CCL). The Board of Directors of CCEP has made a non-binding offer to acquire 69.2% of the entire existing issued share capital of CCL, which is held by shareholders other than The Coca-Cola Company, to be effected by means of a scheme of arrangement; and has entered into a non-binding heads of terms and cooperation letter with The Coca-Cola Company (KO), setting out the terms on which CCEP proposes to acquire KO’s 30.8% interest in CCL, conditional upon Australian regulatory approvals and the implementation of the scheme of arrangement Rothschild & Co are acting as lead financial adviser and Credit Suisse are acting as financial adviser to the Affiliated Transaction Committee (ATC) of the Board of Directors of CCEP. Slaughter and May and Corrs Chambers Westgarth are acting as legal counsel, to CCEP. www.cocacolaep.com","@ID":10}, "EDITOUR PETplanet Insider Vol. 21 No. 11/20 petpla.net 24 The Philippines With more than 7,600 islands (the number increased by more than 500 a few years ago with the help of modern radar technology), the Philippines cover a total area of nearly 340,000km2 , of which 300,000km2 is land mass. It extends 1,127km and 1,850km from north to south and east to west respectively. There are around 880 inhabited islands. 81 provinces grouped together in 17 regions are divided into three archipelagos: Luzon in the north and west, Visayas in the centre and Mindanao in the south. Luzon and Mindanao are the two largest island groups covering around 110,000km2 and 97,500km2 , respectively. The capital is Manila. To the north, the Philippines, which are completely surrounded by water, are connected to the Luzon waterway with Taiwan to the north, to the South China Sea to the west and Vietnam further west, the Sulu Sea with Borneo to the south-west, the Celebes Sea with Sulawesi, Indonesia, to the south and the Philippine Sea to the east. The country’s geographical location means that it is part of the Pacific Ring of Fire, which has repeatedly led to volcanic eruptions and earthquakes. A tropical climate provides the country with an average temperature of 26.5°C, accompanied by regular and sometimes violent tropical storms and typhoons. Changes linked to climate change have been predicted for the region for some time, with the Philippines high in the world rankings for natural disasters which have been caused as a result. The population of the Philippines last year was just over 108 million, most of whom live on the northern islands, with the majority residing in Luzon. It is estimated that Manila’s metropolitan region will be home to just under 14 million people this year. Sugar tax, Covid-19 and modest PET growth The Philippines drinks’ market In 2017, Manila was the starting point for our visit to Coca-Cola’s Philippine subsidiary and affiliated preform supplier, Alpla, at Canlubang in the south. Rodrigo Duterte had become the country’s President only a year earlier and the actions of his administration have resulted in direct foreign investment falling below expectations, while the number of unemployed and people in poverty has remained consistently high. And yet, annual GDP grew by 6.4% between 2010 and 2017, which is nearly 2% more than during the previous decade. Although the Asian Development Bank is expecting a massive 7.3% slump in GDP growth during this Covid-dominated year, the country’s economy should be back on track next year with a forecast of 6.5%. Here, we examine what the current economic situation, the tax on sugary drinks introduced in 2018 and the coronavirus pandemic mean for the drinks’ industry. Tour Sponsors: Macro-economic data Philippines 2017 2018 2019 Population (millions) 105.17 106.65 108.12 Population growth p.a. 1.5% 1.4% 1.4% GDP (current, in billions) 328.5 346.8 376.8 GDP growth rate 6.9% 6.3% 6% GDP per capita (current) in US$ 54,066 57,396 54,907 Imports (goods and services, in billions US$) 126.8 145.5 151.7 Export (goods and services, in billions US$) 97.1 104.8 106.8 National debt of GDP 42.1% 41.8% 41.5% Unemployment rate 2.6% 2.3% 2.2% Inflation 2.6% 5.2% 2.5% Beautiful beaches and bays attract tourists from all over the world.","@ID":26}, "49 PRODUCTS PETplanet Insider Vol. 21 No. 11/20 petpla.net The new MRSjump recycling extruder - PET tray-to-tray recycling in a single extrusion step If a circular economy is to be realised, it will be necessary to consistently recycle post-consumer thermoformed PET trays back into PET trays. The recycling of regrind from post-consumer PET trays to new sheet for PET trays presents challenges for the recycling process: With the new MRSjump extruder, Gneuss offers a system with which it is possible to process post-consumer PET regrind from thermoformed trays directly to sheet for thermoforming trays in one step. Without the need for thermal pre-treatment of the PET regrind, or to make pellets first and then feed the pellets into the sheet extruder and with EFSA and FDA food contact certification. The new MRSjump Extruder combines the high decontamination performance of the MRS degassing extruder with a viscosity boost: The extrusion process does not necessitate any pre- or post-treatment of the input material, such as crystallisation or pre-drying of the recycled material or an IV boost in a solid state polycondensation (SSP). The degassing efficiency makes it possible to comply with EFSA and FDA limits without time- and cost-intensive upstream or downstream material treatment. The set-up direct extrusion process avoids the combination of different material treatments prior or subsequent to extrusion and resulting interface problems. Thanks to the short process chain, the melt remains within a narrow, defined residence time spectrum. The thermal and mechanical stress on the material is kept low. The compact design of the MRSjump Extrusion System: it has a small footprint, it can easily be retrofitted to an existing sheet line within the same spare requirements. It can processes a wide range of input materials, from regrind from mono- and multi-layer trays to material combinations In combination with the Gneuss Rotary Filtration Technology high melt purity is guaranteed. Quality assurance is provided by optional systems for measuring melt viscosity and optical properties (colour and transparency measurement). With the innovative MRSjump Extruder Gneuss offers an optimum solution for post-consumer tray-to-tray recycling, which meets all requirements of completely circular modern food packaging. Recycling and decontamination are for the first time made possible with the MRSjump Extruder, within one single extrusion step without upstream or downstream material treatment steps. This opens up new possibilities for the recycling of tray regrind. www.gneuss.com Building the future in every moment of your business 40 Bar Oil-Free Piston Compressors for PET Applications. hertz-kompressoren.com RECYCLING","@ID":51}, "CAPS & CLOSURES 37 PETplanet Insider Vol. 21 No. 11/20 petpla.net CAPS & CLOSURES 37 Michael Krueger: In the first weeks of the pandemic we saw very high demand, primarily family packs/ supply packs. Very quickly, small containers for on the move or single serve packs dropped as travel was no longer possible. So despite the initial peak, fewer caps were needed. Additionally, after April, stocks were full everywhere so volumes dropped. Since then, we have been returning to normal levels. PETplanet: Finally, a word about tethered caps. Is the bottler already prepared? Michael Krueger: Firstly, not all regulatory details have been defined. We do not expect big surprises. But of course it is harder to prepare for uncertain conditions. Bottlers have a very high level of interest in the topic and certainly do a lot to be prepared. But right now it seems that a significant number of bottlers will try to implement the conversion as late as possible. PETplanet: Is this purely a European topic? Michael Krueger: I don’t have that impression. In many other countries, similar regulations are in the pipeline; some bottlers also see tethered caps as an additional benefit for consumers. For us it is important that we can offer our tethered cap solution to our customers for all relevant neck finishes. This will be the challenge for us over the next few months. PETplanet: Thank you very much! www.corvaglia.com Corvaglia factory was built up in 2018 in the USA. ENDLESS INNOVATION SINCE 1919","@ID":39}, "EDITOUR PETplanet Insider Vol. 21 No. 11/20 petpla.net 27 PETcast In our new Road Show podcast, PETplanet meets industry experts from Down Under to Japan and talks with them about their successes, decisions and current developments. Listen to the full conversation atwww.bit.ly/2HVwbAd Customer Factory INTRAVIS Service PLASTIC PACKAGING VISION INSPECTION WWW.INTRAVIS.COM ALWAYS BY YOUR SIDE . IN PERSON ORONLINE . 91% respectively. It is worth drawing attention here to the impressive 17% growth in PET used for RTD coffee. Covid-19 and consumer behaviour A comparison of the development in bottle sizes shows that despite the pandemic and with more and more time being spent at home, single-serve sizes are still an attractive option for consumers. The 300ml bottle introduced by Coca-Cola Femsa and Pepsi-Cola leads the way with a massive 67% of the CSD market as popularity of this size continues to grow. The number of 1.5 l bottles is also on the rise here. “We can say that while numbers of 0.5 l bottles are not really growing, the same cannot be said for the 300ml and 1.5 l varieties which are on the up. Smaller sizes such as 250ml for RTD coffee and 230ml for RTD tea are also increasing and in line with this trend. This will also help us to determine whether there is a pandemic-related trend for larger bottle sizes for longer drinking times. With long-term temperature rises, more and more consumers are feeling the need to stay hydrated when on the go, which also explains the continuing success of smaller bottle sizes”, said Romano Reyes, Husky Injection Moulding’s Regional Manager for Rigid Packaging in the Philippines. Sources: GTAI, Husky Injection Molding Systems, Market Research Company Euromonitor International, Statista, WKO, World Bank Manila’s waterfront promenade on Roxas Boulevard","@ID":29}, "TRADE SHOW REVIEW PETplanet Insider Vol. 21 No. 11/20 petpla.net 44 A strong signal for the beverage industry, part 1 China Brew China Beverage The need for B2B networking and information was high – it was palpable at the world’s second-largest trade fair in the beverage and liquid food industry. China Brew China Beverage (CBB) took place from October 13 to 16, 2020 in Shanghai. Due to the coronavirus, the trade fair had a largely national focus, although 101 exhibitors were from other countries. “The fact that the CBB took place successfully sends a positive signal for our global drinktec network, as well as the trade fair industry as a whole,” explains Dr Reinhard Pfeiffer, Managing Director of Messe München. “Especially in difficult times, it is important to maintain your business, stay informed and search out new opportunities. CBB has once again confirmed its position as a leading trade fair in the Asian market.” Petra Westphal, Exhibition Group Director at Drinktec, adds, “To us, CBB is an important milestone on the way toward the world’s leading trade fair drinktec 2021 in Munich, with many exhibitors having already firmly booked. This shows that the industry is confident and committed to planning the industry gathering in Munich.” China remains important sales market “China remains one of the most important sales markets for suppliers of machinery and systems for the production, filling and packaging of beverages”, emphasises Richard Clemens, Managing Director VDMA Food Processing and Packaging Machinery Association. “Against the background of the global corona pandemic and the associated travel restrictions, investments in machinery and equipment are temporarily lower than in previous years. The China Brew & China Beverage 2020 trade fair shows that there is a high level of interest in technologies for efficient, hygienic and flexible beverage production. The CBB has sent important signals and we hope that the investment projects discussed can be implemented soon”, says Richard Clemens. A new start for the industry in the Southeast Asia region CBB was seen by many decision makers in the industry as a chance to re-start their business. The trade fair attracted 31,781 visitors comprising around 30 delegations, including those from the National Food Management Center of China Light Industry, the China National Research Institute of Food & Fermentation Industries and","@ID":46}, "PETpatents www.verpackungspatente.de PETplanet Insider Vol. 21 No. 11/20 petpla.net 56 An aseptic bottle European Patent No: EP 3594142 A1 Applicant: Suntory Holdings Ltd., Osaka (JP) Date of application: 6.3.2018 A light thin-walled bottle for hotfilling. Its base is specially designed to absorb internal pressure without deformation to prevent the base from buckling with resultant loss of stability. Bottle with a solid spout Internal Patent No: WO 2018/170365 A1 Applicant: Consolidated Company LP., Atlanta (US) Date of application: 16.3.2018 The plastic bottle’s shoulder section and spout are specially designed to absorb forces “non-destructively” that occur during shipping or when the bottle is dropped accidentally. Preform with several sections Internal Patent No: WO 2020/028424 A1 Applicant: Niagra Bottling LLC., Ontario (US) Date of application: 30.7.2019 In order to be able to best meet a bottle’s various requirements, it is proposed to divide the preform into several “sections” according to thickness of material and shape. Preform with thread Internal Patent No: WO 2020/028405 A1 Applicant: Niagra Bottling LLC., Ontario (US) Date of application 30.7.2019 A preform for creating a lightweight PET bottle. The top side is already moulded as a thread to help provide a better and more reliable way of determining whether the bottle has been opened. Cap holder Internal Patent No: WO 2020/037089 A1 Applicant: Novembal USA Inc., New Jersey (US) Date of application: 14.8.2019 In order to prevent a cap from falling off or being discarded, it is proposed making a recess in the opening/ bottle neck into which the cap can be “wedged”. Lightweight plastic bottle Internal Patent No: WO 2019/245638 A1 Applicant: Graham Packaging Comp., L.P. Lancaster (US) Date of application: 16.4.2019 A weight-reduced bottle with a special moulded base shape and outer wall design to absorb the forces produced during hotfilling or filling with carbonated content “without deformation” in the visual area.","@ID":58}, "PREFORM PRODUCTION PETplanet Insider Vol. 21 No. 11/20 petpla.net 21 Interview with Integrated Plastics Pty. Ltd October 15, 2020 We met: Mr Nicholas Mellen, Managing Director PET bottle handles produced during the preform phase by Kay Barton In the Villawood district some 30 km west of Sydney city centre, Integrated Plastics have been working on an effective, market-ready solution for bottles and containers with integrated handles since 2010 with a view to launching a global licensing business for PET converters and bottle producers. The handle’s material and the process involved are special features of the technology. The patented idea relies exclusively on PET and rPET for the handle and, unlike other more conventional technologies, is produced with the preform at the preform stage. This allows the company to achieve key objectives such as ideal recyclability of the whole container, together with savings in weight and material compared with other combinations of plastics and production output. We spoke to Integrated Plastic’s Managing Director, Mr Nicholas Mellen, about the concept and the development of what he says is a unique product that can be promoted worldwide. Origins and development “Integrally Moulded Handle” or IMH as the company calls it is what experts most closely associate with extrusion processes or subsequently inserted HDPE handles. One occasionally comes across moulded grips which, for process-specific reasons, are moulded rather than recessed for effective finger insertion. The introduction of the IMH means that previous technical limitations should now be a thing of the past with the whole container also guaranteed to be 100% recyclable. The initial IMH idea was developed by the Australian company, B&R, which started production for the first time in 2006 as the licensor. “We were really excited by the idea, acquired the relevant licence in 2012, founded Integrated Plastics and began producing bottles with handles”, explained Managing Director and Co-Founder, Nicholas Mellen. The entrepreneur has 20-years’ experience in the plastics industry and runs the company with David Ramirez, Manufacturing Manager, Lead Innovation and R&D and Ganesh Krishnan, Global Head of Projects, Lead Innovation and R&D. Process and production systems were continually updated over the ensuing years. “We began by using a 140 g preform for 4 l bottles and produced other IMH bottle types up until 2014 such as 2 l varieties weighing between 75 g and 85 g which were produced using an ADS Linear Blow Moulding System. Tour Sponsors: IMH bottles used by Tru Blu Beverages","@ID":23}]}}
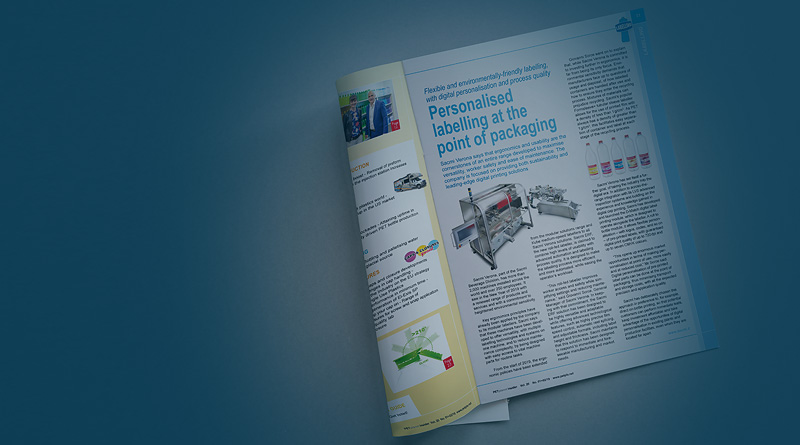